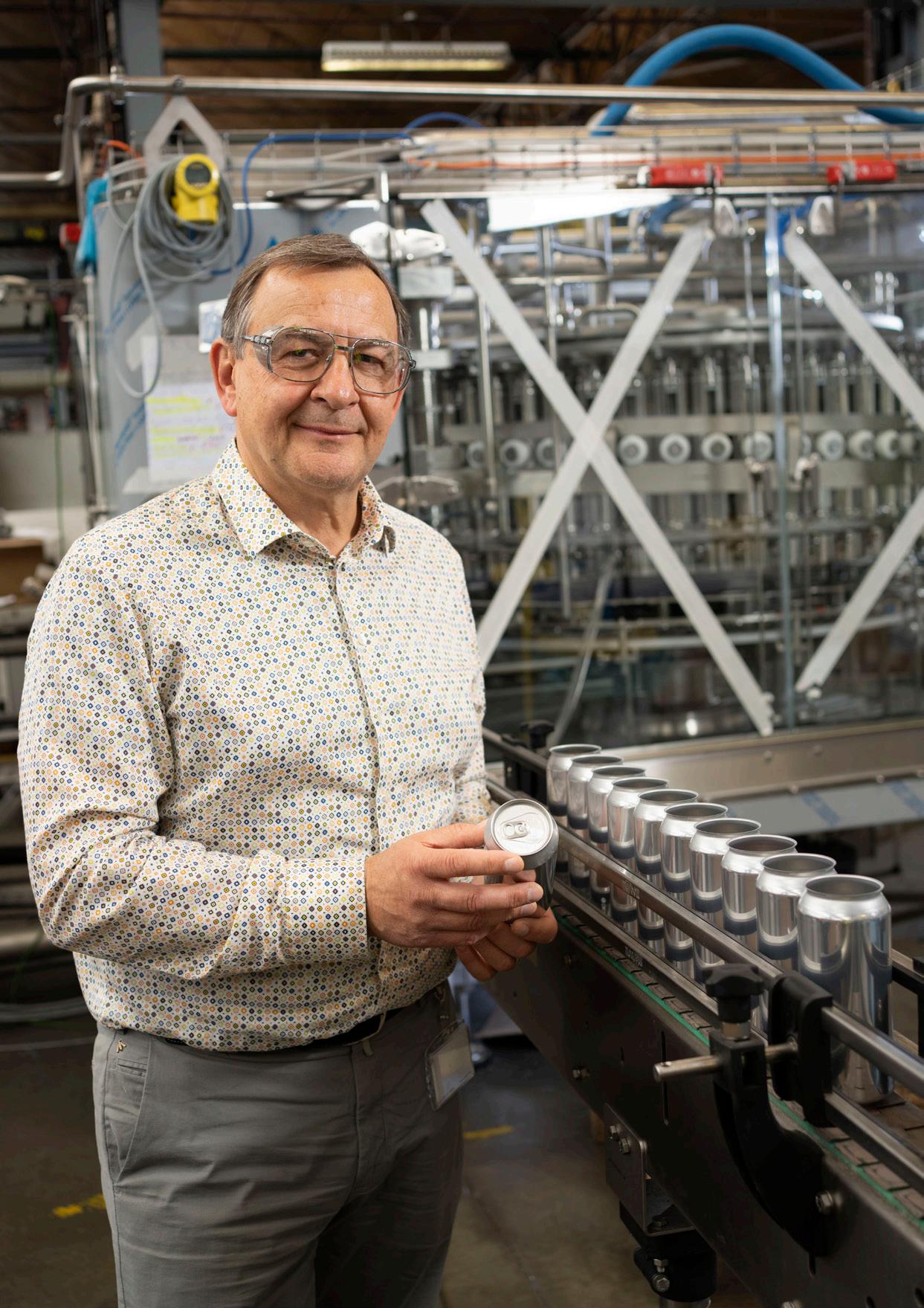
8 minute read
BEDRIJF John Bean Technologies
Deelnemer Voka Charter Duurzaam Ondernemen
Jan Windey, John Bean Technologies
Tussen de woonwijken in hartje Sint-Niklaas ligt John Bean Technologies dan wel wat verborgen, maar dan nog vinden wereldspelers uit de voedingsindustrie zoals Nestlé, Kraft Heinz en Friesland Campina vlot de weg naar zijn 300 meter lange productiecomplex in de Breedstraat. Als fabrikant van machines om voedingswaren in een nietsteriele productieomgeving in blik te verpakken, is het zelfs wereldvermaard.
door Jan Van de Poel fotografie Stefaan Van Hul Met een ontvangst van businesspartners en een familiedag op de site vierde John Bean Technologies net voor de zomer zijn 75-jarig bestaan in Sint-Niklaas. Even terugrekenen leert dus dat zijn Wase verhaal startte net na de Tweede Wereldoorlog. ‘Met het oog op de heropbouw van Europa, nam onder andere het Amerikaanse Food Machinery Corporation (FMC) deel aan het Marshallplan. Dat bedrijf fabriceerde toen al machines voor de voedingsindustrie, zowel voor het vullen en sluiten van voedingsproducten in blik als het steriliseren ervan. Samen met een aantal andere fabrikanten van voedingsblikken en sluitmachines richtte het zo International Machinery Corporation, kortweg IMC, op. De eerste voorzitter ervan was Paul Heymans, ook wel gekend als voormalig minister en stichter van de conservenblikfabrieken Sobemi. IMC is dan eerst begonnen met het maken van machines voor de voedingsindustrie onder licentie van vooral Amerikaanse en Engelse fabrikanten’, blikt Jan Windey even terug in de tijd. Als site director runt hij vandaag de vroegere Wase vestiging van IMC, die begin jaren zeventig eerst een volwaardige FMC-dochter met eigen producten en lijnen werd. Sinds 2008 opereert die onder de naam John Bean Technologies. ‘Door de jaren heen was FMC alsmaar actiever geworden in de petroleumbusiness. Toen die activiteiten meer dan 70 % van de activiteiten uitmaakten, is de machinebouwpoot ondergebracht in het aparte bedrijf John Bean Technologies. Die bedrijfsnaam eert onze founding father, die de fundamenten van de Food Machinery Corporation heeft gelegd (zie kader). Vandaag haalt John Bean Technologies 70 % van zijn omzet uit machinebouw voor de voedingsindustrie. De overige 30 % komt uit de luchtvaartindustrie. Wereldwijd telt de groep een 35-tal locaties en zo’n 7.000 medewerkers en haalt ze een omzet van twee miljard. Met een 200-tal medewerkers dragen we vanuit Sint-Niklaas daaraan zo’n 60 miljoen euro bij’, schetst Jan Windey.
UITBLINKER BINNEN DE GROEP
Jaarlijks fabriceert zijn team een 30-tal vul- en sluitmachines en een 20-tal sterilisatieketels. Los van die cijfers wordt de Sint-Niklase vestiging bovenal beschouwd als het wereldwijde center of excellence binnen John Bean Technologies in vullen en sluiten van blikverpakkingen voor uiteenlopende producten, van melkpoeder tot bier. En aangezien JBT zelf een leidende speler in zijn niche is, kan haar Wase fabriek mooie adelbrieven voorleggen. ‘De productie van machines voor het niet-aseptisch vullen en sluiten van verpakkingen gebeurt binnen onze groep zelfs uitsluitend in Sint-Niklaas. Hierdoor zijn wij de leverancier van machines aan wereldspelers zoals Nestlé, Danone en Kraft Heinz. Zo’n center of excellence word je niet zomaar binnen onze groep. In de loop der jaren hebben we hier veel kennis en knowhow kunnen borgen en overdragen, zowel op vlak van ontwikkeling als in de praktische uitvoering op de werkvloer.
Van sproeimachine tot amfibievoertuig
De sproeimachine die John Bean in 1884 ontwikkelde om een ziekte in zijn amandelboomgaard tegen te gaan, was de hoeksteen van multinational FMC. Vanuit San José veroverde zijn bedrijf na Amerika ook Europa, Australië en Afrika. Naast de productie van machines voor de landbouw- en voedingsindustrie en activiteiten in de petroleumwereld, bouwde dat opvallend genoeg ook een belangrijke poot in de luchtvaart uit als fabrikant van bijvoorbeeld passagiersbruggen en automatische laadtoestellen. Tijdens de Tweede Wereldoorlog herbouwde FMC een aantal productielijnen voor sterilisatoren zelfs om tot productielijn voor amfibievoertuigen. Later leidde dat tot de productie van ander rollend materieel, zoals zelfrijdende oogstmachines en automatisch geleide voertuigen.
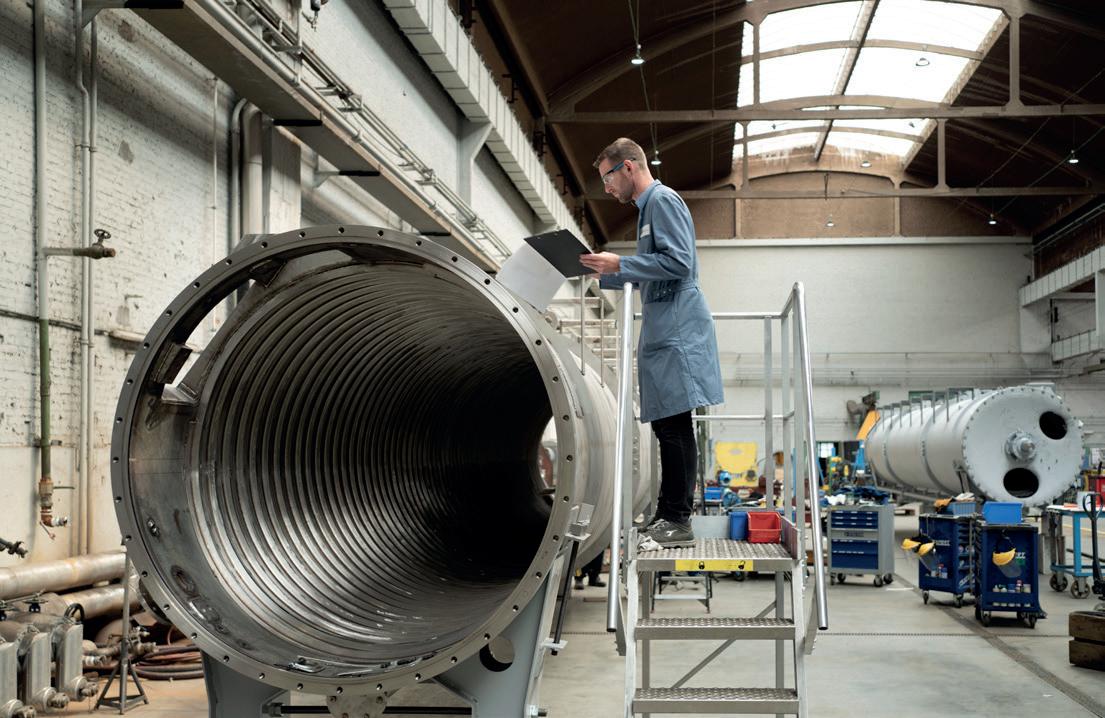
Sommigen hebben weleens geprobeerd om onze machines of componenten ervan na te maken. Zij hebben moeten vaststellen dat het verre van eenvoudig is om gelaste constructies tot anderhalve meter diameter en vijftien meter lang af te leveren met maximaal anderhalve millimeter tolerantie op de maatvoering.
Om dat te bereiken en zo de aansluiting van allerlei componenten hierop nog mogelijk te maken, moet je echt wel weten wat je doet. Vandaag is meer dan de helft van alle geproduceerde voeding in blik met onze machines gesteriliseerd. Bij de productie van citrus- en diepvriesproducten is dat zelfs meer dan 75 %, maar dan met machines van andere JBT-locaties’, stipt de site director aan.
SERVICE OVER HELE LIJN
Hart van de business bij John Bean Technologies in het Waasland zijn nog steeds de roterende drukkokers en bliksluiters; machines waarnaar de voedingsindustrie decennia geleden al greep om haar producten een langere houdbaarheid mee te geven. ‘Aan onder meer Continental Can, dat vooral in de Verenigde Staten actief was, hebben we bliksluiters geleverd die tot meer dan duizend blikjes per minuut konden verwerken. Van die machines hebben we er in totaal 1.200 gemaakt onder licentie, van de jaren 1950 tot 1970. Hoewel het basisconcept van die machines nauwelijks veranderde, zijn die door de jaren natuurlijk aangepast aan wijzigende omstandigheden. Zeker toen we in de jaren 1970 zijn begonnen met de ontwikkeling van eigen producten onder de merknaam FMC. De nieuwe generatie van machines, die elke minuut tot 2.200 blikjes in roestvrij staal kon afwerken, is wereldwijd verkocht. Bijvoorbeeld bij biermerk Fosters in Australië staat zo’n machine die 2.200 blikjes per minuut aan kan. Dat zijn dus 36 blikjes per seconde. Als je weet dat de zijkant van zo’n drankblikje bestaat uit flinterdun staal van ongeveer 0,06 mm, is het een huzarenstukje om tot zo’n verwerkingssnelheid te komen’, geeft Jan Windey mee. ‘We merken trouwens dat onze klanten steeds meer verwachten dat wij hen een volledige oplossing voor de hele productielijn kunnen aanbieden. Ze willen liefst een single source of equipment, met één eindverantwoordelijke. Om ons portfolio aan te vullen en klanten van het begin tot het einde van hun lijn te kunnen bedienen, kijken we met de groep waar nog acquisities of allianties met andere partijen mogelijk zijn. Zo worden we alsmaar meer een partner voor onze klanten en vice versa.’
DUURZAME STAPPEN ZETTEN
Met onder zijn klanten een aantal wereldspelers die willen vooroplopen in de Europese ambitie om klimaatneutraal te zijn tegen 2050, wordt John Bean Technologies door hen meegezogen in dat verhaal. De jongste jaren werkt het binnen het Voka Charter Duurzaam Ondernemen allerhande initiatieven in die zin uit. ‘Dit programma
van de Antwerps-Wase Kamer vormt een dankbaar raamwerk voor onze duurzame inspanningen, die wel al langer lopen. Zo halen we intussen al 300 megawatt per jaar uit de zonnepanelen op de al vernieuwde daken. En in de komende jaren pakken we nog andere daken aan. Stap voor stap renoveren we delen van ons complex, dat oorspronkelijk dateert van begin vorige eeuw. Voorts is onze productieruimte al uitgerust met automatische verlichting met bewegingssensoren en energiegunstigere verwarmingssystemen. Zo hebben we dat energieverbruik in de loop der jaren al tot de helft kunnen reduceren’, merkt HSE-manager Jan Vangansbeke op.
‘Het Voka Charter Duurzaam Ondernemen geeft internationale uitstraling aan onze inspanningen voor meer duurzaamheid’, merkt hr-directeur Niko Parmentier. ‘Bovendien heeft het onze blik nog helpen verruimen, bijvoorbeeld door ook aandacht te hebben voor initiatieven naar armoede of samenwerkingen met lokale leveranciers. Elke audit geeft inspiratie voor nieuwe zaken die we kunnen aanpakken. Dit programma blijft je dus voortdurend uitdagen en dat is alleen maar goed.’
Vanuit zijn streven naar meer duurzaamheid zet John Bean Technologies ook nadrukkelijk in op upcycling. ‘Oude machines nemen we terug over van klanten. Na een update geven we die zo nog een tweede leven. Daarnaast kijken we hoe innoverende technologieën kunnen worden toegepast in ons productaanbod. Dat gaat bijvoorbeeld over het hergebruiken van warmte gegenereerd in de koelers van onze sterilisatoren voor het opwarmen van koud afgevulde producten in het begin van het proces. In een nieuw concept bekijken we zelfs het zelf opwekken van stoom voor het sterilisatieproces door restwarmte te recupereren’, gaat Jan Windey voort.
ONDERSTEUNING VAN TRAPJE HOGER
Op digitalisering en technische ondersteuning vanop afstand was het bedrijf al aan het inzetten, al heeft de coronacrisis wel geleid tot een aanzienlijke versnelling op dat vlak. ‘Dat was ook nodig, want reizen naar Azië was lange tijd gewoonweg onmogelijk. Terwijl dat continent door de bevolkingsomvang toch wel goed is voor 40 % van onze totale afzetmarkt. En met de toenemende levensstandaard in landen als Thailand, Vietnam en Maleisië neemt de vraag naar verwerkte voedingsproducten daar nog toe’, geeft de site director mee. ‘Dus hebben we verder stappen gezet in ondersteuning vanop afstand voor kleinere teams van technici uit het land zelf. Ook monitoring vanop afstand via een dashboard, aan de hand van sensoren in de machines, hoort daarbij. Zulke IoTtoepassingen kunnen interessante zaken aanduiden, bijvoorbeeld dat downtime van een machine vooral terug te voeren is tot de operator die niet attent is. Nodig onderhoud voorspellen op basis van metingen in plaats van periodiek onderhoud uitvoeren, is nog toekomstmuziek. Met alle tandwielen en overbrengingen die in onze machines voortdurend bewegen, is het niet eenvoudig om zuiver aan de hand van sensoren de vinger op de wonde te leggen. Anderzijds willen we daar wel naartoe werken. Want dat past in onze ambitie om klantenondersteuning van een trapje hoger te verzekeren.’
Die ambitie tekent Jan Windey vandaag nog mee uit vanuit zijn eerste stappen binnen het bedrijf als field service engineer, intussen 38 jaar geleden. ‘Waar medewerkers vroeger voor heel lange tijd aan boord bleven, stel ik vast dat er nu wat meer verloop is. Door de schaarste op de arbeidsmarkt worden ook onze mensen aan de mouw getrokken. Om daarop een antwoord te vinden, hebben we uiteenlopende samenwerkingen met scholen’, stipt hij aan. ‘We bieden niet alleen stageplekken, maar schenken ook afgeschreven machines en computers. Daarnaast kijken we verder dan de grenzen. Intussen hebben we al een tiental verschillende nationaliteiten aan boord en werven we momenteel servicemedewerkers uit Mexico aan. Want daar vind je wel nog profielen met de nodige expertise’, vult Niko Parmentier aan.
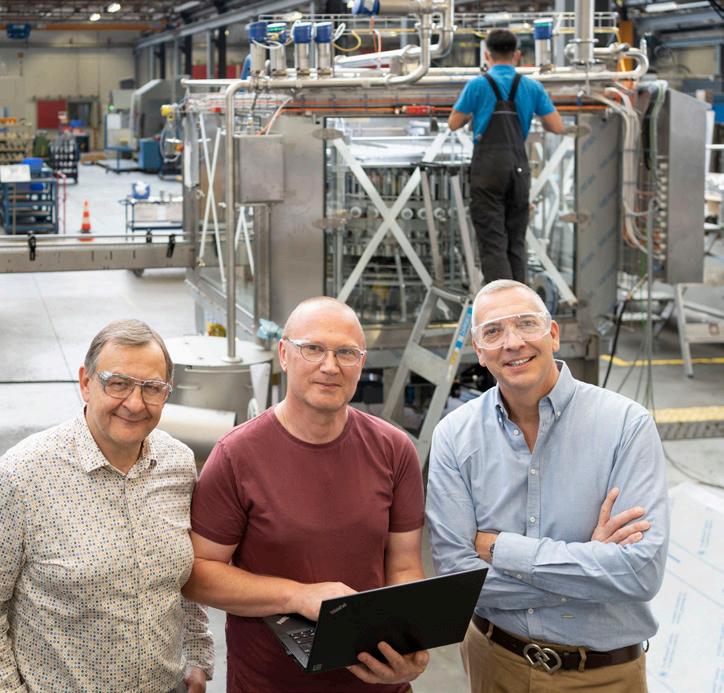