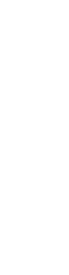
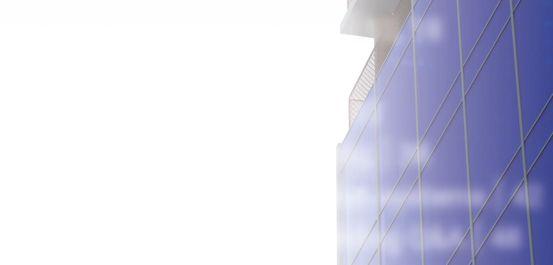
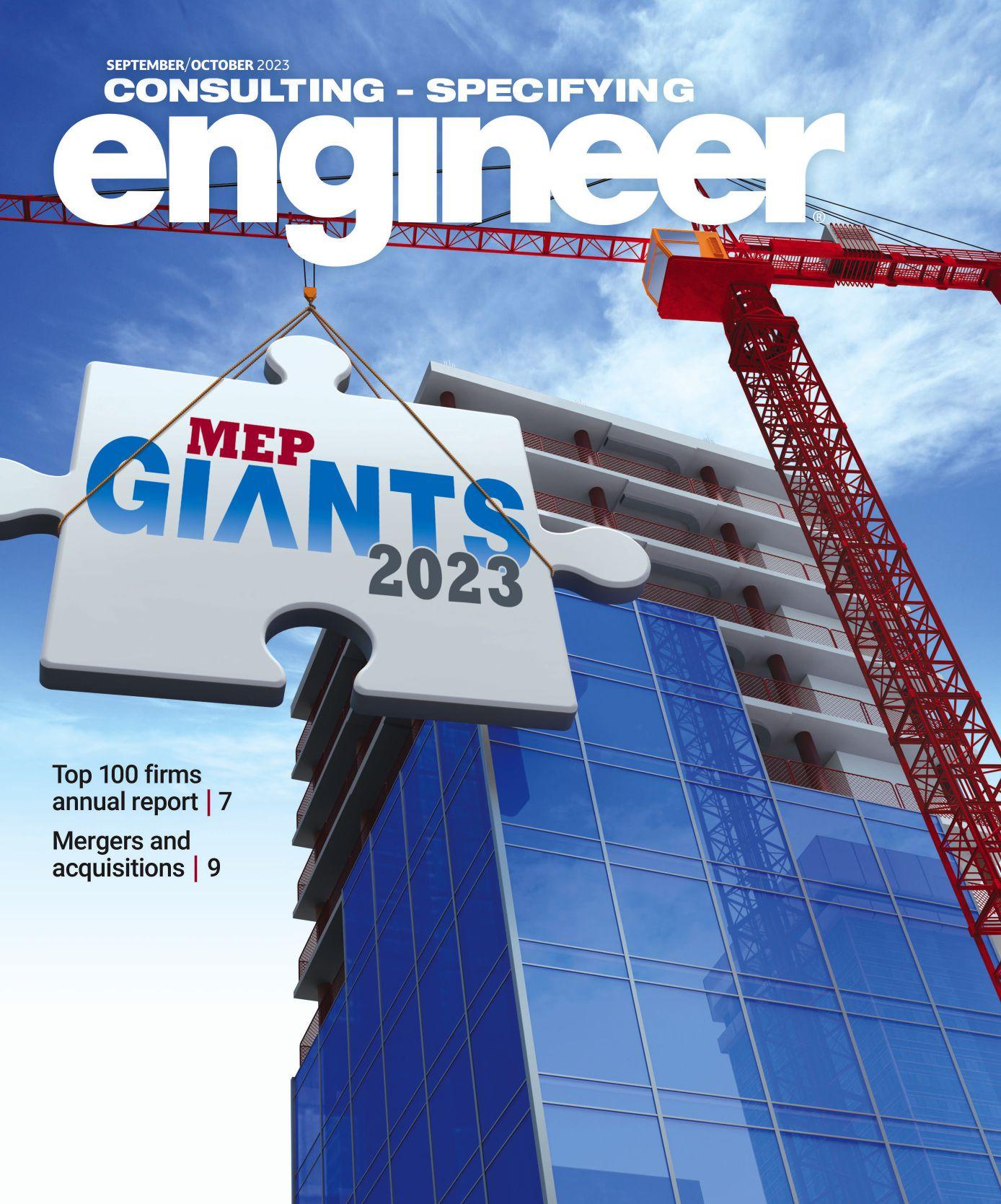

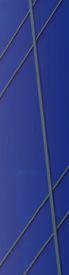
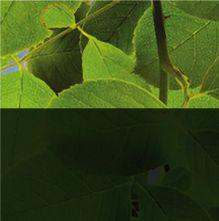
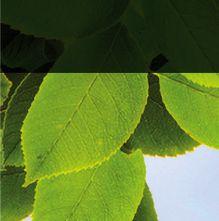


According to the World Green Building Council, we spend 90 percent of our time indoors. Given that statistic, it’s clear the quality of the air we breathe in buildings can dramatically impact our health and well-being. At Reliable Controls we believe sustainable buildings are a key component to reducing the health and environmental impacts of indoor and outdoor air pollution.
Learn more reliablecontrols.com/IAQ
for your next big high commercial heating application
Cascade up to 32 units and common vent up to 4 units for a wide range of heating outputs.
Patented Navien designed and built ASME-Certified “H” stamped stainless steel fire tube heat exchanger.
Intuitive 7" touch screen control for easy set up and diagnostics.
Built-in hardware for boiler pump, 3 heating zones or indirect tank control.
To learn more about all the big things happening at Navien, visit Navieninc.com.
The ultimate in power density just got better. Upgrade from your obsolete DC motor today. The Baldor-Reliance RPM AC motor combines square frame design, efficient cooling and premium insulation systems for ultimate torque performance in a compact package.
abb.com/motors-generators
5 | How is your firm handling hiring, retaining, training?
Learn how your company stacks up and how you can become more appealing
7 | MEP Giants annual design revenue rises, bucking trends
While the economy sits at a slow burn, the 2023 MEP Giants firms continue to do well
9 | What made for another strong year for the MEP Giants?
Following record M&A activity in 2021, 2023 MEP Giants had another active year
12 | Preventing shock and arc flash hazards in electrical systems
Understand electrical hazards to establish electrically safe work environments
18 | Achieving arc flash safety in building electrical systems
Arc flash analysis is important when designing electrical systems for large amperage and utility service equipment
26 | How you can save with hydronic heating systems
Lowering the temperature of heating hot water systems is key to decrease energy used to heat buildings
32 | Considerations from the history of building control systems
Technologies and protocols that allowed for multiple control system integration
38 | Cybersecurity impact on construction, engineering projects
Technology increases in the built environment introduce cybersecurity to the design and construction industry
42 | How to design medium-voltage distribution systems
End user safety, system reliability and equipment maintainability are key for medium-voltage electrical distribution systems
48 | Emerging trends in college and university buildings
Environmental consideration, future flexibility are
considerations for universities
AMARA ROZGUS, Editor-in-Chief/Content Strategy Leader ARozgus@CFEMedia.com
CHRIS VAVRA, Web Content Manager CVavra@CFEMedia.com
ANNA STEINGRUBER, Associate Editor ASteingruber@CFEMedia.com
AMANDA PELLICCIONE, Director of Research APelliccione@CFEMedia.com
MICHAEL SMITH, Creative Director MSmith@CFEmedia.com
DARREN BRUCE, PE, LEED AP BD+C, Director of Strategic Planning, Mid-Atlantic Region, NV5, Arlington, Va.
MICHAEL CHOW, PE, CEM, CXA, LEED AP BD+C, Principal, Metro CD Engineering LLC, Columbus, Ohio
TOM DIVINE, PE, Senior Electrical Engineer, Johnston, LLC, Houston
CORY DUGGIN, PE, LEED AP BD+C, BEMP, Energy Modeling Wizard, TLC Engineering Solutions, Brentwood, Tenn.
ROBERT J. GARRA JR., PE, CDT, Vice President, Electrical Engineer, CannonDesign, Grand Island, N.Y.
JASON GERKE, PE, LEED AP BD+C, CXA, Mechanical Engineer, GRAEF, Milwaukee
JOSHUA D. GREENE, PE, Associate Principal, Simpson Gumpertz & Heger, Waltham, Mass.
RAYMOND GRILL, PE, FSFPE, LEED AP, Principal, Ray Grill Consulting, PLLC, Clifton, Va.
DANNA JENSEN, PE, LEED AP BD+C, Principal, Certus, Carrollton, Texas
WILLIAM KOFFEL, PE, FSFPE, President, Koffel Associates Inc., Columbia, Md.
WILLIAM KOSIK, PE, CEM, LEED AP BD+C, BEMP, Senior Energy Engineer, Oak Park Ill.
KENNETH KUTSMEDA, PE, LEED AP, Engineering Manager, Jacobs, Philadelphia
JULIANNE LAUE, PE, LEED AP BD+C, BEMP, Director of Building Performance, Mortenson, Minneapolis
DAVID LOWREY, Chief Fire Marshal, Boulder (Colo.) Fire Rescue
JASON MAJERUS, PE, CEM, LEED AP, Principal, DLR Group, Cleveland
BRIAN MARTIN, PE, Senior Electrical Technologist, Jacobs, Portland, Ore.
GREGORY QUINN, PE, NCEES, LEED AP, Principal, Health Care Market Leader, Affiliated Engineers Inc., Madison, Wis.
BRIAN A. RENER, PE, LEED AP, Principal, Electrical Discipline Leader, SmithGroup, Chicago
SUNONDO ROY, PE, LEED AP, Director, Design Group, Romeoville, Ill.
JONATHAN SAJDAK, PE, Senior Associate/Fire Protection Engineer, Page, Houston
RANDY SCHRECENGOST, PE, CEM, Austin Operations Group Manager/Senior Mechanical Engineer, Stanley Consultants, Austin, Texas
MATT SHORT, PE, Project Manager/Mechanical Engineer, Smith Seckman Reid, Houston
MARIO VECCHIARELLO, PE, CEM, GBE, Senior Vice President, CDM Smith Inc., Boston
RICHARD VEDVIK, PE, Senior Electrical Engineer and Acoustics Engineer, IMEG Corp., Rock Island, Ill.
TOBY WHITE, PE, LEED AP, Associate, Boston Fire & Life Safety Leader, Arup, Boston
APRIL WOODS, PE, LEED AP BD+C, Vice President, WSP USA, Orlando, Fla.
JOHN YOON, PE, LEED AP ID+C, Lead Electrical Engineer, McGuire Engineers Inc., Chicago
From this report, learn how your company stacks up and what you can do to become more appealing
The 2023 Hiring, Retaining & Training Engineers report has been released by Consulting-Specifying Engineer. In it, more than 350 people provide information about how they are filling jobs, what benefits they offer and on continuing education.
Slightly more than half of respondents work at a consulting engineering firm, and the remaining participants work at architectural engineering firms or are in-house engineers. When asked about responsibility for recruiting and hiring, 62% of respondents have this as part of their job, leaving 38% to respond to training-related questions only.
They’re also actively mentoring junior team members more actively (68%). Firms also support local colleges (read: a great resource for new graduate hires), grade schools, high schools or vocational programs.
Amara Rozgus, Editor-in-Chief
Perhaps not surprising, 53% of companies seeking new hires are looking at candidates with three to five years of experience, 44% six to 10 years and 37% zero to two years (entry level). This means candidates with only a few years of experience are highly desirable.
Hiring firms want to retain these employees. More than half of companies offer the following benefits to their employees: vacation, sick leave, PTO, etc. (79%); health insurance (71%); casual dress code (62%); life insurance (58%); flexible work schedule (57%); work remotely/at-home privileges (53%); regular performance evaluations (51%).
And once they’ve hired these junior-level team members, they offer training and education. While only 44% of respondents have an official education or training program, more than half promote the value of continuing education. Continuing education in particular is considered highly valuable to engineers, with 89% rating it 7 or higher on a scale of 1 to 10, where 1 indicated “no value” and 10 indicated “extremely valuable;” 56% gave a rating of 9 or 10.
Where does this leave your firm? Are you aggressively trying to hire new employees? Are you actively networking to find new people? And what about your current employees — are they happy?
Learn how your firm stacks up and what you can do to become more attractive to future candidates. cse
Register to download the full report: https://tinyurl.com/ CSEhiring
Look familiar?
If your power infrastructure includes renewables, battery storage and/or EV charging, a microgrid may be the missing piece you need to bring it all together.
At the heart of such a system is an intelligent microgrid controller that maintains overall system stability and dynamically manages
generating assets and loads to optimize power flow based on user-defined goals.
Eaton’s Power Xpert microgrid solutions provide reliable power that delivers operational resilience, minimizes carbon emissions and reduces energy costs.
To learn more go to: Eaton.com/microgrid
While the economy sits at a slow burn, the 2023 MEP Giants firms continue to do well
The 2023 MEP Giants generated $11.96 billion in mechanical, electrical, plumbing (MEP) and fire protection engineering design revenue, an increase over last year’s MEP Giants’ revenue of $11.01 billion. This year, the 2023 MEP Giants earned approximately $67.66 billion in gross annual revenue during the previous fiscal year, a decrease of 4%. Gross revenue was down, however MEP design revenue rose 9% over last year’s numbers.
Noticeably absent from the top 10 was AECOM, a regular to this list. There were also some newcomers to the total of 100 companies. Several companies
either joined the list for the first time or returned after time away from reporting data (in alphabetical order): AMA Group; Bard, Rao + Athanas Consulting Engineers LLC; Burdette, Koehler, Murphy & Associates Inc.; Cleary Zimmermann Engineers LLC; The Engineering Enterprise; Interface Engineering Inc.; Kimley-Horn; LEO A DALY; and Lizardos Engineering Associates.
The list this year comprises 54% private companies (down from 59% in 2022), 28% employee-owned companies, 9% public companies and 9% limited-liability companies. The 2023 MEP Giants are made up of consulting engineering firms (63%, up from 60% last
year) and architectural engineering firms (29%, even with last year).
Several mergers and acquisitions occurred in the past year; 26% of the firms reporting acquired another company, a slight dip from last year’s 29% acquisition rate (see page xx for the article “What made for another strong year for the MEP Giants?”).
Table 1 shows the top firms based on MEP design revenue, which is how the MEP Giants are ranked. cse
Amara Rozgus, Editor-in-Chief, and Amanda McLeman, Director of Research, Consulting-Specifying Engineer
After record M&A activity in 2021, the 2023 MEP Giants rode the momentum to another active year
With a continued focus on and investment in sustainability and energy efficiency, Consulting-Specifying Engineer’s 2023 MEP Giants’ deal-making continued in 2022 at levels not seen before 2021. As a group, the largest mechanical, electrical, plumbing (MEP) and fire protection engineering firms completed 65 transactions in 2022 with more than one-quarter (26%) of the MEP Giants completing at least one acquisition.
This pace of deal-making is down slightly after 2021’s record-setting year of 70 deals closed by the MEP Giants, but remains elevated compared to prior years.
As companies seek to expand capabilities, tap into new markets and gain a competitive edge in the ever-changing business landscape, the demand for MEP firms and their respective innovative and sustainable solutions will continue to drive merger and acquisition (M&A) activity.
Fueled in part by publicly traded engineering firms’ access to capital; private equity’s increasing appetite in the architecture, engineering (AE) and environmental industry; a strong economy with ample funding and need for services; and a fierce war for talent, interest in and valu-
ations for engineering firms remain high. In 2022, 36% of all transactions in the AE and environmental industry were made by either a private equity-backed or publicly traded engineering firm, up from 34% the prior year. Looking at the 2023 MEP Giants, publicly traded firms accounted for 49% of deals consummated in 2022, while their private equity-backed and employee-owned counterparts were neck-and-neck at 26% and 25% of all MEP Giants’ acquisitions, respectively.
Why does this trend play out in the data year-over-year? First, publicly traded firms generally have even easier access to capital than private equity firms — that’s why
a firm goes public. Second, public buyers typically self-finance transactions without a need to borrow money or solicit third-party lenders or other stakeholders beyond the board of directors. Third, Morrissey Goodale data indicates that publicly traded firms, all else equal, pay more for deals than even private equity-backed firms, thus making offers more attractive to sellers.
Last year was yet another record-breaking year for M&A activity in the AE and environmental industry with 715 deals globally. This is the second year in a row the industry saw a new high-water mark for consolidation and the seventh year in the last nine that the industry concluded the year with a record number of deals. Bringing things back stateside, the domestic M&A activity within the AE and environmental industry mirrors what is playing out on the global stage. In 2022, U.S. industry M&A activity increased by
more than 7% to 476 transactions. For the first time in five years, U.S. industry M&A activity slowed during the COVID-19 pandemic in 2020 as the world was faced with lockdowns and supply chain crises. Despite these challenges, the domestic M&A saw a decline in deal-making of just 1% from 2019’s record of 324 transactions, signifying the strength and resilience of the industry.
The 2023 MEP Giants have been on an acquisition spree for the better part of a decade and 2022 was no exception. Over the past five years, 26% of MEP Giants on average report making at least one acquisition. The slowdown in deal-making in 2020 in the broader AE and environmental industry did impact the MEP Giants as the number of transactions completed fell by 37% to just 33 from 52 the prior year.
The most prolific acquirers of the MEP Giants in 2022 were as follows: IMEG (Rock Island, Illinois; nine deals), WSP
merger and acquisition activity in the engineering, architecture and environmental industry recognized a record-setting number of transactions in 2022. Courtesy:
(Montreal; nine deals), Bowman (Reston, Virginia; eight deals), Salas O’Brien (Santa Ana, California; seven deals) and NV5 (Hollywood, Florida; six deals). This looked very similar to the most frequent buyers in the 2021 as NV5 accounted for eight deals followed by Bowman (seven deals), Stantec (Edmonton, Alberta) (six deals), Salas O’Brien (six deals) and WSP (five deals).
IMEG was the firm that stepped up its M&A game as the firm accounted for nine deals in 2022, up from three deals in 2021. Other MEP Giants that made more than one deal in 2022 were Tetra Tech (Pasadena, California), Stantec, Jensen Hughes (Baltimore), Stanley Consultants (Muscatine, Iowa), CMTA (Louisville, Kentucky), RTM Engineering Consultants (Schaumburg, Illinois) and Johnson, Mirmiran & Thompson (Hunt Valley, Maryland).
In 2023, we expect MEP M&A activity to remain strong as the MEP Giants seek growth opportunities. That said, we expect the number of transactions to remain flat across the AE and environmental industry given the turmoil in the global economy. Rising interest rates across the globe may tip the scales further to publicly traded buyers. cse
Nick Belitz, CVA, is a Principal with Morrissey Goodale LLC, a management consulting and research firm that exclusively serves the architecture, engineering and environmental consulting industries.
Greenheck's model KSQ roof supply fan is designed, engineered and tested to be the performance leader. Multiple intake and discharge configurations provide application flexibility with a mixed flow wheel that improves airflow and efficiency while reducing sound and footprint. Introduce more clean outdoor air into your application with the KSQ.
Specify with Confidence. Specify Greenheck.
Lilly Vang, PE; and Joshua Hunter, PE, CDM Smith, Maitland, Florida
This article serves as a guide to understanding electrical hazards and establishing electrically safe work environments
Both employers and employees have responsibilities when it comes to safety, particularly electrical safety. It is the employer’s responsibility to provide a workplace that is free of hazards that could result in death or serious harm per Occupational Safety and Health Administration's (OSHA) General Duty Clause. It is the employee’s responsibility to follow and implement the safety protocols provided by the employers.
NFPA 70E: Standard for Electrical Safety in the Workplace creates standards for electrical safety. While the first chapter outlines safety-related work practices, it does not equate to official training.
Electrical safety standards, guides and codes
Standards, industry guides and codes relating to electrical safety include, but are not limited to the following:
• OSHA 29 CFR 1910, Subpart S: Addresses electrical safety requirements and mandates that any employee who might encounter an electrical hazard must receive electrical safety training.
IEEE 1584, 2018: Provides guidelines for performing arc-flash hazard calculations.
FIGURE 1: An example of an approach boundary, showing an open and energized panelboard where energized parts are exposed. Courtesy: CDM Smith
• NFPA 70: National Electrical Code (NEC) 2023: Guidelines for the installation of the electrical equipment.
• NFPA 70E: Standard for Electrical Safety in the Workplace, 2021.
It is crucial to understand who is and is not considered a qualified person to promote electrical safety. A qualified person has skills and knowledge related to the construction and operation of the equipment and installations and has received safety training to identify the hazards and reduce the associated risk. They can perform tasks such as testing, troubleshooting and voltage measuring where an electrical hazard can exist.
Per NFPA 70E, Article 110.6 (A)(3), a person can become unqualified if they are not trained every three years. Additionally, a qualified person is not necessarily qualified to work on all equipment. They may be considered qualified with respect only to the specific equipment and tasks for which they have been trained.
While an unqualified person cannot work on equipment that has potential electrical hazards, they still require training. Per NFPA 70E 110.6 (A) (2), any unqualified person needs to be trained and familiar with any electrical safety-related procedures or practices that are necessary in their work.
Electrical hazards come in many forms including stripped insulation, improperly installed equipment and damage that modified the original equipment installation. These hazards may result in a shock, arc flash or blast event.
A shock hazard is the presence of a potential shock to a person, caused by touching or being near exposed energized electrical conductors or circuits. Shocks occur when parts of a person’s body complete a circuit between an electrical source and ground, with current flowing between the two points through the person’s body. It is not necessary that a person touch the electrical source for a shock to occur as a high enough voltage gradient can create an arc through air or another otherwise insulating material.
The greater the voltage difference between the source and ground, the greater distance a person must be to remain safe. The distance a quali-
fied person is allowed near a source where shock hazard is present is known as the restricted approach boundary, whereas the distance for an unqualified person is known as the limited approach boundary.
Figure 1 illustrates the two approach boundaries for shock hazards.
• Identify what electrical hazards to look out for.
• Understand the basics of existing codes and guidelines for safetyrelated work practices.
• Recognize ways to reduce risk while working on or near electrical equipment.
High-voltage shocks are a serious and deadly matter and it does not take much to cause serious or fatal damage. Even shocks from 120-volt (V) circuits can cause serious injury or death.
It is important to understand the relationship between current, voltage and resistance. Voltage represents an electric potential or difference in charge of two points, resistance is the opposition to the flow of current and current is the flow of charged particles, such as electrons or ions, through a material.
This relationship is represented by the following equation, commonly known as Ohm’s Law:
V = Voltage, in units of volts
I = Current, in units of amperes (A)
R = Resistance, in units of ohms
This equation means that any increase in current or resistance will increase voltage. If there is an established voltage differential in a location, any increase in resistance will also reduce current.
It is important to take the body’s resistance into consideration. The internal body has a resistance of about 300 ohms, while the skin has resistances 1,000-100,000 ohms. This variance depends on which areas of the body make contact, the amount of moisture on the skin, condition of the skin and other factors.
For instance, if someone accidentally completed a 120-volt circuit with their hand and their body resistance at those points totaled to 50,000 ohms, the shock delivered would result in 2.4 milliamperes (mA) of current through the body. While this may cause pain, it wouldn’t be a deadly incident. However, if their body resistance at those points was 1,500 ohms, the resulting current would be 80 mA, enough to cause ventricular fibrillation if the current passed through their heart.
Meanwhile, a common circuit breaker or fuse in a house will only open or trip at 15/20 A. This
‘ Electrical hazards come in many forms including stripped insulation, improperly installed equipment and damage that modified the original equipment installation. ’
is unless the circuit breaker is a ground-fault circuit interrupter, which can trip at 6 mA, based on the difference of the current in the circuits primary path. See Table 1 for a list of effects various amperages can have on the human body.
Understanding how little current it takes to cause harm, drives home the importance that resistance has in electrical safety during design and while working in the field. A person wearing personal protective equipment (PPE), such as electrically rated safety boots or gloves, may increase their resistance and therefore, reduce the risk of a shock hazard.
However, there is a limit to how much protective gear and a good ground system can help mitigate shock hazards. It is important to practice good safety practices, to keep distance, only work on or near
live parts if necessary. If safe working conditions are not possible, shut off equipment before working on it using a lock out tag out procedure. Table 2 shows NFPA 70E recommended distances from various voltage sources.
In certain situations, energized conductors, such as bare overhead lines or platforms, can move due to wind or other outside forces, meaning the distance cannot be controlled by the employee. Due to the lack of control in the distance from the energized and open equipment, the approach distance for an unqualified person will increase. The restricted approach boundary will remain unchanged, however. Whether the energized equipment is moving or not, the qualified person should be equipped with the skills and knowledge to handle different situations. A good rule of thumb is to not stand in front of the energized equipment when it is being opened. If any electrical hazard should happen, it’ll propagate toward the open space.
An arc flash hazard exists when personnel working on or near electrical equipment is exposed to arc flash incidents. An arc flash is the release of energy caused by an electrical arc, producing bright light, high temperatures and a shock wave, at very high arcing currents. An arc flash can be created for several reasons. One major cause is voltage spikes from lightning strikes or switching loads,
which create a large amount of energy over a few microseconds. Other causes can be due to gaps in insulation, worn or loose connections, improperly installed parts or a buildup of dust or corrosion.
An arc flash can blind someone, create deafening sound waves, throw a person across a room, cause third degree burns and result in death. The potential severity of an arc flash incident depends on several factors: the possible size of the arc flash incident, the distance from the arc flash and the PPE worn. The contributors to the potential size of an arc flash incident are the available fault current, equipment shape, electrode configuration and the clearing time.
The available fault current is the amount of current that can be supplied during a fault incident. The fault current available at a given piece of equipment is based on distance from the supply current, resistances in wires and other equipment which will lower the available fault current and step-down transformers which will increase the current. This is why the available fault current must be calculated at each point in the system.
The clearing time is the amount of time it takes for an overcurrent protective device, such as a circuit breaker or fuse, to open during a fault incident. For the same fault current, the longer it takes for the overcurrent protective device to open, the larger the arc flash incident will be. For instance, a high available fault current incident could end up creating a small arc flash incident if opened quickly, while a small available fault current could create a large arc flash incident if opened slowly.
To inform personnel working near or on equipment susceptible to arc flash hazards, it is important for the facility to have an up-to-date arc flash study with arc flash hazard labels placed on the equipment. These labels provide information regarding the potential energy of an arc flash hazard, the appropriate distances to approach the equipment and appropriate PPE that should be worn around the equipment.
To ensure this information is accurate, it is required per NFPA 70E that the arc flash study be updated and reviewed at least every five years and after major modifications or renovations to the electrical system. If identified as necessary, the arc flash labels should be updated and replaced based on the new study.
Like shock hazards, the closer you get to equipment, the greater the risk involved. For arc flash hazards these distances are broken into a working distance, often 18 or 36 inches from the equipment, and an arc flash protection boundary. The working distance is the distance for electrical workers and other trained professionals wearing the appropriate level of PPE. The arc flash protection boundary is the minimum distance required for unprotected personnel to receive no more than second degree burns from a potential arc flash incident, which is equivalent to an incidental energy of 1.2 calories per centimeters squared (cal/cm2). The arc flash boundary is not solely dependent on voltage but is instead calculated as part of the arc flash hazard assessment.
When working within the arc flash protection boundary it is important to wear proper PPE. The PPE equipment is rated based on the potential incident energy, in cal/cm2. This can start with wearing a face shield, a long sleeve shirt, gloves, pants and safety boots at 40 cal/cm2. At 40 cal/cm2 or higher a full body arc flash suit is required.
At exceptionally large arcing currents, a powerful enough arc blast may be created that eliminates many of the protections electrical PPE provides. The blasts can become so powerful that the equipment will explode into shrapnel and propel anything or anyone in its path across the room. Because there are no calculations for determining
FIGURE 2: This figure shows a power terminal cabinet with a plastic cover guarding the live/energized parts.
Courtesy: CDM Smith
the blast hazards that may be present, it is especially important to follow the proper rules and guidelines to ensure safety around electrical equipment.
An electrically safe work condition (ESWC) is a state in which a circuit or equipment has been disconnected completely from energized parts, locked and tagged in accordance with established standards per NFPA 70E 120, tested to verify the lack of energized parts and, if necessary, temporarily grounded for personnel protection.
Any equipment operating at or above 50 V is required per NFPA 70E 110.3 to be completely de-energized if the employee is required to be within the limited approach boundary or the employee needs to interact with the equipment and there is a remote possibility that an injury could result from an exposure to an arc flash hazard — regardless of whether the energized parts are exposed or not.
There are only four allowances for when work on energized equipment is allowed per NFPA 70E, Article 110.4:
• There are additional hazards or increased risk when de-energizing (i.e., exposure to other potential hazards such as chemical, mechanical or environmental when de-energizing equipment).
• It is infeasible to de-energize an equipment due to the equipment design or operation limitations (i.e., performing diagnostics and testing of electrical circuits that can only be performed with the circuit energized).
• The energized circuits do not present an electrical shock hazard. This typically includes equipment less than 50 V. The possibility of risk of exposure to electrical burns or explosions must be considered. If there is potential for an arc flash,
work on equipment is not allowed unless it satisfies the first two allowances.
• Normal operation of the equipment is allowed when it is in a normal operating condition (i.e., equipment door is closed, or equipment cover is placed and secured as manufacturer’s intended purposes). This is assuming that the equipment is properly installed, maintained and used in accordance with manufacturer’s instructions, listing and labeling. In addition, there must be no evidence of arcing, overheating, loose/bound equipment parts, visible damage or deterioration. This allowance is more for the interaction with and not work on the equipment. For example, installing plug-in circuit breakers is not considered normal operation.
When energized work is permitted to be performed, an energized electrical work permit is required per NFPA 70E 130.2(B). The energized electrical work permit must document the description of the equipment worked on, the location of the equipment, the work to be performed, the justification for why the work needs to be performed while the equipment is energized, how safety will be implemented, results from a power system analysis study, the means to restrict access of unqualified persons in the work area, evidence of job briefing and an energized work approval signature from the responsible management or owner. The power system analysis study results must show the voltage, approach boundaries, incidental energy, PPE requirement and the equipment required to safely perform the assigned task.
The most important question that should be considered before any risk control method is, “Do people feel safe, comfortable and confident working on the electrical equipment?” The risk control methods mentioned previously serve to boost the confidence an employee feels for their safety while working on the electrical equipment.
Per NFPA 70E, Article 110.5(H)(3), risk assessment procedures require implementation of preventive and protective risk control methods in the following hierarchy. The risk control methods are ordered from the most effective method to the least effective method. Although every risk assessment isn’t detailed in the following, being able to identify,
analyze and evaluate the risk is important to determine the best risk control method(s).
Elimination: How can potential accidents be stopped? This risk control method removes the electrical hazards at the source and effectively accounts for human errors, such as accidentally brushing against an energized conductor. The best way to remove the electrical hazard is to completely de-energize the equipment and establish an ESWC.
In the case that the equipment cannot be de-energized, other control methods, such as the administration or engineering controls, should also be considered. For example, if work needed to be done to an existing switchgear that provides power to multiple buildings that need 24/7 operation. The building occupants should first be notified of the shut down in advance of the work timeframe and solutions, such as bypassing the switchgear before de-energizing it completely, can be considered to effectively eliminate electrical hazards.
Substitution: What other equipment should be considered for a safe system? Safety should be considered during the design stages and not after everything is built and done. Substitution is a risk control method that considers alternative design options that could limit the number of electrical hazards. For example, the amount of incident energy can be reduced by replacing 120 V control circuits with 24 V control circuit or by installing circuit breakers with a maintenance mode setting switch. Circuit breakers with maintenance mode are designed to temporarily reduce the short-time delay setting of the circuit breaker, typically using a separate analog trip circuit that provides faster interruption times and significantly lowers incident energy level.
This doesn’t necessarily help the employee avoid shock hazards, but by performing a power system study to better understand the electrical system and the amount of energy produced from each equipment in the system, it can help the employer and employee better understand what protective equipment is better for reducing the energy level.
Engineering controls: How can the employee be separated from the hazard? Engineering controls remove hazardous conditions by placing a barrier between the worker and the hazard. For example, a guard using shutters or plastic covers for live or energized parts doesn’t have high chance of arc flash blast (see Figure 2).
Other considerations that could be done, especially during the design stage, are systems with dual feeds, tie circuits or bypass switches that allows planned shutdowns for maintenance. By having a bypass, the employee can effectively isolate and de-energize the equipment of concern.
Awareness: Is there enough information to identify the risk? Identification of the equipment and hazard present will allow the employee to easily identify the potential risk. In addition to an arc flash label that details the boundaries, incident energy and PPE, equipment should also have labels identifying voltage, where it’s fed from and what it feeds (see Figure 3).
Administration controls: How can safety be best communicated? Administration controls improve safety through policies, practices and procedures. Accurate documentation is key for this kind of risk control. Documentation can include verification of proper maintenance and installation, details of the lockout/tagout programs, written electrical safety procedures and training requirements. Communication between employer and employee is important for this risk control method as it can better modify policies, practices and procedures that are suitable for the people working in the facility.
PPE: What should be worn? PPE be considered as a solution only after all other risk control methods have been exhausted. Even then, it should not be the only control element, as it is the least effective and provides the lowest level of safety control.
PPE should be rated for the incidental energy of the equipment as determined from an arc flash study. All conductive material, such as jewelry or belts should be removed when working on an electrical part. Leather work shoes or dielectric overshoes are required when insulated footwear is used. Because one of the biggest worries in shock hazard is completing the circuit, insulated footwear can prevent shock that comes from stepping on energized conductors or parts. cse
Lilly Vang, PE, is an electrical engineer at CDM Smith, focusing on the design of electrical power systems. Joshua Hunter, PE, is an electrical engineer at CDM Smith, experienced in the design and analysis of electrical power systems.
‘ The most important question that should be considered before any risk control method is, “Do people feel safe, comfortable and confident working on the electrical equipment?’
u
csemag.com
u Shock and arc flash hazards can cause serious injury or death. Adhering to the best electrical safety practices can help protect employees.
u Understanding what an electrical hazard is and how to mitigate it is key for any personnel working with electrical equipment or in an electrically related field.
Hunter Koch, EIT, Certus Consulting Engineers, Dallas
Arc flash analysis is an important piece of designing electrical systems, especially in large amperage and utility service equipment applications
There are many concerns and challenges facing the construction industry, not least of which is electrical safety for facilities and the people maintaining those facilities. One of the most dangerous scenarios that can occur in a building is the possibility of electricity arcing from electrical equipment into a room where a person may be working. This poses a significant risk to nearby human life and to the building if a fire is started from the arc flash.
and NFPA 70 (2023): National Electrical Code. All the details of arc flash are not able to be covered within this article, more information can be found in NFPA 70 and 70E.
• Gain an understanding of what arc flash is, what can cause it and why it is dangerous if not considered properly in design.
A reaction to this and a consideration for construction teams is the need for extended shutdowns of major electrical equipment providing power to these facilities during any future maintenance or renovation work. Rising concerns for human safety have caused more electrical contractors to refuse work on electrical equipment that is energized. Many electrical contracting companies even have put policies in place banning live work from being done by any person working for that company. Electrical designers must work around these challenges to provide safe and practical solutions mitigating any risks from arc flashes.
• Review the code dictated safety requirements, such as working areas, key terms and personal protective equipment guidelines.
• Learn the basics of the code recognized arc energy reduction methods and how they are used.
This article will look at the basics of arc flash, what can cause it and the potential hazards if it occurs. It will also cover general code requirements for safety and mitigation techniques. The primary codes referenced in this article will be NFPA 70E (2021): Standard for Electrical Safety in the Workplace
An arc flash occurs when electrical energy is released from a circuit or piece of electrical equipment into the immediate workspace around the equipment. This happens when there is an electrical short or fault current in the intended circuit that causes the energy to exit this circuit and travel to a different nearby circuit or path to ground, such as a person.
There are many reasons an arc flash may happen, including but not limited to an excess of dust or water on the circuit/equipment creating a conductive pathway for electricity, an accidental short caused by metal (such as a tool) connecting across circuits or terminals, degradation of older equipment creating damaged or exposed live parts or poor installation resulting in loose connections that create air gaps where electricity can arc.
Arc flash occurs in the forms of heat energy, both high-pressure and sonic blasts and electrical shock. Arc flashes can cause explosions with shrapnel flying from the electrical equipment in the immediate vicinity, as well as fires that can spread throughout the building.
A person maintaining the electrical equipment and potentially anybody else in the room with
the equipment when an arc flash occurs risks very serious injury, including burns, soft tissue damage, hearing damage, lacerations or dismemberment and death. Any time work is going to be performed on or near live electrical equipment, precautions should be taken to be properly protected. Knowing how to be protected and what precautions to take is very important.
NFPA 70E establishes the guidelines for electrical safety in the workplace. It defines many of the key terms and methods for arc flash in Article 130 (Work Involving Electrical Hazards). It defines three boundaries for working space and safety (130.5(E)).
The first is the arc flash boundary, beyond which serious or permanent injury due to arc flash should not occur. NFPA 70E sets the incident energy value for the arc flash boundary at 1.2 cal/cm2, which is the research-based incident energy that can cause a second-degree burn that will heal without permanent injury. Incident energy above this value can result in permanent damage or more serious injury.
The next boundary set by 70E is the limited approach boundary, which is the closest point any unqualified person, if escorted by a qualified person and in proper personal protective equipment (PPE), should approach a piece of electrical equipment with exposed live parts.
The closest boundary defined by the NFPA is the restricted approach boundary. This boundary is the closest point anybody should approach the equipment, including qualified personnel, unless they meet one of the two conditions established in 130.4(G), which states says anybody entering the restricted approach boundary must either be insulated from the energized live parts at greater than 50 volts with insulating gloves and sleeves or the energized live parts must be insulated from the person.
The limited and restricted approach boundaries are both shock hazard boundaries and are independent of the arc flash boundary. They are determined by the voltage of the equipment per Table 130.4(E)(a).
TABLE 1: Arc flash personal protective equipment (PPE) categories and incident energy ratings using both NFPA 70E methods. This table compares the similarities and differences between both methods. Courtesy: Certus Consulting Engineers
Proper PPE to enter an equipment’s arc flash boundary is determined by that equipment’s maximum incident energy. To gain an understanding of maximum incident energy, a risk assessment must be completed that calculates the energy levels for applicable electrical equipment. NFPA 70E allows two different methods for determining the arc flash boundary/maximum incident energy and required PPE.
The first method is detailed in Section 130.5; this method is to perform a full arc flash analysis on the entire electrical system to calculate the maximum incident energy and arc flash boundary for every piece of equipment in the system. The second method is detailed in Section 130.7 and uses tables and established values by the NFPA to calculate maximum incident energy and arc flash boundary based on the type, size and voltage of the equipment.
These two methods produce different calculated values and have slightly different PPE requirements. NFPA does not prefer either method; it is permitted to use either method for calculations on separate equipment items on the same electrical system. However, both methods may not be used
csemag.com
Arc flash insights
u Designing a building’s electrical system to mitigate arc flash incidents is vital for electrical engineers to understand.
u NFPA 70E, along with other codes, standards and guidelines, guides electrical engineers and electricians in working with electrical equipment.
on the same piece of equipment. For a single piece of equipment, only one of the methods can be used (see Table 1).
While the NFPA does not have a preference regarding which method to use, it is typically best practice to perform a system analysis per Section 130.5. This method will yield more accurate and specific arc flash values for the equipment and system, rather than table generated numbers that are more generic in nature.
To perform an arc flash analysis per 130.5, the entire distribution system is modeled in a power
system analysis program, such as from SKM System Analysis Inc. or ETAP ArcSafety. The entire electrical distribution system must be modeled with the actual equipment that is purchased or installed. The software will then analyze, calculate and produce the results detailing the required information for all the applicable equipment.
The analysis yields exact values for the arc flash boundary and incident energy and provides a more precise understanding of the system. The design engineer must always design the arc energy mitigation techniques used for the electrical system, but it
TO KEEP OCCUPANTS and workers safe in this hospital, electrical engineers used zone-selective interlocking (ZSI) breakers to mitigate arc flash incidents
The project design for a new hospital bed tower will include a new normal power utility service and a new generator system with associated normal and emergency branch panels to serve the building. The new building will use a 480/277-volt, 3-phase, 4-watt plus ground service from the utility. The goal of this example is to design the arc energy reduction system for the electrical equipment over 1,200 amps that is required by NFPA 70 (2023): National Electrical Code to have arc energy reduction.
It is determined a 2,000-amp normal power utility is needed and a 1,600-amp main switchboard is required to feed the emergency power system. From these main switchboards, the rest of the electrical system and downstream equipment is designed and sized to feed the building. The design determines that these two switchboards are the only two pieces of equipment over the 1,200-amp threshold.
The next step for this design is to perform an arc flash analysis to determine the incident energy, arc flash boundary and the necessary personal protective equipment (PPE) for the two pieces of main electrical equipment that require arc energy reduction.
For this example, SKM System Analysis Inc. software is used to perform the arc flash analysis calculations. Important inputs for this calculation are to obtain the available fault current from the utility company, the calculated fault based on the generator contribution, voltage and amperage ratings for all the major electrical gear, motor contributions and transformer impedances (see Table 2).
According to the results from the SKM calculation, both panels are above the 40 cal/cm2 threshold and they both have
TABLE 2: Calculation results of the main switchboard and emergency switchboard arc flash analysis and associated arc flash hazard labels for the equipment. Courtesy: Certus Consulting Engineers
extreme arc flash boundaries exceeding 200 inches. This means that a person working in those electrical rooms is almost guaranteed to be working inside the arc flash boundaries.
Because both switchboards exceed the 40 cal/cm2 incident energy threshold, there is no safe PPE for working on either of these. With no safe PPE and a room encompassing arc flash boundary, neither of these switchboards should be maintained live under any circumstance. Doing so would result in certain permanent injury and/or death were an arc flash to occur while working in the room.
The example arc flash hazard labels from Table 2 need to be placed on each switchboard to ensure the level of danger is known to anybody entering the room and to ensure no work or maintenance is done to the equipment while operational.
Because these two switchboards fall above 1,200 amps, NFPA
is common practice for the design engineer to delegate the short circuit, coordination studies and arc flash calculations to the electrical contractor during the construction phase. In this case, the engineer must carefully review the submittals for these items to ensure the components being purchased match the design intent and that the equipment meets code requirements for safety (see Table 3).
In addition to NFPA 70E, NFPA 70 also has guidelines for arc flash safety. Article 110.16(B) of NFPA 70 requires all service equipment, other than in dwelling units, that is likely to require work
‘ While the NFPA does not have a preference regarding which method to use, it is typically best practice to perform a system analysis per Section 130.5. ’
or maintenance while energized at or above 1,000 amps, to have proper labeling that identifies the level of arc flash hazard. The label must be clearly visible on the equipment so that it is seen before performing any work on that equipment.
FIGURE 1: Final one-line diagram including zone-selective interlocking circuit breakers as the arc energy reduction method. Courtesy: Certus Consulting Engineers
70 Article 240.87 requires them to have arc energy reduction. Article 240.87 describes six different methods for achieving arc energy reduction; this is a new expansion so there are no existing methods for the building already established.
The method chosen for this design will be zone-selective interlocking (ZSI) breakers. This method has been chosen as it is a common, well-understood solution that works automatically. Automatically tripping in a fault condition is preferrable and it does not require a person to activate and deactivate the arc flash mitigation measures, which increases the safety in the system.
An additional benefit of this method is that it will aid in selective coordination by only opening the nearest breakers the fault, reducing the amount of the building that will experience downtime to a breaker trip.
This method is not without drawbacks. There is added cost to the circuit breakers installed in the two switchboards because the ZSI breakers are significantly more expensive than normal electronic trip circuit breakers typically used in switchboards for this type of facility. This method also adds signal circuits between
upstream circuit breaker and the downstream breakers in the equipment enclosure increasing the labor and materials cost.
To accomplish the desired arc energy reduction using ZSI breakers, the ZSI breaker types must be used for the electrical equipment’s main circuit breaker, as well as all other breakers in the board feeding downstream equipment and loads. For this design, all circuit breakers in the two switchboards will be 100% rated, electronic trip circuit breakers with adjustable; long-time, short-time, instantaneous, ground settings; ZSI modules; and a signal circuit to communicate between the main circuit breaker and each downstream breaker in the switchboard.
The final design for ZSI is shown in Figure 1. It shows how this method can be used on contract documents and the symbology/ terminology for ZSI breakers on one-line diagrams.
Following the code requirements set by NFPA 70 and NFPA 70E (2021): Standard for Electrical Safety in the Workplace — and using the proper considerations when evaluating electrical systems for arc flash safety — will ensure a safer, more maintainable building for anybody working in these spaces in the future.
TABLE 3: An example of an arc flash analysis calculation table. The most important categories coming from this table are arc flash boundary and incident energy.
Courtesy: Certus Consulting Engineers
NFPA 70E 130.5(H) requires the arc flash label to contain the following information: system voltage, arc flash boundary distance and either the available incident energy/working distance or the arc flash PPE category (shown previously from NFPA 70E, Table 130.7(C)(15)(a)) or the minimum arc rating of clothing or site-specific level of PPE (see Figure 1).
In addition to identifying the potential risks of arc flash, the codes offer requirements to help limit the potential risk. One of these is the requirement for arc energy reduction found in NFPA 70 Articles 240.67 and 240.87. These articles describe the requirement as well as provide methods that are approved per the code.
The goal of arc energy reduction is to reduce the amount of time it takes to clear the circuit and trip the circuit breaker or other overcurrent protective device (OCPD). Reducing the clearing time reduces the amount of arc flash energy because there are fewer electrical cycles for the arc flash to occur. If there are fewer cycles for the arc flash to release energy, then there will be less energy to cause damage to the equipment and surroundings.
Articles 240.67 and 240.87 require any overcurrent protection device over 1,200 amps (adjustable or static rating) to have arc energy reduction means. Note: An arc energy reduction method must be used for any OCPD where the maximum rating of the device is 1,200 amps or higher, even if
FIGURE 2: An example of an arc flash hazard label. This label has the NFPA 70 130.5(H) required information on the label and meets all code requirements.
Courtesy: Certus Consulting Engineers
the device is an adjustable circuit breaker and is set lower than that for its specific circuit. This section also requires documentation that explains the chosen mitigation method and proves that it reduces the clearing time below the available arcing current. Article 240.67 lists five acceptable methods to reduce clearing time for fuses, while Article 240.87 does the same for circuit breakers with seven methods. While NFPA 70 covers arc energy mitigation requirements for both fuses and circuit breakers, circuit breakers are more common, so the methods focused on by this article will be those methods for circuit breakers.
There are seven methods for circuit breakers to reduce clearing time allowed in NFPA 70 Article 240.87, those methods are listed below:
• Zone-selective interlocking (ZSI).
• Differential relaying.
• Energy-reducing maintenance switching with local status indicator.
• Energy-reducing active arc flash mitigation system.
• Instantaneous trip setting.
• Instantaneous override.
• An approved equivalent means.
ZSI uses circuit breakers in a protected piece of equipment to sense when a fault occurs and reduces clearing time of the fault by opening the breaker very quickly. When using a ZSI to reduce arc flash energy, the ZSIs must be installed on the molded circuit breaker (MCB) and all downstream breakers in that panel and then signal circuits must be installed between the MCB and all the downstream breakers.
If a fault is sensed in one of the downstream breakers it will send a restraint signal to the ZSI breaker and the downstream breaker will open immediately. The upstream ZSI breaker will only trip in a fault scenario when the fault occurs between the upstream and downstream breakers or if the downstream device does not clear the fault in adequate time. An additional benefit of this method, besides being automated, is that it will minimize the amount of equipment that is disrupted in a fault scenario because only breakers sensing a fault will clear the fault.
Differential relaying places a current-sensing differential relay at each point where current can enter or leave a protected piece of equipment or multiple pieces of equipment. This relay measures the amount of current entering the upstream side of the relay and measures the amount of current leaving the downstream side of the relay. If the sum of the currents entering and leaving the zone of protection isn’t zero, it signifies that a fault is occurring somewhere in the protected relay area and the relay will send a signal to the upstream breaker and open that breaker to clear the fault. Because differential relaying doesn’t affect selective coordination, it can operate without intentional delay and can clear a fault very quickly.
An energy-reducing active arc flash mitigation system uses sensors that are designed to detect the onset of an arc flash or fault by sensing the light emitted from a flash. When the sensors detect an arc occurring, they send a signal to open the upstream breaker immediately thereby limiting the incident energy.
Instantaneous circuit breaker trip settings use adjustable instantaneous trip settings in the circuit breaker that can be set based on the available fault current at that breaker. The instantaneous setting must be set to a lower level than the available arcing current calculated for the circuit breaker to meet the NFPA 70 Article 240.87 requirements. Note that when using this method, temporary adjustment of the setting is not permitted.
Instantaneous override describes a fixed setting in a circuit breaker that is intended to open the breaker very quickly in the event of a fault. Like instantaneous circuit breaker trip settings, the instantaneous trip setting for the override must be lower than the available arcing current for the circuit breaker. When the instantaneous trip is set below the available arcing current, most circuit breakers will open and clear the fault in fewer than three cycles (50 milliseconds). It should be noted that both instantaneous circuit breaker trip settings and instantaneous overrides are very low-cost options and simple to install.
FIGURE 3: An example of an energy-reducing maintenance switch with a blue indicator light as part of the electrical equipment assembly. The blue light indicates when maintenance mode is activated for the equipment. Courtesy: Certus Consulting Engineers
ZSI, differential relaying, energy-reducing active arc flash mitigation systems, instantaneous trip settings and instantaneous overrides are all examples of systems that are designed into the electrical system and automatically open the overcurrent protection upstream of a fault so there is no manual intervention required. These systems are practical because they are designed to act immediately upon detection of an arc flash to clear the fault.
‘ It is important to understand that complying with NFPA 70 mitigation requirements does not make it safe to work on energized equipment. The intent of the code is to make energized work less hazardous. ’
ZSI, differential relaying and energy-reducing active arc flash mitigation systems are more aggressive measures to reduce the clearing time of an arc flash and reduce arc energy. These three methods are more expensive than the two instantaneous methods of arc energy reduction.
Energy-reducing maintenance switches are manual devices that are designed to reduce arc energy by overriding a circuit breaker’s normally delayed tripping and switching it into a position to immediately open in the case of a fault. NFPA 70 Article 240.87 requires an indicating light that illuminates when maintenance mode is turned on and should be installed with the switch that it is indicating. The maintenance switch/indicator light is typically provided with the electrical equipment it is protecting.
The maintenance switch should only be switched on during maintenance of the equipment because selective coordination may not be achieved while in maintenance mode because the settings that provide protection to a person working on the equipment are not optimal for the normal operation of the system.
The primary weakness of an energy-reducing maintenance switch is that it requires a person to activate the arc energy mitigation protection and return it to normal operation. Either operation could be overlooked or forgotten by the staff work-
ing on the system, which is not a possibility with any of the automatic methods. This method of arc energy reduction is relatively cheap compared to some of the other methods listed (see Figure 3).
Arc energy mitigation is still relatively new to the electrical construction industry, so an approved equivalent means is provided in the code to be flexible to new, innovative methods to achieve arc energy mitigation and accomplish the intent of the code to provide a safer system.
There are several factors to consider when selecting which arc energy reduction method to design for an electrical system. When working in an existing facility, the existing electrical system may prevent the use of some of the methods that are not easily retrofitted into existing equipment and the cost and ease of retrofitting should also be considered.
In a new building, cost and preferences of the maintenance staff should be the primary consideration. An experienced staff may be comfortable working with an energy-reducing maintenance switch, while a less experienced staff may prefer a more automated approach, such as one of the other methods listed.
It is important to understand that complying with NFPA 70 mitigation requirements does not make it safe to work on energized equipment. The intent of the code is to make energized work less hazardous, not completely safe. Arc energy reduction is not helpful on large service equipment with incident energy above the NFPA 70E based 40 cal/ cm2 where there is no safe PPE to work on energized equipment.
With an understanding of what arc flash is — as well as an understanding of the electrical dangers — it prevents and the code required mitigation techniques, designing the safest and most practical electrical systems possible for both maintenance engineering as well as building occupants can be accomplished. cse
Hunter Koch, EIT, is an electrical designer at Certus Consulting Engineers where he leads design efforts on health care and complicated electrical infrastructure projects.
Ensuring the continuous and reliable supply of power to critical loads is the primary objective of a critical power system. Mersen’s overcurrent and overvoltage protection products are designed to meet the demands of critical power systems and protect equipment, data, and most importantly, people.
• Mersen Amp-Trap 2000 fuses with SmartSpot indicators: Amp-Trap 2000 fuses make it easy to achieve selective coordination to reduce the scope of outages. SmartSpot visual blown fuse indicators simplify identifying faults, helping to reduce system downtime.
• Mersen Pluggable SPDs are nofuse, fail-safe surge suppressors featuring Mersen’s industryleading TPMOV® technology inside. These units are DIN-rail mountable and feature easily replaceable surge units for a costeffective way to prevent damage to sensitive electronics. Available in 50kA and 75kA.
• Mersen STZ Series SPD comes in internally or externally mounted designs, with surge current ratings up to 450kA and standard surge counter and EMI filtering options. Featuring a 15-year warranty and TPMOV technology, this device provides safe, reliable, and longlasting surge protection to keep critical operations running.
• Mersen Compact Fused Switch is suitable for use as main/feeder device and, in conjunction with CC fuses, is rated for branch circuit protection. It has a smaller footprint compared to a traditional Class CC disconnect switch with a max interrupting rating of 200kA.
Dennis Sczomak, PE, LEED AP; and David A. Conrad, PE, Peter Basso Associates Inc., Troy, Michigan
Lowering the temperature of heating hot water systems is a key step toward decreasing energy used to heat buildings, and toward decarbonization and electrification
As buildings move toward decarbonization and electrification, it is increasingly important for engineers to incorporate lower heating water temperatures into the design of building hydronic heating systems to most efficiently apply both natural gas boilers and electric refrigeration machines as heating sources.
Hydronic heating systems have been around for centuries, dating back to what is believed to be the earliest system in a 14th century Greenland monastery fed by a hot spring. Early fossil-fuel-heated hydronic systems relied on gravity circulation, with pumps not introduced until the early 20th century. Over time, hydronic heating systems, along with warm air, have supplanted steam and have become the predominant heating systems for buildings.
Modern hydronic heating systems provide occupants with a dependable, cost-effective and comfortable solution. Over the years, hydronic heating systems have evolved and engineers are continually developing new ways to increase efficiencies, integrate innovative technology, and reduce the impact on the environment.
Hydronic heating systems are commonly heated by a boiler that is fired by natural gas, with heating hot water circulated by pumps through a closed loop piping system. For many years, hydronic heating systems were designed with supply water temperatures commonly on the range of 180°F to 200°F, maximizing the output of hydronic
• Learn how low heating hot water temperature is critical to maximizing the efficiency of condensing gas boilers.
• Learn how low heating hot water temperature is critical to maximizing the efficiency of heat-producing refrigeration equipment.
• Learn steps that can be taken to allow heating hot water temperature to be lowered when designing a building’s hydronic heating system.
heating devices while remaining safely below the system water boiling point. These high temperatures allowed heating devices such as air handling unit heating coils, zone air tempering coils, and perimeter heating devices to produce very ample heat for even the most demanding heating situations.
Over the past two decades, condensing natural gas boilers have become a popular choice among engineers and owners. Condensing boilers are significantly more efficient than noncondensing boilers because they extract more heat from the combusted fuel-to-air mixture by condensing the water vapor in the hot gases. To operate in the efficient condensing mode, condensing boilers require return water temperatures to be 130°F or lower (see Figure 2).
The lower return water temperatures required for the condensing mode limits the associated design supply water temperature to around 150°F to 170°F, in conjunction with hydronic heating device water temperature drops of 20°F to 40°F, respectively. While these 150°F to 170°F supply temperatures reduce the heating output of hydronic heating devices as compared to earlier 180°F to 200°F supply water, the effect is not dramatic, and a modest increase in heat transfer surface provides ample heat for even the most demanding heating situations. Mean water temperature for a hydronic heating device is equal to the average of the supply water temperature entering the device and the return water temperature leaving the device (see Figure 3).
With a hydronic heating system using condensing boilers, it is possible to still achieve high seasonal efficiency even if the hot water heating temperature is required to rise out of the condensing region (higher than 130°F return water
2: This is a graph of a typical condensing boiler’s efficiency versus return water temperature. Courtesy: Peter Basso Associates Inc.
3: This shows a typical hydronic finned tube radiator’s heating output versus mean water temperature. Courtesy: Peter Basso Associates Inc.
temperature) only during the short periods of extreme cold outdoor conditions, and then is reset back down to the condensing region when outdoor conditions are not as extreme. This can be an important design approach when incorporating condensing boilers as a retrofit into an existing hydronic heating system designed originally to operate above 130°F return water temperature.
To take a further leap into decarbonization by moving into electrification, refrigeration machines such as air source heat pumps, ground source water-water heat pumps and heat recovery water chillers are now being used to generate heating hot water. Limiting the heating hot water temperature allows these refrigeration machines to be very efficient, all-electric heat producers.
csemag.com
Hydronic system insights
u By lowering the heating temperature on boilers, water to water heat pumps, and heat recovery chillers, efficiency goals can be met.
u Lowering the heating temperature on water to water heat pumps and heat recovery chillers has a dramatic effect on their efficiency.
Heating hot water temperature is a significant and limiting factor for the application of water-water heat pumps and water cooled heat recovery chillers. While there are chillers that can produce hotter water, for practical purposes the heating hot water temperature should be limited to no more than 140°F for standard machines using standard refrigerants. Even lower temperatures are desirable when possible.
This is because the efficiency of the heat recovery chiller is affected greatly by the “lift” at which
the machine is operating, with lift being governed by the temperature difference between the cold fluid leaving the chiller’s evaporator and the hot fluid leaving the chiller’s condenser. In a heat recovery chiller, the fluid leaving the chiller’s condenser is heating hot water.
As demonstrated in Figure 4, lowering the lift of the heat recovery chiller by lowering the heating hot water temperature has a dramatic effect on the chiller’s coefficient of performance (COP); higher COP means higher efficiency and lower energy use.
A MUSEUM HVAC RETROFIT in a cold climate benefitted from new hydronic heating devices
In this existing museum in Southeast Michigan, the original heating, ventilation and air conditioning (HVAC) system design incorporated a comparatively inefficient district steam system as the primary heating source for the building’s hydronic heating system, making 180°F heating hot water via a shell and tube heat exchanger. High-efficiency, natural gas condensing hydronic boilers are being installed to replace the district steam as the primary heating source for the building.
The original HVAC system design also incorporated an airside economizer, which when paired with the requirement to maintain a minimum of 40% relative humidity (46°F dewpoint temperature) in the building throughout the winter, required extremely large amounts of humidification energy.
The airside economizer mode in the air handling systems is being eliminated in favor of intaking outside air only in the amount required as ventilation air. Note that ASHRAE Standard 90.1-2019: Energy Standard for Buildings Except Low-Rise Residential Buildings provides an exception to its economizer requirement when the building is required to be humidified to more than 35°F dewpoint temperature.
Chilled water will be required year-round as the airside economizer mode is eliminated, and a heat recovery chiller is being incorporated as the winter cooling source and as the first stage of hydronic heat. A heat recovery chiller was chosen to produce chilled water in winter instead of choosing a waterside economizer cycle, which would have rejected heat through the building’s cooling tower. The heat recovery chiller is a very efficient heating device, recovering the building’s heat instead of rejecting it to the outdoors.
To maximize the efficiency of both the new condensing boilers and the new heat recovery chiller, the existing hydronic heating devices in the building — all of which have exceeded their useful life, and all of which were originally designed to operate with 180°F heating hot water supply temperature are being replaced with hydronic heating devices designed to operate with 120°F heating hot water. Most of the existing hydronic heating piping is being reused because it remains adequately sized and is in good condition.
A few rooms along the building exterior wall used hydronic radiant ceiling panels to offset heat loss through the exterior wall. Lowering the supply water temperature to 120°F greatly diminished the heat output of these radiant panels. To mitigate the reduction in capacity, the capacity of the air terminal unit heating coils is being increased in these rooms.
‘
FIGURE 4: This is a graph of a heat recovery chiller’s coefficient of performance (COP) versus leaving hot water temperature based on the minimum efficiency requirements for a 150- to 300-ton water cooled chiller as prescribed in ASHRAE Standard 90.1: Energy Standard for Buildings Except Low-Rise Residential Buildings. Courtesy: Peter Basso Associates Inc.
door conditions subside, the system supply water temperature can be programmed to decrease back to 120°F. Consideration must be given to the maximum heating hot water supply temperature capability if employing a heat recovery chiller, which is commonly 140°F for many machines.
Lowering the water temperature in hydronic heating systems can increase boiler efficiency to a significant extent when condensing natural gas boilers are installed, thus reducing a building’s carbon footprint.’
Lowering the water temperature in hydronic heating systems can increase boiler efficiency to a significant extent when condensing natural gas boilers are installed, thus reducing a building’s carbon footprint. Lowering the water temperature also opens the door to the use of heat pumps and/ or heat recovery chillers as efficient heat sources for the hydronic heating system, making these machines a smart choice for electrification. cse
Dennis Sczomak, PE, LEED AP, is Senior Vice President/Director of Engineering at Peter Basso Associates Inc. David Conrad, PE, LEED AP, is Vice President/Corporate Government Group Leader at Peter Basso Associates Inc.
Now shipping within 48 hours
Fiberglass conduit is a lightweight, durable alternative to GRC in data centers.
> No burn-through eliminates elbow repairs
> Lower coefficient of friction for smooth pulls
> Fault resistance makes repairing cables easy
> Durable and corrosion-resistant for project longevity
> Available with lower material and installation cost
> NOW shipping within 48 hours DOWNLOAD
The low pressure drop LPD-Mag is the industry’s first Y-Strainer solution to pump seal failures caused by iron oxide build-up within the water system.
Neodymium 8000 Gauss Magnet
Tests have proven the 3” LPD Mag can capture 42% of the particles on the first pass. After only 5 passes, a 92% success rate in capturing and removing particles.*
• Captures magnetic particles that range from visible rust/metallic chips to very fine powder.
• The only magnet solution on the market that can be blown down while in-service.
* Test Conducted at Milwaukee School of Engineering
Scan code to view demo video. Visit Metraflex.com/LPDMag or dial 800-621-4347 for more info.
Stuck to Pump Motors vs Removed by the LPD Mag
Joseph Lisowski, LEED AP, HDR Inc., Princeton, New Jersey
Building controls technologies, open communication protocols and networked internet protocol evolved to create a relatively easy means to integrate multiple control systems
Heating, ventilating and air conditioning (HVAC) control systems, also known as building management systems (BMS) or building automation systems (BAS), have changed significantly over the years. The primary function of the BMS is to control air handling units, boilers, chillers, cooling towers, space temperature controls and other related building HVAC control systems.
• Understand the history of building management system (BMS) protocols and how new open protocols/platforms available provide for ease of integration.
As buildings evolve and are increasingly more sophisticated, the requirements of integrating additional control systems to the BMS also increases. This can include lighting control, electrical power monitoring systems and plumbing equipment. Understanding how these various systems can be connected to a seamlessly integrated control system can increase building performance.
• Establish the importance of early owner involvement and how it impacts BMS protocol specifications.
• Gain knowledge of BACnet and Niagara platforms to help specify communication protocols or platforms to obtain the final desired outcome for your client.
One of the most noticeable evolutions with building control systems, is the way information is transferred within their controllers and displayed on the graphical user interface (GUI), such as an operator workstation
(OWS) or a thin client. See Figure 1 for an example of a proprietary BMS network architecture diagram. During the development of the various BMS control systems, it was up to each independent BMS vendor to determine the communication method and protocol in which data would be sent and received.
For example, unique communication protocols would not allow the control system of Vendor “A” to transfer data to the control system of Vendor “B.” As a vendor’s proprietary solution, these communication protocols can be very restrictive. Therefore, a building owner who would like a BMS installed at a facility would need to decide which BMS vendor should be selected, understanding that this would require a long-term commitment. If a building owner later decided to use another BMS, it would be expensive to replace the existing controls in the building, including the BMS controllers, field devices, OWS and wiring.
Alternatively, a communication gateway could be installed to translate the BMS information between two different control systems. This solution would require a significant amount of programming to configure communication links and could have reliability issues, as the gateway is a single point of failure.
An owner might decide to change BMS vendors if they were not satisfied with the control system performance or if there were issues with the service agreement, such as high cost or slow response time. This is not the most desirable solution due to the expense of additional changes to an existing control system. Since there would not be any competition in the selection of a controls system contractor for renovation work, this is typically subject to increased cost for services as well.
Owners of larger facilities could decide to use multiple control systems, which would allow for competition between the vendors. However, this solution can be cost prohibitive as well, since this would require the duplication of the OWS, communication wiring, spare parts and potentially another programming language.
The answer to these common challenges was the creation of a nonproprietary “open” protocol that could be shared among all BMS manufacturers, leading to BACnet International.
Building automation and control networks, or BACnet, was developed by ASHRAE in the 1980s as the open protocol solution for BMS control systems. ASHRAE allowed for the sharing of the BACnet protocol amongst all BMS vendors, as documented in ASHRAE Standard 135: BACnet — A Data Communication Protocol for Building Automation and Control Networks, which granted
building owners more flexibility. To ensure compliance of BACnet communication among the various BMS vendors, the BACnet Testing Laboratories was established as an independent organization to verify that the control devices meet the ASHRAE Standard 135 requirements and confirm communication inoperability.
Both BMS vendors and equipment manufacturers could reap the benefits from using BACnet. For example, the BMS could use the BACnet protocol to communicate with the manufacturer’s factory installed control systems for boilers, chillers and variable frequency drives. Using the BACnet communication with third party equipment is a more cost-effective option, since a communication wire could transmit multiple control signals associated with equipment parameters, whereas previous monitoring of HVAC equipment would require a dedicated wires for each control signal or a communication gateway. See Figure 2 for an example BACnet BMS network architecture diagram.
‘ The
answer to these common challenges was the creation of a nonproprietary “open” protocol thatcould be shared among all BMS manufacturers, leading to BACnet International.
’
‘ Even though the BACnet protocol allows for a nonproprietary communications protocol, it still has limitations. While the use of BACnet establishes a common protocol for communication, it does not solve the problem of allowing building users to modify the system on a controller level.’
Even though the BACnet protocol allows for a nonproprietary communications protocol, it still has limitations. While the use of BACnet establishes a common protocol for communication, it does not solve the problem of allowing building users to modify the system on a controller level. The BMS vendor would still use proprietary software to startup and commission the system, which will not allow the end user to adjust later, on the local controller level. The owner would only have access for adjusting via the GUI. For some building owners that might not be an issue. However, for buildings that have ongoing renovations, this would be detrimental.
There are other protocols that are considered ‘open’ that can be used in BMS networks. One such protocol is Modbus, which was developed by Modicon for industrial programmable logic controllers in 1979. For the commercial HVAC control system industry, Modbus is used for communication with
electrical equipment, such as automatic transfer switches, switchgears, emergency generators and electric meters.
The next progression in creating a truly open hardware system, which could entail hardware solutions, software solutions or both that addresses the limitations of BACnet and other open protocols is seen in the implementation of the Tridium Niagara system.
Tridium created a software solution, called Niagara, that is an open programming platform. The Niagara framework is an operating system that is installed on controllers and servers. Tridium also offers a hardware product, called a Java Application Control Engine (JACE) that the Niagara framework is installed on. However, this framework can be installed on any manufacturer’s controllers. Many of the major BMS providers will carry two product lines: one proprietary system and one Niagara system.
For example, Johnson Controls has their proprietary offering, the Metasys system, and also has a Niagara offering, Facility Explorer. Certain verbiage needs to be incorporated into the specifications to prevent contractors from installing proprietary software on Niagara devices. This is important to guarantee that downstream controllers are programmable from the workbench and that the system remains fully open. This also prevents the contractors from being able to “lock out” competing vendor controllers from communicating with
each other. This verbiage is called the Niagara Information and Conformance Statement (NICS) and is provided by Tridium.
The advantage of many different manufacturers offering a Niagara solution is that all can bid on the same project, with the same solution, while providing a future-flexible hardware environment. When bidding on new projects with the option of either a proprietary system or an open system, there may be an additional upfront cost for an open system that the owner should be aware of.
However, after the open system is installed, it will provide more competitive bidding on future projects and can thereby decrease future cost, since any Niagara certified manufacturer can service the system and controllers. Owners are not locked into one provider. In the event an owner becomes unsatisfied with the service that is being provided from a service provider, the owner can engage with a different Niagara certified service provider that may offer a more satisfactory response.
This is also an advantage when working with a customer with a large global footprint who is looking to maintain consistency across their portfolio. The customer can standardize using Niagara and the system can be installed by any Niagara certified branch, instead of being limited to only local branches in the area the buildings are located. By allowing open programming, Niagara provides the ability to integrate with many different manufacturer’s products and communication protocols. The Niagara framework can be configured and customized to suit the needs of the project. Third-party communication drivers can be installed on the controllers to enable communication with proprietary controllers with protocols from Siemens, Trane, Johnson Controls and others. This is a powerful feature, particularly during retrofit projects. For instance, an owner may wish to upgrade the BMS, but have a prohibitive budget, making it unreasonable to replace all front-end
equipment and field level controllers at one time. Niagara could be used as a potential solution to implement an incremental modernization of the equipment.
A JACE could be used to first replace the supervisory level controllers. The JACE can be equipped with drivers installed to integrate with legacy field controllers in the building. There may be different manufacturers’ controllers in the building that can be integrated to the Niagara front-end. Once this process is complete, the remaining legacy controllers in the building can be replaced over the years as the budget allows.
Another benefit of a Niagara system is the ability to connect to legacy systems and controllers. The Niagara system can either communicate to the controllers through a JACE or a Niagara computer server or supervisor. The legacy controllers may have proprietary software installed, which can limit some of the functions available with a JACE, but these can still be integrated into the Niagara system using drivers. However, a JACE controller that has the Niagara workbench installed will provide more flexibility and enable the end user to use all Niagara benefits.
The flexibility of integrating different manufacturers building automation controllers and packaged mechanical equipment controllers can also be applied to different technologies. Additional gateways may be required, whether it be lighting
FIGURE 4: Control system integration as seen in a children’s hospital. Courtesy: HDR, Dan Schwalm
‘
controls, power monitoring, security or an access control system. The open platform solution of Niagara can again be used as the framework where these systems can all communicate and be visualized at a central location. See Figure 3 for an example of a Tridium Niagara network.
Tridium provides the option for customers to opt in to a Niagara Service Maintenance Agreement (SMA). The Niagara SMA is an offering that
BMS communication protocols and their ability to be integrated with other control systems has dramatically changed over the years, from the initial creation of the BMS vendor proprietary protocols to the “open” systems approach that allows inoperopability with a multitude of control systems.
’
continuously provides technology updates and feature improvements to the system. This enables existing systems to be updated to fix software bugs and to be upgraded to the latest technological developments. While Niagara provides a powerful solution with many different capabilities, there are some factors that need to be considered before pursuing this product.
system manufacturer or vendor can streamline coordination and problem-solving. Although Niagara provides the ability for these different systems to communicate, there are challenges that can be encountered when dealing with multiple manufacturers. Coordination between the numerous parties involved can make it difficult to determine who has ownership when an issue arises. A single source vendor that can provide the different control systems involved has the potential to alleviate this issue.
Each device that the Niagara workbench is installed on, whether it be a server, JACE controller or Edge device, requires a license. The licenses are provided based upon device counts and point requirements. Each of these licenses comes with a software maintenance agreement that provides the updates and improvements previously mentioned. The cost of these licenses and maintenance agreements can add up when there are a lot of controllers in the building. First cost and total cost of ownership should both be presented to the client and should be considered when comparing open versus proprietary systems.
u
csemag.com
Control system insights
u Building control systems have evolved over several years from simple systems that control one aspect of a building to more modern, complex systems that control everything.
u Integrated control systems cannot only control all the engineered systems within a building, they can enhance security and sustainability.
Major BAS providers will typically provide a line of Niagara controllers, yet these are often installed by independent contractors. These independent contractors do not always have the same accountability offered by the main manufacturer branches. The level of expertise of the independent contractors also may not be held to the same standard as a major distributer with local branches.
Additionally, Niagara has many different capabilities and functions, which must be established during design by the engineer of record or building commissioning agent for a project. The contractor must effectively implement the desired features defined by the engineer of record and tested by the commissioning authority during installation. This increases the importance of interviews during the bid process to ensure a contractor is qualified to complete the project.
When dealing with a project involving multiple different control systems, such as building automation, security and lighting, a single source control
BMS communication protocols and their ability to be integrated with other control systems has dramatically changed over the years, from the initial creation of the BMS vendor proprietary protocols to the “open” systems approach that allows inoperability with a multitude of control systems. When designing and specifying a control system for a project, there is no advantage of using a proprietary protocol for new construction.
However, it might be required in a renovation project for the controls to be easily integrated into the existing facility’s control system. This will need to be reviewed with the building’s owner. In some cases, it would make sense to remove the existing control system and install a new one, especially if the BMS is outdated and potentially obsolete. The most desirable solution for the BMS communication protocol is BACnet. This allows for the most flexibility with communication to a multitude of BMS vendors and mechanical equipment vendors. After selecting BACnet as the BMS communication protocol, the owner still needs to decide which BMS platform to use. The BMS platform components include the BMS OWS and BMS control-
lers. Vendor-specific and Niagara platforms are the most common platforms used. The vendor-specific platform is provided by the control vendors such as Johnson Controls, Siemens and Honeywell and uses their proprietary software. The Niagara platform is provided by Tridium with “open” software capabilities, called Workbench, which can be supported by numerous control vendors. Some additional items to consider when deciding on which type of BMS platform to specify are:
• Does the building need to integrate with control systems from different vendors?
• Will the BMS need to expand, such as at a campus or is it restricted to a small environment?
• Is it important to have the freedom to select a BMS service provider and not be locked into a specific vendor?
For any new project, even where there is not a known need for the integration to multiple ven-
dor platforms and the building owner is agreeable with selecting one BMS service provider, having a vendor-specific platform solution might prove to be best choice. For a building owner who would like the freedom to choose a BMS vendor for service and where there is a requirement to integrate to a multitude of unique control systems, the Niagara platform should be considered.
This would allow the owner to have multiple BMS vendors bid their services, leading to a competitive price. The ability to have an open bid situation for BMS vendors can only be achieved if the building is equipped with controllers that do not use proprietary software, as these would require the use of the Niagara Workbench devices. While vendor-specific and Niagara platforms are both viable solutions, each option should be reviewed and considered with the building owner and a subject matter expert. cse
Joseph
Lisowski, LEED AP, is Mechanical Instrumentation and Controls Section Manager at HDR Inc.
The M5900 stops flooding caused by auxiliary drains that freeze and break, are maintained improperly, vandalized, or broken by accidents. They enable facilities to recover faster with less clean-up and expense. Now Available on select COLLECTanDRAIN models.
‘
For any new project, even where there is not a known need for the integration to multiple vendor platforms and the building owner is agreeable with selecting one BMS service provider, having a vendorspecific platform solution might prove to be the best choice.’
David J. Brearley, CISM, GICSP, PMP, HDR, Charlotte, North Carolina
An explosion of technology in the built environment introduces cybersecurity — and its challenges — to the design and construction industry
Imagine a hospital or a military base that have achieved a high level of cybersecurity maturity. Both facilities will have outside dependencies including people, power, water, manufacturing and supply chains, which will not have the same level of cybersecurity maturity. What is the potential impact to their operation, if the nonregulated water or wastewater plant were to become inoperable due to a cyber event? Reverse the dependency, what if we have a health care system that cannot treat patients critical to the operations of a water or power plant?
Even though industries are dependent on each other, the regulations, standards, laws and requirements for securing operational technology (OT) systems used vary greatly. Depending on the industry, these can range from voluntary cyber risk recognition and mitigation, to regulated or expected risk management.
• Become familiar with technologies in the built environment that may be at risk of a cyber incident.
• Understand basic cyber hygiene concepts that can be applied to technology during construction to lower risk potential.
A cybersecurity incident within any of the 16 U.S. government-defined critical infrastructure sectors can disrupt modern society in an instant. The potential of societal impact was recently illustrated in the Colonial Pipeline incident. Colonial Pipeline was the victim of a ransomware attach that resulted in the shutdown of pipeline movements affecting the Southeastern United States. News of the shutdown resulted in public panic and a run on gasoline, which led to gas shortages and increased fuel costs.
• Become familiar with the potential impact of a cyber event on operational technology systems.
Essential functions and mission critical facilities including federal facilities, mili-
tary bases, hospitals, utilities and power generation have deep interdependencies on each other, as well as the OT systems that are essential for operations. OT systems are no longer used as a convenience or efficiency tool for manufacturing. Instead, these are now required to serve the increased production needs for large populations and rely on complex processes that cannot be controlled by humans; and as an enabler to achieve sustainability and resilience initiatives.
For example, a modern building will have OT systems, such as automation systems for heating, ventilation and air conditioning, electrical systems and fire alarm systems. These three system groups include multiple subsystems and sensors connected to operate the building. Each system and sensor represent a potential attack point to an adversary if not secured.
In complex buildings, the number of systems can increase substantially, especially with the increased demand to meet net zero targets to help reduce energy consumption. It is not uncommon for a modern building to have more than 50 systems with thousands of network-connected devices. Many net zero carbon buildings or highly rated U.S. Green Building Council LEED buildings leverage OT technologies such as solar arrays, lighting controls, occupancy sensors, automatic shade controls, smart windows, rainwater harvesting and more to achieve energy reduction goals.
In the not-so-distant past, many of these systems were natively manufactured without intelligent components as an option. Today, components are
manufactured with onboard intelligence included and, in many cases, nonintelligent components are no longer an option.
A lack of cybersecurity is a risk to building systems. However, cybersecurity requirements are often not included in every design due to cost or lack of cyber risk awareness. Some states and regulatory agencies have begun to increase risk awareness and requirements such as:
• March 2023, the Biden-Harris Administration published the National Cybersecurity Strategy and within days the U.S. Environmental Protection Agency and Transportation Security Agency issued updated sector specific cybersecurity requirements.
• In 2022, the states of New Jersey, New York, Maryland, Tennessee and Florida issued legislation applying cybersecurity requirements for utility owners.
• In 2017, the U.S. Department of Defense has required the use of Unified Facilities Criteria (UFC) 4-010-06 for all design and construction projects.
However, many industries have limited budgets or thin profit margins and cybersecurity mitigations often have cost implications in design, construction, system operations and maintenance.
The concept of risk management is not new to design and construction projects. Engineers design to standards and codes that have been adopted to lower risk from incidents such as fire, flooding and wind. Now, industries need to transition traditional planning to include cybersecurity as a risk that should be addressed.
As this industry begins trending toward increased comprehensive cyber risk recognition, the application of cybersecurity requirements within the design of the built environment needs to be included in project plans early in the process. By incorporating proactive solutions for system owners that include cybersecurity considerations into
‘ Cybersecurity requirements are often not included in every design due to cost or lack of cyber risk awareness. Some states and regulatory agencies have begun to increase risk awareness and requirements.’
the design from the beginning, engineers and designers can control design, construction and maintenance costs.
As a starting point, consultants can bring the topic of cybersecurity to the forefront by introducing the concept of “cyber-ready” into a standard master specifications package. Where clients may not specifically require cybersecurity requirements, these master specifications will focus on a few key concepts that are generally recognized as best practices across multiple industry standards (ISA-62443, NIST-800 SP 53, NIST 800 SP82, ISO27001). Examples include:
• Requiring the contractor to share a spreadsheet-based asset inventory of devices and software allows clients and response teams visibility of what devices belong on networks.
• Default usernames and passwords can easily be leveraged by a low-skilled adversary to impact devices. Requiring the contractor to coordinate with the client to change default usernames and passwords to unique usernames and password per device on all programmable devices and software can help combat this risk. Additionally, the contractor should provide a secured password inventory at project close-out.
• Known vulnerabilities in devices and software are both published and shared by adversary communities. Many devices procured by contractors
csemag.com
Cybersecurity insights
u If a cyberattack occurs at a water treatment plant or electric utility, it affects more than just that agency. Buildings and individuals are directly impacted.
u Network security within the building’s systems — such as a building automation system — are required to ensure full functionality.
are received from inventories or sit idle before use, where the firmware in the device is not up-to-date, which could lead to the new system being insecure. Incorporating a requirement for patching to the latest firmware and software at time of commissioning will lower the risk of a new build including known vulnerabilities.
‘ Cybersecurity mitigations implemented during the design and construction process can be more effective than bolt-on solutions after hand-over. ’
• All systems that support access control such as PIN or password should have it enabled to restrict access to specific system functions based on the person's role. Actions and capabilities within the system should be limited to only those that are necessary for the particular person based on their role. It is impossible to design an unhackable system, however, applying mitigations can lower risk to be within tolerance. Therefore, a requirement of a documented transfer of all software and configuration backups for every programmable device, which can be used by clients to recover from an incident, should be implemented. These basic hygiene requirements fall primarily within the NIST Cybersecurity Framework’s (CSF) “identify and protect” stages and provide for a moment in time (at system turnover) backups for potential recovery actions.
Unfortunately, applying design requirements to detect, respond and recover tools beyond a moment in time backup require a more comprehensive engagement with clients to develop solutions, which are cost effective and maintainable. For sectors with a lower risk tolerance, the use of the NIST risk management framework to evaluate and incorporate appropriate security controls is recommended. This allows for alignment with the sector’s risk tolerance for each of the OT systems in the project. The accepted security controls can then be incorporated within the drawings and specifications. Afterall, cyber ready is just a starting point. Cybersecurity mitigations implemented during the design and construction process can be more effective than bolt-on solutions after handover. These may impact cost and schedule. Applying cybersecurity after a system’s functional startup may impact functionality and require retesting of system function. System and component suppli-
ers must recognize and plan for the design requirements, which may include:
• Client coordination.
• Client cyber training on systems or components.
• Increased performance requirements for components (managed network switches, firewalls, encryption).
• Specific configuration requirements (device hardening, network segmentation, least privilege).
• Additional testing and validation efforts related to security of the system in addition to functionality.
• Increased documentation requirements.
• Client provided or configured equipment.
Cyber-ready systems as described above normally do not require contractors or vendors to employ cybersecurity experts for implementation. More complex designs meant to lower risk will require increasing the technical acumen to configure devices and networks for security, in addition to system functionality. Highly secured systems may require contractors to include dedicated cybersecurity staff to work with vendors to implement or verify the system.
Everyone in the planning, design and construction life cycle has a role to play in cybersecurity. Cyber adversaries will continue to implement new tactics and techniques, cyber mitigation requirements will adjust to the changing threat and the design and construction industry will adapt to a new playing field where cybersecurity is an integral part of project risk management and a construction implementation requirement. cse
David J. Brearley, CISM, GICSP, PMP, is director of operational technology cybersecurity at HDR. He has 20 years of international experience providing information technology and operational technology solutions.
ON CALL
If you need assistance with sizing or product selection, our team of Application Engineers is ready to assist you. The Rheem Commercial Water family of brands offers a comprehensive product portfolio designed to meet the needs of any commercial project.
Product application sizing charts for all commercial products
2D and 3D support with creation of project quotes showing relevant specifications
Product application sizing and design solutions within 48 hours
Taha Mohammed, PE; and Robert Magsipoc, PE, CDM Smith, Fairfax, Virginia
When designing a medium-voltage electrical distribution system, the end user’s safety, system reliability and equipment maintainability are key components for the designer to consider.
Several factors must be considered and evaluated, by the designer, when determining whether to use a low-voltage (LV) or medium-voltage (MV) distribution system.
The owner’s satisfaction and safety are the goal of any project. Collaboration and input from the owner on their opinion, operational staff experience and comfort level with MV equipment should be considered when deciding to use a MV versus LV system for a facility. In addition, equipment availability, system capacity, cost, physical space and site constraints are the main factors when selecting the distribution system.
voltage system and equipment accordingly. Similarly, early coordination with the mechanical engineers is needed to determine the expected loads and hp sizes for their pump motors and equipment.
Another deciding factor is cost. Generally, MV equipment is more expensive than LV equipment. However, the using MVs will reduce the amount of current traveling through the conductors, which reduces the quantities and sizes of conduits, conductors and duct banks installed as well as labor costs, especially for long runs on campuses. The designer should consider evaluating the cost effectiveness between LV and MV early during the design.
Physical space considerations and site restrictions could also affect the designer’s voltage choice. MV equipment is typically larger than LV equipment as it requires higher-rated insulation and more separation between the buses within the enclosure. In addition to the equipment itself, the working space clearance in front of MV equipment required by NFPA 70: National Electrical Code (NEC) is greater than LV.
• Identify applicable codes and standards for medium-voltage (MV) electrical distribution systems.
The availability of LV equipment becomes limited when the total electrical load approaches certain sizes. For example, for an LV system, 5,000-6,000 amperes (A) is the threshold for LV switchboards and switchgears that are commonly available by manufacturers. Exceeding this threshold increases the risk of arc flash. Equipment availability also applies to the driven equipment, such as variable frequency drive (VFD) motor starters may not be commonly available at LV for motors 700-800 horsepower (hp) or larger by all the VFD suppliers.
• Learn about MV distribution equipment for industrial applications.
• Learn about best practices to consider during MV electrical distribution system design.
Early coordination with the electric utility is necessary to determine the available voltage rating near the project site. This will allow the designer to select the appropriate
NEC Sections 110.31 and 110.34 cover the minimum distance from fences to live parts and the minimum depth of clear working space at electrical equipment, respectively, for systems more than 1,000 volts, nominal (refer to NEC Tables 110.31 and 110.34(A)). However, as discussed, MV will require less conduits and conductors installed for distribution and between equipment in comparison to LV, which is more effective for project sites with physical space constraints.
Compared to LV equipment, MV equipment is more expensive. Due to a higher system voltage, the amount of power generated during a fault, depending on the system impedance, may be larger and
more damaging. Additionally, with the increase of the voltage, the concern of electrocution increases. Therefore, MV system requires specific considerations including, but not limited to, the following. Protection: The most common form of protection in MV systems is the use of protective relays. Protective relays are devices that provide open and close commands to the associated circuit breakers based on input from current transformers and voltage or potential transformers. The protection can range from time overcurrent, instantaneous overcurrent, over/undervoltage, over/underfrequency, ground fault, etc.
ANSI/IEEE C37.2 assigns standard device numbers to the type of protection a certain relay performs. The following are commonly used protective relays:
• 25 – Synchronizing or SynchronismCheck Device.
• 27 – Undervoltage Relay.
• 32 – Directional Power Relay.
• 47 – Phase Sequence or Phase Balance Voltage Relay.
• 50 – Instantaneous Overcurrent Relay.
• 51 – AC Time Overcurrent Relay.
• 51G – Ground Time Overcurrent.
• 59 – Overvoltage Relay.
• 67 – AC Directional Overcurrent Relay.
• 81 – Frequency Relay.
• 86 – Locking Out Relay.
• 87 – Differential Protective Relay.
Standby generator neutral grounding resistor: For a MV standby generator, it is important to consider using a neutral grounding resistor (NGR) connected to the alternator grounding system. If a fault occurs while the standby generator is running, the NGR will limit the ground fault current that will return to the alternator and protect the generator from damage. See Figure 1 for a field installed NGR for an indoor MV generator.
MV enclosure and assembly: In general, there are two types of MV enclosures, metal-clad (MC) and metal-enclosed (ME). IEEE C37.20.2: Standard for Metal-Clad Switchgear defines MC switchgears as a switchgear that contains drawout electrically operated circuit breakers that is compartmentalized to isolate components such as instrumentation, main bus and both incoming and outgoing connections with grounded metal barriers.
ME is defined by IEEE C37.20.3: Standard for Metal-Enclosed Interrupter Switchgear as a switchgear assembly completely enclosed on all sides and top with sheet metal (except for ventilating openings and inspection windows) containing primary power circuit switching or interrupting devices or both, with buses and connections and possibly including control and auxiliary devices. Access to the interior of the enclosure is provided by doors or removable covers.
Both MC and ME switchgears contain interrupting devices, such as a circuit breaker, fuses (ME only) or load break interrupter switches. The MV circuit breaker switching mechanisms are electrically operated and have no integral protection and require external control power, unlike LV circuit breakers that have integral protection.
The MC switchgear has a higher initial cost in comparison to ME,however, the MC assembly is more robust as it contains insulated buses, does not have exposed parts and the MV and LV sections are completely segregated. Another difference is that MC assemblies require front and rear access, while ME typically only requires access from the front. Therefore, physical space constraints, accessibility and working space clearance requirements should be considered when selecting the type of MV enclosure and assembly during the design phase.
DC control system: As mentioned above, MV operation and protection requires a reliable source of power. Unlike LV, MV uses protective relays to open and close the circuit breakers. The reliability of the control power for protective relays is extremely critical for the system to be always functional and safe. In general, direct current (dc) control power is used for MV protection systems and
FIGURE 1: Field-installed neutral grounding resistor for an indoor medium-voltage generator. Courtesy: CDM Smith
‘Early coordination with the electric utility is necessary to determine the available voltage rating near the project site. ’
csemag.com
MV insights
u Medium-voltage (MV) electrical systems can be used in many commercial and industrial applications.
u While MV equipment can be more expensive, it requires fewer conduits and conductors.
circuit breaker operations, in lieu of alternating current (ac) control power. DC systems are more reliable, less impacted by the inrush of the circuit breaker coils, require less physical space and can store more energy.
Typical DC control systems require batteries, such as flooded lead acid, valve regulated lead acid, nickel cadmium, etc. and 48 V or 120 Vdc control voltages are commonly used. Based on the type and quantity of the batteries, additional ventilation or special storage, such as a dedicated room, may be required. IEEE 485: Recommended Practice for Sizing Lead-Acid Batteries for Station Applications and IEEE 1115: Recommended Practice for Sizing Nickel-Cadmium Batteries for Station Applications are standards that can be used to size the battery system, which is measured in amp-hours (Ah). The
Ah is based on the MV protection system components power usage, such as circuit breaker coil trips, spring charging and closing, steady state loads and the number of circuit breaker operations within a certain period of time, which should be determined during the design.
NEC Article 480, Stationary Standby Batteries, shall be complied with for the battery system, including, but not limited to, protection, accessibility, wiring, illumination and ventilation.
Redundancy: To provide a reliable electrical system, a double-ended (main-tie-main circuit breakers) switchgear assembly should be considered to provide flexibility during maintenance and redundancy to maintain operations in the event of failure from one source. Redundancy should also be considered with respect to the dc control sys-
Water supply system gets a much-needed electrical upgrade
AN 80-YEAR-OLD water system was updated with a new medium-voltage electrical system
The Rocky Gorge Pump Station (RGPS) is a raw water pump station located in Laurel, Maryland, that is owned and operated by the Washington Suburban Sanitary Commission (WSSC). The pump station provides raw water to Patuxent Water Filtration Plant and is a key element of WSSC’s potable water supply system for Prince George’s and Montgomery Counties. Originally built in the mid-1940s, CDM Smith provided engineering services, including design and construction, to upgrade its total flow capacity from 72 to 110 million gallons per day.
As part of the upgrade, the existing medium-voltage (MV) electrical system was evaluated and it was determined that a new distribution system would be required. The electrical distribution system included a 33 kilovolt (kV)-4,160 Volt (V) liquid-filled outdoor substation; 4,160 V metal-clad double-ended indoor switchgear; MV motor control centers (MCCs); and MV pumps with variable frequency drives and reduced voltage solid-state soft starters.
Several factors were considered when deciding on using MV. One of the main drivers for this project was the quantity and size
of the pump motors used in the pump station, which ranged from 200 horsepower (hp) to 1,500 hp. The total estimated maximum operating loads was approximately 8,000 kilovolt amperes, which is outside the practical capacity for a low-voltage (LV) system due to the high short-circuit current available at this capacity and the potential of dangerous arc flash hazards.
Additionally, MV motor starting equipment is more practical and available when motors exceeding 700-800 hp. Physical space limitations of the existing site and reducing quantity and sizes of conduits and copper wires throughout the pump station were also deciding factors to use MV over LV.
To build a robust electrical distribution system, the design incorporated various protection techniques, such as differential protection of the substation transformers and motors, transformer oil temperature and pressure monitoring, switchgear overcurrent, over voltage, differential and other protective measures. Motor protection management relays were used in addition to regular overcurrent, control and permissive interlocks. To harden the reliability and resiliency of the electrical system, redundant transformers, double-ended switchgear and MCCs and direct current voltage control battery system were used.
tem such as including a second dc control system (battery system).
Surge arresters, also known as lightning arresters, are used to protect MV equipment from high-voltage surges and are typically installed to protect transformers and distribution equipment by connecting the line terminal to ground (see Figure 2). When a surge arrester experiences a voltage higher than its maximum continuous operating voltage, it becomes conductive and shunts to ground.
There are three classes of surge arresters commonly used in MV protection: distribution class, intermediate class and station class. NEC Article 242 Part III has requirements for surge arresters rated more than 1,000 V.
outdoor pad-mounted transformer.
As this project was an upgrade to an existing pump station, space constraints of the existing structure and location required continual coordination and consultation with electrical equipment manufacturers and collaborations with architectural, structural and building mechanical engineers during the design. Complying with NFPA 70: National Electrical Code working space requirements, maintaining front and rear access of the switchgear and MCCs for future maintenance and allocating sufficient space to move the equipment in and out of the electrical room were challenges that required extra attention and coordination to overcome.
4: Rocky Gorge Pump Station medium-voltage pumps and motors layout. Courtesy: Washington Suburban Sanitary Commission
The engineering work didn’t end at the design stage, as numerous meetings and continual collaborations with approved manufacturers and the construction contractor were required to optimize the equipment layout and arrangements. As the owner and end user of the pump station, WSSC provided continuous input and feedback that were critical to produce a safe, resilient and maintenance-friendly electrical system. Various workshops and on-site meetings were held with the equipment suppliers, owner’s staff, construction contractors and engineering teams to resolve conflicts and ensure the
supplied equipment would be operable and can be effectively serviced throughout its expected useful life.
The project also involved keeping the pump station functional while the construction was in progress, also known as maintenance of plant operation. This required coordination with the construction contractor to developing a sequence of construction that would minimize facility shutdown while replacing the existing electrical system.
After construction was completed, the upgrade included acceptance testing of all the electrical equipment in accordance with InterNational Electrical Testing Association acceptance testing specifications (known as NETA ATS) and manufacturer standards. The electrical distribution system was also tested using a nondestructive very low frequency testing method.
Lastly, a power system study was completed that included short circuit, protective device coordination and arc flash studies. The protective relay settings that were determined as a part of the study were incorporated in the field and arc flash labels were installed in accordance with NFPA 70E: Standard for Electrical Safety in the Workplace.
Additional information and applications for commonly used surge arresters can be found in IEEE C62.11: IEEE Standard for Metal-Oxide Surge Arresters for AC Power Circuits (>1 kV) and IEEE C62.22: IEEE Guide for the Application of Metal-Oxide Arresters for Alternating-Current Systems. Figure 2 shows a surge arrester connected to the MV side of an outdoor pad-mounted transformer.
NEC Tables 315.60(C)(1) through 315.60(C)(20) provide the ampacities of conductors for the various installation configurations and methods for the different cable temperature ratings (Type MV-90 for 90°C and MV-105 for 105°C).
In addition to properly sizing MV conductors based on full load requirements, MV conductors and terminations are required to have insulation that can withstand the stresses experienced during normal and abnormal operating conditions, including fault events and rated for the environment that they will be installed. NEC Article 315 defines the requirements for MV conductors sizing, applications, installation and other requirements.
Normally, there are two types of MV cables that are used in underground applications, ethylene propylene rubber and crosslinked polyethylene. MV cables have three insulation thick-
ness levels (100%, 133% and 173%) depending on the amount of time it takes to clear a ground fault. According to NEC Article 315, 100% insulation level cables are used with relay protection to clear ground faults as rapidly as possible but within a minute. Cables with 133% insulation levels are used when the ground fault clearing of less than one minute cannot be met but can clear in one hour and 173% insulation class is used when one hour cannot be met and an orderly shutdown is required.
The ampacity of MV cables is dependent on the cable size, conductor material (aluminum or copper), based on the configuration of the cables (single conductor or three conductor) and how they are arranged in a duct bank. NEC Figure 315.60(D)(3) displays different configurations for cables installed underground.
The higher the voltage, the increased concern of electrocution or electric shock (see NFPA 70E: Standard for Electrical Safety in the Workplace). The safety of the end user is of paramount importance and should be incorporated into every design. Operating MV switches and circuit breakers while standing in front of the MV switchgear could potentially cause significant harm to personnel.
Small footprint, big impact
• UL 924 Listed. Supports Normal and Emergency circuits.
• 120 VAC and 277 VAC
• DMX control for Relay or 0-10V
UNDERSTAND the definitions related to medium-voltage (MV) systems, as well as other voltages
Throughout the United States, several different voltages are used to power residential areas, commercial buildings and industrial facilities. These voltages generally range from 120 volts (V) for lighting and appliances that are low-voltage (LV), up to 69,000 V or 69 kilovolts (kV) for campuswide distribution that is medium-voltage (MV). When voltages exceed 69 kV, the system is considered high-voltage (HV), which is more commonly used for transmission lines.
ANSI Standard C84.1: Electric Power Systems Voltage Ratings (60 Hz) defines the system voltage classes as follows:
• LV: 1,000 V or less.
• MV: Greater than 1,000 V and less than 100 kV.
• HV: Equal to or greater than 100 kV and equal to or less than 230 kV.
• Extra-high voltage: Greater than 230 kV and less than 1,000 kV.
• Ultra-high voltage: Equal to or greater than 1,000 kV.
Similarly, NFPA 70: National Electrical Code (NEC) also defines MV equipment as 1,000 V and higher. Before the 2014 edition of the NEC, MV was applied to equipment rated 600 V and higher. This article discusses design considerations for MV electrical systems in industrial applications.
For MV electrical systems, the following codes, standards and references apply:
• ANSI
• NEC 2023 edition
– NEC Article 110 Part III: Requirements for electrical installations over 1,000 V, nominal
• NEC Article 110.34: Working space
– NEC Article 240 Part IX: Overcurrent protection over 1,000 V, nominal
– NEC Article 315.60 Tables: Ampacities of conductors 2,001 V to 35 kV
– NEC Article 450: Vault and fire requirements for transformers and transformer vaults over 35 kV
• NFPA 70B: Recommended Practice for Electrical Equipment Maintenance.
• NFPA 70E: Standard for Electrical Safety in the Workplace.
• Institute of Electrical and Electronics Engineers (IEEE).
• International Building Code (IBC).
• International Electrical Testing Association (NETA) MTS: Standard for Maintenance Testing Specifications for Electrical Power Equipment and Systems.
• International Fire Code (IFC).
• International Mechanical Code (IMC).
• National Electrical Manufacturers Association (NEMA).
One way to mitigate the risk of electrocution and arc flash is to provide a remote racking mechanism or a LV mimic panel to operate the MV switchgear remotely. A mimic panel will have a copy of the MV switches and controls, but at a lower and safer voltage, which allows personnel to operate the MV switchgear operations remotely without having to stand in front of the MV switchgear. cse
Taha Mohammed, PE, is an electrical engineer at CDM Smith. Robert Magsipoc, PE, is an electrical engineer at CDM Smith.
Josam’s PRO-PLUS® system is the perfect solution when installing trench drains.Its Compressive, Tensile, and Flexural strength is unmatched. The material is 1.5 times stronger and 70% lighter in weight, with 1.7 times less thermal expansion than polymer concrete.
✓ Unmatched Strength
✓ Lightweight
✓ Easy-to-Install
✓ Requires Less Manpower
✓ Withstands Extreme
TemperaturesPreventing Shape
Distortion
✓ PRO-SNAP® grates with no bolts
✓ Load Class A-F
Specify the labor-saving PRO-PLUS® with confidence, knowing you specified a high-quality, superior product that owners will be satisfied with and contractors will find easy to install.
View our complete line of drainage
CSE: What's the biggest trend in college and university buildings?
Christopher Augustyn: Electrification of building heating systems continues to gain traction. Institutions are looking for ways to decarbonize their building heating and domestic water heating systems, and to detach from central steam heating plants while utilizing less energy overall. This becomes especially challenging in cold weather climates, since current electrification equipment technology has limited ability to produce high-quality heat when outside air temperatures are subzero for multiple days.
Matthew Goss: The biggest trends in college and university buildings are decarbonization, energy efficiency and resiliency. Institutions are looking for options to decarbonize energy sources and to identify opportunities to electrify. They are also looking to utilize renewable energy technologies and continuing to implement energy efficiency projects. Clients are looking to incorporate additional layers of resiliency, through redundant equipment, cogeneration or energy storage technologies.
Richard Loveland: The biggest trend in colleges and universities is the focus
on amenity-driven campuses. This includes expanding high-end dormitory options and state-of-the-art athletic facilities. Additionally, there’s a growing emphasis on increasing dining options to offer more variety. Another aspect is the integration of technology-driven classrooms, creating a new era of learning environments. When designing these spaces, engineers need to be thoughtful about energy efficiency and carbon footprint reduction.
Tom Syvertsen: We have seen an increase of multifunction buildings that house several programs, to encourage collaboration between departments. Larger buildings offer options to select more efficient systems, but create the challenge of serving varied occupancy, schedules and types of spaces. In some buildings, this may mean applying multiple types of systems to different parts of the building.
Kirstie Tiller: With the advent of Covid-19, the focus and biggest trend in college buildings remains on indoor air quality considerations. These considerations include enhanced filtration systems, disinfection technology, and an increase in air changes per hour.
CSE: What future trends should engineers expect for such projects?
Tom Syvertsen: The largest future trend for heating, ventilation and air con-
ditioning (HVAC) systems is decarbonization. Decarbonization states that heat produced using electricity instead of burning fossil fuels will use less carbon as the electrical grid greens. While electric heat conjures thoughts of expensive electric resistance heating, the latest technologies produce heat using compressors that can have coefficients of performance of 3.0 or greater. These systems become more attractive when the waste heat or chilled water byproduct can be used for applications that otherwise need additional energy.
Matthew Goss: Engineers should be able to design systems that offer efficient and resilient operations. Aside from selecting technologies that maximize the utilization of cleanly generated energy, systems should be energy efficient and provide operational flexibility to account for future modifications. Additionally, engineers should prepare to design for some level of resiliency or redundancy.
CSE: How do changes or new designs from COVID-19 still impact these buildings and projects?
Tom Syvertsen: The HVAC industry is now focusing on equivalent clean airflow rate, which relies on the treatment or filtration of recirculated air in
combination with outdoor air. The new ASHRAE Standard 241: Control of Infectious Aerosols, details methods to reduce risk of airborne disease transmission and looks to become the standard for healthy buildings.
CSE: If enrollment continues to decrease, what changes do you anticipate seeing?
Richard Loveland: In the event of continued enrollment decreases, campuses will have the opportunity to focus on specific target groups. This can have a significant impact on the types of projects pursued and the overall needs addressed. With a decrease in student population, there is opportunity to customize projects, focusing on specific needs and interests.
CSE: How are engineers designing these kinds of projects to keep costs down while offering appealing features, complying with relevant codes and meeting client needs?
Christopher Augustyn: The key to designing appealing systems while maximizing cost-effectiveness is finding upfront cost trade-offs. For instance, using a chilled beam system is very energy efficient, but the cost of the beams and associated piping systems is expensive.
Christopher Augustyn, PE
Senior Project Engineer, Department Facilitator
Affiliated Engineers Inc., Chicago
Matthew Goss, PE, PMP, LEED AP, CEM, CEA, CDSM
Mechanical, Electrical, Plumbing & Energy Practice Leader
CDM Smith, Latham, New York
Richard Loveland, PE
Senior Vice President
BVH a Salas O’Brien Company, Bloomfield, Connecticut
Tom Syvertsen, PE, LEED AP
Vice President
Mueller Associates, Madison, Virginia
Kristie Tiller, PE, LEED AP
Associate, Director of Mechanical Engineering Lockwood, Andrews and Newnam Inc. (LAN), Dallas
However, one of the major advantages of using chilled beams is the potential to significantly downsize the main air handling system and all ducted components, saving on cost. Understanding trade-offs like this are key during schematic design and budgeting.
Matthew Goss: More engineers are often working with their equipment vendors and manufacturers to utilize unconventional or off-the-shelf solutions versus utilizing a custom-engineered solution. In addition, engineers are considering modularity and flexibility and may design a solution that gets built out over time through additional phases of work. cse
Education and personal development are vital to the advancement of the engineering community.
We invite our readers to explore and utilize the educational efforts of this year’s participants in our annual Educating Engineers program.
ABB Motors and Mechanical
AGF Manufacturing
Cambridge Air Solutions
Camus
Cleaver-Brooks
Greenheck
Gripple
Inaba Denko
Janus Fire Systems
Metraflex
Noritz
Reliable Controls
Rheem Commerical Water cse202309_leadHLF_EduEng.indd
Select AGF COLLECTANDRAIN models can now be ordered with a FLOODELIMINATOR Model 5900. The Model 5900 is a fail-safe designed to stop the flood of water that is released into a facility when a dry fire sprinkler system’s auxiliary drain fails due to a freeze and break, accident, improper maintenance, or vandalism. This allows facilities to get back online a lot faster with less clean up and expense.
The Model 5900 doesn’t require a power source and automatically resets when a new auxiliary drain is installed, and the system is restored to operation. It can also be purchased separately to retrofit onto existing small volume low-point drains or auxiliary drains. CLICK here to learn more or SCAN QR at right to watch an informative video.
Improve system efficiency, reliability and sustainability by pairing an inverter duty motor with a variable speed drive
About 45% of the electricity used in industry is consumed by the 300 million industrial electric motors at work around the world, many of them old and inefficient. If 80% of the world’s electric motors were replaced with the most efficient motors available, 160 terawatthours of energy would be saved per year.
Replacing older motors with new, high-efficiency models is one way to improve inefficient systems, and performance can be increased further by pairing motors with variable speed drives. The basic function of a drive is to control the flow of energy from the power supply to the motor, thus controlling speed, power and torque output.
Inverter-duty motor/drive systems provide optimal performance for constant-power, constant-torque and variable-torque applications
As a result, systems can be optimized to deliver the right amount of performance – no more, no less.
Inverter duty motors are designed to be paired with drives, ready to be placed into new applications or as an upgrade to optimize existing systems. If motors in operation were replaced with motor/drive systems, global electricity consumption could be reduced by as much as 10%, resulting in a 40% reduction in greenhouse gas emissions. It’s not enough to wait until a motor needs a replacement — proactively replacing
older motors with new motor/drive systems will result in reduced power consumption, longer equipment life and better process control.
ABB’s ID (inverter duty) motors on demand webinar series provides information about the benefits of pairing motors with drives. The series features an introduction into ID motors and how to choose the correct motors for various applications. Also included with the series, whitepapers, podcasts and videos.
Click here or scan QR for more information
As the expert, you want to deliver top-tier solutions designed to meet your customer’s needs. We provide premium HVAC equipment, known for its energy- efficiency, longevity, and industry-leading lead times.
Our process is enhanced by specialized building assessment tools and expert guidance every step of the way, empowering you with the confidence to seamlessly connect with your customers.
Discover how the Cambridge Air Solutions ESC-Series can help you transform your customers’ experience:
• The ESC-Series evaporative cooling unit offers semi-custom fabrication and can use direct, indirect, or a combination of both indirect/direct (2-Stage) evaporative cooling to meet specific usage and dimensional requirements. It also provides provides heating options for added versatility.
• This unit utilizes 100% outside air to deliver tempered make-up air and cooling for industrial, commercial, and institutional buildings, ensuring improved indoor air quality while avoiding the high equipment and operating costs associated with mechanical cooling.
• Both E- and ESC-Series evaporative technologies are designed to provide an energy efficient solution for temperature relief during hot summer months. With 12 Two-Stage ESC Models ranging from 2,400 to 56,000 CFM and options for indirect, indirect/ direct, and direct evaporative cooling as well as indirect gas fired heat options, these units can offer up to 70% less energy consumption compared to conventional mechanical cooling systems. Additionally, multiple accessories and control options further enhance versatility.energy consumption compared to conventional mechanical cooling systems. Additionally, multiple accessories and control options further enhance versatility.
CLICK here or scan QR below to learn more.
Avenger ® 5000/6000 MBH firetube comes equipped with patentpending technology that fires the boiler with an industry-leading 40:1 turndown ratio, providing seamless high turndown across its entire firing range. Boiler solutions designed with this proprietary technology feature dual gas valves and a 1:1 air/gas ratio control to maximize turndown and control combustion at desired O 2 levels without an O2 trim system.
Avenger Advantages
• Provides engineers the opportunity to design systems with higher turndown for improved system efficiencies during periods of low demand, off-season heating or reheat applications
• Ideal for variable-primary and secondary systems with varyingor low-flow conditions
• Reduces boiler cycling and saves energy associated with over heating and boiler pre/post purge conditions
• Extends boiler life and reduces system maintenance
CAMUS Avenger ® condensing firetube boilers feature a proven rifled tube technology and a low-emissions premix burner.
Other manufacturers require additional devices and controls to monitor and correct for changes in combustion performance. The Avenger burner achieves this through an integrated gas valve/venturi system that automatically adjusts for combustion air density changes, meaning the boilers have inherent O2 trim in a simple-to-operate design.
The self-regulating gas valve/venturi system combined with variable-speed blower technology delivers the lowest energy consumption – advanced linear-modulation control with up to 40:1 turndown per boiler for hydronic systems.
CAMUS Legacy Boilers - Drawing on the success of our legacy DynaFlame/Dynaforce heating and domestic hot water (DHW) boilers, Avenger is also approved for both heating and DHW systems. For systems that require high turndown, engineers, contractors, and end users can standardize their operations with Avenger boilers.
System Design - The modulating premix burner of Avenger offers up to 99% efficiency with ultra-low NOx emissions, available to less than 9 ppm.
The Avenger two-pass, counter-flow design with rifled tube technology was developed from proven industrial technology and modified for use in commercial firetube condensing boilers. The result is a superior and robust design for variable-primary and low-pressure systems. The system is low-flow tolerant and operates more smoothly through varying load conditions while minimizing boiler cycling.
CLICK to learn more or scan QR at right for smartphone access.
TurboFer ® firetube technology revolutionizes boiler design with exceptional heat transfer and condensing capabilities. Boilers with this technology feature a duplex stainless steel tube surrounding an aluminum-alloy finned heating surface. Enhancing turbulence through the patented tube design increases heat transfer, yielding up to 20% greater efficiency compared to standard gas boilers.
• Special injection design increases flue gas velocity, which creates turbulence and enhances heat transfer
• Effective heat transfer surface area 5x greater than other condensing boilers
• 10x greater thermal conductivity compared to stainless steel alone
• Duplex stainless steel construction on the waterside allows for simplified water treatment
Cleaver-Brooks introduces the next generation of ClearFire® -CE condensing boilers, incorporating TurboFer technology, advanced controls, 10:1 turndown ratio, and a low-emissions premix burner. Unlike competitors, the ClearFire burner integrates a gas valve/venturi system, automatically adjusting for combustion air density changes to maximize energy efficiency and 10:1 turndown ratio.
The flagship ClearFire-CE boiler (CFC-E) excels with dual returns, optimizing efficiency and condensing performance even in high-temperature
heating loops. The TurboFer counter-flow heat exchanger enables low-flow return at 10% through the lower inlet connection, and high-temperature returns beyond 140°F through the upper inlet.
ClearFire-CE boasts a modulating premix burner achieving up to 99% efficiency and ultra-low NOx emissions as little as 7 ppm. Integrated controls ensure seamless transfer between connected boilers during downtime, while delta T boiler pump speed control optimizes efficiency under low-load conditions. Engineered for variable-flow primary systems, CFC-E operates smoothly across varying load conditions without buffer tanks. Its adaptability minimizes short cycling and reduces pump electrical consumption.
CLICK for more details, or scan QR code at right for smartphone access.
Greenheck’s online eCAPS® Engineer Application Suite allows you to quickly select and specify the best value products for your project. eCAPS® can also assist you in ensuring the fan products selected will comply with ASHRAE 90.1 or other state energy codes. Just enter a few project requirements and eCAPS® finds and ranks the best products based on cost and performance. From there, you can compare performance, sound levels, operating costs or first costs, and Fan Energy Index (FEI) for all applicable models on a single screen for easy comparison.
Based on ANSI/AMCA Standard 214, the Fan Energy Index (FEI) calculation is intended to compare the fan’s relative wire-to-air efficiency to a baseline efficiency inclusive of fan motors and drives. Values below 1.0 may not meet minimum efficiency levels depending on local codes. Values over 1.0 are more efficient than the baseline. For example, a fan with an FEI of 1.1 is 10% more efficient than the baseline fan. If a standard such as ASHRAE 90.1 requires fans to have a minimum FEI of 1.0, fans with a lower FEI (say 0.85) will not be acceptable as they are using more electrical input power than the baseline power. eCAPS® provides FEI metrics for hundreds of fan models.
eCAPS® allows you to easily create schedules incorporating FEI, download product drawings, share or print product cut sheets, and download AutoCAD® 2-D and 3-D and Revit® drawings.
ClIC k or scan QR code to access Greenheck’s eCAPS®.
ecaps@greenheck.com • 715-359-6171 www.greenheck.com
Code Compliance - Much assurance regarding cable hangers comes from the approvals and listings that establish compliance with U.S. Building Codes and other standards in the construction industry. For example, Gripple cable hangers are listed with International Code Council Evaluation Services (ICC-ES) through a PMG-1408 listing report, which establishes compliance of Gripple hangers with the following codes and standards:
• International Building Code (IBC) through compliance with:
• International Mechanical Code (IMC)
• International Plumbing Code (IPC)
• MSS SP-58 Standard for Pipe Hangers and Supports
• SMACNA Duct Construction Standards
• ASME B31.9 Standard for Building Services Piping
Sway Concerns - Although threaded rod may seem a rigid suspension solution when compared to a cable hanger, on longer drops threaded rod is highly susceptible to lateral forces, which can cause it to move and bend permanently.
This can lead to the failure or even collapse of the suspended systems. In comparison, cable hangers are flexible and lateral forces don’t cause them to bend. Additionally, once ductwork, piping, electrical services, etc. are hung using cable hangers, the full weight of the installed runs impose static gravity loads on the hangers.
Contractor Advantages - And finally, installing with cable hangers instead of threaded rod comes with some key advantages for the contractor:
• Reduced Loading of Interior Structure: 150 lbs of cable hangers (1,000 hangers) replaces over 3,000 lbs of rod and strut.
• Reduced Transporting Costs: 100 cable hangers are packaged in a single small box, easily carried under one arm. Avoids transporting and moving heavy material five or six times prior to hanging.
• Adjustability: Contrary to threaded rod, cable hangers allow easy height and leveling adjustment of the suspended service, during/after installation.
• No Tools: In contrast to the manpower required to measure and cut threaded rod and grind the edges smooth, cable hangers come in pre-cut, ready-to-use lengths.
630-406-0600
grippleinc@gripple.com www.gripple.com/en-us/
During system installation, ductless cassette drain-up condensation drain pipe connections can often be challenging and time-consuming. Issues such as leaks due to an improper seal and even cracks in the unit drain pipe connection can happen due to stress.
Finding the right fittings to navigate an area crowded by structural supports, wiring, other piping, etc. proved to be a difficult task. However, DSH-UP can solve these challenges.
The DSH-UP drain kit contains a flexible insulated drain hose with pre-connected hose fittings that quickly connect to the condensation drain pipe and secured with traditional worm-gear hose clamps. This reduces the number of plumbing fittings which save time, labor and reduce the risks of condensation leaks. The hose comes in both 27 5⁄8 ˝ and 39 3⁄8 ˝ lengths to better meet your connection needs.
• Designed exclusively for drain-up piping
• Flexibility makes it easy to adjust and position
• Hose is pre-insulated for faster installation
• Pre-connected hose fittings eliminate use of cement or adhesives
• Design reduces risk of condensation leakage
• Transparent fittings assure a secure fit
• Water-flow check wrapping for quick leak detection
• Flexible design reduces vibration stress on drain piping
With ceiling cassettes installations on the rise, make sure to specify this time saving solutions on your next project. These insulated drain hoses will greatly reduce install time, since there is no need to cut and cement plastic pipes for the drain assembly.
Clean Agent Fire Extinguishing Systems using halocarbons and fluoroketones have come under scrutiny largely because 3M the US based manufacturer of FK 5-1-12 fire protection fluid brand named Novec 1230 announced that they will cease production of per- and poly-fluoroalkyl substance (PFAS) manufacturing by the end of 2025.
NFPA 2001 Standard on Clean Agent Fire Extinguishing Systems paragraph 1. 4.1. states that the fire extinguishing agents addressed in this standard shall be electrically non-conducting and leave no residue upon evaporation. Paragraph 1.4.1.2 Agents that meet the criteria of 1.4.1.1 shall be shown in Table 1.4.1.2. Table 1.4.1.2 includes FK-5-1-12. FK-5-1-12 is gaseous in use, and does not precipitate to groundwater.* NFPA 2001 design guidelines limit release of all clean agents. FK 5-1-12 is available on the global market.
The US EPA takes a measured scientific approach in evaluating PFAS listing. Currently, there are at least 180 PFAS compounds listed as toxic chemicals on the Toxic Release Inventory (TRI List) . Since Gaseous Clean Agents do not meet adverse human health and environmental criteria, Clean Agents are not included on the TRI List. This has been supported and peer reviewed by an independent panel of experts conducted by SciPinion. Additionally, Congress has not placed any Clean Agents on the TRI List.
In the Significant New Alternatives Policy (SNAP) the EPA has determined that Clean Agents are acceptable for use for total flooding fire extinguishing agents. Based on environmental and health risks, including ozone depleting potential (ODP), global warming potential (GWP), toxicity, flammability, local air quality, ecosystem effects, and human exposure.
Janus Fire Systems personnel can address your questions on this critical topic.
Hildebrandt • +1-219-663-1600
janusfiresystems.com
A healthcare institution underwent renovation of their 50-year-old system, including the replacement of the entire boiler plant and the condensate main running through the facility, totaling roughly ¼ mile of pipe. Once this new system was up-and-running, maintenance noticed large iron particles in the steam condensate system. These particles were making their way to the surge tank, resulting in jet-black water quality — a problem the Low Pressure Drop (LPD) Magnetic Y-Strainer was designed to address.
With the LPD Mag Y-Strainer in place, a regular blow-down process was implemented. Over a period of four months, the system was blown down three-to-four times, daily, SCAN QR CODE TO LEARN MORE.
Solids Removed from Steam Condensate System with LPD Mag Y-Strainer
without shutting off the pumps. The LPD Mag is the only magnet solution on the market that can be blown down while in-service.
This maintenance led to a substantial reduction in debris and sludge, resulting in a significant improvement in water clarity. The LPD Mag captured and eliminated harmful metallic particles, ensuring the surge tank is clear and free of debris.
The blow-down process was maintained on a regular basis to sustain the improved water quality. However, there was a period where the system was left alone. During this time, the water quality experienced a slight deterioration. Luckily the LPD Mag Y-Strainer’s previous cleaning efforts had significantly improved the system’s condition, and despite the lack of maintenance, the water remained in relatively good condition.
The LPD Mag proved to be an effective solution for combating iron particles and maintaining a clean and efficient low-pressure steam condensate system.
In a rapidly evolving field like engineering, staying updated with the latest advancements is crucial. The Noritz Training website offers a game-changing opportunity to enhance your skillset, conveniently fitting into your schedule. The platform hosts a range of self-paced video training modules that cater to various experience levels, from beginners looking to grasp the basics to seasoned professionals aiming to fine-tune their expertise. Introducing the all-new Noritz Training website at www.training.noritz.com — your gateway to comprehensive and convenient learning in the realm of tankless water heating technology.
At Noritz University you can choose between self-paced courses or webinars.
One standout feature of the Noritz Training website is its commitment to accessibility. Whether you’re a novice engineer or a seasoned pro, the self-paced video training ensures you can learn at your own pace, enabling you to delve deep into the intricacies of Noritz tankless water heaters without interrupting your busy schedule.
But learning is just one aspect. For those engaged in the design and planning stages, Noritz has also streamlined the process. With Noritz Building Information Modeling (BIM) files, accessible at www.noritz.com/bim, designing tankless water heater systems becomes a breeze. These detailed BIM files allow for seamless integration into your design software, empowering you to create accurate, efficient, and effective heating solutions that align with your project’s specific requirements.
By offering free, self-paced video training through the Noritz Training website and providing access to BIM files via www.noritz.com/bim, Noritz is not just setting a new standard – it’s redefining the future of tankless water heater education and design. Embark on this transformative journey today and unlock the true potential of Noritz tankless water heaters.
SCAN QR CODE FOR SMARTPHONE ACCESS
To obtain credentials:
1. Click on the [Support] link on our homepage and choose Support Center Login from the dropdown.
2. Click on [Apply for an Account] then choose Consultant / Engineer from the account dropdown.
3. Fill in the Contact Information then click on the Submit Request button. Your request will be automatically sent for processing.
Once you have received your credentials, go ahead and begin to download the benefits!
Guide Specifications - Save time in specifying a complete BTL-Listed native BACnet DDC system by downloading our guide specifications in CSI Master Format 1995 and 2012. Your junior system designers will be enlightened to have the “fully annotated” guide specification that provides valuable references and background information.
BACnet Resources - Download a complete and current list of BACnet Protocol Implementation conformance Statements (PICS), or view the Advanced BACnet Training Manual to help you take full advantage of BACnet for your projects.
Product Drawings - Choose from over one hundred product drawings in *.dwg, *.png, and *.svg formats. Download the entire product drawing library as Visio 2007 Stencils.
Software Official ReleasesDownload and install Free Trial Versions of RC-Archive and
Sign-up for a consultant support center account today to unlock all these benefits and more: reliablecontrols.com/account.php info@reliablecontrols.com • 877-475-9301 • reliablecontrols.com
RC-Reporter software and begin archiving and analyzing a limited number of objects from any accessible IP-connected BACnet facility, or download any of the online software manuals.
Engineering Submittal Sheets and User Guides - Download the complete range of product submittal sheets and hardware user guides. Feel confident that you have the most current and comprehensive engineering and technical documentation produced directly by the manufacturer.
Manufacturers are under constant pressure to remain innovative as pressures mount to increase energy efficiencies within product offerings. This pressure has driven the industry to create and repurpose existing technologies.
One example of repurposing existing technology is leveraging the heat pump technology. Heat pump water heaters (HPWH) have become increasingly popular due to their energy efficiency and operational cost savings compared to traditional water heaters.
Since HPWH are significantly more energy proficient, installing HPWHs results in substantial operational cost savings, decreasing energy costs for a building over the lifetime of the unit. Current trends show the global HPWH market is expected to double by 2031.
HPWHs reduce energy use by up to 75% and can improve building efficiency ratings, which is ideal for green building programs like LEED certification. Available rebates, incentives and tax credits help reduce upfront costs and enhance ROI for interested businesses.
When specifying HPWHs it is important to consider ambient air and water temperatures to properly determine the BTUs needed. HPWHs work most efficiently at temperatures above 40 degrees Fahrenheit to capture waste heat and provide free bonus cooling.
as an automatic defrost and
Also, consider specifying a pre-heat for lower energy efficient equipment and ensure proper storage tank size for the building’s water usage. If you use a unit like Rheem’s Commercial Heat Pump Water Heaters Split Systems, the units possess built-in features for greater peace of mind, such as an automatic defrost and electric tank back-up for lower temperatures.
www.rheem.com/commercialheatpump
ABB Motors US .2 .www .abb .com/motors-generators
AGF Manufacturing, Inc .37 .www .agfmfg .com
BELIMO .C-4 www .belimo .com
CAMUS Hydronics Ltd . .C-3 www .camus-hydronics .com/HigherTurndownHydronics
CDM Smith .64 .www .cdmsmith .com/en
CFE Media LLC .63 .www .cfemedia .com
CHAMPION FIBERGLASS .30 .www .championfiberglass .com
CleaverBrooks .8 .www .cleaverbrooks .com
Eaton .6 .www .Eaton .com/microgrid
ETC .46 .www .etcconnect .com
Greenheck .11 .www .greenheck .com
Hammond Power Solutions .63 .www .hammondpowersolutions .com
JOSAM .47 .www .josam .com
Mersen .25 .https://ep-us .mersen .com
Metraflex .31 .www .metraflex .com
Miura North America, Inc .29 .www .miuraboiler .com
Navien, Inc . .1 .www .Navien .com
Pritchard Brown .46 .WWW .PRITCHARDBROWN .COM
Reliable Controls .C-2 www .reliablecontrols .com
Rheem Commercial Water .41 .www .rheem .com/commercial-hot-water
Ruud Commercial Air .4 .www .RuudCommercial .com
Tjernlund Products .64 .www .tjernlund .com
CDM Smith is hiring mechanical and electrical engineers!
Publisher/Midwest
Matt Waddell MWaddell@CFEMedia.com
3010 Highland Parkway, Suite #310 312-961-6840
Downers Grove, IL 60515
Account Manager
Robert Levinger RLevinger@cfetechnology.com 630-571-4070 x2218
West, TX, OK
Aaron Maassen AMaassen@CFEMedia.com Integrated Media Manager 816-797-9969
Northeast
Richard A. Groth Jr. RGroth@CFEMedia.com 12 Pine Street 774-277-7266 Franklin, MA 02038
Director of Content Marketing Solutions
Patrick Lynch PLynch@CFEMedia.com 3010 Highland Parkway, Suite #310 847-452-1191 Downers Grove, IL 60515
Marketing Consultant
Brian Gross BGross@CFEMedia.com 3010 Highland Parkway, 630-571-4070 x2217 Suite #310
Downers Grove, IL 60515
Jim Langhenry, Co-Founder and Publisher, CFE Media JLanghenry@CFEMedia.com
Steve Rourke, Co-Founder, CFE Media SRourke@CFEMedia.com
McKenzie Burns, Marketing-Events Manager MBurns@cfemedia.com
Courtney Murphy, Marketing and Events Manager CMurphy@cfemedia.com
Paul Brouch, Director of Operations 630-571-4070 x2208, PBrouch@CFEMedia.com
Rick Ellis, Audience Management Director 303-246-1250, REllis@CFEMedia.com
Michael Smith, Creative Director 630-779-8910, MSmith@CFEMedia.com
Michael Rotz, Print Production Manager 717-422-3622, mike.rotz@frycomm.com
Maria Bartell, List Rental Account Director Infogroup Targeting Solutions 847-378-2275, maria.bartell@infogroup.com
Claude Marada, List Rental Manager 402-836-6274, claude.marada@infogroup.com
Letters to the Editor: Please e-mail your letters to ARozgus@CFEMedia.com
Letters should include name, company, and address, and may be edited for space and clarity.
Information: For a Media Kit or Editorial Calendar, go to https://www.csemag.com/advertise-with-us/ Marketing consultants: See ad index.
Custom reprints, electronic: Paul Brouch, PBrouch@CFEMedia.com
TM Technology and
5000 & 6000 MBH
The Avenger® Series II is an advanced two-pass, counter-flow firetube commercial boiler, providing efficient hot water for demanding commercial needs.
» Industry-leading 40:1 turndown
» Thermal efficiencies of up to 96%
» Designed for today’s higher turndown variable primary and low pressure systems
» 3 to 4 week lead-time with stock units available for quick ship
The integration of Belimo’s Thermal Energy Meter with the Energy Valve allows for easy energy control and transparent tenant billing. Designed to EN1434/MID standards ensures high accuracy and reliability, allowing for easy tenant billing. Belimo is stepping into a new era of integrated thermal energy management and bringing together what belongs together.
Discover the advantages www.belimo.us