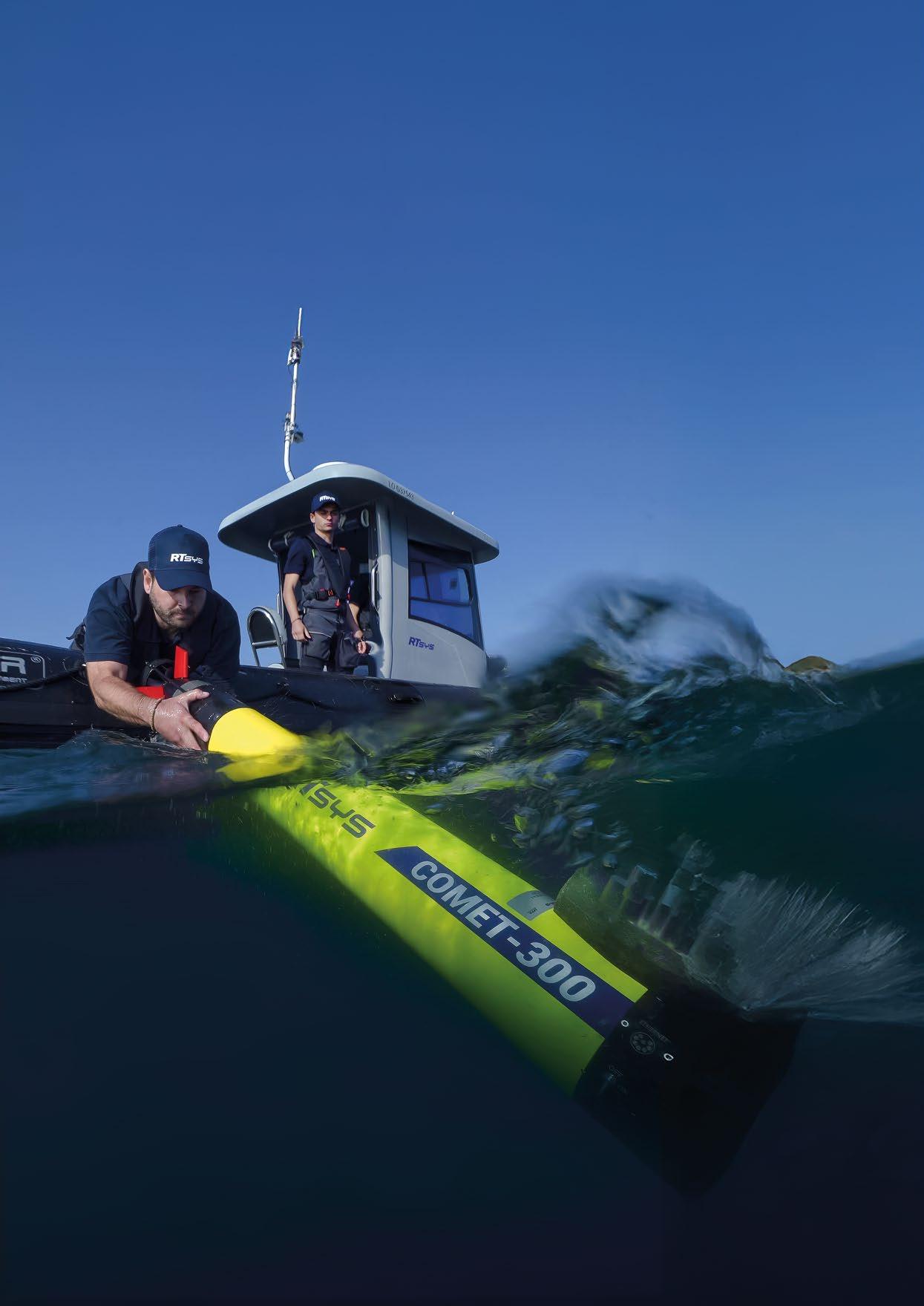
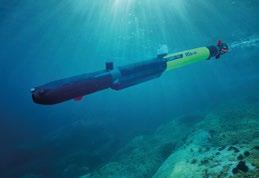
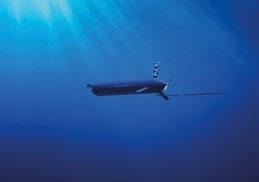

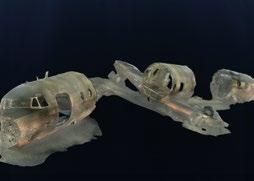
• intelligent vehicles
• reliable communication
• accurate positioning
• modern sensor networks
• diver navigation systems
We deliver safe and precise integrated services that optimize efficiency and keep your operations running smoothly—anytime, anywhere—with our remote and digital offerings.
The ELI-3325 BlueWhale, equipped with ATLAS Elektronik passive and bi-static towed array sonar, has successfully detected submarines in operational exercises across diverse maritime environments, including the Atlantic, Indian, Mediterranean, and Baltic Seas.
BlueWhale is a large, high-endurance, uncrewed underwater vehicle engineered for stealth and autonomous operation. Further mission capabilities include ISR, seabed warfare, MCM, ACINT, SIGINT, and forward scouting for special forces, including real-time video support.
06. Events Calendar & Welcome to Ocean Robotics Planet
09. COMET by RTSYS: A Dual-Use AUV that Redefines the Rules of Underwater Exploration
15. BlueWhale: A True Submarine Force Multiplier
17. Subsea’s Best Kept Secret: Advanced Navigation’s Subsonus USBL2 Empowering the Tech Ecosystem
23. IVM Technologies in Full 3D: Revolutionise Your Subsea Inspections
27. General Oceans Empowering Defence Capabilities Through Advanced Ocean Technology
30. Poster: SRS FUSION ROV
33. MarineNav: North Atlantic Tough. Trusted Everywhere.
35. South Korea Says OK to HD Hyundai for Autonomous Vessel. Mariners Say Oh My!
37. Flexing Muscles: Norway Bulks Up Civilian-Military Co-Operation to Build CUI Security
39. The Cellula Robotics Toolkit for Safe-Guarding Our Vital Shared Assets
43. Leveraging AI-technologies to Make Uncrewed Surface Vessels More Autonomous
45. Accelerating the Journey to Achieve a “Hybrid Fleet”. The Role of Innovative Science and Technology
49. Maritime Drones (USVs) in the Russo-Ukrainian War (2022-24)
55. Ukraine Lessons Learned in Drone Warfare
ISSN 2755-239X
EDITOR-IN-CHIEF
Richie Enzmann
COPY EDITOR
Will Grant
SALES DIRECTOR
Nick Search
DESIGN & LAYOUT
Milan Farkas
CONTRIBUTORS
Richie Enzmann, Alison Pike, George Galdorisi, H I Sutton, Lee Willett, Marc Deglinnocenti, Richard Mills
SPECIAL THANKS TO
Aidan Thorne, Alistair Gibson, Andy Freeman, Anthony Hammond, Audrey Leon, Bill Mallin, Callum Shaw, Charlotte Sherwood, Chris Sundstrom, Curtis Lee, Dawn D’Angelillo, Francisco Bustamante, Jack Rowley, James Acuna, James Colebourn, John Benson, Jostein Jansen, Lee Willett, Karoll Audibert, Marion Seyve, Matt Bates, Michael King, Morgane Ruiz, Pierre-Alexandre Caux, Rachael Reader, Rachel McAlpine, Raymond Ruth, Richard Mills, Willard Balthazar
Advanced Navigation
Alseamar
BAE Systems
Blueprint Subsea
Cellula Robotics
Deepinfar
Digital Edge Subsea
Exail
General Oceans
IAI-ELTA
IVM Technologies
MarineNav
MARTAC
NETmc Marine
Norwegian Navy
Norwegian Offshore Rentals
Oceaneering
QYSEA
RTSYS
Saab Seaeye
Sonardyne
U.S. Navy
MAY COMBINED NAVAL EVENT (CNE)
Farnborough, UK (20–22 May 2025)
JUNE UNDERWATER TECHNOLOGY CONFERENCE (UTC)
Bergen, Norway (10–12 June 2025)
MTS/IEEE OCEANS
Brest, France (16–19 June 2025)
ENERGY DRONE & ROBOTICS SUMMIT
Houston, TX, USA (16–18 June 2025)
KIEL MUNITIONS CLEARANCE WEEK
Kiel, Germany (18–20 June 2025)
JULY MARITIME SECURITY SUMMIT
SEPTEMBER
National Harbor, MD, USA (23–24 July 2025)
OFFSHORE EUROPE
Aberdeen, UK (2–5 September 2025)
DSEI
London, UK (9–12 September 2025)
UNMANNED MARITIME SYSTEMS TECHNOLOGY USA
Arlington, VA, USA (15–17 September 2025)
OCTOBER
MTS/IEEE OCEANS
Great Lakes, USA (29 Sept – 2 Oct 2025)
MATS
Southampton, UK (30 Sept – 1 Oct 2025)
SEABED SECURITY
Troia, Portugal (30 Sept – 1 Oct 2025)
SUBMERSIBLE OPERATORS GROUP
Tenerife, Canary Islands, Spain (7–10 Oct 2025)
NOVEMBER
DECEMBER
OFFSHORE ENERGY
Amsterdam, The Netherlands (25–26 Nov 2025)
UNDERWATER INTERVENTION / WORKBOAT SHOW
New Orleans, LA (3–5 December 2025)
CHANGI NG THE PARADI GM OF SURVEY , SCI ENCE AND SECURI TY THROUGH LONG RANGE MODULAR AUTONOMOUS UNDERWATER VEHI CLES
cell power ed AUVs
Exploring the uncharted depths of our oceans has long been a feat reserved for the biggest and most expensive underwater vehicles. Yet, with changing environmental demands and surging interest in critical undersea infrastructures, there has never been a greater need for efficient, flexible, and reliable underwater exploration tools. Enter the COMET Autonomous Underwater Vehicle (AUV) from RTsys; a revolutionary, dual-underwater vehicle which sets a new standard for autonomous marine operations.
Every year, the ocean reveals a mere fraction of its mysteries to humans. According to the National Oceanic and Atmospheric Administration (NOAA), over 80% of our ocean remains unexplored and unmapped. This vast aquatic world –which hosts marine life, resources, wrecks, and even clues to climate history – offers promise for science, industry, and conservation alike. Increasingly, industries such as offshore energy, biodiversity research, and environmental monitoring require robust tools not just to reach these depths, but to understand and act upon the data gleaned from them.
Traditionally, the limitations of underwater vehicles have hampered progress. Tethered Remotely Operated Vehicles (ROVs) demand hefty support systems and expert crews, while many legacy AUVs are specialised and inflexible. The result often means costly missions, incomplete data, or even vehicles lost at sea. Against this backdrop, RTsys – renowned for their advanced acoustic and subsea technology – have engineered a solution tailored for both versatility and reliability.
At the cutting edge of French marine engineering, the COMET300 AUV stands out for its unique dual-mode design. It’s the only portable underwater vehicle currently on the market that is seamlessly used by research institutes, survey companies in the offshore industry, and navies worldwide. The COMET is engineered not simply to be an exploration tool, but as a platform committed to quality, flexibility, and user-friendliness.
AT A GLANCE: KEY SPECIFICATIONS
ƀ Dual Operation: for civil industry, scientific, and military operations
ƀ Dimensions: two-man portable <2.5m length, <40kg weight
ƀ Maximum Depth: rated up to 300 m
ƀ Endurance: up to 20 hours depending on its final configuration
ƀ Navigation: FOG INS + Doppler Velocity Log + GPS surfacing + RTsys RACAM protocol (sparse-LBL)
ƀ Sensors & Payloads: SSS, magnetometer, camera, CTD, multiparametric probes, OAS, hydrophone…
ƀ Ease-of-use: no need for LARS – ease of transport and deployment
ƀ From coastlines to offshore
Imagine either a team of marine biologists, a reduced survey crew or an EOD team ready for MCM operation stationed off the coast of Brittany. They must conduct a six-hour survey to map the seabed and detect points of interest. In the past, the operation would have required scheduling a vessel with a large crew, days of calibration, and risky descent using delicate equipment. But, with COMET-300 AUV, the story is different.
After having programmed the mission, the COMET can be ready for deployment within minutes. Launched manually by a single operator, the AUV autonomously glides along pre-programmed
transects, gathering high-resolution sonar and imagery data with the highest accuracy of positioning possible (less than 5m constantly with sparse-LBL technology). If an area of interest appears – such as a suspected shipwreck, a rare coral species, or a mine from World War II – the team can reprogram in just a few minutes a new path to more closely inspect the contact of interest for instantaneous investigation and new footage samplings. The operation can be conducted by just two people, directly from a small inflatable boat. And as almost every underwater mission encounters unexpected scenarios, the COMET300 allows immediate operational switch, so mission flexibility is maximised without sacrificing data integrity.
Exploration needs are rarely the same from one mission to the next. That's why the COMET-300 accepts a wide array of sensors and payloads, from side-scan sonar to magnetometer, HD video cameras, CTDs (conductivity, temperature, and depth sensors), and even custom scientific probes. Integrating every payload as one system, facilitated by a modular nose section – a rarity for vehicles of this size – and an incomparable stability makes COMET a reliable platform for higher data rendering, specifically for sonar imageries and magnetic data recovery. Built from marine-grade aluminium
alloys and reinforced plastics, the COMET is both durable and easily portable. At just 40kg, two people can transport, and one single person can deploy the vehicle without specialised winches or cranes. Powered by swappable high-performance lithium-ion batteries, the COMET can perform up to twenty hours on a single charge under typical deployment, with realtime battery monitoring from the surface while the AUV is on duty. For extended operations or under challenging conditions, additional battery modules are easily swapped on deck.
FOR WHOM AND FOR WHAT? INDUSTRIES & MISSIONS
ƀ Scientific Research and Environmental Monitoring: habitat mapping, water quality assessment, marine life census
ƀ Offshore Energy: undersea infrastructure inspection, pipeline/cable route survey, leak detection
ƀ Maritime Safety and Security: wreck localisation, UXO (unexploded ordnance) detection
ƀ Search and Recovery: rapid deployment for search missions, disaster response
COMET’s mission-planning interface is designed for intuitive setup: drag-and-drop waypoints; real-time tracking up to 2km (RTsys’ own protocol); and adaptive mission correction if environmental conditions shift. Onboard routines enhance obstacle avoidance and optimise data quality, without requiring operator oversight. Combined with an easy maintenance procedure (modular design means field repairs are quick) the total operation cost for COMET-300 is among the lowest in its class, reducing both human and financial resource needs.
The quality of underwater data is what determines the success of any exploration mission. RTsys equips the COMET with data logging and onboard data QC (quality control) tools. Coupled with RTsys COUSTO software suite, users can visualise, analyse, and export mission results immediately after having recovered the vehicle. COMET-300 AUV isn’t just another underwater vehicle. It's a comprehensive marine exploration partner: rugged, smart, efficient, and unfailingly reliable. For sectors
where time, data quality, and operational security matter, COMET-300 stands alone as the future-ready choice. RTsys’s ongoing commitment to innovation, and close user support ensures that every new challenge in ocean science, industry, and defence can be met with confidence.
At first glance, the RTsys COMET-300 AUV resembles any number of sleek, torpedo-shaped ocean drones now crisscrossing the world’s seas. But a closer look especially in its COMET-MCM configuration reveals something unique: the military configuration of the COMET-300 AUV has been optimized for Mine Counter Measures (MCM), fighting sabotage against vital undersea infrastructure, and rapid Search and Rescue (SAR) response. In other words, this compact and portable underwater asset is poised to transform how navies and security forces confront underwater threats.
Mine warfare is, in many ways, the original asymmetric threat. Even a single naval mine can block an entire port or isolate a fleet. Traditionally, countering these has been slow, risky, and often requires putting divers directly in harm’s way. COMET-MCM offers a different vision. Outfitted with military-grade side scan sonar (SSS), this vehicle can sweep the ocean floor for mines and unexploded ordnance, capturing razor-sharp images in silty harbours or cluttered coastal zones: scenarios where manned vehicles and divers are at greatest risk.
During one of the NATO exercises which RTsys have been consistently participating in for years, observers watched as a single COMET-MCM unit, deployed from a small RIB, conducted a complete search of a simulated one-squarekilometre minefield in just few hours, automatically mapping and identifying all threats.
It’s not just navies taking notice. COMET-MCM’s sensor suite makes it an ideal silent sentinel for undersea infrastructure protection, covering submarine cables, energy pipelines, or port assets, all of which are crucial to the global economy. Operators can pre-program regular patrols, letting the AUV glide beneath offshore platforms or along lengthy cables, using high-resolution sonar and HD cameras to spot intrusions, tampering, or environmental threats. If something unusual appears –an anchored object or a sign of sabotage – the operator can send an ROV or divers immediately to the points of interest to investigate and document evidence detected originally by the AUV. Multiple COMET-MCM units can even be networked, sharing positioning data securely via encrypted acoustic links for wide-area surveillance.
In a world where both state and non-state actors see undersea assets as targets, such tools offer a blend of persistent vigilance and a rapid response which is difficult to match. As maritime infrastructure grows ever more critical and the underwater domain more contested, experts say COMET-MCM is likely to become a familiar sight in harbours and at sea, silently patrolling, scanning, and responding in real time.
Danger doesn’t always come from conflict. Whether it’s a sunken vessel, a lost airline black box, or marine accidents during bad weather, search and rescue at sea demands speed and accuracy.
Thanks to COMET-MCM’s portability and quick response capability, once launched it can leverage onboard mapping and acoustic tracking to quickly localise wrecks, lost cargoes, or survivors’ beacons. Its internal batteries give it the stamina for hours of work, and should the mission demand more, operators can reconfigure its modular payload section in a matter of minutes.
For Defence and Coast Guards specialists, the promise is obvious: less risk to human life, faster threat identification, and unmatched adaptability in the field. It’s a force multiplier, and a platform like COMET-MCM lets experts rethink how to secure the sea below the surface, whether the mission is military, commercial, or scientific.
In ocean technology, the pressure to do more with less has never been greater. From deterring threats at sea to ensuring that the lifelines of global industry stay connected, COMET300 and COMET-MCM stand out, not as a compromise, but as a breakthrough.
They’re the first man-portable vehicles to truly erase the line between military and industrial subsea operations, not just in branding, but in real-world capability. The result is better value, broader impact, and a new operational freedom for all those whose frontiers lie beneath the waves. Whether requested from a Navy Commander safeguarding critical passages, or a PhD scientist keeping energy flowing under the sea, the dual spirit of COMET ensures they will never have to settle for less than mission excellence.
High resolution sonar system solutions for Mine Counter Measures and other military applications.
Supporting ocean scientists, engineers and the maritime industries overall by providing underwater technology.
Advanced instruments used in oceanography and subsea navigation to help measure movement in underwater environments.
Mission-ready Hybrid ROV system with fully integrated sensors for fast deployment.
Adaptive robotic arms for intervention and control in offshore energy and modern naval landscapes.
Robust, reliable underwater sensors for the planet’s harshest environments and most difficult applications.
Find out more
Seafaring nations face unique challenges in ensuring the safety, security and sovereignty of their nautical frontiers. Even in times of tranquility they must guard against threats such as terrorism, smuggling, illegal fishing, natural resources theft, and uncontrolled mass immigration. And when conflict does arise, these nations must have antisubmarine and anti-surface vessel warfare capabilities to defend against naval incursion or attack. Even before the outbreak of open hostilities, it is imperative that they be able to detect and track hostile naval forces engaged in intelligence gathering and other covert activities.
To contend with this multitude of threats, organizations tasked with maritime security employ maritime patrol aircraft, coastal radars, naval patrol vessels, submarines and a range of surface and subsurface sensors; but resources are always challenged given the tremendous scope of the endeavor. Moreover, few effective solutions are available to detect and track hostile submarines operating at depth.
In response, IAI’s innovative systems and sensors subsidiary, IAI ELTA, developed BlueWhale™, a unique system with onboard capabilities beyond anything seen before on an uncrewed underwater asset. BlueWhale™ is a stealthy, longendurance, large displacement uncrewed underwater vehicle (LDUUV) designed to complement conventional submarines and naval forces with autonomous capabilities.
With its modular design and array of available sensors, BlueWhale™ can be configured for a wide range of critical missions: Anti-Submarine Warfare (ASW); Intelligence, Surveillance and Reconnaissance (ISR); SEABED warfare; Mine Counter Measures (MCM); Acoustic Intelligence (ACINT); Forward SIGINT scout for Special forces, including landing missions; Forward SIGINT scout for naval task force; and piracy, terrorism and illegal immigration detection.
Special attention has been paid to BlueWhale’s ASW capability. IAI teamed with ATLAS ELEKTRONIK, a world leader in the underwater domain, to integrate the company’s Towed Array Sonar (TAS) with BlueWhale™. The synergy between these systems has produced a truly “game changing” solution.
Using Bi-static and Multi-static external active sonar sources, the system delivers the revolutionary ability to extend a submarine barrier over areas that were previously impossible to monitor in an efficient way. Operating undetected with a passive array to a dive depth of 300 meters, BlueWhale™ creates a true dilemma for enemy submarine forces.
The sub-surface sensor suite also includes active and passive Flank Array Sonar (FAS) for the detection of surface vessels and submarines, Synthetic Aperture Sonar (SAS) for mine detection and high-resolution sea bottom mapping, and magnetic sensors for mine detection and verification.
On top, BlueWhale™ features a patented, collapsible mast configured with advanced surface payloads, including a staring radar, electro-optics/IR, R-ESM, and low signature Broad Band SATCOM for real-time data exchange.
Blue Whale’s capabilities were recently demonstrated to great effect by the German Navy within the framework of its Operation OPEX program, geared at introducing innovation to address current and future threats. For two weeks in November 2024, Blue Whale underwent intensive sea trials in the “real world” laboratory of the Baltic. The testing focused on reconnaissance and sonar capabilities, employing a comprehensive and empirical methodology to verify the system’s performance and reliability. The sonar and mast mounted sensors provided a clear, accurate
picture of long-range targets, demonstrating ISR capabilities comparable to those of conventional submarines but without endangering operators.
Regarding the trials, the Inspector General of the German Navy, Jan Christian Kaack, recently stated at the Navy Talks in Berlin that Blue Whale “…exceeded our expectations.” He added “And with two or three of these models, I could seal everything off Fehmarn”.
BlueWhale™ is managed via an efficient Command & Control (C2) system, facilitating a continuous Situation Awareness Picture, Call-to-Action commands, events blogger, remote operation and more. A user-friendly Human-Machine Interface (HMI) enables effective operation by a small team.
With acquisition and operating costs far lower than conventional systems, and the ability to perform critical missions with complete autonomy, proven over 2,000 diving hours, BlueWhale™ is a true force multiplier that empowers maritime nations to secure the integrity of their territorial waters.
Advanced Navigation’s USBL2 is creating a buzz in the industry, offering a high accuracy positioning sensor at an affordable cost compared to the competition. However, to those not yet familiar with their positioning sensors and how they actually work, then the following will cover how you can enhance your navigation accuracy without over-the-top spending.
For a long time the USBL market has been in need of an underwater heading solution that is reliable and cost-effective. Traditionally, obtaining heading has been done through either fibre-optic gyroscopes (FOG) or magnetic heading devices. However, there are two common problems with these solutions.
FOG is typically expensive, heavy and can be complicated to set up, which can have a bearing on the applications it is suited to. Magnetic heading devices, on the other hand, are not as accurate as FOGs, because magnetic north and true north are rarely the same and these devices are more prone to drift and other errors than FOG. Additionally, both types of systems sometimes struggle with accuracy due to magnetic interference and secLat degradation at higher latitudes.
This is where Advanced Navigation’s Subsonus USBL comes in. It was born out of the idea to bridge a clear gap in the market, with a solution that provides accurate and reliable heading, overcomes issues with magnetic interference at high latitudes, while being cost-effective.
USBL2—TRANSDUCERS
Subsonus provides a unique USBL configuration option called “USBL-squared” (USBL 2). The primary difference to other traditional USBL configurations (I.e. Classic USBL and inverted USBL) is having a transducer on both the surface
vessel and on the tracked object. If classic USBL and inverted USBL are considered as having the location of the transducer as the primary differentiator for certain performance reasons, it becomes clear that having a multi-transducer setup will offer significant advantages.
The Subsonus transducer contains a high specification inertial navigation system (INS) alongside its hydrophone array and acoustic sounder. These elements are pre-calibrated during manufacturing, reducing in-field calibration time for operators. The INS provides roll, pitch, magnetic, and gyroscopic heading, as well as heave and acceleration data of the unit, allowing high accuracy dead-reckoning capability in full six-degrees of freedom (6DoF). Data from the inertial sensors is fused and processed using Advanced Navigation’s proprietary algorithmic technology. The hydrophone array is also used to measure the speed of sound through water at the transducer head.
The acoustic signals in the Subsonus USBL system are encoded with data and contain multipath rejection filters inherent to the acoustic signalling. This allows information to be shared between the transducers, rather than a simple ping-response-fix scenario. To initiate the system, the surface vessel Subsonus will emit an acoustic signal that the remote Subsonus will respond to. The surface vessel Subsonus will resolve the range and bearing of the remote unit, and then acoustically send the absolute position and heading to that transducer. Now, the remote Subsonus knows where it is in the world and in which direction it is headed.
The USBL 2 multi-pronged approach offers a multitude of benefits, including:
ƀ ENHANCED NAVIGATIONAL CERTAINTY: Performing USBL calculations at both the tracked object and surface vessel significantly reduces navigational uncertainty as each Subsonus is effectively two components of a single system that is able to accurately resolve the orientation and position of each Subsonus unit.
ƀ IMMUNITY AGAINST INTERFERENCES: Compared to other methods of obtaining accurate underwater heading, such as through adding a FOG to the navigation system, USBL 2 is immune to magnetic interference and has higher tolerances to environmental noise than traditional USBL. USBL 2 is also unaffected by secLat degradation caused by operating at high latitudes.
ƀ ADAPTABILITY AMONG DIFFERENT ANGLES OF COMMUNICATION: The high sensitivity and fine granularity of angular measurement from USBL 2 architecture helps overcome difficulties in precise positioning when dealing with acute slant range, such as in shallow water conditions, and when attached to more dynamic vessels.
ƀ IMPROVED SPEED OF SOUND: Speed of sound through water measurement is improved by USBL 2 as it is measured at each Subsonus transducer and then shared between units for greater precision in range approximation.
ƀ SCALABILITY: USBL 2 is not limited in the number of remote Subsonus units, providing a highly scalable solution. This means that a single surface vessel Subsonus can manage a virtually limitless number of remote Subsonus transducers.
In the USBL market there used to exist a gap between the very high-end systems—which performed with incredible precision but are complex and expensive—and the low end of the market where magnetic heading devices proved to be temperamental. Combined with the complex and costly set-up process, users would struggle to get usable data out of these solutions.
Subsonus was developed to overcome these industry challenges. In addition to the unique USBL 2 approach, it introduces modern quality-of-life upgrades, including a webbrowser-based user interface and ethernet connection. The result is a solution that improves heading accuracy, reduces
complexity and calibration time, and introduces faster integration into vessel designs.
In fact, simplifying integration and reducing operational complexity are key motives that empower Advanced Navigation’s technology ecosystem—in which Subsonus is one critical component working seamlessly with the rest of the company’s subsea product portfolio through real-time data fusion, cross-platform interoperability, and effortless integration of new and legacy products.
The ecosystem’s goal is to have everything automatically configured for the customer with one supplier. This allows for compatibility in a much tighter integration level, leading to much better performance via a process that is much easier, quicker to mobilise, and simpler to operate.
SUBSONUS AND SUBSONUS TAG
Subsonus can be operated just in a regular USBL mode with the Subsonus Tag—an acoustic positioning transponder that operates with the Subsonus USBL—, or with a second Subsonus to operate as USBL 2 and still have the Tags available.
The Subsonus Tag is designed to be interrogated by a Subsonus unit, allowing its position to be identified and displayed on a live map via a web interface. The tags are small, battery-powered, easy to use, and require no connectors and little maintenance. It has an electronic paper display screen that displays the battery life and other quality-oflife features. Multiple Subsonus Tags can be deployed in the same area and tracked using a single Subsonus in surface configuration. Each tag has a unique address and can be assigned a name for easy identification.
In a real-life scenario, a complete ROV suite can be implemented by using USBL2 to provide a navigation solution to the vehicle, along with a Subsonus Tag attached to a tethered float. This setup allows operators to track both the ROV and the tether float, providing full spatial awareness of the entire vehicle system.
Advanced Navigation has customers utilising Subsonus as their primary positioning package. It’s an easy solution with a simple connector. There’s no need for additional expensive custom equipment for its power source and charging systems, only standard items affordably available from a local electronics store. It’s possible to change settings on the Subsonus acoustically if the customer forgets to do that before deployment. It’s even possible to charge the Subsonus Tag wirelessly through a phone.
Apart from Susbonus, the ecosystem consists of the INS, DVL, and time server. It’s also possible to integrate both side instruments and use external INS when there’s a need to upgrade to a FOG solution. And of course there are the GNSS solutions on the topside.
Within the ecosystem there is also Advanced Navigation’s Hydrus, a micro hovering AUV for cost-effective benthic and habitat monitoring and underwater surveying. Hydrus features a full navigation and positioning suite—a lot of AUVs have these options only as aftermarket, but in this case, it’s a tool that makes Hydrus much more powerful. Although Hydrus is an end user product, it is built to take full advantage of the ecosystem to bring down the cost of complexity.
The Subsonus is compatible with Hydrus; there’s no need for additional hardware as Hydrus can leverage the existing capabilities of the Subsonus system. Some Advanced Navigation customers were already using Subsonus Tags for diver tracking before later purchasing Hydrus, which
Seabed Warfare
Underwater Warfare
Special Operations Warfare
MEET US AT CNE 2025 BOOTH E60
equipment rental services!
equipment to the offshore, subsea, and renewable energy industries
Equipment you can count on, people you can trust.
IVM Technologies is transforming underwater photogrammetry with the Hydro Series: fast, accurate, and easyto-use 3D modelling without markers. Paired with IVM SLAM, it enables real-time tracking, reducing costs and inspection time. Looking ahead, AI-driven autonomous navigation will enhance efficiency.
Photogrammetry has been on a seven-century development journey since the concept was introduced by Leonardo da Vinci in the 1400s. He envisaged it as a tool to study how to use projective geometry as a measurement tool. However, it was not until early photographers adopted the concept that it became a well-known process. The first practical use was in the lead up to the First World War for terrain mapping. This was also the only real use for it until after the Second World War. At that point it became widely used for map making; produced via the collation of millions of still photographs.
Historically, photogrammetry was a completely manual process, requiring many hours of work to produce usable 3D images. Even so, the use of photogrammetry for a wide variety of applications grew in popularity across a variety of markets, including the underwater inspection market. The process only started being used for underwater inspections in the late 1960s and for very small areas. As computing power was then very limited, processing still took a long time.
New software developments in the 1990s helped speed up processing, but the methodology for underwater inspections required survey “ladders” and/or markers attached to the asset, and elaborate lighting setups. Such inspections were only performed by specialist survey companies, and they were still very slow and cumbersome.
One such company was Comex A/S, the world-famous and pioneering diving company from Marseille, France, started by Henri-Germain Delauze in 1961. Comex A/S performed its first photogrammetry project in 1998; it was an archaeological survey of a wreck. The company spent many years perfecting underwater photogrammetry culminating in the design of the ORUS3D, the first wholly integrated stereo camera system. ORUS3D included integrated lighting for ROV deployment and was designed to demystify photogrammetric acquisition and data processing at depth.
In 2020, Comex A/S restructured and sold off the photogrammetric development to its in-house development and operations department. This department then started IVM Technologies with the express purpose of continuing to simplify photogrammetric techniques. This would allow nonspecialists companies and operators to perform underwater inspections and easily produce repeatable high accuracy models: anything from small cracks to chain inspections and spool piece metrology, to digital twin production of complete assets. Through a combination of engineering, high specification digital stills cameras, integrated high powered LED lights, and software development, and using today’s faster computers, surveys that could historically take days to perform and weeks to process, can now be performed in a matter of minutes or hours.
This innovative development culminated in the launch in early 2022 of the IVM Hydro series. This is a range of ROV mountable stereo photogrammetry cameras for every class of ROV, from Micro to Work Class. It’s a wholly independent measuring tool that does not require data from any other sensors, ladders, or asset markers for completely noncontact inspections.
The Hydro Series is made up of four models of different depth ratings: 100m, 300m, 1,000m, and 3,000m. All are based on the same platform and are designed for easy installation,
effortless use, and high-accuracy 3D modelling. Unlike traditional methods, it requires no external markers or additional sensor data. The system is supplied as a complete solution, including all cables, control software, and processing hardware and software. Though each system is factory calibrated, a calibration plate for field verification is included with each shipment.
As explained above, IVM Technologies benefits from extensive field experience. This practical knowledge has paved the way for a new product, bringing major improvements in subsea asset inspection. IVM SLAM is an intelligent, costeffective, and time-saving inspection solution. When used alongside our cameras, the IVM SLAM generates a real-time 3D model even in poor visibility conditions. This enables realtime tracking during subsea inspections.
Reducing time at sea is a major cost saving for any underwater project. Sharing a photogrammetric model – with its high accuracy and quality imagery – with each stakeholder providing project teams with crucial insights to improve project planning. For IRM inspections, the speed of survey can drastically reduce the in-water time of an ROV, whilst providing more and higher resolution data. Creating a digital twin of a soon-to-be decommissioned asset that can be
shared amongst all stakeholders can improve the planning and reduce the unknowns which often negatively impact budgets. Many other projects, from UWILD and moorings inspections, to spool piece metrology and dam inspection, can benefit from this cost saving technology. With the Hydro Series, IVM Technologies is setting the standard and leading the way in the ROV photogrammetry market.
Marine Archaeology
As inspections with any Hydro Series equipment is a wholly non-contact operation, they’re ideal for the marine archaeology market. Archaeologists can now create detailed 3D models that preserve artifacts in their discovered state, allowing them to gain more information from the site before recovering the assets.
Historical in-water calliper measurements of mooring have proven to be at best inaccurate and at worst extremely inefficient. This results in several lines being replaced when subsequent in-air inspections proved they were safe. Inspections using IVM Technologies products have repeatably proven to reduce operational risks, costs, and inspection time, while offering certified millimetric precision of every surface of each links inspected and the surface of the trumpet.
Spool pieces require precise measurements for installation and repairs. With IVM Technologies’ solutions, engineers can take measurements, identify alignment issues, and design installations with unmatched accuracy. This is all without the aid of expensive acoustic spreads, reducing the inspection time by up to six times and ensuring cost savings. To validate the Hydro Series' ability to deliver precise spool piece metrology, a certification process with Bureau Veritas is now underway.
Unlike conventional video inspection, which are prone to low visibility and erratic motion, 3D photogrammetric models provide quantifiable data for detecting structural changes, tracking corrosion, and predicting maintenance needs.
Structural integrity assessments are a cornerstone of subsea asset management. With underwater photogrammetry, operators can generate accurate 3D models to analyse defects, monitor material degradation, and verify compliance with safety regulations. From better data comes better decision making, and long-term cost savings.
Regulatory bodies often require UWILD inspections for offshore structures and vessels. Historically, these inspections relied on divers and ROVs capturing low-resolution video footage. IVM Technologies meet these specific needs by offering photogrammetry solutions to create detailed 3D representations of hulls, thrusters, and structural components, ensuring that inspections meet regulatory standards.
Digital stills offer distinct advantages over video in underwater photogrammetry:
ƀ HIGHER RESOLUTION: video frames are compressed, while stills capture sharper images for precise 3D models.
ƀ BETTER EXPOSURE CONTROL: stills allow for optimised lighting per frame, ensuring consistency.
ƀ REDUCED MOTION BLUR: ROV movement and currents blur video, whereas stills ensure clear images.
ƀ OPTIMISED DATA PROCESSING: stills eliminate redundant frames, reducing processing time.
ƀ IMPROVED MEASUREMENT ACCURACY: high-resolution digital stills enhance key feature recognition for metrology and defect analysis.
By using digital stills, IVM Technologies ensures superior accuracy and reliability in underwater inspections.
Building on IVM Slam development, we believe this solution would benefit a broader range of applications within the underwater asset inspection industry. In this regard, at IVM Technologies we are actively exploring how to leverage our real-time 3D modelling solution to enhance autonomous navigation systems.
A major challenge in underwater autonomous navigation is the lack of real-time spatial awareness. ROVs and AUVs work with sensors-based navigation or pre-programed routes, and they are highly dependent on visibility. Therefore, when operating in complex environments, they encounter operational difficulties. By adding real-time 3D modelling technology to underwater robots, we have revolutionised autonomous navigation.
This evolution is crucial for:
ƀ EFFICIENT SURVEY PLANNING: the robot can adjust its trajectory according to live 3D data and guarantee full coverage of the inspection.
ƀ COLLISION AVOIDANCE: 3D modelling ensures obstacle detection and identification with precision.
ƀ OPTIMISED DATA COLLECTION: the system can prioritise scanning areas with detected anomalies, reducing data acquisition and processing time.
The future of underwater photogrammetry lies in intelligent, real-time decision-making. IVM Technologies is at the forefront, pushing the boundaries of subsea inspection through progress in real-time processing and AI-powered navigation. Our goal is to reduce the operational time and costs of subsea asset inspection. The combination of the IVM Slam and autonomous navigation systems strengthens this objective. With minimal supervision required, deployment costs are lowered, and immediate access to 3D data enables faster decision-making.
At the recent Ocean Business 2025 exhibition in Southampton, we took the opportunity to showcase some of our products. Being present at this exhibition for the ocean industry offered meaningful encounters and exciting milestones. Among them was the finalisation of a contract which has accelerated the development of a new addition to our portfolio: the Hydro 6000. The subsea contractor, Deep Ocean Search Ltd., chose us on behalf of a third client to provide a photogrammetry kit capable of pushing the boundaries of asset inspection down to 6,000m. Taking part in this project is a valuable opportunity for us to keep advancing the state of the art in underwater photogrammetry.
General Oceans, a customer-centric group of underwater technology companies continues to solidify its global presence by offering advanced underwater technology to the defence sector, from its brands Klein Marine Systems, Strategic Robotic Systems (SRS), and Reach Robotics. With a focus on military applications, the group's solutions significantly enhance underwater mission capabilities within maritime security, mine countermeasures, and subsea operations.
Klein Marine Systems, recognised worldwide for their highspeed, high-resolution side-scan sonar technology, remain a cornerstone of General Oceans’ defence offerings. Their flagship product, the System 5900, exemplifies quality through continuous enhancements.
Klein’s sonar technology plays a critical role in modern Mine Countermeasure (MCM) operations by providing high-speed, high-resolution seabed imaging. In the initial stages of an MCM mission, Klein’s advanced sonar systems are deployed to scan the seafloor and identify underwater threats or objects of interest with clarity. This capability is crucial for distinguishing between natural seabed features and potential hazards. Klein’s sonars are specifically designed to image mine-like objects with exceptional resolution and precision, enabling faster and more accurate assessments. By delivering highly reliable imagery at pace, Klein’s technology supports safer and more efficient clearance operations. This allows naval forces to make informed decisions to neutralise threats, whilst minimising risks to personnel and equipment. Whether deployed from unmanned systems or ships, Klein’s sonars remain a trusted choice in mission-critical mine countermeasure strategies.
Recently, Klein announced a significant development by integrating Exail’s Octans Nano OEM Attitude and Heading Reference System (AHRS) and Nortek Doppler Velocity Log (DVL) into the 5900 platform. This integration has improved the sonar’s precision and image stability, both of which are crucial for mission-critical operations like unexploded ordnance (UXO) detection, and detailed geophysical surveys. The Octans Nano OEM – known for its compact design, low power consumption, and superior attitude performance –ensures higher accuracy by reducing motion-induced data errors. Ted Curley, Vice President & General Manager of Klein Marine Systems, said, "This advanced motion compensation technology delivers clearer and more reliable imagery for critical missions."
Furthermore, Klein’s reputation is bolstered through strategic partnerships such as with French company RTsys. RTsys recently contracted Klein to supply twenty high-resolution 900kHz side-scan sonar systems for their NemoSens® micro Autonomous Underwater Vehicles (AUVs). The NemoSens® micro AUV, adopted in multiple sectors, leverages Klein’s sonar for unparalleled seabed imaging, enhancing operational effectiveness in for a variety of applications. PierreAlexandre Caux, RTsys’ Business Director, confirmed that this partnership significantly boosts operational efficiencies in both defence and civilian underwater missions globally.
Klein's technological leadership is further evidenced by their collaboration with the Korea Institute of Ocean Science & Technology (KIOST). The institute recently accepted delivery of Klein’s 5900 system to advance their high-resolution seafloor topography surveys. Utilising Klein’s multi-beam side scan technology and integrated AI software, KIOST can now conduct comprehensive, high-speed seafloor mapping with exceptional clarity and detail. This demonstrates the 5900’s critical role in advancing global marine research and defence capabilities.
Strategic Robotic Systems (SRS) have contributed to General Oceans’ defence portfolio with their innovative FUSION Hybrid ROV system. Distinguished by its intuitive design and operational flexibility, the FUSION vehicle operates in both tethered and untethered modes: capable of precise real-time control or fully autonomous missions as required. Its performance in Explosive Ordnance Disposal (EOD) missions and amphibious operations has made it a preferred choice among the Coast Guard units and defence forces around the globe.
The FUSION ROV addresses the needs of Special Operations Forces by effectively removing divers from high-risk scenarios such as mine identification and hull inspections. Designed for rapid deployment and ease of operation, it
enables operators with limited training to perform complex underwater tasks safely and efficiently. This capability is vital for contemporary defence missions that increasingly prioritise personnel safety and operational efficiency.
The recent partnership announcement with RS Aqua – the newest addition to the General Oceans group – as the official distributor for the FUSION Hybrid ROV/AUV in the UK and Ireland expands their global reach. These further cement their position as an indispensable asset in maritime security and underwater intervention.
Reach Robotics complements General Oceans’ defence offerings with their advanced subsea robotic manipulators, designed for demanding military applications. Recently, Reach Robotics secured a significant contract with the Australian Defence Force (ADF) to deliver a custom "deepwater" variant of their Reach X Advanced Intervention System (RX-AIS). This system will be capable of operating at depths up to 1,000m, surpassing any previous Reach Robotics manipulator in terms of operational depth.
Launched in 2023, the RX-AIS was developed in close collaboration with both US and Australian Departments of Defence. Its dual electric manipulators are specifically engineered for high-dexterity tasks on lightweight submersible platforms, enabling safer and more precise subsea intervention. This variant expands the operational capabilities of portable ROVs, significantly enhancing the ADF’s ability to respond to evolving naval threats.
Christian Nyman, Vice President and General Manager at Reach Robotics, highlighted the importance of customerdriven innovation, saying "Reach Robotics maintains a deep engagement with key defence customers in the development of advanced-functionality solutions based on direct military-operator input. These strong relationships continue to drive Reach Robotics forward in capability, and together we chart the course of extraordinary subsea robotic manipulator dexterity.”
The RX-AIS system features two seven-function manipulators, specialised tooling, and advanced controller integration. This initiative underscores Reach Robotics’ commitment to delivering military-grade solutions globally.
General Oceans' integrated defence offering leverages the strengths of each brand, creating a united approach to underwater operations. Klein’s sonar technology initially identifies underwater threats or objects of interest with clarity. Strategic Robotic Systems’ Fusion vehicles then conduct detailed inspections, neutralising risks and collecting vital data. Reach Robotics’ advanced manipulators further enhance these missions by providing precision intervention capabilities in challenging conditions, ensuring personnel safety and operational effectiveness.
Through their brands, General Oceans continue to strengthen defence capabilities in the underwater battlespace. By combining precision sonar imaging, advanced robotic intervention, and highly effective ROV platforms, General Oceans offer robust solutions tailored to modern defence challenges. Their dedication to continuous improvement and customer focus ensures safer, more efficient, and effective defence operations worldwide, solidifying their reputation as a leader in underwater technology.
For almost 25years, NETmc Marine has been at the forefront of video recording technology, with many of the world’s largest, and not so large, inspection companies relying on our technology and technical support to ensure smooth operations and compliant video content. Be it single or multi-channel, structures or pipelines, no matter your video source, NETmc Marine has a cost effective recording solution.
Did you kn ow NE Tmc Ma rine also m anu factu re unde r water ca me ras ?
Ou r inn ovati ve DVCi ran ge of ca me ras a re desi gned to enable full HD/ 4K ov t wis ted pai r, thus all owin g olde r Divin g and ROV u m bili cal to ca rr y these ca me ra si gnals .
By Capt. Marc Deglinnocenti, U.S. Merchant Marine (ret.), oldarmada@gmail.com
At the 2024 Underwater Intervention convention in New Orleans, a marine technology company showcased affordable products, including several advanced Remotely Operated Vehicles (ROVs). Gordon Smith from MarineNav highlighted competitive pricing and the reliability of their inspection-class Oceanus ROV systems. Headquartered in Prince Edward Island, Canada, MarineNav is known for its innovative and budget-friendly product offerings. What goes on in this small part of Northeast Canada?
Their reputation as a manufacturer of inspection-class ROVS particularly caught my attention. Their smallest ROV, the Oceanus Mini-Lite, is priced at USD 20,000. They offer several ROV platforms that provide a range of power and the flexibility to add accessories, accommodating different budgets and dive mission requirements. MarineNav has authorized dealers on every continent except Antarctica and offers post-sale ROV maintenance through a network of certified ROV service technicians.
MarineNav also offers Side-Scan Towfish sonar, including the Towfish-13” (up to 75 meters depth) and Towfish16” Premium (up to 150 meters depth). You can purchase various optional ROV accessories, many of which are designed and manufactured on-site. Options include various tether lengths and tether reels, single-axis or rotating manipulator arms with different attachments, retrieval hooks, and custom camera mounts. They support and providing mounting solutions for many third-party accessories, including sonars, metal thickness gauges, tracking and positioning systems, among others. He emphasized that they have a robust quality control system for producing thrusters and all other components, which allows them to maintain a steady inventory of complete thrusters and other wearable ROV parts. Additionally, Gordon noted that they exclusively adhere to subsea industry standards for their ROV-related connectors.
Aside from ROVs, MarineNav specializes in manufacturing marine-grade computers and displays for global sales to various marine-sector industries. They also provide bespoke design and manufacturing of mil-spec components for various international government agencies, as well as tier 1 defense contractors including Lockheed Martin, Rafael, and Raytheon. Their computers have an impressive mean time between failures of over 100,000 hours, ensuring reliability in demanding conditions. The monitors are designed for maritime use, featuring powdercoated aluminum frames that resist salt air and UV.
In addition to hardware, MarineNav provides software programs for the Canadian Coast Guard that monitor critical vessel engine readings, including oil pressure, engine temperature, RPM, and more. This software supports the maintenance of the Coast Guard fleet and keeps a detailed history of each vessel.
Founded in 2005, MarineNav is committed to delivering high-quality marine technology products at competitive prices.
By Capt. Marc Deglinnocenti, U.S. Merchant Marine (ret.), oldarmada@gmail.com
HD Hyundai lines sought for and was granted approval in principle from the Korean Register and the Liberian International Ship & Corporate Registry for an 8000 teu autonomous container ship. The autonomy level of the 272-meter (892 ft.) M/V Manzanillo Bridge is categorized as an International Maritime Organization (IMO) degree 3 Maritime Autonomous Surface Ship (MASS). That means that this 75,154 gross ton ship will be remotely controlled and sailing the seas with absolutely no crew on board. What does this forebode for future professional mariner jobs, and what could possibly go wrong?
Nothing will go wrong according to their HYUNDAI INTELLIGENT NAVIGATION ASSISTANT SYSTEM (HiNAS) developed by Avikus. HiNAS boasts a multitude of advantages over a human crew. They claim that HiNAS will provide a reduction of human error. The United States, British, and German accident studies claim that most vessel collisions involve some sort of human error. That human error might be in the 80% to 90% range. Avikus says that their software makes faster and better decisions to avoid collisions and groundings. HD Hyundai’s 360-degree surveillance cameras and sensors can detect many hazards and even pirates.
Detecting pirates is one thing; stopping them is another. How they plan on stopping unauthorized boarding is anyone’s guess. They also claim that having better speed controls and computerized optimal courses will save much fuel and therefore save money and the environment. They claim 5% to 15% in fuel savings for the main engine and generators. That’s a great addition to any ship’s on-board bridge electronics.
Saving fuel and automatically initiating anti-collision measures early is a great tool for a human bridge crew to utilize. However, it is not a good tool to replace the crew entirely. After all, Artificial Intelligent Maneuvering (AIM) systems are electromechanical devices that are subject to failure due to multiple reasons. Those failures often happen at the most inopportune times too. Maybe they will have a backup AIM system. How they plan on keeping the main engine, generators, and other equipment running is also another story. No engineers and other crew members on board means that all emergency situations must be handled automatically and/or remotely.
Fire on board must be suppressed by automatic means or by remotely triggered means such as fire doors, sprinklers, gas and liquid fire extinguishing systems, dampers, and other automatic systems. Damage control is probably going to be restricted to multiple compartmental dewatering pumps. Maybe emergency human crews can be transported to the MASS vessel in time to save the day. Maybe not.
All of these concerns and more are being closely considered by the Ministry of Trade, Industry and Energy (MOTIE). That’s the South Korean governmental agency that is responsible for regulating economic policies in the industrial and energy sectors. They are currently monitoring and advising this MASS project in many ways. MOTIE has 17.5 billion won (KRW) in "regulatory sandbox funds" to support the technological innovation activities of companies in cutting-edge fields. So, money is flowing into this project from both HD Hyundai and the Republic of South Korea. We all hope that MOTIE will eliminate as many possible vulnerabilities that they can. Hopefully, that will all happen well before the ship sets sail as a degree 3 MASS vessel.
You can bet that the IMO is also keenly interested in this MASS project. The IMO may not have a lot to say about the project now, but they will certainly have a great deal of influence when it comes to any future MASS regulations. In any case, many professional mariner jobs may soon be lost.
It’s true that some new jobs will be created in the computer software and hardware segments of the ship operations along with its monitoring and controlling aspects. More maritime jobs will be lost than those that will be created though. Will additional separate human controller and human monitoring positions be created with each new construction and deployment of more MASS vessels, or will one remote control center be directing multiple MASS vessels? What are the qualifications of these human controllers and monitors? Will they have actual sea time experience, or will their instruction be strictly in the classroom and hypothetical in nature? Will they be licensed mariners with inherent liability for their human errors?
These are all important questions to ask, because HD Hyundai Heavy Industries just happens to be the world’s largest ship building facility located in South Korea. They claim about 10% of the world’s shipbuilding market. They can and will make a huge impact on maritime safety and careers if they keep heading in the MASS direction.
It will be interesting to see just how well the M/V Manzanillo Bridge fares out there in the real world. It looks as though we will all soon find out. So, if you’re out at sea and spot the M/V Manzanillo Bridge, you might want to keep clear of her just in case she loses her remote-control signal. If you’re in any kind of distress, their call sign is 5LLP3. Unfortunately, there won’t be anyone on board to render aid to you. Just put on your life jacket and write a strong letter to HD Hyundai.
Capt. Marc Deglinnocenti is a maritime technical writer. His sea-time dates from 1974 in a wide variety of roles on sailboats, conventional and tractor tugboats, training ships, barges, warships, cargo ships, passenger vessels and research vessels.
Dr Lee Willett
On 26 September 2022, two Nord Stream gas pipelines on the Baltic Sea’s seabed were ruptured, reportedly by underwater explosions. This was the first of several incidents involving damage to seabed critical underwater infrastructure (CUI) in the Baltic Sea. The incident turned into reality a theoretical risk to CUI that had been a longstanding concern for Western countries and their navies.
Immediately after the incident, several Baltic and North Sea countries quickly got together to surveil CUI across the region, checking for other areas of concern, and demonstrating
collective response to build deterrence against any deliberate efforts to disrupt the CUI network.
For example, Denmark, Germany, the Netherlands, Norway, and the UK worked collectively to check almost 9,000 kilometres of oil and gas pipelines and communications and data cables on the seabed in their sectors. Crucial here was co-operation with the marine industrial sector, especially oil and gas companies. In Norway alone, commercial companies in this sector were found to possess more than 600 uncrewed underwater vehicles (UUVs), providing a deep pool of capability resource that could be drawn from.
The close links between Norway’s navy and its seabed-focused commercial sector have been highlighted as a good illustration of effective civilian-military co-operation in securing CUI. Such integrated, collective operations generate what could be termed ‘applied mass’. As Royal Norwegian Navy (RNoN) chief Rear Admiral Oliver Berdal explained to Ocean Robotics Planet, the commercial sector brings the “big muscle” of UUV numbers, while the navy can harness this mass with its expertise in surveillance, countering military threats, and integrating different stakeholders to apply the required response.
“First, you have to start with the basic facts: where is the big muscle when it comes to seeing things on the seabed and doing things on the seabed?” asked Rear Adm Berdal. For Norway, the Chief of Navy added, “The big muscle is in the private sector.”
Alongside its oil and gas pipeline industry, Norway has significant capacity and expertise on seabed cables, like supplying electrical power and electronic data out to oil rigs and other CUI infrastructure. Alongside sizable shipping and fishing industries, it has growing knowledge in windfarms and other new offshore resource capabilities.
“We have tens of thousands of engineers and people working with seabed problems in private industry every day,” said Rear Adm Berdal. “Over the last 50 to 60 years, we’ve built a huge industry where there’s a lot of people with a lot of knowledge, and their everyday job is to do things on the seabed and below the seabed.”
“If you need to check 8,800 kilometres of pipelines in the North Sea, do you put grey ships in charge of doing it, or do you use the ships that do this every single day?” the admiral asked, adding that the oil and gas companies regularly and routinely check their pipelines.
Second, the Chief explained, while military forces like navies currently have only handfuls of people with deep expertise in CUI security because the threat is only just starting to surface (despite the long-standing risk concerns), military forces bring deep expertise in two other key areas. For expertise in dealing with explosive devices, “Whether it’s historic [ordnance] from the First World War or Second World War, drifting mines, or objects that somebody could place down there, that’s where the military expertise and knowledge comes in,” said Rear Adm Berdal. Moreover, military forces can combine military intelligence with information from various civilian sources, including national authorities, police forces, coastal administrations, and maritime agencies. The military role here is “getting all the available information and getting it fused to create good situational awareness”, the admiral added.
The individual strengths the respective commercial and military stakeholders offer – especially when enhanced today with increased information sharing supported by information database building – can help accelerate CUI security
development, particularly when time is of the essence in deterring or responding to a CUI incident.
“The navy is clearly much better at finding mines than the private sector. The navy is much better at identifying objects and saying ‘this is dangerous or not dangerous’,” said Rear Adm Berdal. “However, when you have 8,800 kilometres of seabed pipelines for oil and gas, thousands of kilometres of fibre-optic cables, and thousands of kilometres of electrical interconnectors, if you check all that using the navy’s capabilities – even using unmanned, remotely operated vehicles –it will take a long time.”
Whether the CUI challenge is responding to an incident in the immediate term or building longer-term deterrence presence, time is of the essence for Western countries, their navies, and the commercial industry they work with. As regards tactical and operational response, and wider strategic impact, “We’ve covered a lot of ground in a very short time,” said Rear Adm Berdal. “When Nord Stream took place, within days an operation was up and running; within weeks and months, a lot of the most important work had been completed,” he explained. “Most importantly, during those days, weeks, and months, all relevant actors – on the government side, and on the industry side – were able to get together and discuss things, liaise, and assist each other in a way we’d never done before.”
Liaison and other assistance activities are enabled by having staff embedded in each other’s operational cells.
“I’m quite sure about one thing,” Rear Adm Berdal continued. “If something were to happen again, we would be much quicker the next time – even though we had a pretty fast and impressive reaction the last time – because now we are mentally prepared for it and organizationally prepared for it.” The civil-military relationship on CUI security continues to remain close, with meetings frequent and regular, to ensure capacity remains current in response to the threat, he added.
The impact of the threat response was both immediate and long-lasting, the Chief said.
“It was not a ‘one-off’ thing that we did and then stood down. It was a ‘one-off’ thing that shook us, that woke us up,” he explained. “To a certain extent our responses were tested, and we did quite well – but now we are in a much better situation, much better prepared for whatever may come in the future.”
Here, he said, national but also multinational co-operation is key.
“We will still work hard together, especially with allies: I think that’s the clue now: one thing is what we do at the national level, but especially now [it’s] what we’re also doing between countries,” the admiral continued. He highlighted bilateral and multilateral co-operation amongst countries responding to several reported and possible CUI cable incidents that have occurred in the Baltic Sea since October 2023.
Richard Mills, Chief Commercial Officer (CCO), Cellula Robotics
Critical Underwater Infrastructure (CUI) protection is a key strategic task for many navies. It is similar in nature to asset integrity management for offshore energy companies, where pipelines and seabed installations are surveyed and inspected at regular intervals. There are a variety of solutions to solve this commercial task, including Remotely Operated Vehicles (ROVs), Autonomous Underwater Vehicles (AUVs), towed sensor bodies and more.
We need to protect undersea cables and pipelines for a myriad of reasons. Energy security, economic stability, healthcare, education, and the dissemination of information all rely on the unobstructed use of pipes, and fibre-optic cables, often in deep water and over very long distances. Cutting just one internet cable could be devastating to a small island nation, for example.
Therefore, there is an immediate need to protect these crucial assets. However, there are many challenges that require a different approach to what has been implemented before. Cellula Robotics has developed a system of systems approach to aid governments, navies, infrastructure owners, and operators that is focused on detection, inspection, and protection. This approach encompasses cable-free networked seabed sensor nodes, survey grade AUVs, and larger payload delivery AUVs, all sharing common elements not least the ability to provide a persistent presence.
Subsea Sentinel is a sensor-agnostic seabed node. With a design battery life of more than twelve months, Subsea Sentinel can be deployed alone or in a network of nodes. It can then provide all sorts of data including pattern of life, marine mammal monitoring, noise monitoring, and oceanographic information. Connected by an acoustic mesh network, anomalies can be transmitted to shore or surface over the network to provide low-latency notification to users. Installations may be placed across a natural choke point or along a linear asset, like a cable or pipe.
Subsea Sentinel nodes include passive acoustic hydrophones as a standard sensor package. These can be augmented by turbulence sensors, echosounders, magnetometers, and more. Not only is Subsea Sentinel sensor agnostic, but it is also algorithm agnostic. Detection and tracking capabilities can be integrated to provide the ability to detect and classify anomalies on the node. This detection can then wake active sensors to aid with identification. The decision to relay information will then be prioritised based on the classification hierarchy.
Subsea Sentinel nodes can be deployed much like a Long Baseline Array (LBL) from a ship. It can also be deployed covertly from Cellula’s Guardian AUV. This is an extra large AUV powered by a hydrogen fuel cell. The Guardian AUV is approximately 11m long, with a horizontal and vertical cross section of 1.7m. The nose and tail are packed with essential AUV sub-systems. The very large central section is modular in construction with a strong-back design philosophy. The frame runs along the top of the AUV, housing the fuel cell gas storage and wastewater tanks. This provides a very large payload bay for off-platform assets such as Subsea Sentinel.
Guardian has several attributes that distinguish it from other larger AUVs. Compared to a rechargeable battery system of equivalent size, Guardian has approximately two or three times the endurance. It’s capable of up to 45-day missions, or 5,000 km range at typical AUV speeds. Fore and aft lateral and vertical thrusters enable Guardian to station keep, hover, and manoeuvre on the spot. For low-power station keeping, the system weathervanes into the current. There are also hard and soft ballast systems for vehicle trim in the water column, and to park on the seafloor if required.
These unique capabilities make Guardian an ideal platform for the deployment and recovery of Subsea Sentinel node networks. Onboard the AUV, the Autonomy, Navigation, Command, and Control (ANCC) Package from Metron Inc. conducts in-mission seabed analysis to select the most appropriate locations for the nodes. The AUV then hovers over the site and lowers the node onto the seafloor, all without the need to surface.
ANCC also works on Cellula’s Envoy AUV® platform. In both cases, ANCC sits on top of the vehicle’s condition-based decision matrix autonomy system that manages waypoint following, fault management, and safety, such as maximum depth and collision avoidance. ANCC includes several modules to provide both extrospective and introspective analyses to the mission commander. Sensor payload data is fused with navigation and positioning data to provide situational awareness. AUV systems and sub-systems are monitored for degraded performance or failure. All of this is combined in an adaptive command and control function to manage the mission objectives, given the dynamic condition of the vehicle and its environment.
Cellula’s Envoy is used for more traditional, periodic survey missions along cables and routes. When surveyed at regular intervals, data can be analysed for changes either on the vehicle or post-mission. These types of data include Synthetic Aperture Sonar (SAS) imagery, bathymetry from a multibeam echosounder, sub-bottom profiles, optical imagery, and millimetric laser data and magnetometry. The fusion of these data for change detection helps remove the need to follow the same mission profile each time a survey is conducted. Temporal
separation also provides the ability to assess trends and changes in the environment, not just the detection of objects placed within proximity of – or the interference with -an asset.
Envoy is also powered by a hydrogen fuel cell. This offers more than two weeks of mission duration at typical survey speeds. Where rapid data collection is required, Envoy can also operate at much faster speeds than other AUVs, doubling the linear kilometres covered in a relatively short mission of just a couple of days.
In addition to detection by Subsea Sentinel, this capability is also provided by the Envoy AUV. Envoy carries a typical geophysical survey sensor suite with in-situ signal processing for on-board data analysis by ANCC. Objects can be detected in the SAS, multibeam echosounder, camera, and laser data in near real-time. Post-mission data analysis and fusion with the on-board magnetometer further aids the detection of anomalies, potentially including buried threats.
Further inspection capabilities are provided by the Guardian AUV. A separate payload module can be installed to deploy an observation class ROV from the AUV. As demonstrated with HonuWorx in 2024, a surface buoy is deployed from the AUV on a tether. This provides position updates, and satellite communication for live tele-operation of the ROV from shore. This enables operators to observe, assess, and potentially interact with objects placed close to cables and pipes.
The general protection of critical assets requires the combination of Subsea Sentinel, Guardian, and Envoy. Over time, the network of Sentinel nodes generates sufficient data to provide a baseline, against which it is easier to detect and classify anomalies, thereby discriminating between non-threats and threats. Periodic survey for the inspection of assets and the detection of physical threats by the Envoy AUV, followed by interdiction by the Guardian AUV carrying an ROV completes the package.
Enhanced protection could be provided by integrating neutralisation systems into either Envoy or Guardian. Both AUVs have the proven capability of deploying small AUVs for in-theatre tasking. These could also include kinetic effectors provided by third parties.
J u n e 1 6 – 1 9
Unprecedented Networking 800+ Attendees 50+ Exhibitors 400+ Technical Papers
The OCEANS 2025 Brest conference is for global mari time professionals to learn, innovate and lead in the protection and utilization of the world’s largest natural resource – our OCEANS.
Visit us at brest25 oceansconference org
By Captain George Galdorisi, U.S. Navy (ret.)
The U.S. Navy’s visionary document, the Navigation Plan forAmerica’sWarfightingNavy, provides a way forward for the Navy to make the maximum contribution to the “Joint Warfighting Ecosystem.” This Navigation Plan embodies Project 33, which sets targets for enabling the U.S. Navy to make strategically meaningful gains in the fastest possible time. This Plan has several components:
ƀ The readiness component of the Navigation Plan has the goal of eliminating ship, submarine and aircraft maintenance delays and restoring critical infrastructure that sustains and projects the fight from shore.
ƀ The people component of the Navigation Plan notes the goal of recruiting and retaining the force needed to fill officer, chief petty officer and enlisted ranks and delivering a quality of service for Navy personnel.
ƀ The operational component of the NavigationPlan involves creating upgraded command centers for the Navy Fleet commanders and training for combat to ensure that the Navy has a warfighting advantage over its adversaries.
ƀ Finally, the goal to scale robotic and autonomous systems to integrate more platforms at speed focuses on capitalizing on the inherent advantages that uncrewed systems bring to any navy.
While the first three components of Project 33 represent areas that the Navy has been seeking to improve for some time, the most intriguing part of the Navigation Plan is the goal of scaling robotic and autonomous systems (UxS) to integrate more platforms at speed.
The U.S. Navy has a rich history of UxS development. The 28th CNO Strategic Studies Group spent one year examining this issue, and its report spurred increased interest in—and emphasis on—uncrewed systems Navy-wide. Leveraging the SSG’s work, recent Navy focus has emphasized the need to enhance UxS command and control (C2) capabilities to allow one sailor to control multiple systems to lower Total Ownership Costs (TOC) of uncrewed systems. This link between increased autonomy and decreased TOC has become an important theme in Navy UxS development. Indeed, there is growing realization in the Department of the Navy that Total Ownership Costs are the key driver in the cost all weapons systems, leading to a strong focus on TOC in the Navy’s “Wholeness Balance Reviews.”
For the past several years, the Navy has invited several USVs manufacturers to bring their commercial-off-the-shelf (COTS) USVs to exercises, experiments and demonstrations to put them into the hands of sailors who employ them for a variety of missions. Mindful of the imperative to break the “many joysticks, many operators, one USV” paradigm, the Navy has given priority to those USV manufacturers who use AI-technologies to train their vessels to operate autonomously by inviting them to participate in multiple events.
This “aspiration” is good as far as it goes, but it begs the question: “how much autonomy is enough?” Another question that is important to consider is the tradeoff between the cost of operators and the cost of AI-technologies. Based on the Navy’s experience of inserting new technologies into its platforms, systems, sensors and weapons, this tradeoff must be a primary consideration. In order to answer this question “how much autonomy is enough?” understanding “levels of autonomy” is key.
Although there is no universally accepted standard taxonomy for describing levels of autonomy in uncrewed systems, individual industries have developed methods for categorizing autonomy levels within their particular area of specialization. One such standard is the Society of Automotive Engineers (SAE) standard J3016, “SAE Levels of Driving Automation.”
This taxonomy breaks down into six levels of autonomy that are generally accepted by uncrewed systems developers. Although the explanations of these six levels are derived from automotive terminology, the parallels with unmanned systems are clear:
1. No Driving Automation: Full remote control from (similar to radio-controlled model aircraft) with some situational awareness provided to the operator by the USV.
2. Driver Assistance: Some USV autonomy. Pre-planned navigation routes requiring operator intervention if a deviation is required.
3. Partial Driving Automation: Sense and avoid features. Craft will autonomously execute avoidance maneuvers and resume route, but may require further operator intervention.
4. Conditional Driving Automation: USV will execute most mission aspects autonomously. Operator intervention in the event of other predetermined conditions or component failures. Specific actions (such as payload deployment) might take place autonomously, subject to operator override.
5. High Driving Automation: Criteria under development.
6. Full Driving Automation: Criteria under development.
Understanding what these definitions mean in the operational environment is key to determining what level of autonomy is best. For example, if uncrewed maritime systems are being used to contribute to port and harbor security (a capability demonstrated by Maritime Tactical Systems, Inc. (MARTAC) with one T12 MANTAS at the Port of Los Angles and with two T12 MANTAS at the Port of Tampa) where the USVs patrolled the harbor while carrying various sensors and linking that
information to a land-based command center, a high level of autonomy with few operators would likely be the best solution.
Conversely, Commander U.S. Fourth Fleet has been experimenting with using MARTAC USVs to locate – and subsequently chase – simulated high speed drug running craft. In this case, where operators will often want to issue commands to these USVs “on the fly” a lower level of autonomy will likely suffice. As another example, for the mine-counter-measures mission, where operators likely will not know the dimensions and density of a minefield, a high level of autonomy is the best solution.
We could provide additional examples, but these should suffice to help understand the opportunities and challenges when it comes to inserting AI-technologies into Navy platforms, systems, sensors and weapons. Given that the U.S. is in an “AI arms race” against our peer adversaries, there will likely be a long-term push within the U.S. military to leverage AI-technologies, understanding levels of autonomy will likely become increasingly important.
The Navy and Marine Corps have plans for an ambitious series of exercises, experiments and demonstrations this year and beyond that are intended to further “wring out” AI-enabled technologies. While USV manufacturers are being encouraged to bring more-autonomous uncrewed surface vessels to these events, the Navy and Marine Corps must do more than say “more autonomy is better” but juxtapose this “aspiration” what level of autonomy is actually needed.
If the uncrewed surface vessel industry is to thrive, it must leverage what the U.S. Navy and Marine Corps learn during these events and find ways to leverage AI-technologies more fully going forward. As the ability of these uncrewed maritime systems to perform a plethora of missions becomes increasingly dependent on a high degree of autonomy, we will likely see more emphasis on what’s inside the craft, not just attributes highlighted at trade shows. Whether used in the military or the private sector, needing fewer operators will ultimately make uncrewed surface vessels increasingly affordable.
By Captain George Galdorisi, U.S. Navy (ret.)
The U.S. Navy has been at the forefront of innovation throughout its history. Whether it was the transition from sail to steam, or the advent of steel warships to replace wooden ones, or the change from the battleship to the aircraft carrier to the centerpiece of the Navy fleet, these changes helped the U.S. Navy dominate at sea.
In the Cold War era, this innovative journey gathered momentum: from the introduction of the first nuclear submarine, USS Nautilus, in 1954; to the first of the Nimitzclass nuclear aircraft carriers in 1975; to the first Aegis-class warship, USS Ticonderoga, in 1983. These innovative technological developments kept the Navy at the forefront of warfighting prowess.
Today, the U. S. Navy stands at the precipice of a new era of technology advancement. In an address at a militaryindustry conference, the then-U.S. Chief of Naval Operations, Admiral Michael Gilday, revealed the Navy’s goal to grow to 500 ships, to include 350 crewed ships and 150 uncrewed maritime vessels. This plan has been dubbed the “Hybrid Fleet.” In an address at the Reagan National Defense Forum, CNO Lisa Franchetti cited the work of the Navy’s Unmanned Task Force, as well numerous exercises, experiments and demonstrations where uncrewed surface vessels were put in the hands of Sailors and Marines, all designed to advance the journey to achieve the Navy’s Hybrid Fleet.
The Navy-After-Next will be a “Hybrid Fleet.” This innovative concept was born out of necessity. The concept of Hybrid Fleet evolved due the U.S. Navy’s ongoing challenge of building enough crewed ships to adequately meet the Navy’s global commitments. The Chief of Naval Operations Navigation Plan for America’s Warfighting Navy put it this way: “We cannot manifest a bigger traditional Navy in a few short years.” Indeed, the price of an ArleighBurke-class destroyer has risen to $2.2B.
A recent report by the Department of the Navy Science and Technology Board entitled The Path Forward on Unmanned Systems, seeks to help accelerate the path to a Hybrid Fleet by offering a path forward to design, develop and field uncrewed systems — especially uncrewed maritime systems — in order to achieve the Navigation Plan’s goal of: “Scaling robotic and autonomous systems to integrate more platforms at speed.”
The quest to achieve a Hybrid Fleet will depend on the same level of innovation. That is why The Path Forward on UnmannedSystemswill prove useful to help guide the Navy’s leadership to turn “aspiration” into concrete actions. Led by the Honorable Christine Fox, former Acting Deputy Secretary of Defense, and including members such as the Honorable Robert Work, former Deputy Secretary of Defense and Michael Brown, former Director of the Defense Innovation Unit, The Path Forward on Unmanned Systems is already gaining traction within the Department of the Navy.
The Report noted that the Navy can achieve a Hybrid Fleet with a strategy of focusing on experimentation, prototyping and learning during the current Future Years Defense Program (FYDP), working on building the infrastructure to support uncrewed systems in the next FYDP and procuring uncrewed systems in numbers during the following FYDP.
The Path Forward on Unmanned Systems puts special emphasis on: “Ensuring that unmanned systems meet the needs of operational commanders.” There is little doubt that the nation’s combatant commanders are eager to add uncrewed systems to their warfighting assets.
In an article in U.S. Naval Institute Proceedings, the U.S. Indo-Pacific Commander, Admiral Samuel Paparo, put the Navigation Plan’s emphasis on scaling robotic and autonomous systems in an operational context, noting:
The CNO is focusing on rapidly developing, fielding, and integrating UxSs. These systems will augment the multi-mission conventional force to increase lethality, sensing, and survivability. Project 33 [part of the NavigationPlan] will allow the Navy to operate in more areas with greater capability. Unmanned systems provide the ability to project fires and effects dynamically, at any time, from multiple axes, and with mass.
Recognizing that the United States is in an “AI arms-race” with our peer adversaries, The Path Forward on Unmanned Systems urges the Navy to fully leverage AI-technologies, noting: “As they design, develop and acquire new systems, DON will want to take advantage of rapidly changing technology such as AI and autonomy.” This builds on the Navy’s desire to lower total operating costs by moving beyond the current “one UxS, multiple joysticks, multiple operators” paradigm that exists today.
Subsequent to the issuance of The Path Forward on UnmannedSystems, Navy officials have provided more granularity regarding how this report is gaining purchase within leadership circles. For example, Maria Proestou, deputy assistant secretary of the Navy for acquisition, policy and budget and executive director of the Department of the Navy Science and Technology Board, noted that uncrewed systems are: “The most powerful technology that, if employed correctly, could really change warfighting,” going on to say that these technologies can: “Create an asymmetric advantage for the warfighter.”
Importantly, The Path Forward on Unmanned Systems injects a sense of urgency if the Navy is going to field a Hybrid Fleet in time to address aggressive moves by peer adversaries, noting: “We see these steps as critically important to a future hybrid fleet but believe they should be taken in parallel rather than in sequence. In the face of potential conflict, we must move as fast as the relevant supporting technologies generate opportunities rather than at a pace that is bureaucratically comfortable.”
In a presentation at a Center for Strategic and International Studies/U.S. Naval Institute forum, Vice Admiral Jimmy Pitts, deputy chief of naval operations for warfighting
requirements and capabilities, put the focus on uncrewed maritime systems in these terms: “We are leading the way with unmanned systems. We are leveraging the success of the Navy’s unmanned task force as well as the disruptive capabilities office. Our goal is to get unmanned surface system solutions to the Fleet within the next two years.” Admiral Pitts went on to ask the questions: “What will unmanned systems do operationally? How will they get to the war at sea and littoral operating areas? How will they stay in those areas and remain ready for conflict?”
Admiral Pitts addressed important considerations. Juxtaposed against the Navy’s plans to accelerate its fielding of uncrewed maritime systems is the fact that the U.S. Congress has been reluctant to authorize the Navy’s planned investment of billions of dollars in USVs until the Service can come up with a concept of operations (CONOPS) for using them. Congress has a point. The Navy has announced plans to procure large numbers of uncrewed systems — especially large and medium uncrewed surface vessels — but a CONOPS has not yet emerged.
An evolving concept of operations is to marry various size uncrewed surface, subsurface and aerial uncrewed vehicles to perform missions that the U.S. Navy has — and will continue to have — as the Navy-After-Next evolves. The Navy can use a large, uncrewed surface vessel such as the MARTAC T82 Leviathan as a “truck” to move smaller USVs, UUVs and UAVs into the battle space to perform several important Navy missions such as intelligence, surveillance and reconnaissance (ISR) and mine-countermeasures (MCM).
How would this CONOPS for a Hybrid Fleet evolve? Consider the case of an Expeditionary Strike Group comprised of several amphibious ships underway in the Western Pacific. This Strike Group includes three large, uncrewed surface vessels (LUSVs). Depending on the size that is ultimately procured, the LUSV can carry a number of medium-sized uncrewed surface vessels (MUSVs) and deliver them to the intended area of operations.
These vessels can then be sent independently to perform the ISR mission, or alternatively, can launch one or more smaller USVs to perform this mission. For the MCM mission, the LUSV can deliver several MUSVs equipped with mine-hunting and mine-clearing systems (all of which are commercial-off-theshelf (COTS) platforms such as the MCM-USV, T38 Devil Ray, Shadow Fox and others tested extensively in Navy exercises). These vessels can then undertake the “dull, dirty and dangerous” work previously conducted by Sailors who had to operate in the minefield.
This is more than an aspirational concept. As one example, the T38 Devil Ray successfully performed the MCM mission in recent Pacific Fleet-organized exercises in the San Diego operating area by leveraging other commercial-off-the-shelf
(COTS) mine-hunting sonars and mine-destroying remotely operated vehicles (ROVs) to demonstrate the ability to destroy mines autonomously and at a distance.
To be clear, this is not a platform-specific solution, but rather a concept to team the crewed ships of a Hybrid Fleet with capable uncrewed maritime systems. When fleet operators see a capability with different size uncrewed COTS platforms in the water working together and successfully performing the missions presented in this article, they will likely press industry to produce even more-capable platforms to perform these missions and thereby accelerating the fielding of a Hybrid Fleet.
By H I Sutton, OSINT Analyst
Following Russia's full-scale invasion in 2022, Ukraine swiftly developed a potent uncrewed naval force. Utilizing explosive-equipped uncrewed surface vessels (USVs), Ukraine has successfully inflicted significant damage on the Russian Navy. These pose such a formidable threat that the Russian fleet into a state of inactivity at port. This grants Ukraine a level of sea denial that was scarcely conceivable just a few years ago.
The cornerstone of this achievement, in my opinion, lies primarily in the implementation of uncrewed platforms. This has allowed operations which would not have been viable with crewed vessels. Uncrewed vessels can be smaller, and expendable.
Ukraine's uncrewed vessel revolution has in turn only been possible because of real-time two-way satellite communications. There have been uncrewed platforms before, but high bandwidth communications allow human-in-the-loop control. This enables faster deployment and rapid adaption to evolving targets and missions. Starlink serves as the primary provider of satellite communications, although Kymeta is also utilized. Automation will improve, likely making this human-in-loop command less necessary, but that is some way off.
We have also seen some development of semi-submerged or fully submerged versions. These fall under the UUV or AUV (uncrewed underwater vehicle, or autonomous underwater vehicle) category.
All current designs are characterized as being relatively small, much smaller than if humans had to be carried. This has many advantages.
There are, for sure, more types under development. This visualization only includes publicly revealed types.
MYKOLA
The first of Ukraine’s USVs to be revealed, the 'Mykola' were used in September 2023 and the dramatic raid on Sevastopol on October 29, 2022. These USVs were used, together with UAVs, to attack the Russian Navy in port. Two warships, the frigate Admiral Makarov and the minesweeper Ivan Golubets were damaged.
The Magura V5 is the main type known to be in service with the GUR (Ukrainian Defence Intelligence). Images were made public until May 24 2023 when some attacked the Russian
Navy intelligence ship Ivan Khurs. This was significant because it occurred far south of Crimea, showing the USV's impressive range. The attack was unsuccessful, as was another on intelligence ship, Priazovye, on June 11. The circumstances of these attacks are unclear, and it appears that some of the USVs may have been inoperable before being engaged by Russian guns. The new version is associated with the designation Magura V5. Magura's have since been involved in multiple missions and sunk several high-value Russian ships.
TOLOKA TLK-150
The small Toloka TLK-150 is a natural evolution of Ukraine’s maritime drones which are uncrewed surface vessels (USVs) packed with explosives. Being an underwater vehicle it is less prone to detection and harder to neutralize with gunfire. Its warhead is also impacting below the waterline so may be more likely to sink its target.
The design is evidently intended to operate as a form of loitering torpedo. It consists of a typical tubular body, but with a large keel and horizontal stabilizers amidships. Thrusters are mounted on the end of each horizontal stabilizer. Intuitively, these are used for steering as well as propulsion. This should allow significant agility. If the mast is always above water then, technically, you could argue that it’s a semi-submersible. In this case however that distinction may be unhelpful. It’s a weaponized UUV.
The trade-off will be range and speed. Also, the communications mast, which may contain an electro-optical camera, will need to be above the surface. Although it has been shown publicly, it is unclear whether it is being used operationally. Multiple versions are expected, including one which is 4 meters long and claimed to have a range of 1200 km or 400 km operation radius.
The Mamai was used by Ukraine's SBU (Security Service of Ukraine) in the attacks on the Ropucha Class landing ship Olenegorsky Gornyak and the tanker Sig. Both attacks, far away from Ukrainian controlled territory, inflicted significant damage.
It is named after Kozak Mamai (Cossack Mamai/Mamay), a Ukrainian folk hero and one of the standard characters in traditional Ukrainian 'Vertep' puppet theatre. The design is much larger than the canoe-like USVs (uncrewed surface vessels) first seen in September 2022. And the Magura family of USVs used by GUR (The Main Directorate of Intelligence of the Ministry of Defence of Ukraine). All the same its overall dimensions are still compact. The increased volume likely allows for a large fuel load, giving its demonstrated long range.
The design uses a planning hull which allows a reported top speed of 60 knots (110 kmph). One, sometimes two, satellite communications antennas are fitted, and there is an electro-optical camera-ball. The warhead is detonated by any of three impact sensors protruding at the bow. These have, on this particular model, proven reliable.
Ukraine's SBU operates the Sea Baby USV. This was reportedly used to attack the Kerch bridge on July 17 2023. The design is larger than the Mykola and Magura types but still overall quite small.
In addition to the main charge, the Sea Baby can carry RPV-16 thermobaric rockets. Variations of two, four and six small rocket tubes have been seen. The rockets are unguided and have a range
of around 1,000 meters. These weapons could serve several purposes. As well as being a primary way to attack a target, they could be used to defend against surface threats. During an attack with a ram-charge, the rockets could be launched to distract or suppress defenses. This latter tactic was used on some Imperial Japanese explosive boats in World War Two.
The improved Sea Baby developed for the SBU was revealed in early March 2024. A single 400 horsepower engine is used in place of the twin jet ski motors of the earlier type. This allows a 400 kg warhead (some reports heavier). It has a range of around 500 nautical miles and a maximum speed in the region of 48 knots. Its reinforced hull can traverse waves 1.5 meters high, while its draft is around 1 meter and height above water 1 meter. Communications includes both a directional Starlink antenna and Kymeta satellite link. Although unconfirmed, it seems likely that like the original Sea Baby it can also carry rockets.
The large white antenna at the stern is Kymeta while the smaller rectangular one is StarLink. Ahead of that is the electro-optical/infrared sensor.
The Stalker 5.0 USV was revealed at the international Black Sea Security Forum 2024 in Odesa. It is approximately 5 meters long and 1.2 meters wide and carries a 150kg payload. The vessel uses a 60 hp outboard motor to achieve maximum speeds of 40 knots. Range is 350-600 km. The type is described as being intended for reconnaissance and patrol and can also be used for transporting supplies. Unit price is stated as 60k USD, making it cheaper than some other designs.
The Marichka (МАРІЧКА) is a new large autonomous underwater vehicle (AUV) developed by AMMO Ukraine. Among the many large AUV projects around the world, it is probably the first born directly from wartime needs. The basic vehicle is 6 meters long and 1 meter in dimeter. Construction is metal with all or most of the hull being a pressure vessel. A keel appears to run along the bottom, and there are the expected towing loops.
Ammo Ukraine have advertised the system as being for antiship, anti-bridge, intelligence gathering and transport. Range is reportedly 1,000km. Unit cost is stated as 16 million UAH, equivalent to 433k USD.
At least one of the prototypes has an X-form rudder configuration. Note the nose cone on the floor at the front of the vehicle.
WEAPONIZED AM-800 RHIB
An unidentified USV was discovered, float capsized, in Romanian waters on April 3 2024. The craft uses an American-built Silver Ships AM-800 rigid-hull inflatable boat (RHIB) as its base. The warhead was from a STYX anti-ship missile. The vessel has not been formally attributed but appears most likely Ukrainian.
MAGURA'FRANKENSAM' AIR DEFENCE USV
Ukrainian uncrewed surface vessel (USV) armed with an improvised air-defense system with two AA-11 ARCHER (R-73) missiles. Produced by Magura and used by GUR.
RIVERINE RESUPPLY USV
Prototype logistics USV observed with two ammunition containers (US type, 120mm or 155mm rounds). The craft is very small, around 1.5 meters long, and has a 30kg payload.
On December 7 2024 the commander of the Ukrainian Navy (VMS ZSU), Vice-Admiral Oleksiy Neizhpapa, shared a video of a new surface drone (USV- uncrewed surface vessel) being used in the Black Sea. The vessel is unique among previously seen types in having a hangar for at least 4 quadrotor FPV drones. It also appears to have a hangar for minelaying over the transom.
The BBKN Dandelion (ББКН «Одуванчик») is a small USV developed by KMZ (Kingisepp Machine-Building Plant) in St. Petersburg. The latest image suggests a very different design to the RK-700 Vizir USVs previously marketed by the company.
Limited information is available. According to reports it can reach 80 km per hour (43 knots) and has a range of 200 km (108 NM). This would mean that it is shorter ranged than the Ukrainian types. Its payload of 600 kg is similar. Most probably this would be a warhead in the bow, although many options can be considered. However, these specifications are remarkably similar to those published for the RK-700 Vizir design. So, a reporting error is a distinct possibility.
The Murena 300S appears generally comparable with Ukrainian types. The Murena (Moray Eel) is approximately the same size as the Ukrainian Magura V5 and Sea Navy designs. The producer, LLC KB Center for Unmanned Systems, advertises it for Defense of Naval facilities, mine laying, mine clearance, patrolling and reconnaissance. On September 19 2024 it was displayed to President Putin while armed with UMT 220mm lightweight torpedoes (in dummy form).
The vessel has a simple metal semi-planing powerboat hull similar to the classic Soviet-era ‘Progress’ series. Unlike most, but not all, Ukrainian designs it has an outboard motor.
Significantly, it appears to have a Starlink antenna. The apparent antenna as been hidden under camouflage netting but its distinctive shape is evident. The corners of the square antenna are also just visible in photographs from the event.
H I Sutton writes about the secretive and under-reported submarines, seeking out unusual and interesting vessels and technologies involved in fighting beneath the waves. Submarines, capabilities, naval special forces underwater vehicles and the changing world of underwater warfare and seabed warfare. To do this he combines the latest Open-Source Intelligence (OSINT) with the traditional art and science of defense analysis. He occasionally writes non-fiction books on these topics and draws analysis-based illustrations to bring the subject to life. In addition, H I Sutton is a naval history buff and data geek. His personal website about these topics is Covert Shores (www.hisutton.com)
The inaugural event of Ukraine: Lessons Learned in Drone Warfare and Tactics Year 3 – Take Aways for the EU and NATO, took place in Estonia between the 4th-6th March. It was organised by the Baltic Ghost Wing Center of Excellence (BGWCOE) and Proving Grounds. The company organising the event runs a 50km2 testing ground for military drones, and is led by James Acuna, a former CIA senior operations officer. As the location is close to the Russian border, it’s under constant jamming and spoofing. This makes it ideal for realistic testing of military unmanned drone technologies.
One might ask the question, in what way is this relevant to readers of Ocean Robotics Planet. The answer is simple. The Russian Navy – the second most powerful naval fleet of the world -was restricted access to Odessa and parts of the Black Sea, by Ukraine, a country that doesn’t actually have a navy. This was achieved mainly by deploying Unmanned Surface Vessels (USVs), alongside Unmanned Underwater Vehicles (UUVs), and even examples of First Person View (FPV) aerial drones that use USVs as mother ships. These FPVs currently have a flight range of 20km, giving USVs an additional strike capability to reach targets inland.
The BGWCOE has a cutting-edge facility located in Johvi, Estonia. Their mission is to test advanced concepts and tactics, techniques, and procedures (TTPs), as well as to provide top-tier UAS training for both civilian and dual-use unmanned aerial systems (UAS) operators. Our own readers can even become the best drone pilot in the world by learning from the best; James Acuna was inspired by the elite training style of Top Gun when opening up this facility.
The proving grounds offer a highly controlled and realistic environment designed to replicate hostile battlefield scenarios: tough working situations that closely match the conditions in Ukraine.
Their facilities include a specialised airfield near Jõhvi, Estonia, for testing fixed-wing UAS, and over 50 km² of uninterrupted land near Sonda, Estonia, for comprehensive real-world testing. These diverse testing areas provide an unparalleled platform for evaluating the full spectrum of UAS capabilities, including flight endurance, navigation precision, sensor functionality, and safety protocols. They also offer advanced weather simulation capabilities, which allows for testing in various conditions such as wind, snow, and winter scenarios.
The BGWCOE are committed to extending the boundaries of UAS operations, ensuring that they can replicate the toughest conditions around the world. Their proving grounds not only enhance the readiness of UAS but also contribute to the safety and success of missions in critical and difficult operational scenarios.
There is the opportunity to test a range of different drone technologies that includes USVs, UGVs, and FPVs. Furthermore, BGWCOE is now opening a new USV range and also coordinates electronic warfare testing.
James Acuna opened the conference with a keynote discussing the reasons for this event, and the great lineup of interesting speakers, whom the audience had the chance to interact with afterwards. He joked that all information
here is unclassified but “Telegram Top Secret”, referring to the various Telegram channels that claim to be in the know, when top secret information doesn’t usually get discussed via open channels. However, this joke didn’t age well with the Signal Chat Scandal happening just only a few weeks afterwards.
The event was held over three days, and the audience had the chance to engage with seasoned military drone operators and designers of drone technologies. These have already proven useful on the battlefield. In Ukraine, solutions that don’t work get filtered out very quickly because lives depend on them. For obvious reasons we can’t go in depth on tactics, but high-level strategy can be discussed.
Some of the key points are that there are now 200+ military UAV groups in the Ukraine, conducting over 4,000 flights per day, and these units have already neutralised over 50,000 enemy personnel. This makes FPV drone warfare a force to be reckoned with.
Another interesting and perhaps troubling trend is the proliferation of these FPV drones outside of the battlefields of Ukraine. These technologies are now being used for smuggling contraband into the USA and elsewhere, as volunteer Mexican and Colombian fighters on both sides of the Ukrainian conflict have taken the piloting know-how to their home countries. Europe could possibly experience something similar in the future.
According to one of the senior Ukrainian drone leaders, the biggest lesson learned was that even their greatest ally and supporter can become unreliable if the political leadership changes and policies shift. Thus, the country must become self-sufficient in the production of weaponry such as military drones and related technologies. As a result of this we can see Ukrainian drone developments are now at the forefront of technological innovation, where the cycle of countermeasure techniques is only 5 days whenever a new tactic is introduced.
After the conference presentations several drone companies and operators showcased their aerial drones on the testing grounds and at an indoor location that was linked to the event.
Several NATO military drone trainers attended the conference along with Ukrainian trainers of FPV drone pilots. The event was an invaluable premise for discussions and learning from real life operations in the field. It’s worth noting that during the event the Russian Federation tried deploying targeted electronic warfare techniques from the other side of the border. However, despite all their efforts to disrupt the flight of allied NATO drones, none of their attempts were successful.