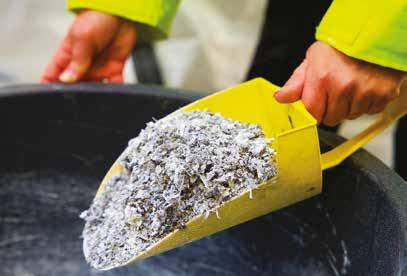
4 minute read
Il Demanufacturing è la nuova sfida per i materiali green
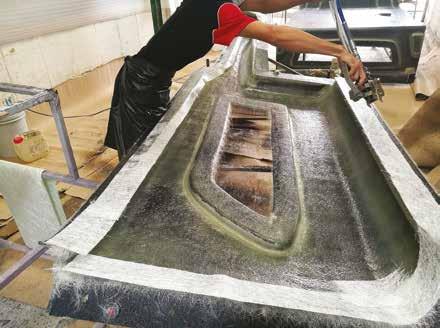
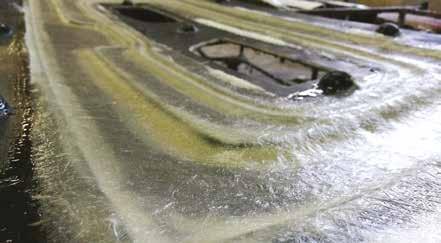
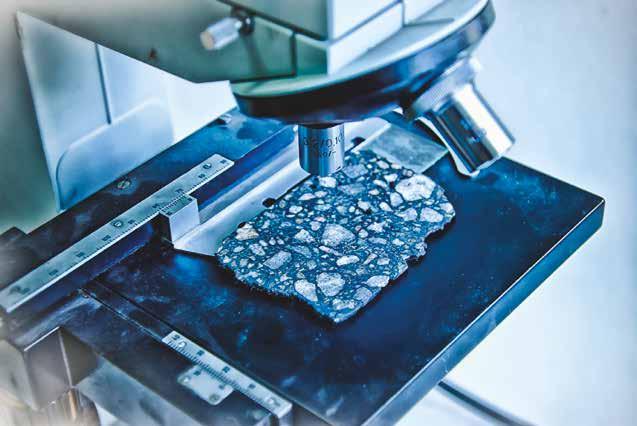
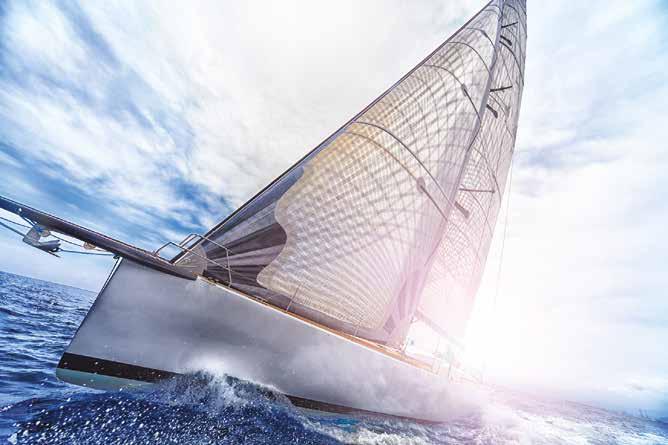
Il tema della problematica degli scarti provenienti dalla filiera delle aziende dei compositi marchigiani e la loro possibilità di impiego in manufatti Green è stato oggetto di una memoria presentata durante il convegno digitale Progettistapiù 2023
Imateriali compositi stanno assumendo una crescente importanza come materiali chiave per la riduzione del peso in molte applicazioni. Tuttavia, sebbene essi siano in grado di coniugare elevate prestazioni con un peso contenuto, presentano diverse problematiche dal punto di vista ambientale. In questo contesto, i biocompositi, possedendo numerose caratteristiche interessanti come basso costo, bassa densità, elevate proprietà specifiche, compatibilità ambientale, riciclabilità e riduzione delle emissioni di CO2, stanno rivoluzionando il settore promettendone uno sviluppo sostenibile. Tuttavia, questi nuovi materiali incontrano diverse difficoltà nell’essere introdotti in applicazioni industriali, soprattutto per la problematica relativa agli scarti provenienti dalla filiera delle aziende che li producono. Per affrontare in ottica green questo tema, durante il convegno digitale Progettistapiù 2023 è stato descritto come nel progetto MARLIC sono state vagliate diverse modalità di recupero degli scarti, così come la loro “preparazione” e trasformazione e reimpiego come materia prima di recupero, con l’obiettivo di avere una panoramica sui materiali compositi tra i più difficili da riciclare e fare luce sugli scenari futuri.
In questa attività le varie università facenti parte del progetto hanno controllato la qualità delle materie prime e, al termine, hanno valutato i materiali che sono stati prodotti.
Secondo la Linea 1 del progetto, il laboratorio MARLIC verrà creato nel comune di Camerino (Mc), e sarà il fulcro della Piattaforma Collaborativa. L’obiettivo finale è quello di realizzare una solida infrastruttura regionale di ricerca a disposizione delle aziende. La Linea 2 dei biomateriali, seguita da HP Composites, si occuperà dello sviluppo di nuovi materiali compositi avanzati partendo dallo sfruttamento di biomasse, sostanze naturali, sottoprodotti e scarti delle lavorazioni industriali per la realizzazione di prodotti innovativi ed eco-sostenibili. Con il progetto di R&D “Demanufacturing” sono state in via preliminare elencati e valorizzati gli scarti di ogni azienda, per poter poi riutilizzarli e dargli una seconda vita. In particolare, è stato studiato il recupero degli scarti di produzione (materiali compositi termoindurenti, materiali compositi termoplastici e Biomateriali), componenti compositi a fine vita e il recupero di materia prima/seconda da cicli di produzione, da reimpiegare per la progettazione/realizzazione di prototipi di nuovi manufatti composti pensati secondo i dettami della logica 4R (Riduzione, Riutilizzo, Riciclo e Recupero delle risorse).
Le problematiche
Il composito per sua natura è difficile da riciclare perché nel momento in cui si produce è necessario che la parte organica e quella inorganica siano legate tenacemente. Quindi, in fase di riciclo, queste due componenti eterogenee sono difficili da separare. Questo è il motivo per cui allo stato attuale il prodotto viene avviato in discarica.
Le aziende che hanno fatto parte di questa partnership provengono da differenti settori industriali, dal nautico, all’edile, dall’automotive all’eolico, dall’arredamento al calzaturiero. Tutti i loro scarti erano conferiti in discarica con determinati codici CER e valutati in matrice e rinforzo di diversa natura: matrice termoindurente a base metacrilica, poliestere, vinil-estere, epossidica ecc.; rinforzo: strati di tessuti di origine minerale (vetro, carbonio, basalto, wollastonite, quarzo, vetro, metalli, fanghi, fibra di carbonio) o vegetale (lino). Tra le possibili tecnologie di recupero sono stati testati i processi chimici (di depolimerizzazione nel caso di compositi acrilici per esempio), processi meccanici (per esempio una macinazione) e processi termici per bruciare questi materiali e ricavarne la parte di rinforzo. Quindi è stata fatta una ricognizione dei ruoli e delle competenze in ambito di economia circolare nelle Marche e proposta di modello organizzativo; una progettazione mediante metodologie e strumenti innovativi di DFD e DFR di prodotti industriali, e realizzazione prototipi; l’identificazione e la caratterizzazione degli scarti/ sfridi e componenti in materiale composito disponibili e identificazione delle tecnologie per il recupero e trasformazione. Funzionale al progetto è stata poi costituita una carta d’identità degli scarti e degli sfridi dei partner, identificandoli per tipologia, caratteristiche, compatibilità e quantità.
La trasformazione meccanica degli scarti Delta produce lavelli da cucina in materiale composito costituito dal 70-80% di carica minerale (quarzo) e il resto di resina metacrilica quindi non recuperabili per riscaldamento. Il primo passo è stato quello di indicare la modalità di macinazione di un prodotto di questo genere la cui principale difficoltà è legata, impiegando un impianto di triturazione bi-albero, al riscaldamento della massa a causa della parte polimerica. Per rendere il composito più fragile è stato, quindi, impiegato azoto riuscendo a ottenere macinazioni differenti dal grano più grande al più fino. L’Università di Camerino si è poi occupata della caratterizzazione chimico-fisica degli scarti macinati visto che questi devono essere utilizzati in un’altra applicazione. Sono state anche eseguite prove di depolimerizzazione mediante impianto di
Marche Applied Research Laboratory for Innovative Composites” (acronimo: MARLIC) è la piattaforma della Regione Marche nell’ambito della “Manifattura sostenibile: eco-sostenibilità di prodotti e processi per nuovi materiali e de-manufacturing”. Il Progetto, finanziato dalla Regione Marche nell’ambito del POR Marche
FESR 2014-2020 , prevede un gruppo di lavoro di 27 soggetti guidati dall’impresa capofila depolimerizzazione coreano che ha lavorato gli scarti dei lavelli per riottenere monomero di recupero e cariche minerali. In questo caso, la strada in termini economici non è percorribile. Mentre, attraverso un processo di pirolisi sono stati ottenuti risultati interessanti ottenendo un syngas composto da CH4 e H2 che alimentava bene un genset che è un generatore di elettricità, In questo caso, il problema è che si formavano tantissime parti minerali da smaltire. Si è partiti poi con l’ultimo obiettivo che era quello di utilizzare questi componenti prototipali di materia prima seconda con il materiale recuperato e loro caratterizzazione. Sono state seguite tre strade, impiegando materiali di scarto dei partner, materiali di scarto Delta, materiali di scarto Delta verso nuove applicazioni con esiti più o meno positivi.
Articolo tratto dalla memoria dal titolo: “Compositi con materie prime di recupero: il De manufacturing è la nuova sfida per i materiali GREEN” - Maria Savina Pianesi, Responsabile R&D della Delta del gruppo Plados Telma, PhD Dottorato di ricerca in Chemical Science (ciclo XXVII) e laureata in Chimica presso Università degli studi di Camerino – Progettistapiù, 24 gennaio 2023
Per seguire l’intera presentazione: www.progettistapiu.it/guarda-video/104/materiali-innovativi-nelle progettazioni-sostenibili
HP Composites, leader a livello mondiale nella progettazione e produzione di componenti in materiale composito avanzato. Insieme ad HP anche 20 aziende del territorio marchigiano, la Fondazione Cluster Marche e cinque centri di ricerca tra cui l’Università di Camerino, l’Università Politecnica delle Marche, l’Università degli Studi di Urbino, ENEA e CNR. Per informazioni: www.marlic.it
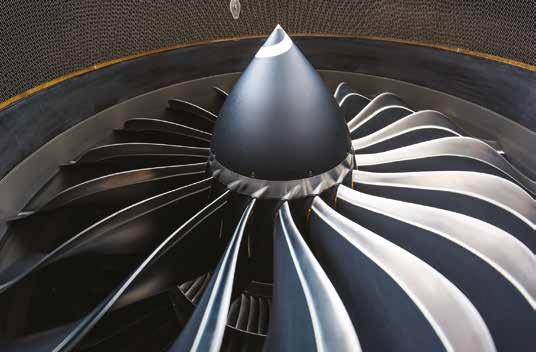