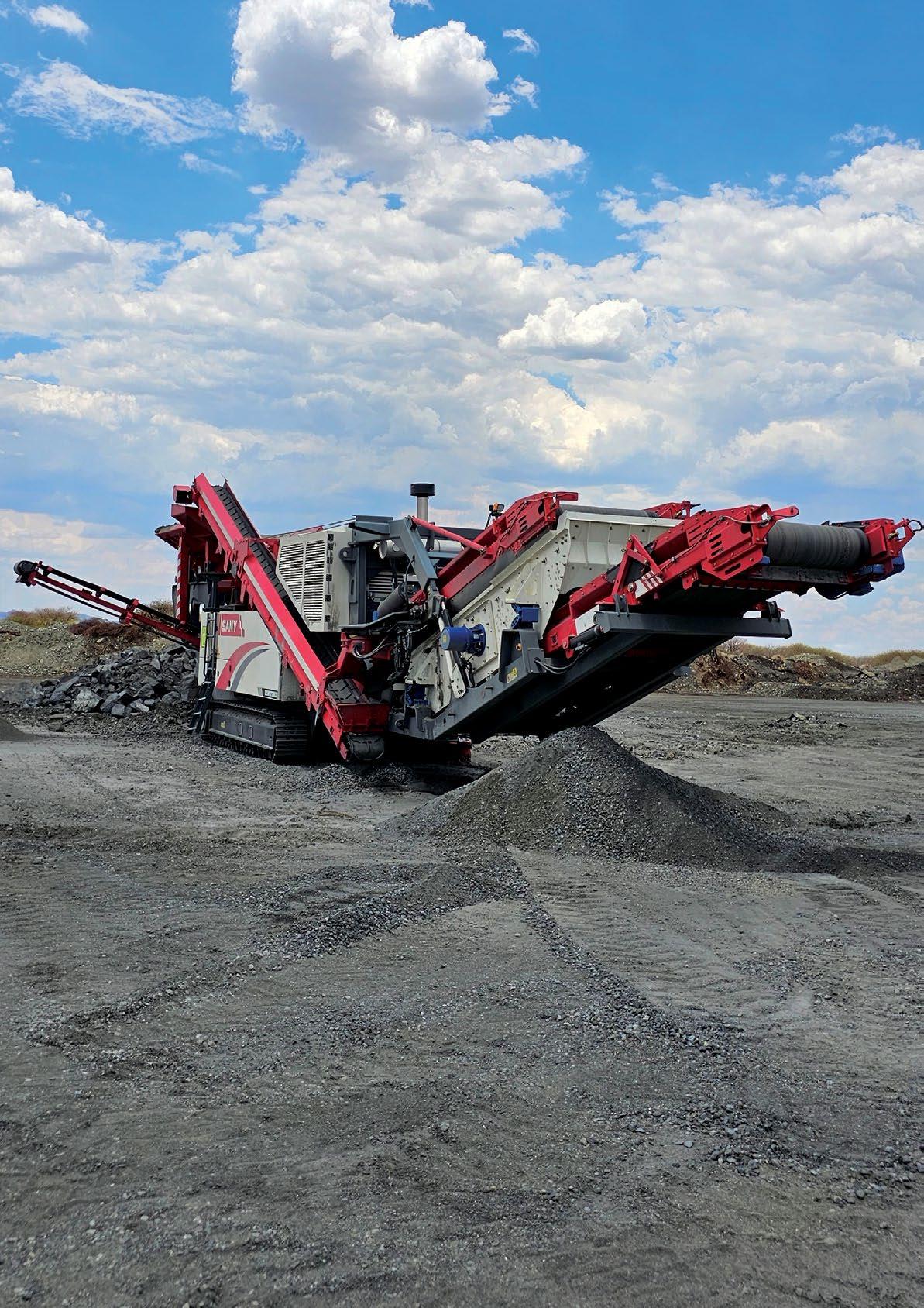
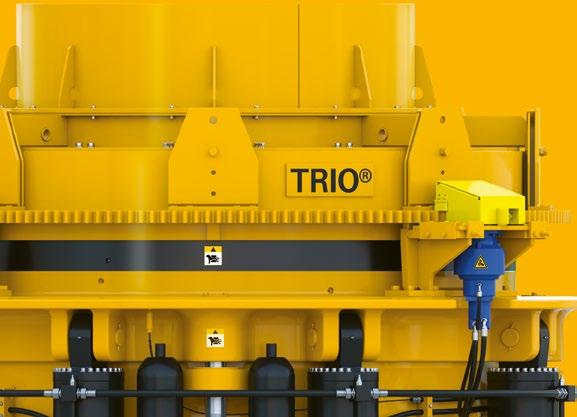

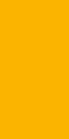

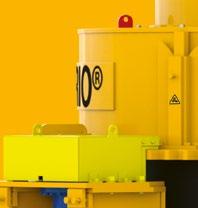
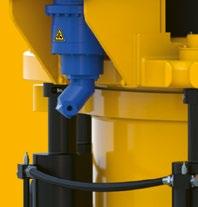

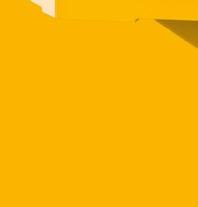
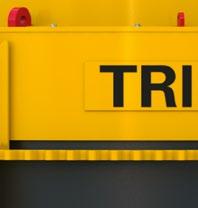
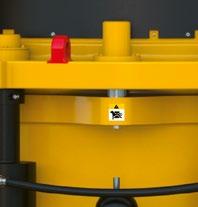
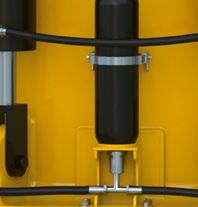
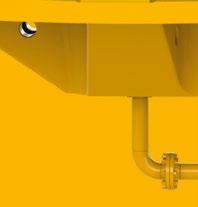
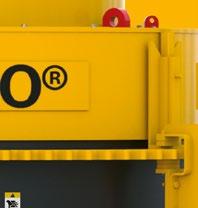


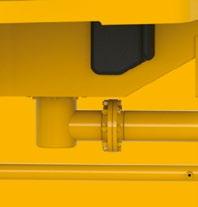
Different quarries need different cone crushers. Weir Minerals is the only global manufacturer that offers both. TRIO ® live and xed shaft cone crushers are made for modern quarries with advanced hydraulics, wear resistant materials and the latest technology. You get what’s right for your circuit. No unnecessary redesigns needed. Plus, with a lifelong commitment from the Weir Minerals global network, we’ve got you covered. Visit info.global.weir/trio
Like many other sectors of the economy, the quarrying sector in South Africa, the most advanced aggregates industry in Africa, is undergoing an intense period of change, and companies – both quarry operators and their supply chain counterparts – have had to adapt to respond to this shift in the market.
With the industry facing the toughest market environments in recent years, the South African quarrying sector is reinventing itself to achieve maximum growth in the face of a constrained construction market.
In a recent chat to Elsie Snyman, CEO of Industry Insight, she noted that despite substantial investments in renewable energy and infrastructure initiatives ahead of the May 2024 elections, the sector experienced an 8% year-on-year decline in investment during the first three quarters of 2024, following a 3,7% contraction in 2023. Factors such as higher interest rates, increased inflation and political uncertainties have constrained private sector investment, a key driver in the building sector.
third quarter of 2024, down from 5,2% in 2023, primarily due to intensified competition.
However, it is not all doom and gloom, with some regions experiencing increased construction activity. In KwaZulu-Natal, there have been several noteworthy construction developments in recent years. For example, the N2 and N3 upgrades, which form part of the national government’s key Strategic Integrated Projects (SIP2), are ongoing. Another significant project is the construction of the Cato Ridge Logistics Hub, a multi-billion-rand initiative aimed at boosting economic growth and job creation in the region. In the Western Cape, SANRAL’s upgrades to the N2 are well underway.
MUNESU SHOKO
Publishing Editor Email: munesu@quarryingafrica.com
LinkedIn:
Munesu Shoko
Quarrying Africa
The civil construction segment also faced difficulties, with a 7,6% year-on-year decline in investment during the same period. However, confidence among civil contractors rebounded in the latter half of 2024, reaching an eightyear high, attributed to government efforts to boost infrastructure spending. Despite these initiatives, the reallocation of funds in the 2024 Budget from transport and energy to water services, coupled with a decline in social infrastructure expenditure, has raised concerns about the government’s investment strategy.
The construction industry also continues to grapple with challenges such as intimidation from groups known as the “Construction Mafia”, corruption, project cancellations and payment delays. In 2024, project postponements increased by 27% year-on-year, affecting over 200 projects, while cancellations rose by 82%, impacting 344 projects. Profit margins also declined, averaging less than 2% up to the
Despite this upsurge in construction activity in these provinces, several suppliers note that the improved business activity has not translated into new capital sales for original equipment manufacturers (OEMs). Having grappled with low demand due to a lack of significant infrastructure spending and incessant tough economic times for close to a decade, quarry operators have changed their approach to procurement decisions.
The market has become increasingly costsensitive, with a big drive to reduce capital expenditure where possible. In a tough business cycle, it is understandable why construction material suppliers are holding their purse strings tight and are being much more conservative in their spending.
In a tough market, aggregate producers are also demanding maximum plant uptime, with unplanned downtime out of the question. They are therefore looking to partner with OEMs and suppliers that can ensure them maximum uptime, efficiency and profitability.
OEMs have responded to this need for uptime through Service Level Agreements (SLAs) and continued investments in aftermarket support. SLAs are a sign of commitment to the customer’s uptime, giving them that peace of mind that their best interests are always top of OEMs’ priorities. a
Publishing Editor: Munesu Shoko
Sub Editor: Glynnis Koch
Admin: Linda T. Chisi
Design: Kudzo Mzire Maputire
Web Manager: Thina Bhebhe
SYNERGISTIC PLATFORM FOR SUCCESS
LOADRITE’S QUEST FOR AFRICAN DEALERS
LINTEC CDP12001M FOR GABON PROJECT
REVOLUTIONISING
MEASURING
Quarrying Africa is the information hub for the sub-Saharan African quarrying sector. It is a valued reference tool positioned as a must-read for the broader spectrum of the aggregates value chain, from quarry operators and aggregate retailers, to concrete and cement producers, mining contractors, aggregate haulage companies and the supply chain at large.
Quarrying Africa, published by DueNorth Media Africa, makes constant effort to ensure that content is accurate before publication. The views expressed in the articles reflect the source(s) opinions and are not necessarily the views of the publisher and editor.
The opinions, beliefs and viewpoints expressed by the various thought leaders and contributors do not necessarily reflect the opinions, beliefs and viewpoints of the Quarrying Africa team.
Quarrying Africa prides itself on the educational content published via www.quarryingafrica.com and in Quarrying Africa magazine in print. We believe knowledge is power, which is why we strive to cover topics that affect the quarrying value chain at large.
Printed by:
Email: munesu@quarryingafrica.com
Cell: +27 (0)73 052 4335
Having established itself as a major player in the yellow metal equipment space, SANY Southern Africa has entered into new territory with the launch of its first ever mobile crushers. Marodew Plant and Services took delivery of the first unit in Africa, a SANY SCIM1213RC6 impact crusher, which has thus far proven its mettle in coal and chrome applications. Quarrying Africa recently visited a chrome mine in Limpopo, South Africa, where the machine is making light work of the abrasive ore.
By Munesu Shoko
There is a new player in the southern African crushing and screening market following SANY Southern Africa’s launch of its first ever range of mobile crushers and screens. At the time of writing, the company had brought the first unit in South Africa, a SANY SCIM1213RC6 impact crusher, owned and operated by Marodew Plant and Services, a young company that specialises in the rental of mobile crushing and screening equipment, as
well as the building of static crushing plants. As is the norm with any new brand, especially in a competitive market such as crushing and screening, the first machine was received with scepticism among some customers. Based on the experience of previously being a crusher operator, technician and eventually supervisor, Rodney Smith, one of the founding directors of Marodew Plant and Services, was from the onset convinced with the build quality and design of the SANY impact crusher.
The SCIM1213RC6 impact crusher is powered by a 371-kW Isuzu engine, a Japanese motor that has proven itself across many functions in mining and construction equipment
There is a new player in the southern African crushing and screening market following SANY Southern Africa’s launch of its first ever range of mobile crushers and screens
Although the SANY machine is completely new to this market segment, the client is convinced by the globally proven components that make up the crusher
Most of the SANY SCIM1213RC6 impact crusher’s components are electrically driven, doing away with hydraulically driven pumps
To ensure uninterrupted operations, SANY brought in a technician from China to support Marodew Plant and Services
Although the SANY machine was completely new to this market segment, Smith and his co-director Wihan van Wyk were both convinced by the globally proven components that make up the crusher. For example, the SCIM1213RC6 impact crusher is powered by a 371-kW Isuzu engine, a Japanese motor that has proven itself across many functions in mining and construction equipment. The crushing chamber is made in Ireland, which is dubbed the “home of crushing and screening”.
By adding the SCIM1213RC6 impact crusher to its fleet, Marodew Plant and Services has increased its crushing capacity by 200-300%
SANY maintains an impressive 99% parts availability in its parts warehouse
All the electrical components are from Schneider, a trusted global specialist in energy management.
When it comes to the build quality of the machine, says Smith, the SANY impact crusher is built on an excavator chassis, ensuring reliability. It also comes with an overload protection for the crusher. When a crusher is overloaded, components such as the crushing chamber, motor and bearings can experience excessive stress, leading to potential damage or failure. Overload protection therefore prevents this by automatically shutting off power when the load becomes too high, thus extending equipment lifespan, enhancing operational efficiency by minimising downtime due to breakdowns, and improving safety by mitigating risks associated with overstressed components.
Most of the SANY SCIM1213RC6 impact crusher’s components are electrically driven, doing away with hydraulically driven pumps. “The absence of hydraulic pumps increases the machine’s reliability and reduces downtime associated with hydraulic failures. In our experience, about 80% of breakdowns in hydraulic machines is related to the hydraulics,” says Smith.
“From the onset, we were convinced by the production capacity of this machine which, as a rental company that also executes contract crushing work, allows us to take on bigger jobs. The machine can take a feed size of up to 600 mm, producing between 150 and 450 tonnes per hour (tph), depending on the characteristics of the material,” adds Smith.
At the time of writing, Marodew Plant and Services had already run the machine for about nine months, initially in a coal application, before moving it into a chrome processing environment. In both jobs, “the machine passed with flying colours”, displaying high levels of productivity, efficiency and ease of maintenance.
“In coal, we crushed between 5 000 and 6 000 t in a 12-hour cycle. The machine punched well above its rated production capacity of up to 450 tph by producing 500 tph. Given that this is a diesel-electric unit, the machine is consuming about 50% less diesel per hour in this application than a competitor machine,” says Van Wyk.
With productivity in mind, the machine incorporates a pre-screen, a crusher and a post-screen, allowing for the production of different product sizes using a single machine. This three-in-one nature of the machine allowed Marodew Plant and Services to produce up to three different sizes of material in coal, eliminating the traditional need for two to three machines in such an application, thus reducing both capital and operational costs.
The pre-screen guarantees accurate fines removal, ensuring both increased productivity and reduced wear in the crushing chamber. The
less fine material that reaches the crushing process, the higher the productivity and final grain quality. During coal processing, Marodew Plant and Services saw particularly an increase in final product quality through the discharge of coarser particles via the side discharge conveyor.
The post-screen processes two screened products and recirculates any oversize back into the crusher. The ability for it to be reconfigured quickly to produce one single-sized finished product, or twosized finished products, depending on the operational demands, maximises the machine’s versatility.
When Quarrying Africa visited the chrome mine in December 2024, the machine had already crushed about 150 000 t of material, clocking some 450 hours in the process. Despite the abrasive nature of chrome, the crusher is offering a 50% fuel saving compared to a same-sized competitor machine previously deployed in the same application.
Given that this machine is dieselelectric, it can also be plugged onto mains electricity. Where infrastructure is available, this provides for a significant reduction in both operational costs and carbon (CO 2) emissions.
The addition of the SANY impact crusher to Marodew Plant and Services’ fleet has given the company new capabilities. Adding the SANY SCIM1213RC6, says Smith, now allows the company to tender for large-volume jobs from bigger mining companies.
“We can now service any high-
production contracts from 40 000 to 150 000 tonnes per month (tpm) with a single machine, be it in coal, chrome or any other hard rock application. With our previous fleet, we could only undertake contracts up to 40 000 tpm in size. In essence, we have increased our crushing capacity by 200300% by adding this machine to our stable,” says Smith.
The efficiency of the machine also allows the company to meet stringent fuel cap limits in contracting. According to Van Wyk, the acceptable standard in the industry is about R1,5 worth of fuel per tonne, and with the SANY machine, Marodew Plant and Services is well below that limit, achieving between 30 cents and 50 cents per tonne in terms of fuel consumption. In addition, being able to produce up to three material sizes using one machine means that the company further saves clients fuel and also helps them meet their sustainability goals.
Fewer maintenance requirements on the machine also translate into high uptime for Marodew Plant and Services, allowing the company to meet its contractual obligations, especially in high-production jobs. The machine is designed with ease of maintenance in mind. For example, it takes about 15 minutes to change the deck. It also comes with an on-board mini-crane for easy changing of blow bars.
“Reduced maintenance equals more production and reduced operational costs. To provide context, we have produced 150 000 t of chrome and 500 000 t of coal with one set of blow bars which, in our experience, is unheard of. The ease of maintenance and the reduced maintenance costs of this machine are ‘dream attributes’ for every contractor,” says Smith.
Both Smith and Van Wyk have been impressed by the support from SANY Southern Africa. From the onset, says Smith, Thabo Lerumo, operations manager at SANY Southern Africa, was supportive of the young company. Despite the lack of a substantive track record, SANY was willing to “take a chance” on the Marodew Plant and
Services and provided the machine on a rent-to-buy basis.
To ensure uninterrupted operations, SANY brought in a technician from China to support Marodew Plant and Services. During Quarrying Africa’s visit in December 2024, the technician, a knowledgeable individual who was part of the team that designed SANY crushers and screens, had been on site for six months which, according to Van Wyk, shows SANY’s commitment to the success of its customers.
Before opting for the SANY crusher, Marodew Plant and Services had already been impressed by SANY Southern Africa’s parts stockholding. The company recently commissioned a new parts distribution centre located in Olifantsfontein, Midrand. The new, bigger warehouse has enabled SANY to increase its spare parts inventory from approximately R170-million to R270-million.
As part of its strategy to further grow its aftermarket capacity, SANY has in recent time opened new branches in Middelburg, Rustenburg and Richards Bay, allowing it to provide faster service turnaround times to customers in these important mining regions.
“These investments are informed by our drive for customer satisfaction and to advance the reputation of the brand in southern Africa, which is important for us. The huge capital investments also exhibit our long-term commitment to the local market and our customers,” says Lerumo. “We are happy that the first SANY crusher has performed beyond expectations. Based on this performance, we have received three more orders, which will be delivered in 2025.”
Van Wyk has also been impressed by the quick turnaround in terms of parts. SANY maintains an impressive 99% parts availability in its parts warehouse. If, for any reason, something is not in stock, the company resorts to air freight to ensure minimal impact on customer operations.
“In a recent incident, we had a problem with the generator of our machine and SANY flew in a new generator from China, which took only a week to arrive. For us, this shows true commitment by the original equipment manufacturer. In future, we are looking at standardising our mobile crushing fleet with SANY a
is a unique quarry that operates
different
A relentless focus on good health and safety practices has not only created a safe working environment for Raumix Queenstown Quarry, but also increased worker morale and ultimately boosted productivity. Equally, an effective environmental management system has been central to conserving resources, thus increasing operating efficiency and reducing the quarry’s environmental impact. By
Munesu Shoko
Located in Queenstown, Eastern Cape, Raumix Queenstown is a unique quarry that operates two pits with different geologies – dolerite and quartzite – next to each other. This gives it unmatched flexibility to serve diverse market needs. For example, its quartzite pit serves the market needs for base materials such as G4, G5, G6 and G7, while the dolerite pit is largely ideal for high-quality material sizes such as road and concrete stone, amongst others.
While it has the capacity to produce an extensive range of materials, from base materials to gabion and everything in between, Malan Zerwick, operations manager: Queenstown Quarry, tells Quarrying Africa that the unprecedented demand for crusher dust in the past four years has been driving the market. Crusher dust, he says, currently constitutes anything between 60% and 75% of the operation’s sales.
In fact, the quarry has traditionally struggled to build a stockpile of crusher dust due to the high
To separate customer trucks from trackless mobile machinery, the quarry laid out roadways using oversized rock from the quarry.
levels of demand from blockmakers in the area. The quarry supplies between 20 and 25 block yards within its vicinity. With upgrades to the plant, which was built and installed by fellow Raubex Group’s sister company, B&E International, back in 2014, Raumix Queenstown has increased plant flexibility to allow it to meet high demand for crusher dust and other material sizes.
For the past few years, the operation has reinforced its flagship status in the South African quarrying space, particularly on the compliance front. If ASPASA audit results – both Health and Safety (ISHE) and Environmental (About Face) – are anything to go by, then Raumix Queenstown is among the top South African quarries that,
95%
Raumix Queenstown has achieved Showplace Status (above 95%) in both the ASPASA audits – ISHE and About Face – for two years running, placing it among the Top 10 operations in each audit
Located in Queenstown, Eastern Cape, Raumix Queenstown is a unique quarry that operates two pits with different geologies – dolerite and quartzite – next to each other
For the past few years, the operation has reinforced its flagship status in the South African quarrying space, particularly on the compliance front
Several safety initiatives have been central to Raumix Queenstown’s safety excellence. One of the key ones to date has been the implementation of a thorough traffic management plan
One of the major environmental initiatives has been the implementation of a water reticulation system, which is designed to recycle process water from the wash plant
despite the cost, place compliance at the centre of their operations. “The ASPASA team of Letisha van den Berg, Anthony Bowen and Marius van Deventer, has played a key role in our success by sharing their knowledge of the industry with us to guide us to where we are today,” says Zerwick.
To provide context, the quarry has achieved Showplace Status (above 95%) in both the ASPASA audits – ISHE and About Face – for two years running, placing it among the Top 10 operations in each audit. In fact, this is a
90%
The entire Raumix Aggregates quarry portfolio has recorded a 12-month-long Lost Time milestone Injury (LTI)-free period
In the pit area, an entry/exit loop, which is currently 90% complete, has been implemented. This eliminates significant risk by creating a loop system where trucks cannot overtake each other on the bench
group-wide achievement which has seen all 11 Raumix Aggregates quarries achieving Showplace Status in both audits during the past few years, demonstrating the company’s excellent focus on compliance.
Apart from ASPASA audit results, the entire Raumix Aggregates quarry portfolio has recorded a year-long Lost Time milestone Injury (LTI)-free. This comes on the back of several health and safety initiatives at both site and group-wide level. In fact, says Zerwick, the Raubex Group is currently running its biggest safety campaign ever, dubbed “I am a safety Leader”, which has seen a significant culture and statistical returns since its implementation.
Several safety initiatives have been central to Raumix Queenstown’s safety excellence. One of the key ones to date has been the implementation of a thorough traffic management plan. Under the guidance of CJ Fourie, regional safety manager – Southern Region at Raumix Aggregates, Zerwick and his team initially identified problematic areas on site that could lead to potential safety issues and addressed them accordingly through the traffic management plan.
“Firstly, we focused on separating customer trucks from our trackless mobile machinery (TMM), which in our investigations presented significant risk through potential collisions. We laid out roadways using oversized rock from the quarry. The rocks were painted white for drivers to easily identify the loading point without getting in the way of our TMM. We also implemented the necessary stop signs, directional signs and speed limits, which ultimately help to reduce accidents and maintain smooth traffic flow on site,” explains Zerwick.
In addition, only two customer trucks are allowed to enter the security gate at a given time. Entrance to the
stockpile area, where loading takes place, is limited to one truck at a time. There is also constant communication between the weighbridge operator and the security personnel to ensure smooth traffic flow.
In the pit area, an entry/exit loop, which is currently 90% complete, has been implemented. This, says Zerwick, eliminates significant risk by creating a loop system where trucks cannot overtake each other on the bench. “We have also established different zones where only specific machines are allowed to enter,” he says. “In addition, pedestrian walkaways, demarcated by painted boulders and signs, have eliminated possible contact between TMM and pedestrians, thus maximising safety on site.”
Apart from the traffic management plan, other safety initiatives include the installation of emergency telephones on site with all the necessary emergency contact details, as well as the building of an automatic tyre inflation station on site – a safety protection cage where operators can easily inflate their machine tyres behind a safety barrier.
In addition, the mine places a high priority on occupational hygiene compliance. Factors such as fallout dust monitoring, noise monitoring, thermal stress monitoring, illumination surveys, ventilation and gasses monitoring, welding fumes monitoring, vibration surveys, ergonomics surveys, plant hygiene facilities monitoring, diesel particulate matters monitoring, and water sampling, form part of the operation’s occupational hygiene systems. Furthermore, Raubex Group has introduced online systems for the management of health and safety incidents as well as its ESG compliance. This has added to the success achieved in Raumix’s health, safety and environmental programmes. Raumix Aggregates achieved top performing company status during Raubex Group’s last auditing cycle relating to ESG management.
Given that the quarry is located close to mountains,
The quarry has achieved Showplace Status in both the ASPASA audits – ISHE and About Face – for two years running.
there is a very high risk of lightning strikes. The team at Raumix Queenstown has therefore invested in a hand-held lightning detector which provides crucial early warning alerts about approaching thunderstorms, allowing miners to take preventive measures such as seeking shelter, halting operations and securing equipment. This significantly reduces the risk of injuries or fatalities from lightning strikes, especially in an environment where weather conditions can change rapidly.
“I commend our regional safety manager for the Southern Region, CJ Fourie for his immense help in getting our safety standards to where they are today. He built our safety systems on the ISO 45001 standard, which correlates with ASPASA’s audit sheet,” says Zerwick. “We also commend the group at large for incentivising safety performance. That has made a huge difference in terms of staff buy-in and taking initiative when it comes to safety.”
Given that the quarry primarily produces crusher dust, the emission of dust on site is a huge problem which not only poses health risks, but also environmental concerns. To address dust on site, an automated haul road dust suppression system has been installed. This is complemented by carefully selected spray nozzles to deal with dust on all transfer points of the plant.
Another environmental initiative of note has been the implementation of a water reticulation system, which is designed to recycle process water from the wash plant. By reusing process water, the need to draw fresh water from natural sources is reduced, helping to protect ecosystems and conserve this scarce resource. Recycling process water, says Zerwick, translates into lower water bills, as less fresh water is required for operations. In addition, less process water discharged into the
environment means less potential pollution.
Given that Queenstown is a high rainfall area, the quarry has also implemented an effective stormwater control strategy. Making use of gabion stone, the team has built filtration berms to slow down stormwater runoff on various sections of the site, thus minimising soil erosion. Using this filtration system, clean water is isolated and redirected around the site into a nearby dam for local communities’ use.
If left to accumulate on site, old conveyors can pose significant waste challenges for quarries. To mitigate this potential environmental hazard, Zerwick and his team donate old conveyors to farmers in the area. These are used to line sheep and cattle kraals to increase safety and comfort for animals. Old crusher sleeves are also used to reinforce kraal gates at farms.
“As they say, ‘your biggest pimple on the nose’ on a quarry is always the scrap yard. As part of our recycling efforts, we have separated our scrap yard from the salvage yard. Scrap metal recycling is a great way to help prevent more damage being done to the environment,” says Zerwick.
Most customer trucks, he says, are responsible for oil spillages/leaks on site, potentially contaminating the soil and the environment. This often occurs due to wornout seals, damaged hoses or improper maintenance on hydraulic systems. To minimise these damaging oil spills onto the quarry site, a dedicated parking area for customer trucks waiting to be loaded has been established off site. A truck only enters the quarry area when it is time to load.
“Another environmental initiative has been the establishment of parking bays for TMM with individual drip trays. When operators are done for the day, they park their machines in their own dedicated parking bays. The drip trays are designed to contain any spillages with a specific end goal to keep the work environment as safe as possible,” concludes Zerwick. a
By putting health and safety at the core of its operations, AfriSam reached a major safety milestone in October 2024 and has in recent years received multiple acknowledgments for its safety performance. Vernon Brown, National Health & Safety Manager Construction Materials, tells Quarrying Africa that the development of a safety culture, with a genuine and visible commitment from both leadership and the workforce, has been central to AfriSam’s strong health and safety performance. By Munesu Shoko.
In the quest for Zero Harm, AfriSam maintains high levels of health and safety standards across its quarry operations. For two years running – 2022 and 2023 – the company was named the Top Corporate Performer in the annual ASPASA ISHE Awards, highlighting a strong commitment to the implementation, promotion and maintenance of the highest level of health and safety in the workplace.
In addition, October 2024 marked a four-year Lost Time Injury (LTI)-free milestone for AfriSam’s Construction Materials division. Brown says reaching the four-year mark without an LTI is a major highlight in the company’s safety journey and is in line with
the vision of zero injuries for every task or action. It is also testament to the commitment and dedication of everyone involved in maintaining a safe and healthy working environment at AfriSam.
“Within our Construction Materials business, and the AfriSam organisation at large, there is an understanding that improving health and safety performance is a long-term goal that requires sustained effort, resources and commitment,” says Brown. “What sets us apart is an executive leadership that shows a genuine and visible commitment to the achievement of a safety culture, treating health and safety as a line management responsibility.”
For AfriSam, adds Brown, compliance to health
2022-23
For two years running – 2022 and 2023 – AfriSam was named the Top Corporate Performer in the annual ASPASA ISHE Awards, highlighting a strong commitment to the implementation, promotion and maintenance of the highest level of health and safety in the workplace
In the quest for Zero Harm, AfriSam maintains high levels of health and safety standards across its quarry operations
For AfriSam, compliance to health and safety is part of the company’s licence to operate
Quarry managers are empowered to take initiative in developing their site-level safety interventions
Over the years, AfriSam has leveraged technological advancements to create a safer work environment
and safety is part of the company’s licence to operate. Lack of compliance with the Department of Mineral and Petroleum Resources’ guidelines can be detrimental to operations through the issuance of Section 54 mine stoppage instructions, for example.
“It is therefore important that we put compliance with health and safety at the core of our operations,” he says. “For us, health and safety compliance is never a box-ticking exercise; it is about making sure that every employee goes back to their families unharmed every day.”
Central to the maintenance of high safety standards across AfriSam quarry sites is a deep understanding
4 In addition, October 2024 marked a four-year Lost Time Injury (LTI)-free milestone for AfriSam’s Construction Materials division
“Within our Construction Materials business, and the AfriSam organisation at large, there is an understanding that improving health and safety performance is a long-term goal that requires sustained effort, resources and commitment.
among every member of the team that they play a big part in the safety performance of the company. According to Brown, when employees understand the hazards associated with their tasks and are equipped with the right knowledge and skills to mitigate those risks, they are less likely to be involved in accidents.
“Management commitment is another important cornerstone for our health and safety performance. Through our Visible Field Felt Leadership programme, the executive management team regularly tours operations to see what is happening on the ground. We also conduct regular internal and external reviews to ensure continuous improvement. Our external reviews come in the form of ASPASA annual audits, which provide an opportunity to reflect on our safety performance and receive guidance on where we need to improve,” says Brown.
As an industry body, ASPASA promotes informationsharing among its members to ensure industry-wide success when it comes to health and safety performance. Sharing information and knowledge with other organisations operating in the same sector allows AfriSam to keep abreast of new developments in the safety sphere. Brown says collaboration and information-sharing are key for the industry to change the course of its safety performance, highlighting that safety is an area where the industry must collaborate.
Commenting on some of the key initiatives that have contributed to the company’s exceptional safety record, Brown makes special mention of the inter-plant safety competition. The main aim of this initiative is to “change hearts and minds of employees” when it comes to safety. The interplant competition focuses on four key areas.
“The first area is statistics, because we need to compare and understand where we are in terms of operations. The second area we look at is audits – both internal and external. For us, audits are not just about the scores, but more about the findings, which give us an opportunity to address any shortcomings that might have been pinpointed by the auditor,” says Brown.
The third area of consideration is housekeeping which, according to Brown, is one of the basic pillars of successful health and safety practices. Good housekeeping can help prevent accidents, such as slips, trips and falls, which are common in quarries and mines.
The fourth area of attention is safety leadership at operations level. Quarry managers are empowered to take initiative in developing their site-level safety interventions. These initiatives are inclusive and speak directly to the people at these operations. As part of the safety leadership approach, AfriSam also cultivates a culture
of understanding each individual’s responsibility and proactiveness in achieving positive safety outcomes.
“We also look at safety as a continuous improvement aspect. Consequently, there are continuous management interventions at operations, making sure that we have controls and mitigations in place to deal with risks. Continuous improvement is important for safety because it helps us keep up with new challenges, comply with regulations and reduce risks to employees. Continuous improvement also helps us ensure that our safety strategy is up-to-date and complies with the latest legislation and guidelines,” says Brown.
Education and training are the foundations for enabling improvement in health and safety. According to Brown, sound basic education for work, refresher training and companyspecific training are crucial for the implementation of effective health and safety hazard prevention programmes.
In line with this approach, AfriSam has a competency-based safety (CBS) programme, a behavioural safety programme aimed at achieving organisation-wide occupational health and safety awareness. One of the key benefits of this programme is that it ensures that employees have the skills they need to perform their tasks safely. It also helps AfriSam to identify skills gaps through assessments and performance reviews.
Technology, says Brown, has dramatically changed the way businesses operate, and its impact on workplace safety is no exception. Over the years, AfriSam has leveraged technological advancements to create a safer work environment.
“The first focus area is blasting operations, where we have adopted technologies such as vibration and noise
monitors. These allow us to ensure that all our operations are in line with the ground vibration and airblast limits recommended by the regulator to ensure both the safety of employees and the protection of surrounding communities,” says Brown.
In addition, AfriSam makes use of weather alert apps to ensure that blasting occurs during favourable weather patterns. For example, blasting should be avoided when there is heavy cloud cover or a temperature inversion, as these conditions can increase airblast overpressure.
The use of blast design programmes also allows AfriSam to simulate blasts before they take place. This offers the blasting engineer even more control over the blast, not only ensuring efficiency, but also better safety outcomes.
The second area where AfriSam has prioritised technology adoption is in trackless mobile machinery. Here, the focus is to eliminate vehicle-to-vehicle and vehicle-to-people interactions. Following a detailed risk assessment exercise in line with the Mining Industry
Occupational Safety and Health (MOSH) guidelines, the company has done its comprehensive traffic management plans for its various quarry sites.
“As part of our risk assessment exercise, we have identified areas with significant risk, which led to the adoption of proximity detection systems (PDS) and collision prevention systems (CPS). We have currently done a full installation at our Verulam Quarry in KwaZulu-Natal. Elsewhere, we have done trials at our Rheebok Quarry in the Western Cape and we are also busy with trials at our Jukskei operation in Gauteng,” says Brown.
Brown is encouraged by the developments in PDS technology in recent years. Now using AI, the technology can distinguish between pedestrians and machinery while providing adequate warning to machine operators in the event that people are in close proximity to the machine or in its blind spots. This eliminates the need for conventional tags for each person on site.
While the prohibitive cost of the PCS/CPS technology was initially a major hurdle for opencast operations, particularly cost-sensitive quarries and other small-scale operations, Brown points out that the cost of the PDS/ CPS technology has in recent years come in line with the expectations of the industry.
Commenting on the company’s safety goals for the next three to five years, Brown says, in line with its vision for “zero injuries for every task and every action”, AfriSam will continue to place value on continuous improvement.
“We need to benchmark our own safety performance against our industry peers to have a grasp of where the industry is in terms of best practices. We also need to learn from industry incident trends so that we can prevent similar issues from happening at our own operations. Continuous safety leadership remains another key focus area to foster a culture of safety across all our operations,” concludes Brown. a
With over 35% of Volvo Construction Equipment’s total product range renewed during the past 12 months, marking the last step in the company’s largest product portfolio renewal in decades, is its ‘biggest and boldest’ articulated hauler launch to date. With advanced technologies at the centre of its development, the seven-model range casts a special design focus on productivity, efficiency, uptime, safety and operator comfort. Munesu Shoko recently attended the official launch at the company’s Braås factory and filed this report for Quarrying Africa
The updated models mark a significant technological leap forward thanks to innovations such as the new electronic system and an in-house developed transmission, delivering fuel efficiency improvements of up to 15% depending on model and industrial application
With its 45-t payload, the all-new A50 delivers 10% more productivity and 8% greater fuelefficiency when compared to the previous generation A45GFS – making it an ideal solution for high-production quarries, mines and large construction sites
The redesigned steering system reduces steering effort by 25% compared with the previous G-Series
With the launch of its new generation articulated haulers, Volvo CE has once again demonstrated its commitment to delivering cutting-edge, safe, efficient and productive solutions to the global mining, quarrying and construction sites. The seven-model lineup represents a compete revamp of the already proven A25, A30, A35, A40, A45 and A60 models – with the major talking point being the introduction of a completely new class size machine, the 45-tonne (t) A50, which fills the gap between the 42-t A45 and the 55-t A60.
Melker Jenberg, President of Volvo CE, says the unveiling of the new range represents the company’s “biggest and boldest” articulated hauler launch since it pioneered the concept with the 1966 launch of the world’s first articulated dump truck, dubbed as ‘Gravel Charlie’. The arrival of the
With the launch of its new generation articulated haulers, Volvo CE has once again demonstrated its commitment to delivering cutting-edge, safe, efficient and productive solutions to the global mining, quarrying and construction sites
The seven-model line-up represents a compete revamp of the already proven A25, A30, A35, A40, A45 and A60 models – with the major talking point being the introduction of a completely new class size machine, the 45-t A50
The updated models are planned for stepwise introduction to international markets. In southern Africa, Babcock, the Volvo dealer in the region, is due to bring in the first units by mid-2025
A key feature on the new A50 is the fully hydraulic suspension concept. Pioneered by Volvo CE in 2007, the full suspension has proved to be a reliable system for the toughest of driving conditions
new range further strengthens Volvo CE’s product lead in the segment, while broadening the model line-up with the addition of the A50 to cover more applications.
“For nearly 60 years, we have been leading the way with our range of articulated haulers and now with the launch of this seven-model range, which includes an entirely new model, we prove that there are no limits to our capacity for innovation,” says Melker. “Our customers expect a first-class product when they get into any of our haulers, but that experience has just got even better with a host of cutting-edge features designed with our customers in mind.”
The updated models are planned for stepwise introduction to international markets. In southern Africa, Babcock, the Volvo dealer in the region, is due to bring in the first units in the near future (estimated arrival May/June 2025). According to David Vaughan, MD of Babcock’s Equipment business, the updated A35, A40, A45 and the all-new A50, will be the first models to arrive, before the rollout of the A30 and A60 – at a later stage (dates to be confirmed).
The new generation Volvo J-series, which replaces the proven G-Series, contains the largest updates in 20+ years. Pre Trozell, product manager in Sales Region Europe and International at Volvo CE, says the updated models mark a significant technological leap forward thanks to innovations such as the new electronic system and an in-house developed transmission, delivering fuel efficiency improvements of up to 15% depending on model and industrial application.
A host of new features guarantees maximum productivity across the most challenging projects in quarrying, mining, construction and more. With its ability
to identify and remember any slippery road segments, the Volvo drivetrain with Terrain Memory ensures superb fuel efficiency without compromising on power. Automatic drive combinations, with 100% differential locks and all-terrain bogie and hydro-mechanical steering, also combine to provide unmatched traction, stability and precision control.
In addition, Volvo Dynamic Drive – with its predictive gear selection – adapts to operating conditions. The downhill speed control function and industry-leading braking systems further enhance efficiency, safety and comfort.
The updated range has been engineered for durability thanks to features such as reinforced axles capable of withstanding heavy loads and high torque, resulting in superior stability and strength. Safety is also a priority, with new harness anchor points in the cab which meet WorkSafeBC and OSHA regulations, withstanding up to 22kN of force.
With simplified servicing, longer change intervals and easy component access, servicing is now quicker and easier than ever before, maximising uptime and reducing costs. Industryleading greasing intervals of 250 hours also eliminate the need for daily or weekly greasing, boosting productivity and reducing downtime.
What is more, Volvo articulated haulers are said to require less fluid volume compared to the competition, benefitting the environment and reducing operating costs.
Customers can boost the performance of their articulated haulers even further with the addition of solutions such as Haul Assist with On-Board Weighing. Powered by Volvo Co-Pilot, it provides real-time payload
The updated range has been engineered for durability thanks to features such as reinforced axles capable of withstanding heavy loads and high torque.
data to prevent overloading and minimise carryback, which not only maximises productivity but also reduces fuel consumption and machine wear.
Traffic flow, vehicle performance and on-site logistics can also be improved with the support of digital and advisory tools such as Connected Map, Performance Indicator and Site Optimisation, while the CareTrack telematics system is designed to help boost machine uptime and reduce repair costs.
Not just a machine for today, the new generation of Volvo articulated haulers is future-enabled thanks to a new software architecture which allows customers to adapt to changing needs and seamlessly incorporate future upgrades and new smart solutions. This ensures that their equipment stays up-to-date with cutting-edge technology.
Already regarded as the operator’s machine of choice, Volvo CE’s updated articulated haulers take operator comfort to a whole new level, thanks to the new cab with a modern styling. The new cab, designed from ground up, gives more space to the operator for superior comfort, leading to higher productivity over the full operating cycle.
Premium comfort and ease of operation are assured by the addition of adjustable seats, Bluetooth connectivity, USB ports and storage solutions, as well as an ergonomic gear lever and a noise-reducing cab design. The redesigned steering system reduces steering effort by 25% compared with the previous G-Series.
The interactive, integrated Volvo Co-Pilot display offers easy control over essential functions such as media, camera settings, climate control, and machine status. This is combined with the dynamic instrument cluster, positioned in front of the steering wheel, which provides crucial vehicle data at a glance.
The major highlight of Volvo CE’s articulated hauler launch is the introduction of the all-new A50 model, which expands customer opportunities in the demanding hauler segment. The addition underscores Volvo CE’s commitment to meeting the evolving needs of its customers by enhancing operational capabilities and offering more choices.
A key feature on the new A50 is the fully hydraulic suspension concept. Pioneered by Volvo CE in 2007, the full suspension has proved to be a reliable system for the toughest of driving conditions. The A50 takes the concept to new heights as the only full suspension machine of its size class on the market. As a result, it offers a significant improvement in cycle times, an increase in hauler production per operator-hour and lower costs when compared to its standard suspension counterparts.
Volvo CE’s full suspension reduces vibration, noise and shocks, which can help prevent repetitive strain injuries to operators. A smoother ride on the hauler and road can reduce unnecessary maintenance costs.
As part of the new generation update of Volvo articulated haulers, the A50 enjoys all the same great features and benefits. Most notably, it delivers unrivalled efficiency thanks to the new in-house-developed Volvo transmission that works in harmony with the rest of the Volvo engine to ensure maximum fuel efficiency.
With its 45-t payload, the all-new A50 delivers 10% more productivity and 8% greater fuel-efficiency when compared to the previous generation A45GFS – making it an ideal solution for high-production quarries, mines and large construction sites.
For the A50, service costs are reduced by up to 6% over 12 000 hours of operation due to simplified servicing, longer change intervals and easy component access.
Developed to be among the most fuel-efficient hauling solutions on the market, the new models have also been built with a focus on sustainability. As part of efforts to reduce carbon emissions across every area of its business, Volvo CE is for the first time implementing in serial production, low carbon emission steel in all its articulated haulers built in Braås, Sweden.
Conventional steel is a heavy emitter – and as one of the main components in Volvo CE’s products, critical to reducing carbon emissions. Steel makes up approximately 60% of Volvo articulated haulers’ total mass and accounts for more than 50% of the machine’s total carbon footprint in the cradle-to-gate scope.
As part of the sustainable transformation, Volvo CE was the first in the world to showcase in 2021, a concept hauler built using pilot deliveries of fossil-free steel,
one type of carbon emission-reduced steel. This took place in partnership with Swedish steel manufacturer, SSAB. The following year, Volvo CE became the first company to hand over to a customer a construction machine built using this fossil-free steel, demonstrating the fast-tracking of innovation to real-world solutions as companies across the value chain come together to drive change.
And now Volvo CE has entered the next phase of its continued exploration into low carbon materials by implementing low carbon emission steel into the serial production of its full range of articulated haulers at its Braås factory.
While the two steel alternatives are produced with close to zero fossil carbon emissions, with production powered by fossil-free electricity and biogas, the key difference is that the fossil-free version is based on iron ore, whereas the low carbon emission steel is produced using recycled steel.
Rickard Alm, Head of Volvo CE’s Life Cycle Assessment programme, says: “We are proud to lead the way in the industry and move forward towards minimising our climate footprint across the entire lifecycle of our products. While emissions from product use represent the vast majority of carbon output in our industry, it is important to also act to cut emissions in the production phase, including materials such as steel, in close collaboration with our global supply partners.”
In the initial phase, around 13% of the total mass of steel in all articulated haulers manufactured in Braås is now replaced with the low carbon emission steel – a number that is set to
increase as availability of the low carbon material is augmented in collaboration with the company’s supply chain.
With this change, Volvo CE is able to reduce the total CO 2 emissions by around 13 000 t annually, or over 5%, in the cradle to gate scope. As an example, for an A40, this represents a reduction of nearly 6 t CO 2 emissions.
No stranger to pioneering new ways of working for the benefit of the environment, Volvo CE Braås was also recently the first of the company’s facilities to reach Climate Efficient Site status. As early as 2014, it became the company’s first carbon-neutral premises, as well as the first construction equipment production facility in the world to be powered
renewable energy. a
The 28-tonne RA30 articulated hauler is made for the toughest jobs and roughest sites, from quarries and infrastructure developments to commercial construction projects.
On the back of projected construction market growth and vast mineral resource wealth, Africa is a market of strong interest for Rokbak, which has been expanding its presence on the continent since its rebrand in 2021. To continue developing its footprint, the articulated hauler manufacturer seeks to align with established, independent dealers who share the same value for strong aftersales support. By Munesu Shoko.
Buoyed by a vast mining industry and a construction market that is projected to grow significantly as the continent seeks to close its infrastructure gap, Africa offers great opportunity for articulated dump truck (ADT) manufacturers. Paul Culliford, regional sales manager at Rokbak, tells Quarrying Africa that Africa is a market that the company has been expanding into since Rokbak rebranded some three years ago, and continues to develop its presence in the region.
As part of this expansion programme, the company recently appointed two dealers, HMD Machinery in West Africa and Machinery Exchange in Zimbabwe. HMD Machinery, says Culliford, is one of the top dealers in Africa, covering a massive territory; from
Mauritania all the way to the Democratic Republic of Congo (DRC). The company has already delivered four Rokbak units to a customer in Ghana, underscoring the brand’s growing prominence on the continent.
In addition to providing durable and efficient ADTs backed by expert technical support, the new partnership between HMD and Rokbak now brings flexible financing options backed by Export Credit Agencies (ECAs) and Private Risk Insurers (PRIs) to West African customers.
Through UK Export Finance (UKEF), the Swedish Export Credit Agency (EKN), and a network of PRIs, HMD customers can now access competitive financing packages. These flexible financing solutions reduce the financial burden of fleet expansion with affordable interest rates, extended repayment periods
261%
Since the launch of a government blueprint in 2019, the mining sector in Zimbabwe has experienced notable growth. In 2021, mineral revenues surged to US$9,77-billion in 2023 –representing a remarkable 261% increase since 2017
As part of its expansion programme, Rokbak recently appointed two dealers, HMD Machinery in West Africa and Machinery Exchange in Zimbabwe
Africa is a market that Rokbak has been expanding into since it rebranded some three years ago
As part of this expansion programme, the company recently appointed two dealers, HMD Machinery in West Africa and Machinery Exchange in Zimbabwe
Rokbak is strengthening its footprint in Africa, capitalising on the region’s growing demand for robust and efficient articulated haulers in mining, quarrying and infrastructure projects
Rokbak seeks to align with established, independent dealers who recognise that, when it comes to desired articulated hauler needs, customers are seeking low total cost of ownership and a good price to performance ratio
and structured payment plans tailored to meet the demands of West African operations.
“Furthermore, we have been keen to develop our presence in Zimbabwe and foster relationships with customers through an established dealer. Machinery Exchange provides essential coverage with branches throughout the country,” says Culliford.
Mining in Zimbabwe, he adds, is a multi-billion-dollar industry, fuelled by the rich and diverse range of key
65%
Africa has a vast resource wealth, and there is a surge in demand for its minerals. Forecasts suggest a 65% increase in market value by 2030, demand tripling by 2040 and growing sixfold by 2050
“Fundamentally, prospective dealers need to share the same value with us for strong aftersales support, and know when it comes to servicing and maintenance, it is about being there and acting responsibly and quickly to any customer requirements.
minerals available locally. These include diamonds, gold, lithium, chrome and iron ore, amongst others. Since the launch of a government blueprint in 2019, the mining sector has experienced notable growth. In 2021, mineral revenues surged to US$9,77-billion in 2023 – representing a remarkable 261% increase since 2017.
“Infrastructure, too, is an area benefiting from huge investment. There are multiple ongoing projects to improve road and transport networks and facilitate regional integration. The construction market in Zimbabwe is currently valued at between US$3-billion and US$4-billion, and, with the staggering size of those
numbers, comes a demand for reliable, high-performance machinery,” says Culliford.
Because of areas such as this, Rokbak is now strengthening its footprint in Africa, capitalising on the region’s growing demand for robust and efficient articulated haulers in mining, quarrying and infrastructure projects.
“We are positioning ourselves on key platforms, including tradeshows such as Mining Indaba in South Africa where we are able to meet potential customers and discuss our solutions alongside our dealer in West Africa, HMD. By appointing the right, trusted dealers such as HMD in Africa, Rokbak is strategically placing itself in important markets where demand for reliable heavy equipment continues to rise,” Culliford says.
With Africa’s construction market projected to grow significantly in the near future, Culliford maintains that Rokbak’s focus remains on delivering high-performance, easy-to-maintain and cost-effective articulated haulers tailored for the region’s rugged terrain. By working with independent dealers who offer strong local support, financing options and aftersales service, Rokbak wants to ensure that customers across Africa will be able to benefit from reliable and durable equipment.
“We are looking to align with established, independent dealers who recognise that, when it comes to desired articulated hauler needs, customers are seeking low total cost of ownership (TCO) and a good price to performance ratio – which our RA30 and RA40 ADTs deliver,” says Culliford. “Fundamentally, prospective dealers need to share the same value with us for strong aftersales support, and know when it comes to servicing and maintenance, it is about being there and acting responsibly and quickly to any customer requirements.”
When it comes to the product, Culliford says Rokbak trucks are reliable, robust and easy to maintain. When customers buy machines, they buy them to perform and do a job. Rokbak trucks are popular with customers
The RA30’s new transmission and high-performance engine improve fuel efficiency, operator comfort and deliver power when you need it.
because they are hardworking, high-performing and durable.
“We understand fuel efficiency and integrate connected services for operation monitoring and reduced idle time. Machine owners also need to keep operators happy, and, alongside ride control and independent front suspension, operators could not be more content than in the comfortable, spacious cabs which we provide for them,” he says.
Looking ahead, Culliford is positive about the business outlook and Rokbak in Africa. The African construction market is projected to grow from US$58,42-billion to US$74,81-billion by 2029, and companies are seeking advanced equipment to enhance efficiency and productivity.
“Africa has a vast resource wealth, and there is a surge in demand for its minerals. Forecasts suggest a 65% increase in market value by 2030, demand tripling by 2040 and growing sixfold by 2050, thus solidifying Africa’s role as a crucial supplier to the global market. As Africa grows, Rokbak wants to grow alongside it,” concludes Culliford. a
One of the major milestones was when the company pioneered the 50-t ADT, the B50, which was the largest on the market at the start of global sales at bauma 2004.
In a year that the company celebrated its 70th anniversary, 2024 also marked another important landmark in the history of Bell Equipment – 40 years of manufacturing articulated dump trucks (ADTs). In a one-on-one with Quarrying Africa, product manager Brad Castle details some of the major milestones in the company’s ADT journey during the past four decades. By Munesu Shoko
With roots dating back to 1954 when Irvine Bell established a small engineering and agricultural equipment repair service in Empangeni, northern KwaZulu-Natal, Bell Equipment has become a formidable name in the global capital equipment space some 70 years later.
A product that has put Bell on the global map is inarguably the ADT, which the company started manufacturing in 1984. In fact, the articulated hauler represents Bell Equipment’s core product, making up a good 80% of the company’s original equipment manufacturer (OEM) business.
Beyond the numbers, says Castle, 40 years of ADT manufacturing represents a commitment to innovation, excellence, resilience and unwavering customer service. The Bell ADT’s 40th anniversary is significant in the sense that the company has been in
A product that has put Bell Equipment on the global map is inarguably the ADT, which the company started manufacturing in 1984
“In terms of models, we have one of the broadest lines in the global market to date, including three 4x4 models, two 6x4 models and seven 6x6 models. In total we have 12 variations of machines available for the global market.
this challenging market for more than 50% of its 70-year existence. This is despite the recognised challenges that manufacturers have to contend with in South Africa, including high energy costs, skills shortage and supply chain issues, amongst others.
“Despite these widely acknowledged obstacles, we remain committed to local production. The impact of our local manufacturing activities is significant, not only to our employees, but also to our suppliers and the economy at large. To provide context, we have a supplier base of over 1 200, and 90% of these are South African entities,” says Castle.
80%
The articulated hauler represents Bell Equipment’s core product, making up a good 80% of the company’s OEM business
The year 2024 marked an important landmark in the history of Bell Equipment – 40 years of manufacturing articulated dump trucks
Along the journey, there have been some important milestones, ranging from the incorporation of technology and setting new standards in product sizes
Investment in R&D has fuelled innovation, which in turn has driven growth by setting new standards in the ADT market
With the increasing focus on sustainability, Bell Equipment believes that hydrogen will play a major role in the alternative fuels drive
With the B60E, Bell Equipment pioneered the 4x4 concept – a hybrid between a rigid truck setup and an ADT.
The 40-year milestone, says Castle, also reflects South Africa’s engineering prowess. For four decades, Bell Equipment has been at the leading edge of ADT manufacturing and the company to date has produced one of the most technologically advanced ADT line-ups in the world. This, he adds, is despite the fact that the ADT is by its nature a complicated machine with over 7 000 different parts.
Along the journey, there have been some important milestones, ranging from the incorporation of
Over the years, Bell has reinforced its agnostic approach to autonomy by working closely with several technology providers such as Pronto AI.
technology and setting new standards in product sizes.
The technology revolution, says Castle, started with the adoption of new manufacturing techniques such as plasma cutting and laser cutting. In addition, investment in research and development (R&D) has fuelled innovation, which in turn has driven growth by setting new standards in the ADT market.
Looking back, the 2001 launch of the D-Series was a step change for Bell Equipment from a global recognition perspective. The introduction of the range provided a springboard into major global markets.
One of the major milestones was when the company pioneered the 50-t ADT, the B50D, which was the largest on the market at the start of global sales at bauma 2004. The size evolution was followed up by the introduction of the 60-t ADT, which was again the largest at the time of its launch in 2014. With the B60E, Bell Equipment also pioneered the 4x4 concept – a hybrid between a rigid truck setup and an ADT.
“In terms of models, we have one of the broadest lines in the global market to date, including three 4x4 models, two 6x4 models and seven 6x6 models. In total we have 12 variations of machines available for the global market. In fact, we have the widest model range of 4x4 models, which I believe shows that innovation is at the heart of what we do and we continue pushing the boundaries,” says Castle.
While Bell Equipment’s current E-series generation, which made its debut in 2014, is to date one of the most technologically advanced ADT ranges on the market, Castle stresses that the technological revolution dates
back as far as the early 2000s.
“In 2001, Bell Equipment became the first ADT manufacturer to incorporate its own on-board weighing system. For over a decade, on-board weighing has been a standard feature on every Bell ADT that we sell. On-board payload weighing is very complicated, but for the past 24 years, we have paid our school fees and perfected our technology to achieve the most accurate measurements,” says Castle. “On-board weighing lets the operator know how much load is in the bin. Load and production information can be transmitted to the owner via our own telematic system, Fleetm@tic ®.”
Speaking of Fleetm@tic, he adds, Bell Equipment was the first ADT manufacturer to launch its own satellitebased telematics solution in 2003. To date, the system is standard on all of the company’s ADTs. Fleetm@tic desktop control allows customers to keep an eye on their machines and receive alerts on a wide range of parameters.
These early core technologies, says Castle, have provided building blocks for other innovations that the company introduced in the later years. For example, when Bell Equipment introduced an inclinometer to improve its on-board weighing accuracy, the company saw an opportunity to improve the safety of its trucks with the 2009 launch of its Hill Hold and Tip Safe features that prevent rollback on slopes and rollovers due to tipping at unsafe angles.
In 2019, Bell Equipment became the first ADT manufacturer to integrate its trucks with third-party pedestrian detection systems (PDS) and collision avoidance systems as standard, well ahead of South
Fleetm@tic® desktop control allows customers to keep an eye on their machines and receive alerts on a wide range of parameters.
Africa’s new mining regulations that came into effect in December 2022.
In terms of the regulations, diesel-powered, trackless mobile machines must be able to automatically detect the presence of pedestrians and other diesel-powered, trackless mobile machines in the vicinity, and provide an effective warning. Where no action is taken to prevent a potential collision, the machine must be able to “fail to safe” without human intervention by means of a system that has the means to retard the machine to a safe speed whereafter the brakes are autonomically applied (Level 9).
Bell provides a PDS gateway controller (ISO 21815-2) for a PDS/CAS to connect to a Bell ADT. The third-party PDS/ CAS then does the detection and gives commands while the execution of these commands and the control of the truck is Bell Equipment’s responsibility.
Bell’s Pin 3 E-series ADTs, introduced towards the end of 2020, are built ready to integrate with a wide range PDS or CAS up to level 9. This was a natural progression for Bell because its earlier E-series trucks introduced huge advances in automation to offer industry-leading levels of driver and machine protection.
A focus on providing more efficient and safer ADTs has over the years consistently kept Bell Equipment at the forefront of autonomy. Since 2019, Bell Equipment’s forward-thinking approach has enabled interoperability between different control systems and its trucks.
By adding layers to its PDS ISO standards, the company has created an autonomous ready platform that uses an open communication protocol principle to integrate easily
with third-party suppliers. Over the years, the company has reinforced its agnostic approach to autonomy by working closely with several technology providers such as Pronto AI and xtonomy, with several Bell ADTs now operating commercially on sites in the Northern Hemisphere.
Commenting on the future of ADT technology, Castle makes special mention of the sustainability drive. To date, Bell ADTs can operate on hydro-treated vegetable oil (HVO) without the need to dilute with diesel or impacting on engine service intervals. HVO can reduce carbon emissions by up to 90%.
However, Castle believes that the migration to fully electric machines will gather pace as some of the developed countries in the world are already demanding net-zero solutions. With this increasing focus on sustainability, Castle believes that hydrogen will also play a major role in the alternative fuels drive.
“However, these solutions are not without their challenges. For example, one of the limitations for hydrogen is the storage, which doubles that of diesel. The need for more tanks on the ADT, which by its nature is designed to be lightweight, makes the adoption of hydrogen a challenge at this stage. A few years ago, one of our engineers also found that to match the power of a diesel engine on a 45-tonne (t) ADT, one would require some 6 t of batteries which, again defeats the drive for lightweight machines for increased payload capacity. Despite these challenges, I believe that technology will evolve and these alternative energy sources will become viable in the future,” concludes Castle. a
To help commercial vehicle operators improve their vehicle uptime, productivity and ultimately profitability, UD Trucks Southern Africa has reiterated its commitment to providing customers with the necessary resources and services to help keep their trucks on the road, where they belong. By Chantelle Kotze
An unpredictable global landscape shaped by rapid technological change, economic fluctuations, geopolitical instability and climate change, combined with domestic energy and logistics issues, has required UD Trucks Southern Africa to be more agile in forecasting customer and market needs – and being able to meet them.
At UD Trucks Southern Africa’s annual press conference held on January 27, 2025, the company highlighted its continued commitment to assisting its customers to gain as much value as possible from their vehicles. This is in the face of rising fixed and variable cost pressures which impact on the total cost of ownership of a vehicle or fleet of vehicles.
While 2024 was a year marked by unpredictable operating conditions, on both the domestic and
international fronts, Filip Van den Heede, MD of UD Trucks Southern Africa, says that despite the prevailing industry conditions, the company had the right resources in place to “go the extra mile for customers to keep their trucks on the road, where they belong.”
To achieve this, UD Trucks Southern Africa has established a strong nationwide distributorship network in South Africa, comprising 39 dealers, that is backed by efficient original equipment manufacturer (OEM) support throughout the life of the vehicle.
The company has also bolstered its aftermarket service offering, which is aimed at maximising vehicle uptime for customers, and continues to work towards enhancing parts availability at dealer premises.
Moreover, the company has significantly increased its service and maintenance contracts (Service Agreements) in 2024, with over 50% of UD Trucks vehicles on the road now supported by service and
90 years
In 2025, UD Trucks is celebrating 90 years of the brand’s existence globally and over 60 years in South Africa
Global and domestic market unpredictability and volatility has required UD Trucks Southern Africa to be more agile in forecasting customer and market needs, and being able to meet them
UD Trucks Southern Africa is committed to helping customers derive maximum value from their vehicles in the face of rising fixed and variable cost pressures
Several resources are in place to improve vehicle uptime and ensure customer vehicles remain on the road, where they belong
UD Trucks emphasises the benefit of regular servicing and maintenance to help reduce breakdowns
maintenance contracts, up from 44% in 2023. “This means that one in every two trucks sold has a Service Agreement contract in place,” explains Van den Heede. With these service and maintenance contracts in place, vehicles benefit from enhanced uptime, efficiency and a longer lifespan, while customers enjoy peace of mind, Van den Heede highlights.
In addition, UD Trucks Southern Africa introduced Euro 5 vehicles to the South African market in 2019, preparing its customers for the switch to cleaner fleets well ahead
50%
In 2024, 50% of UD Trucks vehicles on the road were supported by service and maintenance contracts, up from 44% in 2023
“As we gear up to the remarkable future, we remain dedicated to the success of the southern Africa region and to going the extra mile to provide our customers with ultimate dependability for the next 90 years.
of the legislation. The Euro 5 vehicles reduce nitrogen oxide emissions by 43% compared to Euro 4, significantly lowering the industry’s carbon footprint. These vehicles also have lower maintenance requirements, thus reducing operational costs.
While legislation to support Euro 5 standards in the country continues to be delayed, now anticipated to come into effect around mid-2027, customers can already reap the benefit of owning Euro 5-compliant Quon, Quester and Croner trucks with lower carbon emissions, better fuel efficiency and a lower total cost of ownership (TCO).
In the face of rising fixed and variable cost pressures in South Africa, where the cost of moving goods has increased dramatically over the years, so too has been the total cost of owning a vehicle.
“Understanding TCO for a logistics operation is absolutely key to be able to manage, monitor and be aware of the costs involved in owning and operating a vehicle or fleet,” says Rory Schultz, Project Office (Com & Prod) at UD Trucks Southern Africa.
Fixed costs (incurred regardless of vehicle usage) and variable costs (incurred while the vehicle is in operation) together determine the TCO and affect the profitability of a logistics operation. “Maximising vehicle uptime while managing fixed and variable costs is essential to ensuring customers’ profitability and productivity,” says Schultz.
Profitability is crucial for logistics operations and remains a core focus area for UD Trucks Southern Africa, says Sanjay Naipal, Aftermarket Director at UD Trucks Southern Africa.
“At UD Trucks, we understand that for any fleet owner, the biggest pain points are unexpected breakdowns and downtime. To ensure our customers avoid unexpected interruptions and costly repairs, our uptime solutions allow vehicles to spend more time on the road and less time in the workshop,” says Naipal.
One such solution is the UD Trust Standard or Ultimate Service Agreements, which offers predictable maintenance costs on the vehicle, while guaranteeing uptime, profitability, and increased second-hand value, Naipal explains.
Moreover, Naipal emphasises the benefit of regular servicing and maintenance to help reduce breakdowns and
better organise workshop visits, to improve overall vehicle uptime.
Furthermore, Naipal says UD Trucks Southern Africa is actively working towards reducing customer downtime through improved parts availability at dealerships. “We use predictive systems, a dedicated team to investigate demand patterns, and data from vehicle sales and service agreements to improve management of our parts availability, he explains.
As testament to this, the company achieved a 96% parts availability in 2024, its best in a decade, ensuring dealerships have parts ready at the start of the day. This boosts workshop efficiency and productivity, and demonstrates its commitment to customer uptime.
Naipal says UD Trucks Southern Africa also offers a telematic solution, UD Connected Services, which enables business owners to monitor driver behaviour and vehicle health to ensure immediate action on error codes before something goes wrong.
UD Roadside Assist provides customers with roadside assistance in the event of a breakdown, with a maximum turnaround time of six hours. These services also contribute to getting customer’s vehicles back on the road in the shortest possible time.
In 2025, UD Trucks is celebrating 90 years of the brand’s existence globally and over 60 years in South Africa, producing light, medium, and heavy-duty trucks for the local market.
“As we gear up to the remarkable future, we remain dedicated to the success of the southern Africa region and to going the extra mile to provide our customers with ultimate dependability for the next 90 years,” concludes Van den Heede. a
To increase its speed to market and expand focus on the non-mining sector, Sandvik Rock Processing has appointed S&R Enterprises to distribute and support both the stationary and mobile crushing and screening equipment for the construction and aggregate industry. In a one-on-one with Quarrying Africa, Stephen Smith, MD of S&R Enterprises, outlines how the company plans to change the game for Sandvik customers in the local market. By Munesu Shoko.
Sandvik customers in the aggregate and construction industry can look forward to a new era following the appointment of a dedicated distributor to look after their interests, primarily in South Africa, and eventually in the whole of southern Africa.
Founded in January 2012, the company leverages decades of the team’s experience in the crushing and screening sector. Previously part of the Sandvik capital sales team, Smith has 20 years of experience working with Sandvik and other leading crushing and screening equipment.
Backed by this in-depth industry knowledge, S&R Enterprises has over the years helped customers in
Africa optimise their operations, ensuring efficiency and profitability. The company has built a solid reputation across several industries, including mining, construction, quarrying, demolition and agriculture. During its founding days, S&R Enterprises specialised in the supply of aftermarket wear and spare parts for all crushing and screening plants. The company later extended its portfolio to include refurbishment and rebuilding of mobile plants, a service which has over time become its core business. Apart from the provision of aftermarket parts and refurbished gear, S&R Enterprises has experience in the supply and support of new crushing and screening equipment. In fact, between 2014 and
S&R Enterprises’ focus is on the small to medium-sized static and mobile equipment in the 100-200 tonnes per hour size range
Sandvik Rock Processing has appointed S&R Enterprises to distribute and support both the stationary and mobile crushing and screening equipment for the construction and aggregate industry
Backed by this in-depth industry knowledge, S&R Enterprises has over the years helped customers in Africa optimise their operations, ensuring efficiency and profitability
While the distribution agreement is for southern Africa, initial focus will be on South Africa
With an established headquarters in Tshwane, the immediate plan is to invest in both machine inventory and parts stock to support the projected infrastructure rollout in Gauteng in 2025 and beyond
2015, the company assisted Sandvik Rock Processing to set up its modular range in the local market. In 2017, S&R Enterprises was appointed to distribute and support a range of Australian-manufactured mobile crushers and screens.
“Aware of the build quality, we have always rated the Sandvik product highly. We are therefore excited to embark on this partnership to enable profitable growth for
70%
Given that about 70% of quarries in South Africa are static plant-based, Sandvik, together with S&R Enterprises, have a strong focus on growing this market segment
quarrying and construction customers in southern Africa. Our focus is on the small to medium-sized static and mobile equipment in the 100-200 tonnes per hour (tph) size range,” explains Smith.
While the distribution agreement is for southern Africa, Smith tells Quarrying Africa that initial focus will be on South Africa. The establishment of a regional footprint, says Smith, will be rolled out in a staged approach over the next 24 months.
With an established headquarters in Tshwane, the immediate plan is to invest in both machine inventory and parts stock to support the projected infrastructure rollout in Gauteng in 2025 and beyond.
Thereafter, focus will turn to establishing branches in provinces with a high quarry population such as KwaZulu-Natal and Western Cape. After getting the South African footprint right, says Smith, attention will turn to Botswana and Namibia. The establishment of branches in these markets will allow the company to be closer to its customers to ensure quick parts and service turnaround times. Other markets such as Mozambique and Zimbabwe will probably be supported via sub-dealers.
Given that about 70% of quarries in South Africa are static plant-based, says Smith, Sandvik, together with S&R Enterprises, have a strong focus on growing this market segment through an aggressive aftermarket support strategy.
“At the core of the strategy is to get the aftermarket regime right for the static market. Together with our principal, we have already set the ball rolling with a revised pricing structure for wear and spare parts. This market segment, especially quarrying, is price-sensitive, and we have therefore done extensive work to get the pricing for parts in line with market expectations,” explains Smith.
By January 2025, Smith is confident that the pricing for Sandvik parts for the static market will be on par with 90% of the aftermarket suppliers. “We strongly feel that this will be the first major step in getting the Sandvik brand back to the top, where it rightfully belongs. We commend the Sandvik Rock Processing team, led by Tarynn Yatras, Vice President – Sales Area Africa, for the collaborative effort in this venture,” adds Smith.
The same approach will be adopted on the mobile crushing and screening side of the business. In addition to the aftermarket drive, S&R Enterprises will cast special focus on maintaining proper levels of inventory to ensure that products are readily available to meet
customer demand.
“The plan is to double the Sandvik aftermarket business in the aggregate and construction sector. How do we achieve that? Primarily by doubling up our wear and spare parts stock, as well as getting the pricing structure right. We are also bringing a large inventory of quarrying and construction-focused tracked equipment in the first quarter of 2025,” says Smith. Apart from static and mobile equipment, Smith is excited about the prospects of growth in the wheeled plant market. In addition to ease of mobility on and between sites, Sandvik wheeled plants are cost-effective to run. Because they are electrically powered, the running costs are much lower than their mobile counterparts. Due to the absence of hydraulics, wheeled plants also have lower maintenance requirements than track-type machines.
majority of these tenders fall under SANRAL’s Northern Region, which comprises Gauteng, Mpumalanga, Limpopo and North West. SANRAL’s Northern Region manages approximately 9 500 km of the national road network, making it the agency’s largest region. Some 34 tenders worth R16,5-billion are earmarked for the region and will have a major impact on the economy.
In the Eastern Cape, the roads authority awarded tenders to the value of R1,4-billion for the construction of road infrastructure since the start of the 2024/25 financial year.
Commenting on the outlook of the business, Smith is confident regarding the prospects of growth in South Africa. While KwaZulu-Natal and Western Cape provinces will remain stable in terms of construction activity, he believes that the biggest growth will come from Gauteng and Eastern Cape.
To give context, in September 2024, the South African National Roads Authority Limited (SANRAL), announced that it was evaluating 96 tenders worth R35-billion. The
A further R3,8-billion in contracts was expected to be awarded by the end of 2024. The flagship N2 Wild Coast Road (N2WCR) project has already picked up speed, with three major contracts underway, including the Msikaba Bridge, the Mtentu Bridge and the construction of the road linking the bridges (Package 5).
“While we are upbeat about the infrastructure development prospects, we are equally excited about the strategy we have put in place to re-establish the Sandvik brand in the non-mining sector. We are confident that the aggressive parts pricing strategy, investment in machine inventory and a strong aftermarket regime in general will be central to clawing back significant market share in the aggregate and construction sector. We reckon that this will yield significant impact within the first six months of 2025,” concludes Smith. a
THE CONFERENCE will feature 2 Keynote speakers as well as 14 Quarry industry speakers. This will include presen tations from our Young Professionals within the industry.
Our theme for this year is “Navigating a changing landscape”.As our world changes, so does our technology. As technology evolves, companies and employees will need to continuously upskill and reskill to stay relevant.
EXHIBITION. A static Exhibition will be staged and will be open for the duration of the Conference. This will give the delegates an opportunity to view the latest technology in the quarrying industry from the top Industry suppliers.
Elangeni Hotel Snell Parade, Durban, KwaZulu-Natal
To further develop its business in Africa, Terex Mineral Processing (Terex MPS) has over the past three years embarked on an aggressive footprint expansion, growing its distributorship channel from two to seven dealers. Following the expansion, Terex MPS has seen sizeable growth of its business. To recognise the outstanding efforts of its dealer partners, the company recently held its Terex Dealer Awards in Johannesburg, South Africa, as part of its annual Dealer Conference. By Munesu Shoko.
With its vast mineral resources and infrastructure development potential, Africa remains an important market to Terex MPS. As testament to the significance of the market, Terex MPS has recently expanded its sales and support footprint by appointing capable dealer partners across the continent.
Since his appointment in 2021, Willem du Plooy, regional business development manager – Africa, has overseen the appointment of three new dealers, making it seven in total. The dealers, covering all the important markets in Africa, have been strategically selected, with the criteria based on a number of factors, including the dealer’s financial muscle, technical expertise and infrastructure, among
30%
The strategic dealer partnerships in the past three years have already yielded massive returns for Terex MPS. The company has seen a year-on-year growth of about 30% in the past few years
others.
“When I joined Terex MPS some three years ago, the first thing on my agenda was to understand the existing dealer network and identify areas where we needed to establish representation. At the time, the existing two dealers were ELB Equipment in southern Africa and PowerX Equipment, our partner in the Englishspeaking West African countries such as Ghana and Nigeria,” says Du Plooy.
As part of the footprint expansion programme, Paris-headquartered Tractafric Equipment, the existing Caterpillar dealer in several African countries, was appointed the Terex MPS dealer in parts of North, West and Central
For clinching a £500 000 parts deal, the largest of its nature in the history of Terex MPS, PowerX Equipment took home the Parts Sales of the Year award
Terex MPS is witnessing a trend towards bigger plants, moving away from the common 100-200 tph plant size range to 300-400 tph capacities
Terex MPS has recently expanded its sales and support footprint by appointing capable dealer partners across the continent
The dealers, covering all the important markets in Africa, have been strategically selected, with the criteria based on a number of factors, including the dealer’s financial muscle, technical expertise and infrastructure, among others
In December 2024, Terex MPS held its annual Dealer Conference in Johannesburg, an occasion used for the company’s Dealer Awards ceremony. Tractafric Equipment walked away with the Africa Dealer of the Year accolade
For clinching a sizeable parts deal, the largest of its nature in the history of Terex MPS, PowerX Equipment took home the Parts Sales of the Year award
Africa. With a 90-year history, Tractafric Equipment operates in ten African countries – Burundi, Cameroon, Congo, Gabon, Equatorial Guinea, Morocco, Central African Republic, the Democratic Republic of Congo (DRC), Rwanda and Chad, in addition to having a presence in France and China.
“This was a strategic appointment for many reasons, including proven expertise, existing footprint in several key markets and strong sales and support infrastructure. In addition, being a French company makes it possible for Tractafric to look after our interests in French-speaking African countries. To provide context, there are about 29 Frenchspeaking countries on the continent.
Often overlooked, a language barrier can pose significant challenges to businesses though miscommunication, misunderstandings, lost opportunities, strained relationships and delayed negotiations,” says Du Plooy.
footprint into Angola, a market that we were not previously active in. Within the first three months of our partnership, Consulmet had already supplied its first order to a big quarrying client in Angola. The company is also occupied with another plant for a diamond project, which will bring the first of their kind Terex machines on the continent,” says Du Plooy.
Elsewhere, Hyquip Equipment has been appointed the dealer for the islands of Madagascar, Mauritius and Reunion Islands. This is a French-speaking dealer well known in its markets. The Meta Group has been appointed to look after East Africa, primarily Kenya and Tanzania.
For clinching a £500 000 parts deal, the largest of its nature in the history of Terex MPS, PowerX Equipment took home the Parts Sales of the Year award
Another strategic appointment was Consulmet, which looks after Angola, Botswana and Namibia. Being a specialist engineering group focused on fast-tracked design and construction of minerals processing plants, Consulmet brings a lot of expertise in big Engineering, Procurement and Construction (EPC) projects, opening up new opportunities for Terex MPS. For example, in partnership with Terex MPS, Consulmet designed and built a 600 tonnes per hour (tph) crushing and screening plant for an iron ore client.
“Partnering with Consulmet also gave us an immediate
The strategic dealer partnerships in the past three years have already yielded massive returns for Terex MPS. The company, says Du Plooy, has seen a year-on-year growth of about 30% in the past few years, with prospects for further growth in the coming years.
Partnering with some of these established equipment groups has also changed the game in terms of the size of equipment being sold. In recent years, Terex MPS has seen a shift from the previously prominent 100-200 tph plant size range to 300-400 tph capacities.
To meet this capacity increase, the company has shifted to the development of larger machines. A case in point is the WC1150S cone-screen plant – which made its debut in 2023 – a high-performance, medium-sized wheeled crushing and screening system. At the heart of the plant is
COMBINATION MODULES
WHEELED
Crushing and Screening Modules
Modular or Wheeled Crushing and Screening Solutions
STATIC
•In-country, fully equipped technicians for installation, servicing, maintenance and refurbishment of Terex MPS equipment.
•In-country warehousing of critical spares for Terex MPS equipment.
Jaw, Cone and Impact Crushers, Horizontal and Inclined Screens
terexmpsenquiries@consulmet.com www.consulmet.com/consulmet-equipment
the 225kW Terex TC1150 cone crusher and a 6’ x 20’ tripledeck screen. Following the installation of the first unit in Namibia in 2023, two more units were commissioned in Mozambique during the same year.
“We are witnessing a trend towards bigger plants, moving away from the common 100-200 tph category, to the 300-400 tph capacities. In mining, we have seen demand for plants as big as 600-700 tph. In Angola, we are busy with an 800-900 tph plant for a quarrying project, which is a completely new level for us,” says Du Plooy.
In December 2024, Terex MPS held its annual dealer Conference in Johannesburg, an occasion used for the company’s Dealer Awards ceremony. Tractafric Equipment walked away with the Africa Dealer of the Year accolade. During the past 18 months, the company has made massive inroads into Central and West Africa markets, securing several new complete plant installations in both regions, comments Du Plooy.
Mohammed Zaidane of Tractafric Equipment tells Quarrying Africa that the company has already put in excess of 15 Terex MPS machines to work in 18 months, with notable projects in Gabon and the DRC. “We also have significant projects running in Morocco, helping with the preparations for the 2030 FIFA Soccer World Cup. We have also made an installation in Burkina Faso for a mining contractor,” says Zaidane.
For clinching a £500 000 parts deal, the largest of its nature in the history of Terex MPS, PowerX Equipment took home the Parts Sales of the Year award. “PowerX Equipment is supporting a high-profile mining customer in West Africa where it secured the largest single parts sale in Terex MP’s history. PowerX Equipment’s dedication to service and support with parts backup is key for the success of this project,” says Du Plooy.
For being the Terex MPS dealer for the past 14 years, the longest among all other African dealers, ELB Equipment was awarded the Long Service Award. In addition, Tracy Hugo of ELB Equipment walked away with the Salesperson of the Year award. “Tracy secured the sale for a complex crushing and screening plant in South Africa, which took a lot of hard work and understanding of the application, in order to win,” says Du Plooy.
Sarel von Wielligh of Consulmet was awarded the 2024 Service Engineer of the Year. Having joined Consulmet late in 2023, Von Wielligh was thrown in the deep end, travelling to Angola for the first time in December 2023, where he was tasked with the installation of a new crushing and screening plant. “Sarel performed beyond expectations despite the challenges Angola presents. He went beyond his call of duty to service the customer and held the Consulmet and Terex MPS names high in the process,” concludes Du Plooy, adding that the next Africa Dealer Conference will be hosted by Tractafric Equipment in Morocco this year. a
Sandvik Mining and Rock Solutions brought its first Sandvik DR412i rotary blasthole drill into Africa some two years ago.
Amid a steady move towards the concept of intelligent drilling, Sandvik Mining and Rock Solutions brought its first Sandvik DR412i rotary blasthole drill into Africa some two years ago. A radical upgrade of the previous KS-Series, the DR412i has lived up to its design billing of combining power with intelligence to deliver new levels of process optimisation, efficient drilling and dependable penetration in harsh mining conditions. By Munesu Shoko.
As the mining industry forges ahead on its path towards innovation to improve efficiency, safety and sustainability, the past decade has witnessed a rapid move towards intelligent drilling, particularly anchored by the evolution of autonomous drilling, not only for enhanced precision and productivity, but also to advance efficiency and safety in opencast mines.
Among the global original equipment manufacturers (OEMs) leading this charge has been Sandvik Mining and Rock Solutions with its i-Series range of drills – under which the DR412i rotary blasthole drill falls.
Designed for standard rotary drilling with optional down-the- hole (DTH) hammer drilling power, the DR412i is an automation-ready drill that replaced the previous KS-Series, a range of hydraulic drills which made its name in the market due to its robustness, confirms Trinity Nkosi, sales engineer, Surface Drills Department at Sandvik Mining and Rock Solutions.
“On the back of a trend towards intelligent machines, we responded by introducing the i-Series. As our
platform of the future, the i-Series family comes with an impressive array of advanced features and customer benefits. One of the major talking points is the scalable surface drill automation architecture, which allows for a customised path to the level of automation each customer needs, when they need it. While the DR412i differentiates itself with its automation-ready capabilities, it retains the same robustness as its predecessor range, the KS-Series,” says Nkosi.
Suited for soft to medium/hard rock formations, the DR412i can drill 203 to 311 mm diameter blastholes with a single-pass capacity of 17,65 m or multi-pass capacity of 75,5 m. Primarily used in surface mining, it can also be deployed in oil and gas applications.
One remarkable feature on the DR412i is the scalable surface drill automation which features flexible, customised automation capabilities that allow customers to add the automation modules they need, when they need them.
203-311 mm
Suited for soft to medium/hard rock formations, the DR412i can drill 203 to 311 mm diameter blastholes with a single-pass capacity of 17,65 m or multi-pass capacity of 75,5 m
Sandvik Mining and Rock Solutions brought its first Sandvik DR412i rotary blasthole drill into Africa some two years ago
Primarily used in surface mining, it can also be deployed in oil and gas applications
The first DR412i in Africa has been hard at work in a coal application in South Africa for the past two years, and the customer is particularly happy with the power, precision, productivity and efficiency of the machine
One remarkable feature on the DR412i is the scalable surface drill automation which features flexible, customised automation capabilities that allow customers to add the automation modules they need, when they need them
Sandvik offers various automation levels – iDrill (onboard operation) and AutoMine ® (remote operation). Automated onboard functions allow the rig to work from partial to full autonomy. The operator monitors at fleet level and takes control only when required. The onboard automation functions of Sandvik’s i-Series rotary drill rigs form the basis for remote operation,
30%
The Compressor Management System can save customers up to 30% on fuel, with a proportional reduction in carbon footprint and extension of both engine and compressor life
minimising the risk of human error.
The AutoMine product group – Line-of-Sight, Control Room and Autonomous – offers autonomous and remotely operated drilling. It allows operators to simultaneously control and monitor multiple surface drills from the comfort and safety of a remote control room.
One operator can control multiple drill rigs simultaneously, either by a line-of-sight setup from a van or trailer close to the operating area. Alternatively, a Control Room option may be selected to operate the drill rigs from any location, be it on the mine site, or even from another city. This reduces exposure to noise, dust, vibration and exposure to hazardous environments. The operator monitors the fleet and can easily switch to control the rig requiring detailed attention.
The AutoMine system and intelligent rig control system ensure accurate and efficient drilling operations. The intelligent system helps to use the drill rig’s full potential in the many ways it is designed to be operated. AutoMine includes a safety system designed in accordance with international functional safety standards. This is critical for mines, where operator safety is of paramount importance. When it comes to data monitoring, the MySandvik data portal is available in three subscription levels to access telemetry reports and dashboards. MySandvik Insight is the entry level package, which offers performance reporting for the machine. With insights on fuel consumption and metres drilled, fleet owners can follow production and understand the efficiency of their drilling operations.
MySandvik Productivity gives fleet owners access to fleet utilisation, alerts and service indicators. With this package, customers can follow production, understand efficiency, know their fleet, understand performance, identify bottlenecks and review work practices. My Sandvik Onsite is a monitoring solution that transforms real-time data generated by Sandvik’s i-Series’ surface drill rigs into actionable insights for productivity improvements. The on-premises solution works on a local network and can be integrated into any surface mining system.
With productivity in mind, the Sandvik DR412i uses a CAN bus controlled hydraulic system to monitor the machine, allowing for timely preventative maintenance and delivering higher availability.
Durability is another key design parameter, anchored by the chain-driven feed system. “Whereas most competitors use a cable-driven feed system, which is prone to slippage and has a short lifespan, we make use of a chain-based feed system, which requires less adjustment and has self-
tensioning capabilities. The chain feed system delivers cleaner holes, which improve blast quality at a lower cost,” he says.
The travelling centraliser reduces drill pipe wobble to produce straighter holes faster, extend component life and reduce unplanned maintenance. This feature, says Nkosi, increases the life of drilling pipes.
drilling applications in order to maximise efficiency and reduce fuel burn. The Compressor Management System can save customers up to 30% on fuel, with a proportional reduction in carbon footprint and extension of both engine and compressor life,” explains Nkosi.
Equipping the drill with a large engine, he adds, also means that the motor is not frequently used close to its capacity load. The DR412i therefore averages a 70-80% load on the engine, whereas most pedestal offerings in the size class peak at around 95% load range, which not only increases fuel consumption, but also negatively affects engine life.
Putting operator comfort and control to the fore, the new-generation ergonomically designed cab includes controls on the armrests, touchscreens, angled windows to reduce glare and a safari-style roof to keep the cab cooler.
The wider, 360-degree walkways enable superior drill access for easy pre-shift inspection and routine maintenance. An optional hydraulic main-access stairway can be mounted to provide a parallel step onto and off of the drill.
In Australia, a coal mining operation increased its penetration rate by 18 m per hour by deploying the DR412i, which in turn resulted in a 43,4% reduction in fuel consumption per metre compared to other drills
To withstand harsh operating conditions, the DR412i benefits from a heavy steel body and powerful engine. “Compared with competitor offerings in this size class of pedestal drills, the DR412i is much heavier, largely due to the massive steelwork and a bigger engine. While there might be a concern that a bigger engine uses more fuel, that is not the case. This is made possible by the advanced compressor management system which reduces the load on the engine by isolating the compressor during non-
The first DR412i in Africa has been hard at work in a coal application in South Africa for the past two years, and the customer is particularly happy with the power, precision, productivity and efficiency of the machine.
In a massive feat, a mine in the Mesabi Iron Range in northeastern Minnesota drilled over 1 000 m in a day using a 271 mm drill bit. This was made possible by the drill’s robustness and powerful build.
“In Australia, a coal mining operation increased its penetration rate by 18 m per hour by deploying the DR412i, which in turn resulted in a 43,4% reduction in fuel consumption per metre compared to other drills – a big factor in the mine’s ability to reduce its cost of operation,” concludes Nkosi. a
LiuGong bulldozers will form part of the range of LiuGong equipment available from ELB Equipment in southern Africa.
Having taken over the exclusive distributorship of LiuGong earthmoving and construction Equipment late last year, ELB Equipment has already made significant strides in integrating the brand into its stable. In an exclusive interview with Quarrying Africa, Keon Kardolus, Divisional Director – Earthmoving and Construction Equipment at ELB, says LiuGong’s strong product line-up, combined with ELB’s established footprint, creates a synergistic platform for success.
By Munesu Shoko.
In a major industry development, ELB Equipment, one of the largest earthmoving, mining and construction equipment suppliers in southern Africa, announced the signing of an exclusive agreement to distribute and support the full range of LiuGong’s earthmoving and construction equipment in the region.
The dealership agreement, confirms Kardolus, covers South Africa and neighbouring countries, initially Namibia, with future plans for expansion into other southern African countries. The agreement took effect in December 2024, with operational plans already being executed and team integration underway to ensure a seamless transition.
“Following the announcement of the distributorship agreement, our immediate focus is to integrate LiuGong into our operations,” says Kardolus. “This includes onboarding LiuGong personnel at ELB, training our sales and service teams, as well as rolling out marketing initiatives to create awareness. We are also working on optimising our infrastructure to support LiuGong equipment, ensuring that our customers receive the highquality service they have come to expect from ELB.”
Commenting on what influenced the decision to opt for LiuGong, Kardolus tells Quarrying Africa that the Chinese
original equipment manufacturer’s (OEM) reputation for manufacturing durable, high-performance machinery at competitive pricing played a significant role in ELB’s decision to add the range to its extensive offering.
“Additionally, LiuGong’s commitment to innovation, strong global presence and excellent aftermarket support align with ELB’s strategy to provide reliable and cost-effective solutions to our customers. LiuGong’s expanding footprint in the global equipment market also matches our growth aspirations in southern Africa,” says Kardolus.
LiuGong’s business model of forging long-term relationships with its dealer partners was another attribute that matched ELB Equipment’s operating model. To provide context, LiuGong has partnered with its previous dealer for about 20 years, while ELB Equipment has distributed some of its OEM brands for extended periods, with Powerscreen, Furukawa and Sumitomo all having been part of the company’s stable for over 40 years.
Developments in the automotive sector, adds Kardolus, where Chinese automotive brands have become formidable global competitors through improved designs that incorporate advanced technology, sleek exteriors and well-appointed interiors, are a precursor of what is likely to happen in the construction equipment sector. “I believe that developments in the automotive environment today have set the tone of what
we should expect in the construction space in the next two to three years,” he says.
As part of the agreement, ELB will distribute and support the full range of LiuGong construction and earthmoving equipment, including wheel loaders, excavators, bulldozers, graders, backhoe loaders, mining trucks, as well as compact and compaction equipment.
ELB will also support existing LiuGong equipment supplied by both the previous dealer and LiuGong Southern Africa. LiuGong’s existing customer base, he says, can rest assured that ELB Equipment will uphold the 11
With its robust infrastructure – 11 branches, six sub-dealers and dedicated service teams strategically located across South Africa – ELB is well-equipped to support LiuGong’s growing footprint
856H
In a major industry development, ELB Equipment announced the signing of an exclusive agreement to distribute and support the full range of LiuGong’s earthmoving and construction equipment in southern Africa
The dealership agreement covers South Africa and neighbouring countries, initially Namibia, with future plans for expansion into other southern African countries
LiuGong’s reputation for manufacturing durable, highperformance machinery at competitive pricing played a significant role in ELB’s decision to add the range to its extensive offering
The addition of the LiuGong range also allows ELB to close some crucial gaps in its offering, particularly in the mid-market segment, providing customers with durable, versatile and affordable equipment options
ELB is excited about the addition of the LiuGong 856H wheel loader to the ELB stable, one of the flagship LiuGong products in the market
22-t
Based on the high uptake, the 22-tonne 922E is one of the LiuGong flagship products in the local market
quality and reliability that they have come to expect from the LiuGong brand. With its robust infrastructure – 11 branches, six sub-dealers and dedicated service teams strategically located across South Africa alone –ELB is well-equipped to support LiuGong’s growing footprint.
Leveraging its established support infrastructure in the region, ELB is expanding the LiuGong offering through the provision of other lines that were previously not available to the local market, including pneumatic tyre rollers and asphalt pavers, amongst others.
The addition of the LiuGong range also allows ELB to close some crucial gaps in its offering, particularly in the mid-market segment,
providing customers with durable, versatile and affordable equipment options. It also enhances ELB’s ability to offer comprehensive solutions to its customer base with the addition of mining trucks.
“Previously, we did not offer any mining trucks, which we felt was a limiting factor to our ability to provide a full line of solutions to our customers. With the addition of LiuGong’s wide body trucks (90-t and 100-t models) and a 100-t rigid dump truck – the most prominent size in the contract mining sector – we have closed the gap in our product line-up,” says Kardolus.
Apart from mining trucks, Kardolus is excited about the addition of the LiuGong 856H wheel loader to the ELB stable, which he believes is one of the flagship LiuGong products in the market. Over the years, the 856H has gained popularity in southern Africa, demonstrated by a strong installed base across commodities.
The 22-tonne LiuGong 922E excavator is another model which Kardolus believes stands out, based on the high uptake of the machine in the local market. “The proven performance of the two machines in harsh conditions, coupled with innovative designs and advanced technology, makes them exciting additions to the ELB portfolio,” says Kardolus.
ELB’s approach is to ensure that all brands within its portfolio “remain distinct yet complementary”. Ultimately, customer satisfaction and loyalty will guide the company’s strategy for positioning LiuGong alongside existing offerings.
Kardolus is very optimistic about this partnership. LiuGong’s strong product line-up, he says, combined with ELB’s established presence and customer relationships in southern Africa, creates a synergistic platform for success. He believes that this collaboration will drive significant growth, expand ELB’s market share and strengthen its reputation as a leading provider of earthmoving and construction equipment in the region.
“This partnership marks a pivotal moment for ELB Equipment. By aligning with a globally respected brand of LiuGong’s stature, we are reinforcing our commitment to delivering innovative and reliable solutions to our customers. We look forward to showcasing the advantages this collaboration will bring to the construction and mining industries across southern Africa,” concludes Kardolus. a
Our cutting-edge Lintec CDP12001M mobile continuous asphalt mixing plant has been engineered for superior performance. The CDP asphalt mixing plant delivers topquality asphalt quickly and directly at your job site. Say goodbye to transportation delays and hello to seamless, on-the- go operations. Elevate your projects with our innovative solutions and experience true mobility redefined. — Your road to success starts here.
www.lintec-linnhoff.com info@lintec-linnhoff.com
Amid growing demand for onboard weighing systems and conveyor belt scales in Africa, leading manufacturer of precision weighing solutions, Loadrite, is looking for new dealers in selected African regions to expand its distribution network on the continent. By Munesu Shoko.
As mines and quarries seek to run datadriven operations, the demand for load weighing systems in Africa has over time, grown significantly, Sören Schramm, regional manager EMEA at Loadrite, tells Quarrying Africa . On the back of this uptake is the growing understanding that at the heart of the extractive industry’s efficiency and profitability is accurate weight measurements – a crucial factor that is often disregarded.
Having access to data, in real time, is key to ensuring efficient and productive loadout and crushing operations. The availability of data equips quarry and mine managers with insights that enable them to improve productivity and impact the bottom line.
“In the past few years, the demand for onboard weighing systems and conveyor belt scales has increased significantly, with enquiries from all over Africa. Our existing distributors in southern and West Africa have
The move to the L5000 represents a big step forward for many customers in managing their loading processes CO2
seen a lot of demand for all types of weighing systems,” says Schramm.
“To meet this increased demand, we are therefore looking to appoint capable dealers, especially in Central and East Africa. We also see opportunities to grow our footprint in several countries in North and West Africa. We seek to appoint either in-country dealers or partners who can service the whole region, depending on their capacity and potential,” he adds.
Due to the extensive nature of mining activities in Africa, Schramm says the sector presents huge growth prospects for the Loadrite offering. Mining operations are intricate processes that require meticulous attention to detail, particularly in the area of materials handling. Loadrite weighing solutions play a pivotal role in optimising these operations, ensuring efficiency, accuracy and regulatory compliance.
A reliable weighing system also helps monitor and reduce CO 2 emissions
4G
The L5000’s easy connection to Loadrite InsightHQ with integrated 4G modem and WiFi substantially reduces the cost of connecting data to the office
In the past few years, the demand for Loadrite onboard weighing systems and conveyor belt scales has increased significantly, with enquiries from all over Africa.
“The need for process improvement and management of material flow in quarries and other material handling sites offers growth opportunities for our products in Africa,” he says. “Ports or container handling terminals on the continent also have to comply with the International Convention for the Safety of Life at Sea (SOLAS) regulations and that is an area where Loadrite products can really help.”
In addition, says Schramm, some countries and regions in Africa are just starting to monitor train or truck loading. Monitoring the material and weight loaded onto on-road trucks protects roads from unnecessary damage. When mines install weighing systems on the excavator in the pit, they can monitor payload and improve efficiency. With the price of diesel and maintenance costs rising, it has never been more important to monitor payload and efficiency. A reliable weighing system also helps monitor and reduce carbon emissions.
Commenting on the expected type of partners, Schramm says there is no discrimination between small and large entities. The selection of a capable representative depends on the workforce behind the sales and service of the products. Loadrite, he adds, already has successful dealers running small entities with few employees, often dedicated to the Loadrite brand. On the other hand, the company also
“It is essential that our distributors sell and support our entire product portfolio. This allows end customers to get the best experience with Loadrite products. Having access to weighing data from all parts of a site can be a big step forward. Therefore, selling only one product line is not an option.
As mines and quarries seek to run data-driven operations, the demand for load weighing systems in Africa has over time, grown significantly
To meet this increased demand, Loadrite is looking to appoint capable dealers, especially in Central and East Africa
The company is also seeking to grow its footprint in several countries in North and West Africa
Loadrite seeks to appoint either in-country dealers or partners who can service the whole region, depending on their capacity and potential
The move to the L5000 represents a big step forward for many customers in managing their loading processes.
has successful distributors running larger businesses, and Schramm stresses that the right attitude and commitment are certainly the most important in the success of a dealer.
“The quarrying and mining industries are changing. This makes it challenging, but quite interesting for a distributor. Installers need a diverse set of skills, ranging from hardware installation and electronics to understanding of software/IT systems, modems and cloud data. For an individual, this is a demanding but all-encompassing and rewarding skill to have,” he says. “For growing businesses, managing cash flow is often a common challenge.”
In the face of these challenges, Loadrite supports distributors in all aspects of their businesses. The company trains installers, helps sales staff with quotes, provides training on industry dynamics and customer needs. In addition, the principal can also help its distributors with business planning, marketing, advertisements, setting the right pricing and managing cash flow.
“It is essential that our distributors sell and support our
entire product portfolio. This allows end customers to get the best experience with Loadrite products. Having access to weighing data from all parts of a site can be a big step forward. Therefore, selling only one product line is not an option,” says Schramm.
With the recent launch of the L5000, Loadrite has ushered in a new era in load weighing. The L5000, says Schramm, has been well received in the global market.
“The move to the L5000 represents a big step forward for many customers in managing their loading processes. Key features include a loadout management system which can connect to the weighbridge software, extensive onboard metrics and loadout history. Customers can easily review and reprint their past load tickets. Easy connection to Loadrite InsightHQ with integrated 4G modem and WiFi substantially reduces the cost of connecting data to the office,” concludes Schramm. a
Astec Africa Middle East
China Communications Construction Group Ltd, one of the world’s largest multinational engineering and construction companies, selected a Lintec CDP12001M asphalt mixing plant for a major water supply project in Libreville, the capital city of Gabon. The equipment arrived in December 2022 and was fully installed and commissioned by March 2023.
The project is part of an international assistance initiative that was funded by loans of €75,4-million from the African Development Bank and €42-million from the Africa Growing Together Fund. Launched in Gabon in 2019, the drinking water component of the Libreville Integrated Drinking Water Supply and Sanitation Programme (PIAEPAL) was completed in June 2024.
To help complete this highly ambitious project, the Lintec CDP12001M played a crucial role in developing the transportation network and enhancing road infrastructure in the water supply areas, reinforcing the importance of the highly mobile capabilities of the asphalt mixing plant that easily facilitates movement between job sites.
The plant produced an estimated 50 000 t of asphalt to build a host of roads around the new water supply system. With the road-building projects spread across a wide area, the asphalt plant was required to move multiple times throughout the job, representing a key reason why China Communications Construction Group Ltd., opted for the highly mobile Lintec CDP12001M.
A spokesperson from China Communications Construction Group Ltd, says: “We are thrilled that the
Lintec CDP12001M played such a pivotal role in our major water supply project in Libreville, Gabon. The selection of the Lintec CDP12001M was driven by key factors including its exceptional mobility and ease of installation which is ideal for projects such as the one in Libreville, that required quick relocation and short-term setup.”
With a maximum capacity of 120 tonnes per hour, the Lintec CDP12001M can be assembled without the need for cranes or concrete foundations. The plant has been conceptualised for easy and quick set-up and dismantling. This makes the Lintec CDP12001M particularly suitable for mobilisation from one project to another.
China Communications Construction Group Ltd and Lintec & Linnhoff have a long history of partnering on key infrastructure aid projects.
Between 2010 and 2022, the company purchased several asphalt mixing plants including the Lintec CSM and Lintec CSD series, that contributed to projects in several countries including China, Ethiopia, Cameroon and the Republic of Djibouti. This project marks the first time that China Communications Construction Group Ltd has purchased a model from the Lintec CDP range. a
or more than 80 years, Martin has delivered the cleanest, safest, most productive solutions to countless bulk material handling issues. That history has taught us the value ongoing training can contribute to employee wellness and company profits.
Our Foundations™ Learning Center provides online, aroundthe-clock access to a variety of training modules, webinars and Zoom sessions conducted by factory-trained, certified professionals. And all provided to mitigate risks to workers, premature equipment failure, and unexpected downtime.
Click and log on. Classes now in session.
Manufactured sand production has become a pressing need across southern Africa as natural sand resources near urban growth centres dwindle and environmental restrictions tighten. Responding to this demand in 2024, Pilot Crushtec International introduced the Metso HRC 8 high-pressure grinding roll crusher, a cutting-edge solution for efficient and sustainable sand manufacturing.
“FThe HRC 8 employs inter-particle comminution, where feed material is compressed between two counter-rotating rollers - one fixed and the other floating. This method ensures uniform grain sizes and the desired gradation, critical for concrete and asphalt applications. It is this precision that allows aggregate suppliers to produce a superior finished product.
rancois Marais, sales and marketing director at Pilot Crushtec, describes the Metso HRC 8 as a gamechanger for the manufactured sand market. “The HRC 8 employs interparticle comminution, where feed material is compressed between two counter-rotating rollers - one fixed and the other floating,” he explains. “This method ensures uniform grain sizes and the desired gradation, critical for concrete and asphalt applications. It is this precision that allows aggregate suppliers to produce a superior finished product.”
The Metso HRC 8 delivers excellent cubical-shaped sand tailored to customer requirements. This not only effectively substitutes natural sand but also reduces the need for excess cement and asphalt in mixes, driving down material costs and enhancing sustainability.
Beyond producing high quality sand, the HRC 8 can transform unsellable quarry waste into marketable materials. By correcting particle shape and gradation curves, operators can extract additional value from previously discarded materials.
“The ability to reprocess waste into sellable products adds another dimension of cost efficiency for operators,” notes Marais. “This feature aligns with the industry’s growing emphasis on reducing environmental impact while enhancing profitability.”
Marais is also quick to point out that the Metso HRC 8
is not limited to sand production. It also excels in premilling applications for various minerals, including chrome, lithium, silica, gold, and copper. Traditionally, sizing materials to minus 5 mm has relied on impact crushers, but their high wear costs often outweigh initial savings.
“With the HRC 8, operators benefit from reduced wear costs and increased efficiency, particularly when processing abrasive ores like chrome, silica and lithium,” Marais says.
Establishing new benchmarks in productivity and efficiency, the Metso HRC 8 consumes up to 50% less power compared to traditional technologies for similar outputs. Its patented flange design maximises material engagement within the crushing zone, significantly increasing throughput while reducing downtime. The innovative arch-frame eliminates skewing, ensuring consistent and reliable performance.
Enhanced wear life of components and simplified maintenance processes further contribute to lower operating costs, making the HRC 8 an economical and efficient choice for both sand producers and mining operations.
“The machine’s energy efficiency and robust design make it a cost effective solution, especially for producing manufactured sand. It is a sustainable option that delivers superior performance with a reduced environmental footprint, and we are seeing increased interest from both existing and new customers,” Marais concludes. a
Maintenance personnel should receive advanced conveyor training, so they can analyse cause-and-effect relationships.
Are you just checking the boxes by doing required training hours, or is your goal to get a return on your investment? There can be huge improvements in production, maintenance labour, risk avoidance and cashflow by training employees on how to safely control fugitive materials in bulk material handling and then implementing changes. Unfortunately, half measures do not get half results, so training alone would not be sufficient. Following through on what has been learned is the key. By R. Todd Swinderman, President Emeritus at Martin Engineering.
Training should be robust enough to break the ‘we have always done it that way’ mentality and encourage creativity in problem solving with safety at the forefront of the design. Companies that place a priority on safety – and address fugitive material problems seriously – benefit from fewer safety incidents, less regulatory oversight and higher productivity and profits.
The online Martin Foundations Learning Centre draws from the collective knowledge and expertise gathered over nearly 80 years solving bulk handling challenges. Aimed at apprentice technicians and experienced engineers alike, the non-commercial information is offered at no charge and is accessible by computer, tablet, or smartphone. An extension of the Foundations training curriculum, the Learning Centre uses a mix of text, photos, videos, webinars, online events and live experts available to answer questions.
Everyone operating, cleaning or maintaining conveyors should be trained in the hazards of belt conveyors and bulk material handling. Operators and cleaning crews should have a basic understanding of what is normal conveyor operation and what the common problems are, so they can be aware that there are ways to reduce day-to-day problems such as spillage and belt wander.
Basic training includes topics such as guarding, identifying problems and safe work practices. Appropriate safety training emphasises how the belt can store elastic energy even when Lock-Out Tag-Out procedures are followed and why additional securing of the belt is required. Further, with the retirement of many experienced operators and mechanics – and the difficulty in finding new workers – it becomes critical that new employees understand the basics of conveyor design and operation.
80
The online Martin Foundations Learning Centre draws from the collective knowledge and expertise gathered over nearly 80 years solving bulk handling challenges
2
No two conveyors are identical and even twin conveyors side by side can act differently
A professional safety inspection takes a third-party perspective of aspects that workers often overlook.
Training should be robust enough to break the ‘we have always done it that way’ mentality and encourage creativity in problem solving with safety at the forefront of the design
Companies that place a priority on safety – and address fugitive material problems seriously –benefit from fewer safety incidents, less regulatory oversight and higher productivity and profits
The engineering and maintenance staff should be additionally trained in fundamental conveyor design concepts, so they can analyse cause-and-effect relationships
It is incumbent upon management to take the safety and maintenance training as seriously as the staff, listen to the concerns of employees and fix the problem correctly the first time
The engineering and maintenance staff should be additionally trained in fundamental conveyor design concepts, so they can analyse cause-and-effect
relationships. Quite often the visible signs of poor conveyor operation are not the root cause of the problem. For example, using guide rollers to force the belt to track does not address the fundamental reason for the belt mistracking and usually results in belt edge damage.
Sometimes training is on a specific piece of equipment with the goal of creating trainers who can educate the rest of the maintenance department. This approach works well with certain types of equipment but ends up with one or two motivated and well-versed technicians who can troubleshoot.
A mechanic trained in installing problem solving components will run into a myriad of physical constraints. First, the original conveyor design and subsequent modifications can make it impossible to install equipment according to the manufacturer’s instructions without a complete redesign. Second, often structural obstructions or conveyor arrangements do not allow enough room for installation, clear views for inspection or access for safe and easy maintenance access according to industry standards. Conveyor design training for engineers and mechanics is critical so they can diagnose problems with an understanding of fundamental design methods. Systems are incrementally modified over time to minimise problems when belt speed and capacity exceed the original design
The Martin Conveyor Belt Carryback Gauge is a patented tool for estimating carryback on the return side of a conveyor belt.
specifications. No two conveyors are identical and even twin conveyors side by side can act differently. So, adhering to standard design methods allows one technician to make these slight adjustments and another technician to recognise the intentions even without the prior technician present.
Training alone rarely results in meaningful actions to improve conveyor performance. When management understands the clear links between safety, cleanliness and productivity, it is much easier to turn training into results. There are many variations of how this can work, but most success stories have common threads: Basic training in conveyor hazards and the methods for controlling fugitive materials
• Training in conveyor design fundamentals and the root causes of common problems
• Management participation in the training to show support
• A pilot programme and measured results
• A long-term plan implemented from a successful pilot programme
examples showing similar problems and their solutions. The first day typically starts with reviewing the typical problems and getting the class to talk about their specific challenges. The class identifies a couple of problem conveyors and the class splits into small teams. Each team can look at the same problem or select different ones.
Photos and videos of the issues are taken to be used in the problem-solving discussions.
The rest of day one and the start of day two review basic design principles that relate to the problem conveyors. The discussion centres on possible root causes and solutions. Once the teams reach an agreement on a way forward, they prepare a short presentation with the help of the instructor, using their actual conveyor problems and the knowledge they gained. The presentations may also include an estimate of the cost of the proposed solutions.
A walkdown of one or two "problem belts" and a review of goals the day before the training help the instructor focus on site-specific problems and management's expectations
A walkdown of one or two “problem belts” and a review of goals the day before the training help the instructor focus on site-specific problems and management’s expectations. The survey and interview usually take a few hours to half a day. The goal is for the instructor to have actual examples to show the class their problems are not necessarily unique. An experienced teacher will most likely have
At the end of day two, management is invited to listen to the team presentations and solutions. By participating in the class presentations, management shows a commitment to making improvements and has an opportunity to ask questions.
The trainees, by making the presentations, show the knowledge they gained and support for the proposed solutions. The photos, videos and inspection sheets help shed light on issues and solutions crews experience every day. It is critical at this step that the manager(s) who attend the presentations have the authority to act on the proposals and are willing to commit to a pilot programme to prove the theoretical results can be turned into reality.
One or more conveyors are selected for a trial programme. While it is normal to select the “worst” conveyor, keep in mind that half measures do not get half results, so consider the project’s scope. Once a conveyor(s) has been selected, detailed proposals for retrofit can be obtained. An experienced person from the selected equipment supplier should overview the designs, offer feedback, and supervise the installation. Either outside contractors or in-house personnel can be used. Sufficient downtime must be allocated to properly modify the conveyor.
Measuring results from improvements is important but relatively easy to do. Photos and videos of before and after must be taken. Dust levels are measured using common instrumentation, spillage can be measured by placing buckets or trays in appropriate locations and carryback is measured by placing a tarp under several return idlers close to the discharge pulley.
The collected fugitive materials are weighed for comparison after the conveyor has been modified. Dust and spillage sampling locations should be marked so the tests can be accurately repeated after retrofitting and an improvement percentage can be calculated.
The length of time for collecting samples can vary from a day to a week and should give a good representation of the average or typical operating environment and weather conditions. It is important to keep the dust monitor running even if the conveyor is running empty, as maximum fugitive dust levels are often detected when running conveyors empty long enough that the carryback dries out and becomes airborne.
Usually, the results of the pilot programme are immediately noticeable, but there is a temptation to assume the problem has been fixed and to revert back to delaying maintenance without follow-up maintenance, causing the results to deteriorate. Therefore, the test period should extend to the next scheduled maintenance
shutdown with periodic inspections and adjustments made by the equipment supplier in the interim to ensure optimum efficiency.
To demonstrate the benefit of safety to a company’s bottom line, the U.S. Occupational Safety and Health Administration (OSHA) created the online tool, ‘$afety Pays’, which uses company-specific economic information to assess the potential economic impact of occupational injuries on that firm’s profitability. The programme estimates direct costs (claim cost estimates provided by the National Council on Compensation Insurance) and indirect costs (provided by the Stanford University Department of Civil Engineering) and weighs them against financial details supplied by the company.
Experience has shown that the motivation to take action developed in the classroom often defaults back to prior habits. Sometimes it is a lack of funding, an understaffed maintenance department or a “runtill-broke” mentality. The pressure to get back into production overwhelms the training that emphasises the understanding of the root causes of inefficiency and injuries such as fugitive materials. A productionat-all-costs approach means the problems and safety concerns never go away, and employees just have to accept the poor performance and added risks, which demoralises them.
It is incumbent upon management to take the safety and maintenance training as seriously as the staff, listen to the concerns of employees and fix the problem correctly the first time. As research has shown, companies that prioritise safety, training and updating equipment enjoy fewer safety incidents, less regulatory oversight, higher productivity and greater long-term profits. a
AfriSam
AfriSam is a leading construction materials group in southern Africa. Since establishing its first cement plant in 1934, the company has grown into a formidable construction materials group with operations in South Africa, Lesotho and Eswatini.
www.afrisam.co.za
Babcock
Through several business units, Babcock offers a range of products and services, including construction and mining equipment, engineering solutions for steam generation and power plants, crane hire and gear rental, industrial generators, welding equipment and DAF truck sales and service.
www.babcock.co.za
With more than 16 years of experience in Proximity Detection Systems solutions, Booyco Electronics has supplied over 6 500 sets of mining vehicle equipment installations across southern Africa, as well as more than 55 000 pedestrian RFID installations.
www.booyco-electronics.co.za
Bunting
Bunting’s range of magnetic separators and metal detectors for quarries and mines ensures the protection of crushers, screens and conveyors. Overband magnets, suspension magnets and pulley magnets automatically remove tramp ferrous metal from conveyed quarried rock. www.bunting-redditch.com
IPR is recognised across the SADC region as the pump, heavy duty slurry handling and dredging specialist operating in underground and surface mining, quarrying, construction, wastewater, petrochemical and oil and gas sectors. www.pumprental.co.za
LOADTECH Load cells Onboard Weighing are specialists in onboard weighing providing complete solutions onboard your heavy goods vehicle, primarily in the application of load cell and transducer systems for payload protection and accuracy in the commercial vehicle sector. www.loadtech.co.za
JBI Industrial Solutions specialises in a diverse range of weighing systems in partnership with PFREUNDT GmbH. We provide solutions for both mobile and static weighing needs. The PFREUNDT weighing systems are versatile and deliver significant benefits across various industries, including extraction, disposal, recycling, industry and agriculture.
www.jbisolutions.co.za
Pilot Crushtec International
Pilot Crushtec International (Pty) Ltd is South Africa’s leading supplier of mobile and semi-mobile crushing, screening, recycling, sand washing, stockpiling, compacting and material handling solutions. www.pilotcrushtec.com
Sandvik
As a world-leading mining equipment manufacturer, Sandvik Mining and Rock Solutions is committed to improving your productivity and profitability. Our products and services provide you maximum value in terms of performance, quality, safety, flexibility and total economy. www.rocktechnology.sandvik/en/
Astec
Astec Industries has been a global leader in providing innovative Rock to Road™ solutions since 1972, specialising in equipment for asphalt road building and aggregate processing. www.astecindustries.com
John Deere
John Deere offers a comprehensive range of construction equipment, including ADT’s, excavators, loaders, dozers, graders, skid steers and TLB’s, designed to enhance productivity, efficiency, and performance on job sites of all sizes. www.deere.africa/en/construction
Lintec & Linhoff
Lintec & Linnhoff is a global manufacturer and distributor of leading-edge solutions for the asphalt and concrete industries under the Lintec and Linnhoff brand names. Its products include asphalt mixing plants, concrete batching plants, pavement related technologies, and specialist concrete cooling solutions.
www.lintec-linnhoff.com
Weir Minerals
Weir Minerals Africa offers a wide range of equipment solutions including pumps, hydrocyclones, valves, dewatering equipment, wear-resistant linings, rubber products, screens and crushers – backed throughout the product lifecycle by high levels of aftermarket support.
www.global.weir
SANY
Sany Southern Africa is a subsidiary of Sany Group, a leading manufacturer of construction, mining and port machinery with over 20 R&D centres and manufacturing bases all over the world. www.sanysouthafrica.com
Designed with a unique combination of power and intelligence the TA 230 features market leading technology, an innovative weighing system, automatic traction contre, hill start assist, not to mention the superior cabin design to leave your operator feeling good. Simply put, a perfect mix of agility with outstanding performance.