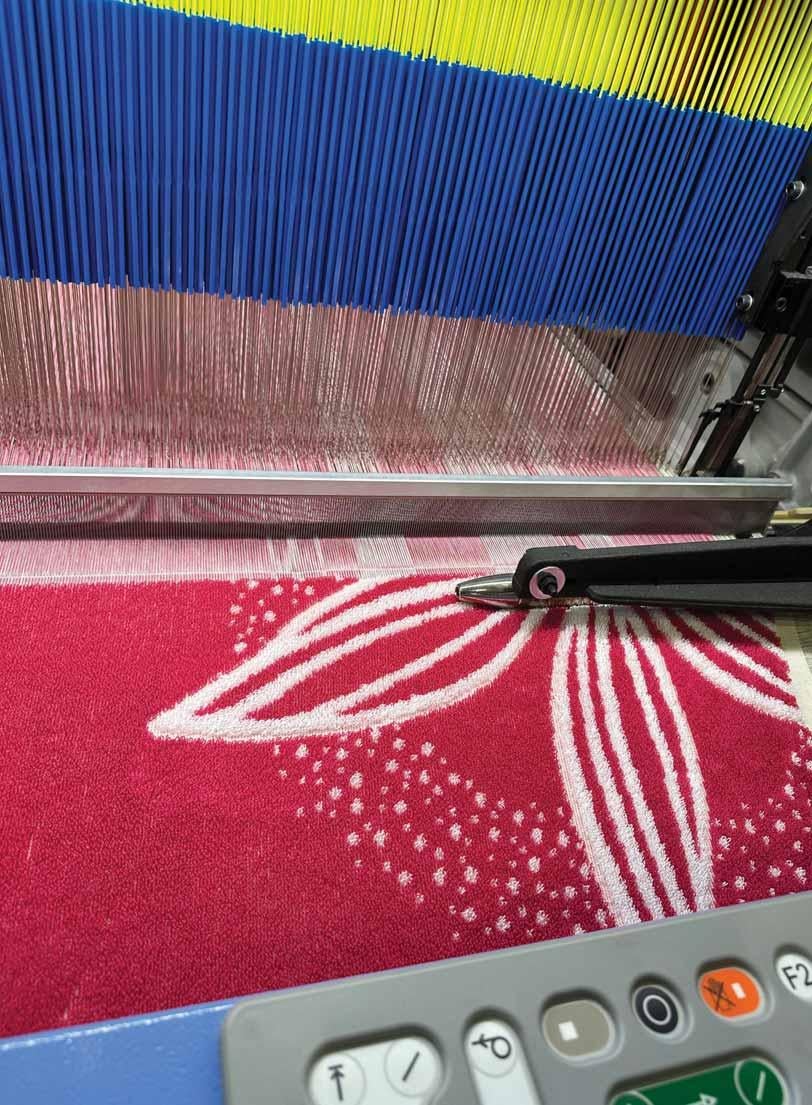





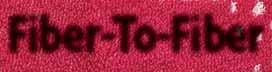


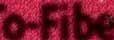



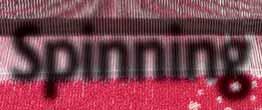
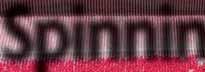

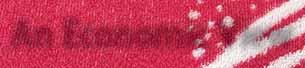


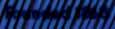
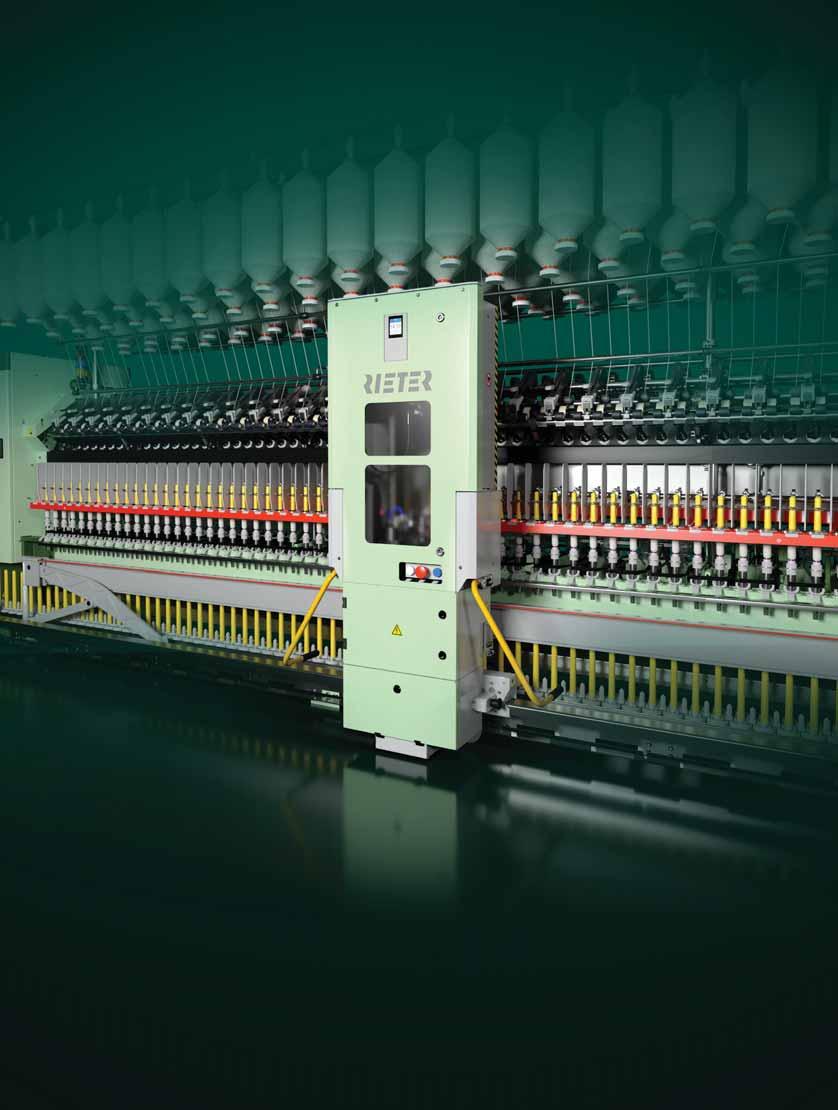
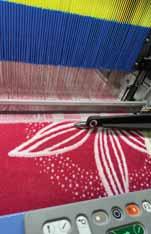
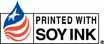
IInnovative textile machinery has been re-crated and shipped on,booths have been carefully disassembled,and exhibitors and attendees have returned home to process the events of a successful ITMA 2023.
The European Committee of Textile Machinery Manufacturers (CEMATEX) hosted 1,709 exhibitors from 47 countries in a net exhibition space of 118,300 square meters while some 111,000 visitors from 143 countries made their way through the halls.All now attempt to absorb what they witnessed at the “world’s showcase for textile machinery.”
By most accounts,ITMA 2023 was lauded a great success by exhibitors and attendees alike.Now digesting the many new innovations becomes the focus of the work at hand. “How will these new technologies impact my manufacturing capabilities?”“What investments could be real game-changers?” and “How does my company evaluate the impact and opportunity of new technologies and their underlying trends?”are just some of the questions that will be considered.
Post-ITMA analysis is never an easy task, but this ITMA has thrown some real gasoline on the technology fire as the industry faces so many challenges of improving efficiencies, going greener,and maybe rethinking entire business models.
Textile World editors get to help with this matter at hand,lending a hand in exploring the many developments offered by this year’s ITMA exhibitors.
The coverage won’t be perfect,but over the next several issues, TW editors will explore sector-by-sector the latest advances in textile technology and the opportunities they present to the industry.
In addition to the regular TW staff,various professors and researchers from North Carolina
State University’s Wilson College of Textiles have offered their expertise in providing TW ’s readers insights and analysis into observations of technology presented at ITMA 2023. TW is grateful for their many insightful contributions and their continuing work at the University.
That said,the one major take-away is the sheer volume of new ideas and technology presented at ITMA — some incremental, some very new — all have a place in the changing business environment U.S.textile manufacturing faces.
And the opportunity for investment comes at a great time.Or does it? Well,timing is in the eye of the beholder,but there is an appetite for new investment and investment that helps tell a company’s story.That story may be a reshoring investment,a green technology investment or even a startup.But of late,most of the investment news has been about expansion and refitting — both ripe for having a look at a new,possibly more efficient ways of producing textiles.
Collaboration is key.Many of the contacts made at ITMA will lead to trial work,product development and new process testing,as well as proof-of-concept projects.
ITMA is never a one-and-done story,— more like a spike in the process,a catalyst for moving forward and looking for new opportunities that capitalize on existing core competencies that need to be renewed and refreshed.It is a shot in the arm that can help stimulate and show businesses a new way or maybe a better way to achieve a textile manufacturing success story.
James M. Borneman jborneman@TextileWorld.comEDITOR IN CHIEF
James M. Borneman
EXECUTIVE EDITOR
Rachael S. Davis
TECHNICAL EDITORS
Dr. Lisa Parillo Chapman
Dr. Peter J. Hauser
Dr. Trevor J. Little
Dr. William Oxenham
Dr. Behnam Pourdeyhimi
Dr. Abdel-Fattah Seyam
Dr. Andre West
CONTRIBUTING EDITORS
Jim Kaufmann
Stephen M. Warner
INTERNET CONTENT EDITOR
Rachael S. Davis
CIRCULATION MANAGER
Julie K. Brown-Davis
ADVERTISING BUSINESS MANAGER
Denise Buchalter
ART & PRODUCTION MANAGER
Julie K. Brown-Davis
OWNER/PUBLISHER
James M. Borneman
ADVERTISING REPRESENTATIVES
UNITED STATES & CANADA Turner Marketing &Media, LLC +864-594-0921 sturner@textileworld.com
EUROPE (except ITALY)
Sabine Dussey +49-171-5473990 sabine.dussey@dussey.de
ITALY
Ferruccio & Filippo Silvera
+39-022-846716 • Fax +39-022-8938496 info@silvera.it
ASIA
James M. Borneman +678-483-6102 jborneman@textileworld.com
MEXICO, CENTRAL & SOUTH AMERICA
Virgilio L. González +58-412-622-2648 • Fax +58-212-985-7921 vlgonzalezp@gmail.com
INTERNET & CLASSIFIEDS
Julie Davis +678-522-0404 jdavis@textileworld.com
Non-contact precision spray technology and plasma treatment for sustainable finish applications.
Providing a wide range of jet, jigger, beam dyeing machines and infrared laboratory dyeing equipment.
Finishing and coating lines for woven and knit fabrics, technical textiles and nonwovens.
Detwisting, opening and web guiding for all fabric constructions.
Scouring and bleaching ranges for wovens and tubular/open width knits. Cold pad batch and vacuum extraction.
Textile calenders for softening, lustre change, embossing and recalipering of textile substrates.
Water treatment and water recovery plants in textile facilities.
Fabric surface finishing equipment: napping, sueding and shearing.
Circular knitting machines for apparel, mattress, home furnishings and footwear markets.
Turbotex Scrim Fabric machine.
In-line vision systems for weaving and warp knitting machines, tenter frames, compactors, coating/laminating ranges.
Automatic dispensing of powder dyestuffs and liquid chemicals for laboratory, and bulk textile production.
Automated inspection and packaging systems for rolled goods.
For additional information on these companies contact Ian Mills at imills@fi-tech.com.
PO Box 683155 | Marietta, GA 30068, USA
Telephone +678-483-6102 | www.TextileWorld.com
The Italy-based Lonati family-owned and founded Santoni Shanghai Knitting Machinery Co.,China, has announced plans to acquire Terrot GmbH,a Germany-based producer of circular knitting machines.The transaction is pending approval from Chinese regulatory authorities.The acquisition is part of Santoni Shanghai’s long-term vision to create an ecosystem that reshapes and consolidates the circular knitting industry.
“The integration of Terrot,which also includes the well-known Pilotelli brand, will bring an immediate and extraordinary boost to our products portfolio,”said Gianpietro Belotti,CEO of Santoni Shanghai.“Terrot’s incredible technical capabilities,extensive product range and vast experience in serving customers all over the world will enable us to better achieve our shared aspirations.We are very excited about this partnership and look forward to working with Terrot as we move towards establishing a pioneering industry ecosystem,realizing our mission to providing customers with an utterly new knitting experience.
“We see our machines not simply as isolated units of production,but rather as parts of a holistic and integrated ecosystem,” Belotti added.“Each part of this ecosystem is interconnected with the entire
industry chain,bolstered by our recent advances in digitalization and our century long expertise.The new synthesis will offer now the largest range of technical solutions available in the market,which we believe will enable us to satisfy the needs of all the investment levels.Through our partnership with Terrot, we are one step closer to fulling our vision of innovatively consolidating the entire industry.”
Shortly after announcing Nufabrx® joined forces with Enventys Partners to establish HealthWear® a patented smart-technology platform aimed at delivering medicine,health and wellness to consumers via clothing — it was publicized that Charlotte, N.C.-based Tallayne has agreed to purchase the Nufabrx brand and its retail unit from the parent company Textile-Based Delivery Inc.Nufabrx/ Textile-Based Delivery was founded by Jordan Schindler who conceived of the idea to use textiles as a delivery mechanism while he was a student at the University of Washington.The Nufabrx brand offers compression braces infused with pain relief ingredients that continue to dose medication into the body over time and are reusable.The move will accelerate expansion of the brand and increase product
The United States Agency For International Development (USAID) recently awarded North Carolina State University’s (NC State’s) Wilson College ofTextiles a $2 million, two-year grant to fund development of a technical textile training program. The program,named Hilando Oportunidades — spinning opportunities — aims to develop skilled workers for the textile industry while transforming the lives of young people in northern Honduras. The goal is to train at least 1,500 Hondurans in yarn spinning,knitting,dyeing and finishing,and apparel production.The grant brings together the Wilson College,Gaston College and Catawba Valley Community College with the Universidad Technológica Centroamericana (UNITEC) in Honduras.
The program will employ the technology of Shimmy,an industrial startup company that offers app-based training.
Melissa Sharp,associate director of the Zeis Textiles Extension (ZTE) at the Wilson College will lead the project.She notes that the program comes with trackable credentials,issued
availability across the United States.Tallayne is known for working with early stage,innovative brands to prepare them for commercial success.
“My involvement with Nufabrx since 2018 has
through Credly and maintained by NC State,that will provide third-party proof of skills obtained through the program.
“Through Hilando Oportunidades,Wilson College and our partners have the rare opportunity to transform the lives of thousands of Hondurans by providing pathways to better employment and brighter futures while simultaneously enabling a sustainable regional textile supply chain with key allies that also drives economic prosperity here in North Carolina,”said Wilson College of Textiles Dean David Hinks.
“UNITEC is delighted that Honduras is receiving support from USAID and our partners to promote the development of skilled labor to support and strengthen the country’s textile industry,“ said UNITEC CEO Rosalpina Rodriguez.“Academic quality and social responsibility are fundamental pillars of UNITEC,and we will bring our full experience in these areas to train Hondurans with the necessary skills and knowledge to build successful careers in the textile industry.”
strengthened my belief in the potential of its technology,brand,and the exceptional leadership demonstrated by Jordan Schindler,”said Glenn Normoyle,Tallayne founder.“This acquisition
opens doors to even greater opportunities as we proactively work to grow awareness following its initial success.”
“The Nufabrx brand was our first line of products available in the commercial market,its consumer success has led to the development of many new health and wellness products coming soon,”said HealthWear CEO and Nufabrx Founder Jordan Schindler.“The sky is the limit on potential use causes and partner collaborations at this intersection between pharmaceuticals and apparel.We’re extremely excited to see where the team at Tallayne takes the brand!”
Auburn Manufacturing Inc.(AMI),Mechanic Falls, Maine,recently hosted President Joe Biden at its plant in Auburn,Maine. The company produces fire- and heat-resistant materials for the defense industrial base,as well as primary metals,power generation and aerospace industries.AMI has been actively involved for years with the Department of Commerce,Customs and Border Protection,and now the current administration to shine light on China’s unfair trade practices.
President Biden was the first sitting president to visit Auburn since 1912. During his visit to AMI, the president praised employees’work ethic and commitment to the community,while also pledging further support
for domestic manufacturers such as AMI.
“The AMI team is incredibly humbled to have hosted an event of such magnitude,collaborating with the White House on behalf of American manufacturing writ large,”said Kathie Leonard,AMI president and CEO.“President Biden’s visit to Auburn is truly a historic event, reminding all Americans that Maine is on the manufacturing map and that domestic manufacturers like us will never stop working hard and fighting back against even the fiercest competition.We look forward to even brighter days ahead for manufacturers across America.”
“We are thrilled and sincerely appreciative of President Biden’s visit to this industry”said Kim Glas,president and CEO of the Washington-based National Council of Textile Organizations.“President Biden’s economic agenda and focus on domestic manufacturing supply chain resiliency,which he highlighted here today, helps bolster this vibrant U.S.textile industry, which has made major investments in state-of-the art manufacturing facilities, produced $65.8 billion in output in 2022,and employed 538,000 workers. Auburn Manufacturing — a leading producer of fireand-heat resistant materials,a major supplier to the U.S.military,and a women-owned certified business — exemplifies the U.S.textile industry’s innovative spirit,diversity, and importance to the U.S.economy.” TW
IITMA 2023, Transforming the World of Textiles, provided insight to current and future issues facing the global textile complex. There were opportunities to learn about new and innovative technologies being developed and implemented to address these issues. There was a notable focus on sustainability and circularity throughout all sectors of the supply chain including new fiber development, processing, yarn production, fabric production, finishing, cut-and-sew operations, and recycling. In addition to numerous exhibitors showcasing their products, there were ITMA live sessions, Innovator Xchange panels and presentations, and ITMA Innovation Awards related to Sustainability and Circularity. During ITMA, Planet Textiles 2023, a two-day conference sponsored by the Sustainable Apparel Coalition (SAC), explored trends and the latest thinking on circularity, sustainability, and identified drivers that will shape the industry of the future. With more than 111,000 visitors and 1,700-plus exhibitors, ITMA provided opportunities to network with all those involved and gain insights on technologies and trends shaping the future of textile recycling.
Reclaiming and reusing postindustrial waste has been a common practice throughout many textile industry sectors for decades. Postconsumer recycling is an emerging area of interest that has unique challenges requiring the development and use of innovative technologies to reach the goal. This article focuses on the drivers, challenges and solutions to post-consumer waste collection, separation, and recycling; and many such solutions were highlighted at ITMA 2023. There were numerous new technologies introduced, as well as innovative uses of existing technology that allow for the steps in textile recycling to be mechanized, automated and combined. Legislation, both in development and soon to be implemented, was reviewed, and noted as a driver in moving toward
fiber-to-fiber recycling and circularity in the global textile value chain. It is also noted that numerous partnerships among companies in various sectors of the supply chain have been formed and are contributing to the transformation of the industry.
Textile production, from fibers to consumer products, often is resource intensive requiring large amounts of water, energy and chemicals depleting the world of natural resources. These processes can pollute the air, and water, and are known to produce greenhouse gas (GHG) emissions and impact the biodiversity of the environment. Recycling textile products at the end of life can reduce this depletion of natural resources, reduce pollution and help reduced the strain on the planet’s environment. In this article, recycling includes breaking the product down to the fiber level or its base molecules/monomers in support of the circular economy and closed-loop manufacturing is the interest and the focus. This level of recycling is completed using chemical or mechanical processes depending on the raw material being recycled and intended future use. Recycling will provide raw materials from which new products can be manufactured.
There is an overabundance of postconsumer textile waste. Carolyn Chun noted that according to McKinsey, roughly 97 percent of all clothing eventually ends up in a landfill and within 12 months of its manufacturing date, 60 percent of clothing is in the landfill. 1 Media pressure, consumer demand, regulations and technology are driving forces behind the move toward fiber-to-fiber circularity.
Waste can be categorized as preor post-consumer. Pre-consumer waste is from the manufacturer and never makes it to the consumer or retailer. It can also be classified as post-industrial waste. Cutting room floor scraps, rejects, trimmings, threading or end of process waste are examples of post-industrial waste. For years, companies have found ways to reuse or sell this waste diverting it from landfills and sometimes it is used in other products. An advantage of pre-consumer versus post-consumer waste when considering reuse and recycling is there is a better understanding of the raw materials in the waste stream.
Post-consumer waste includes items that have been used by the consumer, disposed of, and diverted from the landfill. Post-consumer waste contains mixed material that is difficult to recycle. Although not truly post-consumer, 30 percent of garments produced are not sold and are commonly landfilled or burned, which also are potential raw materials for fiber-to-fiber recycling.2
Numerous challenges have been identified regarding textile and apparel recycling in general and specifically related to post-consumer waste. Some critical challenges for effective fiber-to-fiber recycling include garment disassembly and fiber identification. As apparel and other textile products are commonly
made of multiple components from various materials, a frequently identified challenge is the use of mixed materials within the products. These can include various fasteners and embellishments as well as various fabrics of different fibers within the garment. In many cases, the fabrics are made from unknown fiber blends, which is problematic in the recycling process. Remembering that the different materials are recycled differently, the presence of mixed materials has previously limited effective fiber-to-fiber recycling.
When post-consumer waste is collected, the first step is sorting. Sorting is most commonly a manual process and there are numerous criteria — sometimes up to 60 sorting categories are used. Initially, those products of “high value,” identified as designer goods vintage items, are removed for high-end resale. Then items suitable for resale through thrift shops are identified and removed. The remaining products may be identified as suitable to sell to rag dealers, and fiber content is of importance in determining how functional they will be in this application.3
To move the remaining goods to recycling so the fibers and/or raw materials can be reused, resulting in effective closed loop manufacturing, it is important to accurately identify the raw materials. This is critical in determining appropriate recycling techniques — chemical or mechanical — and potential end-uses.
In 2021, polyester had a market share of 54 percent of total fiber global fiber production, followed by cotton and other natural cellulosic fibers with about a 28 percent market share, man-made cellulosics about 6.4 percent and nylon accounting for approximately 5-percent market share.4 In the clothing industry, more than 68 percent of the fibers used in apparel are synthetic fibers, primarily polyester, 5 followed by cotton. Blends of cotton-polyester — such as 65/35 and 50/50 —are commonly used in apparel products.
The majority of products contain multiple fibers that have been intimately blended and therefore it is difficult to separate the fibers. Historically, determining the materials within the product was cumbersome and has been achieved using a specially trained workforce that can identify fiber content by touch or others who examine the labels for this information. Next, the products need to be disassembled to remove non-textile components as this would interfere with the recycling process. As these processes are completed manually, they are time consuming and create a bottleneck in the recycling process.
Technology was presented at ITMA 2023 that aids in the identification of fibers using near infrared (NIR) spectroscopy. NIR uses the unique signature based on the chemical com-
position of the fiber for sorting that may be completed incredibly quickly. Several companies at ITMA were promoting this technology including Belgium-based Valvan N.V. — a provider of high-tech sorting and baling systems — and Austria-based Andritz AG , among other companies. These two companies also have combined various technologies, partnering with others, to provide sorting and recycling systems.
Valvan has developed a library of fiber signatures and when the NIR signature from the fiber is compared with those in the library, the fiber is identified in milliseconds. The identification system, Fibersort™, uses artificial intelligence (AI) to predict the concentration of fibers. Fibersort can also separate by colors using an RGB camera. The quick identification allows this technology to aid in fast automatic sorting of the product. Valvan has stated that there is 99 percent accuracy on single fiber materials and 95 percent accuracy on blends.
Andritz recently announced a partnership with Pellenc ST and Nouvelles Fibres Textiles, both based in France, to establish the first combined industrial scale automatic textile sorting line in France. Technologies in Pellenc ST’s Mistrial machines use NIR, visible spectrometry, induction, and X-rays with NIR suitable for fiber identification.
Products must be disassembled by removing fasteners — such as buttons, snaps or zippers — and embellishments — including leather patches, studs and sequins — before moving to fiber recycling. The garment pieces are cut and innovative technology capable of identifying and removing the non-fibrous materials from the waste stream was demonstrated at ITMA. The technology pulls any garment components containing non-fibrous materials such button or zippers and removes them from the product stream while
only fabric pieces move forward to the next step, which is shredding.
Both Valvan and Andritz demonstrated technology at ITMA that effectively separated non-textile components from the base fabrics that are found in post-consumer textile waste. Both companies have combined new technology to develop systems that have the potential to transform the textile waste industry and help the move towards a circular economy.
Valvan’s technology first determines the fiber content before clipping the garment into smaller pieces and then feeding them into the Trimclean™, a highly effective system for removing zippers, buttons, labels and other non-textile raw materials (See Figure 1) . The undesirable components are pneumatically separated from the textile. This increases the purity of the feedstock resulting in both quality and reliable feedstock for fiber-to-fiber recycling. Valvan creates solutions for all steps in the recycling process including supply systems, bailing systems and sorting.
Andritz also demonstrated technology that successfully separates non-textile components from the fabrics. Like Valvan, the Andritz system covers several segments in the textile industry from sorting, shredding and mechanical recycling. The equipment shreds the fabric while simultaneously removing heavy and metal parts including buttons zippers, rivets and other embellishments commonly found in apparel. Andritz is moving forward into both chemical and mechanical recycling through collaborations with international partners.
Technology that can instantly identify fiber content in the sorting process and then remove non-textile components from post-consumer textile waste has been described. However, until recently, it has not been possible to separate fibers in multifiber blended fabrics and therefore fiber-to-fiber recycling has been limited to those prod-
ucts of a single fiber. As the push for recycling continues, technology to separate garments containing blends of fibers is critical. Through various panels, presentations and various networking events, companies pioneering fiber separation from mixed textile materials were present at ITMA. Representatives from Circ , Ambercycle Inc. , and Renewcell shared information about their technology that successfully separates the different fibers in fabric blends and the production of new fibers from the recycled raw materials.
Circ, Danville, Va., has flexible technology that is capable of separating synthetic fibers from cellulosic content; capturing the majority of the raw materials so it can be remade into high-quality fibers to be used in future clothing. The company initially focused on biofuel production, but now is applying a technical solution to blended textile fabrics. In an interview with Elle magazine, Peter Majeranowski, Circ CEO, stated: “A key step in a fully circular fashion system is creating technology to break down textile waste and create new fibers from it [and then] creating garments that are using fibers made from recycled textile waste.” 6 Circ uses a hydrothermal processing technology to treat and separate the fibers.
Aksay Sethi and Moby Ahmed founded Los Angeles-based Ambercycle in 2015 as they developed a breakthrough technology using a biological recycling process that enables the molecular separation of different fibers, such as cotton and polyester. This process, known as Ambercycling, produces regenerated materials from post-consumer waste that has been separated and purified at the molecular level. In their process, a whole T-shirt goes into a reactor, and using their patented process, polyester is recovered and reformed into a yarn. These newly regenerated materials can then be made into fabrics for new garments. This not only reduces garments from going into landfills but also reduces the need to use new resources. Ambercycle introduced Cycora ® which has been
designed to serve as a direct replacement for polyester used in apparel. Cycora is a closed-loop circular yarn created using regenerated textile waste. Ambercycle also collaborated with Avery Dennison to create a unique, scannable QR code label, which allows for full traceability, transparency, and authenticity.
Renewcell was formed in Sweden in 2017 and its technology transforms cellulose waste into pulp and allows for the efficient reuse of chemicals. Renewcell’s goal is to recycle more than 1.4 billion T-shirts every year by 2030. The process still has limitations when recycling blends, however Renewcell’s technology can recycle clothes that are made of cotton and up to 5 percent non-cotton material like polyester.
There are numerous drivers moving industry and consumers to a circular economy. Increased awareness of the environmental impact of the global textile complex through scientific reporting, social awareness, and ease of access to information is one of these drivers. Another driver is legislation related to textile waste, both pre-and post-consumer waste, and in some cases the implementation of Extended Producer Responsibilities. Specifically, the European Union’s Waste Directive Framework requires countries to separate all textile waste by 2025, and the Circular Economy Action Plan ensures that circular economy principles are applied to all textile manufacturing products. These actions have pushed forward the technologies discussed here and support their implementation so companies throughout the supply chain will be in compliance with such legislation.
The SAC-organized Planet Textiles conference that took place during ITMA 2023 highlighted upcoming legislation during a panel presentation titled “The Global Legislative Landscape: What to Expect for Fashion, Sport and Footwear.”
The panel was moderated by Baptiste Carriere-Pradal, co-founder and director of 2BPolicy, and featured speakers ESG, Simple Approach General Manager Ilishio Lovejoy and New Standard Institute Director Maxine Bédat. Current and future legislation is expected to impact all sectors of the value chain.
Carriere-Pradal began the session with an overview and noted that 10 years ago it was thought that consumers would be the drivers of a change to more environmentally and
bility of post-consumer textile waste. Following are the pieces of legislation discussed and or mentioned during the Planet Textiles session. It is expected this legislation will drive the development and implementation of innovative technologies leading to a more sustainable industry.
The Fashion Sustainability and Social Accountability Act — also known as the New York Fashion Act — was a bill introduced in the New York Assembly in 2022. However, the bill did not move forward because of
socially sustainable goods, and brands would change things to meet this demand by ensuring the choices they provide to consumers are made with a “fairly minimum impact.” However, Carriere-Pradal noted that is it now the citizens that are requiring change which has resulted in an increase in legislation addressing the way products are designed, sourced, manufactured, marketed and what happens at end of life. Chun1 noted that regulatory trends are also a factor influencing the landscape of sustainability within the global textile complex and regulation will factor into future innovation development and implementation. Many of the legislative acts mentioned during Planet Textiles relate to transparency and traceability of the product. Increased transparency will allow more accurate and easily accessible information regarding product raw material content and processing and will aid in the recycla-
lack of support. A 2023 version of the bill was reintroduced, which stalled in the last session. The act has the four key elements of supply chain mapping, due diligence, adverse impact disclosures and targeted impact reduction.7 During the Planet Textiles panel presentation Bédat noted that this bill includes due diligence language incorporating what has otherwise been voluntary. The approach is requiring the fashion seller and/or brand to set and achieve sciencebased targets. “The idea is not to put the information on the consumer and have the consumer do decide and decipher any labeling,” Bédat said. The brand will set the goals and decide how they will structure their business to meet these goals. There is language within the New York Fashion Act, of not only what the fashion seller/brand has to do, but also what information regulators must provide and make available to prevent lack of
clarity about what is the responsibility of the supply chain and seller.
The aim of the Corporate Sustainability Due Diligence Directive (CSDDD) adopted by the European Commission in February 2022 is to “foster sustainable and responsible corporate behaviour throughout global supply chains …. requiring companies to identify, and where necessary, prevent, end or mitigate adverse impacts of their activities on …. the environment for example pollution and biodiversity loss,” as well as “anchor human rights and environmental consideration in companies’ operation and corporate governance.”
When referring to the CSDDD during the Planet Textiles panel, CarrierePradal stated, “…even if this obligation will be for the people putting the product on the market, it’ll have definitely ripple effect for everybody in the value chain, so there will
References:
be changes throughout the industry.”
The Corporate Sustainability Reporting Directive adopted by the European Parliament in November 2022, strengthens and expands sustainability reporting to move to a green and sustainable economy. This framework will be introduced in phases beginning in 2024. It includes reporting on environmental and social aspects and how related issues impact their business and how their operations affect people and the planet. Items related to environmental areas include science-based targets, E.U. Taxonomy, and climate risk related reporting.8
On March 30, 2022, the proposal for a new Ecodesign for Sustainable Products Regulation (ESPR) was published by the European Commission, which will improve product circularity, energy performance and other environmental sustainability aspects. It
1.Chun, C. (2023, June 11) “The Recycling idea at Levi’s, Adidas, Zara to stop trillions in fast fashion from going to waste”, CNBC. Retrieved from https://www.cnbc.com/2023/06/11/a-recycled-idea-at-levis-adidas-to-stop-clothingfrom-going-to-waste.html
2.Rudenko, O. (2018, December 10) “The 2018 apparel industry overproduction report and infographic” ShareCloth.com Retrieved from https://medium.com/nataliya-makulova/the-2018-apparel-industry-overproductionreport-and-infographic-by-sharecloth-284cda8f1f9
3.Englund, F., Wedin, H., Ribul, M., de la Motte, H., and Ostlund, A. (2017) “ Textile tagging to enable automated sorting and beyond-a report to facilitate on active dialogue within the circular textile industry”, Mistra Future Fashion report number 2018:1, RISE Research Institute of Sweden, 2017.
4.Textile Exchange, (2022), Preferred Fiber & Materials Market Report. Retrieved from https://textileexchange.org/ app/uploads/2022/10/Textile-Exchange_PFMR_2022.pdf
5.Chen X, Memon HA, Wang Y, Marriam I, Tebyetekerwa M. (2021) Circular economy and sustainability of the clothing and textile industry. Mater Circ Econ. 2021;3(1):12. doi: 10.1007/s42824-021-00026-2. Epub 2021 Jul 6. PMCID: PMC8257395.
6.Chong, D. A. (2023, May 5) “The future of fashion is circular- here’s how major fashion brands are adapting. Elle. Retrieved from https://circ.earth/the-future-of-fashion-is-circular-heres-how-major-fashion-brands-are-adapting/
7.Lupo, A.V., Santos, A. M., Roque, R. E., Xu, F.A., and Lewis, E.B. (2023, July 17) “ New York’s fashion sustainability and social accountability act – Round 2 underway”, ArentFox Shiff, Retrieved from: https://www.afslaw.com/ perspectives/alerts/new-yorks-fashion-sustainability-and-social-accountability-act-round-2-underway
8.Crabbendam, N. (2022, December 15) “Corporate Sustainability Reporting Directive (CSRD) Explained”, Carbon Trust. Retrieved from https://www.carbontrust.com/news-and-insights/insights/corporate-sustainability-reportingdirective-csrd-explained
allows performance and information requirements to be set for most categories of physical goods placed on the European Union market. The requirements cover a broad range including product durability, reusability, and reparability, recycled content, carbon, and environmental footprints, including Digital Product Passport. The ESPR proposal will apply to all products placed on the E.U. market whether they are produced inside or outside of the European Union.
ITMA 2023 provided the opportunity to learn about the trends impacting sustainability and circularity within the global textile complex. With increased media attention and consumer awareness on the environmental impacts of textile industry, technology, and legislation, there is a transformational change coming in the future. Innovations that allow the mechanization and automation of textile sorting, fiber identification, and the creation of new fibers from textile pre- and post-consumer waste are being developed and implemented as the textile industry moves to meet this change. Both start-ups and wellestablished companies are taking leadership roles through all sectors of the textile and apparel supply chain to meet the new criteria imposed on the industry. Increased collaboration among non-governmental organizations, industry and academia are tackling the complex issues facing the textile industry. New collaborations, innovative technologies, increased consumer awareness and legislation are driving this transformative change. TW
Editor’s Note: Dr. Karen K. Leonas is a professor of Textile Sciences in the Textile and Apparel, Technology and Management department at Raleigh, N.C-based North Carolina State University’s Wilson College of Textiles, as well as co-chair of the Wilson College Sustainability Committee.
*and experience the futureproof sustainability of the all-new, revolutionary Ultimax.
— items that are still in supply chain recovery mode since 2018. Shortages in some cases lead to “allocation” of equipment to existing or strategic customers only, most definitely not a desirable situation for the industry.
Some themes do emerge in the technology directions despite this economic backdrop.
Cautiously moving forward” appears to be the overarching motto of the spinning sector at ITMA 2023 held recently in Milan, Italy. Of course there were some technical advances on display, but economically speaking, no new innovations that completely shake up existing business models. Some of the incremental investments1 of the 1980s are coming back to mind. Incremental investments allow textile manufacturers to utilize new or improved technologies without having to completely replace existing equipment. This conserves financial resources, which is relevant in uncertain economic times, as well as during times when technological directions are not yet clear. The theme of economic uncertainty was definitely visible and frequently mentioned in many conversations during ITMA.
Many machine manufacturers as well as their clients still mentioned
“surviving COVID” in the postCOVID times. Economic activity is still reduced, and survival is simply more important than innovation, or at least more imminent. For equipment producers, just like for their clients, raw material prices have been very volatile and considerably higher than five years ago2. These kinds of cost increases impact machine prices, thus changing the cost/benefit analysis for new equipment and new technologies. Similar price increases and volatilities have taken place in raw materials for yarn producers — in cotton and polyester 2 prices, for example — making long-term decisions like the purchase of new spinning equipment extremely difficult.
Additionally, like for most other industries, a lot of technological innovation is happening in the integration, control and coordination of textile processes. This upgrade requires computing equipment and semiconductors
Most of the equipment manufacturers at ITMA showed very sophisticated programs that monitor, control, optimize, and integrate processes within and between plants. Cloud computing, remote access and control, and a plethora of data analyses was shown by most of the companies at ITMA. Software programs are key to efficient plant management, and exhibitors integrate maintenance and spare part businesses into their plant management toolboxes. While spare parts have always been an important business component, today these services are strongly promoted, showing how much more important they have become to the suppliers.
MyTrützschler — available from Germany-based Trützschler Group SE — for example, allows users to access to detailed plant information with live feeds from practically anywhere. The MyWires functions help optimize card clothing management, whether the spinning mill conducts its own wire maintenance or utilizes the service provided by Trützschler. Technologically, this kind of real time data allows for optimized plant management, optimized equipment maintenance, and faster and better decision making. Economically, it also shows how much more integrated the supply chain on the textile equipment side is. Not only are the textile equipment manufacturers much more integrated in bale handling through spinning, but also any of the auxiliary suppliers — such as monitoring and maintenance, for example — are tied into the supply chain through acquisitions and strategic alliances.
In similar fashion, digital solutions offered by Italy-based Marzoli
Machines Textile S.r.l. optimize the spinning process and monitor key performance indicators (KPIs) in real time. According to the company, implementing its predictive maintenance program analyses a large volume of company data against benchmark values, resulting in maintenance cost savings of up to 30 percent. Using the cloud based marketing resource management (MRM) software, problems can be analyzed remotely and energy consumption and efficiencies can be optimized.
On the equipment side, Trützschler showed the TC 19i card at ITMA 2023, with the T-GO gap optimizer, which automatically fine-tunes the carding gap to compensate for changing temperatures and conditions during operation, leading to higher production and better quality. The optical sensor of WASTECONTROL continuously monitors the waste quality at the licker-in and automatically optimizes the mote knife setting via the servo motor. With rising raw material costs, any raw material savings are an important cost factor, no matter what textile market is served. NEPCONTROL data is monitored and uploaded to the MyMill system, where any deviation in nep count can be analyzed and addressed at the machine level from anywhere in the world. The TC 30i card has been updated since Barcelona and shows an increased
carding area — with approximately 1/3 more active flats plus a pre-carding and post-carding zone. While an increased carding surface is not a new idea or technology, the existing carding technology has certainly been improved, leading to higher production levels, better quality and more efficient waste management — including minimizing fiber waste and separating waste fibers to optimize the recovered value. Similar improvements can be seen in drafting — like the self-optimization of Trützschler’s TD 10 — leading to higher efficiencies, improved quality monitoring and better integration of mill management.
Switzerland-based Rieter showed very similar directions in its developments, with the C77 and C81 carding machines featuring an increased carding surface — the company reports the C81 sports the “largest active carding area” in the market — automatic Carding Gap Control and optimized fiber yield using its Trash Level Monitor. Improvements in its spinning machines also continue, for example in ring-spinning with the G38 and G37 models; rotor-spinning, like the fully automatic R70; or in compact spinning, like the K48. However, the J70 for air-jet spinning was specifically highlighted at ITMA. With a roughly 25-percent higher production speed compared to ring spinning and unusually high flexibility offered via the VARIOlot option — up to two different lots per machine side — the J70 matches the ever-changing mar-
ket demands for smaller lot sizes. Cost and flexibility remain relevant.
Marzoli showed the FTM320 roving frame with the central headstock in the middle of the machine. This layout not only simplifies managing the machine itself and optimizes automated transport of bobbins to the spinning machines, but it significantly reduces exchange and cleaning times by almost 30 percent, according to the company, thus increasing efficiency and reducing cost — specifically energy cost — which is of course an ongoing concern in the textile industry. The layout of the FTM320 also reduces space requirements, and while looking at productive area versus non-productive area is not always one of the most urgent decision criteria considered, in some cases, space becomes an absolute deal-breaker or deal-maker. Marzoli’s MDS2 spinning frame also offers improved efficiency and reduced energy consumption, inline with the concerns of the industry. Energy consumption, and specifically air consumption, also are the key improvements seen in Marzoli’s comber CMX, with increased productivity and up to 10 combing heads.
In addition to the high degree of automation within each of the machines, from self-correcting adjustments to automated and integrated maintenance, Marzoli also showed the integration between machines. Automated transport and coordination between combing, roving, and spinning are key elements in
addressing concerns about labor availability and reliability.
An overarching theme for Rieter also was automation and integration. Its ROBOspin fully automated piecing robot now is also available for compact spinning machines. Improved control systems allow quality control going into and out of the machines, and Rieter helps mills with its Rieter Digital Spinning Suite to monitor, manage and optimize spinning mills remotely. Service, maintenance, and spare parts, as well as carding wire management are an essential part of the Rieter business model.
Saurer Intelligent Technology AG , Switzerland, also showed automation and process integration as a major theme. Like most equipment producers, it addresses automation as a managerial response to rising labor costs worldwide and independent of cost automation, which helps address reduced availability of skilled labor in the industry. All equipment manufacturers mentioned training programs at ITMA — in person, online, or at the machines — as well as automation in order to address various labor issues — skill levels and ongoing training, availability and cost — that are
an industry concern worldwide. Saurer offers training through the Saurer Academy. Additionally, automation and process integration can improve quality and efficiency by reducing human error.
Saurer specifically showed the Autocard SC7 carding machine — which features automatic gap adjustment for recycling, and increased carding surface area for improved quality and production rates — and automation in automatic transportation or “linking” from one process to the next.
The ZI 72XL compact spinner, the Autoairo air spinning machine, the Autocoro 11 and BD8 with Twinsuction on both ends rotor spinning machines, and ZI 451 worsted compact-spinning machine were on display, as well as twisters, cablers, and winders. Energy efficiency and reduction of energy consumption are an important topic in spinning, where energy cost often exceeds the cost of direct labor. Saurer addresses this through its Texparts product line, which introduced a smaller diameter spindle, Eshape, to reduce energy costs, among other variables.
Automation in process and product monitoring and inspection is of course a key component in any textile manufacturing setting, and Switzerland-based Uster Technologies AG showed the 360Q solution suite as a fully integrated system helping with data generation, analysis, and solutions for quality as well as cost management. This leader in textile testing and monitoring has integrated in-line monitoring at all levels with analysis and decisionmaking tools. Human error is essentially removed from the equation. The RSO3D, Uster Quantum, and Uster Sentinel are key elements in mill management that existing and
new spinning mills need to remain competitive.
The Yarn Master PRISMA from Loepfe Brothers Ltd., Switzerland, offers superior clearing with its dual measurement system — infrared and mass sensors — thus improving quality while saving costs — two key business drivers in yarn production. Using an innovative Autostart feature, set-up times are drastically reduced, allowing for faster and less costly product changes, which is a key aspect of agile manufacturing. Integrating software enables a complete management system, and as additions to existing equipment Uster and Loepfe technologies have always been part of new and incremental investment strategies in the industry.
Italy-based Savio Macchine Tessili S.p.A. also showed trends towards more automation with its Proxima Smartconer automatic winder, for example; and increased flexibility in air-jet spinning with its Lybra Smartspinner, which allows changing fiber blend ratios in the yarn from two slivers via computer (See “Just A Few Of The “Cool” Things On Display — The ITMA 2023 Edition,” T W , July/August 2023)
There was much anticipation surrounding Japan-based Toyota Industries Corp. ’s Helix vortex spinning machine, but unfortunately the machine was not on display at ITMA. Only videos were available to customers. According to company associates, production speeds are in the 50,000 revolutions per minute range with very fast start-up speeds. This technology is something to look forward to seeing in person at ITMA 2027!
Murata Machinery Ltd. (Muratec), Japan, manufacturer of the Vortex spinning system, had only a small booth with videos and chose not to display any machines at ITMA.
France-based NSC/N. Schlumberger SAS showed similar directions of improvement — in automation, energy savings and process integration — for long-staple-fiber yarns.
Spain-based Spinhole® Consulting offers consultancy services to help spinning mills change the configuration of the drafting zone and yarn guides to create a double “multi” balloon, allowing increased production speeds, reduced energy consumption, and thus reduced costs — a true incremental investment as defined above. Italy-based C.P.S.
option from Sahm — as well as remote support and service.
It should be noted that in addition to the traditional spinning machinery producers, there are equipment producers from India — Lakshmi Machine Works Ltd. (LMW®) for example — or China — such as Jingwei Textile Machinery Co. Ltd. — that offer a full range of equipment for spinning mills.
All major manufacturers of spinning equipment showed not only how energy consumption has been reduced, but also how the technologies can contribute to a circular economy. Recycling has moved from an also mentioned ability to a separate business concept that warrants complete business segments within the companies with dedicated equipment from opening through spinning. At ITMA, manufacturers market dedicated product lines specifically for recycled materials — such as TRUECYCLED by Trützschler or the COM4 Recycling process by Rieter, for example — and with raw materials being the biggest cost factor in textile processing, recycling makes sense economically as well as environmentally. Being able to process obsolete products into raw materials is as essential in the circular economy as any other step within this circle.
more complex and difficult to maintain. This is where remote training programs, and service and maintenance programs offered by the manufacturers become an integral part of the business models.
TEX S.r.l. with its Greenspin technology, offers similar retrofitting drafting systems for worsted and woolen ring spinning machines.
Also, in winding, companies — such as Dietze+Schell Maschinenfabrik GmbH & Co. KG and Georg Sahm GmbH & Co. KG , both based in Germany — illustrated the trend towards more automation, higher production, increased flexibility — like the Flexible Traverse
All of the equipment manufacturers also describe reduced energy consumption in their products; this is of course an ongoing trend, and economically highly relevant as energy costs in spinning tend to be more relevant than labor costs. Managerially speaking, cost savings are always easy to justify, especially when these costs are getting more volatile. Additionally, reduced energy consumption results in a smaller carbon dioxide footprint, which is good for the environment and a company’s corporate social responsibility report. While these are all easy concepts to sell, they are not necessarily easy concepts to implement into the equipment, and tend to make equipment
The world economy is still recovering, and supply chain issues — specifically in the electronics areas — impact spinning equipment like any other machinery. In terms of innovation, there is not a completely new mousetrap, but the existing mousetraps are continuously improving — higher efficiencies, more automation and process integration, better controls, and remote access. Most equipment features self-correcting systems that ensure higher speeds, more flexibility, and better quality. Simultaneously, manufacturers are aligning with cultural trends toward sustainability by embracing energy efficiency and product lines for the circular economy. TW
References:
1.H. Hergeth, “Investitionsstrategien für Stagnierende Branchen“, in der Reihe Empirische Wirtschaftsforschung Bd. 1, Münster, 1986. Also, H. Hergeth, Incremental Investments and their Results in the Textile and Apparel Industries, Ars Textrina 26, 1996, pp. 65-79.
2.Federal Reserve Bank of St. Louis, Commodity Prices for various products, https://fred.stlouisfed.org/.
Editor’s Note: Dr. Helmut H. Hergeth is an associate professor in the Wilson College of Textiles at North Carolina State University, Raleigh, N.C.
The Association of the Nonwoven Fabrics Industry (INDA), Cary, N.C., is collaborating with Belgium-based EDANA to implement the nonwoven industry’s first Quality and Audit Program (QAP) in the United States. The program— which grew from the inefficiency of facing multiple audits that assessed similar requirements, but according to different standards — will support manufacturers in the absorbent hygiene products and wet wipes industries, reducing complexity for suppliers and converters. After a testing and piloting phase, QAP initially rolled out in Europe over the summer.
“With this partnership, we believe QAP will become the global quality standard in the hygiene industry, thus ensuring that consumer products across the industry are of the highest quality,” said Tony Fragnito, INDA president.
Turkey-based Lotus Teknik A.S., has chosen a Metris All-In-One digitalization platform from Austria-based ANDRITZ for its new Wetlace™ CP nonwovens line. The platform combines functionalities for production management, simulation and optimization using artificial intelligence methods; condition monitoring using smart sensors; and cyber security.
“We have already gained positive experience with a Metris installation on our spunlace line from ANDRITZ, and so we are confident that the comprehensive Metris All-In-One solution will take the production performance of our new ANDRITZ Wetlace CP line to an even higher level,” said Ceyhun Zincirkiran, co-owner and managing director of Lotus Teknik Tekstil.
Spain-based Textil Santanderina has launched the Advanced Black Denim collection in collaboration with Switzerland-based Archroma. The collection is dyed using Archroma’s new DIRESUL ® Evolution Black LIQ dyestuff — an eco-friendly alternative that offers an overall impact reduction to 57 percent compared to a standard Sulfur Black 1 liquid, according to a life cycle analysis performed by Spain-based Ecoterrae.
“With the DIRESUL Evolution Black LIQ, Archroma is rewriting the future of denim for market leaders like Textil Santanderina that want to produce more sustainable collections with high-value aesthetics and top
fabric quality,” said Umberto De Vita, director, Denim Market Segment, Textile Effects Division, Archroma.
Belgium-based Devan Chemicals NV, part of Pulcra Chemicals, reports it has achieved durability of 50 washes for its bio-based, biodegradable R-Vital ® NTL microencapsulation technology. The product allows textile manufacturers to add active ingredients — including aloe vera, avocado seed oil, CBD, multivitamins and vitamin E — to textile products for added value, and health and wellness functions. When incorporated in textiles, the active ingredients are gradually released to the skin as
The England-based Nonwovens Innovation And Research Institute (NIRI) recently opened Innovation House, a new state-of-the-art headquarters location that expands its capacity for nonwoven and fiber product development. The new facility, which houses seven new laboratories, is more than double the size of its previous location.
“We’ve invested in more equipment, more people, bigger and better-equipped labs, said Chris Fowler, NIRI Group founder. “This move will help enable us to deliver our three-year strategy for growth, with the expansion of our functional chemistry, formulation, and polymer engineering capability; recruitment of 20 additional technical textile scientists; acquisition of complimentary operations, and the expansion of our U.S. and E.U. presence.” TW
the microcapsules burst and release their content over time.
Amsterdam-based Mimaki Europe recently introduced the TxF300-75 direct-to-film (DTF) printer, which increases the print speed by three times compared to its first DTF printer, the Tx150-75, introduced earlier this year. The DTF series printers feature a built-in ink circulation system and a degassed ink pack for reliability.
“We believe in giving customers choice and anticipating their needs, which is why we are expanding our DTF printer line-up hot on the heels of the inaugural system,” said Arjen Evertse, general sales manager, Mimaki Europe. TW
Stoll’s ADF —Autarkic Direct Feeding — series machines feature yarn carriers that are independent of the carriage.
Themes in knitting evident at ITMA2023 include advanced materials, robotics and AI, as well as sustainable production.
By Dr. Andre West, Technical EditorIITMA, a pivotal platform for engaging textile and apparel leaders and machine makers worldwide, gathered 110,000 international participants at its latest edition held in Milan, Italy. This nexus facilitates insights and alliances, extending to a critical component constantly growing and innovating, the knitting machine industry.
During ITMA 2023, with a focus on “Pivoting Towards Digital Transformation and Circularity,” four themes in knitting emerged:
1.Advanced materials with an eye on sustainability are fueling innovative technical textiles with multi faceted functionalities that span fashion, sports, architecture, defense and healthcare.
2.Robotics and artificial intelligence (AI) are fostering automation in knitted textiles while 3D digitization reshapes supply chains. Open AI’s early integration allows for retooling and efficiency that were not possible before, and autonomous machines have started to amplify their reach.
3.Remarkable advancements have propelled textile production, defied pandemic expectations and encouraged technology introspection.
4.Sustainable practices are integrating innovative materials and pro-
cesses, aligning with ecological goals. Creating virtual garments using 3D technology is accelerating prototypes and cutting waste.
The article breaks the knitting industry into key machine markets — flat, shoe/socks, circular and warp knitting. It is impossible to cover every machinery manufacturer’s innovations, and the report focuses on what is new rather than what is best. Some of these machine innovations will prevail and be featured at the next ITMA four years from now as a standard component.
Japan-based Shima Seiki Mfg. Ltd. showcased its innovation prowess at ITMA 2023, unveiling the newly branded R-Series — meaning Reborn. Moving away from the traditional green and blue knitting machines, the new line features nine grey flat knitting machines, including a cutting-edge prototype faster WHOLEGARMENT® machine. Hundreds of intricate fabric samples spanning fashion, sports, medical applications and more, were displayed on a bustling stand.
Shima Seiki embraced the traditional ethos of ITMA by introducing previously unveiled machinery while engaging clients to obtain feedback in this microfactory-oriented testing
ground. The flagship WholeGarment knitting machines finally are part of the Shima Seiki ecosystem after more than 20 years of fine-tuning, streamlining planning, design and production. These machines enable agile sampling and custom knitwear crafting in limited quantities, enhancing efficiency and fit with the sustainable economy of far less waste with superior quality.
Shima Seiki revealed its fifth generation SWG-XR prototype knitting machine. This iteration showcases remarkable speed, quality, efficiency and dependability strides. An homage to the groundbreaking SWG-X, the pioneer four-needle bed device that birthed seamless, WholeGarment knitting, the SWG-XR introduces innovative attributes like a spring-based mobile sinker system, a compact carriage with four knitting systems and automated yarn carriers. These features boost productivity by more than 25 percent compared to the preceding MACH2 XS model. There were three prototype SWG-XR machines, each integrating new facets like needle defect detection, premium 18-gauge fabric knitting and automated yarn end finishing. SWG will now become a household name for knitwear manufacturers, just like the SEC and SES did in previous generations.
Not to be forgotten, Shima Seiki’s esteemed SES series was a pioneering machine in flat knitting, transforming garment creation with single garment, shaped piece innovation. Aiming to redefine the SES’s scope, the new prototype SES-R emerges, incorporating a novel sinker system for dimensional sinker patterns and short-row knitting paired with a pioneering transfer jack system. Enhanced productivity arises through automated yarn carriers, particularly intarsia, combined with loop pressers for inverse plating and inlay knitting. The exhibit showcased two SES-R prototypes, which emphasized the transfer jacks and highlighted the loop pressers.
In this author’s opinion, Dr. Shima’s legacy will always be innovative glove knitting technologies, which were showcased at ITMA in the SFG-R glove-knitting marvel. The machine boasts a new sinker system, beltdriven carriage and automated yarn carriers, which results in gloves that impeccably follow hand contours, enriching fit and design potential. The SPG-R pile glove knitting machine, a stalwart since 1979, also integrates a refreshed sinker system, belt-driven carriage and automated yarn carriers. This revitalization expands color choices, design possibilities, and market diversification into cozy gloves and mittens.
Furthermore, Shima Seiki is integrating its software and cloud presence wherever it can, giving its customers a genuinely virtual seamless online package. The Apex4 series graphic design system has undergone enhancements in knit programming, 3D capabilities, speed and user-friendliness. These augmentations — along with the cloud-based design system ApexFiz, digital yarn
sourcing web service Yarnbank, and Shima’s Datamall digital content web service — enable users to procure valuable data for fashion planning, production, and sales; while Shima KnitManager functions as production management software. In addition, Shimanavi for training and the Shima HelpCenter all contribute to Shima Seiki’s one-stop shop for operations and support.
showcased production data tracking, enhancing transparency in manufacturing and optimizing workflows. The autonomous insertion of NFC chips into fabric patterns, inscribed with unique data by an integrated apparatus, underscores that wearable monitoring of human biomarkers is not far behind.
The ADF 830-24 Ki W knit and wear offers an 84-inch-long bed with a weave-in device with new yarn carriers with exchangeable tips and conical inlet to simplify and speed up the threading process and thus reduce the setup times. Also, ergonomic solutions to streamline a knitter’s daily work, such as a mirror and lighting for the belt take-down and fabrics in the storage area, seem like simple ideas, but their addition increases ease of use.
Germany-based Stoll — now also known as KARL MAYER STOLL Textilmaschinenfabrik GmbH after the company became part of the Germany-based Karl Mayer Group — expanded the renowned adaptability of its ADF series and finds total expression in the ADF 530-32 ki FLEX E7.2, which pushes flexibility to unparalleled heights. This universal machine epitomizes diverse knitted outputs, enabling prompt adaptation to order shifts or emerging business opportunities. Automated needle bed gap adjustment harmonizes varied knitting methods while augmenting fabric thickness and quality. A live demonstration during ITMA 2023
In contrast, the ADF 530-32 ki BCW E20, an actual 20gauge machine, emerged as an ultra-fine marvel, crafting delicate flat-knitted textiles adorned with intricate patterns, promising innovation in flat knitting. In Milan, T-shirts exemplified aesthetics and sustainability. The machine is backed by a compact design, which reduces the ADF’s footprint by 7 percent and allows for expanded capabilities.
Looking to the future, Stoll unveiled the prototype ADF 530-16/4 ki WWK E7.2 — which merges weft knitting, warp knitting and weaving techniques — to yield versatile fabric structures with sectoral enhancements. Innovative yarn guides with 3D mobility underpin this advancement. This machine can be seen as the first significant development that has happened since the purchase of Stoll by Karl Mayer, a leader in warp knitting.
Stoll also offers its Knitelligence® software solutions, which encompasses design systems, automated
and optimized production, and intellectual property protection products. Stoll PPS is a digital tool for flat knitting that contains production planning and manufacturing execution system (MES) functions. Realtime updates on pivotal production events bolster adaptability, while integration with enterprise resource planning (ERP) systems aids automation and remote maintenance. PPS’s display at the trade event highlighted its versatility and bottleneck detection capability. The group of Knitelligence products help facilitate creativity, streamline range development and curtail design-tomarket timelines.
Italy-based Mandarin Knitting Technology S.r.l. unveiled an array of advanced computerized flat knitting machines, featuring its unique “designed in Italy, made in China” technology. Amidst the established machine builders, the company’s innovation garnered significant attention during ITMA 2023.
Founded in 2011 in Conegliano, Mandarin Knitting Technology is situated in northeast Italy’s Veneto region — an area renowned for knitwear production by giants like Benetton and Stefanel. Its ITMA exhibition highlight was the F20 101 TD in 1.5 gauge — a remarkable machine. Presented with a 1.5-gauge needle fitted with an enlarged hook, the machine can be knitted at a half gauge, effectively achieving a gauge of 0.75. Mandarin affirmed this to be the world’s coarsest flat knitting gauge. Notably, a 0.75-gauge F20 101 TD machine has found application in crafting carpets by an Italian rug manufacturer. This machine could be used in the bustling home furnishing market.
Switzerland-based Steiger Participation SA unveiled the four needlebed KS3-60MC-II, which marked a pivotal departure from its China-based parent company Ningbo Cixing Co. Ltd.’s prototype showcased in past textile machinery exhibitions. This momentous step integrates the Steiger brand into the
Cixing Group’s flat knitting machines produced in China, shifting from earlier attempts to establish the Cixing identity beyond Chinese borders.
The Steiger KS3-60MC-II, presented as an 18-gauge model at ITMA 2023, was more than a prototype, but still awaits finalization before its market debut. This machine’s imminent market entry is anticipated at the threshold of the cutting-edge realm of four-needlebed technology. Steiger Sales Manager Gianni Zamarco indicated that meticulous testing involving Steiger’s clientele will precede its official release. Bearing a single head and three-system configuration, the KS3-60MC-II boasts a substantial 60inch needle bed, attaining speeds of up to 1.6 meters per second. Standard models encompass 16 motorized yarn carriers. The takedown mechanism involves a flexible device, comb, and auxiliary roller apparatus complete with segmented adjustments. Steiger also unveiled a novel 3-gauge Antares 2.185 flat knitting machine. This distinct Swiss creation features 24 motorized yarn carriers, which caters to crafting coarse gauge intarsia sweater panels.
Italy-based Lonati S.p.A. exhibited one of the most exciting knitting concepts at the show. Lonati Group, global technology company HP and sporting company Decathlon collab-
orated to unveil an innovative manufacturing paradigm that harnesses 3D printing. Their endeavor represents an eco-conscious approach to shoe production, employing cuttingedge technologies — HP’s Multi Jet Fusion and Lonati’s shoe-upper knitting machines — thereby redefining the creation of sustainable footwear.
Traditionally, the footwear manufacturing process necessitates multiple components, adhesives and extensive labor. However, HP, Decathlon, and Lonati have pioneered a transformative method, presenting a sports shoe that encapsulates the future of footwear. This distinctive shoe seamlessly integrates Lonati’s intricate sock with a 3D-printed midsole and outsole created using HP’s Jet Fusion 5200 printer. Lonati’s XT-MACHINE and Double Cylinder E1530XS knitting machines allow single or doublelayer fabric uppers to be made, blending comfort, performance, lightweight and quality.
The sole is 3D printed using Ultrasint ® TPU01 thermoplastic polyurethane (TPU) powder from BASF for shock absorption, energy return and flexibility.
The collaboration underscores the industrial potential of 3D printing and digital knitting, accentuating the following focal points:
•Personalization — The shoe presents extensive customization options, allowing consumers to
tailor their footwear per individual preferences.
The glue-free assembly approach facilitates seamless shoe repairs, avoiding the need to discard the entire shoe. Segregating cushion and upper components enables targeted fixes, prolonging product life and minimizing waste. Employing a single material, TPU, for grip and cushion elements enhances recyclability, contributing to an ecologically conscious product life cycle.
Taiwan-based Pailung is a global provider of circular textile machinery and solutions with a rich history and a strong reputation in the textile industry. Pailung’s advanced knitting machines, KS3B PLUS HS and KD3.2B PLUS, enhance fabric production speed, energy efficiency and capacity. The KS3B PLUS HS offers versatility with six fabric types and a maximum speed factor of 1350. To boost versatility, the machine can be modified using a conversion kit to further produce terry and 3-end fleece fabrics. On the other hand, the KD3.2B PLUS surpasses its predecessor in crafting six fabric types at an increased capacity.
Pailung’s innovative fabric technology can produce recyclable high pile fabrics without the need for adhesives. The Cozy Collection encompasses eco-friendly, warm, and versatile high-density, two-sided and three-layer high-pile fabrics. Inline with sustainability goals, these
adhesive-free winterwear options ensure recyclability and durability. Pailung’s approach to high-pile fabric involves layered knitting to reduce labor, time, and power consumption, while preserving design flexibility. Enhanced fiber control during knitting amplifies design possibilities and minimizes subsequent shearing. Distinct from sliver knit fabric, Pailung’s high pile fabric achieves similar density using a unique circular knitting production process that directly creates fibers on the fabric, yielding lighter, denser, and fur-like textures that are unique.
To reduce waste and eliminate the chance of faulty fabric reaching a customer, Pailung has developed the Fabric Defect Detection system, which employs advanced computer vision and cameras within the knitting machine to stop fabric defects from continually occuring. Fabric waste translates into economic losses as well as an environmental impact. The system monitors production in real time and if a defect is identified, the machine halts.
Pailung’s AlterKnit is an evolved rendition of inverse plating, functioning by interweaving alternating yarns
into the fabric’s framework. Using circular knitting machines, this process fuses yarns of varying colors or compositions within the same row. AlterKnit caters to the fashion and apparel sector, providing textile designers and manufacturers with the means to create intricate patterns incorporated directly into the knit structure, which eliminates the necessity for post-production printing or dyeing. This technology yields clear patterns with well-defined edges — a noticeable advancement over conventional inverse plating. Elements such as sports team emblems, complete with text and logos, may be created in the fabric. Single-knit AlterKnit styles also are reversible, with two mirrored iterations of the same design — comprising up to four colors — on either side.
Pailung also offers a comprehensive software suite. The Knitting Fabric Management System (KFMS) archives knitting data, facilitating the replication of fabric production. This knowledge transfer to the factory empowers any technician to reproduce saved styles. The Pailung Online Monitoring System (POMS) centrally oversees multiple knitting machines. Linked with KFMS-stored materials and parameters, POMS permits remote control, scheduling, and monitoring using a dashboard. Integration of KFMS, POMS, and the Manufacturing Execution System (MES) enhances textile factory ERP functionality. These systems can supply data to the ERP for resource management, error analysis and operational insights.
Germany-based Mayer & Cie. ’s prominent offering, the Relanit 3.2 HS, stands as a highly favored machine among customers, notably for its superior productivity in elastomeric plating. This mechanical single jersey model handles a diverse spectrum of yarns and qualities, boasting consistent reliability. It excels in energy efficiency, consuming up to 30percent less energy than traditional circular knitting machines. The latest version of Relanit 3.2 HS incorporates an enhanced yarn guide, streamlining
elastic thread feeding and facilitating retrofitting for existing units.
Among Mayer & Cie.’s repertoire tailored for mattress cover fabrics, the OVJA 2.4 EM is preeminent. Within a 38-inch diameter, it produces up to 30 kilograms of coveted 300 grams per square meter fabric hourly. This duallayer apparatus extends its capabilities to encompass spacer fabric knitting in E18 to E20 gauges. Exhibited at ITMA, the machine adeptly crafts spacer fabric with intricate perforations, supported by the thread fluctuation system in alternate units that maintain constant tension and thwart thread irregularities. The OVJA 2.4 EM is further refined with a novel horizontal yarn guide, enhancing its reliability and user-friendliness. Accommodating thicker weft yarns with a larger bore, this innovation eliminates the need for rib dial height adjustments and bolster hold-down function, which is crucial for extended floats.
In response to prevailing trends in the apparel sector, Mayer & Cie. introduced the SF4-3.2 III. This machine ingeniously amalgamates elements from the S4 3.2 II and MBF 3.2, catering to the demand for lightweight elastic three-thread fleece fabrics, including cotton blends. Significantly, its impeccable plating prowess is demonstrated through discreet background yarn, removing the necessity for double dyeing in most cases.
In summation, Mayer & Cie.’s trio of machines — Relanit 3.2 HS, OVJA 2.4 EM, and SF4-3.2 III — epitomize the synergy of innovation, efficiency, and adaptability in contemporary knitting technology.
ITMA 2023 witnessed Karl Mayer ’s introduction of pioneering warp knitting machinery. The RSJFS 4/1 EL, 130 inch, E14 raschel machine stood out. Capable of intricately woven patterns and designs in both flat and circular knit aesthetics, it offers remarkable productivity. Its ability to work with staple fibers enhances sustainability, including
100-percent cotton and coarser yarns in the jacquard bars.
A debutant, the RDPJ 6/2 EL MC, 138 inch, introduces a double-bar raschel machine, revolutionizing spacer fabric design. Innovations in color and jacquard techniques permit vibrant multicolor designs, making these textiles appealing to fashion, footwear, and home sectors. The elimination of dyeing via the use of spun-dyed yarns reduces environmental impact and costs.
The HKS 3-M ON, E 32, 130 inch embodies digital tricot excellence. Leveraging cloud pattern data, this model ensures rapid adaptation to trends with reproducible patterns. Notably swift and efficient, it employs advanced yarn feed innovation for seamless production.
At ITMA 2023, Karl Mayer showcased a myriad of samples to show the capabilities of its machinery. Everything from warp knit seamless garments devoid of seams and a 3D-seamless collection featuring relief-like designs to the warp-knitted crochet-knit fabrics made using 100-percent cotton and next-generation 4D-Knit insulating, twocolor-effect spacer fabrics were on display. Among lace innovations, Karl Mayer showcased elastaneinclusive variants with exceptional wash resistance. Karl Mayer’s presentation encompassed a spectrum
of inventive textiles with diverse applications that will continue to inspire the textile industry.
In conclusion, the recently concluded ITMA 2023, renowned as the pinnacle event in the textile machinery exhibition realm, marked a notable juncture. This ITMA ushered the textile industry into a dynamic phase characterized by its trajectory toward both sustainability and digitalization. Functioning as an avantgarde global showcase, ITMA 2023 substantiated its role as a premier platform for catalyzing innovation within the textile domain. Ranging from eco-conscious materials and processes to waste mitigation and conscientious manufacturing, ITMA 2023 underscored the non-negotiable importance of sustainability for a prosperous future. Knitting in general has always been an industry where technology innovation goes beyond sheer performance and speed. The engineers and technicians at these machinery companies have added amazing features that drive brands in the fashion and industrial world to think differently. It will be interesting to see the developments for consumers when these innovations get into the hands of the knitting designers. TW
totypes, which led to significant loss of production and raw materials.
Sample warpers were advanced to not only produce prototypes, but also small and medium orders for diversified line of production. Today, because of their numerous advantages, sample warpers are used not only by weavers, but also by universities and research institutions.
At ITMA 2023, Germany-based KARL MAYER Group exhibited a compact version of the automatic sample warping machine MULTIMATIC ® 32 Compact with creel capacity 32 wound packages for short and medium length warps. The machine was producing an intricate striped warp. The MULTIMATIC 32 Compact is characterized by its high production, interactive multi-flexible movable creel, fast pattern changes and short setup times. The increase in productivity is achieved by eliminating the stop for leasing and sizing separation.
By Dr. Abdel-Fatah M. Seyam, Technical EditorRResponding to environmental concerns and demand from consumers, textile machinery manufacturers are developing technologies to address sustainability in terms of reducing manufacturing waste, saving in energy and water consumption, and producing yarns and fabrics from recycled and biobased fibers. The technologies exhibited at ITMA 2023 revealed the continued commitment of the machine manufacturers, which started at the previous ITMA show, to focus on sustainability and digitization that light the road to Industry 4.0. It should be noted that sustainability and digitization are highly interrelated.
This paper covers some notable innovations in weaving technologies exhibited at ITMA 2023. As seen at previous shows, machine manufacturers continue to develop and
improve their equipment to form diversified products for apparel, home and technical textiles markets. Several exhibitors demonstrated weaving yarns from recycled fibers at high-speed. At the previous ITMA show, machine manufacturers marketed their technologies as Industry 4.0 ready, which has continued at this ITMA with more development in digitization. The last three decades have witnessed a dramatic increase in automation, control, monitoring of production and performance, and data storage in super computers and cloud and communication to access the data using electronic devices.
Sample preparation technologies were developed forrapid prototyping. Prior to the development of sample technologies, weavers used production machines to develop pro-
The company offers LINKMATIC ® automatic systems to increase the productivity of indigo and sizing machines by up to 30 percent. After completing a warp beam set, the system is used for tying-in the warp yarns from the new warp beam set to the set just completed. LINK-MATIC is designed to be managed by only one operator and reduce material waste.
Karl Mayer’s machines, including warp preparation systems, are networked via cloud for efficient access to machine data and remote service. Production and quality management reports stored in the cloud can be accessed by electronic devices such as mobiles and laptop or desktop computers. Its software offering KM.ON offers customers individual solutions that include production data analysis tools for flexibility and efficiency.
Belgium-based VANDEWIELE NV again showed its Smart Creel that was introduced at the previous show. The creel is very compact compared to
a traditional creel because the large wound packages are replaced with much smaller cells/holders arranged in rows and columns. Robots are used to wind the pile yarns from large wound packages with the exact length needed per weaving pattern.
Germany-based Groz-Beckert KG showed its KnotMaster as well as the WarpMasterPlus drawing-in machine that were on display at past ITMAs. The WarpMasterPlus is equipped with a computer system with swivel monitor or a touch screen user-interface with operator guided visualization that provides instructions on operation and troubleshooting via videos. Two monitors are available as an option to facilitate operator monitoring because the machine is long at between 2.4 and 4 meters. The machine consists of the drawing-in needle, drop wires, heddle wires, reed, and a single yarn from a wound package and their associated modular mechanisms. The yarn is fed to the machine by a feeder that is similar to a weft yarn feeder in weaving. The heddle wires and drop wires, which are loaded by an operator, are fed automatically to the drawing-in zone. The single yarn is fed to the drawing-in needle that threads the yarn through a drop wire eye, a heddle wire eye, and a reed dent. Then the yarn is cut, and the procedure is repeated at up to 150 times/min depending on the yarn type. After the drawing-in is completed, the drop wires are transferred to drop wire bars and the heddle wires to harnesses. The harnesses, drop wire bars, and reed are moved on a trolley to a storage area. When a weaver’s beam is ready, the drawn-in warp from a single yarn is knotted to the corresponding warp yarns using a tying-in machine. Then warp beam, read, harnesses, drop wires bars are moved to the weaving area to supply a new warp to a weaving machine according to production planning. Due to the absence of the weaver’s beam because of using a single yarn, the drawing-in machine occupies less space. However, space is required at
the next step for the weaver’s beam and tying-in process post drawing-in. While the drawing-in process is faster and setup time is shorter as a result of the simplicity of drawing from a single yarn, additional time is needed for knotting the weaver’s beam yarns to the drawn-in yarns.
Switzerland-based Stäubli showed its tying-in machine TIEPRO that was unveiled at ITMA 2019, while unveiling more information about the technology at this ITMA. The machine employs a new method of yarn separation from the upper and lower warp sheets. Two conical-shaped separators are used instead of the traditional method of yarn separation, which
new version of Active Warp Control 0.2 (AWC 2.0) allows the SAFIR machines to detect double-end and manage color and S or Z twist sequence in instances of drawing-in warps without lease. If double-end is detected, the two yarns are returned to the warp sheet and the system tries again for picking one yarn. As for the color/twist sequence, the AWC 2.0 checks the yarn color against the color repeat sequence and if the yarn is out of sequence, it will be kept in a storage area. Yarn in storage will be picked up later and placed in the correct sequence. The color detection system is designed to detect small differences in color to meet the demand of using same color of different shade and depth.
requires a range of needles depending on yarn type and size. The TIEPRO conical yarn separation mechanism is independent of yarn type and size. Additional features of the TIEPRO include: tying-in with or without lease; 3 to 100 Ne yarn count range; double end detection; short knot fringes; up to 600 knots per minute depending on yarn characteristics and size; and it’s suitable for staple yarns, 100-percent cotton yarns and cotton blends. TIEPRO is equipped with an Auto-Reverse function that is associated with detecting double ends. The machine repeats the yarn separating process on its own before tying and it does not cut the yarn. Operator intervention is required to separate the double end and then the tying-in resumes from where it was stopped.
Stäubli again exhibited its SAFIR 60 automatic drawing-in machines for striped warps. The company’s
Germany-based Lindauer Dornier GmbH exhibited the new air jet A2, as well as its rapier P2 weaving machines. The P2 rapier weaving machines were shown at ITMA 2015 before commercialization, and at ITMA 2019 post commercialization. At the Dornier booth, one P2 Type TGV 8/S G20/360 cm with 339 cm width in reed (WIR) machine was weaving plain weave sailcloth fabric at 320 picks per min (ppm) or 1,085 meters per min (m/min) rate of filling insertion (RFI); while an A2 Type AWS 4/E D 10/280 cm with 266 cm WIR was weaving plain woven awning fabric at 900 ppm or 2,394 m/min RFI. At the VANDEWIELE/Bonas booth, a second P2 Type TKN 8/J G/220 cm with 171 cm WIR machine was weaving intricate jacquard scarf fabric at 400 to 450 ppm or 684 to 770 m/min RFI; and on the Stäubli stand, another A2 Type AWS 6/J G/240 cm with 226.5 cm WIR machine was forming jacquard high stretch sportswear fabric from warp and weft yarns containing spandex at 1,000 ppm or 2,265 m/min RFI.
The A2 air jet machines, which is the successor of A1 series that was introduced in 1989, were shown for the first time at this ITMA. The A2 machines are highly digitized. The ErgoWeave ® operating panel was
redesigned with optimal continuous fabric production parameters overview. The more user-friendly high-resolution interface permits monitoring and shortens changeover of woven fabric parameters.
In the vein of digitization, weaving machines may be networked using Dornier DoXNet software, which provides a user-friendly production overview. Networking does not require internet; hence weavers have full control over their proprietary production, optimum machine settings and fabrics’ specifications data. With DoXNet, the optimum machine setting for a given type of fabric can be shared with other machines weaving the same fabric. If so desired, Dornier DoXWeave’s control desk, which centrally manages weaving machine data in a plant or plants, allows remote access to weaving machines’ production data. The Dornier myDoX is a portal that allows customers to shop 24/7 online and provides direct Industry 4.0 connection to experts and information from Dornier.
Discussion with technical personnel at the show revealed that Dornier’s biggest contribution to sustainability is designing sturdy machines work for many years. Dornier still provides spare parts for machines produced in 1978. It is well known fact that weavers have to surplus their machines or seek machine shops for support at extremely high cost because of a lack of spare parts for early machines. The
question that comes to mind is “Can such machines be digitized at reasonable cost to benefit from digitization and readiness for Industry 4.0?”
Itema S.p.A., Italy, unveiled the new EVO Series rapier machines, R9500EVO, and an air-jet machine A9500EVO. A total of 12 machines — 11 EVO 1 R9500-2 and one Hercules — were in operation at ITMA; seven machines at its booth and five machines on partner’s stands. The machines covered the formation of diversified fabrics for apparel, home textiles and technical textiles using natural and high-performance fibers. At its stand, Itema exhibited R9500 EVO/220 cm weaving wool fabric at 600 ppm or 1,320 m/min RFI, R9500EVO/220 cm weaving denim fabric at 750 ppm or 1,650 RFI, R9500EVO/190 cm weaving jacquard tapestry fabric at 600 ppm or 1,140 RFI, R9500EVO/260 cm weaving jacquard terry fabric, R9500EVO/220 cm weaving reinforced sail fabric at 600 ppm or 1,320 RFI, A9500EVO/190 cm weaving bottomweight fabric, and Hercules/380 cm weaving heavyweight filter fabric.
The five machines exhibited at other stands include R9500EVO at the Stäubli booth weaving Jacquard high fashion apparel, R9500EVO at the VANDEWIELE booth weaving Jacquard decoration fabric, R9500EVO at MEI stand weaving label fabric, R9500EVO at Julibao booth weaving label fabric and a R90002 weaving shoe fabric.
In terms of sustainability, Itema offers the mechatronic device iSAVER ® for raw material waste reduction, which has been expanded to several other fabric types after its initial success in denim weaving. At the Itema booth, three machines were equipped with the iSAVER ® device. The technology eliminates the need for auxiliary selvage yarns and cutters and minimizes the fringe on the left-hand side of the fabric. The iSAVER® is compatible with up to six different filling yarns.
In terms of digitization, Itema offers iKNOW™ and MyWeave™ systems. The iKNOW is an expert system loaded with information collected from the field over years. Itema reports the system enhances the user experience and optimizes production. Such systems are useful based on previous experience and therefore may be limited when it comes to developing new fabrics using new materials, especially fabric from recycled and bio-based fibers. The system needs continuous update that requires commitment from Itema and their customers. MyWeave is a new system that provides monitoring and management production data for a plant or plants. The EVO series is equipped with an EVOConsole of 15.6-inch-wide touch screen and can be connected to Wi-Fi and Bluetooth. It is also ready for data analysis and IoT. The EVOConsole allows access to the brand-new customer portal HelloItema, which allows customers to request service, access data and documents, and order spare parts.
Picanol NV , Belgium, unveiled new rapier Ultimax weaving machines that build on the predecessor OptiMax machines. The Ultimax machines are designed with a high degree of digitization to facilitate operation and communication with each other, as well as PicConnect. Picanol also exhibited the OptiMax-i rapier and OmniPlus-i air jet machines that were shown previously. A total of 10 machines were shown at the Picanol stand, one machine was exhibited at the VANDEWIELE/Bonas stand and
one at the Staubli booth. The list of machines along with fabric type, weaving speed and RFI are listed below:
•Ultimax-4-R-220 weaving denim fabric at 730 ppm (1,600 m/min RFI);
•Ultimax-8-R-360 weaving voile fabric at 400 ppm (1,440 m/min RFI);
•Ultimax Terry-8-J-260 weaving jacquard terry towel at ppm (1,417 RFI);
•Ultimax-12-J-340 jacquard flat carpet at 300 ppm (1,020 m/min RFI);
•OptiMax-i Connect-4-R-430
weaving anti-hail fabric at 330 ppm (1,419 m/min RFI);
•OptiMax-i Connect-4-R-540
weaving coating fabric at 275 ppm (1,485 m/min RFI);
•TerryPlus-i Connect-6-D-260
weaving jacquard terry towel at 600 ppm (1,560 m/min RFI);
•OmniPlus-i Connect-4-D-340
weaving sheeting fabric at 1,000 ppm (2x3,400 m/min RFI);
•OmniPlus-i Connect-4-D-190
weaving car seat fabric at 1,200 ppm (2,280 m/min RFI);
•OmniPlus-i Connect-4-P-190
weaving bottom weight fabric from 100-percent recycled yarns at 1,500 ppm (2,850 m/min RFI);
•OmniPlus-i Connect-4-J-220
weaving jacquard african damask at Staubli stand; and
•OptiMax-i Connect-12-J-190
weaving a jacquard fabric at VANDEWIELE/Bonas booth.
The OmniPlus-i Connect-4-P-190
weaving machine was weaving bottom weight fabric from 100-percent recycled warp and weft yarns with fiber content 67-percent polyester/33 percent cotton at and impressive speed of 1,500 ppm (2,850 m/min RFI). The performance, and hence weavability, of yarns from recycled fibers is lower. Despite this, Picanol demonstrated the commitment to develop high-speed machines to handle such yarns containing short fibers and support sustainability initiatives. Picanol reports that the Ulti-
max-4-R-220 is recycled yarn ready. Another notable achievement is weaving sheeting from fine cotton yarns Nm 102/1 warp and Nm 68/1 weft with fabric count (72x41x2) at 1,000 ppm weaving speed or 2x3,400 m/min RFI — the 2 denotes doublepick insertion. As a result of the higher levels of short fiber content in recycled yarns, higher fly is generated that settled on the machine, warp sheet and fabric during demonstration. This fly will require a blowing system to remove the lint. Blowers and suction systems are not unusual in weaving operations.
The Ultimax-8-R-360 and OmniPlus-i Connect-4-P-190 machines were equipped with newly developed leno motion O-Leno. The O-Leno yarns are driven by a timing belt and two time gears that can be programmed to form half-turn or fullturn leno weaves to secure the fabric selvages. It may be programmed to vary form half- or full-turn leno for individual weft yarns depending on their surface characteristics.
Picanol’s highly digitized machines are Industry 4.0 ready. The company developed PicConnect to access data stored in the cloud. It is the gateway to all Picanol digital information access such as Picanol applications, IoT, AI, and customer service.
Smit S.r.l. Italy, exhibited three rapier machines — the new 2FAST 220 C8 D; the GS980 260 F8 J, previ-
new conceptual machine under development, the CONCEPT 190 C8 D. The 2FAST machine was weaving denim fabric at 700 ppm with WIR 222 or 1,554 m/min RFI, the GS980 machine was weaving jacquard terry towel at 500 ppm with WIR 244.4 cm or 1,222 RFI, and CONCEPT machine was weaving shirting fabric at 800 ppm with WIR 172 cm or 1376 m/min RFI. The 2FAST and the CONCEPT machines are designed for quick style Changes. The warp stop motion of the CONCEPT machine uses a laser device, which eliminates the drop wires. Monitoring warp breaks using lasers may be challenging in situations where a high warp density causes the broken yarn to be supported by neighboring yarns instead of falling where it is detected by the laser. The 2FAST machine is equipped with 2SAVE that was shown for the first time at ITMA 2019. 2SAVE eliminates auxiliary selvages from both sides and cut weft fringes collected for recycling. While the machine at the show was weaving denim fabric, it is designed for versatility to weave fabrics for fashion, home textiles, and technical fabrics using range of yarns from different fibers and counts. The rapier uses a previously introduced free flight system — no guide is required to support the rapier during weft insertion.
Japan-based Toyota Industries Corp. showed three of its new JAT 910 air jet series machines at ITMA. A JAT910 4F-230ES-EF was weaving high fabric count (274x526) doublefaced fabric at 1,000 ppm with WIR 210 cm (2,100 RFI), a JAT910 2S340LM-ET was demonstrated weaving side-by-side 261 cm wide sheeting and 20 cm wide pillow fabrics at 900 ppm (3,060 m/min RFI), and JAT910 8T-280JE-EH was weaving four panels of different jacquard terry towel patterns at 950 ppm with 269 WIR (2555.5 m/min RFI). Toyota’s approach to sustainability is in reducing air and energy consumption. Its i-SENSOR technology monitors the leading weft yarn during insertion inside the shed prior to arrival at the right-side selvage. Early arrival — which occurs as the weft package diameter is reduced due to the fact that the weft yarn gets more air friendly with higher traction — will be detected and insertion timing is adjusted accordingly. Toyota reported a 20-percent reduction in air consumption compared to the conventional models. There are no studies in public domain that compares air consumption using adaptive control systems by different machine manufacturers.
Toyota’s factory management support system FACT has been evolved to FACT-plus. The system collects data in real time from weaving preparation, weaving machines and the inspection room, and pro-
poses actions to machines and operators. It monitors different sensors — such as speed, pressure, temperature, and compressor pressure data, for example — and provides instructions for machine maintenance and the next assignments for operators.
Japan-based Tsudakoma Corp. exhibited a new air jet weaving machine series, the ZAX001neo, that was successfully commercialized and sold in 2021. At its stand the company demonstrated a ZAX001neo190-2C-Cam weaving lining fabric at 1,200 ppm (2,280 m/min RFI), and a ZAX001neo-390-4C-Cam weaving awning fabric at 820 ppm (3,198 m/min). A new weft insertion system, designed as a standard for the ZAX001neo machines with optimized auxiliary nozzles positions, led to a reduction of 35 percent in air consumption corresponding to 20-percent reduction in air pressure compared to the previous generation model. Additionally, a direct drive high-efficiency IPM motor, developed for this series, reduces stop marks. The company upgraded its weaving support system to Weave Navigation ® System II. The system has different functions: Weave Vavi® provides user support to best weaving conditions for a given situation; Tune Navigation delivers the best machine setting — including loom timing, tension, easing amount and air pressure — for a given fabric type; and i-start, which eliminates stop marks via controlling the let-off and take-up to
adjust cloth fell position and the warp tension back to its pre-set levels.
3D weaving for fiber-reinforced composites and other innovative applications was a highlight in the weaving area again at this ITMA. At previous shows, companies displayed 3D woven products with variable thickness, distances (spacer), stitched multilayer, and unstitched/stitched double cloth for insertion of electronics and ceramic for ballistic protection.
At ITMA 2023, VANDEWIELE showcased samples and displayed on a large screen several distance/spacer fabrics for automotive and boat applications to demonstrate the capabilities of its weaving technologies.
Optima 3D was a return exhibitor at ITMA. The company exhibited one Series SJ-600-4 3D weaving machine equipped with four shuttles for weft insertion and the SX Staubli Jacquard shedding system. The machine forms one shed at a time and the shuttle is transferred by a magnetized rapier arm for weft insertion. The arm is designed with a magnetized conical space to hold the metal nose of shuttle. The machine is equipped with a linear fabric take-up motion — thick 3D preforms cannot be taken-up on rollers — and touchscreen controls for user interface. Warp yarns are supplied from a compact creel with rotating flanged spools that allow parallel winding for longer yarn packages and hence longer runs to reduce creel changes. The creel capacity is 576 spools, and two or more creels can be set behind the machine if needed. The company product line also includes spool winding machines. Shuttle weaving combined with a jacquard shedding system allows the formation of 3D orthogonal and angle interlocking, stitched/unstitched multi-layer along with a variety of shaped 3D preforms including I, T, Truss, cellular, among other shapes, for fiber-reinforced composites and other applications.
VÚTS A.S., Czech Republic, exhibited the DIFA air-jet weaving machine
weaving 3D distance fabric. The machine can be programmed to form fabrics with variable distances between the top and bottom base, or ground, fabrics to obtain the target shape of the inflatable structure after coating. This type of distance fabric requires a minimum of two warp beams — one dedicated for the warp sheet for the top and bottom ground fabrics and the other is assigned for the pile warp sheet. Applications for the distance fabrics include inflatable structures such as boats of different types, dock, mats, flood protection and lifting bags.The company also showed its CAMEL ADAPTIVE air-jet machine for leno fabrics. VUTS promotes its machine as Industry 4.0 ready.
Switzerland-based Jakob Müller Group has been developing narrow weaving machines for smart textiles applications since ITMA 2011. Back then, the company showed a wireless smart label that consisted of a woven antenna from electrically conductive yarn and a chip with integrated circuit for antifraud identification using radio frequency (RF) technology. At ITMA 2019, the company showed its NFM ® MDW ® — Multi Directional Weaving — machine weaving narrow fabric containing electrically conductive e-yarns from polyester/copper/silver with the aid of e-yarn guides that move the yarns out of the open reed and place them as desired to form fabric-based electronic circuits.
At ITMA 2023, Jakob Müller showed the NFM 53 2/84 MDW. Unlike the previous generation shown in 2019, the updated model uses a different methodology of laying in effect or functional yarns in strategic places to form a desired pattern. The MDW is equipped with effect or functional yarn guides with up to four guide bars available. The effect/functional yarns are moved downward aided by the guide bars. The weft yarn is then inserted to hold the effect/functional yarn in place, then the effect/functional yarn is incorporated to the fab-
ric following the beat-up. A strategic motion can be electronically preprogrammed to move the effect/functional yarn to either side by a specified distance and lower the yarn to interlace with the weft yarn. The steps are repeated to complete the targeted design. The calculated movement of the effect/functional yarn guides results in the formation of area covered with the yarn distributed with the desired pattern. The NFM 53 2/84 MDW machine was demonstrated forming an e-textile from polyester filament base fabric yarns and two conductive yarns containing copper and nickel controlled independently by two guide bars. Potential applications for this technology include e-textiles, fashionable textiles using colored and fancy yarns, and multidirectional yarns for enhanced performance in different directions other than the main directions of warp and weft. Currently, formation of 3D multidirectional preforms for fiber-reinforced composites is achieved by manually stacking of 2D woven fabrics at different angles to form semi-isotropic and other structures with enhanced properties at different directions, which is time consuming, subjected to labor errors, and costly. The MDW technology can be expanded for broad weaving to benefit the fiber-reinforced composite industry for forming wide preforms with laid-in multidirectional high-performance yarns.
On-loom fabric inspection systems have been developed to detect defects at the loom stage and trouble shoot the root cause of defects and thus avoiding the production of off quality fabrics that leads to reduction in fabric waste and increase in profit. One of the early systems was Batch Motion consisting of an off-loom fabric take-up, platform/stage for operator/inspector and inspection station. The inspection station is similar to postweaving manual inspection and relay on the weaver/ inspector’s eye to detect defects. There are several drawbacks associated with the batch motion and to eliminate manual or Batch Motion inspection, several automated on-loom fabric inspection systems with high-speed image capture using cameras and scanners were developed. Examples of these technologies include LOOM-TEX by Elbit Vision Systems , Israel, Cyclops by Duluth, Ga.-based Barco , and Fabricscan by Uster Technologies Ltd ., Switzerland. These systems can captureand store fabric defect images, identify and classify defects, report defects maps, and stop the weaving process based on the severity of the defect. The systems are installed between the front fabric rest and take-up rolls, which was an improvement over the manual post-
weaving and Batch Motion inspection. However, more than one meter of fabric passes the system before detection, which results in late discovery of fabric defects and leads to second quality product and waste. To avoid this serious disadvantage, Uster offers the Q-BAR 2 on-loom automatic fabric inspection system that was exhibited again at this ITMA. The scanner is installed right above the fabric formation area and covers the entire width, including the cloth fell, as well as the fabric length as the fabric is taken up for 100-percent quality fabric quality monitoring. The fabric is scanned right after each weft insertion so fabric inspection is not delayed. The Q-BAR 2 is equipped with a touchscreen visualization system. The system offers options for grading fabric rolls based of defect type, size, and location that can be defined based on the quality required in the end-use product.
While there are high volume instrument systems to measure fiber quality data that spinners use to optimize bale layout for production of high-quality and consistent yarn batches and monitoring quality of yarn of individual positions on winding machines, these data are not utilized by the weavers due to lack of available systems. Warp yarns are numerous and it is extremely difficult to make use of their quality data captured during the winding process during the weaving process. It is envisioned that the Uster Q-BAR 2 system may be used to monitor the warp yarns. Two monitoring locations may be feasible: to monitor the warp sheet between the warp take off point from the warp beam and web roll using additional unit; or, to monitor the warp and fabric quality using one unit. The latter approach is less expensive but more challenging as the reed moves — from the beat-up position to the most back position — and comes between the scanner and the warp sheet up to 1,500 times — equal to loom speed in ppm. However, this may be accounted for since the system uses high-speed cameras.
The ultimate goal of Industry 4.0 is to maximize productivity, efficiency and product quality through automation and digitization of technologies that allow communication between machines, software systems, and people via the Internet of Things throughout different stages of the pipeline required to manufacture a product. This can be achieved by cyber-physical systems and big
shedding systems, and automated style change system. There is a need for integration of the entire technologies required to manufacture wovenbased products from fibers since the productivity and quality are influenced by all the steps required to form them.
data/cloud storage to collect data from sensors and integrate them for analytics and artificial intelligence (AI). In terms of automation, weaving machine manufactures have developed numerous automated systems including warp stop motions, weft stop motions and automatic repair, monitoring stops and efficiency, adaptive weft control systems for airjet weaving for saving energy, automatic weave/pattern change, pre-programmed weft selection for intricacy and hybridization, preprogrammed variable machine speed, preprogrammed weft density, automatic on-loom fabric inspection, automatic smart drawing-in and tying-in machines, individual warp yarn control in jacquard, and individual harness control in dobby, among other automation technologies. More affordable automations are still required to achieve the goal of Industry 4.0, including automatic repair of broken warp yarns, multi-phase weaving that triples or quadruples productivity with dobby/jacquard
At this ITMA, weaving machine manufacturers continued to advance their technologies with high degree of digitization that allows machines to communicate and store big data relevant to the production and fabric quality that are accessible to users via intuitive use-friendly interface. Manufacturers’ software products are broad and varied, which poses challenges to companies housing machines from different manufacturers. Machines are driven digitally by proprietary and elaborate low-level computer code. A company with machines from different manufactures cannot integrate its production and quality data without adding significant cost. The integration must be done by collaboration between machine manufacturers to standardize data access and user interface or by a third party. The demand from customers may lead government agencies to regulation of standardization. Collaboration between companies that are not fully vertically integrated, such as greige fabric producers, are in need to collaborate with their suppliers and customers to take full advantage of digitization and Industry 4.0.
The complexity of the textile industry creates a need for a technical team with collective skills in textile technology and engineering, machine learning, AI models, computer programming language, mathematics, and statistics to achieve the goals of Industry 4.0. Vertically integrated companies may afford to build such a team. Those who cannot afford such a team may collaborate with their business partners or retain consultant firms in the field. How fast the textile industry completes the road to Industry 4.0 depends on the factors discussed above and perhaps more importantly on the economy. TW
While ITMA remains an event with limited composites offerings, plenty of compositerelated innovations were to be found at ITMA 2023.
By Prateeti UgaleTThe 19th international textile machinery show, ITMA 2023 was recently held in Milan. The “Olympics” of textile machinery exhibitions held every four years, has a 73-year history of displaying the latest technology for every single work process of garment making and textiles. Out of the many products specialized in various areas, this article focuses on the latest and existing machinery for textile reinforcement structures, composite processing machinery, and accessories for the same.
A composite is made up of at least two components that possess significantly different physical and chemical properties which when combined forms a material that possesses advantageous properties of all the base components. In textile reinforced composite, the two components are matrix, which is a polymeric bonding component and textile, which is a reinforcement. The resultant composite benefits from tensile strength of the textile reinforcement and compressive strength of the matrix. Common fibers used are carbon, glass, basalt, aramid, or natural fibers to provide strength to the
material whereas, matrix resins include materials like epoxy, polyurethane (PU) and others which function as glue to hold the reinforcement in place1. Braiding, nonwovens, knitting, weaving production techniques can be used to obtain reinforcement architecture. Composites have infinite applications including automotive, sports, aerospace, medicine, construction, and many others. The composite manufacturing process usually includes:
•prepreg — fiber architecture achieved through careful placement of fibers also called tape laying;
•impregnation — fibers and resins are comingled to form a composite; and
•consolidation — intimate contact is made between layers of fibers or lamina.
Composites can also use fillers, additives, and surface finish coatings depending on end-use applications. Lamination technique or process is another class of composite which involves manufacturing a material with multiple layers to achieve enduse properties like appearance and strength.
Braided Reinforcement Structures — Braided composites are at the forefront of the composite market due to their structural integrity and cost efficiency. The France-based Interreg North-West Europe (NWE) Program supported COBRACOMP project aims to develop, test, and validate a new automated textile braiding process to produce preforms for composite materials reinforcement. The organization displayed a section of its braider at ITMA. Higher mechanical performance is achieved with the innovative multilayer 3D axial braid assembly with more axial yarn, fiber fraction, and homogeneity. Composites expert Georges Cahuzac invented new architecture that has no gaps between unidirectional (UD) fibers, a bias to UD ratio of 5:4 equal to 80 percent and introduces four UD sections per layer. Front crash cone is an application that illustrates that this braid can absorb lots of energy due to the presence of UD yarns which help resist crack propagation.
Zhejiang Benfa Technology Co. Ltd., China, showed a hose braiding
machine at its stand. The braids produced from this braider are used as high-pressure wire hoses, Teflon hose, high pressure rubber hose and car airconditioning hose, among other applications. Its machinery can braid using stainless steel and aluminum wire as well as nylon, polyethylene and composite yarn material.
Germany-based HERZOG GmbH displayed SE 1/32-432 and SE 1/32266 rope braiding machines. Its GF 1/32-120 glass fiber braiding machine along with the take-up is used for producing fiberglass sleeving and for overbraiding hoses with fiberglass.
Nonwoven Reinforcement Structures — Germany-based AUTEFA Solutions converts carbon fiber waste by recycling carbon fibers to carbon fiber nonwovens. If the waste is resin-free it can be directly processed on AUTEFA machinery; if not, the resin needs to be removed using pyrolysis. The Aerodynamic Web forming Machine Airlay K 12 can produce a nonwoven with isotropic fiber orientation and medium fiber separation. Autefa Solutions’ Carbon Card can produce incredibly good fiber separation with UD orientation. The fiber orientation, surface weight and width of the nonwoven can be adjusted using Crosslapper TOPLINER in combination with the card. Its Needle Loom Stylus can process 100-percent carbon fibers and enable mechanical web bonding. By adding a thermoplastic, thermal bonded nonwovens can be produced using Thermobonding Oven HiPerTherm. Autefa is the key
supplier for carded-crosslapped needlepunch lines, aerodynamic web forming technology, thermobonding lines and spunlace lines.
Germany-based Dilo Group demonstrated brand new MicroPunch technology as alternative to hydroentangling. This is a “green” needling technology for lightweight nonwovens right from bale opening to final winding step. The technology is classified green because the trimmed material can be recycled within the process therefore there is no fiber loss and no water is consumed. These lightweight nonwovens — in the range of 30 to 40 grams per square meter (g/m 2 ) — may be used for applications including artificial leather and automotive, among other applications. Dilo’s inventions Hyperpunch and Cyclopunch have speed of 150 meters per min (m/min) and stroke frequency of 3,000 per minute. Dilo demonstrated the machine with a needle density of 45,000 needles per m per board, a barb depth of 20 to 40 microns, and throughput speed up to 140 m/min at 2,000 strokes/min. Dilo Group machines can also process aramids, glass fiber, P84 ® and polypropylene (PP), which is useful for composite applications.
Woven Reinforcement Structures — Germany-based Lindauer DORNIER GmbH’s A2 air-jet weaving machine debuted at ITMA 2023 and hence, its stall was very busy. This new machine provides improved efficiency, as well as enhanced flexibility and reliability to technical textiles. Electronically controlled systems
monitor and control reliable weft insertion. DORNIER Composite Systems® is designed to produce highquality reinforcement fabrics. World renowned, the P2 roving weaving machine produces reinforcement fabrics using carbon, glass and aramid fibers. Tritos® PP equipment manufactures multilayer textiles with complex structures for composite reinforcements using digital weave patterning, rapid rapier motion for low filamentation, and flexible shed geometry. Protos® TW is a tape weaving machine that can process strip-like materials such as fiber reinforcement tapes and films using zero twist feeder. Lastly, Protos® TP machine is used for UD tape which can be either be coated with a binder or impregnated with thermoplastic resin.
Switzerland-based Jacob Müller Group exhibited the Narrow Fabric Loom NFM 53 2/130, which can make spacer fabrics, tapes, rigid webbing and elastic ribbons with controlled thread transports suitable for all yarn types.
Knit Reinforcement Structures
— COMEZ International, a member of the Jacob Müller Group presented the DNBF/EL-800, an electronically controlled raschel type warp-knitting machine that can produce 3D knitted fabrics, tubular fabrics and nets for the automotive industry. It operates at a higher speed compared to the previous models. Müller also offers the NH2 53 8/27 needle loom that uses the Z6 weaving system to make spacer fabrics suitable as reinforcements in lightweight composite materials and can provide good compressive stability by incorporating monofilaments.
Germany-based Karl Mayer Group showed new digital developments and applications of artificial intelligence to change patterns without making manual adjustments. It demonstrated the HKS 3-M ON, which is the fastest three-bar tricot machine and a compact warp knitting machine, as well as a warp knitting machine with magazine weft insertion to produce technical textiles with
reduced weft yarn waste and increased working speed and width. The KM.ON dashboard is user-friendly and tackles the issue of global shortage of skilled workers. MULTI-MATIC® 32 Compact was the highlight in the warp preparation area. Karl Mayer also offers composite machines for producing biaxial and multiaxial textiles, fiber spreading lines and fiber reinforced thermoplastic tapes. BIAXTRONIC® II can produce biaxial layer structures; COP MAX 4 can produce multilayer, multi-axial structures; MAXTRONIC® can produce high performance glass fiber composites; and COP MAX 5 can process carbon fibers and lightweight textiles. UD 500 AND UD 700 are fiber spreading machines that can produce fiber tapes from continuous filament yarns. SIM.PLY UD can produce tapes up to a width of 800 millimeters (mm).
At ITMA 2023, Sweden-based IPCO AB highlighted its ThermoPress Systems and Scattering Systems. IPCO’s scatter system can deposit powdered, granular and fibrous materials onto a carrier material up to 1800-mm-wide. Applications include composites, nonwovens and textiles. ScatterPro F can scatter fibers like glass and carbon uniformly using key features such as a special agitator for uniform distribution, optimized scattering roller to hold the fibers, a rigid or adjustable doctor blade, easy change of the brush roller and a scattering roller with digital position display to adjust the distance between the two rollers.
IPCO manufactures double belt presses used in composites production. Its presses include ThermoPress TB, which has Teflon®-coated belts and counter pressure elements to make multi-layered materials, mixed thermoplastics, carbon fiber, glass fiber, and composite sandwich sheets. ThermoPress CB is used in making fiber-metal composites. ThermoPress SB is a high-pressure steel belt-based double belt press technology used to
make high performance metal-plastic composites. IPCO has a 1,600square-meter center of excellence testing center in Germany that has a full range of processes from impregnation, lamination, and consolidation to tempering and cooling. The company can consolidate pre-laminate sheets and impregnate fibers with resin which can be applied in liquid, film, or powder form on a felt or nonwoven material.
Germany-based BRÜCKNER
Trockentechnik GmbH & Co. KG, exhibited innovations for textile coating and finishing at ITMA 2023. Its finishing line for glass mesh fabric and for construction reinforcements
this application Meyer has laminating machines that can generate high pressure linearly as well as surface wise. These prepregs can be used in televisions, notebooks, mobile phones, the aviation and automotive industries and for lightweight construction components. The KFK-P is a high pressure at elevated temperatures laminator used for processing fiber reinforced composites and other composites. Some technical highlights are hydraulic belt tension, hydraulic pressure by the means of pressure rollers and pneumatic surface pressure.
Meyer also offers a production line to make glass mats from glass rovings with the help of a cutting unit
is the Techno-line TT glass fiber finishing line. OPTI-COAT KA/KC coating unit has a simple and compact design with combined floating knife-/knife against cylinder unit. Woven and knitted fabrics can be processed for end-use applications including technical lightweight protection materials and air bags.
Since 1949, Germany-based Maschinenfabrik Herbert Meyer GmbH has been making fusing, laminating, and scattering machines and presses. At its booth a Technical Sales representative mentioned that the company has bonding technology for composites like honeycomb sandwich sheets and fiber reinforcement composites; and for technical textiles like powder coating and impregnation. For prepregs, the flow behavior of the thermoplastic adhesive is important as the fibers need to be optimally encapsulated. Prepreg makes semi-finished products for end-use components. For
that cuts the roving into a defined length and spreads them evenly on a conveyor belt. Then a powder scatterer distributes the adhesive powder. An infrared preheating station helps fast melting of the adhesive to increase the production speed. Applications of the lamination and scattering machines are tempering and sintering of UD-/Machine Direction (MD)-layers, coating of UDtapes, thermoconsolidation of UD-/MD-layers, connecting of single UD-tapes to large-area layers and, production of UD-/MD tapes in different effective direction.
Meyer’s thermoconsolidation press is suitable for carbon layers or any other material that requires high processing temperatures. The temperature can go up to 400°C.
Italy-based Matex S.r.l. has expertise in coating and finishing machines since 1973. At ITMA 2023, it showed a reverse cylinder coating head with fea-
tures including independent driving system, tension control for adjustments with lightweight materials, trays for continuous recirculation, gap control using digital display, removable roller and cleaning tray which help with easy maintenance. The machines can do direct coating and transfer coating with a knife or rotating cylinder. Matex also has impregnation equipment such as Rotocomp for impregnation of composite substrates with carbon, glass, or aramid fibers. Rotocoat, Rotomark, Rotopharm, and Rotosplit are its lamination lines. End-use applications include soundproofing for offices, automotive and filtration.
Zappa Macchine S.r.l., Italy, was founded in 1860, and its long history brings experience and knowledge in hot melt lamination, coating, impregnation, calendaring, flock, prepreg and powder scattering. With coating head model HSM-2, blade in air and blade over roll coating is feasible. This technology is used in applications like prepregs, technical textiles and traditional textiles. The head can be customized per a customer’s requirements and has accurate blade gap settings. Width ranges from 500 to 6,000 mm, and mechanical speed is 0 to 40 m/min. The company also highlighted a rotogravure head that can coat different water-based resins on a fabric for the Brinatura “frosted” effect. It can apply micro-dots of resin using different engraved rollers. The head also may be used to apply special effects such as lamination with metallized film. The web width of this machine is 1,600 to 3,600 mm and mechanical speed is 0 to 40 m/min.
Italy-based COS.T.A. S.r.l. designs industrial lines for applications including synthetic leather, tannery, carbon fiber dip coating and furniture edge banding. COS.T.A. offers high-performance dip coating technology for carbon fiber, fiberglass and Kevlar® that can be used for prepreg preparation. The company also has lab lines for research and development, self-adhesive technology, technical textile laminations and hot melt lines.
Textilmaschinen GmbH & Co. KG presented the Montex®Coat coating unit which can coat using air knife, roller knife, magnetic doctor blade, rotary screen printing, paste and foam coatings — hence, can offer a lot of tailor-made solutions from one source. It has improved features including saving setting time, handheld control device, and automatic edge limiters for immediate adaptation to changing coating widths.
The Netherlands-based Van Wees UD and Crossply Technology B.V. entered the composite industry in 1994. The company is proud to be the only company to offer UD and multi-axial cross-ply technology. It manufactures UD thermoplastic resin impregnation machines, fabric prepreg (thermoset) impregnation machines, crossply machines, lamination lines, creels and other custom-built machines. It also offers product and development services at its Research and Technology Center (R&TC).
Van Wees displayed a variety of samples at ITMA including glass
fiber PP, a crossply roll of carbon fiber PP; materials used for soft applications such as sailcloth and flexible protection materials like bullet resistant vests; and flax fiber reinforced polymer.
At Van Wees, technology offers a spreading section, impregnation section, and final winding using tension control on every yarn. The fibers that may be process on these machines are glass, carbon, aramid fibers and ultrahigh-molecular-weight polyethylene (UHMWPE), which are converted to UD tapes using dispersion resin. These tapes are then used as raw materials for the multiaxial UD or crossply machines to make composites with various fiber orientations and layers.
The three machines Van Wees offers for impregnation of fibers and fabrics are dispersion impregnation, thermoset impregnation by reverse roller coater, and thermoplastic resin impregnation with inline extruder. The dispersion impregnation is stable with high impregnation due to easy penetration at the speed of 20 m/min. The thermoset prepregs are made in one step process by reverse roller coater at a speed of 3 to 10 m/min. For impregnation of thermoplastic resins, the film is made by melting the polymer in an extruder and metering the film thickness on impregnation roller at a speed of 3 to 15 m/min.
VanWees also has equipment for making flakes, which can be compression molded on a press to make make products. For flat panels, it has heated tables on which the materials is consolidated using vacuum pressure only. All the equipment used inhouse is commercially available.
Van Wees also has expertise in testing and consultation, and has inspection machines at its research facility, as well as drumwinders that can mimic the processes as it would take place in actual crossply and UD production.
Texmer GmbH & Co. KG, Germany, specializes in developing and supplying creels for all winding materi-
als that can be pulled off both tangentially and overhead. A motor on the creel calculates and controls tension from full bobbin to empty bobbin. The company developed patented tension balancing systems that provide a substantial number of adjusting possibilities. Texmer has experience with high-quality pneumatically braked creels characterized by short response times, high operational safety and extremely low wear. Diameter control secures trouble-free operations. These creels are made for technical yarns and tapes. Specially coated guide elements help reduce carbon fiber damage to a minimum and increase process reliability. It is particularly important for low yarn tension glass roving creels to have exact control. Pneumatic mandrels have unrolling solutions for glass fiber roving without a twist. The yarn comes in minimum contact with the Texmer creel and can be drawn as far as possible without deflection. A polyacrylonitrile (PAN) precursor creel can hold bobbin diameters up to 1,000 nanometers and weight up to 500 kilograms (kg). All positions are individually controlled. Once the controlling unit of the electronically controlled creels is adjusted it will maintain a required thread tension by accelerating or decelerating the motor during operation.
Topocrom GmbH , Germany, offers Topocrom ® surface structure for wear and corrosion protection that helps extend the service life of machine parts. It is challenging to process technical fibers such as carbon, aramid, glass and basalt fibers because they can be very abrasive. If the fiber filaments break, tear, stick or splice it can lead to interruptions in automated operations, which often happens because of the unsuitable surface of the guiding element.
Topocrom employs a chrome electroplating process. Base materials suitable for chrome plating include steel, steel alloys, cast iron, stainless steel, copper, copper alloys, titanium and titanium alloys. The roughness of the surface can be changed by altering the current during electroplating and
Topocrom coating can prevent splicing, wrapping, adhesion of filaments, reduce dust formation and increase wear resistance.
Van Wees also develops creels with features such as regulated yarn tension with manual or automated adjustment for each individual row or the entire creel. This is helpful when processing yarns like nylon, polyester, aramids, and UHMWPE. In the case of carbon fiber, it supplies special eyelets to avoid twisting the tows. Van Wees’ glass roving creel can handle heavy rolls up to 25 kg.
Switzerland-based Retech AG provides heat treatments for filament yarns with high-quality components, machines and in-process monitoring systems. The company demonstrated intriguing sustainable advancements for heated godets that are crucial in manufacturing synthetic yarns. Retech presented the new “blue line” temperature controller UCR-6/CR-7 and transmitter UTR-4 /UTR-4A The new devices are sustainable as they consume less energy, which reduces the overall cost while producing exceptional results. Retech presented its innovation in a customized draw frame with godet, Internet of Things (IOT) technology and (super) slow speed drive concept. It presented vibration measurements, bearing temperature display and induction temperature measurement; and its demonstration unit explained the negative temperature effects and vibrations. The newly developed algorithms, monitoring devices and sensors can achieve higher productivity, less downtime and a longer lifetime.
Germany-based Osthoff-Senge GmbH & Co. KG demonstrated one of its singeing machines that often is a first step in finishing. Woven and knitted fabrics comprised of cotton, viscose and glass fibers may be treated. The display machine was five feet wide and ran at a speed of 100 m/min.
Textile composites play a significant role as innovations in lightweight performance materials used in sleeves for
electron volt batteries or artificial leather for high-end fashion brands, among other applications. The theme for ITMA 2023 was “Transforming the World of Textiles” and the event featured 20 sectors of innovations including composites, although composite technologies remain a relatively small focus. Some companies specialize in composite technologies, while other companies are focused on manufacturing such as braiding, nonwovens, knitting and woven reinforcement that may be used in composite applications. At ITMA, several companies demonstrated the ability to process high-performance fibers on their machines, provide research and development consultation and testing and contract manufacturing. Overall, this year’s ITMA unveiled remarkable advancements in improving process sustainability by reducing waste and adding smarter and faster technologies to make machines more automated and efficient. TW
References:
1 Romeo RIM. (n.d.). What Are Composites? - Romeo RIM. Retrieved July 19, 2023, from https://romeorim. com/what-are-composites
Editor’s Note: Prateeti Ugale is a Ph.D. student in Fiber and Polymer Science and a research and teaching assistant at NC State University’s Wilson College of Textiles, Raleigh, N.C.
Brent Hyder has joined Denver-based VF Corp. as chief people officer. He reports to President and CEO Bracken Darrell.
The Italy-based Association of Italian Textile Machinery Manufacturers (ACIMIT) has appointed Giorgio Calculli managing director. He replaces Federico Pellegata, who after 25 years as managing director, is moving into a role as CEO of ACIMIT Servizi S.r.l., a company that provides services to its associated member companies to help promote and support the Italian textile machinery at home and abroad.
The board of directors at Albany International Corp., Rochester, N.H., has named Gunnar Kleveland the successor to Bill Higgins as president and CEO. Higgins is retiring, but will remain on Albany’s board.
Tom Gyles is the new senior vice president, Global Distribution Network in Canada, for Portland, Ore.-based Columbia Sportswear Co.
Standard Fiber, Foster City, Calif., has named Trina Solomon to the new position of vice president, marketing and brands.
Macy’s Inc. has joined the U.S. Cotton Trust Protocol, Memphis, Tenn. PrimaLoft Inc., Latham, N.Y., recently launched PrimaLoft® Utility, a resilient, man-made insulation material designed to excel in harsh conditions and last longer.
Blue Ridge Home Fashions, Irwindale, Calif., has introduced a new basic bedding collection — comprised of filled pillows, comforters, mattress pads, mattress toppers and blankets — featuring CiCLO® sustainable textile technol-
ogy from Intrinsic Advanced Materials LLC.
HanesBrands, WinstonSalem, N.C., has announced a multi-year licensing agreement for the design, production and distribution of Champion and C9 Champion outerwear in North America with New York City-based G-III Apparel Group Ltd.
Navis TubeTex, Lexington, N.C., is now a sales agent in Canada, Honduras and the United States for Germany-based SETEX a producer of controllers, sensors and software
Daren Abney was recently named executive director of the U.S. Cotton Trust Protocol.
Dr. Sanjay Patel has joined Navis TubeTex, Lexington, N.C., to lead the chemical applications product line and strengthen the company’s commitment to providing sustainable chemical finishing solutions.
San Francisco-based Gap Inc. has named Chris Blakeslee president and CEO of Athleta
Kontoor Brands, Greensboro, N.C., has appointed Pete Kidd executive vice
president and chief human resources officer.
Cincinnati-based Standard Textile Co. Inc. has named Jonathan Simon executive vice president of Global Growth and Strategy.
Markku Koivisto, senior vice president, Europe and R&D at Helsinki-based Suominen, has been named interim senior vice president, Americas. Lynda Kelly, senior vice president, Americas and Business Development, has left the company for medical reasons. The company has started the search for a new senior vice president, Americas. TW
solutions for textile dyeing and finishing operations.
Cone Denim®, Greensboro, N.C., has joined the CIRCULOSE® Supplier Network. It reports it is the first U.S.-based denim mill to join the network, which comprises yarn and textile manufacturers committed to streamlining and increasing the production of Circulose, a cellulosic fiber made using waste material.
Switzerland-based electronic warp feeding system provider Crealet AG is celebrating its 20th anniversary.
Aurora Specialty Textiles Group, Yorkville, Ill., recently celebrated 140 years of continuously manufacturing products in the United States.
New York City-based denim brand Madewell has become a bluesign® System Partner.
Montreal-based Gildan Activewear Inc. recently published its 19th Environmental, Social and Governance (ESG) report, which highlights the companies 2022 performance against key targets. TW
9-10 :Filter Media Training Course, organized by the Association of the Nonwoven Fabrics Industry (INDA), Navy Pier,Chicago.Visit filtxpo.com /training.html.
11 :Southern Textile Association (STA) Northern Division Fall Meeting, Manufacturing Solutions Center at Catawba Valley Community College, Conover,N.C.Visit southerntextile org.
10-12 :FiltXPO™ 2023,organized by INDA,Navy Pier,Chicago.Visit filtxpo.com.
22-25 :38th World Fashion Convention hosted by SPESA and the International Apparel Federation (IAF),the Bellevue
Hotel,Philadelphia.Visit spesaassociation.org/world-fashionconvention.
24-27 :Intermediate Nonwovens Training Course,organized by INDA Headquarters,Cary,N.C.Visit inda.org.
26-27 :Synthetic Yarn and Fabric Association (SYFA)Fall 2023 Conference,Sheraton Charlotte Airport Hotel,Charlotte,S.C. Visit thesyfa.org.
30-November 2 :CAMX 2023 — the Composites and Advanced Materials Expo,Georgia World Congress Center, Atlanta,Ga.Visit thecamx.org.
1-3 :Advanced Textiles Expo 2023, organized by the Advanced Textiles Association (ATA),Orange County Convention Center,Orlando,Fla. Visit advancedtextilesexpo.com.
13-16 :Hygienix™ 2023,organized by INDA,The Roosevelt New Orleans Hotel, New Orleans,La.Visit hygienix.org.
15 :STA Southern Division Fall Meeting, Courtyard by Marriott Downtown, Greenville,S.C.Visit southerntextile.org.
28-30 :Americas Apparel Producers’ Network (AAPN) Honduras regional meeting and mill/factory tours,San Pedro Sula,Honduras.Visit aapnetwork.net.
Cotton Incorporated’s RESTech COTTON™ technology imparts increased softness, moisture management properties and durability to cotton sheeting for a more restful night’s sleep.
CONTACTS:
For more information on RESTech COTTON™ please visit cottonworks.com /restech-cotton. Go online to TextileWorld.com for archived Quality Fabric articles.
WWhen polled by Cary, N.C.-based Cotton Incorporated as part of a Home Textiles Survey, 79 percent of respondents said quality is a priority when choosing sheets, 70 percent actively seek 100-percent cotton goods and quality bedding translates to better sleep according to 87 percent of people polled. In addition, 71 percent express a desire for environmentally friendly textiles.
Cotton Incorporated’s latest innovation, RESTech COTTON, uses advanced chemistry to create a 100-percent cotton sheeting solution that checks all the boxes to meet those consumer concerns and produce a restful night’s sleep. The company reports the technology brings comfort, durability and softness to sheeting products, while remaining an ecofriendly choice because it’s biodegradable and recyclable.
According to Cotton Incorporated, RESTech COTTON-treated sheets are up to 40-percent softer than untreated cotton sheets, with durability that beats polyester and rayon when tested against ASTM D3885 – Standard Test Method for Abrasion Resistance of Textile Fabrics. In addition, RESTech boosts the natural moisture management and thermoregulating properties of cotton, and may dry up to 50-percent faster on the skin, thus providing cool comfort for hot sleepers. Cotton also is a naturally hypoallergenic fiber that is gentle on the skin for people with skin sensitivities.
The technology is applied as a finish
using a standard pad-dry-cure application after the sheets have either been bleached to a finish white or dyed.
According to Mark Messura, senior vice president, global supply chain marketing for Cotton Incorporated, the cotton-specific innovation was designed for practical implementation and may be licensed from the company with the only requirement that it be used on 100-percent cotton fibers. However, there may be further applications for the technology that will be introduced in the future.
“RESTech COTTON technology takes the best attributes of cotton and cotton finishes to create a unique, durable product with non-fluorine technology,” noted Dr. Hongqing “Mike” Shen, vice president and managing director of product development and implementation for Cotton Incorporated. “It allows sheets to hold less moisture, dry more quickly, maintains remarkable softness and comfort. This combination makes it a triple threat.”
“With our RESTech COTTON technology, we’ve captured the timeless comfort of cotton and enhanced it with modern innovation, redefining the possibilities of a good night’s sleep,” said Jennifer Lukowiak, director, supply chain marketing, for Cotton Incorporated. “This technology is a perfect choice for those seeking not just better sleep but a more sustainable one. It’s another proud milestone in our continuous effort to promote the natural excellence of cotton.” TW