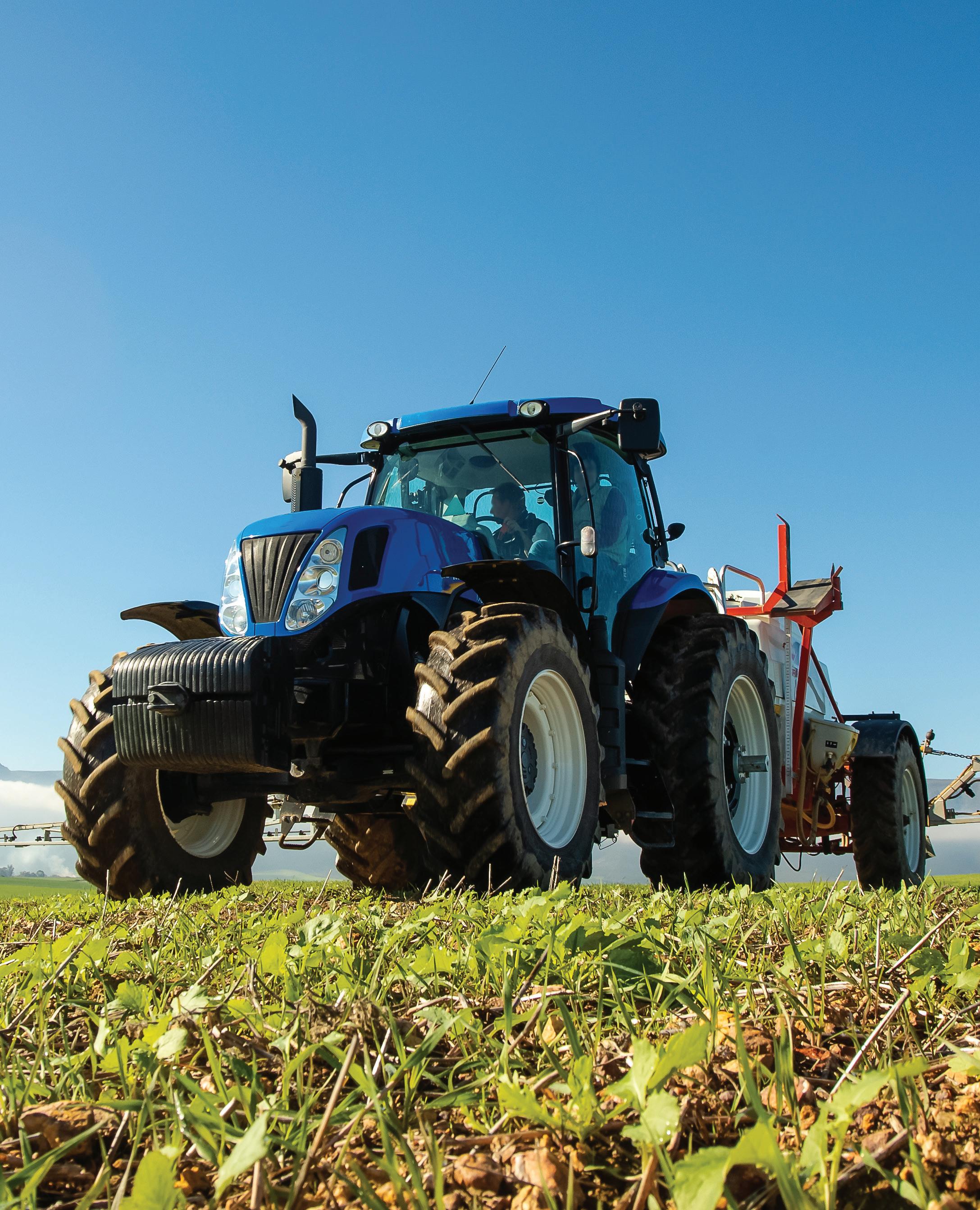
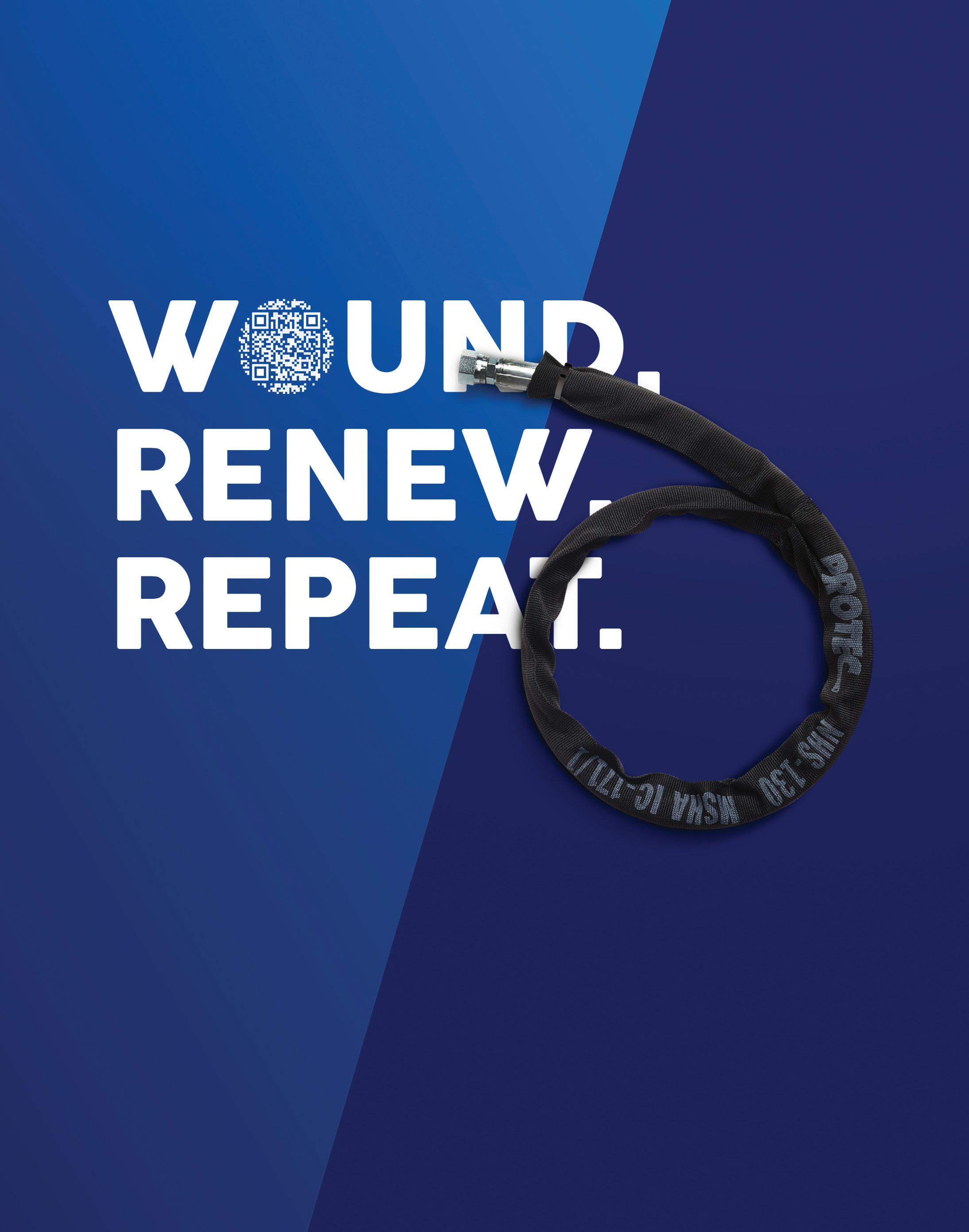
Mary C. Gannon • Editor-in-Chief
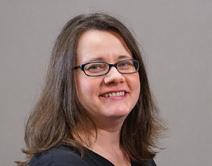
Mary C. Gannon • Editor-in-Chief
I'VE GOT CONTAMINATION ON THE BRAIN.
In the past couple of weeks, I have edited several articles focused on the perils of contamination and how to prevent it. On page 18 of this issue, we talk about the importance of contamination control in agricultural machinery. We also talk industrial contamination control in our June issue, where we tackle both pneumatic and hydraulic concerns.
And just the other day, I moderated a webinar with Josh Cosford about oil analysis and contamination monitoring. This webinar was well-attended and had some of the best questions and interactions of any recent webinars I’ve moderated.
It has been said since I started in this industry 20 years ago that contamination is the cause of most hydraulic failures — between 70% and 90%. These numbers never seem to change, and although everyone claims to be big proponents of proper filtration and doing all the right things to keep your hydraulic fluid flowing freely and cleanly, we still have a problem.
Some say that the manufacturers themselves are to blame due to subpar filtration technologies. Others say it’s the designers, building systems that don’t consider proper filtration and expose critical components to risk. And still others say it’s an education problem, that there are way too many technicians out there not trained in fluid power design and maintenance.
Pointing fingers at one of these issues is not going to solve any problems here, unfortunately. Knowing that contamination has been a problem since long before I entered the industry, no matter what we do, it seems it may continue as long as air and oil are flowing.
So what can we do? We can keep advocating for good designs. There are so many high-tech filtration and sealing components out there — quality seals, filtration, and all the technologies that keep particles, water, air, and other contaminants at bay. Avoid cheaper filters from an online retail shop. Instead, work with your local distributor on the best choice from any number of reputable filter manufacturers. We also must
keep educating the industry that quality should always come before cost, and that good design keeps machines running reliably longer.
And like us here at Fluid Power World, we all need to keep pushing this knowledge out there. If just one new fluid power designer or technician comes across these three pieces of contamination content I mentioned above, we’ve made a difference. So keep choosing better quality and keep advocating for better design. It’s the only way to prevent contamination-related failures. FPW
Mary C. Gannon • Editor-in-Chief mgannon@wtwhmedia.com linkedin.com/in/marygannonramsak
Harvesting
Thomy Leibacher pioneers valve designs with creativity and authenticity
Learn how the Swiss-based founder of Leibacher
EDITORIAL
VP, Editorial Director
Paul J. Heney pheney@wtwhmedia.com @wtwh_paulheney
Editor-in-Chief Mary Gannon mgannon@wtwhmedia.com @dw_marygannon
Technology Editor Ken Korane kkorane@wtwhmedia.com @fpw_kenkorane
Senior Editor Rachael Pasini rpasini@wtwhmedia.com
Contributing Editor Josh Cosford @FluidPowerTips
Contributing Editor Carl Dyke @carlindustry
Contributing Writer Robert Sheaf rjsheaf@cfc-solar.com
www.nfpa.com
PRODUCTION
VP, Creative Services Matthew Claney mclaney@wtwhmedia.com @wtwh_designer
Art Director, FPW Erica Naftolowitz enaftolowitz@wtwhmedia.com
Art Director, FPW Digital Eric Summers esummers@wtwhmedia.com
Director, Audience Growth Rick Ellis rellis@wtwhmedia.com
Audience Growth Manager Angela Tanner atanner@wtwhmedia.com
PRODUCTION SERVICES
Customer Service Manager Stephanie Hulett shulett@wtwhmedia.com
Customer Service Representative Tracy Powers tpowers@wtwhmedia.com
Customer Service Representative JoAnn Martin jmartin@wtwhmedia.com
Customer Service Representative Renee Massey-Linston renee@wtwhmedia.com
Customer Service Representative Trinidy Longgood tlonggood@wtwhmedia.com
FLUID POWER WORLD does not pass judgment on subjects of controversy nor enter into dispute with or between any individuals or organizations. FLUID POWER WORLD is also an independent forum for the expression of opinions relevant to industry issues. Letters to the editor and by-lined articles express the views of the author and not necessarily of the publisher or the publication. Every effort is made to provide accurate information; however, publisher assumes no responsibility for accuracy of submitted advertising and editorial information. Non-commissioned articles and news releases cannot be acknowledged. Unsolicited materials cannot be returned nor will this organization assume responsibility for their care.
FLUID POWER WORLD does not endorse any products, programs or services of advertisers or editorial contributors. Copyright© 2025 by WTWH Media, LLC. No part of this publication may be reproduced in any form or by any means, electronic or mechanical, or by recording, or by any information storage or retrieval system, without written permission from the publisher.
MARKETING
VP, Operations
Virginia Goulding vgoulding@wtwhmedia.com @wtwh_virginia
Digital Marketing Manager Taylor Meade tmeade@wtwhmedia.com @wtwh_taylor
SALES
Ryan Ashdown 216-316-6691 rashdown@wtwhmedia.com
Jami Brownlee 224.760.1055 jbrownlee@wtwhmedia.com
Mary Ann Cooke
781.710.4659 mcooke@wtwhmedia.com
Jim Powers 312.925.7793 jpowers@wtwhmedia.com @jpowers_media
Courtney Nagle 440.523.1685 cseel@wtwhmedia.com @wtwh_CSeel
LEADERSHIP
CEO Matt Logan mlogan@wtwhmedia.com
Co-Founders Scott McCafferty Mike Emich
SUBSCRIPTION RATES: Free and controlled circulation to qualified subscribers. Nonqualified persons may subscribe at the following rates: U.S. and possessions: 1 year: $125; 2 years: $200; 3 years: $275; Canadian and foreign, 1 year: $195; only US funds are accepted. Single copies $15 each. Subscriptions are prepaid, and check or money orders only.
SUBSCRIBER SERVICES: To order a subscription please visit our web site at www.fluidpowerworld.com
FLUID POWER WORLD (ISSN 2375-3641) is published six times a year: in February, April, June, August, October, and December by WTWH Media, LLC; 1111 Superior Ave., Suite 2600, Cleveland, Ohio 44114. Periodicals postage paid at Cleveland, OH & additional mailing offices.
POSTMASTER: Send address changes to: Fluid Power World, 1111 Superior Ave., Suite 2600, Cleveland, OH 44114
Josh Cosford
IT'S HARD OUT HERE FOR A CRIMP. Indeed, the fluid power industry in North America can be described as the USA walking a tightrope spanning Niagara Falls while holding a balance pole opposed by Mexico and Canada at either end. It’s a heavy pole to balance, and getting it right is critical not only for either tip of the pole but also for the tightrope walker.
It’s hard to avoid social media posts where world leaders posture over what is essentially a zero-sum game at best but, more realistically, a negative-sum venture. Every time a spontaneous tweet calling down twenty-five percent fire and brimstone goes viral, we fluid power professionals react by securing Teams meetings with customers or suppliers to discuss the minutia of HS Codes, certificates of origin and whether to bury tariffs or add a costing line to invoices.
We’ve had two across-the-board tariff scares in '25, and we're not yet six months through the year at the time of this writing, although raw material and vehicle tariffs are currently in place, depending on the direction of movement. It's hard to get your ducks in a row when the ducks are three Red Bulls deep, and the row looks like an SCCA autocross course.
The current bilateral tariffs on steel and aluminum are the current threat damaging fluid
power outfits since metal distributors traditionally pull from their favorite mills on either side of border without concern is the 25% tariff. Hydraulic manifolds, steel and aluminum cylinders and valve bodies of all alloys are subjected to huge cost increases for their raw material.
So manufacturers are expected to eat massive cost increases, leading to 10-20% less into the bottom line for finished products. Do we absorb this? Do we increase prices? Do we add a tariff surcharge? And now, realistically, we're going to hit our cross-border customers with a price increase alongside the threat of their own tariffs, which is essentially going to euthanize our international revenue altogether.
Of course, the math isn't so simple and could be different for every product you sell. Your accounting and purchasing team would have to work overtime to run tariff classification analyses on finished components with internationally diverse bills of materials should they not meet USMCA requirements. Do we Canadian manufacturers source American steel and incur the 25% Canadian tariff on raw materials with hopes of favoring regional value content to avoid export tariffs? Or do we keep our costs down by using Canadian raw materials and subsequently working with cross-border customers to help them mitigate their own costs?
It's a sticky situation with no winners. The idea of re-shoring business is great on the surface but difficult in practice. It's not like steel mills, auto plants, and cylinder manufacturers pop up overnight, and even if capital flows into local manufacturing investment, by the time these projects are complete, there is no guarantee that the subsequent administrations will continue to fly the protectionist flag.
As a Canadian businessman, I love my American and Mexican family, friends and customers, of which I have many. I’ve discussed the tariffs with customers and suppliers, and besides the confusion of (happily) delayed timelines, we all agree that applying North American tariffs is akin to childhood friends asking each other to cough up paper route money every time they throw and catch a baseball. FPW
Josh Cosford • Contributing Editor jcosford@higginson.ca linkedin.com/in/joshcosford
Find OFCO’s Equivalents for Your Filtration Parts.
Use our new tool to search by manufacturer, part number or description.
Why wait months? OFCO ships your order from our Ohio factory in days. Email Rob Montgomery or call 740.295.9721 today to find out why.
Edited by Mary C. Gannon • Editor-in-Chief
emits an estimated 400 million tonnes of carbon dioxide per year, according to IDTechEx. With the scale of global construction activity set to increase significantly in the decades to come, decarbonizing heavy-duty machinery is vital to curbing greenhouse gas emissions. Leading crane manufacturer SANY is supporting these efforts and helping its customers achieve zeroemission construction sites through the electrification of its lattice- and telescopic-boom crawler cranes.
Electrifying massive, heavy machinery can be a challenge, as the bigger the machine, the more batteries are required, and thus, extra weight. To balance this extra weight, simplifying the traction and work functions is necessary.
After having previously electrified its lower capacity models with Danfoss Power Solutions’ technologies, SANY partnered with them again to develop fully electric versions of its higher capacity crawler cranes. On Sany’s smaller platforms, Danfoss supplies Editron motors and D1P pumps for its 80- to 150-tonne cranes.
Recently, Danfoss’ Editron division delivered its first eHydraulic Power Module to SANY for the electrification of a 200-tonne lattice-boom crawler crane, to power the traction and work function systems. The eHydraulic system integrates a Danfoss Editron synchronous reluctance assisted permanent magnet motor with a Danfoss variable displacement axial piston pump to maximize performance and efficiency.
Comprising an Editron PMI375-T1100 motor and D1P 260-cc pump, it delivers peak performance and maximizes hydraulic system efficiency, extending machine runtime on a single charge. The hydraulics system also includes Danfoss' series 90 pump and PVG 128 valve.
eHydraulic Power Module combines a synchronous reluctance assisted permanent magnet (SRPM) motor together with axial piston variable displacement technology, which results in enhanced pump efficiency with variable speed drive and the highest motor efficiency throughout the operation range on the market (~96%, said Danfoss).
SANY realized additional benefits with the Danfoss eHydraulic Power Module, including a compact package with mechanical advantages, simple installation, and high reliability. Supplying the electric motor and hydraulic pump as an integrated package eliminates the risk of noise, vibration, and component damage that can arise when using a flexible coupling to join the components. It also simplifies and accelerates installation as there’s no need for the OEM to connect the components. CE marks and Danfoss’ global service network were also key reasons SANY chose to partner with Danfoss on the project.
“Building a solution for SANY’s
high-capacity platform with the Danfoss integrated eHydraulic Power Module marks a milestone,” said Roy Chen, President, Editron division, Danfoss Power Solutions. “eHydraulics represents the future. Together with our Controls division, we have designed a system combining our D1P pump and Editron motor while tuning controls algorithms to maximize efficiency. We look forward to our continued collaboration with SANY and supporting their green journey.”
“Conventional hydraulics still plays a role in the electrification of heavy machinery, particularly machines of this size,” said Henrik Jørgensen, President, Controls division, Danfoss Power Solutions. “By integrating Danfoss’ advanced hydraulic solutions and electrification technology, we are empowering a smooth transition to more sustainable operations. Leveraging our eHydraulic solutions and our application know-how, we aspire to be the partner of choice for visionary OEMs like SANY.” FPW
Danfoss Power Solutions
Danfoss.com/Editron
Edited by Mary C. Gannon • Editor-in-Chief
vacuum pump, the piClassic Neo, Piab has developed a design that minimizes manufacturers emissions and energy costs. Designed to meet the evolving demands of modern industries, the piClassic Neo variants combine efficiency, adaptability and sustainability.
Building on the proven success of its predecessor, piClassic Neo offers the performance and reliability that Piab vacuum technology is known for while minimizing their environmental impact. They come in a familiar footprint so users can integrate them easily, even for existing piClassic users. It features a multi-stage COAX ejector design, based on Piab’s innovative COAX technology, and energy saving functions, available for handling either leaking or sealed applications. This allows manufacturers to minimize their Scope 2 Emissions and energy-related costs.
The air-driven vacuum pump is available in two variants: piClassic Neo, the standard vari-
ant, with all ports accessible from one side; and piClassic Neo Inline with the exhaust direction opposite the vacuum port, for flush mounting directly on profiles. The Inline design is particularly suitable for end-of-arm-tooling (EOAT) and robotic applications, making equipment integration easier.
This new vacuum ejector is suitable for fastpaced packaging lines, high-precision electronics manufacturing, secure automotive production, or general industrial applications. It is designed to integrate effortlessly into a diverse range of industries with its multiple configuration possibilities, installation interfaces and accessories.
In addition, piClassic Neo is built for fast maintenance and long-lasting reliability. Key components are easily accessible thanks to its innovative and modular design, simplifying service efforts and reducing downtime to keep operations running smoothly. Multiple accessories and upgrade possibilities are available
to ensure prolonged lifetime as well as adaptability to current and future application needs.
“By being easy to both install and maintain, piClassic Neo supports operational efficiency for a vast range of industrial applications,” said Christina Storckenfeldt, Product Manager, Vacuum Automation Division, Piab AB.
The piClassicNeo features a design rooted in sustainability, working to fit industries worldwide that are shifting towards environmentally responsible manufacturing. It is designed following eco-design principles, resulting in up to 58% reduction in CO2-emissions cradle-togate compared to its predecessor. These results were determined through a commissioned life cycle assessment report performed in accordance with the ISO 14040 standard.
It uses premium sustainable materials (biobased or recycled) for plastic components, and is designed for optimal material usage without compromising on durability and robustness.
Beyond the pump design itself, energy efficiency is at its core. With optional energy saving functions — piSave ESS or piSave ESL — users can minimize air consumption and reduce operating costs. This ensures a more efficient and responsible approach to vacuum solutions when handling either leaking or sealed materials. Users can achieve top-tier vacuum capabilities, while still reducing their environmental impact as they move towards manufacturing processes in alignment with global sustainability goals. PISave ESS is best used for handling air-tight materials, such as metal, glass or plastic, while piSave ESL is recommended for handling leaky materials, such as cardboard, fabric, bags, MDF boards or wood.
“We've designed piClassic Neo to fit not only today's manufacturing demands but also tomorrow's, helping manufacturers take a simple step toward a more sustainable production process,” Storckenfeldt added. FPW
Piab piab.com
Ron Marshall • Contributing Editor
RUNNING A LUBRICATED SCREW compressor at light loading can lead to a critical issue known as oil carryover, where excess lubrication oil escapes the compressor into the downstream air system. This problem, while often overlooked, can result in costly operational challenges, particularly in food processing plants where air purity is critical.
Lubricated screw compressors rely on oil for sealing, cooling, and lubrication within the compression elements. When operating at light loads — typically below 30% of the compressor’s capacity — the balance between oil injection and air compression becomes disrupted. Reduced air flow through the system causes excess oil mist to accumulate and escape into the air stream. Over time, this oil mist bypasses the separator and downstream filters and contaminates the compressed air.
Additionally, light loading causes frequent start-stop cycles or continuous unloaded operation, leading to incomplete oil separation and reduced effectiveness of oil removal components. This only serves to accelerate the oil carryover problem, creating persistent contamination issues in the air system.
In food processing environments, compressed air often comes into direct or indirect contact with food products, packaging, or processing equipment. Oil carryover poses a significant contamination risk that can compromise product quality and safety. Even trace amounts of oil in compressed air can lead to regulatory violations, product recalls, and damage to your reputation!
For example, oil-laden air used in food conveyance systems can contaminate raw materials, while oil residues in pneumatic tools or process lines may introduce unacceptable risks of food adulteration. These risks, which have happened in the past, necessitated the devel-
opment of stringent air quality standards, such as those defined by ISO 8573-1 for oil-free air.
To prevent or reduce oil carryover, food processing facilities should avoid operating compressors at light loads whenever possible. Consider using a variable speed drive (VSD) compressor to match air supply with demand more effectively. Regular maintenance of oil separators, filters, and drains is also crucial to
maintaining air purity. Additionally, installing high-quality filtration systems downstream can further protect sensitive applications.
Be sure to address the causes of oil carryover and invest in preventive measures. Facilities need to do careful work to ensure reliable, contamination-free compressed air flows into the plant while maintaining compliance with strict food safety standards. FPW
Edited by Mary C. Gannon • Editor-in-Chief
on the agriculture market, Fluid Power World spoke with Vinicius Povineli, Mobile electronics/ connectivity product manager, Bosch Rexroth, to learn how electrification is impacting ag machinery today and tomorrow.
FPW: How are hybrid and electric innovations impacting the agriculture industry and where do you see any challenges arising in the future?
Povineli: From my perspective, hybrid and electric technologies are already making a noticeable impact in agriculture by improving fuel efficiency, reducing emissions, and opening the door for more precise, intelligent machine control. These solutions align well with the industry's growing push for sustainability and automation. However, challenges remain — particularly in infrastructure such as charging availability in remote or rural areas, and in justifying ROI for farmers who operate in cost-sensitive environments. Battery technology is improving, but energy density and runtime under heavy-duty use are still limiting factors for full electrification of larger machines.
FPW: How are electronic control solutions, such as electrohydraulic valves and smart pumps, transforming the performance and efficiency of mobile agricultural machines?
Povineli: I’ve seen firsthand how electronic control systems, especially when integrated through platforms like Rexroth eOC and eEP, are revolutionizing mobile equipment. Electrohydraulic valves and smart pumps enable realtime, adaptive machine behavior that reduces energy loss, improves responsiveness, and supports precision farming applications. This level of control enhances both performance and fuel economy, and it also simplifies diagnostics and predictive maintenance through data collection. In addition to performance and efficiency, electrohydraulic designs greatly improve
ease of controllability. Operators can achieve smoother, more precise movements thanks to programmable logic and proportional control, which allow for fine-tuned adjustments across different functions and load conditions. This not only enhances operator comfort and accuracy in the field, but also enables automation features that reduce dependency on manual
AGDRIVE, AN EFFICIENT COMPLETE SOLUTION FROM BOSCH REXROTH WHICH INCLUDES BODAS SOFTWARE, OPENS UP A WIDE RANGE OF FUNCTIONS FOR SELF-PROPELLED AGRICULTURAL MACHINES WITH A HYDROSTATIC MULTI-MOTOR DRIVE.
input and improve repeatability across tasks — like Bosch Rexroth Kinematic Positioning System (KPS) using our IMU sensors (MM7) to control the movements of excavator implements.
FPW: What types of machines are most impacted by these hybrid and electric solutions? Which are less likely to adopt the new technology and why?
Povineli: Smaller utility tractors, autonomous platforms, and implements with auxiliary drives are among the most impacted so far — largely because they can benefit from electrification without the same power demands as highhorsepower machines. On the other hand, large combine harvesters or 4WD tractors are slower to adopt due to the sheer energy demand and runtime requirements during peak operations. For those, hybrid solutions, such as electrified auxiliaries, are a more realistic near-term path than full battery electric.
That’s where hybrid systems play a critical transitional role. In large machines like harvesters or articulated tractors, full electrification
is often impractical today due to battery size, weight, and charging logistics. However, hybrid architectures — such as using electric drives for fans, pumps, or compressors — can offload work from the engine, improving fuel efficiency and reducing emissions without compromising uptime. These solutions also pave the way for better load management, modularity, and future scalability as battery and charging technologies evolve.
FPW: How do electric solutions and sensor integration in mobile agriculture equipment support improved data analysis, machine output and the precision of mobile agriculture practices?
Povineli: By combining electric actuation with sensor-rich systems, like all Rexroth Bodas Platforms, especially AgDrive, we can achieve highly precise control of field operations. The real game-changer, though, is the data these systems generate. With platforms like Rexroth Bodas Connect, we’re able to collect, analyze, and act on that data remotely, optimizing machine performance and enabling predictive service which is especially valuable for fleet managers and dealers.
Sensor-rich architectures are also foundational to autonomy. Ultrasonic sensors, Radar, cameras, Collision Avoidance Systems, GNSS, IMUs, and other perception technologies allow machines to better understand their environment, respond to changing field conditions, and navigate with minimal human input. This is critical not only for full autonomy, but also for semi-autonomous functions like section control, headland turning, and variable rate application.
From a broader perspective, these IoTenabled systems are transforming decisionmaking in agriculture. By capturing high-resolution operational data, farmers can make more informed choices about planting depth, fertilization rates, soil compaction, and even yield estimation. This leads to improved consistency, resource efficiency, and ultimately higher productivity across the growing cycle.
FPW: What is a barrier to adopting hybrid and electric mobile machines in the agriculture industry?
Povineli: One of the biggest barriers is still the total cost of ownership. Farmers are open to innovation, but the investment must pay off in tangible benefits — either through fuel savings, reduced downtime, or better yields. There’s also a learning curve for both operators and technicians when it comes to maintaining and
troubleshooting these new systems. Training, dealer support, and clear ROI calculations will be essential for broader adoption.
Additionally, as machines become more complex with hybrid and electric technologies, farmers often face challenges when it comes to troubleshooting and repair. The increasing reliance on advanced electronics, software, and specialized components means that traditional repair methods may no longer suffice, and many farmers struggle with the inability to repair these systems themselves. This dependency on external service providers can result in longer downtimes and higher maintenance costs.
Manufacturers can help mitigate this issue by designing more reliable and user-friendly systems that are easier to diagnose and repair. Incorporating predictive maintenance tools and remote diagnostic capabilities can enable farmers to address potential issues before they become major problems. This proactive approach to maintenance can reduce the frequency and severity of breakdowns, ultimately lowering repair costs and improving overall machine uptime. FPW
Bosch Rexroth boschrexroth.com
Edited by Mary C. Gannon • Editor-in-Chief
MACHINE SAFETY IS CRUCIAL for fluid power systems, as anytime you are dealing with highly pressurized fluids you must take extra special care. To this end, the Machinery Directive 2006/42/EC outlines the safety requirements for machinery and equipment in the European Union. The directive sets out specific safety measures and guidelines that
manufacturers must adhere to when designing, manufacturing, and commissioning hydraulic equipment. These measures include the use of safety valves, to promote a safer working environment and maintain operational efficiency of machinery.
The Machinery Directive 2006/42/EC is a foundation of equipment safety within Euro-
pean Union member states. This directive sets forth essential rules for operators’ health and the safety requirements for machinery throughout its entire lifecycle, from initial installation and ongoing maintenance to eventual disposal. By carefully addressing a wide range of safety aspects, the directive ensures that machinery is designed and manufactured with the utmost
priority on the well-being of operators.
Two crucial similar standards play a key role in ensuring the safety of hydraulic systems: ISO 13849 and IEC 62061. These standards provide a framework for manufacturers to assess and mitigate risks by considering various factors like the reliability of components, the architecture of the control system, and the severity of potential hazards.
Performance Level (PL) and Safety Integrity Level (SIL) are two important concepts when evaluating the effectiveness of safety measures in hydraulic systems. These levels measure the ability of safety functions to perform their intended task under specific conditions. By assessing these factors, manufacturers can determine the appropriate PL/SIL required for their specific hydraulic system, ensuring the implemented safety measures are adequate for the intended application.
By understanding the Machinery Directive 2006/42/EC, industrial engineers will have the knowledge and insights needed to revolutionize the functional safety of hydraulic systems,
resulting in increased reliability, improved performance and ultimately, creating a safer industrial environment for operators.
As functional safety becomes increasingly important across industry sectors, the full comprehension of the pivotal role of safety valves and their contribution to achieving compliance with ISO 13849 and IEC 62061 standards assumes ever-greater importance.
Safety valves are specifically designed and tested to meet stringent safety standards and regulations. They ensure the overall safety and reliability of hydraulic systems. They are engineered with advanced features such as monitoring systems and fail-safe mechanisms, meeting the highest level of safety. In practice, safety valves help in limiting potential risks to equipment or operators, preventing dangerous movements of electrohydraulic axes during production cycles or emergency conditions.
However, it must be taken into consideration that overall SIL and PL assessment does not depend solely on the characteristics of a single component. SIL and PL assessments con-
sider the entire chain of safety-related components working together to perform the safety function.
Safety valves can be integrated in redundant double channel systems to achieve higher safety levels, as well as increasing the complexity of the systems. Numbers and types of faults detected can be improved by introducing safety mechanisms into the system architecture, to further increase the overall diagnostic coverage.
Atos has developed a range of safety valves specifically designed for functional safety. They undergo rigorous testing processes, ensuring their quality, reliability, and compliance with industrial safety standards. These safety valves are supplied with certification approved by notified body, facilitating the machine design phase and the system certification process.
Atos’ complete range of on-off valves and cartridges with inductive safety sensors monitor the spool or poppet position, used by the machine central unit to confirm the safe status of the valve. The available range of digital proportional valves with on-board electronics were designed and certified for functional safety.
Atos proportional safety valves meet safety standards by inhibiting the regulation of proportional valve via on-off enable signals. The valve confirms when the safe spool position has been reached by sending on-off digital signals to the machine central unit. Meeting these stringent requirements helps to prevent accidents and protect both machinery and personnel. FPW Atos atos.com
Agricultural machinery is up against a variety of harsh environmental conditions, so proper protection of the hydraulic systems is necessary.
By Josh Cosford, Contributing Editor
DRY, DUSTY ENVIRONMENTS CAN WREAK HAVOC ON HYDRAULIC SYSTEMS, SO PROTECTIVE FILTRATION SYSTEMS ARE NECESSARY TO PREVENT CONTAMINATION INGRESSION.
The agricultural industry is unique in many ways, not the least of which is the source of nourishment for billions of people, which is not something mining or forestry can claim. When it comes to the design and operation of agricultural machinery, the operating environment creates unique challenges that fluid power designers must overcome to ensure machines are effective and reliable.
The challenge of eliminating contamination in ag hydraulics is a daily struggle, as the ambient environment assaults machinery with every possible ilk of damaging stressor. A late-spring Sunday drive in the country could yield vistas of dust clouds as tractors work dry fields or, conversely, nothing at all as machinery sits idle in the rain. And even during heavy rain when fields are inaccessible, there’s always work to be one on the farm, such as livestock care and handling of seed, feed and fertilizer.
Sometimes, the plumes you see stem from dry-spread fertilizers and nutrients. Using hydraulic conveyor and spinner motors to hurl dry nutrients across the field, granular and powdered fertilizers are still relatively common. Lime is used to adjust soil pH, gypsum to improve soil structure, and phosphate fertilizers may be periodically spread on fields, each of which can be dusty.
Because hydraulic systems need to respire during the operation of differential area cylinders (those with a single rod), the reservoir fluid volume lowers during cylinder extension and rises during cylinder retraction. To prevent vacuum or pressure inside a reservoir, a breather cap is installed atop the filler hole in most cases.
However, because farm equipment sometimes operates within a swirling cloud of grit, that reservoir interior needs protection from contaminant inhalation. The filler cap on most reservoirs doubles as a breather device, allowing air to enter while filtering a great deal of the particles doing their best Trojan Horse impersonation.
MUD
IS YET ANOTHER RISK TO AGRICULTURE MACHINERY’S HYDRAULIC SYSTEMS, AS MACHINES ARE OFTEN STORED OUTDOORS.
Despite this common barrier to contamination ingression, there are caveats to the commonly used breather cap. The offthe-shelf twist-lock designs you can buy at the tractor supply store are neither terribly efficient nor configured appropriately to store very much dirt. We rate a filter’s capacity to store contaminants by its Dirt Holding Capacity, and such inexpensive breathers may only hold a few grams of dirt and dust before becoming clogged. Additionally, the budget-friendly breather designs have a poor beta ratio, which describes a filter’s efficiency at trapping particles in a single pass. Contrary to the low micron number claim by breather cap manufacturers, the efficiency of these designs is poor. When you factor in the
A
high-end machine deserves high-end contamination control equipment, so farm machines should use lowmicron, high-efficiency breathers.
construction method using either mesh or foam, you might agree that a 4-micron rating from a $4 breather will offer some compromises.
A high-end machine deserves high-end contamination control equipment, so farm machines should use low-micron, high-
efficiency breathers. Many manufacturers offer synthetic media with ultra-fine mesh down to 3-micron or lower, and the penalties of back pressure are nominal when flowing only air. Additionally, synthetic media’s dirt-holding capacity is exponentially higher than that of inexpensive materials, allowing the element to hold over 100 grams of dirt when so equipped.
Farmers must be mindful of their environment and the potential for quickly loading a breather cap with dirt, even when using high-capacity elements. Spin-on breathers are quick and easy to replace, but they should be replaced regularly. The effects of a clogged breather are often challenging to detect, and the damaging consequences can occur without notice. A
pump may cavitate more quickly should air not quickly replace the reservoir's fluid, as reservoir vacuum occurs when a differential cylinder extends. Here, it's always best to follow the manufacturer's service frequency recommendations.
Of course, there are perhaps just as many chances where rain is the prevailing issue on any given day, depending on climate, of course. Rain presents its own challenges regarding reservoir respiration since mobile hydraulic systems aren’t friends with water. Water, even in the form of humidity, creates a range of problems for hydraulic components, including corrosion, fluid degradation, and increased microbial
growth, among others.
OEMs have been diligent in avoiding reservoir design and placement in such a way as to allow and encourage free water to enter around the filler-breather location. A well-planned location and installation of a breather riser will prevent pooling water from dripping into the tank, but humidity is a serious concern for outdoor machinery.
To combat excessive humidity inside the reservoir, which can be absorbed by hydraulic oil, OEMs now use desiccant breather caps to leech away water in addition to particles. Although expensive compared to traditional breather caps, the protection they provide for the lifeblood of your tractor is invaluable.
THESE FILLER BREATHERS FROM OHIO FABRICATORS CO. HAVE A THREADED FITTING, MAKING THEM EASY TO INSTALL AS FILLER PORTS FOR HYDRAULIC RESERVOIRS. THEY PROVIDE AIR FLOW WHILE KEEPING OUT CONTAMINANTS AND PARTICLES.
The desiccant breather cap is nearly universally a transparent plastic shell with colored silica gel beads. These small beads provide exceptional surface area for the best chance of capturing water molecules as they pass. Modern breathers use methyl violet or iron salts that change the color of the beads when they’re saturated, providing a visual signal to change the breather.
Older technology used a chemical called cobalt chloride, although such versions have been phased out in the farming industry because of environmental concerns. Cobalt chloride is blue when dry but turns pink when saturated. Meanwhile, the modern chemicals, as previously discussed, are more inert and appear orange when dry before changing to green when saturated. When shopping, be sure to locate or ask for the orange desiccant.
High-end machines take contamination prevention to another level by incorporating sealed reservoirs. A reservoir capable of a moderate positive pressure allows for
To combat excessive humidity inside the reservoir, which can be absorbed by hydraulic oil, OEMs now use desiccant breather caps to leech away water in addition to particles.
differential volume control while avoiding any chance of cavitation or contaminant entry. These systems are exponentially more expensive than breather caps but are impervious to even the most biblical dust cloud.
Farm equipment experiences more trouble outside of reservoir humidity, of course, since they're exposed to the elements. In many cases, farms may lack space in the machine shed for all the required equipment, so infrequently used or older machines may sit outside. Besides the obvious filler cap, water can invade through poorly maintained and uncapped quick couplers (Pioneers), damaged cylinder rod seals and from condensation inside the reservoir.
Each of the above options results in free water, which can damage the hydraulic system in ways more severe than humidity alone. Free water can create localized pools of rust as machinery sits for extended periods, which could rust and create iron oxide particles. Those particles could break away during machine startup and create havoc on sensitive components. In cold climates, water will also freeze, leading to possible physical damage depending on its location. When water freezes, its volume expands with such strength that even steel parts may be damaged. The worst damage may occur in late fall and early spring when the mercury waxes and wanes thermoclastic. If the freeze/thaw cycle is strong enough to
heave asphalt and concrete, imagine how easily a seal could be blown out.
Another form of contamination common in agricultural hydraulics originates from an unexpected source: implements. Few farms are fortunate enough to commission only brand-new equipment, and farmers frequently buy, sell and trade to secure the fleet that suits their needs.
Many hydraulic-heavy farm implements consist of various hydraulic cylinders and/or motors. Folding disks, silage wagons, large balers, and auger wagons are machines frequently used by most farms, and with so many hydraulic functions, the machine as a whole stores many gallons of hydraulic fluid. Cylinders, motors, valves and plumbing contain hydraulic fluid, and when buying old machinery, the condition of such fluid is often unknown.
Auction houses often list equipment as-is, so no guarantee is offered to the
Another form of contamination common in agricultural hydraulics originates from an unexpected source: implements. Few farms are fortunate enough to commission only brand-new equipment, and farmers frequently buy, sell and trade to secure the fleet that suits their needs.
state or quality of the hydraulic fluid or the components it’s meant to lubricate and protect. Simply hauling your new-to-you self-propelled sprayer home and connecting up the hydraulics without first purging everything could invite hoards of damaging contaminants into your expensive tractor.
Your tractor is worth far more than some hydraulic oil (or the implement), so be sure to drain all used fluid and then refill and bleed air as required. You dramatically decrease the opportunity for contamination while ensuring your actuators begin their stay with you enjoying fresh oil.
This next part is for the veteran farmers reading. Up until now, the article risks appearing fluffy and irrelevant because we all know farmers with old, rusty equipment who use them every three years with no issues despite looking like a bombedout armored personnel carrier. Also, I like to indulge in the random YouTube videos that appear in my feed with titles like "This Excavator Hasn't Run in Twenty Years. Can We Get It Started?" Clearly, old machines have the capacity to work and run, but that doesn't make them ideal.
If old equipment works for you and your farm and hasn’t hindered your production capacity, then who am I to tell you to focus your time on contamination control rather than putting up hay or caking cows? However, the reality for commercial farming is that productivity, reliability, and automation are necessary to remain profitable with ever-tighter margins. But when advanced, 7-figure machines are expected to make huge returns on investment, being casual about contamination control is not an option. FPW
DESICCANT BREATHERS, LIKE THIS DESIGN OF THE D-AB SERIES FROM SCHROEDER INDUSTRIES, USE SILICA GEL BEADS THAT CHANGE COLOR FROM ORANGE TO GREEN TO INDICATE SATURATION.
THOMY LEIBACHER SHOWS HER WORK ON VALVE DESIGN IN HER COMPANY, LEIBACHER HYDRAULICS+ELECTRONICS.
Learn how the Swiss-based founder of Leibacher Hydraulics+Electronics supports both design and camaraderie in fluid power.
By Mary C. Gannon, Editor-in-Chief
Isay over and over again, it’s the people in the fluid power industry that have kept me here so long. Connecting with entrepreneurs, engineers and innovators is inspiring. But add to that, the kind and welcoming personalities you find at every turn and you can’t go wrong.
You don’t even have had to meet a person in this industry to know them and consider them an industry friend. Thomy Leibacher is one such person. She shines like a beacon of joy, her fire emojis on LinkedIn a testament to her passion for the industry and her support of those advancing the industry.
Like many in the industry, Leibacher got her first taste of hydraulics very young. She was a 17-year-old apprentice with a manufacturer of industrial valves for controlling steam, gas, water or contaminated water in power plants. Her teacher and mentor there worked with her to build a flow rig to measure the pressure loss on the valves. This hooked her and she continued with this work, learning how to design and produce seals on poppet valves and using metallic materials for seals in high-temperature and high-pressure applications.
She worked the gamut of valve design, from machining valve parts, assembly, testing for leaks, and setting up PID controllers on air-driven valves. It was there she learned when and where different highquality materials should be used, such as stainless steel, Inconel and other high strength materials.
Having gotten a taste of the work, Leibacher decided to attend evening school to become a mechanical design engineer. Throughout the 1980s, she worked in mobile hydraulic sales, gaining valuable sales training while on the job. She began to work with more hydraulic technologies over these years, learning stack valves and customized manifolds, pressure-compensated external gear pumps, orbital hydraulic motors, hydraulic cylinders on construction machinery, and even special hydraulic cylinders with integrated positioning sensors for use in hydro power plants.
She spent the next couple decades working in valve design, even relocating from Zurich to Chicago for her dream job. She had met Connie Kosarzecki in 2006, and was inspired by his valve designs. “I never met someone who understood how to keep the
"My job keeps creativity and curiosity vivid. I stay focused and well-organized in project management, staying up to date on standards."
valve design simple and sturdy as he did,” she said.
After nearly four years in the U.S., she returned home to Zurich and eventually started Leibacher Hydraulics+Electronics, working as a reseller for Kosarzecki’s existing product line at Command Controls Corp. She now designs and sells her own cartridge valves, slip-in DIN cartridge valves, actuators, power packs, closed-loop circuits, and test benches.
“My job keeps creativity and curiosity vivid,” Leibacher said. “I stay focused and well-organized in project management, staying up to date on standards.”
Mornings are focused on managing multiple projects, and she often breaks in the day for exercise, whether it is running or ice skating, which she shares with her friends regularly on LinkedIn. “In the morning, I experience a blast of new ideas and focus on tasks and priorities. In this sequence of booting up my working day I need to be undisturbed to organize all this in my project management tools. We keep today’s data and information at our fingertips,” she said.
Leibacher loves the fluid power industry, and has worked at manufacturers both large and small, like her own company, throughout her career.
"The most rewarding part," she asserts, "is the constant evolution and the diverse applications of valves." She acknowledges the challenges — navigating complex standards, cultural nuances, and the evolving
THOMY LEIBACHER HAS BEEN INVOLVED IN VALVE DESIGN SINCE THE START OF HER CAREER. HERE ARE SIMULATIONS OF HER LOGIC ELEMENT SIZE 40 RATIO1:1.06. THIS VALVE RATIO WORKS FOR CHECK VALVE AND DIRECTIONAL VALVE FUNCTION UP TO 9,000 PSI IN HIGH FLOW APPLICATIONS.
landscape of fluid mechanics. Her commitment to diversity and inclusion fuels her belief in cultivating teams that blend varied expertise and perspectives, essential for tackling industry complexities.
“Engineering is everywhere. It is a great place for people who like analytic work and developing new solutions for machinery functions. The work includes materials, design, project management, all the production processes like turning, drilling, milling, grinding, honing, heat treading, forging, powder metal processing, brazing, soldering, welding and many others,” she said. “It is a never-ending playground for creative people.”
She added that while there is value in larger organizations, she believes the varied experiences you gain at small manufacturers is so important. Her vision favors small, agile local production, fostering innovation in a globalized economy. “I believe in small, powerful local organizations and production,” she said. “They keep skills, train-
"The most rewarding part is the constant evolution and the diverse applications of valves."
ing and culture for young talents vivid and it’s a good motivation to push your own new product line.”
As for the future, Leibacher has seen the industry evolve over her career, with more digital electronics in hydraulic applications and valve controls. Reflecting on the industry's evolution, she highlights the transformative role of digital electronics and sensor integration in hydraulic systems. While she embraces technological advancements, she remains a proponent of balanced integration, cautioning against over-reliance on electronics at the expense of robust, mechanical solutions.
“By using digital electronic cards, the remote support process and adjustment
has gotten much easier compared to analog electronics. Sensors and price decreases have pushed the concept of closed-loop circuits in mobile and industrial hydraulic applications. BUS interfaces offer high speeds to drive any hydraulic signal to and from the valves in fractions of second,” Leibacher concluded. “But to be honest, although I am a huge fan of electronics, sometimes, the simple valve without any electronics will be good enough.”
Connect with Thomy Leibacher now at linkedin.com/in/thomy-leibacher-69423514/ or visit her website at leibacher.com/ FPW
Edited by Mary C. Gannon • Editor-in-Chief
AS FLUID POWER SYSTEMS GROW more complex and integrated with electronic technologies, staying ahead means having the right tools to learn, adapt, and excel. The Electronic Controls Specialist (ECS) Study Manual from IFPS has been fully updated to meet the demands of today’s evolving industry.
Designed for professionals preparing for the ECS certification or those working with electronic control systems in fluid power, the revised manual offers enhanced content, clearer explanations, and updated graphics to reflect modern-day applications. Topics include sensors, PLCs, control system design, troubleshooting, and safety — presented in a format that’s both comprehensive and approachable.
Created by industry experts and backed by the International Fluid Power Society, this manual supports technicians, engineers, and specialists seeking to sharpen their skills and validate their expertise in electronic controls.
JUNE IS RECOGNIZED
, making it the perfect time to spotlight the importance of safety in the fluid power industry. The International Fluid Power Society (IFPS) is dedicated year-round to promoting the highest safety standards to protect technicians, mechanics, engineers, and other industry professionals.
IFPS offers comprehensive safety training and resources designed to keep workers informed, prepared, and safe on the job. Developed in collaboration with industry experts, IFPS safety programs are practical, easy to understand, and focused on real-world application — ensuring professionals are equipped to create and maintain safer work environments.
In addition to training, IFPS provides valuable tools like safety cards and posters to serve as daily reminders in high-risk settings. By fostering a strong safety culture, IFPS not only protects workers but also strengthens the overall integrity and reliability of the fluid power industry.
Learn more at ifps.org/safety FPW
Whether you're pursuing certification or looking to strengthen your understanding of control systems, the updated ECS manual is a critical resource to guide your success.
Explore the new ECS Study Manual at ifps.org. FPW
SUMMIT, to be held October 6-9, at the Hyatt Regency Greenville, South Carolina. The event features a variety of presentations, networking opportunities, and special events for fluid power, motion control and sealing distributors, and manufacturers.
The event kicks off Monday, October 6 with meetings, then social activities including a special miniature golfing event, welcome events, and after-party and dinner.
Tuesday, October 7 will kick off with the opening keynote, "Over the Wall Thinking," by Andy Papathanassiou followed by a general session, "My Way Highway: Navigating Uncertainty on the Road to Success," by Alan Amling. Teambuilding events will include a NASCAR-themed Pit Stop Challenge, running concurrently with the vendor showcase. The day continues with both FPDA and ISD annual meeting of members, followed by the vendor showcase and networking reception.
Wednesday, October 8 will begin with a morning keynote, "Reclaim Your Workday: Accelerate Productivity, Navigate Distractions, and Drive Results," by Marcey Rader. Two general sessions, "AI Full Throttle," by Jena Dunham and "Elevate Your Focus: Drive Focus in a Distracted World," by Marcey Rader, will be followed by a closing keynote, "Industry Update," from Conor Lokar. The evening concludes with a dinner at New Realm Brewery.
Attendees can wrap up with golf and lunch Thursday, October 9, before departing.
For details, visit fpda.org FPW
THOMAS WANKE WAS A MONUMENTAL figure in fluid power, active for more than 50 years and influencing generations of fluid power engineers through his work at the Milwaukee School of Engineering, its Fluid Power Institute, and with the National Fluid Power Association.
To honor his memory and ensure that his positive impact on fluid power education continues to be felt, the NFPA Education and Technology Foundation announced that it would administer the Thomas Wanke Legacy Fund, to support fluid power scholarships and education activities at universities throughout the United States.
Total donations exceed $30,000, marking the milestone to qualify for the maximum matching gift of $25,000 that was pledged by the NFPA. The fund now has more than $55,000 to use in supporting fluid power education.
In its second year, three students earned $2,000 toward their tuition expenses. When selecting the awardees of the Tom Wanke Legacy Fund, the judges were looking for students who were:
• Passionate in their academics
• Active in extracurricular activities
• Dedicated to obtaining careers in the fluid power industry
Based on that criterion, NFPA industry member judges selected Emily Bolin, Evan Fender, and Riley Mack.
“As a former competitive Junior Olympic gymnast, I vividly remember a meet supporting the Make-A-Wish Foundation, where another gymnast told her story as a cancer survivor with a hip disarticula-
tion. Despite having a full-length artificial leg to replace the amputated limb, she was still able to compete due to her advanced prosthetic that utilized pneumatics. I was amazed to see her perseverance working with mechanics and fluid systems as she competed and continued to live an active lifestyle. Since then, I have been fascinated with fluid systems working with the human body and want to learn more,” said Emily who is studying, Mechanical Engineering at Grace College.
Evan Fender, also studying Mechanical Engineering at Wright State University, said that “Winning the Tom Wanke Legacy Fund award is a great honor and validation of my dedication to the field. It represents not only recognition but also the opportunity to further my goals in fluid power and engineering. I am extremely grateful for the support this award provides as I continue pursuing my passion and striving to make an impact in engineering.”
“Awards such as this are incredibly beneficial to students like me who are not following the traditional four-year college plan. I have been working since I was 14 years old to help pay my own way,” said Riley Mack, a Service Technician student at Garden City Community College. “In agricultural machinery, hydraulics operate implements and perform various tasks. Fluid power will be present daily as I service and repair different types of equipment."
Since 2023, six students have been awarded a Tom Wanke Legacy Fund Scholarship, totaling $12,000. Donations are still welcome at nfpa.com/donate-now FPW