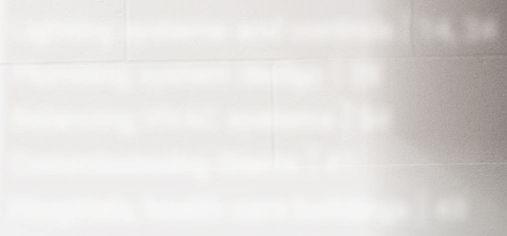

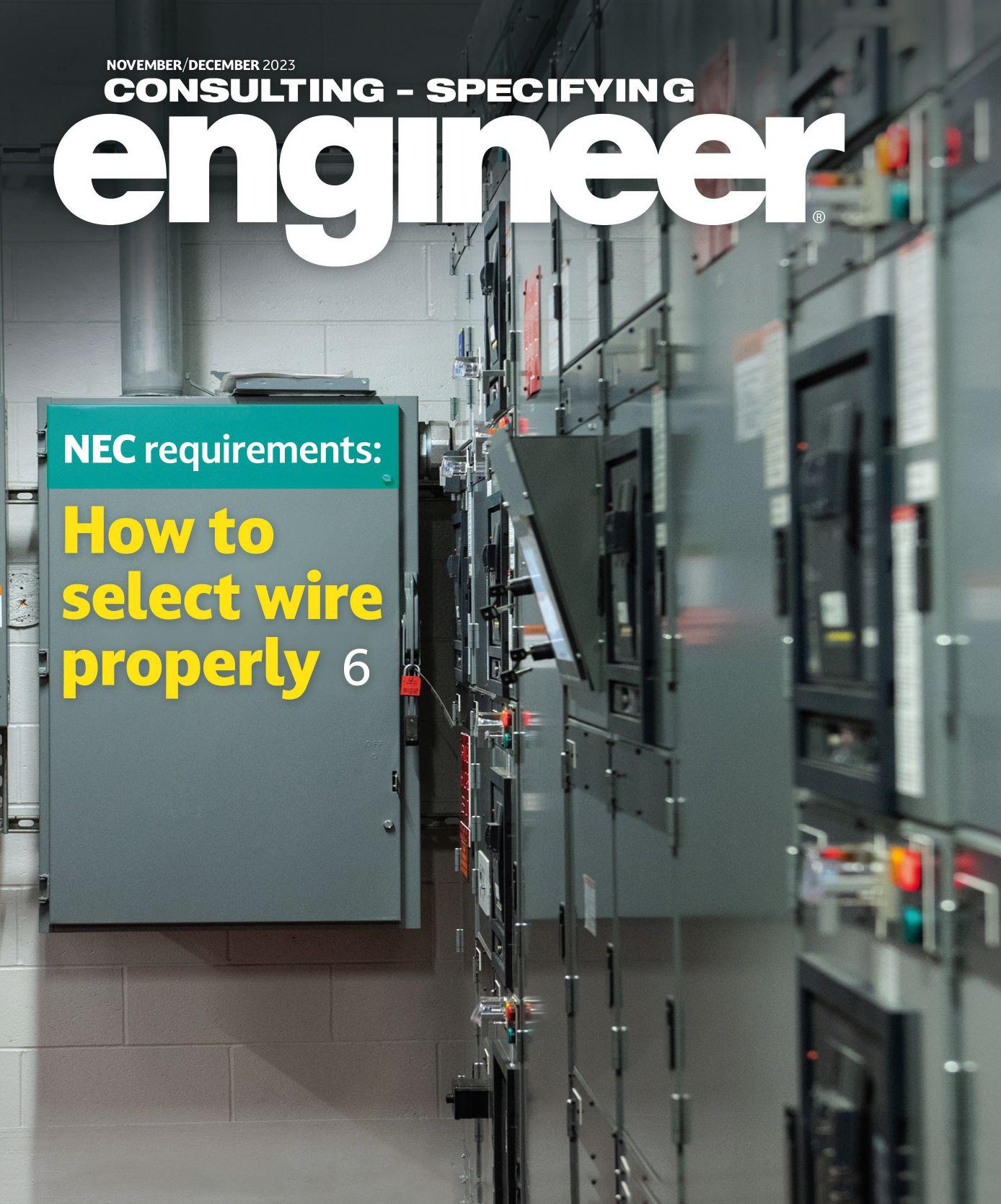
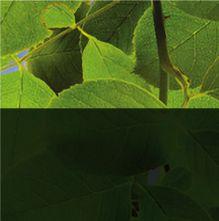
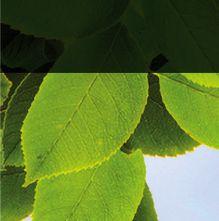
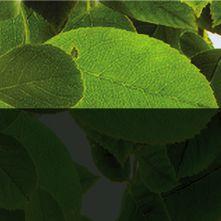
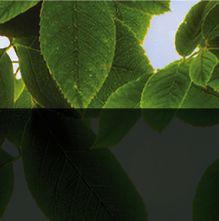
According to the World Green Building Council, we spend 90 percent of our time indoors. Given that statistic, it’s clear the quality of the air we breathe in buildings can dramatically impact our health and well-being. At Reliable Controls we believe sustainable buildings are a key component to reducing the health and environmental impacts of indoor and outdoor air pollution.
Learn more reliablecontrols.com/IAQ
The integration of Belimo’s Thermal Energy Meter with the Energy Valve allows for easy energy control and transparent tenant billing. Designed to EN1434/MID standards ensures high accuracy and reliability, allowing for easy tenant billing. Belimo is stepping into a new era of integrated thermal energy management and bringing together what belongs together.
Discover the advantages www.belimo.com
5 | How COVID-19 made everyone a little smarter
The average population now cares more about HVAC, allowing products and systems to gain more of the spotlight
6 | Back to basics: Sizing low-voltage power conductors for a lift station
Electrical engineers must learn to size electrical conductors appropriately per the NEC
14 | How light systems are evolving to be smarter
As lighting technology continues to evolve, designers and specifiers are faced with the challenge of keeping up with the changes
24 | Designing lighting control systems to meet the needs of all users
When designing lighting control systems, technology, energy efficiency and the user must be considered
28 | Three ways to advance your plumbing system design
Plumbing industry advancements include high-efficiency equipment, digital systems
34 | Creating better HVAC systems in old laboratories and university buildings
The HVAC industry faces challenges to upgrade systems in aging university lab buildings to match modern standards
41 | Commissioning Giants’ revenue surges $100 million over last year
The 2023 Commissioning Giants data reports on the top 25 firms
43 | Building design trends in hospitals and health care facilities
Lessons from COVID-19 have made flexibility and resiliency top concerns when designing for hospitals and other health care facilities
Circulation records are maintained at CFE Media, LLC, PO Box 348, Lincolnshire, IL 60069. Telephone: 630-571-4070. E-mail: cse@omeda.com. Publications Mail Agreement No. 40685520. Return undeliverable Canadian addresses to: PO Box 348, Lincolnshire, IL 60069. Email: cse@omeda.com. Rates for nonqualified subscriptions, including all issues: USA, $120/yr; Canada/Mexico, $150/yr (includes 7% GST, GST#123397457); International air delivery $260/yr. Except for special issues where price changes are indicated, single copies are available for $30 US and $35 foreign. Please address all subscription mail to CONSULTING-SPECIFYING ENGINEER, PO Box 348, Lincolnshire, IL 60069. Printed in the USA. CFE Media, LLC does not assume and hereby disclaims any liability to any person for any loss or damage caused by errors or omissions in the material contained herein, regardless of whether such errors result from negligence, accident or any other cause whatsoever.
AMARA ROZGUS, Editor-in-Chief/Content Strategy Leader ARozgus@CFEMedia.com
CHRIS VAVRA, Web Content Manager CVavra@CFEMedia.com
ANNA STEINGRUBER, Associate Editor ASteingruber@CFEMedia.com
AMANDA PELLICCIONE, Director of Research APelliccione@CFEMedia.com
MICHAEL SMITH, Creative Director MSmith@CFEmedia.com
DARREN BRUCE, PE, LEED AP BD+C, Director of Strategic Planning, Mid-Atlantic Region, NV5, Arlington, Va.
MICHAEL CHOW, PE, CEM, CXA, LEED AP BD+C, Principal, Metro CD Engineering LLC, Columbus, Ohio
TOM DIVINE, PE, Senior Electrical Engineer, Johnston, LLC, Houston
CORY DUGGIN, PE, LEED AP BD+C, BEMP, Energy Modeling Wizard, TLC Engineering Solutions, Brentwood, Tenn.
ROBERT J. GARRA JR., PE, CDT, Vice President, Electrical Engineer, CannonDesign, Grand Island, N.Y.
JASON GERKE, PE, LEED AP BD+C, CXA, Mechanical Engineer, GRAEF, Milwaukee
JOSHUA D. GREENE, PE, Associate Principal, Simpson Gumpertz & Heger, Waltham, Mass.
RAYMOND GRILL, PE, FSFPE, LEED AP, Principal, Ray Grill Consulting, PLLC, Clifton, Va.
DANNA JENSEN, PE, LEED AP BD+C, Principal, Certus, Carrollton, Texas
WILLIAM KOFFEL, PE, FSFPE, President, Koffel Associates Inc., Columbia, Md.
WILLIAM KOSIK, PE, CEM, LEED AP BD+C, BEMP, Senior Energy Engineer, Oak Park Ill.
KENNETH KUTSMEDA, PE, LEED AP, Engineering Manager, Jacobs, Philadelphia
JULIANNE LAUE, PE, LEED AP BD+C, BEMP, Director of Building Performance, Mortenson, Minneapolis
DAVID LOWREY, Chief Fire Marshal, Boulder (Colo.) Fire Rescue
JASON MAJERUS, PE, CEM, LEED AP, Principal, DLR Group, Cleveland
BRIAN MARTIN, PE, Senior Electrical Technologist, Jacobs, Portland, Ore.
GREGORY QUINN, PE, NCEES, LEED AP, Principal, Health Care Market Leader, Affiliated Engineers Inc., Madison, Wis.
BRIAN A. RENER, PE, LEED AP, Principal, Electrical Discipline Leader, SmithGroup, Chicago
SUNONDO ROY, PE, LEED AP, Director, Design Group, Romeoville, Ill.
JONATHAN SAJDAK, PE, Senior Associate/Fire Protection Engineer, Page, Houston
RANDY SCHRECENGOST, PE, CEM, Austin Operations Group Manager/Senior Mechanical Engineer, Stanley Consultants, Austin, Texas
MATT SHORT, PE, Project Manager/Mechanical Engineer, Smith Seckman Reid, Houston
MARIO VECCHIARELLO, PE, CEM, GBE, Senior Vice President, CDM Smith Inc., Boston
RICHARD VEDVIK, PE, Senior Electrical Engineer and Acoustics Engineer, IMEG Corp., Rock Island, Ill.
TOBY WHITE, PE, LEED AP, Associate, Boston Fire & Life Safety Leader, Arup, Boston
APRIL WOODS, PE, LEED AP BD+C, Vice President, WSP USA, Orlando, Fla.
JOHN YOON, PE, LEED AP ID+C, Lead Electrical Engineer, McGuire Engineers Inc., Chicago
The average population now cares more about HVAC, allowing products and systems to gain more of the spotlight
Asegment about indoor air quality (IAQ) recently ran on the TV program “60 Minutes.” The experts interviewed for the piece discussed how COVID-19 brought commercial buildings into a whole new light. Specifically, commercial buildings that don’t usually require specialty exhaust systems — offices, schools, churches and other non-health care structures — were largely ignored until the pandemic.
tion with outside air and added in a dash of HVAC controls to create commercial real estate HVAC systems that are efficient and effective.
Amara Rozgus, Editor-in-Chief
Laypersons who didn’t know anything about mechanical engineering or heating, ventilation and air conditioning (HVAC) systems thought that most buildings were inherently fine, and that breathing indoors would generally be easy and safe. The TV segment focused on a group that attended a “super spreader” event, highlighting their awareness and helping them understand how the HVAC system might affect IAQ.
What can engineers do to bridge the IAQ gap? Experts who understand air changes per hour, dedicated outside air systems, MERV filters and similar systems quickly caught on that these technologies, working in tandem with other solutions, were the answer to people going back to the office, school or the grocery store in the early days of COVID-19 and are now making more extensive adjustments.
To create cleaner air inside, engineers partnered high-quality air filtra-
The Occupational Safety and Health Administration published IAQ guidelines in 2011, and maintains an updated website to help building owners or facility managers. The U.S. Environmental Protection Agency has published IAQ guides for office building occupants. The EPA also has its National Ambient Air Quality Standards.
And, while they’ve been around for several years, engineers started paying very close attention to ASHRAE 62.1: Ventilation and Acceptable Indoor Air Quality and ASHRAE 170: Ventilation of Health Care Facilities.
Fast-forward to now, and the industry knows that proper design, balancing, operation, maintenance and overall use can make a difference for building occupants. The National Bureau of Economic Research and a variety of property managers have gathered data about the relationship between healthy buildings and property value or rental prices.
It’s a real breath of fresh air (pun intended) that these topics engineers have known about for years are now firmly on the general population’s radar. cse
Lilly Vang, PE; and Joshua Hunter, PE, CDM Smith, Maitland, Florida
Electrical engineers must learn to size electrical conductors appropriately per the NEC
Ensuring proper wire selection is an important part of electrical design. While NFPA 70: National Electrical Code (NEC) is not meant to be used as a design book, it does provide minimum requirements to prevent overheating and fire. The minimum requirements for conductors rated up to 2,000 volts (V), per NEC Article 310, includes information regarding the type of conductors, type of insulation, ampacity ratings and application.
When it comes to applications pertaining to NEC Article 310, conductors are required to be aluminum, copper-clad aluminum or copper, unless otherwise specified. Both aluminum and copper are great industrial conductors, but they do have some differences. The primary differences are the current carrying capacity and resistance of the wire.
Because aluminum conductor has a lower capacity for carrying current and greater resistance than copper conductor, a larger aluminum conductor will be required for the same application as a copper wire. Additionally, aluminum will corrode, requiring the use of special compounds at termination points or for the termination lug to be constructed of copper-clad aluminum.
While copper is the better conductor, it is nearly three times heavier than aluminum and much more expensive. It is the designer’s responsibility to determine which material is appropriate for an installation.
After determining the wire material, it is necessary to determine which type of insulation to use. This is important because the wire insulation prevents the current in the wire from encountering other conductors, resisting electrical leakage and preserving the wire material. All bare conductors must be insulated unless specifically permitted elsewhere in the NEC.
The type of insulation to select will depend on the application and maximum operating temperature as there are a wide array of insulation types and materials used in the industry. Applications may require the insulation to be flame-retardant, waterproof, resistant to direct sunlight exposure, high heat resistant, corrosion resistant or contain some combination of these qualities. See Table 1 for a few common
insulation types used during industrial design. For a complete list of conductor insulations included in the NEC and where they are permitted to be used, refer to Tables 310.4(A) and 310.10.
Once the wire material and insulation type has been chosen, the size will need to be determined. The NEC uses two metrics for denoting the size of conductors: AWG and kcmil. American Wire Gauge (AWG) is a standard method for measuring and identifying cable thickness in the United States.
In the NEC, the sizes go from 18 AWG to 4/0 AWG, with the smaller numbers being larger conductors. The 4/0 AWG in this case represents the size 0000, while 3/0 AWG would be 000, working up to size 1 AWG and above.
For conductors larger than 4/0 AWG, the NEC uses the kcmil method of measuring. This method provides a more direct label of size to describe the area of the wire. The “k” represents kilo for 1,000, the “c” represents circular and “mil” represents 1/1,000 of an inch. Therefore, 1 kcmil is 1,000 circular mils, which corresponds to a cross sectional area of approximately 0.5067 mm2
It should be noted that the NEC requires the minimum size of power conductors for voltage ratings up to and including 2,000 V to be 14 AWG when the wire is copper and 12 AWG if the wire is aluminum or copper-clad aluminum, except as permitted elsewhere in the NEC (NEC 310.3(A)).
Additionally, if conductors are being installed within a raceway, conductors that are 8 AWG or larger must be stranded (NEC Article 310.3(C)). The reason for this requirement is stranded conductors are made of multiple small strands grouped together to form a single conductor, allowing greater flexibility over a solid conductor. This becomes important as conductors become larger and need to be bent and maneuvered into place. See Figure 2 for a cross-section illustration of a solid wire and a stranded wire.
Now that the conductor material and insulation has been chosen and sizing units are understood, it’s time to size the conductor. For low-voltage conductors, there are several tables that can be used. The table used depends on the type of insulation and whether the conductors are in free air, in a raceway, in a cable, on a messenger or directly buried in earth.
These tables include Tables 310.16 through 310.20. An additional table, Table 310.21, is included for bare copper and bare aluminum conductors in free air. Refer to Table 2 for an excerpt from the NEC Table 310.16.
Once the correct table is selected, the column with the desired insulation type should be used to determine the correct conductor size based on the amperage needed. For example, using Table 310.16 for no more than three current-carrying conductors in a raceway, cable or earth, copper conductors insulated with THWN rated at 75°C is rated at 50 amperes (A) for size 8 AWG. Conductor amperage ratings must be determined by the design professional and meet the minimum NEC requirements, which vary based on the desired application.
There may be times when the necessary conductor amperage is greater than the rated capacity of the largest conductor included in the NEC or in installations where it is not preferrable to use a given size conductor due to the difficulty of installing certain conductor sizes. Often conductors larger than 600 kcmil will not be used because they are difficult to bend and thus more difficult to install. For these instances, it can be a good idea to install multiple sets of conductors in parallel.
Installing conductors in parallel increases the amperage capacity while reducing the size and difficulty of installing the conductors. To install conductors in parallel the conductors must be at least 1/0 AWG or larger and comply with all the requirements of 310.10(G)(2) through (G)(6). Some of these requirements include the conductors being the same length, the same material, the same kcmil size and being terminated in the same manner.
• Recognize different types of wires included in NFPA 70: National Electrical Code (NEC).
• Know NEC requirements for conductor selection.
• Learn the basics of sizing low-voltage conductors for an industrial application.
As stated in NEC Table 310.16, which was used in the previous example, the table is meant for no more than three current-carrying conductors in a raceway, cable or directly buried. If it is desired to have more than three current-carrying conductors within a raceway or cable, then it will require “derating” of the conductors. The process of derating conductors involves reducing the maximum amperage capacity from the rated ampacity defined in Tables 310.16 through 310.19.
The reason for this adjustment is because increasing the number of conductors within a raceway or cable will increase the heat generation within the raceway. To prevent an excess of heat buildup, an adjustment factor is used to lower the conductor resistance and thereby lower the heat production.
For example, if eight current-carrying conductors were placed within a single conduit, the maximum amperage rating of the conductors would be reduced to 70% of the current rated in the ampacity tables. This adjustment may require upsizing conductors larger than usual. The complete table for adjustment factors for more than three current-carrying conductors can be found in Table 310.15(C)(1).
To ensure conductors and cables can be identified, the NEC requires that the maximum rated voltage, type of wire or cable, manufacturer name or trademark and size in AWG or kcmil are marked on the conductors and cables. Depending on the type of conductors and cables this can take the form of surface marking, marker tape or tag marking. See Figure 3 for a photo of conductor cables with appropriate markings per the NEC.
This case study presents the process for sizing low-voltage insulated power conductors at a wastewater lift station. This does not include the sizing of the equipment grounding conductor, which is in NEC Article 250.122. Although power conductor sizing works hand in hand with various aspects of design such as calculation of loads, sizing of protective devices, size/number of conduits, etc., these topics will not be fully detailed in this case study.
However, it is important to remember that the size of the load (i.e., the demand) is what drives the size of the conductors. Before the type of wire can be selected or sized, it is important to understand the location where the wire will be installed.
A wastewater lift station is commonly used to provide the additional pressure boost to the raw sewage in the wastewater transportation system. Wastewater lift stations are typically located outdoors, in a residential neighborhood or in locations convenient for the piping system. The loads commonly seen at a wastewater lift station are:
• Pumps.
• Grinder.
• 120 V loads (i.e., lights, receptacles, sump pumps, instruments, etc.).
heat and oil-resistant thermoplastic
Thermoset rubber, moisture resistant cable
Thermoplastic, heat resistant cable, nylon jacket outer sheath
Thermoplastic, heat and moisture resistant cable
Thermoplastic, heat and moisture cable, nylon jacket outer sheath
Cross-linked polyethylene, heat resistant cable, nylon jacket outer sheath
Cross-linked polyethylene, heat and moisture-resistant cable
Cross-linked polyethylene, heat and moisture resistant cable
Cross-linked polyethylene, heat and moisture-resistant cable, nylon jacket outer sheath
(167°F)
(194°F)
(194°F)
and wet locations
Moisture-resistant, flame-retardant, nonmetallic covering
and wet locationsNylon jacket or equivalent
and damp locationsNylon
(167°F)
(194°F)
and wet locationsNylon jacket or equivalent
TABLE 1: Excerpt from conductor applications and insulations rated 600 V table from NFPA 70, Table 310.4(A). Courtesy of CDM Smith
Wastewater lift stations require utility power and a secondary standby power. Depending on the criticality of the lift station, the standby power can be in the form of a portable generator connection or a standby generator.
In other words, a wastewater lift station is a critical industrial facility typically located outdoors (i.e., wet, corrosive, hazardous location) that needs reliable and sturdy connections for motor loads in a small space. This also means that wires must be housed in a raceway to allow for extra protection against big equipment and corrosive materials.
In this case study, a standby generator will be considered in tandem with a single utility source. The two power sources feed an automatic transfer switch (ATS) that is normally fed from the utility source and switches over to the standby power source during a utility outage. The ATS then feeds a pump control panel that powers two pumps, a grinder control panel and a lighting transformer that feeds the 120 V loads. The one-line power diagram is shown in Figure 4.
Copper is the most common choice for many wiring applications due to its durability and con-
**Note: Ampacity are underlined based on NEC Article 110.14.
TABLE 2: Excerpt of ampacities of insulated conductors with not more than three current-carrying conductors in raceway, cable or earth (directly buried) from NEC Table 310.16. Courtesy: CDM Smith
ductivity. On the other hand, aluminum is much cheaper and a lightweight material that is more malleable and easier to install. Every material has its advantages and disadvantages. For this case study, copper conductor is the best option because this application requires durable connections that doesn’t take up a lot of space.
Per NEC Article 310.10, some of the types of conductors permitted for use in wet locations are as follows: Types RHW, RHW-2, THHW, THWN, THWN-2, TW, XHHW, XHHW-2, XHWN, XHWN-2, etc. All conductors will be protected by a raceway, therefore, thicker wire types that can be used for direct burial applications such as type USE will not be used in this application.
Due to the wet location type and criticality of the lift station, the service entrance feeder wire will be Type RHW-2 because RHW-2 is rated 90°C for dry and wet locations and has one of the thicker insulations in addition to a moisture-resistant, flameretardant, nonmetallic covering. Type XHHW-2 will be used for the feeders and branch circuits as it is rated 90°C for dry and wet locations but has an insulation thickness that is slightly smaller and cheaper than Type RHW-2.
In addition, type cross-linked polyethylene insulation is lighter than other rubber insulations, which makes it easier to install.
NEC Table 310.16 will be used as a reference because the wires for this wastewater lift station are insulated conductors with no more than three current-carrying conductors in a raceway. The conductor, as mentioned previously, is copper so
the column section for copper in Table 310.16 will be used.
Per NEC Article 110.14(C), unless otherwise indicated on the equipment, termination provisions of equipment for circuits rated 100 A or less or marked as 14 AWG through 1 AWG conductors, shall be used only for conductors rated 60°C along with the other conditions mentioned in Article 110.14(1)(a).
In other words, when sizing conductors using Table 310.16, the ampacity of conductors sized 1 AWG or smaller shall be determined using the column for 60°C in Table 310.16 or as shown underlined in Table 2. Per Article 110.14(C)(1)(b), termination provisions of equipment for circuits greater than 100 A or marked for conductors larger than 1 AWG, shall be used for conductors rated 75°C along with other conditions mentioned (i.e., conductors sized larger than 1 AWG shall be determined using the column for 75 ° C or as shown underlined in Table 2). The following details the design decisions for sizing the lines in Figure 4.
NEC Article 230.42 covers the conditions for selecting the ampacity of the service entrance conductors. In this case study, the service entrance conductors terminate in an overcurrent device where both the overcurrent device and its assembly are listed for operation at 100% of their rating.
Therefore, the service entrance conductor (shown in Line 1) must have an ampacity of 400 A or more. Referring to Table 310.16, column 75°C, the wire would be 600 kcmil (420 A). However, 600 kcmil will not be used because 600 kcmil wires can be difficult to bend and pull in certain installations. Therefore, paralleling conductors will be considered and per Article 310.10(G) (1), only sizes 1/0 AWG and larger can be paralleled. Size 4/0 AWG wires (230 A per Table 310.16, 75°C) will be paralleled to get over 400 A, thus resulting in two sets of three #4/0 (i.e., six 4/0 AWG wires total, three in each conduit).
The 3/0 wire can be used but because the protective device is 100% rated (carries 400 A continuously instead of 320 A), it is recommended to provide conductors with ampacity higher than the protective device ampacity.
All these wires are essentially sized the same because their overcurrent protection device upstream of the wire are the same ratings. Per Article 240.4, conductors, other than flexible cords, flexible cables and fixture wires, shall be protected against overcurrent. Therefore, the conductor must be sized equal to or bigger than the overcurrent protective device, which is 400 A. Paralleling 4/0 AWG wires will result in 460 A; thus, resulting in two sets of three #4/0 AWG.
Additionally, NEC Article 445.13 requires the ampacity of conductors from the output terminals of a generator to the first distribution with overcurrent protection must be 115% of the generator’s nameplate current rating or greater. If the generator design and operation prevent overloading, the conductor’s ampacity must be 100% of the generator’s nameplate current rating or greater. Because the current rating of the example generator is approximately 376 A, at 115% this would require approximately 432 A.
The size of the load determines the size of the conductors and indirectly the size of the protective device. In this case study, the protective device has already been sized to protect the wire and account for the variable frequency drive (VFD) load. The wire is protected by a 200 A circuit breaker, meaning the wires from the pump control panel to the VFD must be rated for 200 A, which is three #3/0 AWG.
Line 6 would essentially be of the same size. However, let’s assume the pump and its respective pump terminal cabinet is around 800 feet away from the VFD. Because of the distance, voltage drop needs to be considered. Due to the resistance of the wire, which correlates to the size of the wire, the voltage can drop down to 3%.
Though not required by the NEC, the NEC recommends that the voltage drop be 3% or less at the farthest load and the maximum total voltage drop on both feeders and branch circuits to the farthest load does not exceed 5% for reasonable efficiency of operation. Other state building codes and standards may require a voltage drop of around 3%-5%. A bigger wire means more copper, which means
less resistance, resulting in a lower voltage drop. In this instance, if the three #3/0 is increased to three #4/0, the 800-foot distance would result in a voltage drop of less than 3%.
Line 7 is cables typically provided by the submersible pump manufacturer and each pump manufacturer recommends different sizes and types that is most suitable for their pumps and application. Therefore, it is crucial to coordinate with the submersible pump manufacturer when it comes to providing the correct cable from the pump terminal cabinet to the submersible pump.
‘ NEC Table 310.16 will be used as a reference
because the wires for this wastewater lift station are insulated conductors with no more than three current-carrying conductors in a raceway.
Line 8 is the wires from the pump control panel to the 15 kilovolt-ampere (kVA) lighting transformer, TX-1. The protective device for TX-1 is rated 30 A. Per Table 310.16, 60°C column, three #10 (30 A) wires should be protected by the protective device.
Line 9 is the wires from the transformer to 120/208 V lighting panelboard, LP-1. Wires on the secondary side of a transformer, per Article 240.4(F), are not considered to be protected by the primary overcurrent protective device if the transformer is a single-phase and multiphase except for two-wire, delta-delta or three-wire transformers. Therefore, the wires on the secondary side shall not be sized based on the primary overcurrent protective device. In this case, the transformer is located within 10 feet of LP-1; thus, the transformer secondary conductor can be sized per NEC Article 240.21(C)(2). The ampacity of the secondary conductors must not be less than the combined calculated loads on the circuits supplied by the secondary conductors, not less than the rating of the equipment containing an overcurrent device(s) supplied by the secondary conductors or not less than the rating of the overcurrent protective device at the termination of the secondary conductors.
csemag.com u
NEC insights
u Electrical engineers should pay particular attention to NFPA 70: National Electrical Code Article 310: Conductors for General Wiring.
u A code-compliant design minimizes the risk of overheating and fire due to excessive electrical resistance.
Line 10 is not shown on the one-line in Figure 4 but the wires fed from LP-1 would typically be shown on a panel schedule. Line 10 includes the wires from LP-1 to the generator enclosure. Panel LP-1 is providing power to the 120 V loads in the generator enclosure, which may include the following:
• Receptacles.
• Lights.
• Oil level control.
• Jacket water heater.
• Battery charger.
• Generator space heater.
TABLE 3: Legend for current-carrying conductor in Figure 4. Courtesy: CDM Smith
In addition to this, Article 240.21(C)(2) details other requirements for the secondary conductors concerning location, protection and installation, which will not be discussed in this article.
As the one-line in Figure 4 does not detail the size of the LP-1, the maximum capacity a 15 kVA, three-phase, four-wire transformer can support can be calculated with the following equation:
A = kVA / (kV x sq rt(3)) = 15 kVA/(0.208 kV x sq rt(3)) = 41.63
APer Table 450.3(B), the maximum secondary protection shall be 125% of the transformer-rated current. Therefore, the secondary conductor is 125% of 41.63 A, which is 52.04 A. This is the maximum protection, therefore 50 A protective device can be used.
However, as 52.04 A does not correspond to a standard rating of a fuse or nonadjustable circuit breaker, a higher rating that does not exceed the next higher standard rating shall be permitted. In other words, a 60 A protective device can also be used as a secondary protective device.
However, for this case study, a 50 A protective device will be assumed for LP-1. This would essentially mean four #6 (55 A per Table 310.16, column 60°C) is the size of the secondary conductors.
For simplicity’s sake, it is assumed these six loads are essentially all 120 V, 20 A circuits that would typically require two #12 (20 A per Table 310.16, column 60°C). Because the loads are in the same location, all the wires can be put in the same raceway.
This is 12 current-carrying conductors. Per NEC Table 310.15(C)(1), 10-20 current-carrying conductors in a raceway or cable have an adjustment factor of 50%. This essentially means that the ampacity of each of the #12 wires has 10 A capacity as opposed to 20 A. For the wires to have a 20 A capacity, the #12 wires will have to be upsized to a #8 wire (40 A per Table 310.16, column 60 ° C). This would not be recommended because the wire size increased by two sizes and although this may work per code, the load may not be able to receive such oversized conductors.
Therefore, the six circuits can be split into two raceways (i.e., six current-carrying conductors or three circuits per raceway). Per Table 310.15(C) (1), 4-6 current-carrying conductors in a raceway have an adjustment factor of 80%. Therefore, #10 wires would be sufficient for all six of the loads.
The size for the wires labeled in the one-lines in Figure 4 are shown in Table 3. cse
Lilly Vang, PE, is an electrical engineer at CDM Smith, focusing on the design of electrical power systems.
Joshua Hunter, PE, is an electrical engineer at CDM Smith, experienced in the design and analysis of electrical power systems.
for your next big high commercial heating application
Cascade up to 32 units and common vent up to 4 units for a wide range of heating outputs.
Patented Navien designed and built ASME-Certified “H” stamped stainless steel fire tube heat exchanger.
Intuitive 7" touch screen control for easy set up and diagnostics.
Built-in hardware for boiler pump, 3 heating zones or indirect tank control.
To learn more about all the big things happening at Navien, visit Navieninc.com.
Richard Vedvik, PE, IMEG Corp., Rock Island, Illinois
As lighting technology continues to evolve, designers and specifiers are faced with the challenge of keeping up with the changes
Lighting controls have seen major changes over the past 20 years and it seems that taking line voltage to a manual switch to control lighting fixtures is a thing of the past. Modern lighting controls are programmable and addressable, connected to either a closed network consisting of relays, power supplies, power packs, sensors and control points.
These systems are “smart” in the way that they offer flexibility for both initial installation as well as flexibility in future revisions, and the next generation of lighting control systems is likely to take advantage of artificial intelligence (AI) for dynamic programming and behavior.
One of the largest changes in this industry is the way lighting controls are specified. Historically, single-line diagrams were used to convey how lighting controls were to be wired and the number of wiring options were fairly limited. There was line voltage, typically 120 volts (V) or 277 V and control voltage, which was usually 0-10 V used for dimming. As digital, programmable lighting control systems became more prevalent, designers started seeing them show up as alternatives during the shop drawing review process. This meant that the manufacturer representatives and suppliers were tasked with developing the wiring diagrams and determining the components required.
As a result, there was a discrepancy between what was specified and what was provided. The primary reason for this difference was the unique way each manufacturer approached lighting control with programmable components. While not intentionally timed, the industry saw a simultaneous shift toward solid state lighting components, now ubiquitously known as LED. Designers were caught scrambling to keep up with rapidly changing technology and the use of detailed wiring diagrams slowly became obsolete.
The most common way for designers to convey the intent of modern lighting controls is with lighting sequence narratives or tables, which describe the system behavior instead of focusing how the system is to be configured. This method is used in lieu of detailed diagrams because the final quantity, arrangement and type of component are now up to the manufacturer and chosen by the construction team, usually determined at time of bid. This new process presents a challenge to designers, as it
removes some of their control over the final product and requires a vague specification.
A distributed lighting control system consists of a network of remote modules connected to a digital network via network hubs. Control is managed through either a central station, system server or isolated within each control area. These modules facilitate communication with lighting control devices through the digital network and the system encompasses associated components like wiring, relay modules, photocells, switches, dimmers, time clocks, occupancy sensors, network interfaces and hubs. The system employs distributed relay modules, allowing placement above accessible ceilings, within lighting fixtures themselves or adjacent to the rooms they control, specifically when access is a concern.
Control devices, such as occupancy sensors (including ultrasonic, internal resistance and dual technology types), photocells, switches and timers, are specified by the engineer and shown on the drawings or described within sequences and narratives (see Figure 2). The vendor then chooses which exact products are compatible with the control narrative to operate on the system network. Additional power packs are supplied as necessary, to facilitate multiple control devices, with relevant details identified in shop drawing submissions. It is uncommon for construction documents to include relays on the plans; thus, the supplier is left to determine what components are necessary for system functionality.
The relay modules are mounted in enclosures or on the outside of junction boxes, with a physical separation of 120 to 277 V wiring compartments from low-voltage control wiring. These relay modules offer low-voltage digital communication to control devices as per drawings and schedules, with dimmable relay modules provided when specified. The relays are typically mechanically held and splitcoil momentary-pulsed types, rated for 20 amps (A) at 125 V alternating current (ac) for tungsten filaments and 20 A at 277 V ac for electronic ballasts, with a typical rated capacity of 50,000 cycles.
A centralized lighting control system is commonly designed as a network of lighting relay panels integrated into a digital network and managed
through a system server or central station. In this system, lighting control devices are connected to the relay panels and communicate with the system server via the panel controller. It encompasses all the necessary components, including network interfaces, wiring, relay panels, control modules, input modules, panel processors, relays, photocells, switches, dimmers, time clocks and occupancy sensors.
To enable seamless communication and coordination, the system includes a server or central station equipped with operating software, a data network and BACnet IP communication capabilities. This ensures compatibility with the building automation system (BAS), like a central controller on a distributed system.
The server or central station allows for programmable operation of lights through the system relays and control devices. The system software facilitates control of relays, control devices, time and sequence scheduling, timed-out and blink light operation and monitoring or reporting of system events and components. Initial programming is set according to the plans and schedules. Designers should coordinate the location of this system and the expected needs with the building owner and operators. Because the operators will want to control schedules and programs, prior experience and proper training are important inclusions in the project specifications.
• Identify types of digital and programmable lighting controls.
• Understand necessary details that designers should include in specifications.
• Use new methods of specifying modern lighting controls.
The system power supplies typically consist of a transformer and full-wave rectifier with filtered direct current output to power the panel, controllers and control devices. Regardless of which type is chosen, the specifier should also consider total harmonic distortion for each type. The system also includes various features to enhance control and operation. The relays are typically mechanically latched, split-coil and momentary-pulsed type. Instead of mechanical relays, the designer can specify a controllable breaker that offers solenoid-operated thermal magnetic breakers to provide control, overload protection and short circuit protection.
Like other system types, the control devices include occupancy sensors, photocells, switches and timers, all designed to operate on the system network. Supplemental power packs are provided for multiple control devices as required.
The digital addressable lighting interface (DALI) control system is designed as a digital lighting control network, connecting DALI-compliant digital addressable ballasts, control modules and lighting control devices directly to a system server or central control station. The individual addressable electronic ballasts, control modules and devices
are operated based on signals received through the DALI-compliant bus from various DALI-compliant digital controllers and interfaces. The system software enables control of DALI ballasts, control modules and control devices, as well as time and sequence scheduling, timed-out and blink light operations, monitoring and reporting of system events and components. Designers should identify initial programming on plans and schedules so the manufacturer and system installers can accurately bid the scope of work.
The system is programmed through the system server or central control station. It encompasses all necessary components, including network bus, wiring, DALI controllers and interfaces, panels, photocells, switches, dimmers, time clock and occupancy sensors. The system makes use of DALI-compliant ballast and dimming modules provided with the light fixtures.
All control devices, including occupancy sensors, photocells, switches and timers, are specified as DALI compliant. The manufacturer representatives will identify additional DALI-compliant signal repeaters and controllers are supplied as required and list them in shop drawing submissions. Designers should consider the location of these components, to ensure accessibility and adequate environmental conditions.
Both centralized and decentralized lighting control systems incorporate various interfaces to provide efficient and flexible control over the luminaires. Manual switches and button stations feature modular, momentary pushbutton switches with addressable capabilities to control specific luminaires. Preset/fader stations that operate using programmable buttons and/or faders can also be provided and the designer should discuss control options with the client (see Figure 3). Integral pilot lights or LEDs indicate the active state or power status. Button and fader labels can be engraved or screened by the manufacturer, usually based on approved text from shop drawing submittals.
This text should be discussed with the owner during design to ensure that there are not additional costs during construction. Station control components offer default or customizable system functions, including preset selection, manual mode,
record mode, station lockout, raise/lower, macro, cue and room join or separate.
Designers can also choose liquid crystal displays (LCD) with or without touch-screen interfaces, enabling operation through programmable control pages with buttons, faders and images. Users can adjust LCD station contrast and brightness, and the station can be programmed to dim during periods of inactivity. The stations can support the import of bitmap image files for customizable pages and branding. Permanently installed LCD stations are semi-recessed in manufacturer-furnished backboxes and trim assemblies without visible fasteners, while portable stations can conveniently nest into wall docking stations provided by the manufacturer, requiring no umbilical cable or plugs for connection. For these systems, the docking station ensures charging and communication with the portable device when docked.
For daylight sensing, network daylight level sensors play a crucial role. These sensors serve as measurement devices, providing ongoing read-backs of sensor settings to the lighting control network or daylight controller. The sequence of operations outlines specific actions to be triggered at various read-back values. The sensors can be mounted on a ceiling or wall and meet application requirements based on range and viewing angle.
Outdoor sensors should be wet location listed and designed for outdoor use. The sensor's output signal is typically linear with light level and its network connection enables remote querying of sensor status and values via control software. Specifications should indicate what parameters are network adjustable and which are manual-only.
The systems support the "blink warning" function, which allows for flashing lights off/on before the lights are turned off, with definable warning intervals for each zone. Occupants can override any scheduled off sweep using local wall switches within the occupied space, with a programmable override time with a maximum of two hours, as required in several adopted energy codes. This “blink warning” is more convenient than letting the lights just turn off, which forces occupants to navigate in the dark to turn the lights back on. To appropriately specify coverage, designers should consider occupancy or vacancy sensor coverage during design, while also considering the typical types of movement each space will see.
When centralized control and programming is desired, the system should include a server/central station equipped with operating software, a data network and BACnet IP communication capabilities with other systems. This communication protocol is compatible with the BAS, allowing for energy-saving features such as heating, ventilation and air conditioning set-back. The server/central station offers a programmable operation of lights through the system relays and controlled with system devices. The system software provides control of relays and control devices, time and sequence scheduling, timed out and blink light operation and monitoring and reporting of system events and components, as initially specified on plans and schedules.
The programming and scheduling of the system can be done locally at the parent lighting control panel and remotely via the internet. Remote connection to the system enables real-time control
5: This conference room has flexible lighting control zones to accommodate presentation or collaboration functions. Courtesy: IMEG Corp.
csemag.com
Lighting control insights
u Lighting controls have evolved significantly over the past 20 years, transitioning from manual switches to programmable, AI-enabled systems.
u Specifying lighting controls has shifted from detailed diagrams to using lighting sequence narratives, reducing designer control but accommodating varying manufacturer approaches.
and feedback, allowing monitoring and commands from a remote PC. The system can retain all programs, schedules and time of day in nonvolatile memory for a specified amount of time, implementing required programs upon power restoration. The system can allow individual users to turn lighting on and off with their PCs, with password-protected software for popular operating systems. These systems can incorporate an RS232 interface for audio/visual or control interface stations, providing an interface for PC and/or A/V connection to the lighting control system through appropriate German Institute for Standardization-style connectors.
The responsibility for coordinating relay modules, network hubs and the control system server/ central station lies with the lighting control system manufacturer, who ensures proper system performance. The server is usually equipped with a monitor, keyboard and mouse and is connected to an equipment emergency circuit with an uninterruptable power supply so no programming is lost.
The network hub houses a processor and astronomic time clock to control and monitor the lighting and associated systems. This hub is usually fed from an emergency circuit when emergency lighting controls exist on the network. Emergency egress lighting can be accomplished several ways. The two most common methods being a “night light” designation or a “switched emergency” des-
ignation. The “night light” method leaves the emergency egress luminaires unswitched, when allowed by energy code and therefore there would be no lighting control for this circuit.
Illuminated exit signs share this circuit, typically. The “switched emergency” method allows the emergency egress luminaires to be controlled with the rest of the space, allowing for dimming or turning-off, but a UL 924 listed transfer device will bypass the controls in the event of a loss of power to the normal circuit, driving the designated luminaires to 100% output.
When specifying lighting controls, it is important for designers to consider where the control components will be located. With each of the control types listed above, the devices controlling the lighting fixtures are no longer at the wall controls, but instead closer to the lighting fixtures themselves (or integrated within the lighting fixture). As a result, designers should specify adequate parameters for components.
For example, electrolytic capacitors, which exist throughout the system, are sensitive to heat and their expected lifetime doubles for every 10°C they operate below their rated temperature. Conversely, if operated at 10°C above the rated temperature, their life expectancy halves and at 20°C above, it reduces to a quarter.
To ensure a minimum 10-year operating life under worst-case field conditions, the dimming equipment should be designed to handle peak currents higher than the rated operating current, which is caused by tungsten inrush, magnetic inrush and lamp burnout. To ensure reliability of components, the maximum current rating of each component should be at least two times the dimmer or relay's rated operating current. Additionally, the dimmers and relays should be capable of withstanding repetitive inrush current of 50 times the operating current without affecting their lifetime and they should be designed and tested to withstand line-side surges without impairment to performance.
It is common for the dimming equipment to incorporate a "soft-start" features for a smooth ramp-up of lights within fractions of a second at initial turn-on. To achieve smooth changes in light levels perceived by the human eye, the dig-
A HEALTH CARE SYSTEM needed modernized lighting design for its headquarters in a historic building, creating unique challenges in retrofitting new lighting systems in an older building
A health care system needed a new home for its mission headquarters and worked with the city and state to renovate a 275,000-square-foot building that started life as a department store in 1904. The building had seven levels above ground and two levels below ground and had seen several owners over its life span.
The $150 million renovation started with a complete demolition of the interior and the exterior precast, which had previously replaced the 350 Chicago-style windows that had originally adorned two sides of the building. The new lighting controls needed to provide useful zoning based on the open office floorplan used along the exterior sides while still being modern, exceeding energy code and meeting the approval of the historical preservation society.
The design needed to maintain an open-ceiling concept to reveal the 350 plaster column capitals, all of which were restored. The lighting design needed to illuminate and highlight these column capitals, which created additional lighting control zones and strategies. All of the lighting was LED, and because of high-efficacy fixture selections, the design was 41% better than required by 2018 International Energy Conservation Code at only .47 watts per square foot.
A distributed networked lighting control system was chosen for its combination of flexibility and scalability while reasonably minimizing cost. Button stations were used for multizone office areas while touchscreens were used for conference rooms and public areas.
The design documents conveyed the lighting control intent though a combination of control identification subscripts on every luminaire and controller on the floor plans, with a sequence of operations identifier in each zone that correlated to a sequence schedule. The control identification subscript allows for each fixture to be assigned to a switch, clearly defining zon-
ital control systems must have enough steps in their light control output. The dimmers must be capable of controlling all light sources in a smooth and continuous manner without visible steps. They should be flexible enough to compensate for the different power levels required to dim various lighting sources, ensuring proper dimming curves for specific light sources. The components should allow for field adjustments to fine tune dimming curves and manage maximum light levels for energy savings.
FIGURE 7: Open office areas feature exposed ceilings that were constructed to allow for conduit and lighting controls to be recessed, while coordinating with historical columns. Courtesy: IMEG Corp.
ing. The sequence of operations allows for a narrative description of how that zone is to be controlled, if occupancy or vacancy is required, if daylighting is a factor, dimming requirements and more. Some sequences included interfacing with the heating, ventilation and air conditioning system for unoccupied modes, with the building security system for override on or with emergency egress transfer controls.
This building included a historical renovation of an adjacent building that became a new restaurant. This space used a combination of decorative and functional lighting, which had 15 interior zones and nine additional exterior, color-changing façade lighting. Instead of a bank of individual controls, a touch-screen controller was provided that interfaced with a combination of digital multiplex, 0-10 volt and reverse-phase dimming modules to accommodate the variety of fixtures provided. Egress lighting was achieved with surface cylinders that have a UL 924 transfer switch controllers to override-on in the event of a power loss and these fixtures are on the building’s standby generator emergency branch.
When specified for specific load types, line voltage dimmers should meet the requirements for magnetic low-voltage transformers, electronic low-voltage transformers, neon and cold cathode transformers, fluorescent electronic dimming ballasts or LED drivers. Coordination between low-voltage dimming modules and line voltage relays is necessary to control different light sources effectively, so designers should consider each lighting type and the specific requirements of each.
Nondim circuits should meet the requirements for switching high inrush loads, preventing arcing at relay contacts to extend their life beyond one million cycles. The rated life of relays at full load should be a minimum of one million
cycles and they must be capable of fully rated output continuous duty for inductive, capacitive and resistive loads.
Designers need to define the types of
conductors to be used and the requirements to install them. For example, specifications require copper conductors to be no smaller than a #16 American wire gauge (AWG), with insulation voltage and temperature ratings equal to that of the line-voltage wiring. For tapping conductors to switches or relays, stranded copper conductors of 16 AWG, solid 16 or 18 AWG with matching insulation ratings are to be used. When tapping conductors to dimming ballasts, solid copper conductors of 18 AWG with insulation voltage rating that is not less than that of the line-voltage wiring and insulation temperature rating of at least 90°C may be specified. The installation of these cables above the ceiling should be defined, with the goal of preventing loose cabling routed on top of ceiling tiles, supported by foreign systems or other carless arrangements. The specifications within CSI Division 27: Communications Manufacturers can be echoed.
Electrical bearing damage causes unplanned downtime
Variable frequency drives (VFDs) are used to control pumping systems. But VFDs create a motor shaft voltage that discharges through the bearings, blasting millions of pits in bearing surfaces. Both motor and pump bearings are at risk. These discharges oxidize the bearing grease and cause bearing uting, premature failure, and costly downtime.
Protect motor bearings with AEGIS® Shaft Grounding Rings
By channeling VFD-induced discharges safely to ground, AEGIS® Shaft Grounding Rings prevent electrical bearing damage. Proven in millions of installations worldwide, AEGIS® Rings provide unmatched protection of motors against electrical bearing damage, motor failure, and unplanned downtime.
Before energizing the system components, a complete functional test shall be performed by a factory-authorized technician. All loads will be tested live for continuity and freedom from defects and control wiring will be checked for continuity and connections. Programming of initial zones, schedules, lighting levels, control station groups and sensor settings will be carried out by a factory-authorized technician, with the lighting control sequence of operations serving as the basis for programming.
However, the final decisions regarding groups and schedules will be made at the owner's discretion. Specific procedures will be followed to confirm the correct operation of occupancy/vacancy and daylight sensors, making necessary adjustments for proper functioning. Regarding training, the manufacturer will provide a competent factory-authorized technician to train owner personnel in the operation, maintenance and programming of the lighting control
Continued on pg. 22 1-866-738-1857 | sales @ est-aegis.com
system. The training duration shall be at least three days, with an additional day scheduled at least two weeks after the initial training.
In terms of documentation, the manufacturer will provide system documentation, including a system one-line diagram showing all panels, control stations, sensors, communication lines and network or building management sys-
tem/BAS interface unit. Additionally, drawings for each panel showing hardware configuration, numbering, panel wiring schedules and typical diagrams for each component will be provided.
As the use of AI grows, it will likely find a home in BAS, including lighting controls. The way lighting controls are programmed is based on a finite set of basic rules and these programs are static. Changes to the programs are time consuming and in some cases, they can be too complex for the building owner or operator, requiring visits from the manufacturer. These controls are also reactionary and cannot predict future issues or functionality. AI can learn patterns and improve energy efficiency of programmable lighting controls through a combination of reactive and predictive assessments of the environment and occupant behavior.
For example, engineers can program in a “dead band for daylight sensors to prevent erratic behavior from fluctuating lighting levels. This dead band is arbitrarily determined at the time of install and remains fixed. Lighting controls using AI may not need a dead band at all, as the behavior of the sun would already be understood and predicted, allowing for smooth lighting transitions that predict behavior, creating a seamless user experience. AI can also find use in reading occupancy or vacancy sensors or could replace them altogether with alternative methods of determining occupancy for a single room, entire suite, floor or building by combining all possible building sensors, cameras and access control. Certainly, the future of smart lighting controls will continue to evolve and designers are likely to encounter a series of exciting new challenges to enhance building performance. cse
Richard Vedvik, PE, IMEG Corp., Rock Island, Illinois
Michael McTavish, PE, LEED AP, Dewberry, Menomonee Falls, Wisconsin
When designing lighting control systems, technology, energy efficiency and the user must be considered
There has been a significant evolution of lighting controls over the past 20 years, from banks of standard light switches, to centralized relay control systems, to digital lighting controls connected to the network via Wi-Fi or low-voltage wiring. Smart lighting controls allow building managers to control the light level of a specific light fixture from across the nation via the internet.
These web-enabled lighting control systems can be programmed to provide cellphone alerts when the status of a room goes from vacant to occupied, triggering the lighting in the space to turn on. Internet-enabled technologies have become a powerful tool in reducing building energy use and improving facility efficiency.
Lighting control systems have gone from complex installations that perform a basic sequence of operations to a very simple installation that can perform complex operations. Detailed wiring diagrams to convey design intent have been replaced by written descriptions of how the space should function as functionality is dictated by system programming.
Given the increase in interest for buildings to achieve zero net electrical use, this progress has made it possible to further reduce a building’s energy use intensity via smart lighting systems. As engineers who interact with this technology daily, it’s easy to overlook the most important aspects of design: the building owner and the end user.
When designing a lighting control system, initial meetings with the owner’s staff are necessary to determine the staff’s level of technical savvy and establish the functional goals. Not every facility requires the level of control that allows a building manager to monitor the lighting status in a specific space through a graphical user interface. Often,
the individual tasked with maintaining the lighting control system is someone who oversees all building functions and has little desire to learn a complex lighting control system, resulting in the need for a system that works and has low maintenance.
As a design engineer, there is a level of education that also needs to take place when discussing the required functions of the lighting control system. Most states and municipalities have adopted an energy conservation code. These codes are specific to what lighting controls are required and how they are to function as a baseline for energy use reduction and must be followed regardless of the owner’s desired functionality.
The engineer should inform the owner of what is required and how that will be accomplished. If the engineer has adequately educated the building owner, then the owner should not be surprised by lights shutting off automatically in response to natural daylight levels. When designers include systems and features that were not requested by or discussed with the owner, frequently work-arounds are established that remove energy-saving features from the system.
For example, occupants may tape over photo sensors to eliminate the automatic functionality. The additional cost of the unwanted features would be better used in other aspects of the project. Designers should try to make the control system an asset to reduce their facility electrical usage rather than an unused icon in the building automation system (BAS). If the owner doesn’t know how to use it, it will not be used.
It’s important to consider that the owner may have additional desires unbeknownst to the design engineer. Perhaps they have multiple facilities under their supervision, for example college campuses, municipalities, corporate campuses or public school districts. If a lighting control system has been standardized, the owner should be alerting the design team that they must specify around that system.
The design engineer should inquire how the current system functions and try to emulate it in the new project while still complying with the current energy conservation code. If there is not an existing standardized system in place, the engineer may consider promoting the current project as an opportunity to create a standard.
Benefits to discuss with the owner include:
• Familiarity of systems between all facilities for maintenance staff. The staff will not need to know multiple system specifics.
• Reduced attic stock of lighting control devices. Replacement devices will work universally across all facilities that have been standardized.
• Opportunity to network all facilities together for monitoring and control from a single location as future upgrades are made. This can also allow for remote access via the internet.
• A single manufacturer or sales representative for technical assistance when issues arise. This single point of contact will be familiar with a system and may be able to troubleshoot the entire system remotely.
• Understand the capabilities of lighting control systems, including smart lighting controls.
• Learn which considerations should be made when designing a system tailored to a particular owner.
• Know how the end user of the lighting control system may impact the features provided.
FIGURE 4: It’s important to understand how a facility manager may operate a system. If that individual is overseeing facilities for an entire school system, they may not have the capacity to manage a complex lighting system.
Courtesy: Dewberry
When assisting the owner in selecting a lighting control system, the engineer should present multiple alternatives. Discuss the pros and cons between each, including:
• The cost for replacement parts and long-term availability of parts.
• Where the professional technical service is located and how quickly it can respond when the system needs repair or reprogramming.
• The ease of which the owner can make changes to scheduling and device functionality on their own.
‘ As an evolving technology, smart lighting control systems regularly become increasingly flexible with fewer installation effort and more features. ’
Design engineers should understand that the owner is the one who will live and interact with the system for the lifetime of the building or campus. Understanding the owner’s level of technical aptitude and discussing how the system will work will not only benefit the design, but also the owner’s comfort with the system provided.
Similarly, the design engineer should consider the end user when designing and specifying the lighting control system. Who are the people using this facility and how will they be using it?
Consider a project that is an upgrade for a local church, which includes a multipurpose room. The owner informs the design team that the space will be used throughout the week by various groups, which may include senior citizens. This group of individuals may be more accustomed to lighting controls that consist of snap switches and rotary dimmers. In this instance, it would be prudent to provide an entry control station that more resembles a standard wall switch with clear on/off labeling versus a digital touch screen, which may be more commonly installed nowadays.
csemag.com
Lighting insights
u Smart lighting systems use controls to help manage specific fixtures in a building or on a campus.
u By understanding the goals of the building owner and needs of the occupant, lighting control systems can meet both needs.
• The amount of information that the system can provide, such as occupancy status, power use profiles and inputs to the BAS.
• The potential for futureproofing the system as improvements are made. The manufacturer should indicate if and how they will be backward compatible with new system releases.
• What is the cost for the added control features and can the project budget accommodate this cost?
How the lighting controls should function is also dependent on the application. In the 2012 International Energy Conservation Code, automatic daylight harvesting control became a requirement. To satisfy this code, the automatic controls may continuously dim or step-dim the lighting fixtures within the daylighting zone. The use of the space should have been considered when selecting the control method. In 2012, continuous dimming controls were more expensive than step-level dimming.
As the designer, it was good design to limit continuous dimming to areas where automatic reductions in light level would be distracting, such as classrooms, meeting rooms and office spaces. Corridors, library stack areas and lobbies could be step dimmed as occupants generally pass through these areas and are not focusing on a task for long periods of time.
Open offices pose a different challenge. In these spaces, individuals are often working under similar conditions. However, everyone has his own light level and temperature preferences. These spaces often span an area of up to 5,000 square feet and are controlled universally throughout the space.
One method to provide individual light level control is to provide task lighting at each space. Alternatively, individual fixture lighting controls allow for each inhabitant of the space to control the fixture directly above their workspace. Benefits to this control solution include:
• Eliminating the need for task lighting in addition to general ambient lighting.
• Providing flexibility for future furniture layouts.
• Providing the ability to add enclosed spaces in the future with little to no rewiring of the existing lighting, rather, reprogramming of the system.
• Minimizing the lighting required to be operating during building “closed” hours when employees are working after hours. Lighting near the worker can remain on, while the rest of the open office space can be shut off or reduced to minimal light output levels for energy savings.
As an evolving technology, smart lighting control systems regularly become increasingly flexible with fewer installation effort and more features. BAS integration will likely become a main component in energy use reduction and decarbonization of the built environment. It will be incumbent on the designers of these systems to make sure they are in line with the desires and capabilities of building owners and managers.
Additionally, the controls need to align with the needs of the end users. If the designer provides an overly complex system, it likely won’t be used as intended and the desired energy savings will not be achieved. cse
Michael McTavish, PE, LEED AP, is an associate vice president and assistant business unit manager for Dewberry’s Midwest MEP group.
SMART. SAFE. TEMPERATURE CONTROL.
Take greater control of your domestic hot water system with Bradley’s new Navigator® Digital Mixing Valve. Dial in and maintain precise temperatures for mid to large scale projects — even during low demand periods. And the self-cleaning ball valve and programmable legionella flush keeps your system safe and maintenance free.
Innovative Water Solutions. Brought to Life.
Richard D. Barbera, CIPE, Fitzemeyer & Tocci Associates Inc., Woburn, Massachusetts
Innovative advancements in the plumbing industry have included high-efficiency equipment and digital systems
Mechanical and plumbing engineers can help a commercial building owner save money by using more advanced systems in their design. By specifying some of the most advanced and effective equipment, long-term savings goals can be achieved.
For example, an engineer would look first at a standard duplex sewage ejector to serve a building’s waste system when the sanitary system is below the invert of the sanitary system exiting a building. The duplex ejector system is designed to efficiently remove sanitary waste from lower-lying areas to higher elevation discharge points.
• Learn how significant savings can be realized by an owner when direct inline sewage ejectors are installed above-grade as opposed to in a traditional wet well.
• Understand the manpower savings with the installation of flexible medical gas piping.
• Review use of an electronic mixing valve, which can be integrated into a building automation system to allow facilities managers to remotely monitor and control water temperatures.
A duplex sewage ejector consists of two pumps, each equipped with a float switch, check valve and motor. The pumps alternate their operation to
ensure continuous and reliable sewage discharge. When the wastewater level in the basin reaches a predetermined level in the wet well, the float switch in one pump is triggered, activating the pump and starting the pumping process. The other pump remains inactive.
As the active pump starts operating it will discharge waste from the basin to the higher gravity sanitary system. The check valve prevents backflow and maintains the forward flow of sewage. The pumps must be designed to provide enough lift to allow the waste to meet the gravity system.
Once the wastewater level in the sump pit decreases below a specified level, the float switch associated with the active pump detects the change and deactivates the motor. At the same time, the float switch in the inactive pump rises, preparing it for the next cycle. For each future cycle, the roles of the pumps reverse. The previously inactive pump becomes active, while the previously active pump remains idle until the wastewater level rises again. There is also a high-water level float switch that will activate both pumps if the first pump cannot maintain the flow entering the basin.
Engineers have an alternative to a standard pumping system located within a wet well: An inline sewage ejector system. This type of system is a game changer that revolutionizes wastewater management by offering efficiency and convenience. Designed to handle sewage and wastewater in a wide range of settings, this technology simplifies installation, optimizes performance and reduces maintenance requirements.
An inline sewage ejector system consists of an inline ejector pump, control panel and monitoring system — all seamlessly integrated to provide
‘ The pumps must be designed to provide enough lift to allow the waste to meet the gravity system. ’
reliable and efficient operation. Unlike traditional sewage ejector systems that require a separate wet well and complex set ups, an inline ejector simplifies installation with its compact design and inline installation capability.
The inline pumping system operates by means of a pressure sensor located beneath the entry chamber of the pumps. The sensor continuously measures the height of the fluid at the inlet into the pumps. The sensor consists of a stainless-steel flush membrane and is highly resistant to wear and tear. It is resistant to deposit build up because of the fluid speed coming into the pumps and the suction of the pump.
The connection from the sensor to the control panel is completed by a rated cable. In addition to the information transmitted from the sensor to the control panel regarding the inlet fluid height, information can be sent by the transmitter for remote observation of the system’s operation without the need for any additional equipment by using an isolated output of the control panel. The panel itself comes with a user-friendly display that indicates speed, intensity, level gauge, motor power, motor torque, flow meters and status readings for remote users.
The benefits of an inline pumping system include:
• Excellent performance and efficiency. The hydraulic design ensures optimal water flow and maximizes energy consumption. The inline pump operates with minimal friction loss, thus providing a constant and reliable discharge.
• The pumping system incorporates smart technology and control features, allowing for real-time data collection, analysis and remote adjustments to maximize operational efficiency. Measurements that can be monitored are predictive automated analysis, tuning, over torque and active factory assistance. All monitoring is globally accessible 24/7.
• An inline pump system can replace an existing system in an existing wet well.
• A compact and space-saving design, making it suitable for installations with limited space. The inline configuration eliminates the need for extensive infrastructure and wet wells, optimizing the use of space when the pump needs to be installed in tight mechanical rooms. This is especially beneficial in a renovation project.
• Environmental sustainability. With the efficient operation and energy saving design, it helps reduce the carbon footprint associated with the entire system. Anticontamination features are incorporated by means of including backflow devices to ensure the safe disposal of the sewage waste.
• The inline system is driven by variable speed drives. Operation is no longer based on “all-ornothing” pumping but on continuous modulated pumping directly from the effluent inlet.
• The cabinets and the control panels are delivered ready to be plugged in. Only the two motors and the sensor require connection for operating the system. All internal connections are made and tested in the factory. Dry contacts for remote surveillance status reports are fitted as standard.
• By pumping gravity-fed effluent directly from the point of entry, without water loading or a wet well, the inline pump overcomes the drawbacks of retaining raw sewage. No dangerous gases (hydrogen sulfide, or H2S), sand and grease accumulation, structural erosion or obstructed float switches are present — the owner or maintenance person-
2: The corrugated piping allows for continuous runs without the need for fittings to provide a change in direction. Courtesy: Omega Flex Inc.
nel always have safe access. The system can pay for itself with reduced maintenance requirements.
No authority having jurisdiction approval is required with the in-line system. Engineers should also consider capital cost and coordination with the architects and civil engineers on the project.
Submersible pump stations around the world share a common enemy, the flushable wipe, which really isn’t that flushable. In a traditional wet well system, these wipes are separated from the pumped liquid, solidify and form clogs that result in costly maintenance service calls. Inline pumping systems help eliminate the main cause, the ejector basin.
In Texas, a 23-story, 30-unit high-rise residence building with a grocery store and restaurant had continuous issues with frequent pump clogs; six clogs in a two-month timeline created costly maintenance issues for staff to remove clogs, fats, oils and grease.
The reason for the constant clogging was flushable wipes. Despite the staff notifying the building occupants on multiple occasions, they could not control what was being flushed into the sanitary system. The clogging continued and maintenance costs continued to rise. The building owner needed a solution to stop the clogging and provide the occupants with a first-class residence.
The building owner’s service team quickly removed the antiquated submersible pumps, piping, rails and control panel. With the equipment removed, the 60-inch diameter fiberglass basin was prepped for the new dry-pit system. The inline pump arrived factory pretested, pre-wired, assembled and ready to be installed.
Within 2.5 hours, the wet well was transformed into a dry pit and the inline pump installation had begun 10 feet below ground. In a safe, clean and dry environment, the team was able to connect the suction directly to the invert and construct the discharge piping. A sump pump was used with the system to handle any water ingress from the hatch. The valve vault was no longer needed and could be removed during future construction.
In just one day, the source of much pain and expense had been converted from a wet well into a dry, clean and reliable pump station.
Until the 2018 edition of NFPA 99: Health Care Facilities Code, the only option for medical gas piping was seamless copper tubing that is cleaned and capped. Included in the 2018 update was the new option of using corrugated medical tubing (CMT). CMT is a semi rigid tubing made from a copper alloy. The corrugated piping allows for continuous runs without the need for fittings to provide a change in direction (see Figure 2).
CMT is available in 0.5-2 inch sizes. The fittings to connect sections of CMT are an axial swaged, sealed quick-assembly brass fitting, which can connect sections of CMT to each other or to standard copper in case of a renovation project or a hybrid standard copper/CMT installation. CMT has rolls of piping in lengths of up to 500 feet (see Figure 3).
CMT must be installed by an American Society of Sanitary Engineering 6010: Medical Gas Systems (or state equivalent) certified installer who has successfully trained through the manufacturer’s installation program.
The benefits of using CMT when compared to seamless copper are significant. With fittings no longer required, the need for hot work is significantly reduced if not removed completely. Not only does this lessen the potential risks of fire damage but it reduces the cost of paying for a fire watch. The speed of installation and lower installation cost also make CMT a viable option. The quicker installation time for CMT will reduce the time onsite for the contractor, in turn reducing the overall cost of the project and minimize downtime for the hospital. CMT also cuts down dust and contaminants that can be harmful in a health care environment. Hangers shall be installed per manufacturer requirements and bending radii shall not exceed installation requirements.
When installing CMT below grade, there are also time and cost savings. All brazed fittings are eliminated while minimizing any potential of contamination of the system. The elimination of below-grade fittings removes the potential for points of failure. With the requirement of the inspection of underground fittings eliminated, the installation process is simplified.
Be mindful of which edition of NFPA 99 a municipality recognizes; some cities/towns require
designing to an earlier version of NFPA 99 (before CMT being accepted). In this situation the Centers for Medicare & Medicaid Services can issue a waiver, QSO-20-40-LSC, which allows the installation of CMT in both new and existing applications. The waiver, introduced in 2020, requires the facility owner to document the use of CMT and that the systems were installed per NFPA 99 requirements.
A renovation project at a local community hospital in Massachusetts included the relocation of an existing zone valve box from the patient care area to a designated area outside of the patient care area, as required per NFPA 99.
The new zone valve box, containing shut-offs for both a vacuum and oxygen line, was located on the other side of a corridor beyond the fire stop roughly 65 feet away. For comparison purposes the vacuum line was done in 1.25-inch hard-drawn copper pipe and the oxygen lines were done in 1-inch CMT. All piping runs were done in parallel taking the same route between connection points.
Approximately 75 feet of piping was used for each run (150 feet per system). The piping run included a vertical rise out of the new zone valve box followed by a series of 90- and 45-degree bends to the 65-foot straight run down the corridor. The piping then turned 90 degrees across the corridor and was tied into the existing supply and distribution lines. Both piping systems used the same existing hanger supports down the 65-foot corridor run.
Table 1 compares the materials required for medical vacuum brazed hard-drawn copper pipe versus the CMT system.
As with all rigid piping installations, elbows are required when turning corners and changing direction to route around, above or below obstacles. CMT can bend around corners and flex to avoid potential obstacles, resulting in no intermediate connections. In this case, two 1-inch CMT lines were pulled together, much like pulling wire or cabling through a hole in the firewall down the entire length of the corridor in roughly 15 minutes. An additional 30 minutes later, the piping rough-in was complete and ready for fitting connections.
There was a significant labor savings between the installation of the brazed hard copper and
CMT. The brazed hard copper was anticipated at 64 person hours to tie in the new valve box and prepare for final tie-ins, so this is not a final installation. The labor estimate for CMT installation was 12 hours to pull and make all final connections.
Overall, the use of CMT resulted in a 79% reduction in joints for the piping system and a minimum of an 82% reduction in labor hours.
Additional benefits of the system included:
• Ease of transport to the job site.
• Reduced cost in support items such as brazing rods and purge gas.
• Contamination possibility was greatly reduced.
• No need for intermediate joints due to the continuous lengths of piping.
• The continuous lengths of piping also resolve fire prevention concerns. No brazing is required in confined spaces, unlike what is required for hard drawn copper systems.
Thermostatic mixing valves are used to keep water at a constant temperature by blending cold and hot water in a steady flow to assure safety while washing hands, showering and/or bathing. The primary goal of thermostatic mixing valves, which are
‘ Engineers should also consider capital cost and coordination with the architects and civil engineers on the project. ’
Standard medical vacuum brazed hard-drawn copper pipe materials required:
150 feet of hard-drawn K copper pipe
Corrugated medical tubing (CMT) system materials required
150 feet of CMT
28 fittings with a total of 56 brazed joints8 fittings total with 4 brazed joints
12 90-degree elbows
4 45-degree elbows
12 couplings
4 CMT fittings
2 couplings
2 axial swaged hard-drawn copper pipe connections
TABLE 1: Materials required for medical vacuum brazed hard-drawn copper pipe versus the corrugated medical tubing system. Courtesy: Fitzemeyer & Tocci Associates Inc.
FIGURE 4: The benefit of digital mixing valves. Courtesy:
designed to manage water temperatures, is to prevent scalding. A mixing valve allows the temperature of the water in the water heater to be increased (to lessen the risk of bacteria growth) while also preventing scalding. Plus, by combining hot and cold water, available hot water supply is more readily available.
A standard thermostatic mixing valve consists of four main parts:
• Thermostatic element: A temperature-sensitive device that expands and contracts when the temperature of the water fluctuates.
• Piston: The piston moves in response to the thermostatic element sensor. The piston will quickly close if the hot or cold water temperature regulation fails.
• Return spring: The return spring of a thermostatic mixing valve pulls the piston back to its original position after it has contracted or expanded.
amount of data that can be stored and communicated through a building automation system (BAS) or locally at the controller, providing intelligence at the foundation of the entire plumbing system.
Digital mixing valves place instantaneous information at an owner’s fingertips to allow for immediate decision making when safety is a concern and for operational decisions to help conserve water, perform more efficiently and reduce system downtime and the associated costs. There are three main technology-driven components in a digital mixing solution:
• The controller’s algorithm.
• Sensors.
• Cloud-based technology and mobile apps.
The benefits of a digital mixing valve include:
• Maintains safe water temperature to prevent scalding and thermal shock.
• Delivers consistent hot water on-demand, wherever and whenever it is needed.
• Conserves energy through efficient water temperature management.
• Integrates with a BAS to provide broad management capabilities.
csemag.com
Plumbing insights
u Commercial building plumbing systems have improved dramatically over the past couple of decades.
u Case studies about an inline sewage ejector, corrugated medical tubing and digital hot water mixing highlight best uses for plumbing advancements.
• Temperature adjuster: The adjuster is used to regulate the outgoing temperature of the mixing valve by turning the external handle of the valve. A thermometer should always be installed on the discharge side of the mixing valve to determine the outgoing temperature.
Recently, there has been a move toward the use of digital mixing valves. Digital water mixing directs hot water delivery through a programmable valve or system that processes temperature, flow and pressure data. The data is obtained from the hot and cold water inlets, mixed outlet and sensors on the mixed water return. High-speed electronic actuation modulates a simple ball valve that allows the setpoint to be maintained. Fast, responsive digital technology enables the collection of a large
• Reduces repair and maintenance costs.
• Minimizes risks and liability for owners, engineers and facility managers.
• Eliminates the need for an aquastat.
• Simple plug and play installation.
• Remote access alerts enable a facility manager to see and monitor the plumbing water system(s) from anywhere.
• Can be used for quick decision making when control of the system matters the most.
• Digital mixing valves that have digital LED touchscreens to allow immediate hot water temperature control.
Hotel plumbing system problems fixed
Hotel staff often receive complaints about the lack of hot water; the highest use is typically early morning when guests prepare for their day. This was the case for several years at a 384-room airport hotel. The hotel would get several calls a week from guests about the lack of hot water. The best explanation that could be given was that “it was being worked on.” The hot water issues lasted for more than two years. Hotel management, along with contractors, did a deeper dive into the issue and it turned out that a large hydronic valve was used for the original domestic hot water system. It was determined the valve had a 120-second response time and couldn’t actuate quickly enough to keep up with the hotel's changing water pressures.
Because of the valve’s longer response time, whenever something went wrong with the pumps, heat exchangers or storage tanks, the entire domestic hot water system would require a time-consuming recalibration. Maintenance was required routinely and became a constant source of disruption for the engineering staff. Once the existing valve was replaced with a digital mixing valve, the hot water issues disappeared. Thus, eliminating the costly maintenance issues along with the hotel guest complaints.
Above are just a few advancements in the plumbing design field. It is recommended that all engineers reach out to manufacturers and manufacturers’ representatives to keep apprised of new technologies and new ways of designing plumbing systems for systems to be smarter, more efficient and longer lasting. cse
Richard D. Barbera, CIPE, is Plumbing Engineering Manager at Fitzemeyer & Tocci Associates Inc.
In Critical Power Facilities, all data recorded during a power outage is vital! Sequence of Event Recorders collect precision data to quickly identify the root cause, providing a clear picture of what happened, and what is needed to restore power quickly!
of what and what is needed to restore power
‘ Digital mixing valves place instantaneous information at an owner’s fingertips. ’
Brian Venn, TBE, CxA, Mechanical Testing, Inc., Clifton Park, NY; Jeremy Johnson, TBE, CxA, American Testing Inc., Ellicott City, MD; Thomas Prevish, Ph. D., PE, CEM, NorthWest Engineering Service Inc., Beaverton, OR
The evolving HVAC industry faces challenges to upgrade complex systems in aging university lab buildings to match modern standards of energy efficiency and performance
As the heating, ventilation and air conditioning (HVAC) industry continues to evolve, there are more opportunities to improve the effectiveness and efficiency of commercial buildings that consume a substantial amount of energy.
A university teaching lab is a great example of a building that relies on complex HVAC design and installation to operate effectively and efficiently. There continues to be a need and desire for university science and lab buildings, both for new construction and existing facility upgrades. As some of these existing buildings approach 30 years or older, the new challenge facing the industry is to properly upgrade the HVAC critical components, such as direct digital controls, air terminals, air handling units (AHUs), energy factors, pumps and chillers. Starting with the infrastructure components, many of these buildings are designed with energy recovery wheels, coils and night or occupancy setbacks, all to reduce the energy costs while still meeting the needs and expectations for a laboratory building. When it comes to determining the current performance of the existing infrastructure, using a testing, adjusting and balancing (TAB) firm that can help assess the current conditions is a must.
Air to air energy recovery wheels are very popular and highly efficient in these 100% outside air laboratory buildings. While very efficient at reducing energy use, they also need proper maintenance on a frequent basis to ensure the proper performance of the system. Many times, wheel degradation can affect the supply and exhaust fan performance. Assessing the purge cubic feet per minute (CFM) and total fan performance is essential. Manufacturers provide performance data with purge CFM that needs to be independently verified. As these laboratory HVAC systems have redundancy, excessive purge CFM can eliminate or considerably reduce system redundancy (see Figure 1).
• Understand the integrity of existing ductwork if being reused for renovations will greatly impact the new systems being installed and must be visually, as well as pressure tested if possible.
• Identify what important pre-survey data should be incorporated into the scope of work.
• Gain better knowledge of how the entire project comes together by using a sound approach from the start and real time data to get better end results.
Variable air volume (VAVs) offer pressure independent control and reliability in these applications. Proper TAB is critical and is required after any building automation system (BAS) controls upgrade. The components of the terminals are simple, but there can be severe consequences if they are not operating correctly. Buildings at least 30 years old usually need BAS upgrades where the local VAV controller is replaced.
However, other components of the controls and duct leakage should also be measured and assessed by a TAB firm. For example, the VAV flow ring is essential for proper operation. If only replacing the existing VAV controller, a designer may miss the condition of the flow ring and include cracked tubing or dirt laden ring, which will have severe consequences to properly TAB the air terminal. To prevent these kinds of instances, a full and detailed assessment is needed (see Figure 2).
Some typical design applications have a campus type of chiller water and steam distribution. Establishing the building gallons per minute, differential pressure and maximum capacity requirements ensures that the building can properly heat, cool, humidify and dehumidify.
Lab fume hoods can most likely be found in university teaching labs. There are many different types of fume hoods that operate at low velocity, 60 feet per minute (FPM), or standard velocity, which is100 FPM. Other controls schemes include VAV with occupancy, night setback or active sash control. The biggest challenge that fume hoods face in the industry is to provide a safe environment for the researchers while still being efficient as possible. This is easier said than done with a system that typically exhausts 100% of its air into the atmosphere and replaces it with outside air being introduced into the building or lab through the HVAC system. Modern products
and approaches to control concepts have changed through the years and should be reevaluated if newer technology can benefit an existing building (see Figure 3).
One of the biggest reasons why HVAC controls are replaced in 30-year-old buildings is that the components or supports are no longer available from the supplier. These are called legacy or outdated controls. So, when a component breaks, it’s up to the maintenance team or vendor to apply a bandage the best they can. This is an absolute injustice to a building that conceptually needs to operate independently for the comfort and safety of its occupants. But even on a more practical note, Band-Aid fixes are temporary, which leads to further patches and systems that become untenable to manage.
Procuring a TAB firm to help assess the existing conditions is an important part of any HVAC building upgrade. Not only will they help identify systems that no longer are working and find ductwork that leads to nowhere, but they also are a vital part of determining whether existing systems have the ability for future capacity planning. When it comes to pre-TAB there are important criteria that should always be considered. One of the first is existing duct integrity; how much of the original duct sealant remains, if any? Are the existing fire or smoke dampers still operational and compliant? These are just two examples of components of the existing HVAC system that are often assumed to be reusable, but in many cases are only partially functional.
FIGURE 2: A commercial heating, ventilation and air conditioning variable air volume terminal that was retrofitted with a new airflow pitot sensing device. Courtesy: Jeremy Johnson, American Testing Inc.
‘ Variable air volume offers pressure independent control and reliability in these applications. Proper TAB is critical and is required after any building automation system controls upgrade.’
FIGURE 3: A high performance, or low flow, laboratory fume hood seen in university buildings. Courtesy: Jeremy Johnson, American Testing Inc.
‘
In the case of an existing laboratory building, open duct chases can be rusted out because of chemical exhaust through the fume hoods that reacts with ductwork installed 30 years ago.’
In the case of an existing laboratory building, open duct chases can be rusted out because of chemical exhaust through the fume hoods that reacts with ductwork installed 30 years ago. These chases need to be examined with cameras, if possible. Static pressure profiles between floors can identify areas of significant static loss.
During the pre-TAB, it is critical to verify that the AHU performance is still intact. Many times, performance values are pulled from old schedules or old TAB reports. In many cases, the report from 30 years ago will not be indicative of current performance. A fresh set of data at the fan must be collected to ensure that the project goals can be accomplished.
Another point of investigation should be the condition of the current energy recovery wheel. How are the seals and brushes? Is the wheel dirty or damaged? This is a great opportunity to meet with the facilities team and review any existing issues that could become hurdles during final TAB. Reviewing existing and known deficiencies allows the entire construction team to be ready for existing challenges in the project(see Figure 4).
Next, the performance at the terminal units needs to be verified on both the air and hydronic sides of the HVAC systems, in conjunction with current controls. During this part of the pre-TAB, building conditions can be noted like accessibility
and serviceability, condition of the control valves, water condition and pipe scaling. With gathering of on-site drawings, HVAC original equipment submittals and other maintenance reports that may also be available. None of this due diligence can be accomplished from a desk and must be part of a field pre-TAB site visit.
Once the on-site visit is conducted and the TAB data has been refreshed, the new design review can be started. This desk review should be inclusive of maximum or peak condition demands for ventilation and minimum flow conditions as well sequence of operation, if the situation calls for it. Modern laboratory HVAC systems have occupancy controls that incorporate proximity sensors on the fume hoods and interaction with GEX (general exhaust registers in the lab) for the purpose of constant pressure control from labs to corridors. Riser airflow diagrams should be compared with contract drawings for the purpose of matching up space discharge cubic feet per minute (DCFM) requirements with the terminal units DCFM serving those areas. Additionally, once verified design feet per minute velocities should be checked for the main and zone ducts to look for possible distribution duct that could be a larger static loss than originally anticipated. During this step it’s also a good idea to look at any diversity that has been built into the new HVAC laboratory design to ensure that the TAB plan incorporates this into its approach for final TAB.
Reviewing the new supply and exhaust fan submittals is an important step to understand the amount of total static pressure the fans can produce. The final step is to make sure the tolerance levels specified that the TAB team will balance to are achievable. Be mindful that sometimes tolerance levels of 5% are not achievable based simply on the terminal units that have been approved for the equipment installed. Terminal units are very accurate when calibrated, however many off the shelf models can only control for a tolerance of +/- 7% to 11%. If these terminal units are applied to a 5% tolerance job it will not work and if found should become a request for information to the design team immediately.
Continued on pg. 38
Discover the advantages www.belimo.com
Belimo’s gas monitors are factory calibrated and measure single or dual gas combinations to help maintain adequate ventilation. The monitors can be used as a standalone system or integrated into a building automation system using BACnet MS/TP.
After all the VAV controls have been modified or replaced and the infrastructure upgrades are complete, the TAB firm can calibrate the new controls and optimize the air system static pressure setpoints and water system differential pressure setpoints.
Controls verification by the TAB firm has great value with the BAS control upgrades for a university teaching laboratory. While the TAB firm is performing the TAB, taking the extra time to verify the controls components and document the conditions can be done during this step. With a BAS controls upgrade, there may not be the same quality assurance as with a new construction process. Having controls verification written into a controls upgrade is valuable to the project and the future of the building.
As filtration of the HVAC duct system and components have evolved over the years, new challenges, such as particulates from forest fires and concerns about coronaviruses, face the industry — requiring higher required filter differential pressures. These frequently have severe consequences on the performance of older fans, especially in a building that was sized for cooling loads decades ago. Measuring the filter differential pressures and comparing to the design provides insight to the performance.
TAB insights
u Testing, adjusting and balancing (TAB) firms are vital for assessing and optimizing complex HVAC systems in lab buildings, which ensures efficient operation and performance.
u Upgrading outdated HVAC controls is essential because of component unavailability. Collaboration between TAB and controls teams is crucial for successful integration and improved system efficiency.
For calibration of the new controls, it’s not just about calibrating the BAS to read the same as the capture flow hood. This process of TAB captures a moment in time that is an important document for future generations to use and benefit from, known as total system balance. Documenting final operating conditions, such as damper positions, component static pressure profile, thermal capacities and motor brake horsepower (BHP) usage are a few of the real measurables on how the HVAC system performance. If the fan motor BHP exceeds the design intent, there may be a bigger issue that needs to be addressed.
Optimizing the pressure setpoints of both air and water has great value in the operating energy of the building. An AHU or engineering fundamentals system that operates with all the air terminal dampers 50% open wastes energy and is not properly set up. For a properly balanced system, the critical run air terminal should be no more than 80%-90% open during a full cooling test. There is usually only one chance to get this right, as the full cooling or max capacity test only happens once.
The specification will sometimes call for TAB planning or project drawings to be completed on as-built drawings. However, this is not realistic because as-built drawings are often not completed or uploaded to today’s construction portals before TAB begins on projects.
Outside air needs to be verified in the peak cooling conditions, at minimum conditions and possibly at some other sequences in between. Today’s buildings operate in more than just minimum and maximum conditions and today’s engineers have developed additional energy saving sequences for different times of the year and regions of the country. Outside air cannot be measured with one reading anymore.
The decision to upgrade building equipment, which is often because of controls, is one that involves a lot more than simple replacement and restart. TAB surveys in advance and early in the design process will help ensure the building owner is satisfied with the investment. cse
Brian Venn, TBE, CxA, Mechanical Testing, Inc. Clifton Park, NY. Jeremy Johnson, TBE, CxA, American Testing Inc., Ellicott City, MD. Thomas Prevish, PhD, PE, CEM, NorthWest Engineering Service Inc., Beaverton, OR.
ON CALL
If you need assistance with sizing or product selection, our team of Application Engineers is ready to assist you. The Rheem Commercial Water family of brands offers a comprehensive product portfolio designed to meet the needs of any commercial project.
Product application sizing charts for all commercial products
2D and 3D support with creation of project quotes showing relevant specifications
Product application sizing and design solutions within 48 hours
By Amara Rozgus, Editor-in-Chief
The 2023 Commissioning Giants provides information on the top 25 firms based on self-reporting for this year’s rankings.
The average percentage of commissioning revenue earned by the 2023 Commissioning Giants was approximately 32.9%, a slight increase from the past reporting year at 30.5% of gross revenue. The top 25 firms earn a great deal of their revenue from commissioning, with four firms earning 100% of their revenue solely from commissioning: Bureau Veritas Primary Integration Inc., Iconicx Critical Solutions, FST-HEA LLC and Rubicon Technical Services.
See Table 1 for the complete ranking, including the six new or previously unranked companies.
For the 2023 report, the top 25 companies made $831.7 million in commissioning revenue, a marked increase from the previous year’s $730 million. The majority (40%) of firms are consultingengineering firms with a commissioning division; about a quarter (24%) are commissioning-focused firms. Firm ownership type fell into four categories: private (32%), public (24%), limited liability company (24%) and employee-owned (20%).
The average commissioning fee per project varied. About a third (32%) of companies earned $100,001 to $300,000, 28% earned $50,001 to $100,000 and 24% earned $25,001 to $50,000. Only 12% earned more than $300,000 per project.
Delivering more flexibility and power in less space!
Get the ultimate in comfort integration with a high-capacity unified platform, for commercial and light commercial applications.
• Expanded outdoor unit capacity, from 6 to 36 Ton
• Larger single module outdoor units – up to 16 Ton
• Up to 26% less space with larger single module outdoor units
• Both Heat Pump and Heat Recovery operation available from one unit
• Increased number of connectable indoor units
• Extended ambient air temperature operating range from -15°F to 126°F
• Intelligent refrigerant control optimizes individual zone comfort
Unified VRF outdoor units allow for heat pump or heat recovery operation for the ultimate in application flexibility.
CSE: What’s the current trend in hospitals, health care facilities and medical campus projects?
John Blanton: Trends in health care continue to move toward shortened stays and increased outpatient procedures. As insurance reimbursement rates change for different types of procedures, so does the type of facilities we are designing and constructing.
For example, when the reimbursement rate for outpatient elective surgeries rose, ambulatory surgery centers become larger and more prevalent. With increased revenue of these facilities, surgeons requested more sophisticated operating rooms (ORs). However, these types of facilities still do not typically have the construction budgets that large hospitals have. Engineers need to be more creative on these types of facilities to meet the requests for things like low temperature ORs that are becoming the norm. These facilities also do not have 24/7 on-site maintenance, so the designs must consider reliability, redundancy and remote monitoring in a limited construction budget.
Brian Evan: Owners are looking at the resilience and performance of their
facilities. These facilities need to function through any emergency, so backup heating sources and power are a must. Because of staffing shortages, designing efficient facilities that are easy to operate is needed to reduce operating costs and maintain functionality. ORs are becoming more sophisticated, especially with robotics involved. To accommodate electrical needs, space and capacity for additional isolation panels and low voltage cabinets need to be accounted for.
Kristie J. Tiller: Many hospitals are at a point where they are no longer seeing an influx of COVID patients. This means they have the ability to strategize and use funds to begin implementing tactical measures that increase effectiveness and safety for another major event. Some of these measures include increased isolation units and new and improved heating, ventilation and air conditioning (HVAC) systems.
Tim Willoughby: Firstly, the industry is experiencing especially long lead times for various hospital equipment. This is forcing owners to make decisions and design to be undertaken earlier to procure equipment. Secondly, increased project
John Blanton, PE
Senior Mechanical Engineer
Certus, Dallas, Texas
Brian Evan, PE Associate
Wold Architects & Engineers, Saint Paul, Minnesota
Associate, Director of Mechanical Engineering Lockwood, Andrews and Newnam, Inc., Dallas, Texas
Tim Willoughby, PE
Mechanical Engineering Principal HDR, Omaha, Nebraska
size and budget are making larger hospital projects more common. While five years ago, a hospital project was considered anything over $300 million, today a large hospital project will typically have a budget of $1 billion or more. Thirdly, smart buildings/equipment and cybersecurity are more and more common. Newer hospital requirements are dictating more sophisticated controls systems, while implementing strategies that consider cybersecurity risks.
CSE: What types of challenges do you encounter for these types of projects that you might not face on other types of structures?
Brian Evan: Hospitals operate around the clock and potential service outages require proper planning. Contractors
FIGURE 1: Operating rooms like this one have specific air pressure, lighting and electrical requirements that create challenges for engineers.
Courtesy: Certus
csemag.com
Health care insights
u Healthcare facilities are shifting towards outpatient procedures and advanced designs due to the demand for more sophisticated and costeffective facilities.
u The COVID-19 pandemic has driven changes in healthcare facilities, promoting flexible design, isolation units and improved HVAC systems to address evolving spatial needs and emergency preparedness.
may have to work during off-hours to install new equipment while existing systems remain operational. This may mean carving out a new electrical room instead of swapping equipment in the same location and extending the outage downtime.
CSE: What are engineers doing to ensure such projects (both new and existing structures) meet challenges associated with emerging technologies?
Tim Willoughby: Even with emerging technologies, there is still a focus on resiliency. Balancing innovation with reliable systems requires an evaluation of pros and cons for each system. While new technologies offer better energy efficiency or greater operational accuracy, they are usually higher in upfront cost and require increased maintenance or higher controls complexity.
Brian Evan:
In both new and existing structures, it’s important to verify the roof’s load-bearing capacity for solar panel installation. Roof obstructions like mechanical units, vents and parapets should be minimized or grouped together to maximize roof space. If roof-mounted panels are not an option, planning for green space on the site is an alternative, however it usually requires more land than the site can accommodate. It’s also important to ensure that the main switchboard has empty conduit and a spare breaker to feed the solar panels.
CSE: How have changes that came about during COVID-19 continued to impact health care facilities or medical campuses?
Kristie J. Tiller: The pandemic helped identify weaknesses in campus facilities. One of the main challenges is ensuring there is flexibility in the use of spaces. The spatial needs of health care facilities are very specific, so changing the usage of each space offers unique opportunities. Engineers and architects work with owners and operators to design flexible facilities, so they are prepared for another major event, can configure facilities as efficiently as possible and maintain the safety of both their patients and staff.
Tim Willoughby: The COVID-19 pandemic caused a shortage of manpower, which led to supply chain shortages and higher supplier and labor costs. With the pandemic seemingly under control, equipment manufacturers are playing catchup with the demand, causing longer lead times. Hospitals also typically aspire to develop an action plan for a
Continued on pg. 46
Greenheck’s eCAPS® online product selection program includes Fan Energy Index (FEI) metrics to help you select fans that meet or exceed ASHRAE 90.1 and state energy code requirements.
Enter a few project requirements and eCAPS® will find and rank the best fans based on cost and performance
Compare FEI metrics side-by-side with sound levels, performance, first cost and operating cost data
Create schedules incorporating FEI, share code-compliant product cut sheets, and download AutoCAD® and Revit® drawings
Continued from pg.
future pandemic. COVID-19 facilitated a knee jerk response, ranging from 100% outside air operation, to makeshift treatment structures, to a triage of patients that needed testing and treatment. These responses created a “lessons learned” playbook for approaches that did and didn’t work. We are now creating strategies that, in collaboration with clients, provide a staged response to design hospitals for the next pandemic.
CSE: How are hospitals, health care facilities and medical campus buildings being designed to be more energy efficient? And, if you have experience in this area, how will new outside air requirements affect this energy efficiency?
John Blanton: For heating systems, we rarely see large steam boilers included in the design for new facilities anymore. Steam systems are costly and inefficient. Maintaining these systems requires maintenance personnel with a high level of experience and expertise, who are hard to find. Most new projects are designed with low temperature heating hydronic boilers that are about 92% more efficient. In addition, we are retrofitting large existing heating systems with high efficiency hydronic boilers. The existing steam systems are downsized to feed only the processes that require steam, such as sterile processing and humidification. Local steam generation for these types of loads can also be evaluated based on total life cycle cost to further reduce the demand for centralized steam.
CSE: Looking ahead with pandemics in mind, how do you think hospitals and health care facilities will be designed? What aspects of the engineered systems will change?
John Blanton: I believe we will see the desire for more dedicated pandemic patient wings and overtly flexible spaces. It generally is not practical to design a negative pressure “pandemic” floor, since typical, non-infectious patient care areas should be positively pressurized. However, pre-pandemic design of a patient floor does not provide necessary flexibility. Designs must allow areas to switch to a negative pressure pandemic mode when needed. These designs require additional equipment and may require upsizing of cooling coils to handle additional outside air. Control systems and sequences will become more complex to provide a cascading airflow between staff and patient spaces. Additional protective securities must be in place to ensure the areas are not inadvertently placed into the wrong mode.
Kristie J. Tiller: The most significant change in health care facilities is the trend toward isolation units. In our projects, we see entire hospitals augmenting their HVAC systems. The medical facilities being designed and renovated are increasing natural ventilation and introducing technology to ensure cleaner air is entering and being recirculated in each space. Hospitals are now funneling more resources and design thought to isolating pandemic patients and treating them in separate quarters. cse
‘ Each reporting firm completed, on average, 371 projects in the previous reporting year, up from 320 commissioning projects (at any level) in 2022.’
Continued from pg. 41
This data reflects commissioning at all levels: new buildings (46%), whole building (13%), emergency power systems (6%), existing buildings (7%), retro-commissioning (6%), building enclosure (envelope, 5%), monitoringbased (3%), fire protection systems (3%), recommissioning (3%) and communications systems (2%). Each reporting firm completed, on average, 371 projects in the previous reporting year, up from 320 commissioning projects (at any level) in 2022.
The average percentage of commissioning revenue earned by these firms fell into a few key building types:
• Data centers: 32%, a drop from 40% last year.
• Hospitals/health care facilities: 6%, a drop from 14% last year.
• Government or military facilities: 12% (no change).
csemag.com
• Office buildings: 6%, a drop from 12% last year. cse Visit www.csemag.com/giants for the full Commissioning Giants report.
Trane® / Mitsubishi Electric VRF heat pumps and heat-recovery systems are strategic electrification solutions that contribute to the greater drive towards the decarbonization of HVAC systems. Trane has an extensive portfolio of innovative VRF products and a team of knowledgeable advocates committed to sharing their expertise. With lower emissions, greater energy efficiency and more optimal use of your building’s space, Trane helps engineers take the benefits of VRF technology further.
Products you can count on, expertise you can trust.
• The right VRF portfolio options for any project, anywhere
• Dedicated VRF applications engineers to help you design comprehensive VRF systems
• On-demand and real-time training for design resources
• Pre-engineered system controls and building automation solutions
SPEC US ON ARCAT
Small footprint, big impact
• UL 924 Listed. Supports Normal and Emergency circuits.
• 120 VAC and 277 VAC
• DMX control for Relay or 0-10V
visual environment technologies etcconnect.com
ADVERTISEMENT
Case studies provide valuable discovery of challenge situations, recommended solutions, and implementation actions to solve specific real-life issues.
CSE magazine invites you to explore the pages to follow while you learn and benefit from the case study success stories and project details shared by the following companies:
Berner International
ABB Motors and Mechanical
Inaba Denko
Noritz
BQE Software
Camus Hydronics
Champion Fiberglass
Cleaver-Brooks
Greenheck
Rheem Commercial Water
Ruud Commercial Air
Trane
Viking Group
challenge: A leading multi-national pharmaceutical packaging corporation sought to implement more environmentally sustainable processes and technologies in its manufacturing facilities, in part by upgrading to more efficient motors.
solution: The company purchased one highly efficient Baldor-Reliance ® EC Titanium™ motor to test against the motors currently running in its plants. The test demonstrated a significant reduction in energy consumption while lowering operating costs, potentially providing a full return on investment in less than two years.
Result: The company purchased additional EC Titanium motors for immediate installation on its high-priority production lines and is in discussions to upgrade all lower-efficiency motors in its main manufacturing facility.
summaRy: This company, with more than 4,500 employees in 140 locations worldwide, has taken a leadership approach to the development of cleaner processes and technologies, including construction of what will be the world’s greenest-ever pharmaceutical plant. Company leadership understands that a large portion of the world’s electricity is used to power electric motors, and upgrading to high-efficiency motors will help reduce energy consumption and environmental impact while lowering costs.
By incorporating new technologies, ABB’s motor system achieves a high level of energy efficiency while using sustainable materials. The packaging company purchased one EC Titanium motor to test against current lowerefficiency motors, and the benefits were instantly recognizable. EC Titanium achieved an energy reduction of 12.59 kWh per day, translating to a cost savings of $520 per year, per motor. This cost savings would realize a complete return on investment in less than two years, while greatly reducing energy usage and environmental impact.
It has been estimated that replacing 80 percent of motors currently in operation around the world with newer technologies that achieve higher efficiency levels could save more than 160 terawatt-hours of electricity each year and cut total global electricity consumption by as much as 10 percent.
479.646.4711
baldor.abb.com
Challenge: High temperatures and humidity in South Carolina, along with constant foot traffic leaving the doors open, led to sweltering indoor temperatures of 85° F and above along with soaring utility bills. Customers thought the AC was broken.
Solution: Berner air curtains over the entrances to keep heat out and AC in when doors are open.
reSult: The 16,000 sq ft indoor facility now maintains year-round temperatures of 70-72°F, resulting in a 20% sales increase attributed to customer comfort and $20,000 annual utility savings.
Summary: Charleston Fun Park, a popular indoor/outdoor family entertainment center in South Carolina, faced challenges with sweltering indoor temperatures and soaring utility bills due to frequent hot and humid weather combined with high foot traffic. To combat this, they installed four Berner air curtains over the main entrances, effectively maintaining indoor temperatures at a comfortable 70 to 72°F year-round as visitors passed through the doors. This energy-efficiency upgrade resulted in annual utility cost savings of approximately $20,000.
The improved indoor temperature also led to a 20% increase in sales within the first year after installation. The indoor facility, housing virtual reality, an arcade, ticket staging, snack area, and restrooms, was previously plagued by high temperatures. The air curtains transformed it into a cool and comfortable space. Customers stayed longer and spent more on gaming. The air curtains not only helped retain current customers but also attracted new ones, as the park’s reputation for comfort and enjoyment grew.
Besides energy savings and comfort, the air curtains also facilitated compliance with health codes in the snack area.
In summary, Charleston Fun Park achieved substantial utility savings, improved indoor comfort, and increased revenue thanks to the Berner air curtains.
Challenge: Infinity Engineering grappled with scaling and reporting issues using their previous big-name software. Amidst growth and escalating project complexity, they needed a more adaptable and efficient time and expense tracking and project management solution.
Solution: After evaluating 8 different solutions, they found quickly generating invoices and improving cash flow gave BQE CORE a distinct advantage. Its reporting capabilities and customization options accelerated the implementation process. The BQE CORE app’s touch-to-talk option made getting in touch with support quick and painless.
ReSult: The changeover was seamless for Infinity’s team, and the time savings, coupled with more efficiency in both systems and processes, have been of immeasurable value, allowing their firm to scale and grow.
SummaRy: Navigating a trajectory of growth and increasingly intricate projects, Infinity Engineering found themselves constricted by the limitations of their then-PSA software, Deltek, particularly in scalability and report customization. As the firm augmented both in staff and project complexity, a discernible gap appeared in their ability to efficiently generate custom reports and meticulously track nonbillable and administrative hours.
The transition to BQE CORE marked a pivotal transformation, unlocking a multitude of capabilities tailored to their needs. BQE CORE allowed them to leverage enhanced scalability, access and formulate one-off and scheduled reports with ease, and attain granular control over the entire team’s billable hours.
Furthermore, they exploited additional utilities for comprehensive customer data querying and an ‘Active History’ function that fortified their time and expense management strategies. This shift not only streamlined their operational workflow, but also embedded a robust platform that could pivot and adapt in tandem with their evolving requirements, ensuring that Infinity Engineering remained equipped with a potent tool that aligned seamlessly with their commitment to delivering unparalleled products and services to their clients.
Sales@bqe.com • 866-945-1595 www.bqe.com
Challenge: To design and install a reliable and efficient heating system for a new middle school building in Alberta, Canada, that also met environmental standards.
Solution: A custom-built, prefabricated skid with two Camus Hydronics Avenger ® 4000 MBH firetube boilers was selected for its high efficiency and low emissions with a 25:1 turndown ratio.
ReSult: The new Avenger boilers reduced both energy bills and greenhouse gases and simplified installation and maintenance. In addition, the new system continues to provide safe, uniform heating throughout the building for student and staff comfort.
SummaRy: A school system located in Alberta, Canada, needed a reliable, efficient heating system for its new middle school building. Constructed in 2023, the new school replaced an existing building that was demolished due to structural concerns. The challenge was to design a system to heat a gymnasium and classrooms serving 600 students while complying with environmental standards.
After considering specifications and background information provided by the school’s engineering team, Camus developed solution recommendations to meet customer needs. The school opted for a custom-built, prefabricated skid with two Camus Hydronics Avenger 4000 MBH firetube boilers, supplied by Camus representative Wesmech Sales. The project contractor was Dee-Jay Plumbing & Heating, an established Alberta company.
The Avenger firetube boilers are hydronic heating units that use water as the heat transfer medium. Designed to provide high efficiency and low emissions with a 25:1 turndown ratio, these boilers modulate their output according to demand. They are equipped with a stainless steel heat exchanger, variable-speed combustion air blower, and a digital control panel.
Avenger boilers deliver significant energy savings by operating at peak efficiency throughout the heating season, and they reduce the school’s carbon footprint by emitting less greenhouse gases than conventional units. These boilers simplify installation and maintenance as they are preassembled on a skid and feature removable side and front panels for easy access.
Available in sizes up to 6000 MBH, Avenger boilers are suitable for schools, hotels, hospitals, offices, and multi-residential buildings.
Challenge: There were supply disruptions and rising material costs at the time of the project. Long lead times were affecting project timelines. Also, the wind farm project involved a complex buried installation requiring minimal disruption.
Solution: This project necessitated a strong and durable conduit capable of adequately protecting transmission lines to the grid. As an alternative to PVC, Champion Duct® was available with shorter lead times. It proved more cost-effective than comparable conduit, improving bottom lines.
ReSult: This project benefited from on-time product procurement and lower material and installation costs. Plus, its complex installation was made easier with lightweight, easy to maneuver electrical conduit and customized help from Champion Fiberglass.
SummaRy: South Fork Wind Farm is New York’s first offshore wind farm. It consists of 12 turbines and a state-of-the-art transmission system that will generate enough clean energy to power 70,000 homes and offset tons of emissions each year. Located 35 miles east of Montauk Point, the underground transmission line will deliver power to the local grid in the town of East Hampton.
Champion Duct®’s high dielectric strength protects cables along four miles of trenched installation delivering power via a single, 138kV alternating current (AC) transmission line.
The project involved a complex installation with unique requirements including open trench excavation along four miles of railway and roadway, buried duct banks and use of conduit spacers. Lightweight Champion Fiberglass® conduit was easy to maneuver into the trenches. (Alternative conduit types such as PVC would have been heavier.) Also, Champion Fiberglass created custom bends that were helpful at certain points of the install.
Better product availability, the conduit’s light weight and ease of installation helped facilitate an on-time, successful completion. Finally, lower material and installation costs helped the project stay within budget.
Tel: 281.655.8900
communications@championfiberglass.com
Championfiberglass.com
Challenge: To identify a reliable condensing boiler to meet sub-30 ppm NOx emissions for boilers between 2,000 MBH and 5,000 MBH at a tech company’s California campus.
Solution: Cleaver-Brooks ClearFire® -CE fully condensing firetube boilers’ proprietary heat exchanger technology met the customer’s requirements of low NOx emissions, high efficiency, reliability, and longevity. The custom-designed outdoor skid, including protective features like a rain hood, made these boilers ideal for the campus
ReSult: Eighteen outdated boilers were replaced in just six weekends, offering reduced natural gas consumption, lower operating expenses, and whisper-quiet operations.
SummaRy: A tech company’s California campus has emerged as a shining example of environmental responsibility. Facing stringent regulations, they sought a solution that would meet the Bay Area Air Quality Management District’s requirement of sub-30 ppm NOx emissions for boilers between 2,000 MBH and 5,000 MBH.
R.F. MacDonald Co., a Cleaver-Brooks representative based in Hayward, Calif., was the key collaborator for this transformation. The company recommended Cleaver-Brooks ClearFire® -CE (CFC-E) fully condensing firetube boilers due to their low NOx emissions, high efficiency, reliability, and longevity. A custom-designed outdoor skid made these boilers ideal for the campus.
Eighteen outdated boilers were replaced in six weekends, offering reduced natural gas consumption, lower operating expenses, and whisper-quiet operations. The customer’s commitment to a sustainable future serves as a beacon for businesses looking to align with evolving environmental standards.
Environmental sustainability is a pillar of Cleaver-Brooks boiler room solutions and continues with our latest generation CFC-E high-mass, fully condensing boilers. They offer exceptional performance by utilizing proprietary TurboFer ® heat exchanger technology that achieves up to 99% efficiency. The ClearFire-CE with TurboFer design creates turbulent flow in the tubes engineered with an expanded heat transfer surface area to deliver unmatched heat transfer and condensing performance.
Count on Cleaver-Brooks to provide safe, reliable, and efficient condensing hydronic boilers that ensure the heat transfer is done right.
Challenge: Improve temperature control for employee comfort and regulate moisture to prevent condensation in a wholesale florist greenhouse.
Solution: Two Greenheck DC-5 overhead HVLS fans installed in the greenhouse addition provide much needed air movement making the facility comfortable for employees and healthier for plants.
ReSult: In addition to creating a more comfortable environment, the fans also provide increased evaporation that has helped decrease mold, mildew, and other disease issues with the plants. The plant scrap level has decreased dramatically while inventory and spoilage have greatly improved.
SummaRy: A 24,300-square-foot greenhouse addition constructed at the Krueger Wholesale Florist distribution facility houses thousands of potted plants that have been transported to the Wisconsin facility from Florida, California, and Washington State. The addition acts as a holding facility for the plants that are then delivered to Krueger’s retail and grocery store customers throughout the Midwest.
The greenhouse includes 80 skylights to help the plants get needed sunlight. However, the sunlight can make the space uncomfortably warm for employees, especially during the summer months. (A typical outdoor greenhouse can reach 110oF inside.) In addition, the combination of sunlight with the daily watering of plants makes the space very humid.
An air conditioning system installed in the greenhouse addition did not provide enough air movement throughout the space to maintain comfort and moisture control.
Two Greenheck DC-5 HVLS fans installed in the greenhouse operate continuously providing additional air movement that helps keep the addition at a comfortable 72oF. The humidity levels in the space are higher in the morning due to the daily watering of the plants, however, the fans also help manage the humidity for a more comfortable environment. The plants can last up to two weeks in the greenhouse addition as the overhead fans allow the facility to mimic more of a home environment.
info@greenheck.com • 715-359-6171 www.greenheck.com
Challenge: VRF installation on the rooftop was exposed to the elements and needed a way to protect the multiple lines while allowing for easy repair and maintenance.
Solution: Slimduct RD, an innovative metal lineset enclosure, was chosen to protect the lines from mechanical and weather damage.
ReSult: The Slimduct RD provided the needed protection for the lines, plus protection for the communication lines, eliminating the need to run a separate conduit. The proper enclosure of the lines, using Slimduct RD adds a beautiful finish and look to the rooftop.
SummaRy: Meadowbrook Place in Ontario, Canada is a high-rise complex designed to provide energy-efficient housing for low-income tenants. The complex uses VRF systems for heating and cooling. Daily Commercial News calls it “Ontario’s largest passive house.”
Protecting the refrigerant pipes is very important. Especially in areas with extreme temperatures or other conditions that could harm the system’s performance and equipment lifespan. This is because insulation can degrade and copper pipes can oxidize.
This projected consisted of the installation of nine outdoor units, rooftop, with each unit serving 16 indoor units per floor. The Slimduct RD was used to protect the refrigerant lines.
“The RD series Slimduct was very important on this project because it provides that protection for our refrigeration lines, especially from UV rays that can deteriorate those refrigeration lines over time. It also provided protection for our communication lines, so we didn’t have to run a separate conduit on those refrigeration lines to each one of these units,” said Travis Gerard of Bryant Heating & Air Conditioning.
Slimduct RD is a strong commercial covering system that can enclose many refrigeration pipes and other system-related items like wiring. The cover is made of metal, and has a coating of zinc, aluminum, and magnesium to prevent corrosion and scratches.
Slimduct RD is more durable and lighter than other metal enclosures.
Oahu Correctional Center safeguards hot water supplies by replacing aging boilers with Noritz tankless water heaters.
Challenge: Replace two failing 23-year-old 1,000,000 BTU boilers with a multi-tankless commercial heater system at Hawaii’s Oahu Community Correctional Center to safeguard reliable hot water supplies for its 1,200 inmates.
Solution: Installed six NCC199CDV gas-fired commercial condensing tankless heaters to improve the resiliency and reliability of the correctional facility’s hot water supply system.
ReSult: Besides providing an uninterrupted flow of hot water, the multiple-tankless option offers the ability to service any of the six units without shutting down the entire system. Furthermore, load balancing ensures that operation is equalized across all units, so one doesn’t suffer undue wear and tear.
SummaRy: Officials at the Oahu Community Correctional Center (OCCC) in Honolulu were faced with a hot water crisis when their aging boilers and storage tanks failed, posing a risk to staff and inmate hygiene. To address this essential need for hot water, a solution was urgently devised in partnership with Hawaii Gas. They decided to replace the failing boilers with a system of commercial condensing tankless water heaters to ensure a continuous and reliable hot water supply.
The project was executed in three phases to accommodate the facility’s 24/7 operations. The first phase involved installing six gas-fired commercial condensing tankless heaters to serve a portion of the inmate housing modules. The second phase added two prefabricated water heater banks to provide hot water to the remaining inmates. The final phase introduced 12 more tankless units to support the center’s laundry and kitchen operations, ensuring redundancy and uninterrupted hot water supply.
The choice of tankless water heaters, specifically the Noritz NCC199CDV models, offered higher energy efficiency, greater flexibility in meeting demand, and significant cost savings compared to traditional boilers. With a focus on operational redundancy, this approach ensures a continuous supply of hot water even if one or two units are temporarily offline.
Cl IC k or scan QR to download the study.
The installation of tankless water heaters eliminated the need for bulky storage tanks, simplified maintenance, and significantly reduced operating costs, offering a reliable and efficient hot water solution for OCCC. commercial@noritz.com
Challenge: Looking to modernize its operation, Olson’s Greenhouse of Colorado sought to replace its existing heat system. The owners wanted to install a more efficient, cost-effective and reliable option for their business.
Solution: Olson’s installed a new system powered by Raypak®, a division of Rheem Commercial Water, using their XTherm Condensing and MVP non-condensing boilers.
ReSult: By replacing the old steam heat system with Raypak Boilers, Olson’s Greenhouse has upgraded to a more reliable system that can be easily monitored by greenhouse staff. Additionally, Olson’s goal was to increase efficiency. The previous steam system ran at 45% efficiency, the new Raypak boilers operate at efficiencies up to 97%. Beyond aiding with reliability and efficiency, the new system also saved Olson’s money by significantly reducing any downtime and impact on their plants.
SummaRy: With 13 acres, Olson’s Greenhouse of Colorado is a renowned grower of flowers and bedding plants for regional wholesalers. Olson’s Greenhouse operations have moved into the modern era by upgrading their old steam heat set-up with a new modulating, high-efficiency boiler system.
Working with BioTherm, an exclusive partner for Raypak boilers in the greenhouse market, Olson’s revamped its system, installing numerous Raypak products including one condensing boiler alongside four non-condensing boilers.
With this new, easy-to-use Raypak system up and running, Olson’s staff was afforded a newfound peace of mind. Now, if the system requires servicing, individual units can be isolated from the heating system without having to worry about major malfunctions or having to shut the whole system down, which can have major impacts on their plants and flowers. Plus, the system provides Olson’s with beneficial cost savings through reduced gas usage.
Additionally, with Olson’s new heat system minimizing downtime thanks to redundancies created by the boiler operation, the greenhouse staff noted they have seen faster plant rooting times and more consistent plant growth, helping their business’s bottom line.
Email Tim Badger, Commercial Product Support Specialist at: Tim.Badger@Rheem.com www.rheem.com/commercial-hot-water
Challenge: The multiuse, 31,500-square-foot church building did not have heating and air conditioning that kept all areas of the building comfortable.
Solution: Focus Heating & Cooling and Mar-Hy Distributors built an HVAC system that featured almost 100 tons of equipment across nine units from Ruud, including Renaissance™ and Resolute™ commercial packaged units, to deliver ultimate comfort.
ReSult: The new HVAC system included zoning the building’s two floors separately for better control. The building’s temperatures are now balanced across the two floors. No matter where you are, the Ruud system provides comfort to every person who walks through the church’s door.
SummaRy: In Salem, Oregon, Trinity Covenant Church brings together around 120 people on any given Sunday. But in the community, they help so many more. From resources for the homeless to free after-school programs, the church is a pillar of Salem.
The only problem: The church building itself did not have a working HVAC system that offered balanced, comfortable temperatures throughout the multiuse space.
With a large foyer, sanctuary, classrooms, community gym and offices across two floors, the building had been zoned for the north and south, so the two floors were controlled by one piece of equipment. The result was that the classrooms on the upper level would routinely reach 80 degrees, while the offices below would freeze.
Local contractor Focus Heating & Cooling partnered with Mar-Hy Distributors to install almost 100 tons of equipment from Ruud Commercial Air, including Renaissance™ and Resolute™ commercial packaged units. With installability and serviceability top of mind, the Ruud equipment was an easy choice.
With the church’s new HVAC system, the building was rezoned to better meet the needs of both levels. The result is comfortable, balanced temperatures throughout the church, creating a welcoming gathering space for the Salem community.
Challenge: Built in 1956, the school needed a system upgrade that would provide flexibility in temperature control, reduce classroom noise and lower costs without massive renovation.
Solution: The school selected a Trane® /Mitsubishi Electric VRF system that allowed for simultaneous heating and cooling across different zones, providing for temperature control in each classroom, increased overall efficiency, and ease of use for school staff.
ReSult: After installation, the school was able to reduce utility bills by one-third, convert the existing boiler room into additional conference room space, and ultimately create a more comfortable and energy efficient space where teachers have control of their individual learning environments.
SummaRy: St. James Catholic School has been a staple in its Oklahoma City community since it was built, serving age three through eighth grade. They have created a community over the last 50 years, but the building itself had aged less than gracefully.
Teachers, students, and administrators alike had long struggled with climate-related issues in the building. Teachers would struggle to balance the classroom temperature or be heard over loud noise from the unit. The school needed a system that could help keep rooms climate controlled, reduce disruptive noise, and lower costs without damaging the character of the older building.
The Trane® /Mitsubishi Electric VRF system was able to transform the school into a comfortable learning environment for everyone. The system can centrally heat and cool while requiring less renovations due to less piping and ductwork. It also allows for temperature control in each classroom, higher efficiency, and greater ease of use. The upgrade provided the school an opportunity to eliminate the old boiler and repurpose the space as a fully functioning conference room.
In addition, teachers can easily adjust the fan speed, direction and temperature from their individual classrooms, allowing the school to get back to what matters most: their students.
Cli C k or scan the QR to read full Case Study.
www.trane.com
Challenge: To protect a proposed atrium with a multi-story glass wall and floating stairs along the side with window sprinklers.
Solution: Viking conducted a series of spray pattern coverage demonstrations of the VK960 Vertical Sidewall Sprinkler when installed on 24° and 30° slopes.
ReSult: The testing proved that there was total coverage of the glazing at all pressures and at both slopes, however, the 30° slope had slightly more impact than the 24° slope in overspray from the middle sprinkler, and a more significant rundown of water on the underside of the slope onto the sprinkler stub.
SummaRy: Three VK960 Vertical Sidewall Window Sprinklers were installed to spray on the glazing at a distance of 4 inches from the surface of the glazing. The rig was set so that the slope of the sprinklers could be adjusted from 24° to 30°.
A baffle was placed between the top sprinkler in the horizontal position and the middle sprinkler. No baffle was placed between the middle sprinkler and the lower sprinkler.
As a result of the observations, a baffle was located between the lower and middle sprinkler approximately 24 inches up the slope from the lower sprinkler. During the initial demonstrations, this appeared to be where the sprays of the lower and middle sprinklers collided.
It was observed that this baffle had a significantly positive impact on protecting the lower sprinkler from the spray of the middle sprinkler at both 7 psi and 12 psi but most significantly at 7 psi.
2024 AHR EXPO
.47 .www .ahrexpo .com
ABB Motors US .2 .www .new .abb .com/motors-generators
BELIMO .1, 37 .www .belimo .com
BERNER AIR CURTAINS .40 .www .Berner .com
Bradley Corp .27 .http://bradleycorp .com/digital-mixing-valve
CAMUS Hydronics Ltd . .C-3 www .camus-hydronics .com/HigherTurndownHydronics
CleaverBrooks .4 .www .CleaverBrooks .com/HeatTransferDoneRight
CYBER SCIENCES .33 .www .cyber-sciences .com
Electro Static Technology Inc .20 .www .est-aegis .com/resources/case-studies ETC .50 .www .etcconnect .com
Fujitsu General America, Inc .42 .www .fujitsugeneral .com
Greenheck .45 .www .greenheck .com
Hammond Power Solutions .48 .www .hammondpowersolutions .com
IEC . . . . . .23 .www .iec-okc .com/EnviroKIT
Navien, Inc . .13 .www .Navien .com
Pritchard Brown .48 .WWW .PRITCHARDBROWN .COM
PVI Inc . . . . . . . .22 .www .pvi .com
Reliable Controls .C-2 www .reliablecontrols .com
Rheem Commercial Air .21 .www .RheemCommercial .com
Rheem Commercial Water .39 .www .rheem .com/commercial-hot-water
Tjernlund Products . .64 .www .tjernlund .com
Trane . . . . . . . . . . . . . . .49 .www .trane .com/vrf
ULINE . . . . . . . . . . . . . . . . .50 .www .uline .com
Yaskawa America, Inc . . . . .C-3 www .yaskawa .com
Publisher/Midwest
Matt Waddell MWaddell@CFEMedia.com PO Box 471 312-961-6840
Downers Grove, IL 60515
Account Manager
Robert Levinger RLevinger@cfetechnology.com 630-571-4070 x2218
West, TX, OK
Aaron Maassen AMaassen@CFEMedia.com Integrated Media Manager 816-797-9969
Northeast
Richard A. Groth Jr. RGroth@CFEMedia.com 12 Pine Street 774-277-7266
Franklin, MA 02038
Director of Content Marketing Solutions
Patrick Lynch PLynch@CFEMedia.com PO Box 471 847-452-1191
Downers Grove, IL 60515
Marketing Consultant
Brian Gross BGross@CFEMedia.com PO Box 471 630-571-4070 x2217
Downers Grove, IL 60515
Jim Langhenry, Co-Founder and Publisher, CFE Media JLanghenry@CFEMedia.com
Steve Rourke, Co-Founder, CFE Media SRourke@CFEMedia.com
McKenzie Burns, Marketing-Events Manager MBurns@cfemedia.com
Courtney Murphy, Marketing and Events Manager CMurphy@cfemedia.com
Paul Brouch, Director of Operations 630-571-4070 x2208, PBrouch@CFEMedia.com
Rick Ellis, Audience Management Director 303-246-1250, REllis@CFEMedia.com
Michael Smith, Creative Director 630-779-8910, MSmith@CFEMedia.com
Michael Rotz, Print Production Manager 717-422-3622, mike.rotz@frycomm.com
Maria Bartell, List Rental Account Director Infogroup Targeting Solutions 847-378-2275, maria.bartell@infogroup.com
Claude Marada, List Rental Manager 402-836-6274, claude.marada@infogroup.com
Letters to the Editor: Please e-mail your letters to ARozgus@CFEMedia.com
Letters should include name, company, and address, and may be edited for space and clarity.
Information: For a Media Kit or Editorial Calendar, go to https://www.csemag.com/advertise-with-us/ Marketing consultants: See ad index.
Custom reprints, electronic: Paul Brouch, PBrouch@CFEMedia.com
TM Technology and
External events influencing power quality can interrupt equipment and cause failure of electrical components. A lack of redundancy potentially puts patient care at risk. For example, a lightning strike or even a planned generator test could interrupt delivery of critical air to an operating room.
Our HV600 Redundant VFD Solutions help to insure that these external events are one less thing to worry about. They provide seamless automatic switchover during the primary failure of any fan, pump, chiller, or cooling tower application.
Yaskawa has over 35 years experience in delivering quality HVAC VFD solutions and our products are built in U.S.A.
Want to learn how Yaskawa benefits healthcare? Call us today.
5000 & 6000 MBH
The Avenger® Series II is an advanced two-pass, counter-flow
firetube commercial boiler, providing efficient hot water for demanding commercial needs.
» Industry-leading 40:1 turndown
» Thermal efficiencies of up to 96%
» Designed for today’s higher turndown variable primary and low pressure systems
» 3 to 4 week lead-time with stock units available for quick ship