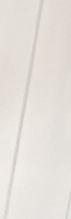
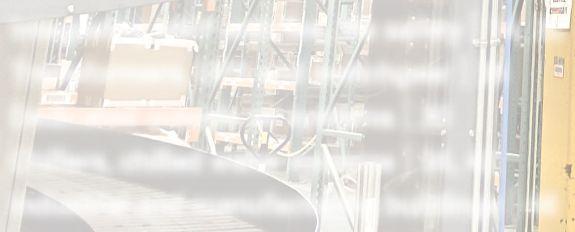
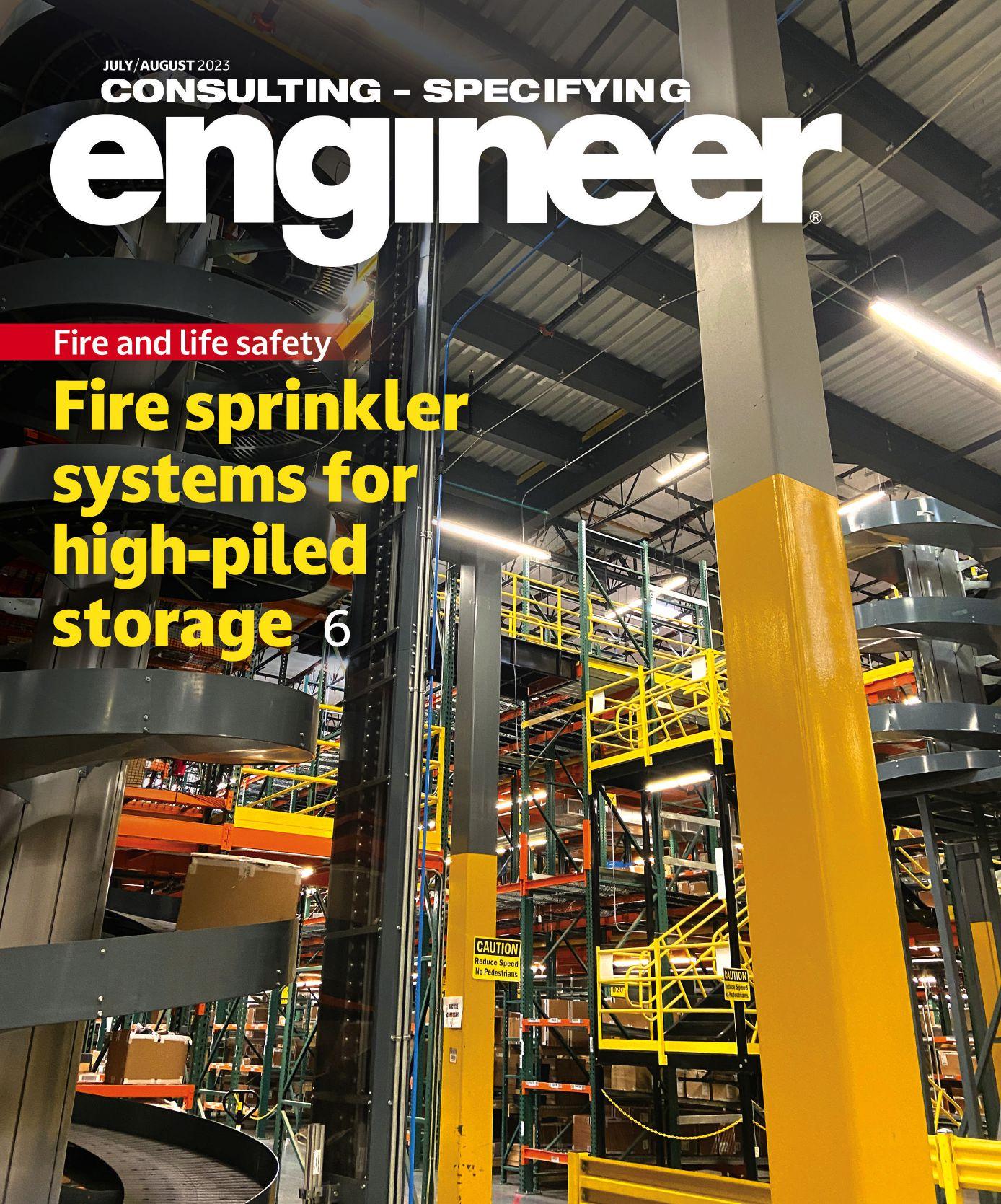

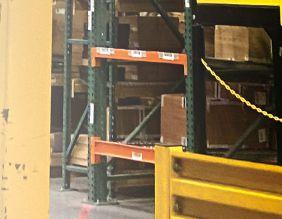

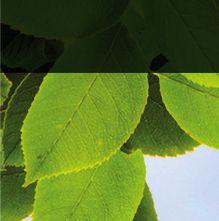
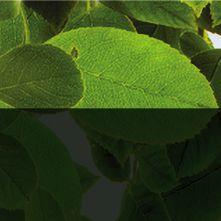
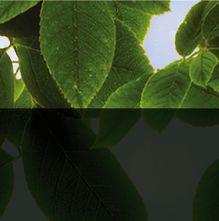
According to the World Green Building Council, we spend 90 percent of our time indoors. Given that statistic, it’s clear the quality of the air we breathe in buildings can dramatically impact our health and well-being. At Reliable Controls we believe sustainable buildings are a key component to reducing the health and environmental impacts of indoor and outdoor air pollution.
Learn more reliablecontrols.com/IAQ
• Navien cascade system continuously matches operation to demand
• Meets temperature demands up to 185°F
• Redundancy allows servicing one unit, while others handle demand without interruption
• Cascade up to 32 units and common vent up to 12 units
• Navien EZNav™ multi-line intuitive control for easy set up and diagnostics
• Same day easy to install Navien Ready-Link® manifold system for wall or rack mounting
To learn more, visit Navieninc.com.
Sustainable non-toxic environmentally friendly components
Plug and play
Quick and easy motor and drive set-up
A greener solution
Reduce your power consumption with industry leading rotor technology
Upgrade to ABB’s Baldor-Reliance® ultra-premium EC Titanium™ integrated motor drive, and lower your overall energy cost. These motors are specifically designed for VFD operation that help optimize overall performance at reduced speeds and loads, ideal for fans, pumps, and compressors.
•More than 10% efficiency gains compared to NEMA premium
•Reduce power consumption by 25%
•Higher power density for a smaller footprint
Efficient. Innovative. Environmentally friendly. baldor.abb.com/ec-titanium
5 | Do you need to move your firm to another country to recruit the right talent?
Are you nervous about being unable to fill your next engineering opening? You’re not alone
6 | How to design fire sprinkler systems for high-piled storage
Learn the fire sprinkler code and requirements for high-piled storage systems design
14 | How to design mechanical fire protection systems
A clarifying framework for understanding both active and passive fire protection systems
20 | A team approach for integrating MEP systems with fire, life safety
Successful mechanical, electrical and plumbing integration with fire and life safety systems
26 | Transformer, switchgear and UPS design considerations
Engineering decisions to consider when designing a power distribution system
30 | Back to basics: Introduction to dedicated outdoor air systems
Outdoor air is an important component of a building’s overall health and well-being
36 | Heat recovery chillers can help recover valuable, rejected heat
Chillers also can be considered as part of the heating system, minimizing lost heat
42 | Where and how to specify pressure-independent control values
Commercial hydronic systems are generally reliable and efficient
48 | Automation, sustainability drive manufacturing buildings
Automation, logistics,
IL 60069. Telephone: 630-571-4070. E-mail: cse@omeda.com. Publications Mail Agreement No. 40685520. Return undeliverable Canadian addresses to: PO Box 348, Lincolnshire, IL 60069. Email: cse@omeda.com. Rates for nonqualified subscriptions, including all issues: USA, $120/yr; Canada/Mexico, $150/yr (includes 7% GST, GST#123397457); International air delivery $260/yr. Except for special issues where price changes are indicated, single copies are available for $30 US and $35 foreign. Please address all subscription mail to CONSULTING-SPECIFYING ENGINEER, PO Box 348, Lincolnshire, IL 60069. Printed in the USA. CFE Media, LLC does not assume and hereby disclaims any liability to any person for any loss or damage caused by errors or omissions in the material contained herein, regardless of whether such errors result from negligence, accident or any other cause whatsoever.
ON CALL
If you need assistance with sizing or product selection, our team of Application Engineers is ready to assist you. The Rheem Commercial Water family of brands offers a comprehensive product portfolio designed to meet the needs of any commercial project.
Product application sizing charts for all commercial products
2D and 3D support with creation of project quotes showing relevant specifications
Product application sizing and design solutions within 48 hours
AMARA ROZGUS, Editor-in-Chief/Content Strategy Leader ARozgus@CFEMedia.com
CHRIS VAVRA, Web Content Manager CVavra@CFEMedia.com
ANNA STEINGRUBER, Associate Editor ASteingruber@CFEMedia.com
AMANDA PELLICCIONE, Director of Research APelliccione@CFEMedia.com
MICHAEL SMITH, Creative Director MSmith@CFEmedia.com
DARREN BRUCE, PE, LEED AP BD+C, Director of Strategic Planning, Mid-Atlantic Region, NV5, Arlington, Va.
MICHAEL CHOW, PE, CEM, CXA, LEED AP BD+C, Principal, Metro CD Engineering LLC, Columbus, Ohio
TOM DIVINE, PE, Senior Electrical Engineer, Johnston, LLC, Houston
CORY DUGGIN, PE, LEED AP BD+C, BEMP, Energy Modeling Wizard, TLC Engineering Solutions, Brentwood, Tenn.
ROBERT J. GARRA JR., PE, CDT, Vice President, Electrical Engineer, CannonDesign, Grand Island, N.Y.
JASON GERKE, PE, LEED AP BD+C, CXA, Mechanical Engineer, GRAEF, Milwaukee
JOSHUA D. GREENE, PE, Associate Principal, Simpson Gumpertz & Heger, Waltham, Mass.
RAYMOND GRILL, PE, FSFPE, LEED AP, Principal, Ray Grill Consulting, PLLC, Clifton, Va.
DANNA JENSEN, PE, LEED AP BD+C, Principal, Certus, Carrollton, Texas
WILLIAM KOFFEL, PE, FSFPE, President, Koffel Associates Inc., Columbia, Md.
WILLIAM KOSIK, PE, CEM, LEED AP BD+C, BEMP, Senior Energy Engineer, Oak Park Ill.
KENNETH KUTSMEDA, PE, LEED AP, Engineering Manager, Jacobs, Philadelphia
JULIANNE LAUE, PE, LEED AP BD+C, BEMP, Director of Building Performance, Mortenson, Minneapolis
DAVID LOWREY, Chief Fire Marshal, Boulder (Colo.) Fire Rescue
JASON MAJERUS, PE, CEM, LEED AP, Principal, DLR Group, Cleveland
BRIAN MARTIN, PE, Senior Electrical Technologist, Jacobs, Portland, Ore.
BEN OLEJNICZAK, PE, Senior Project Engineer, Mechanical, ESD, Chicago
GREGORY QUINN, PE, NCEES, LEED AP, Principal, Health Care Market Leader, Affiliated Engineers Inc., Madison, Wis.
BRIAN A. RENER, PE, LEED AP, Principal, Electrical Discipline Leader, SmithGroup, Chicago
SUNONDO ROY, PE, LEED AP, Director, Design Group, Romeoville, Ill.
JONATHAN SAJDAK, PE, Senior Associate/Fire Protection Engineer, Page, Houston
RANDY SCHRECENGOST, PE, CEM, Austin Operations Group Manager/Senior Mechanical Engineer, Stanley Consultants, Austin, Texas
MATT SHORT, PE, Project Manager/Mechanical Engineer, Smith Seckman Reid, Houston
MARIO VECCHIARELLO, PE, CEM, GBE, Senior Vice President, CDM Smith Inc., Boston
RICHARD VEDVIK, PE, Senior Electrical Engineer and Acoustics Engineer, IMEG Corp., Rock Island, Ill.
TOBY WHITE, PE, LEED AP, Associate, Boston Fire & Life Safety Leader, Arup, Boston
APRIL WOODS, PE, LEED AP BD+C, Vice President, WSP USA, Orlando, Fla.
JOHN YOON, PE, LEED AP ID+C, Lead Electrical Engineer, McGuire Engineers Inc., Chicago
Are you nervous about being unable to fill your next engineering opening? You’re not alone
While dining with a fire protection engineer recently, he shared something that nearly every other engineering firm owner or manager has said: He cannot find enough good candidates to fill open positions.
This is the same thing I have been hearing for 15 years, though it seems to have gotten worse recently. It’s the perfect storm, and there is no easy solution.
als from outside the U.S. who lack the necessary visas have created a significant obstacle for these firms, hampering their ability to tap into a diverse talent pool.
Some firms prefer to hire people right out of college and mold them into the employee they want them to be. They train them in the “style” in which they do business, and ensure they get their EIT and PE so they can contribute on all levels.
Amara Rozgus, Editor-in-Chief
One of the primary challenges faced by firms is the limited availability of certain visa categories, such as the H-1B visa. These visas are designed for highly skilled workers in specialized occupations, and the annual cap set by the U.S. government restricts the number of individuals who can be hired.
The challenge that not a lot of U.S. citizens are graduating with science, technology, engineering or math (STEM) degrees will have repercussions for years to come. While not the lowest in the world, only 19.6% of graduates in the U.S. obtain a STEM degree, less than half of graduates in Malaysia, in which 43.5% of graduates get a STEM degree.
So where does that leave a hiring manager? Do they move the firm to a different country, one with more plentiful candidates? Or do they hire from countries that graduate more engineers?
The challenges of hiring individu-
Additionally, the lengthy and complex visa application process adds another layer of difficulty for engineering firms. The bureaucratic hurdles and paperwork involved in sponsoring a foreign worker often deter companies from pursuing international talent.
To combat all of this, a multipronged approach is the only way to go. Some firms have the structure and money to recruit internationally, while others must go the route of onboarding U.S. graduates. Some companies start recruiting via college internships, while others acquire entire companies with specialties they do not have.
What is your firm doing to stay on top of the recruiting shortage? cse
Patrick Veldenian, PE, CET, CDM Smith, Los Angeles
Learn the fire sprinkler code and requirements for high-piled storage systems design
The use of fire sprinkler systems for protection of storage materials has been around for more than 100 years. The first recognized patent for a sprinkler system was issued in early 1700s and the National Fire Protection Association (NFPA) was established in New York City in 1896. A few years later, NFPA standards were endorsed and employed in the United States and Canada. NFPA 13: Standard for the Installation of Sprinkler Systems continued its evolution and during the 1950s, the “Red Book” (NFPA 13) was the to-go reference for installation and inspection of fire sprinkler systems.
Fire sprinkler systems are one of the most effective and economic options for protection of property and people against fire hazards. They are also the first choice for protection of warehouses due to their simple mechanism, fast responsiveness, efficiency, high success rate and vast availability for alternatives and equipment selection.
• Learn about the codes and standards reference sections as they apply to fire sprinklers.
No other type of fire protection system can perform comparable when considering overall benefits and effectiveness of fire sprinkler systems for warehouse and storage protection applications.
• Understand the advantages of storage type fire sprinkler systems.
• Obtain a summary of developments in the high-piled storage fire sprinkler industry.
Fire sprinkler reference tools
There are several applicable codes, standards and references as it relates to fire sprinklers and suppression in general.
• Computational Modeling of Fire Sprinkler Spray Characteristics Using Fire Dynamics Simulator by Matthew J. Bourque, Thomas A. Svirsky.
• International Building Code (IBC).
• International Fire Code (IFC).
• NFPA 13: Standard for the Installation of Sprinkler Systems.
Significant progress has been made in warehouse and storage industry with the ongoing evolution of advanced structures and modern construction materials. New generations of warehouse buildings have morphed into much taller and larger areas for racking up increasing amounts of goods in more easily accessible arrangements.
As a result, fire protection schemes for distribution and warehousing industry sometimes equates to an extremely challenging task due to the complexity of assemblies and frameworks.
Standard spray sprinklers perform an outstanding job for protection of most of the commercial light and ordinary occupancies, including business and residential buildings and have served greatly to cover this necessity for many decades.
However, for challenging warehouse fires they fall short due to physical characteristics of water spray droplets, the size and consequently insufficient velocity that give rise to momentum for pen-
etration into fire plumes. Droplet velocity is an important spray characteristic when determining if the sprinkler will be able to extinguish a fire. Fire plumes have an upward velocity and if the water droplet does not have enough downward vertical velocity and momentum, it will not be able to penetrate the plume and reach the base of the fire.
‘ There are several applicable codes, standards and references as it relates to fire sprinklers and suppression in general. ’
Moreover, the longer it takes the droplet to penetrate the fire plume, the higher the chance the droplet will evaporate.
Because rooms with higher ceiling will have higher fire plumes, the velocity will need to be larger than in rooms with lower ceilings. Contrary to standard sprinklers, storage application sprinklers with larger orifices and resulting larger K-factors and advanced deflector designs, have been developed and tested to provide enhanced water distribution, increased drop sizes and amplified velocities for producing higher densities of water at the same or very close pressures as standard sprinklers perform.
Based on the performed tests on spray drops velocities and water spray pattern development, it has been determined that droplet diameter has a direct correlation with terminal velocity and Reynolds number: the larger the droplet diameter, the higher the terminal velocity and the higher the Reynolds number can be obtained. As a reminder, the Reynolds number represents the effect of air (friction) on the droplet and the terminal velocity is an important characteristic to determine if the droplet will end up with enough velocity to penetrate the upward plume velocity.
These fire sprinklers with larger K-factors of 11.0 through 34.0 are designed and listed for storage applications. Considering their advanced design and significantly larger orifices, storage sprinklers can reduce the call for higher water pressures generally required for the high-density systems demand.
The sprinkler types used in high-piled storage applications include the following:
• Early suppression fast response (ESFR).
• Control mode specific application (CMSA).
• Control mode density area (CMDA).
ESFR sprinklers requirements for storage applications can be tracked down in Chapter 23 of NFPA 13. In addition to specific guidelines found in Chapter 23, general criteria for ESFR sprinklers must be practiced in accordance with Chapter 20 of NFPA 13 standard.
Purpose: In the 1980s, ESFR sprinklers were developed and designed to extinguish the fire and eliminate the need for extinguishment and final mop-up by firefighters.
Design considerations: ESFR sprinklers are listed for use in wet systems only. They are also recognized to protect light and ordinary hazard occupancies, as well as any storage setup designed per ordinary hazard I and II and extra hazard I
csemag.com
u There are several types of fire suppression systems available and fire sprinklers are widely used.
u Warehouse and storage buildings have unique requirements for fire suppression, specifically when it comes to highpiled storage.
and II design criteria. In addition, ESFR sprinklers are the favored choice for protection of highpiled storage of class I-IV commodities, including solid piled, palletized, rack storage; and group A plastics, rubber tires, rolled paper, plastic motor vehicle components and high-bay record storage applications.
The ceiling-only ESFR sprinkler are not allowed to protect storage on solid shelf racks in ceilingonly applications and storage with open-top containers. In case of installation of ESFR sprinklers adjacent to systems with standard-response sprinklers, a draft curtain of noncombustible construction and at least 2 feet in depth must separate two sprinkler systems and a clear aisle of 4 feet, centered below the draft curtain, required for systems
separation. Lastly, the clearance between the ESFR sprinkler deflector and the top of storage shall be 36 inches.
Design area and hydraulic calculations: According to Section 14.2.8 of NFPA 13, the maximum area of coverage of any ESFR sprinkler cannot exceed 100 square feet, unless existing obstructions created by structural members result in moving a sprinkler along the branch line not more than 1 foot from its allowable spacing. The consequent area of coverage cannot exceed 110 square feet per sprinkler and average actual floor area protected by the moved sprinkler and adjacent sprinkler head should not exceed 100 square feet.
Additionally, adjacent branch lines will maintain the same pattern of spacing and spacing between
IN THIS EXAMPLE, a high-piled storage warehouse included many different aspects
The following sample case study represents the code analysis produced for an existing high-piled storage warehouse. The warehouse under consideration contains crates of household products holdings in rack storage and solid-piled storage on floor arrangement. The analysis in details exhibit the requirements referenced in International Fire Code (IFC), International Building Code (IBC) and NFPA 13: Standard for the Installation of Sprinkler Systems 2019 edition, for this specific storage warehouse.
Warehouse area: 24,400 square feet.
High-piled storage area: 15,800 square feet.
Building construction type: III-B.
Occupancy class/use group:
• Business occupancy (B).
• Storage occupancy moderate-hazard (S-1).
Ceiling height: 28 feet, 8 inches.
Sprinkler system: Yes, fully sprinklered building.
Selected design criteria: Early suppression fast response (ESFR) 25.2
K-factor, minimum operating pressure: 15 psi, reference NFPA 13 Table 23.3.1, maximum storage height 25 feet, maximum ceiling height 30 feet.
Sprinkler head type: ESFR 25 K-Factor = 25.2.
Temperature rating: 212°F.
Maximum coverage area: 100 square feet.
Minimum coverage area: 64 square feet.
Maximum spacing: 12 feet for building heights up to 30 feet.
Minimum spacing: 8 feet.
Minimum clearance to commodity: 36 inches.
Deflector-to-ceiling distance: 6-18 inches.
Hose stream allowance and water supply duration: 250 gallons per minute for 60 minutes.
Maximum ceiling height: 48 feet (UL listing).
Maximum storage height: 43 feet (UL listing).
Storage arrangement: Palletized, solid pile, open frame; single row or double row rack.
Storage method 1: Single- and double-row rack storage of household appliances in cartons and on wood pallets
Storage method 2: Wood crates (vaults) solid pile on floor for storage of household products
Packaging materials:
• Rack storage: corrugated cartons.
• Wood crates on floor: exposed storage.
two sprinklers never exceed 12 feet. By the same token, the minimum permitted protection area of coverage for ESFR sprinklers cannot be less than 64 square feet.
For the purpose of establishing design area, Section 27.2.4.4 of NFPA 13 standard is the proper reference; design area for ESFR sprinklers shall consist of the most hydraulically demanding area of 12 sprinklers, consisting of four sprinklers on each of the three branch lines, unless other specific numbers of design sprinklers are indicated in other sections of the standard (e.g., rubber tire protection with 20 sprinklers in four adjacent branch lines).
For design densities, sprinkler minimum pressure and design area requirements, Chapter 20 and 23 must be consulted.
The design area will be comprised of the hydraulically most demanding in accordance with Chapters 19 and 20 in most cases, but for special design approaches, the outlined directions per Chapter 26 shall be sought. For ESFR gridded systems, and all other gridded fire sprinkler systems, a minimum of two additional sets of hydraulic calculations at immediately adjacent areas on each side along the same branch lines will be produced to demonstrate peaking of most demanding area friction loss referencing the main design area.
In case of using computerized hydraulic calculations programs, rather than providing two sets of hydraulic calculations, a single set of calculations is acceptable. Notes that include peaking information for calculations performed by computer program,
‘ The ceiling-only ESFR sprinkler are
not allowed to protect storage on solid shelf racks in ceiling-only applications and storage with open-top containers.
’
Storage height and aisle width:
• Rack storage: 21 feet.
• Wood crates on floor: 21 feet.
• Aisle width: larger than 8 feet.
Commodity classification:
Rack storage: Class I commodity per IFC Section 3203.2, noncombustible products in ordinary corrugated cartons, with or without single thickness dividers or in ordinary paper wrappings with or without wood pallets. The amount of Group A plastics shall be limited in accordance with Section 3203.9 such that the commodity is not classified as a Group A plastic.
Wood crates on floor: Class I-V commodity and unexpanded Group A plastics in accordance with Section 3203.8 and Table 3203.8, furniture and beddings (Group A plastics).
Further considerations
Section 3205: housekeeping and maintenance
For housekeeping and maintenance, requirements of the Section 3205 will be referenced, including rack structure integrity, clearance from ignition sources and no smoking signs,
as well as aisle maintenance per Section 3205.4 shall be provided.
Section 3206: general fire protection and life safety features
In reference to Table 3206.2: Commodity class: high hazard (high-piled commodity class I rack storage).
Size of high-piled storage area: 2,501-300,000 square feet (15,800 square feet actual).
Automatic fire extinguishing system: Yes, fire sprinkler system per Section 3208 rack storage (3206.4 and Table 3206.2).
Fire detection system: Not required (3206.5 and Table 3206.2).
Building access: Required (3206.6 and Table 3206.2).
Access doors: Required (3206.7 and Table 3206.2); location, access, marking, number of doors, door size and type, locking devices, key box, per Section 3206.7.2 to 3206.7.8.
The fire safety feature shall be extended to 15 feet beyond high-piled storage area as indicated on the following plan per Section 3206.1
Aisles per Section 3206.10.1 has been provided (more than 44 inches wide).
must be among the hydraulic calculations “Summary Sheet” information.
Control mode specific application
CMSA sprinklers specific requirements for storage applications can be found in Chapter 22 of NFPA 13. Additionally, general design criteria for CMSA sprinklers is scattered through the different sections of Chapter 20.
Purpose: Contrary to ESFR sprinklers, CMSA sprinklers have been designed and developed to control the fire; they do not necessarily extinguish the fire. In essence, they provide greater flows with lower pressures with larger K-factors and as a result, the minimum allowable K-factor for CMSA sprinklers is K-11.2 to achieve better plume penetration.
Design considerations: CMSA sprinklers can be used in wet, dry or preaction systems and must be installed in accordance with their listings. Quick-response CMSA sprinklers can be used to protect light and ordinary hazard occupancies, whereas standard-response CMSA sprinklers are permitted for use in ordinary hazards in addition to storage occupancies. Both quick- and standard-response sprinklers are allowed to be used to meet criteria in Chapter 20 through Chapter 25, including general storage (Chapter 20), high-piled storage (Chapter 21), CMSA-specific requirements (Chapter 22), alternative systems (Chapter 24) and rack storage systems (Chapter 25).
Storage conditions that can influence greatest water demand in a building include pile height, clearance to ceiling, pile stability and array of storage and shall be considered for the design of CSMA sprinkler systems. To a great extent, CMSA sprinklers rely on direct attack to gain rapid control of both the burning fuel and ceiling temperatures. Therefore, interference with the discharge pattern and obstructions to the distribution should be avoided.
Design area and hydraulic calculations: The design area for CMSA sprinklers must comply with the specific requirements of Section 27.2.4.3.1. Per this section, the design area will consist of a rectangular area having a dimension parallel to the
branch lines at least 1.2 times square root of the area protected by the number of sprinklers to be included in the design area. The design area protected by the number of sprinklers to be used by the 1.2 rule shall be based on the maximum allowable area per sprinkler and any fractional sprinkler shall be carried to the next higher whole sprinkler.
In systems having branch lines with an insufficient number of sprinklers to comply with 1.2 requirement, the design area will be extended to include sprinklers in adjacent branch lines supplied by the same cross main. Moreover, the minimum area of coverage of any CMSA sprinkler may not be less than 80 square feet and the maximum area may not be more than 130 square feet. Design must account for minimum operating pressure and number of sprinkler heads in the design area obtained from Chapter 22.
Specific requirements for the storage applications of CMDA sprinklers can be found in Chapter 21 of NFPA 13. Additionally, general design criteria for CMDA sprinklers can be found in assorted sections of Chapter 20.
Purpose: Like CMSA sprinklers, CMDA sprinklers have been designed and developed to control the fire; they do not extinguish the fire like ESFR sprinklers.
Chapter 32 of International Fire Code (IFC) presents conditions for recognizing various classes of commodities and other features of fire and life safety systems regarding to high-piled storage occupancies as defined in Chapter 2 of the IFC. It also sets down requirements for protection of high piled storage on pallets, in racks or on shelves where the top of storage is greater than 12 feet in height or 6 feet for high-hazard commodities.
It should be noted that in addition to the requirements of Chapter 32, the material-specific conditions should comply with the following chapters (or with NFPA 13 for paper records):
• Aerosols: Chapter 51.
• Flammable and combustible liquids: Chapter 57.
• General storage of combustible material: Chapter 3.
• Hazardous materials: Chapter 50.
• Storage of combustible fibers: Chapter 37.
• Storage of combustible paper records: NFPA 13.
Commodity classification in Chapter 32 of IFC lines up with NFPA 13 standard’s high-piled class I, II, III, IV, storage classifications and plastics in A, B and C grouping. In addition, the amount of group A plastics in class I, II, III and IV commodities without resulting in a Group A plastic classification is limited to the quantities specified in Section 3203.9.
However, to regulate the main commodity classification of the products and materials, IFC Table 3203.8 must be referenced. Table 3203.8 considers the product and the packaging if listed with the item. Products with additional packaging consisting of Group A plastics shall be classified in accordance with Section 3203.9. The system designer or consulting engineer should keep in mind that in case of conflicts occurring between requirements of fire code and NFPA 13 standard, requirements of the IFC applies.
High-piled storage areas, considered for storage of a different commodity class than adjacent areas, must be designed and correctly contain Class I, II, III, IV or high-hazard commodities. The selection of a high-piled storage area must also be according to the highest hazard commodity class stored in the area with exception to engineering analysis referenced in Section 3204.2.
Fire protection and life safety features for highpiled storage areas are referenced in Section 3206. Table 3206.2 specifies type(s) of protection required based on the commodity classification, size of storage area, whether they are open to public (e.g., department stores), storage type, pile dimension, storage height and pile volume (application to solid-piled, shelf and palletized storage).
The size of each high-piled storage area includes the footprint of the actual high-piled storage racks, shelves or piles. It also includes the interior aisles
within the footprint of the storage area, and an aisle around the perimeter of the footprint with a minimum width as indicated in Section 3206.10.1 or the dimension to a wall or full height wall, whichever is less.
If a building contains multiple high-piled storage areas, the aggregate of all high-piled storage areas may be used for the application of Table 3206.2 unless the high-piled storage areas are separated by fire barriers with a minimum fire-resistance-rating of one hour. In the case of sprinklered buildings, high-piled storage areas must be separated by 100 feet or more of free of high-piled combustible storage area. In addition to general requirements of Section 3206, for specific requirements of high-piled storage areas, the following sections of IFC shall be consulted:
• Solid-piled and shelf storage: Section 3207.
• Rack storage: Section 3208.
• Automated storage: Section 3209.
• Specialty storage: Section 3210.
Unexpected changes and scheduled modifications are anticipated in storage occupancies. It is a common practice to frequently alter the storage arrangement within storage warehouses. The storage layout and heights are always changing and, as a result, a more adaptable sprinkler protection that affords flexibility is highly desired.
Storage application sprinklers with notably large K-factors permit ceiling-only sprinkler system installations (e.g., ESFR sprinklers), which provide a greater water density without a significant increase in minimum required listed discharge pressure. This is a great advantage over design and installation of complex in-rack sprinkler systems and puts the facility owners in more workable position for their new storage setup and provid-
ing maximum operational flexibility while minimizing risk of accidental discharge. In addition to change in storage layout, the ceiling sprinkler system densities can be regulated and changed through implementation of sprinklers with alter-
native larger K-factors closely designed for same application with an increased density requirement.
As an example, replacing of ESFR K-14.2 sprinkler heads with ESFR K-16.8 sprinklers after the removal of permis-
Electrical bearing damage causes unplanned downtime
Variable frequency drives (VFDs) are used to control pumping systems. But VFDs create a motor shaft voltage that discharges through the bearings, blasting millions of pits in bearing surfaces. Both motor and pump bearings are at risk. These discharges oxidize the bearing grease and cause bearing uting, premature failure, and costly downtime.
Protect motor bearings with AEGIS® Shaft Grounding Rings
By channeling VFD-induced discharges safely to ground, AEGIS® Shaft Grounding Rings prevent electrical bearing damage.
Proven in millions of installations worldwide, AEGIS® Rings provide unmatched protection of motors against electrical bearing damage, motor failure, and unplanned downtime.
FIGURE 6: Fire sprinkler protection overhead and below obstructions wider than 4 feet. Courtesy: MAG Material Handling
Fluting Damage
1-866-738-1857 | sales @ est-aegis.com
sion of K-14 sprinklers use in buildings greater than 35 feet in NFPA 13-2016 and later editions, allows the implementation of K-16.8 through direct replacement for smaller K factors (K-14.2) for least financial impact and same hydraulic requirements. cse
Patrick Veldenian, PE, CET, is a licensed fire protection engineer and certified system designer at CDM Smith. He performs fire and life safety systems code review, design, hydraulic analyses, site surveys and plan reviews for buildings and systems in the industrial, commercial and energy sectors.
Easily commission and troubleshoot actuators with your smartphone. Near Field Communication (NFC) allows assisted configuration by a smartphone, even if the actuator is not connected to power.
Discover the advantages www.belimo.us
Justin P. Milne, PE, WSP, Irving, Texas
This article provides a clarifying framework for understanding both active and passive fire protection systems and life safety systems
The coordination and integration of modern fire protection, life safety and mechanical systems require a common understanding of these systems’ performance objectives to ensure effective and successful planning, design, construction, inspection, testing, maintenance and operation. Rich examples where many fire protection and life safety system types require careful integration include fire pump rooms and fire command centers. Beyond these, there are many other technical nuances to fire protection and life safety system types.
For instance, there are three active fire protection system classifications: fire protection, fire suppression and fire extinguishing. There are many more passive fire protection systems. A detailed understanding of these system types is necessary for every team.
• Learn more about passive and active fire protection and life safety systems.
• Understand how to better coordinate and integrate fire and life safety systems with mechanical systems in health care facilities.
• Review some key coordination and integration considerations for mechanical, fire protection and life safety systems.
This article stresses that a common understanding of fire protection and life safety systems’ performance objectives will help better orient mechanical, fire protection and life safety system (MFPLS) designers to successfully address health care coordination and integration challenges, especially in the case study the article considers — a life safety atrium smoke control system. Note: A future article will discuss the integration of electrical, fire alarm, smoke control and life safety systems.
Fire protection systems typically encompass specific mechanical design elements, such as sprinkler systems, standpipe systems and fire pumps. But to exclusively hone in on sprinklers, is to bely the full scope and nature of the fire protection discipline. For example, the fire protection pump room in Figure 1 includes nine active and passive fire protection system elements with coordination issues involving architectural, structural, civil, mechanical, electrical and plumbing scopes of work. Six active fire protection systems include:
• A site underground fire service main system.
• A fire and jockey pump system.
• Multiple automatic wet pipe fire sprinkler systems.
• Multiple automatic dry pipe fire sprinkler systems.
• Multiple single interlock preaction systems.
• Associated drainage systems.
Note: There is no standpipe system in the rendered image.
Separately, three distinct passive fire protection system elements include a mechanical incidental use fire separation, a stairwell vertical opening fire separation and a fire pump room fire separation. As a discipline, fire protection engineering strategically approaches internal and external fire safety challenges for the built environment. Fire protection engineering does this by integratingall key stakeholders to achieve performance objectives for a specific hazard.
In the case of a fire pump room, numerous critical elements are needed to mitigate active and passive fire protection system hazards. Active fire protection systems may be life safety systems depending on the system’s role and function (see definition below). Similarly, passive fire protec-
tion systems may also be life safety systems working together with active systems to protect people. Active and passive fire protection concepts are crucial to an ordered understanding of fire and life safety. They are defined by the NFPA Glossary of Terms, 2021 Edition, as follows:
Active fire protection system: A system that uses moving mechanical or electrical parts to achieve a fire protection goal (for definition, see NFPA 3: Standard for Commissioning of Fire Protection and Life Safety Systems, 2018 Edition Article 3.3.20.1). Active fire protection systems must move mechanically or be initiated to move by an electrical means. These active fire protection system elements include fire sprinklers, valves and pumps.
Passive fire protection system: Any component of a building or structure that provides protection from fire or smoke without any type of system activation or movement (for a definition, see NFPA 3 Article 3.3.20.5). Passive fire protection systems rely upon the compartmentalization spaces within the built environment to control the spread of fire or smoke. Passive fire protection systems include:
• Fire or smoke assembly type.
• Associated opening protectives.
• Penetrations protection.
• Joints sealant.
• Thermal and sound insulation.
• Fire-resistance features.
When requiring a rated passive fire protection system, some opening protectives may also include active and life safety system elements such as:
• Fire, smoke, combination, ceiling radiation and corridor dampers.
• Balanced, low-energy power-operated, power-assisted, power-operated, exit access, fire exit.
• Glazing for fire door and window assemblies.
• Smoke guards and adjustable door floor sweeps.
In addition to clarifying the roles of active and passive fire protection systems, it is vital to understand the three main goals active systems aim to achieve as they relate to mechanical systems: fire protection, fire suppression and fire extinguishing. Fire protection: Methods of providing for fire control or fire extinguishment (for a definition, see
NFPA 801: Standard for Fire Protection for Facilities Handling Radioactive Materials, 2020 Edition Article 3.3.13). Fire protection systems are designed for normal hazard classifications and intended to control fire size by covering the fire, limiting its heat production and wetting adjacent combustibles to prevent structural damage.
Fire suppression: Sharply reducing the heat release rate of a fire and preventing its regrowth by means of direct and sufficient application of water through the fire plume to the burning fuel surface (for a definition, see NFPA 13: Standard for the Installation of Sprinkler Systems, 2019 Edition Article 3.3.76). Suppression systems are engineered for a specific hazard and listed based on full-scale fire testing. Fire suppression systems forcefully knock down the fire while breaking up the fuel source and limiting its consequential effects.
Fire extinguishing: The complete suppression of a fire until there are no burning combustibles (see NFPA 750: Standard on Water Mist Fire Protection Systems, 2019 Edition Article 3.3.8). Extinguishing systems are engineered for a specific hazard and listed based on full-scale fire testing. Extinguishing systems quench burning by cooling the fire, smothering the air supply, removing the fuel source or interrupting the chemical reaction.
The overarching goal of all active and passive fire protection systems is to protect people and property.
1: Fire pump room with more than nine active and passive fire protection system elements. Courtesy: WSP USA
‘ Active fire protection systems may be life safety systems depending on the system’s
role
and function.’
When an active or passive system has historically protected people and property against near misses, injury, loss events, mission continuity, environmental protection or preservation of cultural resources, it is a sign that the system is achieving its goal. The surest sign an active or passive system must reconsider how it has been designed is if the building envelope encounters something called "flashover”:
“When the upper layer temperature reaches approximately 1,100°F, pyrolysis gases from the combustible contents ignite along with the bottom of the ceiling layer … those present in the room are unlikely to survive.”
Evaluation of active or passive systems that have failed to achieve their performance objectives are reevaluated by code authorities and codes and standards development committees and addressed in the code development process. In addition to the fire prevention efforts of active and passive fire protection systems, life safety systems also play a critical role in ensuring the life safety of occupants, first responders, neighbors and nearby communities.
Life safety systems typically encompass specific mechanical design elements, such as elevator systems, emergency generators, fire alarm systems, smoke control and dampers. Like the discussion of fire protection systems, this is a siloed view of life safety systems. There are also nonmechanical life safety systems, such as means of egress and emergency lighting. As noted previously, active and passive fire protection systems may also be life safety systems depending on their goal and function. Life safety systems are defined in the NFPA Glossary of Terms, 2021 Edition, as:
Life safety systems: Those systems that enhance or facilitate evacuation, smoke control, compartmentalization and isolation (for a definition, see NFPA 4: Standard for Integrated Fire Protection and Life Safety System Testing Article 3.25.6).
A fire command center is a rich example of a life safety system. Fire command centers require more than 18 critical life safety elements to ensure a facilitated emergency response. These fire command centers employ active and passive life safety system elements.
A more specific example of a mechanical life safety system is where initiation controls actuate a combination fire/smoke damper. Integrating either fire pump rooms or fire command centers requires significant coordination between MFPLS stakeholders.
Specifying mechanical engineers focus on heating, ventilation, air conditioning (HVAC) and/ or thermal and fluid system applications. In con-
trast, specifying fire protection engineers focus on active smoke control systems, explosion protection and prevention systems, passive building systems, egress systems and human behavior to design the building envelope for fire events. In health care, mechanical system equipment components may trigger active or passive fire and/or life safety system requirements (see Table 1).
Air distribution system are among health care's most prevalent mechanical systems. For a typical air distribution system, NFPA 90A: The Standard for the Installation of Air-Conditioning and Ventilating Systems, 2021 Edition, Chapter 5 helps to clarify specific passive MFPLS integration challenges. Chapter 6 details controls requirements for active MFPLS components.
For a more unique atrium smoke extraction system, NFPA 92: The Standard for Smoke Control Systems, 2021 Edition, Chapter 6, clarifies passive and active MFPLS integration challenges. Note: Both standards impact nondedicated systems. Implementing these safe practices is further complicated for the mechanical systems in defendin-place health care facilities, as articulated in NFPA 99: The Health Care Facilities Code, 2021 Edition, Chapter 16, and NFPA 101: Life Safety Code, Chapters 18 and 19.
Passive fire protection systems must be inspected or tested per NFPA 3 Article 5.4.1.2 and active fire protection systems must be inspected and tested in accordance with NFPA 4 per NFPA 3 Article 5.4.1.3. These considerations are evaluated in the following case study of a three-story atrium smoke extraction system.
With any fire protection and life safety system, beginning with the end in mind is recommended. For this reason, the framework of this case study is based on a confidential client's real-life atrium smoke control system example. System coordination and integration efforts will follow NFPA 3. The framework
of this standard illustrates benchmark activities to be conducted for commissioning fire protection and life safety systems in the planning, design, construction and occupancy phases.
The fire protection and life safety planning phase has three primary purposes:
• To detail the owner’s project requirements (OPR) with the relevant stakeholder team.
• The formation of the commissioning team.
• The development of the commissioning plan.
At the minimum, the commissioning team should include the owner and the fire commissioning agent. An ideal team would consist of a testing and balancing professional, a registered mechanical engineer and a registered fire protection engineer. The commissioning team or a third-party entity approved by the local authority may perform special smoke control inspections.
Atrium smoke extraction integration challenges that the commissioning team should consider in the planning phase of a project include the following:
• Applicable and conflicting codes, standards, guides and technical references such as ASHRAE, ICC, NFPA, SFPE.
• Specific user requirements: Building management, remote testing, emergency lighting
Fire command center with more than 18 life safety system elements. Courtesy: WSP USA
‘ Active and passive fire protection systems may also be life safety systems depending on
their goal and function.
’
• Training requirements: Fire protection engineering, mechanical engineering and testing and balancing training for smoke control. Other training modules, such as enclosures, energy code issues and emergency management, should also be considered.
• Warranty requirements:
–Active systems: Firefighter’s smoke control station, exhaust system components, supply system components, door components, fire and smoke dampers, fire alarm initiation devices, access control devices, fire alarm notification devices, fire sprinkler system zoning.
–Passive systems: Building enclosure façade system, fire shutters, fire and smoke doors, air barriers, stairwells.
‘ The fire protection and life safety design phase follows the same three precepts as the planning phase as informed by the owner's project requirements.’
• Integrated testing requirements: All active and passive fire protection systems require integrated testing in new structures if two or more fire protection or life safety systems are integrated. Following system acceptance, periodic testing is also required, as indicated in the test plan, but no less than every 10 years.
• Performance criteria: Acceptance tests for an atrium exhaust system include requirements for detection devices, ducts, inlets and outlets, fans, smoke barriers and controls.
• Third-party requirements: Smoke control system testing shall be by approved agencies for smoke control testing with expertise in fire protection engineering, mechanical engineering and certification as air balancers.
The fire protection and life safety design phase follows the same three precepts as the planning phase as informed by the OPR:
• Development of the basis of design (BOD).
• Guidance and input are to be taken from the commissioning team.
• The commissioning plan will be updated accordingly with particular attention to scope and design issues.
The rational analysis report is the other important smoke control document for consideration in the design phase. Design effect considerations for successful MFPLS coordination and integration of active and passive systems include:
Passive fire protection and mechanical system design coordination and integration: Fire sprinkler system: MFPLS coordination of fire protection sprinkler systems may be influenced by a phenomenon known as stratification in spaces with high ceilings and glass glazing. Depending on how a mechanical engineer designs the HVAC system or informs architects of building envelope energy performance issues, solar radiation may cause hot air to become more buoyant than a smoke plume in a fire event, prohibiting sprinklers’ activation. Note: Fire detection systems are also influenced by stratification.
Passive fire alarm and mechanical system design coordination and integration: Fire alarm emergency voice and communications system (EVACS): MFPLS coordination of acoustical systems is one mechanical area that often impacts an EVACS design. Frequently, atrium spaces are subject to acoustically distinguishable space (ADS) requirements. The voice fire alarm system in an ADS is required to be intelligible. Mechanical HVAC and acoustical engineers must coordinate noise, reverberation and echoes, which may impact the fire alarm system’s design intelligibility.
Active fire protection and mechanical system design coordination and integration: Fire sprinkler system: MFPLS integration of fire protection sprinkler systems requires that the sprinkler sys-
tem be zoned with the atrium space to ensure that if a sprinkler activates, the system’s interconnected water flow alarm will know to trip the atrium smoke control system. Note: Fire alarm systems may also be influenced by atrium detection, initiation and notification system zoning requirements.
Active fire alarm and mechanical system design coordination and integration: Fire initiation and detection system: MFPLS coordination of detection and initiation systems within the built environment may impact fire system detection capabilities. Ducted and indoor air quality designs may influence ducted air velocity, air humidity, air temperature and the system’s final exhaust flow rate may influence smoke color and density. Depending on indoor air quality design provisions, design specification of thermodynamics, psychometrics, heat transfer, fluid mechanics, energy and mass balance and heating and cooling loads may affect fire system detection capabilities.
Active smoke control and mechanical systems design coordination and integration: MFPLS integration of HVAC systems is vital to a functional smoke control system:
• Makeup air is sized based on exterior openings, interior forced air, leakage into the atrium building envelope or other mechanical system sources. Note: Makeup air must be limited below the exhaust air condition to ensure the atrium environment remains negatively pressurized.
• Exhaust air is sized based on natural ventilation from the space or mechanical means. The steps in this sizing are the specification of a design fire and the evaluation of visibility, velocity, temperature and asphyxiant tenability thresholds.
• Exhaust air inlets incorrectly located may cause plughole effects.
• Exhaust system temperatures will influence damper fire rating requirements.
• Extraction fans associated louvers, door controls and dampers are controlled by a dedicated firefighter’s smoke control station.
• Fire and smoke damper systems are typically required at smoke control shaft and smoke compartment boundaries duct openings. The damper closing influences the speed at which makeup air may be injected into an atrium space.
• The building automation system provides additional monitoring of the system.
• The graphics annunciator panel is observable from a fire command center.
• The smoke extraction system must integrate with testing elements for other smoke control systems.
• The smoke extraction system must integrate with testing elements for other HVAC systems.
• Additional considerations for HVAC systems include structural fire ratings of system support, exhaust air conditioning temperature, facade penetration requirements and fire-rated housing for variable frequency drives.
The above provisions must be coordinated in the planning and design phases.
Successful system integration requires a holistic understanding of the place and purpose of MFPLS systems within health care buildings. Fire protection systems are divided into active and passive system types. Fire protection, fire suppression and fire extinguishing systems are all mechanical systems specifically focused on addressing fire hazards by protecting people and property. Life safety systems also serve other building system concepts to amplify their goal of preserving life.
This case study illustrates a smoke control system design's fire, life safety and mechanical integration elements. Integrating the fire, life safety and mechanical systems, especially smoke control systems is challenging but achievable with the right skills, perspectives and objectives working together as a team.
A future article will further evaluate this case study from the perspective of integration of electrical, fire alarm, smoke control and life safety systems. cse
Justin P. Milne, PE, is a senior fire protection engineer at WSP.
3: Fire dynamics simulator (FDS) atrium smoke control tenability analysis. Courtesy: WSP USA
csemag.com
Fire protection insights
u The article applies fire and life safety foundational knowledge to some notable mechanical equipmentspecific issues relevant to health care buildings.
u In addition, fire protection engineers can take a deeper look at some coordination and integration challenges specific to atrium smoke control.
John M. Herboth, PE, CxA, BET-CP, Affiliated Engineers Inc., Portland, Oregon
Successful mechanical, electrical and plumbing integration with fire and life safety systems require significant investment from all angles
One of the most vetted systems in buildings is the fire and life safety system, which includes fire protection sprinklers, fire/smoke rated assemblies for containment, detection and alarming and smoke control or evacuation. Yet, after a building receives its certificate of occupancy, it is the assumption that because it worked once when it was demonstrated for an authority having jurisdiction (AHJ) that it is set up to respond correctly in every scenario, including all the mechanical, electrical and plumbing (MEP) and controls com-
ponents integrated within the building that support fire and life safety.
Ensuring all the individual components, equipment and systems are designed and set up to be failsafe is one of the biggest challenges that requires extensive consideration and practical experience. This is key when integrating all the MEP equipment and systems so the monitoring stations and an operator are given direct notice when any one component doesn’t operate correctly or isn’t providing confirming feedback. If components, equipment and systems are not set up in this manner, as the building and its components age over time and receive different levels of attention and care, there will be unknown failure points.
From fire and life safety system installation and completion, to the end of the one-year warranty period, to five years down the road, some components may be found to be failed or defeated, wired incorrectly, have inaccessible components or incomplete documentation or even have unsafe conditions due to required updates or replacements to connected systems.
FIGURE 1: Mechanical, electrical, plumbing and fire/life safety drawing of a medical office building with smoke evacuation control mode relays for the building automation system. Courtesy: Affiliated Engineers Inc.
While most project teams typically aim to create high-quality buildings, some systems are not always set up to be maintained easily either due to accessibility, facility team knowledge or experience or a lack of available time needed to keep things from becoming deferred maintenance items. Life safety systems require as much or more time to maintain than was spent on its design, installation and verification upon completion.
Setup for system longevity with ease of maintenance in mind will always remain a best practice for project teams as it is rare that facility operations team have as much experience with the individual MEP or fire and life safety systems or have access to the wealth of knowledge.
It is the building owner and operator’s responsibility to periodically test its life safety systems, connected components and document it for the AHJ. It takes knowledgeable project team members and facility operators to coordinate, plan, execute and document efforts to set up the system for success and periodically perform required maintenance regardless of the enforcement environment. Enforcement does make a huge difference for what gets done studiously versus what may get overlooked on a budget due to the apparent risk to operations.
Testing should occur at the following rates: fire dampers and fire smoke dampers every four to six years per NFPA 80: Standard for Fire Doors and Other Opening Protectives and NFPA 105: Standard for Smoke Door Assemblies and Other Opening Protectives or semi-annually for dedicated smoke control systems dampers and annually for nondedicated dampers per NFPA 92: Standard for Smoke Control Systems (see Figure 2).
Design thoughtfulness, coordination, installation, testing and good documentation pays dividends to the operations team and anyone that performs system maintenance. For smoke control systems, semiannual and annual testing doesn’t get regular review by an AHJ in the Northwest region but it is still a responsibility based on national and local fire code requirements which are all based on the International Fire Code (IFC) Chapter 909.20.
Use of the project commissioning provider and/ or a smoke control special inspector to review design plans and shop drawings, verify installed components and equipment and oversee the dif-
CHAPTER 7
International Building Code and International Fire Code containment dampers periodic testing requirements
Retesting at the end of the first year after certificate of occupancy date.
Complete retesting every four years, except in hospitals, which is every 6 years.
CHAPTER 9
International Fire Code Smoke Control System Dampers periodic testing requirements
Dedicated dampers Nondedicated dampers
Semiannually Annually
FIGURE 2: Periodic testing requirements table, life safety dampers, dedicated and nondedicated dampers for smoke control. Courtesy: Affiliated Engineers Inc.
ferent integration of MEP systems while leading coordinated testing is one of the most valuable quality assurance and quality control roles there are for a building project (see Figure 3).
For this reason, a good portion of state and local fire code requires, based on IFC Chapter 909.3 and International Building Code Chapter 1705.18 that a special inspector is responsible for the smoke control system.
‘ Ensuring all the individual components, equipment and systems are designed and set up to be failsafe is one of the biggest challenges that requires extensive consideration and practical experience. ’
For example, in Portland, Oregon, a smoke control special inspector is requirement for all smoke control systems including a simple certified panel focused on just stairwell pressurization. That special inspector works with the engineer of record (EOR) to review the smoke control design, inspect its installation, verify its performance and co-stamp the final report with the EOR.
After a building enters its operational occupied phase, most building owners and operators must rely on their fire alarm maintenance provider to keep systems up to date and meet facility code requirements. However, the fire alarm maintenance provider doesn’t have MEP equipment and systems scope other than to maintain any existing tiein points from their side of the fire alarm system, which can cause major challenges when only one system is being work on, changed or altered without having team members responsible for the entire systems operation.
• Understand the value of oversight and verification for fire and life safety systems and mechanical, electrical and plumbing (MEP) integration.
• Identify the value of knowledgeable team members for fire and life safety projects and facility operations.
• Discover lessons learned from fire and life safety projects.
A facility operations or service team lead is needed that understands how these systems are integrated or is knowledgeable enough to delegate and require responsibility to avoid unintended impacts and consequences. There are many available published documents and guides out there to help in-house teams and service providers.
NFPA 3: Standard for Commissioning of Fire Protection and Life Safety Systems and the AMCA Guide for Commissioning and Periodic Performance Testing of Fire, Smoke and Other Life Safety Related Dampers include two accessible and descriptive ways to set up processes to maintain fire and life safety systems and their MEP connected components.
There are also a wealth of replacement instructions available from manufacturers, along with technical representatives to guide in the process. Should someone find themselves in a situation where UL listing is debated and a party wants to replace damper assemblies as a whole versus replacing the failed component, Dampers - UL Marking and Application Guide can be referenced.
For example, a major health care provider’s existing hospital in Portland, Oregon, underwent fire and life safety upgrades to reduce actuated and fusible link fire dampers as they reconfigured their
egress paths and fire-rated corridors. This could take place only after an engineering-led review of their life safety plans, which had accurate fire smoke damper testing documentation and required field verification of ductwork and components. This life safety project required significant planning, after-hours work and documentation of field work to ensure ongoing hospital operations were not interrupted.
By hosting a coordination meeting with hospital department heads early in the project, the owner representative, facilities lead, general contractor and engineering team resolved several issues immediately. With the right people in the room, questions were answered in about an hour with a detailed spreadsheet as the output. After a postmeeting debrief was completed with the organizer, the engineering team set an inspection and test schedule together, planned a support structure to reduce risks when executing the tests and pushed out the plan to the project team
During this project, as a result from the risk assessment discussion, the team supported creating test buttons at the fire alarm control panel (FACP) to trigger alarm functions and operate the panel versus activating field devices directly. This was due to the nature of a 24/7 hospital, where the team couldn’t trust initiating field devices such as area detectors or duct detectors as the system had numerous revisions and additions to the fire alarm system programming and field wiring over the decades of operation. In addition, the FACP programming had inconsistent naming conventions for relays, devices and equipment. The risk profile was too high to trust manually activating field devices that could potentially impact live systems adjacent to the one the team planned to test. Integrated fire alarm testing could not be done by level or individual system without potential to significantly impacting operations regardless of the time of day when conducted. It was decided that testing would be performed as individual electrical, controls and heating, ventilation and air conditioning (HVAC) components then triggered by system relay programming for an encompassing inspection and testing program.
This would mean that for an individual fire alarm relay device, electrical terminations were reviewed when triggered and all the system interac-
‘ The most important lesson learned is that it is imperative to have an experienced and responsible party to validate building systems and interactions with the support of the design team to meet code requirements. ’
tions verified from the fire smoke damper closing to the HVAC equipment turning off, status notifications generated within the building automation system for the position switch and alarm notification generated at the FACP for the specific area and device alarm.
On one evening, it was discovered a bevy of simple termination errors at several relay devices during a failure condition would not depower the fire smoke dampers for smoke compartmentalization, trigger an alarm or shutdown the equipment as intended. Essentially, in a fire or smoke event condition, no shutdown or closures would be initiated and no way to identify there was a response problem would be provided. What ensued was a discussion with the electrician, the fire alarm system operator and general contractor night leads about the potentially disastrous situation that was avoided due to team integrated testing as a result of the commissioning effort.
Commissioning providers’ top priority is to identify issues upfront and avoid unwanted call backs years later, not just for an individual party, but the whole team.
The team continued to run into other minor issues from bad end switches and some exhaust equipment not shutting down as planned due to fire alarm programming errors, but overall, it was a resounding success because of efforts made to verify components and the system interactions. As a result of the team coordination and planning or ongoing operations were not impacted over the course of the team’s time on the project, including all of the hospital’s surgery suites.
In addition, the commissioning final report was reviewed and sign off by the AHJ without any cor-
rections or revisions required. It pays dividends to have a good team, with members who support each other, especially when each individual trades’ work impacts others and the system. Integrated testing allows for the vetting of the building’s life safety system and when coordinated and executed as a team, not only ensures individual systems are fully functional, but responses are appropriate and notifications provided when a component fails to do its job.
The most important lesson learned during this project is that it is imperative to have an experienced and responsible party to validate building systems and interactions with the support of the design team to meet code requirements (see Figure 4). There are high levels of effort needed to execute projects and many unforeseen challenges can occur when dealing with life safety systems that are composed of different systems working together. Commissioning providers are a critical component, but without the general contractor and subcontractors as part of the project team, key interval reviews and inspections won’t get the job done alone.
It’s key to require thorough documentation and testing requirements for projects, have a team full of dedicated professionals who coordinate effec-
csemag.com
Fire insights
uThe design, installation and testing of fire and life safety systems are key to ensuring building occupants are safe.
uIntegrated testing of the fire protection system must be done before occupancy, preferably by a professional knowledgeable with the system.
FIGURE 5: Building automation system smoke evacuation and shutdown control relays. Courtesy: Affiliated Engineers Inc.
tively, execute cooperatively and ensure systems are functioning properly and who conduct pretesting efforts before final inspection by the AHJ. There are many opportunities for individuals to miss things, from the planning and design stage through construction and project completion. The best way to catch these mistakes is a strong oversight and verification process integrated within a supportive project team environment, where buy-in is a must. Systems aren’t getting less complicated; integration of those systems and their different components will be the crux of every project whether it is a new or existing building. Focus on getting the right group together that can plan and execute as a team, exclude those with large egos and who set defensive postures regularly due to budget or personality, so that a critical building systems functions now and years down the road. cse
John Herboth, PE, CxA, BET-CP, is a senior commissioning engineer at Affiliated Engineers Inc. and is actively involved in leading fire and life safety testing and inspection services.
In Critical Power Facilities, all data recorded during a power outage is vital! Sequence of Event Recorders collect precision data to quickly identify the root cause, providing a clear picture of what happened, and what is needed to restore power quickly!
Compact, 1600-2000 MBH water heater
- Up to 65% less footprint vs. the competition
Advanced Edge® Controller with O2 Trim technology
- Self-adjusts and maintains optimal air-fuel ratios for peak efficiency, low emissions and maximum reliability
Durable, corrosion-resistant AquaPLEX® duplex stainless steel - Fire tube heat exchanger backed by a 15-year warranty
| pvi.com/centurion
Sha Eshghi, PE, Jacobs, Portland, Oregon
Several key and common engineering decisions to consider when designing a power distribution system are highlighted in a case study example.
Transformers, switchgears and uninterruptible power supplies (UPS) equipment are crucial parts of the electrical power system. Transformers step up or down the voltage level to facilitate the transmission and distribution of electricity. Switchgear provides protection of electrical circuits and a means of disconnection. UPSs protect equipment during voltage fluctuations and outages by providing backup and conditioned power.
These three systems, when properly applied together, help ensure the reliability, protection and safety of the electrical system and the personnel maintaining them. There are several engineering design considerations involved in selecting this equipment for an industrial facility.
• Understand electrical engineering design principles surrounding transformers, switchgear and UPS systems.
• Learn about the importance of ensuring existing electrical infrastructure capacity meets the design demand load requirements.
• Understand the relationship between transformer impedance rating and the available fault current at secondary side of the transformer.
A major industrial facility plans to expand its campus by adding an additional building. This expansion includes manufacturing, offices and data centers as the main functional areas. This expansion would require power to various electrical loads, such as lighting, general/critical/life safety power, HVAC, manufacturing machinery and electrical appliances.
During the design phase of the project, the electrical engineering team needed to consider various design decisions to specify equipment for different operational scenarios to create the power distribution system for this expansion.
As part of the continuous support and services provided on this site, the electrical engineer-
ing team had made provisions for future expansion during site master planning for this campus. The utility substation yard was designed to accommodate additional buildings in the future, this was done by including additional medium voltage transformers in prior design packages for future use. The underground duct bank was also installed from the utility transformer to a manhole outside of the substation utility yard for future tie in. The electrical engineering team had to determine the existing service has sufficient capacity for this expansion. In order to determine the requirements, NFPA 70: National Electrical Code (NEC) Article 220.87 (Determining Existing Loads) was utilized, which states:
“The calculation of a feeder or service load for existing installations shall be permitted to use actual maximum demand to determine the existing load under all of the following conditions:
(1) The maximum demand data is available for a 1-year period.
(2) The maximum demand at 125 percent plus the new load does not exceed the ampacity of the feeder or rating of the service
(3) The feeder has overcurrent protection in accordance with 240.4, and the service has overload protection in accordance with 230.90.”
This metered maximum demand data, combined with the expansion load projections, allowed the team to conclude the existing service was properly sized.
The design team first step was to estimate the demand load for this expansion to ensure existing equipment can be utilized. This included the medium voltage transformer from the utility yard feeding the primary power to the building, and the secondary source being fed from an existing air insulated medium voltage switchgear providing secondary source of power to multiple buildings on site.
The engineering design team reviewed the basis of design, list of equipment with their specifications, civil site drawings, architectural equipment schedules, mechanical/plumbing schedules, and general power/lighting loads. The design team also needed to identify power requirements for critical data/controls, life-safety and security system. Utilizing the client measured data from their existing facilities, the expected load was determined using the data shown in Table 1.
Transformers: Liquid-filled less flammable fluid type medium voltage (MV), and low voltage (LV) dry-type transformers were specified for this project. The design team had to consider various factors in designing the transformers at different levels in the electrical distribution:
• Reviewed containment and type of insulating fluid requirements for the liquid filled MV transformers to meet national and local site-specific codes/standards.
• MV transformers were designed with vacuum fault interrupters along with relays to enable low arc flash mode, providing safety during maintenance.
• MV transformers were specified as KNAN/KNAF (fluid natural air natural/ fluid natural forced air) for cooling.
• The design team had to revise the LV transformers within the power distribution units, because initially the impedance rating of the LV transformers was causing higher fault values compare to capacities of the equipment ratings downstream. Since the lead time on downstream equipment was not accommodating the construction schedule, the design team specified higher impedances for the LV transformers to lower the available fault after calculating the worst-case peak fault current at the secondary side of the LV transformers.
• Design team specified K4-rated LV transformers to step down 480V UPS power to feed critical loads. The K4 rating uses electrostatic shield to reduce the transient noise harmful to
‘ Transformers, switchgears and uninterruptible power supplies (UPS) equipment are crucial parts of the electrical power system. ’
nonlinear loads such as computers and IT equipment. In addition, K4-rated transformers can withstand overheating caused by harmonics from nonlinear loads.
Switchgear: Medium voltage (MV) switchgear and low voltage (LV) switchboards were specified in this project. Several factors had to be considered during design:
• Air insulated MV switchgear (AIS) 27 kV class was specified, although gas-insulated switchgear (GIS) was also considered due to smaller footprint and lower maintenance requirements. The AIS was chosen due to upfront costs, lead times, no space restrictions in the field and ease of expansion.
• LV switchboards were specified based on demand loads with consideration for N+1 redundancy and future expansion. LV switchgear was considered but rejected, because a 30-cycle rating was not required to achieve selectivity between the main and the feeder breakers, and the switchboard would be maintained during outage times.
• Notice in Figure 2 the secondary rated ampacity of the transformer is lower than the main breaker and switchboard bus rating. Since the transformer rating is based on a thermal limit, having the secondary current rating of the transformer being the limiting provides greater flexibility for expansion in the future, versus the bus rating on the switchboard to be the limiting factor.
• Switchgear and switchboards fault current equipment ratings were specified to withstand maximum available faults based on the short circuit study. Specifying equipment with proper ratings can prevent significant safety hazard to personnel and protect the space beyond the equipment enclosure during a fault.
• MV switchgear control power was initially overlooked and not planned properly to provide UPS backed power to the switchgear enclosure. The engineering team added a control power transformer internal to the switchgear enclosure switched via an external circuit.
FIGURE 3: MV Switchgear fed from MV utility transformer, and incoming shore power for critical loads internal to the switchgear enclosure. Courtesy: Jacobs
The expansion also contains both a small data center and a significant industrial load addition. The industrial loads are primarily motors fed by variable frequency drives (VFDs). Due to mechanical redundancy, short duty-cycle loads and demand factors, the system size to support the loads was reduced when compared to the connected load. Articles 430.24 (Several Motors or a Motor(s) and Other Load(s)), and 430.26 (Feeder Demand Factor) were utilized with supporting data from the existing facilities and all findings were provided to the authority having jurisdiction (AHJ) for approval.
Uninterruptible power supply (UPS): Modular type UPSs with lithium-ion batteries were specified by the engineering team. Below are steps taken by the engineering team to specify the UPS equipment:
• After the critical power demand load was calculated, the design team had to determine the runtime required to power critical loads during outages. The duration time plus maximum critical load power demand determines the size of the UPS and batteries required.
• The design team specified modular type UPSs to run in parallel to meet the critical power demand loads, also considering N+1 redundancy on the number of modules to prevent downtime during maintenance.
• The design team specified UPSs with 480V output to be stepped down via transformers as needed, this was due to voltage drop considerations for certain loads.
• The design team coordinated with the architectural and mechanical design teams to meet space requirements for the lithium-ion batteries. The batteries had to be isolated in a separate room with fire rated walls. Proper ventilation and fire safety measures had to be taken into consideration.
• Lithium-Ion batteries have advantages, but also come with additional requirements due to some cases involving issues with fires. A full discussion of this topic is beyond the scope of this article, but NFPA 855 and the local fire marshal were consulted.
• Design team then calculated the proper DC cabling between the battery cabinets and the UPS modules.
• The engineers worked with the mechanical team to ensure proper air flow, and temperature were maintained for UPSs in the electrical room. Also taking into consideration all other equipment to be installed in the same room. This included a computational fluid dynamics (CFD) study to identify potential hot spots or areas of dead air flow. Based on this study, the electrical engineers had to modify the equipment layout inside the electrical room to allow for better airflow, and derated the cables running in cable tray above the UPS cabinets.
When it comes to designing industrial power systems, many design decisions must be made. This case study shows some of the common key design decisions that must be made in an industrial setting.
Other factors such as site-specific standards, regional codes and standards, equipment lead time and client expectations would impact the overall design decisions to specify a complete and functional electrical distribution system that meets the client’s construction and operational targets. cse
Sha Eshghi, PE, is an electrical engineer with Jacobs with experience in power distribution design on advanced facilities.
csemag.com
Power generation insights
u A power distribution system has many different aspects that need to be considered because a fault or mistake can lead to major issues regardless of the type of facility.
u The case study highlights several challenges the electrical engineering team faced and how they had to work through these problems by revisiting or revising what they had done to ensure the project would be successful.
Alexandria Stuart and Caley Johnson, CDM Smith, Maitland, Florida
Most building codes require mechanical ventilation with few exceptions. Many building occupancy types require large volumes of outdoor air. Dedicated outdoor air systems (DOAS) provide 100% fresh outdoor air to a building or space. Unlike traditional heating, ventilation and air conditioning (HVAC) systems, which usually recirculate air inside the building, DOAS units bring in outdoor air and condition it before distributing it throughout the building.
DOAS usually run alongside other HVAC equipment serving the building or space to meet the need for outdoor air. Where traditional cooling and heating equipment can’t meet latent loads, special equipment is needed, increasing costs and space requirements.
ing the fresh air to occupied spaces. DOAS units are also effective dehumidifiers. DOAS units can help keep building pressurized properly. This can prevent unwanted odors, moisture and impurities from entering the building through infiltration. Because DOAS units can handle larger latent loads, other local or central HVAC units can be reduced in size to just handle the building’s sensible load. Preconditioning outdoor air at the DOAS unit can also lead to significant energy savings, which can lead to monetary savings when implemented correctly.
The requirements for ventilation rates by building codes and other standards are the main driving factors for installing DOAS. With the growing popularity of DOAS to meet ventilation needs, these systems are provided by various manufacturers and suppliers. Manufacturers are beginning to provide an array of configurations that meet different design needs.
Learningu
• Become familiar with the selection process for determining the appropriate dedicated outdoor air system (DOAS) arrangement.
• Understand the various components that make up a DOAS unit.
• Review the codes and standards that govern a DOAS unit design and specification.
According to the ASHRAE Handbook 2020: Heating, Ventilating and Air Conditioning Systems and Equipment, DOAS can help bridge that gap by centralizing the conditions of the outdoor air and in some cases incorporating an energy recovery ventilator (ERV).
Although the main reason for using a DOAS unit is to meet minimum ventilation requirements, these systems also provide other benefits. Conditioning the outdoor air separately from recirculated air makes it easier to verify that each zone is being provided with sufficient outdoor air.
DOAS also improve indoor air quality (IAQ) by filtering outdoor air contaminants before dispers-
The type of equipment used with a DOAS unit may vary depending on building type, spatial constraints and end-user needs. The benefit of a DOAS is that it, unlike a lot of other HVAC equipment, can meet these high ventilation rate requirements.
DOAS units are provided by several manufacturers in the HVAC industry. These manufacturers offer units in multiple configurations such as a split option or packaged. The split option is composed of an indoor unit with a remote condenser. The packaged options are self-contained and located outside on a building’s roof or on a concrete slab on the ground. Hydronic DOAS units can be installed within a building with outdoor air ducted to the exterior through a louver.
DOAS units are designed to accommodate a diverse range of entering air conditions, ranging from the hottest summer days to the coldest winter nights. Units can temper the outdoor air using different methods. The system configuration types include water source heat pumps, air source heat pumps, water-cooled direct expansion, air-cooled, direct expansion or chilled water. These configuration options are chosen based on client site utilities, client preference and even an energy model’s leastcost estimates.
Manufacturers also provide customization options for DOAS units. Cabinets can be outfitted with insulated foam to reduce heat transfer losses and corrosion-resistant coatings to withstand challenging environments. There is also the option to provide human machine interface, which allows a simpler way to program different unit settings such as temperature and humidity.
The DOAS unit typically cools and dehumidifies air in the summer and humidifies and heats air in the winter. The most basic unit consists of a preheating coil, a cooling coil, a reheating coil and a humidifier. DOAS units can also be provided with a wide range of additional components to meet specific design needs and climate conditions. The below outlines common equipment components:
Supply and/or exhaust fans. DOAS units come standard with supply fans and also can be equipped with an optional exhaust fan and/or heat recovery component. Plenum supply fans are also common in DOAS applications.
Variable-speed drives or electronically commutated motors (ECM). Fans equipped with ECMs offer 10:1 turndown. This allows for fan speed reduction as ventilation needs vary. Variable speed compressors allow for the DOAS unit to adjust its heating and cooling capacity to match the required load. In doing this, the unit provides a consistent temperature throughout the space and avoids large temperature swings.
FIGURE 1: This figure displays a typical dedicated outdoor air systems (DOAS) unit configuration. Courtesy: CDM Smith
‘ Unlike traditional HVAC systems, which usually recirculate air inside the building, DOAS units bring in outdoor air and condition it before distributing it throughout the building.’
Cooling modules. Cooling modules are useful for cooling and/or dehumidifying outdoor air. Heating modules. When a space requires heat greater than what the base unit can provide, DOAS units can be provided with electricity, natural gas, liquefied petroleum gas (propane), steam or hot water as a heating source. The heating systems have multiple options for control including multistage, silicon-controlled rectifier or modulating.
Humidifiers. DOAS units can be fitted with humidifiers to be used during the dry outdoor conditions to bring moisture into the air, providing greater occupant comfort.
Hot gas reheat. Manufacturers offer hot gas reheat options on their units for dehumidification purposes. On a mild but humid day when air needs to be dehumidified, the only way to remove moisture is to cool the air. To avoid creating cold clammy air if it is not warm enough, this additional option allows cooled, dehumidified air to be heated to a more comfortable temperature, providing neutral dry air. Heating and heat recovery of air above 60°F in DOAS units that provide ventilation air to multiple zones and operate in conjunction with zone heating and cooling systems when building loads or outside air temperature indicate the majority of zones are in cooling is prohibited by ASHRAE Standard 90.1: Energy Standard for Buildings Except Low-Rise Residential Buildings. In other words, heated “room neutral” air from a DOAS can cause energy waste when downstream units must recool it to meet zone temperature setpoints.
csemag.com
DOAS insights
u Building codes and industry standards are requiring minimum volumes of outdoor air. To meet these ventilation requirements, dedicated outdoor air systems (DOAS) are needed to address the conditioning capacity associated with the ventilation requirements.
u These systems most often run in parallel with other systems to provide 100% outdoor air and handle latent loads. DOAS also improve indoor air quality through filtration, further increasing occupant comfort.
Air-to-air energy recovery devices. Energy recovery for these units is typically air-to-air. This can be provided through polymer enthalpy wheels, aluminum enthalpy wheels or enthalpy plate heat exchangers. Energy is recovered when two streams of air — fresh air and return air — pass through the energy recovery device and transfer moisture and heat from one air source to the other.
Filters and other cleaning devices. Air purity can be improved through different filtration options provided for units including MERV 8, 11 or 14 filters; metal mesh filters; or some manufacturers even offer bipolar ionization. Bipolar ionization systems generate positively and negatively charged particles to help HVAC systems remove them from the airstream.
Space/building air temperature and humidity sensor. This component helps in monitoring the air temperature and humidity within a space or building and is available in various measurements, which include, outdoor, discharge, space and return humidity and air temperature measures.
Unit configurations. Unit orientations can be modified to meet space requirements. This is especially useful in retrofit applications where available space is limited. Manufacturers typically allow either vertical or horizontal supply air discharge placement and vertical, horizontal or no return air arrangements.
When designing a building’s HVAC system, the engineer or designer may opt to provide multiple
smaller units to have more zone controllability in lieu of single, large units.
DOAS units can be integrated with almost any type of heating and cooling system design. DOAS units are often used in conjunction with fan coil units, variable air volume (VAV) systems, variable refrigerant flow systems or packaged terminal air conditioners.
In any configuration type, the DOAS selection would consider the outdoor air and latent loads for the building and the local equipment would be sized for each space’s sensible loads. This allows for a reduction in the local equipment’s sizing because it will only need to be sized to handle the sensible load generated within the space. One configuration type is ducting directly from the DOAS unit to each space the unit serves.
Another system configuration for the DOAS is to duct the outdoor air directly to the return of the local unit. When the DOAS is ducted directly to the return, it allows the local unit to mix the outdoor air with the recirculated air and condition this mixture.
The final HVAC system configuration discussed occurs where the DOAS is ducted to a ceiling plenum, closet or mechanical room plenum, which the local unit uses as an intake. This method is typically not recommended as it is challenging to guarantee that each space receives its allotted outdoor air requirement.
In different design climates, DOAS can provide different modes of operation. For hot and humid areas, the DOAS unit should run in dehumidification and cooling mode. In other climate zones where ambient conditions are hot and dry, the DOAS unit may only need to run in sensible cooling mode. In cold climate areas, the DOAS may need to heat the incoming outdoor air in heating mode and provide humidification.
During occupied hours, the DOAS may need to run in these different operating modes and provide ventilation air. During unoccupied hours, because ventilation is not required, the DOAS may only need to provide dehumidification to ensure the building stays dry. This is done by closing the
A WATER treatment plant expansion required DOAS to serve buildings that needed a lot of outdoor air
Houston, in association with four regional water authorities, is expanding its Northeast Water Purification Plant (NEWPP) from 80-million-gallons-per-day (mgd) to 400 mgd — dramatically increasing its ability to support steady residential and commercial growth while reducing dependency on groundwater. The NEWPP expansion project is the largest water treatment plant project in the world being delivered using a progressive design-build delivery methodology.
This project is being performed by the Houston Waterworks Team, a 50/50 joint venture comprised of CDM Smith and Jacobs operating as one team to bring this exciting project to fruition.
Dedicated outdoor air systems (DOAS) were implemented for spaces that required a high volume of outdoor air. These DOAS units are used to serve chemical buildings, administration buildings and maintenance buildings.
The first unit in Figure 4 is a ground-mounted, packaged, unit ducted into a chemical building. The unit uses natural gas as a source to heat the air. It is supplying 5,175 cubic feet per minute (cfm) to chemical storage areas. Due to the corrosive nature of the space, the system does not provide any exhaust to the DOAS unit. The unit has a cooling capacity of 204 MBH (thousand BTUs per hour) and a heating capacity of 316 MBH. The unit is supplied with an aluminum mesh and MERV 8 filter.
Some additional accessories include stand-alone controller, plenum curb with horizontal duct connection, stainless steel gas heat exchanger, inverter scroll compressor, electronically commutated motor (ECM) premium efficiency motor and a 1-inch injected foam, R-7, galvanized steel liner.
The unit in Figure 5 is a roof-mounted, packaged, bottom-discharge, unit ducted into an administration building. The unit uses natural gas as a source to heat the air. It is supplying 1,710 cfm to a control room, office and a break room and returning/exhausting 1,575 cfm to the DOAS unit. The unit has energy recovery in the form of an energy wheel, a cooling capacity of 83.80 MBH and a heating capacity of 160 MBH. The unit is supplied with a MERV 8 prefilter and MERV 13 filter.
Some additional accessories include 1-inch injected foam, R-7, galvanized steel liner, ECM premium efficiency motors, inverter scroll compressor, modulating control on inverter compressor, stainless steel gas heat exchanger, at least 5:1 modulating turndown, provide with horizontal duct connection or plenum curb
with horizontal duct connection, standalone controller, multiple exhaust airflow conditions based on a control sequence and an internally mounted nonfused disconnect with external service handle.
Comparing the two units, some of the required accessories are similar between them, regardless of the application. Other accessories vary due to the difference in application, serving a chemical storage space versus serving an administrative space. Some of the main differences are due to whether the unit is receiving exhaust/return air, the discrepancy in unit size and installation location.
It is important to note that the chemical building DOAS unit does not require multiple exhaust airflow conditions, but the DOAS unit that serves administrative spaces does and has energy recovery associated with it. The staggered setpoints for exhaust are due to conditions in which kitchen exhaust hoods and exhaust fans are activated.
The unit controller and overall building automation system will be programmed to allow that functionality. This is not necessary for the chemical building DOAS unit as it only has interlocked operation with exhaust fans serving that building and no return air provided to the unit.
‘ ASHRAE Standard 62.1 is continuously updating and evolving to ensure minimum IAQ is provided for building occupants. ’
outdoor air intake damper and just recirculating return air to allow it to be dehumidified. This control method reduces wasted energy and provides cost savings for the building owner.
ASHRAE Standard 62.1: Ventilation for Acceptable Indoor Air Quality was first published in 1973 and provides industry standards for outdoor air requirements for various occupied building types and spaces. ASHRAE Standard 62.1 is continuously updating and evolving to ensure minimum IAQ is provided for building occupants.
In some cases, there is a benefit to providing more outdoor air to a space than minimum required by code. One U.S. Green Building Council LEED point can be achieved by providing 30% more outdoor air to each breathing zone than the minimum required by ASHRAE Standard 62.1.
LEED Certification is the most widely used global rating system that recognizes the design and construction of high-performance buildings that are
better for occupants and the environment.
Another benefit of providing more outdoor air than is required by code minimums is an increase in employee production by reducing quantities of carbon dioxide. Studies have shown that higher concentrations of carbon dioxide may lead to slower reaction times and increased tiredness. Providing additional outdoor air can also help reduce the infection rate of viruses. By providing fresh air, the concentration of viruses in the space also decreases. DOAS units that provide 100% ventilation air are becoming more widely used. In building spaces where outdoor air requirements are high due to energy codes and ASHRAE standards, DOAS units are often most efficient. DOAS units are also best used for buildings with large occupancies or zones that require all or large amounts of air to be exhausted, such as commercial kitchens. The below are common building and space occupancy types that are best served by DOAS:
• Animal shelters.
• Churches and religious buildings.
• Conference rooms.
• Dormitories.
• Hotels.
• Institutions.
• Locker rooms.
• Multifamily housing.
• Nursing homes.
• Restaurants.
• Retail stores.
• Schools.
• Veterinary hospitals.
DOAS systems are an innovative approach for HVAC design that have proven to be highly efficient while providing occupant comfort and meeting the needs for outdoor air requirements. Many design applications benefit from the use of DOAS systems and these systems can be used in a wide variety of building types. cse
Alexandria Stuart is a mechanical engineer at CDM Smith, focusing on the design of HVAC and plumbing systems for wastewater and water treatment plants. Caley Johnson is a mechanical engineer at CDM Smith, focusing on the design of HVAC and plumbing systems for wastewater and water treatment plants.
Greenheck's comprehensive line of Dedicated Outdoor Air Systems, available in models RV, RVE, and RVC, deliver up to 100% fresh outdoor air and industry-leading features that are pre-engineered and factory-tested to meet the demands of your projects. Offering airflow up to 18,000 cfm, cooling, heating, and energy recovery options , Greenheck’s DOAS products elevate ventilation performance.
Specify with Confidence. Specify Greenheck.
Dennis P. Sczomak, PE, LEED AP, Peter Basso Associates Inc., Troy, Michigan
Chillers, previously used only to cool buildings, also can be considered as part of the heating system, thus minimizing lost heat and reducing fossil fuel consumption
Water chillers remove heat from chilled water, which is used to cool a building or process. With a water-cooled chiller, the chiller transfers that heat via a refrigeration cycle from the chilled water to a separate condenser water loop, typically that heat is rejected from the condenser water loop to the outdoors via a cooling tower.
The valuable heat being rejected from the building could be recovered by a water cooled, heat recovery chiller (see Figure 1). This can substantially reduce the building’s carbon footprint by decreasing heating energy requirements, whether from a fossil fuel boiler or from an electric heating source. Cooling tower water makeup and chemical treatment is also reduced.
Operating a chiller in heat recovery mode requires more compressor energy than operating a water-cooled chiller with heat rejection to the outdoors via a condenser water loop and cooling tower.
• Understand how a heat recovery chiller can reduce a building’s carbon footprint.
• Review scenarios in which a heat recovery chiller can be applied.
• Know about the design considerations for heat recovery chillers.
For example, using the minimum efficiency requirements in the 2019 edition of ASHRAE Standard 90.1: Energy Standard for Buildings Except Low-Rise Residential Buildings, a 150-300-ton water cooled
chiller uses 0.462 kW/ton when cooling, based on the standard’s required integrated part load value. Operating a chiller with similar capacity in heat recovery mode using the minimum efficiency requirements in ASHRAE 90.1-2019 with a leaving heating water temperature of 120°F increases the chiller’s cooling energy use to 0.650 kW/ton.
However, a heat recovery chiller operating at this minimum efficiency is an extremely efficient heating machine, with an effective heating coefficient of performance of 22.2, when considering only the incremental compressor energy increase between operation in cooling-only mode and operation in heat recovery mode.
Three scenarios for application of a heat recovery chiller are highlighted.
First, during summer, many building heating, ventilation and air conditioning (HVAC) systems reject heat through a cooling tower, via a watercooled chiller, at the same time fossil fuels are being consumed to generate heat for tempering cool air supplied for ventilation and/or dehumidifcation. The valuable heat being rejected by the cooling tower could instead be recovered via a water cooled, heat recovery chiller, assisting in the decarbonization of the building.
Second, during winter, many buildings have rooms that require cooling at the same time rooms along the exterior of the building require heating. The rooms that require cooling are typically located in the interior of the building and/or are rooms with high heat gains from lights and equipment.
The most common building HVAC systems address the cooling needs of interior or high heat gain rooms in winter by supplying them with cool winter outdoor air, which is then exhausted to the outdoors. While the valuable heat in the warm exhaust air can often be recovered to reduce the heating requirements of the incoming outdoor
makeup air, a more effective approach may be to decouple the ventilation air supply from the cooling and heating of the rooms. This allows heat to be removed directly from the rooms which need cooling, via a sensible cooling device such as a chilled beam and then that heat can be transferred to the heating system by a heat recovery chiller and used to heat exterior rooms that need it, thus reducing fossil fuel use.
Third, buildings in cold climates that have high indoor relative humidity requirements will significantly reduce humidification energy use by limiting their outside air intake to the amount required for ventilation, instead of incorporating an airside economizer cycle. This is because an airside economizer cycle will take in a large volume of outside air during moderate winter conditions, often far in excess of the amount required for ventilating most buildings, which must be humidified to the indoor humidity level.
The elimination of the airside economizer cycle typically requires the chilled water system to provide chilled water throughout the winter. A common method to accomplish this without running a chiller is to employ a waterside economizer system in which the cooling tower fan(s) are operated during winter to produce cooling tower water, which is colder than the required temperature of the chilled water. The cold cooling tower water is then used to produce chilled water via an intermediary heat exchanger. Valuable heat being rejected by the cooling tower could instead be recovered via a heat recovery chiller, which transfers the heat from the chilled water to the building’s heating hot water system used to heat the building.
While it may seem somewhat counterintuitive to energize the much larger electrical load of a heat recovery chiller instead of a cooling tower fan for winter chilled water production, because the heat recovery chiller can transfer in the range of 4-7 times its compressor energy into the heating hot water and also capture its own compressor energy as heat, the heat recovery chiller is effective at both reducing carbon footprint and saving energy cost in nearly all cases.
There are several important design considerations when incorporating a heat recovery chiller into a building HVAC system:
‘ The most common building HVAC systems address the cooling needs of interior or high heat gain rooms in winter by supplying them with cool winter outdoor air, which is then exhausted to the outdoors. ’
Heating hot water system temperature is a significant and limiting factor for the application of water-cooled heat recovery chillers. While there are chillers that can produce hotter water, for practical purposes the heating hot water temperature should be limited to no more than 140°F and lower when possible. This is because the efficiency of the heat recovery chiller is affected greatly by the “lift” at which the machine is operating, with lift being governed by the temperature difference between the cold fluid leaving the chiller’s evaporator and
the hot fluid leaving the chiller’s condenser. In a heat recovery chiller, the fluid leaving the chiller’s condenser is heating hot water.
For new construction and renovations in a northern climate, we target the HVAC system’s hydronic heating devices to provide the maximum required capacity at no greater than 120°F heating hot water supply temperature. This typically requires more rows and larger face area in airside heating coils than when hotter water temperatures are used.
A MUSEUM NEEDED an updated HVAC system, including a modular chiller
In this existing museum, most of the HVAC system had surpassed its useful life and required replacement. The original HVAC system design incorporated an airside economizer, which, when paired with the requirement to maintain a minimum of 40% relative humidity (46°F dewpoint temperature) in the building throughout the winter, required extremely large amounts of humidification energy. Note that the 2019 edition of ASHRAE Standard 90.1: Energy Standard for Buildings Except Low-Rise Residential Buildings provides an exception to its economizer requirement when the building is required to be humidified to more than 35°F dewpoint temperature.
The airside economizer mode in the air handling systems is being eliminated in favor of intaking outside air only in the amount required as ventilation air. Chilled water will be required year-round as the airside economizer mode is eliminated.
A modular heat recovery chiller that has the capability to simultaneously heat and cool is being provided to replace the existing cooling-only chillers. The modular chiller will be operated year-round. When building heating and cooling loads are balanced, module(s) will operate in heat-recovery mode (see Figure 3). When cooling loads are dominant over heating loads, additional module(s) will simultaneously operate in cooling-only mode (see Figure 4).
Should the museum install a geothermal ground loop in the future in addition to having modules operate in heat recovery mode at times when heating loads are dominant over cooling loads, additional chiller modules could be operated in heating mode to draw heat from the ground loop (see Figure 5).
The modular chiller was chosen because:
• Each module could automatically switch between heat recovery and cooling modes and allow a varying number of
3: Modular chiller with simultaneous heat-cool capability during heat recovery only mode. Courtesy: Peter Basso Associates Inc.
modules to be operated in each mode as dictated by load. This helped to effectively increase the capacity of the chiller in each mode within much less of a footprint than would have been required by separate, dedicated heat recovery and cooling-only chillers. This allowed both modes to be accommodated within the constrained space of the existing mechanical room.
• Each chiller module can be separately brought into the existing mechanical room, greatly reducing the complexity as compared to bringing larger chillers into the room.
Reduced heating hot water supply temperature limits its use for indirectly heating domestic hot water to preheat duty, requiring booster heaters for domestic hot water in most cases.
For existing buildings with heating hot water supply temperatures greater than 140°F, a heat recovery chiller is generally impractical until the heating system is retrofitted to work with a lower water temperature. We plan to discuss design considerations for the application of low temperature heating hot water systems in new and retrofit applications in a future article.
‘ While there are chillers that can produce hotter water, for practical purposes the heating hot water temperature should be limited to no more than 140°F and lower when possible. ’
• Each chiller module has two small, independent refrigerant circuits, which are smaller than the allowance of the local municipality’s refrigeration ordinance.
• The evaporative cooling tower’s open water loop is being decoupled from a closed condenser water loop, which circulates through the chiller by means of a plate and frame heat exchanger. This would allow the closed condenser water loop to be adapted in the future, if needed, to circulate through a closed-geothermal ground loop. Because the selected modular chiller has internal automatic valves that gives it the capabili-
ty to send the geothermal loop water to selected evaporators in heating mode (see Figure 5), this would allow chiller modules to draw heat from the earth into the heating hot water, in addition to other modules recovering heat from the chilled water into the heating hot water.
To coordinate with the heating capabilities of the heat recovery chiller, the existing hydronic heating devices in the building, all of which have exceeded their useful life and all of which were originally designed to operate with 180°F heating hot water supply temperature, are being replaced with hydronic heating devices designed to operate with 120°F heating hot water.
Chilled water supply temperature should also be kept as warm as possible to minimize the required chiller lift, thus improving heat recovery chiller efficiency. This is a parallel consideration to keeping heating hot water supply temperature as low as possible when using a heat recovery water chiller. This means chilled water temperature should automatically be reset by the HVAC control system to be as warm as possible, especially when dehumidification is not required in winter conditions.
‘ For a heat recovery chiller to function, the HVAC system into which the heat recovery chiller is applied must have concurrent chilled water and heating hot water demands. ’
The use of chilled beams as sensible-only cooling devices in rooms provides an ideal system for the application of a heat recovery water chiller. With a chilled beam system, chilled water temperatures must be kept warmer than the room dewpoint temperature, thus also reducing the required lift of the heat recovery chiller. Because most or all room heat gain in both summer and winter is removed by the chilled beam into the chilled water, the amount of recovered heat is optimized. The heat recovery chiller moves the heat from the chilled water circulated through the chilled beams into the heating hot water, which can then be supplied to heating devices.
ery chiller is limited by the concurrent cooling load on the chilled water system; if the cooling load is less than the heating load served by the chiller, minus the chiller’s compressor heat, then the chiller’s operating capacity must be lowered to match the load.
To maximize the fossil fuel reduction achieved by the heat recovery chiller by means of its heating output, the chiller can be piped to load it before loading other cooling-only chillers. A side stream chilled water piping arrangement for this is indicated in Figure 2. With this piping arrangement, when the cooling load exceeds the cooling capacity of the heat recovery chiller, the cooling-only chillers must maintain the system leaving chilled water temperature.
There are other possible piping arrangements for incorporating a heat recovery chiller with cooling-only chillers — this side stream arrangement minimizes the lift on the heat recovery chiller and allows it to be fully loaded when the cooling-only chillers are not.
If there is potential for inadequate heating demand as needed to balance the heat recovery chiller’s chilled water production, it can sometimes be beneficial to add heat rejection capability to the heating hot water system that can be activated when needed (making sure that other heat sources on the heating hot water system, such as boilers, have already been turned off).
u
Heat recovery chiller insights
uHeat recovery chillers can recover heat being rejected from the building. This process can aid in decarbonization.
uDecoupling ventilation air from the cooling and heating of a building’s rooms can also reduce fossil fuel use.
Concurrent heating and cooling demands: For a heat recovery chiller to function, the HVAC system into which the heat recovery chiller is applied must have concurrent chilled water and heating hot water demands. The heat recovery chiller moves heat from its evaporator (chilled water) to its condenser (heating hot water, see Figure 1). The heat recovery chiller’s compressor heat is also rejected through the condenser and into the heating hot water.
The cooling provided by the heat recovery chiller is limited by the concurrent heating load on the heating hot water system. If the heating load is less than the cooling load served by the chiller, plus the chiller’s compressor heat, then the chiller’s operating capacity must be lowered to match the load. Similarly, the heating provided by the heat recov-
Among the ways to accomplish this is by adding a heat exchanger that transfers heat out of the heating hot water loop and into the cooling tower loop, where it can be rejected by the cooling tower (or by the geothermal ground loop, if one exists).
It is important to consider that a heat recovery chiller typically consumes more power, due to its greater lift, than a cooling-only chiller that is rejecting heat to a cooling tower. Because of this, the amount of heat being rejected to the outdoors from the heating hot water system should not be allowed to exceed the tipping point where the beneficial heat being recovered into the heating hot water system is less than the increase in compressor energy between the heat recovery chiller and the coolingonly chiller.
Careful consideration should be given to concurrent heating and cooling load profiles to avoid oversizing heat recovery chillers.
Another approach for systems with inconsistent heating demands would be to provide smaller increments of heat recovery and cooling-only chiller capacity, allowing them to be staged as heat recovery and cooling-only demands vary. An example applying specialized modular heat recovery chillers that are available on the on the market, is described in the case study: Retrofit requires modular chiller with heat recovery.
When heat recovery chillers are incorporated into an HVAC system, their cooling and heating capacities can be factored in when determining the required capacity of other cooling-only chillers and heating boilers, but important considerations must be taken, including:
• If heating hot water temperature is seasonally adjusted, the heat recovery chiller’s capacity must be derated to the capacity it can provide at the heating hot water temperature for which the boiler capacity was selected.
• There could be an imbalance between heating and cooling loads at certain times, as described above, which could limit the heat recovery chiller’s cooling and/or heating capacity at the time the cooling-only chillers and/or boilers are required to provide their maximum capacity.
Chillers should no longer be considered only as machines that remove heat from the building for it to be rejected to the outdoors. Heat recovery chillers can be employed to capture that heat, reducing the building’s carbon footprint. Designing the building heating system to work with low heating water supply temperatures, designing the building cooling system to effectively capture internal heat gains and careful evaluation of concurrent cooling and heating load profiles are among the complexities that need to be considered when employing heat recovery chillers. cse
Dennis P. Sczomak, PE, LEED AP, is a senior vice president at Peter Basso Associates Inc. He has 38 years of engineering experience and leads PBA’s technical staff as Director of Engineering.
CHILLED BEAMS are working in conjunction with a heat recovery chiller to move heat to the hot water system
In this large laboratory building, a heat recovery chiller is being incorporated to transfer heat from the chilled water being returned from chilled beams into the heating hot water system. The benefit of applying the heat recovery chiller directly to the chilled beam water return — as opposed to applying it to the mixed return water from chilled beams and air handling unit (AHU) coils is that the chilled beam return water is much warmer, reducing the required lift on the chiller and improving its efficiency.
Chilled water is supplied by the heat recovery chiller to the chilled beams at a temperature that is slightly above the room dewpoint temperature, but below the room’s dry bulb temperature. The room sensible heat that is absorbed into the beam water is transferred by the heat recovery chiller into the building heating hot water system.
Cooling-only chillers provide chilled water to AHU cooling coils at a temperature that is cold enough to dehumidify the incoming outside air when required. The cooling-only chillers can also serve as an additional cooling source for the warmer chilled beam cooling water through a blending valve arrangement.
Outside air is heated, cooled and dehumidified (or humidified, depending on season) at the central AHUs before it is supplied to the laboratories and office spaces at a temperature that is just below the room design dry bulb temperature. The heating, cooling and dehumidifying process at the central AHUs is done very efficiently, using air to air heat recovery devices to transfer heat to/from the exhaust air (depending on season) and to transfer heat from upstream of the chilled water coil to provide “free” reheat downstream of the chilled water coil, reducing the load on the cooling coil in the process.
The near neutral temperature air is then supplied in an amount required by each room for the greater of the code required ventilation air, volume of dry air required for the latent cooling load, minimum air change rate for laboratory rooms or makeup air for fume hood exhaust. In some laboratories there are large equipment heat gains, which, if a conventional HVAC system had been used, would have required an additional quantity of supply air for cooling and thereby an additional amount of dehumidification and supply fan energy would have been consumed.
Instead, in these rooms the chilled beams remove this additional sensible heat, without adding dehumidification or supply fan energy and the heat is recovered by the heat recovery chiller.
Another benefit of the chilled beam system, as compared to a “conventional” HVAC system in which ventilation air delivery is not decoupled from room cooling is that exhaust air energy recovery can be maximized at the AHU. In a conventional, coupled HVAC system, exterior rooms receive the same cool supply air as interior rooms, so the air being supplied to exterior rooms cannot fully benefit from exhaust air energy recovery devices that are employed at the central AHU to heat incoming outside air.
Further, the cool air supplied by a coupled HVAC system to exterior rooms must be reheated to room temperature before additional heat is added to offset the heat loss through exterior walls. By incorporating a decoupled HVAC distribution system using chilled beams, AHUs can fully use the benefit of exhaust air heat recovery devices to heat incoming ventilation air to near room-neutral temperature before it is supplied to all rooms, including exterior rooms, greatly reducing the need for additional reheat energy.
By John Song, PE, McGuire Engineers, Chicago
While commercial hydronic systems are generally reliable and efficient, they can experience a range of issues that can impact performance and lead to increased energy costs and equipment failure
FIGURE 1: The differential pressure regulator within the pressure independent control valve is a key component, which consists of a diaphragm, spring and the valve. Together these components work to maintain a constant flow regardless of changes in the system pressure or load. P3 is the high-pressure side and the small capillary tube connects the high-pressure side to the bottom of the spring-controlled a. P2 shows the flow, controlled by the plug modulated by the actuator and P1 is the low-pressure side of the valve.
Courtesy: IMI Hydronic Engineering
Hydronic systems operate to maintain flow through a system and typically at the end of a project, flow to different devices and units are balanced to maintain the flow required.
However, as demand from the different coils within the system changes, the pressures throughout the hydronic system also change. As filters become clogged, increasing pressure drop, different pressures are seen within the system, which also affect flow at each coil. If additional coils are added or removed from the system, the entire hydronic system should be rebalanced but is rarely done.
Low delta T syndrome is a condition that can occur in commercial heating, ventilation and air conditioning (HVAC) hydronic systems when the temperature difference between the supply and return water is lower than expected or designed. This condition results in poor performance and increased energy consumption as additional equipment is required to operate.
When water temperature difference decreases, more flow is required and since pump energy is a cubic function of flow, pump energy costs increase substantially. In addition, more chillers may be required to operate to maintain the flow requirements through the system.
This is expressed by the typical heat capacity equation we are familiar with when accommodating for water:
Eq 1: q = m x C x ΔT
Or, converting for water:
Eq 2: Btuh = 500 x gpm x ΔT
One of the causes of low delta T syndrome is poor water control, which can be caused by several factors:
• Poorly balanced system: If the system is not properly balanced, some areas may receive more water flow than others. With improper balancing, typically the coils hydraulically closest to the pumps overflow to meet the flow requirements for coils that are hydraulically furthest away.
• Oversized pumps: If the pumps in the system are too large and unable to turn down to appropriate requirements, they may push water through the system too quickly, which can lead to poor heat transfer and low delta T.
• Air in the system: If there is air in the system, it can also prevent proper water flow with improper heat transfer, which can cause low delta T syndrome.
Although low delta T syndrome can occur throughout the day, it is more prevalent during unoccupied hours when cooling load is typically lower. When the building is unoccupied, the heat generated by occupants and the equipment is reduced and the outside air temperature may also be lower. As a result, the chilled water supply temperatures remain the same, but the return water temperature is reduced.
Low delta T syndrome can lead to several negative impacts on the system, including reduced heating or cooling capacity, reduced efficiency and increased energy consumption.
Pressure-independent control valves (PICV) are a type of control valve used in hydronic systems that can more accurately maintain the necessary flow rate, regardless of changes in the differential pressure across the valve. One type of PICV operates using a combination of a control valve and a differential pressure regulator. The differential pressure regulator is located downstream of the control valve and maintains a constant differential pressure across the valve. This ensures that the flow rate remains constant, even if the system pressure changes due to varying demand or other factors.
In a variable volume hydronic system, the pump increases and decreases in speed to maintain a system differential pressure depending on the flow requirements of the individual coils. At an individual control valve, as the pump increases in speed and flow, the control valves adjust the flow by closing or
FIGURE 2: The iconic main entrance to The Art Institute of Chicago, where the installation of pressure-independent control valves in the chilled water system reduced chilled water energy usage by mitigating low delta T syndrome. Courtesy: McGuire Engineers
FIGURE 3: A simple chilled water flow diagram is shown for The Art Institute of Chicago project where proper balancing would provide a temperature difference of 7°F. Secondary return water temperatures match the primary water return temperatures through the boilers. Courtesy: McGuire Engineers
opening the orifice to allow flow. As the system pressure changes, the valve must modulate to maintain a constant flow.
If the valve does not modulate, an increase in pressure translates to an increase in flow through the valve. A decrease in pressure translates to a decrease in flow. To maintain a constant flow as the pressure changes, the actuator on the control valve moves the plug up and down to close or open the orifice. By decreasing or increasing the opening, flow is controlled.
PICVs are typically controlled by a building automation system that monitors the temperature in different zones of the building or monitors a coil discharge temperature
• Review how low delta T syndrome can affect performance and energy usage in chilled water systems.
• Learn how pressure-independent control valves (PICV) operate to maintain constant flow with system pressure changes.
• Understand how pressureindependent control valves can solve low delta T syndrome.
FIGURE 4: Chilled water flow at The Art Institute of Chicago shows the results of low delta T syndrome during unoccupied hours where the secondary loop chilled water flow provides only a 4°F temperature difference. Flow through the bypass also incorrectly flows backward as the secondary loop flow is greater than the primary loop. Additional chillers on the primary loop must operate to maintain the necessary flows. Courtesy: McGuire Engineers
csemag.com
Hydronic insights
u Hydronic systems are typically balanced to ensure the proper flow in an HVAC system.
u Pressure-independent control valves (PICV) can help optimize heat transfer and ensure that the temperature difference or delta T, between the supply and return water is consistent.
u Low delta T syndrome can be a common occurrence that can be solved using pressureindependent control valves.
and adjusts the flow rate to maintain the desired temperature — like a standard modulating two-way control valve. The difference is with the differential pressure regulator, which is the key component and typically consists of a spring-loaded diaphragm in combination with the valve assembly. The spring in the cartridge provides a constant force on the diaphragm, the diaphragm senses the differential pressure across the control valve and adjusts the regulator to maintain a constant pressure drop, allowing it to maintain a set flow over a range of system differential pressures.
The control valve within the PICV operates in the same fashion as a conventional modulating control valve with the valve plug moving up and down to adjust the flow based on the coil requirements. By decreasing or increasing the opening, flow is controlled.
In a PICV, the differential pressure regulator use a small capillary tube to operate the spring-loaded diaphragm, which adjusts an orifice to maintain a constant pressure. As system pressure increases, the diaphragm moves toward a closed position to maintain constant pressure.
As pressure in the system decreases, the diaphragm increases the flow area to maintain the constant pressure again. The spring controlling the movement of the diaphragm is selected and cali-
brated to maintain the constant pressure. This means that the control valve can be fully modulated to control flow while the differential control valve maintains pressure.
By combining the function of a control valve and a differential pressure regulator, a PICV can provide precise control over the flow rate while maintaining a constant pressure drop across the valve.
An additional benefit of the PICV is to limit the movement of the actuator, prolonging its life. As the system flow and pressure continuously change throughout the system as, the actuator on a conventional two-way modulating control valve must constantly adjust to maintain a constant flow. As the differential pressure regulator maintains the constant differential pressure, the actuator can remain in the same position and movement is limited.
The differential pressure regulator is typically set to a specific differential pressure during installation, based on the requirements of the system. This pressure drop will vary depending on the flow rate and the specific system requirements, but maintaining a constant differential pressure across the control valve is what allows for accurate flow.
There are many types of PICVs, some of the more common types include:
• Fixed orifice: A fixed orifice PICV has a fixed flow orifice size that provides a constant flow rate regardless of pressure variations. It is the simplest and most economical types of PICV and is commonly used in small or low-flow applications.
• Dynamic balancing: A dynamic balancing PICV incorporates a pressure regulator that adjust the valve opening to maintain a constant flow rate as the system pressure varies. It is an ideal choice for systems with variable pressure drops, such as those with multiple coils.
• Self-acting: A self-acting PICV has a control element that responds to changes in the system pressure to maintain a constant flow rate. It does not require external power or a control signal and is an excellent choice for systems with no power supply.
• Electronic: An electronic PICV uses an electronic actuator to control the valve opening, providing precise control of flow rate regardless of pressure variations. It is commonly used in large or complex systems where accurate control is critical.
• Ball valve: A ball valve PICV has a flow control cartridge that maintains a constant flow rate
THE ART INSTITUTE of Chicago incorporated pressure-independent control valves to improve energy efficiency
The Art Institute Chicago has been proactive in reducing its energy usage and operating its systems efficiently. Maintaining both temperature and humidity is critical when storing and displaying artwork as they can affect the physical and chemical properties of the materials used in the artwork.
High temperature and humidity can cause materials to expand, contract, warp and degrade, leading to permanent damage to the artwork. High temperatures can accelerate chemical reactions and cause paint to crack, fade or become brittle. Low humidity can cause materials to dry out and become brittle, while low temperatures can cause condensation and damage to delicate surfaces.
Maintaining temperatures within an appropriate deadband requires precision control of the cooling, heating and humidification systems.
Additionally, energy costs have only increased and demand charges by the local utility company represented approximately 22% of the energy cost in 2013 and was projected to be approximately 42% in 2016. Opportunities to reduce energy usage and increasing energy efficiency were a driving factors by the decision makers.
With a chilled water temperature difference of 7°F to 9°F and even worse during unoccupied hours, any increase in temperature difference would save both pumping energy and potentially
FIGURE 5: The Art Institute of Chicago’s Modern Wing Building was also included in the pressure-independent control valves upgrade to reduce the central chiller plants energy usage. Maintaining strict temperature and humidity controls requires more energy than typical commercial buildings so The Art Institute has an innate interest in reducing energy consumption. Courtesy: McGuire Engineers
reduce the quantity of operating chillers. The chilled water plant operated at an average of 0.93 kW/ton before any changes were made to the system.
Pressure-independent control valves were introduced to the operating team as an opportunity to increase energy efficiency and reduce energy consumption. As a result, an implementation cost of approximately $350,000 was met with a simple payback of 2.4 years before any utility incentives. The operation of the plant was reduced to an average of 0.73 kW/ton. Temperature differences were also greater than originally specified for the system.
FIGURE 6: Chilled water supply and return temperatures at The Art Institute of Chicago show temperature differences between 7°F to 9°F before the implementation of pressure-independent control valves. After 85% of the pressure-independent control valves were installed and calibrated, temperature differences between 10°F to 15°F were realized — even greater than the temperature differences originally specified for the system. Courtesy: McGuire Engineers
regardless of pressure changes. It is often used in high-flow applications.
When comparing the total installed cost of pressure-independent control valves to the cost of conventional two-way modulating valves, components such as circuit setters may no longer be required and time on-site calibrating each valve is reduced.
Pressure-independent control valves can be a helpful solution to address low delta T syndrome in HVAC hydronic systems. PICVs can help maintain
a constant maximum flow rate through coils they serve, regardless of changes in the system pressure or load, which can help prevent low delta T syndrome and ensure efficient operation.
By maintaining a constant maximum flow rate, PICVs can help to optimize heat transfer and ensure that the temperature difference (delta T) between the supply and return water is consistent. This can be particularly helpful in systems that are prone to low delta T syndrome, as it can help to overcome issues related to poor water flow, such as oversized pumps.
THE FIELD MUSEUM in Chicago will incorporate pressure-independent control valves to help regulate its chilled water system
As The Field Museum in Chicago implemented its master plan, its chilled water system would change as more and more air handling units were consolidated onto the system over the past 20 years. The net result was an improperly balanced system, which became worse over time.
During a recent investigation, the twoway modulating valve controlling flow to the coil hydraulically closest to the distribution pumps were operating as on-off valves. With its location so close to the distribution pumps, the valves would crack open and the pressure would immediately overflow the coils, which also prevented good heat transfer. This wasted energy was prevalent at nearly all the units, which were tested.
A balancer was called out to the site to calibrate the valve to meet the specified flow requirements. After doing so, the valve was able to operate as intended and modulate flow to the coil in lieu of acting as an on/off valve before balancing. Further, more flow was seen at the coils hydraulically furthest away from the distribution pumps.
Air handling units serving critical storage rooms with tight temperature and humidity controls were experiencing issues maintaining values within the required range. While the chilled water valve would open to 100%, discharge air temperature was still not met further verifying issues that flow through the system was compromised.
FIGURE 7: A chilled water valve at Chicago’s Field Museum was shown to open drastically to 100%, unable to maintain the necessary discharge air temperature and operates as an on/off valve due to improper balancing. Flow through the valve and coil are improperly balanced as the system flow and pressures have changed as additional chilled water coils have been consolidated onto the central chilled water plant. Courtesy: McGuire Engineers
The goal is to install pressure-independent control valves moving forward so a properly balanced system can be maintained as air handling units throughout the building are upgraded. During these replacement projects, complete system rebalancing is not necessary after future equipment upgrades.
PICVs can also help maintain system balance even after changes in the system are made. Any changes to the system, with an addition or a removal of a coil, can change the dynamics of the system. In this way, PICVs are beneficial as the system does not have to be rebalanced after any changes as the differential pressure regulator allows the valve to continue to maintain the proper flow.
When low delta T syndrome is present in a chilled water system, additional chillers may be required to operate based on the system flow requirement but not necessarily the load. Meeting building cooling requirements can be difficult when on a design day if the hydronic system is not properly balanced.
It is important to properly size and commission these hydronic valves. If not done, the following are items to consider:
• Valve sticking or binding: Over time, debris or mineral buildup in the system may cause the valve to stick or bind, resulting in poor control and reduced flow rates.
• Incorrect valve sizing: PICVs are easy to size based on the flow rates and will always maintain good controllability. However, always ensure that the design flow is within the recommended gallon per minute range for a given size.
• Inadequate maintenance: Lack of proper maintenance may lead to valve failure or malfunction. Regular visual inspections and general cleaning can help prevent unnecessary issues from general dirt and grime buildup.
• Control system integration: The PICV is a critical component of the HVAC system and must be properly integrated with the control system.
Issues with communication, calibration or control algorithms may result in poor performance or instability, like typical control valves.
As with all control valves, proper sizing and commissioning is critical to ensure optimal performance and longevity. cse
John
Song, PE, is a Mechanical Engineer and Vice President at McGuire Engineers.
‘ By maintaining a constant maximum flow rate, PICVs can help to optimize heat transfer and ensure that the temperature difference (delta T) between the supply and return water is consistent.’
AIR SOLUTIONS READY EVERY
AIR CONTROL SOLUTIONS READY FOR EVERY CHALLENGE
Air control solutions from Ruskin® give the freedom to do more. With innovative damper, louver and air measuring systems, Ruskin continues to lead the industry with solutions to meet the most demanding air handler requirements.
you to more. louver and air systems, continues to lead the with solutions to meet the most air
Automation, logistics and sustainability are pushing mechanical, electrical, plumbing and fire protection engineers to design industrial and manufacturing buildings differently
CSE: What’s the current trend in industrial and manufacturing facilities?
Jarron Gass: Automation, automation, automation! As companies seek to minimize operating costs, efforts to automate manufacturing processes continue to increase. Automation creates opportunities for engineers to innovate and streamline these processes. The advancements with interconnection of various aspects of manufacturing and shipping processes com-
bined with co-locating of different parts of the supply chain are providing the conditions for a more streamlined process from raw source to finished product to end user. These types of efficiencies are working to flatten some of the supply chain issues that have been hampering industry the last few challenging years of the pandemic.
Matthew Merli: There is certainly a large push right now in semiconductor and supporting industries, with CHIPs act as well as private venture capital. That means
research/development, manufacturing, as well as supporting academic institutions pushing money into these types of facilities. Additionally, there are huge advances in automated industrial and manufacturing facilities. Things like robotics, automated manufacturing and support functions are growing exponentially. Lastly, more homegrown (i.e., in the U.S. or neighboring countries) manufacturing seems to be happening with supply chain concerns.
CSE: What future trends should engineers and designers expect for such projects?
Alex Engelman: We believe automation and robotics will continue to develop and will play an even bigger role in industrial and manufacturing facilities, with the help of artificial intelligence (AI) and self-driving cars. As far as building design, many jurisdictions will continue to encourage or introduce legislation toward decarbonization, eliminating and reducing fossil fuels and encouraging renewable energy and energy storage.
Jarron Gass: Following on the automation theme, the next steps will be bridging gaps in the entire supply chain, from raw materials through the manufacturing process and end user acquisition. There is increased scrutiny on inventory manage-
FIGURE 2: First building as part of a bigger industrial development in Brooklyn, New York, providing sortation facility with fleet parking and rooftop photovoltaic (PV) panels. Courtesy:
ment and maintaining lean principles. This means that every individual at every part of the process is feeling pressure to be more exact in predictions and production. Automating as much of the process as possible combined with predictive analytics, to look at and compare current inventory levels against expected and historical needs for any given period, can maximize efficiency and minimize disruptions in the supply chain.
Matthew Merli: Additional automation in these facilities needs to be considers and thought about. Additionally, adaptation to AI and whatever that brings about for our clients will, of course, be important. Changes will happen quickly and engineers and consultants need to be ready to react.
CSE: How is the growth of immediate-delivery services impacting industrial and manufacturing facility projects?
Jarron Gass: Inventory management or supply chain logistics has really magnified the lean approach. On-demand services have presented challenges to efficient lead times and delivering products and services within a reasonable timeframe. From an engineering standpoint, I believe that the challenge is to deliver on the design efficiently and effectively and ultimately construction of new or upgraded facilities. Finding the balance between speed and quality is the defining characteristic of the industry. The ability to deliver cutting-edge and innovative solutions to meet the increasing demands of customer needs is what also often defines the success and profitability of a project.
Alex Engelman: The speed of project delivery for last-mile delivery centers is a highly competitive developer-led marker. Speed to market have led developers to innovate with their engineering, architectural and build teams to accelerate project delivery. To achieve that, a lot of the deliver sortation facilities must be built in dense cities which comes with atypical challenges for industrial facilities. You are now building facilities that cost more, take longer to build and typically have more stringent authority having jurisdiction (AHJ) requirements.
CSE: What are professionals doing to ensure such projects meet challenges associated with emerging technologies?
Alex Engelman: The two major challenges we run up against is coordinating with AHJs and vendors with respect to newer technologies, case in point use of lithium-ion batteries. Additionally, for things such as electric vehicles (EV), the power demand for such facilities has potential to increase dramatically, requiring detailed discussions and planning with the utility companies. Another challenge is making sure the water services can support early suppression fast response (ESFR) or other storage type occupancies. In early planning with the client/developer, understanding the target tenant we can assist in preplanning the needs and making sure anything that should or must be installed with the core and shell and what can wait for final tenant requirements, are valuable discussions.
Jarron Gass, PE, CFPS
Fire Protection Discipline Leader
CDM Smith Pittsburgh
Alex Engelman, PE, LEED AP, CEM
Associate Principal
Syska Hennessy Group New York City
& Technology Market Leader
Fitzemeyer & Tocci Associates Inc.
Woburn, Massachusetts
Jarron Gass: It is a delicate balancing act to identify upgrades or replacements in both facilities and infrastructure and identify when existing facilities should be fully replaced or relocated based on life cycle analysis of existing equipment and the logistics of maintaining service or production during a renovation. This provides ample opportunity for architectural and engineering consultation. Using the newest software and design tools, integrating design teams at the earliest possible stages and collaborating openly with all stakeholders early and often can allow a design and build teams to optimize both the time or downtime associated with construction with the most return on investment for the actual money being spent.
CSE: In what ways are you working with information technology experts to meet the needs and goals of an industrial or manufacturing facility?
Matthew Merli: We invest a lot in our IT and building information modeling (BIM) technologies here. We work on highly advanced facilities like high-tech, labs, manufacturing and health care, and those designs can be complex and the models can be quite busy. Ensuring we
Josam’s PRO-PLUS® system is the perfect solution when installing trench drains.Its Compressive, Tensile, and Flexural strength is unmatched. The material is 1.5 times stronger and 70% lighter in weight, with 1.7 times less thermal expansion than polymer concrete.
✓ Unmatched Strength
✓ Lightweight
✓ Easy-to-Install
✓ Requires Less Manpower
✓ Withstands Extreme TemperaturesPreventing Shape
Distortion
✓ PRO-SNAP® grates with no bolts
✓ Load Class A-F
have a live, Revit/BIM model helps our design team coordinate and makes life easier during construction.
Jarron Gass: CDM Smith has an analytics division to address and bridge the gap from data acquisition with how to use that data. The data is used to analyze and identify vulnerabilities and inefficiencies, understand processes and enable or automate those solutions, stopgaps or other processes to be streamlined. If you understand historical data with multiple variable inputs and understand trends (be it seasonal or consumer sentiment) and pull together all aspects of your supply chain, it allows you to increase efficiency along the journey from all the various source materials to that final consumable product.
Alex Engelman: Many of our clients have a large portfolio and aggressive energy performance target and commitments. We work closely with their environmental, social and governance (ESG) teams to understand their reporting platforms and goals so that our designs align. Key piece of this is the data aggregation from the mechanical, electrical and plumbing (MEP) metering.
Specify the labor-saving PRO-PLUS® with confidence, knowing you specified a high-quality, superior product that owners will be satisfied with and contractors will find easy to install.
CSE: In what ways are you helping manufacturers and suppliers deal with supply chain issues?
Alex Engelman: We have started to work directly with vendors evaluating specific equipment with respect to it not only meeting project requirements but also improving the lead times. For a recent facility, we have redesigned our heating, ventilation and air conditioning (HVAC) distribution while it was already under construction to accommodate different type of equipment and meet stringent schedule. It’s not uncommon to swap out manufacturers for equivalent types but typically we wouldn’t have redesigned major portions of the distribution even when it may be a bit less efficient. cse
Air-cooled heat exchangers for process cooling are challenging applications. While a heat exchanger is a simple device, maintaining a high operational tempo with minimum downtime to support continuous operation of industrial processes is often difficult to achieve with conventional motor and power transmission systems. Whether using belts or gearboxes, these setups require regular maintenance. Belts must be tightened or replaced, and gearboxes require monthly oil checks and semi-annual oil changes. Conventional motors also require regular lubrication.
ABB’s Baldor-Reliance RPM AC direct drive motor solutions offer a unique approach to maintaining operation of air-cooled heat exchangers. Direct drive motors allow exchanger fans to be mounted directly to the motor shaft, eliminating the need for speed reduction devices. The motor’s low operating speed means that lubrication cycles can be extended to an annual basis requiring only a brief shutdown once per year to apply grease to the bearings.
RPM AC direct drive motors operate at low speeds with high torque outputs, and a matched variable speed drive provides the ability to regulate fan speed to maintain specific process cooling requirements. Running at a reduced speed means less power consumption, providing an immense opportunity for power savings and greenhouse gas reductions.
Derived from one of the toughest motor platforms used in the most demanding industrial applications, the RPM AC direct drive motor is right at home inside a heat exchanger’s hot and humid environment. The totally enclosed, air-over, (TEAO) design reduces maintenance, and the electrical system is manufactured using an insulation process that ensures long motor life even in the most extreme environmental conditions.
By combining the technologies of a field-proven, high-performance, permanent magnet rotor with the matched performance of a variable speed drive, the RPM AC direct drive motor reduces energy consumption and maintenance. The realization of these benefits means improved reliability and a lower total cost of ownership.
Engineering a Better Sensor Solution Automation Components, Inc. (ACI), an ISO-9001:2015 certified manufacturer of high-quality sensors for the building automation industry, has developed an ECM current switch with an industry leading 0.075 A minimum adjustable trip point. ECMs have a unique operating profile that includes a small standby current when the motor is powered but not actively spinning compared to no current draw on traditional PSC motors. Power to the switch is induced from the monitored conductor without the need for external power supplies or additional wire loops used to increase the minimum operating current level thus simplifying the installation process.
The ECMCS25-A can be used on both variable and multispeed ECM motors to accurately monitor the motor status and improve your return on investment (ROI) and predictive maintenance. Key features include a finely adjustable 0.075 to 0.500 A trip point, split-core design, small size with 35 mm DIN rail mounting clip, and optional LED indicator tool to reduce installation time.
ACI has additional energy efficiency related products:
• Current Sensors and Switches
• Power Monitoring Meters and Current Transformers
• RH, Temperature, Gas, and Pressure Sensors
• NIST Certifications
Contact Senior Sales Executive, Mike Bollant at 1-888-967-5224, or email: ecm@workaci.com workaci.com
At Cummins, innovation is at the forefront of everything we do. We’ve meticulously designed and built our integrated power systems to offer the highest levels of design and performance control. Offering you unmatched reliability with reduced complexities.
From generator sets and paralleling controls, to system level controls, switchgear and transfer switches, to microgrid components, and digital solutions for remote monitoring, Cummins is with you every step of the way.
No matter your goals, together we can power your future.
Designed and manufactured entirely by Cummins, our latest innovation, the PowerCommand ® B-Series is a marvel. Combining a draw-out automatic transfer switch with an isolation mechanism and a manual bypass transfer switch, the B-Series was designed to meet and exceed UL1008’s stringent endurance testing.
Available from 1200A to 3000A, B-Series features include:
• Cummins-exclusive High-Endurance Mechanism (HEM) Blow-On Technology, which improves product reliability and allows for the ability to survive severe fault current conditions
• Advanced PowerCommand® 80 transfer switch control, a sophisticated LED backlit colored LCD display which includes integrated networking, power quality metering, and power control capability
• Best-in-class Withstand and Closing Ratings (WCR) , 0.05s (3-cycle) time-based WCR which is up to 150kA and 0.5s (30-cycle) short-time WCR, which is up to 125kA
• Heavy-duty opening springs enable fast opening times, extinguishing an arc faster
• Durable automotive grade microswitches for higher reliability
• Dependable modular architecture utilizing stacked high-performance switching cassettes with arc suppression technology designed for maximizing contact life
Built to support your performance, connectivity, and reliability needs, the B-Series went through rigorous testing and complies with the latest applicable codes and standards, such as NFPA70 (NEC), NFPA110, and NFP99.
More than one product, with Cummins, you’re backed by more than 80 years of experience in power transfer control. We’re with you every step of the way in your power journey, offering unrivaled peace of mind.
CLICK to learn more about the B-Series.
From the company that pioneered two stage infrared heaters in the 1990s comes the next big thing in infrared….
Meet the Re-Verber-Ray REV Series.
With a host of innovative and patent pending features never before seen in the marketplace, the REV Series is here to revolutionize building heat. The adjustable reflector and pre-heated combustion air mean the REV Series leads the pack in heater efficiency. High quality materials and superior workmanship ensure years of reliable and efficient operation for heaters that are truly in a class of their own.
Features Include:
• Revolutionary adjustable reflector with variable configurations, allowing for a 12–18% higher radiant output vs. our standard tube heaters.
• Pre-heated combustion air and 18-point reverberatory facets.
• Insulated air pockets for decreased clearances to combustibles.
• Hangerless sliding track & floating tube design.
• 0.075, 14 ga. Aluminum extruded reflector.
• Single Pass or Dual Pass geometry with models capable of achieving an Infrared Factor up to 15 and REV in excess of 110.
Single Pass vs Dual Pass – What’s the Difference?
Also known in the market as “100% design efficient,” Single Pass reflectors direct 100% of radiant rays off the reflector and back to the floor without contacting the radiant tube.
Dual Pass reflectors redirect a small portion of infrared rays back to the radiant tube. The resulting increase in tube temperatures dramatically increases radiant output, meaning more heat is felt at the ground level. While the heat spread is slightly narrower, the increase in radiant output equals higher overall heater efficiency and greater comfort levels.
Each configuration is suited to various applications in different ways, and with the REV Series, you don’t have to choose between them. Click here to learn more.
Efficiency Engineered
We have been innovating infrared heating technologies for over 65 years, and are proud to make high quality, energy efficient heating products right here in the USA.
See the video here: https://vimeo.com/685555945
Maintaining precise humidity levels is crucial in commercial applications. Protect sensitive instruments, mitigate the risk of equipment failure, preserve valuable materials and artifacts, and ensure a safe and healthy environment with comprehensive HUMIDITY CONTROL solutions from DriSteem.
Remove Excess Humidity with DriSteem’s New RL Series Dehumidifier
The RL series dehumidifier complements DriSteem’s existing lineup of world-class humidification, evaporative cooling, and water treatment systems, helping you implement comprehensive humidity control solutions like never before. Dehumidification removes moisture from the air, decreasing condensation and frost, as well as protecting against mold, mildew, and fungus.
Add Humidity with an Energy-Efficient Ultrasonic Humidifier
Enhance your humidity control system with the energy efficient Adiatec ® ultrasonic humidifier, which offers significant energy savings up to 93% compared to isothermal humidifiers while reducing cooling loads. Benefit from the flexibility of in-room and AHU/duct models, allowing you to customize the system according to your specific requirements. Add DriSteem Hydrotrue ® RO and DI water treatment solutions for a complete package that produces high purity adiabatic humidification.
Maintain a Humidity-Controlled Environment to:
• Minimize the risk of equipment failure in manufacturing facilities, as controlled humidity prevents moisture-related issues that can lead to costly downtime and repairs.
• Support the plant growth cycle in indoor agriculture, such as cannabis cultivation, by providing ideal humidity conditions for healthier plants, increased yields, and consistent crop quality.
• Preserve important materials and artifacts in storage spaces and museums by preventing moisture damage, ensuring their longevity, and maintaining their value.
• Safeguard against the spread of viruses and bacteria in dry storage areas and warehouses, creating a safer environment for both goods and personnel.
Available for immediate shipment, get the equipment you need without the long wait. Select models of DriSteem humidifiers and dehumidifiers are in stock for immediate shipment. Don’t miss out on the benefits that the RL series dehumidifiers and Adiatec ultrasonic humidifiers offer. Contact your local DriSteem Representative today to discuss your humidity control needs: www.dristeem.com/find-a-rep.
ETAP is a global leader in software solutions for electrical systems. Through its integrated electrical digital twin platform, ETAP unlocks total efficiency and sustainability at all stages of the lifecycle across infrastructure, building, industry, and utilities.
ETAP empowers engineers and operators to build and manage resilient and reliable power systems with advanced tools to meet design and operational challenges. Our state-of-the-art software offers real-time insights, enabling informed decisions that maximize efficiency, reduce emissions, and promote renewable energy integration.
ETAP continues to revolutionize the way organizations optimize their electrical systems while prioritizing safety and compliance. We proudly announce that our software, ETAP ArcSafety™ , has received the esteemed Gold Award and our ePPC ™ has been honored with the distinguished Bronze Award at the Consulting-Specifying Engineer’s Product of the Year Program for 2023.
ETAP ArcSafety, an all-in-one solution to perform AC and DC arc flash analysis on low, medium, and high voltage systems, equips electrical engineers with unrivaled tools for arc flash analysis, risk assessment, and mitigation.
ETAP ePPC, our model-driven hybrid power plant controller and eSCADA system enables operators to optimize power generation, ensure grid code compliance, and drive efficiency. With ETAP’s innovative energy management solutions, you gain the ability to effectively monitor, control, and optimize power plants, resulting in a lower carbon footprint and accurate forecast of yield.
The latest release, ETAP 2023 offers innovative solutions and features with numerous enhancements and timesaving improvements, providing ETAP customers with technology and best practices to be safer, more reliable, efficient, compliant, and sustainable. New modules and features include:
• Energy Reducing Line Side Isolation (ArcBlok™ )
• Arc-Flash Analysis using IEC Short-Circuit Standards
• Fast & efficient modeling of Zone Selective Interlock (ZSI) settings
• Unbalanced Network Harmonic Distortion Mitigation using Active Filters
Contact us today for a free quote.
Greenheck offers the industry’s most comprehensive line of ventilation equipment including fans and ventilators, make-up air units, energy recovery ventilators, kitchen ventilation systems, dedicated outdoor air systems, indoor air handlers, dampers, louvers, and laboratory exhaust systems. The recent addition of air distribution products to Greenheck’s growing product portfolio makes it even easier for specifiers to schedule a complete ventilation system from one supplier.
Greenheck’s air distribution product line includes an extensive selection of product types that meet performance as well as aesthetic requirements in a wide range of building applications. Greenheck air distribution products, many available with industry-best lead times, include:
• Grilles and registers
• Ceiling diffusers
• Linear diffusers and grilles
• Plenum slot diffusers
• VAV diffusers
• Displacement ventilation for spaces with ceiling heights of 9 feet or greater
• Stainless steel GRDs for applications needing improved corrosion resistance and durability
• Fire-rated air distribution packages that are UL-Listed
• Engineered polymer air distribution products ideal for environments with nonferrous requirements like MRI rooms, pools, and water treatment plants
• Air terminal units (ATU) including single duct, constant volume, variable volume, dual duct, and retrofit ATU models
A new line of healthcare, laboratory, and cleanroom (HLC) air distribution products is also available. This line includes laminar flow diffusers, radial flow diffusers, and surgical air curtains that are ideal for use in cleanrooms, hospital operating rooms, and patient isolation rooms, as well as laboratories and manufacturing facilities. Greenheck HLC products are designed, engineered, and tested to meet or exceed today’s critical environment standards for performance and energy efficiency.
As a single-source supplier of complete ventilation systems, Greenheck prides itself on being the easiest company to do business with. The addition of air distribution products to our comprehensive product line makes it that much easier to create safe, healthy, and comfortable spaces in commercial, industrial, and institutional buildings.
For more information on Greenheck’s complete line of air distribution products please visit www.greenheck.com/products/air-distribution
info@greenheck.com 715-359-6171 www.greenheck.com
Noritz has launched the innovative Hybrid Hot Series, a solution that combines the benefits of hot-water storage with the efficiency of tankless water heating, specifically designed to meet the demands of high-volume commercial applications. This groundbreaking technology is ideal for establishments like restaurants and hotels, where large quantities of hot water are required in short bursts, followed by extended periods of zero demand.
The Hybrid Hot Series storage tanks feature a specially designed heat trap that enhances the stratification of hot water within the tanks. This heat trap, resembling an elephant nose, enables maximum hot-water efficiency and achieves optimal stratification. As hot water tends to rise to the top due to its lower density, the trap facilitates the central withdrawal of hot water from the tankless water heater, while preventing unwanted convection flow during standby periods. Additionally, the tank’s concrete lining and polyurethane insulation minimize heat loss, resulting in reduced energy consumption.
Noritz’s Hybrid Hot tank boasts a half-inch-thick cement lining, offering superior corrosion protection compared to traditional glass linings, eliminating the need for frequent anode rod maintenance. Furthermore, the tank’s two inches of polyurethane foam insulation ensure excellent heat retention, leading to significant energy and cost savings.
The Hybrid Hot Series incorporates a dedicated ¾-inch MNPT recirculation return port, strategically placed on the side of the tank. This feature simplifies installation by allowing plumbers to connect the recirculation return line to the incoming cold-water line without requiring complex plumbing configurations.
With an industry-leading 10-year warranty for both the tank and tankless components, the Hybrid Hot Series ensures long-term reliability and customer satisfaction. The tankless water heater achieves a remarkable thermal efficiency rating of 98%, accompanied by a 0.96 uniform energy factor (UEF).
Noritz’s Hybrid Hot Series is revolutionizing water heating in commercial settings by providing a seamless combination of hot-water storage and tankless technology. This innovative solution guarantees an abundant supply of hot water, eliminating the need to heat the entire tank, thereby reducing energy consumption and costs.
How part obsolescence and supply-chain challenges helped Reliable Controls improve some of its best-selling products
The pandemic continues to interrupt global supply chains. For Reliable Controls, the impact of interruptions to the flow of raw materials drove the company to pivot its design and manufacturing processes in support of its mission to have the most satisfied customers in the building automation industry. That meant a complete redesign of two of its bestselling products: the MACH-ProView™ LCD controller and the SMART-Sensor™ EPD device.
Redesigning the popular MACH-ProView LCD gave Reliable Controls an opportunity to improve controller performance in several meaningful ways, with a new processor, new memory, and other revisions. Start-up time is almost half that of the previous version of the controller; users can switch themes 10 times faster; and EQUIPMENTview–a customizable screen that lets users display and access objects on the LCD–performs more efficiently. The MACH-ProView is a freely programmable BACnet Building
Controller and BACnet Operator Display that provides customizable, high-resolution graphical interfaces facility managers can use to access, monitor, and control comfort and energy performance in their buildings.
Supply-chain challenges also affected production of the SMART-Sensor EPD, a networked-sensor device that allows building occupants to control 10 parameters related to their space.
Reliable Controls switched the processor, ported the firmware, and implemented a new printed circuit board – all without affecting what the customer sees or how they interact with the device. “We took a big risk with the redesign since we can’t upgrade the firmware in the field,” says James Puritch, VP of R&D.
“I’m very proud of our team’s ability to pivot and take on uncertainty to deliver products that are even better than before – in as short a time as possible.”
Manufacturers are under constant pressure to remain innovative as pressures mount to increase energy efficiencies within product offerings. This pressure has driven the industry to create and repurpose existing technologies.
One example of repurposing existing technology is leveraging the heat pump. Heat pump water heaters (HPWH) have become increasingly popular due to their energy efficiency and operational cost savings compared to traditional water heaters. HPWH are quickly becoming a leading product for commercial installs and Rheem has over 10 years of experience with this HPWH technology.
Since HPWH are significantly more energy proficient than traditional water heaters, installing HPWHs results in substantial operational cost savings, decreasing energy costs for a building over the lifetime of the unit. Current trends show the global HPWH market is expected to double by 2031.
HPWHs reduce energy use by up to 75% and can improve building efficiency ratings, which is ideal for green building programs like LEED certification. Additionally, available rebates, incentives and tax credits help reduce up-front costs and enhance ROI for interested businesses.
Godfrey Vaughn Commercial Water Product Specialist Godfrey.Vaughn@Rheem.com
When specifying HPWHs it is important to consider ambient air and water temperatures on location to properly determine the BTUs needed. HPWHs work most efficiently at temperatures above 40 degrees Fahrenheit to capture waste heat and provide free bonus cooling. Also, when specifying, consider a pre-heat for lower energy efficient equipment and ensure proper storage tank size for the building’s water usage. If you use a unit like Rheem’s Commercial Heat Pump Water Heaters Split Systems, the units feature elements such as an automatic defrost and electric tank back-up for lower temperatures, to ensure solutions to potential challenges are built within the unit to allow for peace of mind.
Champion FiberglassⓇ values innovation, as evidenced in products and tools for customers and environmental stewardship in manufacturing. The ISO 14001:2015-certified company strives to be a responsible corporate citizen in terms of the byproducts created in fabrication.
In fact, the company’s water and solid waste systems not only protect natural resources, they have beneficial results for customers too.
The filtration system cleans water used in manufacturing for reuse in the cooling system, a process that has helped lower water consumption. It has also lowered the cost of disposal, savings that flow to customers in competitive fiberglass conduit pricing.
Manufacturing conduit also creates solid waste in broken and unusable fragments. The company’s hammer mill machine grinds these pieces for a dramatic reduction in solid waste. Landfill contributions have decreased 80-90% saving thousands of dollars in chemical and landfill disposal costs.
In developing quality products for customers, these environmental systems allow Champion Fiberglass to innovate and fabricate more efficiently, effectively and sustainably while passing along savings to customers. See your savings by estimating project needs with the company’s proprietary calculator tool at https://championfiberglass.com/calculators/ info@championfiberglass.com | 281.655.8900 | championfiberglass.com
Many chemical processing applications involve the presence of potentially explosive gases. In these applications, variable frequency drives (VFDs) are often used to control electric motors for precise control and energy savings. VFDs, however, produce a capacitive voltage on the motor shaft, which can discharge through the bearings, causing electrical pitting damage and premature bearing failure. This damage can be mitigated by electrically bonding the motor shaft to the frame with a shaft grounding ring. This is complicated by the presence of potentially explosive gases, though.
Underwriters Laboratory (UL) developed a set of procedures for installing AEGIS ® Shaft Grounding Rings inside of explosion proof (XP) motors. Several motor manufacturers offer XP motors with shaft bonding rings factory installed.
IEEE 841-compliant motors are often used in Class I, Division 2 areas. Per the recent IEEE Standard 841-2021, shaft grounding devices are now acceptable options for “841 Standard” motors. Shaft grounding is permitted in Class I, Div. 2 areas when the application has been properly evaluated.
Electro Static Technology has published a technical bulletin to help you understand the relevant code and standard changes, and determine whether AEGIS ® Shaft Grounding Rings are acceptable in a specific application. Download a free copy at www.est-aegis.com/841
info@est-aegis.com Tel: 866-738-1857
www.est-aegis.com/841
PVI’s Centurion ® is a high-efficiency, direct-fired domestic water heater designed for maximum performance, longevity and reliability. Featuring state-of-the-art technology and the advanced Edge ® Controller, Centurion streamlines and simplifies operation from setup and configuration to maintenance and diagnostics. Centurion provides more effective and efficient management of the building’s domestic hot water system.
The advanced Edge ® Controller incorporates dynamic feed-forward sensing for precise modulation of its high turndown air/fuel delivery system. The Edge Controller fires the unit to accurately match load requirements and produce tight hot water outlet temperature control. Centurion includes onboard multi-unit sequencing logic for up to 16 units, eliminating a need for a separate sequencing panel. Wasteful overshooting and cycling are virtually eliminated as is the need for storage tanks, mixing valves and other temperature averaging components in most applications.
With its compact design (65% smaller vs. the competition), Centurion is able to be installed with zero side clearance and through a standard 36”doorway making it ideal for both retrofit or new applications where space savings and installation flexibility are essential. Available in 1600 and 2000 MBH, Centurion is fabricated with the revolutionary AquaPLEX® duplex stainless steel and proprietary manufacturing process that provides superior corrosion-resistance and extended product life.
817-335-9531 pvi.com/centurion
ABB Motors US .2 .http://baldor .abb .com/ec-titanium
BELIMO .13 .www .belimo .com
CFE Media GSI Database .63 .https://gspplatform .cfemedia .com/si/home
CFE Media NPE Database .63 .https://gspplatform .cfemedia .com/pe/home
Cummins .C-4 www .cummins .com
CYBER SCIENCES .24 .www .cyber-sciences .com
Electro Static Technology Inc .12 .www .est-aegis .com/resources/case-studies
Greenheck .35 .www .greenheck .com
Industrial Cybersecutiy Pulse .51 .www .industrialcybersecuritypulse .com
JOSAM .50 .www .josam .com
Navien, Inc .1 .www .Navien .com
PVI Inc . .25 .www .pvi .com
Reliable Controls
.C-2 www .reliablecontrols .com
Rheem .4 .www .rheem .com/commercial-hot-water
RUSKIN .47 .www .ruskin .com
Tjernlund Products .64 .www .tjernlund .com
Yaskawa America, Inc .C-3 www .yaskawa .com
Publisher/Midwest
Matt Waddell MWaddell@CFEMedia.com
3010 Highland Parkway, Suite #310 312-961-6840
Downers Grove, IL 60515
Account Manager
Robert Levinger RLevinger@cfetechnology.com 630-571-4070 x2218
West, TX, OK
Aaron Maassen AMaassen@CFEMedia.com Integrated Media Manager 816-797-9969
Northeast
Richard A. Groth Jr. RGroth@CFEMedia.com 12 Pine Street 774-277-7266 Franklin, MA 02038
Director of Content Marketing Solutions
Patrick Lynch PLynch@CFEMedia.com 3010 Highland Parkway, Suite #310 847-452-1191 Downers Grove, IL 60515
Marketing Consultant
Brian Gross BGross@CFEMedia.com 3010 Highland Parkway, 630-571-4070 x2217 Suite #310
Downers Grove, IL 60515
Jim Langhenry, Co-Founder and Publisher, CFE Media JLanghenry@CFEMedia.com
Steve Rourke, Co-Founder, CFE Media SRourke@CFEMedia.com
McKenzie Burns, Marketing-Events Manager MBurns@cfemedia.com
Courtney Murphy, Marketing and Events Manager CMurphy@cfemedia.com
Paul Brouch, Director of Operations 630-571-4070 x2208, PBrouch@CFEMedia.com
Rick Ellis, Audience Management Director 303-246-1250, REllis@CFEMedia.com
Michael Smith, Creative Director 630-779-8910, MSmith@CFEMedia.com
Michael Rotz, Print Production Manager 717-422-3622, mike.rotz@frycomm.com
Maria Bartell, List Rental Account Director Infogroup Targeting Solutions 847-378-2275, maria.bartell@infogroup.com
Claude Marada, List Rental Manager 402-836-6274, claude.marada@infogroup.com
Letters to the Editor: Please e-mail your letters to ARozgus@CFEMedia.com
Letters should include name, company, and address, and may be edited for space and clarity.
Information: For a Media Kit or Editorial Calendar, go to https://www.csemag.com/advertise-with-us/ Marketing consultants: See ad index.
Custom reprints, electronic: Paul Brouch, PBrouch@CFEMedia.com
TM Technology and
consulting-Specifying
HV600 drives and packages are available in a variety of styles and enclosures to meet all your HVAC requirements:
• Standalone: UL Type 1, UL Type 12
• Bypass/Configured Package:
UL Type 1, UL Type 12, UL Type 3R
Bypass and configured packages are offered in space-saving Narrow or option-rich Enclosed designs with an array of power and control options in a “right-size” package design, allowing you to customize a package to suit your application needs.
What type of conditions are you looking to meet? Call Yaskawa at 1-800-927-5292 today.