LSFA GUIDESUSTAINABILITY For Light Steel Frame Construction www.lsf-association.co.uk
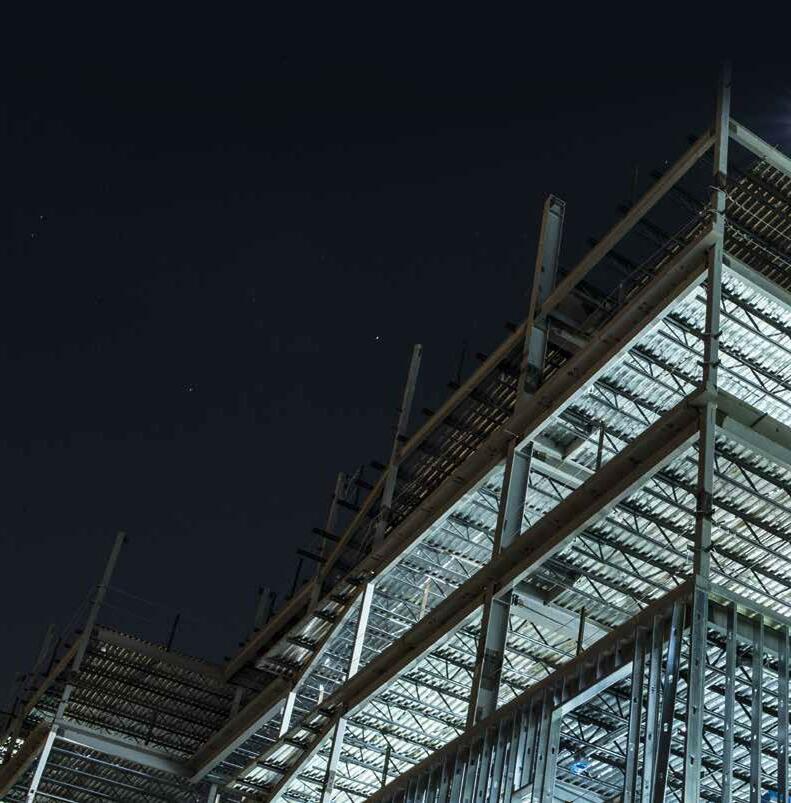
2 Sustainability Guide Contents Sustainability in LSF Construction ....................................................................................................................................... 3 Key Sustainability Benefits of LSF Construction 4 Embodied Carbon ........................................................................................................................................................................ 5 Design Guide for Reducing a Building’s Embodied Carbon ............................................................................... 6 Accommodating Environmental Enhancements 6 Sustainability into the Future ................................................................................................................................................7 Contact Information ................................................................................................................................................................... 8 Further Reading ........................................................................................................................................................................... 8
Items covered in this document include sustainability in LSF construction, key sustainability benefits, embodied carbon, means of reducing embodied carbon, accommodating environmental enhancements and looks at sustainability now and in the future. There are also references for further reading which cover the subject of sustainability in more detail.
Introduction
Further information can be found on the websites of LSFA members and at www.lsf-association.co.uk
Refer to the contact details on page 8.
The Light Steel Frame Association (LSFA) was established to influence legislation/regulation, and to support the overall objectives and growth of the sector. The LSFA collaborates closely with its members to raise awareness of the benefits of using steel framing systems and provide access to industry contacts, technical expertise and market intelligence.
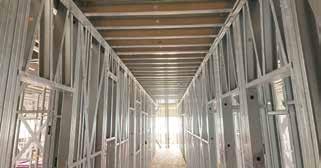
how LSF technology meets the demand for an environmentally friendly method of build.
LSF technologies are shown to perform well in embodied carbon assessments and the key sustainability benefits show this to be a construction method which is highly sustainable and suitable for sectors of the construction industry including residential, commercial bedspace, education and healthcare.
The benefits of light steel frame construction depend on the application and project specific details. When a designer is selecting the build system to be used structural stability, fire/ thermal/acoustic performance and cost are key drivers. However, sustainability and means of protecting the environment must also be taken into account. This document outlines the key sustainability indicators and looks at
Light steel frame (LSF) technology is widely utilised throughout UK construction industry and LSFA members have demonstrated that LSF is a highly sustainable method of construction. LSF technologies include load bearing and non-load bearing elements which can be formed from panelised/modular systems or as steel studs for erecting as infill or oversail wall solutions.
www.lsf-association.co.uk 3
Sustainability is quantified in terms of various measures of environmental, social and economic performance. These issues can be addressed through the use of light steel framing systems, however, the benefits of using these systems are not widely understood. This document seeks to address these issues and outline the environmental credentials of the technology.
The LSFA passionately believe that the answer to these complex sustainability questions is
HM Government ‘Construction 2025 (July 2013 Report)’ stated that LSF was “an industry that has become dramatically more sustainable through its efficient approach to delivering low carbon assets more quickly and at lower cost, underpinned by strong, integrated supply chains and productive long term relationships.”
As time has progressed steel has become part of a carbon neutral solution and sustainability is back at the top of the construction agenda. However, when budgets come into play it is safety, cost, programme, design adaptability and structural integrity which are more often the deciding factors, but the importance of sustainability must not be overlooked when assessing the build system to be used.
When looking at LSF against other offsite technologies timber may appear to have a ‘softer/green’ image, whereas light steel frame is often seen as having less sustainable credentials. However, it is well known that steel is one of the world’s most recycled materials with a potential recovery and re-use factor in excess of 90% so performs better than timber when all factors are taken into account over the whole life of the building.
that a lightweight structure is required and this lightweight technology is clearly LSF. This is particularly relevant when looking at lifecycle analysis including recycling at the end of a building’s life which must be factored in to any sustainability discussion with the highly recyclable nature of steel. Steel Construction Institute (SCI) publication ‘Protocol for reusing structural steel’ concludes that the environmental advantages of re-using reclaimed structural steel are considerable, compared to the common practice of recycling by re-melting scrap. There are also potential cost savings to be considered which influence the system selected.
Sustainability in LSF Construction
This protocol notes that material characteristics declared under CE marking procedures are designed to ensure that the material is as specified in design. When using reclaimed steel, the design is based on the material properties (tested or conservatively assumed), maintaining the relationship between design assumptions and material resistance. It is therefore appropriate that re-fabricated, reclaimed structural steelwork may be CE Marked in accordance with EN 1090, which demonstrates its suitability for re-use.
It is also worth noting that the steel manufacturing environment is more automated than more traditional build technologies and the industry has become incredibly efficient at value engineering and minimising waste through Design for Manufacture and Assembly (DfMA) approaches. This is assisted by the advances in digital engineering with better use of Building Information Modelling (BIM).
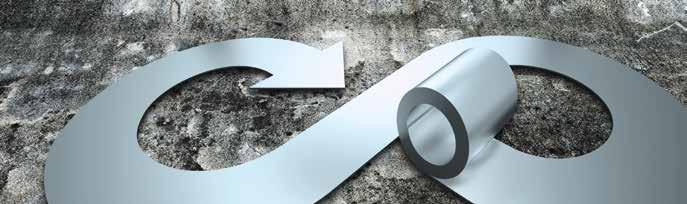
LSF construction has many benefits including cost-effective structures, durability, site safety, quality, predictability of delivery and versatility. However, in a world where a green, sustainable way of living/operating is essential the sustainable nature of LSF offers many benefits which include:
•
• Lightweight:
• Design
• Construction
4 Sustainability Guide
• Recycled
• Reduced
• Durability:
To maximise the benefits of offsite construction, early identification of the type of offsite system to be used leads to more cost-efficient construction. The benefits of early incorporation of LSF technology is noted in LSFA publication ‘Specification & Engineering Guide for Light Steel Frame Construction’. This Guide clearly demonstrates that LSF is the product to choose. Refer to LSFA document for more detail.
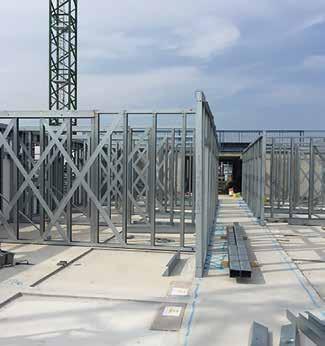
• Production
Key Sustainability Benefits of LSF Construction
• End
• Speed of build: Productivity and the speed of construction on the build site due to components being manufactured offsite reduces the impact on the local environment. Faster construction brings an earlier watertight envelope, which allows earlier access to follow on trades. This leads to reduced build programmes of circa 20% reduction compared to traditional construction. Energy/Thermal performance: Embodied Carbon Assessments show Operational Energy is 67% of the overall carbon total –the high levels of thermal insulation and airtightness achieved in LSF construction assist greatly in this area. Carbon Emissions: Substantial reduction (circa 20%) in the overall carbon footprint of a building. Content: LSF structures are built using steel with a high level of recycled content – circa 40% recycled content based on manufacturers data. of Life Recyclability: It is well known that steel is one of the world’s most recycled materials with a potential recovery/re-use factor in excess of 90%, and there is no waste at all. Steel components can also be unbolted/disconnected and dismantled for reuse in the future. Light gauge framed steel structures are substantially lighter than traditional steel framed buildings allowing a significant reduction in the construction of foundations, circa 70% reduction relative to concrete and masonry according to SCI data. waste: Steel wastage is minimised by the efficient use of materials. In factory production, all steel off-cuts and drill swarf are sent for re-cycling back into new steel components. Site Waste: Site waste is virtually eliminated using pre-engineered and fabricated product so contributes to zero waste targets on site. for Reuse: This may be a new discipline to some designers – however, the process is not difficult. For example, deconstructed sections are inspected and tested to verify their dimensional and strength properties. The section is then shot or sandblasted to remove any coatings, refabricated and primed to the requirements of the new project. Lightweight structures can be modified, easily extended and repurposed as they can be dis-assembled. Light steel walls and floors in warm frame applications have a predicted design life of up to 250 years. transportation: As the volume of material which can be included on a typical delivery is increased with LSF, there are less vehicle deliveries to the project (reduced by typically 60%). This assists in reducing the impact on the environment and minimises pollution.
• Reduced
There is a misconception about LSF construction and steel in particular in the embodied carbon debate, that steel is not as good an option as timber where sustainability is concerned. However, the strength of the LSF structure when assessed against the low weight of the steel used equates to improved efficiencies as a lot of structure can be formed with not a lot of weight. This reduces embodied carbon and is where LSF technologies come to the fore as lighter structures not only reduce material consumption but reduce the concrete required in the ground*
It is clear that the ‘big wins’ are in the operational energy and product/materials and these areas are where benefits of LSF technology can be seen. Embodied Carbon Assessments and LCA’s may be available from manufacturers which can demonstrate the green credentials of the relevant LSF system.
*Manufacture of concrete generates 9% of the world’s carbon emissions - almost much as industry.
used to quantify the environmental impacts of construction products.
Embodied carbon assessments (also known as carbon foot-printing) look at materials used, energy use/performance, waste, transportation and are based on RICS and British Standard guidance and include information from relevant Environmental Product Declarations (EPDs) and publicly available embodied carbon data. These assessments review the structure from facilitating works/demolition through to fixtures and fittings/ building services as part of the 60-year whole-life embodied carbon assessment including: product, construction process, in use – maintenance/repair and refurbishment, in use – water and energy and end of
To validate these positive statements, whole-life carbon cycle analysis have been carried out to assess credentials/performance when compared to structures formed using other methods of construction. These assessments show that light steel frame structures demonstrate a substantial reduction in the overall carbon footprint of a building of up to 20%.
CarbonEmbodied
carbon assessments are quite straightforward involving the multiplication of quantities of construction products and materials (generally on a weight basis) with embodied carbon coefficients or carbon emission factors. Quantities are generally derived from a ‘take off’ from construction drawings or directly from Bills of Quantities. Increasingly, design software is being developed to automate the assessment process.
3 times as
Embodiedlife.
Operational Energy 67% Product Materials 21% Maintenance 8% Transport 2% End of life disposal 1% Construction <1%
the entire aviation
An assessment of a medium scale residential property has been carried out by the LSF industry and can be found in a report on the SteelConstruction.info website. The figures in this report show the breakdown of the key elements are as follows:
www.lsf-association.co.uk 5
Embodied carbon assessment is a subset of a full Life Cycle Assessment (LCA) which is the tool used to develop Environmental Product Declarations (EPD) which are increasingly
• Biomass heating - Services from heating systems can be run through the LSF structure – locations should be agreed at design stage to avoid redesign/modifying the structure
6 Sustainability Guide
• Wind turbines - Locations to be agreed in advance with the LSF designer
• Design to use resources efficiently over the design life of the building
Incorporating the benefits of Embodied Carbon and Life Cycle Assessment (LCA) into building and infrastructure projects is critical for making informed decisions which can achieve real sustainability improvements and cut project carbon and cost.
• Design for durability avoiding the need to demolish
These technologies include:
• Design adaptable, dynamic spaces, anticipating future changes in their use
• Solar hot water - Solar technology can be accommodated within or on the roof structure – loads should be advised to the LSF manufacturer at design stage
Design Guide for Reducing a Building’s Embodied Carbon
• Combined Heat and Power (CHP)
Buildings using LSF technologies can accommodate environmental enhancements and integrate renewable and low-carbon technologies in exactly the same way as traditional construction.
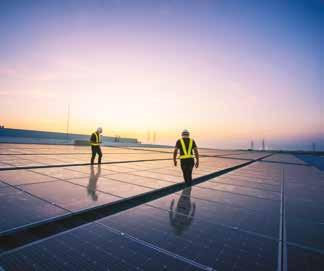
If these design principles are followed and light steel frame technologies are specified early in the design process, there will be a reduction achieved in the buildings carbon footprint.
EnvironmentalAccommodatingEnhancements
Seek advice from the system manufacturers design and engineering team to ensure these elements can be efficiently incorporated (as required).
Elements relevant to sustainability and reducing embodied carbon can be achieved through efficient design. Areas to be considered by the designer (preferably at Stage 2 of the RIBA Plan of Work) include the following:
• Design the structure to reduce the weight imposed on to the foundations
• Design for the long not short term
• Design floors with reduced thickness of concrete or use joisted floors
• Limit the amount of hot rolled steel required by good vertical alignment of structural elements
• Design to minimise energy use in all stages of a building’s life-cycle
• Air source heat pumps
• Design for disassembly and re-use at end of life
• Design to reduce waste
• Design to optimise the buildings architectural design for energy efficiency
• Solar photovoltaics (PV)
• Ground source heat pump
TATA are also working on radical new technologies which will completely transform the way steel is made. These processes will use 50% scrap steel and reduce carbon emission by 80%. The steel industry is united around the recycling and reuse of components and are working together to offer significant embodied carbon benefits.
The UK is largely self-sufficient in steel, in that it can produce the steel needed through recycling the latent stock to satisfy market demand so well placed for the future.
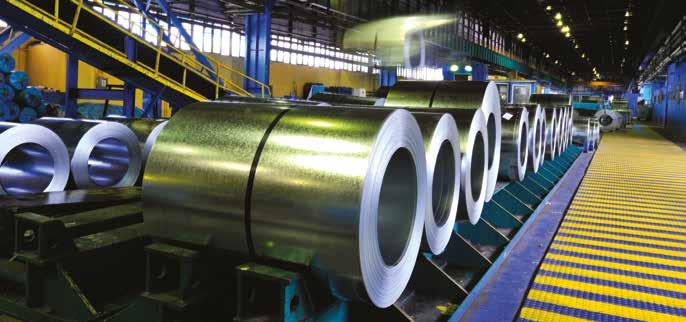
Looking to the future manufacturers are further developing a fabric first approach which allows the system users to achieve exceptional energy performance in their buildings. LSF manufacturers seek to partner with like-minded specialists to help their clients achieve and surpass their sustainability goals. This is achieved through early project engagement which enables clients to benefit from industry expertise to help deliver environmental solutions.
Sustainability in the future
Sustainability now
Steel has a well-developed and efficient recovery infrastructure, with current recovery rates from demolition sites in the UK at 99% for structural steelwork and 96% for all steel construction products. These figures far exceed those for any other construction material. Research carried out by the LSFA’s technical partner, the Steel Construction Institute (SCI) has estimated that there are around 100 million tonnes of steel in buildings and infrastructure in the UK. This ‘stock’ of steel is an important and valuable material asset that will be reclaimed and either reused or recycled in the future.
www.lsf-association.co.uk 7
Sustainability into the Future
Each manufacturer has design and engineering teams who maximise the structural benefits of the products by using the smallest amounts of material possible and minimising waste. They use digital technology at the design stage of a project in conjunction with the quality processes used by the manufacturer. This ensures that all steel components used are formed from steel which is traceable back to the coil from which it was formed. This allows the gauge, grade and level of galvanising of the steel used to be clearly identified to ensure it can be repurposed in a safe and structurally sound manner.
Sustainability is already a key driver for the use of LSF technology, with manufacturers who have quality and environmental procedures integrated into all their business processes to ensure that waste is minimised. Manufacturers actively manage the products they use to minimise waste and ensure they are sustainably-sourced.
Steel, being the core element of the LSF technology is provided by suppliers who are investing heavily in steel production and the likes of TATA are working in partnership with the LSF industry to develop the largest cluster of hydrogen powered plants in Europe to meet the goal of being carbon neutral by 2050.
VERSION 1 - SEPT 2022
Eco-efficiency of the cold roll formed product supply chain Journal of Materials Processing Technology, Vol. 177 www.sciencedirect.com/science/article/abs/pii/S0924013606003505
CONTACT INFORMATION
LSFA (Light Steel Frame Association) www.lsf-association.co.uk
Cogent Consulting Ltd - Offsite Construction Consultants 1 www.cogent-consulting.co.uk
SCI P370 - Sustainability of steel in housing SCI Technical Information Sheet ED020
Protocol for Reusing Structural Steel www.steel-sci.com/assets/downloads/steel-reuse-protocol-v06.pdf
Profiles and data for LSFA members can be found on their websites –LSFA members are listed at the following link: www.lsf-association.co.uk/members
UK Government Renewable and low carbon energy Guidance www.gov.uk/guidance/renewable-and-low-carbon-energy
Further Reading
LSFA Members
Steel Construction Institute 2 www.steel-sci.com
TATA Steel Shaping a sustainable society for generations to come www.tatasteeleurope.com/sustainability
Steel for Life embodied carbon report www.steelconstruction.info/File:Leti_WLC_Breakdown.jpg
1 Cogent Consulting Ltd have authored this document on behalf of the LSFA 2 Steel Construction Institute are technical partners of the LSFA www.lsf-association.co.uk
World Steel Association Steel Companies Performance www.worldsteel.org/steel-topics/sustainability/sustainability-indicators/
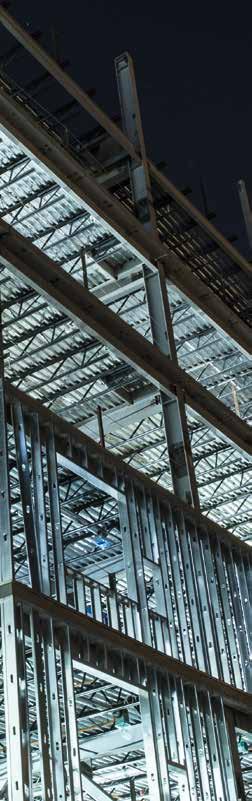