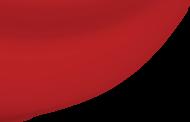
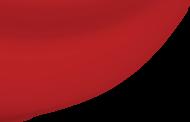
Rosehill Wine Cellars
Crafted for Collectors
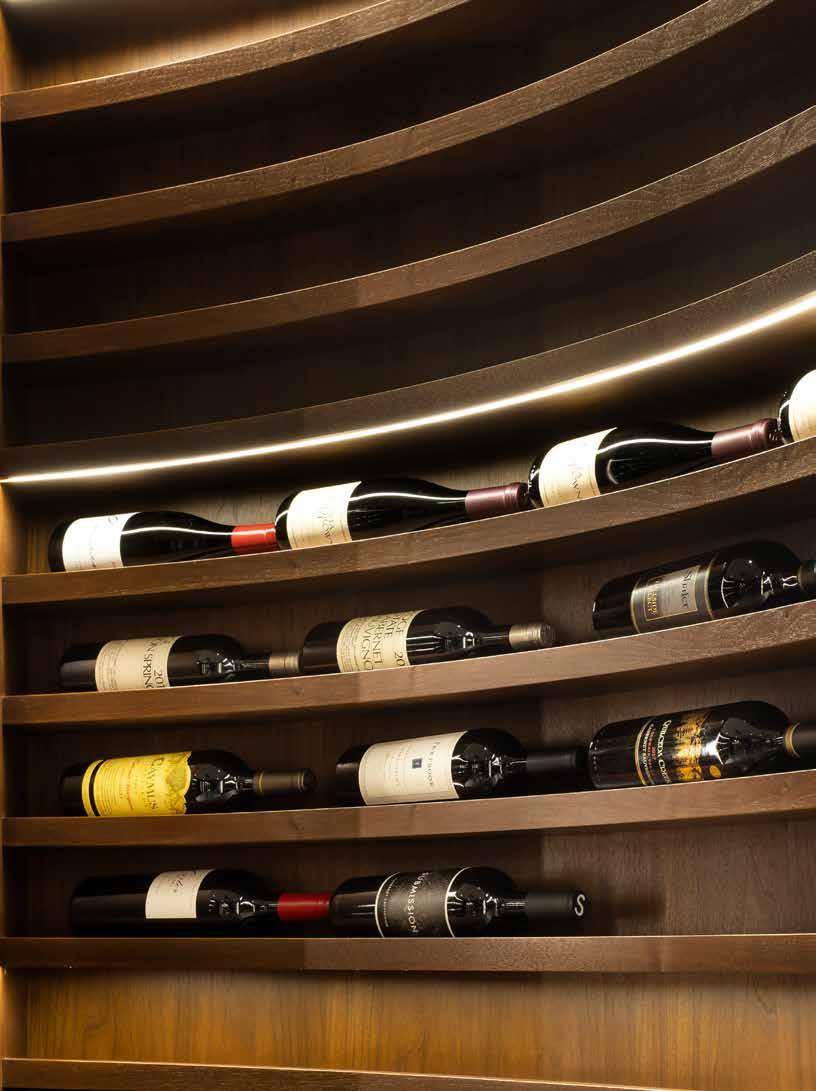

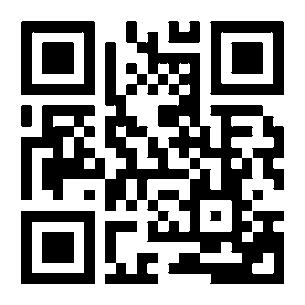
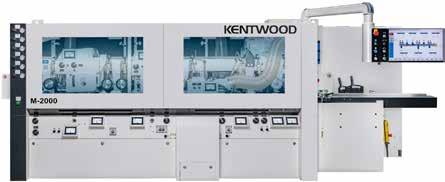
• HSK-85WS spindles
• 24” touchscreen driven by the ProLink Advanced Power Control
• Rapid hood set-up reducing set up time by 50%
• Highest finish quality possible due to 6,000-12,000 variable RPM spindles
• CNC controlled spindle positioning with digital information displays
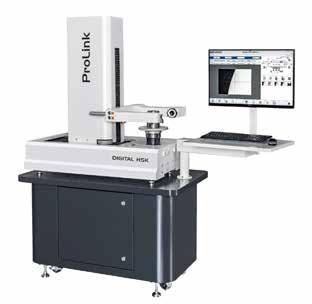
• 2-axis non-contact tool inspection and measurement
• Automatic min/max radius and angle measurement
• Contour to DXF and ghost profiling knife alignment functions
• Tool database (up to 10,000 tools) & profile database (up to 2,000 profiles)
• Remote set up and production scheduling directly uploaded to up to 10 moulders
KENTWOOD M2000 CNC
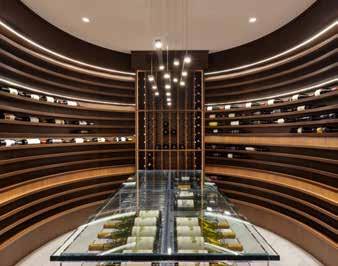
REVOLUTIONIZING CONSTRUCTION
From classrooms to high-rises, prefabrication offers faster, greener, and smarter building solutions—reshaping infrastructure development across North America’s healthcare, education, industrial, and housing sectors.
20
WISDOM, STRENGTH, LONGEVITY
Nu-Way Kitchens has thrived for over 60 years by staying small, serving locally, and evolving through generations—proving that adaptability, family values, and passion are the pillars of lasting success.
36
PREVIEWING AWFS FAIR 2025 Innovation, Talent, and Opportunity in Las Vegas. Canada’s woodworking community heads to Las Vegas for AWFS Fair 2025—highlighting new technologies, educational tracks, workforce strategies, and international collaboration in a dynamic, future-focused trade environment
42
THE POWER OF ACTIVE LISTENING IN MANUFACTURING LEADERSHIP:
Sunrise Kitchens transforms leadership on the shop floor by embedding active listening into training, coaching, and culture—building stronger teams, improving communication, and fostering respect-driven collaboration in a fast-paced environment.
CRAFTED FOR COLLECTORS
Specializing exclusively in wine storage, Rosehill Wine Cellars combines precision millwork, modular solutions, and design-forward innovation to deliver high-quality, custom cellar experiences across North America.
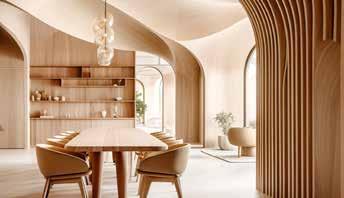
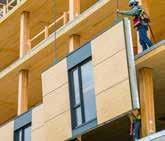
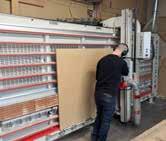
NOW IS A GOOD TIME TO INVEST. THERE IS
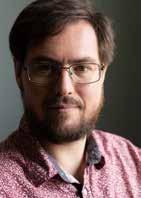
NO OTHER TIME.
Hello Industry Partners, We are entering a season not just of change, but of potential. As uncertainty continues to ripple across global markets and technologies evolve at an accelerating pace, it’s tempting to hesitate. But investing is not for when the road is smooth. It is for now. Now is the time to invest in your business, in your people, in your values, and in yourself.
In this issue of Wood Industry, we explore what investment looks like in practice. From legacy shops to national associations, each feature reflects a mindset of purposeful growth.
At Rosehill Wine Cellars, Mike and Stefania Domazet have aligned their strengths and passions with precision process design. Their work illustrates how personal investment—when rooted in purpose—can drive business transformation and long-term differentiation.
At Nu-Way Kitchens, investment takes a different form. In Sandra Wood’s profile, we see a business grounded in continuity. Jake Wolters and his family demonstrate that sustainability is not only environmental. It’s also financial, operational, and personal. Their approach proves that staying small can still mean staying strong.
Amrita Bhogal of Sunrise Kitchens reminds us that one of the most powerful investments we can make is in those around us. Her piece on active listening, grounded in real leadership practice, shows that culture is built through everyday actions, not slogans.
Chris Leonard of Kaizen Learning Partners, writing on behalf of the Canadian Kitchen Cabinet Association’s Advanced Manufacturing Peer Group, explores how Jidoka—the principle of “automation with a human touch”—is guiding CKCA members toward smarter, human-centered modernization. The CKCA’s approach emphasizes shared learning, pilot projects, and peer support, helping shops modernize without losing their soul.
Looking ahead, our Q&A with Angelo Gangone on AWFS Fair 2025 previews the ideas and technologies shaping tomorrow’s shop floor. The fair will spotlight AI, automation, circular economy tools, and talent development—all critical areas where investment now will shape competitive strength later.
Until next time, Take care of yourself and each other.
ART DIRECTOR
PUBLISHER
Jake Blanchard jakeb@mediaedge.ca
EDITOR
Tyler Holt tylerh@mediaedge.ca
PRESIDENT Kevin Brown kevinb@mediaedge.ca
PRODUCTION MANAGER
Ines Louis Inesl@mediaedge.ca
Published by
Annette Carlucci annettec@mediaedge.ca
GRAPHIC DESIGNER Thuy Huynh-Guinane roxyh@mediaedge.ca
CIRCULATION circulation@mediaedge.ca
Wood Industry is published four times annually, Spring, Summer, Fall, Winter, for the secondary wood products manufacturing and marketing industries in Canada. Subscriptions are free to qualified participants in Canada’s secondary wood processing industry. Subscribe at www.woodindustry.ca. Paid subscriptions rates: $40 to Cana dian addresses, $60 U.S. and foreign, $20 student rate. Please mail payment to Wood Industry, 251 Consumers Road, Suite 1020 Toronto, Ontario M2J 4R3. For subscription inquiries, e-mail circulation@mediaedge.ca
© 2025 by MediaEdge Communications All rights reserved. MediaEdge Communications and Wood Industry disclaim any warranty as to the accuracy, completeness or currency of the contents of this publication and disclaims all liability in respect to the results of any action taken or not taken in reliance upon information in this publication. The opinions of the columnists and writers are their own and are in no way influenced by or representative of the opinions of Wood Industry or MediaEdge Communications
Tyler Holt
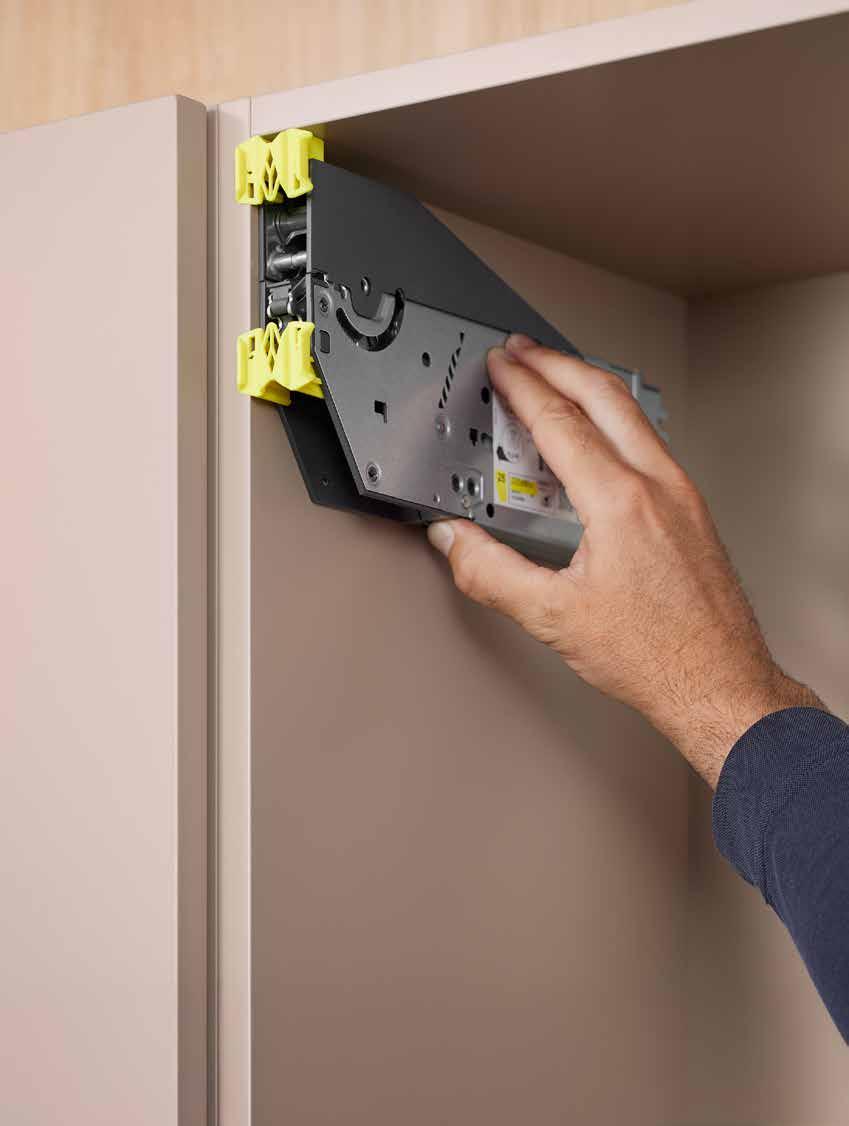
AVENTOS top: Install with ease
The all-new AVENTOS top lift systems are engineered to make your life easier. No need for complex calculations anymore. Simply align the AVENTOS yellow markers with the frame of the cabinet and slide all the way to the top, secure the hardware with screws and job done!
Available for AVENTOS HL, HK, and HS. Want more information?
www.blum.com/aventos
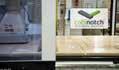
KCD Software Acquires CADCode to Expand CNC Automation Tools a move that expands its capabilities in CNC machining, nesting, labeling, and production automation for custom cabinet and closet makers. Based in Skillman, NJ, CADCode is known for its optimization tools that help manufacturers reduce waste and improve material yield. KCD President Cadman Campbell called the acquisition a strategic fit to “empower everyone from designers to manufacturers.” CADCode founder Ned Brown will stay on to collaborate on future projects. KCD will integrate CADCode’s technologies while continuing support for existing customers. The acquisition strengthens KCD’s designto-manufacture platform and reaffirms its commitment to delivering industry-specific software tools developed by professionals with deep cabinetry experience.
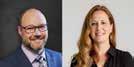
Thermwood Appoints New President and EVP to Drive
Continued Growth Thermwood Corporation has promoted Jason Susnjara to President and Jennifer Watt to Executive Vice President, following the retirement of longtime President David Hildenbrand. Susnjara, with over 30 years at Thermwood, previously served as EVP and brings extensive operational and strategic experience. Watt, who joined as Chief Legal Officer in 2019, has led legal and governance functions and serves on the company’s Board. These executive shifts aim to support Thermwood’s continued innovation and expansion across CNC machining and Large Scale Additive Manufacturing. Based in Dale, Indiana, Thermwood operates a 175,000-square-foot facility and remains a global leader in advanced manufacturing systems for woodworking, aerospace, defense, and automotive applications.
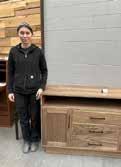
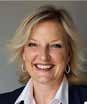
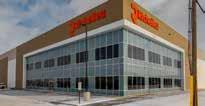
Richelieu Hardware has opened a new 260,000-square-foot distribution and laminating facility in Calgary, merging two previous locations into a centralized Western Canada hub. Now the company’s largest logistics site in the region, it supports Richelieu’s 114-location North American network. The new facility includes an in-house Evans Midwest laminating line capable of pressing panels in under 90 seconds and stocks over 23,000 SKUs. An 8,000-square-foot showroom and warehouse management software further improve order accuracy and fulfillment, with typical turnaround in under 12 minutes. A second laminating line is scheduled for Surrey, B.C. Richelieu says the investment will strengthen service efficiency and product access for both industrial and retail customers.
Conestoga Students Showcase Woodworking Excellence Graduating students from Conestoga College’s Woodworking Technician program presented their final projects at the Woodworking Centre of Ontario on April 16. Industry sponsors FS Tool and Rampa Tec joined the showcase, awarding top honours to three standout creations. First place went to Samantha Stamp for a walnut console cabinet featuring high-end fittings and expert joinery. Jesse Koonstra earned second with a hand-crafted oak dresser, praised for dovetail joinery and mitred rails. Third place and the Rampa Tec Design Award went to Kwok Kit Lam for a multifunctional Chinese games table in oak and cherry. Faculty praised the projects as evidence of the program’s high standards and students’ craftsmanship.
Cienapps has named Freya Hannah as Head of Business Development and Partnerships for its Cieblink platform, a key move to drive digital adoption in the woodworking and building supply industries. Hannah, a long-time advocate of Cieblink, now formally joins the company to expand its network of suppliers, OEMs, distributors, and end users. Cieblink streamlines operations and boosts sales efficiency through e-commerce and process automation. “It is time for our industry to be unified with technology,” said Hannah. Cienapps called her a “pillar of the woodworking world,” citing her strategic insight and influence. Her leadership is expected to accelerate platform adoption and support Cienapps’ broader mission to modernize manufacturing and distribution operations.
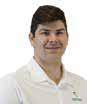
Kyle
Hubner Named
Central Canada
Regional Manager at SamesThe Architectural Sames North America has promoted Kyle Hubner to Regional Manager for Central Canada, recognizing his 12 years of service and consistent leadership. Hubner started as a Service Technician and has recently supported distribution growth while upholding strong customer service standards. The company praised his commitment to operational excellence, noting that his approach reflects Sames’ customer-first values. “His unwavering dedication and commitment to providing the highest level of support to our customers exemplifies doing what’s best for the customer,” the company stated. Hubner’s appointment underscores Sames’ strategy of advancing internal talent and affirms confidence in his ability to lead a core regional market.
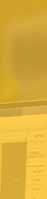
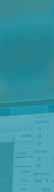
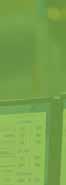
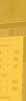
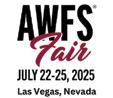
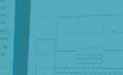
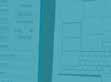
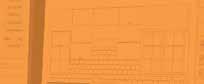


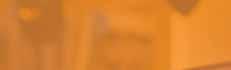
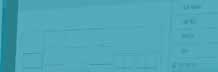
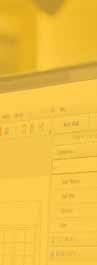
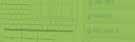
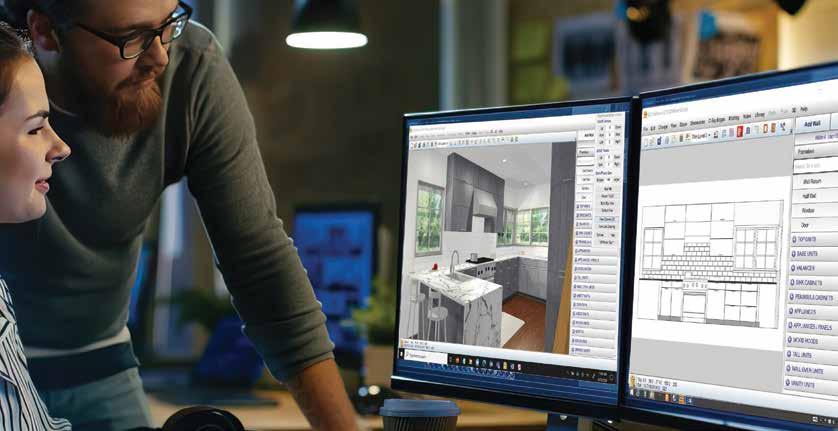
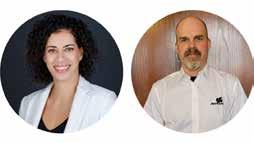
AWMAC Ontario has announced its 2025/2026 Board of Directors following its Annual General Meeting, with two new additions: Lesley Morris of ISPA Store Fixtures and Tim Scholman of Microvellum, both joining as Directors at Large. The chapter also acknowledged the departure of Ian Rowe (Alexandria Mouldings) and thanked him for his contributions. The new board, led by President Nick Anastas (Svend Nielsen), includes leadership from Akhurst, Upper Canada Forest Products, RGA Woodworking, and others. AWMAC Ontario expressed enthusiasm for the incoming directors and the year ahead, emphasizing continued collaboration and support within the architectural woodwork community.
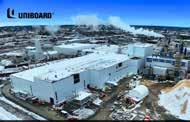
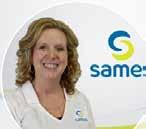
Rhonda
Joslin
Named Marketing Director for the Americas at Sames North America
Sames promotes Rhonda Joslin to Marketing Director for the Americas, expanding her role across North and South America and reinforcing strategic alignment, digital transformation, and sector growth initiatives.
Uniboard Invests $5.5M in Robotics at Val-d’Or Facility
Uniboard has invested $5.5 million in robotic material handling at its Val-d’Or plant, introducing autonomous guided vehicles (AGVs) to streamline particleboard production. The upgrade marks Phase 3 of the $350 million Val-d’Or Renaissance Project, aimed at modernizing operations by summer 2025. President and CEO James Hogg said the investment reinforces Uniboard’s leadership in engineered wood and enhances client service and market reach. Supported by Quebec’s Programme Innovation Bois, the move reflects the company’s commitment to innovation and productivity. Val-d’Or’s strategic location enables wide North American distribution, while its integration of TFL production and resin manufacturing makes it one of the region’s most advanced composite panel sites.

INNERGY Acquires Microvellum to Advance Millwork Software Integration
INNERGY has acquired Microvellum in a move to unify ERP and design-formanufacturing solutions for the millwork industry. Both companies will continue to operate independently, with leadership teams remaining in place to ensure continuity. The partnership aims to enhance operational visibility and workflow efficiency by integrating INNERGY’s ERP systems with Microvellum’s drafting and manufacturing tools. “This is about unlocking new possibilities for our customers,” said Microvellum President David Fairbanks. INNERGY owner Marc Sanderson added the merger supports innovation and profitability for woodworking professionals. Joint efforts in the coming year will focus on developing cloud-based solutions to modernize operations while preserving industry-standard workflows.
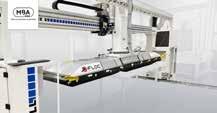
Akhurst Machinery Group has announced a strategic partnership with German insulation machinery leader X-Floc, aiming to deliver advanced pneumatic insulation solutions to the North American market. X-Floc, known globally for its blowing machines since 1994, will now be represented by Akhurst—parent company of Cantek America and Leadermac USA. The partnership enables Akhurst to offer solutions ranging from stand-alone machines to full modular factory installations. “We aim to set new industry standards,” said VP Graham Akhurst, citing affordability and efficiency as key benefits. As X-Floc’s primary distributor in North America, Akhurst strengthens its position in supporting prefabricated and modular construction sectors with cost-effective, high-performance insulation technology.
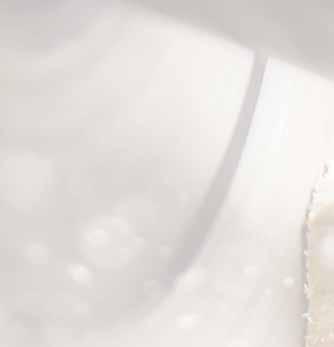
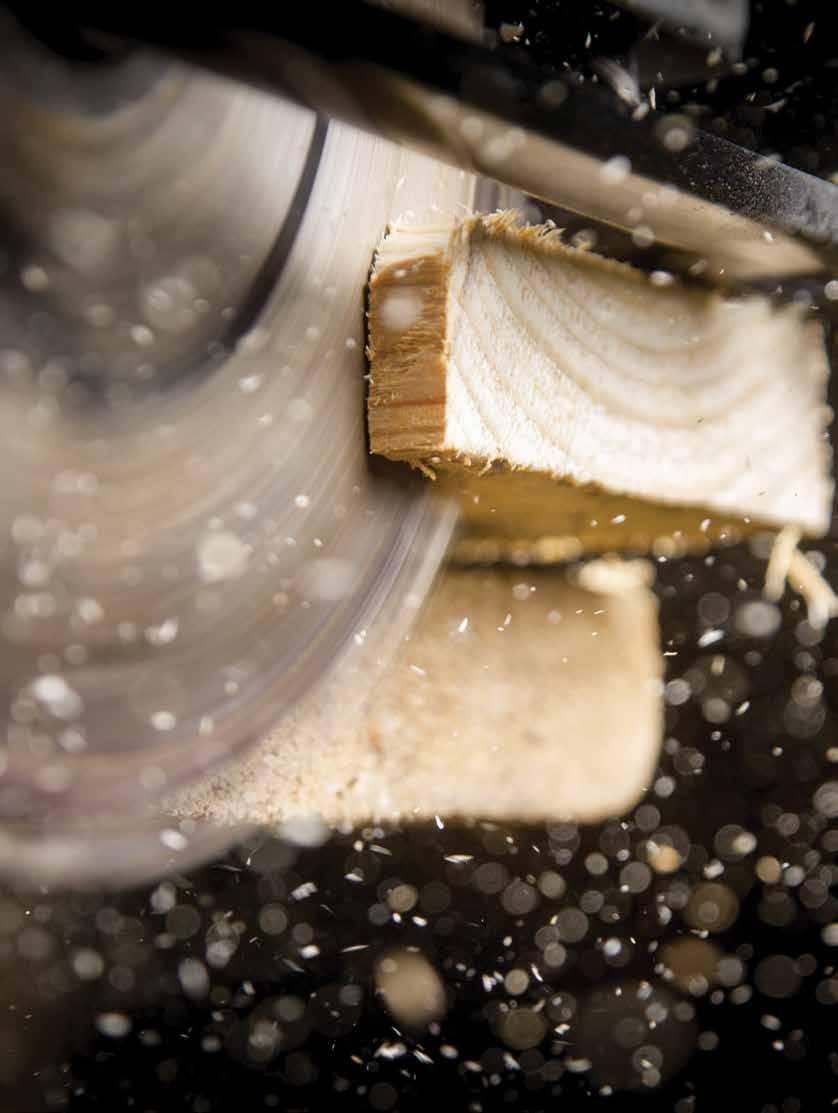
November 12-14, 2025
Toronto Congress Centre
Etobicoke (Toronto), CA
WMS, Canada’s premier woodworking event and marketplace, is making a move to the Toronto Congress Center, promising an enhanced experience for the Canadian woodworking industry!
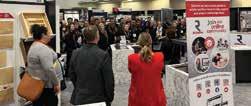
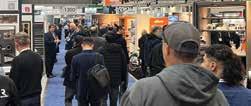
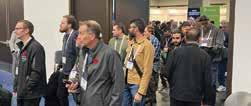
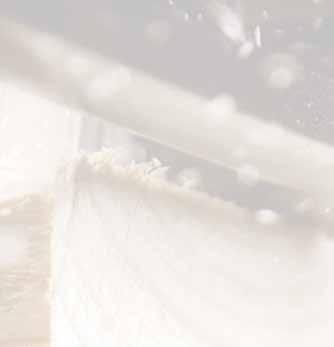
• Experience a spacious and easy-to-navigate expo floor. See the latest advancements in machinery, materials, supplies, hardware, software and more on an expanded show floor.
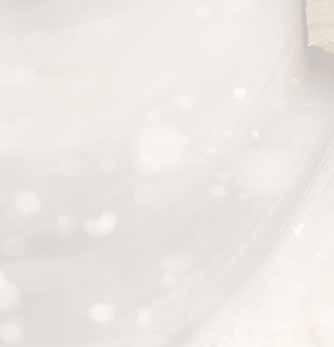
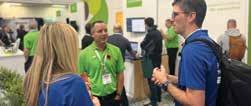
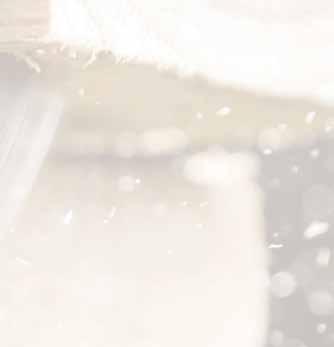
• Unlock greater profits and a stronger competitive edge. Three days of FREE, expert-led educational sessions right on the show floor. Dive into best practices for Adopting New Technology, Lean Manufacturing, Cyber Threat Protection, Leadership Development, and other vital topics. Plus, earn your CEUs.
• Acquire valuable items at competitive prices. The WMS Live Auction, in partnership with Boss Auctions, allows attendees to bid on a variety of woodworking equipment, materials, and supplies, both on-site and online. It’s the must-attend event for Canada’s professional woodworker! For general conference and show information: Kim LeBel |
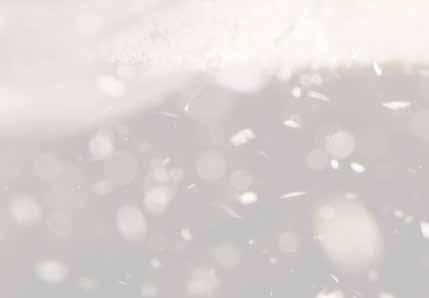
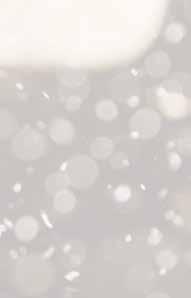

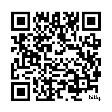
12-14,
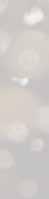
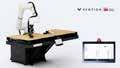
Vention has introduced the Rapid Sanding Solution (RSS), its first turnkey robotic sanding system, aimed at helping cabinetmakers and woodworkers address labor shortages through automation. Featuring up to eight sanding stations, laser-based panel measurement, and a touchscreen interface, the plug-and-play unit integrates seamlessly into existing shops with its 95 x 69-inch footprint. Powered by a FANUC CRX-30iA robot and optimized for 3M™ abrasives, RSS is designed for precision, safety, and ease of use. Sales are underway, with initial deliveries expected in May 2025. Developed in partnership with 3M, the RSS builds on proven success—such as a 31% sanding efficiency boost reported by Quebec-based Fabridor—offering small and mid-sized firms a practical path to automation.
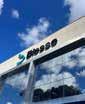
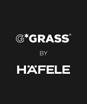
Häfele Canada has announced it will now distribute the full range of Grass movement systems, expanding its hardware portfolio through a new strategic partnership. The agreement grants Häfele customers exclusive access to Grass’s premium Europeandesigned solutions, known for precision engineering, ergonomic performance, and aesthetic appeal. Grass products—ranging from drawer slides to hinge systems—are recognized globally for enhancing the function and feel of cabinetry and furniture. Häfele stated the partnership reinforces its commitment to offering top-tier movement technology that delivers smooth, smart, and seamless operation for designers and manufacturers across Canada.
Biesse has officially opened its Toronto Material Hub, part of a global rollout of five new hubs worldwide designed to showcase advanced multi-material processing technologies. The initiative marks the launch of Biesse’s expanded machinery portfolio and reflects a strategic shift toward supporting industries beyond woodworking—including glass, stone, and composites. Located in Toronto, Sydney, Osaka, Lyon, and Porto, the hubs offer hands-on demonstrations and digital tools to explore the company’s latest innovations. Unveiled during the global “Embrace the Evolution” event on March 26, 2025, the hubs emphasize sustainability, design collaboration, and Biesse’s new Human Machine Interface, unifying control across machines. The initiative aims to reshape how manufacturers interact with technology and materials in an evolving industrial landscape.
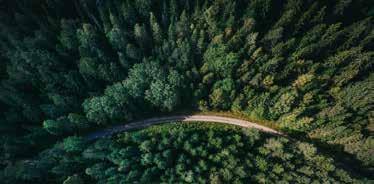
The Clean Air Company
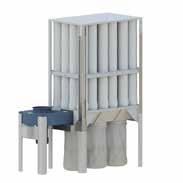
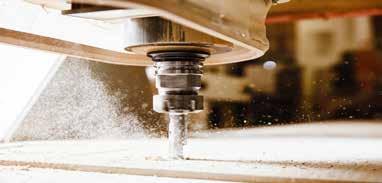

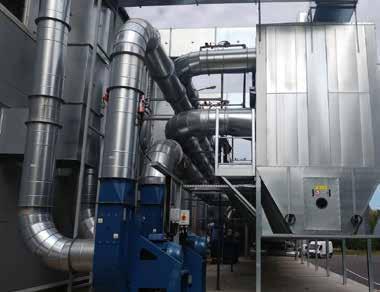
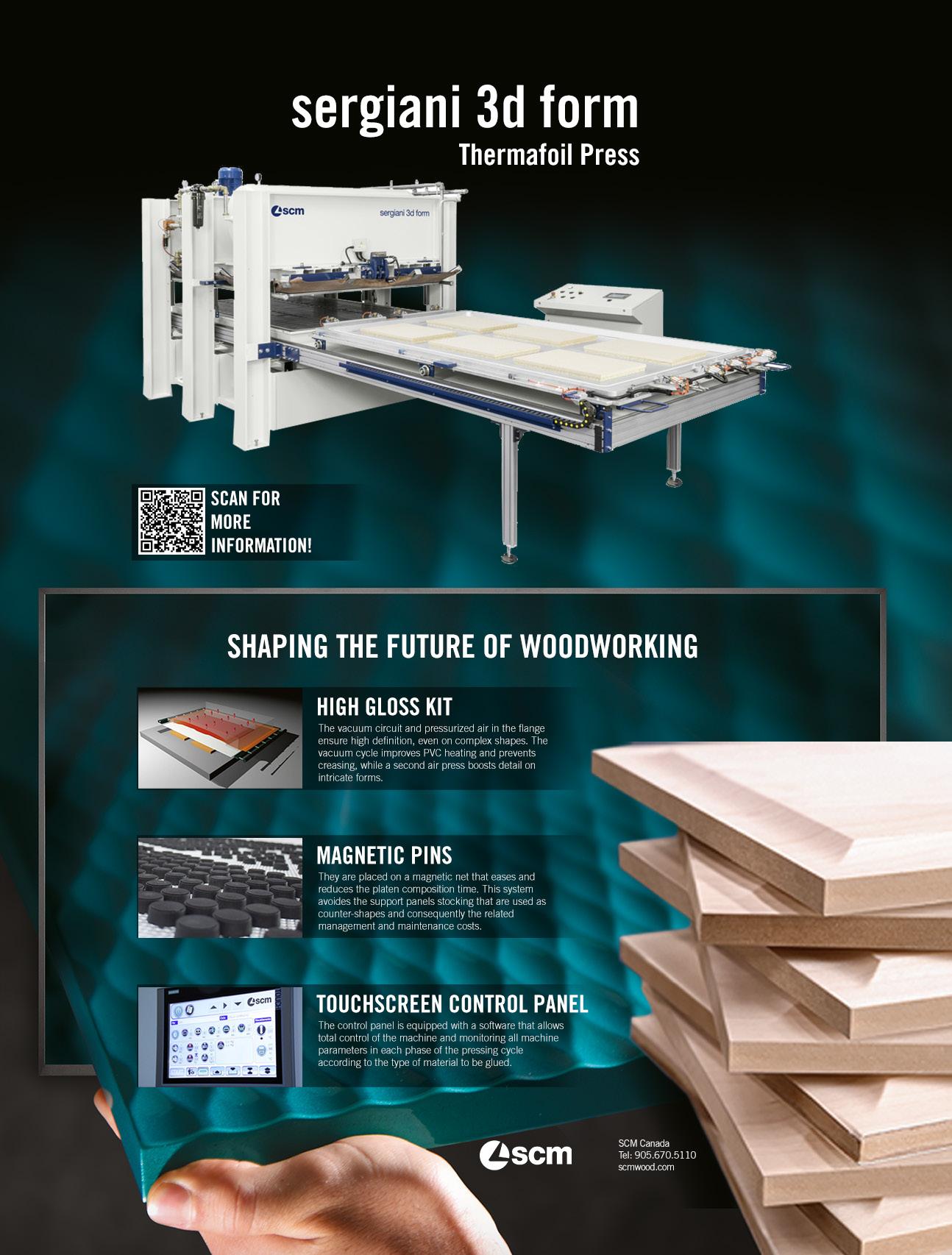
REVOLUTIONIZING CONSTRUCTION
Prefabrication in Healthcare, Education, and Urban Development
:: By Jayden Campbell, Product Manager, Akhurst Machinery
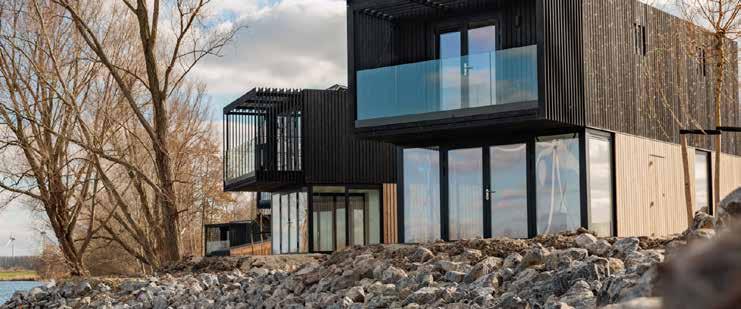
The construction industry across North America is experiencing a paradigm shift. As cities grow in population, infrastructure ages, and demand intensifies for more efficient and faster building methods, prefabrication – also known as offsite construction – is gaining momentum as a reliable and industry-defining solution. Manufacturing components in a controlled environment and assembling them onsite offers faster delivery, greater cost control, and improved quality and consistency. From healthcare and education to commercial spaces and urban infill, prefabrication reshapes how North America builds.
PREFAB IN HEALTHCARE AND EDUCATION: RAPID SOLUTIONS FOR CRITICAL INFRASTRUCTURE.
Healthcare and education sectors across the U.S. and Canada are under significant pressure to modernize and expand capacity, often within tight timelines and budgets. Traditional construction methods have been unable to parallel population growth and changing needs, putting stress
on major cities to accommodate the lack of opportunity specifically in underserved or remote regions. Prefabrication steps in as a highly effective method to deliver quality facilities with reduced disruption, faster timelines, jobs, and infrastructure growth.
In the United States, modular construction has led the charge in rapidly building clinics and outpatient centers, enabling faster turnaround times and
improved infection control through factory-built, high-spec environments. In June 2020, NYC Health + Hospitals deployed modular COVID-19 testing and vaccination centers across New York City, demonstrating prefab’s ability to respond swiftly in times of crisis.
On the education front, American school districts in states like California, Texas, and Florida are leveraging modular classrooms to combat overcrowding and address disaster recovery. After Hurricane Katrina, New Orleans schools used modular construction to reopen quickly. More recently, the Clark County School District in Nevada has turned to prefab to accommodate surging enrollment in Las Vegas suburbs, operating over 2,100 classrooms and moving 450,500 annually to accommodate changing demands.
Barli, Netherlands | Revolutionizing Modular Construction – Roompot Lakeside Resort Brielle Project
In Canada, modular classrooms and entire school wings are being deployed from British Columbia to Nova Scotia. At UBC’s (University of British Columbia) Brock Commons Tallwood House, one of the tallest of its kind globally, is an 18-storey hybrid mass timber structure offering accommodation to 404 students and completed in a staggering 70 days.
With growing emphasis on green building standards across both countries, prefabricated educational and healthcare buildings can be certified or net-zero ready, making them a cornerstone of future-ready infrastructure. These systems offer flexibility, reusability, and energy efficiency – key traits for managing fluctuating student populations – while showcasing sustainable design, reduced carbon emissions, and rapid construction methods that position institutions like UBC as leaders in innovative, eco-conscious building practices.
COMMERCIAL AND INDUSTRIAL PREFAB APPLICATIONS: DELIVERING SPEED AND ROI
Across North America’s commercial and industrial sectors, prefabrication is being embraced for one core reason: speed. Developers of hotels, office buildings, distribution centers, and manufacturing facilities use prefab to reduce construction times, lower financing costs, and fast-track revenue generation.
In the U.S., hotel chains such as Marriott and Hilton have invested heavily in modular builds. Marriott’s Folsom, California project—the Fairfield Inn & Suites—was completed 25% faster than traditional methods using fully finished room pods manufactured off-site. Entire
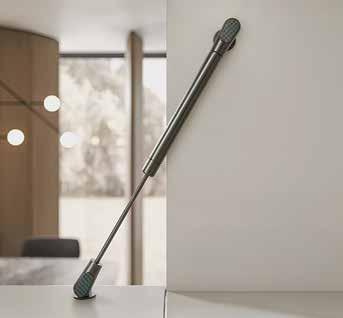
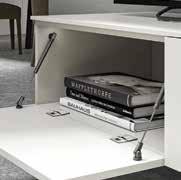
SMOOTHER, BOLDER, BETTER MEET LIDO.
An opening system arm that comes in 3 lengths, a titanium-colored finish and is easy to install. German engineering meets Italian design with 2 opening options available, upwards and downwards, to ensure maximum accessibility and ease.

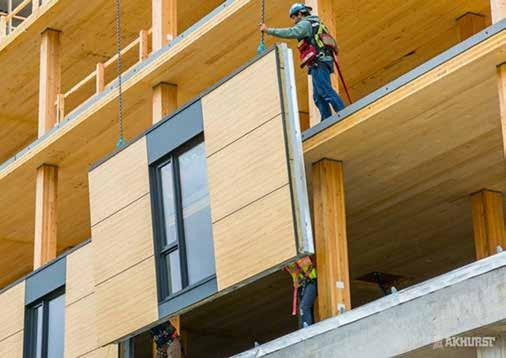
guestrooms, including finishes and furniture, were stacked in place in days. These preassembled components reduce labour requirements and ensure higher quality control in urban sites with limited access and tight schedules.
In the industrial sector, Canada’s Stack Modular partnered with Bird Construction to deliver workforce housing in remote areas, including a 204-room complex for LNG Canada in British Columbia – constructed overseas and assembled onsite in weeks.
Prefabrication in commercial and industrial settings reduces weather delays, minimizes waste, and offers developers greater predictability – essential advantages in a high-stakes, low-margin environment.
URBAN INFILL AND PREFAB: SOLVING THE DENSITY PUZZLE
Urban centers across North America face a dual challenge: growing populations and limited space. Prefabrication is proving to be a powerful tool for infill development – building on underutilized land within existing cities – offering a path to densification without long construction disruptions or inflated costs.
In Canada, newly elected Prime Minister Mark Carney has introduced an ambitious national housing strategy centered on mass timber and prefabricated construction, aiming to more than double the country’s annual housing output to 500,000 units. The new ‘Build Canada Homes’ plan will provide $25 billion in financing support to Canadian
prefab companies to help achieve this bold target. While associations such as MHABC and BC Modular continue to drive industry growth, innovation, and adoption, they also play a critical role in addressing key economic challenges, advocating for updated building codes and liaising with government to ensure the successful implementation of this transformative initiative.
San Francisco and Los Angeles are turning to modular developers to deliver affordable housing and infill solutions faster. Large companies in this industry are now producing entire apartments in off-site facilities and completing projects in half the time of conventional builds.
Private developers are increasingly using prefab to build mid-rise apartments on constrained sites. These projects allow cities to meet housing goals without sacrificing neighbourhood character, parking, or access. Additionally, the environmental advantages –fewer truck trips, lower emissions, and less waste will support these municipal sustainability goals.
THE FUTURE OF CONSTRUCTION: STANDARDIZING SMART, SCALABLE SOLUTIONS
Prefabrication is no longer a niche solution – it’s rapidly becoming a core strategy for smart construction across North America. Integrating digital modelling, advanced materials, and automated manufacturing opens new opportunities in scale and complexity.
As urban density increases, populations expand, and climate pressures intensify, North America demands building solutions that are fast, adaptable, and future-ready. Strategic partnerships – like those between Akhurst Machin-
“Prefabrication is no longer a niche solution – it’s rapidly becoming a core strategy for smart construction across North America.”
UBC | Brock Commons Tallwood House, Vancouver, BC – Mass Timber & Prefabricated Panels
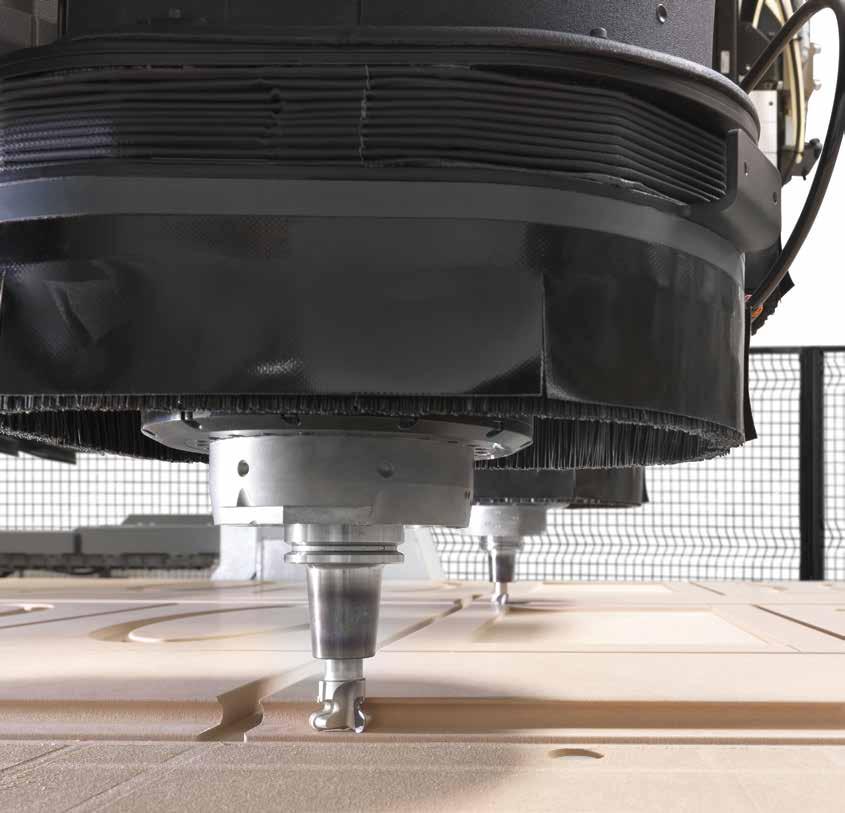

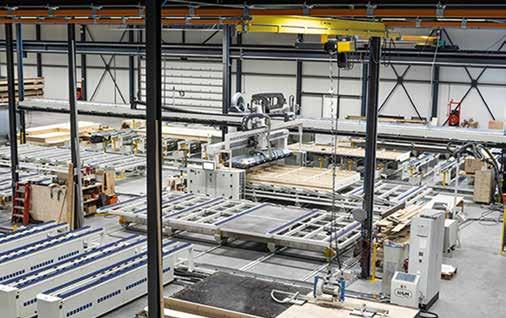
ery, Modular Building Automation, and X-Floc are driving this transformation by delivering the advanced machinery and support systems needed to construct and meet the demands of health-
care, education, commercial facilities, and urban development.
The public and private sectors are seeing the benefits: reduced build times, enhanced safety, lower costs, and improved environmental performance. However, for prefabrication to reach its full potential, key challenges must still be addressed: building code harmonization, supply chain resilience, and skilled workforce development.
Learn more about Offsite Construction and stay tuned for our next post –From Automation to Adoption: The New Era of Building, Training, and Regulations.
Akhurst Machinery. Building Trust. Creating together.
Jayden Campbell is a dedicated Product Manager at Akhurst Machinery, where he leverages his industry expertise to drive product innovation and streamline operations. With a passion for machinery and technology, he is committed to delivery solutions that empower clients and support Akhurst Machinery’s growth in the industry.
HOLZ-HER CANADA POWER-PIN 7505
Fully automatic drilling and dowel insertion in one machine
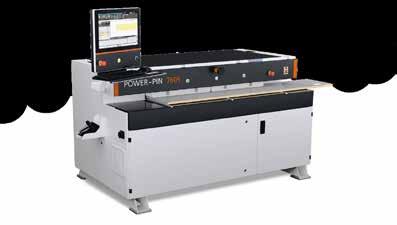
Split pressure beams allow for multi-area loading, for a smooth workflow.
• Just 4 m³, fits any workshop layout easily.
• Fully automatic dowel insertion boosts production speed.
• Handles multiple dowel and panel types, sizes, and lengths.
• Multi-area loading and intuitive controls maximize output.
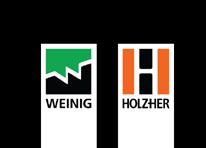
WEINIG HOLZ-HER CA
4317 Autoroute des Laurentides E, Laval QC H7L 5W5 Unit 4 210 Brunel Rd Mississauga, ON L4Z 1T5 holzher.ca
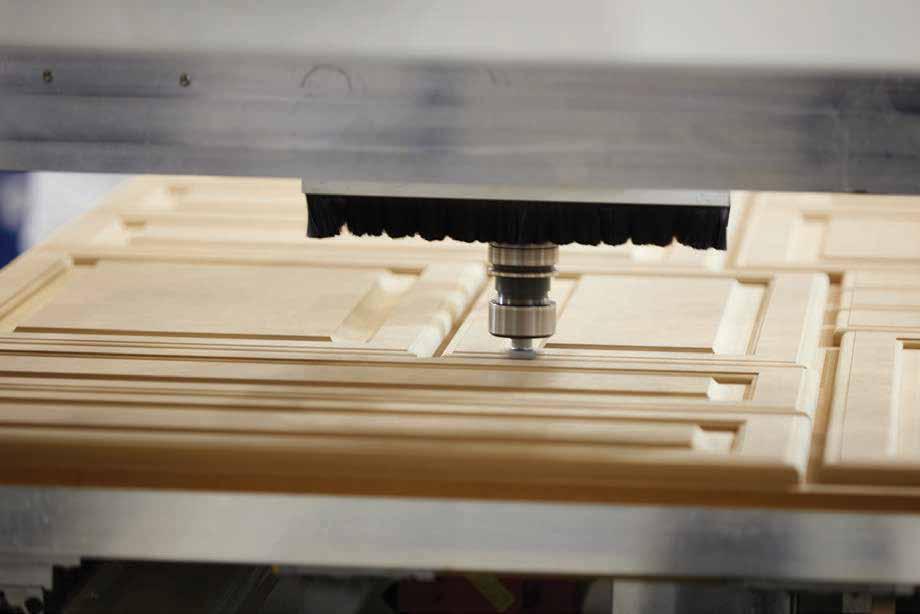
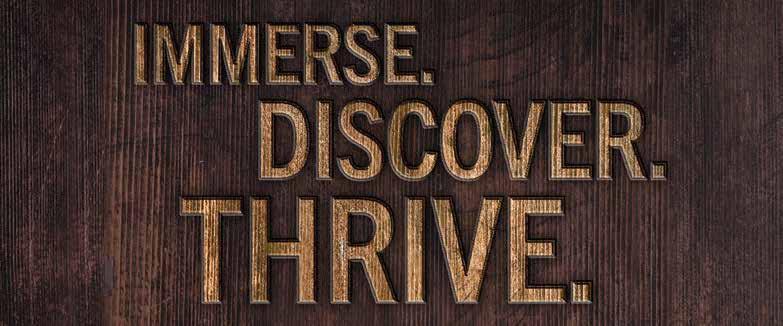
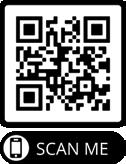
Wisdom, Strength, Longevity
Nu-Way Kitchens defining continuity
:: By Sandra Wood, Executive Director of the CKCA
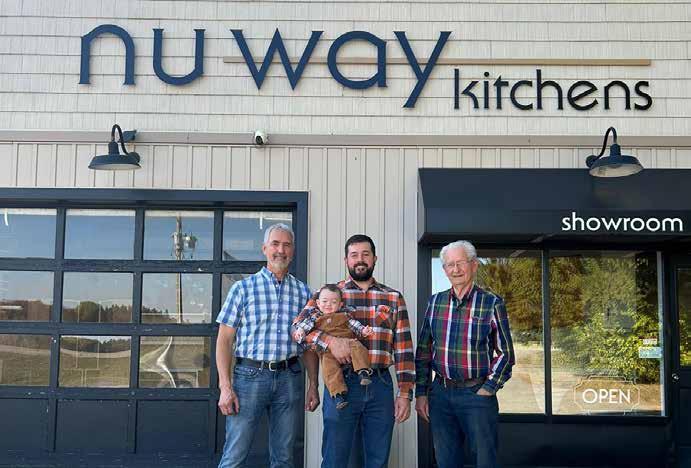
Travel to Guelph, Ontario and you’ll come across a kitchen cabinet business that has been operating since 1964. Nu-Way Kitchens Inc. has a long standing history and is one of the oldest continuously running kitchen cabinet shops in the country! We spoke to Jake Wolters, Owner at Nu-Way Kitchens Inc. to learn more about the company and their ingredients for staying in a successful business for more than 60 years.
CKCA: What’s the story behind Nu-Way?
Jake: My dad, Clarence, worked as a home builder in the late fifties installing all the baseboards, casings, closets and all cabinets including kitchens and bathrooms. That was the trim carpenters job at that time. I joined full time in 1979 and then my brother Andy came on board in 1985. My brother and I bought my Dad out in 1992. Andy left the business in 2014 and that void was filled by my son Ryan that same year who is now owner with me
CKCA: What’s your market?
Jake: We sell only to our local geographical area. Usually within an hours drive from our shop. Seventy percent of our sales are residential and the rest are builders.
CKCA: How large is the shop?
Jake: Our shop and showroom is a total of 4,000 sq. ft. with 5 employees. All employees have been with us for over 10 years.
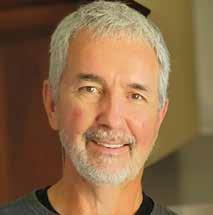
Four Generations(Right to left): Jake, Ryan and his son, and Clarence Wolters
CKCA: Tell us about the family run business.
Jake: My son does all the books and is the head installer. My dad is 92 so his involvement is very minor. He will still do some occasional pickups and deliveries for us just because he likes to get out of the house. I kind of have my hands in all areas of the business just to keep everything in order.
CKCA: What type of equipment do you have in your shop?
Jake: We are still a little old school with our equipment. A panel saw, edgebander and line boring machine. Our guys are quite efficient with them so it hasn’t been a problem for us. A CNC machine is in our sights, but we haven’t pulled the trigger on that yet.. Our company has not changed in size for most of the 60 years that we have been in business.
CKCA: What do you think has been a key reason why you have stayed in business all these years?
Jake: We love what we do. I think I would struggle if I had to work for someone else. There have been some lean years for sure and they can be stressful. But overall I couldn’t see myself doing anything else.
MANAGEABLE PROBLEMS
CKCA: Tell us about your business challenges?
Jake: Don’t over extend yourself. When the market is hot it’s easy to borrow a lot of money for expansion, but you have to be prepared for a downturn in the market as well. You need to have money set aside for those lean years because they will come.
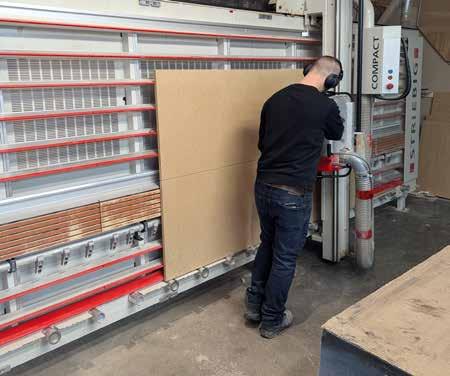

TOP: Nu-Way Kitchens Inc., A Striebig Compact panel saw. BOTTOM: Crafted with care by Nu-Way Kitchens—family-owned and serving Guelph since 1964.
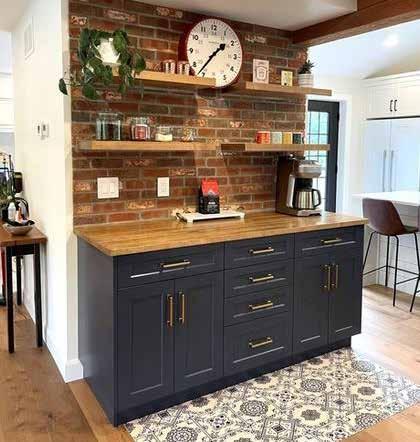
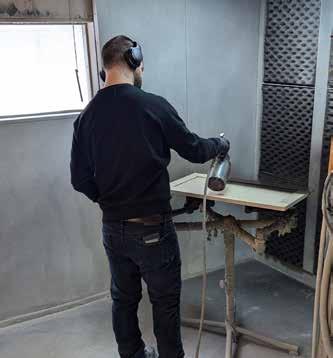
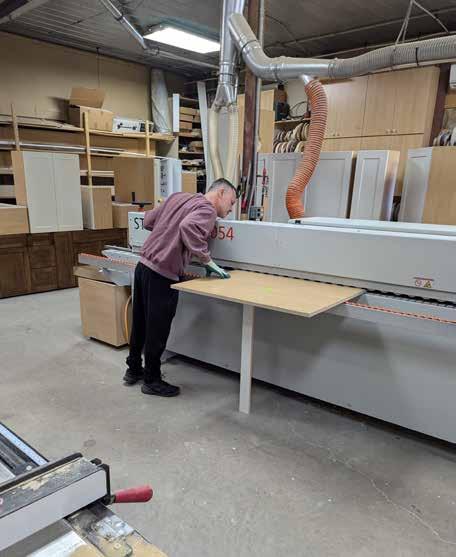
CKCA: You got involved with the CKCA and became President, why?
Jake: I joined the CKCA in 2002. That was after my Richelieu rep hounded me for over a year to come out to a meeting. After that first meeting I could see the benefit to being involved. I’ve never looked back. I was proud to be President of CKCA from 2011 to 2014 and would encourage anyone to get involved.
CKCA: What are your thoughts on the industry?
Jake: The kitchen cabinet business is ever changing. That’s one of the things I like about it. We do things so different now compared to when my dad started in the sixties. I’m sure things will keep on changing. Each cabinet shop will have it’s own strengths and weaknesses. You will have to adapt your business to serve the customers you are selling to. A small shop like ours has to serve our local geographical area which will be different than a large shop with multiple showrooms across the country.
CKCA: In these trying times with market fluctuations, what do you tell our son to encourage him to keep going with the business?
Jake: My son is very smart. He keeps his eyes on things that will have an impact on our business which, in turn, can be stressful. I see the same things coming, but my attitude towards those changes is more like “this too shall pass”.
CKCA: Your company has built a lot of resilience, what does that look like?
Jake: The strong years we’ve had in business are good problems to have. Those are manageable problems. The tough years are a challenge of a different type. Trying to get through some lean years is about survival and going home with a smaller paycheck or no paycheck at all and living off your savings. We were fortunate to not have too many of those years.
CKCA: What do you say to people entering the industry or taking over a business?
Jake: Being adaptable is very important. We are in our third generation now and each of us have different strengths and weaknesses. If we stick to our strength in the business and hire people that will fill in our weakness then we will have a strong company. My dad was happiest when he was working on cabinets. He didn’t like the sales process or dealing with customers. He did that because he had to. I, on the other hand, enjoyed the sales process and the finishing of cabinets. Ryan is much more business minded and is all about seeing profits. Trust me, that is a good thing. I wish I had more of that!
CKCA Final Note: On behalf of the CKCA we would like to congratulate Nu-Way Kitchens Inc. for being an inspiration to the industry. From your humble roots you have stayed the course longer than most, driven by a genuine passion and
commitment to serve the community keeping your business steady and strong. Your ingredients for success are uniquely yours and they have served you
well. Now with a fourth generation born in 2024, it will be exciting to see how the future will unfold at Nu-Way Kitchens Inc.. We wish you continued success.
Sandra Wood is the Secretary and Executive Director for the CKCA. She enjoys “connecting the dots” and facilitating strong networking opportunities to engage members. She believes associations are about fostering strong business relationships fueled by an empathic and sound business approach.
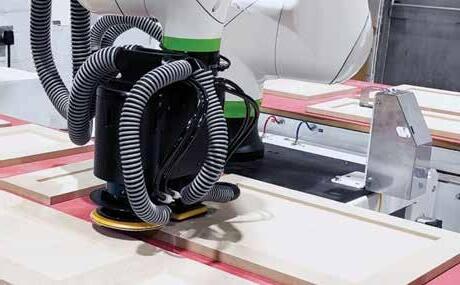
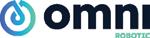
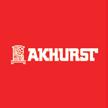
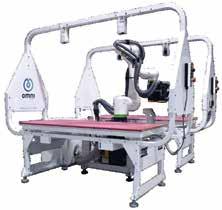
PSA-80 PRO Panel Sanding Assistant.
The fastest sanding machine on the market, now with DUAL SANDING UNITS engineered to elevate your productivity like never before.
The Omnirobotic PSA-80 PRO Panel Sanding Assistant offers autonomous sanding quality and performance in its simplest form. Specially designed for kitchen cabinet manufacturers, this advanced sanding machine will help you overcome the skilled labor shortage and boost your productivity. Powered by AutonomyOS™, an AI platform for robots, it autonomously performs every sanding task with a quality that is second to none.





Q1 2025 HOUSING STARTS
Regional Growth Offsets Urban Slowdowns
:: By Tyler Holt, Editor of Wood Industry Magazine
Early 2025 housing data tell a story of contrasts rather than competition. According to the Canada Mortgage and Housing Corporation (CMHC), 45,302 new homes began construction in Q1 2025 across centres of 10 000 people or more—an 8.6 percent dip from the same period last year. Yet that headline masks pockets of strong expansion. Several provinces recorded substantial gains, particularly in multi unit rental projects, while some of Canada’s largest metropolitan areas experienced a pause after an unusually active 2023. For secondary wood manufacturers, the takeaway is not who is “winning” or “losing,” but where momentum is shifting and how to align supply chains with evolving regional demand.
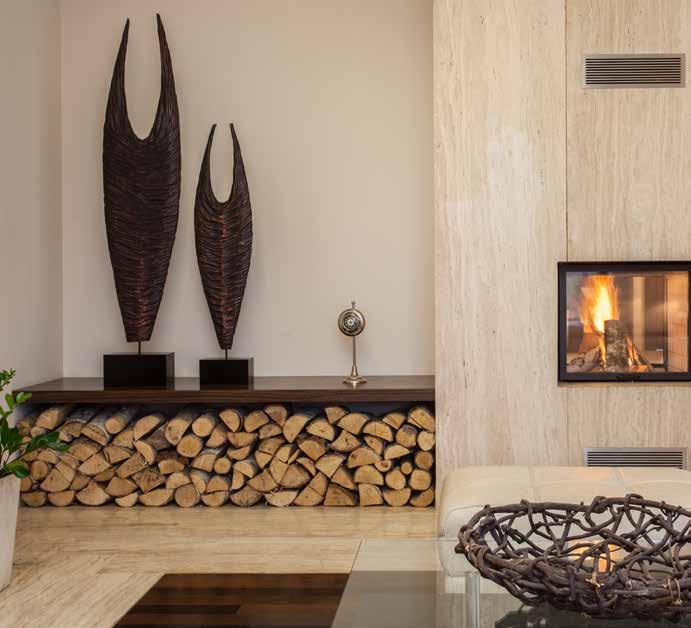
PROVINCIAL OVERVIEW
DIVERGING TRENDS
Figure 1 and 2 summarizes Q1 2025 compared with Q1 2024. Saskatchewan nearly doubled its starts (+97 percent), while Quebec (+50 percent) and Alberta (+18 percent) registered notable gains. Ontario (–38 percent) and British Columbia (–30 percent) saw fewer projects break ground, though each remains a large share of national demand.
The Canadian Home Builders’ Association observes, “Ontario starts declined 38 percent year over year, reflecting both financing challenges and the timing of project approvals.” The same report stresses that activity levels remain above pre pandemic norms in many medium sized markets.
Rather than signalling defeat, slowdowns in large provinces indicate a market rebalancing after recent peaks, while growth elsewhere points to new opportunities for housing supply and wood product demand.
THE PRAIRIE UPLIFT
Alberta: Sustained Expansion
With 11,470 starts in Q1, Alberta accounted for roughly one quarter of all Canadian housing starts this quarter. Purpose built rental complexes in Calgary and Edmonton—a segment relying heavily on engineered wood floor systems and factory finished millwork—led the way.
Alberta’s Minister of Seniors, Community and Social Services called the numbers “evidence that policy changes to streamline approvals are translating into shovels in the ground.”
Saskatchewan: Rapid Acceleration
Saskatchewan’s 1,295 starts nearly doubled last year’s tally. Many six storey wood frame apartment blocks— enabled by the National Building Code’s mid rise provisions—are driving that growth in Saskatoon and Re-
HOUSING STARTS Q1 2024 BY PROVINCE
STARTS Q1 2025 BY PROVINCE
gina. Suppliers of laminated beams, pre hung doors, and modular kitchens are seeing lead time compression as developers race to meet rental demand.
Manitoba: Steady Climb
Manitoba added 1,362 starts (+38 percent), continuing a three year upward trend. Winnipeg remains the hub, with single detached and townhouse projects providing consistent demand for custom cabinetry and trim packages.
Prairie provinces collectively produced 24 percent of national starts, up from 17 percent a year ago—an important sig-
nal for manufacturers considering distribution hubs west of the Great Lakes.
Quebec’s Rental Driven Growth
Quebec logged 10,137 starts, a 50 percent year over year increase that underscores the province’s focus on rental supply.
The Association des professionnels de la construction et de l’habitation du Québec (APCHQ) notes, “Eighty percent of new units in Q1 were purpose built rentals, reflecting both demographic demand and tax incentives.”
Montreal, in particular, saw a 138 percent jump in March starts, bringing new
HOUSING
HOUSING STARTS OCT 2023 - MARCH 2024 (SAAR, LCA)
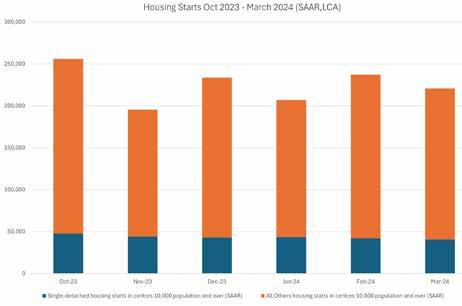
HOUSING STARTS
opportunities for millwork shops specialising in multi unit interiors. With provincial and municipal programs expediting permitting for affordable rentals, Quebec’s market appears poised for sustained, if moderating, growth through 2025.
SLOWER STARTS IN ONTARIO AND BRITISH COLUMBIA
Ontario: Adjusting After a Strong Cycle Actual starts in Ontario fell to 10,938, the lowest first quarter total since 2018. While striking, the decline follows an elevated multi year run. Developers cite high interest rates, labour cost pressures, and a recalibration of condo pre sales.
Economist Mike Moffatt notes, “The pause is partly cyclical. Once borrowing costs ease and existing inventory absorbs, many of these shelved projects are likely to re activate.”
Manufacturers should therefore treat Ontario’s pullback as a temporary reprieve rather than a permanent contraction.
British Columbia: Moderated Activity
British Columbia registered 7,511 starts (–30 percent), with Vancouver accounting for much of the decline. Builders report that financing for large towers tightened in late 2024; several phased developments opted to push groundbreaking into the second half of 2025. Smaller interior markets such as Kelowna and Kamloops, however, continue to launch wood frame townhome clusters.
Ontario and B.C. still represented roughly 40 percent of national starts despite the quarterly slowdown. Their medium term outlook hinges on the pace of interest rate adjustments and municipal planning reforms.
ATLANTIC CANADA –MIXED BUT MEANINGFUL
• Newfoundland and Labrador initi-
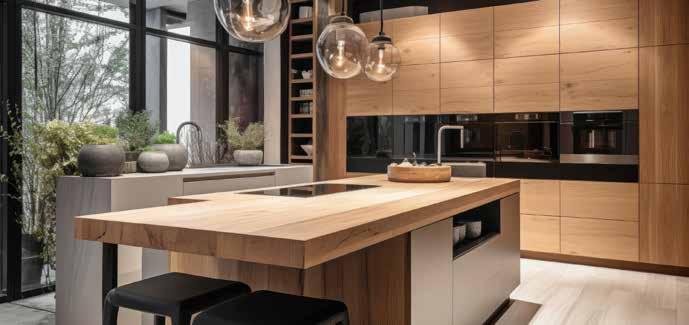
ated 123 starts (+18 percent)—small in absolute terms yet indicative of a stable recovery in St. John’s infill construction.
• New Brunswick added 673 starts (+11 percent), buoyed by Moncton’s expanding rental pipeline.
• Prince Edward Island recorded 289 starts (–12 percent), largely reflecting project timing rather than waning demand.
• Nova Scotia saw 1,504 starts (–24 percent) after two robust years; Halifax developers cite higher financing costs and construction trades capacity constraints.
For wood product suppliers, Atlantic demand may be uneven quarter to quarter, but the region’s multi unit emphasis keeps a dependable baseline.
SAAR Context and Project Pipeline
Looking at the six month rolling average (SAAR) from October 2024 to March 2025, national starts stood at 220,043 units— only 2 percent below the prior period. Single detached activity edged up 5 percent, while multi unit starts eased 4 percent. Importantly, completions declined 17 percent nationwide, suggesting that inventories will remain tight, especially in provinces with growing populations and robust rental demand.
IMPLICATIONS FOR SECONDARY WOOD MANUFACTURING
1. Re balancing Supply Chains – Firms may consider expanding Prairie and Quebec distribution while maintaining capacity for eventual rebounds in Ontario and B.C.
2. Labour Allocation – Trades shortages are most acute in Calgary, Saskatoon, and Montreal; project timelines may stretch unless prefabricated solutions increase.
3. Product Mix – Increased rental construction favours durable, high volume wood components, whereas slower condo segments may delay demand for premium custom millwork.
4. Logistics Planning – Westward freight costs are rising; wholesale manufacturers are consolidating shipments or exploring rail to contain expenses.
POLICY LANDSCAPE AND MARKET OUTLOOK
Federal targets call for 580,000 annual housing starts to close the affordability gap—a target the current SAAR undershoots. Provinces are tackling the challenge differently:
• Alberta is expanding secondary suite allowances.
• Quebec offers tax credits for affordable rentals.
• Ontario is reviewing development charge structures to reignite condo pipelines.
• Federal regulators are signaling cautious rate cuts, which may restore financing confidence by late 2025.
Manufacturers should track policy changes closely: a modest reduction in borrowing costs can rapidly reopen paused projects, particularly in big ticket condo markets.
A NUANCED GROWTH PICTURE
Canada’s housing starts landscape in Q1 2025 resists simple binaries. Urban giants paused, giving mid sized provinces and Prairie newcomers room to expand. For secondary wood manufacturers, the message is clear: opportunity exists across the spectrum—from large rental complexes in Montreal and Calgary to steady low rise builds in Manitoba and New Brunswick. By calibrating production lines and logistics to this evolving mosaic, the industry can support—and benefit from—the next wave of Canadian homebuilding.
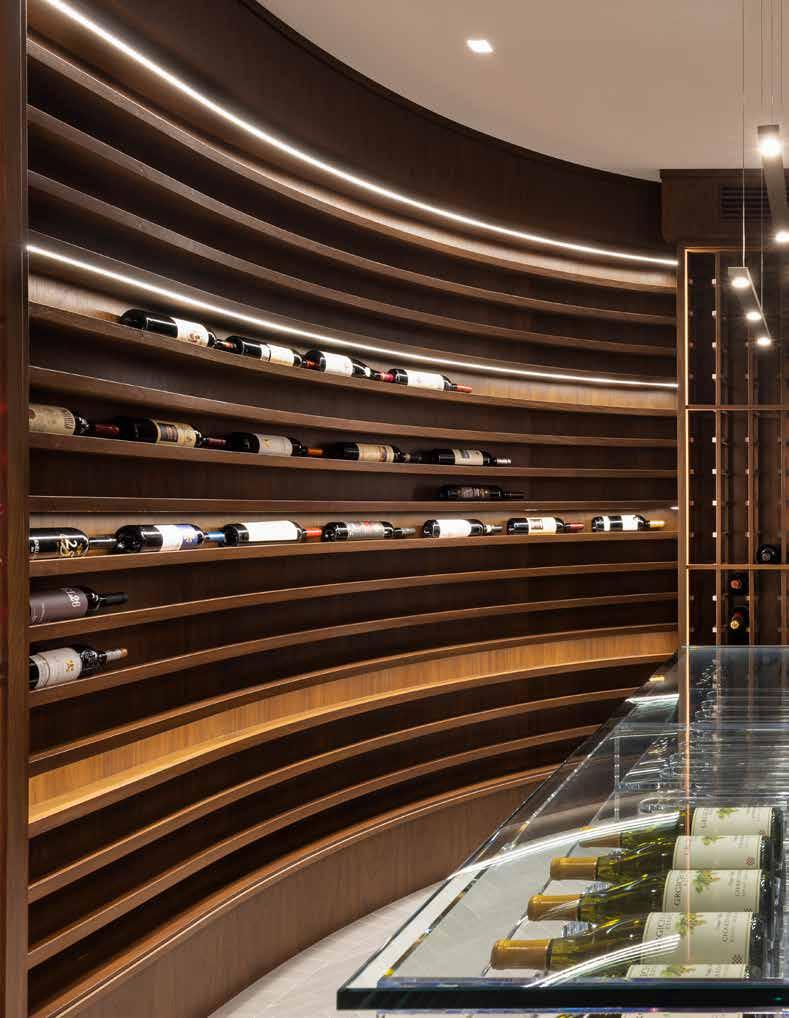
CRAFTED FOR COLLECTORS
Inside Rosehill Wine Cellars
:: By Joy Doonan, Wood Industry Writer
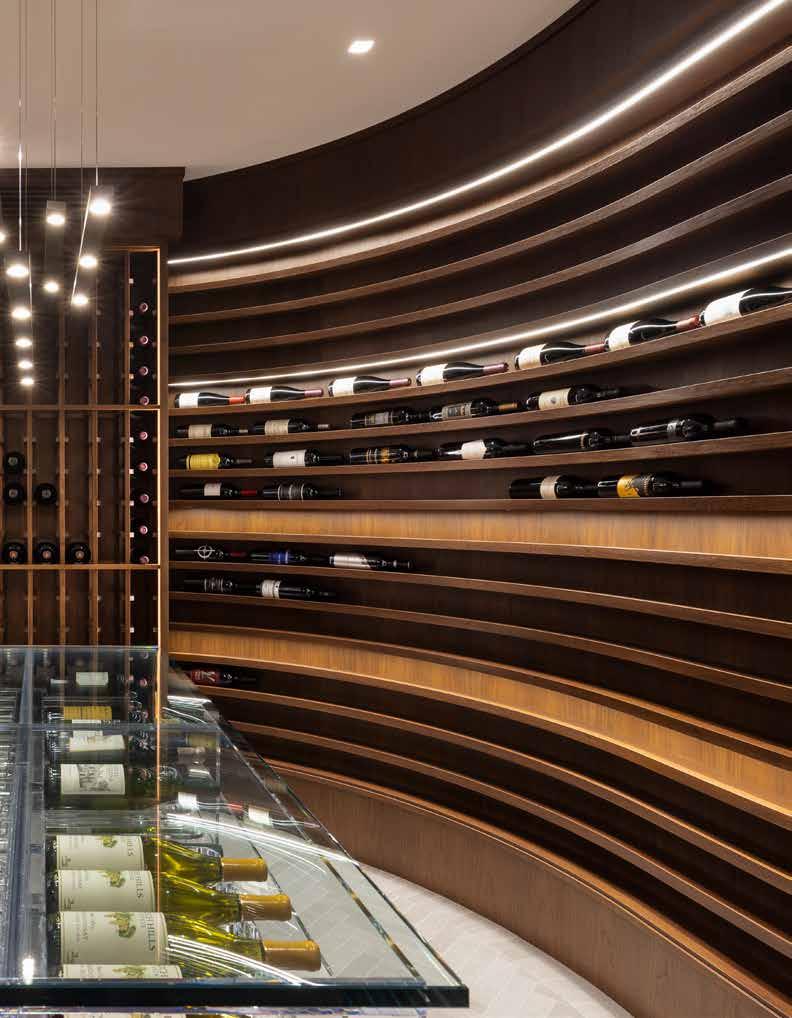
Photo
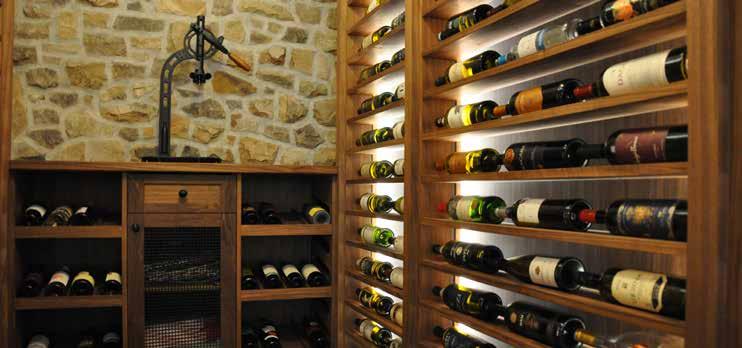
A LEGACY REIMAGINED
Celebrating 30 years of business in 2025, Rosehill Wine Cellars has steadily built a reputation as one of Canada’s most specialized providers of custom wine cellars. While the company operates predominantly in the Greater Toronto Area, they have taken on projects across North America. Since 1995, Rosehill has completed over 3,000 wine cellar projects, bringing collectors’ visions to life in unique, elegant, and functional turnkey spaces.
Rosehill entered a new phase in 2022, when Mike and Stefania Domazet took ownership of the company. Each with family histories rooted in the winemaking business, they were excited to continue the tradition Rosehill had started. Under their leadership, the business has only grown in scale and efficiency, as well as in vision.
Today, Rosehill offers customers a full range of services, from complete turnkey custom wine cellars to mod-
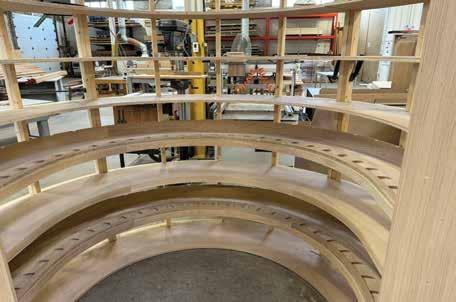
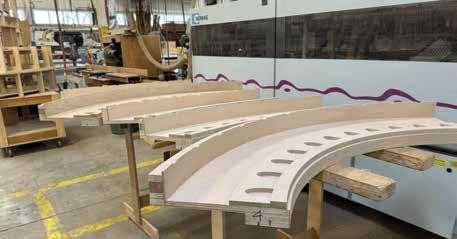
Outfitted with Homag CNC machinery, planers, molders, drum sanders, and hand-finishing tools, along with in-house CAD design and refrigeration technicians, Rosehill maintains full control from design to installation.
ular, do-it-yourself racking kits, wine cellar cooling systems, glassware, and wine accessories. In a recent conversation with Wood Industry, Mike shared his perspective on the brand’s evolution, how it’s positioned to grow, and what makes Rosehill stand apart in a competitive marketplace.
A SHOP BUILT FOR PRECISION AND PURPOSE
What makes Rosehill distinctive is not just what it produces, but how it produces it. While many woodworking companies focus on high-volume cabinetry or generalized millwork, Rosehill is devoted exclusively to wine storage, both custom and modular, giving it an unusual level of control over quality and customer experience.
“Our wine cellar construction business is a full-service millworking operation,” Mike explains, “but we focus our attention on wine cellars only. I’ve been approached many times to do bars, vanities, full kitchens… we’ve done vanities
and bars in certain situations. But it’s all geared towards the wine cellar being the focal point of the space, with these ancillary features attached to that.”
This specialized focus has led Rosehill to develop a production operation that balances the demands of artisanal craftsmanship with efficient modular manufacturing. The company’s 25,000-square-foot facility houses a dedicated 15,000-square-foot workshop, outfitted with a Homag machinery: CNC router, an 18-foot edge bander, gang ripper, CNC crosscut saw, planers, molder, drum sanders, and large-scale finishing tools. Four CAD designers work on staff, translating client concepts into production-ready designs, and all finishing is done by hand using Kremlin spray guns for staining and lacquering.
As Mike describes it, the shop runs in two distinct but complementary modes. One side focuses on high-production modular kits—DIY racking systems with features like tasting niches, angled
“Our wine cellar construction business is a fullservice millworking operation… but we focus our attention on wine cellars only.”
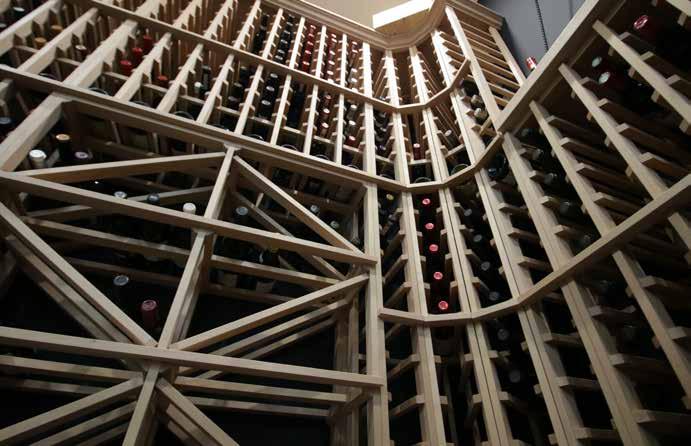
Rosehill creates both completely custom and modular storage solutions.

displays, individual bottle slots, and case storage, all manufactured to consistent standards. The other side is dedicated to custom projects, working with homeowners, designers, contractors, and architects to create one-of-a-kind installations. Whether shipping DIY racks
to a customer across North America or designing a fully integrated cellar for a private collector’s residence, Rosehill maintains complete oversight from start to finish.
This end-to-end control is something Mike believes sets Rosehill apart. “We’re
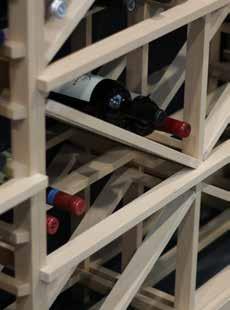
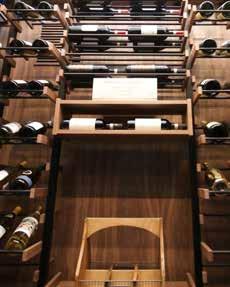
the only provider out there that does everything from start to finish,” he says. “We control the quality of the output. We’re not relying on a third party. My team members have direct control over their quality, their output, and we’re able to deliver a much better
“We’re the only provider out there that does everything from start to finish.”
product based on the fact that they’re Rosehill employees.”
Beyond the millwork, Rosehill also operates a thriving retail division, offering wine fridges from Vantaggio and other brands, as well as bespoke wine cabinetry, glassware, and accessories. Since 2022, Stefania Domazet has taken the lead in revitalizing this side of the business, applying her earlier background in technology sales and administration. Under her direction, the retail division has undergone a strategic refresh, with updates to the website, a refined product portfolio, and a stronger overall market presence. The company also outfits cellar spaces with custom cooling units, supported by in-house refrigeration technicians—an uncommon feature among wine cellar builders who normally hire 3rd parties. It is clear that Rosehill has taken very thoughtful initiative in becoming a complete turnkey provider of a holistic building experience.
A STEWARD TO THE BRAND
For Mike Domazet, the journey into the world of custom wine cellars wasn’t just a business opportunity—it was the culmination of a lifelong passion.
“At the end of the day, I’m a wine collector myself,” Mike says. “I’m passionate about the industry. I buy wine. I store wine. I enjoy wine.
Coming from a manufacturing background, Mike brought with him a natural inclination toward process optimization and operational efficiency. “I’ve got an engineer’s brain,” he explains. “When I look at manufacturing processes, I’m constantly thinking of ways to do things better and faster and more efficiently.” This mindset has allowed Rosehill not only to uphold its reputation for craftsmanship but to strengthen its capacity for innovation and growth.
A key element of Rosehill’s custom work lies in its material choices. The company predominantly uses White Oak, African sapele—a type of mahogany—and Black Walnut. For particularly
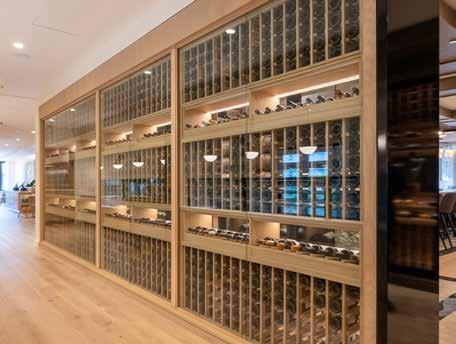
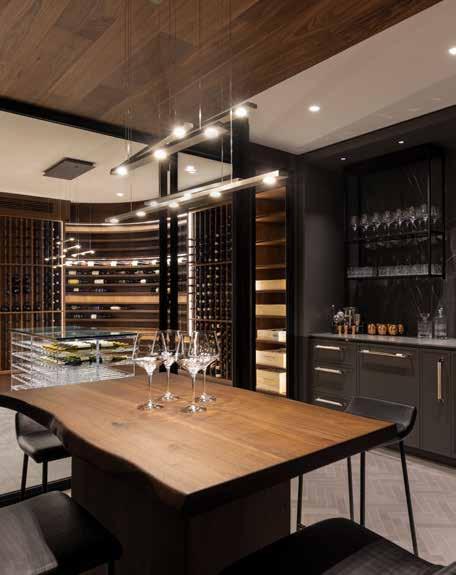
Photo: Rosehill Wine Cellars
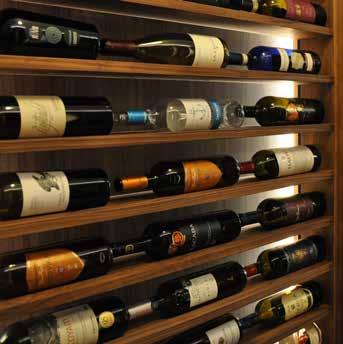
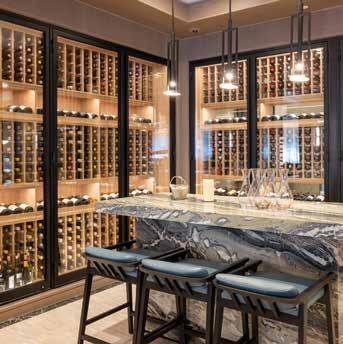
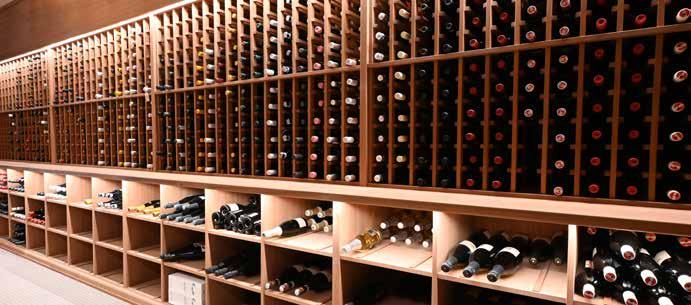
specialized projects, the team occasionally works with hickory or cherry, the latter often requested by more traditional collectors. “Cherry isn’t as popular as it was years ago,” Mike notes, “but we still have clients who want that traditional feel, and of course we want to bring their vision to life.”
Rosehill’s design lines reflect this blend of heritage and innovation. The Premier Cru Classic series is an all-wood racking system designed for traditional collectors, evoking the timeless aesthetics of old-world cellars. In contrast, a new line Rosehill has launched recently, the
Premier Cru Modern series integrates wood and metal elements, offering a more contemporary look that appeals to younger tastes and design-forward homeowners.
Through all of this, Mike’s role has been to act as both a guardian of Rosehill’s legacy and a driver of its future. His background in sales and marketing leading large teams, particularly his experience working with high-profile clients, has helped position the company to attract new clientele and explore opportunities beyond its core market.
NOT YOUR GRANDFATHER’S BRAND
While Rosehill has deep roots in tradition, its recent trajectory has been unmistakably forward-looking. Since taking the helm in 2022, Mike has overseen a period of rapid growth.
“Since we bought the business three years ago, we’ve doubled in revenue and in resources,” Mike reflects. “It’s all been a result of the decisions made on the marketing side to rebrand the business and refocus us on growth. That’s made the brand more approachable for a wider group of people and ‘not your grandfather’s brand.’ It’s more like your father’s
brand, and I think that’s been a game changer.”
Those changes have included reimagining the company’s image to appeal to a broader demographic, investing in digital platforms, and bolstering the in-house marketing team—moves that have expanded Rosehill’s reach well beyond its historical base. The company has seen steady growth across North America, including major projects in Florida, Massachusetts, Washington and other parts of the U.S.
Looking ahead, Mike has his eyes on international expansion. While tariffs remain a consideration, Rosehill has already laid groundwork for a stronger U.S. presence, including establishing it’s US operations in Florida.
For Mike, these developments aren’t just about capturing new markets— they’re about ensuring that Rosehill remains a relevant, dynamic force in an evolving industry. “Our ability to
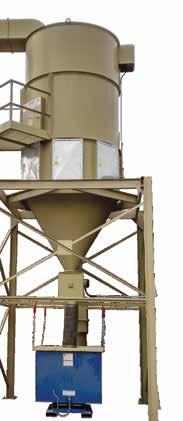
“It’s an approach that honors the company’s past while keeping its eyes on the horizon.”
execute from a marketing perspective really puts us in a position where we’re going to be able to open up new markets quickly,” he says. It’s an approach that honors the company’s past while keeping its eyes on the horizon.
GUIDED BY CRAFT, DRIVEN BY VISION
Rosehill Wine Cellars stands as a rare example of a company that has carved out a distinctive niche and flourished within it—not by chasing every opportunity, but by focusing deeply on what
it does best. Under the Domazet’s leadership, Rosehill has balanced tradition and innovation, maintaining the artisanal quality that made it a respected name while charting an intentional course for growth. As the company prepares to expand its footprint at home and abroad, it remains guided by the same values that first inspired Mike to take the leap into the wine cellar business: a passion for craftsmanship, a commitment to quality, and a vision for what’s possible when those two things come together.
Joy Doonan is a writer from Ottawa. She has a degree in Sociology and a certificate in Technical Writing, and she takes a special interest in small business sustainability.
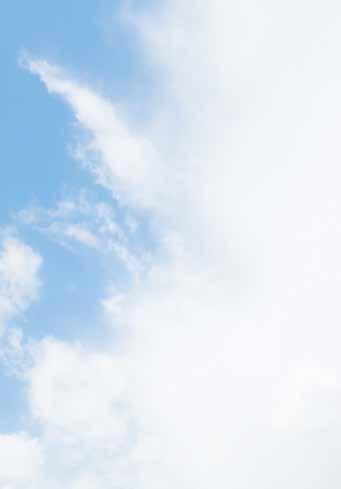
MURPHY MEANS MORE
QUALITY
STRENGTH IN NUMBERS
Our cluster thrives on the collaborative model of sharing best practices, gathering new ideas, and working together. Join us and become part of a dynamic and supportive community dedicated to helping each other succeed.

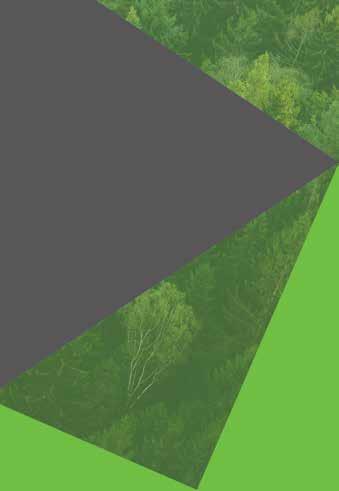

Previewing AWFS Fair 2025
INNOVATION, TALENT, AND OPPORTUNITY IN LAS VEGAS
:: By Tyler Holt, Editor of Wood Industry Magazine
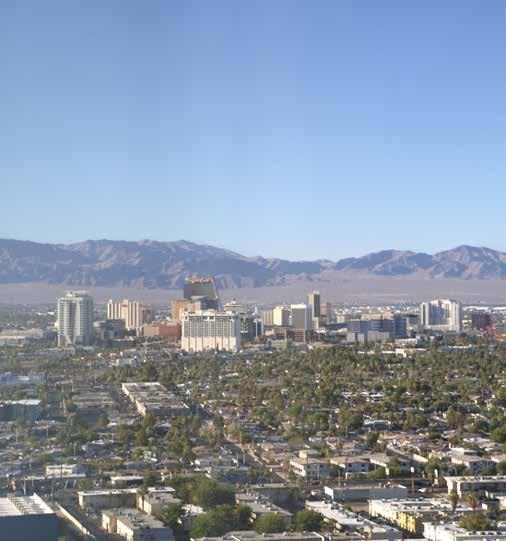
The AWFS Fair, one of North America’s most significant events for the woodworking and furnishing supply industry, returns to Las Vegas from July 22–25, 2025. Held at the Las Vegas Convention Center’s West Hall, this biennial showcase brings together over 500 exhibitors and thousands of attendees from across the woodworking spectrum—cabinetmakers, furniture producers, educators, and machinery suppliers alike. For Canadian manufacturers it’s a premier chance to see what’s next and who’s leading the charge in woodworking innovation.
AWFS Fair 2025 kicks off with preshow activities on Monday, July 21, including an in-depth symposium hosted by Woodworking Network. Focused tracks like the CNC Bootcamp and Closets Symposium offer a full day of learning, capped with a leadership reception. When the exhibit floor opens Tuesday morning, the show transitions into a high-energy, four-day experience packed with live demos, product launches, competitions, and hands-on engagement.
“CNC Bootcamp is a program that was designed to educate participants that are relatively new to this technology or are looking to buy their first CNC,” says Angelo Gangone, AWFS Executive Vice President. “The workshop is going to be moderated by Will Sampson … and will cover selecting the right CNC machine, integrating it into your operation, choosing the right tooling, dealing with dust collection and finding the right software for your operational needs.
Anyone that may be interested in purchasing a new CNC will find that attending this workshop … will provide them with some valuable information … and make them a much more informed buyer when examining the numerous options available on the show floor.
The Closets Symposium will be an all day workshop, moderated by Michaelle Bradford … [and] targets designers, retailers and installers, with topics including the most current designs, marketing and business topics of relevance to all professionals that seek to benefit from this growing market niche.”
One of the major draws is the AWFS Fair Live stage, located directly on the show floor and open to all attendees. The programming is diverse and dy-
“It is hard to overestimate how game changing the introduction of Generative AI is to the future of so many industries, particularly manufacturing.”
namic. Expect TED-style WED Talks featuring voices from design, manufacturing, and education; rapid-fire presentations by exhibitors introducing new products; and guest speakers like Brian Hamilton (New Horizons Data), Geoffrey Finkel (Source Book.com), and Matt Buell (M Buell Studio). On Thursday, the stage hosts two marquee events: the Fresh Wood Student Competition Awards and the Visionary New Product Awards. These sessions celebrate emerging talent and groundbreaking technologies that are shaping the future of woodworking.
EDUCATION AND SEMINARS
Beyond the stage, the College of Woodworking Knowledge (CWWK) seminar series provides a deeper dive into essential topics. More than 70 sessions are organized into tracks covering Business Management, Technology, Production, Workforce Development, and Education. This year’s programming puts a
strong emphasis on artificial intelligence, sustainability, succession planning, and talent pipelines.
The Business Management track includes workshops on pricing, M&A strategies, and green branding—highlighting how shops can evolve for younger, climate-conscious buyers. In the Technology track, AI takes center stage with sessions on design automation, predictive analytics, and robotics integration. Production-focused offerings feature handson learning, from CNC tooling strategies to advanced finishing techniques and lean manufacturing SOPs.
Educators and school leaders will find targeted programming on modernizing woodworking curriculum, grant writing with AI tools, and vocational succession planning. The Education track also highlights emerging tech like digital fences and 3D printers in school shops. Complementing this is the new Field Trip Program, offering guided show floor tours for
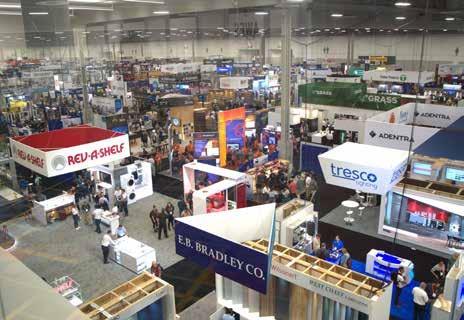
newcomers, niche builders, and educators seeking supplier connections.
“We have always had a very strong emphasis on workforce development in our CWWK program. It is a critical topic, not only for our industry but for all manufacturing.… As a result of these rapid technological changes in manufacturing, we know that our industry’s future workforce will need a different skill set in order to ensure our industry remains competitive.
In fact, at each of our shows we dedicate an entire track to educators as part of our effort in helping them train the next generation of industry leaders.…
This year, among the seven seminars featured under our Teacher Track, we will introduce a seminar that will give educators hands on experience in the latest AI tools like ChatGPT, Claude, Gemini, HeyGen, Suno, Eleven Labs and Adobe Firefly.
I do know this: it is hard to overestimate how game changing the introduction of Generative AI is to the future of so
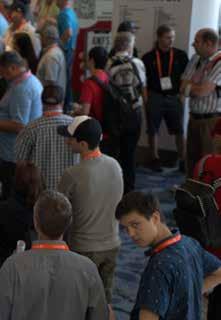
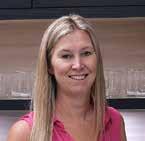
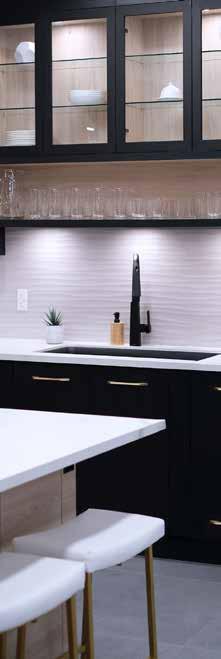
As a CKCA member I’ve participated in round table discussions and national network events where we’ve toured various manufacturing facilities and made new connections in the industry.
I’ve brought all the learning back and also leaned on my connections for best practices, and software updates and sometimes just for a cup of coffee!
CKCA allows members to form lasting relationships across the country in an industry that is small but mighty. I’m thrilled our company is part of CKCA.
RISHELLE TARR
DIRECTOR, BUSINESS OPERATIONS
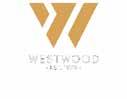
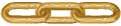
LEADS. OPPORTUNITIES. CONNECTIONS.
LEARN MORE AT
many industries, particularly manufacturing.… some of those AI capabilities … will inevitably filter down to medium sized and smaller shops… Only this time, I have a hunch that this process will happen much faster than we have witnessed in the past because of how rapidly AI is progressing.”
New for 2025 is the Biomass Block, a showcase dedicated to equipment for turning wood waste into energy and biochar. Alongside it, the Safety Zone will focus on workplace safety innovations, PPE, and emergency readiness—both reflecting critical shop-floor priorities across the industry.
“The Biomass Block is an information and resource center developed to inform Fair participants about the potential profits that could be gained from recycling wood waste. Every year shops must pay to dispose of wood waste which most often ends up in landfills. This show feature was designed to inform our audience about the advantages that the Circular Economy offers and how wood waste can be recycled into end products such as biochar and energy that shops can then use to power their facilities.
In addition to the Biomass Block, CWWK will also feature a seminar titled There’s Cash in that Trash: Profit Driven Circularity. This seminar will be led by Circular Economy and Supply Chains expert, CJ Nord. We are very excited about this initiative and its potential for our industry. I have known CJ for well over a decade and she is one of the most knowledgeable authorities on this subject. I highly recommend this seminar for shop owners and operations and production managers/directors. In the end, it’s a great way to learn how shops can take an operational cost and ultimately transform it into a revenue source or utilize the recycled wood waste as a means of reducing utility costs.” Said Gangone
The CWWK series not only delivers technical expertise but also supports broader business strategy. For Canadian attendees looking to benchmark processes or train team leaders, these sessions offer
a valuable opportunity to upskill with real-world, shop-floor takeaways.
AWARDS AND COMPETITIONS
Product innovation remains a cornerstone of the fair. The Visionary Awards recognize standout technologies in areas like CNC machinery, Industry 4.0 software, raw materials, and ergonomic hardware. Finalists are showcased in a dedicated exhibit at the front of the hall, and attendees can visit winning booths to see the products in action. Previous winners have included robotic sanding cells, IoT-enabled dust collection systems, and AI-assisted table saws—evidence of the rapid evolution in shop-floor automation.
Interactive features enhance the attendee experience. The Tool Tour encourages visitors to explore hand and power tool exhibitors across the floor. Completing the tour earns participants a commemorative t-shirt. Make-n-Take stations offer another form of engagement, where attendees can test tools and leave with small projects. These experiences help demystify new tools and foster direct product comparisons.
For students and educators, the Fresh Wood Student Competition is a cornerstone of the fair. It brings finalist projects from woodworking programs across North America to Las Vegas, where they are displayed, judged, and celebrated. Awards are given for craftsmanship, complexity, and design, with categories for both high school and post-secondary students. The Best of Show award—often a highlight of the Thursday afternoon ceremony—represents the highest level of student excellence and is judged by a panel of industry experts.
CANADIAN PARTICIPATION AT AWFS
Canada routinely delivers the Fair’s largest international turnout. Executive Vice President Angelo Gangone puts the numbers in perspective:
“4 % of our exhibitors in 2023 were from Canada and this year we are tracking at that same 4 %. … Canadians have
always been our largest international market… We hope to see even more Canadians represented at this year’s event and AWFS® will be looking at ways we can continue to strengthen that cross border connection in the future. It isn’t difficult to see how important international representation is to our show.” Remarked Gangone
For those travelling south, the metric is less about percentages than practical return:
“We would like [Canadian companies] to walk away from the show with some new ideas that can help their shops become more efficient, productive, safer and more profitable… and to find new suppliers—maybe even several they never knew existed.”
That invitation remains steady, regardless of broader politics or currency swings:
“We have always appreciated and enthusiastically welcomed our Canadian neighbors, and that will never change.”
AWFS is exploring additional networking and information sharing initiatives to make that cross border exchange even stronger in future cycles. The message is clear: Canada’s presence is integral to the Fair’s success, and the doors to Las Vegas remain wide open.
The scale of the exhibit hall is immense. Canadian companies are well represented among the 500+ exhibitors, showcasing the country’s technical depth and market reach in wood manufacturing. Companies like Richelieu Hardware Ltd., Royce//AYR Cutting Tools, Stolbek Machines, Ventless LLC, and Vancouver Automation bring unique innovations in edge banding, automation, and precision tooling. Coatings specialists like Envirolak, Fantastic Wood Coatings, and Fuji Spray highlight Canada’s growing presence in finishing systems, while Com-Pleat Filters and Paper and Lorchem International offer solutions in air quality and industrial cleaning. Machinery and hardware firms such as Taurus Craco, Williams & White, and Hardware Rebels also anchor Canada’s footprint at the show.
And of course, Wood Industry / Le monde du bois (Booth 4478), will be exhibiting and on-site covering trends, technologies, and stories shaping the secondary wood manufacturing space.
For Canada’s woodworking sector, AWFS Fair 2025 offers more than just a trade show floor. It’s a moment to gauge industry momentum, eval-
uate new technologies, and connect with peers from across the continent. Whether you’re a millwork shop looking to automate, an educator exploring curriculum trends, or a business owner preparing for your next capital investment, AWFS provides unmatched access to the people and ideas moving the industry forward.
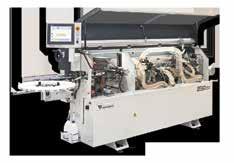
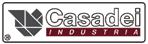
E550 AUTOMATIC EDGEBANDER
The Casadei E550CRT is an automatic edge bander with chain panel feeding, pre-milling and corner rounding units featuring superior hot melt glueing technology which allows the use of EVA/PUR glue with the same glue pot.
“At last, perfect glueing for every level of investment.”

CONCEPT 350 PLUS SAW
Introducing the Concept 350 Plus: top-tier performance for precise and efficient panel and wood processing. Up to 50% space savings, 40 m/min cutting speed, single-operator efficiency, full blade safety, superior cut quality, quiet operation, and reduced dust.
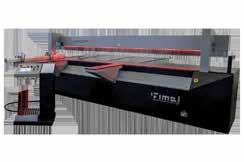
Toll Free: 1 800 386 5222
Open: Monday - Friday 8 am - 5 pm tauruscraco.com
The new Format4 tempora F1000 sets new standards in the field of comprehensive edge processing and combines exceptional durability, precision and efficiency to ensure maximum performance.
Thanks to its length, stability and large dimensioned machine frame, this machine ensures exceptionally smooth running of all units and guarantees the highest level of adjustment precision and maximum service life - even and especially when working in multi-shift operation.
The F1000 is equipped with a belt feed drive on the upper pressure bar to ensure careful material handling of surfacesensitive materials. Compared to a pressure roller infeed, the belt feed drive provides uniform pressure distribution over the entire length of the workpiece, guaranteeing more precise machining results and minimizing cleaning effort by eliminating abrasion and dust.
The edge jointing unit impresses with its powerful motors and automatic, centric adjustment to the workpiece height, which prevents one-sided wear and significantly extends the service life of the router. The top-mounted glue pot ensures faster heat-up and the integrated drain function makes cleaning much easier.
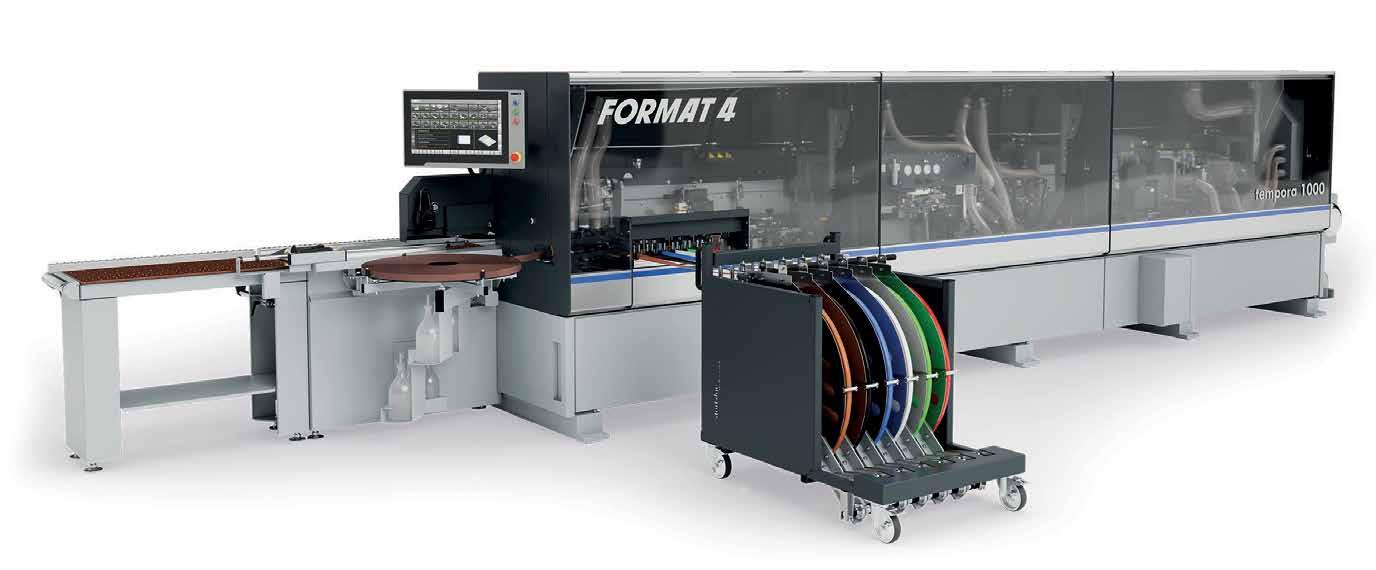
















































Top-mounted, controlled glue pot including cleaning fuction Application cpntrolled pneumatic pressure unit e-motion with 4 pressure rollers
The all-new, completely redesigned corner rounding unit with CNC-controlled positioning axes delivers even more precise results, minimizes maintenance and increases efficiency. The patented multi-radius router cutters ensure a uniform edge radius even when processing thin edges.
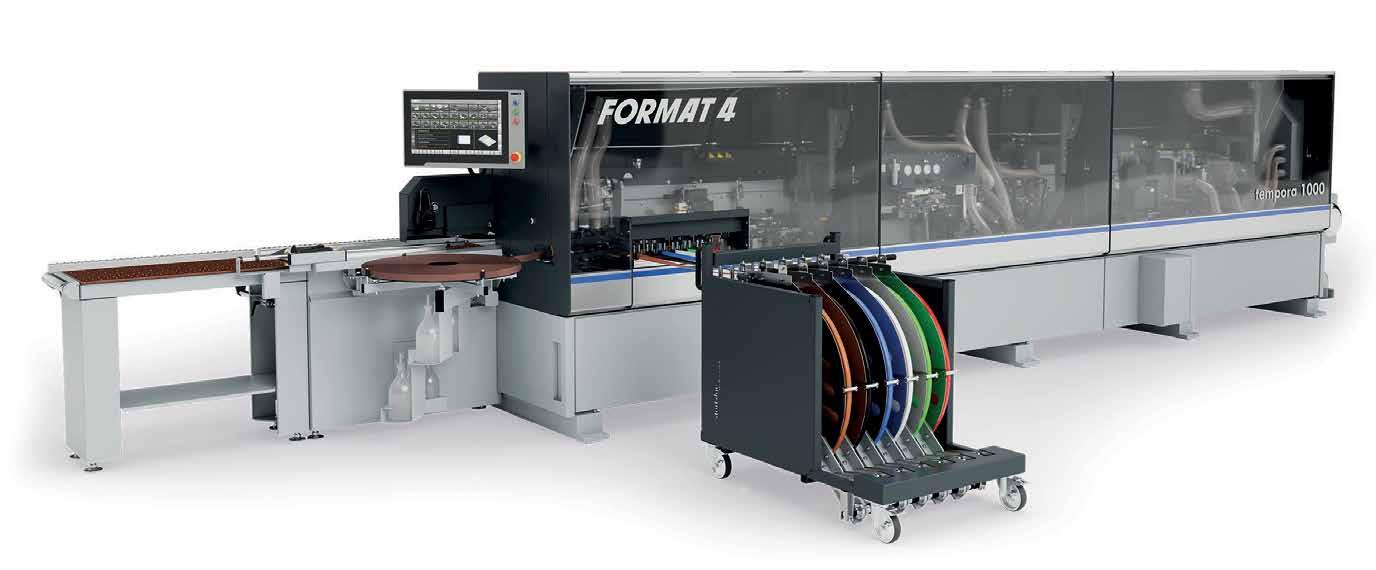
The F1000 equipment packages Classic, Professional and Performance offer targeted customization to meet your individual operational requirements. Opt now for a Format4 machine – You will be impressed!
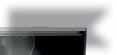
YOUR BENEFITS
Installation length: 8000 mm
Edge thickness 0.4–12 mm,
Workpiece height: 8–60 mm
Feed speed: 12–25 m/min
Top-mounted applicationcontrolled glue pot
Automation: e-motion
Corner rounding unit (CNC controlled)
Complete edge processing
Top pressure belt
Premilling unit “professional”
Multifunction trimming unit “professional”
Radius scraping unit “professional”
Twin-engine linear end trimming unit
Feed speed: 12 & 25 m/min
THE POWER OF ACTIVE LISTENING IN MANUFACTURING LEADERSHIP
:: By Amrita Bhogal, People and Culture Leader, Sunrise Kitchens
In the fast-paced, hands-on environment of kitchen cabinet manufacturing, clear communication is a cornerstone of productivity, safety, and collaboration. Yet one of the most undervalued — and underutilized — leadership skills is also one of the most powerful: active listening.
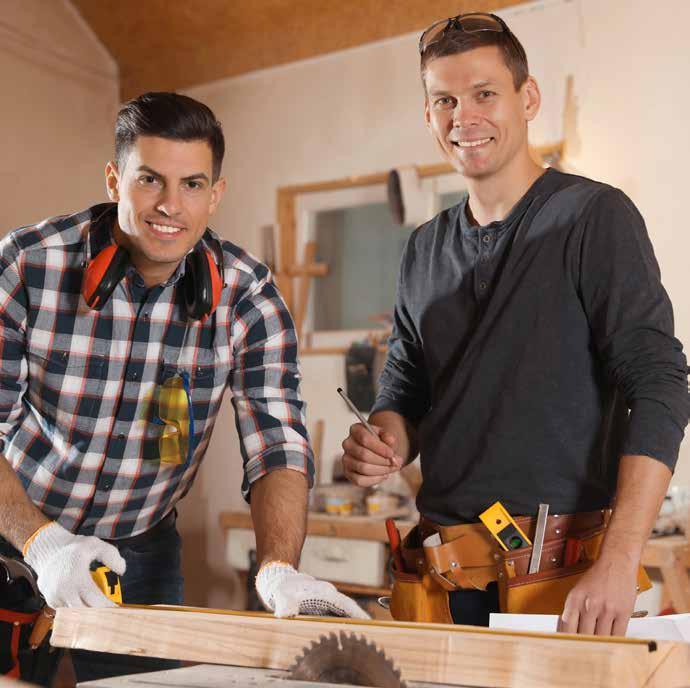
At Sunrise Kitchens, we recognized that active listening was not just a soft skill — it was a critical leadership competency. Through the development of our Living Our Values Recognition Program, we identified specific actions that bring our core values to life. Under the value of Respect, one key action stood out: Active Listening.
To help bring this value to life on the production floor and beyond, our HR team developed and delivered an internal workshop specifically for team leads, focusing on the practical, daily application of active listening in a manufacturing environment.
WHY ACTIVE LISTENING MATTERS IN MANUFACTURING
In a production-based setting like ours, team leads are the linchpin between operations and people. They’re responsible not only for meeting deadlines and quality expectations but also for keeping their teams safe, motivated, and heard.
Too often, communication flows in one direction: top-down. Team leads give instructions, correct mistakes, and push for productivity. But when the reverse is true — when a team member brings forward a concern, an idea, or even a frustration — the quality of that moment depends entirely on the leader’s ability to listen.
Active listening isn’t just about hearing words. It’s about being present, suspending judgment, and acknowledging the speaker’s perspective. It’s a discipline that builds trust, reduces conflict, and drives engagement — outcomes that are especially vital in a busy production environment where small miscommunications can lead to bigger problems.
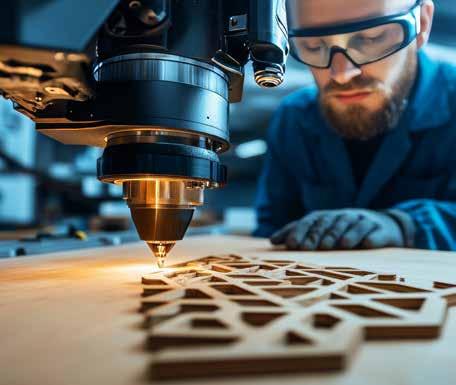
WHAT WE COVERED IN THE ACTIVE LISTENING WORKSHOP
Our internal workshop, created specifically for Sunrise Kitchens’ team leads, focused on four essential pillars of active listening:
1. Pay Attention Be fully present. Minimize distractions and give the speaker your full attention.
2. Show You Are Listening Use verbal and non-verbal cues — like nodding or short affirmations — to show engagement.
3. Seek Clarity and Paraphrase
Check for understanding. Paraphrase what you heard and ask questions to confirm.
4. Respond Thoughtfully Pause before reacting. Consider both the content and the emotion behind what’s being said.
During the session, we placed significant emphasis on seeking clarity and paraphrasing, as well as on how to respond thoughtfully. This was informed by insights from our 1-on-1 conversations with team leads over the past year, where a recurring theme emerged: team leads often were faced with miscommunication that led to conflict within their teams. By focusing on these two areas, we aimed to build confidence in navigating emotionally charged conversations and ensuring alignment in understanding — before jumping to solutions or making assumptions.
FROM DIRECTING TO EMPOWERING: THE IMPACT
By the end of the workshop, our team
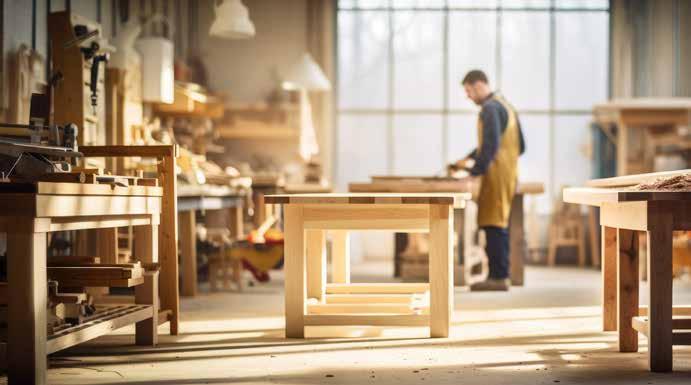
leads began to shift from a communication style rooted in directing to one focused on empowering. This change reflects a growing culture of trust, respect,
Here are some of the practical outcomes we’ve observed over the past few months:
Listening more, talking less Team leads shared that they now spend more time actively listening to their team members’ perspectives before offering guidance — creating space
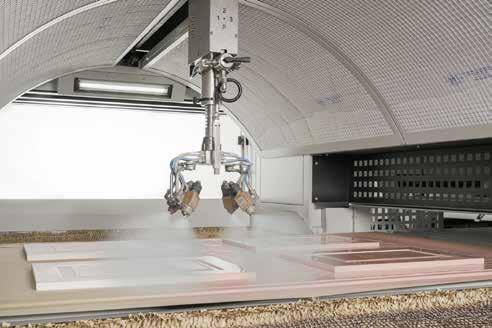

Cefla’s Canadian Distributor:
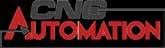

for shared problem-solving and deeper understanding.
Asking clarifying questions instead of assuming understanding A subtle but powerful shift occurred in language. Phrases like “Just get it done” have evolved into “What do you need from me to move forward?” This simple change signals openness, curiosity, and partnership.
Responding with empathy Leaders now more consistently recognize emotional cues such as frustration or overwhelm. Rather than overlook these signals, they acknowledge them with reflective responses like “It sounds like you’re feeling stretched — let’s prioritize together.”
This training didn’t end at the workshop — in fact, it sparked an ongoing conversation. Active listening has now become a recurring topic in our 1-on-1s with team leads, where we reflect on real examples and identify where additional support may be needed.
These continuous check-ins allow us to tailor guidance to each team lead’s communication style and comfort level, en-
Scan to Learn More:
“The most effective leaders aren’t the ones who talk the most.
They’re the ones who listen best.”
suring that the learning is personalized, practical, and sustainable. In doing so, we’re not only developing stronger leaders — we’re fostering a culture where every team member feels heard, understood, and valued.
Three months after the training, the real value of active listening is becoming clear. Team leads have noticed that taking a moment to confirm the team member truly understands the instruction or topic of discussion has prevented several misunderstandings. In fact, many shared that employees would sometimes paraphrase the instruction in a way that revealed a completely different understanding.
Rather than letting that miscommunication fester and result in poor performance or conflict later, team leads now clarify in the moment, reducing frustration and increasing accountability on both sides.
This simple shift — from assumption to verification — is creating a more respectful and proactive culture across teams.
CONNECTING BACK TO PEOPLE & CULTURE
Active listening isn’t a standalone skill. It is a reflection of culture in action. At Sunrise, our commitment to a respectful workplace goes beyond policies — it’s embedded in how we communicate every day.
By teaching and reinforcing active listening, we are reinforcing a deeper cultural message: every voice matters. When team leads practice these skills, they model respect, build stronger relationships, and create environments where people are more likely to speak up, innovate, and stay engaged.
CONTINUING THE JOURNEY
At the conclusion of our Active Listening workshop, we equipped our team leads with reflection tools and practical resources in a take-home workbook — reinforcing that leadership growth doesn’t end in the training room. Like any core competency, active listening is built over time and strengthened through intention and practice.
In our fast-paced manufacturing environment, where priorities shift by the hour and decisions impact workflow, the ability to pause, listen, and understand is not a luxury — it’s a leadership necessity. Whether you’re managing
a production schedule, supporting a colleague on the floor, or navigating cross-departmental goals, how you listen influences how others feel, respond, and perform.
That’s why active listening is more than a communication skill at Sunrise Kitchens — it’s a cultural commitment. And it’s one we’re choosing to nurture daily through ongoing 1-on-1 coaching, peer support, and value-based recognition.
The most effective leaders aren’t the ones who talk the most. They’re the ones who listen best.
And that’s something we’ll continue to build — one conversation at a time.
Amrita Bhogal is the 3rd generation at Sunrise Kitchens. With a focus on People and Culture. She is leading change through lean principles and continues to strengthen culture through values and behaviours.
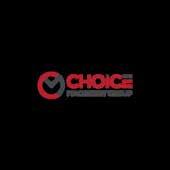
PROUDLY BUILDING AMERICAN MACHINERY BRANDS
choicemachinerygroup.com | 616-546-8225 | info@choicemachinerygroup.com

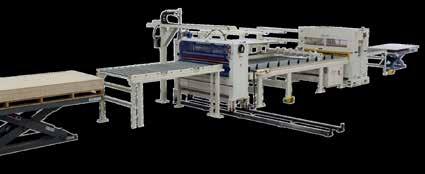

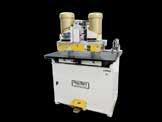


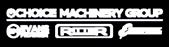
Demanding Real Sustainability in the Wood Industry
How to Spot the Difference Between Action and Optics
:: By Jaime Álvarez, Vice President of Marketing at Garnica
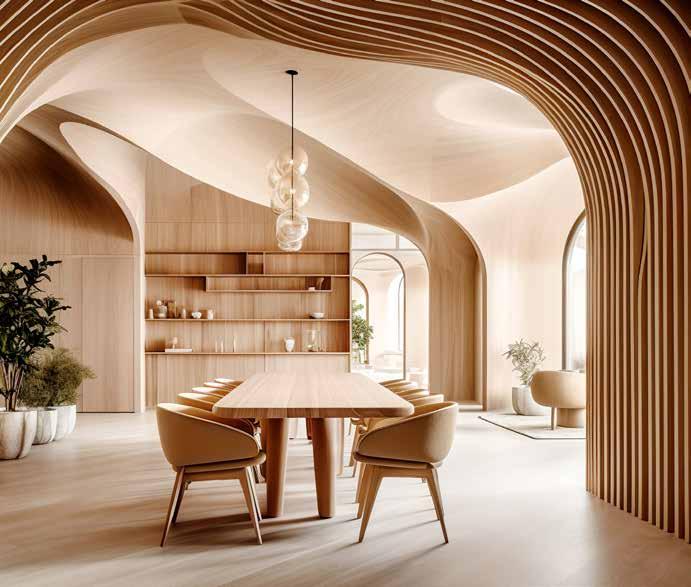
Sustainability is now a baseline expectation in the wood industry—but not all claims are created equal. For millworkers, cabinet makers and fabricators who rely on responsibly sourced materials, the challenge isn’t finding products that say they’re sustainable; it’s figuring out which ones truly are.
With customer scrutiny rising and global regulations tightening, the stakes are higher than ever. Here are three key indicators to help evaluate whether a brand’s environmental commitments are real, replicable, and relevant to your own sustainability goals.
1
Third-Party Accountability and Continuous Improvement
A critical test of genuine sustainability is external accountability. Are companies not only making environmental claims, but inviting others to scrutinize and validate them?
Third-party audits, environmental per-
formance reports, and research partnerships demonstrate that a manufacturer is committed to long-term improvement— not just short-term optics. These companies are often engaged in research and development efforts to improve material efficiency, reduce waste, and explore alternatives to traditional wood inputs. For example, engineered panels made with lower-impact adhesives or bio-based resins. Additionally, they actively participate in collaborative sustainability efforts—working with governments, universities, and other companies to improve industry-wide standards.
2
Traceability and Transparent Sourcing
The foundation of any credible sustainability claim starts with traceability. Can a company prove where its wood came from, how it was harvested, and whether those practices are ecologically responsible?
The ongoing conflict in Ukraine has highlighted just how crucial traceability is. Once widely used across North America, Russian Baltic birch plywood has come under scrutiny following sanctions imposed on Russian exports. Despite these restrictions, investigations by the Environmental Investigation Agency (EIA) have revealed that Russian birch is still making its way into North American markets—often rerouted through Southeast Asia to mask its origin and evade duties.
This practice not only undermines international sanctions but also puts companies at risk of losing key sustainability certifications, such as those from the Forest Stewardship Council (FSC®), which no longer
recognize Russian timber. It shows why traceability must go beyond surface-level claims. Buyers and manufacturers need full transparency at every stage of the supply chain to ensure they’re not unintentionally supporting unethical practices.
This is where the role of independent certifications becomes critical. Certifications like PEFC™ (Programme for the Endorsement of Forest Certification) and FSC® ensure that wood comes from sustainably-managed forests that meet strict environmental, social, and economic standards. They also provide assurance that the wood has not contributed to illegal
logging, deforestation, or degradation of high-value conservation areas.
Garnica is an example of a company that actively prioritizes sustainability at all levels of its operations. All wood used in its plywood panels is sourced from fast-growing, sustainably managed European tree farms. These forests are carefully monitored and operate under EU forest management regulations. Garnica’s supply chain is fully documented and externally verified, with certifications including:
• FSC® and PEFC (responsible forest management)
• CARB Phase 2 and EPA TSCA Title VI
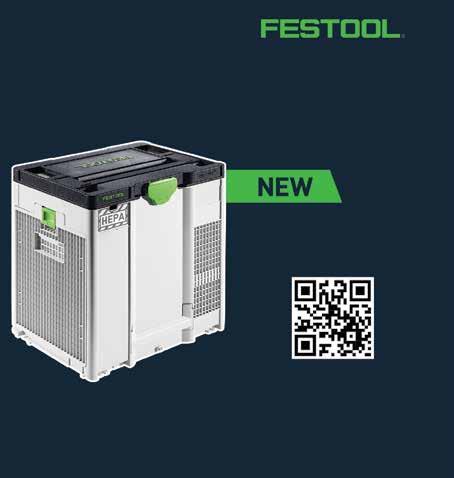
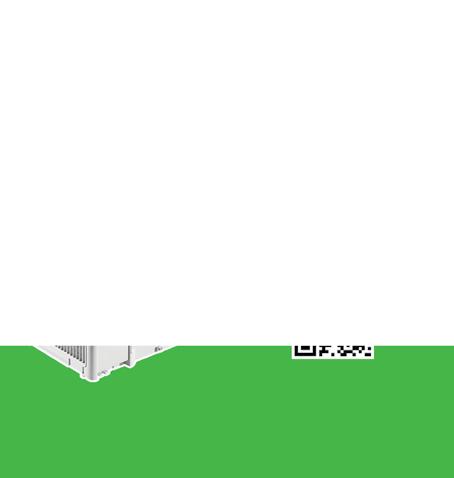
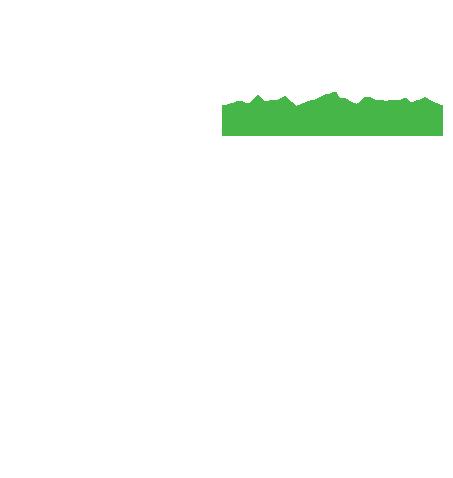
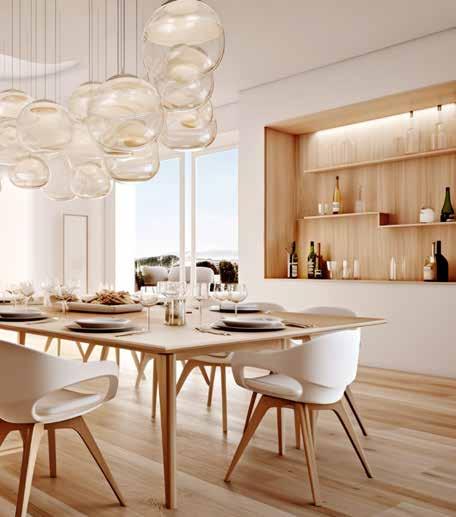
(low formaldehyde emissions)
• ISO 14001 (environmental management systems)
• ISO 50001 (energy management systems)
When you specify or source Garnica products, you’re choosing materials with a transparent, verified environmental footprint. And when your clients ask: “Where does this wood come from?”, you’ll have the answer.
3Full Life Cycle Responsibility
True sustainability doesn’t stop at the
forest line. It extends through the entire product life cycle—from harvesting and transportation to manufacturing, use, and eventual disposal or reuse.
Leading manufacturers are adopting Life Cycle Assessments (LCAs) to understand and minimize environmental impact across each stage of production. They’re also investing in processes that reduce emissions, water use, and energy consumption in their factories. Others are developing recyclable or biodegradable components, extending product life spans, or designing for disassembly.
For professionals in the cabinetry, furniture, or prefab housing sectors, these considerations matter. A plywood panel with a low carbon footprint and minimal off-gassing doesn’t just reduce environmental impact—it improves indoor air quality and contributes to healthier living and working spaces. When clients care about WELL, LEED, or Passive House standards, these product choices carry weight.
Choosing suppliers who are looking at the big picture—from tree to panel—underscores your own commitment to responsible design and long-term value.
ASK THE RIGHT QUESTIONS
If you’re sourcing materials for a modular home project, furniture line, or millwork package, don’t just ask whether a product is sustainable. Ask:
• Where was the wood harvested?
• Is it certified by an independent organization?
• What emissions standards does the product meet?
• How is the manufacturer reducing its environmental footprint?
• Are sustainability claims backed by data or third-party verification?
By digging deeper and asking the right questions, you’ll not only protect your own business and reputation—you’ll help push the industry toward higher standards of integrity, transparency, and environmental stewardship.
In a marketplace crowded with eco-labels and lofty claims, real sustainability will always stand up to scrutiny. And in the wood industry, where the stakes include both the health of forests and the trust of consumers, that distinction has never been more important.
Jaime Álvarez is the Vice President of Marketing at Garnica and has been with the company for over 10 years. Fluent in Spanish and English, Jaime lives and works in La Rioja, Spain overseeing marketing initiatives for both the European and North American divisions. He studied Economics at the University of Zaragoza and also obtained a master’s degree in marketing Management from the ESIC Business & Marketing school.
AUTOMATION WITH A HUMAN TOUCH
What Jidoka Can Teach Us About the Future of Cabinet Manufacturing
:: By Chris Leonard, Director at Kaizen Learning Partners and Chair of the CKCA Advanced Manufacturing Peer Group
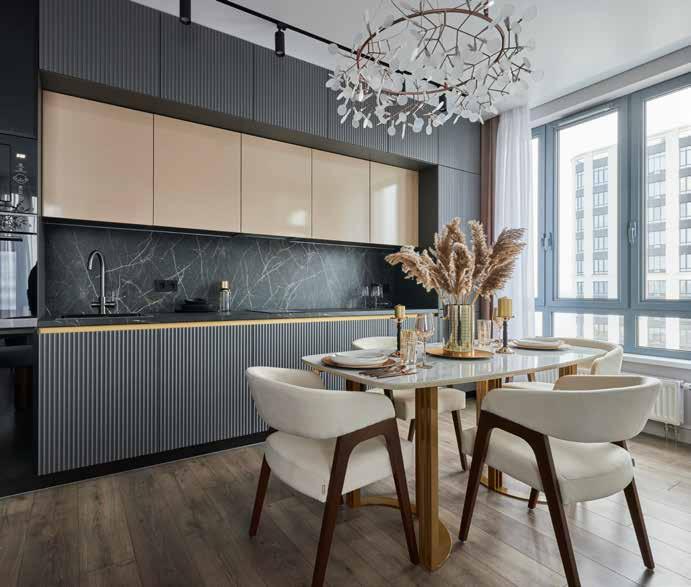
In today’s manufacturing world, buzzwords like “smart factory” and “advanced manufacturing” get a lot of attention. But long before those concepts became buzzwords, Toyota laid out a principle that still shapes how we should think about automation today. They called it Jidoka = automation with a human touch.
Jidoka isn’t about replacing people with robots. It’s about empowering machines to recognize when something isn’t right and to stop production so that humans can intervene. The result is not just faster output, but smarter, safer, and more consistent production, while keeping people at the center.
Toyota builds this principle into everything it does. Machines detect abnormalities. Workers are empowered to stop production instantly. The system is designed to expose problems, not conceal them. This leads to higher quality, less waste, and more engaged employees.
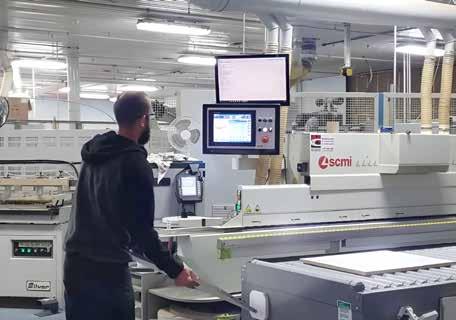
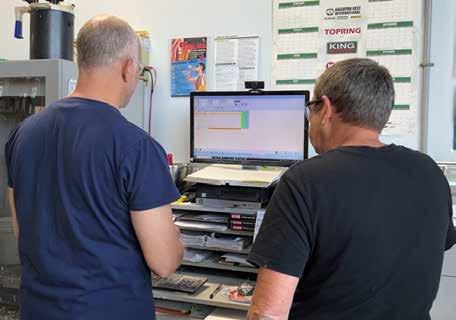
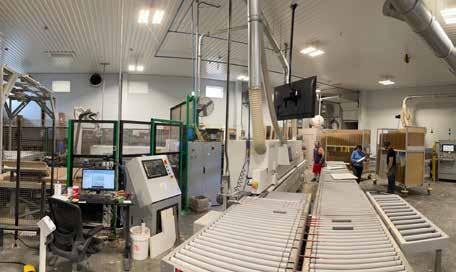
FROM CARS TO CABINETS
So, what does all this mean for Canadian cabinet manufacturers?
Traditionally, our shops are high-mix, low-volume, every kitchen is a custom job. That nurtures creativity and craftsmanship but can make standard process and overall efficiency hard to achieve. Now imagine applying the same discipline of a food processing factory, where uptime, yield, and standardization are at the core of what they measure to that of custom manufacturing shop.
That’s the future AMPG is helping build, and it’s already underway at companies like Muskoka Cabinet Company.
VISION-DRIVEN AUTOMATION
Muskoka Cabinet Company, a founding member of the CKCA Advanced Manufacturing Peer Group, is pushing the boundaries of automation in a custom environment, and Jidoka is right at the core.
Luke Elias, President of Muskoka Cabinet Company, explains:
“We’re not automating to remove people — we’re automating to eliminate non-value-added activities. This allows skilled operators to focus on real work, not wasted motion or rework.”
Muskoka’s production front-end, including panel processing, routing, drilling, and edge banding,is being integrated into a semi-autonomous line designed with Jidoka in mind. A key feature is their new vision inspection system, which combines a camera array with data-driven analysis software. This setup identifies defects like misaligned panels or incorrect parts in real-time, halting the line when necessary and alerting operators immediately.
The software aggregate’s fault data into a growing “defect causation library”, enabling root cause analysis and continuous process improvement. Over time, the system learns to recognize more patterns, leading to smarter stops and fewer recurring issues.
The entire package, including the vision system, software, IoT gateway, and support tools is being piloted across select CKCA member facilities this spring.
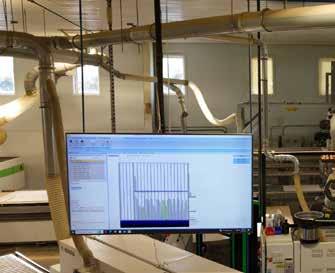
BEYOND THE VISION SYSTEM: THE INNOVATION PIPELINE
The vision system is just one piece of a growing innovation pipeline. Muskoka is also prototyping a fully automated box assembly line, designed to integrate seamlessly with upstream processes. This will further reduce manual handling, speed up throughput, and ensure more consistent final product assembly.
Another exciting development is the Part Porter 100, an autonomous mobile robot built to tackle one of the most overlooked efficiency drains in a cabinet shop, the movement of service parts. Instead of relying on people to move service request materials across the floor, the Part Porter 100:
• Follows pre-programmed routes using smart mapping and LiDAR
• Carries up to 225 lbs of material on a charge that lasts up to 16 hours
• Includes touchscreen navigation, real-time location monitoring, and cloud integration
• Can be customized and API-connected to existing shop floor systems
Manual material handling is one of the largest hidden costs in a shop. And as Luke Elias puts it:
“If a skilled operator spends even 20 minutes a day walking parts, you’re losing not just time — you’re potentially losing hundreds of cabinets a year in missed output.”
STRONGER TOGETHER: THE POWER OF COLLABORATION
The CKCA Advanced Manufacturing Peer Group was created to close the innovation gap, not just through tech, but through community.
Sandra Wood, CKCA Executive Director, puts it best:
“This is about putting manufacturers in the driver’s seat to create solutions for our industry. Sure, you can go it alone — but it’s more costly and more time-consuming. AMPG brings like-minded manufacturers together to share what works, solve common problems, and move faster — together.”
AMPG isn’t a separate group, it’s a core part of the CKCA, open to any member committed to growth and modernization. Some are early adopters piloting AI, robotics, and automation. Others are just starting out with small process changes. All are welcome.
JOIN THE MOVEMENT
If you’re already exploring automation, we want to hear from you. If you’re unsure where to begin, AMPG can help you get started with audits, best practices, peer support, and funding advice.
And if you’re a supplier, integrator, or innovator — the AMPG network is actively looking for pilot partners and scalable tech that can transform the shop floor.
Because the gap between a traditional cabinet shop and a fully modernized process manufacturer may be wide, but it’s not unbridgeable.
And together, we can cross it faster.
That’s Jidoka. That’s AMPG. And that’s the future of cabinet manufacturing in Canada.
Chris Leonard is the Director at Kaizen Learning Partners and Chair of the CKCA Advanced Manufacturing Peer Group.
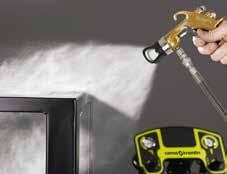
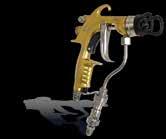

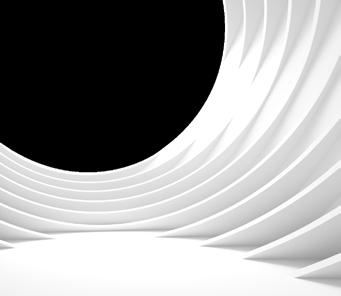
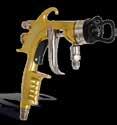
Blum ECODRILL – Compact Hinge Boring Tool for On-Site & Workshop Use
The newly redesigned Blum ECODRILL offers enhanced efficiency and convenience for precise hinge boring. Its compact, ergonomic design makes it ideal for both workshop and on-site use. Compatible with electric or cordless drills (14V or higher), the ECODRILL allows for effortless assembly of Blum hinges, including CLIP top, MODUL, and AVENTOS HF/HK-XS systems. Each drill bit operates independently and retracts automatically, ensuring clean, accurate bores every time. It supports variable boring distances from 2 to 8 mm and clamps securely to door materials up to 40 mm thick. Pre-installed drill bits and two Torx drivers are included for immediate use. Engineered for professionals seeking portability, precision, and time-saving functionality in one durable tool.
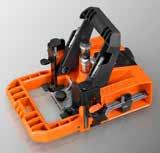
Dynapro Undermount
Slide System – Smooth, Synchronized Precision
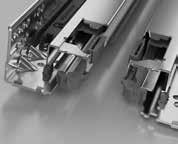
The Dynapro Undermount Slide System delivers full-extension, soft-close performance with silent, synchronized motion. Engineered for wooden drawers up to 48” wide and 132 lbs, Dynapro’s rack-and-pinion system ensures smooth gliding without binding. Available for 16mm and 19mm drawer materials, it supports 3D and optional 4D adjustment—height, side, depth, and tilt— without tools. Ideal for modern cabinetry and heavy-duty applications, Dynapro provides exceptional stability with wide 31mm drawer members and robust front-locking cleats. Its bottom-mount version is perfect for appliance garages, pull-out shelves, or oversized drawers, maintaining smooth operation under heavy loads. Built for performance and precision, Dynapro is a reliable, adaptable solution for kitchens, closets, and high-use environments.
Format4 tempora F1000 Performance – 25 Years of Edgebanding Excellence
Celebrating 25 years of Format4 innovation, the new tempora F1000 Performance redefines precision edgebanding for demanding production environments. Built with a massive, stable frame and extended machine length, it ensures smooth, vibration-free operation across all processing units—even in multi-shift settings. A belt-driven upper pressure bar provides uniform pressure on sensitive surfaces, while the centric edge jointing unit automatically adjusts to material height for extended tool life. The topmounted glue pot heats quickly and features an integrated drain for simplified cleaning. The newly redesigned, CNC-controlled corner rounding unit with patented multi-radius cutters boosts accuracy and efficiency. Customizable in Classic, Professional, or Performance packages, the F1000 is built to deliver uncompromising results with maximum uptime and machining precision.
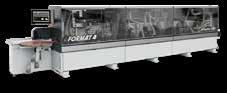
TigerStop Pro™ – Precision Positioning with Zero Setup Time
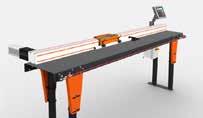
The all-new TigerStop Pro™ delivers highprecision automated positioning, now with a refreshed touch screen and brushless motor for unmatched reliability. Capable of pushing, pulling, and positioning material up to 240 lbs with ±0.004” accuracy, it transforms manual equipment into a lean, fully automated system. The TigerStop Pro™ supports up to 30 ft lengths with a 32 mm belt and integrates easily with saws, drills, or punches. Enhanced with optional Dynamic Optimization, Cut List Downloading, and Label Printing upgrades, it maximizes raw material usage and boosts throughput. Eliminate rework, reduce setup time, and improve operator efficiency—even in compact shops. Whether retrofitting or scaling up, TigerStop Pro™ ensures precision, consistency, and productivity from day one.
Kentwood M-2000 – HighSpeed CNC Moulder with HSK Precision
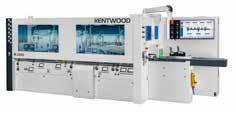
The Kentwood M-2000 is the brand’s flagship highperformance moulder, engineered for rapid setups, superior finish quality, and operator ease. Equipped with variable-speed HSK 85W spindles (6,000–12,000 RPM), the M-2000 delivers exceptional surface results at high feed rates. CNC-controlled spindle positioning and rapid-adjustment hoods minimize changeover times, while a robust feed system and chrome table surfaces ensure smooth material handling. Powered by Siemens IE3 motors and managed through a 24” touchscreen with APC ProLink software, it supports seamless tool integration and real-time production tracking. With pneumatic pressure elements, integrated table lubrication, and advanced safety features, the M-2000 sets a new standard for moulding and profiling efficiency. Available in multiple spindle configurations across select global markets.
SprayTwirly™ Rotating Spray Table – Precision Painting Made Easy
The SprayTwirly™ (SPTY) is a versatile, rotating spray table designed to simplify and perfect cabinet door and part painting. With 360-degree rotation, it allows painters to reach every angle without moving around the table— delivering consistent, precision finishes from a fixed position. Retractable arms and adjustable magnetic spikes accommodate a wide range of door sizes, making it ideal for varied cabinetry projects. Designed for convenience, the SprayTwirly assembles in minutes without tools and packs up easily for transport. Now upgraded with increased table height (Lot #104), it enhances ergonomics for improved workflow.
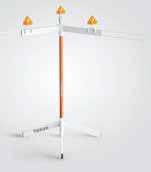
piGRIP® FLC – Flexible Level Compensation for Custom Vacuum Solutions
The piGRIP® FLC (Flexible Level Compensator) is a versatile vacuum system component engineered to expand the performance range of Piab’s piGRIP® suction cups. Ideal for off-angle picking and height variance applications, the FLC allows integration of suction cups with unique sealing or friction properties—even those with limited stroke length. Its secure clamp interface minimizes the risk of detachment during operation, while enabling a wide variety of bellow combinations for fully customized setups. Compatible with piSAVE® sense valves and compliant with REACH and RoHS standards, the FLC is designed for safety, flexibility, and optimal handling efficiency. Clamp fittings are recommended for heavy-duty tasks or applications requiring added operational security.
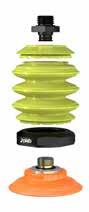
Rev-A-Shelf Vanity Drip Tray –Prevent Cabinet Damage from Leaks
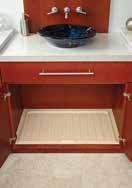
The Rev-A-Shelf SBVDT Vanity Drip Tray offers essential protection against undersink water damage in bathroom vanity cabinets. Crafted from rigid, durable molded polymer, the tray holds up to 0.92 quarts of liquid and features a smart design that channels overflow to the front of the cabinet—providing a visible alert when leaks occur. Ideal for 21” and 24” vanity sink base cabinets, it can be trimmed with a utility knife for a custom fit. While it can be installed in existing cabinetry, adjustments may be needed for plumbing or center dividers. Available in multiple sizes and finishes, the SBVDT is a simple, effective first line of defense against costly cabinet damage.
AkzoNobel Launches RUBBOL WF 3350 with 20% BioBased Content
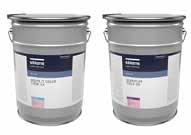
AkzoNobel has introduced RUBBOL WF 3350, a waterborne wood coating featuring 20% bio-based content, developed by its Sikkens Wood Coatings business. Designed for interior and exterior use, the sprayable opaque coating delivers high performance and durability without compromising sustainability. Its renewable content, derived from plant-based materials, has been independently verified using ASTM D6866 C-14 testing. Manufactured in Malmö, Sweden, RUBBOL WF 3350 is backed by the Sikkens Extralife warranty, ensuring long-term protection. “We’re helping reduce environmental impact while supporting our customers’ sustainability goals,” said Sustainable Innovation Manager Tessa Slagter. The launch reflects AkzoNobel’s broader strategy to incorporate bio-based materials across its product lines, including automotive and interior paints with significant renewable content.
Biesse Rover B FT HD – Fastest CNC for Nesting with TwinHead Design
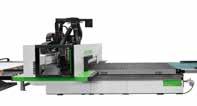
Biesse has introduced the Rover B FT HD in a twin-head configuration, delivering the fastest CNC performance for nesting and panel processing. Each head operates independently in shared space, enabling mirror-mode machining or secondary operations during tool changes—boosting productivity while reducing space and equipment costs. Engineered with a restructured chassis and enclosed open-table design, the machine eliminates vibration and enhances safety. Upgraded components allow rapid acceleration (10 m/sec²) and cutting speeds up to 128 m/min. Even in single-head mode, it’s 30% faster than standard models. Ideal for highvolume, standardised production, the Rover B FT HD offers unmatched speed, efficiency, and performance—outpacing two machines with a single footprint.
OptiPockit DM 2025 Edition – Dimmable 24V/3W LED Puck Light with Recessed Trim
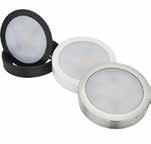
The 2025 OptiPockit DM is a versatile, dimmable 3W LED puck light designed for smooth, warm 2700K illumination. Compatible with Freedim controllers, in-line dimmers, and aftermarket hardwired dimmers, it offers seamless integration into new or existing lighting setups. This 24V fixture includes interchangeable recessed trims in nickel, white, and black, making it easy to match any design aesthetic. The 79” lead provides ample wiring flexibility for under-cabinet, display, or accent lighting. Designed for performance and ease of installation, the OptiPockit DM is ideal for residential and commercial applications seeking energy-efficient, adjustable lighting with a clean, modern look. Rated 4.2 by users, it blends style and functionality in a compact form.
DEWALT® 20V MAX GRABO LIFTER – Built for Heavy Lifting
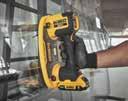
The DEWALT® 20V MAX* GRABO LIFTER delivers high-performance suction for lifting heavy, awkward, and delicate materials across the jobsite. With a 265 lb capacity and a powerful vacuum pump, it grips smooth, textured, and semi-porous surfaces like plywood, tile, sheet metal, and glass. Designed for professional use, it features a built-in pressure sensor for real-time grip monitoring, helping reduce damage and increase safety. Ideal for solo or team lifts, the GRABO LIFTER improves handling efficiency across wood, tile, glass, and HVAC applications. As part of the 20V MAX* system, it runs on DEWALT’s trusted battery platform for seamless jobsite integration and consistent power. Grip, grab, and get to work—this lifter is made to move.
stats and facts
In February 2025, Canadian lumber production saw a 15.3% decrease from February 2024 (Statcan)
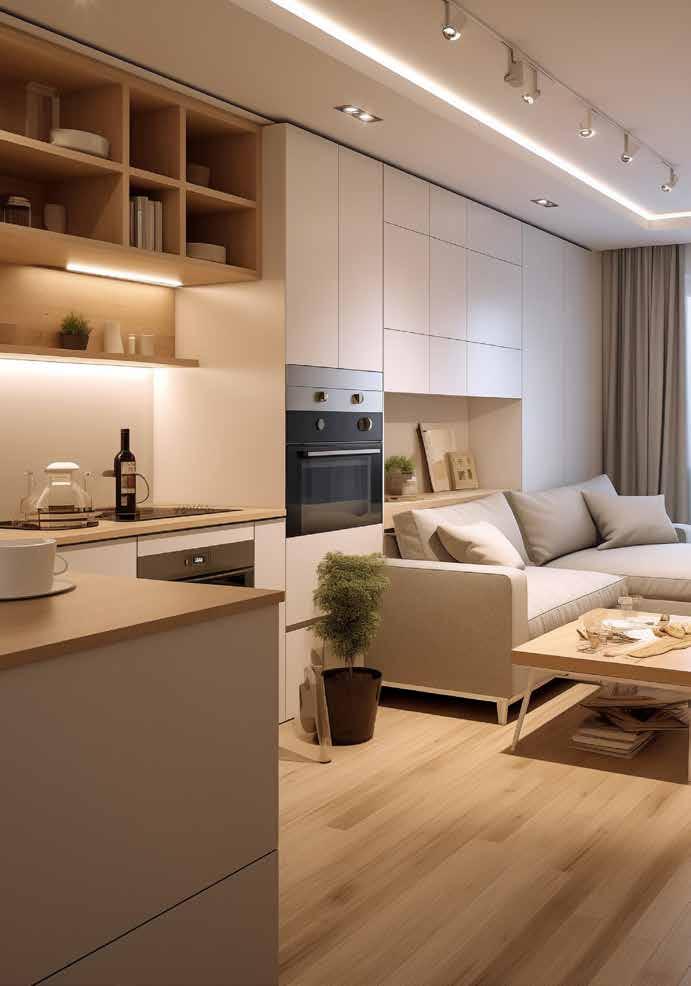
In March, Natural Resources Canada also announced $13.3 million in funding for 28 forest sector projects in Quebec (Natural Resources Canada)
In March, Natural Resources Canada announced $20 million in funding for 67 projects “that support the growth and resilience of British Columbia’s forest sector” through the Green Construction through Wood (GCWood) program (Natural Resources Canada)
The 2024 Canadian federal government budget earmarked $409.6 million over four years, starting in 2025–26, to the Canada Mortgage and Housing Corporation to launch a new Canada Secondary Suite Loan Program, enabling homeowners to access up to $40,000 in low-interest loans to add secondary suites to their homes (CKCA)
Investment in multi-unit construction rose $241.5 million to $8.4 billion in February, largely attributable to gains in Ontario (+$357.8 million) and British Columbia (+$53.1 million) (Statcan)
The Canadian Occupational Projection System predicts a total of 44,700 job openings in carpentry between 2024–2033, with job creation accounting for 35% of openings and replacement demand accounting for 65% (ESDC Canada)
In 2024, FedDev Ontario pledged $2.9 million to support the Wood Manufacturing Cluster of Ontario. The funding aims to help with industry modernization efforts, particularly digital transformation, and to date, has generated $12.5 million in total project value (WMCO)
Ontario’s Achievement Incentive Program offers up to $17,000 to eligible employers in the trades, helping them reduce the cost of apprentice training (Ontario.ca)
As of April 30, 2025, the City of Hamilton issued building permits totaling $1.016 billion, marking the highest construction value for the first four months of any year in the city’s history and surpassing the previous record set in 2021 (City of Hamilton).
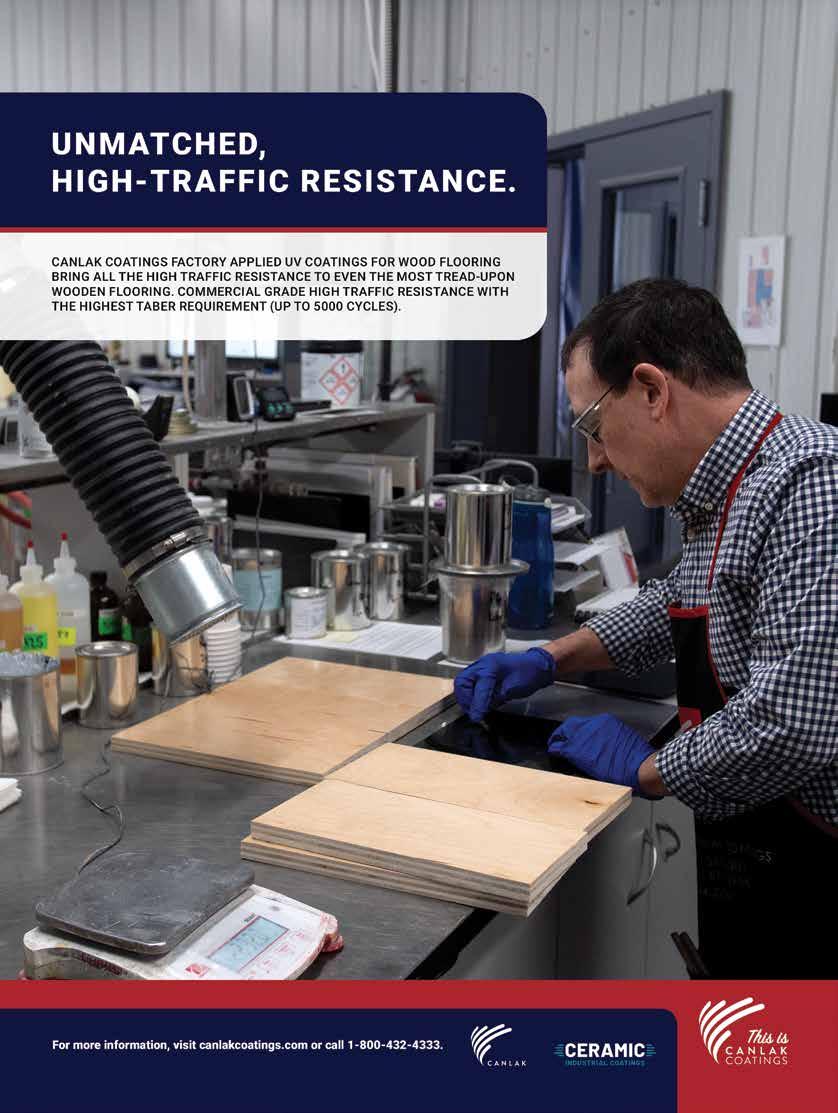

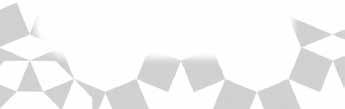
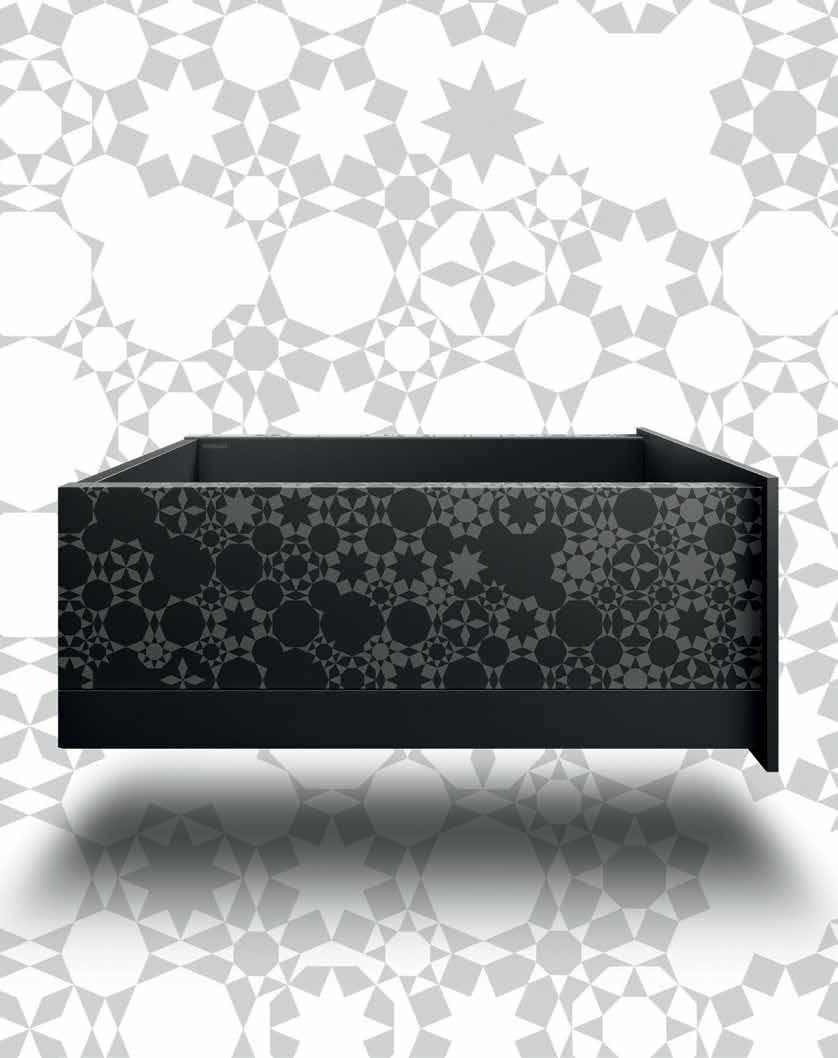
Nova Pro Scala Moved
by Art
VITRUM ARTE
Art by Valcucine
Printed designer panel