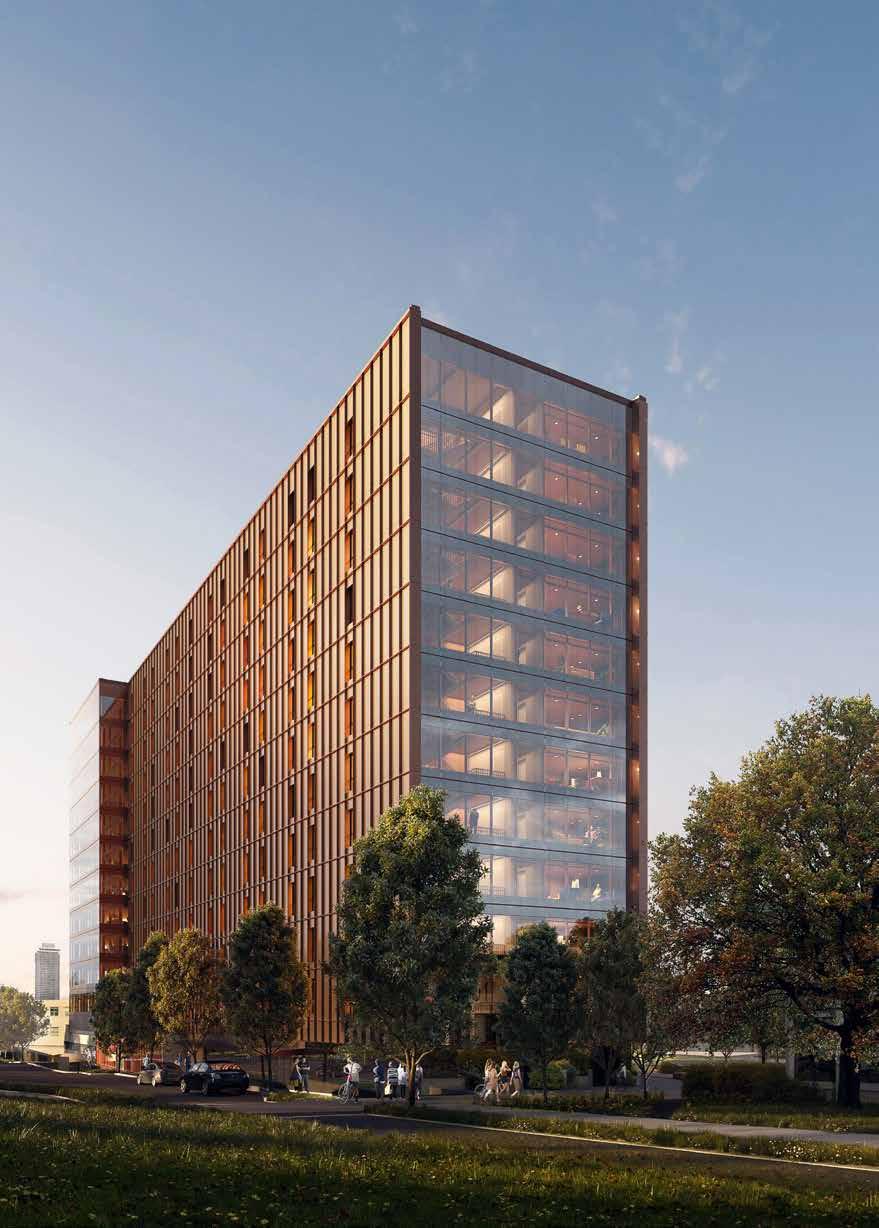
BCIT TALL TIMBER STUDENT HOUSING
BYRON TARBY, PRESIDENT, MAKON PROJECTS | TECHNOLOGY
VIBI AWARDS OF EXCELLENCE — VICA WINNERS
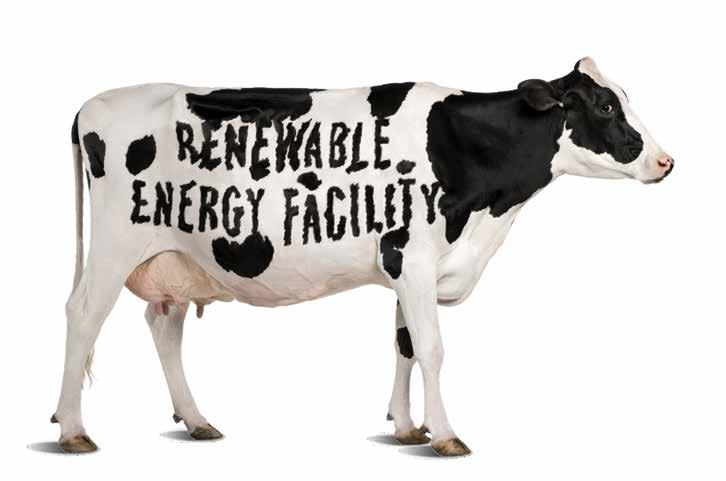
BYRON TARBY, PRESIDENT, MAKON PROJECTS | TECHNOLOGY
VIBI AWARDS OF EXCELLENCE — VICA WINNERS
Like biogas captured from cow manure to create Renewable Natural Gas1 (RNG). It’s a low-carbon2 energy that can help reduce overall greenhouse gas emissions, with more RNG projects underway.
Customers can sign up for the voluntary RNG program to designate five, 10, 25, 50 or 100 per cent of the gas they use as RNG.
Find out more about RNG at fortisbc.com/rngbuild.
Byron Tarby, president of Makon Projects, is passionate about construction and is growing his company in Nanaimo.
BCIT Tall Timber Student Housing is a showcase of innovations in mass timber construction, prefabrication and sustainability.
19 Technology Innovation with Digital Strategies The Power of Trenchless Technology Unlocking the Power of Data
04 Message from the Editor
22 The Legal File Construction Challenges in 2025
Cover Photo
BCIT Tall Timber Student Housing, courtesy of BCIT.
A significant project that recently completed was the new $39 million Canfor Leisure pool in Prince George. The city is also seeing strong residential development, which has increased significantly over the last few years. Earlier this year, the city reported 2022 saw record-high building permit values at a little over a quarter of a billion dollars.
When Scott Bone announced his retirement in 2022, he encouraged Bryant to put her hat in the ring. He was at the helm of the association as CEO for seven years.
“In Prince George, we don’t have as many capital projects but residential is very busy,” says Bryant.
The NRCA represents 211 members including general and trade contracting companies, manufacturers, suppliers and professional service providers. The association covers the largest geographical region in B.C., spanning from Williams Lake to the Yukon border and from the Alberta border to the West Coast.
“Given my combined knowledge of business development and the construction world, I thought the position was a good fit,” says Bryant, who just completed her bachelor’s degree in marketing at UNBC in April and is now working on a post-graduate certificate in non-profit management at SFU.
Our Awards issues are always fun to put together. Recognizing the hard work and ingenuity that result in sustainable and beautiful buildings or critical infrastructure is a great way to draw attention to companies, individuals and the industry.
“ We are a staff of three and being a small team, we have to work twice as hard to pull off what we need to do to serve our members,” says Bryant, who knows the region well.
While Bryant juggles a range of industry priorities, the issue of prompt payment is a major focus for the association.
for the multi-phase Sunrise Ridge Resort in Parksville. For our profile, I spoke with Byron Tarby, president of Makon Projects. Passionate about construction, he is focused on growing a young team at his company, which he started five years ago.
demand grows. The situation is particularly acute in northern B.C. with the large number of major projects and small population.
Labour reports indicate B.C. will be short 23,000 skilled workers by 2029.
“ Our focus is filling that labour shortage and helping our members become employee of choice so that we can attract more people to the construction industry,” says Bryant.
The association launched its Women in Construction committee last year to address barriers that prevent women from getting into and staying in the construction industry. One of the initiatives was to host a construction camp last summer to provide young women with practical hands-on skills and other training.
As we do every year, all the Vancouver Island Construction Association Award winners are showcased in this issue. Pomerleau won the top Prime Contractor Award for a project over $25 million. The highly complex B Jetty recapitalization project at the CFB Esquimalt meant working in a marine environment requiring careful coordination and technical expertise.
Born and raised in Prince George, Bryant was exposed to the construction industry at an early age through her grandfather. He had an electrical contracting company called Bryant Electric which he founded in 1960.
“I grew up in the industry and was involved in estimating and project management in both construction and manufacturing,” she says.
Makon Projects was also a winner this year, taking home a Prime Contractor Award
Before joining NRCA, Bryant was an account executive at Bell Mobility. She knew many of the NRCA members by offering services and education through an affinity partnership with the association.
“One of the top priorities province-wide is prompt payment,” she says. “It’s an important piece of legislation that’s been tabled time and time again. We are working to push that boulder uphill to see if we can get the attention of the provincial government. Construction is one of those industries where it can take up to 120 plus days to get paid. It’s time that changes.”
On our cover is another impressive building — the BCIT Tall Timber Student Housing project. It showcases significant strides in tall, hybrid, mass timber construction. A unique structural design and prefabrication are a couple of the key features of this project, which is set to open in the fall to meet student housing demand on the Burnaby campus. The use of technology in design and construction allowed the project to achieve its goals of sustainability, efficiency and affordability.
Taking advantage of technology continues to be touted in the construction industry by experts, but more needs to be done to accelerate adoption. From prefabrication to AI, using digital tools can make a difference — especially in uncertain market conditions. Learn more in our technology section inside this issue.
Procurement practices are another area of concern where the construction industry continues to call for accountability, transparency and fairness.
“Contractors are bidding on prices good for seven days and the tender doesn’t get decided on for nine days so by the time the contract is awarded, those prices are out of date. That’s how volatile it is,” says Bryant.
Of course, labour shortage remains a pressing challenge and will increase in severity as project
“ We conducted a high school youth building program where women came together to build a shed — planning, project management and construction,” says Bryant. “We will auction the shed at the awards gala. It’s an opportunity for them to take pride in the project.”
As the number of industry veterans hang up their hardhats over the next decade, recruitment and retention of skilled tradespeople from all underrepresented groups will be critical.
Cheryl Mah Managing Editor
“ We need to really empower our equityseeking groups, who are actively involved in construction or who want to be involved in construction, to see that it is a career choice. It’s not a boys’ club anymore. We’re looking at an equal and open environment,” says Bryant.
BY CHERYL MAH
For Byron Tarby, watching his young team and company grow over the last five years has been tremendously rewarding.
“We have invested a lot into training and mentorship within our company and seeing these young and new workers transform from zero experience to carpenters and project managers has been phenomenal,” says Tarby, founder and president of Makon Projects.
Hiring young and new workers was a necessity when Makon undertook its largest project to date in 2021: the Sunrise Ridge Resort. The company was tasked to deliver 64 luxury townhome units across 10 construction phases (6-15) for the multiresidential development in Parksville. Additionally, Makon provided construction management services for all underground civil infrastructure, ensuring the project’s success from the ground up.
“The industry was booming when we landed this project and labour was extremely hard to find,” says Tarby. “So we had to hire young and new workers. It was a risky challenge but it has been amazing to see them learning… with many of them growing into greater levels of responsibility in the company.”
The successful execution and hard work on the project earned Makon a Prime Contractor VICA Award at the annual Vancouver Island Building Industry (VIBI) Awards.
“The award means a tremendous amount to the team,” says Tarby. “It shows our expertise — that a smaller, relatively new company has what it takes to execute sophisticated large projects. Being nominated was already a big surprise.”
Aside from having to overcome a labour shortage, the other major challenge on this project was building in an Oceanside resort that remained fully operational during construction. Makon had to implement careful coordination and safety protocols to minimize any disruptions to guest experience. The project was completed on time and on budget in 2024. The project also won a Vancouver Island Commercial Building Award.
“At the end of the day, it’s all about building relationships and having a happy client who will recommend us and work with us again. That was the case on this project,” says Tarby.
Makon is continuing to establish its reputation and brand on Vancouver Island, focusing on
commercial, multi-residential and light industrial projects. Current projects include a new fire hall for the Village of Tahsis, a watermain upgrade in Nanaimo and an ice arena mechanical upgrade in Comox. Makon also completed the Vancouver Island University gathering place (Shq’apthut) ex-
pansion, which added 2,750 square feet of new ceremonial spaces, offices, and accessible washrooms.
“Business is good and we have a few multi-family projects in the pipeline. Vancouver Island is experiencing strong growth so there are lots of opportunities,” says Tarby, who discovered his interest in construction when he moved to Nanaimo from South Africa.
Like many on his team, Tarby knew little about construction when he started. Building his own home in 2008 with his wife sparked a passion for construction that led him to explore carpentry at Vancouver Island University.
“I had no experience but going through the construction process for our home, I was basically project managing. My strength is working with people, leading people and managing teams,” recalls Tarby, who began his career at the bottom with a local company and moved his way up to gain carpentry experience.
When the residential market downturn hit, he moved to Alberta and spent two years with an industrial piling company where he was a project manager and worked as a site superintendent on one of the company’s largest projects. During that time, he obtained his Project Management Professional (PMP) certification.
In 2016, he moved back to Nanaimo and worked for a couple of general contractors, gaining experience in the ICI sector by working on projects for major brands like 7-Eleven, Starbucks and Tim Hortons.
“I always knew I wanted to start my own business but I also knew I needed the skillsets... so working with these different companies in diverse industries allowed me to build practical and managerial knowledge,” he says.
Taking the entrepreneurial plunge, he and his wife founded Makon Projects in 2020 in their basement. It was the height of the global pandemic — full of uncertainty and lockdowns but also opportunities. Demand for home renovations spiked during COVD-19.
“It was scary venturing out on our own during COVID, but fortunately people were renovating their homes. We landed a couple of jobs right away and hit the ground running,” says Tarby, 45.
His decision has paid off. Today, the Nanaimo-based company has grown to more than 25 employees, offering general contracting, construction management, and design build services.
Tarby’s leadership and commitment to shaping the future of construction extends outside his company. He serves as a board director for both the B.C. Construction Association and the Vancouver Island Association.
“I am passionate about the industry. I want to see our industry grow and flourish. I know how much the industry has given to me. If I can give back, I’m
BY CHERYL MAH
Innovative strategies are being used to deliver a new benchmark for mass timber construction on BCIT’s Burnaby campus.
Set to complete this fall, the BCIT Tall Timber Student Housing will not only meet the demands of a growing student population but also showcase encapsulated mass timber construction, sustainable design and prefabrication.
The new 12-storey building will more than double the supply of on-campus housing and include 470 beds in studio and single units; common spaces and support areas; shared kitchens; and an outdoor accessible plaza.
The use of mass timber construction was a key objective on this project as well as ensuring this is a
highly sustainable building by targeting BC Energy Step Code 4 and Zero Carbon Building certification. The project received Zero Carbon Building certification in December 2024.
“From the very beginning, the team was focused on the environmental and innovative aspects of the design. This project was an opportunity for including mass timber hybrid systems and prefabricated construction,” said Slavica Puzovic, senior architect, Perkins&Will, at Buildex Vancouver.
Specific sustainability features were implemented to achieve low carbon targets including a high performance envelope designed to reduce heat transfer, a low window to wall ratio using triple-glazed windows, and increased insulation in the roof and walls.
Puzovic described how the design focuses on modularity with the studio and single bedroom suites stacked floor-to-floor.
“The repetitive nature of this program and the modularity of layout worked extremely well with the prefabrication requirements. The units are repeating throughout the floorplan but they are completely stacked vertically including all services,” said Puzovic.
The mass timber and structural steel hybrid building with a fully prefabricated envelope is configured as two rectangular wings positioned at 90 degrees. The CLT point-supported structure is comprised of 11 storeys of cross-laminated timber (CLT) floors supported by steel hollow structural section (HSS) columns, on a concrete podium. The building in-
cludes a below-grade basement for services and additional storage.
“Besides the efficiency of the construction, another benefit of having a prefabricated envelope is reduction of embodied carbon and minimizing waste,” said Puzovic. “The CLT had to be encapsulated as the building was being erected. The only way to keep enclosing the building as you’re installing the structure is to use a prefabricated envelope. All CLT panels with steel columns and all prefabricated envelope panels were installed within 25 weeks.”
The use of steel HSS columns is one of the notable features on the BCIT project, according to Jamie Pobre Sullivan, associate, Fast+Epp.
Sullivan explained that the columns fit within a standard party wall assembly, allowing for a higher net-to-gross floor space ratio to maximize occupiable space and layout efficiency. The steel also allowed for shop-installed, prefabricated components that could be lifted into place, reducing the need for temporary shoring during construction.
Another unique aspect is the use of Western Hemlock in the CLT, which is underutilized and historically not specified due to the complexity of drying. The decision to use a Hem-Fir option was driven by on-site delays and to address material supply chain challenges at the time.
“This is the largest commercial use of Hem-Fir in CLT to date,” said Sullivan, noting they were able to find a CLT supplier that “is a long standing lumber mill and has a history with drying Hemlock and producing Hem-Fir lumber.”
Each mass timber level comprises of flat, two-way spanning, Hem-Fir CLT floor plates, point-supported on steel columns without beams, and uses 3.5-metre wide CLT panels.
“The cores were another big consideration on how do we speed up construction and simplify the structural design,” she said, explaining the project has a steel concentrically braced frame for the lateral resisting system at the stair and elevator cores which help speed up construction and acted as egress during construction.
Cole Edwards, senior project manager, Ledcor, emphasized how quickly the building went up, noting they broke ground in 2022 and it was about 30 weeks from transfer slab to enclosing the building. He credited the project constructability and success to a self-supporting superstructure, prefabrication, preconstruction and moisture mitigation planning.
“It was a very rapid pace of construction only possible through these four things,” he said, adding Ledcor spent a year in preconstruction planning before mobilizing on site. “We did clash detection, detailed all the penetrations in the CLT and built 4D models to help the construction teams plan out the execution of the work and steel erection sequences.”
This early involvement allowed the team to address potential challenges and optimize the construction process.
The CLT panels, point supported systems as well as the façade were all prefabricated which expedited construction. Prefabrication meant greater quality control and there were significant safety benefits, said Edwards citing no silica work, no loud noise, no swing stages and reduction in crew sizes.
“Multi-storey lifts reduced the amount of welding on site so quicker and safer,” he said.
The project topped out in July 2024 and was fully enclosed by September 2024. The construction schedule was planned to optimize efficiency.
Edwards explained the CLT was installed approximately on a two week cycle (taking into account for delays) — first was the CLT panels and then the façade and structural columns.
“As soon as panels came to site we could immediately put them in place. No single step in this erection could be delayed. It was challenging with all the different scopes but we were able to understand the process and time everything out,” he said. “The construction team was able to maintain that tight schedule.”
One of the most important aspects of mass timber construction is managing moisture. On this project, passive protection was used for the moisture mitigation planning.
“The most important thing you can do to keep wood dry is get the building enclosed quickly,” said Edwards, explaining they used Home Depot gutters for the slab edges and solid pipe to help drain the building out. “A lot of our efforts were spent on passive protection that doesn’t require workers on site.”
While encapsulation went well, Edwards said maintaining the sequence can be challenging and without careful planning and execution, it can “derail your project if you can’t get the panels dry enough.”
Cole emphasized prefabrication benefits were significant. “You can build mass timber building — prefabricated buildings this fast and you can build them year round,” he said. “For the next project, we would
like to prefabricate more. Prefabrication went fast. Traditional construction went conventional speed. The more prefabrication, the better.”
The project has already garnered international attention for its structural engineering ingenuity. It won Outstanding Structure at the NCSEA 2024 SEE Awards. It also earned a ACEC-BC Merit Award.
Endor sed by the leading construc tion, design and architec tural associations, Construc tion Busines s is the publication of choice by adver tiser s who want to reach the decision maker s in the multi - billion dollar B C. and Alber ta construc tion marketplace To adver tise your produc t s, ser vices and exper tise or for more information on customizing an adver tising program, please contac t: Dan G noc
dang@mediaedge.ca
2025 marked out fifth annual VICA Awards, a celebration of the year’s past building and individual achievements. As the premiere industry association on the island, the Vancouver Island Construction Association (VICA) Awards showcase the outstanding achievements and contributions of our members: the prime contractors, trade contractors, and individual construction professionals from the south to the north, and everywhere in between.
Dan Gnocato Publisher
Construction Business Magazine 1/3 page -
CONGRATS
VIBI
Inspired by the resilience of Vancouver Island’s construction industry and its continued strength as an economic driver, we shifted from a traditional sit-down dinner to an Oscars-inspired evening featuring cocktails, canapés, and entertainment. This new format allowed us to celebrate our members in a fresh, engaging way while reflecting the energy and adaptability of our industry.
This year, we received almost 60 submissions for 16 categories, highlighting the pride our membership takes in their work. The projects that were recognized represent only a small portion of the bustling construction activity on Vancouver Island
and the Sunshine Coast, however, that does not take away any of the achievement and quality of these projects. The effort, proficiency, and collaboration of these projects are a testament to the abilities of these companies and their teams, and are considered exemplary within our highly competitive industry.
The individual awards acknowledged local industry and business leaders, recognizing their continued contribution to our sector through mentorship, volunteer work and business achievement. The Woman in Construction (WiC) of the Year Award and the U40 Person of the Year Award showcase the committed leaders within our WiC and U40/Young Builder committees, and we’re excited to be a part of their leadership journey.
On behalf of VICA staff, board and our membership, congratulations to all the nominees, and award recipients. We are already looking forward to next year’s awards!
Rory Kulmala CEO, VICA
Congratulations to all the nominees, and award recipients. We are already looking forward to next year’s awards!
BY CHERYL MAH
THE $1.1B A/B jetty recapitalization project at the Canadian Forces Base Esquimalt was a challenging undertaking in a marine environment that required overcoming complex logistics and pandemic constraints while meeting rigourous specifications.
The replacement of two aging jetties consisted of extensive dredging, demolition and construction to deliver larger, more modern and robust berthing facilities that will meet current industry standards that address climate change, tsunami risks, and seismic resiliency. The project supports Canada’s National Shipbuilding Procurement Strategy, which will deliver modern ships to the Royal Canadian Navy over the next 30 years.
Pomerleau has been working on A and B Jetty since 2017, initially awarded the contract for the deconstruction of B Jetty and environmental remediation. They were awarded a second contract to rebuild B Jetty and began construction in late
2019. Substantial completion was achieved on August 8, 2024.
The new B Jetty construction is a multi-purpose marine jetty that extends 270 m from the existing shore and is 26 m wide. The jetty structure is supported by 273 large-diameter steel pipe piles with depths varying from 15 to 100 m drilled into rock. The connection to the future A Jetty is 36 m long and 59 m wide.
“This project was extremely complex and challenging from both a technical and logistic perspective,” says Tomy Drolet, project director at Pomerleau.
Challenges included executing very specialized and complex marine construction on an active military base and extensive in water work requiring environmental measures and mitigations that had to be in place throughout the project. Foundation, reinforcement, formwork, and concreting work had to be carried out by diving teams.
The new jetty required more than 30,000 m3 of concrete cast in place, with a large portion of the concrete construction completed inside the tidal zone daytime and nighttime.
A significant amount of work was performed during the pandemic, adding additional sanitary measures and supply chain challenges, notes Drolet. ” Having specialized supplies coming from everywhere in the world, we had to reorganize some of our work to allow for the pandemic-
delayed deliveries without creating a negative impact on the critical path of the project.”
The project was delivered by a small army of more than 200 employees on-site during peak periods. Planning of work required significant coordination with subcontractors, suppliers, deliverers, and onsite trades. All activities also had to be executed according to the plans developed and approved by Defence Construction Canada to ensure base operations were not impacted by construction — particularly on the water where large ships and significant traffic were present. Security clearance management was also a priority.
Work is now focused on the A Jetty expansion project, which is the final phase, and is expected to be completed in 2031.
The successful delivery of this extremely challenging project earned Pomerleau a Prime Contractor VICA Award.
“It is huge honour for us to receive this recognition from VICA and in front of our peers. Pomerleau has been working on the Island since 2017, and are committed to making the communities of Vancouver Island better places to live, work, and build. This award recognizes that commitment,” says Drolet.
MAKON PROJECTS served as the general contractor for this multi-residential development at Sunrise Ridge Resort in Parksville. The company delivered 64 luxury duplex units across 10 construction phases at Sunrise Ridge Resort—all while the Oceanside resort remained fully operational. With careful coordination, safety protocols, and a strong focus on guest experience, Makon balanced quality with efficiency. Another major challenge was overcoming a labour shortage at the time, requiring the hiring of new and young workers. The project fostered industry growth by training emerging talent, making it a standout in both execution and impact.
Designed by Praxis Architects, key features include wood-frame building construction with durable metal roofing, custom interior finishes, and thoughtfully designed landscaping and hardscaping. Additionally, Makon provided construction management services for all underground civil infrastructure, ensuring the project’s success from the ground up.
OPENED IN 2024, the Hulitan Early Years Centre in Colwood is B.C.’s first trauma-informed, Indigenous-focused childcare facility. This one-storey, 6,000-square-foot space supports daycare, after-school care, and the Journeys of the Heart cultural program. Through strong community and stakeholder collaboration, the $4.3 million centre blends modern amenities with cultural care—creating a welcoming, purpose-built environment for Indigenous children and their families.
PML Professional Mechanical Ltd. Nanaimo Correctional Centre Replacement Project
SITUATED ON THE traditional territory of the Snuneymuxw First Nation, this correctional facility redevelopment expanded to 180,000 square feet with 11 new buildings and a community-focused design. Phased construction kept operations running while enhancing spaces for education and rehabilitation. With sustainability in mind, a high-efficiency VRF system was installed—supporting reintegration through thoughtful design and long-term energy performance
Located next to the original correctional centre, the new campus-style Nanaimo Correctional Centre (NCC) is architecturally inspired by traditional Coast Salish plank houses and designed to ensure safety and security, while supporting a strong connection to the natural environment and an operational model focused on healing, recovery and change.
In addition to expanding remand capacity for Vancouver Island, the new centre includes a unit for women and features modern purpose-built spaces for programs such as the Guthrie program, which combines work, addictions treatment and counselling. The new centre features specialized areas for working with people with complex mental-health needs and a sophisticated healthcare centre.
AT CLAYOQUOT Wilderness Lodge, Hakai Energy Solutions delivered B.C.’s largest off-grid solar and battery microgrid. The 824kW solar field and 1.66MWh battery system cut diesel use by 80 per cent, transforming energy use at the remote lodge. Completed ahead of schedule despite rugged conditions, the project sets a new benchmark for renewable innovation in off-grid environments.
Skytec Contracting Canada Ltd. Port Alberni Child Care Center
THIS PROJECT UNITED the historic Rollins Art Building with a new, energy-efficient childcare facility — blending heritage with innovation. Skytec Contracting delivered a high-performance building enve-lope that met the B.C. Step 4 Energy Code standards, skillfully managing the complex integration of old and new structures. Through precise craftsmanship and strong collaboration, the team preserved character while creating a vibrant, modern community space.
Jordin Dillon, Knappett Projects Inc.
Jordin Dillon, a Red Seal carpenter with more than 22,000 hours at Knappett Projects, started as a labourer and rose to foreman on a $60-million site. Known for his infectious positivity and dedication, Jordin overcame personal challenges with the help of mentorship and now pays it forward, supporting others on their journey. He’s a true example of growth, leadership, and heart.
Jayna Wiewiorowski
Jayna Wiewiorowski is the heart of VICA volunteerism. A longtime YBN leader and last year’s chair, she’s also an active force in Women in Construction and a key contributor to the first Women’s PPE Showcase that took place last fall. Always engaged and always smiling, Jayna’s energy, dedication, and leadership make her an exceptional choice for our inaugural Volunteer of the Year.
SUPPLIER OF THE YEAR
Harbour City Kitchens
Harbour City Kitchens sets the standard for what a construction supplier should be—skilled, proactive, and reliable. On projects like Kentwood Place, their technical expertise, collaborative spirit, and exceptional service made them a true partner. With consistent delivery, problem-solving foresight, and a customer-first mindset, HCK is a standout for Supplier of the Year.
Caitlyn Bruce, Green Island Builders
Caitlyn Bruce is transforming construction culture with bold, equity-driven leadership. As people and operations manager at Green Island Builders, she’s introduced inclusive policies—from menstruation leave to flexible work—and helped earn the company major workplace accolades.
Kerr Controls Inc. (1 – 20 Employees)
A dedicated VICA member since 2003, Kerr Controls is a familiar and valued presence at events and initiatives. Co-owner Christy Kerr’s leadership extends beyond the company, with her active role on the BCCA Employee Benefits Trust Board. Their long-standing commitment to industry support and engagement makes Kerr Controls a standout Member of the Year.
Copcan Civil LP stands out as a true champion of the VICA community. They attend every event, proudly sponsor select initiatives, and have made a major investment in workforce development by enrolling their team in VICA’s education programs. Their ongoing commitment to industry engagement and employee growth makes Copcan Civil LP a standout Member of the Year.
Cap Canada (21 – 50 Employees)
A dedicated VICA member since 2006, White Cap Canada has been a consistent and enthusiastic supporter of the community. From sponsoring to showing up at nearly every event, their commitment goes beyond presence—it’s partnership. Their unwavering support strengthens our industry connections and spirit, making White Cap Canada a valued and outstanding Member of the Year.
UNDER 40 OF THE YEAR
Brett Willsie, Green Island Builders
Brett Willsie is a rising leader in Vancouver Island’s construction industry. Known for his technical expertise, strong communication, and collaborative leadership, Brett builds trust across teams and delivers complex projects with precision. From major developments to day-to-day site success, he brings energy, insight, and a drive to continuously learn and lead by example.
VICA MEMBER OF THE YEAR (ASSOCIATE)
Coast Capital Investment Management
Coast Capital has been an incredible supporter of VICA, backing nearly every initiative the association undertakes. From sponsoring major events to showing up at golf tournaments, Trades Night, the VICA Conference, and the VIBI Awards, their presence is felt across the entire community. Coast Capital’s dedication and partnership make them a truly deserving Member of the Year.
EMPLOYER OF THE YEAR
Heritage Masonry
At Heritage Masonry, every detail matters—on the job and in the workplace. With a passion for tradi-tional craftsmanship, they foster creativity, community, and well-being. From meaningful restoration projects to tailored benefits and handson mentorship, Heritage Masonry supports its team like family.
Path Group Properties Corp.
Flynn Canada Ltd.
Casman Projects Ltd.
Omicron Construction Ltd.
Kerr Controls Inc.
Western Grater Contracting Ltd.
Prep Energy Limited
EllisDon Corporation
Tsolum & Tsable OHS
BY HAMMAD CHAUDHRY
In construction, profitability often hinges on decisions made long before any concrete is poured. Project managers frequently ask, “We won the job, but what did we miss?” The old adage, “When it rains, it pours,” rings especially true on the job site, as small problems often cascade into larger ones if left unchecked. Issues like weather delays, design changes, coordination errors, and equipment downtime can quickly erode projected profits.
Recognizing these challenges, the National Research Council of Canada and UNB Offsite Construction Research Centre released the “Roadmap to Transform the Canadian Construction Industry” (2025). The Roadmap identifies key barriers, including fragmented regulations, limited digital adoption, and cultural resistance. It offers strategies to accelerate industrialized construction and productivity through innovation. It aims to shift the industry from reactive firefighting to proactive planning, laying the groundwork for Canada’s construction sector to modernize, digitize, and scale.
Many companies instinctively cut innovation budgets when problems arise, expecting field teams to find solutions on their own. While this seems prudent, it often results in higher costs down the road. Instead, leading contractors are investing in digital strategies that service risks early and protect profits throughout a project’s lifecycle.
Disconnected tools, 2D drawings, fragmented databases, and siloed communication often lead to expensive errors that surface only once construction is underway. Canada’s regulatory complexity compounds the issue, as codes and approvals differ across jurisdictions. The Roadmap calls for national harmonization and digital standardization to reduce delays and unlock innovation at scale. As Frank Lloyd Wright said, “You can use an eraser on the drafting table or a sledgehammer on the construction site.”
1.
Building Information Modelling (BIM) and Virtual Design and Construction (VDC) enable teams to coordinate designs virtually, resolving issues before they hit the job site. Large and mid-size general contractors, including PCL, DPR, EllisDon, Suffolk, Turner, and Skanska, now maintain dedicated BIM/ VDC teams. A part of how they do business.
A 2011 ASCE study found BIM coordination can yield a 634 per cent ROI. The Roadmap also flags early modelling as a proven tactic to reduce rework, compress timelines, and facilitate prefabrication.
2. Reality Capture and Monitoring
Tools like laser scanning, drones, fixed position
cameras, and 360 degree photography provide accurate, up-to-date views of the job site. During a Vancouver project I supported from 2019 to 2020, weekly scans helped our team stay on the critical path. We caught deviations early, preventing rework and delays.
This isn’t anecdotal. Studies show that reality capture can reduce project durations and costs by 15 per cent or more. It builds trust, improves communication, and keeps progress measurable against the plan.
3. Prefabrication and Modular Construction
Off-site construction reduces labour demands by 25–35 per cent, improves safety, and mitigates weather delays. According to the Roadmap, prefabrication is critical to addressing Canada’s labour shortages and housing demands.
Modular methods can cut total project costs by up to 20 per cent and compress timelines by nearly 50 per cent. But they depend on accurate models and integrated teams, something digital workflows make possible.
4. Mobile Field Management Tools
Mobile apps for reporting and documentation reduce administrative tasks by around 30 per cent (Dodge Data & Analytics, 2019). They give foremen and project managers real-time access to data, improving agility and reducing lag in decision-making.
5. Advanced Analytics and AI
Leaders like Turner, Mortenson, Suffolk, and Pomerleau are using AI and predictive analytics to forecast risks, automate bidding, and optimize schedules. These tools enhance human judgment with data-backed insights.
The Roadmap encourages more R&D investment in AI applications for productivity, cost forecasting, and design optimization, particularly when
paired with digital construction and sensor-based monitoring.
Technology adoption fails when it feels bolted on rather than built in. Construction culture typically evolves through predictable stages: beginning with resistance, then moving to cautious adoption of targeted solutions for immediate pain points, followed by integration across departments, and finally reaching a breakthrough where digital becomes the new standard. Success hinges on pairing experienced field staff with digital talent and involving teams in technology selection. Demonstrating real wins early, like announcing “we avoided rework on level 7 and saved $20,000” during site meetings builds momentum and trust. The fundamental principle is simple: ensure change happens with your teams, not to them.
The Roadmap envisions a modernized construction sector that is collaborative, data-driven, and integrated. But technology alone isn’t enough. Contracts must evolve, too. Traditional agreements often create silos, making data-sharing feel risky. Unless we update how projects are structured with more collaborative or IPD-style contracts, many digital tools won’t reach their full potential. Construction is changing. Forward-looking companies are adopting technology not only to build faster, but also to build correctly with the new talent pool — the digital nomads. With the right tools, culture, and frameworks in place, we can solve risk before it pours and build a more profitable future.
Hammad Chaudhry is vice-president of market development and partnerships at Timescapes, a con-struction technology firm. He has more than a decade of experience driving digital innovation across Canada’s construction industry.
BY TONIA JURBIN
Imagine a city growing so fast that 28 new residents arrive daily. This is the reality facing the City of Surrey, British Columbia. Measuring over 300 km2 with a population of more than 600,000, it is the fastest-growing municipality in the province. So fast in fact that Surrey is on track to outpace Vancouver by 2040. With growing population comes the need for growing and upgrading the existing infrastructure.
Enter “Guilford the Greatest,” an ambitious development that’s creating a great opportunity to upgrade and grow the capacity of Surrey’s aging sewer system. This 20-unit townhome development is just one of the many new developments in the area that will need to be serviced by upgraded and new municipal infrastructure. In this case the challenge is to figure out where and how the new sanitary capacity should be built?
Initially, the developer pitched a new 350mm sewer main in a new alignment in the road along 148th Street. A main arterial, 148th Street, is already congested with underground services. Fearing months of traffic disruption to both residents and businesses, the city didn’t want to dig up the road and suggested their consultant to look at alternatives.
PW Trenchless Construction offered an innovative proposal to double the capacity of the existing pipe without digging up the road using pipe bursting technology. Picture a large high-tech bursting head burrowing through the old 200mm asbestos cement pipe, simultaneously splitting it and pulling a new 400mm HDPE pipe into place along
the same alignment. All this happening 3 metres below the bustling street above, with only a few strategic excavations needed.
The prime contractor sole-sourced PW Trenchless to pipe burst the existing 200mm (8”) asbestos cement pipe and replace it with a 400mm (16”) HDPE pipe over a length of about 130m (425’) with minimal excavation.
Before the work could begin a sewer bypass was installed using 2 — 150mm (6”) hoses under pressure to contain the contents of the existing 200mm (8”) pipe. The second hose was used as a standby bypass in case something went wrong. PW Trenchless also had to bypass one 200mm (8”) gravity sewer that intersected the existing main, which happened to be located along an easement that was not abandoned but had been forgotten about because it was hidden under vegetation on private property. The crews found the service connection and redirected the contents from the unexpected 200mm (8”) gravity sewer to the upstream end of the pipe bursting project so that the contents of the pipe was treated with the rest of the contents of the existing AC sewer.
Even though all the work trucks have an M-Scope utility locating device, it was still necessary to retain a subsurface utility engineering (SUE) contractor because of the large number of services and the fact that the M-Scopes that are used cannot pick up the fiber optic cables.
There were three manholes along the existing alignment and several light standards, the sidewalks, a major driveway to a park, and hydro poles that had to be managed. Even though the project was a trenchless pipe bursting project, excavations are necessary at the entry and exit pits; these are usually located at existing manholes. The existing pipe was buried over 3m (10.5’) deep, so the excavations of the entry and exit pit were about 14m (45’) long. A third excavation was necessary to access the centre manhole. This centre manhole was initially going to be replaced; however, the contractor was able to jackhammer 2 - 1050mm (40”) holes into the sides of the existing middle manhole to accommodate the new HDPE pipe. The excavation for the middle manhole was about 2 metres (6’) long and just over 3 metres (10’) deep.
Additionally, because the pipe size was being doubled, some heaving was expected, and a few of the lamp standard foundations had to be adjusted after the pipe bursting work was complete.
Another challenge along the alignment was the height of the communications conductors that were under-built on the B.C. hydro poles. The wires were only about 5.5 meters (18’) at the project’s north end. Threading the layout through all the obstacles, both below and above the ground, required careful placement and staging of the excavators supporting the HDPE pipe during the actual pipe pulling stage of the work.
For this project, the developer considered both open-cut and trenchless methods. In the end, the trenchless method proved not only less disruptive but also more cost-effective than traditional open-cut techniques. More importantly, the prime contractor liked handing it over to PW Trenchless, knowing there would be less restoration necessary with the sidewalks, hydro poles, and light standards.
The developer was also attracted to PW Trenchless because of their excellent relationship with the City of Surrey which led to smoother sailing through the inevitable hurdles of urban construction. There was also a high confidence that PW Trenchless would capably manage the sewer bypass, traffic control and all other construction-related issues — which they did. Offering a predictable lump sum to carry out and manage the work was the cherry on top.
As Surrey continues its impressive growth, the tale of “Guilford the Greatest” stands as a testament to the power of trenchless technology in solving the growing and the aging pains of a booming city.
Tonia Jurbin, P. Eng. (retired) is a geotechnical engineer and freelance writer in Greater Vancouver www.toniajurbin.com
BY MARK DEVEREUX
Canada’s construction sector faces mounting pressures — labour shortages, housing short-falls, and stagnant productivity. Among the most promising solutions is prefabrication, and now, a new digital tool makes the growing prefab ecosystem far more visible.
Developed by Scius Advisory, the Prefab Construction Navigator is the first public-facing dashboard that maps the national prefab landscape. Drawing on verified data from over 830 companies in more than 1,000 locations, the Navigator sheds light on a previously opaque part of the industry, supporting a more coordinated and evidence-based approach to con-struction modernization.
Prefabrication isn’t new. Panelized systems, modular homes, and volumetric builds have long been used in Canada. What’s changed is the scale and complexity of prefab applications. From mass timber walls in British Columbia to steel-framed volumetric modules in Ontario, these approaches are increasingly being adopted for mid-rise and institutional projects — not just single-family homes.
Yet the sector remains hard to define. Firms use different terminology to describe similar systems, and many operators fly under the radar. Sector-wide data has been fragmented and difficult to access. The Navigator solves this by combining open data, industry interviews, and spatial analysis into an interactive, filterable platform. Users can search by prefab method, material type, location, and enduse market, making it easier to understand regional capacity and identify potential partners.
Built using Esri’s ArcGIS technology, the dashboard offers a clean, intuitive interface. A national map displays company locations, while filters enable users to drill down by method —panelized, volumetric, hybrid — and material: wood, steel, or concrete.
Regional patterns quickly become apparent. British Columbia shows a growing cluster of timber panelizers, many working in partnership with Indigenous communities and public-sector housing authorities. In Ontario, the landscape includes steelbased volumetric builders and MEP subcontractors using prefab to streamline hospital, hotel, and affordable housing developments.
Importantly, the data reveals that prefab extends well beyond housing. Strong uptake is evident in institutional, commercial, and industrial (ICI) construction, where prefabricated risers, HVAC pods, and electrical closets help reduce delays and minimize on-site labour needs. Several of these systems are fabricated in highly controlled shop environments, then delivered to project sites just-intime.
Four key trends shaping prefab in Canada:
1. Hybrid systems are gaining traction, as companies combine volumetric and panelized elements to strike a balance between factory efficiency and design adaptability.
2. Regional specialization is becoming more pronounced. Timber-based construction dominates in the West, steel in Central Canada, and concrete prefabrication in urban centres where heavy-load capacity is key.
3. First Nations engagement is growing, with more Indigenous communities investing in or partnering on prefabrication initiatives to meet local housing needs, build skills, and support economic development.
4. Digital integration is accelerating, with a growing number of firms using BIM, CNC fabrication, and parametric design to link design directly to manufacturing.
Yet despite these positive developments, the data also highlights gaps, especially in regional production capacity and workforce readiness. Some provinces, particularly in northern or rural areas, have strong demand but few local manufacturers or trained workers. Others, mainly urban regions, are facing factory bottlenecks and labour constraints, threatening to slow project timelines even when funding is in place.
These mismatches have real consequences. Long transportation distances increase project costs. Limited capacity means lead times can stretch unpredictably. And in some regions, pre-fab options are so scarce that developers are forced to revert to conventional construction.
Without targeted investment in workforce development and regional infrastructure such as small-scale factories or mobile manufacturing units, many areas will continue to miss out on the full benefits of prefabrication.
By making the sector visible, the Navigator supports more informed planning and investment. Developers can identify regional partners and suppliers. Governments and procurement agencies can design more effective prefab programs. Funders can assess which clusters are ready to scale and where strategic investment could catalyse growth. Researchers can track regional performance and innovation over time.
The tool also allows users to distinguish between different business models and production types —whether a firm provides full
delivery or simply assembles
racks off-site. That nuance is critical in a sector often mischaracterized as monolithic.
And because the data is presented visually, patterns emerge quickly: underserviced areas, emerging hubs, or duplicative capacity in saturated markets. These insights can help shape everything from zoning policy to industrial land use planning.
As Canada accelerates its efforts to build more housing, lower emissions, and modernize its construction sector, prefab will play a central role. But its success hinges not just on technical capacity — it also depends on coordination.
That includes coordination of training systems, so more tradespeople are familiar with factory-based workflows and digital fabrication tools. It includes investment in regional infrastructure, so smaller communities can access prefab solutions without relying on distant suppliers. And it includes more agile procurement and code pathways that recognize the efficiencies of off-site construction.
The Prefab Construction Navigator offers a national foundation for this coordination. For the first time, Canada’s dispersed prefab sector is visible as a system—with defined players, capacities, and opportunities for connection.
Prefab is no longer operating at the margins. It’s expanding. It’s evolving. And now, with tools like the Navigator, it’s ready to deliver at scale.
Mark Devereux is principal and managing director at Scius Advisory, a Vancouver-based re-search and strategy firm focused on accelerating innovation in construction, housing, and clean technology. Their work spans national prefab initiatives, Indigenous-led housing partnerships, and digital transformation projects across Canada’s building sector.
BY NORM STREU AND CHRIS HIRST
The construction industry is facing challenging times. Not long ago, the oft-repeated phrase in the industry was to “wait until 2025.” The general expectation in the industry then was that rapidly declining interest rates would reinvigorate the industry. The mood has since deeply soured and many in the industry are now saying “just get through 2025.”
Despite rapidly declining interest rates, the U.S. tariffs have introduced so much uncertainty into the market that fewer projects are proceeding. Some have been cancelled altogether. Many now say that this is the most challenging market they have seen since 2008. Some say it is the worst in their lifetimes.
What can be done? There is much that is unfortunately out of our hands. However, there are some things that industry participants can do to protect themselves in these challenging times.
Steps that construction industry participants can take to ensure that they get through 2025 might include:
1. Watch costs and spending. In a strong market, companies can lose sight of the importance of strong cost management and spending controls.
As the market changes, those companies with
poor cost controls and loose spending habits are often the first to fail. Start treating each dollar as though it is critical to the success or failure of your business.
2. Carefully watch your inventory purchasing and closely follow inventory pricing trends. What commodities will do in this market is anyone’s guess. The best you can do is ensure that you are watching your inventory closely and ensuring you are reducing exposure to both escalation and the potential for a general fall in the price of input commodities.
3. Determine where your supply chain is at greatest risk for tariff related cost escalation. Do what you can to explore reasonable alternatives that allow you to minimize that risk.
4. Consider carefully whether now is the best time to invest in expansion. On the one hand, it is critical to avoid spending money that would place you in a weaker financial position in the event of a long downturn. A strong balance sheet is what will carry you through adversity. On the other hand, downturns can create some of the most exciting expansion opportunities, as your competitors struggle and the overall playing field shifts.
5. Consider contractual protections. Before you execute new contracts, consider how the tariffs and a market downturn may impact the agreement and whether you can add language to protect yourself. For example, in the last downturn many owners sought to renegotiate executed construction contracts to reflect new market pricing. Your contracts should include clauses now that directly address what happens if market pricing changes. You should carefully consider all of your tariff risks and consider what language you should include in your contracts to protect yourself.
6. Closely monitor pricing trends on projects you are bidding. Many contractors are slow to react to changing realities. If pricing begins to tighten, ensure your pricing is immediately reflective of the new reality. In a falling market, the longer you wait to fill your book the worse it is likely to get.
7. Avoid financially weak or problematic customers. The wrong job with the wrong customer could mean the difference between success and failure in a challenging market. Only provide aggressive pricing to customers that have earned your trust.
8. Chase accounts receivable. The assumption that a customer “always pays eventually” can be very dangerous in a changing market.
9. Cut deadwood but protect your human assets. Examine your team early and objectively and determine whether your team is as efficient as it should be and make changes where necessary. At the same time, ensure that you secure enough work to keep the team you value employed through a downturn.
10. Identify and secure cornerstone projects. In a good market, projects are plentiful. In a challenging market, you will want to ensure you have lined up a few key projects to carry you through.
11. Solidify key relationships. The construction business is about relationships, and you want to ensure that the right people are on your side and will want to help you through adversity.
2025 has so far not been the year that many in the industry had hoped to see. However, with attention to the details and good business practices you can do your best to ensure that your company is in the best possible position to weather the storm.
Norm Streu is associate counsel with the law firm Harper Grey LLP and past chair of the Vancouver Regional Construction Association. Chris Hirst is a partner and leader of the Construction and Engineering practice group at the law firm Alexander Holburn LLP.