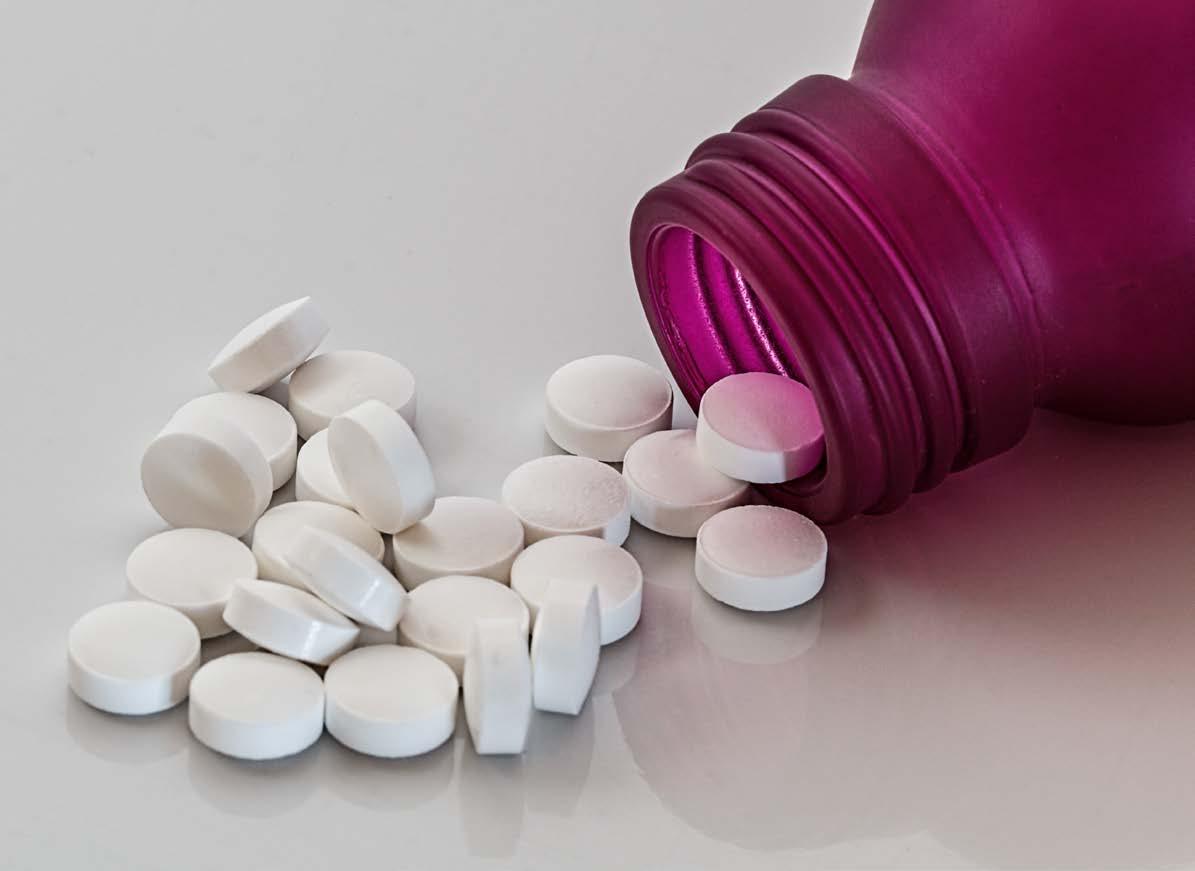
9 minute read
Child resistant packaging
from SPN April 2021
by spnews.com
New ‘tamper-proof’ packaging - childs play
New solid advances in child resistant packaging. For many years Sanner Atmo has been at the forefront of the development of speciality closures and child-proof pharmaceutical packaging.
Advertisement
Philip Yorke takes a closer look at its latest unique offering.
The company’s TabTec® CR is a child-resistant pharmaceutical packaging product designed for solid drugs with a novel and patented child-resistant function. The Press & Flip child safety mechanism in the closure prevents accidental opening, and the certified child-resistant packaging meets all international regulatory requirements.
The TabTec® CR prevents medicines from getting into children’s hands. The unique, innovative re-closure of the child-resistant function, makes the medication packaging ultra-safe. In addition, the integrated desiccant and the appropriate colour selection not only make the contents childproof, but also protects them at all times from moisture and light. The integrated pouring assistance feature also offers a particularly hygienic and easy-dosage delivery of the medicines.
An additional advantage is that no extra desiccant capsules or sachets need to be added to the childresistant tablet packaging during filling. The childresistant tablet box also offers other key advantages, such as the application of a warranty function by means of a label with an integrated TE band. Further information is available in Braille, QR codes, and advertising, which can easily be integrated into the booklet label. This saves costs in secondary packaging and opens up new communication channels to end users.
A perfect alternative to blister packs
In an independent consumer study, Sanner’s novel child-resistant packaging for tablets was given an excellent rating. Consumers between the ages of 18 and 50 in particular were convinced of the need for a childproof tablet box for most medicines. The new packaging also scored very well in other criteria compared to child-resistant blister packs. In addition to the childresistant opening mechanism, these include hygienic removal and ease-of-use when on the go. Furthermore, the need to open the TabTec® CR packaging with both hands visually reinforces the message of child safety. More differentiation at the point of sale with the TabTec® Cr is its novel design, which also enhances the look and feel of the brand enhances the differentiation and recognition of Sanner’s child proof medical packaging. The new packaging clearly stands out from the crowd of existing child resistant pharmaceutical packaging.
Senior friendly
Another key benefit of this new product is its unique opening mechanism which is not only childproof, but also senior-friendly. The TabTec® CR is unique, and unmistakable as well as being ‘senior proof’ and child proof right down to the last tablet. The new ‘Sanner Atmo Guard System®’ also combines the company’s expertise and quality in a comprehensive, safety-first product. To recommend the ideal amount and type of desiccant, Sanner takes all relevant moisture ingress factors into account and works with real product data to develop a tailor-made desiccant solution. This in turn ensures reliability, cost-effectiveness and maintains the product’s required shelf-life.
With the focus today on sustainability and safety, the packaging industry has clearly stepped up to the plate in order to provide the best possible solutions. Accordingly, SPN is pleased to showcase the work of some of the most innovative pharmaceutical packaging companies.
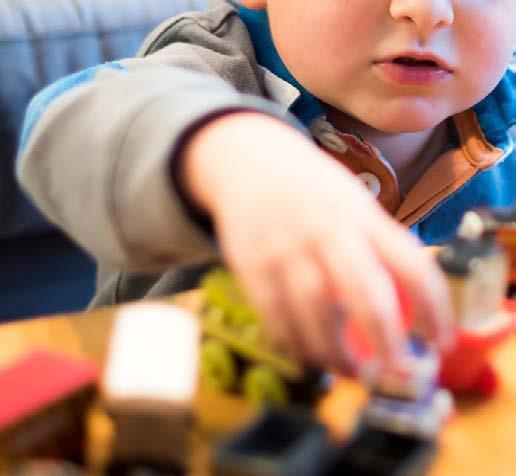

Putting waste medical packaging in its place
Anyone involved with the Pharmaceutical industry will know that it has its own highly specific requirements, regulatory bodies and diverse manufacturing constraints. With the Covid 19 pandemic and sustainability foremost in our thoughts, the industry has come under greater scrutiny than ever before, as Philip Yorke reports.
Although it is acknowledged that pharmaceutical packaging represents a small percentage of total packaging waste, it is still significant enough to warrant the world health organisation (WHO) to make a variety of recommendations and encourage nations to enact new laws regarding the proper disposal of medical packaging waste.
Recently Michael Greenwood M.Sc. made the following observations concerning sustainability in the pharmaceutical industry. In the interest of sustainability, uncontaminated waste can be recycled depending on the availability of local facilities, with paper, plastics, glass, and metals often recycled directly. Contaminated waste, however, is usually incinerated, or otherwise taken to a landfill if incineration is not possible. Other environmental concerns associated with the manufacture of a drug include the availability of active ingredients, many of which are sourced from plants, thus encouraging deforestation, the inclusion of toxic ingredients in the drug or packaging that then escape into the environment, and the use of chemicals that aid in the application of a drug, such as chlorofluorocarbons used in propellants.
Sustainability is the ability to sustain something indefinitely, and in this context refers to the number of materials consumed by a process, and the ability to regenerate the materials in an environmentally friendly way.

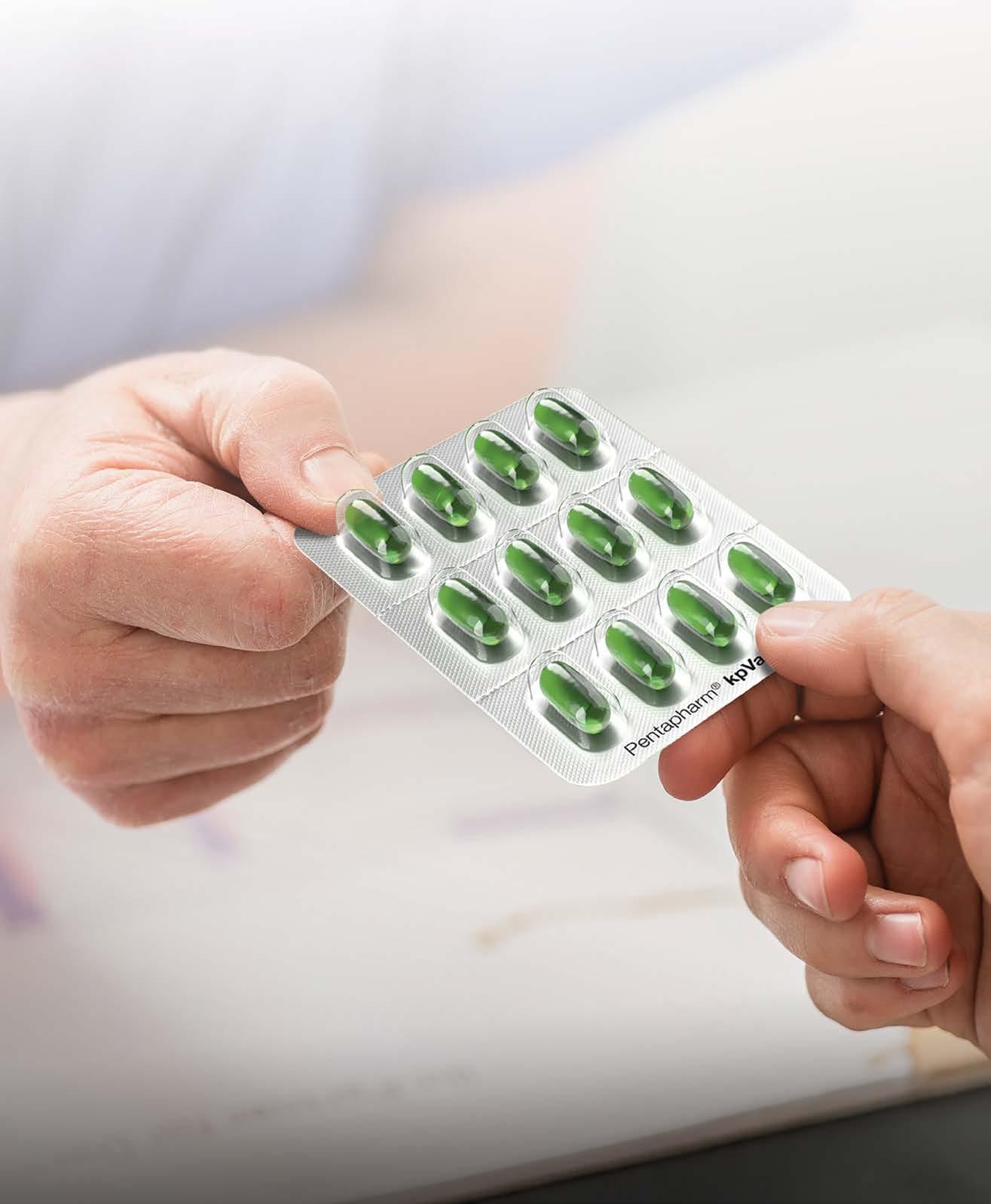
A toxic subject
The world health organisation identified three directives to help reduce and eliminate waste: reducing packaging that is not essential to the protection of the drug, making as much of the packaging as possible recyclable, and making contaminated packaging incinerator-safe. For example, some plastics are more toxic than others when incinerated, while some plastics are significantly more toxic when undergoing incomplete combustion, highlighting the importance of disposal facility infrastructure development. In 2005 the Sustainable Packaging Coalition defined sustainable packaging as safe for individuals throughout its life cycle, meets criteria for performance and cost, is manufactured and transported using renewable energy, uses recycled materials, uses materials that are friendly in likely end-of-life scenarios, and is physically designed to minimise materials and optimise energy use.
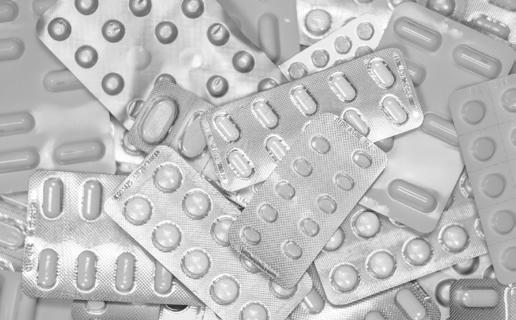
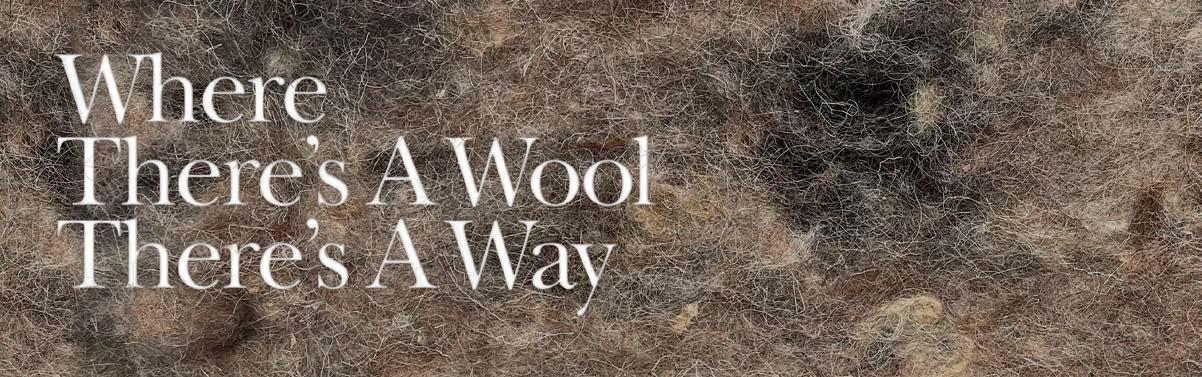
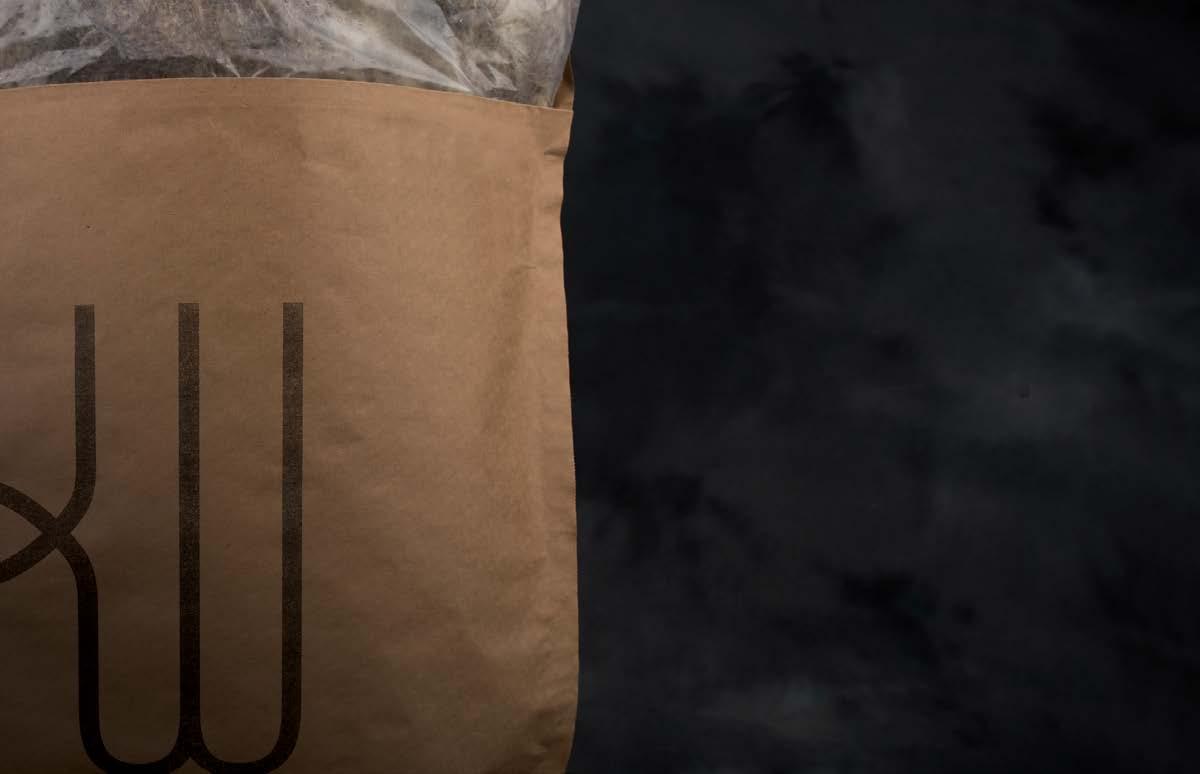
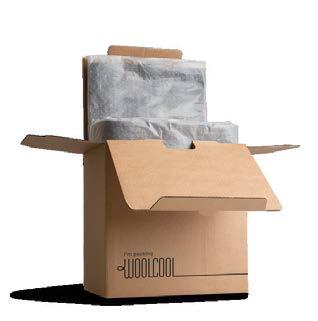
The Marchesini Group is an Italian packaging Corporation which designs and builds stand-alone machines and customised lines for the packaging of pharmaceutical and cosmetic products. For more than ten years the company has been developing advanced paperboard tray solutions for the packaging industry.
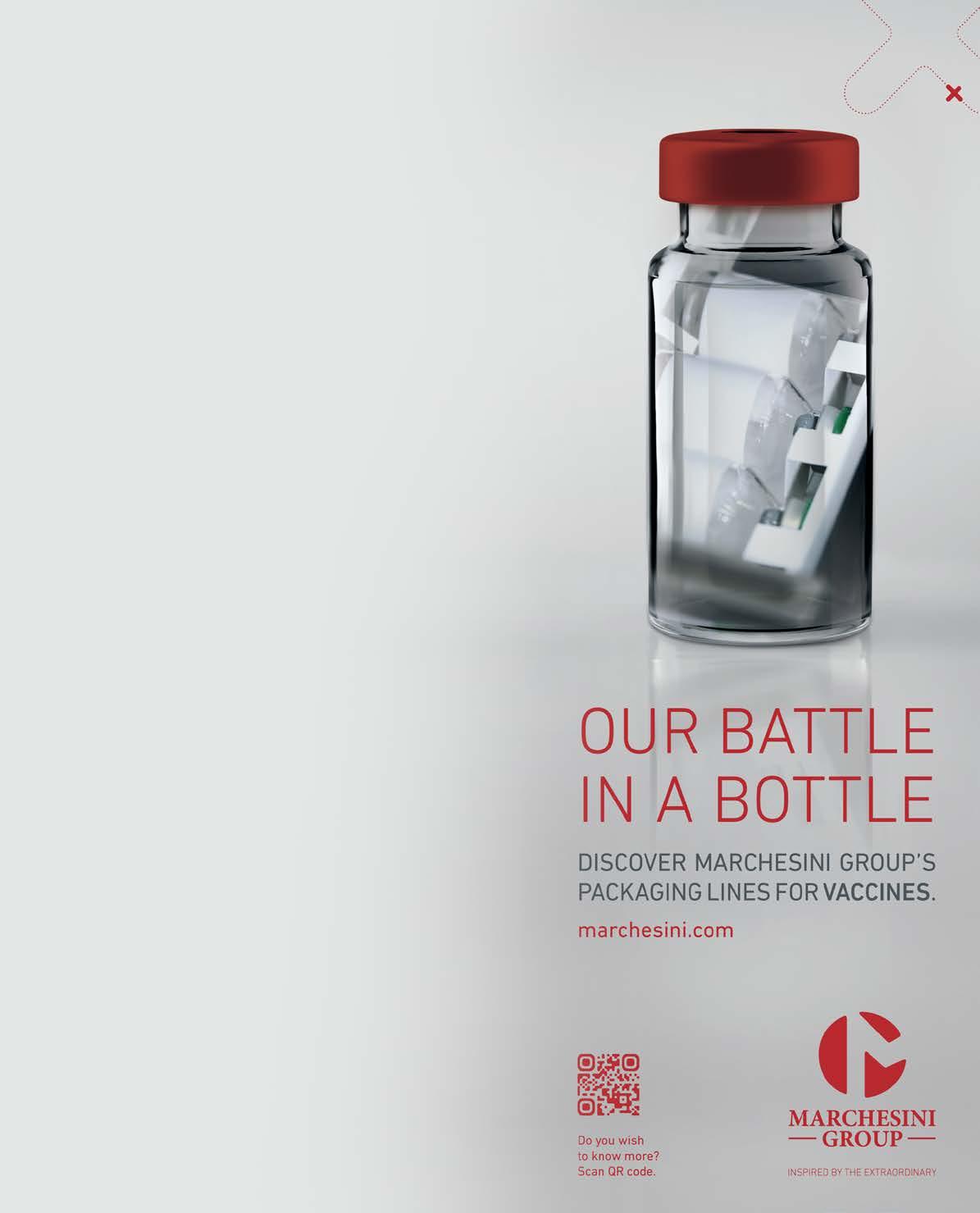
Marchesini’s paperboard trays offer all the benefits of modern, single-material packaging as each tray is made from identical material to the carton. This eliminates the need for a second material, such as plastic and this key benefit means a reduction in material ordering and storage logistics by up to 50%. However, it is also well known that protecting fragile products, such as syringes and vials, can be a very costly business. Fortunately, by using Manchesini’s paperboard trays, customers can benefit from reduced operating costs and floor space, as well as increasing their broad operational efficiency. These valuable solutions provide further added benefits by ensuring that the packaged products are well-protected and secure throughout their lifespan. This also translates into big savings for customers in reduced storage and transportation costs, as well as presenting products to the end user in a modern and most attractive way.
Today Marchesini is globally recognised for its unrivalled expertise in design and production, which focuses on creating customised trays and cartons for specific product types, sizes and quantities. Using prototypes and mock-ups, the trays and cartons are fine-tuned to ensure that customers can optimise their entire packaging line, from the handling of components, to the cartoner and subsequently to the case-packer and palletiser.
Finally, it is important to appreciate that paperboard tray loaders can be fitted in multiples on any Marchesini cartoner ranging from low speed to high speed machines that are capable of producing over 450 trays per minute. So when looking to the future, customers can look forward to optimised production efficiency and value, with Manchesini’s world-class engineering and packaging innovation.

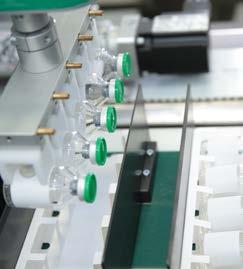

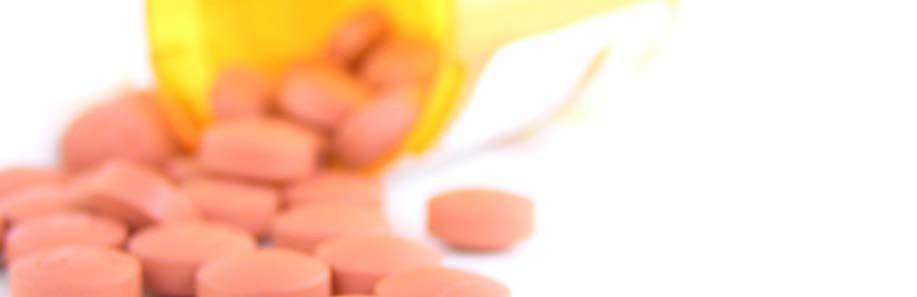
Gauging the benefits
As many restrictions limit the use of recycled materials in pharmaceutical package production, manufacturers are encouraged to consider the recyclability of their product at the end of its life, making up for where laws do not allow for best sustainability. Additionally, the ability to sustainably source any packaging materials must be considered, as if demand is high even renewably sourced materials may not be sustainable.
Many pharmaceutical companies are achieving reduced packaging by lessening their weight. Modern plastics can be made thinner while maintaining strength, and advances in structural design thanks to computational engineering methods allow new designs that use far less material while maintaining the function and purpose of the packaging. Competition between overthe-counter drug companies has led to an increase in the variety, size, and visual appeal of packaging, which may encourage the use of unnecessarily-sized and coloured packaging. Regardless, packaging must maintain the information regarding contents, dosing, and safety precautions.
Reducing accelerants
Another source of waste in pharmaceutical packaging is the use of accelerants and solvents that are damaging to the environment, for example, chlorofluorocarbons. Many pharmaceutical companies are researching and developing alternatives to these solvents, one example being Cyrene (di-hydro levoglucosenone), developed by Merck as an alternative to N-methyl-2-pyrrolidone or dimethylformamide.
These chemicals are common intermediates in the pharmaceutical industry, used to enhance the absorption of topical drugs and as formulating agents, and can potentially pose an environmental hazard if allowed to accumulate. The functionality of the product must always be the first priority when it comes to medicines, with some requiring high levels of moisture and light protection that necessitate sophisticated packaging. Insufficient packaging will inevitably, ultimately, generate more waste, as damaged goods must be disposed of and replaced.
Trend towards personalised medicines
Sustainability may also be implemented to a greater degree during manufacture. Large manufacturing runs of drugs are becoming less commonplace for new pharmaceuticals as generic manufacturers around the world begin to take over the production of off-patent drugs. Modern personalised medicine also forces smaller manufacturing runs that are inherently more wasteful, as down-time between producing batches is wasted time and energy that is spent setting up for the next run.
Companies are becoming increasingly streamlined and optimised in this regard, with, for example, the amount of heat applied to blister-packs being finely tuneddown to conserve energy, water consumption being closely monitored, and ventilation systems carefully optimized. Tracking through the supply chain can also improve sustainability by optimising the manufacturing rate and distribution of products, ensuring that it is not overproduced, minimizing energy-consuming storage time and that it is not transported more than is necessary.
Today the Pharmaceutical industry leads the field in many aspects of its practices developed to improve sustainability and the recycling of medical waste. In its on-going mission to achieve 100% sustainability, SPN will continue to monitor the latest innovative solutions that have been created in partnership with the pharmaceutical companies throughout the world.