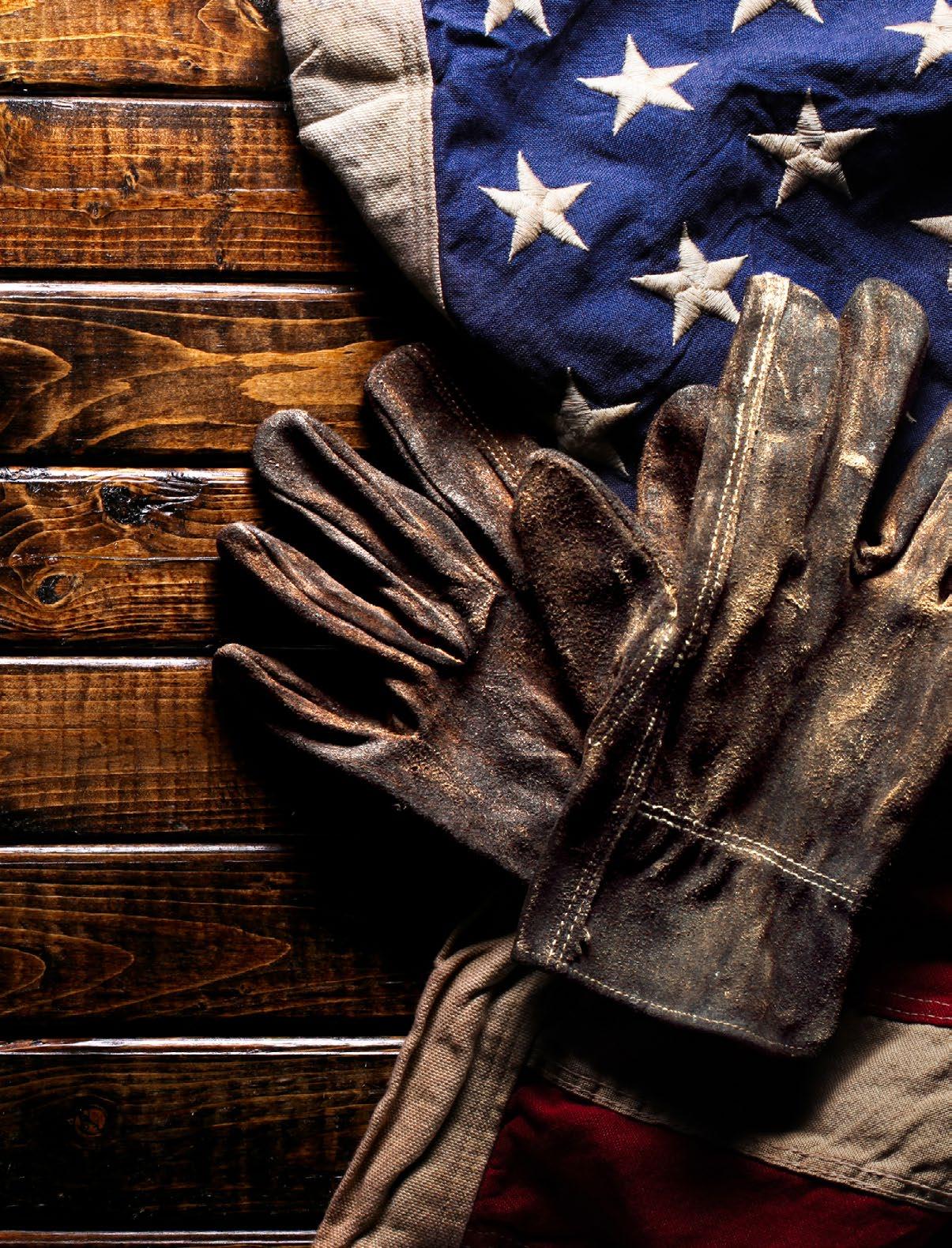

North America’s Manufacturing Resource for Industry Professionals Since 1986
North America’s Manufacturing Resource for Industry Professionals Since 1986
AI, Autonomy, and the Rise of Smart Factories in North America
From Spare Parts to Smart Design
How Additive Manufacturing Is Redefining Industrial Machinery
Lifting Smarter: How Sky Hook Combines Ergonomics, Customization, & Craftsmanship to Revolutionize Manual Material Handling
IIoT and Machine Learning shape the future of predictive maintenance
Materials Matter: Enhancing Quality and Durability Through Material Selection
EMAG MSC 5 DUO: A Twin-Spindle Turning Center Engineered for Productivity and Precision
Empowering Small Manufacturers in the Digital Era: Siemens' Scalable Solutions for Real-World Challenges
Precision Tools Supporting North America’s Manufacturing Momentum
Running your operation comes with enough challenges. Managing your industrial filtration systems doesn’t have to be one of them.
Partnering with Donaldson is like having the industry leader in filtration on your team. Custom solutions, performance insights, replacement filters and parts, and unrivaled service and support. Complete coverage from a single source.
THAT’S PEACE OF MIND. DELIVERED BY DONALDSON.
SCAN to schedule a free consultation with a Donaldson expert.
SETTING NEW STANDARDS FOR SAFE LIFTING
• Large range of sizes, up to M1000/UNC 4 "
• Embedded RFID creates easier inspections
• Replaceable bolt extends use, saves money
• Spring mechanism prevents sagging and transverse loads
• Huge selection of sizes are IN STOCK!
THE
TURNADO
Mathieu Pérennou,
maximizing equipment performance and longevity, wireless condition monitoring helps industrial enterprises boost productivity and improve the
North America’s Manufacturing Resource for Industry Professionals Since 1986
William C. Strickland III, Publisher william.strickland@indmacdig.com 800-366-0676 ext. 103 | Fax: 866-826-5918
Adrienne Gallender, Associate Publisher/Media Advisor agallender@indmacdig.com 847-612-1572 | Fax: 847-559-2909
Brian Self, Associate Editor/Podcast Producer brian@indmacdig.com 800-366-0676 ext. 104 | Fax: 866-826-5918
Shane Bell, Creative Director sbell@indmacdig.com
Lisa Hanschu, Sr. Account Executive lisa@indmacdig.com 785-965-9159 | Fax: 785-965-7199
William C. Strickland III, National Sales 205-903-9178 | fax 866-826-5918
Susan Strickland, Accounting susan@indmacdig.com 205-542-1098 | Fax: 866-826-5918
CIRCULATION & SUBSCRIPTIONS
IMD, 3590-B Hwy 31 South, Suite 233, Pelham, Al 35124 circulation@indmacdig.com | Fax: 866-826-5918
REPRINTS
To purchase article reprints please call 800-366-0676 ext. 103 or email wstrickland@indmacdig.com
Rethinking What’s Possible in
North American manufacturing is at an inflection point—not defined by crisis, but by transformation. The stories in this issue make one thing clear: we're not just making products faster or cheaper—we're reimagining how things get made at every level.
The rise of intelligent automation, whether in the form of collaborative robots, autonomous logistics platforms, or AI-driven safety and control systems, signals a deeper shift underway. It’s not simply about plugging in new machines— it's about weaving together physical processes, digital systems, and human ingenuity to solve complex challenges.
From robotic torque control to AI copilots that orchestrate entire fleets of autonomous vehicles, we're witnessing a shift in mindset: where the factory floor is no longer a static space, but a dynamic, data-connected ecosystem. Add to this the growing importance of safety technologies, ergonomic tools, and precision workholding— and the message is unmistakable: operational excellence in North America is now being built from the inside out, powered by software, insight, and scalable innovation.
What unites all of these advancements isn’t a singular technology—it’s a shared purpose: to create smarter, safer, and more sustainable systems that work in harmony with the people who use them. This issue captures the momentum, the ambition, and the spirit of what’s next.
As always, thank you for being part of the IMD community.
Onward,,
William Strickland, Publisher, IMD
AMT is bringing back its popular Meetup series for 2025 with a seven-city tour across the united States. These casual after-hours networking events are designed to connect professionals from across the manufacturing technology ecosystem, featuring new partnerships with Women in Manufacturing (WiM) and the National Tooling and Machining Association (NTMA).
The AMT Meetup series offers unique opportunities to build brand visibility and expand social capital among AMT’s technology builders and distributors, NTMA’s precision manufacturers and job shops, and WiM’s expansive network of professionals advancing careers in manufacturing.
“This is what happens when the right people—and the right partners—show up,” said Bill Herman, AMT’s Vice President of Membership and Sales. “These meetups prove that manufacturing isn’t just evolving—it’s becoming more connected and community-driven.”
Major sponsors for the 2025 series include Okuma America, Stratasys, Epicor, Vollmer of America Corp., Tata Technologies, Milltronics, and Advanced Machine & Engineering, among others. Attendees can enjoy free food and drinks at each event, with stops scheduled in:
» Detroit, MI (July 16)
» Indianapolis, IN (July 30)
» los Angeles, CA (Aug. 20)
» St. louis, MO (Sept. 24)
Registration is free but space is limited.
For More Information: www.AMTonline.org/events/AMT-meetups
Boston Metal has appointed Eduardo Bartolomeo, former CEO of global mining giant Vale, to its Board of Directors as the company nears revenue generation from its Critical Metals business and advances toward commercializing its Molten Oxide Electrolysis (MOE) steel technology.
Bartolomeo, who led Vale from 2019 to 2024, brings over 30 years of industrial leadership experience. At Vale, he introduced the Vale Production System and advanced the company’s sustainability strategy. His appointment signals Boston Metal’s growing global relevance and the viability of its zero-emissions MOE platform for steelmaking and critical metal recovery.
“Eduardo’s decision to join our board is a powerful signal that Boston Metal’s technology and team have the potential to transform how metals are made,” said Tadeu Carneiro, CEO of Boston Metal.
Boston Metal recently commissioned its multi-inert anode MOE industrial cell—a significant step toward full-scale deployment of its emissions-free steel process. With operations in Massachusetts and Brazil, the company is redefining sustainable metals production through innovation.
For More Information: www.bostonmetal.com
Hypertherm Associates is reaffirming its commitment to workforce development by sponsoring the welding competition at this year’s SkillsuSA National leadership & Skills Conference, taking place June 23–27 at the Georgia World Conference Center in Atlanta.
As an in-kind sponsor, Hypertherm is donating nine Powermax45 S yNC® plasma cutting systems and 100 S yNC drag cut cartridges for use in the competition. In addition, Hypertherm professionals will volunteer as judges and mentors, providing expertise and support to student competitors throughout the event.
“Advancing technology through a student-mentor connection is core to Hypertherm Associates’ origin story,” said President and CEO Aaron Brandt. “We take an active role in SkillsuSA each year to honor our history while investing in the future.”
Hypertherm will also exhibit at TECHSPO, the event’s accompanying tradeshow, where attendees can explore the Powermax45 S yNC® and learn about innovations in consumable cartridge design, RFID-enabled torch communication, and simplified operations that benefit the next generation of skilled trades professionals.
The company’s participation highlights its commitment to narrowing the skills gap while showcasing cutting-edge plasma cutting technology for industrial and educational settings alike.
For More Information: www.hypertherm.com
At the AGMA/ABMA Annual Meeting in Austin, Texas, the American Gear Manufacturers Association (AGMA) and the American Bearing Manufacturers Association (ABMA) officially merged to form the Motion and Power Manufacturers Alliance (MPMA). The newly unified organization introduced its first Executive Committee and Board of Directors, representing leadership across the power transmission industry.
Sara Zimmerman of Sumitomo Machinery Corporation of America was elected as incoming Chair. Other key Executive Committee members include Matt Frady of Dodge Industrial, Steve Janke of Brelie Gear, Jason Daubert of Fl Smidth, Michelle Maddox of B&R Machine and Gear, Brian Parsons of NSK Americas, and outgoing Chair Michael Cinquemani of Master PT.
The Board of Directors includes representatives from more than 20 companies, including Gleason Corporation,
Schaeffler, Nachi Technology, NTN Bearing, and The Timken Company.
“On behalf of the 425+ companies that now make up the MPMA, I look forward to working with these leaders to keep moving our industry forward,” said MPMA President Matthew Croson. “These dynamic leaders will explore new ways to add value across the power transmission supply chain.”
NETZSCH Pumps uSA celebrated the official reopening of its remodeled headquarters in Exton, PA, on February 26, 2025. The 119 Pickering Way office now reflects a modern, collaborative work environment designed to enhance innovation, efficiency, and employee satisfaction.
With open layouts, flexible workstations, and dedicated collaborative zones, the redesign encourages communication and agility. Company leaders including President Thomas Streubel, Moritz Netzsch, and Giuliano Albiero joined employees and special guests for the ribbon-cutting ceremony and facility tour.
“This transformation represents a new era for our team,” said Streubel. “It’s more than a physical update— it’s a strategic investment in our people and how we work together.”
The remodel is part of NETZSCH’s broader commitment to continuous improvement and providing high-performance workspaces that foster innovation and collaboration.
For More Information: pumps-systems.netzsch.com
Annual
244,000 U.S. Manufacturing Jobs From Reshoring and FDI
The Reshoring Initiative’s 2024 Annual Report revealed that over 244,000 u.S. manufacturing jobs were announced via
reshoring and foreign direct investment (FDI), continuing a trend toward rebuilding domestic production. However, early 2025 data suggests momentum may slow without stable policy support.
Since 2010, over 2 million jobs have been announced due to companies and investors bringing operations closer to u.S. customers. In 2024, reshoring by u.S. firms significantly outpaced FDI, with high-tech industries driving the growth—especially in computer electronics, EV batteries, and transportation equipment.
President Harry Moser emphasized the need for sustained industrial policy. “We must level the cost playing field and build a skilled workforce to truly compete globally.”
The Initiative advocates for strategies such as uSD devaluation, expanded apprenticeships, retention of capital investment expensing, and smarter tariff applications.
For More Information: www.reshorenow.org
TRuMPF Inc. marked a major milestone with the grand opening of its new Smart Factory in Farmington, CT, on May 20, 2025. The $40 million, 55,800-square-foot
facility is dedicated to high-tech production of TRuMPF sheet metal machinery for the North American market.
The Smart Factory integrates automation, digital connectivity, and real-time manufacturing demonstrations. It also supports TRuMPF’s local-for-local strategy by boosting u.S. production of press brakes, tube laser machines, and related systems.
TRuMPF also announced three strategic initiatives:
Expanded Production: A new press brake line will launch in summer 2026, adding capacity and jobs.
Training Center Growth: A larger facility will serve more students with advanced automation training.
Apprenticeship Consortium: A new regional workforce development partnership will include other Connecticut manufacturers and leverage TRuMPF’s in-house programs.
Governor Ned l amont applauded the opening, calling it “a model for advanced manufacturing.” TRuMPF also became the first recipient of Connecticut’s Strategic Supply Chain Initiative funding.
For More Information: www.trumpf.com
Inspire your team with durable, comfortable and wellfitting workwear — and we’ll take care of your laundry list, too. With an Apparel+ program, we’ll pick up your team’s dirty clothes, wash and repair them, and deliver the fresh garments back to your business. Cintas gives you the complete package, with no upfront investment.
Discover the innovative tools and technologies shaping today’s manufacturing landscape. Highlighting processes that transform raw materials into precision-crafted products, from advanced cutting and forming systems to welding and finishing techniques, the focus remains on efficiency, accuracy, and innovation driving modern fabrication.
From advancements in automation and sustainable manufacturing practices to the latest developments in material processing, gain insights into trends and solutions that enhance productivity, improve quality, and maintain competitiveness in a rapidly evolving industry. This overview showcases the equipment and expertise behind the products powering industries worldwide.
By Mathieu Pérennou, Additive Manufacturing & Nexus Solutions Director, Hexagon Manufacturing Intelligence
The way manufacturers design, build, and maintain industrial machinery is changing— quietly but fundamentally. One of the key drivers behind this shift? Additive manufacturing (AM).
Once seen as a niche tool for prototyping or “innovation labs,” AM is now carving out serious value on the production floor. It’s not replacing traditional machining, but it’s complementing it in smart, strategic ways—reducing downtime, accelerating time to market, and extending the lifespan of legacy systems. With today’s ongoing supply chain uncertainty and labor shortages, that flexibility is more valuable than ever.
Industrial machinery has always walked a line between repeatability and specialization. Whether you’re building packaging lines, custom automation rigs, or heavy-duty forming equipment, there’s rarely a one-size-fits-all solution. This is where AM truly shines. Because it’s a tool-less process, AM allows manufacturers to design
and produce machine components that are highly customized, structurally optimized, and built on demand. From conformal cooling channels in injection molds to lattice structures in lightweight mounts, the design freedom of AM opens new doors for improving performance without adding complexity to production.
We’re seeing this play out in advanced manufacturing sectors like semiconductor equipment. For example, ASM l , a leading semiconductor equipment
manufacturer, publicly credits AM as a way to maintain its technological edge. By incorporating additive parts into their machines, they’re able to reduce weight, increase thermal efficiency and part performance, and iterate faster—all without needing to redesign entire systems from scratch.
Speed is another reason AM is gaining traction among manufacturers. Time-to-market is often limited not by innovation, but by the lag and the siloed situation between design and production. Traditional prototyping cycles involve long waits for tooling, machining, or outsourced fabrication. AM shortens that loop dramatically.
Design teams can rapidly prototype new parts, fixtures, or assemblies in-house, test for fit and function, and iterate in days rather than weeks. This kind of agility is especially valuable for OEMs that offer machine customization or work in low-volume, high-complexity segments. With AM, they can validate designs faster,
engage customers earlier, and move from pilot to production more confidently.
In many cases, this rapid prototyping doesn’t stop at form and fit. It can also involve functional testing. High-performance polymers like PEEK or carbon-fiberreinforced materials are increasingly used to print working machine parts that withstand mechanical or thermal stress.
The benefits of additive manufacturing aren’t limited to new machinery. AM also plays a critical role in extending the service life of existing assets.
One of the most practical applications of AM today is in producing spare parts for legacy equipment, especially parts with long lead times, high costs, or no digital CAD data. Through reverse engineering and additive manufacturing, machine shops can reproduce components that are otherwise impossible to source, keeping critical systems online and reducing dependency on external vendors.
This isn’t just theoretical. Several metalworking shops have begun building internal “digital warehouses” of legacy parts—3D-scanned, digitally archived, and ready to print as needed. That means shorter wait times for OEMs to ship discontinued parts or expensive rush orders from third parties.
Some go a step further by upgrading those legacy components using Design for Additive Manufacturing (DfAM) principles. Instead of simply replicating a worn-out bracket or housing, they redesign it to be lighter, stronger, or easier to manufacture. It’s a cost-effective way to improve equipment reliability without a complete overhaul.
While additive is powerful, it doesn’t exist in a vacuum. In metalworking, many machine shops are seeing success by integrating AM with conventional machining processes. The usual approach is to print a near-net-shape part, such as a rough geometry of a mounting plate or fixture, and then finish key surfaces with CNC milling.
This hybrid workflow delivers the best of both worlds: the design freedom and agility of AM as well as the precision and surface finish of subtractive methods. It’s efficient, scalable, and particularly valuable in scenarios where time, material savings, or complexity are at a premium.
We see this trend accelerating as more machine builders look to diversify their in-house capabilities. Shops that can handle both additive and subtractive processes are better positioned to serve their customers and respond to disruptions without relying solely on outside suppliers.
The full potential of AM is unlocked when it’s part of a connected digital workflow. Many organizations are starting to support this through cloud-based environments that connect the design, simulation, build, and quality inspection processes into one streamlined thread, like Hexagon’s Nexus.
With connected data, teams can move faster and more collaboratively. A design engineer can simulate thermal performance and stress tolerances, validate the print path, and share real-time feedback with manufacturing and QA teams. AI tools integrated into the workflow help predict
build outcomes, reduce trial and error, and even assess the viability of AM for specific parts based on geometry and material needs.
This level of integration helps accelerate adoption and reduce risk, especially for machine builders entering the AM space for the first time.
Additive manufacturing is no longer a future-facing experiment. It’s already proving its worth as a reliable tool for building, maintaining, and enhancing industrial machinery. As the technology matures, we expect to see continued improvements in printing speed, material diversity, and post-processing automation.
The next frontier? Scaling beyond prototyping into full production, particularly for spare parts, tooling, and machine components that are traditionally slow to source or expensive to make in low volumes.
For now, the smartest move for machine builders is to start small: identify a pain point, pilot a solution, and build from there. The entry barrier is lower than it’s ever been–and the payoff, in terms of flexibility and resilience, is growing every day.
Amada Weld Tech has unveiled a dedicated webpage for its advanced wire compacting heads, supporting critical applications in automotive, aerospace, and electronics manufacturing. These systems transform stranded wires into solid, cuboid forms, reducing contact resistance, enhancing reliability, and eliminating the need for terminal lugs—streamlining assembly and reducing overall weight and cost.
Designed for copper wires (with or without tin or silver plating), the technology supports various wire sizes and
is used in applications such as battery distribution, airbag initiators, and safety sensors. Engineers can filter options based on compacting force and braid cross-section to find the right solution quickly.
For More Information: www.amadaweldtech.com
E-Z lOK offers threaded metal inserts that reinforce plastic 3D printed parts for repeated use. Options include press-in (E-Z Press™ and E-Z Fin™) and heat-staking (E-Z Sonic™) inserts that work with thermoplastics to provide strong, reusable metal threads.
Installation is fast and straightforward, and kits are available with both metric and imperial options. These inserts are ideal for prototyping and production runs where durability and reusability are key.
For More Information: www.ezlok.com
ESAB introduces OK Autrod 42 l SW, a low-slag ER70S-9 solid MIG wire formulated for robotic applications. This copper-coated wire minimizes slag and silica islands, improving weld appearance and reducing post-weld cleanup.
Engineered for automotive and structural welding, it produces fewer oxide inclusions, allowing paint or galvanizing processes to proceed without added labor.
Available in multiple diameters and packaging sizes, the wire also offers a smooth weld puddle and excellent spatter performance.
For More Information: www.esab.com
Fronius continues to lead arc welding innovation with its intelligent gas controller, which reduces shielding gas consumption by up to 40%. By stabilizing gas flow and preventing the surge typically seen at weld start, it eliminates waste while preserving arc quality.
Whether using argon, helium, or mixed gases, the system delivers precisely what is needed for each welding job and adjusts in real-time. Available as a retrofit to TPS/i and iWave machines, this upgrade significantly lowers operating costs and environmental impact.
For More Information: www.fronius.com
HSG l aser debuts its STORE PRO automation solution at FABTECH Booth #A3592. Paired with the new GH Series 2D fiber laser cutting system (3kW to 60kW), STORE PRO integrates smart material handling with high-speed, high-power laser performance.
The GH Series cuts carbon steel up to 100mm, stainless up to 120mm, and aluminum up to 90mm. It features AT+ Visual Edge Detection and AR+ Visual Residual Functionality. FDA and CE certified, this platform is supported by local u.S. service.
For More Information: www.hsglaser.com
Hypertherm Doubles Warranty Length for Powermax® Series
Hypertherm has extended the warranty on Powermax® plasma cutters from three to six years, retroactive to all units delivered on or after January 1, 2025.
Known for their reliability and versatility, Powermax systems handle manual and automated cutting and gouging up to 1.5" thick. Customers don’t need to take any action to benefit—just retain their purchase record.
For More Information: www.HyperthermAssociates.com
Automated 6-Axis Structural Steel Robotic Beam Cutting Machine with Seamless 3-Spindle Drill Processing
Machitech introduces the Beamcut BC50 with Drill at FABTECH Booth #A5467. With three drilling heads and integrated plasma cutting, this compact machine supports drilling, milling, tapping, and countersinking in one inline operation.
Its robotic 3D CNC platform cuts mild steel, stainless, and aluminum profiles up to 48 inches wide, with customizable length configurations ideal for shops with space limitations. For More Information: www.machitech.com
At FABTECH Booth #A5478, Tecoi uSA showcases its THOR® and l S Series machines, designed for large-format plate processing. THOR integrates plasma and oxyfuel cutting with full mechanical processing including drilling, tapping, and beveling.
The l S Series features dual drill heads, 22 hp motors, and rapid tool changes. Coupled with StockTec automation for plate storage and material flow, Tecoi’s systems offer complete fabrication line integration. For More Information: www.tecoiusa.com
W.F. Wells Inc. Celebrates 75+ Years of Excellence in Bandsaw Manufacturing
Celebrating over 75 years in business, W.F. Wells Inc. continues to lead in American-made twin post bandsaw production. With 40+ standard models and a reputation for durability, the Michigan-based manufacturer serves aerospace, energy, defense, and fabrication industries. In addition to metal, W.F. Wells bandsaws have cut everything from wood to emeralds. The company is committed to custom solutions and lasting craftsmanship.
For More Information: www.wfwells.com
Material handling is at the heart of efficient industrial operations, focusing on the movement, storage, and organization of materials. This section highlights strategies and technologies that streamline these processes, from automated storage and retrieval systems to advanced conveyor solutions. Readers can explore innovations like forklifts, cranes, hoists, and magnetic lifters, which play a pivotal role in optimizing material flow across warehouses, factories, and supply chains.
In addition to hardware advancements, this area emphasizes cutting-edge solutions like warehouse management systems and parts tracking technologies, which integrate seamlessly into modern production environments to enhance operational control. Topics also cover sustainable practices, such as energy-efficient lift equipment and ergonomic tools designed to improve workplace safety while reducing strain. Whether tackling inventory management or enhancing material logistics, this section provides the insights and tools needed to excel in today’s industrial landscape.
In the world of material handling, safety and simplicity often collide with operational realities. Overexertion injuries, awkward loads, and outdated equipment continue to pose risks on the factory floor. But for Sky Hook, a fourth-generation, family-owned company founded in the late 1960s, these challenges have long served as the foundation for innovation. At the heart of Sky Hook’s mission is a clear focus: to create lifting devices that not only meet rigorous ergonomic standards but are also designed so well that operators actually want to use them.
Thomas Christensen, VP of Design and co-owner of Sky Hook, brings both heritage and modern design insight into every solution the company delivers. “Most lifting injuries happen not because of how much is being lifted, but because of how it's being lifted,” he said in a recent interview. “Our goal is to offer a solution that allows operators to lift safely, without using their backs or risking injury.”
Founded by Christensen’s greatgrandfather, Sky Hook was born from a personal mission to reduce workplace injuries by rethinking manual lifting. What began as a simple device intended to alleviate strain on workers has evolved into a robust catalog of customized lifting solutions serving industries such as aerospace, semiconductor manufacturing, and general industrial production.
industry-specific constraint, Sky Hook thrives on tailoring its designs to solve real-world problems.
“Our customers are driving our design,” Christensen emphasized. “When they come to us with a specific lifting challenge, our talented design and sales teams come together to simplify that complex situation into a reliable, easy-to-use solution.”
That design flexibility doesn’t just extend to dimensions or configurations. It also influences the very way Sky Hook thinks about manufacturing. With the entire production process kept in-house at their u.S. facility, the company can rapidly iterate and pivot to meet specific requests—a key differentiator in a global market increasingly reliant on offshore or third-party sourcing.
under the leadership of his parents, Dean & Twilla Christensen, Thomas and his brother are the fourth generation to steward the company, continuing the legacy of craftsmanship and practicality that has defined Skyhook from the beginning. “Our grandfather wasn’t just solving a problem—he was designing something that looked and felt like an extension of the operator. That’s always been the heart of our philosophy,” Christensen explained.
unlike larger and more complex lifting systems that often require specialized certifications or additional infrastructure, Sky Hook’s devices are manual, compact, and intuitive. They’re specifically designed to lift objects that fall within the range an operator might otherwise attempt to handle alone—but in a safer, ergonomically sound manner.
“Our focus is to make a manual lifting device that an operator actually wants to use,” said Christensen. “That comes down to simplicity. It’s not a big overhead hoist or a complicated piece of machinery. It’s a practical tool that’s easy to integrate into day-to-day operations.”
Sky Hook’s approach addresses a long-standing issue in industrial ergonomics: compliance. Even the best equipment is useless if operators avoid it because it’s cumbersome or inconvenient. By streamlining operation and maximizing mobility, Sky Hook's devices increase both safety and adoption on the factory floor.
Sky Hook’s product line has expanded considerably since its inception, thanks in part to the company's deep commitment to customization. Whether it’s a unique mounting interface, a specialized reach requirement, or an
“Being made in the uSA and manufacturing in-house allows us to move fast,” said Christensen. “When a customer has a unique request, we don’t have to wait on external suppliers or international shipping timelines. We can act quickly and stay competitive.”
Sky Hook's pivot toward ergonomic design in the early 2000s marked a turning point in the company’s evolution. As industrial safety regulations tightened and awareness of musculoskeletal disorders (MSDs) increased, the need for reliable, easy-to-use material handling solutions grew in parallel.
“Back then, we really dove deep into ergonomics,” Christensen said. “It became clear that if we wanted our solutions to have a lasting impact, we needed to ensure they were not just functional but also human-centered.”
The company’s design language began to incorporate operator feedback more heavily. Handles were repositioned for ease of use, lifting mechanisms were optimized for smooth operation, and mobile bases were introduced for better floor navigation. Today, that human-focused philosophy is embedded into every Sky Hook product.
One of Sky Hook’s key design philosophies is ensuring that each device feels like a helpful extension of the user—not a hindrance. “If a lifting device is too heavy, too complicated, or too slow to deploy, it doesn’t get used. That defeats the purpose entirely,” said Christensen.
To combat this, Sky Hook has engineered its systems for rapid deployment, minimal training, and intuitive operation. The goal is to reduce the cognitive and physical load on the operator while still meeting performance requirements.
This approach is particularly valuable in industries with high labor turnover or where new operators may lack the training or strength to safely handle materials using traditional means. In such environments, Sky Hook’s accessible design becomes an equalizer—empowering more employees to perform critical tasks safely and effectively.
Another point of pride for Christensen and the Sky Hook team is the level of craftsmanship that goes into every product. “From the very beginning, our goal wasn’t just to build a functional tool—it was to build a great one,” he said. “Something that looks like it belongs in the hands of someone who takes pride in their work.”
This artisan mindset echoes throughout the company, from initial design sketches to final assembly. Even as Sky Hook serves high-tech sectors like semiconductor fabrication and aerospace, the company maintains its commitment to high-touch, high-quality manufacturing.
That blend of aesthetic and function is more than a vanity metric—it plays a direct role in product adoption and operator satisfaction. “When someone sees our lifting device and thinks, ‘Wow, that’s well-made,’ they’re more likely to engage with it,” said Christensen.
Sky Hook’s commitment to customization, ergonomics, and quality craftsmanship continues to inform its future roadmap. As industries demand more specialized solutions, Sky Hook is leaning into its strengths—agility, in-house design, and a direct connection with the customer.
“We’re in a position where we can still be hands-on with every project,” Christensen said. “That means we’re not just building a product—we’re solving a problem with the person who’s going to use it in mind.”
In a material handling landscape dominated by automation and mass production, Sky Hook’s personalized approach may seem like an outlier. But for thousands of operators across manufacturing, aerospace, and R&D, that individual attention translates directly to fewer injuries, greater efficiency, and higher morale.
As Christensen sees it, that’s the real legacy of Sky Hook: a company where every customer challenge sparks innovation—and safety is never sacrificed for speed.
This article was developed from an interview with Thomas Christensen, Vice President of Design at Sky Hook, conducted by Industrial Machinery Digest as part of its ongoing coverage of ergonomic innovations and custom solutions in the material handling space.
Bison®
Bison®, a leader in air-moving and power-transmission technologies, highlights its ROTRON® CP and EN Regenerative Blowers, designed for the most challenging environments. With aluminum construction and stainlesssteel hardware, these blowers offer natural spark and corrosion resistance. The proprietary Chem Tough™ process further enhances chemical durability and lubricity.
The lo-leak™ option and double-faced carbon seal reduce gas leakage, improving safety and gas usage. Explosion-proof motors rated for Class 1, Division 1, Group D ensure safe operation in hazardous areas—outperforming competitors who use lower Division 2 ratings.
Virtually maintenance-free and built for over 25,000 hours of service, these blowers are ideal for environmental, chemical, and industrial use.
For More Information: www.rotron.com
CMETB
Combilift marked the 10-year anniversary of its OEM Engineering Traineeship, developed in partnership with the Cavan and Monaghan Education and Training Board (CMETB). Since its launch in 2015, over 150 trainees have gained QQI level 5 qualifications, with more than 80% achieving job placement.
Blending 26 weeks of classroom instruction at Monaghan Institute with 12 weeks of workplace training at Combilift, the program includes modules in lean Manufacturing, Hydraulics, and Mathematics. Fully government-funded, it provides a €300 weekly bursary and added certifications like City & Guilds Hydraulics and lean Six Sigma.
The milestone celebration featured testimonials from past graduates and renewed commitment to expanding employer participation.
For More Information: www.combilift.com
Coxreels® has surpassed industry standards in salt spray testing, achieving 20% more corrosion resistance hours than the recommended benchmark. Independent lab testing confirmed that their powder-coated products rank among the highest tiers for uV and corrosion protection— outperforming finishes used in automotive under-hood environments and heavy-duty equipment.
This achievement reflects Coxreels’ commitment to continual product improvement and delivering top-tier durability across their hose, cord, and cable reel lines.
For More Information: www.coxreels.com
l antek and TCI Cutting have introduced a jointly developed automated sheet unloading system, integrated with l antek Expert software. using TCI’s Automation Systems load & unload® platform and a smart suction cup grid, this system enables precise, unattended unloading of laser-cut parts.
The system detects each part’s shape, activates only the necessary suction cups, and deposits parts at a common point, eliminating operator error and minimizing cycle interruptions. Manual configuration is also available for complex geometries or micro-joint handling. This flexible, modular solution enhances safety, reduces workload, and increases production speed—now available for wider industry adoption.
For More Information: www.lantek.com | www.tcicutting.com
Numina Group and SAPNEXX have teamed up to connect Numina’s Real-time Distribution Software (RDS™) with SAP WM and EWM using ready-made BAPI templates and a RESTful API for fast, low-risk deployment.
The integration enables advanced automation—voice picking, conveyor control, sortation, and AMRs—cutting labor costs and boosting speed and accuracy. It’s especially effective for high-volume operations in healthcare, electronics, and e-commerce.
Together, they offer a scalable solution that streamlines fulfillment and supports same-day shipping demands.
For More Information: www.numinagroup.com | www.sapnexx.com
The Cornerstones of Operational Excellence
The Safety & Maintenance section is dedicated to creating safer workplaces and ensuring equipment longevity. Covering everything from cutting-edge machine guarding systems to advanced air filtration and dust collection solutions, this section provides actionable insights into workplace protection and preventative maintenance. Whether you're exploring ergonomic tools to reduce operator strain or electrical systems that enhance reliability, this section focuses on products and practices that prioritize both people and machines.
In addition to highlighting safety innovations, this section delves into essential maintenance strategies, including retrofitting, rebuilding, and remanufacturing, ensuring that machinery operates efficiently and reliably over time. Maintenance supplies, facility equipment, and accessories are explored alongside new safety technologies designed to meet evolving compliance standards. Readers will discover how a proactive approach to safety and maintenance not only minimizes risks and downtime but also fosters a culture of care and continuous improvement within industrial settings.
By maximizing equipment performance and longevity, wireless condition monitoring helps industrial enterprises boost productivity and improve the bottom line
By Lorenzo Amicucci, Business Development Manager, Nordic Semiconductor
In factories, facilities and other industrial settings, millions of machines power the production of everything we need, from food and medicine to cars and computers. But even the best machines can’t run forever. Wear and tear take their toll. And when internal faults such as bearing wear, electric motors overheating, or external conditions like humidity and temperature cause these critical assets to fail or falter, even for short periods, the impact on organizations can be severe.
For example, data from a 2022 report by Senseye Predictive Maintenance, a Siemens AI-powered machine health-management platform, suggests an average large plant loses 25 hours per month to unplanned machine downtime[1]. The
cost of just a single lost hour of downtime ranges from an average of $39,000 for factories producing fast moving consumer goods, to more than $2 million in the automotive sector, the report states. Elsewhere, consultant Deloitte says unplanned machine downtime is costing industrial manufacturers an estimated $50 billion each year[2].
Such statistics mean waiting for a piece of equipment or machinery to break before fixing it is not a viable maintenance strategy. yet neither is repairing or replacing it without genuine cause. Predictive maintenance provides the answer.
Predictive maintenance (traditionally known as condition monitoring) is not a new concept extending back until at least the early 1990s. Its goal is to trigger machine servicing when the maintenance activity is most cost-effective but before the equipment’s performance becomes unsatisfactory. In practice, when a nominated threshold for machine health is reached an alert is raised and engineers carefully check a machine’s condition to catch defects and fix things before they escalate.
The value of the methodology is significant. Deloitte claims that implementing predictive maintenance leads to material cost savings of five to 10 percent a year on average; a 10 to 20 percent increase in equipment uptime and availability; a 5 to 10 percent cut to overall maintenance costs; and 20 to 50 percent reduced efforts for maintenance planning time. And according to McKinsey Global Institute, Industrial Internet of Things (IIoT)-based predictive maintenance typically reduces machine downtime by up to 50 percent and increases machine life by up to 40 percent[3].
The benefits of predictive maintenance are not limited to manufacturing. Virtually any industry that depends on physical assets for service or production could take advantage of the tech. For example, utility companies could implement predictive maintenance and monitoring tools to prevent costly power outages that would otherwise cause enormous disruption.
In the early years of predictive maintenance, the lack of suitable sensors to gather data and limited computational resources to collate and analyze the information made it difficult to implement. Today, because of advances in the IIoT, Cloud computing, data analytics and Machine learning (Ml), predictive maintenance is common among small and medium enterprises (SMEs) and large firms alike. Around three-quarters of respondents in the Siemens report saw predictive maintenance as a strategic priority.
Robust, low power wireless technologies like Bluetooth lE power sensors that gather data across networks of
hundreds, thousands or tens of thousands of devices. These IIoT sensors monitor parameters such as equipment temperature and vibration, pressure, gas levels and energy consumption, enabling service teams to gain greater insights into the predicted future state of equipment and respond proactively to problems before they arise.
“Data is the fuel of any predictive maintenance engine. Its quality and quantity are the limiting factor for analyzing root causes and predicting failures well ahead of time,” says Deloitte in its Predictive Maintenance positioning paper. The IIoT provides a continuous stream of this ‘fuel’. Sensors continuously gather data and then transmit the critical information back to a central server or the Cloud for analysis, via a gateway.
Wireless networks bring other advantages. For example, they make it possible to monitor assets in hazardous environments and hard-to-reach locations from which humans are advised to avoid. Wireless networks also significantly reduce the costs associated with the installation, maintenance and performance of the predictive maintenance systems.
Gauge Steel Design Press Bed bolted on, not welded, to prevent distortion.
Large press bed to accommodate a variety of tooling other than just punching.
Pump, motor, valve and reservoir are all easily accessible for maintenance.
Large rectangular tubes used at base of machine to give safe, instant portability.
Building a wireless network that can generate millions of data points a day, every day, is one thing. But making sense of all that data in time to react to problems demands is quite another. To minimize the cost and energy of transmitting large volumes of data (much of which will be unremarkable) much of the computing is done within the network itself using a technique called edge processing. That demands lots of computing power and memory, sensor fusion and, increasingly, Ml
Sensor fusion is the process of combining sensor data such that the resulting information has less uncertainty (i.e. is more precise or complete) than would be possible if the sensor sources were used individually. Ml is an application of Artificial Intelligence (AI) that allows computers to learn without direct programming or instruction. Ml algorithms learn from data and then generalize to unseen data and thus make decisions without explicit instructions. The result is a continual enhancement of a machine’s capabilities and a high degree of autonomy.
Edge processing and sensor fusion enables IoT devices to locally sift through data to decide which is mundane and which indicates things are changing and should be flagged. By adding Ml to the mix, edge devices move beyond just checking data to see if it has exceeded preset thresholds to inferring (drawing a conclusion about a future state of something from information already known about it) what the change means – and then doing something about it.
One example relevant to predictive maintenance is a temperature sensor monitoring a machine bearing. The sensor could use an Ml model to infer that a gradual temperature increase in the bearing is simply the machine warming up and not something about which to be concerned. But a more rapid bearing temperature increase could be indicative of lubrication failure and trigger the sensor to shut the machine down before mechanical damage occurs.
Many of today’s advanced Ml models require significant computing resources and high power consumption to perform inference. But a huge number of today’s IoT-connected devices, while able to perform some edge computing and sensor fusion, lack access to those resources.
A solution comes in the form of Tiny Machine learning or TinyMl . The technology is a subsector of Ml that streamlines the software such that battery-powered, microcontroller-based embedded devices such as wireless Systems-on-Chip (SoCs) can run it.
Nordic design partner, Edge Impulse, provide TinyMl software to run on the company’s nRF52840, nRF5340 and the latest nRF54H20 SoCs. Nordic provides an app that can be used to train and deploy embedded Ml models on the company’s Thingy:53 IoT prototyping platform. The app allows the developer to upload raw sensor data via a mobile device to the Cloud-based Edge Impulse Studio
and deploy fully trained Ml models to the Nordic Thingy:53 over Bluetooth lE.
This capability has led to development of sensors such as the Atomation Atom, powered by Nordic’s nRF52840 SoC. The sensor measures oscillations to determine if a machine motor is vibrating more than it did yesterday, or monitors temperature to check if a bearing is running hot when the machine is in operation. Each Atom functions for up to three years using a 3.6-volt li-ion battery.
The sensors monitor and process information locally, instead of sending a constant stream of data back to a central system. When thresholds are exceeded or equipment is acting outside of normal parameters, data is sent to a gateway via Bluetooth lE wireless connectivity. For example, the Atom devices can determine and answer questions such as, “is the device on or off?”, “is the motor vibrating more than it did yesterday?” or “is the bearing temperature too high when the machine is in operation?”.
“The Nordic SoC is the true ‘brain’ of our Atoms, and that brain has to take in raw sensor data, convert it to useful information and make independent decisions before communicating in a tough RF environment,” explains Steve Hassell, CEO at Atomation.
Predictive maintenance is increasingly using automated analytics powered by Ml . That will mean even better results with less human engagement. But it also increases the demand for computing power at the edge. Nordic has anticipated this demand with its next generation of shortrange SoCs, the nRF54 Series.
The new SoCs integrate multiple Arm Cortex-M33 processors and RISC-V coprocessors, with each processor optimized for a specific type of workload. Combined with embedded high-capacity, non-volatile memory and RAM, the nRF54H20 SoC equips the developer with the increased computing and memory resources needed to run complex Ml-powered predictive maintenance applications. Better yet, using the nRF54H20 combined with a Power management IC (PMIC) such as Nordic’s nPM1300 results in ultra low power consumption extending battery life, lowering maintenance requirements and reducing waste.
Tomorrow’s predictive maintenance solutions powered by a new generation of SoCs such as the nRF54H20 SoC will be even more flexible, efficient and sustainable. That will enable operators of all types of machines to maximize the potential of their assets while extending their operating life. Predictive maintenance has come a long way in just thirty years.
lorenzo Amicucci is a Business Development Manager at Nordic Semiconductor and is based in Oslo, Norway. He supports the Nordic sales team in creating innovative solutions together with leading partners and
customers across different industries. Before joining Nordic, Amicucci worked in the telecom industry, focusing on wireless (microwave) network equipment, and serving leading customers deploying critical wireless infrastructure.
He has studied in world-renowned universities in Italy, China, and Sweden, and holds a Master’s in Electronic Engineering from Politecnico di Milano, with specialization in Analog/RF IC design.
1. “The True Cost of Downtime 2022”, https://blog. siemens.com/2023/04/the-true-cost-of-downtime/ 2. “Predictive Maintenance”, https://www2.deloitte. com/content/dam/Deloitte/de/Documents/ deloitte-analytics/Deloitte_Predictive-Maintenance_ PositionPaper.pdf
3. “Manufacturing: Analytics unleashes productivity and profitability”, https://www.mckinsey.com/capabilities/ operations/our-insights/manufacturing-analyticsunleashes-productivity-and-profitability
Cementex Highlights
Cementex showcases its 15" double-insulated Reset Tool, designed to improve safety and precision for electrical professionals working in energized environments. With Cementex’s signature orange-over-yellow insulation for clear wear indication, the Reset Tool provides protection up to 1,000 VAC / 1,500 VDC and is tested to 10,000 volts. Featuring a round tip and cushion grip handle, it offers comfort and control in tight spaces. The tool meets OSHA, NFPA 70E, and CSA-Z462 standards and is made in the uSA using both domestic and global materials. A lifetime mechanical guarantee and two-year insulation warranty add long-term value for safety-conscious professionals.
For More Information: www.cementexusa.com
Dart Controls has launched its new MicroDrives—compact, microprocessor-based SCR DC drives with programmable digital displays. Available in two versions—MD for continuous operation and MD Plus for start/stop needs— these drives support motors up to 2 HP and offer RPM control, process timing, or synchronized “Follower” mode across multiple motors.
The MD Series is ideal for applications like ovens and continuous flow systems, while the MD Plus version includes PID control and 4–20 mA signal following for high-response environments such as filling stations or product mixing. Built-in logic controls can eliminate the need for PlCs, making them a versatile solution for industrial automation.
For More Information: www.dartcontrols.com
Securis Selects Twiceme Technology as Its Connected Safety Partner for Entire
Twiceme Technology has partnered with Securis, a Velotec Sports brand, to integrate its digital safety platform across all Securis industrial helmets. l aunching in July 2025, the helmets will include Twiceme chips, allowing workers to store critical health and work documents accessible to first responders via smartphone scan.
The integration helps jobsite managers streamline certification tracking and incident response using Twiceme’s Safety Management Portal. This partnership enhances both user-level protection and organizational safety oversight, reflecting a shift toward connected PPE solutions in industrial settings.
For More Information: www.securisprotect.com
Quality control and assurance are the backbone of manufacturing, ensuring every product meets rigorous standards for precision, performance, and reliability. This section delves into the tools and technologies that enable manufacturers to uphold the highest quality standards. From advanced coordinate measuring machines (CMM) to vision systems and laser inspection equipment, the spotlight is on innovations that enhance accuracy and efficiency in measurement and inspection.
Nondestructive testing (NDT) equipment and positional measuring machines are also featured, allowing manufacturers to evaluate products without damage. Tools such as form measurement gauges, cutting tool inspection systems, and tool condition monitoring devices refine production processes and reduce errors. Whether through shrink-fit technologies or video inspection systems, this section highlights the importance of advanced solutions in maintaining precision, ensuring compliance, and driving continuous improvement in industrial operations.
Making a reliable, high-quality product starts with choosing the optimal materials for the task at hand. While design and workflow considerations also deserve attention, the raw resources in an item determine its quality and durability ceiling. Consequently, getting these decisions right is crucial.
Manufacturers must also recognize that ideal characteristics are not always as black-and-white as they initially seem. Materials impact the product and its workflow through several avenues, all of which must play into sourcing decisions.
The most obvious factor to consider is
a resource’s strength and longevity. However, even these properties are more multifaceted than some may realize.
For example, carbon fiber has a tensile strength of up to 7 gigapascals, which is more than twice that of many steels. Still, its axial compressive strength can be as low as 10% of
that figure. Consequently, carbon fiber may be the more durable option for low-impact applications like vehicle panels, but steel is better for structural integrity in the frame or for construction.
Designers must also think of the specific product’s end use when choosing materials. Some applications require unique properties that may outweigh structural strength and longevity.
Copper is often the resource of choice for electrical wires, but silver is more conductive, so it may be better for sensitive, high-frequency electronics. Similarly, most semiconductors today use silicon, but gallium nitride enables more efficient power conversion and can work at higher voltages, making it better for some niche use cases.
How easy it is to manufacture something out of a resource also demands attention. The primary reason gallium nitride hasn’t overtaken silicon is its production complexity. A workflow not equipped to handle additional difficulty may produce more errors when using a higher-functioning but less workable material.
Manufacturers must consider their goals and existing equipment to make the right choice. For example, 300 Series stainless steels are only hardenable by cold methods, requiring specific production workflows. However, 400 Series steels, which can use conventional heat-treating, are not as corrosion resistant, which may impact product longevity in some cases. Which is best depends on the specific item and its value statement.
Naturally, a material’s cost must also play into the equation. Organizations should be careful to understand the entire expense picture, though. Some resources may be cheap to source but have high production costs by virtue of their low workability.
Supply chain considerations impact costs, too. Just over half of the refined copper used in the u.S. comes from domestic sources, and 90% of the remaining copper comes from just three nations — Chile, Canada and Peru. Consequently, reliance on this resource can lead to higher costs amid high tariffs or other supply disruptions among these countries.
Manufacturers should consider sustainability as climate issues become increasingly prominent. Some materials rely on environmentally destructive processes for resource extraction, giving the company’s supply chain a bigger carbon footprint. Choosing greener alternatives may improve the business’s public image and help comply with regulations.
Sustainability can also produce cost benefits. The textile industry could achieve a $700 billion boost in
economic value by embracing a circular economy, which requires a switch to more easily recyclable materials. These setups typically take time to show a meaningful return, but the long-term advantages are often worth the initial investment.
Every choice in manufacturing and product design has a cascading effect on all future decisions and results. Consequently, material selection is one of the most crucial decisions a producer makes, as it’s one of the most foundational and earliest in the value chain.
Manufacturers should consider these five factors, at minimum, when choosing the optimal material for their products. Taking a comprehensive look at how resources affect product costs, functionality, durability and more will lead to better decisions for both the company and its clientele.
FARO® Technologies has introduced the Quantum X FaroArm® Series to transform quality assurance and inspection in sheet metal stamping. This portable 3D metrology solution replaces cumbersome fixed CMMs, allowing direct inspection at the die or part location and reducing setup and downtime.
The Quantum X’s advanced l aser line Probes (llPs) with Continuous light Rectification allow high-resolution scanning of complex surfaces—without requiring sprays or coatings. Integrated CAM2® software enables GD&T analysis, trend tracking, and real-time reporting. The system's 8-Axis Max rotary table supports 360° scanning, cutting inspection times by up to 40%.
Manufacturers adopting this solution report over 50% reduction in inspection time, improved throughput, and enhanced quality control—transforming stamping workflows into more efficient and data-driven operations.
Hexagon’s Manufacturing Intelligence division has partnered with PRAGMA to deliver the first fully integrated portable NDT (Non-Destructive Testing) solution using Hexagon’s Absolute Arms and leica laser trackers. This breakthrough allows engineers to perform high-precision NDT directly on components, eliminating disassembly and enabling real-time positioning in 3D coordinate space.
Applications include corrosion mapping, composite flaw detection, additive manufacturing inspection, and weld evaluation—performed with absolute positioning accuracy. This system also offers tailored aerospace and automotive kits, retrofit options for existing Hexagon equipment, and multi-sensor modularity.
Hexagon will distribute PRAGMA’s NDT instruments across North America, expanding inspection capabilities in critical industries like aerospace, nuclear, and wind energy.
For More Information: www.hexagonmi.com
lK Metrology has released eight new Altera SF bridge-type CMMs designed for shop-floor environments. These machines deliver laboratory-grade accuracy while offering large measuring volumes (up to 4,000 x 1,500 x 1,500 mm), making them
ideal for inspecting bulky parts without moving them to a separate QC room.
Built with a ceramic bridge, air bearings, and glass-ceramic optical scales, the Altera SF ensures thermal stability, low interpolation error, and robust performance in uncontrolled environments. Features include passive or active anti-vibration systems, temperature compensation sensors, and real-time system monitoring.
Integrated with the NMC300 controller and CAMIO software, the systems are ready for automation and come with a 10-year accuracy warranty.
For More Information: www.lkmetrology.com
Nikon has introduced limited Angle CT, a powerful new scanning option for its VOXl S and XT H 225 industrial X-ray systems. This technology achieves high-resolution imaging without requiring full 360° rotation—allowing manufacturers to inspect larger or complex components like EV battery cells, PCBs, or composite parts with unmatched precision.
Benefits include faster scans, smaller voxel sizes, and Nikon’s proprietary reconstruction algorithms, which match conventional CT quality. Automated centerof-rotation calculation streamlines setup, eliminating manual adjustments.
limited Angle CT complements Nikon’s broader CT toolbox and represents a leap forward in speed and accuracy for non-invasive industrial component analysis.
For More Information: www.nikonmetrology.com
Robotics and automation are transforming modern manufacturing, redefining efficiency, precision, and versatility across industrial processes. From welding robots and robotic tooling to autonomous technology and cobots (collaborative robots), innovations are seamlessly integrating robotics into diverse manufacturing workflows.
Key advancements include automated cells and press transfer robotics, enabling streamlined operations and reduced cycle times. Solutions like material handling systems and end effectors highlight the adaptability of robotics in tasks ranging from machining to assembly. With a focus on enhancing safety and productivity, the integration of RFID and enclosure systems, along with comprehensive training, empowers manufacturers to harness the full potential of robotics in an increasingly automated world.
From reshoring efforts to next-generation warehouse automation, robotics is no longer a supplement—it’s central to North America’s manufacturing resurgence. As shop floors evolve into digital ecosystems, robotics technologies are taking on increasingly strategic roles: driving efficiency, enabling autonomous logistics, and blending physical and digital operations into unified, intelligent systems.
This month’s Robotics section highlights a wave of solutions pushing automation forward. l ogic Robotics reimagines the humble pallet as a fully autonomous transport agent capable of reshaping multi-facility logistics. u niversal Robots opens the door for torque-sensitive cobot applications in research and industry. Siemens, meanwhile, continues its push toward “automating automation” with AI copilots and safer, more adaptable AGV systems.
AI-powered interfaces and digital twins are no longer futuristic concepts—they’re active tools
bridging data, motion, and decisionmaking in real time. From Sinequa’s AI agents pulling engineering insights from scattered systems, to Siemens’ Safe Velocity software ensuring dynamic AGV safety, and Hexagon's new CNC motion control platforms improving performance at the edge—robotics today is smarter, safer, and more connected than ever before.
The companies featured here are not just building robots— they're architecting a future where intelligence is built into every layer of motion, from torque-level control to fleet-level orchestration. As North American manufacturers face mounting pressure to deliver speed, precision, and adaptability, robotics is answering with innovation that transforms how factories move, think, and scale.
LOGIC ROBOTICS
Logic Highlights the Logic Pallet: The First Autonomous Mobile
logic Robotics introduces the logic Pallet, the first autonomous mobile pallet designed to fully automate goods movement across and between facilities.
Replacing traditional pallets and forklifts, the logic Pallet is a self-driving, self-loading robotic platform with a 2,000 lb payload, 160-hour battery life, and AI-powered navigation via logic’s l INK warehouse OS.
Supporting aisleless, high-density storage and real-time inventory tracking, the logic Pallet enables advanced logistics functions like autonomous stacking, cycle counting, and trailer loading in under five minutes. As a made-in-America solution, logic Pallet sets a new benchmark for scalable warehouse automation.
For More Information: www.logic-os.com
Sinequa will showcase its AI-powered Search platform at Siemens Realize lIVE 2025, demonstrating how its intelligent agents retrieve engineering knowledge buried
across PlM, MES, MRO, and enterprise systems. Powered by GenAI and Retrieval-Augmented Generation (RAG), Sinequa helps engineers and quality teams quickly access specs, documentation, and compliance records.
With support for over 200 enterprise applications including Siemens Teamcenter, SAP, and SharePoint, Sinequa's cognitive digital thread accelerates design, reduces downtime, and connects product data across the lifecycle for faster decision-making.
For More Information: www.sinequa.com/industries/manufacturing
At Automate 2025, Siemens unveiled an upgraded motion control system featuring SINAMICS S200/S210 servo drives, the new SIMATIC S7-1200 G2 controller, and SIMOTICS motors. This cost-optimized solution supports up to 31 PROFINET devices, provides fast axis synchronization, and includes advanced safety up to SIl 3.
Ideal for basic handling, positioning, and processing tasks, the system supports NFC diagnostics, motion control objects, and seamless TIA Portal integration— delivering flexibility, performance, and easy configuration for modern automation environments.
For More Information: usa.siemens.com/servo-drives
Siemens announced new capabilities for its Operations Copilot, enabling real-time interaction with autonomous mobile robots (AMRs) and automated guided vehicles (AGVs). The Copilot now assists in commissioning, configuring, and managing entire fleets using AI agents and sensor-based environmental mapping.
Complementing this is Siemens’ new Safe Velocity software, which enables fail-safe AGV speed monitoring and dynamic protective field adjustment—reducing hardware needs and simplifying system architecture while ensuring compliance with safety standards.
For More Information: www.siemens.com
universal Robots has launched a Direct Torque Control interface, giving researchers and advanced users access to control cobot joint torque at 500 Hz. This interface supports
precise force control ideal for assembly, screwdriving, and AI-driven applications, and integrates natively into uR's PolyScope software.
Available for all uR e-Series and uR Series cobots, the interface allows faster development of sensitive, forceaware tasks—enabling research teams to skip low-level implementation and focus on application design.
For More Information: https://ur.centercode.com
Metalworking encompasses the tools, technologies, and processes that drive precision manufacturing. This area highlights advancements in machining, grinding, lathing, and cutting systems, along with innovations like EDM (Electronic Discharge Machining). It captures the synergy between precision equipment and skilled craftsmanship, essential for producing high-quality components across diverse industries.
Focusing on the integration of controls, machining tools, and accessories, metalworking emphasizes the efficiency and accuracy demanded by modern manufacturing. From contract manufacturing to heat treating and gear machinery, it reflects the essential techniques and equipment shaping today’s industrial landscape. Whether utilizing traditional methods or cutting-edge innovations, metalworking celebrates the pursuit of excellence in every detail.
In an environment where cost pressures, labor shortages, and energy concerns continue to challenge the manufacturing sector, EMAG introduces a game-changing solution: the MSC 5 DuO. Officially debuting at EMO 2025 in Hanover, this front-loading CNC turning center is purpose-built for high-productivity soft turning in automated batch production—delivering exceptional performance while keeping capital investment in check.
Part of EMAG's Classic series, the MSC 5 DuO reflects the company's commitment to essential functionality without compromise. It offers dual-spindle turning within a compact,
front-loaded footprint, optimized for standard production requirements. Peter Gröner, Product Manager of the Turning Business unit, emphasizes, “The Classic series stands for optimized basic machines at attractive capital investments… the MSC 5 DuO offers precisely the technical functions that our customers need for their specific production tasks—no more and no less.”
This design philosophy translates into real-world savings: the MSC 5 DuO costs significantly less per spindle compared to higher-end machines, yet delivers identical productivity for routine soft turning applications.
Precision begins at the base. The MSC 5 DuO’s split-bed construction isolates each work area mechanically, minimizing vibration transfer during simultaneous operations. This leads to consistently accurate results across both spindles—even during demanding machining cycles.
Each A2-5 spindle reaches speeds up to 4,500 rpm, with 5.5 kW of continuous power or 7.5 kW available for shorter high-load intervals (a more powerful option provides up to 11 kW). The machine maintains constant torque from 1,125 to 4,500 rpm, ensuring consistent cutting conditions for a wide range of materials.
Thermally optimized spindle bearings and active temperature monitoring preserve tight concentricity and extend operational life under continuous use.
Two servo-controlled BMT turrets, each with 8 tool stations (expandable to 12), improve machining stability and tool longevity. Hydraulic clamping and quick indexing reduce tool change times while boosting repeatability. Tooling capacity includes boring bars up to 40 mm and external shanks up to 25 × 25 mm.
A fully integrated 3-axis gantry loader ensures rapid, precise part handling with minimal downtime. Servodriven axes handle both loading and unloading. The built-in workpiece turner enables complete dual-side machining in a single setup—cutting down on cycle time and material flow complexity.
Handling, moving and working with large dies or molds can present a ton of problems. Damage to equipment, dies or molds, as well as worker safety are just the beginning.
With EMH Overhead Cranes, count on safety, efficiency, and precision accuracy, while you dramatically reduce the chance of damage. Then, with virtually unlimited tonnage capacity and availabiltiy in varied congurations to suit almost any application need, you can count on all the lift you need.
The MSC 5 DuO’s stacker system is a standout feature. Fully integrated without requiring extra floor space, it accommodates a wide range of part geometries and enables hours of unmanned production. For facilities aiming to maximize output in a compact footprint, this design provides both space and labor savings.
Equipped with a FANuC 0i-TF Plus control, the MSC 5 DuO allows programming while the machine is running, supports process monitoring, and is ready for integration into digital manufacturing systems. Its compatibility with MES and ERP platforms enables seamless data acquisition and optimization within smart production environments.
The MSC 5 DuO isn’t just another CNC machine—it’s a targeted solution for today’s production realities. With its split-bed architecture, dual-spindle design, automationready features, and cost-efficient build, it is ideally suited for shops looking to scale throughput without scaling overhead.
As EMAG’s Gröner puts it, the machine’s power lies in its simplicity: “We do not create complexity for the sake of complexity. The MSC 5 DuO offers exactly what is needed to get the job done.”
Flex Machine Tools will showcase its advanced manufacturing solutions at FABTECH Booth #A5920 in Chicago, Il , from September 8–11, 2025. Highlights include the FlexJet Waterjet Fl-0404, featuring IGEMS CNC control, Tilter 5-Axis head, Snapper camera, and proprietary tools like Rounder and Straighter. Flex is the only u.S. provider offering this complete suite for intricate waterjet applications.
Also on display will be the FlexCNC C-10-02, a cantilever-style vertical machining center capable of handling parts from 10' to 50'. It’s designed for high-speed milling, drilling, and tapping with a monobloc steel frame and precision guideways.
The FlexArm line of tapping arms, including the REM-16 Electronic Tapping Arm and GH-45 Hydraulic Tapping Arm, will be demonstrated. These solutions offer unmatched versatility for both vertical and horizontal tapping needs.
Grizzly introduces the G0994 10" Vertical Metal-Cutting Bandsaw, designed for small shops and hobbyists. Compact yet powerful, it features variable blade speeds (85–265 FPM), a tilting cast-iron table, laser guide, lED work light, and quick-release blade tension.
Built for precision and convenience, the G0994 also includes a pullout dust drawer, ball-bearing blade guides, and rack-and-pinion adjustments—bringing pro-level cutting accuracy to entry-level users.
For More Information: www.grizzly.com
America’s Cutting Edge (ACE), a national initiative led by IACMI, is transforming how manufacturers find and train CNC machinists. Offering free online and in-person bootcamps, ACE equips participants with foundational machining skills. Companies like Pace Machine & Tool and Seyer Industries now use ACE as a reliable pipeline for talent.
Bootcamps include CAD/CAM software training and hands-on CNC machine work. Employers report reduced hiring costs, better employee retention, and improved shop floor readiness. ACE is fast becoming a strategic workforce development tool for companies nationwide.
For More Information: www.iacmi.org/aces
Niigata’s HPN800 horizontal machining center combines high-speed operation with rugged reliability. Equipped with a 75-horsepower, high-torque spindle and hybrid guideway system, the HPN800 offers rapid traverses up to 2,362 ipm and a tool-to-tool change time of 2.5 seconds.
Its ultra-rigid T-shaped base, advanced lubrication/ cooling systems, and Niigata’s Intelligent Cell Controller
(ICC) make it ideal for demanding production environments. With multiple pallet and tooling options, the HPN800 ensures high productivity and a low cost of ownership.
For More Information: https://niigatausa.com
In an era where innovation drives productivity, the Software section explores the cutting-edge tools empowering manufacturers to streamline operations, enhance precision, and optimize performance. From CAD/CAM/CAE design platforms to CNC simulation and process verification, this category reveals how digital solutions are revolutionizing the way products are conceptualized, created, and delivered.
Covering a broad spectrum of applications—such as ERP systems, factory floor software, and industrial IT—this section emphasizes the importance of connectivity and real-time data in achieving operational excellence. Topics like quality control, job tracking, and program optimization showcase how software bridges the gap between vision and execution, enabling manufacturers to stay competitive in a fast-evolving industry.
In today’s manufacturing landscape, small to mid-sized enterprises (SMEs) face a unique confluence of challenges. From limited IT resources and tight margins to a persistent labor shortage, these businesses are often operating under pressure—with little room for costly missteps or sprawling digital overhauls. But according to Dale Tutt, Vice President of Industry Strategy, scalable digital tools and a thoughtful adoption path are making transformation not only possible for SMEs—but practical and profitable.
Speaking from Realize lIVE, Siemens' flagship user conference, Dale brings deep insight into how
digital solutions are empowering even the leanest operations to compete in an increasingly complex market.
Dale’s background spans over three decades in aerospace and defense, where he led engineering, manufacturing, and test programs before joining Siemens six years ago. Now overseeing industry strategy across multiple verticals—including aerospace, automotive, consumer products, pharmaceuticals, and electronics—he has a front-row seat to the digital needs and pain points of manufacturers of all sizes.
“Our role in strategy is to understand what’s happening in the market, where we should be investing, what’s important to our customers, and how we can help communicate those needs inside the company,” he explained. “It’s not just about large enterprise customers; we work closely with small and mid-sized businesses as well.”
For SMEs—many of which operate without a dedicated IT department—digital transformation can seem daunting. Dale noted that it’s not unusual for the “IT department” at a job shop to consist of a relative with a knack for computers. This is precisely where SaaS (Software-as-a-Service) platforms like Siemens' Teamcenter X and NX X make the most impact.
“With SaaS, we’re managing the software for them,” Dale said. “That means it’s easier to deploy, and we handle updates and backend management. It really eliminates the need for a large IT team.”
This model mirrors the now-familiar experience of Microsoft Office or Google Workspace, where updates happen automatically and new capabilities appear without disruption. For small manufacturers, that means access to cutting-edge tools without infrastructure headaches—or capital-heavy investments.
Digital transformation doesn’t have to be an all-at-once affair. Dale emphasized that Siemens’ Xcelerator portfolio is designed to grow with a company.
“ you adopt what you need based on the problems you're trying to solve,” he said. “ you might start with CAD, add simulation tools later, then bring in Teamcenter for data and workflow management. It’s not a rip-and-replace model.”
This flexibility is crucial for SMEs who may already rely heavily on spreadsheets, whiteboards, or homegrown systems. Transitioning from such rudimentary setups is possible through connectors and migration tools that help shift data into Siemens’ platforms with minimal friction.
And while Excel might work for now, Dale pointed out the limitations: “Spreadsheets aren't purpose-built for change management or release workflows. With tools like Teamcenter, you get best practices embedded. you're not creating or maintaining workflows on your own.”
Cost concerns remain a top barrier for small manufacturers considering digital upgrades. Dale acknowledged this, particularly with regard to large capital expenses.
“Historically, on-premise solutions required significant upfront investment. With SaaS, it's an operating expense. That’s a huge shift,” he said. “ you get predictable monthly costs, and you don’t get surprise spikes from unexpected IT needs.”
For many SMEs, this subscription-based model not only makes budgeting easier but also enables quicker
ROI. “ you can start small, get value quickly, and then build on that,” Dale added. “The first step might take a year or two to pay back, but it’s scalable and targeted to your business goals.”
Perhaps the most pressing issue among SMEs—beyond budgets and infrastructure—is workforce availability. From shop floor technicians to engineers, finding qualified talent has become a nationwide challenge. Dale, who previously led engineering teams of more than 1,600 people, knows the problem firsthand.
“There were years when we needed to hire 450 people just to meet demand, and we couldn’t do it,” he recalled. “That’s where digital tools help—not by replacing workers, but by closing the gap.”
Siemens is embedding AI and automation into its platforms to reduce the burden on limited teams. By automating data management, enabling conversational interfaces, and incorporating best practice workflows, these tools free up employees to focus on higher-value tasks.
“It’s not about pushing a button and having a part pop out of your factory,” Dale joked. “But it’s about enabling your workforce to be more productive, to solve more complex problems, and to do it with fewer administrative headaches.”
AXIAL PISTON PUMPS… Oilgear open loop
axial piston pumps are offered in a variety of models and displacement sizes to match required performance. Models include both medium and high horsepower, medium and heavy duty, low viscosity pumps, plus a series of multiple fixed delivery pumps. Of the many industries Oilgear serves, a primary one is mobile and off-highway applications. Oilgear pumps are recognized for high performance in the toughest environments. Their heavy duty designs resist contamination as well as operating on low viscosity specialty fluids.
VARIABLE PUMPS…
Whatever the application, Oilgear has the ideal pump to fulfill the requirements.
MULTIPLE FIXED DELIVERY
CHECK VALVE PUMPS…
• High pressure to 15,000 psi
• Heavy duty construction
• High contamination tolerance
• Operation on low viscosity fluids
• Multiple deliveries up to three displacements from a single pump
He views the narrative around AI replacing jobs as largely misguided: “It’s augmenting, not replacing. Especially in manufacturing, AI can take over the mundane tasks so your people can do the meaningful work.”
Another common challenge for SMEs is decades of archived data—often in paper form. That historical knowledge is valuable, but difficult to access or leverage without digitization. Dale noted that Siemens works with partners who specialize in scanning, contextualizing, and migrating that data into usable formats within Teamcenter and related tools.
“There are companies sitting on 20 years of paper data they still need,” he said. “By digitizing and contextualizing it, they can make it part of their operational and decisionmaking process again.”
While this step may take more time and effort than migrating Excel files, it’s increasingly in demand. “The business value is clear,” Dale affirmed.
For current Siemens customers—or those evaluating their options—events like Realize lIVE offer unmatched value. Beyond product demonstrations or keynote announcements, the real benefit, Dale says, is user-to-user connection.
“The greatest thing about Realize l IVE is how customers talk to each other,” he said. “Sometimes, the best insight comes from someone in a non-competing industry who has solved the same problem you're facing.”
Dale recounted a recent conversation with a Northrop Grumman engineer who attended Realize lIVE a decade ago. At the time, he was struggling with a technical limitation—only to have the solution announced live on stage. “That kind of moment is why people come,” Dale added.
The conference isn’t just for engineers and managers, either. From software updates to hands-on training and AI showcases, Realize lIVE serves as a nexus for Siemens' evolving ecosystem—backed by good food, a lively atmosphere, and a sense of shared purpose.
“It’s about building a community,” Dale emphasized. “And about helping customers see what’s possible, often from someone just like them.”
For small to mid-sized manufacturers navigating the demands of modern production, the message is clear: Digital transformation is no longer just the domain of Fortune 500s. Thanks to scalable SaaS offerings, embedded AI, and a commitment to customer-focused design, Siemens is delivering tools that meet businesses where they are—without overwhelming their resources.
And as Dale suggested, the future may hold even more seamless integration. “In a few years, I don’t think we’ll be talking about AI so much—it’ll just be part of the tools we use every day.”
For manufacturers ready to grow, adapt, and compete, that future is closer than ever.
Cetec ERP has partnered with QBuild Software to simplify and accelerate the data transfer process between engineering and production. Traditionally, manufacturers using Cetec ERP were manually entering data from CAD software into their ERP system—a time-consuming process prone to error. Through this integration, customers can now use QBuild’s CADlink to transfer data directly from SolidWorks/PDM into Cetec ERP.
This streamlines the design-to-manufacture workflow, reduces duplicate entries, and ensures real-time data accuracy. CADlink supports custom and revision-controlled BOMs, make-to-order and engineer-to-order operations, and MES integration. This integration empowers engineering and production teams to collaborate more effectively and bring products to market faster—with fewer errors and reduced rework.
For More Information: www.cetecerp.com
Hexagon’s Manufacturing Intelligence division has unveiled MAESTRO, a ground-up reengineering of the coordinate measuring machine (CMM) designed for speed, scalability, and intuitive use. Tailored to meet modern manufacturing demands, MAESTRO offers unmatched throughput, ease of programming, and seamless IIoT integration.
Its digital-first architecture supports real-time data sharing, automation compatibility, and modular upgrades. With new sensors, a redesigned controller, and cloud-native metrology apps powered by Hexagon’s Nexus platform, MAESTRO enables both expert and novice users to perform precision quality checks with sub-micron tolerances.
MAESTRO is ideal for aerospace, automotive, and high-precision manufacturing environments where speed, data integrity, and scalability are essential. It will be available in multiple configurations beginning June 30, 2025. For More Information: https://hexagon.com/products/maestro
LBS -
LBS INDIVIDUALLY SERIAL NUMBERED FOR BETTER TRACEABILITY ORDERS SHIPPED SAME DAY
Tooling and Workholding is the cornerstone of precision manufacturing, ensuring that materials are securely held and processes are executed with unparalleled accuracy. This section highlights the latest innovations in clamps, chucks, collets, and magnetic workholding, alongside advancements in rotary tables, toolholders, and modular fixturing systems. Together, these solutions enable manufacturers to achieve repeatability, reduce setup times, and enhance overall productivity.
From versatile milling and turning tools to specialized threading and gear-cutting instruments, this category delves into the diverse range of equipment designed to meet the unique demands of every operation. Whether exploring robotic end-effectors for automation or custom fixtures for intricate designs, Tooling and Workholding underscores the critical role these components play in driving efficiency and precision across the manufacturing spectrum.
As North American manufacturers strive for increased productivity, precision, and flexibility, tooling and workholding innovations are proving essential in maximizing machine uptime, reducing rework, and pushing output further. In this issue, we spotlight companies delivering enhancements in
clamping systems, modular tooling catalogs, and next-gen carbide drills—all designed to serve the evolving needs of high-mix, high-performance operations.
Whether it’s simplifying chuck changeovers with sealed quickchange systems, supporting delicate parts with floating clamps, or improving surface finishes and drill
life with smarter geometries, this selection of solutions underscores a common theme: better tooling equals better parts, faster. As reshoring trends gain steam and lead time pressures mount, North American shops are seeking tools that empower adaptability without compromising performance—and that’s exactly what this lineup delivers.
HAINBuCH is redefining the chuck changeover experience with its centroteX quick-change systems and TOPlus sealed chucks. Designed for ease, versatility, and repeatability, these systems reduce setup time, increase rigidity, and minimize maintenance—making switching chucks both efficient and enjoyable.
The TOPlus system features contamination-resistant sealing, vibration damping, and optimized lubrication grooves, supporting higher metal removal rates without sacrificing part quality. With adaptability across machines and part types, HAINBuCH encourages operators to optimize setups more frequently, unlocking better results and greater process reliability.
For More Information: www.hainbuchamerica.com
norelem has expanded its range with a new in-house manufactured compact floating clamp—ideal for securing thin-walled or complex components sensitive to distortion. Available in two versions (Form A with fixed jaws, Form B with replaceable jaws), these clamps offer spring-loaded support with clamping forces up to 8000 N. By allowing flexible, vibration-reducing workholding at overdetermined points, these clamps improve machining outcomes for irregular geometries. Built from nitrocarburized steel and black anodized aluminum, they offer robust performance with simplified operation.
Platinum Tooling, a master distributor of precision tools, has released its latest catalog featuring comprehensive lines from Heimatec, Tecnicrafts, Henninger, Hommel + Keller, Rineck, Dunner, and REV. The offering includes live and static tools, Swiss-type collets and bushings, speed increasers, knurling tools, shrink fit holders, and broaching solutions.
Highlights include Heimatec’s live and angle heads for difficult applications, Tecnicrafts ultra-precision bushings, and Henninger's high-speed spindles. The new catalog aims to simplify selection across a wide array of tooling needs, helping shops match tools to specific machine platforms for maximum output and efficiency.
Walter has launched the Drivox∙tec™ IKON DD170 Supreme solid carbide drill, engineered for high-performance drilling in steel and cast iron. Featuring a Krato tec® coating, 12 internal coolant grooves, and a 140° tip angle, this drill delivers smoother surface finishes, greater hole roundness, and extended tool life.
Capable of eliminating pilot drilling and performing at up to 12×Dc, the DD170 is optimized for process reliability in cross-hole and inclined exit scenarios. Applications include mold & die, automotive, aerospace, and general mechanical engineering.