

howtouseadhesivesfor hermetic wire feedthroughs
The hermetic sealing of electrical and optical feedthroughs is critical for the longevity and reliability of electronic devices. Depending on the degree of hermeticity required and the constraints of the application, techniques such as gasket sealing, adhesive sealing, and ceramic or glass sealing are used. By comparison, epoxy adhesive sealing or potting offers exceptional processing flexibility — particularly for hermetically sealing wire feedthroughs composed of many conductors through a small diameter housing.
Commercially available non-hermetic connectors can also be back-filled with epoxy around the conductors to provide a wire feedthrough that’s quickly fabricated while delivering hermetic performance.*
Process and adhesive requirements
The factors to consider when using epoxies to create a hermetically sealed wire feedthrough include:
• Viscosity
• Cure schedule
• Adhesion
• Chemical and temperatureresistance
• Shrinkage-upon-cure
• Coefficient of thermal expansion (CTE)
For back-filling wire feedthroughs, a lower viscosity is typically preferable such that the adhesive readily flows and fills the internal space of the electrical connection. There are one and two-part epoxy systems. For two-part systems, the mix ratios must be followed closely, and the components thoroughly
mixed before use. It’s also critical to vacuum degas the epoxy to avoid the entrapment of any suspended air. Improper mixing and/or an improper cure schedule will compromise the physical integrity of the epoxy seal, reducing the cross-link density and chemical resistance while potentially increasing the permeability of the epoxy.
Epoxies have a high degree of adhesion to most substrates. However, all parts bonded with an epoxy must be appropriately degreased and cleaned to ensure a strong bond and avoid the inclusion of any weak boundary layers.
For an epoxy, high-glass transition temperature, Tg (the temperature at which the adhesive will start to soften), indicates superior resistance to high-temperature resistance. The permeability of the adhesive to atmospheric gases must be minimized. Typically, epoxies offer a low permeability, making them ideal
for hermetic sealing and potting applications. They also exhibit some degree of shrinkage upon cure. Selecting an epoxy with minimal shrinkage upon cure helps alleviate stresses that may build up within the joint, which could result in debonding or the formation of cracks or channels, compromising hermeticity.
Epoxies can be formulated with various fillers tailored to their CTE for a particular application. As epoxies are inherently electrically insulative, nonconductive fillers can modify the CTE of the formulated system.
For an ideal feedthrough, there should be no major difference in the CTE between the housing material, epoxy, or conductors. A significant CTE mismatch could result in a differential in expansion and contraction while the part undergoes temperature changes. This could lead to an accumulation of stress, resulting in cracking and a loss of adhesion and hermeticity. This
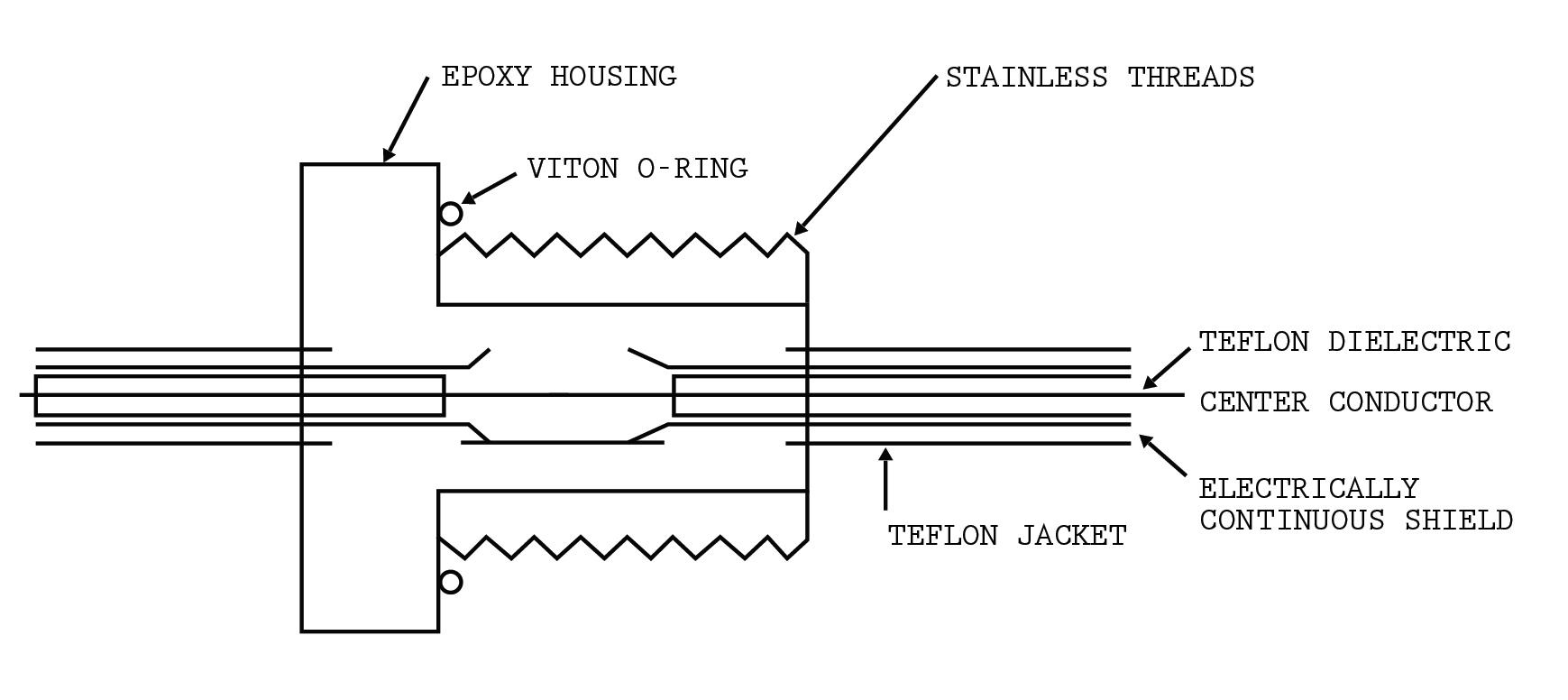
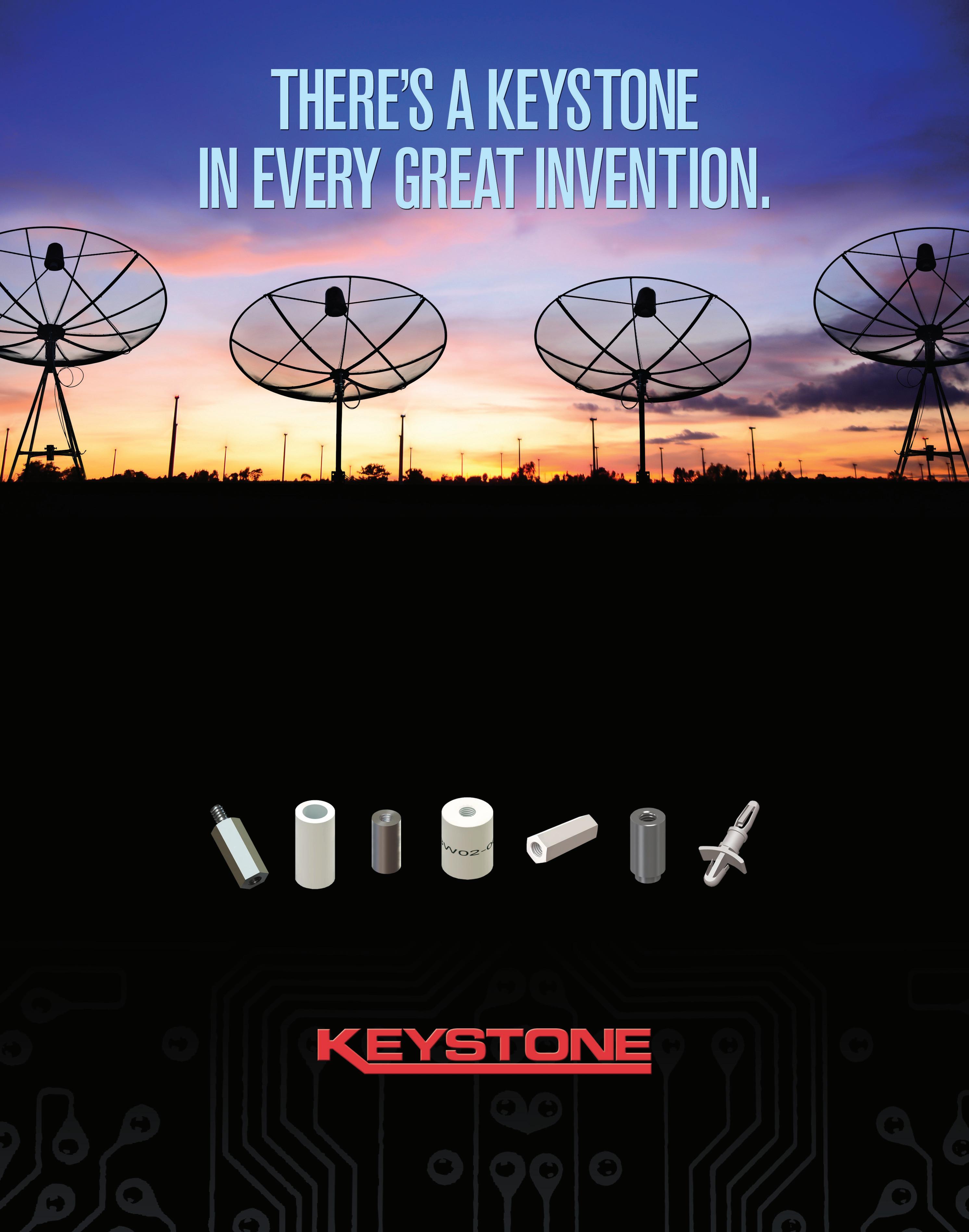

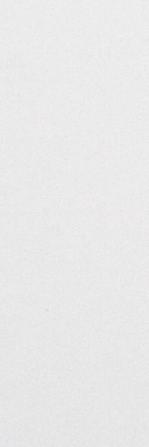
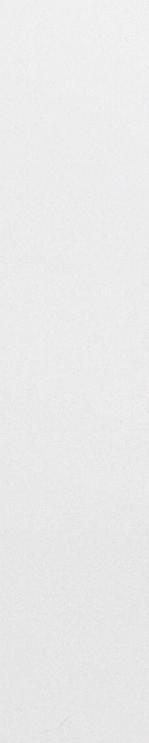


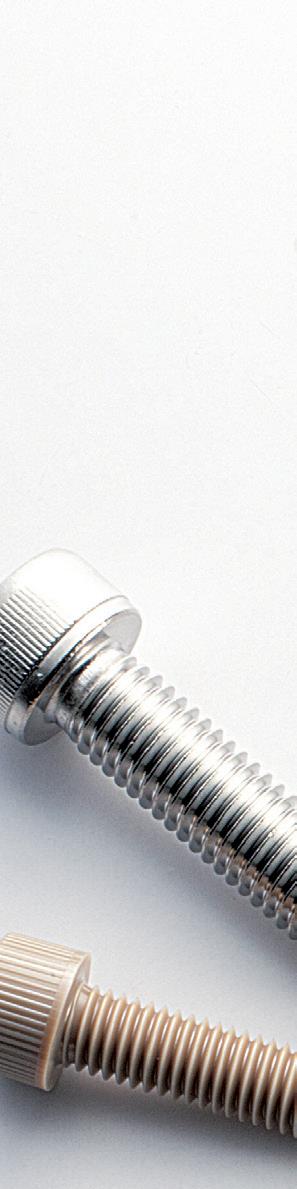
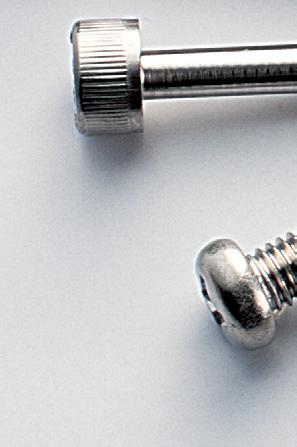
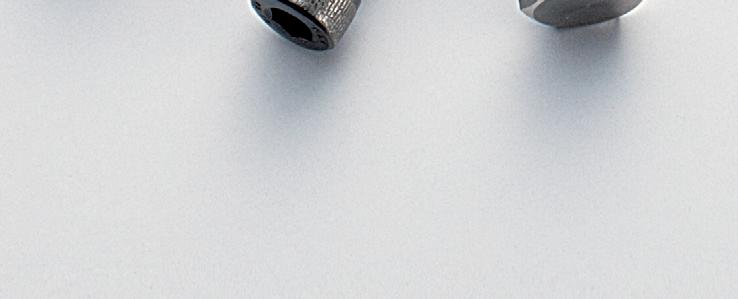

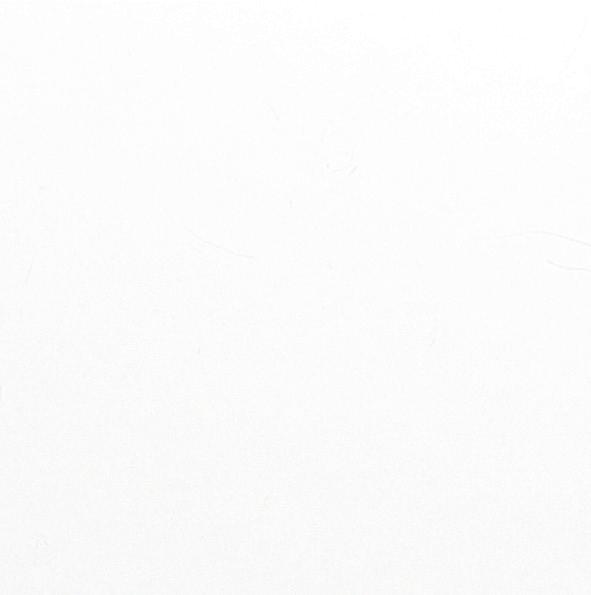
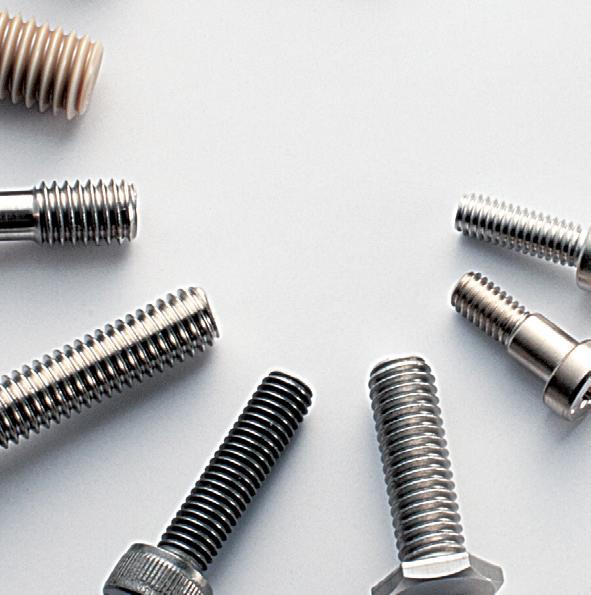
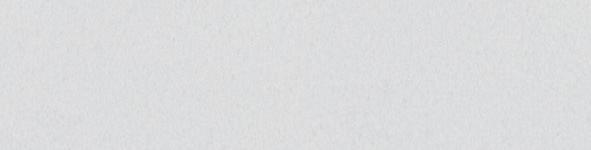

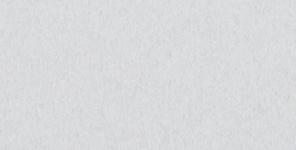

is relevant throughout the operating life of the part and during the initial fabrication of the wire feedthrough (i.e., during thermally catalyzed epoxy curing and the subsequent cool-down process).
Case study 1: MIT-LIGO
The LIGO Team (Laser Interferometer Gravitational-wave Observatory) at MIT required a hermetic sealing method that allowed for a high number of electrical and optical conductors to construct their prototype five-meter vacuum system. The hermetic sealing method must be vacuum clean, bakeable, cost-effective, and use welldeveloped technology.



The conductors in question include optical fiber, instrumentation feedthroughs carrying low and high-voltage connections withstanding up to 1 kV. The traditional method of using glass-to-metal or ceramicto-metal seals was deficient regarding the efficient use of flange space, cost, and lead time. Due to these limitations and the lower conductor density provided by the traditional hermetic sealing method, the LIGO team desired an alternative solution.


Epoxy adhesives, due to their hightemperature resistance, electrical resistivity, tailorable CTE, and flexibility of use, constructed the hermetical seals through potting. Additionally, epoxies can be formulated to meet NASA’s low-outgassing requirements, rendering them suitable for vacuum applications.


Two types were tested: a stainless-steel shell with an epoxy plug and an all-epoxy version with stainless threads. The researchers found that all passthroughs leaked no helium from the factory. However, after thermal cycling and baking, leaks developed in the stainless-steel shell-type seal. The all-epoxy seal did not exhibit these problems.

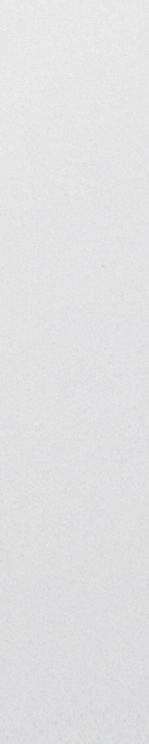
Figure 1 illustrates a cross-section of the all-epoxy seal with stainless-steel threads. It can be hypothesized that the leak present in the stainless-steel shell design post-thermal baking was due to a mismatch of the CTE between the steel and the epoxy, resulting in a loss of adhesion or allowing for the development of leaks.
This work was performed in 1988, and since then, more work has been done. In particular, the inclusion of non-conductive
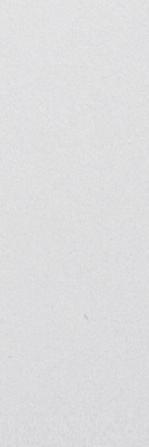
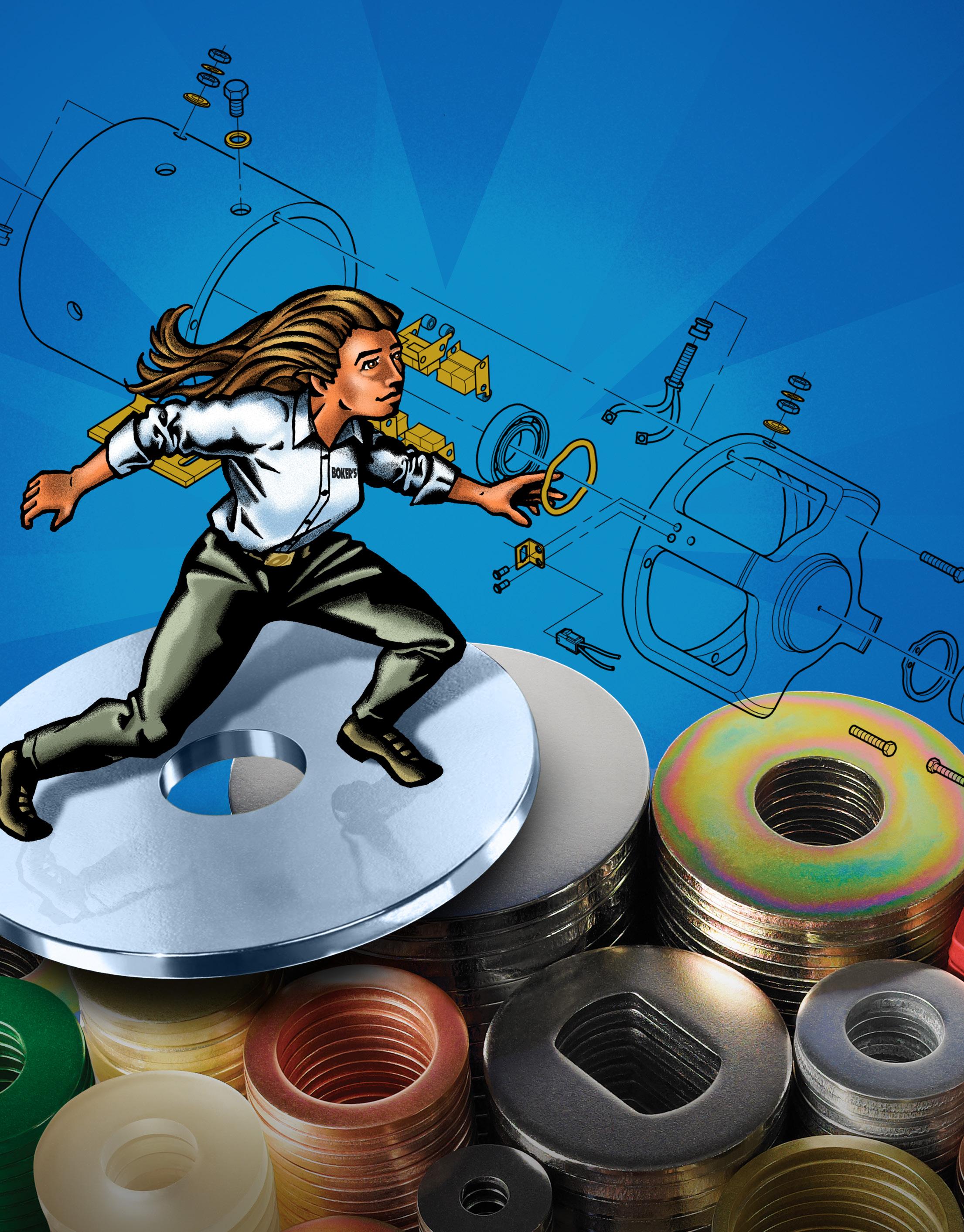
adhesives
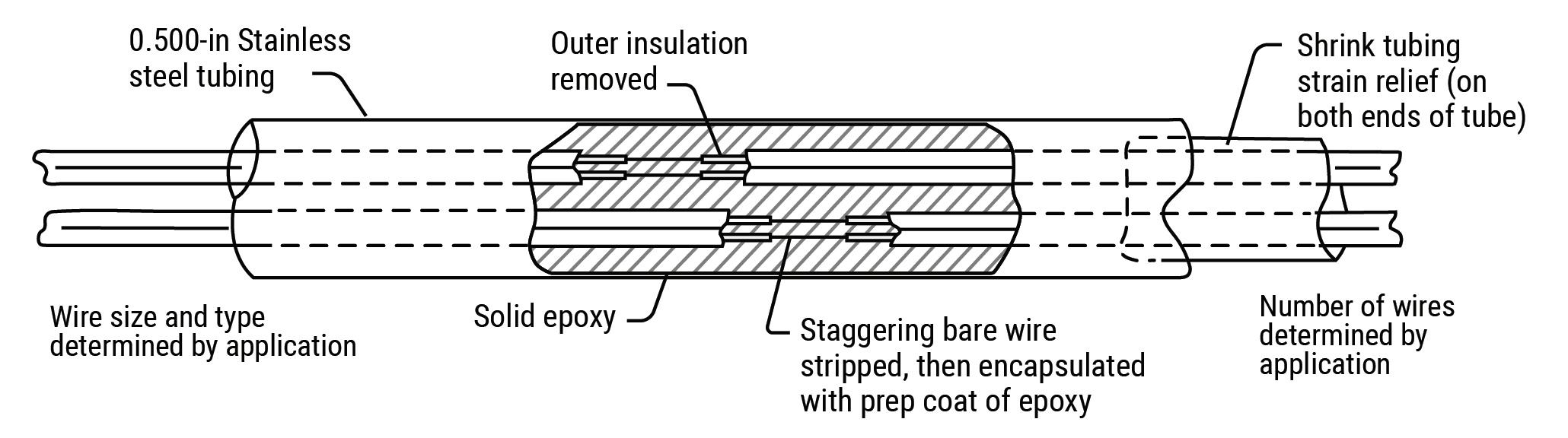
fillers can be added to the epoxy to match its CTE to the seal’s housing. The LIGO team found that the all-epoxy seal with stainless-steel threads provided a cost-effective means to construct hermetic seals for isolated ground co-axial feedthroughs without causing problematic outgassing.
Case study 2: NASA
NASA employed an epoxy potting technique to address a common problem: wicking refrigerant fluid into the insulation of thermocouple wires. A feedthrough within the compressor’s casing can allow for fluid to leak into the adjacent disconnect box outside of the compressor casing — leading to fluid contamination and creating unfavorable operating conditions.
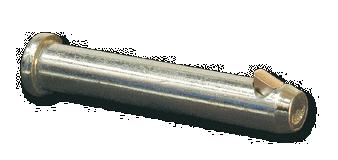


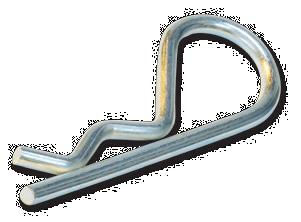
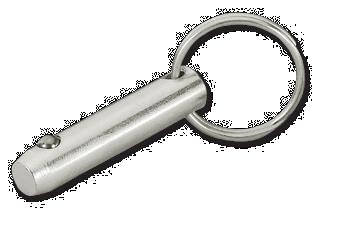

To address this, NASA constructed a customized, epoxy-based, hermetic feedthrough for thermocouple routing on a bank of Worthington compressors. Thermocouples monitor bearing temperatures. The thermocouple is routed into the compressor casing via a hermetic feedthrough and embedded within the bearings. As the casing is filled with R12 refrigerant fluid and operates at an elevated temperature, the selected epoxy was chosen to resist these conditions.
Figure 2 shows the design
epoxy after the thermal couple wires were bonded and sealed with an epoxy prep coat.
Due to the inherent flexibility of this method, NASA employed this design in various other feedthroughs with different wire-types, wire-gauges, and configurations.
The construction of epoxy-based hermetic feedthroughs accommodates a range of applications, including vacuum, pressure, or for the isolation of fluids.
*Referencesavailableuponrequest.
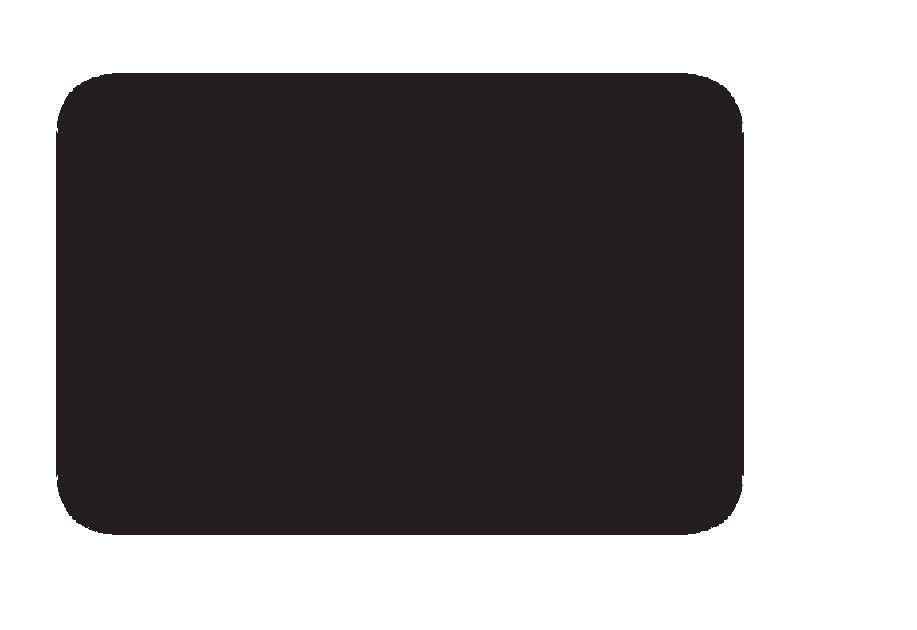



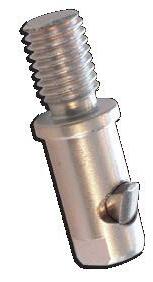
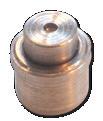
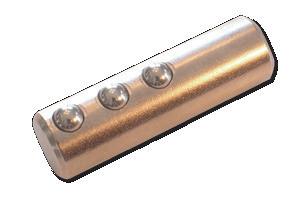
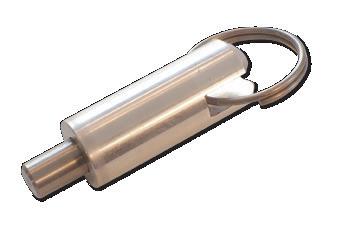
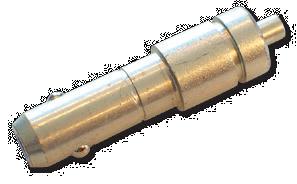



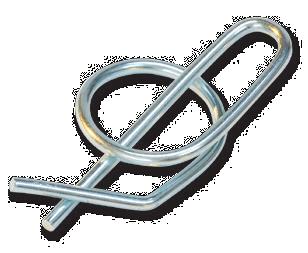


Selecting the Optimal Washer
Flat: Generally used for load disbursement
Tab/Lock: Designed to effectively lock an assembly into place
Finishing: Often found on consumer products

Wave: For obtaining loads when the load is static or the working range is small
Belleville: Delivers the highest load capacity of all the spring washers
Fender: Distributes a load evenly across a large surface area
Shim Stacks: Ideal for simple AND complex applications
Boker’s Inc.
3104 Snelling Avenue
Minneapolis, MN 55406-1937
Phone: 612-729-9365
TOLL-FREE: 800-927-4377
(in the US & Canada)
bokers.com
Keystone Electronics Corp.
A World Class Manufacturer of precision electronic components & hardware for over 70 years. Keystone’s design and engineering experts are fully integrated with their in-house precision tool & die division supported by advanced manufacturing systems to produce close tolerance Stamping, Machining, Assembly, CNC and Injection Molded parts.
Keystone utilizes state-of-the-art software to support the thousands of standard products found in their Product Design Guide M70 and Keystone’s Dynamic Catalog on-line.
Product Overview: Battery Clips, Contacts & Holders; Fuse Clips & Holders; Terminals & Test Points; Spacers & Standoffs; Panel Hardware; Pins, Plugs, Jacks & Sockets; Multi-Purpose Hardware.
As an ISO9001:2015 certified manufacturer, Keystone’s quality control system, responsive customer service and custom manufacturing division can meet your challenges with a standard or custom design solution.
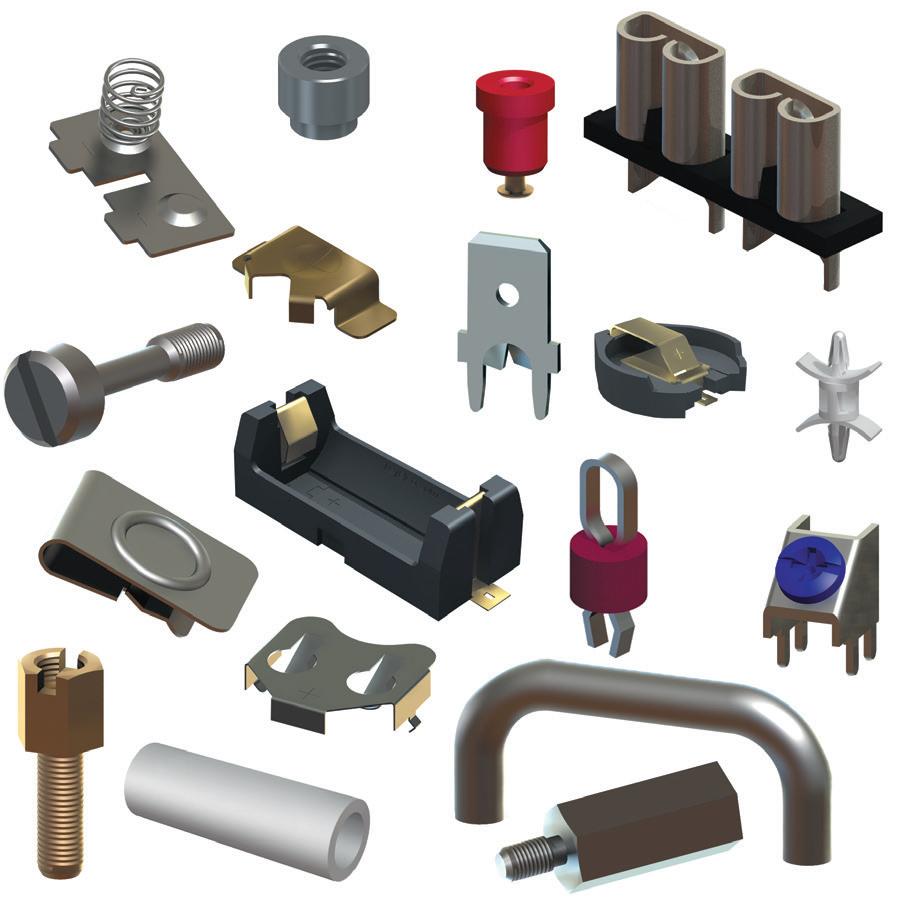
www.keyelco.com
www.keyelco.com
NBK Acquired Solid Spot’s Plastic Fastener Business and Expanded Lineup
NBK is a manufacturer of Specialty Screws including Plastic Fasteners. In this April, NBK acquired Solid Spot LLC’s plastic fastener business and then, more various product lineup are available such as PEEK, RENY, PC, PVDF, PTFE, POM, etc.
NBK manufactures not only plastic screws but also low profile (low head), miniature size(less than M3), vacuum application, anti-galling, chemical resistance, non-magnetic, and more.
Flexible customization is available.

Assemble Faster with SLIC Pins
Pin and Cotter All-In-One
Eliminates Cotters, Clips, Nuts
Speeds Assembly Time
No Tools Needed
Safer Retention, More Secure
As Strong as Corresponding Cotters
The SLIC Pin from Pivot Point features a strong, springloaded plunger that acts as an automatic cotter. Upon insertion, the plunger automatically ramps down to pass through the application, springing back up to lock the pin in place. More consistent and easier to install, SLIC Pins eliminate the wasted motion to install a cotter, clip or nut. With separate pin/clip systems, clips can be mis-installed, forgotten altogether, or fall off later. The one-piece design of a SLIC Pin eliminates those risks, reducing product failures in the field and leading to a more consistent product. Manufactured on automated equipment, SLIC Pins are affordable, making them an ideal solution for optimizing high-volume assembly.
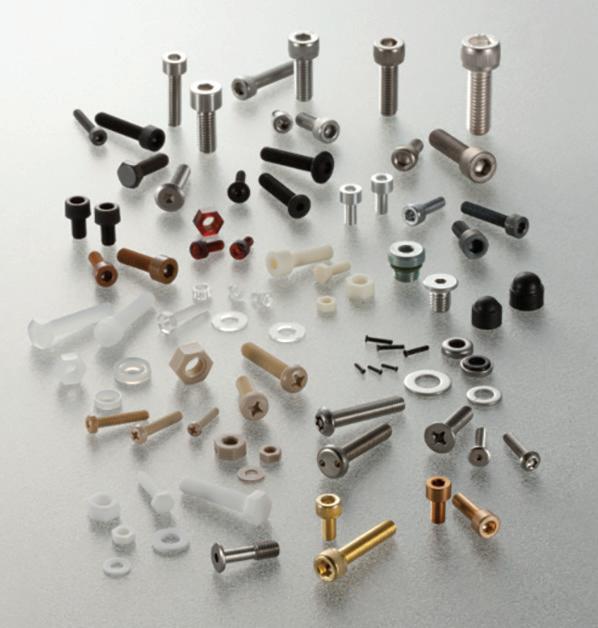
Phone: 484-685-7500
https://www.nbk1560.com/en-US/
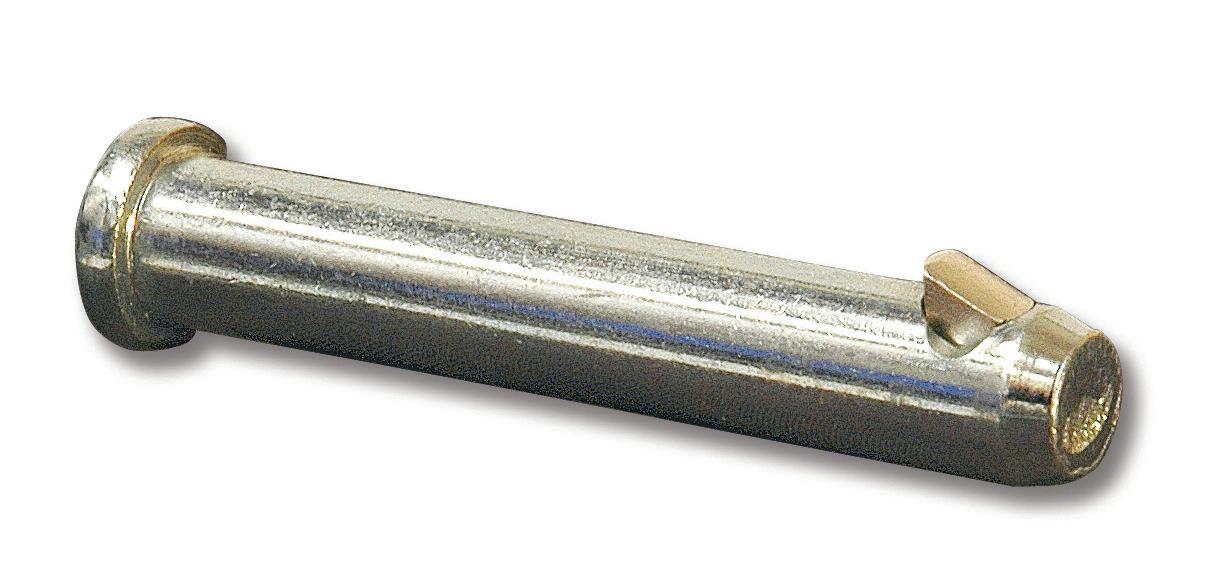
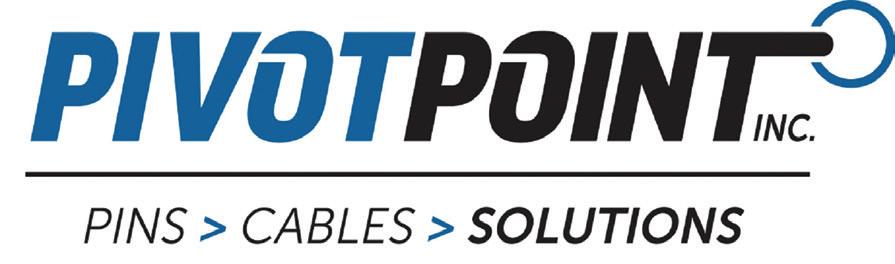
Tens of millions of SLIC Pins are installed each year, touching every industry and saving countless hours.
Explore SLIC in your application today.