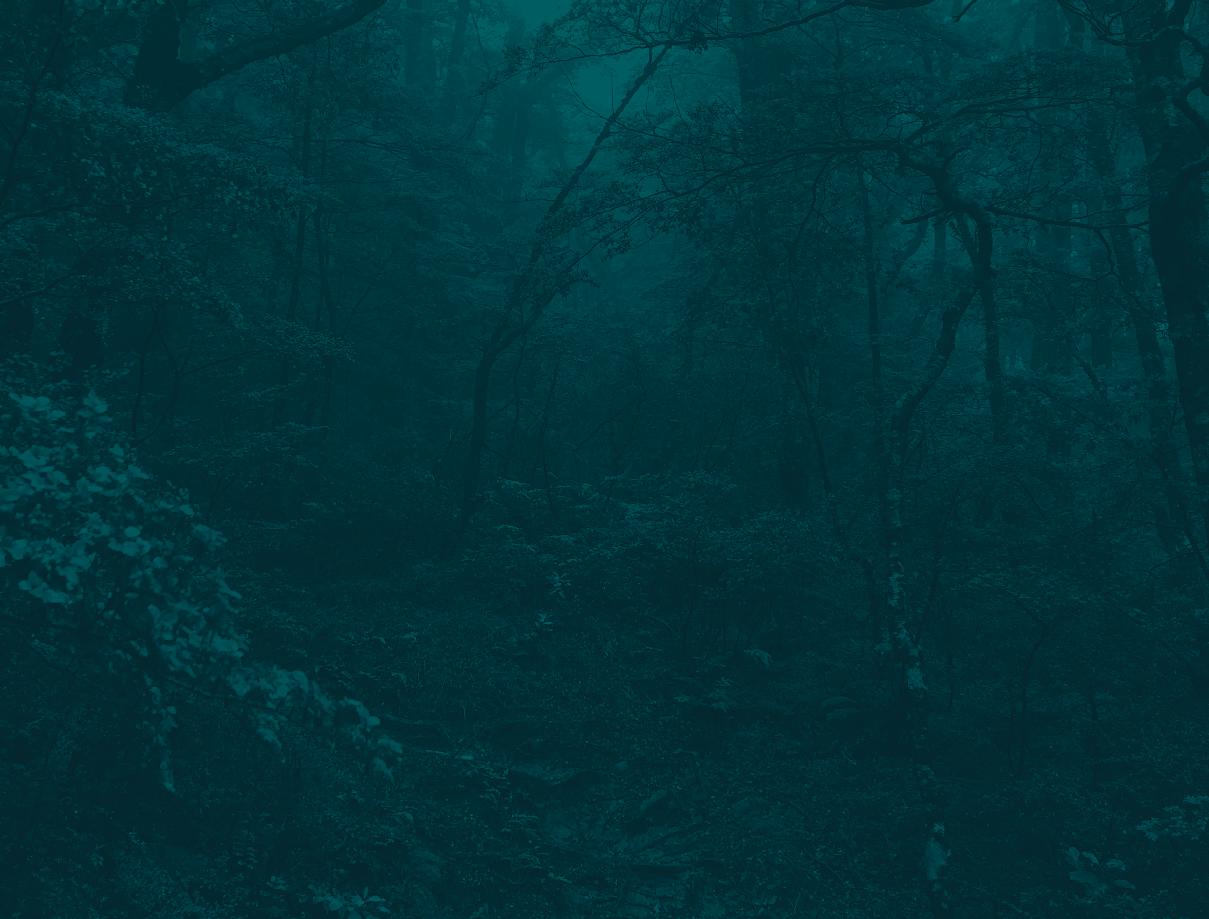
K FEED
I S K
HUNGRY
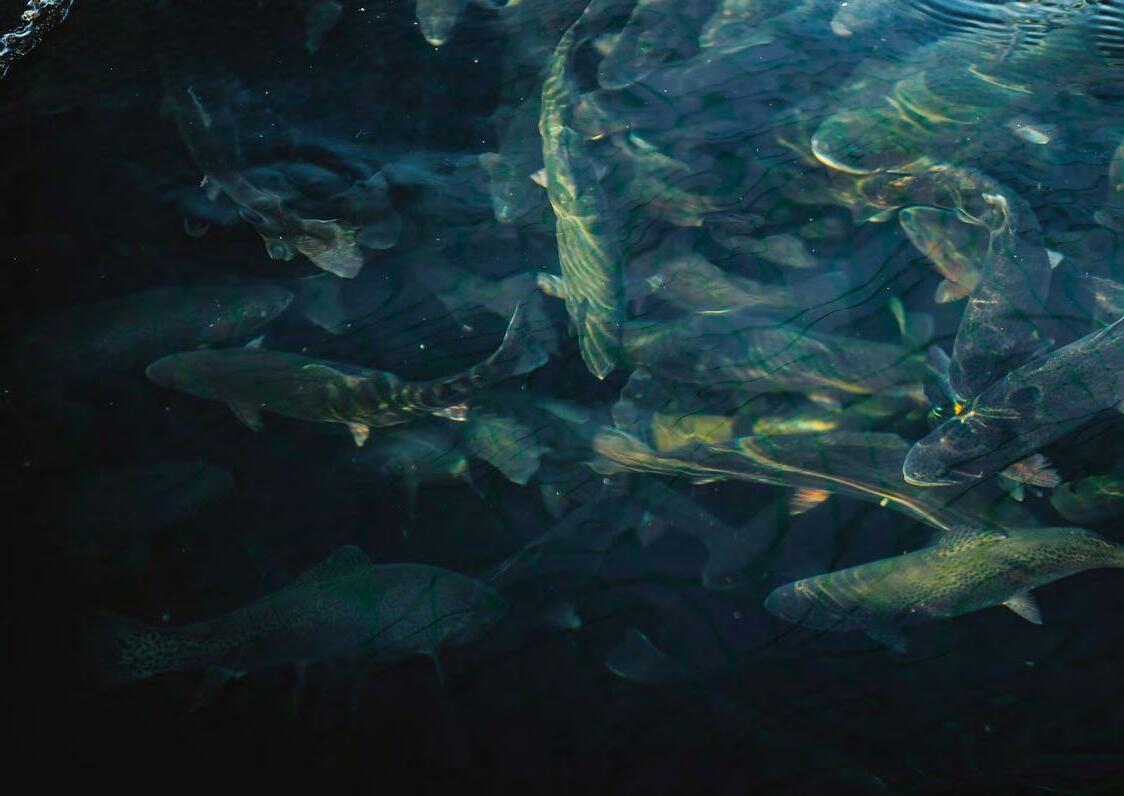
K FEED
I S K
HUNGRY
By the year 2050, the world's population will be expected to grow to 9 billion people. In addition, Norwegian salmon farming must triple the value creation by the year 2030 and fivefold by the year 2050.
This growth, both nationally and globally, is not sustainable if the fish are to be fed on soy, fish oil, or fish meal. There simply aren't enough fish feed in the sea to feed all the farmed fish. Corn and soy are also used as food for humans, and it can be debated whether they should be used as animal feed. Soy production also contributes to the deforestation of the rainforest in South America. Therefore, we need new, sustainable protein sources that are part of a circular economy, e.g., single-cell protein (SCP) produced from wood-based sugar. An important challenge will be to understand the characteristics of the feed and how it affects the fish’s health. Sustainable growth of the aquaculture industry requires an increased focus on preventive fish health, and new production technology to solve environmental challenges so that Norwegianproduced seafood products can be associated with quality, sustainability, and high ethical standards.
The objective of the FISK project has been to produce an economical and sustainable replacement for to day's products, and at the same time to to investigate
– without contribute various technology routes along the axis from forest to feed proteins and thereby pro vide a necessary basis for further technology choices when establishing the production of fish feed. Furthermore, the project wanted to increase the degree of utilization and value creation from the forest biomass that does not consist of construction wood, by using GROT (e.g. branches and tops) and side streams from the forest industry. The project will iden tify key obstacles that will require further R&D to secure the future technology choices that must be made.
The results from the project will contribute to quality assurance of technology and economy in a value chain that is new and highly innovative both in a regional, national and international context. A successful project will be of great benefit to society and have significant economic effects both in the forest-based industry, the aquaculture industry, as well as derivative businesses in the Nordic Green Belt region.
development of single-cell protein (SCP) production from forest-based
that
with food
THE PROJECT WILL BE ABLE TO PROVIDE THE FOLLOWING IMPACT TARGETS:
Value creation through profitable production of protein for a fish feed from forest-based biomass, preferably by processing residual streams, such as GROT.
Increased supply security for the fish farming industry through local production of protein for fish feed. Improved sustainability of the fish farming industry by increasing the proportion of sustainable protein sources in fish feed.
During the project, calculations and research results have been produced and discussed back and forth between actors in the supply chain, and it appears that in the short term an integrated process in an existing process would be the most cost-effective. Then it would mean fewer logistics, use of exist ing resources such as personnel, steam, and purification of the process water.
If you look at the effects in the long term, there is the possibility of being able to build up a process where several products are produced, for example, lactic acid and SCP to get a profitable business for more difficult raw materials such as GROT. Today's calculations will not be the same due to the prevailing climate changes, with poorer harvests, defishing of the ocean, and unrest in the world, which will lead to higher prices for raw materials, and thus this alternative may become attractive on the market.
Develop the basis for
The project will be
of the
in the Nordic Green Belt region forestry and aquaculture industry by contributing to the establishment of production of
feed,
on
raw
project
a
contribute to
industry companies, smaller companies or
companies closely connected to the industry within the program area,
marketing of their products and that the fish farming industry gets access to a new, sustainable protein source.
The goal of this work package was to investigate the production of high yield
from
To reach a cell concentration in bioreactors of 20 g/L, as well as reach a productivity of 2//L/h in continuous cultivation. In addition to that, separation, washing and drying of SCP is optimized.
The produced SCP will be evaluated in fish feeding trials with focus on investigating which effect it has on fish health and meat quality compared to soy protein.
WORK PACKAGE 4 Business development. Investigate techno/economic model for protein production.
To contribute to the region's transition towards a bioeconomy and strengthen a central part of the region's business life, the project has focused on several different activities.
Communication has been one of the activities with the aim of spreading the results in a wider circle. Activities relating to communication have included the creation of project pages on ri.se and rise-pfi.no, articles, press releases, presentations, and graphic material. Unfortunately, seminars, workshops, and other types of meetings have been difficult to implement as the global pandemic has made it difficult to travel and meet physically.
A meeting and workshop that could be carried out was the meeting that took place in September 2022 in Trondheim when the project group met to discuss the project and future collaboration opportunities.
The project was divided into four main activities: Pre-treat ment (WP1), Protein production (WP2), Cultivation and testing on fish (WP3), and Business development (WP4). Each main activity has a goal and sub-goals, described in the work pack age description in the report. FISK had received support from the EU of €341,029, gov ernment IR funds of NOK 1 million and SEK 1.8 million from Region Västernorrland, NOK 500 from Trøndelag County Municipality, and NOK 500 in contribution from industry in Norway. The total budget for the project was €938,441, which was worked up to almost the entire amount and stayed within the scope of the project budget. The project had to make two budget changes largely due to the uncertainty surrounding the Covid pandemic. Staff became ill, planned trips were canceled and long deliveries of materials.
Number of companies receiving support.
Number of companies that receive support to introduce new products to the market.
Number of companies receiving support to introduce new products to companies.
Number of companies participating in cross-border or interregional research projects.
Number of research institutes participating in cross-border or interregional research projects.
Number of participating organizations in cross-border research projects.
Demonstration and test projects.
Long-term cooperation agreements between different research institutes.
3 The project collaborates with Domsjö Fabriker AB, Synergifabrikken AS and Sveaskog AB.
0 In the long term, we see that several of our partners can be involved in introducing SPC within the Nordic green belt.
3 The project has worked with a new assortment for Domsjö Fabriker AB, Sveaskog AB and a new product for Synergifabrikken AS.
3 Domsjö Fabriker AB, Sveaskog AB and Synergifabrikken AS.
RISE PFI AS, RISE Processum AB, ekonomiska föreningen Norra Skog och Wood Works! skogsand tränäringskluster.
GROT was tested on a 3-liter scale due to low raw material. The goal was to test on a 50-liter scale.
RISE PFI AS and RISE Processum AB
The project has been managed by two project managers, the Main project manager Yvonne Söderström Nordin from RISE Processum in Sweden, and the Sub-project manager Mihaela Tanase-Opedal from RISE PFI in Norway.
The task of the project managers has been to be responsible for and lead the project in its entirety and to support the work package managers. Their task has also been to coordinate and follow up on the project's resources as well as to dialogue with and report to the project's financiers. The project managers have had the support of controllers, project administrators, a communicator, and a buyer.
managers being able to have continuous meetings with the project partners.
WRITTEN BY YVONNE SÖDERSTRÖM NORDINDespite the global pandemic that struck shortly after the start of the project, the collaboration between the project leaders has worked well and the work with the activities in the lab has been able to be carried out despite restrictions and difficulties in obtaining materials from suppliers. The digital changeover that took place during the pandemic contributed to the project
FISK is an environmentally oriented project that aims to find new sustainable opportunities to produce fish feed from residual streams from the forest industry.
In the work for sustainable development, both equality and diversity are important pieces of the puzzle. The forest indus try is a male-dominated industry. However, the industry has started working on changing attitudes and promoting women to apply to the industry, FISK has supported this process.
The research institute sphere looks different in comparison, especially in recent decades, when women and men are more evenly distributed. The project intended to greet young women to show them how you can work with forest issues from a research and sustainability perspective. Unfortunately,
this could not be carried out as the global pandemic made it difficult to receive visits to workplaces. Parties to the project, however, have received students who were allowed to com plete their master thesis, a man and a woman.
The project managers have also participated in focused train ing on gender equality in the forestry industry. Having project managers with updated information on how to work with gender equality is important for the project to work effectively with these types of questions. A total of 4 different nationalities have worked on the project. It is important to have diversity in terms of nationality, gender, age, and junior/senior research ers. With this kind of diversity, the project has continuously re ceived various thoughts and ideas which benefited the project.
The steering group for FISK project consists of the group manager for Innovation Systems at RISE Processum, RISE PFI's CEO and representatives from Synergifabrikken. The steering group has held digital meetings approximately four times a year where they discussed how the project is progressing and developed proposals for measures.
”Two project managers are better than one”
It has been important for the project to have digital plat forms where it is easy to spread information and where you can also reach an audience adapted to the target group. To create such platforms, a project page was created early in the project on ri.se and a page about the project on rise-pfi. no. Ri.se is RISE's official website where RISE Processum also has a subpage (ri.se/processum). Since RISE Process um is a subsidiary of RISE, projects that RISE Processum is involved in are on ri.se. The website rise-pfi.no is owned by RISE PFI, where there is information about the FISK project and available infrastructure. On ri.se there is information not only about various projects but also about equipment and expertise. This has made it possible to further increase the visibility of the project as the pages relate to both test and demo pages as well as personnel pages.
Communication is an important measure to have the opportunity to create a sustainable future. Raising public awareness has been an important part of the FISK project. Various communication initiatives have taken place continuously throughout the project period.
The project is not only visible on ri.se but also on the websites: https://bioeconomyregion.com/protein-fran-sko gen-blir-fiskfoder-genom-norsk-svenskt-samarbete/ and https://www.nkfv .se/news/soon-can-protein-from-the-fo rest-be-used-as-fish-feed. The fact that the project is visible on the internet is of great value. There has been a major shift in how society collects information, and the internet is the leading actor.
In addition to the project page and other websites, the project can also be seen on social media. The project ow ners have shared information about the project on one of their LinkedIn channels, which currently has 1223 followers.
A following that is largely interested in bioeconomy and biorefinery. WRITTEN BY AMELIE KARLSSON
The pandemic made it difficult for the project to have physical meetings and attend physical events to talk about the project. As the digital meeting tool Teams became a new meeting place, a new teams-background was created that the project participants could use on occasions where the project was presented or represented. During a digital department meeting for the Biorefinery and Energy depart ment at RISE on March 31 2022, Yvonne Söderström Nordin, project manager at RISE Processum and Philip André Reme, CEO at RISE PFI gave a presentation about the project to their colleagues in the department. The aim was to inform their colleagues about the project and create new contacts. During the same day, project manager Mihaela Tanase Ope dal presented the FISK project during the hybrid seminar “Tøffe råstoffer for økt bærekraft i fôrproduksjon”. (https:// arktisklandbruk.no/seminar-31-03-01-04-toffe-rastoffer-forokt-baerekraft-i- forproduksjon/).
The aim of the seminar was to increase and share expertise on the use of blue and green bioresources for feed ingredi ents and at the same time increase cooperation between industry and R&D.
Sveriges Television has a show called Vetenskapens värld that educates the Swedish people in various scientific subjects. On September 21, 2021, the program had an episode that dealt with the theme Food of the Future. The program traveled around Sweden to take part in the latest on sustainable food.
From Örnsköldsvik to Skåne, both researchers and farmers are trying in different ways to produce more sustainable food with lower emissions. During this episode, Björn Alriksson, Group Manager at RISE Processum, took part and talked about the project and how it can contribute to a sustainable transition.
During the project period, an article and a press release were also published. The article published on February 8, 2022 described the project and also described the progress made in the project. This article was published on ri.se/processum and was also shared via social media.
On June 17, 2020, a press release was issued describing the purpose and goals of the project. This press release received good circulation and was picked up by two external news sites.
The production of protein from forest-based biomass requires complex processes, and it will be difficult to compete with soy-based protein in terms of price. In order to succeed, it is therefore essential that the market is willing to pay a higher price for a fish feed with increased sustainability, increased self-sufficiency and high quality.
The raw materials used for production of Single Cell Protein (SCP) in FISK project are a side stream from a biorefinery process industry called sulfite liquor and GROT called branches and tops. In this study we assumed that using available sulfite liquor on the market it’s easiest to come up to commercial scale while GROT is a future raw material for production of SCP. Per today GROT is usedfor the energy pur poses, with a huge potential to be used as raw material for value-added products depending on the regions and wood type. The logistics costs are high in Norway and therefore GROT is mainly exported to Sweden.
GROT spruce and GROT birch material were produced in Norway, while GROT mix was produced in Sweden. The GROT material produced in Norway was special grinded to be used in FISK project. The raw material was collected, mechani cally treated to reduce the particle size, dried and chemical characterized for the chemical composition. The particle sized required for further used in the pretreatment process are thickness ≤ 2mm and dryness >90ºC. The results shows
that GROT spruce consists of 39% cellulose, 22% hemicellu lose, 33% lignin and 1,56% extractives; GROT birch consists of 37% cellulose, 25% hemicelluloses, 27% lignin and 2,9% extractives and GROT mix consists of 36% cellulose, 23% hemicelluloses, lignin 29% and 2% extractives. The chemical composition of GROT spruce and GROT birch fractions is in accordance with the chemical composition reported in liter ature for spruce and birch while the GROT mix is a mixture of spruce and birch, where birch is the predominant one. The composition of the hemicellulose fraction is also different: spruce consists of C6 sugar components, such as mannose and galactose, while birch consists of C5 sugar components, such as xylose and arabinose.
An overview over relevant pretreatment methods has been done in the beginning of the project. Based on this, the pretreatment method chosen to be used in FISK project is based on a strong acid hydrolysis. The method consists of 1) in the first stage biomass is treated at high acid concentra tion (55-72%), low temperature (35-40ºC) under
continuous mixing for 30 minutes; 2) stage two the material is treated with low acid concentration (4%) at 120ºC for 3 hours. After the second hydrolysis step, the liquid is filtrate, and the sugar solution is neutralized to the wanted pH. The lignin will follow the fast material. One of the challenges correlated with strong acid hydrolysis is the chemicals costs. Therefore, an efficient chemical recycling system is central to such a process being able to be defended, both environmentally and economically. We believe that the tech nology chosen to be used in this project has what it takes to be scale up. A strong acid-based hydrolysis process is an at tractive pre-treatment process for Norwegian forest-based biomass, as it can provide a high sugar yield with minimal formation of chemical components that inhibit subsequent fermentation (e.g. hydroxymethylfurfural, furfural and for mic acid). Flow chart for an integrated process to produce SCP from forest-based biomass is described in figure 2.
The optimization of the pretreatment process has been done to obtain: 1) high yield of carbohydrate; 2) carbohydrates in a form that can be sent directly to fermentation; 3) low inhibitor formation and 4) optimal sugar concentration for the microor ganism and to give a SCP with wanted aminosyre profile to be used as component in feed to fish.
As described in AP1.2, the strong acid hydrolysis process con sists of several steps: 1) first hydrolysis step, 2) sugar precip itation and acid separation, 3) second hydrolysis step and 4) neutralization. In the first hydrolysis step, very good mixing between acid and biomass, particle size of the biomass, acid concentration and acid:biomass ratio are extremely important to achieve a high sugar yield and low formation of inhibitors.
After several trials, it was found that the optimum acid con centration is 70%, using a sulfuric acid:phosphoric acid (2:1) mixture. Sugar precipitation and acid separation is an impor tant step to achieve profitability within the process. Different organic solvents were tested in the project, and we found that
FIGURE 2. Schematic draw of SCP production process
methyl ethyl ketone (MEK) gave the best results in sugar precip itation and acid separation. In addition, this 98% of this solvent can be evaporated with rotavapor and recovered and 95% of acid could be used back in the process. In the second hydrolysis step, oligomer sugar is broken down to monomer sugar (important in the further fermentation step where SCP is produced).
In the neutralization step, model sugar solutions of GROT spruce and GROT birch were made at RISE PFI and the effect of neutralization chemicals in the fermentation process was inves tigated. Furthermore, RISE Processum has investigated cultiva tion on the sugar solution which was neutralized with different chemicals. When calcium carbonate and calcium hydroxide are used, gypsum is precipitated which must be filtered before fur
ther cultivation/fermentation of the sugar solution. This leads to a small part of the sugar being lost with the gypsum. When sodium, potassium hydroxide or ammonia is used in neutrali zation, the salt is dissolved in the water, and we believed that it could be consumed on to cultivation/fermentation. However, our hypothesis was wrong. The results shows that by adding Na, K and ammonia, the sugar solution was slightly more diluted by 20-30g. The lower biomass yield for Na, K and ammonia can be explained due to the more dilute sugar solution and the conductivity. The results show that with high conductivity, the cell growth rate is reduced.
Raw material Sulphuric acid Phosphoric acid Impregnation stage First stage hydrolysis Liquid fraction Solid fraction Acid/sugar separationOptimization of the strong acid hydrolysis process used in the FISK project was done so that a sugar concentration in the filtrate of 20-25 g/L gives a biomass concentration of 15g/l for GROT birch and 18 g/l for GROT spruce.
There is a great potential for GROT collection and uses for value-added products in Norway, and thus a potential for increased value creation based on a biomass resource for which there is currently little demand for uses other than energy production. To be able to develop a cost-effective process for the production of SCP from forest-based biomass, one must 1) have a raw material that comes from reasonable sources so that such an SCP can compete with soy/fishmeal on price or 2) that the SCP from forest-based biomass contains other active biocomponents so that the market is willing to pay a higher price.
Within the scope of this project, hthe project team has addressed many of these parameters, and calculated the production price for 1 ton of product from forest raw material. In work package 1 (WP1), the raw material (point 1 above) and the pretreatment method (point 2) was evaluated and in WP2 we focused on optimizing the SCP organism (point 3) and investigated the harvesting and drying procedures (point 4).
The available equipment, including the instruments that were purchased within the project, has mostly worked well for their purpose. The experiments were performed in scales from small shake flasks to bioreactors of 3, 50, and 600 liters. Upscaling worked well, but not perfect since the bioreactors in pilot scale was limited in stirring and aeration capacities. The dissolved oxygen in the cultivation media is a very important parameter when growing a filamentous fungus. When the SCP organism reaches high biomass levels, the broth becomes vis cous, which results in difficulties in stirring and aeration. This type of SCP organism is easily harvested by filtration and for the larger bioreactor cultivations in this project (50-600 liters) a filter press was used. There are different types of equipment for drying of the harvested material in pilot and demo scale, for example a belt dryer, spray dryer, and a tornado dryer. In the scale used in the present project and with the funding available, manual drying in drying cabinets were used.
To investigate and optimize the productivity of a microorgan ism, a bioreactor system must be run in continuous mode, where new cultivation media is fed to the reactor at the same speed as cultivated media is harvested. After a few hours or days of continuous operation an equilibrium is reached, and thereafter representative samples of the cultivated media can be harvested until all fresh media is consumed. The equipment (4 bioreactors at 3 liter each, Fig. 1) that was invested in during the project did not perform as planned. The harvesting pumps were unable to pump the highly viscous broth containing the
SCP cells out of the reactors, instead removing only the liquid media; this resulted in accumulation of SCP within the reactors. Continuous fermentations (2) were instead run in a 50-liter bio reactor (Fig. 2) with 40 and 30 liter of cultivation media and a dilution rate of 0.1 (i.e. 4- and 3-liter feed/hour respectively). The larger reaction volume meant that larger tubing and pumps could be used. The cultivations were allowed to proceed for 6 and 4 days respectively, and the harvested material was analyzed for biomass, protein content, sugar- and acid con centrations. Practically, the experiments went well overall, but the results did not meet the expectations. Productivity was 1,5 g/L/h at most, and the protein content was only about 43% at the best harvest (the goal of the project was a productivity of 2 g/L/h and protein content at above 60%). The low produc tivity and protein content is probably the result of low oxygen transfer to the cells due to insufficient stirring and aeration of the cultivation media. Sugar analysis of the media confirmed the decreased growth of the cells, since there was significant amounts residual sugar in the harvested media.
Spent sulphite liquor (SSL) from the Domsjö Fabriker was used in all the productivity optimization experiments since a large volume was needed. The SSL is a well-known model substrate and is used in many applications by RISE Processum.
To address the optimization of fast and efficient cell growth of the SCP organism, we focused on increasing the cell biomass (g SCP/ L of cultivation media) through strain development. The fungus was modified either by long-term adaptation or by random mutagenesis with UV-light during the whole project period. Small and compact colonies on agar plates is the pre ferred morphology of the microorganism and these colonies were cultivated with liquid media in shake flasks. The theory for this selection is that the long filaments (hyphae) of the fungus will likely result in higher viscosity in liquid media,
FIGURE 1. A bioreactor system in stainless steel containing four reactors of 3 liter each. FIGURE 2. A 50-liter bioreactor that is working very well for cultivation of the SCP organism. FIGURE 3. A 3-liter bioreactor system in glass used for the adaption experiments.and thereby decrease stirring, aeration and oxygen transfer into the media. Since good oxygenation is crucial to the growth of the fungus, higher viscosity leads to decreased overall biomass is the result. A shorter filament should thereby lead to higher possible biomass content.
In the adaptation experiments the filamentous fungus was cultivated in 3-liter bioreactors (Fig. 3) for an extended time (3 weeks), and portions of the cultivation media were replaced with fresh media every 3 days. After the cultivation period, cells were cultivated on agar plates and the size of the result ing colonies were evaluated. The best (small and compact) colonies were used for a second round of adaptation experi ments. This procedure was repeated a third time before the evolved strain was analyzed for biomass production. With the final adapted strain, a biomass of 25 g/L of dry cell weight was reached, compared to about 7-8 g/L for the wildtype strain. Mutation experiments with UV-light were also performed during the project and these also resulted in elevated biomass concentrations, but none of the produced strains in these mutation experiments exceeded 20 g/L of SCP.
Within this part of the project, a number of other parameters were also investigated to increase the efficiency and decrease the cost of production of SCP in large scale. The explored parameters were cultivation of the microorganism at lower pH, increased concentration of the substrate (spent sulphite liquor), and optimization of the nutrient solution composition.
It is potentially beneficial to cultivate the cells at lower pH, since many pretreatment reactions (in this case others) are performed under acidic conditions; therefore the amount of base needed to neutralize the media before cultivation is decreased. Cultivation at low pH would then improve the economics by decreasing the cost of chemicals, while also decreasing the amount of chemicals used which is beneficial for the environment. Before the project was initiated, the optimal pH for this fungus was around 6, but after optimization and adaptation during this project, the microorganism could be cultivated at pH 4.5 with no loss in productivity. Cultiva tion at even lower pH was also investigated, down to pH 3.0, but at these conditions the microorganism grew slower and produced less biomass.
Experiments to cultivate at a higher substrate concentration were also performed. The initial concentration of the spent sul phite liquor was 50% (diluted with water, nutrient solution and inoculation culture) and experiments using 75-94% of substrate were performed. Many experiments with increased substrate concentrations were successful, but not all, which indicates that more research must be done to get consistently better performance. It is important to be able to cultivate the microor ganism at as high concentration as possible to reduce the water consumption and to get increased economic viability.
Another interesting parameter to optimize is the nutrient solution composition (mainly nitrogen and phosphorus content). The goal with the optimization is to determine the lowest amount of added chemicals that will maintain good cell growth and high protein content. The first experiments indicated small differences in the composition would result in slightly higher biomass, but more experiments are needed to evaluate and confirm these results. It is important for a future factory to minimize additions of chemicals, both for the cost and for the environment.
In order to investigate the options for harvesting and drying of the cellular SCP biomass, a filter press (Fig. 4), a shredder (Fig. 5) and five drying cabinets (Fig. 6) in pilot scale, was purchased, installed and used during the project. Many separation and washing experiments were performed in the filter press to optimize the harvesting of SCP. The filter press has a built-in function to squeeze the filter cakes after all the material is filtered. This squeezing is done first with water pressure (the filter cakes are protected by the filter membranes) and then by air to increase the dry content from around 20 up to 35-40%. This function results in much drier and cleaner filter cakes, and a slightly higher protein content was also detected when compared to harvesting in a conventional filter press.
After the harvesting procedure with the filter press, filter cakes with dimensions of 30 x 30 cm and up to 4 cm thick are obtained. These filter cakes are broken into smaller pieces with a shredder, and the shredded material was subsequently distributed onto metal sieve trays and dried in a drying cabinet for around 6 hours. The drying cabinets purchased within the project are equipped with several excellent functions, such as an efficient fan system within the cabinets, removal of the moisture, temperature interval up to 150 ˚C, and temperature control with a timer. The filter press, shredder, and the drying cabinets are all working very well.
Additionally, the digestibility of the SCP product was investigated by an in-vitro method to evaluate the effect of drying conditions. Digestibility is an important parameter in the feed industry since it is an indication of how well the animals can absorb the feed nutrients in their gut. Drying at three different temperatures was studied (60 ˚C, 75 ˚C,
and 90 ˚C) and out of these the lowest temperature gave the best result, i.e. the protein in the material dried at the lower temperature was the most digestible.
Within the scope of the project, different techniques for large scale harvesting and drying has been performed in cooperation with equipment producers. One of the techniques, a belt drier, was found to work very well together with the SCP organism used in the project. In the pilot/ demo facility that is under construction in Örnsköldsvik, the acquisition of a demo-scale belt dryer is planned as a result of the FISK-project.
Within the project, spent sulphite liquor was used in opti mization studies for cellular biomass and productivity, but pretreated tops and branches from birch and pine were also evaluated and used as a substrate for SCP production. In WP 1, PFI sorted and selected representative samples of birch and spruce, which were used in pretreatment experiments to produce a fermentable substrate with high sugar content and with low concentrations of inhibitors. These samples were sent to Processum to evaluate the fermentability of the media using the SCP microorganism. The first samples contained too low amount of sugar for the organism to grow at high biomass content, but the inhibitor content was also negligible. PFI continued with optimizing the pretreatment experiments and produced a slurry with high sugar content and low amounts of inhibitors after a concentration step. The microorganism grew well on the concentrated substrate from tops and branches (birch 14.9 g/L and spruce 18.0 g/L SCP). An upscaled exper iment was also performed using this material with 2-liter
FIGURE 4. A pilot-sized filter press. FIGURE 5. Shredder used for grinding SCP before drying. FIGURE 6. A set of drying cabinets to produce the final dry SCP product.cultivation media in 3-liter bioreactors using tops and branch es from both birch and spruce, and with a substrate composed of theoretical amounts of monomeric sugars present in the trees as a control substrate. The microorganism grew as well or even better in the pretreated material of tops and branches than in the control media (Fig. 7).
The questions that have been addressed within WP 2 of the project are growth and productivity of the SP-organism, and also optimization of the harvesting and drying procedures. During the project, the biomass production of the cultivated filamentous fungus has increased three times and the produc tivity has also been increased, but to a lesser extent. Future plans might be to investigate how well the fungus would grow at optimal conditions with perfect aeration and stirring and an optimized nutrient solution. To reach economically viable production of SCP, the microorganism must be able to grow on substrates containing fermentable carbon sources of at least
50 g/L to get a biomass content of 25 g/L. The protein content also needs to be increased in order to have an economic pro duction process. Harvesting and drying have worked very well in the scale examined in this project, but for a large-scale facili ty another type of drying equipment is more suitable, i.e. a belt dryer with 2-4 segments with different drying temperatures.
7. An experiment with the comparison between tops and branches from birch and spruce and control samples.
The trial was designed as digestibility of nutrients and energy in a new feed ingredient by means of substitution and control trials with benchmark feed. The latter was formulated based on a standardized diet. Trial feed was formulated by repla cing 30% of the benchmark feed mix with the trial ingredient (SCP). This is a standardised method to measure digestibility in feed ingredients. Intake of trial feed was good and growth rate was almost as good as with benchmark feed, but better than according to Skretting´s standardised growth table.
Protein content in SCP is currently too low, but appetite was good. Growth and appetite indicates good health. We have to further develop our production technology of the substrate, research, test and improve Wood SCP in order gain better digestibility and feed factor.
WRITTEN BY OYSTEIN SELENResults are promising despite the fact that protein contents were in the lower bracket of the scale. The feed batch used in this trial did not result in reduced feed intake despite high content (30%) mix of SCP which is an indication that Wood SCP has a potential for being used as a main ingredient in commercial salmon feed. Such a process will require more trials, research and documentation in order to pave the road for commercialisation of Wood SCP.
project has analyzed the business potential of various biorefinery concepts with forest raw material to produce SCP. Those reported in this report are:
Pre-study: SCP Demo plant from brown liquor
SCP, production on a larger scale from brown liquor
Biorefinery for the production of bio-based monomers with SCP as a by-product from pulpwood or sawdust.
WRITTEN JONAS MARKUSSONThe project has analyzed the business potential of some business models that include the production of SCP. The study demonstrates that large-scale production is necessary to be able to meet assumed market prices and shows the impor tance of focusing on maximizing the valorization of value streams from a biorefinery.
The plant was calculated to use a partial flow of brown liquor from a pulp mill to a smaller semi-commercial sized produc tion facility (DEMO) to produce SCP. An overall picture of flows in and out of the facility is illustrated below in Figure 1.
In a technical feasibility study, a process concept was created. The costs for the process and its necessary infra structure were defined together with machine suppliers and engineering companies. See Table 1 for an image of the investment estimate.
The financial performance of the investment was analyzed by creating a cash flow-based investment model. The assump tions used are listed in Table 2.
SCP production brown liquor SCP CO2 Process return Steam, electricity Chemicals, water etc Brown liquorThis demonstrates that the economics-of-scale effects for the demo plant were too negative and that these facilities must be constructed on a larger scale to be potentially
Based on previously stated assumptions, it was concluded that approx. 1950 EUR/ton SCP is required to break even. To be com pared with an estimated market price of approx. 950 EUR/ton. A few scenarios were created to analyze various effects.
Future development for organism efficiency.
Maximum investment support
Streamlining of the process. None of these scenarios gave an effect where a profitability in the demo plant could be reached. The analysis shows that with 50% investment support, the facility would need addi tional support amounting to at least EUR 2.5 million per year.
The project did not conduct a technical feasibility study but chose to convert the data from the preliminary study to an approximately 5.5 times larger facility. The investment for this larger facility was estimated at 73.3 MEUR. The economic performance of the investment was analyzed by creating a cash-flow-based investment model. The assumptions used are listed in Table 3.
This analysis does not have the same accuracy as the smaller scale plant and should be regarded as uncertain. Based on previously stated assumptions, the conclusion was reached that approx. 740 EUR/ton SCP is required to break even. To be com pared with the estimated market price of approx. 950 EUR/ton.
Estimated profitability using the stated market price is used is good, with an IRR close to 17%.
The biorefinery concept uses formed solid phase residue (primarily lignin) for the production of electricity and steam used internally within the refinery. The analysis shows a biorefinery with potentially very strong profitability even with modest price assumptions for the main products even without attempting to valorize lignin.
The FISK project has contributed to increase awareness for alternative sources for sustainable feed and beenessential for Synergifabrikken in establishing and formalised a complete value chain for possible production of SCP for use in fish feed. An important challenge with SCP from “surlut” or other suitable wood biomass is to increase share of protein in order to make SCP competitive. We have therefore worked hard to ensure to include companies that have required qualities to improve manufacturing efficiency, substrate quality and value chain.
An improved value chain can also be achieved by establis hing complimentary value chains which can contribute to optimisation of resource sharing by taking an overall view by analysing major input factors such as raw materials, man po wer, energy, know-how and refinery processes. Synergifabrik ken has conducted a number of meetings and entered into agreements with potential partners as well as meetings with authorities to assess potential locations for establishing a production line. Such a location must allow for developing an eco-system based on SCP production supported by compli mentary value chains. In Norway WoodWorks Surnadal and central Eastern Norway such as Elverum represent potential areas with respect to availability of raw materials and logis tics. Sweden and North-America are also of interest.
Financial challenges and some questions related to SCP manufacturing based on “surlut” as raw materials has delay ed our application for salmon research concessions due to uncertainty related to when volume production of SCP will be available. Synergifabrikken has therefore chosen to establish a formalised cooperation with some specially selected Sal mon fish farmers to apply for salmon research concession by establishing a company named Bærekraftig Laks (ie Sustaina ble Salmon) in which fish farmers also are shareholders. This company is now awaiting a revised raw material strategy (ref. conclusion from techno economic analysis).
WRITTEN BY OYSTEIN SELENOn September 13 to 14, the project group meet in Trondheim to have a joint meeting and discuss future cooperation opportunities. There were intense days that opened up for exciting discussions and fruitful conversations.
Early in the morning on September 12, RISE Processum's project group drove from Örnsköldsvik towards Trondheim, and more specifically towards the colleagues at RISE PFI. The days that lay ahead would include study visits, meetings, and several new lessons learned. After years of the pandemic, it felt important for everyone in the project to have time to see each other physically and discuss how the project went, what happened and what lessons were learned during the three years the project had been running.
Physical meetings often open up for more creative and open discussions, something that was really noticeable during the days in Trondheim. Attended did RISE Processum, RISE PFI, Synergifabrikken, and WoodWorks. The various work packages were presented and the results from them were discussed. It is important that everyone can get an overview of the work that was done in the project and together be able to have a dialogue about the results.
FISK has been a project that has consisted of both success and setbacks and what the project members could agree on is that there are more aspects to investigate and more research attempts to implement.
The visit to Trondheim consisted of more than meetings. The project group went on a study visit to SeeSalmon and got to learn more about how salmons are brought up, how fish health is affected by farming, and also learn about myths that exist about salmon and salmon farming. A visit that gave more perspectives on salmon farming than just what feeds the salmon eat.
Experiences, networks and knowledge were spread between managers, researchers, companies and support functions, so as project manager and communication