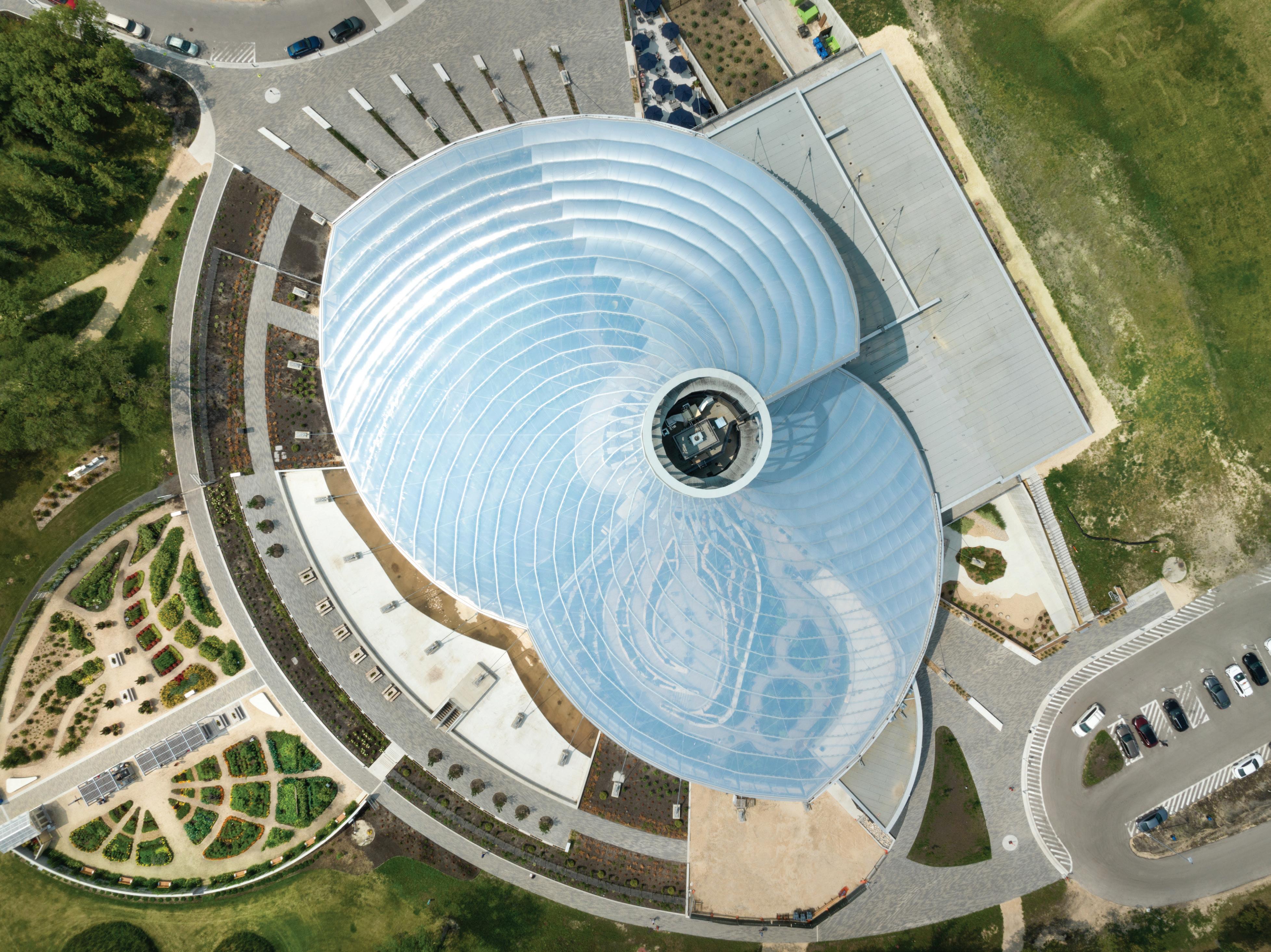
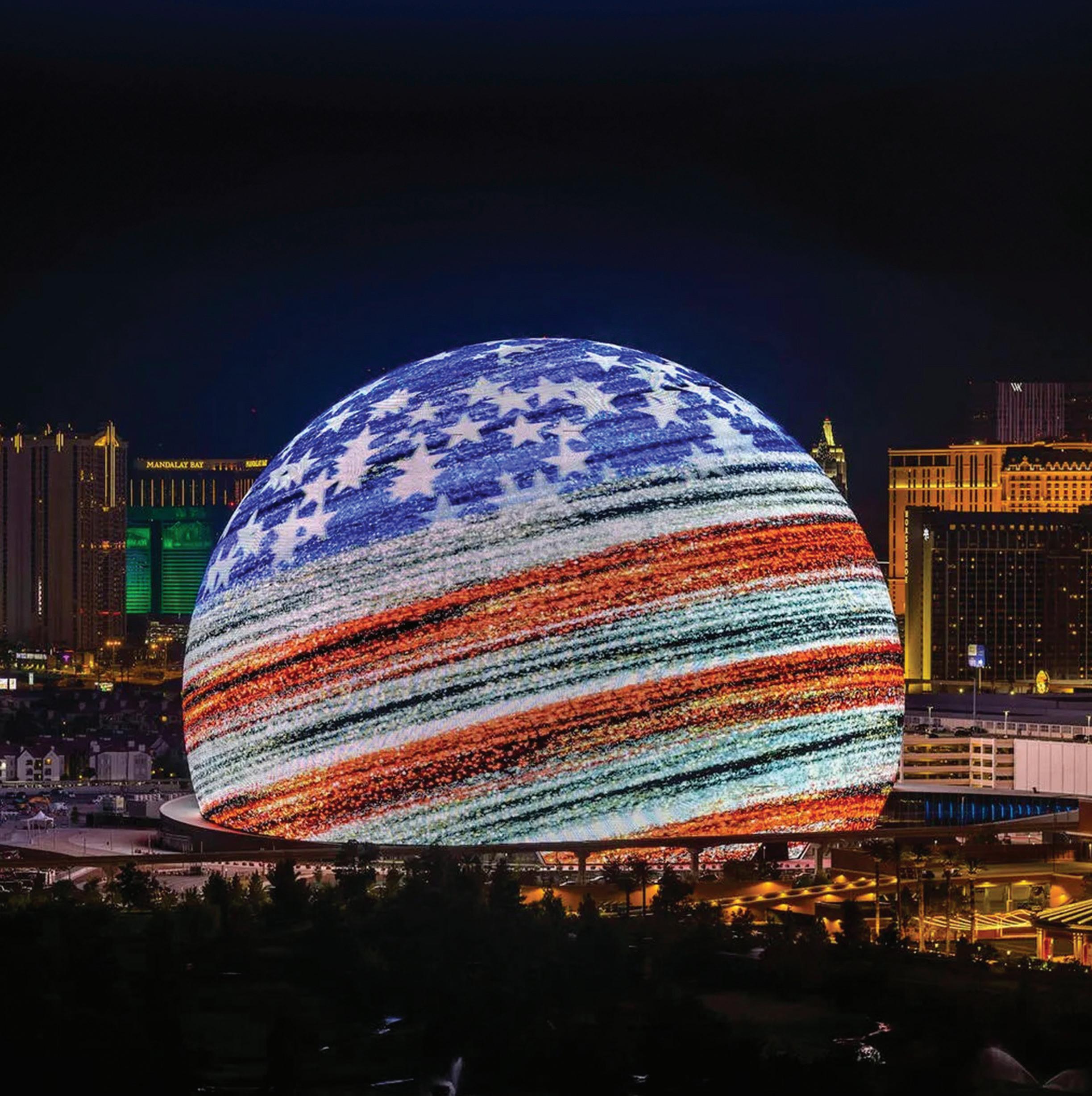
The venue’s massive, semispherical frame sits just south of Sands Avenue and east of Las Vegas Boulevard. The Sphere’s revolutionary design takes up 750,000 square feet and comfortably seats 18,500 concertgoers. It boasts an eye-catching steel frame that has quickly become a landmark representative of the world-class entertainment and recreation that Las Vegas has to offer.
To meet the Sphere’s aesthetic requirements, the engineering design called for unique sizes of round hollow structural sections (HSS) Atlas Tube was chosen as a partner due to its ability to quickly tool up, produce, and deliver those unique sizes within North America.
Atlas’ Engineering Support team had worked with fabricator W&W | AFCO on challenging projects before, and the existing partnership paved the way for collaboration that made the project a success. Achieving the intended vision of the Sphere required HSS sizes that are listed in the AISC Steel Manual but have never been rolled by Atlas Tube. Atlas invested in the necessary tooling to create the full range of required sizes for W&W, ultimately producing 2,460 tons of HSS The strict quality standards of Atlas’ 100% domestically made steel combined with its wealth of experience and expertise with custom tooling and logistics helped W&W | AFCO deliver the project on time.
Though simple from the outside, the Sphere is composed of several interacting structural systems:
• A pile-supported foundation
• A structure supporting interior seating and vertical transportation
• The parametrically designed exterior skeleton, known as the geosphere
• A domed roof below the geosphere that supports an all-encompassing screen over the concert venue
The round HSS members of the geosphere are connected to custom nodes produced by Cast Connex, which reduced fabrication cost and provided precise, repeatable geometry at each of the many connection points.
These parts work in perfect balance to create a unique, jaw-dropping superstructure that greatly benefits from the HSS compact profile and its unique ability to accomplish the engineering and architectural goals of the project.
In addition to the Sphere itself, the venue features a 1,200-foot-long off-site pedestrian bridge with a unique serpentine pattern that connects the Sphere to the larger Las Vegas Strip. The bridge features a metal walking deck and a metal deck roof, founded on pipe piles just like the Sphere.
Ultimately, Atlas Tube’s ability to quickly set up custom tooling for uncommon sizes of HSS, close relationships with fabricators, and its speed of delivery helped to make the Sphere one of the world’s premier concert venues and a contemporary American icon.
Owner: Sphere Entertainment Company
General Contractor: MSG LV Construction LLC
Architect: Populous
Structural Engineer: Severud Associates
Erection Engineer: Stanley D. Lindsey and Associates Ltd.
Steel Team
Fabricator and Erector:
W&W | AFCO Steel
Detailer: Prodraft Inc.
Bender-Rollers: Max Weiss Co.; Chicago Metal Rolled Products
Casting Manufacturer: Cast Connex
750,000 SQUARE FEET
18,500 SEATS
2,460
Scan for a downloadable copy of the project highlight. More on the design and engineering of Las Vegas’ Sphere is covered in Modern Steel Construction and Informed Infrastructure. To learn more about Atlas or to discuss your design ambitions, call 800.733.5683 or visit atlastube.com
Chair John A. Dal Pino, SE Claremont Engineers Inc., Oakland, CA chair@STRUCTUREmag.org
Marshall Carman, PE, SE Schaefer, Cincinnati, Ohio
Erin Conaway, PE AISC, Littleton, CO
Sarah Evans, PE Walter P Moore, Houston, TX
Linda M. Kaplan, PE Pennoni, Pittsburgh, PA
Nicholas Lang, PE
Vice President Engineering & Advocacy, Masonry Concrete Masonry and Hardscapes Association (CMHA)
Jessica Mandrick, PE, SE, LEED AP Gilsanz Murray Steficek, LLP, New York, NY
Jason McCool, PE
Cool Country Engineering PLLC,Cabot, AR
Brian W. Miller
Cast Connex Corporation, Davis, CA
Evans Mountzouris, PE Retired, Milford, CT
Kenneth Ogorzalek, PE, SE KPFF Consulting Engineers, San Francisco, CA (WI)
John “Buddy” Showalter, PE International Code Council, Washington, DC
Eytan Solomon, PE, LEED AP Silman, New York, NY
Jeannette M. Torrents, PE, SE, LEED AP JVA, Inc., Boulder, CO
EDITORIAL STAFF
Executive Editor Alfred Spada aspada@ncsea.com
Managing Editor Shannon Wetzel swetzel@structuremag.org
Production production@structuremag.org
MARKETING & ADVERTISING SALES
Director for Sales, Marketing & Business Development
Monica Shripka Tel: 773-974-6561 monica.shripka@STRUCTUREmag.org
subscriptions@structuremag.org
CAST CONNEX ® custom steel castings allow for projects previously unachievable by conventional fabrication methods.
Innovative steel castings reduce construction time and costs, and provide enhanced connection strength, ductility, and fatigue resistance.
Freeform castings allow for flexible building and bridge geometry, enabling architects and engineers to realize their design ambitions.
Custom Cast Solutions simplify complex and repetitive connections and are ideal for architecturally exposed applications.
SALESFORCE TRANSIT CENTER, CA
Architect: Pelli Clarke & Partners, and Adamson Associates
Structural Engineer: Thornton Tomasetti, and Schlaich Bergermann Partner
Structural Steel: Skanska
Photography by Jason O’Rear Photography
By David Bowick, P.Eng.
The structural systems and details of “The Leaf" at Canada’s Diversity Gardens, Assiniboine Park in Winnipeg, reflect biophilic design.
By Kevin Shelley, AIA, LEED AP, Scott Clore, PE, and Michael Roach, PE
Structural engineers and architects collaborated on a year-round multi-purpose venue at Indiana’s historic pavilion.
By Kurt Bloch, SE, and Julie Shaw, PE
The structural systems at the new Washington University School of Medicine Jeffrey T. Fort Neuroscience Research Building needed to accommodate ever-evolving needs of the research groups.
ASTERI ITHACA By Cody Gibbens, PE
The project delivered a conference center as well as affordable housing to the growing city.
Edmond Saliklis, Ph.D,
By Andrew Lovenstein, PE, SI
One of the things that I enjoy about being a professional engineer is the sense of community. As with all communities, there is a social contract where along with the benefits to be gained is a responsibility to give back. The benefits gained include sharing our collaborative knowledge to strengthen building codes and industry standards, as well as receiving continuing education to keep current with our profession. As for giving back to the community, one way that I’ve found to help our larger community is through disaster response. There are two primary ways to help with disaster response, and I have been active in both for many years.
When a natural disaster has a large area of effect, many buildings may become damaged. The local Building Departments, as well as state or regional Emergency Operations Centers have to check buildings to make sure they are habitable and/or have to be evacuated until repairs are made. SEER volunteers make a quick evaluation of the homes or commercial structures, notify the owners of the building’s status, and provide that status to the local Building Department.
How to Join: The first step is to take one of two classes on how to evaluate structures. One class is “When Disaster Strikes,” presented by The International Code Council (ICC). The other class is the California Office of Emergency Services’ Safety Assessment Program. These classes are offered several times a year by industry groups, including local state structural engineers associations. NCSEA offers training through its CalOES Safety Assessment Program, which is compliant with the requirements of the Federal Resource Typing Standards for engineer emergency responders. The next training will take place this fall.
How the Process Works: After a natural disaster, the local Building Departments or Emergency Operation Centers (AHJ) determine how many SEER volunteers will be needed. They will then reach out to the Disaster Response Alliance, which will review the database of volunteers. After the volunteer has been contacted and agreed to be deployed, they will travel to the area of the natural disaster and work with the Building Departments to evaluate the buildings. The inspection plan and locations will be provided to the volunteers by the local Authority Having Jurisdiction (AHJ). The volunteers will conduct their inspections on the structures designated by the AHJ and report their data back to the AHJ each evening. Typical deployment occurs a couple weeks after the natural disaster for a week or two.
Who Can Volunteer: A volunteer does not have to be a Professional Engineer, but Professional Engineers are greatly appreciated. A volunteer must complete one of the two classes listed above, and the volunteer must be signed up on the Disaster Response Alliance database.
efforts are underway, and provide advice on shoring damaged elements of the structure so that the rescuers are in the safest conditions possible. Other specialists on a USAR team include medical doctors, rescue dog handlers, experts in crane lifting, and drone pilots.
How to Join: The first step is to find the closest Urban Search and Rescue team. Every USAR team has a lead Structural Specialist whose name can be found by contacting the USAR team. A volunteer should contact the Lead Structural Specialist and express interest in joining the team.
After joining a team, the volunteer will be sent to Structural Specialist Training conducted by the U.S. Army Corps of Engineers. This training is a week-long class focused on using building monitoring equipment, shoring techniques and guidelines, and hands-on experience in conducting building evaluations and search operations.
The ICC and NCSEA together created the Disaster Response Alliance, which maintains a single, national database of skilled volunteers willing to help with response and recovery activities. After taking one of the two classes on how to evaluate structures, a volunteer can sign up to be placed in this database, which is located at the Disaster Response Alliance website: Disasterresponse.org/register.
Urban Search and Rescue (USAR) teams deploy after natural disasters, such as earthquakes and hurricanes. They also respond after a building collapses. The teams are organized by individual states. Some state teams are also designated to be Federal Government FEMA teams. USAR teams are typically made up of firefighters who conduct rescue operations, as well Structural Specialists, who assist the rescuers with the evaluation of buildings, monitor damaged buildings while rescue
How the Process Works: After a natural disaster or building collapse, states and FEMA will activate the USAR teams. This can actually occur before the disaster, in the case of a hurricane. The Structural Specialists deploy with the rescue teams to conduct search and rescue operations. Some FEMA teams deploy internationally for disaster response, as well. When a USAR team is activated, the team and all its gear are loaded onto transportation and sent to the affected area. A typical deployment can last between one and three weeks.
Who Can Volunteer: A volunteer must be a professional engineer with experience in buildings, construction, and building evaluations.
Disasters happen, and we as engineers are uniquely qualified to help save additional lives and infrastructure by ensuring rescue and recovery efforts are performed safely. Volunteering is rewarding both on a professional and personal level. ■
A city-owned site in Boulder, Colorado, is a success story for deconstruction, stockpiling, and reuse of structural steel.
By Alexis Feitel, PE, and Dan Bergsagel, C.Eng., MICE
Boulder, Colorado, is one North American city advancing circular economy practices. Aiming to reduce its emissions by 80% by 2050 and become “zero-waste,” Boulder passed Deconstruction Ordinance 8366 in 2020, which requires residential and commercial deconstruction projects to divert 75% of materials by weight from landfills, via recycling or reuse. This case study describes Boulder’s exemplary circular economy project, focusing on the deconstruction, stockpiling, and reuse of salvaged structural steel from the Boulder Community Hospital for Boulder’s new Fire Station 3.
A circular economy prioritizes sharing, leasing, reusing, repairing, and recycling existing materials and products (i.e. structural components) for as long as possible, reducing environmental impacts compared to the prevailing linear economy, which relies on a limitless supply of cheap, easily accessible materials and energy. Extending the lifecycle of construction products prevents waste to landfill, resource extraction, and embodied carbon emissions associated with manufacturing. Often, buildings are demolished and their components landfilled— not because they are in deterioration but because they have lost their aesthetic or functional value. Many buildings are deemed too costly to convert to a new occupancy type, requiring major structural modifications and material replacement. The building may no longer have value, but what about its components?
Components such as structural steel beams and columns can be recovered through deconstruction, which is the intentional disassembly of a building or structure to prevent damage to components. Although a typical hot-rolled structural steel section contains 93% recycled content on average, 89% of the product’s manufacturing emissions are attributed to the melting and processing of the raw material, billet casting, and rolling to shape according to the American Institute of Steel Construction’s industry average Environmental Product Declaration (EPD). The emissions from high-energy processes to produce molten steel and form shapes are avoided by reusing components directly. While some companies such as Rheaply, Building Ease, and All for
Reuse have developed material exchange databases for non-structural salvaged components, North America lacks circular economy infrastructure and at-scale salvaged material markets. A few North American municipalities have reuse and landfill diversion legislation, mainly for non-structural materials or dimensional lumber. This policy landscape contrasts with Europe’s recent policies and expansion of commercial markets that enable structural component reuse in London, Belgium, and the Netherlands. The reuse of structural components is unique in that geometry, material properties, and structural integrity must be well documented or at least discoverable, to enable reuse in structural applications due to life-safety requirements. This adds burden to structural materials that is not present for non-structural materials.
The city-owned Boulder Community Hospital (BCH), a roughly 250,000 square-foot building, was sustainably deconstructed in 2023. For this building, the goals were to achieve 90% waste diversion, prioritize reuse, and illustrate the potential for a circular economy and long-term material stockpile within the city. The project achieved 93.5% landfill diversion of all interior and exterior materials by
optimized for localized loading conditions and are therefore inappropriate for general structural reuse, requiring reverse engineering. Steel members that have experienced cyclical loading, plastic deformation, or other unique loading conditions may not be suitable for structural reuse. Component characteristics and installed conditions affect the ease and challenges of recovery and reuse. A member may be easy to recover and lack reuse application. Inversely, a member may be challenging to recover but have high value.
KL&A authored a Steel Deconstruction Specification that detailed cut locations, level of cleanup, and piece-marking requirements. It defined the resulting condition of the steel pieces which allowed new construction projects to bid the fabrication scope appropriately. The purpose of defining cut locations was to balance the ease of deconstruction with recovering as much of the members’ length as possible. It was anticipated that 12 inches would be removed from each end at some point during the process. An average of 27 inches total was removed from the original length of Source A pieces.
The deconstruction team recovered 30 beams per day. The “flying time” of the Source A beams was 12 minutes, from removal to setting on the ground. Source B recovery was much faster, primarily because it was a single-story structure, and the team was familiar with having completed Source A. It is estimated that fewer than 30 pieces (5%) were damaged and therefore unsuitable for structural reuse. These pieces were either recycled, used for material testing then recycled, reserved for non-structural applications, or used as stockpile dunnage.
At the time of this writing, the BCH deconstruction costs are still being analyzed and cannot be reported in detail. The total cost of deconstruction (interior plus core and shell) was $9.2 million, compared to an estimated demolition cost of $7.7 million, a $1.5 million (19%) premium. The floor area of Source A and B was roughly 18% of BCH.
The order of operations varied between the two sources, primarily due to the availability of structural drawings for Source A and lack thereof for B. For example, fireproofing was removed from Source A steel, and each component was piece-marked to match the digital inventory before deconstruction. However, Source B fireproofing was removed in situ, further cleaned off while on the ground, then
piece-marked, and then inventoried.
Member cleanup consisted of removing fireproofing and accessory material (plates, appendages, etc.). 90% of fireproofing, within any 6 square-inches of surface area, was removed onsite. This is not considered unique to deconstruction versus demolition, as metals recycling facilities typically do not accept steel with fireproofing, or they accept it at a lower value because it must be removed eventually. All accessory material that extended beyond the boundary of the member’s cross-sectional area was removed onsite, except for material that extended a significant length along the member, such as welded deck-edge angle. The purpose of cleanup was to ease handling during recovery, vertical stacking at the stockpile, transportation, and processing by fabrication equipment which often uses rolling conveyors. A stockpile endeavor should balance cleanup effort against the intended end-use, time, cost-sharing, and ease of handling. New projects may be unconcerned about extraneous material or even decide to highlight those features as part of their aesthetic and project brand.
A physical and digital inventory was created to document, track, and identify individual pieces of steel. The digital inventory housed component characteristics, as well as logistical information like the specific location in the physical stockpile, if it was to be sampled for material testing, and claims by new projects. The inventory tracked total tonnage, embodied carbon savings, and estimated cost compared to standard new steel.
Measurements and photos were taken onsite, and descriptive information was recorded, such as general condition (finish, corrosion), accessory material and holes (connections, penetrations), observed damage (excessive bend, missing material), and observed geometry (camber, sweep, tilt). This was used to develop individual cut sheets, assign historic AISC Manual of Steel Construction shape categories (e.g. W14x22), and flag any noteworthy conditions for the end-user.
There is no industry standard or code requirements for testing and validating salvaged steel for structural reuse in North America,
This case study is part of a new database of circular economy projects published by the ASCE SEI Sustainability Committee’s Circular Economy Working Group. For more information about the database and for information on submitting case studies please visit https://se2050.org/ resources-overview/case-studies/.
although protocols have been developed for other regions. KL&A developed a testing protocol, based on recommendations from ASCE 41-13: Seismic Evaluation and Retrofit of Existing Buildings and the Steel Construction Institute’s Structural Steel Reuse: Assessment, Testing and Design Principles.
Samples were taken and tested to estimate the properties of size categories within each source rather than from every piece. ASTM A370 tension testing was performed on 10% of the pieces in each size category and ASTM A751 chemical analysis testing, to verify weldability, was performed on 10% of the total quantity of pieces. The third-party laboratory required 1x8” samples and cost about $100 per sample. Additional testing may be necessary based on the source and end-use.
Based on the dates of construction and available documentation, it was anticipated and validated by testing that the wide-flange members are equivalent to ASTM A36 and tube members equivalent to ASTM A500 Gr. B. All the samples confirmed weldability, with some results recommending preheating procedures.
The financial feasibility of deconstruction is directly tied to connecting an end-use of the recovered material, whether it be specific or a general resale market opportunity. Understanding the ability of Fire Station 3 to utilize pieces from BCH was critical to moving forward with recovery.
The uncertainty of logistics, cost, and risk is a significant barrier to innovation. The cited motivations of projects that engaged with the stockpile were sustainability goals (embodied carbon reduction), appetite for innovation, project brand differentiation, and material cost savings. It was evident that the reliability of member sizes, geometry, and material testing results of salvaged structural components are highly desirable to new projects before design implementation.
The Fire Station 3 structural design team claimed pieces from the inventory during Design Development to incorporate into roof framing over the apparatus bay and mechanical screen framing atop the roof. The sizes and anticipated strength were incorporated into the analysis model. The structural Construction Documents noted in plan the locations for the intended use of the steel. Full Metal Iron retrieved and transported the pieces from the BCH stockpile to their fabrication shop. After a final cleaning, the fabrication process was reported to be seamless and like that of new steel. It was successfully installed in 2023. There were no reported differences in fabrication or installation costs and schedules, and the steel was procured at zero cost to Fire Station 3. This resulted in net cost savings of 0.5% of the total steel contract because the material savings outweighed the fabricator’s cost to transport and clean the steel. In the future, policy requirements and consumer demand will be strong motivations to consider salvaged structural materials. It is
and HSS pieces rest at the BCH stockpile (credit:
reasonable to speculate that the use of salvaged steel in new construction can be cost-competitive, even when considering a resale value.
This project illustrates that at-scale deconstruction and reuse of structural steel components is possible and financially feasible. The necessary change in behavior, priorities, and incentives is more challenging to overcome than the technical and logistical aspects. To advance structural material recovery and reuse, several topics arisepolicy and incentives, protocol and code development, Environmental Product Declaration development, collaboration among building stock and new construction, specialty business opportunities, technology opportunities, and design for deconstruction (DfD). Through concerted efforts, strategic initiatives, collaboration, and reinvention the construction industry can pave the way for circular economy, embodied carbon reductions, and environmental stewardship.
Full references are included in the online version of the article at STRUCTUREmag.org .
Alexis Feitel is the project manager for the Boulder Community Hospital salvaged steel. She co-founded and leads KL&A Engineers & Builders’ Team Carbon. She is on the steering committee of ASCE Structural Engineering Institute’s (SEI) Sustainability Committee and a contributing Circular Economy Working Group member. (afeitel@klaa.com)
Dan Bergsagel leads schlaich bergermann partner’s sustainability brief from their NYC office and is a visiting scholar at Cornell AAP’s Circular Construction Lab. He chairs the ASCE Structural Engineering Institute’s (SEI) Sustainability Committee Circular Economy Working Group. (d.bergsagel@sbp.de)
See how high-strength steel is enabling sustainable design. nucor.com/madeforgood
Developers can see end-of-life profits from deconstruction by considering engineering pre-planning in new structure builds.
By Steven Anastasio, PE
"Built-to-last” has been an underlying mantra in the field of structural engineering. When we pen structures onto the boards, we draw them to be more durable than any of the other building systems, so we can’t fathom the end of life of the building. We design with the expectation that the structures will become fixtures on earth indefinitely, or at least to outlive ourselves.
Because of this, there is less motivation to plan for the back end of the building life cycle, especially in a developer driven industry, and when it can seem daunting to even predict the trends 20 years out.
Some trends are apparent right now, though. Buildings are becoming lighter and more efficient, technology and trends are changing more frequently, and methods of construction, deconstruction, and reconstruction are improving.
While recycling is a good strategy, it is not the overall goal. The overall goal is to have a circular economy where materials are reused for similar items as many times as they can before they are recycled.
The practice of incorporating deconstruction into the lifecycle of a building has been around for decades, albeit on the fringes because of the speed and lower cost of the wrecking ball and landfill placement. Now with sustainability requirements and lower carbon mandates, along with rising landfill prices, the time for serious consideration of building end-of-life and recycling has become imperative to consider early in the construction process. As the Urban Land Institute/PWC’s 2024 Emerging Trends Report recently stated, “Real estate professionals can no longer ignore the embodied carbon elephant in the room, and stakeholders are putting on the pressure from all angles to address the issue.”
In a 600,000 square-foot multi-family high rise of 48 stories which utilizes cast-in-place concrete, the embodied carbon makes up 38% of the total carbon in the building with the structure itself making up 63% of the 38%. So, if you look at the overall operational and embodied carbon in the entire building—the structure alone makes up 24%. Traditionally, when the lifecycle of that building expires, the owner has the option to reallocate for a different purpose, if the structure and systems make that feasible. If not, the structure will be demolished, taking with it all of that embodied carbon and sending it to the landfill. This is a huge waste and potentially a missed opportunity to gain the associated revenues for reusing, recycling, and reallocating materials. More developers are now exploring strategies for deconstruction of a building from the onset of the construction cycle. This early focus allows them to see the potential for reselling the materials at the terminus of the building, while incorporating sustainability practices. This has led to active conversations with architects and engineers about planning for deconstruction.
In 2018, the EPA estimated that 600 million tons of Construction & Demolition (C&D) debris were generated, and the average building demolition created 155 pounds of waste per square foot of building area. A 50,000-square-foot building creates 3,875 tons of debris when it is demolished and carted away. Currently, the industry is selectively recycling building components.
If the debris is elected to be directed to a recycling plant in broken rubble form—the components are separated and resold either in the component’s same use or downgraded for other uses. This recycling process is laborious and mechanically intensive. For instance, concrete is crushed down, and an Eddie current separator sorts the metals. Wooden material and foams are separated in a water bath. It is estimated that three-quarters of construction waste can be recycled; however, about one-third is recovered.
Recycling construction materials is difficult. That's why deconstruction is so important. The structural materials take up a huge portion of the landfill, often making it more impactful. The architectural products are certainly more complex to deal with, but when everything goes into a landfill and isn't considered for recycling, the size matters most.
To bridge this gap, it is on the design professionals to specify and design buildings that facilitate reuse and recycling after demolition.
Demolition is complete disposal, whereas the EPA Resource Conservation and Recovery Act (RCRA) defines deconstruction as “the selective disassembly of buildings to facilitate the reuse or recycling of valuable materials.” Focused on salvage, this method takes whole, or partial, components of a structure and carefully disconnects them. For example, a connection that can be unscrewed is much easier than a welded one which requires more invasive disconnection measures that could compromise reuse. It’s essentially going in the reverse order of building a structure. You start first by removing finishes and fixtures and then progress to the structural elements, like electrical and plumbing infrastructure, and then to the core structural elements such as beams and trusses. Reuseable/recyclable elements are then resold or stored for reuse.
Good candidates for deconstruction are buildings with short life cycles, or re-location cycles, such as those for retail, health-clinics and task-oriented buildings (storage, showroom, military, classrooms and agriculture). By assessing the lifespan of the building—is it more permanent or temporary—a developer can get an idea of the kind of construction that lends itself to deconstructability. For a use that will change frequently (yearly), a highly temporary construction—like a shipping container—works well and provides flexibility for new uses. A use that will be maintained for one to five years can use modular box construction and panelization of components for easy disassembly. For a building that will have a low turnover frequency—five to ten years—conventional and durable materials can be bolted together and disassembled in part, or as a whole.
A fine example of deconstruction reuse can be found at the Terrain Gardens at Devon Yards in Devon, Pennsylvania. Terrain is a garden center and restaurant that has incorporated indoor/outdoor event space into
their operations. Focused on creating an immersive natural experience for their retail space and events, Terrain reused steel trusses from a University of Maryland structure that had used bolted connections for easy disassembly and then reconnected them in the new space to form the framework of their new venue. The result was a one-of-akind, sustainable setting that supported the values of the organization.
To effectively plan for deconstruction from an engineering perspective, the original building concept needs to include:
The world‘s largest database of 400,000+ pre-designed 2D/3D connections, base plates, HSS connections, steel-to-timber, and other connection types
Model and design any bolted or welded connection
Comply with AISC checks, including advanced analyses
Fully customizable reports with equations and graphics
BIM integrations with SAP2000, STAAD.PRO, SDS/2, RISA, TEKLA, REVIT, export to IFC, and many more
Enabling parametric design with IDEA Open Model
• Materials assessment—Implementing durable and non-toxic materials
• Easily separable—Use of mechanical fasteners instead of adhesives and glue
• Simplicity—Simple components that have limited material types and sizes
• Limited components—Small numbers of large components
• Clear plans—Labeling and providing diagrams as a roadmap for future removal
• Transparency—Systems need to be visible and identifiable, not hidden behind walls
• Regularity—Similar and repeatable systems throughout the building
• Disassembly safety—Worker safety during deconstruction.
Architects and engineers play a key role in guiding developers through a property assessment for deconstructability. The following questions provide an outline for working with building owners to decide deconstruction pros and cons for a property.
Why are you considering deconstructability? If your business’ mission is focused toward sustainability, then it’s clear that deconstructability is a good avenue to consider on every project. If it’s not so clear cut, taking the time to find a building application where shorter, modular building lifecycles lends itself to reuse/recycling of materials may serve the dual purpose of making a profit at the end of building lifecycle while shining a positive sustainable light on the developer. What is the anticipated end use of the building (including sub-lifespans)?
The longer the anticipated lifespan of the building the more difficult it becomes to anticipate the long-term trends and therefore, uses and value of the construction materials. The shorter life buildings have end of life uses that can be predicted more easily and with more tangible markets and buyers for the building components. Who is on the back end using the building or materials, and who is deconstructing it? Likely, the same contractor who builds a structure will not be the same one who deconstructs it. In that circumstance, simplicity of design and connection is incredibly important to the successful deconstruction and materials in the future. Additionally, is there already a market for recycling the reuse of materials that are being used? If there is, there’s a better opportunity for projecting values in the future.
These are just some of the questions that should be considered when choosing whether to pursue a deconstruction strategy on a new build. Pre-planning with a qualified, experienced deconstruction engineer will help ensure a smooth structure transition at end of life and the successful capture of associated revenues from materials reuse/resale.
Full references are included in the online version of the article at STRUCTUREmag.org .
Steven Anastasio, PE, is the Director of Structures for Bala Consulting Engineers, Inc. Anastasio concentrates on industrial and residential markets, with a keen focus on structural dynamics, blast engineering, and earthquake engineering.
The tools enable engineers to design CLT per U.S. codes quickly and accurately for common applications.
By Matt Kantner, PE, SE
Cross-laminated timber (CLT) is an engineered wood product that is growing quickly in popularity both in the United States and abroad. It is just one product in a suite of products and, in fact, an entire method of construction that is known as mass timber. A patent for CLT was first issued on August 21, 1923, to Frank Walsh and Robert Watts of Tacoma, Washington (Fig. 1). Like many great innovations, the world was not ready for this game-changing product at the time, and it largely went forgotten for decades. Then, in the 1990s, Austrian engineer Gerhard Schickhofer wrote his PhD thesis on CLT and went on to develop CLT as a commercially viable product with government approvals first granted in 1998. CLT grew in popularity in Europe in the early 2000s and has since exploded into a globally manufactured and utilized product.
CLT is growing in popularity for a variety of reasons. For one, when CLT lamstock is harvested from sustainably managed forests, it has serious green credentials. Replacing more carbon-intensive materials with CLT can drastically reduce a building’s embodied carbon, especially when taking biogenic carbon into account. Organizations such as the American Society of Civil Engineers, via its SE 2050 Commitment Program, recognize structural engineers’ outsized role in lowering embodied carbon in buildings; low-carbon materials such as CLT have a significant role to play. Building occupants love exposed CLT due to its warmth and its biophilic properties. (Biophilia is our innate desire to be surrounded by nature and natural materials.) Architects love it for the warm and beautiful spaces it can create. Builders love it because panels are prefabricated and get erected quickly and easily on-site. CLT has inherent two-way spanning capabilities that can be used for perimeter cantilevers or even point-supported systems. Cross laminations make CLT dimensionally stable in both in-plane directions and allow it to function as a diaphragm.
Today, many CLT manufacturing facilities are located all over the world. Six facilities in the United States are certified to sell CLT as a structural building product with more planned, and a growing number of international suppliers in Canada, Europe, and South America are gaining U.S. approvals (Fig. 2). CLT factories are busy… according to Woodworks, as of March 2024, 2,115 mass timber projects are built, in construction, or in design across the United States
since they began tracking in 2013; 1,197 of these include CLT. Prior to 2013, either of these numbers would have likely been in the single digits. The 2021 International Building Code has helped usher in a new era of tall, mass timber buildings by allowing mass timber buildings up to 18 stories. But mass timber and CLT are equally at home in single-family homes. CLT is also commonly used in office buildings (Fig. 3), multifamily residential buildings of all sizes, schools, fire halls, higher education buildings, and more.
Being an engineered wood product, the design of CLT in the United States is governed by the American Wood Council’s (AWC) National Design Specification for Wood Construction (NDS). CLT first appeared in the NDS in the 2015 Edition in Chapter 10. CLT also made its first appearance in AWC’s Special Design Provisions for Wind and Seismic (SDPWS) standard in its 2021 edition (see STRUCTURE July 2021 article) for use as shear walls and diaphragms.
Reference CLT design values are a bit different than for other wood products—this is due to the unique properties of CLT that are inherent because of the transverse layers. For uniform orthotropic materials like sawn lumber or glulam, an engineer simply divides the bending moment by the section modulus (i.e., M/S) to calculate the bending stress and
divides the axial force by the cross-sectional area to find axial stresses (i.e., P/A). CLT, however, is a composite material with layers that are oriented perpendicular to the direction being evaluated, so this simple calculation is not directly applicable. The design of CLT per the NDS takes these unique properties into account in Table 10.3.1. Some key properties from that table include:
• Fb(Seff ) for bending. Manufacturers calculate this allowable bending capacity for the CLT layup using the shear analogy method as prescribed in ANSI/APA PRG 320: Standard for Performance-Rated Cross-Laminated Timber, 2019 Appendix X3 for both the minor and major direction of their panels. These values, which are known as Fb(Seff ), are published in CLT product code reports.
• (EI)app for out-of-plane stiffness. This is where CLT gets really fun. In most materials and situations, engineers can reasonably ignore the impacts of shear deformation (or take them into account with rough approximations). This is not the case in CLT. Due to the influence of the transverse layers, shear deformation in CLT is significant even at high span-to-depth ratios. A term known as (EI)eff, which considers flexural stiffness only, is calculated using the shear analogy method per PRG 320 Appendix X3. Similarly, (GA)eff, the effective out-of-plane shear stiffness, is calculated. Both of these values are published in manufacturer code reports. (EI)app is an apparent out-of-plane stiffness that takes both the flexural stiffness, (EI)eff, and shear stiffness, (GA)eff, into account. (EI)app can be calculated per NDS 2018 equation 10.4.1 for a given span length, loading type, and end fixity condition.
• Ft(Aparallel) and Fc(Aparallel) for axial loading (tension and compression respectively). Aparallel represents the cross-sectional area of plies parallel to the direction being considered. Transverse plies have a negligible impact on the axial capacity of CLT as wood is far weaker and less stiff perpendicular to the grain, plus most North American CLT is not edge-glued.
• Fs(Ib/Q)eff for rolling shear capacity. If you are not familiar
with rolling shear, the name is quite intuitive. Imagine wood as a bundle of straws. For sawn lumber or glulam, parallel-to-grain shear governs the shear capacity of a section. Parallel to grain shear can be imagined by taking some of your straws and sliding them in a direction along their primary axis. Rolling shear is when you take some of the straws and slide them perpendicular to their primary axis. Due to the transverse layers in CLT, rolling shear is developed from out-of-plane loading. Also, since rolling shear allowable stresses are one-third that of allowable parallel-to-grain shear stresses, rolling shear capacity governs the out-of-plane shear capacity of CLT. PRG 320 2019 Appendix X3 provides equations for determining rolling shear capacity, and in practice, manufacturer code reports simply list a value Vs, which can be used directly as an allowable shear strength per one-foot width of the panel.
CLT is often used in building types that require structural elements to have fire-resistance ratings of one or two hours. Due to its inherent beauty and biophilic properties, it is desirable to leave CLT exposed visually, which also leaves it exposed to fire (Figure 4). Design provisions for CLT exposed to fire exist in the 2018 NDS Chapter 16 as well as in the recently published Fire Design Specification for Wood Construction (FDS) by the AWC, 2024. Technical Report No. 10: Calculating the Fire Resistance of Wood Members and Assemblies (TR10) by the AWC is another good reference since it contains worked example problems.
At a high level, designing timber elements for fire is relatively simple—wood chars in a fire at a predictable non-linear rate. For a given fire duration, an engineer can calculate how much wood is considered ineffective as it heats up and turns to char. The remaining cross-section is evaluated for strength. Only imposed gravity loads are considered, and the reference ASD strengths for bending, shear, etc., are multiplied by an adjustment factor, which effectively makes them ultimate strength values. Things get more complicated at connections. For a brief primer on this, see the May 2023 STRUCTURE Magazine article, “Fire Protection of Mass Timber Connections Based on the 2022 Fire Design Specification.”
When it comes to designing for vibrations, a couple of factors can create challenges for CLT floors. First, CLT has lower stiffness than an equivalent thickness of a concrete slab. Second, CLT has a great strength-to-weight ratio; the primary downside of this is that CLT floors have less modal mass. It also means that a CLT floor has lower overall loads compared to a concrete slab… this is good for strength design, of course, but makes it more likely that vibration
considerations can govern the design. As a seasoned mass timber engineer once told me, a concrete slab’s primary job is holding itself up. Consider a typical residential floor; the ratio of self-weight to all superimposed loads is roughly 1.5 for a typical post-tensioned concrete flat plate floor and roughly 0.15-0.25 for a 5-ply CLT floor. Vibrations due to human activity are a serviceability criterion that is not addressed directly in the building code. The U.S. Mass Timber Floor Vibration Design Guide by Woodworks, published in 2023, is a tremendous resource for the vibration design of CLT floors. It includes some simplified provisions for CLT panels on rigid supports and provides calculation methods for floor plates supported on flexible (e.g., beams) framing as well.
Two new CLT design tools enable engineers to design CLT in accordance with U.S. codes quickly and accurately for many common applications. These tools are wrapped up into a single Excel workbook and are available for free at https://eqcanada.com/design-resources/. Within the workbook, one tab performs calculations for floor/roof panels: cold strength, fire strength, deflections, and vibrations are all checked (Fig. 5). The other tab performs calculations for CLT walls loaded axially, including provisions for eccentric loading, out-of-plane wind loading, and P-delta effects. Cold strength and fire strength are checked.
The CLT Design Tools allow users to input any symmetric CLT layup from three to nine plies. While this can be done manually with ease, it is even more efficient to select layups from the built-in database. The layups are called up directly on the calculation sheet from a layup database that exists on a separate tab and includes every commercially available PRG 320 certified layup in the U.S. market at the time of publication. EQUILIBRIUM is committed to maintaining this layup database and making any other critical updates to the tools for the next two years and perhaps beyond pending additional funding. Less refined versions of these tools have been used by EQUILIBRIUM engineers for years to design CLT on our projects, including some of the projects shown in the images within this article. The CLT design tools were officially launched on August 29, 2023. The first update was made on February 29, 2024. To date, the tools have been downloaded over 1,100 times. In a recent user survey, over 70% of respondents ranked the tool's Floor/Roof designer as the best tool they have used for design of CLT floors and roofs.
The development, release, and promotion of these new tools was funded by the U.S. Forest Service by way of a Wood Innovation Grant. Additional funding was received from the Softwood Lumber Board. Holmes Structures performed a peer review. Early versions of the tool were originated at Katerra.
Matt Kantner, PE, SE, is an Associate Principal at EQUILIBRIUM, where he leads the company’s U.S.-based team from their office in Atlanta. Like his colleagues, he designs in all materials but is especially passionate about mass timber and sustainability-focused design. Kantner is a member of the SEI’s SE 2050 Committee and the American Wood Council's Wood Design Standards Committee. (mkantner@eqcanada.com)
The Modern Müller-Breslau Method is a geometric way to establish equilibrium in 2D and 3D structures.
By Edmond Saliklis, Ph.D, PE
The Modern Müller-Breslau (MMB) Method is a new, purely geometric means of establishing equilibrium in two-dimensional and three-dimensional structures. It builds off the work by Heinrich Müller-Breslau (1851–1925), which is well known by civil engineers around the world as the Influence Line Method.
The impetus of creating the new MMB theory was driven by the author’s experience teaching many architecture and engineering students at California Polytechnic State University (Cal Poly), while trying to address the curious phenomenon of a growing gap between design students’ knowledge of form creation, and their limited understanding of how load flows through the forms they create. The MMB Method demonstrates visually, with no statics at all, how load flows to a support or how an internal force or moment equilibrates external loads. While it can be drawn by hand, even on the proverbial “napkin sketch,” the method lends itself best to precise simple line drawings done parametrically on a computer.
Several examples of the new MMB method will be shown in this article, along with a brief review of the classic Müller-Breslau (MB) Method.
In the classic Müller-Breslau (MB) Method, to find an Unknown reaction or internal force or moment, Heinrich Müller-Breslau first removed the Unknown, be it an external or internal force or moment equilibrator, then he “perturbed” the structure a unit displacement or rotation amount Δ in the assumed direction, or sense, of the Unknown. The MB and the MMB Methods agree perfectly for any scale of Δ as shown in Figures 1, 2, and 3. In Figure 1, a simply supported beam contains point loads at each of the free cantilever tips. To seek either Unknown Reaction, such as the Right Reaction (RR in the classic MB Method), the RR is removed and a geometric perturbation of 1 unit is applied vertically, because the reaction is vertical. Since the perturbation is purely vertical, the entire beam stretches, i.e. it elongates. This is known as the “Influence Line” for the Right Reaction. In Figure 2 for the MB method, the geometric displacement known as the perturbation is 1 unit and the “loft” or the movement of each load is -0.3 and 1.1 for F1 and F2 respectively. In Figure 3, the MMB Method does not stretch the beam. Rather, it respects all boundary conditions after the perturbation is applied. While the perturbation Δ is still measured in the direction of the Unknown, the path of the entire perturbed structure is circular, as shown in Figure 3. Notice in Figure 3 that the loft of each load is measured solely in the direction of the load. Both methods agree with theory, and the result is not earth-shattering, so why go through the trouble of drawing the perturbed shape without stretching the beam? The answer arises with lateral loads.
Consider now the slanted, simply supported beam shown in Figure 4. To seek the Unknown Right Reaction RR using the classic MB Method, the “loft” or movement of the applied load is zero in the perturbed configuration, regardless of the size of Δ, because the beam stretches. This would imply that the Right Reaction RR is zero, which is incorrect. If there is no horizontal movement of the external load,
then there is no work done by it, so there would be a zero reaction. But, there is indeed a vertical reaction on the slanted beam, induced by the horizontal load.
Using the MMB Method, one simple work equation can be applied to any structural problem. Work is force multiplied by a distance. The distance is either Δ for an external reaction, or it is a Loft for an applied external force.
1 Unknown ∙∆+ ∑Fi ∙ Lofti=0
Figure 6 shows the solution to this problem for a large perturbation Δ, and Figure 7 shows the solution approaching the theoretical value as Δ gets small. The circular path is evident, yet the perturbation Δ of the Unknown and the Loft of any load is only in direction of those loads.
Consider now, a slightly more complicated structure, a threehinged arch subjected to a partial live load projected uniformly along a horizontal line, as shown in Figure 8. Suppose the Unknown moment in the left “elbow” shown in Cartesian Coordinates at (2,5) is sought. Most students would balk at this problem if asked to solve it algebraically. Yet, with the MMB Method, the problem requires as minimal effort as the previous examples show. The Unknown, which here is the moment in the elbow, is removed. That juncture is perturbed some amount Δ. All pieces must remain straight, and all other boundary conditions must be respected. Then, the Loft of the loads is simply measured. One necessary rule is to break a distributed load into separate parts if the load passes over a kink in the perturbed structure. Figure 9 shows the perturbed structure for a large Δ.
Reducing Δ by an order of magnitude shows that the solution rapidly approaches theory. This is demonstrated in Figure 10. Notice that the right elbow does not get distorted in the perturbed configuration. All boundary conditions are respected, and only one violation occurs at the Δ for the Unknown being sought. The first part of the distributed live load passes through Ld1 in the original configuration and through Ld1’ in the perturbed configuration. The second part of the distributed live load passes through Ld2 in the original configuration and through Ld2’ in the perturbed configuration. Since those loads are vertical, the lofts associated with each load are vertical. If the sign of the load vector agrees with the sign of the loft, that work, or product of two terms, is positive. If the signs disagree, that product of two terms is negative. The Unknown internal moment is a double negative, so Equation 1 can be used as-is.
Finally, Figure 11 shows a problem that many engineering students would most likely answer incorrectly if attempting to solve it algebraically via statics. A frame is pinned at the lower left end, roller supported at the lower right end, hinged at the Crown connecting the two frame members, and a tensile tie cable that begins at a distance of 1/3 of each of the lengths of the frame members, starting from the base supports. The load is a dead load, uniformly applied along the length of each frame member and downward. The Unknown tensile force in the cable is sought.
The power and the efficacy of the MMB Method is shown in this example because once again, Equation 1 finds the solution. Since the Unknown force in the tensile tie is sought, it must be perturbed some
amount Δ in the direction of the tie itself. The perturbation Δ here means that the tensile tie gets longer. Yet all other boundary conditions must be respected, and the frame members do not stretch. Students delight in solving the purely geometric puzzle of understanding the perturbed shape. The free children’s software GeoGebra, which is meant to teach children Geometry and Algebra, is ideally suited for such problems and available in many languages. The lofts are immediately found using GeoGebra as a easy to find measurement in the Geometry window of the program.
Figure 12 shows the solution for a large Δ, and Figure 13 shows the solution approaching theory for a small Δ. Δ is the difference in lengths of the perturbed tensile tie and the original tensile tie. The lofts are always in the direction of the load. The only difference is that for an internal force, we slightly modify Equation 1 to account for the fact that any Δ is always opposed by the internal force, i.e. that product is always negative. If we stretch the cable, the internal force pulls back in the opposite direction of the Δ. The same phenomenon happens with internal moment, but those details are not shown here, and Equation 1 can solve for an internal moment because the Unknown product has a double negative.
Many other types of problems can be quickly solved using this method, including trusses and three dimensional simple spatial structures. In each case for any statically determinate problem, the MMB Method approaches theoretical values as Δ gets small. The method also can be applied to indeterminate problems, albeit in an approximate manner.
The method’s power arises from the fact that it is purely geometrical. No algebraic or graphic statics are used. The perturbed shapes clearly demonstrate that some loads have significant flow to a reaction, whereas other loads have negligible flow.
Duane K. Miller, PE, ScD, is a recognized authority on the design and performance of welded connections. Elected to the National Academy of Engineering in 2024, Miller is a past chair of the American Welding Society (AWS) D1 Structural Welding Code Committee and a past co-chair of the AASHTO-AWS D1.5 Bridge Welding Code Committee.
STRUCTURE: What led you to study welding engineering?
Miller: I had decided to attend LeTourneau University in Texas before I settled on Welding Engineering (WE), although I had heard of its WE program. Originally, I was a Mechanical Engineering major. But there was an excitement and uniqueness associated with their Welding Engineering program, so I took a WE elective as a freshman. I liked the tangible aspects of welding engineering, and I was always inclined toward hands-on activities. WE graduates had a 100% job placement record, and they were getting the top offers in terms of pay. Ultimately, I chose to double-major in WE and ME.
STRUCTURE: How did Omer Blodgett, the author of "Design of Welded Structures," influence you as an engineer?
Miller: Mr. Blodgett is one of the five most influential individuals in my life. He taught me how to approach a problem, look beyond first impressions (which are often wrong), and identify the fundamental causative factors. In his heart, he was a mathematician, so he always looked for a mathematical explanation. He often said, “math doesn’t lie.” He loved welding (he first welded when he was ten) and wanted others to know how to use it properly. He viewed knowledge as an inheritance, something to be held and protected for a time, and something we were to pass along to others, hopefully in a better condition than what we received.
STRUCTURE: What do you think is the biggest misconception engineers have about welded connections?
Miller: Many engineers view welding as just another way of joining materials, but it is far more than that: welding is a method of design. Welding revolutionized the design of bridge girders as compared to the riveted alternative. Gone are all the angles and lap plates associated with making riveted connections. Welded connections are lightweight, highly efficient, and dependable when designed, detailed, and constructed properly. Welding is far more than an alternative to rivets and bolts.
STRUCTURE: What would you consider some of the major surprises that you have found in your research/development of welds/welding design?
Miller: Early in my undergraduate studies, I learned that fatigue was the number one cause of the failure of welded connections. Yet, I was not taught “why” (or, at least I didn’t listen to that part of the lecture). As I studied the work of others, I learned the “why” behind fatigue failures. Additionally, I learned how to design welded connections to overcome fatigue problems. Then, there was the issue of fracture. I learned that constraint and notches are the key contributors to fracture. Eventually, I came to realize that problems associated with welded connections were usually associated with cyclic or impact loading, notches, and constraint. What was typically presented as a “welding problem” was almost always a design-related problem.
STRUCTURE: Of all the initiatives you’ve been involved in,
Miller: The Northridge Earthquake in 1994 was a career-changing event. I was named Chair of the AWS Presidential Task Group, a member on the Project Oversight Committee for the Federal Emergency Management Agency-sponsored SAC Steel Project, and the first Chair of the AWS D1.8 Seismic Welding Committee. All of these activities “moved the needle” and changed engineering practices. On a personal level, I was able to associate with and learn from some of the most brilliant engineers in practice. It was an honor to associate with these people, most of whom have become personal friends of mine.
STRUCTURE: Who inspires you?
Miller: I have had the good fortune to associate with many amazing people. At the top of my list is my late father who instilled in me a belief that I could do anything I set my heart and mind to do. My LeTourneau professor Dr. David Hartman inspired me to pursue graduate school and learn about Fracture Mechanics. Dr. John Barsom is “Mr. Fracture Mechanics” to me, having written the book that I studied in graduate school. Dr. Barsom is an amazing person who has encouraged me on a professional and personal level. Dr. Barsom’s best advice to me: “Duane, don’t neglect your family.” Mr. Donald Hastings hired me at Lincoln Electric; he was an inspiring leader who eventually became CEO. He convinced me to join the company and to go into sales for a while; both were wonderful suggestions. I’ve already mentioned Mr. Blodgett. These five individuals all changed the trajectory of my life in positive ways.
STRUCTURE: What do you think you will be remembered for in terms of your personal legacy, and/or what are you most proud of?
Miller: I hope I’ll be remembered as a good husband, a good father, a good grandfather, and one who was a consistent follower of Jesus Christ.
STRUCTURE: We don’t often see engineers featured on TV. Can you speak about your experience on the History Channel and Discovery Channel?
Miller: The directors of these programs conceptualized shows that featured welding, so it was natural for them to contact Lincoln Electric for information. We opened our doors and allowed them to film the welding processes and interview our people. I was identified as someone who could answer some of their questions. The directors and I talked with each other for an hour or so, all while being filmed. I was surprised to see what they chose to keep and cut. Some of my best replies ended up on the cutting room floor!
STRUCTURE: As a speaker or a professor, how would you describe your style of teaching?
Miller: I start with where my audience is. What do they know? What do they need to learn? What steps are needed to get them from point A to point B? Mr. Blodgett was passionate about making sure our customers and audiences learned the lessons we taught. He had no desire to impress others with his knowledge; he wanted to transfer his knowledge to others. I’ve tried to emulate that approach in my teaching. I also try to make learning fun.
STRUCTURE: What are the most important attributes of
Miller: The most important attribute is integrity. An engineer must deal with the facts in an unbiased and objective manner. The second most important attribute is to maintain a focus on the advancement and betterment of human welfare. Engineering is a noble profession; every engineer must maintain the highest standards of professional conduct.
STRUCTURE: What advice would you give to young engineers?
Miller: Be honest. Keep learning. Never guess. Read Petroski. Write papers. Make presentations. Join technical committees and become an active contributor. Seek to learn the “why” behind the “what” and “how.” Find a mentor. Be a mentor. Become a specialist (an expert in a narrow field of engineering). Realize that there is more than one solution to a problem. Be professional. Give 20% more than anyone else in the office.
STRUCTURE: What do you think is the biggest challenge facing our profession in the next ten years?
Miller: Artificial Intelligence (AI) will transform many aspects of our life, including engineering. I’m concerned about the potential effect of AI on engineering. In some cases, AI will give us answers that are just plain wrong; hopefully, we’ll realize when that happens. In other cases, AI will give us the correct answer, but we’ll not know the “why” behind the answer. When this happens, engineering progress will be hampered. We must understand the physics behind our engineering principles and equations. We must know more than just the answer, particularly as we push the limits with our designs. AI will help us with what exists but will mislead us when it comes to developing what does not exist. AI will not replace thinking engineers.
STRUCTURE: What do you think is the biggest opportunity moving forward in this industry or something exciting and new that you’re looking forward to?
Miller: Additive Manufacturing (AM) (sometimes called 3-D printing) holds great promise in the area of structural engineering, particularly in the realm of connections. Traditional steel members, whether they be rolled shapes or hollow structural shapes (HSS) have been joined with nodes made with steel castings. Where castings are impractical due to limited volume, AM parts can be made instead. The technology exists today and is being used in other industries. I look forward to the first building and the first bridge that will incorporate additively manufactured components. ■
The structural systems and details of “The Leaf" at Canada’s Diversity Gardens, Assiniboine Park in Winnipeg, reflect biophilic design.
By David Bowick, P.Eng.
he Leaf at Canada’s Diversity Gardens in Assiniboine Park in Winnipeg, Manitoba, has been described as a “horticultural sanctuary for the 21st century.” Interior biomes celebrate the flora of Mediterranean and tropical climate zones, and a butterfly garden allows guests to interact with a wide range of butterflies. The principals of biophilia, which is the human tendency to interact or be closely associated with other forms of life in nature, inform every aspect of the design of the building.
The structure of the building, which must be non-combustible due to its public program and scale, takes advantage of biomimicry—the emulation of elements of nature in design. Biomimicry can take two forms. Formal biomimicry emulates natural forms, while functional biomimicry emulates natural systems to solve functional problems. The Leaf employs functional biomimicry with resulting biomimetic forms using state-of-the-art technologies.
The most striking formal element of the Leaf is the sweeping spiral cable net of the roof. The roof supports inflated pillows of ethylene tetrafluoroethylene (ETFE), a fluorine-based plastic with high corrosion resistance and strength over a wide temperature range. Technologically, the pillows follow directly from Frei Otto’s soap bubble experiments in the early 1960s.
ETFE was chosen for the project for its high light transmissibility, particularly the plant-critical UV light, and economy, particularly when compared to glass. While ETFE is not “vision clear,” it diffuses light slightly in its passage through the membrane, so shapes and forms are easily distinguishable, and it reflects or absorbs only around 5% of the light. This is a critical factor when designing an indoor botanical garden at a latitude of 50° where the shortest day is barely more than 8 hours.
The striking spiral cable net of The Leaf's roof consists of inflated pillows of ethylene tetrafluoroethylene (ETFE), which is a plastic with high corrosion resistance and strength over a wide temperature range. ETFE also has high light transmissibility which is crucial for the plants within the building—especially in a city with short days. ETFE only reflects or absorbs around 5% of light.
The functional objective of the roof was to minimize shading. A cable net was considered ideal because, with a light transmissibility of 95% in the membrane, most of the shading is structural shading. Cables, by virtue of their high strength (fully locked strand cable has a breaking strength in excess of 180 ksi) can be dimensionally small when the form allows. ETFE as a system can accommodate large movements without a reduction in performance. A large deformation structural system allows each element to be fully utilized for strength (demand/capacity ratio close to 1) minimizing its size.
ETFE, the foil, is extremely economical and the surface area of the foil is a minor contributor to the cost of the system. Working with Vector Foiltec in the early stages of the project, the design team learned that the cost of the system is largely in the extrusions, which form the boundaries, and in the labor to install them. The key to an economical system, as well as the key to minimizing shading, is to minimize the boundary to surface ratio. This constraint suggested two possibilities: long parallel pillows and large discrete rhomboid or hexagonal “tiles” (similar
to Grimshaw’s Eden Project in the UK).
ETFE pillows are leaky and require a constant supply of air to remain inflated. A tiling of discrete pillows would require a system of ducts to bring air to the pillows, adding cost and shading to the system.
The planning of this building placed the mechanical equipment, including the inflation fans, in the central core. To avoid air distribution ducts, each pillow must terminate at the core. Conventional planning would orient the pillows radially, requiring over 100 pillows, tapering from a minimum width of around 1 foot to a maximum around 10 feet at the perimeter (the approximate maximum span of the ETFE cushion in a oneway system). This would result in almost 50% shading near the core.
Reducing the number of pillows to limit shading would require two or more subdivisions of the pillows over their length—the strategy employed at Foster’s Khan Shatyr Entertainment Center in Kazakhstan. This solution would require air distribution ducts to bring air from the core to the subdivided pillows.
The solution chosen for this structure borrows from the mollusc. The mollusc builds its shell by laying down a single continuous strip of calcium carbonate in a spiral form to create an everexpanding cone of constant proportion. These cones might be acute and wound like a snail or flat like a clam. In this project, rather than one, the design team chose 36 pillows, one for each 10 degrees of cardinal direction, each pillow following a continuous spiral path from the core to the perimeter. The choice of 36 pillows allows each pillow to intersect the boundary at an angle that is not so acute that it is essentially flat, maintaining a minimum slope for drainage.
The spiral form of the roof also borrows from phyllotaxis, the arrangement of leaves on a plant stem. When the angle between the spawning of sunflower seeds from the central meristem is equal to Fibonacci’s “golden angle” (the smaller of the two angles created by sectioning the circumference of a circle according to the golden ratio) the result is an optimal packing of seeds and a pattern closely resembling the roof of the Leaf, which was optimized to a near constant 10 feet pillow width.
As an aside, the hairy ball theorem of algebraic topology states that “there is no nonvanishing continuous tangent vector field on even-dimensional n-spheres.”
In other words, you can’t comb a coconut. Any parallel-sided pillow solution on a compound curved surface was likely to lead to spirals.
ETFE foil is very thin—less than 0.5mm—but strong. As a membrane, it has no flexural stiffness and relies on prestress and curvature to span. Prestress is maintained by the inflation
pressure of the pillows, similar to a soap bubble. Two pressure equalized chambers make up the assembly to provide good thermal performance with an R-value in the range of 2.0. Internal pressure is maintained at about 5 psf in the summer and 10 psf in the winter to resist modest snow loads. Heavy snow fall (up to 30 psf in this case) will cause the pillow to deflate with the snow load to be shared by all three layers of foil. With the three layers in contact, the R-value drops to something around 0.1 and the heat from the biomes quickly melts the bottom of the snow forming a slick boundary layer of water. This precipitates sliding of the snow to the perimeter, after which the pillow reinflates.
The cable net for the roof is a triple layer spiral cable net supporting the spiralling pillows. The spirals were derived from the complementary diagonals associated with a radial/annular grid of 36 radials and annular parallels at 10’ c/c.
Like membranes, cables have no flexural stiffness, yet in this case the system must span as much as 150 feet. Cables rely on curvature and prestress to span. The job of the compression chord in a bending system is done by the boundaries in a cable net. If a cable experiences compressive forces, it will instantly buckle, losing all stiffness. Prestress is applied to ensure that all cables remain in tension during all
loading conditions.
The form of the roof is anticlastic, derived from a rotational hyperboloid, meaning at any given point, the surface curvature is convex in one direction and concave in the other. An anticlastic curve has the benefit that the prestress in the convex layer is balanced by the prestress in the concave layer and can be maintained in the absence of external forces such as inflation pressure.
In order to provide the large east-facing, overlooking window at the butterfly garden, the rotational form was split and, rather than revolving around a continuous ring, the curve was revolved around a helix. While the net remains anticlastic, the break from the pure form complicated the loads in the boundaries.
The plan of the building, resembling a pair of overlapping beech leaves, was derived by trimming the rotated form along selected spirals, chosen to optimize the interior spaces to their respective programs.
Introducing three layers to the grid (as opposed to simple radialannular or two complementary diagonal spirals) adds indeterminacy and complication to the behavior. While the spiral net was crucial for supporting the spiral pillows, any tailor knows that fabric cut on the bias is stretchier. Radial cables were required in addition to the spiral net to provide stiffness.
The three layers of the net were described as the Radials, the
Positive Spirals, and the Negative Spirals, positive and negative determined based on the “right hand rule.” Negative spiral cables by Redaelli are single 24mmØ Locked Strand cables and were designed to have constant prestress over their length of around 15 kips. Positive spirals are pairs of 16mm locked strand cables, prestressed at roughly 7.5 kips to balance the negative spirals. Radial cables, locked strand cables ranging from 52mmØ to 64Ø, accumulate load at each “node” (the points where the spirals intersect the radials) at roughly 40 kips per node to a maximum tension of about 250 kips in the longest radial. Under balanced load conditions the pillows pull equally horizontally on their extrusions and little lateral force is resolved into the net. But in a snowfall event, the snow can’t be relied on to be uniformly distributed nor to slide at
the same time in adjacent pillows. A condition with full snow on one pillow and none on the adjacent pillow is a very real possibility. Additionally, the pillows must be lifted roughly 18 inches above the negative cables to ensure that they don’t bear on the crossing cables which would result in premature wear. The result is that unbalanced loads place large torsional forces on the extrusions and the paired positive cables. Anti-rotation cables complete the net, installed below the negative cables. The node elements, resembling huge prehistoric bugs, consist of a top and bottom clamp plate with a machined cable groove affixed to the radial cables with torqued high strength bolts. A third clamp plate clamps the negative cables in place in a curved groove. Positive cables, lifted roughly 10 inches above the negative cables, are clamped in place atop a steel post.
The final piece, an S-post, is bolted to the bottom to connect the antirotation cables. The geometry of each of the 333 nodes is unique, accommodating the subtle differences in cable incidence angle and forces. Geometries were precisely determined to attempt to limit the “kink” as the cable passes in and out of the clamp to less than 1.5°.
Like the roof, the interior partitions separating the biomes consisted of ETFE foil supported by cables. Rather than pillows and spirals, however, the structure of the partitions resemble a bat’s wing, consisting of a single layer of tensioned foil membrane spanning between vertical cable stiffening elements. The vertical cables themselves are supported from catenary cables below the roof.
The cable wall was designed to limit the lateral movement under an interior wind pressure of 5 psf to H/36, requiring significant prestress. Those vertical cable forces would result in enormous catenary cable forces should the catenaries follow the roof profile—a requirement to achieve environmental separation of the biomes. To address this, the vertical cables were supported by a very deep catenary cable, and a second set of vertical cables span between that and a shallow catenary cable that follows the roof profile. The upper set of cables span a much shorter distance and, as a result, require less prestress. The prestress on the 16mmØ lower and upper wall segments are roughly 10 kips and 2.5 kips, with the large catenaries carrying up to 150 kips of prestress. While the ETFE system is strong with excellent light transmission characteristics, it is vulnerable to
contact damage and is not “vision clear.” Glass was chosen for the bottom 3m of the partitions to allow views into the biomes.
The partition enclosing the Butterfly Garden presented a sepa rate challenge. While the height of the partition is much shorter, the partition curves in plan to follow the edge of the leaf-shaped platform. Lateral stay cables were installed following the radial lines of the roof to pull partition into its correct alignment.
The diagrid core is the spine of the building. It contains the vertical circulation to access the event spaces and the Butterfly Garden, as well as housing the mechanical equipment for the inflation of the pillows and environmental controls for the building and biomes.
The structure of the diagrid does the heavy lifting for the building, resisting the gravity and lateral loads for the roof and providing the tension ring function to anchor the cables of the cable net.
The diagrid form was developed for its structural rigidity as much as its aesthetic impact. The horizontal elements within the diagrid form a pair of parallel helixes, each rising 30 feet per revolution. The formal reference to the DNA molecule is evident.
Less evident is the functional precedent in the grain of trees. According to The Gymnosperm Database, It (spiral grain) has also been noted that spiral grain may make the tree stronger and better able to withstand stresses caused by wind, particularly if the direction of the spiral is periodically reversed." (https://www.conifers. org/topics/spiral_grain.php)
A further functional solution borrowed from dendrology is the soft flaring of the branches at intersections. The diagrid incorporates 81 six-limbed ductile cast steel nodes weighing between 1,500 lbs. and 2,500 lbs. each. The branch intersections of the cast node geometries mimic this
natural aesthetic with softened fillet transitions. These fillets reduce stress risers and improve the performance and reliability of the joints.
The freeform capabilities of cast steel geometry further enabled the diagrid form by facilitating the helical revolutions along the height while allowing the intermediate elements to remain straight-cut pieces. The castings, designed and supplied by Cast Connex, included precision-machined branch-ends to minimize tolerances and support fabrication. Each branch-end included a bevelled nose to create grooves for the circumferential welds to the incoming HSS members. The diagrid was shop fabricated in large assemblies, carefully planned based on shipping constraints, to minimize field welding.
A unique feature of the cast nodes, proposed by Cast Connex, is the centerline eccentricity. Rather than a single concentric work point, the node has two works points, eccentric from one another by slightly less than one pipe diameter. This eccentricity results in bending (which every good engineer tries to avoid), but as a fully welded frame, some bending is inevitable. Casting use precludes local HSS connection limit states enabling smaller member sizes than otherwise needed, which in turn helped reduce overall tonnage. Introducing this eccentricity also dramatically shortened and
lightened the casting, making the whole system more economical. Rather than attempting to conceal this eccentricity, the design team elected to celebrate it with a continuous soft vertical groove. The unique geometry of the nodes earned them the nickname “hockey pants,” an appropriate metaphor for a Canadian winter city.
Where the transparent partitions provide visual access to the biomes, the skywalk provides a physical connection to the tree canopy, Cantilevering out of the elevator lobby, it loops back to terminate at the Butterfly Pavilion passing the top of the waterfall. The load is primarily carried by the shorter inner girder, a torsionally rigid square hollow steel section, connected for both moment at torsion at each end. Purlins cantilever from this inner girder to pick up the floor and are connected at the outer end by a continuous curved channel.
Roughly halfway along the length of the bridge it is propped by a pair of round hollow steel struts terminated with CastConnex Universal Pin connectors. These struts significantly increase the stiffness of the bridge in normal service conditions. In order to keep them visually light and maintain a high-quality finish, these elements received no fire protection. In the event of a fire, these elements are considered to have failed. The bridge has been designed to maintain its integrity in the absence of these elements to allow safe exit for the occupants.
Approaching The Leaf, one is first struck by the gentle sweep of the spiral roof. Moving closer, the angled cable stays radiating from the perimeter of the building come into view.
In a cable net, the job of the compression chord is done by
the boundary. Often this consists of a compression ring around the perimeter. Sometimes these boundary forces are taken into the earth, a strategy employed by the Banyan tree.
A compression ring at the eave was not possible on this project because of the desired visual lightness of the eave and the complications created by the split. The soil conditions in Winnipeg are challenging and not suitable for resisting large tension loads. The solution was to create a closed system, with all forces resisted
internal to the structure, below the ground, so that the foundations carry only the weight of the building. Transferring the horizontal loads through a raft diaphragm wasn’t feasible because the raft would interfere with the interior landscaping. A pile supported raft compression ring was buried below the ground, outside the footprint of the building, with the forces transferred to the ring with diagonal stay cables. The raft acts as ballast, balancing the vertical components of the stay forces, as well as transferring the horizontal
components around the building. At the rear of the project, the supporting “bar” building fulfils the function of the raft slab, transferring the loads through the building structure to the foundations.
The conception and design of this project was a tremendous technical challenge. Equal to that was the erection planning. Design is done as though the structure materializes instantly
and perfectly. In reality, the structure is erected piece by piece, and cables are installed one at a time. Each element is imperfect, and each dimensional variance has an impact on the distribution of forces in the structure.
The key to success is tolerance. Providing broad guard rails ensures the car stays on the road. Each cable was terminated with an adjustable pin fitting. The pins allow rotation about their axis; adjustable fittings can correct length tolerance and facilitate tensioning. Nonetheless, the
guard rails are not always wide enough. Cables and pillows were fabricated concurrent with the structural steel based on objective perfect geometry. Pins allow rotation only about one axis, and steel tolerances in a project with a complicated geometry are difficult to achieve. Extensive surveying and some amount of field rework was required to ensure that the structural supports were compatible with the fabricated net and pillows. Where rework was impractical, the net was recalibrated to suit the existing
boundary conditions.
Each step in the erection redistributes forces in the structure, and each element must be confirmed, which the design team did, working on behalf of the contractor.
Cable contractors, Redaelli and Tensile Integrity, would propose a sequence of installing and tensioning cables. The design team then would analyze each step to verify strengths and calculate movements in the structure. If a step created an unacceptable condition—such as overstress—the plan would be adjusted.
The goal was to develop a sequence of installing and tensioning cables that would result in an acceptable final prestress condition in the net that is safe and rigid, and as close as possible to the target model.
The net was tensioned in roughly 39 steps, each cable being adjusted up to three times and each step tensioning six cables until the predicted tensions and set-outs (the predicted position on the adjuster
associated with the desired prestress) were reached. The erection proceeds in a forward direction, adding tension and taking up adjustment in order to reach the correct target; the analysis steps were completed backwards, starting with the target model and relaxing each stage. For each stage of the erection, the strength of each member was verified, as was the slip of each node clamp and the kink angle of the cable at the clamps. Movements of the supporting columns and stays were calculated and reported. These values, along with the measured tension from the tensioning jacks, were used to validate each stage. This information was reported to the contractor in a single spreadsheet exceeding 100 MB in size. They distilled this into a series of field work sheets to inform each day’s work.
Two approaches were taken in
the design and representation of this project.
The cable net, diagrid, and supporting elements were modelled and designed using NDN, a large deformation non-linear finite element package specifically created for the engineering of membrane structures. The ETFE pillows themselves were a delegated design, with engineering completed by the contractor, Vector Foiltec. The design team worked closely with Vector Foiltec to ensure that the cable net provided adequate torsional rigidity to maintain stability of the pillows and extrusions under unbalanced load conditions.
These components were modelled and drawn for the construction documents using Solidworks, which is effective for complex, non-orthogonal geometries and multi-level assemblies. Solidworks models can be exported to .ifc and other formats to integrate with Revit, Tekla and other software used
by coordinating disciplines and trades.
The bar building was analysed and designed using Etabs with input loads at the interface coming from NDN. The bar building was also incorporated into the NDN model for validation of the Etabs results. This portion of the project was modelled for representation using Revit which allowed close coordination with the architects and was also used by the steel fabricator to assist in preparation of shop drawings. ■
Reduce material costs and simplify construction. New Millennium flush-frame connections feature a more efficient design that eliminates beam torsion concerns. Our published set of standard flush-frame connections simplify design and specification. Now, structural engineers can quickly and accurately specify flush-frame connections, streamlining fabrication and erection. Together, let’s build it better.
Indiana Farm Bureau's original Swine Barn, which was just a roof and floor and only occupied for two weeks out of the year, was transformed into a year-round, multipurpose space—just in time for the 2023 Indiana State Fair.
STRUCTURAL ENGINEERS AND ARCHITECTS COLLABORATED ON A YEAR-ROUND MULTI-PURPOSE VENUE AT INDIANA’S HISTORIC PAVILION.
BY KEVIN SHELLEY, AIA, LEED AP, SCOTT CLORE, PE, AND MICHAEL ROACH, PE
The complex design of the Indiana Farm Bureau (INFB) Fall Creek Pavilion project on the Indiana State Fairgrounds campus was a collaborative effort between architects at Schmidt Associates and structural engineers from Lynch, Harrison & Brumleve, Inc. and Complete Structural Consulting, Inc. Over 18 months, from 2021 to 2023, the group designed a notable example of creative structural engineering. The structural elements shared in this story not only highlight the firms’ work but also offer chances for insight and learning through observation and lessons. Seven years in the making and with $50 million from the Indiana General Assembly, the INFB Fall Creek Pavilion opened in July 2023 and preserved history with structural engineering. The structure is a 196,000-squarefootbuilding that caters to the State of Indiana with expanded possibilities. During the Indiana State Fair, it serves as an exhibition facility, providing an environment for livestock competitions, historical exhibits, and education. With a 120,000-square foot show floor, exhibitors and visitors can interact, promote agriculture, and participate in various state fair events. Beyond its livestock focus, the Pavilion’s flexibility can be seen through consumer and sporting events.
Features include:
• Clear-span space: Boasting 212 feet of clear-span, column and brace free area, this open expanse allows unobstructed views.
• Ceiling heights: The 28-foot ceiling heights can accommodate regional and national track and field, basketball, and volleyball tournaments.
• Agricultural education: Inspired by Indiana’s agricultural history, Schmidt Associates architects, structural engineering partners, and a construction administrator designed a 5,000-square-foot mezzanine inside the main entrance overlooking the show floor that can be used as display and demonstration space for fair and show producers.
• Green innovation: To curb odors, 22 overhead doors, scentrepelling floor surfaces, and a bi-level ventilation system with one exhaust system for daily use and another for use during the state fair are part of this design.
• Historic preservation: A restored 1923 north façade with reclaimed wood from the historic Seine Barn adds to the building’s 100-year lineage. Four limestone sculpture panels were added to the south façade to continue the legacy .
The INFB Fall Creek Pavilion created a multifunctional space for hosting events as varied as NCAA indoor track meets, large car auctions, and annual Indiana State Fair swine competitions. What sets this project apart is its versatility and the engineering achieved during challenging times such as the COVID-19 pandemic, supply chain disruptions, and the requirement to maintain the historic 1923 north façade. At the time of bidding this project, the production market for open web steel joists was at capacity, mainly due to the construction of warehouse facilities for online retailers such as Amazon. The limited supply for steel joists, especially 200’, three-piece, double-field-spliced super longspans, presented a significant problem for the design team. Allocating the necessary production time for a complex and demanding project made costs prohibitive for a traditional joist supplier. Realizing the need to keep the project on track, a specialty engineer, Complete Structural Consulting, Inc., was brought on-board so that the joists could be produced by the steel fabricator using the specifications of a traditional Steel Joist Institute (SJI) supplier. To achieve this goal, several design and fabrication procedures were documented and reviewed among the design team. A quality manual was developed by the specialty engineer and steel fabricator to document the shop standards instituted to ensure the SJI requirements were maintained. The clarity and thoroughness of the documentation provided design team and the Owner peace of mind while allowing the project to continue. The tailored design solution ensured the joists and large trusses, adhered to standards of The SJI, The American Institute of Steel Construction (AISC), The American Welding Society (AWS), and the Society for Protective Coatings.
Preserving the historic street-level main entry structure on the north side of the building was identified early on as a critical aspect of the project. The existing street level was 10 feet higher in elevation than the exhibition floor and connecting these two elevations while preserving the entry proved to be a significant challenge. Three options were discussed among the design team and construction manager.
• Building a concrete retaining wall —One option was to construct a concrete retaining wall to separate the entry from the exhibition floor. While efficient in design and concept, construction of the retaining wall would have required significant excavation, which could have led to set-back issues due to the proximity of the existing building.
• Temporary H-piles and wood lagging —Another concept that was originally favored by the construction manager and design team, was to install H-pile shoring, pour a concrete wall against shoring as the finish surface, and eventually abandon the shoring once the slab on-grade was installed.
• Steel sheet piling —During construction, the shoring contractor proposed installing steel sheet piling, a similar sequence as the H-piles and wood lagging but would allow for a faster schedule since the sheet piles provided the retainage as a single unit while the H-piles and wood lagging was a two-part system The downside to this option was that the fluted shoring profile would need to be filled with concrete to create a finished concrete surface. Filling the flutes required a substantial volume of concrete to fill the void. The extra material cost was offset by the gains of construction schedule and this option was chosen by the construction and design teams.
The sheet pile shoring option allowed construction of the new exhibit and administration areas without compromising integrity. This
Creating an HVAC system that met the needs of different events and addressed the requirements of hosting 1,300 swine meant using 100% outside air to design a system catering to three zones within the building. The fairgrounds, facilities, and maintenance department constitute Zone One, which is served by a high-efficiency gas-fired DX rooftop unit. This unit provides conditioned ventilation air to Variable Air Volume boxes equipped with electric reheat to give precise control over the indoor climate. Similarly, Zone Two, housing the office area for the Indiana State Police and emergency personnel, follows the same HVAC setup as Zone One. Both zones are designed to accommodate daily use with a single level of exhaust that isolates fumes from the livestock environment.
The show arena is the third zone. It is a multifunctional space with six 140-ton high-efficiency gas-fired DX rooftop units to provide conditioned ventilation air, accompanied by 12 CFM low-intake exhaust fans and 20 high-volume/low-speed paddle-type fans. This setup offers flexibility for the State Fair Commission leadership to control rooftop units based on the type of event being hosted.
“We collaborated with the Owner to fully understand their expectations and vision of what the Pavilion would be,” Schmidt Associates Senior Mechanical Designer and HVAC Project Lead Brad Wallace said. “As a team, we communicated regularly both internally and with our partners to strike a balance, talk through challenges and develop solutions.”
For the show floor, a concrete broom finish suitable for livestock and easy to clean while controlling odors was ideal for a multi-use building. Additionally, air conditioning, power, and wash bays on the show floor could keep people and swine comfortable. Finally, biosecurity measures were implemented to reduce the risk of infectious diseases being carried onto the premises. This was done through a multi-level design with a separation between spectators and exhibitors. Spectators entering on-grade at the Main Street level get a view 15 feet over the show floor, and there is space for exhibiting different livestock breeds without entering the show floor. Bleachers overlooking the show floor also provide a view for visitors.
approach, which used an entire bay to protect the façade, blended new developments with historic preservation. As such, the historic north entry elements, including the entry portals, two restroom towers in the northeast and northwest corners, and office space, were preserved. The original brick masonry veneer on the north entry was restored by repointing joints and replacing damaged brick with colorful porcelain tile cornice, utilizing masonry maintenance guidelines from the National Park Service. The decision to restore the north entry required that the entire Pavilion be constructed with a closely matched brick. The design team was able to find a suitable brick, seamlessly connecting the new construction to the original look. The design team also integrated restored and reclaimed wood from the original structure’s roof deck into the arched ceilings from the original Swine Barn’s three north entry portals .
The 212-foot clear-span was realized using 126-inch deep, three piece, double-field-spliced, open-web steel joists. Uniform in their configuration, these structural members extend across the ceiling, combining functionality with aesthetics. This integration of form and function reflects an interpretation of traditional craftsmanship and a tailored design solution.
The structure presents a simple façade from below, concealing the robust engineering behind its construction. Early in the design process, it was decided to use the joists and girders on the primary grids as key elements in the Main Wind Force Resisting System (MWFRS). Incorporating the joists into the lateral system eliminated the need for diagonal bracing, thereby maximizing usable floor space. Continuity was achieved by field welding the top chords of the joists and girders at the supports, along with the bottom chords at the stabilizer plates. The connections at the top and bottom chords restrict rotation, creating a force couple at the ends of the joists and girders. Close coordination between the designer of record and the specialty engineering team ensured that all structural members—the girders, joists, columns, and their respective connections—worked together to provide adequate
resistance and a clear load path for all gravity and lateral loads. At several locations, the joists and girders meet at different elevations at the columns, causing a combined effect of biaxial bending in the columns. Additionally, the joists were designed for various gravity load cases to cater to specific event requirements. This included incidental 5-kip bottom chord bend-loads to accommodate rigging and signage, as well as the capacity to support multiple 40-kip RTU loads without extra web members that would disrupt the consistent web layout.
The consistent truss geometry also helped to streamline the construction process for the steel erector. This standardized design allowed for the development of repeatable methods in the splicing and erection of trusses, contributing to efficient and expedited completion. The long-span joists were delivered to the site in three separate pieces, then assembled in pairs on the ground before being lifted into their final position and bolted to supporting members. To ensure precise and consistent geometry, the erector built a large jig for assembling each three-piece joist on the ground.
Erecting the initial pair of trusses posed a challenge, requiring exact coordination to keep the first truss stable while positioning and bolting the second truss with bolted X-bracing to form a stable pair. The initial lift required four large cranes, one crane to stabilize each half of the truss pair. Once the stable pair was erected and bolted, each subsequent truss could be individually erected and braced to the others with the bolted X-bridging. One the roof deck was welded to the joists, and provided lateral restraint for the top-chords, the trusses were fully installed and ready for their full design loads.
The 200’ joists were designed with a 2-inch chord gap to increase rigidity in the weak axis. This design provided more stability during erection and minimized the necessary bolted bridging. This design feature also allowed for larger single-member webs, resulting in fewer web members. The fabricator, using techniques common for SJI joist suppliers, crimped up to a 3-inch single-angle rather than using double angle sections. 2” HSS were also used as web members at critical locations and vertical web members. This approach provided more room at each panel point for aligning concentric members as the single members are in the chord gap, and the double angle webs are on outside of the chords, resulting in less secondary bending,
fewer double angle sections, and further enhancing the openness of the expansive area.
Like any large project with multiple teams, the INFB Fall Creek Pavilion project faced challenges, notably the need to adapt to various uses. This required coordination and upfront research from stakeholders. The original joist span, planned at 116 feet, was extended to 212 feet during design development to accommodate program requirements to enable the Pavilion to host USA Track and Field events.
The onset of the COVID-19 pandemic also halted the project, with a rebid in 2021. While challenging, this delay provided the teams time to reassess and refine the project’s design and logistical plans that led to a more efficient outcome.
The project team also learned valuable lessons in flexibility and adaptation. An example was the work with the Indiana Bridge fabrication shop, which brought the project to life. This hands-on experience and the Owner’s involvement led to a smooth and transparent process, highlighting the importance of open communication. Permanent shoring on the north side of the building proved beneficial. The team initially proposed a temporary steel H-pile and wood lagging system, but the contractor proposed sheet metal piling for efficiency. As a result, even though more concrete was required due to the depth of the sheet piles that also served as formwork for the lower wall, the installation proceeded faster, helping to keep the project on schedule.
The INFB Fall Creek Pavilion partnership between Schmidt Associate’s architects, Lynch, Harrison, and Brumleve, Inc., Complete Structural Consulting, Inc. engineers, and Indiana Bridge Fabricators was a multidisciplinary approach to collaboration and problemsolving. The project not only met functional goals but also did so on budget, ahead of schedule, and with a level of quality that may be seen by the public eye.
According to the Owners, air handling and movement of odors, the loading and unloading of swine, the broom finish on the showroom floor to provide the right balance of traction for the livestock footing, cleanability to control surface odors, and the separation of the public
from the exhibitors had to be planned and coordinated before the 2023 Indiana State Fair.
Transforming the previous Swine Barn, which was just a roof and floor and only occupied for two weeks out of the year, into a yearround, multi-purpose space, Schmidt Associates architects designed a facility with a lower grade elevation.
“When the Indiana State Fairgrounds were constructed in the late 1890s, they were built for fairgoers to bring their animals by train, and they didn’t have to worry about 55-foot trailers,” Indiana State Fair Commission Executive Director Cindy Hoye said. “This is something a lot of people don’t consider, but to solve this challenge, Schmidt Associates considered livestock and people.”
Despite the project’s scope, the team kept costs within the $50 million budget. This discipline was achieved through strategic decisions, resulting in over $1 million in savings.
The INFB Fall Creek Pavilion is a win for Indianapolis and the State of Indiana due to its ongoing annual economic impact of over $200 million and the vitality to various sectors, from hospitality and transportation to local businesses and job creation. In its short life, the Pavilion has not only enhanced the capacity of the campus, but it also shows how challenges can become opportunities.
“Undoubtedly, the highlight of the 2023 Indiana State Fair was the Indiana Farm Bureau Fall Creek Pavilion. The building exceeded all expectations,” said Indiana State Fair Commission Chief Development and Strategy Officer Ray Allison. “Through countless conversations during the Fair, I heard praise for the work we did. People were speechless when they walked in, and long-time swine exhibitors were emotional.” ■
Kevin Shelley, AIA, LEED AP, is chief operations officer | principal for Schmidt Associates. He loves helping Owners realize their visions, and working with them to achieve more than what they thought was possible. He serves clients in the firm’s K-12, higher education, community, and healthcare studios.
Scott Clore, PE, became a member of the Lynch, Harrison & Brumleve, Inc. (LHB) team in 2003 and a principal in 2015. Throughout his time at LHB, he has worked on large industrial facilities, churches, office buildings, multi-use structures, and educational facilities.
Michael Roach, PE, is President of Complete Structural Consulting, Inc. (CSC). CSC specializes in delegated design for connections and misc. metals, industrial design, and protective structures design. Michael began his career in the steel joists industry where he authored technical digests, the Special Profile Joists Catalog. His expertise includes connections, cold-formed, dynamic analysis for protective structures, and steel joists and deck design.
The project delivered a conference center as well as affordable housing to the growing city.
By Cody Gibbens, PE
On the south shore of Cayuga Lake lies the city of Ithaca, New York. The home of Cornell University, this city faces the best of times—a high quality of living and steady growth. With this growth comes a need for more parking, more meeting spaces, more amenities, more housing, and like many cities across the nation, more affordable housing. With these challenges in mind, BW Architecture and Engineering partnered with the City of Ithaca to develop a three-phase project which consisted of adding affordable housing to the area, the construction of a new conference center, and the renovation of the existing Green Street Parking Garage.
STAND Structural Engineering teamed with BW Architecture & Engineering and delivered a three-story conference center with nine stories of affordable housing stacked on top. The lower three stories house a 55,000 square foot conference center with multiple large meeting rooms, a two-story ballroom, full commercial kitchen, management offices, and a ground floor retail space. The upper nine stories consist of 181 affordable housing units, 40 of which remain reserved for people in need of supportive services per the New York State Empire State Supporting Housing Initiative (ESSHI). The residential tower also houses a full community room, fitness space, outdoor patio, and conference room on the top floor with a full balcony.
The design team initially performed an extensive system selection exercise to determine and select the best structural system for the project. Early on in this process, the team determined that the main challenge was laying out a column grid so that the columns would have a minimal impact within the ballroom spaces. The primary options explored were: Option 1: Utilize a conventional
composite steel framing system. Although a natural place to start, the downside of this system is that to maximize the spans, a deeper structural depth is required in the residential tower portion of the building. This deeper structural depth would result in eliminating an entire floor since the overall building had already been near the code specified height limit.
Option 2: Utilize precast hollow-core planks with upset support beams. This would entail creating custom T-shaped members that would span the units for the precast planks to bear on. This option minimized the depth of structure needed, but it did not maximize the spans and overall created a heavier system as compared to other evaluated systems.
Option 3: Design a four-story composite steel podium designed to clear-span over the ballrooms below. This hybrid system uses 4 stories of composite steel framing, paired with 8 stories of load-bearing cold-formed walls stacked above. This structural scheme would allow for the individual requirements of the two main zones of the building to each be met. Throughout the conference center the composite steel system allows for the flexibility to design around a non-repetitive layout, as compared to a cold-formed wall system above which better suits the repetitive nature of the apartment units.
After evaluating the three systems, as well as additional options not discussed, the design team chose to move forward using Option 3—the Hybrid Steel Podium.
After selecting the overall general structural system for the building, designing an element to clear span the ballroom and support eight stories of residential space above presented the next challenge. The design team chose to explore various custom steel truss designs
Structural Engineer of Record: STAND Structural Engineering
Architect of Record: BW Architecture & Engineering
Contractors: Vecino Construction—Tower
Construction, Welliver—Conference Center
Construction
Steel Fabricator: JPW Companies
that would span between columns located along the exterior edges of the ballrooms.
One of the primary concerns with the truss design was deflection throughout the construction of the project. If the trusses deflected too much during the construction process, the cold-formed strap bracing in the shear walls could buckle and require refastening or the gypsum wall sheathing could crack as the lower levels begin finishing.
The design team made two critical design decisions at this point.
First, they reduced the overall weight of the residential tower by using lightweight concrete for the construction of the tower floors rather than conventional normal weight concrete. Even by doing this, since the design live load for residential spaces is 40 psf, roughly 75% of the load applied to the trusses consisted of dead load. Second, they designed the trusses to a very stringent deflection limit of L/600 for the total load deflection and a max deflection of 3/4 inches for dead load deflections. With these two decisions in mind,
the team decided on a one-story deep wall truss.
As seen in Figure 1, the wall trusses spanned an entire floor, with the 4th floor being the bottom chord and the 5th floor being the top chord. At the south ern portion of the truss outside of the ballroom area, the truss deepened from 15 feet deep to 23 feet deep. The overall length for each truss measured 115 feet with a maximum clear span between supports of 75 feet. Four of these trusses were used spaced at 30 feet on-center with composite floor framing spanning between them. For the fabrication and erection of the trusses, the steel fabricator responsible for the trusses and all steel throughout the project, JPW Companies out of Syracuse, New York, elected to shop fabricate the wall trusses in four separate sections for easier transport. Per standard practice in the New York area, all connections on the trusses were to be bolted connections. Once on site, the crane would hoist the sections of the truss into location and workers would field bolt them into place.
For the lateral force resisting system, the team used a combination of cast-in-place concrete shear walls, light gauge cold-formed shear walls, and steel braced
frames. Between all these systems, the full height concrete shear walls making up the stair towers and elevator cores function as the lateral element that resists most of the lateral load from the residential tower. The light gauge shear walls primarily resist the wind loading from the nearly 20-foot-tall parapet and screen walls. And finally, the steel braced frames act as the main lateral element for the steel podium for the lower five stories. During the bidding process, contractors Vecino Construction and Welliver elected to bring Vulcraft on board with its Vulcraft RediCor system in place of the previously designed cast-in-place concrete shear walls. By making this change, the stair towers and elevator cores would be premanufactured in modules at an offsite facility that would then be transported to the site and could
quickly be erected. One of the benefits of switching to the RediCor system included the immediate stair access to all floors once workers installed the modules. At the time of construction, this project utilized the tallest RediCor stair core to date at a height of 152’-6” and the tallest four-sided elevator shaft RediCor had produced to date at a height of 145’-6”.
The project site provided its fair share of challenges. Three sides of the building contained utility easements, sewers, or electrical and telephone vaults located within 12 inches of the face of the pile caps. Due to the location of these elements, the building needed to incorporate cantilevers into the design since foundations could not
be installed in these areas. These conditions led to the development of one of the signature focal elements of the building—the double skewed columns at the Southeast corner of the building as seen in Figure 4.
The foundation design of the building also posed considerable hurdles. Even though the existing building located across the street bears directly on bedrock, preliminary borings at the start of the project revealed that rock
was not located within 100 feet of finished grade on our site. With the columns that support the main trusses supporting loads upwards of 2,000 kips, the team decided to use 100-ton steel H-piles as the primary foundation system. During the bidding process, the initially designed foundation system switched to the Menard USA’s proprietary controlled modulus columns. These controlled modulus columns are 18-inch diameter vertical grouted elements which
displace soils laterally, producing little spoils. With this being a drilled system versus the driven H-piles, the disturbance to the surrounding building and neighborhood was greatly reduced, as well. That decision alone saved the project nearly $400,000.
The Asteri Ithaca project overcame many challenges throughout
its design including design constraints and economic hurdles, not to mention a pandemic sweeping the nation at the start of construction. Upon its completion this project now stands as a pillar to help support the City of Ithaca, be it through the city’s new conference center and its ability to bring
new commerce and events to the city or the residential tower and the opportunity it brings to help house more of the ever-growing community of Ithaca, NY. ■
Design for the modern scientific workplace is most successful when the architectural and structural configuration of a building is directly linked to its purpose. This philosophy dictates that a research facility should be much more than a controlled environment for academic study; it should actively support and promote the science within.
Seeking to become the nation’s leading research program for National Institutes of Health
The structural systems at the new Washington University School of Medicine Jeffrey T. Fort Neuroscience Research Building needed to accommodate ever-evolving needs of the research groups. By
Kurt Bloch, SE and Julie Shaw, PE
(NIH) funding, stakeholders in the Washington University School of Medicine (WUSM) in St. Louis, Missouri, envisioned a laboratory facility that could readily adapt to the rapidly evolving science happening within. They wanted a building with dynamic spaces for research collaboration across a broad range of diverse but related disciplines to accelerate the development of “bench-to-bedside” treatments and improve patient outcomes.
Now completed, the Jeffrey T. Fort Neuroscience Research
Building (NRB) is one of the largest facilities of its kind in the United States. The 11-story, 609,000-square-foot NRB is home to more than 100 research teams working together in a building where architectural and structural design is intrinsically tied to the goals and needs of the institution.
One of the most important guiding principles of the design was to
create a research environment with the flexibility to adapt as needs evolved. Rather than the typical approach of assigning space based on departments, WUSM planned the layout of the research spaces around specific themes to facilitate team-based science beyond that of traditional departmental boundaries. As a result, the structural systems were required to accommodate the ever-evolving needs of these research groups throughout the life of the building. Given these requirements,
reinforced concrete proved to be the optimal structural system for the project. In keeping with local construction practices, the design features a one-way pan joist floor system that spans between concrete beams. In addition to providing a vibration-resistant floor that efficiently balances damping and self-weight, a pan joist floor can accommodate future floor openings and penetrations more easily than a comparable two-way flat slab system.
As part of a broader strategy to
maximize flexibility, all laboratory spaces were designed to meet a Vibration Criteria (VC) of 2000 µ-in/s, or VC-A, to satisfy typical requirements for sensitive equipment. A 10-foot cantilever along the building perimeter at each floor was reserved for office spaces and designed to satisfy an acceleration limit of 0.5%g for occupant comfort.
The use of RAM Structural System and RAM Concept guided the design toward a cost-effective solution with an optimized column grid of 21 feet by 31.5 feet. A
Owner: Washington University School of Medicine
Architect: CannonDesign, St. Louis, MO, and Perkins+Will, Chicago, IL
Lab Planning: CannonDesign, St. Louis, MO, Perkins+Will, Chicago, IL, and Jacobs, New York, NY
Structural Engineer: CannonDesign, St. Louis, MO
MEP/FP Engineer: CannonDesign, St. Louis, MO and AEI, Madison, WI
Vibration and Acoustical Consultant: Colin Gordon Associates, Brisbane, CA
General Contractor: McCarthy Building Companies, Inc, St. Louis, MO and KAI, St. Louis, MO
6000-psi concrete mix was used for the structural framing to optimize the size of the columns and improve the vibration and deflection performance of the slab and framing due to the higher stiffness properties. Typical lab space floor system consisted of a 6-inch slab over 14-inch-wide by 14-inchdeep concrete joists (22-inch total structural depth) utilizing 53-inch wide pans. 42-inch-wide girders spanning between the columns matched the 22-inch joist depth. The vibration performance of this design was initially evaluated using RAM Concept and then verified by vibration consultant, Colin Gordon Associates (CGA), using their own proprietary finite element modeling software. To balance efficiency and adaptability, floors dedicated to mechanical systems were only designed to meet strength and deflection requirements. Despite the higher applied load to the floor to accommodate the mechanical systems, the concrete joist web widths were reduced from 14 inches to 10 inches and the concrete girder web widths were reduced from 42 inches to 36 inches with the structural depth remaining consistent at 22 inches.
Unlike the 15.5-foot story heights for the typical lab spaces, the mechanical rooms located in the basement, second-floor, and eleventh-floor feature 22-foot to 24-foot story heights to accommodate double stacked air handling
units. Additional concrete beams were required to support the localized heavy equipment on the second floor and eleventh floor, and supplemental reinforcement was provided in the slab above to support the substantial point loads imparted by suspended piping and ducts. Planned plumbing penetrations on all floors were accommodated by sizing and reinforcing the girders to include an allowance for 4-inch diameter sleeves.
The depth of the basement level, coupled with the effects of surcharge loads, required 22-inchthick concrete walls around the perimeter of the building. The first structured floor above the basement was designed to support an extensive system of steel-framed catwalks, mechanical equipment, and suspended elevator pits. Because the basement has a larger footprint than the structure above, portions of the first-floor slab were designed to accommodate drive lanes that provide access to a new garage located immediately south of the research building. These portions of the structure feature closely spaced pan joists to support multiple topping slabs, soil, sidewalks, and vehicle traffic.
Despite the challenges posed by the construction of the basement level, a significant benefit was realized from the improved soil conditions, rock bearing, and skin friction capacity present at the depth of excavation. Even with the heavy loads applied to each column, drill pier sizes for the foundation system were on average
42 inches in diameter with 9-footdeep rock sockets. In addition, the geotechnical investigation of the subgrade conditions established that a soil site classification of B would be appropriate for the NRB, which lowered the Seismic Design Category from typical C in St. Louis to B. This development provided the welcome benefit of reduced seismic loading, which was particularly beneficial given the mass of the building, and reduced requirements for nonstructural seismic bracing within the facility.
The building’s design needed to provide spaces for both laboratory research as well as collaboration/ knowledge transfer. A grand atrium space and an auditorium
on the first floor were central to realizing a building that actively fosters knowledge sharing. The program needs for each of these spaces could not be accommodated within the standard column grid, so story-high transfer beams were designed to support the eleven stories above that could be constructed within the secondfloor mechanical space. Above the atrium, a concrete beam cantilevers 11 feet from the shear walls that wrap around the elevator core. At the auditorium, a story-high beam spans 72 feet between columns to support a column above that transfers near the middle of the span. The design of the transfer beam above the auditorium was complicated by the need to accommodate a door through the member. Analysis of each transfer beam was performed using the strut and tie method with validation from RISA 3-D.
Near the facade, the grand atrium is open further from the first level to the underside of the fourth level, resulting in a ceiling height of nearly 76 feet. Rising unbraced through this space, large 44-inch diameter concrete columns at the perimeter of the building support wind girts to which the curtain wall is attached. Given these considerations, it was essential to cast each column in a single pour or incorporate moment splices at each cold joint. Leveraging their previous experience, McCarthy chose to construct each column monolithically using a specialized self-consolidating concrete (SCC) mix.
WUSM is affiliated with BJC HealthCare, which includes the nationally recognized
Barnes-Jewish Hospital and St. Louis Children’s Hospital. These facilities are connected across the medical campus by an extensive system of skywalks. To connect the NRB visually and physically with the rest of the campus, this
network needed to be extended through the construction of a new pedestrian bridge that, in addition to enhancing movement across the campus, serves as a bold design statement.
To replicate the aesthetic of the
current pedestrian skywalk system, the new bridge incorporates cantilevered concrete columns that support long-span steel girders, the longest of which spans 120 feet. Because the columns supporting the bridge are categorized
as a cantilever column lateral force resisting system and designed to meet Seismic Design Category C, the 2018 International Building Code and Chapter 12 provisions of ASCE 7-16 restricts the permitted column height to 33 feet, 11 feet below what the design required.
Posed with this challenge, the team turned to the 2009 AASHTO Pedestrian Bridge Code for guidance. Unlike IBC, this design code does not have a prescriptive height limit for the seismic design of cantilevered column systems, though its application to a building structure required engineering judgement. To overcome this hurdle, the design team sought a variance from the City of St. Louis, which proposed using the most stringent design forces and detailing requirements of both ASCE and AASHTO. Ultimately, the approach was accepted by the AHJ. RISA 3D was used for
design of the steel sections, and use of SP Column was required for the slender column design.
Although the pedestrian bridge is structurally independent from the parking garage it connects to, structural upgrades of this existing building were required. Linking the end of the bridge to the rest of the pedestrian walkways required the construction of an enclosed pathway across the parking structure. The higher live load within this zone coupled with the need for a topping slab to create a level walking surface exceeded the design capacity of the existing parking deck.
Collaborative efforts from CannonDesign, McCarthy, and specialty engineer Norton and Schmidt determined that the most economical solution was to reinforce the existing garage using fiber-reinforced polymers (FRP). The applied loads along the planned walkway were given
to Norton and Schmidt for analysis and design of the FRP system. The top of the existing slab was scored so that FRP rods could be inserted to provide negative flexure reinforcement. The bottom of the slab and sides of the existing post-tensioned beams were reinforced with a carbon fiber wrap to resist positive flexure and shear.
Every aspect of the Jeffrey T. Fort Neuroscience Research Building represents a meticulous response to the institution’s goals, exemplifying the harmonious
marriage of form and function between architectural and structural design. While the design of this massive building frequently posed new challenges, each one offered an opportunity to implement a creative solution. With construction complete, the researchers who now call this building home can address more profound sets of challenges as they seek a deeper understanding of the human neurological system with the ultimate goal of improving patient outcomes. Today, this magnificent structure stands as a beacon of hope and a testament to the relentless pursuit of scientific progress and medical excellence. ■
The changes to flood design should significantly strengthen the flood load resistance for structures designed to these new provisions.
By William L. Coulbourne, PE; Daniel Cox, Ph.D; and Jessica Mandrick, PE, SE
ASCE 7-22 Minimum Design Loads and Associated Criteria for Buildings and Other Structures Supplement 2 was published in May 2023 and incorporates a complete revision of the flood load provisions of the standard. Prior to the supplement, the flood load provisions that are part of ASCE 7 Chapter 5, had been minimally changed since 1998. In contrast, communities in coastal and riverine areas have experienced extensive damage and loss from extreme storms with nine of the 10 costliest Atlantic hurricane seasons occurring since 2004. As a result, many jurisdictions have sought to increase flood standards locally. Figure 1 shows severe damage to two recently constructed houses, both of which were damaged from Hurricane Michael in 2018 when both were outside the 100-year floodplain. Building to the new flood provisions would have either made these houses more robust or they would have been elevated to minimize flood damage. With many lessons learned and new research conducted since 1998, the ASCE 7-22 Flood Load Subcommittee strongly felt that the standard needed to be replaced with up-to-date formulas and methods. The subcommittee developed a new approach for addressing the reliability of building design for flood considering climate change effects, particularly sea level rise. All references in this article to ASCE 7-22 flood loads are to Supplement 2.
The current design requirements in ASCE 7-16 for flood elevation only required designs to the 100-year flood (the 1% annual chance flood) plus some amount of freeboard. The use of the 100-year flood was largely based on the National Flood Insurance Program (NFIP) Base Flood Elevation (BFE) and did not meet the reliability targets of ASCE 7. This freeboard added to the Base Flood Elevation was a fixed amount based of the requirements of NFIP, ASCE 24, or the local jurisdictions; it was not risk-based and had no particular connection to the importance of the facility to the community. Dependent upon site conditions such as the topography and presence of waves, the freeboard provided inconsistent levels of protection above the 100-year flood. Moreover, ASCE 7-16 applied only to structures located within the 100-year flood area. Even as some attempts were
made to increase elevation requirements via freeboard, none of this applied to structures immediately adjacent to the 100-year flood area, creating a ‘waterfall’ effect.
ASCE 7-16 and earlier editions recognized that the 100-year flood load did not meet the reliability targets of the standard and assigned a load factor of 2.0 to coastal A and V zones in an attempt to increase the reliability. This presented a similar issue to the addition of freeboard. The load factor of 2.0 scaled the magnitude of the horizontal flood force but did not scale the elevation of the flood water. The Flood Load Subcommittee wanted flood design to be based on risk and to be risk consistent across the country.
One of the most significant changes in ASCE 7-22 Supplement 2 is the change in the definition of the flood hazard area. Previously, structures within the 100-year flood area, or the Special Flood Hazard Area in the terminology of flood plain management, were subjected to ASCE 7. However, the new definition calls for the 500-year floodplain to be the new area of applicability for Risk Categories II, III, and IV structures. For Risk Category I structures, the 100-year floodplain remains as the designated flood hazard area. This change has significant implications for all new construction and substantial improvements to structures lying between the maximum extents of the 100-year and the 500-year flood areas.
The new approach can be described as going beyond the National Flood Insurance Program regulations and requirements. The new flood load provisions do not tie the loads to a fixed regulatory elevation but instead use a risk-based approach to determine the flood hazard and then use the hazard levels to calculate the loads for the selected flood hazard. The new definition in the revised standard for the design flood is “The flood corresponding to the design mean recurrence interval assigned by risk category in accordance with Table 5.3-1, including
relative sea level change.” This revised definition includes references to two major changes in the ASCE 7-22 provisions. One is the link between flood design, flood return periods, and building risk category. The second is the inclusion of relative sea level change as part of the design flood. A reduced version of Table 5.3-1 is shown in Table 1.
The revised ASCE 7 Flood Load chapter now requires the use of a return period for design based on the Risk Category that ASCE uses to define use and occupancy classes. As evidenced by the amount of flood damage, losses, and claims in areas beyond the special flood hazard area, as shown in Figure 1, the regulatory minimum elevation that uses the 100-year event is no longer sufficient to reduce losses caused by flooding.
The solution to the problems of under-estimating the flood hazard and improving risk consistency is to require flood designs for each Risk Category to a specified flood return period. The risk categories and their corresponding mean recurrence intervals are shown in Table 1.
The advantage of using this method is that most buildings fall into Risk Category II and federally published Flood Insurance Studies (FIS) typically have 500-year flood elevation data in addition to the 100year data and many FEMA Flood Insurance Rates Maps (FIRMs) also delineate the extent of the 500-year flood plain. The disadvantage of this method is that the 750- and 1000-year MRI elevations and flood conditions are typically not published in the FIS or on the FIRM. In order to determine these larger return period floods, scaling factors were developed for both riverine and coastal conditions to convert the 100-year flood elevation to the desired mean recurrence interval. The table of scaling factors is shown as Table 2. These scaling factors are also part of the standard Table 5.3-1.
The amount of flood information available from federally published flood studies varies depending on the amount and type of information collected and developed regarding the local floodplain and the date of the study. Table 2 assumes that 100-year flood elevation data is available and thus can be used to scale from. The revised standard addresses the issue of unavailable data, so the user knows how to proceed to obtain the required design flood elevation. Flood velocity and wave heights are also part of the flood hazard. Scaling factors are also provided for those parameters for return periods greater than 100 years. These are shown in Table 3 and are in the standard as Tables 5.3-2 (velocity) and 5.3-3 (wave height). These changes now require the user to select the Risk Category, determine the flood hazard level and calculate flood loads based on the design flood depth. In many instances, especially coastal, the designer may elect to elevate the building above the expected flood level instead of fortifying the building sufficiently to ‘resist’ the flood. Another significant change is the inclusion of climate change effects in the determination of the design flood. The ASCE 7-22 equation
for design stillwater flood depth is: df = (Stillwater elevation for design MRI—Ground elevation including effects of erosion) + Δ sea level rise.
The revised standard now requires that climate change in coastal flood plains be considered by adding the change in sea level rise to the flood depth. The user is to consider the SLR effect over a 50-year period, the minimum of this change effect is to be a straight-line extrapolation of the historical SLR. Other more conservative approaches may be used including projections made by the U.S. Army Corps of Engineers (USACE) a link to the Corps projections is provided in the standard. The Corps data makes projections for a low, intermediate or high rate of SLR until the year 2100. Those projections allow the user to make a choice of which rate is the most appropriate for their design condition or which rate best suits the needs of the client.
The new chapter also includes guidance on the amount of scour to consider for columns and walls under breaking and nonbreaking wave conditions.
There are changes to several flood load formulas in addition to the changes made in defining the flood hazard.
1. Flood velocity has been reduced to: V = Cv√gdf, where C v is a velocity coefficient taken as 0.5, g is acceleration due to gravity, and df is the design stillwater flood depth. This change was made based on extensive study by the USACE on velocity of coastal floods; the method previously used in ASCE 7 was thought to be very conservative and the recent Corps study has confirmed that thought. Figure 2 illustrates the results of the velocity study data points in comparison to ASCE7-22 and ASCE 7-16 formulas.
2. Calculation of wave loads was changed to follow the Goda method. This method depends on adjusting the wave load effect on a building with the height of the wave and the depth of the building in relation to the still water level. Wave wash up on a wall is also considered if the wall is located such that the wash up effect can occur. Figure 3 is one of the new wave conditions showing the bottom of a building partially submerged below the stillwater level. The Goda equations
allow the determination of the pressure profile acting on the building, as opposed to the previous breaking wave formula which was applied as a concentrated force at the stillwater elevation.
3. Flood-borne debris design criteria has been added; the provisions and methods are patterned after those used in Chapter 6 on Tsunami loads. Risk Category I structures are exempt from the debris design criteria, as are one- and two-family dwellings, and Risk Category II buildings outside of the special flood hazard area. The chapter specifies the types of debris and their properties (threshold depth, mass, stiffness) to be considered for each risk category. Engineers should note that for a debris impact, the stiffness of the impacted structural element (weak axis bending stiffness of a wall or bending stiffness of a column) may often be considerably less than the axial debris stiffness. Considering the stiffness of the impacted object, as permitted by the standard can significantly reduce the debris impact load.
4. A method has been added to be able to determine if the site is subject to either non-breaking or breaking waves. The difference in wave loads from these two conditions can be significant.
5. Load combinations for various flood conditions have been determined so that the total flood load is used in the application of the appropriate load combination from ASCE 7, Chapter 2. The combinations cover both riverine and coastal floods. For example, the flood load combination for coastal flooding is the sum of loads from hydrostatic, hydrodynamic, and waves or debris impact applied to the design element of interest. This sum is Fa in the load combination used in Chapter 2.
6. Additional provisions are included to determine if either a sliding or overturning condition might affect global stability. Both of these stability load combinations are in addition to those in Chapter 2.
7. A section has been added for Performance-based Design (PBD) for Flooding. This section points to the already permitted use of PBD in ASCE 7 and provides some guidelines on how to follow the PBD process for flooding.
The calculations for hydrostatic loads are included in the supplement, and they require that the soil be considered fully saturated unless a seepage analysis in the geotechnical report determines otherwise. The calculations for hydrodynamic load are included in the supplement and the reduction in the maximum velocity can significantly reduce the hydrodynamic pressure as the velocity term is squared in the equation. There are new provisions for determining the impact of debris damming, which is the accumulation of debris between columns of an open foundation, which results in an increased area for the application of hydrodynamic loading.
The last significant change is the reduction of load factors used in load combinations that include flood. The LRFD flood load factor has been reduced from 2.0 in V Zones and Coastal A Zones to 1.0 for all zones; the ASD load factor has been reduced from 1.5 in V Zones and Coastal A Zones, to 0.70 for all zones. These reductions are possible because of the use of a higher return period for the design flood; the resulting loads on structural elements now achieve the target reliabilities assigned in ASCE 7 for each of the Risk Categories.
There are a lot of changes to ASCE 7 Chapter 5, and after years of minimal changes, it will likely take some time for the practice to incorporate all these changes into their designs. The new chapter is published in ASCE 7-22 Supplement 2 and is available for free download on the ASCE website. The recently published Building Designer’s Guide to Calculating Flood Loads Using ASCE 7-22 Supplement 2 by FEMA walks users through several examples and is also available for free download. FEMA continues to work on a Future of Flood Risk dataset and user tool so that in the future designers will be able to retrieve flood hazard data for various MRIs and risk probabilities. The changes to flood design that are now in ASCE 7-22, Supplement 2, should significantly strengthen the flood load resistance for structures designed to these new provisions.
William L. Coulbourne, PE, F.SEI, F.ASCE, Coulbourne Consulting, has 50 years of experience as a manager, designer, and building professional. He is a member of ASCE 7 standards committees on flood loads.
Daniel Cox, Ph.D, M.ASCE, is a professor at Oregon State University. His research focuses on community resilience to coastal hazards, including tsunami and hurricane surge and waves inundation.
Jessica Mandrick, PE, SE, M.ASCE, is Partner at Gilsanz, Murray, Steficek. She has a wide range of experience in multiple disciplines with specialties in education facilities, renovations, and buildings in the floodplain. Mandrick is also a member of the STRUCTURE magazine Editorial Board.
This article reviews global balustrade practices and how one can specify a project to meet best practices to keep occupants safe.
By Richard Green, SE, PE, P.Eng.,CPEng, IntPE
In general, global building/loading codes are in close agreement for most loading types, with variations of +/- 20% for comparable conditions. However, the loads for handrails, barriers, and guards in the United States (ASCE 7, IBC, ASTM E985 and ASTM 2358, NAAMM AMP 521-01 et.al.) do not currently reflect values for crowds and assembly areas that are in widespread use elsewhere in the world, in particular Canada (NBC), Europe (EN), the UK (BS), Brazil (ABNT) and Australasia (AS/NZS).
Comparison of the loads for typical cases, without assembly or crowd loading, have good agreement with the 50 pounds force/foot (lbf/ft) (0.73 kilonewtons/meter (kN/m) versus the 51.5 lbf/ft (0.75kN/m) distributed loads; however, for crowd and stadium loadings, ASCE 7 and IBC have no additional requirements, whereas NBC, EN, BS, ABNT and AS/NZS require 3 kN/m (~200 lbf/ft) for stadiums. Additionally, EN, BS and AS/NZS also have an intermediate level of 1.5 kN/m (~103 lbf/ft) for specific areas of assembly, but this is not in the NBC code. In total, of 45 countries in which balustrade loadings were able to be found at the time of submission: 40 countries have a maximum crowd loading of 3 kN/m (~206 lbf/ft) or greater (>4x U.S. code loading), one country (India) has a loading of 2.25 kN/m (~154 lbf/ft) (~3x the U.S. code loading) and none have a lower loading.
A historical study of U.S. documents pertaining to loading yields three main references: ASTM International ’s ASTM E985 Standard Specification for Permanent Metal Railing Systems for
Buildings , the American Society of Civil Engineers’/Structural Engineering Institute’s ASCE/SEI 7 M inimum Design Loads and Associated Criteria for Buildings and Other Structures, and the International Building Code . Significantly, ASTM E985 was originally released in 1984 and its references include Australian Standard AS 1170.1 Structural design actions, Part 1: Permanent, imposed and other actions, and British Standard BS6399 Loading for buildings – Code of practice for dead and imposed loads which at the time also showed 0.75 kN/m (~51 lbf/ft), but the last technical update to E985 was in 2000, and it was withdrawn from 2012 through 2024. (ASTM E985 was recently reinstated, ostensibly as it was in 2000, for the purpose of bringing it up to date.) Crowd and assembly loadings were adopted by BS6399 in 1996, AS/NZS 1170.1 in 2002 and EN1991 Eurocode 1: Actions on structures—Part 1-1: General actions—Densities, self-weight, imposed loads for buildings in 2002. In the interim period, without maintenance of standards in the U.S., balustrade loadings have languished; thus the question becomes: “Why did they change elsewhere, and are those changes justified?”
The balustrade load categories proposed here were introduced in BS6399 – 1996. The history of its introduction is unknown to the author; however, it was possibly a reaction to the 1989 Hillsborough Disaster (UK) where 96 people died in conditions of overcrowding, following a collapse of a crowd barrier at an FA Cup semi-final soccer
Table 1. Summary of Handrail and Guard Design Categories per AS/NZS1170.1 and EN1991 With Rounding to Convenient Imperial Numbers.
Occupancy Use Examples
Handrail, Top Rail, and Guards Infill Handrail and Guard Design
A Light duty Interior residential and access gantries
B Basic Areas not subject to assembly or overcrowding
C Assembly Areas where assembly and congregation may be anticipated
D Crowd Areas susceptible to overcrowding.
One and two family dwellings excluding external balconies and edges of roofs, and; safe working places and access normally used by operating, inspection, maintenance, and servicing personnel with an occupancy of less than 50.
Areas not susceptible to overcrowding: external residential, office and institutional buildings, also industrial and storage buildings.
All retail areas including public areas of banks/credit unions; Areas with fixed seating adjacent to a balustrade, restaurants, bars, etc. (See also D for areas where overcrowding may occur)
Theaters, cinemas, grandstands, discotheques, bars, auditoria, shopping malls (see also C), assembly areas, schools, universities, studios, etc.
* Actual value in AS/NZS and EN is 0.25kN = 56lbf; the current value in ASCE 7 is proposed for convenience.
** Value summarizes AS/NZS and EN but does not comply with OSHA 1910.28.
match. The investigation listed several other precedent collapses. Railing collapses have also been reported at a Philadelphia (PA, USA) stadium in 1998, in Maryland (USA) in 2022, and at the Public University of El Alto in Bolivia in 2021, which resulted in at least six deaths and multiple injuries. The latter item is relevant as the Bolivian loading standard for Actions on Structures (NB 1225002-1) requires 1.0 kN/m (69 lbf/ft), which is greater than the maximum balustrade loading in ASCE 7/IBC/ASTM E985.
Other collapses without serious injury included events at NFL football games. These are significant because there was not a great depth of people pressing behind the barriers.
The Hillsborogh Disaster was thoroughly investigated and is well documented by R.A. Smith from University of Sheffield in “The Hillsborough Football Disaster: Stress Analysis and Design Codes for Crush Barriers,” published in Engineering Failure Analysis (1994). In the paper, Smith quotes the investigation report by Lord Taylor, noting that similar investigations had occurred in 1924, 1946 (33 deaths), 1972 (66 deaths), and 1986 (56 deaths). Smith (writing in 1994) also noted other crowd crushing events in 1990 (Mecca, 1,426 deaths), 1991 (Shanghai, 105 deaths) and 1992 (Madras, 65 deaths). The Wikipedia page https://en.wikipedia.org/wiki/ List_of_fatal_crowd_crushes#21st_century summarizes hundreds of events and thousands of deaths due to crowd crushing. While all of these do not include details of barrier collapse, they demonstrate that fatal crowd loading is sufficiently frequent to be a design consideration; we know that if a barrier collapses it is more likely to cause crowd collapse and fatalities. It is important to prevent crowd loading situations from turning into fatal ones.
In a report “Going Off the Rails” (2021), The National Center for Spectator Sports Safety and Security (NCS4 at the University of Southern Mississippi) notes a history of fatalities and serious injuries at U.S. sporting arenas, both old and new.
While the Hillsborough Disaster was attributed in part to overcrowding, post-failure analysis indicated that the railing failed at approximately 8 kN/m; thus, the proposed loads of 3 kN/m (~200 lbf/ft) for crowd loading and 1.5 kN/m (~100 lbf/ft) for assembly spaces is not excessive for reasonable design load situations. The El Alto incident reinforces that elevated rail loading exceeding 1kN/m (69 lbf/ft) is possible at assembly areas other than at stadiums, so the approach in AS/NZS and EN, which is broader than in NBC, is justified. Eurocode includes a range of 3-5 kN/m (~200 lbf/ft – 340 lbf/ft) with 3 kN/m (~200 lbf/ft) recommended. This approach highlights some circumstances in which the designer may wish to select a loading greater than 3 kN/m (~200 lbf/ft) if it is considered appropriate.
R.A. Smith includes the formulation of a “leaning crowd” model used to estimate loads generated on a barrier on a stadium with terraced seating.
Studies of crowd crushing by Fruin (1993) indicated that crush forces of up to 3430 N (766 lbs) can be applied to a single person in overcrowding situations; hence, similar loads should be anticipated at barriers that contain crowds. This is important because the collapse of a barrier can lead to people falling over an edge, or by falling down and being crushed by those that land on top of them (Fried and Grant JASM Venue Safety Strategies, 2023).
An animation at CrowdRisks.com/research.html provides a computer simulation of “crowd collapse,” a situation in which a disturbance causes one person to fall and be unable to shift and regain balance without pressing on the person next to them, who is then also pushed off balance, creating a domino effect—with increasing mass and synchronous dynamic effect and/or multi-cyclic impact as the wave passes through the crowd. Review of the video of the El Alto incident indicates that there were “pressure waves” within the crowd
and that a scuffle added a dynamic component to the static load at the time of collapse.
An Australian Study by C.T. Styan, M.J. Masia, and P.W. Kleeman “Human Loadings on Handrails” in the Australian Journal of Structural Engineering takes an experimental approach to measuring the horizontal loads possible on rails and finds that the loads in the BS, EN, and AS/ NZ standards are reasonable and that in a significant number of cases, exceed the loads in ASCE 7. The Australian study also documents other failures due to overloading in the introduction to their study. In the 1998 Philadelphia barrier collapse professional reports stated that the failure was due to overloading, not a design fault (relative to the design loading) and further notes that the audience was only one or two rows deep. The test simulated loadings associated with various types of occupancy and compared them with the design loading. Testing found that a single row of people could generate static loads of 1.43 kN/m (98 lbf/ft), two rows generated 2.12 kN/m (145 lbf/ft) and three rows generated 2.66 kN/m (182 lbf/ft); adding dynamic “bouncing” and a single row at the barrier generated 2.43kN/m (167 lbf/ft). In each case, test results showed the design loads were appropriate; the results also found that in circumstances subject to “unruly behavior,” such as kicking the barrier, loadings higher than the design loading were possible. The testing also confirmed a 1.5 kN/m (~100 lbf/ft) loading for an occupancy with assembly but without crowd loading.
As the occupancy categories used in the U.S. are different than in the other standards referenced, the tables in BS, AS/NZS and EN have been grouped and summarized by load. Notably, in Table 1 Category “A” there is a reduced point load relative to ASCE 7 for interior single residential usage, but a 25 lbf/ft uniform load is required where ASCE 7 would exclude a requirement. The loading in the U.S. is concentrated load based on a “grab load” and “soft body slip impact load” as investigated by ANSI; hence, reductions are not proposed, and the table is a conservative bounding of the criteria. Additionally, concentrated loads do not match the 200 lbf point load requirements in the Occupational Safety and Health Administration (OSHA) Regulations 1910.28.
The proposed design loads in Table 1 are an amalgamation of the referenced EN and AS/NZS standards and the existing precedence in ASCE 7. The load categories do not align directly between the standards; whereas ASCE 7 has concentrated loads for the top rail and the components, and a uniform load for the top rail, the AS/ NZS standard has all of these, and a distributed load applied to infill panels. The EN/BS standards have a concentrated load applied to the infill only (albeit that this is similar to or greater in magnitude than the ASCE 7 concentrated loads for top rails.) The reference standards’ inclusion of distributed loads applied to infill components is incorporated in the recommendation as it is likely important for barrier walls and fences. Canada’s National Building Code has incorporated allowances of 0.5 kPa (~10 psf) for walls as barriers.
ASTM E985 continues to be referenced and was recently reinstated in its prior form so that it can be updated. As such, it is noteworthy that not only does it not recognize assembly or crowd loading, it regards the 50 lb/ft as a test load for both the balustrade system and the attachments to structure as tested in ASTM E894 Test Method for Anchorage
of Permanent Metal Railing Systems and Rails for Buildings and E935 Test Methods for Performance of Permanent Metal Railing Systems and Rails for Buildings. Such testing protocols do not currently allow any variability in the materials or testing to provide a safety factor. For example, the National Design Specification (NDS) for wood recommends a safety factor of 5 for withdrawal of fasteners relative to test data to allow for system variation. For post-installed concrete anchors under static loading a factor of safety of 4 is common but is greater for dynamic loading. Post-installed concrete anchors should pass the requirements of American Concrete Institutes’ ACI 355.2 Qualification of PostInstalled Mechanical Anchors in Concrete and Commentary. As noted in a report “Going off the Rails” by The National Center for Spectator Sports Safety and Security, where railings fail, failures at the anchors are the most common cause. The Australian Standard 1170.0 Structural design actions, Part 0: General Principles Appendix B provides proof load testing factors based on sample size and coefficients of variation. Following ASTM methods, the combination of lack of crowd loading and safety factor for testing results in metal railing systems attached to a wood structure, tested and approved to ASTM E985 and E935, are one fifteenth of the loads prescribed by AS1170.1 and testing to AS1170.0 Appendix B . Even for the current ASCE 7 design loads, the lack of a safety factor in testing means that systems approved by testing potentially have a significantly lower strength than systems justified by calculation to the relevant materials standards.
The proposed loads in Table 1 are reasonable and validated. The reference in Eurocode EN 1991 indicates a range of crowd loads between 3 kN/m (~ 200 lb/ft) and 5 kN/m (~ 340 lb/ft) and the post-failure analysis of the Hillsborough barriers indicated failure at ~8 kN/m (~ 550 lbf/ft); however, the latter was in a case of extreme overcrowding which might be considered greater than a reasonable design case. Crowd loading of 3 kN/m (~ 200 lb/ft) has also been adopted by the Canadian code for stadiums.
Justification by testing to meet standards needs to incorporate suitable safety factors based on the materials they are being attached to as well as testing variations. For testing with samples of 6 or more, a proof load factor of 2.5x for steel, 4x for concrete, and 5x for wood is consistent with achieving statistical significance consistent with the respective materials’ standards and coefficient of variation.
There is a large discrepancy between balustrade loadings in the United States and most other countries. Changes elsewhere were based on multiple disasters, investigation of those events, and validation by testing. The balustrade loads similar to Table 1 have been adopted in over 40 counties. These loads have been proposed to ASTM and ASCE for future incorporation. In the interim, design professionals and project specifiers have the option to follow international best practice when selecting appropriate testing and design loads for balustrades and guards. Full
The 16th Edition AISC Steel Construction Manual marks nearly 100 years in publication.
By Margaret Matthew, PE, and Yasmin Chaudhry, PE
AISC recently released the 16th Edition Steel Construction Manual. The 16th edition celebrates nearly a century of publishing one of the most respected design aids in the construction industry.
The big changes in this edition are outlined here. While not everything new is mentioned here, a full list of changes and updates are included in the Preface to the 16th edition.
The AISC Committee on Manuals has dedicated the 16th edition to Dr. William (Bill) A. Thornton, former Chairman and longtime member of the committee. From 1985 until 2011, Bill served as the Chairman of the Committee on Manuals and oversaw the development of numerous Manual editions, including the First edition LRFD Manual and the 14th edition Manual. The 16th edition is only the second Manual ever to be dedicated and honors Bill’s many contributions to the industry.
The big story in the 16th edition starts in Part 2, General Design Considerations, which includes a wide range of guidance applicable to the design and construction of steel buildings. Significant changes
AISC Specification for Structural Steel Buildings
AISC Code of Standard Practice for Steel Buildings and Bridges (ANSI/AISC 303-22)
RCSC Specification for Structural Joints using HighStrength Bolts
Minimum Design Loads and Associated Criteria for Buildings and Other Structures (ASCE/SEI 7-22)
AWS D1.1/D1.1M Structural Welding Code—Steel
ASTM A6/A6M Standard Specification for General Requirements for Rolled Structural Steel Bars, Plates, Shapes, and Sheet Piling
were made to the tables that help guide users when specifying material: Table 2-4 includes the available grades of standard structural shapes, Table 2-5 includes available grades of plate and bar material, and Table 2-6 includes available grades of structural fasteners.
In addition to available material grades, the tables show preferred grades for different components. For every new Manual, AISC reviews the materials that are commonly used in steel construction to develop a list of preferred materials that reflect factors like ready availability, ease of ordering and delivery, and pricing. The use of preferred materials will help avoid material procurement issues and the potential for added cost.
An important distinction—preferred does not mean required. Any of the other applicable material specifications can be used successfully on a project, but the availability and cost-effectiveness of grades other than the preferred material specification should be confirmed with a fabricator prior to their specification.
Here are the major changes in the tables:
• The preferred material specification for M-, S-, and L-shapes has been updated to ASTM A572/A572M Grade 50 from ASTM A36/A36M.
• The preferred material specification for C- and MC-shapes has been updated to ASTM A992/A992M from ASTM A36/A36M.
• The preferred material specification for round HSS is still ASTM A500/A500M Grade C, however the yield strength has increased from 46 ksi to 50 ksi.
• The preferred material for plates and bars up to 4 in. thick has been updated to ASTM A572/A572M Grade 50 from a dual preference of ASTM A572/A572M Grade 50 and ASTM A36/ A36M. There is now a row in Table 2-5 listing ASTM A36/ A36M as a preferred material specification for “All other applications.” This row is for elements like toe-kicks, edge plates, and other miscellaneous steel where the additional yield strength of A572 Grade 50 is not necessary.
All shear connection design tables found in Part 10 have been updated from 36 ksi to 50 ksi connection material. Designers can use the tables to aid the design of typical shear connections using higher strength materials that are regularly used today.
The 2022 AISC Specification and 2020 RCSC Specification have adopted a new bolt specification, ASTM F3148. This new bolt grade has a tensile stress of 144 ksi, which puts its strength between Group 120 and Group 150 bolts. These new Group 144 bolts are an option in the shear connection tables throughout Part 10.
The Part 10 shear connection tables received a major revamp. The tables affected are:
• Table 10-1—All-bolted double-angle connections
• Table 10-4—Shear end-plate connections
• Table 10-10—Single-plate connections
• Table 10-12—Bolted/welded single-angle connections
Each of these tables is split into three subtables—one to verify the connection material strength, one to verify the shear transfer strength at the bolt holes, and one to verify the strength of the supported member when coped. The new tables will allow for an easier determination of the effective bolt shear transfer strength and the shear strength of the supported beam web when coped. See Table 10-1a in Figure 1.
Part 2 of the 16th edition includes expanded guidance for corrosion protection. A new section on galvanic corrosion was added to help identify situations where galvanic corrosion may be an issue when joining dissimilar metals. The new section lists conditions where galvanic corrosion is unlikely and where risk is high. A new table, Table 2-8 shown in Figure 2, provides a matrix of common construction metals and their steady state electrode potential as a basis to identify the potential for galvanic corrosion.
Fig. 1 (left). New tables, such as Table 10-1a allow for easier determination of the effective bolt shear transfer strength. Fig. 2 (above). This new table provides a matrix of common construction metals and their steady state electrode potential.
The 16th Edition Manual is not all that’s new. Accompanying its release are several useful, free resources available at www.aisc.org/manualresources.
The new version 16.0 Companion to the AISC Steel Construction Manual is a two-volume set containing nearly 1,800 pages of material to supplement the Manual. Manual Companion, Volume 1: Design Examples v16.0 includes more than 160 complete design examples illustrating commonly used provisions in the 2022 AISC Specification and the16th edition Manual for designing members, connections, and structural systems.
The v16.0 Manual Companion, Volume 2: Design Tables, contains 20 design tables that supplement the Manual with additional material grades, including ASTM A913 Grades 65 and 70 W-shapes and ASTM A1085 HSS members.
The v16.0 Shapes Database is a Microsoft Excel spreadsheet that compiles the dimensions and properties of all shapes printed in Part 1 of the Manual.
The new v16.0H Historic Shapes Database is updated with all dimensions and properties consistent with the 15th edition Manual. This resource provides a complete list of historical shape information recorded from 1873 to 2016.
The Basic Design Values Cards are a set of pocket-sized cards presenting some frequently used limit state equations for checking members and connections from the 2022 Specification in an abbreviated format.
The Interactive Reference List is a complete listing of all the references found in both the 2022 Specification and 16th Edition Manual. Many of the references are available from the AISC website, while others are linked to the outside organization where the listed publication can be accessed or purchased.
Additional changes in Part 2 includes a new section, Using the Manual Tables, that alerts users about interpolation within design tables, and a section on Simplified Determination of Required Strength that presents a simplification of the effective length method when a quick, conservative solution is desired.
When preparing contract documents, start with the updated section on Contract Document Information, which summarizes the requirements from the AISC Specification, the AISC Seismic Provisions, and the AISC Code of Standard Practice.
Solutions for a first- and second-order analysis of two beam-columns are now provided in Part 6. The new Table 6-5, shown in Figure 3,
conveniently includes benchmark solutions for bending moments and deflections of a simply supported beam subjected to an axial load and transverse uniform load (Case 1), and a cantilevered member subjected to an axial force and transverse point load (Case 2).
These solutions are intended to validate solutions from computerized structural analysis or facilitate computation of required forces and deflections during design when the member configuration matches the given configurations.
Part 11, which in previous editions contained information for partially restrained (PR) moment connections, and Part 12, which included information for the design of fully restrained (FR) moment connections have been merged into the new Part 11, Moment Connections.
The new Part 12, Design of Simple Connections for Combined Forces, provides guidance on the design of typical shear connections subjected to axial or torsion forces in addition to shear forces.
Part 13, Design of Bracing Connections and Truss Connections, has several updates in the 16th edition. The Uniform Force Method has been expanded with a new “Special Case 4” that utilizes a single plate at the column connections. The new special case is useful where braces framing into the column web can create erection difficulties in the field, especially when columns have stiffener (continuity) plates in the web. Part 13 also includes a new section covering chevron bracing connections, which require special consideration during both member and connection design due to a phenomenon called the “Chevron Effect.” Lastly, Part 13 includes new material covering the design of horizontal bracing connections.
Part 9, Design of Connecting Elements, contains a new “Plastic Section Modulus for Coped W-Shapes” table as a companion to the coped beam elastic section modulus table in previous editions. The procedure for checking the available flexural strength of a beam with a cope at the top flange provided in Part 9 requires the calculation of the plastic bending moment of the coped section. This calculation is much simpler now using the coped beam plastic section modulus taken directly from the new table.
Tables 10-2 and 10-3 are used for the design of bolted/welded or all welded double-angle connections. For the weld between the angles and the support (“Welds B”), the weld design method was changed from the elastic method to the instantaneous center of rotation method. The updated design method will provide higher connection strengths. Additionally, these tables have a new weld geometry (“Welds C”) that includes additional lines of weld at the bottom of the angles, providing additional connection strength where needed.
The new Manual can be purchased at www.aisc.org/16thedition.
O’Donnell & Naccarato (O&N), a structural engineering firm headquartered in Philadelphia, celebrated the grand opening of Broad + Noble, a luxury apartment tower in Center City, PA. With views of the city skyline, the 19-story, 326,000-square-foot residential high rise offers top-of-the-line amenity spaces, as well as a blend of retail and office space and secure below-ground parking.
O&N provided structural engineering services for the $112 million project, in partnership with developer Toll Brothers Apartment Living and architect Barton Partners. The building, which broke ground in 2021, features a traditional brick exterior in a nod to the historic industrial architecture of Philadelphia’s Callowhill neighborhood and overlooks a sprawling landscaped plaza with a separate, two-story retail space, nestled between its massive L-shaped footprint.
Residents of the 344-unit apartment complex will also enjoy a sky lounge with private dining, outdoor terraces, and a rooftop deck created by setbacks at the building’s upper levels.
Broad + Noble is constructed almost exclusively with 8-inch precast plank floors, using the Girder-Slab structural system to maximize space relative to the building’s height. The top-floor sky lounge is designed with a plank floor system on steel wide-flange beams, and large steel transfer beams interrupt the spacing of columns and highly
coordinated brace frames within the residential floors to permit a transition to amenity spaces and below-grade parking on the first and second floors below.
Student engineers from the University of Florida secured their fourth straight firstplace overall win in the 2024 Student Steel Bridge Competition (SSBC) National Finals on June 1, breaking the consecutive titles record they set themselves in 2023.
Louisiana Tech University in Ruston, LA, served as the host school for the 2024 competition.
This year’s SSBC participants were challenged to design, fabricate, and quickly construct a scale-model steel bridge that would span a man-made river in a large disc golf course. Competitors had to find innovative ways to navigate new rules and challenging assembly constraints, including one of the widest conceptual rivers in the competition’s history.
In addition to winning the overall prize (and $5,000 in scholarships), the University of Florida placed first in economy and lightness and came in second for efficiency. They achieved an 11-minute, 37-second assembly
NIST announced two of its own are finalists for the Samuael J. Heyman Service to America Medal for their work on tornados and designing structures that can withstand them. Long Phan and Marc Levitan have "played a critical role in changing minds about designing for tornadoes by conducting groundbreaking research and advocating for changes to building codes and standards," according to a post on NIST's Taking Measure blog.
The Samuel J. Heyman Service to America Medals are given to career federal employees and chosen through a selection process led by a panel of leaders in academia, business, philanthropy, government, and media. Winners will be announced in the early fall.
"In 1997, a big tornado hit Jarrell, Texas.
At the time, the National Weather Service rated tornadoes using the Fujita scale. The Fujita scale estimates tornado wind speed by assessing the damage it caused. It assumes that more damage means there was a higher wind speed. The Jarrell tornado was rated as an F5, the highest possible Fujita rating.
As a structural engineer with experience in structural failure, when I looked at the Jarrell tornado, I just didn’t think that the damage was necessarily caused by extremely high wind speed. So, I began to think, 'OK, the Fujita scale might not be accurate.'" —Long Phan as told to NIST's Taking Measure Blog.
time with only two builders.
“I was nervous coming into the main competition,” said Anthony Perez Ortegon, co-captain of the University of Florida steel bridge team. “These teams spent just as much time–if not more–as we did, putting in so much work. Seeing their bridges and how much they love them really puts this pressure on you that’s like, ‘man, they brought the competition.’”
University at Buffalo came in second overall, winning second place in construction speed and third place in economy—plus $3,000 in scholarship funds.
Lafayette College won third place overall and brought home $2,000 in scholarship support. They received the Frank J. Hatfield Ingenuity Award, which recognizes innovative approaches to competition rules. Lafayette’s student engineers took advantage of a new SSBC rule requiring the use of rigid containers for loose nuts and bolts by wearing the containers on their arms for efficient access to the bolts.
“All 47 teams impressed us with their creativity, willingness to compete, and togetherness,” said AISC President Charles J. Carter, SE, PE, PhD. “They made it such a wonderful weekend for all of us.”
The final results of the 2024 competition are as follows:
Overall
Economy
University of Florida
William Jewell College
University at Buffalo
University of Florida
University at Buffalo
Lafayette College
Construction Speed
William Jewell College (0:4:30)
University at Buffalo (0:6:06)
University of California, Davis (0:6:22)
Lightness
University of Florida
Liberty University
University of Connecticut
Aesthetics
Virginia Tech
University of Michigan
University of Texas at Tyler, Houston
Engineering Center
Stiffness
University of Wisconsin, Platteville
University of Alaska, Fairbanks
University of California, San Diego
Cost Estimate
University of Texas at Tyler, Houston
Engineering Center
University of Connecticut
Pennsylvania State University, University Park
Efficiency
University of Alaska, Fairbanks
University of Florida
University of Wisconsin, Platteville
Team Engagement Award
University of Nevada, Las Vegas
Robert E. Shaw Jr. Spirit of the Competition Award
South Dakota School of Mines and Technology
Frank J. Hatfield Ingenuity Award
Lafayette College
John M. Yadlosky Most Improved Team Award
Arizona State University
Video Awards
University of British Columbia
Universidad Nacional Autónoma de México
University of North Carolina at Charlotte
The SSBC planning committee also announced that Iowa State University is the official host of the 2025 SSBC National Finals (May 30-31, 2025, in Ames, IA).
Hatfield Group Engineering (HGE), a New York-based, WBEcertified, multidisciplinary engineering firm, announced the launch of its Chicago studio. HGE Chicago is led by Koz Sowlat, SE, PE, and Robert J. Diebold, SE, PE, who have co-led their firm, Sowlat Structural Engineers, since its founding in 2004. HGE Chicago was established on May 4, 2024, to better serve HGE clients, by leveraging Sowlat and Diebold’s structural expertise, and by bringing HGE’s structural, MEP/FP, and facade engineering services to the Midwest. Sowlat, Diebold, and HGE founding partner, Erleen Hatfield, PE, FAIA, F. ASCE, worked together while at Perkins and Will and Thornton Tomasetti and are reunited to provide their expertise in the design of large, complex buildings with fast-track schedules, leading to high-quality built projects.
HGE Chicago is currently delivering structural engineering services for the following projects:
• The Lake View, 333 Superior Street, Duluth, MN, a 16-story residential building, under construction
• Hilton Chicago Renovations, Chicago, under construction
• The Chicago Housing Authority, North Lawndale Building Renovations, Chicago
• 424 South Wabash, Chicago, a 26-story Sonder Hotel.
Construction is underway on the University of Michigan's College of Pharmacy building. The project, designed by RDG Planning & Design alongside Alvine Engineering (mechanical, electrical and plumbing), TD2 Engineering & Surveying (structural engineering) and Midwestern Consulting (civil engineering), is utilizing mass-timber structures to reduce greenhouse gas emissions, increase the speed of construction and provide well-being benefits. RDG’s design combines fire detection and suppression systems that go beyond baseline fire codes and standards to further improve fire performance. Plus, mass timber enhances fire safety by creating a char layer on the surface of the wood that insulates and protects the inner core from burning. The building is scheduled to be completed in the fall of 2025.
Architecture and Engineering firm, IDOM, has completed a successful final design review for one of the largest mechanized smart buildings in the world.
The Giant Magellan Telescope, which is now 40% under construction and on track to be operational by the early 2030s, is the work of the GMTO Corporation, an international consortium of 14 universities and research institutions representing the United States, Australia, Brazil, Chile, Israel, South Korea, and Taiwan. The telescope is being built in America and will be reassembled and completed in Chile by the early 2030s.
Once completed, the 65-meter-tall enclosure will be one of the largest mechanized buildings ever constructed and will represent a true feat of modern engineering and precision manufacturing. At over 5,000 metric tons, the enclosure will be able to complete a full rotation in four minutes and be equipped with 46-meter-tall shutter doors that reveal the 25.4-meter telescope for unobstructed scientific observations. The smart building is designed
Once completed, the 65-meter-tall enclosure will be one of the largest mechanized buildings in the world. Credit: Giant Magellan Telescope - GMTO Corporation
Two leaders at Lockwood, Andrews & Newnam, Inc. (LAN) have been appointed to significant positions within the American Council of Engineering Companies (ACEC) state and local chapters. President Wayne Swafford, PE, will serve as president-elect for the 2024-2025 ACEC Texas Officers, and Chief Operating Officer Steve Gilbreath, PE, will serve as director for the 2024-2025 ACEC Houston Board of Directors. Swafford and Gilbreath will bring their extensive expertise and leadership to their respective roles.
Swafford, a structural engineer with more than 30 years of experience, is responsible for the direction and operation of LAN.
to control the telescope’s operating environment by protecting seven of the world’s largest mirrors as they track celestial objects across the sky more than a billion light years away.
IDOM began developing the Giant Magellan Telescope enclosure design over two years ago following a competitive, global search and extensive evaluation process.
“Our team approached the challenge of the Giant Magellan Telescope enclosure knowing that this structure would be responsible for enabling some of the most important scientific discoveries of our lifetimes,” said IDOM North American President Tom Lorentz. “We are proud to have delivered a successful design and look forward to the Giant Magellan Telescope’s success.”
With the enclosure design milestone complete, the Giant Magellan Telescope is now preparing a global search for a firm to leave their mark on the future of astronomy with construction of the enclosure.
Gilbreath currently serves as the chief operating officer of LAN, where he oversees the firm’s day-to-day operations.
ACEC is the business voice of America’s engineering and design services industry.
ACEC Texas is a statewide organization representing over 300 member firms in the engineering industry.
To solidify ICC-ES as a one-stop-shop for testing, inspection, and certification, services offered by the ICC-NTA Building and Plumbing Products division, including inspections, testing, and certification engineering, are being branded as ICC-ES, effective immediately.
The acquisition of NTA into the ICC Family
of Solutions in 2019 expanded the services the Code Council provides by adding testing and inspection capabilities. This addition streamlines the technical evaluation process provided by ICC-ES. Both teams working together simplifies the process for clients as verified resources can readily be shared across companies, eliminating the need for additional communication steps.
The company is working with the respective accreditors to ensure a seamless transition to the ICC-ES brand and with no disruption to current report holders.
The ICC-NTA brand will remain associated with off-site construction services, including plan review, inspection and certification of modular home systems.
Test laboratory locations span several states to offer local testing options to customers, from Texas to Indiana. For more information and frequently asked questions, visit www.icc-es.org.
Arizona lawmakers passed Bill HB2253, ensuring the continuation of the Arizona Board of Technical Registration (BTR), with Governor Katie Hobbs signing it into law on June 18. This decision ends the uncertainty that arose when the bill stalled in the Senate, threatening the BTR’s existence beyond July 1, 2024.
The BTR regulates licensure, applications, renewals, complaints, and disciplinary actions for structural engineers and other professionals in Arizona. Its continuation is vital for maintaining high standards and protecting the health, safety, and welfare of Arizona citizens. The passage of HB2253 ensures the BTR will continue its crucial role in safeguarding public interests and upholding professional standards in Arizona. Moreover, the preservation of the BTR underscores the importance of professional regulation, which benefits structural engineers nationwide by reinforcing the significance of rigorous licensure and regulatory oversight.
NCSEA, as part of the Structural Engineering Licensure Coalition with CASE and SEI, supported the SEA of Arizona in advocating for the bill.
Tricia Ruby, President of the NCSEA Foundation Board, is the recipient of the 2024 Horace H. Rackham Humanitarian Award from the Engineering Society of Detroit (ESD). This prestigious accolade recognizes outstanding humanitarian achievements through technical accomplishments or exceptional contributions to civic, business, public-spirited, or humanitarian endeavors.
Ruby is a strong advocate for diversity and inclusion within the engineering and construction industries. Her leadership roles in the NCSEA Foundation and ACE Mentor Southeast Michigan highlight
her commitment to these causes. Her dedication has earned her multiple awards, including the AFP Distinguished Volunteer Award and the ACEC National Community Service Award. Ruby was presented with the Rackham Award, ESD’s highest honor, at the organization’s annual dinner on June 26.
The NCSEA Foundation recently announced the launch of the “Structural Engineer Spotlight Series: Something From Nothing,” a webinar series created by esteemed filmmaker Dilip Khatri. The series showcases the remarkable journeys of members from the Structural Engineers Association of Southern California (SEAOSC) as they rise from humble beginnings to become influential figures in the field. The series kicked off with Episode 1 on July 19, featuring Lorena Arce, who shared her journey, struggles and achievements. Episode
2, airing on Aug. 16, will highlight Adena Geiger’s story of moving from Iran, navigating a rigorous education process and earning her master’s degree in civil engineering. It concludes with Episode 3 on Sept. 20, featuring Daryl Frigillana’s path to becoming a structural engineer. Each webinar will take place at 10 a.m. PT/12 p.m. CT/1 p.m. ET and will include a live Q&A with the featured engineer. The webinar series is made possible by the NCSEA Foundation and is complimentary to attend.
NCSEA recently released results from its survey of structural engineers about their biggest concerns for communities and the built environment.
Topping the list of concerns was the speed of construction projects (42 percent of respondents) followed closely by deferment of important structural improvements and repairs (41 percent of respondents).
“The increased pace of design and construction can pose challenges to detailed coordination and project quality, but it also opens up new opportunities,” says Andrew Podojil, P.E., S.E., Associate at Veitas Engineers. “Involving structural engineers early and expanding contracted scope allows deeper collaboration; better risk management; and, ultimately, elevates project outcomes. Also, discussing concerns with your engineer will better serve the needs of the building owner and future occupants, leading to improved overall quality and reduced construction costs.”
Structural engineers are dedicated to ensuring the stability and safety of buildings and bridges in communities all over the world. Factors such as site location, environmental conditions, building material characteristics,
and load demands all influence the structural design and are considered from concept through completion of every project they are involved in.
After construction speed and lack of important improvements and repairs, survey respondents (37 percent) indicated that aging infrastructure was also a major area of concern.
“Investing in the rehabilitation and retrofit of existing buildings and infrastructure may not be the easiest sell to decision makers, but these are necessary investments for the safety and resilience of our communities,” says Ed Quesenberry, S.E., Founding Principal of Equilibrium Engineers LLC and NCSEA Past President. “Structural engineers have the knowledge and tools to make these critical improvements as economically feasible as possible.”
The survey was part of NCSEA’s We SEE Above and Beyond campaign, which illustrates how structural engineers create safe, vibrant, and resilient communities and provides valuable resources for architects and building owners.
Structural engineers attending the NCSEA 2024 Structural Engineering Summit can kick off their experience with a special preconference symposium on Nov. 5 in Las Vegas. “Existing Buildings Assessments: Lessons Learned and Best Practices for Structural Engineers” is a half-day event packed with valuable insights.
Attendees will learn about advanced investigation methods like non-destructive testing, surveying, monitoring, and scanning. The symposium will cover common structural failures in materials such as steel, concrete, wood, and masonry, and building parts
like parking garages, balconies, and decks. There will also be tips on report-writing, including rating systems, assessment levels, and legal aspects. The symposium, sponsored by DEWALT, will award 4.75 PDHs to attendees.
The event is open to everyone, with a registration fee of $249 for NCSEA members and $449 for non-members. You don’t need to attend the full Summit to join this symposium. To sign up, create a profile at NCSEASummit.com/register and select “Existing Buildings Assessments” at checkout.
Purchase an NCSEA webinar subscription and get access to all the educational content you’ll ever need! Subscribers receive access to a full year’s worth of live NCSEA education webinars (25+) and a recorded library of past webinars (170+) – all developed by leading experts; available whenever, wherever you need them!
CASE has committees that work together to produce specific resources available to members, from contract documents to whitepapers, to help your business succeed.
If you are a member of CASE, all CASE publications are free to you. NCSEA and SEI members receive a discount on publications. Use discount code - NCSEASEI2022 when you check out.
Check out some of the new CASE Publications …
In today’s world, survey after survey has listed flexible work schedules and work location as a top desire of employees at all levels. Many companies are currently struggling through this shift and trying to determine what works best for the company in the long term as there are many pros, cons, and important considerations. In addition, structural engineering firms are having more difficulty filling positions and expanding the candidate pool beyond the local office locations could yield high quality employees. These options do create business, insurance, technical, IT/security, productivity, training/mentoring and cultural challenges. This Tool attempts to provide some guidance in these areas.
A critical component of talent management is succession planning. Training, development, career planning (employee-centered), career management (organization-centered), and replacement planning are all key elements of succession planning. Successful succession planning helps an organization cope with talent scarcity, identify skill gaps and training needs, promote knowledge transfer to retain institutional knowledge, increase morale and retention by investing in employees, and create bench strength for unique and highly specialized skill sets.
This tool provides guidelines and tips for the verification of analysis and design software results. It focuses on linear elastic structures and small deformation/small strain analysis which represent the vast majority of design office work.
An important aspect of a joint project pursuit between a contractor or design professional and a structural engineer is an agreement covering the activities of the parties prior to contract award. This agreement is commonly referred to as a teaming agreement. Teaming agreements are often associated with design-build projects but can be used on any project pursued jointly by two or more parties. Many organizations familiar to structural engineers provide a standard form teaming agreement. This commentary summarizes the contents and typical clauses of the standard form teaming agreements offered by these four organizations:
• American Institute of Architects (AIA): Contract C102-2015
• Engineers Joint Contract Documents Committee (EJCDC): Contracts D-580 and E-580
• Design-Build Institute of America (DBIA): Contract No. 580
• Consensus Docs: Contract Nos. 296 and 498.
You can purchase these and other Risk Management Tools at https://www.acec.org/member-center/get-involved/coalitions/case/resources/
Is there something missing for your business practice? CASE is committed to publishing the right tools for you. Have an idea? We’d love to hear from you!
August 8-9, 2024, Minneapolis, Minnesota
The CASE Summer Meeting will be in Minneapolis, Minnesota this year. The meeting will feature breakout sessions for the CASE Committees, interactive discussions on structural engineering and business resources, education sessions, and more. Registration is open now. https://www.acec.org/event/case-summer-meeting/
Now more than ever we need to support the upcoming generation of the workforce. Give to the CASE Scholarship today!
The past year has been transformative for the Professional Community (PC) in SEI, marked by growth and exciting new procedures. Under the leadership of its dedicated executive committee, the PC has navigated the shifting landscape of the SEI reorganization, leveraging the collective expertise of its subcommittees to drive meaningful progress. Current Chair Nicole Baer P.E., F. SEI., M. ASCE., emphasizes the PC’s pivotal role in disseminating knowledge and nurturing future leaders, stating, “The way I was kind of looking at it is the technical community creates content, but the professional community is the one that gets that content out to the world.”
A significant development this year has been the ongoing global initiatives within the PC. These initiatives, including the establishment of Interorganizational Collaboration Committee, represent a major expansion of the PC’s reach and impact. The goal is to foster strong connections and collaborations with structural engineers worldwide, promoting cooperation and knowledge exchange. Currently, the committee is undergoing a name change and will be calling for new members who are passionate about forging global partnerships and driving innovative projects.
The PC ExCom has introduced several operational enhancements to improve communication and collaboration among the committees and graduate student chapters. By assigning liaisons to each committee, the ExCom ensures that these groups stay connected, share progress, and collaborate effectively.
Vice-Chair Trevor Walker P.E., S.E, M. ASCE., highlights, “I’ve been very pleasantly surprised at how much appreciation there is now for the PC ExCom” and stating “it [PC Ex Com] ties everyone together.” These changes have led to a marked increase in productivity and alignment among groups previously working in silos. Reflecting on the procedural changes, the PC acknowledges the challenges of adapting to new systems, such as submitting detailed meeting notes and updating charge statements regularly.
However, these practices offer long-term benefits by fostering a more collaborative and productive environment that serves the broader structural engineering community. As the year concludes, the PC is primed to continue its mission of empowering structural engineering professionals and shaping the future of the profession.
The SEI Futures Fund, in collaboration with the ASCE Foundation, is offering scholarships to students and young professionals to attend Structures Congress 2025, taking place from April 9-11 in Phoenix, Arizona. These scholarships cover registration and travel costs, providing emerging engineers with the chance to gain insights from industry leaders, enhance technical knowledge through hands-on workshops, and network with a diverse group of professionals. Additionally, student membership to ASCE/SEI is free, with the first-year post-graduation also complimentary, emphasizing support for the next generation of structural engineers. Application details available at structurescongress.org
In June, Managing Director of SEI, Jennifer Goupil, spoke at the ASCE-NOAA Taskforce Workshop about the process of incorporating NOAA data into ASCE standards. The workshop focused on using NOAA datasets to enhance ASCE 7 and other standards, aiming to improve the accuracy and reliability of engineering practices through this collaboration.
Learn more about the NOAA ASCE Taskforce: go.asce.org/asce-noaa-taskforce
Want to shape and inspire the next generation of engineers? SEI invites you to apply for a position on the SEI Education and Leadership Committee. As a member, you will influence the direction of structural engineering education by developing state-of-the-art curricula and programs, leading initiatives that promote leadership skills and professional growth within the SEI
community and collaborating with a diverse group of professionals dedicated to advancing the field.
Apply online with QR code! Select “SEI Professional Community” from drop down and then select “SEI Education and Leadership Committee.”
Following the publication of ASCE/SEI 41-23 Seismic Evaluation and Retrofit of Existing Buildings, the committee is reconstituting its roster to begin work on the 2029 edition. ASCE/SEI 41 is now accepting new members for the next edition of the standard.
Applications for committees are being accepted until Sept 1, 2024. Select SEI from the Institute drop-down, and then select the standard title.
Full access to all ASCE standards referenced in the 2024, 2021, and 2018 editions of the International Building Code (IBC) is now available with our new ASCE Referenced Standards: IBC Collection! This comprehensive package includes essential standards like ASCE 7, ASCE 24, ASCE 41, and more. Ensure your projects meet the highest industry standards. Visit https://amplify.asce.org/ibc.
ASCE is conducting a reaffirmation public comment period on the ASCE/ SEI 32-01 Design and Construction of Frost-Protected Shallow Foundations. The 45-day reaffirmation public comment period will be held from June 21, 2024 – August 05, 2024. Visit go.asce. org/standardsballoting
Accessing the Public Comment System will require using or creating an ASCE web user account. For additional questions contact James Neckel, ASCE’s Codes and Standards Manager, at jneckel@asce.org
Application details available at structurescongress.org
ASCE standards provide technical requirements for promoting safety, reliability, productivity, and efficiency in civil engineering. The new ASCE Referenced Standards: IBC package offers users secure access to all ASCE standards referenced in the 2024, 2021, and 2018 editions of the International Building Code. The subscription includes:
Access to all 14 ASCE standards referenced in the IBC.
Referenced standards include key structural engineering guidelines including minimum design loads for structures, use of steel cables, cold-formed stainless steel design, flood design, structural fire protection, shallow foundations, wind tunnel testing, tensile strength, and seismic analysis.
The suite of interactive tools and feature-rich functionality that come standard with the ASCE AMPLIFY platform.
View the full list of standards at asce.amplify.org/ibc
In addition to the IBC-referenced standards, the AMPLIFY platform includes ASCE’s new Standard Practice for Sustainable Infrastructure, ASCE/COS 73-23, which provides design guidance to infrastructure owners, engineers, and contractors, to minimize the environmental impact and protect natural ecosystems, while simultaneously meeting the diverse needs of communities.
ASCE AMPLIFY is a powerful digital interactive platform designed to revolutionize your experience with ASCE’s engineering content. With ASCE AMPLIFY you receive onestop access to the most in-demand standards. You will experience the ease of working with the robust suite of interactive tools with a wide range of features and functionality.
One-click synchronizing between Provisions and Commentary with side-by-side display.
Redlining feature to quickly spot changes to previous editions.
Two-level search functionality: Site-wide search and product search.
Critical real-time incorporation of supplements and errata with date stamps.
Individual and corporate subscriptions available.
Building skills in creativity can complement the logical side of the engineering profession for better problem solving.
By Mark Riley, Ph.D.
The methods used by educators to train future engineers creates analytical thinkers who can deconstruct complex challenges into manageable tasks. Through lectures, readings, homework, and experiments, engineering students develop their analytic thinking skills but often do not fully develop their communication skills. In my 27 years as an educator, I and my colleagues have incorporated more communication exercises into curricula but despite these efforts, employers continue to seek improvements in the student communication skills. Here I share an idea that I believe has potential for meaningful improvement.
Recall the old saying that “if a tree falls in the forest and if no one is there to hear it, does it make a sound?” If no one is around, then there are no tympanic membranes which would convert the pressure waves into what we know as sound. A related concept applies to communication. If an individual talks at another and the receiver does not understand what is being said, has communication occurred? Good communication likely has not.
The 1970s tune, "The Logical Song," by the band Supertramp exemplifies the challenge facing engineering educators. To quote,
“But then they sent me away to teach me how to be sensible Logical, oh, responsible, practical Then they showed me a world where I could be so dependable Oh, clinical, oh, intellectual, cynical.”
We teach our students to be logical and, in the process, we restrict the exercise of uninhibited creativity, which is needed to produce well-rounded, engaged problem solvers who can communicate with a variety of audiences. I suggest that the engineering community look to the tools of improvisation, or improv, to improve communication skills.
Improv is founded on two rules: “yes” and “and.” The concept is that an improviser accepts the situation that has been presented to them (the “yes”) and adds information to the situation (the “and”). These rules are simple to learn but challenging to put into practice.
The skills of improv can be learned through a series of games which on the surface seem quite silly; however, they serve to practice active listening (the first part of good communication) and removing mental filters that restrict us from speaking our minds. One simple example is a game called “Introductions.” Participants are paired up and introduce themselves by answering questions: what their name is, where are they from, what kind of music do they like, and what is one location they have not yet visited but hope to travel to someday. These pairs match up with another couple and introduce their partner to the new tandem.
Many improv games have a history that connect with the works of Viola Spolin, often considered the mother of Improv. In Chicago in the 1930s, Spolin created The Educational Playroom for children in recognition that recent immigrants were not comfortable
in speaking English.
Spolin developed a series of games which encouraged all the children to participate and to gain confidence in speaking. The games became popular and eventually her son, Paul Sills, brought the games to adults as part of workshops intended for enjoyment of the participants. The workshops gained an audience and eventually begat the Second City comedy club and then Saturday Night Live, SCTV, and others. Improv skills have been learned by many communicators, comedians, and in recent years business professionals.
Improv is not inherently about comedy or being funny. Sometimes funny happens, but that’s not the point.
The tools of improv are helpful in improving the communication skills especially of individuals who are reluctant to speak their minds. This includes introverts, non-native English speakers, and engineers who have been trained to not speak on any topic that is outside of their area of expertise. For the past two years the University of Nebraska-Lincoln has been teaching improv skills to our graduate students.
Another game to build active listening skills is the “One sentence story.” The participants arrange in a circle and start with a prompt including the profession of a protagonist and a challenge they must overcome. The group creates this individual hero’s journey by each participant adding one sentence. They should agree and accept what was said previously (yes) while adding new information (and) to move the story along to resolution.
I am not suggesting abandonment of good practice in engineering, but rather that we place some effort to exercise parts of our brains that in many cases have not had the opportunity to flourish. Bodybuilders who focus on growing their biceps, pecs, and shoulders exclusively tend to look out of proportion with tiny, under-developed legs. Don’t skip leg day!
The concept of “yes, and” can apply to many layers of communication. Contrast the effect of hearing “yes, and” relative to “no, but.” For example, if an individual goes to a supervisor suggesting that they add a popcorn machine to the breakroom as a perk for employees. The supervisor’s natural instinct ought to be to support hearing creative ideas from their staff even if they have misgivings. A response of “no, but, we should encourage healthy eating” will not be well received since after the word “no” the listener is likely to shut down. The word “but” often invalidates all of the words that came before; that “no” already has turned off the receiver. A better response is “yes, and, we
should encourage health eating." Same words at the end, but the start of the sentence changes what is communicated.
Similarly, the “yes, and” approach is useful in the design process. When developing new concepts, use this instead of brainstorming, or association-based ideation. Start with one idea, accept that this idea is worthy of discussion, then build out the concept as far as it can go. Don’t critique the concept immediately. Start with another seed idea and run it out to completion.
After the SEI Congress 2023, a survey of participants asked for suggested programming at future meetings. Communication skills and leadership skills were in the top 5. “Structural Engineering Improvisation” made the list as a desired topic for leadership development.
At NASCC24, we held a workshop on “Building a better structural engineer through improvisation.” About 100 individuals participated in a series of games to encourage active listening and to remove communication filters. They seemed to have a good time especially in the “One sentence story” that arose about a heroic chemical engineering savant who realized the error of his/her ways and switched to structural engineering. For this activity each participant had to accept what was already established in the story and add one more sentence to advance it. This was a good example of building upon what has come before, of teamwork, of creativity, and of a willingness to speak without concern for saying the wrong word in a non-judgmental space. These are important lessons best learned through practice.
There is not yet a wealth of literature on engineers or scientists using improv to advance their communication skills.
I encourage you to seek out activities that take you out of your comfort zone and allow you to gain experience using the practices of improvisation. Local community colleges often have improv or theater classes which may be useful. That’s how I got my start down this path and have enjoyed it tremendously.
Additional resources are included in the online version of the article at STRUCTUREmag.org .
ASDIP Structural
Software
Phone: 407-284-9202
Email: support@asdipsoft.com
Web: www.asdipsoft.com
Product: ASDIP STEEL
Description:
Intuitive and reliable software that performs the structural design of steel members, such as anchor rods, composite & non-composite beams, steel columns, base plates, shear lugs, shear connections and web openings. You may complete any anchor design within minutes with only a few clicks using ASDIP STEEL.
ENERCALC, LLC
Phone: 800-424-2252
Email: info@enercalc.com
Web: https://enercalc.com
Product: ENERCALC SEL/ENERCALC 3D
Description: Streamline the design and calculations of anchor and anchor bolts with ENERCALC. ENERCALC SEL can assist in determining loads and performing analyses of full structures and connected components through its Loads & Forces modules and its many analysis and design modules including the Base Plate by FEM module.
RISA Tech, Inc.
Phone:949-951-5815
Email: info@risa.com
Web: risa.com
Product: RISAConnection
Description: RISAFloor, RISA-3D, and ADAPTRISAConnection is at the cutting edge of nextgeneration connection design software and now features full anchorage design as well as expandable reports and full 3D visualization. RISAConnection includes complete integration with RISA-3D and RISAFloor, as well as partner software packages such as Tekla Structures and Hilti Profis for anchorage design.
As a transformative, high-performance alternative to traditional low-slope roofing assemblies, OneDek® features include:
• Tapered insulation, parapet wall scuppers and internal drains
• Fewer total roof assembly components, which result in fewer labor hours
• Minimized through-fasteners, decreasing the likelihood of water infiltration, thermal loss and points of failure
• Full system, industry exclusive weathertight warranty