
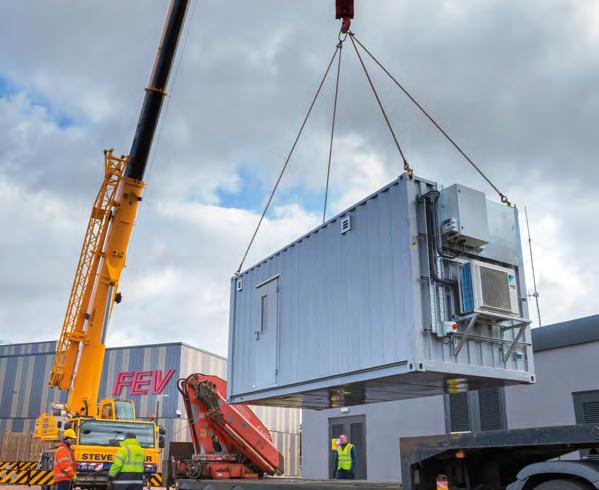
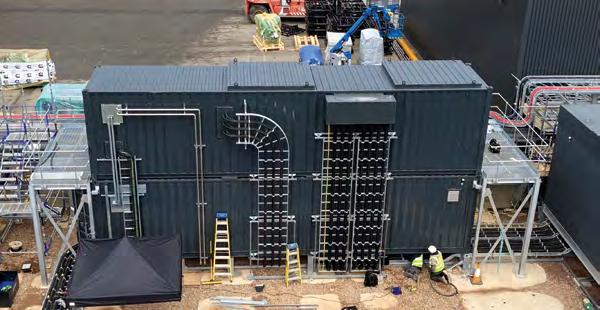
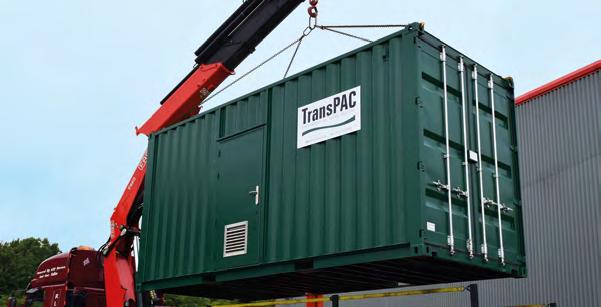
S Jones Conversions division is the UK’s leading container conversions specialist. We design and manufacture bespoke containers, enclosures and plant rooms for the safe and compliant housing of engineering processes, equipment and machinery.
For decades, we have specialised in providing clients with Contained Space Solutions®. This brochure contains a small selection of the thousands of container conversion projects we've completed for some of the most reputable engineering companies in the UK.
In 2019, Coventry University collaborated with global engineering specialist FEV Group to develop a stateof-the-art low carbon technology centre.
Named C-ALPS (Centre for Advanced Low-Carbon Propulsion Systems), the £50m centre enables leading international automotive and aerospace organisations to develop the next generation of electric, hybrid and internal combustion engines.
As part of their mission to build, test and further improve on future-proof powertrain concepts, Coventry University reached out to our specialist shipping container conversions team for a 20ft fire-resistant lithium battery store.
This needed to come complete with ATEX Zone II interior electrical and HVAC installations, explosion venting and fire protected storage shelving.
After working with Coventry University on the specification, we used our CAD (Computer Aided Design) expertise to generate an accurate visual representation of the shipping container that would ensure full functionality prior to build.
Building from this design, we then fabricated the battery store in our purpose built workshop before repainting it in our professional paint booth.
What Coventry University Had To Say:
“It has been over five years since I worked with S Jones on the very first bespoke container for battery storage. Having the ability to store our new and used Lithiumion batteries safely plays a key part in the operations of our research centre. I am very pleased to see how the design of the container has evolved over the years to include many new features to meet the latest safety requirements, making it the industry’s best practice for battery storage. Thank you so much for doing a great job!”
ProfessorYueGuo,ChairofBattery Systems–CoventryUniversity
Culligan, a leading water treatment supplier, is committed to delivering state-of-the-art products and water solutions while minimising the impact on the environment. The company has been working to provide better water for their customers in their working environments around the world for over 80 years.
Culligan contacted us with a requirement for secure temperature controlled enclosures for their equipment to be housed in.
After discussions with our conversions specialists, two 20ft double door containers were chosen. Vinyl floor was fitted for easy cleaning, HVAC and gland plate pipes were built into protected recesses and finished with twin pack paint to enhance UV protection as the containers will be located in Afghanistan.
“We find that our customers are requiring a ‘Plug and Play’ solution for their water treatment systems more and more. Culligan has the expertise to provide these solutions. With our inhouse team we have the capabilities to provide a complete turn-key solution to suit the customer’s requirements.
We wanted to use a professional company for our container conversion project, which is why we partnered with S Jones Conversions. They demonstrated early on in the project that they could deliver the design and high-quality finish we required. Their technical expertise is extensive, which means if we have a problem, they will have a solution!”
AndrewWoods–Culligan(UK)Ltd
As part of their sustainability efforts, Cummins wanted to house equipment for a ground-breaking solution that would recover electricity from their diesel engine generator test process.
Involving the stacking of two containers, the project provided a welcome challenge for our talented team, seeing us design and manufacture the containers entirely in-house.
The two bespoke 40ft high cube containers allow Cummins to safely and compliantly house the equipment necessary to sell back energy to the national grid at a time when sustainability has never been higher on the national agenda.
“S Jones’ designers were engaging and contributed creative ideas to help us achieve this challenging project.”
“S Jones were adaptive and flexible throughout the engineering phase, especially considering the effects of Covid-19 and the lockdown at the time.”
CharlesPetersen,ProjectCoordinator–CumminsPowerSystemsLtd
June 2018 saw the official opening of the world’s first liquid air energy storage plant, designed and developed by Highview Power and housed at project partner Viridor’s, Pilsworth site in Bury.
The plant is enhanced with Siemens technology, to provide instant energy on demand. The combined system can store enough energy for around 5000 homes for several hours, with fast response.
Given their durability and versatile interiors, Siemens recognised that there would be many benefits to housing their technology inside of a shipping container. As a result, Siemens reached out to S Jones directly to ensure their requirements for a containerised solution could be fully met.
Utilising a wealth of experience, S Jones delivered a number of innovative and vital elements to this revolutionary project, including:
Agile Digital Visualisation: S Jones created a detailed 3D CAD design model of the container which imported the relevant Siemens technology needed to power the plant.
This visualisation was used in Siemens virtual reality simulator enabling S Jones to guide the customer around the art of the possible, enabling quicker decision making and stakeholder engagement for the customer.
Risk Mitigation: S Jones installed sound attenuated linings and a fire alarm system to ensure compliance with health and safety standards, alongside corporate mitigation measures, throughout the operational lifespan of the container plant.
Expert Engineering Knowledge: One of the biggest challenges of the container was creating enough space to accommodate the sheer scale of the technology required to run the plant efficiently.
We provided complex structural modifications such as a galvanized steel roof platform and a sub floor stiffening structure to ensure our client had peace of mind that the plant would run safely and effectively.
In-house Proofing and Fabrication: S Jones provides end-to-end customer experience, from initial concepts through to the final design sign off.
We completed the fabrication of the container in our workshop in the West Midlands, offering Siemens the opportunity to see their vision turned into a reality, every step of the way.
“S Jones provided a flexible approach to this prototype design, allowing multiple design changes to be included throughout the build. This allowed our engineers to fully develop this world-first concept. The results are a high quality solution, fully meeting our requirements”
KevinPatterson,ProjectManager–Siemens
To assist rapid re-development of a water abstraction and treatment site required by the HS2 project, CEMA were asked to supply and deliver circa 25m cable between two Motor Control Centres (MCC in separate, repurposed shipping containers. This was carried out in collaboration with the S Jones Conversions team.
Given the pandemic, it was agreed to complete all the build and MCC installation off-site to minimise risks by performing the majority of the work in a controlled environment.
S Jones customised designs and paid special attention to provide a non-standard height product capable of being installed in the reduced space available. Certified designs of the busbar systems had to be maintained and incorporated, together with bespoke design and build of a Power Quality Filter (PQF) system within the space limitations. Special measures for environmental monitoring and control within the containers were also necessary to provide effective heating and cooling for the equipment, alongside the PQF, contained Variable Speed Drives and other significant heat-generating equipment.
The original concept of providing high-volume forcedair ventilation of the container was dismissed as being too noisy and not cost-effective. As a result, we modelled the worst-case heat-gain scenario, taking into account insulation values of the custom container build (including the solar gain relative to the geographical location and external colour of the container) to identify the most economic airconditioning solution for the buildings.
Field cabling access to the MCC was developed with an innovative approach adopted for cable glanding. Given the height restrictions within the container cable, glanding space within the MCC had become compromised. To counter this, we applied our out-ofthe-box thinking by relocating the gland plates to the underneath of the containers, which were to be suspended above ground to provide cabling access from below.
To assist with the turn-key solution, the container had to be equipped with a certified Fire Alarm system (interconnected with the MCC) to effectively cut the power by tripping the Mains and Generator Air Circuit Breakers in the event of an alarm. Together with the alarm system, general domestic services were built into the container customisation and connected back to the MCC.
Following the build and witness-testing by the clients, the MCCs were installed into the containers at CEMA's factory, re-built and re-tested prior to delivery. Specialist lifting and transport equipment was employed to enable the completed units, weighing twelve tonnes each, to be delivered to the site on schedule.
“S Jones presented themselves and their capability far in excess of their competitors. Their understanding of the client requirements and the attention to detail was paramount to the success of the project. Working directly with Andrew and Les meant we had direct access for timely and knowledgeable decisions and guidance. We would highly recommend S Jones for all partners on future schemes.”
GraemeMorley,ManagingDirector –CEMALtd
Highlighted below are many of the elements we change to provide enclosures and work spaces that clients need:
3D CAD design – A modified container with a lot of specialist equipment involved can be a very crowded space. Not only is there the equipment for controlling the internal environment, but also the client’s own equipment together with adequate access requirements. To ensure that everything fits appropriately, and to greatly assist in the design process, we have used 3D CAD for many years. This is an area of our specific expertise and has also been used to seamlessly integrate with client's own VR suite facilities.
Surface treatments – We are one among the very few companies with a ‘whole container’ heated and air filtered paint booth. This facility enables us to apply a variety of specialist coatings recommended by the manufacturers, ensuring optimal application and maximum performance lifespan.
Our multi-stage preparation and application processes enable us to control both the coating of new structures and the overcoating of existing container paint systems. We can, for extreme requirements, shot blast containers back to bare steel to SA2.5 before reapplying client required paint systems
Shell and structure – To a greater or lesser extent, we can modify the original designs of shipping containers. Where this has structural implications, we design reinforcements whilst also enabling the required 'functionality' of the shell in terms of connection and access points for services, personnel, equipment and its maintenance. When required, we can have the modified container proof-lead tested and certified using accredited suppliers. We can design and certify modified containers so that they can be shipped under container CSC regulations.
Ancillary equipment – As part of creating enclosures for equipment operations, environment control and risk/hazard management, we use a variety of technical solutions to provide: power supply and delivery, temperature and humidity control, ventilation (including positive pressure enclosures), gas detection, smoke and fire control, ESD (electrostatic discharge) control, etc.
Lining treatments – As part of controlling the internal environment of an enclosure, it is likely that a lining will be required. This will include a combination of: temperature, sound, hygiene, fire containment/ exclusion, vapour control, etc. Where specific performance is required, especially for temperature, sound/acoustic and fire management, these will be to an engineered specification.
Transvac are the world’s leading provider of awardwinning Ejector Solutions and have been using S Jones Containers since 2015.
Transvac purchased 20ft containers painted in a green RAL colour to match their logo. Previously, they used containers with a single side opening but have progressed their end product design to include a double opening as it provides easier access to both sides for installation and maintenance purposes.
As evident in the photo above, a stud wall was installed into the container, as good access from both ends is key. Converting shipping containers into water treatment plants is yet another demonstration of the huge flexibility of design the S Jones Conversions team can deliver.
“The product we built using S Jones Containers is called the ‘TransPAC’. The TransPAC is a fully mobile, all-in-one, ‘plug and play’ system that doses Powdered Activated Carbon (PAC) at a specified rate into water treatment works sites. PAC is used to tackle taste and odour issues, remove pesticides (including the notoriously difficult Metaldyhyde) and algae blooms.
The main benefits of having the full system installed into a container are that it is kept secure, vandal resistant, takes up a small amount of space on site, requires no groundwork to install and can be literally picked up and moved elsewhere if problems arise on other sites of a more urgent nature.”
CraigFavill,SalesManager–TransvacSystems
Our relationship with Uniflare goes back to 2008. Over the years, we’ve delivered 13 projects for the global environmental technology company.
The Challenge and Solution
Our latest project involved delivering a bespoke containerised renewable energy system that has been shipped to Thailand.
The 40ft high cube shipping container is being used to process methane waste gas on landfill gas sites and houses three gas compressors and a control room.
The compressors are used to compress bio gas 55% methane and 45% carbon dioxide, at the rate of 4500 cubic metres per hour, feeding a CHP (Combined Heat & Power generator.
The extent of works covers external structural modifications, six sets of cargo doors on the sides, louvres and fan vents, together with an insulated lining designed to work in high temperature and high humidity climates.
Previous Uniflare projects include an equipment container enclosure in the desert sands of Saudi Arabia, demonstrating how we are able to deliver costeffective solutions to the most remote locations.
What Uniflare Had To Say:
“Uniflare completes projects for the UK, Europe and worldwide. We work with S Jones Containers because of their ability to deliver completely bespoke units using 3D CAD modelling expertise.
This complements our way of working as all Uniflare projects are a bespoke build to exacting customer requirements.”
TrevorBeardsmore,Purchasing –Uniflare
We were approached by construction group Galliford Try to design and provide dual-purpose cabins at their client’s SUEZ, Knowsley Rail Transfer Loading Station.
The Transfer Station is part of an operation which handles up to half a million tonnes of residual (currently non-recyclable) waste collected annually from homes in Merseyside and Halton.
Waste that has been collected by local councils is transported to the site by both large road vehicles from existing waste transfer stations and by a limited number of refuse collection vehicles.
These vehicles deliver their waste to the Rail Transfer Loading Station where it gets transferred into sealed shipping containers inside the building. The containers are then transported onwards by rail to an energyfrom-waste facility at Wilton on Teesside.
Our remit was to provide a control cabin for crane operations and meeting rooms with large viewing panels of specialised fire retardant glass.
There was also a requirement to meet the compulsory specifications for two-hour fire-rated personnel refuges.
Project Manager Les Newick said, “This was an extremely challenging brief. The rail head has been modified as a waste compaction site where residual waste is compressed into containers and then loaded onto trains. The operation is scheduled to handle 90 HGVs delivering into the facility and two trains transporting waste out per day.”
Critical to the project was the two-hour integrity of the external fire cladding, large glass windows with 30-minute fire protection rating and two-hour rated internal fire shutters over the windows designed to shut automatically in the event of a fire alarm.
Working from Galliford Try’s initial concept drawings and the fire protection specifications, the S Jones Conversions team designed and manufactured the three bespoke enclosures.
As a result, once the compacted waste leaves the Knowsley rail head, it is now transported to the Teesside facility where it is thermally treated under
controlled conditions to generate electricity and heat. This offers a far more environmentally-friendly and cost-effective way of disposing of Merseyside and Halton’s waste than landfill.
“S Jones Containers got to grips with the brief immediately and understood the safety critical nature of the commission. The risk of fire in this kind of installation is something that can be mitigated but never eradicated and we need to ensure first and foremost that staff are protected.
S Jones Containers rose to the occasion and delivered a technically challenging solution on time and on budget. We have already approved S Jones Containers to work on our next project.”
KenO’Hare,ProjectManager–
GallifordTry
el: +44 (0) 1922 741 756
Email: andrew.nicholls@sjonescontainers.co.uk
www.sjonescontainers.co.uk/container-conversions
S Jones Containers Ltd. Anglian Road, Aldridge, Walsall, West Midlands, WS9 8ET