R & D SOLUTIONS
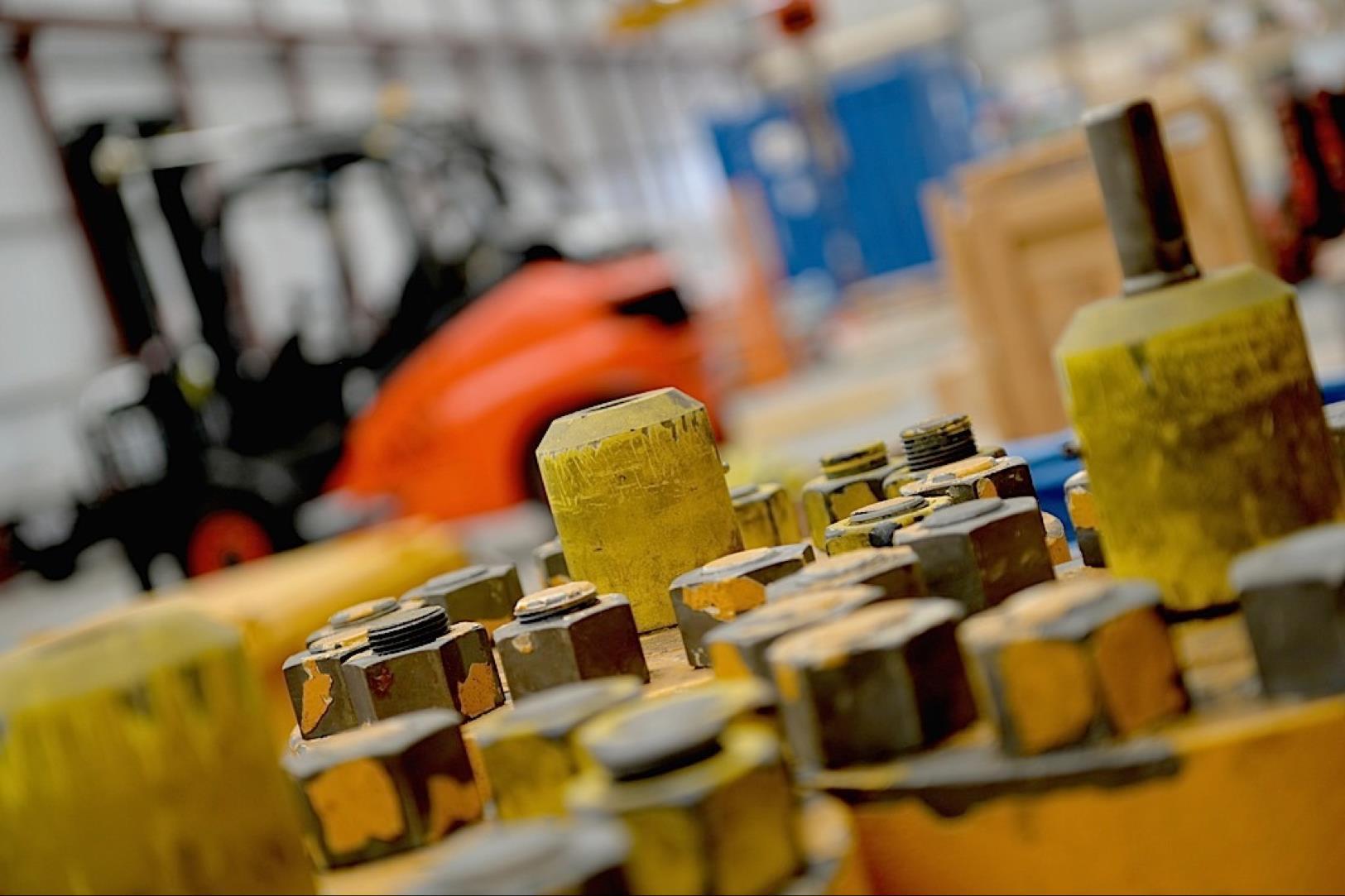
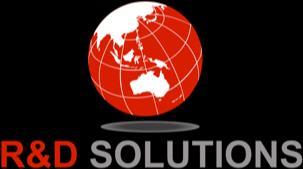
R&D Solutions is a privately owned oil, gas, and renewable energies equipment and services provider.
Based in Perth Western Australia, R&D Solutions prides itself on providing a broad spectrum of equipment and technology solutions. From the remote outback of Australia to offshore Asia and Europe.
We are available around the clock to assist service and support your operations.
We are the representative agents for a range of suppliers of proven drilling, completion and monitoring technology. Whether your requirements are for geothermal renewable energies, or traditional oil and gas, locally and internationally, our track record proves we will deliver on time and to budget.
In addition to product supply our locally based engineering group is well positioned to assist you with one off tool requirements that may arise during operations.
We also facilitate heavy industry machine repairs of damaged equipment or refurbishment.
R&D Solutions prides itself on being able to take on special build items and turn these round in a timely manner from concept to delivery.
In alliance with independent training providers, R&D Solutions provides industry training on all of the following:
• Slickline Operations
• Well Completion
• Basic Completions
• Overall production & exploration overviews
• Induction type courses for new hires
• Slickline course for supervisory personnel
Our customers engage us for our proven history of delivering responsive and cost competitive solutions. R&D Solutions’ Directors bring significant local and international experience. Russell Furner is formerly of BBL Bits and Doug Gillespie is exWeatherford Completions.
Our history of continued repeat business from our client base of major oil and gas companies is testament to our commitment to outstanding service, including Apache Energy, Chevron, Esso Exxon, Hess, Horizon Energy, Inpex, Santos, Shell, Vermilion Oil and Gas, Weatherford and Woodside.
Local highlights since establishment include the award of the Chevron Wheatstone contract for the supply of drill pipe protectors and service, the Shell prelude contract for the supply of Matrix Low Friction centralisers, drill pipe protectors and service and a Master Services agreement with Santos to provide Packers Plus technology and services.
The bigger, new R&D Solutions warehouse is conveniently located at Welshpool near Perth City airport to provide accountable Equipment Storage and Inventory Management with prompt receipt and delivery to and from customer’s mobilisation point or workshop.
4 Riversdale Road Welshpool Western Australia 6106
• Full service Office with access 24/7
• 2000m² fully enclosed, high truss, air conditioned warehouse and workshop
• Double overhead cranes
• 2000m² outside hardstand
• 30 minute drive from Perth CBD. 15 minutes from Perth airport.
• Fully equipped workshop with hand tools
• Total Inventory management
• All good stored under cover
• Fully fenced, secure yard with parking and lay down area
• Monitored alarm and security cameras
• Forklifts and qualified staff to conduct equipment load outs and receivals
For small shipments R&D Solutions can deliver to customer’s facilities at short notice. For larger goods R&D Solutions use local transport and shipping specialists to ensure quality service at a competitive cost.
Chapter 2
Since 1989, WWT International group of companies has been providing services to operators around the world, helping them overcome many of the challenging conditions encountered during drilling and completion operations, including torque, drag, casing and riser wear, heat checking and drillpipe buckling.
Since 1989, WWT International group of companies has been providing services to operators around the world, helping them overcome many of the challenging conditions encountered during drilling and completion operations, including torque, drag, casing and riser wear, heat checking and drillpipe buckling.
WWT NRP create a standoff, effectively isolating the drillstring while preventing damage to the critical contact areas of the casing. In most cases, WWT NonRotating ProtectorsTM will measurably improve drilling performance and wellbore casing integrity.
WWT Non-Rotating Protectors (NRP) effectively prevent drillstring contact with the wellbore and riser. You may benefit from using WWT NRP if you are faced with one or more of the following challenges:
• Deep Directional Wells
• Extended Reach Drilling
• Horizontal Wells
• Unplanned Doglegs
• Deepwater Riser Operations
• Deepwater Sub-Salt Wells
• Re-Entries and Sidetracks
• Shallow Kickoffs
• Production Riser Applications
• Slow, Difficult Drilling
• Deep, S-Shaped Wells
• Underpowered Top Drives
• Offset Well Heads
• Casing Patches
• Adverse Ocean Currents
WWT Non-Rotating ProtectorsTM (NRP) prevent casing wear by creating a standoff between the tool joint and the casing. The rotating tool joint can severely wear the casing, resulting in damage, expensive repairs, tie-backs and downtime. Installing a WWT Protector directly above the tool joint prevents tool joint contact.
Installing WWT NRPs on each joint of pipe in the high contact areas of the wellbore provides optimal casing protection for every hole section where applied. If contact forces exceed the side-load rating for an individual assembly, another can be installed to share the load, thereby allowing any measure of contact force to be accommodated.
Placement flexibility, along with no added connections, keeps operations simple and safe. In addition there is no need to remove and store the Protectors each time you pull out of hole. Simply manipulate the protected drillpipe to maintain continued placement in the critical zones of the well.
WWT Non-Rotating Super Slider ProtectorTM (Model SS) features low-friction pads on the outside of the sleeve that reduce sliding friction between the drillstring and the casing.
The sleeve slides easily along the casing while the drillpipe rotates in its ID, isolated from contact with casing. As a result, slack-off weight is increased and pickup weight is decreased at the surface.
WWT Non-Rotating ProtectorsTM (NRP) reduce rotational friction between the drillstring and the casing by creating a standoff between the two surfaces. The unique, patented inner sleeve geometry allows fluid to flow into the interior of the sleeve.
Rotation of the drillpipe draws fluid across the sleeve flats, creating a fluid bearing within the sleeve, reducing rotating friction by 50 to 90% even at low rpms and in almost any drilling or completion fluid. The result is that surface torque is significantly reduced allowing more torque to be distributed to the bit improving drilling performance and the rate of penetration (ROP).
Description
WWT Non-Rotating Protectors (NRP) reduce rotary torque and drag, and provide casing and riser protection during directional, extended reach, sidetracking, and deep-water drilling operations. The sleeve is made from advanced polyurethane with improved fluid bearing, and low friction polymer inserts.
• Reduce torque up to 50%
• Reduce drag +/-25% (Model SS)
• Limit casing wear by maintaining tool joint stand-off
• Protect riser, production riser and LMRP in adverse offshore conditions
• Reduce buckling
• Prevent heat checking
• Reduce vibration at surface
• Operate without the need for expensive mud additives
• Proactively reduce downtime expense related to equipment stress.
The NRP assembly consists of an aluminum stop collar above and below a reinforced polyurethane sleeve that has an OD greater than the tool joint.
The assembly is installed directly above the tool joint and creates a friction-reducing standoff between the tool joint and casing/riser. The NRP sleeve’s patented design creates an effective fluid bearing within its ID.
The combination of the tool joint standoff, fluid bearing and WWT placement analysis significantly reduces rotary torque, drag and casing/riser wear.
Click to Play
NeoTork is a newly patented downhole technology that offers improved drilling performance whilst reducing downhole vibrations including stick-slip. The tool is purely mechanical and its action is automatic and instantaneous.
NeoTork is located in the BHA, generally on top of the directional assembly, and it relies on a combination of disc springs and a swivel mechanism to automatically control drill bit depth of cut on the basis of torque.
When torque exceeds a preset limit, NeoTork contracts to reduce the drill bit depth of cut. The excess torque is 'stored' in the system and is slowly released as the bit drills off.
As a result, vibrations remain limited and drilling parameters can be optimized, delivering improved ROP while protecting all BHA components, particularly the drill bit.
• Performance Drilling in all sizes up to 17 ½”
• Directional Drilling including horizontal
• Coiled Tubing Milling
• Hole Enlargement
• Casing Milling
• Coring
• Faster ROP
• Longer bit life
• Reduced vibrations & Stick-Slip
• Smoother borehole
• Reduced equipment damage
NeoTork is downhole tool that manages torque generated by the drill bit as well as mitigating axial and torsional vibrations, protecting critical downhole equipment.
The simple, unique design automatically controls downhole torque. When torque exceeds a preset limit, the tool contracts to reduce the drill bit depth of cut. The excess torque 'stored' in the system is slowly released as the drilling structure drills off.
There has been a rise in the use of PDMs over recent years, mostly thanks to increased horizontal drilling in shale developments. Although PDMs are effective, they are at risk of stalling if torque levels exceed their operational limits.
Once a PDM stalls, the coil needs to be lifted from bottom to allow the PDM to restart rotating. The coil is then slowly returned to the bottom to resume milling. This costs time and money.
To avoid stalling, operators limit parameters, or use mill bits generating lower torque (roller cones). Whilst this does reduce stalling, it impacts on ROP and the completion time for the well.
NeoTork manages downhole torque and prevents PDM stalling. Any excess torque, from a peak on WOB or a change in milling material is 'stored' by the tool. NeoTork contracts, automatically pulling up the mill bit and allows milling to continue without stalling the PDM.
Running NeoTork when using a PDM allows optimization of milling parameters as well as the use of more aggressive milling structures instead of roller cones, removing the risk of lost cones downhole.
• Less downtime
• Faster ROP
• Longer bit life
• Smoother borehole
• Reduced number of stalls
• Reduced equipment damage
4 Riversdale Road, Welshpool, Perth, WA 6106 Australia
Website: www.randd-solutions.com
Welshpool & Canning Vale Australia
Mobile: +61 450 663 908
Office: +61 8 9486 8350
allan.paterson@randd-solutions.com