PILOT
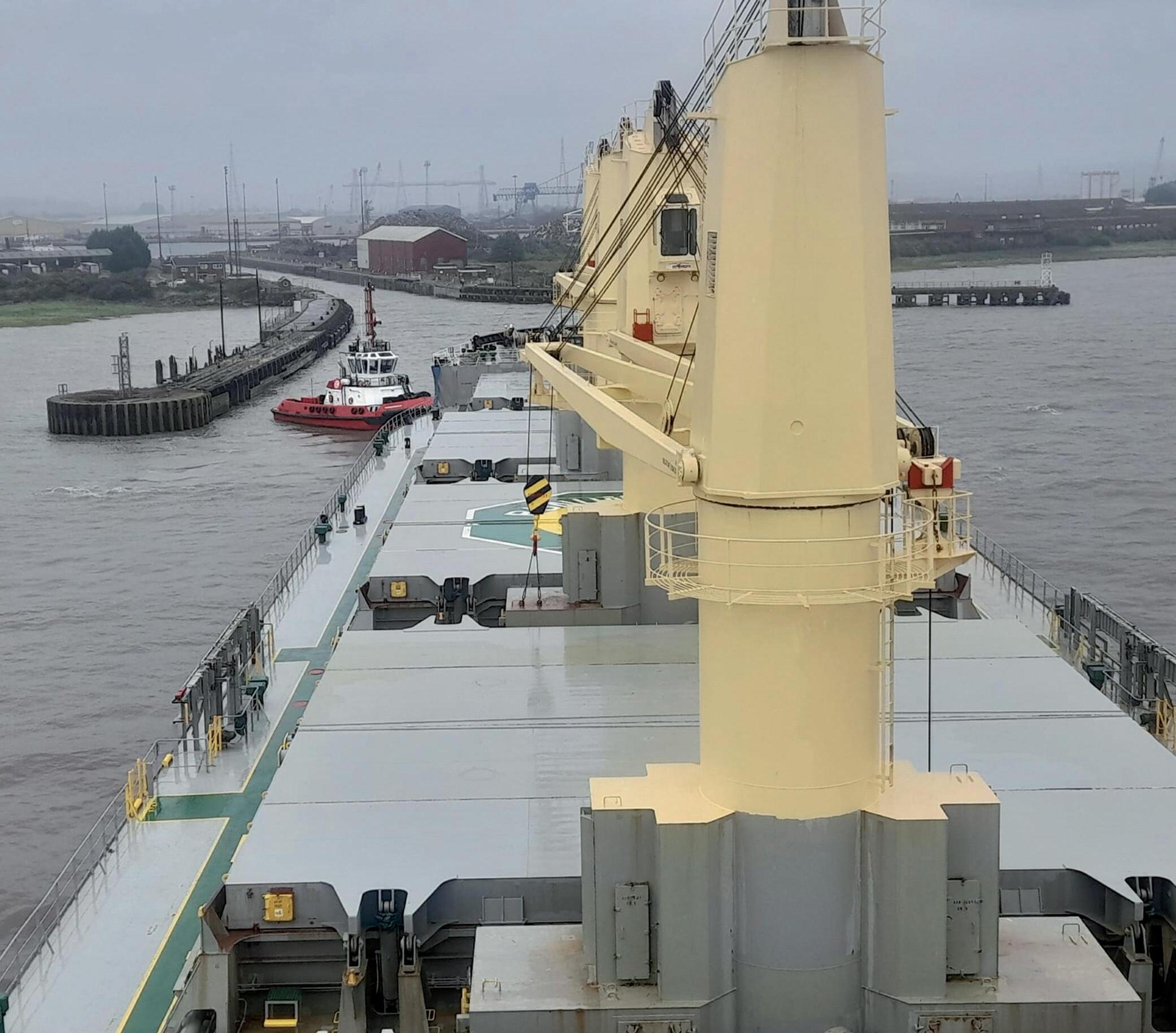
Conference & Port Reports / Canal Pilotage & Towage / Fatigue, Are You Aware? / What Makes Human Factors? /
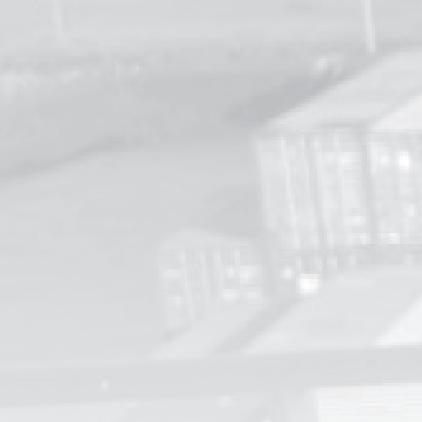
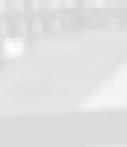
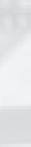
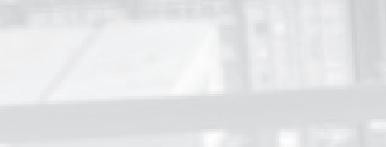
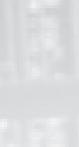
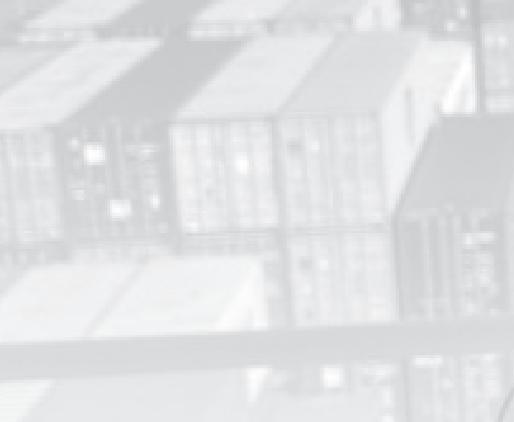

Conference & Port Reports / Canal Pilotage & Towage / Fatigue, Are You Aware? / What Makes Human Factors? /
oun all r helmets of UK po Supplied
POR • protect TheMa otectipr
R
o a has been designed t nt
own. o the cr on t ection with 100 joules ot d pr ers 90 joules f s, Unlikeothermarine ts or o the majority globally and t theMH4of A
Technica S EN16473 Y RTS/QU eas wing ar ollo the pilot in the f
th Hltthi
thep pilot the p Resc Ithasthesameimpact It has the same impact por y or ound the qua ving ar mo
ARDING A •
ety goggle sameassaf ound the second all ar est of 120 met impact t It also has otpr moltenmetalandelec helmet plus it also has ationtesta and penetr l s: ection.
thisisthec EN12492
w. o vie ction t
ers the v cue Helmet – this co t. oval limbing appr s c it’ es t h giv d whic standar – this is the c In EN16473, a the Mant
s on w
e bing a ladder and ther thehelmetcanbeused metreladderclimbtestto
oafieldofvisiontest PERA TBO
CLIMBING/BO operations ve – thisco Ma AS028 A MARINEO • estric is no r limb while c makesure anda10m thereisals limbing GSHIP es e helmet es per tr a ballistic ctrical chemical, asthesafety P sonwater rstheMantaforall andard ety St arineSaf
AT TIONS/PILO T
First, I would like to thank Alan Stroud for his dedicated time and effort on arranging the UKMPA conference in Harrogate last November. The conference delivered high-standard presentations from excellent speakers, some of whom have written articles for this edition. The UKMPA would again like to thank those who attended and spoke at the event.
Second, I would like to congratulate the following: Chris Hoyle for his promotion to UKMPA Chairman, Jason Wiltshire for his promotion to Vice Chairman and Alan Stroud to Treasurer. Also, congratulations to Neville Dring and James Musgrove who have become Region 5 & 6 representatives respectively.
Thank you to the outgoing chairman Hywel Pugh for his dedicated service to the UK pilotage Industry. Hywel is a fountain of pilotage knowledge and has represented the UKMPA exceptionally well over the years.
The theme for this edition is tugs and towage along with human factors in our industry. The magazine has not covered towage within pilotage in great detail for many years. I felt it was time to look closer at this aspect of our industry, coinciding with the 2024 UKMPA conference theme.
The theme of the magazine also coincides with the release of the MAIB report on the tragic Biter accident. On a personal note, I have been fortunate to work alongside some excellent tug crews and masters in my career; one was when I was working with a Hull company taking a project cargo all the way inland to Gainsborough in 2020. The unique skills when using conventional towage were clearly demonstrated by the experience of the tug crews.
Questions do arise regarding the use of these types of tug, the training of tug crews, pilots and when to make fast the tug. However it also has to be remembered the type of ports which require these unique size and type of tugs.
This edition has articles from the MCA about the need to report pilot ladder defects, fatigue management and Goodchild, the launch manufacturer explaining launch specifications.
Reporting of defective pilot ladders remains vital in maintaining the safety of pilots. The Maritime & Coastguard Agency clearly outlines this in this magazine. In a future edition, I plan to cover the latest pilot ladder developments.
I welcome Claire Pekcan to this edition. Claire made an excellent presentation at the EMPA conference in Antwerp and again at the last UKMPA conference on fatigue management. Pilots who are fatigued are a danger to themselves and to others. There are many reasons for this and these are highlighted in this edition.
John Slater, who has spent considerable time and effort writing his article on climb zone criteria, appears in the membership section. John is passionate about this matter and one of the reasons for appearing in this edition is for readers to have a closer understanding of the mindset of climbing ladders. This matter is very much up for future discussion in the interests of future safety.
I thank James Musgrove for his updated article about mental health. His dedication to this service is exemplary and all pilots should be aware of this important service at their disposal.
Congratulations to Hywel Pugh and James Musgrove on receiving their service awards at the UKMPA conference last November.
Thank you for reading. Safe piloting and thank you once again to all those of
Matthew Finn / Editor UKMPA
It has continued to be a busy year since my last report, culminating with the 136th AGM and conference in Harrogate, which was a resounding success. Conference is always an opportunity to engage with the membership and this conference saw several members attend conference for the first time. The feedback was very good and I would encourage all to attend where possible.
The shipping minister was unable to attend in person but did send a video message where he highlighted our importance to the UK’s economy and future growth. Thank you to all the sponsors, exhibitors and speakers for their support.
The MAIB has released the report into the girting of the tug Biter. I hope you have all read it. It highlights that we sometimes operate within very small margins. The UKMPA in partnership with BTA/UKHMA/BPA and the Workboat Association has been asked to develop guidance for inclusion in the Port Marine Safety Code’s Guide to Good Practice and other appropriate publications that emphasise the importance of conducting a pilot/tug exchange, in addition to the master/pilot exchange, to ensure that the pilot, bridge team and tug crew have a common understanding of the intended arrival or departure manoeuvre, the potential hazards and their respective roles in managing them.
The new pilot ladder performance standards are progressing well through the various committee stages at the IMO and we have been receiving regular updates from IMPA. The next step is adopting the amendments in June 2025 to allow entry into force on 1 January 2028.
EMPA is holding its next conference in Krakow Poland, next year. EMPA has also launched the EMPAsafe app for reporting defects.
Engagement with stakeholders has been good in the past few months, with members of the executive attending various meetings, conferences and seminars. These are, to name a few, MCA, IMO, DfT, UKMPG, BPA, BTA and the Chamber of Shipping.
Our very own James Musgrove –Tees Bay pilot and now a member of the executive – attended and spoke on the Safe Haven project at the AMPI Conference in Papua New Guinea.
It has been over three years since I took up the role of chairman. I stood down at the conference in Harrogate and handed over to Capt Chris Hoyle. It has been an honour and a privilege to chair the UKMPA. I would like to thank the executive for all their support and wise counsel; for the families of the executive it is always difficult balancing the workload and I really appreciate the time they have given to me. So, I wish Chris and the executive a bright future as I step back into the ranks of the membership.
Hywel J Pugh
THANK YOU
TO THE EXECUTIVE FOR YOUR SUPPORT DURING MY TENURE AS UKMPA CHAIRMAN, IT HAS BEEN AN HONOUR
Awarm welcome to 2025. Exhausted but satisfied after a hugely successful AGM and conference in Harrogate, your volunteers at the UKMPA have taken some welldeserved downtime over the holiday period to recharge with family and friends.
We say a fond farewell to our outgoing Chair, Hywel Pugh, and extend our gratitude to his 14 years of selfless dedication to our profession.
I was honoured to be elected as Chair in Harrogate and as such I have taken some time to reflect on the UKMPA’s progress over the past few years. With our membership numbers at a record high, and with increasing interest from wider stakeholders, I am proud to say our recognition and engagement across the industry is stronger than ever. It is through this strong engagement that we can continue to deliver on our mission of supporting pilots and protecting trade.
Within our own ports sector there is no more stable occupation than maritime pilots retaining that essential specific expert knowledge. The ever-increasing demand for the expert knowledge that maritime pilots possess reiterates the recognition of their ability to maintain the integrity of the ‘last blue mile’.
It is crucial that continuity, and the collaboration between pilots and industry, is maintained so that we can support the profession, keep our shores and infrastructure free from pollution and damage and support the end goal of protecting our vital seaborne trade flowing as an island nation.
In a short time the UKMPA has been able to deliver many successes, notably our mental health support and industry engagement programmes. As we move into to 2025, we will strive to maintain a stable and engaged association to benefit both our members and the continued success of the ports and maritime sector, recognising that we should always seek to improve on best practice and not acquiesce.
Your UKMPA committee will look forward to supporting the membership and acting as a vital conduit with its partners and wider stakeholder group to ensure the success and strength of shipping and ports. After our hugely successful debut in 2023, we look forward again to taking part in London International Shipping Week (LISW), partnering with Maritime London to highlight the critical work of pilots to the wider industry.
Before I sign off, I would like to welcome Jason Wiltshire CMMar (Bristol) as our new Vice-Chair, who now takes responsibility for running our association’s day-to-day activities. Jason has spent the past eight years as our diligent and respected treasurer and clearly brings a wealth of experience to his new role. The Treasury is now under the care of Alan Stroud (Medway). Adding to the Executive is always an exciting time and I would like to welcome two new board members: Neville Dring (Liverpool) and James Musgrove (Tees).
I would like to express our sincere thanks for the work of all our volunteers on the Board and those that stand by as deputies and work on our Technical & Training Committee. To commit family and leisure time as volunteers, working to support fellow pilots and influence the broader industry, shows a strong moral fabric. Our volunteers give up their time because they feel they can make a difference, and I have the utmost respect for this. In signing off, I would like to also pass a special thanks to those colleagues in the districts of our volunteers who support their peers in this priceless work.
Yours Aye
Christopher F Hoyle / UKMPA Chairman
In the insurance industry, effective communication can be challenging. From navigating the complexities of policy wordings to the relatively recent shift towards underwriters working remotely, the industry has a unfair reputation of muddying the waters, despite billions being paid in claims annually.
A broker’s job is to bridge these channels and overcome this unwanted reputation by mastering the oftenforgotten skill of interpreting policy wordings, building strong personal relationships with underwriters and communicating with their policyholders effectively. We rely on these skills and experiences to maximise value for our clients. Similarly, your role as a maritime pilot is critical. You ensure the safe navigation of extremely large ships through narrow, sometimes hazardous waterways. Pilots must continuously develop essential skills and strategies for effective communication, especially in challenging circumstances, to benefit their ‘customers’.
While we all agree on the vital role of a pilot, we have witnessed pilot skills questioned by crew members, leading to communication breakdowns that can result in near misses, collisions or injuries.
Successful passage requires pilots to bridge communication gaps among various crew members, minimising the risk of incidents. Pilots must also co-ordinate with port authorities, harbour masters and tug operators to ensure a perfectly synchronised operation. So, how can we learn from these interactions to keep improving?
To facilitate effective communication, the IMO has developed Standard Marine Communication Phrases, which help ease language barriers and reduce misunderstandings. In our own roles, we must ensure that we are:
• Accurate and concise in our communications.
• Assertive but not overbearing to prevent hierarchical structures from stifling information flow.
• Open to information flow in both directions to support effective decision-making.
Lastly, and perhaps most importantly, we must learn to listen actively. Many of us have been guilty of making assumptions based on limited information, only to discover there was more to learn. I continuously encourage my colleagues to listen more and speak less. I’ve learned the most about our clients when I’ve allowed them to speak, rather than filling every pause in our conversation.
With all this in mind, I’d like to address Circle’s communication with you, the pilots. There seems to be some confusion around why you need insurance to be a member and vice versa. We place this insurance on behalf of the UKMPA membership with two guiding principles: it must be costeffective and it must respond promptly when called upon.
We administer approximately 75 incident reports annually, most of which require minimal intervention. However, in those cases where significant assistance is required, pilots have consistently expressed gratitude for the support we provide during difficult times.
If you’re uncertain about the need for insurance, please take the time to fully read the Frequently Asked Questions document we have prepared, which is also available online at the UKMPA site. If questions remain, don’t hesitate to reach out to either Roger Darkins or me. We’re happy to discuss cover details and share real examples you may find relevant. As a team we are always here to help. We’re at your side so please communicate with us effectively and politely.
Ian Storm / Circle Insurance
Chairman Christopher Hoyle chairman@ukmpa.org
Vice Chairman Jason Wiltshire vice.chairman@ukmpa.org
Region 1 Executive Alan Stroud region1@ukmpa.org
Region 2 Executive Chris Grundy region2@ukmpa.org
Region 3 Executive Peter Lightfoot region3@ukmpa.org
Region 4 Executive Robert Keir region4@ukmpa.org
Region 5 Executive Neville Dring region5@ukmpa.org
Region 6 Executive James Musgrove region6@ukmpa.org
Treasurer Alan Stroud treasurer@ukmpa.org
Secretary & EMPA VP Peter Lightfoot secretary@ukmpa.org
Membership Robert Keir membership@ukmpa.org
Mental Health James Musgrove region6@ukmpa.org
IMPA VP Paul Schoneveld paul.schoneveld@ukmpa.org
“The Pilot” Editor Matthew Finn Editor@ukmpa.org
Technical & Training Chair John Slater technical@ukmpa.org
Web Captain James Musgrove webcaptain@ukmpa.org
Region 1 Deputy Simon Lockwood deputy1@ukmpa.org
Region 2 Deputy Mike Robarts deputy2@ukmpa.org
Region 3 Deputy Alan Jameson deputy3@ukmpa.org
Region 4 Deputy Ross McCauley deputy4@ukmpa.org
Region 5 Deputy Paul Schoneveld deputy5@ukmpa.org
Region 6 Deputy Matthew Finn deputy6@ukmpa.org
Circle Insurance Ian Storm Ian.storm@circleinsurance.co.uk M: 07920 194970
Insurance Queries Claire Johnstone claire.johnstone@circleinsurance.co.uk
Incident Reports Via UKMPA app insurance@ukmpa.org
UNITE Maria Ball maria.ball@unitetheunion.org
Web Captain James Musgrove webcaptain@ukmpa.org
Editor Matthew Finn photos@ukmpa.org
Minor incident 0141 249 9914 insurance@ukmpa.org
Major incident 0800 6446 999 insurance@ukmpa.org Incident Reports insurance@ukmpa.org
Safe Haven Hotline 0800 433 2163 Visit www.ukmpa.org for further details
Tony Fisher –01480 495848 / 07703 279214 –tony@spectrumcreative.co.uk
Sergio Panzini London
Daniel Tolley London
Patrick Kelly London
James Terry London
Caroline Palmer London
Leuan Clark South Wales
Asley Williams Southampton
Rob Hugh Southampton
Daniel Stevens Plymouth
Leslie Maines Tyne
Michael Lynch Workington
Jaimie Fisher Humber
Michael Paterson Associate
Dean Stores Associate
Thursday 1st May 2025
Lee-on-the-Solent Golf Club
We are very pleased to receive continued sponsorship from Ben Huggins and the team at Svitzer Marine Limited, for the 3rd Golf Day in support of the Cachalots Captains charity which for 2025 is Solent Dolphin. www.solentdolphin.co.uk
To book your place, contact - Bruce Thomas bruce.cachalotsgolf@gmail.com
20.11.24
By James Foster / Class 1 Pilot, London Medway / Secretary of the Medway Pilot’s Association
The 136th UKMPA conference was held in the heart of UK’s Historical Turkish Bath and spa town of Harrogate in North Yorkshire. The venue was the grand Victorian 137 guestroom of The Old Swan Hotel.
Having spent the day travelling, five Medway Pilots’ and I experienced heavy snow on the roads, coupled with train and transport delays. It was idyllic and comforting to be greeted by a warm log-burning fire, surrounded by cosy Victorian period features, on such a cold winter’s night.
The evening started with the Chairman’s Reception at the Sun Pavillion, which held a perfect backdrop overlooking the wintery valley and gardens. It was an ideal time to greet face’s old and new, in not only pilotage, but the whole Marine Environment. The current chairman Hywel Pugh, gave a warm welcome and introduction to what was going to be an enjoyable couple of days. In total, the conference consisted of 126 delegates, 16 exhibitors and 17 speakers.
The morning of Day 1 consisted of the UKMPA section committee, giving members’ presentations and reports on current affairs. This included where the association is currently standing and the direction the association is taking. It all appeared positive feedback, and there have also been some internal position changes. I join along with all the members in congratulating them on their current achievements. An official article detailing committee matters will be published shortly.
It was reassuring that the UKMPA has an array of professional associates and contacts to support pilots as part of their membership package.
Day 1 started with Mike Paterson (MD, Svitzer UK) and Scott Baker (head of marine standards at Svitzer) both giving valuable presentations, which included a brief history of Svitzer from its roots and up to what it does and how it partners worldwide. Svitzer operates in over 142 ports worldwide, covering over 137,000 towage jobs, which equates to one towage job every 4 minutes. I’m sure you would agree that these are impressive figures.
One of the interesting reports that was dissected in Scott Baker’s presentation was that of an unfortunate incident involving a conventional tug (the Gray Test) and a feeder container ship in a UK port that nearly resulted in the capsize of the Gray Test tug.
The next presentation was from John McCorquodale of the MAIB, who shared an MAIB report on the unfortunate Biter incident on the Clyde. The sad incident resulted in the loss of two experienced seafarers’ lives. It was almost unbelievable that that it took a mere 10 seconds for the Biter tug to capsize and, just like most incidents, it was never one element that contributed but several. In this case, 14 contributory factors were identified. It puts into perspective just how much towage operations and pilotage continue to be hazardous tasks for seafarers and pilots.
I would highly recommend reading the presentations on both incidents, along with the MAIB report, which the
UKMPA has published on its website. No matter how experienced pilots become, reading about past incidents and taking note of the lessons learnt reminds us all of the dangers involved and of the evolution of safe operating practices that both tugs and ships can employ to minimise certain risks.
Mike Kane, Parliamentary Minister for the Department of Transport (DFT), presented a personal video to the attendees on future developments involving de-carbonisation and how its policy will unlock investments and further growth of the UK economy. It was reassuring to see and hear that the UKMPA and DFT have a good professional relationship, given the fact he had a clear understanding of the important role that pilots have and how they contribute to the economy.
There were four memorable presentations involving new technology, aimed directly at pilotage. The first by Peter Farthing of Sensor Technologies showcased ‘Sureline’ a rope monitoring system that gives tug masters and pilots real-time data on tug lines and mooring ropes. It is able to record and transmit the line tension.
The company’s developments are expanding, which would enable it to use this technology to inform ships and ports with accurate real-time data, the forces applied to fenders and forces applied to vessels and with tugs pushing alongside.
Scott Tonks of Zelim showcased the company’s new technology for Maritime Search and Rescue. 40% of manoverboard (MOB) incidents are reported to be fatal (MAIB) and Zelim has
developed a system that employs Artificial Intelligence in the identification and tracking of MOB casualties. This, coupled with its ‘Swift Rescue Conveyor’, was fascinating to see, whereby something that looked relatively simple and cost-effective could retrieve MOB casualties from the water so effectively and quickly. So it’s no surprise that various workboats are ditching their rescue lines, tripod set-up and means of recovery lifts in favour of this excellent piece of minimalistic and effective lifesaving equipment.
The closure of Day 1 resulted in some refreshments, while patiently waiting to see if any of the attendees had won any of the raffle prizes. Most of us had our eyes on winning the Port and Ship Lego City Box set – oh well, better luck for me next time. But happy building to the lucky pilot who won. However, the raffle and auction raised an impressive amount for the Sailors’ Society charity.
The evening held at the Royal Baths Chinese restaurant gave ample time to socialise, discuss the various presentations of the day and catch up with old and new acquaintances. Although there were many legendary and experienced individuals present, it was great to see new up and upcoming attendees, reflecting a change of generations in our respective pilotage districts.
Day 2 continued on the theme of new technology, with John Cumming of Artemis presenting the latest in pilot boat technology. Hybrid and fully electric hydrofoil pilot boats demonstrated how personnel could be transported at 25-30kt speeds in three-metre seas, in complete comfort, reducing any impact from waves while emitting zero emissions and ensuring sustainability. It was a great insight into what can be achieved today in the marine world. I’m all for a comfortable, seasickness-free feeling of transport
Dr Clare Pekcan gave a first-class, medically proven presentation on the causes and consequences of fatigue in our roles as pilots and what we can do to help. Repeated sleep deprivation has some serious health issues and risks while engaging in pilotage acts but also before and after the job. Clare’s presentation is on the UKMPA website and I strongly encourage pilots to read and familiarise themselves with the content.
It's impossible to go through every presentation and mention all the speakers, as quite frankly, I would be writing a novel on the two-day experience. But that is what I would call it, an experience, and one I would encourage people to attend in the future.
For myself, what stuck out at this conference, compared with others, was the subject and content of the presentations. All of the speakers were confident, enthusiastic and extremely knowledgeable, covering current hot topics in our maritime world, be it, pilotage incidents, best practice, new guidance, fatigue, new technology or how artificial technology could influence the maritime industry and society (thanks to Patrick Galvin of Shannon Pilots for the thought-provoking presentation on Artificial Intelligence).
Iwould like to say a big thank you to all the speakers and attendees for making the 136th UKMPA conference a triumph. And, finally, congratulations to Alan Stroud (treasurer UKMPA /Medway), who spent considerable time organising this successful conference.
The third International Maritime Human Factors Symposium (IMHFS) was held at the IMO Headquarters in London, and I was privileged to attend as a representative of the UKMPA’s Technical and Training Committee, alongside James Musgrove from the Section Committee. The event brought together approximately 160 participants, featuring 47 high-quality presentations across 12 expert panel sessions over two days. The attendees comprised both academics and industry professionals. Key figures included the Chief
Inspector of the MAIB as well as lead representatives from CHIRP Maritime, the International Chamber of Shipping, the MCA, Inmarsat, the Seafarers’ Charity, and the Nautical Institute, which co-hosted the event with the University of Strathclyde.
A significant focus was placed on decarbonisation, with it becoming clear that there is no single, definitive solution regarding which ‘alternative fuel’ is the most viable. One of the more unusual and potentially controversial options discussed was nuclear power. A presentation was delivered by a
company claiming to have developed a reactor that is safe, insurable and efficient, and does not produce nuclear waste.
One of the main concerns, however, centred on the shortage of trained seafarers and how the industry will address the training needs for these new power systems.
Many of the presentations explored the role of AI, autonomy, and emerging technologies, particularly in terms of reducing the human element in maritime operations. Discussions also revolved around how autonomous vessels would interact with the existing COLREGs. One particularly impactful presentation highlighted the importance of mental wellness. The speaker shared a deeply personal and emotional account of a tragic tanker explosion that led to a catastrophic fire on his vessel. Through his experience, he underscored the long-lasting effects of trauma on mental health, stressing that mental health challenges can persist for years, even with professional support.
The MAIB provided insightful statistics on the most common types of accident, while CHIRP emphasised the critical importance of incident reporting. They also highlighted the ongoing issues caused by the lack of a global reporting network and the insufficient number of near-miss reports, which limit the industry'’s ability to learn from such incidents.
The symposium provided a wealth of valuable insights. James and I made every effort to engage with the wider audience and convey the unique perspective and concerns of pilots within the maritime sector.
By Jon Smith / UKMPA Technical & Training Committee
24
The UKMPA Executive are delighted with the attendance of the 2024 Conference and would like to express our sincere gratitude to the organising team, speakers, delegates and sponsors for making the 136th conference in Harrogate, such a great success.
Special thanks to Chevron, our headline Sponsor
THANK YOU!
The EMPA Board convened its most recent face-to-face meeting in Brussels on the 1st and 2nd of October. In addition to this, the Board continues to meet regularly via monthly Teams calls. This report highlights key discussions from the October meeting not covered in the EMPA newsletter, along with updates from various EMPA subcommittees and other relevant topics affecting European maritime pilotage.
In Germany, due to a declining number of applicants from the traditional recruitment route, the German Pilots have commenced their own in-house training.
Applicants will have an equivalent Officer Of The Watch certificate before starting a more extensive training scheme in their respective ports. Most of the current applicants will become pilots before their 30th birthday. The scheme will eventually cover the seven pilotage areas and, although the entry requirements will be lesser, the training will be more extensive to cover the shortfall in experience. Other European countries are also experiencing difficulties in recruiting suitably qualified
officers from the traditional route, so it will be interesting to see how the German model progresses.
In Spain, environmental group Oceancare has advocated for a speed limit of 10 knots for vessels in the waters around Barcelona, Valencia and the Balearic Islands to protect migrating whales and dolphins. According to Oceancare, ships traveling above 10 knots pose a much higher risk of lethal collisions with marine mammals, despite the fact that the probability of such collisions remains low. Oceancare’s data suggests that in 2023, 80% of ships in the northwestern Mediterranean exceeded this speed threshold.
The proposal has led to discussions within the Spanish government regarding the possibility of introducing mandatory speed limits in the region. This is a significant development for the maritime sector, as it highlights the growing intersection between environmental concerns and maritime operations.
There are two EMPA sub-committees. The Technical and Training and the Deep-Sea Pilots sub-committees.
Miguel Castro, who chairs the T&TC recently, attended the Remote Pilotage Days in Helsinki in September.
From an EMPA perspective, we do not like the term Remote Pilotage as we feel that Pilotage only refers to the physical presence of a pilot on the bridge of a ship. We see many of the proposals currently being put forward as enhanced VTS, but that is a whole other debate.
The meeting was well attended by pilots from around the world as well as government officials and industry developers. The main countries looking to introduce remote pilotage are Denmark, Sweden, Finland and Singapore. All currently have projects ongoing with enhanced technology onboard vessels. These include cameras, iPad and even using drones. It should be mentioned that most of these projects are related to fairways, channels and approaches to ports and not to actual docking manoeuvres, however, there have been many challenges detected in implementation so far.
You may ask why these countries are driving this. The reasons given include the following points, increased safety, the safety of crew and pilots in bad weather conditions, emission reductions and cost reductions. Also mentioned on several occasions was a lack of new pilots, with the German training programme mentioned several times. The T&TC in conjunction with Amura has also been working hard in developing the new EMPAsafe app, which went live in October. Our UKMPA app will integrate with EMPAsafe so members do not need to take any action, but I must mention the many hours of work done by our own T&TC committee and extend our thanks to John Slater and his team for their efforts so far.
Those of you who attended last year’s UKMPA conference in London may recall me mentioning the concerns raised by the UK and other European deep-sea pilots. They reported that several deep-sea pilots were operating out of Cherbourg and selling their services as marine advisors to some of the major shipping companies despite being uncertified.
Following reviews of our EMPA recommendations on deep -sea pilotage and in response to concerns raised, we issued a position paper on deep-sea pilotage at our conference in Antwerp (May 2024).
This was sent to all relevant stakeholders around Europe. In that document we recommended that:
“The North Sea-adjoining countries re-form the North Sea Pilotage Commission or an alternative committee to work together for the improvement of DSP services in the Channel and North Sea areas, and to maintain the highest level of professional qualification and certification of DSP.”
Here I must thank Kim Sykes, a DSP and member of the Elder Brethren of Trinity House Newcastle, for acting quickly to re-form this committee. Kim organised the first in-person meeting of the NEDSPA to be held for many years.
Erik Daleg (EMPA president) and I attended in person, and we were joined by over 25 other delegates at Trinity House in Newcastle. The delegates represented the main DSP providers as well as UK, German and Dutch government officials, the three UK Trinity Houses responsible for authorising DSPs and representatives from Nautilus, the Honourable Company of Master Mariners and the North Standard P&I Club.
We discussed several options to highlight the need for properly certified pilots and how to counter the use of non-certified pilots using the recommendations laid out under MGN506(M) and IMO 1080(A).
Carien Droppers, a co-ordinating specialist advisor from the Netherlands, presented insights into how Dutch authorities manage the growing network of wind farms in the North Sea and how they identify the need for DSPs to mitigate risks in these increasingly congested waters.
This meeting was a significant step in maintaining high standards for deep-sea pilotage and will be repeated annually, with the next meeting set to take place at Hull Trinity House in 2025.
It is worth mentioning that the deep-sea pilotage companies here in the UK maintain the highest standards and in fact their current recruitment entry criteria are much higher than many UK ports. Most deep-sea pilots are former ship masters with at least three years’ command experience who undergo an extensive training period before being certified by Trinity House.
Those who attended this years UKMPA conference in Harrogate will recall that I had hoped this year’s EMPA conference would go ahead as planned in Batumi Georgia. Unfortunately, due to the worsening political situation in the country and the ongoing political issues in the region the EMPA board have decided to cancel the EMPA conference in Georgia.
This decision was made following close communication with our member associations and major conference stakeholders. We hope that Georgia will be able to host in the future once the political and global politics in the region are resolved.
Following several excellent alternative applications the EMPA board have decided to hold this year’s conference in Poland. The venue city will be Krakow with conference being held from the 27th-30th of May. Full details will be published on the EMPA website once finalised.
By Peter Lightfoot Vice President - EMPA
By Captain James Musgrove
Our ‘Safe Haven’ initiative has continued to grow. Pilot wellness is crucial to ensuring the safe and efficient operation of vessels, particularly in challenging conditions. Our support services have gained recognition not only domestically but are now inspiring organisations worldwide to prioritise mental health and break down the stigma surrounding it.
I’m pleased to report that, over the past year and a half, there has been a 10% increase in the number of members utilising our ‘Safe Haven’ services to support their wellbeing during difficult times. This underscores the vital importance of mental health support and reassures our members that help is available when they need it most.
In October, we took an important step forward by launching the UK’s first Pilot Wellness Coaching Programme, made possible through our partnership with the Sailors’ Society charity. This programme is not designed for counselling but is aimed at individuals seeking to enhance their overall wellbeing. All sessions are completely free and confidential, and are conducted one‐on‐one with our dedicated wellness coach, Daniel Taljard.
A holistic approach to wellness
Well‐being is a cornerstone of success, both on the job and in personal life. The UKMPA’s Wellness Coaching Programme focuses on nurturing the whole individual, addressing five key dimensions of personal well‐being: physical, emotional, social, intellectual and spiritual health. By guiding members through strategies and practices designed to improve each area, the programme ensures that participants lead balanced, fulfilling lives. The emphasis on holistic wellness is more than just physical health – it’s about fostering resilience, reducing stress and cultivating a sustainable lifestyle that supports long‐term success both on and off the water.
As maritime pilots, leadership is a crucial part of daily life. The Wellness Coaching Programme goes beyond personal wellbeing by also addressing professional development. Through specialised coaching sessions, members gain valuable leadership and management skills, enhancing their ability to lead teams, handle complex challenges and navigate their careers to the next level. These skills are essential in an industry where effective decision‐making, communication and crisis management make all the difference.
Personal growth through proven coaching techniques
Personal growth is at the heart of the UKMPA Wellness Coaching Programme. Built on well‐established psychological principles, the coaching model empowers participants to set meaningful, actionable goals and achieve them. Whether it’s improving work‐life balance, advancing in the maritime field or overcoming personal obstacles, the programme helps members foster self‐awareness and cultivate a mindset for lasting growth and success.
Tailored coaching to fit your needs
One of the key features of the UKMPA Wellness Coaching Programme is its flexibility. Recognising that every individual has unique challenges and goals, the programme offers tailored support that fits diverse needs. Whether a member is seeking a one‐time session to address a specific issue or prefers ongoing coaching to support sustained progress, the programme can be customised to suit the pace and objectives of the individual. This adaptability ensures that the support provided is relevant and effective, regardless of where the member is in their personal or professional journey.
Crisis support when you need it most In the demanding world of maritime pilots, moments of crisis can arise unexpectedly. The UKMPA Wellness Coaching Programme acknowledges this by offering critical crisis support.
In situations where immediate intervention is needed, trained coaches are equipped to connect members with the Sailors’ Society Crisis Team. This support system ensures that members facing urgent issues receive timely assistance, providing them with the resources and guidance to navigate through difficult times.
The UKMPA Wellness Coaching Programme is a significant milestone for maritime pilots in the UK. By addressing the interconnected aspects of personal wellness, career development and crisis support, it equips members with the tools needed to thrive in all areas of life.
With the UKMPA’s commitment to wellbeing and professional growth, members now have an invaluable resource to support their journey towards a healthier, more fulfilling career in the maritime industry. Whether you're looking to improve your personal wellness, develop leadership skills or need support in a challenging moment, the Wellness Coaching Programme is here to guide you every step of the way.
The UKMPA is dedicated to eliminating the stigma surrounding mental health. Our 'Safe Haven' initiative in partnership with the 'Sailors' Society' has been a resounding success, and we remain committed to highlighting this critical issue to support our members during challenging times. We will continue to enhance our support services and elevate the standards of wellbeing for marine pilots, always prioritising their wellness and safety at the core of our mission.
I am delighted to share that at our conference and AGM, our members, delegates, stakeholders, sponsors and speakers generously raised an incredible £2,400 for our partner charity, the Sailors’ Society. A heartfelt thank you to everyone for your kind donations. Every penny raised will go directly towards supporting the invaluable services provided to our members.
Scan the QR code to access the members' area for any enquiries related to our pilot wellness programme.
Mental health professional support service – Call : 020 4577 4313 Safe haven hotline – speak with a fellow pilot – let’s talk Call : 0800 433 2163
By Kerrie Forster / Workboat Association Chief Executive Officer
Within the past 24 months, I have been involved in post-incident proceedings involving pilots and workboat interactions. The workboat industry and the pilot service working closely together, can help to minimise the number of dangerous and fatal incidents in this important port service sector.
Factors involved in those incidents include:
1) Vessel design
Modern tugs are designed to remain extremely stable and stiff throughout their towing work. The tug’s buoyancy is not comprised as it is designed to return quickly to the upright position once the tipping forces are removed. The acting forces applied by the tow are positioned on board in places that contribute the least tipping forces and the most opposing force.
Older tugs, not necessarily designed directly for ship’s towage work, have different properties. They are often built with a soft curve and so a more traditional hull shape, mixed with the alternative, more traditional placement of the towing apparatus and forces. Often, they are single - or twin-propeller driven with a hull design focused on longitudinal efficiency and primarily in the forward direction.
Sadly, it is a fact speed does kill. The greater the speed, the greater the energy mass, the greater the pressure on the tug and associated towing apparatus and the greater the towing risk. The construction and material of any piece of towing equipment that is subject to such pressure is tested for its maximum working load.
For example, each tug along with its towing apparatus and tow line are tested to their maximum working load. The above information may, however, be used in contrary form. The bollard pull of a tug (the Safe Working Load or SWL) is often used to highlight a tug’s ability, not its weakness. A procurement team will look at the SWL of a tug and use that information as a comparison index to judge that vessel against another.
I would like to ask the following:
• How many pilots’ passage plans have the SWL of the tug(s) detailed on them?
• How many plans have the speed at which the ship will make the working load of the tow rise above the SWL under force?
As users and operators, we use that data to create a risk-assessed Safe Working Limit for the conditions. This enables us to make dynamic operational decisions knowing the maximum safe towline limits. It has to remembered that ‘safe working load’ and ‘maximum load’ are different. The tug and its associated equipment tire with age, the propulsion and engines will not be as powerful as when built.
Towing apparatus will require replacing throughout its lifetime, so the safe working load and maximum load of the tug will change (positively or negatively) based on the variables related to the technical condition of the vessel and its equipment. As a consequence, if the tug changes characteristics then the tow will also change.
How many times have you chosen to look away or chosen not to get involved when something unsafe is happening?
At no point should anyone find themselves unable to speak up if they see something going wrong and stop the job. If you are not happy to commit to the job or see something going wrong, stop the job. Do not wait for an accident to occur.
The training requirements for workboats and tugs have gone through big changes in the past 24 months. The introduction of Workboat Code 3 has been one of those catalysts, along with the current revision of STCW that is taking place at the IMO. Digitalisation, new technology and simulation continue to be some of the key considerations for updates. As of the end of 2024, and depending on the size and operation of the vessel you are going to command, there are three main routes to gaining your certificate(s) of competence (CoCs) and becoming a Master of a workboat or tug.
A. Having served deep sea and holding your full STCW Master certificate(s)
B. Workboat-specific routes
C. Tug-specific routes
Option B requires you to meet the requirements of the Workboat Code. This was re-published as Edition 3 in December 2023. All crew have until 12 December 2028 to comply with
the new edition of the code and some may be required to comply earlier depending on the certificate date of the vessel. Many training requirements will become mandatory from 13 December 2026.
Briefly speaking, a Master of a Workboat Code 3 vessel requires the following:
1. A CoC, depending on operating area and tonnage of vessel, such as:
• STCW Master 200 < unlimited
• RYA/MCA Yachtmaster (any variation)
• MCA Boatmasters’ Licence
• RYA/MCA Powerboat Advanced
• Certificate of competency for appropriate area issued by Competent Authority
• RYA/MCA Powerboat Level 2
• RYA/MCA Day Skipper
• Local Authority Licence for appropriate area
2. Sea Survival training
3. First Aid training
4. Firefighting training
5. GMDSS or Radio Operator licence
6. Radar training (if Radar is fitted)
7. Stability training (if the vessel is required to have a stability information book)
8. Electronic Chart System training (if ECS is fitted)
9. ECDIS training (if ECDIS is fitted)
10. Basic food hygiene training (if preparing food)
11. Dangerous Goods training (if vessel is certified to carry DG)
12. Lithium-ion Battery training (if Li batteries are fitted)
13. MGO transfertraining (if performing MGO transfer)
14. General vessel familiarisation training
Option C) is to complete a MCA Tug COC, either 500gt or 3,000gt (following a more conventional, college-based approach)
1. Complete the required tug service
2. Complete the MCA-approved Training Record Book Level 4
3. GMDSS Operator’s Certificate
4. Medical Care (STCW A-VI/4-2)
5. Pass the required MSQ units (Master 500gt Tug) Vessel navigation and tides Unit 11
• Ship Construction Unit 37
• Chart-work and tides Unit 41
• Contribute to stability and watertight integrity Unit 43
• Control tug operations Unit 44
• Control vessel anchoring mooring and securing operations Unit 46
• Interpret Meteorology in the near coastal area Unit 48
• Provide Fire Fighting response on board a vessel Unit 59
• Provide Medical First Aid on board a vessel Unit 60
• Take charge of a watch in the near coastal area Unit 63
• Respond to navigational emergencies Unit 62
• Control Marine Radar and Automatic Identification systems Unit 88
• Control Marine Electronic Navigation Systems Unit 89
• Control Electronic Chart Display Information Systems (ECDIS) Unit 90
• Control Bridge Resources Unit 91
• Direct Tug operations Unit 47
• Manoeuvre a tug Unit 55
6. Hold an OOW (Tug) less than 500gt CoC
7. Pass oral N (T) – Master (Tug) less than 500gt near coastal, or
8. Pass the required additional MSQ units on top of Master 500gt Tug (Master 3,000gt tug)
• Manage personnel on board a vessel UNIT 51
• Manage Vessel navigation UNIT 52
• Manage vessel maintenance UNIT 53
• Manage vessel operations UNIT 54
• Take charge of medical care on board a vessel UNIT 66
9. Navigation Aids, Equipment and Simulator Training (NAEST) Management for <3,000gt Tug
10. Pass oral P (T) – Master (Tug) less than 3,000 GT near-coastal
As shown in the training requirements, the Master (Tug) route includes many tug-specific modules. It also incorporates relevant experience (sea time on Tugs) and the completion of a training record book.
All of these specifically evidence and nurture the candidate’s understanding of tug-specific operations and scenarios.
The training under Workboat Code 3 does not, so the MCA has an additional voluntary training requirement: the ‘Voluntary Towing Endorsement’. This endorsement can be added to any regular CoC but endorses the holder to evidence their understanding of tug-specific operations and scenarios.
This includes the following:
• A minimum relevant experience (sea time on tugs)
• A focus on any of: General Towage, Sea Towage, Ship Assist Towage
• The completion of a VTE Training Record Book
• A practical assessment
The practical assessment covers the areas of the tug-specific MSQ units but in an on board and live setting. This can be more suitable for the style of learning or assessment that some candidates excel in.
The downside is that it is not mandatory. Although 190 VTE certificates have been awarded since the first successful candidate in 2014, there remain many practising tug operators without tug-specific training or assessment.
The Workboat Association has noted this and we are doing things to correct it. Together with the industry and led by the MCA, we recently reviewed the Port Marine Safety Code guidance. One of the biggest chapters to be updated relates to the management and safety of small harbour craft (Tugs and Workboats). Another way we are bridging the gap is the development of training for those vessels engaged in towage that are not contracted as ‘tugs’: for example, vessels that perform a one-off tow to move a floating object or vessel around a harbour or loch or a workboat that could tow but the crew are not often contracted to do so.
By Edward Pentney / Class 1 Manchester Ship Canal Pilot
The four Victory Class tugs were built between 1973 and 1976 by James W. Cook and Co. in Wivenhoe, Essex. They are the last purpose-built tugs for the Manchester Ship Canal and when they entered service, they replaced early twin-screw designs dating from the 1940s. They joined the Manchester Ship Canal Company’s fleet of approximately 12 working traffic tugs and were based at Runcorn. They are very similar in mechanical design and outward appearance to the older Sovereign Class tugs that entered service in 1956. In the 1980s, Peel bought the Manchester Ship Canal Company and all its assets, including the tugs. By this time, traffic in the upper reaches was in steep decline and the old Manchester Docks had closed completely in 1982. Peel closed the yard at Runcorn and rationalised the tug fleet to just four vessels, these being the Victory Class. They would now be based at Eastham, where they remain to this day. Trade has since been concentrated in the lower reaches, primarily serving the oil refinery at Stanlow and dry bulk trades to Ellesmere Port and Runcorn. © John Eyres
In 1989, the Carmet Tug Company took over the crewing and management of the tugs, although Peel retained ownership of these critical assets. Carmet continues to operate the tugs and is currently the sole contractor for towage on the canal. All four of the tugs – MSC Victory, MSC Viking, MSC Viceroy and MSC Volant – remain in serviceable condition, although spare parts must now be custom-built. They typically operate in pairs, with two tugs working for a week, before spending the following week on standby duties only.
Tug Specifications
The tugs are conventional twin-screw designs, and do not have bow thrusters or winches. They are fitted with twin Allen 640bhp diesel engines for a total of 1,280bhp and a maximum bollard pull of 16 tonnes when towing over the stern. When towing over the bow, only 10-11 tonnes of bollard pull is available. Their chief advantage is their shallow draught of around 3.5 metres, which permits them to get very close to the canal bank. This is often required both on transit and during swinging manoeuvres at Stanlow and Runcorn.
The tugs measure 28.6m LOA by 7.8m beam. The propellors are fixed, four-bladed and measure 2,310mm in diameter – clutched in with conventional gearboxes. Towage is achieved via a 28mm steel wire, secured on mooring bitts (forward) or a towing hook (aft). The hook has a quick-release mechanism built in so the wire can be released quickly under tension if required. As no winch is fitted, the length of the towing wire cannot be adjusted but it is also possible to rig a towing ‘bridle’, which will be discussed below.
The basic requirements for towage date back to the earliest days of the canal in the 1890s and are based on the experience of the first pilots. Any vessel of 113m LOA (370 feet) or greater must take two tugs for the entirety of its transit, regardless of manoeuvring characteristics. Due to the narrow width of the main channel – 36 metres – the tugs are an additional safety measure and can assist with correcting the vessel’s desired centre position should it find itself closer to one bank than the other.
Smaller vessels also require tugs to run astern, which is regularly done between Stanlow and Ince – a distance just over half a mile. Some LPG tankers that visit Stanlow do not have bow thrusters and in these cases the head tug is used to control the bow when swinging and running astern. In other cases, a pilot may simply decide that a smaller vessel below the required parameters may require a stern tug if it is heavily laden, has poor astern power or suffers from extreme transverse thrust when astern movements are given.
The main drawback of the tugs is their lack of power when handling the largest vessels on the canal. The larger tankers (150m LOA x 23m beam x 8m draught) that visit Stanlow are often fitted with air-start main engines and fixed-pitched propellors, giving a ‘dead slow ahead’ speed of 5-6 knots. When slowing down prior to berthing, swinging or entering Eastham Lock, the stern tug is positioned bow-to-stern and thus only has a maximum of 10-11 tonnes bollard pull available. In these cases, the main engine of the piloted vessel must be stopped at least once so that the stern tug can achieve enough ‘grip’ to slow the vessel. CPP vessels are much easier to slow down as the pitch can be fine-tuned to achieve minimum steering speed.
When swinging inbound at Stanlow, the vessel almost always swings bow to port, with the stern of the ship staying in the main channel. The stern tug first slows the vessel down but must then transfer its wire from the forward bitts to the aftertowing hook. This is done by hand by the tug’s crew and is the most critical moment of the operation. It may take up to one minute to transfer the wire and during this time large ahead or astern movements should be avoided on the piloted vessel’s engine / pitch.
When departing Stanlow, the vessel must usually swing bow to port. The stern tug in this case makes fast stern-to-stern with the wire made fast on the after towing hook. Once the piloted vessel has completed its swing, the stern tug must be let go before any significant headway is gained. If the tug is towed stern-to-stern by the piloted vessel above 2 knots, it will be susceptible to girting. Once it has been let go, it will turn around and make fast bow-to-stern for the remainder of the transit to Eastham Lock.
Normal towing arrangements make use of a single towing wire passed through the fore or aft centre leads of the piloted vessel. However, on heavily laden vessels, a ‘bridle’ may also be employed –with two wires sent through both the port and starboard leads. This is especially useful for dead towage, which happens occasionally when a vessel loses propulsion. A gob rope is often used when towing over the stern. During a swing, the head tug remains fast and will push with its stern to assist the often-underpowered bow thruster, assuming one is fitted. Likewise, the tug can also check the swing towards the end of the manoeuvre.
The primary risk to the tugs is that of girting – which is why gob ropes are employed when towing over the stern. Quick-release mechanisms are also fitted to the towing hooks for use in emergencies. It is normal for the pilots to communicate frequently with the tugs, especially when large ahead or astern movements are required on the main engine. The piloted vessel must also avoid towing the aft tug stern-to-stern under all circumstances.
Fresh winds can severely hamper towing operations, more so than with a modern ASD or tractor tug. They do not have bow thrusters and can struggle in a strong cross wind, which means that
unwanted weight must be applied to the towing wire for them to maintain their position. The transfer by hand of the towing wire from fore-to-aft of the stern tug when starting a swing presents a risk of loseing control. The tugs cannot change their position nearly as quickly as an ASD or Voith-Schneider design.
Another risk is that of a wire parting, which fortunately is a rare occurrence. Spare wires are carried on board and can be rigged quickly by the tug’s crew. To summarise, the tugs are more vulnerable than modern ASD or tractor varieties and clear communication between the pilot and tug master is essential. Before any manoeuvre is undertaken, the pilot will confirm the exact details, whether a swing is involved and the destination berth.
Trainee pilots must complete several trips on the tugs during manoeuvres so that they get a good idea of the operations from the tug’s perspective. Wooden model boards are also used to teach and assess pilots moving through the classes –Class 2 is the level when working with tugs becomes more commonplace on the canal. There are no simulators or electronic training aids because of the unique nature of the canal.
Perhaps the best training comes from doing the jobs under supervision of a Class 1 pilot. Vessels over 112m LOA must carry an ‘assistant pilot’ whose job it is to hand-steer the vessel on transit. The assistant pilot is often of a more junior class and, when he is close to moving up a class, he can perform the manoeuvre himself under the watchful eye of the Class 1 pilot. Roughly one third of the vessels on the canal carry an assistant pilot so this is an excellent way to gain experience for junior colleagues.
In summary, I enjoy working with these tugs as I believe they are unique for a major port in the UK, with similar designs elsewhere being phased out in the 1990s. They are now 50 years old and are expected to be the mainstay of our towage for many years to come. The tug masters have decades of experience between them and as pilots we have developed an excellent working relationship with them.
By Captain Henk Hensen / FNI
Tug power has increased considerably over recent decades. Today, some ship handling tugs have a bollard pull of more than 100 tonnes. In addition, high tug power can be installed in ever smaller compact hulls. As a consequence, the composition of tug fleets is changing and, increasingly, pilots are complaining about the absence of the smaller tugs that are needed to handle smaller ships in a smooth, safe and efficient way.
Change in tug fleet composition
The increase in maximum tug power is a consequence of the need to assist and escort very large tankers, bulk carriers and gas carriers, while the latest container carriers have such a large windage that much tug power is needed in case of strong winds. While in previous years, a fleet of conventional tugs would be made up of less powerful tugs than today, it would also – importantly here – include a number of smaller tugs to assist smaller vessels. For the purposes of this article, we will assume that a ‘modern’ tug fleet consists of azimuth stern drive (ASD) tugs, although the discussion that follows applies to most other tugs with azimuth thrusters as well, such as azimuth tractor drive (ATD) tugs. ‘Small or medium‐sized ships’ refers to vessels up to about 160 metres in length. Let us take the tug fleet of the port of Rotterdam as an example. Before the arrival of modern tugs with greater power in around 1980, there were five classes of tug in the Eastern part of the port, with an additional class in the Western part of the port.
Present situation
With a tug fleet consisting solely of modern, powerful ASD tugs, it is frequently the case that these powerful tugs also have to handle smaller ships. Even when the tug is not equipped with slipping clutches, an experienced tug master can manoeuvre these modern tugs very gently. This is a prerequisite when handling smaller and light ships, otherwise the ship manoeuvres may be spoiled. Proper training is therefore essential – but there are other consequences of the use of large and powerful tugs to handle small and medium‐sized ships, which will be discussed below.
Response time
In the Western part of the port where the largest deep‐draught tankers and bulk carriers berth, stronger tugs were available: 6 x 30 tonnes, 4 x 35 tonnes and 2 x 40 tonnes bollard‐pull Voith Schneider tugs.
It is amazing how small tugs handled large ships. For instance, tugs of only 600 hp were assigned to ships of over 200 metres in length, if in combination with one 900 hp tug. Even with the relatively small difference in tug power across the tug fleet, small ships were handled by the smaller tugs and larger ships by the more powerful tugs.
Short response times are an important factor in the smooth handling of small and medium‐sized vessels. This is one of the reasons why smaller tugs are preferred. Tugs with a high bollard pull regularly have to operate with reduced power to avoid overloading the ship’s deck equipment due to high forces in the tow line. This is often needed when handling large ships but always for smaller ships. See Figure 1, where an ASD tug with a bollard pull of 80 tonnes is assisting a relatively small vessel with deck equipment with an estimated Safe Working Load (SWL) of around 30 tonnes. This needs the powerful tug to reduce its pulling power by more than 60 per cent – although reduced power can also be used in combination with tension control on the towing winch, if tugs are equipped with it. The reduced power will lengthen response times. Today’s small ASD tugs are much more powerful than the old ones listed in the table left, with a bollard pull of, let us say, 20 tonnes. The Safe Working Load of deck equipment of ships up to approximately 160 metres is around 30–45 tonnes. In other words, a smaller tug will not need to reduce its power to keep ship bollards and fairleads intact.
It can therefore be expected that small tugs will be able to react considerably faster than large, powerful tugs when assisting smaller vessels. Another reason for that is that tug masters of powerful tugs have to apply the high power carefully, which is less of a concern for smaller tugs.
Another important aspect is the availability of slipping clutches (also called speed modulating clutches) and controllable‐pitch propellers. If an ASD tug is equipped with slipping clutches, it can regulate propeller rpm stepless to zero or from zero up.
When decreasing speed to a minimum, the thrusters stay in the same position (as shown in Figure 4, overleaf), while propellor rpm is decreased gradually till the required speed has been achieved. If a tug equipped with controllable‐pitch propellers decreases speed, rpm or propellor pitch is regulated in such a way that the required minimum speed will be achieved.
A tug that is not equipped with slipping clutches or controllable‐pitch propellers manoeuvres differently. This is shown in Figure 3, where an ASD tug without slipping clutches is approaching a ship that has some headway. During the approach the thrusters remain clutched in and propeller rpm is at its minimum. To reduce speed further, the thrusters are set at an angle. Finally, the thrusters are set almost perpendicular to match the speed of the ship (see Fig 3). Steering is still possible by setting one thruster somewhat ahead and the other somewhat astern. At the final approach (Fig 3), the propeller wash is hitting the ship’s hull –this is clearly visible in Figure 1. Especially with a light ship, this can disturb the planned manoeuvre.
The strength of the effect depends on whether the tug has high‐ or medium‐speed engines. The effect is greatest with high‐speed engines, and of course high power. An example:
RPM (engine) Min Max
Medium‐speed engine 250 1200
High‐speed engine 500 1800
Assuming propeller rpm at maximum speed is 200, propeller rpm at minimum speed with the same reduction is then: Medium speed engine (reduction i = 6): 250/6 = 41.6 rpm. High‐speed engine (reduction i = 9): 500/9 = 55 rpm.
If we take an ASD tug of 70 tonnes bollard pull with a high‐speed engine, towing force at idle speed is then: 552/2002 x 70 = 5.3 tonnes, which means 2.6 tonnes for each thruster. This is the same as a class A or B tug of the type mentioned above pushing with half power against the ship hull. Furthermore, depending on the angle of inflow, the propeller wash may create an area of low pressure along the port side aft of the ship, pushing the stern to port. All are unwanted influences on the ship. The effect of lower‐powered tugs will be proportionally less. For example, a small, low‐powered tug of 20 tonnes will create a side wash force of, in this case, only about 0.7 tonnes. It can be concluded that, for handling small or medium‐sized ships, less powerful tugs are needed, preferably equipped with slipping clutches.
If the assisting tugs are towing on a line, for instance one at the centre lead forward and one at the centre lead aft, they can give steering assistance or control the ship’s speed. They are not in contact with the ship and how they operate depends on the tug master’s experience. Do these tugs have an effect on the manoeuvring of the tanker? This may well be the case –although again, the extent of the effect will depend on the size of the tugs in relation to the size and displacement of the tanker. When tugs towing on a line operate with utmost care, there will be no problems. But it may happen that for some reason the tug makes an uncontrolled movement, causing the line to tighten. This may result in unwanted movement of the ship, for instance a speed increase or a course change.
The tugs can also operate with the push‐pull method. In that case, when the ship is approaching the berth, the tugs are usually made fast and are lying alongside as shown in Figure 4, above. In this situation, the tugs may hinder course‐keeping or delay course changes. For instance, when making a turn to starboard the forward tug has to move with the ship and the aft tug has to be pushed away, causing a lower rate of turn. The effect will be even more pronounced if the towline of the forward tug is coming tight. In addition, when the tugs shown in Figure 4 are proceeding with the ship under an angle, hydrodynamic effects will play a role and will also affect ship’s course‐keeping ability or course changes. Skegs underneath the tugs will increase this effect.
The larger and more powerful the tugs, or the smaller the ship’s draught, the larger the disturbing effect can be.
Let us have a look at the impact of tug size, in this case displacement. A tanker of 145 metres has an estimated displacement when loaded about 27,000 tonnes; when ballasted approximately 17,500 tonnes. Large ASD tugs such as the Damen ASD 3212 have a displacement of 800 tonnes. With two tugs, as in Figure 4, this is a total of 1,600 tonnes. In case of a ballasted ship, almost 9% of the ship’s displacement is hanging alongside. Where smaller tugs are used, for instance the ASD 1810, it is only 3%. That is three times better.
In other words, the impact of the larger tug on the ship is three times higher than that of the smaller type of tug, assuming the same approach speed. This applies to situations as discussed where the tug comes, or lies, alongside a ship and when towing on a line. The higher power of the larger tug may even worsen the situation. So, again, smaller tugs are preferred for handling small and medium‐sized vessels.
Due to the high power installed in present tugs, stability – which was already an important concern for tugs – has become even more important. To increase stability, tugs with azimuth thrusters have become wider. However, such wide tugs have become course unstable as a result. It is a risky situation for a tug when operating close to a ship having headway and coming under the influence of interaction effects. It requires a tug master to be attentive because frequent steering actions are needed, particularly for the more course‐unstable widerbodied tugs. A moment of inattention from the tug master may bring the tug in contact with the ship. Near the bow of the ship this can become catastrophic for the tug and problematic for the ship, while contact at other locations may disturb the ship’s manoeuvre or cause damage to the ship unless the tug is equipped with good fendering. Again, the smaller the tug, the smaller the disturbing effect on the ship, and the lower the ship’s speed, the lower the risks.
This again shows how important it is that tug masters have a good practical training.
Height
Another point is the height of the tug’s bow. The bow of a large tug pushing at the side of a small ship may be too high for it, or may damage the ship’s railing (see Figure 5).
What has to be done?
It has already been shown how important tug master training is. Proper ship handling with tugs requires thorough training by qualified instructors and optimal communication and cooperation with the pilot. Some of the negative effects of large tugs assisting small or medium‐sized ships can be prevented or minimised through good training, but certainly not all. At the same time, if either training or communication is lacking, the negative effects of handling small ships with large tugs will increase considerably. ‘Big is Better’ is certainly not true when it comes to tug assistance for small and medium‐sized ships. Such ships should not be handled by large, powerful tugs, such as today’s ASD and ATD tugs or similar of 40–100+ tonnes bollard pull, because of the risks outlined above, especially when thorough training of tug masters is lacking.
Ships up to approximately 160 metres in length should ideally be handled by more suitable tugs, smaller and less powerful, and preferably having speed modulating clutches or controllable‐pitch propellers. These tugs are also less costly to purchase, and the cost of fuel and maintenance is lower.
A trend of building smaller ASD tugs can already be observed in the Netherlands, France and some other countries. These tugs have enough bollard pull to handle the ships in question safely. Of course, the economic viability of developing a fleet including smaller, less powerful tugs depends on the number of small and medium‐sized ships that call at the port. The more smaller and medium‐sized ships that call at the port, and the more frequently such ships use tugs, the larger the possibilities for smaller and less powerful tugs.
THANKS TO: THE NAUTICAL INSTITUE
This article was previously published in Seaways and now re-published in the Pilot magazine, with the permission of The Nautical Institute.
By Brendan Smoker & Andy Read
When some readers think of escort towage, they may recall those wellknown images of tugs heeled over to extreme angles, decks immersed, wondering if at some point the tug will capsize. Towage industry leaders would like to think things have come a long way since then, namely in the improved capability of modern escort tugs along with training and competence of those they employ on the controls.
What constitutes an escort tug is often misunderstood. In many cases, people assume that any tug connected to a moving ship is escorting, but this is not the case. In situations where the tug is not imparting any force on the ship and the speed of the connected vessels is less than 6 knots, this situation is properly defined as a ship-assist mode. To be truly considered escort- capable, a tug must
be able to safely and effectively provide steering or braking forces via a towline to the ship at speeds greater than 6 knots. This is typically done in an indirect towing mode, utilising a combination of hydrodynamic lift and drag from the hull and skeg providing towline tension and thrust from the drives to maintain position.
The justification for escort towage has always been a ‘sensitive’ control measure for harbour authorities, weighing the balance between protecting the local environment, port interests and operational necessity against the commercial sensitivities of ever-rising port costs to shipping lines.
When assessing the requirement and parameters for escort towage, harbour authorities should engage with their towage providers (and tug masters) and ask, “What is it we want the tugs to do and what is the added margin of safety that they will provide?” Clarify expectations, limitations and suitability of assets available for the task.
With a clear understanding of escorting speeds, rates of turn and localised requirements from the trials team (pilots) to support this process, effective research and development through simulation, modelling and trials have proven a critical process when validating performance data.
The design of an escort tug is a balancing act between various competing features. The most appropriate tugs result from clearly defined operational requirements, such as, the maximum-rated escort speed (typically 8 or 10 knots), and the maximum steering and braking performance. It is also worth defining if the tug is to operate in calm or heavy weather and if it will be a dual-purpose tug used for both ship-assist and escort duties.
The starting point is typically a proven escort tug 'platform', but with hull dimensions adjusted to provide the stability needed to counteract the expected escort forces. With the centerline skeg being so critical in the generation of escort forces, its shape, size and location are carefully analyzed in CFD or scale model testing. The working deck is carefully laid out so that the escort towline staple is positioned optimally, and is visible to the tug captain.
The longitudinal position of the staple needs to be carefully studied. Too far forward and the tug will not generate the full escort capability of the hull and too far aft and the tug may not be 'fail safe' in the event of a propulsion failure.
Towage operators have made significant investments in fleet renewals to provide high-quality (and appropriate) assets within the ports where they operate. With the significant variety in escort tug requirements, naturally there is also a wide range of escort tug capabilities. Therefore, it is critical for both the tug master and ship pilot to understand the escort performance and limitations of each escort tug on the job.
The escort butterfly diagram below shows the performance envelope of the particular tug when tethered in the center lead aft position at the indicated speed and loading condition. The green region indicates the steering and
braking forces the tug can achieve at heel angles equal or less than the class heel angle limit. The red region, if shown, indicates forces the tug can generate but at a heel angle greater than allowable by class.
It is the job of the tug master to adjust position throughout the escort operation to maximise potential and thus effectiveness of the tug during the assist phase.
The four key characteristics of an escort tug are:
• The rated escort speed (typically 8 or 10 knots)
• The maximum steering and braking performance (typically shown in an escort performance butterfly diagram)
• The maximum allowable heel angle while conducting indirect escort
• The Towing System Load Rating (TSLR) that dictates the maximum towline tensions for each wrap angle zone
The rated escort speed, maximum allowable heel angle and TSLR are defined in the Escort Placard, included in the official tug stability book. The placard is meant to be posted in
the wheelhouse to ensure the master is aware of the tug stability and towing equipment strength limits while escorting. The size and position of the skeg, coupled with the hydrodynamic characteristics of
the hull, have a significant effect on the amount of steering and braking force that the tug can generate. It must also have sufficient propulsive thrust to enable proper positioning at all required speeds. With regard to safety, there are several aspects to consider: primarily stability and towing equipment.
The tug must have enough reserve stability in this dynamic situation to properly counteract the extremely high heeling moment that is generated in extreme escort situations. Additionally, all the towing equipment – winch, line and staple, etc – must be engineered for the intended service. For winches, this may include an active payout and retrieval system to prevent slack lines and shock loads that may occur as the tug manoeuvres or moves in heavy seas.
With all towage operations, the exchange between pilot and tug master is a fundamental process to ensure the safe execution of the act. Control of speed throughout the passage is critical to ensuring the safety of the operation. Escort tugs running at their upper escort speed of 10 knots only have limited power reserves to keep pace with the assisted vessel and to manoeuvre into an assist position. It is vital (but sometimes forgotten) to consider the high lateral speeds generated aft as a large vessel rounds a turn. To maintain optimal position, balancing the yaw angle due to the ahead and athwartship speed components can be a challenge for even the most experienced tug master. Because of the high forces involved, selecting appropriately rated deck
fittings is important and the additional loading forces that can be caused by the angle of the towline towards the lead need to be considered. For example, a tug towing on a towline with an angle up to 45° to the vessel, can generate 140% of its bollard pull force on the deck fitting. Pilots should be aware of and communicate any limitations or restrictions these fittings may pose to the escort operation.
The final, and among the most critical aspects of escort tug design and operation, is training. The most successful escort operations around the world involve frequent simulator and live training, with both tug masters and pilots working together. The best escort tug in the world is only as good as the training of the Master and pilot.
P.Eng., M.A.Sc.
Manager, Escort Tug Performance
Robert Allan Ltd
Andy Read
Southampton Pilot Cl.2
• Prior to career in pilotage, 10 years’ experience in towage industry.
• Offshore, harbour & escort towage on deepsea, ASD, tractor & rotor tugs.
By Scott Baker, CMMar / Head of Marine Standards –Europe, Svitzer
We live in a world of modern, powerful and innovative tugs, yet conventional towage is a widely used and necessary aspect of today’s maritime operations and, regardless of developments in tug design and technology, it looks set to remain so for many years to come.
The recent release of the report on the investigation of the capsize and sinking of the tug Biter has once again highlighted some key issues that should act as a stark reminder to tug operators, pilots and harbour authorities concerning the dangers of conventional towage.
Girting is the term used to describe a tug being capsized by the action of a ship or other vessel it is towing. Capsizing may occur when the towline is abeam of the tug (at 90 degrees to its centreline)
and sufficient force is generated by the action of the tow to pull it over bodily. Also described as ‘girding’ (Gaston, 1996). “Many tugs have capsized due to girting and often with dramatic consequences. Girting itself is most often not the root cause. The basic cause is the disregard for, or even the lack of knowledge about, the capabilities and limitations of the tug. This includes, on more than one occasion, a lack of proper communication between the pilot/captain and the Tugmaster” (Hensen & van der Laan, 2016).
Speed has been highlighted as one of the most important and influential factors affecting conventional towage, especially in the context of assisting with the arrival, manoeuvring and departure of larger vessels (ship assist towage).
The conventional tug is particularly vulnerable to girting when acting as the stern tug or as a brake at higher
speeds in a towed situation. Ideally, conventional towage operations on the stern of an assisted vessel should be completed at approximately 2-3 knots in accordance with general industry guidelines. Equally, consideration should also be given to connecting speeds that effectively start the operational element of the towage evolution.
This article will not discuss the fundamentals of Tugmaster training, pilot training or the use of specific equipment such as gog arrangements. It will consider the on-scene towage operation and associated communication, backwards through the opportunities that all pilots, Tugmasters and harbour authorities have in their existing arsenal of tools designed to assist with the provision of a common understanding in a bid to prevent incidents.
Many modern vessels are designed in such a way that is very difficult if not impossible for a pilot on the bridge to maintain visual awareness of the position and activities of supporting tugs.
This factor, along with shortfalls in communication, has played out time and again through a series of incidents, such as “the pilot was unable to see… [the tug] from where they stood on the bridge”… “the pilot assumed… [the tug] was following stern-to-stern.” (MAIB, 1999)
“The… investigation found that the [tug’s] coxswain was not advised that [the assisted vessel] was about to come ahead.” (MAIB, 2017)
“The pilot and [tug’s] coxswain did not share a common, detailed understanding of the plan and, once the operation commenced… opportunities were missed for key information to be exchanged.” (MAIB, 2016)
There are three crucial factors required to establish a common mental model for pilotage and the associated towage operation: communication, communication, communication.
The Port Marine Safety Code (PMSC) guide to good practice states that “it is essential that the pilot/ship master agrees with the Tugmaster, as part of the pre-operation interchange, what the ship’s speed through the water will be when the tug is made fast and thereafter. Excessive speed will cause dangerous interaction between the ship and tug and could be fatal for the tug.”
§10.3.6 (DfT, 2018)
This is reiterated in the Code of Safe Working Practices for Merchant Seafarers (COSWP) [§25.5.3], which states: “prior to towing operations being undertaken, the master should establish suitable means of communication, exchange relevant information (e.g. speed of vessel), and agree a plan for the tow with the Tugmaster.” It goes on to state [§25.5.7] that “the Tugmaster should be kept informed of engine movements, proposed use of thrusts etc [during operations].” (TSO, 2015).
COSWP [§33.1.2 (Port Towage Industry)] clearly explains that: “Before beginning towing operations, a comprehensive plan of action should be prepared, taking account of all relevant factors, including sea-state, visibility and the findings of the risk assessment.” (TSO, 2015).
The PMSC Guide to Good Practice [§10.3.8] sets clear expectations regarding local port liaison meetings: “Pilots and Tugmasters should conduct regular liaison meetings, safety workshops, visits including pilots tripping on tugs and tug masters accompanying pilot… It is recommended that, as a minimum, liaison meetings between facility representatives, pilot associations and towage providers take place every quarter.” (DfT, 2018).
The PMSC Guide to Good Practice (DfT, 2018) [§10.3.8] also includes comments concerning training:
“Guidelines should be used to ensure that tug crews are appropriately trained and qualified… They should also include the need for tug crews to train with pilots… and all parties attending simulator training and refreshers together. Trips should cover as varied a selection of towage activities as possible including escorting (where applicable).”
The European Tugowner’s Association again draws a parallel with its own guidance for training and visits that strongly recommends “that pilots should periodically attend on-board tugs during harbour towing operations and ideally should find time to attend on both the bow tug and the stern tug.” It also highlights that “Pilots may have done so [visiting/training on conventional tugs] during their initial training period, but as they progress further through their career whilst qualifying to handle larger vessels, they may tend to forget how it feels to be at the other end. Therefore, by attending periodically on board a tug during a live harbour towing operation and, if opportunity exists, by attending simulator sessions ideally together with the Tugmasters, they will constantly keep in mind the Tugmaster’s concerns and the Tugmaster can gain insight in the pilot’s concerns. This will eventually work to the benefit of the tugs’ crews and the crews of the assisted vessels because it will undoubtedly have an effect on the safety of all parties concerned.” (ETA, 2015)
DfT, 2018. A Guide to Good Practice on Port Marine Operations. London: Department for Transport.
ETA, 2015. Guidelines for safe harbour towage operations. Bruxelles: European Tug owners’ Association.
Gaston, M. J., 1996. Tugs Today. 1st ed. London: Patrick Stephens Limited.
Hensen, H. & van der Laan, M., 2016. Tug Stability: A practical guide to safe operations. 1st ed. Trowbridge: The ABR Company Limited.
MAIB, 1999. Girting, capsize and sinking of workboat/tug Trijnie, while assisting petroleum products tanker Tillerman, with loss of 1 life, Southampton: Marine Accident Investigation Branch.
MAIB, 2016. Report on the investigation into the girting and capsize of the mooring launch Asterix, Southampton: Marine Accident Investigation Branch.
MAIB, 2017. Girting and capsize of tug Domingue while assisting container ship CMA CGM Simba with loss of 2 lives, Southampton: Marine Accident Investigation Branch.
MAIB, 2024. report on the investigation of the capsize and sinking of the tug Biter with the loss of two lives, while assisting the passenger vessel Hebridean Princess off Greenock, Scotland on 24 February 2023, Southampton: Marine Accident Investigation Branch.
TSO, 2015. Code of Safe Working Practices for Merchant Seafarers. As Amended ed. London: The Stationary Office.
There is clearly so much guidance out there. It is the author’s contention that there is little, even no requirement for anything new. The industry has the guidance and frameworks in place; perhaps the only thing remaining is to add a little more detail to standardise practices and to implement the training, visits and meetings that we are already expected to do.
Sensor Technologies has enabled tug operators and pilots to undertake safer towage operations while having real-time data at their fingertips.
UK-based technology developer
Sensor Technologies has developed Sureline, a sensor that is discreetly located within the rope core, for monitoring loads in towage and moorings applications. Sureline gives real- time data to tug masters, allowing them to clearly monitor load tensions, slew angle and vertical angles of the towage rope during operations.
Tug masters can now instantly see and respond to any abnormal loads and rope angles, helping them to reduce or prevent rope incidents that may otherwise occur without this data. The use of Sureline has been readily identified as a step change to safety and has been welcomed by marine
pilots who also need to have safety data at hand in real time.
At the recent 2024 UKMPA AGM & Conference, it was suggested by sharing this data between the tug master and pilot there would be much more awareness of the stresses being seen within the tow ropes. This would help the pilot and tug master to have better real-time situational awareness.
// Cloud-based data for onshore visualisation and monitoring. (real-time or historical)
Access to real-time rope usage data means users are now able to review a rope’s length of service by working within MEG 4 and SOLAS guidelines, helping identify peak loads, time under tension
and critical vertical and slew angles.
The sensor offers up to 10 data points per second with a calibration or +/- 5% accuracy. Each sensor can store up to 48 hours of data and at the same time
The recent two-day event in Harrogate highlighted the need for clear open lines of communication between stakeholders. The overwhelming opinion of the gathered forum was that data is critical to safer operations and that collaboration between all parties is the way forward.
Sensor Technologies MD Peter Farthing said, “It was a great honour to present Sureline and to be able to bring advancements in technology to such a global business sector.” He went on to say the UKMPA leads the way in recognising safety first and safety foremost when it comes to operations.
The sensor package will allow the operator to better assess the life cycle of the towage ropes and in turn this should help reduce the premature line failures due to shock loads or stress fatigue that cannot be identified with current procedures.
transmit the data to the MCU when further data storage is available, and simultaneously send the data to the Sureline hub for visualisation onshore.
Available for trials from Q3 2025
While manoeuvring a large vessel on-to its moorings, several areas of possible concern have been identified. When considering the safe mooring of the vessel, factors such as wind direction, wave height and swell height and period, along with fendering forces, can all be classed as contributory factors in the prevention of incidents.
Having completed the necessary towage manoeuvre, the importance then switches to fendering. This ensures the vessel is carefully positioned into the correct location for mooring, and at this point the emphasis on safety is transferred to the forces being applied from the tug fenders to the push points on the vessel’s hull.
As highlighted in the images opposite, Fenderforce identifies the position of the force on the fender arrangement by angle, but also shows the load being applied at that point.
Simple-to-use screens allow the tug crews to monitor forces and position of the tug during the fendering operation.
Locating the correct position for the fendering manoeuvre is critical in maintaining the stability and momentum needed to place the ship alongside without incident.
The bottom image shows how Fenderforce can map out and help identify the correct position and applied forces being used to render a safe fendering.
Data collected during this manoeuvre can help support the drive for reducing carbon emissions by helping reduce engine revolutions and cut fuel costs.
By Peter Farthing / Sensor Technologies
The Technical & Training (T&T) Committee has had an active year, focusing on various initiatives that support the Section Committee and UKMPA members. This year’s efforts culminated in full attendance at the recent conference in Harrogate; a testament to our dedication and collaboration.
Stakeholder engagement
At the T&T meeting held before the Harrogate conference we were delighted to welcome several esteemed guests, including Patrick Galvin from EMPA, who introduced the newly released EMPAsafe reporting app. Discussions focused on integrating the new app with our own reporting platform to facilitate the exchange of noncompliant vessel data. This session also sparked a lively discussion with Arie Palmers, who, alongside our own Kevin Vallance, continues to advocate for enhanced pilot transfer safety through the #dangerousladders forums.
Our relationship with Port Skills and Safety has grown significantly this year. The T&T team provided expert input into their recent reviews, including the evaluation of Hadrian’s Rail usage. We remain ready to contribute further as projects evolve.
In partnership with Grant Walkey of Trident Training, the Maritime Immediate Emergency Care course has expanded its reach, now being offered across Ireland and with increased availability in the UK. This initiative still underscores the importance of proper PPE and a unified recovery plan, enabling critical decision-making during the vital golden hour of emergencies.
The T&T team remains at the forefront of discussions on emerging technologies, such as Maritime Autonomous Surface Ships (MASS). Members regularly participate in seminars to ensure the pilot’s perspective is represented
during these formative discussions.
Vice chair Simon Lockwood recently attended the Autonomy Industry Meeting, hosted by the MCA in Southampton. The meeting highlighted the MCA’s global leadership in developing MASS regulations and ensuring comprehensive safety measures for such operations.
Another key engagement this year was Jon Smith’s attendance alongside James Musgrove at the International Maritime Human Factors Symposium at IMO headquarters in London. Topics included MASS and the growing emphasis on decarbonisation and alternative fuel technologies. This event also provided an excellent platform to educate the broader maritime community on the critical role and responsibilities of pilots.
These examples represent just a portion of the T&T team’s efforts to support and advocate for our members. Together, we remain committed to driving progress and ensuring the voice of pilots is heard across the maritime industry.
By James Suffield / Maritime & Coastguard Agency Nautical Manager
We’ve all done it. We’ve all spent time filling in a paper STOP card or an online safety observation reporting tool and then thought to ourselves, “What’s the point?” Does anyone read them? Does it really matter or is it just another form to add to the ever-increasing number of forms we’re required to complete these days? We’ve all heard the term ‘silence is consent’ but is that just a catchy phrase dreamt up by an HSE advisor or does it really mean something?
It may be easy to consider the UKMPA reporting app within the same category: yet another piece of paperwork to complete, especially after a hard pilotage through marginal weather and without good coffee. But really it shouldn’t be considered as such. This short, easy-to-fill-in form produces insights that actively improve pilot safety as well as help shape future regulation.
At the Maritime and Coastguard Agency (MCA), the safety of pilots is a continuing priority and a cornerstone of what the Agency is here to achieve. Pilot transfers are, while seen as routine for many, an operation fraught with risk and unimaginable consequences should it go wrong.
If we compare pilot transfer operations with transfer of personnel in either the offshore oil and gas or the wind industry, we can see that when ship operators must transfer their own personnel the technical and operational barriers put in place (such as surfer landings, fall arrest systems or even motion-compensated gangways), which are designed to mitigate the risk, are treated as a priority and a necessity. Those same vessels, however, may have little concern or regard for using an unsuitable or damaged pilot ladder, or a deck officer not confirming the rigging of a ladder prior to a transfer, or even cutting corners with inadequately placed lifesaving
appliances. Why is this? Is transferring pilots seen as just a formality; a simple task that’s been done for hundreds of years? Is it lack of training, poor historic policing, or is it poor vessel or ladder design? These are the questions that need to be answered.
These questions are being asked internally at the MCA with the aim to improve pilot transfer operations. So how do we determine the root cause of poor pilot transfer practices so corrective actions can be taken either within the MCA, within domestic industry or even internationally? The answer to these questions lies in gathering data. Reports from pilots, attending vessels (pilot boats, tugs) and surveyors, are key if data-driven insights are to be made.
This leads us in a roundabout way back to the UKMPA reporting tool. This simple form is being used to not only deal with immediate areas of concern, which may require a surveyor or port state control officer to attend a vessel, but also to build a database of reports that can be used to determine trends that are laid as the foundations for future regulatory change.
When you make a report of a dangerous occurrence inbound into a UK port, the first link in the chain is the report being received and reviewed by the inspection team and, if deemed necessary, it’s forwarded to the local Marine Office for actioning.
At this point a local surveyor will follow up directly with the offending vessel to ensure any immediate concerns are rectified. This helps to ensure an immediate improvement to safety, either to yourself or to another pilot who may be attending the vessel on a future leg of its passage. This is the part you have likely seen in action, but it only makes up half the story.
The other half of the story relates to the data gathering and assessment of the data that is carried out by a department within the MCA, which you may never have heard of. While the Marine Offices and their teams of experienced mariners lead the way in the public-facing part of the Agency, especially when a number of them appear on the Channel 5 documentary series “Coastguard: Search & Rescue”, there are other teams of former mariners dotted around the country. One team in particular, UK Technical Services Navigation, has a wide range of technical expertise and is responsible for a plethora of areas ranging from Hydrography & Meteorology, Ports & VTS, Marine Licensing, Space Launch, Radio & GMDSS and Navigational Safety. While Ports & VTS have a vested interest in pilot transfer operations, it’s the Navigation Safety team that takes the lead.
One of our primary roles is to be the technical focal point for SOLAS Chapter V by means of maintaining the Merchant Shipping (Safety of Navigation) Regulations 2020: the statutory instrument that brings SOLAS Chapter V into UK legislation. The focal-point role includes being responsible for ensuring the legislation is working as intended, the guidance to industry is suitable and that the underpinning text within SOLAS is relevant, which is achieved by representing the UK at the IMO.
In June 2024, the IMO sub-committee on Navigation, Communication and Search & Rescue (NCSR) spent 10 days reviewing, amending and ultimately agreeing the output from a review of SOLAS Chapter V/23 and supporting IMO performance standard. Representatives from all major administrations were involved in this work at NCSR, as well as professional bodies ranging from IMPA and the Nautical Institute to BIMCO and the International Federation of Shipmasters’ Associations.
The proposed changes include but are not limited to: removing most of the technical text from the main body of SOLAS Chapter V/23 and placing it in a more detailed and more concise performance standard, giving clearer guidance on the use of trapdoor arrangements, fundamental changes to the design life of pilot ladders, maintenance routines (no more onboard step changes or repairs) and a clear push to ensure ships and shipowners ensure crew familiarisation and competence, even on non-ISM Code vessels.
You may be wondering where your reports fit into the work being carried out at an international level within the IMO building. While the Navigation Safety team is made up of experienced master mariners and deck officers from Merchant and Royal Navy backgrounds who draw on many years operational experience with pilot transfer arrangements, our role is not to dictate regulation based purely on our experiences but to represent UK stakeholders and give them a voice on an international stage. This is where the UKMPA reports become vital. Building a database of reports that give insights of recurring themes with pilot ladder or fixed equipment design, operational failings such as failure to correctly rig or manage a pilot transfer operation, or even the performance of other flag state or vessel types, is vital. This information helps in providing quantifiable evidence at IMO when potentially controversial or costly amendments are proposed and require support from leading flag states to even be allowed into wider discussion.
At the time of writing this article, the proposed amendments to SOLAS Chapter V/23 and its supporting performance standard are due to be ratified at the Maritime Safety Committee in December 2024 at IMO. Once ratified, it will become a mandatory instrument in 2028 and it is hoped will help improve the safety of pilot transfers for years to come. These changes are in part due to the continued reporting made by UKMPA members.
It's also easy to forget that when the MCA represents the UK at IMO, we are not only representing Great Britian and Northern Ireland but also the wider Red Ensign Group (REG), which includes Bermuda, Isle of Man and Gibraltar among others. The reach therefore of the UKMPA reporting data is not limited only to the UK flag and UK waters but also much wider, throughout the REG.
While not as high-level or potentially as interesting as thinking about discussions at a United Nations specialised agency, the use of UKMPA reports to help shape domestic guidance is just as important. Domestic guidance can consist of Marine Guidance Notices, which are intended for wider industry and can help provide clearer interpretations of specific legislation as well as focus industry on key issues raised on assessment of the insights gathered from pilot transfer reports.
Another key element of domestic guidance is ensuring that surveyors and port state control officers are given clear instruction on what should be, and can be, assessed with regard to pilot transfer arrangements. This internal surveyor guidance needs to be targeted and precise, something only possible when there are clear data insights into what is failing or causing concern out in the wider world.
So, with all of this in mind, when you’ve finally stepped off the pilot boat onto the jetty or down the accommodation ladder onto the quay after a long shift, consider whether it’s worth spending five minutes to open the UKMPA app to write down an observation on a potentially unsafe act or condition.
Just remember how far-reaching your five minutes might actually be. How your simple report could start a snowball effect where a vessel is forced to replace a pilot ladder or amend an operational routine, which, in a sliding-doors moment, saves a colleague from a major accident. Where the snowball grows larger when it opens a change in domestic guidance that improves the safety of UK ships, and then even larger when it’s followed by a major change to international regulation at IMO level that ultimately reduces the risk to all involved with pilot transfer arrangements.
So, when the data does get recorded, it does get used. The only time an issue or incident won’t count towards enforcement or aiding future legislation, and ultimately safety, is when it is not reported in the first instance. When you think of it like that, I’d say those five minutes are worth it.
By John Slater / Chairman of UKMPA Technical & Training
The image of a pilot climbing a rope ladder alongside a ship remains emblematic of the maritime industry. It embodies resilience, precision and the quiet courage required to navigate this essential yet potentially perilous task. However, as ships grow larger and pilotage operations continue seamlessly, the inherent hazards of pilot transfers often fade into the background.
Despite low incident rates relative to the sheer number of transfers completed, the consequences of accidents during these operations are on occasions fatal. Alarmingly, statistics reveal that, on average, a pilot loses their life every six months worldwide during transfers. While some degree of risk is intrinsic to the process, we must take every possible measure to reduce it to as low as reasonably practicable.
A case study: The Van Star Incident
In April 2021, a French pilot sustained severe injuries after falling four metres from the combination ladder of the bulk carrier Van Star while navigating the River Seine. The pilot’s fall onto the pilot boat deck resulted in multiple fractures and months of recovery. Upon investigation, the French Marine Accident Investigation Bureau (BEA MER) identified numerous non-compliances in the transfer arrangements:
• The ladder exhibited a poorly repaired step with missing chocks
• The accommodation ladder overlapped a side rope
• The setup lacked an inboard stanchion and was not secured to the hull
Alarmingly, two other pilots had accepted these substandard conditions on this passage before the incident occurred.
BEA MER’s findings also highlighted a broader systemic issue:
• A poor reporting culture regarding non-compliant transfer arrangements
• A lack of specific training for pilots on transfer safety
• Inconsistent approaches to pilot boat manoeuvres across varying transfer heights
Learning from accidents: a call for proactive measures
In response, the French Pilots’ Association (FFPM) produced 20 Years of Accidentology, a compelling film underscoring the dangers of falling onto solid surfaces. The research revealed that:
• A three-metre fall can cause severe injuries
• A five-metre fall often results in permanent disability
• An eight-metre fall can lead to fatality
Over the study period, 20 falls onto solid decks caused serious injuries, while ten falls into water led to significantly less severe outcomes, demonstrating the importance of appropriate personal protective equipment (PPE) and adequate transfer safety measures.
Parallels and challenges in the UK
In the UK, the UKMPA already offers a reporting structure through its app. However, participation remains limited to a small core of pilots, despite the critical safety implications.
The facts speak for themselves: climbing only safe and compliant ladders should be a non-negotiable standard.
The Boarding & Landing Code emphasises the importance of preparing for longer climbs by positioning pilot launches away from the ship’s side. In fostering a ‘climb zone’ mindset, collaborating with the coxswain to plan and mitigate risks in advance of the transfer will assist in formalising the process.
Reducing risks through regulatory and practical measures
‘Red Zone Transfers’ (those approaching nine metres) present the greatest severity. Recent reports indicate that ultra-large container vessels (ULCS) in ballast condition have presented ladders exceeding this height due to the trim.
‘Orange Zone Transfers’ remain extremely hazardous and with high severity that is often overlooked, given the reduced height transfer, but the risks associated with these arrangements can often be further mitigated by reducing climb heights even further whenever possible.
IMO Resolution A.1045(27) recommends a global standard: a minimum of five metres from the waterline for lower platforms in combination rigs. While some ports adhere to this guideline, local practices vary. For instance, some ports increase the combination rig transfer heights based on swell conditions, while calmer waters, such as some areas of Eastern Canada, often allow for lower transfer heights, reducing the climb exposure.
Exposure
During the recent NCSR 11 subcommittee session of the IMO Maritime Safety Committee, proposals from certain flag states to reduce the maximum permissible climb height from nine metres to five metres failed to achieve consensus. This outcome was probably influenced by concerns related to swell conditions coverage and the significant operational changes required to implement such a reduction. Nonetheless, the critical issue of fall height exposure remains a pressing concern. It is essential that shipping, harbour authorities and pilot bodies work collaboratively with the aim of reducing transfer heights to the minimum safely achievable wherever possible.
Ultimately, the responsibility for ensuring safe pilot transfers rests with all stakeholders. Pilots must assess risk exposure for each climb, reduce climb heights when safe rigging is possible and formalise transfer plans with their coxswains. The Maritime and Coastguard Agency strongly supports pilots who report non-compliant arrangements, reinforcing the need for accountability across the industry.
(FFPM) –20
code.
Safety in pilot transfers is not just a regulatory matter – it is a moral imperative. With continued vigilance, robust reporting and adherence to best practices, the industry can work towards a future where no pilot risks their life climbing a ladder that fails to meet safety standards.
Iwas asked the question recently, “What keeps you awake at night when it comes to pilotage?” My immediate answer was, “Pilots working when they are tired.” This article is a report of the presentation I made at the European Maritime Pilots’ Association General Meeting in Antwerp about pilot fatigue and the steps that can be taken by individual pilots, their associations and their employers to mitigate the risks of fatigue. As I see it, there are two challenges that need to be addressed. The first concerns how the human body is designed and the second concerns the changing business context. I propose that fatigue risk-management practices can help meet both those challenges.
By Dr Claire Pekcan
The maritime industry operates 24/7 and accordingly pilotage acts are conducted day and night. The problem for all those individuals working in ports, around the clock, is that the human body was not designed for 24/7 working.
Even though we are now well into the 21st century, the human body still functions as it did millennia ago . It follows a 24-hour cycle, known as the circadian rhythm (the blue line in the picture).
Our sleepiness and our alertness levels are governed by a complex cocktail of chemicals as well as by the time of day, how long we have been awake and how much we have slept. From the moment that we wake up, we are on a downward slope in terms of our alertness (the red line in the picture). At the same time, our risk of falling asleep increases and is at its greatest between the hours of midnight and 6 in the morning (the green dotted line).
Fortunately, a good sleep of 7 hours is usually sufficient to restore us back to full alertness. If, however, our sleep is disrupted or insufficient, we start to accrue a sleep debt.
Much like when we make a withdrawal from our bank accounts, our sleep debt will continue to grow, reducing our alertness and creating numerous cognitive problems, such as those in the table, until such time as we make a credit: we have at least 7 hours of uninterrupted sleep.
For industries that are not safety-critical, the consequences of working when tired are likely to be inefficiencies rather than catastrophes. In the maritime industry, as accident statistics bear witness, driving ships when sleep-deprived is a high-risk strategy. For example, a National Transportation Safety Board accident report on the collision between a tanker and a container ship revealed that the pilot had worked five nights in succession in the deep trough of his circadian rhythm. Both the pilot and the pilotage authority appeared unaware of the impact of the pilot’s lack of sleep on his performance. When we review the pilot’s work hours and the table of cognitive problems associated with sleep deprivation, it is easy to see that the pilot’s performance was going to be degraded.
How could fatigue riskmanagement help?
Unfortunately, the invidious nature of sleep deprivation means that the more tired we become, the less we can monitor our performance and catch our mistakes.
Fatigue riskmanagement practices are designed to mitigate the risk of performance
impairments associated with sleep deprivation. There are proactive measures and there are reactive measures that pilots and their organisations can instigate.
Proactive measures include assessing the risks associated with the roster and designing them so that night-time working is
The changing business context
The second challenge that a pilotage service must contend with is the changing business context. In short, the number of pilots entering the profession is reducing, leading to a depletion of experience and expertise. Simultaneously, ships are getting larger, reducing the margins for error.
The simple solution would be to recruit more pilots so that night working is reduced to a minimum. In tight recruitment markets and competitive commercial situations, this is impractical. Additionally, fatigue risk- management cannot change the operating environment.
What it can do, within the context of a supportive culture and the adoption of progressive people-management practices, is aid in the attraction and retention of highly skilled professionals, increase productivity and work quality, increase the health and wellbeing of the workforce and offer individuals a better work-life balance. However, to be effective, fatigue risk-management requires both pilots and their employers to take actions; both have responsibilities to reduce the likelihood of the performance decrements that are an inevitable part of sleep deprivation.
balanced by adequate recovery time. Another measure is to instigate fatigue self-assessment and reporting (see example from Energy Safety Canda below).
Reactive measures include, but are not limited to, monitoring and investigating the role fatigue plays in near misses and incidents.
Employers’ responsibilities
• Safe work practices
• Adequate resources to sustain a Fatigue Risk Management programme
• Work shift design that allows for adequate recovery periods
• Adequate assessment, control and monitoring of fatigue related hazards and risks
• Policies and procedures that support fatigue risk management, e.g., overtime, napping, commuting, etc.
• Building competency and disseminating information regarding fatigue risk management
• Stop work when the activities are unsafe due to fatigue
Employees’ responsibilities
• Arriving at work fit for duty
• Managing lifestyle to minimise fatigue
• Reporting all fatigue-related near misses and incidents
• Maintaining an awareness of fatigue supporting and participating in risk mitigation strategies
• Stopping work when the activities are unsafe due to fatigue
Cognitive problem
Decreased vigilance
Slowed reaction time
Impaired decision-making
Memory problems
Narrowed attention
Microsleep
Time on task decrement
Adoption of simpler but riskier strategies
Pilotage examples
• Incorrect reading of navigation equipment
• Failure to respond quickly enough to avoid adverse effects
• Inaccurate navigational actions / calculations
• Forgetting to check ship’s position at critical times
• Perseverance with inappropriate responses
• Delayed response to stimuli
• Increased errors in judgement as work period continues
• Over-reliance on radar and other automated equipment
1. Smolensky, M., & Lamberg, L. (2001). The body clock guide to better health: How to use your body's natural clock to fight illness and achieve maximum health. Macmillan.
2. Åkerstedt, T., Ingre, M., Kecklund, G., Folkard, S., & Axelsson, J. (2008). Accounting for Partial Sleep Deprivation and Cumulative Sleepiness in the Three-Process Model of Alertness Regulation. Chronobiology International, 25(2–3), 309–319. Available: https://doi.org /10.1080/ 07420520802110613
3. Australian Maritime Safety Authority (2020). The work practices of Marine Pilots: a review. Available: https://www.amsa.gov.au/sites/ default/ files/the-work-practices-of-marine-pilots.pdf
4. Collision of the Tankship Elka Apollon With the Containership MSC Nederland Houston Ship Channel, Upper Galveston Bay, Texas October 29, 2011. Accident Report NTSB/MAR-12/02 PB2012-916402. Available: https://www.ntsb.gov/investigations/ AccidentReports/Reports/MAR1202.pdf
5. Energy Safety Canada (2015) Individual fatigue likelihood assessment. Available: https://www.energysafetycanada.com/Energy SafetyCanada/media/ESC/Resources/ESC_ FatigueWalletCard-BleedCrops.pdf
By Tony Birr / Goodchild
The ORC range of pilot boats built by Goodchild Marine Services (GMS) is designed by French company Pantocarene and provides fuel-efficient running at service speed, combined with excellent seakeeping, allowing surprisingly high transit speeds even in rough weather.
The trademark beak bow is designed to increase the waterline and reduce slamming and vertical accelerations; this along with the remotely mounted wheelhouse to reduce noise and vibration results in less fatigue for pilots and vessel operators. Through over 30 years of design development, Pantocarene has been able to significantly reduce the drag of the
hull form while maintaining best-of-breed qualities. The drag reduction therefore improves fuel efficiency and reduces emissions. The ORC 171 hull is a refinement of over 30 years’ knowledge of designing beaked-bow vessels.
The design is like the many fast pilot boats designed by Pantocarene operated by other operators within Europe and Australia.
An advanced double chine hull with forward ‘BEAK’, which acts as a hydrodynamic shock absorber in head seas, was developed following an extensive tank testing development programme resulting in a hull design with good internal volume and roll damping.
The double chine hull combines several other advantages: finer entry in the forward sections (to dampen motions in heavy seas) and a more sea-friendly shape in the forward slamming area, with a chine shape at the aft end to give stability in following seas. This also provides fuel-efficient, economical operation at all speeds. The hull has excellent manoeuvrability and has been proven by the vessels in service, at slow speed for harbour operation, at service speeds for pilot boarding or rescue operations and at high transit speeds. This is due to the shape of the hull, together with careful balancing of the lateral water-plane area.
Its modular, resiliently mounted wheelhouse reduces noise and vibration levels in the personnel areas. This is assisted and kept as low as practicable using sound absorption materials on engine compartment boundaries, and purpose designed resilient mountings on main engines, remotely mounted gearboxes and couplings. The result is both lower engineroom and wheelhouse noise levels even at cruising speeds.
The ORC 171 vessels achieve a continuous service speed of at least 25 knots with the vessel fully fitted, with 100% fuel and water and nine persons, while the smaller vessels achieve slighter less cruising speed.
upright position. Deployment is instantly ready should an emergency occur. In addition, a stainless-steel transom ladder is fitted within a moulded recess. A self-contained hot and cold airconditioning plant is installed, providing cooling and heating to the wheelhouse.
A compressor driven from one engine power take-off with a seawater pump provides the ability to cool the cabin and keep the temperature constant. A diesel-powered heating system is combined with the selfcontained hot and cold air climate plant as the vessel is likely to spend some time operating alongside without the main engines running.
These ORC vessels are self-righting by design. To our knowledge, none of the 160-plus ORC vessels worldwide have ever capsized.
The wheelhouse is designed to ensure ease of use and very good 360° visibility during navigation, but above all for repeated coming alongside manoeuvres. A ‘Hadrian’ safety rail and pilot system is provided around the perimeter of the wheelhouse handrail. A man overboard recovery system is provided by means of a hydraulically operated stern recovery platform to ensure casualties are quickly and safely lifted from the water in a horizontal manner to minimise cardiac arrest, which is common with vertical lifts from cold water when in shock.
During normal operations the platform is stowed vertically, providing a means of protection from falling overboard and the ladder/propeller guard sits neatly within the platform assembly. Stowed position is locked automatically and does not require any mechanical means of securing in the
Both heating and cooling work in tandem offering climate control, drying the moist air within the wheelhouse.
To summarise, these vessels are built to be operationally effective and fuel-efficient, meeting the latest emission regulations, and provide a safe-as-possible working environment for crews and pilots. Finally, they offer increased comfort while inside the wheelhouse in terms of ride, noise and temperature quality. Since their introduction to the UK market in 2012, they number over 30, with many of the country’s ports both large and small operating an ORC pilot boat because of their proven suitability in UK waters.
By Dr Jim Price / BMT
Most people understand human behaviour in the same way as they do gravity; they know it’s there and see the effects of it every day. But ask people to explain gravity and how it works and not many can tell you. By gaining a better understanding of behaviour, we can improve our responses when things get tricky. First, let’s clarify some definitions to ensure we are talking about the same thing.
A crisis is defined as a time of intense difficulty or danger, when a difficult or important decision must be made. Under normal conditions, we can make sound, predictable decisions and choices. Most people spend most of their day on autopilot and behave habitually, performing actions they have repeated over time and received a favourable outcome. During a crisis, autopilot is suddenly and unexpectedly switched off; subsequently not only are we faced with danger but, if we are unprepared, we simply don’t have habitual behaviour to rely upon to provide a favourable outcome.
Behaviour is an act or action. It is something physical we can see or hear happening, for example a smile. We can’t see happiness or a positive attitude because someone can have these things going on inside their head. If they are smiling, we have a tangible behaviour to witness. It’s worth noting that, if somebody is faking a behaviour, how would we know? It’s best to stick to the facts, for example, when I ask my wife “how are you?” and she replies, “I’m fine”, but in that tone of voice (you know the one), then I take it that she’s fine – because I’m not a mind reader. And I spend a lot of time sleeping on the couch.
Consequences are how we influence our environment through our behaviour. For example, when we hit a key on the keyboard, we are rewarded with the character we wanted appearing on the screen. When we eat tasty food, we are rewarded with tasty flavour and our hunger is satisfied. Of course, there are also negative consequences that can come from our behaviour. For example, we deliver the punchline of a joke, and nobody laughs. We drink too much beer and feel awful the next day. The important things to remember about consequences are that every behaviour delivers the person doing it with a consequence and consequences are felt individually – behaviour might have an impact on others, but only the individual experiences the consequences.
If you are starting to think of Pavlov’s Dog, then you are on the right track. If you have no idea what Pavlovian Theory is, don’t worry, it’s not vital to understand this article. Just know that it proves behaviour is not as unpredictable as it seems, and even humans can be trained to respond to certain stimuli. Dogs train their humans by standing at the back door and looking like they are about to poo. The well-trained human opens the door and lets the dog out.
Now that we know there is a science to the way we behave, let’s look at what the research says about the human response in a crisis. In November 2016, Jerzell Black from the Centre for Disease Control published an article in which he explained the three-stage predictable response humans have in a crisis.
• Denial
• Deliberation
• Decisive Action
Denial is the first stage, where we try to avoid acknowledgement of the danger. The first thing to understand is that this is perfectly normal. We will often look for what is called social proof – how are the people around us responding? We will try to avoid the consequences of looking silly by overreacting. The research also shows that we are less likely to take responsibility when other people are present. Diffusion of responsibility is when we assume that others are owning the situation.
always comes second, even if we don’t recognise that we’ve been through denial. Once the crisis has been recognised and accepted, we begin to consider our options. The more information we have gathered about our environment, the more options will be available to us. Have you considered, for example, how you would leave the room you are in if it went dark or suddenly filled with smoke? How far is it to the nearest exit? What obstacles are in your way? What alternative exit could you use?
Decisive action – now it’s time to go! You’ve acknowledged there’s a crisis. You’ve considered your options. The next step is to act. Call for help or take cover, whatever it is you decided to do. In most situations, there is no definite right or wrong. There is no perfect plan, only the best we can do under the circumstances. In most situations, an imperfect action is better than no action at all. Whatever you do will be judged by others later – usually by someone who wasn’t faced with the exact same situation. Push that future judgement to the back of your mind.
Survive first, worry about being alive to be judged later. How quickly you move through the stages depends on a wide variety of factors, but prior experience of the situation will help immensely. When faced with a building fire, for example, a trained and experienced firefighter will reach Decisive Action much faster than the rest of us. The right training environment can provide this experience.
Practice make permanent not perfect. As marine pilots, how can you prepare yourselves to cope with a crisis? There are some general tips that anyone can do to ensure they cope better:
Stay fit – having confidence in your physical ability to deal with just about anything will remove doubt at the time when you need your body to cope with stress.
Manage fatigue – make sure you are at your most alert at times when a crisis is most likely to arise.
Mentally prepare – pay attention to your surroundings. Become familiar with alternative modes of operating or escaping and the capabilities and limitations of the people around you. Behavioural scripting – if you’ve ever wondered ‘what would happen if…’ during normal operations, explore that situation and, if possible, try it out. Training simulators are a great place to explore your ability to cope with denial, analyse your options and see if your actions would deliver the success you hope for. It’s an opportunity for you to gain that all-important experience in a safe place, then practise it over and over and over. This will dilute the shock of a crisis and make your instant behaviour closer to an autopilot response.
In conclusion, don’t get caught out. Even when facing a crisis you haven’t rehearsed for, the preparation you will have put into dealing with possible situations will stand you in good stead when the unexpected happens. Pilots work in a high-stress environment where a moment of crisis is always a possibility; it’s why you’re there. Make sure you are the one keeping your head when all around you are losing theirs.
By Malcolm Watts / Manchester Pilots
Agathering of pilots, (not clans!) took to the field at Penrhos Golf Club for the 49th. Marine Pilots Golf Societies golf match. Three games were played over the three days in changeable weather conditions. There were pilots from the Forth, the Humber, Liverpool, Manchester and Milford Haven, with handicaps ranging from the low teens to the high twenties. There are trophies to be played for but it is a social gathering more than serious golf. Names on the trophies show that pilots have come from other ports.
In the past they have come from Fowey, Southampton, Kings Lynn, the Clyde, the Tyne and other ports.
We have two events each year, two days in May and three days in September and always we meet at a golf course with hotel accommodation so that we can park the car on arrival and leave it until it is time to head home. The venues we meet at are courses in Scotland followed by the east coast area the next year and then farther south and towards Wales for the third year, although this is not ‘cast in stone.’ In the past we have played at The Belfry, St. Andrews, Breadsall Priory, Ullesthorpe Manor, St. Mary’s and the Forest of Dean, to name a few.
The May games are played at Shawhill Golf Course, which is near to Preston.
The pictures show the 17th hole at Penrhos with Steve Watson, Joe and Jim Fortnum putting out (I put my ball in the water!) and some of the pilots waiting to tee off on the first tee.
We would really welcome any UK pilot to join us. I am sure that we would welcome colleagues from Ireland or the near continent as well.
Contact Chris Harding, whose e-mail address is pilots06@btinternet.com
By Hywel Pugh / (past) UKMPA Chairman
Captain Nick Lee, Merchant Navy Medal for Meritorious Service. Presented by Princess Anne, Her Royal Highness The Princess Royal, at Trinity House London, 5 November 2024.
The citation reads: Captain Nicholas Lee for services to safety, training and education.
Captain Nicholas Lee is 64 years old and went to sea in 1977. For the past 26 years Nicholas served as a Port of London
Authority Pilot, specialising in handling vessels of up to 400m in length. As an active member of the United Kingdom Maritime Pilots’ Association (UKMPA), he chaired the Technical and Training committee for over 13 years. His focus was pilot safety, training and professional development.
During his tenure Nicholas was responsible for the conception and development of the highly acclaimed UKMPA immediate emergency care
course, the UKMPA pilot ladder reporting app and the updating of the United Kingdom pilot boarding and landing code. Additionally, Nicholas worked with Port Skills, developing the original Marine pilot apprenticeship scheme.
Having recently retired, Nicholas is spending a more leisurely time with his wife Carole, navigating and exploring the UK canal system on their narrow boat Lotse.
It has been another busy year on the Clyde and if I had to choose three words to sum up our year, they would be projects, bridges and barges.
Over this past year, many plans for the future development and expansion of the port came to fruition. The pilots were consulted on many of these waterborne plans and were integral to their successful outcomes. One of the most visible projects that we were part of was the delivery and installation of our two new Leibherr container cranes (officially named Craner Swift and UCrane Bolt) at Greenock Ocean Terminal. The successful arrival and offload of these new cranes has dramatically altered the skyline of Greenock (for the better) and will increase the size of container ship that we can receive at our deepwater container berth.
Within this past year we have towed two new bridges up-river to span the Clyde. One of these is a new footbridge linking Govan and Partick and one a road bridge linking Renfrew and Clydebank. The planning, safe arrival and transit of these new bridges was only achieved by the good working relationships held between the pilots, tug masters and marine managers within the port. The work for us didn’t stop there though. As the road bridge is located 1.5 miles downstream from our main berth in Glasgow, we have had to develop and risk assess stringent opening and closing procedures for the bridge to allow shipping to safely pass to and from our berths in Glasgow.
With all of the bridge moves plus a few more non-standard tow’s, many of us were exposed to the elements on barges throughout the year. One of the most anticipated and technically difficult jobs that we undertook was the tow of the CD01 barge with the new Type 26 frigate
(HMS Cardiff) loaded on deck. Once again the success of these non-standard moves was down to the good working relationships (barge team management) between the pilots, tug masters, tow masters and barge team (Forth Logistics).
We have continued to use and develop the EMPX program on the Clyde. We have found the program very useful, easy to use and customisable to suit our specific needs. The feedback that we get from ships’ Masters on EMPX is usually very good.
And finally, this year we have welcomed a new head of Marine Department to the Clyde. Our new marine manager is a former Clyde pilot so understands a lot of the marine issues from a pilot’s point of view. We all look forward to continuing working with her in the future.
Ross MacAulay, Pilot, Peel Ports, Clydeport
The year 2024 has seen an increase in acts of pilotage over 2023 numbers, including over 140 acts in support of the Dover Western Docks infill project. This has seen the Granville dock and tidal basin reclaimed for future landbased uses including space allocated for the European Entry/Exit System infrastructure. We’ve maintained a diverse selection of customer vessels with our usual cruise, reefer cargo, bulk cargo, bunker tankers, heavy lift, aggregate vessels and a few windfarm support vessels joining the mix.
We now have six Class 1 Pilots, five of whom cover a 24/7 shift pattern and the role of Duty Harbour Master, and one office-based as Deputy Harbour Master. There are also over 70 PEC holders whom we authorise and regularly assess.
During 2024 we have collaborated with various external partners. These include Carnival Cruises, with whom we carried out joint simulator studies at “Csmart” for large cruise vessels using Dover, plus more recently a collaboration with the Viking Maritime Skills Academy in Dover. This was for theoretical and practical pilot ladder training using their training pool facility and custom-built pilot ladder set-up. Summer 2024 saw the arrival of our new pilot vessel, the DHB Diligent, which brings our total to three and gives us some much-needed resilience. Winter 2024/25 sees our cruise terminals closed for some muchappreciated upgrades to our mooring infrastructure;
Again another steady year with a total of approximately 3,000 acts by six pilots. We are still strong in the Oil & Gas Offshore sector as well as renewables. Overall, business is steady with slight ups and downs in various commodities. Being connected to a largely agricultural region on an industrial scale, we see a good number of vessels engaged in fertiliser and grain trades.
we are replacing the existing, in some cases antique, bollards with much stronger and better-placed quickrelease hooks. Domestically, the pilots have continued with their various hobbies (see last year for details), kept their number of offspring at a static level, and professionally five out of six of us have got used to the slight look of disappointment on ship’s Masters faces when the realise they’re not getting the lady pilot for this job.
Best wishes for 2025 from all at Dover / Guy, Chris, Tom S, Fran, Tom H and Kirk.
The new Great Yarmouth third River Crossing (GY3RC) was officially named as ‘Herring Bridge’ in homage to the port’s past history with the herring fleets. This opened in March and has been very beneficial to the port and town.
It’s been a good year for aggregates. In December, the port welcomed its largest ever visitor (Yeoman Bridge), which discharged 55,000 tonnes of crushed aggregate destined for various projects throughout East Anglia, including the new nuclear power station (Sizewell-C) on the Suffolk coast. This helped the port to a new record year for one single commodity handled through our outer harbour, as it passed the 1,000,000 -tonne mark.
We’ve seen quite a few cruise liner visits this year including the Seabourn Ovation, with many American veterans and families doing site visits as part of the 80th D-Day anniversary celebrations.
There is also an offshore wind service base currently being constructed, due to open late 2026. Along with the new bridge, it is hoped to continue positive growth of the area.
We are looking forward to the use of an in-house vessel simulator combined with a re-location of pilot station to the main harbour building in the near future. All six pilots have been issued with and trained with PPUs.
Best Wishes / Great Yarmouth Pilots
Another year of growth for the Liverpool Pilots. Trade within the port is steadily bouncing back following a marked downturn in trade during 2023. Within this return to growth, there is a steady upturn in larger vessels utilising the port. The addition of MSC’s Brittania service has brought us into the world of ULCS pilotage following years of detailed preparation. In addition, other new container services from Samskip and Boluda alongside various new RoRo operations have brought yet more business for our members. Our most recent intake of trainees (2021/22) are now mostly Class 2 authorised, which has bolstered our ability to handle this increased tonnage.
The acquisition of the Liverpool City Cruise Terminal by Global Ports Holdings took place over the summer and promises to stimulate yet further growth. As a part of a busy summer programme, the terminal hosted the naming ceremony of Cunard’s Queen Anne at the heart of Cunard’s historic home port. Liverpool Pilots were at the forefront of planning and executing this spectacular event on the river following months of intensive simulator work and liaison with key stakeholders.
Our in-house simulation facilities have played an increasingly prominent role in our consultation work with the CHA and other parties wishing to utilise our expertise and facilities as part of preparation for new services, berthing trials and event planning. This year has seen a cohort of Kuwaiti Pilots travel to use our facilities as part of a bespoke training package delivered by our members. To further enhance this work, we have fully upgraded our two simulation suites following a major investment. Away from the river, we waved goodbye to two of our colleagues this year at our annual ‘Hot Pot’ in the Royal Liver Building. We are now looking to the future with plans to recruit to maintain our current manning level, which stands at a healthy 52. Our now informal ‘Retired Pilots Section’ continues to meet and has again hosted a successful annual Ladies Luncheon while serving pilots have yet again represented the service at Liverpool’s annual Merchant Navy Day commemorations. In summary, it has been a successful year for us here at Liverpool Pilots, which has seen us promote the importance and value of Maritime Pilots both within the Port of Liverpool and further afield.
Sam McDougall, secretary / Liverpool Pilots
The Peterhead Port Authority’s pilotage service is a critical element of our operations, ensuring safe and efficient navigation for vessels entering and leaving the port. Our pilot team consists of four unrestricted pilots, one of whom serves on a part-time basis, and two Class 2 pilots. This experienced team handles a range of maritime traffic, contributing to smooth operations for a diverse range of stakeholders.
The Port Authority currently has 32 pilot exemption certificates in force, all issued to either platform supply or pelagic vessels. The port’s current trade comes from approximately 55% fishing sector and 45% merchant. This means the pilots manage a diverse range of movements ranging from general cargo, pelagic and construction vessels, all the way to the larger of the vessels going into the North part of the harbour. Pilot transfers are conducted primarily using our dedicated pilot cutter, the Blue Toon. Blue Toon’s keel was laid in February 1993 and it was built by Buckie Shipyard. It has a heavy steel hull and handles well in the unforgiving North sea. It is well looked after by our team of boatmasters, many of whom were recruited from the fishing sector. We also run a small workboat/tug, Ugie Runner, which is certified as a pilot cutter, strengthening our operational resilience.
Looking ahead, we are working closely with the Acorn project team, which we hope to see bring in a regular trade of liquid CO2 carriers. It is an exciting time for the port, as the port authority has not handled tankers of this size since the closure of the last oil-fired power station in September 2006. The proposed Petermax tanker would be up to 220m in length and would carry liquefied C02. Although smaller and more manoeuvrable than the largest vessel to enter port, the Aframax tanker Kitty Knutsen in 2011, the pilots are looking forward to this new challenge.
Overall, Peterhead Port Authority's pilotage service plays an essential role in ensuring navigational safety and operational efficiency for the varied and evolving traffic demands within
the port. The essential role is supported by a professional team of experienced mariners who are excited to see what the future holds.
It’s been another record year for passenger vessels in 2024 with close to 500 vessel calls, with 58% over 300m in length, showing the growing trend in larger vessels. The overall number of acts shows a steady trade in all sectors.
Dredging work took place again in the early part of 2024 to widen the channel off the western docks, which, combined with simulator work and risk assessment, allowed the largest ULCVs to service all parts of the container port. Capital dredging is expected to start again late in the year to expand access to the Solent Gateway site on the Marchwood side of the port in anticipation of an expansion of trade using the site.
Recruitment and initial training of two pilots in the early part of the year, followed by a further recruitment later with one retirement, takes the total number of pilots to 40.0 FTE.
Best wishes / Southampton Pilots
In South Wales we are currently 16 active pilots and one apprentice pilot. UKMPA members total 12 and UNITE members 15. Pilots now hold authorisations across the various ports in South Wales.
Once again we are seeing big changes, with Port Talbot harbour seeing the last Tata vessel in September. The Tidal Harbour is now destined for big changes, with the FLOW (Floating Offshore Wind) project really gaining momentum.
With steel production ending in Port Talbot, both Cardiff and Newport have seen an increase of imports of steel slab and coil. This is set to continue until the new electric arc furnace is built. Both ports have also seen an increase in scrap trade, with four berths now available for scrap export.
Swansea is likely to see an increase in export of the surplus cargo remaining in Port Talbot. Otherwise it remains quiet, with paper and fertiliser import being the main trades.
Barry still has import and export of chemicals for Dow Corning but remains quiet.
The new joint Pilot/RNLI building was officially opened this year and the new pilot boat for SE Wales, the Terra Nova, is now fully operational. Pilot boat cover for SW Wales is via an ex-Humber Pilot Vessel, the Humber Saturn.
With a new Harbour Master in place, things have settled in South Wales, and we are awaiting the appointment of a new pilotage manager in the near future. The pilotage service looks in a very good place, with a young and enthusiastic workforce.
We wish you all well from South Wales. Stay safe out there.
It’s been an eventful year so far at Tees Bay Pilots, filled with steady trade, evolving experiences and fresh developments.
Our team of pilots has seen notable growth with four pilots achieving the rank of senior first class in 2024. As we look ahead to the early retirements of two seasoned members next year, we’re preparing to recruit in the upcoming winter to keep our operations strong and well-manned.
A major highlight of this year’s continued professional development (CPD) was a simulator training day at South Tyneside College, which focused on managing Capesize bulk carrier entries. These large carriers, which were a familiar sight
Trade on the River Thames in 2024 has remained at a similar level to 2023. There has been a slight decline in river traffic but an increase in the ultra-large vessels, both containers and tankers.
Recruitment and training continue at pace: in 2023/2024, 12 trainee pilots achieved their first pilotage qualification and 14 trainee pilot positions have been advertised for 2025. Retirements and leavers now leave us with 102 full-time sea pilots, which is three more than the same time last year.
Marin completed a software upgrade to the simulator based in Gravesend. Further investment has been planned in 2025/2026 when it is hoped a new full bridge and tug simulator will be installed.
DP World has almost completed work on Berth 4 at London Gateway; currently 250 metres are available with full berth capacity expected in the first quarter of 2025. Simulations are already planned for Berths 5 and 6 in January 2025.
London VTS will shortly be moving to a new home, not far though: the building next door to their current location. The reason for the move is that their current home will be refurbished and new state-of-the-art VTS equipment will be installed.
during the peak operations of the Redcar steelworks, are less common now. The training day offered a fantastic opportunity for experienced pilots to pass down valuable insights to our younger members, bridging the knowledge gap for those who hadn’t previously encountered these vessels.
We’re pleased to share that James Musgrove has joined Peter Lightfoot representing us on the UKMPA section committee. Our support for their involvement ensures our voice is heard on key matters affecting the industry.
A unique operational challenge came early in the summer with the arrival of the Allseas’ Pioneering Spirit, here to deliver the massive Brent Charlie platform for recycling, using the Iron Lady barge. The team met the demands of this complex operation with skill and preparedness.
This year, we also saw the completion of the new Steel River Quay at South Bank, a development that harkens back to our region’s rich industrial past. The quay is now operational and has already received its first vessels, marking a new chapter for the area.
Meanwhile, we’re adapting to shifts in traditional cargo traffic along the river. Emerging trade related to the Dogger Bank wind farm has brought in ‘walk-to-work’ vessels, installation ships and component delivery vessels, frequently docking around the Tees and Hartlepool. This shift represents an exciting diversification of our usual trade activities as we continue to handle our staple shipments of crude oil, various bulk cargoes and feeder container trade.
As we close a strong year, we remain energised for the challenges and opportunities that 2025 is sure to bring. We’re proud of the dedication our team brings to every assignment and look forward to serving the dynamic needs of Tees and Hartlepool with the same commitment in the year ahead.
Best regards / from the Tees Bay Pilots
And finally, we are very proud of our fellow pilot and former college Capt Nick Lee, who, on Tuesday 5 November, became the first PLA pilot to receive the Merchant Navy Medal for meritorious service, presented by HRH The Princess Royal at Trinity House: a truly well-deserved honour for all his hard work on pilot safety over the years.
Kind regards / Nick Brown Chairman, LPC
In 2024, our contingent of 24 authorised pilots across various classifications experienced a steady flow of trade, which returned to a more typical pace. Recruitment efforts compared with the past four to five years have slowed, with future appointments expected to be made in response to part-time working arrangements and retirements.
The port has welcomed a new freight service from Finland and an additional cement works, both contributing to an increase in visiting vessels. The primary sources of trade continue to include cars, LNG, aviation fuel, containers, paper, aggregate, cement, steel, timber, bananas and the occasional project cargo. A notable highlight of the year was the assignment to tow a 1,000m floating pipeline from the Medway, where it had been constructed, to its new location in the Thames Estuary.
Following a successful trial, all pilots have now been equipped with a Portable Pilot Unit, with plans to implement an EMPX system in the future. The Medway Channel has recently undergone a successful dredging campaign aimed at enhancing the operational window for deep-draught tankers and bulk carriers.
This year has been very much ‘steady as she goes’ for the Forth, with trade much the same as 2023. Crude oil exports from Hound Point Terminal have remained steady, with VLCC traffic heading for the Far East being the main feature.
Cruise ship traffic in the summer hit record levels and is likely to remain the main feature of summer 2025.
Traffic related to renewable energy continues to increase, with the first ships calling at the new renewables hub at Leith Outer berth. The berth is also being used for cruise ship traffic, which allows larger cruise vessels to tie up alongside rather than anchor in the river.
Ineos has announced that the Grangemouth Oil Refinery will close in early 2025. It is expected that there will be little change in shipping numbers, as oil products will have to be imported. However, it will result in 450 direct job losses and be a severe blow to the local economy. Scotland is the second largest oil producer in Europe but will have no oil refinery.
The Forth Green Freeport project has been announced, which it is hoped will bring increased investment to the Forth area. Green freeports are areas of operational and development land linked to a port where normal tax and customs rules are varied to promote growth and trade.
Looking ahead to 2025, the year promises significant developments.
The port is investing £30 million in a new ro-ro berth at Sheerness, the reopening of Chatham Number Three Basin and an increase in storage capacity at Grain LNG contracted to Qatar Gas.
Jon Smith / Medway Pilots
Ineos continues to import fracked gas from the US for the production of chemicals and plastics.
Container and dry bulk traffic remain steady, with Grangemouth continuing to handle more containers than any other Scottish port.
The Dali incident in Baltimore has resulted in a review of bridge transit operations, with the speed limit for vessels transiting the Forth Bridges reduced to 8 knots and active escort towage compulsory for vessels in excess of 180 metres.
On the naval front, the aircraft carrier Queen Elizabeth unexpectedly visited Rosyth for repairs and is due back for a scheduled docking in mid-2025. Assembly of Type 31 frigates is well underway with the first hulls floating in 2025.
Pilot numbers are steady at 24. Five are still working their way to unlimited authorisations and two pilots are now part-time. We find the part-time option to be a great benefit to pilots looking to wind things down a bit before full retirement, while retaining them helps the service as new pilots work towards full authorisation.
Bob Keir continues to represent the Scottish Region on the UKMPA executive, Neil Walker is alternate trustee of the PNPF and Tim Wingate is on the International Standard for Pilot Organisations (ISPO) board. All are supported by Forth Pilots.
Best wishes / Forth Pilots