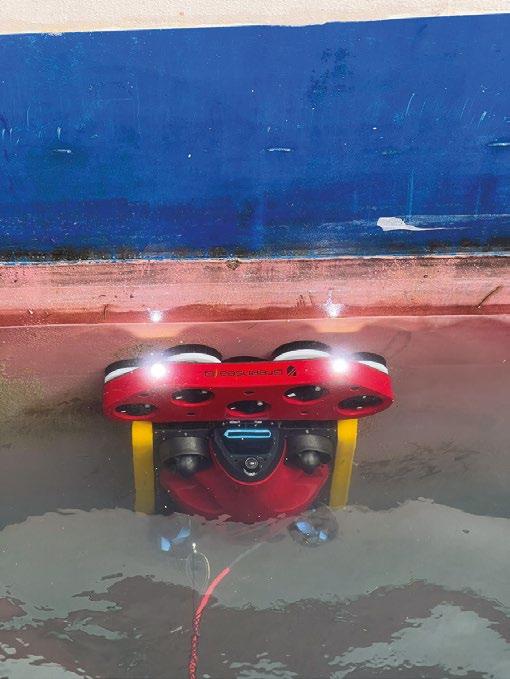
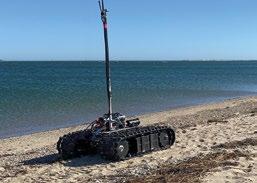
9.
Greensea IQ Delivers High Impact Dual-Use Technologies
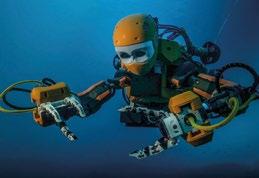
21.
Robotic Mermaids of the Deep


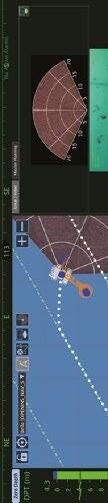
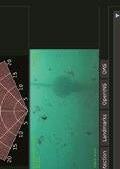
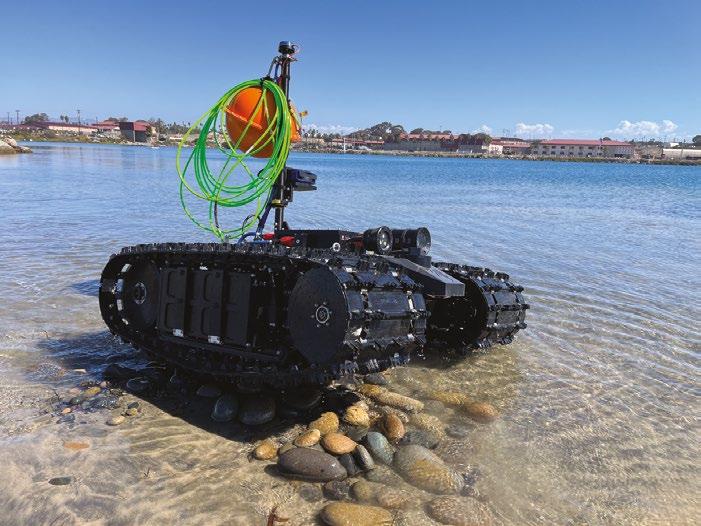

25.
Pioneering Complex Underwater Exploration and Inspection

37.
Think Weaponized Drones are a New Idea?
38
9.
Greensea IQ Delivers High Impact Dual-Use Technologies
21.
Robotic Mermaids of the Deep
25.
Pioneering Complex Underwater Exploration and Inspection
37.
Think Weaponized Drones are a New Idea?
38
• Delivering data in most adverse conditions: underwater acoustic modems with advanced communication technology and networking
• Accurate USBL, LBL and hybrid positioning of underwater assets, navigation for divers
• Modem emulator and multiple cost-saving developer tools
• Sonobot 5 - the autonomous surface vehicle for bathymetry, monitoring, search & rescue, and AUV support
• Quadroin - the novel bionic AUV for surveys and monitoring
Hydrus takes the drone revolution underwater with the most advanced navigation and communication systems of any subsea vehicle. Its ability to detect obstacles, avoid collisions and deliver high-quality georeferenced imagery makes Hydrus an excellent tool for underwater exploration, surveying and research.
Learn more about Hydrus. www.advancednavigation.com
06. Events Calendar & Welcome to Ocean Robotics Planet
09. Greensea IQ Delivers High Impact Dual-Use Technologies
13. Reaching the Future of Remote Operations
17. Goby: Limitless Energy and Autonomy Powered by Waves
21. Robotic Mermaids of the Deep
25. Pioneering Complex Underwater Exploration and Infrastructure Inspection
31. Offshore Wind Inspections: A Comprehensive Approach through the AROWIND Project
34. Poster: Drone Anti-Submarine Helicopter (DASH)
37. Think Weaponized Drones are a New Idea?
43. Sea Duty Suits Versatile Skeldar V-200 VTUAV
47. The Importance of Uncrewed Vessels for Naval Operations
51. Filling the Open Ocean Autonomy Capability Gap
55. Unlocking the Potential of Subsea Resident ROVs with Cutting Edge INS/DVL Tech
59. ROV Multiplexing: Past, Present, and Future
ISSN 2755-239X
EDITOR-IN-CHIEF
Richie Enzmann
COPY EDITOR
Will Grant
SALES DIRECTOR
Nick Search
DESIGN & LAYOUT
Milan Farkas
CONTRIBUTORS
Richie Enzmann, Alberto Lopez, Bjorg Mathisen Doving, Bob Christ, Edward Lundquist, George Galdorisi, Marc Deglinnocenti, Mike Tinmouth, Maxime Le Roy, Terje Ollestad
SPECIAL THANKS TO
Audrey Leon, Bill Mallin, Bopha Le Guernic, Brian Storie, Curtis Lee, Dawn D’Angelillo, Francisco Bustamante, Freddy Knutsen, Jack Rowley, James Colebourn, James DellaMorte, Jeroen Romijn, John Benson, John DellaMorte, Jostein Jansen, Julian Lalanne, Kieran O’Neill, Marion Seyve, Matt Bates, Patricia Sestari, Paul Fletcher, Rob Howard, Siv Tveit, Willard Balthazar
Advanced Navigation
AQUA Ocean
BEC Plastics
Blueprint Subsea
DeRegt Cables
Digital Edge Subsea
DWE
EvoLogics
Norwegian Offshore
Oceaneering
Popoto Modem
QYSEA
Reach Remote
RTS
Saab Seaeye
Spectis Robotics
Sunfish
UMS Skeldar
U.S. Navy
VideoRay
Voyis
Zetechtics
MARCH OCEANOLOGY INTERNATIONAL
London, UK (12–14 March 2024)
WINDEUROPE
Bilbao, Spain (20–22 March 2024)
APRIL SEA AIR SPACE
National Harbor, MD, USA (8–10 April 2024)
UNDERSEA DEFENCE TECHNOLOGY (UDT)
London, UK (9–11 April 2024)
MCEDD
Amsterdam, The Netherlands (9–11 April 2024)
MTS/IEEE OCEANS
Singapore (14–18 April 2024)
MARITIME RECONNAISSANCE & SURVEILLANCE TECHNOLOGY – USA
Arlington, VA, USA (29–30 April 2024)
MAY UNCREWED MARITIME SYSTEMS TECHNOLOGY UK
Wokingham, UK (8–9 May 2024)
AQUACULTURE UK
Aviemore, Scotland, UK (14–15 May 2024)
COMBINED NAVAL EVENT (CNE)
Farnborough, UK (21–23 May 2024)
JUNE ANNUAL ENERGY DRONE & ROBOTICS SUMMIT
Houston, TX, USA (10–12 June 2024)
INTERNATIONAL UNDERWATER GLIDER CONFERENCE
Gothenburg, Sweden (10–14 June 2024)
GLOBAL OFFSHORE WIND
Manchester, UK (18–19 June 2024)
AUGUST
SEPTEMBER
ONS 2024
Stavanger, Norway (26–29 August 2024)
UNCREWED MARITIME SYSTEMS TECHNOLOGY – USA
Arlington, VA, USA (23–25 September 2024)
MTS/IEEE OCEANS
Halifax, NS, Canada (23–26 September 2024)
WINDENERGY
Hamburg, Germany (24–27 September 2024)
OCTOBER
FLOATING OFFSHORE WIND
Aberdeen, UK (9–10 October 2024)
GLIDER SCHOOL 2024
Gran Canaria, Spain (21–25 October 2024)
EURONAVAL Paris, France (4–7 November 2024)
UNDERWATER INTERVENTION / WORKBOAT SHOW
New Orleans, LA (12–14 November 2024)
MAST Adelaide, Australia (19–21 November 2024)
OFFSHORE ENERGY
Amsterdam, The Netherlands (26–27 November 2024)
My name is Richie Enzmann. Allow me to welcome you all to the latest issue of Ocean Robotics Planet!
On the front cover of this issue, we have the new Greensea IQ logo. Their business includes robotic systems, Bayonet crawlers, and the EverClean robotic hull cleaning service, to name but a few. You can read about these in more detail in our lead article.
We also have an in-depth piece covering the DASH (Drone Anti-Submarine Helicopter). It was developed by Gyrodyne in the 1960s to counter the Soviet nuclear submarine threat. This little known project was the first attempt to use drones in the maritime domain.
At the end of last year, I met Captain Lundquist in Washington DC. We decided to set the historical record straight after we saw several large defence contractors publicly claiming to have developed the world’s first drones to deliver torpedoes: a feat already achieved many decades ago. This provided the inception for the article “Think Weaponized Drones are a New Idea?”.
In a separate article Captain Lundquist looks at the Vertical Take-off and Landing Unmanned Aerial Vehicles (VTUAV) that are extending intelligence, surveillance, and reconnaissance (ISR) capabilities for the navy, coast guard, and other maritime operations. Also, on the military side of things, Captain Galdorisi talks about other unmanned systems. These offer the promise of providing the U.S. military with an asymmetric advantage over potential adversaries. He also discusses TECHNET Indo-Pacific, a recent major international military-industry event held in Honolulu, Hawaii. This issue is packed with technology; we look at the newly developed Goby Wave Charger buoy from RTS that could power remote assets, such as sensors and even resident ROV/ AUV platforms in the future. We then take a deep dive into the the past, present, and future of ROV multiplexing technology.
You will also read about the groundbreaking humanoid robot named OceanOne; Reach Remote’s new USV-ROV concept, featuring an integrated Kystdesign electric work class ROV as part of a large, unmanned surface vessel; and the Sunfish AUV that was developed for complex underwater exploration and infrastructure inspection.
Finally, we are very much looking forward to attending Oceanology International in London. This is in addition to a selection of other great events, including three defence focused sessions both in the UK and the USA. If you see us there, please say hi and tell us what you thought of this quarter’s issue. Enjoy!
Best regards,
Richie EnzmannDeRegt delivers
Feel free to reach out and connect
Working in oceanic depths under great pressure requires cables and connections you can rely on. At DeRegt Cables we provide outstanding technical solutions and custom-engineered cable solutions for the most challenging of circumstances. When you are raising the bar, we deliver the right solution.
• Top notch cable design
• Reliable cable manufacturing
• High end cable termination
• Thorough cable testing
• Outstanding field service Call us for the best connection +31 180 66 88 00
Zaag
2024 picks up where '23 left off as Greensea IQ continues to “MTFB” (move the ball) towards the transformation into a higher impact company leveraging dual-use technology. This advancement aims to significantly enhance oceanic operations, prioritising both the safety of maritime workers engaged in hazardous tasks, and the protection of the marine environment.
Greensea IQ is entering 2024 with a strategic plan to transition autonomous robot technology developed with and for the defense industry into the commercial space.
Our work within the explosive ordnance disposal (EOD) and special operations forces (SOF) communities continues to maximise the safety of our service members by providing autonomous solutions that make their missions safer. Utilising that technology to provide scale and safety in other parts of the blue economy has become our focus in growing the potential of Greensea IQ’s technology.
Our EverClean service is a perfect example of this dual-use technology. Originally developed under the Small Business Technology Transfer (STTR) program under the Office of Naval Research (ONR), a novel, hull-relative positioning system for use in a hull crawling robot that could be used to keep naval ships free of biofouling was born.
The commercial applications of this technology are huge. There are more than 50,000 commercial ships in the world’s ocean going fleet, each one of them slowly accumulating biofouling. According to a report from International Maritime Organization (IMO) GloFouling Partnership in October 2022, protecting ships from biofouling would enable the industry to cut CO₂ emissions by as much as 19%.
EverClean is the first commercially available service of its kind where, through a Robot as a Service "RaaS" subscription, robots are delivered as a service to ship owners and operators. This lowers the cost to engage this new technology, and provides an efficient, safe, and scalable tool for lowering their fleet’s fuel consumption and emissions.
EverClean also harnesses another Greensea IQ Dual use technology known as Safe C2 to provide the next generation of service. This is a one to one residency where the service robot lives on the ship and is supervised over the horizon as it cleans the ship wherever it might be.
Safe C2 was originally developed under a Small Business Innovation Research (SBIR) ASAP grant. It’s a technology suite that provides Standoff Command and Control of ROVs. In 2021 when the SBIR Phase II award was announced, Greensea stated, “standoff command and control…will be invaluable to industry users who want to centralise all types of unmanned platform operations, reduce personnel who have to go to sea, and migrate to fully unmanned offshore services.” Several commercial marine companies are currently using Safe C2’s technology in their remote operations today.
Most have experienced the power of a wave first hand. Working in the environment of the surf zone is notoriously dangerous. Surface and subsea vehicles are rolled and buffeted by the wave forces making it hugely challenging to accurately control or maneuver. What’s needed are low profile, bottom heavy vehicles that are impervious to the waves’ forces.
Greensea IQ manufactures the first line of autonomous underwater ground vehicles that are perfect for working within the surf zone. The Bayonet product line consists of three sized vehicles that are selected based on the conditions that they will work under. The Bayonet 150 is the smallest of the three vehicles and it’s designed to be used under lighter sea conditions, and when it needs to be launched from a small craft. It also has a lighter footprint so it’s more suited to being used in sensitive environments like salt marshes and estuaries. The Bayonet 250 is a versatile workhorse capable of working in heavier sea conditions, yet still being two-person portable. The largest vehicle is the Bayonet 350 which has a deck carrying capacity of nearly 160 kg. Each Bayonet vehicle can work on dry ground and to a depth of 100 m. The motors are battery powered and operate 4-6 hours (model dependent).
Equally adaptable and capable of both defense and commercial roles, the Bayonet AUGVs can be outfitted with mission specific sensors. The vehicles are built on Greensea IQ’s OPENSEA robotics platform that supports thousands of commercially available sensors. Think of the Bayonet vehicle like a truck, ready to be loaded with required sensors for the task at hand. A variety of environmental, oceanographic, hydrographic, benthic, and industry-specific sensors are already compatible with OPENSEA.
The OPENSEA autonomy platform includes Greensea IQ’s proprietary inertial navigation system and is capable of manned, semi-autonomous, and fully autonomous control. Vehicles can be pre-programmed with a search pattern, and the vehicle will perform the pattern without intervention. Equipped with Greensea IQ’s OPENSEA Edge, the vehicle’s autonomy can be further enhanced by adding AI and machine learning libraries on the vehicle.
Applications of the Bayonet AUGVs include EOD, mine detection and identification, and minefield surveys for defense markets. Commercial applications include beach profiling and RTK surveying for dredging operations, UXO site clearance for cable transit lanes in offshore wind, and the rapid environmental assessments and surf observations for scientific research.
As discussed above, Greensea IQ’s EverClean service was born to solve the age-old problem of biofouling. As soon as a ship enters the water, life in the ocean starts to attach to it. This starts with a thin coat of slime called microfouling. Over the course of a few days to a few weeks, when enough slime accumulates, larger organisms are able to attach and propagate. Throughout history, ship owners have grappled with the problem of biofouling. How we solve the problem hasn’t changed much in the past two thousand years; we try to slow the process down (by adding toxic coatings), and then when biofouling becomes too much, the ship is put in dry dock to be cleaned. This is a dirty, dull, and difficult job.
An alternative approach is deploying divers to clean ships while they are in port, a method that is not only arduous, but also presents inherent risks. In instances where tasks are characterised by monotony, dirt, and danger, utilising robotic solutions presents an ideal strategy.
EverClean is a service that provides regular, proactive cleaning of ship hulls by supervised robots. EverClean robots are specialised to have a high performance sensor suite that optimises autonomy, navigation, and hull intelligence. Their modular brush head and specialised treads are designed to not cause any damage to the hull coatings. With high-resolution sonar and multiple cameras, the robots collect an incredible amount of hull data with each cleaning. EverClean IQ is the reporting portal for customers to review this collected data in order to make crucial decisions about preventative maintenance and repairs. This level of data collection requires the precise on-hull navigation that only EverClean can provide.
The IMO GloFouling 2002 publication, Analysing the Impact of Marine Biofouling on the Energy Efficiency of Ships and the GHG Abatement Potential of Biofouling Management Measures, said this about services like EverClean:
“Proactive hull and propeller cleaning has the potential for economic and environmental benefits, not only because it can proactively eliminate the possible penalties of biofouling, but it can also save the cost associated with intensive hull cleaning while in dry dock. Proactive cleaning is less aggressive and thus causes less damage to the anti-fouling coating. It also reduces the risk of transporting invasive alien species.”
Greensea IQ through products and services – such as EverClean, Bayonet AUGVs, OPENSEA, and Safe C2 – have the potential to change the way we work within the ocean: making it safer, more efficient, and providing solutions for some of the most difficult problems facing us today. All of the Bayonet AUGVs and EverClean robots will be on display at Oceanology International, March 12-14, 2024 in Greensea IQ’s stand, G200.
–
– 19 channels
– Remote operation for web interface
– Depth rated to 4500 m
– Proven technology based on Gen 5 reliability
– Software resettable fuse on every channel
A high-tech marathon is taking place in the inner forests of Kongsberg. About 100 technologists and engineers are working tirelessly to complete the Reach Remote: the world's first Norwegian-registered, unmanned, and remotely operated vessel. Reach Remote is packed with Norwegian technology, designed by engineers with Kongsberg on the chest and Reach on the shoulder. In the summer of 2024, the plan is to sail in Norwegian waters without a single sailor on board.
Reach Remote is about to give birth to a brand new Kystdesign e-WROV concept. Once again, the partnership with Reach Subsea will bring to the market a completely new way of solving subsea tasks.
The underwater robotics available are the result of a hightech evolution over the past century, made possible by the ecosystem of customers and suppliers that make up the industry. If we go back 30 years, we hear people discussing whether it’s realistic to imagine that all intervention will be conducted solely with remote-controlled technology. Readers will already know the answer to that. AI, automation, and digitization are changing our lives, both privately and at work. Development has accelerated significantly in recent years.
In the robotics race, we will introduce drone strategies, regulations, and guidelines. In the meantime, both priest and bailiff must deal with new variants of AI technology that are introduced every single day, whether it be at the airport check-in desk, or wielding the scalpel in the operating theatre. This creates challenges for both financial and educational institutions: where should we place our bets, and what guidelines should we follow?
FACT BOXES
Norwegian listed company headquartered in Haugesund, globally represented in the Americas, Asia, Australia, Brazil, and Europe. Offers maritime services with emphasis on ROV operations, surveys, and surveillance. It has 370 employees with international expansion plans.
The business sector is definitely in a restructuring phase. But history shows that those customers who have shown a willingness to put money on the table to stimulate their digitization journey (as Equinor did by remotely controlling Valemon back in 2017) benefit greatly from this. And when Europe wants to be a pioneer in the development and use of drone technology, surely everything should be in place to welcome the robots to the farm.
Reach Subsea was established in 2008, and was founded by people with robust experience from the development of underwater robotics dating back to the 1980’s. The contribution to industry development is holistic; from the development of new ROVs and tools, to establishing frameworks for both ROV operations (NORSOK U-102), and not least the ROV certificate education. Now Reach Subsea wants to use this experience to accelerate the use of new maritime robotics. Automation combined with AI makes it possible to place the sailor ashore.
The motivation for doing this has many facets. Reach Subsea is not doing this to replace its other, owned and conventional, vessels. Rather, it’s designed to increase its portfolio of services, knowing
Contact: bma@reachsubsea.com | +47 92880416
Unmanned vessels to be remotely controlled from the control room operated by Massterly.
The vessels are owned by Reach Subsea, which will remotely control the ROV operations over the horizon. Two vessels are under construction and will be delivered by Kongsberg Maritime in 2024.
Vice President of the Reach Remote initiative. Educated as an engineer from Western Norway University of Applied Sciences and has 20 years of experience from the subsea industry. She is an experienced speaker and keynote speaker.
that there are still many maritime operations that require a conventional solution. The unmanned option has many advantages: in terms of environment, personal safety, and cost. In addition, this opens up further opportunities for new employment, and stimulus for a forest of subcontractors hungry to prove that remote control is the future. Reach Subsea – backed by KONGSBERG and the Wilhelmsen Group – calls it a new maritime adventure that calls for justified attention.
But what does this mean for the competence profile of those who will handle the robots? Do they need to have sailed at sea, or have played PlayStation since the age of 5? The conventional solutions will exist for many more years, and a healthy ecosystem is essential in all industries. So how does the R&D industry acquire sufficient access to important human resources with a new and correct competence profile?
For almost ten years, researchers at the Nordic Institute for Studies in Innovation, Research and Education (NIFU) have mapped the competence needs of Norwegian companies. There is a great need for expertise in automation and robotics. In 2022, 65% of companies report having an unmet need for expertise. This unmet need has consequences for companies, and 45% of the companies that lack expertise report that they have lost customers and market shares, and almost as many report that they have shelved or postponed expansion of their activities. Around 25%also say they have had to reduce their business.
But on the coastline of Western Norway, very exciting things are happening. Based on the popular model from Kuben in Oslo, Ganddalen High School already has a fully subscribed course for robotics and automation in the fall of 2023. Combined with projects such as iMaster at the University of South-West Norway – which has a focus on simulator and control room training – perhaps we see the outlines of the future competence profile we are looking for?
However, there is still a missing link. The R&D industry is not active enough in the educational environment, and there is a lack of teachers and teaching skills. Increased attention to this topic is encouraged, so that we ensure that we have the right and necessary expertise at the right time. Reach Subsea rolls up its sleeves and invites the rest of the industry to offer guest lectures, internships, and company visits: both to update teachers and excite our children who are at the crossroad of choosing the right education….
… so that our adventure will have a happy ending, with humans winning over the robots in the end!
In the tree of life, finding ways to ensure continued survival often produces some remarkable outcomes. It also often produces some strange bedfellows. Take for example the symbiotic relationship between the pistol shrimp and the goby: the shrimp builds and maintains a burrow that both animals live in, and the goby offers the shrimp protection from predators. This relationship is simple and both creatures benefit.
The accelerating drive towards renewable, clean energy sources presents a similar (potentially existential) problem; one that also requires remarkable and unconventional solutions. The most pressing demand for emerging wave technology energy companies is the development of a wave powered energy source to generate power for local electricity grids. As a company, RTS have explored different concepts of wave energy systems over the years, and concluded that most of these theories were too complex, inefficient, and costly to manufacture.
RTS believe that in order for wave energy to become a commercial success it requires a simple, sustainable, inexpensive, and small-scale solution. Based on this initial design criteria, the outline for the “RTS Goby® Wave Charger” system was first developed.
Rental Technology & Services (RTS) was established by partners, Freddy Knutsen and Odd Kåre Øygarden in 2002, and have since designed and manufactured industry leading solutions, recognised as the best-inclass by the ROV and subsea communities around the world. With over 50 employees located in Norway, Spain and the UK, RTS comprises departments in administration, sales, logistics, engineering and development.
The initial concept for the Goby ® was to have a piston forcing sea water through a turbine. A number of variations were tested, but none produced sufficient energy to drive the turbine efficiently. Then a new idea was pitched: why not move the generator through the water column?
A preliminary design concept was formulated by RTS and simulated using a number of mathematical models. Several in water test trials followed, resulting in a solution that was simple yet functional. RTS named this solution “Hydropower in Reverse”.
This model features a moving turbine travelling out of phase from the prevailing motion of the waves. The moving turbine rotates and spins whenever seawater is forced through its blades.
RTS continued working with this initial concept, and a scale prototype model was manufactured. At the beginning of 2022, a meeting was held with the experts from Stadt Towing Tank (STT). STT is one of the leading hydrodynamic test facilities in Northern Europe, located in Måløy, Norway. They have extensive experience working and testing a number of different wavepower concepts.
The overall test results of the scale prototype Goby ® allowed RTS to generate a mathematic model. This provided the company with enough test data to show that the Goby ® design principle could be scaled up for future applications.
Conventional wave powered devices can be both expensive and complex. Meanwhile the Goby® Wave Charger boasts:
ƀ A low cost solution, with limited moving parts.
ƀ Access to almost infinite supplies of wave energy.
ƀ Reduced weight and physical size, with fewer storage batteries and no requirement for solar panels.
ƀ The ability to power a larger number of surface and/or subsea sensors.
ƀ System scalability to suit customers’ individual power needs.
ƀ Reduced installation costs and a smaller deployment vessel requirement.
So, what are these future applications? There is an immense need for local power where no infrastructure is currently in place. RTS’ aim is to manufacture a standardised wave powered generator platform; one that’s flexible and scalable enough to meet the customer’s individual power specifications.
The Goby ® will be a bespoke solution able to power any sensor package configuration. It will also include data communication infrastructure to accommodate the client’s subsea monitoring requirement. Here are just a few examples of where Goby ® could be utilised:
ƀ Sensor spreads for hydrographic and oceanographic monitoring. Traditionally these packages are powered using solar panels and batteries with some inherent limitations. By using subsea wave power generation, the range of sensors can be increased, and the surface buoys can be made smaller and lighter. It’s worth noting that the Goby® is very light as it carries no fuel; it is a zero carbon technology with no net CO2 emissions.
ƀ Charging of subsea battery banks where Goby® would be able to provide both charging and data communications to resident underwater drones via AUV platforms; to match the industry’s drive towards autonomy, you need reliable and persistent charging infrastructure. This could be beneficial for both mature and emergent fields, and new areas without infrastructure, all of which may need external charging facilities.
ƀ Observation of critical infrastructure (Infrastructure Seabed Surveillance – Leak Detection, Asset Management and Aquaculture). The Goby® Wave Charger is equipped with monitoring devices both above and below the surface for this purpose. In a similar manner, it coulld also be harnessed as an Oceanographic and Environmental monitoring solution.
ƀ It can also be used as a data interface hub for a network of subsea sensors.
These are only a small number of Goby® Wave Charger application examples. Further opportunities in oil and gas, aquaculture, oceanographic research, and the military are limitless.
The European patent application for Goby ® was filed in September 2022, and the Patent Cooperation Treaty (PCT) filed the following July. The very first models are currently under construction, and RTS already have a project with the Norwegian Ocean Research Institute. They have been tasked with providing power and real-time communication for an Acoustic Doppler Current Profiler (ADCP) spread.
The aim of the trial is to ultimately replace the current battery configuration with a Goby ® Wave Charger. This will save the client operational time and maintenance costs, whilst providing real-time data transmission from the ADCP sensor. Utilising the environmentally friendly Goby ® Wave Charger on this research project will allow the client full control of the sensor spread information in real-time, and offer a considerable saving in both vessel operational time and cost.
RTS are aiming to install their first Goby ® Wave Charger this spring, and will obtain valuable feedback on its performance and operation following this first project. RTS are also
targeting several other underwater projects. They intend to use these operational experiences to develop a fully scalable Goby ® Wave Charger instrumentation platform to support the emerging world of underwater autonomy.
These are exciting developments, and point to a promising road map for both this product and its end users. RTS are confident from what they’ve seen so far that the Goby ® Wave Charger will create the perfect symbiosis between customers’ vision and the demands of their various industries.
World leading family of large and small fibreoptic multiplexor solutions for survey, data collection and control system tasks of any scale.
Connected with our fibre optic LINK™ boards for ethernet, serial, video and much more!
More than 100 units sold last 2 years
8 station Tool Control Unit
Subsea valve pack with up to 8 NG4 valves. Available with any combination of solenoid and proportional valves.
6 station Tool Control Unit
Subsea valve pack with 6 channels with bidirectional, proportional solenoid controlled valves.
Valve Driver & Ethernet
Remote I/O
The core controller in “intelligent valve packs”.
If mermaids aren’t real and cannot be found, then we’ll just have to make one of our own! That’s exactly what Leland Stanford Jr. University of Palo Alto, California did under the direction of Oussama Khatib. He is the Professor of the Computer Science Lab and the Director of the Robotics Lab at Stanford University. In 2014 Dr. Khatib started a project that turned a mythical mermaid into a real underwater robot. That first iteration had a 200 metre depth rating which soon increased to 1000 metres in 2022. He calls his creation OceanOne. Others call it revolutionary.
It is a new and exciting approach to Remotely Operated Vehicles (ROVs) because it takes manipulating underwater objects to a whole new level of dexterity. That level of dexterity is something we humans can relate to a lot better than your standard underwater manipulator arm clamps. OceanOne uses two humanlike arms and two humanlike hands. It has a head and torso like a human too. This human upper body design emulation is something that we can all relate to intrinsically, and therefore we can manipulate it much more naturally than other ROVs. OceanOne’s unique control system along with its eight thrusters helps the oper ator in a big way.
The control system for OceanOne is also a bit revolutionary in its design. It uses “haptic” interaction. Simply put, you get a physical feeling of touch when the robot touches an object with its fingers. These sensory responses are fed back to your own fingertips in a delicate and sophis ticated way. This feedback allows the operator to manip ulate and recover delicate marine archeological objects without breaking them. You can feel when contact is first and continually made. Even the robotic arms are equipped with two stages of feedback responses. Each arm has seven joints with each joint having one degree of freedom (DOF) movement. An operator can apply gradual arm movement pressures with feedback. It’s similar to your foot feeling the braking of an automobile. Haptic arm and hand controls along with stereo camera vison is revolu tionary, because it’s just like being there to grab the object yourself. Grabbing those objects is just what OceanOne has been doing too.
In 2016 OceanOne dove 20 miles off the coast of France into the flagship of King Louis XIV. That 100 metre dive resulted in OceanOne recovering an extremely delicate vase without damaging it. In 2022 OceanOne dove at La Ciotat, off Côte d'Azure, Corsica, and Cannes, France. A P-38 aircraft was observed in 40 metres of water and a Beechcraft twin engine aircraft in 67 metres of water. Many shipwrecks both modern and ancient were also explored during that particular expedition. The modern era submarine Le Protée was visited in 124 metres of water. The modern era passenger ship Francesco Crispi was found at a depth of 507 metres. An ancient unknown Roman shipwreck was explored in Aléria, Corsica at a 334 metre depth. So, OceanOne is a proven viable marine archeological ROV of unparalleled value. The next question is, will it be available for us to purchase?
Yes, the oil-filled, deep diving, OceanOne is available for purchase at Force Dimension through the www.forcedimension.com website. So, you see, mermaids are real after all.
FIND US AT
Manufacturing custom-machined components for ROV and associated applications. Any quantity of components at a competitive cost.
Our components can operate in extreme conditions and offer high levels of reliability. Fast efficient response to quotes, and a high level of customer service. Our level of expertise in this field is a benefit to our customer base.
www.becplastics.co.uk
enquiries@becplastics.co.uk
+44 1236 781255
Developing Autonomous Underwater Vehicles (AUVs) to survey simple underwater terrain is a field that has seen considerable advancement over the past seventy years. However, when it comes to cluttered, complex, or overhead 3D environments, the challenge intensifies significantly. Here autonomous exploration is much more demanding.
Over the past two decades, the team at Sunfish has significantly advanced AUV technology, enabling it to excel in complex environments. Initially motivated by the ambition to plumb the depths of water-filled caves on Earth, and later pursuing the goal of exploring potential subsurface oceans in the outer Solar System, the development of the SUNFISH® AUV marked a major breakthrough in maneuverability, exploration, and autonomy.
This AUV is capable of operating autonomously far beyond pre-programmed missions. It is equipped to understand high-level objectives, and make independent decisions to fulfill them. With its advanced technology, the SUNFISH AUV navigates through both intricate mazes of natural caves and complex man-made structures.
The SUNFISH AUV can trace its roots back to a project in 1999. A private patron and the National Geographic Society funded a team of explorers to build a three-dimensional map of the flooded cave system that gives rise to Wakulla Springs, one of
the largest and deepest freshwater springs in the world. This team, led by Dr. Bill Stone, developed the digital wall mapper.
This instrument mounted as a front module to a diver propulsion system, and captured a 3D map of the surrounding environment as a technical diver steered it through the waterfilled tunnels. The map produced was the first of its kind.
Then, in 2001 Stone founded Stone Aerospace, a research and development company focused on developing tools to explore the frontiers of space.
Around the same time, a scientific field called “astrobiology” was gaining traction with researchers at NASA and universities around the world. The endeavor of the field is to understand the origins of life on Earth and to investigate the potential for life, past or present, on other planetary bodies in our solar system. This could include Mars, or the ice-covered moons of Saturn or Jupiter.
Some of the work involves using cutting edge technology to study remote and extreme environments on Earth to better understand potentially similar locales beyond Earth. Stone Aerospace was one of the first companies to be funded by NASA to develop AUV technology, in order to search for signs of life outside of Earth.
DEPTHX was the first AUV system developed by Stone Aerospace for this purpose. This four degree-of-freedom hovering AUV was the first to implement 3D real-time sonar Simultaneous Localization and Mapping (SLAM) navigation in a complex 3D environment. DEPTHX was about the size of a VW bug and weighed approximately 1 metric ton. Development occurred over three years and was successfully tested over two field seasons in cenotes (naturally occurring pits or sinkholes) near Tampico, Mexico.
The second AUV system, ENDURANCE, built upon the successes of its predecessor. The DEPTHX AUV was reconfigured to operate in Antarctic conditions with an integrated aqueous chemistry sensor suite.
ENDURANCE added to the DEPTHX 3D mapping capabilities with the ability to localize data from an advanced sensor suite within the just-created map. This capability enables not only autonomous navigation based on the geometry of the environment, but also from physical and chemical data. This ultimately enables the AUV to make decisions based on environmental conditions. The AUV was successfully deployed over two field seasons under ice in Lake Bonney, Antarctica. It traversed more than 70 km under ice and created a 3D chemistry map of the subglacial lake.
The success of the DEPTHX and ENDURANCE AUVs led to the development of ARTEMIS, a novel hovering AUV capable of autonomously acquiring scientific data from an array of biological and chemical sensors over a 20-km-range
trajectory in a confined sub-ice environment. ARTEMIS included advanced robotic behaviors such as obstacle avoidance, range standoff, station keeping, and autonomous rendezvous and docking. These capabilities were tested and demonstrated in late 2015 beneath the McMurdo Ice Shelf in Antarctica. The vehicle conducted 20 missions, returning each time to a 1.2 m diameter drill hole.
Transitioning from space-focused exploration technology to terrestrial applications, Stone Aerospace went on to develop the SUNFISH AUV. The underlying technology of this AUV was based on the lineage of vehicles developed by Stone, but was miniaturized and adapted for uses closer to home. In 2019, Sunfish was founded to adapt space exploration technologies developed by Stone Aerospace for exploration, science, and infrastructure inspection on Earth.
The SUNFISH system is a lightweight and person-portable hovering AUV designed for automated inspection and 3-D mapping. It excels in overhead environments and utilizes the geometry of the environment itself for feature-based registration of the maps it creates, as well as to correct drift in its guidance, navigation, and control system.
It also features a multi-beam sonar and proprietary dead reckoning navigation system for its exploration, obstacle avoidance, and auto-egress behaviors. These provide a means for assessment of submerged tunnels.
The SUNFISH AUV can be operated in one of three modes:
1. Under servo-level remote control, via a data fiber that can optionally be deployed from the surface or from the vehicle.
2. Under supervised autonomy, where the vehicle can accept scripts or higher-level goals and make its own local decisions on how to achieve those objectives (Personnel at mission control can view vehicle actions using data coming from the fiber and intervene if desired).
3. Fully autonomously without fiber.
Each of these modes can be used in different contexts to support complex operations. The SUNFISH AUV carries a suite of sensors which can be used for survey, precision inspection, underwater intervention, and exploration and mapping of complex 3D geometries.
A notable application for the SUNFISH AUV are inspections of raw and potable water infrastructure. These inspections provide the foundation of a high-quality asset management plan by supplying the information necessary to make informed decisions. Such assessments provide insight into the nature and timing of possible failures, and guide maintenance/repair planning and funding allocation.
However, physical and financial barriers associated with gaining access to underwater infrastructure (tunnels, gates, valves, etc.) present a major obstacle for utilities attempting to remain safe and compliant while performing these condition assessments. Although tremendous advances have been made in diving and underwater robotics access methods, these methods are greatly restricted by safety and industrial regulations which limit in-water time at depth, and require constant communication through tethering. These regulations are particularly restricting when dealing with long enclosures such as buried transmission or intake tunnels.
Today, the SUNFISH AUV makes it possible to autonomously navigate hard-to-access environments without the cost and service delays associated with traditional dewatering methods for inspection. AUVs are not subject to submersion time limits like a diver, and operate with far less restrictive tethers than those required by traditional ROVs. In some cases, completely umbilical-free operation is possible.
Sunfish currently deploys its AUV with either diver-assisted or unassisted operations to inspect infrastructure using behaviors that perform SLAM, exploration, path planning, precision docking, and underwater communication. This use case typically requires high-resolution sensors onboard to produce 3D data products acquired when performing visual and non-destructive inspections.
Some of Sunfish’s clients that chose to perform their detailed inspection with an AUV have seen a reduction of 60% of the traditional inspection cost, alongside a 96% reduction in service outage time.
Another benefit of utilizing the SUNFISH AUV is the enhancement of water resource management, particularly in karst aquifer systems (underground watercourses typically formed from layers of sedimentary rock). There is a great need to map freshwater springs that feed karst aquifers given their challenges such as saltwater intrusion. Environmental agencies currently rely on course data to determine where these aquifers are; what their spatial extent is; and to assess their recharge levels.
SUNFISH AUV is a great tool for enhancing water resource management at accessible sites by providing comprehensive, accurate data to inform conservation and restoration efforts. By adding water quality sensors to the AUV – such as a nitrate sensor or water sampling – pollutant loads to the karst aquifer can be quantified and located. The AUV provides knowledge of these complex aquifer dynamics in order to properly mitigate water quality and quantity problems from the surface.
To date, the SUNFISH AUV has assessed numerous underwater cave sites around the world, moving through and producing 3D maps of these complex structures that scientific divers cannot always safely access. The AUV is able to
acquire high resolution physical, hydrological, and chemical data, thus overcoming the limitations of data collection.
The SUNFISH AUV has also enabled new exploration and research in the field of marine archaeology, particularly exemplified in NOAA's "Our Submerged Past" project. This groundbreaking project aimed at exploring submerged Late Pleistocene caves in Southeast Alaska; areas that are hypothesized to hold clues about human migration to the Americas during the last Ice Age.
The SUNFISH AUV's role in this project was multifaceted. It performed detailed 3D surveys of complex seafloor terrain; identified underwater caves and rock shelters; and created high-resolution 3D maps that were previously unobtainable. Its ability to autonomously navigate through these complex environments allowed archaeologists and scientists to explore and analyze areas that helped fill a historical gap in human migration to the Americas.
Small ROVs have long been used in marine archaeology to visually scan and explore underwater environments – such as caves, ruins, or wrecks – with complex 3D geometries or overhead obstacles. Traditionally, more advanced work –such as detailed inspection or sampling – was generally performed by human divers due to the advanced perception
High resolution imaging in turbid water for improved situational awareness and target identification. Available in 375kHz to 3.0MHz. Depth rated to 500m, 1000m, or 4000m.
and maneuvering capabilities required. The real-time sonar SLAM system of the SUNFISH AUV has the unique ability to autonomously explore underwater caves.
Using this capability and an exploration behavior to expand the SLAM map, SUNFISH is able to safely find a path through previously unknown 3D environments, and return to previously visited locations. In addition, the vehicle can collect sediment samples through action scripts behaviors at a location determined in the 3D map.
During a Spring 2023 field deployment on the continental shelf west of Prince of Wales Island in Southeast Alaska, Sunfish demonstrated these capabilities. The AUV successfully found, explored, mapped, and sampled submerged caves and rock shelters to look for evidence of prehistoric human habitation in now submerged caves. This work was supported by NOAA Ocean Exploration.
The SUNFISH AUV's journey from extraterrestrial exploration to a tool for commercial and ocean science highlights its advanced capabilities and potential. As underwater exploration and infrastructure demands grow increasingly complex, Sunfish continues developing innovations that pave the way for future advancements in autonomous underwater technology.
Offshore wind energy has become a pivotal resource in the transition towards sustainable energy, offering an economically viable avenue for meeting the escalating global energy demand while curbing environmental impact. The expansion of offshore wind farms signifies a paradigm shift in the offshore survey industry, introducing new inspection challenges that necessitate innovative technological solutions. This article explores the evolution of offshore wind, its growing significance, the challenges it poses, and the technological breakthroughs that will revolutionize how these assets are effectively monitored.
A revolution for sustainable energy offshore, wind energy has become a beacon of hope in the quest for sustainable and renewable energy. Unlike traditional wind farms located on land, offshore wind farms harness the power of winds
over open waters. This shift addresses concerns related to land use, enhances energy production efficiency, and minimizes visual impact. The growing interest in offshore wind is underscored by its potential to unlock vast energy resources, significantly contributing to reducing reliance on fossil fuels.
While offshore wind presents a promising solution, it comes with its own set of unique technical needs. Harsh environmental conditions limit access to wind farms, while the corrosive nature of seawater degrades the submerged assets. Also, the sheer number of turbines at each site requires significant improvements in inspection efficiency compared to oil and gas. Traditional General Video Inspection (GVI) methods – deployed from large and expensive crewed vessels – fall short in addressing these challenges, and lead to increased operational risks due to lack of monitoring.
To overcome the cost challenges inherent in offshore wind inspections, a completely integrated solution is required. Optical inspections must leverage recent innovations in 3D modelling and change detection. Vessels have become much smaller, uncrewed, and capable of autonomously deploying observational class Remotely Operated Vehicles (ROVs). Underwater laser scanners and high-resolution cameras provide a keen eye below the surface, capturing high-resolution imagery and enabling real-time monitoring of critical infrastructure. This innovation not only ensures the structural integrity of offshore wind installations, but also enhances the safety and efficiency of inspection processes with shore-based personnel.
Optical sensors play a pivotal role in addressing the challenges posed by offshore wind inspections. These sensors, equipped with advanced imaging technologies, deliver unparalleled clarity in subsea environments. By integrating these sensors into subsea vehicles, inspection processes become more efficient, accurate, and less dependent on human intervention. This not only reduces operational costs, but also mitigates safety risks associated with human presence in challenging offshore conditions.
The integration of optical sensors with subsea vehicles brings forth a seamless synergy, allowing for real-time data acquisition and analysis. The high precision and reliability of these sensors contribute to enhanced decision-making processes, ensuring that potential issues are identified and addressed promptly. As a result, the operational lifespan of offshore wind installations is extended, and the overall efficiency of energy production is optimized.
In response to the pressing need for advanced offshore wind inspection technologies, Voyis, in collaboration with industry leaders and funded by Canada’s Ocean Supercluster (OSC) has spearheaded the Autonomous Remote Offshore Wind Inspection, Navigation and Deployment (AROWIND) Project. This groundbreaking initiative developed an uncrewed surface vessel (USV)-based subsea inspection solution specifically tailored to offshore wind farms.
The AROWIND Project represents a monumental leap in the evolution of offshore wind inspections. With a total project value nearing $6.7 million, it is poised to redefine industry standards by leveraging innovative technology. This initiative harnesses the expertise of Canadian companies, including Voyis Imaging, Deep Trekker, and HydroSurv Unmanned Survey. These companies will be working alongside international partners EVIA, Sonardyne, and Saipem.
Voyis, as the lead partner, has brought a wealth of experience in underwater optical sensor design, vehicle integration, and algorithm development to the AROWIND Project. The project capitalizes on Voyis's proven engineering prowess, with a focus on developing core optical sensor products essential for the success of the solution.
The success of the AROWIND Project hinges on the integration of Voyis's compact Insight Laser Scanner and Imaging Systems for ROV horizontal inspection scopes. To meet inspection requirements and drive qualitative preventative maintenance, the highly compact 3D optical sensors from Voyis will be developed and integrated with Sonardyne’s Sprint-Nav Mini navigation system to deliver the first survey grade payload for small ROVs. In addition, all systems will be powered by EIVA’s navigation and processing software, for improved data visualization and analysis.
Additionally, the project leverages the Voyis Discovery Stereo Camera, to facilitate ROV vertical inspection and navigation. Optical payloads developed by Voyis will seamlessly integrate with Deep Trekker's and Saipem’s vehicle platforms, establishing a new standard for offshore windfarm inspection methodologies.
The AROWIND Project is a testament to effective collaboration, with each partner playing a crucial role. Deep Trekker contributed with the robust REVOLUTION ROV; an inspection class vehicle built tough to survive harsh underwater conditions, allowing it to accomplish complex missions. HydroSurv Unmanned Survey will also contribute with their USV. This will be designed as the first commercially available remote ROV deployment system. Saipem’s role was to develop resident vehicles to offer a complimentary remote solution for wide-area cable surveys.
The AROWIND Project is set to redefine offshore wind inspections by introducing remote and autonomous deployment solutions. For localized inspection – with the goal of eliminating the use of the large Service Operations Vessel – the HydroSurv USV will deploy the Deep Trekker ROV with Voyis sensors and EIVA software. For wide area cable survey, the Saipem resident vehicle will deploy the Voyis optical inspection payloads.
By reducing vessel costs and minimizing the number of personnel on board, AROWIND not only enhances costeffectiveness but also addresses safety concerns associated with human presence in challenging offshore environments. This project, backed by the Ocean Supercluster, stands as a beacon of innovation, paving the way for the future of offshore wind inspections worldwide.
As the AROWIND Project progresses, its potential legacy extends beyond the boundaries of a singular initiative. The innovative solutions developed through AROWIND have the potential to set a new industry standard, not only in Canada but globally. The integration of innovative optical sensor technology with autonomous subsea vehicles not only revolutionizes inspection processes for offshore wind, but also opens the doors for similar applications in diverse sectors, from marine research to underwater infrastructure inspections.
The AROWIND Project emerges as a meaningful change in the realm of offshore wind inspections. As the industry grapples with challenges unique to offshore environments, this comprehensive solution promises to usher in a new era of efficiency, safety, and sustainability. With its innovative approach, the AROWIND Project paves the way for the widespread adoption of remote and autonomous inspection solutions, contributing significantly to the growth and success of the offshore wind energy sector. The collaboration among industry leaders and the infusion of innovative technology positions the AROWIND Project as a beacon of hope, illuminating the path towards a more sustainable and efficient future for offshore wind energy.
Unmanned aerial vehicles (UAVs) are no longer a novelty. They are becoming commence on surface combatants as another tool to extend their sensor range. Today, U.S. Navy ships employ the small Puma, Scan Eagle, and the vertical-launched Fire Scout to conduct intelligence, surveillance and reconnaissance (ISR) missions) form ships at sea.
Recently a team of BAE Systems and Malloy Aeronautics claimed to have flown the first unmanned aircraft to launch a torpedo. A BAE Systems/Malloy Aeronautics T-600 Uncrewed Air System (UAS) deployed an exercise Sting Ray torpedo as part of the recent demonstration at the NATO REP(MUS) (Robotic Experimentation and Prototyping using Maritime Uncrewed Systems) exercise in Portugal.
While the T-600 accomplishment is an important milestone and a major step in creating a vital tactical at-sea capability, it is not the first-time torpedoes have been deployed by drones. Not even close.
The T-600 and other contemporary maritime UAVs were preceded by a Vertical Takeoff Unmanned Aerial Vehicle (VTUAV) that operated from surface combatants that date back more than a generation. The Drone Anti-Submarine Helicopter, better-known as DASH, operated from destroyers and destroyer escorts in large numbers more than six decades ago.
In the 1950s, anti-submarine warfare meant getting on top of a sub, or very nearly so, to use torpedoes, depth charges and “hedgehogs.” As both the threat from new, better submarines increased, along with the availability of long-range sonar, the Navy sought an anti-submarine weapon that could match the greater sensor range.
DASH was built by Gyrodyne of Long Island, NY. It had a bare-bones appearance that lacked any kind of shrouding or attempt at a streamlined aerodynamic design. Its coaxial rotor system featured two counter-rotating rotors, with one set of blades above the other. But it wasn’t built for looks. It was designed to deliver a torpedo to a location far from the ship and drop it in the water where it would activate and actively hunt down the enemy sub. The requirement was to be able to launch on short notice and proceed at 80 knots to deploy a torpedo within 200 yards of a plotted submarine contact at a range of 10,000 yards (or 400 yards at twice the range).
With the DASH coaxial rotor system, the rotors turned in opposite directions, eliminating the need for a boom and tail rotor to counter the torque from the main rotor. It also provided more lift in less space. Power that might otherwise be needed for the tail rotor could be used for the main rotors in providing lift for greater payloads. The two twin-blade rotors had a diameter of only 20 feet. The total blade area with the coaxial blade system was similar to that of comparable single rotary system, but had a smaller footprint, a desirable characteristic when operating off very small destroyer flight decks. Hovering and controlling DASH was made simpler by the coaxial rotor system, and there were fewer parts due to the absences of the powered tail rotor system.
After World War II, the U.S. Navy has a lot of destroyers, and they needed to be updated with the newer sensors, weapons and capabilities. The ships were upgraded as part of the Fleet
Rehabilitation and Modernization (FRAM) program. The Navy had such faith in DASH that they began modifying destroyers to have small flight decks and hangars to accommodate the drones. Modernized World War II-era destroyers receiving the FRAM I and FRAM II conversions were given flight decks and hangars, as were newly constructed destroyer leaders (DL), missile frigates (DLG), and the DE 1037 and DE-1041 escorts. Altogether, nearly 200 DASH-capable flight decks entered the fleet.
DASH was remotely piloted by a member of the ship’s company located in the ships Combat Information Center (CIC), using an AN/SRW-4 DASH control system. The control system received inputs from the ship’s radars. The ship and aircraft communicated using radio signals.
DASH developed a bad – if not undeserved – reputation of flying out but not coming back. Many officers were trained to operate the system and became highly proficient, but officer turnover was an issue, as were problems with the telemetry link. If a DASH destroyer were operating in the screen or on plane-guard duty with a carrier, the DASH would be unable to fly because of air space confliction. Some commanding officers were overly cautious in employing DASH for fear of losing a valuable asset, and that meant operators didn’t get the flight time needed to become proficient. However, as an ASW weapons system, DASH worked. It could be employed in pairs, and it gave a surface combatant a standoff ASW weapons delivery system that, in most, cases exceeded the range of the surface ship sonars of that time.
Successive generations of the aircraft, first designated DSN-1, then QH-50A, got longer legs, a higher ceiling and a heavier payload. The initial aircraft had barely enough endurance, about 25 minutes, to fly out to the submarine’s position and release its weapon. A subsequent version, the QH-50C, had
Boeing T-50 turbine engines and a larger 33-gallon fuel tank. Still later, the QH-50D model had a 52-gallon fuel tank and a more powerful engine. By the time the last DASH was being built, it had a 325 hp Allison T-63 power plant, giving the QH-50E a combat radius of more than 150 miles and a top speed of 70 knots, with a payload of nearly 1,000 pounds.
DASH could carry a pair of 12.75-inch (32 cm) MK 46 lightweight torpedoes, or a torpedo and a sonobuoy. The MK 46 system needed inputs, but would proceed to its preset depth and begin searching. When it acquired its target, it would proceed to intercept and kill.
While DASH was entering the U.S. fleet, the Navy also installed the Anti-Submarine Rocket (ASROC) system on combatants. FRAM I destroyers received both ASROC and DASH. FRAM II conversions received only DASH. ASROC did not have the 25-plus-mile range that DASH had, nor could it loiter or reposition to drop a weapon on an updated position (ASROC’s maximum range was 10,000 yards, or 9,144 meters ASROC could be launched in any weather. ASROC was a better
quick-reaction system, able to deliver a torpedo or depth bomb payload to a water entry point faster than it took to launch a DASH and fly it to the target. DASH was reusable, and could return to the ship with its weapon. ASROC was neither recallable nor reusable. Together, the two systems provided a complimentary set of capabilities.
DASH lent itself to experimentation. The “DESJEZ” modifiedDASH drones carried passive “Jezebel” sonobouys, which were normally dropped from P-2 Neptune and P-3 Orion maritime patrol aircraft, as well as torpedoes, giving the destroyerbased system both sensor and weapons-delivery capabilities.
During the Vietnam conflict, some DASHs were modified with cameras for the tactical reconnaissance role, known as “Snoopy,” contributing to the naval gunfire support mission by acquiring targets and providing battle-damage assessments. The USS Orleck, (DD 886) for example, used her drone for “Snoopy” photo reconnassaince missions on a regular basis in 1969 and was the last warship to use her DASH in this combat role. The destroyer-based Snoopy aircraft could also support other fire support platforms, such as the USS New Jersey’s (BB 62) 16-inch guns. Snoopy could evaluate the effectiveness of a fire mission, but it could also acquire targets.
The Marine Corps developed a pair of light-armored, day/night reconnaissance QH-50 drones as part of the Nite Panther project, carrying extra fuel tanks (80 gallons), a “low light-level”
TV cameras, and a laser rangefinder. The system was controlled with a Jeep-mounted, modified shipboard DASH control station. Nite Gazelle was another experiment, which mounted bomblet dispensers and grenade launchers on a QH-50D. Yet another development was the use of a pair of QH-50Ds working in tandem. One was an “attack drone” and the other a “gun ship” model. The GAU-2B mini-gun on the gunship would clear a drop zone for the attack ship, which would deliver ordnance on the target. Three of these test aircraft deployed to Vietnam, and two of them operated from the USS Blue (DD-744).
At one point Gyrodyne was producing more 100 QH-50D aircraft a year. About 700 DASH were ultimately delivered to the Navy (and the Japanese Maritime Self Defense Force taking delivery of another 16). Let that number sink in for a moment. That’s probably more than all unmanned aircraft deployed on naval ships in all fleet combined today.
DASH was eventually replaced by manned helicopters, such the Kaman SH-2 Seasprite Light Airborne Multi-Purpose System, or LAMPS (and later the SH-60 and MH-60 Seahawks). The DASH hangars and flight decks had to be enlarged to handle the larger manned aircraft. The last few drones were transferred to the Army’s White Sands Missile Range in New Mexico, and the Navy Air Warfare Center at China Lake, Calif., where they served towing targets. Nevertheless. DASH had a lasting impact on the destroyer fleet an ASW tactics. They were ahead of their time. Way ahead!
Today, seagoing VTUAVs include the UMS SKELDAR V-200, Scheibel S-100 Camcopter and the Northrop Grumman MQ-8A, MQ-8B and MQ-8C (the MQ-8A and MQ-8B is no longer in service).
These systems are much more advanced, and have the autonomy to fly mission profiles without constant operator commands, unlike the radio-controlled DASH systems.
The original MQ-8A Fire Scout was intended for the U.S. Navy’s littoral combat ships, and was based on the Schweizer 330 manned helicopter. The platform was later “upsized” to a Schweizer 333 airframe, becoming the MQ-8B, and is currently built upon the Bell Jet Ranger 407 platform as the MQ-8C.
The UMS SKELDAR systems have been used by navies and coast guards, and are currently part of the combat systems on the German K130 corvette and Belgian-Dutch rMCM mine warfare ships, which rely heavily on offboard systems.
The Schiebel systems are operated by a number of western navies, as well as China and Russia, although they reportedly have different sensors.
Kaman Aerospace has worked with the U.S. Marine Corps on the autonomous USMC K-MAX® VTUAVs used for logistics, and is currently developing a more capable K-MAX TITAN aircraft, primarily intended for commercial work.
Giving those in offshore energy the ability to create high-accuracy digital representations of their subsea assets in real-time to reduce risk and enable survey autonomy.
Simplified integration with pre-configured payloads
Increased survey efficiency by enabling autonomy
Lower costs by owning your own survey
Gain a clearer understanding with high-res data
The SKELDAR V-200 vertical take-off and landing (VTOL) unmanned aerial vehicle (VTUAV) is extending intelligence, surveillance and reconnaissance (ISR) capabilities for navy, coast guard and other maritime operations. The V-200 is an automatic take-off and landing (ATOL) UAV made by UMS SKELDAR Sweden AB, a company owned by Saab Sweden, with headquarters and manufacturing facilities in Linköping, Sweden.
UMS Skeldar also makes the slightly smaller V-150 aircraft, but the company is currently focusing on the V-200 because of its suitability for shipboard use.
The V-200 is ideally suited for maritime missions. Depending on the payload, the V-200 can conduct Search and Rescue (SAR) missions, provide initial sensor information to queue followon investigations, and serve as a communications and data relay between dispersed nodes in a network, as well as act as a gateway to transmit data received from underwater systems.
The system is available with standard baseline sensor configuration. With a typical EO/IR sensor payload, the V-200 endurance is around five hours. Because of the modular open architecture design, changing payloads doesn’t take long, and new payloads can be readily integrated.
“We work with the customer to understand the mission determine what the optimum sensor payload should be,” said UMS Skeldar Flight Manager Per Malmström. “Because we built the interfaces into the aircraft from the beginning, it’s relatively easy to integrate a new sensor with the system. That would require some flight testing to validate performance, but it’s very achievable.
The V-200 has also demonstrated the ability to participate in anti-submarine warfare (ASW). UMS Skeldar and Ultra Maritime have jointly developed a new ASW sonobuoy dispensing capability for rotary-winged unmanned aircraft systems (UASs), as part of the Canadian Department of National Defence's Innovation for Defence Excellence and Security (IDEaS) program. The effort included the placement of sonobuoy dispenser on the V-200 aircraft. The six-sonobuoy payload is significant considering the compact size of the V-200 platform.
“Up until now, only manned helicopters or larger fixed-wing unmanned aircraft with access to airfields could previously deploy sonobuoys. As a result, there has been a lack of a rapid ship-based responder that can support recognition efforts using passive sonobuoys, which is necessary for complementing ASW operations,” said UMS SKELDAR's VP of Business Development Richard Hjelmberg.
Another unique payload has resulted from a collaborative effort between UMS Skeldar and Green Valley, Ariz., based Hydronalix, to carry and deploy its compact unmanned surface vessels (USVs) from the V-200. The autonomous Hydronalix USVs can carry sensor packages, serve as communications links, and deliver supplies.
“The USVs offered by Hydronalix are such versatile pieces of technology, which we saw a great many uses for including supporting covert surveillance missions and acting as a critical communications link” said Ted Ackerstierna, UMS Skeldar’s vice president for the USA market. “Attached to our Skeldar V-200, which has which has a significant endurance with a payload, the complete system will be able to provide a wide range of enhanced capabilities for Marine Corps and Navy war fighters across their operational domains.”
Hydronalix CEO Anthony Mulligan called the combination a “gamechanger.” “The future distributed force concepts require innovative solutions that can provide the domain awareness for effective decision making. From rescue to ISR assignments, the UMS Skeldar UAV / Hydronalix USV platform combination with advanced mesh networking promises to serve Expeditionary and Special Forces under new distributed force designs.”
The V-200 has earned its sea legs performing diverse missions for different customers. The aircraft has demonstrated its ability to fly in the challenging maritime environment by conducting aerial inspections of merchant ships for emissions for the European Maritime Safety Agency (EMSA). “We provided a VTUAV that could land and take off from EMSA's ships,” said UMS Skeldar CEO Lars Sjöberg.
The Finnish Coast Guard has also successfully demonstrated Skeldar V-200 operations to support day and night search and rescue missions from the Patrol Vessel Turva as part of the Valvonta2 project led by the Finnish Border Guard and funded by the European Maritime and Fisheries Fund.
The V-200 can take-off and land on an area of 9x9 meters, which is smaller than most ship flight decks, and has been selected for use by the joint Belgian Dutch rMCM mine countermeasures ships and the German Navy’s K130 Braunschweig class ocean-going corvettes.
The Belgian and Dutch navies share a critical requirement to ensure the high-traffic environment protecting the approaches to some of the busiest ports and waterways in the world are free of mines. Together they are procuring 12 mine countermeasures vessels-- six for each navy -- which will carry a “toolkit” of unmanned and offboard systems. That toolkit suite, provided by Exail, includes two Skeldar V-200 aircraft. The ships will also have unmanned surface and unmanned underwater vehicles and towed sonars for mine detection. The toolkit includes the MIDS system (Mine Identification and Disposal System) for mine identification and neutralization; SEASCAN remotely operated vehicles (ROV); and K-STER expendable mine disposal vehicles (EMDS).
Very few mine warfare ships can embark a helicopter, and most do not have the ability to launch and recover organic UAVs. The Belgian and Dutch ships are designed for unmanned systems from the beginning, including UAVs, as opposed to adding that capability later.
“Exail selected us as the result of an open procurement, which shows we have a strong product and we can be very competitive,” said Sjöberg.
The German Navy refers to their V-200s as “Sea Falcons.” Each K130 will receive a “system” consisting of two V-200s, along with a ground control station integrated on the corvette to control the aircraft, and equipment with tools and spare parts.
The V-200 is operated with a twin-console remote control station (RCS), which can be at a fixed location, in a container, truck-mounted, or on a ship and integrated into the ships combat system. Launch and recovery is accomplished autonomously.
The V-200 uses a reliable Hirth two-stroke engine that uses spark plugs and runs on heavy fuel, which is much safer than Av Gas on ships. The aircraft can use Jet A1, F44 JP-8 or JP-5, which are all readily available jet aviation fuels that are safe to use aboard ships. The fuel is compressed, vaporized and then ignited with the spark plug. The two side-mounted fuel tanks are cross connected. The engine is water cooled, with a radiator visible at the front topside of the aircraft. The throttle control regulates the engine to run at a fixed 6,100 RPM, and adjusts itself depending on the air temperature or load.
“The ‘high level controls’ tell the aircraft what to do, but the system figures out how best to do it,” said Malmström. “I tell it to take off, and it engages a centrifugal clutch and the tail rotor and adds collective slowly until it’s airborne.”
The system has redundancy and backup systems. The flight control unit uses dual computers, in case one of the central processing units (CPUs) fails. Navigation inputs include global navigation satellite system (GNSS), AIS (automatic identification system), INS (inertial navigation system) and IMU (inertial measurement unit), and a magnetometer that provides a heading reference for additional redundancy. There are two different datalinks, as well as dual power supplies and generators.
The control system gets a lot of information from the host platform ship, such as course, speed, sea state, wind, temperature barometric pressure, and the status of the deck landing system, which indicates how the ship is moving.
Malmström said the aircraft is normally operated with one pilot and one payload operator. “We train with two pilots. The two consoles are completely the same, but we train with the primary pilot on the left. We have a standard course that provides both individuals with the same level of knowledge. Each operator knows what’s happening, and what needs to get done. We have found that works more effectively and efficiently for normal operations than having separately trained payload operators,” said Malmström. “We also provide training for maintainers.”
Malmström said the SKELDAR system is intended to be used often by customers who require airborne surveillance on a regular basis. “Good training and operational usage are extremely important to maintain the capability of any UAS.”
The informed readership of Ocean Robotics Planet understands that emerging technologies have changed the character of warfare through the ages. Whether it was the transition from sail to steam, or the advent of steel warships to replace wooden ones, or the change from the battleship to the aircraft carrier to the centerpiece of the Navy fleet, these changes helped the U.S. Navy dominate at sea.
For those who follow military matters, it is impossible to miss the impact of emerging technologies on changing the character of warfare through the ages. From the time that our cave-dwelling ancestors figured out how to fasten a sharpened stone to the end of a sturdy stick, advances in weaponry have decided the outcome of battles and the fate of nations.
Today there are numerous technologies that have the promise to make an enormous impact on warfare in the third decade of the twenty-first century. Some of the most prominent include next generation fighter aircraft, quantum computing, stealthy bombers, artificial intelligence and unmanned technologies in all domains.
The U.S. Navy stands on the precipice of yet another monumental technological advancement. The Navy’s Force Design 2045 document envisions a fleet of 500 ships, to include 350 crewed vessels and 150 uncrewed maritime vehicles. This represents a once-in-a-generation shift in the composition of the Navy fleet and one that will place big bets on emerging technologies that can make uncrewed maritime vehicles more autonomous.
For the U.S. Navy, unmanned systems – especially uncrewed maritime systems – offer the promise of providing the U.S. military with an asymmetric advantage over potential adversaries. Ukraine’s use of weaponized uncrewed surface systems to attack Russian naval vessels has demonstrated just one use of these – as one wag described them – “Swiss Army Knife” platforms.
The U.S. Navy has taken several actions to define and accelerate its journey to have uncrewed platforms populate the fleet. These include publishing an UNMANNED Campaign Framework, standing up an Unmanned Task Force, establishing Surface Development Squadron One in San Diego and Unmanned Surface Vessel Division One in Port Hueneme, CA, and conducting a large number of exercises, experiments and demonstrations to evaluate uncrewed platforms, including the recently completed Integrated Battle Problem 2023.
This U.S. Navy’s emphasis on uncrewed maritime vehicles was on full display at a recent major international
military-industry event. Held in Honolulu, Hawaii at the Hilton Hawaiian Village in mid-November 2023, TECHNET Indo-Pacific drew over 4,000 delegates from throughout the Indo-Pacific region. As in previous years, the conference featured keynote speakers as well as breakout panels. Among the highlights of this three-day event were a keynote address as well as panel remarks.
Rear Admiral Eric Ruttenberg, Reserve Deputy Commander, U.S. Pacific Fleet, delivered the event’s opening keynote address. His presentation covered a wide range of challenges and opportunities facing the U.S. Navy in the Indo-Pacific region. A substantial portion of his remarks were focused on uncrewed maritime vehicles.
Rear Admiral Ruttenberg noted that the most pressing need for U.S. Pacific Fleet is innovation, that the velocity of innovation must accelerate, and that Pacific Fleet is looking for ways to get unmanned surface vehicles forward to desired areas of operations. He highlighted Pacific Fleet’s emphasis on unmanned because these platforms will enable warfighters to conduct missions in a contested environment that manned systems cannot do due to adversary anti-access/area denial (A2/AD) capabilities.
The admiral also noted that the Navy must continue to evaluate unmanned systems in national and international exercises, experiments, and demonstrations. He placed special emphasis
on the Navy’s Integrated Battle Problem series – providing details of some of these events. He noted that these represent the pinnacle of experimentation with uncrewed maritime systems, and that these will continue into 2024 and beyond.
Rear Admiral Ruttenberg explained that the U.S. Pacific Fleet, which is responsible for dealing with the United States principal adversary in the region, is leaning forward to leverage uncrewed maritime vehicles to perform a plethora of missions for a number of reasons, among them: their ability to reduce the risk to human life in high threat areas, to deliver persistent surveillance over areas of interest, and to provide options to warfighters that derive from the inherent advantages of unmanned technologies.
Later that day, a panel of subject matter experts in the field of uncrewed maritime vehicles highlighted many of the strides the Navy has made in getting these technologies into the hands of Sailors and Marines who evaluated them in the operational environment.
The panelists noted that International Maritime Exercise 2022, held under the auspices of Commander Fifth Fleet and Commander Task Force 59 (CTF 59) in the Arabian Gulf, set the standard for uncrewed maritime vehicle experimentation and included operations with several regional partners. Navies of these nations explored the capabilities of USVs such as the Saildrone, the MARTAC MANTAS and Devil Ray, and many other USVs from participating nations.
A key theme of the panel – and something that resonated with TECHNET attendees from throughout the Indo-AsiaPacific region – was the fact that RIMPAC/Trident Warrior 2022 was a major coming out for uncrewed surface vehicles (USVs) operating with the fleet. Building on the success of RIMPAC/Trident Warrior 2022, the Integrated Battle Problems are increasingly evaluating USVs in broader and more intense set of missions.
Panelists explained that Australia has become a leader is USV experimentation. Autonomous Warrior 22 (AW22) expanded the evaluation of USVs from Australia, New Zealand, the United Kingdom and the United States and featured 30 autonomous systems, including Saildrone, MANTAS and Devil Ray. Autonomous Warrior 22, the Australian Defence Force (ADF) organized, Royal Australian Navy (RAN)-led, two-week exercise was built around a simulated, next generation naval battlespace. Its purpose was to test and evaluate uncrewed, robotic and autonomous systems.
Finally, the panel noted that, building on the recent successes of uncrewed maritime vehicles in international exercises, experiments and demonstrations, a plethora of events designed to continue to place these systems in the hands of naval operators are planned for 2024 and beyond, especially those that feature uncrewed maritime vehicles performing increasingly autonomous missions.
These, as well as other, discussions during TECHNET Indo-Pacific made it clear that the Department of the Navy – and especially the U.S. Pacific Fleet – have a strong commitment to an accelerated development path for uncrewed surface systems so that they can complement the Navy fleet and perform missions that keep Sailors and Marines out of harm’s way.
George Galdorisi is a career naval aviator and national security professional. His 30-year career as a naval aviator culminated in 14 years of consecutive service as executive officer, commanding officer, commodore, and chief of staff. He is a 40-year Coronado resident and enjoys writing, especially speculative fiction about the future of warfare. He is the author of 18 books, including four consecutive New York Times bestsellers.
Product market fit. It's the biggest killer of early-stage technology companies – they build something that no one wants, needs or is willing to pay for. Despite the ever-increasing profile of ocean tech, and billions of dollars flowing into the sector, end-user adoption of autonomous systems has remained slower than expected.
At ACUA we’re completing the build of the world’s first autonomous vessel powered by hydrogen. Our zero-emission platform will replace expensive crewed vessels with smaller scalable platforms meeting the needs for power, endurance and stability but costing less than a fifth of the price to operate.
Over the past three years we’ve spoken to almost a hundred potential users across the maritime security, offshore energy and marine conservation sectors and in every customer discussion the same three challenges preventing the scaling of maritime autonomy kept coming up:
Time is money – and time on site means more coverage, more data and faster project delivery. Across all sectors, the target number has been +720 hours and was even formalised as a Congressional requirement in the 2021 National Defense Authorization Act.
Currently, the biggest challenge has been the maintenance cycles and reliability of diesel generators. Moving parts, oil and filter changes and constant failures mean that most USVs are struggling to achieve more than 6-10 days at sea – a fraction of what is commercially required.
The other challenge with endurance is operational time vs time on site. In open ocean sea states, simply “surviving” at sea is not a commercial solution. Discussions with end users highlighted weather downtime is a major challenge to projects. A recent data harvesting project in Norway with a USV was delayed by over a week due to rough sea states. To be truly scalable USVs need to be stable enough to deliver meaningful capabilities in sea states of 2.5m and up.
To achieve endurance, USV operators have traditionally gone down the wind, wave and solar power route – but as end users have explained time and again, endurance without payload capability is meaningless.
The second autonomy challenge is the collection, processing and communication of high-quality, near-real-time data. Simply being at sea, whether 30 days or 365 days a year isn’t a commercial solution. Platforms need to have both the stability and power for payload to collect high-quality data, through the launch and recovery of sensors and sonars.
This data collection is further impacted by seakeeping performance. Smaller USVs, or medium-sized monohull or catamaran USVs designed foar heavier or more complex payloads can be inefficient, unreliable or even incapable of completing their tasks in moderate sea states. This is principally due to the excessive pitch and roll, preventing useful data gathering or causing comms blackouts; or preventing the effective deployment or recovery of payloads.
Finally, the scalability challenge. How can you cost-effectively build, mobilise and operate vessels to deliver increased operational capabilities whilst always driving down costs? Solutions increasingly need to be low-cost, modular and rapidly deployable with the interoperability to conduct Distributed Maritime Operations. This scalability also needs to take into account localised fuel sources, regulatory requirements and operational logistics such as data handling.
A wide variety of maritime agencies and operators have, or will have, a requirement for systems that can gather a broad spectrum of ocean data and can monitor wide areas of ocean, economically, reliably, environmentally sustainably, and ideally in a manner which presents an integrated and fused data picture.
We saw a clear market space for automated and uncrewed marine systems that have long-endurance capabilities, that can function without loss of sensor performance or
communications blackouts in heavy sea states and adverse weather, and that showcase zero-downstream greenhouse gas emissions.
The modular hydrogen powertrain which has been built and factory acceptance tested enables the H-USV to be futurefuel agnostic, acting as a range extender to the battery system which manages peak power requirements. By moving to a PEM fuel cell which requires a visual inspection every 6 months we remove the reliability challenge of diesel engines and deliver enhanced acoustic, thermal and chemical signature capabilities.
The H-USV uses a Small Waterplane Twin Hull (SWATH) design to increase stability, using a similar vessel design to the US Navy Tagos-class survey ships. The H-USV design increases ACUA’s utilisation rates – meaning more operational days at sea than competitors, who lack the stability needed to operate in larger open ocean sea states due to the reduced unstable which can significantly impact the quality of the data collected with other platforms like experiencing as much as 15-30 degree roll reducing operational efficiencies and data quality.
Independent studies by the University of Southampton showed that ACUA’s 13.5m SWATH vessel has operational limits similar to or better than a 36m monohull vessel which would be required to be minimally crewed. Increased operational limits mean less weather downtime and a greater potential operating period than existing USVs – this, in turn, means higher potential profit, and more data coverage.
The modularity of the H-USV delivers applications across a wide range of sectors and individual use cases within them. Due to its quieter propulsion, long endurance and autonomous capabilities, the defence and security sector has uses for the H-USV across Intelligence Surveillance and Reconnaissance, Anti-Submarine Warfare as well as Border Patrol and security.
It is equally well placed for offshore national infrastructure maintenance and monitoring, including wind farms, pipelines and data cable, due to its clean energy source without compromising its ability to endure long periods offshore. The H-USV also has emerging use cases in the marine conservation sector; with emerging legislation being ratified such as The High Seas Treaty and UN 30x30. The versatility across these sectors due to flexible payloads has captured the interest of a range of businesses. This potential is multiplied through the scope of using swarms. The distributed nature of the swarm operation amplifies the capabilities of the H-USV, enabling simultaneous coverage of expansive ocean areas, critical for all areas.
While the integration of liquid hydrogen as a fuel source brings numerous advantages, challenges still exist in establishing a robust infrastructure and supply chain for widespread adoption, as well as a chronic talent and knowledge gap in the UK marine engineering sector.
Despite this, the modular powertrain lays the groundwork for guiding the maritime transport sector away from fossil fuel use with a 4-week short-sea shipping pilot funded by the UK Department of Transport under the Clean Maritime Demonstration Competition taking a payload from Aberdeen to Orkney.
Before the North Sea crossings, the H-USV will undergo a series of dry and wet HAT and SATs from ACUA’s HQ at Turnchapel Wharf in Plymouth.
As we navigate the opportunities and hurdles of innovation, the H-USV not only addresses the longstanding challenges of existing workboat-sized USVs but also aligns seamlessly with the maritime aspirations outlined in Maritime 2050. Its SWATH hull design, liquid hydrogen and electric powertrain, paired with versatile payload capabilities position it as an adaptable solution for a myriad of applications, from ocean exploration and environmental monitoring to security operations.
Traditional Remotely Operated Vehicles (ROVs) have long been used for underwater tasks, connected to surface vessels through umbilicals. However, the limitations imposed by tethered systems has prompted the development of subsea resident ROVs (R-ROVs). These autonomous vehicles can remain deployed on the seabed, ensuring a continuous presence and swift response to subsea infrastructure needs.
In recent years, subsea R-ROVs have seen increased use in underwater inspections, providing a unique solution for continuous monitoring and maintenance of subsea infrastructure. To unlock their full potential, high-performance equipment, particularly advanced navigation sensors, are crucial. The Rovins 9-DVL from Exail, an all-in-one INS/DVL system, stands out as the leading solution, integrating the latest navigation technology for optimal performance.
In today's underwater inspection landscape, subsea R-ROVs are revolutionising operations by addressing operator challenges effectively. Remaining stationed on the seabed for
extended periods, R-ROVs facilitate real-time monitoring, immediate event response, and prolonged data collection without constant deployment and retrieval. This capability allows operators to conduct continuous surveillance missions and gather data over extended periods, proving invaluable in oceanographic research and subsea pipeline monitoring.
Their autonomous capabilities and adaptability reduce vessel days, minimising the carbon footprint and mobilisations associated with frequent movements. Overall, this contributes to cost reduction and operational efficiency. This in turn enhances underwater operations across diverse applications, from offshore platform maintenance to subsea infrastructure inspections and environmental monitoring.
R-ROVs rely on precise underwater navigation for swift interventions, allowing prompt responses and timely inspections. Equipping R-ROVs with high-performance navigation systems is crucial, and Exail's Rovins 9-DVL excels in this regard. Integrating a Fiber-Optic Gyroscope (FOG)-based Inertial Navigation System (INS) and a Nortek Doppler Velocity Log (DVL), it efficiently meets R-ROVs' objectives for rapid intervention and effective task execution.
With a heading accuracy of 0.04° (deg secant latitude RMS), the Rovins 9-DVL significantly enhances navigation precision, offering unparalleled positioning and navigation capabilities. The direct coupling of INS and DVL facilitates real-time data fusion, providing operators with instantaneous and accurate data for continuous adjustments to the R-ROV's route. This enables R-ROVs to follow a direct and precise path to target locations, thus minimising diversions. Combining INS and DVL measurements significantly enhances navigation precision compared to using either system alone. The system's satellite connectors enable seamless integration with external sensors, such as pressure or sound velocity sensors, ensuring comprehensive data collection for even greater accuracy.
Tailored for rapid deployment, the Rovins 9-DVL is pre-calibrated and plug-and-play, eliminating the need for on-thefield calibration and ensuring seamless integration into vehicles. With self-alignment in motion, it guarantees the R-ROV's readiness for immediate deployment, essential in critical situations requiring quick action, such as risk mitigation, or urgent underwater assessments.
To execute missions such as inspecting underwater infrastructures or collecting samples in areas inaccessible to human divers, R-ROVs may be deployed at considerable depths and in challenging conditions. Navigating underwater currents and topographies poses significant challenges to maintaining precision during inspections.
The Rovins 9-DVL is highly resistant to high pressure with its robust titanium housing, and is operational down to 6,000 meters. This proves highly effective for meeting R-ROVs' navigation precision needs in harsh environments. Its ability to reduce drift over time and compensate for external disturbances ensures accurate positioning even in dynamic underwater conditions.
With a bottom range detection capability of up to 175 m and a frequency of 500 kHz, the integrated DVL can operate at higher levels in the water column and closer to the seabed (up to 0.3 m) compared to similar equipment. This capability enables R-ROVs to maintain optimal control even in areas with complex or irregular seafloor conditions, crucial for ensuring stability and safety, avoiding collisions, and conducting thorough inspections.
The Rovins 9-DVL represents a pivotal solution to address the imperative need for autonomous capabilities in R-ROVs. As these vehicles are specifically designed to endure extended periods stationed on the seabed, ranging from weeks to months, the demand for autonomous functionalities becomes paramount. The Rovins 9-DVL not only meets but exceeds these expectations by operating on low power consumption (< 18 W). This provides a strategic advantage for R-ROV operators striving to conserve energy resources without compromising on essential data processing power. By leveraging Exail solid-state FOG technology, it ensures seamless operations and reduces maintenance requirements, thus enhancing overall efficiency. Its compact, lightweight, and versatile design simplifies integration into all subsea platforms, requiring fewer cables for installation.
In conclusion, the rapid growth of underwater exploration in residential areas, driven by the widespread adoption of ROVs, highlights the crucial role of precise navigation. Advanced navigation sensors, as showcased by the Exail all-in-one Rovins 9-DVL, are unlocking the full potential of subsea R-ROVs, significantly enhancing the accuracy and dependability of residential ROV monitoring. These advancements go beyond mere technological enhancements; they are fundamental drivers in the evolution of underwater exploration and intervention capabilities, promising a future where autonomy and precision redefine the possibilities of subsea operations.
In the 1980s and well into the 1990s, the term "mux" (short for multiplexer) was commonly used to refer to the part of the ROV control system that handled the remote control of the vehicle, i.e. a package with digital and analog inputs/ outputs. Video was transmitted on separate coaxial cables as "baseband" video, and all other controls on shielded twisted pairs. These conductors ran in the same umbilical and tether all the way down to the TMS and the ROV.
Cameras were the most bandwidth-demanding devices at that time. Meanwhile sonars and similar devices managed well with some form of serial communication.
In cases where there was a shortage of coaxial cables in the tether/umbilical, frequency multiplexing of three video channels was used, utilising components originally designed for cable TV systems. Digital multiplexing for video was not available, and video existed solely in "analog" form.
The shift towards using fibre was influenced by several factors:
ƀ The desire to dive deeper, necessitating a longer umbilical. Analog video and RS 422/485 are generally suitable up to around 1,000 m of cable;
ƀ Increased bandwidth requirements;
ƀ Safety-related demands: electrical regulations only allow limited mixing of conductors with different voltages in the same cable, especially with signal conductors alongside high voltage;
ƀ Growing availability of fibre optic slip rings and other components fitting within the control pod of an ROV.
Early solutions with optical fibre in the umbilical were based on multimode (MM) fibre, addressing safety and – to some extent – bandwidth, but only to a limited extent in terms of range requirements. As single-mode fibre and electrooptical converters became more accessible, the industry predominantly adopted them.
Some ROVs incorporated fibre in the early 90s, such as Oceaneerings’s AIS and Slingsby's Trojan. They would often utilise a mix of standard fibre optic components from other industries and/or custom-made circuit boards to address specific interfaces.
Stolt Comex Seaway (SCS) were early in building at least two specialised survey-focused ROVs, named SOLO. These systems had extensive external equipment connection capabilities. The control pod for SOLO MkII – built by Innova AS around the turn of the millennium – had in addition to analog video, a total digital bandwidth of 3Gbps. This is less than what a single modern SFP can provide.
The first manufacturer to focus on cards dedicated to multiplexing and the transition from electrical to optical interfaces specifically for ROV applications was Prizm Inc. in the USA. Their first representative outside of the USA were Prosys AS. This took place around 1993, led by one of Innova AS's founders. Prosys AS were later acquired by a larger industrial company with little interest in that part of Prosys's business, and Prizm Inc. became the first agency signed by the newly established Innova AS in autumn of 1997.
With the emergence of sensors with higher bandwidth, usually sonars, in the late 90s, several companies received requests for custom-built pods for specific sensor configurations. Some of these early sensors also had unique power supply requirements, including high DC voltages, or both positive and negative (relative to 0V). This led to an increasing number of requests for the construction of special electronic
pods to accommodate specific sensor packages. Over time, these specifications evolved into "standard" solutions designed to cover 80-90% of all possible configurations.
Innova AS were possibly the last of the major suppliers to introduce standardised solutions. However, significant experience had been gained from a wide range of custom pods. Innova AS had also received feedback from customers regarding deficits in other suppliers, especially in terms of power supply and diagnostic capabilities.
A "standard" ROV typically has relatively few extra interfaces for external equipment. To perform a job requiring more than basic equipment, one will have to expand the interface capacity. For comparison, if more hydraulic functions are needed, an additional valve pack and possibly a Dirty Work Pack (DWP) –essentially a hydraulic isolating transformer – can be installed. Such a solution may be regarded as a hydraulic expansion kit.
If more connectors are required to plug in sensors and the like, the solution is a dedicated multiplexer, providing expanded capacities for both signal and power management. Sometimes a separate multiplexer is used even if direct connection to the ROV's original control system is theoretically possible, for the reasons mentioned below.
Drivers behind this separation can be:
ƀ It’s costly to build all ROVs with large extra interface capacity when traditionally only a limited percentage of the vehicles are used for such work;
ƀ On a survey job, there may be one contractor for the ROV itself and another contractor responsible for data collection. When installing lots of different equipment on the vehicle, and electrical faults, signal problems, etc. occur it can quickly become a debate over whether the fault lies with the vehicle or the new components mobilised, including both cabling and sensors. A dedicated survey multiplexer simplifies both troubleshooting and contractual matters, especially if the multiplexer is designed to monitor the condition and troubleshoot cabling, etc. associated with this;
ƀ The entire survey setup can be almost completely tested in the workshop before being brought on board. Furthermore, it’s usually easier and significantly cheaper to repair faults in a workshop environment, without using vessel time for this.
During both mobilisation and operation, it’s important to monitor the condition of equipment. A water alarm should be standard on all high-cost equipment installed on an ROV, but one should also be able to monitor both the optical and electrical aspects as much as practically possible.
SFPs (Small Form-factor Pluggable), which are standard telecom devices, are used to convert the signals between the electrical and optical domain. The SFPs has a diagnostics interface providing various information: data on temperature; optical level in; and optical level out. Ideally, these data should be made available to the user through the topside unit.
There is also occasionally a desire to integrate an Optical Time Domain Reflectometer (OTDR) to locate faults in the fibre link through to the surface. However, since historically these have been very expensive, they have had limited use as an integrated part of a standard multiplexer so far.
The point that has had the greatest potential for improvement compared to solutions from the 90s has been the power supply and its management (popularly called Power Management). A large percentage of faults visible during mobilisation on board are those that cannot be tested in a dry workshop, i.e. faults caused by the combination of power and seawater. Most of these faults relate to cabling and connectors and can be very time-consuming to resolve if the multiplexer is not built with this in mind.
On a typical multiplexer, there are usually one or two connections providing 110/120 VAC routed directly from the host ROV. These are not galvanically isolated from the source and must be monitored by the ROV's ground fault system. All other external connections to the multiplexer, as well as internal systems, go through separate power supplies with galvanic isolation and will be monitored locally.
Based on close dialogue with several key customers, there was a quick agreement that as much disconnection as practically possible should be incorporated, and in addition to the ground fault system, it is also advantageous if there are:
ƀ Fuses that can be "reset" remotely;
ƀ Adjustable fuse characteristics (trip limits);
ƀ Measurement of current and voltage per output.
In early 2000, Innova implemented electronically resettable fuses. This removed the need to resurface the ROV to reset fuses, and significantly aided troubleshooting. The other key features mentioned above where included from the introduction of the Matrix MkII; and has – according to customers – been an essential requirement for their mux acquisitions since then.
Available building blocks and basic technologies have made significant progress since Innova AS's founders became involved in this field more than 30 years ago. It’s now possible to fit a considerable amount of bandwidth, many channels, and also compact and efficient power supplies into a relatively small volume.
The one component that remains as large as ever are the connectors used on the end cap. This means that when one wants more of any particular interface, one must prioritise to find space for it.
In the early days of Multi Beam Echo Sounders (MBES), some key manufactures agreed on Positive-referenced EmitterCoupled Logic (PECL) communication. At the time, the highest speed of Ethernet commonly used on ROV’s was 100 Mbit/s, and these new sonars needed quite a bit more. 1,000 Mbit/s Ethernet was defined, but not commonly used on ROVs. PECL more or less disappeared when 1 Gbps Ethernet became practically available, and Innova AS stopped offering it as a standard option four years ago.
Serial lines (RS 232/485) were predicted to be near the end of their life cycle a few years ago, but it still seems to be the simplest and most robust way to connect most low-bandwidth sensors.
Analog Video (AV) is in a similar position, where there is a clear trend toward more IP-based cameras. One reason AV persists is that IP-based cameras will always have some latency, and the pilot and manipulator operator require near real-time video. The latency in IP cameras has gradually decreased over the years and can now be below 200 ms to almost 100 ms.
HD-SDI and 3G-SDI has been the biggest consumer of bandwidth for many years, initially driven by high-resolution requirements and zero latency.
Ethernet (10/100/1000/2500… etc.): In short, all users moving from something (RS232/485, Analog Video, 3G/HD-SDI) covert to IP, and this is most likely to be the preferred solution going forward. However, on that path, there are some elements that must be addressed and that we, to some extent, need to consider as an industry.
When running 1,000 Mbps directly point-to-point, timing can be maintained without problem since it does not involve an Ethernet switch. This mainly applies to multibeam sonars –since in many cases they need this bandwidth – but also some cameras.
All other equipment mainly operates at 100 Mbps, and this is realised in a multiplexer that divides a 1,000 Mbps line via a switch. For timing to be deterministic through a switch, it must be able to handle PTP (Precision Time Protocol).
Furthermore, we should be able to begin the introduction of PoE (Power over Ethernet). It can help reduce the number of different connectors necessary to cover all possible types of sensors to a maximum of two. Then a relatively inexpensive 8-pin connector can cover everything up to about 71 W power requirements and 100 Mbps, and a 10-pin connector for those needing either more power or more bandwidth. The two additional pins can be used for the extra required power, and the eight other pins can be physically placed in a configuration that allows up to 2,500 Mpbs.
Innova AS has been a central developer and supplier of multiplexers and fibre optic components since we started our business. In 2022/23, we have sold over 100 larger multiplexers in total. This is in addition to selling a large number of components to several leading ROV manufacturers, and going forward we will intensify our efforts to develop even more new solutions in this area.
After a three year pause due to Covid, Underwater Intervention came back like a whirlwind at the end of last year. UI23 took place between November 29th through December 1st 2023. The event returned to its traditional venue of New Orleans, Louisiana, but has moved to a different timeframe in order to join forces with The Workboat Show. This move worked out very well, with the two events complimenting one another perfectly and encouraging tremendous synergy.
In early-2023, the UI track chairs and I went back to the drawing board. We wanted to address some of the floor traffic issues for exhibitors, whilst also helping to promote the technical program, and still enjoying the social aspect of this wonderful event. We worked with our new show management team, Diversified Communications (Divcom), to plan how to move the technical rooms to the show floor. This proved to be a huge success.
Foot traffic at the show had increased considerably from the last show in 2020. By the end the exhibitors were all completely exhausted from the sheer amount of client face time.
The expansive food court was another component of the UI sector of the exhibition hall. Its inclusion allowed visitors to stay at the show instead of having to leave the Convention Center at lunch time.
Another benefit was the location of the registration entrance. This was positioned on the UI side, funneling everyone through our sector before they reached the Workboat Show.
The technical program centered on two technical rooms, one on each side of the stage where the Think Tank would be held. A total of six technical tracks filled the two rooms, with spill-over onto the stage. We eventually pushed one of the tracks upstairs due to inadequate room on the floor itself.
The show concluded on the 1st of December with a straight run into the Christmas Holidays. In January, I had to issue an HSE warning to all the track chairs and show management for shoulder injuries caused by patting ourselves on the back so hard! Joking aside, we now feel we have a very strong plan looking ahead at UI24. We’re planning an expansion of the total number of technical rooms (again, on the show floor), and extended exhibit space for more exhibitor booths.
There are also some further changes in the handover from UI23 to 24. As part of the conclusion of this successful event restart, Chuck Richards has retired as the Marine Technology Society’s ROV Committee Chair. In turn, I have been appointed by MTS President Justin Manley to take over this role.
This position has a very storied history. It was first filled in 1992 by Bob Wernli, then continued by Drew Michel, before being taken over by Chuck. Chuck has been a wonderful leader and mentor to me along the way, and I hope to do this position justice by carrying on his legacy. Many thanks to Chuck for the years of hard work and wonderful service to our industry.
As for my vacated position as UI Technical Chair, that role will be filled by a combination of Nancy Summers and Jami Cheramie, both of whom are with Oceaneering International.
I am anticipating a huge expansion of the show following 2023’s successful restart, and I hope to see all of you in New Orleans later this year for another fun and thought-provoking get-together.
PHINS 9 COMPACT
World's most compact high-performance inertial navigation system
Unmatched navigation accuracy: heading 0.04°, roll & pitch 0.01°
Easy integration through optimized SWaP-C
Unrivaled reliability in harsh environments
Meet us at Oceanology International
Booth #E100-200