MODULAR
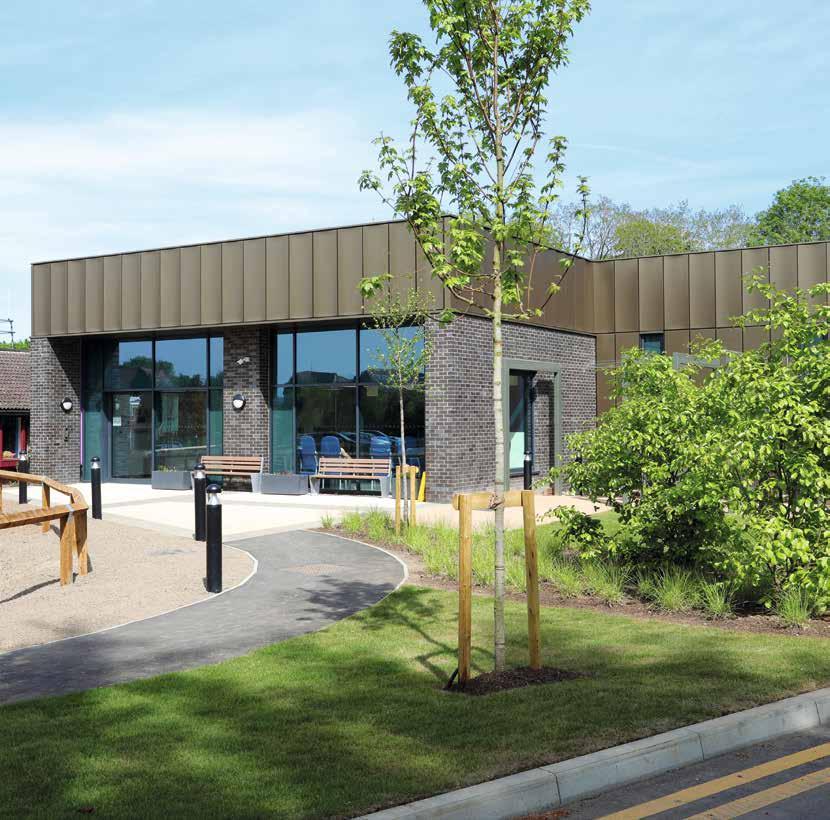
MILFORD COMMUNITY HOSPITAL
TRANSFORMING HEALTHCARE USING
MODULAR DESIGN AND BUILD
ROYAL RECOGNITION
Integra Buildings receives King’s Award for Enterprise for its sustainable approach to construction
P12
UTILISING AI
Reds10 discusses AI in action and how it can transform construction efficiency and precision P14
EDUCATION DELIVERY
Rapid and reliable solutions for schools needing more teaching space and specialist classrooms


Welcome to one of our regular sections covering the volumetric modular sector, where we provide a very quick run through some recent projects and developments
The sector has spent the last few years going through a rebalancing act of sorts, with several big name and well publicised business exits – even as we went to press Elements Europe were the latest to falter and enter administration. But as seasoned observers and industry commentators will know – irrespective of individual internal and various external forces – those businesses have been beset by problems that have
For anyone that read last issue’s ‘Volumetric Voices’ industry survey, undertaken by ARV Solutions and Cogent Consulting – although there has been an exodus of businesses from the volumetric homes sector – the survey revealed that whilst there is an air of trepidation from departing personnel about the factory environment they had been operating in, the overwhelming response was that volumetric technology and the prospect of returning to work inside that industry were resoundingly positive. The way in which the businesses were structured,
While the volumetric modular homes industry has taken a hit, the technology and potential it holds is still huge. Market dynamics may have exposed weaknesses but there is still a compelling case –especially with component standardisation, pattern book repeatability and a DfMA approach – that volumetric modular can play a transformative role in delivering the housing targets that successive
But for all the housing talk, it is in the healthcare and education sectors where many successful projects are being delivered at scale, on-time and on-budget to the highest standards. Lots more of these success
OVERLEAF…
04 08 10 12 14
MTX
A Community Diagnostic Centre at Milford Community Hospital using volumetric modular methods is helping reduce waiting lists and deliver more rapid treatment for patients.
INTEGRA BUILDINGS
Recently named as a recipient of The King’s Award for Enterprise 2025, CEO Gary Parker, reflects on one of the proudest moments in Integra’s 28-year history in its sustainable approach to construction.
CPAC MODULAR
With four decades of developing and delivering the highest quality building systems, Managing Director Sean Murphy provides an update on its customer-centric ethos.
AI IN ACTION
AI has the potential to revolutionise construction, delivering significant gains in efficiency, quality, and productivity. However, the industry risks missing out on these benefits as Scott Laird, AI & Technical Director, Reds10 explains
WERNICK BUILDINGS
When it comes to rapidly expanding a school estate, time, disruption and long-term value are key considerations. These elements are all under control with a specialist modular approach.
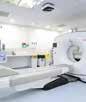



Contracts Ltd - Milford Community Hospital

MILFORD GOES MODULAR
A Community Diagnostic Centre designed to reduce waiting lists and deliver more rapid treatment for patients has been created at Milford Community Hospital as a design and build project by MTX Contracts Ltd.

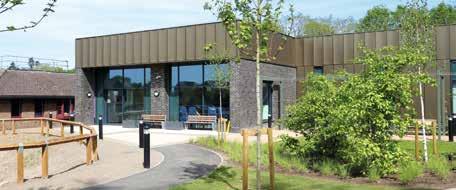
MTX used modern methods of construction (MMC) to complete the fully compliant facility faster, safer, greener and more cost effectively than conventional building techniques. The new Community Diagnostic Centre (CDC) includes two MRI scanners and a CT scanner, along with consulting rooms and offices and is set deliver an extra 11,000 MRIs and 9,500 CT scans as part of a ‘one-stop-shop’ for Royal Surrey NHS Foundation Trust.
The new facility will widen the scope of available diagnostic imaging services across the region.
MTX faced considerable challenges undertaking groundworks on the site adjacent to the Milford Community Hospital. Development of the site required rerouting water and gas mains and amending the plans for the foundations after the discovery of substantial sandstone deposits.
However, the MTX site team worked with the Trust and P&HS architects to overcome the issues, creating a poured concrete slab which forms a stable base for scanning equipment which is highly sensitive to movement or vibration.
With the slab formation and concrete pour completed, MTX craned into position a total of 27 precisely engineered structural steel modules which were factory-manufactured offsite while the groundworks were underway, to speed up project delivery. The groundworks package also included hard landscaping to the building entrance, a filtration pond and work on a new access road.
The CDC incorporates specialist features required because of the sensitive equipment it houses –including a Faraday cage installation incorporated into the structure around the MRI rooms to avoid interference
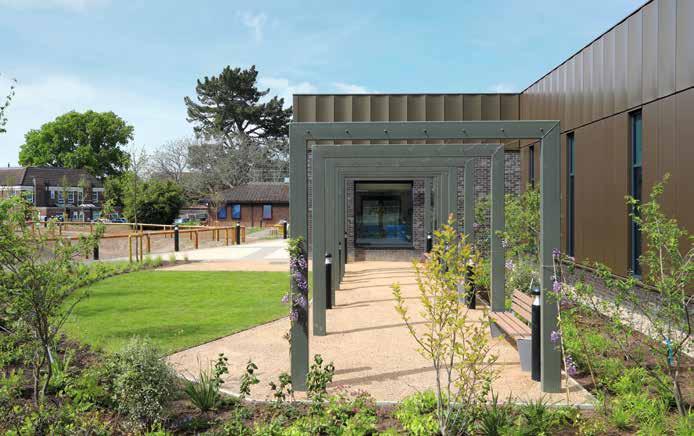
with other electrical equipment, and a lead lining to the CT Scanner room. The new building also includes roofmounted solar panels to provide green energy. An independent link corridor constructed by MTX connects the new CDC to the Milford Community Hospital.
Ross Dunworth, Royal Surrey NHS Foundation Trust Deputy Chief Executive, said: “We were pleased to work in partnership with MTX on this project as they have extensive experience of constructing similar facilities at other NHS trusts. The new unit became operational at the end of March and patients are now benefiting from this state-of-the-art facility. This will improve health outcomes by helping to speed up diagnosis and access to potentially life-saving treatments, whilst providing a more convenient service to patients closer to home.”
Milford is one of five CDC projects completed by MTX in the space of 18 months. The urgent need for fast-track build of bespoke medical facilities is encouraging NHS Trusts to partner with specialist provider MTX for more rapid and cost-effective delivery, which ensures a quicker return on investment.
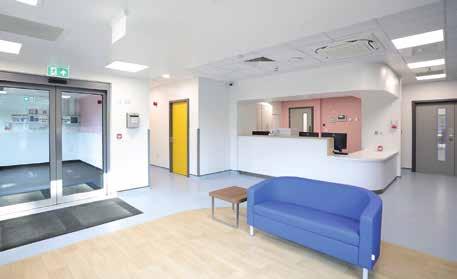
MTX Managing Director David Hartley added: “MTX has been privileged to partner with a number of NHS Trusts which recognise the benefits of using MMC to ensure rapid delivery, high quality and good value. Our team brings a huge amount of experience and expertise to these CDC projects and while they often share characteristics, each facility is designed and built to prioritise the requirements of the individual NHS Trusts.”
MTX has partnered with the NHS for more than 40 years providing vital specialist facilities and ward accommodation for hospitals and during that time has created more than 300 operating theatres and 2500 compliant bed spaces.
For more information visit: www.mtx.co.uk 3 4
Images: 01-04. The CDC at Milford Community Hospital has transformed healthcare locally and used cutting edge MMC to do it
BOUTIQUE MODERN CONTRACTED FOR LANDMARK EASTBOURNE DEVELOPMENT
Boutique Modern has signed contracts to deliver its most significant project to date when it builds 100 affordable homes at the Grade II Listed Victorian Pump House in Eastbourne. The scheme will deliver 100 affordable homes, including 59 houses and 41 apartments. Of these, 20 will be for shared ownership and the remainder for affordable rent.
Eighty of the homes will be newbuild and delivered using modular construction, while the rest will be created by converting the site’s historic Victorian Pump House.
Originally constructed in the 1880s for the Eastbourne Waterworks Company, the building will be sensitively repurposed by Boutique Modern’s specialist partners as part of the main contract works. This major regeneration project will transform the landmark building in Bedfordwell Road which has been derelict for many years. Dick Shone, Managing Director of Boutique Modern, said: “We’re proud to begin work on our
largest project to date – a scheme that marks an important next step for our business. Thanks to the increased capacity of our new factory, we’re able to take this on while continuing to deliver for other clients alongside the recent launch of our ModernHome product.
“We’ve worked closely with Eastbourne Borough Council on several successful schemes, so we’re very pleased that this milestone project will be delivered in the town. It’s another step forward in our relationship with the council and we hope it will give other local authorities confidence in our ability to deliver schemes like this one.”
All the newbuild homes are targeted to achieve an EPC A rating, which will be delivered through a combination of solar PV, MVHR, air source heat pumps, electric heating, and Boutique Modern’s fabric-first design approach, which keeps homes warm in winter and cool in summer.
Boutique Modern secured the scheme through the Lewes District Council Modular Housing Framework, with Councillor Peter Diplock, cabinet member for housing at Eastbourne Borough Council, saying: “I am incredibly pleased to see

this ambitious project move from planning to reality.
“Developing a brownfield site like Bedfordwell Road presents unique challenges, but our perseverance has paid off. This development of 100 affordable homes represents the most significant council-led housing initiative in our borough for decades and underscores our commitment to delivering much-needed homes that local people can afford.” Enabling works are already underway, with full construction due to start towards the end of 2025.
Source: www.boutiquemodern.co.uk
MERIT DELIVERS CRUCIAL COMPONENTS FOR BEDFORD HOSPITAL

Merit has announced a significant milestone in the construction of the new Same Day Emergency Care (SDEC) Unit at Bedford Hospital. Appointed by the Bedfordshire Hospitals NHS Foundation Trust, Merit has successfully delivered seven major UltraPOD ® units that will form the core of this state-of-theart facility. During May a 450-tonne crane expertly lifted and positioned the seven UltraPODs® on site, marking a substantial advancement in the project's timeline.
Merit’s proprietary UltraPOD® SFS variant is at the heart of this cutting-edge facility. This customisable, full-building solution harnesses advanced offsite manufacturing techniques, enabling faster and more cost-effective construction. By pioneering an industrialised approach to building, Merit addresses the urgent demand for efficient healthcare delivery while prioritising sustainability.
This project milestone follows Merit’s approval to commence offsite manufacturing at its factory in December 2024, underscoring the team’s dedication to rapid project delivery. Leveraging their expertise, Merit’s team pre-manufactured 85% of the UltraPOD® units, incorporating all mechanical, electrical and plumbing (MEP) services. This innovative approach not only accelerates construction timelines but also ensures exceptional quality control at every stage. Once operational, the new SDEC Unit will encompass consultation rooms, clinical management rooms, examination rooms, assessment areas and other supporting services, to provide a comprehensive range of healthcare services at Bedford Hospital.
Tony Wells, CEO at Merit, said: “We are thrilled to reach this crucial project milestone in the delivery of the new SDEC Unit at Bedford Hospital. At Merit, we are proud to be at the forefront of innovative offsite construction solutions that not only meet the urgent needs of healthcare facilities but also prioritise sustainability and efficiency. Reaching this important project milestone is a testament to our commitment to delivering high-quality healthcare environments quickly and effectively.”
Melanie Banks, Director of Redevelopment and Strategic Planning at Bedfordshire Hospitals NHS Foundation Trust, added: “The Trust is pleased to be delivering this new facility which will provide critical improvements in both emergency capacity and patient flow through our extremely busy Emergency Department at Bedford Hospital. The true extent of Merit’s offsite manufacturing is beyond what we have seen with other modular manufacturers and have dramatically reduced both the extent and duration of the impact to our operational site from the construction process. We look forward to continuing our ongoing work with Merit on what is a fast-tracked project with limited budget.”
Source: www.merit.co.uk
MCAVOY SECURES PLACE ON NHS SBS FRAMEWORK FOR THIRD CONSECUTIVE TERM
McAvoy is proud to announce its successful appointment to the NHS Shared Business Services (SBS) Modular Building Framework for the third consecutive term, marking a sustained commitment to delivering high-quality modular building solutions across the UK public sector.
The four-year framework, which facilitates the procurement of modular buildings for public sector clients, sees McAvoy awarded six Lots, encompassing both permanent and rental modular solutions. This includes standard and bespoke buildings tailored to the needs of the education, healthcare, and wider public sectors.
McAvoy’s continued presence on the NHS SBS Framework underscores its reputation for excellence in offsite manufacturing, providing clients with efficient, sustainable, and costeffective building solutions. McAvoy’s modular approach offers significant advantages, including reduced construction timelines, enhanced quality control, and greater certainty in project delivery.
Commenting on this latest framework appointment, Stephen Clayton, Preconstruction Director at McAvoy said: “Being reappointed to the NHS SBS Framework for a third term is a significant achievement for McAvoy. We’re proud to continue supporting the UK public sector with innovative modular solutions that prioritise sustainability, quality, and speed of delivery. This achievement is a testament to the hard work and dedication of our entire team.”
Procuring through the NHS SBS Framework offers a range of benefits to public sector clients, including access to prequalified suppliers, the option to procure via mini-competition or direct award, reducing procurement time and associated costs, greater price predictability through not-tobe-exceeded framework rates and opportunities for early contractor involvement and collaboration, ensuring projects are delivered on time and within budget.
Over the past eight years, McAvoy has successfully delivered numerous projects under the Framework, ranging from state-of-the-art educational facilities to advanced healthcare units.

The reappointment to the NHS SBS Framework reflects McAvoy’s ongoing dedication to innovation and excellence in the modular construction sector.
Source: www.mcavoygroup.com
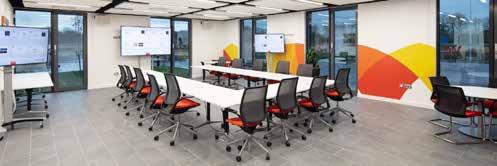
Modular Solutions when
you need them most
From schools to wards, research labs to office spaces, McAvoy delivers high quality modular buildings tailored to your needs.
With over 50 years’ experience, we work across education, healthcare, commercial, and pharmaceutical sectors, offering both permanent and temporary modular solutions designed for performance, speed, and sustainability.
Our
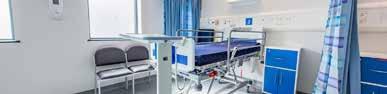
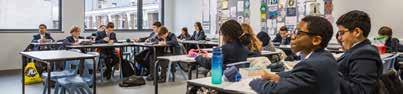




ROYAL RECOGNITION FOR MODULAR BUILDING
Integra Buildings was recently named as a recipient of The King’s Award for Enterprise 2025 and is seen as royal seal of approval for its sustainable approach to construction.
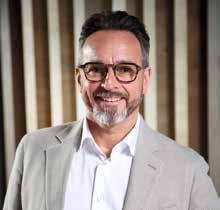
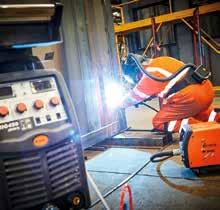
Recognised in the ‘Sustainable Development’ category, the award underlined Integra’s position as a pioneer in offsite construction, putting sustainability at the heart of its current and future strategy. Reflecting on what CEO Gary Parker, described as one of the proudest moments in Integra’s 28-year history, he said: “We are challenging the boundaries of what is possible in sustainable construction, through bespoke design and offsite manufacturing. This is a nice tribute to Integra Buildings and from a very credible source – the judges of The King’s Award for Enterprise.
“Being royally recognised in the Sustainable Development category was a milestone moment in our history, now dating back almost three

decades. Beyond that, we see it as significant for the offsite construction sector as a whole. It shone a light on what we’ve long believed is one of modular’s greatest USPs – its inherent sustainability compared to traditional methods of construction.
“Factory manufactured buildings provide an increased level of quality control, efficiency and sustainability that cannot be replicated by traditional methods. A crucial element of that is the flexibility, and reusability, of modular buildings. A perfect example was our involvement in the revived Channel 5 series ‘Challenge Anneka.’ We donated an ex-hire classroom building to be re-purposed and used as a community food bank. It gave the building a new lease of life, extending its lifespan and providing a sustainable solution. You certainly wouldn’t be able to do that with a traditional building.
“At risk of preaching to the converted, offsite construction means every stage of project delivery – from design and manufacturing, to install and fit-out – can be impeccably tracked and monitored. By embracing digitisation through platforms such as SafetyCulture, Viewpoint and Asite, we have accelerated our evolution from a modular builder to a full turnkey modular construction company.
Everything we do is underpinned by professional standards. We now hold four ISO certifications and strive for BREEAM in more of our buildings.
“Across our headquarters site, you’ll find lots of sustainable investments –from large-scale solar installation and waste compactors to EV chargers and electric welding inverters and forklifts. We have set a bold net zero target of 2038 and, by the end of this year, will have removed gas from our site as another significant step towards that goal. But a business is nothing without its people. Our team has embraced sustainable change, new ways of working, and shown a real dedication to helping us achieve our ambitions. We passionately believe modular is the future of construction. The King’s Award is further endorsement that our sustainable approach is not just good for our business, but good for the industry.”
For more information visit: www.integrabuildings.co.uk
Images: 01. Gary Parker, CEO, Integra Buildings 02-03. Gary Parker and Managing Director Chris Turner are at the helm of a hugely successful and expanding volumetric modular business



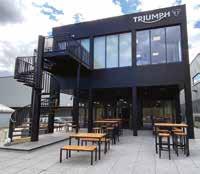
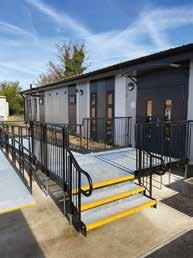
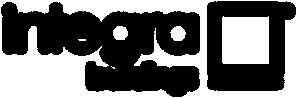
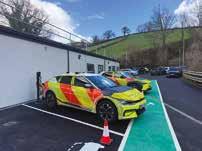
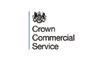



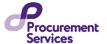
A LEGACY OF INNOVATION
CPAC Modular was founded over four decades ago with the goal of developing and delivering the highest quality building systems. “The ethos was always customer-centric and high quality,” says Managing Director Sean Murphy.

Over the last four years, CPAC Modular has embarked on a major innovation drive, investing in new technologies, materials, and people with the new goal to redefine modular construction and take it beyond traditional preconceptions.
Hybrid Modular: a game-changer
One of CPAC Modular’s most significant innovations was the introduction of hybrid modular construction. “We developed a product that was not just a step up from prefab buildings, but a complete evolution,” explains Sean Murphy. “We raised the bar using better materials, with longer lifespans, and placed a huge emphasis on structural integrity and fire compliance.”
A strategic vision for innovation and growth, coupled with the rebrand, drove CPAC Modular forward to another level. “We looked at our potential and realised we could do so much more,” says Sean. “We had the capacity and the ambition, to adapt to a changing market and we shifted towards a permanent modular offering.”
1
The company’s expansion has been nothing short of remarkable. CPAC Modular has grown from 40 employees to a workforce of over 120, with a strong focus on quality, sustainability, and efficiency. “The transition wasn’t without its challenges,” admits Sean. “Change is always difficult – but our team recognised the opportunity for growth and embraced it wholeheartedly.”
A revolution in construction
CPAC Modular has positioned itself as a leader in construction, including the education and healthcare sectors, with projects ranging from modular school buildings to hospital extensions. “Our permanent modular schools offer significant time savings compared to traditional methods,” says Sean. “This means students get access to state-ofthe-art learning environments much faster.”
The company has delivered critical projects such as Enhanced Community Care (ECC) hubs and hospital extensions in healthcare. “Modular construction is ideal for healthcare because it allows us to create high-

2
quality, fully compliant buildings in a fraction of the time,” adds Sean. “Speed of project delivery and reducing the time on site is crucial to our healthcare clients.”
CPAC Modular is not just about faster construction – it’s about smarter construction. The company is pioneering smart modular technology and integrating predictive maintenance systems into its buildings. Sustainability is also a key focus with significant investment in lean training, ensuring its production processes are as eco-friendly as possible.
The Road ahead
The company is currently investing €16million in a new state-of-the-art production and office facility, which will significantly increase its production capacity. With its focus on quality, efficiency, and sustainability, CPAC Modular is not just keeping pace with the construction industry - it’s leading the way “This new facility will allow us to scale up even further. We’re doubling down on our commitment to innovation,” says Sean. “We’re just getting started. The future is modular, and we’re proud to be at the forefront of that transformation.”
For more information visit: www.cpacmodular.com
Images: 01-02. Modular schools offer significant time savings compared to traditional methods and means students get access to learning environments much faster
Built Better.
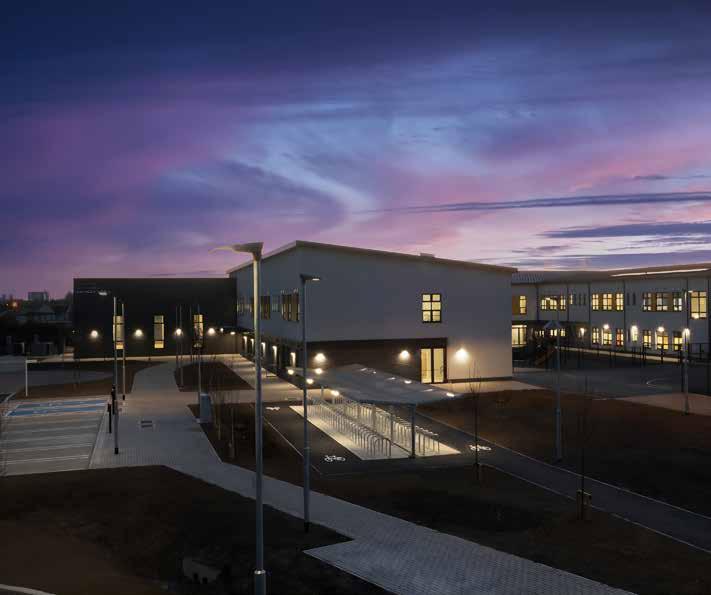
Our passion can be seen in every construction detail, every material choice, every ISO certified quality process, every safe working day, and in every smile by the students and staff of Ireland’s first permanant, modular-built, school for Lucan East ETNS. Co. Dublin.
ARTIFICIAL INTELLIGENCE MEETS OFFSITE MANUFACTURING
AI has the potential to revolutionise construction, delivering significant gains in efficiency, quality, and productivity. However, the industry risks missing out on these benefits—not only because it has historically been slow to embrace change -housebuilding, for instance, still relies on methods that are over a century old, but also because its prevailing economic model poses a major barrier to progress, as Scott Laird, AI & Technical Director, Reds10 explains.
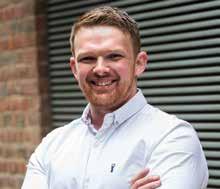
AI depends on clean, consistent, and centralised data to function effectively. Yet in construction, vital information—ranging from design and compliance to performance—is often fragmented across a complex web of subcontractors. This disjointed structure, where Tier One contractors manage an ever-growing chain of subcontractors, makes it difficult to harness AI’s full potential or integrate it seamlessly into project workflows.
AI in action – transforming construction efficiency and precision At Reds10, we’re taking a different approach. By managing design in-house and standardising our processes, we’ve been able to harness AI’s power with impressive results. For instance, we now use AI to optimise cladding design, reducing what once took 8–10 weeks to just minutes. This leap in efficiency is only possible because we control and refine our data internally.
We’re also exploring tools like Autodesk Forma, which enables rapid planning and layout optimisation. While currently focused on mass modelling, its future lies in linking with AI-driven generative design.
Images: 01. Scott Laird, AI & Technical Director, Reds10 02. Imjin Barracks SLA 1 2
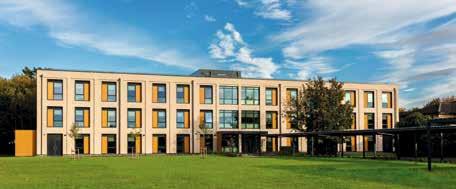
This could revolutionise how buildings are conceived—automating layouts, improving coordination, and freeing designers to focus on creativity rather than technical constraints.
Our use of Autodesk Construction Cloud (ACC) and LOD 500 3D models further enhances precision. These models aren’t just visual aids—they’re machine-readable and can be interpreted directly by CNC machines, streamlining fabrication and prefabrication.
On-site, AI-powered 360° cameras like OpenSpace are transforming documentation. These tools automatically capture and map site conditions, allowing AI to track progress, flag discrepancies, and support quality assurance in real time.
Reds10 can maximise the integration of AI because of the increasing levels of standardisation and industrialisation across our products, as we deliver sustainable high-quality buildings for the public sector, including homes for the armed forces, schools, and new buildings for the NHS and the prisons system.
Intelligent by design – powering a new era in construction
Just as consistent data is essential, high-quality, standardised models with structured information will be critical for fully harnessing generative design and AI in the future. Looking ahead, it’s easy to envision a future where centralised models generate detailed building designs automatically, streamlining the entire construction process. But to get there, the industry must embrace a more programmatic, industrialised approach.
AI offers construction a rare opportunity to leap forward. But unless the sector reforms its outdated business model and commits to standardisation, it risks missing out—again. At Reds10, we’re proving that with the right structure and a commitment to industrialisation of construction, the AI revolution isn’t just possible—it’s already underway.
For more information visit: www.reds10.com
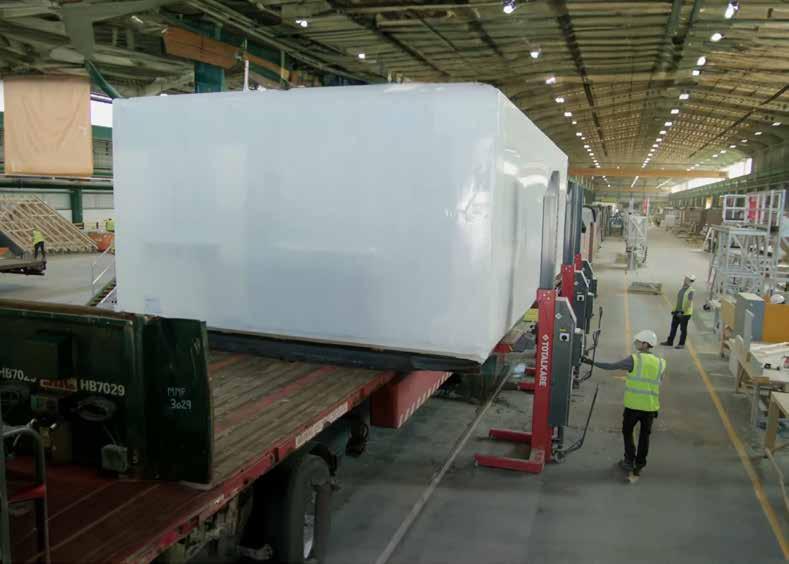
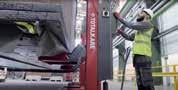
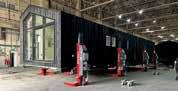

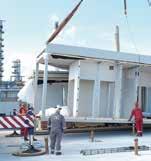
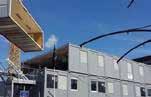


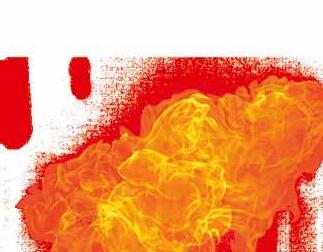
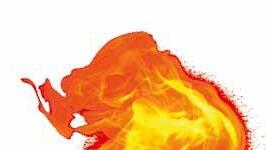
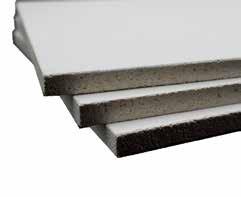

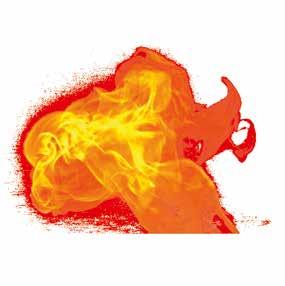
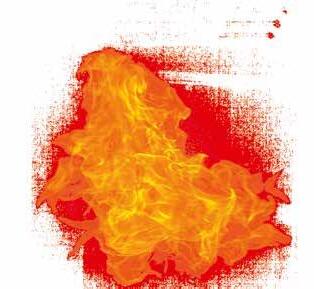
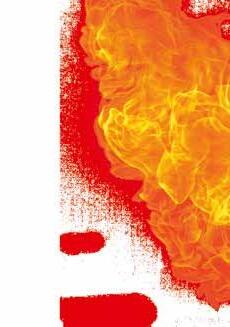
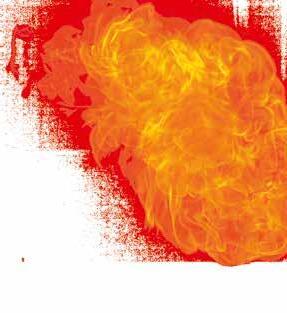
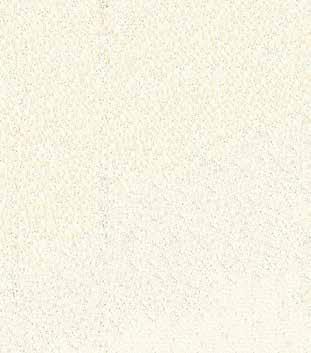
RAPID EDUCATION ESTATE DELIVERY
When it comes to expanding a school estate, time, disruption and long-term value are key considerations. These elements are all under control with Wernick Buildings and a modular approach.
For many schools across the UK, the summer holidays present an ideal opportunity to undertake construction works without impacting daily operations. Modular buildings offer a rapid and reliable solution for schools needing additional teaching space, specialist classrooms or support facilities. Modular construction offers faster project delivery, reduced on-site disruption, and high-quality, compliant buildings. This enables educational institutions to adapt to growing demands within the tightest of timeframes.
Why are more schools choosing modular buildings to expand their estates during the summer break?
Fast-track construction with minimal disruption
Traditional construction projects on school sites can be lengthy, disruptive and often require works to continue during term time. For many schools, this can raise concerns around safety, noise and interruption to teaching and learning. Modular construction solves these issues by relocating the bulk of the work offsite.
At Wernick Buildings, each module is manufactured in our dedicated facility in South Wales, where we can control quality and schedule with precision. While modules are being built offsite, enabling and groundwork can proceed simultaneously on school grounds. This parallel approach dramatically reduces the overall project timeline. Once the modules are complete, they are delivered and installed in a matter of days, often over a single weekend or during the school holidays. This ensures schools return to education in September with new spaces ready to use.
This streamlined process not only accelerates delivery but also minimises the impact on staff, students, and
parents. A crucial factor for schools looking to maintain continuity and wellbeing across the academic year.
A future-ready solution tailored to your estate
The beauty of modular buildings lies in their flexibility. Whether you require additional classrooms, science laboratories, PE facilities or SENDspecific spaces, modular solutions can be tailored to your school’s unique requirements with no compromise on design or functionality.
Wernick modular buildings are built to permanent building standards, incorporating energy-efficient features, natural daylighting and modern finishes that promote an excellent learning environment. Our buildings are fully compliant with BB103 guidelines, Part L building regulations and all other educational design standards. Modular systems also offer room for growth. With repeatable designs and scalable layouts, schools can add more modules in future phases or relocate them entirely to other parts of the estate if necessary. This long-term adaptability provides great value to local authorities, trusts and independent schools alike.
Whether you need temporary teaching blocks or permanent expansions, modular construction allows you to respond quickly and cost-effectively to rising student numbers or curriculum changes.
Sustainable, compliant and costeffective
We understand the importance of value for money and environmental responsibility in the education sector. Modular buildings offer schools a more sustainable way to expand, with significantly reduced material waste, fewer carbon emissions, and improved energy performance when compared to traditional builds.
All our modules are built using responsibly sourced materials in a low-waste factory environment. Our projects can incorporate features such as photovoltaic panels, highperformance insulation and heat recovery systems to support net zero goals. For many schools and trusts, these sustainability credentials are not just important for regulatory compliance, but for delivering on their own climate commitments and fostering environmental awareness among students.
The programme certainty offered from modular reduces the risks of weather delays and any on-site complications. This means more assurance and better control over costs. This will therefore result in a high-quality building delivered on time and within budget, all during a window that suits your school calendar.
Plan now for summer installation
With the summer holidays not far away, schools looking to expand should soon begin their planning and procurement processes to ensure their project is ready for installation during the break. Our expert team can guide you from design through to handover, offering a full turnkey service that includes planning applications, groundwork, landscaping and interior fit-out. With decades of experience delivering school buildings across the UK, we understand the pressures schools face, and we are here to help you find a solution that works.
For more information visit: www.wernick.co.uk/buildings
Images: 01-03. Modular construction can provide education facilities, sustainably, quickly and with reduced disruption
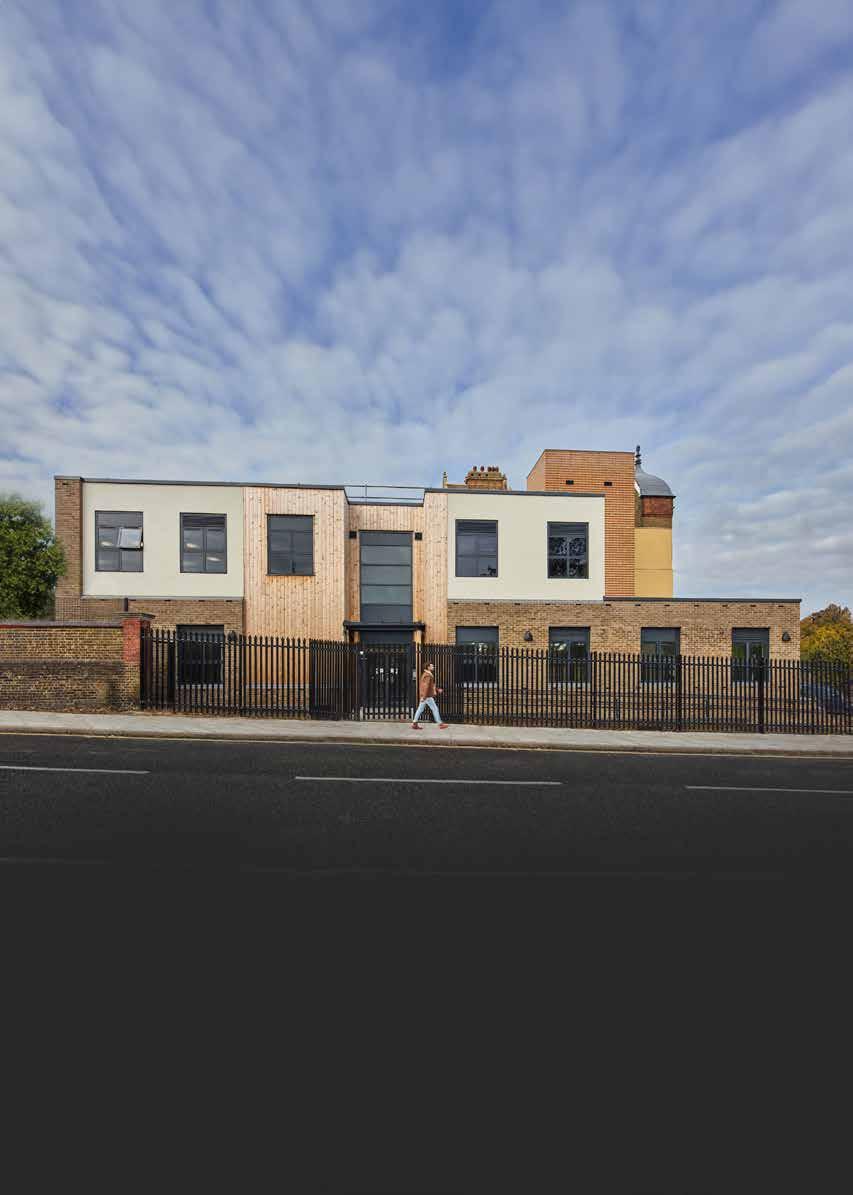

BUILDING STRONGER TOGETHER: SOLVING SUPPLY CHAIN CHALLENGES
Volumetric modular construction continues to gain traction as a highperformance solution to some of the built environment’s most pressing challenges, but while manufacturers are innovating rapidly at the design and delivery level, one of the most persistent obstacles remains at the foundation: supply chain selection and integration.
Stefan Prychidko, Supply-Chain Consultant with Cogent Consulting, explores some of the challenges and the potential solutions.
Volumetric modular systems rely on a wide array of components — from structural frames and insulation to MEP services, interior finishes, and digital systems. Unlike traditional construction, however, volumetric manufacturers need their supply chains to deliver with precision, repeatability, and synchronisation to meet factory-driven timelines and quality standards. This presents a unique challenge: finding suppliers that are not just cost-effective, but deeply aligned with the manufacturer’s methods, pipeline, and long-term vision.
A New Kind of Supply Chain
Volumetric modular manufacturing demands a shift from transactional procurement to strategic partnership. Rather than sourcing materials on a project-by-project basis, manufacturers need long-term collaboration with suppliers who understand and support their production systems. This means shared R&D, co-developed products, and in some cases, joint investment in machinery, logistics or packaging innovations.
Critically, this model depends on pipeline visibility. Suppliers need confidence in future demand to commit to high volumes or tailor their production processes. Without a stable, visible pipeline, suppliers are less willing to invest — and modular manufacturers can struggle to secure pricing, availability, or innovation at scale.
Leveraging Volume Through Collaboration
To address this, the sector needs to embrace collaborative procurement
models. Volumetric manufacturers — many of whom are SMEs or midsized enterprises — could significantly improve their supply chain leverage by pooling their procurement needs through buying clubs, consortia, or shared framework agreements. These models are common in sectors like housing and healthcare, where volume aggregation reduces costs, strengthens negotiating power, and increases supplier commitment.
This kind of cooperation requires trust and transparency — not just between manufacturers and suppliers, but between competitors. In some cases, it may mean standardising certain elements of design or specification in order to create shared demand for key components, such as bathroom pods, floor cassettes.
The Role of Platform Thinking and Standardisation
The adoption of platform-based construction and manufacturingwhere standardised components, interfaces, and manufacturing principles are used across multiple projects — enables far more efficient and predictable procurement. Standardisation doesn’t mean one-size-fits-all. Instead, it allows manufacturers to develop a kit of parts or repeatable solutions that can be configured to suit different projects while relying on the same supply chain backbone.
With consistent specifications, suppliers can plan ahead, invest in process improvements, and deliver better pricing and performance. This makes it easier for manufacturers to scale, innovate, and ensure consistent quality - all essential for volumetric delivery.
To deepen supplier relationships, volumetric manufacturers must also rethink how they approach intellectual property and innovation. In traditional models, IP is closely guarded, and R&D happens in silos. But in modular construction, innovation often emerges at the intersection of disciplines — a smarter fixing system, a more efficient assembly method, or a fully integrated MEP pod can transform productivity.
Shared IP agreements, codevelopment projects, and transparent collaboration models can unlock new value — not just for the manufacturer, but for the entire supply chain. These arrangements need careful management but can significantly accelerate innovation and drive mutual benefit.
Building Long-Term Resilience
Ultimately, the success of volumetric modular manufacturing depends on building resilient, integrated supply chains based on partnership, not procurement. Manufacturers must shift their mindset from short-term buying to long-term collaboration — sharing risk, insight, and opportunity with their suppliers. By doing so, they can reduce costs, improve quality, unlock innovation, and scale their businesses with greater confidence.
The future of volumetric modular construction isn’t just about building differently — it’s about partnering differently. And those who embrace that change will be best placed to lead the industrialised construction revolution.
For more details on supply chain development support offered by Cogent Consulting, visit www.cogent-consulting.co.uk or email stefan.prychidko@cogent-consulting.co.uk
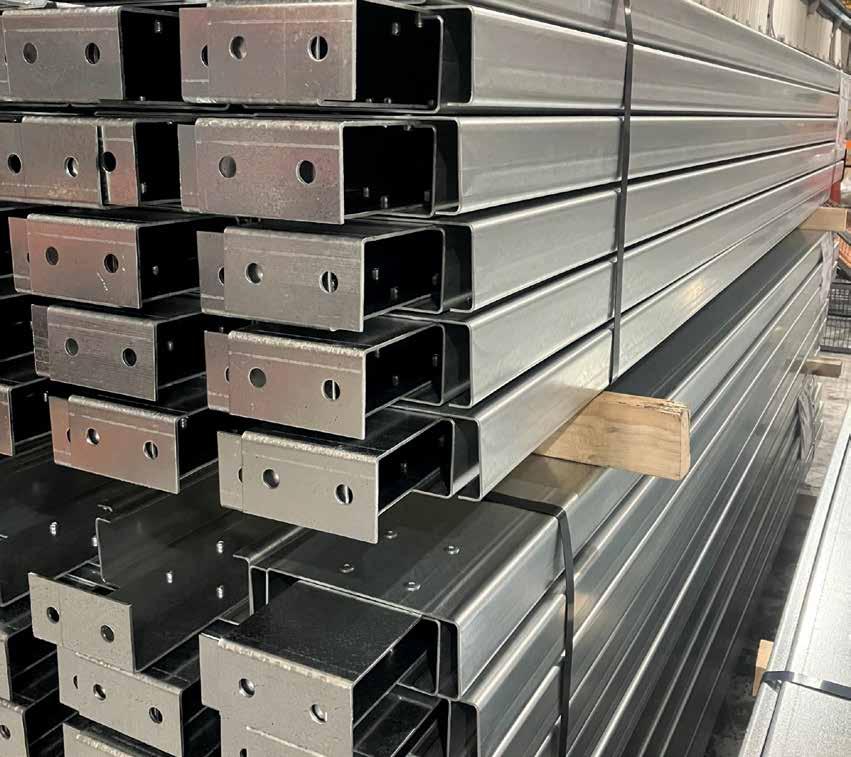
Modular Building Solutions
Built to Fit. Engineered to Perform.
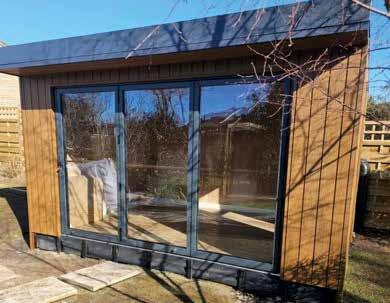
Steadmans is one of the UK’s leading manufacturers of roofing and cladding systems, offering complete solutions for modular builds, from structural steelwork to high-performance cladding and custom accessories.
STRUCTURAL STEEL JOISTS
For floors & roofs: precision-engineered from S450 pre-galvanised steel
Riveted, bolted, or loose cleats for rapid assembly
Custom cut, punched, & prepared offsite
CLADDING SYSTEMS
Insulated composite panels & single skin profiles
Thermal efficiency with custom colours & surface finishes
Ideal for classrooms, pods, offices, garden rooms & more
ACCESSORIES
Bespoke flashings, trims & fasteners
Colour-matched finishes
Streamlined installation
Why modular builders choose Steadmans
• Fast lead times with large UK stockholding
• Nationwide delivery
• Seamless integration with design & procurement workflows
• Expert support from concept to completion
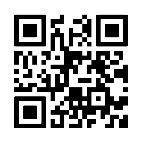
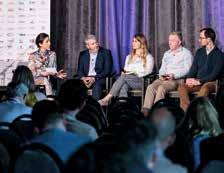


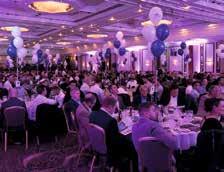
The focal point of Offsite Construction Week, taking place from 15-19 September –OFFSITE EXPO is a dynamic open source event that offers unparalleled opportunities to look to new horizons to address the issues that have plagued the construction industry for decades.
Join industry pioneers, innovators, and thought leaders at the forefront of modern construction. The OFFSITE AWARDS are more than a celebration—they’re your gateway to game-changing insights, connections, and opportunity. Visit page 52 to discover this year’s shortlist.
In partnership with the Structural Timber Association, the STRUCTURAL TIMBER CONFERENCE will provide a focal point for celebrating timber’s success and steering discussions that will define its future. The event will feature a wide-ranging programme of keynote speakers, technical seminars, and forward-thinking expert panel discussions, tackling subjects including sustainability, industrialised construction and timber supply capability.
Featuring compelling examples of what can be achieved using the most natural and sustainable of materials, the STRUCTURAL TIMBER AWARDS are returning on 01 October 2025 to celebrate outstanding projects, inspiring individuals, and the coming together of an industry. Winners will be announced at the prestigious awards ceremony celebrating architectural achievements and engineering ingenuity in timber construction.
To gain insight from those who are shaping the future of the offsite housing sector, the EXPLORE OFFSITE HOUSING Conference brings together technology leaders to discuss the growing opportunities that the housing shortage presents for offsite construction.
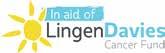
Partnering with the Lingen Davies Cancer Fund, we will be increasing our fundraising efforts in 2025 to support those who need it most.
To donate use the following QR

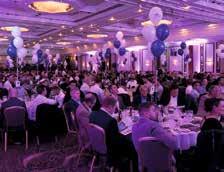
Where High Performance Meets High Efficiency
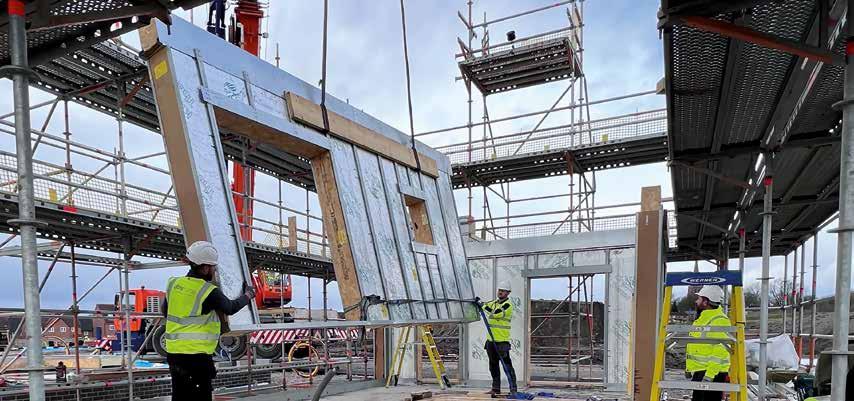
Ultrapanel patented SIP systems are future-ready solutions designed to deliver high quality new homes at scale.
Experience the Future of Housebuilding
Later this year, Ultrapanel will be unveiling a state-of-the-art demonstration home that brings together cutting-edge construction technology and sustainable design.
Smarter, Faster, Greener Building – Powered by Ultrapanel
We will be hosting live and virtual experiences and sharing regular updates. To register your interest, please email hello@ultrapanel.co.uk
Ultrapanel Building Technologies Ltd
Salthill Road, Clitheroe, Lancashire, BB7 1PE
© Ultrapanel Building Technologies Ltd 2025
Steal the advantage in construction with Howick steel roll-forming machines and technology.
You want a system you can trust. One that delivers speed, accuracy and control without locking you in.
That is the Howick difference.
Machines 100% built in-house in New Zealand for quality you can rely on
No toll fees, royalties or software lock-ins
Open integration with your preferred CAD framing software
Proven performance, precision and repeatability across global projects
Personal support from people who know your machine inside out
nearly
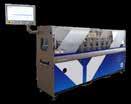
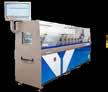
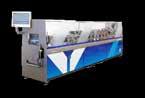
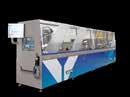

Visit howickltd.com today.
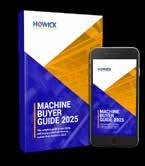
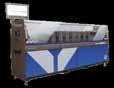
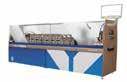