
2 minute read
GLASS MANUFACTURE
from AEOLIAN - AADRL
by Salim Hilles
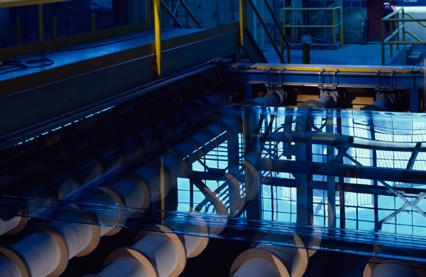
The glass used for domestic purposes increased the growth of the industrial revolution. During the 19th century, people prefer to use glass as material for windows and doors for decorative purposes. Architectural designers apply glass for stained glass in decorative windows. In the 20th century, the versatile purpose in the glass was widely used for windows on skyscrapers, houses and offices. There are two common ways to manufacture glass: Float Glass and Glass-blowing.
Advertisement
I) Float Glass1
Sheet glass
Batching:
Raw materials, including soda lime glass, silica sand (73%), calcium oxide (9%), soda (13%), and magnesium (4%), are weighed and mixed together in batches, which also includes recycled glass (cullet).
Melting:
The raw materials are then moved to a five-chambered furnace where they are heated to approximately 1500°C, turning them into a molten state.
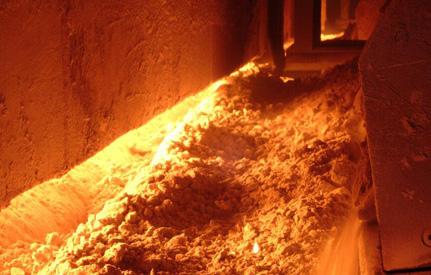
Drawing:
The molten glass is “floated” onto a bath of molten tin at a temperature of about 1000°C, forming a ribbon with a width of 3210mm and a thickness between 3 and 25mm.
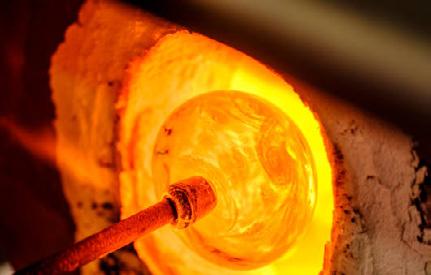
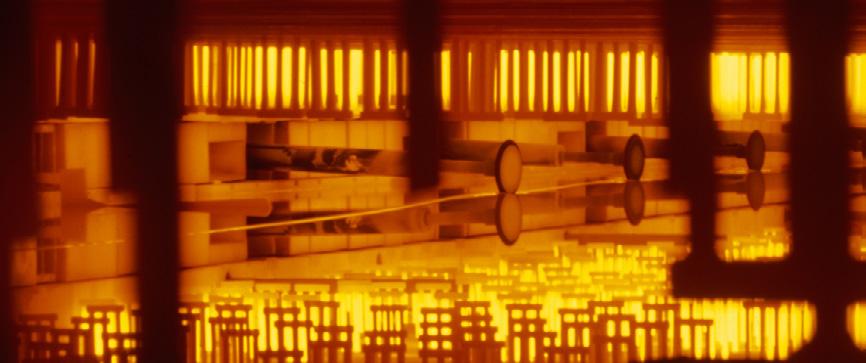
Cooling:
After leaving the tin bath, the glass cools to 600°C, it is then passed to an annealing chamber, which modifies the internal stresses and ensures flatness of the glass.
Cutting and Storage:
After cooling, the glass goes through a quality check, is washed and then cut into sheets of up to 6000mm x 3210mm, which are stacked, stored and ready for transport.”
1"Glass Academy - Float Glass Production Process." last modified September 10th, 2022. http://glass-academy.com/float-glass-production-process/
II)
Finishing:
The final shape is achieved by using compressed air.
Moulding : Heated liquid glass is dropped into a blank mould
Forming : Shaping the neck part
Blowing: A blast of air is introduced through the formed neck, expanding the liquid glass into the walls of the partition mould. The reheated glass takes on its final shape in the moulds.
The most important take away from this research is the evolution and applicability of making glass, a vital element to consider in the team’s research as various methods are explored for strategizing the fabrication of such elements.
Stone Spray
ANNA KILIK, INDER SHERGILL, PETR NOVIKOV for IAAC
Student from Institute for Advanced Architecture of Catalonia have built a robotic 3D printer that creates architectural structures from sand. The Stone Spray robot sprays the grains of sand or soil out of one nozzle and glue out of another to make a mixture that solidifies as it hits a surface. The robot’s arm moves multi-directionally and can also print onto vertical surfaces.
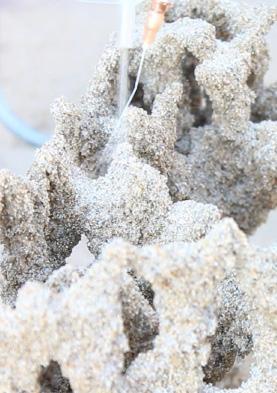
The use of robotic systems to fabricate complex and generative morphology using sand mixture as a material. The disadvantage of the technique is a lack of scalability as the printer uses glue to bind sand particles, therefore the system cannot be autonomous to work on site
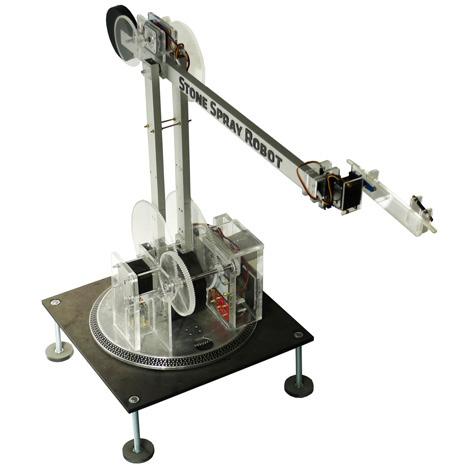
The glass 3d printer made by MIT Media Lab has the ability to fuse sand into glass however it is very limited with the scale as the model should fit into the bounding box of the printer. The research resulted into the working version of the tool being capble of actually printing glass with the layering to be able for the model to grow in z direction.

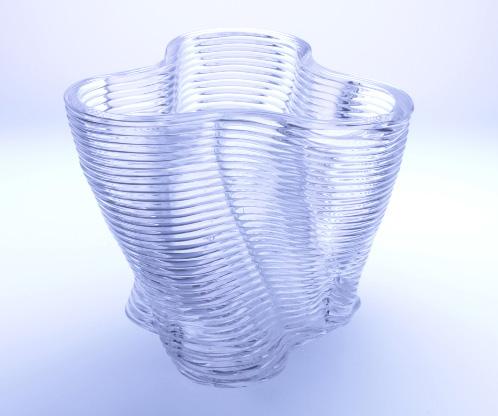

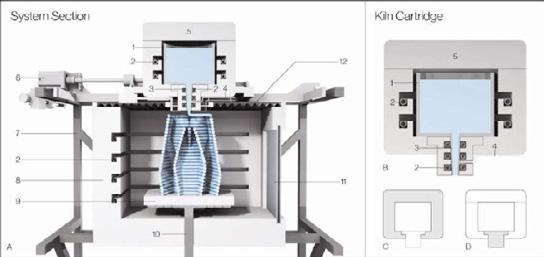
The properties and intricate knowledge regarding the properties of glass and how automative mechanisms can be used as a method of interactive with the material contengincy of glass was an essential in this research.
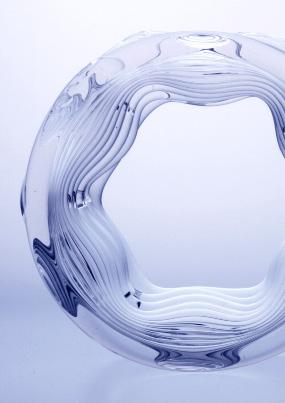