HealthcareFacilities
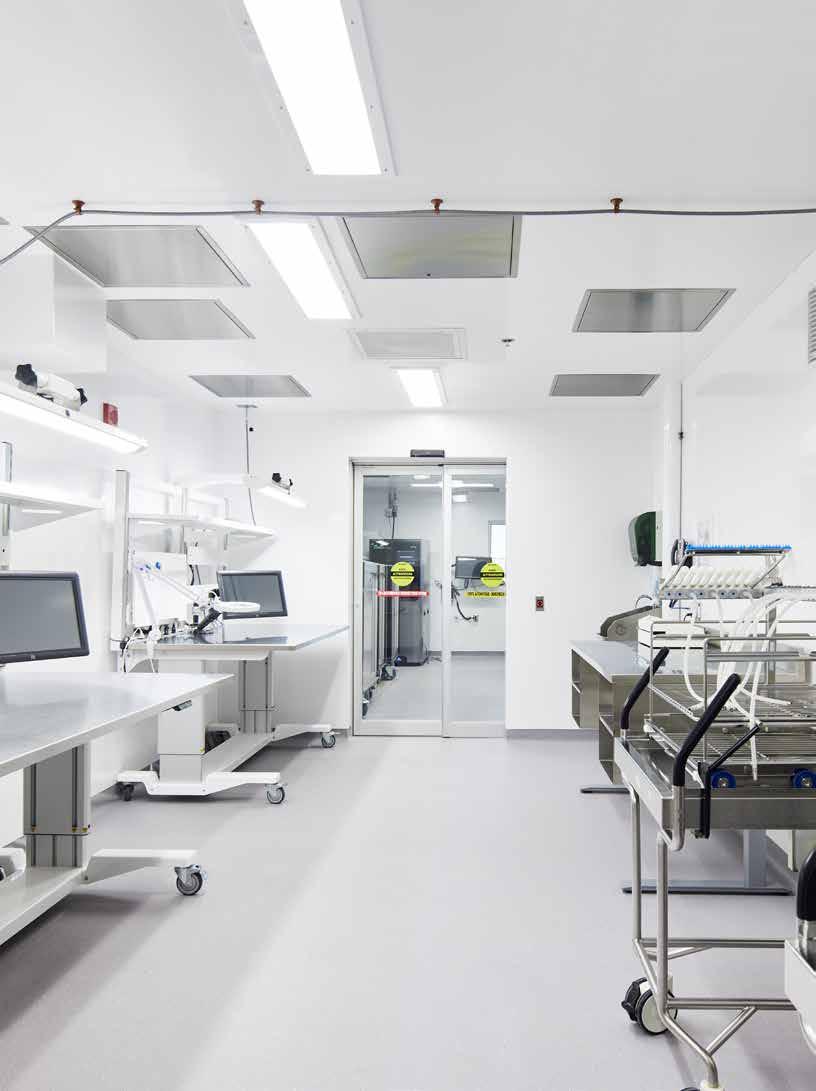
CISSS of the Laurentians’ adoption of MMDRU a first for Quebec
Implications of IoT for healthcare
Addressing IPAC in long-term care
Hospital water damage preparedness
We are pleased to announce that now monitors 50 plus hospitals Ontario region.
We are pleased to announce that now monitors 100 plus hospitals Ontario region.
Labour Canada has fully “acknowledged” the scope of work provided in the semiannual inspection program. In addition, the written documentation contributes greatly to the hospital accreditation programs.
Labour Canada has “acknowledged” the scope work provided in the semiannual inspection program. In addition, the written documentation contributes greatly to the hospital accreditation programs.
Further we are always pooling the knowledge resources of Infection Control and Engineering Groups like CHES, the ventilation inspection program is in a evolution to meet future healthcare needs for patients and staff.
Further we are always pooling the knowledge resources Infection Control and Engineering Groups like CHES, the v inspection program is in evolution to meet future healthcare patients and staff.
and inspection of the hospital
ventilation fire dampers may be part of
h l ti and inspection of the hospital building audit this year. Some of u have already taken advantage f our new software program which in conjunction with our patented robotics, allows us to minimize ceiling access requirements.
building audit this year. Some of u have already taken advantage f our new software program which in conjunction with our patented robotics, allows us to minimize ceiling access requirements
To da t e , o f t h e t h o us a n d s o f fi r e d o o r s i n spec t e d a p p r o x im a t e l y 3 0 % a r e n o t h u m a n l y acces s i b l e f r o m tr a d i t i o n a l ce i l i n g acces s p o i n t s O u r p a t en t e d r o b o t ove r co m e s i s o b s t acl e , a l l ow i n g m p l e t e d o c u m e n t a t i o n o f a l l o o r s w i t h i n t h e ve n t il a t i o n F u r t h e r, o f t h e t o t a l , 7 % h ave b ee n f o u n d de f ec t ive , b l o c ke d w i t h wo o d , w i r e d u p , o r si m p l y c l o s e d s h u t t i n g o ff a i r f l ow.
To da t e , o f t h e t h o us a n d s of fire dampers inspected a p p r o x im a t e l y 3 0 % a r e n o t h u m a n l y acces s i b l e f r o m tr a d i t i o n a l ce i l i n g acces s p o i n t s . O u r p a t en t e d r o b o t ove r co m e s i s o b s t acl e , a l l ow i n g m p l e t e d o c u m e n t a t i o n o f a l l fire dampers within the ventilation em. Fu rt h er , of th e t ot a l , 15 % f o u n d de f ec t ive , b l o c ke d r e d u p , o r si m p l y c l o s e d w
“Setting the Standard for Commercial Ventilation Care”
EDITOR/RÉDACTRICE Clare Tattersall claret@mediaedge.ca
PUBLISHER/ÉDITEUR Jason Krulicki jasonk@mediaedge.ca
PRESIDENT/PRÉSIDENT Kevin Brown kevinb@mediaedge.ca
SENIOR DESIGNER/ Annette Carlucci CONCEPTEUR annettec@mediaedge.ca GRAPHIQUE SENIOR
GRAPHIC DESIGNER/ Thuy Huynh GRAPHISTE roxyh@mediaedge.ca
PRODUCTION Ines Louis COORDINATOR/ inesl@mediaedge.ca COORDINATEUR DE DE PRODUCTION
CIRCULATION MANAGER/ Adrian Hollard DIRECTEUR DE LA circulation@mediaedge.ca DIFFUSION
6 Editor’s Note
8 President’s Message
10 Chapter Reports
INNOVATION & TECHNOLOGY
14 Mobile Specialized Equipment a First for Quebec
Première Québécoise en fait d’équipement mobile spécialisé
18 IoT in Healthcare
Harnessing data to improve patient care, facilities operations
INFECTION PREVENTION & CONTROL
22 Fair Warning Infection control red flags during hospital construction
24 A New Standard for Long-term Care CSA Z8004 addresses shortcomings exposed by pandemic
EMERGENCY PREPAREDNESS & RESPONSE
26 Navigating an Unexpected Crisis Hamilton Health Sciences’ COVID-19 pandemic response
28 Dealing with Water Damage Tools, techniques to protect patients when flooding occurs
CANADIAN HEALTHCARE FACILITIES IS PUBLISHED BY UNDER THE PATRONAGE OF THE CANADIAN HEALTHCARE ENGINEERING SOCIETY. SCISS JOURNAL TRIMESTRIEL PUBLIE PAR SOUS LE PATRONAGE DE LA SOCIETE CANADIENNE D'INGENIERIE DES SERVICES DE SANTE.
CHES SCISS
PRESIDENT Craig B. Doerksen
VICE-PRESIDENT Jim McArthur
PAST PRESIDENT Roger Holliss
TREASURER Reynold J. Peters
SECRETARY Beth Hall
EXECUTIVE DIRECTOR Tanya Hutchison
CHAPTER CHAIRS
Newfoundland & Labrador: Colin Marsh
Maritime: Robert Barss
Ontario: John Marshman
Quebec: Mohamed Merheb
Manitoba: Reynold J. Peters
Saskatchewan: Melodie Young
Alberta: Mike Linn
British Columbia: Sarah Thorn
FOUNDING MEMBERS
H. Callan, G.S. Corbeil, J. Cyr, S.T. Morawski
CHES
4 Cataraqui St., Suite 310, Kingston, Ont. K7K 1Z7 Telephone: (613) 531-2661 Fax: (866) 303-0626
E-mail: info@ches.org www.ches.org
Canada Post Sales
Product Agreement No. 40063056
ISSN # 1486-2530
Reproduction or adoption of articles appearing in Canadian Healthcare Facilities is authorized subject to acknowledgement of the source. Opinions expressed in articles are those of the authors and are not necessarily those of the Canadian Healthcare Engineering Society. For information or permission to quote, reprint or translate articles contained in this publication, please write or contact the editor.
Canadian Healthcare Facilities Magazine Rate
Extra Copies (members only) $25 per issue
Canadian Healthcare Facilities (non members) $30 per issue
Canadian Healthcare Facilities (non members) $80 for 4 issues
A subscription to Canadian Healthcare Facilities is included in yearly CHES membership fees.
La reproduction ou l’adaptation d’articles parus dans le Journal trimestriel de la Société canadienne d’ingénierie des services de santé est autorisée à la condition que la source soit indiquée. Les opinions exprimées dans les articles sont celles des auteurs, qui ne sont pas nécessairement celles de la Société canadienne d’ingénierie des services de santé. Pour information ou permission de citer, réimprimer ou traduire des articles contenus dans la présente publication, veuillez vous adresser à la rédactrice.
Prix d’achat du Journal trimestriel
Exemplaires additionnels (membres seulement) $25 par numéro
Journal trimestriel (non-membres) $30 par numéro
Journal trimestriel (non-membres) $80 pour quatre numéros
L’abonnement au Journal trimestriel est inclus dans la cotisation annuelle de la SCISS.
The CHES 2023 National Conference will be held in Winnipeg MB at the RBC Convention Centre, September 17-19, 2023. The RBC Convention Centre is conveniently located in the downtown core and close to local amenities.
The 2023 CHES National Conference will be held in Winnipeg, Manitoba, at the RBC Convention Centre, September 17-19, 2023. The RBC Convention Centre is conveniently located in the downtown core and close to local amenities.
A block of rooms has been reserved at the Delta Hotel, starting at $202 plus applicable taxes standard Queen/King single/double occupancy
A block of rooms has been reserved at the Delta Hotel, starting at $202 plus applicable taxes standard queen/king single/double occupancy.
The theme of the 2023 conference is “Rejuvenating Healthcare Infrastructure”
The theme of the 2023 conference is “Rejuvenating Healthcare Infrastructure”
The CHES 2023 Education Program is well underway and will once again feature dual tracks with talks on relevant industry topics from high-profile experts in the field. Isha Khan, CEO, Canadian Human Rights Museum will be our Keynote Speaker
The 2023 education program is well underway and will once again feature dual tracks with talks on relevant industry topics from high-profile experts in the field. Isha Khan, CEO, Canadian Museum of Human Rights will be our Keynote Speaker
The Call for Abstracts for program submission closes on November 18, 2022. You may submit your completed form at (https://www.xcdsystem.com/ches/abstract/index.cfm?ID=9AqVARj) and/or any inquiries by email to info@ches.org
The Great CHES Golf Tournament will be held at Quarry Oaks Golf Course on Sunday, September 17, 2023.
The Great CHES Golf Tournament will be held at Quarry Oaks Golf Course on Sunday September 17, 2023
Join us for the CHES President’s Reception and Gala Banquet at the RBC Convention Centre. The banquet will celebrate the accomplishments of our peers with the 2023 CHES Awards presentations, while enjoying great food and entertainment with friends.
Join us for the CHES President’s Reception and Gala Banquet again in 2023 at RBC Convention Centre. The banquet will celebrate the accomplishments of our peers with the 2023 Awards presentations, while enjoying great food and entertainment with friends.
See you in 2023 in Winnipeg!
For more info visit our website at
For more info visit our website at www.ches.org
www.ches.org
Follow us on Twitter!
Follow us on Twitter!
Joins us on!
Joins us on!
THIS TIME LAST YEAR was very different for my family. In February 2022, my dad slipped and fell on some ice while out walking early one morning, hitting his head on the pavement. Thankfully, someone found him whilst he lay in a puddle partially conscious on the side of the road and called an ambulance. He was rushed to Canada’s first and busiest trauma centre, Sunnybrook Health Sciences Centre, where he spent several days in the intensive care unit. He had suffered a brain injury. The days he spent in hospital were filled with a lot of unknowns, as was the first month after he was discharged. He required around the clock supervision and assistance, and my thoughts inevitably went to long-term care. Instead of focusing on the benefits of this type of healthcare option should the need arise, my mind whirled with the tragedies suffered by many in these homes during the pandemic, including the appallingly deplorable conditions in which residents lived in some cases. Thankfully, my thoughts remained just that — my dad recovered in the ensuing months and while not yet 100 per cent, you would never know he suffered such an unfortunate accident.
Since the early days of COVID-19 when the horrors of long-term care were brought to the fore, governments have taken steps to improve the provision of services at these facilities. This has included the development of national standards, one of which is explored in this issue. CSA Z8004 addresses the design, operation, and infection prevention and control practices in long-term care homes. You can read all about it in A New Standard in Long-term Care.
Keeping with the topic of COVID, Navigating an Unexpected Crisis reviews Hamilton Health Sciences’ pandemic response from a facilities management point of view. It delves into requests the team stickhandled, operational impacts of COVID and projects implemented.
But to begin is our English-French feature on the first-ever use of a mobile medical device reprocessing unit (MMDRU) in Quebec. Implemented by the Laurentians Integrated Health and Social Services Centre, the high-performance sterilization unit has proven to be an indispensable tool. Mobile Specialized Equipment a First for Quebec delves into why the health authority decided to introduce the mobile unit and the design process, including criteria and obstacles.
Other topics tackled in this issue are the use of Internet of Things for space optimization, infection control red flags during hospital construction and how to manage flooding in the event it occurs.
If you are interested in contributing an article to the publication or there’s a topic you’d like to see covered, please contact me.
Clare Tattersall claret@mediaedge.caCanadian Healthcare Engineering Society
Société canadienne d'ingénierie des services de santé
CHES is seeking both sponsors and candidates for the 2023 Young Professionals Grant. The application forms for Sponsors and Candidates are available on the CHES Website.
Call for Sponsors:
• The YPG sponsorship application form must be completed by the sponsoring organization/company and submitted to the CHES National Office.
• CHES National Office will invoice sponsoring organization/company for $2,000 once candidate applications have been received and approved.
Call for Candidates:
• Young professionals who are or will become architects, engineers (i.e. mechanical, electrical, power, and civil, etc.), technicians or similar technical disciplines are eligible.
• Eligible candidates are those working within a healthcare organization or a company supplying goods or services to healthcare facilities or organizations.
• Eligible candidates must be working in the healthcare field for less than 5 years.
• The YPG application form must be completed by the eligible candidate and submitted to the CHES National Office. In this form, the eligible candidate will be required to provide information on their recent employment and future career aspirations.
• Confirmed candidates will receive complimentary registration for the 2023 National Conference and complimentary membership for the remainder of the 2023-2024 membership year.
For Nomination Forms, Terms of Reference, criteria, and past winners
www.ches.org / About CHES / Awards
Send nominations to; CHES National Office info@ches.org
Fax: 866-303-0626
WE’RE HEADING INTO ANOTHER Canadian spring, which usually evokes feelings of growth, renewal and some would say hope. The adage of the healthcare facility in which I worked for more than 30 years is, “Hope flourishes in this place.” Hospitals are seen as a place for healing. However, long-term care (LTC) facilities, including hospice and palliative care, support residents on a path that normally leads to the end of life. This could be viewed as a strong dichotomy within healthcare. It leads me to talk about healthcare, hospitals, LTC, healthcare standards and our personal responsibility in offering hope to those in our care.
In late January, both the Health Standards Organization and CSA Group released new standards related to LTC. HSO’s new standard, CAN/HSO 21001:2023 Long-Term Care Services, focuses on the delivery of high-quality long-term care services. This includes “promoting good governance; upholding resident-centred care and enabling a meaningful quality of life for residents; ensuring highquality and safe care; fostering a healthy and competent workforce; and promoting a culture of quality improvement and learning across long-term care homes.”
Often, the perception is facility staff are solely focused on the facilities within which they work. But the CHES members I know in LTC keenly realize and support that residents are in ‘their home.’ It has only been in the past eight years that the word ‘resident,’ not ‘patient,’ and the ‘home’ aspect of LTC has begun to resonate with me, as my parents made their journeys through LTC. Following my personal experience, I have begun to relate more to LTC management.
CSA Group’s fourth standard in the Z8000 series, Long-Term Care Home Operations and Infection Prevention and Control (IPAC), focuses on creating safer physical environments. It provides guidance on “safe operating practices, design and IPAC in LTC homes while incorporating a personcentred approach.” It also takes into consideration “what is required during both normal, day-to-day circumstances and catastrophic events.” Having been privileged to be part of the standard’s technical subcommittee, I witnessed people from across Canada with different skills, education and experience come together to quickly build a new standard, including use of other technical standards, particularly the 15 CSA Group standards for healthcare facilities. While Z8004 is an essential resource for all designers, facility managers and operators of LTC facilities, it is a must-read for the rest of the healthcare industry, too. I look forward to more conversations with the LTC community and CHES members as we “build member expertise in healthcare.”
I am eagerly awaiting to attend this year’s chapter spring conferences where I will get to see many of you. I am also excited to go to IPAC Canada’s national conference in Vancouver, May 28-31, on behalf of CHES, as well as the Canadian College of Health Leaders conference June 4-6, in Toronto. When we gather together, our combined skills and personal experiences bring hope to healthcare.
Craig B. Doerksen CHES National presidentMembers of the Canadian Healthcare Engineering Society can earn free continuing education units (CEU) by reading the Spring 2023 issue of Canadian Healthcare Facilities and passing a quiz based on articles in the issue. Once you’ve read the issue from cover to cover, simply go online to www.surveymonkey.com/r/MXD2THY to take the quiz. CHES members who pass the quiz will be able to claim one contact hour (0.1 CEU) on their CanHCC or CCHFM certificate renewals.
According to the World Green Building Council, we spend 90 percent of our time indoors. Given that statistic, it’s clear the quality of the air we breathe in buildings can dramatically impact our health and well-being. At Reliable Controls we believe sustainable buildings are a key component to reducing the health and environmental impacts of indoor and outdoor air pollution. Learn more reliablecontrols.com/IAQ
2022 was a quiet yet dynamic year for the Saskatchewan chapter. We held a mini conference in October, in Regina, with a successful turnout that created great conversations and dialogue around our current supply chain challenges. Our annual general meeting included the election of myself as chapter chair, John Megenbir as vice-chair, Steve Kemp as secretary/treasurer and Jim Allen as past chair (retired). A number of new members were also brought on to the executive committee that we look forward to working with alongside retired members that have graciously remained on. This collaboration is a huge asset as we plan our fall conference in Saskatoon. Throughout this year, one of the Saskatchewan chapter’s objectives is to promote the benefits of CHES to increase our membership.
—Melodie Young, Saskatchewan chapter chairIt’s full steam ahead in planning our spring conference, which will be held May 7-8. After last year’s record-breaking event, the bar is set high to meet or exceed people’s expectations. Although we are one of the smaller CHES chapters, we deliver a large conference. For those who have been involved in the planning process, you know there is much more to this event than meets the eye. The chapter executive has been engaged in strategizing how to better deliver CHES events to our members. Like last year, there will be education sessions and training opportunities at the conference. We are looking at incorporating a roundtable discussion and possibly live demonstrations.
Looking back on the last half of 2022, fall was relatively quiet. It seems people were exhausted with the COVID-19 pandemic and took some time off to recharge. The same applied to our chapter. Beyond a couple of meetings, the executive remained low-key. But we are back and ready to go.
Chapter membership is status quo, which is positive news. We continue to find new ways to encourage CHES membership to those who have not joined. We are also reaching out to people who have not renewed their membership and actively pushing recruitment on vendors/suppliers, consultants and others to improve enrolment. We are seeing uptake from those that are part of our multi-disciplinary teams. The number of people involved in infection prevention and control that attend our conferences has grown in recent times. This shift illustrates CHES is not just about facilities and for facilities personnel.
Financially, the chapter is in a solid position. The executive team wishes to invest in the betterment of our members. Whether that is providing more education opportunities, sending additional members to the CHES National conference or paying for more webinars, we want to give back to our membership.
As we move into spring, the Quebec chapter’s energy will continue to be focused on attracting new members and relaunching following the COVID-19 pandemic. We are bringing back our in-person dinner conferences this year. For the time being, our goal is to offer three to four events throughout 2023. Dates will be confirmed soon through the CHES website.
We have successfully added a new executive member to the Quebec chapter. The new person will represent the chapter on the national committee for membership. We are looking to add another person who will represent the chapter on the professional development committee. Both additions are essential as they will help fulfill our mission of ‘building member expertise in Canadian healthcare engineering.’
Do not forget to follow us on social media and to regularly check the Quebec chapter page on the CHES website for updates.
The Maritime chapter’s spring conference will be held April 30-May 2, in Moncton, N.B., at the Delta Beausejour hotel. The theme is Maximizing the Patient Experience Through the Physical Environment. Current events, such as the pandemic and climate change, have added more demands on already stressed facilities support groups. The public depend on us to ensure healthcare infrastructure is strong, flexible, robust and safe. Being aware of mitigation strategies posed by changing risks is essential to the resilience of healthcare facilities. The conference will discuss standards, procedures, processes and the challenges faced by healthcare facilities and how to develop positive outcomes. It will kick-off with a networking reception on April 30. The second day features internationally renowned speaker Greg Kettner, who will give the keynote address and ensure delegates are motivated, and the chapter’s annual general meeting. Education sessions are scheduled for May 1-2.
Planning is underway for the 2024 CHES National Conference in Halifax. Much has already been completed. We encourage members from across Canada to join us Sept. 6-10, 2024, for some homegrown Maritime hospitality and an exceptional conference program.
The Maritime chapter will host the Canadian Healthcare Construction Course (CanHCC) May 30-31, in Halifax, at the Prince George Hotel. The chapter is working closely with the Construction Association of Nova Scotia to promote the CanHCC to its members. I encourage all healthcare managers, architects and engineers to consider the program as part of their professional development or orientation to the healthcare industry.
The chapter continues to offer several financial incentives to members in the way of student bursaries, contribution to Canadian Certified Healthcare Facility Manager exam fees, and covering the cost of webinars and the fall education day, among other benefits.
—Robert Barss, Maritime chapter chair
tion québécoise continuera de se concentrer sur l’attraction de nouveaux membres et la relance après la pandémie de COVID-19.
Nous ramenons cette année nos dîners-conférences en personne. Pour l’instant, notre objectif est d’offrir trois à quatre événements tout au long de 2023. Les dates seront bientôt confirmées sur le site Web de la SCISS.
Nous avons réussi à ajouter un nouveau membre exécutif à la section du Québec. Cette nouvelle personne représentera la section au sein du comité national des membres. Nous cherchons à ajouter une autre personne qui représentera la section au sein du comité de développement professionnel. Ces deux ajouts sont essentiels, car ils nous aideront à remplir notre mission, qui est de ‘développer l’expertise des membres en ingénierie des soins de santé au Canada.’
N’oubliez pas de nous suivre sur les médias sociaux et de consulter régulièrement la page de la section du Québec sur le site web de la SCISS pour obtenir des mises à jour.
The Ontario chapter executive continues to meet virtually every quarter. Our focus is membership development, member benefits, including bursaries and the YPG grant, and providing educational offerings. Building on growth in membership over the past year, we are engaging in analytics to identify opportunities for further membership development.
The chapter executive continues to engage in networking and advocacy opportunities. We are looking forward to attending the ASHE Region 6 conference in Rochester, Minn., and ASHE PDC summit in Phoenix, both in March, as well as local CHES conferences this spring. Thank you to the host chapters for accommodating our participation.
CHES Ontario’s conference planning committee is busy planning our first in-person chapter conference in four years, to take place June 4-6, in Windsor. Built around the theme, Engineering Sustainability and Resilience in Healthcare Facilities, we have an engaging program. I look forward to reconnecting with members.
The next CHES Alberta Clarence White Conference & Tradeshow will take place June 12-13, at the Red Deer Resort and Casino. The conference will be followed by an added educational component — the Canadian Healthcare Construction Course, June 14-15, at the same venue.
The first call for nominations for the chapter executive closed Jan. 29. Positions up for election are vice-chair, secretary and treasurer. Thank you to everyone who put their name forward or nominated others.
A big shout out to those who were involved in the completion of the new Calgary Cancer Centre. The $1.6 billion stateof-the-art facility will provide cancer treatment services and serve as a hub for cutting edge cancer research. I suspect a nomination will be coming soon for the Wayne McLellan Award of Excellence in Healthcare Facilities Management.
The Manitoba chapter continues to work with the CHES National conference planning committee in preparation for this year’s conference in Winnipeg. Registration will open soon, along with sponsorship and trade show booth bookings. I’d like to thank Events & Management Plus Inc. for working with the conference planning committee to keep us moving ahead.
Speaking of Events & Management Plus, on behalf of the Manitoba chapter I’d like to congratulate Donna Dennison on her retirement. Donna has been a huge part of CHES for longer than the Manitoba chapter has even been around. She has been a constant support for all things CHES, not only nationally but for us in Manitoba. Thank you, Donna, for your commitment to CHES. We will miss you and your leadership.
The Manitoba chapter, together with the Winnipeg Construction Association (WCA), will hold its next Canadian Healthcare Construction Course (CanHCC) April 27-28, at the WCA office. We will hold a second two-day CanHCC session in conjunction with the CHES National conference Sept. 20-21, at the WCA office. Thanks again to the WCA for partnering with CHES Manitoba and providing their fantastic facilities. And to our CanHCC faculty, thank you for providing the training instruction that so many of our people working in healthcare construction need.
—Reynold J. Peters, Manitoba chapter chairÀ l’approche du printemps, l’énergie de la sec-—Mohamed Merheb, chef du conseil d’administration du Québec —John Marshman, Ontario chapter chair —Mike Linn, Alberta chapter chair The 2023 CHES National Conference will be held in Winnipeg, Sept. 17-19.
Over fall and into winter of last year, the chapter executive was busy planning and preparing for our 2023 conference in Penticton, May 28-30. The theme, Healthcare Facilities: Managing through Crises, provides an opportunity to discuss many relevant topics, such as succession planning, lack of qualified personnel, climate change and impacts from past weather events, including lessons learned and future-proof planning. We have received 18 submissions from the call for abstracts. The education committee, led by Caroline Reid, is busy reviewing them. I encourage all industry partners to continue to submit to present at the conference. Trade show booths are selling fast and great interest is building among delegates. New sponsorship opportunities were created due to an increase in requests. The conference planning team is using the Yapp app to help promote the event.
The chapter executive has implemented centralized document storage, setting up a cloud-based Google shared drive that allows all executive and committee members to store files and collaborate. This option was free and has been working well so far. We are looking at ways to update CHES B.C. processes and are considering adding a financial tracking software to record financial details for audit purposes. These changes will support the chapter in moving away from paper-based processes.
The B.C. chapter continues to find new ways to encourage CHES membership. Membership executive director Arthur Buse is doing a great job connecting with potential and current members, and reaching out to those who may have forgotten to renew.
The chapter executive is discussing potential dates to host the Canadian Healthcare Construction Course (CanHCC) in the fall.
An expression of interest has been drafted and will be issued shortly for volunteers to support chapter directors. These opportunities will provide mentorship and pathways to fill future executive positions.
Members of the B.C. chapter are actively working on CHES National committees, including partnership and advocacy, membership, social and the CanHCC, as well as those that support CSA Group.
I’d like to thank everyone for their hard work and dedication this past year to our industry. I look forward to engaging in the important work ahead of us in 2023.
2023
Hans Burgers Award
For Outstanding Contribution to Healthcare Engineering
DEADLINE: April 30, 2023
To nominate: Please use the nomination form posted on the CHES website and refer to the Terms of Reference.
Purpose: The award shall be presented to a resident of Canada as a mark of recognition of outstanding achievement in the field of healthcare engineering.
Award sponsored by
2023
Wayne McLellan Award of Excellence
In Healthcare Facilities Management
DEADLINE: April 30, 2023
To nominate: Please use the nomination form posted on the CHES website and refer to the Terms of Reference.
Purpose: To recognize hospitals or long-term care facilities that have demonstrated outstanding success in completion of a major capital project, energy efficiency program, environmental stewardship program, or team building exercise.
Award sponsored by
In 2019, the Laurentians Integrated Health and Social Services Centre (CISSS) in Quebec was faced with an urgent need to modernize its protocols for the cleaning, sterilization and reuse (reprocessing) of medical instruments and equipment. CISSS retained Quebec-based engineering firm, gbi, whose mandate was to design the province’s premier mobile medical device reprocessing unit (MMDRU). Initially, the MMDRU would be used at Mont-Laurier Hospital. It would then be moved and installed at St. Jerome Hospital, to remain on-site and in operation for eight years. After this period, the MMDRU will be utilized as needed throughout CISSS’s network for the duration of its estimated 15-year lifespan.
A high-performance sterilization unit is indispensable for keeping hospital operating and emergency rooms open and available for patients. The design of the MMDRU had to provide increased and modernized sterilization capacity for at least two
En 2019, le Centre intégré de santé et de services sociaux (CISSS) des Laurentides à Québec a été confronté à un besoin urgent de moderniser ses protocoles de nettoyage, de stérilisation et de réutilisation (retraitement) des instruments et équipements médicaux. Le CISSS a donc retenu les services de la société d’ingénierie québécoise gbi pour concevoir la première unité mobile de retraitement de dispositifs médicaux (UMRDM) de la province. Cette UMRDM sera utilisée, dans un premier temps, à l’hôpital de Mont-Laurier. Elle sera ensuite déplacée à l’Hôpital de Saint-Jérôme, où elle restera en service pendant huit ans. Par la suite, l’UMRDM sera utilisée au besoin dans l’ensemble du réseau du CISSS pour le restant de sa vie utile estimée à 15 ans.
Une unité de stérilisation performante est indispensable pour maintenir les salles d’opération et d’urgence des hôpitaux
hospitals without interrupting essential services, while maintaining full reprocessing capacities during regular maintenance or retooling of the existing fixed reprocessing units.
This innovative customized approach to provide mobility, flexibility and autonomy of use for the patient care facilities and their operators is a first of its kind in Quebec.
The design team initially explored the possibility of renting a similar trailer-based unit from the United States, but it was not well-adapted to the specific needs or local operating methods and required connections to the hospitals’ HVAC, purified water and purified instrument air systems, which was not possible. Further, renting the unit for eight years was estimated as being more expensive than the development of a custombuilt MMDRU.
ouvertes et disponibles pour les patients. La conception de l’UMRDM devait permettre d’augmenter et de moderniser la capacité de stérilisation d’au moins deux hôpitaux sans interrompre les services essentiels et tout en maintenant des capacités de retraitement complètes pendant la maintenance régulière ou le réoutillage des unités de retraitement fixes existantes.
Cette nouvelle approche personnalisée vise à offrir mobilité, flexibilité et autonomie d’utilisation aux établissements de soins aux patients et à leurs opérateurs. C’est la première du genre au Québec.
L’équipe de conception a d’abord étudié la possibilité de louer une unité sur remorque aux États-Unis, mais elle n’était pas bien adaptée aux besoins spécifiques ou aux
During the design of the MMDRU, local expertise and suppliers were retained, resulting in the injection of more than $1.6 million into the provincial economy.
The MMDRU is also more sustainable compared to temporary units that have to be deconstructed and produce massive amounts of environmental waste. As well, the MMDRU is a ‘greener’ option than the rental of a trailer from the U.S., which consumes significant amounts of fuel to operate.
The flexibility and autonomy of the MMDRU allows quick connection to any hospital for large-scale use. For instance, during its first six months at Mont-Laurier Hospital, the MMDRU was able to sterilize and reprocess more than 10,000 medical devices.
The project was aimed at finding a solution to the healthcare facilities’ lack of space. The first challenge was to maintain mobility while designing a fully operational reprocessing unit inside a limited square footage.
Namely, the mobile unit needed to house sterilizers, washer decontaminators, an ultrasonic sterilizer, ventilation unit, osmosis unit and instrument air unit. It also had to respect protocols and provide efficient and ergonomic installations for hospital technicians.
In addition, due to the Laurentians’ northern climate, protection against condensation buildup and the freezing of electromechanical systems and various medical devices had to be incorporated into the operating design criteria.
During the design team’s drafting process, blueprints were intentionally created with limited piping to reduce cross-over connections to the hospitals’ fixed mechanical rooms. Also, early in the design, it was decided the MMDRU would have to be moved in several smaller components since a single ‘slide out’ module would not be able to contain all the mechanical equipment needed to ensure high-performance and reliability, and would be too big to transport on Quebec’s roads. Consequently, the number of modules had to be maintained to a minimum while still allowing for a regrouping of services to minimize the connections between each module.
Other design criteria and obstacles included purified water and purified instrument air had to be produced inside the unit to meet
méthodes d’exploitation locales. En outre, cette unité sur remorque nécessitait des connexions aux systèmes CVC, d’eau purifiée et d’air purifié des instruments des hôpitaux, ce qui n’était pas possible. De plus, la location de l’unité pour huit ans avait été estimée plus coûteuse que le développement d’une UMRDM construite sur mesure.
Le recours à des experts et fournisseurs locaux a entraîné l’injection de plus de 1,6 million de dollars dans l’économie provinciale.
L’UMRDM est également plus durable que les unités temporaires qui doivent être démontées et produisent des quantités massives de déchets. De plus, l’UMRDM est une option plus écologique que la location d’une remorque, qui consomme des quantités importantes de carburant pour fonctionner.
La flexibilité et l’autonomie de l’UMRDM permettent une connexion rapide à tout hôpital pour une utilisation à grande échelle. Par exemple, au cours de ses six premiers mois d’existence à l’Hôpital de Mont-Laurier, l’UMRDM a pu stériliser et retraiter plus de 10,000 dispositifs médicaux.
Le projet visait à trouver une solution au manque d’espace des établissements de santé. Le premier défi était de maintenir la mobilité tout en concevant une unité de retraitement entièrement opérationnelle pouvant tenir dans un espace restreint.
Ainsi, l’unité mobile devait abriter des stérilisateurs, des laveurs-décontaminateurs, un stérilisateur à ultrasons, une unité de ventilation, une unité d’osmose et une unité d’air pour les instruments. Il fallait également respecter les protocoles et fournir aux techniciens hospitaliers des installations efficaces et ergonomiques.
En raison du climat nordique des Laurentides, la protection contre l’accumulation de condensation et le gel des systèmes électromécaniques et de divers dispositifs médicaux devait être intégrée aux critères de conception de l’exploitation.
Les plans prévoient un minimum de tuyauterie afin de réduire les connexions croisées avec les salles mécaniques fixes des hôpitaux. De plus, dès le début de la conception, il a été décidé que l’UMRDM devrait être déplacée en plusieurs petites composantes. En effet, un seul module ‘coulissant’ n’aurait pas pu héberger tout l’équipement mécanique nécessaire pour assurer la haute performance et la fiabilité. Un tel module aurait été trop gros pour être transporté sur les routes du Québec. Par conséquent, le nombre de modules devait être maintenu à un minimum tout en permettant un regroupement des services pour minimiser les connexions entre chaque segment.
Parmi les autres critères et obstacles de conception, l’eau purifiée et l’air purifié des instruments devaient être produits à l’intérieur de l’unité pour répondre aux normes de qualité et de pression actuelles. De plus, le taux d’humidité à l’intérieur de l’unité devait être maintenu en permanence en dessous de 60 pour cent. Au-delà de ce niveau, les dispositifs médicaux peuvent devoir être restérilisés. Comme la plupart des appareils médicaux génèrent une quantité importante de vapeur, une unité de ventilation a dû être installée pour fournir une charge élevée de déshumidification et de climatisation.
current quality and pressure standards. Additionally, humidity levels within the unit needed to be maintained below 60 per cent at all times. Above that level, medical devices may need to be re-sterilized. As most medical appliances generate a significant amount of steam, a ventilation unit had to be installed to provide a high dehumidification and air conditioning load.
The engineering firm was also confronted with airflow direction requirements. The ducts had to be airtight to allow airflow from sterile to non-sterile areas. The only junctions to the existing buildings were for drainage, domestic water supply, steam and electricity. As well, engineers had to overhaul the whole concept of the unit’s wiring connections. Since a part of the roof and ceiling are separated between the smaller modules, the conduit could not simply be installed vertically to the junction boxes. The team had to come up with a way to have the wiring rolled up and to limit access traps. A horizontal band was reserved at the top of the walls where wires could be laid parallel.
Since the MMDRU was to be installed at two or more facilities, compatibility and flexibility with different buildings’ existing structures and equipment had to be taken into account. This required the installation of flange joints on the piping along the intersection of each module, which also served to protect the unit during moves.
In 2022, the Association of Consulting Engineering Companies Canada recognized gbi with an Award of Excellence for the design of the MMDRU, citing the project will help lead the way toward more adaptive medical infrastructure. That same year, the specialized equipment earned the engineering firm first prize in the mechanicalelectrical building category at the Quebec Consulting Engineering Grands Prix, nudging out 61 other engineering projects.
Alexandre Blain, P.Eng., is director of mechanical and electrical at gbi. Since 1963, gbi offers professional consulting engineering services in various sectors for both public and private clients. Alexandre can be reached at ablain@gbi.ca.
Le cabinet d’ingénierie a également été confronté aux exigences en matière de direction du flux d’air. Les conduits devaient être étanches pour permettre la circulation de l’air entre les zones stériles et non stériles. Les seules jonctions avec les bâtiments existants servent au drainage et à l’alimentation en eau domestique, en vapeur et en électricité. En outre, les ingénieurs ont dû revoir l’ensemble du concept des connexions de câblage de l’unité. Comme une partie du toit et du plafond est séparée entre les modules plus petits, la conduite ne pouvait pas simplement être installée verticalement jusqu’aux boîtes de jonction. L’équipe a dû trouver un moyen de faire enrouler le câblage et de limiter les trappes d’accès. Une bande horizontale était réservée au sommet des murs, où l’on pouvait poser des fils parallèles.
Comme l’UMRDM devait être postée dans deux ou plusieurs installations, il fallait tenir compte de la compatibilité et de la flexibilité avec les structures et les équipements existants des différents bâtiments. Cela a nécessité l’installation de joints à brides sur la tuyauterie le long de l’intersection de chaque module, ce qui a également servi à protéger l’unité pendant les déplacements.
En 2022, l’Association des sociétés d’ingénieurs-conseils du Canada a décerné à gbi un prix d’excellence pour la conception de l’UMRDM, citant que le projet contribuera à ouvrir la voie à une infrastructure médicale plus adaptable. La même année, l’équipement spécialisé a valu à la firme de génie le premier prix dans la catégorie des bâtiments mécaniques et électriques aux Grands Prix du génie-conseil du Québec, devançant 61 autres projets de génie.
Alexandre Blain, P.Eng., est directeur de la mécanique et de l’électricité chez gbi. Depuis 1963, gbi offre des services professionnels de génie-conseil dans divers secteurs pour des clients publics et privés. Alexandre peut être joint à l’adresse ablain@gbi.ca.
Smart buildings, smart cities, Internet of Things (IoT), 5G, digital twins, single panes of glass. The healthcare industry is full of tech buzzwords and the challenge for facilities is to figure out how to leverage these technologies, and to optimize existing and future infrastructure. More than ever, the adoption and integration of technology can help ease the immense strain on healthcare facilities in Canada.
IoT is a relatively mature technology in the industrial and manufacturing sectors. These highly process-driven environments benefit greatly from incremental change and process improvement that is to be gained from collecting and analyzing data. Healthcare facilities are starting to incorporate smart building technology into new build projects; however, there is limited integration with existing facilities, even with
major retrofits/renovations. Much like industrial and manufacturing, healthcare is also a highly process-driven sector and it stands to reason that facilities can benefit from IoT technology in much the same way.
HH Angus and Associates Ltd. has been working closely with a health network in the Greater Toronto Area to explore the use of IoT for space optimization. The engineering and consulting firm was tasked with finding
use cases that could show value for the health network. Following a series of discussions, a variety of different use cases were identified around gathering data for presence and space utilization within clinical and administrative spaces.
Healthcare facilities’ needs change over time and spaces within existing facilities are often repurposed to meet evolving requirements. It is also of paramount importance that existing space is used in an optimal way. With this in mind, two short-term data collection use cases were developed along with one long-term use case. The ultimate goal in all cases was to use data to drive decision-making.
The short-term use cases looked at near real-time data acquisition to examine clinical space usage on a room-by-room resolution, as well as historical data analysis to optimize the distribution of administrative spaces.
Current space usage data comes from the healthcare facility’s health information system; alternatively, data is gathered by direct observation of a space within the facility. Using simple wireless infrared-based presence sensors and a custom dashboard, the HH Angus team was able to visualize specific data on how a clinical space was occupied throughout the day. By grouping data from similar room types, hourly, daily and weekly trends could be easily seen.
While this data was interesting, it lacked true insight. Healthcare facilities can look at the various data sets but a user would need to spend time sifting through it in order to make observations based on this data.
As the data collection continued, HH Angus and the healthcare facility looked at the individual usages within similar roomtype groupings to determine if any difference could be observed. There was anecdotal feedback from the clinicians that there would be distinctions. For instance, many of the blood draw rooms were used at a significantly
higher rate than other rooms. From a functional perspective, these are adjacent rooms with no specific differences.
This begs the questions: Why are patients assigned to the blood draw rooms at different rates? And where is this bias originating?
Ultimately, in the short-term, there is no impact on the function of the space but longterm, there is more wear and tear on building assets due to the uneven distribution in usage. Could a change in procedure at the clinical level remove this bias? Or could changes to the functional program prevent this bias in future?
Based on learnings from the first use case, the second short-term use case had a very specific goal. The healthcare facility wanted to understand the overall usage for various administrative spaces. Typically, there is limited data available for administrative space usage. A healthcare facility can harvest card reader data, which is a viable data source for this use case; however, it is limited to areas that have controlled access. Not all areas have card reader data available. Further, card reader data needs to be anonymized and it does not account for tailgaters.
The healthcare facility considered the collection of accurate data important, as the current understanding of space usage came from anecdotal observation and feedback from departments occupying the spaces. Hybrid and remote working due to COVID19 had fundamentally changed how administrative spaces were being used, and the healthcare facility felt there was opportunity to optimize how spaces across their campus could be utilized.
Again, using a custom data visualization, historical data on administrative space usage was displayed with specific insights on, for example, most favoured days of the week, and the three most and least popular days in a given time period that could be used to make data-driven decisions on space usage.
With this data, the healthcare facility can work with the various departments occupying the space to determine if there are options to reorganize, reschedule or combine departments.
The final use case looked at long-term space utilization. When it comes to a new build, the functional programming is a complex challenge that needs to be solved. Functional programming is largely driven by design architects and the clinicians who will be using the space. Both these groups have valuable insight into the spaces, particularly clinicians who want to improve how their existing spaces operate and are programmed. However, by gathering data over a long period to inform future space planning and functional programming, the current process for functional programming and space design can be strengthened with real data. This could be applied when planning a large infrastructure renewal or major retrofit.
There is incredible potential for IoT technology to improve healthcare facilities. The healthcare sector is at the tip of the iceberg in making data-driven decisions as it relates to space usage. As project experience confirms, the focus should be on making sure the right questions are asked to derive the correct use cases to drive value. As vital as the technology is to gathering data, it is secondary to determining the right use case and application. With immense pressure on health systems, engineers can still find new ways to help solve problems and challenges facing Canadian healthcare facilities.
Akira Jones is a principal and director, digital services, at HH Angus and Associates Ltd., which provides engineering and information, communication and automation technology consulting services to healthcare facilities across Canada. Akira can be reached at akira.jones@hhangus.com.
Clorox HealthcareTM Hydrogen Peroxide Cleaner Disinfectant Wipes
• A one-step, ready-to-use cleaner & disinfectant wipe that kills 56 pathogens and made with no benzyl alcohol
• Kills bacteria, viruses and TB in 1 min or less
• Designed for use on common healthcare surfaces: Multipurpose Wipes 17.1 cm x 22.8 cm (6.75” x 9”)
Designed for: Everyday cleaning and disinfecting, daily patient room cleaning, hard, high-touch surfaces
Terminal Wipes 30.5 cm x 27.9 cm (12” x 11”)
Designed for: Terminal cleaning and disinfecting of hard surfaces
Together, we’re ready for anything.
While we are still processing the ways COVID-19 has transformed infection control approaches, there is no doubt that its impact reinforced the notion that prevention is preparedness. Nowhere is this mindset more relevant than when it comes to healthcare-associated infections (HAIs), including antimicrobial-resistant organisms (AROs).1
New U.S. research released this past July from the Centers for Disease Control and Prevention (CDC) may offer a helpful preview – and perhaps a head start for Canadian infection control specialists navigating the prevention of HAIs post 2019-2020.1,2
Resistant hospital-onset infections and deaths among seven pathogens increased 15% from 2019 to 20201
According to the COVID-19: U.S. Impact on Antimicrobial Resistance, Special Report 2022 , the pandemic pushed back years of progress made combating antimicrobial resistance (AMR). It was reported that resistant HAIs increased at least 15% during the first year of the pandemic, and that AMR infections had gotten worse.1
The CDC report showed an increase in resistant HAIs from 2019 to 2020 among these seven pathogens:1
• Carbapenem-resistant Acinetobacter (↑78%)
• ESBL-producing Enterobacterales (↑32%)
• Vancomycin-resistant Enterococci (VRE) (↑14%)
• Carbapenem-resistant Enterobacterales (↑35%)
• Multidrug-resistant Pseudomonas aeruginosa (↑32%)
• Antifungal-resistant Candida (↑26%)
• Methicillin-resistant Staphylococcus aureus (MRSA) (↑13%)
As many as 1 in 12 patients admitted to Canadian healthcare facilities, and 1 in 8 patients in an ICU, developed an HAI.4,5 HAIs in Canadian hospitals are prevalent. A recent study reported:
• antimicrobial-resistant organisms, while low in prevalence, are rising;6
• antimicrobial-resistant pathogens to watch are carbapenamase-producing Enterobacteriaceae and Candida auris ; and
• a rise in vancomycin-resistant Enterococci (VRE) infections over time may be linked to recent discontinuation of targeted VRE control strategies in some hospitals in Canada3,4
There is some good news – the 2021 Canadian Antimicrobial Resistance Surveillance System Report found that there was a decrease in Clostridioides difficile (C. diff) infections.6-8 This decrease was attributed to:
• hand hygiene compliance3,8
• environmental cleaning 3,8; and
• antibiotic stewardship3
Hard surface disinfection of immediate environments plays a major role in reducing HAIs7 – making CloroxPro® Canada your ideal go-to partner in disinfection. Our wide range of CloroxPro® disinfecting and sanitizing products can help you fight HAIs in your facility.
The power to stop the spread of HAIs in Canada
CloroxPro® offers many Health Canada-approved products that are effective in killing the microorganisms that spread HAIs in your healthcare facility, particularly on hard, non-porous surfaces. Kill the microorganisms that can spread HAIs on your hardest to clean surfaces in as little as 30 seconds with CloroxPro®.
Our infection control specialists are equipped to review your current outbreak protocols, recommend products based on clinical evidence and customize your protocols to the needs of your facility.
To see the efficacy and kill times for specific bacteria, virus, fungi/VET and spores, visit https://www.cloroxpro.ca/products/clorox-healthcare/
DIN:02473151
DIN:02465671
DIN:02406225
References: 1. DC. COVID-19: U.S. Impact on Antimicrobial Resistance, Special Report 2022. Atlanta, GA: U.S. Department of Health and Human Services, CDC; 2022. 2 . Boulanger V, etal Divergences between healthcare-associated infection administrative data and active surveillance data in Canada. CanCommunDisRep2022;48(1):4–16. 3. Canadian Nosocomial Infection Surveillance Program. Healthcare-associated infections and antimicrobial resistance in Canadian acute care hospitals, 2014–2018. CanCommunDisRep2020;46(5):99–112. 4 . Johnstone, Jennie, etal . “Health Care-Associated Infections in Canadian Hospitals: Still a Major Problem.”
CanadianMedicalAssociationJournal , vol. 191, no. 36, 2019. 5. Mitchell, Robyn, etal . “Trends in Health Care–Associated Infections in Acute Care Hospitals in Canada: An Analysis of Repeated Point-Prevalence Surveys.” CanadianMedicalAssociationJournal vol. 191, no. 36, 2019. 6. Public Health Agency of Canada. CanadianAntimicrobialResistanceSurveillanceSystemReport:Protectingand EmpoweringCanadianstoImproveTheirHealth pp. 90. Published 2021. 7. MacLaurin, Anne, et al. “Measuring and Monitoring Healthcare-Associated Infections: A Canadian Collaboration to Better Understand the Magnitude of the Problem.” HealthcareQuarterly , vol. 22, no. SP, 2020, pp. 116–28. 8. Weiner-Lastinger, L., etal . ”The impact of coronavirus disease 2019 (COVID-19) on healthcare-associated infections in 2020: A summary of data reported to the National Healthcare Safety Network.” InfectionControl&HospitalEpidemiology , vol. 43 no. 1, 2022. pp 12-25.
© 2023 The Clorox Company
Construction, renovations and maintenance (CRM) projects within healthcare settings can cause serious issues for patients and staff. For this reason, infection prevention and control practitioners (IPCPs) have become more involved in the CRM process, which requires steps be taken to ensure those on-site are protected from dust and stagnant water.
Dust can carry mould spores, such as Aspergillus species, and stagnant water can have microorganisms like Legionella species. The control of dust during CRM is vitally important. The amount of dust, or the duration and complexity of the CRM activity, can indicate what level of precautions are required. As for water, remediation after a flood needs to be performed in such a way that mould does not have a chance to proliferate.
CRM projects require an infection control risk assessment that analyzes what is to be done and where. This is conducted by a multi-disciplinary team to ensure the safest outcome is provided to both patients and staff.
An IPCP will frequently do a walk-around during a project to assess safety from their perspective. Most IPCPs also tour their entire site to remain visible and to help with other aspects of infection prevention.
During these walk-abouts, IPCPs are looking for red flags. Finding a hose hanging from a ceiling and draining into a bucket is an indication there is a leak. Once the area has been dried, the IPCP will become involved in the remediation. Seeing dusty footprints or the dusty tire track of a wheelbarrow are also red flags that something is happening without proper precautions.
In the case where the infection control risk assessment has determined barriers are
SEEING DUSTY FOOTPRINTS OR THE DUSTY TIRE TRACK OF A WHEELBARROW ARE RED FLAGS THAT SOMETHING IS HAPPENING WITHOUT PROPER PRECAUTIONS.
required for the CRM, the IPCP will inspect these frequently, even daily in higher risk or long projects. If the construction zone is to be under negative pressure, the pressure differential will also be regularly monitored. The negative pressure can fluctuate based on numerous issues with hoarding, the air handling devices, or improperly sealed doors and windows.
Contractor meetings can help bring issues to the IPCP’s attention. Meetings can address infection control issues early in the agenda to free up the IPCP who may be handling the project along with routine dayto-day duties. Regular updates can help keep the IPCP in the loop on larger maintenance projects being done by the facility’s staff.
Other red flags are walk-off mats that are either no longer sticky (if using sticky mats) or saturated with dust (if using a short pile carpet). During the demolition phase of a project, dust control will be audited through several means. The simplest detection measure is to wipe surfaces outside the construction zone daily with a white wipe to see if dust has escaped the previous day. (A background of ‘daily’ dust can be established before the project gets started.)
Ductwork needs to be kept sealed as much as possible before, during and after installation. Use of HEPA filtered air blown into the ductwork can create a positive pressure to keep dust out of ducts during subsequent CRMs.
Wet drywall or cement board is another red flag. It can occur before the building is sealed to the elements. Any wetness that is not dried within 24 to 48 hours will allow mould to grow. This should not be encapsulated within walls during CRM activities.
Gross construction dust should never be covered within wall cavities. The IPCP will need to inspect wall cavities before they are insulated or sealed, as well as ceiling elements. This may require the IPCP to have fall arrest training in order to use scissor-lifts. Insulation should never be cut on a dusty floor because this will allow dust to be sealed into the walls.
Electrical and computer cabling should be protected as much as possible from dust during and after installation.
The IPCP role is to keep patients and staff safe from infectious agents, which can be liberated during CRM activities. Almost none of these trained professionals are skilled in any of the building or maintenance trades, so questions need to be addressed, even if they seem simplistic to a tradesperson. Once all involved in construction and maintenance understand everyone’s role, red flags will not pop up.
Jim Gauthier is senior clinical advisor, infection prevention, with Diversey Inc., a manufacturer of cleaning and disinfection products. He is also a microbiology technologist and board certified in infection control.
The pandemic taught many hard lessons but few so heartbreaking as the need to improve long-term care (LTC) in Canada. Too many vulnerable people died, became sick or suffered terribly because they were isolated
from loved ones. The deficiencies in LTC were known for years; however, COVID-19 laid them bare for all to see. It became clear there was a pressing need for standards to address the challenges facing LTC.
In early 2021, CSA Group and the Health Standards Organization (HSO) were called upon by the Standards Council of Canada to develop two complementary LTC standards. HSO’s standard focuses on the delivery of high-quality LTC services,
while CSA Group’s standard focuses on creating safer physical environments.
In December 2022, CSA Z8004, LongTerm Care Home Operations and Infection Prevention and Control, was published after a 21-month development process that
involved consultation with those most affected: residents, families, caregivers, staff, academics and owners of LTC facilities.
The standard seeks to address some of the most troubling shortcomings exposed by the pandemic. Facilities were inadequately designed to support residents, not only in stopping and containing infections but in dealing with the consequences of outbreaks, too. Residents suffered from social isolation during lockdowns. There were gaps in care due to short staffing as well as gaps in procedures, leaving frontline workers with insufficient knowledge of how to provide care while also preventing the spread of COVID-19.
CSA Z8004 covers many aspects of LTC. Yes, there are sections on the most obvious areas, such as the physical plans, along with heating and ventilation. And there are procedures for hand-washing and other types of cleaning to prevent the spread of infection. But the standard goes deeper and wider.
What separates Z8004 from standards for other healthcare facilities is the recognition that LTC facilities are people’s homes — often their final homes. These facilities must not be viewed the same as hospitals. People live there and the design should reflect this reality. The atmosphere must be home-like, not institutional. The standard sets out design parameters to facilitate the containment of infection and how residents can be safely isolated to protect others. But those isolation areas must retain elements of comfort and home, with a way of safely facilitating contact with loved ones.
The standard also addresses technological advancements and the need to leverage currently available technology, such as tablets, to facilitate social interaction, while reaching for the vast potential of future innovations, including robotics and arti-
ficial intelligence. Nothing can replace human interaction but technology can do much to ease the burdens on overworked staff.
Cultural issues were explored, too. In consulting with Indigenous people, for example, the deep significance surrounding the preparation of food and sharing meals was revealed. Facility operators and caregiving staff should be sensitive to these kinds of concerns.
In developing the standard, there was awareness of the challenges and limitations facing facility operators. It is one thing to incorporate the latest best practices in a new building; it is quite another to retrofit a facility that is 20 to 30 years old. Rural facilities often have different issues than those in an urban setting. While CSA Z8004 is the standard to which all should aspire, older buildings cannot be expected to adopt everything.
While the standard is now available, the work is not over. The larger task at hand is adoption and implementation. CSA Group intends to work with operators, community groups and all levels of government to help them understand the standard and put it into practice. There is already a substantial amount of formal outreach underway, with a series of workshops and training programs.
After the tragedies of the pandemic, there is an extraordinary opportunity to improve the care of Canada’s most vulnerable citizens, while making an investment in everyone’s future well-being. CSA Z8004 can play an important role. Now is the time to seize the moment and work together to make a difference.
When COVID-19 began its spread across Canada, Hamilton Health Sciences (HHS) and its five hospitals had to respond quickly to adapt to the new realities.
At the start of the pandemic, HHS facilities management (FM) and capital development teams were called upon to provide support to clinical departments for a
variety of COVID-related projects. There were copious requests for barriers for patient care areas, cafeterias and screening spaces. Using the ingenuity of the trades staff, many variations of protective screens were developed. Installation of screening booths in main entrances that remained open had to take into consideration the flow of patients waiting to be screened, provision of electrical
for the booths and the comfort of staff subjected to cold weather from the opening and closing of doors. New covered shelters were also installed at all sites to protect patients from the elements, which allowed them to wait in relative comfort while maintaining physical separation.
The operational impacts of the pandemic were multifold. One such impact was the
FM team had to attend daily operation briefings and provide updates on the engineering aspects of the COVID response. An upside was getting to know many clinical and medical staff during these briefings that otherwise would not have happened. Other impacts included additional inspection and repair of many new pieces of equipment like beds and stretchers that arrived on a daily basis; addressing restrictions on contractors’ access to all HHS sites and ensuring enough qualified contractors were able to continue to work; dealing with COVID-related illness in staff and ensuring a minimum number of staff were always available; and obtaining required materials and spare parts in a timely manner in the midst of supply chain shortages.
Many major projects were implemented in support of COVID. One was the installation of an additional bulk oxygen tank at Hamilton General Hospital. After an initial meeting between intensive care unit (ICU) medical staff and FM and respiratory teams, it was determined the existing system could not keep up with a potential increase in patients. A design was quickly developed and tendered, followed by installation and connection to the existing pipeline system. An additional benefit of this was the need to ensure Hamilton General Hospital had a backup oxygen tank in case one was ever out of service. Other projects included turning trauma rooms at the hospital’s emergency department into temporary airborne isolation rooms (AIRs); construction of two new AIRs in the ICU; and the installation of a mask reprocessing machine in the hospital’s medical device reprocessing department. This last project was accomplished over the 2020 Easter weekend with HHS’s mechanical contractor WalterFedy and the FM team working on the fly to ensure rapid completion.
HHS was home to one of the mobile health units (MHUs) erected in the province as a rapid response to the pandemic. The MHU had multiple tent structures that were put up in one of the parking lots at the Hamilton General site. The MHU had its own power, HVAC, sanitary and water systems with a direct connection to hospital infrastructure for IT and fire safety. The planning and construction of the MHU created challenges at the site with respect to
fire department and ambulance drop-off routes; however, these were resolved by collaboratively working with the City of Hamilton.
Early in the pandemic, HHS worked in partnership with St. Joseph’s Healthcare Hamilton to establish a satellite healthcare facility for non-COVID patients to make room for the increasing number of COVID patients at acute care sites. Working with multiple stakeholders, a downtown hotel was selected as the preferred site. Work swiftly began to improve the lighting, fire alarm and HVAC systems, replace washroom fixtures and improve millwork to suit the patients intended for this facility.
The initial stages of the COVID pandemic were a flurry of activity, which required FM and capital development teams to learn to be flexible and always prepared for the next request. This served the team well then and has readied everyone for the next pandemic, whenever it may be.
George Pankiw, P.Eng, is director of capital development at Hamilton Health Sciences and formerly facility manager for Hamilton General Hospital. Dave Thompson, P.Eng, is a partner with WalterFedy, a multi-disciplinary design and construction firm with offices in Toronto, Kitchener and Hamilton, Ont.
NEW COVERED SHELTERS WERE INSTALLED AT ALL SITES TO PROTECT PATIENTS FROM THE ELEMENTS, WHICH ALLOWED THEM TO WAIT IN RELATIVE COMFORT WHILE MAINTAINING PHYSICAL SEPARATION.
Flooding is a concern that’s top of mind for many facility managers, most of whom are already stretched thin trying to keep up with routine maintenance and repairs. While some flooding can be forecasted, such as that from snowmelt, it can also happen at a moment’s notice from burst pipes. Of course, this is troublesome in any environment but flooding in healthcare facilities poses unique challenges and calls for expert solutions.
It’s easy to see flooding solely as a facilities problem. After all, when it occurs, maintenance teams must dry the building, remove damaged materials and renovate affected areas. And this is certainly part of the picture.
However, in healthcare facilities, the primary concern is protecting patients.
Flooding poses a number of risks to patients and mould is at the top of the list. Capable of growing in 24 to 72 hours after flooding, mould can quickly become a major threat to immunocompromised patients and those struggling with respiratory illnesses. To protect patients, the first order of business is to remove them from the affected areas. Remediation teams can then pivot to focusing on the facilities. They must stop fungal growth when possible, contain mould once it has grown and eliminate it from affected areas.
Mould thrives on moisture and when flooding occurs, moisture is in no short supply. The
moment flooding starts, the clock is ticking. To prevent mould growth, the building must be dried to eliminate the moisture needed for it to grow. To do this, contractors use air movers to get moisture off surfaces and into the air. They then use dehumidifiers to capture the moisture in the air.
While this process is effective for drying a building, if harmful particulates are in the air, the air movers can blow these throughout the building. This is a risk that healthcare facilities can’t take. So, before drying the building, healthcare facilities must begin by containing the affected area.
In the past, contractors would erect drywall walls to contain flooded areas. However,
depending on the scope of the flooding, these walls can take two to three days to build, giving mould plenty of time to grow. Further, these walls are not reusable, they’re labour intensive to construct and require stud frames, and they must be painted. Because of this, they’re less cost-effective and can lead to further mould growth.
Instead of using drywall, contractors are increasingly turning to modular containment walls. By comparison, they’re easier to set up, lighter, reusable and impermeable to water. For these reasons, CSA standards now include them as a permissible option.
Once contractors put containment walls in place, they’ll need to negatively pressurize the containment area. Negative air machines or portable air scrubbers are the tools of choice for this task. These devices prevent contaminated air from leaking into adjacent areas by ensuring airflow is directed into the contained area rather than away from it.
If mould has grown inside the affected area, teams will often have to remove damaged drywall and other materials.
Simply knocking mould off the surface isn’t enough. The mould will continue to grow, naked to the visible eye, creating further problems down the road.
When removing these materials, mould spores and other harmful particulates can enter the air. To clean the air, contractors turn to HEPA portable air scrubbers, which remove 99.97 per cent of particulates from the air. These machines draw air in, run it through filters and then exhaust the filtered air outside the building through ductwork that fits seamlessly with the modular containment walls.
It’s one thing to think about how to manage flood damage theoretically. Dealing with it in real life is another matter entirely.
Recently, at one of Northern Health Region’s locations in Manitoba, 70,000 gallons of water poured into an operating room overnight when a pipe burst. The facility brought in a team of restoration and remediation experts to handle the situation. They installed 100 linear feet of modular containment walls. Then, they used nega-
tive air machines to create negative pressure in the contained area. Finally, they filtered and exhausted the air while teams worked to dry and replace materials in the affected area.
In healthcare facilities, flood damage is a constant concern. Despite the best efforts of maintenance teams, flooding cannot always be prevented. Accordingly, teams must have a plan for how to quickly, effectively and safely respond to flood damage. Additionally, they must have the right tools for the job, empowering them to protect patients, restore the building and allow the healthcare facility to continue caring for patients.
Elizabeth Lamb is the national healthcare and construction manager at Abatement Technologies. Abatement Technologies is a leader in the design and manufacture of powerful abatement products. Since its founding in 1985, tens of thousands of environmental abatement and HVAC contractors, commercial building owners, facility managers and hospital infection control specialists have trusted the company’s products.
Our Integrated Facilities Management solutions incorporate all aspects of Hard & Soft Services, Energy Management & Sustainability, Project Delivery, and Strategic Procurement into one streamlined solution.