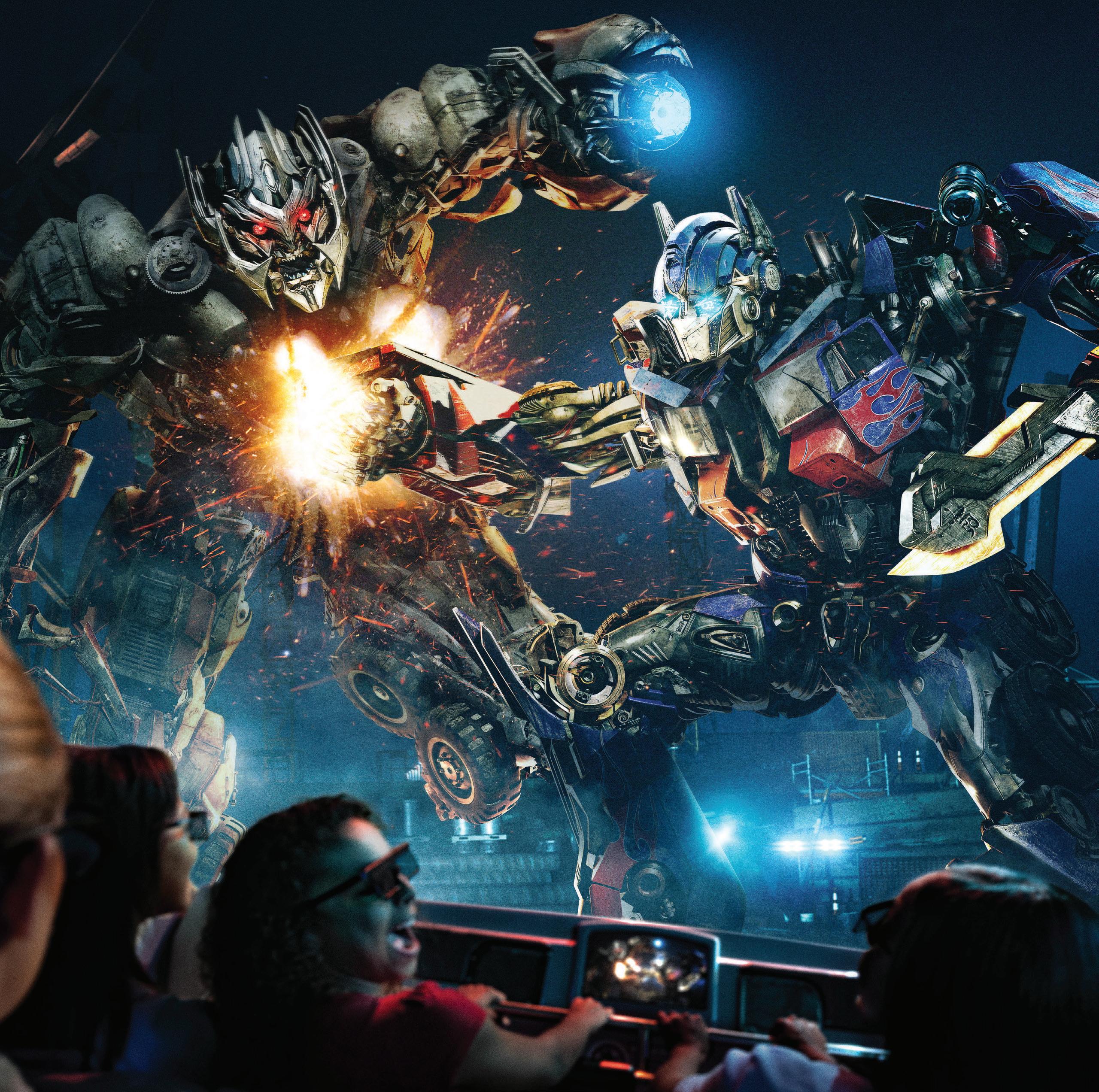
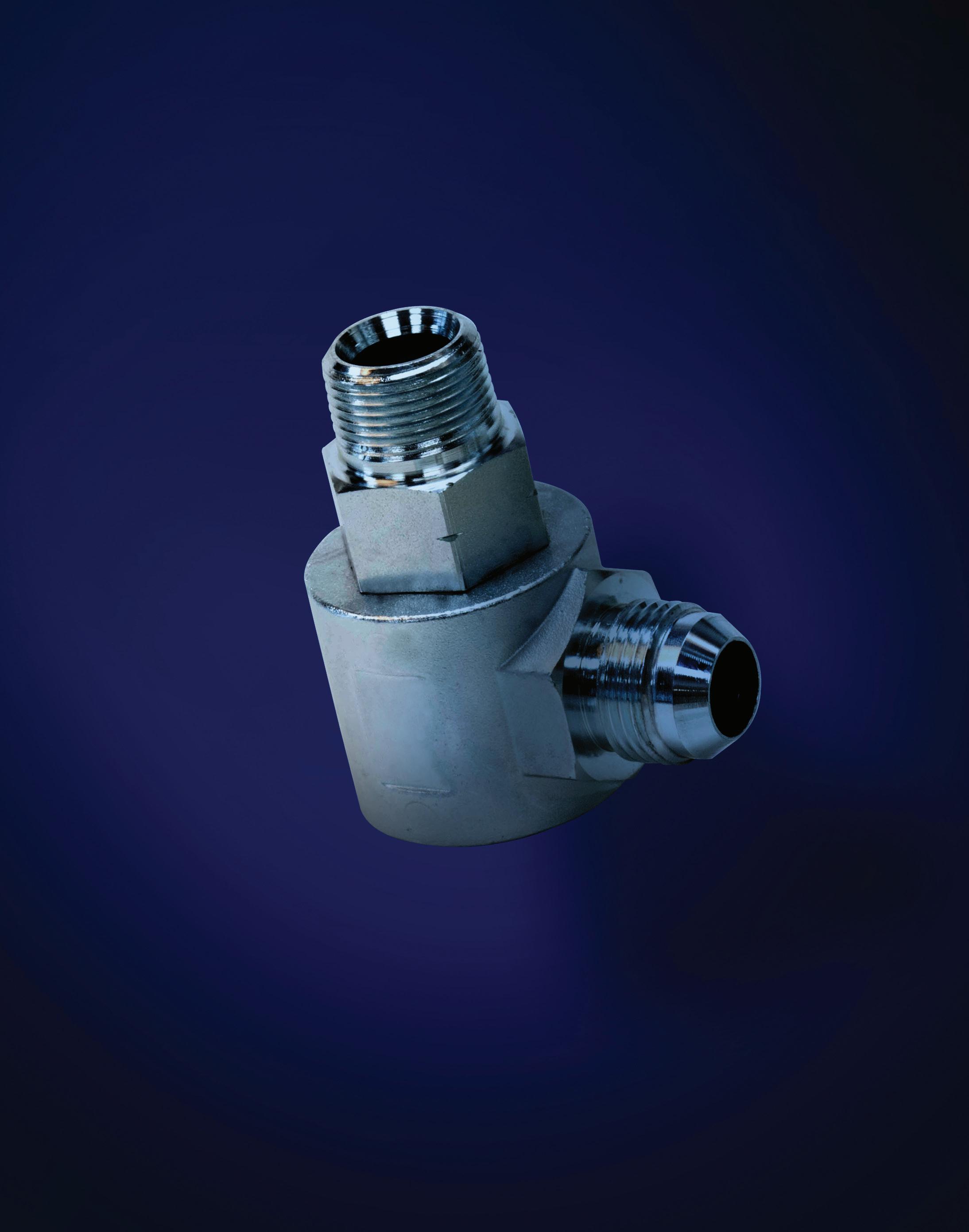
Mary C. Gannon • Editor-in-Chief
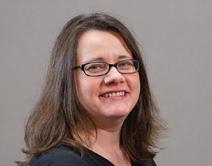
Mary C. Gannon • Editor-in-Chief
LAST WEEK, I HAD THE OPPORTUNITY to visit Continental’s ContiTech headquarters here in North America and spoke with Andreas Gerstenberger, CEO of ContiTech USA, as well as Luis David Almanza Padilla, Product Manager of Digital Solutions Americas ContiTech. Stay tuned for more updates from these conversations in the coming weeks. But speaking about all things digital with Padilla got me thinking.
Padilla showed me ContiTech’s Shop in a Box, which includes all necessary systems for completing a hose assembly — saws, cleaning tools, reels and, of course, crimpers. Most importantly, it features smart crimping technology, which allows manufacturers to send updates through the cloud to the crimper, resulting in fewer mistakes in hose and fitting assemblies. Gone are massive catalogs containing every crimp spec known to man. The machine knows exactly what die to use and exactly how long to hold the crimp for the proper design.
This makes so much sense for crimping technology — if there is an update to a product line, ContiTech sends it to the crimper, eliminating the risk of a technician not knowing which die to use or losing a printed update card.
When I started covering fluid power 20 years ago, massive catalogs were every-
where. They contained technical details on products, installation and assembly instructions, engineered illustrations and sometimes technical engineering briefs that could educate the user on some basics of the technology. But these are mostly gone, supplanted by online catalogs.
This is good in many ways, as the online catalog should be more easily searchable and saves countless trees. Most books are available in an online format, whether as a PDF or web-based. But do paper catalogs still have their uses?
Recently, I’ve seen several conversations on LinkedIn by folks loyal to such catalogs and engineering handbooks. Pages would be dog-eared where they referenced critical information more than once. Most of the engineering information contained therein is still accurate today. And some of that useful text may be more difficult to find online through search functions versus a bookmark of some sort.
As someone in the business of publishing, I hold paper copies of my work dear. Not because I am old-fashioned and hate change, but because I know how easily online work can be erased. My earliest work predated most online journalism, so I still have every newspaper page with my byline. However, much of my early writ-
ing about fluid power was erased when my name was completely removed from all articles because I went to write for a competitor. It’s easy to erase things online. But if you have that tangible copy, no one can take it from you.
I know that just because it’s in a book doesn’t mean it’s true. But if it’s in a book and it IS true, it’s hard to disprove that with online inaccuracy and misrepresentation. Anyone can publish just about anything these days, including AI and disinformation. And changing content online or hacking in is very easy. But a book, a journal, a catalog? Those words will hold true as long as someone still reads them.
Let me conclude by asking you this: Are you strictly an online reader? Or do you hold on to your books, journals and other items as frequent reference in your daily lives? FPW
Mary C. Gannon
• Editor-in-Chief mgannon@wtwhmedia.com linkedin.com/in/marygannonramsak
Fluid power brings the fun
Without the power of hydraulics or the snappy precision of pneumatics, much of the fun in theater and amusements parks wouldn’t be possible.
Dan Fernandes never looked back after his hydraulics internship
For Dan Fernandes, his mechanical engineering degree was the ticket into a successful fluid power career.
EDITORIAL
VP, Editorial Director
Paul J. Heney pheney@wtwhmedia.com @wtwh_paulheney
Editor-in-Chief Mary Gannon mgannon@wtwhmedia.com @dw_marygannon
Technology Editor Ken Korane kkorane@wtwhmedia.com @fpw_kenkorane
Senior Editor Rachael Pasini rpasini@wtwhmedia.com
Contributing Editor Josh Cosford @FluidPowerTips
Contributing Editor Carl Dyke @carlindustry
Contributing Writer Robert Sheaf rjsheaf@cfc-solar.com
www.nfpa.com
PRODUCTION
VP, Creative Services Matthew Claney mclaney@wtwhmedia.com @wtwh_designer
Art Director, FPW Erica Naftolowitz enaftolowitz@wtwhmedia.com
Art Director, FPW Digital Eric Summers esummers@wtwhmedia.com
Director, Audience Growth Rick Ellis rellis@wtwhmedia.com
Audience Growth Manager Angela Tanner atanner@wtwhmedia.com
PRODUCTION SERVICES
Customer Service Manager Stephanie Hulett shulett@wtwhmedia.com
Customer Service Representative Tracy Powers tpowers@wtwhmedia.com
Customer Service Representative JoAnn Martin jmartin@wtwhmedia.com
Customer Service Representative Renee Massey-Linston renee@wtwhmedia.com
Customer Service Representative Trinidy Longgood tlonggood@wtwhmedia.com
FLUID POWER WORLD does not pass judgment on subjects of controversy nor enter into dispute with or between any individuals or organizations. FLUID POWER WORLD is also an independent forum for the expression of opinions relevant to industry issues. Letters to the editor and by-lined articles express the views of the author and not necessarily of the publisher or the publication. Every effort is made to provide accurate information; however, publisher assumes no responsibility for accuracy of submitted advertising and editorial information. Non-commissioned articles and news releases cannot be acknowledged. Unsolicited materials cannot be returned nor will this organization assume responsibility for their care.
FLUID POWER WORLD does not endorse any products, programs or services of advertisers or editorial contributors. Copyright© 2025 by WTWH Media, LLC. No part of this publication may be reproduced in any form or by any means, electronic or mechanical, or by recording, or by any information storage or retrieval system, without written permission from the publisher.
MARKETING
VP, Operations
Virginia Goulding vgoulding@wtwhmedia.com @wtwh_virginia
Digital Marketing Manager Taylor Meade tmeade@wtwhmedia.com @wtwh_taylor
SALES
Ryan Ashdown 216-316-6691 rashdown@wtwhmedia.com
Jami Brownlee 224.760.1055 jbrownlee@wtwhmedia.com
Mary Ann Cooke
781.710.4659 mcooke@wtwhmedia.com
Jim Powers 312.925.7793 jpowers@wtwhmedia.com @jpowers_media
Courtney Nagle 440.523.1685 cseel@wtwhmedia.com @wtwh_CSeel
LEADERSHIP
CEO Matt Logan mlogan@wtwhmedia.com
Co-Founders Scott McCafferty Mike Emich
SUBSCRIPTION RATES: Free and controlled circulation to qualified subscribers. Nonqualified persons may subscribe at the following rates: U.S. and possessions: 1 year: $125; 2 years: $200; 3 years: $275; Canadian and foreign, 1 year: $195; only US funds are accepted. Single copies $15 each. Subscriptions are prepaid, and check or money orders only.
SUBSCRIBER SERVICES: To order a subscription please visit our web site at www.fluidpowerworld.com
FLUID POWER WORLD (ISSN 2375-3641) is published six times a year: in February, April, June, August, October, and December by WTWH Media, LLC; 1111 Superior Ave., Suite 2600, Cleveland, Ohio 44114. Periodicals postage paid at Cleveland, OH & additional mailing offices.
POSTMASTER: Send address changes to: Fluid Power World, 1111 Superior Ave., Suite 2600, Cleveland, OH 44114
Josh Cosford
ACCORDING TO Globe Newswire, the global hydraulics market is going to expand from $39.4 billion to $44.3 billion over the next five years. We’re not talking about finance industry-level revenues here, but I can happily handle 2.4% compound annual growth rates in what is supposed to be our “mature industry.” It's even more promising when I see that, through various sources, the North American market is projected to expand by 5-6% CAGR, which is expected to stem from the oil & gas, construction, and automation sectors.
If we bring pneumatics into the equation and consider the top five fluid power corporations alone (Parker Hannifin, Danfoss, Bosch Rexroth, SMC, and Festo), they collectively pool around $47 billion in 2024 (across all business segments, not just fluid power). These are impressive numbers, and their combined workforce of nearly 177,000 employees is a significant contributor to their local economies. When the zombie apocalypse eventually unfolds, it will be them and us who rebuild the world while social media influencers perish, so I've got no hate for any of the big guys.
Still, I’m part of an SME (Small to Medium Enterprise) just like many of you reading this article. We don't design or build landing gear or motion control systems, nor do we offer any products advertised with Industry 4.0 in the verbiage. I boldly estimate the Top 5 take home 50% of the fluid power market share, while another 25-30 percent stems from the medium enterprise and up camp, such as your Hydacs and Motion Industries of the world. Does that leave the worldwide market for the little guy to just 20-25% of the $55 billion total fluid power market? Indeed, it does, but I'm less concerned about absolute numbers and the distribution of wealth than I am with
real, hardworking people trying to make the best life for themselves and their families. So, rather than framing it as a David vs. Goliath scenario, like the tales of small-town shops closing their doors when a Walmart moves into town, we need to consider what value the smaller fluid power shops bring to their local customers.
Small shops can provide the dynamic and versatile service that the big guys cannot. Bosch Rexroth has no interest in setting up a small hose shop near the local steel mill, and Danfoss has bigger fish to fry than to repair used salter spreader trucks at the side of the road. And even if Parker did have market saturation in every geographic location, Amos is buying that power unit from Jeremiah in Lancaster County, PA, anyway.
The two-to-twelve-employee fluid power distributor remains common today because they offer fair prices with local representation and have the experience and expertise to support the community’s relevant industries. Whether offering support for the automotive parts plant or paper mill, the team at these shops will know the buyers, millwrights and maintenance managers by name.
The threat more likely to affect the local shop is the looming buyout by Motion Industries and Applied Industrial Technologies of the world. It's not to say this is a bad thing, because in many cases, big brother allows the shop to keep its team in place while providing training resources and an expanded product offering. In many cases, the previous owner will stay on board to manage the branch, changing little as far as customers and team members are concerned.
Whereas the big manufacturers work on smart technologies, Industry 4.0 applications and corporate mergers to grow their business,
the large players in distribution (such as SunSource and Grainger as well) acquire smaller chains or shops to expand their revenue potential and grow their physical market. And there’s nothing wrong with this approach because the aging fluid power experts who run these shops are just as likely to close when they retire if it wasn’t for a looming buyer. These big distributors have a more secure and steady stream of talent to help replace veterans or train newbies.
Calling the local Motion fluid power shop a “little guy” might be a stretch, but their function matches the definition, despite the consolidated HR channels and sophisticated ERP software. Tow truck drivers will still show up with a busted hose in hand to be remanufactured while he shops for new work gloves and ponder the three-dollar fundraiser candy bars.
A unique aspect of this industry is the respect that exists between major manufacturers and their distributors, regardless of their size. Sure, you may see the big five snipe the local OEM to attempt the direct sale now and again. But they'd much rather leverage hundreds of small shops than hire a salesforce to cold-call a small-town machine shop or AG repair garage. So long as manufacturing and industry at large will function in decentralized pockets, so too will the little guy. FPW
Josh Cosford • Contributing Editor jcosford@higginson.ca linkedin.com/in/joshcosford
Find OFCO’s Equivalents for Your Filtration Parts. Use our new tool to search by manufacturer, part number or description.
Why wait months? OFCO ships your order from our Ohio factory in days. Email Rob Montgomery or call 740.295.9721 today to find out why.
Ron Marshall • Contributing Editor
HOW DO YOU DECIDE WHEN TO REMOVE your compressed air filter elements? If you are using the differential gauge to tell you when, that could be a mistake.
Compressed air is widely used in manufacturing, but contamination is a major concern. To maintain air quality, compressed air systems rely on filters — particularly coalescing and dry particulate filters — that remove oil, water aerosols, and solid particulates. These filters use replaceable elements that degrade over time due to harsh operating conditions like pressure variations, high humidity, and chemical attack.
Filter media is constantly bombarded by contaminants, weakening its structure. If the media is damaged — even with a pin-sized hole — it compromises filtration, allowing contaminants to pass downstream. Thus, filter elements have a finite life and should be replaced regularly, typically every 12 months, regardless of usage duration. This ensures consistent air quality and protects downstream equipment.
Many users mistakenly rely on differential pressure (DP) indicators to determine when to replace filter elements. However, DP devices are imprecise (±25% accuracy) and are designed only to detect premature blockages — not as reliable indicators for routine maintenance or air quality. In fact, a torn filter may show no DP change at all, falsely indicating that the system is functioning well.
Using clogged or damaged filters can increase system pressure losses, leading to higher energy costs and reduced equipment efficiency. Every 1 bar of extra pressure can raise energy consumption by approximately 7%. Additionally, contamination due to filter failure can result in costly damage to equipment and product spoilage.
A white paper, "Why Should I Change My Compressed Air Filter Element?" by Parker
Hannifin stresses that preventative maintenance — changing filter elements and float drains annually with proper parts safeguards system integrity, ensures compliance with ISO 8573-1 standards, and preserves manufacturer guarantees. Washing or reusing filters is ineffective and damaging.
Timely replacement of compressed air filter elements is essential for maintaining air quality,
operational efficiency, and long-term cost savings. DP indicators should not be used as the sole maintenance trigger. Instead, users should follow manufacturer guidelines to avoid contamination risks and ensure system reliability. FPW
For training in compressed air optimization visit: compressedairchallenge.org
Edited by Mary C. Gannon • Editor-in-Chief
THE OFF-HIGHWAY INDUSTRY is undergoing great change lately, in particular with autonomous technologies advancements. For hydraulic engineers developing systems for mobile construction machinery, this transformation represents both challenges and opportunities. While autonomy may not aim to replace human operators entirely, it is redefining their role, improving productivity, safety, and efficiency.
Modern off-highway machines incorporate features that reduce operator workload, enhance safety, and streamline processes. However, full autonomy remains rare outside controlled environments, leaving room for innovation, said Adam Khaw, Head of Autonomy, Senior Director of Danfoss, during the company’s annual distributor meeting last fall.
Sam Long, sales developement manager with Danfoss' autonomy, said there are five levels of autonomy, with level 0 being fully manual machines with no automation.
• Level 1: Basic operator assistance, such as automatic braking
• Level 2: Partial automation, where some functions (like cruise control) are managed by the system
• Level 3: Conditional automation, allowing machines to handle all functions under specific conditions but requiring the operator to remain nearby
• Level 4: High automation, where the machine controls all functions but still requires on site supervision
• Level 5: Full automation, with no human supervision necessary
"We’re just beginning to see Level 5 systems in action," he said. "But to make them viable, factors like reliable internet connections and safety protocols must be flawless."
While Levels 4 and 5 offer the greatest potential, most development currently focuses on Levels 3 and 4. These systems provide sig-
nificant benefits without the complexity and cost of full autonomy.
The goal of autonomy is not to replace operators but to assist them and augment their work. Machines equipped with operator-assistance systems use technologies like cameras, LiDAR, and GPS to simplify challenging tasks.
For example, Khaw detailed one application for ground-support at airports. The most highstress job for cargo loaders occurs when docking machinery close to aircraft. Even a minor bump or misalignment can cause downtime and thus delay flights, not to mention financial losses of about $250,000 per incident. By automating the final docking steps, Khaw said, these systems improve accuracy and reduce anxiety, preventing costly errors.
Additionally, construction machinery outfitted with sensors can establish “virtual fences” using cone markers or other inputs. These fences restrict equipment to operate within
predefined zones, preventing collisions with buildings, traffic, or people. Systems can also detect human presence, stopping operations if someone enters the boundary.
Some manufacturers are introducing fully autonomous machines designed to perform entire tasks without human intervention. For example, Khaw said a soil compactor can define its operating boundaries, generate an optimal path, detect obstacles, and adjust its behavior to avoid disruptions. Such innovations enhance productivity by minimizing rework and error and elevating safety.
By utilizing LiDAR, radar, GPS, and position sensors, these systems enable seamless coordination between the machine’s electronic and hydraulic components.
“Autonomy is growing most in Level 3 systems. These allow machines to do much of the work while a human handles unexpected situations," Khaw said. "For instance, if a cow unexpectedly crosses into the operating area, the operator can intervene to ensure safety."
While autonomy brings electronic control systems into the spotlight, hydraulic systems remain fundamental to the operation of heavy machinery. The integration of autonomy and hydraulics presents opportunities for innovation for fluid power manufacturers.
Hydraulics provide force and precision. Autonomous technologies enhance this by introducing advanced control algorithms. For instance, with automated path generation and obstacle avoidance, machines can make instantaneous adjustments to hydraulic actuators, maintaining stability and accuracy while optimizing efficiency.
To support autonomy, hydraulic systems are increasingly tied to modular electronic architectures said Long. Tools like Danfoss’ Plus+1 Guide software integrate perception, navigation, and control layers within hydraulic-powered machines. "Think of it as visual coding," Long said. "You don’t need a computer science background, but you do need to understand the systems. Prewritten code blocks make it accessible to most engineers."
Telematics can add a data-driven layer to hydraulic systems. By monitoring parameters like pressure, flow rate, and actuator performance, telematics allows for predictive maintenance, reducing downtime and prolonging the lifespan of hydraulic components. In autonomous machines, this data also informs decisionmaking, enabling machines to adapt dynamically to changing conditions.
While these systems are changing the way they work, they are not without their challenges. Addressing challenges starts with the sensors, Long said. Sensors detect obstacles and gather data. However, sensors like LiDAR may not be as effective in adverse conditions, such as dust, fog, and heavy rains. To mitigate this, filters and advanced algorithms are being developed to refine data, ensuring machines operate effectively in all environments.
"Consider the machine stopping safely if geese suddenly land in its path. It’s all about safety first," he said, emphasizing the importance of robust operational design domains. Khaw noted that as autonomy becomes more widespread, engineers will need to rethink hydraulic systems’ design and integration, focusing on:
1. Increased system intelligence: Adding more sophisticated sensors and controls to hydraulic systems will allow for realtime adjustments, improving precision and responsiveness.
2. Improved safety mechanisms: Autonomous features must include fail-safe designs to prevent accidents. For hydraulic systems, this may involve redundant circuits or pressure-relief mechanisms that ensure operations stop safely if control systems fail.
3. Energy efficiency: Autonomous systems can optimize hydraulic energy use, reducing waste and improving overall efficiency. This includes incorporating hybrid systems that leverage electric actuators alongside hydraulics for lighter tasks.
4. Seamless human-machine interaction: Operators will still play a crucial role. Interfaces must simplify complex operations, providing intuitive controls and real-time feedback for tasks requiring manual intervention. FPW
Danfoss danfoss.com
Josh Cosford • Contributing Editor
could run off highly crude forms of hydrocarbons, without a complement of additives, the performance and longevity of your hydraulic machine would suffer. Welcome to Part Seven of the Hydraulic Oil Analysis series, where we dig deep into the various additives that are always or usually used to keep your hydraulic machines performing at their best.
Through various techniques such as spectroscopy and elemental analysis, labs can check the condition and/or quantity of the hydraulic oil additives. Most of the benefits hydraulic oil provides are because of the additional chemicals added during manufacture. Although basic mineral oil makes a great lubricant, we shouldn’t forsake other fluids not using an oil base — water-glycol and high water-based fluids need these additives and more to perform well.
With the above in mind, be on the lookout for zinc, which provides a protective layer on metal surfaces to help reduce physical wear from metal-on-metal. Zinc is especially important when high-pressure parts are forced together while rotating or sliding, such as piston slippers on the wear plate or vanes on the cam ring. In a similar vein, the various compounds of molybdenum help reduce the friction where it’s needed, increasing hydraulic efficiency.
Rust and oxidation inhibitors are more than just products to prevent water from doing its nasty deed on your metal internals. Oxidation leads to rust, and oxidation may come from many sources. Phenolic and aminic additives help prevent the formation of acids, sludge and varnish, each of which degrade the performance of the oil while possibly damaging system components.
If you’re not taking advantage of an oil analysis program and fail to realize your antioxidants are depleted, you will have to rely on detergents to help neutralize acid and wash away deposits. You’ll see chemicals repre -
sented in your test report such as calcium sulfonate, which your lab can advise is either low or totally absent. Also, to help keep compounds suspended so they can be washed away, dispersants like succinimide should be present in your test.
Of course, we need to be careful with emulsifying additives, which, when too concentrated, could result in excessive water retention in your hydraulic oil. Demulsifiers such as polyalkylene glycols or silicone-based versions must be wellbalanced to prevent free water without excessive retention of moisture.
You’d be surprised at how poorly mineral base stock performs when the temperature varies outside of its ideal range. Depending on the base stock, manufacturers will add chemicals such as polymethacrylates or olefin copolymers to increase the viscosity index of the oil. Although synthetic base stock gets a head start with VI, you won’t see any oils over 140 VI achieving the task without additives. For machines used in all-weather conditions and extremes, be sure to confirm which VI-improvers are present should the VI test come back lower than expected and you need to replenish them.
When oil foams easily, the chance of cavitation and the related damage are accelerated.
Polydimethylsiloxane (don’t worry, it’s not on the quiz) or olefin copolymer helps prevent the bubbles from sustaining past simple aeration, thereby preventing cavitation, which is one of the most catastrophic causes of damage to hydraulic pumps. Labs can test for foaming characteristics, but just as with VI-improvers, knowing what additives you have or need will help you decide how to proceed should foaming become an issue.
Finally, for fluids offering the potential for microbial growth, various additives such as isothiazolinones (definitely on the quiz) or formaldehyde-releasing chemicals will prevent bacteria and fungi from degrading your oil, clogging filters, or just plain smelling funky. Not all fluids come with biocides, but can also be added when you’re working with high-water based fluids or bio oils.
I need to be clear that not every fluid has every additive, and not every sample needs every additive tested for every time. Some standard lab tests imply additive health when results are positive, such as the Viscosity Index. However, when things go wrong, you want to know what can be changed or added to reinvigorate old oil. FPW
Check Valves
Flow Control Valves
Needle Valves
Flanges & Adapters
Bar & Custom Manifolds
Pressure Gauges & Snubbers
SSW Power Unit Systems
Transfer Pumps
Industries Served:
• Oil & Gas
• Industrial Hydraulics
• Mining
• Forestry
• Chemical & General Processing Plants
• Medical
• Aerospace
• Factories
• Mobile Equipment
• Defense
• Machine Tool
• Testing Equipment
• Ocean Depth Technology
• Automotive
• Food Processing
• Agriculture
• Industrial
• Aviation
• Petrochemical
• Marine
• Subsea
Alex Ng, CES Application Engineering Manager • ContiTech USA Inc.
SELECTING THE RIGHT HYDRAULIC HOSE on a piece of industrial equipment is often an afterthought — if it gets any thought at all — even though a hose failure can be catastrophic. A ruptured hose can be life threatening, harmful to the environment, costly and substantially disruptive to operations, and is almost entirely avoidable.
Understanding why hose failure happens, industry standards, hose selection best practices, and working with a knowledgeable distributor or application engineers of hose manufacturers can help companies choose the right hose for the job — and keep workers safe and production running on track.
1.Why hose failure happens
Hydraulic hoses are essential components on a vast array of machine types, from construc-
tion to manufacturing, and they are susceptible to wear and tear like many workhorse components. Common causes of hose failure include:
• Abrasion and external damage – Exposure to rough surfaces, sharp objects, and environmental conditions can wear down hoses over time.
• Improper selection – Using the wrong hose coupling or termination and incorrect hose and coupling sizes for a specific application can lead to premature failure, could be life threatening to the operator or others, and can negatively impact the environment.
• Incorrect installation – Twisting, kinking, or incorrect couplings can weaken hoses and their connections. Improper routing and the wrong torque on the appropriate termination could also cause issues.
• Age and material degradation – Over time,
rubber and other hose materials degrade, reducing their effectiveness and increasing the risk of failure. Different types of polymer have different effects with hydraulic fluids. There are also biodegradable hydraulic fluids that have different impacts on polymer types.
Hose failures can lead to severe consequences for operators, other employees and for the operation. Ramifications of a hose failure can include fluid leaks that could cause environmental contamination and costly cleanups, personal injury from hot and pressurized fluid that can pose risks of severe burns or high-pressure injection injuries, or machine downtime which leads to productivity losses and expensive repairs.
Visual inspections of hydraulic hose assembly should be part of routine equipment main
tenance and should be carried out regularly, depending on how often the machines are used. The older the machine, the more frequently it should be inspected.
2. Using STAMPED, ISO to get the right hose for the job
Experts rely on the STAMPED selection process, the industry-wide practice used by engineers and operators, to determine the right hydraulic hose for the job. STAMPED considers:
• Size: inside diameter, outside diameter, and length
• Temperature: operating and ambient temperatures
• Application: specific usage conditions
• Material: the substance being conveyed
• Pressure: working pressure and pressure surges
• Ends: fitting types and connections
• Delivery: special requirements such as certifications or custom specifications
By considering the seven variables identified using the STAMPED acronym and consulting with a knowledgeable equipment dealer or distributor, businesses can prevent hose failures and enhance operational efficiency. Selecting the right hose from a trusted manufacturer ensures reliability, safety, and compliance with industry regulations.
ISO-18752 certified hoses represent the latest standard in the industry. With a minimum requirement of 200,000 cycles, these hoses provide consistent durability and reliability. This standard has been in place for over 20 years, proving its effectiveness in ensuring the highest performance. Companies that choose ISOcertified hoses benefit from increased longevity, reduced downtime, and enhanced safety.
Why reliability matters more than ever in hydraulic
Reliability is a top priority for OEMs that design machines with specific performance requirements. In hydraulic systems, hoses must meet strict specifications to ensure they function properly under high-pressure conditions — often 3,000 to 6,000 psi.
Meeting industry specifications is critical to reliability. Before releasing a hose to production, manufacturers must validate both design and manufacturing processes to ensure compliance, including running rigorous tests to confirm performance under specified conditions, following strict guidelines and specifications of ISO quality management systems and appropriate industry specification such as SAE or ISO for production, and conducting ongoing quality control checks to maintain consistency.
For example, standards like SAE J517 or ISO 18752 indicate that a hose has been validated and passed all required tests. When end-users see this certification, they can trust that the product meets the highest industry requirements.
Reliability can also take form in the basic engineering of a hose, which happens at the manufacturing level. Continental’s five decades of experience manufacturing hydraulic hoses, for example, has enabled the company to hone its processes and meet customer standards and requests with precision. In today’s environment, where labor shortages and downtime are critical concerns, reliability is more important than ever.
Reliability testing can be expensive, but it is an essential investment. Partnering with a high-end manufacturer ensures quality control, superior performance, and long-term dependability. Continental recommends working closely with the distributor or dealer and asking for a hose that not
only meets industry standards but exceeds them.
Hose failures are more than just an inconvenience, they can be life-threatening. Many people underestimate the risks associated with a broken hose. High-pressure hoses operate at extreme psi levels, and a ruptured hose can release a powerful burst capable of cutting through materials — and people.
By investing in high-quality, reliable hoses, companies can protect their workforce and minimize risks. Safety should always be a priority, and selecting the right hose is a key step in preventing accidents and injuries.
If a hose fails in the field, the standard practice is to take the failed hose assemblies to a hose dealer for proper servicing and replacement. Dealing with professional hose dealers ensures the replacement is selected and installed properly, minimizing the risk of recurring failures.
Hose failure is a serious issue, but with proper selection, adherence to ISO standards, and expert engineering, businesses can enhance reliability and safety. Consulting with experts and using the STAMPED method ensures the right hose for each application, while high-quality materials and manufacturing expertise help prevent costly failures. When safety, efficiency, and reliability matter, choosing the right hydraulic hose makes all the difference. FPW ContiTech USA Inc. continental.com
TRANSFORMERS: THE RIDE – 3D IS BASED ON THE POPULAR TRANSFORMERS FILMS AND CREATED ALONG WITH THE AWARD-WINNING DIRECTOR OF THE FILM SERIES, MICHAEL BAY. IT FEATURES HYDRAULIC MOTION CONTROL, 3D PROJECTIONS AND TRACK-MOUNTED CARS FOR UP TO TWELVE PASSENGERS.
Without the power of hydraulics or the snappy precision of pneumatics, much of the fun in theater and amusements parks wouldn’t be possible.
By Josh Cosford, Contributing Editor
There are few industries entirely devoid of fluid power actuation, but some could have never existed without it. Even if some other technologies, such as mechanical transmission, could have created a similar result, the power, reliability and smoothness of fluid power have provided the top solution for entertainment machines for nearly a century.
Although lights, cameras, and special effects get all the awards from awing crowds who attend movies, stage shows, theme parks, and even rock concerts, hydraulic and pneumatic technology is a critical component of the spectacle. From the rapid actuation of pneumatics to the powerful and precise control of hydraulics, you can expect to experience the hidden magic provided by fluid power when you’re dazzled by entertainment.
Fluid power offers up advantages making it ideal for high loads, repeating movements and dynamic actuation. Hydraulics, in particular, excels where compact, highforce cylinders and motors are tasked to move entire stage platforms, massive animatronics and amusement park safety systems. While not as force-dense, pneumatics provide speed, simplicity and economical options for everything from animated movie beasts to lifting systems on aerial carousels.
To fully understand how fluid power aids the entertainment industry, it's best to talk about some choice applications that our industry best serves. The Cirque Du Soleil Kà show, which previously ran at the MGM Grand in Las Vegas, is a tour de force of hydraulic technology. Its signature 25x50 ft deck tips the scales at over 50 tons and stands 75 feet from the basement floor. The platform rotates 360° while tilting up to 100°, where performers appear to walk unaided up its vertical surface.
Although designed and built over 20 years ago, the Kà production used the most advanced hydraulic and control systems available at the time. It used four 12 in. bore x 52-ft stroke cylinders rated for
4,000 psi and fed by (now discontinued) Parker PE series axial piston pumps. Ten of these 145-cc bad boys were driven by 1,250 horsepower, and with the help of 34 50-gal accumulators, offered up 2,200 gpm to the platform lifting system.
Although an electric motor handles the rotating function, designers chose four 12 in. bore by 110-in. stroke cylinders for the stage tilting function, which can cycle from completely horizontal to over-center at 100°. The combination of lift, tilt, and rotate functions with sophisticated control systems allows for over a hundred axes of motion and requires highly advanced valves to achieve the task. Parker D3FH high response, proportional servovalves combined with Atos slip-in proportional valves control lift functions, while D81HF zero-overlap proportional valves control the slant angle.
Although lights, cameras, and special effects get all the awards from awing crowds who attend movies, stage shows, theme parks, and even rock concerts, hydraulic and pneumatic technology is a critical component of the spectacle.
As you'd expect, such a complex set of high-performance components isn't controlled by push buttons and toggle switches. Delta motion controllers employed PID programming to ensure the entire array of valves and actuators performed smoothly and accurately. PID stands for proportional, integral and derivative. Using various sensors, it essentially controls the various axes of motion with a correction profile that looks at how far off in position the actuators are (proportional), how long they've been out of position (integral) and smoothness correction if things are changing too fast (derivative).
Of course, not all fluid power applications in the entertainment industry are so sophisticated and expensive. Amusement parks use an array of hydraulic and pneumatic technology, from the hydrau- NILS
HYDRAULIC RESTRAINT SYSTEMS ARE BUILT TO A NEAR-AEROSPACE LEVEL OF QUALITY AND SAFETY, ESPECIALLY AS THE COASTER SPEED AND G-FORCES RISE. TWO ACTUATORS ON EACH SEAT PROVIDE REDUNDANT PROTECTION SHOULD ONE FAIL.
lic catapults that previously powered the Top Thrill Dragster at Cedar Point to simple pneumatic locks for restraint systems. Although many rides use a ratcheting lock system for their lap or shoulder bar, these older systems require park employees to release the pins manually car by car, so now many parks prefer fluid power activation, which is infinitely adjustable and semi-automatic.
Rather than manual release, the evolved cars were installed with levers attached to the pin release that was actuated by a long bar under the coaster, itself powered by pneumatic cylinders. This allowed the control operator to simultaneously release the spring-loaded bars, which sped up the rider changeover process. However, the system still used a ratcheting system with discrete positions that were not suitable for every body type. The hydraulic restraint system would improve the experience even further.
Perhaps I should add the caveat regarding hydraulic locking systems since
these are not traditionally powered actuators. Hydropneumatic accumulators provide the stored energy to operate the restraint cylinders in a simple circuit that also includes a 2/2 solenoid poppet valve, for example. The lap or shoulder bar can be pulled into place while fluid exits the cylinder’s cap port, passes through the poppet valve and into the rod port, kind of like a float function. Excess volume is directed to the accumulator.
Once adjusted to a snug yet comfortable position, the restraint cylinder is locked in place because fluid cannot move backward through the poppet valve. The poppet prevents the backward motion of fluid from the rod port of the cylinder, keeping the restraint locked and firm until the ride ends.
When the car is stopped on the power rail (essentially a brush contact), power
A 6-DOF system is able to produce linear (translational) movement, which is described as surge, sway, and heave.
and control are provided to the solenoid valve, which opens when all the safety criteria are met. It's quite a simple hydraulic circuit that essentially allows the restraint to move freely or to lock, aided by the accumulator.
Hydraulic restraint systems are built to a near-aerospace level of quality and safety, especially as the coaster speed and G-forces rise. The above combination of cylinder, accumulator and valves is a single assembly with no external plumbing, ensuring no tube or hose could leak or fail. Combining two actuators per seat provides redundant protection should one fail, which is a testament to the commitment parks take to safety.
Across the world, there are myriad older theme parks with rides and attractions that remain very close to their original design and configuration, making them popular for theme park fans looking for a legendary thrill. Besides the applications already mentioned, pneumatic cylinders were a common solution for powering safety gates and slow-speed motion effects, for example, due to their simplicity and low cost. For safety gates — such as those at ride entrances, exits, or loading platforms — small-bore double-acting cylinders (typically 1 to 1.5 in. bore, 4 to 8 in. stroke) were mounted to hinged gates to control their opening and closing. These cylinders were often tied to basic solenoid valves triggered by operator controls or proximity switches, ensuring gates only moved when conditions were safe. For slow-speed motion effects in themed dark rides or gentle attractions, pneumatic cylinders were used to animate lightweight props, such as rocking animals, swaying lanterns, or slowly rising figures. In these applications, speed control was handled by needle valves or inline flow restrictors, and cylinders operated at low pressures (40–60 psi) to reduce wear and maintain smooth motion.
If you’ve ever ridden through a haunted house for example, you’ve likely heard the unmistakable sound of air hissing upon release, which indicates that a skeleton or other similar character has ADOBE
just jumped at you, made possible by pneumatic cylinders.
You can expect to see the compact stainless cylinders made famous by manufacturers such as Bimba and Norgren, who supplied many of these rugged, interchangeable components. Though limited in precision due to air compressibility, these pneumatic systems were reliable, easy to maintain, and inexpensive to replace — making them ideal for non-critical functions in long-running park attractions still in use today.
If you’re the kind of person who loves movies and theme parks, then it’s likely you’ve already had the pleasure of experiencing the immersive attractions such as the Ratatouille ride at Disney or the Transformers: The Ride 3-D at Universal Studios. The latter is a stunning and immersive experience using hydraulic motion control, 3D projections and track-mounted cars for up to twelve passengers.
The story has riders escaping Decepticons while riding an EVAC (short for evac-
uation) and aided by Autobots. Each of these EVAC hexapod cars tips the scale at up to 12,000 lb when fully loaded and is controlled by an onboard 6-DOF motion control system. 6-DOF stands for 6 degrees of freedom and describes the movement axes possible using six hydraulic cylinders.
A 6-DOF system is able to produce linear (translational) movement, which is described as surge, sway, and heave. These directions translate to forward/ backward on the X-axis (Surge), left/right on the Y-axis (Sway) and up/down on the Z-axis (Heave). The next three movements are the more familiar pitch, roll and yaw, each of which centers around one of the above translational axes. Pitch tilts forward or backward about the Y-axis, roll tilts side to side about the X-axis, and yaw rotates clockwise or counterclockwise around the Z-axis.
The 6-DOF system uses six sophisticated hydraulic cylinders with low breakaway (low static friction), linear differential transducers and integrated servo valves for the quickest possible response. Accu-
mulators assist with surges of high flow, empowering the EVAC with up to 2Gs of acceleration. The cutting-edge computer controllers can simulate many real-world experiences, such as crashes, drops and earthquakes. For example, a rapid combination of left sway, left roll and clockwise yaw simulates a heavy impact to the rear right of the EVAC vehicle.
What’s impressive about watching a 6-DOF system in action is the orientation of the six cylinders, which appears visually as a double-leg tripod, is how the default 45-degree angle of the cylinders can still recreate the forward and backward surge movement without changing any other linear or rotational axis.
As you can see, fluid power applications within the entertainment industry span everything from economical pneumatics to the most sophisticated hydraulics. It’s easy to see why fluid power has permeated into every corner of entertainment, provide fast, safe and reliable solutions from the oldest rollers coasters to newest stage shows. FPW
FERNANDES IS SEEN RECORDING A SUN HYDRAULICS NEW PRODUCT LAUNCH VIDEO WITH HYDRA-POWER SYSTEMS.
The future of fluid power is in the hands of our young engineers and technicians. And while we all are concerned about the need for more young people in our industry, there’s great hope with the ones who are currently shaping the future.
For Dan Fernandes , his mechanical engineering degree was the ticket into a successful fluid power career.
By Mary C. Gannon, Editor-in-Chief
I met one of these young engineers for the first time in 2022. Although it was our first time actually shaking hands, I felt like I knew Dan Fernandes, CFPA AI well already. He was about a decade into his career at Sun Hydraulics and was making his name known by publishing informative educational content about hydraulics on his LinkedIn page as part of his role in business development. He left Sun shortly after that but like so many fluid power professionals, it was just to move to another hydraulics company, HAWE Hydraulik. Now, he’s Vice President of Product at HydraPower Systems.
While he was still a student at the University of South Florida in the Mechanical Engineering department, Fernandes jumped at a chance for a summer internship at Sun Hydraulics’ Sarasota manufacturing facil-
ity. “Steve Weber was instrumental in building this internship program and the connection to USF,” he said. “Given the pressure of finding quality, full-time employment after college, I quickly applied to the internship, interviewed, and secured the position. That internship led to an 11-year career at Sun and built a passion for fluid power solutions.”
Although he recognized there were several career paths open to him while studying engineering at University of South Florida, he learned quickly that fluid power was his future. “Mechanical engineers can design fluid power components, develop manufacturing improvements, conduct research in a laboratory environment, support customer applications, develop into front line sales engineers, and more,” Fernandes said. “The ME degree is a great ticket into the door of a fluid power company. It allowed me to pursue a customer
DAN
facing role where my value proposition is product competency which helps solve customer challenges.”
Fernandes relates engineering to being a superhero, as it allows you to anticipate problems and then solve them. He encourages young engineers and students to open their eyes to the fluid power industry as it has so much to offer. “Fluid power has been called ‘The Hidden Giant.’ It is not the dream of many students to join the fluid power industry, but I believe that is because of lack of exposure or awareness,” he said. “Once you’re in fluid power, many times you stay in fluid power due to the wide range of opportunity.”
Fernandes is very active in industry associations. He volunteers as the VP of Education for the International Fluid Power Society, where educational materials are created to improve fluid power competency across the industry. He strongly advocates for the Hydraulic Specialist certification and the impact it can have on young professional’s careers. He also noted that the IFPS and National Fluid Power Association can truly help introduce third- and fourth-year engineering students to the industry and help launch their career.
“I am involved with the IFPS and NFPA because of the excellent work they do in promoting, educating, certifying, and standardizing our industry, as well as the events that they organize which bring fluid power colleagues together to one place,” he said.
Currently, Fernandes works to continuously improve the product strategy at HydraPower Systems. As a fluid power solution provider, he said they succeed best when they understand the latest market trends, creatively solve fluid power challenges, and partner with leading vendors in their respective product category. The most exciting aspect is bringing new products to the Hydra-Power Systems’ team and to the OEM market, he said.
With nearly 15 years’ experience working in fluid power, Fernandes said the rewards of the industry are twofold. “First, the industry has a great network of colleagues with a long tenure in fluid power. This allows deep relationships to be formed,” he said. “The other reward is the exposure to many different technologies. From stationary manufacturing machinery to municipal trucks, and construction equipment to wind turbines, the wide variety of applications exposes fluid power colleagues to learn how manufacturing, mining, and agricultural industries operate.”
As for the biggest challenge? He said it’s simply the length of the sales cycle. You may be part of innovations but may not see them take off. “When the greatest new fluid power component is developed, it can take years to realize high volume production on OEM machinery,” he explained.
Challenges and change have a part Fernandes noted that no career is without challenges, but if you view them in a positive light, they can bring great growth. Midway through his career at Sun Hydraulics, he relocated to Vietnam in a business development role. “It was an incredible learning experience where I had to bring the latest technology from America to the emerging markets in Southeast Asia. We were successful in bringing new proportional valve solutions to OEMs in Southeast Asia through persistent training and technical support,” he said. “The lesson learned was that industry around the world relies on hydraulic equipment. With fluid power know-how, we can help peers around the world be successful in their own careers.”
More recently, he had an opportunity to modernize a customer’s system which took some convincing. In this project, they
were encouraging an OEM that was using purely manual controlled valves to switch to an electrohydraulic CAN-bus solution.
“The technology is higher priced, more complex, more compact, but it provided enough value in safety, remote operation, and automation to be a viable option,” he said. “We ensured success through communication and technical support.”
He's seen changes like this firsthand throughout his career. “For the first 10 years of my career, energy efficient products did not get much attention, as the prime mover remained a diesel engine,” he concluded. “Now with electrification and hybrid machinery, efficiency is finally being prioritized in a big way.” FPW
Connect with Fernandes at linkedin.com/in/ dan-fernandes-cfps-ai-4571a480/ or visit hpsx.com/
Edited by Mary C. Gannon • Editor-in-Chief
TWO INDIVIDUALS WERE NAMED TO THE FLUID POWER HALL OF FAME on Fluid Power Professionals’ Day. Dr. Andrea Vacca was named for this year’s class, while Jerome B. Komendera was also inducted post-humously.
Vacca is the director of the Maha Fluid Power Research Center, the largest academic research center dedicated to fluid power research in the United States. His research focuses on several aspects of hydraulic control technology including new concepts to perform hydraulic actuations, new designs and modeling of positive displacement machines, electrification of fluid power systems, modeling of the properties of hydraulic fluids, and reduction of noise emissions from hydraulic components. His research has been funded by the U.S. Department of Energy, the U.S. Department of Agriculture, the National Science Foundation, and several industry partners like Bosch, Bobcat, Casappa, Caterpillar, Case New Holland, Collins Aerospace, Danfoss, Eaton Aerospace, RollsRoyce, Parker Hannifin, and Tesla, among others.
Vacca holds 24 patents/patent applications and he is author of more than 200 technical papers (including 14 prize papers), and of the textbook “Hydraulic Fluid Power.” He is the Editor in Chief of the International Journal of Fluid Power, one of the directors of the Global Fluid Power Society, and a former chair of the Society of Automotive Engineers (SAE)- Fluid Power Division and of the American Society of Mechanical Engineers (ASME)- Fluid Power System and Technology Division.
In 2019, Vacca was awarded the 2019 Joseph Bramah Medal from the Institution of Mechanical Engineers for his contributions to global fluid power research, particularly related to gear pumps. He is also a fellow of the American Society of Mechanical Engineers (ASME) since 2024. Vacca received his Master’s degree in Mechanical Engineering with honor from the University of Parma (Italy) and his Doctoral degree in Energy Systems from the University of Florence (Italy).
Jerome “Jerry” B. Komendera’s legacy in the fluid power industry is one of innovation, leadership, and mentorship. A Detroit native, he graduated from the University of Detroit in 1950 with a degree in aeronautical engineering. Following his service in the Army Air Corps during World War II, he began a distinguished career that would span over four decades and leave a lasting imprint on the industry.
Komendera held prominent positions at respected organizations, including Greer Hydraulics, Bellows Valvair, Mac Valves, and Hydromation Filter. Most notably, he served as President of Automatic Valve Inc. from 1963 to 1990, continuing to consult in the industry until his full retirement in 1993. Under his leadership, Automatic Valve became a key player in advancing solenoid and reversing valve technologies. He was named as an inventor on multiple U.S. patents, showcasing his commitment to innovation and technical advancement throughout his career.
Beyond his commercial success, Komendera was a driving force in industry education and advocacy. He was a founding member and past president of the Fluid Power Society Detroit Chapter 1, where he championed programs to train and develop young engineers. He also helped establish the Detroit Chapter 1 Education Foundation and served on the board that launched the Detroit Area Fluid Power Shows. His passion for mentorship shaped countless careers, making him a true ambassador for fluid power.
Those who knew Komendera described him as intellectually curious, humble, and always eager to understand and support others. His growth mindset, people-first leadership style, and genuine generosity were central to his impact. Whether collaborating with customers, supporting colleagues, or mentoring the next generation, he led with integrity and purpose.
For more details and to see previous recipients, visit www.fluidpowerhalloffame.org FPW
LAST MONTH, WE REPORTED ON PRELIMINARY SESSIONS for the National Fluid Power Association’s Advanced Hydraulics Conference at iVT Expo in Chicago next month. Now, show organizers and NFPA have announced the full program, which runs from noon on August 20 and wraps up at 12:40 with the final session on August 21. iVT Expo (the Off-Highway Vehicle Technology Expo) will be held at the Donald E. Stephens Convention Center in Chicago.
Below are all session titles. Visit ivtexpo-usa.com/nfpa-advancedhydraulics-programme for complete information.
Wednesday, August 20
12:00-12:20 - Optimizing packaged electrification systems for mobile equipment, presented by Andy Cailteux, product management and business development and Justin Hernan, project engineer - Parker Hannifin
12:20-12:40 - Off-highway power transmission methods, presented by D J O'Konek, engineering manager - Nott Company
12:40-1:00 - Efficiency improvements in a mini-excavator using a distributed independent metering valve system, presented by Aaron Jagoda, systems engineer - Danfoss Power Solutions
1:00-1:20 - Unlocking efficiency in electrified hydraulic systems, presented by Chase Younker, electronics product manager - HAWE Hydraulik
2:30-2:50 - Remote diagnostics and support using connected devices, presented by Cory Fisher, director of engineering shared services - Sun Hydraulics
2:50-3:10 - Hydraulic data from the heart of the circuit: pump output digitalization, presented by Mark Preissig, general manager - Casappa Corp.
3:10-3:30 - Fully digital electrohydraulic systems: integrating real-time control, AI-enabled safety and MISRA-C compliance, presented by Michael Terzo, founder and CEO - Xirro
3:30-3:50 - The power of IoT in fluid power: driving performance and innovation through ecosystem partnerships presented by Adam Livesay, co-founder - Elevāt
3:50-4:10 - Thermal management architectures for electrified vehicles, presented by Zach Weis, application engineer - HYDAC
4:10-4:30 - The value in working with a systems integrator, presented by Adahm Faehn, P1 engineering manager - Applied Engineered Systems (Applied Fluid Power)
Thursday, August 21
10:00- 10:20 - Integration of hydraulic work functions on a batteryelectric backhoe loader, presented by Simon Nielsen, staff engineerDanfoss Power Solutions
10:20- 10:40 - Advancing software-centered systems in hydraulics, presented by Rafael Cardoso, engineering manager, mobile systems and software - Bosch Rexroth
10:40-11:00 - Data-driven dissection of an excavator machine cycle, presented by Corey Quinnell, VP of global engineering - Husco
11:00-11:20 - Efficiency-forward approach to electrohydraulic design, presented by Chase Saylor, group product manager for compact and mobile hydraulics - HYDAC Technology Corp.
11:40-12:00 - Control system architectures for electro/hydraulic vehicles, presented by Brad Johnson, electronic controls supervisor - JEM Technical Marketing Co.
12:00 12:20 - From hydraulics to human: Why smart interfaces are the next frontier in electrohydraulic equipment, presented by Jason Looman, president, and Andy Gray, director of sales - Scanreco North America
12:20-12:40 - Advancing Hydraulic Efficiency in ePTO Idle Mitigation Systems, presented by Reinhold Herrman, Director of Business Development and Marketing - IFP Motion Solutions FPW