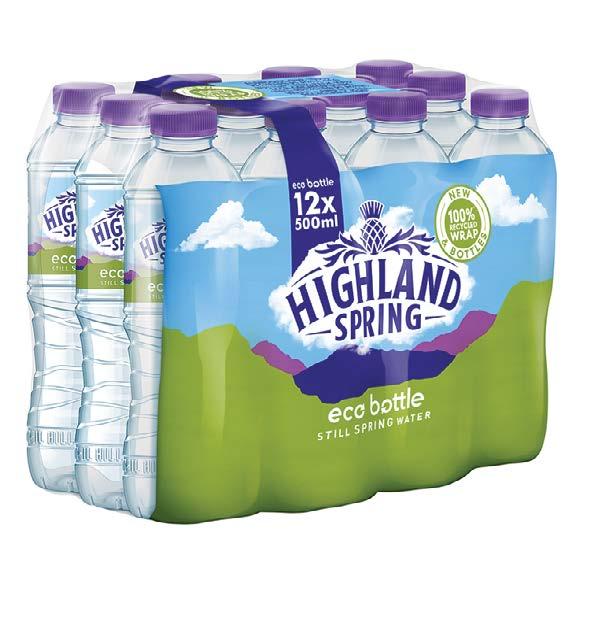
32 minute read
Plastic innovation
from SPN April 2021
by spnews.com
Spring forward
to 100% film recyclability
Advertisement
The quest to achieve the 100% recyclability of packaging film took a major step forward recently when the Highland Spring Group, launched its most environmentally sustainable ‘Eco Pack’ to date using Coveris’ Duralite R film. The next generation, 100% recycled and fully recyclable Duralite R shrink-film supports the company’s journey to reach 100% recycled materials across its entire packaging portfolio.
The Highland Spring 12 x 500ml multipack launched in January this year is being trialled at 270 Sainsbury’s stores across the UK. Following the introduction of its range of 100% recycled and recyclable eco bottles. The Highland Spring Group has continued its use of 100% recycled materials as part of its commitment to providing healthy hydration in an environmentally sustainable way.
Coveris’ award-winning, fully recyclable polyethylene film for the Highland Spring multipacks, features 100% recycled content comprising 50% post-consumer recyclate (PCR) and 50% post-industrial recycled material (PIW). Supporting a circular economy for plastic packaging, the 50/50 blend of recycled content achieves a 54% carbon footprint reduction compared to the use of virgin materials.
Highland Spring’s Eco Pack is the first major brand launch using a complete 100% recycled film from the Coveris Duralite R range. Simon Oldham, Chief Commercial Officer of the Highland Spring Group said: “We want consumers to understand that plastic is a valuable resource that should not be treated as waste. We are taking a holistic approach to our packaging and want to create a truly circular plastics economy in the UK to ensure these materials stay in the loop.
“That’s why we are delighted to introduce our next generation 100% recycled shrink wrap, which offers a significant step forwards in ensuring all our packaging uses recycled materials and is designed in a way that makes it easy for consumers to embrace positive plastic behaviours.”
Tim Frost, Coveris Louth Sales Director, added: “Coveris has been able to support Highland Spring Group’s forward-thinking approach to packaging sustainability with the development of our innovative, next generation Duralite R shrink film. Through our ‘No Waste’ strategy, Coveris is focussed on a sustainable future for plastic packaging by the advancement of high-quality recyclable materials, innovative use of recycled content and a ‘No Waste’ operating model.” In November 2020, Duralite R was awarded Flexible Plastic Pack of the Year in the UK Packaging Awards for achievements in carbon footprint reduction, innovation in recycled content and development of sustainable plastic packaging.

Smart enzymes
break down plastic film barriers
The Spanish company, Film Solutions has developed a technique that uses enzymes to break down plastic film, thus allowing for both the composting and recycling of its film.
The REBICOM (REcyclable, BIodegradable and COMpostable film) project has been funded by the European Union Horizon 2020 programme. Innovative Film Solutions has led the project that developed a new range of plastic films that contain enzymatic technology that accelerates the breakdown of the plastic in order to enable them to be recyclable, biodegradable or compostable.
The researchers encapsulated certain enzyme complexes in a polyolefin matrix to obtain a masterbatch that was incorporated into the formulation of plastic films during the production process. Following this, the technology was proven at scale, producing prototype films that met the EN 13432 standard as well as European legislation for food contact materials. Potentially, these new films can be biodegradable, compostable or recycled using current plastic recycling technologies. REBICOM coordinator Joaquín Buendía said: “Plastics take hundreds if not thousands of years to degrade, breaking down into ever-smaller pieces. Adding certain compounds to plastics could act as a culture for microorganisms. The enzymes secreted by organisms initiate material depolymerisation, feed on carbon bonds, thereby speeding up biodegradation.
“The plastic films carry within an inactive load that is 100% recyclable. When these plastic films end up in the environment in contact with microorganisms, their load triggers an enzymatic reaction that converts them into a biodegradable product in a relatively short period of time, given the proper temperature and humidity levels.”
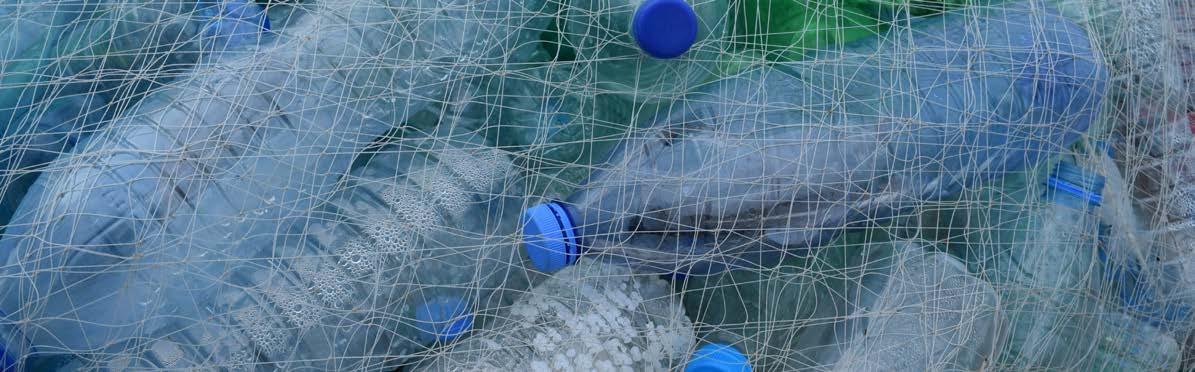
Boosting recycling and collection
In another move to increase the levels of plastic recycling, the EU launched its latest plastics strategy, which has since become the driving force behind the steady increase in European plastic recycling.
In 2018 it pledged that by 2025 PET plastics would have a minimum of 25% recyclable content. This pledge has now become law. In this issue, SPN looks at the latest recycling developments and how the strategy has dramatically improved the recyclability of soft drinks beverages and why the industry is still calling for enhanced recycling processes and improved feedstock recovery in order to meet their goals.
Boosting the collection and recycling of PET bottles is a key goal for both the EU and UNESDA. In addition to reducing plastic in the waste stream, it will also create a reliable supply of food-grade quality rPET. Soft drinks companies have been instrumental in setting up and running many of the packaging collection schemes across Europe.
The sector supports both deposit return schemes (DRS) for beverage packaging and extended producer responsibility (EPR) schemes which cover various packaging types and materials.
Harnessing rPET potential
There are a several different recycling technologies in operation today and companies must leverage each of them if they are to achieve their goals:
• Mechanical recycling – the grinding, washing, separating drying, re-granulating, stripping and compounding of plastics as widely used today; • Solvent purification – dissolving plastic in a solvent with a series of purification steps to separate the additives and impurities before the plastic is reused; • Enhanced recycling – the process of depolymerisation which breaks down the molecular bonds of the plastic into its original monomers and oligomers; • Feedstock recovery – heating the plastics to convert them back into basic petrochemicals so that they can be used to produce new plastic.
Jindal Films, a global leader in the development and manufacture of specialty films is expanding its broad OPP films portfolio to help the industry move towards easier to recycle laminates. In-line with the CEFLEX design guidelines issued in 2020, Jindal Films has been deploying its Technology development in 3 specific areas: outer print webs, barrier webs and sealant webs.
1. Printable OPP solutions
With the increasing need to remove from flexible packaging “hardto-recycle” printable substrates such as PET and Paper, Jindal is proposing a range of non-heat sealable OPP films either in a glossy (Bicor NND/NNH) or matt (Bicor CSRM) appearance. A new OPP platform with improved heat resistance is currently under development to have low shrinkage in the heat seal areas, high Modulus for efficient rotogravure printing while maintaining high clarity. This performance improvement would allow some customers to maintain packaging and filling rates in some demanding applications where previous attempts with conventional OPP failed to replace PET or Paper.

2. Barrier OPP solutions
With the growing need to remove Aluminum foil and metallized PET films from flexible packaging laminates, Jindal Films has developed a thin version of its well know Ultra High Barrier (UHB) OPP film technology. Metallyte 16MM883 provides barrier performance at the level required for numerous market segments typically resorting to Alu foils. Current applications extend from dehydrated foods and beverages, to roast & ground coffees, sensitive nuts and dry pet care typically in 3-ply lamination for products requiring 9 to 24 months of shelf life. Vacuum metallized OPP films in a fully printed laminate have b een shown not to interfere with NIR techniques commonly used in sorting plants.
For transparent barrier applications, Jindal Films has expanded its Aluminum Oxide vacuum coated OPP film offering. Alox-Lyte 16AO894 and 16AO893 can be used in 2-ply or 3-ply applications across a broad range of packaging formats, delivering improved recycling alternatives compared to harder to recycle thicker EVOH coextruded sealant films or to clear vacuum coated PET films.
3. Sealant OPP solutions
Jindal Films recently introduced a significant upgrade to its “Enhanced Seal” technology with the introduction of a new high seal performance “Ultra Seal” OPP film technology. Bicor 30, 40 & 50MB344US provide the inherent advantages of OPP (e.g. clarity, stiffness, puncture resistance, notched-tear propagation) with a seal performance approaching that of cast or blown PP or PE films. Seal strengths upwards of 15N/15mm can be measured on Ultra Seal based laminates, which allows for significant opportunities to replace blown PE films and design PP-rich alternatives for improved recycling.
RECYCLABLE POLYPROPYLENE PACKAGING
EXCELLENT BARRIER
(Moisture, gas, aroma and mineral oil )
HIGH STIFFNESS GOOD HEAT RESISTANCE
GREAT OPTICS
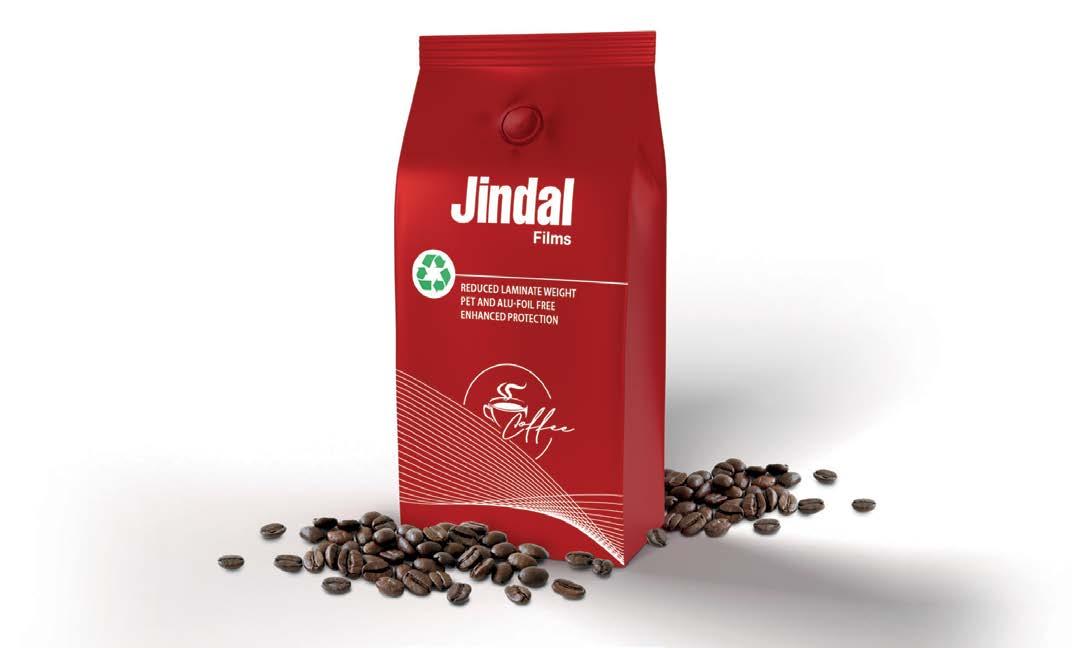
GREAT PUNCTURE RESISTANCE

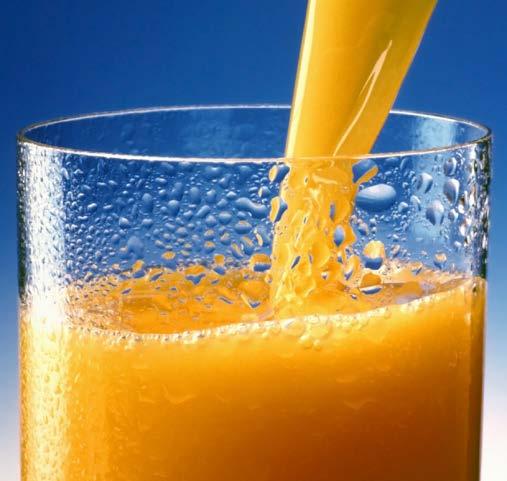
By combining the use of mechanically recycled PET, enhanced recycled PET and renewable PET, it is possible to reduce the carbon footprint of packaging while delivering products in a safe and sustainable packaging manner. Through harnessing all recycling technologies it is possible to unleash the full potential for rPET and also capture other plastics such as polyolefins which currently cannot be recycled mechanically.
Ensuring quality, safety and availability
Increasing the use of rPET will depend on its quality, safety, availability and affordability. The different recycling processes need to adhere to a standard set of principles that allow us to foster new technologies and infrastructures and ensure that all recyclates are safe and of a quality that is suitable for the production of food-grade quality rPET.
The European Commission’s ambition to increase the uptake of recycled plastics is an essential step towards realising a circular economy. With a harmonised, legal framework and measures to assure availability and affordability of recycled materials compared with virgin materials, Europe can realise more sustainable packaging in a circular economy.
By combining each of the different recycling technologies we will be able to realise our ambition of sustainable packaging. Harnessing the very latest innovations we will build the bottle of the future – a bottle that is virtually free from virgin-plastic.
Today the soft drinks industry is calling for:
• swift authorisation of mechanical recycling techniques • an unleashing of innovation in driving new recycling technologies • a harmonising of definitions and approaches across EU markets • a supportive legal framework for alternative plastic recovery technologies like enhanced recycling and feedstock recycling • simplification and harmonisation of those processes to unleash the full potential of the new technologies under the REACH registration • traceability – through verification and certification schemes
Re-defining sustainability
ProAmpac is a global flexible-packaging company that is re-defining sustainable packaging though a combination of collaboration and innovation. With its extensive, sustainably-driven portfolio, the company provides creative packaging solutions, unrivalled customer service and award-winning innovative packaging.
ProAmpac’s global success can be defined by its four core values: Integrity, Intensity, Innovation and Involvement. Today the company is moving flexible packaging forward by redefining innovation through collaboration within its own company and in partnership with its customers and suppliers. ProAmpac brings brand owners and packaging experts together to accelerate advanced technologies and increase speed-to-market, as well as package customisation and consumer differentiation.
ProAmpac shares its 5 top Guidelines for those transitioning to recyclable, sustainable packaging in Form, Fill & Seal applications.

1. Packaging Performance
When evaluating materials, product protection is first and foremost. Packaging engineers need to understand moisture and oxygen barrier properties as well as resistance to puncture and scuffing. Product weight is also critical since it will determine the required strength of the package. All of these criteria are important to understand as moving to an all-PE material set, can require tradeoffs vs. a conventional multi-material laminate.
2. Packaging Format
After isolating product protection requirements, the packaging format needs to be chosen. Critical factors include shelf presence, distribution considerations - especially for e-commerce, and graphic presentation. Different formats have a varying degree of challenges when changing to an allPE recyclable structure. Packages that run on form/fill/seal equipment can be especially challenging and may require that the film has high heat resistance, in order to obtain optimal line speeds and good-locking seals.
3. Machinability
When transitioning to recyclable film, machinability is critical. The goal is to run at the same line speed as current multimaterial laminates since a reduction causes increased costs and loss of manufacturing capacity. In many cases ProAmpac has proved that maintaining current line speeds with a recyclable product is possible, but machine setting commonly needs adjusting. It is important to control heat radiating from the seal bars during pauses in production and also to control film tension along the length of the machine. Stiffer films with higher heat resistance will typically perform best in form/fill/seal operations.
4. Reclose Features
Flexible packaging often has open and reclose capabilities like zippers, press-to-close, hook and loop, or INNO-LOK® pre-zippered rollstock. For the package to be recyclable, the zipper must also recyclable and compatible with the film. Generally, zippers with a thinner profile and lower mass per lineal foot are easier to seal because they require less heat and dwell time when attaching to film. Additionally, a dedicated zipper crush station on form/fill/seal equipment will allow heat to be targeted on a single area rather than potentially overheating the entire side seal.
5. Sustainability Claim Considerations
When considering moving to a recyclable format, companies with a variety of products often take a phased approach. They may start with a higher-value product where sustainable packaging is most valued by consumers such as in the natural and organic market space. Or theymay start with 1 SKU of a low-risk product and evaluate consumer feedback. In all cases, it is recommended that manufacturers work with packaging suppliers to determine the best recyclable structure for their speicific product and filling process. One of the most important aspects of recyclable packaging is communicating the sustainability story to the consumer. Brands should consider clearly communicating why they chose to change the packaging and the resulting environmental benefits. The package should also clearly indicate recycling methods since flexible films are not collected in all recycle streams.
Films are on a roll
While plastic bottles get all the media attention and infrastructure investment, plastic films are quietly sitting there, being useful and, sometimes, recycled. With only 9% of all plastic film currently being recycled, the less visible cousin of the plastic bottle has a valuable role to play in the circular economy, particularly with regards to consumer understanding of standard recycling collections.
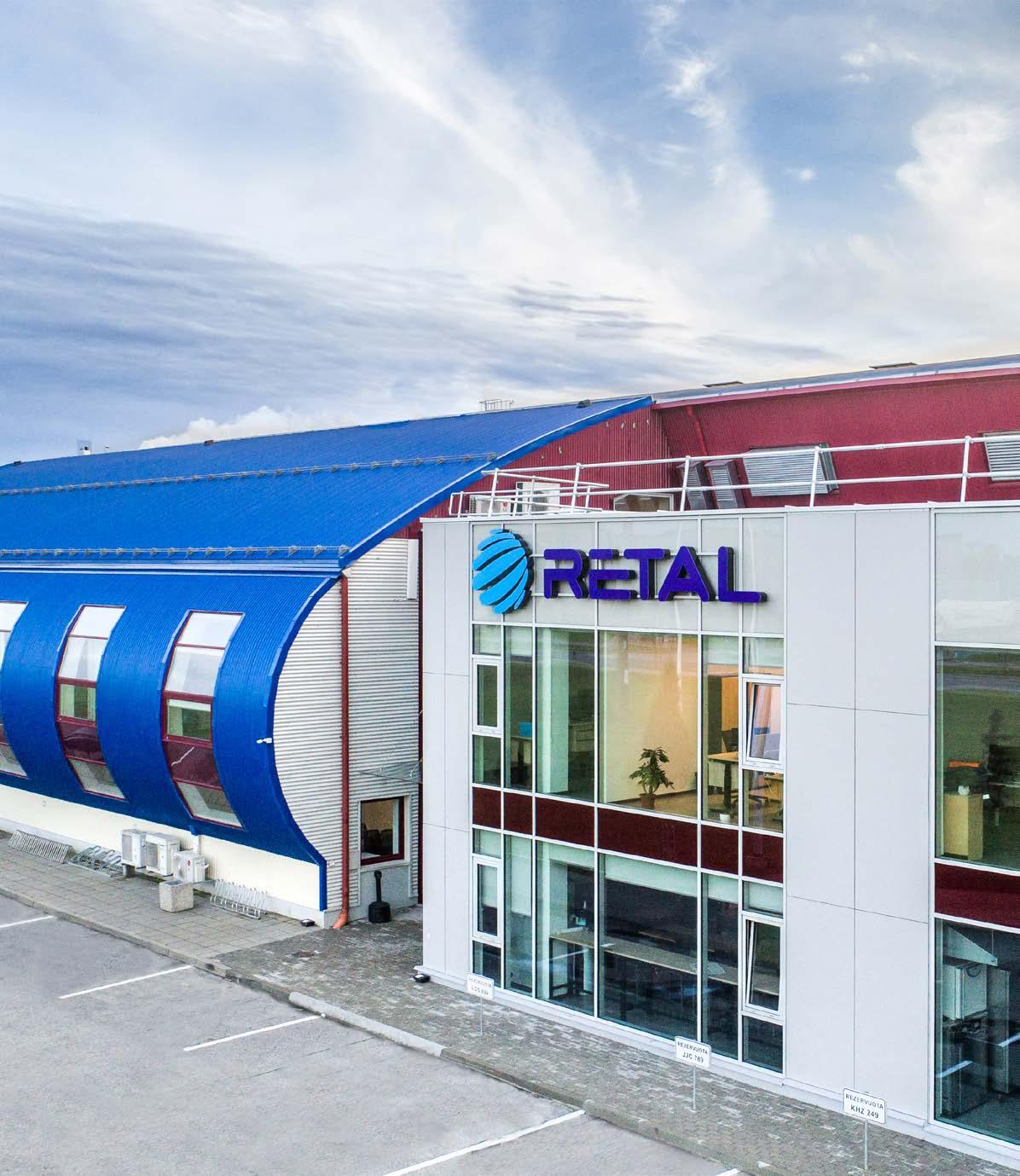
With nearly 5million tonnes of packaging films produced worldwide every year and only just over 9% being recycled, it’s no wonder that alternatives such as compostable and biodegradable films are widely touted as the best thing since the bag that previously wrapped sliced bread. But the convenient consumer disconnect of buying ‘more responsible’ packaging vs what happens to it after they put it in with the rest of their recycling means that vast problems are stored up for recycling collection schemes a little further down the chain.
Compostable and biodegradable films don’t just happily wilt in normal curbside recycling bins. They contaminate the rest of the haul. So while they’re great if consumers have their own compost bin and use it properly, if they throw compostable or biodegradable films into their standard recycling bin, thinking they’re doing the right thing, they’ve actually contaminated the whole of the batch, rendering it impossible to recycle and so more ends up in landfill than before.
Plastic packaging film is a huge growth industry, with a predicted 8% year on year global growth taking it to around $46.2bn by 2025. As always, with possibility comes responsibility and, just because the plastic bottles are the ones under the current spotlight, that’s not to say that films are getting away easily. Consumer understanding of standard recycling systems could certainly be improved, yet with costly advertising campaigns such as the ‘possibilities are endless’ from the Waste & Resources Action Programme over a decade ago certainly helping to get recycling into consumer consciousness, the highly specific technical details have, understandably, got some way to go.
Viktorija Griziene, general manager at RETAL Baltic Films, the dedicated films division RETAL Industries Ltd, a global plastic packaging manufacturer, explains how integrating responsibility right from the first stage of films development is integral to the responsible and profitable future of the industry. Griziene says, “It’s not enough to rely on very particular consumer behaviour regarding plastic packaging when it comes to a viable circular economy. Every stakeholder must understand and action their own sphere of influence; for us, it means developing films from recycled material, with added performance benefits, that can be recycled again in the standard collection schemes.”
Good growth
RETAL Baltic Films has recently invested over €3m in a third production line that allows it to produce films with up to 100% recycled content as well as permitting a greater use of post industrial waste (PIW) from various hard-to-recycle PET films such as metalised, multilayer, laminated and dark colours. Griziene adds, “This new equipment lets us create new food-grade packaging from all these different materials, which delivers a more circular solution to our customers for their PIW than incineration.”
Design for Recycling (DfR) plays an important role in the long-term viability of packaging film not relying on uncontrollable consumer behaviour by integrating greater practical solutions before the packaging has even reached the consumer.
If the aim is that whatever is thrown into the recycling bin can be recycled as standard, investing in equipment that allows for greater use of recycled content and readily accepts the unpopular materials and turns them into food-grade packaging, the worry of whether an item is the ‘wrong’ material lessens considerably and ensures the maximum volume of recycled content and minimum landfill.
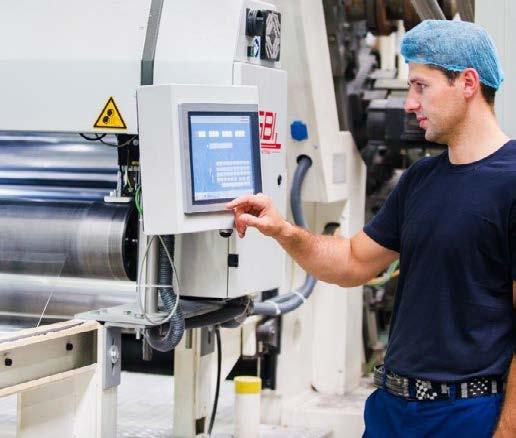
Contract Killers
When it comes to Contract Manufacturing there are many examples of where a watertight contract, has proved to be anything but, and where promising partnerships have died overnight. On many occasions this has been due to different interpretations of the small print. Today’s prime example of a ‘real-time’ conflict is that of Astra Zeneca’s well publicised contract with the EU.
Thankfully nothing quite so dramatic currently afflicts the packaging industry and companies both large and small continue to build upon the strength of their mutually beneficial partnerships. In any event, so much depends upon the reliability and commitment of the supplier, that new contracts still require the utmost diligence, for as always, the devil remains in the detail. Whilst researching the most constructive and forward-looking trends in the Contract Manufacturing Industry sector, SPN discovered a new report by ‘Grand View Research’ of the USA, which offers readers some interesting projections and trends for the period 2021 to 2028.
Healthy growth in pharma
The new ‘Grand View Research Report’ has highlighted the positive outlook for the future of the Contract Manufacturing segment and in particular the pharma sector. It states that the global healthcare contract manufacturing market was valued at USD 177.9 billion in 2020 and is expected to expand at a compound annual growth rate (CAGR) of 7.7% from 2021 to 2028. An increase in offshoring to emerging countries and the changing regulatory landscape are the prominent trends currently present in the marketplace.
Pharmaceutical and medical device companies are outsourcing low-end services to third parties to reduce the overall cost of production and to speed-up time to market. This trend is expected to contribute to the growth of the contract manufacturing market in the foreseeable future. The presence of end-to-end service providers that are engaged in providing value-added services for an integrated or risk-sharing business model is expected to boost the market growth. Pharmaceutical and medical device companies are outsourcing manufacturing activities to CMOs to reduce their manufacturing footprint. This allows manufacturers to be more dynamic and cost effective in their manufacturing process.
In addition, the increasing prevalence of noninvasive surgical procedures is driving demand for pharmaceutical drugs and medical devices. To meet such increased demand, OEMs are outsourcing manufacturing of non-core manufacturing activities as it assists them to reduce labour costs, free up capital, increase worker productivity, and improve manufacturing lead times.
For many large, medium and small pharma firms, outsourcing turns out to be an economic option as a fixed cost for manufacturing biologics products account for around 60% - 70% of the cost of goods sold (COGS) and cannot be avoided even during idle demand. Therefore, the use of multi-product facilities to produce biologics has been proven economically efficient and safe as there is negligible to no risk with respect to product carryover, thereby supporting market growth.
The COVID-19 pandemic has forced many pharmaceutical and medical device companies to increase the manufacturing of drugs and medical devices needed by infected patients worldwide. The U.S. FDA has observed that over 60% of FDA-regulated products imported from China are medical devices, making the U.S. medical device industry highly dependent on China’s supply chain. Medical device manufacturers are facing severe supply bottlenecks, which will ultimately reduce the company’s scope of revenue generation.
Since the medical device industry is highly regulated, making rapid changes in the supply chain may not be manageable. Medical device manufacturers distributing products in the U.S. are not required to report actual or potential supply chain shortages to the FDA. Despite this, the FDA is actively addressing potential shortages in the medical device supply chain. Some of the products facing shortage are aluminium products, integrated circuits, lithium-ion batteries, and special components, including pneumatic fittings, black body radiation source, and platinum.

Unprecedented demand
This has created an unprecedented demand for the manufacturing of active pharmaceutical ingredients (APIs), finished doses, and medical devices in order to maintain supply. According to Medical Product Outsourcing, manufacturers expect outsourcing to yield cost savings and faster time to market. According to various reputed tabloids, companies are expected to outsource more work, based on a 2020 Global Managed Services Report. This report has performed a survey with 1,250 executives across 29 countries, which stated that 45% of organisations will outsource more in the coming years. However, the limited production capacity of the CMOs may pose a major challenge by restraining the market growth.
Image courtesy of Clean-Room Technology
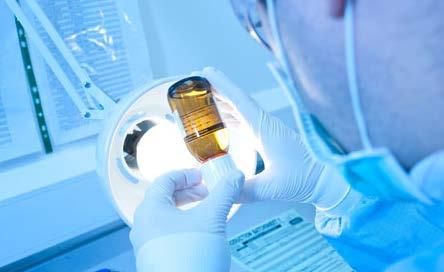
Segmented Insights
Based on type, the industry is segmented into pharmaceutical and medical devices, where the pharmaceutical segment accounted for the largest revenue share of 75.2% in 2020. The medical device segment is further divided on the basis of service and therapeutic area. The service segment includes accessories, assembly, component, and device manufacturing. The device manufacturing segment is anticipated to dominate the contract manufacturing market over the forecast period owing to the increasing outsourcing of device manufacturing due to lack of inhouse manufacturing facilities and complexity.
On the basis of therapeutic area, the medical device segment is segregated into cardiology, diagnostic imaging, orthopaedic, IVD, ophthalmic, general and plastic surgery, drug delivery, dental, endoscopy, diabetes care, and other areas.
The cardiology segment held the largest share in 2020. Rising demand for cardiovascular devices as a result of increasing cases of associated conditions is contributing to the growth of outsourcing of these devices. Moreover, the high complexity of cardiovascular devices and the need for technical expertise result in higher outsourcing of these devices.
The pharmaceutical segment is divided by service into Active Pharmaceutical Ingredients (APIs), advanced drug delivery formulations, packaging, and finished dose formulations. Being the key component in drug development, APIs captured the largest share in 2020 and are expected to witness significant growth over the forecast period. Several companies are opting for the outsourcing of drug development due to limited capacity, insufficient resources, lack of skilled professionals, and cost saving. Various CMOs offer customized services. Services offered by CMOs range from the manufacturing of API/bulk drugs to finished dose formulations.
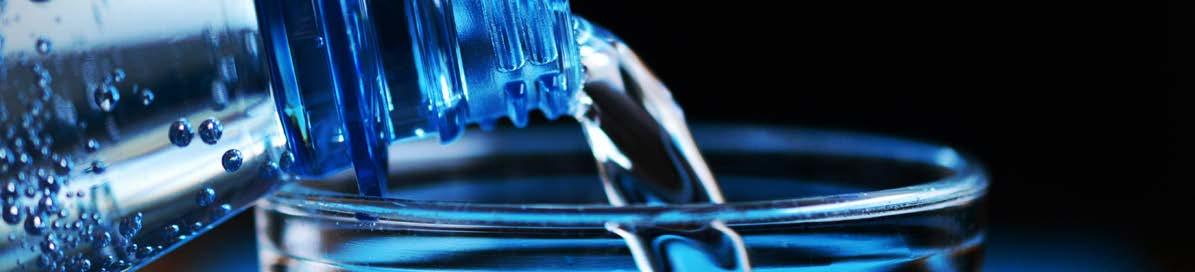
Challenges driving investment and growth

The diverse beverage market is encouraging the modernisation of contract packaging with new technology thus making a big contribution to greater efficiency and sustainability.

Iberia Coconut Water, is packaged by Brooklyn Bottling in the US and uses a carton for its packaging, acknowledged by experts as being more sustainable than many other forms of packaging.
Monster 100% Outsourced Portfolio
Today the ‘Monster Beverage Corp’ contract packs 100% of its product portfolio, according to Beverage Marketing Corporation. With manufacturing norms upended by the pandemic, manufacturers are taking a step back to assess these changes. Mordor Intelligence’s “Contract Packaging Market: Growth, Trends and Forecasts to 2025’ shows that the contract packaging market was valued at $52.28 billion in 2019. With a compound annual growth rate (CAGR) of 15.33 percent, the report predicts that the market will reach a value of $118.94 billion by 2024.
Gary Hemphill, managing director of research for New York-based Beverage Marketing Corporation (BMC), states that, in the beverage industry, carbonated soft drinks, PET bottled water and RTD tea are the Top 3 categories that are contract packed. Close behind them are beer, fruit juice and sports drinks.
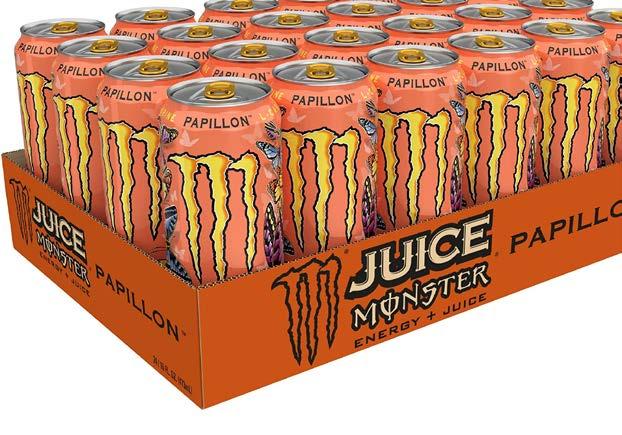
Influential Trends
As consumers increasingly express their environmental concerns, along with the producers’ demand for economical packaging options, contract packers are adopting eco-friendly alternatives and eco-sensitive package designs. Mordor’s latest report states: “Sustainability and customisation are likely to continue to positively impact the contract packaging market, leading to growth in use in consumer packaged goods, such as personal care and food and beverages, over the forecast period, 2020-2025.
John Moran, chief executive officer and founder of SourceHUB, Chicago, notes that sustainability, supply chain resiliency and automation are trends impacting contract packaging right now, plus the rate of change in SKUs. “From marketing changes to regulatory/legal requirements, SKU change velocity has increased significantly over the past few years, which in turn adds pressure on teams to do more with equal or fewer resources.”
Trade restrictions as well as the fall-out from the Covid pandemic also continues to affect the supply chain. As such, utilising a single source of contracting and workflow automation will be critical to building supply chain resiliency in manufacturing. Moran added, “Packaging has a history of poor specification management. So, when there are major shocks to the system, it is nearly impossible to respond at the speed that today’s climate requires.
In addition, companies are recognising that supply chain resiliency is necessary to thrive in the current climate.” Highlighting the importance of this aspect, manufacturers quickly woke up to the reality of disruptions in packaging operations”. Moran added, “Looking back, we were spoiled in a very stable global supply chain for 20-plus years. We enjoyed a stability that, quite frankly, is shocking. Today, being reliant on single-sourcing strategies is no longer an option.”
Increasing workflow automation
For example, 60 percent of flexible intermediate bulk container (FIBC) bags come from India, Moran notes. When shut down, 60 percent of the global supply for these bags disappeared overnight, he explains. However, workflow automation and collaboration tools can provide a single source of truth throughout the entire packaging value chain and by getting everyone on the same page, companies can build a resilient supply chain and stabilise production schedules.
Furthermore, by owning your specifications, you can respond instead of reacting to disruptions, whether it is geo-political, trade or something like Covid, you can respond quickly and make error-free adjustments much faster than with management by Excel, email and other informal processes.”
Moran also said that managing artwork, specifications and orders the “old way” can involve scrambling to expedite freight, move production schedules, and more, whereas automating the upfront artwork and specification processes provides breathing room. While SourceHub focuses on automating at the front end to reduce the pressure on production schedules. Moran says bringing everyone onto a single platform where automation is involved has significant synergies with contract packaging.
Tooling-up for global success
There is a new kid on the block when it comes to moulded fibre tooling. HP’s Advanced Moulded Fibre Tooling Technology puts all predecessors in the shade with its high-speed, high-performance products and special tooling production service.
The latest moulded fibre tooling solutions from HP have opened up entirely new packaging opportunities for the industry and there are many good reasons why. Among them is the fact that the latest solution offers the fastest-ever enhanced design and fabrication of moulded fibre tooling. It takes just two weeks, which compares very favourably with the current four-to-six weeks using traditional tooling methods. This new, end-to-end solution also delivers greater production efficiencies via its increased ‘up-time’ offering, and it doesn’t end there. In addition, the new technology offers customers significantly reduced maintenance costs and unlimited customisation capabilities.
Global ‘first’
In launching its global ‘first’, HP is partnering closely with ‘Pulp Moulding Dies Inc (PMD) to deliver the next generation of durable, lighter, faster and easier-to-use tools. The company is also working in tandem with leading packaging solutions companies such as Veritiv, which works with customers to accelerate the adoption of more innovative and sustainable moulded fibre designs for clients across the entire packaging spectrum including every kind of consumer product, as well as medical and industrial markets.
HP’s global head of Moulded Fibre Solutions at HP Inc. Mariona Company, told SPN in an exclusive interview just a few days ago, “Businesses around the world, including HP, are making the commitment to create new, plastic-free packaging initiatives - and the moulded fibre industry is leading the field with its production of renewable, recyclable and natural fibre, for both products and packaging”. When asked by SPN how HP is bringing sustainability and recyclability to the rest of the industry? Mariana Company said. “Where do we start? We are a baby in the moulded fibre packaging business. However, HP is a father of great innovation and as such is able to offer entirely new sustainability packaging possibilities to the industry. In the food and beverage sectors for instance, we can help significantly with improving efficiency and reducing timelines, as well as reducing materials and enabling the addition of textures and logo’s to packaging.
This new digital trend will change the industry dramatically over the next five years or so. However, despite today’s challenging constraints, the new technology announced by HP and our latest advances in 3D printing potential has been very well received in the marketplace”.
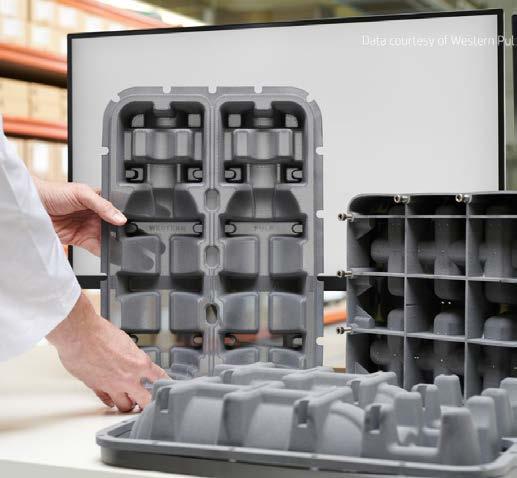

Staying focused
Mariona Company continued, “Every business has different ambitions and expectations and we like to stay focused and to keep our feet on the ground. In doing so we don’t wait for Covid to retreat, as this will not prevent us from engaging with our customers to provide them with the optimal and personalised solutions that they need”.
In looking at the global rollout of this ground-breaking new product, we asked Mariona Company where HP plans to start. “Our new HP moulded fibre tooling division is based here in Barcelona and we have identified two global markets that we wish to target first, with our unique and unrivalled moulded fibre tooling technology. These are Europe, closely followed by Asia. It is really important to engage with customers in these regions and to take our world-beating innovations to these important markets where we can provide the best and most comprehensive support”.
Diverse capabilities
SPN looked at the vital role that PMD has played in the development and realisation of the new tooling technology and innovative contributions made by them. Their latest advanced software package, clearly takes 3D printing to the next level. The company’s in-depth expertise in moulded fibre tooling, along with the advanced design, data, software and production of HP’s new tooling technology, has made a huge difference in achieving the ground-breaking results. Mariona Company commented: “The diverse capabilities of HP’s digital manufacturing platform, has led to advances in the production of custom screens, which was previously impossible. This also applies to the complex packaging geometries needed and further improvements to the overall dewatering process. In fact, as a result of this collaboration we have been able to produce moulded fibre tools that are 10-20 times lighter than conventional tools”
In a recent press release HP added that its new moulded fibre advanced tooling solutions, eliminates the timeconsuming and intensive manual fabrication involved in the traditional moulded fibre tooling manufacturing process, Leveraging proprietary HP innovations in digital manufacturing software and data intelligence, has resulted in a new digital design platform along with advanced industrial 3D printing technology. These unique solutions enable more efficient design options and replace the need for hand-crafted screens, as well as avoiding the need for CNC machining, and manually drilled form tools.
Following the HP interview, SPN believes that this latest technology from will set new standards throughout the moulded fibre tooling industry and make a significant contribution to sustainability and the circular economy, an outcome for which we are all grateful.
Music to our ears
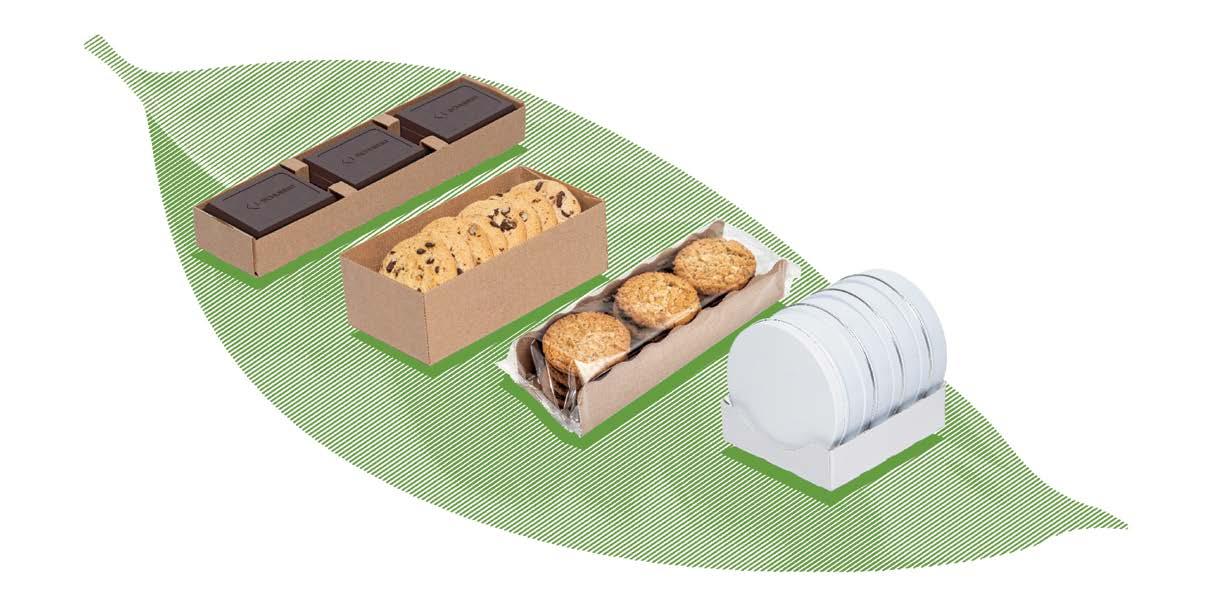
Schubert’s future-proof packaging machines play a pioneering role in the global quest for sustainability
The consumption of resources and the way we treat our environment affects people and companies worldwide. Consumers are now more eco-aware than ever and thereby critical when shopping, thus making environmentally friendly and sustainable packaging an important sales argument. Gerhard Schubert GmbH, with its core competence in cardboard packaging, has been dedicated to reconciling sustainability and cost-effectiveness in packaging for over 50 years.
The renowned packaging machine specialist from Crailsheim, Germany, takes this claim very seriously and has committed itself to adopt six of the key proclaimed sustainability goals of UNESCO. These must be implemented by the year 2030. To achieve this, two years ago, an internal sustainability expert group was established. This dedicated focus group collates information concerning all developments and innovations from across the Schubert Group aimed at achieving these vital goals. Michael Graf
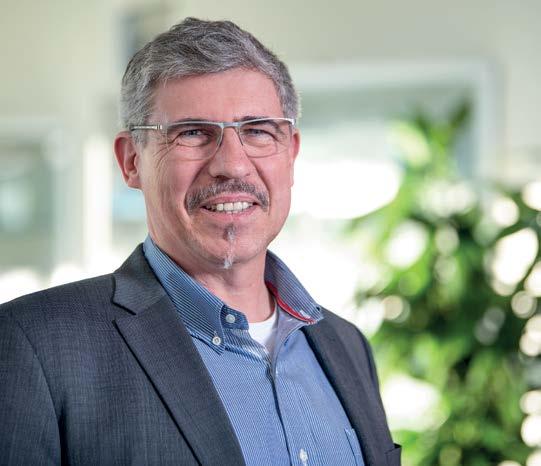
Close-up of water jet machine cleaning Director of Schubert-Consulting and Head of the Sustainability Expert Group at Schubert
Schubert’s 5 Rs
As a committed sustainability partner, Schubert is able to optimise its customers’ processes throughout their entire supply chain, ranging from raw materials, packaging and logistics to recycling. The basis for this strategy is the company’s “Five R’s”, which represent its five principles for recycling and waste prevention. Schubert’s Five R’s are: Refuse: Eliminate unnecessary and unsustainable packaging materials. Reduce: Create innovative packaging solutions for using less materials and transportation. Reuse: Convertible, modular packaging machines Recycle: Recyclable and conventional materials in one plant, and Rethink: Resource-saving supply chain from A to Z.
Focus on Robotics, AI and Cobot Devlopment
Michael Graf, Director of Schubert-Consulting and Head of the Sustainability Expert Group at Schubert, has already chalked up a number of major successes for the company: “We are already successfully implementing six of the UNESCO Sustainability goals. For example, we use geothermal energy to air-condition our offices and generate our own electricity using photovoltaics. As a well-known innovation driver for outstanding packaging and robotics technology, we are also strongly positioned in the areas of digitalization, networking and the integration of artificial intelligence.
“This is symbolised by the many pioneering projects of our subsidiaries in the field of Cobot development, Schubert Motion, Schubert Additive Solutions and Schubert Consulting. The concept of sustainability can be found in all areas of our company and is practised in equal measure at all levels, from purchasing through the entire production process and training, to cooperation with service providers and partners”.
Future-proof flexibility
Anyone who walks attentively through the production facilities in Crailsheim, will immediately notice that all machining centres attach great importance to the recycling of waste material and, wherever possible saving energy. The packaging systems for the customers are developed according to the latest state of the art technology. Even at the design stage, the aim is to achieve a machine design that is as simple and excluding processes that are not essential, thus also saving resources and raw materials. Schubert offers further advantages with the modular machine concept itself and the extensive use of robotics. The company’s unique modular systems are so flexible that packaging machines can be tailored precisely to suit a customer’s specific requirements. In addition, new formats can also be implemented in the machines at a later date. This even applies when switching to more sustainable packaging materials: Simple substitutions such as cardboard trays instead of plastic trays can be implemented in an existing Schubert plant without any major effort.
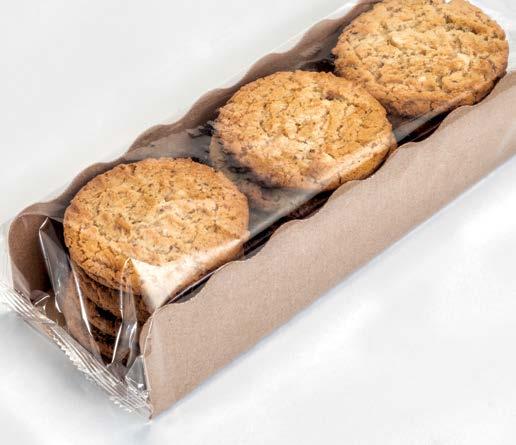
Independent consulting services
Because Schubert pursues a high standard of sustainability in its own operations management, all customers who want to manufacture packaging sustainably and economically as part of the global trend towards more ecological packaging, are now able to make packaging processes more efficient and sustainable in their entirety.
The experts at Schubert-Consulting specialise in providing targeted advice at the strategic earlyplanning phase. Michael Graf explains: “Thanks to our manufacturer-independent consulting services, we are already in a position to help customers make the switch to sustainable packaging materials. Right from the outset, we pay attention to the perfect interplay of materials, technology and know-how - from cardboard trays to paper-based films. The concepts provide flexibility, quality and efficiency and thus set high standards throughout the industry.”