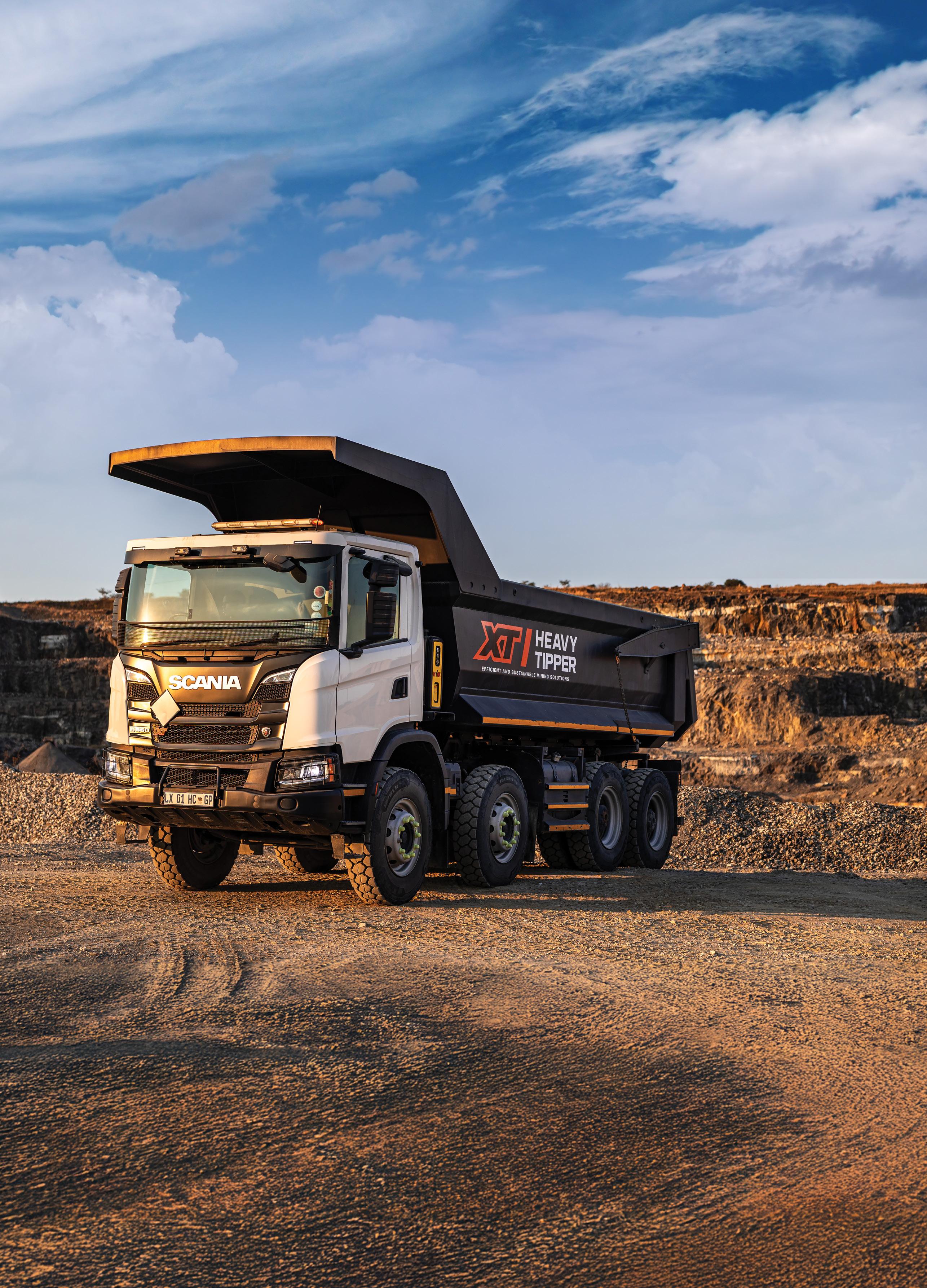
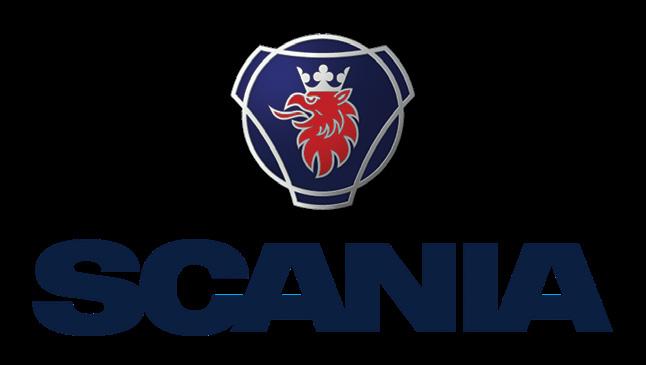
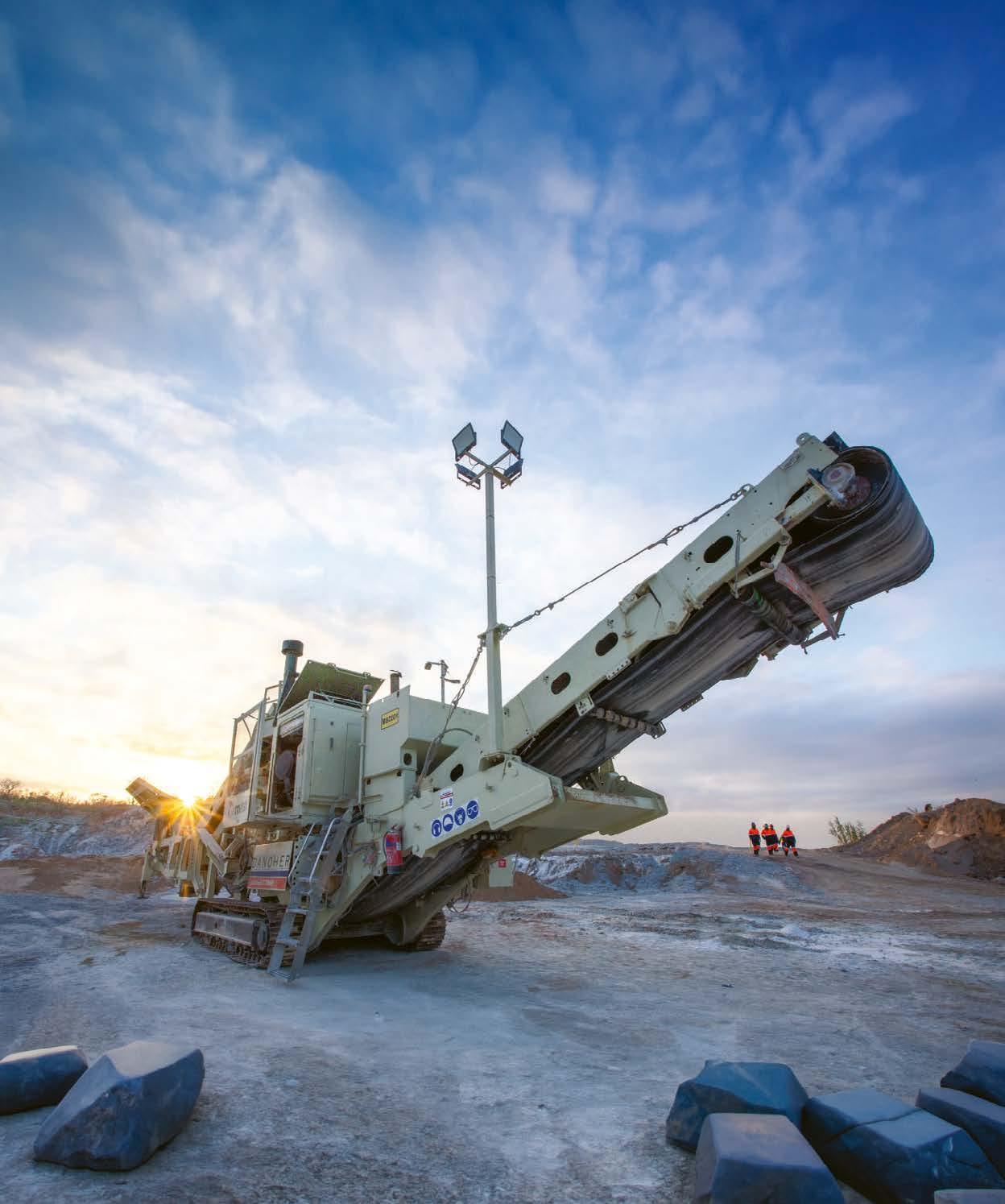
For every business, product quality is a key parameter that earns customer loyalty, helps establish brand recognition and manage costs. Customers often buy more from companies they know and trust, and businesses can reduce costs that result from product returns, defects and losses through quality claims.
This particularly rings true for aggregate producers, which is why, as you will see in this edition, we cast the spotlight on quality control in aggregates – why it is important and how to develop a quality control strategy, plus we take a look at the common methodologies of product testing and the relevant industry standards that guide quality control in quarrying.
In our quest to become a true industry information hub, we have in the past two years taken a deliberate approach to tackle key topics of critical importance to the industry. One that came to mind when we reconfigured our Features List was quality control.
Trending of results on a daily basis helps aggregate producers get an understanding of how consistent the crushed material is and whether any adjustments are required in the production process. If done well, one should be able to determine the rate at which the material is changing and make adjustments accordingly before any major issues occur.
One of the key takeaways from this discussion was that paying attention to quality allows producers to sleep peacefully at night as they are confident that their product complies with the specification. Capital channelled towards quality control/assurance is money well spent; it can lead to overall cost reductions based on lower percentages of materials produced that are out of the product specification limits. The investment pays for itself by reducing the percentage of rejected materials per annum, thus helping meet the needs and expectations of customers, and those invested in the quarrying activities.
MUNESU SHOKO
Publishing Editor Email: munesu@quarryingafrica.com
LinkedIn:
Munesu Shoko
Quarrying Africa
I recall speaking to Barry Pearce, who leads ASPASA’s Technical Quality Committee, who said that it is unfortunate that quality often receives the least attention, yet it should be the parameter that governs all the other activities. Without some form of quality assurance, he said, aggregate producers have no idea of where they are in real terms, besides the “gut feel” which often depends on an individual’s experience. This can be a good starting point if one is experienced but without a definitive test result, one cannot determine if the quality of the product is trending towards the edge of the specification limits, which is problematic.
Unfortunately, with production being seen as the main driver behind profitability, it often gets the lion’s share of the attention, while quality tends to be overlooked. Consequently, laboratory setups at many quarries remain understaffed, underequipped and are just there to provide results that preferably always pass. It is, however, encouraging to see the growing focus on quality control in the industry. As you will see in this edition, leading construction material suppliers such as AfriSam and Afrimat do not leave anything to chance when it comes to their quality control regimes. They employ stringent testing regimes to ensure ongoing conformity to standards and product specifications.
ROKBAK ADTS PROVE THEIR METTLE
SANDVIK CH430 CRUSHING IT AT AFRISAM’S RHEEBOK QUARRY
THE QUEST FOR ZERO-EMISSION TRANSPORT
RENEWED FOCUS ON OFF-ROAD MISSIONS
A ‘ROLLERCOASTER HEADING DOWNHILL’ THAT NEEDS TO ‘LEVEL OUT’, SOON!
Publishing Editor: Munesu Shoko
Sub Editor: Glynnis Koch
Admin: Linda T. Chisi
Design: Kudzo Mzire Maputire
Web Manager: Thina Bhebhe
Quarrying Africa is the information hub for the sub-Saharan African quarrying sector. It is a valued reference tool positioned as a must-read for the broader spectrum of the aggregates value chain, from quarry operators and aggregate retailers, to concrete and cement producers, mining contractors, aggregate haulage companies and the supply chain at large.
Quarrying Africa, published by DueNorth Media Africa, makes constant effort to ensure that content is accurate before publication. The views expressed in the articles reflect the source(s) opinions and are not necessarily the views of the publisher and editor.
The opinions, beliefs and viewpoints expressed by the various thought leaders and contributors do not necessarily reflect the opinions, beliefs and viewpoints of the Quarrying Africa team.
Quarrying Africa prides itself on the educational content published via www.quarryingafrica.com and in Quarrying Africa magazine in print. We believe knowledge is power, which is why we strive to cover topics that affect the quarrying value chain at large.
Printed by:
Email: munesu@quarryingafrica.com
Cell: +27 (0)73 052 4335
During a month-long trial, both the management and operations teams at Blurock Quarries were ‘pleasantly surprised’ by the Scania mining tipper’s aptitude in in-pit haulage.
Having endured tough market conditions in the past three years, KwaZulu-Natal-based Blurock Quarries has been investigating efficiency improvement initiatives to reduce operating costs and enhance profitability. One area that is receiving attention is in-pit haulage, a major cost driver for any quarry or mining operation. As part of rethinking haulage, Blurock is one of the first local quarries to trial the Scania G460 XT mining tipper at its operation. During a monthlong trial, both the management and operations teams were ‘pleasantly surprised’ by the truck’s aptitude in such an arduous application. By Munesu Shoko.
Saying that in-pit haulage is one of the major cost drivers in quarrying and open-pit mining is not making an overstatement. In fact, transportation, on average, accounts for about 30% of total mining costs at most opencast mining operations, which is why operations
8,2 l/h
Deployed to haul run-of-quarry material from the muckpile to the primary jaw crusher, the mining tipper consumed about 8,2 litres of diesel per hour
The Blurock team generally loaded between 35 and 37 t payload.
As part of rethinking in-pit haulage, Blurock Quarries is one of the first local quarries to trial the Scania G460 XT mining tipper at its operation
During a month-long trial, both the management and operations teams were ‘pleasantly surprised’ by the truck’s aptitude in such an arduous application
The Scania mining tipper’s massive 40-t payload enables consolidation of loads and thus reduces the amount of vehicle movement required to distribute a given quantity of material on site
While the haul roads at Blurock are designed for downhill hauling of loaded trucks, the team was impressed at how the Scania mining tipper made light work of hauling uphill at gradients of up 11 degrees (24%) with a full 35-t load during testing
such as Blurock Quarries are at the forefront of investigating ways to reduce costs directly linked to this function of their operations.
In an environment where market conditions have been depressed for the past three years, Jeremy-Hunter-Smith, CEO of Blurock Quarries, and his entire team, have been
40%
While the fuel consumption was pretty much on par with the 30-tonne ADTs that the quarry has been running, the Scania tipper achieved 40% more payload
42%
In terms of purchase price, the Scania mining tipper costs about 42% less than a premium 30-t ADT, and this is bound to be even more when compared with a 40 t articulated hauler
“Given our challenges as an industry, exacerbated by the generally low business activity in the past few years, we must think outside the box and start looking at new ways to increase efficiencies. Let us not be afraid to try new things, such as the Scania mining tipper. I encourage other quarry owners to test this truck and see if it works for their operations.
“For operations to achieve maximum value with a Scania mining tipper, it is important to ensure well-maintained, debris-free haul roads. While this offers numerous benefits, including increased productivity and efficiency, reduced costs and enhanced safety, it is particularly key to reducing tyre loss.
hard at work identifying areas of improvement, with haulage being one of the principal areas of consideration. Why haulage? Hunter-Smith tells Quarrying Africa that improving haulage efficiency directly impacts productivity and, ultimately, profitability. Optimising haulage reduces costs, increases production and minimises environmental impact, making it a key factor for quarry success.
As part of optimising haulage efficiency, the quarry has implemented a number of initiatives, including shortening hauling distances, designing haul roads for downhill hauling of loaded articulated dump trucks, and focusing on creating stable, well-maintained haul routes.
In addition to these initiatives, Blurock Quarries has also started investigating the possible change in hauling gear to squeeze more efficiencies. This drive was behind the recent decision to trial the Scania G460 XT mining tipper.
“Having come out of a very difficult business cycle, the timing to put the Scania mining tipper to test was just perfect for us. In the past three years, we have endured a difficult period, especially with an onsite asphalt plant being mothballed due to lack of meaningful road projects in the area. We therefore started looking at potential cost-cutting initiatives and efficiency improvement projects and one of the areas we
considered was in-pit haulage, which is why we jumped at the opportunity to try the mining tipper and see how it compares with the traditional articulated dump trucks (ADTs) we have always run,” explains Hunter-Smith.
The overall impression from the operations team on site, from the driver to the quarry manager, is that the Scania mining tipper performed beyond expectations. Given that the drive was all about efficiencies, the first area of consideration was fuel consumption. Deployed to haul run-of-quarry material from the muckpile to the primary jaw crusher, the mining tipper consumed about 8,2 l of diesel per hour.
While this was pretty much on par with
The Scania mining tipper was deployed to haul run-of-quarry material from the muckpile to the primary jaw crusher.
the 30 tonne (t) ADTs that the quarry has been running, the Scania tipper achieved 40% more payload, confirms Hunter-Smith. The 30-tonne ADTs offer a 25-t payload capacity, while the Scania mining tipper, with its 60-t gross vehicle mass (GVM), has a rated payload capacity of 40 t. However, the Blurock team generally loaded between 35 and 37 t payload, which is 10-12 t more than that of the 30-t ADT, yet the trucks still had the same fuel consumption figures.
In fact, says Vinesh Kalu – key account manager –Scania Mining at Scania South Africa, there was room to squeeze more efficiencies, given that 57% of the fuel consumed was through idling. According to Scania’s fleet management system, of the 8,2 l of diesel the truck consumed per hour, only 5,9 l was dedicated purely to driving.
The excessive waiting times at the loading and tipping points were purely because the site was not geared for an extra truck in its hauling system as this was just a trial session. In an environment where these bottlenecks are non-existent, there is room to haul more for even less.
For Hunter-Smith, it would be ideal to pit the Scania mining tipper against a 40-t ADT. While the two trucks would ideally move the same payload, about 35-36 t on average, the Scania mining tipper would be much more fuel efficient. The massive difference in the capital cost would also be another big cost factor to consider. To provide context, in terms of purchase price, the Scania mining tipper costs about 42% less than a premium 30-t ADT, and this is bound to be even more when compared
with a 40 t articulated hauler.
However, Kalu is quick to point out that for operations to achieve maximum value with a Scania mining tipper, it is important to ensure well-maintained, debris-free haul roads. While this offers numerous benefits, including increased productivity and efficiency, reduced costs and enhanced safety, it is particularly key to reducing tyre loss.
Commenting on the truck’s productivity, Avinash Mahabeer, TMM team leader at Blurock, says the truck’s massive 40-t payload enables consolidation of loads and thus reduces the amount of vehicle movement required to distribute a given quantity of material on site.
“For example, we generally run with two 30-t ADTs in our hauling cycle. One day we decided to stop the two ADTs and deployed the Scania mining tipper alone. The large payload capacity and faster cycle times meant it could easily feed the plant with no issues, effectively replacing the two ADTs in the hauling system,” says Mahabeer. The truck’s high payload yields economic, safety and environmental benefits. In addition, fewer trucks on site translate into less operating costs related to maintenance. To sustain the increased payload, explains Kalu, the new XT mining tipper benefits from a robust suspension. It is equipped with heavy-duty rear axles with cast-iron housings to stand the test of challenging, rough mining conditions. Both rear axles are equipped with shock absorbers to improve traction and comfort.
Apart from the fuel efficiency, David Hadebe, production manager at Blurock, was impressed by how effortless and comfortable it is to operate the vehicle. One of the contributing factors to this is the Scania Opticruise gearbox, which ensures smooth, automated gear changing, thus reducing driver fatigue. Scania Opticruise, one of the first automated gear changing systems on the market, has over the years been refined, and is said to be one of the smoothest and smartest systems on the market.
When the truck first pulled up on site, quarry manager Morne Conradie was sceptical of its ability to take on the rugged conditions of in-pit haulage. One of his hesitations was the truck’s ability to haul downhill with a full load. “At first, I was concerned about the braking capacity of the truck going downhill with a full load. After driving it for the first time, I was pleasantly surprised by the retarding capacity of the truck,” says Conradie.
The five-stage Scania Retarder (hydraulic auxiliary brake that acts directly on the drive shafts) improves braking performance and reduces wear on the wheel brakes, especially on downward slopes. The retarder works independently of the standard wheel brakes and provides additional braking power, particularly useful in downhill situations.
While the haul roads at Blurock are designed for downhill hauling of loaded trucks, Conradie was also impressed at how the Scania mining tipper made light work of hauling uphill at gradients of up 11 degrees (24%) with a full 35-t load during testing. In addition, Conradie was immediately happy with the fact that the truck’s speed could be governed to meet Blurock’s 25-km speed limit requirements.
While there is a general belief that yellow metal haulers are principal hauling solutions for in-pit haulage, Hunter-Smith believes it is time for quarries to start opening up to new ideas. While quarrying has always been referred to as ‘other’ within the mining sector, he says, it is governed by the same legislation as the mainstream mining sector.
Given that the industry mines a low-value, high-volume product, the constant change in legislation, which by its nature is very expensive to comply with, has meant that aggregate operations have found it extremely onerous to stay on top of costs and need to look at new ways to improve efficiencies.
“In fact, everything comes down to efficiencies,” stresses Hunter-Smith. “Given our challenges as an industry, exacerbated by the generally low business activity in the past few years, we must think outside the box and start looking at new ways to increase efficiencies. Let us not be afraid to try new things, such as the Scania mining tipper. I encourage other quarry owners to test this truck and see if it works for their operations.” a
Nomthandazo ‘Nomthi’ Gumede has established NTC Drilling and Blasting, a specialist provider of a comprehensive range of opencast mining services.
With a wealth of experience in the mining sector, Nomthandazo ‘Nomthi’ Gumede has established NTC Drilling and Blasting, a specialist provider of a comprehensive range of opencast mining services. In a one-on-one with Quarrying Africa, she unpacks the drive behind the venture, target markets, challenges faced by young entrepreneurs to venture into this market and how NTC seeks to change the game in the industry. By Munesu Shoko.
There is a new player in the drilling and blasting game in southern Africa following the formation of NTC Drilling and Blasting, a 100% Black, Female-Owned drilling and blasting contractor. Targeting quarries and opencast mines in South Africa and the southern African region at large, the company goes beyond the bench, offering a full suite of specialised opencast mining services, including land clearing and mine stripping, drilling and blasting, secondary breaking, load
Newly-formed NTC Drilling and Blasting is a 100% Black, Female-Owned drilling and blasting contractor
Nomthandazo Gumede’s career began in 2008 at AfriSam as a production plant operator, where she was responsible for overseeing and controlling machinery and production processes
and haul operations, as well as quarry rehabilitation.
At the helm of the newly formed company, which opened its doors in January 2025, is MD Nomthandazo Gumede, who brings a wealth of experience in the mining sector. Affectionately known as ‘Nomthi’ in the industry circles, she has 15 years of experience across various roles in surface mines and quarries.
Gumede’s career began in 2008 at AfriSam as a production plant operator, where she was responsible for overseeing and controlling machinery and production processes. Over the next six years, she took on various production roles at the leading construction materials supplier, while sharpening her craft in drilling and blasting.
At the time she left AfriSam in 2014, she had already assumed the role of trainee superintendent, having earned her blasting licences and certifications. She then joined Lafarge (now Afrimat) as a quarry blaster, where she spent six years, executing blasting operations across all of the company’s sites in KwaZulu-Natal.
In December 2019, she took a career break to focus on family responsibilities before returning to the mining industry in January 2021 as a mine manager at Matsopa Minerals in the Eastern Cape, a role she held for a year.
Nomthandazo Gumede brings a wealth of experience in the mining sector, particularly in drilling and blasting.
There is a new player in the drilling and blasting game in southern Africa following the formation of NTC Drilling and Blasting, a 100% Black, FemaleOwned drilling and blasting contractor
The company offers a full suite of specialised opencast mining services, including land clearing and mine stripping, drilling and blasting, secondary breaking, load and haul operations, as well as quarry rehabilitation
At the helm of the newly formed company, which opened its doors in January 2025, is MD Nomthandazo Gumede, who brings a wealth of experience in the mining sector
While the company has not secured any contracts yet, it has over the past few months focused its efforts on extensive engagements with potential clients across all the markets that it is targeting
Nomthandazo Gumede has 15 years of experience across various roles in surface mines and quarries.
Following another year-long career break, she joined Brauteseth Blasting in 2023, a leading drilling and blasting company, where she worked until the end of 2024, before deciding to take the entrepreneurial route, leading to the formation of NTC Drilling and Blasting.
She tells Quarrying Africa that her time at Brauteseth Blasting was a valuable learning experience, which equipped her with the necessary capacity to establish her own drilling and blasting company in 2025.
Commenting on the decision to establish the company, she says: “I believe the desire to start my own business was driven by a sense of having reached a career ceiling. I wanted a more challenging opportunity – one that would allow me to fully utilise my experience
in mining. I also felt a strong need to challenge the status quo and break traditional boundaries by fostering greater diversity, driving innovation, and ultimately setting new, higher standards of excellence in industry practices.”
Gumede believes that the company’s competitive edge lies in the operational expertise of the whole team, from the founder to the executive team and the highly-skilled operational staff. “We prioritise human resources, fostering a skilled and dedicated team that is equipped to tackle the most complex challenges in opencast mining operations. That drives our success and ensures the highest standards of service,” she says.
The company’s commitment to production efficiency, she adds, enables it to offer highly-competitive service rates without compromising on quality. “The combination of experience, commitment to people and efficient operations makes us the ideal partner for mining and quarrying needs,” Gumede explains.
While the company has not secured any contracts yet, it has over the past two months focused its efforts on extensive engagements with potential clients across all the markets that it is targeting. These discussions, she says, are in their final stages and Nomthi is optimistic that the company will be able to announce new projects soon.
On the capital equipment front, the company has already secured the necessary gear to execute projects. To date, the drilling fleet comprises premium top hammer hydraulic rigs, the Pantera DP1500i and the Ranger DX800 from Sandvik Mining and Rock Solutions.
The Sandvik machines, she says, were chosen for their versatility, making them well-suited for both mining and quarrying operations. Additionally, the NTC team has extensive experience with these machines. She also highlights Sandvik’s reputation for reliability, which further reinforced the decision.
In addition, NTC Drilling and Blasting makes use of hydraulic hammers from Epiroc for secondary rock breaking operations. According to Gumede, Epiroc hydraulic hammers are a popular choice for rock breaking in mining due to their high efficiency, durability and adaptability to various tasks and carrier types. They offer a robust, reliable solution for tough jobs, with
features such as the Solid Body concept and maintenancefree accumulators that ensure consistent performance and extended lifespan.
While the building blocks are in place, Gumede points out some of the challenges associated with setting up a business of this nature. “One of the biggest challenges we have faced as entrepreneurs in this sector is the high barrier to entry. Establishing an opencast mining services company requires significant capital investment, as the equipment is extremely expensive,” she says.
Beyond the financial hurdles, adds Gumede, the conservative nature of clients in this industry presents another major challenge. Many operations are said to prefer to work with long-established ‘legacy’ companies, making it difficult for new entrants to secure contracts. “Because of this, we have had to work hard in our engagements with potential clients to prove beyond doubt that we can deliver,” explains Gumede.
Fortunately, she adds, the extensive experience of the team members has played a key role in demonstrating that the company is not only just as capable as legacy companies but, in many cases, it is better positioned to bring fresh, innovative approaches to the industry.
Commenting on what can be done to support young companies of this nature to find their feet in such a competitive market, Gumede says there are already several funding and development initiatives in place, but she believes that these could be more effective. For example, she says, while various funding options exist, the application and disbursement processes often take too long.
“Fast-tracking approvals and fund delivery would make a significant difference. Additionally, industry leaders and major clients can play a crucial role by actively embracing and supporting new entrants, creating a more inclusive and competitive industry landscape,” she says.
Despite these challenges, she hopes that her journey with NTC Drilling and Blasting serves as testament to the capabilities and impact that women can make in the mining industry.
“At NTC Drilling and Blasting, we are excited about the future and the many opportunities that lie ahead, both in South Africa and across the continent. Through our work, we are committed to driving Africa’s growth and creating lasting value for our clients, communities and partners,” concludes Gumede. a
That quality control is an indispensable parameter in successful aggregates production is no overstatement. Based on this understanding, leading construction materials supplier, AfriSam, employs a stringent testing regime to ensure ongoing conformity to standards and product specifications. During Quarrying Africa's recent visit to AfriSam Jukskei Quarry, Nithia Pillay, Regional Product Technical Manager at AfriSam, provided us with the lowdown on the company’s quality control processes. By Munesu Shoko.
It is imperative to employ a rigorous quality control regime that ensures compliance with requirements and specifications on a consistent basis
To comply with standards and specifications, AfriSam performs various aggregate tests – both internally and externally
While there is no stipulation in terms of frequency, AfriSam commits to at least once a quarter for each of the quality control tests, highlighting the company’s dedication to quality assurance
To influence industry standards, the AfriSam technical team provides critical input to industry bodies. For example, the company is part of the COTO Review Committee and provides feedback through surface mining association, ASPASA
Consistent aggregates quality is a key competitive edge for every quarry operation. That is the view of Nithia Pillay, Regional Product Technical Manager at AfriSam, who stresses that a strong quality control regime ensures that quarries supply products that meet the required standards and specifications. High-quality products result in satisfied customers, often translating into customer loyalty, repeat orders and positive references.
Traditionally, there has always been a trade-off between
AfriSam’s Jukskei Aggregate Quarry.
“In fact, no other process is inextricable from quality control. Driving a high production process of 500 tph, for example, means nothing if the product is out of spec and you cannot make revenue out of it. It is therefore imperative to employ a rigorous quality control regime that ensures compliance with requirements and specifications on a consistent basis.
production and quality control in the industry, with the former gaining more preference. However, driving production alone and neglecting the necessary quality checks can be even more detrimental, possibly resulting in materials that are out of spec and ultimately rejection or reclassification to a lower quality material and a lower sales price per tonne. The result is potential loss of income and reputational damage.
“It is important to understand that quality control informs many other processes in the production process of aggregates. For example, insights from quality control inform other pertinent areas of the value chain such as face-mapping and overall equipment efficiency (OEE),
3.0
The apparent relative density of aggregate generally varies between 2.7 and slightly above 3.0
amongst others,” says Pillay.
“In fact, no other process is inextricable from quality control. Driving a high production process of 500 tonnes per hour (tph), for example, means nothing if the product is out of spec and you cannot make revenue out of it. It is therefore imperative to employ a rigorous quality control regime that ensures compliance with requirements and specifications on a consistent basis,” Pillay adds.
To comply with standards and specifications, AfriSam performs various aggregate tests – both internally and externally. Internal tests, which are conducted
Course and fine aggregates used in concrete should comply with SANS 1083, which includes requirements for various physical properties of aggregates, such as flakiness index, relative density and abrasion resistance
SANS 1090 focuses on fine aggregates for plaster and mortar, addressing properties such as grading, cleanliness and clay content
To comply with standards and specifications, AfriSam performs various aggregate tests, both internally and externally.
in an AfriSam laboratory, include Grading, Flakiness Index, Apparent Relative Density (ARD) and Average Least Dimension (ALD), amongst others, and these are considered to be part of process control.
External tests, undertaken by independent South African National Accreditation System (SANAS) accredited labs, include Petrographic Examination, X-ray Diffraction Analysis (XRD), Aggregate Crushing Value (ACV) and 10% FACT (Fines Aggregate Crushing Test), and these form part of the quality control process. AfriSam acknowledges the need for accurate and relevant testing to meet and surpass industry requirements and as a result the company has embarked on process enhancement by seeking SANAS accreditation for the process control testing currently in place.
“There is a difference between process control and quality control. Process control entails proactively managing the production process to ensure consistent quality, while quality control involves inspecting and testing the final product to verify it meets specifications. With process control, samples are taken on an ongoing basis and are subjected to necessary tests such as grading and flakiness index to ensure that nonconforming aggregate does not leave the quarry. In the event of non-conformance, we conduct extensive analyses and forensic investigations to determine the root causes of shortcomings and develop solutions accordingly – this forms part of AfriSam’s continuous improvement initiative,” explains Pillay.
AfriSam conducts several process control tests, and these tests are an integral part of the daily production processes. A grading test, also known as sieve analysis, determines the particle size distribution (PSD) of an aggregate sample. This test is crucial for quality control and compliance in civil engineering projects, ensuring that aggregates meet the specified requirements for a
particular application.
Flakiness Index measures the flatness of an aggregate. A high flakiness index suggests a higher percentage of flat or thin particles, which can affect the workability of concrete and the performance of road surfacing aggregates.
The ARD test is used to determine the density of the aggregate particles. This test is crucial for determining compliance of the density with applicable specifications, thus understanding how an aggregate will perform in various applications, such as road construction and concrete. The apparent relative density of aggregate generally varies between 2.7 and slightly above 3.0.
The ALD of an aggregate is the average thickness of a group of aggregate particles, determined by measuring the smallest dimension of each particle and calculating the average. It is a key parameter particularly in road surfacing, as it influences the quantity of bituminous product needed and the spread rate of surfacing aggregates.
The XRD test is one of the major quality control tests undertaken at AfriSam quarries. It is used to determine the mineralogical composition, identify potentially deleterious phases and assess the quality of the material.
“An XRD test will tell us how the rock type is changing. If it is changing, is it getting better or worse? It gives us the opportunity to better manage the resource. If, for example, there are intrusions of ‘brown’ material in our granite deposit it gives us the opportunity to make informed decisions on which products can be produced with the current resources,” explains Pillay.
A petrographic test involves microscopically analysing samples to assess their quality, composition and potential for durability in concrete. It helps identify rock types, mineral constituents and their condition, including weathering, alteration and presence of reactive materials
such as chert.
ACV and 10% FACT tests measure the crushing strength of aggregate for concrete, surfacing (chips) and asphalt, as well as for crushed stone base. These results do not necessarily relate to the flexural or compressive strength of concrete made with that aggregate, but are a useful index of overall quality. There is generally good correlation between ACV and 10% FACT values.
While there is no stipulation in terms of frequency, AfriSam commits to at least once a quarter for each of the quality control tests, highlighting the company’s dedication to quality control. “While we adopt a threemonth frequency – which by all means is costly on our behalf – some competitor quarries do it once every two to three years. For us, it is about keeping the finger on the quality pulse and passing the confidence to our customers,” says Pillay.
There are various standards that govern aggregate production in South Africa. AfriSam complies with the new Committee of Transport Officials (COTO) standards for road and bridge works. These came into effect on August 18, 2020, replacing the Committee of Land Transport (COLTO) standard specifications for road and bridge works of 1998, and became mandatory for use in procurement documents for South African road authorities by March 1, 2021.
“The COTO standards for aggregates used in asphalt – referred to as Class 1 and Class 2 – are particularly stringent. These classes are very strict by their nature and require high quality compliance requirements for shape and grading. The shape of the individual particles must be properly measured and should be cubicle, which creates a ‘bottleneck’ in the production process,” he says. “Typically, we cannot produce asphalt stone as much as we would produce, for example, concrete stone, which has a wider envelope and does not have a stringent shape requirement.”
AfriSam offers materials that meet the evolving needs of the construction industry and contribute positively to infrastructure development.
Course and fine aggregates used in concrete should comply with SANS 1083, while sands used for mortar and plaster should comply with SANS 1090. SANS 1083 includes requirements for various physical properties of aggregates, such as flakiness index, relative density and abrasion resistance. Equally, SANS 1090 focuses on fine aggregates for plaster and mortar, addressing properties such as grading, cleanliness and clay content.
Nithia Pillay,
Regional Product Technical Manager at AfriSam,
highlights how quality control ensures conformity to standards.
When Quarrying Africa visited AfriSam Jukskei Quarry, Pillay highlighted the extensive nature of the process and quality control practices at this operation, which are duplicated across the company’s operations. Quality control here starts well before the planned blast.
“From the previous blast, we collect drill chips, which we send for an XRD test. This gives us an idea of what to expect from the upcoming blast, which then informs our selective mining processes and allows us to map the various benches for future blasts. This is done before every single blast so that we have a grasp of what type of material to expect and what we can make with it. Current sales and demand trends determine the material we need to produce; the latter is overlaid onto the bench mapping to confirm blasting activity,” says Pillay.
After material has been processed and stockpiled, AfriSam lab personnel collect samples from each stockpile, and regular testing is carried out in accordance with standard test methods for compliance of all aggregate products from each plant with relevant internal and national specifications. Grading results are captured daily to a central computerised system for continuous analysis to ensure consistence in product quality.
“Our protocol is very strict and entails the collection of several samples at frequent intervals. In fact, we take two to three samples per day per product to ensure production consistency. If any deviations occur, we can pick it up quickly and initiate corrective action,” says Pillay. All results are logged onto a database called LIMS. Data generated
is constantly analysed and interpreted to inform decisions. The data, he says, is analysed not just for hypothesis purposes, but to come up with solutions to problems.
“There is a lot of information generated from the process control and quality control protocols, and what we do with it is very important to make processes better.”
To influence industry standards, the AfriSam technical team provides critical input to industry bodies. For example, the company is part of the COTO Review Committee and provides feedback through surface mining association, ASPASA. “We recently provided feedback on the review process of the SANS 1083 standard. The industry is considering combining into one the various standards that govern various materials, such as concrete stone, plaster mortars, asphalt and granular materials,” says Pillay.
Another current industry discussion is the implementation of testing frequencies. In recent times, he says, project engineers have started to demand quality control test results that are not more than three months old, which is in line with AfriSam’s current practice, yet some competitor quarries only test once in every two to three years.
“Being part of the industry bodies ensures that we stay up-to-date with new requirements and trends. This allows us to offer materials that meet the evolving needs of the construction industry and contribute positively to the infrastructure development agenda of the country,” concludes Pillay. a
Afrimat’s North Cluster central lab, located at Lyttleton Dolomite Mine, oversees quality control processes for the seven Afrimat quarries in the region.
Quality control is of fundamental importance in Afrimat’s aggregate production processes. In a oneon-one with Quarrying Africa, Christopher Vermeulen, Aggregates Quality Manager, Construction Materials – North Cluster, outlines how quality control is ensured at every stage of production – from source material evaluation to final product testing – and is supported by good systems, skilled personnel and continuous improvement practices. By Munesu
Shoko
At Afrimat, quality control plays a crucial role in aggregate production, helping identify potential defects, inconsistencies or impurities in construction materials.
According to Vermeulen, accurate testing and stringent quality control protocols guarantee that the company’s construction materials meet both industry standards and project specifications, contributing directly to the durability, integrity and safety of infrastructure projects.
The in-depth quality assurance regime at Afrimat entails two tiers – process control and quality control. Every quarry, says Vermeulen, has its own site laboratory, which tests
material on a continuous basis, and that forms part of the process control regime. Afrimat also operates two Central Laboratories in two regions; one is situated in Gauteng at Lyttleton Dolomite Mine and the second in the Western Cape at Worcester, which oversees the quality control aspect of each quarry located in that cluster.
Following the recent successful acquisition of Lafarge, Afrimat has reconfigured its regional clusters into five, namely the South Cluster (Western Cape), South East Cluster (Eastern Cape), East Cluster (Coastal KwaZulu-Natal), Central Cluster (North of KwaZulu-Natal and Free State) and the North Cluster (Gauteng, Limpopo and Mpumalanga). Each of these clusters operates its own satellite laboratory, headed by the aggregate’s Product Technical team.
Quarrying Africa recently visited the North Cluster’s central lab, located at Afrimat’s Gauteng-based Lyttleton Dolomite Mine. The laboratory is responsible for overseeing quality control processes for the seven Afrimat quarries in the region, namely Lyttleton (Gauteng), Glen Douglas (Gauteng), Eckraal Quarry (Gauteng), Lephalale (Limpopo), Hartebeesfontein Quarry (Mpumalanga), Dingwell Quarry (Mpumalanga) and Karino (Mpumalanga).
As the aggregates quality manager for the North Cluster, Vermeulen is responsible not only for managing the central laboratory, but also for overseeing the satellite laboratories at each of the seven quarries, including training of personnel, ensuring adherence to testing standards and frequent auditing of these facilities.
The company’s meticulous approach to quality assurance involves rigorous testing procedures and adherence to stringent quality control protocols. Afrimat complies with a range of national standards across its laboratories.
At satellite level, laboratory personnel are trained to collect samples and run tests in accordance with standards such as TMH5, a set of methods for sampling road construction materials, detailed in the Technical Methods for Highways series. It provides guidance on how to collect samples from various sources such as natural rock masses, gravel pits, stockpiles and pavement layers for testing purposes.
The ultimate goal of TMH5 is to ensure that representative samples are collected for accurate testing, which is crucial for quality control in road construction. For example, for sampling of material such as G5 from a conveyor belt, explains Vermeulen, the minimum requirement under TMH5 is 120 kg of sample material, allowing site personnel to conduct parameters such as grading and flakiness index.
“Site laboratories are basically responsible for compliance. For example, for every certain number of tonnes produced, they need to take a test sample. For smaller quarries that produce, let us say, 30 000 t per month, they need to take a test sample for every 250 t produced. For larger quarries, site labs need to take a test sample for every 500 t produced. If for example, an operation produces 80 000 t per month, it means that they are supposed to take 160 test samples per month –that is how rigorous the process control regime is,” says Vermeulen.
In addition, Afrimat also complies with SANS (South
Afrimat complies with SANS (South African National Standards) 1083 for readymix concrete aggregates and SANS 1090 for plaster and mortar
Afrimat’s meticulous approach to quality assurance involves rigorous testing procedures and adherence to stringent quality control protocols.
At Afrimat, quality control plays a crucial role in aggregate production, helping identify potential defects, inconsistencies or impurities in construction materials
The in-depth quality assurance regime at Afrimat entails two tiers – process control and quality control
Site laboratories are basically responsible for compliance. For example, for every certain number of tonnes produced, they need to take a test sample
Afrimat performs a comprehensive range of tests. These start from source material evaluation to final product testing
85%
Coarse aggregates are those with a nominal size greater than 5 mm, and 85% of aggregate products falls in this category
500 t
For larger Afrimat quarries, site laboratories need to take a test sample for every 500 t produced
African National Standards) 1083 for readymix concrete aggregates and SANS 1090 for plaster and mortar, as well as COLTO/COTO (Committee of Land Transport Officials) standards for road construction materials.
Increasing requirements for certified quality aggregates has also led surface mining industry association, ASPASA, to introduce its own guidelines and auditing systems to ensure testing of aggregates and crushed granular materials is carried out in accordance with the South African National Standards (SANS) 3001-AG and -GR series of test methods.
“AG methods are test procedures conducted on both coarse and fine aggregates. Coarse aggregates are those with a nominal size greater than 5 mm, and 85% of aggregate products falls in this category. Fine aggregates are those with a nominal size smaller than 5 mm. The test methods range from AG1 to AG23 and test various parameters such as flakiness index, grading and relative density, amongst others,” explains Vermeulen.
GR methods are testing procedures for gravels. These range from GR1 to GR57 and primarily focus on assessing the physical and mechanical properties of aggregates, ensuring they meet the necessary standards for construction and engineering applications. These tests include sieve analysis for gradation, specific gravity and absorption tests, soundness tests, abrasion resistance tests, aggregate crushing value tests and impact tests, amongst others.
Compliance to the relevant standards is achieved through sampling methods and frequency; strict adherence to testing protocols and calibration
schedules; a trained and certified team conducting regular sampling and testing; internal audits and thirdparty verification (SANS-accredited labs); real-time tracking of test results to ensure immediate corrective action if deviations are identified; and ongoing training and awareness to keep staff updated on standards and best practices.
All non-conforming materials are immediately quarantined and investigated through a root cause analysis. The process includes reviewing test data and production logs, as well as site inspections if required. Team debriefs to assess procedures or equipment faults may also be carried out. Corrective actions may involve adjusting processing configuration, retraining staff, or equipment servicing. Preventive measures are also put in place to avoid recurrence, and all actions are logged onto the company’s quality management system.
“All testing and production data is logged in a centralised Laboratory Information Management System (LIMS). Each batch is traceable through unique batch identifiers, linked test results and material specifications, and corrective actions. The system ensures secure archiving, easy retrieval and compliance with audit requirements. Access is role-based to maintain integrity and confidentiality,” explains Vermeulen.
Customer feedback is also critical in improving the quality control regime. Feedback from customers is collected through client surveys and postproject reviews, as well as direct liaison with quality representatives on-site.
“Feedback is acquired through collaboration in technical meetings and audits. This feedback is analysed for improvement areas, and actions are prioritised based on impact. We then update test methods, provide targeted training, or adjust specifications accordingly based on industry changes,” explains Vermeulen.
Driving
At Afrimat, quality control teams drive continuous improvement efforts to enhance quality control processes. These include Tabular Report principles to identify and reduce variation, as well as regular training programmes and certification refreshers.
“In addition, we do cross checks with SANS-accredited external labs. Effectiveness is measured through reductions in non-conformance rates, improved turnaround times for test results and positive client feedback. Datadriven reviews are conducted through weekly Business Performance Reviews (BPR) to evaluate these key performance indicators (KPIs),” explains Vermeulen.
Afrimat performs a comprehensive range of tests. These start from source material evaluation to final product testing. “We start with the XRD (X-ray Diffraction) test, which gives us the geological composition of the parent rock. From those results we can determine what we can
produce with the available rock, for example, base materials or concrete stone, depending on material properties,” says Vermeulen.
Particle Size Distribution (sieve analysis) ensures the grading of aggregates meets required specifications for concrete, asphalt and base products.
Apparent Relative Density and Water Absorption test determines the density and porosity of aggregates, which affect strength and durability.
Flakiness Index, one of the common tests in aggregate production, measures the shape of particles, impacting compaction and workability.
Atterberg Limits are carried out to determine the moisture contents at which fine-grained cohesive soils transition between solid, semi-solid, plastic and liquid states.
Compaction (Modified AASHTO / Proctor) test evaluates the optimal moisture content and density for layers under roads and structures. Moisture Content test is critical for controlling mix designs in concrete production. Each test provides key insights into aggregate suitability and supports compliance with client and statutory standards.
In addition, Ultra Fine Content and Clay Content & Methylene Blue tests are important for readymix concrete. This determines the proportion of very fine particles (such as silt and clay) within a sample of fine aggregate. High levels of fines can negatively impact concrete strength and workability, making this test crucial for quality control in construction.
“At Afrimat, quality control is not just a checkpoint – it is a mindset worked into our operations. Our laboratory’s role is both technical and strategic, ensuring that the materials we produce contribute to the success and longevity of infrastructure across South Africa. We are proud of the standards we uphold and the team that drives them forward,” concludes Vermeulen. a
To service clients across the three plants, the company currently operates a total of 26 readymix trucks, of which 18 are owned by Afri Readymix and the rest by contractors.
Founded in 2021 following the acquisition of its Rustenburg readymix plant from one of the major construction material suppliers in South Africa, Afri Readymix has grown in leaps and bounds. As part of its rapid expansion, the company has not only added two other readymix plants, but also opened its first hardware store, allowing it to extend its service portfolio from the ‘foundation to the roof’. Munesu Shoko was recently on site and filed this report for Quarrying Africa.
While the 2020 COVID-19 pandemic was a global pandemic of huge proportions which wrought havoc across global businesses and economies, it did, in fact, also have some positive spin-offs. A case in point was the establishment of Afri Readymix, a business that came into being in 2021 following the purchase of a readymix plant from a major construction materials supplier.
As part of a rationalisation strategy to sidestep the tough market conditions brought about by the pandemic, the leading construction materials supplier mothballed some 23 readymix plants across its national footprint, of which the Rustenburg plant was one.
Having worked for the company for 20 years at the time, Gerhard Maree, who is now the MD and founder of Afri Readymix, grabbed the opportunity to acquire the plant from his previous employer, in partnership with
800 m³
Afri Readymix Rustenburg has the capacity to produce 800 m³ of concrete per day
Founded in 2021 following the acquisition of its Rustenburg readymix plant from one of the major construction material suppliers in South Africa, Afri Readymix has grown in leaps and bounds
Within a year of its formation, Afri Readymix quickly expanded its horizons with the addition of the Afri Readymix Boshoek plant in 2022
This was followed by the establishment of Afri Hardware and Building Supplies, a hardware store which officially opened its doors on August 3, 2024
The hardware store was soon followed by the establishment of Afri Readymix Limpopo – a plant based in Northam – in December 2024
60%
While mines constitute about 60% of the company’s readymix concrete business to date, some 30% still comes from the cash-on-delivery clients
“From the onset, we had a vision to become a one-stop construction materials supplier, offering our customers anything from concrete to hardware, and this became reality when we successfully invested in our hardware store, which is also located in Rustenburg.
fellow directors Werner Weiss and Christie van der Mescht. The acquisition went through in March 2021, marking the birth of Afri Readymix, a company that has been on a positive growth trajectory for the past four years.
Within a year of its formation, Afri Readymix quickly expanded its horizons with the addition of the Afri Readymix Boshoek plant in 2022. This was followed by the establishment of Afri Hardware and Building Supplies, a hardware store which officially opened its doors on August 3, 2024.
“From the onset, we had a vision to become a one-stop construction materials supplier, offering our customers
anything from concrete to hardware, and this became reality when we successfully invested in our hardware store, which is also located in Rustenburg,” explains Maree.
“When customers build a house, for example, they also need bricks, plumping, electrical and roofing materials. Given that we are the customer’s first point of contact for the concrete for foundations, we realised that we could also talk to them about the rest of the materials they need to build, from the foundation to the roof, and this was central to the hardware store venture,” says Maree, adding that, if successful, the hardware model will be replicated across the company’s readymix plant footprint.
The hardware store was soon followed by the establishment of Afri Readymix Limpopo – a plant based in Northam – in December 2024, bringing to three the number of readymix plants owned and operated by Afri Readymix.
To date, the company has a workforce of 40 permanent employees and 20 contractors across these sites. In terms of capacity, Afri Readymix Rustenburg has the capacity to produce 800 m³ of concrete per day, while the Boshoek and Northam plants are both rated at 400 m³ per day. To service clients across the three plants, the company currently operates a total of 26 readymix trucks, of which 18 are owned by Afri Readymix and the rest by contractors.
In addition, the company also provides mobile concrete batching plant services. These are particularly useful for projects requiring on-site concrete production, such as road construction, solar farms or those in remote locations. By reducing the need for concrete transport, these plants minimise carbon emissions and waste.
Commenting on the company’s quick growth, Weiss tells Quarrying Africa that one of the key success factors is the consistent, high-quality service to all customers, regardless of size, which has been central to building a positive business reputation. Diversifying the customer base with both large and small clients, adds Weiss, also reduces reliance on a few large clients, which has led to a more stable and resilient business.
“In the face of a constantly changing construction market, the corporate approach to customer service has lost relevance. That is why we have a face-to-face approach to every deal. It does not matter whether the customer is buying 4 m³ or 100 m³ of concrete from us –we always seek to establish personal relationships with our customers. This fosters deeper connections, trust and personalisation of service, leading to increased customer satisfaction and loyalty,” explains Weiss.
While mines constitute about 60% of the company’s readymix concrete business to date, Maree says that some 30% still comes from the cash-on-delivery (COD) clients, which provides a balanced customer base to the business. The market is diverse, and includes civil projects, property developers, private home developers, chicken houses for the food industry and solar farms, amongst others.
According to Maree, one of the early success drivers has been the relentless focus on providing top quality readymix concrete at the best rate possible. Working closely with suppliers allows Afri Readymix to negotiate better input pricing and reduce overall procurement costs. This, in turn, allows the company to offer competitive rates to the market.
“Collaborative relationships with suppliers can lead to joint identification of cost-saving opportunities. On the cement side of things, which is a crucial input in what we do, we commend Sephaku Cement for walking the journey with us in the quest to reduce costs and ultimately put back better rates into the market,” says Maree.
“We also get our aggregates from third-party suppliers who source from Sibanye Stillwater and Glencore, where legacy material is processed. This process is a win-win situation for all parties involved – we help them get rid of excess material as part of their rehabilitation efforts, while we also get access to cost-effective, quality aggregates and also drive our own sustainability agenda in the process,” adds Maree.
In addition, Afri Readymix is not just about selling
readymix concrete – the business prides itself on being an active citizen in communities in which it operates.
Community engagement and social responsibility are at the core of the company’s values, embodied in its ‘Giving Back Drive’. This initiative reflects the commitment to empowering and enriching the communities of which the company is an important part.
“Key aspects of our ‘Giving Back Drive’ include building stronger community connections, encouraging active participation from customers and employees, nurturing a positive image, promoting economic progress and tackling local issues. These endeavours are geared towards making a substantial difference, nurturing ethos of empathy and communal responsibility within our company,” says Maree.
Commenting on some key trends in the market, Maree believes that, like any other sector of the economy, the readymix concrete business is seeing a technological shift, starting with the concrete batching plants themselves. The technological revolution in concrete batching plants is characterised by increased automation, digitalisation and the use of advanced sensors and control systems. This, he says, leads to improved efficiency, quality control and output capacity in concrete production.
“Concrete batching plants are increasingly becoming technologically advanced. For example, we make use of advanced systems such as Command CE Systems, which helps optimise mix designs, ensures raw materials meet specifications and streamlines quality control processes. Additionally, Command CE provides real-time insights into material performance and mix efficiency, enabling better decision-making and greater operational control,” explains Maree.
The adoption of technology also extends to concrete properties themselves. The advent of new admixtures has
been a key trend in readymix concrete production. Afri Readymix works closely with CHRYSO Southern Africa to continuously introduce new admixtures in its designs. The addition of these admixtures has been instrumental in reducing the water/cement ratio, which leads to several benefits, primarily increasing the strength and durability of the concrete. It also improves the long-term performance of the concrete, reduces costs of production and the environmental impact.
Technology, adds Maree, has also allowed flexibility in concrete mix designs. Through its partnership with concrete specialist, Go Consult, Afri Readymix offers in excess of 300 mix designs. “Through our partnership with Go Consult, a reputable name in concrete consulting services, we can offer a full suite of mix designs and special mix designs such as durability W-mixes, self-levelling, high strength and pool, amongst others,” says Maree.
As part of its growth strategy, Afri Readymix has plans to expand its readymix concrete footprint, particularly into smaller towns with high demand and minimal competition. At the start of this year, plans were underway to establish a plant each in Potchefstroom and Marikana, a decision that has been put on hold due to the prevailing economic conditions and a projected reduction in construction activity.
In addition to constrained economic conditions as a result of a generally weak business environment and political uncertainty around the Government of National Unity (GNU), Maree is wary of the strained relations with the United States, which he says could negatively impact economic growth this year and beyond.
“We had several plans in the pipeline, but these have been put on hold. We will maintain what we have at the moment and wait to see what will happen with the South African economy in the near future,” concludes Maree. a
The major highlight of the new articulated hauler launch is the introduction of the all-new A50 model, which expands customer opportunities in the demanding hauler segment.
Following their global introduction earlier this year, the new-generation Volvo excavators and articulated dump trucks (ADTs) are making their southern African debut. At an official launch event to be held at Babcock’s Middelburg branch this June, customers will have the first glimpse of these much-anticipated new arrivals. By Munesu Shoko.
In the past 12 months, Volvo Construction Equipment (Volvo CE) announced its largest product portfolio renewal in decades, with 35% of the company’s total product range renewed during that time. As part of the historic product rollout, Volvo CE introduced its ‘biggest and boldest’ articulated hauler line-up to date at a global launch event attended by Quarrying Africa in January this year at the company’s Braås factory in Sweden. At the same time, a new range of excavators in the competitive, but lucrative 21-30 tonne (t) market segment, rolled off the production line, pushing
the boundaries with a modern design and updated features – just what customers in southern Africa and elsewhere in the world need to get ahead of the competition.
At a time when capital equipment owners across sectors, including construction, quarrying and mining, are looking to gain a competitive edge by enhancing efficiency, productivity, safety and profitability in their operations, Babcock is introducing these new ranges for the very first time in southern Africa.
David Vaughan, MD of Babcock’s Equipment business, says with advanced technologies at the centre
The updated ADT models mark a significant technological leap forward thanks to innovations such as the new electronic system and an in-house developed transmission, delivering fuel efficiency improvements of up to 15% depending on model and industrial application
Babcock is introducing the new-generation Volvo excavators and articulated dump trucks in southern Africa
Of the seven-model line-up, the updated A40, A45 and the all-new A50, are the first models to arrive in southern Africa
The major highlight of the new articulated hauler launch is the introduction of the all-new A50 model, which expands customer opportunities in the demanding hauler segment
When it comes to excavators, Babcock will initially unveil three new models comprising the EC210, EC220 and EC300
““We are excited about the local launch of the new generation Volvo articulated haulers. The arrival of this new range will further strengthen our marketleading position in the segment, while broadening our model line-up with the addition of the new A50 to cover more applications.”
The ADTs’ automatic drive combinations, with 100% differential locks and all-terrain bogie and hydromechanical steering, also combine to provide unmatched traction, stability and precision control
of their development, these new-generation machines cast a special design focus on productivity, efficiency, uptime, safety and operator comfort.
Since it pioneered the concept with the 1966 launch of the world’s first ADT, dubbed as ‘Gravel Charlie’, Volvo CE has for the past 60 years reinforced its leading position in the global articulated market. With the arrival of its new generation articulated haulers, the company is once again demonstrating its commitment to delivering cutting-edge, safe, efficient and productive solutions to the global mining, quarrying and construction sites.
The seven-model line-up represents a complete revamp of the already proven A25, A30, A35, A40, A45 and A60 models – with the major talking point being the introduction of a completely new class size machine, the 45-tonne (t) A50, which fills the gap between the 42-t A45 and the 55-t A60.
“We are excited about the local launch of the new generation Volvo articulated haulers. The arrival of this new range will further strengthen our market-leading position in the segment, while broadening our model line-up with the addition of the new A50 to cover more applications,” says Vaughan. “Our customers expect a first-class product when they get into any of our Volvo CE haulers, but that experience has just got even better with a host of cuttingedge features designed with customers in mind.”
Of the seven-model line-up, the updated A40, A45 and the all-new A50, will be the first models to arrive in southern Africa, confirms Vaughan, before the rollout of the A30 and the A60 at a later stage (dates to be confirmed).
The new generation Volvo ADT range is said to contain the largest updates in 20+ years. “The updated models mark a significant technological leap forward thanks to innovations such as the new electronic system and an inhouse developed transmission, delivering fuel efficiency improvements of up to 15% depending on model and industrial application,” explains Vaughan.
A host of new features guarantees maximum productivity across the most challenging projects in quarrying, mining, construction and more. With its ability to identify and remember any slippery road segments, the Volvo drivetrain with Terrain Memory ensures superb fuel efficiency without compromising on power. Automatic drive combinations, with 100% differential locks and all-terrain bogie and hydromechanical steering, also combine to provide unmatched traction, stability and precision control.
In addition, Volvo Dynamic Drive – with its predictive gear selection – adapts to operating conditions. The downhill speed control function and industry-leading braking systems further enhance efficiency, safety and comfort.
“The updated range has been engineered for durability
thanks to features such as reinforced axles capable of withstanding heavy loads and high torque, resulting in superior stability and strength. Safety is also a priority, with new harness anchor points in the cab which meet WorkSafeBC and OSHA regulations, withstanding up to 22 kilo newton (kN) of force,” says Vaughan.
With simplified servicing, longer change intervals and easy component access, servicing is now quicker and easier than ever before, maximising uptime and reducing costs. Industry-leading greasing intervals of 250 hours also eliminate the need for daily or weekly greasing, boosting productivity and reducing downtime. What is more, Volvo articulated haulers are said to require less fluid volume compared to the competition, benefitting the environment and reducing operating costs.
Customers can boost the performance of their articulated haulers even further with the addition of solutions such as Haul Assist with On-Board Weighing. Powered by Volvo Co-Pilot, it provides real-time payload data to prevent overloading and minimise carryback, which not only maximises productivity but also reduces fuel consumption and machine wear.
Traffic flow, vehicle performance and on-site logistics can also be improved with the support of digital and advisory tools such as Connected Map, Performance Indicator and Site Optimisation, while the CareTrack telematics system is designed to help boost machine uptime and reduce repair costs.
Not just a machine for today, the new generation of Volvo articulated haulers is future-enabled thanks to a new software architecture which allows customers to adapt to changing needs and seamlessly incorporate future upgrades and new smart solutions. This ensures that their equipment stays up-to-date with cutting-edge technology.
Already regarded as the operator’s machine of choice, Volvo CE’s updated articulated hauler range takes operator comfort to a whole new level, thanks to the new cab with a modern styling. The new cab, designed from ground up, gives more space to the operator for superior comfort, leading to higher productivity over the full operating cycle.
The major highlight of the new articulated hauler launch is the introduction of the all-new A50 model, which expands customer opportunities in the demanding hauler segment. A key feature on the new A50 is the fully hydraulic suspension concept. Pioneered by Volvo CE in 2007, the full suspension has proved to be a reliable system for the toughest of driving conditions.
“The A50 takes the concept to new heights as the only full suspension machine of its size class on the market. As a result, it offers a significant improvement in cycle times, an increase in hauler production per operator-hour and lower costs when compared to its standard suspension counterparts,” says Vaughan.
Volvo CE’s full suspension reduces vibration, noise and shocks, which can help prevent repetitive strain injuries to operators. A smoother ride on the hauler and road can reduce unnecessary maintenance costs.
As part of the new generation update of Volvo articulated haulers, the A50 enjoys all the same great features and benefits. Most notably, it delivers unrivalled efficiency thanks to the new in-house-developed Volvo transmission that works in harmony with the rest of the Volvo engine to ensure maximum fuel efficiency.
With its 45-t payload, the all-new A50 delivers 10% more productivity and 8% greater fuel-efficiency when compared to the previous generation A45– making it an ideal solution for high-production quarries, mines and large construction sites. For the A50, service costs are reduced by up to 6% over 12 000 hours of operation due
With its ability to identify and remember any slippery road segments, the Volvo drivetrain with Terrain Memory ensures superb fuel efficiency without compromising on power.
to simplified servicing, longer change intervals and easy component access.
When it comes to excavators, Babcock will initially unveil three new models comprising the EC210, EC220 and EC300. The 21-t EC210 replaces the previous EC200DL, while the EC220 replaces the old-generation EC210DL, ushering in a new era in the 20-22 t market, the most popular size class in the southern African excavator market. The two models are ideally suited for general construction, plant hire and earthworks applications. The larger 30-t EC300 fits the bill for mid-size construction sites, sand works and small-scale quarrying operations.
The new Volvo excavator range combines cutting-edge technology, robust design and industry-leading efficiency to benefit various industrial applications. Each of the models integrates engine-pump optimisation technology, delivering up to 15% fuel efficiency compared to previous models.
With enhanced production and reduced emissions, the excavators help provide greater cost savings while maintaining exceptional performance. A brand-new cab design has also been implemented to increase operator support.
efficiency,” explains Vaughan.
The new range features increased hydraulic flow for responsive, accurate control in digging and loading operations. Operators benefit from smoother, easier movement when digging as well as travelling and lifting simultaneously, due to the harmonised boom and arm movement.
The revamped cab offers improved ergonomics, intuitive controls and advanced human-machine interface (HMI) systems, providing operators with a comfortable, productive working environment, with enhanced visibility, reduced noise levels and efficient HVAC systems. “The cab adopts a totally new design with a more intuitive layout,” explains Vaughan. “While Volvo has prioritised productivity and power, it is not at the expense of operator comfort.”
The new Volvo excavators come at a time when the South African construction sector, an industry that has generally endured a protracted downturn during the past decade, anticipates a potential record R1-trillion infrastructure rollout programme
“The new excavators benefit from a simplified, yet innovative hydraulic system, resulting in smoother, faster, powerful and efficient operation. The range is designed to lower fuel consumption and reduce operating costs. The powerful Volvo engines work in harmony with the machines’ proven hydraulics to provide high torque at low revolutions per minute (rpm) for the ultimate combination of performance and improved fuel
All models are compatible with Volvo Dig Assist, an optional intelligent machine control system that improves excavation precision and productivity. Operators can utilise tools such as real-time weighing, automated digging, and smart monitoring, which enhance efficiency, with Volvo Smart View producing 360° machine visibility. Additional features such as preset depth, height, and swing limits further enhance on-site safety.
“The new excavators come at a time when the South African construction sector, an industry that has generally endured a protracted downturn during the past decade, anticipates a potential record R1-trillion infrastructure rollout programme. We are looking forward to providing these new tools to our customers to enable them to achieve greater efficiency, reduce costs and improve safety, ultimately leading to higher profitability,” concludes Vaughan. a
Our new range of excavators will help you push the boundaries of productivity, fuel efficiency and total cost of ownership. You will enjoy modern features in a modern design. From more space, to space that matters. A place for your boots and place to breathe. Easy to use technology for easy control. Just what you need to get ahead of your competition. Connect with your Volvo-dealer today.
Following record rainfall in KwaZulu-Natal, South Africa, in the first four months of 2025, quarries and surface mines in the province have had to contend with excessive water accumulation in their pits. Equipped with high-performance dewatering solutions and leveraging Atlas Copco Specialty Rental Division’s extensive infrastructure in the region, IPR (Integrated Pump Rental) is playing a critical role in helping operations address water management challenges. By Munesu Shoko.
While rain is vital for replenishing water resources such as lakes, rivers, and aquifers, which are essential for both human and ecological survival, heavy rainfall can pose significant challenges for surface mines and their quarrying counterparts, potentially leading to flooding, operational disruptions and increased costs.
That is exactly the situation in KwaZulu-Natal, a province that has experienced prolonged rainfall patterns and resultant flash floods in recent years – a trend which has become the new normal and is attributed to the pressing effects of climate change. In fact, KwaZulu-Natal has experienced 12 devastating floods over the past nine years,
With its flexible rental options, highquality equipment and 24/7 support, IPR is well-positioned to meet the challenges faced by the mining and quarrying industries in the KwaZulu-Natal region
Two Atlas Copco PAS150HF diesel-driven dewatering pumps in operation at a customer site in
Requiring effective solutions to mitigate the impact of excessive water accumulation in pits and desilting settling ponds, quarries and mines in KwaZulu-Natal are taking advantage of the comprehensive and flexible dewatering and dredging solutions from IPR
Leveraging Atlas Copco’s extensive provincial footprint, advanced logistics and technical prowess, IPR has proven to be the dredging and dewatering specialist of choice for operations operating in the region
IPR’s integration into Atlas Copco’s Specialty Rental Division, has significantly enhanced the company’s offering in KwaZulu-Natal by providing access to a broader range of equipment, advanced technology and a stronger service network
IPR’s flexible rental model is designed to meet both short- and long-term needs by offering access to advanced technologies and supporting operations with expert maintenance and logistical services
0,4-65 kW
The Atlas Copco submersible pump range for dewatering available from IPR starts at 0,4 kW to 65 kW
2,2-450 kW
IPR’s Toyo heavy duty slurry pump offers ranges between 2,2 kW and 450 kW, depending on application
“While it is true that the selection of a dewatering pump largely hinges on application requirements, we believe that the principal consideration should always be the expertise of the supplier, which is why many operations in the KwaZulu-Natal area prefer IPR for their dewatering and dredging needs.
to the detriment of both households and businesses.
This year has not been any different, with Durban, the metropolitan capital of the province, exceeding its average annual rainfall of 1 009 mm within the first four months of 2025, according to the South African Weather Service (SAWS). This equates to approximately 69 mm of rain per month.
Requiring effective solutions to mitigate the impact of excessive water accumulation in pits and desilting settling ponds, quarries and mines operating in the province are taking advantage of the comprehensive and flexible dewatering and dredging solutions from IPR, now part of Atlas Copco’s Specialty Rental Division.
Herman van Rooyen, business development manager KZN at IPR, says that by leveraging Atlas Copco’s extensive provincial footprint, advanced logistics and technical prowess, IPR has proven to be the dredging and
Trailer-mounted diesel-driven dewatering pumps can be quickly and easily relocated on site to wherever pumping is needed.
dewatering specialist of choice for operations operating in the region. Offering both the correct product and the right expertise, the company is playing an integral role in keeping mining areas free of flooding.
“IPR’s integration into Atlas Copco’s Specialty Rental Division, better known as Rand Air in South Africa, has significantly enhanced our offering, not only in KwaZuluNatal, but within the southern African region at large, by providing access to a broader range of equipment, advanced technology and a stronger service network,” he says.
“Quarrying and surface mining operations now benefit from a more comprehensive and reliable rental solution that not only meets immediate dewatering and dredging needs but also offers cost-effective solutions to support long-term growth and success. Through Rand Air, we have professionals in each province, bringing us even closer to our customers and servicing them more effectively,” adds Van Rooyen.
In quarries and surface mines, water accumulation –whether from rain, groundwater seepage or both – can wreak havoc to operations through flooding of mining areas, structural and equipment damages, as well as health and safety hazards. Dewatering, says Van Rooyen, therefore plays a crucial role in preventing flooding and keeping site operations running smoothly.
“While it is true that the selection of a dewatering pump largely hinges on application requirements, we believe that the principal consideration should always be the expertise of the supplier, which is why many operations in the KwaZulu-Natal area prefer IPR for their dewatering and dredging needs,” says Van Rooyen. “IPR provides quality pump solutions and dewatering equipment, playing a key role in supporting dewatering efforts for quarrying and surface mining operations.”
IPR, he adds, offers a versatile range of products that meet the dewatering and slurry needs for quarrying, surface mining and industrial operations. These include Atlas Copco diesel self-priming and submersible pumps, as well as Toyo heavy duty slurry pumps. The Atlas Copco submersible pump range for dewatering starts at 0,4 kW to 65 kW, while the Toyo heavy duty slurry pump offers ranges between 2,2 kW and 450 kW, depending on application.
Where constant pump relocation is a principal requirement, IPR’s skid or trailer-mounted dewatering pump solutions offer the benefit of ease of mobility. These systems can be easily installed in open pits and be moved across different areas of the mine, adapting to changing conditions and requirements.
This is complemented by the in-house designed IPR SlurrySucker dredging system, which is suitable for the regular cleaning of process water ponds, return water dams or other water storage areas. It is also ideal for dredging and cleaning water capture areas where silt or slimes are an issue or where water retention and water holding capacity are being threatened.
“From diesel-driven pump sets for heavy-duty applications to electric submersible pumps for more energy-efficient dewatering, and the SlurrySucker for specialised dredging, IPR provides tailored solutions that ensure smooth water management and slurry removal activities. With our flexible rental options, high-quality equipment and 24/7 support, we are well-positioned to meet the challenges faced by the mining and quarrying industries in the KwaZulu-Natal region,” says Van Rooyen.
Before selecting a pump for dewatering needs, Van Rooyen reiterates that it is important to assess site-specific conditions. By combining detailed site assessments, expert recommendations, customised
Dewatering is frequently required directly within the pit and IPR’s trailer-mounted dewatering pumps offer easy mobility and quick positioning on site for immediate action.
solutions and continuous support, IPR ensures that each dewatering or dredging solution is perfectly matched to the specific conditions of the quarry or mine site.
“This tailored approach helps maximise efficiency, maintain safety, meet environmental standards and minimise operational downtime. Whether it is handling heavy slurry, managing high flow rates, or operating in remote areas, our diverse range of equipment and expertise guarantees that each solution is the right one for the job,” he says.
In an environment where capital is not always available, IPR’s flexible rental model makes sense for quarries. Renting pumps from IPR eliminates the need for substantial upfront capital expenditure, freeing up capital for other pressing operational needs. In addition, says Van Rooyen, renting pumps provides unmatched flexibility and scalability for mining operations.
“IPR’s flexible rental model is designed to meet both short- and long-term needs by offering access to advanced technologies and supporting operations with expert maintenance and logistical services,” he says.
“Whether a mine or quarry needs equipment for a few weeks, several months, or an ongoing project, our rental approach ensures they get the right equipment without the financial burden of ownership, while also enjoying the flexibility to adapt to changing site conditions and project demands. This combination of cost savings, flexibility and expert support makes IPR’s rental model a perfect fit for quarrying, mining and industrial operations,” adds Van Rooyen.
Apart from offering a reliable and cost-effective product, IPR’s technical support and maintenance
IPR’s KwaZulu-Natal operation maintains a good stockholding of diesel-driven dewatering pumps, including this Atlas Copco PAS150HF, enabling a rapid response to customer needs across the region.
service plays a critical role in ensuring pump reliability and uptime, especially in remote or high-demand quarry and mine sites.
“IPR’s technical support and maintenance services are fundamental to ensuring that pumps and equipment remain reliable and operational, particularly in remote or high-demand quarry sites. By offering preventative maintenance, rapid on-site support, predictive monitoring and tailored solutions, IPR minimises downtime and maximises equipment uptime. This is critical for quarry operations that rely on continuous, efficient water management to ensure smooth and uninterrupted production,” concludes Van Rooyen. a
Tru-Trac used bauma 2025 to officially launch its groundbreaking intelligent belt scale that combines advanced AI technology, real-time diagnostics and automated calibration.
True to its innovation culture, Tru-Trac Rollers used bauma 2025 to officially launch its groundbreaking intelligent belt scale. Integrating AI-driven continuous calibration check and real-time load cell monitoring, amongst other pioneering functions, the belt scale not only accurately measures and detects tonnes per hour (tph) but also provides advanced conveyor belt monitoring by integrating AI-driven analytics with traditional belt scales. By Munesu Shoko
0,5 mV
To function properly, the belt scale’s load cells must be balanced within 0,5 mV of each other, and having individual load cell signals now allows Tru-Trac to monitor those stringent parameters
Tru-Trac Rollers used bauma 2025 to officially launch its groundbreaking intelligent belt scale
At the heart of the system is the real-time load cell monitoring feature, designed to ensure that millivolt signals remain within their optimal range and balance
One of the most remarkable features of Tru-Trac’s intelligent belt scale is its ability to automatically detect and correct any inaccuracies without the need for manual calibrations
The intelligent Tru-Trac belt scale system goes beyond simple weighing to monitoring of the health of the entire conveyor system, thus ensuring material flow consistency
In an environment where data-driven decisions have taken root, particularly in mining and industrial operations, having access to highly detailed, real-time data has always been a priority – but traditionally this has always come with the significant cost of installing and maintaining an array of complex instruments.
This conventional approach, though effective, was generally cumbersome and resource-intensive. In a departure from this traditional approach, Tru-Trac has introduced an intelligent belt scale that eliminates the need for an intricate network of instruments and replaces this with a more effective, single, unified system.
According to Tinus Ludik, sales manager – Bulk Materials Handling Division at Tru-Trac, the system, which made its grand international debut at bauma 2025 (April 7-13) in Munich, is “the pinnacle of advanced technological innovation, offering unparalleled accuracy and efficiency.”
The belt scale integrates with yet another Tru-Trac innovation, the Rip Prevent+ system, which made its local debut at Electra Mining Africa 2024, where it also won the Innovation Award, highlighting the gamechanging nature of this technology.
The Tru-Trac Rip Prevent+ system allows mines and other bulk material handling operations to optimise their conveyor lines’ performance by preventing costly interruptions due to rip events. Using a data-driven model and artificial intelligence (AI), the Tru-Trac Rip Prevent+ system can detect anomalies or rip events on any conveyor belt type, including steel cord, pipe and fabric belts.
KPIs
By continuously monitoring key performance indicators (KPIs), the new intelligent belt scale from Tru-Trac offers customers real-time insights into their plant’s efficiency
“Integrating the proven capabilities of the Tru-Trac Rip Prevent+ system, we have created a groundbreaking intelligent belt scale that is technologically advanced, yet still easy to use, while offering an immense amount of data that was never previously available from any of the available belt scales in the market.
“Integrating the proven capabilities of the Tru-Trac Rip Prevent+ system, we have created a groundbreaking intelligent belt scale that is technologically advanced, yet still easy to use, while offering an immense amount of data that was never previously available from any of the available belt scales in the market,” says Ludik. The belt scale and Rip Prevent+ combination is connected to the clients’ internal networks, allowing them to monitor all the parameters on a Tru-Trac designed dashboard installed in the control room, and is available via ethernet connection. While the system can be made available online, most customers, says Ludik, prefer to keep all their critical information within their organisation, for security reasons.
At the heart of the system, says Ludik, is the real-time load cell monitoring feature, designed to ensure that millivolt (mV) signals remain within their optimal range and balance. Load cell health is continuously monitored, and if any discrepancies or deviations from the norm are detected, the system sends proactive warnings. The early detection allows for timely interventions, significantly reducing the risk associated with inaccurate or inconsistent readings.
This preventive monitoring is essential to ensure repeatability and accuracy of the scale. By providing insights into load cell performance, the system empowers customers to track and maintain their equipment, enhancing overall operational reliability and longevity.
physically measure the millivolts on each load cell with a multimeter. Now all this information is accessible remotely, in real-time and continuously monitored against historic patterns” says Ludik.
The new smart junction box, which averages out the values from the load cells and speed sensor, allows for monitoring of individual cell signals. To function properly, the belt scale’s load cells must be balanced within 0,5 mV of each other, and having individual load cell signals now allows Tru-Trac to monitor those stringent parameters. Having balanced load cells enhances repeatability of results, which in turn increases accuracy.
“From a productivity point of view, the biggest improvement comes from the high level of accuracy and repeatability because we are now able to monitor a wide range of parameters that we were never able to monitor in the past. Previously, one had to
One of the most remarkable features of Tru-Trac’s intelligent belt scale is its ability to automatically detect and correct any inaccuracies without the need for manual calibrations. Through the use of advanced AI algorithms, the system continuously analyses and cross checks the belt scale readings against mass flow measurements to identify any deviations in measurement accuracy. If any anomaly is detected, the system is capable of automatically initiating earlystage corrective measures such as remotely recalibrating the belt scale.
This feature greatly improves reliability and reduces maintenance, as it eliminates the need for personnel to conduct routine calibration or perform manual adjustment corrections.
With the system working autonomously, human intervention is only necessary when critical issues arise, thereby reducing human error and operational disruptions.
“The main aim is to increase accuracy and repeatability,” explains Ludik. “Once the system senses that there is deviation, it will automatically calibrate itself without human intervention. Some of the alerts
triggered when a deviation occurs include inaccuracy alerts, belt misalignment alerts, imbalanced load cell alerts, possible future load cell failures and belt scale under- or over-reading.”
The intelligent Tru-Trac belt scale system goes beyond simple weighing to monitoring of the health of the entire conveyor system, thus ensuring material flow consistency. Through continuous load cell mV readings, it assesses the alignment of the conveyor belt, detecting potential misalignment caused by off-centre material distribution. This real-time monitoring feature that tracks individual load cells and detects deviations while measuring weight distribution per load cell ensures even material loading.
This helps prevent costly damage to the belt and related components, reducing maintenance costs and prolonging the life of the customer’s equipment.
In addition, the Tru-Trac intelligent belt scale system does not only focus on immediate operational accuracy, but it also provides insightful long-term data that helps with decision-making and productivity forecasting. By continuously monitoring key performance indicators (KPIs), it offers customers real-time insights into their plant’s efficiency. This allows for more accurate production forecasts and a clear understanding of the overall productivity percentage, which is directly correlated to profitability.
“By having access to such detailed, actionable data, plant managers can make informed decisions that optimise operations, improve throughput and ultimately drive better bottom-line results,” says Ludik.
In addition, the system incorporates advanced anomaly detection capabilities that continuously monitor and analyse all operational parameters of the conveyor in real time. Should any irregularities or discrepancies arise, the system is capable of flagging them immediately for further investigation, ensuring that potential issues are addressed before they develop into more significant challenges. This real-time oversight fosters an environment of constant optimisation and operational excellence.
“The system helps customers manage their preventative maintenance regimes better because they have a continual understanding of what is happening with their conveyor belts. This offers numerous benefits, including reduced downtime, increased conveyor belt lifespan, improved safety, enhanced efficiency and significant cost savings, by preventing costly repairs and extending belt lifespans,” says Ludik.
The Tru-Trac intelligent belt scale, says Ludik, can integrate with existing Tru-Trac belt scale solutions. The system is good news for all industries that run conveyor belts and have accuracy, repeatability and production at the top of their priorities. Well before the official launch at bauma, several potential customers had already expressed interest in the system, and installations were imminent.
“In terms of the early adopters, I think the system will appeal to high-value commodity operations such as platinum, gold and copper mines, amongst others, where the plants run at millions of rands per hour and any form of inaccuracy and downtime are out of the question. Having such an advanced solution that ushers in a new era in belt weighing is critical for their operations,” concludes Ludik. a
HMD, Rokbak’s newly-appointed dealer for West Africa, has successfully deployed its first Rokbak articulated dump trucks (ADTs) in Ghana, where they are excelling in demanding mining and construction applications. By Munesu Shoko
HMD has built a reputation as a trusted distributor of premium heavy machinery across Nigeria, Ghana, Senegal, Benin, Guinea and Côte d’Ivoire. The company’s portfolio features a diverse range of premium heavy machinery from industry-leading brands, including Bobcat, Bomag, Epiroc, Hitachi and Rokbak.
“We select brands based on market demand, proven reliability and strong
aftermarket support,” says HMD CEO Mathew Khouri. “Rokbak’s durability and performance align perfectly with our customers’ needs, particularly in mining and large-scale construction.”
HMD’s first Rokbak RA40 units hit the ground in early 2025, tackling Ghana’s rugged terrain with ease. The 38-tonne haulers have already earned praise for their reliability, efficiency and ability to enhance
HMD’s first Rokbak RA40 units hit the ground in early 2025, tackling Ghana’s rugged terrain
The 38-tonne RA40 haulers have already earned praise for their reliability, efficiency and ability to enhance project timelines while reducing operating costs
project timelines while reducing operating costs.
“Customers are highly satisfied – these machines are built for Africa’s toughest conditions,” says Khouri. Backed by HMD’s renowned aftermarket support, including mobile technicians, stocked spare parts and maintenance training, Rokbak operators benefit from minimised downtime and optimised productivity.
Beyond equipment supply, HMD and Rokbak now offer flexible financing options backed by Export Credit Agencies (ECAs) and Private Risk Insurers (PRIs). Through UK Export Finance (UKEF) and Sweden’s EKN, customers can secure competitive rates and extended payment terms, making fleet expansion more accessible.
“ECA-backed financing is a game-changer,” says Khouri. “It is not just about selling machines – it is about enabling our customers’ success with tailored financial solutions.”
HMD’s first Rokbak RA40 units hit the ground in early 2025, tackling Ghana’s rugged terrain with ease
Backed by HMD’s renowned aftermarket support, including mobile technicians, stocked spare parts and maintenance training, Rokbak operators benefit from minimised downtime and optimised productivity
Rokbak’s durability and performance align perfectly with customers’ needs, particularly in mining and large-scale construction
Beyond equipment supply, HMD and Rokbak now offer flexible financing options backed by Export Credit Agencies and Private Risk Insurers
The Rokbak range – featuring the RA30 and RA40 models – has generated significant interest across West Africa. With class-leading fuel efficiency, advanced telematics and operator-friendly designs, Rokbak haulers are poised to become a staple in the region’s infrastructure and mining sectors.
“We see tremendous potential for Rokbak in West Africa,” Khouri adds. “As infrastructure projects expand, we are committed to driving customer success through superior equipment and support.”
West Africa is making giant strides towards industrialisation and free regional trade in order to drive inclusive growth. The success of these initiatives, however, depends largely on improved infrastructure. This presents tremendous opportunities for businesses.
courtesy of the Spatial Development Initiative promoted by the African Development Bank (AfDB). The 1 028-km transnational coastal motorway will connect Côte d’Ivoire to Nigeria, while crossing through Ghana, Togo and Benin. Work is due to commence in 2026 and is earmarked for completion in 2030, according to the AfDB.
The toll-free motorway will boast four to six lanes, with up to eight lanes in Lagos. After a drive of 82 km through Nigeria, the road will cover 520 km in Ghana, 144 km in Cote d’Ivoire, 90 km in Togo, and 127 km in Benin. There are also plans to build 63 interchanges. Construction of the road is expected to generate up to 70 000 direct and indirect jobs. Most of the work will be carried out in the form of PPPs.
US$180billion
According to PwC, infrastructure spending in West Africa is estimated to reach US$180-billion per annum by 2025. While there is a growing focus on private sector involvement, particularly through public-private partnerships (PPPs), a significant funding gap remains, with annual needs estimated between US$130-$170-billion, compared to the current US$80billion invested annually.
According to PwC, infrastructure spending in West Africa is estimated to reach US$180billion per annum by 2025
The project will link an urban population which is expected to reach 173-million people by 2050 and connect the most densely populated metropolitan areas in West Africa, from Abidjan, Takoradi and Accra, to Lomé, Cotonou, Porto-Novo and Lagos.
On the mining front, a Fitch report notes that West Africa’s mining sector will experience robust growth over the next decade, driven by a strong project pipeline. Large untapped resources, elevated commodity prices and improving infrastructure are set to encourage investment in new projects.
Transportation is one area that is attracting investment, with regional corridors taking centre stage. A case in point is the Abidjan-Lagos Corridor Highway, which will link the cities of five major West African countries by 2030 and is set to become a powerful economic and industrial hub
As these projects come to market, more and more contractors in the region will be able to benefit from Rokbak haulers’ robust and reliable performance. HMD sees enormous potential for Rokbak in West Africa, where infrastructure development and mining activity are set to accelerate.. a
Leading construction materials company AfriSam has upgraded its Rheebok Quarry plant near Malmesbury in the Western Cape with the high-capacity, advanced-design Sandvik CH430 cone crusher from Sandvik Rock Processing.
Desmond Jacobs, AfriSam’s senior engineer for the Western Cape, explains that the replacement crusher is driving operational efficiency while enhancing sustainability and reducing maintenance. The upgrade, part of the company’s long term capital investment strategy, was executed ahead of schedule during the builders’ shutdown from late 2024 to early 2025.
AfriSam’s Rheebok Quarry mines a granite deposit to produce aggregate stone, crusher
sand, base, sub-base, roadstone and ballast.
“After a thorough selection process evaluating both technical and commercial considerations, the Sandvik CH430 proved to be the best fit for our operational requirements,” says Jacobs. A key factor in the decision was the Sandvik CH430’s footprint which closely matched that of the previous crusher, minimising structural modifications.
“This was a brownfields project, meaning we had to work within existing site constraints,” he explains.
“The CH430 fitted seamlessly into our setup, significantly reducing installation time and costs.
““This was a brownfields project, meaning we had to work within existing site constraints. The CH430 fitted seamlessly into our setup, significantly reducing installation time and costs. Time was critical, as we had to install the new crusher during the year-end shutdown.”
AfriSam has upgraded its Rheebok Quarry plant with the Sandvik CH430 cone crusher from Sandvik Rock Processing
The crusher is driving operational efficiency while enhancing sustainability and reducing maintenance
One of the key considerations was safety and efficiency, which the Sandvik CH430 delivers through its hydraulic Hydroset system, allowing for precise and automated closed-side setting adjustments
The Sandvik CH430’s design allows for better dust control, with more space between the crusher base and the support base to install and maintain dust suppression systems
The upgrade, part of the company’s long term capital investment strategy, was executed ahead of schedule during the builders’ shutdown from late 2024 to early 2025
Recommending the CH430 for AfriSam was based on careful alignment with the crusher’s expected duty at Rheebok Quarry
Another key consideration was energy efficiency. While the previous unit operated with a 160-kW motor, the Sandvik CH430 is powered by a 132 kWunit
Time was critical, as we had to install the new crusher during the year-end shutdown.”
Key considerations
He also highlights the importance of safety and efficiency which the Sandvik CH430 delivers through its hydraulic Hydroset system, allowing for precise and automated closed-side setting adjustments.
“Manually adjusting crusher settings can be time consuming, but with this technology we can optimise output with the push of a button,” he says. “This also improves safety as operators do not need to be near the machine.”
For Sandvik Rock Processing, recommending the CH430 for AfriSam was based on careful alignment with the crusher’s expected duty at Rheebok Quarry, explains PC Kruger, business line manager for Crushing Solutions at Sandvik Rock Processing. He says that Sandvik’s 400 Series cone crushers are known for their flexibility and reliability in the quarrying sector.
“The most important aspect of any process design is identifying a solution that meets the client’s needs,” he says. “AfriSam’s Rheebok Quarry produces different product sizes ranging from aggregate stone, crusher sand, roadstone and ballast, so meeting those specifications was imperative.”
To assist in this task, Sandvik Rock Processing specialists used the Sandvik Plant Designer platform which leverages industry data and expertise to strategically plan plant operations. This platform calculates material flow and output levels, assisting in crusher selection and optimisation.
Another key consideration was energy efficiency. While the previous unit operated with a 160-kW motor, the Sandvik CH430 is powered by a 132 kW-unit.
“Reducing power consumption was a critical factor for us,” Jacobs says. “Lower energy demand translates to direct cost savings and supports our sustainability goals in terms of our People, Planet,
The successful installation of the
was made possible by strong collaboration between AfriSam and Sandvik Rock Processing teams.
and Performance commitment.”
Kruger notes that the motor’s maximum power demand was set at 132 kW but the design aimed to stay well below this limit, enhancing energy efficiency while improving crusher output.
He also explains that the Sandvik CH430 features the Automatic Setting Regulation (ASRi) system, which continuously monitors and optimises crusher performance.
“This advanced feature minimises operator intervention and allows real-time adjustments, improving consistency in product size and quality,” says Kruger. “The system also tracks key parameters like temperature and pressure, enabling proactive maintenance to prevent unexpected breakdowns.”
The new unit enhances product quality by reducing oversized material in the feed stream. Jacobs says that by early 2025, this benefit was already evident with the Sandvik CH430 in operation.
“Our initial assessments showed a dramatic reduction in oversize material being sent for secondary crushing,” Jacobs notes. “This optimises throughput and may allow us to remove redundant processing steps in the future.”
Despite the new unit’s compact size and lighter weight, the AfriSam Rheebok Quarry team was immediately impressed by its performance, throughput and advanced digital features. Predictive maintenance, facilitated by the ASRi system, adds further value.
“We can now digitally monitor crusher liner wear, avoiding significant manual intervention until maintenance is required,” he explains. “This helps us plan maintenance more effectively within the broader quarry operation.”
The Sandvik CH430 cone crusher can be fitted with a variety of mantles and concaves, making it highly versatile. “Operators can choose different mantles and concaves to suit specific processes, using different eccentric throws and bushings,” Kruger explains.
Jacobs adds that the Sandvik CH430’s design allows for better dust control, with more space between the crusher base and the support base to install and maintain dust suppression systems.
AfriSam also values Sandvik Rock Processing’s strong local presence and support capabilities. “AfriSam has a longstanding relationship with Sandvik Rock Processing, and its Cape Town-based team provides critical support within easy reach of our operations,” Jacobs says. “We also appreciate the local stockholding of spare parts ensuring minimal downtime – a vital aspect of our operations.”
Kruger notes that Sandvik Rock Processing’s Cape Town office offers a range of support services including plant audits to identify opportunities for further efficiency improvements in the crushing circuit. a
Haulage in mining and quarrying, and the road transport of aggregates and commodities, contributes majorly to carbon emissions, exacerbated locally by shifting from rail to road. There is definite merit in decarbonising, which cuts carbon emissions, limits fuel cost volatility, improves the total cost of ownership, and meets environmental, social and governance targets. Volvo Trucks clearly demonstrates that electric trucks result in more sustainable haulage and transport, with the company having already sold over 5 000 trucks in a range of industry segments worldwide, including construction. By Chantelle Kotze.
5 000
Volvo Trucks has sold more than 5 000 electric trucks in a wide range of transport segments worldwide to date
The shift from rail to road transport for commodities to their destination in South Africa is a major contributor to carbon emissions
Volvo Trucks South Africa is positioning electric trucks in the country as a more sustainable haulage and transport alternative to traditional dieselpowered trucks
Electric trucks are already being used in South Africa in regional applications, running between 300-400 km/ day and returning to a home base after each day
Volvo Trucks South Africa’s extra-heavy electric truck range can be customised for the quarrying, mining and construction sectors, with a wide range of superstructures, such as tippers, mixers, tankers and cranes, depending on the application
2040
In a bid to reach its global net-zero emissions by the 2040 target, Volvo Trucks has a three-path technology strategy that embraces a mix of technologies to suit different transport applications and customer needs globally
“Although the newly introduced Volvo FH
Aero Electric truck is very much designed for the European market, it would be possible for local customers to request it for specific applications.
In mining and quarrying operations, efficient haulage and on-road transport are vital to productivity when moving raw material from extraction points to processing plants or transporting aggregates to end users and construction sites.
Traditional diesel-powered trucks still dominate the South African transport sector due to the country’s outdated emission standards for heavy-duty vehicles. South Africa still adheres to Euro 2 emission standards despite the availability of trucks with Euro 6 engines in the domestic market.
While South Africa’s domestic transport sector is starting to adopt cleaner, more fuel-efficient technologies, the shift to electric trucks still faces several barriers – including high upfront costs, limited charging infrastructure, grid constraints and range limitations.
“Customers are increasingly willing to invest in their own off-grid or hybrid charging solutions to support electromobility and meet their sustainability goals.
Driven by its value of ‘environmental care’, Volvo Trucks has offered electric trucks since 2019 and has eight electric truck models in production today, sold mainly in Germany, the Netherlands, United States, Norway and Sweden. Electric trucks have been available in South Africa since 2023, with internal testing and homologation (Type Approval) work being undertaken.
More recently, Volvo Trucks announced the introduction of a new long-distance electric truck – the Volvo FH Aero Electric – that has a range of up to 600 km and batteries that can be charged in 40 minutes. Volvo Trucks will formally launch and start taking orders for this truck in the second quarter of 2026.
Waldemar Christensen, MD of Volvo Trucks South Africa, who addressed customers at an event in Paarl, Western Cape in May, says that although the newly introduced Volvo FH Aero Electric truck is very much designed for the European market, “it would be possible for local customers to request it for specific applications”.
“From a South African perspective, we see it as an indicator of how Volvo Trucks’ technology is advancing and what is possible in the future, also here locally,” Christensen says.
In a bid to reach its global net-zero emissions by the 2040 target, Volvo Trucks has a three-path technology
The introduction of Euro 6 engine technology echoes the growing demand for cleaner transport solutions in the country.
strategy that embraces a mix of technologies to suit different transport applications and customer needs globally. The strategy is built on:
• Battery electric trucks: These trucks are already being deployed globally with ongoing battery range, payload and battery energy density improvements being made.
• Fuel cell electric trucks: These trucks are a mid- to long-term electromobility solution that are typically fuelled by hydrogen, to generate electricity on-board using a fuel cell to power the electric motor.
• Renewable fuels: These renewable fuels, such as green hydrogen, biogas, biodiesel or hydrotreated vegetable oil, allow combustion engines trucks to run on renewable fuels and provide customers with the flexibility to reduce emissions while investing in full electrification.
This diversified strategy enables Volvo Trucks to support emission reduction across different geographies, industries and duty cycles, including mining and quarrying.
Demonstrating the global demand for electromobility trucks, Volvo has sold over 5 000 electric trucks in over 50 countries and over 8 000 gas-powered trucks that can switch between using renewable biogas and regular liquified natural gas fuel.
Eric Parry, Sustainable Solutions Manager for Volvo Trucks South Africa, is excited about the company's electromobility future in South Africa.
He says electric trucks in South Africa work well in regional applications, running between 300-400 km/day but returning to a home base after each day. This includes distribution centres delivering to multiple stops a day or a factory delivering to distribution centres.
In South Africa, the first electric FM 4x2 tractor was presented to Volvo customer, KDG Logistics, for use in its Durban operations to move new passenger vehicles between factories/storage facilities and Durban Port. Another early adopter of electromobility was cold chain logistics provider, Vector Logistics, which acquired two battery electric FH 6x4 truck tractors (paired with a custom refrigerated trailer) to undertake domestic
deliveries and distribution, Parry says. To accommodate electromobility, Vector Logistics invested in two high speed DC charging stations, coupled to the solar power available at its home bases in Cape Town and Johannesburg where the trucks have been deployed to ensure that when fully charged, each truck has a range of between 200-300 km.
Moreover, Parry says that South African freight company, Strategic Transport, which manages the material handling and transport for Volvo Trucks South Africa, has two FM 6x4 truck-tractors in operation. The trucks undertake component deliveries between the warehouse and manufacturing factory in Durban, doing multiple round trips a day and being charged using solar power, he explains.
Volvo Trucks South Africa’s extra-heavy electric truck range includes FH, FM and FMX models in truck-tractor or rigid configurations in 4x2, 6x2, 6x4 and 8x4 axle combinations.
Speaking to Quarrying Africa on the side lines of the Western Cape customer event, Parry said: “Given the ability to customise our electric trucks depending on the application, these conventional trucks can be customised for the quarrying, mining and construction sectors with a wide range of superstructures, such as tippers, mixers, tankers and cranes, depending on the application.
“In mining and quarrying, our electric trucks are extremely capable of transporting material from processing plants to rail sidings,” he says.
Parry says that one of the key considerations when adopting electromobility is whether it makes economic sense for specific operations. “The ability to control their own charging infrastructure gives some customers greater certainty over energy costs – an advantage in times of fluctuating fuel prices and higher fuel taxes,
which supports a lower total cost of ownership over time,” he says.
Despite the applicability of electric trucks in South Africa, there are concerns surrounding power supply constraints, charging infrastructure and range and performance limitations, especially in remote or heavyduty applications and how operators can work around this challenge to efficiently operate electric trucks.
Parry says this all comes down to planning by the truck operators. “We will provide operators with the necessary tools to guide their charging infrastructure options according to their workload and routes and potential loadshedding,” he says.
“Customers are increasingly willing to invest in their own off-grid or hybrid charging solutions to support electromobility and meet their sustainability goals,” says Parry. This is despite barriers such as high upfront costs and limited energy infrastructure.
As an alternative ownership structure, Volvo Trucks South Africa offers electric trucks through an equipment-as-a-service rental model, reducing upfront costs. To support this, it has partnered with a service provider to provide nationwide charging infrastructure for rental customers.
As the mining and quarrying industries navigate growing cost pressure amid increased global pressure to reduce emissions across their value chain, the transitioning to cleaner, more sustainable transport is increasingly important.
The ability to shift to zero-emission haulage in heavy duty applications or remote areas is already a reality, with global applications proving that it can be both operationally effective and economically viable, even in South Africa. a
IVECO South Africa is expanding its footprint into loadhaul-dump operations with the introduction of its
Following the arrival of its T-Way range of off-road trucks in 2024, IVECO South Africa has reiterated its renewed focus on construction, quarrying and surface mining industries. As these sectors continue to place a high value on improved productivity and efficiency, the company is also expanding its footprint in load-haul-dump operations with an 8x4 truck that offers a payload capacity of 40 tonnes (t). By
Munesu Shoko
Construction, quarrying and surface mining industries are inarguably the bedrock of South Africa’s economy. Their strategic importance cannot be overstated, states Elvis Mutseura, product manager at IVECO South Africa.
While they may ebb and flow due to a wide range of factors such as international pricing, demand and local policy, he says, these industries have continually delivered returns for the economy for over a century and will continue to
do so well into the future.
Given the strategic importance of construction, quarrying and surface mining industries, Mutseura says IVECO South Africa has in recent times renewed its focus on these sectors through the provision of innovative off-road solutions that speak directly to the needs of the industries.
“IVECO is very excited about the solutions that we offer to construction, quarrying and surface mining industries. We are even more excited about our renewed focus on these sectors. We launched
IVECO South Africa has started some pilot runs in load-haul-dump operations with its 8x4 truck, and the results are extremely positive to date.
IVECO South Africa has renewed its focus on construction, quarrying and surface mining through the provision of innovative off-road solutions that speak directly to the needs of the industries
The company launched its T-Way range of off-road trucks in 2024 to replace the previous Trakker range, which places it in good stead to offer effective solutions to these sectors
With its combination of robustness, reliability and comfort, the T-Way is designed to meet requirements for high productivity, payload capacity and safety
our T-Way range of off-road trucks in 2024 to replace the previous Trakker range, which places us in good stead to offer effective solutions to these sectors,” says Mutseura.
The IVECO T-Way is said to provide strong performance in tough off-road missions. With its combination of robustness, reliability and comfort, it is designed to meet requirements for high productivity, payload capacity and safety.
The T-Way range boasts a new 13-l common-rail diesel engine that significantly improves fuel economy and has a longer service interval. A new generation 16-speed automated transmission provides enhanced control and performance through responsive and precise gear
13 l
selection to tackle challenging underfoot conditions and terrain.
“We offer an array of Power Take-Off (PTO) options that are programmable to accomplish a multitude of tasks efficiently, intelligently and safely. Available in 4x4, 6x4, 6x6, and 8x4 configurations, there is a T-Way for any task,” says Mutseura.
One of the major talking points on the T-Way is IVECO’s Hi-Traction, a hydrostatic drive system that provides
One of the major talking points on the T-Way is IVECO’s Hi-Traction, a hydrostatic drive system that provides additional hydraulic front-wheel traction when needed, improving grip, handling and driving safety 40 t
IVECO South Africa is expanding its footprint in load-haul-dump operations with an 8x4 truck that offers a payload capacity of 40 t
The T-Way range boasts a new 13- l commonrail diesel engine that significantly improves fuel economy and has a longer service interval 16
A new generation 16-speed automated transmission provides enhanced control and performance through responsive and precise gear selection to tackle challenging underfoot conditions and terrain
additional hydraulic front-wheel traction when needed, improving grip, handling and driving safety, especially on slippery surfaces and in off-road conditions.
“The Hi-Traction system is automatically activated to provide additional hydraulic front-wheel traction when needed to overcome the skidding of the rear axle on slippery surfaces. It delivers all the grip, manoeuvrability and driving safety advantages of all-wheel drive,” explains Mutseura.
The Hi-Traction system can be activated manually with a button in the cab, switching from ‘Inactive’ to ‘Ready to engage’ mode. The system is running in the background, ready to activate when needed. When needed, the system automatically switches to ‘Active’ mode and provides front-wheel traction if the rear axle slips. The Boost mode is activated at every standing start (0 to 3 km/h) to improve traction and reduce wear and tear of the clutch.
One of the major advantages is its versatility – the T-Way can be deployed across applications, including concrete (pumps, mixer, mixer pumps), tipper, heavy haulage and public utilities. The IVECO T-Way cab line-up offers a choice of cabs to match the mission at hand: the AT sleeper cab with low or medium roof, and the AD short cab with low roof.
The modular, mission-oriented approach of the range, with a wide choice of features and components, together with the structural strength and low kerb weight, provides ultimate flexibility in customising the vehicle to the specific requirements of a wide variety of applications.
In addition, IVECO South Africa is expanding its footprint into load-haul-dump operations with the
introduction of its 8x4 truck that has a body and payload capacity of 40 t. “We appreciate that there are operations where we cannot displace a traditional articulated dump truck (ADT), for example, but we recognise other areas where we can deliver superior productivity and efficiency at a significantly lower cost,” says Mutseura.
IVECO South Africa has started some pilot runs in this space and the results are extremely positive to date. The company will also tap into the experience of its sister operations in markets such as Indonesia where IVECO has a long history of success in such operations. Mutseura also sees tremendous potential in support services such as dust suppression and other specialised maintenance and support functions.
“In addition, mining and quarrying products need to be transported over long distances to ports, or processing facilities. Medium and long haul is a job that we understand very well and support via a dealer network that covers all the major shipping routes in South Africa. Our T-Way truck tractor can haul up to 100 t. Performance based standards (PBS) allow operators to harness this pulling power to increase their returns and we are here to help them do so,” he adds.
The PBS approach, as certified by the Road Transport Management System, offers flexible design rules, allowing truck and trailer combinations to perform safely while carrying larger payloads. Some of the key benefits of PBS include increased gross combination mass, increased cubic capacity, improved productivity and freight efficiency. a
‘Demography is destiny’, credited to French philosopher Auguste Comte (1798-1857), encapsulates a great deal about the dynamics of our economy, construction sector and the suppliers to the latter. There are many nuances to the saying, but in our context, what is available per person, or gross domestic product/income per capita holds the key.
The logic is straightforward; total production/ income in the economy divided by the population. The size of the country’s production/income is an indication of its wherewithal to afford infrastructure (houses, hospitals, roads etc.) for its people, and the number of people is an indication of the needs of the population. Graph 1 shows the correlation between GDP/per capita and the size of ‘construction’ infrastructure.
But the connection also runs in the opposite direction; the more is spent on infrastructure, the faster an economy grows! It is a well-known fact that a country needs overall fixed investment to be in the order of 25% of gross domestic production for it to grow and expand. Graph 2 shows that it has never been higher than 22% (for South Africa) and currently averages around 14% of GDP. The impact of this, since the middle 2000s, on the SA economy is difficult to
ignore. Minister Ramokgopa (of Electricity and Energy) calls it ‘South Africa’s infrastructure emergency’.
Of greater concern is that the share of construction related investment of total fixed investment declined by 2% on average per year from 51% (2009), to 41% (2020), and even faster (-4% per year) to only 34% by 2024.
Spending on construction related infrastructure is directly proportional to the demand for construction materials. The trends observed in construction fixed investment data show (and should have) a high correlation with construction material sales (Graph 3).
The SA Reserve Bank’s diagnoses of the 3,7% contraction in fixed investment in 2024 (which was at odds with general business sentiment) is due to private sector investment declining by 3,2%, public corporations’ spending contracting by 5,1% and which were not countered by higher general government investment spending (+2%) during the second half of the year. Overall, this the state of affairs is ascribed to low (economic) demand and supply shocks (load shedding and logistics) since 2019.
The political or policy environment clearly acts as a brake on both economic growth and the appetite for fixed investment. Graph 4 shows the correlation between construction fixed investment data and political confidence. The overwhelming majority (+50%) of respondents to the BER manufacturing confidence surveys rated the latter as highly ‘obstructive’. The Government of National Unity partners’ recent non-alignment on fiscal policy clearly shows in the increased uncertainty, over the last quarter (Q1, 2025). Confidence has a direct impact on construction fixed investment and that in turn on construction materials sales. Graph 5 shows the extent to which administered prices, caused by public sector inefficiencies, are impacting on/ aggravating sector input costs (components petroleum products (22,6%), electricity and water (15,6%) transport and
25%
It is a well-known fact that a country needs overall fixed investment to be in the order of 25% of gross domestic production for it to grow and expand
2%
Of greater concern is that the share of construction related investment of total fixed investment declined by 2% on average per year from 51% (2009), to 41% (2020), and even faster (-4% per year) to only 34% by 2024
storage (34,8%), and government services (27%)). Declining fuel prices contributed to slower cost increases lately, but is no indication of structural costs declining; in fact, it is contributing to uncertainty due to its volatility. With all the above said, the question then is about the future prospects for the sector. Taking a three-year view, economic growth is expected to slowly improve from about 1% (2025) to around 2% (2027), driven by growing consumption expenditure, helped by investment, better exports and steady commodity prices in the outer years, as well as the gradual positive impacts of alleviating energy and logistical bottlenecks. Overall investment is expected to
Sources : SA Reserve Bank, Statistics SA, Quantec
Sources : SA Reserve Bank, Statistics SA, Quantec
grow by 2,1% this year, rising to 3,6% in 2027. Construction fixed investment (housing, non-residential and construction works) is expected to grow by 3,5% (2025), 5% (2026) and 2,5% (2027). There are (albeit weak) indications that the lagged effect of lower (and stable) interest rates will have a positive impact on the residential building market, and that improved economic growth and the ‘return to the office’ trend after Covid, will stimulate demand for non-residential buildings. Private sector spending on embedded energy generation plants as well as public sector spending on energy related projects (+60% over three years) will boost construction
works. Public sector spending on water and sanitation (+24% over three years) and transport and logistics (+11% over three years), barring delays in project execution, will also enhance construction works demand for construction materials.
However, the short-term trends emerging from high frequency datasets are ‘directionless’, clearly reflecting the uncertainties around domestic and international geo-politics, and virtually all markets. Linking confidence indicators to the relevant actual performance datasets give some indication of possible immediate future trends.
The ‘expected building activity’ confidence index shows more optimism (reading above neutral) than reflected in the
Sources : SA Reserve Bank, Statistics SA, Quantec
Sources: BER Manufacturing Survey, SA Reserve Bank, Statistic SA and Quantec
actual production trends. The civil engineers’ confidence index did the opposite and dropped below neutral. Builders’ confidence is more directly linked to sector production/ products, than those of civil engineers (due to the diverse products demanded by the latter, as well as higher market concentration in this sub-sector of the contracting fraternity).
The resurgence of loadshedding probably had a detrimental effect on production recently, but sector data is delayed, so it is not possible to gauge the impact with certainty, at the time of writing.
Although actual production in January was higher than in January 2024, and still grew over the last 12 months, January deeply disappointed (-7,5%) against December 2024.
Builders are more optimistic about expected business conditions, but although actual sales rose (3,4% in January on December), when inflation is taken out, it declined. Confidence about expected construction activity by civil engineers declined strongly (since middle 2024), in line with total (building materials and non-metallic) sales’ declining trajectory since 2022 already. The trend in wholesale volumes is also on a downward trajectory, despite seasonal volatility.
Not surprisingly, the production/selling price index for the sector has slowed down, from near 5% during 2024, to just below 3% on average for the first two months of 2025. The input cost index for the sector shows that input costs (an
Sources: Statistics SA, SA Reserve Bank, Quantec
Sources: SA Reserve Bank, Quantec Research.
average) have been rising slower than selling prices.
All of the above are sensitive to the implementation of structural reforms in energy and logistics and the evolution of the global economy. Tariffs and trade restrictions present serious threats to the global economy, and the resulting uncertainty will undoubtable spill over into the fixed capital (and therefore growth) environment in South Africa. The successful navigation of the myriad economic and geo-political uncertainties, as well as domestic policy resolve/execution to ‘restart’ (construction) fixed investment, are indispensable for underpinning future higher economic growth in SA. Such an outcome will be positive for construction materials sales and production. a
AfriSam
AfriSam is a leading construction materials group in southern Africa. Since establishing its first cement plant in 1934, the company has grown into a formidable construction materials group with operations in South Africa, Lesotho and Eswatini.
www.afrisam.co.za
Babcock
Through several business units, Babcock offers a range of products and services, including construction and mining equipment, engineering solutions for steam generation and power plants, crane hire and gear rental, industrial generators, welding equipment and DAF truck sales and service www.babcock.co.za
Booyco Electronics
With more than 16 years of experience in Proximity Detection Systems solutions, Booyco Electronics has supplied over 6 500 sets of mining vehicle equipment installations across southern Africa, as well as more than 55 000 pedestrian RFID installations. www.booyco-electronics.co.za
Bunting’s range of magnetic separators and metal detectors for quarries and mines ensures the protection of crushers, screens and conveyors. Overband magnets, suspension magnets and pulley magnets automatically remove tramp ferrous metal from conveyed quarried rock. www.bunting-redditch.com
IPR is recognised across the SADC region as the pump, heavy duty slurry handling and dredging specialist operating in underground and surface mining, quarrying, construction, wastewater, petrochemical and oil and gas sectors. www.pumprental.co.za
LOADTECH Load cells Onboard Weighing are specialists in onboard weighing providing complete solutions onboard your heavy goods vehicle, primarily in the application of load cell and transducer systems for payload protection and accuracy in the commercial vehicle sector. www.loadtech.co.za
JBI Industrial Solutions specialises in a diverse range of weighing systems in partnership with PFREUNDT GmbH. We provide solutions for both mobile and static weighing needs. The PFREUNDT weighing systems are versatile and deliver significant benefits across various industries, including extraction, disposal, recycling, industry and agriculture. www.jbisolutions.co.za
Pilot Crushtec International
Pilot Crushtec International (Pty) Ltd is South Africa’s leading supplier of mobile and semi-mobile crushing, screening, recycling, sand washing, stockpiling, compacting and material handling solutions. www.pilotcrushtec.com
Sandvik
As a world-leading mining equipment manufacturer, Sandvik Mining and Rock Solutions is committed to improving your productivity and profitability. Our products and services provide you maximum value in terms of performance, quality, safety, flexibility and total economy. www.rocktechnology.sandvik/en/
Astec
Astec Industries has been a global leader in providing innovative Rock to Road™ solutions since 1972, specialising in equipment for asphalt road building and aggregate processing. www.astecindustries.com
John Deere
John Deere offers a comprehensive range of construction equipment, including ADT’s, excavators, loaders, dozers, graders, skid steers and TLB’s, designed to enhance productivity, efficiency, and performance on job sites of all sizes. www.deere.africa/en/construction
Lintec & Linnhoff is a global manufacturer and distributor of leading-edge solutions for the asphalt and concrete industries under the Lintec and Linnhoff brand names. Its products include asphalt mixing plants, concrete batching plants, pavement related technologies, and specialist concrete cooling solutions.
www.lintec-linnhoff.com
Weir Minerals
Weir Minerals Africa offers a wide range of equipment solutions including pumps, hydrocyclones, valves, dewatering equipment, wear-resistant linings, rubber products, screens and crushers – backed throughout the product lifecycle by high levels of aftermarket support. www.global.weir
Sany Southern Africa is a subsidiary of Sany Group, a leading manufacturer of construction, mining and port machinery with over 20 R&D centres and manufacturing bases all over the world. www.sanysouthafrica.com
For over 40 years, BME has been at the forefront of mining innovation, delivering cutting-edge solutions in commercial blasting and mining chemical processing. As a trusted partner in the industry, we provide a comprehensive range of products and services designed to enhance safety, efficiency, and sustainability in mining operations worldwide. www.bme.co.za
Only ENDURON® HPGR comes with a 10-year bearing warranty. Not that you’ll need it. After all, there hasn’t been one premature bearing failure to date.
ENDURON® HPGR delivers unmatched grinding efficiency, even when processing the hardest rocks, boosting mineral recovery. Expect ≥95% equipment availability, so operators can rest assured production targets will be achieved whilst using the lowest possible resources.
With lowest energy consumption and no water or grinding media required, typical operating costs for HPGR based circuits are over 20% lower compared to conventional SABC circuits whilst reducing comminution CO2 emissions by 30%. It’s no wonder we say ENDURON® on and on and on.
Find out why. www.global.weir/ENDURON
Designed with a unique combination of power and intelligence the TA 230 features market leading technology, an innovative weighing system, automatic traction contre, hill start assist, not to mention the superior cabin design to leave your operator feeling good. Simply put, a perfect mix of agility with outstanding performance.