
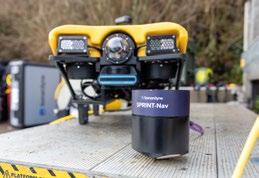
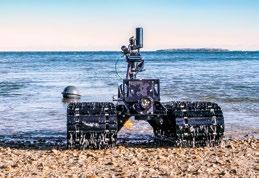
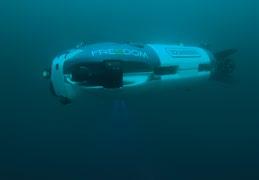
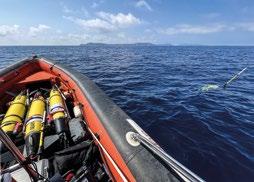
• intelligent vehicles
• reliable communication
• accurate positioning
• modern sensor networks
• diver navigation systems
April 8-10, 2025
High resolution sonar system solutions for Mine Counter Measures and other military applications.
Supporting ocean scientists, engineers and the maritime industries overall by providing underwater technology.
Advanced instruments used in oceanography and subsea navigation to help measure movement in underwater environments.
Mission-ready Hybrid ROV system with fully integrated sensors for fast deployment.
Adaptive robotic arms for intervention and control in offshore energy and modern naval landscapes.
Robust, reliable underwater sensors for the planet’s harshest environments and most difficult applications.
Find out more
06. Events Calendar & Welcome to Ocean Robotics Planet
09. Unlocking New Possibilities for Small Robotic Vehicle Operations
15. Greensea IQ Pioneering Subsea Robotics
21. Freedom AUV Performance Delivers Military Precision
25. Keeping a Complex Warship Fighting Fit – An Industry View
31. Enhancing the Capability of Intervention Class Vehicles
35. Diving Deep: The Role of Testing and Certification in Subsea Vehicle Buoyancy Performance
38. Disruptive Defence Tech Startups Making a Debut at Masschallenge
40. Poster: Alseamar SeaExplorer
43. SeaExplorer: Alseamar’s Leading System for Advanced Underwater Exploration
47. Impact Subsea Unveils ISP360: A New Era in Subsea Profiling
51. What Available and Appropriate Technologies Exist for Critical Underwater Infrastructure Monitoring and Protection
55. Balancing Security and Profits with New Realities: Why Being Compliant is No Longer Enough
59. UDT2025 Shaping the Future of Undersea Defence Technology
61. Sulmara Discover New Age for USVs
65. The U.S. Navy Publishes a New Navigation Plan and Advances the Fielding of a “Hybrid Fleet”
69. Exercise Archipelago Endeavor 2024 is an Opportunity for Experimentation
72. The Self-Propelled MEDUSA Mine System can Clandestinely Seed an Underwater Minefield
73. Leveraging AI-Technologies to Enable Uncrewed Maritime Vessel Autonomy
77. Should You Take a Chance with Chance Maritime Technologies?
ISSN 2755-239X
EDITOR-IN-CHIEF
Richie Enzmann
COPY EDITOR
Will Grant
SALES DIRECTOR
Nick Search
DESIGN & LAYOUT
Milan Farkas
CONTRIBUTORS
Richie Enzmann, Alan Anderson, Alison Pike, Cathrine Lagerberg, Edward Lundquist, George Galdorisi, Jami Cheramie, John Zimmerman, Matthew Chapman, Stephen Sloan
SPECIAL THANKS TO
Aidan Thorne, Alistair Gibson, Andy Freeman, Anthony Hammond, Audrey Leon, Bill Mallin, Callum Shaw, Carl Brendtson, Charlotte Sherwood, Chris Sundstrom, Colin McKinnon, Curtis Lee, Dawn D’Angelillo, Francisco Bustamante, Gill Vosper, Guy Frankland, Jack Rowley, James Colebourn, John Benson, Jostein Jansen, Kieran O’Neill, Matt Bates, Michael King, Morgane Ruiz, Oda Ryggen, Paul Fletcher, Rachael Reader, Rachel McAlpine, Raymond Ruth, Richard Mills, Rob Howard, Sophie Hudson, Tom Smith, Willard Balthazar
Advanced Navigation
Alseamar
BAE Systems
Base Materials
BEC Plastics
Blueprint Subsea
Cellula Robotics
Chance Maritime Technologies
Deepinfar
DeRegt
Digital Edge Subsea
EvoLogics
General Dynamics
General Oceans
Greensea IQ
Impact Subsea
IVM Technologies
Norwegian Offshore Rentals
Oceaneering
QYSEA
Saab Seaeye
Silicon Sensing
Sonardyne
SubC Tech
Sulmara
Teledyne Valeport U.S. Navy
MARCH
UNDERSEA DEFENCE TECHNOLOGY (UDT)
Oslo, Norway (25-27 March 2025)
APRIL SEA AIR SPACE
National Harbor, MD, USA (6-9 April 2025)
OCEAN BUSINESS
Southampton, UK (8-10 April 2025)
MAY COMBINED NAVAL EVENT (CNE)
Farnborough, UK (20-22 May 2025)
JUNE UNDERWATER TECHNOLOGY CONFERENCE (UTC)
Bergen, Norway (10-12 June 2025)
MTS/IEEE OCEANS
Brest, France (16-19 June 2025)
GLOBAL OFFSHORE WIND
London, UK (17-18 June 2025)
SEPTEMBER
OFFSHORE EUROPE
Aberdeen, UK (2-5 September 2025)
DSEI
London, UK (9-12 September 2025)
UNMANNED MARITIME SYSTEMS TECHNOLOGY USA
Arlington, VA, USA (15-17 September 2025)
OCTOBER
NOVEMBER
DECEMBER
MTS/IEEE OCEANS
Great Lakes, USA (29 Sept – 2 Oct 2025)
OFFSHORE ENERGY
Amsterdam, The Netherlands (25–26 Nov 2025)
UNDERWATER INTERVENTION / WORKBOAT SHOW
New Orleans, LA (3–5 December 2025)
My name is Richie Enzmann. Allow me to welcome you all to the latest issue of Ocean Robotics Planet!
Dear Reader,
I’m happy to announce that this is our longest issue to date! And as usual, it’s packed with interesting content for our faithful readers. On the front cover we have the SPRINT-Nav U acoustic-inertial navigation system launched by Sonardyne, which is the smallest in the world and well suited for inspection grade robotic vehicles. This compact system combines the power of INS and DVL technology in a unique way. Its reduced size and ability to operate close to ferrous materials opens up operational capabilities for smaller vehicles working in a variety of fields.
Another interesting technological solution in this issue is Sulmara’s way of using USVs for surveys. They have been pushing innovation to their survey setups to acquire data in a more efficient and faster way. They achieve this by designing innovative techniques & methodologies and joining forces with leading technological partners.
This issue’s centrefold shows the Alseamar SeaExplorer as it’s being launched from a helicopter in a spectacular way – allowing the rapid deployment of this military grade ocean glider.
In the world of defence, Captain Lundquist reports on the Archipelago Endeavor 2024 exercise in Sweden, where Swedish and U.S. Marines improve their combined warfighting skills with the use of unmanned systems. He also reports on the new and secretive MEDUSA unmanned self-propelled mining system that can clandestinely seed an underwater minefield. Meanwhile Captain George Galdorisi shines light on the newly published navigation plan of the U.S. Navy. He also has a new interesting column that looks at Artificial Intelligence (AI) and its implementation into unmanned maritime systems.
Finally, we look at Critical Underwater Infrastructure (CUI) monitoring and protection, which has become a very relevant topic recently due to world events. We have a very detailed article on this topic written by a group of academics and experts, lead by John Potter. I encourage you to read the article to have a better understanding of the challenges and potential solutions to this problem. Cathrine Lagerberg also has an interesting piece on the need for export control of underwater technologies. She explains how important this is, if we want to keep our technological edge and our underwater infrastructure secure in the future.
You can read about all of this in more detail and much more besides. I very much hope you enjoy this quarter’s issue.
Best regards, Richie Enzmann
Working under high pressure DeRegt delivers
Working in oceanic depths under great pressure requires cables and connections you can rely on. At DeRegt Cables we provide outstanding technical solutions and custom-engineered cable solutions for the most challenging of circumstances. When you are raising the bar, we deliver the right solution.
• Top notch cable design
• Reliable cable manufacturing
• High end cable termination
• Thorough cable
•
We deliver safe and precise integrated services that optimize efficiency and keep your operations running smoothly—anytime, anywhere—with our remote and digital offerings.
New capabilities for small, inspection grade, robotic vehicles can now be achieved through the addition of the world’s smallest hybrid acoustic-inertial navigation technology payload.
Introducing SPRINT-Nav U from Sonardyne, the world’s smallest hybrid acoustic-inertial navigator built on the pedigree of its bigger SPRINT-Nav predecessors. This compact and versatile system tightly combines INS and DVL technology to provide robust real-world data. Engineered to increase operational capabilities of any vehicle, this brand-new addition to the SPRINT-Nav family opens a world of opportunities for big performance from small vehicles and towed platforms.
SPRINT-Nav U is the world’s smallest hybrid acoustic-inertial navigator allowing smaller robotic platforms to succeed at more complex and extended missions that weren’t possible before. Its class leading navigation provides robust guidance and control for missions such as geophysical surveys and civil engineering inspections. These were previously limited to larger vehicles due to the size of available true north seeking navigation instruments.
Based on over ten years of proven hybrid acoustic-inertial navigation excellence, SPRINT-Nav U provides an all-in-one turn-key solution at a mere 600 grams in water. Its Inertial Measurement Unit (IMU) contains true north seeking, fibre optic gyroscopes and accelerometers alongside Sonardyne’s trusted Syrinx DVL and a high-performance pressure sensor.
In subsea environments where GNSS signals cannot penetrate, accurate orientation and heading data are crucial for navigation. While both fibre optic gyroscopes (FOGs) and magnetic sensors alongside Micro-Electro-Mechanical Systems (MEMS) can provide motion sensing capabilities, only FOGs, as used in SPRINT-Nav U, can reliably find and maintain heading accuracy in any environment, in such a small form factor.
Demanding surveys require the highest accuracy sensors available, maintaining accurate control of pressure and therefore depth is crucial. The utilisation of the same 0.01% (full scale) pressure sensor as used across the SPRINT-Nav family ensures that survey deliverables which rely on accurate 3D position can always be produced.
Accurate velocity estimation when using a DVL relies on good knowledge of sound velocity. Ideally an external sensor would provide this, however on small vehicles this isn’t always possible. With small vehicles in mind, every SPRINT-Nav U has a calibrated platinum resistance thermometer (PRT), thermally isolated from the SPRINT-Nav U and directly exposed to water, so that as soon as your vehicle is deployed it will compensate accurately for sound velocity.
Sonardyne’s class leading DVLs are designed by application experts with the user in mind, featuring the largest element aperture possible for the SPRINT-Nav they are intended for. This leads to narrower, more focused beams which more precisely measure velocity and maximise high altitude performance.
The tight DVL integration and pre-calibration in the factory means SPRINT-Nav U can align itself to North within five minutes. It’s fast to set up and ready to deploy almost as soon as you’re on site. In fact, it’s the world’s fastest aligning subsea navigator.
SPRINT-Nav U’s design holds the key for unlocking new small vehicle capabilities and operations. Its size optimised FOG, unaffected by ferrous environments, tightly integrated with its world class leading sensor suite, makes it a true selfcontained navigator for any marine environment.
“SPRINT-Nav U can turn any AUV or ROV into a survey grade platform. It unlocks operations that were not previously possible for subsea vehicles. As part of the proven Sonardyne SPRINT-Nav family, customers can be assured of reliable, accurate navigation and positioning every time, no matter the operating environment.” John Houlder, Senior Product Manager, Sonardyne.
Small enough to fit seamlessly on any vehicle, the SPRINT-Nav U is in a navigation payload class of its own.
As you’d expect from over ten years of subsea navigation expertise and innovation, SPRINT-Nav U features an intuitive web UI, an industry standard application programming interface (API), comprehensive guidance control and survey outputs. This provides reassuring familiarity and ease of use for operators alongside compatibility with a range of other systems whilst bringing the accuracy and size weight and power (SWaP) optimisation of the SPRINT-Nav family to smaller vehicles.
SPRINT-Nav U’s reduced size and ability to operate close to ferrous materials opens up operational capabilities for small subsea vehicles working in a variety of fields. Its compact form and weight in water makes it ideal for use on towfish without affecting their deployability whilst delivering robust navigation. Its low power and space requirements ensure ease of integration while providing precise pitch, roll and heading data to support sonar imaging etc.
With increasing demand for autonomous marine defence operations, SPRINT-Nav U can provide easy to deploy, accurate, reliable positioning and navigation for any number of small, covert, autonomous vehicles.
Civil engineering projects along coastlines, in harbours and inland waterways can be undertaken by small, inspection class-sized, vehicles with survey grade precision and without interference from any ferrous infrastructure simply by integrating SPRINT-Nav U into their payload.
SPRINT-Nav U’s ability to provide precise location data even in the presence of ferrous materials makes it perfect for offshore renewable energy operations. Accurate positioning data is needed to enable return visits year on year to conduct surveys of the turbine infrastructure. Smaller subsea vessels are able to get closer to turbines and monopiles for more thorough inspections. SPRINT-Nav U enables them to position themselves precisely without disruption from the structures themselves.
As with all new products prior to their launch, SPRINT-Nav U has undergone extensive testing and trials. Alongside Sonardyne’s in-house testing at their facilities in Hampshire and in the water off Plymouth, SPRINT-Nav U has been through customer testing on ROVs, AUVs and ROTV.
A flooded quarry in Somerset, UK, containing the wreck of a plane and other ferrous objects in depths of up to 36 metres, provided the ideal testing ground in January 2025. Atlantas Marine supplied and operated a VideoRay Defender observation class ROV, which measures 75cm × 39cm × 26cm (L × W × H) and weighs just over 17kg, to put SPRINT-Nav U through its paces.
Launched manually from quayside, and after taking less than five minutes to align, the Defender was soon navigating the quarry with its SPRINT-Nav U payload. Using Greensea software, the Defender was able to successfully perform precise box and lawn mower survey patterns – with less than 0.1% error as a percentage of distance travelled – over the plane wreck without the ferrous materials affecting the navigation.
“The size and weight advantages of the SPRINT-Nav U make it ideal for small observation grade ROVs to perform operations that would previously been beyond their capabilities due to the size of the payload. But perhaps its biggest advantage for us is its ability to maintain precise, accurate positioning around ferrous objects, like monopiles, enabling repeat surveys to be undertaken year on year, with our clients confident that they are returning to the exact same location.” Mark Salter, Senior Project Manager, Atlantas Marine.
UK AUV developers ecoSUB Robotics integrated a SPRINTNav U into their survey grade vehicles to improve the accuracy. SPRINT-Nav U, alongside an 1800 kHz Marine Sonic Technologies Scout ARC MkII side scan sonar kept the
ecoSUBm5-Power+ AUV within a navigational accuracy of 0.45% error as a percentage of distance travelled in a straight line. Initial testing was conducted in Vobster Quay, Somerset before moving to open water work in Chichester Harbour.
“As a small vehicle manufacturer, we have always worked to develop our navigation solution to ensure the greatest utility of our AUVs for the end-user. Having a SPRINT-Nav product available to vehicles in the small to medium range creates a step change in the performance we can get out of our systems, and the value they can add to end users. The results of our trials have proven that SPRINT-Nav U provides reliable navigation and accurate geo-referenced data.” Iain Vincent, Director and General Manager, ecoSUB Robotics.
SPRINT-Nav U has also been successfully integrated with towed survey equipment. In February, as part of their continuing mission to lead innovation in offshore operations, Sulmara mobilised SPRINT-Nav U to a vessel and survey setup in the US to perform various data acquisition tasks with a range of sensor equipment. The sensor payload was towed behind a vessel and aided by a Sonardyne Ranger 2 USBL system. This combination of USBL with the new INS DVL provided the towed platform with a heading accuracy of better than 0.15°.
"SPRINT-Nav U’s performance is really impressive for equipment with such a small form factor. This is something we value at Sulmara, as we're always seeking efficient hardware options to support our innovative survey efforts. We're also increasing the adoption of uncrewed and remote technologies, and it is essential that we do not compromise on the quality of the data we collect. Having the power of SPRINT-Nav products available to deliver guidance for our ROTV operations gives us the reliability needed.” Jim Gardiner, Technology and Innovation Portfolio Director, Sulmara.
“SPRINT-Nav U has been designed with our customers in mind. We’ve been speaking to them for a number of years about their aspirations for operations with small platforms. These trials have demonstrated a variety of use cases for this new, compact navigator and we’re excited to work on many more innovative uses in future.” Aidan Thorn, Business Development Manager – Marine Robotics, Sonardyne.
The successful trials of SPRINT-Nav U in challenging conditions demonstrate its potential to revolutionise small AUV and ROV operations. By combining the accuracy of fibre optic gyroscope technology with an impressively compact design, this innovative navigator allows smaller, more cost-effective vehicles to perform complex missions previously reserved for larger platforms. Its ability to maintain precise positioning near ferrous materials, rapid alignment capabilities, and survey-grade accuracy every time make it particularly valuable for offshore renewable energy inspections, marine defence operations and civil engineering projects amongst many others. WWW.SONARDYNE.COM
CHANGI NG THE PARADI GM OF SURVEY , SCI ENCE AND SECURI TY THROUGH LONG RANGE MODULAR AUTONOMOUS UNDERWATER VEHI CLES Fuel cell power ed AUVs
The maritime industry faces increasingly complex challenges that demand robust technological advancements to ensure operational efficiency, safety, and environmental sustainability. Operators in defense, commercial, and scientific sectors require innovative, adaptable solutions capable of withstanding extreme conditions while improving mission success. Greensea IQ engineers state-of-the-art subsea robotics, autonomous navigation systems, and operatorfocused software platforms that empower teams to work smarter and safer in challenging underwater environments.
Greensea IQ’s suite of advanced technologies—including the Bayonet Autonomous Underwater Ground Vehicles (AUGVs), IQNS Navigation System, EOD Workspace, and Safe C2— sets a new standard for autonomous maritime operations. Designed with precision, modularity, and user-centric control, these products provide defense and commercial operators with a fully integrated ecosystem for safer, more effective missions in complex underwater environments.
The Bayonet series of Autonomous Underwater Ground Vehicles (AUGVs) represents the pinnacle of mission-ready versatility for complex subsea and amphibious operations. These rugged vehicles thrive in environments where traditional ROVs and AUVs face limitations, offering unmatched stability and payload capacity for a range of defense, commercial, and scientific applications.
Bayonet AUGVs operate seamlessly from the seabed to the surf zone and onto shore, making them ideal for nearshore and amphibious operations such as underwater beach surveys, unexploded ordnance (UXO) detection, and coastal mapping. They are engineered to maintain operational stability even in high-energy surf zones, capable of withstanding wave heights up to 6 feet.
Key Features:
ƀ Amphibious Performance: Designed to navigate through surf zones and operate in water depths up to 100 meters.
ƀ Payload Flexibility: A modular design with a large open deck accommodates diverse payloads such as forwardlooking sonar, magnetometers, and sub-bottom profilers.
ƀ Rugged Construction: Built to withstand harsh marine conditions for extended missions.
The Bayonet AUGV is widely utilized for UXO inspection, providing defense operators with a reliable, autonomous tool for detecting and mapping underwater hazards. Its precise navigation system and compatibility with advanced sensor payloads ensure enhanced situational awareness during EOD operations, improving safety and operational success.
At the core of Greensea IQ’s technological advancements lies the IQNS (Inertial Navigation System)—a powerful, compact system combining navigation, control, and perception capabilities for autonomous marine operations. IQNS builds on Greensea IQ’s legacy of advanced inertial navigation and combines INS capabilites with edge processing, delivering reliable performance in dynamic underwater environments.
Key Technical Highlights:
ƀ High-Performance Processing: Powered by the NVIDIA Orin NX, delivering 100 TOPS of AI performance.
ƀ Exceptional Accuracy: Achieves precise navigation using fiber-optic gyroscopes, Doppler Velocity Logs (DVL), and GPS integration.
ƀ Modular and Scalable: The system’s modular design allows for daisy-chaining to expand computational power for complex missions.
IQNS goes beyond standard navigation—it’s a hub for autonomous decision-making. Its support for AI, machine learning, and advanced perception systems enables real-time obstacle avoidance and enhanced situational awareness, crucial for fully autonomous missions.
When integrated with the Bayonet AUGV, IQNS provides a comprehensive solution for EOD missions. Its combination of precise navigation and real-time data processing allows operators to detect, classify, and neutralize threats more effectively while enhancing mission safety.
Greensea IQ’s approach to subsea innovation extends beyond hardware—it’s about developing technologies that meet the evolving needs of the maritime industry. A focus on modularity, interoperability, and operator feedback ensures solutions that adapt to a variety of missions, including environmental monitoring, defense, and scientific research.
ƀ Coastal and Environmental Surveys: The Bayonet AUGV’s high-accuracy RTK (Real-Time Kinematic) survey capability enables precise beach mapping, habitat monitoring, and shoreline assessments.
ƀ Maritime Defense Operations: The Bayonet AUGV and IQNS combination provides a scalable platform for EOD, ISR, and UXO operations in near-shore and shallow water environments.
Greensea IQ is redefining the limits of what’s possible in subsea robotics. The Bayonet AUGVs and IQNS exemplify Greensea IQ’s commitment to providing robust, intelligent tools for safer, more effective maritime operations.
As the industry advances toward greater autonomy and sustainability, Greensea IQ remains dedicated to driving innovation—on the surface, beneath the waves, and at the forefront of technological advancement.
Greensea IQ’s EOD Workspace software is a comprehensive solution for modern explosive ordnance disposal, revolutionizing how EOD technicians interact with data and manage complex underwater tasks. Built with direct input from EOD professionals, this software provides an intuitive, all-in-one platform for mission planning, data analysis, and postmission reporting.
Key Capabilities:
ƀ Centralized Mission Control: Provides a unified interface for planning, executing, and reviewing EOD operations.
ƀ Sensor Integration: Seamlessly integrates with a variety of sensors, including sonars and magnetometers, for enhanced target detection and classification.
ƀ Automated Data Management: Automatically compiles and categorizes mission data, reducing operator workload and improving situational awareness.
EOD Workspace simplifies the complexity of underwater EOD operations by reducing manual data handling, improving coordination between operators, and ensuring a clearer understanding of the underwater environment. When paired with Bayonet AUGVs and IQNS, EOD Workspace provides a complete mission support system for complex defense operations.
Safe C2 revolutionizes the command and control of subsea assets by providing over-the-horizon (OTH) capabilities. This plug-in for EOD Workspaces enables operators to pilot remotely operated vehicles (ROVs) from anywhere in the world,
allowing ROVs to be deployed from unmanned surface vehicles. By maintaining real-time communication and control through secure, encrypted channels, Safe C2 ensures seamless coordination in multi-domain operations, including Explosive Ordnance Disposal (EOD), Mine Countermeasures (MCM), and Intelligence, Surveillance, and Reconnaissance (ISR).
Designed to enhance operational flexibility and safety, Safe C2 minimizes the need for personnel to be physically present in hazardous environments or at sea on research vessels. Whether remotely piloting EverClean robots for proactive hull cleaning or deploying ROVs for critical defense missions, Safe C2 delivers reliable, long-range command and control. This technology empowers warfighters and operators to achieve mission success with confidence while keeping personnel safely out of harm’s way.
Key Features:
ƀ Secure Communications: End-to-end encryption ensures secure data transmission between assets.
ƀ Real-Time Mission Management: Allows for live mission adjustments and data sharing across teams.
ƀ User-Friendly Interface: Intuitive design tailored for use in high-pressure operational environments.
Greensea IQ’s technology suite—Bayonet AUGVs, IQNS, EOD Workspace, and Safe C2—works together as a fully integrated
ecosystem designed for maximum operational effectiveness in complex underwater environments. This cohesive approach provides defense, commercial, and scientific operators with tools that streamline mission planning, execution, and data analysis.
Real-World Applications Include:
ƀ Defense: UXO inspection, EOD operations, amphibious reconnaissance, and ISR missions.
ƀ Commercial: Coastal mapping, harbor inspections, and offshore infrastructure monitoring.
ƀ Scientific Research: Habitat monitoring, sediment analysis, and nearshore environmental surveys.
At Greensea IQ, we are redefining the boundaries of subsea autonomy through intelligent design, operator-driven innovation, and a commitment to environmental sustainability. Our Bayonet AUGVs, IQNS, EOD Workspace, and Safe C2 represent the future of autonomous operations—delivering safer, more effective tools for complex missions across defense, commercial, and scientific domains.
As maritime technology continues to evolve, Greensea IQ remains dedicated to empowering operators with cuttingedge systems that enhance safety, performance, and mission success—above, below, and beyond the waterline.
H I G H - R E S O L U T I O N
PROVEN TECHNOLOGY DELIVERS ADVANCED MANEUVERABILITY, AUTONOMOUS DEPLOYMENT, AND
By Alan Anderson, Matthew Chapman, Jami Cheramie, and John Zimmerman, Oceaneering International
Nations and commercial operators face serious challenges maintaining and protecting critical subsea national infrastructure. They require capable and more advanced technologies to safeguard pipelines and cables. Autonomous underwater vehicle (AUV) technology must deliver better maneuverability and longer residency subsea while providing rapid data transfer. Oceaneering’s Freedom™ AUV technology has been enhanced to meet changing industry expectations that, today, is enabling complex autonomous subsea operations that far exceed what was previously thought possible.
AUVs have carried out simple mapping and high-altitude inspection tasks traditionally in conjunction with a surface support vessel, executing preplanned missions during the dive and delivering data only on their return. This approach required multiple sorties to be planned and executed to address the findings generated in post-survey processing.
The Freedom™ AUV’s advanced technology is now enabling far more complex missions, offering the ability to react to and interact with subsea objects and to remain at depth for long periods without a vessel in attendance. The flexibility provided by subsea residency combined with the ability of re-tasking by shoreside operators enables immediate monitoring and datagathering so decision-makers can make critical determinations to address infrastructure issues or neutralize threats.
Revolutionizing performance in this way requires unconventional thinking and deep domain expertise. Drawing on decades of experience using subsea robotics systems to perform complex and demanding subsea construction, inspection, repair and maintenance tasks, Oceaneering started down a new path more than a decade ago to develop advanced capabilities in the Freedom™ AUV.
This process began with rethinking AUV design and focusing on improved maneuverability. The goal was to develop an AUV capable of high speed and long endurance that could function more flexibly than traditional AUVs by sensing its surroundings and positioning itself closer to objects of interest. The ability to stop, hover, orbit, and reverse, linked with payload informed flight control and onboard decision intelligence enables autonomous single sortie interactions that previously required multiple sorties to survey, process, and analyze, before taking any actions.
The unique autonomous capabilities, combined with two other proprietary developments – namely the field proven Liberty™ subsea resident system and Onshore Remote Operations Centers (OROCs), where experts weigh in on missions in near-real time to quickly make decisions –provide comprehensive mission support planning and shorten postmission processing.
Recent developments with the Freedom™ AUV’s technology have focused on improving endurance, accelerating recharging capability and improving subsea data exchange operations. These capabilities will be incorporated within a new Freedom system, which is due to be delivered to the Defense Innovation Unit (DIU) of the U.S. Department of Defense in 2025 along with an Onshore Remote Operations Center.
Prior to this agreement, in February 2024, the Freedom™ AUV was selected to demonstrate its capabilities to the U.S. government. The DIU contracted Oceaneering to develop and test the Freedom™ AUV as a potential Large Displacement Unmanned Undersea Vehicle (LDUUV) prototype for the U.S. Navy’s Program Office for Advanced Undersea Systems.
Two, one-week AUV demonstrations were completed in March and June 2024 at Oceaneering’s subsea autonomy testing facility in Norway.
The March program included several days of at-sea demonstration that successfully presented the AUV’s unique capabilities and showcased the company’s portfolio of capabilities to design, engineer, operate, and maintain subsea solutions. For the June Program, the DIU set a number of stretch targets for the team to demonstrate the flexibility of the modular architecture and define areas where the capabilities of the Freedom™ AUV could be refined to meet the DIU’s exacting requirements.
Deployed from a suspended cage, the Freedom™ AUV demonstrated exceptional maneuverability—stopping, hovering, station keeping, orbiting and reversing. Its payload-informed flight control employed a camera, multibeam echo sounder, laser imaging system and forwardlooking sonars throughout the missions. The onboard perception stack weighed the data quality, selecting the most trusted data to inform the flight path. The AUV executed orbital inspections and multidirectional obstacle avoidance (including onboard 3D path planning) and proved adept at visual positioning, visual locating, precise, autonomous object deployment, and deployed object position recording.
At the end of the mission, the unit located the suspended cage, re-entered it, and latched itself in.
In June, Freedom’s capability was extended, removing the need for Operator-On-the-Loop and demonstrating its ability to conduct a mission without a support vessel. The AUV was able to “chain together” multiple tasks, moving from transit to survey to deployment and switching instruments on and off as needed to maximize battery life.
Exceptional execution throughout these demonstrations confirmed the reliability of the Freedom™ AUV and its ability to repeatedly execute missions as planned, consistently collecting mission critical, high-resolution data.
In addition to demonstrations for the U.S. Navy, the Freedom™ AUV has completed a number of commercial projects, including exceptionally demanding missions carried out in shallow, high-current areas that historically have been challenging using traditional AUVs and ROVs. One of these projects, was a pipeline inspection industrial pilot for TotalEnergies in the North Sea that demonstrated the unit’s efficacy for sustainable commercial pipeline inspection missions.
The pilot included inspection of more than 120 km of submarine pipelines, adding to an earlier inspection of 60 km of near-shore pipelines inspected to demonstrate the AUV’s ability to detect and track a pipeline while maintaining a defined flight envelope. Employing onboard adaptive behaviors developed to provide additional insights into subsea features, the unit acquired the required data in a single pass.
Onboard autonomous capabilities ensured the AUV remained directly above the pipeline at a low altitude. The onboard high-spec instruments, including a laser imaging system and multibeam sonar technology, delivered a detailed external inspection of the pipeline and surrounding seabed features.
In collaboration with TotalEnergies, onboard automated data processing assessed the effectiveness of the mission and confirmed the pipeline condition via high-quality datasets gathered faster than legacy WROV pipeline inspection methods can deliver. This is a step change in inspection performance. Freedom’s success confirms its ability to conduct rapid pipeline inspection, proving that it can deliver cost-effective surveys.
Additional near-shore and deepwater deployments validate the unit’s ability to execute surveys across a range of environments and conditions, The unit has to-date successfully executed more than 200 km of commercial pipeline survey proving it can consistently execute precise movement, gather quality data, and effect expedient data transfer, paving the way to deploying the AUV for other applications.
Oceaneering’s track record of innovation has laid a foundation for continuing technology development that will further extend subsea robotics capability and performance in the energy and defense industries. Oceaneering will continue to transform subsea operations with the integration of advances in digital twinning and artificial intelligence that will enable better target recognition and more precise execution to improve remote assessment, enhance operational efficiency and transform end-to-end digital and physical subsea robotic services.
Formulated to produce ultra-high strength-to-weight characteristics, our low-density syntactic buoyancy materials are engineered for use in seawater depths down to 11,500 metres.
Low density
Maximum uplift
Full ocean depth
Excellent water ingress resistance
Available as material blocks or completed modules to your design specifications
Not quite ready for a new set of buoyancy modules yet? Our subsea buoyancy repair and refurbishment service provides an alternative solution as modules get worn and damaged, extending life to give you maximum usage.
Visit our website or scan the QR code to find out more base-materials.com
The latest evolution in bathymetric measurement
Density corrected depth data directly from one instrument
The Type 26 frigate: delivering world leading Anti-Submarine Warfare (ASW) capability, combat proven Local Area Air Defence, flexible surface warfare capability, and a large mission bay to support multi-mission and autonomous operations.
As the world's geopolitical landscape and climate changes, so do national defence and security strategies. The reduction of the ice sheet in the Arctic means once denied routes are now accessible by our adversaries. Countering this growing threat requires a continuous deterrent to protect Sea Lines of Communication (SLOCs), provide freedom of passage for world trade, and to ensure that Critical National Infrastructure (CNI) remains protected and secure.
This requires assets being ready for deployment with up-todate platform and weapons systems to meet that threat. The deployment of comprehensive Through Life Support (TLS) strategies combined with continuous Industry Capability
Development plans can deliver enhanced capability at pace. With the evolving threat, there is a growing need to adopt a more offensive position, requiring the ability to search, detect, classify and attack at range, thereby rebuilding the traditional layered approach.
Traditionally, a platform and its systems were designed and procured to meet a defined set of requirements through a specified set of capabilities, applicable to that point in time. Through the platform’s life, new capabilities would be applied on a piecemeal basis as operational urgency dictated and budgets allowed.
Recent operational experiences from Ukraine and the Red Sea have proven the need for continuous development of systems with capability upgrades and insertions to meet the rapidly evolving battlespace. Sporadic, often mid-life capability approaches from the past, cannot maintain defence readiness at the required rate.
Today, navies including the Royal Navy, are seeking to progressively add capability through a Spiral Development Strategy. For the Type 26 Frigate, this ensures that this complex ASW Warfighting Frigate remains fit for purpose as existing threats evolve, new threats emerge and mission profiles change. The need to adapt and complement a platform’s capabilities at pace requires a continuous development and capability upgrade strategy, supported by a shared vision between the military and industry.
The UK regards the Spiral Development vision as a key component of warship sustainment, and is investing significantly in this strategy. This enables the deployment of capability upgrades as they become available rather than waiting for a complete solution as part of a ship mid-life update, which may be too late or no longer fits the purpose.
The Spiral Development strategy for the Royal Navy’s surface fleet ensures its overt and defensive capabilities are match fit for combat operations, as recently evidenced in the Red Sea by the Type 45 Destroyer Sea Viper and Type 23 Frigate Sea Ceptor air defence systems. The Type 26 is being fitted with the Sea Ceptor air defence system along with other, combat-proven systems that are part of the Spiral Development strategy.
The Type 26 has been designed from the outset as a class leading ASW Frigate. Designed to meet the UK’s low acoustic signature requirements to maximise performance of the platform’s underwater sensors and capabilities. The ship’s mission bay, the largest amongst comparative Frigate classes, allows for a wide range of standalone or integrated multi-mission capabilities to support operational requirements, including augmented sensors and effectors deployed
from uncrewed vehicles. The Type 26 industrial enterprise, comprising of some of the world’s leading defence suppliers, is central to the platform’s Spiral Development vision.
As the primary provider of Combat Management Systems (CMS) to the Royal Navy for over 30 years, BAE Systems is developing the in-service support solution to maintain constant capability through life. The solution will continuously remove obsolescence, maintain cyber resilience and further develop capability to match the evolving threat.
The Schiebal Uncrewed Air System (UAS) for the UK MoD’s peregrine programme, is the first UAS to be successfully integrated into an existing UK Warship CMS, an area of capability that could be considered for incorporation into Type 26. In addition, BAE Systems have also successfully integrated an autonomous surface vehicle capability into the same CMS.
BAE Systems is leading the implementation of Maritime Multilink (MML) across the UK fleet. This will enhance the effectiveness of data linked force situation awareness for the Royal Navy and NATO forces, for P-8A ASW operations and the combined multi-domain sea, air, space and land picture.
The Type 26 Frigate will replace the long serving ASW Type 23 frigate, which itself has been subject to capability development programmes through life. The primary towed array Sonar 2087 has been developed for the Royal Navy through the Type 23 programme and will be fitted to the Type 26.
The low acoustic signature of Type 26 fully exploits Sonar 2087 capability, with greater emphasis on the passive capability to provide considerably improved performance over the standard
CAPTAS 4 sonar used on many other International Frigate programmes. Sonar 2087 capability insertions will include software-based enhancements with improved detection and tracking, enhancements to the operator human-computer interface, as well as new decision aids and training tools.
Part of the Type 26 ASW suite is the Leonardo AW101 (Merlin) maritime helicopter providing acoustic processing linked to the dipping sonar and sonobuoys, which can be augmented by UAS in the future.
The new Ultra hull mounted Sonar 2150 will be fitted to the Type 26 replacing the existing Sonar 2050 on the Type 23 fleet. Sonar 2150 will use open systems architecture and will publish/ subscribe inter-process communications to support future capability spirals and facilitate insertion of third-party applications.
The BAE Systems Sting Ray lightweight torpedo, used by both the Royal Navy and the Royal Norwegian Navy, will be upgraded as part of the UK Spiral Development
strategy, which would be applicable to Norway. Airborne and surface platform launched; Sting Ray was recently successfully launched from the BAE Systems Malloy UAV. Work is also underway to integrate Sting Ray to the P8 maritime patrol aircraft, operated by both UK and Norway. The Royal Navy is also investigating options to launch lightweight torpedoes from the Type 26 Mk-41 vertical launch silos, to provide stand-off defence against submarines and surface targets.
The Type 26 Local Area Air Defence capability is provided by the MBDA Sea Ceptor surface to air missile (SAM) weapon system, to protect itself and other units in its immediate vicinity. Sea Ceptor utilises the Common Anti-air Modular Missile (CAMM) used by both the Royal Navy and British Army for air defence of the UK and on deployed operations. CAMM is being developed to provide two longer range variants, CAMM-ER (extended range) and CAMM-MR (medium range), which will increase the maximum operational range of the CAMM family. CAMM can be deployed from a range of launchers including plans for multi-pack solutions from the Mk 41 Vertical Launching System. CAMM is also being fitted to the Royal Navy’s Type 45 Destroyers to provide an enhanced intermediate air defence capability.
In 2023, BAE Systems signed a £270 million contract to enhance the Royal Navy’s radar capabilities to meet the evolving threat. This contract includes the development of the area surveillance Artisan radar fitted to the Type 23 and Type 26 frigates. The contract combined industry funded investment from BAE Systems and UK MOD to develop next generation radar technology. The result will be a family of Artisan radars, which will include sensors for patrol vessels, such as envisaged for Norway’s future standardised vessel program, up to complex frigates.
The Artisan family includes two higher-powered variants for detecting very small targets, such as that encountered recently in the Red Sea, against which Artisan, Sea Ceptor and the BAE Systems CMS are now a combat proven kill chain. The Next Generation Artisan is evolving to provide detection ranges of 300+km, for super/hypersonic missiles and antiship ballistic missiles.
In addition, the Dragonfire Laser Directed Energy Weapon (LDEW) has recently carried out successful trials leading to a UK announcement to bring forward the entry into service of LDEW. After UK evaluation trials are complete, it’s anticipated that Dragonfire will be an option for Type 26.
The Type 26 capability path includes a Future Cruise AntiShip and Land Attack missile, deployed from the MK41 VLS. Kongsberg’s Naval Strike Missile (NSM) is being deployed across the Royal Navy escort fleet, and has also been selected by Australia and Canada for their variants of the
Global Combat Ship (GCS). While only recently announced by Kongsberg, the UK is reviewing the feasibility of a Type 26 MK 41 launched Super Sonic Strike Missile (3SM).
The Mk45 Mod 4 127mm Medium Calibre Gun (MCG) is fitted to the UK Type 26 and has been selected for Australia’s Hunter Class frigate. There are over 200 installations worldwide including over 130 on US Navy platforms. The 127mm is the Standard NATO Calibre for Naval platform MCG’s. The extended range ammunition is evolving including High Velocity Projectiles, which are currently being evaluated by the US Navy. NATO partners are additionally testing unguided and guided Ballistic Extended Range munitions for the MK45 127mm MCG. Other novel effectors under development include the BAE Systems concept Kingfisher, which fires a projectile with an ASW payload that could include small depth charges, sonobuoys, small UUVs, data nodes, acoustic decoys or hydrographic sensors.
With the transition to a continuous capability development strategy that moves away from the traditional mid-life update approach, the Type 26 will be well placed to deal with the pace of the evolving threat and adapt to changing mission profiles. It also enables the Type 26 to remain technically advanced to support the ever-growing need for interoperability with allies for joint operations.
Manufacturing custom-machined components for ROV and associated applications. Any quantity of components at a
Large
Engineered
Lowest
As the demands upon the world’s oceans increase year on year General Oceans a global group of underwater technology companies - has set its sights on addressing the complex needs of the ocean technology user and offering key support to the Blue Economy.
Founded in 2021, General Oceans brings together a portfolio of innovative ocean technology companies dedicated to delivering cutting-edge solutions for global maritime industries. Since its inception the group has grown from founding members Nortek and Strategic Robotic Systems to include Reach Robotics, Tritech International Ltd, and the legendary side-scan sonar designer and manufacturer Klein Marine Systems. This suite of highly respected, industry leading technology companies grew further in 2024, with the addition of Portsmouth based technology distributor RS Aqua. This is an acquisition that will increase the opportunities of all the General Oceans companies operating in the UK.
General Oceans have also invested in two startup companies: the transducer manufacturer Echosonics - who share a base in sister-brand Tritech’s manufacturing facility in Ulverston, UK - and Hefring Engineering, who design and manufacture gliders on the outskirts of Boston, USA.
United by a shared mission, General Oceans’ companies focus on developing innovative technologies that enable their customers to better observe, navigate, and intervene underwater. Every new development - from Reach Robotics’ electric arms to Tritech’s latest multibeam imaging sonar - is designed with the customer at heart.
Australian based Reach Robotics design and manufacture electric robotic arms for underwater intervention in complex environments. Robotic intervention has evolved to tackle tasks once performed exclusively by commercial divers, and with Reach Robotics at the forefront of this revolution. The Reach X empowers smaller ROVs to undertake tasks such as valve turning and shackle removal, previously reserved for work-class systems.
Reach Robotics are working hard to meet the customer requirements of today and of the future. They have hinted recently that they’re working on the design and manufacture of a deeper rated set of underwater robotic arms. This increased depth rating – keeping in mind that the standard electric Reach X has a maximum depth of 300m – will greatly increase capabilities for customers to use these versatile manipulators at much greater depths.
In January 2025, Tritech International Ltd announced the launch of its much-anticipated Gemini 1200id: a 4,000m depth rated dual frequency multibeam imaging sonar. Gemini products include forward-looking imaging and navigation sonars, designed for both shallow and deep-water operations. Gemini sonars are versatile and robust, ideal for integration with ROVs, AUVs, and drones. The Gemini 1200id is the latest addition to the Gemini suite of multibeam imaging sonars, and is designed with Work Class ROVs in mind. The sonar offers the reliability, robust design, and familiarity of the industry standard Gemini 720is, but with dual frequency capability.
The Gemini 1,200id will offer users the frequency of 720 kHz seen previously with the Gemini 720is alongside a second frequency of 1,200 kHz. This allows for closer, more detailed inspection at a much higher resolution.
The new sonar features a wide 120° horizontal field of view when operating at both 720 kHz and 1,200 kHz acoustic frequencies. It also actively attenuates external waterborne noise from other subsea equipment in the vicinity of the sonar. These are some of the enhancements which enable the Gemini 1,200id to produce sonar images with sharp and bright acoustic returns on a noise reduced background, meaning crisp sonar images with impressive clarity.
The Gemini 1200id boasts a range resolution of 2.4mm and importantly, has a depth rating of up to 4,000m. This makes it ideal for Work Class ROV operations in any sector, though commonly seen in underwater energy operations.
The power of a dual frequency sonar unlocks both the collision avoidance capability at longer ranges, and the ability to navigation close range around complex structures and undertake inspections in low visibility waters. At short range, sonars are also an important tool in gaining situational awareness when undertaking complex operations with manipulators and other tools.
The cornerstone of the General Oceans group, Norwegian ADCP and DVL designer and manufacturer Nortek, continues to work tirelessly with customers to solve industry issues.
Offshore survey contractor Modus Subsea Services Ltd (now part of Manta Systems) chose Nortek’s DVL to help maintain navigational consistency for their subsea vehicles while proving the capabilities of resident autonomous subsea systems.
Persistently deployed, or “resident” AUVs and ROVs represent significant environmental and operational challenges, particularly for navigation sensors. Nortek’s DVLs are recognized for maintaining reliable bottom lock in demanding
conditions, which enabled Modus Subsea Services Ltd to successfully demonstrate proof of concept through reliable navigation in acoustically complex subsea environments.
General Oceans also delivers fully integrated systems, combining navigation, imaging, and intervention technologies. The FUSION hybrid ROV/AUV designed and manufactured by Strategic Robotic Systems exemplifies this approach. It offers a mission-ready platform with advanced imaging, navigation, and manipulation capabilities. Designed for both military and security sectors, FUSION is a game-changer for dive teams, coastguards, and special forces worldwide.
The SRS FUSION was recently deployed after the Baltimore Bridge collapse in the USA. The ROV was used to inspect the wreckage of the bridge, and to find victims who had died. This difficult but important work helped to identify the location of two of these victims, and aid in the recovery effort.
The integrated sensor design of the FUSION, facilitates deployment of the vehicle through seamless integration into the software, viewable via a custom-built controller.
In the future, other General Oceans systems can be used to speed disaster recovery efforts. Klein’s 5900 system
leverages multibeam imaging to deliver near-SAS-quality imagery for identifying underwater mines in mine countermeasure applications. This can then be partnered with the SRS FUSION platform to offer unmatched efficiency in verifying and neutralizing underwater threats.
Expanding beyond classic ROVs to hybrid vehicles and AUVs, the growing use of these vehicles for operations has led to a demand for better quality imaging capability on tetherless vehicles. Klein’s side scan sonars are renowned for producing the highest quality sonar images, and the UUV3500 OEM payload continues that trend.
As customer requirements evolve and an ever-expanding array of offshore tasks are performed, General Oceans is committed to developing next-generation solutions to meet these needs, and to ensure customers can meet the challenges of a rapidly changing subsea landscape.
By Stephen Sloan, Head of Commercial at Base Materials
As industries such as renewable energy, marine research, and underwater tourism continue to grow, the need for reliable and efficient subsea vehicles has never been greater. Innovations in design and materials are enabling these vehicles to dive deeper and operate more efficiently, opening new frontiers in both commercial and scientific applications. The subsea vehicle market is not just evolving; it's poised for a transformative leap that will redefine how we interact with our oceans and harness their resources.
But with heightened safety concerns fuelled by recent events in the industry, coupled with ever-increasing operational costs and more stringent environmental regulations, there are a multitude of challenges for owners, operators, and manufacturers.
As a result, subsea vehicle OEMs, owners, and operators must look to guarantee the performance, reliability, and quality of their equipment. Subsea buoyancy modules are missioncritical equipment that ensure the stability and performance of underwater vehicles, enabling them to maintain desired depths and navigate challenging environments. By providing
essential buoyancy control, these modules enhance safety, efficiency, and reliability of subsea vehicles during exploration and research missions.
It is therefore crucial that the quality and performance of the materials used to manufacture buoyancy modules is verified through independent testing and certification.
Buoyancy modules play a critical role in the operation of a subsea vehicle. So how can owners and operators guarantee that the modules they use perform as required during operations?
Buoyancy materials and modules should undergo comprehensive testing to guarantee their quality and reliability. For materials, these are primarily assessed via water absorption tests, hydrostatic crush pressure testing, and density checks. These evaluations are conducted during material development and qualification as part of the manufacturer’s R&D process.
When it comes to the buoyancy modules, these should typically be subjected to calibrated weight-in-air and weight-in-water measurements to verify their performance. Additionally, dimensional checks using laser scanning technology ensure that the modules conform to the specifications outlined in the original CAD drawings. Buoyancy modules can also undergo full-size pressure testing to determine their performance at maximum operating depths, providing suitably sized facilities are available.
The current industry practice of verifying the performance of buoyancy materials and modules is predominantly carried out by the buoyancy manufacturers themselves. The reason this is so readily accepted is that most manufacturers own the required testing equipment. There is however no industry-wide requirement for such testing to be conducted or witnessed by a third party. There is also no requirement for a manufacturer’s testing equipment to be reviewed, unless a manufacturer is ISO 9000 accredited, where it would be included within the quality management
system (QMS). This could be said to represent a potential conflict of interest, given that manufacturers are essentially certifying their own products.
Widely recognised as one of the world’s leading classification societies, DNV is an independent expert in assurance and risk management for the maritime industry. While DNV certification is not a mandatory requirement within the subsea industry, it serves as a crucial benchmark for quality performance assurance.
Organisations that achieve its certification demonstrate a commitment to adhering to rigorous standards and best practices, which enhance the reliability and safety of their solutions. DNV certification involves comprehensive assessments and audits, ensuring that systems and processes meet strict criteria for design, manufacturing, and operational performance.
When it comes to subsea buoyancy, DNV type approval is only awarded to a handful of companies. This rigorous process includes the witnessing of successful testing of a buoyancy materials’ mechanical and hydrostatic properties. It also involves a manufacturer performing pressure tests on samples of the material at a variety of pressures through a variety of timescales. In addition, a range of mechanical tests – such as tensile, shear, and flexural strength – are also conducted on samples of the buoyancy material.
DNV certification undoubtedly provides subsea vehicle owners and operators with a greater level of confidence in the performance and durability of the materials they are relying on. But, while the DNV certification of buoyancy materials isn’t necessarily essential for all applications, it should be mandated across applications like human-operated vehicles (HOVs) where reducing risk should always be paramount.
Triton Submarines are a cutting-edge submersible design and manufacturing company, dedicated to challenging conventional thinking, and pushing the boundaries of innovation to increase ocean awareness and advocacy. They recently approached Base Materials to support the upgrade of the Triton 7500/3, the world’s deepest diving three-person acrylic submersible.
The Triton 7500/3 offers passengers a remarkable 360-degree view of the underwater wonders, enabling an immersive experience during dives that can reach depths of 2,286m (7,500 feet) for durations exceeding 10 hours.
To enhance the submersible’s capabilities, six additional DNV certified buoyancy modules were required to achieve the necessary uplift to allow the vessel to dive over 1.4 miles
subsea. This necessitated a collaboration with a strategic partner who not only boasts in-depth knowledge of subsea buoyancy solutions but could provide DNV certified machined modules ready for installation. These would fit seamlessly within the composite structure of the submersible.
The designs of the new modules were provided by Triton Submarines and manufactured from Base Material’s DNV approved Subtec® 3,000 buoyancy material. This is a lowdensity, high-performance syntactic foam material, which is qualified for use in seawater depths down to 3,000m.
In addition to providing the Subtec® 3,000 buoyancy material, Base Materials delivered a full end-to-end solution. It leveraged its network of trusted partners to conduct CNC machining of the modules to ensure they were built to meet the project’s precise design specifications, ready for installation.
Prior to shipping the buoyancy modules to Triton Submarines’ facility in Barcelona, Spain – where the submersible was being constructed – DNV personnel witnessed the calibrated buoyancy checks, dimensional surveys, and stringently reviewed
documentation from Base Materials. All of this was to ensure that the supplied modules complied with the customer’s specifications and met DNV requirements to maintain the vessel’s certification.
As the subsea vehicle industry continues to grow, the importance of ensuring the quality and reliability of buoyancy materials cannot be overstated. While DNV certification is not mandatory, it offers a vital benchmark for performance assurance, providing manufacturers, ROV owners, and operators with the confidence needed to navigate an increasingly complex operational landscape.
Independent testing and certification not only enhance safety and efficiency but also help mitigate the risks associated with deploying subsea vehicles in challenging environments. As the industry continues to advance, prioritising rigorous quality standards is essential for fostering innovation, whilst ensuring environmental compliance and safeguarding the lives of those who work in these demanding underwater environments.
Richie Enzmann, Ocean Robotics Planet
The 15th MassChallenge BlueTech cohort had an interesting line up of companies this year that are aiming to disrupt the traditional defence robotics sector. MassChallenge’s mission is to equip bold entrepreneurs to disrupt the status quo and create meaningful change. It boasts a network of over 3000 experts, 300 investors, 200 corporate partners, and a pool of 4000 start-up alumni that have collectively raised over $9 billion. The organisation connects startups, experts, corporations, and communities to grow and transform businesses and economies.
Recent startups Havguard, HavocAI, American Tenet, Codective One, and SkylineNav AI were selected out of over 1000 applicants to present their solutions to an audience of tech afficionados that included investors, journalists, and experienced mentors from large defence corporations such as Raytheon, Mitre, and BAE Systems. Each of these startups had the chance to give a 3-minute pitch to the audience to give a flavour of their companies’ technology and market outlook.
HAVGUARD AS, headed up by Emilie Åsberg, are developing an AI driven wireless multi modal underwater communication network, combining acoustics, optical and magnetic modes of communication. Their goal is to provide real-time surveillance of critical infrastructure. Havguard is a dual-use case start-up based out of Norway, with technology designed for mesh networking, for instance where swarms of drones will collaborate on surveillance and detection missions.
HAVOC AI, cofounded by Joe Turner, are building a fleet of AI driven, USV swarm. The company already manufactured a 10 strong fleet of vessels that they are trialling. They aim to bring scalable maritime autonomy solutions and our ultra-low cost, high-rate production USVs to the defense and commercial markets at the
speed of relevance. They claim to be able to increase production up to even 30 units a month if it is needed to be.
AMERICAN TENET, headed up by James Oleen, have developed an engineless, autonomous, and indefinitely loitering drone platform. The system silently detects, tracks, and leverages atmospheric thermals to maintain its altitude with limited radar exposure. Computer vision and advanced sensor packages power propulsion with naturally occurring energy.
CODECTIVE ONE, led by Anton Gera, develop software that utilizes innovative and lean approaches mainly operating in AI/DS/ML. They are applying their vast knowledge of software into drone development in the Ukraine.
SKYLINENAV AI, headed up by Kanwar Singh, have built a GPS-independent precise navigation solution for ground vehicles, drones, boats and aircraft. Their Skyline Match AI harnesses the power of computer vision algorithms and reference datasets to navigate and position effectively without relying on GPS, cellular, or Wi-Fi.
Although the final demo day took place in Boston, MA, the event also included a visit to the new BlueTech Test Tank facility run by the MITRE Corporation. We are very excited to see these startups progress and wish them great success in their endeavours!
Spool piece metrlogy
Intergity management
Mooring inspections
Decommissioning
Fits all sizes of ROVs
Diver held system
For over 15 years, ALSEAMAR has been dedicated to develop small, very long range Unmanned underwater Vehicles. The mission is to provide high-performance, innovative systems for underwater data collection that meets the following challenges: system autonomy and endurance, collected data quality, cost management, ease of use, integration capacity into a larger system of systems. Given these considerations, ALSEAMAR kept developing its underwater gliders as a provider of a smart global solution answering operational needs.
SEAEXPLORER gliders, with months of endurance can scout the ocean over wide areas. Powered by changes of buoyancy, the vehicles pump oil in and out of their central hulls to vary their buoyancy. Under pitch, and thanks to hydrodynamic principles, the gliders move forward as it sinks or rises back to the surface. To follow a specific trajectory, internal low-power actuator roll the vehicle as it glides, enabling
accurate heading and hence precise route following even in the current.
The gliders are equipped with modular nose-cones that can be fitted with a large number of possible sensors, enabling the adaptation of a single vehicle to multiple type of missions by simply interchanging this front section, or even more interesting, using fleets of gliders equipped with different payloads.
The SEAEXPLORER integrates a rechargeable Lithium-Ion battery, allowing optimum global persistence at sea. It only takes three days of interruption in the mission to recharge and considerably reduces the risk of leakage.
Communicating by satellite, the gliders are fully autonomous and remotely monitored by the supervision system GLIMPSE (C2), enabling piloting and data analysis gathered by fleets or potentially shoals of hundreds of vehicles, by a limited number of people.
As it merges data for global operational needs, the GLIMPSE database used by the SEAEXPLORER Community stores over 500 million measurements from 4,000+ missions and is one of the largest datasets in this field.
One of the defining features of the GLIMPSE system is its ease of use, thanks to its modern Web-based graphical interface. This intuitive interface allows users to operate the glider remotely, receive real-time data, and make adjustments to missions as necessary. With GLIMPSE, glider users have access to enhanced data visualizations, performance metrics, and real-time decision-making tools.
Recently, with no additional cost for the user, a model of the different vehicles and payloads was introduced, allowing detailed simulations and predictive analysis, helping pilots to anticipate the glider's behavior and optimize missions before they even begin. The simulator uses digital twins of both the vehicles and the environment (models of currents) to provide accurate estimations. Different scenarios can be simulated and compared before being used as a mission plan.
Automatic data import and export modules were also developed to simplify the publication of the acquired data. The system is now able to publish CTD data to Coriolis (Science), or to connect to NATO command and control systems to receive mission plans and shared acquired data (Defense). Such modules are modular, allowing implementation of others if needed.
The ongoing development of this system ensures that the system capabilities are continually expanding, making it an indispensable tool across a wide range of applications.
The launch of the X3 generation of gliders in 2024 brings improvements and new features implemented on a wider product range, all piloted by the same supervision system. The shared electronic core was optimized to reduce power consumption and acoustic noise both for the navigation and payload CPUs, and made compatible with the use of the hybrid propulsion.
Endurance being a key parameter to minimize at-sea interventions and glider recharging, the control command and sensors power consumption were optimized. One impressive gain was obtained by removing the payload-dedicated CPU, logging the sensor data directly on the navigation one. Thanks to a collaboration with RBR-Canada, an ultra-lowpower CTD-Oxygen-Fluorometer combo was implemented. This solution saves a lot of energy compared to the use of independent sensors from different manufacturers.
Efficiency of the ballast is also a matter of depth, as it is proportional to the operating depth. Some customers working in shallow areas like the Baltic Sea (example: methane leak monitoring by University of Gothenburg using its fleet of SEAEXPLORERs) look for a ballast engine with maximum efficiency at 200m, while others wish to increase the vehicle’s maximum depth.
Based on the same X3 generation core, a family of four products were released in 2024:
ƀ SEAEXPLORER-1000: designed for use down to 1000m, new version of X2 with optional hybrid propulsion;
ƀ SEAEXPLORER-1250: designed with 25% depth increase, down to 1250m
ƀ SEAEXPLORER-1000M: Military version of SEAEXPLORER-1000 optimized for security missions: quieter, securing of data and stealth color;
ƀ SEAEXPLORER-SHALLOW-200: designed for shallow waters (<200m), featuring larger 1.6L ballast, and the option to add a secondary battery, doubling the onboard energy, and optional hybrid propulsion.
Each of this product is compatible with AURIS acoustic payload and back-seat driving system, both developed by ALSEAMAR. With this portfolio, ALSEAMAR offers a complete range, covering shallow to deep-sea operations, allowing the implementation of heterogeneous fleets piloted by the same GLIMPSE interface.
While the SEAEXPLORER system was initially developed for oceanographic use, over the years, ALSEAMAR kept integrating more and more sensors to its modular payloads. Its versatility has been extended far beyond physical oceanography. One of the most notable advances is the integration of biogeochemistry and acoustic sensors, including for example fluorescence sensors and fish sounders. Many new capabilities are in the works, fitting more and more the customers’ needs (DNA samplers, etc).
Meanwhile, the glider’s acoustic capabilities have been enhanced by ALSEAMAR's development of AURIS. This advanced sensor system improves the glider's ability to
monitor and detect underwater noise and marine life. This technology, which integrates real-time data collection and analysis, has proved highly valuable for projects such as the PIAQUO project (which focuses on the study of marine ecosystems using physical and biological data) as well as defense and security missions.
The SEAEXPLORER’s months of endurance in the water enables more comprehensive data collection and better assessment of environmental impacts. For example, it can be used to monitor the impacts of climate change, track pollutants, and measure ocean health over long periods of time. The glider’s persistence in the water makes it an ideal tool for missions requiring sustained observation and data collection.
Starting from an oceanographic tool in 2007, ALSEAMAR, current and future customers now have a full system ready to answer numerous challenges:
Firstly, in a wide variety of scientific domains, such as meteorology (in-situ measurement of temperature and currents in the water column, hurricane and storm forecasting),
geography (monitoring of underwater volcanoes activity, communication relay for seabed stations) and climate change (CO2 absorption assessment and oceans acidification, monitoring of marine heatwaves, biodiversity and eDNA, ocean health and pollution monitoring);
Gliders can also be deployed for marine energies surveys, including oil & gas (natural seeps detection, oil pollution, seismic receivers, far-field measurement and marine mammal detection during seismic surveys), wind energy (ambient noise monitoring, pile driving noise measurement, impact on marine life) and specific regulations (ambient noise and ship noise level measurement, fish stock assessment).
Last but not least, the gliders capacities offer many opportunities for defense and security applications: acoustic intelligence (ACOUSTINT), Underwater Warfare (UWW, including Passive acoustic and multi-static detection), Seabed Warfare (detection near infrastructures), Rapid Environmental Assessment and “Non-Acoustic" wake detection.
Many other detection missions can be considered, such as localization of civil and military aircraft black boxes, etc.
In addition to manufacturing gliders and providing access to the GLIMPSE supervision system, ALSEAMAR has a Survey division that carries out data collection missions. Since 2016, the company has led numerous missions around the world and has acquired a perfect control of the system, as it regularly prepares, deploys and pilots its own fleet on behalf of their customers or as part of funded projects.
ALSEAMAR's survey missions are ideal for offshore companies wishing to de-risk their operations through cost-effective upstream in-situ exploration missions without having to acquire equipment.
Surveys also enable researchers or scientists to test the glider for specific one-off or permanent missions, or to integrate new sensors to push scientific research forward.
Additionally, they enable navies to test the equipment through demonstrations and manipulations in an operational context, before acquiring the gliders. As a matter of fact, ALSEAMAR's ability to develop and operate complex systems of systems ensures optimum interoperability of gliders with other detection systems, and facilitates their integration within a naval force.
Impact Subsea, a pioneer in underwater sensor technology, has unveiled its groundbreaking ISP360 Profiling Sonar and its innovative IS3 acoustic signalling scheme. The ISP360 is a high-performance, mechanically scanned profiling sonar that sets a new standard in measurement precision and range capability.
FEATURES
ISP360 is a highly compact and power efficient 1° to 2° profiling sonar, with up to 80m range and a 0.35mm timing accuracy. The ISP360 provides profiler points of its surroundings, and sonar imagery is also available.
Unlike an imaging sonar a profiling sonar has a very narrow conical acoustic beam. This is ideal for taking a slice of the surroundings and creating a set of range measurements across the scanned area. As the ISP360 moves, these measurements can be stacked together. This enables the creation of a 3D points cloud of the underwater environment.
The ISP360 is depth rated to 4,000m / 13,123ft and is provided in a Titanium housing to enable many years of operation. The profiling sonar provides a full 360° field of view, or a narrower definable sector that can be configured by the user. The acoustic transducer utilises inductive coupling to the profiler electronics which enables operation without the use of slip rings. This ensures excellent longevity in operation without the need to periodically return for slip ring replacement.
Acoustically the ISP360 can operate over the frequency range of 650kHz to 1.25Mhz using Continuous Wave (CW), Compressed High Intensity Radar Pulse (CHIRP), or the Impact Subsea Signalling Scheme (IS3).
IS3 signalling uses advanced phase modulation and coding techniques coupled with CHIRP technology. IS3 also allows multiple ISP360 profilers to operate at the same frequency with significantly reduced interference. This removes the requirement for the ‘ping syncing’ traditionally required for multiple mechanically scanned profilers, thus enabling much faster scanning capability when using multiple profilers and leading to decreased survey times.
“We are excited to introduce the ISP360 Profiling Sonar to the market,” said Ben Grant, Managing Director of Impact Subsea. The ISP360 is a game-changer for underwater profiling and positioning.”
“With integrated IS3 signalling technology coupled with a highly sensitive broadband composite transducer, the ISP360 delivers unparalleled accuracy for sonar profiling with optional pitch and roll, all from a single device.”
The ISP360 offers a number of key features and benefits, including:
ƀ 1° or 2° acoustic angular resolution;
ƀ 80m range capability;
ƀ 0.35mm timing accuracy;
ƀ IS3 acoustic signalling for minimised noise between multiple profilers;
ƀ Optional integration of pitch and roll for even more flexibility and control;
ƀ Integration with seaView software for operation and data generation;
ƀ 4,000m depth rating;
ƀ Software development kit for direct integration into third party systems.
The ISP360 is perfect for a wide range of underwater applications, including:
ƀ Pipeline profiling;
ƀ Trench profiling;
ƀ Positioning of a vehicle in a tank;
ƀ Internal pipe and tank profiling;
ƀ Asset positioning;
ƀ Bridge foundation survey.
ƀ “The ISP360 is a valuable asset for anyone who needs to collect accurate and detailed data about the underwater environment,” said Ben Grant of Impact Subsea. “With its advanced features and versatility, we are confident that the ISP360 will quickly become the industry standard for mechanically scanned sonar profiling.”
Optionally
roll sensing capability. The pitch and roll sensing is based on Micro-Electrical-Mechanical-System
Within the ISP360 there are three MEMS based gyros and accelerometers. The outputs from each of these MEMS devices are fused together, providing highly stable pitch and roll. The integrated sensing capability allows for automatic compensation for vehicle roll during surveys.
In the demanding reliability are both paramount. For those seeking a powerful
and versatile solution for sonar profiling, the ISP360 is a game-changer.
Developed by Impact Subsea, a leader in cutting-edge subsea technology, the ISP360 offers a compact and robust package. Its ease of use is further enhanced by readily available resources on the Impact Subsea website, including informative videos to streamline the learning curve.
Impact Subsea's commitment to innovation extends beyond the ISP360, encompassing a comprehensive suite of subsea sensors and systems. From sonar technologies like the ISS360 and ISS360HD, to altimeters, depth/temperature sensors, AHRS, and Flooded Member Detection Systems, their offerings cater to a diverse range of underwater applications.
With distribution available around the globe, Impact Subsea ensures access to its cutting-edge solutions. The ISP360 and Impact’s entire product portfolio represent a significant advancement in subsea technology, empowering researchers, surveyors, and operators with the tools necessary to navigate the underwater world with greater precision
John R. Potter 1, Jan Petter Morten2 and Steinar Bjørnstad3
1 Centre for Geophysical Forecasting, Institute of Electronic Systems, Norges teknisk-naturvitenskapelige universitet (NTNU)
2 Alcatel Submarine Networks, Norway
3 Tampnet, Norway
In this short commentary we address the issues of who owns, maintains and is currently responsible for Critical Underwater Infrastructure (CUI) with an appraisal of effective technical options that are currently available to monitor and protect them. We conclude that there is a gap in providing coherent protection and that the full power of available solutions is far from realised, largely due to a lack of integration of the disparate parts and the rapid evolution of new technologies yet sparsely appreciated across the stakeholder landscape.
We consider CUI to consist primarily of cables, pipelines and seabed energy production structures. Offshore electrical cables, oil and gas pipelines and seabed production structures are generally owned by large energy corporations with a variety of ownership structures based on specific agreements and regional regulations, which may include national interests and ownerships. Many of these elements
are equipped with Fibre-Optics (FO), embedded in the mixed core of power cables, as a separate cable attached to the exterior of power cables and pipelines or otherwise installed to monitor and communicate with the structures.
Stand-alone subsea FO cables are typically owned by telecommunications companies and consortia formed by these operators. Additionally, major hyperscalers such as Google, Meta, Amazon, and Microsoft invest in and own such infrastructure to support their global data networks.
The responsibility for protection and maintenance of FO cables lies with the owners. Inspections and monitoring of FO cables are generally only conducted when telecom performance degradations occur, meaning damage control is often reactive rather than proactive. Organisations such as the Atlantic Cable Maintenance Agreement (ACMA) and Global Marine perform cable repairs and maintenance when initiated by the owners.
In the case of offshore pipelines, the owners are responsible for routine monitoring and maintenance, carried out according to structured maintenance programs. Specialised subsea inspection companies use Remotely Operated Vehicles (ROVs) and Autonomous Underwater Vehicles (AUVs) to perform periodic inspections, ensuring the integrity of the infrastructure.
Despite their critical importance and relevance to national security, subsea FO cables and oil and gas pipelines are not continuously monitored for or protected against potentially malicious activities in their vicinity. FO cable damage is typically only identified when telecom network performance degrades, while minor oil and gas pipeline damage is usually only discovered during scheduled inspections.
Despite a long history of clandestine cable and pipeline mapping and interference throughout the Cold War, it seems that in the decades of globalisation following the age of détente, little attention was given to the risk of hostile action against the rapidly growing, and often civilian-owned, CUI.
In the light of recent events and geopolitical developments, we now find ourselves motivated to rapidly adapt from focusing on natural hazards to security risk monitoring. This requires a proactive and predictive approach, including deterrence. To achieve this, we need to develop real-time monitoring, with proactive alarm mechanisms.
As shown by recent incidents, trawling and anchor dragging can cause severe damage to submarine cables and pipelines, particularly in areas where cables are insufficiently buried. While some of these incidents are undoubtedly accidental, anchors on some offending vessels have been observed with their tips cut off, so they drag across the seabed rather than dig in as intended by their original design. With only a moderate increase in sophistication, commercially available ROVs can easily be used to deploy explosive charges next to pipelines and other structures.
For oil and gas pipelines, real-time proactive monitoring can both help to prevent damage and reduce inspection costs by enabling targeted inspections when and where an object impact or suspicious activity is detected. Implementing proactive monitoring solutions enhances the resilience of subsea infrastructure, ensuring both operational continuity and cost efficiency.
This commentary is too short to be able to list all applicable technologies, so only those that are newly emerging and/or poorly leveraged will be touched upon.
As much as we might like, we cannot be in all places at all times, so traditional crewed platforms must be augmented with a fleet of smaller, less expensive uncrewed robotic platforms if we are to achieve the required spatial coverage, temporal resolution and timely intervention that is required. We have seen an explosion of capability in maritime robotics in recent years, maturing from research-level systems to an increasingly complete range of vehicles of all sizes and capabilities for use underwater, on the sea surface and in the air. The range and quality of sensors have also improved dramatically, with smaller, lighter and cheaper sensing systems now available to meet a wide range of requirements. A handful of long-range AUVs could now survey the entire Western European CUI network in a few weeks, compared to the several months that it took to do so following the Nord Stream pipeline incident in 2022. NATO has begun to leverage this potential with TASK FORCE X, but this initiative is still in its early stages and needs to be scaled up to cover a much broader area to be effective for CUI protection across European domains of interest.
A significant enabler to maritime robotics is the availability of compact, low cost (in financial, size and weight terms) computational power and memory, combined with advanced miniaturised sensors. These elements in turn allow AI-driven recognition and decision processes to evaluate the environment sensed by the platform to create a local situational awareness in real-time. The crucial benefit of this next-level autonomy is that platforms can now make smart choices about adapting their operational activities in response to their findings, no longer having to wait to pass their data to the outside world and await updated instructions. This dramatically improves the effectiveness and timeliness of robotic platforms.
While AI-driven edge computing is critical to shorten the active control loop for uncrewed systems, AI in the cloud (or, at least, in the outer, supervisory layer of an integrated system of systems) can be used effectively to identify suspicious trends or patterns arising from a disparate number of minor cues that would go unnoticed to human oversight. There are already both military and commercial risk assessment systems being built and offered, based on these ideas. Yet none to date exploit the full range of possible input sensory systems, spanning robotic platforms, shore-based radar, space-based hyperspectral imaging systems, AIS receivers, directional radar antennas, SAR, etc. In addition, AI can infer and predict potentially high-risk scenarios and dubious actors from scouring deep databases of vessels, weather, ports of call, registrations, crew and officers, past incidents, etc. The strength of
synergistic integration lies in the massively increased discriminatory power to reject false alarms, which arise frequently when evaluating the products from only one or a few sensory systems. Data integration enables the detection and flagging of unusual and potentially threatening behaviours in context.
Distributed Acoustic Sensing (DAS) uses light backscatter in an optic fibre to measure real-time strain variations along the cable on the metre-scale. In the last few years, DAS has proven capable of detecting earthquakes, explosions, avalanches, meteors, lightning, trawling, anchor dragging, ships, whales, tsunamis, and a great deal more. The list of potential applications is growing rapidly. Specifically, for CUI monitoring, it is possible to detect, identify and track ships and seabed gear, and to separately detect the seabed interface waves caused by the dragging of bottom trawls and anchors across the seabed in the vicinity of FO cables. This can both enable preventive action and remove deniability on the part of the offending vessel.
Most CUI have FO cables as part of the infrastructure, and existing FO cables can be used with a DAS interrogator to monitor activities in the vicinity, with ranges of few km (in the case of bottom dragging) to tens of km (for the detection of surface ships). DAS is not only able to sense propagating acoustic energy but also stresses associated with surface gravity waves. This allows DAS to detect ships not only by their radiated acoustic signature, but also by the pressure signature of their bow and stern waves, which provide an estimate of their speed and length. Any direct interaction with the cable on the seabed can be pinpointed with high accuracy.
Furthermore, measuring the State of Polarisation of laser pulses in a FO cable adds additional information, confirming if a FO cable has indeed been hit or moved. While FO cable owners and operators have been using these technologies for some time, it is still poorly appreciated and only sporadically applied to CUI protection in general.
Satellites can be equipped with Automatic Identification System (AIS) receivers, Synthetic Aperture Radar (SAR), Hyperspectral optical imaging and directional radar antennas, all of which are powerful tools to detect and identify surface vessels. Optical imaging is now of sufficient resolution to identify the type of vessel being imaged, if the sky is clear. Hyperspectral imaging helps fill in the gaps, while SAR works in all conditions. Directional radar antennas can be used to locate ships that are using radar, of particular interest if that radar source does not correspond with a valid series of AIS packets.
Perhaps the most powerful, yet largely unrealised, technical value is derived by the systemic integration of the many streams of heterogeneous sensing data to provide a coherent
situational awareness. This requires not only the synthesis of many different sensed fields (all with their characteristic ranges, latencies and resolutions) but in the informal inferential Bayesian probability estimation of the probability of a particular vessel, or CUI, being associated with a threat. Several groups, commercial, academic and military, including NATO (e.g. the ‘Mainsail’ program), are beginning to explore this potential and are finding it to be a rich enabler.
A suitable integrated system must provide sufficient information to support informed decisions. The data must have both the sensitivity to detect all important interactions and events associated with a developing incident or anomalous behaviour and the discriminatory power to recognise anomalous behaviour in context. This requires high spatial resolution to detect e.g. a cable interaction that is essentially local, on the metre-scale, in addition to a more global appreciation of context. The resolution requirement, together with spatial coverage that could exceed 100 km, enables accurate localisation at considerable distance from the source. This means that we require data with full coverage for very large areas. The combined requirements of high resolution and high coverage drives us to a very high cumulative data rate. For example, FO sensing for a single cable can amount to several TB of data per day. If we are to monitor many cables, with high spatial resolution and at high acoustic bandwidth then we must find a way to deal with massive data flows. It is impractical to continually stream such data rates to a central processing facility, even if it were desirable. The obvious solution is to process automatically at the edge and transmit only important findings.
Edge computing allows us to process data at or near the sensor so that limited digested output can be transmitted and made available to an operations center in near real-time for timely alerts. The output should provide the basis for classification of the type of incident that is developing and, if possible, identify vessels involved. This supports decision making in case an intervention is required.
Fig. 1 illustrates the range of spatial scales of the problem. We need both high resolution and broad coverage, and no single sensing modality can deliver across the vast range of scales, more than eight orders of magnitude. Only a synthesis of many sensing systems can give us the situational awareness we need.
With efficient high coverage sensing we would be able to target the deployment of drones or vessels, including uncrewed, which would be sparsely distributed over the large scales in question. Instead of patrolling the cables or pipelines, high spatial coverage data of sufficient resolution enables efficient use of drones or vessels, both crewed and uncrewed, by directing them directly to the location where any anomalous event is developing. Efficient and cost-effective
intervention could be implemented by uncrewed surface vessels that can deploy and recover autonomous underwater vehicles and aerial drones.
We consider FO sensing technologies to be a key component, because they provide a data stream that is always on, everywhere on the infrastructure and which does not require any offshore components. When integrated with other sensing modalities, it becomes possible to identify the vessels and mariners involved, who can then be contacted and warned off. Deterrence is the least confrontational and most desirable first-step intervention. Even if the vessel(s) in question continue, denying them deniability is an important component of deterrence and subsequent prosecution of guilty parties.
We also believe that satellite data will be an important component of integrated data interpretation. Satellite optical and radar information have very wide spatial coverage and can be used to track dark vessel activity via several independent sensing modalities, although their temporal resolution may be on the scale of hours and not always useful for real-time situational awareness. Sensors integrated on drones patrolling an area will be characterised by only local coverage but will provide ground truth. These sensors should be of different types that complement the full coverage sensing, e.g. optical (hyperspectral), acoustic, magnetic, EM, to enable appropriate bases for interpretation.
The integrated sensing system envisioned here would provide a very large and dense information pool, with multiple sensing modalities spanning very different spatial
and temporal resolutions and coverage and with different latencies. Automated analysis and integration, coupled with AI data mining will be necessary to provide a robust system to raise alerts for important anomalous events and provide support for intervention decisions. A high false alarm rate would reduce operator capacity to follow up on high-risk events and waste resources. Integrating many independent sensing systems with complementary modalities greatly reduces false alarms arising from any individual system. The AI inferential risk profiling we propose will also serve to provide strong guidance for detecting anomalous behaviours in context.
Existing technologies could be mobilised to address the current gaps in CUI monitoring and protection, but some of these are relatively new and have not yet been deployed at scale. Examples include FO sensing on existing cables, which provides high resolution monitoring over large spatial scales with real-time data streamed to shore at moderate cost. It is also clear that no single sensing system or platform will suffice, due to limitations on resolution, coverage and falsealarm rate. Multiple sensing systems with different modalities, if appropriately integrated, would be capable of delivering the resolution and coverage required, at much lower false-alarm rates, creating more value than the sum of the parts. AI is a key component, both at the edge (to reduce data volume and provide more intelligent and flexible behaviours) and in the overarching situation assessment, where deep mining for patterns will be necessary to identify anomalous behaviour in context.
by Cathrine Lagerberg, Dual-use, Technical & Strategic Risk and Security Expert, Crown Defenze
How can we defend ourselves if we continue selling underwater technology and leaking knowledge to nations we are planning and building defenses against? Most Western companies enforce export control by complying with laws and regulations. However, compliance is no longer enough. The current threat picture demands stricter export controls to remain competitive and safeguard our defense capabilities. Updated decision support, security measures, intelligence-based due diligence and strategic risk assessments: these are all crucial in addressing long-term risks when exporting or exposing critical information to maintain competitiveness and safeguard defense interests.
Western technologies are vital for adversaries' military programs and development, hence the establishment of Coordinating Committee for Multilateral Export Controls (CoCom) in 1949 at the beginning of the Cold War. As the Soviet Union once relied upon Western technologies, China is likely facing the same challenges within certain underwater technologies. Until these nations master series-production of similar quality, they will continue to depend on Western components for their military systems. This underscores the necessity for stringent export controls to prevent the transfer of sensitive technologies to countries that the West do not have security cooperation with.
Modern defense systems, industry, and underwater technologies rely on advanced microelectronics for precise navigation and positioning, reliable communication, target accuracy, and safe and efficient operations. The most advanced microchips are predominantly manufactured in Taiwan on design specifications and orders from U.S. tech companies. Therefore, the U.S. and Western allies currently enforce strict export restrictions to maintain strategic advantage.
As a result, sanctioned nations must acquire much of this technology through illicit and covert means by circumventing the sanctions. If physical goods cannot be obtained, the next targets will be decision-makers, know-how, R&D, and critical intellectual assets: leveraging collaboration, academia, and industry expertise to gain sensitive access, trade secrets, and strategic information.
Companies developing dual-use (both listed and not-listed) technology must understand that they are part of critical supply chains and make strategic risk assessments accordingly. This includes much more forward-looking and holistic security and risk assessment of employers, research collaborations, supply chains, investors, physical and digital access, in addition to the export itself. All of which can constitute unwanted knowledge transfer to countries that we do not have security cooperation with. Sanctioned entities will pursue vulnerabilities as they arise and target their resources with any tool available to whatever company they’re after. Therefore, security must be lifted and holistically assessed and implemented according to today’s threat picture, and how we foresee adversaries targeting our technology tomorrow.
Underwater technologies are critical for national security and military strategy, from the High North and Arctic – key to NATO and U.S. interests, to the South China Sea and Indian Ocean, where global strategic competition between U.S. and allied forces, including Taiwan, and China is intensifying.
Nations like Russia and China are developing advanced underwater capabilities. Strategic nuclear assets and autonomous systems rely on high-quality Western microelectronics
and sensors for mapping, collection, intelligence gathering, and autonomous operations. Some of these technologies are under the limit of ITAR and Wassenaar specifications, or contain items that are not considered “very critical”.
It's impossible to create an exhaustive list of microelectronics and inertial navigation systems (INS). However, without the best of them, your underwater assets will drift off, you can miss your targets, end up with inaccurate maps or positions, lose communication between mothership, modem, transponders and platforms being operated, or conduct unsafe and hazardous operations.
Given the strategic importance of underwater technologies, current export control measures are inadequate if we want to prevent adversaries from acquiring critical technologies.
Unauthorised transfers of Western technologies and knowledge could enhance adversaries' military capabilities and pose significant security and strategic risks. And there is really no such thing as a civilian end user. All civilian vessels and equipment are likely to be placed at state or military disposal if needed. According to the Norwegian Intelligence Service’s annual report Focus 2025:
“The use of civilian technology in military weapons programmes challenges traditional export controls. Civilian technology can be used in weapons and military surveillance, detection, monitoring, planning, construction, and maintenance systems. Russia, China, Iran, and North Korea […] use a variety of methods to obtain and exploit civilian Western technology for military purposes”.
Hence, the likelihood of exporting to a civilian end-user that ends up being used military will always be high.
Many businesses in Europe struggle to navigate China. The export of “listed” dual-use goods for military use to China is not permitted, however, it is highly challenging to ensure export for civilian purpose since China’s national law, Article 7, obligates Chinese individuals and organisations to support national intelligence work.
It's therefore imperative to:
ƀ Include a broader range of dual-use technologies, encompassing also commercial items and non-listed/non-ITAR items;
ƀ Take the Chinese national law into account: the risk of diversion to intelligence and military purposes can never be less than 50%;
ƀ Extend risk assessments to include comprehensive strategic and intelligence-based due diligence and screening, to identify potential threats associated with technology transfers, and assess the risk of diversion to military end-use. These assessments must include employees, sub-vendors, third party contractors, R&D, and any exposure that critical defence suppliers and tech companies have towards entities and companies we do not have security cooperation with.
Complying with laws and regulations is not enough, as regulations are often the result of reactive and long bureaucratic processes and regime consensus.
International frameworks established to define and regulate export of dual-use goods and technologies, like the Wassenaar Arrangement and Missile Technology Control Regime (MTCR), face inherent limitations due to the diverse and sometimes conflicting interests of their member countries with opposing defense strategies and national priorities.
As Chris Lade (Saab UK)’s emphasises in his article “Fortifying Undersea Security”, there is an urgency in joining forces between commercial and defence sector since most of the technology for safeguarding critical undersea infrastructure (CUI) is delivered by the private and commercial industry. Since the same technology can be used against CUI; to detect, map and collect information for intelligence purposes and future offensive military missions, these companies have become our last line of defence.
Companies must therefore embrace their responsibility by enforcing stricter export control and security routines.
Turning a blind eye and continuing business as usual will not only weaken our defense and military strategies, but also lead to loss of market, lost competitiveness, and adversaries gaining crucial technology: ultimately risking the West’s technological lead.
By adopting more strategic security, risk, and export assessments, companies will not only gain a competitive advantage against your competitors, but they will also be in a stronger position to increase market position, and expand market share while mitigating long-term risks. But this will require more than just compliance.
No department or service will do it for you. They may warn you, fine you, or, in the worst case, put you in jail if you fail to comply. But ultimately, the responsibility lies with the company itself, which is perhaps the core of the problem: disclaimer of responsibility.
The authorities must establish requirements and regulations that follow the threat landscape, so it becomes easier for businesses – and not up to the company – to decide when and how to secure the values that will ultimately affect national and international security interests.
Loopholes exist to be circumvented. We cannot rely on disclaimers and written end-use, re-export, prohibited use, or third-party restrictions clauses. These are easy to bypass, and adversaries don’t care.
Next time you wonder whether to export or not, maybe the answer is in the question itself. It’s better to consult an expert one too many times and do some extra due diligence, than finding your sonar on an adversary’s research ship mapping your nation’s/allies’ infrastructure.
There's a lot to think about, but if each of us takes slightly more responsibility for our exports, it accumulates and makes a real impact. One thing is for certain: compliance alone is no longer enough.
25 - 27 March 2025
Oslo, Norway
25 - 27 March 2025
NOVA Spektrum, Oslo, Norway
Undersea Defence
Designed
As global maritime security challenges continue to evolve, the need for advanced undersea defence solutions has never been more critical. In response, the Undersea Defence Technology (UDT) event returns to Oslo from 25th to 27th March 2025, bringing together the world's foremost experts, innovators, and decision-makers in the field of naval and undersea warfare. Hosted at the NOVA Spektrum Convention Centre, UDT 2025 promises to be the premier gathering for those shaping the future of undersea security.
UDT 2025 is the world’s largest dedicated event for undersea defence technology, fostering innovation and collaboration across the industry. This three-day exhibition and conference will welcome over 1,500 attendees, including military end-users, researchers, and defence industry leaders. With key stakeholders from NATO, leading defence companies, and international navies in attendance, the event is set to be an essential platform for discussions on cutting-edge technological advancements and global security strategies.
This year’s theme, “Innovate, Collaborate, Deliver”, underscores the importance of bringing together expertise from different sectors to drive real-world defence solutions. Attendees will engage in high-level discussions about the latest developments in submarine platforms, autonomous undersea vehicles (AUVs), sonar technology, and undersea surveillance systems.
UDT 2025 is not just a conference—it’s an interactive experience. The exhibition will feature pioneering solutions from some of the most renowned defence suppliers, including Babcock, BAE Systems, Kongsberg, and SAAB. Visitors will have the opportunity to witness first-hand the latest innovations shaping naval warfare and maritime security.
The event will also host a series of keynote addresses and panel discussions, offering unique insights from senior military officials and industry pioneers. These sessions will explore pressing topics such as AI integration in undersea defence, advances in stealth technology, and the evolving role of unmanned underwater systems in naval operations.
With geopolitical tensions on the rise and technological advancements accelerating, collaboration among allied nations has never been more crucial. UDT 2025 will provide an unparalleled opportunity for networking, allowing professionals to build partnerships that drive innovation and enhance operational effectiveness. The event will also facilitate discussions on how international cooperation can help nations stay ahead of emerging undersea threats.
For naval professionals, defence contractors, and researchers, UDT 2025 is an unmissable event. Whether you are looking to showcase cutting-edge technologies, gain insights from industry leaders, or expand your professional network, this event offers an invaluable platform for progress in undersea defence.
Join us in Oslo from 25th to 27th March 2025 and be at the forefront of the next wave of undersea innovation. For more details and to secure your place, visit udt-global.com.
Courtesy of Sulmara
At the forefront of these efforts is Sulmara, a Scottishheadquartered international services provider, who specialise in site investigation, construction support, subsea survey and inspection across the offshore energy and utilities sectors. The company has supported a wide range of projects using tailored setups that incorporate innovative technology, aimed at achieving the best quality data possible while significantly reducing carbon emissions and the number of hours people are exposed offshore.
By designing innovative techniques and methodologies, and joining forces with leading technology partners, Sulmara are helping to drive the decarbonisation of offshore services. This has resulted in their development of a new suite of services- known as Sulmara Discover
During 2024, Sulmara executed a number of USV projects in the Gulf of Mexico, including various campaigns of data acquisition on the Bayou Bend Carbon Capture and Storage
While uncrewed surface vessels (USVs) are redefining the way data is collected across a range of marine environments, new thinking is required to get the most out of technology development, and push innovation to survey setups and sensors as well as the uncrewed platform itself. Innovating around USVs requires investment of time, expertise and finance – and a leap of faith in new technologies and approaches.
(CCS) project, a joint venture between Chevron, TotalEnergies and Equinor. Bayou Bend CCS in southeast Texas saw Sulmara work with the project stakeholders to successfully apply some technology innovations for the first time, while also gaining valuable insights and opportunities to how they could be further developed and applied.
Using one of their fleet of WAV-V16 USVs, Sulmara conducted an archaeological and subsurface geohazard assessment of the export pipeline route from the future offshore platform to the beach, supporting a scheme that will reduce the environmental impact of local industrial facilities by isolating carbon dioxide underground. The WAM-V16 is a 4.9m (16ft) uncrewed catamaran from Ocean Power Technologies, with electric propulsion for zero emission data acquisition, and independently articulated hulls separated by a gimblecorrected platform for sensor mounting. The ability of the hulls to independently ‘ride’ over waves, and the stability of the sensors once installed, allows data acquisition in higher sea states than traditionally capable with a USV of similar size.
For the initial survey, the USV was equipped with a full suite of geophysical sensors, showcasing Sulmara’s USV towing capability for side scan sonar and magnetometer data, and providing “some of the best data quality ever seen, even in comparison with conventional methods”. With the survey area around 15km from shore, a Starlink Maritime system was integrated with the command-and-control package on the USV to achieve higher speed communications with the mobile remote command centre. This is the first time Sulmara’s USV of this size has been able to go this far offshore, ensuring improved quality of data and reducing the time needed to collect the information when compared to a conventional survey vessel.
In addition to the USV, an inshore survey vessel was also used during the survey, allowing a direct comparison between the two methodologies. The two vessels acquired largely similar datasets over similar areas, with the USV achieving 38% uptime against poor weather conditions, while the conventional vessel achieved 28% uptime in the same environment. The data was of high quality from both vessels, but the USV required less infill acquisition to meet the scope requirements.
However, there were limitations to the project execution with the USV – the battery life reduced the length of survey windows, and more maintenance was required to keep the vessel and sensors operational, but its encouraging to see a direct comparison showcase the capabilities of USVs towing commonly required survey equipment.
In parallel with development of USV towing capability, since 2022 Sulmara have been working with EdgeTech to bring their Buried Object Sonar System (eBOSS) to the commercial market, building it into a suite of services including various industryleading hardware, custom software packages and exclusive deployment methodologies known as Sulmara Discover
With a long track record in military and defence applications, eBOSS is an advanced 3D sub-bottom and swathbased version of the Compressed High-Intensity Radiated Pulse (CHIRP) sonar system, which generates high-resolution
images of the seabed and the subsurface sediment layers beneath. It is capable of imaging up to 20m below the seabed, depending on the geology., and resolution of 0.05m voxels in all three dimensions throughout the 3D volume allows detailed object detection and imagery in a way not before seen in the industry. As a full-spectrum CHIRP swathbased system, exhibiting survey swath widths up to 60m depending on the sensor height, it is easier to imagine the system as a ‘multibeam echosounder meets sub-bottom profiler’, using some similar technology to provide results. Accurately positioned imagery of surface targets is also acquired, allowing verification of the positioning of objects of interest seen on data from other sensors.
Thanks to the swath-based operation and beam steering options, there is no acoustic blanking, allowing images to be produced beneath assets, giving highly useable information from the surface right down to the extent of the subsurface penetration. Data is available in real time for immediate use, making the system ideal for campaigns where immediate appraisal of the subsurface is required, or for post-installation verification of asset positions. Fully navigable and measurable 3D volumes are produced from post-processing for more detailed imagery of objects, but thanks to the software development undertaken by Sulmara, this is part of the delivery that takes hours or days, as opposed to weeks. Once these 3D volumes are acquired, slices at 5cm intervals in any dimension or direction can be taken, allowing a very high level of interpretation without averaging or interpolating as with other 3D seismic systems.
The year 2024 saw development of Sulmara Discover alongside a USV, offering a unique way of acquiring detailed 3D seabed and subsurface information in shallow water. Following the successful towed geophysical campaign, Sulmara worked with the project partners to realise some of the benefits of Sulmara Discover at Bayou Bend CCS and prove the use of the system from the WAM-V16. Two specific challenges existed within part of the CCS project area that Sulmara Discover was able to support.
Firstly, subsurface depressions from previous jack-up barge spud-can emplacements were not showing up on conventional side scan sonar or sub bottom profiler datasets. The ground conditions and age of some of the subsea infrastructure in this part of the Gulf of Mexico, combined with the age of the anticipated spud-can depressions meant that their location was not known. Thanks to the detailed 3D dataset acquired from the USV, and the advanced processing and imagery available, several of the spud-can depressions were clearly visible in Sulmara Discover , whereas previous survey campaigns had failed to identify them.
Secondly, it was believed that somewhere in the local area there was a buried wellhead that had been abandoned some time ago. The exact location, and critically the depth of burial, of this wellhead was not known – and this posed a potential risk to the CCS project. With a single-channel sub-bottom profiler, discerning the difference between subsurface features can be tricky, and in this case, a previous survey had identified what looked to be shallow gas pockets in the area where the wellhead was believed to be buried. With the additional information available through SulmaraDiscover , the difference between a nearby shallow gas pocket and what is believed to be the grout seal on the wellhead was visible. It can be seen on the data that the grout seal looks very similar to the shallow gas, and with no advanced system to provide greater insight, would have been labelled as such.
The style of wellhead construction and grouting from the 1960s is well known, and the imagery from the USV survey supported the anticipated findings, with the top of the submerged structure likely to be seen just above the level of the grout seal that was clearly visible. In addition, the rest of what is thought to be the wellhead was visible in the 3D volume, right down to the plug at the base. Until further investigation takes place, nothing can be confirmed, but SulmaraDiscoverhas given an insight to what will likely be found in the subsurface. It is worth noting that the
surrounding geology was fairly simple, exhibiting a uniform ‘layer cake’, but the usefulness of the 3D data was clear, even in a simple subsurface environment.
A USV-deployed setup of Sulmara Discover has also been employed to provide shallow water cable tracking and postinstallation depth of burial verification. During late 2024, the use of conventional-only techniques was holding up installation of a small fluid-filled umbilical in a very shallow, turbid environment in the Eastern Mediterranean. These techniques were unable to verify the installation depth of a cable previously branded ‘undetectable’ and requiring the manual efforts of divers until Sulmara Discoverwas used to image the cable. The use of the same survey setup as initially proven in the Gulf of Mexico proved successful once again, and a comprehensive cable profile was produced.
With the resolution and quality of the data acquired, future shallow water projects are anticipated to include pipeline outof-straightness surveys, pre-dredge risk mitigation, UXO detection, buried boulder mapping, landfall cable and pipeline route surveys, marine archaeology, geohazard assessment and asset monitoring campaigns – all performed from a range of platforms that Sulmara is developing.
SulmaraDiscoverbrings together industry-leading hardware and software, and combined with the expertise of Sulmara’s team, has the potential to revolutionise the way sub-surface information is gathered. However, adoption of new technologies come with their own challenges that need to be overcome and the resistance to change is an obstacle often encountered with innovation, despite the potential upside. Sulmara are known for challenging the industry to think differently, to embrace new methodologies, and realise the benefits of doing so – something they will continue to do as Sulmara Discover continues to redefine what can be achieved in the future.
Sulmara is an international services provider specialising in site investigation, construction support, subsea survey and inspection across the offshore energy and utilities sectors. They drive the decarbonisation of offshore services through the development and use of innovative technologies and methodologies. The Glasgow-headquartered business was founded in 2019 and has grown rapidly to more than $70m annual revenue, and building a global footprint with offices in Glasgow, Aberdeen, Norwich, Houston, Singapore and Taipei.
The U.S. Navy has been forthcoming and transparent in its strategies designed to ensure peace and stability on the global commons working with allies and partners. These strategies have contributed to the security and prosperity of all nations touched by the oceans.
Whether manifested in documents such as the Department of the Navy Strategic Guidance, Advantage at Sea: Prevailing with Integrated All Domain Naval Power, or Americas Warfighting Navy, these high-level documents provide a clear vision of how the U.S. Navy intends to accomplish these goals.
While these strategic visionary documents remain important, achieving these goals requires documents with more granularity that describe ways, means, and ends to achieve the desired outcomes.
Over the past decade, these ways, means, and ends have been articulated in Navigation Plans issued by successive Chiefs of Naval Operations. These Navigation Plans serve two purposes. One is to be transparent to the nation and to U.S. Congress regarding the Navy’s goals and objectives. Another is to assign responsibilities to senior flag officers on the CNO staff, as well as to other commands and commanders throughout the Navy.
In September 2024, the 33rd Chief of Naval Operations, Admiral Lisa Franchetti, issued her Chief of Naval Operations Navigation Plan for America’s Warfighting Navy. Admiral Franchetti describes this Navigation Plan as the strategic guidance to the U.S. Navy that builds on the one-page document, America’s Warfighting Navy issued in January 2024 that describes who we are, what we do, and where we are going as the U.S. Navy.
This Navigation Plan embodies “Project 33” in recognition of the fact that Admiral Franchetti is the 33rd Chief of Naval Operations. Project 33 articulates two overarching objectives: an imperative to be ready for the possibility of war with the People’s Republic of China by 2027, and enhancing the Navy’s long-term advantage. Project 33 embodies several components.
The readiness component of the Navigation Plan, has the goal of eliminating ship, submarine and aircraft maintenance delays and restoring critical infrastructure that sustains and projects the fight from shore and are areas that require attention from the Navy shore establishment.
The people component of the Navigation Plan notes the goal of recruiting and retaining the force needed to fill officer, chief petty officer and enlisted ranks and delivering a quality of service for Navy personnel shows a strong focus on balancing quality of life and quality of work for all Navy people.
Finally, the operational component of the Navigation Plan involves creating upgraded command centers for the Navy Fleet Commanders and training for combat to ensure that the Navy has a warfighting advantage over its adversaries.
Finally, the goal to scale robotic and autonomous systems to integrate more platforms at speed focuses on capitalizing on
the inherent advantages that uncrewed systems bring to any navy. This is perhaps the most intriguing part of the CNO’s Navigation Plan for America’s Warfighting Navy.
Momentum to do this has been building for almost two decades, beginning with the Navy’s Strategic Study Group report titled The Unmanned Imperative and other reports and studies up to and including the Navy’s UNMANNED Campaign Framework with its overarching guidance for how unmanned systems might help the Navy achieve its warfighting goals.
These aspirational documents have now found purchase in the Navigation Plan for America’s Warfighting Navy with specific goals and objectives for inserting unmanned and autonomous systems into the Navy inventory.
Admiral Franchetti’s predecessor, Admiral Michael Gilday, articulated the goal of a “500-Ship Navy,” which includes 350 crewed vessels, and 150 uncrewed vessels. Admiral Franchetti has embraced this goal of a “hybrid fleet” and her plan to scale robotic and autonomous systems and integrate them with crewed platforms points directly to the goal of a 500-ship hybrid fleet.
Two recent real-world events have worked to accelerate the U.S. Navy’s development and fielding of uncrewed vessels. The first is the Ukrainian Navy’s use of uncrewed surface
vessels to deny the Russian Navy the use of the Western Black Sea, as well as threaten Russia’s supply lines to occupying forces in Crimea. The second is Yemen’s Houthi rebels use of drones against commercial vessels as well as against U.S. and partner navies in the Red Sea.
Uncrewed capabilities not only keep sailors out of harm’s way, but they provide opportunities to greatly expand the sea service’s warfighting capacity at less cost than traditional Navy vessels. Like their air and ground counterparts, these uncrewed surface vessels are valued because of their ability to reduce the risk to human life in high threat areas, to deliver persistent surveillance over areas of interest, and to provide options to warfighters that derive from the inherent advantages of unmanned technologies.
The Navigation Plan for America’s Warfighting Navy adds more granularity to the “why” behind the Navy’s commitment to uncrewed surface vessels. It notes that robotic and autonomous systems, by augmenting the multi-mission conventional force, will provide opportunities to expand the reach, resilience, and lethality of the combined creweduncrewed Navy team.
A short-term goal, articled in the Navigation Plan, is to integrate proven robotic and autonomous systems for routine
use by the commanders who will employ them. The overarching goal is to integrate mature uncrewed capabilities into all deploying carrier and expeditionary strike groups by 2027. The anticipated use of these uncrewed capabilities will focus on key operational challenges across critical mission areas such as surveillance, fires, networking, logistics, and deception.
The Navigation Plan puts special emphasis on the Hybrid Fleet. As Admiral Franchetti noted, absent a large infusion of resources, it will not be possible to build a bigger traditional navy in a few short years. Therefore, the hybrid fleet concept explained above is seen as a viable path to put enough hulls in the water to accomplish the Navy’s myriad global missions.
The Hybrid Fleet is moving forward. Navy officials have been laying the keel for the future hybrid fleet via experimentation and other efforts, such as standing up Task Force 59 and Task Force 59.1, establishing the Disruptive Capabilities Office, and “operationalizing” the integration of uncrewed platforms into numbered fleets beginning with the U.S. 4th Fleet. Importantly, the Navy is moving from experimentation to integrating robotic and autonomous systems across numbered fleets and Navy Special Warfare to accelerate their integration into the Fleet.
One of the reasons that the Navigation Plan describes the Navy’s confidence in the ability of uncrewed surface systems to perform as expected next to the Navy’s crewed vessels is the fact that over the past decade, the U.S. Navy, along with allied and partner navies, have inserted commercial-off-theshelf (COTS) uncrewed systems into Navy and Marine Corps events to perform a wide range missions.
That said, small and medium uncrewed surface vessels (along with their air and undersea counterparts) must get to the area of operations to perform their various missions. Given that there is limited space aboard Navy ships already loaded with systems, sensors and weapons, another means must be found. This requires a large uncrewed surface vessel as a craft to move
these smaller uncrewed vessels to the area of operations. The Navy wants LUSVs to be low-cost, high-endurance, reconfigurable ships based on commercial ship designs, with ample capacity for carrying various modular payloads. Some potential candidates for this mission include the Navy’s program of record LUSV, the MARTAC T82 and the Ranger and Nomad USVs operated by Unmanned Surface Vessel Division 1.
Rather than speak in hypotheticals, since it will be in the water next year and will be built from the keel up to transport, launch and recover smaller uncrewed surface vessels of various sizes, the Devil Ray T82 is likely a leading candidate to serve as the truck most capable of carrying, launching and recovering smaller uncrewed craft. With a maximum payload of 35,000 pounds, the T82 could carry eight eighteen-foot T18 USVs configured for various Navy missions such as intelligence surveillance and reconnaissance (ISR) and mine countermeasures (MCM).
This is not a platform-specific solution, but rather a concept. When Navy operators see a capability with different size unmanned COTS platforms in the water successfully performing the missions presented in this article, they will likely press industry to produce even more-capable platforms to perform these tasks.
While evolutionary in nature, this disruptive capability delivered using emerging technologies can provide the U.S. Navy with near-term solutions to vexing operational challenges, while demonstrating to a skeptical Congress that the Navy does have a concept-of-operations for the unmanned systems it wants to procure.
Captain George Galdorisi is a career naval aviator and national security professional. His 30-year career culminated in 14 years of consecutive service as executive officer, commanding officer, commodore, and chief of staff. He enjoys writing, especially speculative fiction about the future of warfare. He is the author of 18 books, including four consecutive New York Times bestsellers. His latest book, published by the U.S. Naval Institute, is Algorithms of Armageddon: The Impact of Artificial Intelligence on Future Wars.
By Capt. Edward Lundquist, U.S. Navy (Ret.)
Swedish and U.S. Marines gathered in Sweden’s rocky coastal archipelago to improve their littoral warfighting skills and enhance interoperability during Exercise Archipelago Endeavor 2024 (AE 24).
“This is an annual exercise between Sweden and U.S., and it is the seventh time we conducted it, but it's the first time that we are conducting the exercise as an ally. Before that, we have conducted the exercise as a partner,” said Lt. Col. Patrik Berge of the Stockholm Marine Regiment, representing the host nation.
The Stockholm Marine Regiment operates “where the sea meets the land,” and serves as a vital link between naval and army forces. Using small units, fast boats, mines, missiles, and mortars, the regiment is the Swedish Armed Forces' foremost resource in defending the country's many coastal archipelago areas.
The exercise took place over a several week period in August and September 2024 at the Berga Naval Base south of Stockholm, in and around the Stockholm Archipelago. Berge said approximately 500 Swedish and U.S. Marines and Sailors took part in the exercise, including approximately 225 U.S. personnel from the Marine Rotational Force-Europe (MRFE), which operated alongside Sweden’s (SWE) 1st and 4th Amphibious Regiments.
“The big thing is interoperability. We want to make sure that our systems work together; our people work together; and our leadership can command, control and plan together effectively. We need to test our equipment so we can test different equipment, different techniques and tactics to be better together,” said Berge.
Two Swedish naval vessels took part in the drills: the 234-feet, 2,100 ton, HMSwS Trossö (A264), a patrol craft tender, and HMSwS Loke (671), a 600-class supply vessel equipped for amphibious landings, as well as numerous CB 90 amphibious assault boats.
According to a statement from the Swedish Marines, “AE 24 demonstrates Sweden’s readiness to engage in joint operations, and its commitment to maintaining security in the Baltic Region through pro-active, asymmetric maritime operations.”
“The main aim of the exercise is to enhance the interoperability between Sweden and the U.S., especially regarding warfighting in the littorals. Our training and exercise scenarios have become increasing more challenging and tactically realistic.” Berge said.
AE24 is not only about military readiness. According to a statement from the Swedish Navy, AE24 is a “vital annual exercise between Sweden and the U.S. aimed at developing joint combat capabilities, particularly in coastal and archipelago areas. It is crucial for building interoperability and deepening the military cooperation between the two nations.”
The exercise provides all participants the opportunity to develop, experiment and showcase new joint combat capabilities and future amphibious systems and the ongoing technological advancements between Sweden and the U.S., particularly in coastal and archipelago areas.
That included unmanned systems in the air and on the water.
“We brought several of our unmanned surface vessels to Sweden, which the Marines used for logistics and surveillance,” said Anthony Mulligan, CEO of Hydronalix, a U.S. company based in Suarhita, Arizona. “Our vessels are highly adaptive, small, portable and can be configured to carry food, water and ammunition; or carry a radar, and sonar. The Marines were able to experiment with our boats operating in an austere archipelagic environment. This provides them -as well as our team- valuable realworld experience in how to integrate our vehicles into their distributed maritime operations and best take advantage of our capabilities.”
The Hydronalix boats were developed -and have continuously evolved- through a Navy Small Business Innovation Research (SBIR) investment. The U.S. Marines received training and were certified to operate the Hydronalix systems both before arriving in Sweden and during the exercise.
Testing was conducted using a new configuration of multiple Hydronalix USVs connected together to create an emergency medical evacuation system.
“We adapted our existing Amy USVs and connected them together into a wider and more stable platform to provide a transportation system that can carry one medical patient as well as a medic to provide care enroute to a medical station in a safe area,” said Mulligan. “The vessel is autonomous, so the caregiver only has to be concerned with the patient.”
“It’s important to learn what works and what doesn’t work. We can see how the Marines are using our boats, and what tasks they really need to perform, and we can adapt them and make our platforms perform better and provide even more utility,” Mulligan said.
Sweden’s coastline is referred to as an “extreme littoral” environment, which makes it an ideal place to train.
“Although we are now allies, we had already have established a great relationship with our Swedish counterparts,” said 2nd Lt. Spencer Tidwell, speaking for the U.S. Marines.
“We take a multi-domain approach to warfare in the littorals, from the seabed to space, and including cyber and information warfare. Marines are the only force that can master the littorals -the coastlines and the archipelagos- because we have the ability to control and affect targets on land and sea at the same time.”
During the exercise, Tidwell cited the importance of honing such skills as signature management and self-sufficiency in the field so units can remain in remote and austere locations for extended periods without resupplying.
A Swedish Defence Ministry statement said that, “The Swedish Navy has long maintained a deep and extensive bilateral cooperation with the U.S., and for the Marine Corps, Archipelago Endeavour 24 is a strategically important example of international unit development.”
“Swedish and U.S. Marines have strong bonds,” Berge said. “This exercise makes those bonds even stronger.”
“We're both going to come away from this exercise with a lot a lot more knowledge on both sides,” Tidwell concluded.
By Capt. Edward Lundquist, U.S. Navy (Ret.)
The U.S. Navy has selected General Dynamics Mission Systems to develop the next-generation Mining Expendable Delivery Unmanned Submarine Asset (MEDUSA) system. MEDUSA is a medium-class unmanned underwater vehicle (UUV) with offensive mining capabilities, and is launched from the torpedo tube of a submarine, or, potentially future UUVs.
MEDUSA exemplifies the Navy’s renewed interest in both autonomous unmanned systems and offensive mining capabilities. It can deliver its mine payload accurately and clandestinely to positions far from the launch location or platform, and is designed as an expendable system once deployed.
“MEDUSA is an exciting leap forward for our Navy, aligning with Chief of Naval Operations’ updated NAVPLAN and the evolving nature of warfare,” said Rear. Adm. Kevin Smith, Program Executive Officer, Unmanned and Small Combatants. “This innovative mining system enhances our capabilities, allowing us to stay one step ahead in a rapidly changing environment. By empowering our warfighters with cutting-edge unmanned technology like MEDUSA, we’re ensuring they have the tools they need to thrive in complex situations and protect our interests at sea.”
The initial $15.9 million research and development contract is for the design, fabrication, and testing of the MEDUSA prototypes and associated risk reduction activities. The contract provides options for prototype production and support work through 2032 with a total contract value of up to $58.1 million.
“The award of the MEDUSA contract represents our commitment to advancing unmanned technology and integrating it into Navy operations,” said Capt. Matthew Lewis, program manager of the Unmanned Maritime Systems program office. “Innovation is critical to our national security and directly contributes to the readiness of our fleet. This contract enables us to invest in future operational capabilities and to push the boundaries of what we thought possible.”
The capabilities of General Dynamics Mission Systems Bluefin Robotics platforms and systems are a good fit for the project.
“By leveraging our mature Bluefin Robotics UUV platforms, submarine platform integration experience, and our expertise in launching various torpedoes and payloads from submarines, General Dynamics Mission Systems will provide exceptional capability, military utility, and mission reliability to MEDUSA operators,” said Dr. Laura Hooks, vice president and general manager of the Maritime and Strategic Systems business at General Dynamics Mission Systems.
General Dynamics Mission Systems has brought together a world-class team to support the Navy’s MEDUSA program, including General Dynamics Electric Boat, General Dynamics Applied Physical Sciences, General Dynamics Ordnance and Tactical Systems, EaglePicher, and MIKEL.
“With such an aggressive schedule, each of our partners will have an essential role in ensuring we can deliver on our commitments to the U.S. Navy.” said Paul Dalton, vice president for Autonomous Maritime Platforms at General Dynamics Mission Systems.
Development of the MEDUSA system will occur primarily at General Dynamics Mission Systems’ Quincy, Massachusetts facility, which has become a focal point for rapid prototyping and development of autonomous maritime systems in recent years.
“We’ve recapitalized manufacturing space in our Taunton, Massachusetts, facility to handle the larger scale production of our systems, optimizing our waterfront operations in Quincy as an accelerator for development and prototyping of new UUVs and other novel autonomous maritime systems,” said Michael Guay, director of growth for Autonomous Maritime Platforms at General Dynamics Mission Systems.
“Our initial collaboration with the U.S. Navy on MEDUSA has been very promising and we are poised to move quickly on this urgent operational need.”
By Captain George Galdorisi, U.S. Navy (ret.)
The U. S. Navy stands at the precipice of a new era of technology advancement. In an address at a military-industry conference, then-U.S. Chief of Naval Operations, Admiral Michael Gilday, revealed the Navy’s goal to grow to 500 ships, to include 350 crewed ships and 150 uncrewed maritime vessels. This plan has been dubbed the “hybrid fleet.” More recently, the current CNO, Admiral Lisa Franchetti, has stressed the importance of the hybrid fleet in her Navigation Plan for America’s Warfighting Navy.
The U.S. Navy (as well as other worlds navies) has signaled intense interest in uncrewed maritime vessels. Like their air and ground counterparts, these systems are valued because of their ability to reduce the risk to human life in high threat areas, to deliver persistent surveillance over areas of interest, and to provide options to warfighters that derive from the inherent advantages of unmanned technologies.
One of the most pressing challenges for all navies is to reduce the prohibitively burdensome manpower footprint currently necessary to operate uncrewed systems. Manpower makes up the largest part of the total ownership cost of naval systems. If uncrewed maritime systems are to make up a significant part of any navy the need to move beyond the “many operators, many-joysticks, one-vehicle” paradigm that has existed during the past decades for most unmanned systems is clear and compelling.
There is a strong aspiration to do just that. During a presentation at the U.S. Navy’s Surface Navy Symposium, the Commander of Naval Surface Forces, Vice Admiral Brendan McLane, articulated a goal of having one operator control up to eight uncrewed maritime systems. This is an admirable—and necessary—goal, but one that cannot be accomplished by blunt force. It will require leveraging big data analytics, artificial intelligence and machine learning that is “baked into” these systems.
The keys to controlling multiple uncrewed vessels per operator are:
ƀ The vessel can navigate autonomously on planned mission routes without the concern of hitting other contacts.
ƀ The vessel can detect contacts of interest using artificial intelligence and machine learning and inform the operator: a) that a contact of interest is found, b) that it is implementing the pre-planned or learned behaviors and c) informs the operator of suggested actions.
ƀ The high concept of all of this is trustable autonomy, reliable perception, and an event-based man-machine interaction that is “intelligent” related to the situation and learned/trained tactics and rules of engagement.
With this in mind, a small number of operators could conceivably operate hundreds of USVs with the need for manpower driven by:
ƀ The number and level of adversarial engagements
ƀ Maintaining the vessels
ƀ The logistics of getting vessels in theater and refueled.
Few technologies have dominated the public and defense media as much as big data analytics, artificial intelligence and machine learning. Political and military leaders, CEOs of technology companies, academics and pundits have heralded a new era where AI-technologies will provide people and nations with manifest benefits.
This is good as far as it goes but it begs the question—just how will these technologies enable uncrewed maritime systems to obtain, if not total autonomy, than a substantially reduced human footprint. Unless or until designers can find a way to insert these technologies into uncrewed maritime systems to achieve this goal, the future of these systems may be severely proscribed.
Sadly, there does not appear to be sufficient motivation by navy or industry professionals to insert AI-technologies into their uncrewed maritime systems. While defense organizations worldwide have conducted a plethora of exercises, experiments and demonstrations to evaluate uncrewed maritime systems, most have been focused on the basics of the platform (what missions it can perform, how much can it carry, how fast can it go, what is its endurance, and other attributes). To borrow a U.S. football analogy, this doesn’t advance the ball down the field.
The conflicts in Iraq and Afghanistan spurred the development of unmanned air vehicles and unmanned ground vehicles to meet urgent operational needs. As a result, the lion’s share of previous years’ DoD funding for uncrewed systems has gone to air and ground systems, while funding for uncrewed maritime systems has lagged. However, this balance is shifting, as increasingly, warfighters recognize
the need for uncrewed maritime systems in the fight against high-end adversaries, as well as against nations to whom these nations export their weapons systems.
For this reason, for the past decade, the U.S. Navy and Marine Corps have evaluated uncrewed maritime systems in exercises, experiments and demonstrations. While, as mentioned above, these evaluations have focused primarily on the craft themselves, recently, industry USV manufacturers have begun to bring uncrewed maritime systems with some degree of autonomy or semi-autonomy to these events.
While several industry partners have showcased these autonomous crafts, article length constraints do not allow for a full recounting of all these examples. For simplicity, I will detail the efforts of one manufacturer, Maritime Tactical Systems, Inc. (MARTAC), because they have been invited to participate in the most Navy and Marine Corps exercises, experiments and demonstrations.
If there is a secret to how MARTAC has been able to “bake in” autonomy into each of their various sized uncrewed maritime vessels, it is that each of these boats was designed, tested and fielded at a sufficiently high technical readiness level (TRL) that the basic hull, mechanical & electrical (HME) properties of the MARTAC craft needed little or no additional work and the company could focus on making their boats more autonomous.
While a comprehensive listing of all the ways that MARTAC was able to field USVs with various levels of autonomy is beyond the scope of this article, some highlights reveal that designing uncrewed maritime systems with some degree of autonomy or semi-autonomy is not a bridge too far for industry.
ƀ If there is one reason that some in the maritime community remain skeptical of uncrewed maritime systems, it is their concern that these craft will pose an unacceptable hazard to crewed vessels. These concerns stem from the world of aviation with several near-misses and verified collisions that have involved hobbyist drone operators flying in violation of aviation safety regulations.
ƀ In the maritime domain, crewed vessels abide by the Convention on the International Regulations for Preventing Collisions at Sea (COLREGS). This Convention is similar to the terrestrial rules of the road. MARTAC has inserted software into its various sized USVs to enable them to strictly follow COLREGS so that they do not pose any danger to other craft. While MARTAC craft maneuver according to COLREGS as a default, their algorithms will make an adjustment when the contact to be avoided may itself not follow COLREGS.
ƀ Over a decade ago a MARTAC craft ran a 25-waypoint autonomous mission around San Diego harbor, demonstrating not only COLREGS compliance, but also the ability to follow pre-programmed directions. The capability demonstrated was that the craft’s control system was designed for full autonomy with the ability, but not necessity, for operator intervention.
ƀ During Exercise Trident Warrior in the Hawaii OPAREA, four operators controlled six high- speed MARTAC USVs as “Red Force.” In another exercise, four operators controlled nine MARTAC USVs.
ƀ During the U.S. Pacific Fleet exercise Integrated Battle Problem 21, a MARTAC T38 Devil Ray made a 156-mile round trip autonomous transit from San Diego to San Clemente Island while autonomously dropping two objects, one within two meters of a perfect position.
ƀ A MARTAC T38 Devil Ray craft made a high-speed autonomous run from the coast of Florida to the Bahamas and back in under an hour each way with a cross-track accuracy of under two meters with AI-powered navigation.
ƀ Operating under the auspices of Commander U.S. Fifth Fleet and CTF-59, a T38 Devil Ray made multiple runs through the Strait of Hormuz covering over 1300 nautical miles in nine days. Over ninety-five percent of the mission was run autonomously.
ƀ Working with U.S. Fourth Fleet, a T38 Devil Ray made repeated autonomous high-speed intercept more than 70 knots as well as follow-on demonstrations designed to show how autonomous craft could trail and intercept drug-smuggling vessels.
ƀ In the Philippines, a MARTAC T38 Devil Ray was loaded with an autonomous mission package, directed to arrive at a set destination, and featured an on-board, AI-driven collision avoidance system. It navigated in congested waters, avoiding multiple boats and obstructions without operator intervention. Also, MARTAC’s alt-PNT capability was also demonstrated in combination with MARTAC’s advanced passive perception system in a representative A2/D2 environment.
To be clear, this is not a tip-of-the-hat to one uncrewed maritime systems manufacturer. Rather it is compelling evidence that AI-technologies can be readily inserted into high-TRL craft to enable them to operate autonomously or semi-autonomously. This represents an important breakthrough for uncrewed maritime systems and frees them from the old paradigm of too many people required to operate too few USVs.
Most military-industry conferences include numerous industry booths where platforms, systems, sensors and weapons are on display. Increasingly, these include uncrewed maritime systems. Companies typically explain the attributes of these platforms regarding their basic functions: speed, endurance, carrying capacity and the like.
A visitor to any of these booths is unlikely to hear a discussion regarding the software inside of the USVs that makes it autonomous or semi-autonomous. As the ability of these uncrewed maritime systems to perform a plethora of missions becomes increasingly dependent on a high degree of autonomy, we will likely see more emphasis on what’s inside the craft.
J u n e 1 6 – 1 9
50+ Exhibitors
800+ Attendees
400+ Technical Papers
The OCEANS 2025 Brest conference is for global mari time professionals to learn, innovate and lead in the protection and utilization of the world’s largest natural resource – our OCEANS.
Visit us at brest25 oceansconference org
Unprecedented Networking
4,810 42% 34% 150+ 72%
THE HANDS-ON OCEAN TECHNOLOGY EXHIBITION AND TRAINING FORUM THE HANDS-ON OCEAN TECHNOLOGY EXHIBITION AND TRAINING FORUM TRANSFORM YOUR BUSINESS
3 DAYS HUNDREDS OF SOLUTIONS VISITORS IN 2023 FROM OVER 59 COUNTRIES OF VISITORS FROM OVERSEAS DIRECTOR LEVEL OR ABOVE SPEAKERS, INDUSTRY EXPERTS & THOUGHT LEADERS AUTHORISE OR INFLUENCE BUYING DECISIONS
By Capt. Marc Deglinnocenti, U.S. Merchant Marine (ret.), oldarmada@gmail.com
It’s a chancy world that we live in especially when it comes to some startup unmanned surface vehicle (USV) companies. I happened upon one such startup at the 2024 Underwater Intervention convention in New Orleans, Louisiana, USA. It might have been a “chance” meeting, but the young 34 year old founder and CEO Stuart Chance was surprisingly well versed and experienced in his line of business. He might be standing in the shadow of his father, Thomas Chance who is a retired marine technology entrepreneur best known for selling ASV Global in 2018. However, we must give credit where credit is due. Stuart is no slouch himself.
Stuart Chance worked for the U.S. Army contractor L3 HARRIS as an engineering manager, a project engineer at AVS Global under the tutelage of his father, and as a survey engineer at C & C Technologies which is now owned and operated by Oceaneering. Stuart also holds a Bachelor of Science degree from Louisiana State University. So, his company had a great foundation to start from in 2022. What has all his experience and education along with the additionally impressive resumes from his coworkers produced?
Chance Maritime Technologies offers three USVs. Their 29 foot (8.84 meters) MC-29 has a 2150 nautical mile range at 4.5 knots. Its draft is 2.8 feet (0.85 meters), and its endurance is 20+ days. It has a moon pool for dropping various sensors into the water, a deck mount for equipment, A Frames, and a redundant propulsion system. Since this USV had some A Frames, I asked him if any of his USVs could launch and retrieve Remotely Operated Vehicles (ROVs) or Autonomous
Underwater Vehicles (AUVs). The answer he gave was that this launch and recovery USV capability was currently under development but was very soon to be a reality. It was obvious to me that the A Frames were intended to serve that very purpose, and that capability may already have been achieved by the time of the publication of this article. I then asked him if his USVs could support various types of data collecting sensors currently on the market today. “Of course!” he answered in the positive way to that question. I then tried to trip him up by explaining to him that many of his potential customers already had purchased all sorts of these sensors and other equipment. All these things, I explained, operate on a wide range of Voltages and Amperages as well as 60Hz or 50Hz cycles. He was way ahead of me. His USVs can handle a multitude of equipment power needs. Having been thwarted in finding fault in the MC-29, I moved on to his next largest USV.
Their 30 foot (9.14 meters) LR-30 has a 2150 nautical mile range at 7 knots. Its draft is 3 feet (0.91 meters), and its endurance is 14+ days. It has a modular keel and an A Frame. I noticed that this vehicle had the highest top speed of them all at 12 knots. Having been in some pretty rough sea states myself, I wanted to know if this USV’s hull could take repeated poundings in rough seas for extended periods of time. I mean not just the two weeks endurance either. I meant over the years of use. To my surprise he said that all of Chance Maritime Technologies USVs have aluminum hulls. They are tough and not easily damaged. However, they are easily repaired and modified. He said that you can cut a hole in the hull for mounting a specific piece of equipment. When you remove that piece of equipment, all you have to do it weld a patch into the hull, and it’s just as tough as before. Fiberglass, carbon
fiber, and other exotic material hull repairs are not so simple or as fast. I then asked him about his largest USV.
Their 39.2 foot (11.95 meters) MC-40 has a 9700 nautical mile range at 4.5 knots. Its draft is 4.3 feet (1.31 meters), and its endurance is 90+ days. It has what he calls an astern mission bay. It also has an on-board electrical generator to help achieve such a remarkable endurance. Since this USV was probably going to be weighted down with the most equipment, I asked Stuart if a customer had to drill and cut multiple holes in this hull to mount various sensors. He told me that they had already anticipated this need. The MC-40 has a long aluminum plate keel about 4 to 6 inches (10 to 15 cm) tall that you can drill holes through, weld on, grind on, cut out on, and modify to your heart’s content without compromising the watertight integrity of the hull itself. Mount what you want, where you want, and how you want until all of your mission goals are met with the MC-40 USV. These customer expectations as well as many more such as over the horizon communications have already been thought out and met by Chance Maritime Technologies. They also supply training and customization needs.
I was impressed when I chatted with Stuart Chance and his managers in New Orleans. The National Oceanographic and Atmospheric Association (NOAA) of the USA has also been impressed with Chance Maritime Technologies. Chance has been awarded three NOAA Indefinite Delivery, Indefinite Quantity contracts. Those contracts could total well over 22.5 million U.S. dollars for Chance. I walked away from Stuart’s impromptu interview with the definite feeling that you could indeed take a chance with Chance.
Set against the ocean backdrop at Verftet in Bergen, UTC 2025 will explore the future of subsea technology while acknowledging past achievements. The industry has evolved from tackling deep-water challenges to addressing global energy demands with costefficient, sustainable solutions. While renewable energy gains momentum, reducing emissions from existing resources remains vital. This year’s theme, *Subsea into the Future*, will highlight how subsea solutions can contribute to a more sustainable energy landscape.
Innovation is key, from extending field life and integrating offshore wind to leveraging AI and advancing carbon capture. UTC 2025 will bring together experts from Petrobras, TechnipFMC, and the Northern Lights CCUS project for collaboration and knowledge-sharing. Attendees can join a field trip to Northern Lights and TechnipFMC, industry keynotes & technical presentations as well as not to miss networking events. Whether you’re an industry veteran or new to the field, this is the perfect opportunity to connect, learn, and help shape the future of subsea technology. USF Verftet in Bergen, Norway 10 - 12 June, 2025
A selection of speakers at UTC 2025
MAIN SPONSORS
SPONSOR PARTNERS
MEDIA PARTNERS
ORGANISING PARTNER
HOSTED BY