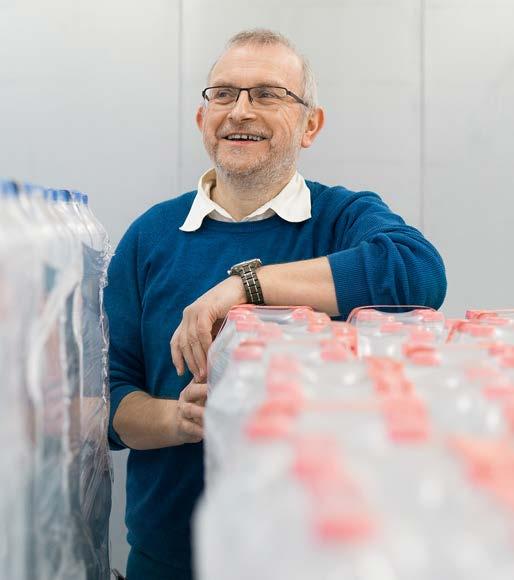
16 minute read
KHS
from SPN April 2021
by spnews.com
A new first in secondary packaging
The latest technology developed by systems supplier KHS, means that cans of food as well as beverages can both be successfully wrapped in paper. This offers a perfect alternative to film or wrap-around cardboard and offers many other advantages.
Advertisement
Benefiting from this new, eco-friendly technology is KHS’s well-known Innopack Kisters tray system. Other key benefits apart from being eco-friendly and energy saving, include lower raw material costs, with only minor adjustments required for conversion to the new set-up. Regarding its stability, the results are the same if not better than those compared to cardboard or film-based wrappers.
However, at KHS the idea of using paper as a secondary packaging material is not a new one. The company first experimented with this concept around 20 years ago. Karl Heinz Klumpe, packaging product manager at KHS told SPN, “Back then, this technology didn’t catch on, as paper was a cost-intensive raw material and wrapping containers in film yielded better results regarding stability. The beverage industry thus opted for different systems and solutions to those available today. Currently our customers want green alternatives to the usual packaging systems such as film and these should be as eco-friendly as possible.”
In order to achieve this, new paper wrapping material has now been developed together with an international beverage producer. This type of pack can replace shrink film or wrap-around carton packaging for transportation or sale, on packs of 12 or 24 cans in the high-capacity range of up to 90,000 cans per hour.
Modular machines require minimal adjustments
In order to wrap cans in paper instead of film just a few adjustments are needed to the Innopack Kisters tray packer. “KHS is increasingly supplying modular systems and solutions that enable and ease the appropriate conversions to our machines. In this case, we’ve simply reengineered the process module for folding and wrapping,” Klumpe explains. Karl-Heinz Klumpe
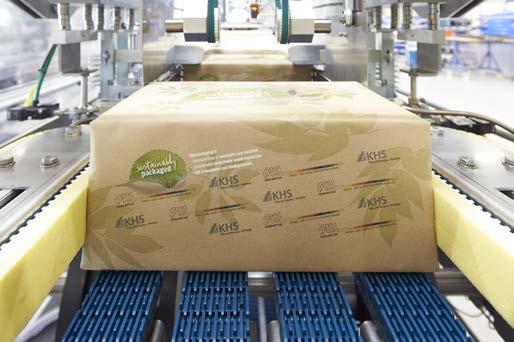
packaging product manager at KHS
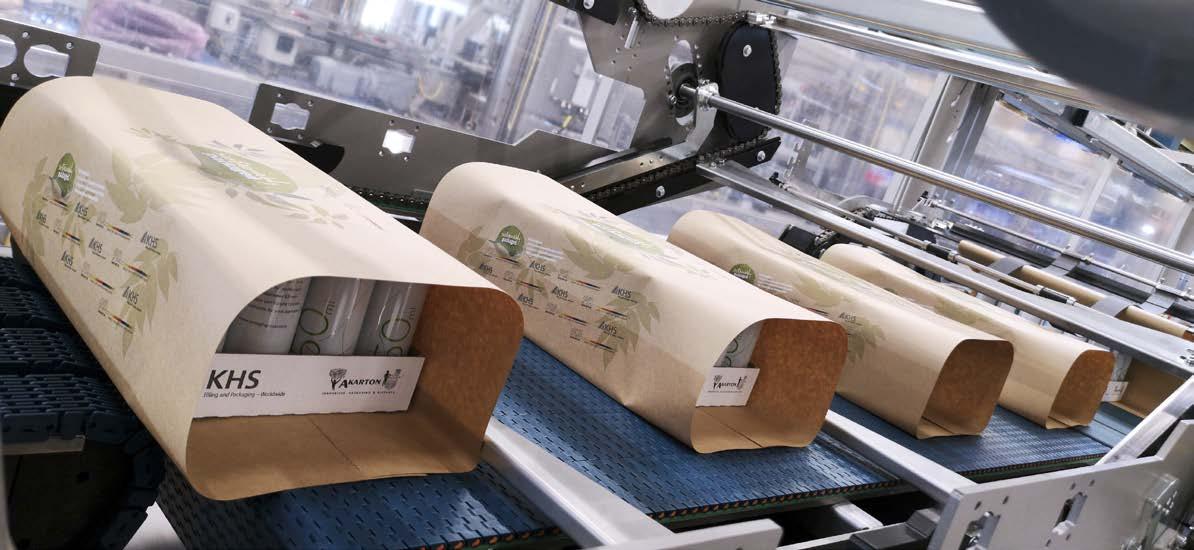
“The standard components such as tray separation from the magazine, gluing or can-feed are identical to those on the hundreds of proven KHS machines already on the market.” This allows beverage producers to have the tray packers already in operation at their plants converted simply by adapting certain modules, making a full new investment unnecessary.
Wrapping cans in paper has many advantages over other materials, believes Klumpe: “On the one hand, paper is kinder to the environment than film with respect to ocean pollution, for instance.” On the other hand, fewer packaging materials are used. Instead of a sturdy wraparound carton or film packs on trays, packaging cans in thinner paper only needs a flat, stable corrugated card pad as a base – with identical results regarding stability. Costs are also cut by the new paper pack: compared to a wrap-around carton by up to 15%, with outgoings about the same as for film. Overheads are also considerably reduced by the low energy consumption of about 14 kWh an hour at 80 cycles a minute. The folding process is such that the pack is also fully enclosed.
Savings and efficiency all wrapped up
Klumpe sees huge potential for the new KHS technology. “When I think how much food is canned all over the world, with our paper pack we offer a useful alternative to conventional secondary packaging. With our system we can significantly help to cut down on the amount of plastic waste being generated.” According to Klumpe, this will support the efforts being made throughout the entire sector to protect the environment. “Sustainability is also always a cost factor, however. With our new approach we’re catering for both aspects here.”
Combined expertise leading the field
The KHS Group is one of the world’s leading manufacturers of filling and packaging systems for the beverage and liquid food industries. The KHS Group includes the parent company KHS GmbH, KHS, Corpoplast GmbH and numerous subsidiaries outside Germany, which are located in India, the USA, Mexico, Brazil and China.
KHS manufactures modern filling and packaging systems for the high-capacity range of products at its five stateof-the-art production facilities in Germany. Today the KHS Group is a wholly owned subsidiary of the SDAXlisted Salzgitter AG Corporation. In 2019 the KHS Group and its 5,149 employees achieved a turnover of almost €1.3 billion.
UR10 Cobot From Raruk Automation
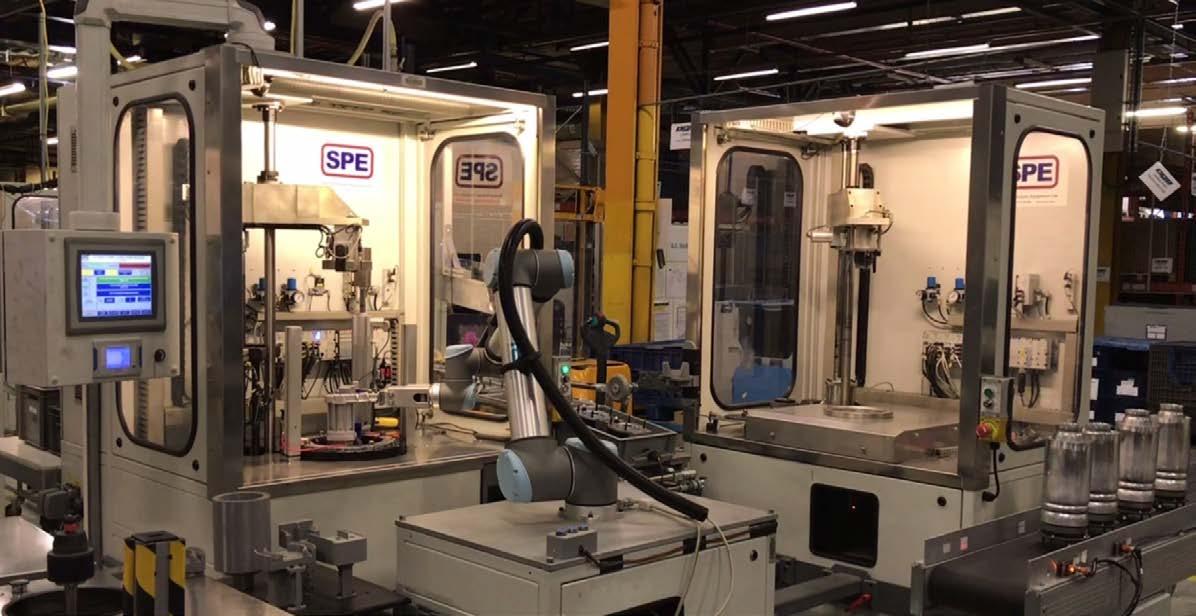
Where flexibility
meets compatibility
Raruk Automation has supplied Plymouth-based industrial control systems manufacturer Oakmount Control Systems with an automated pick and place solution to eliminate a host of labour-intensive processes.
A FlexiBowl parts feeder and Shibaura Machine THP700 SCARA robot are now working in unison at a customer of Oakmount, where they are feeding, picking and placing a medical product into individual plastic packaging trays.
This task was previously performed by a human operative and the new solution has enabled the end user to redeploy its labour resource to a more valueadded task.Initially, cycle time studies of the existing operation set a goal for a proposed automated solution. Using this information, Oakmount worked with technical partner RARUK Automation to discuss the optimum way of reducing the cycle time and improving process repeatability.
“RARUK Automation used Shibaura Machine’s simulation software to evaluate the optimum cycle time that could be achieved,” said John Dawe, business development manager, factory automation at Oakmount Control Systems.
Shibaura Machine

“The software allows CAD drawings to be integrated and therefore get real-time simulations, which in this case turned out to be faster than the manual operation. “We’d used FlexiBowl before, but this was our first project with a SCARA robot. “Once the simulation phase was complete we returned to our customer with the proposal, the estimated cycle time and the cost. “They were pleased with our recommendation and placed the order.” FlexiBowl has been designed to be compatible with any robot and vision system. A single unit can handle entire families of parts within a 1-250mm and 1-250g range.
Furthermore, the system’s lack of dedicated tooling and intuitive programming allow product changeovers in seconds. The THP700 SCARA robot offers a 700mm reach and a maximum payload of 10kg. It is capable of up to 120 cycles per minute in 24-hour continuous operation. Working in a cleanroom environment at Oakmount’s customer, the hopper-fed FlexiBowl feeds awkwardly shaped medical products on to the rotating flat surface of the FlexiBowl. Oakmount positioned a camera-based vision system above the FlexiBowl’s picking area, which then instructs the robot which parts are available to pick.
The SCARA robot then picks up the medical products individually using a vacuum pad and places each one into the required plastic packaging pocket as they emerge from a thermoforming machine. As the trays fill (five trays per row) they move along the production line to a vacuum bagging operation, after which further Oakmount-supplied vision systems confirm that the parts and labels are in place.
A single control panel – also designed and manufactured by Oakmount – oversees the entire operation. There are two variants of the medical product that require packaging. However, the system devised by Oakmount has been purpose-designed to accommodate both with an extremely short changeover time. According to Oakmount, the only aspects that need to change when switching products are the robot programme and the image of the part to pick. Installed and commissioned in June 2020, the system has been running continuously since.
“Our customer has taken a big step forward with this project,” said Dawe. “Aside from the inherent accuracy and continuous placement of parts that the system provides, our customer has been able to release their operator to undertake more technical tasks and reduce any risk of RSI due to repetitive action”.
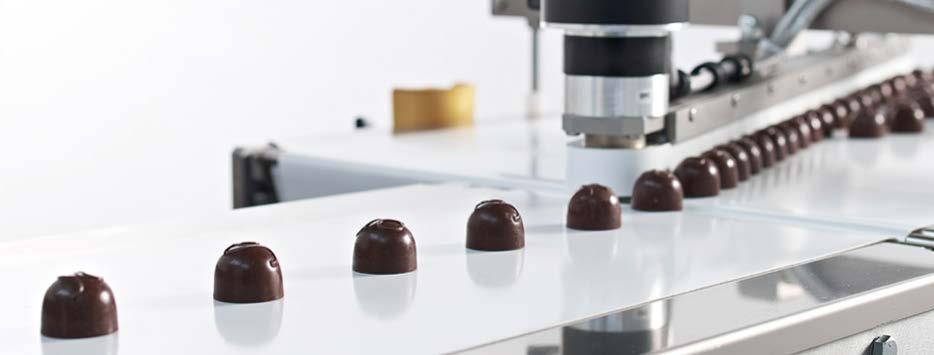
New ‘sweeteners’ for chocolate
German-based equipment specialist Theegarten-Pactec has unveiled a new suction support sealing system offering greater precision for the packaging of chocolate, as well as significant savings on materials. The company said that its latest process has been designed with environmental benefits that have been designed to make manufacturing processes more stable.
Development of its new system follows a recent European study on consumer preferences for packaging carried out in March 2020 revealed that almost 70 percent of respondents were actively trying to reduce their use of plastic packaging (Two Sides: “The Packaging Report 2020”).
Particularly in the market for flexible packaging, sustainable and recyclable packaging is becoming increasingly important. This has led to interest among brand owners, and thus among players in the packaging industry, to switch to sustainable materials such as recyclable mono-materials and to packaging processes that have been designed precisely for these materials. This is a switch that is challenging to implement, especially in the packaging of chocolate products. A variety of bars are packaged using composite materials, such as a base of plastic or paper in combination with an aluminium layer. The products can therefore be easily packaged by fold wrapping and do not require any additional securing of the packaging by sealing or glue. However, packaging materials made of composite materials are not recyclable and are therefore not sustainable in view of market developments.
It therefore makes sense to switch to the use of recyclable mono-materials for packaging processes. However, these materials have poor dead-fold properties, i.e. the packaging must be closed and fixed after folding by sealing or with the aid of glue so that it cannot open again.
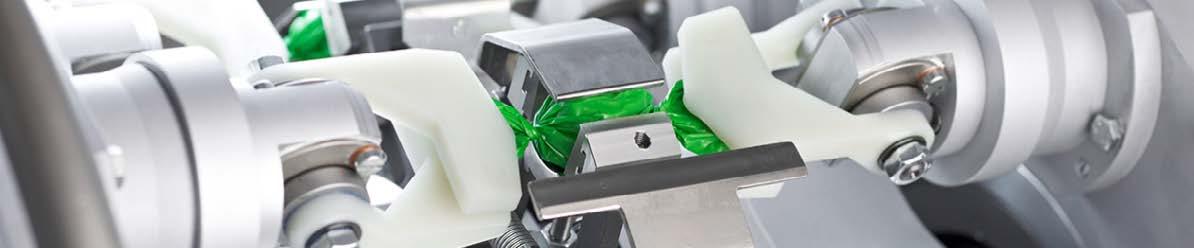
For well-known brand products, a second packaging variant is traditionally used: a combination of two packaging materials – aluminium paper laminate and plastic packaging. This first “packaging layer”, the inner wrap of aluminium paper laminate, is required as a barrier to protect the sensitive chocolate products during the actual packaging process.
When closing the outer wrap using contact sealing technology, the chocolate could otherwise be damaged by the heat that is generated or by the sealing tools used. As an alternative to this process, packaging has been glued with hot melt. The packaging specialists at Theegarten-Pactec have now developed a technology called “suction supported sealing”, which offers numerous advantages over these conventional processes.
Risks of sealing or gluing with hot melt
As the Dresden-based business explained, the chocolate is packaged in a material such as plastic, by means of fold wrapping. However, since plastics have poor deadfold properties, i.e. the packaging opens again after folding, it must be actively closed and fixed by sealing or with the use of glue.
For this purpose, during the sealing process, the sealing tool is pressed against the packaging material from the outside to connect the outer and inner flap of the plastic packaging with each other. This ensures that the packaging is fixed after folding but is still easy for the consumer to open. The problem with this procedure is that when the sealing tool is applied, the packaging material lies close to the product. In order to effectively dissipate the heat generated, the inner wrap of aluminium paper laminate is used. However, the use of two packaging materials – aluminium paper laminate plus plastic packaging is neither environmentally friendly nor particularly costsaving or recyclable. Therefore, the use of a sealable, and ideally even recyclable, mono-film is recommended.
The alternative, which involves the application of glue dots, ensures a permanent closure of the plastic packaging, but also has disadvantages. Clogged glue nozzles or contamination can lead to an increased susceptibility to malfunction and to the need for additional work with respect to cleaning and maintenance of the packaging machine. This reduces the efficiency of the packaging process and generates additional costs.
Furthermore, the application of glue not only involves risks for the machines and aggregates, but also for the product itself. Incorrectly adjusted glue nozzles and the resulting distortion of the packaging material due to excessive glue application can result in the glue being transferred to the chocolate product causing contamination.
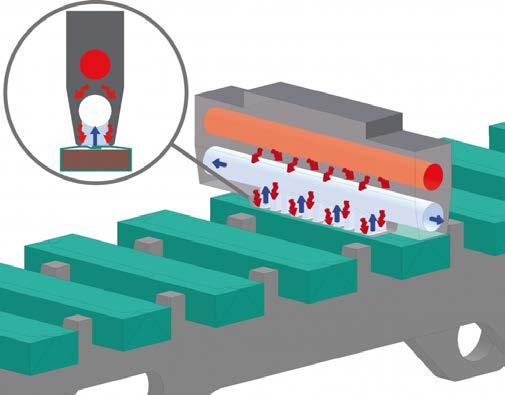
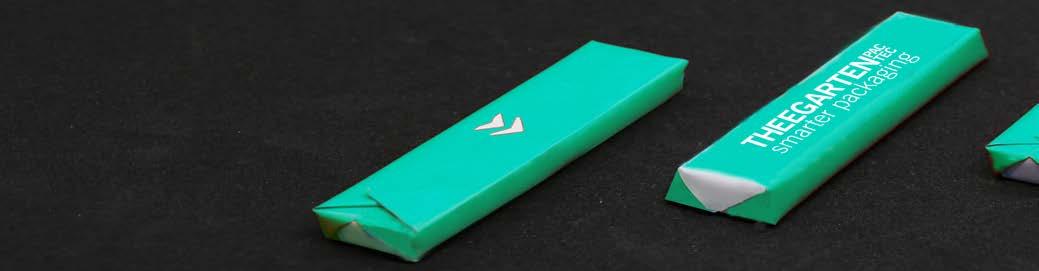
New suction-supported sealing technology
The sealing station developed by Theegarten-Pactec is located directly after the actual wrapping or packaging station. As soon as a product has reached the sealing station, the sealing tool moves to the product to be sealed at a distance of 0.5 mm to 1 mm. Negative pressure then causes the package to be sucked onto the sealing stamp. In this way, there is no direct contact between the packaging and the product during the sealing process.
The heat required for the sealing process is thus distributed selectively and evenly over the entire sealing surface, thereby ensuring that there are no pressure marks or other damage to the chocolate product. Active cooling of the environment ensures additional product safety. After sealing for approx. 50 – 60 milliseconds, the contact between the packaging material and the sealing jaw is terminated when the sealing stamp moves away – which may be assisted if required by switching off the vacuum.
The packaging material detaches from the sealing station and once again rests directly on the chocolate product which has now been completely packed. The sealing seam only comes into contact with the product again after it has sufficiently cooled. The innovative technology can be easily integrated into the standard packaging machines of the Dresdenbased company, with implementation being possible for various service areas and products such as chocolate bars and pralines. In addition to the compact and flexible CWM2 wrapping machine for chocolate products with a capacity of up to 600 products/min, the sealing station can also be integrated into the CFW-S for chocolate bars in letter fold with or without packaging band with up to 850 products/min. Implementation in the CFW-D double-lane high-performance packaging machine for chocolate products in letter fold with packaging band and up to 1,400 products/min is also possible without great effort. Moreover, even existing machines such as the U1-C high-performance packaging machine can be retrofitted with this new technology.
The sustainable alternative
Theegarten-Pactec’s innovative technology offers numerous advantages: Material costs can be reduced by eliminating the need for aluminium laminate to dissipate heat and protect the chocolate. At the same time, negative environmental influences caused by the production of the material are reduced. In addition, there is no need for an unwinding unit for aluminium paper or aluminium-PP composites in the packaging machine. This saves set-up and adjustment times and makes the packaging process more stable and therefore less susceptible to faults.
each detail matters for unrivalled performance
Only a company who has a constant focus on the productivity of its customers thinks ahead and creates extrusion solutions that leave the rest standing. SML specialises in the development of extrusion lines for film, sheet, coating and lamination as well as multifilament spinning lines.
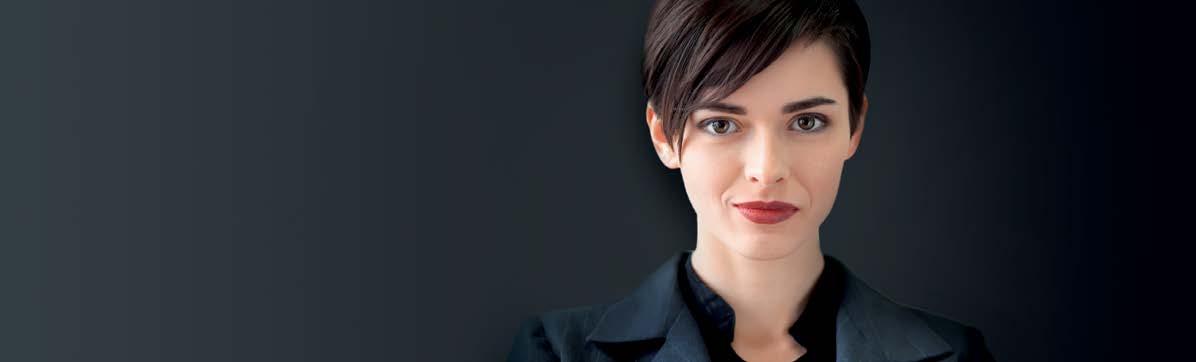
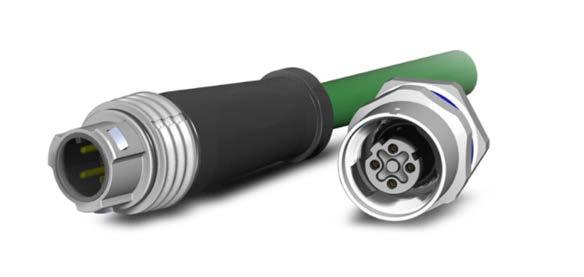
SML’s SmartCast Infinity:
Unchallenged recycling capacities in stretch film production
SML improved the usage of post-industrial recyclate to an optimum at its SmartCast Infinity stretch film line. “We have succeeded in producing film with an ultimate elongation value of 400% by using up to 80% post-industrial recycled materials.
The film’s quality is totally in line with market requirements, the optical properties are excellent,” says Thomas Rauscher, Product Managerfor stretch film. Stretch film, which was already used and collected after usage for re-pelletizing, has also been successfully processed in high quantities on SML’s SmartCast Infinity line. With high-quality recycled material of postconsumer stretch film, SML reaches re-feeding rates of up to 60%. However, in a sustainable circular economy, wherecast stretch films are frequently recycled, a general recommendation is a ratio of 30% post-consumer recycled material in combination with 70% virgin material.
New Sensory Perceptions
Sensors and corresponding connector components go hand-in-hand in factory automation applications. M12 connectors are therefore a flexible option.
Combining the physical world with IIoT requires proper interfacing between the hardware (connectors, cordsets, sensors, etc.) and the software. Sensors play an integral part in this exploding market as well as the components around them which are now at every level of the automation pyramid. Yet, in order to leverage a sensor’s full potential, you must take connectors and cord-sets into consideration together.
It’s important to use cord-sets and cable assemblies that enable proper use of automation sensors and doing so will help provide the network architecture required to fully enable Industry 4.0.In addition, systems continue to get smaller as miniaturisation grows in popularity.
For space-saving reasons, there’s an increased need for components that are both small and help increase sensor accuracy and response time. That’s what makes M12 connectors a primary driver of IIoT and new machine design. There are multiple styles of M12 connectors available on the market today, and they’re all suited for different purpose. A-code through D-code connectors have been around the longest in the industry, and can be found in a variety of applications.
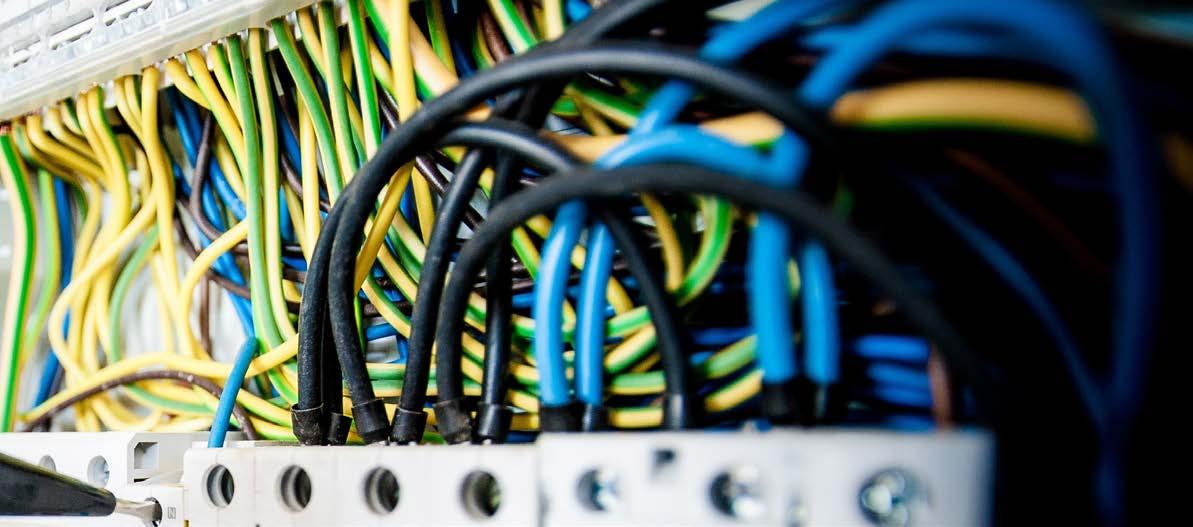
The M12 X-code 8-pin cable assembly meets multiple requirements in order to allow smooth, clean data transfers through the cable. With the 10 GB/second transmission rate, it stops functioning only as a cable and connector. It is truly an essential part of the industrial automation industry to capture and transmit data in a quick and precise manner.
In addition, TE Connectivity now manufactures a rightangle X-code cordset that maintains the 10 GB/second transmission rate—a feat in overcoming molding and shielding challenges. They’re quite compact at only 36 mm high, so they can fit into confined areas.
New line-up for Power Applications
A recent extension to the M12 connector line-up is the M12 L-code power connectors. L-code connectors offer a compact high-power solution for automation devices. They can handle up to 16A per pin (these come either in 4-pin or 5-pin (4+FE) delivering four times the power of standard M12 connectors while providing reliable and efficient power supply. The L-code is ideal for factory automation and use in harsh and wet industrial environments.
They also take up to 40% less space than traditional 7/8-in. connectors typically used for high-power connections, allowing for a more compact build. Its small footprint helps customers embrace the miniaturization trend without sacrificing quality.
Push-pull connectivity
Push-pull connectivity is a trend across the industry in different styles, configurations and materials. However, earlier versions used secondary components and adapters to make it a true push-pull configuration. This was time-consuming and complex.
Now, M12 push-pull configurations have been standardized with IEC 61076-2-012. By establishing a worldwide industrial industry standard for circular connectors, we can add a faster, easier and more reliable installation and connection method to the M12 market.
In addition, the new standard is fully backwardscompatible with pre-installed M12s.International standardisation benefits all applications in which M12 push-pull would be used, as it enables the lower levels of automation sensors and actuators on the production floor to be connected to higher levels where data is transmitted and communication network protocols are occurring.
M12 push-pull connectivity also allows for significant space savings with the plug-and-play style connection, which is critical as components get smaller to meet miniaturization demands. It is spaced well for applications where there are significant space restrictions—either in the machine itself or the operating area in which the machine will be used.