
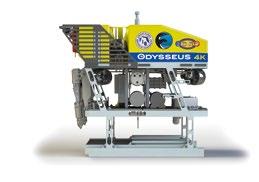
Odysseus 4K: Pelagic’s New ROV for Deep-Sea Science
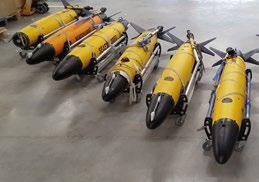

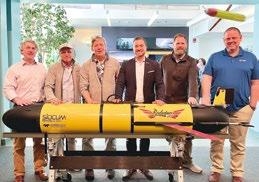
Odysseus 4K: Pelagic’s New ROV for Deep-Sea Science
Delivering data in most adverse conditions: underwater acoustic modems with advanced communication technology and networking
Accurate USBL and LBL positioning of underwater assets
Modem emulator and other cost-saving developer tools
Autonomous surface vehicle for bathymetry, monitoring, search & rescue, and AUV support
New MULTIBEAM SONAR for the Sonobot 5 vehicle available now!
06. Events Calendar & Welcome to Ocean Robotics Planet
09. RTsys Integrating Manned and Unmanned Systems for Greater Outcomes
13. Odysseus 4K: Pelagic’s New ROV Provides Cutting-edge Support for Global Deep-Sea Science
17. Reagan National Defense Forum and Uncrewed Maritime Systems
21. The SeaExplorer Way: Redefining Shallow Water Exploration
25. VideoRay: An American ROV Revolution – Part 1
30. Poster: VideoRay Defender
33. Fortifying Undersea Security: Collaborative Strategies for Subsea Warfare
35. Towards Autonomous Seas: Embracing the Potential of Remote Piloting
37. Uncrewed Surface Vehicles (USV) Network in Support to EOOS
41. Sea-Lift: Connecting Topside to Subsea
45. Digital Edge Showcases New ROV Products
49. Science Fiction Becomes Reality: The Sentinel Mission
53. The ROV Artist: Gaizka Garay
55. ROVAR: Remotely Operated Vehicle for Asset Recovery
ISSN 2755-239X
EDITOR-IN-CHIEF
Richie Enzmann
COPY EDITOR
Will Grant
SALES DIRECTOR
Nick Search
DESIGN & LAYOUT
Milan Farkas
CONTRIBUTORS
Richie Enzmann, Chris Lade, Daniel Baugh, George Galdorisi, Karoll Audibert, Marc Deglinnocenti, Richard Stevens, Roger Moore, Shea Quinn
SPECIAL THANKS TO
Audrey Leon, Bill Mallin, Carlos Barrera, Chris Gibson, Curtis Lee, Darioosh Naderi, Dawn D’Angelillo, Edward Cassano, Francisco Bustamante, Gaizka Garay, Helene Cox, Jack Rowley, James Colebourn, Jeff Mahoney, Jeremy Sitbon, Jeroen Romijn, John Benson, Jostein Jansen, Margo Newcombe, Matt Bates, Paul Fletcher, Pierre-Alexandre Caux, Rob Howard, Willard Balthazar
Alseamar
Blueprint Subsea
DeRegt Cables
Digital Edge Subsea
Enginuity
EvoLogics
Greensea IQ
IMCA
Norwegian Offshore Rentals
Oceaneering
Pelagic Research Services
PLOCAN
QYSEA
RTsys
Saab Seaeye
Silicon Sensing
Smarter Subsea
Handling
Teledyne
U.S. Navy
VideoRay
Zetechtics
MAY COMBINED NAVAL EVENT (CNE)
Farnborough, UK (21–23 May 2024)
SUBMARINE NETWORKS
London, UK (29–30 May 2024)
JUNE INTERNATIONAL UNDERWATER
GLIDER CONFERENCE
Gothenburg, Sweden (10–14 June 2024)
UNDERWATER TECHNOLOGY CONFERENCE (UTC)
Bergen, Norway (11–13 June 2024)
GLOBAL OFFSHORE WIND
Manchester, UK (18–19 June 2024)
OCEAN TECH EXPO
Plymouth, UK (26–27 June 2024)
SEANERGY
Nantes, France (26–28 June 2024)
AUGUST ONS 2024
SEPTEMBER
Stavanger, Norway (26–29 August 2024)
UNCREWED MARITIME SYSTEMS TECHNOLOGY – USA
Arlington, VA, USA (23–25 September 2024)
MTS/IEEE OCEANS
Halifax, NS, Canada (23–26 September 2024)
WINDENERGY
Hamburg, Germany (24–27 September 2024)
OCTOBER
SUBMERSIBLE OPERATORS GROUP
Oslo, Norway (8–10 October 2024)
FLOATING OFFSHORE WIND
Aberdeen, UK (9–10 October 2024)
GLIDER SCHOOL 2024
Gran Canaria, Spain (21–25 October 2024)
NOVEMBER
EURONAVAL
Paris, France (4–7 November 2024)
UNDERWATER INTERVENTION / WORKBOAT SHOW
New Orleans, LA (12–14 November 2024)
MAST
Adelaide, Australia (19–21 November 2024)
OFFSHORE ENERGY
Amsterdam, The Netherlands (26–27 November 2024)
2025 MARITIME RECONNAISSANCE & SURVEILLANCE TECHNOLOGY
London, UK (27-29 January 2025)
NAVY TECH
Helsinki, Finland (11-13 February 2025)
SUBSEA EXPO
Aberdeen, UK (18-20 February 2025)
UDT 2025
Oslo, Norway (25-27 March 2025)
OCEAN BUSINESS
Southampton, UK (8-10 April 2025)
My name is Richie Enzmann. Allow me to welcome you all to the latest issue of Ocean Robotics Planet!
Dear Reader,
On the front cover of this issue, you can see divers performing mine clearance operations with the use of RTsys robotics equipment. One of the takeaways from this article is that there are many cases, such as mine countermeasures, when it can be beneficial to still have humans in the loop. On the other hand, AUVs can also be used to replace actual submarines in training exercises to save on cost. The pros and cons of this match up are explored in more detail within.
Sticking with the defence theme, George Galdorisi reports on the Reagan National Defense Forum where some of the topics include lessons learned from the use of disruptive technologies in the conflicts in Gaza and Ukraine, and especially the relevance of innovative technologies such as uncrewed systems on the battlefield. Ukraine’s use of armed USVs to destroy or disable numerous Russian ships were also highlighted. These are key technologies: vital for future conflicts, and the matching of manned-unmanned components will potentially make a huge difference on the battlefield.
When it comes to the mapping of the vast oceans, gliders are an ideal tool, supplying conductivity, temperature, and depth data to oceanographers. Such a major task could not be undertaken without robots. At the Oceanology International Event, Alseamar introduced the ShallowExplorer, while Teledyne showed of the Slocum Sentinel. Both of these gliders are helping to push the capabilities and endurance of glider operations, and you can find out more inside.
Furthermore, in this issue we are showcasing some interesting new technologies such as the Sea-Lift developed by Enginuity, This piece of kit could make AUV recovery easier and more efficient compared to traditional methods. There’s also a new mini ROV tooling kit launched by Digital Edge Subsea that can be fitted to smaller ROVs to enhance their capabilities. And the ROVAR system that uses liquid nitrogen to vary its buoyancy, and is poised to become the choice of tool for future heavy lifting and decommissioning operations.
Finally, Captain Marc Deglinnocenti visited VideoRay at their HQ in Pottstown, PA. There, he learned about the history of this 25-year-old company, and interviewed Scott Bentley, Chairman, to learn more about their industry leading miniROVs. You can also see a spectacular image of the VideoRay Defender in this issue’s centrefold.
You can read about all of this in more detail, and I hope you enjoy this quarter’s issue.
Best regards, Richie Enzmann
Working under high pressure DeRegt delivers
Working in oceanic depths under great pressure requires cables and connections you can rely on. At DeRegt Cables we provide outstanding technical solutions and custom-engineered cable solutions for the most challenging of circumstances. When you are raising the bar, we deliver the right solution.
• Top notch cable design
• Reliable cable manufacturing
• High end cable termination
• Thorough cable
•
“Humans at the centre of operational decisions.” It is in the spirit of this adage that the French company RTsys has grown its success in the world of Naval Defence since 2010.
In a world of underwater technology that is increasingly instrumented and automated (rightly), the place of humans, their manual dexterity, and their instincts have sometimes been pushed aside in favour of technical developments (wrongly). Whether operator or diver, decision-maker or supervisory expert, humans have intrinsic capabilities evolved through their own experiences. This makes for safer, more timely decisions: choosing whether to act now or postponing further actions until later.
So why should we simply think in a combative spirit and push man against machine, pitting versatile thinking against binary AI, and totally manned versus unmanned operations? There are many factors that will influence this nuanced argument. Through their experience, RTsys has been able in less than 15 years to become the world leader at the center of this balancing act, allowing technology to develop quickly but not to the extent that it leaves humans out of the loop yet.
Let’s take the example of clearance divers. They have been an integral part of the world’s navies for over 70 years. This example shows the vital need to combine human assets with the use of underwater robotics in order to improve performance: securing the diver under the water, as well as reducing their action time overall.
These divers are essential assets in a range of different operations. They can be used in any external theatre for mine warfare countermeasures, as well as for the protection of combat vessels; clearing assaults in live-force recovery operations; opening channel assaults before landing operations; and many other scenarios.
To reach the maximal safety and efficiency levels required by navies, RTsys has created a complete ecosystem for and around the diver in order to reach three specific operational goals: the divers’ safety; the maximum efficiency of any operational missions; and diver discretion in every operation.
These underwater divers have a range of advantages: their level of expertise and identification of targets; their rapid analysis of data for instant decision making; and their dexterity for the neutralisation of different types of ordnance whether bottom laid or floating. The main limitations of divers under the water could be identified mainly as their lack of visibility in shallow water missions, as well as in limitations in terms of safety and speed of action (palming and endurance due to the limited amount of air or nitrox gas in the bottles).
How can divers be supported in all operations in order to improve their performance and exceed those limitations? Underwater robotics is the obvious answer, in a mannedunmanned technical partnership where each part of the team brings its strengths and eliminates its partner’s weaknesses. One example is through the integration of lightweight and portable AUVs, operated by two operators and configured with the necessary sensors for the required operations. These can be side scan sonar, TV cameras and lights, or multi-parameter probe and magnetometer for mine warfare missions, amphibious operation preparation, search and locate, or rapid environmental assessment.
The AUVs extensive endurance – between 10 and 20 hours depending on the models and their required configurations –makes it possible to tackle monitoring, identification, and contact locations over tens of km². Thus, the operator will be
able to analyse the data recorded by AUVs faster and with very high-quality image resolutions. This means that they can concentrate on the actions and responsibilities where the operators themselves present added value: classification and neutralisation of mines; decisions relating to beaching operations; etc.
By combining the respective strengths of robotic underwater systems and human skills, manned-unmanned teaming makes it possible to optimise the overall efficiency of diving operations, while minimising the risks to nearby personnel. This can also increase the speed of operations and reduce the overall cost of missions, thanks to costs that are controlled for by RTsys.
Whereas conventional AUVs have been typically heavy, expensive, and operated independently, RTsys' specialised vehicles now offer a more complementary role to critical diver’s operations from a simple RHIB. This removes the need for a dedicated Launch And Recovery System (LARS) from a support ship. This has been fully recognized for a decade by clearance divers, combat divers and by special operations forces (SOF) throughout the world who are also very sensitive to the capabilities of portability ease in every theatre of operations.
Manned-unmanned teaming does not apply only to divers. It’s also relevant to the growing threat of anti-submarine warfare (ASW), something that has become a subject of utmost importance for all navies. This threat is not limited to classic security matters but is a danger that has evolved through the strategy of asymmetric and hybrid warfare apparent in more recent conflicts. Thus, dedicated training for ASW has been introduced to numerous units as realistic potential scenarios that are carried out by various navies. This has been done either in standalone or international collaborations, such as through NATO exercises intended to consolidate the capabilities of navies in this specific area of combat.
This training contributes significantly to high-intensity operational preparation. This could take the form of integration of the main theme of ASW into a hypothetical scenario, for example conflict in a coastal zone with the intervention of a naval force. It could also be through multiplying the number of participating units, thereby increasing interactions between assets, and allowing the simulation of two realistic opposing forces. Potentially it could also involve unplanned exercises intended to stimulate the creativity of the crews and their tactical spirits, whilst developing their responsiveness.
This type of multi-disciplinary training emphasises preparation for highintensity naval combat. As an example, the French Navy – one of the most recognised experts in the field of ASW – constantly strives to improve the knowledge of its crews. And this is where manned-unmanned teaming takes on its full meaning: using underwater robotics in order to optimise human capabilities in the search, tracking, and neutralisation of submarines, in any possible time frame and location.
The tracking of enemy submarines is an essential task for navy frigates, helicopters, and maritime patrol aircraft (MPA). However, personal training is expensive. Similarly, training time with submarines is also limited and expensive. Therefore, in recent years, ASW training targets have become a more accessible, cost-effective means of sharpening the required tactical skills in the field.
To create real-world simulations, navies need a solution that provides affordable, realistic, and accessible training anywhere in the world: one that operates on every low-frequency active and passive sonar to comply with new generations of ASW sonar and torpedoes. RTsys ASW underwater targets accurately simulate a submarine during training; they are more affordable, portable, reusable, and give a realistic acoustic response within their peripheral frameworks. Sonar operators from 'real' submarines, surface frigates, or on aircraft patrols can then enhance their capabilities in various domains. These trainings range from basic to more advanced: detection, tracking, classification, target motion analysis, torpedo firing exercises, application of procedures, naval force management and coordination of assets. It can also involve water space management and prevention of mutual interference, safety rules in exercises, and anti-torpedo reaction.
While there are obvious advantages to incorporating unmanned systems into various domains, the inclusion of human operators alongside automated technologies in the underwater field are still the only reliable, safe, and efficient configuration to reach optimum results at sea. Manned-unmanned systems simply leverage the strengths of both humans and robotics, leading to synergistic outcomes. By combining experienced human intuition and creativity with the robustness and efficiency of automation, operations are simply optimised for effectiveness and performance.
RTSYS FULL RANGE OF MANNEDUNMANNED SOLUTIONS
According to the U.S. National Oceanic and Atmospheric Administration (NOAA), as of 2023, 24.9% of the global seafloor has now been mapped using high-resolution technology revealing the seafloor in greater detail. While that may sound like we’re gaining ground on what many researchers call “the final frontier,” it’s important to note that these are, in essence, just maps. We don’t actually know the intricacies and critical details of what’s going on down there.
“Seafloor maps can provide information about potential habitats,” NOAA states on their Ocean Exploration site, “but they can’t identify species on the seafloor or in the water column, or provide information about how they interact with each other and their environments. Scientists estimate there may be between 700,000 and 1 million species in the ocean... roughly two-thirds of these species, possibly more, have yet to be discovered or officially described,”
As we are well aware, deep sea Remotely Operated Vehicles (ROVs) remain by far one of the best tools to explore, document, and perform research in these still unknown environments. However, there remains a growing need for flexible, science based ROV systems. Last year, Pelagic Research Services (PRS) created a new effort focused entirely on this model of supporting academic and government research.
“When I formed Pelagic Research Services with my business partner Jim Sloan, our primary goal was to provide affordable, efficient, mobile and highly-capable deep-sea assets to the broad research community,” says Edward Cassano, CEO of
PRS. “Our technology has matured and our team expertise is successfully working with, and supporting, science. This naturally led us to a new model of business where we build and provide the primary ROV asset, and then operate and maintain the system for the client over the long term.”
As the name states, Pelagic Research Services (PRS) was founded on, and continues to support, the scientific community. Our ROV’s are fundamentally designed to support multidisciplinary operations on every dive. We make it a point to get as much done in every dive as possible.”
On a recent project with Ocean Networks Canada (ONC), PRS was tasked with multiple deployments of equipment and instrumentation in support of ONC’s NEPTUNE observatory, located off the west coast of Vancouver Island, using the Odysseus 6K system.
While also installing research experiments like Running Tide, an observational platform designed to investigate changes over time to carbon-capturing biomass on the seafloor
and its potential impacts on the deep-sea environment, Odysseus 6K was also integrating multiple sampling tasks (Niskin bottles, vent plume sampling, push cores, and gas tights), along with horizontal and vertical transects — all in between heavy-lift installations and extensive cable wiring.
“We got a lot of science done on that mission,” says Kate Moran, President and CEO of Ocean Networks Canada.
“Our engagement with scientists during their research project planning allows us to build, when required, research tools and specialized equipment to achieve their particular objectives,” says Cassano.
“Our exciting inaugural project is currently the design and production of ROV Odysseus 4K in partnership with Florida Institute of Oceanography (FIO),” says Cassano. “This cooperative endeavor will highlight our ability to not only provide an exceptional asset for deep ocean research, but to showcase
how cost-effective and time saving this approach can be, both here in the U.S. and on a global level.”
As an integral asset of the research vessel Western Flyer, the sophisticated Odysseus 4K is designed on the proven success of the PRS Odysseus 6K, a 6000m medium class work/science ROV that has earned its stripes as a top-class research vehicle.
“The new 4K ROV system opens up opportunities for the institute to investigate areas beyond scuba depth by providing a highly capable platform for sensors, tools, and sample collection, piloted by a professional team, to maximize research time,” states Cassano. “The ROV's design lends itself to both scientific research and the development and testing of new technologies—allowing researchers to work with engineers to improve deep-sea research methods.”
Launching through the R/V Western Flyer’s moon pool, an opening in the hull that allows scientists to deploy the ROV, Odysseus 4K will be used to livestream video, data, and
shipboard activities using remote science technologies, with the goal of allowing people on land and on board the vessel to cooperatively conduct research in real time.
“The live video and data feeds from the ROV, and supporting data and communications technologies on the Western Flyer will also enable people who are unable to sail to participate via remote science. Thus, expeditions can include a wider range of expertise, and better support multidisciplinary research goals,” Cassano continues.
“This cooperative effort was designed to not only reduce overhead costs – by building, operating, and maintaining the ROVs – but to also provide our ongoing expertise,
while greatly decreasing build and integration times,” notes Cassano.
The Odysseus 4K will be integrated onto the Western Flyer in May, and the science verification cruise will commence in June.
“We’re very excited to be bringing this new, permanentlyinstalled ROV asset to their very capable and highly stable research ship, the Western Flyer, “ Cassano states. “This will open up new opportunities to explore the depths of the South East Coast of the USA, Caribbean, and the Gulf of Mexico while we continue to provide our operational expertise to all of the future science missions. This is definitely a win-win for the research community.”
Pelagic Research Services (PRS) is a company dedicated to providing cutting-edge subsea research tools and services to the global ocean community. The company's team boasts decades of experience in managing and supporting offshore, multi-disciplinary projects in the fields of conservation and marine science. Their expertise extends to collaborating with universities, government agencies, and private companies.
Founded by experienced ocean professionals, PRS has a long track record of success in expedition planning, execution, and scientific support.
PRS specializes in deploying and operating ROVs, like their flagship Odysseus 6K System. This is capable of operating at depths of 6,000 m and offers its services worldwide.
It has mobile equipment that can be transported by air, land, or sea to support projects anywhere around the globe. This flexibility allows them to cater to diverse needs, from scientific research expeditions to search and rescue operations.
In 2023, PRS played the crucial role in the high-profile rescue attempt and ultimate recovery mission of the OceanGate submersible, Titan, which tragically imploded near the site of the RMS Titanic in the north Atlantic. The Odysseus 6K ROV was instrumental in locating, assisting, and retrieving critical submersible debris, demonstrating their capabilities in complex deep-sea operations.
PRS joined an international effort with hopes of saving the crew of Titan. From activation for rescue through mobilization,
via air transport to St. Johns, Newfoundland, through to integration and transit offshore on the Motor Vessel Horizon Arctic, and finally to the sea floor at 3838m at Titanic.
PRS is also prequalified by the University of Victoria to provide ROV services for deploying, maintaining, and repairing Ocean Network Canada’s underwater observatories, showcasing their expertise in supporting crucial scientific infrastructure.
PRS, with its experienced team, advanced technology, and global reach, plays a vital role in advancing our understanding and exploration of the vast and complex ocean environment. From supporting scientific discovery to assisting in critical recovery missions, PRS is a key player in fostering a deeper connection with the depths of our planet.
The Reagan National Defense Forum, held every December at the Ronald Reagan Presidential Library, is one of the most important national security dialogues of the year. “Everyone Who is Anyone” in the national security space is either an invited speaker or an in-person attendee. This includes the Secretary of Defense, secretaries of the military services, uniformed chiefs of the military services, key innovation and acquisition leaders such as the DIU Director, as well as senators and congressmen from key defense committees and others.
As the informed readership of Ocean Robotics Planet knows, uncrewed surface vehicles (USVs) represent one of the most cutting-edge and innovative technologies in today’s defense space. Given the scope of the Reagan National Defense Forum, not every speaker’s remarks were directly focused on uncrewed surface vehicles. That said, what was discussed regarding national security were gaps that the U.S. military needs to fill. Unsurprisingly, discussions regarding technology, innovation and other issues had a strong emphasis on these USVs.
During his remarks, the Director of the Defense Innovation Unit, Mr. Doug Beck, described lessons learned about the use of disruptive technologies in the conflicts in Gaza and Ukraine, and especially the relevance of innovative technologies on the battlefield, particularly uncrewed systems. He highlighted Ukraine’s use of armed USV to destroy or disable numerous Russian ships.
Mr. Beck noted three lessons about the use of disruptive technologies in the conflicts in Gaza and Ukraine:
ƀ The relevance of new technologies on the battlefield, especially unmanned systems.
ƀ The power that alliances and partnerships can bring to the table.
ƀ The need for smart operators to fully exploit emerging technologies.
Mr. Beck noted that these are lessons that the United States is leveraging as it looks to help the United States prepare for conflict anywhere in the world, but especially in the IndoPacific region. He noted that MANTAS and Devil Ray boats have been invited to Pacific Fleet Integrated Battle Problem events over the past several years (and into 2024) due to their usefulness in the high-end fight in the Pacific theater.
As the PACOM Commander, Admiral John Aquilino, pointed out during this event, referring to the ways that Ukraine was able to synchronize the effects of legacy and new platforms, systems, sensors, and weapons, he noted that one lesson for the United States is that the ability to synchronize the efforts of uncrewed surface vehicles.
During her remarks at this event, Chief of Naval Operations, Admiral Lisa Franchetti, called out uncrewed surface systems, which were used with deadly effect in the war in Ukraine, as key assets in any conflict with a peer competitor. She cited the work of the Navy’s Unmanned Task Force as well as numerous exercises, experiments, and demonstrations to put uncrewed surface systems in the hands of Sailors and Marines to determine their usefulness. Admiral Franchetti spoke explicitly about the work of Commander Task Force 59 in the Arabian Gulf, as well as the Pacific Fleet’s Integrated Battle Problem series of exercises where platforms such as Saildrone, MANTAS and Devil Ray boats performed several missions.
During his remarks at the Reagan National Defense Forum, Secretary of the Air Force, Mr. Frank Kendall noted that a key technology vital for future conflicts, especially in the Indo-Pacific region, is the ability to implement mannedunmanned teaming to fully exploit the best attributes of both the human and the machine. He went further to state that the need for more autonomy is so acute in a potential conflict with China that if U.S. platforms, systems, sensors and weapons are not autonomous and there is a human in the loop, we will lose a conflict with China which is rapidly developing fully autonomous weapons systems (as is Russia). Maritime Tactical Systems, Inc. (MARTAC) has scaled up its ability to have MANTAS and Devil Ray boats work autonomously.
During his remarks at the Reagan National Defense Forum, Representative Mike Gallagher, Chair of the House Select Committee on the Chinese Communist Party, noted that other speakers had talked about the DoD’s “Replicator” program (a favorite program of DEPSECDEF Hicks). While noting that it was a good program in concept, he was concerned that the United States does not yet have the technology to control a thousand or more drones simultaneously. He also noted that a key U.S. vulnerability vis-à-vis new technologies is the U.S. hesitance to pick technology “winners and losers”. By inviting MARTAC to every Integrated Battle Problem, Pacific Fleet is, in effect, picking winners and losers for uncrewed surface vehicles.
Many people might be surprised that a conference featuring such senior officials would include discussions of technology as specific as uncrewed surface vehicles. However, in an era of great power competition, USVs have begun to take center stage and are now on an accelerated development path. Like their air and ground counterparts, these uncrewed maritime systems are valued because of their ability to reduce the
risk to human life in high threat areas, to deliver persistent surveillance over areas of interest, and to provide options to warfighters that derive from the inherent advantages of uncrewed technologies.
Future articles in Ocean Robotics Planet will provide updates on this rapidly emerging technology that has the potential to transform warfare. As the Navy and Marine Corps embark on an ambitious series exercises, experiments, and demonstrations throughout 2024 and beyond, more uncrewed surface vehicles will be put into the hands of Sailors and Marines, further accelerating their development and fielding.
Captain George Galdorisi (USN – retired) is a career naval aviator whose 30 years of active-duty service included four command tours and five years as a carrier strike group chief of staff. He is the author of 15 books, including four New York Times best-sellers.
Over the past two decades, Alseamar have been at the forefront of long-range ocean glider development, enabling researchers to unlock the secrets of our planet's oceans. Building on the success of their well-established SeaExplorer line, Alseamar have recently introduced the ShallowExplorer, the next generation of underwater glider, designed specifically for shallow water environments.
The SeaExplorer glider is an autonomous underwater vehicle (AUV) created back in 2007. It’s propelled by its own buoyancy change without a propeller: the vehicle pumps oil in and out of the central hulls every two hours to increase and decrease its volume. Using the Archimedes’ and Hydrodynamic principles, the robot moves forward as it sinks or rises. To be able to follow a trajectory, this vehicle is fitted with wings, and its batteries are mounted on two actuators, allowing for heading and pitch control. The SeaExplorer is optimised to navigate in waters down to 1,000m where its buoyancy engine is at its most efficient. An onboard computer fuses data and makes the glider go wherever the pilot directs it using satellite communications.
The SeaExplorer vehicle is divided into two subsystems: navigation at the back and payload at the front. This early design decision makes the platform very modular, as users can swap the front payload section without touching the navigation. This makes carrying many different payload shapes and sizes possible. The ease of use is also enhanced by the onboard rechargeable battery. The glider doesn’t need to be opened between missions, which significantly reduces leak risks.
To make the SeaExplorer a complete system, Alseamar have developed a piloting interface called GLIMPSE. This is currently the most user-friendly glider piloting tool on the market. With this intuitive interface, operators can effortlessly pilot; monitor the robot’s health; and receive near realtime data from shore, maximising operational efficiency.
For the past ten years the SeaExplorer has been a widely disseminated tool, used for many applications ranging from acoustic monitoring, biochemistry (temperature, salinity, chlorophyll, dissolved gas, etc.), physical oceanography (currents and turbulences) and many others. The SeaExplorer benefits to and from a large community of users.
These gliders have now been used in every world ocean by more than 50 different institutions and companies. But the journey is only just beginning.
The continental shelf waters (up to 200m deep) cover about 27 million km² (10.5 million square miles). Around 90% of the world’s fishing takes place in this region, as well as 70 to 80% of its wind farming. In addition to that, about 50% of
the world’s population lives in coastal areas. These figures are only a few examples of why we need to monitor water pollution, physical oceanography, and biological activities in these shallow waters.
For all of these reasons and more, Alseamar, in partnership with Voice of the Ocean (VoTO), started the development of a new glider in 2022. VoTO, a Swedish foundation, is working towards making the oceans more accessible to all sectors of society. VoTO’s current focus is the Baltic Sea and they have been using a large fleet of 15 SeaExplorers there for many years. However, they identified the need for an optimised solution for shallow water and the strong currents and highdensity gradients characteristic of the continental shelf. Thus, the concept of the ShallowExplorer was born.
The ShallowExplorer is a glider specifically designed to reach a maximum depth of 200m. By changing the ballast technology to increase its efficiency at a lower pressure, this new glider is capable of navigating for more than three months with its “double battery”. Meanwhile, its system platform the SeaExplorer (designed for 1,000m) can fly for about three weeks in these environments.
When working with autonomous vehicles, energy is always a concern. The platform is known for its payload modularity, and this mindset was then applied to its energy reserves. On the ShallowExplorer users can remove one of the two battery packs, reducing the length and weight of the vehicle but only
reducing endurance from three to two months. The Alseamar R&D team not only made the ballast more efficient at 200m, but they also increased its volume from 1 to 1.6l, enabling the vehicle to go through very high-density gradients of about 20-24∆σ. This allows safe navigation in fjords and estuaries, generating a higher thrust in order to navigate in stronger currents, and can withstand the drag of large payloads such as acoustic arrays or microfluidic sensors.
The Shallow Explorer can glide in waters as shallow as 20m. However, reaching areas of such limited depth can be challenging for a buoyancy glider. To address this, Alseamar has developed a unique dual thruster system. This innovative system features folding blades, allowing the vehicle to maneuver effectively in waters as shallow as 6m.
Leveraging the shared components between the ShallowExplorer and its predecessor, the SeaExplorer, Alseamar were also able to develop and de-risk the thruster system before the ShallowExplorer's launch. This hybrid technology ensures reliable performance, and is already in operation on the SeaExplorer.
This capability will propel the glider during normal operation, and it will also help traverse density gradients or fresh water lenses. Another function, this propulsion system unlocks, is the capability to fly horizontally, or “propelled
drift”. This capability employs the glider’s ballast system less often and increases endurance. During horizontal flights, the glider consumes a constant amount of power, whereas when in standard operation the ballast power consumption depends on the mission’s depth. In shallow water, the ballast is used repetitively, increasing the overall power consumption.
Using propelled drifts instead of standard dives, the SeaExplorer will use less battery per kilometer for dives up to 180m. This significantly expands operational applications for the glider. This system also allows users to operate the vehicle horizontally on the surface.
Gliders have been known for years to be the perfect autonomous platform for passive acoustic monitoring (PAM). Indeed, the minimal actuation and slow speed of the vehicle produces extremely low self-noise ensuring an optimal acoustic monitoring configuration.
Over the years, Alseamar have been developing passive acoustic instrumentation and data processing capabilities using gliders and other platforms. All of this expertise was combined in the launch of the 2023 AURIS payload (Acoustic Underwater Recorder Intelligent System). This payload has been specifically crafted for acoustic data recording as well as AI onboard processing.
The AURIS payload encloses an acoustic recording system composed of hydrophones (piezo ceramics), custom preamplifiers and an acoustic Analog to Digital Convertor (ADC) in addition to a dedicated computer that acts as a recorder, signal processor, and open backseat driver. This payload has a user-friendly open architecture design and embeds the well-known middleware ROS, as well as a convenient application user interface.
A backseat driver is a computer that can communicate to the main glider computer to control the vehicle. The term is akin to a passenger in the back seat of a taxi directing the driver where to go. On the SeaExplorer this computer is used in place of the standard payload board. Thus, the system has full access to real time sensor data. With this information, the computer can perform complex onboard calculations and log new information that is shared with the user.
In standard operation, a glider only sends a subsample of data every time it reaches the surface. This constraint is inherent to satellite communication cost and speed, as well as glider positioning and safety. The longer the glider stays on the surface communicating, the more it drifts and could be damaged by an approaching vessel. Having the capability to run onboard processes means that calculations can be done based on a full dataset and the users do not need to wait to recover the glider.
The backseat driver can also be used to change the course of a mission after receiving information from the sensors. Indeed, in standard operations a glider receives a new set of actions
while it is on the surface, communicating with the pilot via satellite. Using the backseat computer on the SeaExplorer means that decisions can be made by the onboard intelligence while underwater. A glider direction or behaviour can now be dynamically adjusted based on onboard sensor data. For example, the glider can be tasked to follow a minimum sound velocity, a maximum level of chlorophyll, or to come back to the surface if specific conditions are met. This is a new era for the SeaExplorer as it unlocks full modular adaptive sampling and autonomous decisions.
When we couple the onboard processing capabilities with an acoustic recorder and a backseat driver, the possibilities become endless. Indeed, acoustic datasets are large and very difficult to be sent to shore via satellite This is especially the case for the AURIS payload, recording up to 785kHz (mono channel) with up to eight acoustic channels simultaneously. In standard operations, the user can only obtain the data upon completion of the mission. This could mean missing important real time phenomena that may have changed the course of the research.
With the AURIS payload the user is now able to add its own onboard processing, and for example, calculate real time ambient noise, detect specific acoustic signatures such as marine mammals or maritime traffic, or to calculate the direction of specific sound sources. With the AURIS and backseat capabilities, the SeaExplorer can even follow individual acoustic sources.
Fuelled by the ever-growing demand for underwater data in environmental monitoring, defence applications, and the energy sector, this past year Alseamar have gone through a period of intense growth. The team at Alseamar is thrilled to be part of this changing world, and to push the boundaries of ocean engineering and science by developing transformative, state of the art solutions in marine autonomy. While the latest developments focus on shallow water monitoring, adaptive sampling and intelligent passive acoustic monitoring, we are looking towards a future of even greater possibilities.
For more information, please visit: or contact us via alseamar13@alseamar-alcen.com
America was founded in 1776 amidst a revolution with an innovative form of government for its time. VideoRay is an American company founded in 1999 that develops and builds innovative Remotely Operated Vehicles (ROVs) for the current technological ROV revolution. Even their first ROV, released in 2000, was considered revolutionary with a 152 metre (500 ft.) depth rating. The VideoRay Pro only weighed 3.6 kilograms (8 Lbs.) and was equipped with dual thrusters, lights, and a video camera. That may not sound like much in today’s ROV market, but it was a big hit with Fish and Game Departments
and Law Enforcement Agencies all over the USA. Soon the VideoRay Pro was upgraded to the VideoRay Pro II in 2002. It had an 80% increase in thrust to combat river currents better, brighter lights, and a higher definition camera. Their Pro 3 had more add-ons, and in 2004 their Deep Blue had a 305 metre (1000 ft.) depth rating with an on-board sonar. They added more horizontal thrust in 2005 and then even more vertical thrust in 2009. Complete autonomous computer controls were offered in 2012 with the VideoRay CoPilot by Seebyte. Those previous product innovations were prompted by the demands of their customers. Those product demands started the VideoRay revolution that hasn’t ended to this day. Today VideoRay offers three main ROVs which they placed in their Mission Specialist category. Even though they may have been released at different times, one newer Mission Specialist ROV was never really designed to replace the other older ROVs within that category. These three Mission Specialist ROVs are more like not-so-identical triplets with each having their own area of expertise.
The first Mission Specialist triplet was “born” in 2017. It is the seven thruster Defender which has a more traditional rectangular frame. That practical equipment frame and racks along with its slender rectangular body affords the Defender a staggering 500 plus specific equipment configurations. That amount of versatility along with its 1000 metre (3281 ft.) depth rating makes the Defender an industry leading ROV. It would be impossible to list all of its optional equipment and functions here, but there are a few that stand out that cannot be ignored. Just one of those functions that stands out is the Defender’s ability to couple up with VideoRay technology or other brands of technology like that of Reach Robotics. They offer single or dual robotic arms from Australia. That attachment is a great addition for underwater archeological research and recovery operations. Experimentation continues with Defender using
1000 metre depth rated, 7 Degree-of-Freedom prototype dual robotic arms which the U.S. Navy is interested in for MCM and EOD applications under its military use category. Defender can be modified to dispose of Water Borne Improvised Explosive Devices (WBIEDs) and Underwater Hazardous Devices (UHDs) which are commonly known as underwater mines. It is also used to observe possible terrorist threats. Non-military or civil industry applications include, but are not limited to, liquid storage tank inspections, hydroelectric dam inspections, and waterway lock structure inspections. The offshore oil industry uses Defender because of its versatile tooling capabilities and deep diving depth rating. The nuclear energy industry can use Defender to inspect underwater areas where it’s not safe to send human divers. Defender can carry a myriad of underwater testing equipment, and it certainly rates as an excellent scientific tool. The options list goes on and on.
Their next Mission Specialist ROV came out soon after the Defender in 2018. The Pro 5 never tried to outdo the Defender. It was designed to be more of an economical ROV option for that same market that boosted VideoRay to fame in the first place. If anything, the Pro 5 builds on their past lines of ROVs. It has three thrusters opposed to the two thrusters of the Pro 4. It can be disassembled and reassembled to a certain degree making it more modular than its ancestors. This modular capability gives it 125 possible configurations. Its forward speed is 4.4 knots, and its depth capability retains the 305-metre rating. It, of course, has all the high-tech controls and software of their modern ROVs.
The third triplet in the Mission Specialist category is the Ally ROV. It has four powerful thrusters that are perfect for lifting heavy objects from the seafloor. It even has two floatation options to aid in that endeavor. The squared off floatation provides more lift with room for the interchangeable
batteries. The rounded floatation is for pipeline observations and for getting into other tight spots. It is important to note that the rounded floatation will not accommodate the batteries. You have to use tether power if you want to get into tighter places. That’s just a fact of life. It can lift up to 11 kilograms (24 Lbs.) though which is great for an ROV that only weighs 13.6 kilograms (30 Lbs.). The Ally can sport a multibeam sonar and a robotic arm at the same time with ease. The Ally ROV does have a genetic link to its two sisters. It also has that common Mission Specialist capability of being modular in the field for versatility. These Mission specialist ROVs are a great lineup for customers with different needs and different budgets, but is that lineup all that VideoRay has to offer? Of course not. VideoRay never rests on its past or current laurels. So, what do they have to offer for the future, and can we all have a peek?
With a strong desire to learn more about VideoRay’s inner workings and future prospects, I decided to conduct a quick over the phone interview with their Executive Chairman Scott Bentley. I started out by asking the most pressing and direct question of the interview:
CAPT. MARC: VideoRay has a glorious history of innovation as well as many capable ROV products currently available. If your past pattern of innovation is any indication of the future, you should have a few new products coming out soon. We already know about your working with Reach Robotics of Australia and their dual robotic arms for Defender. Can you tell us about some of your other innovations?
CHAIRMAN BENTLEY: Our latest product line, as you know, is based on what we call Mission Specialist Technology. It’s a cutting-edge approach that defines the highest performance, most rugged and reliable, and most portable vehicles that
you can buy. Our Defender, Pro 5, and Ally models feature this technology. The Defender, our most sophisticated ROV to date, has proven itself with the U.S. Navy, which has entered into multi-million dollar contracts with VideoRay to develop, define, and deploy new technology for explosive ordnance disposal operations. The Pro 5 has been the go-to ROV for search and rescue teams around the world.
CAPT. MARC: Following up on your success with the U.S. Navy, I now understand that VideoRay has a much larger customer base than I had originally thought. Can you tell us in a little more detail why that is?
CHAIRMAN BENTLEY: Our largest sales are those that have the most difficult missions. That tends to be the military, who require tools that absolutely perform when needed and can accomplish missions that are on the edge of what is possible. VideoRay meets those requirements. So, we have been busy and very successful in that market segment, not only for the U.S. Navy, but with navies and other military organizations around the globe.
Capt. Marc: Another thing that took me by surprise is your assertion that your ROVs are extremely useful in the aquaculture industry. I’m not doubting you about that, but I am curious to know in what ways that is true.
CHAIRMAN BENTLEY: Aquaculture is another market segment where reliable and robust products are essential. Operations go on 24/7. A hole in a fishing net, fish feeding, or fish health problems require immediate attention. The aquaculture industry has relied on VideoRay’s ROVs to help address these issues. In particular, accessories that we have available such as our Sonde instruments that are small yet are capable measuring tools for a wide variety of underwater
applications. That includes, but is not limited to, testing the pH, salinity, conductivity, and dissolved oxygen of the water.
CAPT. MARC: It’s already obvious to me that the Mission Specialist Defender would make an excellent scientific research ROV among other things. I can see where that deep-diving ROV being equipped with a Sonde probe would be of great scientific data collection value. Can you tell us of any other scientific data collection devices that can be installed on Defender?
CHAIRMAN BENTLEY: The Defender is an excellent vehicle for a variety of sensors. The large payload capacity, significant propulsion power, and the multiple Ethernet and RS-485 interfaces allow for the easy integration of several devices useful for scientific data collection. Water samplers, core and water samplers, multiple camera systems, laser measurement systems, and many other devices have been added to the Defender.
CAPT. MARC: I have been a master mariner, a qualified engineer, as well as having worked on ships both in dry dock as well as repairing them underway. I know that the maritime industry would be grateful for any innovations that would aid mariners and sailors with their vessel repair and maintenance tasks. Can your ROVs help in that area too?
CHAIRMAN BENTLEY: There have been several innovations developed to help with ship husbandry and other marine structure inspection, repair, and maintenance. For instance, VideoRay worked with ABS Conoco Phillips, and other interested industry partners on a Joint Industry Project or JIP to develop a solution to remove men from confined-space, ballast tank inspection using suitcase ROV technology. These tools were developed in 2013 and are available in our Mission Specialist Pro 5 systems. They include an articulating Ultrasonic gauge that is capable of rotating to place an ultrasonic thickness sensor on each plate of steel in the ballast tank. The system displays the sensor readings on the video overlay. Recordings not only capture the ROV video with the steel thickness readings, but also the voice annotations of the pilot. Additional tools such as cathodic protection probes, eddy current sensors, flooded member detectors and camera and laser measurement systems have been added as payloads to our Mission Specialist arsenal. Cavitation cleaning systems, which use high pressure water and specially designed nozzles to generate cavitation that can aggressively clean surfaces without damaging them, have seen successful in-the-field use in multiple types of operations.
CAPT. MARC: I’ve had the fortunate opportunity to pilot several types and brands of ROVs both in test tanks and in open waters. Some of those were worth several
thousands of dollars, and some were worth several hundreds of thousands of dollars. I’ve gotten pretty good at over the years, and I feel confident at piloting ROVs. I even piloted your own Pro 4 in San Diego Bay. Do you ever get customers that buy your ROVs without any ROV piloting experience? If so, how do you alleviate their concerns about damaging or even losing their new VideoRay ROV?
CHAIRMAN BENTLEY: We have sold quite a few systems based on our reputation and recommendations. It is not uncommon for our salespeople to receive inquiries such as, “We need a Pro 5 with a multibeam sonar. How much does it cost, and when can you deliver it?" In each case we explain that training is needed before they can operate the ROV and its accessories. Buying an expensive system like that without any training is like a car owner jumping into a full-size tractor trailer rig and driving it away. The odds that you will be successful at operating the rig are pretty low. The chance of disaster, on the other hand, is pretty high. That’s why we develop our systems to be easy to understand and intuitive. We continually work with our customers to understand how they use our products and what challenges they face, and we bring this knowledge as we make continual product improvements. We also believe that training is an important part of the process to ensure optimal operation. We offer both onsite and offsite open enrollment classes with experts who can explain how to plan and execute your mission properly. For instance, attendees will learn that in many cases it is not so much as to where the ROV is located, but as to where the tether is located and what it is routed through. They learn to use navigation and search tools. They also learn how to deploy and recover ROVs from small boats in high velocity currents. Our training and technical support teams are a part of the way we ensure success for our clients.
That was a great interview that taught us all a bit more about VideoRay’s products and personnel. However, I wanted to prod a bit further into this highly successful ROV company. So, I decided to pay them a visit.
I found VideoRay’s large nondescript headquarters building right in the middle of the commercial downtown district of the city. The door was locked and had to be opened by an employee with a keycard. I was immediately met and escorted into their conference room by some highly ranked members of VideoRay’s management team. That’s where I wasted no time at all to begin my face-to-face interview with Chief Executive Officer, Chris Gibson, Chief Product and Innovation Officer, Marcus Kolb and Chief Operating Officer, Paul Czachor. That’s where I hit the pure gold information about what’s coming up with VideoRay. That golden info is coming up in Part Two of my VideoRay report. To be continued in Part Two...
High resolution imaging in turbid water for improved situational awareness and target identification. Available in 375kHz to 3.0MHz. Depth rated to 500m, 1000m, or 4000m.
In September 2023, the NATO REPMUS and DYNAMIC MESSENGER exercises were hosted by the Portuguese Navy. These exercises are focused on ways to protect Critical Undersea Infrastructure (CUI) from potential threats. They benefitted from the participation of over 2,000 personnel from 16 NATO nations, including Ireland, and their newest member, Sweden.
With the growing tensions both in Ukraine and the Red Sea, the vulnerability of CUI has never been more profound, prompting urgent discussions on how best to protect it. These NATO exercises are integral in supporting those discussions. Undersea infrastructure is crucial to the growth and prosperity of nations all over the world, even more so for the socio-economic progress of developing nations. It's essential for everyone –government agencies and industries alike – to collaborate and find new ways to keep our undersea infrastructure safe.
Let's take a closer look at a crucial aspect of CUI: undersea communication cables. These cables are the unsung heroes of our modern connected world, carrying around 99% of global internet traffic. Their fast transmission speed ensures that we can enjoy quick and reliable connectivity, linking continents and enabling real-time communication. They're the backbone of international trade, research collaborations, and even cultural exchanges. With over 500 cables laid and planned globally, stretching over 1.4 million km, they are everywhere.
The catch: some of these cables sit as deep as 8,000m. This depth, coupled with their extensive length and crossing multiple jurisdictions, makes monitoring and defending them a challenge. Who's responsible for keeping them safe? Is it the government, the CUI owners, or perhaps the defence agencies?
If something were to happen to these cables – similar to what was seen with the Nord-stream pipeline damage in 2022 – the consequences could be dire. Despite their importance, these vital pieces of infrastructure often lack proper protection. With recent tech advancements, the sabotage of these cables has become a real threat, giving rise to what's now known as Seabed Warfare.
The commercial underwater industry pioneers cutting-edge tech for safeguarding CUI, using tools like multibeam sonar systems, LiDAR, and underwater robotics (AUVs and ROVs). These innovations boost protection and encourage collaboration between commercial and defence sectors to develop increasingly effective safeguarding.
When it comes to safeguarding CUI, teamwork between the commercial and defence sectors is key. This partnership brings multiple benefits that are important for making sure this vital network stays strong. The commercial industry is great at innovating and moving fast, while the defence experts have the knowledge when it comes to the threat and operational aspects. By working together, they can create a solid defence strategy that includes a range of tactics like advanced sensor systems, and underwater resident AUVs and ROVs, an area in which Saab is at the forefront.
The REPMUS and DYNAMIC MESSENGER exercises focused on the integration of new maritime technologies into NATO operations, and the ability of uncrewed underwater vehicles to operate together in a range of scenarios, including Seabed Warfare.
During the exercises, Saab deployed and operated the AUV62-AT anti-submarine warfare training target and the Seaeye Falcon. Sponsored by the Royal Navy, the Falcon was used primarily to showcase its versatility by aiding in tasks such as identifying and neutralising simulated Underwater Explosive Devices. The AUV62-AT, in collaboration with Sweden's defence procurement agency, supported AntiSubmarine Warfare (ASW) systems by mimicking the acoustic profile of submarines. This then fed-back valuable data about how the ASW battle had been conducted. Saab’s participation in these events helped enhance underwater capabilities, as well as strengthening international security efforts.
This collaborative approach between industry and defence encourages knowledge exchange, enhancing understanding, preparation, and resilience against evolving risks to undersea infrastructure. Ultimately, this alliance fosters a continuous cycle of innovation and readiness, essential for addressing the ever-evolving challenges faced by CUI.
Walking the floor at Oceanology International, the leading marine technology show in London in March, highlighted just how quickly our industry is changing. A huge number of autonomous vessels – whether surface or subsea – new and ever more impressive communication solutions based around satellites and data, and huge flying drones which can deploy a Remotely Operated Vehicle (ROV) out at sea at a moment’s notice were on display.
Alongside them were comfortable ROV piloting stations and increasingly sophisticated mock Remote Operations Centres (ROC). Delegates could sit down, run a simulation, and get a real feel for the technology and how it might work for their own operations.
ROCs can play a pivotal role in improving subsea activity by enabling efficient and safe ROV operations from onshore locations. They ensure flexibility and reduce risk to employees, while contributing to environmental
sustainability, by minimising the offshore presence required. Thanks to improved technology and communication, ROCs are becoming increasingly important to ROV operations.
Technology is always evolving, and the latest ROCs can integrate with real-time monitoring and enhanced decisionmaking thanks to the integration of Artificial Intelligence (AI). Even without these cutting-edge innovations, remote piloting – by its very nature – brings additional layers of complexity to offshore operations.
If piloting remotely, there is a need for reliable connectivity and low-latency data connections and IT security becomes fundamental to any project’s success. More than this though, there is often a reluctance to totally trust remote operations with industry concerns around reliability, safety, and performance.
The increasing importance of ROCs for ROV programmes, and the need to build trust in remote operations, has not been lost on the International Marine Contractors Association (IMCA) and its ROV committee. This is why the latest major
revision of IMCA Guidance, The Safe and Efficient Operation of ROVs (R004), includes recommended best practice around ROCs for the very first time.
A new dedicated chapter highlights the differences between remote and standard ROV operations, covering issues such as access and security, tasks, pre and post dive checks, launch and recovery, remote handover, situational awareness, emergency protocols, network and verbal communications, working periods, team size, and documentation requirements. All of which are crucial to ensuring the safe and consistent use of remote operations for ROVs through ROCs.
This is one-way that IMCA is aiming to help support the industry build confidence in ROCs, their successful deployment, and increased reliability of remote operations more generally. We also hope our approach will provide a framework for future revisions which acknowledge upcoming changes in technology and regulation in an ever-evolving arena.
Recognising the potentially seismic shift of MASS (Maritime Autonomous Surface Ships), IMCA has also been engaging with the International Maritime Organisation (IMO) to ensure that the specific requirements of our industry are recognised in the upcoming global regulation around autonomous vessels.
For remote piloting, this could have a range of impacts. Taking just one aspect of ROV operations – training and accreditation – could we see a shift from the traditional ROV Pilot Technician to a ‘leaner’ role of ROV Pilot? In our new and emerging world, many working onshore will not regularly need to see a ROV, could it also mean the return of a Submersible Engineer role which specialises in offshore
maintenance? These are some examples of the types of questions we will need to find answers to.
While we have a way to go, the course charted is completely clear – the future is increasingly automated and increasingly remote, and we will, as an industry, need to be ready.
Roger Moore is Technical Adviser, ROVs and Offshore Survey at the International Marine Contractors Association (IMCA). Find out more at www.imca-int.com
The ocean is a key component of the Global Earth System that influences the global/regional climate, weather, ecosystems, living resources, and biodiversity. It also plays a key role in many human activities such as coastal protection, tourism, defense and security, and countless others. Ocean observation enables us to better understand ocean functions and meet societal needs related to these activities.
The Intergovernmental Oceanographic Commission (IOC of UNESCO) developed the Global Ocean Observing System (GOOS) more than two decades ago. It was designed to coordinate different national efforts in terms of sustained ocean observations throughout the world, and to maximise the societal benefits of ocean observations.
A wide range of programs and projects are currently aimed at implementing effective ocean observation capacities, operating at different geographic and time scales. These capabilities are, by their nature, highly fragmented and complex. While there is a recognised coordination at the global level under the auspices of GOOS, a strengthening in coordination is still necessary at the regional scale. This will ensure that the right observations are made on a systematic and sustained basis.
An overarching strategy across all measurement platforms is required to ensure that the best use is made of limited resources from Member States and at the European level. The European Ocean Observing System (EOOS) links the currently disparate components of the observing system
in Europe, promoting novel technology and infrastructure development, standardisation, open access to data, and capacity building. EOOS is a coordinating framework designed to integrate Europe’s ocean-observing capacity, whilst promoting a systematic and collaborative approach to collecting information on the state and variability of our seas, and to underpin sustainable management of the marine environment and its resources.
Some of EOOS’s specific responsibilities are:
1. to align and connect existing initiatives, ensuring efficiency and value for money;
2. to identify gaps in the European observation capacity, and foster initiatives to fill those gaps;
3. to promote observation capacities that can benefit multiple sectors;
4. to ensure that Europe’s ocean observing system is integrated into the global observation system(s), by providing a focal point for interaction with international programs and partner initiatives outside of Europe.
In-situ observations provide key information about the physical, biogeochemical, and ecological ocean characteristics. To ensure the long-term stability of ocean information, the totality of the underlying in situ ocean-observing system needs to be recognised as a critical infrastructure network. This mostly publicly funded infrastructure generates open data as a global public good, from which specific products and knowledge are created. This allows delivery of direct and indirect benefits to society by informing public policy, governance, and business decisions.
Such infrastructure needs a strong mandate, including a legal basis to secure binding commitments in a sustained way and in accordance with international standards, including an appropriate data policy for open access and data sharing. National observing systems and roadmaps should be better aligned and deeper cooperation with regional governing bodies is needed. The required growth of the system urgently needs to be matched with more innovative, holistic, and integrative thinking about how to sustainably finance and coordinate these observations.
Several organisations and initiatives at the international level are promoting and developing Ocean Observing Networks through different approaches from their members (government support, research working groups and task teams, etc.). In this context, key references could be ARGO, EMSO, Ocean-Gliders, OceanSites, EuroGOOS, among others. The GOOS Observations Coordination Group (OCG) coordinates across the major, sustained, global
oceanographic, and marine meteorological observing networks. The requirements for ocean observations are expanding and new technologies, variables, platforms, and networks are being developed, deployed, and measured. Observing networks need sufficient maturity and scale to engage with OCG, and the coordination towards supporting GOOS and GCOS.
The proper operation and management of cutting-edge technologies for ocean observation requires both facilities and appropriate equipment, as well as highly qualified technical staff. That is the case with the Oceanic Platform of the Canary Islands (PLOCAN). PLOCAN is a multipurpose service infrastructure with land-based and novel sea-based infrastructures to support research, development, and innovation in the marine and maritime sectors. Its mission is to promote long-term ocean observation and sustainability, providing a cost-effective combination of services through an observatory, a marine test site, a base for underwater vehicles, a training and an innovation hub.
PLOCAN is a member of the Spanish Map of Unique Scientific and Technical Infrastructures (ICTS) and its main objective is the construction and operation of a fixed offshore platform located close to coast and the edge of the continental shelf in Gran Canaria. It’s part of a wider infrastructure designed to act as a test facility and is available for industry and research groups to conduct trials and experiments.
PLOCAN has dedicated assets known collectively as VIMAS (Vehicles, Instruments and Submarine Machines). Its main objective is to provide a permanent service of operational support through a multidisciplinary fleet of cutting-edge autonomous vehicles, platforms, and instruments to all those activities related to ocean monitoring. This has helped provide the motivation and framework to launch the EuroSea’s USV Network initiative.
Autonomous ocean-observing platforms that can enable measurements over a wide range of parameters are a more efficient and sustainable approach than traditional shipbased technologies. Observations range from large-scale processes to small-scale variabilities in salinity, temperature, nitrate, pressure, etc., depending on the needs of the user.
Autonomous technologies for ocean observations in use today include aerial, surface, and subsurface vehicles, satellites, buoys, subsea moorings, and bottom nodes. True autonomy is still unavailable, and all of these observing systems still require a significant deal of human interaction. The largest platforms now support payloads that many years ago would have required manned research vessels. These platforms are still quite expensive and complex. Conversely, systems of numerous, small, and inexpensive observation platforms can increase spatial-temporal coverage, but only for a limited number of ocean variables as small size and limited power implies a limited scientific payload.
All manner of mobile “water-platforms” have been by far the most sophisticated machines developed by humans. As
a key element of exploration, commerce, and war, ships have always involved engineering solutions to difficult problems, and talented individuals to build and operate them.
For thousands of years sailors have placed their trust and their lives in artificial constructions in the face of a challenging ocean. It could be said that the age of “autonomy” has been slow to come to ships. But this is changing. Nowadays there are many small and medium-size unmanned boats in routine use, paving the way toward fully autonomous vessels.
A large list of institutions, universities, and companies have been developing Uncrewed Surface Vehicles (USVs) over the last three decades. Their aim is to cover a wide range of applications and services. With growing worldwide interest in commercial, scientific, and military issues associated with both open-ocean and shallow waters, there has been a corresponding growth in demand for the development of more complex USVs with advanced functionalities. The development of fully-autonomous USVs is underway, aiming to minimise both the need for human control, and the impacts of potential human errors.
An USV is defined as an unmanned vehicle which performs tasks in a wide range of environments without any human intervention with highly nonlinear dynamics. Further improvements on USV technology are expected to bring tremendous benefits, such as lowering development and operation costs, improved safety, extended operational range and precision, and greater autonomy, as well as increased flexibility in sophisticated environments and dangerous missions.
With the inclusion of more robust, available, and affordable navigation equipment (GPS, IMU, etc.), wireless telemetry systems the applications range for USVs has significantly increased and improved in key domains and sectors. These include fields such as scientific research, environmental missions, ocean exploration, the military, and other applications.
After some experimental first steps with limited capabilities, significant progress has been made in recent years in all USV subsystem components (hull and structural elements, propulsion, and power, GNC, telemetry, payloads, data management and ground station). This has enabled a leading commercial technology solution in several applications and services beyond military and research. Improved USV capabilities allow us to undertake missions both in coastal and open-ocean areas for long periods of time due to more efficient power and propulsion systems, in some cases based on renewable energy sources.
State-of-the-art broadband telemetry systems enable remote real-time operation and decision-making. In parallel with the mechanical and electronic system architecture improvements for USVs, software has also advanced rapidly, with a special focus on autonomous navigation methods and techniques. This was done in compliance with ocean digitalisation and e-navigation framework initiatives.
Rent from our inventory of almost 1000 products
Two locations for greatest accessibility Norway and the UK
Up to date, autonomous, and remotely operated platforms at sea have mainly been used as sensor carriers and for other measuring devices. However, nowadays we are facing a step further towards a new paradigm associated with cyber-physical systems, big data, and autonomy, as part of Shipping 4.0 and Digital Ocean international trends and strategies. Efforts in transport cost reduction, the global need for ocean decarbonisation, and the demand for improving safety at sea are three primary reasons why autonomous shipping is currently in the early phases of consideration and implementation.
With these considerations in mind, the development and future implementation of vessels as MASS (Maritime Autonomous Surface Ship) by IMO will represent an inflexion point for this paradigm shift in the industry and maritime shipping as a whole. Therefore, for a successful and smooth settlement of MASS, key aspects related to autonomous shipping and its potential impacts should be envisaged.
Therefore, despite the rapid development of science and technology in the ocean industries, USVs indisputably need to be subject to the international regulations required for vessels to operate safely across international waters. Although some regulatory aspects of manned vessels may be compatible with their unmanned counterparts, such as certain clauses of the International Safety Management (ISM) Code, there is a need for specific international regulations considering the characteristics of unmanned vessels as well. While technology and market demand are required for any innovation to take hold, regulation aspects are still a major consideration. This is especially true in the case of USV developments.
The need to develop the bases for the creation of a coordinated international USV technology network in Europe has been enabled within the framework of the EU’s project EuroSea. The initiative, under the coordination of PLOCAN, has had the direct support of leading institutions such as NOC, MARUM and FEUP-LSTS, as well as the interest and involvement of public research organisations, industry leaders, and government agencies. Since EuroSea finished, its legacy has continued through national and international initiatives, such as DGMM, EuroGOOS, GROOM-II, OASIS, etc.
While small USV developments are usually deployed within sight of the operator, there are many others that go further. Considering hull dimension and propulsion systems as classification factors, several flagship developments have been released in the last two decades, highlighting Sailbuoy (Offshore Sensing, Norway), Wave Glider (Liquid Robotics, USA), AutoNaut (Autonaut-Seiche, UK), C.-Enduro (L3 Harris, UK); Saildrone (Saildrone, USA), DriX (eXail, France), Mayflower (IBM, USA), Sphyrna (SeaProven, France), XO-450 (XOCEAN, UK), SeaTrac (USA), SeaSats (USA); S10- Submaran (Ocean Aero, USA), DataXplorer (OpenOceanRobotics, Canada), SB100-PRO (GPASeabots, Spain); Otter and Mariner (Maritime Robotics, Norway), among many other currently existing USV technologies.
It was on the back deck of a boat in the Gulf of Mexico, while overseeing the installation of a deep-water mooring system, a young marine engineer was witnessing firsthand a rather cumbersome connection of two mooring line components. The operation involved multiple hands, a gaff, and a forklift. The mission was more dangerous than it needed to be, there had to be a better way.
Back on shore, he recounted the story to his colleagues at creative engineering firm Enginuity and the team promptly put their heads together. As many of Enginuity’s engineers and technicians shared a deep marine pedigree, they all had a vested interest that these connectors were safe and reliable. Helmed by engineer Ben Garvey, Enginuity’s earlier clients were purveyors of mooring components for large oil and gas assets, as well as other components such as small connectors, shackles, and H-Links.
Knowing that among even permanently installed mooring systems, there is always a quick connector integrated into the system, the team determined that there must be a better way to make the connection. And since it is necessary that people are safe and assets secure, necessity, as they say, is the mother of invention. But how do you remotely connect two components deep beneath the sea, with almost no visibility simply, safely and with absolute certainty?
It was not a matter of re-inventing the wheel, there really was no wheel. There were other devices on the market, but due to many moving parts, dissimilar materials, and challenging installation procedures, these devices had limitations, high costs and reliability issues.
Back at the Enginuity shop, the challenge was presented to Gleb Sekretta, an engineer with a penchant for solving the seemingly impossible. His initial inspiration came from an unlikely place, the American TV show, Myth Busters. “I had thought of a harpoon type of approach” explains Sekretta, “I had seen a guy fire a harpoon into a 45-gallon drum on TV and I took that as a starting off point.”
Gleb took the simple idea of a barbed hook and ingenuously modified the concept by articulating the barb, making a pawl and stem system that would engage into a receiver. Brilliant in its simplicity, the SEA-Stab was born. From some scrap pieces of stainless steel, a rudimentary design was fleshed out.
Inserted into the top of a 2-litre bottle, the concept was proven. The male end would insert and engage with the receiving side under its own weight. No additional force was needed, hydraulic, mechanical, or otherwise. Furthermore, when not under load, the device could be disengaged with the simple pull of a string. The genius of the SEA-Lift/SEA-Stab derives from a design that allows it to engage using only its own weight (even at depth) and yet can only be released when not under load.
But what kind of force could it handle? Gleb’s colleague, Mechanical Engineer Lou Manuge ran it through comprehensive Finite Elements analysis, finalising the design. Subsequently, with considerable amount of confidence, the nascent device was put under the rigors of NDT’s bigger brother – destructive testing. The testing resulted in the attaching shackle failing well before the coupling itself, proving that the prototype had real potential.
It was in response to the needs of the oil and gas industry where SEA-Stab found its initial market, as an integral component in mooring line assemblies. Incredibly simple to use, demand for the SEA-Stab was high. Straightforward, resistant and robust, it could handle extremely high loads (100-3500Te WLL) and would last 30-40 years.
However, mooring platforms was only the beginning. It soon became apparent that there were many other applications for the device. Tanking oil prices and stalled capital projects added a little “dynamism” to the connector and her inventors.
As natural resource companies were divesting their operations towards other markets, Enginuity accompanied them. James Fisher Decommissioning sought out the SEA-Stab design and incorporated it into their patented SEABASS™ wellhead removal tool. The quick release design of the SEA-Stab allowed decommissioning teams to immediately abort the mission should things go awry, eliminating any potential danger to personnel or environmental impact. Crews could now execute operations with complete confidence in almost any sea state.
Taking the identical design principles of the Sea-Stab, and with the humblest of modifications, the SEA-Lift was born. Enginuity had pivoted from oil platform mooring devices to offering rapidly deployed, high-load dynamic lifting connectors that could be repeatedly used time after time in the most challenging of marine environments.
It is well understood that launch and recovery is one of the highest risk operations at sea. The risk is compounded when the target asset is unmanned. Towed and autonomous vehicles have the inherit challenge of not having a crew to receive a retrieval line.
At launch, the asset can be deployed at any depth or distance from the launch vessel. And upon retrieval, the SEA-Lift is easily directed to a receiver cone pre-fitted on the asset whereupon it engages with the “female” cone and engages under its own weight.
The SEA-Lift product line is a fully scalable series of dynamic connectors that are customisable to any sized asset. Initially used by companies such as Kraken Robotics and Anduril Industries for AUV (Autonomous Underwater Vehicle / Launch and Retrieval), the rapidly deployed dynamic connector has found its home among many defence and surveillance operators. But the utility of SEA-Lift translates across multiple use cases.
Spanning the gamut of various equipment and payloads, from lifeboats and buoy retrieval to cargo loading and subsea asset deployment and retrieval, SEA-Lift and SEA-Stab are an ingeniously simple, economical solution that allows payloads and assets to be brought upon efficiently, without damage and most importantly, in complete safety.
Secured under the trade name SEA-Line™, the two styles of connectors service an array of industries. Operators of all distinctions from platform decommissioning companies to surveillance detection to ocean renewables are adding SEA-Line products to their daily operations.
Current developments in subsea docking for AUV operations are opening the door to for deep-sea recharging and highspeed data transfer. This innovative approach will reduce operating costs and mitigate many inherit associated risks. Incorporating SEA-Line into these technologies will further increase efficiencies considerably. Additionally, the possibility
of integrating “smart deployment” and on-board vision systems to SEA-Line, will even further improve launch and retrieval operations.
Every deployment and retrieval affirm SEA-Lift as an essential means of caring for not only the asset, but the project and all personnel involved. And as the industry grows and horizons broaden, Enginuity and SEA-Lift will continue to find itself simplifying launch and recovery operations for marine operators around the globe.
Rotary Docking interfaces conforming to BS EN ISO 13628-8:2006 ROV interfaces on subsea production systems.
The ETT operates through a dedicated web browser interface, which enables seamless integration with both electric ROV’s & The Jupiter Electric Torque Tool (ETT) is designed for Class 1-4 conventional ROV’s via an Intelligent Power Pod (IPP). The standard
communication interface is Ethernet 10/100 Base-T.
Specification
Max Working Torque: 30Nm to 2,711Nm
• Max Working Speed: 6RPM (fully variable)
• Torque Control Accuracy: ±2% of Torque Demand (271Nm to 2,711Nm)
±10Nm (30Nm to 270Nm)
• Size: 580 x 227 x 215mm
• Lightweight
Depth Rating: 3,000 msw (options to 6,000 msw)
• Power: 115VAC @ 800W (other options available)
• • Communication:
Ethernet: 10/100 Base-T
Serial: RS232 / RS485
For further information, contact sales@zetechtics.com
Digital Edge Subsea, the leading supplier of digital video recorders and inspection systems to the offshore industry, are delighted to announce the expansion of their range of products, with the addition of the ROVTools product line.
The ROVTools’ RTK-01 ROV toolkit is a flexible and highly versatile array. It provides ROV operators with a modular set of tools, and allows them to perform common tasks with greater ease and efficiency.
Compact in size but big on performance, the RTK-01 has the tools to take on a wide range of jobs. This includes cutting ropes up to 25mm in diameter; taking cathodic protection readings; measuring marine growth; and cleaning subsea structures.
Combining 316 stainless steel and tough, corrosion resistant materials with sound engineering principles, the RTK-01 tools are prepared for tasks in the harshest of conditions. With the packaged ROV mounted clamp and tool post system, the modular tool heads can be changed and re-positioned within a matter of minutes. This means less downtime between tasks.
Housed in a custom Pelicase that contains a mounting clamp, adjustable tool pole, adapter brackets, and seven modular tool heads, it’s highly transportable. The tools can also be supplied individually and without the Pelicase.
CLAMP: At the heart of the ROVTools system, the clamp assembly is securely attached to the ROV with six heavy duty bolts and a load-spreading back plate. The tool pole is inserted and quickly clamped into position using two securing bolts and locking nuts.
CUTTER: Efficiently cuts through rope up to 25mm thick, with spring-loaded retractable safety guards, the cutter ensures that the standard STANLEY® blades remain covered until required. Guards can be locked in place when not in use, and changing the blades requires only a pair of pliers.
CP PROBE MOUNT: Designed for the ‘Buckley’ industry standard cathode protection probe, CP readings can be taken quickly and efficiently using this tool.
MARINE GROWTH GAUGE: For visual inspections of underwater structures, this tool provides high contrast and large numerals to allow easy measurement of marine growth up to 300mm deep, in all three axis.
BRUSH: Assembled with six industry standard replaceable wire-brushes on a bracket, that allows five different mounting orientations, the brush tool can be adapted to clean in any direction.
CROOK: The crook’s simple design – a 75mm opening rugged construction – affords the ROV operator a very versatile lifting and positioning tool. Meanwhile the ramped barb ensures that ropes and cables are captured easily and retained.
HOOK: The forward-facing barbed hook design is ideal for collecting, pushing, pulling, or working with finely detailed objects such as netting or ropes.
MARINE GROWTH REMOVER: Using an innovative locking design for quick assembly, the marine growth remover holds an 880mm braided stainless steel or nylon cable between two rods and has been designed to clean up to 26-inch diameter pipe work.
BRACKETS: The 90° and 45° brackets can be used in combination with any of the other kit tools to increase the mounting
orientation options on the tool pole, or as a basis for attaching job specific custom tooling onto.
ELECTROMAGNETS (24VDC): These have been designed to fit to the multi tool adaptor of the ROVTools RTK-01 Toolkit but can also be used independently. With a 50kg pull, these will allow the user to energise the magnet for holding position when conducting stationary work such as hull surveys.
CASSION CLEANER: This prototype subsea cleaning tool has been designed to aid the cleaning of vertical risers and caissons. Two sizes are available, with 400mm and 200mm twin cleaning brushes respectively.
THERE ARE CURRENTLY TWO POWER OPTIONS: 250VDC and 500VDC, with RS-485 communications. A 1U rackmounted topside controller is supplied that allows the user speed and directional control. Two 24VDC motors power the simple modular replaceable cleaning brushes. This will be available once offshore trials have been completed.
EDGE EXTEND: To reduce tool change-out time, we have developed a simple extending ram system tooling skid for medium sized inspection and work class vehicles. The 24VDC extending rams allow the user to install up to four tools on each ROV or skid. These can be extended and retracted as required and are matched to the existing ROVTools RTK-01 toolkit.
A 2U rack-mounted topside controller is supplied to allow the user to extend/retract four rams and control up to four subsea 24VDC relays. Systems will be available for customer trial in June 2024.
Digital Edge Subsea Ltd looks forward to supporting our customers in the subsea industry in 2024 with our new ROVTools product lines, as well as our industry leading digital video recording and inspection systems.
For more information contact info@digitaledgesubsea.com
September 23-26
Halifax, NS
100+ Exhibitors
2,000 Attendees 500 Technical Papers Unprecedented Networking
Shea Quinn, Slocum Glider Product Line Manager, Teledyne Webb Research
If you’ve never read The Slocum Mission by Henry Stommel, it’s absolutely worth the 15-minute read for anyone interested in oceanography, subsea technology, or science in general. Published in the April 1989 issue of Oceanography magazine, the article is a science fictional view of the world of ocean observing in the distant future; it’s written from the perspective of a man in the year 2021 reflecting on the achievements of the oceanographic community over the course of the previous 25 years in bringing to life a network of persistent autonomous subsea vehicles to monitor the world’s oceans.
If that sounds familiar, it’s because it is: over the past 25 years, we’ve seen the rise of gliders – autonomous underwater vehicles with buoyancy-driven engines used for oceanographic research and data gathering – just as predicted in Stommel’s feature. I’ll admit the first time I read The Slocum Mission I was especially confused because I was reading the article in 2021. It was almost read as a history lesson rather than a prediction of what was yet to come. It’s remarkable the foresight Stommel had into the direction and growth of ocean observing – and how much has since come true.
Stommel’s colleague and neighbor, Doug Webb, the “pioneering ocean engineer” in the article, conceived and later developed the first underwater gliders which Stommel named Slocums – in honor of Joshua Slocum, the first man to ever sail around the world solo. By the 1990s, scientists and engineers were busy developing the technologies that Stommel predicted in his article. Webb founded Webb Research (later Teledyne Webb Research) and commercialized the Slocum glider, expanding its reach within the scientific community and making it the backbone of global ocean observing systems. Now 25 years later, as Stommel predicted, there are over a thousand gliders delivered to users worldwide for all types of oceanographic missions.
Earlier this year, we at Teledyne Webb Research launched a new glider vehicle named the Slocum Sentinel Glider, a nod once again to The Slocum Mission article, in which Stommel references the “Sentinel” series of Slocums – gliders designed to achieve the longest missions and most persistent monitoring. This new glider greatly expands upon the capabilities of the Slocum brand, introducing a larger vehicle, greater buoyancy drive, and much higher energy available for longterm and long-distance deployments.
Armed with this new platform, Teledyne Webb Research has partnered with Rutgers University on bringing yet another prediction from Stommel’s science fiction into reality: an international round-the-world voyage of a Slocum Sentinel glider.
On April 23, 2024, Teledyne Webb Research and Rutgers University formally announced this collaborative effort, dubbed The Sentinel Mission, at the Rutgers University Center for Ocean Observing Leadership (RU COOL) in New Brunswick, NJ, USA. Though the Slocum Sentinel glider’s journey won’t begin until later this summer, already there has been several years of planning and coordination between Teledyne and Rutgers on this effort. We agreed to undertake this project in summer of 2022, and since that time the Rutgers faculty have engaged their students with mapping the journey, planning for natural and man-made obstacles to the flight, and using the mission as an opportunity for outreach to the international science community. Teledyne has dedicated resources toward the development and building of a glider that is capable of such a mission.
This partnership builds upon decades of collaboration between Teledyne Webb Research and Rutgers. Doug Webb conducted the first sea trials of the Slocum glider in Tuckerton, New Jersey, working with Rutgers oceanographers. In 2009, Rutgers and Teledyne partnered on the firstever oceanic crossing by an autonomous underwater vehicle when they piloted a Slocum glider from New Jersey to Spain. Since that time, our institutions have continued to partner on new technologies, mission capabilities, and creative solutions for oceanographic research and exploration.
Naming the glider for the Sentinel Mission was no easy task –we wanted a moniker that captured several of the goals we had for the journey: to encourage scientific and educational
outreach, to acknowledge the global reach of the mission, and to honor our founder and glider originator Doug Webb. Ultimately, we decided upon the Research & Education Doug Webb Inter-National Glider, or “Redwing” for short. At the RU COOL ceremony, Redwing was christened with seawater from Falmouth, Massachusetts – where the Sentinel Mission will begin later this year.
As the ceremony concluded, it was impossible not to feel the buzz of excitement in the room for the next step – launching Redwing and undertaking the journey. Undergraduate students, many of whom have spent several semesters dedicating time to the Sentinel Mission, had the opportunity to interact with the vehicle and get an up-close look at the beneficiary of their hard work. Rutgers faculty and Teledyne staff couldn’t help but walk around with large grins as the goal of our collaboration finally felt more real.
In that moment, I couldn’t help but think once again about The Slocum Mission and in particular a passage in which Stommel encourages reserving a percentage of the Slocum glider fleets to pursue projects of “inspiration” – was this not exactly the kind of undertaking he would consider worthy?
It also made me think – if The Slocum Mission was written today, what would the predictions be for the next 30 years of ocean observing? Which new platforms will become available? What advancements in technology will enable
alternate methods of gathering data for the most remote areas of the ocean? What technology being developed in the next 5-10 years will dominate the scientific community in the 2050s?
Time will tell – but for now, we are looking forward to making the science fiction of 1989 a reality 35 years later as we launch Redwing and the Sentinel Mission.
Artistic talent sometimes develops in unexpected places. Gaizka Garay is a fine example of this. While Garay’s lifelong career has been in offshore and marine industries, at a young age he taught himself how to draw and paint.
Garay found his artistic inspiration while working on industrial sites. He started as a marine engineer on board tankers, bulk-carriers, and cable ships. He then became a cable plough and ROV tech/supervisor, before finally moving onshore to work as a technical and subsea manager.
Back in 2017, Garay decided to pursue art as a sideline. In order to technically improve his art skills, he enrolled at the Taller de Arte Mingos Teixeira (the Mingos Teixeira Art Workshop). Finally in 2022, he decided to retire from the industry in order to pursue art full time. Currently, he is studying silk screen painting at the EMAO, a local arts school located in Vigo, Spain.
Here you can find examples of Gaizka Garay’s art, some of which are also for sale. His paintings would make a great addition to any office in the offshore industry.
Richard Stevens, CEO, Smarter Subsea Handling (SSH).
Oil & Gas decommissioning and Offshore Wind construction necessitates a momentous amount of underwater lifting work conventionally conducted by highly specified offshore construction and diving support vessels with large subsea cranes, but this always comes with a hefty price tag, especially in an ever-tightening vessel market where oil & gas and offshore wind are competing for larger vessels.
Smarter Subsea Handling (SSH) is targeting its novel ROVAR subsea lifting device to meet the demands of the decommissioning, offshore wind and undersea defence sectors. ROVAR is an acronym for Remotely Operated Vehicle for Assets Recovery.
The novel ROVAR cleantech range of cryogenic variable buoyancy systems have been designed for the underwater and seabed lifting and handling of offshore energies and defence infrastructure.
The core ROVAR system, ROVAR-20 designed to produce a 20-tonne lift, is based on a small lightweight underwater vehicle consisting of three chambers – a central liquefied gas storage tank, or 'dewar', flanked by a pair of buoyancy caissons. Vectored thrusters, positioning and load sensing, and
a range of interchangeable tooling and grabs add enormous operational versatility in terms of load shapes and sizes that can be recovered from or deployed to the seabed.
A focus of ROVAR’s development is the use of lightweight materials, wherever possible, that would withstand the harsh subsea environment. The system therefore uses a combination of Glass Reinforced Plastic (GRP) composites for nonload bearing parts of the structure and carbon fibre for load bearing, or pressure resistant, components.
Liquid nitrogen is stored in the dewar at around -196°C (-231°F). Gaseous nitrogen occupies a volume around 690 times greater than liquid nitrogen at atmospheric pressure, and it is the exploitation of this physical property that provides greater lift efficiency, and greater versatility and repeatability compared to compressed gases.
SSH is working actively with alternate vessel operators such as SFF Services, the commercial arm of the Scottish Fishermen’s Federation, to use their under-utilised vessels, achieve lower marine emissions and provide a lower cost of deployment and recovery. In addition, the operational flexibility and capacity of smaller offshore vessels, such as Pelagic Fishing Vessels that do not carry heavy lift back deck cranes, will be expanded. This is made possible by the fact that all critical lifting is carried out subsea, controlled from the support vessel via power and data umbilical, without the need for vessel DP.
In terms of operation, as ROVAR is lowered into the sea, with or without a load, dump valves are opened allowing seawater into the buoyancy caissons until such time as it becomes slightly negatively buoyant, allowing it to move downwards under control.
To control the rate of descent towards the seabed, a dewar valve is opened allowing liquid nitrogen to flow through a pipe enveloped by the surrounding seawater facilitating thermal exchange, vaporising the nitrogen and displacing seawater within the caisson, controlling descent and enabling ROVAR to momentarily hover in a neutrally buoyant state. The dump valves are then opened allowing gas to vent and water to enter the caissons, thereby returning to negative buoyancy. Through accurate adjustment of gas ingress and gas egress, the rate of descent can be fully controlled.
ROVAR, using its vectored thrusters, can manoeuvre horizontally allowing it to navigate from the vertical axis to its desired location, constrained only by the length of its power and data umbilical.
Depending on whether ROVAR is in deployment or recovery mode, different adjustments to the level of buoyancy compensate for the change in payload mass, both positive and negative.
All of these operations are managed by ROVAR’s control system which captures various real-time telemetry data
feeds, including load cells, sonar measuring distance from seabed and pressure sensors measuring depth, enabling it to meter liquid nitrogen flow and vaporisation in concert with the venting of nitrogen vapour, thereby maintaining precise levels of buoyancy throughout, irrespective of whether or not the ROVAR is carrying a load. The system is designed to operate to 2000 msw using nitrogen with further studies suggesting the potential of 4000 msw using liquid hydrogen.
Numerous repeat operations are possible without the need to replenish ROVARs internal liquid nitrogen storage. On an indicative basis, ROVAR-20 can perform 8 separate 20-tonne seabed to surface lifts at 100msw and 4 lifts at 200msw, with many more lifts for smaller loads and also where handling around seabed without ascending to surface. This becomes particularly useful for hub and spoke operations, whether ‘hunting and gathering’ debris and items for recovery into a single location, or ‘picking and placing’ from a central location and distributing individual items repeatedly to a desired location.
Since the initial development, SSH have consulted widely with the oil & gas sector and the industry regulator (OPRED), as well as numerous offshore wind project developers. As a result, they have developed two new products which, like the core ROVAR product, can be deployed independently from a conventional multi-use vessel as part of the backdeck equipment, or from vessels of opportunity such as Pelagic Fishing Vessels.
ROVAR-BB, or Buoyancy Beam has been designed to provide dynamic buoyancy for handling elongated structures such as the removal of oil & gas pipeline bundles, and the handling (and repositioning) of dynamic cables, mooring lines, umbilicals, and tubulars at any stage of a project lifecycle across all marine sectors.
Variably buoyant caissons along its beam allow the controlled lifting of elongated structures with different longitudinal weight distributions.
Integrated with cutting and crimping tooling, ROVAR-BB can cut and lift sections of pipeline bundles into, for example, 100m sections using multiple ROVAR units to spread the elongated load and recover the sections to surface.
Once at surface, the sections can be supplemented with fixed buoyancy for wet-tow to recycling yards, while the ROVAR units can remain onsite to continue the sectioning operation.
In circumstances where shorter sections of pipeline are cut (typically around 20m sections), it may be preferable to recover to a submersible barge. ROVAR-WB, or buoyant Wet Basket product, has been designed to collect multiple pipeline sections, or other items requiring recovery to surface.
Once full, the ROVAR-WB’s buoyancy would be activated for lift-to-surface and transfer to a submersible barge for eventual tow to recycling yards. ROVAR-WB can be designed to any practical length and weight bearing capacity and can be deployed as a “seabed trailer”, attached to a ROVAR master unit as a “seabed truck”, to be shunted or towed into position.
Following their participation at the Underseas Defence Technology event, SSH are developing, in collaboration with partners, a mobile and variably buoyant recharging station for underwater military assets (Project MARS).
Under the High Patronage of Mr Emmanuel MACRON President of the French Republic
26>28 June, 2024 Nantes, Pays de la Loire • France
LEADING INTERNATIONAL EVENT ON OFFSHORE RENEWABLE ENERGY
Book your participation among the
stakeholders in offshore
and MRE and check out the full programme
Submarine Networks EMEA is the leading annual subsea connectivity event in the region, bringing together 800 senior leaders from the global subsea market for two jam-packed days of learning, collaboration and networking.
In addition to o ering plenty of networking opportunities, attendees will be able to enjoy thought-leading panels, technical presentations, workshops and cable project and connectivity hub updates.
Gather high-quality survey data at a lower operational impact. Our integrated USV services deliver an efficient, environmentally friendly alternative to vessel supported operations.