
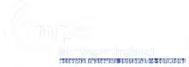
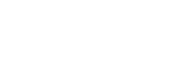
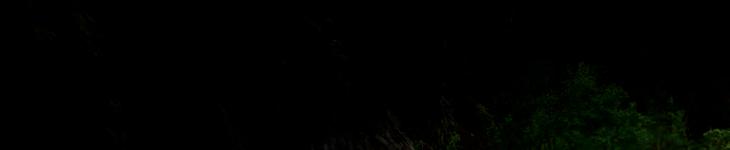
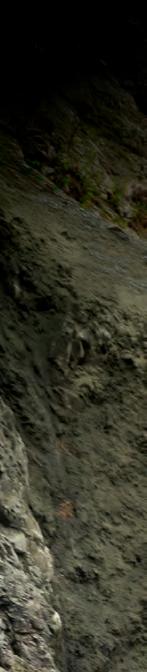

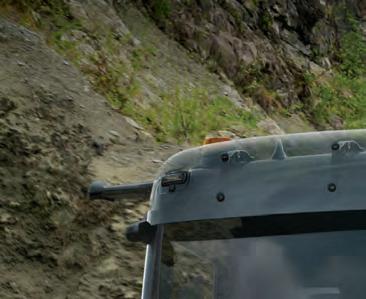
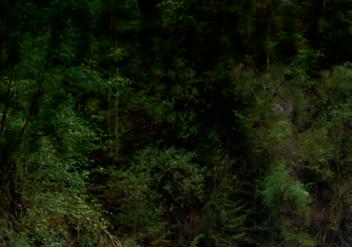
From 18 to 50 tonnes, MAN TGS trucks are built for the toughest construction jobs, combining reliability, performance, and durability. Powered by fuel-efficient, high-torque engines and available with two to five axles, they offer tailored load capacities, wheelbases, and frame overhangs to suit any task.
20 Bobcat launches new ‘V-Drive’ telehandlers for agriculture
22 Kilsaran instruct Wilsons Auctions to host major quarrying and construction auction
36 Latest advancements in highways and roads
56 Dennison JCB’s Ian Calderwood, and his father, John, on their similar plant sales paths
72 Behind the wheel of the Mercedes-Benz Arocs
106 ReCon Concrete’s environmentally-friendly solution in focus
112 Develon unveils Next Generation ‘-9’ Excavators
Golda Burrows General Sales Manager
Sarah Nelson Editor
Martin Elliman General Manager
Joel Byers Production Manager
Catherine Bulling Accounts Administration
Helen Beggs Chief Operating Officer
Plant & Civil Engineer is Published by:
4 SM (NI) Ltd, The Old Coach House, 12 Main Street, Hillsborough BT26 6AE
CONTACT Golda: 07724 192032 or Martin: 07985 887171
Email: golda@4squaremedia.net
Email: martin@4squaremedia.net
4SM (NI) Ltd is part of the North West News Group
COPYRIGHT NOTICE: © Plant & Civil Engineer 2025. All material in this publication is copyright, including advertisements which have been prepared for advertisers. No part of it may be reproduced in any way whatever or stored in electronic retrieval systems without the written permission of the publishers. We are a completely independent voice and are not connected to any Institutes or Associations within the industry. Our aim is to publish accurate, specific and dedicated information, targeting each sector of the industry, throughout Ireland. The publishers cannot be held responsible for any inaccuracies supplied by the contributors. All rights reserved.
12 Ryan Fay Contracts discuss their new Takeuchi TB290-2 Excavator
58 What has the Balmoral Show got in store for 2025?
83 A sneak peek into the ICE Expo’s itinerary and exhibitors FROM THE DESK OF
20 Gordon Best, Regional Director, MPANI
46 Karen McShane, Past President, CIHT SALES AND SERVICES
113 Plant sales
116 Buyers guide COVER STORY
26 Liebherr has expanded its wheeled excavator portfolio
2025 PLANT & CIVIL ENGINEER AWARDS
49 Submit your entries and showcase your expertise
Welcome to the April-May edition of PCE – the first of the publications in which I have been fortunate to step into the post of editor!
It’s been an exciting few months getting to grips with the role and immersing myself in the plant, construction, quarrying and recycling worlds – thank you to everyone I have spoken to so far for being so friendly. However, like many things worth doing, the transition initially felt a little daunting, because PCE boasts a deeply-entrenched legacy, and it’s a legacy which I am eager to do justice. It felt only appropriate, then, that work on my first edition entailed significant learning of other legacies spanning the various facets of the sector – from familial heritages to machinery histories. I’m excited for you to find out more about them, too, over the following pages! In this issue, Niall Kennedy of W.R. Kennedy & Company, reflects on the company’s early beginnings under his grandfather, and continued evolution since. Meanwhile, Dennison JCB’s Ian Calderwood and his father, John, delve into the alignment of their plant sales careers – years apart. It’s another father and son team, from Ryan Fay Contracts, who participate in this issue’s View from the Cab – reflecting on how the purchase of their latest Takeuchi TB290-2 Compact Excavator has been influenced by the brand’s own impressive heritage.
As momentum builds, we are proud to preview two core industry events – Balmoral Show and ICE Expo 2025. Get a peek into the events’ itineraries, as well as an insight into some of the esteemed exhibitors who will be on showcase. The PCE team will also be in attendance at both, so make sure to say hello if you spot us!
Don’t forget that the 2025 Plant & Civil Engineer Awards – taking place on 20th November – are now open for entry, too. Check out the categories and grant us the chance to celebrate your team’s excellence!
I do hope you enjoy the read, and remember that you can remain on the pulse of the profession’s news 24/7 by logging on to our website at www.plantandcivilengineer.com. Our free weekly newsletter is also distributed every Tuesday – subscribe on our website now if you haven’t already.
See you next month!
Sarah Nelson Editor
Email: pceeditor@4squaremedia.net
M: 07789 756 815
Elaine Morphew recently marked a significant career milestone – celebrating 45 years of dedicated service in sales administration at MBNI Truck & Van.
Throughout her impressive tenure, Elaine has expertly managed her sales administration processes, ensuring that everything runs seamlessly. Testament to her commitment to tradition and thoroughness in the role, Elaine is steadfast in the use of her trusty typewriter – affectionately known as her ‘iPad’ – and employs it to create T-Cards for all of the trucks and vans she has ordered. The T-cards are subsequently moved along the board as they progress through the order process, ready for registration and delivery.
Boasting unwavering loyalty and dedication throughout the years, Elaine is highly-regarded by all of the colleagues and customers she encounters.
Commenting on the milestone, Elaine said: “I’ve really enjoyed my 45 years at MBNI, working across service, accounts, and sales. No two days have ever been the same, and I’ve had the
pleasure of meeting so many amazing people – many of them are still part of the team today. As I look ahead, I’m excited to reach my next milestone of 50 years before retiring!”
CPAC Modular, Ireland’s leading modular main contractor, has proudly welcomed the Chartered Institute of Building (CIOB) to Ireland’s first permanent modular school at Lucan in Dublin. This state-of-the-art permanent structure hails a new era for modular construction in Ireland, offering permanent, sustainable and innovative facilities for the educational sector.
Ireland’s first permanent modular school at Lucan spans 3,600 square metres over two floors and comprises of 24 classrooms, as well as a library, multi-use group recreational space and a special education needs wing.
The first-of-its-kind in Ireland, the project was completed within 18 months from start-to-finish, which features cuttingedge amenities, making it a beacon of modern educational infrastructure.
Sustainability is another feature of Ireland’s first permanent modular school with less
time needed on-site, resulting in less fuel for transportation to and from site, combined with a focus on more sustainable materials including light gauge steel. Approximately 85 per cent of the construction for Ireland’s first permanent modular school at Kishoge was constructed off-site at CPAC Modular’s facility in Dunshaughlin, Co Meath.
Mark Whitehead, Construction Director of CPAC Modular, was delighted to welcome the CIOB to Kishoge, where they had the
opportunity to experience first-hand the innovation and efficiency behind Ireland’s first permanent modular school.
“The CPAC is on a mission to change the perception of modular construction in Ireland with projects like this,” said Mark Whitehead.
“The evolution of modular construction has transformed the building industry, and the CIOB’s visit today reinforces this progress. With Ireland’s first permanent modular school here in Kishoge, we’ve proven that modular buildings are a fully viable competitor to traditional structures across various sectors, providing permanent, stateof-the-art solutions. They deliver faster turnaround times and a more sustainable alternative to conventional construction. This project marks a turning point for the industry and signals the beginning of a new era for modular construction in Ireland.”
The new TB370W is a powerful compact 7.5 tonne wheeled excavator and versatile tool carrier designed for maximum productivity on busy construction sites.
Its offset two-piece boom delivers an increased working range and added in-field lifting capacity, complete with lift overload alarm and arm, swing and boom holding check valves, all as standard.
The powerful and responsive load sensing hydraulic system supplies up to four auxiliary ports with hi-flow and proportional control, with optional multifunction grip allowing the operator to assign buttons to frequently used functions.
Its three different work modes Std, Eco and Eco Plus offer the best efficiency. Eco Plus switches between Std and Eco dependent on load. Operators can also switch to cruise
control for consistent travel speed while simultaneously operating attachments.
As a multi-tool-carrier, the new TB370W with DPF, 4WD and four speed transmission delivers fast powerful productivity. The heavy-duty undercarriage with mudguards, switchable difflock and intelligent auto digging brake delivers excellent safety and stability on site. The TB370W is available with optional outriggers.
The large comfortable cab puts the operator in control with touchscreen and jog dial technology for every function complete with maximum safety and visibility with three auto cameras and full LED lighting all-round.
The unique Takeuchi tilt-up cab provides unrivalled ground level access to all service and component parts. The TB370W is supported by a five-year telematics subscription to Takeuchi Fleet Management. Takeuchi now feature three-year/ 3000hour full warranty across the range.
Viki Bell has become the new Chief Executive Officer (CEO) of the Construction Equipment Association (CEA), following a successful first year as Director of Operations. Her appointment marks the next chapter in the association’s evolution, building on a strong foundation of operational reform, strategic renewal, and a clear commitment to supporting members and the broader industry.
Over the past year, Viki has led a major internal transformation. This has included welcoming new team members, refining the CEA’s structure, and modernising key operational processes – from finance and HR, to communications
and digital platforms. A fully integrated CRM and website have been launched, alongside a comprehensive refresh of member materials, to improve clarity, accessibility, and support for members at every stage of their engagement.
Looking ahead, the CEA will continue to focus on the key priorities set out in its manifesto, including decarbonisation, machinery theft, lobbying, a clear industrial strategy, and tackling the industry’s skills shortage.
The association will continue to push for policies that support innovation, incentivise the uptake of greener machines, and address the infrastructure challenges that come with electrification
and alternative fuels. At the same time, education and skills development remain central to this mission.
Planning is also well underway for the UK to host the CECE Congress in 2026 – a significant moment for the sector and an opportunity to bring global leaders together to explore the future of construction equipment in Europe and beyond.
Viki Bell commented: “I am delighted to be taking on the role of CEO. The past year has been exciting – not only in terms of what we’ve achieved behind-the-scenes but in the energy and momentum we’ve built. I’ve also been hugely encouraged by the support of our members, industry partners,
and other associations – as well as the backing of the trade press, which continues to shine a light on the important work being done across the sector
The CEA remains focused on progress and delivering real value to our members and the wider industry. With a strong team, new partnerships, and a clear plan for 2025 and beyond, I’m looking forward to the challenge.”
Sleator Plant, the heavy machinery specialist which provides Rokbak articulated haulers in Northern Ireland, has expanded into the Republic of Ireland.
With a commitment to deliver top-tier construction and earthmoving equipment, the expansion is set to enhance Sleator Plant’s presence, solidify its position as one of the leading premier plant dealerships across Ireland, and provide customers in the region with greater access to Rokbak trucks.
Key to extending its footprint into the Republic of Ireland is the establishment of a specially designed €1.2 million depot in north Dublin, built to enhance accessibility and support for customers throughout Ireland. Located near Dublin International Airport in the Dublin Inland Port, the facility will mirror Sleator Plant’s current Belfast operations, ensuring that clients across Ireland receive consistent, high-quality service and support.
“Ireland has emerged as one of the leading players in the European Union and the market is strengthening, particularly in the quarrying, civil engineering and housing sectors,” explained Sleator Plant Managing Director, Jonathan Campbell.
“Seeing huge opportunity in Ireland, we targeted a prime location in the greater Dublin area and created a team that merged our Northern Ireland operation to work as an all-Ireland outfit.”
Scottish articulated hauler manufacturer Rokbak has long had a trusted partner in
Sleator Plant, having recently celebrated 10 years of collaboration. The partnership has been instrumental in introducing Rokbak trucks to prominent projects in Northern Ireland. Sleator Plant has provided customers in construction, quarrying and mining applications with Rokbak articulated haulers and offered outstanding after-sales support.
A notable example is the integration of a Rokbak RA30 truck into Loughran Rock Industries’ operations, a move that has significantly enhanced productivity and efficiency at its Co Armagh quarry. The partnership exemplifies the synergy between Scottish engineering and Irish industry, setting a precedent for future collaborations across Ireland.
“Our expansion into the Republic of Ireland is a testament to our commitment to meet the evolving needs of our customers,” added Jonathan.
“By offering Rokbak trucks across the entire island, we aim to support the growth of Ireland’s industries.”
Central to Sleator Plant’s ethos is a dedication to customer satisfaction. A customercentric approach has been fundamental to its operations in Northern Ireland and will be seamlessly integrated into its services in the Republic. With access to the supply of Rokbak RA30 and RA40 articulated haulers and a close connection to Rokbak’s Motherwell factory, Sleator Plant is wellequipped to meet the diverse needs of Ireland’s various industrial sectors.
The expansion into the Republic of Ireland marks a significant milestone in Sleator Plant’s growth trajectory. By unifying its operations across the island, it is poised to offer unparalleled products, service and support to both existing and new customers.
“The biggest challenge for any company when they are experiencing a period of growth is to ensure that it maintains the values that has brought it the success to date,” said Jonathan.
“We’re here for the long-term. Our vision is to become the leading plant dealership in Ireland. We are committed to delivering top-quality products such as Rokbak trucks, alongside exceptional customer service, backed by our core values of respect, honesty and ownership.”
DEVELON Europe and the waste disposal corporation, LOGEX System GmbH, have agreed to co-operate to support medium-sized waste disposal companies in Germany and Austria. From their very first conversation, LOGEX System GmbH was enthusiastic about DEVELON’s solutions. The wheel loaders with their transparent bucket system immediately improve occupational safety when in use at LOGEX’s partner companies and meet the needs of the recycling industry. For LOGEX, DEVELON wheel loaders offer a really convincing solution.
DEVELON, formerly Doosan Construction Equipment, is pleased to have gained a strong partner in LOGEX to together support German mediumsized companies with suitable
(L-R): Marc Glesius, District Manager GSA,
innovative solutions. With DEVELON’S strong GSA dealer network in Germany, Switzerland and Austria (GSA) and its many rental and service locations, the
company is in the immediate vicinity of many LOGEX partners – the medium-sized set-up is an ideal fit for DEVELON dealers, with its regional proximity.
Based in Ingolstadt in Bavaria in Germany, LOGEX offers services and advice in all areas of the waste management industry for branches and subsidiaries of centrally-organised companies. The DEVELON machinery range offers the highest performance and enormous efficiency in recycling and waste disposal. In addition to crawler and wheeled excavators and wheel loaders, the product range also includes material-handling machines. The company continually presents innovations with real added value. The range is continually developing with further innovations, including the new Version 2.0 of the Transparent Bucket, intelligent autonomously operating construction machines or alternative drives in construction machines.
DEVELON construction machines are designed for tough and intensive use and are extremely durable. The close support for LOGEX partner companies from the DEVELON dealer network in conjunction with the DEVELON Fleet Management wireless telematics system ensures operational reliability in handling.
Komatsu has released news of their allnew WA700-8 wheel loader, a machine they describe as a “perfect match with their 60-tonne rigid dump truck”.
Engineered to deliver unparalleled levels of safety, increased productivity, exceptional durability, and impeccable environmental credentials, Komatsu claims that “with its performance, large cabin, and wealth of safety features, the ‘re-invented giant’ WA700-8 is now fully ready to claim its place in quarries across the UK, Ireland, Europe and beyond after more than a decade in development”.
The all-new unit complements Komatsu’s existing range of large wheel loaders, “incorporating their key attributes to boost customer value through performance, safety, operator comfort, efficiency, and digital technology,” they say.
Equipped with a robust 578 kW Komatsu engine, the WA700-8 delivers the power needed to deliver optimal efficiency in demanding quarry and mining applications.
A combination of increased engine power and torque mated to a new efficient cooling system and reduced hydraulic losses results in fast cycle times and exceptional fuel efficiency. Designed with environmental sustainability in mind, the WA700-8 complies with EU Stage V emissions regulations, thereby guaranteeing its eligibility in tender situations.
To enhance productivity and operator comfort during V-shape loading, the WA700-8 features a convenient throttle
lock/rpm set function. Furthermore, it can be filled with B20 biodiesels and is 100 per cent compatible with paraffinic fuels such as Hydrotreated Vegetable Oil (HVO) to significantly reduce CO2 emissions.
Commenting, Denis McGrath, Sales Director with Komatsu’s Irish distributor, McHale Plant Sales, said: “All that Komatsu knows about the development of giant wheel loader development has been incorporated in the new WA700-8.
“Though the market in Ireland for such a heavy-duty machine is somewhat ‘select’ compared to mainstream loaders, there can be no doubt that its arrival will be seen
by quarry owners, aggregates producers, and the like as a true game-changer.”
Before commencing development, Komatsu engineers actively collected input from customers who identified safety, cost per tonne produced, CO2 emission, maximising uptime, and operator well-being as key concerns. Integral to the development process, their input has resulted in a powerful machine equipped with advanced features and technologies, including unrivalled power and stability, extreme durability, and substantial load capacity and bucket volume (9.2 cubic metres heaped / 8.0 cubic metres struck).
The NEW COMPACT TAKEUCHI TB370W, a versatile multi-tool carrier with 2-piece boom as standard.
Delivering fast powerful productivity on busy construction sites.
Amidst the ever-emerging landscape, Takeuchi has cemented its status as a world-leader in the compact construction industry.
Fueled by this long-time awareness, Ryan Fay Contracts has been steadfast in the incorporation of the units to its fleet, and recently opted to upgrade its TB290-2 Compact Excavator with the same model. Reliable, robust, and a reaper of both efficiency and power, the Plant & Civil Engineer team were
thrilled to be invited along to witness the formidable excavator’s impact first-hand.
HIGH STANDARDS
At the company’s headquarters in the Dungannon area, father and son team, Ryan and Charlie Fay, expressed how their excavator requirements align with the diverse scope of the projects which they regularly undertake.
“The company originally started with my own father, and I then took over. At
Ryan Fay Contracts we focus on general groundwork, shuttering, all types of drainage, chicken house sites, a few industrial jobs, the building of dwelling houses, a lot of farm work, and many other jobs. There are eight-to-nine of us in the team, along with subs,” said Ryan. Within its impressive fleet, Ryan Fay Contracts runs two Takeuchi excavators at a time, refreshing each every three-to-four years. Currently, the company features a 3-tonne TB230, and in the case of their
latest purchase, were motivated to upgrade their 9-tonne TB290-2 several months ago. Delving into the drivers behind this decision, Charlie explained: “As a family business, my dad and I are both involved in the decisions of buying the diggers – and in this size, I wouldn’t buy anything else. There is no comparison. It has power, speed, efficiency, and is smooth-running, efficient and easy to fuel. As well as being comfortable, it looks well, with a great finish too. We have been able to use it successfully for a mixture of jobs, including rock-hammering, drainage, general work, large excavations, and more.”
Although impressed by the operational success of the compact excavator, its seamless performance comes as no surprise to the Ryan Fay Contracts team, given their prior awareness of the brand behind its brilliance.
Founded in Japan, Takeuchi manufactures highly precision engineered component parts utilisng the latest design engineering technology and expert tooling. Despite being a modern innovator in today’s construction industry, Takeuchi’s standing in product development is steeped in history – tracing back to its cultivation of the world’s first 360° compact excavator in 1971 (TB1000).
Ryan Fay Contract’s affiliation with the brand is entrenched in its own longevity, too.
Ryan said: “We started buying Takeuchi machines in 2000. I was friendly with an individual who sold for Alan Milne Tractors, and he informed me that the company was working with Takeuchi, and asked whether I wanted to try one. I did, and soon agreed the deal and made the purchase of the machine. We have been buying Takeuchis ever since, up to 9-tonne. We bought a 3-tonne Takeuchi in 2020, and the machine prior to this upgrade was purchased four years ago.”
To secure the machinery, Ryan Fay Contracts turned to a renowned dealer – Alan Milne Tractors. Located in Newry, the dealer has been embedded in the machinery business for 45 years, and has adopted the role of a Northern Ireland representative for the Takeuchi range for a quarter of a century. Since then, hundreds of customers have granted the dealer their trade and custom. Testament to Alan Milne Tractors’ reputation among the industry, for Ryan, the decision to purchase the latest excavator through the dealer was an obvious one.
He explained: “We have been dealing with Alan Milne Tractors as it’s not only local, but the team are great to work with. For any services required, they are very quick to help.”
When witnessing the magnitude of the machine first-hand, it’s glaringly clear why the Takeuchi TB290-2 Compact is deemed a sector spearheader. The 9-tonne excavator
offers a versatile excavating performance with superb breakout force of 59.1 kN. Its rounded, contemporary design has been crafted with optimisation at its core, and the compact tail delivers excellent stability,
with only 1650mm tail swing radius with a 540mm overhang at 90° to track.
The speed and scope of projects undertaken by Ryan Fay Contracts, at times in challenging conditions, mean that a unit that also priorities safe site operation is a necessity – and the Takeuchi excavator exceeds this brief. The machine is equipped with a twin boom and arm holding check valves, along with a crane switch and audible lift overload alarm. For bolstered reassurance, LED workzone lighting, travel alarm and auto-activating wide-angle rear-view camera are featured as standard.
Ryan explained: “The beauty of the machine is that it has a full spec with regards to auxiliaries and the different implements which we are putting on – again adding to the reliability.”
From encouraging productivity and focus, to mobilising morale, it’s critical that the comfort of machinery isn’t hindered by optimised performance – but they are wellmatched in the case of this excavator.
“The excavator is extremely reliable, with great visibility. It has the power to ensure that we can get a lot done, while also being a comfortable machine to sit in and use for
the operator. I’m quite tall and there is plenty of legroom space. We also work in a lot of hot weather and dusty environments, so it’s important that the cab is fully-air-conditioned and climate-controlled,” said Ryan.
The latitude of the machine’s impact doesn’t stop there – the new Kawasaki hydraulic system delivers 140 l/min enhanced power and faster cycle times, while the machine’s upgraded pump output provides a smoother and more effortless performance, allowing for multiple operations to occur simultaneously.
Before Ryan Fay Contracts recommenced its brimming work schedule, one more allimportant question had to be posed: do the father and son team have any advice for others who may be considering the addition of the model to their own fleet?
“I would highly recommend the Takeuchi models. The brand gets better all the time and we will no doubt be considering them again in the future. For us, I have to say, hand on heart, Takeuchi has always been excellent,” Ryan said.
Charlie echoed this verdict: “I would definitely go for Takeuchi. Everything is down to personal preference but I would give them a try at least. They’re a leader in the market. You get what you pay for.”
As Plant & Civil Engineer’s visit to Ryan Fay Contracts came to a close, along with
the knowledge gleaned from the visit, two unshakeable certainties powered the return journey back. One: the addition of the TB290-2 to Ryan Fay Contracts’ fleet is further elevating its already soaring operations. Two: Takeuchi’s success as an industry giant shows no signs of abating.
Founded in Ballymena in 1962, and located in Pennybridge Industrial Estate, W.R. Kennedy & Company has grown and expanded to become a frontrunner in the supply of wholesale fuels and lubricants, sharing their expertise and premium products with a wide range of customers, many in the construction, quarrying and agricultural sectors, throughout Northern Ireland. The company distributes premium Texaco commercial fuels along with automotive, agricultural and industrial lubricants from its depot in Ballymena. A significant portion of the domestic heating oil business operates out of its Ballymena depot, while the majority of the commercial and wholesale operations span their Belfast locations –reinforcing the reliability of W.R. Kennedy’s supply, even in the emergence of adverse events or turbulent climate conditions.
Throughout its years in business, W.R. Kennedy has been a cornerstone for the customers and communities it serves. But Niall Kennedy, who joined the business in 2017, attributes its path to success to his family’s own touchstone – his grandfather, the company’s namesake, who was known to his loved ones as Bertie.
It was Bertie who first forged the company all those years ago, and who subsequently instilled in Niall the importance of running a company founded on hard work and trust. Bertie sadly passed away in February this
year, and is much-missed by all who knew him. However, his presence very much permeates through every corner of the company today, and his legacy is reflected in its integrity-rooted commitment to the local areas, sectors, and individuals it serves.
Depicting the extent of the company’s progression with Bertie at the helm, Niall explained: “My grandfather established W.R. Kennedy initially as an owner-driver, with his first truck being a Thames Trader. By 1975
the company had grown to include three Ford D-Series trucks, and relocated to its present location in Pennybridge four years later. In 1984, the company acquired its inaugural Volvo truck from Dennisons and has maintained a Volvo fleet ever since.”
The 1990s represented a period of significant evolution for the business, too. Niall’s father, Terence, joined in 1990 – and within 12 months W.R. Kennedy had extended to six trucks, with the addition of its first
artic, a Volvo F12. The expansion of the Pennybridge depot with the purchase of adjoining land and warehouse, and the introduction of diesel refuelling by card to Ballymena, followed just a few years later.
A standout component of the W.R. Kennedy business, which has been managed by Lyle Foster, and recently also steered by Niall Kennedy’s brother-in-law Mark Bill, is the provision of lubricants such as engine oils, coolants, hydraulic oils and greases. Recognising the intrinsic role of lubricants to the industry, and their necessity in keeping equipment running smoothly and efficiently, W.R. Kennedy, as an Authorised Texaco Lubricants Distributor in Northern Ireland, passionately responded to the need with a supply of a full range of premium lubricants. They have built up a wealth of technical knowledge and provide technical support, product recommendations and even oil sampling and laboratory testing services. Their provisions are designed to deliver reliable performance and protection, while optimising fuel economy, for a broad scope of construction and agricultural machinery, in addition to commercial vehicles. Notably, constructors know that they can rely on W.R. Kennedy’s offering of Texaco Delo engine oil, coolants and workshop products for delivering equipment protection, performance and reliability all whilst conforming to OEM specifications.
After more than six decades in business, W.R. Kennedy has built up a loyal customer base – indeed, many have been with the company since those early days, and understandably so. The familial origins of the company have been helpful in shaping their approach to customer service, and resulted in considerable long-standing collaborations with leading names in the construction industry, as well as airports, ports, local authorities and various other businesses throughout the country. Niall’s recognition of the benefits reaped from continued and personalised communication, in addition to the adoption of networking opportunities, has also been
prompting an influx of new connections to W.R. Kennedy’s customer base.
He explained: “There’s a lot to be said about customers trusting who they are speaking with, rather than receiving an automated response to their queries. They have the reassurance that they will get an immediate answer from us and know who they are working with.”
Having been an authorised distributor of Texaco fuels and lubricants since its inception in 1962, W.R. Kennedy’s relationship with Texaco, too, goes from strength-tostrength – yielding numerous benefits for the company and its customers alike. By leveraging the brand’s quality product ranges, fused with its global presence and recognition, W.R. Kennedy has been able to reach a broader customer base.
Niall affirmed: “People know what they’re getting with the quality brand. The product sells itself in a sense.”
Looking ahead, Niall stresses that W.R. Kennedy is passionate about staying true to its roots, while simultaneously amplifying
its impact further, including actively pursuing opportunities to broaden its presence in the quarrying and construction sectors, which have been essential to the company’s growth over the past 60 years.
Niall explained: “In recent times, the largest portion of our business has been wholesale. However, in the last few years, we have been trying to do more direct business with the construction and quarrying sectors. Rain or shine, we know that they will need continued supplies and we can assist with this.”
Excitingly, 2024 also marked the refurbishment of W.R. Kennedy’s depot and forecourt – contributing to the consolidation of its company-wide offerings. This also includes “continuing to get recommendations from those we already work with, as well as spreading awareness of both sides of the business to customers who have been unaware before, and only had a fuel focus or a lubricants focus.”
Niall asserted: “It’s not about reinventing the wheel, but continuing to provide quality, service and good pricing to our customers – both old and new.”
The construction industry, traditionally dominated by men, is now evolving towards greater inclusivity and diversity. Companies are actively creating inclusive workplaces that support women, recognising that diversity is key to the sector’s success – especially amid a skills shortage.
Jackie Janssen, Head of Communications at the Considerate Constructors Scheme (CCS), the champions for change in the construction industry, highlights five best practice strategies being adopted by the construction industry that are helping to make the sector more accessible to women.
Creating dedicated support networks for women within construction firms provides a platform for discussion, professional development, and advocacy. A number of CCS partners have introduced Women’s Networks, allowing female employees to connect, share experiences, and discuss challenges they face in the industry. These networks can help to foster a sense of community, build confidence, and promote a culture of mutual support. Mentorship programmes also play a vital role in helping women advance their careers. By pairing less experienced employees with senior professionals, these programmes offer valuable career advice, encouragement, and practical guidance on navigating an industry that has historically been male-dominated. Structured mentorship ensures that women not only enter the sector, but also thrive in leadership positions.
One of the biggest barriers preventing women from joining or remaining in the construction industry is the lack of flexible working arrangements. However, this is beginning to change. Many construction firms are already adapting by introducing part-time roles, job-sharing, and hybrid working models. These initiatives enable women – especially those with caregiving responsibilities – to balance their careers with family commitments. By offering
Jackie Janssen.
flexible working from the outset, construction companies can demonstrate their commitment to inclusivity, while ensuring they do not miss out on talented professionals.
Creating a more welcoming environment for women should go beyond policies and include practical changes on construction sites. Some positive examples include investment in gender-inclusive facilities, including self-contained, lockable toilets and private nursing rooms for new mothers. Another essential consideration is Personal Protective Equipment (PPE). Traditionally, PPE has been designed for male body shapes, often making it uncomfortable and unsafe for women. Companies that provide PPE in women’s sizes send a clear message that they value and respect their female workforce. Simple yet impactful steps like these help break down barriers and create a more comfortable and professional working environment for all employees.
Cultural change starts with education. Unconscious bias training is being adopted by forward-thinking companies to help employees recognise and challenge stereotypes.
Gender equality workshops are another powerful tool. These sessions typically cover workplace inclusion, leadership development, and breaking down barriers that prevent women from progressing in their careers. Investing in regular training not only creates more inclusive workplaces, but can also improve team dynamics and overall productivity.
By tackling unconscious bias, construction firms can shift mindsets and ensure that hiring, promotion, and leadership opportunities are truly based on merit rather than outdated perceptions of gender roles.
Visibility matters. Actively highlighting female leaders through case studies, social media, and leadership programmes are popular ways to challenge industry stereotypes. Meanwhile outreach efforts, including school visits, career fairs, and mentorship programmes can help to introduce young women to construction careers.
At the CCS, our annual gala event showcases some inspiring female leaders in the Hall of Fame and Rising Star categories
We have also launched the Guardians of Construction comic book series. This initiative is designed to engage younger audiences and showcase the exciting possibilities within the industry. By illustrating a wide range of careers – from hands-on trades to health and safety management – we want to inspire the next generation and ensure that more women view construction as a rewarding and achievable career.
Find out more about registering with the CCS, and becoming a leader in responsible construction by visiting www.considerateconstructors.com.
To say we have been on an economic rollercoaster this past couple of months would be an understatement. The word “tariff” has been used more times than any word in the English dictionary this past while. I am many of you, like me have been keeping an eye on your pensions and wondering what on earth is going on and what will happen next.
The UK Government has said they will take a "calm and considered" approach in dealing with the fall out from the US trade tariffs. The Secretary of State confirmed that the government has carried out an impact assessment on how businesses in Northern Ireland might be affected.
MPANI members, like all businesses will be watching the impact on financial and energy markets and will be urging the UK, RoI and EU that our unique trading circumstances are taken into consideration in any negotiations with the US and next steps that they are taking. It is also vitally important that both the British government and the EU are working closely together because divergence is not good for us in NI.
The Executive has agreed the 2025/26 Budget which will see increased investment in cutting waiting lists, in Special Educational Needs, Skills for growing the economy, Lough Neagh and Safer Communities.
Announcing the 2025/26 Budget Minister O’Dowd said: “The Budget reflects our Programme for Government commitment to ‘Doing What Matters Most’ and shows this Executive’s determination to work together to deliver. MPANI will take time to study the budget outcomes and assess what it means for our Industry and we will be responding to the Budget according along with other business organisations.
In another development The UK government has been urged to address ‘crippling’ underfunding which has left public services
here in a ‘state of crisis’. Options such as water charges and a review of the rates system have also been suggested. A report published by the cross-party Northern Ireland Affairs Committee in Westminster has recommended a review of the current levels and mechanisms used to fund Northern Irelands public services. Options put forward to the committee include water charges and a review of the rates system, with one witness stating that the latter could raise an additional £615 million. The committee agreed that while it may be “politically contentious” and take a number of years for a domestic water charge system to be implemented, it concluded that “the discussion should not be avoided”. The report warned of the impact the “continuing state of crisis” is having on people’s quality of life. It found that education, health and policing were facing particular pressures and that little had changed since the committee reviewed the issue last year. They said that the “key objective must be to ensure fully funded services” based on need through allocations from the UK government which are “stable, sustainable and predictable”.
The Association has written to the five main Assembly parties requesting the opportunity to meet with them individually to highlight the importance of our sector to the local economy and appeal for their help as “enablers” on improving the planning process, revenue raising for investment in our crumbling water, sewerage and road infrastructure and modernising our energy grid to help our sectors journey to net zero, energy security and cheaper energy prices. We are awaiting their response.
MPANI has also written to the Minister of Health, Mike Nesbitt, regarding the Public Health Agencies role in the planning process. It has recently been brought to our attention by a number of our member and associate
member companies that Council Planning Departments have extended their list of consultees and are now consulting with the Public Health Agency (PHA) with regards to quarry extraction applications, greenfield and extensions, sand and gravel and hard rock. This is a relatively recent development with the first consultation, we are aware of, being made by Mid Ulster Council in May 2022. However, more recently Armagh Banbridge and Craigavon, Ards and North Down and Antrim and Newtownabbey have followed suit in that order. To date the response times, on each occasion, have exceeded 6 months which you will appreciate only exacerbates, what is already the slowest land use planning system within the UK Regions and runs contrary to Central Government's and indeed the NI Assembly’s strategy to speed up the planning process. Furthermore, it is apparent from consultation responses issued, that the PHA are unclear as to why they are receiving these requests, what their role is, given that they are not consultees within the planning process and that their input in a regulatory role for extractive operations is delivered via parallel legislation. The PHA is not a statutory body within the planning process and their input to regulation lies elsewhere and the response to two separate applications follows the same format, that we would be keen to agree a methodology as to how future requests to the PHA can be dealt with to ensure that response times are expedited, in line with the legislative consultation period.
It is unclear to MPANI whether this new approach from Council’s is part of a wider programme to seek a consultation on all major applications that contain multiple vehicle movements or have processes that are subject to PPC licensing regime, such as logistic hubs / food distribution centres and anaerobic digesters, or whether the extractive industry is being singled out for some reason?
We would also take the opportunity to discuss the well establish regulatory framework covering our industry, the associated industry specific guidance published by the Institute of Air Quality Management and the continuation and effective transition to low emission vehicles and low carbon fuels, which should provide further comfort to the PHA that their stated position is the appropriate response.
MPANI met with the head of the Department for Infrastructure Planning Reform Team, Rosemary Daly, on 10th March. The Regional Director met with Rosemary and her team previously at a recent CBI Infrastructure Committee meeting at Titanic Quarter where we heard about the work ongoing on reforming the planning process in NI.
At that meeting the Regional Director highlighted an important MPANI proposal to form a “shared service” for minerals planning across the 11 local councils. We stated that minerals planning is a very specific skills set and the original decision to move minerals planning from the old minerals unit within DoE to planning offices within 11 councils was, in our view, the wrong one.
MPANI has also been active in working with a number of local councils and strategic planning within DfI to improve the skills set and mineral planning knowledge within the Councils by promoting the now widely recognised “Mineral Planning for Mineral Planners” training course developed by the Institute of Quarrying UK and endorsed by the RTPI.
We also highlighted and discussed the changes to planning that have been
proposed via the NI Audit Office 2022 report, the 2022 Assembly Public Accounts Committee report, the 2023 Turley NI Chamber report and the 2019 Irvine Report on statutory consultees. Many of the recommendations are the same and we would support the vast majority, if not all.
The Association will also be hosting new Infrastructure Minister, Liz Kimmins, on the 25th June at Northstones Craigantlet Quarry where the Minister will have the opportunity to view the extensive quarry operations and the companies new asphalt plant.
MPANI have submitted our response to the Department for the Economy Call for Evidence on the socialisation of grid connection costs. The MPANI welcomes the opportunity to respond to this important Call for Evidence (CfE) on increased socialisation of connection costs in the electricity distribution network.
An effective, efficient and value for money connections framework in NI is crucial to delivering a just transition and improving Northern Irelands competitiveness. This is essential to achieve the 2030 decarbonisation, renewable electricity, heat and transport targets and ambitions, encourage economic growth in NI and will have a positive impact on fuel poverty.
MPANI believe we must have a just transition that takes into account the needs of consumer and business. We believe given the importance of this potential policy change for all consumers but also in helping to delivering Northern Irelands climate change targets and decarbonisation goals then there is not only a responsibility but an onus on both local and national Government to help finance development
and strengthening of the electricity grid. The socialisation of grid connection costs as outlined in the Departments choice of Option 4 is in our view the best option. Achieving the renewable energy capacity required to meet the Climate Change Act targets is essential so that we don't fall further behind both of our nearest neighbours while also creating a drain of various resources including skilled employment. Without changes to the current distribution connection charging regime many customers, including our members, will not be able to afford the connections costs to install Low Carbon Technologies due to the level of network reinforcement required. It is also worth highlighting that a change to distribution connection charging would increase the competitiveness of NI as a place to do business.
MPANI would call for a specific higher cost cap for NI given our more rurally based economy, the nature of rural industry where we can only locate where the minerals are and the fact that our processing / manufacture of concrete and asphalt takes place in rural quarries rather than standalone concrete and asphalt plants that are common in GB. MPANI would call for flexibility in assessing rural quarrying and manufacturing businesses.
If you’re interested in becoming a full or affiliate member of MPANI and get access to up to date Industry news and guidance don’t hesitate to give me a call on 07876136929. It would be great to have you on board. Take care and stay safe!!
Ireland’s largest independent manufacturer of concrete products, Kilsaran, have entrusted Wilsons Auctions to sell over 150 assets of quarry equipment and construction machinery this May.
The upcoming auction is set to take place on Friday 16th May at Wilsons Auctions Dublin, with the first lot getting underway at 11am. The catalogue offers bidders with unique opportunities to acquire high-quality items featuring a comprehensive selection of wheel loaders, crushers, rock breakers, screeners, excavators, dump trucks and trailers, conveyors and much more.
Located across various locations in Ireland, the heavy equipment assets promote some of the bestknown machinery manufacturers in the world. Top lots noted in the catalogue include a 2022 Roco Icon 1100 Impactor, a 2021
Caterpillar 972M Loading Shovel, a 2021 Volvo L260H Loading Shovel, a 1997 Volvo L120C Loading Shovel, a 1999 Volvo A30C Dumper, a 2021 Komatsu
WA470 Loading Shovel, a 2005 Dennison Trailers Concrete Mixing Trailer with Euromixer and a 1999 Finlay 312 Mobile Screener on Single-Axle.
The Kilsaran Group currently employs circa 1,000 people and have been in business since 1964. The company’s decision to auction their business assets underscores their dedication to supporting the circular economy. By reintroducing these assets into the marketplace, Kilsaran promotes a sustainable approach to resource management, reducing waste and contributing to environmental stewardship. This initiative reflects their forward-thinking ethos and aligns with the growing demand for innovative, sustainable practices within the industry.
Wilsons Auctions, Ireland and the UK’s and largest independent auction company, is proud to be at the forefront of facilitating this vision. With decades of expertise in managing large-scale auctions and a reputation for providing first-rate remarketing services, the auction company is fully
prepared to ensure this event meets the highest standards of professionalism and success.
This major event will be held at Wilsons Auctions Dublin with physical bidding and live online bidding available to all registered bidders for the auction.
Ricky Wilson, Director and Auctioneer at Wilsons Auctions, said: “It was 14 years ago when Wilsons Auctions first hosted a major auction on behalf of Kilsaran, and I am thrilled that the two Irish family businesses are back in collaboration again.”
“Bidding is open and welcome to the public. I would encourage everyone to book a viewing slot and register as early as possible ahead of the auction. This auction will be a great opportunity for
the construction community, quarry businesses and as well as private buyers.” he added.
Derry McKeown, Co-CEO of Kilsaran, went on to comment:
“Kilsaran are delighted to be working with Wilsons Auctions on this major auction event. This acts as an ideal opportunity for companies and individuals in the industry, and others, to purchase additional quality stock or upgrade their existing portfolio. The inventory of machinery and equipment has been well maintained on behalf of Kilsaran.”
Viewings will be strictly by appointment only on Saturday 10th May and during the week beginning Monday 12th May, allowing prospective buyers the chance to thoroughly inspect the items before the auction.
To book your viewing appointment please contact Wilsons Auctions Dublin on +353 (0)1464 2800 or email shantalawlor@wilsonsauctions. com to arrange your time slot. Videos of all working machinery, plant and equipment are available to view via the online catalogue. Full details of the assets, their condition, and the viewing arrangements are available at www. wilsonsauctions.com.
Interested bidders can register online via Wilsons Auctions’ website or by emailing leegeary@ wilsonsauctions.com.
To view the auction catalogue, visit www.wilsonsauctions.com
Wilsons Auctions is a familyowned business that has grown to become the largest independent auction company in Ireland and the UK. Established in 1936, it specialises in plant and machinery and agricultural equipment and has over 89 years of auctioneering experience in this industry across Ireland and further afield. With over 3,200 auctions held annually across the group, Wilsons Auctions holds over 450 dedicated commercial auctions annually across the UK and Ireland.
For further information, go to www.wilsonsauctions. com, follow on Facebook @ wilsonsauctionsltd or go to @wilsonsauctions on Instagram, Twitter and TikTok.
2014 Caterpillar 336ELH Excavator
2022 Roco Icon 1100 Impactor
1997 Volvo L120C Loading Shovel 19169 Hours
2013 Volvo Loading Shovel L120G 14256 Hours132D12956
2004 Fintec 540 Screener 8721 Hours
Nordbery C3054 Jaw Crusher 170 x 145 x 130 cm, Refurbished Electric Motor
2021 Caterpillar 980 Loading Shovel 8224 Hours PSP Primary Jaw Crusher
Shanta Lawlor
+353 (0) 8683 61148 shantalawlor@wilsonsauctions.com
Lee Geary
+353 (0) 8681 66809 leegeary@wilsonsauctions.com
Bauma provided the platform for a special première: as Liebherr – one of the largest construction equipment manufacturers in the world, and the provider of high-quality, useroriented products and services in a wide range of other areas – presented two new wheeled excavators to the public for the first time.
The A 909 Compact and the A 911 Compact are two new models in the nine and 11-tonne classes, respectively, that expand the Liebherr wheeled excavator portfolio. The A 909 Compact and the A 911 Compact are powerful machines that set new standards in their respective classes and offer customers an optimal solution for demanding applications.
Excitingly, with these two machines, Liebherr is increasing its extensive portfolio of wheeled excavators: for the first time, there will be two wheeled excavators operating in the nine and 11 tonne class. The new wheeled excavators stand out
LIEBHERR COMPACT POWER
LIEBHERR INNOVATION
with their combination of a well-thoughtout machine concept and user-friendly operation. Notably, due to their robust construction and high-performance, they are particularly applicable for efficient work, while their versatility means that they can be optimally adapted to different operating conditions and requirements. Further standout features of the machines include their compact design and small tail swing radius (1.50 m and 1.60 m, respectively) and front swing radius (2.00 m and 2.10 m, respectively). The dimensions of the turning circle of just 3.86 m also underscore the compactness of the two machines, while this applies to the minimum turning circle, too. In combination with the total weight of 9.7 tonnes for the A 909 and 10.8 tonnes for the A 911, both wheeled excavators can be used safely and flexibly – even in confined spaces.
HIGH FLEXIBILITY IN USE THANKS TO MAXIMUM PERFORMANCE
The significant stability and enormous digging forces of the two wheeled excavators ensure high handling performance and productivity – even when working in hard soils. The powerful engine has an output of either 55 kW or 80 kW and, depending on the version, is equipped with an SCR system and intercooler. The perfectly co-ordinated hydraulic system enables flexible, parallel work movements with an optimal supply to all users.
At the same time, it ensures maximum performance of both machines and has a positive effect on fuel consumption.
As a result of the perfectly co-ordinated overall design of the machine, both the A 909 Compact and the A 911 Compact are perfectly placed for the sector with their sufficient refuelling intervals – therefore promoting efficient work with low operating costs.
OPTIMAL DRIVING PERFORMANCE THROUGH STABILITY AND EXCELLENT OFFROAD CAPABILITIES
The robust and reliable undercarriage design with integrated travel drive offers the best possible acceleration due to
the high drawbar pull. The resulting high travel speed reduces the time required for transport, which in turn saves costs. The Liebherr standard tyres ensure comfortable driving performance. These ensure maximum stability and are available in several versions, such as twin or single tyres (optional). Speeder versions enable speeds of up to 37 km/h.
In addition, new designs in the uppercarriage area provide maximum offroad capability: the wheels can move further in the direction of the uppercarriage during an oscillating motion of the axle. In combination with the ground clearance and the pendulum angle of the undercarriage, this provides the A 909 Compact and A 911 Compact with maximum traction.
With their intelligent and service-oriented machine design, the new small excavators feature a well-thought-out maintenance concept. The durability of the high-quality components ensures low service costs and thus minimal downtime for maintenance and servicing. Considering the entire life cycle of the new wheeled excavators, the total costs from purchase to sale are ultimately low – without compromising on quality. A large number of components are also maintenance-free, meaning that no daily maintenance is required here. However, should maintenance be necessary, the most important parts can be reached from the ground, allowing for simple, fast and, above all, safe maintenance. This also applies to refuelling the A 909 Compact and A 911 Compact. The high availability of spare parts and the proven Liebherr service quality round off the excellent overall package when it comes to maintenance and service.
Crucially, the machine operator is able to garner numerous benefits from usage of the machines. In particular, the comfortably designed cab offers sufficient space in the head and foot area, as well as driver-specific setting of the
control elements. The new INTUSI (Intuitive User Interface) operating system, which is installed as standard, allows individual assignment of the functions and thus maximum flexibility in daily work. The intelligent arrangement of the cab ensures that all relevant control panels and joysticks are easily accessible and operable, while the generously-designed glass surfaces provide the best possible overview in all
directions and thus contribute significantly to the safety of the working environment. Bolstering communication, the additional sliding window on the side enables the operator to interact optimally with people outside. In terms of ergonomics, the A 909 Compact and A 911 Compact also offer the operator a comfortable working environment due to consoles that move with the machine, as well as low noise emissions and vibrations.
BY MARTIN ELLIMAN, PLANT & CIVIL ENGINEER’S GENERAL MANAGER
In my role at Plant & Civil Engineer, I am fortunate to be at the forefront of the industry’s machinery advancements and spearheading showcases –engaging with renowned brands and companies everyday. But recently, I was able to gain a deeper understanding and broader context of one of these esteemed brands, being invited to partake in a Merlo Ireland press trip to Cuneo, Italy, for a Merlo factory visit – a leader in the design and construction of innovative operating machines.
The three-day duration of our press visit featured a packed itinerary which paved the path of our understanding from Merlo’s early beginnings, to its trailblazing recognition today. In addition to our tour of the Merlo Group factory in Cuneo, we attended a presentation centring on the company’s progress, embarked on a Merlo ride and drive experience, and had the opportunity to explore the beautiful area the factory is based in, all the while staying at the Hotel Palazzo Lovera.
Founded in 1964, the Merlo Group is familyrun, with its management today being in the hands of the third generation of the family. Paolo Merlo is the President and CEO, responsible for sales, marketing, design and after-sales; Silvia is CEO and responsible for the administrative and financial part; and Andrea is CEO and responsible for production and industrial innovation. Being not just a brand but a family name that has guided its leadership for 60 years enables the Merlo Group to establish a long-term vision to plan the company policies with an unfaltering commitment to the design and production of high-tech machinery. The expansive product range in question includes telehandlers, attachments, tracked carriers, self-loading concrete mixers, dumpers, toolcarrier tractors and waste compactors.
As the central purpose of our visit, the Merlo factory visit was a particular catalyst of our press group’s excitement – notably because the Merlo Group manufactures
92 per cent of its components in-house. This choice is strategic as it allows the main components of Merlo vehicles to be developed, manufactured and developed in-house. The chassis, telescopic boom, cabin and bridges are entirely made here and offer unique advantages in terms of visibility, safety and performance.
This philosophy has over the years prompted the creation of tailor-made key components, such as hydraulic cylinders, plastics, hydraulic distributors, in addition to the various software used, from management software for vehicle operation to safety monitoring software.
The sheer scale of the production plant is an astoundingly impressive sight – it covers an area of about 330.000 sq.m, and resulted in me attaining almost 20,000 steps during the tour alone! Throughout this process, we also learned from the Merlo
experts that more than 1,700 people are employed, and in 2024 8,000 machines were produced. Additionally, 81 per cent of the machines produced are exported.
Although this Italy base represents its headquarters, the brand also comprises eight branches across the world – located in Ireland, France, UK, Spain, Germany, Poland, Australia, and America. And in these settings, as well as the focus on product innovation, Merlo ensures that the wellbeing of the employees and attention to the environment form firm pillars of their business and industrial development.
A further benefit to our visit was gaining a glimpse into Merlo’s future endeavours, and learning how the business is poised for significant growth and innovation.
Representative of this, in March 2025 the works for the creation of the new assembling lines commenced, which will allow the company to expand the assembly lines, granting more space to their production and allowing them to give a new home to the machine-shipping department.
Many new products are going into
production this year, too, such as Roto 16-18, Roto 22-27, Treemme «MC» Boom, New TF III, and New Cingo.
After getting the chance to embark on the Merlo ride and drive experience, and engage in photo opportunities galore, we wrapped up our visit and returned back to Dublin the next day, equipped with newfound knowledge and appreciation of the complexities and expertise driving Merlo’s operations.
A special thanks to Helen, Shaun and Mattia, and the whole Merlo team, for their fantastic hospitality on a truly memorable visit.
Shining under the spotlight of the ever-demanding construction and events industries, the comprehensive nature of Norspace’s rental fleet means that it has become a premier provider of site accommodation and modular buildings throughout Ireland. The company specialises in providing antivandal cabins, modular buildings, jackleg
cabins, welfare cabins, and portable toilets for hire, whether it’s for long-term or shortterm purposes, or a more permanent solution. Alongside their expansive range of products, Norspace provides trusted service and reliable delivery in order to ensure timely set-up and support for their customers across the whole of Ireland.
From initial vision to continued fruition, the company has been embarking on an exciting brand ‘refresh’ journey – which was majorly marked with the recent relaunch and overhaul of its website. And with a stream of further brand promotion plans also in the pipeline, the temporary site accommodation specialist looks set to further eclipse its own success.
Founded 40 years ago, Norspace commenced as a small, locally-focused operation which responded to the escalating demand for flexible and efficient temporary site accommodation. The company’s success was soon set in motion as it became the go-to solution spanning multiple industries – from construction and events, to education and healthcare.
Rooted in its family-run, local origins, Norspace continues to thrive on the values of trust, dedication, approachability, and ultimately a commitment to excellence in all areas of the business.
With an ever-expansive client base and a portfolio of projects in collaboration with some of the most renowned companies across the construction and event sectors, Norspace’s position as a leader in the market across Ireland has been solidified. And it’s this steadiness which sparked inspiration for the company’s brand revitalisation.
Norspace Managing Director, Matthew Smyth, explained: “Norspace has been around for a long time. We know what we do, we love what we do, and we do it extremely well, and this brand refresh was the natural next step for us. Our product offering is more impressive than ever before, as are the quality of the products and the industries that we’re in. We wanted to visually reflect this and present ourselves as the modern, contemporary professional brand that people want to do business with.”
Before the direction of the company’s new design concept could even begin to be carved out, key conversations had to be conducted internally.
Marketing Manager, Aoiffe McConaghy, who joined the team six years ago, and has headed up Norspace’s brand journey, explained: “Over 12 months ago, we sat down to define the branding that would reflect our identity and tell our story.
We wanted our branding to showcase the full package of what we have to offer, while still honouring the heritage the company was built on. As a result, we’ve kept our familiar colour palette but refreshed it in a way that positions us as a trusted, professional partner for our customers –both today and in the years to come.”
In addition to design solutions, delivery, installation, and maintenance, Norspace customers also benefit from the support of experienced professionals with a customerfirst approach. It was integral that their brand elevation portrayed these unique attributes. Matthew commented: “In this industry, you’re only as good as your last job. At Norspace we pride ourselves on our products, which are strengthened by the services we
provide. Our points of differentiation are our reliability, expertise, and knowledge, which compliment our broad spectrum of products. The branding had to reflect this.”
Equipped with the refreshed branding and a clear vision, work on Norspace’s website became the primary area of attention.
As progress on the platform got underway, there was no doubt that the creation and use had Norspace's customer requirements at the forefront. Regardless of the customer’s industry role and specific needs, the website was crafted with them in mind.
Aoiffe explained: “Building our new website was an important step. Our website is a crucial part of business – it often offers a
first impression of the business, and can be our customers’ first point of contact.
It was therefore key that its standard was strengthened to reflect the quality services and products which we provide.
“The website had to be easy to use, while promoting our products and services, and ultimately being fit for today’s modern digital-savvy clientele.”
Translating these aspirations into the final product, Norspace’s website reflects the strong new look and is a user-friendly source for learning about the company, the products and their services. And, crucially, it is representative of the company’s commitment to, and investment in, their refreshed brand journey and start-to-finish customer experience.
As for the next step on Norspace’s revitalised brand journey? There isn’t just one.
Its multipronged approach means that signwriting of Norspace’s vehicles is well underway, as is production of the product stickers, so the new logo will have travelled across the country before long.
Alongside the branding refresh, Norspace continues to invest in its product range. Their products are purpose-built and intended for end use – designed to create comfortable, safe, and practical workspaces for customers. Strong partnerships with supply chain partners, built on years of trust and a shared commitment to quality, contribute to this success.
At the heart of Norspace’s brand refresh – and indeed every step of the business’ journey and offerings – is a team wholeheartedly dedicated to its customers, and striving to exceed their expectations with every interaction.
Just like everything else they do, the Norspace team is embracing this new brand look with open arms and enthusiasm – excited that every facet of the company’s offering propels their customer-first commitment forward.
“We needed to be all in to make the brand refresh happen. All the parts have to work together – the people, the systems, the products – with the overall aim of creating a better experience and better value for our customers. And from a company and team perspective, we are most definitely all in,” emphasised Matthew. For more information, visit www.norspacehire.com
BY STEPHEN BRADSHAW – CIHT NI CHAIR 2024-26
Belfast took a major leap forward in 2024 with the opening of two landmark transport facilities: Belfast Grand Central Station and the newly redeveloped York Street Station.
Belfast Grand Central Station, the largest integrated transport hub in Ireland, opened its doors in September 2024. With a £340 million investment, the station features eight railway platforms and 26 bus stands, designed to handle up to 20 million passenger journeys annually. More than just a transport hub, it offers cafes, shops, and cutting-edge passenger information systems, ensuring a seamless travel experience.
Meanwhile, York Street Station unveiled its transformation in April 2024. Serving as a key gateway to North Belfast, it now provides better links to Ulster University, Sailortown, and the Cathedral Quarter. The redevelopment includes modern facilities, enhanced platforms, and improved public spaces – strengthening connectivity for thousands of daily commuters.
These milestone projects signal a new era in Belfast’s transport infrastructure, easing congestion and providing world-class travel facilities for residents and visitors alike.
The Department for Infrastructure has been making significant progress on a new Regional Transport Strategy, with a public consultation expected in the
coming months. This strategy will guide Northern Ireland’s transport development, ensuring it aligns with local development plans and long-term sustainability goals.
A major highlight in 2024 was the launch of the Active Travel Delivery Plan, which outlines a 10-year strategy to create over 200km of high-quality cycling and walking routes across 42 urban and rural areas. The plan prioritises safe, accessible routes to schools, transport hubs, and town centres, promoting sustainable travel options. CIHT Chief Executive Sue Percy CBE attended the launch, emphasising the benefits of active travel for health, congestion reduction, and environmental sustainability.
Several large-scale infrastructure projects moved forward over the past 12 months, demonstrating a strong commitment to improving Northern Ireland’s road and transport network.
A1 Junctions Phase 2 Road Improvements – an investment anticipated to be over £120m, aimed at enhancing road safety and traffic flow along the A1 between Hillsborough and Loughbrickland.
A4 Enniskillen Southern Bypass – a long-awaited project that will reduce congestion in Enniskillen by providing a direct transport link around the town. Lagan Pedestrian & Cycle Bridge – a £25 million project set to create a modern, accessible river crossing connecting the Gasworks to the Ormeau Embankment. One of the most ambitious projects, the A5 Western Transport Corridor, will deliver over 80km of new dual carriageway between New Buildings and Aughnacloy. While legal challenges remain, strong political backing and public support are pushing the project closer to reality.
Northern Ireland’s road network faces increasing pressure due to funding shortages and ageing infrastructure. A report by the Northern Ireland Audit Office revealed a £1.2 billion backlog in road maintenance, with
current funding levels falling far short of what’s needed for long-term sustainability. Potholes, deteriorating surfaces, and drainage issues continue to be a major concern. The past year has highlighted the urgent need for sustained investment to keep roads structurally sound, safe, and reliable.
One of the standout moments in Northern Ireland’s transport sector was the CIHT NI Annual Gala Dinner, held on March 20th, at the Clayton Hotel, Belfast, attended by the CIHT President Professor Glenn Lyons.
This event not only brought together industry professionals, but also celebrated outstanding achievements through the CIHT NI Awards.
Infrastructure Project of the Year (Under £5m)
Winner: Bay Road Bridge – FP McCann
Infrastructure Project of the Year (Over £5m)
Winner: Belfast Grand Central Station – Translink
Active Travel Project of the Year
Winner: North West Greenway Network – McAdam Design
Infrastructure and Civil Engineering
Ulster University: Taylor Rainey
Queen’s University Belfast: Ben Marsden
Emerging Professional of the Year
Winner: Christine Friel – Amey
Runners-up: Jackson Touhey – Translink
Emma Doherty – AECOM
As the professional body for those working in highways, transport, and infrastructure, CIHT plays a crucial role in career development and qualifications. It offers accreditation for professionals at various levels, including:
Chartered Engineer (CEng)
Incorporated Engineer (IEng)
Engineering Technician (EngTech)
Chartered Transport Planning
Professional (CTPP)
CIHT also runs technical seminars and CPD opportunities, open to both members and non-members. For the latest updates on events, networking opportunities, and professional development, visit the CIHT Northern Ireland events page.
With a year full of progress, innovation, and challenges, Northern Ireland’s transport and highways sector continues to evolve. Looking ahead, investment, planning, and collaboration will be key to building a modern, sustainable, and efficient transport network for the future.
For more information, visit www.ciht.org.uk.
Projects based in Co Kildare and Co Galway have benefited from two innovative solutions which have recently become part of the Groundforce range of products.
Coir Infrastructure used the Groundforce Dual Access Platform for safe access and egress to a water treatment plant and Breffni Group facilitated the safe movement of Road Plates by choosing the Road Plate with LiftSafe.
These two new offerings represent a significant design boost to similar products already established within the industry, so let’s begin by taking
a deep dive into what’s new and discover how they positively impacted safety and efficiency.
As the name suggests, the Dual Access Platform provides access to both sides of a structure or excavation. This ‘up and over’ solution makes the platform ideal for projects, such as the one used by Coir Infrastructure in Co Galway where access was required over an elevated concrete structure. Also able to accommodate walls and pile caps, the platform has a robust mounting system for clamping walls up to 600mm
wide, with the option to bolt into the wall for additional security: a central, self-closing gate completes the safety rich nature of this popular product.
The symmetrical design of the Dual Access Platform means that Tuffsteel Ladders can be mounted both left and right within the hoop. In addition, Groundforce is the only company with the ability to fit a StepSafe Stairway to either or both sides of the platform.
The StepSafe, which can also be used with Groundforce’s Premier LadderSafe, delivers increased stability and safety to enable a confident ascent and descent, essential for added reassurance when negotiating high elevations.
With a strong focus on improving safety in the workplace, Groundforce has introduced a new lifting system for handling Road Plates which provides a much safer and efficient method of lifting and relocating. Designed with operator safety in mind, a lifting cassette
is fixed centrally into the plate to allow a balanced lift using a single-leg chain. This fully eliminates the need to use a conventional four-leg chain, but more importantly means the Road Plate can be
lifted and manoeuvred with a greatly reduced risk of hand injury and finger trapping. With the four corner holes still available if required, this adapted Road Plate was widely used by the Breffni Group in Co Kildare who saw first-hand the gains in efficiency and safety that this fresh innovation brought. For more information, visit www.vpgroundforce.com
The construction industry is at a turning point, driven by the need to reduce emissions, improve air quality, and enhance efficiency. As the exclusive sales and service agents for Volvo Construction Equipment in Ireland, Pat O’Donnell & Co. is championing the shift towards zeroemission machinery, particularly in highways and maintenance contracts across the island of Ireland.
A key factor in this transition is lifecycle performance of the machinery – evaluating a machine’s total environmental impact from manufacturing to operation and disposal. By comparing diesel and electric machines, the benefits of electrification become clear in reducing Scope 1 and Scope 3 emissions, as well as NOx pollution.
www.volvoce.com/global/en/productsand-services/environmental-declarations
A Life Cycle Assessment (LCA) comparing electric and diesel excavators reveals the long-term sustainability advantages of electric alternatives:
• The ECR25 Diesel emits over 11,170 kg of CO2 before leaving the factory, while the ECR25 Electric has a higher manufacturing footprint, 14,570kg of Co2 due to the battery
• Over its 10-year lifespan, a diesel machine emits 10.8 kg of CO2 per operational hour, whereas the ECR25 Electric emits zero emissions per operational hour
• When powered by renewable energy, the ECR25 Electric operates with nearzero Scope 1 emissions, eliminating carbon output from fuel combustion
Electric machines are also more efficient over time, with fewer moving parts, lower maintenance requirements, and reduced energy consumption per cycle, making them a cost-effective and environmentally responsible investment.
Government and private sector contracts are increasingly moving towards low carbon emission solutions for highway maintenance and infrastructure projects. The ECR25 Electric and EC230 Electric are particularly suited for:
• Urban roadworks and nighttime operations, thanks to their low noise levels and zero exhaust emissions
• Tunnelling, bridge repairs, and enclosed spaces, where diesel fumes pose a health risk to workers
• Sustainability-driven projects, helping contractors meet public sector emissions targets and secure future tenders
Nitrogen oxides (NOx) from diesel engines contribute to smog, acid rain, and respiratory diseases, posing a significant issue for high-traffic urban projects.
The ECR25 Electric and EC230 Electric produce zero NOx emissions, leading to:
• Improved air quality for workers and nearby residents
• Compliance with tightening emission regulations
• Healthier and safer job sites
The move to electric construction equipment is no longer just about reducing emissions – it’s about delivering long-term value.
Lower lifecycle emissions, reduced operational costs, and the ability to meet
strict environmental regulations make electric machines the future of highways and infrastructure development.
At Pat O’Donnell & Co., we are committed to supporting our clients in this transition with industry-leading Volvo electric solutions, helping to future-proof Ireland’s construction industry while delivering cleaner, more sustainable operations.
For more information, contact Tim Armstong on +44 7584 123103, or email tarmstrong@patodonnell.com
Complete Weed Control has long been a trusted name in landscape management across the UK and Ireland. Specialising in a wide range of services, including weed control, invasive species management, fine turf applications, grounds maintenance, arboriculture, site clearance, and winter services, the company consistently seeks innovative solutions to improve safety and efficiency in its operations.
In an effort to reduce the risks associated with working at height within the arboriculture division, Complete Weed Control explored
mechanised alternatives for tree removal.
The continuous rotating Merlo ROTO with tilting cab and equipped with the GMT TTC grapple saw, emerged as the perfect solution. Keith commented: “This machine offers exceptional reach, allowing operators to handle limbs from various angles without repositioning the equipment. Moreover, its compact footprint means it has zero tail-swing and so, instead of closing the whole road, work can be safely carried out with minimum disruption to traffic flow.”
Given the company’s focus on highways and roadside tree work, the Merlo ROTO’s ability to move quickly and efficiently made it a standout choice compared to other machines.
He continued: “The devastating effects of Storm Eowyn in January 2025 left a significant clean-up operation in its wake.The Merlo ROTO played a crucial role in safely and efficiently removing hazardous trees. By enabling operators to work from a distance, the machine made it possible to sectionalise and remove dangerous trees that would have been nearly impossible to handle without mechanisation. The tilting cab is invaluable for looking up at the grapple saw in the canopy.” This streamlined approach significantly accelerated the clean-up process while ensuring operator safety.
One of the most significant advantages of the Merlo ROTO is its ability to eliminate the risks faced by chainsaw operators, particularly the dangers of working at height. Injuries and fatalities in arboriculture often stem from these hazards, making mechanised solutions invaluable. Unlike human workers, the Merlo ROTO doesn’t suffer from fatigue, maintaining consistent performance throughout long and demanding tasks. The impact on his operators is not lost on Keith: “Field teams appreciate its efficiency, often struggling to keep pace with its rapid work rate.”
The Merlo ROTO has proven particularly valuable in the company’s roadside tree surgery, where tree removal is a primary focus. Its road-legal design enhances versatility, allowing for seamless road travel – up to 40kph – between job sites. This feature gives it a significant advantage over alternative equipment, making it an indispensable asset in day-to-day operations.
On attachments, Keith is impressed with the GMT TTC050 grapple saw, which he believes enhances precision and control. His operators particularly appreciate the machine’s extensive capabilities and adaptability, making it a vital tool in the field.
Owning a Merlo ROTO has positioned Complete Weed Control as an industry leader in safer tree removal. Keith believes that the investment has not only attracted new clients but also demonstrated the company’s commitment to improving safety and operational efficiency. By embracing innovation, Complete Weed Control continues to set benchmarks in arboriculture, ensuring a safer and more effective approach to tree management.
Keith’s team has been operating a Merlo ROTO 50.26SPLUS since acquiring the machine from local Merlo dealer, Wm Rose, in January 2023. Wm Rose cover Peebleshire, East Lothian and the Central Belt of Scotland. Complete Weed Control’s ROTO is maintained with regular servicing, every 500 hours.
Alan Rose, Director of Wm Rose, commented: “We’ve been Merlo dealers for the past five years and are impressed with Merlo’s dedication to continuously innovate and develop their telehandler range. The ROTO is market-leading, and we continue to be excited by the interest north of the border.”
Keith summed up the interview by emphasising the transformative impact of Merlo’s ROTO in arboriculture: “As the industry
continues to advance, the ROTO is setting new standards for safety, efficiency, and reliability. Its ability to handle even the most demanding conditions demonstrates why mechanisation is the future of tree management.”
Rotating telehandlers provide unparalleled advantages over fixed models, making them ideal for arboriculture. The Merlo ROTO offers:
• 360° rotation, allowing full access to trees without repositioning the machine
• Tilting cab for optimal visibility and operator comfort
• Extended reach, enabling operators to work at height safely and efficiently
• Multi-functionality, acting as a telehandler, rough terrain crane, and aerial work platform in one
• Smart operator features, including adaptive load control, and a 10” terminal for customised settings
• Remote operation capabilities, increasing safety by allowing work from a distance
As seen in the aftermath of Storm Eowyn, the Merlo ROTO’s versatility and power make it an indispensable tool for modern tree management, setting new industry standards for safety and efficiency.
From casting a light of wellearned recognition on the region’s offerings across the pinnacle areas of highways and transportation, to providing a prime outlet for networking opportunities, the CIHT Northern Ireland Gala Dinner recently marked its glittering return.
This year, the annual event took place at Belfast Clayton Hotel and once again boasted a guestlist comprising an array of the industry’s key representatives and spear-headers, including the CIHT President, Professor Glenn Lyons. Expertly compered by broadcaster and journalist, Claire McCollum, the evening also featured the unveiling of the high-achieving CIHT Northern Ireland Awards winners.
Inspiration was further sparked throughout the evening by special guest, Aimee Fuller – a two-time Team GB Winter Olympian, broadcaster and sport and media personality.
The last few months have seen significant changes in our landscape, both physically and metaphorically. Foundation work has started on a new student accommodation block in Belfast City Centre and a local public house on Dublin Road has been demolished to facilitate this development. It is good to see regeneration and change, but is this going to become outdated?
We have seen significant changes internationally over the last month, and as I draft this article, we have just started a 30-day ceasefire negotiated between Puttin / Trump / Zelenskyy. Let us hope that by the time you read this it has led to a better world. But what is happening nationally that may impact upon how we live our lives?
Mid-March was the first announcement of the UK government on changes to our
health system and they have outlined that NHS England is to be scrapped, with management of health service returning to government under the control of the Department of Health and Social Care.
The Prime Minister says that bringing NHS management back under the control of ministers will slash waiting times and added the result would end the duplication from two organisations doing the same job, freeing up staff to focus on patients and putting more resources on the frontline.
What implications is this likely to have to the construction industry here in Northern Ireland and will our devolved government be forced to consider differently how we manage our different Departments?
The aim of this change is to shift resources away from hospital-centric care to more community-based, preventive services. This change is expected to help reduce the burden on hospitals while delivering care closer to patients’ homes and allow for improved patient care.
So far, there are no proposed changes here, but we do have a Department for Heath and regional Health & Social Care Trusts, as well as dental and doctor surgery issues. Is it time to consolidate these systems?
Two of my current projects are part of a team delivering a new health and care centre and a new mental health hospital. Will we see more of these developments in the future, and if such a change takes place, will we see more funding into infrastructure?
No-one likes change but if we want to balance our financial budget and look to the future, is it time to act and follow the lead of the government and NHS England? Our new Programme for Government, ‘Doing What Matters Most’, only sets out a plan to 2027 and there is potential to reform what we do after this. We do have an infrastructure crisis and no prospect of delivering
further development like the redevelopment of Dublin Road.
Our pothole crisis has reached over £1 billion in Northern Ireland and over £17 billion in the UIK. In other areas of Northern Ireland there is a lack of sewerage and potential future water supply infrastructure restrictions as well. Without investment in these sectors, we will not see other new developments coming forward in an appropriate timescale. Is it time to think differently on how we manage and fund our other departments to ensure there is enough budget to allow for our infrastructure, arts, and community activities? Is it time for change?
As a professional institution CIHT does not make a political viewpoint but we are always aware of the issues impacting upon our members and the highways and transportation
sector and we do have to consider what is happening with government as we develop new policies and review our business plan.
The Council of CIHT met in Bristol this quarter to do this and it was a terrific opportunity for representatives from all over these islands to consider the future of our institution. It also offered an opportunity to spend time in the city which has recently introduced a new low emission zone, the reduction in traffic from my last visit was notable.
Locally CIHT held a professional qualifications event focusing on contractors and routes to professional membership. CIHT is open to anyone working in the highways and transportation sector and we offer a series of online courses to allow our members to achieve their CPD. Your level of experience will help select the grade of membership for which you can apply. Further guidance can be found by simply
searching “CIHT Membership” in any search engine.
CIHT held a joint meeting with the Institute of Asphalt technology and had a debate on the performance and specification of surface dressing. We have just held our annual Awards dinner, and this is covered elsewhere in this publication. In April we have a presentation on the now complete Northwest Green way and Pennyburn Bridge.
As well as my role on Council, I Chair the Board of the Rainbow Project and this month I was honoured to present the Northern Ireland Tolerantia Award. These are annual European honours established in 2006 to recognise individuals, institutions, or groups demonstrating exceptional commitment to promoting democratic values, such as equal rights, solidarity, social diversity, and tolerance, as well
as combating homophobia, racism, and other forms of group-focused enmity. This year’s recipient was NI Civil Servant Gareth Johnston who gives so much of his time to creating an equal society within the NI civil service, and is a very deserving recipient for this year’s award. I also get the opportunity to meet and debate with visitors to Northern Ireland and this quarter was no exception when I got to spend an evening with Stuart Milk from the Harvey Milk Foundation, an international human rights activist and youth advocate. I also managed an evening and morning session with the wonderful musician, Kate Nash, who delivered an immensely powerful speech on equality and diversity in Belfast. Her hit single ‘Foundation’ seems a very appropriate end to this piece as it recognises that we do need a solid foundation to create an equal society here. I look forward to further debate next quarter.
Fines amounting to €450,000 were recently handed down to two companies – a manufacturer and an operator – at Central Criminal Court following an incident on 14th August 2019 where a haulier at Dublin Ferryport Terminal was struck and killed by a vehicle.
The manufacturing company had previously pleaded guilty to failing to ensure that the vehicle, an empty container handler, was designed and constructed so as to be safe and without risk to health when properly used by a person at a place of work in that it failed to provide
appropriate devices to remedy hazards due to restricted visibility from the driving position of the container handler, being a breach of section 16(1)(a) of the Safety, Health and Welfare at Work Act 2005.
The operating company had also pleaded guilty to failing to identify the hazard of restricted visibility from the driving position while operating the empty container handler, assess the risks presented by the hazard, and be in possession of a written assessment at the place of work while work was in the course of being carried on, being a breach of Section 19(5) of the Safety, Health and Welfare at Work Act 2005.
Mark Cullen, Assistant Chief Executive of the Health and Safety Authority, commented: “Working in and around plant and machinery is a well known hazard and has been a contributing factor in a significant number of fatal work-related incidents. It is vital that employers carry out a risk assessment for this type of work and identify the appropriate control measures to ensure the safety of employees and others working in and around areas where plant and equipment is being operated. As can be seen from this case, failure to do so can lead to a tragic consequences.”
At the Central Criminal Court, a judge imposed a fine of €400,000 on a Co Laois-based company arising from a fatal workplace incident.
On 23rd November 2017, a fourperson team was tasked with installing plant and equipment
on a site in Dublin. The system of work deployed involved the employees manually handling a section of the LV switchgear (weighing 772Kg) into an upright position inside the plantroom.
An employee was fatally injured when he was crushed between the side panel of
the plant and equipment, and the wall of the plant room .
The company had previously pleaded guilty to four charges in breach of Safety, Health and Welfare legislation.
In the same case, the judge imposed a fine of €5,000 on a director of the company, who
had previously pleaded guilty to two charges in breach of Safety, Health and Welfare legislation. Mark Cullen, said: “It is vital for employers to ensure that all works being undertaken by their employees are planned, organised, managed and conducted in a safe manner. Where there is a risk of serious injury, employers must take appropriate measures to avoid the need for manual handling of heavy loads. As can be seen from this case, failure to do so can lead to tragic outcomes.”
Following an investigation by the Health and Safety Executive for Northern Ireland (HSENI), and after pleading guilty at Laganside Crown Court, an employer was fined £27,500 for failing to ensure the safety of his employee who died during hedgerow cutting operations
The case arose following the death of the employee, who was electrocuted as he was trimming a hedgerow at a residential property. The company was
engaged by the property owner to trim the hedgerow along the edge of the garden.
An 11kV electricity transmission power line was located immediately above the hedgerow. The employee was fatally electrocuted while he worked from a raised mobile working platform located underneath the powerline.
Speaking after the hearing, Kevin Campbell, an inspector within HSENI’s Major Investigation Team, said: “This tragic incident resulted in a family man
losing his life. It is vital that all tree surgeons and arboriculturists properly identify the location of overhead power lines before starting any work.
“Where it is not possible to avoid working close to energised power lines, robust systems must be put in place to minimise and control the risks. The network operator should be contacted, as part of the control measures, to request an outage before work commences. Safe systems of work need to be implemented, communicated to the workforce, supervised and maintained.”
The Plant Hire Company of the Year award celebrates excellence in the plant hire industry.
This award recognises a company that excels in providing topquality equipment, prioritises safety, delivers exceptional customer service, and demonstrates a commitment to sustainability. The Plant Hire Company of the Year sets the standard for excellence, innovation, and leadership within the industry.
The Excellence in Customer Service Award recognises businesses who exemplify an unwavering dedication to providing unparalleled customer service experiences. This award honours those companies who consistently surpass expectations, demonstrating a profound commitment to understanding and addressing the diverse needs of their customers.
The Environmental Initiative Award celebrates outstanding efforts in innovative resource management, environmental impact mitigation, and sustainability across various sectors. Whether through pioneering projects in biodiversity conservation, ethical business practices, charitable initiatives, or other means, this award honours companies, organisations, and initiatives that are making a tangible difference in preserving our planet and fostering sustainability.
This category is for the individual or company that has achieved outstanding success such as in sales, contract wins, company expansion/development or other areas of business over the past 12 months.
Open to any individual or company currently active in the construction, civil engineering, quarrying, waste management and plant & machinery industries. The entrant must highlight the area in which they operate, level and type of achievement as well as outline any relevant factors or reasons that contribute to that success.
The Construction Company of the Year award recognises excellence, innovation, and leadership within the construction industry. This award showcases companies that have consistently demonstrated outstanding achievements in various aspects of construction, including but not limited to residential, commercial, industrial, and infrastructure projects. The recipient of this award embodies the highest standards of professionalism, integrity, and excellence.
This award celebrates the exemplary achievements of individual quarries, spanning the spectrum from hardrock to sand and gravel operations.
Entrants to this category showcase a commitment to fostering safe working environments, employing the highest standards of pollution control, and prioritising sustainability initiatives. Notably, contenders distinguish themselves through their dedication to biodiversity preservation and operational efficiency, setting benchmarks for industry best practices.
The award recognises sites that go beyond mere extraction, presenting a robust portfolio of products and services to meet diverse market demands.
The Wastes Management & Environmental Excellence Award celebratesexcellence within the resources and Wastes Management industry. We seek to honour those who demonstrate exemplary best practices and innovation across various commercial and public sectors.
Nominations are open to companies and organisations who have showcased outstanding contributions in waste management, resource conservation, and environmental sustainability.
The Health & Safety Award acknowledges companies and organisations that demonstrate remarkable dedication and innovation in safeguarding the health, safety, and wellbeing of individuals across varied environments.
This award celebrates entities and initiatives that exhibit exceptional commitment to cultivating safe practices, mitigating accidents, and advancing overall wellness.
The Special Recognition Award acknowledges individuals who have demonstrated outstanding service and remarkable contributions to the construction, quarrying, plant & recycling sectors.
The Construction Project of the Year Award celebrates excellence and innovation, in the construction industry across the island of Ireland and the UK.
Open to all construction companies, including contractors, developers, architects, and engineers, this prestigious award recognises outstanding projects completed within the last 18 months.
This award recognises exemplary leadership and dedication within the quarry sector. It honours individuals who play a pivotal role in quarry management teams, showcasing outstanding contributions to various aspects of quarry operations.
The Circular Economy Award celebrates innovative initiatives and outstanding achievements in advancing the principles of circular economy within various sectors. This prestigious award recognises organisations and businesses, who demonstrate exceptional commitment in rethinking traditional linear economic models, reducing waste, and promoting sustainability throughout the product lifecycle.
The R&D Innovation Award celebrates exceptional innovations that have revolutionised the plant, construction, civil engineering, quarry, and recycling industries. This award recognises products that have transformed traditional practices, enhanced efficiency, and elevated industry standards. Entrants for this award are invited to spotlight groundbreaking machinery, equipment, or solutions that have redefined the game in the past 18 months.
Whether it's a cutting-edge excavator, a state-of-the-art crusher, or a pioneering recycling technology, the focus is on industry impact – has your product reshaped operations, optimised workflows, or opened new possibilities for growth and sustainability? From advanced construction materials handling to sustainable recycling processes, the R&D Innovation award honours innovations that have demonstrated exceptional performance, reliability, and versatility in their field.
The Top Team of the Year award celebrates the outstanding collaborative efforts within companies and businesses across various sectors, including plant, construction, quarry, civil engineering, and recycling industries. This award acknowledges teams within companies that have demonstrated exceptional teamwork, innovation, and dedication in executing a project, initiative, or strategy, resulting in a substantial and positive impact. Teams considered for this award have not only achieved remarkable results but have also overcome obstacles and challenges through effective collaboration and synergy.
This Award will be presented to the organisation that can report on successful involvement within a wide variety of civil engineering projects including planning, construction, infrastructure and maintenance of fixed structures or public works throughout the the island of Ireland and the UK.
The information provided should demonstrate high levels of skill within project management, procurement, innovation and specialist projects. Customer testimonies may also be submitted.
The Waste Management Team of the Year Award recognises outstanding achievement and innovation. This award honours a team that has demonstrated exceptional commitment, leadership, and creativity in addressing the challenges of waste reduction, recycling, and sustainable waste disposal.
Entries for this award should have exhibited exemplary teamwork, collaboration, and dedication to implementing effective waste management strategies. As well as a proactive approach to environmental stewardship, promoting responsible waste practices within their company, organisation or community.
Entries should not exceed word count of 1000 words.
A minimum of two high res images that best depict your entry to be supplied.
Supporting material can be supplied over and above.
Entries must be made by emailing a Word/PDF document stating the award category to: golda@4squaremedia.net
Separate award entries to be emailed for each category entered.
Large files can be sent via WeTransferemail to be sent to golda@4squaremedia.net to advise thereof.
Award Entry enquiries can be made to Golda Burrows - golda@4squaremedia.net
Creagh have once again teamed up with Galliford Try’s Investments and Building to deliver a £52 million BTR development at Guildford Crescent in Cardiff. This apartment block is set to become the tallest building in Wales upon completion.
This development will see the creation of 272 new homes in a 30-storey tower, which will provide attractive, modern, open-plan living with full-height windows in a mix of one and twobedroom apartments reflecting the current demand within Cardiff city centre. The building will be split into three levels, of 29, 25 and 21 storeys, and there will be a roof terrace on the 26th floor.
Creagh’s full Rapidres® MMC solution is being utilised on this project, which includes: etched sandwich panels, internal walls, lift shafts, landings, stairs, and hollowcore. Creagh provided a full design, manufacture and install package.
This project is now scheduled to be delivered well ahead of the projected end date – a testament to the incredible
work of the install team, engineers and logistic partners. Rapidres® from Creagh Concrete Products Ltd is ideally suited to multi-storey projects where the layout is replicated consistently across each floor. Each unit is a highperformance insulated sandwich panel built offsite with a highquality internal finish ready for decoration, with cast-in conduits, electrics, and ventilation.
Creagh provide a wide range of external finishes that can match virtually any other build type.
These now include a versatile range of finishes, including smooth, etched, patterned and even printed concrete. Any brick or brick slip can be cast in, dual brick faces can be cut in half, reducing the quantity required.
Rapidres has a two-hour fire rating and complies with Part L building regulations. They now use a CEM II-A-L cement replacement which has significant reduction in embodied carbon, helping them further achieve their sustainability goals.
Rapidres produces the robust quality of traditional style construction at the speed of a modular build for significant programme savings and produces a fast weather tight build which allows for early access for follow on trades.
Rapidres offers individuality and a maintenance-free alternative to render systems. Every concrete piece is designed with their unrivalled engineering expertise and coupled with their innovative production methods to deliver concrete solutions with outstanding quality and reliability.
• Reduced preliminary costs due to shortened programme times
• Pre-installed doors and windows
• BBA Certification
• Inherent thermal mass Reduced heating and maintenance costs
• No on-site waste. All elements are manufactured off-site
• Improved health and safety. No requirement for external access, such as mast climbers or scaffolding
• Enhanced site co-ordination by cutting follow-on trades, allowing early access for essential ones
• Wide range of external finishes, including brick, cladding and architectural concrete
• Reduced carbon in all their precast units
• Cast in conduits, electrics and ventilation ducts. Walls are ready for direct decoration
• Acoustic separation is minimised due to the density of the floors and walls
Find out more here: www.creaghconcrete.com info@creaghconcrete.com
Animation of the build project is available at: www.youtube.com/ watch?v=J0YXLTPpJGI&t=175s
Images credit: Lee Ballard (Anwick Photography)
As Sales Manager at Dennison JCB, Ian Calderwood’s daily to-do list includes expertly leading his team, steering effective sales strategies, and – crucially – communicating with key representatives from across the construction and plant industries in order to fulfil their machinery needs.
During these meetings with his customers, Ian has found that one key theme frequently arises, as nestled among the technical questions raised to Ian is one that poignantly stand outs: “Is your father John Calderwood?”And it is always with pride that Ian gets to respond his confirmation. Ian stepped into his post as Sales Manager at Dennison JCB in 2018 – a significant career shift, given that it succeeded 32 years in the automotive industry, a period in which Ian progressed from the mechanical side of operations, to sales executive, and subsequently sales manager. Although with the adoption of the role, Ian was marking the beginning of a new chapter in his career, the sector which he was to be immersed in was infused with familiarity – it’s one which his father, John, knows all too well.
John Calderwood was a stalwart in the plant sales industry, and in many areas of the business, he was indeed a trailblazer, too. His own extensive career mirrors his son’s in many ways – with initial beginnings in the mechanical work of machinery,
before transitioning to sales for more than 40 years, and retiring in 2002.
John reflected: “I worked at Harry Ferguson Tractors; it was then in 1962 Massey Ferguson introduced their 710 digger (pictured) and I was offered the job selling them. This was the start of my sales career and from
there I received the opportunity to join TBF Thompson (Garvagh) in 1967, when they had just taken on the agency for JCB. In 1976 a job came up with Caterpillar and it was ideal. I lived beside the premises and the manager even lived close by in the next cul-de-sac! I ended up staying in this role for 26 years, until my retirement, working across my designated areas of Co Down, Co Antrim and Co Armagh.”
Throughout his tenure, John was renowned for his impressive forward-thinking sales ability, to the extent that he was awarded five consecutive top Caterpillar accolades over a span of five years by successfully entering new markets that Caterpillar had never ventured into before, including the farming sector.
For John, the evolution of the industry since these sales days has been extraordinary to witness: “When I was carrying out my role, the machines were a lot different – they didn’t have any radios in the cab. Back in those days, diggers would have cost you £1,900. You just had a book with names in it of people to visit, and if you wanted to ring back to work, you would go to a phone box somewhere and reverse the charges.”
Despite these changes to the wider nature of the business, a successful sales performance ultimately embodies the same
values. As such, Ian has been able to draw on the lessons and experiences of his father while navigating the demands of the job.
“My dad’s advice has always focused on the importance of getting out and seeing people face-to-face. He understands that the role is very different now and we rely heavily on different forms of communication, be it email or WhatsApp etc. But he instilled in me that you still can’t beat a face-to-face conversation – as well as the significance of listening.”
John elaborated on this ethos: “My motto was that I didn’t just have to sell machines, I had to sell myself and my service too. At the end of the day, it’s the service and the residual value which customers receive. As a result of this, a lot of my customers ended up becoming friends.” The generational continuation of this personalised approach is most evident when the customers that Ian now deals with strike a familiar chord. John said: “It’s incredible to see that while I sold to certain customers – Ian is now selling to their sons. For example, going way back to the early 1980s, I sold to John Dan O’ Hare,
and Ian is selling to John Dan O’Hare’s family now. There are loads of cases of this.“
Despite occupying different stages of their career trajectories, Ian and John still enjoy being able to revel in shared industry experiences together – such as their visit to the JCB headquarters in Rocester, Staffordshire – the first time John had returned in 30-to-40 years. John recounted: “We flew over and experienced the background story and tour of JCB. I got to see a lot of the original machines and sit in Joseph Cyril Bamford’s old office. The headquarters look so new and impressive – they’ve changed a lot since the last time I was there.”
Balmoral Show is also a prompter of special memories for John and Ian alike – having both carved out a great presence in their sales roles at the event throughout the years.
Ian said: “I took great pride in being at Balmoral Show for the first time, and still do all these years later. There’s not a
show that goes by that people don’t look at my name badge and ask whether I’m related to John Calderwood. Everyone is so positive in recalling their experiences of my dad’s integrity, loyalty and honesty – qualities I hope that people would one day relay when reflecting on their experiences of working with me, too.”
As for this year’s Balmoral Show, Ian assures us that the JCB impact will be as impressive as ever – with its dancing diggers set to be showcased.
Engulfed in the support from his father, and confidence in Dennison JCB’s continued growth, Ian is excited for all that’s to come.
“Dennison JCB is a great company to work with – I really enjoy my role and the team I get to work with. We also have a very strong relationship with the JCB national brand. Since the company took on the franchise, the business has grown every year and continues to populate the marketplace extremely well.”
Excitement is continuing to build as the 156th Balmoral Show edges increasingly closer. In partnership with Ulster Bank, Northern Ireland’s must-attend agri-food event is set to return to the Eikon Exhibition Centre, Lisburn from Wednesday 14th-to-Saturday 17th May 2025. Once again, the event will be playing host to a plethora of families, foodies, and farmers as they join in celebration of award-winning livestock, a broad selection of local food and drink, along with the friendly entertainment featured across the packed programme.
Joining this year’s line-up in the Main Arena will be the mesmerising JCB Dancing Diggers who are returning to the Balmoral Show for the first time in over 30 years. After stunning crowds at the King’s Hall back in 1993, the JCB team are making their return with up to eight mighty diggers to wow a whole new generation of machinery enthusiasts. Of course, the Main Arena’s timetable wouldn’t be complete without the fantastic full programme of show jumping classes, Pony Cub Games and the unmissable spectacle of the Cattle Parade as the fitting finale to the festivities.
Recognised as a must-attend day out for families, too, the Children’s Area will be back due to popular demand. Located beside the Poultry and Rabbit Pavilion, the Kidz Farm will host an array of farmyard and exotic animals, providing endless learning opportunities for everyone. The Glenarm Castle Mini Land Rover Experience, sponsored by Property
Pal, will be back to help future farmers get into the driving seat and explore a bespoke adventure trail alongside their parents. For older children, there will also be a climbing wall to challenge even the most adventurous visitors. A new addition to this popular area in 2025 is a sensory activity zone for the show’s younger guests who are ready to take time out from the bustling aisles and explore a variety of wellbeing activities. The vast showgrounds will be sparking entertainment for the whole family and in the Cattle Rings, former National Champion, Robert Goligher, will be sure to round up crowds of spectators as he demonstrates the art of herding sheep with his trusty dog by his side. The Start Solar Sustainability Village will be back to help us all explore the latest green innovations and, as always, keen shoppers will be spoilt for choice as they browse
hundreds of stands, including the popular Makers’ Market and Eikon Shopping Village. For food enthusiasts, the show wouldn’t be complete without the tantalising tastes of the NI Food & Drink Pavilion, as well as the catering areas across the showgrounds. From mini tasters to food on the go, you’re sure to get a sweet treat or savoury snack to remember. The Healthy Horticulture Marquee and NI Food & Drink Pavilion will also host cooking demonstrations throughout the show for budget and family-friendly meal inspiration, so don’t forget to nip in and check them out. As always, animals and agriculture form a key part of the Balmoral Show and visitors can expect to see over 3,500 head of livestock across the highly competitive classes. The calibre and quality of entries year-on-year is a testament to the exceptional quality of local produce in Northern Ireland and
the competitive spirit only adds to the excitement across the showgrounds.
Rhonda Geary, RUAS Group Operations Director, commented: “We are so excited to welcome everyone back to the 2025 Balmoral Show in a few weeks! The ‘Balmoral Buzz’ is already taking hold and our packed programme is sure to be one to remember. With outstanding local food and drink, live music from the Downtown Show Stage, first-class entertainment, remarkable livestock, sheep shearing, show jumping and much much more we can’t wait to celebrate our proud agri-food industry with you all. We’ll see you at the Eikon!” For more information, and to purchase tickets, visit www.balmoralshow.co.uk. You can also find out more about the 2025 show via Facebook, Instagram and TikTok, or by downloading the 2025 Balmoral Show app.
At this May’s Balmoral Show, at the Eikon Exhibition Centre, Lisburn, Merlo will showcase an impressive range of telehandlers on stand B10.
The event will feature a comprehensive line-up of Merlo’s innovative machines, designed to enhance efficiency, performance, and sustainability for the agricultural and construction sectors. From compact models to stabilised and high lift solutions, Merlo, a global leader in telehandlers, continues to set new standards in material handling.
TF27.6 – This ultra-compact model is perfect for working in tight spaces, with a width of only 1.86m and a height of 1.96m. Despite its small size, it offers a 2.7-tonne lift capacity and a 6m lift height. Powered by a 75hp Kohler Stage V engine, it delivers impressive performance without sacrificing agility.
TF30.7 – A versatile, compact telehandler measuring just 2m wide and 2.10m high (2.00m with Low Cab option), it delivers a 3-tonne lift capacity and 7m lift height. Powered by a 100hp Deutz Stage V engine, it combines manoeuvrability with impressive performance and optional cab suspension for superior comfort.
TF33.7 – Striking the perfect balance between performance
and size, the TF33.7 offers a 3.3tonne lifting capacity and almost 7 meters of lift while maintaining a reduced overall footprint. Powered by 115hp Deutz engine, the TF33.7 is one of the most popular machines in Merlo’s compact agricultural range.
TF42.7CS – Features a Perkins Stage V 136hp engine with a responsive load-sensing 139 l/ min hydraulic pump, ideal for more demanding tasks, such as clamping silage and general duties around the farm. Offering a 4.2-ton lift capacity and 7m reach, its high ground clearance and cab suspension (CS) ensures smooth operation across rough and uneven terrain, while the high cab position provides 360-degree visibility, enhancing safety and precision when handling bales, loading feed, or moving heavy materials. TF42.7 combines power, control, and
comfort, making it the top choice for modern farming operations.
P40.17 – Combines 4 tonne lift capacity with 17m lift height, making it the ideal telehandler for housebuilding and construction. Perfect for lifting roof trusses, positioning pallets of bricks and blocks, and placing materials on scaffolding or rooftops. Merlo’s advanced stabilisers, boom side shift, and chassis levelling coupled with the compact stabiliser design ensures maximum manoeuvrability on busy job sites and unmatched safety and performance for construction professionals.
50.26SPLUS – A high-performance rotating telehandler designed for demanding job sites. With a 26-meter lifting height and a 5-ton capacity, it offers exceptional reach and strength. Its tilting cab enhances operator visibility, while
the dual hydraulic pump ensures faster cycle times. Equipped with continuous 360° turret rotation and an out-and-down stabiliser system, it provides superior stability and efficiency. Ideal for construction, forestry, and infrastructure projects, the 50.26SPLUS delivers precision, power, and versatility in every lift.
Cingo 500DM – Powered by a 5.5hp Honda petrol engine, this versatile compact tracked carrier offers 500kg capacity and narrow width of only 690mm. It is designed to handle materials in tight spaces, ideal for agricultural, construction and landscaping operations.
Merlo’s telematics system offers proactive maintenance capabilities, enhanced security through real-time data, accessible via desktop or smartphone apps, allowing operators to monitor performance and maximise uptime.
The Balmoral Show is the perfect opportunity to meet the Merlo team and discover how Merlo can help improve efficiency and productivity in your operations. Merlo is proud to be at the forefront of the agricultural and construction industry with a range of innovative material handlers.
Part of the stabilised range, Merlo’s P40.17 PLUS delivers 4-ton lifting capacity and a 17m reach, with advanced stabilisers, boom side shift, and chassis levelling for precision handling. Merlo’s advanced stabilisers, boom side shift, and chassis levelling coupled with the compact stabiliser design ensures maximum manoeuvrability on busy job sites and unmatched safety and performance for construction professionals.
Dennison JCB is gearing up for an actionpacked Balmoral Show, showcasing a wide range of construction equipment – from mini excavators to access equipment, telehandlers to generators, and much more.
The iconic JCB Dancing Diggers will be performing their choreographed routine every morning and afternoon in the main arena, showcasing the power, agility and precision of JCB machinery!
Whether you’re looking to invest in a new machine, learn more about JCB parts and service offerings, explore their fantastic range of merchandise or simply enjoy the show, drop by and visit stand D1 to get in on all the Dennison JCB action. See you at the show!
Sleator Plant is the perfect ally for the industry –whether it’s tackling the daily challenges encountered on the construction site, or seeking trustworthy assets for the completion of crucial projects, the team is a go-to choice for assistance with your fleet’s expansion.
As a trusted local provider of capital equipment, Sleator Plant specialises in machinery for the construction and material rehandling industries, among others.
Since 2015, and adhering to its determination to be a leading construction dealer in Ireland, Sleator Plant has been strategically cultivated to incorporate world-class OEM partners and currently stands as a proud supplier of Genie Access Equipment, Rokbak, Mecalac Construction Equipment and SANY excavators.
Jonathan Campbell, Managing Director of Sleator Plant, explained: “We represent premium, reliable brands – but it’s up to our team to back them up with our after-sales approach. It’s important that every time a customer purchases a machine from Sleator Plant, they can see how effective our support is.”
Fuelling their confidence, this full-package commitment has led to many customers returning to Sleator Plant time and time again, including FP McCann and AG Wilson.
Reflecting the far-reaching impact and popularity of its services, Sleator Plant has recently embarked on expansion into southern Ireland – opening a secondary purpose-built depot just off the M50 beside Dublin Airport. The depot is tailormade for the company with a bestin-class vision at its heart.
Discussing the company’s excitement at the major endeavour, Jonathan said: “This is a new territory than what we’ve been used to – it’s a marketplace with different nuances. As a result, we’ve been fairly aggressive in our recruitment of the people we’ve had join the team of late – seven so far –with more to join in the future.
“We want to employ people who have the ability to do the job, but also have a personality that
fits into our set-up, and we’re really excited about everyone who has joined us so far.”
The expansion plans are set to be conducted closer to home, too – Sleator Plant will be moving into a larger depot in Northern Ireland later in the year.
Although currently embedded in a rapidly evolving chapter, Sleator Plant’s aspirations are firmly tied to its foundations.
Jonathan said: “Maintaining our values while accommodating our growing team is essential. Our core values – respect, honesty, and ownership – help set us apart from the competition. Respecting ourselves, as well as our teammates, suppliers, and customers; prioritising honesty in our dealings and how we approach our customers’ needs; and taking ownership of our own roles and responsibilities.”
A key contributor to Sleator Plant’s continued success and future growth is the Ballyvesey Group – which has provided substantial support to the team in a variety of ways.
Jonathan explained: “As a result of the Ballyvesey Group, we are in the fortunate position to retain the values of a small team, while being part of a larger, receptive group with financial stability that not a lot of dealerships may have. We know our industry and the group gives us the tools to perform to our optimum level. It’s the best of both worlds.”
Joining the line-up of exhibitors at the 2025 Balmoral Show, Sleator Plant’s expertise will soon be in the spotlight.
Jonathan commented: “Balmoral Show has always been very good to us. We do business at it, but that’s not the be all and end all – the most important thing is getting to see many of our customers in-person and give them a warm welcome.”
Later in the year, Sleator Plant will be attending the National Ploughing Championships for the second time – and throughout it all, strengthening its mark in the sector.
Jonathan added: “We have fairly lofty ambitions at Sleator Plant but our feet remain on the ground, and we are fully focused on our customers’ wants and needs.”
The all-new updated Isuzu D-Max is going to turn heads at the Balmoral Show, proudly showcased on the Isuzu stand. Built for strength, performance, and reliability, the latest D-Max combines rugged durability with refined comfort and luxury – making it the perfect partner for farmers, builders, and adventurers alike.
This year’s model features enhanced safety technology, improved towing capacity, and a bold new design, all while maintaining the exceptional build quality Isuzu is known for. Whether you’re navigating off-road terrain, hauling heavy loads or on a weekend adventure, the D-Max delivers with ease.
Eakin Bros, one of Northern Ireland’s leading Isuzu dealers, are on hand at the stand to provide expert advice and walk you through the D-Max’s impressive capabilities. With decades of trusted service and a passion for customer care, Eakin Bros ensure your Isuzu experience is second-to-none.
Tel: 028 7186 0601 www.eakinbrosltd.co.uk
MBNI Truck & Van recently achieved a clean sweep of Gold Awards at the Dealer of the Year Awards with Mercedes-Benz. In addition to retaining the title of Mercedes-Benz Vans Customer Service Dealer of the Year (Gold Award), it went one step further by topping last year’s Bronze Award for Mercedes-Benz Vans Sales Dealer of the Year, and secured Gold in that category too. The achievements are in recognition of the exemplary dedication, expertise, and passion showcased by the wider MBNI Truck & Van team every day.
This year’s prestigious Dealer of the Year Awards took place at Hampton Court Palace, the historic home of Henry VIII –and successfully cast a light of recognition on the extraordinary achievements of Mercedes-Benz Van dealers from across the UK.
CEO, Pauline McKeating, commented on the teams’ triumphs, saying, “We are incredibly proud of both our sales and aftersales teams. This is testament to their hard work, dedication, and passion. Every member of our team plays a crucial role in upholding our high standards, and this recognition affirms the progress we’ve made on our journey. Here’s to 2025 – onwards and upwards!”
Service Manager, Mark Getty, also spoke extremely highly of his team, saying, “Winning the Mercedes-Benz Vans Gold Award in Customer Service for the second year in a row is an incredible achievement, and I couldn’t be prouder of my team! Their dedication, passion, and commitment to excellence continue to raise the bar. This award is a reflection of their hard work and the outstanding
service they deliver every day. Well done, team – this success is truly deserved!”
Van Sales Manager, Robert Walker, added: “The MBNI team has always strived for excellence, and winning Best Sales Team 2024 was an incredible achievement. The award was based on the highest dealer scorecard across 12 KPIs, and after finishing third last year, we were determined to go even further.
“On awards night at Hampton Court Palace, the anticipation was high – third place was announced (no MBNI), then second (still no MBNI). Just as I was getting my phone ready to capture the winner, I was blown away to hear MBNI had won! The pride and excitement, both personally and for the team, were unforgettable.
“Now, as we set our sights on 2025, we’re ready to build on this success.”
Bobcat has completed the company’s agricultural telehandler range with three new machines. The new large high flow models - the TL34.65HF V-Drive, TL38.70HF V-Drive and TL43.80HF V-Drive – all utilise the ‘V-Drive’ continuous transmission system. They are designed to offer more comfort and productivity while improving operators’ peace of mind and reducing the total cost of ownership (TCO) of equipment during its lifecycle.
Florian Hilbert, Product Manager for Telehandlers, Bobcat EMEA, said: “With the V-Drive models added to the existing range, Bobcat still offers the current gearbox transmission for the high flow models, so customers can choose between the existing gearbox system or the new V-Drive continuous transmission. The innovative and smart functions on the new V-Drive models provide an excellent solution for customers requiring a high-performance alternative for their applications.”
Using dual hydraulic motors in series, Bobcat has been able to maintain the same performance as the current gearbox transmission.
Contrary to the current transmission, the V-Drive transmission allows the operator to drive from 0 to 40 km/h without the need to stop the machine or think about changing
the gear before starting. As a result, the simplicity and efficiency of the V-Drive transmission offers the highest comfort and peace-of-mind for the operator. It also removes any jolts that might happen when moving from one speed range to another.
The hydraulic tank has also been redesigned, resulting in a higher capacity (70 l instead of 59 l in the current transmission).
In the new V-Drive models, the Turtle and Rabbit hydrostatic speed ranges are still available and are always selectable through the joystick. Both hydraulic speed ranges have been optimised with specific curves according to the requirements of the application:
• Turtle speed = Loader mode, from 0 to 20 kph
• Rabbit speed = Drive mode, from 0 to 40 kph
The new V-Drive models also offer noise reduction, following work with external acoustic experts to significantly reduce the noise (inside and outside the cab). Among the main changes made, the hydraulic motor has been suspended with four rubber mounts, resulting in a decrease of 60 per cent in vibrations, and the whistle sound of the transmission has been fully eliminated. Coupled with Smart functions like Cruise Control or ECO-Ride, operator comfort is optimal.
Another benefit of the V-Drive transmission is its exceptional traction, providing a smoother, quieter and more efficient ride – free from jerks, even when hauling fully loaded trailers. It effortlessly adapts to any terrain, offering best-in-class grip and stability. Even when the operator is tackling rough ground or slippery surfaces, they can rely on consistent, seamless performance every time.
Based on the most popular options and assuming the V-Drive models are the premium models in the agricultural telehandler range, the following features are included in the base models:
• Tractor homologation
• 40 km/h transmission (max speed with 24 inch tyres)
• Alliance tyres – set of 4 x 460/70R24 inch
• Fan inverter with manual and auto modes
• 7 inch touch display (Bluetooth radio with microphone and Job Manager)
• Hand throttle and flex drive
To further enhance operator comfort, productivity, and to considerably reduce TCO, Bobcat has developed several smart functions which are available as standard in the base models, such as Maximum Speed Limiter, Stop and Start, Cruise Control, and ECO-Ride.
Finning has confirmed a deal to supply Flannery Plant Hire with £65,000,000 worth of Cat® machinery in 2025.
Over the past four years
Finning UK & Ireland, the world’s largest dealer of Cat machines and equipment, has supplied long-standing customer Flannery with over £250,000,000 worth of Cat machinery. The company’s most recent multi-million-pound investment includes 100 Cat Excavators, 70 Cat Bulldozers, 86 Cat ADT Trucks and 20 Cat Rollers, demonstrating that demand for plant hire shows no signs of slowing down.
Similarly, demand in the construction industry itself shows no signs of waning as Glenigans Construction Industry Forecast predicts a growth of eight per cent by the end of 2025. The industry is poised for progression, with government initiatives, housing market recovery and
improved economic conditions all set to drive further need for hard-working heavy machinery.
Its 15-year partnership with Finning has seen the company make significant investments in Cat machinery, technology and support services, to ensure quality, efficiency and sustainability in its fleet.
return on investment, not only are they hard-working machines, but they are incredibly efficient, saving up to 35 per cent on fuel compared to other models. We are committed to achieving our sustainability goals and having machines with lower fuel consumption helps us reduce our carbon footprint as well as save money in the long-term.
“We know from our relationship with Finning that Cat machines are more than capable of tackling the challenges of modern construction. We service the whole industry and need machines to be robust for work in a variety of heavy-duty applications.
Patrick Flannery, Managing Director at Flannery Plant Hire, explained: “As a result of the growth in the industry we are seeing increasing demands for efficient, sustainable and reliable plant machinery that can service the breadth of the industry.
“The Cat XE models in particular have shown us a significant
“Our recent investment shows our commitment to servicing the industry with versatile and innovative plant hire options but also represents our assurance to customers that we will continue to provide efficient and sustainable machines to suit their needs.”
As the government continues to invest in large-scale infrastructure projects and housing developments, access to a variety of plant equipment is integral to the industry’s success this year.”
It’s been four years since Enda Keenan made the career-altering decision to align his extensive technical service expertise and experience with his industrious capabilities to found Crushing & Screening Services NI (CSSNI). And the strides which the business has secured since are setting it up for sustained success.
Located in Clogher, Co Tyrone, CSSNI operates across Ireland and the UK, supporting quarry plant equipment, and with an emphasis on customer service and mitigating the impact of downtime in the industry at its core.
Among CSSNI’s portfolio of provisions, the company specialises in plant set-up, repair, electrical and hydraulic diagnostics, engine diagnostics, machine health checks,
machine rebuilds and major component inspections, preventative maintenance, and a wide range of quarry services.
In the short time-frame since its establishment, the company has experienced expedited expansion in both its client base and referral rate. In response to this demand for CSSNI’s services, and to maintain its high standards of excellence and speed, Enda has already extended his team to incorporate three experts – with impending plans for a fourth member of the team, too.
Owner and Managing Director, Enda, who worked at Terex prior to cultivating his own company, explained: “I worked on my own for the first three years at CSSNI, but then the customer base got busier and busier – between factory work, manufacturing
work, dealer work, and quarry work. I took Sam Badger on in September 2023 as a service technician, but then I ended up back to square one as things got busier again – so I added Luke Keys to the team, too. But again, as the company grew, the demand built up, and now I’m actively seeking another team member.
“Four years ago, I never thought that I would have three vans and be providing services for some of the biggest companies in the world.”
The projects undertaken by Enda and the team are varied in nature – ranging from assisting with basic-to in-depth hydraulic systems, to advising customers and operators on plant maintenance and machine health and safety. The response from customers has been
resoundingly positive – with many remaining steadfast to CSSNI’s services. Enda said: “It’s all down to going above and beyond for customers. I will always answer my phone to them – even working on Sundays and providing 24/7 services when required. On the back of this, a lot of them stay loyal to me. I always say to my team how important it is to interact with a customer at the level they need, and build a relationship with them based on trust and the quality of work provided.”
CSSNI’s rapid rise up the industry’s radar has also been recognised to the extent that the team achieved finalist status in a number of categories at last year’s Plant & Civil Engineer Construction, Quarry & Recycling Awards.
“I rarely get time to look back and reflect on my success to date, but during the awards I was able to do so. I had initially questioned entering the categories, wondering as to whether I was established long enough. But I knew how hard I had worked and how much the company had grown, so I did enter, and I am so glad I did. To come back with three shortlisted titles was unbelievable. It has meant a massive amount to me,” commented Enda.
Although the trail blazed by the business so far has been landmarked with substantial feedback and success, Enda also emphasises the strength and strain which it has taken.
“I was always brought up to work hard – it was a big part of my family’s life. My father’s passing has been a massive driving force for me too. He worked really hard, and always saw in me what I sometimes didn’t see myself.
“Everybody sees the vans, the tools, the successful projects – but what they often don’t see is the work that it has taken to get there – 24 hours a day, seven days a week.
I have had to push myself mentally and physically but it has been worth the effort.”
And does the pressure imposed on Enda as a result of his burgeoning workload detract at all from the benefits of the role? Not at all, as he details the favourite parts of the post.
“It’s the freedom of getting to make the decisions myself, as well as having the responsibility of looking after my own employees, and working with customers who I always thought were unattainable. I absolutely love the job and getting to build the relationships – not one night do I go to bed dreading the prospect of work the next day.”
The future of the business is shaping up to be busy too. Bolstered by all that’s been achieved so far, Enda is far-reaching in both CSSNI’s, and his own, future aspirations.
“I want the business to continuing growing, keeping relationships with small companies, as well as the bigger ones. Long-term, I would also love to become a dealer for some sort of manufacturer or product.
“I want to show my three sons that if you work hard, you can achieve whatever you want. We are continuing to push the limits at CSSNI – the world is our oyster.”
Demonstrating a powerful performance prowess since its inception – and having packed in an even greater innovative punch since – the MercedesBenz Arocs has firmly established itself as a construction forerunner. The Arocs notably stands out with its exceptional resilience, regardless of the challenges posed by different terrains. You can choose from robust steel spring suspension or a blend of steel spring and air suspension, offering remarkable flexibility and optimal chassis configuration. The all-wheel drive options, available in configurations from 4x4 to 8x8, combined with ample ground clearance, enable the Arocs to tackle even the most demanding landscapes with ease. With efficiency a crucial element for managing construction traffic, the Arocs excels in this regard. Equipped with the innovative Hydraulic Auxiliary Drive, it provides extra traction in challenging terrains and supports the vehicle at speeds of up to 30
km/h. This advanced technology ensures smooth traction transfer and decreases vehicle weight by up to 575 kg, resulting in higher payload capacity and reduced fuel consumption. The Arocs effectively balances efficiency and maximum traction precisely when it’s needed most, making it perfect for navigating the toughest landscapes. Providing a broader insight into why the truck is the optimal solution for enhancing efficiency, comfort, and addressing the requirements of any construction project, Tim Moore, Truck Sales Executive at MBNI Truck & Van, reflects on his firsthand experience behind the wheel of the premium Mercedes-Benz Arocs.
The Mercedes-Benz Arocs is a truck built for heavy-duty and construction work. Since it launched in 2013, it’s been all about toughness and reliability, packing features like Euro VI engines, the PowerShift
3 transmission, and smart safety tech like MirrorCam and Active Brake Assist. The newer models are even better, with intelligent drive systems, digital controls, and a surprisingly comfortable cabin. It’s made for tackling the hardest jobs while keeping things safe and efficient – definitely a solid choice if you need some real muscle.
From my first-hand driving experience, the standout features of the latest MercedesBenz Arocs are its advanced safety systems, superior comfort, and significant improvements over previous models. With cutting-edge safety tech and a more comfortable cabin, the Arocs offers an enhanced driving experience, making it the perfect choice for heavy-duty operations.
The Mercedes-Benz Arocs optimises tasks in the construction industry by offering versatile solutions across a range of applications, including tippers, tankers, mixers, and brick bodies. Its adaptability ensures it can handle a variety of challenges, from tough terrain to heavy loads, making it the ideal choice for increasing efficiency and tackling the demands of any construction project.
The power and engine output of the Mercedes-Benz Arocs are impressive, delivering a smooth and responsive performance with excellent torque. This ensures the truck can handle heavy loads and demanding conditions with ease, providing both power and reliability for any job.
The design of the Mercedes-Benz Arocs is built with reliability and safety at its core. It features class-leading safety systems, including Brake Assist 6, which ensures optimal braking performance in critical situations. Additionally, the Arocs is now equipped with the extended safety features of GSR2, offering even greater protection and contributing to its exceptional reliability on the road.
HOW DOES IT PERFORM IN TERMS OF EFFICIENCY AND COST-EFFECTIVENESS?
The Mercedes-Benz Arocs excels in efficiency and cost-effectiveness, thanks to its fuel-efficient Euro 6 engine and advanced engine systems. Designed to perform in challenging terrains, the Arocs delivers impressive fuel economy while maintaining power and reliability. This makes it one of the leaders in its segment, offering businesses a cost-effective solution without compromising on performance.
WHAT IMPRESSES YOU MOST ABOUT THE OVERALL FINISH OF THE TRUCK?
What impresses me most about the overall finish of the Mercedes-Benz Arocs is its rugged, robust style, combined with its in-cab refinements, that ensure a comfortable and enjoyable driving experience.
The truck’s exterior is built to withstand tough conditions, while the interior offers thoughtful features that prioritise driver comfort, making it a perfect blend of durability and luxury.
WHAT TECHNOLOGICAL INNOVATIONS HAVE BEEN INCORPORATED INTO THE DESIGN – AND HOW HAS YOUR EXPERIENCE BEEN ELEVATED AS A RESULT?
The Mercedes-Benz Arocs incorporates several technological innovations, including class-leading Brake Assist 6, Front Collision Assist, and Side Assist. These advanced systems provide enhanced safety and support, giving drivers the confidence to tackle even the most hazardous conditions or demanding tasks. My experience has been significantly improved by these technologies, ensuring not only safety but also a smoother, more controlled driving experience in challenging environments.
HOW DOES THE CAB’S COMFORT ADD EASE TO THE OPERATOR’S JOB?
The cab of the Mercedes-Benz Arocs is designed with operator comfort in mind, featuring a range of creature comforts like air-conditioning, sat nav, Apple / Android Play, and comfort seats. Additionally, the option of comfort cab suspension further enhances the driving experience, ensuring a smoother ride, even on rough terrain.
These features combine to make the operator’s job easier and more enjoyable, ensuring they remain comfortable and focused, no matter how long the shift.
HOW DOES THE AROCS COMPARE TO OTHERS IN THE MARKET?
The Mercedes-Benz Arocs is a premium truck that excels in every aspect, making it a formidable competitor in the market. With its exceptional build quality, cuttingedge technology, and advanced safety features, it consistently outperforms rivals in both reliability and efficiency. Whether it’s handling tough terrain or providing a superior driver experience, the Arocs stands out as a leader in its segment.
The International Powered Access Federation (IPAF) has launched its Global Safety Campaign for 2025: Stop Overturns – Safety Starts on the Ground!
IPAF’s annual safety campaign, informed by data from its global Accident Reporting Portal, delivers a crucial message to the powered access industry. This year’s campaign focuses on the serious and often fatal consequences of mobile elevating work platform (MEWP) overturns. These incidents can result in operators and occupants being ejected from the platform and create complex rescue scenarios for those trapped at height during a partial overturn.
The latest statistics informing this year’s campaign revealed that: Fatal overturns increased by 50 per cent from January 2021-to-December 2023
The occupation most affected was MEWP operators, with a small number from delivery drivers, technicians / engineers, company staff and the public
The most common places for incidents to occur are construction premises, public areas, roads and highways, and rental yards
Reflecting on the Global Safety Campaign release, IPAF’s Head of Safety & Technical, Brian Parker, commented: “MEWP overturns continue to be a major cause of serious injuries and fatalities in our industry. With the launch
of IPAF’s 2025 Global Safety Campaign – Stop Overturns: Safety Starts on the Ground! – we are reinforcing a crucial message: ground conditions matter. By understanding the risks and implementing proper safety measures, we can prevent overturns, protect lives, and create safer work environments worldwide. Let’s work together to make a significant impact and
aim for a measurable decrease in MEWP overturns globally.”
Led by Brian Parker, Head of Safety & Technical at IPAF, and Alana Paterson, Head of Health, Safety & Environment at Taylor Woodrow and Chair of the IPAF International Safety Committee, the campaign emphasises when overturns occur, the hazards and risks – from injuries and fatalities to disruption of worksite and psychological impact –along with ways to manage and minimise the risks.
Recognising the global reach of the campaign, IPAF has developed new industry guidance: The Assessment of Ground Conditions and Supporting Structures for the Safe Use of MEWPs. It is split into two parts: guidance for MEWP users, with sections on dewatering, suspended floors, and temporary works, and guidance for MEWP operators, focusing on the MEWP travelling on uneven ground, elevated, stowed position, slopes and positioning.
MBNI Holdings Ltd, the parent company of M-B Truck & Van Ltd and Rossetts UK Ltd, has announced the successful completion of its full ownership to Pauline McKeating. This significant milestone marks a new chapter for the company, reinforcing its long-term vision for growth, stability, and excellence in the commercial vehicle industry.
With commercial facilities in Northern Ireland and the South of England, MBNI Holdings employs over 300 people and boasts a turnover exceeding £90 million.
Pauline McKeating, who has been with the company for over 25 years, has played a pivotal role in its growth.
Having served as Finance Director and later as Chief Executive Officer, she took over majority ownership in 2023. Her leadership was instrumental in the company’s recent expansion, including the opening of a state-of-the-art £6 million after-sales facility in Dungannon in October of last year.
Reflecting on this achievement, CEO Pauline McKeating shared: “This is an incredibly
proud moment for me. My journey with the company began 25 years ago in 2000, when I joined what was then Agnew Commercials as an Assistant Accountant. Over the years, I have had the privilege of growing with the business, and in 2020, I became a minority shareholder through a Management Buy-In. By 2023, I had acquired majority ownership, and today, I am thrilled to take full ownership of MBNI Holdings.”
This transition has been carefully planned alongside Neil McKibbin, whose leadership and industry expertise have been instrumental in the company’s success.
Pauline added: “Neil’s unwavering commitment has played a pivotal role in shaping the strong foundation upon which our business stands today. I want to extend my sincere gratitude to him for his trust, mentorship, and dedication over the years.”
Under the new ownership of Pauline McKeating, MBNI Holdings will maintain its commitment to operational excellence, customer satisfaction, and team development.
“While ownership has changed, our mission remains steadfast – to deliver industry leading service and to build on the incredible success we have achieved together. Our team is our greatest asset, and I am deeply grateful for their hard work, dedication, and passion. This is an exciting new chapter, and I look forward to leading MBNI Holdings into a bright future,” concluded Pauline.
Take a look at what Search Workshop Supplies (SWS) can do to help.
From a cable tie to a column lift – not to mention the superb Boxo modular storage system – SWS are strategically placed to be able to not only supply but give you all the advice you need to make 2025 the year that your workshop is brought right up to date and fully compliant.
A well-sorted and organised workshop is essential to the smooth running of a logistics operation. SWS stress that they can be relied on to do a whole lot more than supply everything that’s needed from their extensive stock holding in Ireland. The experience gained from over 50 years of trading uniquely position them to be able to offer advice on what’s required; to ensure all current and future legislation is met; and to provide the training and certification to ensure compliance and the safe running of the workshop in the months and years to follow.
The Boxo modular storage system is a central part of this. Built to withstand the toughest workshop environment the range incorporates a whole host of features to ensure the tools that are needed for the job are where they are needed, when they are needed.
Through an ambitious R&D strategy, SpreadTec has recently refined its range of Soil Stabilisation TBM (trailed binder meter) automatic cement and lime spreaders.
The rising costs of materials, reduction of input costs, sustainability, high accuracy and tracability, and environmental pressures are all key drivers in geotechnical engineering, with an everincreasing demand for high specification binding agent precision spreaders.
“SpreadTec is a young, dynamic and evolving brand.” said David Murphy, MD of SpreadTec.
“The design and engineering team are continuously refining the technology through testing and listening to market needs.” he added.
A highlight of the TBM range is the design of a new fully-integrated rear sealed cabinet onset to the existing series hopper which now safely houses the electronic and hydraulic control components. This new design, however, primarily includes the provision for the option of an automatically self-cleaning dust separation compressor and cartridge filtration system.
SpreadTec has an in-house design team who developed the software and electronic control system. The software features an automatic control system that dynamically adjusts the application rate to the ground speed, for consistent material application rates and control of cement, lime and binding
agent materials spread via a metering rotor regulator and auger applicator.
Unique features include operator optimal ground speed guidance control indicator and automated cleaning cycles for each main spreader component. The system can be remotely accessed to debug, monitor and screen shared with SpreadTec or Dealer support teams to both diagnose issues and guide the operator when required.
Key features include an intuitive in-cab main screen, dynamic application rate control, multiple product calibrations, data logging and remote telematic diagnostic support.
SpreadTec’s automatic hydro-electrical system incorporates a full suite of hydraulic controls and a vast array of safety interlocks. Every access panel to moving
parts has been fitted with an interlock sensor, which does not permit the machine to run unless in the safe closed position. The in-cab HMI display monitor indicates to the operator which specific access panel is not in its safe working position preventing accidental operation. The control system also monitors hydraulic pressure, stopping the system if there is a sudden pressure loss, also preventing trailed tractor driven machinery from inadvertent startups when spool valves are not set correctly.
A bird’s eye view of the working surroundings of the machine can be achieved with the optional surround view 360-degree camera system. In addition, a reversing camera gives the operator a clear view of the critical blind spot to the rear of the machine, vital when working in confined site areas along with an audible buzzer sound alarm.
SEAN MCKEE of J & S McKee Ltd. Civil Engineering Contractors in Portglenone, Co Antrim, Northern Ireland, has recently taken delivery of an automatic TBM 10 Auto as supplied by Laurence McMullan of McMullan Agri in Ballymoney.
“What stands out is the technology behind the user interface and the accuracy of the hydraulically driven metering wheel and auger. We can record and export data very easily and log different jobs as tracebaility is a major part of any project we undertake. SpreadTec is a solid addition to the fleet,” said Sean McKee.
The SpreadTec automatic and manual range of spreaders consists of trailed single and tandem axle along with truck/ADT chassis mounted models available in 10 – 18m3 capacity sizes and can achieve spread application rates of 1kg/m2-50kg/m2.
The next steps for SpreadTec is to exhibit at ICE EXPO on 24th-and-25th May in
Punchestown at stand 93 - 94 located in the Outdoor Equipment Pavillion. SpreadTec will showcase trailed single axle models at their stand where all visitors are welcome.
For enquiries, contact Terry Reilly, SpreadTec, on +353 89409189, email terry@ spreadtec.net, or visit www.spreadtec.net.
IPS Ireland is your leading Irish partner for powered access parts, service, workshop supplies and construction plant spares. The company – which was established in 2013 – started off with one staff member operating out of a shared rented office space on a drop shipment basis, building a network of customers and suppliers within the powered access industry.
Today IPS Ireland operates in a stateof-the-art facility centrally located in Dundalk, stocking a vast inventory of parts, enabling the team to provide a nationwide service throughout Ireland.
IPS Ireland is an independently-owned Irish company and proud to be the exclusive Irish distributor for numerous top-tier brands within the industry. Recently the company established strong partnerships with UK-based SafeMewp Safety Attachments, Aresta Safety Products, and The Crane Pad Shop as the sole Irish distributor of their range of products. Upholding the highest standards of quality assurance is integral to IPS Ireland’s operations, solidifying its reputation within the industry’s landscape.
IPS Ireland’s IPAF trained, CAP certified engineer carries out service, repairs and certification of machines nationwide. The company offers an all-inclusive solution encompassing servicing, parts, and installation.
To maximise convenience, the team have developed an online portal. This modern platform facilitates customer access to certificates at their convenience, regardless of their location or device used. For security and ease of use, individual logins are provided – customers can view or download their certificates at any time.
IPS Ireland’s comprehensive inventory boasts over 10,000 parts, strengthened by its solid connections with top-tier manufacturers and suppliers. This allows the team to assure swift delivery times coupled with highly competitive pricing.
By choosing IPS Ireland as your provider, equipment downtime is significantly reduced. Regardless of the specific part you require or the time-frame in which it is needed, rest assured that if it is not already in the warehouse, the team will go the extra mile to get it for their customers.
The company’s close connections with manufacturers have given them the opportunity to supply new and certified used powered access and material handling equipment. Each used machine is meticulously selected and fully serviced by their CAP accredited engineer, complete with a fresh GA1 certification.
If IPS Ireland hasn’t got it, the team can source
and offers assurance that they are buying from a trusted reliable supplier.
IPS Ireland supplies and installs stands and shelving for your workshop or mobile service vans. The stands are supplied with a collection of parts and workshop essentials which can be tailored for specific machines depending on the fleet. The team complete weekly or monthly stock checks for their customers and replenish any stock that has been used, with frequent reviews to update the inventory of stock as requested. The service was set up to take the hassle out of workshop management for customers and ensures they have what they need to keep operation running avoiding waiting for parts to be delivered.
An array of both current and potential customers representing different areas of the industry participated in Dennison JCB’s Demo Dig Day. The Dennison JCB team hosted the much-anticipated test drive event at its Ballyhartfield demo yard to showcase the new JCB Mini Diggers and new 145XR. In addition to providing special event exclusive offers on the company’s range
of new / used stock diggers, attendees garnered further information and insights from the expert Dennison JCB team who were on hand to help, and even had the opportunity to enjoy a burger in the sunshine.
As JCB’s construction dealer covering sales, service and parts for the Northern Ireland and Co Donegal markets, Dennison JCB continues to be recognised for its quality provisions and focus on customer service and after-market care.
Caterpillar Inc. has announced the launch of the next generation ultrahigh demolition excavator, the Cat® 330 UHD, designed to be a highly versatile machine with uncompromised functionality and enhanced safety for emergency responses, urban and city operations.
Focused on urban residential demolition, where it will compete in the 30 MT size class, the 330 UHD features a UHD boom with a maximum pin height of up to 20 m (65’ 6”) to make it comfortably capable of five-to-six-story work.
It is essentially two machines in one – while the UHD boom accommodates all standard demolition work tools, the machine also accepts two types of retrofit booms (single and variable angle (VA) boom
type). The changeover to deploy traditional buckets and work tools in the role of a ‘standard’ construction excavator takes a short amount of time.
“Caterpillar built the 330 UHD to withstand difficult demolition of tall structures. Careful attention-
to-detail has seen the 330 UHD designed to reach even the trickiest inner-city worksites, with a transport width of less than 3m (3’10”). The machine is quickly and easily reconfigurable, allowing operators to extract maximum return from the
machine by deploying it for general construction when not required for demolition contracts,” explained Vincent Migeotte, Senior Product and Sales Consultant at Caterpillar.
The 330 UHD offers operators best-of-class performance with its capability of carrying a large demolition 3300 kg (7,275 lb) work tool at great height up to 20m (65’6”). To optimise its utilisation with the retrofit boom, it is also configured with up-todate technology such as Cat Payload, Cat 2D Grade control system, and Cat 2D E-fence. The latter helps keep the front linkage within a predefined work area, helping provide operator confidence while protecting the machine from damage and monitoring jobsite safety.
Takeuchi, one of the world’s favourite brands of excavator, has recently hit the 50,000th sales milestone in the UK and Ireland.
The 50,000th Takeuchi, a TB217R mini excavator, was sold by a Takeuchi dealer in the south CBL to L-Lynch Plant Hire & Haulage as part of a recent order for over 100 machines, including the latest third generation 3-Series excavators. It’s not Lynch’s first Takeuchi; in fact, they have been running Takeuchi excavators for decades. The first order in the year 2000 included the original Takeuchi TB175, both tracked and wheeled. Since then, Takeuchi excavators in all sorts of sizes have always been part of the Lynch fleet. Lynch remains one of the UK’s best known plant hirers and has always
been attracted by Takeuchi’s promise of “designed and built for hire”.
From the outset, Chairman and Founder, Liam Lynch, always considered Takeuchi an important part of his fleet. He said: “Our customers and service fitters liked the machine and that’s why over the years we have probably invested in more than 1000 Takeuchi units.”
Charlotte Barford, Managing Director of CBL, expressed her pride in the milestone, stating: “This is a truly special moment for CBL, and we couldn’t be more delighted to share it with Lynch. The sale of the 50,000th Takeuchi mini excavator is a testament to the strength of the Takeuchi brand, the trust of our customers, and the dedication of the CBL team. At CBL, we’re passionate about supporting our customers with the
very best equipment and service, and we look forward to continuing to work closely with Lynch and all our valued clients.”
Excitement is rife and the industry is ready – with the ICE Expo 2025 soon sweeping across the sector and making its mark upon attendees and exhibitors alike!
Ireland’s leading innovative construction and equipment show is set to kick off at Punchestown Racecourse, Co Kildare, on Friday 23rd May and Saturday 24th May. Attracting visitors spanning the globe and a line-up of renowned exhibitors, the show is the brainchild of industry expert, Danielle McSorley, founder of DMC Consultancy, and Managing Director of Quarryplant International.
In a bid to reflect the evolving sector and showcase the latest improvements shaping the future of construction, the event is providing a platform for industry professional manufacturers and designers to exhibit and explore cutting-edge technology and equipment.
The forward-thinking mission of the event has been crafted
in response to the new Environmental Social Governance (ESG) legislation which is heralding in a new era, and meaning that companies will have to align with mandatory and regulated sustainability reporting.
The expo will therefore be a key source of assistance for companies to implement ESG, along with measures that help make construction quicker, increasingly costeffective, and safer.
Free admission
Esteemed exhibitors
Networking and meeting areas
Industry-leading speakers
Live interviews
Q&A panels
Live demonstrations
Food truck catering
On-site catering
Live entertainment on Friday evening
Children’s entertainment on Saturday …and much more!
REGISTER NOW
Don’t miss the chance to be part of the must-attend construction event and experience the technology and ideas that will shape tomorrow’s infrastructure today.
The free-of-charge tickets can be reserved via Eventbrite.
Prior to the ICE Expo 2025’s arrival in Punchestown on Friday 23rd May and Saturday 24th May, Danielle McSorley, founder of DMC Consultancy, and organiser of the pinnacle industry event, grants Plant & Civil Engineer a peek behind-the-scenes of the show’s execution – as well as a preview of the exciting advancements which attendees of the expo can expect.
WITH THE ICE EXPO 2025 EDGING INCREASINGLY CLOSER, HOW ARE YOU FEELING?
I’m very excited and delighted with how everything is coming together as we approach ICE Expo 2025. The support from the industry has been phenomenal, and it’s incredible to see the enthusiasm from exhibitors, ICE Expo staff, and attendees alike. The momentum behind this event is truly inspiring, and I can’t wait to be a part of delivering an experience that reflects the strength and progress of our sector.
REFLECTING BACK, CAN YOU OVERVIEW THE INSPIRATION WHICH UNDERSCORED THE CREATION OF THE EVENT –AND THE STEPS YOU HAVE TAKEN TO MAKE IT HAPPEN?
The inspiration behind ICE Expo stemmed from my deep passion for plant equipment and the industry as a whole. I knew that
Ireland, particularly given that over 65 per cent of the world’s crushing and screening equipment is manufactured in Tyrone, needed a dedicated platform to showcase this innovation and expertise. As I spoke with industry leaders, many of whom approached me expressing the need for such a show, it became clear that this was something the sector truly wanted. That support and encouragement solidified my decision to make ICE Expo a reality. From the initial concept to now, the journey has involved extensive collaboration, meticulous planning, and a shared vision with industry leaders. Seeing it all come together has been incredibly rewarding, and I’m proud that the event is providing a stage for companies to showcase their latest advancements to a global audience.
HOW HAS YOUR HERITAGE PLAYED A ROLE IN THE JOURNEY?
My heritage has played a huge role in this journey. With my family being involved in the industry for over three generations, it’s truly in my blood. I was quite literally
born into it – attending plant shows before I could even walk – so it was inevitable that my path would lead me here. Beyond family, this industry has given me life-long friendships that feel just as close as family. The connections, experiences, and shared passion over the years have shaped my perspective and fuelled my drive to create an event like ICE Expo. It’s more than just business; it’s a community, and I’m proud to be playing a part in bringing everyone together to celebrate and showcase the best of what we do.
One of the biggest highlights of this journey has been reconnecting with people I haven’t spoken to in years – catching up, sharing stories, and seeing how much the industry has evolved. The support and excitement from both old friends and new connections have been incredible. At the same time, as a perfectionist, there’s something deeply fulfilling about ticking off the boxes during the planning stages. Seeing each element come together, from securing exhibitors to finalising event details, has been incredibly rewarding. Every milestone reached brings us one step closer to delivering an event that truly represents the strength and innovation of this industry.
HAVE THERE BEEN ANY CHALLENGES FROM AN ORGANISATIONAL STANCE WHICH YOU HAVE HAD TO OVERCOME?
Of course, there have definitely been challenges – some of which I couldn’t possibly mention in this interview! But honestly, if life didn’t have challenges, it’d be pretty dull. Overcoming obstacles is what makes the journey exciting and rewarding. One thing I will say is that my measuring skills have definitely improved throughout this process, something I didn’t expect to be such a big focus! Though, I’m still not quite ready to claim expert status just yet. I’ll also admit, I didn’t realise at the start just how much this would explode. It’s been a wild ride, but I feel so incredibly blessed to have the most amazing team of staff working alongside me.
There are too many to name, but they all know who they are, and their hard work and dedication have made all the difference in making ICE Expo what it is today.
The feedback from the industry has been absolutely incredible. The support I’ve received has been overwhelming, and it has truly filled me with confidence. Through this process, I’ve not only strengthened existing relationships but also made lifelong friends, which has been one of the most rewarding aspects of this journey. From day one, my goal was to create a show that truly serves the industry and its exhibitors. That has always been at the heart of ICE Expo. I started my marketing company, DMC Consultancy, because I love helping people and seeing them grow,
and I genuinely believe that by running ICE Expo, I’m doing just that – just in a different way. Seeing businesses gain exposure, connect, and thrive because of this event makes all the hard work worth it.
We are pulling out all the stops to make sure the attendee experience at ICE Expo 2025 is truly unforgettable. From face painters and bouncy castles to free entry, we want this to be an event for everyone. One of the biggest highlights will be the demo area, where attendees can watch machinery in action up close – bringing the industry to life in a way you won’t see anywhere else. We’re also hosting the largest Operators Challenge, where the best in the business
can put their skills to the test, and of course, there will be a fantastic selection of food and a fully stocked bar – because let’s be honest, some of the biggest deals in this industry are done over a drink! On top of all that, we have top industry leaders speaking on stage, sharing insights and expertise that you won’t want to miss. It’s not just an expo – it’s an experience, and we can’t wait to welcome everyone!
I’m most looking forward to seeing the smile on exhibitors’ faces – when all their hard work, planning, and effort come together, and they see real engagement and success at the event. There’s nothing better than that moment when they realise it’s all been worth it!
The latest equipment innovations, automation technology, and sustainable solutions on display will reflect future advancements across the sector. Our aim is to look into the future of construction and see where it will be in 10 years’ time.
ARE THERE ANY FURTHER
YOU CAN GRANT OUR READERS AHEAD OF THE ICE EXPO?
Get ready for some equipment launches at ICE Expo that’ll be even more exciting than NASA’s! Seriously, we’re lucky to have such brilliant engineering innovators in such a small country, constantly pushing the limits.
Merlo is excited to exhibit at the inaugural ICE Expo this May at Punchestown Racecourse.
Visit Merlo at Stand 23, where we will showcase an impressive range of telehandlers designed to enhance efficiency, performance, and sustainability in the construction industry. From compact models to high-capacity solutions including Merlo’s flagship ROTO, Merlo has the perfect machine for every job.
50.26SPLUS – A high-performance rotating telehandler engineered for demanding job sites. With a 26-meter lifting height and a 5-tonne capacity, it delivers exceptional reach and strength. Featuring a tilting cab for enhanced operator visibility, a dual hydraulic pump for faster cycle times, continuous 360° turret rotation and an out-anddown stabiliser system for superior stability and efficiency. Ideal for construction, forestry, and infrastructure projects, the 50.26SPLUS delivers precision, power, and versatility in every lift.
P40.17PLUS (Stand 23) & 40.14PLUS (Parade Ring) – These telehandlers offer 4 tonne lift capacity with 17m and 14m lift height, respectively. Perfect for housebuilding and construction, they excel in lifting roof trusses, positioning
pallets of bricks and blocks, and placing materials on scaffolding or rooftops. Merlo’s advanced stabilisers, boom side shift, and chassis levelling combined with a compact stabiliser design provide maximum manoeuvrability and unmatched safety on busy job sites.
P120.10 – Designed for the toughest lifting tasks, this powerhouse features a 170hp FPT engine, a maximum lift capacity of 12 tonnes and lift height 9.8m. Its high-capacity axles with epicyclic reducers and oil-immersed brakes ensure smooth and controlled handling under heavy loads. The elevated cab position enhances visibility, and boom side-shift and frame levelling provide precise and efficient operation.
P27.6PLUS – Despite its compact dimensions – only 1.86m wide and 1.96m high – this 75hp telehandler offers an impressive 2.7 tonnes lift capacity and a 6 meters lift height.
TF33.7G – Striking the perfect balance between performance and size, the simple gear pump TF33.7G offers a 3.3-tonne lifting capacity and almost 7 meters of lift height. Powered by 75hp Kohler engine, it remains a top choice in Merlo’s compact construction range.
Cingo M500DM – Powered by a 5.5hp Honda petrol engine, this versatile compact tracked carrier offers 500kg capacity
and narrow width of only 690mm. It is designed to handle materials in tight spaces, ideal for agricultural, construction and landscaping operations.
Merlo’s telematics system offers proactive maintenance capabilities, enhanced security through real-time data, accessible via desktop or smartphone apps, allowing operators to monitor performance and maximise uptime.
Merlo’s 2025 line-up at ICE Expo underscores Merlo’s commitment to deliver versatile, high-performance, and sustainable solutions. Whether a compact telehandler for tight spaces on busy jobsites, a materials handler offering exceptional reach, precision or stability, or a powerful machine for the toughest tasks, Merlo integrates advanced levelling technology, intelligent control systems, and industry-leading safety features to meet every construction challenge.
ICE Expo is the perfect opportunity to meet both the Merlo team and Merlo’s dealer representatives in Ireland. Visitors will see how a Merlo can enhance efficiency and productivity in construction operations.
Originally established in 1991 as a plant hire company, Shannon Valley Group is a family-operated and owned business that has rapidly grown and diversified over the years, evolving into one of Ireland’s largest and most progressive civil engineering and plant hire companies undertaking construction and civil engineering projects both in Ireland and abroad. With its dedication to quality, efficiency and client satisfaction, Shannon Valley strives to complete projects to the highest standards, on time and within budget.
Innovative solutions and adherence to the highest safety and quality standards and professional construction management are the hallmarks of Shannon Valley.
The company is certified to I.S. EN ISO 9001:2015 Quality Management System, ISO 14001:2015 Environmental Management System and ISO 45001:2018 Occupational Health and Safety Management System standards and is committed to ensuring that continual improvement is a part of every employee’s job through the setting of standards and the reviewing of practice at regular intervals.
The scope of the work undertaken varies in type and size, from multimillion euro projects to small and medium-sized contracts covering all sectors of the industry. Projects undertaken include the construction of motorways and regional and local roads, coastal defence works, tidal works, hospitals and construction of water attenuation systems.
The company has also undertaken various types of groundworks, including deep large diameter drainage, utility installations, site
clearance, commercial/industrial/residential development works, landfill facilities, major earthworks, rock breaking and the processing of subsequent materials for re-use and more recently soil stabilisation works. It is also involved in recycling works, quarry works and demolition projects. Shannon Valley has a comprehensive and modern fleet of civil engineering plant machinery, equipment and lorries. The fleet covers the full spectrum of civil engineering needs and requirements and provides it with the flexibility to meet the daily demands of individual projects nationwide.
Shannon Valley employs high calibre individuals from a broad skills base and selects and assigns individuals with the precise mix of skills and experience demanded by each project thereby earning Shannon Valley a reputation for
professional excellence and delivering projects on and ahead of schedule without compromising quality or safety.
Shannon Valley is focused on the sustainable construction practices, such as soil stabilisation and ground improvement. Soil stabilisation provides an opportunity to employ value engineering and maximise the re-use potential of these low strength soils. The process of enhancing the existing properties of soil onsite, as opposed to engaging in the disposal or importation of aggregates, encapsulates a practical and environmentallysound methodology to significantly reduce a project’s carbon footprint.
Shannon Valley will initiate and manage the project, co-ordinate soil testing prior and field testing during works, engage with an accredited laboratory
and geotechnical consultants. The team of experts will survey a site and carry out health and safety risk assessment and compile a Construction Quality Assurance report and project sign-off.
SITECH will showcase its expertise in providing cutting-edge machine guidance solutions and hands-on technology demonstrations to customers at this year’s ICE Expo.
Visitors to ICE Expo, which will be held on 23rd and 24th of May in Punchestown, Ireland, will be able to get first-hand experience of the latest innovative site survey equipment that promises to deliver project efficiencies across the construction industry.
According to the Construction Industry Forecast for the Republic of Ireland (CIS) the industry is set to grow by 11 per cent in 2025, due in large part to the Irish government’s ambitious housebuilding target of completing 30,000 units by the end of 2025. As a result, the quarry and aggregate industries face mounting pressure to ensure efficient delivery of high-quality materials, whilst supporting sustainable practices.
SITECH will be offering visitors the chance to view the Trimble
Connected ‘field to finish’ workflow including Trimble Stratus, Works Manager, and Works OS while also providing hands-on demonstrations with the Trimble Civil Construction portfolio.
Brian Core, Regional Sales Manager at SITECH UK & Ireland, said: “The Trimble Connected Site integrates both on and off machine solutions while streamlining workflows making it an essential tool for businesses
looking to meet the increasing demands of the industry. By combining data management with fleet management capabilities this technology enables a seamless workflow, improving project visibility and efficiency.
“We are really looking forward to bringing this technology to visitors at the ICE Expo. Our experts will be on hand to showcase how our technology solutions bridge the gap between survey data and machine performance, and to advise on how to marry up that data with the improvements and efficiencies our customers want to see in their businesses.
“With demand in the construction industry booming it is vital companies are doing all they can to maximise their efficiencies, and we are passionate about the benefits this technology can bring – particularly in sectors where safety and environmental impact are high-priority.”
Meet SITECH’s experts at Stand 123 to explore how precision technology can transform on-site operations from datacapture to efficiency gains.
The Trimble® Siteworks Machine Guidance Module is a powerful surveying tool on and off machine. Now you can use the same hardware and software to perform a variety of tasks on the job site.
Contact us to find out how to get the best of both worlds—machine guidance and construction surveying at a fraction of the cost.
Rapid International is proud to announce the successful installation of a state-ofthe-art, bespoke concrete batching plant at Coshla Quarries in Galway. Designed and constructed to meet the growing demand for high-quality concrete in the region, this custom-built facility is set to revolutionise the quarry’s concrete production capabilities.
With a focus on modernisation and efficiency, Coshla Quarries partnered with Rapid to develop a solution tailored specifically to their needs. The heart of the plant is the powerful R3000, a 3m³ output Rapid pan mixer, renowned for its ability to deliver consistent, high-quality mixes with every cycle. The facility boasts an impressive array of features, including five 50-tonne aggregate bins, providing ample capacity to handle a wide range of material requirements. This is complemented by three silos – two 80-tonne and one 60-tonne – for maximum storage flexibility, ensuring that the plant remains operational even during peak demand periods.
The plant also includes a Rapid Jetwash high-pressure mixer washout system, designed for quick and efficient cleaning, reducing downtime and ensuring the facility operates at peak performance. Additionally, a specially designed shutoff device on the readymix chute prevents drips and ensures a cleaner, more hygienic working environment.
With this bespoke batching plant, Coshla Quarries is poised to elevate its concrete production, significantly reduce operational downtime, and improve overall efficiency. Rapid’s innovative approach to concrete batching continues to set industry standards, and this project is another example of how bespoke solutions can drive progress in the concrete sector.
NML Solutions is setting a new standard in the truck-mounted crane and hook loader sector, bringing tailored solutions and exceptional service to transport managers across Ireland. As the exclusive importer and supplier of Hiab equipment on the island, NML leverages its extensive industry knowledge to provide customers with complete, customised solutions that drive operational efficiency.
Led by industry veterans Colm Browne, Luke Carberry, Greg Thompson, and David Gibson, the company’s management boasts over 150 years of collective experience. This expertise enables NML Solutions to deliver streamlined processes from concept to completion, encompassing chassis
selection, crane integration, and body building. Clients benefit from a single point of contact, ensuring a seamless and hassle-free experience.
“We’re not just providing a crane or a truck body,” says Colm Browne, Sales Director
at NML. “We work closely with our clients to understand their operational needs and create bespoke solutions that maximise productivity while minimising downtime.”
NML Solutions prides itself on its close partnerships with
leading bodybuilders and truck manufacturers, ensuring the right components are matched to meet the precise needs of its clients. The company’s in-depth knowledge of industry regulations and operational requirements means transport managers can rely on their expertise to optimise fleet performance while remaining compliant.
Operating from a cutting-edge 45,000-square-foot facility in Toomebridge, Co Antrim, NML Solutions offers a comprehensive range of services, including equipment assembly, testing, and operator training. Their state-of-the-art LOLAR testing facility ensures all cranes meet safety and operational standards before delivery. This emphasis on quality assurance is a hallmark of NML’s service, giving clients confidence in their investment.
The company’s commitment to operational excellence extends beyond product delivery. NML Solutions provides an extensive support network, featuring in-house experts and mobile service vans that deliver on-site assistance across the island. This proactive approach reduces downtime, keeping customers’ operations running smoothly. Additionally, regular crane testing and maintenance services ensure longevity and safe operation, fulfilling regulatory requirements for clients in sectors, such as waste management, construction, and forestry.
A significant advantage for NML Solutions clients is the holistic approach the company takes to project management. By managing the entire process, from the initial concept and design to manufacturing, installation, and servicing, NML eliminates the need for transport
managers to co-ordinate multiple suppliers. This streamlined experience translates to faster delivery times and greater operational efficiency.
The company’s partnership with Hiab, a globally renowned leader in load-handling equipment, further solidifies its reputation as a trusted provider in the Irish market. Hiab’s innovative products, combined with NML’s expertise, ensure clients receive cutting-edge technology backed by local, knowledgeable support.
Training and safety are integral to NML Solutions’ offering. The Toomebridge facility includes a dedicated training centre where clients receive handson instruction in the safe and efficient use of their new equipment. By empowering operators with the skills they need, NML helps clients maximise uptime and minimise risk. Looking to the future, NML Solutions remains committed to expanding its capabilities and refining its offerings. With ongoing investments in staff training, technological
advancements, and service enhancements, the company is poised to continue leading the way in the truck-mounted crane and hook loader market. For transport managers seeking a comprehensive solution backed by exceptional expertise and service, NML Solutions provides the assurance of quality, innovation, and reliability. Whether navigating the challenges of waste and recycling, construction, or specialised transport, clients can count on NML to deliver tailored solutions that elevate operational performance.
NML Solutions is excited to announce its participation at the ICE EXPO on 23rd-and24th May 2025. Visit them at stand numbers 116 and 122 in the outdoor area to explore their latest innovations and speak directly with their expert team about how they can support your operational needs.
range of high-quality parts to keep your crushing and screening equipment running at peak performance! Whether you need wear parts, screens, or other essential components, the team have got you covered.
Crusher Screen Parts is committed to delivering the highest quality products and services to its customers. The team of experts continuously strive to create new and innovative solutions that
enhance performance and maximise efficiency.
Believing that the company’s success is intertwined with the success of its customers, the team are dedicated to supporting them in achieving their objectives.
CRUSHER SCREEN PARTS STOCKS:
• Wear parts
• Jaw liners
• Blowbars
• Screenbox parts
• Electrical parts
• Rollers
• Skirting rubbers
• Filters
• Hydraulic motor and pumps
• Hydraulic cylinders
• Wide variety of couplings
• V belts and pulleys
• Bearings
• Conveyor drums
• PTO / clutch
• Oil coolers
• Mesh
• Springs
Call Crusher Screen Parts or email the team today for a quotation or to discuss your spare parts requirements.
Introducing the innovative Screenpod REVO 1200T Reversible Impact Crusher, a groundbreaking mobile crushing solution that sets a new standard in aggregate processing technology. This newly engineered tracked impact crusher combines versatility with a unique hybrid design, seamlessly adapting to a variety of job site conditions while delivering exceptional efficiency and flexibility.
The Screenpod REVO 1200T is designed to operate independently on its own generator or can be connected to an external power source, providing ultimate convenience and effortless integration into any crushing operation. It’s particularly effective in secondary and tertiary crushing of rock and the recycling of building materials.
Key design features include a 6-hammer reversible rotor that operates bi-directionally within the chamber. This innovative mechanism ensures consistent geometry between the hammer and the nine impact bars as they wear down, maximising throughput consistency and performance
while promoting even wear across the blow bars. This results in a significantly extended service life and improved product quality, particularly in sand production (0/4mm), yielding better grain shape and notable energy savings. The REVO 1200T is an excellent alternative to cone crushers and VSI (Vertical Shaft Impactors), accommodating a maximum feed size of up to 120mm.
With customisable crushing gaps and variable speed drive (VSD) control, the Screenpod REVO 1200T allows for precise adjustments in material size and consistency, making it ideal for a wide range of applications, including:
• Aggregates
• Oversized gravel
• Asphalt
• Concrete
• Construction
• Demolition waste
• Glass recycling
• Aerated concrete
• Natural rock
• Sand
• Stone
• Secondary Feed – Tertiary Output
• Lower energy requirements versus VSI
• Large in feed up to 120mm
• 6 hammers – even wear with unique adjustment system
• Reversible rotor for maximised wear part usage
• 9 impact areas – 9 hits, for reduction / shaping
• 60% + passing 0-6mm single pass
• Unparrelled cubicity on sand & chip produced
• Minimised filler/fine sand vs VSI
• Mobile and static solutions
The Screenpod REVO 1200T is the preferred choice for industries focused on maximising material value, reducing operational costs, ensuring material consistency, and enhancing overall performance.
Engcon Ireland are very pleased to be exhibiting at the inaugural ICE Expo 2025 – with the team hoping that the new show proves to be a success and will act as showcase for the latest in construction and plant technology.
Engcon will have on display a number of their newest products, including their DC3 control
system, their next generation control system for excavators.
Engcon Ireland will also be displaying their all new generation 3 tiltrotators Engcon will additionally have their most advanced offering for mini diggers the all new EC204. Now available with EC-Oil on top and underneath, built in tilt and rotation sensors for integrating with dig systems, and also a new option for detachable gripper allowing you to drop off the weight of the gripper when it is not required, allowing for maximum lifting capacity and compactness when working in tight spaces.
Furthermore, Engcon Ireland will have a full working demonstration at the show and be running a number of special offers for customers on both days.
The Engcon Ireland team look forward to welcoming you to ICE Expo.
Our EC-Oil quick coupler lets you switch tools quickly and easily— all from the comfort of your cab. When you buy your next tiltrotator from us, EC-Oil is included*. Switching between hydraulic tools has never been easier.
Call us about EC-Oil: +44 1684 29 71 68 or visit engcon.com for more information.
At the forthcoming ICE Expo taking place in Punchestown in May, McHale Plant Sales will open a window on the world of Komatsu and Metso in what their Marketing Manager, Sean Ryan, says: “will be one of the most exciting shows of construction equipment we have ever put on exhibition”.
The expansion that has been taking place at McHale Plant Sales in recent years – not just in Ireland but across the Irish Sea in England, Scotland and Wales resulting from
their appointment in 2023 as UK distributor of Metso crushers – will be reflected in large in their exhibit.
As distributors of Komatsu construction plant and equipment and Komatsu forest harvesting equipment, the Birdhill, Co Tipperary and Rathcoole-based company enjoys a close relationship with most of Ireland’s leading contractors – in civil works, construction, and infrastructure development – and in the forests of Ireland, north and south, which are now
making such an important contribution in capturing CO2 emissions while helping to achieve net-zero targets.
Flag bearers in Ireland, Northern Ireland and across the UK for Finland’s acclaimed Metso stone crushers favoured by quarry owners and aggregates producers across the globe – McHale Plant Sales has the favoured position of having been the first European distributors chosen by Metso to receive their gold standard award and a recipient also for an award for marketing.
Depending on ground surface conditions at Punchestown, the McHale Plant Sales team hopes to exhibit some of the heaviest and most impressive units from their Komatsu and Metso portfolios, including also units from the Irish-made, MDS trommel range of bespoke units that are building an enviable reputation both in home and export markets.
On the Komatsu front, it is likely that their latest PC228 and PC138 excavators will have pride of place. With them will be units from their
micro-mini-midi diggers range favoured by utilities contractors and leading equipment rental outlets across the country. There too on the McHale Plant Sales stand also will be units from Komatsu’s latest skid-steer range machines, equipment that their Marketing Manager, Sean Ryan, says: “embody all of the knowledge, technology, and operational effectiveness that Komatsu could introduce in machines of this design and calibre”.
Mindful that roads to the ICE Expo will likely be crammed, not just with construction and civil works ‘afficionados’ and major corporates, but with Komatsu users and a host of others, the advice from Sean Ryan is: “invest sufficient time to see all that McHale Plant Sales has to offer”.
Calling out to agricultural and forestry contractors, plant hire specialists, utilities services providers, and plant and machinery fans from all walks of life – including those
diorama builders who fascinate themselves by constructing table-top displays of real-life worksites – Sean Ryan and McHale Plant Sales is filling their exhibit with what they say
will be: “as wide a choice of exhibits as ground conditions and display space will allow”.
Summing it up, Sean Ryan said:
“In addition to the warm welcome that will await visitors to the McHale Plant stand will be a selection of the very latest and most popular units from Komatsu and Metso, two of the world’s leading construction plant and equipment manufacturers”.
“In addition to the enjoyment and welcome visitors to our McHale Plant Sales exhibit can expect, space and ground conditions permitting, we hope also to include in our display a Komatsu forest harvester and, hopefully, a tracked dump truck or forest mulcher from our recently-acquired Prinoth range,” Sean added.
Leading construction equipment dealer, HES Enterprises, of Irlam, Manchester, has received the 2024 Best Market Coverage UK & Eire award from Hyundai Construction Equipment Europe.
The business, which offers the full range of Hyundai machinery across a wide range of industry sectors, celebrated 25 years with the manufacturer in 2024 and is working towards continued success in the future.
“We joined forces with Hyundai in 1999 and we’ve never looked back,” said HES Managing Director, Andrew Shaw.
“2025 has started really strongly and we are looking forward to another successful year.”
Anthony Hogben, Regional Sales Manager for the UK and Eire, presented HES with the award, adding: “This is going to be a massive year for Hyundai, with a broadening of the line-up that will take the company into new market sectors, many in answer to customer request. With highquality dealers like HES, who have built such strong relationships with customers over many years, we are anticipating further growth across the market during 2025.”
Hyundai Construction Equipment Europe continues to recognise the achievements of its sales and after-care network, through its annual Dealer Awards. Celebrating sales and service success across Europe, the awards recognise the dedication, expertise and experience within the distribution network.
McHale Plant Sales has confirmed the imminent availability on the Irish market of two new fully-redesigned Komatsu skid-steer loader and compact track loader machines which ‘prototyped’ at the bauma 2025 exhibition: a new 4-tonne skid steer loader and a new 5-tonne compact track loader.
According to their Sales Director, Denis McGrath, who attended their introduction, the new units join Komatsu’s Dash-8 range to bring, what he calls, “unbeatable customer values to the loader sector”.
Specifically focused on the European market, both units provide “outstanding capacity and hydraulic specification powered by a low emission and low maintenance stage V engines to deliver one of the highest operating capacities in their category, merged with superior lifting, breakout, and traction force,” Denis McGrath said.
Features to benefit operators, include low emissions operation from their 53,7 kW Stage V compliant engine with diesel particulate filter; outstanding stability
and weight distribution in all conditions; manoeuvrability and highest driver comfort; all backed by powerful performance, lift pin height, and category-leading lifting capacity.
Other enhancements include redesigned hydraulics: reduced maintenance cost; a new cab layout with pull-up sliding door for comfort and non-stop working in all conditions; and new operator comfort functions that include an airsuspended seat, pressurised cab,
easiness of operation functions, such as slow speed system, cruise control, adaptive steering, return to dig, and other drive modes.
A rear-view camera with ‘human’ detection system, radio, LED lights and an optional front hydraulic quick coupler add to what McGrath says are “two worthy additions to the Komatsu portfolio, engineered for applications in which skid-steer units are deemed the most effective, most economical, and most cost-value choice”.
SANY UK has released a next generation of operator’s cab for its larger excavators, designed to enhance comfort, safety, and productivity.
The new generation of cabs for machines 13-tonne and above has been engineered with the operator at its core and is tailored to meet the demands of modern construction sites. Every detail, from the seating to the control layout, has been created with the aim of enhancing the user experience and providing greater levels of safety.
SANY has additionally utilised ergonomic design, automotive quality materials, and engineering excellence to deliver exceptional comfort.
Key features include a premium heated air suspension seat (cooling optional) that adjusts its position based on the weight of the operator and provides high levels of comfort throughout the workday.
New wide armrests with multipositional locations also allow for an optimal working posture.
Other features include:
• Smart technology integration: the cab comes equipped with a large 10” highresolution touchscreen, integrated telematics for easier fleet management and 20 programmable work modes to optimise performance for specific tasks
• Automatic climate control: maintains internal cab temperature settings, regardless of external ambient temperatures, ensuring optimal comfort in all weather conditions, allowing operators to maintain focus and productivity
• Noise and vibration reduction: stateof-the-art insulation and dampening technology significantly reduces noise (69 dB(A) / 70dB(A) and vibration levels, creating a quieter and more comfortable working environment
• Safety first: the cab features a rear, rear/side or 360O degree camera, to ensure operator safety at its highest. Keyless start and immobiliser pincode, linked directly to EVI Telematics, ensure complete peace of mind
“At SANY UK, we understand that the operator’s experience directly impacts the success of every project,” said Jonathon Smith, Product Manager of SANY UK.
“This latest-generation cab is a testament to our commitment to our customers. By listening to their feedback, we’ve created a cab that delivers greater levels of comfort, safety, and performance. There’s many more exciting things to come for SANY excavators, and this is just the start.”
The new operator’s cab will be available across a range of SANY’s excavators from 13T plus. Customers can explore the new features first-hand by visiting their nearest SANY dealership or booking a demo.
ECO
ECO Soil Improvers
ECO
ECO Lego Blocks
Sustainable
BS3882 Certified Engineered Topsoils
ReCon Resources is accelerating its mission towards a more sustainable infrastructure sector – with the launch of its new readymixed concrete business, ReCon Concrete. The new arm of the business is dedicated to delivering more environmentally-friendly concrete solutions across communities. Whether it’s a small DIY project or a large construction endeavour, the latest move by the business means that highquality concrete made from eco-friendly materials is easily accessible.
Darragh McConville, Business Development Manager for ReCon Resources, explained that the formation of the latest company branch was a logical progression for the
team, as he outlined the initial steps and inspiration that propelled the idea forward.
“ReCon Concrete is a spinoff from ReCon Resources,
which was founded in 2011 by Managing Director, Daniel Connolly. With over a decade of experience in waste management and
material recycling, the move into sustainable concrete production was a natural progression. Recognising the potential to repurpose waste materials into high-quality construction products, ReCon Concrete was established to provide an environmentallyfriendly alternative to traditional concrete.”
The sustainable concrete solution distinguishes itself in the market by significantly reducing environmental impact, particularly by repurposing recycled aggregates from various waste sources, including construction and demolition waste and other materials, reducing landfill waste and the demand for virgin aggregates.
In fact, the innovative nature of this process has already earned the product esteemed accreditation.
Darragh explained: “In early 2025, we were awarded End of Waste status by the NIEA, officially recognising our recycled materials as a high-quality alternative to traditional concrete materials. This approval ensures compliance with environmental regulations and reinforces our commitment to sustainability. By integrating recycled materials, we significantly lower the carbon footprint of concrete production while supporting
a circular economy. With growing demand for sustainable building materials, ReCon Concrete provides a competitive, eco-friendly alternative that helps developers meet sustainability targets without compromising performance.”
The extensive versatility of the sustainable concrete is evident by the impressive scale of work the resource has already lent itself to – and which it continues to contribute to. ReCon Concrete has so far been successfully employed in a wide range of projects, including foundations, slabs, laneways, and reinforced steel shuttered walls. Already emerging as a popular go-to option for construction, as well as driving the company’s sustainability vision, the product was also created with the industry’s interests in mind.
Darragh shed light: “Our quality control system ensures the concrete is durable, workable and versatile enough to be used in the same applications that traditional concrete can be used in. We have also developed a range of concrete ‘lego’ blocks for modular construction and decorative pillars for landscaping and architectural use.
“Our collaboration with customers has been extensive, working closely with contractors and developers, to provide tailored solutions that meet structural and aesthetic requirements while supporting sustainability goals.”
The highly positive response from the customers in question, who have been incorporating the product into their work, is testament to the quality behind it – in which the clients have been “appreciating both the environmental benefits and performance of our concrete.”
“Customers have also praised the cost-effectiveness of our solutions, as well as the added benefit of reducing their project’s carbon footprint. As demand for sustainable building materials continues to grow, ReCon Concrete is gaining recognition as a trusted partner in eco-friendly construction,” said Darragh.
“The long-term impact extends beyond supplying sustainable building materials – it actively supports the circular economy by transforming waste into valuable resources. For our customers, this means they can meet environmental targets without compromising on quality or performance.”
ReCon Concrete is a key marking on ReCon Resources’s roadmap towards a more environmentallyfriendly future – but it isn’t the only one, as the award-winning Portadown-based company continues to alleviate the burden on local councils and businesses by seeking industrious ways to achieve recycling targets.
Darragh asserted: “ReCon Resources continues to push the boundaries of innovation in waste processing across Northern Ireland, driving advancements in environmental efficiency and circular economy solutions.
Our focus is on ‘difficult to treat’ waste streams, where traditional disposal methods fall short, and we have successfully developed End of Waste solutions
for materials originating from the construction, agriculture, and utility industries.
“Beyond our own operations, we play a pivotal role in enhancing the waste management sector across Ireland by providing specialist support and services to other waste management companies. This collaborative approach expands recycling and recovery opportunities, ensuring that more materials can be repurposed, rather than discarded. By fostering innovation and knowledge-sharing, we are actively contributing to the development of a truly circular local economy, where waste is not an endpoint but a resource for future use.”
To help achieve these objectives, ReCon Resources is also working closely with customers to develop tailored waste solutions and sustainable materials that align with their operational and environmental goals.
“By understanding their specific needs, we provide innovative recycling and recovery strategies that enhance efficiency while reducing environmental impact.”
Co-operation extends beyond clientele too – the team actively engage with third parties in order to help further cultivate a shared, sustainable vision.
Darragh explained: “We also engage with industry bodies, including Recycle NI, to promote best practices in waste management and drive positive change across the sector. Through these partnerships, we contribute to the development of policies and initiatives that support a shared sustainable vision, ensuring that businesses across Northern Ireland can adopt practical, effective, and environmentallyresponsible waste solutions.”
As well as building on the success of the sustainable concrete, the landscape of ReCon Resources’s endeavours is continuing to enhance and diversify – while always aligning with the company’s commitment to a sustainable future.
“We are continuously developing innovative waste recycling solutions, with many more advancements on the horizon. We aim to expand our range of eco-friendly construction products, further strengthening our commitment to sustainable resource management and environmentally-responsible building materials,” said Darragh.
Although highly suited to primary aggregate production in quarries and sand and gravel plants, Screencore’s mobile and modern range of mobile solutions has found a real niche in processing materials arising from construction operations. Possessing exceptional productivity, but at the same time being fuel efficient, the crushers, screens and stockpilers are now at work throughout the world processing a variety of materials, turning what was once considered to be waste into a valuable resource.
Companies working in the demolition and recycling industries have been quick to see how Screencore material processing and handling equipment can aid their business operations. Playing a major part in the success of Screencore has been the company’s extensive international distributor network.
The relationship forged has led directly to a number of compact Screencore tracked jaw crushers, Trident scalper-screens, Orbiter trommels and radial stockpilers being used to recycle construction and demolition materials.
To this can now be added a bespoke selection of stationary recycling plants. All of these solutions are designed to benefit users,
helping them to turn waste into high quality aggregates and other valuable products.
The adoption of Screencore equipment by distributors in such countries as America, France, the UK, Australia and South Africa (often alongside existing product portfolios) directly points to the versatility and processing efficiency of the Screencore range.
“The Screencore product range was developed in order to meet the needs of the modern contractor and material-handling operation. We have set out to build to the highest standards equipment that helps people in the field be more profitable, efficient and effective in what they do. We have also incorporated environmental efficiency into every step of our processes to minimise customers’ carbon footprint.
All this has meant that working with our distributors has seen Screencore equipment adopted on numerous projects, turning construction waste into reusable and /or resaleable products,” explained Screencore Director, Ciarán Ryan.
A typical application – in this case in America – sees, in the first instance, a Screencore XJ Dual-Power Crusher being fed the demolished or excavated material, usually by an excavator or loading shovel. The Screencore XJ itself
is a dual-power 1000mm x 650mm (40” x 27”) jaw crusher designed with a compact footprint. It has proved to be ideally suited to the modern demands of a recycling contractor, rental fleet or inner-city demolition / recycling site. It weighs in at just 30,000kg (65,000lbs) which means that it can be easily relocated without the need for permits It is designed to be both environmentally and acoustically friendly, while delivering impressive throughput even on hard rock applications or concrete with rebar. Following crushing to -100mm (4”), the material is then fed into a 17,000kg (37,500lb) Trident 124 scalper / screener to produce 0/25mm,25/60mm and +60mm (1”, 2.36” and +2.36”) products. In addition, any ferrous metals such as rebar or wire, are easily removed for resale/recycling by the overband magnet on the XJ crusher’s discharge conveyor before being fed into the screen. In many applications the 0/25mm material is generally used for pipe bedding; 25-60mm directly as road subbase or as feed material for secondary crushing for concrete production, while the +60mm is used as drainage stone. The combined set-up time for this crushing and screening combination is less than 30 minutes.
Due to the easily transportable and modern nature of the equipment, contractors and rental fleets have found that the Screencore crusher and screen combination can be readily transported to where the material is. This means that the material can be processed where it originated, and generally where it is needed, resulting in no unnecessary emissions, material handling or transport costs. In addition, the local environment is not subject to unnecessary traffic disturbances and the overall carbon footprint of the contract is dramatically reduced.
“Quick set-up times, easily-adjusted closed side settings, fuel efficiency (dual-power) and ease of transport are just some of the reasons that has seen contractors and recyclers adopt Screencore equipment,” explained Ciarán Ryan.
For some operations, however, mobility is not essential. This has led Screencore to use its expertise to develop a range of bespoke stationary solutions based around its Orbiter trommel range working alongside Screencore stockpilers and scalpers.
“Screencore provides a variety of customised stationary solutions tailored to suit individual applications. Our dedicated in-house design team collaborates with our distributors and their customers to develop an efficient and long-lasting material handling system. Leveraging our electrical power expertise, we ensure that any system satisfies requirements.
“Screencore will custom-design conveyors, stockpilers and feeders to meet any application requirements. Our designs are renowned for their quality and ease of assembly, arriving in neatly packed containers and specified to over-deliver on throughput expectations. We also supply a range of air separation systems for use in both stationary and mobile plant.
Engineered for plastic or ‘lights’ contamination removal from C&D, compost and mulch, the Revac and AirKnife units are available in diesel or electric power to suit customer requirements,” explained Ciarán Ryan.
Screencore’s stationary and mobile equipment come with power solutions to suit various customer requirements. Stationary, and increasingly mobile plants, are electrically powered which makes efficient and costeffective use of main electricity to provide a low cost and low emission solution.
“Screencore has gained a great deal of experience in using electric power from a variety of sources. Mains electricity has proved to be an ideal power source delivering a cost effective and environmentallyefficient solution. Through the use of this power source, or the dual-power solution, precision processing of materials is accomplished without producing the emissions that would be of concern, and at the same time, at a low cost,” concluded Screencore Director, Ciarán Ryan.
Minister of Agriculture, Environment, and Rural Affairs of Northern Ireland, Andrew Muir, recently visited ReCon’s facility, located just outside Portadown, and was accompanied by officials from his department (DAERA NI) and local MLA for the area, Eoin Tennyson.
Following a tour of the facility demonstrating the circular economy in practise, the ReCon team discussed a number of differing innovations which ReCon can offer, that will provide significant solutions to the agri, environmental and construction sectors within Northern Ireland, including:
• Ammonia emissions mitigation in poultry and piggery units from dietary supplementation
• Ammonia emissions mitigation in livestock slurries and anaerobic digestate
• Phosphate emissions mitigation in livestock slurries and anaerobic digestate
• Remediation of legacy soil phosphorous in agricultural land across Northern Ireland
• Sustainable solution for in-situ remediation and re-purposing of subsoils from earthworks, excavation during construction and larger infrastructure projects
• The production of sustainable soil products
• The production of sustainable construction products using recycled resources
• Economical and sustainable waste water treatment solutions that could be implemented to enable more localised regional development to proceed
The ReCon team thanked the Minister and his colleagues for visiting the company and
for providing them with the opportunity to demonstrate the various technical innovations that ReCon can provide as solutions to the agri and environmental sectors within Northern Ireland, that will deliver real benefits to the circular economy moving forward.
CDE, a leading provider of wet processing solutions for the natural and waste recycling sectors, has launched a vodcast series designed to share insights on latest industry trends.
Hosted by CDE’s Senior Marketing Manager, Lauren McMaster, there will be new episodes every month which will feature CDE’s experts from across its five strategic regions talking about industry issues and opportunities.
Lauren McMaster commented:
“At CDE, we share a common purpose to create our best world a ton at a time. We have over 30 years of experience, and unmatched expertise in the industry and with that we are passionate about not only delivering pioneering technology but sharing our
expertise to support the creation of a circular economy.
“We certainly do have tons to talk about, and the launch of the vodcast today signifies our
dedication to equipping our team, customers, and the wider industry with the knowledge to drive meaningful change across the sectors we operate in.”
The first episode sees Lauren joined by three of CDE’s regional experts, Eunan Kelly who oversees Europe, Regis Marty who focuses on the French, Belgian and Swiss markets, and Garry Stewart who manages Ireland.
In the episode, the team discusses quarry waste, and how the industry has evolved in its view of overburden, scalpings and crushed rock fines and that quarry operators are now seeking to process this material to reduce the volume of quarry byproduct that is being stockpiled. To register to listen to the TalkingTons vodcast, visit www.CDEGroup. com/talkingtons.
Hyundai Construction Equipment is introducing the HW250A MH, a dedicated materials handler for the recycling and waste handling industries. With a choice of booms and an elevating cab structure, the HW250MH combines productivity with fuel efficiency.
The HW250MH builds on the success of Hyundai’s popular wheeled excavator range. Weighing 26.1-tonnes, the machine comes as standard with front and rear outriggers, providing maximum stability when lifting.
Equipped with a 6.5m mono boom, the handler has a 4.5m gooseneck arm as standard, for use with an orange peel grapple or a clamshell bucket. Alternatively, customers can opt for a 4m straight arm if using a sorting grab. Maximum working height is 12m with either configuration.
Sitting on a 2.8m wheelbase, the materials handler has a parallel lift cab that delivers up to 2.9m of additional height, to allow operators to see into the working area. The support frame
is constructed as a box structure for maximum durability. There is a manual lift control in the cab and a second control at ground level in case of emergencies.
The robust upper structure is further protected by standard side bumpers, to protect against
impact and a falling object (FOGS) guard is available as an option.
Twin side-mounted main lift cylinders are used for the main boom, delivering increased stability and balance, when compared to a single central cylinder. The machine is equipped
Two new JCB Hydradigs have been earning their keep from day one of their delivery to a waste management company in Northern Ireland – thanks to their ability to do multiple jobs.
Purchased by Portadown-based ABC Waste Management, the JCB Hydradig 110W Plus was supplied by dealer Dennison JCB. It joins a JCB TM320 Wastemaster, a JCB 56080 Wastemaster Loadall, a JCB JS20MH materials handler and JCB 150X tracked excavator in the company’s fleet.
ABC Waste Management Managing Director, Bobby Jameson, said: “JCB machines are superior in build quality which we need as we operate in a harsh environment. We like to spec them up, so they’re well protected for what they have to do.
“One of the biggest plusses of the new Hydradig is the versatility – in a single day it may bale cardboard, work on our picking line and clean up the yard. The new model’s ability to handle material, dig and travel at speed means there is no limit to the number
of jobs it can do. Everything has been well thought through so it can do many different tasks, powering multiple attachments.
“Health and safety was also one of the main reasons for choosing the Hydradig Plus. The 360° visibility means the driver can see anyone standing behind him as he can see all around the machine. The manoeuvrability is excellent too, the machine can move all around the yard with ease. We’re really impressed with it.”
The JCB Hydradig Plus offers a tailored mix of specification to suit customers and boost comfort levels for operators. The machine has the JCB Smooth Ride System, single point axle greasing, reverse steering and two low-flow auxiliary lines as standard.
In the upgraded cab, the operator gets a deluxe air suspension seat and a Bluetooth radio with an LED work light package and a refuelling pump. ABC have added a bucket ram guard and reversible fan for added protection in the harsh waste environment.
with additional steps on the front outrigger and on the cab, to make it easier for the operator to enter and exit safely.
The operator’s seat and controls can be adjusted to suit all sizes of driver, with independent height options for the seat and console. There is a high-capacity air conditioning system and the well-known Hyundai wheeled excavator cab has extensive glazing for maximum visibility. A 7” colour monitor and toggle switch allow the operator to select individual machine preferences. The monitor also provides real-time operating data and various diagnostic functions and can be used to display the rear- and side-view camera feed.
The HW250MH builds on Hyundai’s presence in the market and pushes into new sectors across Europe, in demolition, recycling, forestry and dockside bulk handling. The machine benefits from the company’s expertise in the wheeled excavator market, building on that experience to deliver a dedicated materials handling solution, with the backing and support of Hyundai’s European dealer network.
The machine is powered by a Stage V compliant EcoMAX diesel engine, delivering 81kW, with a hydrostatic transmission. With an operating weight of 11-to-13 tonnes, depending on specification, the Hydradig provides a maximum roading speed of 40kph, making it easy to transfer between work sites. Established in 2008, ABC Waste Management offers a range of waste management services, including skip hire, hazards disposal and baling to both residential and commercial customers from its base in Portadown, Northern Ireland.
The centrepiece of the first appearance at bauma 2025 by DEVELON, formerly Doosan Construction Equipment, was the unveiling of the first models from the company’s new Next Generation ‘-9’ Smart Crawler Excavator range. The Next Generation -9 range represents the latest stage in a proud legacy at Develon that can be traced back through five generations of excavators that began with the Solar range in the 1980s. At bauma, Develon revealed two new -9 smart heavy crawler excavators which were presented for the first time in Europe at a special ceremony on the company’s stand. With the -9 range, Develon is aiming to set a new standard for future products and technologies in construction equipment. Like all -9 models, the DX230LC-9 and DX260LC-9 models achieve this goal by combining 10 ground-breaking technologies and will redefine and set new industry levels of productivity, safety, operator convenience and sustainability.
The Smart All-Around Viewing Monitor is an AI-based Object Detection technology to effectively identify both moving and stationary individuals in close proximity to the machine. Upon detection, the system promptly alerts operators through a combination of visual signals and audible alarms on the monitor, ensuring a heightened awareness of the surrounding environment. The Advanced Lift Assist system provides clear and immediate visibility of the
machine’s tip-over possibility, serving to mitigate accident risks and keep the operator focused on driving.
The innovative E-Stop and Virtual Wall functions prevent accidents the operators are not aware of. To help ensure safety, the area surrounding the machine is clearly defined into specific zones: a yellow warning zone (Zone 2) and a red danger zone (Zone 1).
The -9 machines feature an ergonomicallydesigned user interface that enhances ease of use. It includes a thoughtfully arranged keypad, a jog shuttle and a monitor that is easily accessible, among other features. One standout aspect is the wide and intuitive 12.8-inch monitor, available in dual configurations for diverse needs. Additionally, the machine comes with a comfortable
seat that has a built-in cooling function, as well as a cab designed for improved visibility, providing operators with bestin-class convenience in the industry.
Develon provides customised solutions through its FEH (Full Electric Hydraulic) system on the -9 models.
Compared to the previous -7 models, the new -9 machines provide a 12 per cent increase in productivity and an eight per cent reduction in fuel consumption. This enhancement is primarily attributed to the powerful output of Develon’s selfdeveloped engine, which significantly boosts digging power and lifting capacity.
The incorporation of a FEH control system –featuring electronic pumps, electronic Main Control Valves (MCV), and electronic Relief Control Valves (RCV) – has resulted in fuel savings of between 1700 l (for the DX230LC-9) and 2700 l (for the DX260LC-9) for every 1500 hours of operation compared to earlier models. In addition, the new -9 generation machines offer unparalleled lifting capacity and machine stability within their categories.
The external design truly encapsulates Develon’s vision of SMART construction equipment. Notable features include the industry’s first welcome light, strategically placed horizontal beacon lamps at the four corners of the cab’s upper surface, and signature lighting that adapts to the work environment by changing colour.
Tracked Dumpers & Attachments Hydraulic Breakers & Attachments
DISTRIBUTOR OF: Ammann rollers & compaction equipment, Ausa mini dumpers, Beton concrete vibratory equipment, Radiodetection cable and pipe detection equipment, Hycon hydraulic power packs and tools, Rotair tools and compressors, Yanmar mini excavators.
90a Blackisland Road, Annaghmore, Portadown BT62 1NH Tel. 028 3885 2540 Fax. 028 3885 2541 E: info@crumlinplantsales.co.uk
• Excavators 1 – 45 tonne • 6 – 8 Wheeled Tippers • Mini Digger Hire • Rockhammers
• Rollers
FORTHILL ROAD • DROMORE • CO. DOWN BT25 1RF Tel/Fax: (028) 9269 2542 • Mob: 07860 704502 Email: info@dandds-contracts.com
UNDERGROUND SERVICES
90a Blackisland Road, Annaghmore, Portadown BT62 1NH Tel. 028 3885 2540 Fax. 028 3885 2541 E: info@crumlinplantsales.co.uk