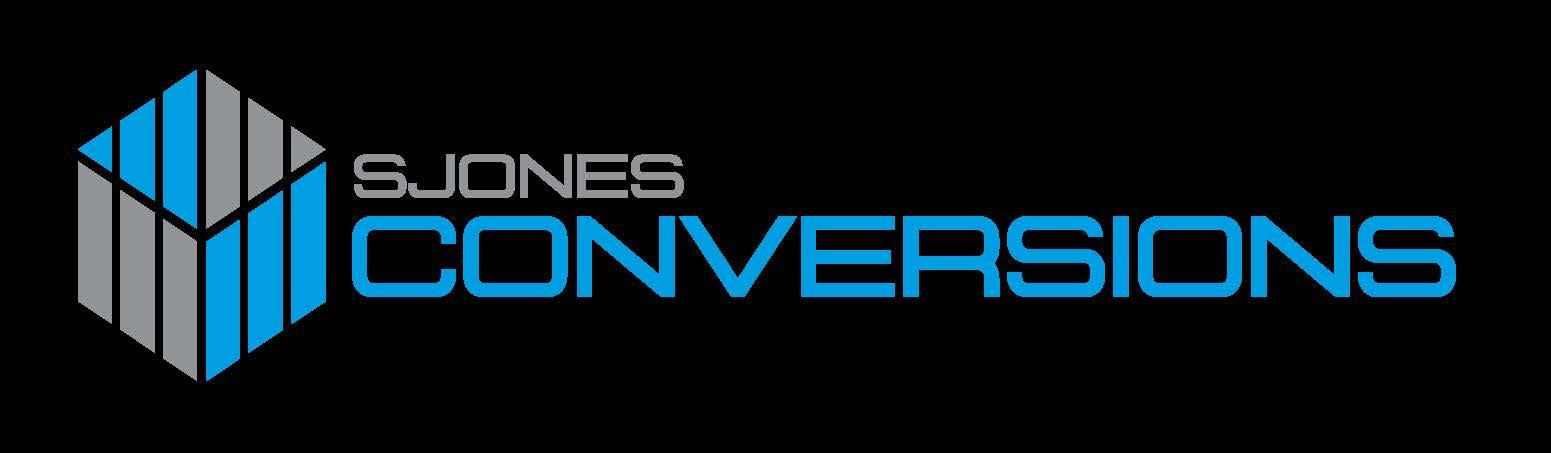
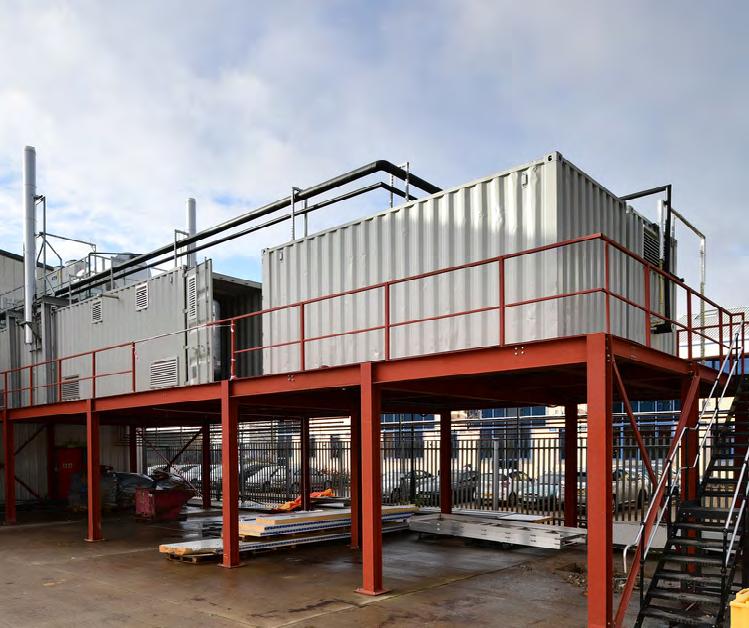

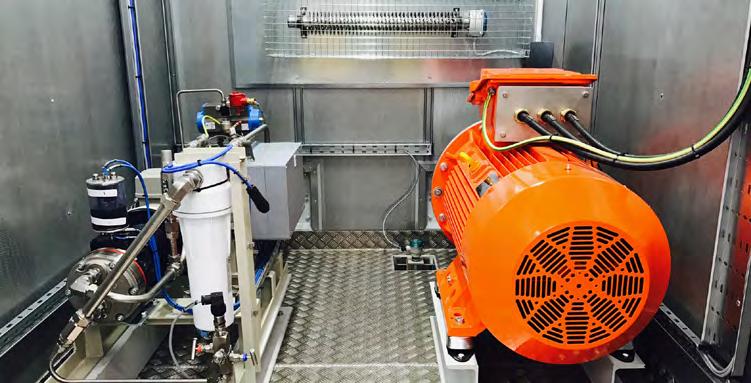
Deliver Your Capability with S Jones Conversions
As the UK’s leading container conversions specialist, we enable our customers to deploy their equipment and deliver their capabilities to places that would otherwise be less viable or even impossible, as temporary or long-term solutions.
S Jones Conversions designs and manufactures controlled environment modular enclosures for industrial equipment, machinery and processes and for specialist work spaces.
See why so many trusted and respected organisations choose S Jones Conversions.
S Jones Conversions specialise in converting shipping containers into bespoke enclosures and plant rooms to provide perfect operating environments for equipment and processes, and to enable equipment to be operated in challenging or high-risk environments. Our modular solutions also enable you to extend and expand existing facilities.
We use a variety of ‘treatments’ to control internal environment aspects such as; temperature, sound, humidity, air flow/supply, fire control, hygiene, structural loading, accessibility, power supply (including ATEX and multiple voltages), service connections, blast risks, etc. These can be from a basic temperature control lining to fully monitored and controlled enclosed environments, together with safety systems to manage and control a variety of hazards.
What sets us apart from other container companies are our industry-leading engineering capabilities and ability to safely containerise almost any industrial process by designing appropriately engineered solutions.
While there are other container conversion companies out there, only with S Jones do you benefit from extensive inhouse expertise, facilities, and experience in delivering complex container solutions for engineering and research organisations.
Tel: +44 (0) 1922 741756
Email: andrew.nicholls@sjonescontainers.co.uk
Web: https://www.sjonescontainers.co.uk/ container-conversions/
Highlighted below are many of the various elements we change to provide enclosures and work spaces that customers need:
3D CAD design – A modified container with a lot of equipment involved can be a very crowded space. Not only is there the equipment for controlling the internal environment, but also the customer’s own equipment together with adequate access requirements. To ensure that everything fits appropriately, and to greatly assist in the design process, we use 3D CAD. This is an area of our specific expertise and has also been used to interface with customer’s own VR suite facilities.
Surface treatments – We are one of very few companies with a ‘whole container’ heated and air filtered paint booth. This facility enables us to apply a variety of specialist coatings in the environment the coating manufacturers intended for best application and lifetime performance. Our multi-stage preparation and application processes ensure we control both the appropriate coating of new structure as well as correctly overcoating the existing container paint system. We can, for extreme requirements, shot blast containers back to bare steel to SA2.5 before reapplying customer required paint systems.
Shell and structure – To greater or lesser extents we modify the original design of shipping containers. Where this has structural implications we design reinforcements accordingly whilst at the same time enabling the required ‘functionality’ of the shell in terms of connection and access points for services, personnel, equipment, and its maintenance. When required, we can have the modified containers proof-load tested and certified using accredited suppliers. We can design and certify modified containers so they can be shipped under container CSC regulations.
Ancillary equipment – As part of creating enclosures for equipment operation, environment control and risk/hazard management we use a variety of technical solutions to provide: power supply and delivery, temperature and humidity control, ventilation (including positive pressure enclosures), gas detection, smoke and fire control, ESD (electrostatic discharge) control etc.
Lining treatments – As part of controlling the internal environment of an enclosure it is likely that a lining will be required. This will include combinations of; temperature, sound, hygiene, fire containment/exclusion, vapour control, etc. Where specific performance is required, especially for temperature, sound/acoustic and fire management, these will be to an engineered specification.
CEMA were asked to supply and deliver two Motor Control Centres to assist with the rapid redevelopment of a water abstraction and treatment site required by the HS2 project.
S Jones Conversions supplied a number of repurposed shipping containers for the project.
Given the altered working arrangements caused by the Covid pandemic, it was agreed to complete all of the build and MCC installation off-site in a controlled environment to minimise the risks of working on-site.
We had to provide a non-standard height product capable of being installed into a restricted space, together with ensuring that CEMA’s equipment, to their certified designs, was incorporated within the space limitations of the modified container.
Special measures were necessary for environment monitoring and control within the containers to provide effective heating and cooling for CEMA’s equipment, which included significant heat generating and heat sensitive equipment.
The original concept of providing high-volume forcedair ventilation of the container was dismissed as being too noisy and not cost-effective. As a result, we needed to model the worst-case solar heat-gain scenario, taking into account; geographical location and external colour of the container and the insulation U-values of the bespoke modification, to identify the most economic air-conditioning solution for the enclosures.
Field cable routing to the enclosure was facilitated by an innovative design for the cable glanding. Given the height restrictions within the container the chosen solution involved locating the gland plates underneath the containers, which were then raised above ground on supports manufactured by S Jones Conversions to provide cable access from below.
To assist with the turn-key solution, the container had to be equipped with a certified Fire Alarm system interconnected with the customer’s equipment to effectively cut the power in the event of an incident. Together with the alarm system, general domestic services were built into the container modification and connected back to the customer’s equipment.
Following manufacture and witness-testing of the completed container conversion by the clients, the equipment was installed into the containers at CEMA’s factory and re-tested prior to delivery. Specialist lifting and transport equipment was employed to enable the completed units, weighing twelve tonnes each, to be delivered to site on schedule.
“S Jones Conversions presented themselves and their capability far in excess of their competitors. Their understanding of the client requirements and the attention to detail was paramount to the success of the project. Working directly with Andrew and Les meant we had direct access for timely and knowledgeable decisions and guidance. We would highly recommend S Jones to all partners on future schemes.”
Graeme
Morley, Managing Director
Advanced CAD capabilities – Our design and manufacturing capabilities are some of the most advanced in our industry and include; 3D CAD modelling, bespoke fabrication and manufacture, and a ‘whole container’ paint booth for controlled surface coatings.
From a full understanding of your technical requirements for the container conversion project, through to CAD concepts and proofing to manufacture, we give you complete visibility on lead times and control over the end-product.
Our team of expert engineers will turn your ideas into realistic, viable designs, working with you every step of the way. This allows you to see exactly what your containerised solution will look like before manufacturing takes place in our on-site workshops.
Productisation – By using a modular container enclosure solution, we can help customers expand their product reach and customer base, including exporting to foreign markets. We can assist with design and repackaging of existing customer solutions into fully containerised versions, complete with bespoke branding as necessary.
S Jones only employs highly qualified and experienced engineers with a focus on engineering projects. Building on decades of experience in delivering bespoke container conversions for a wide range of blue-chip companies and reputable organisations, we are renowned for adding value to your converted shipping containers at every stage with:
Extensive product knowledge of containers and ancillary equipment
Significant Design experience with structural assessment and 3D Computer Aided Design modelling
Thorough project investigation to ensure suitable specifications, high quality workmanship and customer service
State of the art in-house facilities including a paint shop and dedicated workshop
The Trusted Choice Across Industries:
Power and Energy Generation
Control Instruments and Switchgear
Plant Room and Ventilation
Chemical Process and Water Treatment
June 2018 saw the official opening of the world’s first liquid air energy storage plant, designed and developed by Highview Power and housed at project partner Viridor’s, Pilsworth site in Bury.
The plant is enhanced with Siemens technology, to provide ‘instant energy on demand’. The combined system can store enough energy to power around 5000 homes for several hours, with immediate response, as required by National Grid.
Given their durability and versatile interiors, Siemens recognised that there would be many benefits to housing their technology inside modified shipping containers. As a result, Siemens reached out to S Jones directly to ensure their requirements for a containerised solution would be fully met.
Utilising our wealth of experience, we delivered a number of innovative and vital elements to this revolutionary project, including;
Agile Digital Visualisation: We created a detailed 3D CAD design model of the container which imported the relevant Siemens technology needed to power the plant.
This visualisation was used in Siemens virtual reality simulator enabling us to guide the customer around the art of the possible, enabling quicker decision making and stakeholder engagement for the customer
Risk Mitigation: We installed sound attenuated linings and a fire alarm system to ensure health and safety, combined with corporate mitigations, are adhered to throughout the life of the container plant.
Expert Engineering Knowledge: One of the biggest challenges of the container was creating enough space to accommodate the sheer scale of the technology required to run the plant efficiently.
We provided complex structural modifications such as a galvanized steel roof platform and a sub floor stiffening structure to ensure the customer had peace of mind that the plant would run safely and effectively.
In-house Prooing and Fabrication: We provide an end-to-end customer journey, from initial concepts through to the final design sign off.
We completed the fabrication of the container in our workshop in the West Midlands, offering Siemens the opportunity to see their vision turned into a reality, every step of the way.
“S Jones provided a flexible approach to this prototype design allowing multiple design changes to be included throughout the build. This allowed our engineers to fully develop this worldfirst concept. The results are a high quality solution, fully meeting our requirements.”
Kevin Patterson, Project Manager –Siemens
Agile Digital Visualisation – bespoke 3D
CAD models enable our engineers to guide you through the art of the possible, leading to quicker and better decision making and improved customer involvement and engagement throughout the creative design process.
Expert Engineering Knowledge – over 20 years’ experience and extensive industry knowledge enables us to provide intricate structural modifications and create bespoke conversions that fully address your specific challenges. As a result, our solutions often prove ground-breaking in their industry.
In-House Proofing and Fabrication – our experts are involved end-to-end, throughout the entire customer journey, from initial concepts through to final build, quality inspection and sign-off. We complete our customers’ fabrication in our own workshops based in the West Midlands, offering customers the chance to see their vision turned into a physical reality, every step of the way.
Packaged Solutions – if you don’t currently offer your end-users turnkey containerised solutions, we can help you ‘package’ your solution accordingly. As containers can be shipped, we can help you expand your customer base and make the most of export opportunities.
In-House ‘Bake-On’ Paint Facility – our large whole container paint booth enables the professional painting of containers and bespoke units for the high-quality finish you require. We can also decal and brand your containers to meet your end-users exact needs.
RiskMitigation – for complete peace of mind, all of our bespoke container solutions are completed to appropriate health and safety and engineering standards, with all electrical installations certified as required. We can also install a range of services / capabilities into containers such as ventilation, electrics, gas detection, and fire suppression.
Quality Control – we carry out our services in accordance with ‘ISO9001’. We also invest heavily in R&D, which is proven through our continual contribution to the development of market-leading brands and projects worldwide with clients such as; Siemens, Centrax, King’s College and Jaguar Land Rover.
No Need To Outsource – with an in-house depot, workshop facilities, and experienced sales and hire teams, we supply many of the UK’s container companies. In fact, most UK conversions companies actually outsource their work to us, so why risk things being lost in translation when you can come directly to the experts?
As part of their sustainability efforts, Cummins wanted to house equipment for a ground-breaking solution that would recover electricity from their diesel engine generator test process.
Involving the stacking of two containers, the project provided a welcome challenge for our talented team, seeing us design and manufacture the containers entirely in-house.
The two bespoke 40ft high cube containers allow Cummins to safely and compliantly house the equipment necessary to sell back energy to the national grid at a time when sustainability has never been higher on the national agenda.
“S Jones were adaptive and flexible throughout the engineering phase, especially considering the effects of Covid-19 and the lockdown at the time. Their designers were engaging and contributed creative ideas to help us achieve this challenging project.”
Charles Petersen, Project Coordinator –Cummins Power Systems Ltd
www.sjonescontainers.co.uk/container-conversions
Walsall,