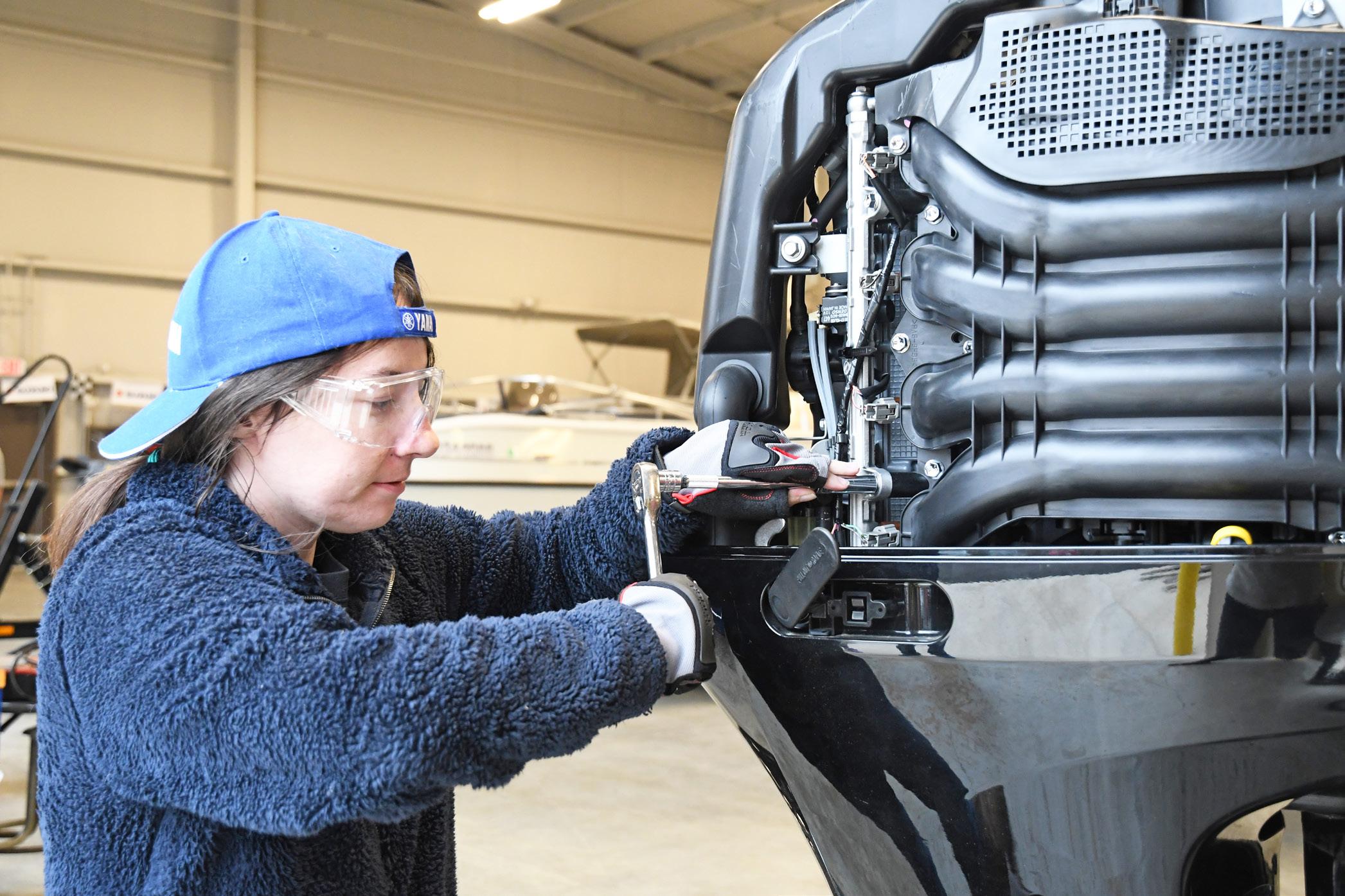
5 minute read
HELP WANTED!
from BluePrint 2023
Arkansas Companies Desperate for Skilled Labor
There’s never been a better time to be a skilled worker in Arkansas.
Skilled labor — also known as “the trades”— is in short supply in The Natural State, and Arkansas’s not alone. Skilled workers have been declining in numbers nationwide for decades as not enough young people have gone into jobs such as electricians, plumbers, construction, welding and a variety of manufacturing fields to help companies keep up with growth.
Contributing to the situation are the millions of existing skilled workers looking to retire and companies struggling to catch up with hiring after COVID. About 10,000 baby boomers reach age 65 every day, according to the U.S. Census Bureau, and by 2030 all members of this generation will be at least 65 years of age. This has reduced the boomer labor force by an average of 2.2 million workers each year since 2010, or about 5,900 workers daily, according to analysis by Pew Research Center.
The COVID-19 pandemic further complicated things by driving millions out of the trades overnight. According to the U.S. Bureau of Labor Statistics, nearly 8 million skilled labor jobs were eliminated during the pandemic, only about half of which have been refilled since.
But perhaps the most stubborn problem facing skilled careers has been an image problem 40 years in the making. Beginning in the 1980s, parents and guidance counselors preached to young people a four-year degree was the only path to long-term career success. Working with one’s hands, meanwhile, was often portrayed as low-skill, low-tech, dead-end work that was hot, dirty and dangerous. Many high schools even did away with shop and ag classes altogether, reinforcing the negative stereotypes about skilled careers.
However, as many high school graduates found out the hard way, four-year colleges are not for everyone, causing many to drop out before attaining a degree, limiting job prospects (but not before racking up considerable student loan debt).
Fortunately, things are starting to turn around in Arkansas as more and more kids are being exposed to skilled careers at younger and younger ages. Community colleges across The Natural State have strengthened partnerships with local school systems to offer training classes during a student’s high school years. This allows more students to get at least part of their training out of the way before high school graduation.
Companies in need of skilled workers have also stepped up to the plate, with high wages; clean, safe working conditions; and career pathways that give employees looking to advance something to work toward. And, the nature of blue-collar jobs themselves has changed, with much more technology in play than ever before. As with every other area of life today, computers and digital technology are everywhere on the job site and in the factory, requiring a new generation of skilled workers to operate them and keep them running.
The future of skilled careers is one of immense opportunity, and while the shortage of skilled workers won’t be solved overnight, there are signs things are headed in the right direction. That’s good for companies, good for workers and great for the state of Arkansas.
HAROLD HOUNWANOU
Engineer
Little Rock Water Reclamation Authority
Home country: West Coast of Africa
Age: 35
BLUEPRINT: You’re from West Coast of Africa?
HAROLD HOUNWANOU: Yes, I grew up in a small town on the West Coast of Africa to the west of Nigeria. We speak French over there. I aspired to come to the United States because of the water access and sanitation issues we have in my country. Those are issues we face on a daily basis, and that inspired me to want to learn more.
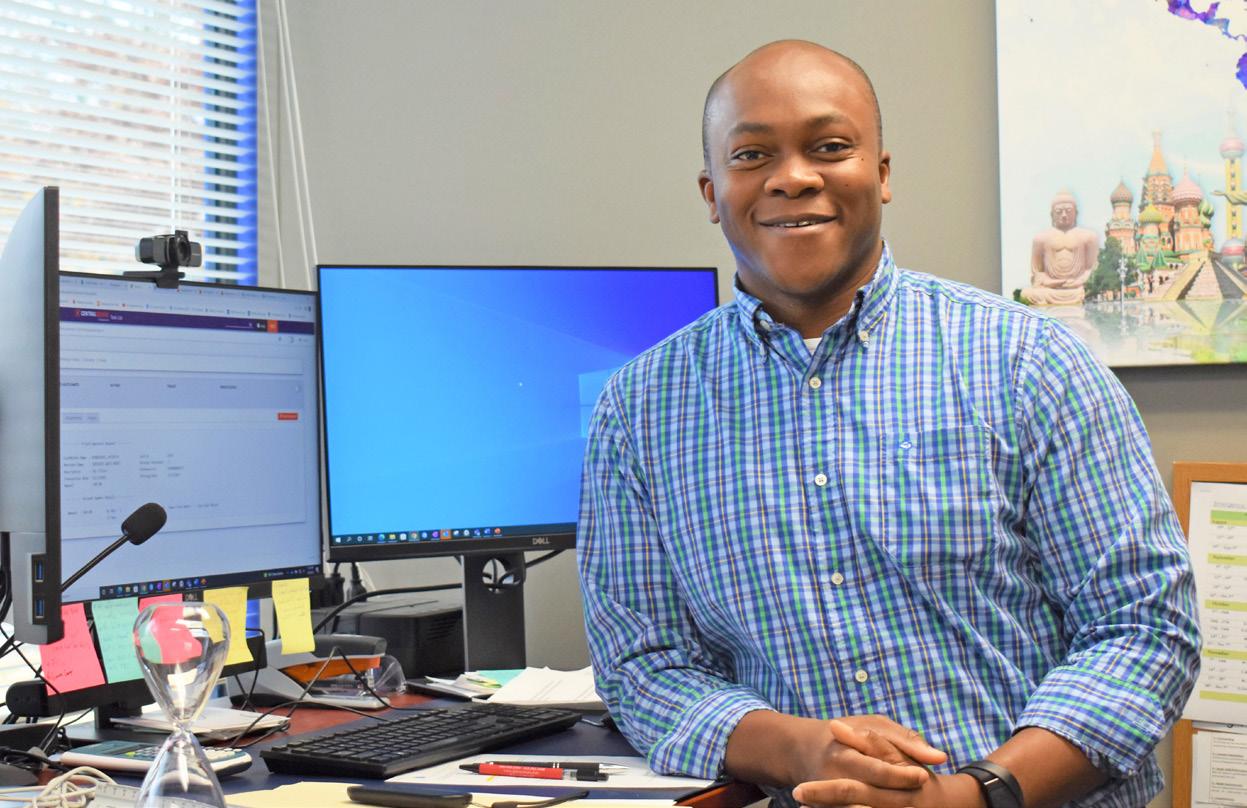
In 2012, I moved here and went to Henderson State University where I learned English, then moved to North Carolina State University and earned a master’s in environmental engineering before moving back to Arkansas.
BP: You joined LRWRA as an engineer then?
HH: I’ve climbed the ladder. I started in 2017 as a utility worker, which is in the field doing manhole work, sewer line work, all kinds of repairs. It gave me the opportunity to learn about the field and what we do to provide sewer service to our customers in the city. It was somewhat of a foot into the door to get that exposure and learn what we do. After doing that for about 18 months I moved to the engineering department.
BP: Are there similar job opportunities there now?
HH: Over the last 18 months, we’ve had 12 retirements in my department alone, and when you have retirements you have to replace those people. People also get promoted and vacancies are created.
The entry level positions, the utility worker position where I started, right now we still have a few vacancies we are trying to fill. We have some commercial driver positions and it’s difficult to find drivers now.
BP: What are the most important skills you look for in a candidate?
HH: I like to call them human skills because ultimately we are in the business of developing relationships with people. Attendance, respect of others, the way you handle yourself and your work are all huge. You can teach hard skills; we have to make sure the employees that we hire are in alignment with our values.
JARRED MARTINEZ
Equipment Operator
Little Rock Water Reclamation Authority
Hometown: Bauxite
Age: 25
Years with LRWRA: 4
BLUEPRINT: How long have you been with the company?
JARRED MARTINEZ: This is going on my fourth year. I’ve been an equipment operator for almost a year now.
BP: What’s your background?
JM : My dad owns his own tile company and I worked for him in high school. I went to college to play baseball, and when that didn’t work out, I kinda didn’t know what I was going to do. I ended up joining the National Guard after one semester of college and then I just worked and did my Guard stuff.
The military helped me grow up a little bit. It also has multiple career paths you can do, and it ended up leading me into a good group of friends that helped me get this job.
BP: What’s your typical day like?
JM: When I get to work, I meet up with my crew leader and we go over the plan for the day. We get the supplies we need and we restock our truck. I operate a 3030 Cat trackhoe and we dig up sewer lines and line mains. We do mains that are located in front yards and backyards or out in the woods, so we can be anywhere digging two-and-a-half feet deep on a six-inch main to 15 feet deep on a 22-inch main.
BP: What training have you received to improve your skills?
JM: When I first got here, I didn’t have my commercial driver’s license and the company paid for me to get that. I also got hands-on training with heavy equipment so now I can operate anything from forklifts to front-end loaders to skid steers and trackhoes. I’ve done an internal class on shoring safety and trenching; every year we complete multiple safety classes that really help you understand what can go wrong and what to look out for to keep everybody safe.
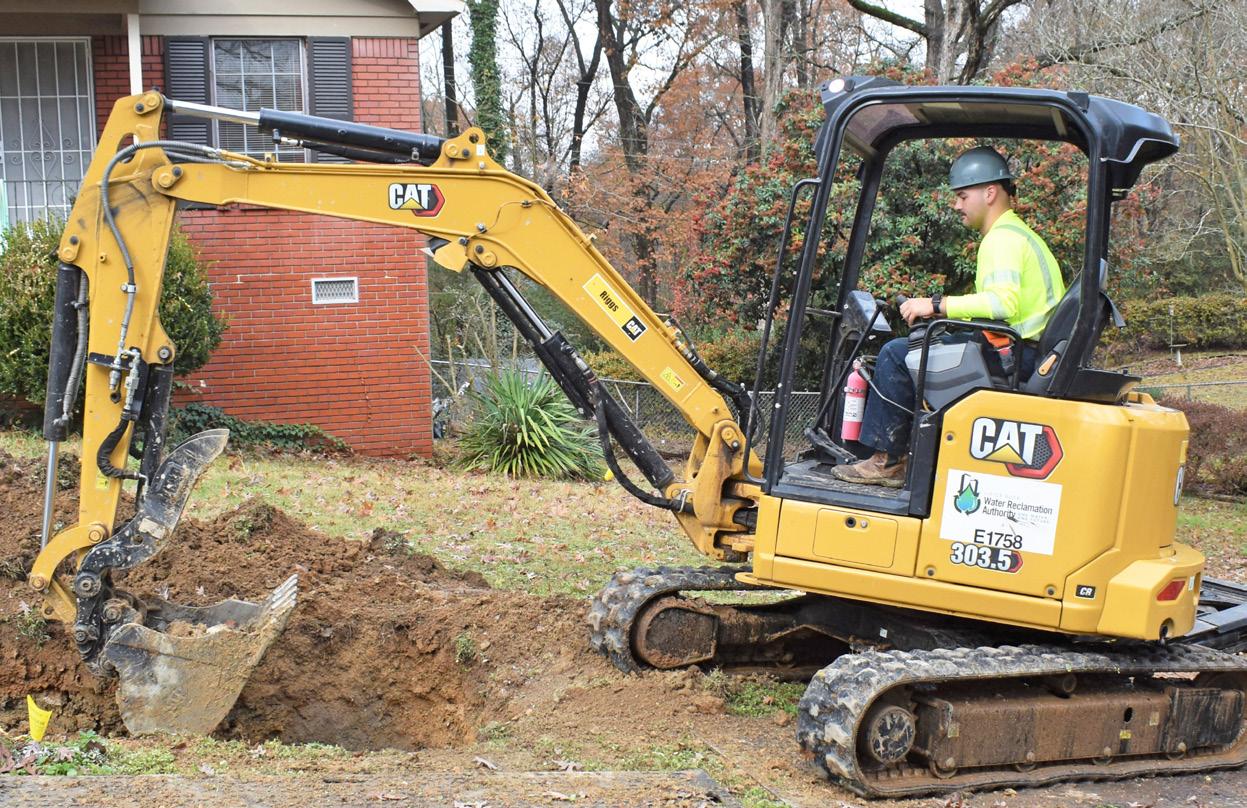
BP: If you could go back to your high school and talk about what it takes to be successful on the job, what would you tell students?
JM: What I’d really like to tell them is they need to have a good work ethic and they need to be able to adapt and overcome differences because no one you’re going to work with is going to be exactly like you. You have to be open-minded and make sure that you can work well together and listen to instructions.