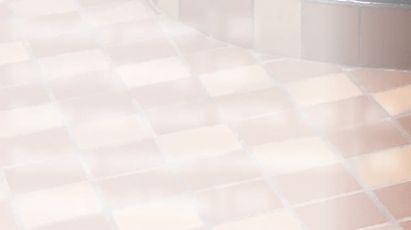
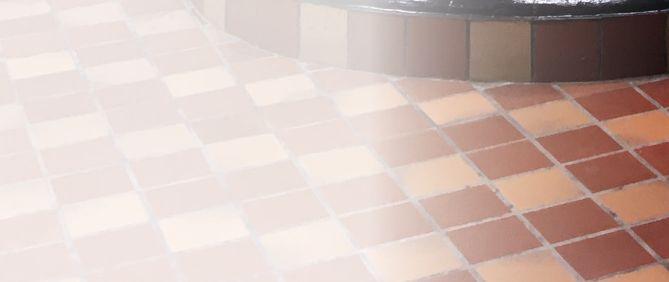
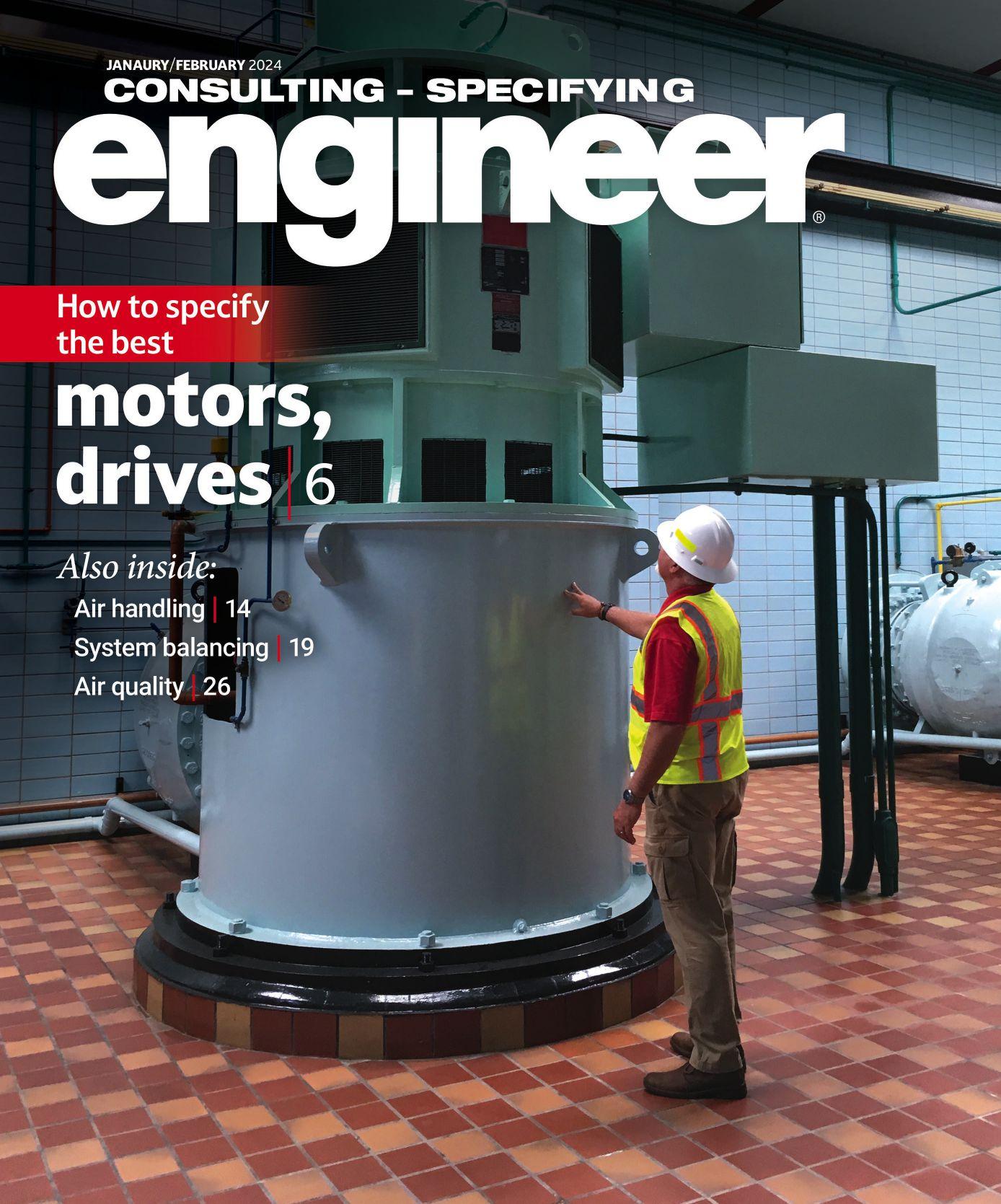
The NPF Advantage: The NPF heats water by burning the gas in a sealed combustion heat exchanger, completely isolated from the airstream. The heated water is then pumped through a hydronic heat exchanger that gently transfers the heat into the air. The fully enclosed Ultra-Low NOx premix burner provides extremely quiet operation, high efficiency of 97% AFUE, and allows for an industry-leading variable capacity that can modulate down to 15% for a next-level comfort experience.
Explore the new NPF at Navieninc.com.
Maintaining CO2 levels below 1000ppm in classrooms is critical to the well-being, productivity, and comfort of students. Belimo room sensors provide real-time air quality monitoring with an intuitive CO2 LED traffic light system, making it easy to verify that the room environment is healthy and comfortable at a glance. Featuring dual channel auto-calibration, altitude and pressure compensation, Belimo room sensors deliver reliable, accurate CO2 readings without the need for manual tuning. Setup is quick and easy using the Belimo Assistant App, which communicates with the sensors via NFC. Use Belimo room sensors to ensure a safe and healthy learning environment for students of all ages.
Belimo’s room sensors accurately measure temperature, humidity, dew point and CO2 Available with or without ePaper touch display.
Are you striving for more sustainable data center solutions?
Liquid cooling keeps your equipment at the perfect temperature, preventing unnecessary energy consumption and reducing your carbon footprint. Danfoss solutions and expertise can help you design and create cutting-edge liquid cooling technology.
Unmatched portfolio and expertise in missioncritical applications.
5 | Thirteen ways to meet energyefficiency goals in buildings
A new year presents the opportunity to focus on innovation
6 | How do you specify the best motor? It depends
Selecting the most appropriate motor depends on many things for an engineer
14 | How to design for cost-effective air handling redundancy
Redundant or standby air handling units are highly beneficial
19 | HVAC system balancing reports: A roadmap to effective design
Testing and balancing reports are key tools to identify issues and create effective solutions
JANUARY/FEBRUARY 2024
26 | Industrial and commercial air quality design considerations
An introduction to the Industrial HVAC Design Guidelines for Commercial HVAC Design Engineers
30 | Do you know the vital requirements for standby power?
Providing power to a building or load when utility power is lost is critical for a facility to support vital operations
35 | How to keep smart lighting from being stupid
Engineers to understand the pitfalls and problems that may come with smart lighting
42 | How to utilize suites under NFPA 101 requirements
Suites allow for operational flexibility in health care facilities under NFPA 101 requirements
46 | Understanding compartmentation as a passive fire safety technique
NFPA 101 outlines compartmentation requirements that are important to prevent the spread of fire and smoke.
55 | Adaptability, sustainability important for office building design
Key trends in the design of office buildings encompasses environmental regulations, the “flight to quality” and the evolving nature of hybrid workspaces
6
ON THE COVER:
This is one of six 2,500-horsepower motors driving three-stage vertical turbine pumps providing 65 million gallons per day of raw water from Lake Huron to water treatment plants several communities. Courtesy: Lockwood Andrews & Newnam Inc.
ENGINEER copyright 2024 by CFE Media, LLC. All rights reserved. CONSULTING-SPECIFYING ENGINEER is a registered trademark of CFE Media, LLC used under license. Circulation records are maintained at CFE Media, LLC, PO Box 348, Lincolnshire, IL 60069. Telephone: 630-571-4070. E-mail: cse@omeda.com. Publications Mail Agreement No. 40685520. Return undeliverable Canadian addresses to: PO Box 348, Lincolnshire, IL 60069. Email: cse@omeda.com. Rates for nonqualified subscriptions, including all issues: USA, $120/yr; Canada/Mexico, $150/yr (includes 7% GST, GST#123397457); International air delivery $260/yr. Except for special issues where price changes are indicated, single copies are available for $30 US and $35 foreign. Please address all subscription mail to CONSULTING-SPECIFYING ENGINEER, PO Box 348, Lincolnshire, IL 60069. Printed in the USA. CFE Media, LLC does not assume and hereby disclaims any liability to any person for any loss or damage caused by errors or omissions in the material contained herein, regardless of whether such errors result from negligence, accident or any other cause whatsoever.
Alan Jones | senior director of product management, Xylem
Mike Licastro | training & education manager for commercial building services and the Little Red Schoolhouse, Xylem
Addressing decarbonization challenges through hydronic HVAC systems
A wave of new building codes, policies and regulations are driving change and creating new challenges for today’s commercial building market. In the quest to build better, engineers, architects and building owners are embracing modern solutions that advance sustainability and decarbonization.
As the largest contributor of CO2 emissions in commercial building operations globally, reevaluating HVAC system design is at the forefront of this movement. Amidst rising energy prices and new legislation escalating demand for more efficient buildings, modern hydronic systems present a viable solution to reduce HVAC systems’ negative impact on the environment and promote renewable energy sources.
With more than a century of success, hydronics is a demonstrated heating and cooling solution that operates on a closed loop whereby the same water is recirculated and heated again. When it comes to shrinking carbon footprint and maximizing return on investment, water is a winner and adaptable to all technology.
What’s more, the legislative, cultural and economic incentives encouraging electrification and decarbonization, and the accompanying demand for low-energy and net-zero buildings, collectively represent one of the greatest opportunities for the U.S. hydronics market in decades.
Bell & Gossett explores all of this and more in its white paper on the value of hydronics as the modern heating and cooling system of choice.
As part of its Building Better platform representing Bell & Gossett’s commitment to advancing sustainability, decarbonization and efficiency across all aspects of the built environment, Bell & Gossett remains an industry thought leader in fostering collaboration to address modern building challenges and shape the systems of the future.
Download the paper: http://tinyurl.com/8ecbz8y5
AMARA ROZGUS, Editor-in-Chief/Content Strategy Leader ARozgus@CFEMedia.com
CHRIS VAVRA, Web Content Manager CVavra@CFEMedia.com
ANNA STEINGRUBER, Associate Editor ASteingruber@CFEMedia.com
AMANDA PELLICCIONE, Director of Research APelliccione@CFEMedia.com
MICHAEL SMITH, Creative Director MSmith@CFEmedia.com
DARREN BRUCE, PE, LEED AP BD+C, Director of Strategic Planning, Mid-Atlantic Region, NV5, Arlington, Va.
MICHAEL CHOW, PE, CEM, CXA, LEED AP BD+C, Principal, Metro CD Engineering LLC, Columbus, Ohio
TOM DIVINE, PE, Senior Electrical Engineer, Johnston, LLC, Houston
CORY DUGGIN, PE, LEED AP BD+C, BEMP, Energy Modeling Wizard, TLC Engineering Solutions, Brentwood, Tenn.
ROBERT J. GARRA JR., PE, CDT, Vice President, Electrical Engineer, CannonDesign, Grand Island, N.Y.
JASON GERKE, PE, LEED AP BD+C, CXA, Mechanical Engineer, GRAEF, Milwaukee
JOSHUA D. GREENE, PE, Associate Principal, Simpson Gumpertz & Heger, Waltham, Mass.
RAYMOND GRILL, PE, FSFPE, LEED AP, Principal, Ray Grill Consulting, PLLC, Clifton, Va.
DANNA JENSEN, PE, LEED AP BD+C, Principal, Certus, Carrollton, Texas
WILLIAM KOFFEL, PE, FSFPE, President, Koffel Associates Inc., Columbia, Md.
WILLIAM KOSIK, PE, CEM, LEGACY LEED AP BD+C, Lead Senior Mechanical Engineer, kW Mission Critical Engineering, Milwaukee
KENNETH KUTSMEDA, PE, LEED AP, Engineering Manager, Jacobs, Philadelphia
DAVID LOWREY, Chief Fire Marshal, Boulder (Colo.) Fire Rescue
JASON MAJERUS, PE, CEM, LEED AP, Principal, DLR Group, Cleveland
GREGORY QUINN, PE, NCEES, LEED AP, Principal, Health Care Market Leader, Affiliated Engineers Inc., Madison, Wis.
BRIAN A. RENER, PE, LEED AP, Principal, Electrical Discipline Leader, SmithGroup, Chicago
SUNONDO ROY, PE, LEED AP, Director, Design Group, Romeoville, Ill.
JONATHAN SAJDAK, PE, Senior Associate/Fire Protection Engineer, Page, Houston
RANDY SCHRECENGOST, PE, CEM, Austin Operations Group Manager/Senior Mechanical Engineer, Stanley Consultants, Austin, Texas
MATT SHORT, PE, Project Manager/Mechanical Engineer, Smith Seckman Reid, Houston
MARIO VECCHIARELLO, PE, CEM, GBE, Senior Vice President, CDM Smith Inc., Boston
RICHARD VEDVIK, PE, Senior Electrical Engineer and Acoustics Engineer, IMEG Corp., Rock Island, Ill.
TOBY WHITE, PE, LEED AP, Associate, Boston Fire & Life Safety Leader, Arup, Boston
APRIL WOODS, PE, LEED AP BD+C, Vice President, WSP USA, Orlando, Fla.
JOHN YOON, PE, LEED AP ID+C, Lead Electrical Engineer, McGuire Engineers Inc., Chicago
To meet sustainability and energy-efficiency goals in commercial buildings, mechanical, electrical, plumbing (MEP) and fire protection engineers play a pivotal role. The coming year presents another opportunity for professionals to elevate their practices, incorporating innovative technologies and methodologies to enhance energy and resource efficiency.
2. Power factor correction: Integrate power factor correction devices to enhance system efficiency.
3. Smart grid integration: Explore opportunities for smart grid integration to optimize electricity consumption.
The convergence of these engineering disciplines can yield significant gains in optimizing building performance and reducing environmental impact. Manufacturers are meeting and exceeding efficiency goals, making it less difficult to provide the right system to building clients.
Mechanical engineers:
1. Variable refrigerant flow (VRF) systems: Consider implementing VRF systems, which offer precise control over heating and cooling.
2. Energy recovery ventilation (ERV): Integrate ERV systems to recover and reuse energy.
3. High-efficiency boilers and chillers: Specify boilers and chillers with high-efficiency ratings.
4. Building automation systems (BAS): Implement advanced BAS to enable real-time monitoring and control of HVAC systems.
Electrical engineers:
1. LED lighting systems: Transition to energy-efficient LED lighting systems.
4. Renewable energy integration: Evaluate the feasibility of integrating renewable energy sources.
Plumbing engineers:
1. Water-efficient fixtures: Specify water-efficient fixtures and appliances.
2. Greywater systems: Explore greywater systems.
3. Rainwater harvesting: Integrate rainwater harvesting systems.
Fire protection engineers:
1. Water mist systems: Consider water mist fire suppression systems.
2. Occupancy-based design: Employ occupancy-based fire protection design strategies.
The efforts of MEP and fire protection engineers hold the key to achieving greater energy and resource efficiency. The new year presents an opportunity for engineers to spearhead transformative change in the way commercial buildings are designed, ensuring a more sustainable and resilient future.
This content was enhanced with ChatGPT. Due to the limitations of AI tools, all content was edited and reviewed by our content team. cse
Jeff Thomas, PE, CEM, CEA, CHC, Lockwood Andrews & Newnam Inc., Houston
Navigating the complexities of motor selection is about more than matching horsepower. It’s about deciding what makes the most strategic sense for the entire electrical distribution system. Choosing the right motor hinges on its intended application, load requirements, available voltage and the surrounding environment. Whether it’s a corrosive setting, a high-temperature zone or an air conditioner in an office building, the motor needs to be up to the task.
Motors come in many different sizes and configurations, from tiny, precision control motors to immense propulsion motors. No matter the size, they all share common characteristics and operating parameters.
The history of motors is closely linked to the evolution of electricity. In 1821, Michael Faraday made a pivotal discovery when he found that a current-carrying conductor could rotate around a magnet, essentially creating the first motor. Commercialization started in the late 19th century when Nikola Tesla pioneered the development of the
alternating current (AC) motor while Thomas Edison aided in the invention and commercialization of the direct current (DC) motor.
DC motors are easier and cheaper to control than AC motors. Controlling the speed and direction of a DC motor is simpler and more cost-effective than AC motors, especially in scenarios where precise motion control is required.
DC motor functions include:
Higher starting torque: Generally speaking, DC motors provide a greater torque at startup than comparable AC motors. In a DC series motor, the field is connected in series with armature. This connection allows the torque to be to be proportional to the square (hyperbolic) of the current, making them suitable for applications that require a strong initial force.
Ability to start and stop quickly: Being able to control the speed of a DC motor is advantageous in applications that demand precise motion control, such as in robotics or conveyor systems.
Good at reversing: The direction of rotation in a DC motor can be easily reversed by simply changing the polarity of the power supply. This is useful for bidirectional operations such as elevators, baggage claim belts and other similar applications
Variable speeds with voltage input: The speed of a DC motor can be varied smoothly from zero to its maximum, providing dynamic control options. By adjusting the voltage input, you can directly control the motor’s speed, making it versatile for various applications.
Entrenchment in the control space: DC motors are foundational in control systems because of their ease of control and reliability. Many legacy systems, particularly in industries like manufacturing, still rely heavily on DC motor setups.
Use in emerging markets: There’s surging interest in DC motors in the fields of automotive drives, particularly in electric direct compatibility of DC motors with battery-driven systems and photovoltaic sources. Without the need for inversion makes them ideal candidates for these developing areas.
A commutator and brushes to achieve an alternating current internally to the motor: These brushes are sacrificial. The carbon they are typically made from creates a small arc every time the commutator goes by. This makes them a bad choice for explosive environments and each arch removes a small amount of the brush. They are usually spring loaded to maintain contact with the commutator as they age. Research varies here, but between 1,000 and 3,000 hours on a set of brushes is about normal. One alternative is brushless DC motors. These use a different architecture which requires the alternating magnetic fields to be created externally to the motor. In other words, a controller is required to alternate the DC voltages supplied to the field magnets of the motor. This adds complexity, but also control. Hard disk drives are a common user of brushless direct current motors.
AC motors are robust, well entrenched and versatile machines with a track record in many industrial applications. They are commonly used in air handlers, pumps, blowers and vacuum systems. Basically, anywhere there is need for continuous rotation to produce work of some kind. Their inherent reliability and compatibility with existing systems make them a “go-to” choice. Strengths include:
They are very reliable and known for their long-lasting durability: Their simpler construction, with fewer moving parts, often means a longer life span with fewer breakdowns. For example, while AC and DC motors typically have a rotor, a stator, bearings and a housing, the DC motor adds a commutator and brushes. The commutator is essentially a series of contacts spaced around the shaft that the brushes make contact (commute) with as they pass. This action effectively chops the DC current, reverses it and sends alternating pulses to the rotor. This induces a changing magnetic field that interacts with the stator magnets, causing rotation. This is exactly how an AC motor works, we
just leave all the chopping and reversing out by providing an alternating current source.
Up to a certain size, they’re disposable: Like many commodity appliances, it’s cheaper to replace smaller motors than to have them rewound or repaired. For example, how often do you repair the motor in a tabletop fan? Even the blower in the air handler of many small to medium units is simply replaced rather than repaired. And let’s be realistic — most equipment motors run to fail with very little to no maintenance. Bearings are sealed, totally enclosed fan-cooled (TEFC) motors have no accessible parts and they seem to run forever. Until they stop.
They have a large installed base: AC motors have dominated many industries for decades and are used in conveyance, air-handlers and water pumps, for example. This widespread use means lots of knowledge, spare parts and expertise are available.
Able to match existing infrastructure: In many facilities, the electrical infrastructure is set up to support AC power. This makes integrating AC motors straightforward without needing converters.
They have variable speeds with frequency input: An AC motor’s speed can be controlled by adjusting the frequency of the input power. Variable frequency drives (VFDs) are commonly seen coupled with motors in a variety of applications to provide precise control over motor speed and torque. VFDs also provide significant energy
2: Located in a commercial mechanical room, 15 horsepower motors are used for chilled water pumps. Courtesy: Lockwood Andrews & Newnam Inc.
• Learn about the typical types of motors: induction, synchronous, stepping, specialty.
• Know the NEMA motor types and their main differences
• Consider the client’s requirements and general trade-offs when selecting a motor.
savings by allowing the motor to run where it needs to rather than at full speed. According to some studies, electric motors are responsible for about 45% of the total consumption of electric energy. If we focus the analysis on the most energy-consuming sector, the industrial one, the percentage attributable to motors rises to around 67%. It becomes easy to see why energy conservation through motors is important.
With designs tailored for specific tasks, motors are essential components in various applications. The choice is usually between induction or synchronous motors. The debate over induction versus synchronous motors arises from their distinct operational characteristics, with operators weighing factors such as efficiency, cost, maintenance and application-specific performance to determine the most suitable motor for a given task.
So, which to choose? Each has its own uses and advantages.
Induction motors are asynchronous, which means the rotor (the spinning part inside the motor) doesn’t spin at the same speed as the magnetic field created by the stator (the stationary part outside the rotor). It is always a bit behind.
The rotor current is induced by the stator current. The rotor doesn’t get its electric current directly. Instead, the current in the stator produces a changing magnetic field, which then creates (or “induces“) a current in the rotor, making it spin.
Induction motors, therefore “slip.” Because the rotor is always trying to catch up to the stator’s magnetic field but never quite does, there’s a small difference in their speeds. This difference is called “slip.”
Induction motors operate at a lagging power factor. Simply, the power used by the motor doesn’t perfectly match the power coming in from the electrical supply. This mismatch is referred to as a “lagging” power factor.
Induction motors are less expensive to manufacture and maintain. Because they don’t have certain parts that wear out quickly, like brushes or commutators that makes them simpler, more durable and cheaper to produce and to keep running.
Most motors in commercial applications are induction motors. Because of their cost-effectiveness, reliability and simplicity, induction motors are a prime choice for many commercial tools and machines.
Synchronous motors, in contrast, maintain a steady speed regardless of load, running in synchronization with the power source. They are designed for precision, efficiency and improved power management, but they often come at a higher initial cost.
Unlike induction motors, synchronous motors often get their rotor current from external sources or magnets, rather than relying on induction from the stator. Synchronous rotors turn in sync with the stator frequency. The rotor’s speed matches exactly with the speed of the stator’s magnetic field, which means there’s no difference or “slip” in their speeds.
Small horsepower synchronous motors are used for precision control (timing). When precise movement or timing is essential, like in clocks or some manufacturing processes, these motors are ideal because they move in sync with the electrical supply’s frequency.
VFDs and enclosures ensured reliable motor performance
Lockwood Andrews & Newnam Inc. (LAN) recently completed a design project for a large municipal water authority in Texas. The project involved moving treated drinking water from a large ground storage tank to its water distribution system. This facility accepted finished water from the water district and pumped it out to the city’s distribution piping that serves the customer base. In a typical installation, water is provided at various points in the system and used by many customers throughout the city and surrounding areas. The distribution is very much like the electrical grid.
The basic installation and site requirements dictated that the nine motors deemed necessary for this operation had to be 400 horsepower, 480-volt, 1,800 revolutions per minute motors. Working with the client, the LAN team defined the important factors for installation. The first was motor protection. LAN wanted vibration and temperature sensors to monitor the large motors, considering their use case and importance in the system. The loss of any of the client pumps could mean long lead times if any of the motors had to be replaced and hamper the system. This would have operational impacts on their distribution system and most significantly, on customers throughout the city.
‘ Another key requirement was satisfying the regulations of the local electric provider.’
Now, with the remote monitoring of these sensors, the city is alerted if any one motor is showing any signs of distress or premature failure so corrective actions can be taken before there is a full malfunction.
LAN also recommended that each motor management unit include a variable frequency drive (VFD) that could also monitor temperatures and vibrations. By keeping the control and monitoring elements integrated within the VFD, it keeps the responsibility for driving and protecting the motor within the realm of a single manufacturer. This is critical when services are required for routine maintenance or repair.
Another key requirement was satisfying the regulations of the local electric provider. In this case, the VFD had to maintain acceptable total harmonic distortion in accordance with the standard set for electrical power systems by the Institute of Electrical and Electronics Engineers (IEEE 159). To achieve this, LAN selected 18-pulse drives for this project.
Finally, to protect the VFDs and motors from the elements, LAN constructed a simple metal building over the existing pump cans to accommodate the new pumps and motors. The pump room is ventilated, while the electrical room is air conditioned to prolong the life of all the equipment, as well as provide a sheltered location for maintenance and repair.
Synchronous motors are more energy efficient because they often convert more of the electrical power into useful mechanical power, wasting less energy. They operate between a unity (1.0) power factor and 0.8 leading power factor. This means they can better match the power they use with the power they receive or even give some power back to the electrical grid, helping to balance electrical systems and potentially reduce costs. While they offer benefits like precision and efficiency, they usually cost more initially than induction motors.
NFPA 70: National Electrical Code (NEC) provides the standards for determining the electrical load for a specific installation and the appropriate sizing and safety considerations. The NEC guidelines also detail the proper sizing, protection, control and installation of motors and their associated circuits.
The National Electrical Manufacturers Association (NEMA) also designates motor types based on their torque-speed characteristics:
• Type A: General-purpose motors, with medium starting torque and normal starting current. Suitable for most applications.
• Type B: Standard design with high slip, low starting torque and low starting current. Common in applications like fans and pumps.
• Type C: High starting torque with low starting current. Often used with hard-to-start load applications such as compressors.
• Type D: High slip motors with high starting torque. Commonly used in applications like hoists, oil well pumps and punching presses.
• Type E: High-efficiency version of Type B motors.
Motor enclosure types: Each motor is also housed in different protective enclosures fitted to the specific operational environments. These different types of enclosure ensure motor safety, longevity and optimal performance. They are:
Open drip-proof: Allows for ventilation through the motor but is designed to prevent liquids and solids (like water drops) from entering from above or the sides.
TEFC: Completely sealed against external contaminants. It uses an external fan to cool the motor, which blows outside the motor casing without interacting with internal components.
Totally enclosed nonvented: Like TEFC, but doesn’t have the external cooling fan, relying on the motor’s housing to dissipate heat. It’s suitable for applications where minimal contamination is possible.
Totally enclosed air over: Designed to be cooled by external airflow, often from a system in which the motor is installed, like a fan blade that blows air over the motor.
Totally enclosed wash down: Suitable for environments requiring regular cleaning or washing, preventing water and contaminants from entering the motor during washdown processes.
Explosion-proof: Built to withstand and contain internal explosions without causing external hazards, commonly used in environments with flammable gases or dust.
Hazardous location: Like explosion-proof casings, these enclosures are designed for locations with specific hazardous conditions and have certain design attributes unique to the particular hazard they’re addressing. There are also several classifications of hazardous locations motors. Class I deals with gases and vapors, Class II with dust and Class III with fibers and “flyings” (particles, debris, dust).
Motor design letter classification: NEMA uses a motor design letter classification system to categorize the torque and currents for motors.
These letters (design A, B, C, etc.) give insight into a motor’s performance, particularly its starting torque, starting current and slip. NEMA tables detail how these ratings relate to energy and horsepower.
Other factors to consider
The duty cycle: The duty cycle describes the operation time and rest period of a machine or system. For continuous duty, the motor runs continuously without stopping. Periodic duty consists of identical run and rest cycles with constant load. The motor starts, runs for a specific period, stops, rests and then the cycle repeats. Short-time duty means the motor runs continuously with a constant load for a short time and doesn’t repeat once the operation is completed. Most commercial applications, fans, pumps, etc. are continuous duty motors.
Service factor and insulation class: The service factor is a motor’s cushion for temporary overload; for instance, a service factor of 1.2 means the motor can handle 20% more power than its rated capacity without incurring damage. Insulation class tells us how much heat the motor’s internal wiring insulation can withstand before deteriorating, with each class (like A, B, F, H) indicating a specific temperature limit.
For motors, understanding the parameters of efficiency, slip and the power factors is vital for ensuring efficient motor operation, optimizing performance and managing operational costs.
Efficiency: Efficiency is the ratio of the useful power output (mechanical power) to the power input (electrical power) of the motor. A motor with higher efficiency converts a larger portion of the electrical energy it receives into mechanical energy, wasting less as heat. It’s desirable to use high-efficiency motors, especially in continuous operations, as they reduce energy costs in the long run.
Slip: In induction motors, there’s a phenomenon where the rotor’s frequency lags behind the stator frequency (F). This delay, which is linked to the physical attributes of the motor’s components, is termed “slip.” Slip is crucial for torque production in an induction motor. A motor with zero slip (i.e., rotor speed equals the magnetic field speed) would produce no torque. In typical scenarios, the slip can range anywhere from 5% down to a mere ½%, shedding light on the intricate balance of power and performance in motor design.
Power factor: For motors, maintaining a highpower factor ensures optimal efficiency and reduced electrical losses.
The power factor is the cosine of the phase angle between the current and voltage in an AC circuit. It measures how effectively electrical power is converted into useful work. It ranges between 0 and 1.
A power factor of 1 means all the electrical power is effectively converted into work, while a lower power factor indicates inefficiencies and results in a higher current draw for a given power output.
It’s important to note that a low power factor can lead to increased power loss in the distribution system and can incur additional utility costs. Correcting the power factor (using capacitors, for instance) can lead to more efficient power use and reduced electricity costs.
Supplementary components: Other things to consider include mounting methods, lifting rings for larger motors, sensors for monitoring things remotely, availability of service and spare parts, familiarity with the maintenance staff, standardization of units across a large enterprise and other logistical concerns.
The systems and devices employed to initiate, control and protect electric motors are varied. Picking the right one depends on the purpose.
Motor starters are used to safely start and stop a motor by providing the necessary initial current and then cutting off or limiting it as needed. These are the different types:
Direct online starters are suitable for small motors. The motor is directly connected to the power supply. In smaller motors, this is often a simple capacitor to provide that extra boost to get things running. Many an air conditioner has failed in the hottest part of the summer due to a bad capacitor. Fortunately, they’re relatively inexpensive and easy to replace.
Star-delta starters turn the motor on in a “star” configuration for reduced voltage and current, then switch to “delta” for normal operation. Used for larger motors to reduce starting current.
Soft starters gradually increase the voltage to the motor, ensuring a smooth start and reduced initial current. VFDs fall into this category.
‘ For motors, understanding the parameters of efficiency, slip and the power factors is vital for ensuring efficient motor operation, optimizing performance and managing operational costs. ’
u Motor selection is a complex, detailed process that requires the engineer to understand the application.
While traditional motor starters turn a motor on or off, a VFD controls the speed of the motor by varying the frequency of the supplied voltage. This reduces the mechanical and electrical stresses on a motor during startup, leading to extended equipment life and reduced maintenance costs. This functionality means that a VFD not only starts and stops a motor, but dynamically adjusts speed and torque during operation. VFDs can also be integrated so they can be controlled and monitored remotely, allowing operators to adjust motor operations and receive performance data or alerts from a distance. In many applications, VFDs can replace or work with traditional motor starters to provide more precise and energy-efficient control.
leading to more efficient power usage and potential cost savings on electricity bills.
Overall, selecting the appropriate motor for industrial applications is extremely important. The right motor choice guarantees optimal efficiency, leads to energy savings and reduces operational costs. The right motor ensures the reliability of processes, reducing unforeseen downtimes that can disrupt production schedules. By minimizing wear and tear through the proper motor selection, maintenance intervals can be extended, leading to further cost savings.
u There are many factors to consider before specifying a motor, such as guidelines, regulations and energy efficiency requirements.
VFDs are most used in pumping systems; heating, ventilation and air conditioning fan and blower systems; conveyor belts; and other machinery where variable speed and torque are beneficial. They can improve the power factor by ensuring that the motor only draws the current it needs,
Ultimately, the right motor can extend the equipment’s overall life span, ensuring a better return on investment. In the end, the correct motor selection directly impacts productivity, operational expenses and the financial health of an industrial operation. cse
Jeff Thomas, PE, CEM, CEA, CHC, is VP and Business Group Director at Lockwood Andrews & Newnam Inc. MOTORS AND
Lower material and installation costs
Fault resistance for easy cable repairs
Durable and corrosionresistant for project longevity
No burn-through eliminates elbow repairs
Gavin Green, PE, Smith Seckman Reid Inc. (SSR), Nashville, Tennessee; and Lee Nordholm, PE, LEED AP, Smith Seckman Reid Inc. (SSR), Dallas
Redundant or standby air handling units, which include cooling and dehumidification, are highly beneficial
When the operations staff at a facility with critical loads, such as hospitals, research labs or large data centers, gets an alert that air conditioning has stopped in an area, it sets a lot of urgent activity in motion. Technicians rush to the air handling unit (AHU) and begin troubleshooting for the cause. It may be a simple fix or it may involve significant downtime to remedy the situation.
Highly critical facilities that require 2N redundancy, in which there is twice the amount of equipment needed with no single point of failure, may use backup or spare AHUs that can be quickly activated to serve while the problem unit is being serviced. That redundancy comes at a high cost — more mechanical room area, equipment and controls to procure, install and maintain.
Hospitals, large laboratories and some research or industrial facilities can keep going if some reduced level of air conditioning is still available, even if it’s not full cooling. A spare or redundant AHU would accomplish this goal, but the available mechanical space and the project budget often do not accommodate a full spare AHU.
Objectives Learningu
• Become aware of facility types that greatly benefit from maintaining some level of cooling and dehumidification if the air handling unit serving an area is down.
• Understand two equipment arrangements for connecting air handling units and the advantages and disadvantages of each.
• Recognize the nuances and details of how connected air handling units operate in normal versus connected modes.
In the meantime, the occupants begin to experience discomfort, heat-sensitive equipment may begin to overheat or room air pressure relationships, critical to a healing environment, may be compromised. In these situations, minimizing downtime is priority one.
If the problem is in an AHU and the unit has multiple supply fans, air movement can continue. However, if the problem is the cooling coil, cooling and dehumidification may be out of service for an extended time. Temporary room spot coolers can help in some situations but not in rooms that require high levels of filtration, for example. The noise, reduced cooling and distraction of temporary units are not acceptable for the time it may take to replace a fan motor or, even worse, replace a coil. Even if there is no sudden urgency, there are still maintenance tasks that must be done that require the unit to be down, such as cleaning coils and changing filters.
For facilities that need to continue operating but can accept a lower level of service for a limited period of time, is there a more cost-effective solution?
An alternative to full backup AHUs is to connect two AHUs to serve the same areas. Each AHU is sized for some percentage of the total load. The operational intent is that, if one unit goes down for an extended period, the other unit can back-feed the areas served by the down unit to maintain not only air flow but some amount of temperature and humidity control as well. This alternative omits the need for allotting space in the mechanical room and for the installation and maintenance costs for a spare AHU.
While connected AHUs do not provide the full backup capacity of 2N redundancy, they do reduce the number of single points of failure:
• There are two independent air paths.
• If properly planned with the electrical engineer, the two units can be served by different electrical sources, as far upstream as practical (back to
main switchgear if desired). Thus, an electrical outage in the source for one AHU would not result in a total loss of air movement and temperature/humidity control. Further redundancy can be provided by using multiple variable frequency drives (VFDs) on each fan in a fan array. In this arrangement, each fan can be served by a different electrical source path, further removing a single point of total failure. This provides more redundancy than using a VFD for the entire fan array and one standby VFD, in which case one source of electric power can be a single point of failure.
While the idea sounds relatively simple, there are several impacts to the design of the mechanical system. In developing the concept, questions and concerns arise:
• What special components and additional controls will be needed? How much of the connected operation can be remotely activated and how much must be manual?
• What are the unintended consequences? Will operation of connected units result in additional operational concerns on the equipment?
There are two ways to connect two AHUs: a cross-connect arrangement and “twinned” units. This engineering team has designed both types of systems and picked up some lessons learned along the way.
In a cross-connected arrangement, two units are located independently and connected with ductwork. The units could serve different areas or the connecting ductwork could enable both units to serve the same areas. If serving different areas, the units could be sized differently.
In normal operation, each unit operates independently. The supply fans modulate to maintain duct static pressure setpoint, the return fans track the supply fans minus the exhaust/outside air quantity and return dampers modulate to maintain outside air quantity. The control valves for each unit’s coils modulate to maintain the discharge air temperature setpoint for that unit. When in airside economizer, each unit operates independently in damper modulation.
As shown in Figure 1, the cross-connect dampers are normally closed.
FIGURE 1: Schematic layout of multiple air handling systems serving different areas. Control dampers (CD) are indicated for connecting the systems and for prioritizing specific areas as required. Courtesy: Smith Seckman Reid Inc. Twinned units
If one unit goes down, cross-connect mode is manually activated. The cross-connect dampers open to allow the operating unit to serve areas of the downed unit.
Several operational and control changes are needed for this mode:
• The supply fans now must look at duct static pressure of both systems to determine fan operating points.
• Because one unit is now serving two areas, there may be a need to prioritize the areas served for the limited amount of air available. This may require some combination of additional control dampers, closing selected smoke dampers or commanding terminal boxes to close or reduce air flow.
• A big question to consider is what happens to the exhaust fans in both areas. Do they fully stop? Fans serving hazardous areas, such as isolation rooms, must continue to operate. If those fans are in the area of the “off” unit, how does that impact the air balance at the “on” unit? This may require the building automation system (BAS) to poll the operating exhaust fans and provide a new outside air total for return fan operation, since return air flow is often controlled to match the differential of supply air minus exhaust/outside air.
• This is further complicated if there is exhaustto-outside air heat recovery. Additional controls would be needed to isolate the heat recovery component of the down unit.
• Because the units serve different areas and possibly different smoke compartments, the response of the AHUs to a fire alarm may change. For example, looking at the cross-connect in Figure 1, if AHU 1 is down and AHU 2 is serving areas A as well as C and D and there is a fire alarm in area A, AHU 2 now responds as if there was a fire alarm in the area it normally serves. A detailed description of what happens when a unit is serving an additional smoke area is needed to coordinate the correct action of the fire alarm and the AHU.
While this arrangement is more complex to operate, there are a few advantages:
• Unit sizes can be different due to different loads served.
• If there is a need for emergency ventilation requiring 100% fresh air, one unit can go into this mode while the other unit runs in a normal mode of return and outside air.
Best practice suggests using a cross-connect arrangement in a situation where, after the design documents have reached a “point of no return” completeness, the owner requests “some means of backup cooling to certain areas”. There is likely no opportunity to redesign mechanical rooms or even make substantial changes to the AHUs due to being different sizes and serving different areas. Crossconnecting provides the capability to direct a limited amount of air to prioritized areas. A graphical interface on the BAS makes it quick and easy for the facility staff to select which areas to prioritize.
There may also be situations in which an owner needs to add cross-connection capability to existing AHUs. While this is feasible, be aware of the nuances and details noted above that must be anticipated for successful implementation.
A simpler, more straightforward arrangement is to closely align two units in parallel. The units are equally sized and serve the same areas. The units are close enough to share common return and discharge plenums (see Figure 2).
Generally, the two units “operate as one.” The supply fans in both units modulate to maintain the same duct static pressure setpoint. A different twist of this arrangement is that the return fans modulate to maintain a negative static pressure setpoint in the common return plenum. This was done to accommodate real life conditions; ideally, each return fan would track the supply fans minus the exhaust/outside air differential.
However, the tolerances of air flow measurement at two supply fans results in return fans operating at different setpoints, with the unintended consequence of the two return fans fighting each other to pull enough return air to meet airflow setpoint. By controlling all fans to a common static pressure setpoint in the return plenum, this single setpoint is a simple operating target.
One nuance is that the use of a dedicated outdoor air system (DOAS) or, at minimum, an outside air fan, helps maintain correct airflow when using return plenum pressure to control return fan speed; changes in wind direction or atmospheric pressure don’t have an effect on air flow from the outside air intake to the mixing plenum. Each unit’s cooling coil modulates to maintain the discharge
air temperature setpoint for that unit. When in airside economizer each unit operates independently. When one unit goes down, the twin unit begins to automatically ramp up to its maximum capacity to try and meet the supply duct static pressure setpoint. As in the cross-connected scenario, there are deeper operational issues to resolve:
• Because one unit is now serving a larger area, there may be a need to prioritize the areas served. This may require some combination of additional control dampers, closing selected smoke dampers or commanding terminal boxes to close or reduce air flow.
‘ A graphical interface on the BAS makes it quick and easy for the facility staff to select which areas to prioritize. ’
• As with cross-connected units, a big question to consider is what happens to the exhaust fans in both areas. Do they fully stop? Fans serving hazardous areas, such as isolation rooms, must continue to operate. Maintaining correct air flow presents a challenge. In full unit shutdown of one unit, there will be a loss of control of building pressure due to half the minimum outside air (OA) being cut off from the system essentially. This is alleviated with the use of the airflow measuring station on the minimum OA duct from the DOAS. The BAS can open the operating unit OA damper more to meet the air flow demand of both units if needed. This is the advantage of using a DOAS or outside air fan when using twinned units.
• Unlike the cross-connected layout, one of two units in a twinned arrangement would not be able to go to 100% outside air in an emergency ventilation scenario — both units would need to operate at 100% fresh air because they share a common return plenum.
While the original and primary purpose of connected AHUs was to find a cost-effective way to provide some level of cooling in the event of an AHU going out of service, owner feedback has focused on the increased efficiency of maintenance.
u Some building types, such as large corporate data centers, have the budget and mechanical room space to provide total backup or spare air handling units. However, other occupancies such as hospitals, some types of labs and industrial facilities need some amount of spare capacity but usually do not have the budget or building area to accommodate a full “spare” air handling unit.
u A cost-effective solution is to connect air handling units so that, in the event one unit is down for maintenance, some reduced level of both air movement and cooling and dehumidification is still available.
‘ Connecting AHUs to serve multiple areas can provide enough cooling and air movement to maintain some level of acceptable indoor conditions. ’
Routine tasks, such as changing filters, are done more quickly, resulting in less downtime and loss of service. The benefit of less downtime is magnified when considering more extensive maintenance or repair such as cleaning coils or replacing coils or fans.
By having the option of scheduling timeconsuming service in mild weather, the maintenance staff can perform tasks on one unit while the other AHU can come closer to fully meeting a reduced load during those mild conditions.
Connecting AHUs to serve multiple areas can provide enough cooling and air movement to maintain some level of acceptable indoor conditions if one unit is down without the additional cost or mechanical room area of a totally spare AHU.
Considering the additional complexity of cross-connected units, a twinned approach offers a simpler operational approach than a cross-connected arrangement to remove a single point of failure in cooling availability.
There is less downtime when maintenance, such as cleaning coils or changing filters, is performed when a unit is down.
If the twinned units or cross-connected units are served by separate electrical power sources, another single point of failure can be removed.
The use of twinned units has been positively received on several projects and one owner is incorporating the use of twinned units in future projects. They consider twinned units a cost-effective means of providing air movement as well as cooling and dehumidification while acknowledging the reduced downtime for maintenance. cse
Gavin Green, PE, is a Senior Mechanical Engineer at Smith Seckman Reid Inc. (SSR) with more than 35 years of experience in HVAC design, with 25 of those years specializing in health care facilities.
Lee Nordholm, PE, LEED AP, is a Senior Mechanical Engineer at Smith Seckman Reid Inc. (SSR) with more than 15 years of experience in HVAC systems, and hydronic and steam systems for health care facilities.
Peter Diperna, Mechanical Technical Specialist, Fitzmeyer & Tocci Associates Inc., Woburn, Massachusetts
A testing and balancing report can be a key tool for design engineers in buildings to identify issues and create quick, effective solutions
All design engineers at some point in their career have received a call from a client stating, “Our system is not performing as designed.” Whether that means a space is hot or cold, three pumps are running when it should only be two, system temperatures do not align with design or there are room pressurization issues.
After gaining experience dealing with these types of calls, the first question is always “Do you have a copy of the testing, adjusting and balancing (TAB) report? Did you call the balancer?” The information contained within the TAB report and building control system will almost always provide the information needed to resolve the problem.
The information in the TAB is obtained from a host of different pieces of equipment that are within the balancer’s arsenal. This includes, at a minimum, the airflow capture hood, anemometer air velocity meter, hydronic manometers, infrared thermometer and additional specialty equipment for fume hood testing.
The balancing technician requires expertise in airflow dynamics, system design and the use of specialized testing equipment. These professionals ensure that the heating, ventilation and air conditioning (HVAC) system operates optimally and efficiently. Key responsibilities of the technicians include:
• Measurement and analysis: Technicians accurately measure airflow rates and analyze data to identify discrepancies and areas that require adjustment.
• Adjustment and calibration: Based on the analysis, technicians adjust dampers, fans and other components to achieve the desired airflow rates and temperature distribution.
• Problem-solving: Technicians troubleshoot issues with the HVAC system and address any malfunctions or inefficiencies that may hinder proper balancing.
• Communication: Effective communication with the design team, building owners and installing mechanical contractors is necessary to understand the design intent and to report issues before completing the balancing. This will allow the technician to address any concerns.
HVAC systems rely on complex instrumentation to function properly. The instrumentation includes sensors of varying types to provide inputs to the direct digital control (DDC) system, which includes, but is not limited to, air and water temperatures, air flow rate and volume, water flow and the operational status of each piece of equipment. Part of the balancing technicians work is to use several different hand-held devices that test the function of a system’s instrumentation and compare the two bits of information. The devices used by the technician must be calibrated on a regular basis to ensure accuracy.
Information obtained with the balancing technician’s devices will be used as a baseline and compared to the information from the DDC system, which is obtained from the field mounted instrumentation. Discrepancies between the two inputs
• Identify the equipment used for HVAC system balancing.
• Understand the advantages to pre-balance and post-balance reports on retrofit systems.
• Learn how to collaborate effectively with a balancing technician during a case study to identify and resolve system issues.
must be resolved and typically the field mounted devices are re-calibrated by the DDC technician.
The report should have a section on instrumentation with a minimum of the following for each piece of equipment used:
• A list of the test instruments that are planned to be used in the testing and balancing process. Each instrument manufacturer, model number and test application should be included.
• A description of the testing procedure for each HVAC system. A list of all the equipment that will be tested for each system as well as the techniques to be used for the testing procedure.
• A list of the contractors that are required to assist with the testing and balancing process along with the expectations of each of the contractors to successfully complete a total system balance. Most importantly, the expectations of the DDC technician should be described.
The basic instrumentation and methods to obtain the information include:
• Airflow measurement devices: Central to air balancing is accurate airflow measurement. When a balancing hood cannot be used, balancing technicians use various instruments, such as anemometers, to gauge air velocity at supply, return and outdoor air intakes. Vane anemometers, favored for their versatility, use small blades that rotate by the air current to provide precise readings. A vane anemometer works on the principle that a freely spinning turbine will rotate at a speed directly proportional to the wind speed. The hand-held device will count the revolutions per minute and calculate the velocity of the
air and ultimately convert to cubic feet per minute. Thermal or hot wire sensors calculate air flow based on the amount of heat removed from the surface or from the thermal resistive element with one or more temperature sensors.
• Pressure gauges and manometers: To assess the pressure differentials between spaces and ductwork, a balancing technician will employ pressure gauges and manometers. A manometer is based on the hydrostatic balance principle, where a space or section of duct work will be connected to the reservoir so that the pressure can be measured in relationship to a neutral space. These instruments can be used to help identify potential obstructions, high loss duct fittings or imbalances within the system. The differential pressure measurements aid in adjusting dampers, registers and diffusers to achieve the desired airflow rates. Pressure gauges and a manometer can also provide room cascading pressurization maps when measured against a neutral location. Cascading room pressure control is used in laboratory and clean room design, when the room is required to be positively pressurized compared to the anti-room and then to the clean or dirty corridor.
• Temperature and humidity sensors: Comfort is not solely dependent on airflow; temperature and humidity also play critical roles. Balancing technicians use temperature sensors, often thermocouples or resistance temperature detectors, to monitor air temperature at different points within the system. Humidity sensors, like hygrometers, help assess moisture levels and ensure the indoor environment remains conducive to human well-being and equipment functionality.
• Balancing hoods: Balancing hoods are employed to determine the air volume supplied and returned by individual vents and diffusers. These specialized devices allow a balancing technician to measure airflows directly, enabling precise adjustments to achieve the required air distribution in each zone.
The air side balancing process for an HVAC system includes:
• System design analysis: The first step in HVAC system balancing involves a thorough review of the design. This includes reviewing the architectural plans, equipment specifications and ductwork layout. By understanding the system's intended design, technicians can identify potential issues that may impact airflow distribution.
A pharmaceutical client requested a review of a recently completed system as they were experiencing low humidity in the clean rooms, room pressurization fluctuations and an inability to maintain cascading pressures from clean rooms to anti rooms. The heating, ventilation and air conditioning (HVAC) system that serves the clean suites was based on a custom dual-tunnel air handling unit (AHU). For system redundancy, variable volume terminal units were used on the supply and exhaust valves. The cascading room pressures differential ranged from a 0.02 inch water gauge (WG) to 0.08 inch WG, depending on the room configuration. Each tunnel section of the AHU was provided with a dedicated gas fired steam humidifier.
The design documentation and the original balancing report were reviewed. The original testing, adjusting and balancing (TAB) report provided an indication that the system was not functioning correctly from the start. However, low humidity issues arose during cold dry weather and the turnover was in the spring. The initial discrepancies were provided in the report and apparently overlooked. A simple calculation verified the issue.
The steam humidifier was reportedly operating at 100% capacity, however when the return air and outside air values were used to calculate the mixed air and relative humidity at the mixed air sensors, where there was a large discrepancy.
The next step was to calculate the grains of moisture in the airstream before and after the humidifier dispersion tubes. The humidifier was reported to be operating at 100% capacity, yet the calculated values indicated the humidifier was only increasing the relative humidity by 3%. The small increase in humidity meant more than 100 pounds per hour of steam were unaccounted for.
The balancing report documented a very high motor amperage on the supply fans and a very high static pressure. The pressure loss from the 30,000 cubic feet per minute air handing unit to the first variable volume terminal unit was calculated to be a 1.2 inch WG loss, yet the supply had a discharge static pressure of 4.8 inch WG. The balancing technician was tasked to perform a static pressure profile along the supply duct, as the system had been installed differently than the design. The static pressure loss within the first 50 feet of duct work was nearly 2.6 inch WG. The turbulence created by the duct fittings created noise and system inefficiencies. Therefore, a duct design was provided that eliminated the 2.4 inch WG of the 2.6 inch WG loss.
After the sections of the ductwork with excessive pressure loss were replaced, the calculations were revised. The revised calculation included mixed air conditions. The calculated values were similar to the previous and indicated the mixed air condi-
4: Balancing supply and exhaust airflow for an urgent care suite during the COVID-19 pandemic to ensure patient safety.
Courtesy: Fitzemeyer & Tocci Associates, Inc.
tions were different from the direct digital control (DDC) system. Working with the balancing technician, the team developed means to verify the outside air flow rates. As suspected, the outside air was 25% higher than stated by AHU’s airflow measuring devices.
Corrective measures were made to the outside air damper controls and the economizer cycle was eliminated from the DDC strategy. When trying to maintain a humidity level of more than 30% relative humidity, an economizer cycle can use more energy to produce steam than it may save from not running the cooling equipment. If the designer chooses to use an economizer cycle, the humidifier capacity must be sized to handle the increased airflow.
The reduced static pressure and revisions to the outside air quantity resolved the downstream room issue. However, despite the efforts of the team, the existing humidifiers would not function. The humidifier was replaced with a similar unit, which resolved the issue. Although there are several theories on what caused the problem, the team never found the root cause. The team believes it to be a combination of high static pressure in the AHU and undersized steam piping from the steam generator to the steam dispersion tubes.
3: A differential pressure sensor is a key part of any testing, adjusting and balancing kit. Courtesy: Fitzemeyer & Tocci Associates, Inc.
For example, during the design review, a balancing technician may discover issues that can hinder proper balancing, such as inadequate duct sizing or improperly located diffusers. The reviewer may discover a lack of accessibility to the equipment that could lead to the addition of access panels or equipment relocation. Identifying issues at this stage allows for early corrective measures and prevents complications later in the balancing process.
• Adjusting dampers and registers: Closing dampers and registers will add static pressure to the system, which then reduces the airflows. However, maintaining an artificially high static pressure in a system is a waste of energy. Before adjusting the dampers, the technician should reduce the motor speed via a variable frequency drive or the speed controller on an electronically commutated motor. After the system global static is set, the dampers and registers can be adjusted to regulate the air distribution to different zones and rooms.
The completed certified TAB report, which typically follow National Environmental Balancing Bureau standards, is typically sent to the engineer of record, the building owner and a commissioning agent. Upon receipt of the completed testing and balancing report, the design team will review it to verify that the HVAC systems are operating as designed. There are many circumstances in which the testing and balancing reports indicate that the system did not achieve the design parameters.
csemag.com
uTAB reports provide crucial information about HVAC system performance and discrepancies from design parameters.
uBalancing technicians play a critical role in HVAC system optimization. They require expertise in airflow dynamics, system design and the use of specialized testing equipment. Through precise measurements and analysis, technicians can adjust dampers, fans and other components to achieve desired airflow rates and temperature distribution.
• Airflow measurements: Accurate airflow measurements are critical for determining the existing air distribution in the HVAC system. Technicians use a variety of tools, including flow hoods, anemometers and pitot tubes, to measure airflow rates at different points within the system.
Airflow measurements are taken at supply air outlets, return air inlets, diffusers, grilles and other critical locations. The data collected provides valuable insights into airflow patterns, which help identify necessary adjustment areas.
• Equipment inspection: During the balancing process, technicians thoroughly inspect all components of the HVAC system to ensure they are in good working condition. This includes examining fans, coils, filters, dampers and other relevant parts.
If any equipment is found to be malfunctioning or damaged, it is repaired or replaced by the mechanical contractor before proceeding with the balancing process. Access is key to maintaining equipment which will extend the useful life and maintain higher efficiency.
It is incumbent upon the balancing technicians to provide an explanation of the issue and what corrective actions were invoked in the field to rectify the issue. If they cannot resolve the imbalance, the expectation is that the engineer of record will provide a solution. The on-site investigation typically involves the balancing technician and the system control integration specialist.
The goal is for the system testing performance data to be within the design parameters specified in the project documents (typically plus or minus percent of the design value). Large discrepancies between the design and installed systems are obvious by reviewing the TAB report and stand out as items to be corrected. The experienced reviewer will not only be looking at the information for compliance between the testing and balancing report and design documents, but also looking for the less obvious patterns to determine if there are hidden installation issues that may create system component failures in the future or limit modification/expansion of the system. This is where an experienced engineer’s review is invaluable.
One of the most common bits of information the engineer reviews is motor data. The reason to high-
Greenheck’s eCAPS® Bridge for Revit® plugin provides access to the most complete catalog of HVAC LOD 200 and 300 product content - without leaving Revit®
Download eCAPS® Bridge for Revit® here: greenheck.com/revit
supply side, the reviewer of the TAB should verify that the static pressure set point is approximately 5-10% above the last variable volume terminal unit in the system. The maximum flow requirement is when the terminal unit has the internal flow damper at 100% open. The design static pressure setpoints are a calculated value based on ideal design parameters. The installed ductwork may differ from the design due to coordination issue. The changes in ducts can add fittings or transition thus changing the design set points.
light the motor section of the testing and balancing report is that motors are a critical part of nearly every piece of equipment in an HVAC system. The reviewing engineer will look closely at the motor amperage. Motor amps are an electrical parameter representing the flow of electricity. If the current is above full load, it may be working harder than it was designed to and may point to an underlying issue. If the amperage is above the design requirements, it could be that there are increased pressure losses in the duct work or piping that were created by poor installation methods, partially blocked pipes or partially closed valves in a piping system.
Motors within systems operate on a continuous basis for 20 years or more. If the motor is operating in the service factor, it will shorten the life expectancy of the motor. In addition, as the system ages and becomes less efficient there are no means to overcome the loss. This small, but very important bit of information is the key to a design or system installation.
It is important to ask, "Was the system balanced with all the variable volume terminal units open or did the design engineer include diversity of the main air handling units (AHUs) or exhaust systems?” If there is diversity on the main systems, the balancing technician can identify a percentage of the variable air volume (VAV) terminal units to be partially closed while other units are set to max cubic feet per minute (CFM). All of the diffusers associated with the VAV must be balanced with the unit set to maximum CFM.
To give a simple example, assume the airside system is operating at 100%. When the balancing technician and the control specialist calculate the AHU
Determining the outside air values and damper controllability at the AHU is a critical component of HVAC system functionality. In many cases, however, the values provided in the TAB for the outside air, return air and mixed air temperatures are overlooked. An increase in outside air above design considerations can lead to cooling problems in summer and mixed air temperatures below freezing in winter. Airflow measuring stations on outside air dampers can be unreliable. When placed over a large damper, this is used for both minimum ventilation and airside economizer.
The percentage of outside air can be calculated from the return supply CFM and temperatures provided in the balancing report. The calculation has a higher level of accuracy than a balancing technician taking reading across the damper or the air flow station.
To obtain the outdoor air flow, the balancing technician must use test ports in the AHU, which does not provide enough space to do a profile across the entire damper or use an anemometer across several areas and take an average of readings. If an airside economizer cycle is used at the AHU, it’s recommended to install two dampers — a minimum damper and a maximum damper. The maximum damper will be used for the economizer. Air from the minimum outside air damper will be appropriately sized, which will increase the controllability and opportunity for accurate measurements of outside air.
Both the design and construction industries agree on the benefits of testing and balancing all
HVAC systems. The same benefits occur when requesting a pre-design balancing report for retrofit projects. The only difference is that the balancing technician only records the data and does not adjust the system. It should be noted that ASHRAE Standard 62.1: Ventilation for Acceptable Indoor Air Quality recommends a TAB audit be performed every five years to ensure efficient operation of the HVAC and control systems. Unfortunately, these 5-year audits are seldom performed. If there is an existing report, it is often from the completed project, which makes it hard to compare the existing and new reports to look for an indication of how the system aged and where the system may be failing.
Before testing an AHU, it is recommended to change filters to minimize external pressure loss. Data should be collected at each filter, noting airside coil pressured drop, outside air CFM values and mixed air temperatures. Also, a main duct pressure profile should be requested. The water side data collection includes flow rates and temperature differential at that moment in time for both the water and
the air side, pre and post coil. The data will provide insight into the current performance of the system and how it uses fan or pump curves. The design engineer can plot the system curve and determine the system performance and expandability.
In addition to the data collection, this may be the right time to work with the control technician to verify the control sequence of operation for the different systems being modified.
Obtaining the system performance information before design and construction will allow the project team to understand the current state of equipment and operations, thus creating an opportunity to take corrective actions or include them in the design. The pre-balance report will help to protect the design firm from perceived errors and omissions. The proposals “assume” the existing system has the ability for increased capacity, however without test data the firm can be held accountable for a lack of system performance. cse
Peter Diperna is a Mechanical Technical Specialist for Fitzmeyer & Tocci Associates Inc.
‘ Obtaining the system performance information before design and construction will allow the project team to understand the current state of equipment and operations. The pre-balance report will help to protect the design firm from perceived errors and omissions.’
Hafiz Rafey, EIT, PMP, and Sunondo Roy, PE, LEED AP, Barry-Wehmiller Design Group, Oak Brook, Illinois
The majority of heating, ventilation and air conditioning (HVAC) design engineers are familiar with the importance of indoor air quality/indoor environmental quality (IAQ/IEQ) in commercial buildings. These two criteria in commercial buildings primarily focus the design effort on the health, safety, and comfort of the building occupants.
Designing commercial building HVAC systems well requires a thorough understanding of ASHRAE Standard 62.1: Ventilation for Acceptable Indoor Air Quality relative to ventilation requirements, ASHRAE Standard 55: Thermal Environmental Conditions for Human Occupancy for indoor comfort conditions including air movement and how humans react to temperature and humidity and the International Green Construction Code. Much of this experiential knowledge also relates to many of the key IAQ/IEQ considerations in industrial manufacturing and packaging facilities.
However, even in such settings, occupant safety is the one design consideration that takes precedence over the production process. Especially within the IAQ/IEQ realm, hazards to occupant respiration are the top priority.
In specialized industrial facilities, such as pharmaceutical production, chip-set fabrication, biological testing or biologic production facilities, the design may also need to address the cleanliness of the ambient production environment with stringent requirements on the acceptable quantity and size of particulates in the air. When the manufactured product can be microscopic in scale, such as with computer chip set integrated circuits, the presence of otherwise negligible dust and lint particles may invalidate the product being manufactured.
Objectives
• Understand how IAQ/ EAQ design features in commercial buildings can be used in industrial facilities.
• Identify the various governmental and thirdparty agencies that provide guidance for industrial facility design.
The design of industrial facilities focuses primarily on the process being carried out more so than on the comfort of occupants running or monitoring the processes, though the latter is still important. Industrial facilities, such as chemical processing, food production, packaging and warehousing, consumer product manufacturing, or a combination of these operations, tend to give primary attention to temperature, humidity and the presence or concentration of certain gases that affect the processes occurring in the building.
In certain classes of drugs that are injected directly into the body, or in the production and laboratory testing of gene and cell therapy lines, the concerns extend beyond the particulates to encompass pathogens that might be carried into the process on those airborne particles.
Overall, the concerns for indoor air and environmental quality within industrial facilities can have much greater stakes than in commercial buildings. Where the impact in a commercial facility may extend to hundreds or thousands, of occupants and their comfort, the impact in an industrial facility can affect tens of millions of consumers. Additionally, the economic and reputational cost to manufacturers can be astronomical.
The ultimate goal of IAQ/EAQ design in commercial facilities such as offices, malls, educational facilities and transportation centers is to engineer a healthy, comfortable environment for human habitation within the building. ASHRAE Standard 62.1, ASHRAE Standard 55, the International Green Construction Code and other standards, guidelines and codes serve as a yardstick, prescribing the minimum acceptable IEQ/IAQ criteria or enhancing them.
In addition to direct air and environmental impact, overall IAQ/IEQ must also address indirect impacts including the energy efficiency of the equipment creating the acceptable indoor conditions. Thus, compliance to ASHRAE Standard 90.1: Energy Standard for Buildings Except Low-Rise Residential Buildings, is an integral design aspect of the overall design as well.
As responsible design professionals implementing the aforementioned features in the design of buildings, it is imperative to focus on the following key elements, provided by Whole Building Design, as applicable:
• Adequate indoor air quality through filtration and quantity of ventilation air supply and exhaust for acceptable indoor air quantity
• Temperature and airflow controllability for thermal comfort
• HVAC systems that manage moisture sources and provide indoor humidity control
• Achieve indoor environmental quality through the design of efficient systems, construction adherence to design documents, commissioning, operation and maintenance practices
• Designing a properly illuminated environment per Illuminating Engineering Society (IES) recommendations
• Designing energy efficient systems relative to the use of individual spaces or buildings
• Provide for high-quality, potable water
In comparison to occupant-centric commercial IAQ/IEQ design, the primary focus of industrial design is on the manufacturing process, as it can potentially affect the quality and consistency of mass-produced products. Deviating from product criteria due to unacceptable variations in IAQ/ IEQ can cause entire batches of product to be out of acceptable specifications, thus invalidating massive
1: This diagram shows a typical food or beverage manufacturing facility and how transition zones separate high-care (high and medium hygiene areas) from basic hygiene and non good manufacturing practices (GMP) areas. Courtesy: Barry-Wehmiller Design Group
quantities of product that may cost millions of dollars in raw material, production labor, packaging or materials. In industrial processes like chip fabrication or pharmaceutical drug manufacturing, being out of mandated tolerances, even for short periods of time can have catastrophic economic impact to the business and end-users.
Occupational Safety and Health Administration (OSHA) has established average exposure limits for acceptable levels of contaminants, temperature or humidity for humans over an eight-hour window. However, industrial processes generally do not have such tolerances since the products are precisely measured and processes are developed for producing consistent, uniform and safe products in mass quantities. Fluctuating environmental conditions can lead to product specification or quality variability, which is unacceptable. When sterility is an additional requirement, any duration of exposure to pathogens beyond limits can also void the entire process, cause serious harm and be fatal to end users.
The key design elements for good industrial IEQ/IAQ design include the following:
FIGURE 2: This diagram shows the required pressurization to ensure conditioned air flows from higher hygiene spaces to lower hygiene spaces down to non good manufacturing practices (GMPs). Courtesy: Barry-Wehmiller Design Group
• Adequate quality and quantity of ventilation air supply and exhaust for acceptable indoor air quantity
• Temperature and airflow controllability for stable process and production consistency
• HVAC systems that maintain hygienic zoning, proper management of moisture sources and adequate indoor humidity control
• Achieve indoor environmental quality through the implementation of good manufacturing practices (GMPs), construction adherence to design documents, commissioning, operations and maintenance practices
• Designing a properly illuminated environment per IES and production specific requirements
• Designing energy efficient systems relative to the use of individual spaces or the building as a whole
• Provide for high-quality, potable water
• Facilitating the production process to operate in as hygienic and sterile environment as required to ensure the highest quality end product
• Maintaining an acceptable level of airborne contaminants by controlling their entry and removing them from the production environment.
Depending on the type of industry and the product, the level of implementation of design strategies may vary, but the following are common design considerations for most industrial facilities:
• Hygienic zoning: This is an operational strategy to segregate various areas within the building into high care, medium care and basic care zones, based on the type of product and by controlling the movement of materials and personnel across these zones based on their risk factors, as shown in Figure 1. The designed system needs to maintain the zone-by-zone segregation through appropriate air filtration and pressurization. Controlled transitions zones and drop zones keep the flow of air from high-risk areas to low-risk areas can be done with controlled transitions zones and drop zones. Parts of the building where production doesn’t occur are designated non-GMP areas.
• Dilution ventilation and local exhaust: For worker protection in industrial facilities, there are two basic types of ventilation systems — pollutant dilution and local exhaust. Dilution ventilation mixes large amounts of clean, outside air with process air to keep the concentrations of contaminants below the allowable limits set by industrial hygienists. Local exhaust systems are designed to capture contaminants at the source and remove them from the workspace through a ducted system. An industrial plant typically has both systems, with greater emphasis on one or the other depending on the hazard risks of the contaminants. The health hazard potential of an airborne substance is characterized by the acceptable time weighted average threshold limit value as published by American Conference of Governmental Industrial Hygienists (ACGIH) or permissible exposure limit per applicable OSHA and industry standards.
• Process air movement: In addition to worker safety, there are also considerations for the production process. For most industrial applications, the higher the hygiene requirement, the higher the air exchange rate to minimize the concentration of contaminants to the process. Where typical air exchange rates for commercial buildings are six air changes per hour (ACH) for human ventilation dilution, process applications require air exchange
rates of 10 ACH up to 30 ACH. Clean room applications require air exchange rates near 50 ACH. The volume of air movement becomes more confined as the environment is subject to more stringent criteria. Otherwise, the absolute air movement quantity in cubic feet per minute become untenable for large volume spaces. Figure 2 depicts air pressurization strategy for air movement in a properly hygienic zoned facility.
Responsible designers are expected to be aware of the specific industry requirements pertaining to the process being designed. Following are some of the agencies relevant to industrial processes and their codes, standards and/or guidelines:
OSHA: Under the U.S. Department of Labor, OSHA ensures safe and healthy working conditions for workers by setting and enforcing standards and by providing training, outreach, education, and assistance. Specific to IAQ/IEQ, it has published ventilation standards including the four standards in OSHA Standard 29 CFR 1910.94 dealing with local industrial exhaust systems. Additionally, it publishes Standard 1910 Subpart Z: Toxic and Hazardous Substances, Table Z-1. This publication includes occupational exposure limits (OELs) for approximately 500 substances with either a maximum instantaneous value, a 15 minute time weighted average or an exposure limit — based on an eight-hour time weighted average exposure. OELs for hundreds of additional substances have been adopted by OSHA, The National Institute for Occupational Safety and Health (NIOSH) and ACGIH.
NIOSH: This U.S. Government research agency focuses on the study of worker safety and health, and empowers employers and workers to create safe and healthy workplaces. NIOSH is part of the U.S. Centers for Disease Control and Prevention, in the U.S. Department of Health and Human Services. It has published several useful criteria documents, current intelligence bulletins, reports, fact sheets and impact sheets. These provide technical guidance on controlling worker exposure to airborne contaminants, nanoparticles, tobacco smoke, heat and to various chemicals and biological agents.
ACGIH: The ACGIH Industrial Ventilation Committee publishes “Industrial Ventilation, a
This manual is recognized worldwide as one of the key design guides for all aspects of industrial ventilation design and applications. The topics covered include equipment fundamentals, associated system design, local exhaust system design, general industrial ventilation principles and design, supply air system design and special design considerations. The manual compiles references and aggregates data, recommended practices, and code references from many different resources into one compendium.
Additionally, ACGIH publishes an annually updated version of a booklet of threshold limit value occupational exposure guidelines for more than 700 chemical substances and physical agents. There are also more than 50 biological exposure indices that cover more than 80 chemical substances. ACGIH also publishes the Guide to Occupational Exposure Values, which supplements threshold limit value and biological exposure indices exposure guidelines with an accessible reference of the most recently published values.
Prioritizing IAQ/IEQ considerations in both commercial and industrial setting is vital. The former places more emphasis on the occupants’ health and comfort whereas the latter places it on maintaining precise conditions to ensure product quality and occupant safety. Compliance with standards and guidelines such as ASHRAE, ACGIH and OSHA, are essential to create safe and efficient industrial environments. Incorporating the appropriate design approach with adherence to industry-specific requirements is the key to a safe, sustainable and successful industrial environment while safeguarding the health and well-being of workers and consumers. cse
Hafiz Rafey, EIT, PMP is a senior mechanical designer in Barry-Wehmiller Design Group’s Chicago office.
Sunondo Roy, PE, LEED AP, is Director of Architecture, Engineering and Process in Barry-Wehmiller Design Group’s Chicago office. He is a member of the Consulting-Specifying Engineer editorial advisory board.
‘ Incorporating the appropriate design approach with adherence to industry-specific requirements is the key to a safe, sustainable and successful industrial environment while safeguarding the health and well-being of workers and consumers.’
u
csemag.com
Ventilation insights
u In commercial buildings, the focus of HVAC design is on the health, safety and comfort of the occupants, whereas in industrial buildings the focus shifts to the production process while still prioritizing occupant safety.
uMany industrial facilities will often have stricter guidelines dependent on the kind of product being made.
Erika L. Bolger, PE, LEED AP, Design Group Facility Solutions, Oak Brook, Illinois
The ability to provide power to a building or load when utility power is lost can be a critical need for a facility to support vital operations or building and occupant safety
Owners, architects, contractors and engineers tend to use the terms emergency/backup/standby power interchangeably to indicate that during a utility power outage, there is a need to have specific loads or even an entire structure’s power maintained for facility operation.
There are distinct differences in the requirements for legally required standby power systems. The first step in designing a robust and code-com-
pliant standby power system for a project is understanding the project requirements.
Legally required standby power system loads are generally described as loads, which upon failure of the normal power source, could create hazards or hamper rescue or fire-fighting operations.
Depending on the project, there may be a need for various types of loads to be served by alternate power sources. These loads can include emergency loads that are loads legally required by governmental agencies for the purposes essential for safety for human life.
Legally required standby loads can also be present in a facility; these include loads that could create hazards or hamper rescue or fire-fighting operations if power is lost.
Additionally, optional standby systems may be present that include loads that, when stopped, could cause discomfort, serious interruption of the process or damage to the product or process.
Lastly, there may be additional loads that do not neatly fall into one of the above categories, but are still required based on an owner’s request to be supported by an alternate power system mainly for reasons of convenience, comfort or financial impact. These load types could be considered optional standby loads.
There is some overlap between the various power systems above for the same load type. These loads should be classified based on the occupancy of the space as well as the function of the load. Additional clarification and guidance can be found in many of the codes and standards required for the proper design and construction of a building.
NFPA 70: National Electrical Code (NEC) Arti-
cles 700, 701 and 702 provide directions as to the electrical safety of the installation, operation and maintenance of emergency, standby and optional standby systems. That is to say, the NEC dictates the technical requirements for electrical installations that include: commissioning, testing, capacity and rating, transfer equipment requirements, wiring methods, identification, etc.
These NEC articles provide guidance in general for the emergency power supply systems (EPSS) themselves along with other NEC code articles; other codes and standards such as the International Building Code (IBC), the NFPA 101: Life Safety Code, the International Mechanical Code and International Fire Code (IFC), local building codes and amendments, federal and military codes and standards, the Environmental Protection Agency, FM Global and other insurance company requirements, to name just a few, also have specific design criteria requirements.
These codes and standards provide further clarity on how loads within specific facilities should be treated. While the NEC is the code that electrical engineers reference most regularly, the designer or engineer cannot rely solely on the NEC for direction; in fact, there are many other sources in which
criteria for the proper application of alternate power systems can be found.
NFPA 110: Standard for Emergency and Standby Power Systems defines the following:
“EPSS: A complete functioning emergency power supply system coupled to a system of conductors, disconnecting means and overcurrent protection devices, transfer switches and all control, supervisory and support devices up to and including the load terminals of the transfer equipment needed for the system to operate as a safe and reliable source of power.”
The terms EPSS and standby power supply systems include but are not limited to:
• Emergency power systems.
• Alternate power systems.
• Standby power systems.
• Legally required standby systems.
• Alternate power sources.
NFPA 110 specifies the installation, performance, maintenance and test requirements for EPSSs in terms of types, classes and levels for the
‘ The NEC dictates the technical requirements for electrical installations that include: commissioning, testing, capacity and rating, transfer equipment requirements, wiring methods, identification, etc. ’
• Determine the proper classification of loads requiring an alternate power source.
• Learn about alternate power source terminology and code requirements of different alternate power sources and systems.
• Understand where to look to determine the requirements of standby power systems.
‘ NFPA 110 provides excellent guidance in understanding the requirement when classifying the requirements of different types of emergency power supply systems. ’
categories above, therefore the category terms used depend on the application involved. These types, classes and levels are essential in helping to distinguish the proper classification of the alternate power distribution system.
An EPSS class refers to the length of time required for an EPSS to provide power to a load (duration the load can be served) without being refueled (NFPA 110 Table 4.1(a)) as well as the maximum time allowed for the load terminals of transfer equipment to be without acceptable power (how quickly the load needs to receive power, (NFPA 110 Table 4.1(b)).
Further, NFPA 110 defines levels for EPSS equipment installation, performance and maintenance requirements. A Level 1 system is where
failure of the equipment to perform could result in loss of human life or serious injuries. A Level 2 system is where failure of the EPSS to perform is less critical to human life and safety. NFPA 110 Appendix A is a reference to assist the designer in understanding the intent of what loads might qualify as either Level 1 or Level 2.
NFPA 110 provides excellent guidance in understanding the requirement when classifying the requirements of different types of emergency power supply systems, but how does the designer know which components of a building or project are applicable to these classifications? Start with the understanding of the project and its occupancy and use classification in the applicable building code or standard.
The building code or standard for a given municipality is dictated by the authority having jurisdiction (AHJ). The AHJ, whether that is the local building department or other governmental agency will determine the building code that is applicable at the time of design. The IBC is a common compliance requirement for many buildings.
The IBC defines the following terms:
THIS FOOD PRODUCTION FACILITY was broken into three areas, each of which achieve specific power needs
A new flagship refrigerated food production facility is being constructed. The facility is 250,000 square feet, primarily single story (36-foot high production and warehouse space) with a three-story office area including an atrium.
The building requires a fire alarm system and given the refrigerated production areas, a large machine room is present that uses anhydrous ammonia refrigeration compressors to provide cooling to the process spaces. In addition, the owner has requested that the entire office area operate during a power outage.
During design, it is determined that the building occupancy areas include: business (B-1), factory (F-1) and storage (S-1). The applicable codes per the municipality include:
• 2021 International Building Code (IBC).
• 2021 International Fire Code (IFC).
• 2023 NFPA 70: National Electrical Code (NEC).
Building code requirements
IBC requirements:
Per Article 2702.2, the smoke control system required for the three-story office atrium is required to be provided with standby power (2702.2.17 and 404.7). Further, the standby power source and its transfer switches shall be in a separate room from the normal power transformers and switch gears and directly ventilated to and from the exterior (per 909.11.1).
Per Article 2702.2.14, emergency power is required for the building egress illumination and fire alarm systems.
IFC requirements:
Per Article 916.5 and ANSI/IIAR CO2-2021 Safety Standard for Closed-Circuit Carbon Dioxide Refrigeration Systems as well as good engineering practices, standby and emergency power shall be provided to serve the gas detection system and emergency ventilation system within the ammonia machine room.
“Emergency power system: A source of automatic electric power of a required capacity and duration to operate required life safety, fire alarm, detection and ventilation systems in the event of a power failure of the primary power. Emergency power systems are required for electrical loads where interruption of the primary power could result in the loss of human life or serious injury.”
These systems are required to make power available within 10 seconds per NFPA 70 Section 700.12.
“Standby power system: A source of automatic electric power of a required capacity and duration to operate required building, hazardous material or ventilation systems in the event of a failure of the primary power. Standby power systems are required for electrical loads where interruption of the primary power could create hazards or hamper rescue or fire-fighting operations.”
These systems are required to make power available within 60 seconds per NFPA 70 Section 701.12.
NEC Article 701.1, Informational Notes 4 and 5 further correlate the intent of standby system loads as being loads that any interruption of could create a hazard or hamper rescue or fire-fighting efforts and could result in loss of human life (Level 1) or less critical to human life and safety (Level 2).
Understanding the intent of the various codes and standards is interesting, but as designers, why should we care? We care because based on the types of loads, different requirements are required for different load types including but not limited to: operation, location and installation.
Per Article 1203.1.4, emergency power systems shall automatically provide secondary power within 10 seconds after the primary power is lost. Standby power systems shall automatically provide power within 60 seconds after primary power is lost. Additionally, emergency and standby power systems shall be designed to provide the required power for a minimum duration of two hours without being refueled or recharged.
The IBC and IFC, as well as the owner's project requirements, have dictated all the required loads that require an alternate source of power during the loss of normal power, these have been formally categorized (see classifications).
National Electrical Code requirements:
Per Part III of NEC Article 700 Sources of Power, the selection of a power source should be based on the consideration of the occupancy and type of service to be rendered. This includes the type of power source, the run-time duration of load, reliability of the alternate power source fuel type and type of loads.
csemag.com
Standby power insights
u Understanding the differences, intended use and limitations between legally required standby power systems and other alternate power systems is critical to meeting a project’s goals and maintaining code requirements of loads being served.
u This article will focus on specifics with respect to legally required standby power systems.
Emergency power Legally required standby power Backup power
Egress lightingSmoke control systemsOffice power and HVAC
Fire alarm systems
Gas detection and emergency exhaust for the compressor room Fire pump
Example of alternate power source load classifications for a largescale industrial project. Courtesy: Design Group Facility Solutions
In this example, a standby, exterior diesel generator was selected because of the types of loads (motor loads serving the smoke control systems and exhaust fans as well as the compressor loads serving the air conditioning). While this facility was designed with a single emergency power generator, separate and distinct branches of emergency power distribution were provided (code required emergency, legally required standby and optional standby) to meet the intent of Article 700.10(B).
The First Center-Guided Check Valve Specifically Developed for VFDs.
Tests Show Improvement in the Cv by 38%
Re-Engineered, Hydrodynamic Disc Design Increases Flow
Flow Provides Superior Functionality in Low-Flow Conditions, Common with VFD drives
For example, IBC Chapter 909.11 requires that for smoke control systems, the standby power source and its transfer switches shall be in a separate room from the normal power transformers and switchgears.
NEC Article 701:
• Indicates a legally required standby system shall have the load capacity calculated in accordance with Parts I through IV of Article 220 or other approved method.
• Dictates the design of the transfer equipment of the standby power system to include allowing the ability to bypass the transfer equipment and the requirement for the transfer equipment to be electrically operated and mechanically held.
• Mandates signage at the service entrance identifying each legally required standby power source.
• Defines the maximum time allowed for the legally required standby source to become available to support the required loads (60 seconds, or per NFPA 110, Type 60).
• Defines the minimum operation time before refueling (two hours, or per NFPA 110, Class 2).
• Provides an approved list of alternate power sources that can be used for standby power systems (some of which require AHJ approval). These include:
– Public gas system.
– Municipal water supply.
– Storage batteries.
– Generator sets.
– Stored energy power systems.
– Separate service.
– Connection ahead of the service disconnecting means.
– Microgrid systems.
• The standby power source should be carefully evaluated based on the loads supported and their purpose.
It is important to understand that the NEC, IBC, NFPA 110 or other codes and standards are to be used as a guide and minimal compliance standard only. It is impossible for these documents to be comprehensive for every situation, so it is up to the design professional with approval by the AHJ to determine the proper classification of the electrical loads on each project while meeting the owner's project goals.
It is the responsibility of the electrical designer to stay current with the understanding of the ever-changing code requirements. The major building and construction codes typically provide changes on a three-year code cycle. The requirements for standby power systems are no exception. cse
Erika L. Bolger, PE, LEED AP, is a director at Design Group Facility Solutions and has more than 30 years of consulting engineering experience.
John Yoon, PE, LEED AP, McGuire Engineers, Chicago
As smart lighting becomes more commonplace, it is important for engineers to understand the pitfalls and problems that may come with it
The most efficient light is the one that is turned off when it is not needed. The least efficient light is the one what is still turned on when it is not needed.
This simple guiding principle for lighting control systems has been at the core of energy conservation codes since their inception. However, with the emergence of new lighting control technologies and their wildly expanded functionality, engineers often get lost in the minutia of the various available control solutions and lose sight of this guiding principle.
Frequently, the result is a control system that is not cost-effective, performs erratically and does not meet the client’s needs. In some cases, it may be that the controls did not perform as expected because there was not a clear understanding about what controls could and couldn’t do.
Changes in technology have allowed for dramatic reductions in energy use, such as the replacement of incandescent and fluorescent light sources with LED. For example, 20 years ago, the 2003 International Energy Conservation Code (IECC) and ASHRAE Standard 90.1: Energy Standard for Buildings Except Low-Rise Residential Buildings mandated a maximum allowable lighting power density (LPD) of 1.3 watts (W) per square foot for commercial office buildings. Now, in the 2021 IECC, the LPD number is 0.64 W per square foot. This represents almost a 51% reduction. Such reductions were easily achieved with the transition to LEDs. However, these types of improvements require revolutionary changes in technology
and are usually the exception. Instead, incremental, marginal gains in lighting system efficiency and energy savings with each energy code revision are usually the norm. Without some other type of transformational change like the adoption of LEDs, the only way to achieve persistent incremental improvements is by increasing the controllability of lighting — to turn it off when it’s not needed.
Or, in the parlance of current design trends, to increase granularity of control (i.e., be able to adjust light levels to the minimum intensity needed and to perform that control only in the exact area where it is needed). The ideal solution would be to bring that controllability down to individual lighting fixtures – to have luminaire level lighting con-
• Review the role of energy conservation codes in the adoption of smart lighting.
• Examine the functional requirements of smart lighting.
• Explore factors that influence the cost of smart lighting.
FIGURE 2A/B: Many wireless sensors are now battery powered which can provide significant flexibility in placement. However, batteries do not last forever and future maintenance must be factored into any design. Courtesy: McGuire Engineers
can vary widely. Some are standalone devices, others are networked. Some have cloud-based controls while others rely on a direct Bluetooth connection to an iOS/Android app. Some allow for automation, others do not. Without a consistent definition to set clear, realistic expectations about the functional capabilities of smart lighting, confusion among the general public is unavoidable.
trols (LLLC). This LLLC concept where anyone can turn individual fixtures on or off was introduced as an additional efficiency package option in the 2015 IECC (C405.2 and C406.4).
The term “smart lighting” is used and abused. Perform a search for smart lighting on the website of any big-box home improvement store, and there will be a multitude of products, usually with wireless control. However, does simply having that capability make something “smart”?
Beyond the singular characteristic of having wireless control, the functionality of those products
Absent standardization by the manufacturers, the driving force in dictating smart lighting functionality requirements, has been the prevailing energy conservation codes. While the term smart lighting is not used in IECC or ASHRAE 90.1, the IECC does have a basic framework for lighting control functionality that could be considered smart.
IECC lists the following definition for LLLC:
“A lighting system consisting of one or more luminaries with embedded lighting control logic, occupancy and ambient light sensors, wireless networking capabilities and local override switching capability where required.”
IECC Section C405.2 Lighting Controls and C406.4 Enhanced Digital Lighting Controls further expanded on this definition with specific functional requirements. These requirements essentially push the required granularity of control down to small groups, or individual light fixtures as in the case of LLLC. A notable omission from functional requirements listed for “Enhanced Digital Lighting Controls” is a lack of a requirement for wireless communication. Wireless capability is specifically called out in the description for LLLC. We will see that the incremental cost associated with adding LLLC functionality is a significant barrier to adoption and eliminating costly physical infrastructure, such as network cabling in lieu of wireless, is critical.
Beside industry wide standards from manufacturers, what is the driving force for developing consistent functionality standards for smart lighting? The answer is money.
The DesignLights Consortium (DLC) is an association of utility and regional energy efficiency organization through the U.S. and Canada. Its members are the same groups that control utility energy efficiency rebate programs across the country. One of its major goals is to create rigorous criteria that substantiates the inclusion of new lighting technologies in energy efficiency incentive programs.
Utility rebates are frequently used to help enable projects that otherwise would not have been financially viable. DLC’s requirements have successfully accelerated the adoption of LEDs by making compliance a condition of utility rebates. It is expected that this same implementation model will be applied to networked lighting controls/LLLC.
DLC has developed formal technical requirements for networked lighting control systems. Version 5 (NLC5) of these requirements was released in 2020 and updated in June 2023. The technical requirements include both “required” and “reported” capabilities. While reported capabilities are not currently required inclusions, their presence or absence needs to be documented by the manufacturer.
Many of these requirements have already been incorporated into the IECC. NLC5 also has some provisions for interoperability, but those are typically limited to communication with other systems beyond lighting.
Any mention of requirements for nonproprietary implementations of industry standard communication protocols (i.e., ZigBee, Bluetooth, DALI2, etc.) for individual control components are notably absent. This lack of standardization is perceived as being a significant barrier to the wider adoption of NLC5/LLLC technology.
FIGURE 4A/B: Pictures of lighting control stations with and without labeling. Courtesy: McGuire Engineers
Networking of Luminaires and Devices Control persistence
Occupancy Sensing Scheduling
Daylight Harvesting/Photocell Control Device monitoring/remote diagnostics
High-End Trim
Zoning
Individual Addressability
Continuous Dimming
Cybersecurity
Energy Monitoring (except room-based systems)
Type of user interface
luminaire level lighting controls
Personal control
Plug load control
Emergency lighting
Color changing/tuning
Ease of implementation
Scene control
Energy monitoring (room-based system)
Load shedding/demand response
External system integration
TABLE 1: Required versus reported capabilities as laid out in the Networked Lighting Controls standards. Courtesy: McGuire Engineers
FIGURE 5: Integrated sensors with wireless control can offer enhanced control capabilities in retrofit situations such as in this 2x2 foot edge light LED panel, which replaced a standard 2x2 foot acrylic lensed fluorescent troffer. Courtesy: McGuire Engineers
In 2022, the U.S. Energy Information Administration (EIA) estimated that lighting represents 11% of total electricity use for the commercial building sector. While increasing light fixture efficiency and controllability can significantly reduce that, what is the value of that electricity? Unfortunately, the primary barrier to LLLC adoption is that the incremental cost associated with increased lighting control granularity is not fully offset by energy cost savings.
The first challenge is being able to quantify potential energy savings in a statistically defendable manner. The U.S. Department of Energy is required, per the Energy Conservation and Production Act of 1976, to make a determination as to whether the latest version of consensus-based building energy conservation standards will improve energy efficiency as compared to the previous edition. As part of this determination, an economic analysis to quantify the associated energy cost savings is also performed.
Nationally aggregated energy cost index (ECI) savings for the 2021 IECC code revision were estimated at 10.6% (reduction from $1.32 a square foot per year to $1.18 a square foot per year). Although not specifically quantified, it is understood that the ECI savings associated with lighting are only a fraction of that total. A key point was that the analysis excluded enhanced digital controls since it did not have quantifiable impact through energy modeling.
While studies have been performed by third parties, they have not yet been able to quantify LLLC energy savings relative to code baselines in a statistically significant way. A Northwest Energy Efficiency Alliance (NEEA) and DLC joint study attempted to quantify the potential energy savings associated specifically with LLLC. The study identified an average energy savings of 63% during normal business hours compared to a “do nothing” scenario, which does not meet code. As such, the quoted savings are not directly comparable to a building with a lighting control system that met
the minimum requirements of one of the prevailing energy conservations codes.
Additionally, there were significant limitations in the NEEA/DLC study. The total savings were based on a sampling size of only 98 buildings with LLLC. Of the total energy savings, 37% was attributed to high-end trim, or the capability to reduce the maximum light output of a light fixture at the time of installation or commissioning, and had nothing to do with the adjustments associated with lights turning on-off and dimming during the day.
Beyond these issues, the primary downfall of this study was that the buildings included in this study were not a random sampling and the overall sample group was relatively small. While the average savings of the sample group may be valid, the savings from building to building varied widely. It is generally suggested that there are potentially significant energy savings, but a broader study with direct comparison to minimum code compliant buildings is needed to demonstrate defendable statistical trends.
The next question is: What is the material cost associated with LLLC? In 2021, NEEA published a study examining the incremental cost associated with LLLC. The study found that while costs were steadily dropping year over year, they were still substantial. The incremental cost of adding “clever” or “smart” functionality compared to the code minimum installation ranged from $29 to $70 per light fixture.
As seen above, smart lighting is not a compelling investment, based on solely on energy cost savings. There are other, potentially more cost-effective energy efficiency solutions, such improving building envelope thermal performance. However, there is a real estate concept known as the 3/30/300 rule that may provide a more compelling reason for smart lighting adoption. This concept states that there is an average order of magnitude between a company’s costs for utilities, rent and payroll per square foot per year:
• $3 for utilities.
• $30 for rent.
• $300 for payroll.
While the exact values will vary, it is expected that the relationships and orders of magnitude difference between these three items are generally valid. Based on this relationship, an incremental percentage improvement in employee productivity can have an outsized impact compared to a similar percentage improvement in energy consumption.
Numerous studies have examined the impact of tunable lighting on circadian rhythms and educational outcomes. The consensus is that controllability is a positive influence on those outcomes. However, similar evidence-based research for commercial office environments is lacking — for now.
Why would a utility company actively encourage its customers to use less electricity if its revenue is tied to selling electricity? The simple answer is that the capacity that one customer does not use can be sold somewhere else. A rebate program makes sense if the utility company can buy that capacity through energy efficiency rebates at a lower cost than what would be required to purchase that capacity from somewhere else.
EIA studies have demonstrated that economic growth in the U.S. decoupled from energy usage long ago. EIA projected that between 2019 and 2050 gross domestic product will grow at an annual rate of 1.9%, but that energy consumption will have an annual average growth of 0.3%. The net result has been reduced investment in the grid.
It is also expected that carbon dioxide emissions will continue to increase, furthering the associated risks of climate change. To this end, the federal government has passed legislation that included decarbonization efforts. So, while overall energy usage growth across the entire U.S. economy may be limited, the fuel mix (coal, gas, solar, nuclear, wind, etc.) will change to emphasis electrification and utilizing renewable generation sources.
The change in the country’s fuel mix will have severe consequences. The intermittent and limited duration nature of wind and solar generation means that replacing thermal generation with renewables is not a one for one swap. Typically, multiple megawatts of renewables are needed to replace a single megawatt of traditional thermal generation. As existing thermal generation assets are retired, it is unclear
• Monitoring occupant activity to brighten or dim lighting when occupied or unoccupied, respectively.
• Monitoring ambient light, both electric light and daylight, and brighten or dim artificial light to main desired light level.
• For each control strategy, configuration and reconfiguration of performance parameters including: bright and dim setpoints, timeouts, dimming fade rates, sensor sensitivity adjustments and wireless zoning configurations.
• Luminaries shall be configured for continuous dimming.
• Luminaires shall be addressed individually. Where individual addressability is not available for the luminaire class type, a controlled group on not more than four luminaries shall be allowed.
• Not more than eight luminaires shall be controlled together in a daylight zone.
• Fixtures shall be controlled through a digital control system that includes the following function:
• Control reconfiguration based on digital addressability.
• Load shedding.
• Occupancy sensors shall be capable of being reconfigured through the digital control system.
if the new renewables will come online at a sufficient rate to make up this shortfall.
PJM, a regional electrical transmission organization responsible for coordinating the reliable transmission of electricity between generation companies and local utilities, issued a study that examined this shortfall issue, and the conclusions were not encouraging. While demand response and distributed energy storage are important tools in helping bridge the gap, additional resources are still needed.
Making this shortfall worse, the problem extends beyond the commercial and residential building market. The EIA typically separates energy usage into four broad categories: industrial, transportation, commercial and residential. While a significant percentage of the total energy consumption in the commercial and residential sectors already comes from electricity, that is not the case for industrial and transportation sectors. If those markets take significant steps toward electrification, the electrical capacity situation will worsen.
The solution to demand outpacing supply in a market-based economy is to raise prices. If the cost for electricity increases, some technologies such
as smart lighting may become more economically viable. The logical extension of DLC’s efforts to develop NLC/LLLC guidelines, is standardizing functional requirements, so it will be easier to quantify the associated energy savings. While energy costs may increase, implementation of smart lighting may also result in energy savings for consumers and recovery of some valuable grid capacity for utility companies.
Lighting control concepts may seem natural to an engineer, but they often are not for the general population. Most engineers assume that building occupants generally want more control over their environment. However, that ability to have extensive controllability is often more confusing than enabling. As such, in a well-designed lighting control system, most functions are automatic, and the need for direct user interaction is kept to a minimum. Where interaction is required, clear and consistent identification of what the controls are supposed to do is critical.
‘ As lighting control systems become more complicated with additional granularity of control, these last two problems will become a reoccurring theme. ’
In the first example, a U.S. Green Building Council LEED Gold corporate headquarters project was designed with lighting system sensors controlling 50% of plug loads within offices areas. Plug load control is commonly integrated into lighting control systems per 2021 IECC and ASHRAE 90.1. The associated receptacles were properly marked “controlled” in accordance with NFPA 70: National Electrical Code Article 406.3(E).
A short time after the client moved into their new offices, complaints started. Many of the executives rarely worked in the office. As they started to use their offices, they would plug laptops, phone chargers and other equipment requiring constant power into whatever receptacle was most readily accessible. The key problems were:
• The occupants had no previous experience with lighting-sensor controlled receptacles.
• Occupants did not know what the markings meant.
• The receptacles were usually located under desks and behind other obstructions where markings were not clearly visible.
This situation could have been made better by improved training and supplemental labeling or color coding to help the occupants to determine that these receptables were different from what they are used to.
In a second example, a networked wireless lighting control system for a commercial office space had been in service for multiple years. After what was assumed to be a power surge, the network controller rebooted unexpectedly. After the reboot, multiple wireless sensors started to function erratically and could not maintain consistent communication with the controller. The controller reported no errors after the reboot. In addition, some wireless occupancy sensors started to report low-battery conditions and it was unclear exactly which sensors were dying. They key problems were:
• “Control persistence” was not present. Control persistence is defined as the ability to execute three energy saving strategies (occupancy sensing, daylight harvesting and highend trim) in the absence of communication with the next higher networked element in the system. This functionality is a reported capability of network lighting systems as defined by DLC’s NLC5 requirements.
• The individual wireless devices did not have an obvious method, such as a different colored blinking light on the device, to identify which one had a low-battery condition.
• The naming convention used to identify devices in the lighting control software interface was convoluted and did not necessarily reflect where the devices were located.
• Lack of knowledge about how to interpret error messages and interact with the software made troubleshooting difficult.
The first two problems reflect possible limitations with the lighting control equipment itself. Hopefully as standards evolve, functional requirements will become more consistent across the industry. The second two problems are more indicative of insufficient training and interaction with the client during the system setup and commissioning process.
In the last example, a tenant noted issues with trying to turn lights on/off in its offices while in the process of moving in. The lighting control system was straightforward with a dedicated button assigned to each control zone. However, the contractors were rushing to complete their work before move-in and it was noted during the punch list that only some of the control stations were properly labeled.
Once the tenant realized that all the unlabeled buttons throughout their space had something to do with lights turning on and off, they resorted to button mashing to figure out what each button did.
In addition, the contractor had programed a placeholder time-of-day schedule for certain common area lighting that was not approved by the tenant. As such, the lighting within the space would turn on or off at time that didn’t match their normal business hours. The key problems were:
• Installation, commissioning and training activities did not take place in a timely manner.
csemag.com u
• Labeling of controls, which would have made the intended functionality of the system more readily apparent to the occupants, was inconsistent leading to confusion.
As lighting control systems become more complicated with additional granularity of control, these last two problems will become a reoccurring theme. cse
John Yoon, PE, LEED AP, is lead electrical engineer at McGuire Engineers. He is a member of the Consulting-Specifying Engineer editorial advisory board.
Smart lighting insights u Smart lighting technologies, while offering potential energy savings, require clear user understanding and proper training to prevent confusion and ensure effective use.
u Rising energy prices and the need to address climate change could make smart lighting more economically viable and contribute to grid capacity optimization.
Mike Chrisman, Henderson, Overland Park, Kansas
Suites are a great design option that allow for operational flexibility in health care facilities, while still meeting NFPA 101 requirements
• Explain suites and their use in health care facilities.
• Review NFPA 101 requirements for suites.
• Understand the types of suites allowed in health care facilities and their uses.
or health care facilities complying with the conditions of participation for Centers for Medicaid & Medicare Services (CMS), the 2012 edition of NFPA 101: Life Safety Code is required to address life safety requirements within a facility. NFPA 101 provides a flexible design and an operational option for a collection of rooms, called suites.
While this option is also described in the International Building Code, this article will be focused only on NFPA 101 requirements. The use of suites is unique to health care occupancies and is often a term that is used generally and misunderstood.
In general, a suite is a collection of rooms that are grouped together or adjacent to each other. NFPA 101 Section 3.3.272.5 defines a patient care suite as, “a series of rooms or spaces, or a subdivided room separated from the remainder of the building by walls and doors.” While this definition has been tweaked in newer editions of NFPA 101, it remains somewhat general to allow flexibility in its use.
By grouping rooms together in a suite, the code permits certain exemptions from other requirements typical to a health care occupancy that may otherwise negatively impact patient care procedures, increase cost or result in additional inspection, testing and maintenance impacts for certain features of the facility.
NFPA 101 defines three different types of suites — patient care sleeping suites, patient care nonsleeping suites and nonpatient care suites:
• Patient care sleeping suites: Thes will contain “one or more sleeping beds intended for overnight sleeping” as defined by NFPA 101. An example in a hospital may include an intensive care unit (ICU).
• Patient care nonsleeping suites: These are used for treating patients, but are not intended for overnight sleeping, according to NFPA 101. Examples in a hospital may include a radiology department, an outpatient clinic within a hospital or, potentially, an emergency department.
• Nonpatient care suites: These are for suites that do not treat patients. Examples in a hospital may include administration departments, staff locker rooms or the facilities department. Each suite type has specific requirements because of the different occupants located within each suite.
Habitable rooms: NFPA 101 Section 18.2.5.6.1 requires, “every habitable room to have an exit access door leading to an exit access corridor.” This
is because most occupants in a health care facility are incapable of self-preservation and require a defend-in-place evacuation strategy. Staff is required to support evacuation, either horizontally or vertically in the facility.
Corridors, which lead to exits, become a very critical component of egress, and this requirement for discharge limits how certain departments/units in hospitals can be designed. One way to get around this requirement is by utilizing suites. Suites permit occupants to exit through several rooms to get to a point where an exit access door is required, meaning that not every habitable room within the suite is required to have direct access to a corridor. This allows designers and staff more flexibility to support patient care while still maintaining a safe environment.
Corridors: An important feature of suites is that corridors are not required within suites. In new health care facilities, corridors are required to be a minimum of 8 feet wide with limited allowances for fixed furniture, wheeled equipment or projections.
In a suite, these circulation spaces (often called halls or something similar) indicate to the authority having jurisdiction that corridors are not part of the suite and that those requirements do not need to be met. This allows these circulation spaces to be reduced to a width that is needed for evacuation, to functionally support the space or is at least 36 inches. This also allows for some amount of equipment to be located within the space so long as there is a plan to promptly remove or relocate during an evacuation event), which is not allowed in a corridor.
Every corridor also requires access to two approved exits, without passing through any intervening rooms or spaces other than corridors or lobbies per NFPA 101. Suites will allow intervening rooms to be utilized before entering a corridor.
Operationally, the removal of corridors and their associated requirements are a positive for facilities staff. In a corridor, walls must be sealed to limit the transfer of smoke under NFPA 101. Additionally, corridor doors are required to:
• Resist the passage of smoke.
• Maintain an undercut of 1 inch or less.
• Maintain positive latching.
For rooms located around a circulating space in a suite, there are no corridor walls or doors, which allows for doors that meet the functional requirements of the space (e.g., pressurized spaces) with-
An example may include an opening area with treatment bays that would require walls and doors (physical separation) for each bay if located directly on a corridor. There are some exceptions for nurse stations or waiting spaces that are allowed in a corridor, but the flexibility of a suite will allow many other spaces to also be open within the suite.
Separation: NFPA 101 requires that all suites are separated from other portions of the building by walls and doors meeting the requirements for corridor separation. Internal walls within the suite are required to be noncombustible, limited-combustible or partitions constructed with fire-retardant treated wood enclosed with noncombustible or limited-combustible materials. They shall not be required to be fire rated unless required by other portions of the code (e.g., hazardous area).
Patient care sleeping suites: This suite type allows for patients that will be sleeping overnight; therefore, requirements are enhanced to address additional defend-in-place and/or evacuation time required.
Criteria includes the following:
• Constant staff supervision is required.
• Direct supervision is required from a “normally attended location within the suite” for the patient sleeping rooms. Any patient sleeping rooms without direct supervision requires smoke detection.
csemag.com
101 insights
uSuites in health care facilities offer design flexibility and exemptions from certain requirements, allowing for patient-centered room grouping.
uCorridors are not required within suites, leading to more efficient use of space and fewer restrictions on corridor width and features. This can simplify facility design and reduce the need for corridor walls and doors, improving operational efficiency.
out requiring the additional inspection, testing and maintenance listed above. Walls may contain gaps for equipment or other items required for patient care or treatment.
For example, it is common to see ICU patient rooms utilizing horizontal sliding doors in lieu of traditional swinging doors. These types of doors can be provided with a latching function, but run into challenges operationally due to the need to move beds in and out of these spaces often. By utilizing suites, these doors are allowed to only meet the requirements needed for functionality or for other code requirements (pressurization, etc.).
Flexibility: Rooms in a suite do not require separation from the circulating space (unless for other code reasons, such as a hazardous room). If these rooms were outside a suite, they would need to be located directly off a corridor, which has a requirement for physical separation with a wall and door.
• Maximum size of 7,500 square feet or 10,000 square feet where both direct visual supervision and total smoke detection is provided.
• Sleeping suites exceeding 1,000 square feet require two remotely located exit access doors. One exit access door shall be direct to a corrido. The other can be into an adjacent suite, an exit stairway, exit passageway or an exterior door.
• Exit travel distance from any point of the sleeping suite to an exit access door is limited to 100 feet. However, the number of intervening rooms within the suite is not limited.
Patient care nonsleeping suites: Patients treated in this suite type do not sleep overnight, which means requirements differ somewhat from patient care sleeping suites. Some considerations include the following:
• Maximum size of 10,000 square feet. Newer editions of NFPA 101 have modified this requirement to allow up to 12,500 square feet or 15,000
A HOSPITAL utilized suites for cesarean section operations to increase operability and flexibility
Working with a health system on a life safety survey and plan update, Henderson Engineers identified an issue involving a patient care nonsleeping suite. The specific area involved a cesarean section (C-section) suite adjacent to an area with patient sleeping rooms.
According to staff, the C-section area was an ideal space for a suite because it had high traffic and included patient beds and other equipment required for treatment that remained in the circulating space for a period. After identifying the space as a suite, another NFPA 101: Life Safety Code issue was identified by requiring a corridor to exit through a suite. This is not permitted because corridors are required to provide access to an approved exit. In this case, the scenario resulted in a dead-end corridor, which is only permitted to be 30 feet in existing sprinklered health care occupancies.
Figure 5: A diagram demonstrating the challenges engineers and designers faced when created a patient nonsleeping suite.
Courtesy:
Henderson Engineers
After confirming with staff that the C-section suite is critical for patient care/treatment, the team identified that creating another suite adjacent to the cesarean section suite would be a good option. By doing so, they were able to maintain NFPA 101 compliance and offer additional flexibility to staff for patient care in the identified area.
The new suite was compliant by:
• Allowing suite to suite egress between adjacent suites.
• Providing each suite with an exit access/corridor door.
• Separating suites from other suites and the remainder of the building by construction required for corridor walls.
square feet. However, this is not currently allowed by CMS.
• Nonsleeping suites exceeding 2,500 square feet require two remotely located exit access doors. One exit access door shall be direct to a corridor. The other can be into an adjacent suite, an exit stairway, exit passageway or an exterior door.
• Exit travel distance from any point of the nonsleeping suite to an exit access door is limited to 100 feet. However, the number of intervening rooms within the suite is not limited.
Figure 6: Designers utilized adjacent suites in this health care facility to increase flexibility and guarantee code compliance. Courtesy: Henderson Engineers
• Having a dead-end corridor that is allowable by NFPA 101.
• Allowing the cesarean section suite to remain a suite thus enabling maximum flexibility for patient care/treatment.
Understanding the types of suites and their respective requirements in addition to working with facilities and their staff to understand how spaces are used can result in identifying appropriate areas that will be incorporated into a project. While suites are not a requirement of the code, they are an option that allows for greater flexibility while maintaining a safe environment, allowing staff to focus on patient care and treatment.
As the newer editions of NFPA 101 have continued to adapt to new conditions, suite requirements also adjust accordingly. It is, however, important to remember that health care facilities under the current Centers for Medicaid & Medicare Services requirements must follow the 2012 edition.
Nonpatient care suite: This suite type does not contain patient treatment or sleeping uses. NFPA 101 requires that the egress provisions for this suite type follow the primary use and occupancy contained within. For example, Figure 4 shows a pharmacy suite and an office suite (staff only, no patients) that are permitted to follow business occupancy requirements for egress. cse
Mike Chrisman is a health sector executive at Henderson Engineers.
Maddy Doyle, CDM Smith, Boston and April Musser, PE, CDM Smith, Atlanta
requirements that are important to prevent the spread of fire and smoke. It is necessary to understand the correct terminology and intent of the requirements to identify when inspections should be completed.
At the time of its initial publication in 1927, NFPA 101: Life Safety Code was titled the Building Exits Code and was primarily focused on methods to safely affect exit burning structures. In the following decades, NFPA 101 became the Life Safety Code, and grew to contain over 40 chapters. While the effective means of egress covered in NFPA 101, Chapter 7 cannot be taken for granted, a lack of familiarity with further topics in the code causes confusion and lack of clarity.
NFPA 101 dictates the collection of fire protection features that are intended to work together to protect people in the event of an emergency. These systems include fire suppression systems, fire alarm systems, egress systems and building compartmentation. Many architects and engineers struggle to understand the differences between fire and smoke barriers and when each are required. People frequently call fire resistance-rated construction a “firewall,” not realizing that what they mean is “fire barrier” and that a firewall is an entirely different construction element.
There are two types of fire protection: active and passive. Compartmentation falls under the category of passive fire protection, which is integral to the building’s construction and aims to control a fire and limit the spread of its effects to other areas of the structure by using fire and smoke resistant materials in specific walls, ceilings and floors.
Compartmentation is defined in NFPA 101, Chapter 8, Features of Fire Protection as the practice of separating a structure into “compartments” to reduce the spread of fire and smoke. Fire and smoke make up the two main categories for classifying compartments, as defined in NFPA 101, Chapter 3, Section 3.3.49. Within the sections for either fire or smoke, NFPA 101 specifies
and references the classifications and constructions of the architectural and structural elements designed to resist the spread of fire and limit its detrimental effects.
Active systems, on the other hand, trigger a response or are applied under conditions that indicate the presence of fire or its byproducts. This kind of system is represented by what is often associated with fire protection overall; i.e., smoke detectors, sprinkler systems and fire extinguishers. Active systems are likely the ones to detect or extinguish a fire, while passive systems are the ones to reduce or limit how much of the structure a fire reaches or damages. These features help limit occupant exposure to the effects of a fire and are intended to help protect egress paths.
Including both active and passive fire protection in a structure’s design helps limit the impact of a fire, and while active systems are often more obvious, best results come from understanding the uses and expected results of passive fire protection. Containing the fire allows more time for egress and fire department activities. By slowing down a fire, even temporarily, passive systems can save lives and lessen property damage.
Fire barriers are defined in NFPA 101, Chapter 3, Section 3.3.32.1 as a continuous membrane or a membrane with discontinuities, created by a protected opening with a specified fire protection rating, where such membrane is designed and constructed to limit the spread of fire. Doors in fire barriers must be rated in accordance with the opening protective requirements of NFPA 101, Section 8.4.3, and must be self-closing with positive latching.
Where penetrations are required in fire barriers, they must be sealed with fire-stop using an approved, assembly-tested and installed in accordance with the manufacturer’s instructions. There is often confusion about whether recessed fixtures or equipment may be installed in a fire barrier. NFPA 101, Section 8.3.4.7 allows certain articles to be recessed into fire barriers if they only penetrate one membrane of the rated wall and meet specific limitations on size and type of penetration.
Where fire barrier systems join exterior walls, other fire barriers, floor, ceiling or roof assemblies, joints are required to be constructed using a
tested joint system assembly that is appropriate for the construction type and meets the minimum fire resistance rating requirements.
Smoke barriers, per NFPA 101, Chapter 3, Section 3.3.32.2, are a continuous membrane or a membrane with discontinuities, created by protected openings, where such membrane is designed and constructed to restrict the movement of smoke. The definition of smoke partition in NFPA 101, sounds like that of a smoke barrier, which often leads to confusion. However, there are a few key differences.
Smoke barriers are constructed as a continuous membrane, like fire barriers, but have the additional requirement of limiting air transfer. This generally necessitates the inclusion of smoke detection and automatically closing smoke dampers at duct penetrations and air transfer openings. Because smoke barriers oftentimes are also required to carry a fire resistance rating, they are commonly thought of as fire barriers with additional protections to prevent smoke movement.
Smoke partitions, on the other hand, require means to prevent air transfer across the barrier, but may omit smoke dampers in the case of duct penetrations. They may have doors that are self-closing but not positive latching.
Typically, NFPA 101 requires the subdivision of certain occupancies into smoke compartments with smoke barriers. These smoke barriers often require a minimum fire resistance rating of 30 minutes or one hour. Smoke partitions are required most at
FIGURE 2: A penetration in a rated fire barrier that has not been provided with the required opening protective. Courtesy: CDM Smith
• Understand terminology related to compartmentation elements in NFPA 101.
• Identify the different goals of different compartmentation elements in NFPA 101.
• Learn the requirements for inspection and maintenance of facility compartmentation as required by NFPA 101 and related standards.
corridor walls or ceilings when a fire resistance rating of the corridor is not required due to the presence of sprinkler protection.
Like fire barrier walls, where smoke barriers and partitions create joints with wall and floor, or ceiling and roof assemblies, the joint system must be capable of resisting the passage of smoke. Where a smoke barrier is also required to have a fire resistance rating, the joint system must meet the requirements for fire barriers.
Smoke- and fire-resistant assemblies are not only limited to vertical applications, like walls. Horizontal assemblies, such as floor or ceiling assemblies, are required at building openings in the conversely vertical direction to limit the spread of smoke and fire. As such, horizontal fire barrier and smoke barrier assemblies are used between floor levels to limit the vertical spread of fire and smoke.
Openings through the floor assemblies that serve as these fire and smoke partitions are required to be enclosed with fire barrier walls or smoke partitions that are continuous from floor to
floor or floor to roof, and openings are required to be protected. Exceptions allowed to this requirement are listed in NFPA 101, Section 8.6.3. These exceptions include penetrations for building utilities, conveyors, escalators, moving walks and at expansion or seismic joints.
In non sprinklered facilities, areas of the building that have a higher degree of hazard than what is normal to the general occupancy of the building are must be provided with fire barriers, in accordance with NFPA 101, Section 8.7. Where sprinkler protection is provided, these required separations for special hazards can be reduced to smoke partitions unless one of the exceptions listed in Section 8.7.1.2 applies.
The terms firewall and fire barrier are often used interchangeably, but they are not the same thing. In fact, firewalls are not addressed or defined in NFPA 101, but instead are covered by building codes and defined in Chapter 3, Section 3.3.15.6 of NFPA 221, Standard for High Challenge Fire Walls, Fire Walls, and Fire Barrier Walls. Firewalls are required to be structurally independent, allowing the building on each side to collapse without the wall coming down. A firewall is oftentimes used to separate structures that are connected to each other, but managed as separate buildings.
A party wall is a type of firewall that is constructed on a property line where two buildings managed by separate owners might be connected. Both firewalls and party walls are prohibited from having penetrations or openings interconnecting the buildings they separate.
Fire barriers, smoke barriers and smoke partitions are part of the collection of systems designed to work together with active fire protection features, such as fire sprinkler protection, fire detection, alarms and smoke control. It is important to review the design of fire protection systems in conjunction with a review of passive fire protection systems.
In one case study, a client had a building designed that included a control area, which needed to be separate from the remainder of the building by a smoke barrier. As a result, air transfer openings in the smoke barrier were required to
THE MGM GRAND HOTEL FIRE in 1980 demonstrates the real dangers that can come from a failure to design comprehensive passive fire protection systems
One of the most well-known case studies that demonstrates the importance of compartmentation is the MGM Grand fire that occurred in Las Vegas on Nov. 21, 1980. Though the fire did not spread past the ground level of the facility, inadequate compartmentation allowed smoke to spread upward through the hotel tower, contaminating exit stairs and corridors. Over 70% of the fatalities were located more than 14 stories away from the fire. Of the 85 fatalities, 61 of them occurred above the 15th floor.
The fire is believed to have started in a deli on the first floor and rapidly spread through the ground-level casino. The deli and casino did not have fire sprinkler protection. However, other areas of the ground level were provided with sprinklers. When the fire began to spread past the casino, the automatic fire sprinkler system activated and prevented further spread into the facility.
Unfortunately, the damage was already done. By the time the sprinkler system stopped the forward progression of the fire, smoke had contaminated exit stairs and guest room corridors with smoke. This prevented many occupants from being able to safely exit the facility. The heating, ventilation and air conditioning (HVAC) systems further spread the smoke and as a result, 61 victims were in corridors, elevators, stairs and guest rooms through a 10-floor span that extended from the 16th to the 26th floor.
The NFPA report identified the lack of proper compartmentation as one of the leading contributing factors to the high number of deaths. Unprotected vertical openings, including stair shafts and seismic joints, allowed smoke to move through the building while HVAC systems continued to operate, spreading smoke through corridors located remotely from the fire.
NFPA reported that the stairwells were not enclosed with twohour rated construction and identified significant gaps in the stair construction that allowed smoke to penetrate the stair enclosure. In addition, at least one stairwell was provided with an unprotected access hatch to the space above the casino ceiling. The fire spread to the catwalks that allowed casino security to monitor activities below, creating a direct path for smoke to pollute the stairwell. It traveled vertically through the building in conjunction with unprotected vertical openings, including seismic joints. Smoke infiltrat-
have smoke dampers. The arrangement of these smoke barriers made the installation of duct smoke detection at the openings impractical, so the design team provided area smoke detection in this space to trigger the smoke dampers to close and prevent the passage of smoke across the smoke barrier in the event of a fire.
FIGURE 4: Over the life of a facility, the fire barrier walls must be regularly inspected to ensure new work is properly protected. This photo shows several new penetrations that have not yet been firestopped. Courtesy: CDM Smith
ed the penthouse, contaminating air handlers, which lacked smoke detection designed to shut down upon detection. They continued running, spreading smoke into guest room corridors.
This fire illustrates how important it is to carefully evaluate compartmentation in facility design and why inspection and maintenance of those elements is vital in limiting deaths in the event of a fire.
A fire alarm reviewer later identified that, because of the presence of sprinkler protection, the building was not required to have area smoke detection (based on its specific use and occupancy). However, the reviewer didn’t recognize that the area detection in this location was required to close the smoke dampers at the smoke barrier walls
as duct detection was not provided at the air transfer openings. The reviewer directed the removal of area smoke detection from the design drawings as part of the value engineering process.
The fire protection consultant identified this error and prevented the mistake from being carried out into the construction drawings, illustrating why it’s important to review fire protection features as a collection of systems, including passive compartmentation fire protection systems.
Owners are frequently unaware of the importance of the passive fire protection systems in their buildings, and may direct renovations that undermine facility compartmentation. An example of a common compartmentation pitfall is the removal of a corridor wall to allow direct light from an open office area. There have also been cases of clients directing the removal of a hard ceiling to access equipment for repair or replacement, but then deciding to replace that hard ceiling with a ceiling cloud system that does not form a continuous smoke partition.
It is important for architects, consulting engineers and building owners to ensure that a thorough review is completed of compartmentation
requirements before making changes for utility or cosmetic reasons that might otherwise better allow the spread of fire and smoke should a fire start.
As buildings go through changes in use and occupancy, compartmentation requirements can also change. However, in existing structures, this can sometimes be overlooked. During changes in use or occupancy, building code analysis should be conducted by a qualified engineer or architect to determine the compartmentation requirements. They should then be reviewed holistically with the entire fire protection plan for the facility, which will ensure compliance with all applicable compartmentation requirements.
This can be especially troublesome in historic or older buildings that may not have been subject to modern compartmentation requirements during their original construction. Often the necessity of modifying the facility to provide compartmentation may be infeasible or impossible in such buildings. Likewise, when only a portion of a building is being modified, compartmentation may not remain continuous, as it would have to extend beyond the renovation area.
Consider a facility where a second floor is being renovated but occupants must traverse an existing lower level to reach an exit. If the lower level isn’t in the renovation scope, compartmentation may not be continuous to an exit for occupants of the renovation area. In these cases, it is important to work with the authority having jurisdiction and a qualified fire protection consultant to determine the best path forward.
Where fire barriers, smoke barriers and smoke partitions are required, building owners are responsible for the maintenance of those barriers and partitions in accordance with NFPA 101, Section 4.5.8. While NFPA 101 doesn’t specifically outline an inspection, testing or maintenance schedule for compartmentation elements such as these, it does have requirements for inspection and testing of fire door assemblies.
Additionally, fire rated doors, smoke dampers and other opening protectives are required to be inspected and maintained in accordance with
NFPA 80: Standard for Fire Doors and Other Opening Protectives. Smoke door assemblies also require regular inspection and testing in accordance with NFPA 105: Standard for Smoke Door Assemblies and Other Opening Protectives. Where adopted, NFPA 80 and NFPA 105 apply to both new and existing construction.
Over the life of the building, fire and smoke barriers are frequently penetrated to route new equipment, and these barriers and partitions may not be properly fire-stopped where new penetrations are created. Where ceilings make up part of a smoke partition, elements like missing sprinkler escutcheons, ceiling tiles or access holes that have not been properly repaired can be addressed through these required inspections. Without a valid annual inspection schedule and proper documentation of them, building owners may find it difficult to comply with the inspection, testing and maintenance requirements in NFPA 80, and NFPA 105, or the maintenance requirements in NFPA 101.
Fire compartmentation is an important part of the collection of systems that make up the entire fire protection envelope for a facility. Understanding the requirements for fire barriers, smoke barriers and smoke partitions can help architects, engineers and facility owners ensure that their facilities remain code compliant.
Ensuring that a facility is protected requires a holistic approach that includes the active systems, like fire alarm and sprinkler systems and passive systems, such as compartmentation. These systems must be maintained over the life of the facility and reevaluated when changes to the facility are made, even if the changes might appear only cosmetic, such as removing a ceiling or a wall. A regular inspection program can help owners ensure that these systems integral to fire protection and life safety are maintained. cse
The voice of the engineering community speaks loudly and clearly in the following corporate profiles featuring those companies taking part in the 2024 Executive Voice program.
We offer our sincere thanks to these advertisers:
NFPA 101 insights
• Compartmentation, including fire barriers and smoke barriers, is vital for limiting fire and smoke spread, to ensure the safety of building occupants.
• Active systems detect and respond to fires, while passive systems are integral to the building's construction and aim to control the spread of fire and smoke. Understanding how both types of systems work together is essential for effective fire protection
Belimo, established in 1975, stands as the global leader in the development, production, and sale of field devices for energyefficient HVAC system control. Specializing in damper actuators, control valves, sensors, and meters, Belimo is committed to advancing sustainable building practices to counter the significant environmental impact attributed to the 40% of global CO 2 emissions generated by buildings.
Our consistent focus on market and customer needs underscores our dedication to delivering superior value, surpassing customer expectations, and outpacing competitors. A testament to this commitment is the allocation of approximately 7% of sales toward research and development, ensuring Belimo’s solutions consistently set new industry benchmarks.
The Belimo Energy Valve® is an IoT, cloud-connected pressure independent valve that monitors coil performance and energy consumption while maintaining Delta T. It features patented glycol monitoring and compensation, ensuring precise flow measurement and compliance with design requirements. Integration with the Belimo Thermal Energy Meter facilitates energy control and efficient billing.
Belimo Room Sensors further enhance comfort with maintenance-free devices accurately measuring temperature, humidity, and CO 2 . The streamlined design, optionally equipped with an ePaper touch display, integrates NFC for quick setup and adjustments through the Belimo Assistant App. This app provides easy data access, field adjustability, commissioning, and troubleshooting, even without power.
With Belimo’s RetroFIT+ we can help you maximize energy savings, reduce carbon emissions, and boost comfort without disrupting existing systems significantly or incurring substantial costs.
“Our consistent focus on market and customer needs underscores our dedication to delivering superior value, surpassing customer expectations, and outpacing competitors.”
Whether you’re looking for a simple improvement, a significant overhaul, or something in between, we have the technology and expertise to help.
For more information on Belimo solutions, or to speak with your local representative, visit belimo.com or scan the QR code.
The Future of Data Centers is Carbon-Free.
Danfoss is leading the way in decarbonization.
With our broad portfolio of low-carbon, energyefficient solutions, we strive to be our customers’ preferred decarbonization partner. We have the expertise to offer data center cooling products for solutions that decrease emissions, energy usage and operating costs.
As part of our ESG (environmental, social, governance) goals, we have pledged to become carbon-neutral by 2030. In 2022, we reduced our emissions from global operations by 7% while experiencing 15% business growth. Throughout our facilities, we are adopting energy-efficient HVAC solutions, recycling and reusing heat where possible, and procuring energy from renewable sources.
In 2023, we signed an agreement to purchase 75 megawatts of solar power from a Texas solar farm, beginning in 2025. This will enable us to fully replace our annual electricity usage in North America with renewable energy through at least 2037 and will reduce our carbon footprint in North America by 75%.
With society’s increasing reliance on data transmission and cloud storage, the demands and numbers of data
centers will continue to grow. According to the International Energy Agency, data centers consume about 1% of the world’s total electricity and account for 1% of global greenhouse gas emissions. Implementing sustainable cooling solutions will be critical to meeting our climate goals.
Business Development Director — Data centers, Danfoss
At Danfoss, we have transformed our headquarters in Nordborg, Denmark. In 2015, they were heated entirely by fossil fuels. The Danfoss headquarters are now carbonneutral and by next year, excess heat from our data center will provide 25% of the overall heat supply for the 2.7 million ft 2 (250,000 m2) of factories and offices at company headquarters.
We have the solutions and expertise to help data centers in their decarbonization journey. Our broad portfolio of low-carbon, energy-efficient data center cooling solutions includes:
· Danfoss Turbocor ® oil-free, magnetic-bearing compressors including for low-GWP refrigerants and high temp applications
· Inverter scroll compressors
· Variable-speed drives
· Microchannel and Plate heat exchangers
· Energy transfer stations for data center heat recovery and reuse
· Universal Quick Disconnect (UQD) couplings and hoses
· Refrigerant flow control and safety devices
Danfoss solutions and application expertise enable data centers to improve PUE, reuse excess heat and minimize water use while decreasing maintenance and energy costs. Learn more at: Datacenters.Danfoss.us .
The Department of Energy (DOE) requires states to certify that they have reviewed and updated their commercial building energy codes to meet or exceed ANSI/ASHRAE Standard 90.1-2019. The deadline to certify compliance with 90.1-2019 was July 28, 2023.
While some states have adopted 90.1 directly or met requirements through IECC-2021 or their state energy code (e.g., CEC T24), many states missed the July deadline. However, $1 billion in funding is available through September 30, 2029 from the Inflation Reduction Act to assist states and local governments in achieving compliance and meeting DOE requirements related to commercial building energy codes. This funding can be used to support the adoption and implementation of qualifying energy codes.
Fan selections based on the Fan Energy Index (FEI) during building design can help meet or exceed energy code requirements while optimizing fan efficiency. Both ASHRAE 90.1 and IECC require a minimum FEI of 1.00 for fans with a motor nameplate of 1.0 hp and above.
FEI represents a fan’s electrical input power relative to a baseline fan at a given duty point. For example, a fan with an FEI of 1.10 requires approximately 10% less power than the baseline model. Selecting fans below 1.00, like one
rated at 0.85 FEI, will fail to meet minimum energy code requirements.
Specifying thirdparty certified FEI values assures the fan will perform as advertised. IECC mandates third-party certification to meet the requirements of the code. Validated ratings give engineers, architects, and owners assurance that fans will operate as designed to assure efficient and effective ventilation of the building.
Mike Wolf P.E., Director, Industry/ Regulatory Relations, Greenheck
Greenheck’s eCAPS® online product selection program includes AMCA-certified FEI values to facilitate codecompliant fan selection. To optimize fan selections and assure code compliance, engineering fan schedules must list the design FEI value and note that “FEI must meet or exceed the listed value in the fan schedule”. Some utilities also provide rebates on fans with FEI ratings that exceed minimum code limits. These incentive programs also usually require third-party certified FEI ratings to assure maximum savings are achieved.
Selecting fans based on FEI ratings during design, while specifying AMCA-certified performance through eCAPS, will ensure both code compliance and ventilation system energy performance that maximizes savings to the owner and provides comfortable, safe air to building occupants.
Visit www.greenheck.com/resources/software/ecaps to access Greenheck’s eCAPS program.
CSE: What’s the biggest trend you see in office buildings?
Mark J. Richter Sr.: Environmental and net zero carbon legislation is a significant trend around the world. As we address the impacts of climate change, it will increasingly become central to the narrative of how the global community shapes the built environment. Many U.S. cities and states are enacting or initiating legislative policies built upon similar European policies already in place. These policies regulate and enforce annual greenhouse gas generated level compliance metrics through severe noncompliance fines. As such, design professionals will need to consult and lead their clients to cost-effective building solutions that will provide long-term regulatory compliance and sustainable results.
Mark Walsh-Cooke: One of the biggest trends I see is the “flight to quality.” The office buildings that have many amenities with options for wellness, food and outdoor space tend to lease well. Recently completed, leased examples in Boston include One Congress and Winthrop Center.
CSE: How are engineers designing office facilities to keep costs down while offering appealing features,
complying with relevant codes and meeting client needs?
Peter Syntax: A lot of office space designs include more adaptable lighting controls and daylight harvesting at a local level. There’s also a trend to design more open office spaces toward the interior. This allows more natural light to enter the space, which conserves energy. Giving individual employees the ability to control the lighting in their office locations without impacting others has been difficult to navigate. Working with building owners, Kimley-Horn has developed standard control systems that can be used in a multitude of spaces to allow the flexibility tenants need.
Mark Walsh-Cooke: Many of the cities we work in have goals either around zero net energy, operational carbon reduction or requirements for full electrification. To help meet this need, one tool we are using is parametric energy modeling. This analyzes of thousands of options, which helps the owner make a more data-driven decision on which design options to proceed with.
As the technology develops for cold weather climates, one solution that is becoming more popular is air source heat pumps for both space heating and domestic hot water. For commercial life science
Mark J. Richter Sr., PE, LEED AP
Client development leader, Principal
HDR Inc.
New York
Peter Syntax, PE, LEED AP
MEP Practice Lead
Kimley-Horn Phoenix
Mark Walsh-Cooke, PE
Principal, Americas east property business leader
Arup
Boston
projects specifically, this strategy can offset over 90% of the annual carbon emissions from fossil fuels.
Mark J. Richter Sr.: COVID-19 had a significant impact on the corporate real estate market, specifically in the reevaluation of the workplace space model for corporate office buildings. This has resulted in adjustments on multiple fronts, including hybrid work schedules, hoteling coworking environments, lower-density workplace programs, communicable and dynamic amenity-driven program spaces, occupier health and safety concerns and employer and employee environmental stewardship. Unlike owners of newer offices, iconic and class A buildings, landlords of older, less desirable offices find themselves facing significant challenges due to aging infrastructure or a lack of new technologies and upgrades. cse
BELIMO .1 .www .belimo .com
BERNER AIR CURTAINS .18 .www .Berner .com
CDM Smith .56 .www .cdmsmith .com/en
CFE Media GSI Database .41 .https://gspplatform .cfemedia .com/si/home
CFE Media LLC .25 .www .cfemedia .com
CFE Media NPE Database .41 .https://gspplatform .cfemedia .com/pe/home
CHAMPION FIBERGLASS .12 .www .championfiberglass .com
Danfoss .2 .www .danfoss .us Greenheck .23 .www .greenheck .com
Industrial Cybersecutiy Pulse .13 .WWW .ICSPULSE .COM
Lafert North America .C-4 www .lafertna .com
Metraflex .34 .www .metraflex .com
Navien, Inc .C-2 www .Navien .com
Tjernlund Products .56 .www .tjernlund .com
ULINE .25 .www .uline .com
Yaskawa America, Inc .C-3 www .yaskawa .com
CDM Smith is hiring mechanical and electrical engineers!
XYLEM GLOBAL HEADQUARTERS .4 .http://tinyurl .com/8ecbz8y5 Join us. We are leading the way for sustainable, resilient solutions. What are you waiting for?
Publisher
Matt Waddell MWaddell@CFEMedia.com PO Box 471 312-961-6840
Downers Grove, IL 60515
Sales Account Manager
Richard A. Groth Jr. RGroth@CFEMedia.com 12 Pine Street 774-277-7266
Franklin, MA 02038
Sales Account Manager
Robert Levinger RLevinger@CFETechnology.com PO Box 471 630-571-4070 x2218
Downers Grove, IL 60515
Sales Account Manager
Brian Gross BGross@CFEMedia.com PO Box 471 847-946-3668
Downers Grove, IL 60515
Sales Account Manager
Mike Workley MWorley@CFEMedia.com PO Box 471 331-277-4733
Downers Grove, IL 60515
Jim Langhenry, Co-Founder and Publisher, CFE Media JLanghenry@CFEMedia.com
Steve Rourke, Co-Founder, CFE Media SRourke@CFEMedia.com
McKenzie Burns, Marketing-Events Manager MBurns@cfemedia.com
Courtney Murphy, Marketing and Events Manager CMurphy@cfemedia.com
Paul Brouch, Director of Operations 630-571-4070 x2208, PBrouch@CFEMedia.com
Rick Ellis, Audience Management Director 303-246-1250, REllis@CFEMedia.com
Michael Smith, Creative Director 630-779-8910, MSmith@CFEMedia.com
Michael Rotz, Print Production Manager 717-422-3622, mike.rotz@frycomm.com
Jeff Mungo, List Rental Account Director DataAxle 402-836-6278, Jeff.Mungo@data-axle.com
Claude Marada, List Rental Manager 402-836-6274, claude.marada@infogroup.com
Letters to the Editor: Please e-mail your letters to ARozgus@CFEMedia.com
Letters should include name, company, and address, and may be edited for space and clarity.
Information: For a Media Kit or Editorial Calendar, go to www.csemag.com/connect/advertising
Marketing consultants: See ad index.
Custom reprints, electronic: Shelby Pelon, Wright’s Media, 281-419-5725 x138 cfemedia@wrightsmedia.com
HV600 drives and packages are available in a variety of styles and enclosures to meet all your HVAC requirements:
Electronic bypass and configured packages are offered in space-saving Narrow or option-rich Enclosed designs with an array of power and control options in a “right-size” package design, allowing you to customize a package to suit your application needs.
What type of conditions are you looking to meet? Call Yaskawa at 1-800-927-5292 today.