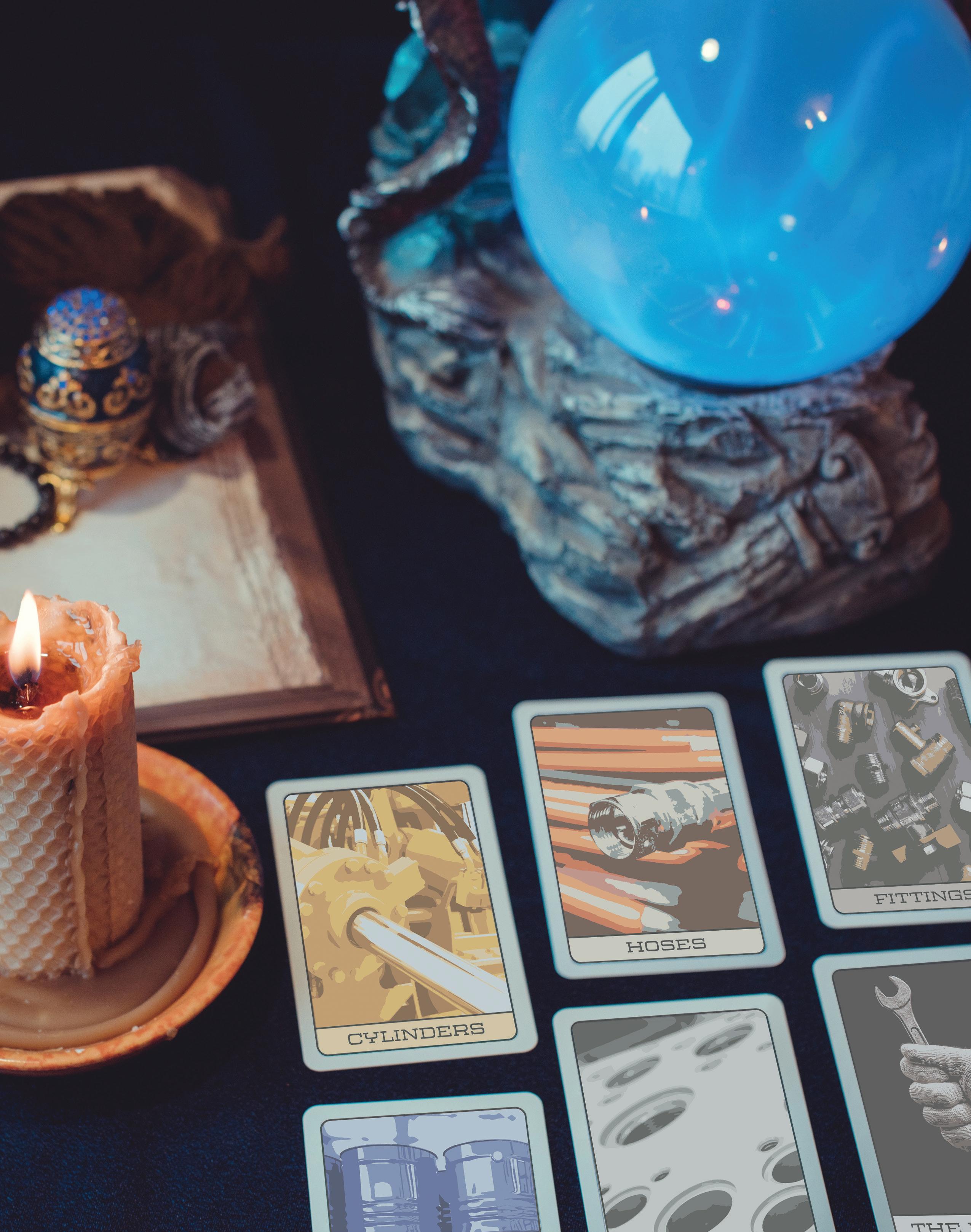
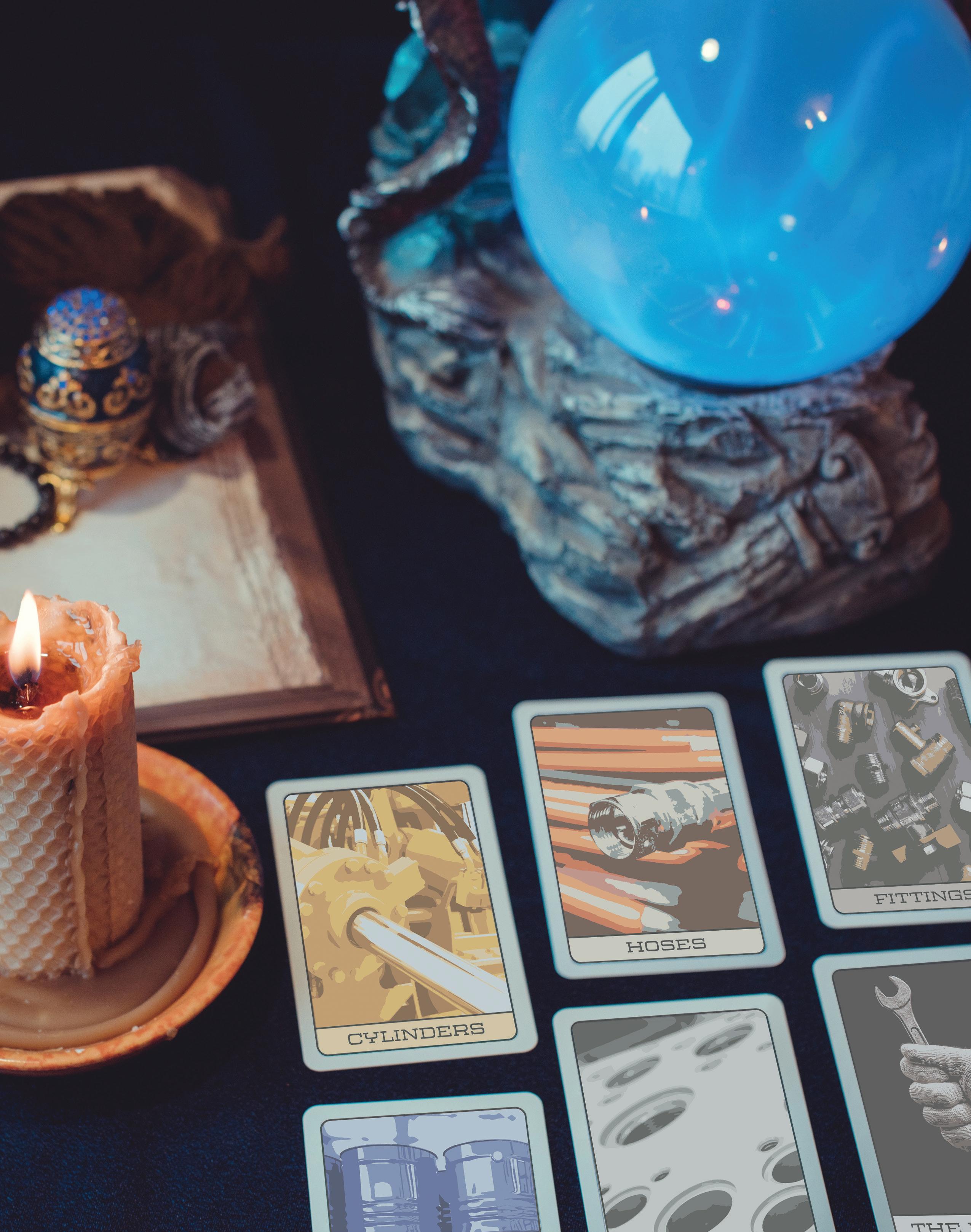
WHAT'S IN THE CARDS FOR LEAKAGE?
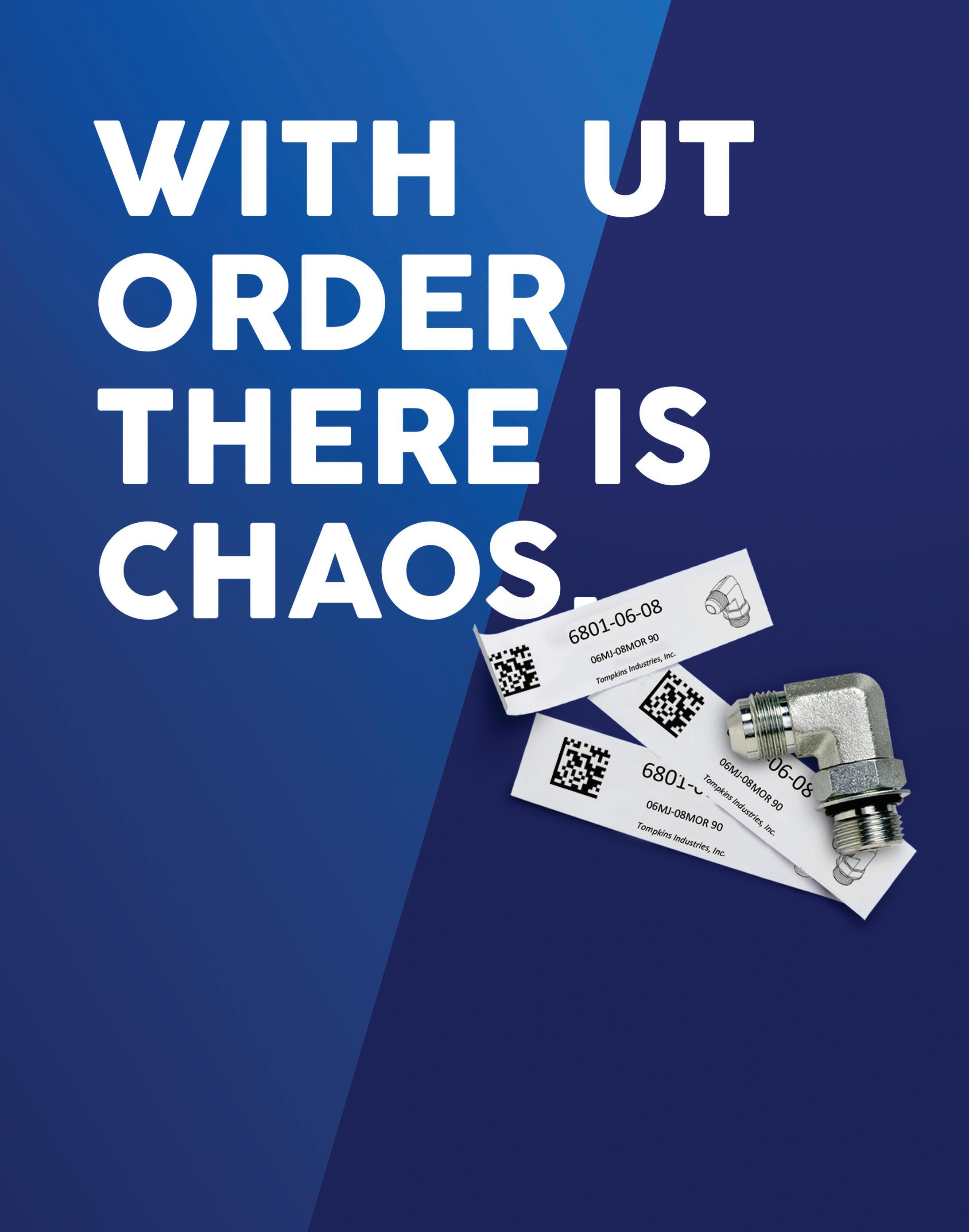
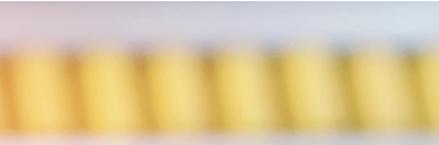
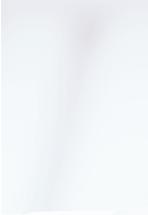
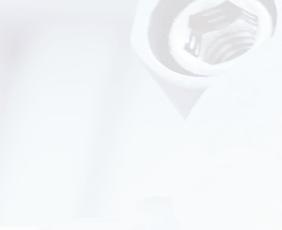
Need Pneumatic Components?
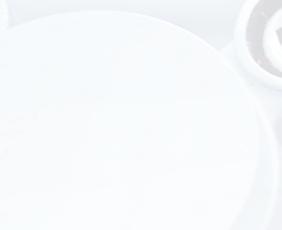

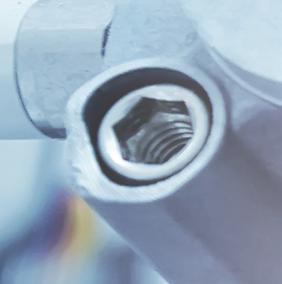
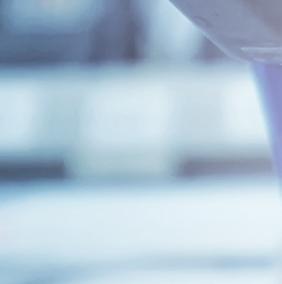


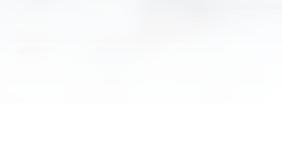
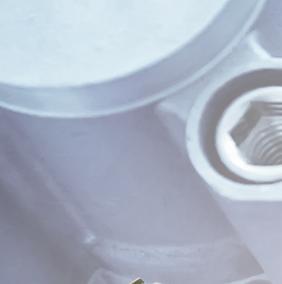
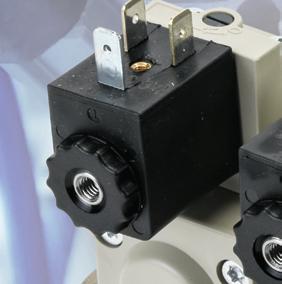
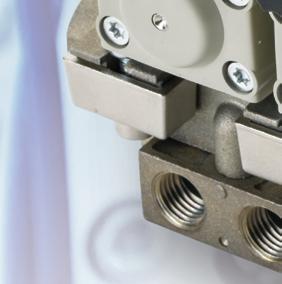

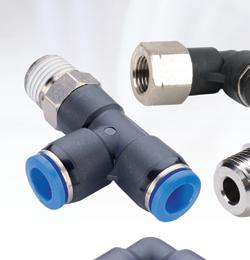
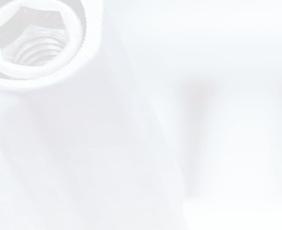
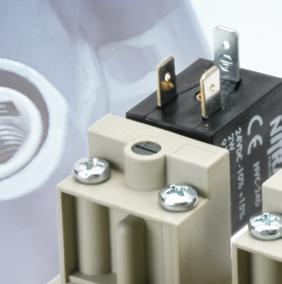
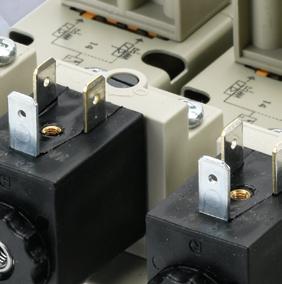

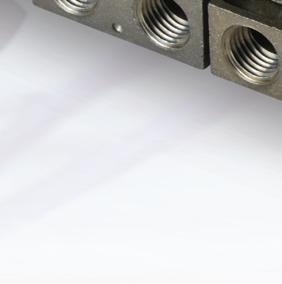
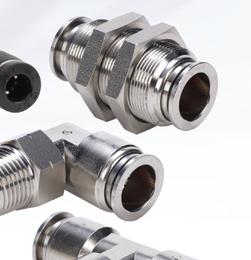

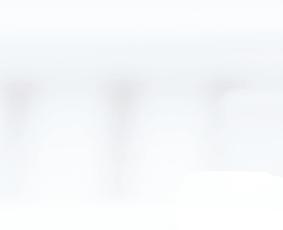

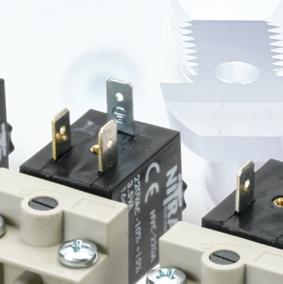
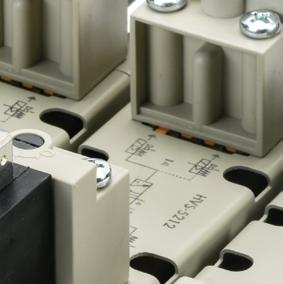

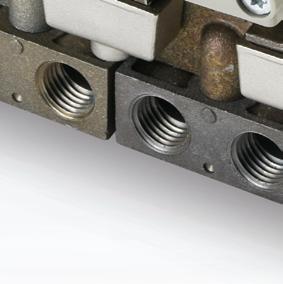
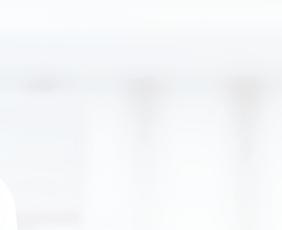
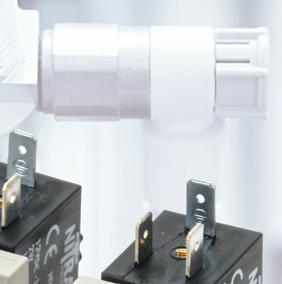
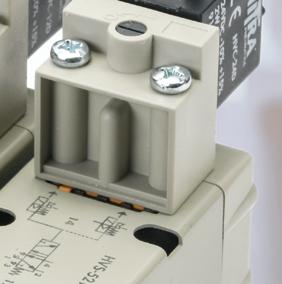
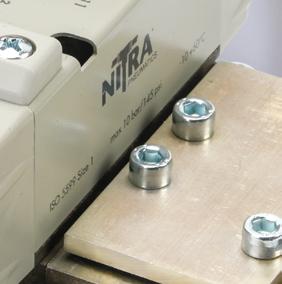
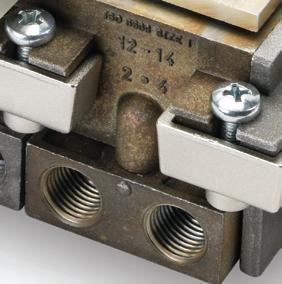
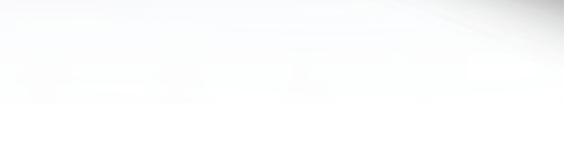
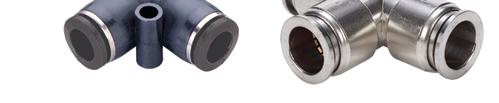
Push-to-Connect Fittings
starting at $3.75/5 pk. (PLUG532)
NITRA pneumatic push-to-connect
fittings are easily installed and work well with flexible tubing to make sealed connections.
• Threaded connections available with NPT, G-thread, and BSPT R-thread types
• Union-style fittings
• Available in thermoplastic, nickel-plated brass, or stainless steel bodies
• Configuration options include male straight (hex and round body), bulkhead female, long male elbow, tee reducers, and much more
• High working pressure and temperature
• Threaded elbow and tee fitting bodies can be rotated after installation
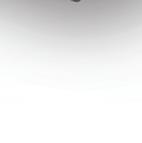

Starting at $86.00 (HVS-5211)
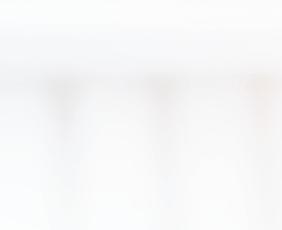
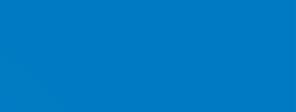



Everything you need at great prices, in stock, and ready to ship

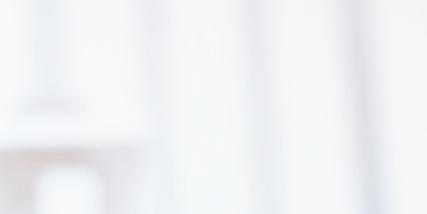
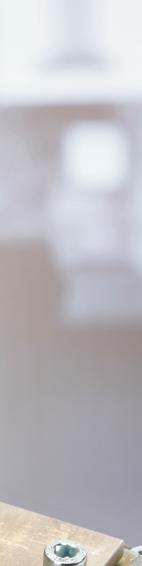
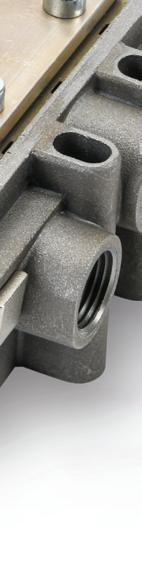
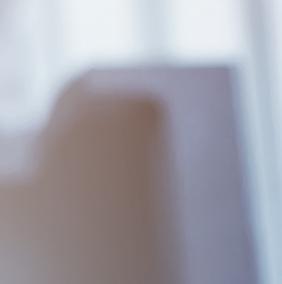
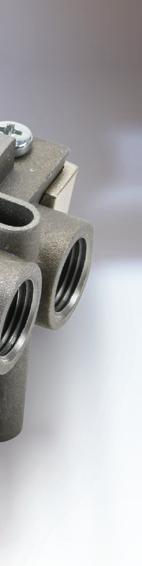
ISO 5599/1 Standard Pneumatic Solenoid Valves
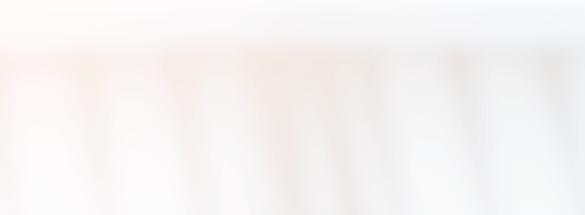


ISO 5599/1 SOLENOID VALVES

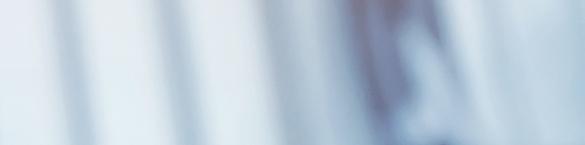
STARTING AT $86.00 (HVS-5211)
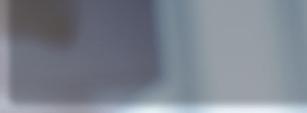
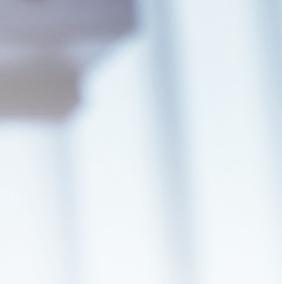
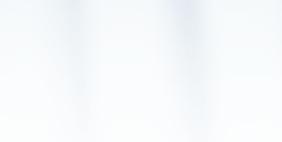

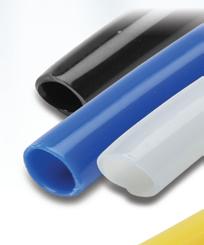
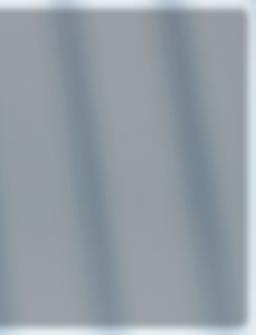
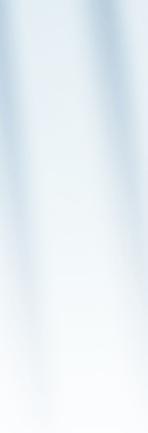
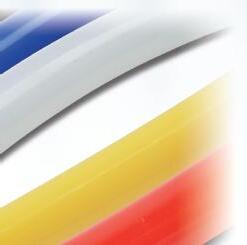

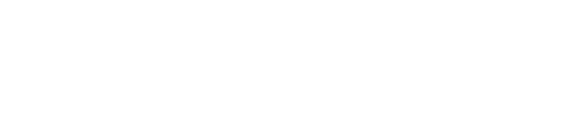
NITRA ISO 5599 valves are a robust directional air control solution that conforms to the ISO 5599/1 standard. They are sold as separate components, so you can buy what you need to replace existing equipment or purchase all the components needed to build a new system.
• ISO 5599/1 sizes 1 and 2 are interchangeable with all other brands meeting the ISO 5599/1 specification
• 5-port / 2-position and 5-port / 3-position valves available
• Solenoid coils sold separately in 12 & 24 VDC and 24, 110, & 220 VAC options
• Order stand-alone bases or manifolds separately
• Bases and manifolds are available in either G-thread (BSPP) or NPT thread types
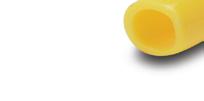
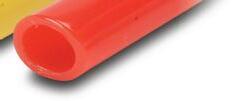
Flexible Pneumatic Tubing
starting at $17.00/100 ft. (N532BLK100)
Strong, kink-resistant NITRA straight flexible tubing is available in a range of diameters and colors in 100ft packages or 500ft reels.
• Inch (up to 1/2in) and metric (up to 12mm) outside diameter tubing sizes
• Multiple colors available including black, clear, and dark green UV stabilized
• Straight polyurethane tubing
• Straight nylon 12 tubing
• Straight PTFE tubing
• Straight bonded polyurethane tubing
• Made in the USA
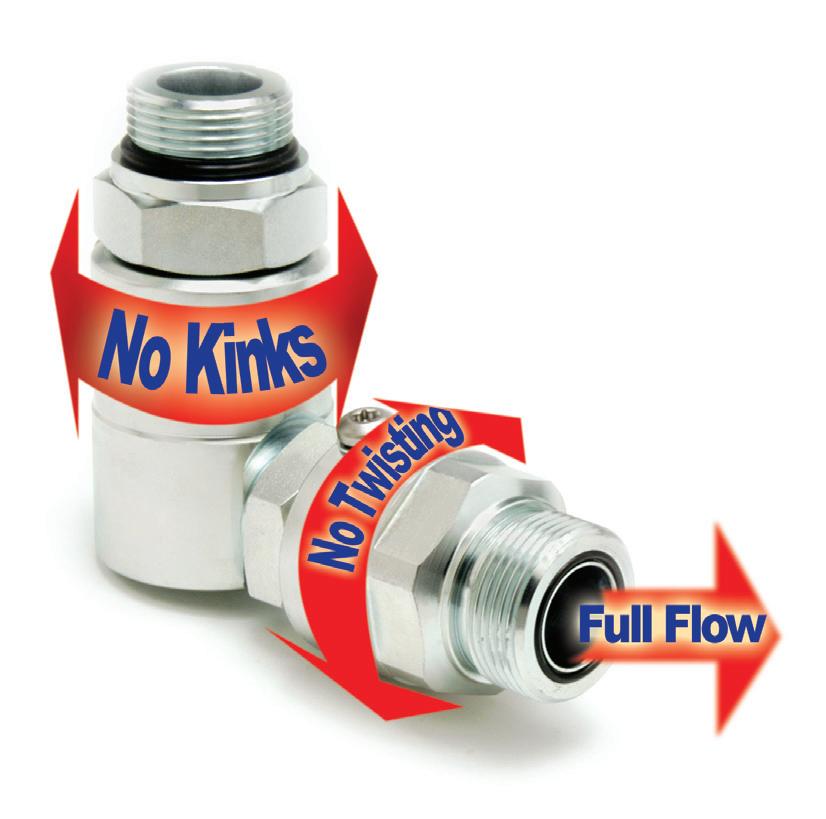
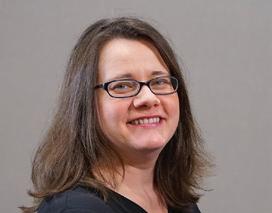
Introducing our blockbuster issues
If you notice a theme throughout this copy of Fluid Power World, you’re not imagining things. With this April issue, we are introducing a new concept to our readers — blockbuster issues that take a trend in fluid power and examine it from several angles.
A few years ago, Paul Heney, our VP, Editorial Director, mentioned an idea he’s had for some time — to do a survey of users and manufacturers to learn if hydraulic leakage is still the problem many see it as. Last year, as we developed our editorial calendar, we decided to take this article a step further and build a whole print issue around the topic.
Paul’s survey and the resulting article came together surprisingly in the negative end of things — showing that leakage is still a problem for many hydraulic systems. What we learned, however, was that it’s more a user issue than technology issue. That means advances in component design ensure more leak-tight cylinders, seals, and hose assemblies but system design and maintenance are often at fault when machines start to leak. Turn to page 22 to read thoughts from dozens of respondents, and how they view hydraulic leakage.
Internal leakage is also a concern, and while the survey discussed this, we felt this would be better served as an online exclusive article in the future, so stay tuned for more thoughts on that topic at fluidpowerworld.com. However, Technology Editor Ken Korane delves into internal leakage research news in our R&D department, page 18.Here, he highlights Chinese research into how neural networks can be used to gauge leakage within electrohydraulic actuators.
Compressed air leakage cannot be ignored, either, as our pneumatics feature points out. Here, Pascal van Putten, CEO of VPInstruments, underscores how wasteful compressed air systems can be if not maintained and monitored properly. Turn to page 36 to learn how detecting and repairing air leaks can immediately result in an energy gain of 10 to 20% and once expanded with compressed air monitoring and optimizations, the savings can even reach 50%.
Finally, we offer our usual technology basics in our Fundamentals department, page 14, where Josh Cosford, Contributing Editor, offers tips for leakage prevention through proper cylinder seal selection and design. And learn about a leakage prevention program for hose assemblies in our Design Notes section, page 12, as I introduce readers to XonKen’s ZeroLeaks program.
Throughout the year, we will continue with these blockbuster print issues. Stay tuned as we take show coverage of the iVT Off-Highway Vehicle Technology Expo in our June issue and MinExpo in our August edition and provide in-depth reviews and tutorials on mobile trends, electrification and the ruggedness that hydraulics offers in these key markets. And watch for our content in December, where our updated Fluid Power Handbook finds its new home. FPW

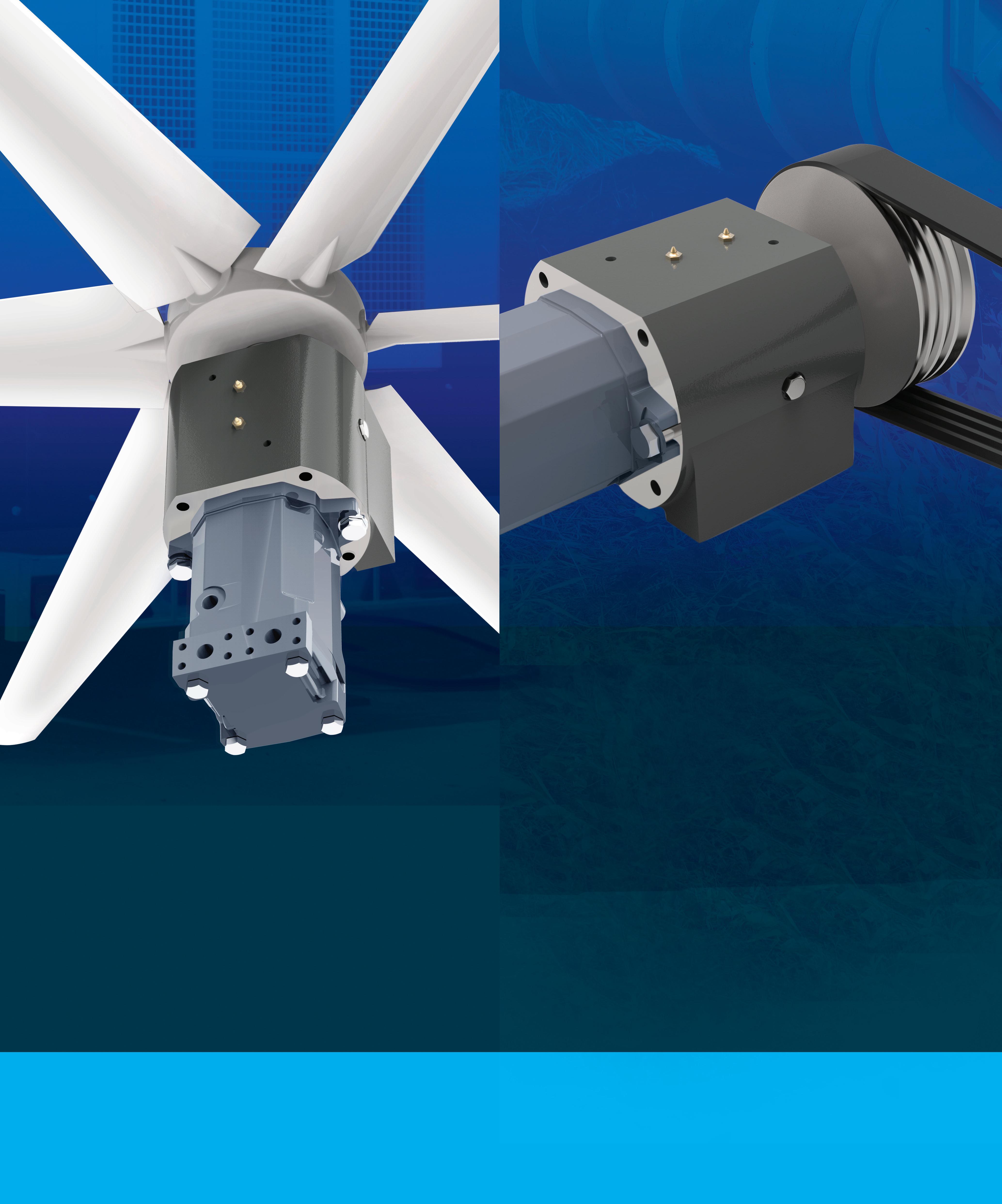

Leakage, perceptions, and projections
For the quarter century that I’ve been covering fluid power, I’ve heard about how leakage (specifically for hydraulics) is the industry’s biggest problem and challenge. And while I agree that leakage problems are something that designers and users have to be aware of — how to avoid them, how to deal with them, what to watch for, etc. — I think that the worries are a bit overblown. Leakage happens, but it’s generally the fault of the person who incorrectly designed the system or the technician who physically put the components together.
With some issues, people project so much onto them that it’s hard to have real, substantive discussions about the causes and solutions. Let’s move outside fluid power for a moment to a different technology: electric vehicles. I’m not here to debate whether EVs are the ultimate answer to our energy/pollution issues (they’re not). But as a fairly new EV owner myself, my experience the last year has been overwhelmingly positive.
Does my battery charge slower in very cold temperatures? Sure. Do I get less range in those cold temperatures? I do. But at the same time, for my driving lifestyle, it’s wonderful. I plug it in when I’m at home, so I never leave the house without a “full tank,” so to speak. That’s something I didn’t enjoy when I drove an ICE. I rarely have to use chargers out on the road, but they are plentiful and usually get me back to 80% in a very reasonable amount of time, say 15 minutes.
But back to the projection. Recently, an acquaintance posted online about how she had rented a Tesla on a business trip. She drove it for two days before noticing that the car needed charging. She drove to the closest charging station (but not a Tesla supercharger) and realized she needed an adapter. At this point, she had only enough charge to get to a Tesla supercharger with 4% battery left and didn’t want to chance it — so a call with the rental company ensued and they eventually offered to tow her to the charging station.
The responses to this situation were filled with vitriol and drama about how awful EVs were because of this type of thing. I kept thinking: Wasn’t this at least partially user error? Why hadn’t she paid attention to her “fuel tank” as she drove for two days? If she’d been driving an ICE and noticed she was down to E, and then panicked because the nearest gas station was 10 miles away, would that have also been the ICE vehicle’s fault?
Similarly, I think some people like to project all their lack of knowledge or comfortability with hydraulics onto the technology. I’ve heard the technology dismissed “because its leaky” more times than I can count. The cover story in this issue delves into the leakage issue, why it persists, and what we can do from both engineering and marketing standpoints to better represent this powerful and important technology. FPW
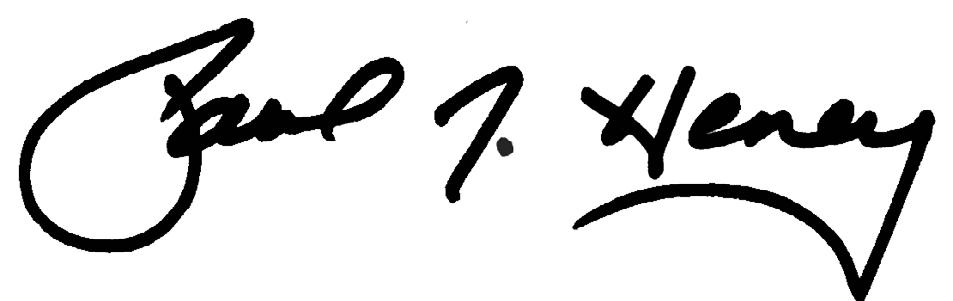

What’s in the cards for leakage? Hydraulics is a mature technology, but the negative connotations continue to follow it everywhere.
ALTERNATIVE ENERGY
Hydraulics at work in the waves
Wave-generated power can be more reliable and consistent than other forms of alternative energy.

OTC PREVIEW OTC shifts the mix for offshore industries Energy professionals reconvene at the Offshore Technology Conference held in Houston’s NRG Park, May 6-9, 2024.
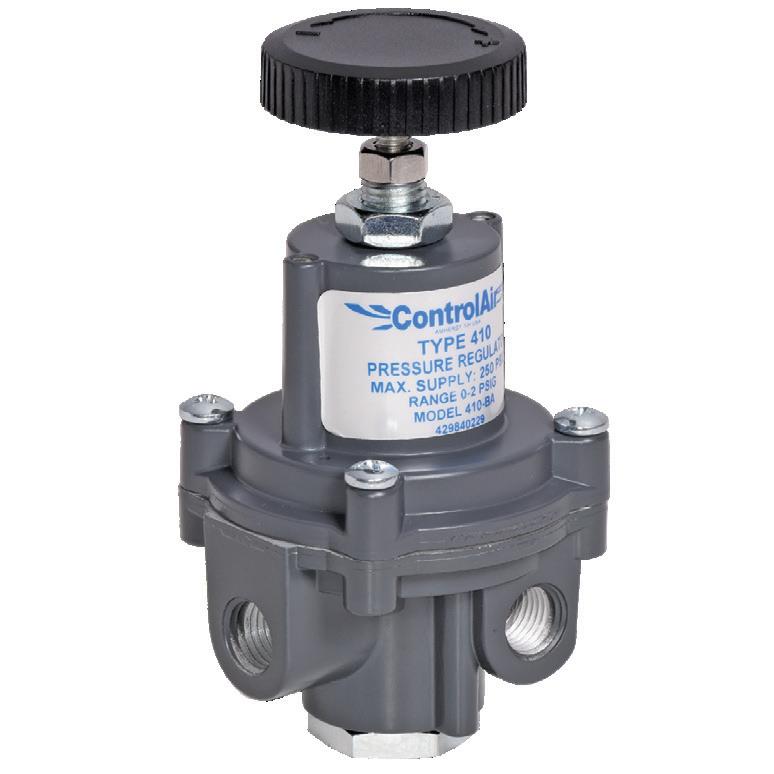
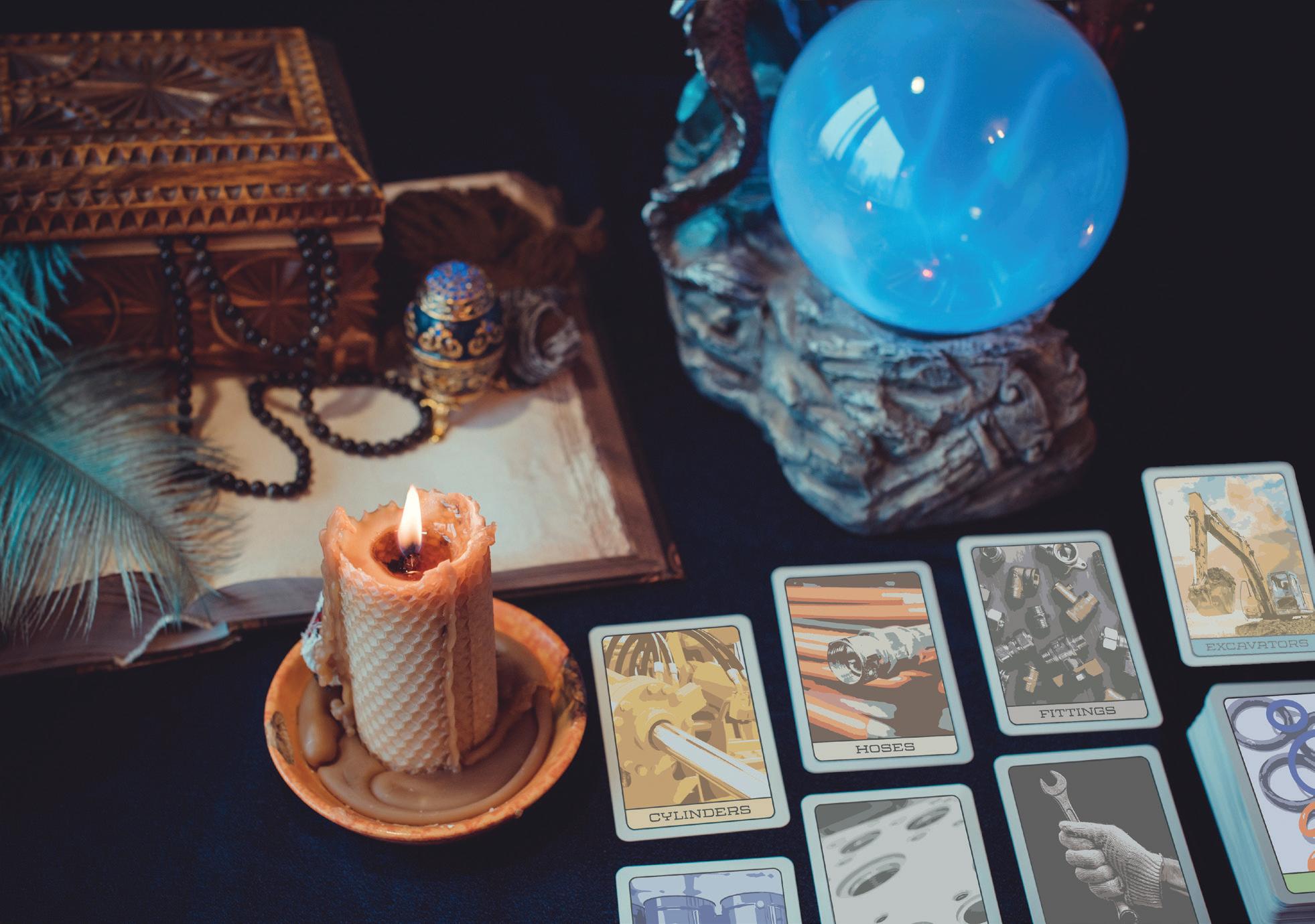
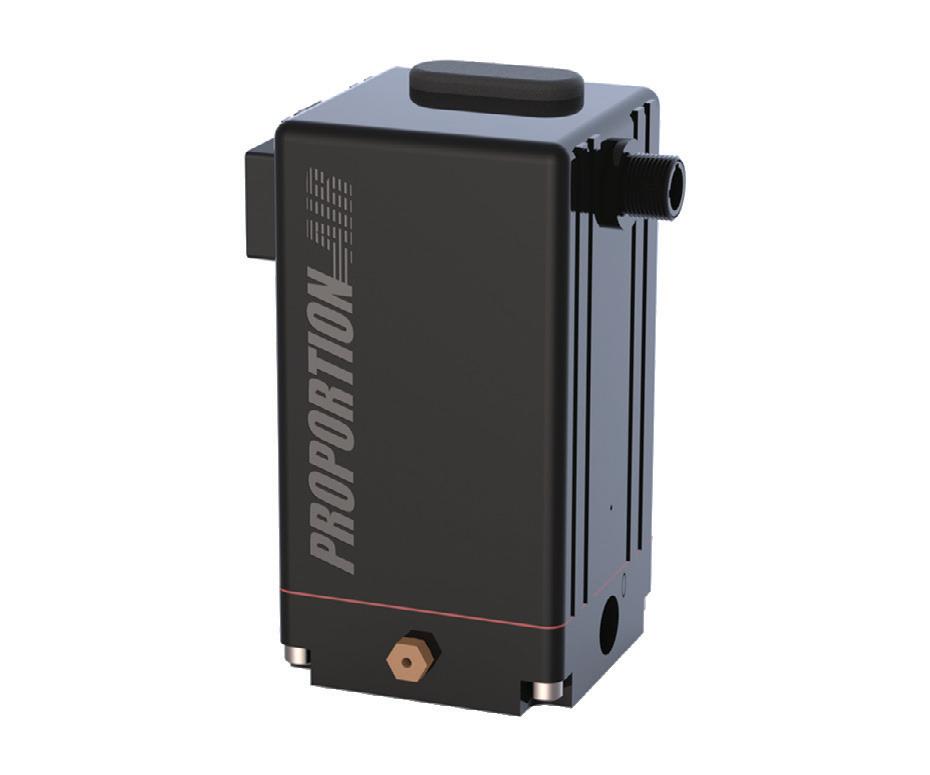
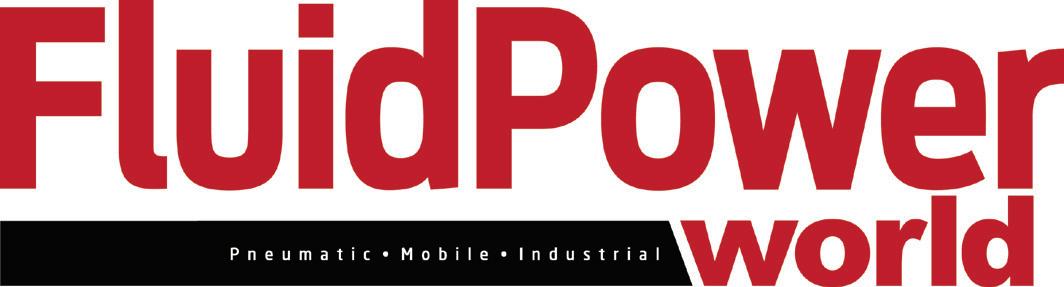
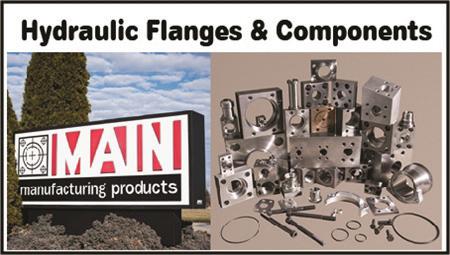
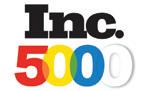





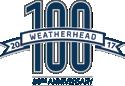
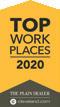
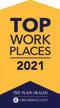
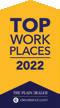
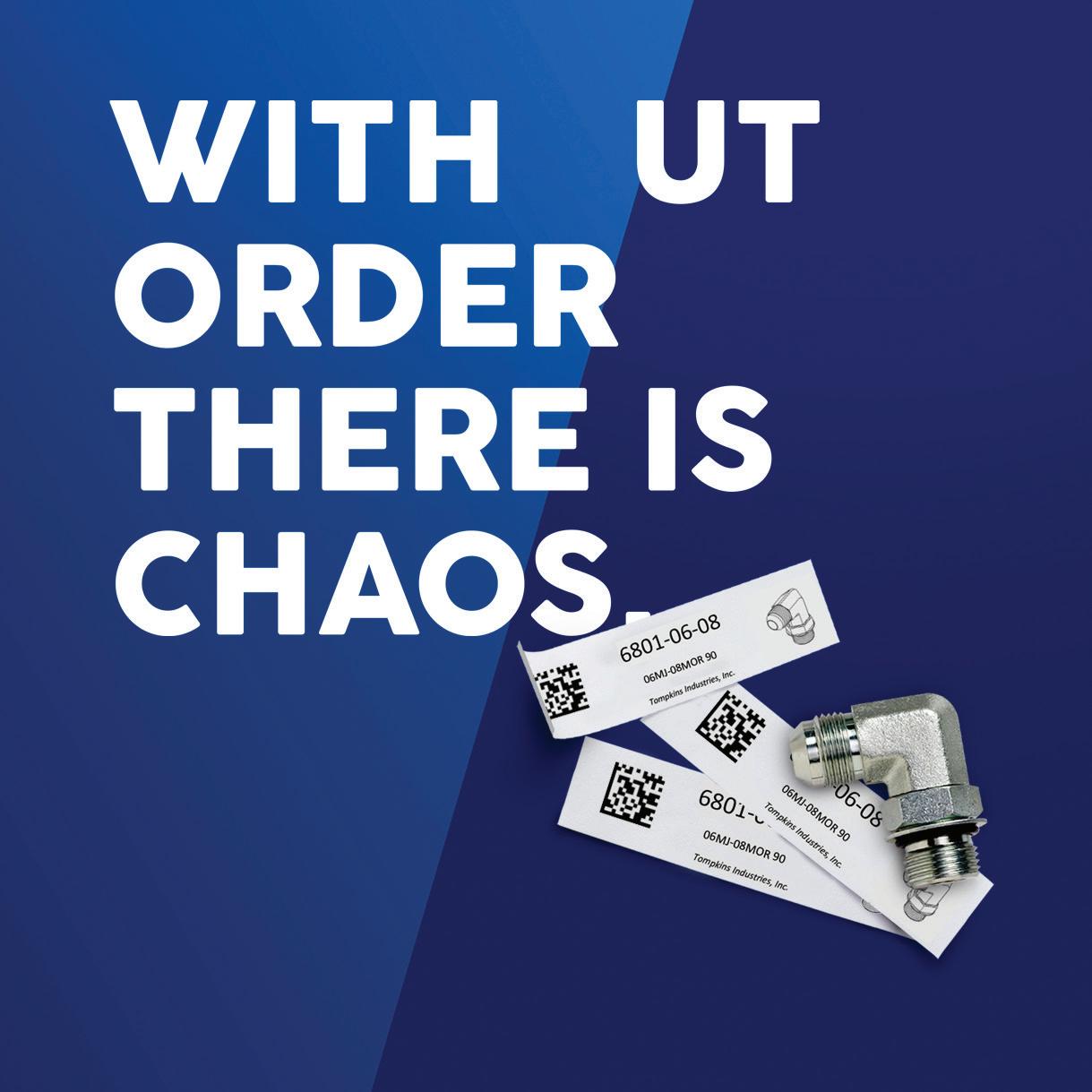
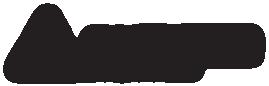






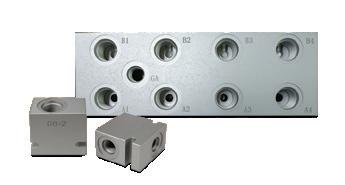
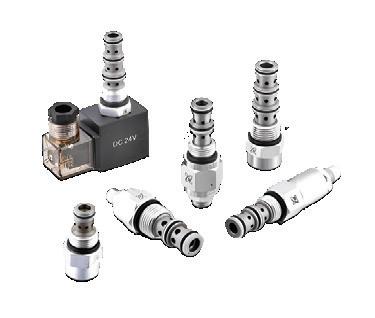
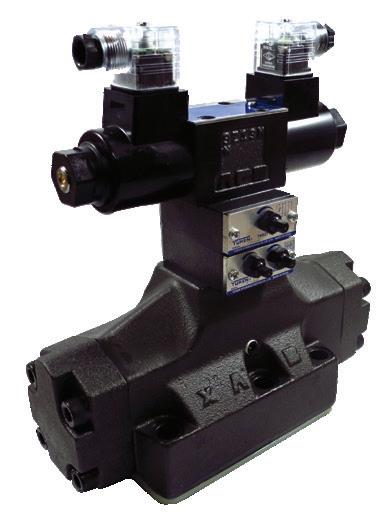
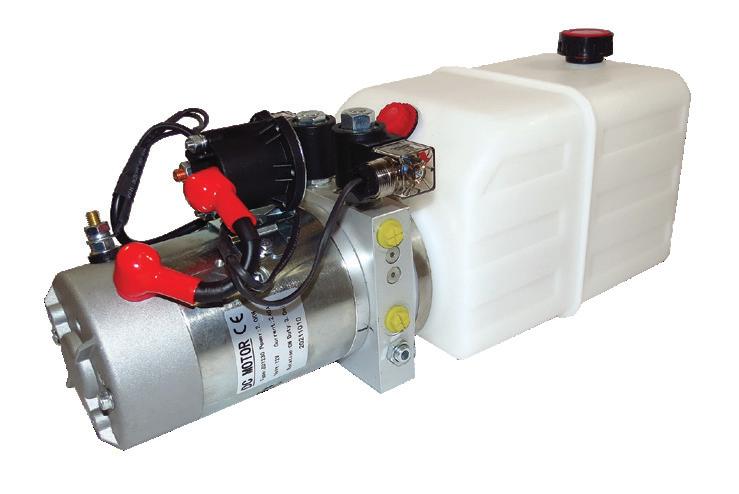

NFPA to present Advanced Hydraulics Conference at iVT EXPO 2024
The National Fluid Power Association (NFPA) has entered into a partnership agreement with UKI Media & Events to convene and co-locate an advanced hydraulics conference for off-highway vehicle and fluid power engineers at iVT EXPO, to be held August 21-22, in Chicago.
iVT EXPO is an annual exposition for the off-highway vehicle design and engineering community, which first took place in the United States in 2022. The event is focused on all types of industrial and off-highway vehicles, with exhibits that are highly focused on a number of key technologies, including new powertrains, electric and hybrid systems, control systems, sensors, and autonomous technologies. With hydraulics serving as a key enabling technology for these vehicles and many of these systems, iVT EXPO offers an ideal platform for growth and expansion of hydraulics, both in its affiliated education program and on its show floor.
NFPA will plan and deliver a two-day conference, running in parallel with the trade show, that will offer iVT EXPO attendees and exhibitors with information on the latest advances in hydraulic technology. Some of the sessions envisioned for the program will focus on the role of hydraulics in key vehicle objectives like thermal management, energy efficiency, noise reduction, preventative maintenance, functional safety, and autonomous operation.
NFPA members are now encouraged to submit session proposals for inclusion in the conference. Special consideration will be given to proposals that address:
• Performance comparisons between hydraulic and electromechanical actuation technologies on off-highway vehicles
• Hydraulic system designs optimized for performance on electrified off-highway vehicles
• Thermal management strategies for hydraulically-actuated, electrified offhighway vehicles

• Improvements in hydraulic system efficiency, especially those that help to increase battery life on electrified offhighway vehicles
• Strategies for reducing the volume and harshness of hydraulic noise on electrified off-highway vehicles
• Hydraulic data collection and utilization strategies that provide system or machine-level performance improvements
• Strategies for meeting the functional safety requirements of electrified offhighway vehicles
• Hydraulic systems that operate in partial or fully autonomous modes
To submit a session proposal, send proposed title, presenter, and 250-word abstract of presentation to elanke@nfpa.com before April 12.
Learn more about the conference and show at nfpahub.com/events/trade-shows/ ivt-expo. FPW
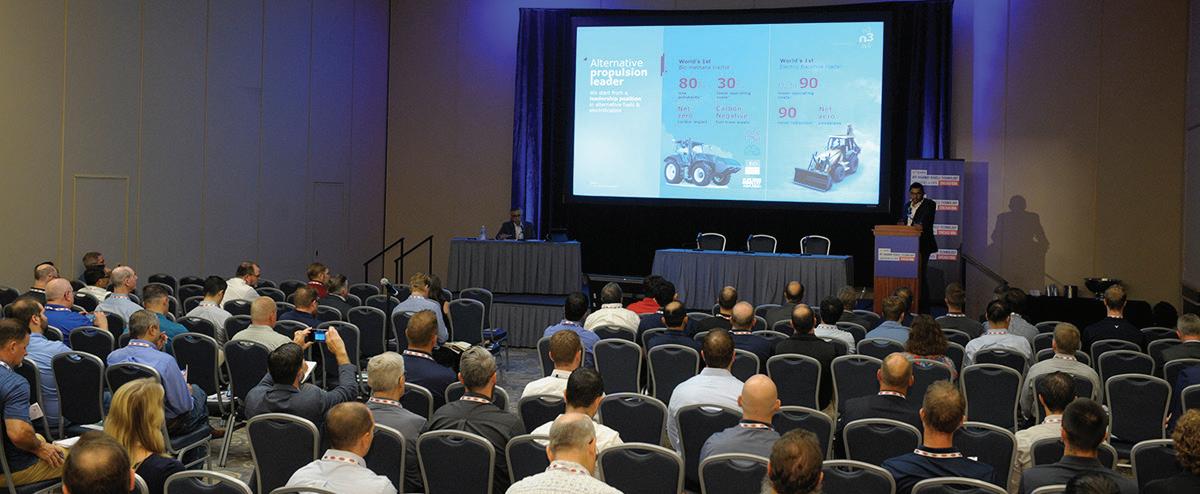
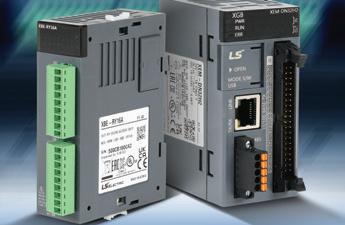


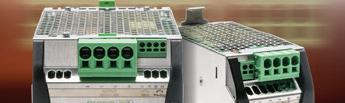
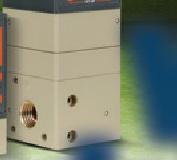

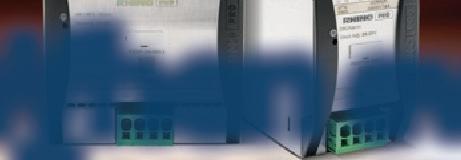
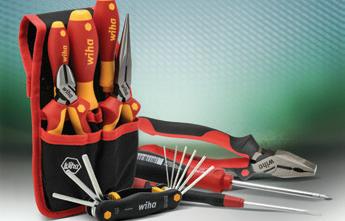
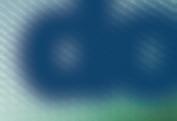

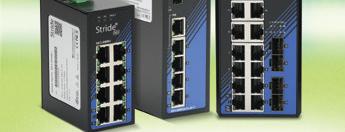
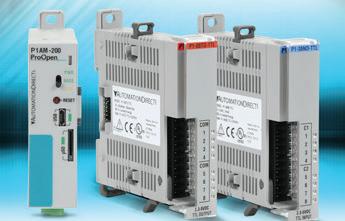
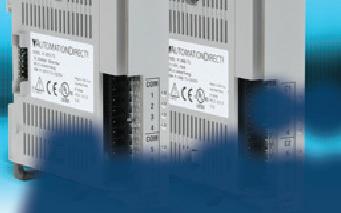


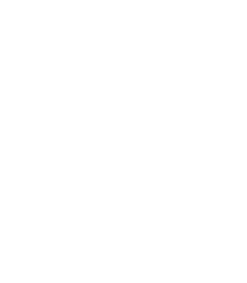


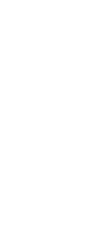




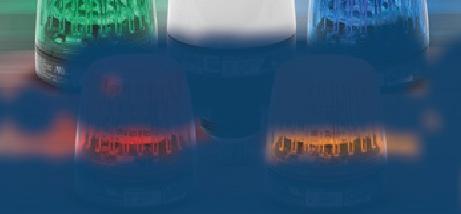

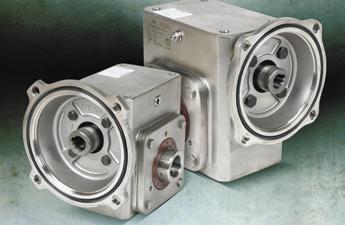
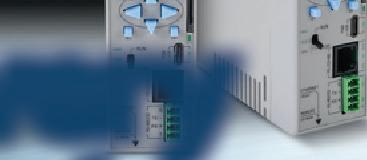



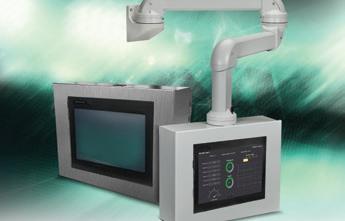
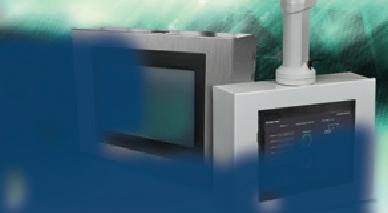


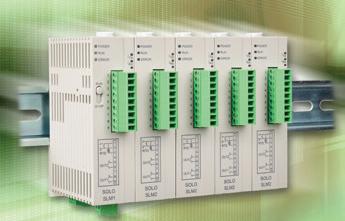




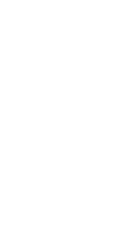






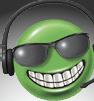
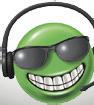
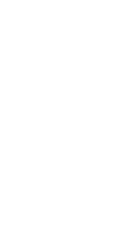


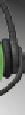
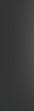
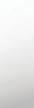



Over 35,000 quality industrial control products at great everyday prices are available on our webstore 24/7/365, and each one comes with the customer service you deserve.

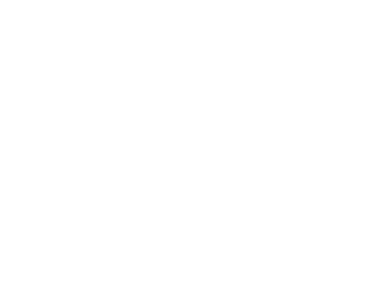










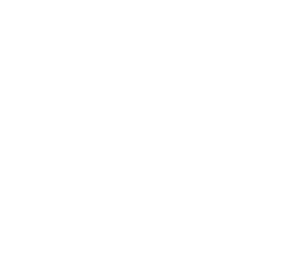

We’ve shopped around to bring you the most practical, reliable industrial control products at the best prices!!
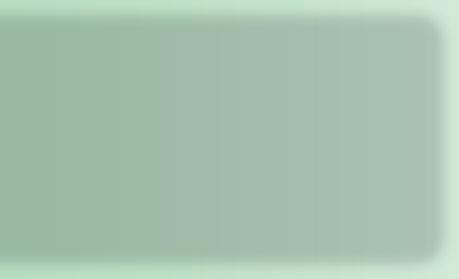
BRIAN in CLEVELAND, TN:
“I love having a single website that I can use for selecting and purchasing everything I need for our industrial automation projects. With fast shipping times, an active support forum, and competitive prices, there’s nothing else that compares. Thanks!”
CODY in MOORESVILLE, NC:

“Best phone support I’ve gotten from a supplier yet, answers the phone quickly and has a very knowledgeable staff.”
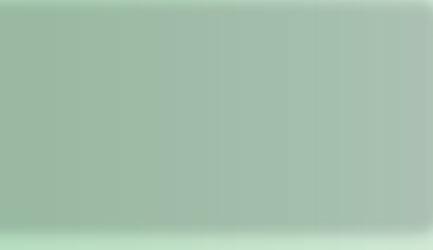

DAVE IN MITCHELL, SD:
“In 10 years of using the company products and services I’ve only had a few returns. The products are reliable and the customer service has always been second to none. I plan to continue using the company into the future.”
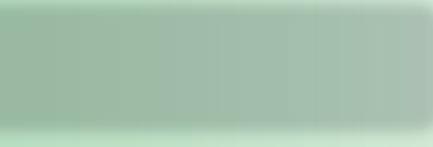
JOHNNY IN NEW CANEY, TX: “Excellent company. Use it regularly and highly recommend it to others.”
BEN IN PAHRUMP, NV:
“We use AutomationDirect as a standard supplier for many of our UL508 control panel components, and have never had a single issue! Automation Direct has an incredible stock of inventory and product selections, and the two day shipping gets us the parts we need right on time!”

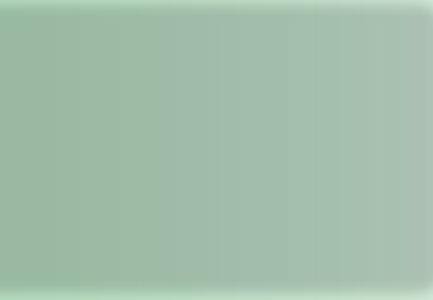
Mark in AYLMER, ON:
“We have been buying from Automation Direct for quite a few years now and we have been really happy with the service and range of products available and the prices are usually as good or better than elsewhere.”
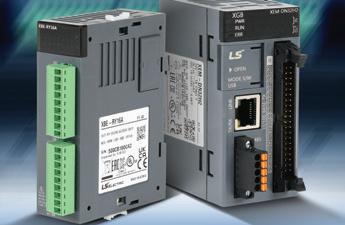
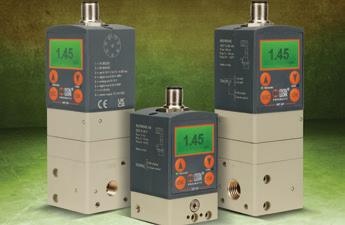
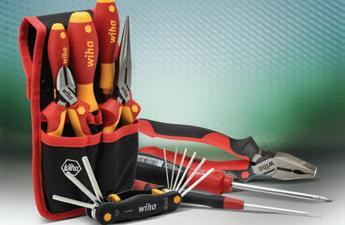


Daniel in ALLIANCE, OH: “They are the best game in town for industrial PLCs”

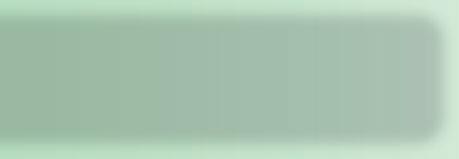
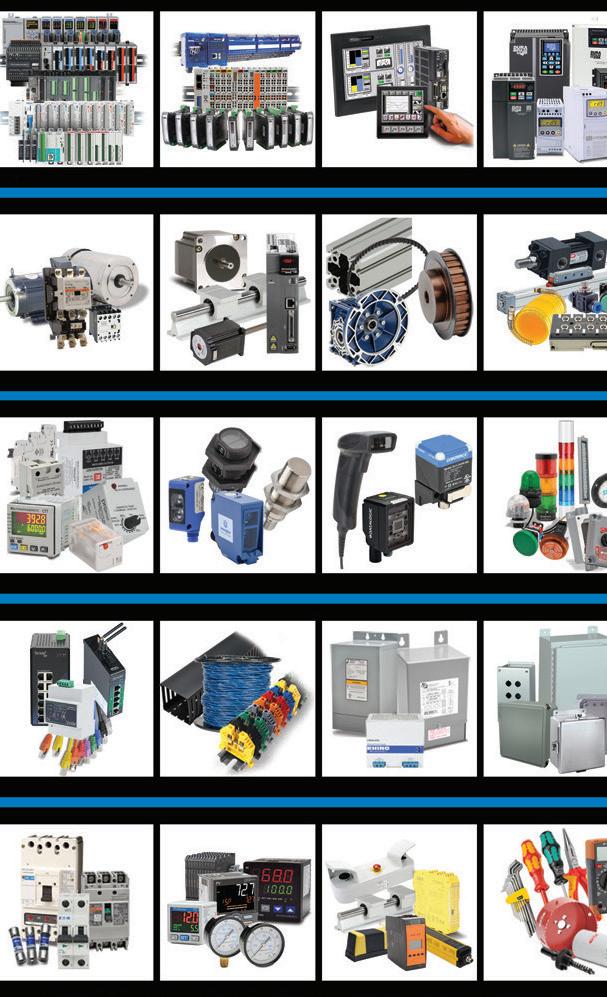
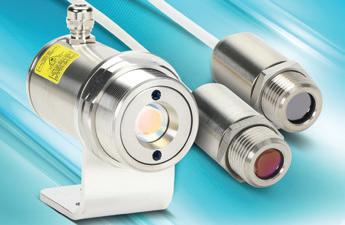
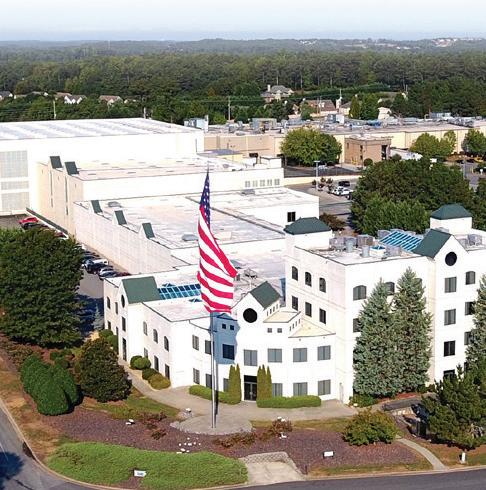
AutomationDirect:
much more than just a “.com”
AutomationDirect is a non-traditional industrial controls ideas from the consumer world to serve your automation quality products fast for much less than traditional suppliers, every step of the way. See below . . .
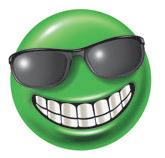
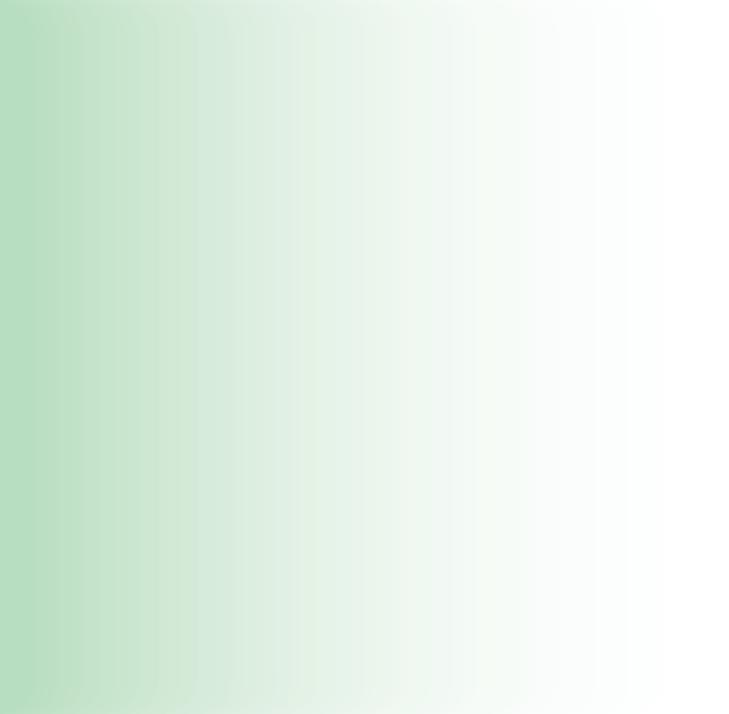
You want complete product information to make the right purchase decision.
Whether you’re deciding on purchasing our products or learning our products after you buy, why jump through hoops or even pay for the information you need?
We have exhaustive documentation all freely available online, including overviews, technical specifications, manuals and 2D and 3D CAD drawings.
We have over 1,500 videos online to get you up to speed quickly. We even provide FREE online PLC training to anyone interested in learning about industrial controls.
http://go2adc.com/videos
http://go2adc.com/training



You need quality products at great

For over 25 years, we’ve been offering a better by running our direct business efficiently and you. No complex pricing structures or penalty everyday prices on everything from fuses to Programming software for controller products can be costly, so we help you out by offering FREE downloadable software for all our latest PLC families and C-more HMIs. No license or upgrade fees to deal with!
http://go2adc.com/why
You don’t want to wait for your We have fast shipping, and it’s FREE if your order is over $49.*
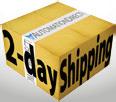
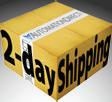
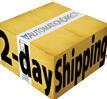

At AutomationDirect, we strive to have what you it. We’ve invested heavily into infrastructure, inventory, automation so that we can continue to provide you products, at great prices, extremely fast!
*Order over $49, and get free shipping with delivery in 2 business the U.S. (Certain delivery time or shipping cost exceptions may Conditions online for complete details.
http://go2adc.com/terms
You insist on getting better service and you want it FREE.
Our technical support team provides superior assistance and has consistently received high ratings from satisfied customers. And it won’t cost you a cent!
Before, during, and after any sale, contact us with questions and we’re glad to help,
http://go2adc.com/support-ss
“.com”
company using the best automation needs. We deliver suppliers, and support you

need, when you need inventory, and warehouse you with quality
Our primary focus has always been customer service — practical products, great prices, fast delivery, and helpful assistance. But the intangible value of customer service is something that cannot be faked, automated or glossed over.
Our team members here at AutomationDirect approach every day with one goal in mind - serve the customer. If the answer to any decision is “Yes, this is good for our customers”, then we do it, whether personally or via self-serve features on our site.
We want you to be pleased with every order. That’s why we offer a 45-day money-back guarantee on almost every stock product we sell. (See Terms and Conditions online for exclusions.) great prices. better value on industrial controls and passing the savings on to penalty for small orders, just low motors.
business days (or less) within may apply; see Terms and http://go2adc.com/terms) your order.
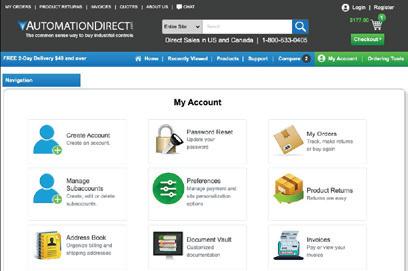
Easy access to account and order history, online returns

You want to be confident in our products and our commitment to you.
We stand behind our products and guarantee your satisfaction.


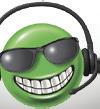
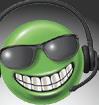
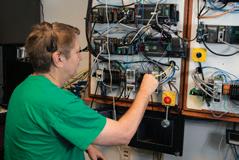



Proportional valves make crane precision possible
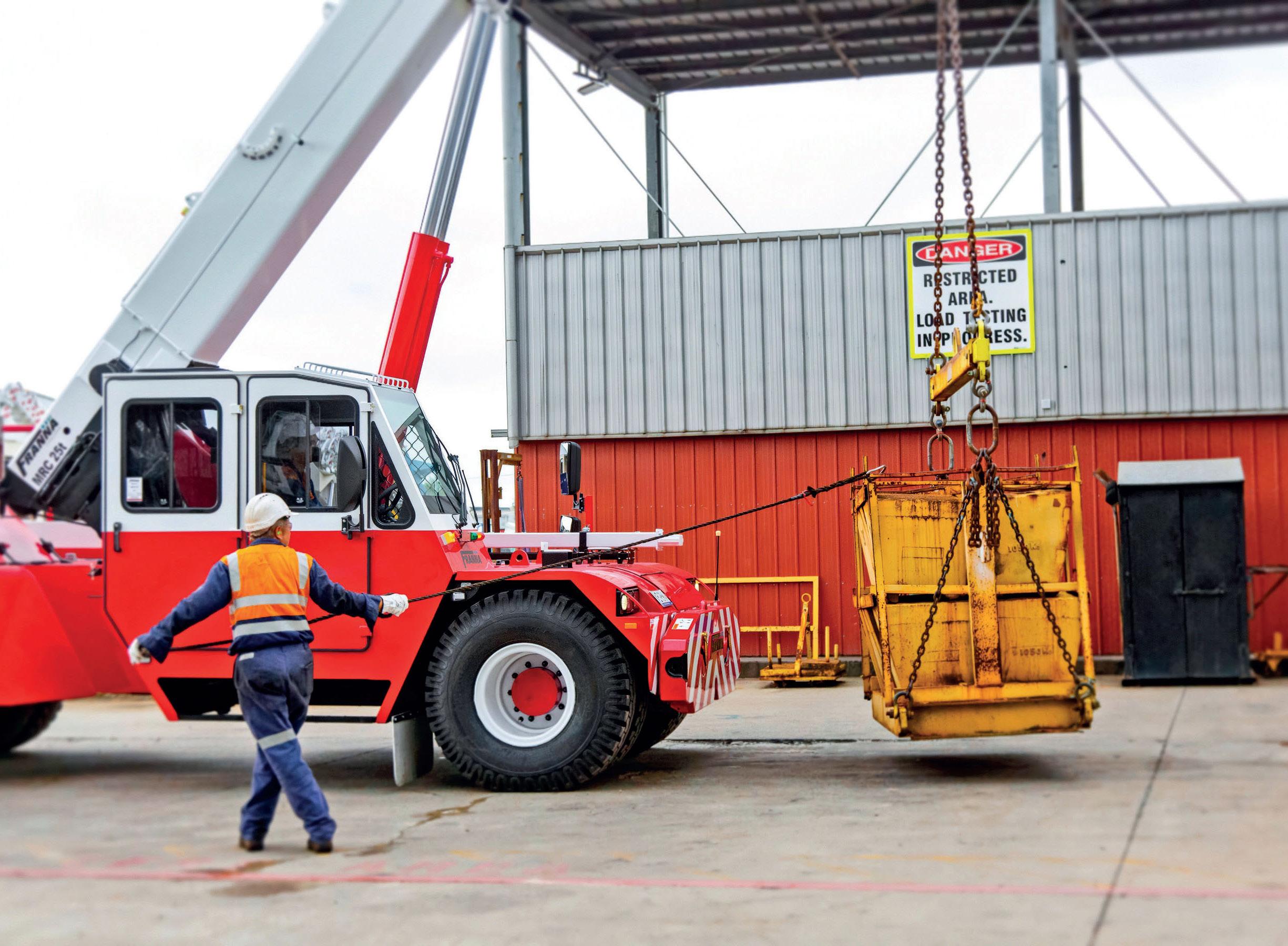
Cranes lift heavy loads, and precise control of the lifting process is paramount for safety and efficiency. Proportional valves fine-tune the hydraulic pressure applied to the lifting mechanism so that operators can control speed and force while lifting and lowering.
In 2021, Australian crane manufacturer Franna sought to improve the performance of its MAC 25 pick-and-carry crane by replacing its main control valve. The MAC
25 mobile articulated crane features a maximum lifting capacity of 27 tons (25 tonnes) and a maximum boom length of 60 ft (18.4 m). The company partnered with Danfoss Power Solutions and selected the PVG 48 proportional valve as the heart of the work and steering subsystems. Danfoss launched the PVG 48 valve to the general market in June 2023, with Franna as a key pilot customer. On the MAC 25, the valve turns operator joystick inputs into quick, accurate boom movement.
PVG 48 is a pre-compensated proportional control valve for applications
requiring flow rates up to 47.6 gpm (180 lpm). This latest PVG load-sensing valve is suitable for machines such as wheel loaders, aerial lifts, and cranes in which precise flow and controllability are essential.
“The PVG is extremely precise and reliable. It does what you want it to do repeatedly,” said Adam Murchie, project engineer at Franna. “It’s the ideal choice for MAC 25 and likely to end up in other of our cranes, too — not least in future launches where more advanced electronic controls are key. We wanted a future-proof valve. PVG 48 is it.”
The PVG 48 valve integrates easily with electric actuators, sensors, and digital controls, opening various possibilities. One of them is to automate certain machine functions so the crane assists or even takes over from the operator. Such a function can be advantageous in many situations, particularly when instant reaction is required to ensure safety.
With the change to PVG 48, Franna also switched to Danfoss counterbalance valves. Together with PVG 48, they ensure smooth and safe activation of the crane’s boom.
“Controllability is smooth and even — very refined,” said Quentin Bourke, product support technician at Franna. “The initial tiny bounce on the front tires, which you sometimes see when operators raise or lower the boom, is completely gone. Extension or subtraction of the boom is impressively smooth, too.”
Bourke added that initial feedback
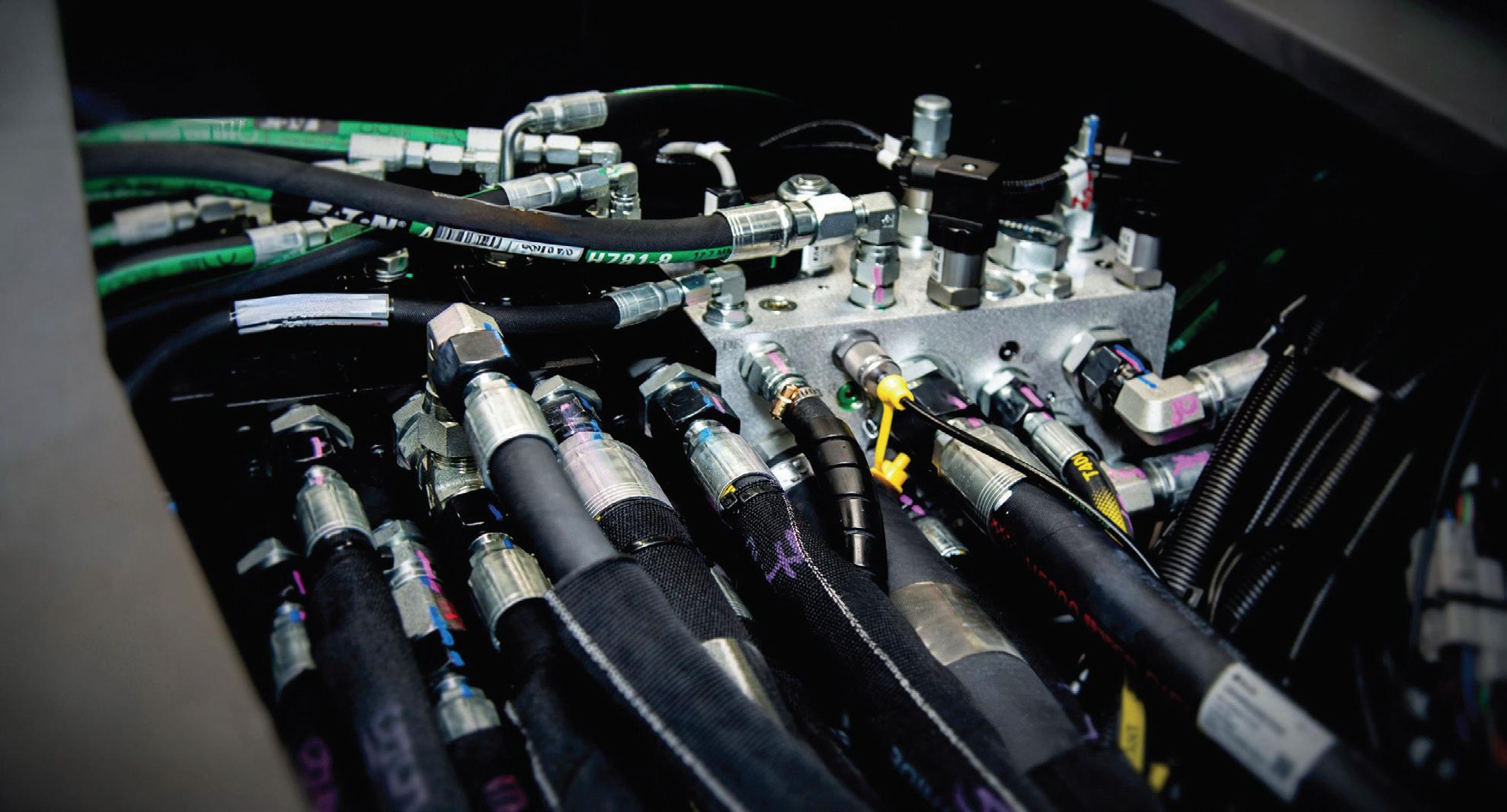
The
is already at work in
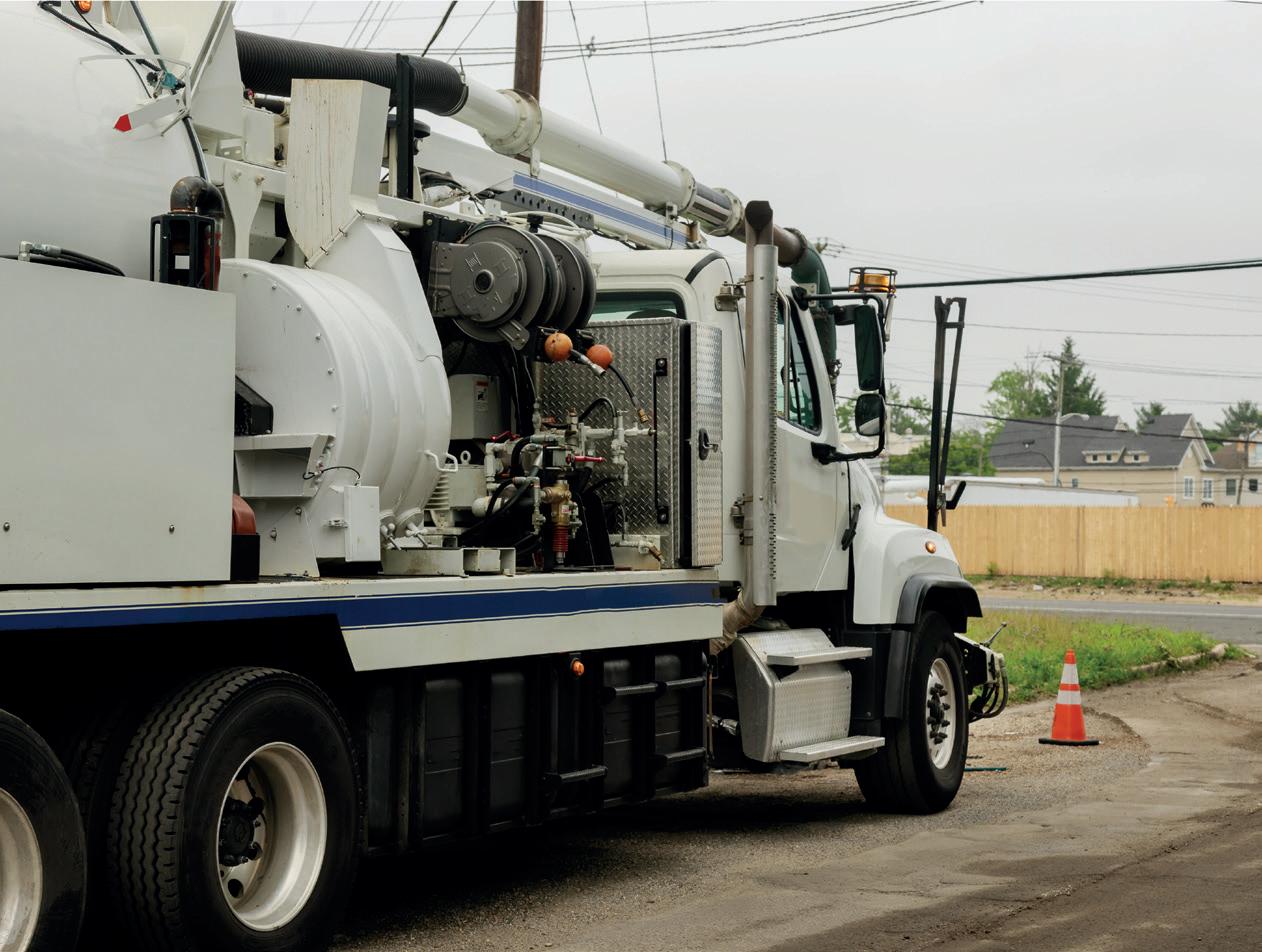

Danfoss danfoss.com



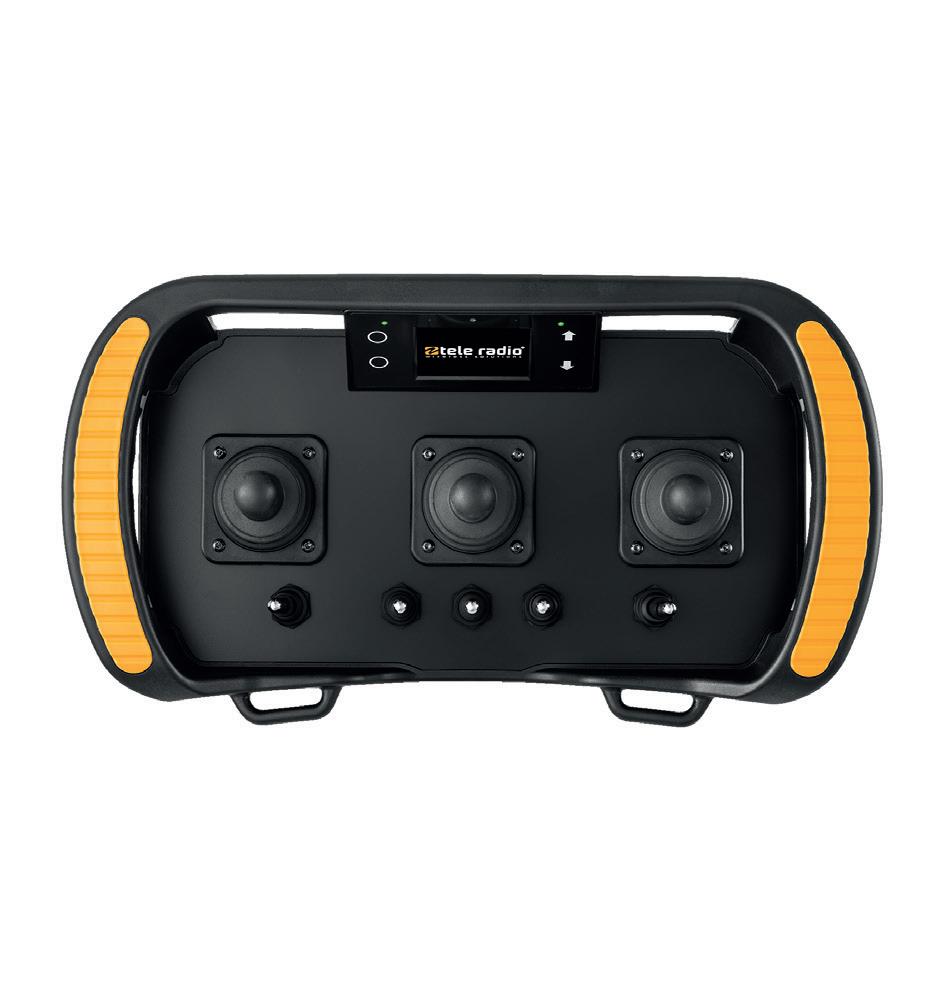
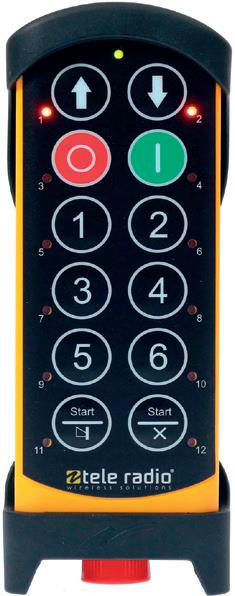


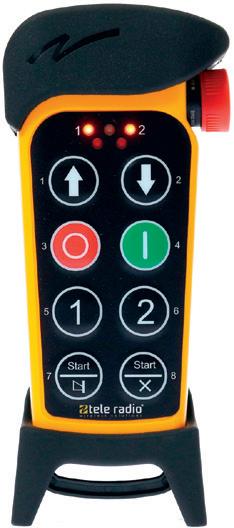
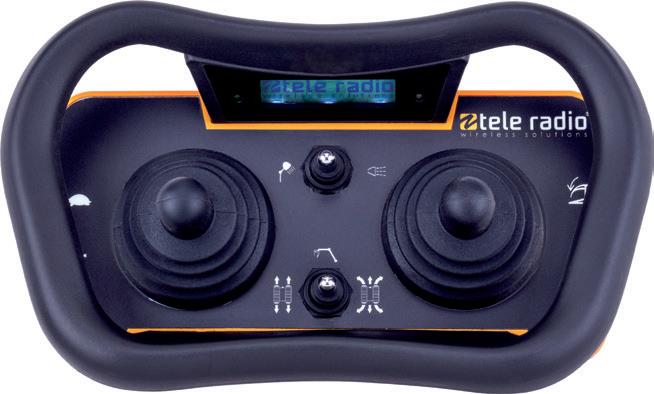

Program aims to stop hose assembly leaks in their tracks
As most users of fluid power technologies know, one of the most vulnerable systems for leakage is within hose assemblies. This is not because hose, fittings, and couplings are poorly designed but, most often, the result of improper assembly design and maintenance.
That’s why XonKen, a Chinese manufacturer of hydraulic hose and fittings, has developed its ZeroLeaks program to stop leakage once and for all. This comprehensive initiative addresses the challenge of sudden leaks in hydraulic hose assemblies. The program encompasses hose assembly design and installation, maintenance, repair, and training.
According to Luis Alberto Leon,manufacturing not only hose but belt products and others as well.
“XonKen is committed to the environment in our process and product social responsibility,” said Leon. “This has led us to innovate and share tools, technology, knowledge, and experience in the operational hydraulic system of corporate high-end users and large users of hydraulic hose.”
The ZeroLeaks program aims to significantly reduce ecological risks due to hydraulic fluid leaks, minimizing the leaks of hydraulic hose assemblies by applying the best practices for crimping, installing, and maintaining hydraulic hose replacements. Reducing such leaks will prevent unexpected process stoppages. This, in turn, generates a substantial cost reduction for the overall operations.
The program encompasses five key objectives:
1. Achieve a strategic alliance between end users and distributors that supply hydraulic hoses, fittings, and components to obtain competitive prices, optimize inventories, and guarantee a timely 24/7 service for emergencies, technical training, and technical support.
2. Adopt a proactive maintenance philosophy implementing root cause analysis (RCA) and reliability-centered maintenance (RCM) methodology for diagnosing, analyzing, and troubleshooting leaks in hydraulic components.
3. Implement best practices for storing, preparing, crimping, inspecting, installing, and maintaining hydraulic hose assemblies.
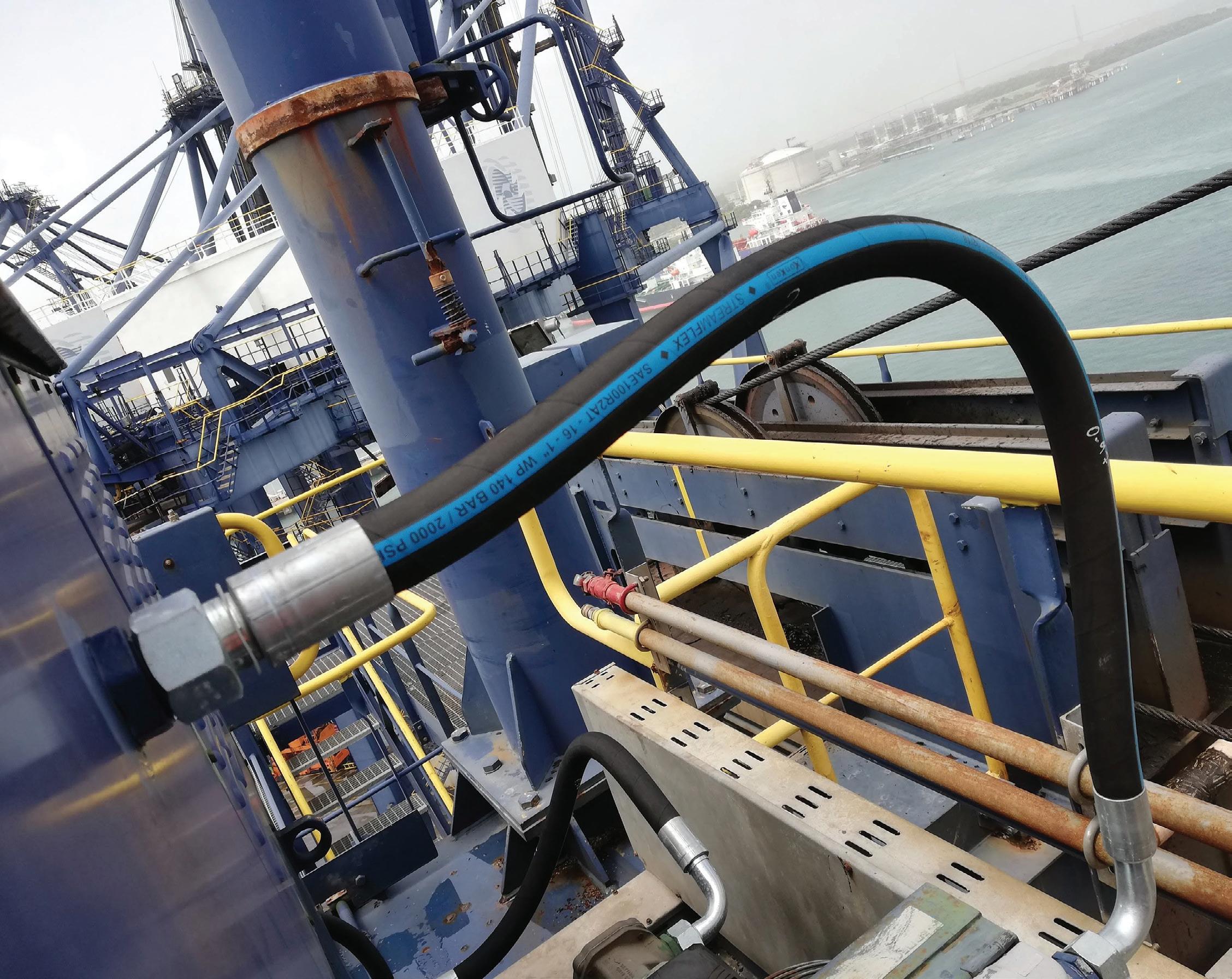
Implement the ZeroLeaks mobile app for the registration, control, and monitoring of hose assemblies in terms of identification, crimping data (operator, crimping machine, external crimping diameters), installation data (date, location, operator), hours in service, scheduling frequency of inspections, and scheduling for replacements.
Provide technical support prior to environmental audits, as well as to resolve non-conformities found, and for waste management, particularly with points and actions associated with hydraulic oil leaks in equipment and processes.
The program is currently being implemented at the Hutchison Port in Panama for the many hoses running throughout the port’s two dozen or so cranes. XonKen is installing and monitoring data for all hoses and hydraulic oil throughout the equipment while providing ongoing training for the technicians, operators, and as many personnel who install and use hose assembly equipment. The full program implementation is three years from installation to complete data monitoring year over year.


In the Hutchison Port program, Leon said that the hose inventory is now split between the port, its distributor, and XonKen’s warehouse, which reduces on-site inventory needs while ensuring rapid deployment of new hose as needed. Additionally, the distributor has committed to resolving any emergencies within an hour, he noted.
One of the key objectives in training is to ensure that operators understand the correct amount of torque needed to install a hose, as that is often the number one point of failure. “With this product, we want to collect and summarize all the data to send to management and the operator. The data needs to be open to all personnel concerned with the operation — the operators, maintenance, distributor, and others.
“You need to establish this confidence with the end user to get the best result of every product,” Leon said. “It’s a philosophy.

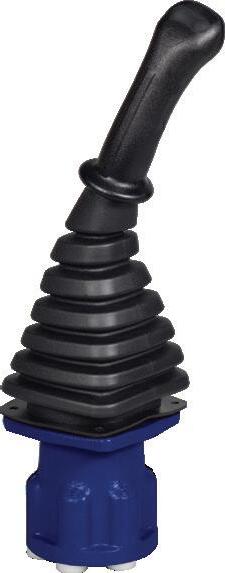

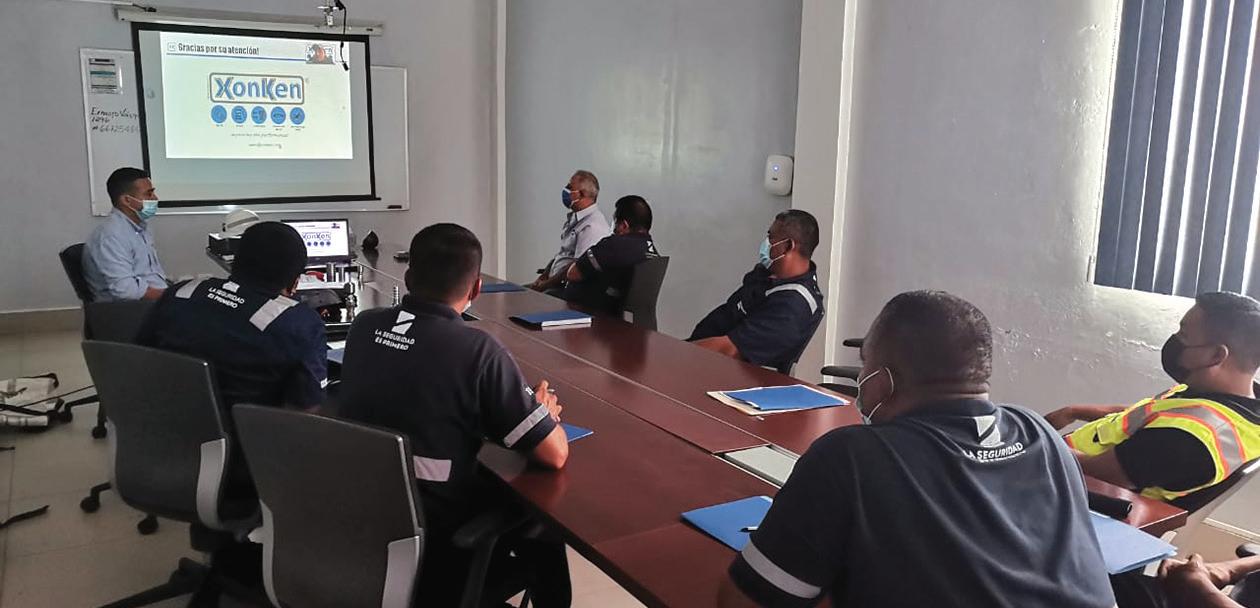
The hydraulic hose assembly is vital for the operation. It’s not a commodity or just a part that they replace. We need to be more professional in every aspect of the hose process, from the start of the raw material production in China, to when our distributors receive the hose in their
warehouse, to when we deliver it to the end user. And when we deliver it to the end user, we need to monitor it to ensure that they crimp and install the hose properly.”
For more information, contact Luis Alberto Leon, Business Development Manager, XonKen Inc. at lleon@xonken.com. FPW
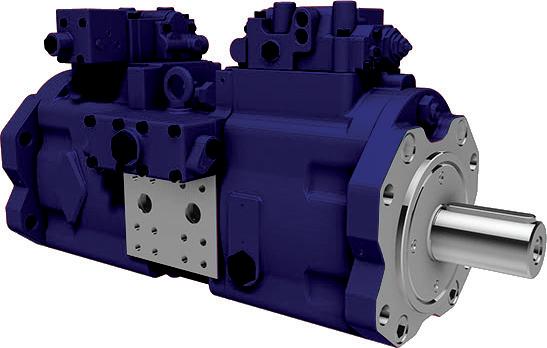
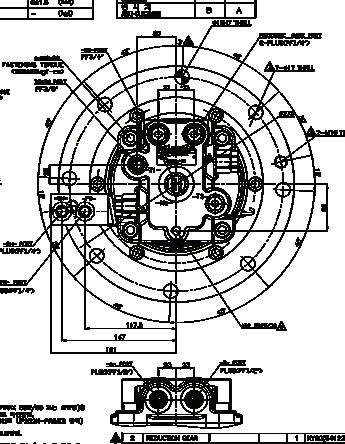
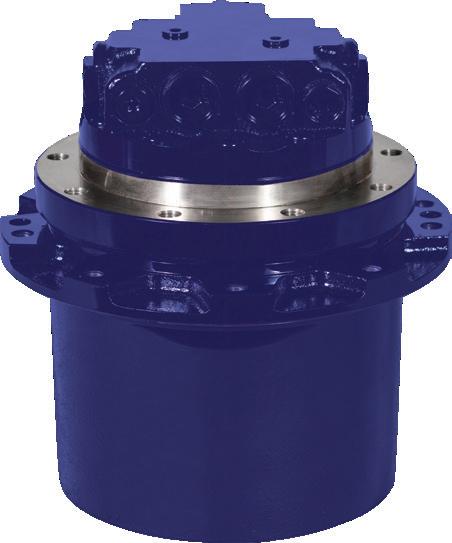


12 tips for leakage prevention
through proper sealing design and selection
Seals used for fluid power applications are highly varied and specific to each component and application. From simply sealing pressurized air from atmospheric air for pneumatic valves to preventing hydraulic oil from leaking into waterways from the rudder cylinder on watercraft, there are few conditions in which a fluid power seal doesn’t operate.
It goes without saying that the primary role of a seal is to contain fluid (yes, air is a fluid). Although an engineered amount of leakage is occasionally required, such as for lubrication purposes, leakage is generally considered a failure mode. Fluid leakage not only leads to operational inefficiencies but can also result in safety hazards and environmental concerns. We must understand the importance of proper sealing design and selection in preventing
and controlling leakage in hydraulics and pneumatics systems, focusing on the design considerations for the seals and the pockets or cavities into which they’re installed.
Leakage in hydraulic and pneumatic systems can occur due to various factors, including wear and tear, temperature fluctuations, pressure differentials, incompatible media, and poor sealing design. The consequences of leakage extend beyond mere inefficiencies, encompassing increased energy consumption, decreased system performance, and, in extreme cases, equipment failure.
In hydraulics, where liquid is used to transmit power, even a tiny leak can result in a significant loss of fluid over time. This not only raises operational costs but also poses environmental challenges. Pneumatic systems, which use compressed air, face similar issues with leakage affecting overall efficiency. To address these challenges, engineers must focus on sealing solutions that are not only effective and durable but

also tailored to the specific needs of each system.
I’ll first discuss the application side of sealing and the four points you must consider to select seals best suited for your pump, valve, actuator or other component. Then, I’ll move along to specialty seals that improve specific applications and the benefits of each. Finally, I’ll wrap it up with practical tips on improving the reliability of any seal used in your application.
Application and Engineering:
1. Material selection:
The choice of sealing material is critical in designing effective seals for hydraulic and pneumatic systems. Different applications demand different materials based on chemical compatibility, temperature resistance, and wear characteristics. Common sealing materials include nitrile rubber, polyurethane, fluorocarbon, and PTFE. Understanding the operating environment and the nature of the fluids involved is essential in selecting the most suitable material for a given application.
For both hydraulics and pneumatics, Buna nitrile offers a great all-around seal polymer suitable for most applications, although other technologies are preferred when extreme conditions present themselves. Urethanes excel in high-pressure applications, while Viton (fluorocarbon) is a top choice for hightemperature environments.
2. Geometry and profile:
The design and geometry of a seal play a vital role in its performance. Engineers must consider factors such as groove dimensions, seal cross-section, and contact pressure distribution. The choice between dynamic and static seals depends on the specific application requirements. Dynamic seals, which experience relative motion
between mating surfaces, are commonly used in hydraulic and pneumatic cylinders, while static seals are employed in areas with no relative motion.
Even when dynamic seals are required, manufacturers offer myriad choices for the same application, such as piston seals, for example. A piston seal can range from a simple O-ring to exotically-shaped lip seals. Depending on application and designer preference, a piston may employ energized U-seals, U-seals with bonded backup, T-seals, multiple buffer seals, vee packings, piston cups, crown seals, or multi-piece assemblies.
3. Pressure and temperature ratings:
Hydraulic and pneumatic systems operate under varying pressure and temperature conditions. Seals must be capable of withstanding these extremes to ensure longevity and reliability, and
how a seal performs in extremes comes down to many factors. Understanding the pressure and temperature ratings of seals helps with selecting components that can withstand the demanding conditions of industrial applications.
Although fluorocarbon generally handles hot ambient conditions up to 400°F, it’s not like any hydraulic oil can withstand such extreme conditions. When you factor in the reduced pressure rating limitation of the softer Viton, perhaps a urethane with a meaty cross section would be suitable, especially with high-temperature polyurethane rated for 250°F.
4. Friction and lubrication:
Friction between sealing surfaces can lead to wear and heat generation, impacting the overall efficiency of a system. Proper lubrication is essential to
reduce friction and extend the life of seals. Engineers must consider the compatibility of lubricants with sealing materials and ensure that the lubrication method aligns with the application’s specific requirements.
Aside from lubrication, which is obviously favorable for hydraulic components bathed in oil, the construction style also affects friction, subsequently influencing velocity limitations. A pneumatic cylinder with a loaded T-seal provides excellent leakage protection but, when dry, will be subject to high friction, where repeated high-velocity cycles may quickly soften and wear the seal, ironically leading to leakage. Choosing a softer U-cup for high-velocity applications may give up some load-holding capacity. Still, with less friction, the seal will be maintained within its ideal operating temperature, leading to leak-free reliability.

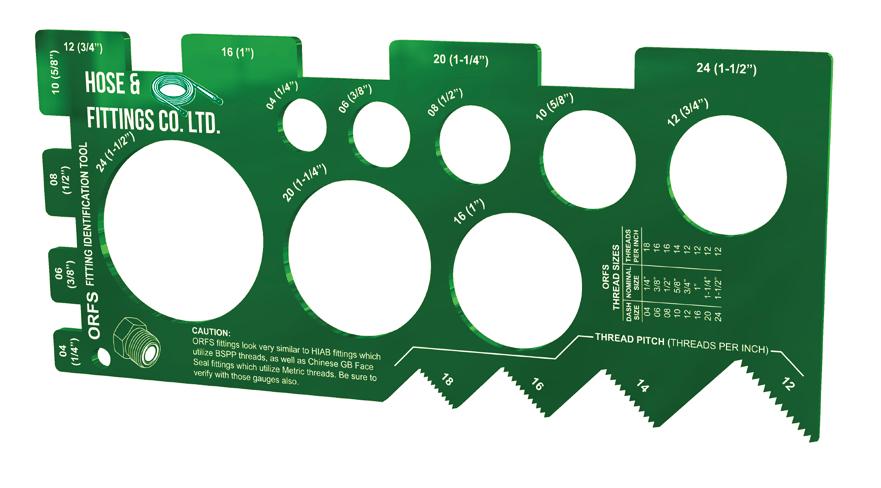
Specialty seal options:
5. Polymeric seals with enhanced properties: Recent advancements in material science have led to the development of polymeric seals with enhanced properties, such as improved wear resistance, flexibility, and chemical compatibility. These advanced materials contribute to longer seal life and better overall system performance. For instance, polytetrafluoroethylene (PTFE) seals are known for their low friction, high-temperature resistance, and chemical inertness, making them suitable for demanding applications in possibly corrosive and caustic conditions. Thermoplastic elastomers (such as Hytrel) offer sealing, pressure capacity, and friction characteristics similar to other choices but with a broader temperature range.
Even within the realm of traditional seal materials, such as urethane, advancements have resulted in sophisticated compounds offering superior pressure capacity, wider operating temperature operation range and even capacity to work with exotic fluids previously incompatible with older technology.
6. Self-lubricating seals: Self-lubricating seals incorporate materials that inherently reduce friction, eliminating the need for external lubrication. They are particularly beneficial where frequent maintenance is challenging or costly. Self-lubricating seals contribute to energy efficiency and extend the intervals between maintenance cycles by minimizing friction. Common self-lubricating compounds are bronze-filled PTFE or carbon/graphite-impregnated rubber.
7. Smart seals with monitoring capabilities:
Integrating sensors and monitoring technologies into seals allows for realtime performance analysis and is on the cutting edge of Industry 4.0 technology. Smart seals can provide data on factors such as temperature, pressure, and wear, enabling predictive maintenance strategies.
By identifying potential issues before they escalate, smart seals increase system reliability and reduce downtime.
8. Seals with low-compression set: Compression set refers to the permanent deformation of a seal after prolonged compression. Seals with low compression set characteristics maintain their shape and sealing effectiveness over extended periods, even under high pressures. This property is particularly crucial in hydraulic and pneumatic systems where seals are subject to continuous compression and decompression cycles. A compressed seal will not correctly fill out the groove or pocket, leading to leakage.
Practical tips:
9. Regular maintenance and inspection:
Implementing a routine maintenance schedule is essential for preventing and identifying potential leakage issues. Regular inspections allow operators to detect wear, damage, or misalignment of seals early, enabling timely replacement and avoiding more extensive damage. Although many leaks are internal (think piston seals), these failures can be monitored or observed, such as when a cylinder drifts or fails to hold a load stationary. It goes without saying that visual leaks are the most apparent form of leakage.
10. Proper installation techniques:
Seals must be installed with precision to ensure optimal performance and leak prevention. Proper installation involves attention to correct alignment, lubrication, and torque specifications. Sometimes, a seal will roll inside its machined pocket after it’s installed, especially when it isn’t prelubricated, such as with rod seals subjected to dry friction of the chromed surface. As well, end seals should be prevented from interference with potential pinching surfaces, burrs or sharp edges. A pinch seal will result in immediate leakage during operation in most cases.
11. Pressure and temperature control:
Operating hydraulic and pneumatic systems within specified pressure and temperature ranges are crucial for seal integrity, as exceeding these limits can lead to seal failure, leakage, and, ultimately, system breakdown. Implementing pressure and temperature control measures, such as efficient circuit design and cooling systems, contributes to the longevity of seals. Also, heat from fluid, friction or ambient conditions softens the seal, making it more likely to extrude through even the smallest gaps.
12. Training and education:
Adequate training for operators and maintenance personnel is crucial for effective system management. Training programs should cover proper handling, installation, and troubleshooting of seals. A well-informed team is better equipped to promptly identify and address potential leakage issues, not only once equipment is installed, but to help prevent the previous two examples from occurring.
Leakage prevention and control in hydraulic and pneumatic systems are paramount for efficient and reliable industrial operations. Advances in sealing technology, coupled with best practices in design and maintenance, contribute to the longevity and performance of seals in these critical systems. As industries continue to evolve, integrating smart seals and innovative materials will play a pivotal role in enhancing overall system efficiency and reducing the environmental impact of fluid leakage. Engineers and operators must remain vigilant in their approach to sealing design and selection, embracing the latest advancements to ensure the seamless operation of hydraulic and pneumatic systems in future years. FPW


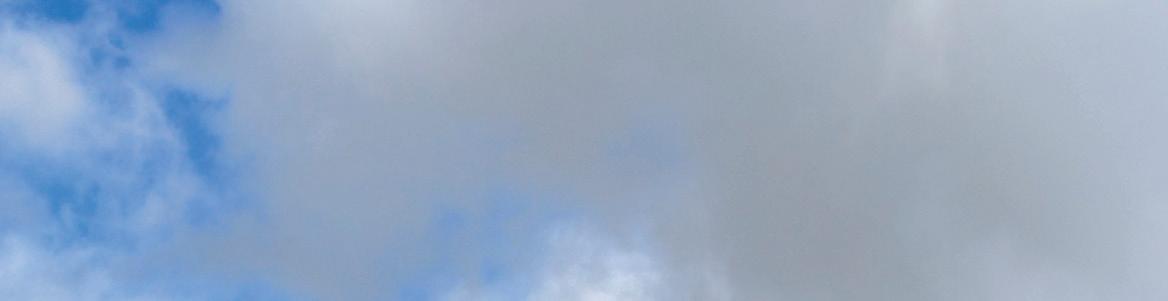
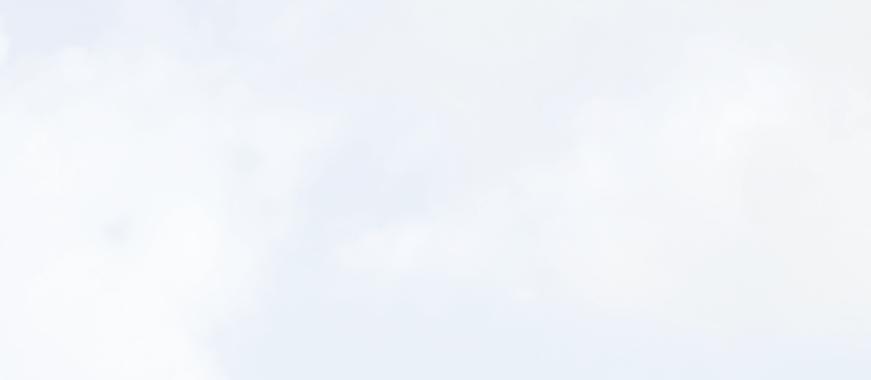
OUTPERFORMING FILTRATION DEMANDS OF TODAY’S HYDRAULIC SYSTEM TECHNOLOGY

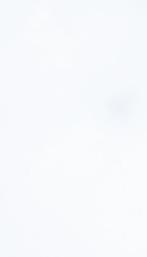

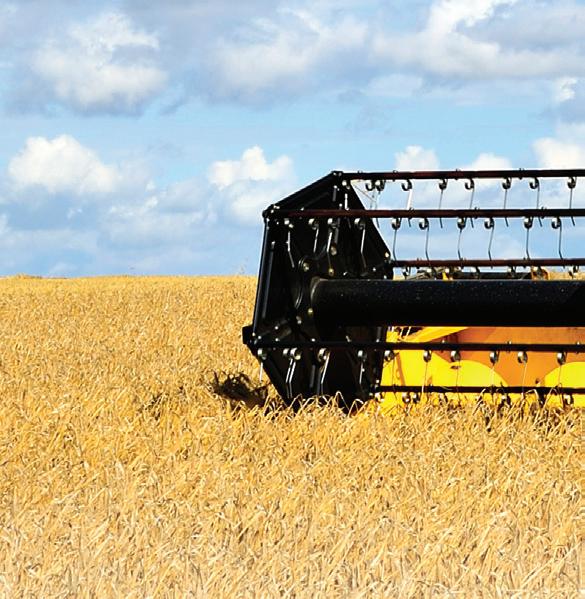
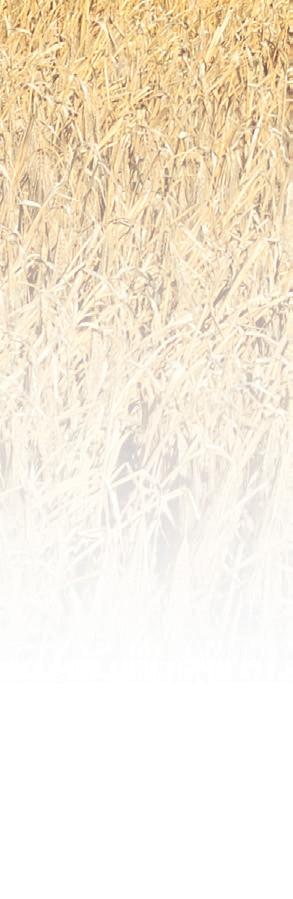
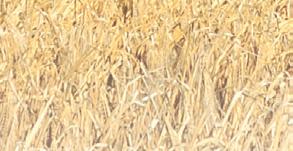

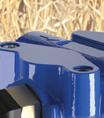
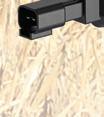
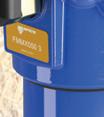
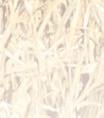
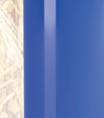
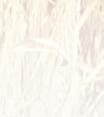
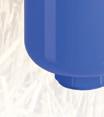
FMMX
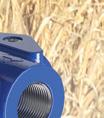
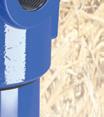
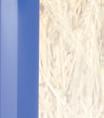
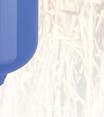
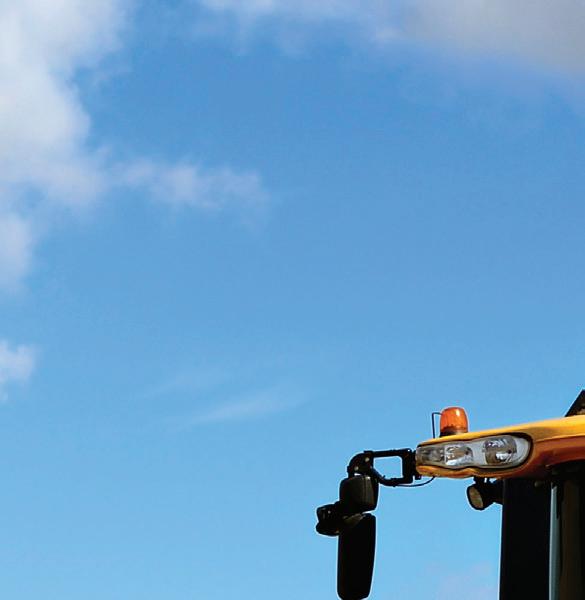




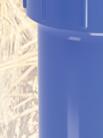

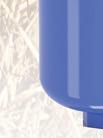
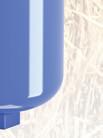

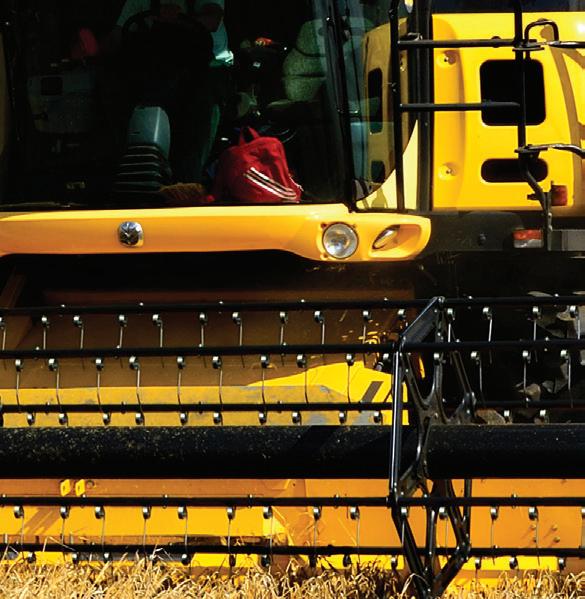
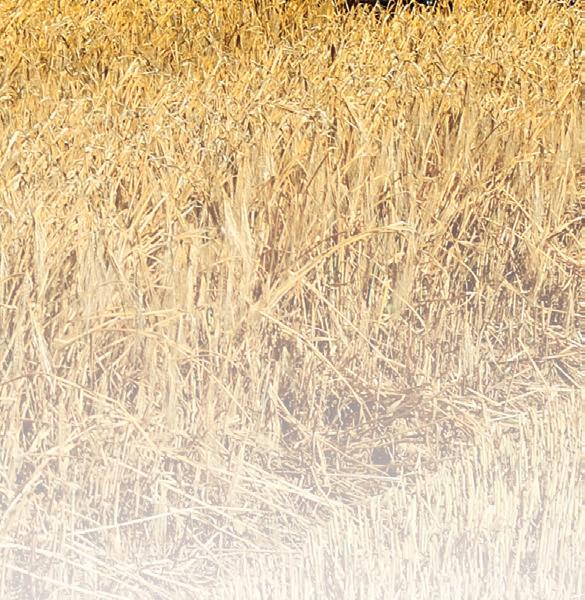
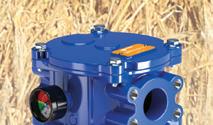
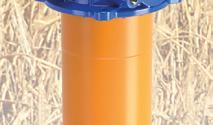
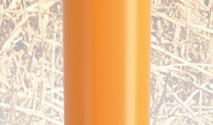
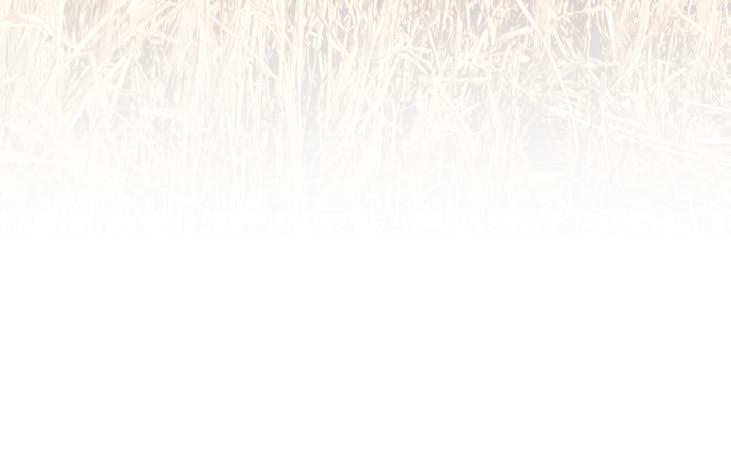
NEW High pressure in-line lter series, pressure to 6090 psi and ow to 40GPM. Patented MYclean lter element design assures original elements over machine life.
ELIXIR HFEX

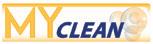

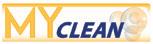

508 psi in-line lters and ow to 80 gpm. Spiral ow head design, and patented lter elements provide longer service life and assures original elements over machine life.
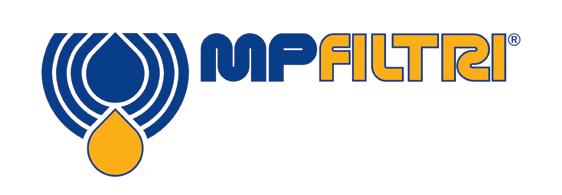
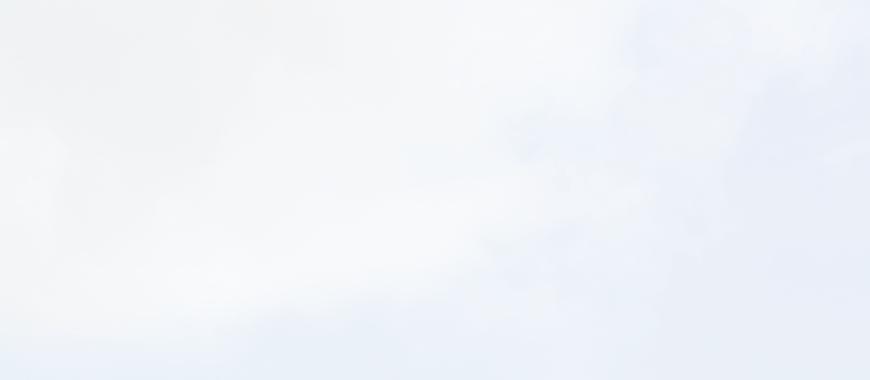
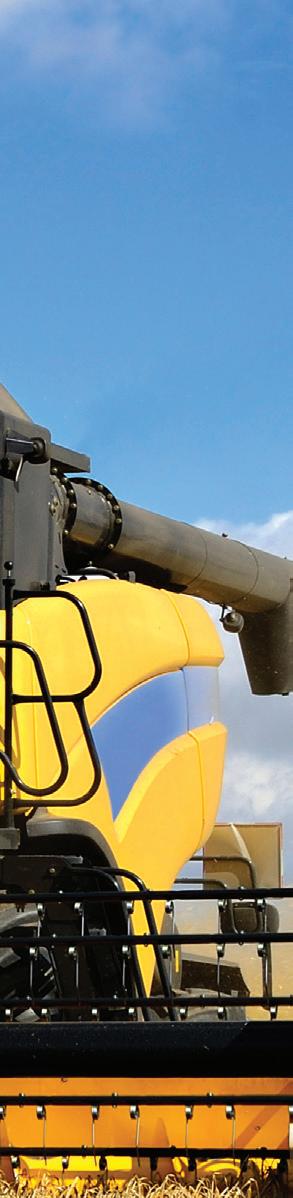
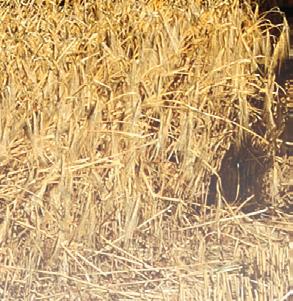
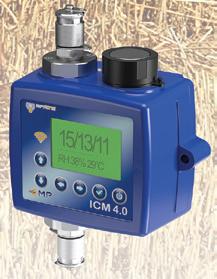

MPFX Series
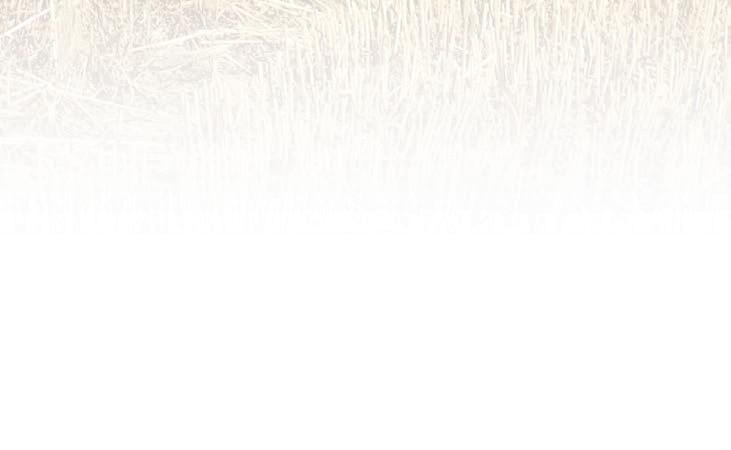
ICM 4.0
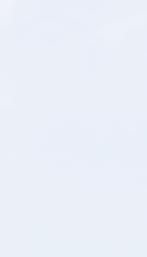
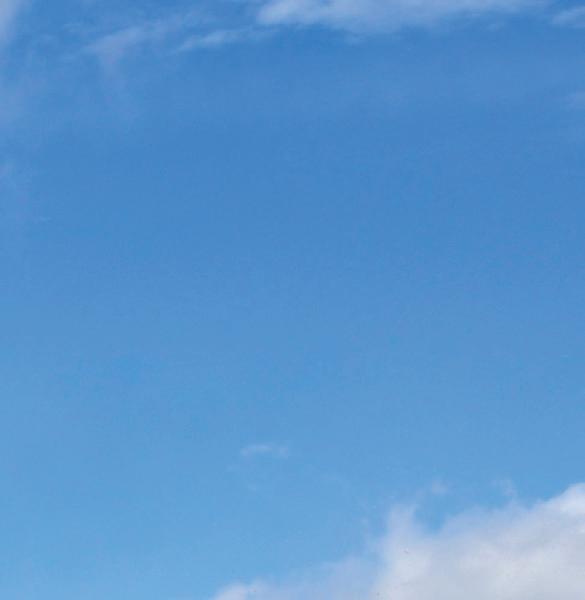

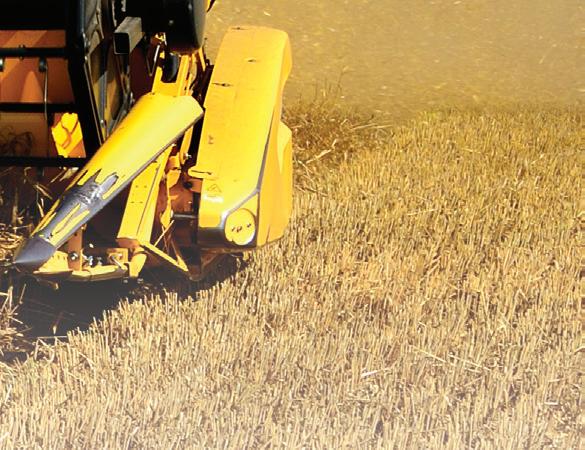
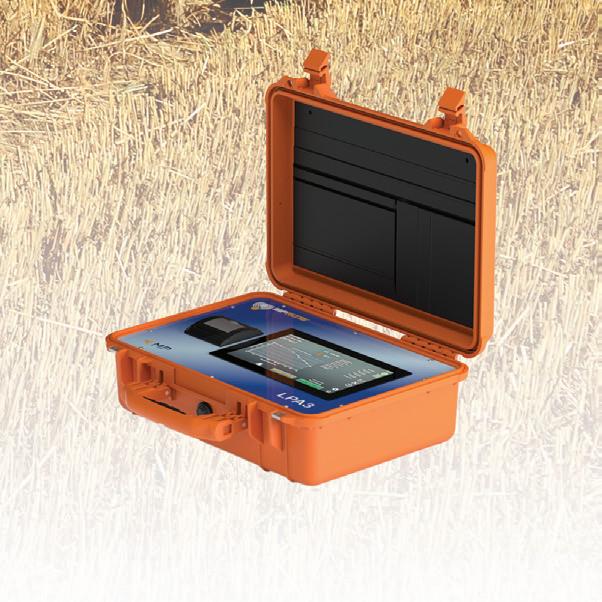
LPA3
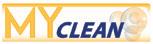

Tank mount return lters with working pressure up to 116 psi and ow to 238 gpm, multiport options, removable bowl and patented MYclean element with OEM speci c design capabilities.

WIFI capable sophisticated software suitemonitors the status of your hydraulic ltration system in continuous real-time, with critical early warning detection. MYclean
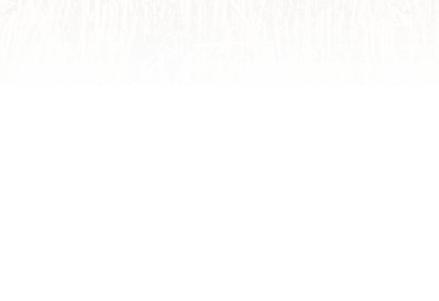
Portable optical and photodiode APC for fast and accurate particle monitoring of hydraulic uids to identify risks before they impact the performance of the hydraulic system.
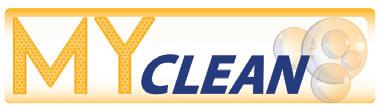
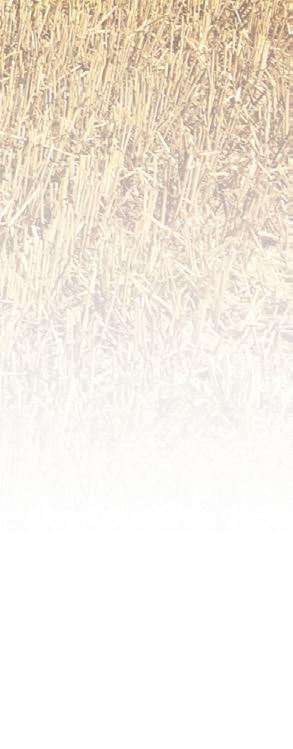





Will AI soon predict internal cylinder leakage?
External hydraulic cylinder leakage is usually very obvious to spot, as you can see from the darkened oil sludge on this machinery.
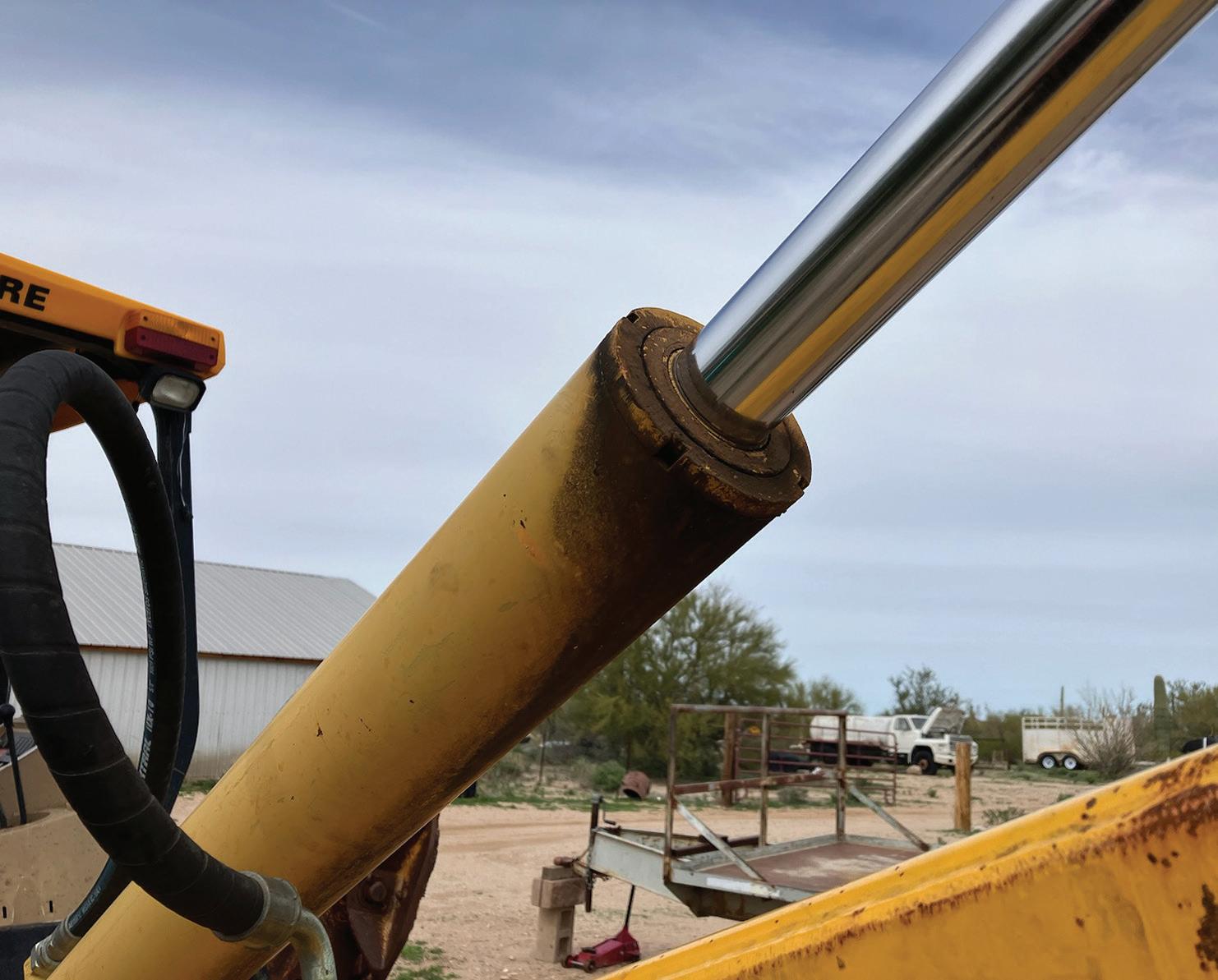
Electrohydraulic actuators are standalone, self-contained systems that perform powerful tasks without external piping. They typically include an electric servomotor driving a hydraulic pump — often an axial-piston unit. Other components include a hydraulic cylinder, tank, valving and charging circuits.
Because they are fitted with their own closed fluid circuit, they require only a small amount of hydraulic fluid and they eliminate a central hydraulic power unit. As a typical unit is quite compact and lightweight, the electro-hydrostatic actuator (EHA) has been used extensively in aircraft. But it is increasingly being used in industrial, marine and offshore applications, as well as for agricultural tasks. Researchers are also
considering EHA use to electrify mobile equipment operations.
However, a serious concern with EHAs is leakage. External leaks, typically caused by rod seal and wiper failures, are easy to spot with a visual inspection. But internal leaks, usually the result of piston seal wear and tear, often go unnoticed. But they can lead to control issues, loss of performance and potentially serious malfunctions.
Researchers in China recently offered a novel method to detect internal EHA leakage using artificial intelligence methods. In a paper published by London-based The Institution of Engineering and Technology titled “A method to detect internal leakage of hydraulic cylinders by combining data augmentation and multiscale residual CNN” the authors, Qingchuan He of Zhejiang SciTech University and Xiaotian Lyu of Zhejiang CHR Intelligent Equipment Co. proposed a way to solve the problem with more than 99% accuracy.
Undetected leaks
According to the authors, at present internal leakage in an EHA cannot be accurately detected by using operational data alone. Some studies have been carried out on detection of internal leakage in hydraulic cylinders by monitoring pressure or other signals. But in general, the proposed methods depend on high-precision pressure gauges, flow sensors and complex leakagemeasuring devices. The EHA is a compact hydraulic system, and it is usually impossible to install high precision and complex measuring devices due to space constraints and weight limitations.
Moreover, said the authors, the amount of internal leakage changes with load and velocity of the rod, and also with hydraulic oil temperature. Detection accuracy cannot be guaranteed by analyzing changes in pressure signal features when a hydraulic cylinder operates under nonstationary load and velocity conditions. Therefore, they said, it is necessary to develop an internal leakage detection method in hydraulic cylinders with no additional complex measuring devices.
Neural networks
Instead, they propose a convolutional neural network (CNN) method to detect internal leakage based on the relationship between operational parameters of the EHA and leakage in the hydraulic cylinder.
A neural network is a method in artificial intelligence that teaches computers to process data much like the way a human brain works. It is a type of machine learning, called deep learning, that uses interconnected nodes or neurons in a layered structure.
According to Arm Ltd., a technology company based in Cambridge, England, a CNN is a type of artificial neural network used primarily for image recognition and processing, due to its ability to recognize patterns in images. A CNN is a powerful tool but requires millions of data points for
training. CNNs must be trained with highpower processors, such as a GPU or an NPU, if they are to produce results quickly enough to be useful.
While CNNs are designed to solve problems with visual imagery, they also have many applications outside of image recognition and analysis, including natural language processing, drug discovery, and health risk assessments. CNNs also help provide depth estimation for self-driving cars.
In recent years, said Qingchuan and Xiaotian, convolutional neural networks are gradually being developed as a computational framework to detect faults in mechanical and electrical products.
Tracking data
A typical EHA system is mainly composed of one permanent magnet synchronous motor (PMSM), an axial piston pump, oil
tank, hydraulic actuator, and corresponding circuits. The PMSM is controlled through closed-loop vector control. Motor dynamics can be described by a model that includes parameters like load torque, viscous friction of the rotor system, rotation speed, total inertia of motor, number of pole pairs, flux linkage caused by permanent magnets, motor current, theoretical pump volumetric displacement, and the inlet and outlet port pressures under working conditions.
Other considerations are the force balance based on the piston surface, velocity and displacement of the hydraulic actuator, the total inertia mass applied to the actuator, viscous friction, stiffness, external applied force, and the internal leakage flowrate in the hydraulic cylinder.
The authors presented a method to align these multi-source signals with different forms by using the motor current
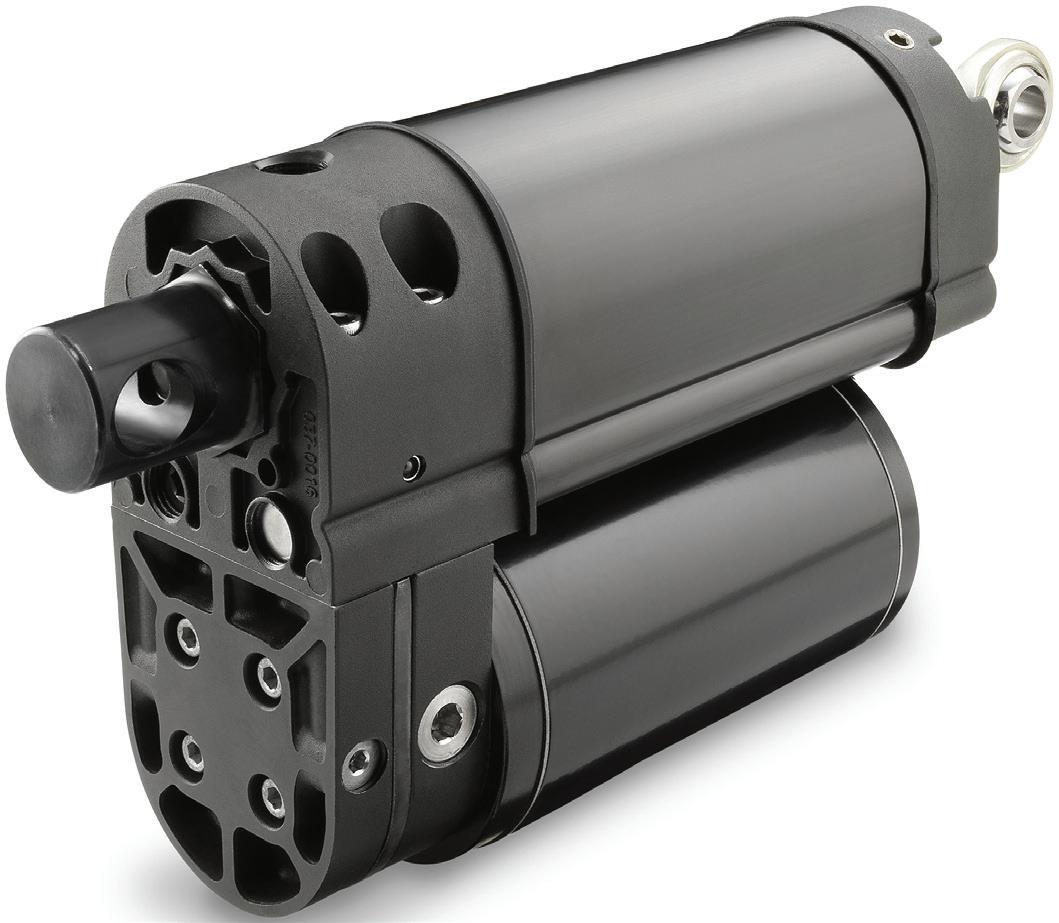
It is more difficult to pinpoint internal leakage, especially with EHAs. Internal leaks here are usually the result of piston seal wear and tear, often go unnoticed. But they can lead to control issues, loss of performance and potentially serious malfunctions.
| Courtesy of Thomson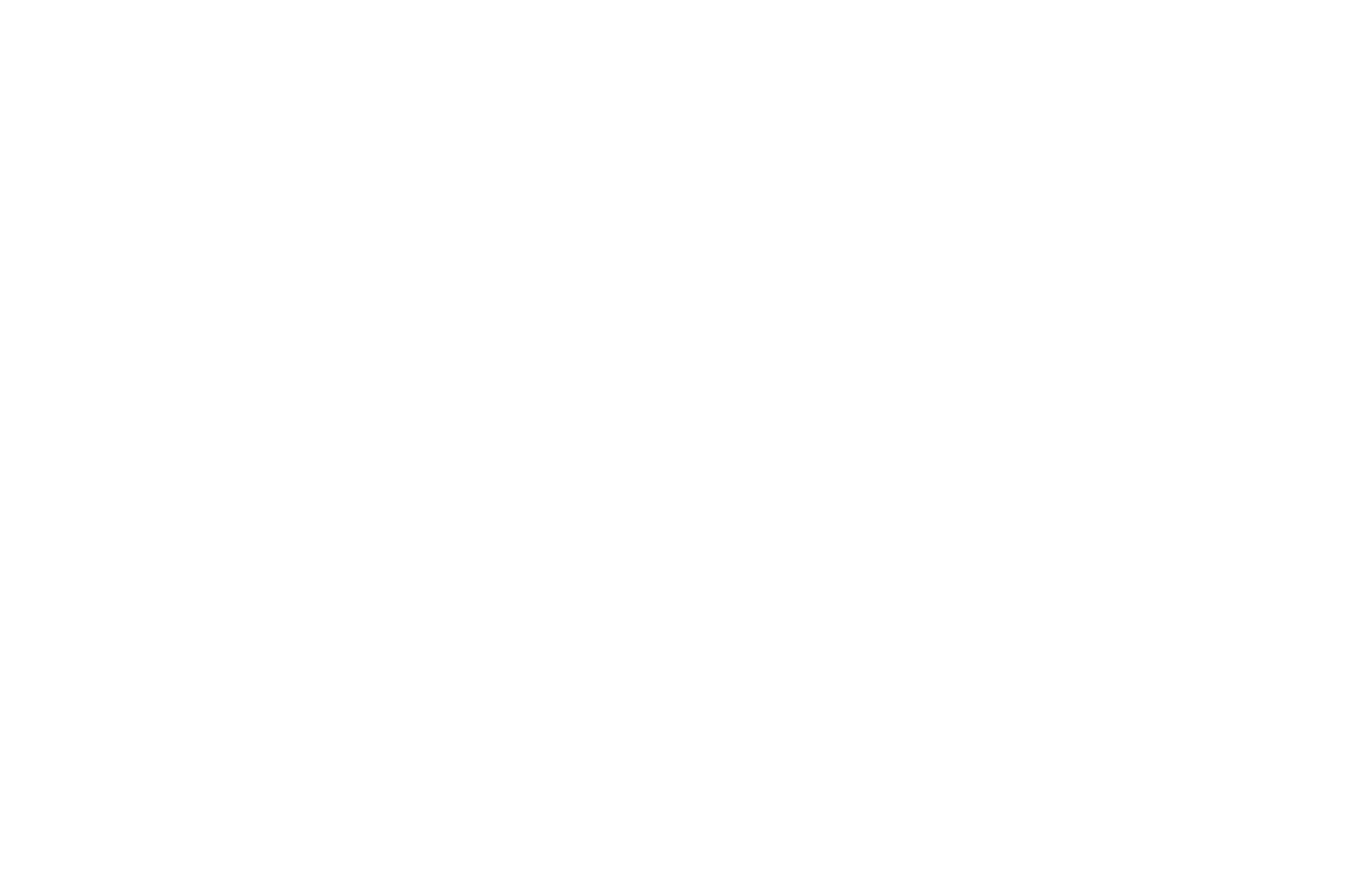
as a benchmark. The raw monitoring signals of an EHA usually include inlet and outlet port pressure of the hydraulic cylinder, motor currents, rotation speed and displacement of the hydraulic actuator. The signals also change greatly with the amplitude and frequency under variable load and velocity condition.
Because the number of monitoring signals are relatively small, a feedforward neural network (FFNN) based data augment method was developed to increase parameters of the input data set. The variables, including velocity and differential pressure, were set as the input of FFNN model, and rotation speed or current was set as the output. Construction of the neural network used MATLAB. And a general method on how to detect internal leakage by combining signals alignment, data augmentation and multiscale residual CNN was proposed. Complete details are found in the authors’ paper.
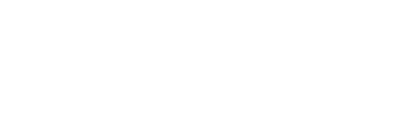
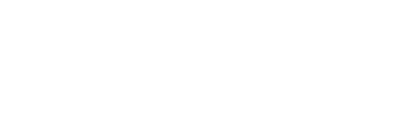
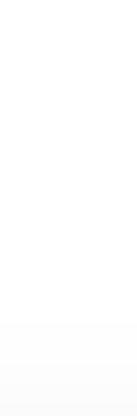
Experimental results
The basic theory and mathematical models were subsequently tested via an experimental setup. The test bench mainly consists of the motor, pump, tank, and actuator, one bidirectional throttle valve, two safety valves and some sensors. The PMSM directly drives the pump; and pressure sensors detect pressure in the chambers of the hydraulic actuator. An LVDT linear position sensor measures movements of the hydraulic actuator and feeds back position information to the control system. Rotation speed and current of the PMSM were collected from the motor driver.
Different degrees of internal leakage of the hydraulic cylinder were simulated by adjusting the bidirectional throttle valve. The signals from displacement, velocity, pressures, motor current and rotation speed were collected synchronously.
The velocity signals note obvious differences between serious leakage and
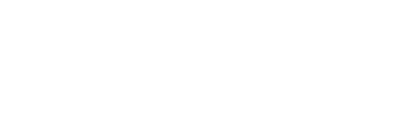

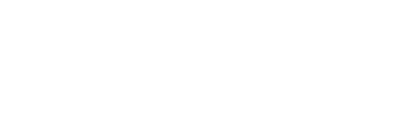
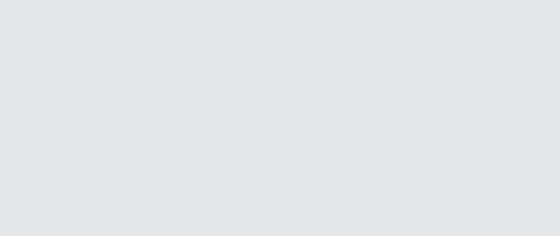
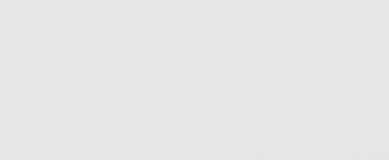
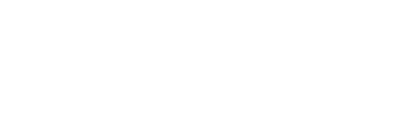

normal states. This means that serious leakage has a major influence on control accuracy. Generally, motor speed and current increased with the leakage when pressurized oil enters the hydraulic actuator. Similarly, the motor speed and current decreased with the severity of fault when oil output exits the hydraulic actuator. However, the changes are not always proportional to the serious leakage because the actual condition is relatively complicated. For example, even a small fluctuation of the load will result in changes in motor speed and current. Therefore, the detection accuracy of leakage cannot be guaranteed by visually tracking the changes in signals. Thus, all the data collected were used for training the FFNN model, repeated over numerous trials.
In the end, predicted values neared the actual measured values. Four experimental datasets were used to train the multiple residual CNN and validate the effectiveness of the proposed approach. They included processed signals such as velocity, pressure difference, motor current and rotation speed, and also predicted motor current and rotation speed, and it obtained test accuracy of 91.2% to 99.8%.

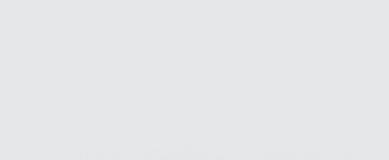
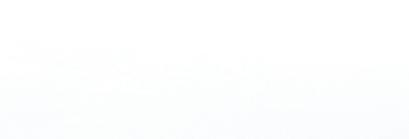
light compact tight

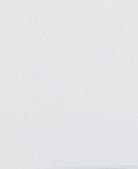
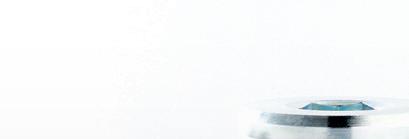

HN P | SCREW PLUG
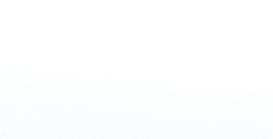

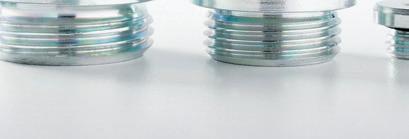
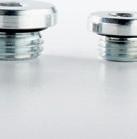
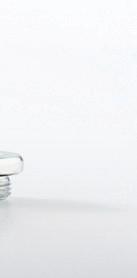
Our solution for tight systems
Screw plugs to avoid wasteful loss of compressed air. For connection dimension comply with ISO 16030. With assembled o-ring, available from M 3 and up. Developed especially for the requirements in the field of pneumatics.
By combining methods of signals alignment, data augmentation and multiscale residual CNN modelling, the detection accuracy of internal leakage control signals was impressive. The results show that the proposed method can effectively improve the accuracy under nonstationary load and velocity conditions.
Moreover, multiscale residual CNNs are usually seen as a black box, where it is unclear what features of a model are used for internal leakage detection decisions. In the future, researchers could focus on how to develop an explainable deep learning algorithm which can visualize the CNNs’ model.
In addition, this article only studied the internal leakage fault in a hydraulic cylinder and did not explore internal leakage in the pump. The next step will be to study multiple internal leakage faults in an EHA. FPW
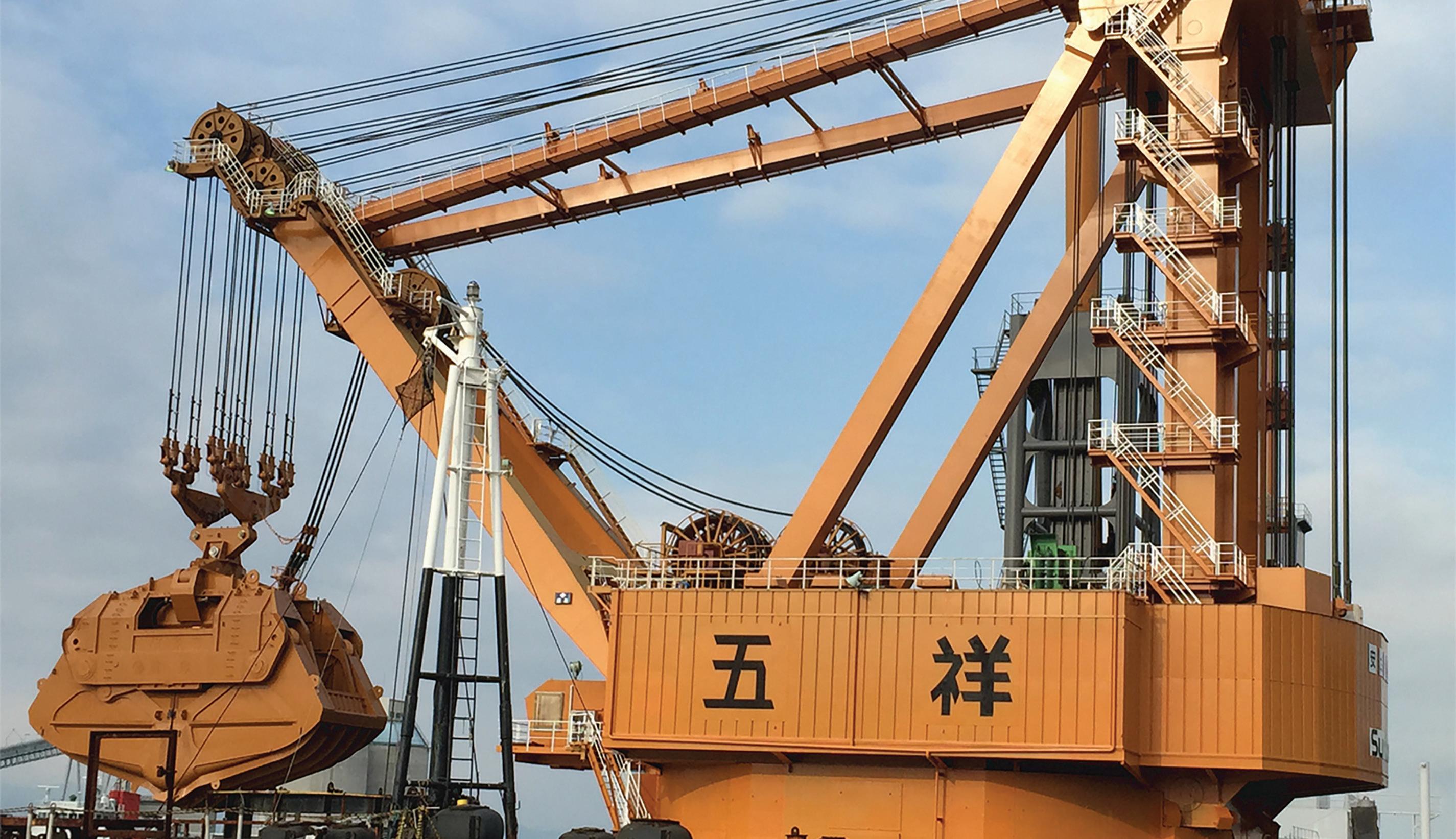
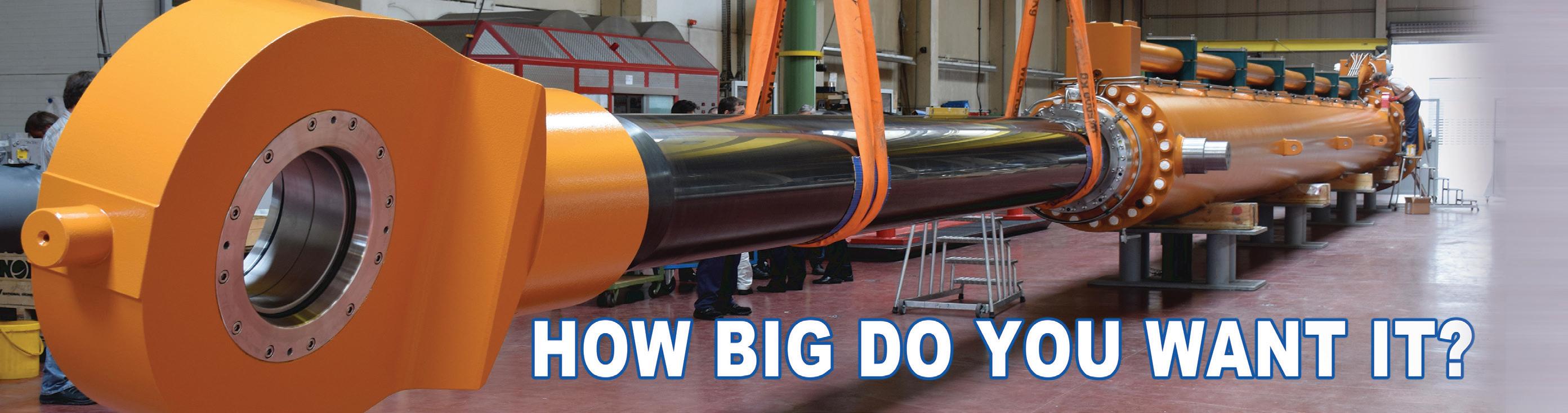

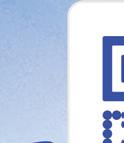
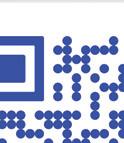
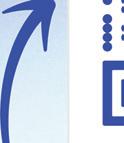
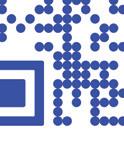


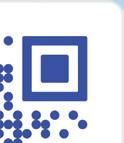


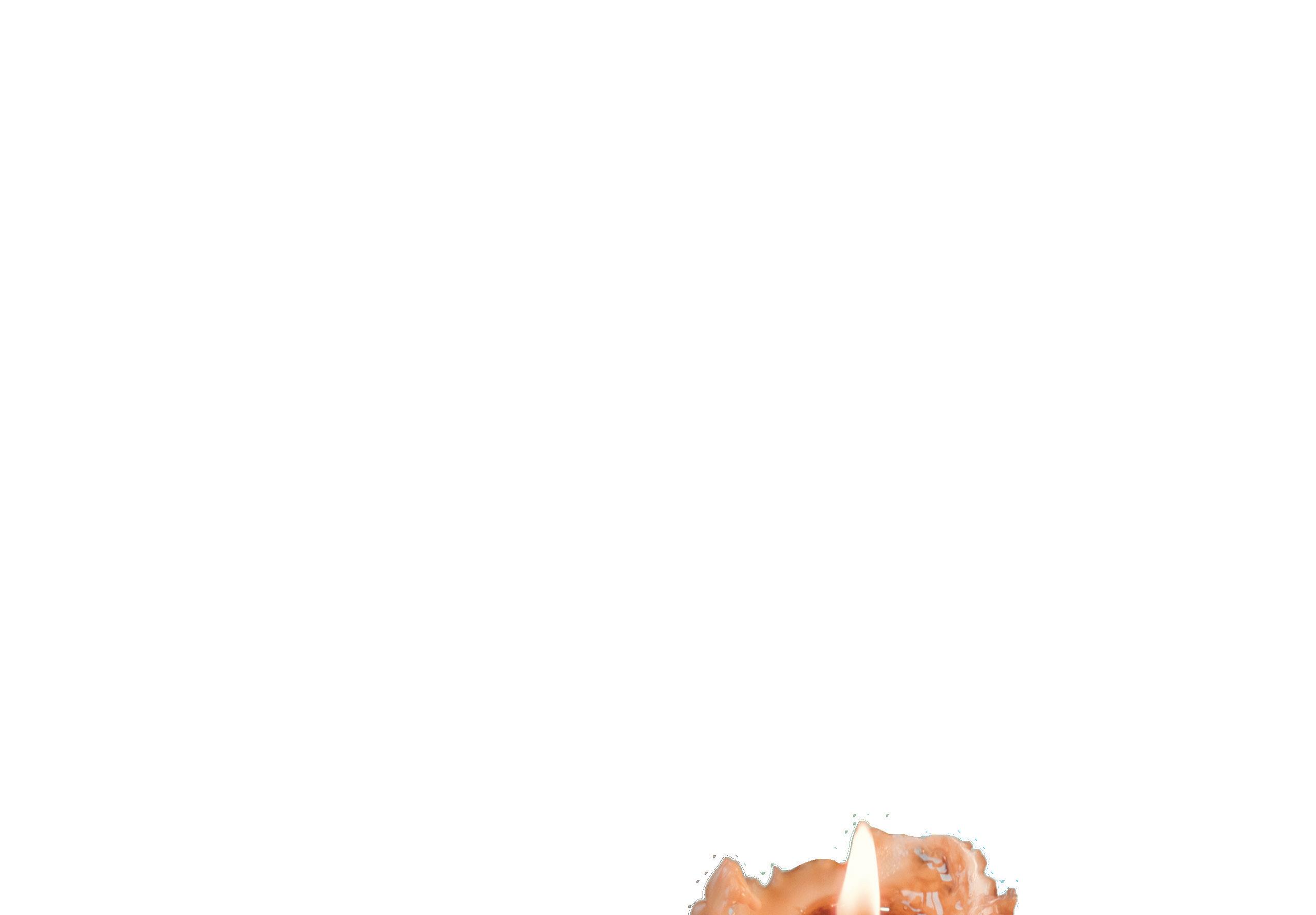
HYDRAULICS IS A MATURE TECHNOLOGY, BUT THE NEGATIVE CONNOTATIONS CONTINUE TO FOLLOW IT EVERYWHERE.

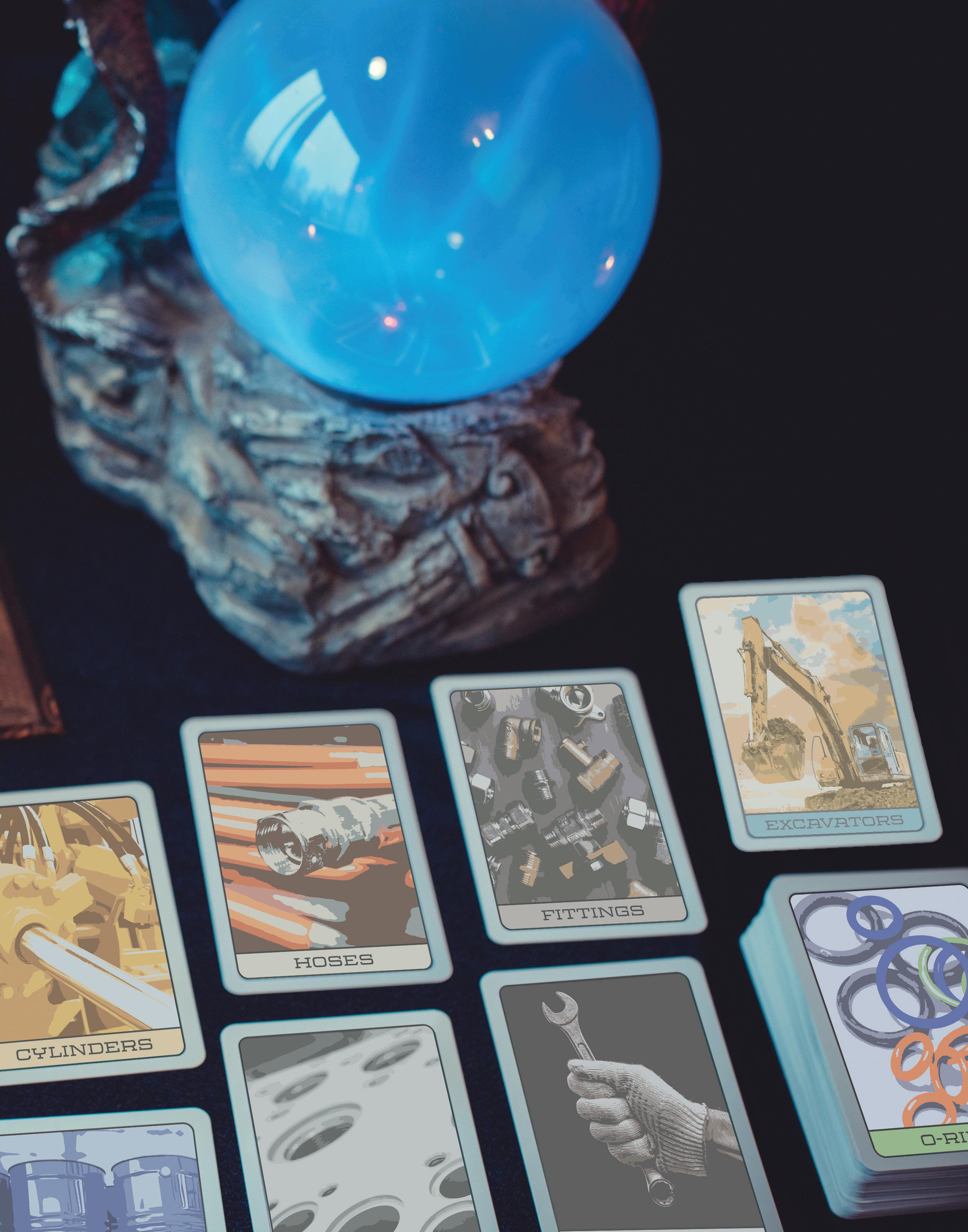

The editors of Fluid Power World decided to tackle this question head on, examining the industry’s vexing scarlet letter and asking what can be done, both from a technology and a marketing standpoint. We asked users, readers, manufacturers, and industry experts for their thoughts. In all, almost 50 people responded to our survey questions or were interviewed by our staff members about the topic. Here’s what we discovered.
Is the problem real?
Concerning external leakage, some of our respondents did see positive steps forward for the industry. Billy Goodman, a Mechanic for DOD, believes today’s hydraulic systems are built more with leakage prevention in mind than older systems were.
an issue of leakage, we have many products that can 100% leak free permanently seal. But our goal is more than just to stop the leak. It is to offer our customers the most cost competitive overall sealing solution.”
But a vast majority of respondents said that leakage is still a major issue.
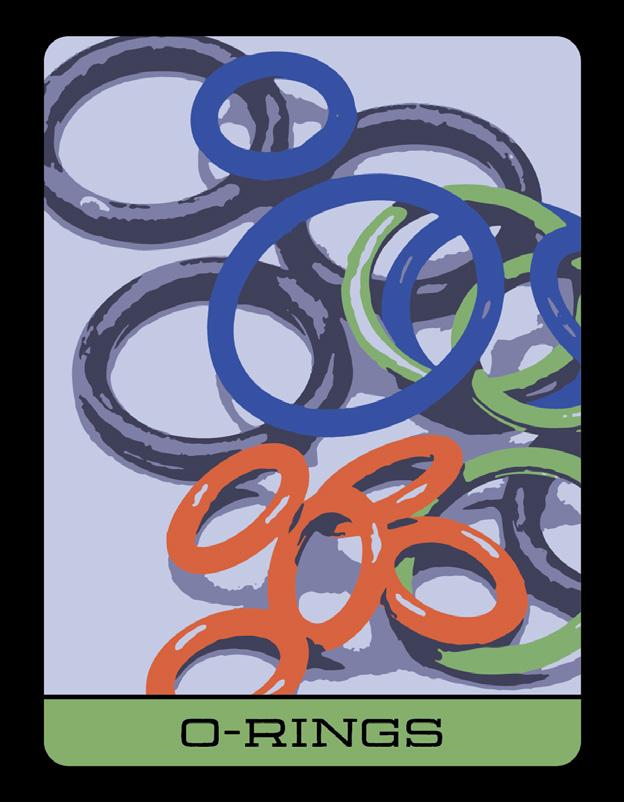
“Better sealing materials and better hose materials have taken care of a lot of the leakage issues. Stopping leaks before they start is stressed more today,” he said.
And Burk Schmidt, Fluid Power Consultant for Creative Hydraulic Solutions, explained that while external leakage could be a problem for some installations, it surely does not have to be a problem today.
“We have good components and fittings at our disposal,” he said. “Therefore, with the use of good components and fittings — as well as proper system design, this really does not have to be a problem. By good fittings, I mean quality fittings with an elastomeric seal. When properly tightened, they do not leak. Have you ever seen hydraulic oil dripping from a commercial airplane? They use hydraulics for flap control as well as the landing gear extension and retraction. By good system design, I mean correct hose routing, use of the right valves, and control sequences to avoid shocks in hydraulic pressure.”
Brian Krieger, North American VP of Sales & Global Marketing Manager for Engineered Inserts & Systems Inc., said that their entire business is to avoid leakages with respect to cross drilled ports.
“When a customer comes to EIS to solve
“Many manufacturing facilities spend significant economic resources on mitigation products (kitty litter). I have seen some shops with pallets full. All this material must be considered HazMat when used for its purpose. Walking around a lot of facilities, you can see mounds of it collected around leak points or under machines. Most never gets disposed of until the machine is dismantled,” said Robert Scaggs, Instructor at Lone Star College.
And Ron Claus, Director of Engineering, System Seals Inc., expressed similar concerns.
“Leakage in hydraulic systems today is a very big problem that affects many varying aspects of the industry,” he said. “Whether it’s a ball valve leaking in the oil & gas market, or leakage from a hydraulic cylinder on a backhoe, the higher-level concerns are environmental impact, safety concerns, immediate and long-term expense, and a high probability of reduced performance.”
For Casey Ruttan, a Territory Manager for Power Systems Inc. of Florida, leakage is still a major problem in his experience, and proper training may be at the core.
“Daily, I see systems with drips, wet hoses, oil coated valve stacks, and seeping fittings and cylinders. Lack of knowledge, training, awareness, and attention is really the root problem. Many of the folks I meet in maintenance capacities have had little to no training in fluid power concepts, let alone maintenance or safety practices,” said Ruttan.
“I had a customer just
last month tell me how he never changes O-rings anymore because they still leak. When I asked him if he had a 900 series O-ring kit, his response was, ‘No what’s that?’ I’d seen this before, so I make sure to ask in a way that doesn’t embarrass anyone. Expecting someone to know this is just not reasonable. Usually that opens the discussion to training. There really isn’t enough training on basic fluid power.”
And leakage is serious business, as Matt Zalick, Director of Business Development at System Seals Inc. noted. “I believe leakage is the number one issue in hydraulic systems across all equipment types. If a leak exists, the problems are many: lost power, environmental hazards, unsafe working areas, increased fire risk, lost product, unplanned downtime to repair, and cost of leaked oil/ grease. Just one or two of these issues can greatly affect the bottom line.”
Rob Klohs, Ops Manager and Senior Fluid Power Engineer at Fluid Power N.T., stressed that it really does depend upon the industry.
“I have been lucky enough to work in 18 different industries in several countries. One client lost more than $5 million a year in fluid loss. Some mining clients lose thousands of gallons per year. At one time, the loss of fluid through leakage in the European mobile market amounted to $25 million per year. The impact on the environment is unknown and can only be speculated. On the one hand, the loss itself presents an increase in the cost of goods and services as the cost of lost fluid will be passed on to the consumer. Although oil itself is an abundant resource (not dwindling as you have been made to believe), the impact on the planet through continued manufacture is problematic for a number of reasons.”
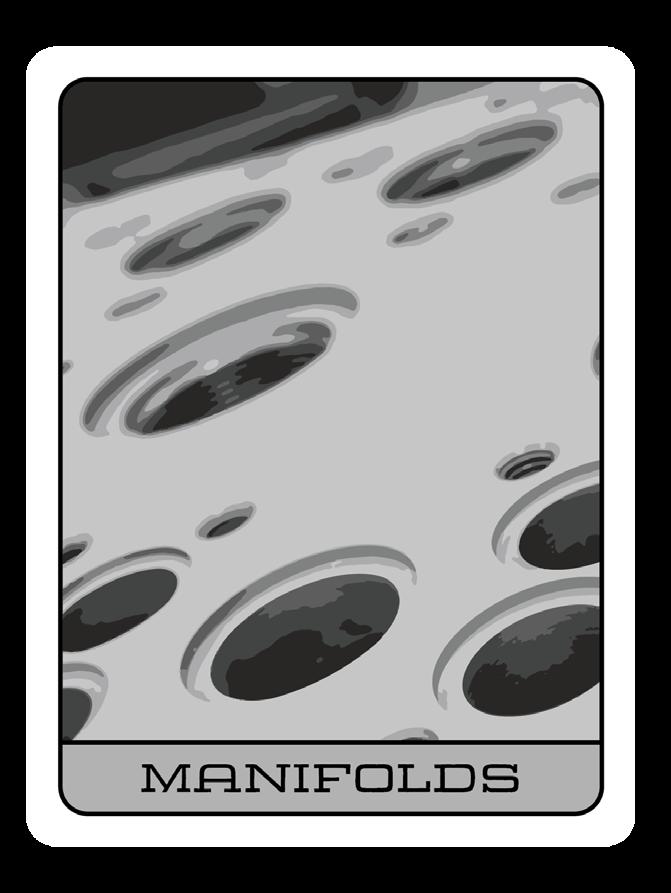
Several industry colleagues mentioned the leakage problems associated with NPT fittings. One was Mark Paxton, CEO of HANSAFlex USA.
“External leakage is a tremendous problem for fluid power and probably
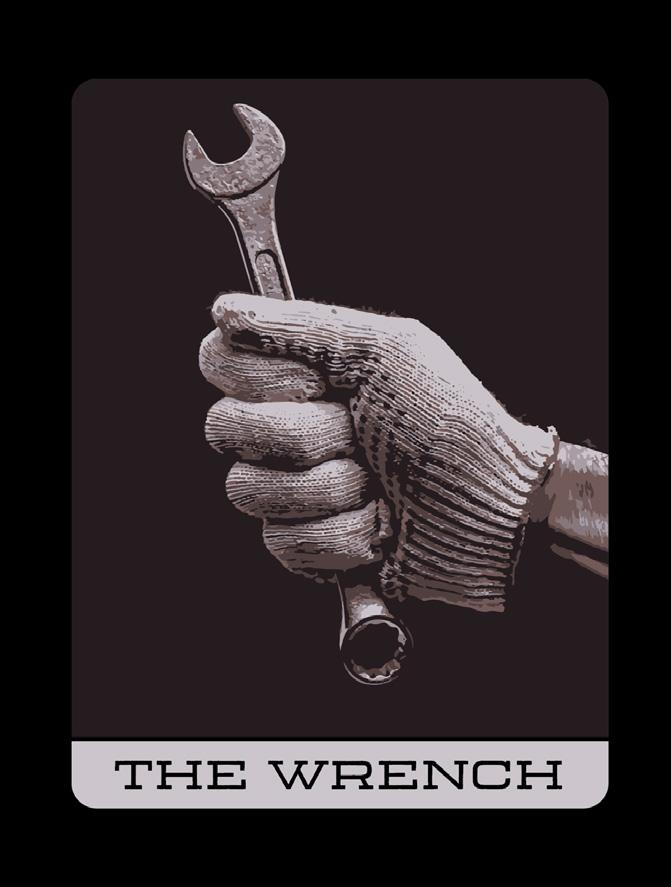
one of the primary reasons why alternative power transmission strategies are coming forward. The industry is always on the defensive, especially in power transmission applications where electromechanical actuators can be effectively applied — for example, turf care. The resolution, while seemingly simple in my eyes, has decades of momentum that prevents companies to make an about-face with their fluid conveyance and port to port connection schemes away from NPT and JIC,” said Paxton.
And while not shying away from the issue, Carl Dyke, President, CD Industrial Group Inc. (and a longtime contributor to Fluid Power World) tried to stay positive.
“Hydraulic system leakage is a very large problem,” said Dyke. “The good news is that this problem is being solved fairly quickly now. Witnessed on newer systems, the problem is primarily a lack of sound installation and maintenance practices — where on older systems, the problem is often the fit and style of hydraulic connections.”
Getting to components
When asked what components were most responsible for leakage, users mentioned a couple of them over and over: hose and fittings. Cylinders and their seals, directional valves, O-rings, pump shaft seals, and flanges were also called out.
“In correctly assembled and maintained systems, the connections between hose and end fittings are the most subject to leakage failures. For systems not assembled correctly, it would be every threaded connection, regardless of the type,” said William Ketel, an Engineer with Number 28 Engineering.
or assembled systems still use JIC fittings. These fittings are prone to incorrect tightening, vibration failure, scratches on the flare face, and other issues. They are used so extensively because they are lower cost than, say, a flat-face O-ring fitting ... the industry has basically decided that the value of lower priced machines outweigh the issues of leakage in many applications.”
Similarly, Will Morris and Joseph Smiley, RS Category Manager and Nachi Distribution Sales Manager (respectively), for RS and Nachi Hydraulics, said that connections are where leakage problems are most likely to happen. “Major contributing factors to leakage in a hydraulic system are its connections. Every pipe, tube, and hose connection becomes a potential leak point for external leakage ... Leakage from hoses is also common if connections are not maintained or if pressures exceed the rating of the hose. Hydraulic hoses can also burst due to unnecessary abrasion or degradation over time, due to lack of maintenance. Again, correctly installing and maintaining these items can prevent many problems. The issues are more often caused by not addressing these issues, rather than the components themselves,” Morris and Smiley said.

“I think hoses and seals are the most common components responsible for leaks,” said Marc Schonhoff, Account Manager, Idemitsu Lubricants America. “These can fail for a number of reasons, and although they are not typically very expensive to repair, the potential for lost revenue leads to a delayed response.”
Michael Terzo, Founder and CEO of Xirro, LLC, agrees. “I would say the number one issue responsible for the vast majority of leaks is incorrect fitting use. Many lower-cost, custom,
For Gene Mitocky, President, Emmco Inc., most of the issues are related to the plumbing of the hydraulic systems; he noted that pipe threads are still being used and these are prone to leaking.

“Welded pipes that have leaks at the welded connections [can result from] fatigue cracks or improper fabrication to begin with,” he explained.
Other areas that Mitocky noted to be wary of for leakage are hoses that are rubbing, exposed to heat or environmental conditions, or have been in service beyond their useful life; piping/tubing that is not properly clamped; and seals that are exposed to higher operating temperatures.
“Shock in the system plays a big role in piping and component failure,” Mitocky said. “Components definitely contribute to the leakage issue, hydraulic cylinders being one of the common sources because of the rod seal failure. The other components, valves, and pumps usually leak because of seal failures, typically due to heat, or because they are used in a dynamic application and wear out.”
Issues with seals were mentioned by many respondents. Michael Cook, Global Segment Director Off-Highway, Trelleborg Sealing Solutions, explained that seals are going to be one of the most associated components with leakage, as they are often times the last line of defense between the enclosed hydraulic system and the external environment.
“Old style sealing technologies at the threaded connection are the #1 culprit in my experience,” said Dan Detweiler, Value Added Systems and Technical Services Manager –U.S., Parker Hannifin Corp. He explained that metal-to-metal connections, combined with application challenges, such as vibration, are high on the list of failure modes.
“During our onsite evaluations of fluid conveyance systems, a common issue is the number of connections used in order to get the job done,” Detweiler said. “In some instances, three or more stacked adapters are used to get from one connection to another. Our goal is always to reduce the number of threaded connections in every system, which eliminates or reduces the
number of leak points. Another key area is the quality of the installation process at the assembler level. For example, more torque is typically not the answer, but it is the most common ‘fix’ for a fluid power leak.”
Improvements over time
Claus explained that there have been advancements in many areas to control leakage. For example, on the polymer science side, improvements have been made to elastomers and thermoplastics to make them more robust. These are material formulations available to us now that simply weren’t a decade ago.
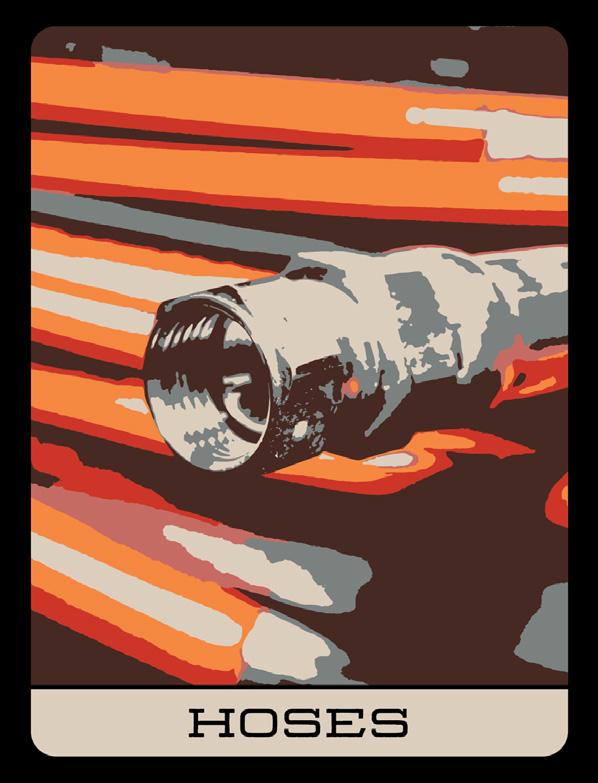
Another longtime contributor to Fluid Power World, Josh Cosford, VP of Sales & Marketing, Higginson Equipment Inc., said that he thinks the biggest improvements have come from precision engineering and machining.
“We’re now able to hold near-microscopic tolerances so that perfectly mated pistons, bearings, wear plates and other items fit so precisely without interference that little room for excess oil to leak remains,” Cosford said. But Klohs took a sour note on the state of things.
Improved sealing materials/designs, better maintenance/installation practices, and more efficient design of components, are some of the improvements that Michael Cook, Trelleborg Sealing Solutions mentioned.
“In addition to the polymer science, there have been advancements in technical resources to better understand failure modes, offering solutions to legacy problems. Higher level manufacturing processes are producing more reliable components all while improving their quality control mechanisms and statistical capabilities,” Claus said.
Dyke was among the many who also highlighted the increased use of elastomer seals in fitting technology, along with manifold technology.

“The CAD/CAM machined manifold, where handfuls of screw-in or slip-in cartridge valves can be integrated — along with other valve assemblies directly attached and sealed to the manifold surface — has removed many hoses, and more importantly, countless fittings and external connection points. This is huge step in the right direction in order to minimize leakage,” Dyke said.
“There has been no improvement — if anything it is worse, not better,” he said. “CAD/CAM manufacturing has made things less robust due to less material being used in many components. [There are] smaller systems running at higher pressures in extreme conditions and a lack of real world understanding of component operational envelopes by many design engineers. No real understanding by mechanical engineers with no fluid power or very little fluid power knowledge.”
User failure is key
Bill Hartwick, Technical Director, Filter Specialties Inc., said that after 40 years of seeing different scenarios, he feels that 90% of leakage is due to user error (improper maintenance or operation) versus 10% where components are underperforming.
"Any component that fails in a short period would typically be replaced with better quality parts to correctly fix the issue,” he said.
Morris and Smiley weighed in here, explaining that user error occurs when the level of workmanship is not at a high enough level and the system plumbing is cobbled together — and not well thought out.
“Fittings are sensitive to torque considerations for tightness. Misapplied components will present excess pressures on the performance of components and systems, which exacerbates wear and leakage
concerns. No product is 100% failure proof, but as in most things, there are various levels of quality; often times, lowest cost products can suffer from a lack of quality. In general, it is probably more common for leaks to be caused by incorrect installation, exceeding ratings, and lack of maintenance,” they said.
“70% of what we see is user error, improper installation of a hose or tubing, or improper connection or improper seeding of the fitting (size is incorrect),” added Fred Mercuri, VP of Sales – Western Region, Brennan Industries.
One industry veteran who works for a major manufacturer said that they think leakage has more to do with laziness and/ or a money saving maintenance strategy of ‘don’t fix it until it’s broken.’ Then someone decides to put a band-aid on it or buy the wrong replacement parts because the new or right ones have a long lead time — or are too expensive.
“Oftentimes, we don’t receive enough of the operating requirements because
Internal leakage woes
External leakage gets most of the attention, because you can easily spot the evidence around systems. But internal leakage robs systems of efficiency and can have long-term consequences.
Pavankumar, a Senior Engineer/ Product Engineering, at Ajax Engineering, noted that, "Internal leakages directly depend on the components used in the hydraulic system, which is directly dependent on the tolerances given in components assembled in the working system,” he said. “Internal leakages are harmful for the system but not fatal ... [they] can be reduced by improving design and material quality in the component manufacturing by analyzing application temperature, working media, and duty cycle.”
Keep reading at fluidpowerworld.com
they are not known,” he said. “Buying the lowest cost could result in a component under-performing or prematurely failing, depending on the application.”
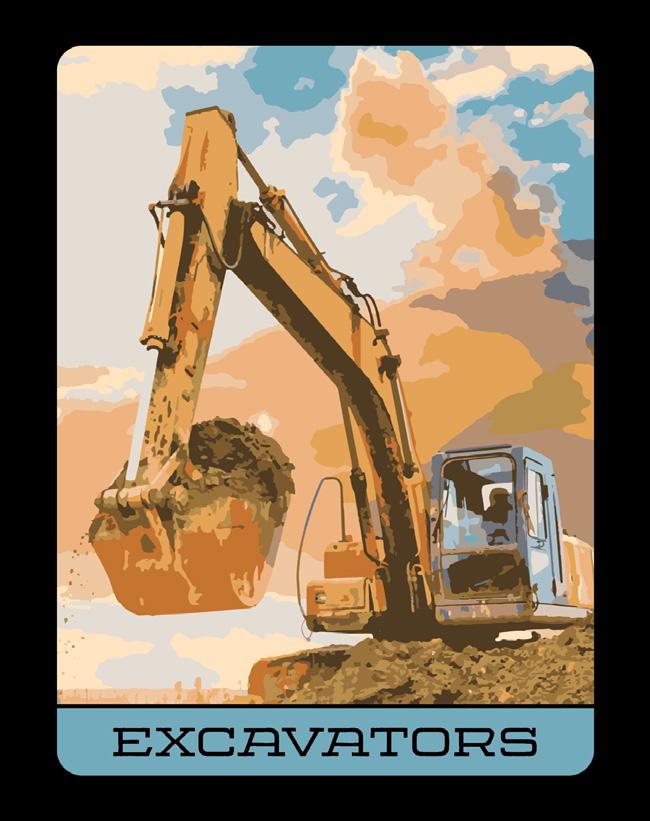
Schonhoff thinks components underperform due to lack of knowledge or user error. He explained that if the proper materials are selected and components are used correctly, many issues could be avoided. “Proper education and training can be costly and time consuming, but the benefits are typically much greater,” he said.
“Lack of technical knowledge is an overwhelming factor,” said Rory McLaren, Instructor, Fluid Power Training Institute. “However, cheap design is a close second. The fluid power industry seems to be satisfied with the status quo. It earned the reputation of being inherently dirty‚ and seems to be satisfied with its image.”
Perception issues
Zalick believes that hydraulics is seen as a “dirty” technology by many people outside our industry.
“Increasing education on things like seals and hoses can go a long way in understanding why quality parts are important,” he said. “Once we can stand by the safety and show you can cleanly operate hydraulic equipment, people will start to drop the misconceptions on our industry.”
Jeff Zimmerer, Manager/Designer, Automated Hydraulics, feels that the typical industrial worker sees hydraulics as a last resort, because they do not want to deal with the potential leak issue. “Most people do not recognize that of all of the technologies available to us, hydraulics has the highest power density (power/volume) of any technology,” he said.
Detweiler said the perception that all hydraulics will leak is a significant drag on fluid power.
“The industry needs to respond in two ways: improving the education and best practices knowledge base of fluid power
users on fluid conveyance systems and in some instances using localized fluid power solutions where the actuator and hydraulic power unit are combined into a single component,” he said. “Localized power eliminates the need for a centralized HPU and long fluid conveyance lines. Depending upon the market and application, one or the other solution may be best.”
Dyke stressed that the perception of leakage continues to be extremely damaging to the hydraulics industry. He said that those who purchase and operate hydraulic systems in any form need to reject the notion of ‘acceptable leakage’ — and hold the machine designer and manufacturer to account for a high integrity design. But that said, users should then be prepared to pay for this high quality. Those same hydraulic system users need to adopt a maintenance mindset and goal of zero-leakage and work towards it.
“Unfortunately, I think the perception of leakage is prevalent in the marketplace and falls under an easy target. You could have 1,000 cylinders that are leak-free, but [there’s] one troublemaker and the perception runs wild,” said Claus. “To solve the problem, approach the leakage issues with proven problem-solving solutions. Understand the leakage issue, or failure mode, by using FE analysis, conduct technical calculations, have in-depth applications and material knowledge to offer innovative sealing products that not only solve the leakage issues, but promote long life and high performance.” FPW

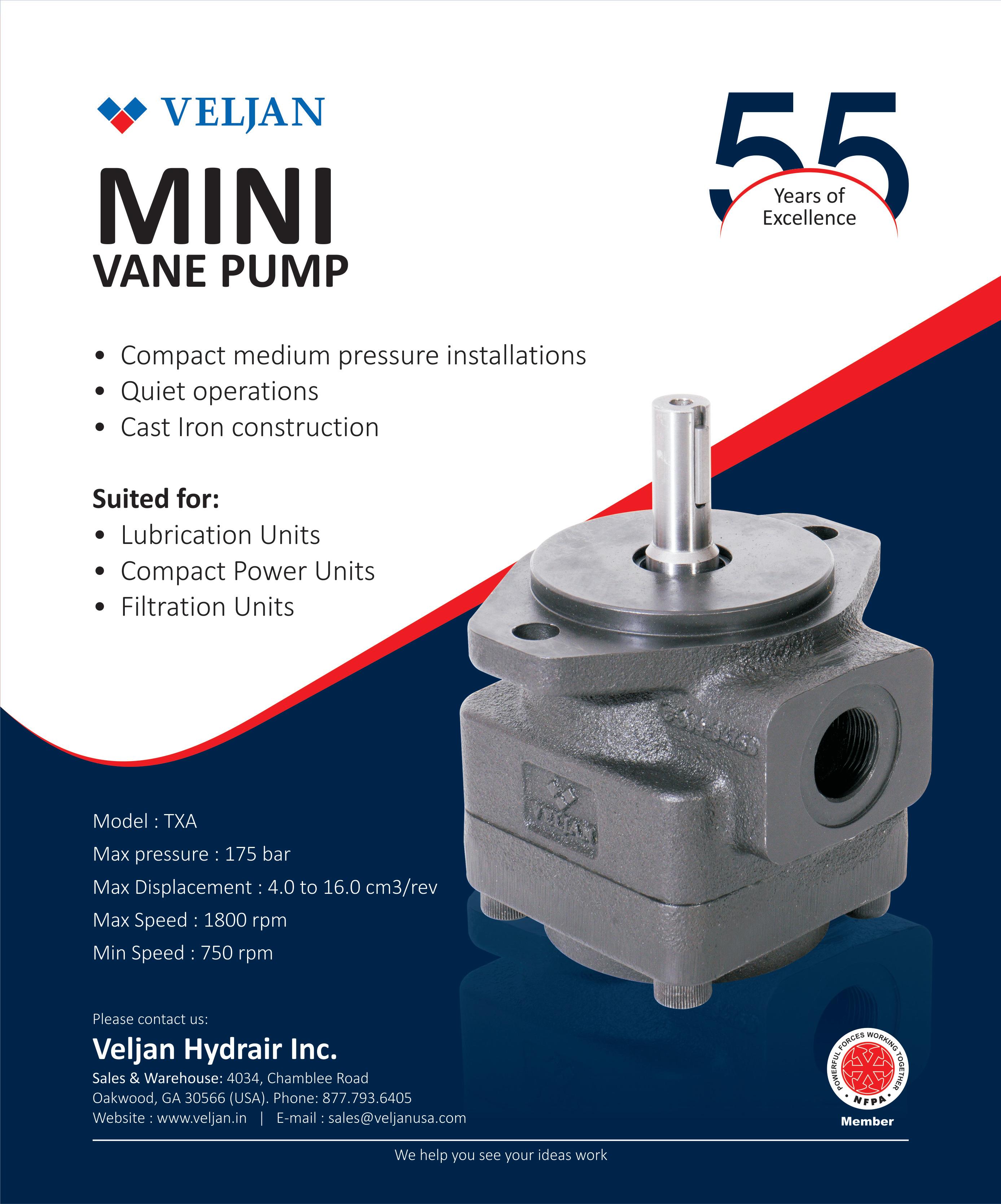
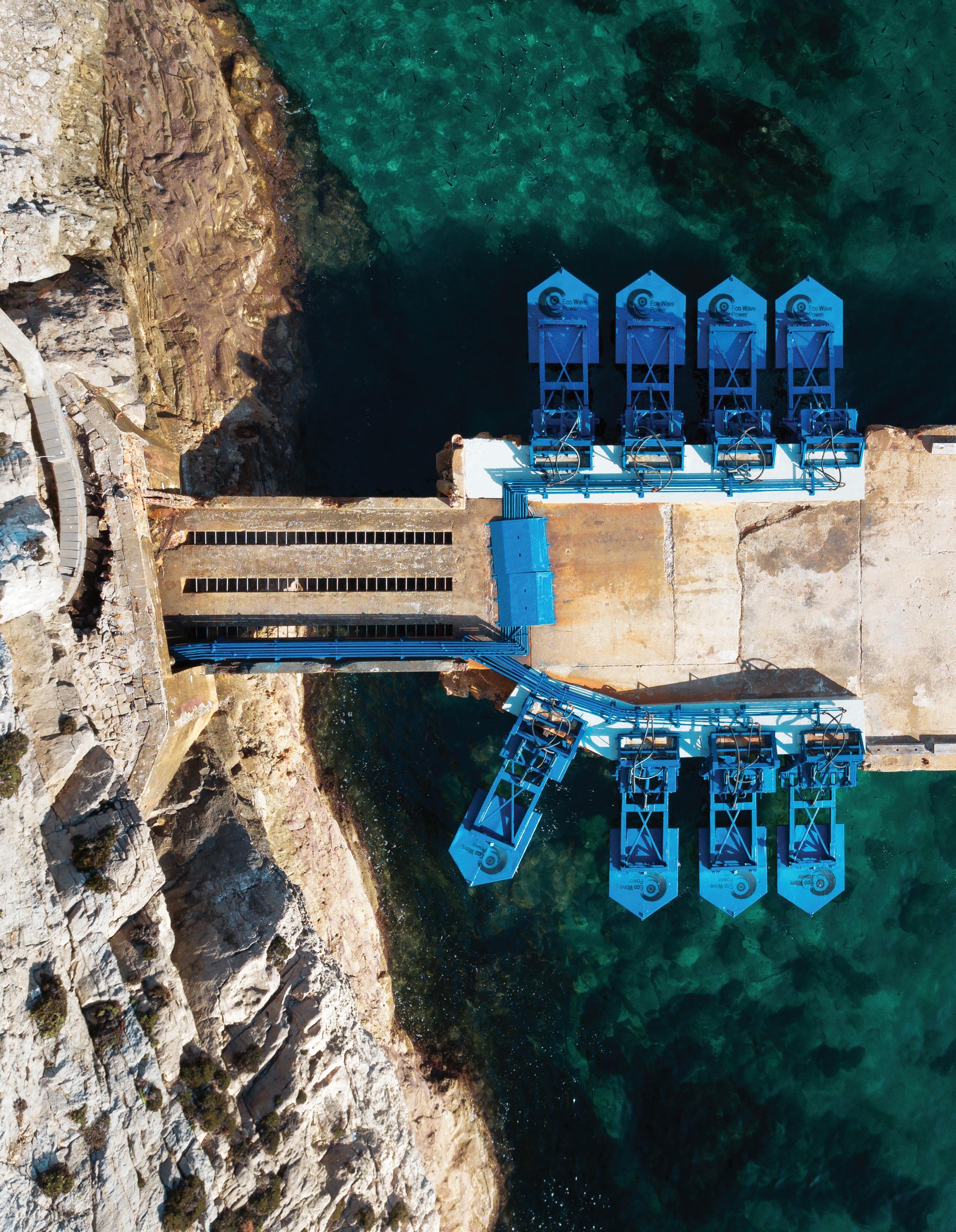
Hydraulics
waves at work in the
Wave-generated power can be more reliable and consistent than other forms of alternative energy. Here, we look at how they work.By: Josh Cosford, Contributing Editor
The
need to address climate change by creating and implementing alternative energy projects remains the most critical objective of our generation. Traditional sources of energy, especially those producing electrical power, range from non-renewable coal and oil and gas to infinitely renewable nuclear and hydro sources. However, nuclear energy has experienced contentious support due to safety concerns over spent radioactive material or potential meltdowns.
Hydroelectric power comes with its own restrictions, of course, since it’s limited to locations with flowing water potential.
Alternative energy explores renewable sources outside the venerable options we inherited from our well-intended ancestors. Although hydroelectric power is an ancient technology and still relevant today, nuclear power is beginning to make a comeback as the establishment’s initially ephemeral caution is sidelined in favor of clean energy.
The two most common alternative energy sources are wind and solar, which highlight the challenge experienced by most alternative energy machinery — intermittent operation. Wind requires moving air, which, luckily for us, stems from our incessantly rotating planet, albeit with calm days producing little or no power. There are fluid power systems used in wind turbines, although we’ve covered those systems in the past. Believe it or not, solar power arrays often use compact hydraulic systems to power guidance systems that track the sun for the highest possible exposure.
The power of water
Stepping outside the ordinary, we can find hydraulics in many new alternative energy projects. Wave power, biomass energy and geothermal projects all use fluid power systems to some degree. The most intriguing, in my opinion, are the methods collecting energy from waves, currents, and tides using powerful hydraulic systems. It’s just not possible for competing power transmission technologies to absorb and control the powerful movement of waves in such harsh conditions.
Harnessing power from water makes

During operation, buoyant “floaters” harvest energy by converting the rising and falling motion of incoming waves. Floater motion extends and retracts hydraulic cylinder pistons which, in essence, act as linear pumps. Courtesy of Eco Wave Power
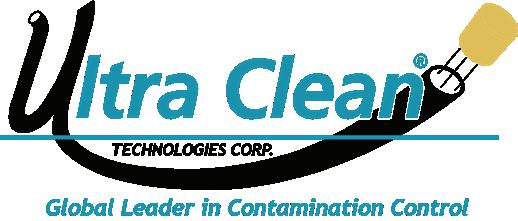
much sense since it covers 70% of our planet, and we have a propensity to find settlements near shorelines. In fact, only 10% of the world’s population lives more than 6 miles (10 km) from water, so it makes sense to generate power closer to where we turn on our TVs at night. And where there is water, you’ll likely find it move or wave.
Also, water packs a punch compared to air –energy density is orders of magnitude higher, and mass is hundreds of times greater per volume. If you’ve ever stuck your arm deep into water from the side of a small boat, you understand the vigor at which currents can act upon a surface area.
There are nearly as many methods to harness moving water as companies are creating them. Various turbine systems, reciprocating methods, and myriad unique methods exist that use flow, gravity or bladders, and each method has a unique and ingenious take on collecting energy.
Reciprocating cylinders at work
The point absorber buoy is a floating station converting the crests and troughs into energy via linear generators. With the buoy fixed to the sea floor using a cable (or rod
Solutions for Contamination
Hydraulic hoses are used across various industries. It is vitally important to use contaminant free hose assemblies. Removing contamination from the hose tube during the fabrication process will prevent premature wear and tear and a possible catastrophic failure. When hydraulic hose is cut with a scalloped blade or abrasive wheel, tremendous heat is generated causing rubber and metal contamination to stick to the ID of the hose tube. To avoid this, it is important to clean the hose immediately after it is cut.

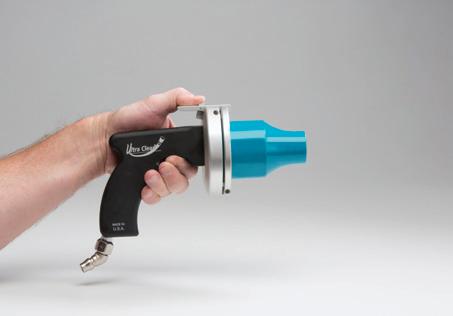

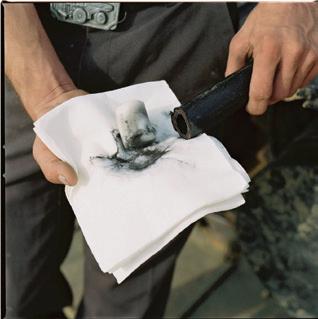
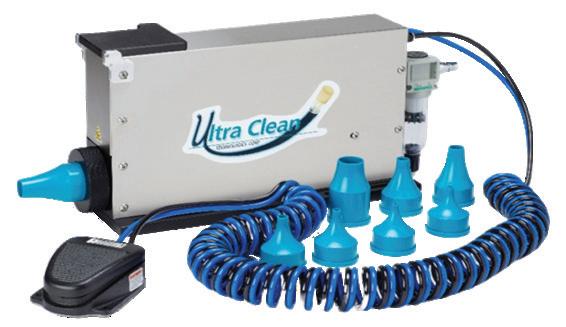
Ultra Clean Technologies offers the perfect solution to help prevent machine failures related to contamination with just three easy steps:
1.)Fire one projectile in each direction through the length of the hose prior to installation of end connections.
2.)After crimping or swaging a fitting, an Ultra Clean projectile should be fired through the entire hose assembly to remove metal flash.
3.)Apply a Clean Seal Capsule to each end to avoid re-contamination during transportation or storage, protect the hose thread, and provide a tamper-proof seal.
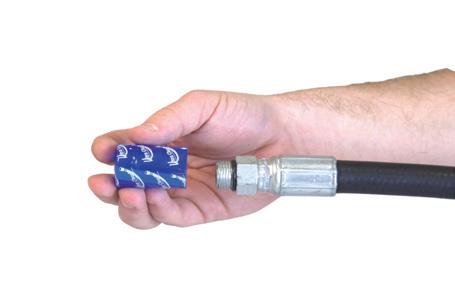

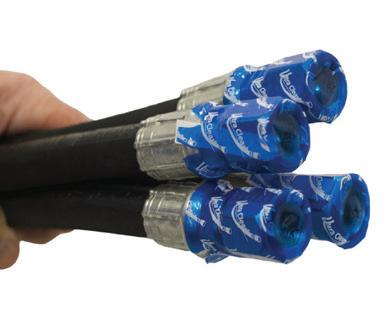
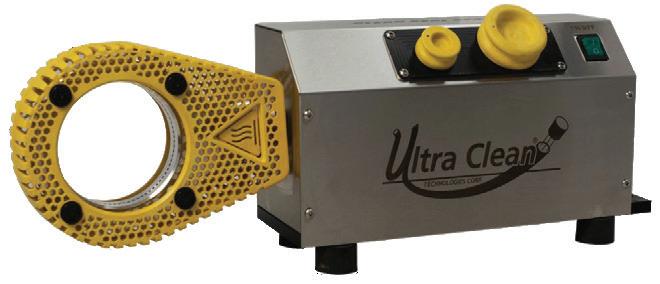
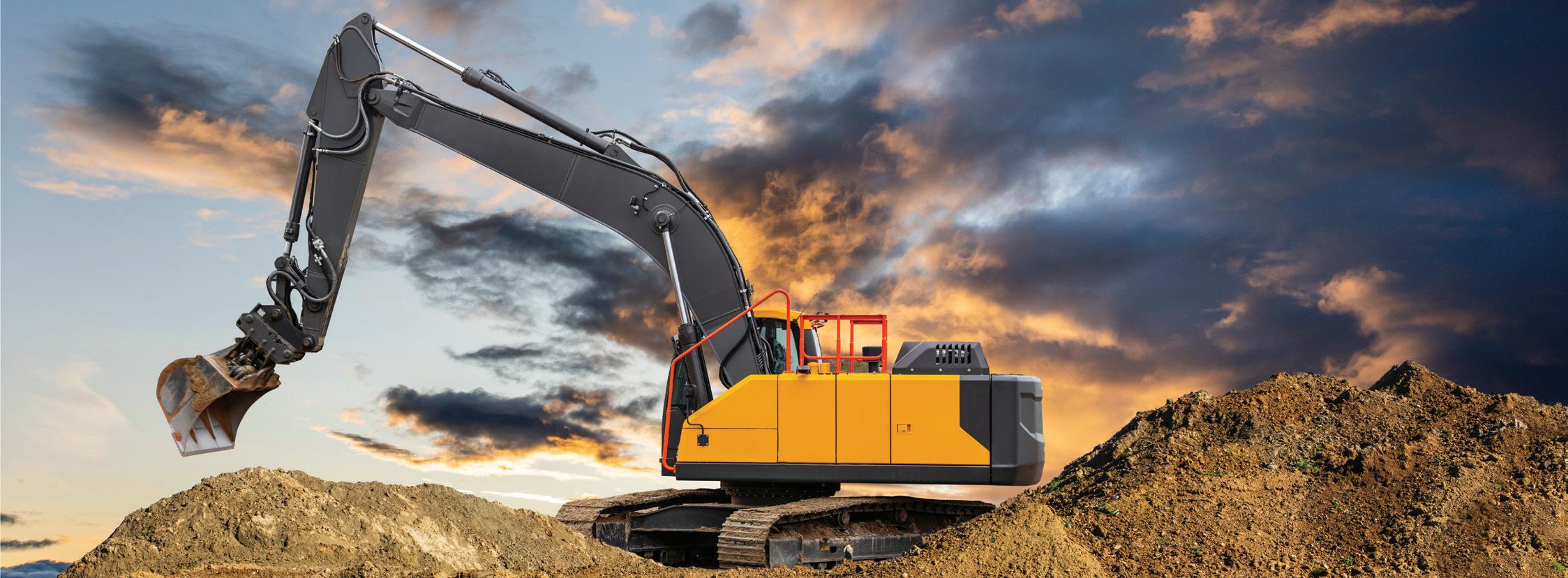
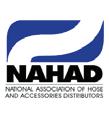
for shallow water), the up and down motion reciprocates either a series of hydraulic cylinders or a rack and pinion system. If you picture toy cars with the pinion zip cord you’d pull through the center to spin up the wheels before release, you’re on the right track.
The reciprocating cylinders act as hydraulic pumps and use a series of check, pressure, and flow control valves alongside accumulators to smooth out the flow rate. The output flow turns hydraulic motors, which in turn drive electric generators. In some cases, the hydraulic motor first turns a heavy flywheel to store energy as inertia, which in turn powers the generator.
Prime choice components for converting mechanical energy into hydraulic energy and back again should only apply. The decades of efficient operational potential mean a piston motor easily covers the spread against its investment cost. By most calculations, wave energy converters are not cheap, so acting penny-wise would prove to be pound-foolish in the long run.
Other point absorber buoys may use a sophisticated rack-and-pinion system to rotate a hydraulic pump instead of reciprocating cylinders. As expected, the hydraulic pump transforms the energy and sends it to the motor-driven generator. The net effect is generally the same as with cylinders, although perhaps more energy is lost through a gear-driven pump than the highly efficient cylinders.
Eco Wave Power is an onshore wave-energy technology company that has developed a cost-efficient system for turning the motion of ocean and sea waves into electricity. The company has taken the next step towards commercialization by finalizing the assembly of the hydraulic energy conversion unit for its Jaffa Port project.
The hydraulic conversion unit is an integral part of the Eco Wave Power system as it transforms pressure (created by the waves) into clean electricity. During operation, buoyant “floaters” harvest energy by converting the rising and falling motion of incoming waves. Floater motion extends and retracts hydraulic cylinder pistons which, in essence, act as linear pumps. Cylinder action transmits high-pressure biodegradable fluid
Infographic
demonstrates how tidal power is converted to on-shore power generation.
TIDAL POWER
to accumulators that are mounted onshore. Pressurized fluid is stored in the accumulators and subsequently routed to a hydraulic motor. The motor turns a connected electrical generator which supplies electricity into the grid via an inverter. The fluid, after decompression, flows back to the hydraulic tank where it is then reused by the pistons, thus creating a closed-circuit system.
Rugged and reliable
Using the bobbing effect of waves, other systems use a series of floating segments, looking like a gigantic toy snake. Each segment pivots relative to the next as the waves oscillate, which strokes the cylinders mounted to the opposing segment. As with the absorber buoy, the reciprocating cylinders create flow and, with the help of similar accoutrement, create the flow that powers the hydraulically driven generators.
On the topic of hydraulically driven generators, if you had asked me in the past about choosing hydraulics to transfer energy for energy production, I’d have told you not to waste your time. Even the best combination of pump and motor running at ideal pressure and flow rates is lucky to achieve 90% efficiency.
However, due to the formidable conditions of oceans and seas, which exert a powerful influence on anything within their realm, all-electrical technology simply doesn’t suffice. It’s not just the corrosive effects of salt water but also the forces from
pounding waves at the surface and crushing pressure below. A failure or breach to the hull or body of a hydraulically actuated wave converter won’t result in a catastrophic write-off of the entire apparatus, as could be possible with electric-only actuators.
Near-shore oscillations
Continuing with cylinder-operated wave energy generators, my favorite is the oscillating wave surge converter. These units look like giant paddles attached to the sea floor, which capture energy from the to-and-fro movement of waves around 20-30 feet below sea level. Working best near shore, wave generators use the same hydraulic components as other reciprocating systems to create flow that subsequently powers generators.
Also known as oscillating wave surge converters, these individual generators may constitute a farm many miles long, installed end-to-end. Unlike wind farms, where the net energy removed from the passing wind does little to affect generators downwind, wave converters do poorly when tiered row by row. Because of the energy density of water waves and the harvesting capacity of the wave converters, these units create a significant energy shadow shoreward of their installed location. There’s simply not enough wave energy left to power a second converter closer to land, although the principle may affect some deep-water versions less.
WAVE POWER DEVICES
Easy to scale
Although it’s been shown that deep water wave energy generators benefit from more consistent average power output, the nearshore generators have some advantages. Instead of installing generators at each station,
some pumps send their output flow to nearby onshore hydroelectric power plants. Imagine sending high-pressure sea water from many collectors to a single plant to power larger electric generators with the benefits of dry land maintenance, repair and distribution.
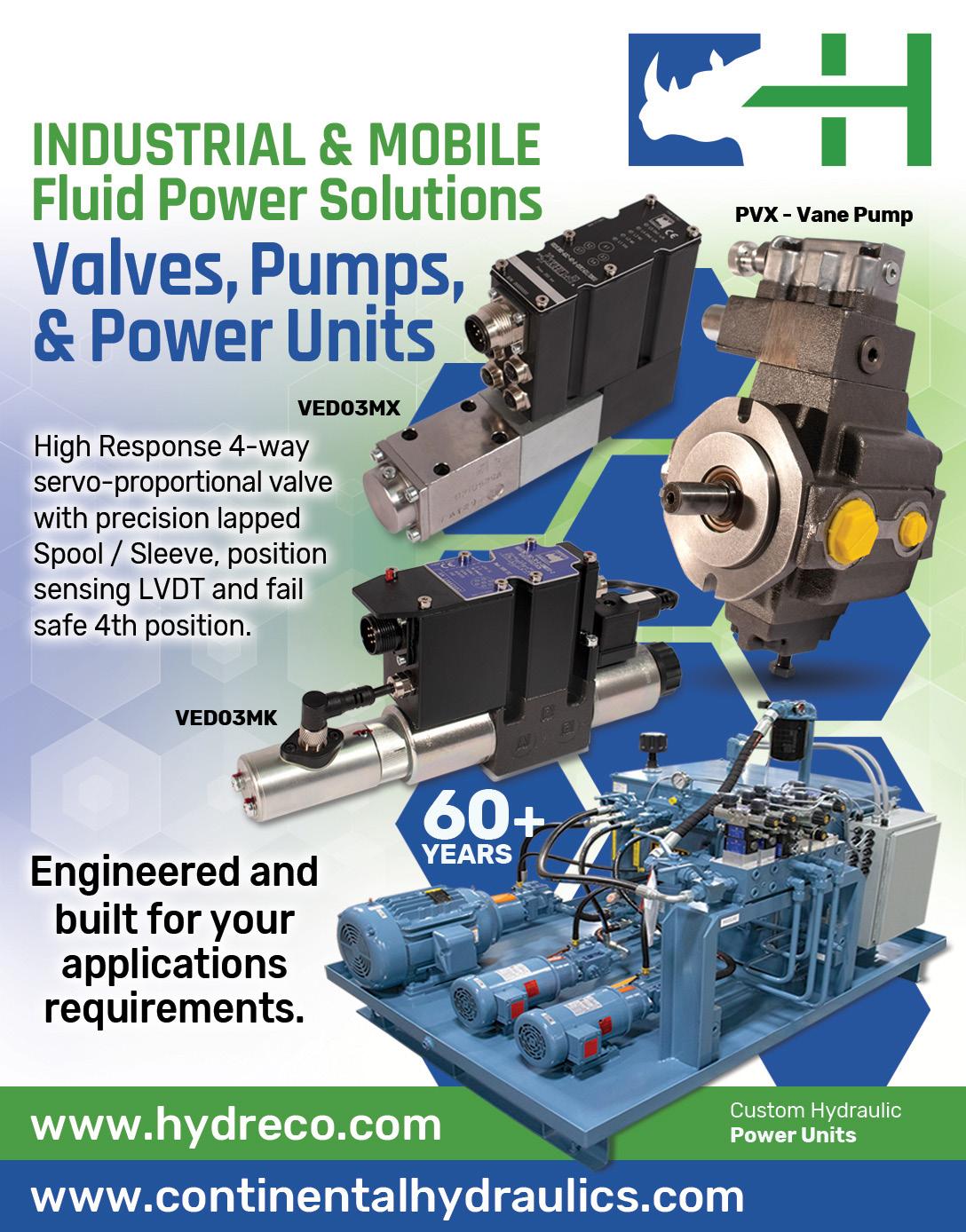
Although wave energy generators are enormous, I feel they offer the most potential for homemade or portable units for low capital investment. A couple of hydraulic cylinders mounted to a flap atop a heavy base could be installed on a beach, where cresting waves oscillate the converter to pump water or oil with fair energy potential. Any reciprocating cylinder can be turned into a pump with a handful of check valves, and output flow is sent to a hydraulic motor turning a heavy flywheel. The flywheel helps maintain the constant and desired speed for the generator to which it is attached.
These small generators could power communities disconnected from any power grid and offer an easily maintained power source compared to wind and solar plants, which are more specialized and complex to maintain. Wave generators of all types can be made small enough for portable operation, making them perfect for emergency response teams working with shore-side communities after a natural disaster.
That hydraulics are so prominent in the various methods of wave energy converters provides reassurance to my theory that hydraulics will never die. Fluid power is fundamentally simple, powerful and easily accessible as a technology. Rather than become obsolete, we continue to dream up creative methods to adopt technology to take advantage of the inherent strengths of hydraulics.
For extreme, demanding applications that require smooth yet powerful conversion of energy, hydraulics are hard to beat. Inherently robust and environmentally resilient, hydraulics are the power transmission method of choice for wet and watery conditions.
As a prominent and growing alternative energy source, wave energy conversion will continue to expand beyond the already dozens of technologies to provide one of the power-dense sources of renewable electricity in years to come, and expect hydraulics to be there every step of the way. FPW
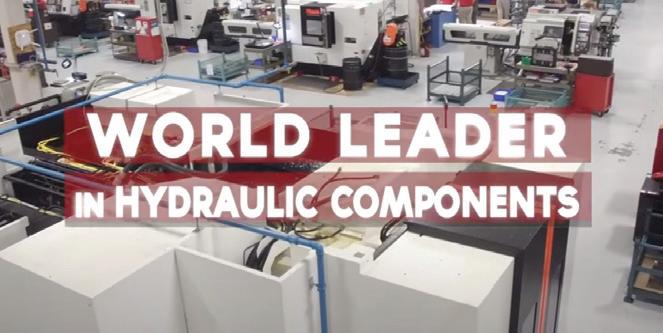
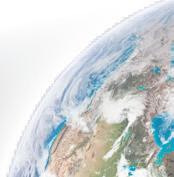



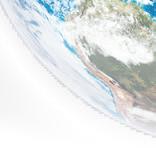
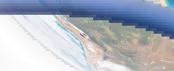
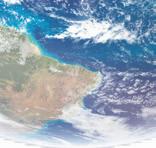


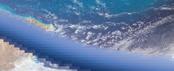
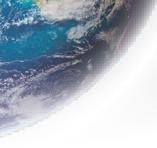
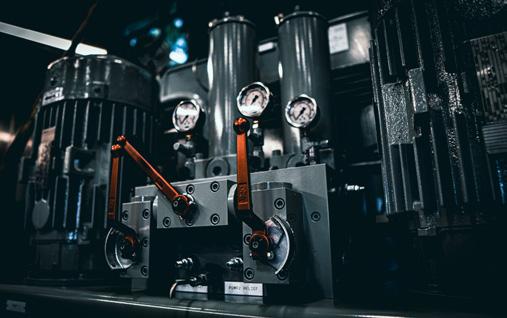
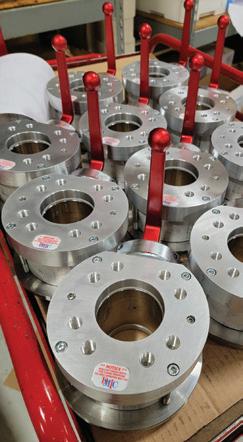
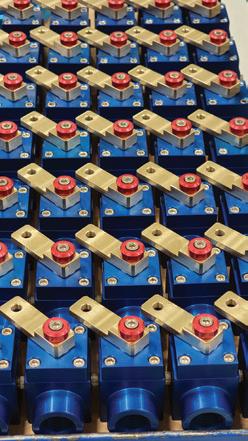
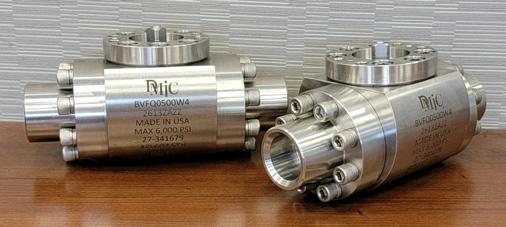
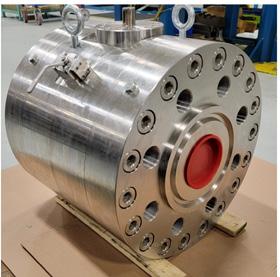
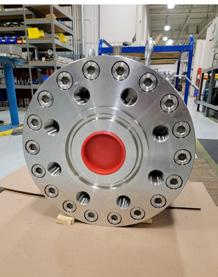
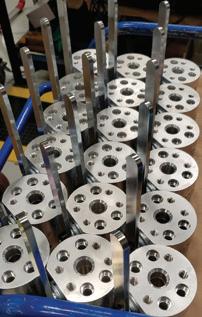

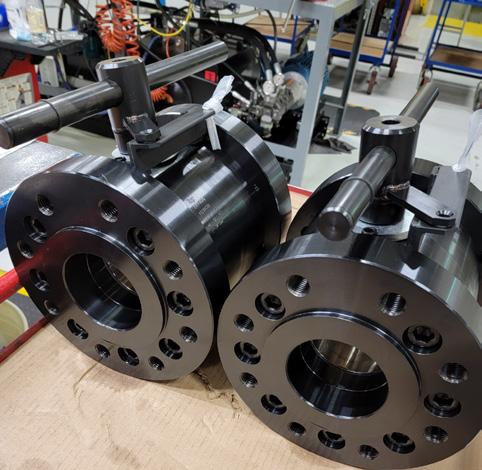
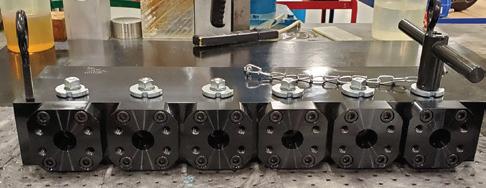

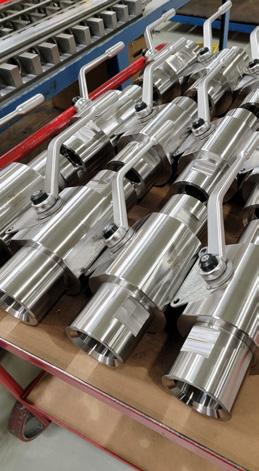

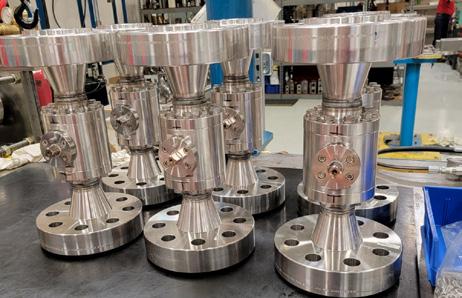
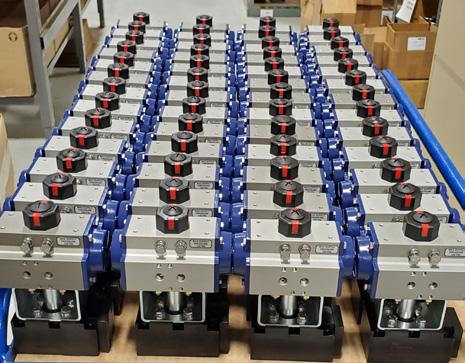
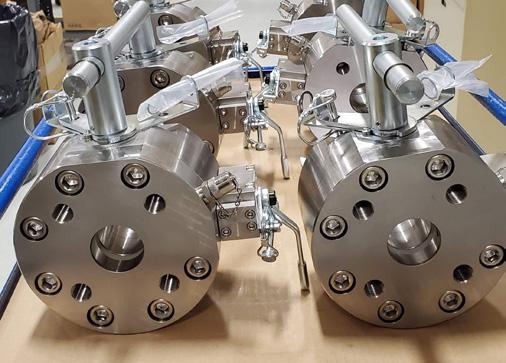
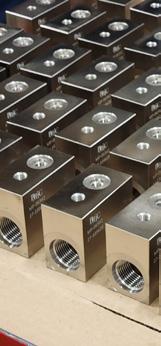
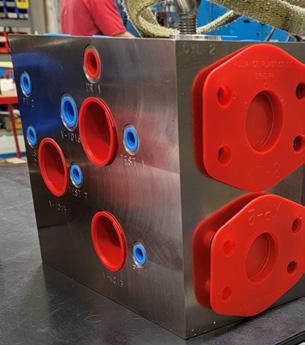

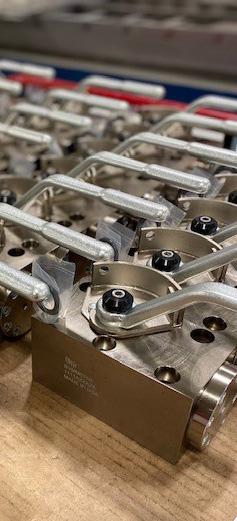
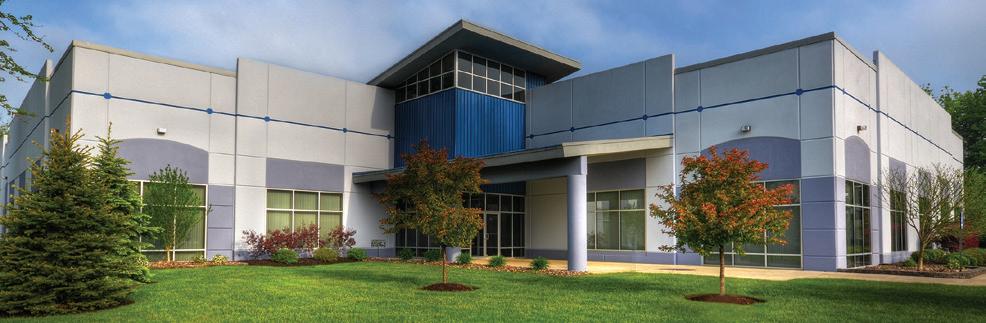
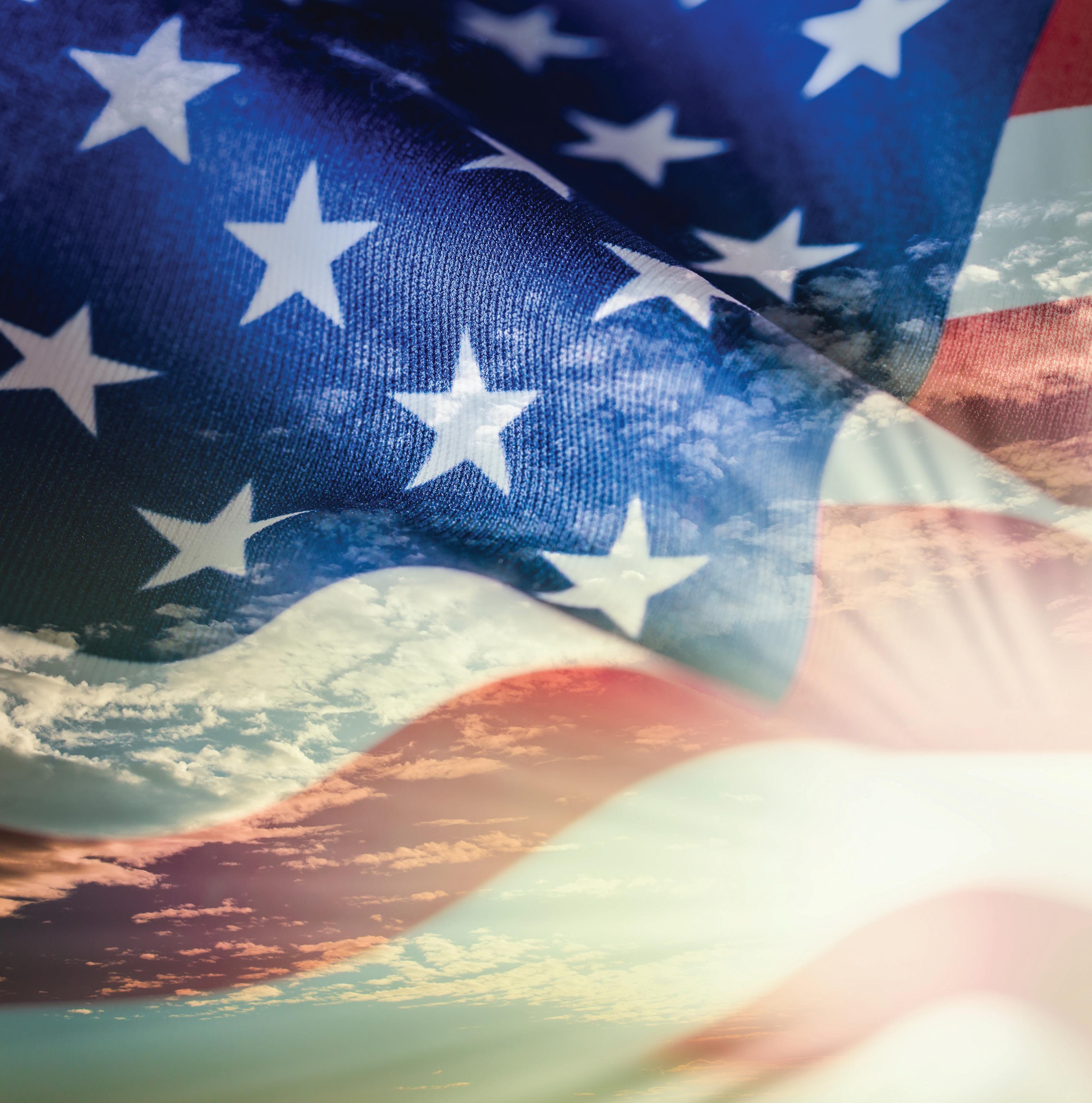
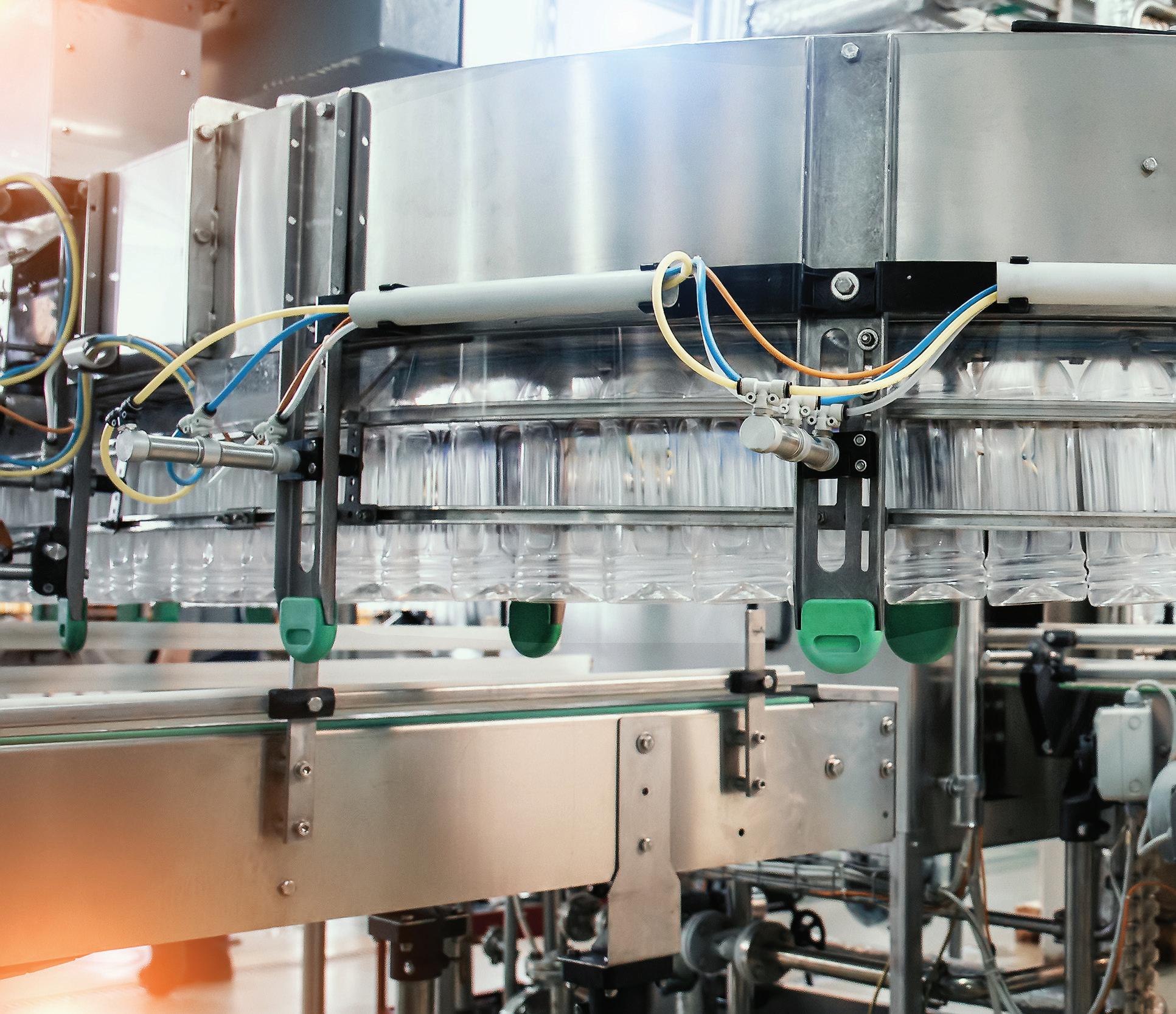
Creating a compressed air leak management plan
Measuring and repairing compressed air leaks can easily reduce energy costs by 10 to 20%.
Edited by Mary C. Gannon, Editor-in-Chief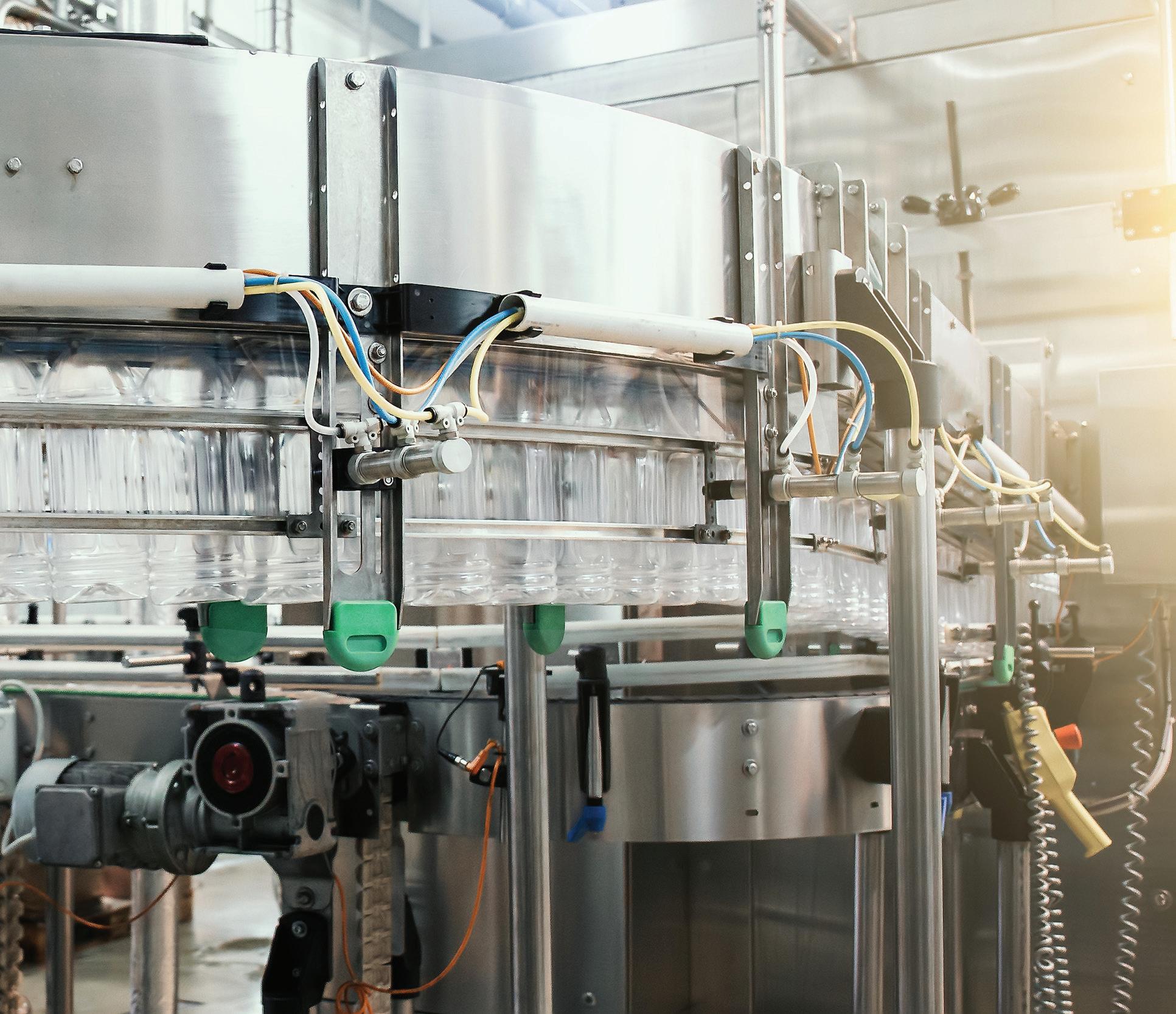
Compressed air is used in factories all over the world to control machines, processes, and pneumatic equipment. It is a safe and easily available medium and can be used in all possible places via hoses and pipes. However, compressed air is one of the most expensive energy carriers. Still, significant savings can be made on compressed air costs with proper compressed air leakage management and monitoring. To start simply: detecting and repairing leaks can immediately result in an energy gain of 10 to 20% and once expanded with compressed air monitoring and optimizations, the savings can even reach 50%.
What makes compressed air one of the most expensive energy carriers?
Pascal van Putten, CEO of VPInstruments explained it this way. “When compressing atmospheric air to a pressure of 90 to 100 psi, 75% of the electrical energy absorbed in the compressor is lost as heat. Pressure loss and leaks, among other things, ensure that the electrical efficiency of the entire compressed air installation is only 7.5 to 15%. This can be improved, and you would expect companies to do everything they can to achieve this. Yet, this is not the case and every year billions of dollars in energy are wasted worldwide, simply because many companies neglect to repair leaks and to optimize the efficiency of their compressed air installation.”
Approximately 5% of all electrical energy used worldwide is converted into compressed air; within the industry itself, this is more like 10%. The generation of this enormous amount of energy contributes to CO2 emissions and climate change. For that reason alone, it is sensible
Every second many dollars will disappear into thin air if compressed air leaks are not repaired. Courtesy of VPInstruments
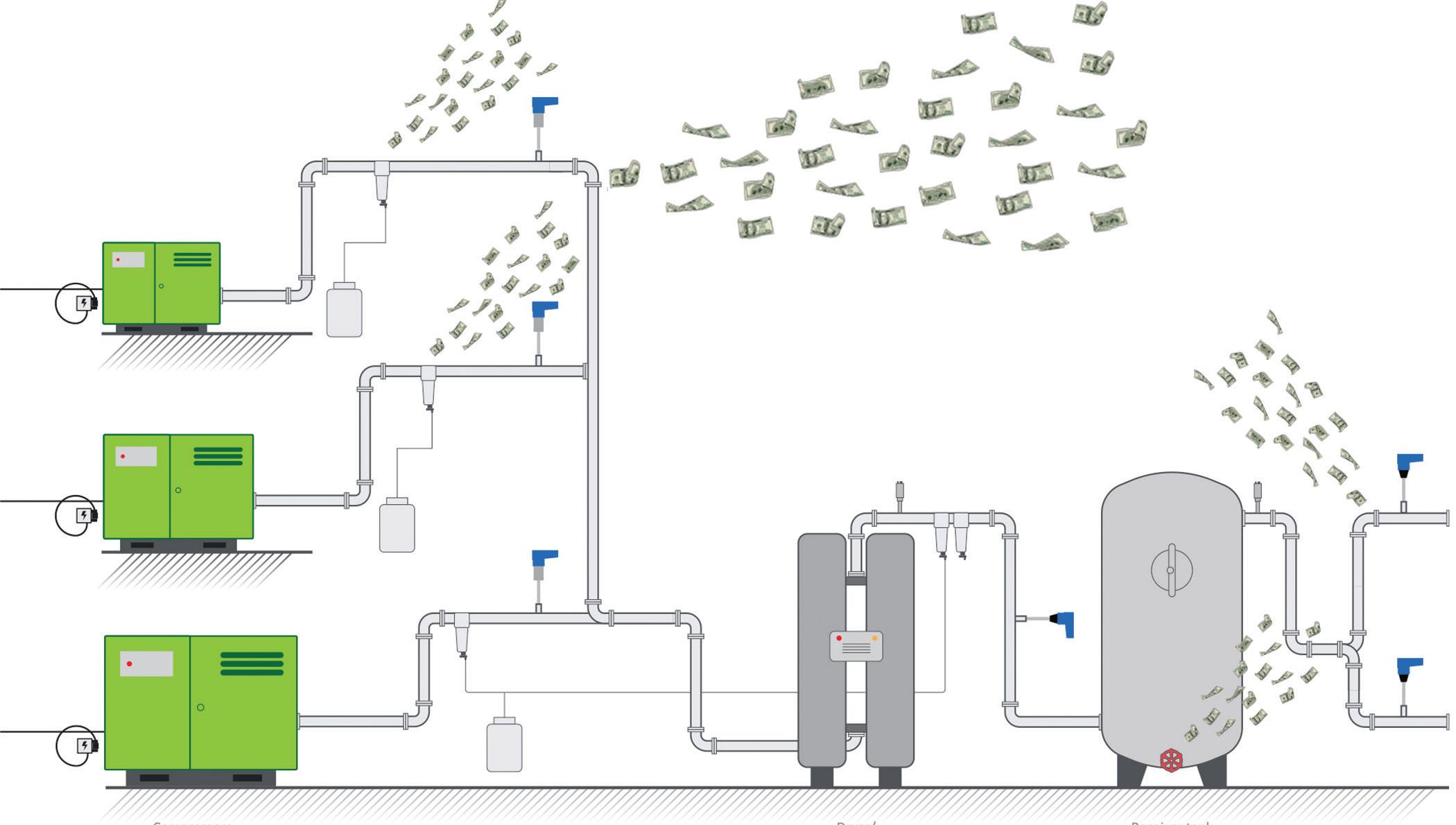
and even necessary to reduce compressed air consumption. Additionally, improving compressed air installation efficiency goes straight to the bottom line.
Leakage management: low hanging fruit
Addressing compressed air leaks is a critical, yet often overlooked aspect of optimizing energy efficiency in industrial settings. Despite its simplicity and relatively low investment requirements, detecting and repairing leaks can yield significant cost savings. Van Putten underscored the straightforward nature of leak detection and repair. “It is absolutely not complicated and does not require high investments to start detecting and repairing leaks,” he said.
Van Putten referred to an example
installation that operates 8,760 hours/ year. The system pressure is 100 psi and the electricity costs are $0.10 per kWh. In this instance, ten holes of just 1/16 in. cost the company $10,500 per year. If the ten holes were 1/8 in., the costs increase to $41,900. “In practice we often encounter hundreds of leaks of all different sizes, and also larger than 1/8 in.! You can imagine what the total financial losses in that case will be,” van Putten said.
Prevent production downtime
Apart from the financial benefits, an even more important reason exists to ensure that the compressed air system functions optimally and efficiently. A reliable compressed air supply is crucial for the continuity of production processes. The right amount of flow and pressure determine the correct operation of production machines. However, leaks contribute to pressure loss.
Insufficient pressure can not only lead to machine downtime, but also affect the quality of products. Errors in packaging or inconsistent texture/taste of foods can inevitably lead to costly recalls. Not to mention the damage to your image. In addition, if pressure drop is incorrectly diagnosed as an equipment defect, there is a chance that investment in new equipment will be required. This entails (unnecessary) additional investments that could have been better utilized elsewhere. Optimizing compressed air systems not only increases energy efficiency, but also establishes the foundation for a reliable and well-performing production process.
Leak detection methods
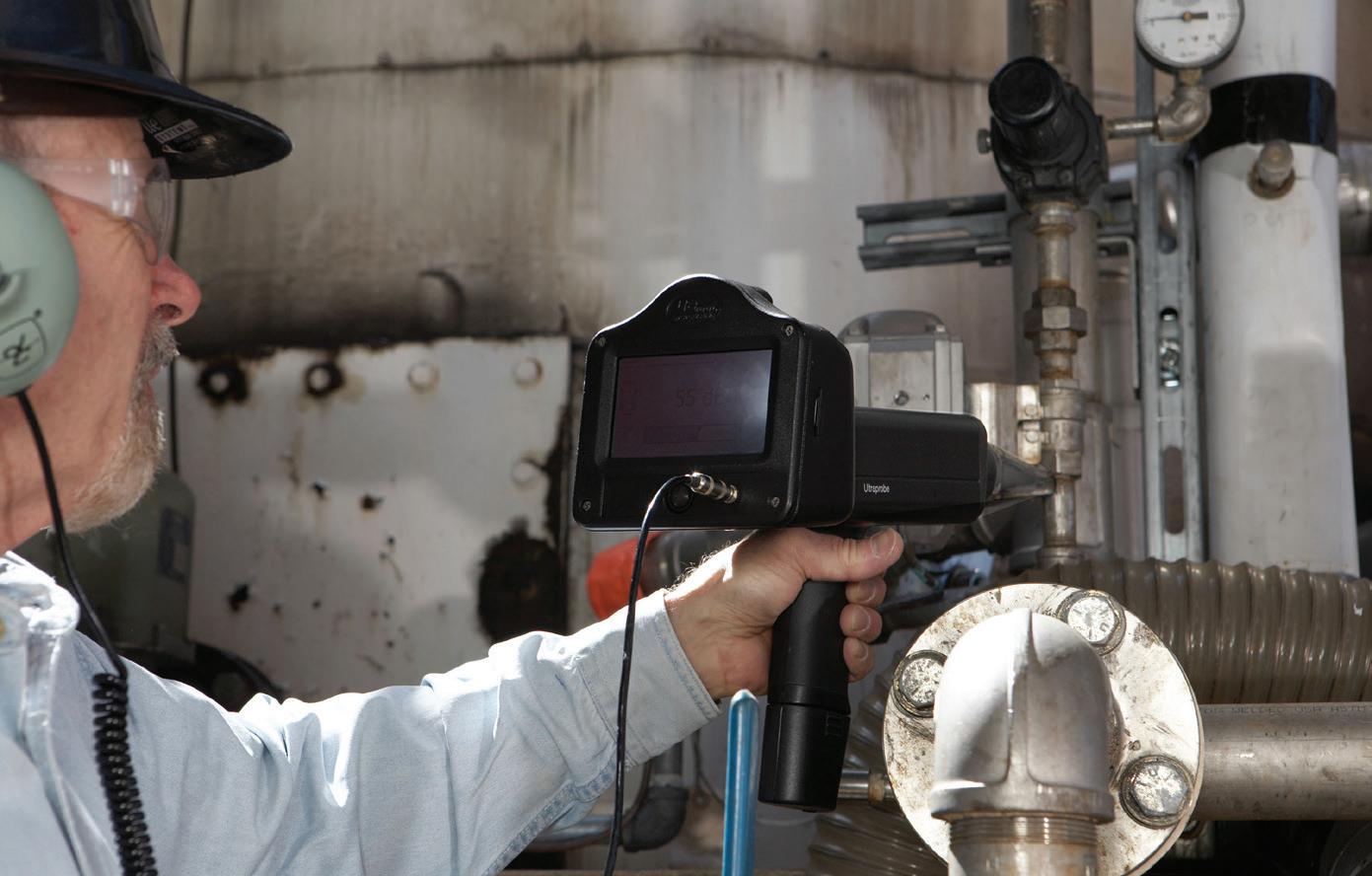
“To detect and repair such leaks, you will spend a few thousand dollars on a simple measuring system and parts such as gaskets, hoses, and quick couplings. We therefore call leaks the ‘low hanging fruit’ in compressed air installations. Easy to detect, easy to repair — and repairing them produces immediate financial profit. Companies often have an external agency carry out a leak audit in which all leaks found in the factory are marked with TAGs. It is not uncommon that when the auditor returns to the factory a year later, the TAGs he applied are still there. So, nothing has been done about it while the leaks and associated costs continue as normal.”
When a hydraulic line leaks in a factory and the puddle of hydraulic fluid on the floor continues to grow, it is evident the problem should be solved as quickly as possible. Not so with compressed air leaks. After all, it is “just air,” so it isn't considered an emergency. It will get taken care of “some day.” Postponement leads to cancellation and the financial and (possible) operational consequences of such a nonchalant attitude will now be clear.
There are various techniques and leak detection methods to detect leaks quickly and easily in compressed air systems, ensuring minimal disruption to operations and maximum cost savings. The most common are: Ultrasonic leak detection — This is a commonly used method for locating compressed air leaks. Ultrasonic detectors can capture high-frequency sounds produced by air leaks and make them audible to humans, allowing maintenance teams to accurately locate, mark and repair the source. Compressor monitoring — A commonly used additional method for detecting (the risk of) leaks is to carefully
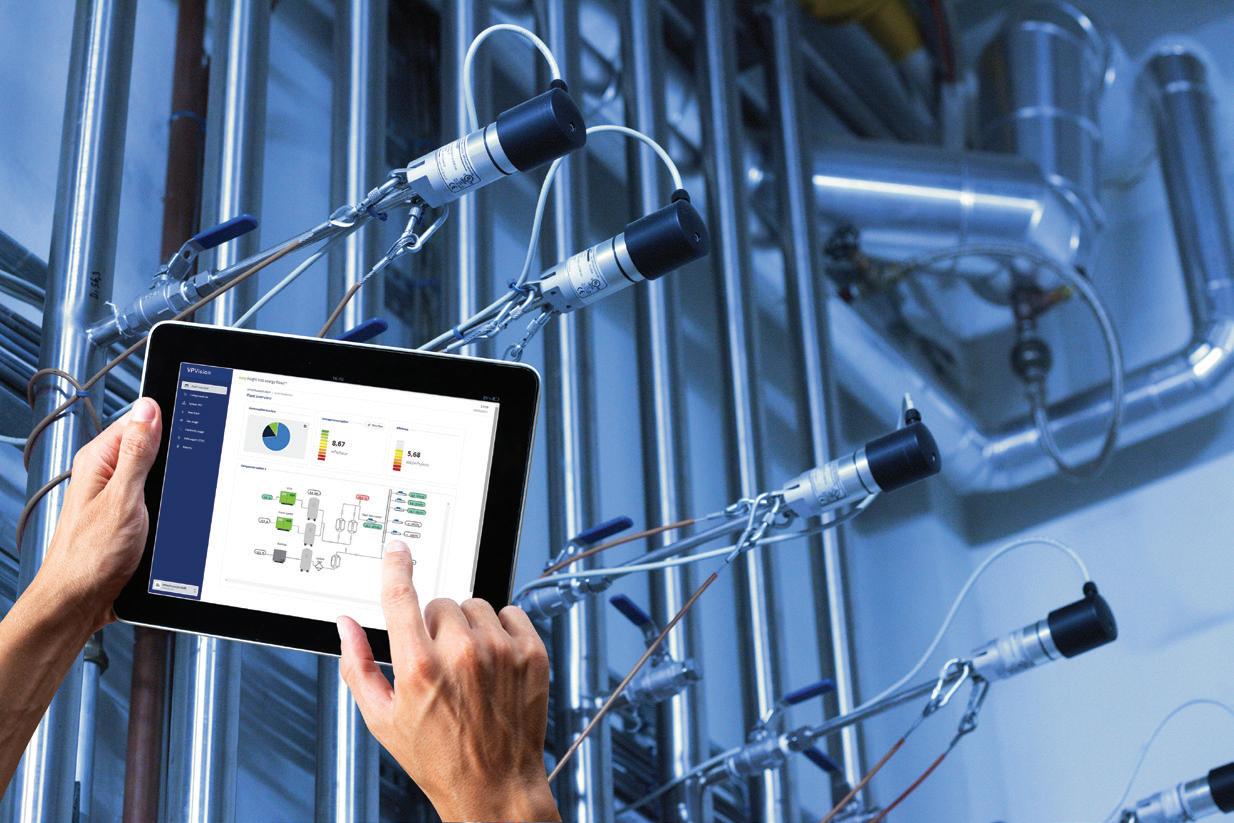
With VPVision (here with six flow meters) the entire compressed air network can be monitored and optimized, covering power, flow, pressure, temperature, dew point and more.
Courtesy of VPInstruments
check/monitor the compressor. This method compares the current performance of the compressor with the achievable/expected performance according to specification. Structural deviations in a negative sense can directly indicate leaks.
Venting test — This method measures the time it takes for a compressed air system to reach a specified pressure drop. If this is carried out periodically, a trend-based insight can be obtained into the overall system efficiency.
Trend analysis — The use of flow meters and monitoring systems provides valuable data about possible leaks. By analyzing the measured and trended data, it becomes possible to identify areas within the plant where significant changes have occurred over time or acutely. This may be caused by (sudden) leaks. This suspicious zone can then be specifically examined using ultrasonic measurements.
Downtime consumption — Plenty of factories still do not produce on weekends. But nevertheless, they still see their compressors kick in during the weekend. Measuring compressor power consumption during downtime is a good indicator of the amount of leakage in a factory.
Leaks in compressed air systems can occur anywhere. They often occur at couplings and in (older) hoses. But incorrectly mounted or corroded pipes, fittings, filters, regulators, and lubricators (FRLs) are also common locations. Leaks can also occur in production lines at control and shut-off valves, flanges, cylinder rod gaskets, and thread seals.
“It is crucial that the maintenance team can independently carry out leakage repairs
without the need for approval ‘from above’ every time,” van Putten said. “After all, this has a very slowing and demotivating effect. It would be useful to introduce a guideline stating that repairing something that costs less than three to six months of energy waste can be carried out immediately and without formal approval. In addition, the savings accrued after repairs in the subsequent period can be added to the energy savings budget. This creates a self-sufficient, cyclical fund within the organization, with the result that solving leaks and further optimizing the compressed air network will make an essential contribution to increasing profits.”
Pressure reduction
After leaks have been resolved, it is important to analyze and optimize the compressed air installation in a targeted manner. With the
help of permanent monitoring, for example, the current compressed air consumption is measured and monitored, and changes are signaled in a timely manner. VPInstruments has developed the real-time VPVision monitoring system that, in combination with VPFlowScope flow, pressure and temperature meters, provides information that allows a maximum cost-effective compressed air system to be achieved.
For safety reasons, a (too) high working pressure is often set, for example 7 bar. But is that necessary? Sometimes machines that require high pressure have long been replaced. By reducing the pressure in small steps and monitoring the system and machine performance full-time for correct operation, it is often possible to reduce the pressure by 14.5 to 21 psi. Remember that every 14.5 psi pressure reduction means a 7% reduction in energy costs. FPW
VPInstruments vpinstruments.com
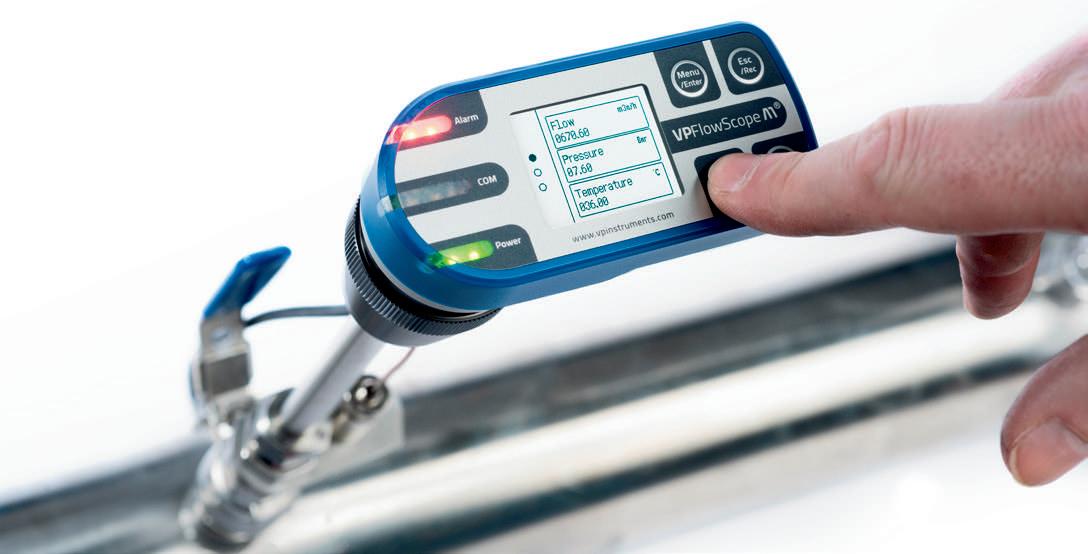
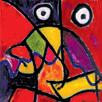
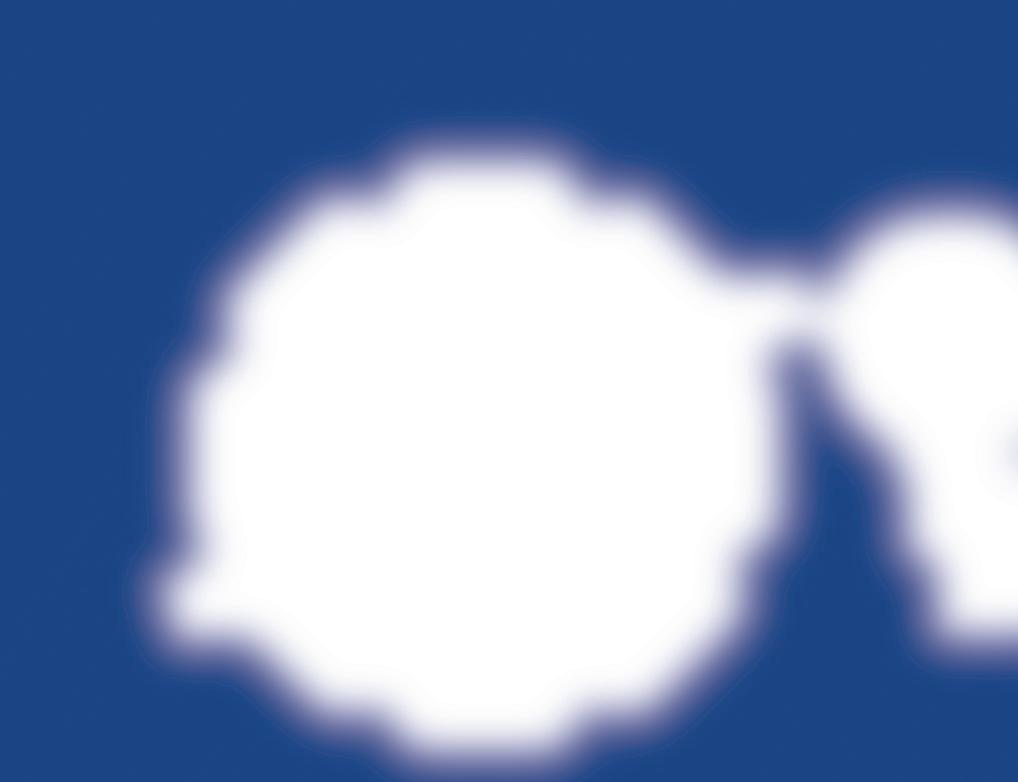
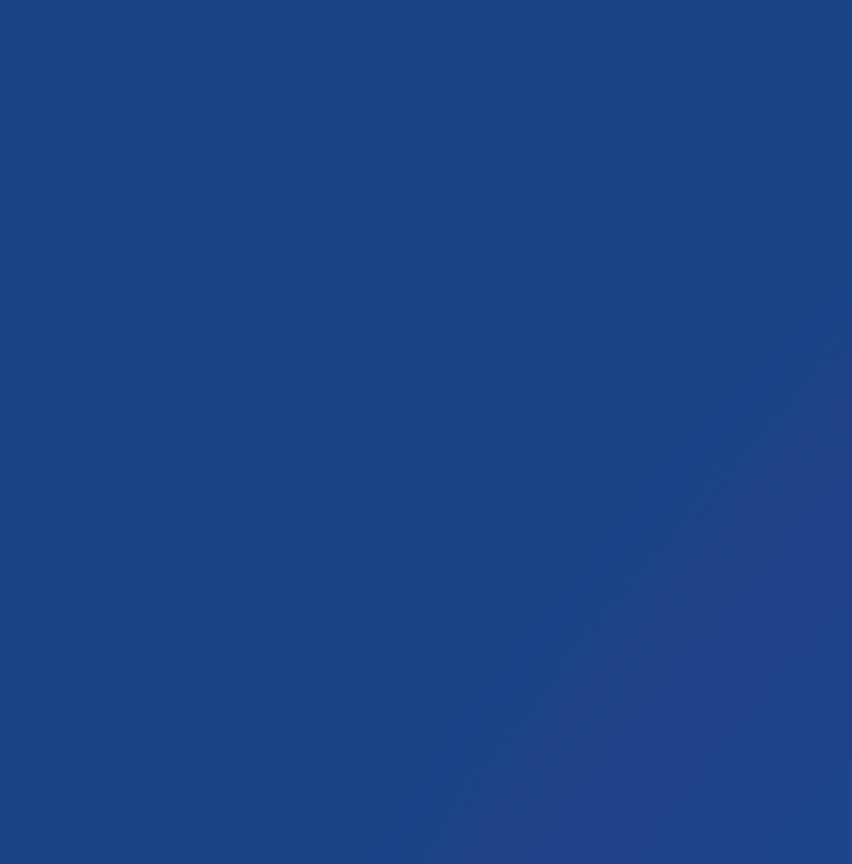

THE EAGLE HAS LANDED
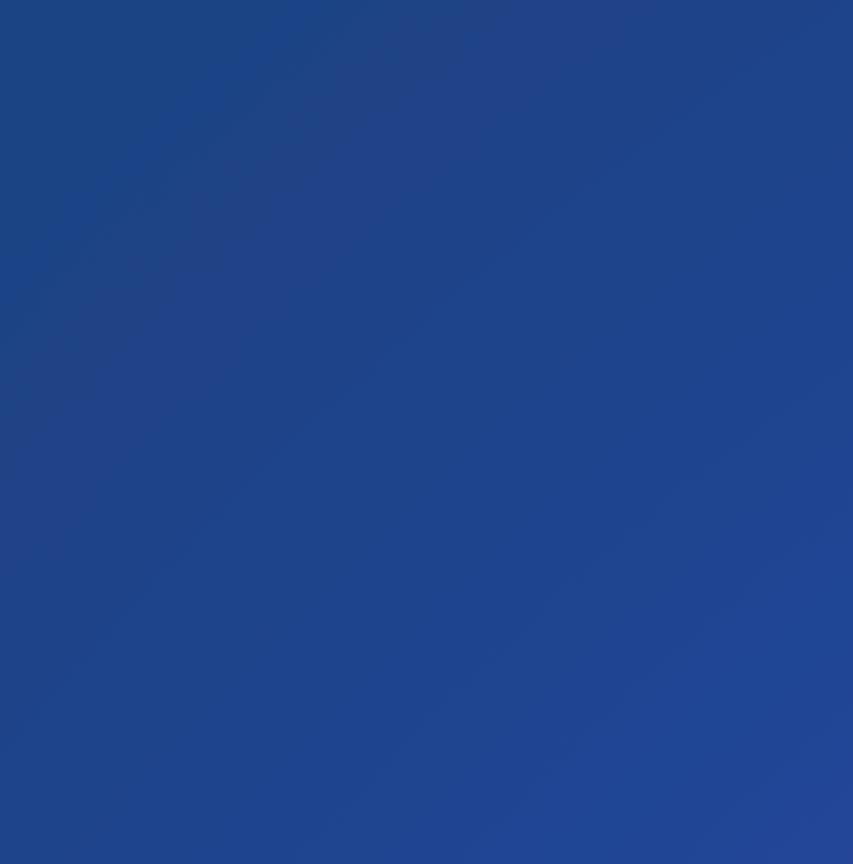
GAUDENT TECHNOLOGY IS A MANUFACTURER OF ELECTROMECHANICAL AND HYDRAULICS DEVICES

More than half of our total production is used in Europe
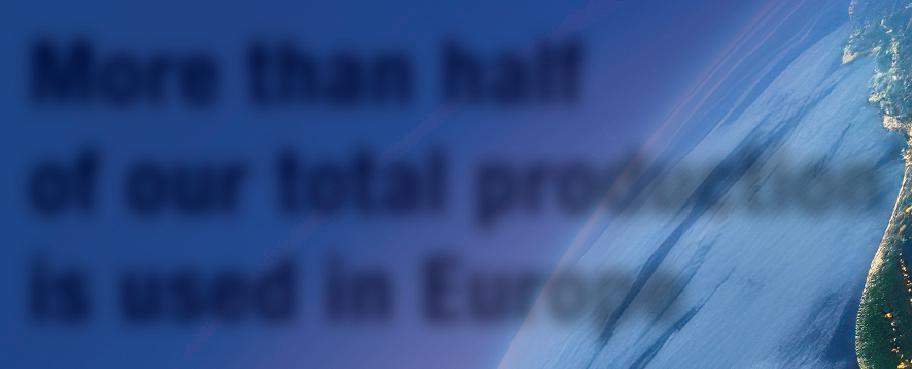
Qualified for the EU market since 2014


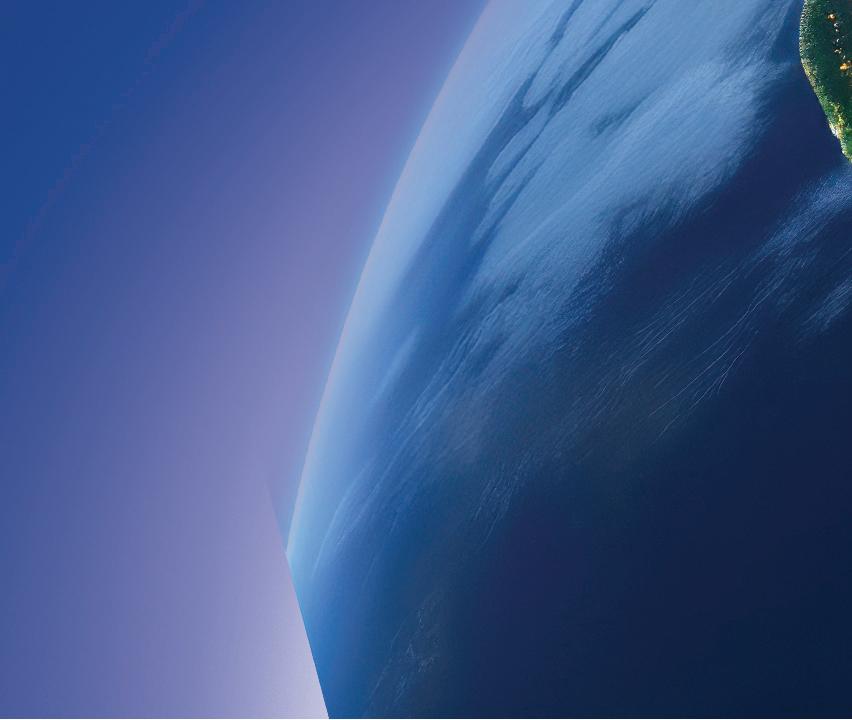

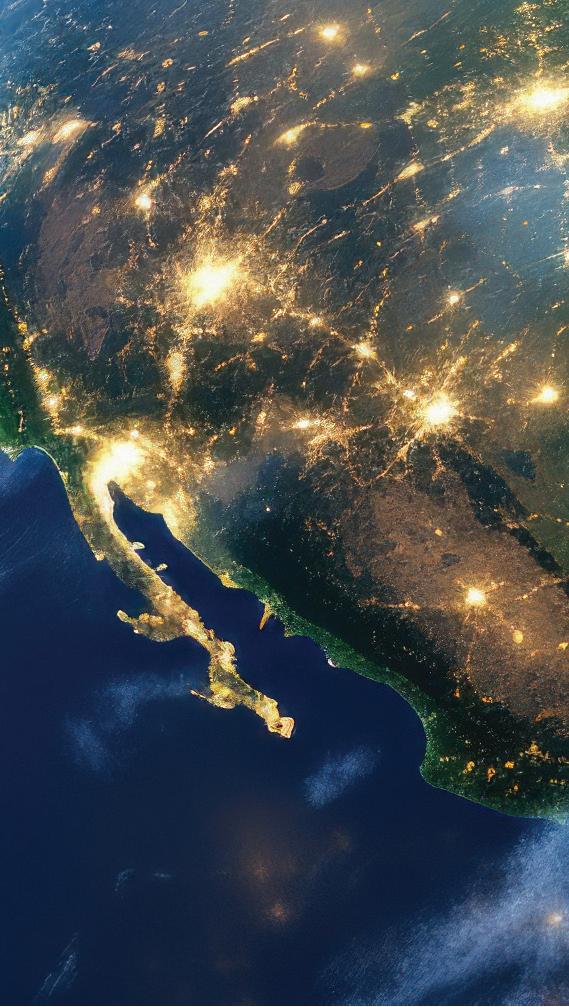


CALL TODAY FOR YOUR CUSTOM SOLUTIONS: (219) 706-8521

OTC SHIFTS THE MIX FOR OFFSHORE
INDUSTRIES
ENERGY PROFESSIONALS RECONVENE AT THE OFFSHORE TECHNOLOGY CONFERENCE HELD IN HOUSTON’S NRG PARK, MAY 6-9, 2024.
BY: RACHAEL PASINI, SENIOR EDITORSince 1969, the Offshore Technology Conference (OTC) has gathered thousands of experts from the oil and gas, solar, wind, hydrogen, and marine industries to discuss global energy advancements and needs. Last year, the theme was “Delivering the Future of Offshore Energy,” where drilling technology, digital transformation, decommissioning, and carbon capture, usage, and storage were key topics. OTC 2024 continues its future-focused thread with an aim to shift and drive the world’s energy mix by “Leading the Global Energy Evolution.” With more than 45 technical sessions, 450 technical presentations, 1,300 exhibitors, and 31,000 attendees, NRG Park will become a haven for knowledge exchange and idea sharing.
Leaders from BP, Shell, Chevron, Enauta, SLB, Geothermal Rising, and other top companies, academic and research institutions, and non-profit organizations will speak on today’s pressing topics and technologies throughout the Technical Program. There will also be a thread dedicated to offshore wind energy technology with speakers from Ørsted, Atlantic Shores Offshore Wind, TotalEnergies, SBM Offshore, Technip Energies, and the U.S. Department of Energy.
On May 5, the OTC board of directors will present the 2024 Distinguished Achievement Awards to Kerry J. Campbell for individual achievement and Petrobras’ Marlim and Campos Basin for institutional achievement. The board will also recognize the EnerGeo Alliance with a Special Citation. On May 7, OTC will celebrate the 2024 class of Emerging Leaders, young professionals demonstrating exceptional talents, commitment, and promise in the offshore energy sector.
“This year’s recipients embody the essence of what it means to be a young professional. Their commitment to excellence, relentless pursuit of knowledge, and unwavering passion for their work have set them apart. They have not only excelled in their field but have also shown remarkable leadership qualities, inspiring those around them to
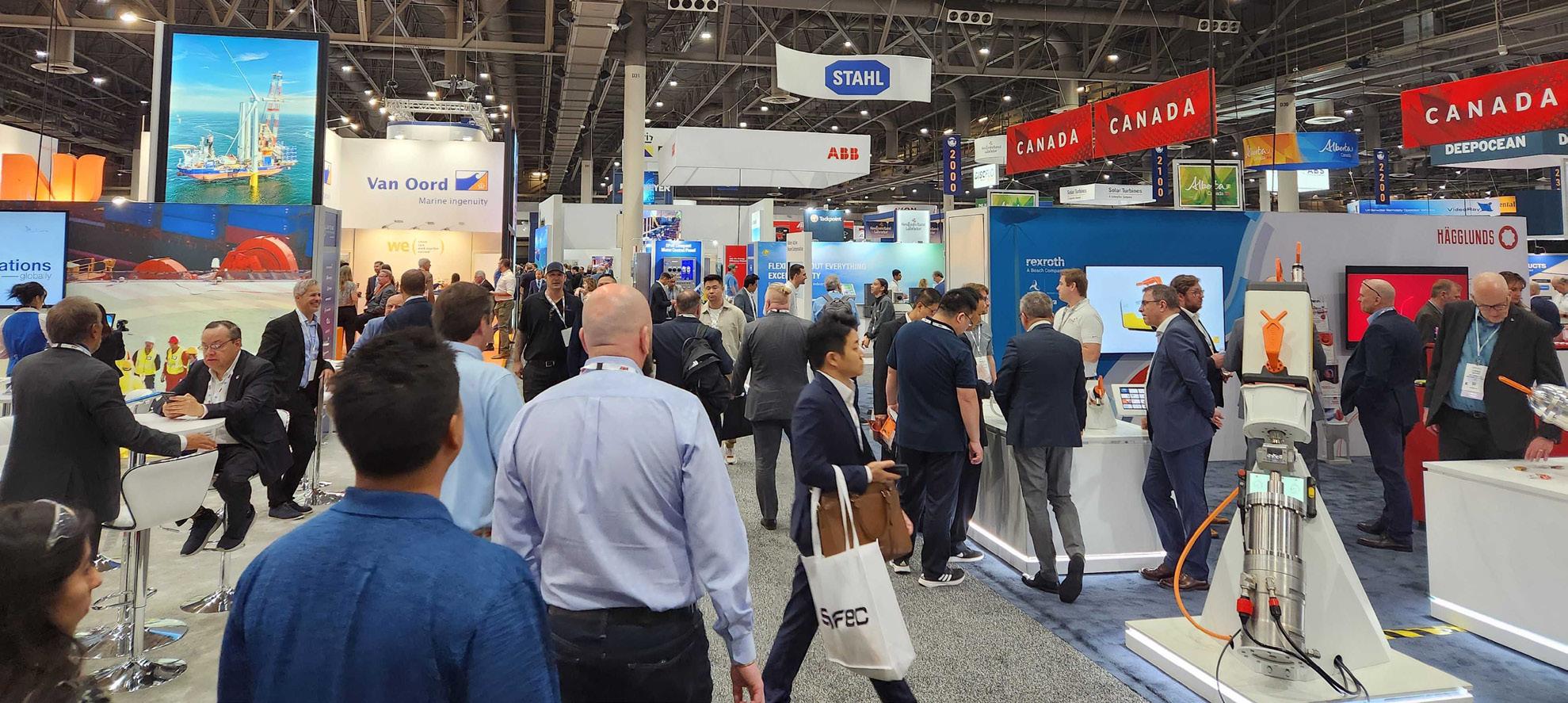
push beyond boundaries and explore new horizons,” said Alex Martinez, chairperson of the OTC board of directors.
Fluid power exhibitors and technology
On the fluid power side, close to 50 companies from around the globe will showcase their technologies on the
exhibition floor. Read this article at fluidpowerworld.com to see a full list of fluid power exhibitors.
Last year, Bosch Rexroth earned a Spotlight on New Technology Award for its Hägglunds Atom gearless direct drive. This year, Hägglunds Quantum Power motor earned the award. The Hägglunds CB motor
evolved into the Hägglunds Quantum, then the company added a connection block with more ports for faster speeds and higher efficiency. The Hägglunds Quantum Power is compact and achieves the power density required in mining and mobile applications.
“Revolutionizing the field is no easy task. It requires collaboration, intense consistency, and the brightest minds in the industry to drive innovation,” said Martinez.
Other exhibitors will display new and updated products, such as Famic Technologies’ Automation Studio 8.0, intended for the design and simulation of multi-technology systems. Especially with the higher level of electrification of fluid power components and equipment, it places greater emphasis on features required for the design of hydraulic manifold blocks, training, and technical publications.
Visit 2024.otcnet.org to learn more and register. FPW
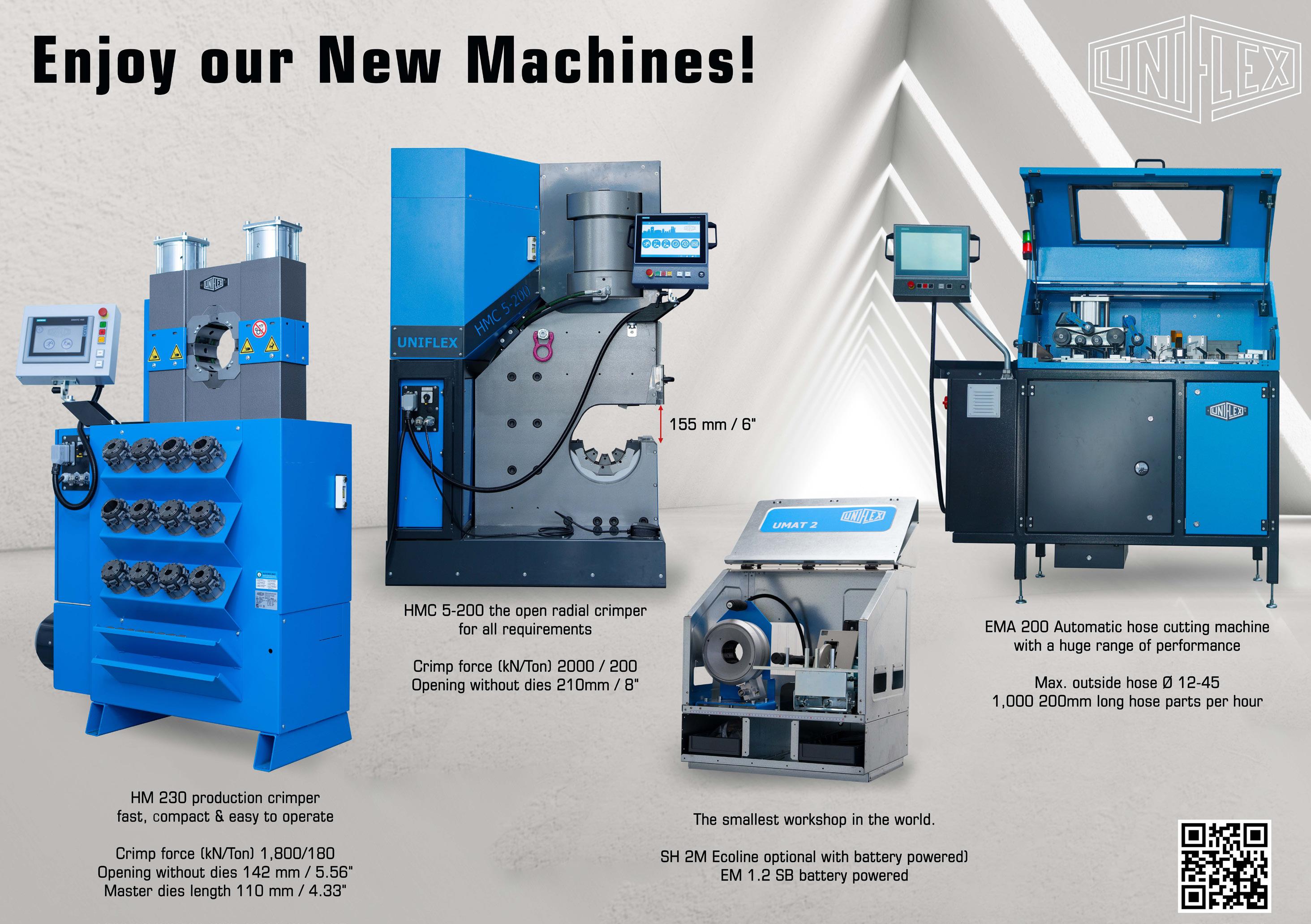
Fluid Power World
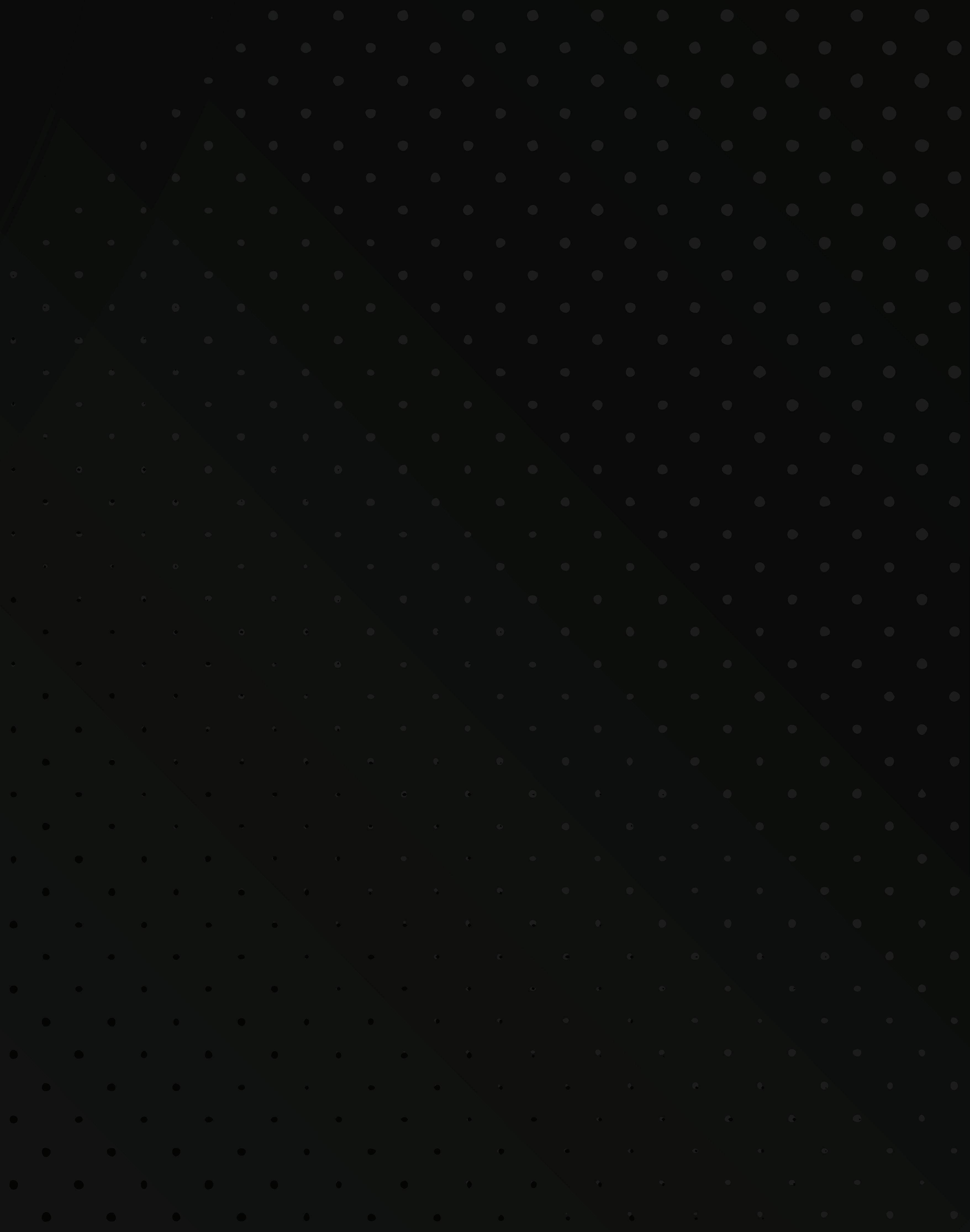
HAPPY ANNIVERSARY, HAWE HYDRAULIK!
An aerial ladder for the fire brigade that transports the fireman to dizzying heights in seconds and in a stable manner. A tunnel boring machine that digs its way through the hardest rock. Countless solar panels that continuously follow the desert sun and bundle the energy of the future. Huge gearboxes that are safely manufactured in one piece on a machining center. Whenever hydraulics are used to move the big things: HAWE is there.
As a responsible development partner with experience in over 70 branches of mechanical and plant engineering, we work with our customers to
develop intelligent solutions that actively shape our environment. With our highly flexible modular system of hydraulic power packs, pumps, valves and sensors, the matching electronic components and our software expertise, we are the ideal partner to tackle global requirements together.
Behind this are more than 2,600 employees in national companies in over 20 countries around the world who make their daily contribution to reducing costs and effort and conserving resources and the environment. It is our employees who make HAWE solutions unmistakable: Solutions for a World under Pressure.
Series 5000 operator system
Spartan Scientific spartanscientific.com
The Series 5000 Operator System is designed to meet the demands of applications requiring higher pressures and increased flow rates, filling a void in the market for reliable, high-performance solenoid solutions. Featuring a range of orifice sizes from 0.6 to 4.0 mm, and available in both 2-way and 3-way configurations, the Series 5000 offers versatility to suit a wide range of industrial fluid applications. With options including DIN spaded or flying lead coils, and a future provision for a 12 mm connection option, the system provides flexibility and ease of integration into existing setups.
Constructed with all stainless-steel tubes and multiple seal materials, the Series 5000 is engineered for durability and reliability in demanding environments.
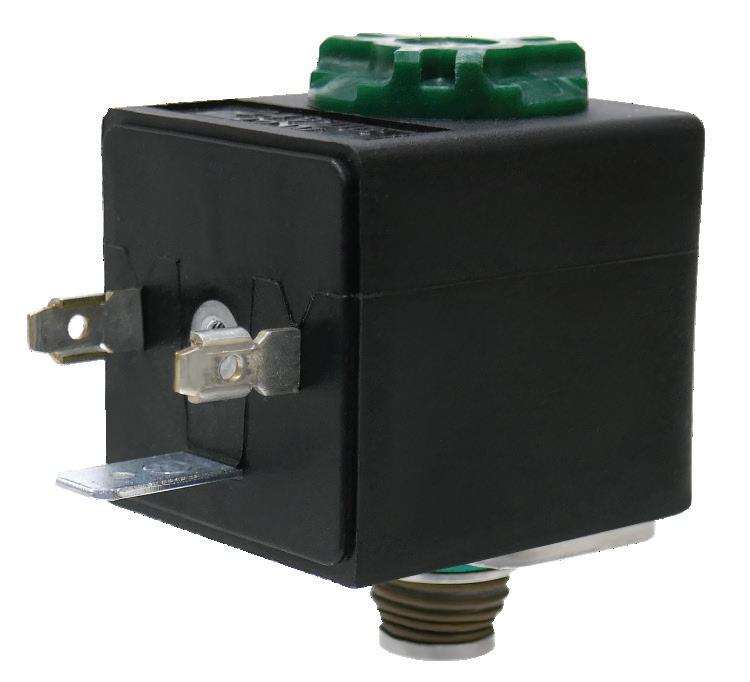
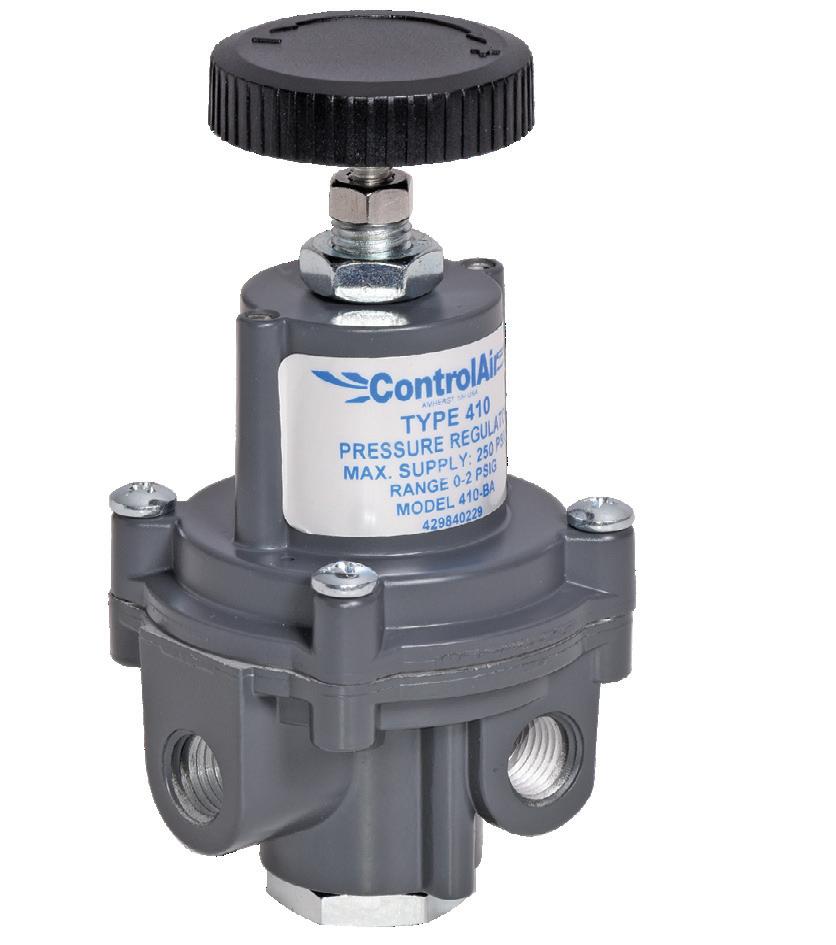
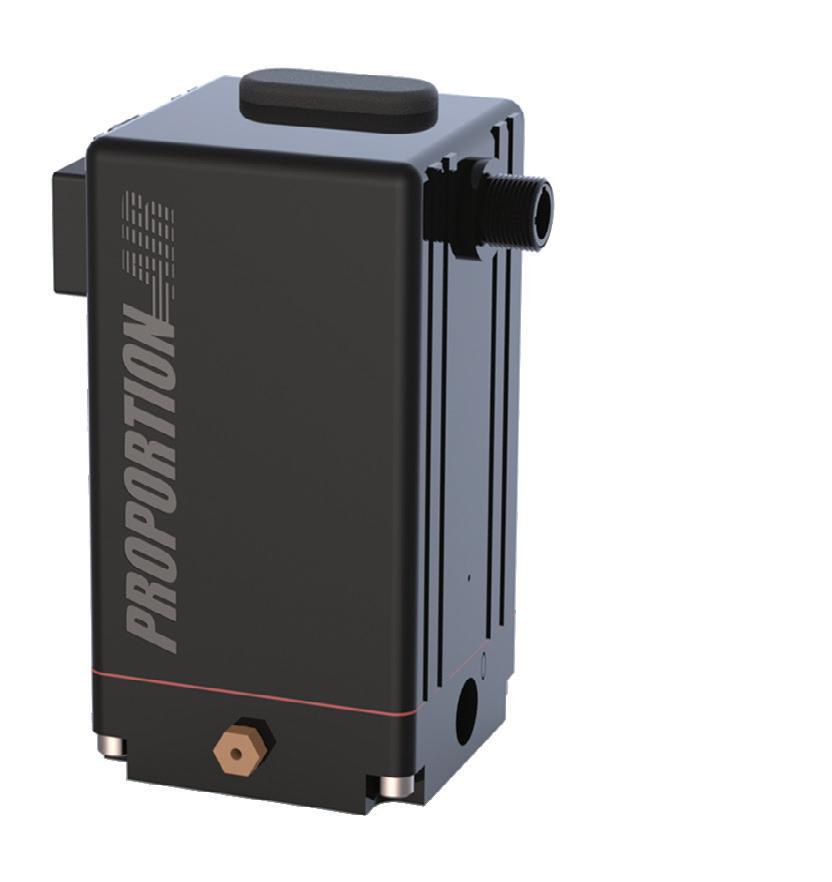
Tractor valve platform
Danfoss danfoss.com
Built on the PVG 32 proportional valve platform, the tractor valve offers a variety of components and features specific to agricultural applications. A range of valve modules — inlets, working modules for auxiliary functions, hitch modules, top-mounted modules, and endplates — enable customization for each specific application.
Zero-leak electrohydraulic PVBZ 16, 40, and 48 modules have been added to the platform, enabling the valve to cover flow rates of up to 170 lpm (44.9 gpm). The new sizes help customers to tailor the flow rate for each service more accurately. All PVBZ modules are based on the PVG 32 platform, eliminating the need for interface plates, and allowing them to be combined in numerous configurations to match customer needs. The new modules are compatible with PVE electrohydraulic actuators.
Low-speed, high-torque motors
FluiDyne Fluid Power fluidynefp.com
The FM4 series motor is the newest addition to the motor product line and is now available in stock alongside the FM1, FM3, and FM50/51 models. The series geroter gear set and spool valve flow distribution make these hydraulic motors compact, highly efficient, and perfect for low-speed, high-torque applications. Whether you’re using parallel or series systems, these motors deliver exceptional performance.
Offered in displacements of 80 to 500 cc (4.88 to 30.5 in.3), these are rated for speeds of 850 to 144 rpm continuous and 956 to 246 rpm intermittent. They are rated for maximum torques of 1,575 to 6,363 lbf-in. continuous or 2,522 to 7,612 lbf-in., intermittent. Maximum pressure ratings range from 2,538 to 1,730 psi continuous or 4,060 to 2,175 psi intermittent.
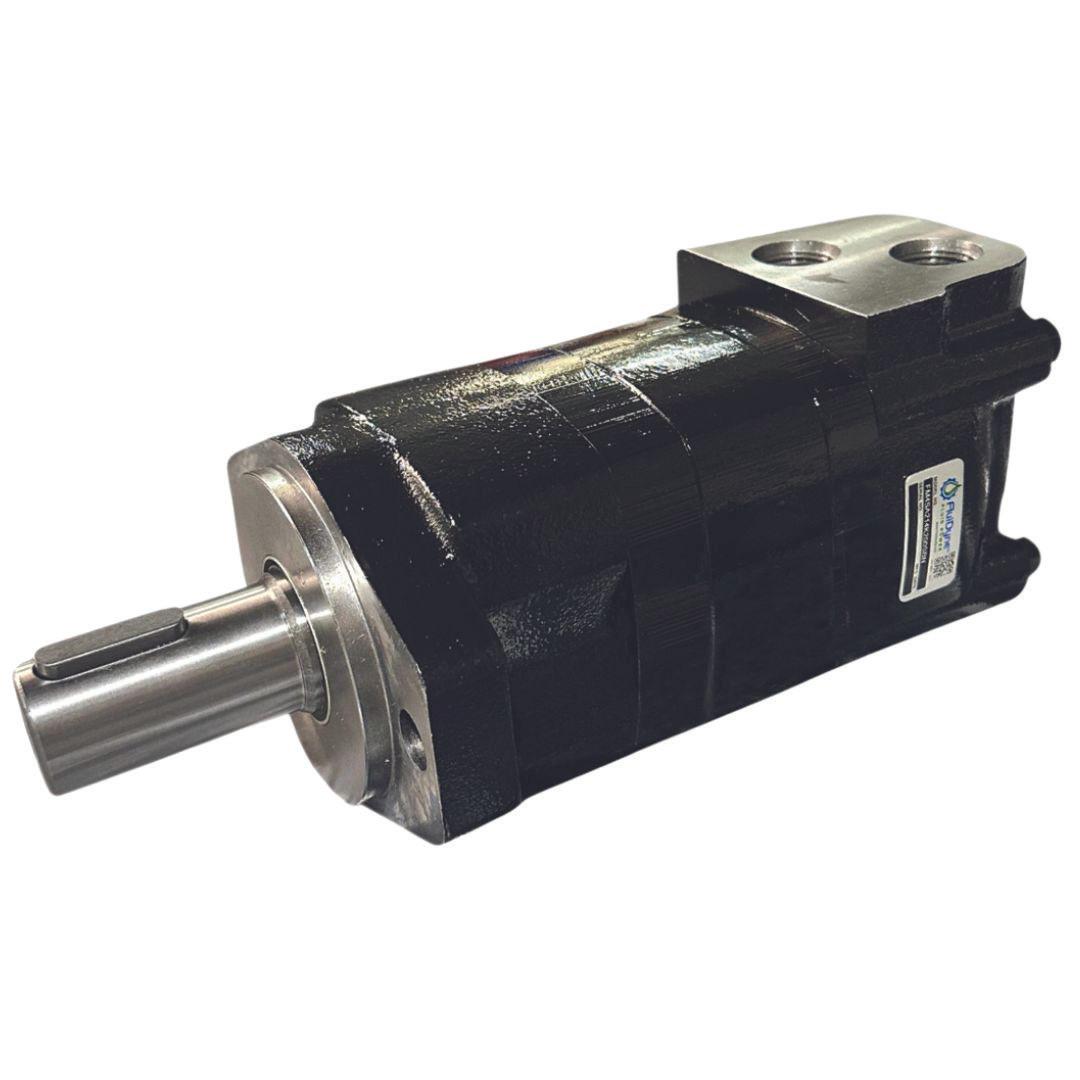
High-precision pressure regulator
ControlAir LLC controlair.com
The new Type 410 high-precision pressure regulator provides high regulation accuracy and repeatability during variable operating conditions. Designed with precision and reliability in mind, the regulator serves as a costeffective yet highly efficient solution for controlling industrial processes. With its superior regulation characteristics, the Type 410 consistently meets control requirements, even amidst fluctuating operating conditions. Built to withstand the harshest industrial environments, the Type 410 features die-cast housings protected with a chromate finish and epoxy paint, ensuring long-lasting durability and performance. Every regulator undergoes rigorous pressure, leak, and flow tests at the factory before shipment, guaranteeing exceptional quality and reliability straight out of the box.

Portable hydraulic hose service workshop
Uniflex
uniflex-hydraulics.com
This new mobile workstation, the size of a dishwasher, answers the need for smaller, more portable hose service tools. The battery-powered UMAT 2 hose service workshop can cut, crimp, and process hydraulic hose up to 1 in. 4 SP and 1 ¼ in. 2 SN anywhere, from the raw material to the ready-to-install hose assembly.
The UMAT 2 includes the SH2 M Ecoline workshop press, the EM 1 SB hose cutting machine including battery and a 700-bar hand pump. Depending on the equipment, crimp dies from 06.8 to 047.0 mm are contained in two separate compartments, suitable for Euroboxes. There is also space for a charger, cordless screwdriver, pop lock kit, and wrench. The UMAT 2 is optionally available with the 700-bar battery pack PUM 0.8/3.2.
Long-stroke pinch valves

Clippard clippard.com
Clippard’s NPV-7
Series high flow pinch valve provides the same functionality as the standard series but with the added benefits of a longer stroke. This makes it suitable for applications that require greater flow or those that use viscous or particulate-laden media. As with all Clippard pinch valves, each valve comes pre-installed with 12 in. (30 cm) of your choice of standard medical/laboratory grade or sanitary food grade silicone tubing.
• Solenoid-operated
• Unobstructed flow path
• Tubing is easily replaceable
• High flow, long stroke
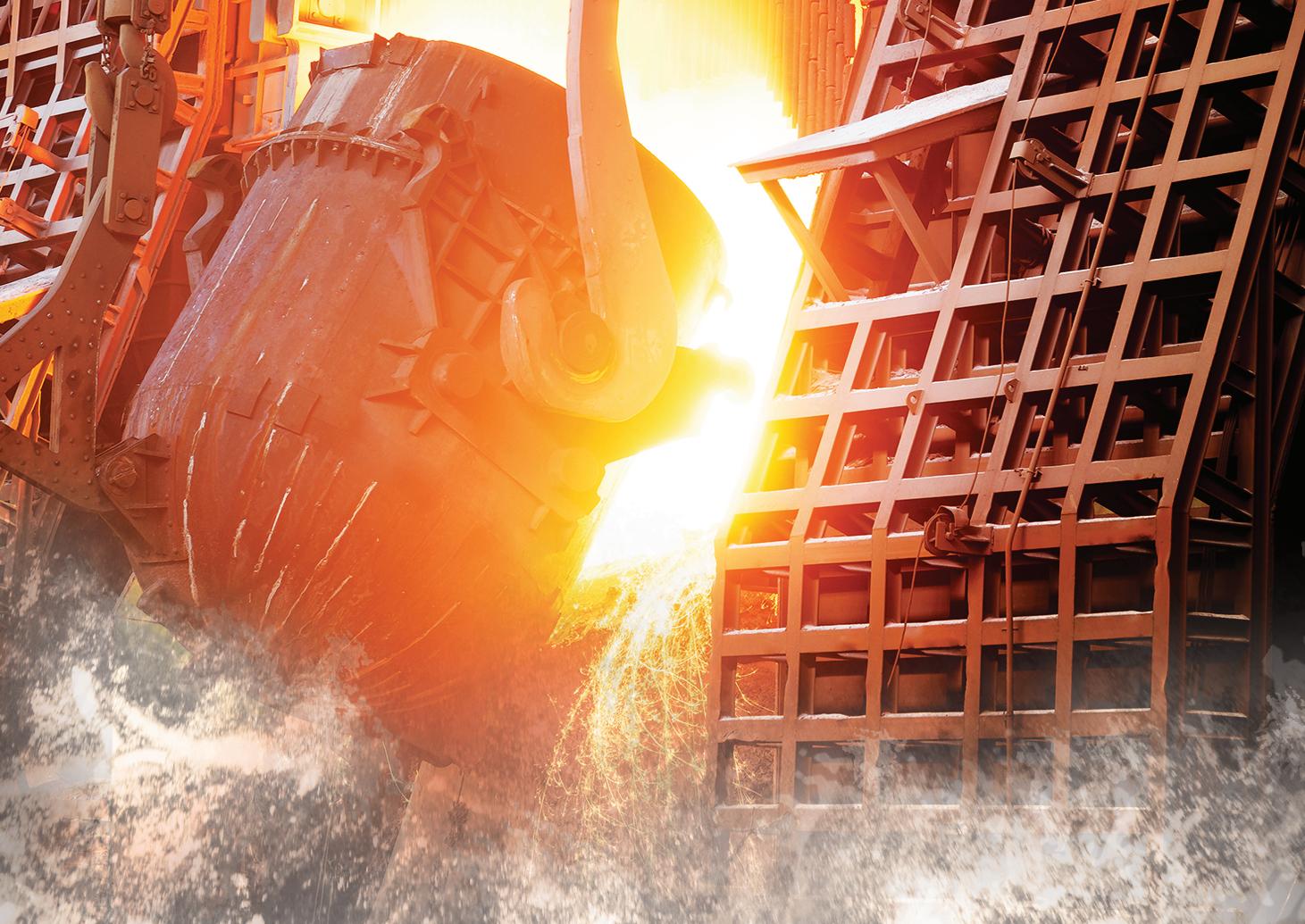
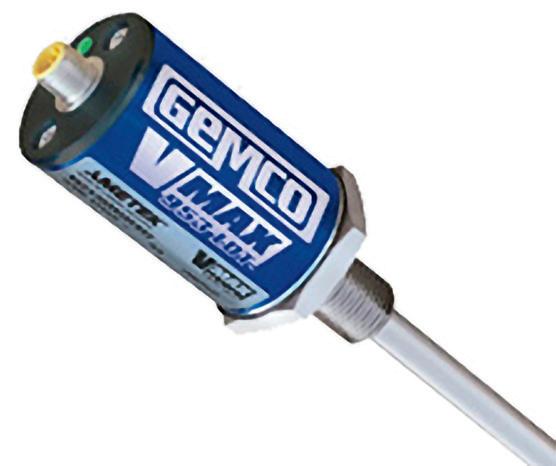
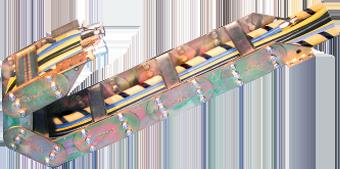

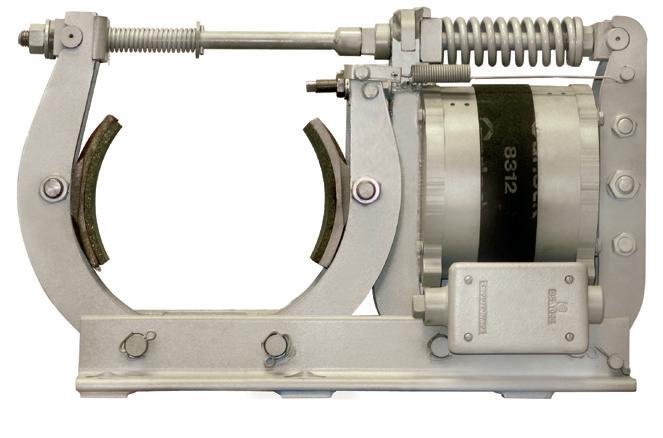
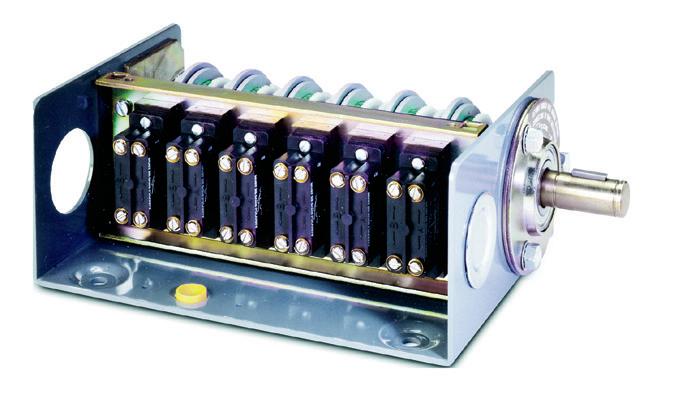
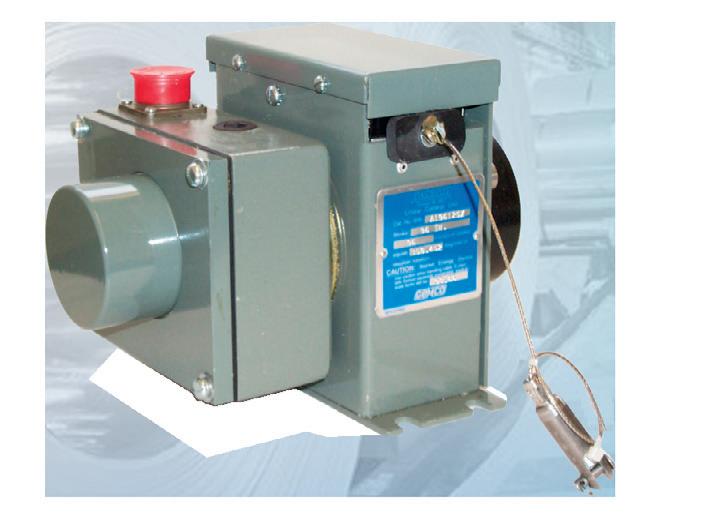
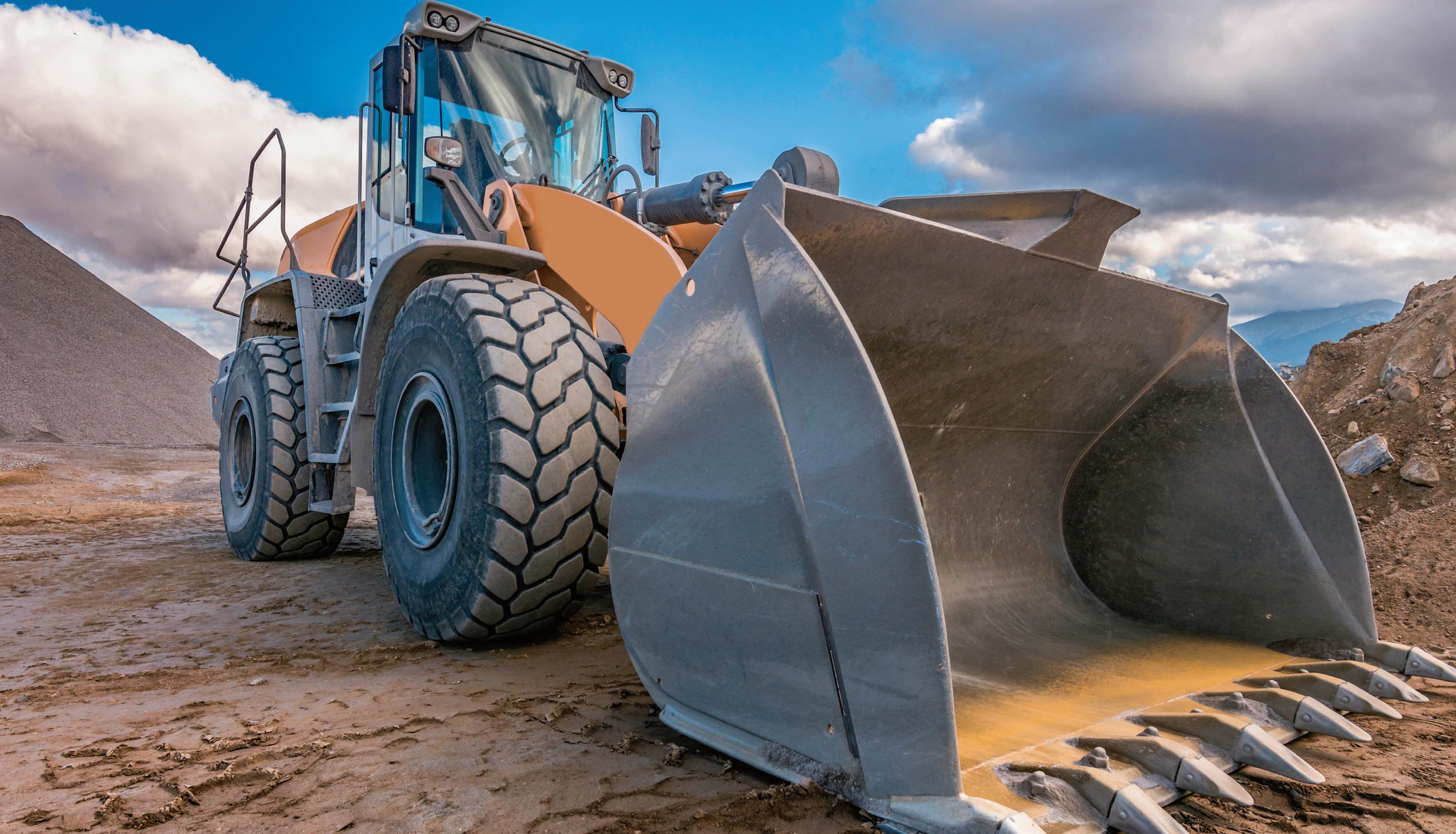
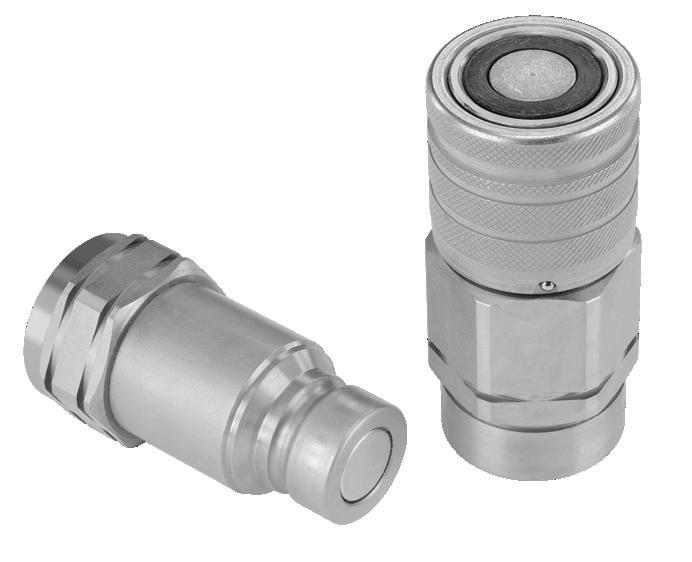
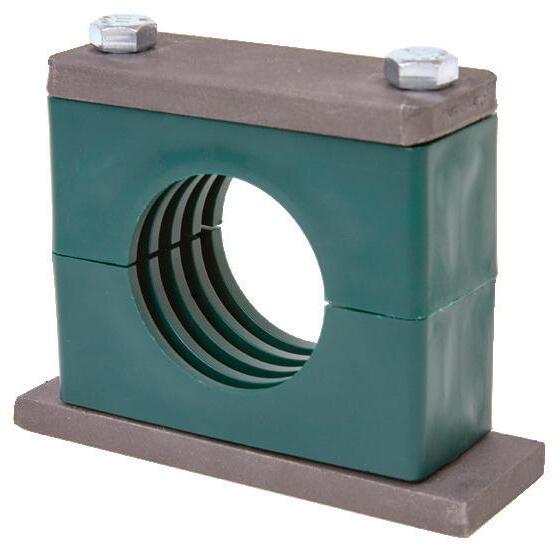
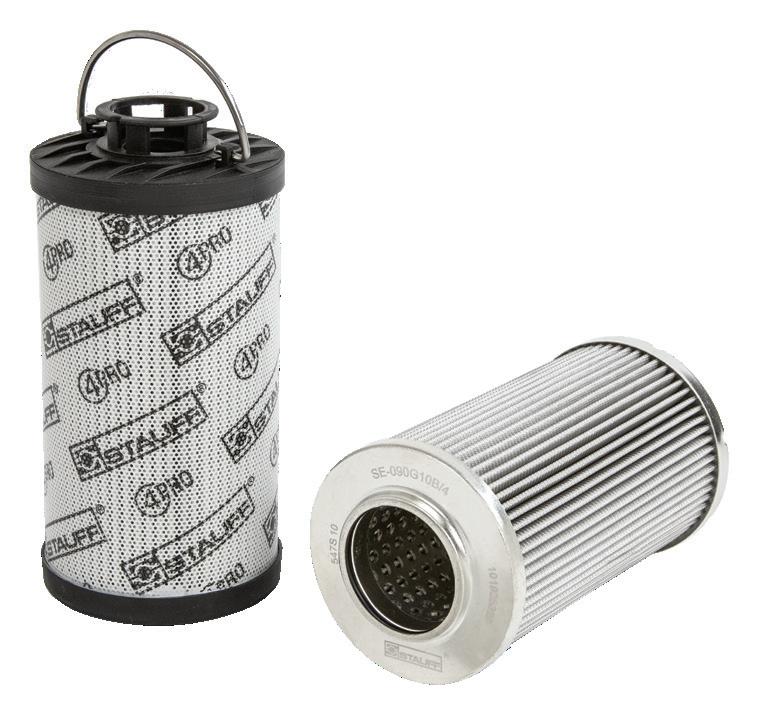
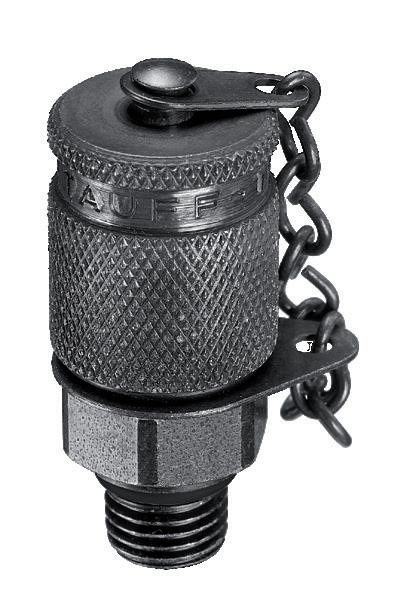
We offer thousands of critical components designed to help our customers operate more efficiently.
Look to STAUFF for Quick Couplings, Clamps, Hydraulic Filters, Test Points and many other components to keep machines—big and small—moving you forward.
416.282.4608 stauffusa.com
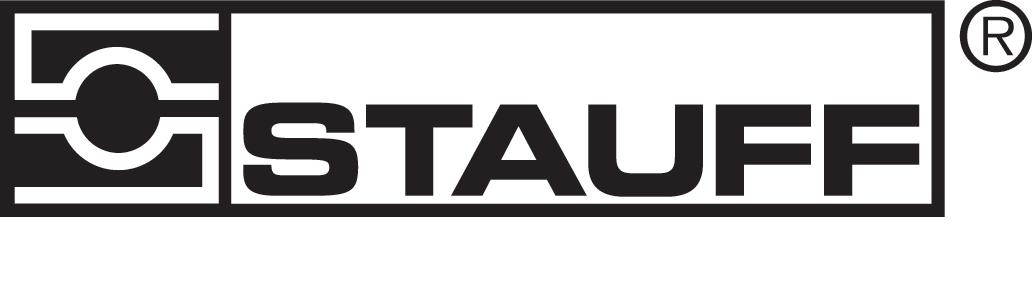
310.279.3844 smccafferty@wtwhmedia.com @SMMcCafferty EVP Marshall Matheson 805.895.3609 mmatheson@wtwhmedia.com @mmatheson CFO
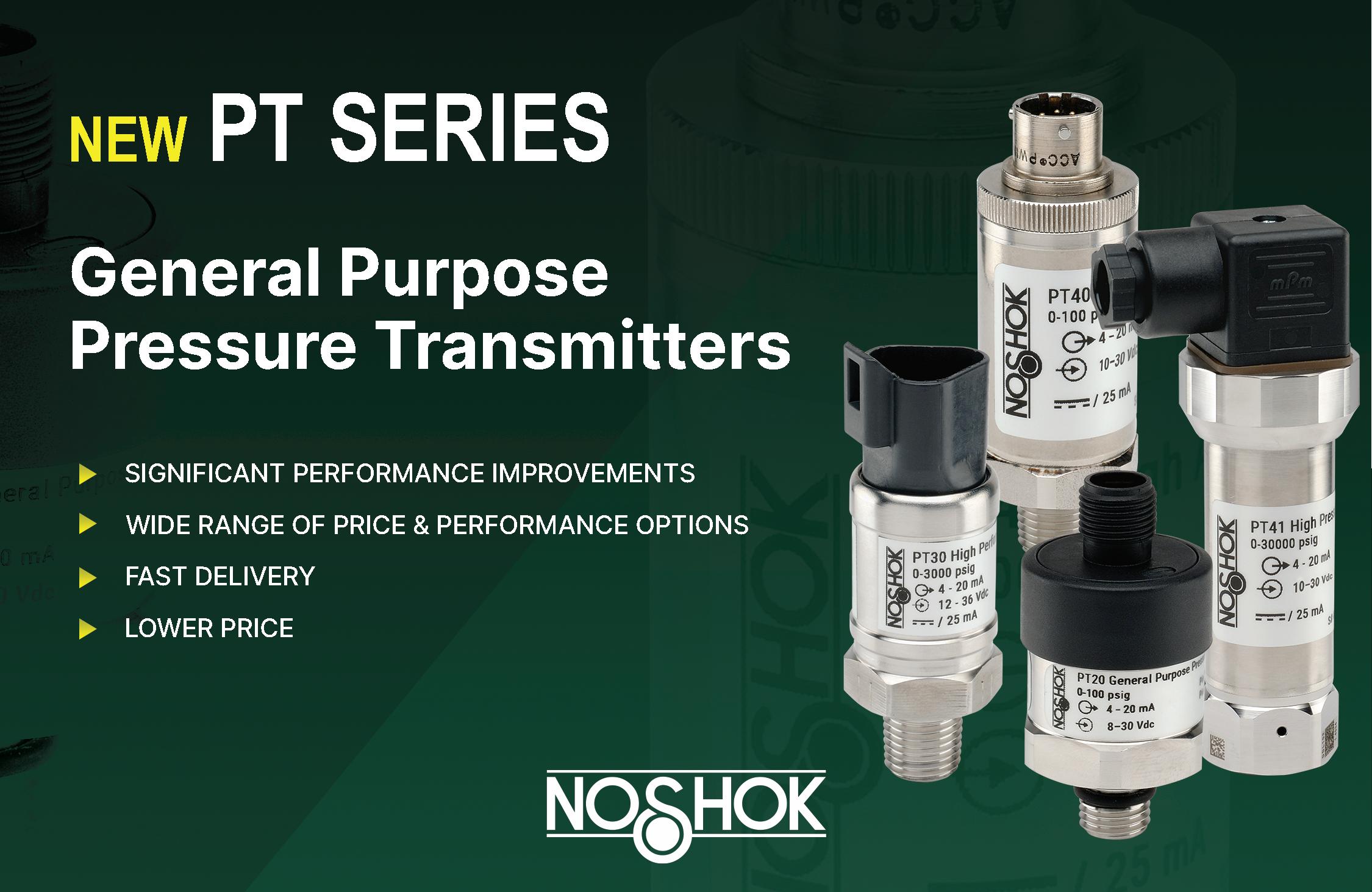
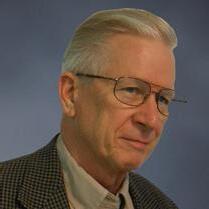
New valve locks up on rod threading machine Solution to cold, weak batteries impact tractor startup
A customer of mine has a machine that threads both ends of a straight piece of rod stock which then is fed into a second machine to bend it in a “U” shape. This creates a clamp for various round pipe sizes.
They had a problem with their large D08 pilot-operated directional valve. This older design with air-gap designed coils kept seeing the coils burn. To eliminate this issue, they decided to replace the D08 valve with a newer design featuring a pilot with wet armature solenoid coils. Everything went fine for about 10 to 12 cycles, but then the valve would lock up. If they held the shifted position for 1 to 2 minutes, it would shift and run the threading motor. However, when given the order to stop, the motor will run briefly and then slowly stop.
Can you identify what was the problem? We welcome responses of all kinds directly to Robert Sheaf at rjsheaf@cfc-solar.com or to mgannon@wtwhmedia.com. The solution will be provided in conjunction with our June 2024 issue. FPW
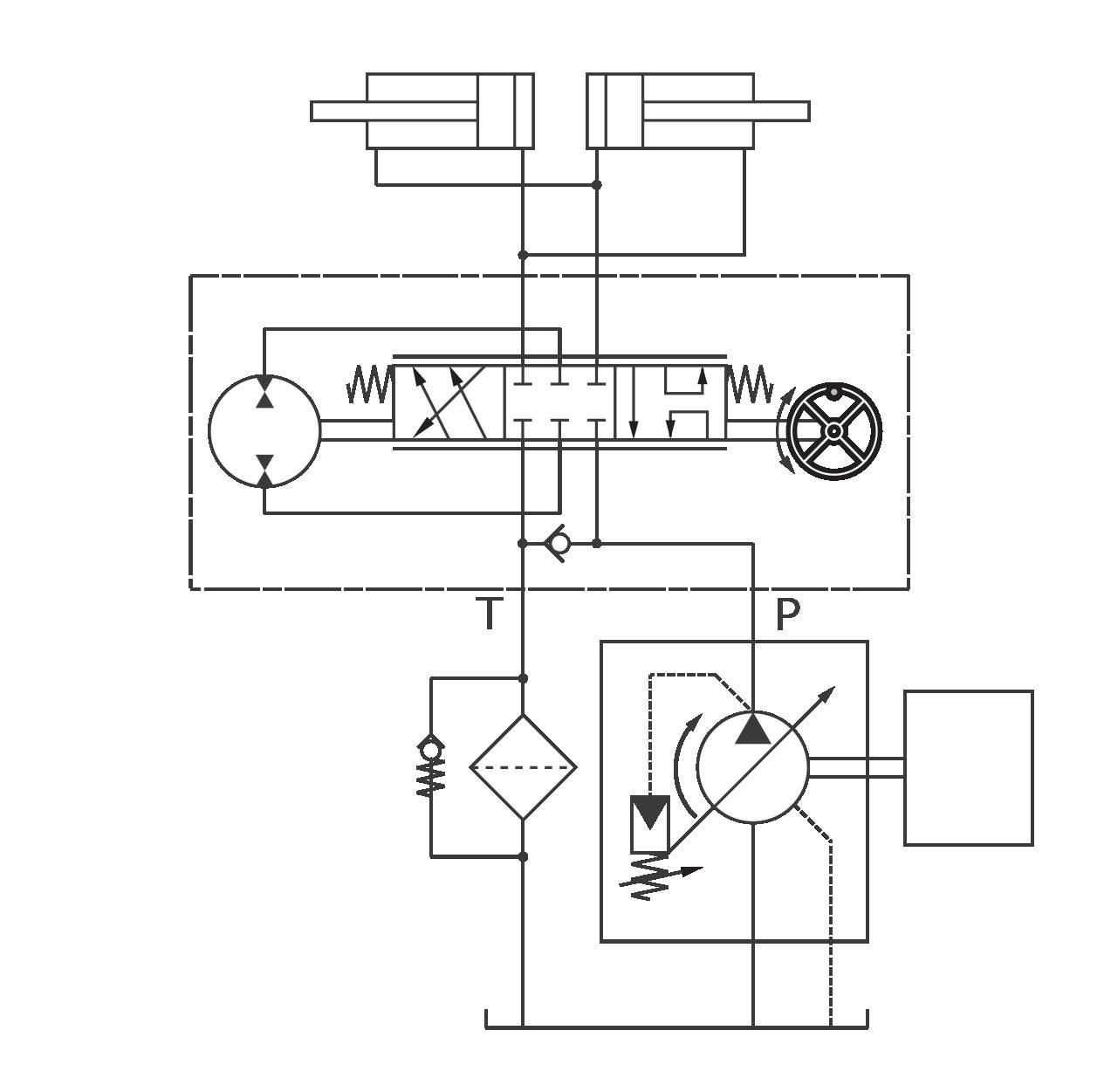
Closed-centered hydraulic systems with pressurecompensated pumps require additional horsepower at start-up because the pressure-compensated pump is fully stroked to the maximum flow position when at rest. The flow increases as the pump speed increases but it has nothing to do but to increase pressure. This increasing pressure continues to put additional load on the system input until the pressure compensator setting starts de-stroking the pump to a low flow condition, which in turn, drops the input horsepower needed.
Turning the steering wheel back and forth reduces the maximum start-up pressure because the wheel cylinders move at a much lower pressure. This usually results in additional horsepower to rotate the engine at a higher start-up speed. FPW


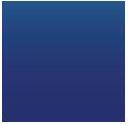
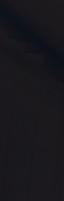
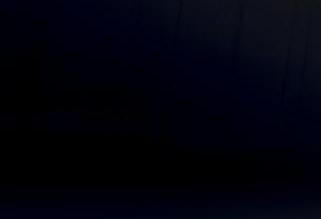
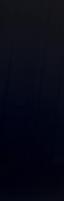






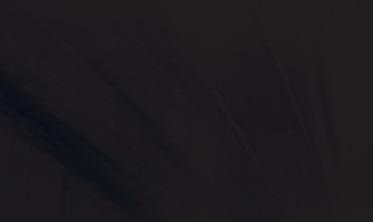
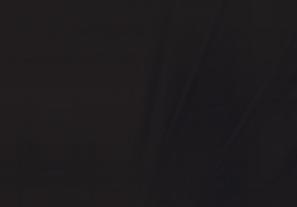
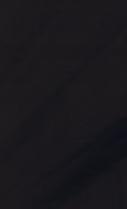
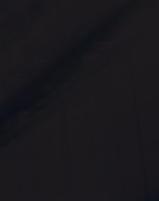

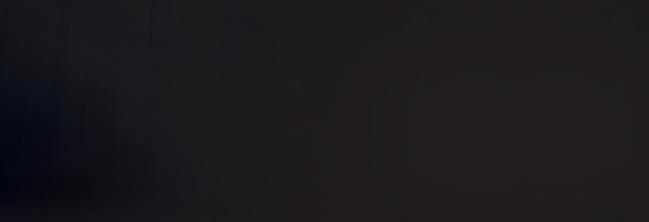

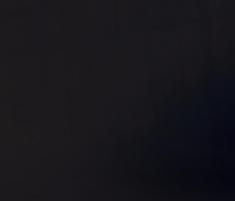
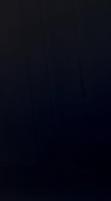

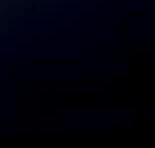

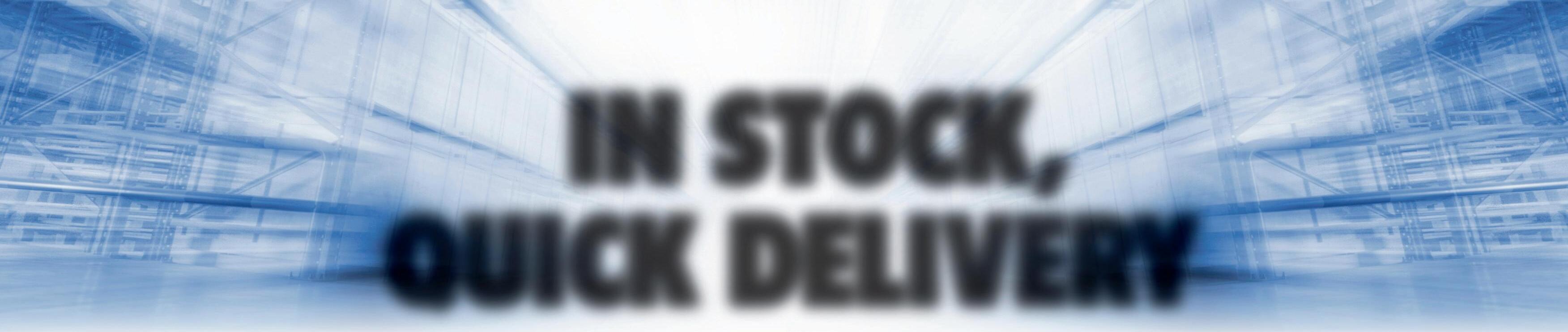


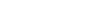
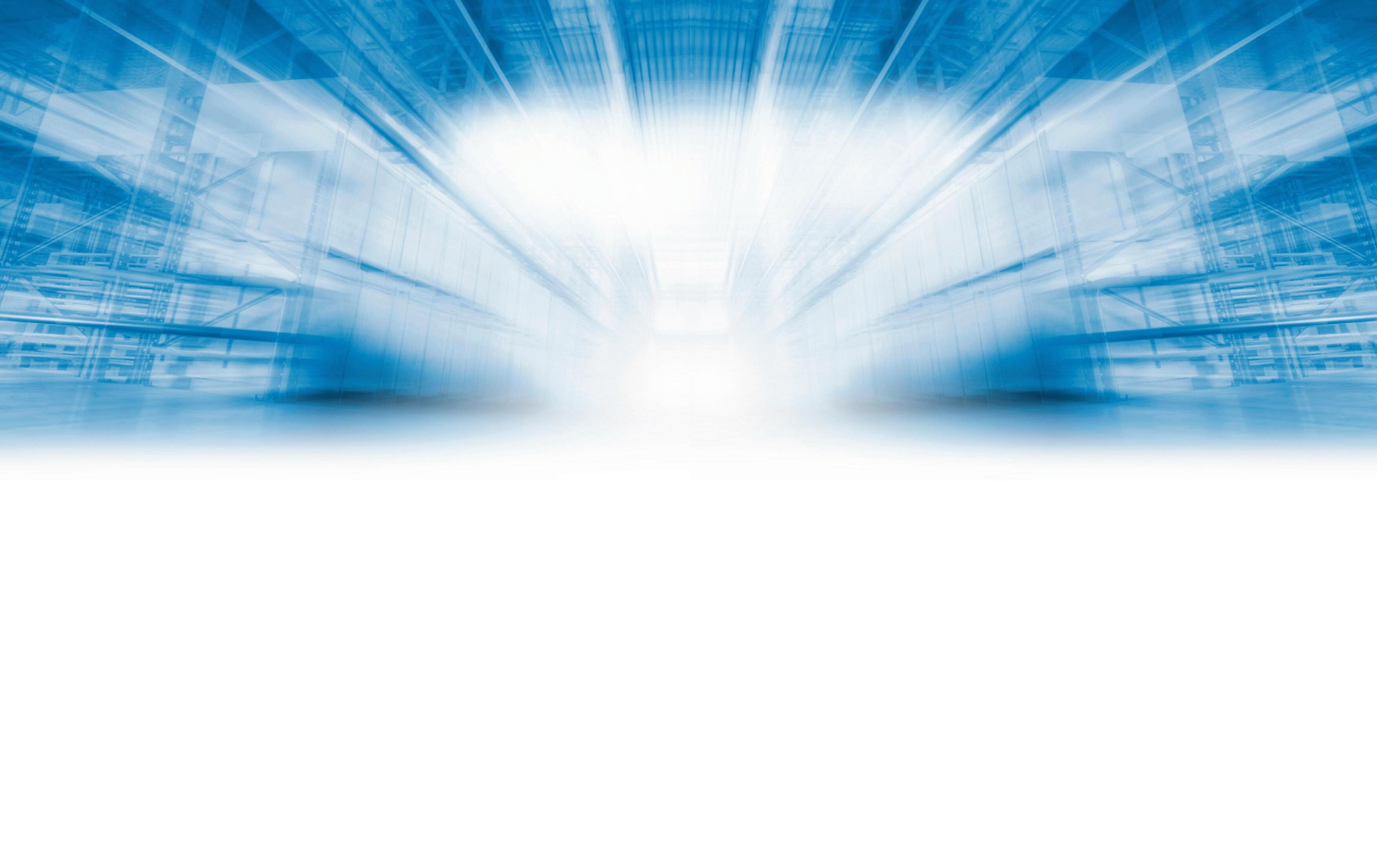
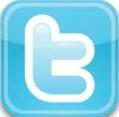

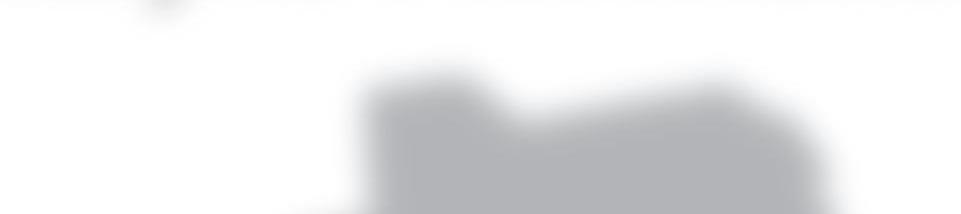
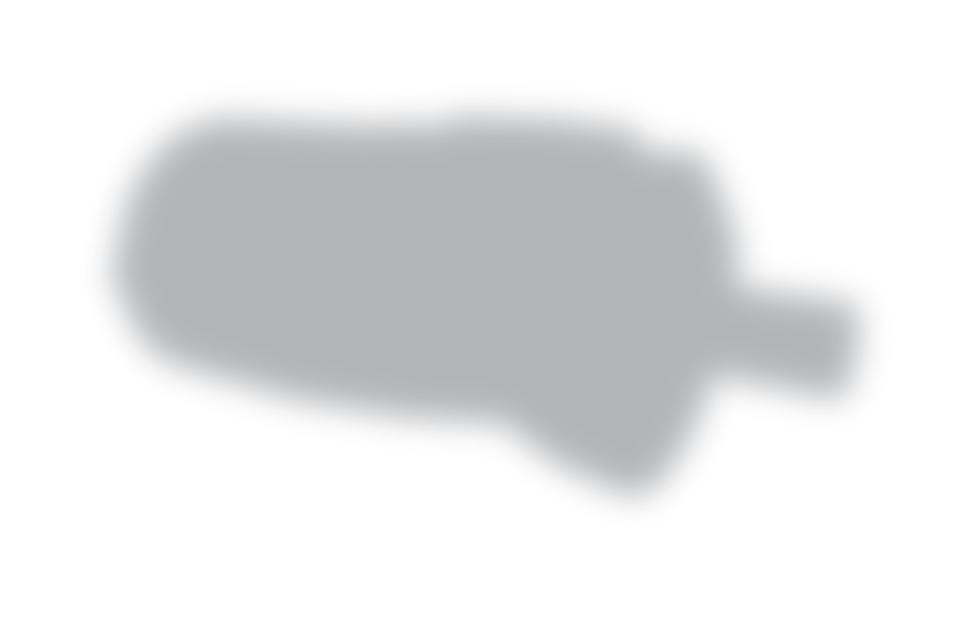
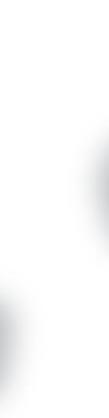

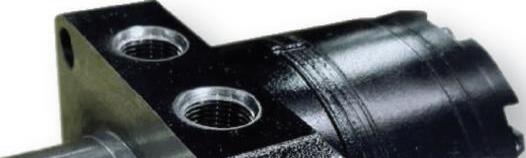
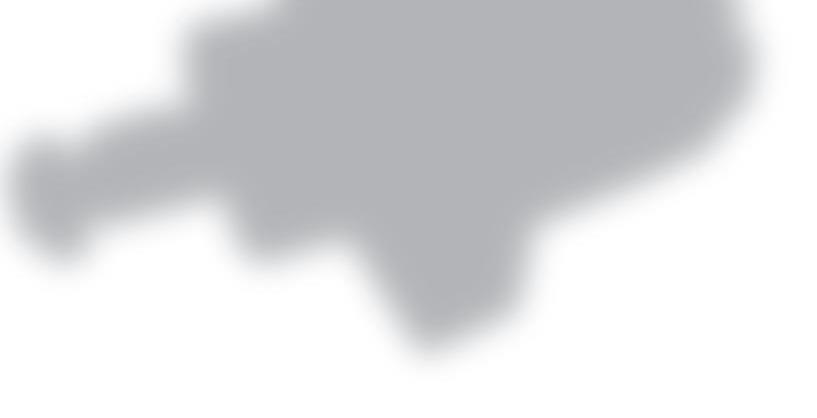


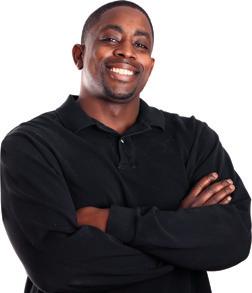
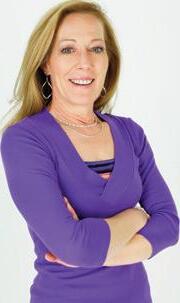
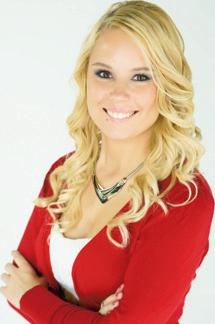
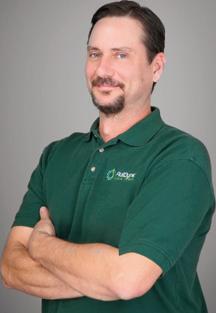


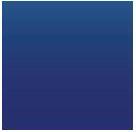
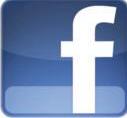


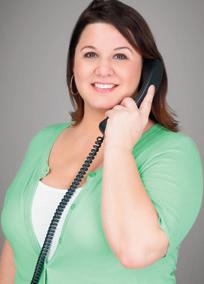




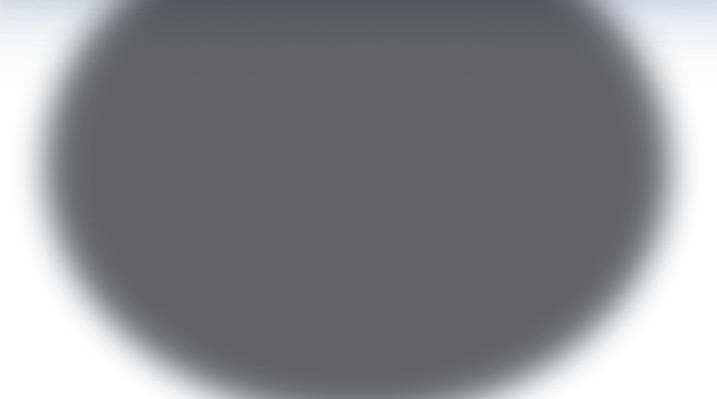

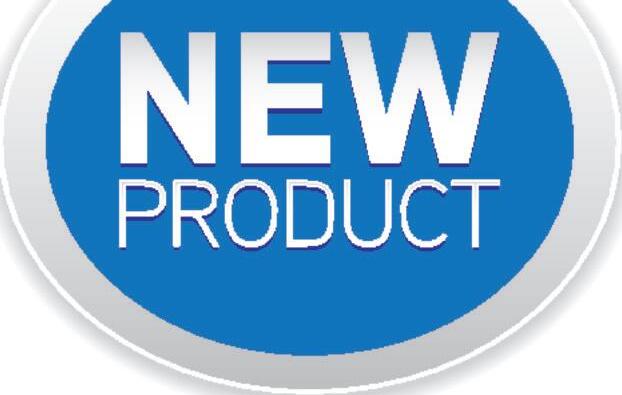
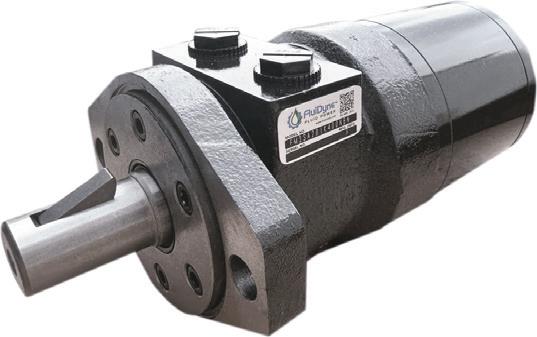
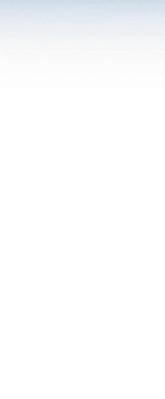

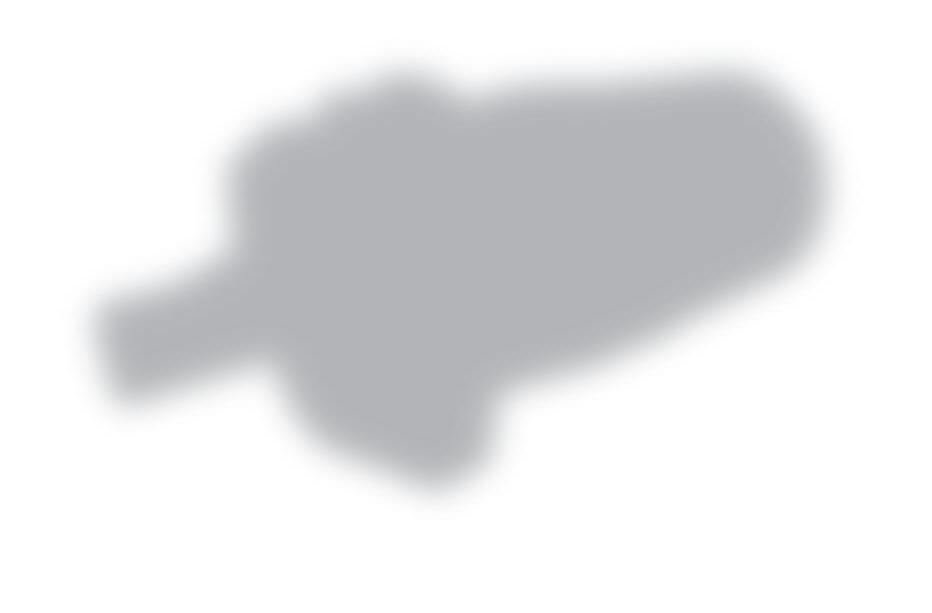
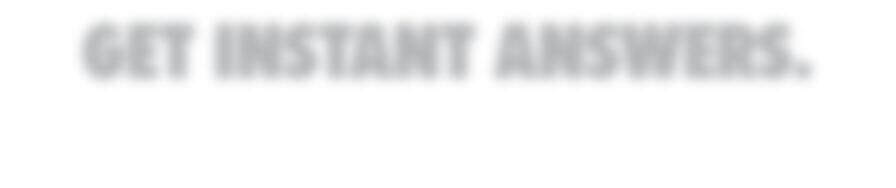




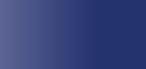
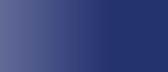
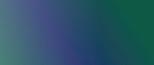


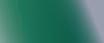



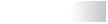




