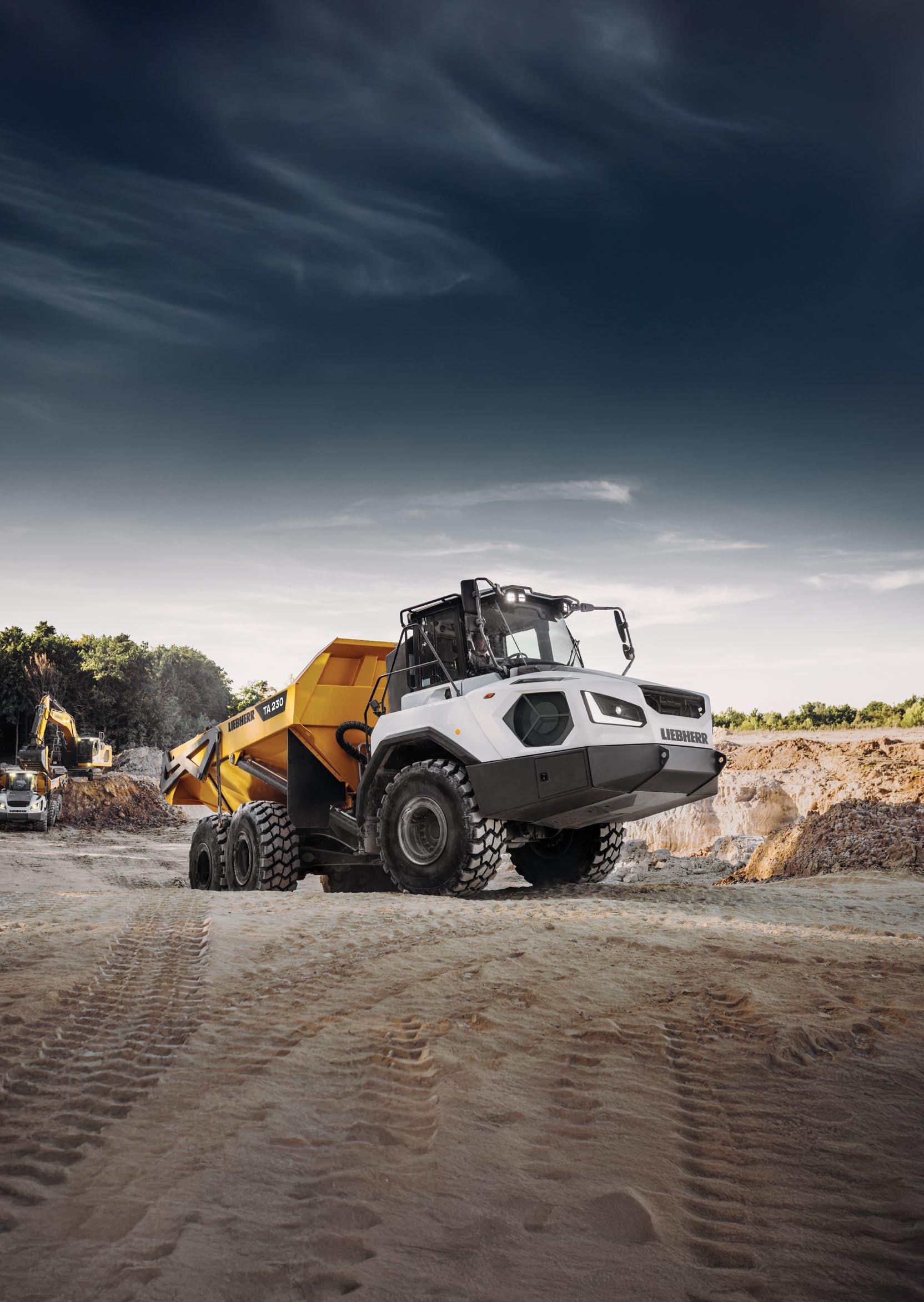
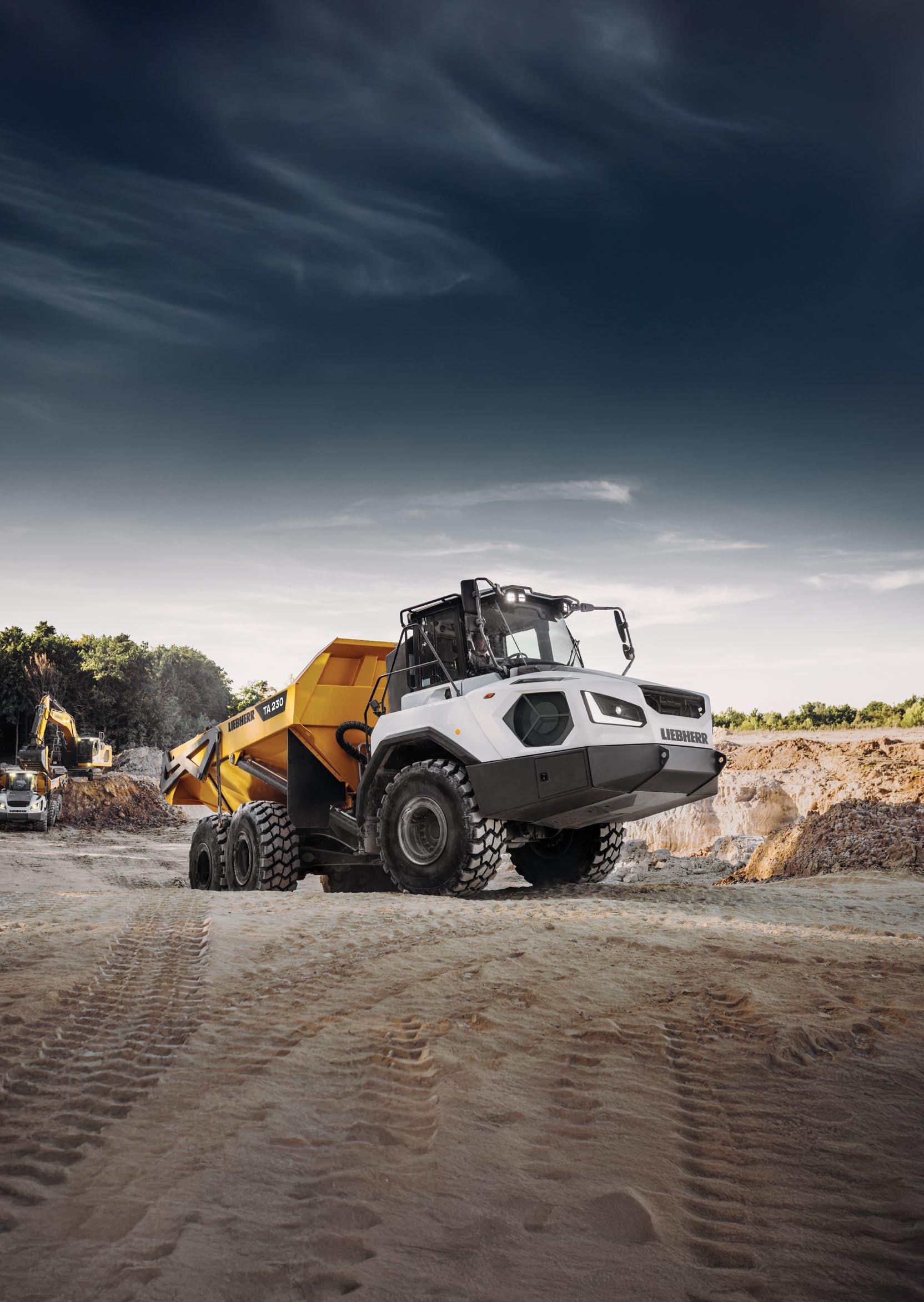
RAPID FLEET EXPANSION
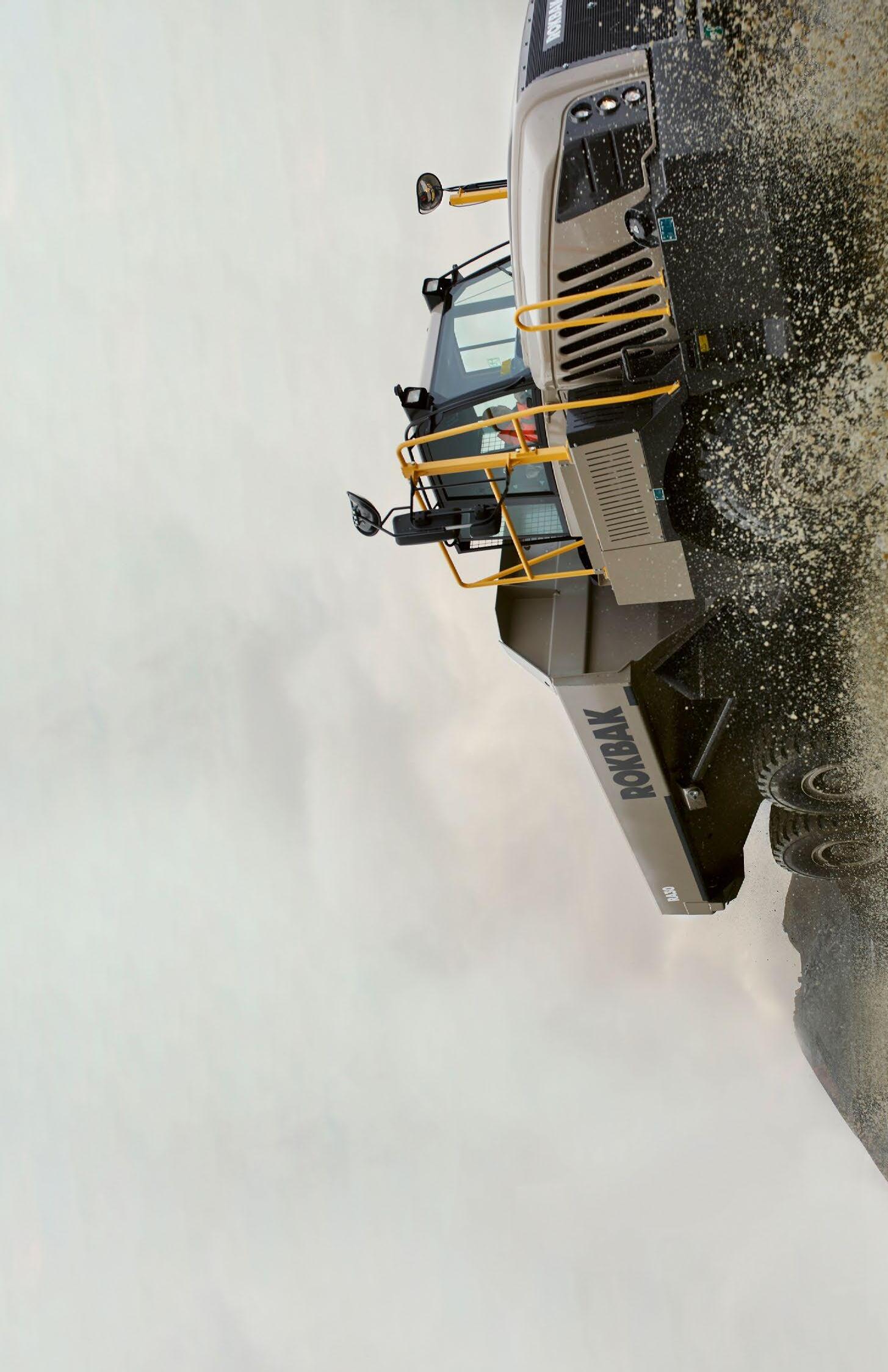
TIME FOR DATA- DRIVEN OPERATIONS
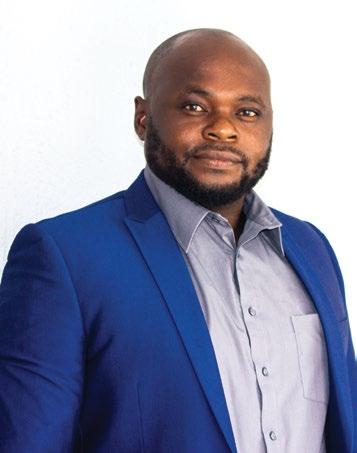
In a recent conversation with a respected captain of industry, my key takeaway from that interaction was that often quarries and their mainstream mining counterparts contend with balancing efficiency and safety in mining operations.
The question is, are they able to prioritise both effectively?
The importance of both parameters to the success of any operation cannot be reiterated enough. Efficiency in quarrying and mining is crucial for operational success, balancing high output, reduced downtime, maintained equipment, enhanced safety and minimised costs, leading to increased profitability and sustainability.
Equally, safety in mining is paramount because it protects workers from inherent hazards, reduces accidents and associated costs. A strong safety culture fosters a more productive and efficient workforce, as workers feel secure and are more likely to focus on their tasks without fear of accidents.
However, there is almost always a trade-off between productivity/efficiency and health and safety, and in most cases the latter wins, and it must not always be the case. Operations can find balance between their productivity/ efficiency drive and their safety efforts without in some way or other neglecting either of these operational parameters.
and predictive analytics, thus simultaneously reducing risks for miners and improving operational outcomes.
Although the quarrying sector is traditionally renowned for being resistant to the uptake of new technologies, it is encouraging to see the new-generation becoming a hi-tech industry that uses vast amounts of data and data insights to enhance efficiencies and improve safety.
Gathering this data is the province of the Internet of Things (IoT), where smart devices, cameras, wearable health tech, satellites, drones, sensors and onboard computers are used to track vehicles, material, staff and equipment. All of this technology enables insights that can enhance safety, boost production and ensure efficient operations.
Locally, data technologies are now taking root in the quarrying sector. For operations to be viable, teams must move earth as efficiently as possible by monitoring fleets constantly, designing routes and usage rosters, conducting training and managing performance output in order to ensure the most effective deployment of staff, equipment and fleets in real time.
MUNESU SHOKO
Publishing Editor
Email: munesu@quarryingafrica.com
LinkedIn: Munesu Shoko Quarrying Africa
How? Firstly, developing a robust safety culture is vital for balancing efficiency and safety. A safety culture is more than just rules and procedures; it is a holistic approach to safety that permeates the entire organisation. In a mining environment, a safety culture encompasses the shared values, attitudes, perceptions and behaviours of an organisation that prioritise safety in all aspects of work, aiming to create a safe and healthy environment for all employees.
Secondly, leveraging technology can significantly enhance both safety and efficiency in mining operations. Technology hugely enhances safety and efficiency in mining through automation, real-time monitoring
In addition, the industry has already seen the benefits of automation in dangerous working conditions, enabling the removal of people from harm’s way. For example, automated drilling rigs enable for remote control, enhancing safety especially when rigs are operating close to a highwall, or when there are unstable geological conditions on the bench. In addition, automated drills follow pre-determined instructions without exceeding limitations, thus helping to extend the life of consumables and components, leading to a lower total cost of ownership.
In the quest to achieve data-driven operations, this year’s IQSA Conference will especially highlight the importance of technology under the topical ‘Navigating a Changing Landscape’ theme. With the industry constantly evolving, it is important for quarry operators to be adaptable – to be open to new ideas and willing to adjust strategies as needed.
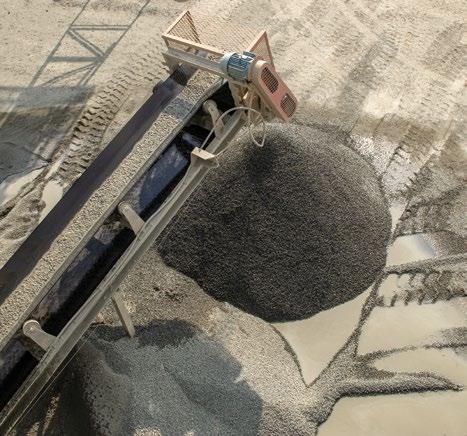
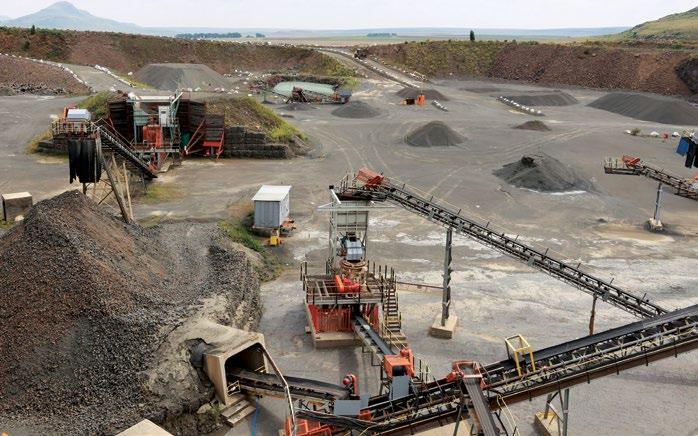
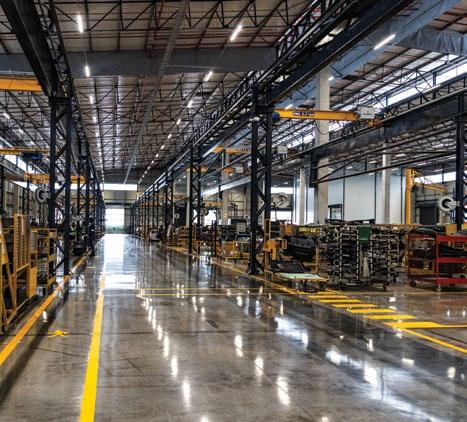
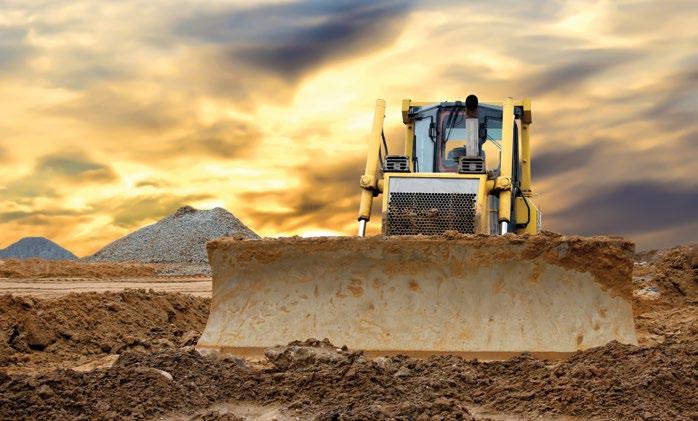
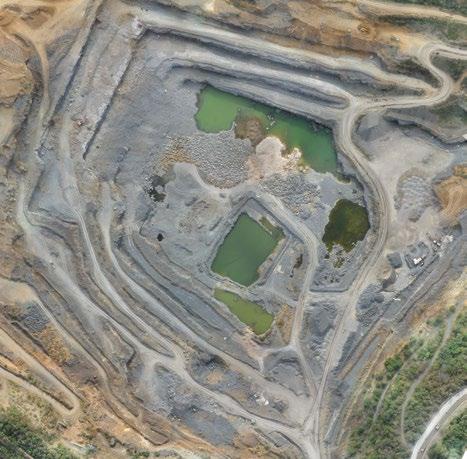
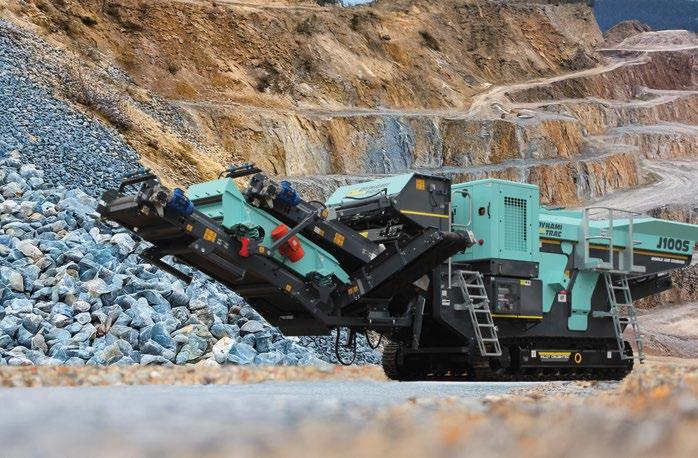
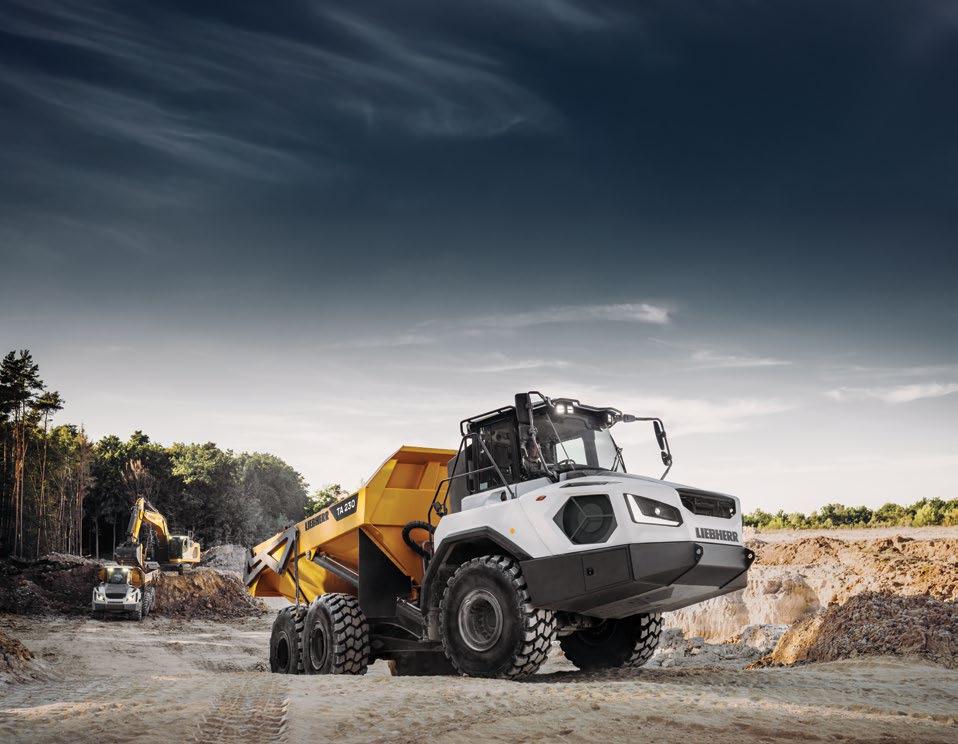
Publishing Editor: Munesu Shoko
Sub Editor: Glynnis Koch
Admin: Linda T. Chisi
Design: Kudzo Mzire Maputire
Web Manager: Thina Bhebhe
DRILLING
MAKING
EMBRACING
ADAPTING
ADDRESSING
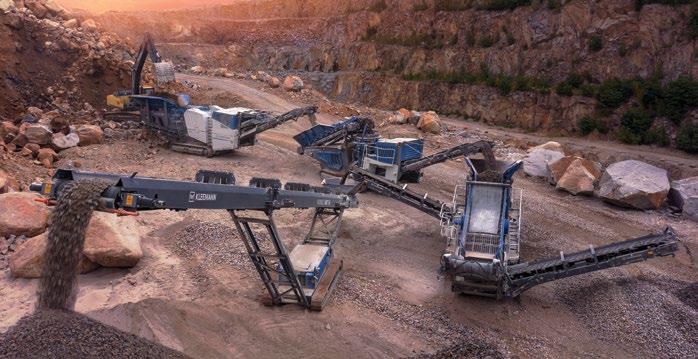
Quarrying Africa is the information hub for the sub-Saharan African quarrying sector. It is a valued reference tool positioned as a must-read for the broader spectrum of the aggregates value chain, from quarry operators and aggregate retailers, to concrete and cement producers, mining contractors, aggregate haulage companies and the supply chain at large.
© Quarrying Africa
Quarrying Africa, published by DueNorth Media Africa, makes constant effort to ensure that content is accurate before publication. The views expressed in the articles reflect the source(s) opinions and are not necessarily the views of the publisher and editor.
The opinions, beliefs and viewpoints expressed by the various thought leaders and contributors do not necessarily reflect the opinions, beliefs and viewpoints of the Quarrying Africa team.
Quarrying Africa prides itself on the educational content published via www.quarryingafrica.com and in Quarrying Africa magazine in print. We believe knowledge is power, which is why we strive to cover topics that affect the quarrying value chain at large.
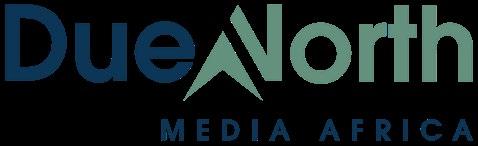
Printed by:
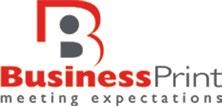
Contact Information
Email: munesu@quarryingafrica.com
Cell: +27 (0)73 052 4335
Several customers running the TA 230 to date have expressed satisfaction with Liebherr’s new machine concept, which has been developed especially for challenging off-road applications.
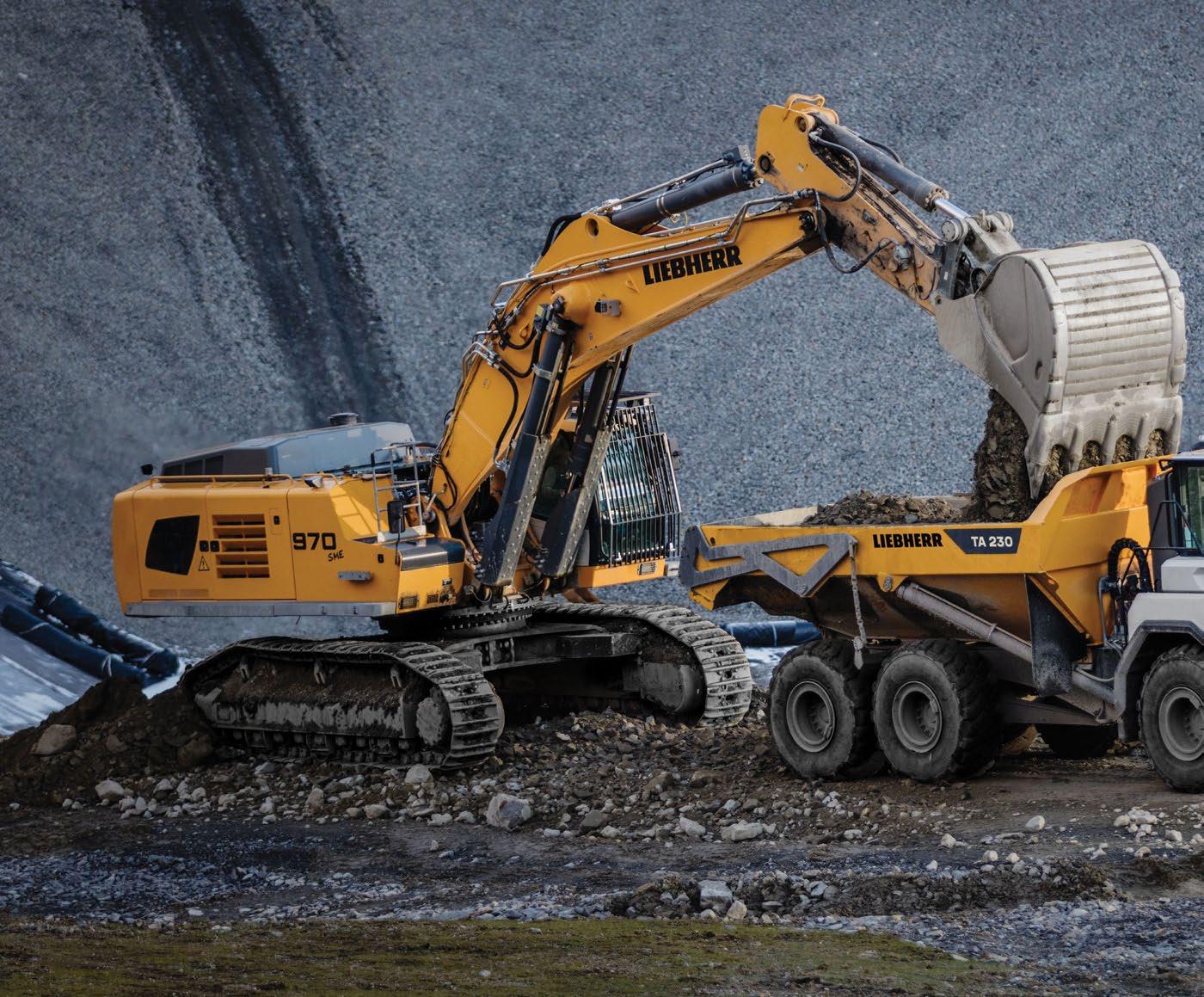
RAPID FLEET EXPANSION
Having taken delivery of its first Liebherr TA 230 articulated dump truck (ADT) in November 2023, a leading construction, plant hire and contract mining company based in Burgersfort, Limpopo province, South Africa, has rapidly grown its fleet to four, becoming the secondlargest TA 230 operator in southern Africa. By Munesu Shoko.
In June 2022, Liebherr-Africa made its local debut in the highly-contested ADT market in southern Africa by launching its first ADT model, the 28-tonne (t) payload Liebherr TA 230. Since then, the company has deployed a sizeable number of units in the market.
One of the companies running several units in its fleet is a well-known construction, plant hire and contract mining entity based in Burgersfort, a small mining town located in the Limpopo province of South Africa, near the border with the Mpumalanga province. In less than 18 months, the company has grown its fleet to four TA 230 units.
Proving their mettle
According to Papa Olifant, key account manager at Liebherr-Africa, the machines have been deployed at a major platinum mine in the Burgersfort area, where the client is executing one of its major mining contracts. While the 28-t payload was initially a concern for this type of application, the client has offset this limitation with the truck’s quick cycle times and fuel efficiency in tough underfoot conditions, thus driving maximum productivity at a lower cost of operation.
From the onset, says Olifant, the deal was a combination of “luck and opportunity” for Liebherr-
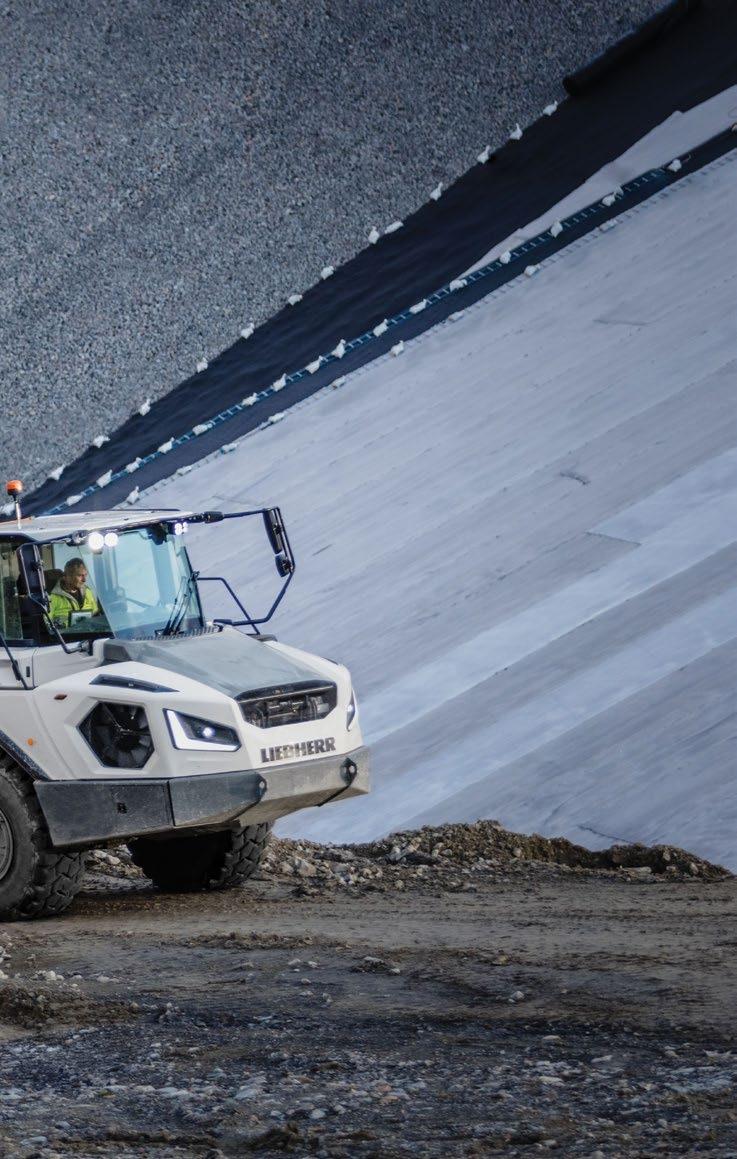
KEY TAKEAWAYS
Since the launch of the first Liebherr TA 230 in June 2022, several units are now operational across southern Africa
Having taken delivery of its first Liebherr TA 230 in November 2023, a Burgersfort-based mining contractor has rapidly grown its fleet to four
Feedback from the customer suggests that they have been impressed by the Liebherr machines’ performance to date, which explains the rapid expansion of the fleet
Based on the recent discussions, there is an indication that the client will ‘beef up’ their Liebherr ADT fleet significantly in the near future
Africa and its dealer partner, Kanu Equipment, which delivered the trucks and also looks after the client’s Liebherr fleet. In late 2023, the client went into the market for two ADTs, and one of the previous preferred suppliers did not have any stock available.
At the time, Liebherr-Africa had several units in stock and the client, who has a long-standing relationship with Kanu Equipment, opted to take one TA 230 on a trial basis in November 2023. Within two weeks of operation, the client decided to buy the demo and also placed an order for the second TA 230 unit, which was delivered in January 2024. During the course of last year, the client added a further two units, bringing to four their total TA 230 fleet.
“In fact, during the past 16 months, the client has grown not only their TA 230 fleet, but their Liebherr fleet at large. In less than two years, the client now operates a large number of Liebherr machines, including excavators, wheel loaders and dozers,” explains Olifant.
Beyond expectations
Feedback from the customer, says Olifant, suggests that they have been impressed by the Liebherr machines’ performance to date, which explains the rapid expansion of the fleet. In addition, he says, this demonstrates the importance of relationships in any capital equipment buying decision.
“While the client had never run Liebherr machines before, they were at ease making the decision to purchase because of their longstanding relationship with Kanu Equipment. While the equipment has proven its mettle, the complementary support from Kanu Equipment has also been central to the client’s decision to expand their fleet of Liebherr machines in a short space of time,” says Olifant.
Based on the recent discussions with the customer, Olifant tells Quarrying Africa that there is an indication that they will ‘beef up’ their Liebherr ADT fleet significantly in the near future. This will also be complemented by a large number of Liebherr excavators.
While size has been a limiting factor for LiebherrAfrica in the ADT market, currently offering only the 28-t payload model, Olifant is encouraged by the increased uptake of the TA 230 in southern Africa. “We are aware that the ADT market is currently driven by the 40-t and 45-t model sizes, and we are glad that Liebherr will soon be competing in that market segment, which will allow us to address the local market’s needs,” says Olifant.
4
Having taken delivery of its first Liebherr TA 230 in November 2023, a Burgersfort-based mining contractor has rapidly grown its fleet to four 28-t
While the 28-t payload was initially a concern for the type of application, the client has offset this limitation with the truck’s quick cycle times and fuel efficiency
265-kW
Powered by a 265-kW 6-cylinder Liebherr engine with a 12-litre displacement, the TA 230 is driven by an automatic 8-speed powershift transmission which ensures optimal force distribution
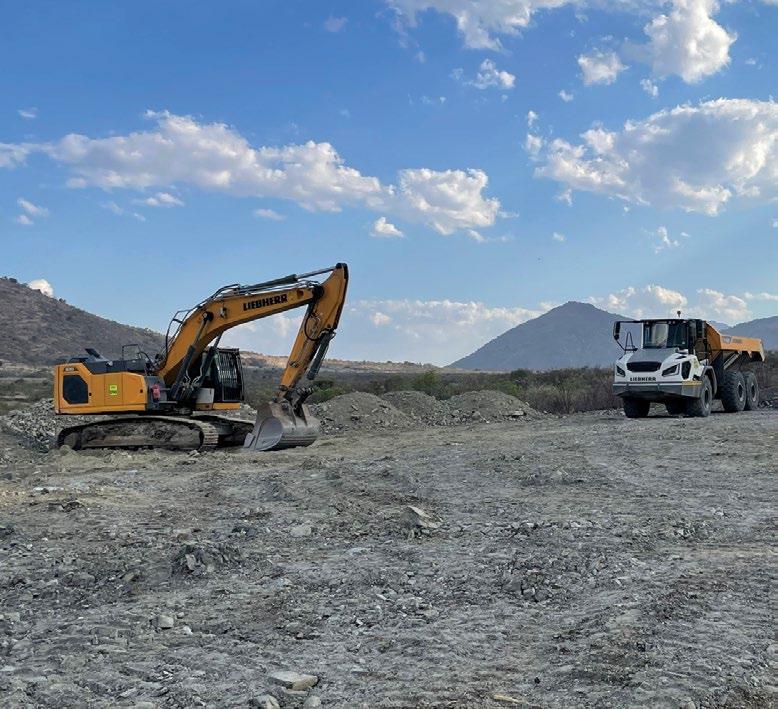
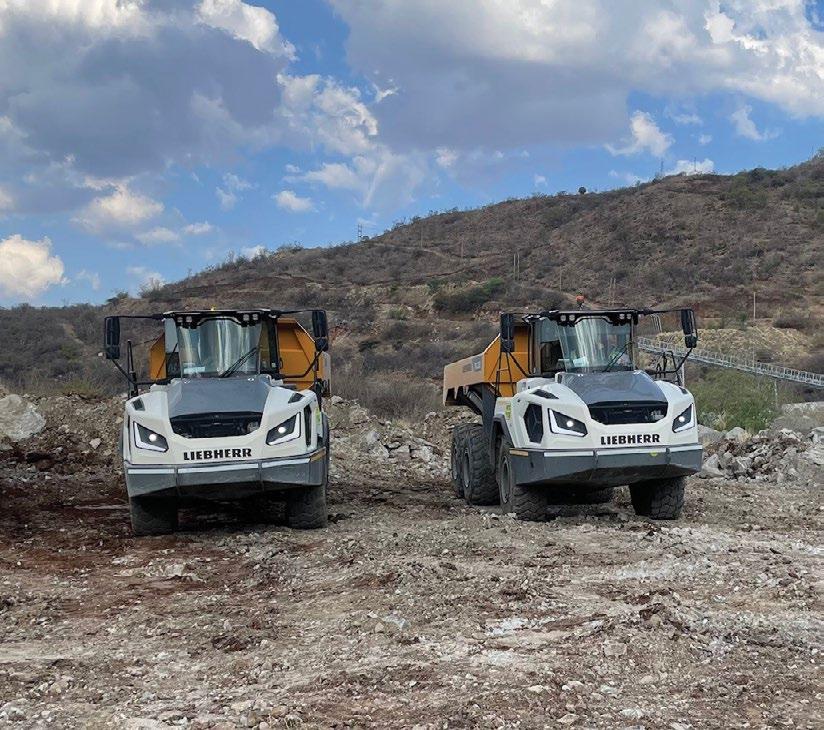
TA 230 in detail
Several customers running the TA 230 to date have expressed satisfaction with Liebherr’s new machine concept, which has been developed especially for challenging off-road applications. Modern designs in the front-end area create maximum ground clearance for greater off-road performance.
The newly designed articulated swivel joint creates sound off-road capability; it allows independent movement of the front and rear ends, thus ensuring maximum manoeuvrability. The positive-locking swivel joint with tapered roller bearing is perfect for the shear stresses associated with tough underfoot conditions, while it also withstands maximum loads and provides optimal force distribution.
The front and rear axles of the machine are secured using sturdy A-rods at the articulated swivel joint and at the rear end. On front, the truck uses hydro-pneumatic suspension for maximum comfort, which is key to the
smooth driving. The shock absorbers at the articulated swivel joint and the position of the separate and oscillating A-rods of the rear axles at the rear end, provide maximum ground clearance.
Powered by a 265-kW 6-cylinder Liebherr engine with a 12-litre displacement, the TA 230 Litronic is driven by an automatic 8-speed powershift transmission which ensures optimal force distribution. The machine impresses with great driving performance and massive pulling force, even in the most difficult ground conditions and on challenging gradients.
A combination of balanced weight distribution, permanent 6 x 6 all-wheel drive, solid, flexible mounting and large bank angle as well as the machine’s high ground clearance, enable the TA 230 Litronic to deliver unparalleled performance on uneven terrain.
The actively controlled inter-axle differential locks mean that the Liebherr TA 230 has automatic traction control. As soon as one axle experiences wheelspin, it is decelerated, and the traction is intelligently redistributed to the other axles. In addition to maximum forward drive, this reduces the power requirement and therefore translates into lower fuel consumption.
Efficiency is further enhanced by the smart gear selection, which enables the machine to adjust automatically to its current speed and load to ensure optimum torque and fuel consumption at all times. The machine therefore automatically reduces its fuel consumption per tonne of transported material.
With productivity in mind, the optimised trough ensures that more material can be moved in a short time. The front of the trough – designed for the effective transport of a 28-t payload – is straight and the sills are low so that loading with a wheel loader, for example, is easily possible across the entire length of the truck.
A standard Liebherr weighing system shows the current payload during loading on the display in the operator’s cab, helping eliminate guesswork in loadout processes. An optional loading light on both sides at the back of the operator’s cab shows the loading level outdoors.
“In order to accelerate the release of the material during unloading, the inner edges of the new trough are tapered. The two tipping cylinders at the side give the TA 230 Litronic high tipping pressure. The load can be tipped against the slope easily and quickly,” concludes Olifant. a
The machines have been deployed at a major platinum mine in the Burgersfort area, where the client is executing one of its major mining contracts.
Feedback from the customer suggests that they have been impressed by the Liebherr machines’ performance to date.
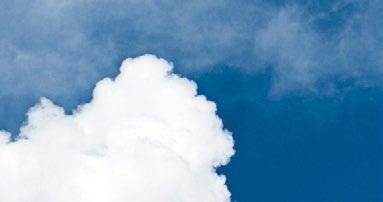
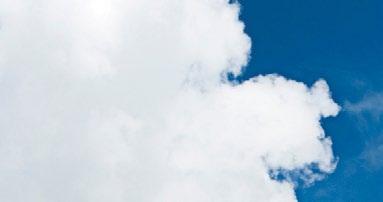
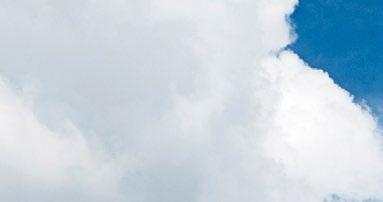


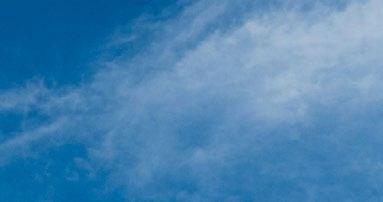
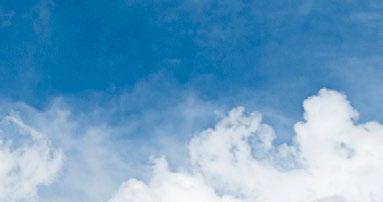
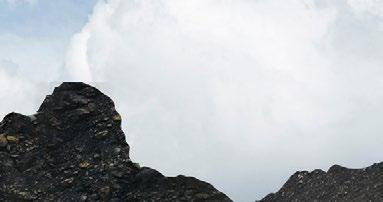
Designed with a unique combination of power and intelligence the TA 230 features market leading technology, an innovative weighing system, automatic traction contre, hill start assist, not to mention the superior cabin design to leave your operator feeling good. Simply put, a perfect mix of agility with outstanding performance.

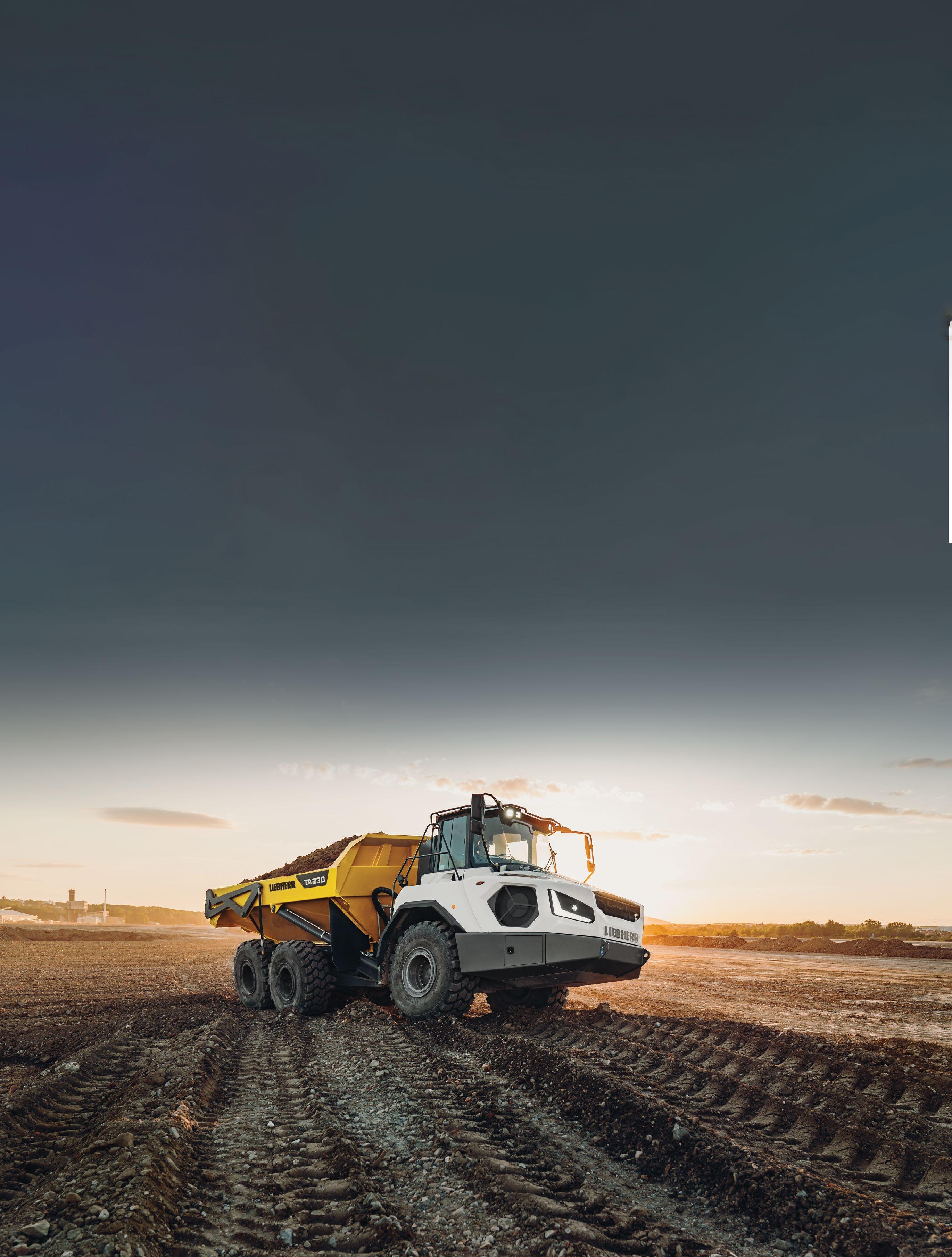
Articulated Dump truck
SARS contended that ‘bulk’ in terms of the ordinary dictionary meaning, suggests that the condition of aggregates does not change in the process of beneficiation.
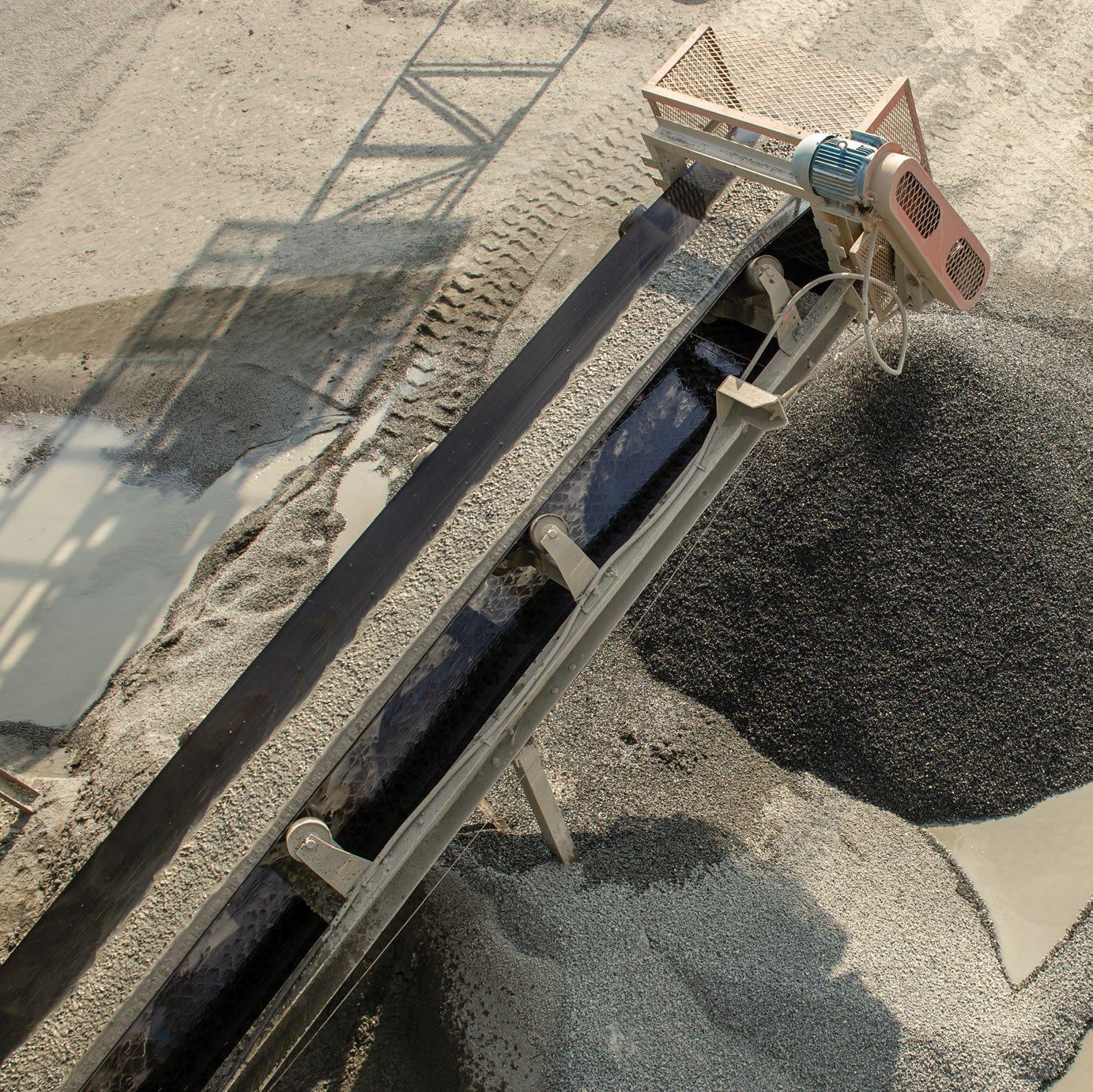
ROYALTY TAX RELIEF FOR AGGREGATES INDUSTRY
Following a protracted legal dispute between ASPASA, the surface mining industry association, and the South African Revenue Services (SARS), regarding the calculation of royalties for the extraction of aggregates, the High Court of South Africa – Gauteng Division, has granted relief in favour of ASPASA. The ruling marks a significant milestone for the aggregates industry. By Munesu Shoko.
For many years now, payment of royalties has been a hotly contested issue between quarry owners in South Africa and SARS, as to where the value of a mined product needs to be determined in order to calculate exact payments.
Letisha van den Berg, director of ASPASA, explains that the industry’s dispute with SARS existed over the first point of sale at which the value of royalties
needed to be calculated. The ‘taxman’ argued that royalties should be calculated from any ‘stockpile’ from which the relevant aggerate product is sold, while the industry insisted that it should be from the ‘muck’ pile.
Background
ASPASA has always engaged in productive discussions with SARS and National Treasury since
Photo courtesy of Afrimat
28
ASPASA has always engaged in productive discussions with SARS and National Treasury since the introduction of the Mineral and Petroleum Resources Act 28 of 2008
KEY POINTS
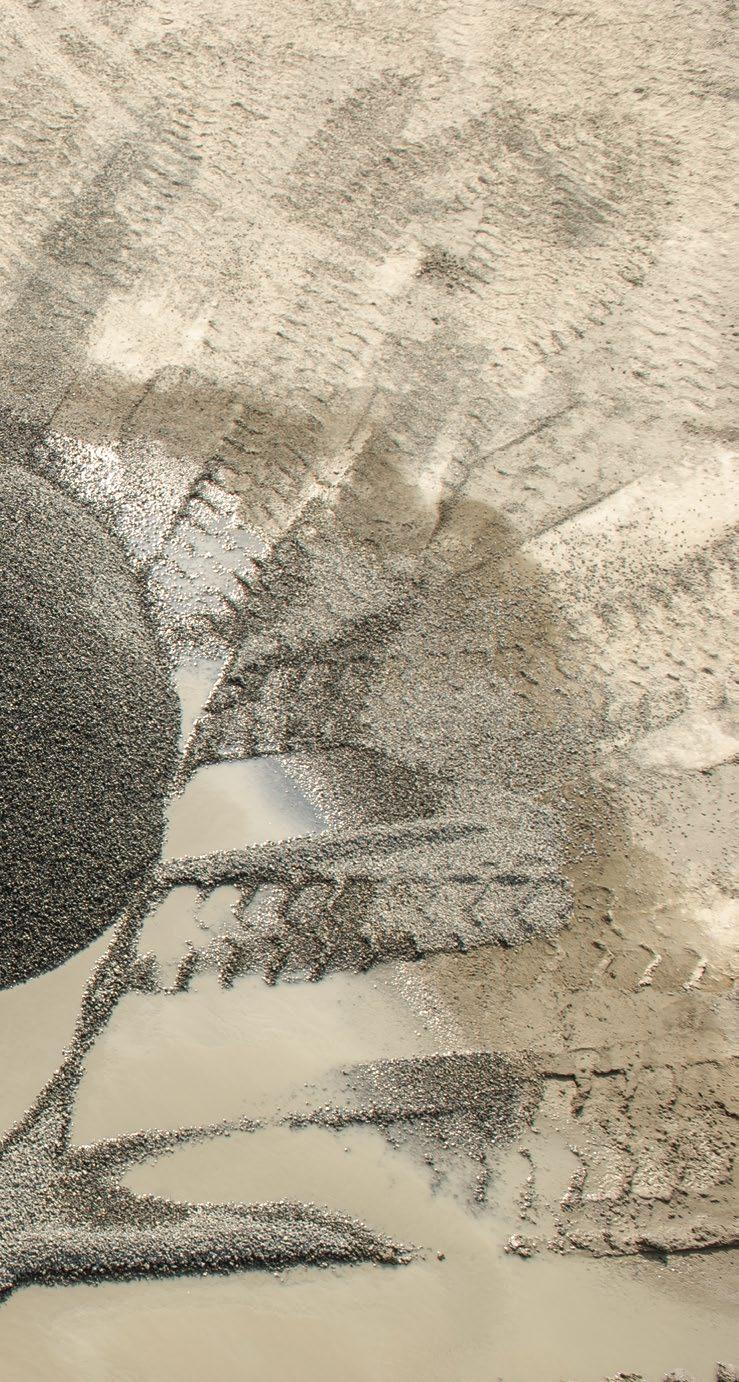
2012
In 2012, an ASPASA member obtained a non-binding opinion confirming that, according to SARS, the condition specified in Schedule 2 of the aggregates pertains to the bulk rock on the quarry floor post-extraction, commonly referred to as the muck pile
For many years now, payment of royalties has been a hotly contested issue between quarry owners in South Africa and SARS
The point of contention has been as to where the value of a mined product needs to be determined in order to calculate exact payments
Following a protracted legal dispute between ASPASA, the High Court of South Africa – Gauteng Division, has granted relief in favour of ASPASA
SARS applied for leave to appeal the High Court judgment to the Supreme Court of Appeal (SCA).
ASPASA opposed the application and on March 5, 2025, SARS’ application for leave to appeal to the SCA was dismissed with costs
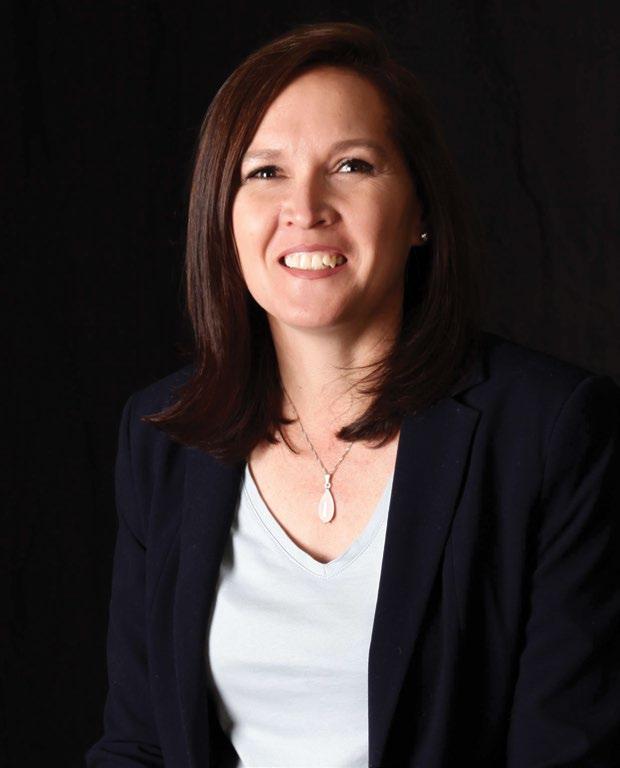
the introduction of the Mineral and Petroleum Resources Act 28 of 2008. The discussions were aimed at ensuring that ASPASA members, primarily small businesses and individual stakeholders operating small surface mines, remained compliant with the Act.
In 2009, ASPASA commissioned the independent multinational auditing firm KPMG to develop a memorandum outlining the appropriate approach for aggregate producers to implementing the Act. The resulting document was disseminated to members as an Industry Practice Note (IPN), which was also shared with SARS for its consideration.
The concept of ‘muck pile’ was introduced to National Treasury in 2009 to clarify its significance.
In 2011, ASPASA requested KPMG to finalise the draft IPN, which was subsequently submitted to SARS. Notably, there were no objections raised by either SARS or National Treasury regarding the IPN. Furthermore, SARS was invited to present at the IQSA Conference that same year.
In 2012, an ASPASA member obtained a nonbinding opinion confirming that, according to SARS, the condition specified in Schedule 2 of the aggregates pertains to the bulk rock on the quarry floor post-extraction, commonly referred to as the muck pile. Thus, gross sales calculations were to be based on this definition.
“In 2023, ASPASA proactively sought a Declarator from the High Court to clarify this matter for its members. The court date was scheduled for November 29, 2024, and on December 6, 2024, relief was granted in favour of ASPASA. This favourable ruling marks a significant milestone for the aggregates industry.
To provide context, where the aggregate producer sells beneficiated aggregate products after the muck pile, they had to calculate their gross sales for royalty purposes on “what they would have received” if they had sold the aggregate product in the muck pile condition. So, it is a deemed gross sales value and not what they actually receive when the beneficiated aggregate product is sold.
However, in 2019, SARS issued Interpretation Note 108, indicating a departure from the initial interpretation and stating that tax should be calculated after the beneficiation of the aggregate, specifically on the stockpile.
“In 2023, ASPASA proactively sought a Declarator from the High Court to clarify this matter for its members. The court date was scheduled for November 29, 2024, and on December 6, 2024, relief was granted in favour of ASPASA. This favourable ruling marks a
Letisha van den Berg, director of ASPASA
The question for the court’s determination was whether the word ‘bulk’ refers to, firstly, aggregates upon extraction (i.e., at the socalled muck pile), or secondly, to the beneficiated state of the aggregates stockpile at the time of the disposal of aggregates.

significant milestone for the aggregates industry,” says Van den Berg.
Point of contention
Andries Myburgh, Executive – Tax at ENS Attorneys, the legal company that represented ASPASA and its coapplicants, tells Quarrying Africa that the case concerned the meaning of the word ‘bulk’ in relation to aggregates (a mineral resource) listed in Schedule 2 of the Mineral Royalty Act.
It was a common cause fact that aggregates at the so-called ‘muck pile’ (the blasted rock at the quarry floor) are already commercial and this is the first saleable point for the mineral resource (aggregates), explains Myburgh. Products sold directly from the muck pile include gabion, armour rock and various other products used in public infrastructure such as bridges and roads.
SARS contended that ‘bulk’ in terms of the ordinary dictionary meaning, suggests that the condition of aggregates does not change in the process of beneficiation. It further argues that bulk remains bulk at whatever stage of beneficiation the aggregate is found at the time of transfer. Therefore, in SARS’ interpretation, gross sales were to be determined in terms of section 6(2)(a) and not section 6(2)(b) of the Royalty Act.
In its defence, ASPASA contended that aggregates in their unprocessed form (at the muck pile) is the first saleable point. Beneficiation of aggregates after the muck pile results in the transfer (i.e., disposal) of aggregates in a condition other than as ‘bulk’. Therefore, gross sales are supposed to be determined on aggregates as extracted –at the muck pile.
The question for the court’s determination was whether the word ‘bulk’ refers to, firstly, aggregates upon extraction (i.e., at the so-called muck pile), or secondly, to the beneficiated state of the aggregates stockpile at the time of the disposal of aggregates, explains Myburgh.
Court’s findings
On December 6, 2024, relief was granted in favour of ASPASA and its co-applicants and made a declaratory order as follows: ‘Bulk’ as used in respect of aggregates in Schedule 2 to the Mineral and Petroleum Resources Royalty Act, 28 of 2008, means the condition in which shot rock (blasted rock) exists at the muck pile prior to processing (i.e., crushing or other form of beneficiation). Accordingly, aggregates as at the muck pile is the condition stipulated by Schedule 2.
Myburgh explains that the court adopted a purposive approach – analysing the purpose, text and context, in this sequence. The purpose of the Royalty Act presents a vantage point that assists in the consideration of both text and context.
The ostensible purpose of section 6(2) of the Royalty Act is to, firstly, set a base condition for purposes of determining the royalty to avoid manipulation of the royalty by extractors, and secondly, not to penalise beneficiation where the condition has changed through a process of beneficiation.
Therefore, the dual purpose of the Royalty Act is to promote beneficiation, and to prevent undercompensation of the State by setting a base condition at which the royalty is determined. The court referred to the preamble read with section 3(1) of the MPRDA, out of which the Royalty Act was promulgated: South Africa’s mineral resources belong to the nation and the State is the custodian thereof.
In terms of text, SARS contended for the ordinary grammatical meaning of ‘bulk’ in ordinary parlance. However, the court found that the word ‘bulk’ in Schedule 2 is used in a technical context in the schedule in which it appears. In such an instance, the presumption is that the technical meaning of the term is to be interpreted. The list of the contents of Schedule 2 demonstrates that the term is used in respect of mineral resources in scientific terms.
ASPASA contended that aggregates in their unprocessed form (at the muck pile) is the first saleable point.
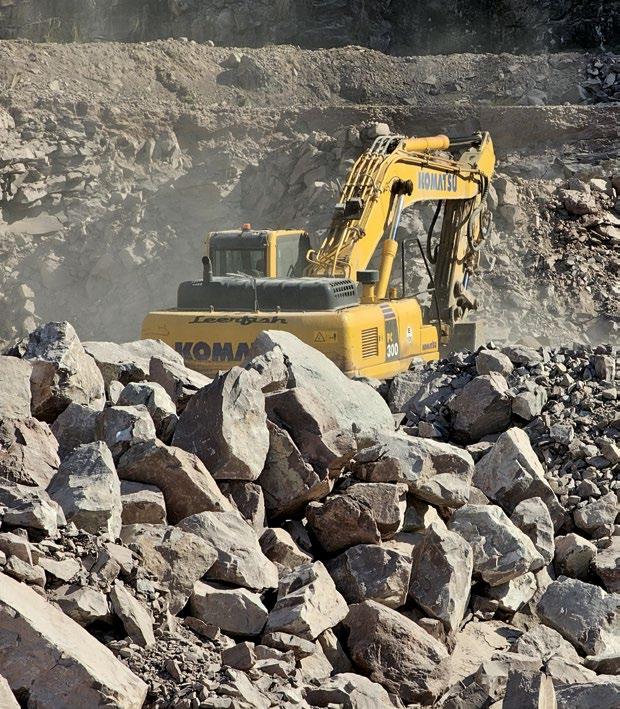
The Royalty Act is passed with reference to the mining industry and the words used need to be understood by those in that industry, even if it differs from the ordinary meaning of the word.
In terms of context, the court noted that Schedule 2 of the Royalty Act is the immediate context of the term ‘bulk’. The Royalty Act distinguishes between refined and unrefined mineral resources: refined minerals and their conditions are specified in Schedule 1; other minerals are defined into subcategories of concentrating, containing mineral and materials that do not contain any metal; aggregates fall within the unrefined minerals category and are referred to in Schedule 2 in the conditions specified for such materials as ‘bulk’.
SARS contended that its interpretation did not penalise beneficiation or value adding processes and that any beneficiation required to bring unrefined metals to the condition specified was already recognised and incentivised in the rate for unrefined minerals, which is lower than the rate that would be leviable on those minerals had they been transferred at the mine face.
The court held that aggregates are already commercially viable at the mine face (at muck pile) and as such, the royalty must recognise it as the first stockpile. The beneficiation of aggregates is achieved after the muck pile by crushing, washing and screening. The court found that SARS’ interpretation lost sight of the difference in price between aggregates at the muck pile and those that have undergone beneficiation. This interpretation renders section 6(2)(b) totally redundant in the context of aggregates.
State of affairs
Following the December 6, 2024 court ruling, SARS applied for leave to appeal the High Court judgment to the Supreme Court of Appeal (SCA) before the judge (Judge Labuschagne J). ASPASA opposed the application and on March 5, 2025, SARS’ application for leave to appeal to the SCA was dismissed with costs.
According to Myburgh, unless SARS petitions the SCA directly for leave to appeal the High Court judgment to the SCA, the matter ends here, and it becomes a final binding legal precedent on the meaning of the word ‘bulk’.
“From a financial standpoint, this is significant for aggregate producers because it confirms that the calculation of the mineral royalty on the value of aggregates at the muck pile as opposed to on the value of beneficiated products sold after the muck pile, is the correct approach. Based on SARS’ approach, the royalty would have been significantly higher, which impacts the financial viability of quarries, especially smaller operations,” concludes Myburgh. a Wacker Neuson excavators set the standard with efficient engines and zero-emission options for more sustainable construction. Visit your nearest dealer in South and SubSaharan Africa to explore cleaner, smarter excavation solutions.
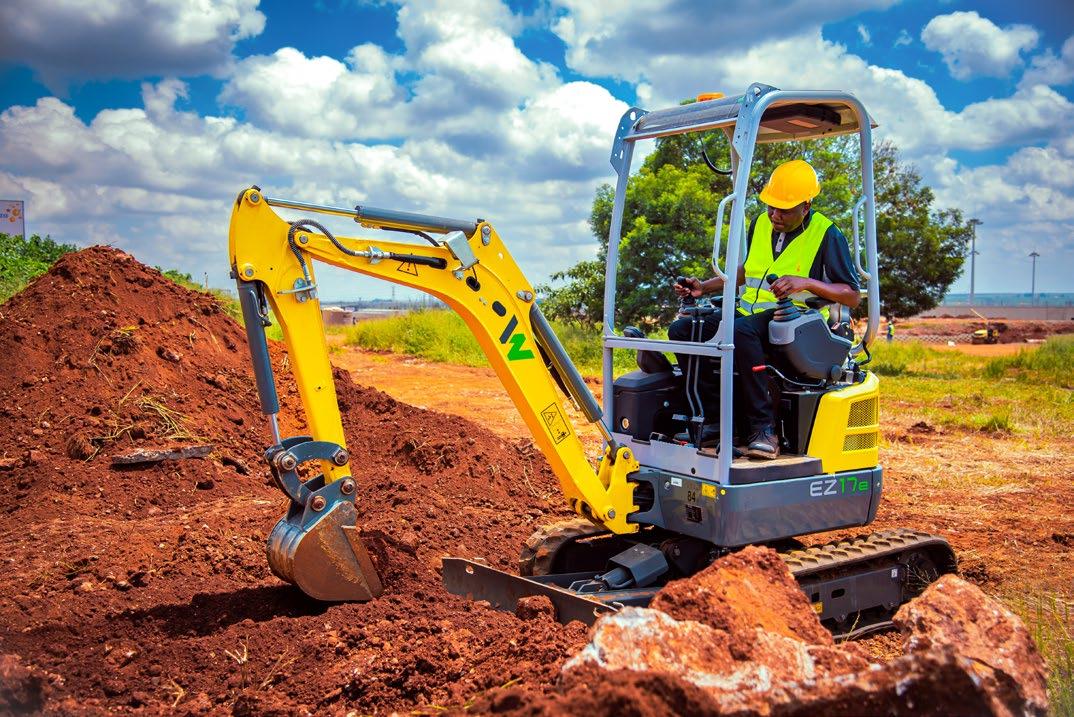
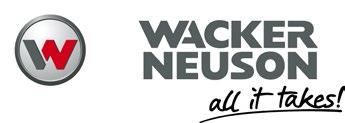
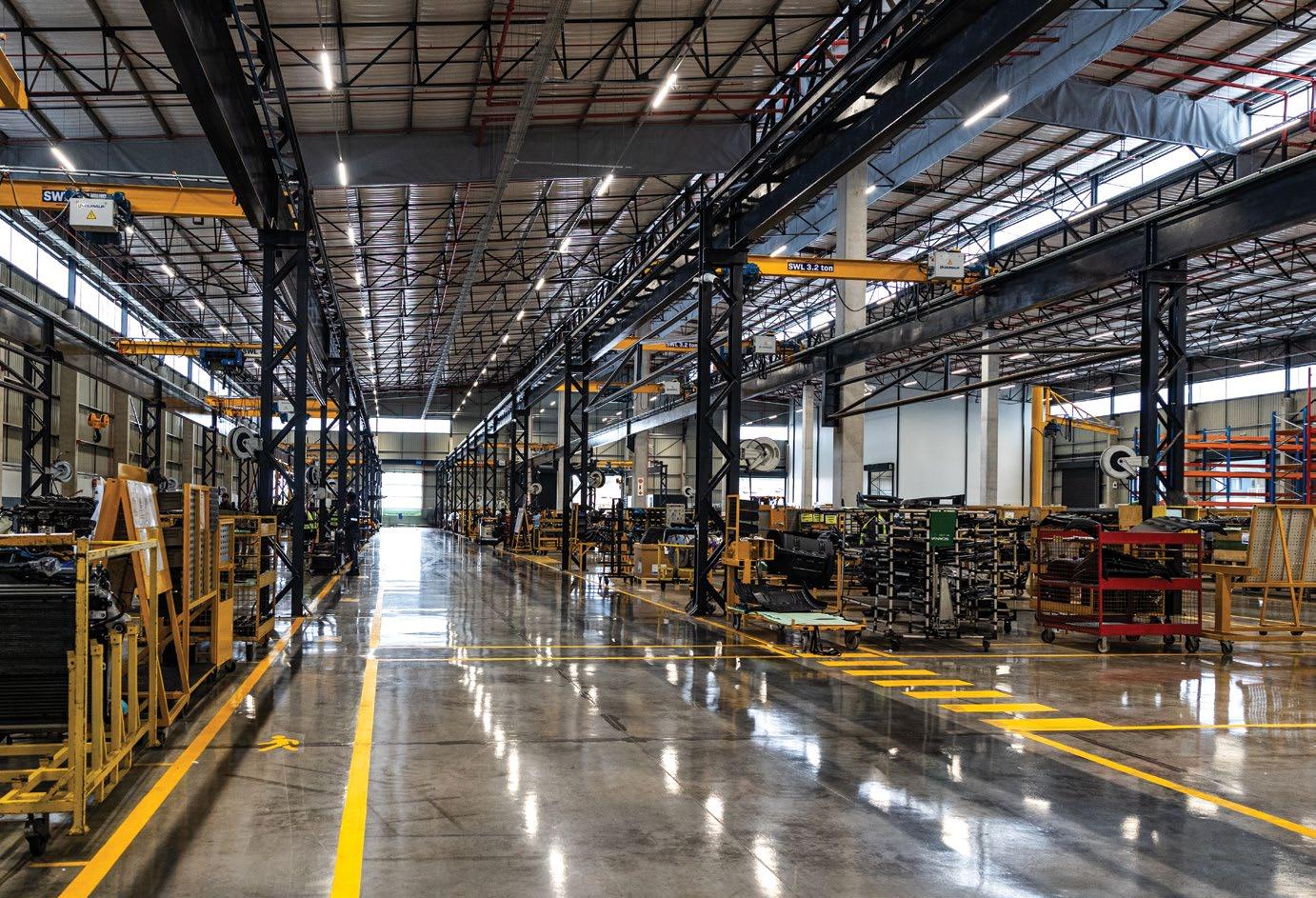
BOOSTING PRODUCTION CAPACITY AND EFFICIENCY
In a year that Scania celebrates 30 years in South Africa, 2025 marks yet another milestone following the company’s inauguration of its new Regional Product Centre (RPC). Officially opened on February 18, 2025, the facility boosts production capacity and efficiency, thus ensuring faster delivery times and enhanced customer support.
Munesu Shoko attended the inauguration and filed this report for Quarrying Africa
Testament to its longstanding commitment to the southern African market and to its dedication to driving progress in the local transport industry,
Scania Southern Africa has invested in a new RPC.
The investment comes exactly a year after the company relocated its head office from its long-time Aeroton base to a state-of-the-art facility in Constantia Kloof, reflecting its commitment to growth and innovation in the region.
“For over 30 years, Scania has been a steadfast partner to the local automotive, transport and logistics industries in southern Africa. Our dedication to this market extends beyond selling
KEY POINTS
Testament to its longstanding commitment to the southern African market, Scania Southern Africa has invested in a new Regional Product Centre
The investment comes exactly a year after the company relocated its head office from its long-time Aeroton base to a stateof-the-art facility in Constantia Kloof
With this facility, Scania is positioning itself to best serve its customers with high-quality, locally assembled products, ensuring faster delivery times and enhanced support
By consolidating various functions at one location, including parts warehouse and logistics, the facility maximises production efficiencies and reduces environmental impact
Scania Southern Africa has invested in a new Regional Product Centre.
30
In a year that Scania celebrates 30 years in South Africa, 2025 marks yet another milestone following the company’s inauguration of its new Regional Product Centre

“By consolidating our warehouse and assembly plant on the same site, we are reducing our carbon footprint significantly. To provide context, we are currently recycling 98% of all waste at the facility, and our target in 2025 is to further improve on this number through new packaging technologies.
vehicles; we are here to create lasting solutions to the industry and contribute meaningfully to the economy and local communities in which we operate,” says Erik Bergvall, MD of Scania Southern Africa.
Scania’s presence in southern Africa, adds Bergvall, is more than just a business; it is about partnerships, investments and trust. The company, he says, has over the years collaborated with its customers, employees and industry partners to shape the future of industry in southern Africa. The opening of the RPC reflects the company’s confidence in the region’s long-term potential and its ambition to support economic growth,
3 200
With 10 500 m² under roof, the new Scania RPC has the capacity to assemble 3 200 units a year, encompassing both trucks and bus chassis on the same line
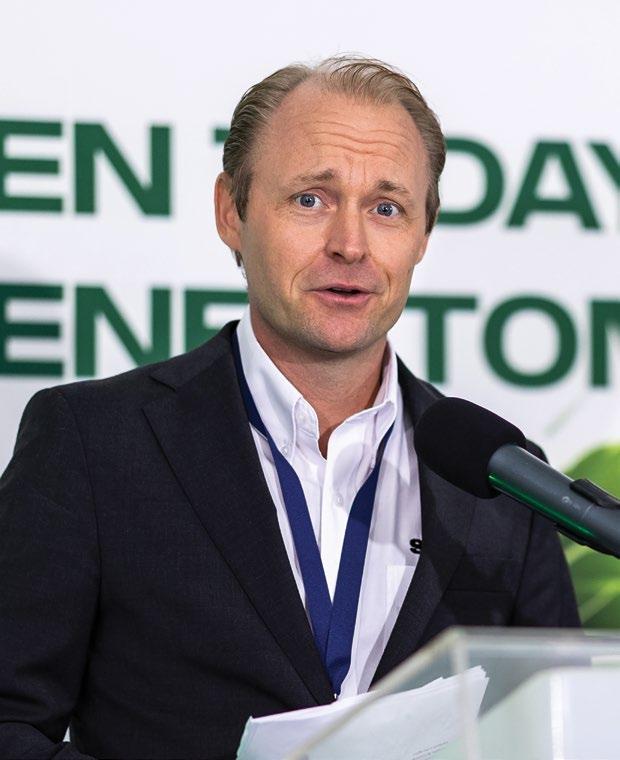
“One exciting aspect about this development is the increased capacity and efficiency of our assembly operations. As demand for Scania’s sustainable solutions grows, we must have the infrastructure to meet this demand in an efficient way.
job creation and sustainable development.
“With this facility, we are positioning ourselves to best serve our customers with high-quality, locally assembled products, ensuring faster delivery times and enhanced support,” says Bergvall. “One exciting aspect about this development is the increased capacity and efficiency of our assembly operations. As demand for Scania’s sustainable solutions grows, we must have the infrastructure to meet this demand in an efficient way. This plant provides us with the capability to increase production, ensuring that we remain agile and responsive to the needs of our customers across southern Africa.”
Erik Bergvall, MD of Scania Southern Africa
Christian Håkansson, RPC manager at Scania Southern Africa
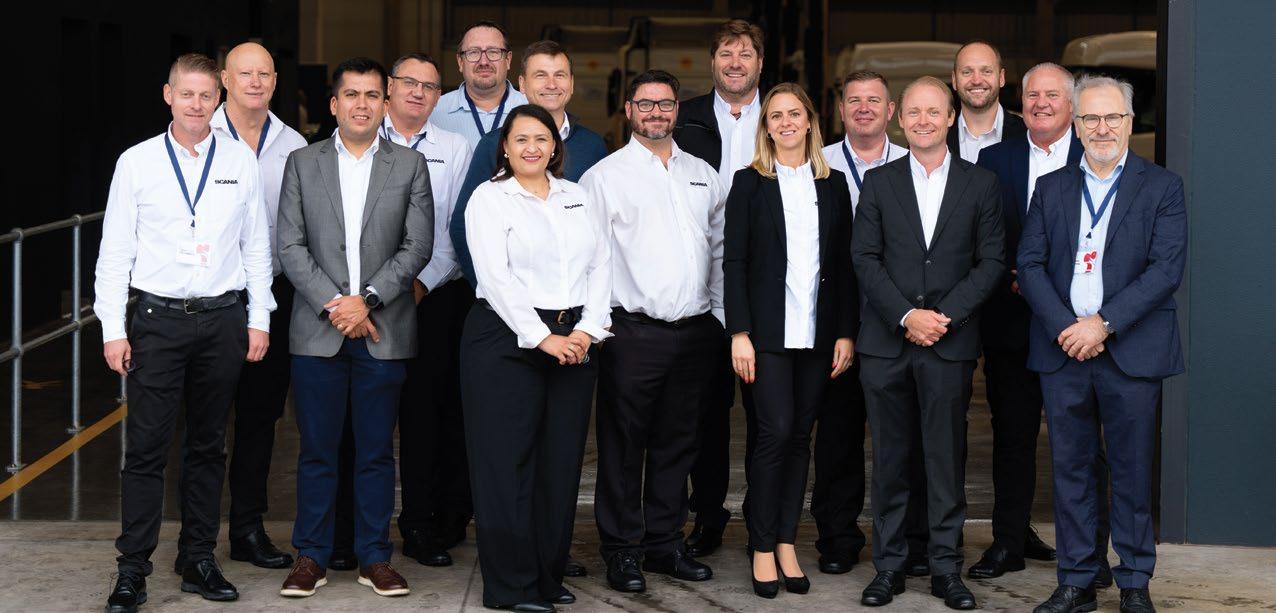
On time and within budget
The project, which commenced in mid-2023, was successfully completed in late 2024, with occupation taking place just before Christmas last year. Built under a strategic collaboration with Redefine Properties, the project was completed on time and within budget, confirms Christian Håkansson, RPC manager at Scania South Africa.
“When the decision was made to relocate our head office from Aeroton to Roodepoort, we carefully considered various options within South Africa,” explains Håkansson.
“After a thorough evaluation, we chose to consolidate Scania’s administrative operations into a single site and build a new production plant in Nasrec, Johannesburg.”
As the years passed, the previous assembly plant in Aereton was expanded as market needs dictated. However, the expansions were just added on, and the facility was never purpose-built, thus impacting efficiencies. One of the benefits of moving the assembly plant within the same area is that Scania managed to retain 100% of its staff, meaning that the company retained all of its important production skills.
Facility overview
With 10 500 m² under roof, the new Scania RPC has the capacity to assemble 3 200 units a year, encompassing both trucks and bus chassis on the same line.
With a staff complement of 83 people, the facility has a 14,5% female representation, which Cornelius Viljoen, workshop manager RPC South Africa at Scania South Africa, is proud of. While there is room for improvement, Viljoen says this achievement has taken greater effort to achieve and the company has plans to further improve in its quest to put more women into ‘blue collar’ working environments.
By consolidating various functions at one location, including parts warehouse and logistics, the facility
maximises production efficiencies. “Our new assembly plant is strategically located next to our parts storage and distribution centre, which strengthens synergies between our assembly operations and parts supply chain,” says Bergvall. “This integration translates into faster turnaround times, improved logistics and customer experience.”
Consolidating various functions at one site has also helped Scania reduce its environmental impact. “By consolidating our warehouse and assembly plant on the same site, we are reducing our carbon (CO2) footrpint significantly. To provide context, we are currently recycling 98% of all waste at the facility, and our target in 2025 is to further improve on this number through new packaging technologies,” explains Håkansson.
Evolution in operation
Commenting on the significance of the new assembly plant, Bergvall says the facility represents an evolution in Scania’s operations. The expansion, he adds, also means greater job opportunities, youth development and a stronger contribution to the South African economy. By investing in local talent and infrastructure, Scania is not only supporting economic growth, but is also helping shape the future of transport in the region.
Bergvall says the investment is proof of Scania’s commitment to strengthening its presence in key markets in the world. This, he says, reflects the confidence the company has in the African market – its potential to drive sustainable and innovative transport solutions.
“Scania’s focus on efficiency, sustainability and innovation will not only benefit the local market, but also contribute to our overall worldwide mission to drive the shift towards sustainable transport solutions. As we look ahead, our goal is to be at the forefront of a future where transport is smarter, cleaner and more efficient,” concludes Bergvall. a
Scania Southern Africa executives during the inauguration ceremony of the new RPC.
98%
Scania is currently recycling 98% of all waste at its new assembly facility, with a target to further improve on this number in 2025 through new packaging technologies
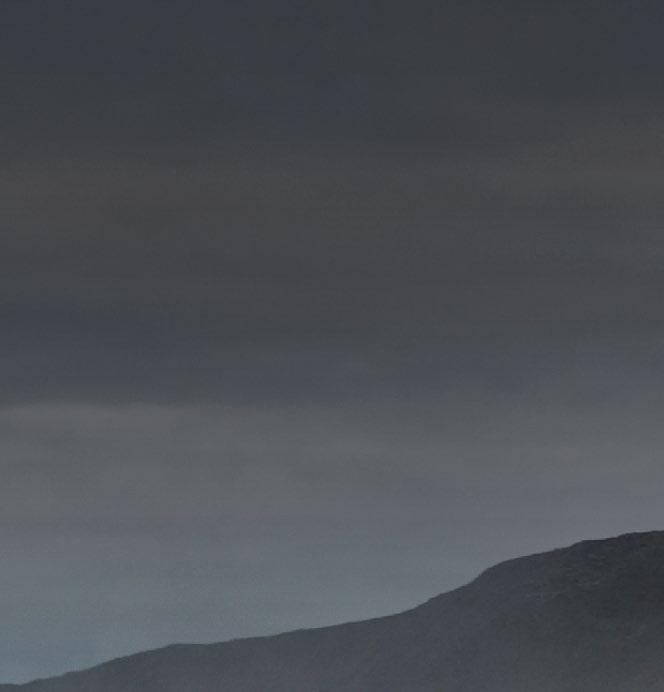
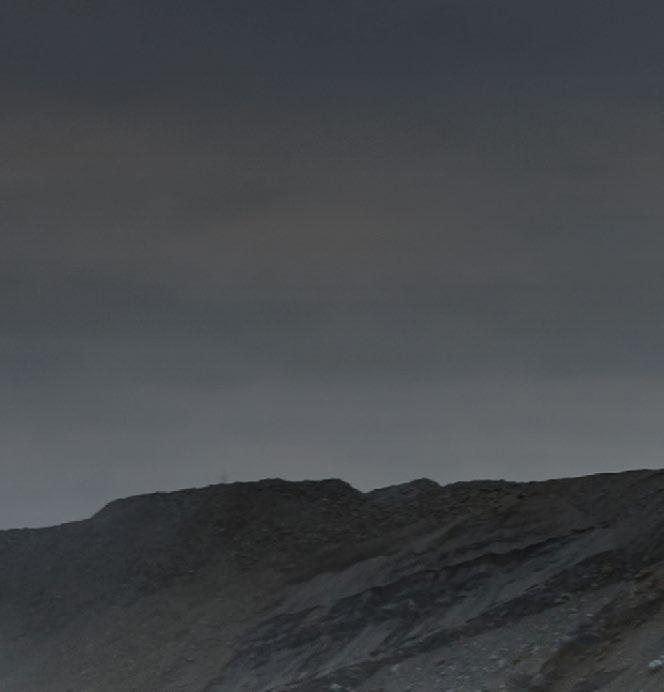

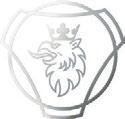
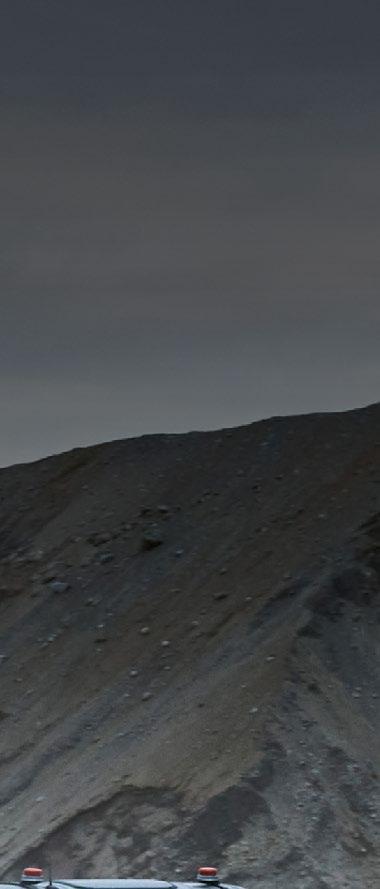

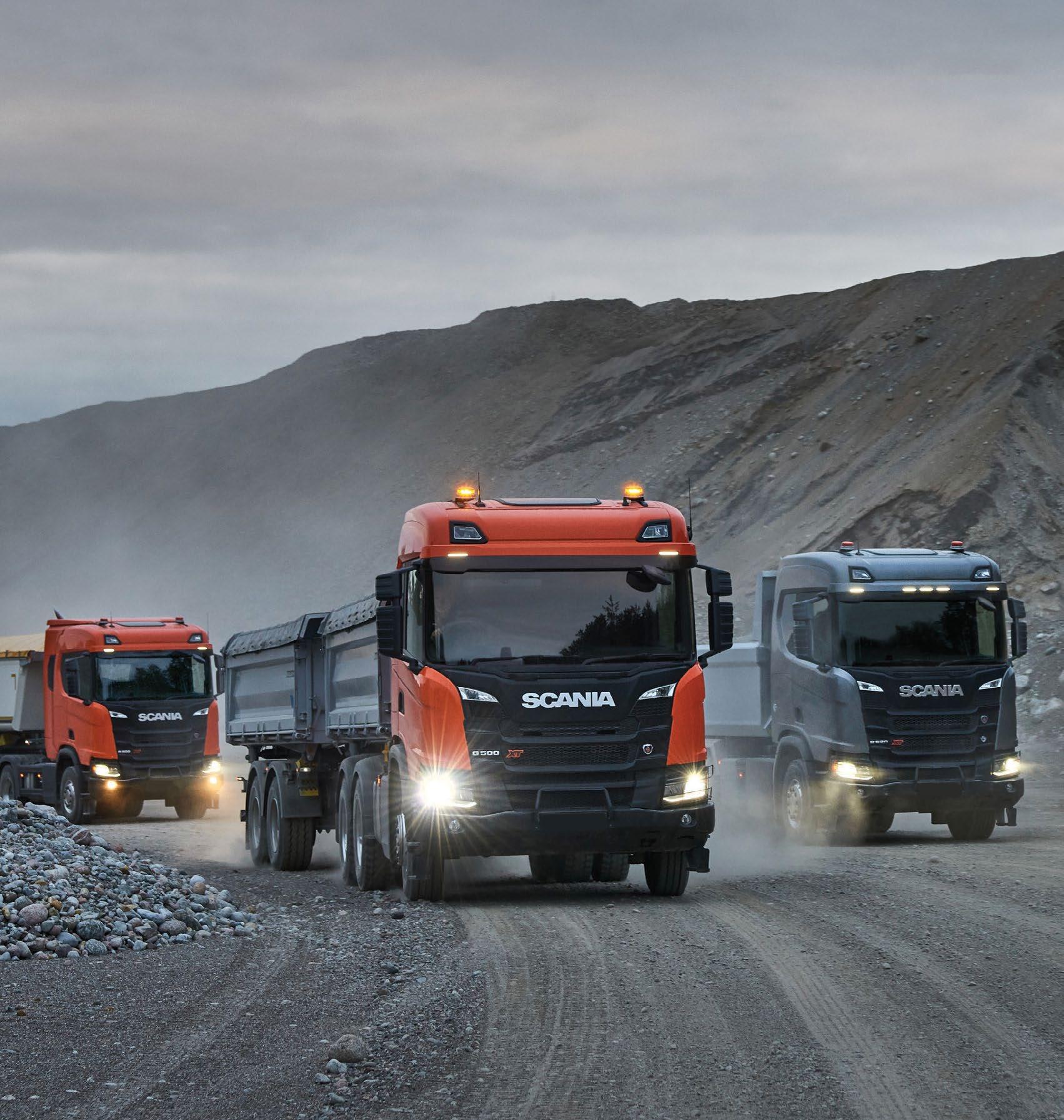

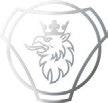
Industry associations such as IQSA and ASPASA have been commended for their role in moulding a resilient quarrying sector in South Africa.
NAVIGATING A CHANGING QUARRYING LANDSCAPE
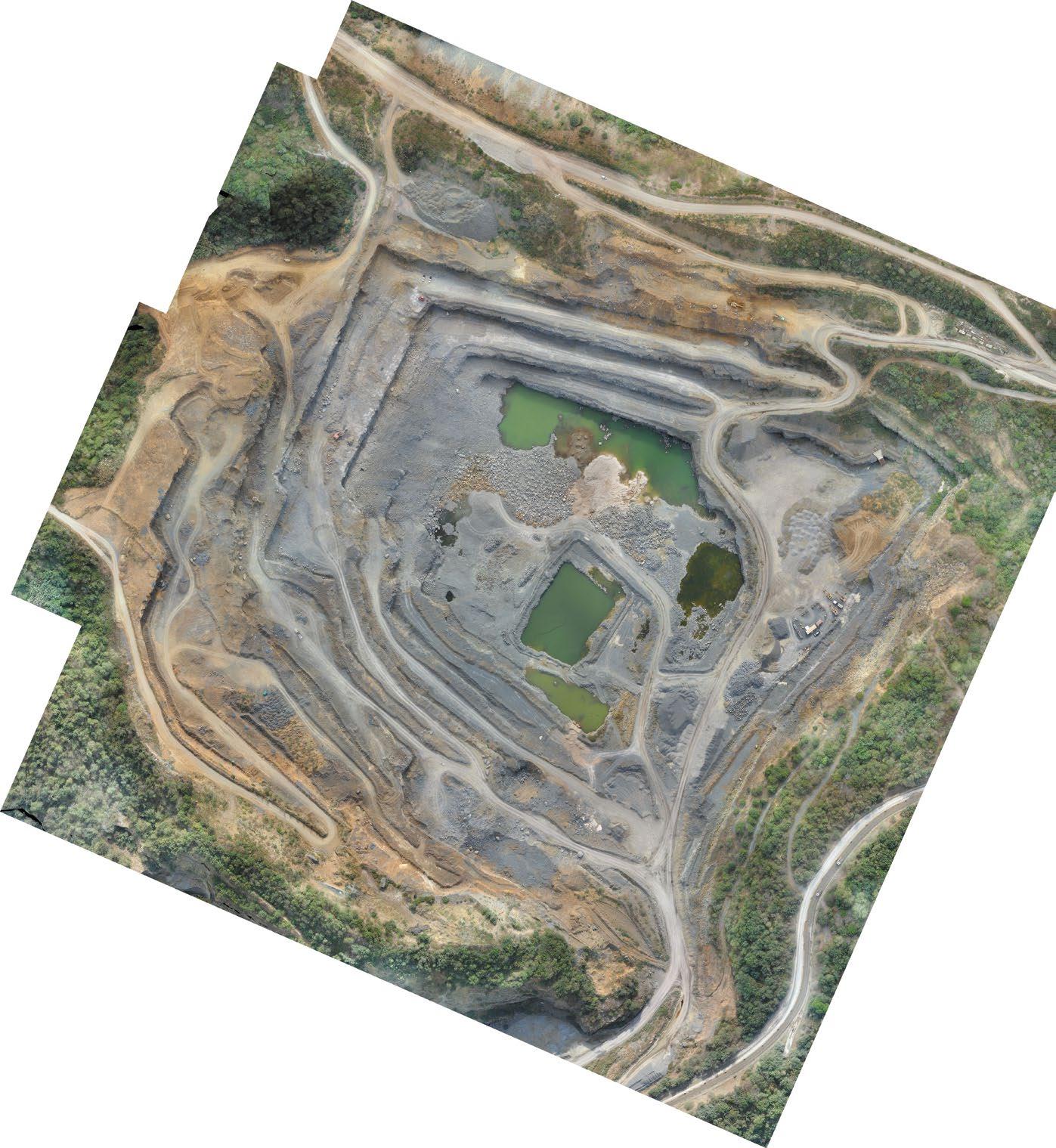
With the quarrying sector, and the mining environment at large, constantly evolving, it is important for quarry operators to be adaptable – be open to new ideas and be willing to adjust strategies as needed. In line with this approach, this year’s IQSA Conference, taking place in Durban on April 3-4, will be held under the theme, ‘Navigating a Changing Landscape’. Chairman Jeremy HunterSmith unpacks some of the changes in the industry and how operators can adapt. By Munesu Shoko.
There is a general agreement that the quarrying sector is evolving, with a renewed focus on the environment and energy efficiency, amongst other areas of attention. However, HunterSmith notes that quarrying is fundamentally the same process as it was in years gone by, but it is what individuals working in the industry have
learned through years of experience, that is shaping the industry. That is what this year’s conference will highlight to help create a safer, healthier and productive quarrying environment.
“While quarrying has always been referred to as ‘other’ within the mining sector, it is governed by the same legislation as the mainstream mining sector. Given that we mine a low-value, high-volume
3-4
This year’s IQSA Conference, taking place in Durban on April 3-4, will be held under the theme, ‘Navigating a Changing Landscape’
KEY POINTS
This year’s IQSA Conference will be held under a ‘Navigating a Changing Landscape’ theme
To navigate some of the challenges facing the industry, new technology is coming to the fore, simplifying some of the daily tasks
Operations are encouraged to fast-track their traffic management plans and identify areas where significant risk exists
Delegates to this year’s conference can also look forward to a full programme, with some formidable guest speakers
product, the constant change in legislation, which by its nature is very expensive to comply with, has meant that aggregate operations have found it extremely onerous to stay on top of costs,” says Hunter-Smith.
To navigate some of the challenges facing the industry, he says, new technology is coming to the fore and it is encouraging to see many operations adopting technology to simplify some of the daily tasks. For example, the use of drones for quarry mapping and surveying, belt scales for data at the quarry operator’s fingertips and better blasting systems for optimal blasts, are some of the new approaches redefining tasks in quarrying.
“It is, however, important to note that quarries are only able to adopt these new technologies once the construction industry improves and more substantial contracts come to market across South Africa. In turn, this stimulates the economy. Yes, there are some fantastic projects on the go, such as the N3 highway upgrade between Pietermaritzburg and Durban, but there needs to be a drive from government to create a conducive environment for private construction investment as well,” says Hunter-Smith.
Respond to changes
Hunter-Smith reiterates the need for quarry owners to prioritise the adoption of technology to enhance safety, improve efficiency, reduce costs and minimise environmental impact through data analysis, and remote operation, ultimately leading to a more sustainable and productive industry.
He also urges operations to fast-track their traffic management plans and identify areas where significant risk exists. This, he says, will inform whether there is need
PDS/CAS
South Africa is a global leader in the adoption of PDS/ CAS in mining, driven by legislation mandating the use of this technology on trackless mobile machinery in order to enhance safety and prevent accidents
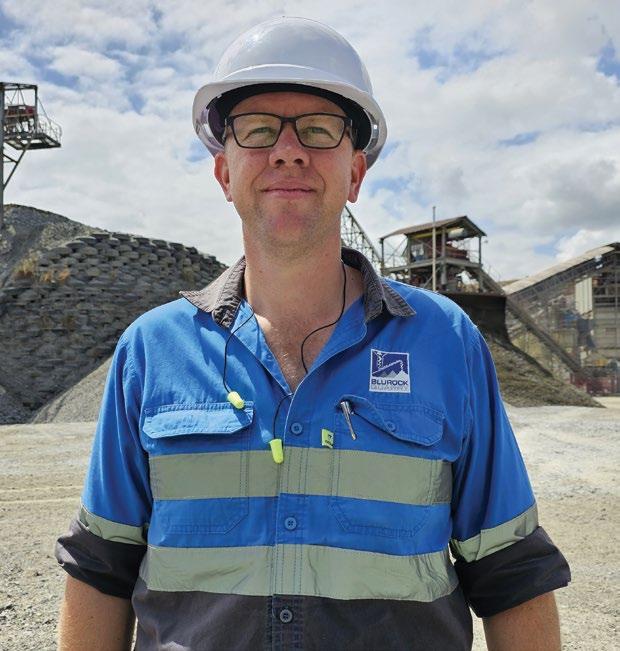
“Our commodity is not valued in thousands of dollars as do the likes of gold and platinum, but rather a few hundred rands per tonne, and this makes big, quick changes difficult in our environment. That is why we have adopted a longterm game with moderate, but constant improvement to our operations.
Jeremy Hunter-Smith, chairman of IQSA
to adopt new technology such as proximity detection systems (PDS) and collision avoidance systems (CAS). South Africa is a global leader in the adoption of PDS/ CAS in mining, driven by legislation mandating their use of this technology on trackless mobile machinery (TMM) to enhance safety and prevent accidents.
While there is a better understanding and commitment to the entire PDS/CAS rollout process, Hunter-Smith highlights some of the challenges for the quarrying industry. One of the major ones is that the technology does not come cheap, yet quarries do not make large amounts of money.
“Our commodity is not valued in thousands of dollars as do the likes of gold and platinum, but rather a few
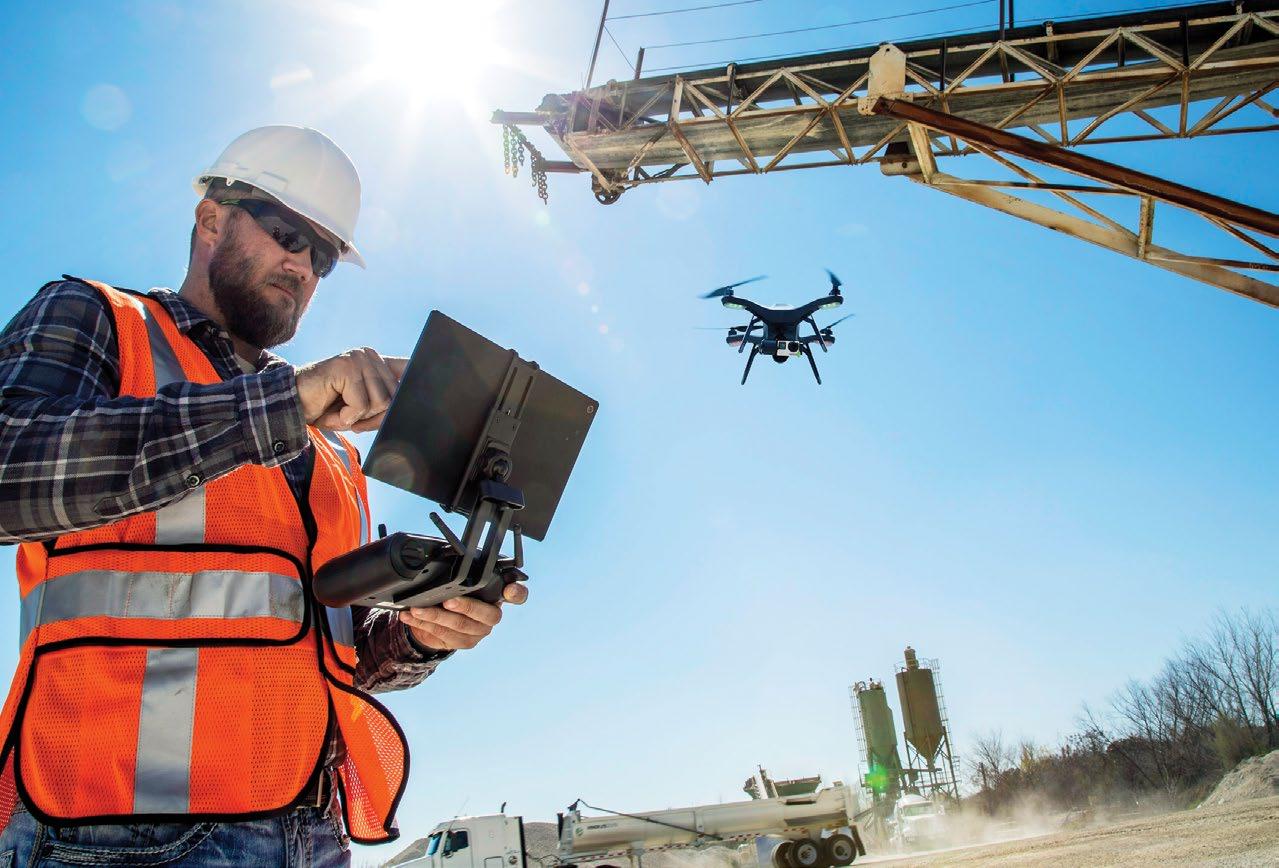
hundred rands per tonne, and this makes big, quick changes difficult in our environment. That is why we have adopted a long-term game with moderate, but constant improvement to our operations. These can be observed in the amazing results of the ASPASA audits. Hats off to the ASPASA auditing team and the great work they do to make a difference in the quarrying industry – to guide and share positive practices that make the difference,” says Hunter-Smith.
Big role
Hunter-Smith commends industry associations such as IQSA and ASPASA for their role in moulding a resilient quarrying sector. ASPASA, he says, has its hands full, helping its members navigate the changes that affect their operations, as well as lobbying with the various governmental bodies on behalf of the industry.
“Letisha van den Berg and her team at ASPASA are doing a remarkable job navigating these changes and also paving the way forward for a sustainable industry,” says Hunter-Smith. “IQSA is there to promote the training and education that is required to ensure the next set of leaders are ready for future changes and how possibly to deal with them. The new, young members should look within the IQSA membership for a mentor to assist and guide them in their career path within the industry.”
More expectations
Delegates to this year’s conference can also look forward to a full programme, with some formidable guest speakers. Peter van Kets, a renowned keynote speaker, will kickstart the conference. Van Kets is one of the world’s top professional endurance adventurers, a conservationist and an international keynote and inspirational speaker.
“The industry can also look forward to a presentation by David Msiza, Chief Inspector of Mines at the Department of Mineral and Petroleum Resources, who will give insights into some of the new developments from a regulator’s perspective. We will also have a political and policy analyst, Theo Venter, who will paint the political and policy picture for the industry,” explains HunterSmith.
In addition, the awards dinner, where the top performing operations in environmental management and health and safety are recognised, is always a major highlight of the conference. “We will also use the evening to recognise individuals who go the extra mile to add value to the industry. This year, we will also honour some IQSA members with the longest membership – some of them having been part of the association for more than 20 years,” concludes HunterSmith. a
This year, IQSA will also honour some of its long-serving members – with some of them having been part of the association for more than 20 years
It is encouraging to see quarries adopting technology to simplify some of the daily tasks, for example, the use of drones for quarry mapping and surveying.
We are proud of our Free Statebased Qwa Qwa Quarry for being recognised as the Top Performer in the ASPASA ISHE Audit 2024.
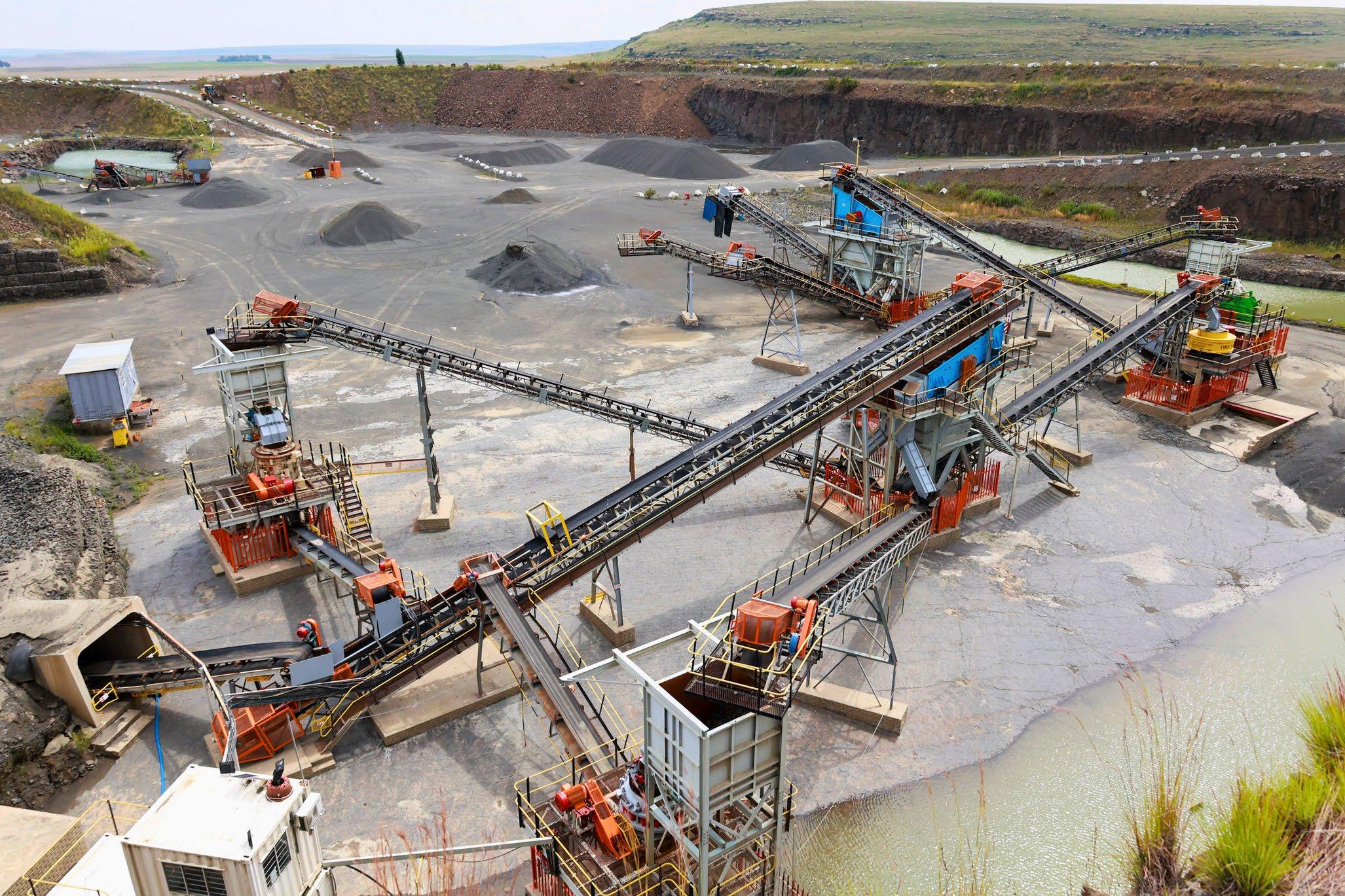
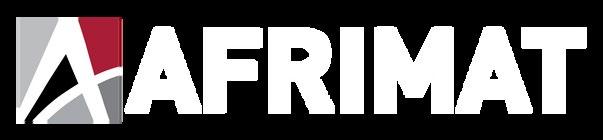
At Afrimat, our responsibility extends to both our people and the planet. We are deeply committed to providing a safe and healthy workplace for all, employing proactive risk management to prevent health and safety incidents.
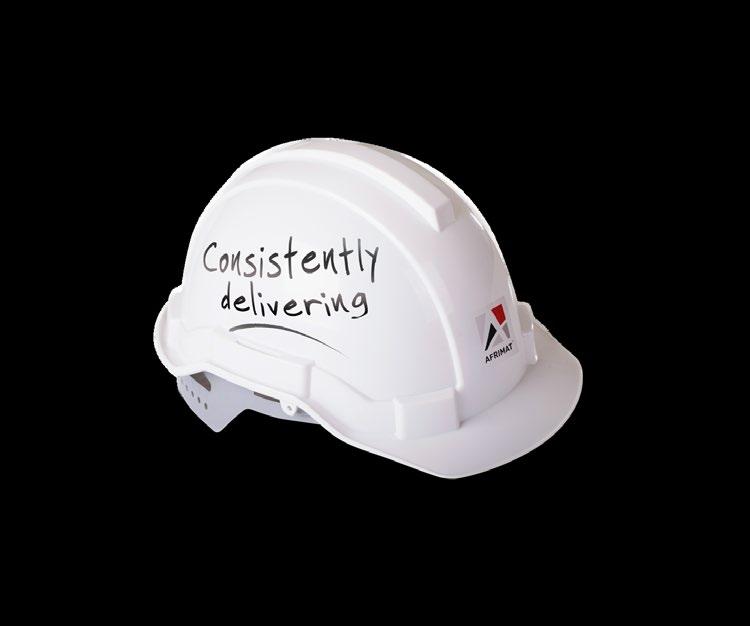
This commitment to our people is mirrored in our dedication to environmental sustainability, as we strive to unlock the earth's mineral potential responsibly and build a better world.
DEMONSTRATING COMMITMENT TO ZERO HARM
Findings from the 2024 ISHE Audit, an annual health and safety audit conducted by ASPASA, demonstrate that members of the surface mining industry association are committed to the zero harm objective, aiming to ensure that every worker returns home unharmed every day. By Munesu Shoko.
ollowing another round of ISHE audits in 2024, ASPASA auditor Marius van Deventer tells Quarrying Africa that members of the association have once again demonstrated high levels of compliance to ensure employee occupational health and safety in the workplace.
A total of 74 audits was conducted on member operations in 2024, with an average score of 90,16%, achieving the highest score of 98,24%. In addition, 13 more audits were conducted at non-mining operations operating under the Health and Safety Act. The average score achieved by these operations was 88,56%.
Both audit protocols were reviewed in 2024, with some scores and weight of scores changed to put emphasis on compliance issues that the Department of Mineral and Petroleum Resources (DMPR) Inspectorate deems pressing for the industry. While compliance with these new requirements proves to be difficult for members operating in multiple DMPR regions due to different interpretations by the Inspectorate, Van Deventer is encouraged by the great effort that ASPASA members have made to comply.
“The general takeaway from last year’s audit is that compliance among all audited quarries and other operations is of a very high standard. Every year the audit casts the spotlight on areas of improvement and it is encouraging to see the continuous improvement efforts by members to meet these audit protocol requirements,” says Van Deventer.
Scope
The ISHE audit covers all operations at the quarry that fall under the legal requirements of the Mine Health and Safety Act and other applicable regulations. Audits are also conducted on member
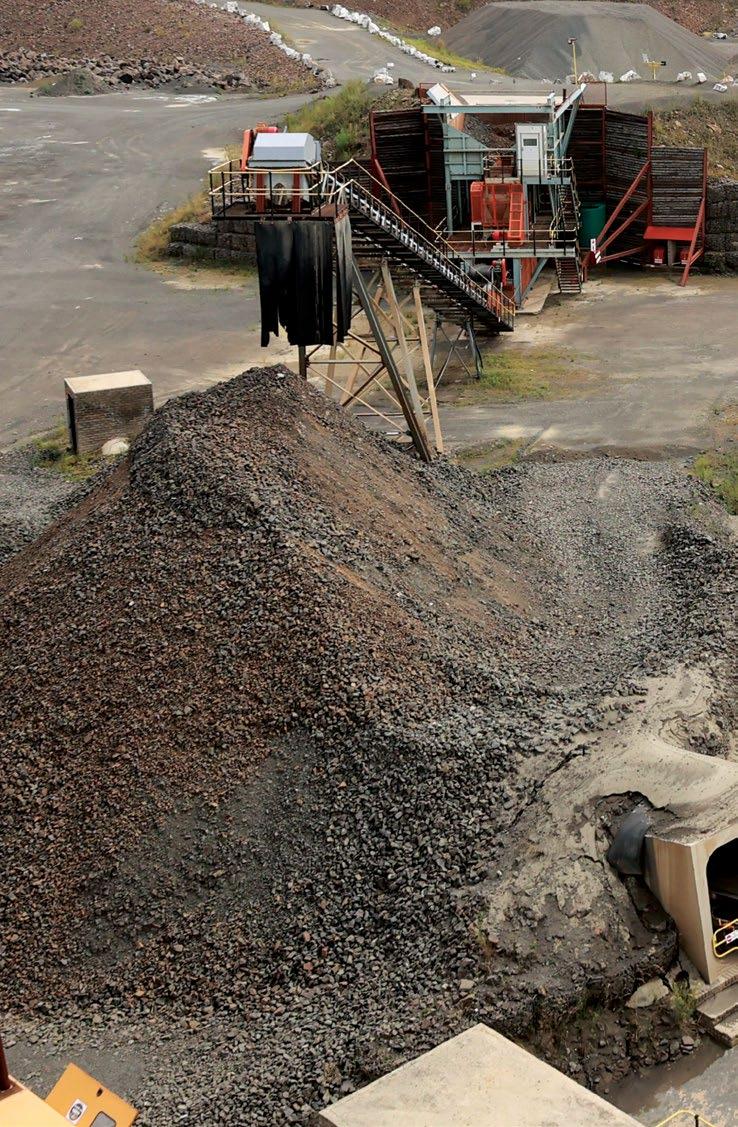

The results of the 2024 ISHE Audit are of extremely high standard. All participating members should be commended for their exceptional efforts, commitment and performances during the year.
Marius van Deventer, ASPASA ISHE auditor
For the fourth year running, Afrimat Qwa Qwa was named the Top Overall Performer in the 2024 ISHE Audit.
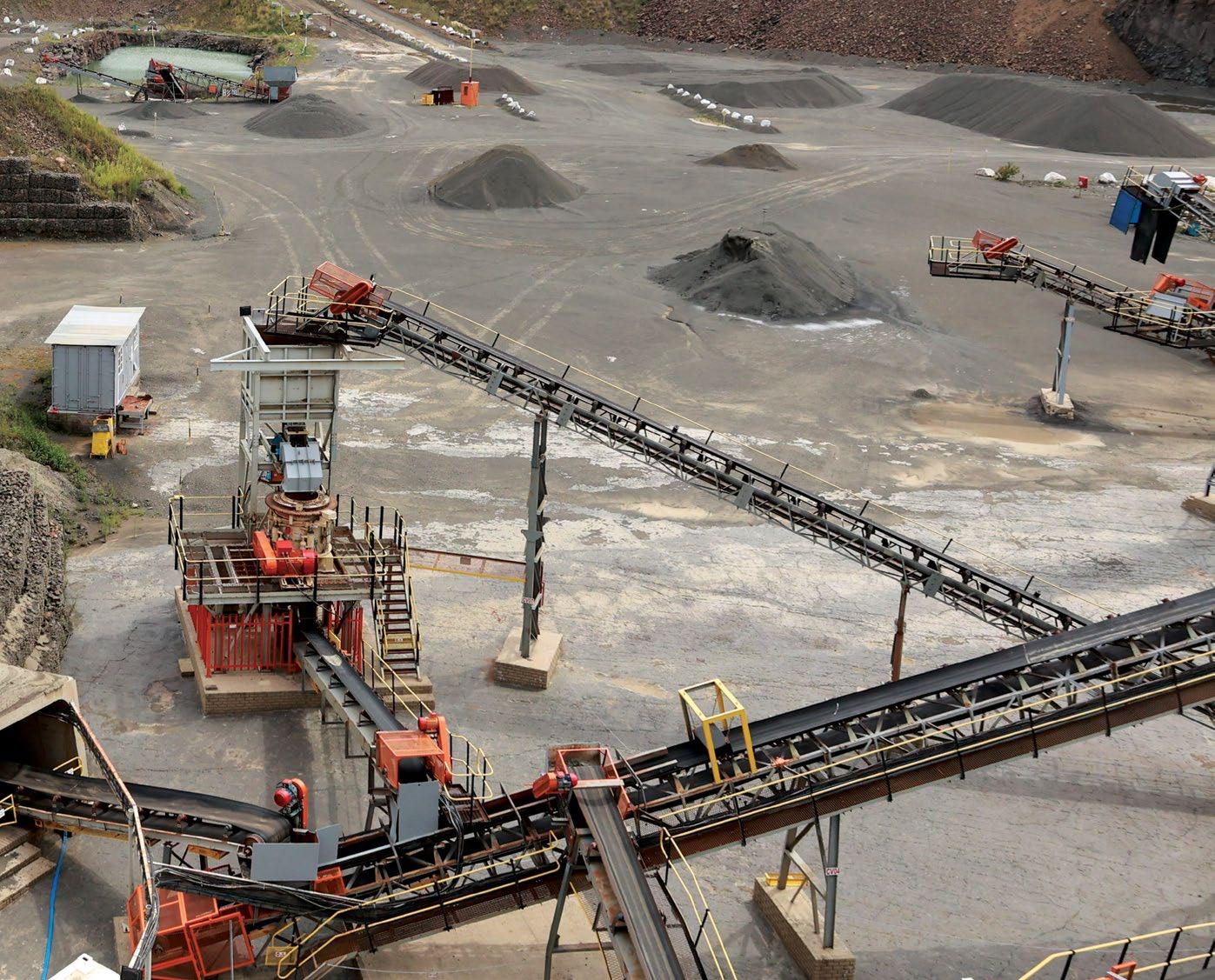
operations that are governed under the Occupational Health and Safety Act.
A structured audit process is followed by in-depth inspections of facilities on site. The auditor then inspects the documentation of the operation’s health and safety system. Legal registers, inspections, pre-start checklists, licences to operate machines and isolation records, amongst others, are some of the important documents that form part of an operation’s health and safety system. The audit process also evaluates employee knowledge on technical, plant, machinery and mining area legal requirements, which is key to maintaining a safe working environment.
98,24%
A total of 74 audits was conducted on member operations in 2024, with an average score of 90,16%, achieving the highest score of 98,24%
KEY POINTS
Following another round of ISHE audits in 2024, ASPASA members have once again demonstrated high levels of compliance to ensure employee occupational health and safety in the workplace
The ISHE audit covers all operations at the quarry that fall under the legal requirements of the Mine Health and Safety Act and other applicable regulations
Audits are also conducted on member operations that are governed under the Occupational Health and Safety Act
The overall health and safety performance of ASPASA members was exceptionally good in 2024, demonstrated by the highest number of operations achieving Showplace Status (95% and above) since the introduction of the audit protocol
Both audit protocols were reviewed in 2024, with some scores and weight of scores changed to put emphasis on compliance issues that the DMPR Inspectorate deems pressing for the industry
20
A record 20 operations achieved Showplace Status (95% +) during the 2024 ISHE Audit
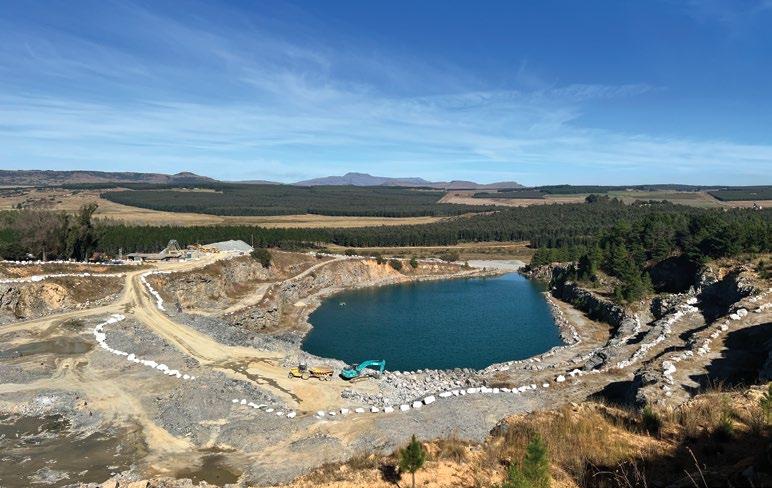
Breakdown of achievements in the 2024 ISHE Audit (Mining)
Showplace Status (95% +) 20 operations
5 Shield Status (90-95%) 34 operations
4 Shield Status (80-90%) 13 operations
3 Shield Status (70-80%) 6 operations
2 Shield Status (60-70%) 1 operation
1 Shield Status (50-60%) None Participation (< 50%) None
Breakdown of achievements in the 2024 ISHE Audit (Non-mining)
Showplace Status (95% +) 2 operations
5 Shield Status (90-95%) 5 operations
4 Shield Status (80-90%) 5 operations
3 Shield Status (70-80%) None
2 Shield Status (60-70%) 1 operation
1 Shield Status (50-60%) None
Participation (< 50%) None
Van Deventer confirms the addition of a new protocol to the 2024 audit process, which was aimed at testing and educating employees on their ability to conduct major accident investigations and respond to enquiries by the DMPR. The audit protocol was based on actual industry accidents that occurred during the previous year. The protocol has been revised again for the 2025 audit and extensive changes have been agreed by members.
“A key role of the audit process is to provide guidance and add impetus to the industry’s drive for zero harm. Knowledge and experience are shared right across the industry to uplift the understanding, attitude and behaviour of all employees responsible for managing health and safety,” explains Van Deventer.
Audit findings
The overall health and safety performance of ASPASA members was exceptionally good in 2024, demonstrated by the highest number of operations achieving Showplace Status (95% and above) since the introduction of this audit protocol.
“Total commitment is required in the industry’s quest for zero harm, and ASPASA members audited in 2024 have demonstrated just that,” says Van Deventer. “The audit outcomes have again shown that ASPASA members
are fully committed to the health and safety of their employees and interested parties affected by their operations.”
Van Deventer says there was a general improvement from the previous year’s audit at most of the sites, with members plugging the compliance gaps that had been identified during the 2023 audit. These operations, he says, need to be applauded for their continuous efforts to improve and dedication to health and safety.
One of the positive takeaways from last year’s audit was the appetite for information-sharing in the industry, which has become a crucial aspect of the audit. Quarry managers are eager to learn from each other’s best practices to improve their own health and safety performance.
“There were a number of positives to write home about in the 2024 audit. One of them is the general improvement in the compliance to machine guarding requirements. In addition, mine development in accordance with mine planning and no serious incidents of mine failure recorded is something that members of ASPASA should be commended for. In general, employees are better informed about requirements and knowledge of safe working conditions. More importantly, no fatalities were recorded among ASPASA members during the audit period,” says Van Deventer.
Areas of improvement
While the industry generally exhibited high health and safety standards, there were several areas of concern cited in the audit report. Van Deventer says one of the major concerns was the several serious injuries recorded during the auditing period.
“This is very unfortunate, but action steps have been taken to prevent recurrence,” he says. “In some instances, proper investigations of accidents and incidents remains unsatisfactory, with operations failing to establish the root cause of the accident, which is key to closing the loop and establishing control measures to prevent it from happening again.”
Other areas of concern highlighted in the 2024 audit, which will receive special attention during the 2025 audit, include compliance to own standards and procedures; liaison with local communities and neighbours, especially when it comes to blasting events; too many lost time injuries, disabling injuries and reportable injuries recorded; and identification of risks
Eskay Crushers was named the Top Independent Performer and the overall runner-up in the 2024 ISHE Audit.
Marius van Deventer (far right front) with the Eskay Crushers team during an audit last year.
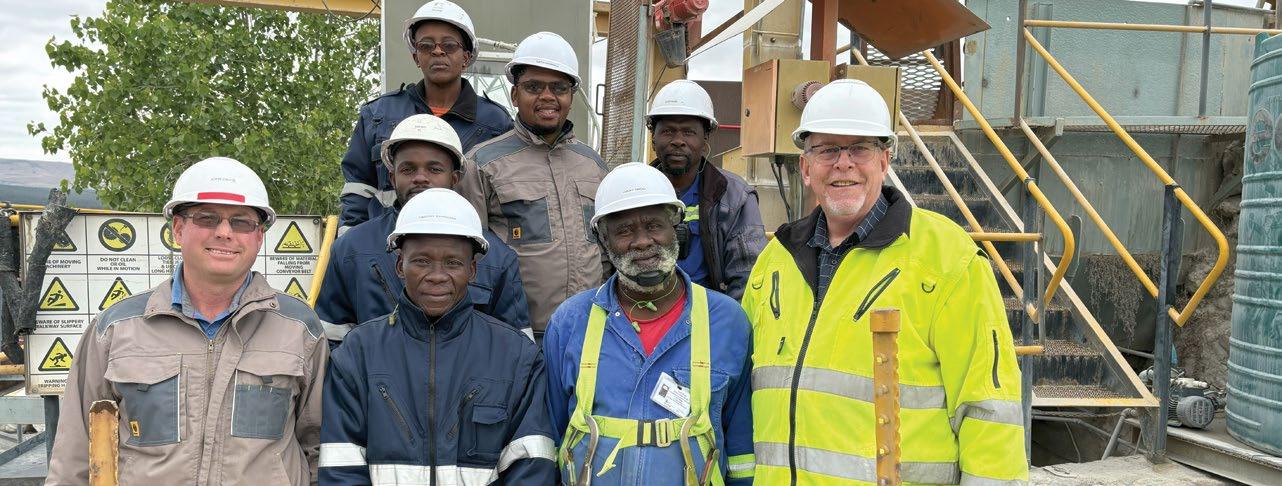
and/or non-compliances. Operations should also improve on their pre-start inspections of plant and trackless mobile machinery (TMM), stresses Van Deventer.
Other areas of focus include the need for full implementation of traffic management plans; improving housekeeping in plants; repeat findings from previous audits; full compliance to isolation and lockout requirements; attention to accident/incident investigations to establish root causes; near miss reporting; contractor management; and emergency training and mock drills.
Audit results
In the quarrying space, a total of 74 audits was conducted on mining operations, with an average score of 90,16%, up from the 89,84% achieved during the 2023 audit. For the fourth year running, Afrimat Qwa Qwa was named the Top Overall Performer with a 98,24% score, highlighting the operation’s unparalleled focus on health and safety performance. Afrimat Qwa Qwa also achieved a Showplace Status for the fifth consecutive year.
Eskay Crushers was named the Top Independent Performer and the overall runner-up with a 97,7% score. Located in Piet Retief, a small town situated in Mpumalanga province, Eskay Crushers has continuously set the bar high in terms of compliance. “I have been auditing Eskay Crushers since 2008, and every year the operation has demonstrated continuous improvement to its health and safety standards. Mine manager John Davis and his team are committed to ensuring a safe and healthy environment for all,” says Van Deventer.
On non-mining operations governed by the Occupational Health and Safety Act, 13 audits were conducted during 2024, with an average score of 88,26% achieved. Van Deventer commends the achievement, highlighting that it was the first time for most of these operations to be audited under the ASPASA audit protocol.
“The results of the 2024 ISHE Audit are of extremely high standard. All participating members should be commended for their exceptional efforts, commitment and performances during the year,” concludes Van Deventer. a
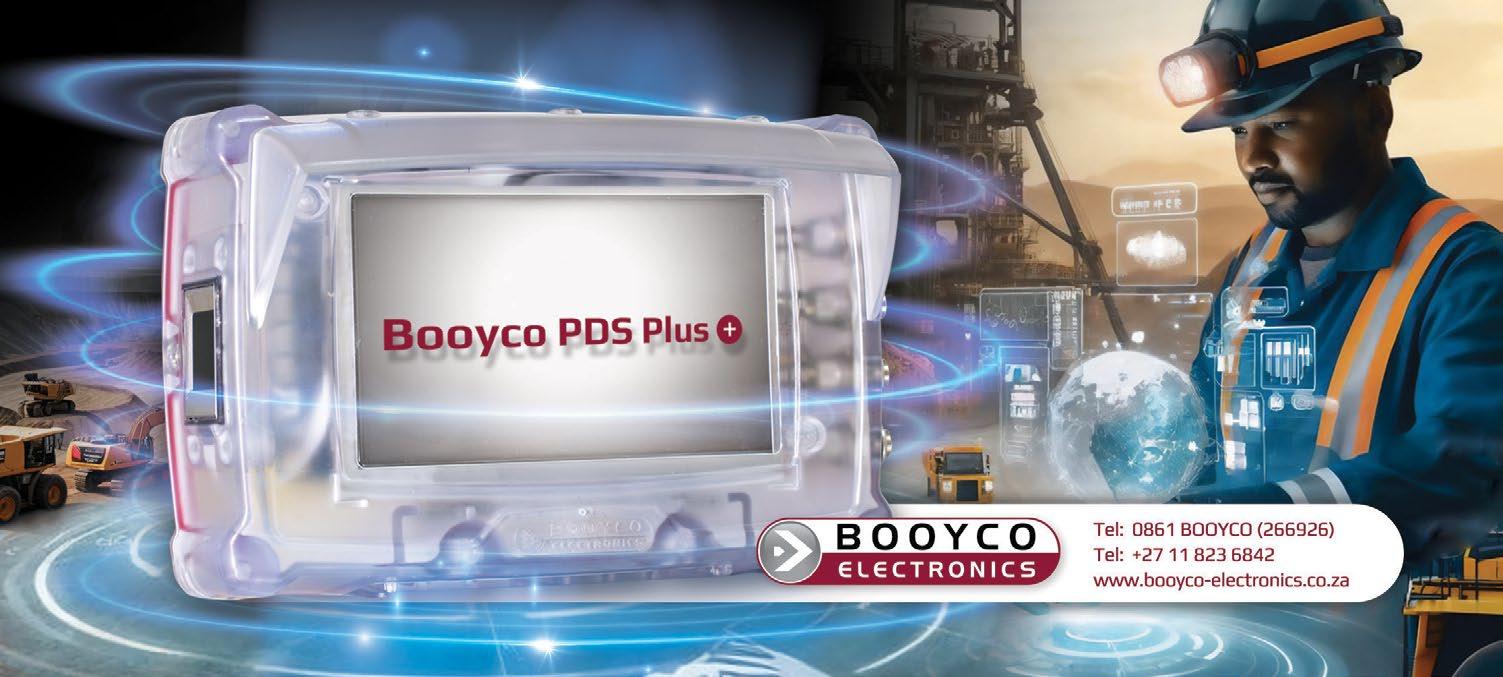
Despite significant challenges in recent years, the South African construction industry remains a critical pillar of the domestic economy.
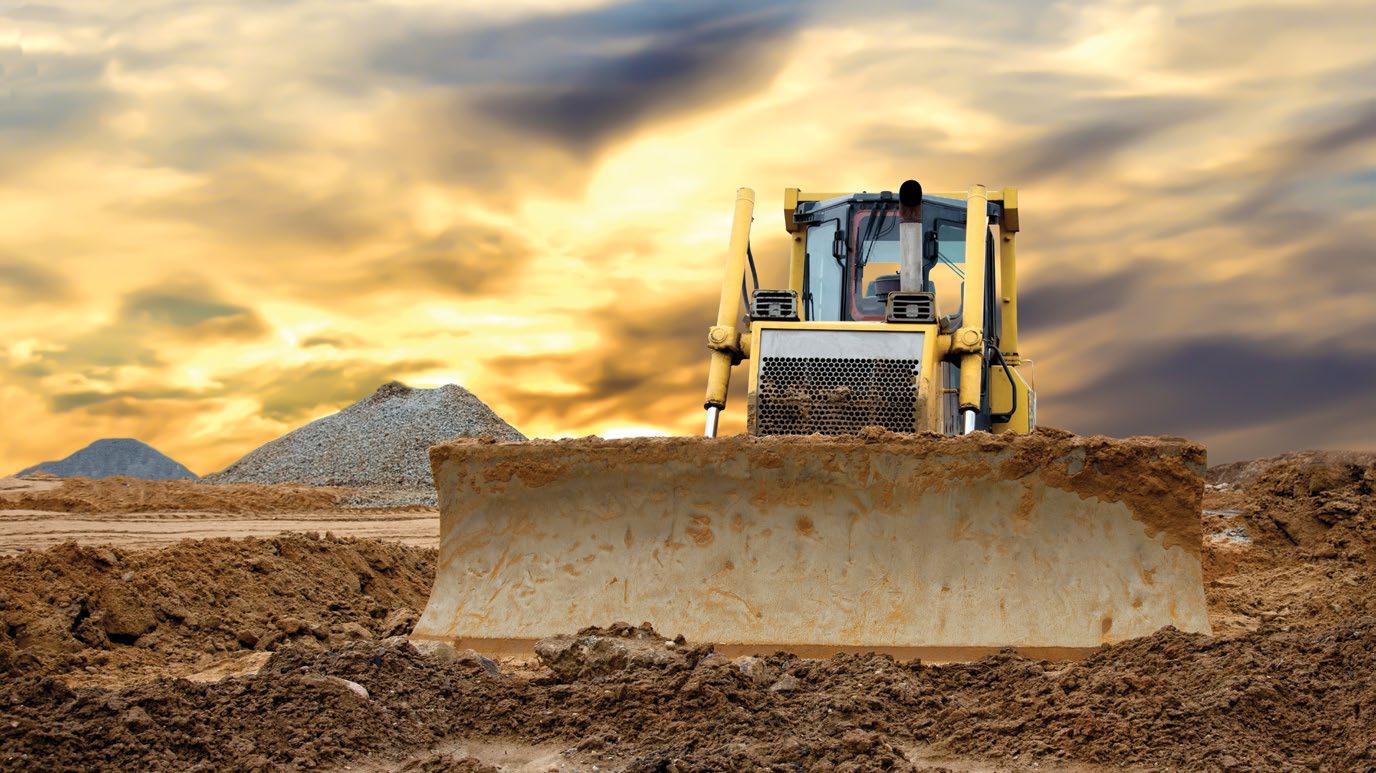
INSIGHT INTO THE STATE OF CONSTRUCTION IN SA
While the South African construction sector remains a vital component of the economy –contributing approximately 5% to the country’s GDP and employing over 1,3-million people – it faces numerous challenges that require strategic interventions to stimulate investment. Elsie Snyman, CEO of Industry Insight, unpacks the state of affairs and provides insight into what needs to be done to stimulate construction investment. By Munesu Shoko.
The significance of the construction sector to any economy cannot be emphasised enough. By creating jobs, stimulating investment, improving infrastructure, contributing significantly to gross domestic product (GDP) and facilitating economic growth through its intersectoral linkages with other industries, construction is the physical foundation needed for the economy to thrive.
Despite significant challenges in recent years, the South African construction industry remains a critical pillar of the domestic economy, contributing 5% to the nation’s GDP in expenditure terms, with a labour force exceeding 1,3-million as of the third quarter of 2024.
Notably, the sector has a high employment multiplier effect – for every R1-million invested, it generates employment for more than four individuals, and this figure rises to an estimated nine jobs when including associated roles in the material manufacturing sector. These figures, says Snyman, underscore the industry’s significant role in both economic output and job creation within South Africa.
State of affairs
After enjoying an historic growth phase during the run-up to the 2010 Soccer World Cup, the South African construction industry has generally withstood a rocky period during the past decade. Despite substantial investments in renewable energy and a political push to enhance infrastructure ahead of the May 2024 elections, the performance in building and construction remained weak, with the construction sector experiencing an 8% year-on-year decline in investment during the first three quarters of 2024, following a 3,7% contraction in 2023. Factors such as higher interest rates, increased inflation and political uncertainties were key constraints to private sector investment, a key driver in the building sector.
The challenges were not only unique to the building sector, with the civil construction segment also facing difficulties, with a 7,6% year-on-year decline in investment during the same period. However, confidence among civil contractors rebounded in the latter half of 2024, attributed to government efforts to boost infrastructure spending.
The South African construction sector experienced an 8% year-on-year decline in investment during the first three quarters of 2024, following a 3,7% contraction in 2023
KEY POINTS
Despite significant challenges in recent years, the South African construction industry remains a critical pillar of the domestic economy
The construction industry contributed 5% to South Africa’s GDP in expenditure terms, with a labour force exceeding 1,3-million as of the third quarter of 2024
Factors such as higher interest rates, increased inflation and political uncertainties have been key constraints to private sector investment, a key driver in the building sector
Despite these challenges, sentiment towards the listed construction sector improved during the latter part of 2024. Notably, cumulative market capitalisation values increased by 76% year-on-year in the second half of 2024
“The civil industry presented a mixed scenario, with weak investment growth alongside improved confidence. Investment in construction works fell by 1,7% year-onyear in 2023, which accelerated to a 7,6% year-on-year decline in the first three quarters of 2024. Yet, confidence levels among civil contractors showed a notable rebound during the second half of 2024, reaching an eight-year high of 50 in the third quarter of 2024, according to the FMB/BER Confidence surveys,” says Snyman. This follows a concerted effort by the government, prior to the May 2024 elections, to increase infrastructure expenditure, given the debilitating economic impact of failed economic infrastructure deeply entrenched across all government spheres.
Spending priorities
Despite these initiatives, the reallocation of funds in the 2024 Budget from transport and energy to water services, coupled with a decline in social infrastructure expenditure, has raised concerns about the government’s investment strategy.
“Infrastructure spending priorities announced in the 2023 Budget, which included the 2023/24 financial period, suggested higher levels of investment in the transport and energy sectors, with an encouraging overall real increase of 4,5% projected over the Medium-Term Expenditure Framework (MTEF) period (2023/24 to 2025/26),” says Snyman.
“We also observed an 11% year-on-year increase in public sector civil tender activity during the first six months of 2024, compared to the same period in 2023. However, 8%
50
Confidence levels among civil contractors showed a notable rebound during the second half of 2024, reaching an eight-year high of 50 in the third quarter of the year
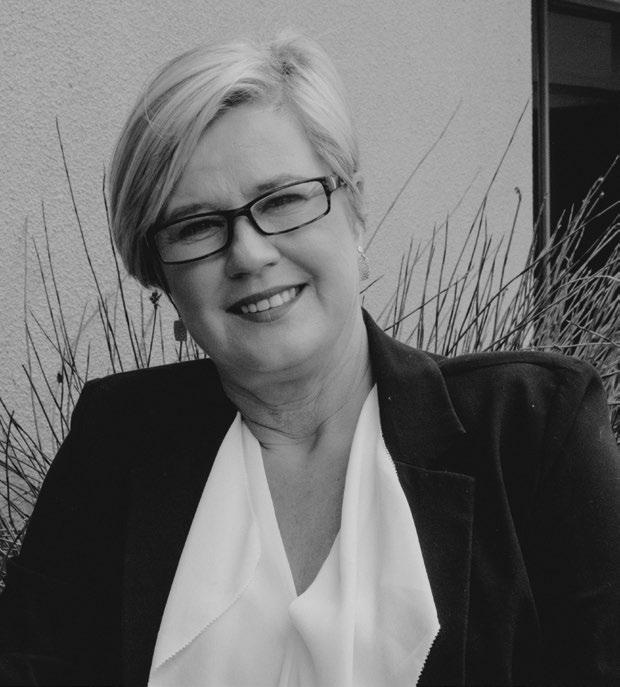
“We observed an 11% year-on-year increase in public sector civil tender activity during the first six months of 2024, compared to the same period in 2023. However, this was followed by a post-election slump, as tender activity fell by 17% year-on-year during the second half of 2024.
Elsie Snyman, CEO of Industry Insight
this was followed by a post-election slump, as tender activity fell by 17% year-on-year during the second half of 2024,” she adds.
In the 2024 Budget, the government reallocated infrastructure funding, shifting focus from transport and energy sectors towards water services. This shift coincided with a continued real decline in social infrastructure expenditure estimates, notably in housing, education and health sectors.
Overall, projections for total public sector infrastructure expenditure indicate an average 0,1% decline in real terms over the MTEF period up to 2026/27, suggesting a governmental approach contrary to widely advocated investment strategies.
Year-on-year change in the estimated value of projects out to tender (2023 vs 2024).

Key challenges
The industry, says Snyman, continues to grapple with challenges such as intimidation from groups known as the “Construction Mafia”, corruption, project cancellations and payment delays. In 2024, project postponements increased by 27% year-on-year, affecting over 200 projects, while cancellations rose by 82%, impacting 344 projects, as reported by industry sources such as Databuild. Profit margins also declined, averaging less than 2% up to the third quarter of 2024, down from 5,2% in 2023, primarily due to intensified competition.
reaching 979 000 tonnes, with a notable 43% year-on-year growth in the second half of the year.
“The surge in cement imports poses a significant threat to domestic cement producers, who are already contending with higher input costs and logistical challenges. These developments underscore the pressing need for strategic interventions to bolster the competitiveness of South Africa’s manufacturing sector and safeguard its role in the country’s infrastructure development initiatives,” notes Snyman.
A few bright spots
Despite these challenges, sentiment towards the listed construction sector improved during the latter part of 2024. Notably, cumulative market capitalisation values increased by 76% year-on-year in the second half of 2024, indicating renewed investor confidence in the sector.
R658-billion
The decline in public sector tender activity in both building and civil sectors during the latter half of 2024 may adversely affect turnover in the short to medium term. The extent of this impact will largely depend on how swiftly the new Government of National Unity (GNU) can rejuvenate tender processes, particularly at provincial and local government levels. Early 2025 has seen increased friction within the GNU, linked to the signing of the Expropriation Act in January 2025. This development has the potential to undermine investor confidence, thereby slowing private sector investment.
In addition, the manufacturing sector in South Africa is grappling with numerous challenges, including escalating input costs, logistical constraints and the threat of imports, all of which adversely affect suppliers of construction materials. A prominent example is ArcelorMittal South Africa’s recent announcement to wind down its long-steel operations, a decision expected to impact approximately 3 500 direct and indirect jobs.
The local cement manufacturing industry faces similar hurdles. Cement imports increased by nearly 20% in 2023,
“On a more positive note, building approvals for new private sector construction appear to have reached a low point, with demand for non-residential buildings and housing gradually improving towards the end of 2024. This trend is partly attributed to a more favourable interest rate environment. However, considering that project approvals typically have a lead time of 12 to 18 months, the building sector may continue to face challenges at the start of 2025,” says Snyman.
The outlook for further interest rate cuts in 2025 has become more uncertain due to renewed global economic uncertainties. Following three consecutive cuts, the South African Reserve Bank reduced the key interest rate to 7,5% on January 30, 2025. While further reductions are anticipated throughout the year, with projections suggesting a rate of approximately 7,25% by year-end, these expectations are contingent upon the absence of unforeseen economic shocks.
Unlocking investment
Commenting on what needs to be done, Snyman says, to address the significant fiscal challenges and reduce escalating debt levels, increasing private sector investment is essential.
“This will require bold actions by the government to restore investor confidence, reduce regulatory obstacles and create a conducive environment for private sector participation. Despite over R658-billion in new project announcements in 2024, the uptake has been slow, indicating the need for effective implementation strategies,” she concludes. a
Despite over R658-billion in new project announcements in 2024, the uptake has been slow, indicating the need for effective implementation strategies
North West: -429
North Cape Province: 1 387
Free State: -3 464
North Cape Province: 1 387
Eastern Cape: -1 396
KwaZulu Natal: -1 931
Limpopo: -201
Mpumalanga: -3 422
Gauteng: -4 206
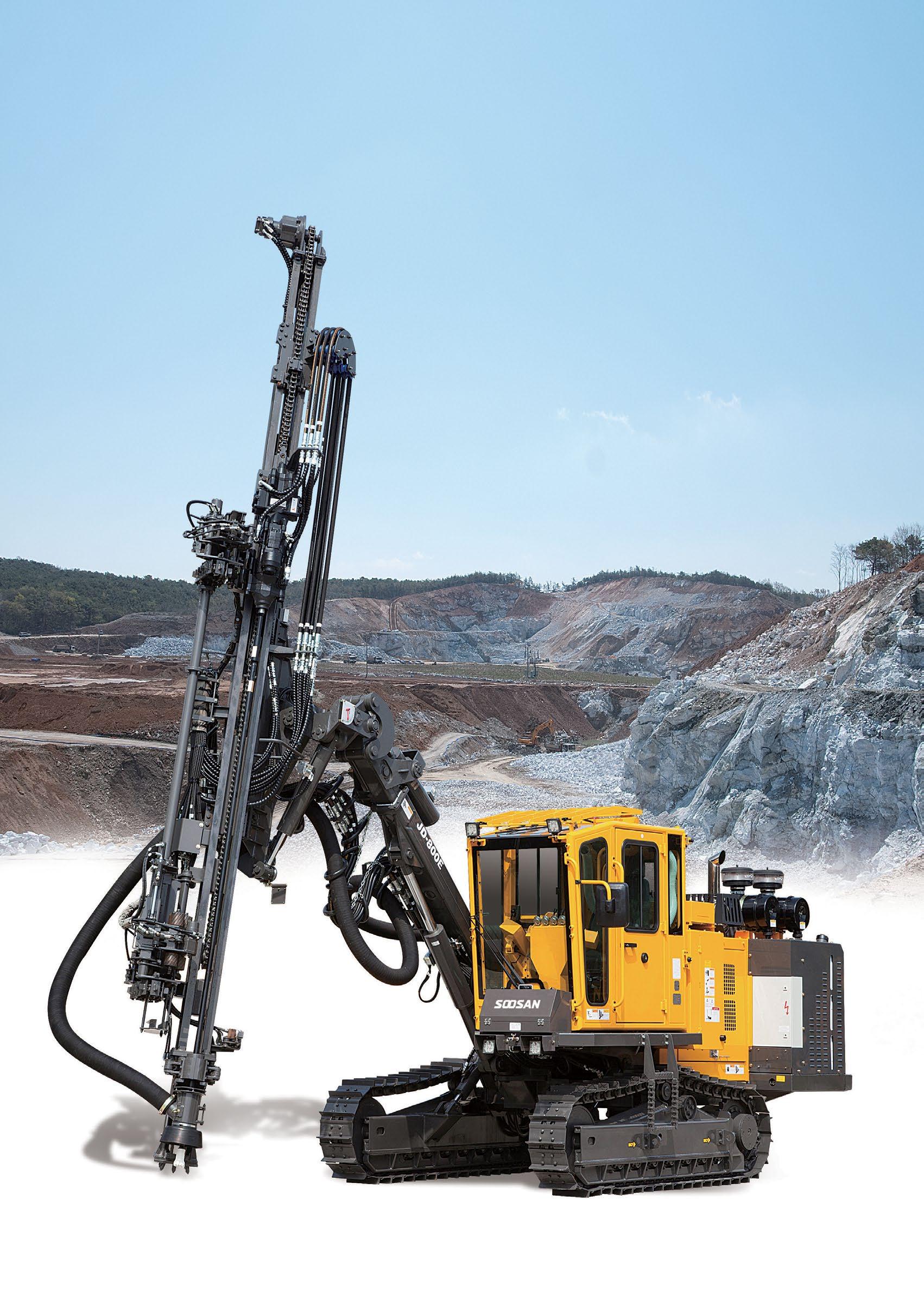
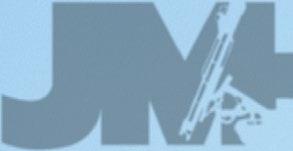
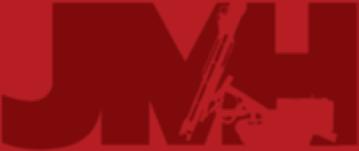


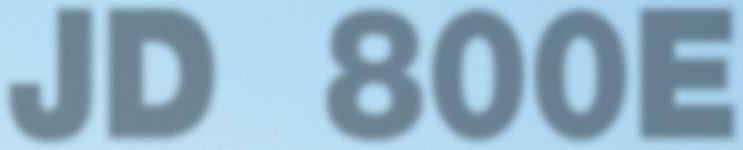
Drilling Diameter ø65~102mm
Drifter 22hp / 17kw
Air Flushing 5.5 m3 / min Drill Steel T38, T45
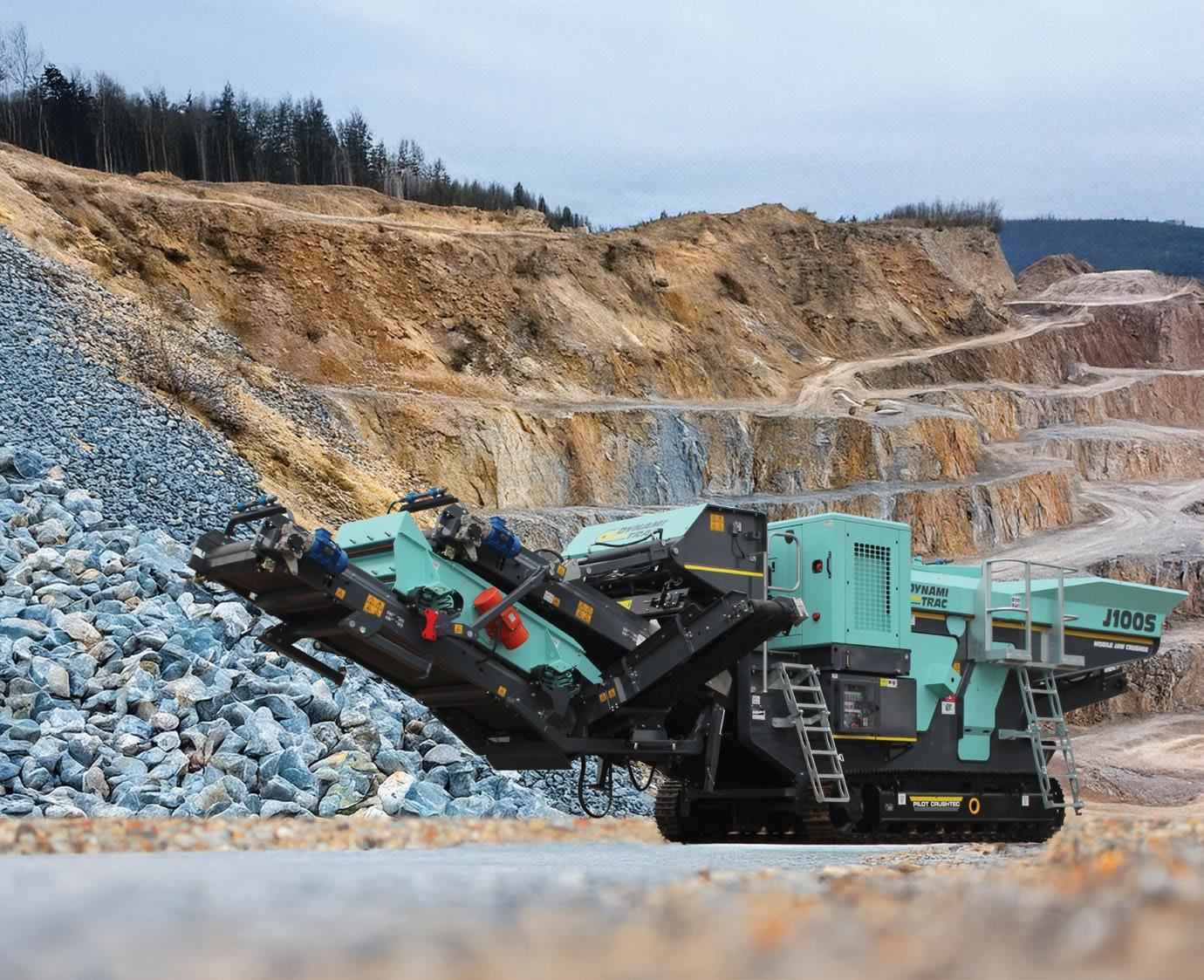
Pilot Crushtec has launched the DynamiTrac J100S – a compact dual-power mobile jaw crusher with a 40 to 100
CRUSHING NEW VOLUMES
To meet the need for compact crushing gear in selected applications, Pilot Crushtec International is launching the DynamiTrac J100S, a self-sustaining, dual power, compact mobile jaw crusher with a hanging screen. With a throughput range between 40 and 100 tonnes per hour (tph), the J100S is particularly suited for construction, recycling and small-scale mining operations. By Munesu Shoko.
Latest from Pilot Crushtec is a costeffective, compact mobile jaw crusher that is set to offer new capabilities in the sub-100 (tph) mobile crushing environments. Taking feed sizes up to 400 mm, the DynamiTrac J100S offers throughput from 40-100 tph, depending on material properties and feed size, amongst others. With a crusher feed opening of 700 mm x 500 mm, the machine has a closed side setting (CSS) range of 30-110 mm, as well as a 2 m³ heaped hopper capacity and a feed height of 2,5 m.
Charl Marais, sales manager South Africa at Pilot Crushtec, says the machine fits the bill for
construction and recycling applications. “In South Africa, this is a typical infrastructure machine. It gives construction contractors a cost-effective tool to keep on site for crushing material on demand, particularly backfill material. Given that it also comes with a double-deck hanging screen, contractors can also deploy it for on-site re-crushing of construction materials into required product sizes,” explains Marais.
Recycling is yet another area where the DynamiTrac J100S will find application. Using a single machine, demolition contractors can now break down material into manageable sizes, screen it into preferred sizes (using the double-deck
tph throughput, ideal for construction, recycling and small-scale mining.
40-100 tph
Taking feed sizes up to 400 mm, the DynamiTrac J100S offers throughput from 40-100 tph, depending on material properties and feed size
KEY POINTS
Pilot Crushtec International is launching its DynamiTrac J100S, a self-sustaining, dual-powered compact mobile jaw crusher
The J100S is particularly suited for construction, recycling and small-scale mining operations
The dual-powered, compact mobile crusher offers many benefits, including no permits to transport due to weight, cost savings and reduced maintenance costs
To provide even more flexibility to start-up mining customers, the J100S comes to market together with its static counterpart – the DynamiTrac MJ100
hanging screen) and remove metal/rebar using a standard overband magnet.
In addition, the J100S will also offer costeffective crushing capabilities to smallscale, low-production mining operations. In the past few years, says Wayne Warren, Africa sales manager at Pilot Crushtec, there has been a growing number of startup mining companies in southern Africa and this machine speaks directly to their operational needs.
Best of both worlds
A major talking point on the J100S is the fact that it is a self-sustaining, dualpowered machine that comes with an on-board generator. In addition, this machine can also be plugged into mains electricity, offering contractors the best of both worlds – the cost-efficiency of a static plant and the mobility of a tracked machine.
“This dual-powered, compact mobile crusher offers many benefits, including environmental friendliness, cost savings and reduced maintenance. The electric drive saves contractors money on fuel, which is generally a big operational cost in mobile crushing. Additionally, the electric motor is easier to maintain and has fewer
30-100 mm
With a crusher feed opening of 700 mm x 500 mm, the machine has a closed side setting range of 30-110 mm

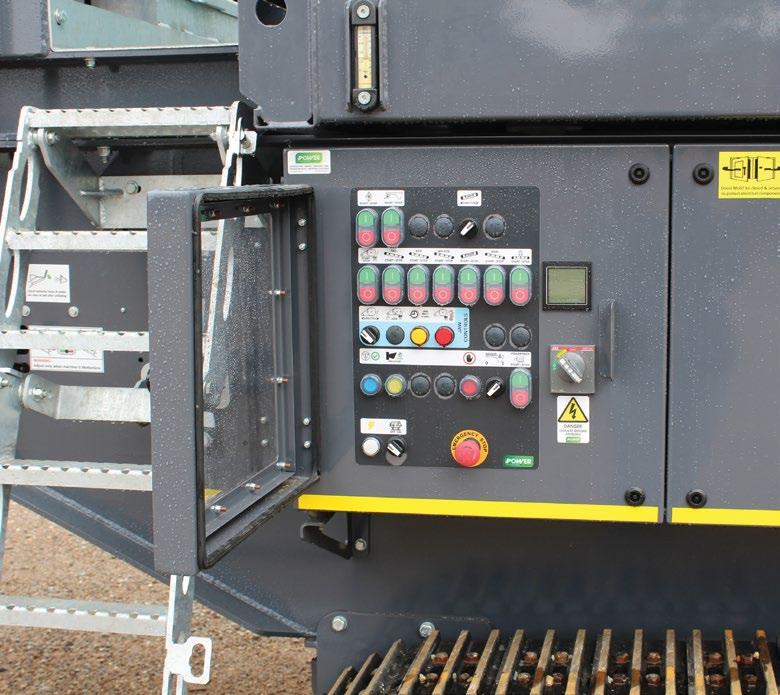
breakdowns than the diesel-powered counterpart,” explains Warren. The generator of the machine is driven by a Cat C3.6 engine which balances compact size, reliability and performance. This engine is offered in ratings ranging up to 106 kW (142 hp) @2 200 rpm. It is an efficient motor which is renowned for its fuel economy.
The DynamiTrac J100S features a hanging screen for efficient material separation, enhancing versatility in compact crushing applications.
The DynamiTrac J100S is equipped with an intuitive control panel for seamless operation and precise crusher management.
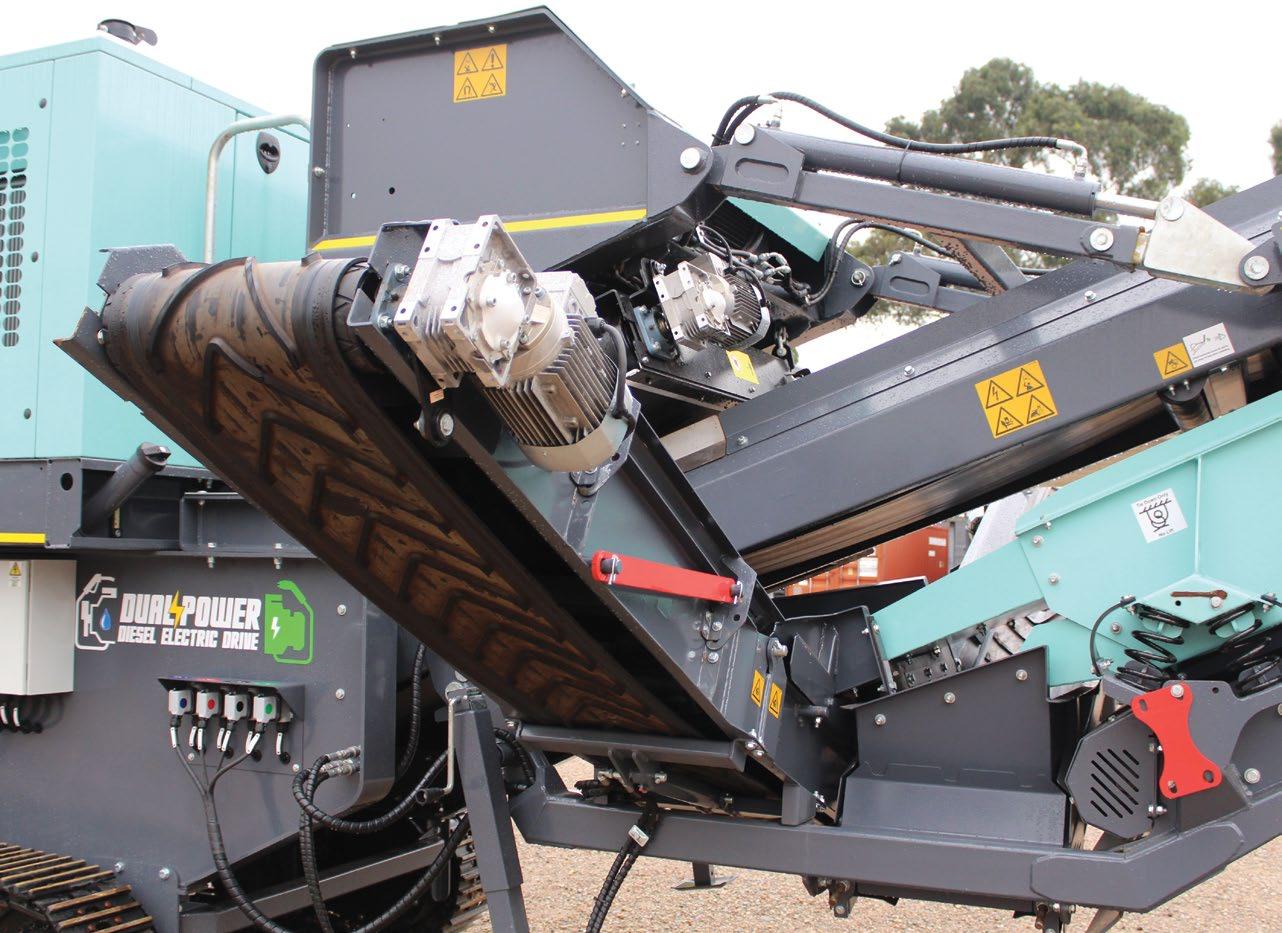
Benefits abound
The option of a two-deck screen maximises the machine’s versatility. The detachable screen enables the production of two screened products and any oversize material is recirculated back into the crusher using a return conveyor. The compact machine is therefore essentially a jaw crusher, a screen and a conveyor on one tracked chassis. This eliminates the need for another machine to work in closed circuit with the jaw crusher. Having a single machine doing the job of two machines, says Warren, offers significant cost benefits for the customer – both from a capital and operational cost perspective.
2,5 m
“The machine also benefits from some of the features found on larger mobile crushing offerings. For example, it comes with a hydraulic CSS adjustment. This allows for fine adjustments to the crushing force through precise control of the hydraulic pressure, enabling adaptation to different material sizes,” says Warren, adding that the push-button mechanism makes the machine simple to operate, with all the necessary parameters displayed.
More flexibility
To provide even more flexibility to start-up mining customers, the J100S comes to market together with
its static counterpart – the DynamiTrac MJ100, which is basically the same machine without tracks and the hanging screen. Having previously offered Pilot Modular solutions in the smaller 5-30 tph capacity range and at the large end of the crushing scale –120 tph and above – the MJ100, with a capacity of 40-100 tph, offers new capabilities, allowing Pilot Crushtec to offer a comprehensive modular solution for crushing needs in the sub-100 tph bracket.
Francois Marais, sales and marketing director at Pilot Crushtec, says the arrival of the MJ100 and the J100S highlights Pilot Crushtec’s commitment to developing solutions that expressly address customer needs. For the past 35 years, he adds, the company has built a reputation for its quality of products and outstanding service levels.
“In today’s dynamic business environment, flexibility, reliability and cost-effectiveness are essential parameters for achieving operational excellence, especially in cost-sensitive environments such as construction and small-scale mining. The addition of the MJ100 and the J100S allows us to expand our product footprint and help our customers achieve their production needs. The range will benefit from the same level of support that our customers have become accustomed to,” concludes Marais. a
The DynamiTrac J100S is equipped with an oversize belt for efficient discharge of larger material, ensuring smooth operation and productivity.
The J100S comes with a 2 m³ heaped hopper capacity and a feed height of 2,5 m
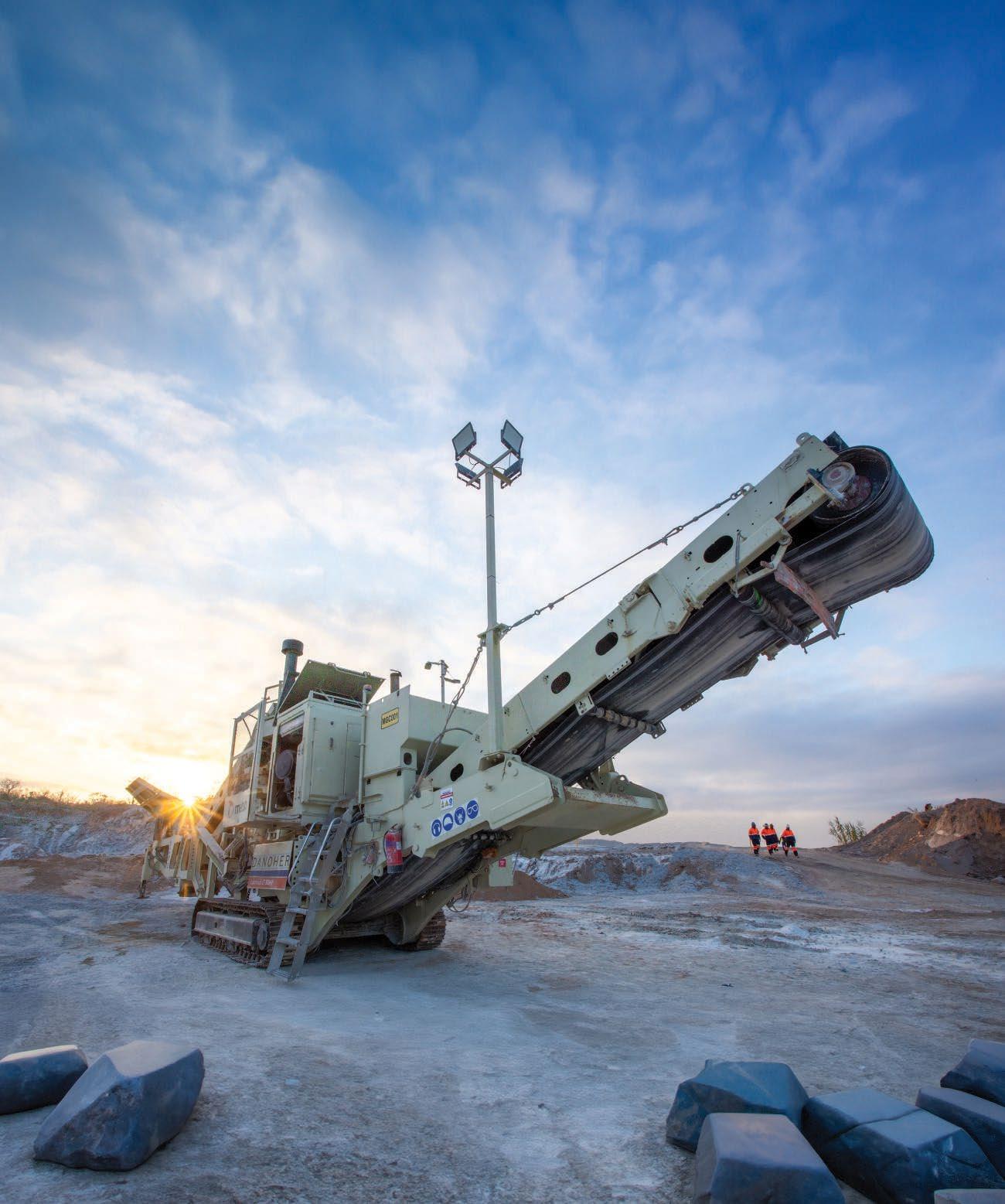
Compared with some of the competition’s machines, a Kleemann train is said to achieve on average up to 40% reduced fuel consumption.
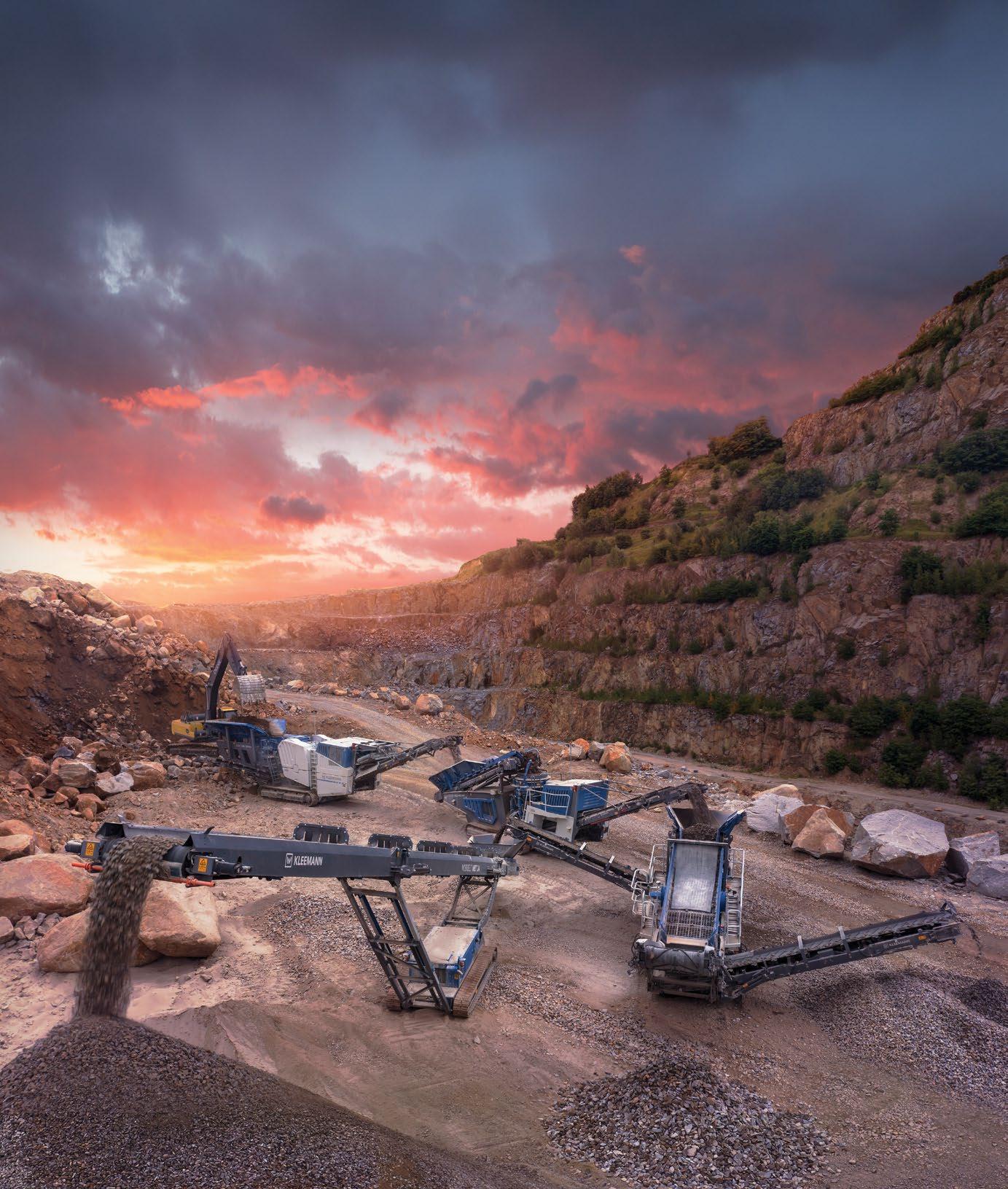
UNLOCKING NEW COMMINUTION GROWTH
To unlock the next phase of market share growth in a different area from its traditional stronghold, i.e., the road-making equipment market, Wirtgen Group South Africa is making its Kleemann mobile crushing and screening range a special focus. In a one-onone with Quarrying Africa, sales manager Waylon Kukard unpacks some of the initiatives to grow the brand and what makes the Kleemann range tick. By Munesu Shoko.
Having launched the first Kleemann units in 2010, Wirtgen Group South Africa has to date put some 80 units into the local market
250 tph
With the arrival of the 250-tph MR 100 NEO, Kleemann now has an impactor suited for smaller crushing operations, such as brickyards and recycling applications
13 l
Kleemann jaw crushers operating in the field are averaging 13 litres of diesel per hour

The Kleemann MOBISCREEN MSS 502 EVO screen has just won the 2025 German Design Award for its technically innovative approaches.
Traditionally, the Wirtgen Group has established itself as a market leader in the road-making equipment market, not only in Africa, but globally. Brands such as Wirtgen, Hamm and VÖGELE, amongst others, dominate the various segments of the road construction equipment market.
“Being such a well-established road equipment manufacturer with such high market shares across various product groups, the focus has always been on maintaining our leadership position in those traditional domains. However, at a group level, we are confident that our next wave of market share growth will come from Kleemann, a product that has already proven its prowess in Europe, but is still to find the same level of acceptance in the local market,” says Kukard.
Installed base
Having launched the first Kleemann units in 2010, Wirtgen South Africa has to date put some 80 units into the local market. While the majority of these machines are operating in South Africa, several machines are also hard at work in neighbouring countries.
Beyond South Africa’s borders, Wirtgen South Africa has capable dealer partners in markets such as Zimbabwe and Botswana. Under the stewardship of Machinery Exchange, the brand is on a growth trajectory in Zimbabwe, with some two trains – each comprising an MC 110 EVO2 jaw crusher, an MCO 9 EVO2 cone crusher and an MSC 703 EVO screen. In total, six Kleemann machines have been delivered in Zimbabwe in the past two years alone, with prospects to commission more trains in the near future.
While Botswana has in recent years turned its infrastructure development attention to water and pipelines, Parts Sales Botswana, the Wirtgen dealer in the country, has enjoyed good success, with an installed base of seven Kleemann machines, confirms Kukard.
Growth initiatives
While the installed base in southern Africa is fairly encouraging, Kukard believes that the brand remains uncommon, especially among some of the major mining contractors who undertake large crushing and screening
KEY POINTS
Wirtgen South Africa is making its Kleemann mobile crushing and screening range a special focus
The company has appointed two experienced sales personnel to drive the Kleemann brand in key mining regions of South Africa
The company believes it has the right product and support to grow its market share in the large contracting market
As part of the renewed focus on Kleemann, Wirtgen South Africa is launching a demo programme to give prospective customers first-hand experience of the performance of the Kleemann machines
jobs. Traditionally, the uptake has been high among construction contractors who are already familiar with the company’s road construction product range and the aftermarket support that comes with it.
“Those customers have come to understand the capabilities of the Kleemann range and are also aware of the Wirtgen quality and what we stand for,” says Kukard. “The target is to penetrate the large contracting market. We have the right product and support to grow our market share in this market segment, which is why we are placing a huge focus on the Kleemann offering.”
Consequently, Wirtgen South Africa has put its dedicated approach in motion with the appointment of two experienced sales personnel to drive the Kleemann brand in key mining regions of South Africa. Based in Mpumalanga, the first Kleemann sales specialist, Christo Kotze, looks after the Mpumalanga and Limpopo provinces. The second Kleemann sales specialist, Morne Oelofse, has been deployed in Kimberley, from where he looks after customers in Northern Cape and Free State territories. Kukard says these deployments are strategic in the quest to broaden Kleemann’s foothold in these important mining regions.
Wirtgen South Africa is particularly excited about the MOBIREX MR 100 NEO impact crusher, which closes a crucial gap in the company’s impact crushing offering.
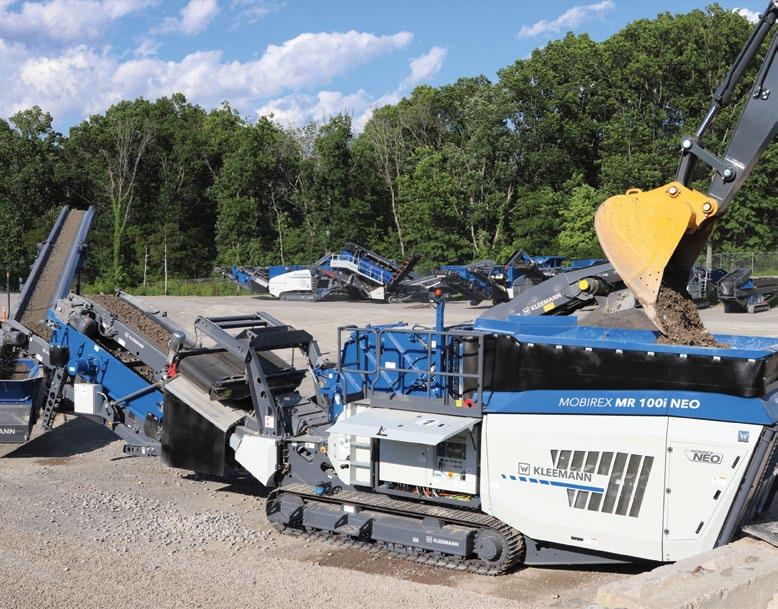
As part of the renewed focus on Kleemann, Wirtgen South Africa is launching a demo programme to give prospective customers, especially the big mining contractors, first-hand experience of the performance of the machines. In addition, the company is also introducing a rental facility which, according to Kukard, provides customers with the opportunity to test the brand before they commit to any outright purchasing decisions.
Model range and strengths
While Kleemann offers a large range of crushers and screens, the most common models locally are the MC 110 EVO2 jaw crusher, the MCO 9 EVO2 cone crusher, the MSC 703 EVO classifying screen and the recently launched MSS 802 EVO scalping screen.
The Kleemann range has to date distinguished itself with a range of capabilities. Firstly, says Kukard, it is a sturdy machine – the stability of the chassis results in better crushing performance, and this has been proven on many reference sites where the machines have been deployed.
Another key competitive edge of the Kleemann offering is its lower fuel consumption, largely driven by new technology engines combined with on-board generators that drive most components. This is particularly important for customers in southern Africa, where fuel prices are known to be very high.
“Compared with most of our competition’s machines, a Kleemann train achieves on average up to 40% reduced fuel consumption,” he says. “To provide context, the annual fuel saving on one train will cover the customer’s full capital cost of a screen, which contributes to lower cost per tonne. The productivity of the machines has also been exceptional, with production rates on par with some of the best in this market, if not better, at a 40% reduction in fuel consumption.”
Kleemann jaw crushers operating in the field are averaging 13 l of diesel per hour, while cone crushers are running at about 21 l per hour, which is “unheard of”, according to Kukard.
As with other Wirtgen Group offerings, the Kleemann range boasts some of the most innovative technologies. One of the major talking points is the SPECTIVE CONNECT digital platform. With this technology, all relevant process information and reporting are displayed on customers’ smartphones without the operator having to leave the feeding device.
SPECTIVE CONNECT also comes with the Smart Job Configurator, which helps in the selection of the correct machine settings. For this purpose, the operator simply enters the data of the planned application in the SPECTIVE CONNECT App. It calculates the optimum machine settings
automatically, which the operator then transfers to the machine via the SPECTIVE touch panel. The new configuration tool also supports the operator in the selection of the best possible crushing tools as well as the recognition of the tools and tracking of their service life. This significantly simplifies the typical workday.
In addition, Kukard is excited about the new Operations Centre telematics platform which now integrates both Wirtgen Group and John Deere systems. Operations Centre is a digital solutions platform that allows users to manage their sites and equipment, including those from Kleemann, through real-time monitoring, fleet management and data analysis, improving efficiency and productivity.
“Operations Centre is more than just a telematics platform. It provides access to a wealth of data, enabling operators to make data-driven decisions that lead to improved project outcomes. It also promotes transparency and efficiency in crushing operations, allowing for better planning, monitoring and decision-making. By providing real-time insights into machine performance and job site activity, the Operations Centre helps to improve productivity and reduce costs,” explains Kukard.
The future
Looking ahead, Kukard is excited about the imminent arrival of new Kleemann machines, which will officially be introduced at bauma 2025 in April this year. These include the MOBIREX MR 100 NEO impact crusher and the MOBISCREEN MSS 502 EVO screen.
Kukard is particularly excited about the MOBIREX MR 100 NEO impact crusher, which he says closes a crucial gap in the company’s impact crushing offering. Previously, the smallest impact crusher in the Kleemann stable was the 350 tonnes per hour (tph) MR 110 EVO2. With the arrival of the 250-tph MR 100 NEO, Kleemann now has an impactor suited for smaller crushing operations, such as brickyards, reclaimed asphalt pavement processing and recycling applications.
In fact, the two machines, the MOBIREX MR 100 NEO impact crusher and the MOBISCREEN MSS 502 EVO screen, have just won the 2025 German Design Award for their technically innovative approaches. The two new products from Kleemann received the coveted design award in the “Excellent Product Design” category. a

The Sandvik UJ313 wheeled jaw crusher delivers powerful, reliable crushing combined with excellent mobility for maximum on-site productivity.
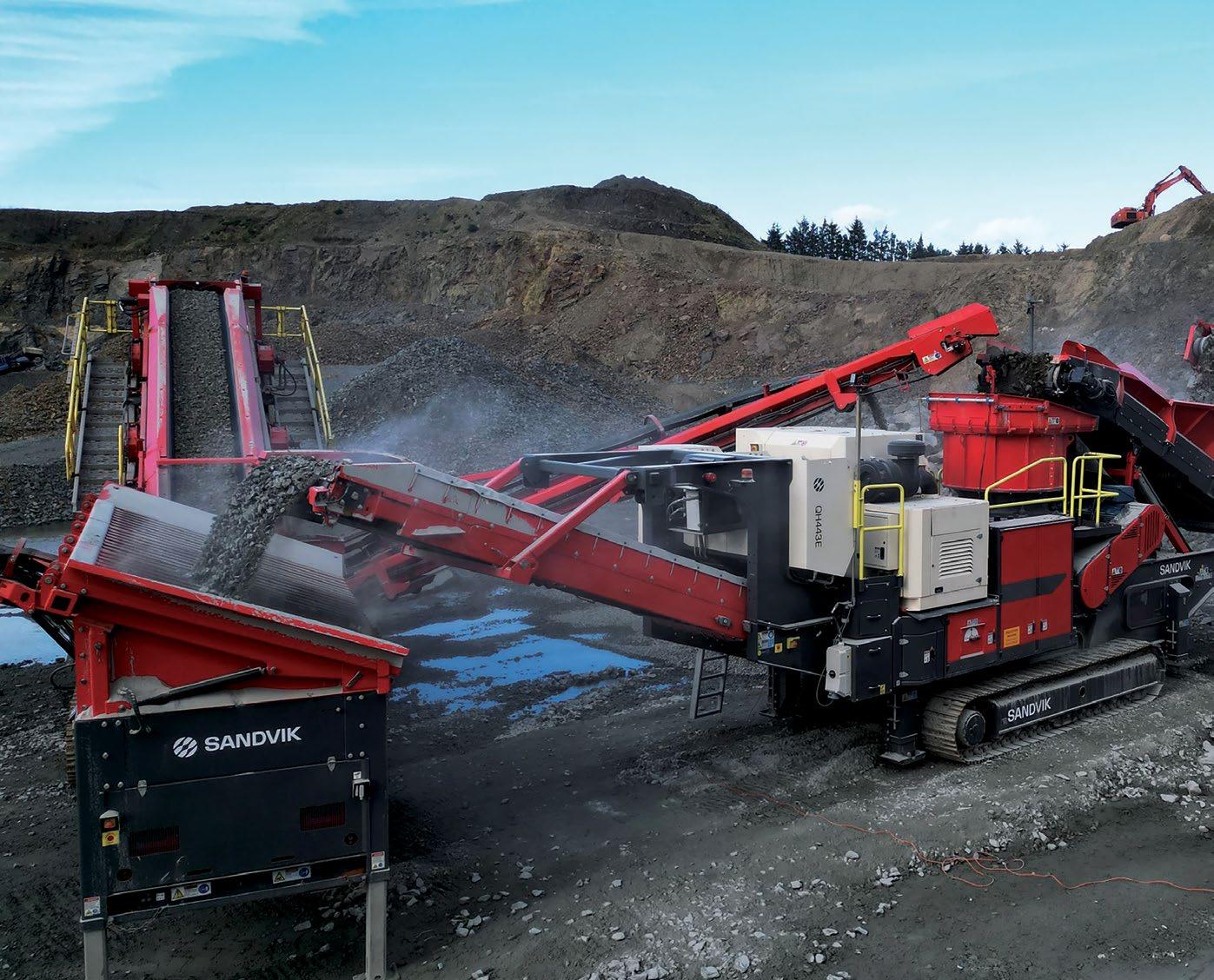
COVERING ALL BASES
With its comprehensive mobile crushing equipment range, Sandvik Rock Processing covers a broad base of crushing needs for quarries and surface mines. This provides customers with the convenience of accessing a wide range of crushing solutions –primary jaw crushers, open and closed circuit cone crushers, as well as impact crushers – from a single source, streamlining their purchasing processes and saving them time and effort. By Munesu Shoko.
Crushing is a vital step that reduces the size of large rocks and ores in quarrying and mining so that they can be further processed into valuable minerals and other products. Dealing with a supplier that places a high value on not only a comprehensive crushing range, but also critical parameters such as efficiency, reliability and high productivity, is nonnegotiable. With Sandvik Rock Processing’s mobile crushing range, all these boxes are easily ticked, says PC Kruger, business line manager Crushing at Sandvik Rock Processing.
Sandvik Rock Processing manufactures a comprehensive range of primary jaw crushers, open and closed-circuit cone crushers, as well as impact crushers – which are all available on crawler tracks or wheels to address the industry’s need for ease of mobility.
The company has plants to suit most process needs, ranging from entry level units weighing in at 35 tonnes (t) to larger units weighing in at a whopping 138 t. In terms of capacity, this ranges from the QJ241 jaw crusher that takes a maximum feed size of 520 mm with a capacity up to 225 tonnes per hour (tph), to the larger UJ640E that takes a maximum feed size of 975 mm, producing up to 1 000 tph.
Withstanding harsh environments
Sandvik Rock Processing’s heavy duty U-range features the company’s trusted stationary derived crushing chambers, jaws, hydrocones and the S-type gyratory, designed for hard rock crushing. These units,
35-138 t
The company has plants to suit most process needs, ranging from entry level units weighing in at 35 t to larger units weighing in at a whopping 138 t
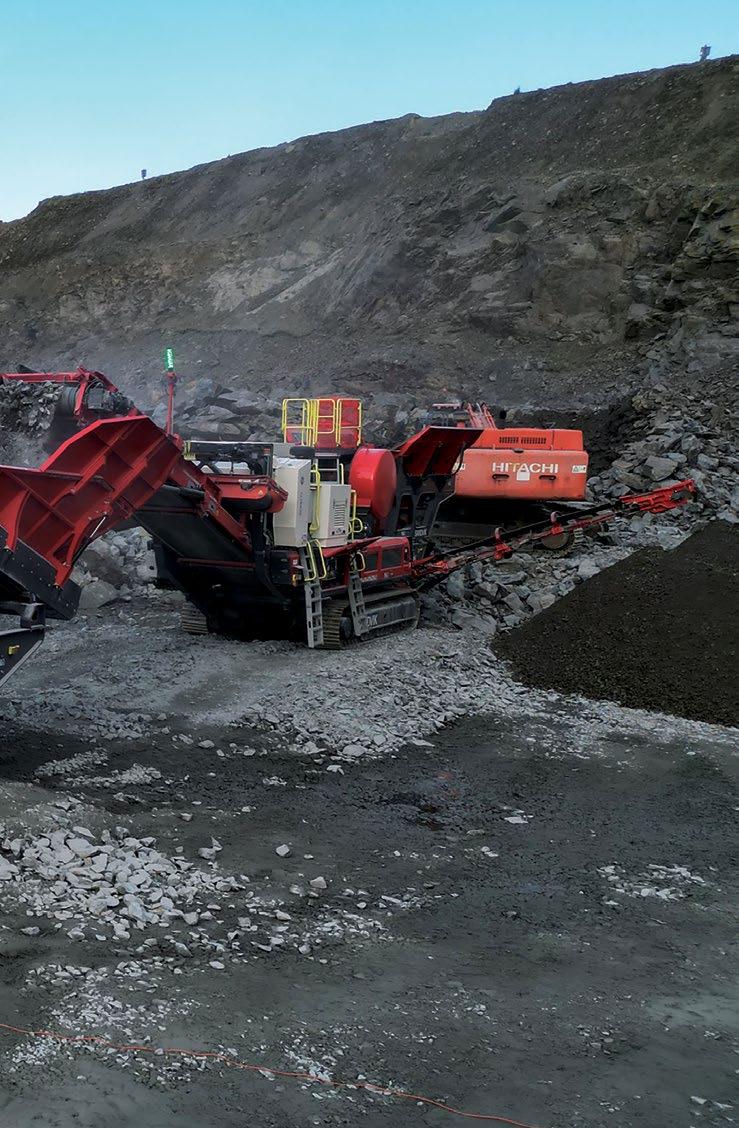
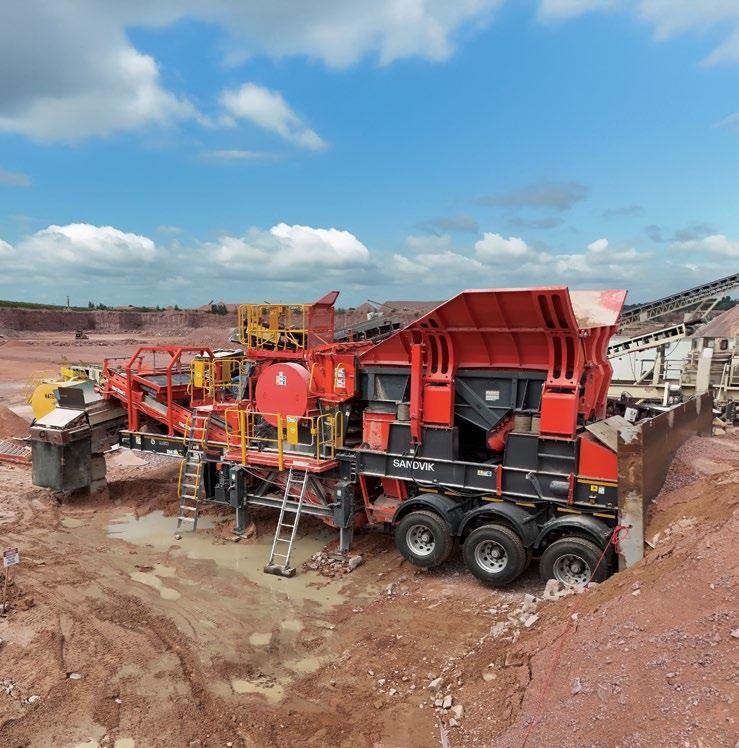
91%
The UJ443E heavy duty jaw crusher unit, using fully electric track drives and final drives, is said to decrease the use of hydraulic oil on the plant by up to 91%
KEY POINTS
Sandvik Rock Processing manufactures a comprehensive range of mobile primary jaw crushers, open and closed-circuit cone crushers, as well as impact crushers
Sandvik Rock Processing’s heavy duty U-range features the company’s trusted stationary derived crushing chambers, jaws, hydrocones and the S-type gyratory, designed for hard rock crushing
To help industry meet its energy efficiency and sustainability obligations, Sandvik Rock Processing is one of the crushing OEMs at the forefront of fully electric mobile crushers to ensure lower operating costs and reduced environmental impact
The performance of the crushers can be easily monitored through the remote monitoring system, which optimises equipment to exact operational requirements
says Kruger, are built to last, operating in the toughest of working conditions. The crushers are built from premium quality components, including high-spec materials used in the chassis to withstand both cold arctic operating conditions and the hot climate in some parts of Africa.
“Deployed in a variety of mining and quarrying applications to handle both tough ores and hard rocks, Sandvik crushers are designed to deliver increased levels of productivity, while maximising operator comfort and cost efficiency. Several of the larger tracked units feature on-board diesel generators, allowing customers to choose their preferred energy source – mains grid power or diesel,” adds Kruger.
Maximising reliability
The importance of efficiency, reliability and productivity in crushing cannot be stated enough. With that in mind, most Sandvik Rock Processing mobile units come with innovative features as standard for improved efficiency and high productivity. These include automated systems such as feeder control, jaw level sensors to optimise the feed rate, and dust-proof components to maximise durability and ensure long life.
As part of a wide range of wear solutions, all Sandvik Rock Processing jaw plates have been developed to deliver high reliability and durability. For example, the Sandvik Optitooth jaw plates, available for the Q-range of tracked jaw crushers, have been designed to achieve optimum performance of the crushing chamber.
The Sandvik UJ313 wheeled jaw crusher delivers, powerful, reliable crushing.
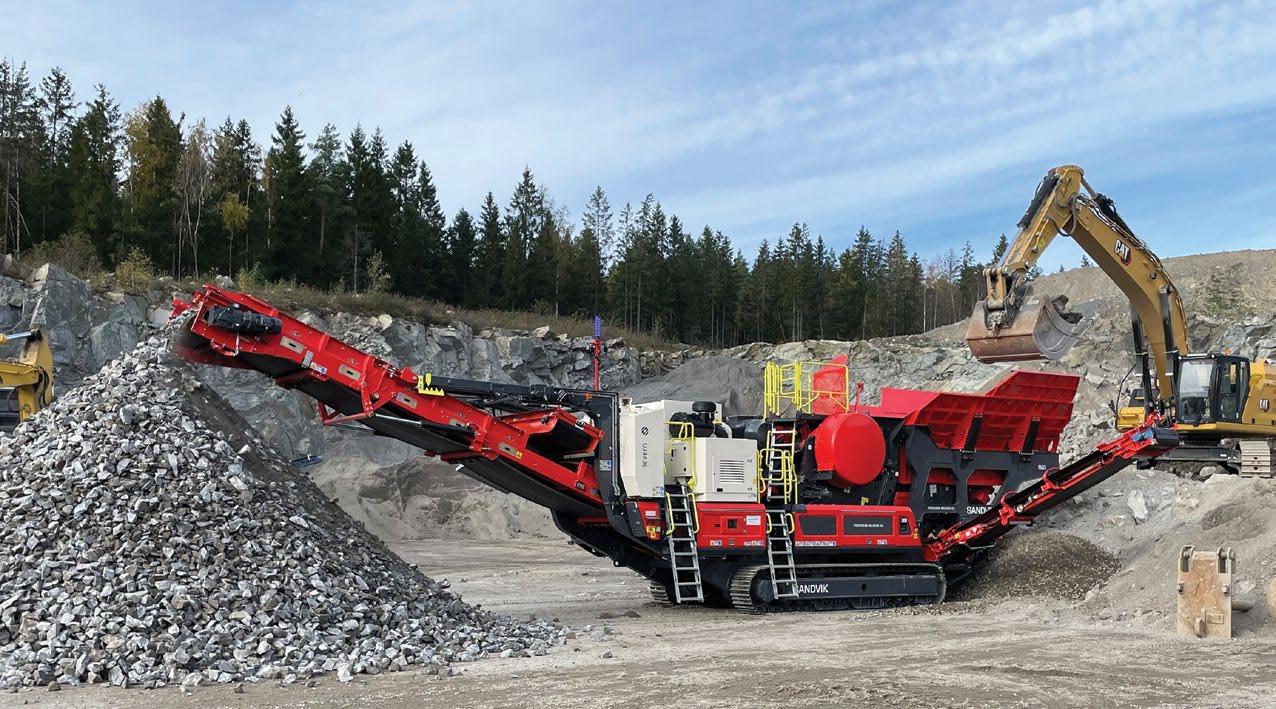
The Sandvik Optitooth jaw plates ensure that a higher percentage of the jaw is utilised, resulting in longer wear life and less manganese waste. The innovative design enables better breakage and a faster distribution of fines through the crushing chamber. This results in lower engine loading and consequently, a reduction in fuel consumption, thus lowering operating costs. According to Sandvik Rock Processing, the Optitooth jaw plates have been proven to last up to 30% longer and to be up to 20% more productive than conventional offerings.
“In addition, Sandvik long-lasting rubber wear plates with full steel backing or extruded aluminium profiles are available for all-round wear protection. These can be tailor-made to fit most applications, from light to extra heavy duty,” explains Kruger. “Due to a long wear life and impact-absorbing properties, service intervals are longer, less maintenance is required and unscheduled breakdowns are avoided. These rubber wear plates also extend equipment lifetime through reduced vibrations and dampened impact forces, while the reduction of noise levels leads to a better working environment.”
Efficiency and sustainability
Processing is one of the crushing original equipment manufacturers (OEMs) at the forefront of fully electric mobile crushers to ensure lower operating costs and reduced environmental impact.
The most recent addition to the tracked electric range of crushers is the UJ443E heavy duty jaw crusher. This machine is built on a new, ‘fully electric’ track platform. It features electric final drives and on-board genset, which can be operated more sustainably, either by an external electricity supply, hydrotreated vegetable oil (HVO) or diesel.
Powering the machine using an external electric source can bring several advantages, including lowering running costs, extending drivetrain service intervals, reducing time spent refuelling, reducing onsite emissions and lowering noise levels. Using fully electric track drives and final drives, the unit is said to decrease the use of hydraulic oil on the plant by up to 91%.
225-1 000 tph
Mines and quarries are actively pursuing energy efficiency due to the significant financial benefits of reducing their energy consumption, which is often a major operational cost. In addition, they are fulfilling the need to improve sustainability by lowering their carbon footprint. Essentially, by using less energy, the industry can save money and operate in a more environmentally responsible way. To help industry meet its energy efficiency and sustainability obligations, Sandvik Rock
The company also manufactures a wheeled range of crushers that has been made to meet the same high standard as its tracked counterparts, operating at maximum efficiency and designed for high-capacity production. Electrically powered, these units offer lower cost per tonne operation, as well as lower emissions, thus minimising the environmental impact, which speaks directly to the industry’s sustainability drive.
“In addition, our range of hybrid mobile crushers also saves energy and reduces the climate impact of rock processing. These dual-powered crushers offer several benefits, including increased efficiency, reduced operational costs and lower environmental impact thanks
The Sandvik UJ443E jaw crusher is built for tough quarry applications, delivering high performance and durability in demanding conditions.
Sandvik Rock Processing’s mobile range starts from the smaller QJ241 jaw crusher with a capacity up to 225 tph, to the larger UJ640E that produces up to 1 000 tph
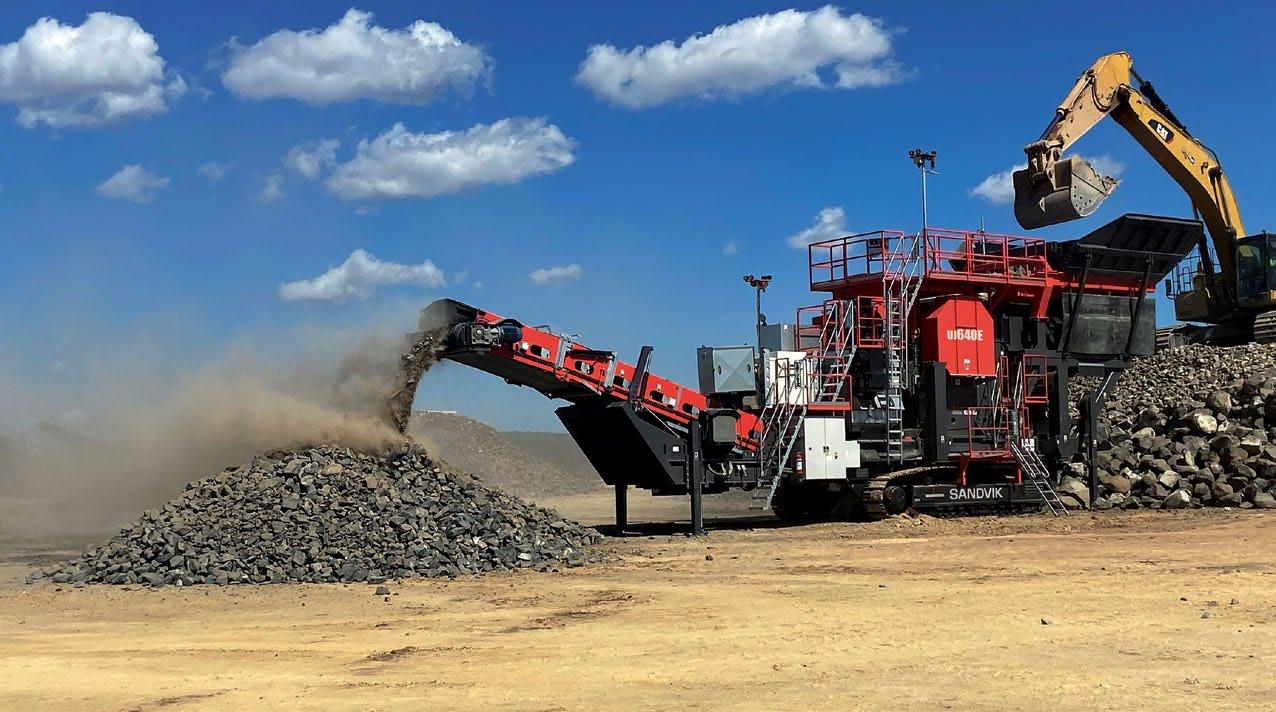
to the potential for using electric power sources,” explains Lodewyk Louwies, field service technician at Sandvik Rock Processing.
Safety to the fore
All Sandvik Rock Processing mobile crusher models place safety at the centre of their design. The units are built with spacious platforms for ease of access to all necessary components. The units are fitted with safety guards over moving componentry as well as emergency stop buttons around the machine.
“User-friendly by design, the operation of our mobile crushers is easy to master and makes processes much simpler to action,” explains Kruger. “The tracked units can be operated by radio remote control for easy and safe operation, while the majority of our best-selling models within our product offering are fitted with My Fleet remote monitoring systems to help optimise operation.”
Optimising performance
The digital solutions developed by Sandvik Rock Processing go a long way in helping customers improve productivity and performance. For example, performance can be easily monitored through the remote monitoring system, which optimises equipment to exact operational requirements.
By using Sandvik Rock Processing quality OEM parts, customers can keep their plants operating at peak performance with minimal downtime. Tested to the extremes, says Kruger, these parts are designed to fit Sandvik equipment perfectly and ensure higher equipment uptime and greater efficiency than nonoriginal parts.
Maintenance and support
For Sandvik Rock Processing, customer support
is an essential element of its business. This starts right from decision-making through to the lifetime of the equipment. To support customers with their decision-making, Sandvik Rock Processing mobiles are fully integrated into the company’s Plant Designer programme – a crushing and screening simulation software.
“This proprietary software platform calculates quantitative and qualitative material flow and output levels, assisting customers in the decisionmaking process of crusher and screen purchasing and ownership. Users can qualify their equipment investment easily through Plant Designer’s state-of-theart simulations, improving profitability and efficiency,” says Kruger.
When it comes to maintenance, Sandvik Rock Processing has recently introduced its Essential Maintenance Packages for its range of mobile crushers and screens. These packages have been designed as an effective self-service solution for customers to maintain their Sandvik mobile units, providing all the necessary parts for up to 1 000 hours of operation all in one convenient package. This helps customers to stock essential spares in advance and minimise downtime.
“Our large pool of skilled service technicians, decentralised across various regions of the continent, ensure uptime, equipment reliability and productivity for customers,” says Jody Vermaak, aftermarkets sales manager at Sandvik Rock Processing. “This is complemented by local equipment and parts inventory across our regional hubs. Apart from our main hub in South Africa, we have entities in Zambia, the DRC, Tanzania and Ghana. We have also placed a premium on training, not only for our employees, but also for other partners that work with our equipment, such as distributors and customers themselves.” a
The Sandvik UJ640E jaw crusher is designed for high capacity primary crushing, delivering exceptional performance and reliability for demanding applications.
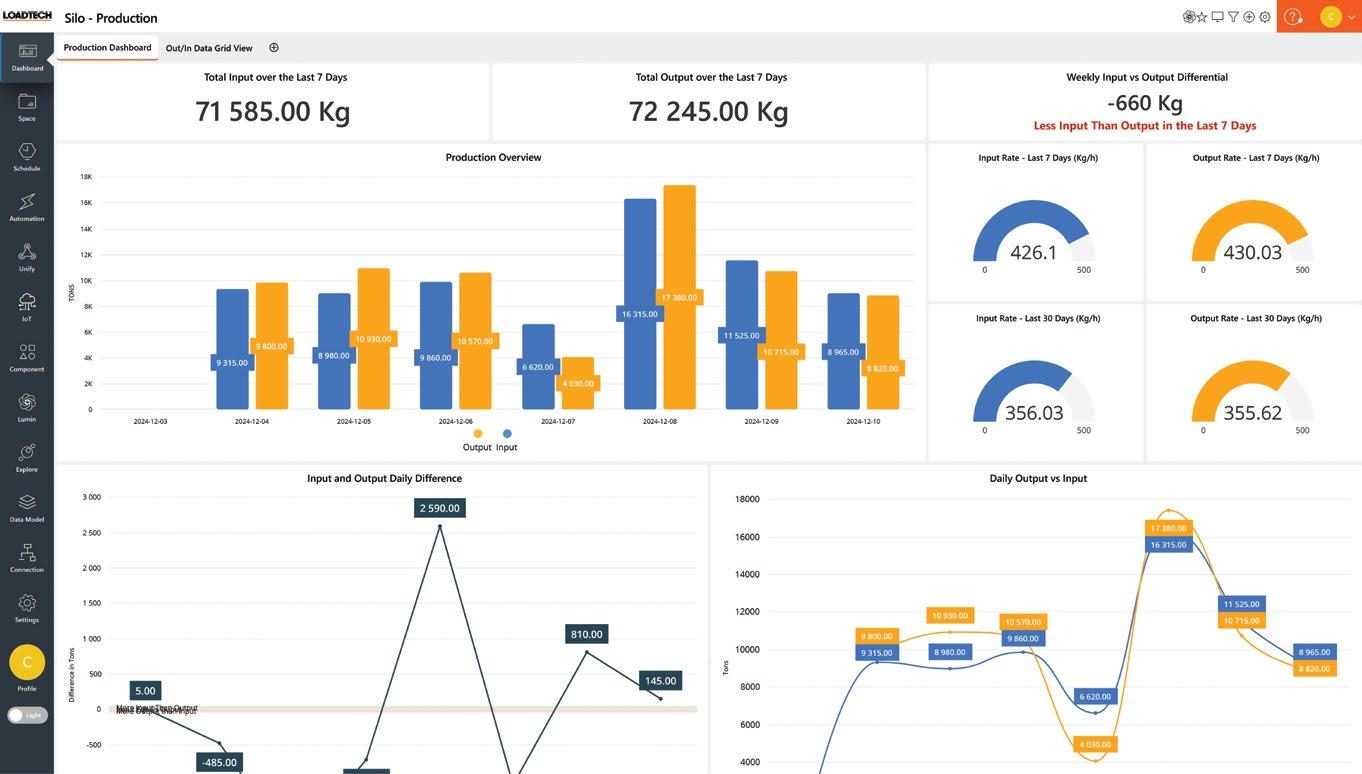
Loadtech ViewIT provides businesses with an easy-to-use data intelligence platform.
MORE DATA, MORE VALUE
Mines and quarries are increasingly running data-driven operations, leveraging data analytics and insights from various sources to optimise processes, predict equipment failures and improve overall efficiency and safety. In response to this trend, Loadtech has launched its Loadtech ViewIT, an Artificial Intelligence (AI)-powered remote monitoring system that brings together data ingestion, storage, visualisation, analysis and trend prediction in one unified interface. By Munesu Shoko.
Having gone through an extensive research and development system, leveraging decades of experience in payload management systems, Loadtech launched Loadtech ViewIT, an inhouse developed online productivity tracker, in mid-2024. Following extensive field tests, several quarrying customers, including some established quarrying groups and independent operations, are already running the system on a number of assets, including silos and conveyor belts, amongst others.
According to Glen Webster, operations director at Loadtech, early feedback from the first adopters shows that the system is adding value to customer’s sites across applications. At the time of writing, several new installations were planned for the start of 2025, highlighting the acceptance of the new technology in the market as operations seek to achieve new levels of efficiency and
KEY POINTS
Loadtech has launched its Loadtech ViewIT, an AI-powered remote monitoring system that brings together data ingestion, storage, visualisation, analysis and trend prediction in one unified interface
The platform seamlessly integrates business intelligence, data automation and machine learning capabilities, offering real-time insights and predictions to support decision-making
Accessible anytime, anywhere and on any device, Loadtech ViewIT enables businesses to stay ahead with intuitive tools for comprehensive data analysis
The integration of the AI algorithm now allows for minor remote calibrations, which ushers in a new era in preserving uptime and maximising production
2024
Loadtech launched Loadtech ViewIT, an in-house developed online productivity tracker, in mid-2024
ChatGPT
One of the remarkable features of the system is the integration of ChatGPT for data analysis and trend prediction
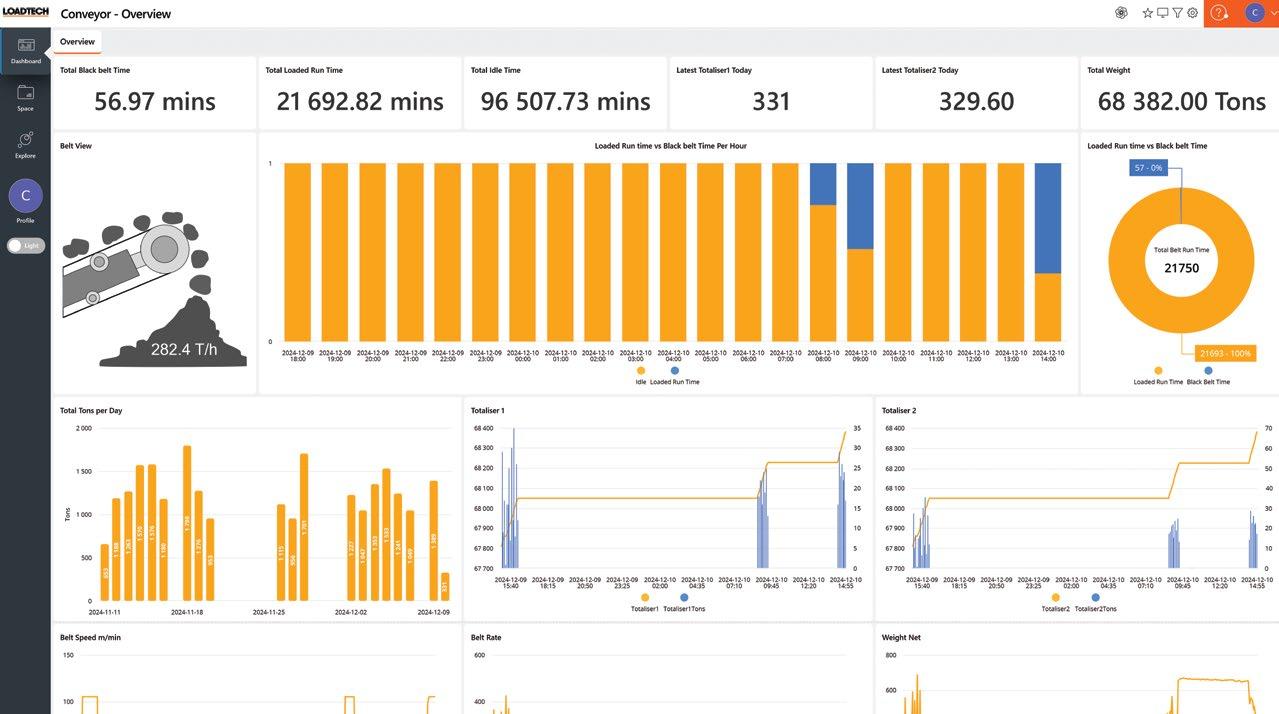
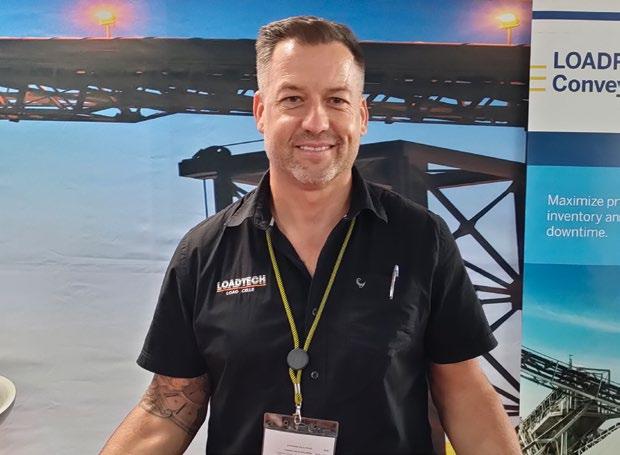
“The integration of the AI algorithm now allows for minor remote calibrations, which ushers in a new era in preserving uptime and maximising production. We are now able to perform calibrations remotely without the need to send a technician to site.
productivity though data-driven decisions. The system will also be one of the major highlights at the Loadtech stand at the 2025 Institute of Quarrying Southern Africa (IQSA) Conference in April.
ViewIT in detail
Available on both Apple and Android platforms, Loadtech ViewIT provides businesses with an easyto-use data intelligence platform that brings together data ingestion, storage, visualisation, analysis and trend prediction in one unified interface.
The platform seamlessly integrates business intelligence, data automation and machine learning capabilities, offering real-time insights and predictions to support decision-making. Accessible anytime, anywhere and on any device, Loadtech ViewIT enables businesses to stay ahead with intuitive tools for comprehensive data analysis.
“Loadtech ViewIT is our in-house developed remote monitoring system that allows customers to view any of their assets from anywhere, be it a silo, weighbridge, wheel loader or mining truck, or others,” explains Webster. “In an environment where mines and quarries generate loads of data from their assets, the system helps them to interpret the raw data into actionable insights. Dashboards can be tailor-made to meet each customer’s
Glen Webster, operations director at Loadtech
Loadtech ViewIT enables businesses to stay ahead with intuitive tools for comprehensive data analysis.
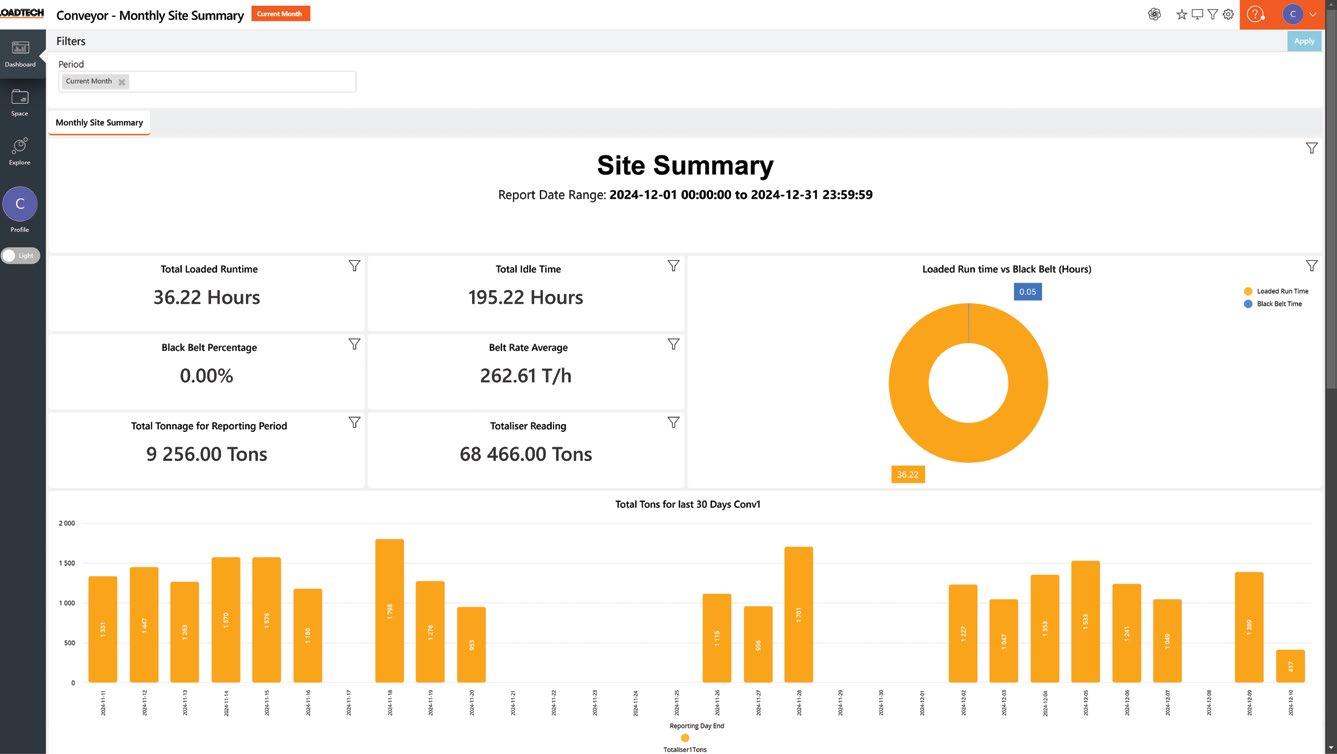
data viewing and reporting needs.”
One of the remarkable features of the system, adds Webster, is the integration of ChatGPT for data analysis and trend prediction. By integrating an advanced AI algorithm, the system continuously analyses a range of operational parameters to identify any deviations.
“The integration of the AI algorithm now allows for minor remote calibrations, which ushers in a new era in preserving uptime and maximising production. We are now able to perform calibrations remotely without the need to send a technician to site,” explains Webster. “No matter the application, ViewIT is the industry’s data solution to solving the ‘where has your product gone?’ question. Backtracking reports are also extractable to PDF, Word or Excel, depending on each customer’s individual needs.”
Data drive
“The Loadtech ViewIT system is our response to the industry’s need for an easy-to-use, cost-effective online productivity tracker at the customer’s fingertips,” says Webster. “Remote monitoring in mining and quarrying offers numerous benefits, including enhanced safety, increased efficiency, proactive maintenance and improved operational decision-making, leading to reduced downtime and costs.”
Beefing up support
2025
The launch of Loadtech ViewIT, says Webster, is directly aimed at the mining industry’s growing appetite for data-driven operations. Mining companies and their quarrying counterparts can leverage historical data to forecast future events, optimise resource allocation and minimise unnecessary spending.
Data analytics enables real-time monitoring of assets, allowing quarry and mine managers to make timely decisions and respond proactively to potential issues. Analysing data from various stages of the mining process, from extraction to processing, also helps operations to identify bottlenecks, optimise efficiency and improve product quality.
As part of its product expansion programme, Loadtech has invested heavily in its data department to look after the Loadtech ViewIT and the development of other complementary data solutions in the future. The dedicated data department streamlines data management, ensuring data quality, security and proper usage, ultimately leading to better support for customers.
In addition, Loadtech is investing heavily in its aftermarket support regime in 2025. Central to this strategy is the opening of the Cape Town branch in March. This is complemented by the appointment of two experienced sales personnel to look after the growing customer base in the Western Cape area.
“While we provide some of the best technology in our line of business, Loadtech has always been built on providing exceptional aftermarket support to our customers. Prompt and reliable aftermarket support builds trust and satisfaction, leading to increased customer loyalty,” concludes Webster. a
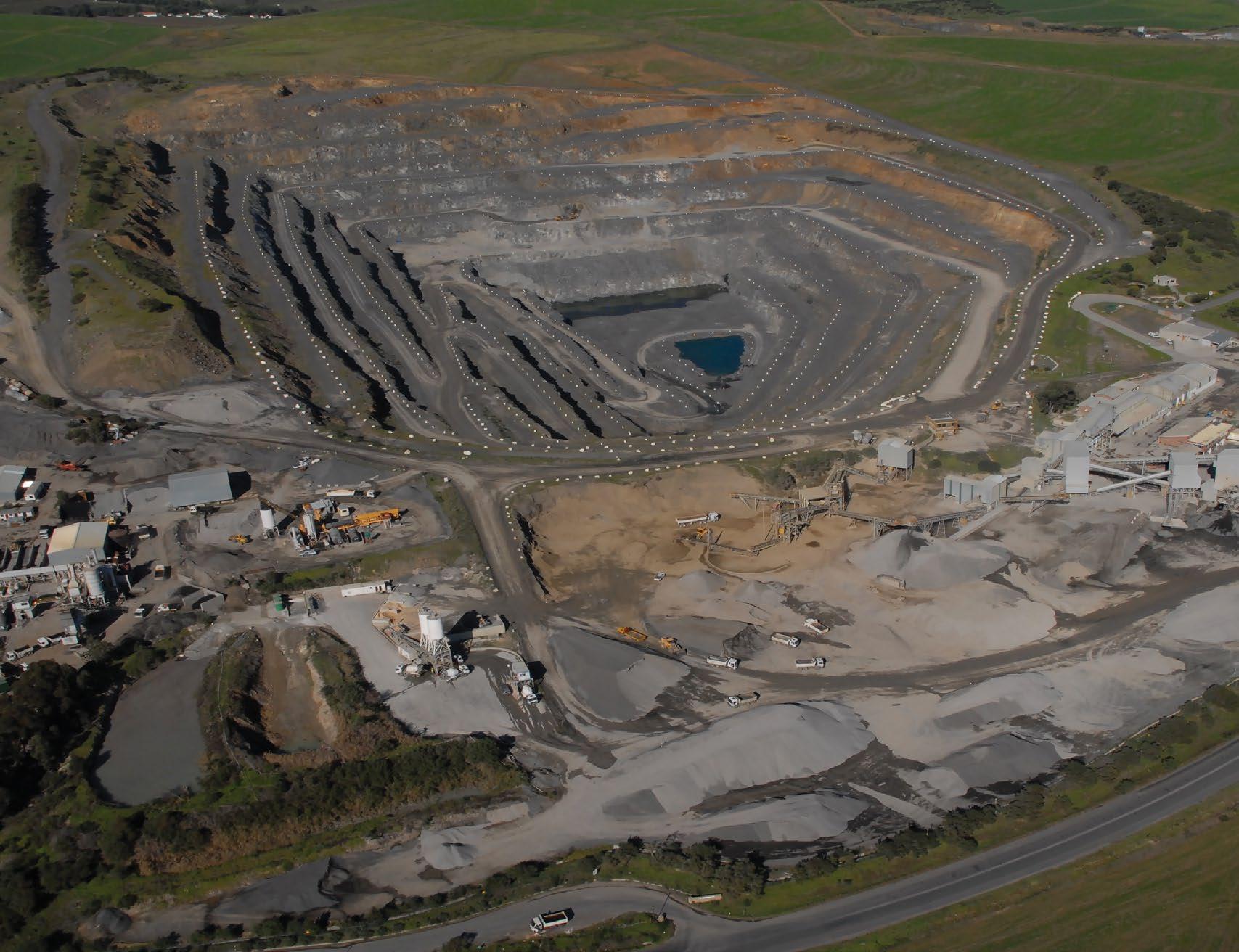
Loadtech is investing heavily in its aftermarket support regime in 2025. Central to this strategy is the opening of the Cape Town branch in March
The platform seamlessly integrates business intelligence, data automation and machine learning capabilities.
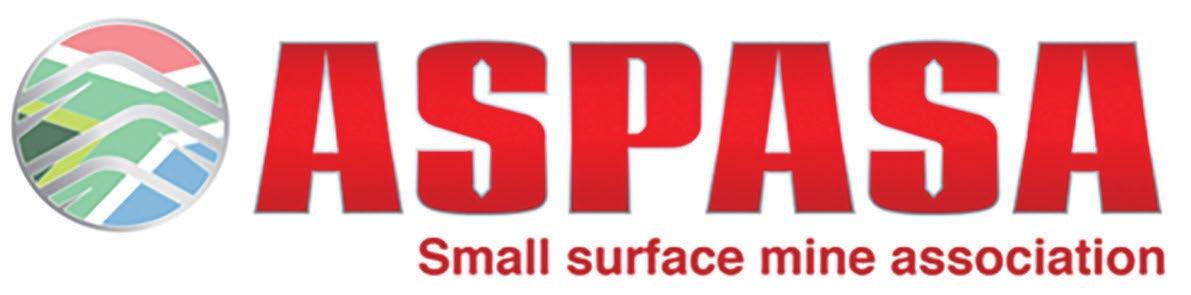
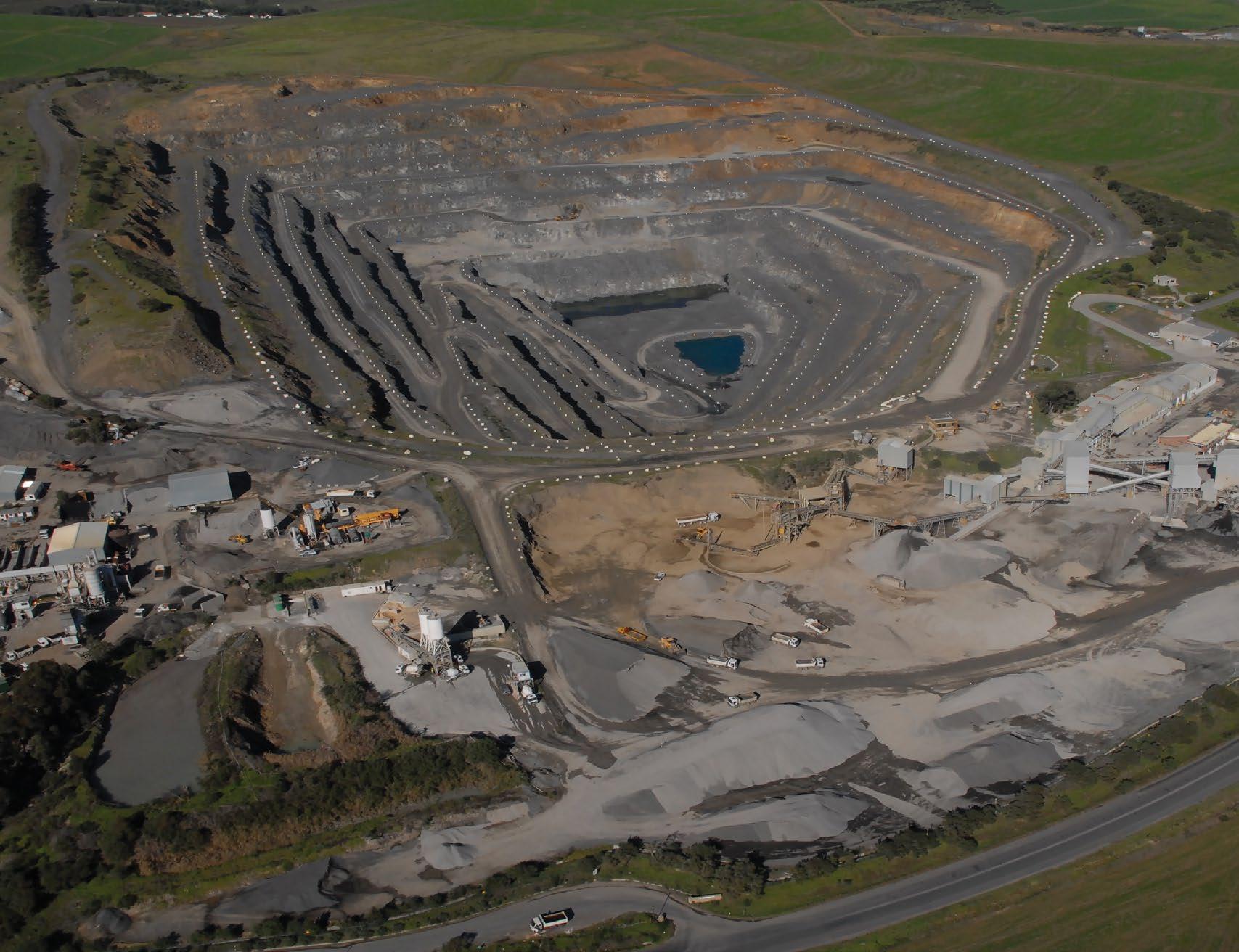
•
•
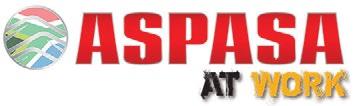
•
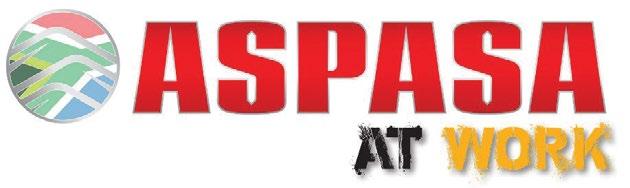
Liaison
International
•
External
•
•
•
•
•
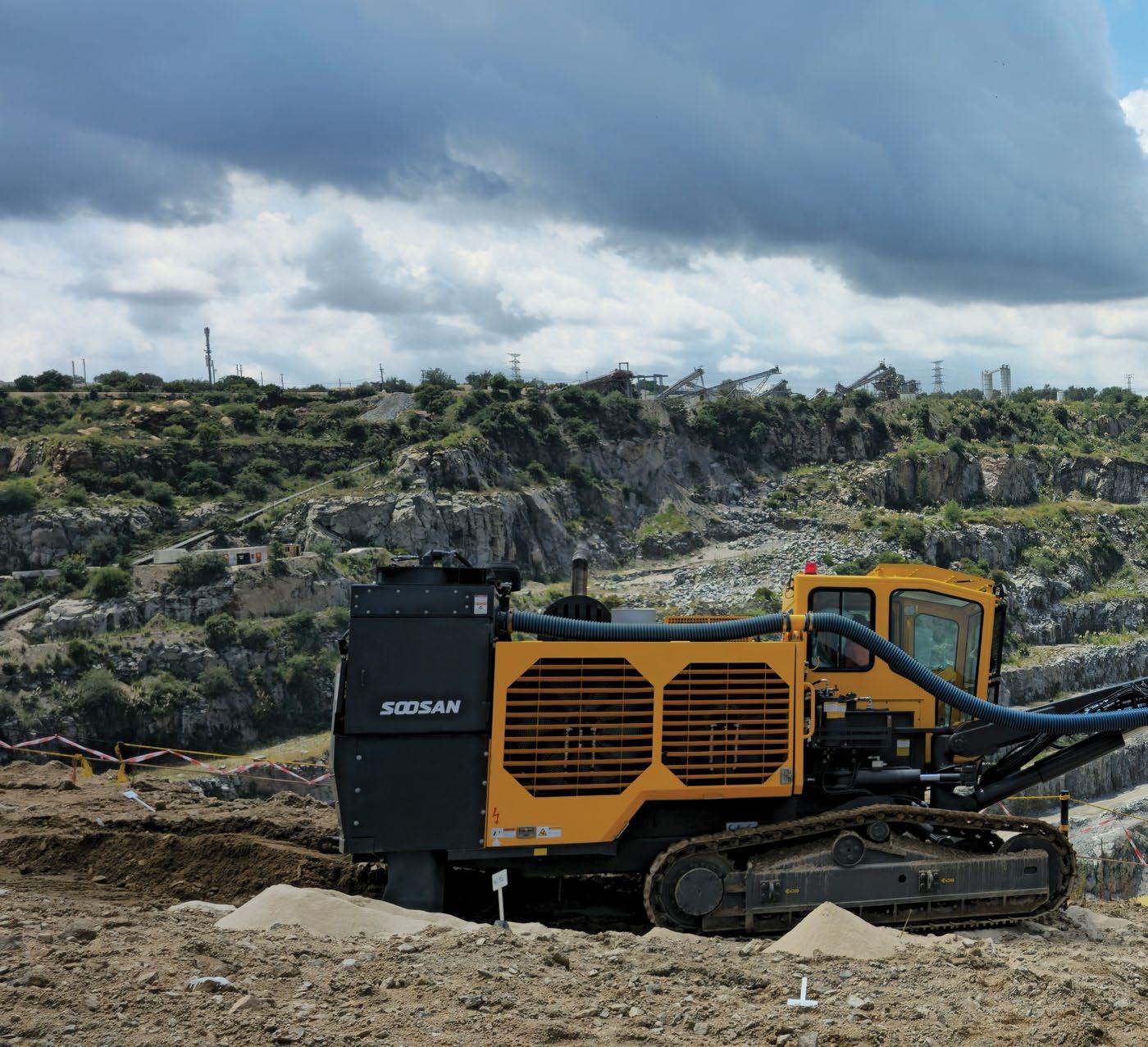
DRILLING INTO QUARRYING
Having traditionally proven popular in the mainstream mining sector, the Soosan CSM range of hydraulic crawler drills, supplied and supported in southern Africa by JMH Equipment since 2007, is gaining a strong foothold in the local quarrying sector. MD Maurits Holtzhausen tells Quarrying Africa that several units are already operational in the aggregate environment, with a few more set to be deployed this year. By Munesu Shoko.
A new Soosan JD-1400E drill has recently been handed over to a quarrying customer.
10-15%
The Soosan CSM range is competitively priced, coming in at about 10-15% less than some of the premium offerings in the market
64-102 mm
The JD-800, the smallest in the range, comes with a hole range of 64-102 mm
89-127 mm
The JD1400-E is the latest and more popular model in the range, offering a hole range of 89-127 mm
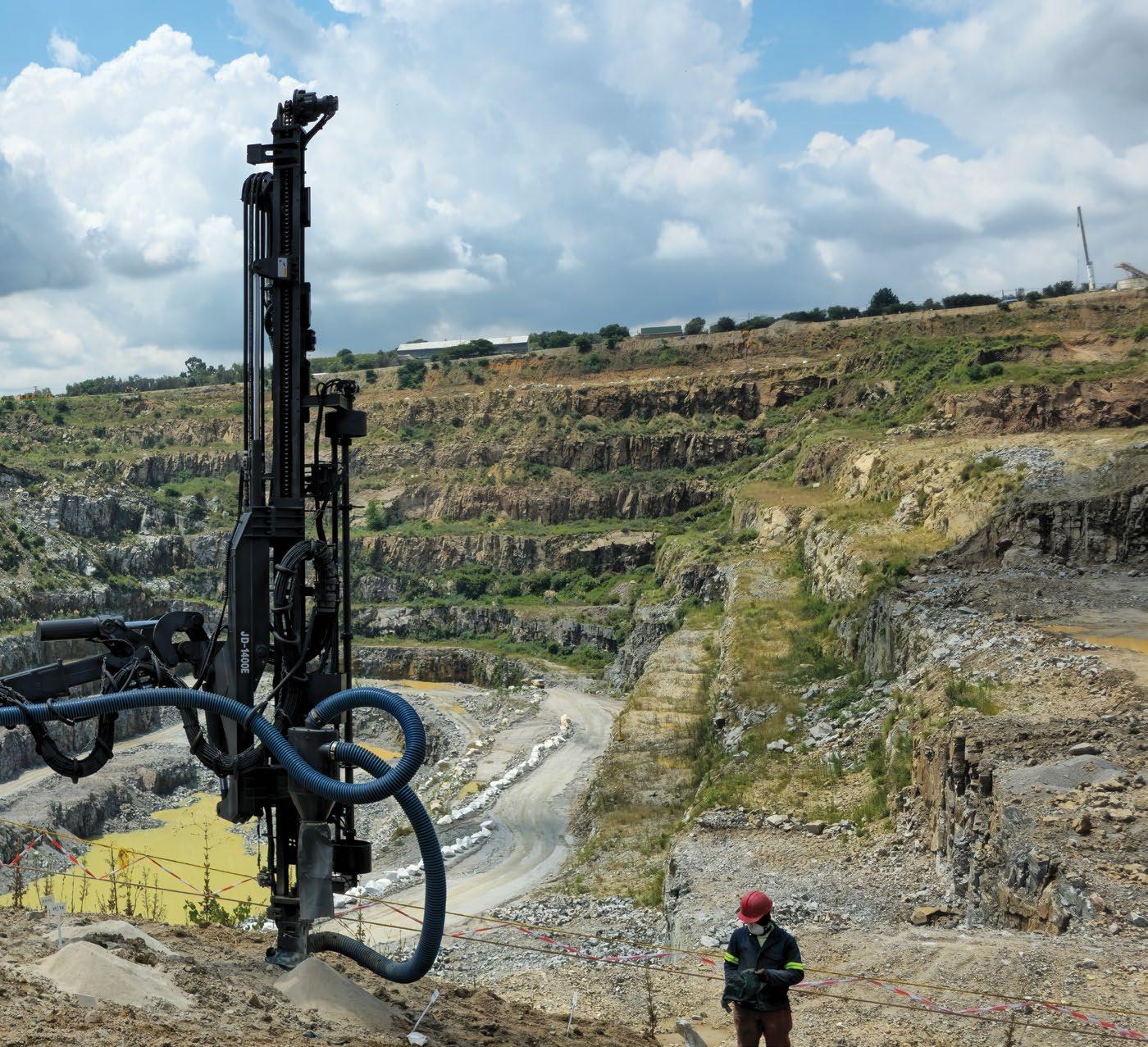
With a large installed base in southern Africa – particularly South Africa, Namibia and Botswana – the Soosan CSM has proven its mettle across commodities, becoming a hit among major mining houses and their contracting counterparts.
Some of the established names that run this Korean-made range of hydraulic crawler drills include Botse Drill & Blast, Profrag Drill & Blast, Explo Energy and Surface Blasting Services, amongst others.
A significant portion of the range’s installed base currently operates in surface mining, particularly in the Rustenburg area, where a large population of opencast mines is present. Headquartered in Rustenburg,
With a large installed base in southern Africa –particularly South Africa, Namibia and Botswana – the Soosan CSM has proven its mettle across commodities in mining
Traditionally, quarrying has never been a major market of focus for JMH Equipment. However, in recent times, the company has started to make strong inroads, with five units supplied last year alone
JMH Equipment offers three hydraulic crawler rig models – the JD-800, JD-1300E and JD-1400E
In addition, JMH Equipment supplies complementary aftermarket drifter spare parts for any make and model of both underground and top-hammer drill rigs
KEY TAKEAWAYS
JMH Equipment has seen increased uptake of its Soosan CMS range of drills in quarrying.
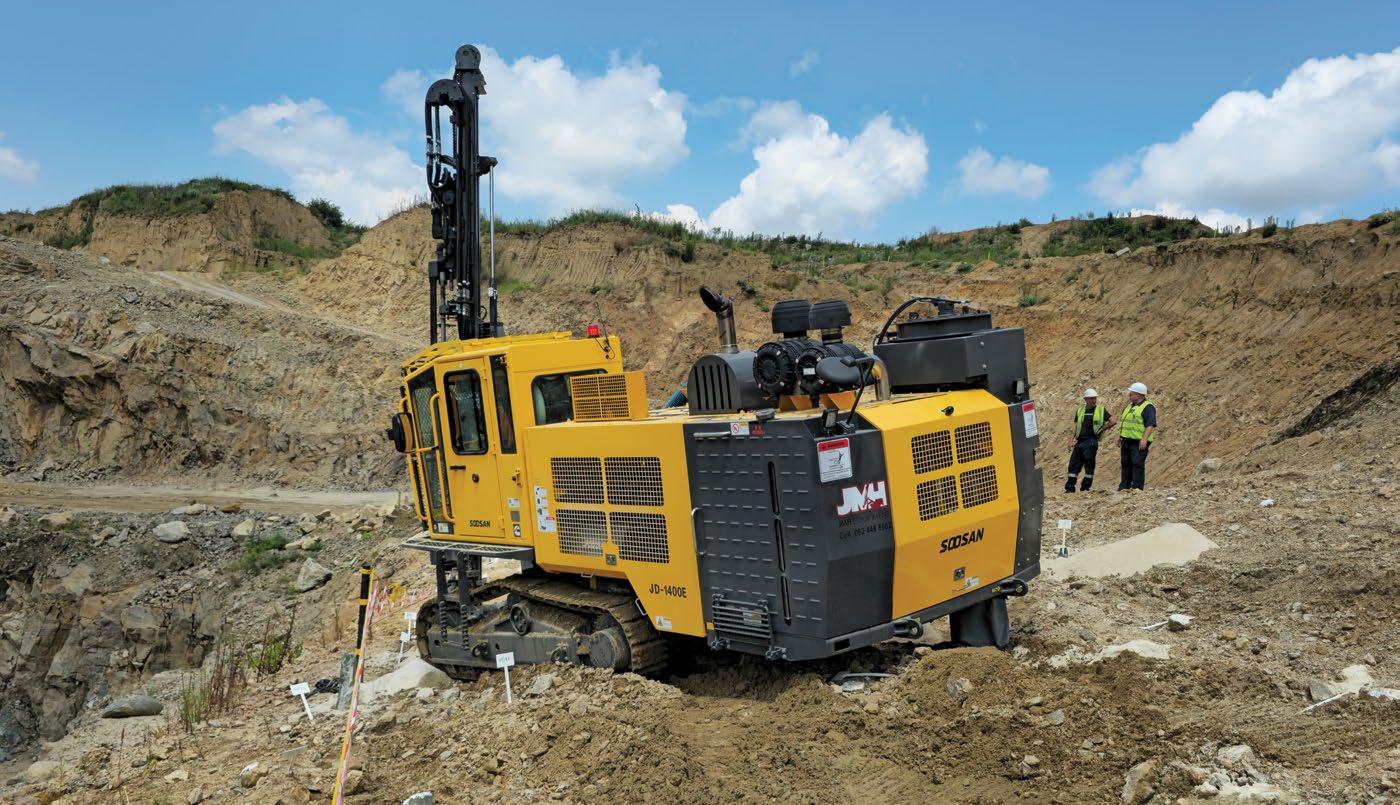
JMH Equipment has forged strong relationships with several mines and contractors operating in the area, hence the large population of Soosan drills in this mining town.
Into quarrying
Traditionally, quarrying has never been a major market of focus for JMH Equipment. However, in recent times, the company has started to make strong inroads, with five units supplied last year alone. At the time of writing, Holtzhausen was expecting to deliver another unit to a repeat customer, highlighting the growing uptake of the range in the aggregates sector.
“We are starting to see a lot more enquiries from quarrying customers who are increasingly becoming aware of the build quality and ease of maintenance of the Soosan CSM range of hydraulic crawler drills. In addition, quarries by their nature are cost-sensitive, and the Soosan range, a simple mechanical drill that is designed to get the job done with no extra ‘bells and whistles’, speaks directly to this group of customers with its competitive pricing,” says Holtzhausen.
The range
JMH Equipment offers three hydraulic crawler rig models – the JD-800E, JD-1300E and JD-1400E. The JD-800E, the smallest in the range, comes with a hole range of 64 mm to 102 mm. The mid-size JD-1300E offers a hole range of 76 mm to 115 mm.
The JD-1400E is the latest and most favoured model in the range with a 400-490 cubic feet per minute (cfm) Airplus compressor, Yamamoto YH135 drifter and a hole range of 89-127 mm. It is fitted with a Cummins CTAA8.3 or QSL9 engine, which is warranteed by Cummins Southern Africa, as well as Kawasaki hydraulic pumps.
89-127 mm
To further grow its footprint into the sector, JMH Equipment will use the upcoming Institute of Quarrying Southern Africa (IQSA) Conference – taking place 3-4 April at the Elangeni Hotel in Durban – to interact with the quarrying community about the key benefits of going the Soosan route to meet their drilling needs.
Its powerful dust collector, fitted with six filters, has a suction capacity of 40 m³ per minute.
The JD-1400E also comes with a Turnstile type auto-rod charger which can carry six rods with an auto-grease to lubricate the rods at the push of a button from inside the cab. The cabin can be certified with Roll-Over Protective Structure (ROPS) and Falling Object Protective Structure (FOPS) as optional, and also includes an air conditioner for maximum operator comfort.
Competitive edge
A key competitive edge of the Soosan CSM range is the favourable price point. The machines are competitively priced against some of the premium offerings in the market, yet they offer the same quality, durability and performance, if not better, according to Holtzhausen.
The JD-1400E is the latest and most favoured model in the range with a 400-490 cubic feet per minute (cfm) Airplus compressor, Yamamoto YH135 drifter and a hole range of 89-127 mm
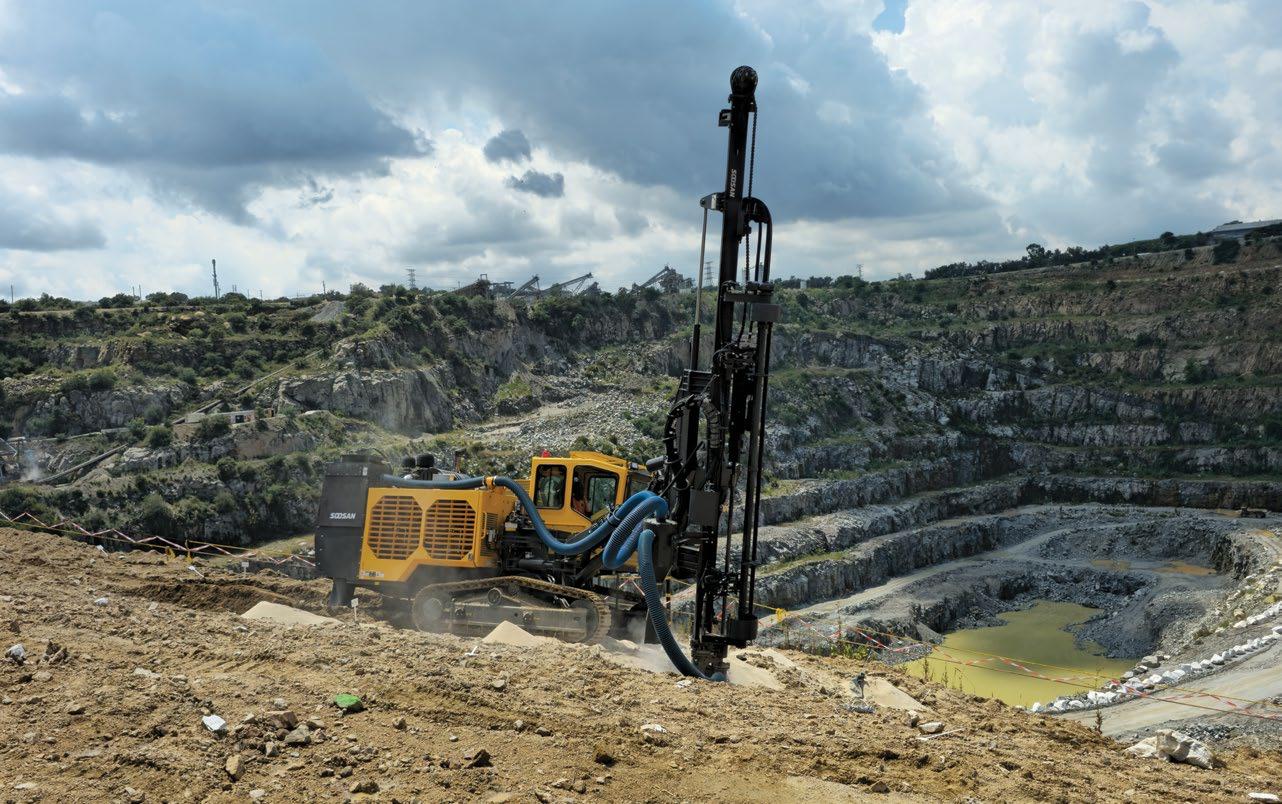
The range comes at about 10-15% less than some of the premium offerings in the market.
Another key selling point is that the Soosan CSM range is easy to maintain, which makes it ideal for companies grappling with the present scarcity of technical skills. In fact, most of JMH Equipment’s customers service their own machines. This is complemented by a strong aftersales support regime developed by the company over the past 18 years.
“With the mechanical layout and absence of computers, the drills are easy to maintain, ensuring minimum downtime for drilling operations,” explains Holtzhausen, adding that for ease of serviceability, the panel-type bonnet and vertical-type fuel tank make ample room for machine inspection and services.
Other key features include an anti-jamming system, collaring and automatic rod changer (ARC). The antijamming system stabilises operation of the rig across all kinds of rock, making the rig easy to operate for novice operators. Collaring makes it easy to take a correct position for drilling and for unskilled operators to drill holes correctly.
With ARC, the operator connects or disconnects the rods by controlling only one lever in the cabin, without an assistant. This automatic rod exchange can be performed by means of sequential hydraulic schematic. Five rods (including the first rod) can be equipped in the cartridge of the ARC.
Complementary offering
In addition, JMH Equipment supplies complementary aftermarket drifter spare parts for any make and model of both underground and top-hammer drill rigs, offering costsensitive customers a cost-effective, yet quality alternative. Over the years, the company has supplied these parts to some of the largest contract miners operating in the region.
Holtzhausen is aware of the disdain with which aftermarket parts have been viewed for many years. As a matter of fact, he says, the build quality of aftermarket parts has significantly improved during the last couple of years. Several equipment owners are therefore starting to choose these affordable, yet efficient options.
Advantages of aftermarket parts include cost, selection and quality. The main reason why there is a large preference for JMH Equipment’s aftermarket parts is that they are significantly more affordable than OEM parts. “In terms of price, our parts cost about 30-40% less than OEM parts, yet the quality is exactly the same,” he says.
Apart from price, these aftermarket parts have also proven themselves in terms of quality. “We have become well-known for the quality of our aftermarket drifter parts. Our parts are imported from Europe and the factory that we buy from is one of the biggest suppliers for reputable names such as Montabert in France, which is testimony to their good quality control and ability to manufacture parts to OEM specifications,” concludes Holtzhausen. a
For the past 18 years, JMH Equipment has developed a strong support regime for the Soosan range of surface drills in southern Africa
The JD-1400E is the latest and most favoured model in the range.
MAKING THE CUT
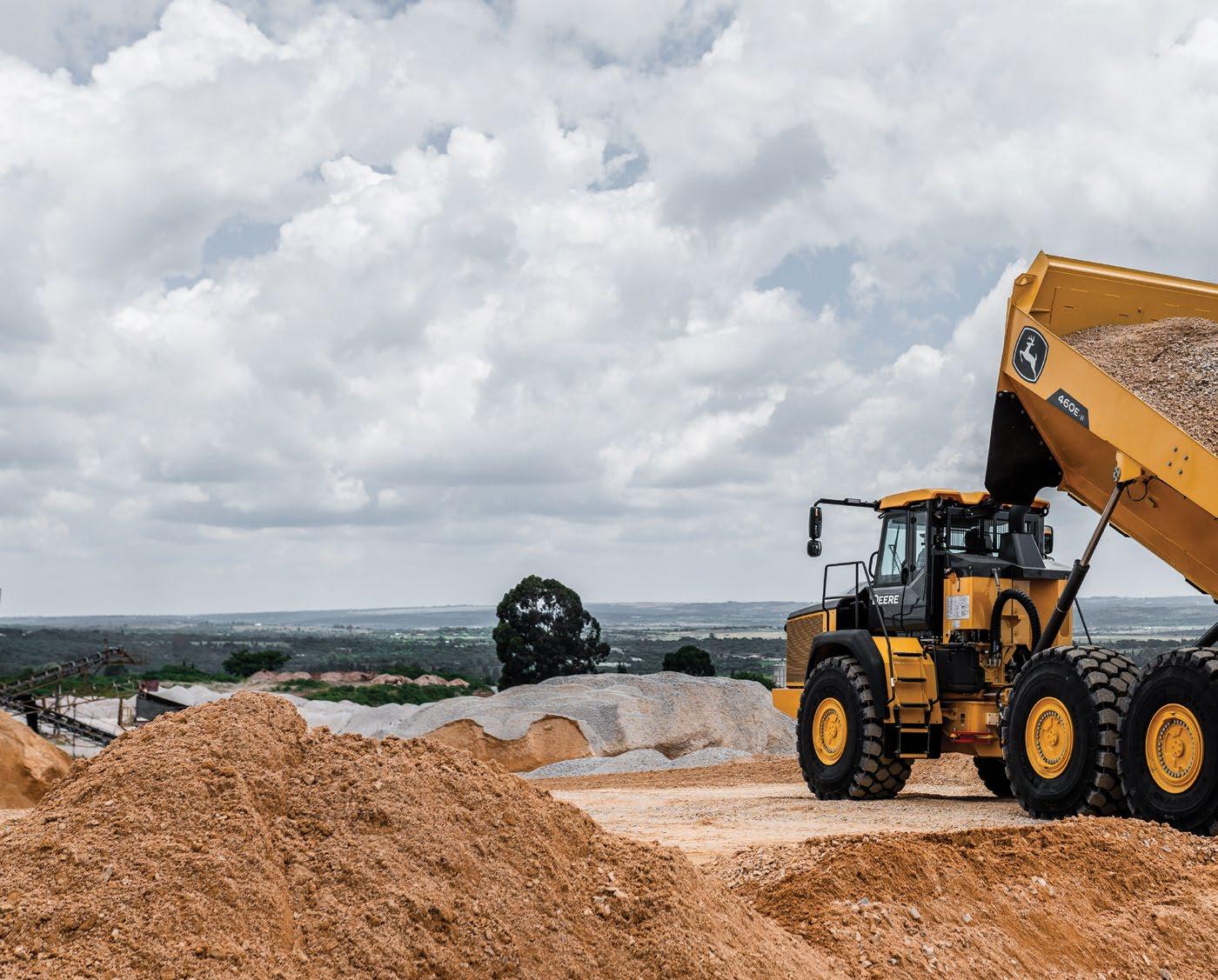
Having bought its first John Deere machine in 2023, a 460E-II articulated dump truck (ADT), Lewcor Mining, Namibia’s largest mining contractor operating some 550 pieces of equipment, has in just two years bolstered its John Deere ADT fleet to 25. In a one-on-one with Quarrying Africa, CEO Helmuth Lewis explains the various factors that influence the company’s buying decisions. By Munesu Shoko.
Founded in 1988 by the late CJ Lewis, Lewcor Group has its roots in civil construction. A major oil exploration project contracted by the Overseas Petroleum and Investment Company (OPIC) Malaysia, marked the beginning of an era, and the rest is history. Over time, the family-owned and -operated business has expanded its portfolio to include other complementary divisions such as mining, plant hire and transport.
Under the stewardship of Helmuth Lewis, who joined the company in the late ‘90s and eventually took over from his father CJ Lewis, the company has become a formidable name in the Namibian mining sector. In fact, Helmuth was central to the formation of the mining division in 1999.
His passion for yellow metal equipment was unmatched from a very young age. And as they say, “once it is in the blood, it is for life”. However, Helmuth was not just into yellow metal, he liked his machines big, which influenced the formation of the mining division upon joining his father in the family business.
Into mining
In 2000, the company went on to execute its first small-scale mining project, before being awarded its first extensive mining project by a major global mining house in 2001. In the following years, the mining division grew significantly, becoming the core business for the company. With the growth of the mining arm of Lewcor Group came the expansion of services from just load and haul to

Lewcor Mining took delivery of its first John Deere ADT in 2023.
550
Lewcor Mining, the largest contract mining company in Namibia, operates 550 pieces of equipment
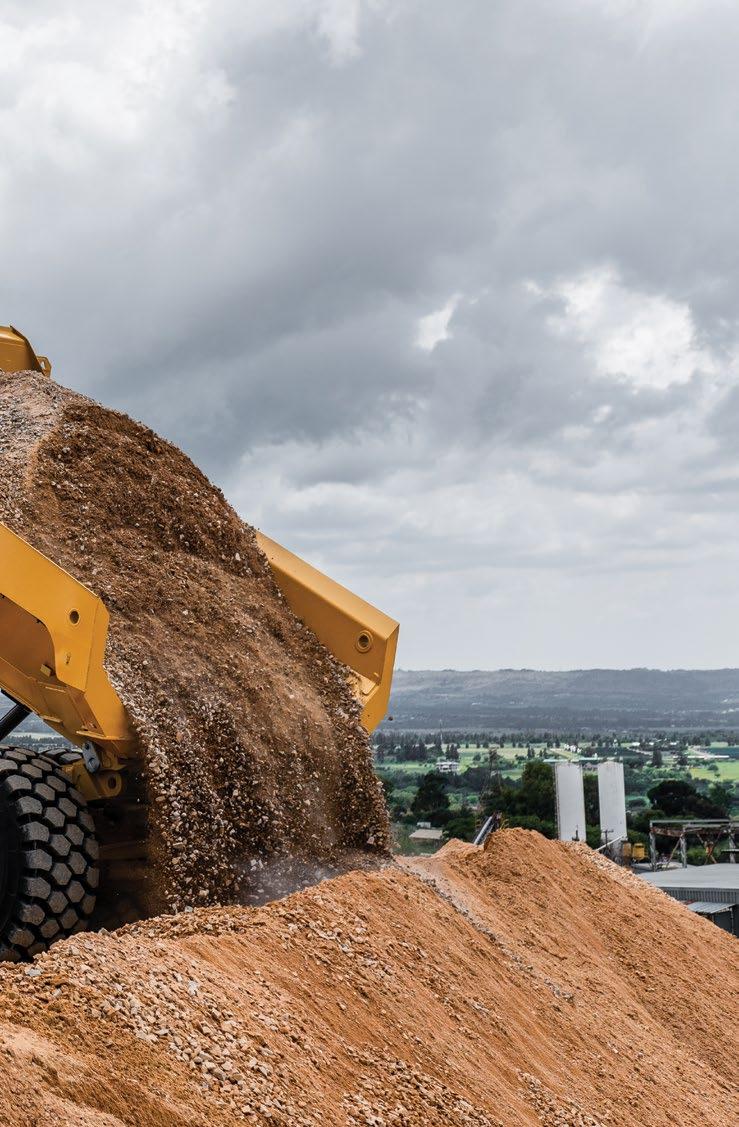
30
In the past two years, Lewcor has bolstered its fleet with a total of 30 John Deere machines
KEY POINTS
Lewcor Mining, Namibia’s largest mining contractor, has in just two years bolstered its John Deere ADT fleet to 25
In addition, Lewcor has taken delivery of three John Deere 850L dozers and a John Deere 670 motor grader, bringing to 30 the total number of John Deere machines in the Lewcor fleet in just under two years
From a fuel efficiency perspective, the company has found John Deere to be a fierce competitor and one of the cheaper machines to run
Given the commitment from both John Deere and its dealer, AFGRI Equipment, Lewcor envisages to boost its John Deere fleet to 100 machines in the near future
Because we run a multi-brand fleet, we have adopted an internal audit and scoring system. Some of the factors to take into account include price of the machine, operator comfort, fuel efficiency, aftermarket support, tonnes per hour and trading values, amongst others.
Helmuth Lewis
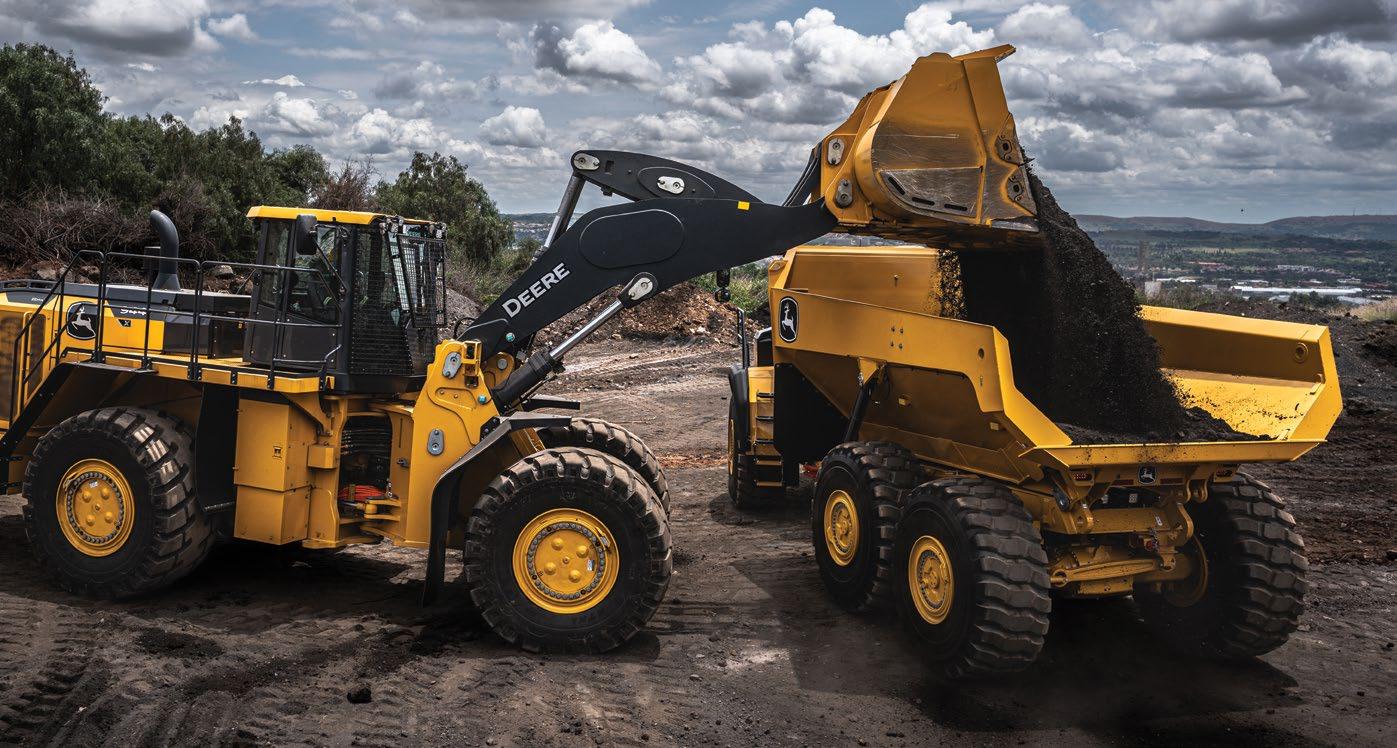
Lewcor recently became the first recipient of the first John Deere 944 X-Tier wheel loader in Africa.
Lewcor recently added a motor grader to its expanding fleet of John Deere machines.
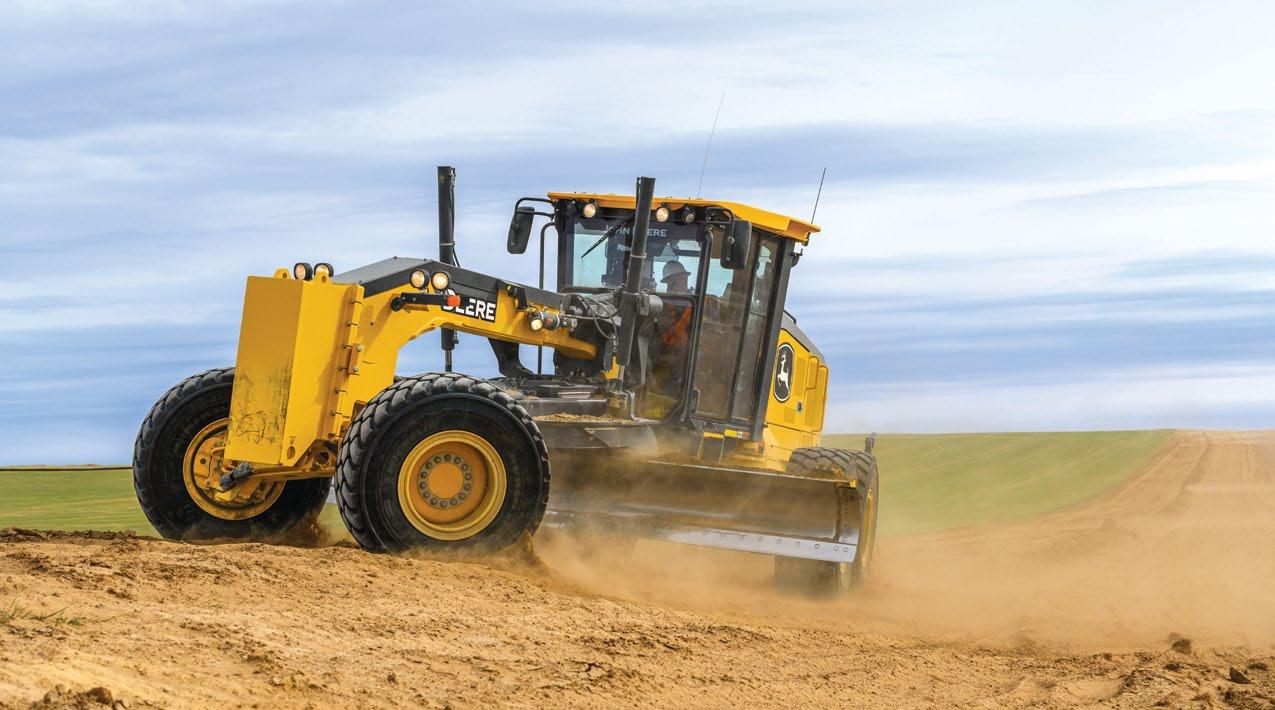
include drilling and blasting, and eventually crushing and screening, establishing Lewcor as a one-stop mining services provider to the Namibian mining fraternity.
“During the following ten years to 2010, we achieved significant growth, mainly because of our unparalleled service delivery, staying close to our customers and the fact that we are a 100% Namibian corporation, with almost all our employees and managers being Namibian citizens. To date, we have about 2 000 people in our ranks, of which 99% are Namibians,” explains Lewis.
However, mining contracts are not always guaranteed, especially given the fact that mining by its nature is notoriously cyclical. To cushion the business against bust cycles, the company started considering buying its own mines, which would allow it to keep its 550 pieces of equipment and its 2 000 strong workforce busy during downward mining cycles. Based on that approach, the company is to date a shareholder in three mines, spread across gold, uranium and diamonds.
“The idea of investment in mines was purely a diversification strategy to keep our staff in jobs and our large fleet running when contracts were few and far between. By going this route, we have managed to keep ourselves busy during the past decade,” says Lewis.
Enter John Deere
In contract mining, success largely hinges on the reliability, productivity and efficiency of the fleet. With that in mind, Lewcor does not leave anything to chance when it comes to the selection of its missioncritical assets. Traditionally, the company used to predominantly run a single premium brand which, at the time, constituted almost 95% of its fleet. As years went by, a decision was made to diversify the fleet with four other premium offerings.
For any new brand, breaking into the Lewcor fleet is no
easy feat. The company has a rigorous vetting process informed by a number of factors, including equipment pricing, cost per tonne of operating the equipment and, more importantly, aftermarket support, especially parts availability.
“Based on this model, John Deere, through its dealer AFGRI Equipment, made the cut into our fleet. It was not a decision taken lightly, especially given that our technicians and operators are already trained to work on certain brands and we already carry massive parts inventories for those brands,” explains Lewis. “Based on what AFGRI was putting on the table from a support perspective, we were convinced to bring John Deere on board, initially on a trial basis.”
Following the local introduction of the John Deere production class equipment in July 2022, Lewcor became one of the first companies to demo the 460E-II, which has since been upgraded with the new 460P. After putting the unit through its paces for several months, the company eventually bought the demo unit, a decision Lewis says was supported by both AFGRI’s commitment to the relationship and the convincing operational performance of the machine. The demo unit purchase was immediately followed by the acquisition of a further four 460E-II units.
During the past two years, this fleet has been bolstered with 20 more units, bringing to 25 the total number of John Deere ADTs running in the Lewcor fleet to date. In addition, Lewcor has taken delivery of three John Deere 850L dozers and a John Deere 670 motor grader, bringing to 30 the total number of John Deere machines in the Lewcor fleet in just under two years.
Recently, Lewcor became the first recipient of the first John Deere 944 X-Tier wheel loader in Africa. Introduced locally in February this year, the machine sets itself apart with its industry-exclusive E-Drive system, which
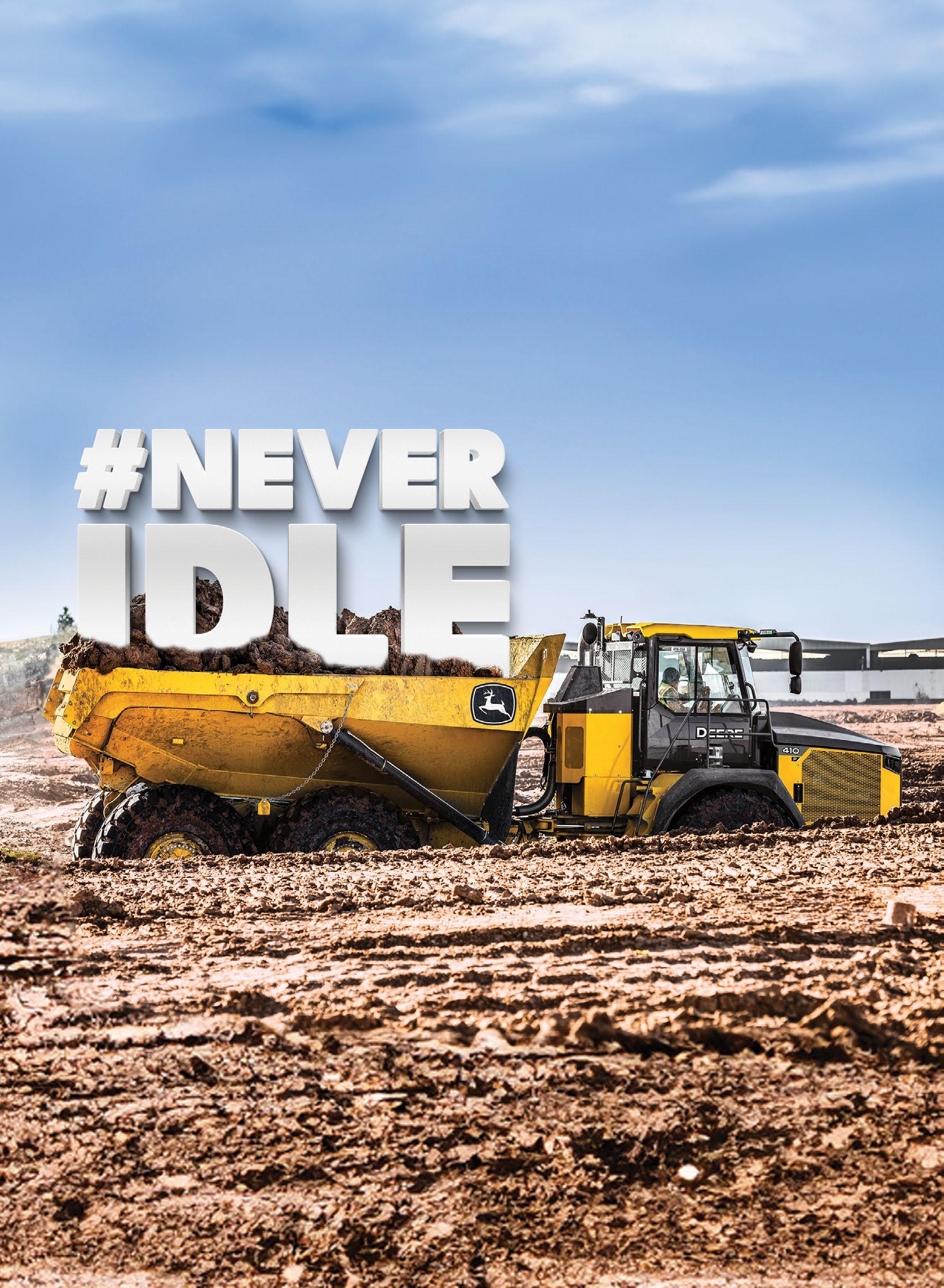
The newly-acquired John Deere 944 X-Tier wheel loader loading a John Deere 460P dump truck.
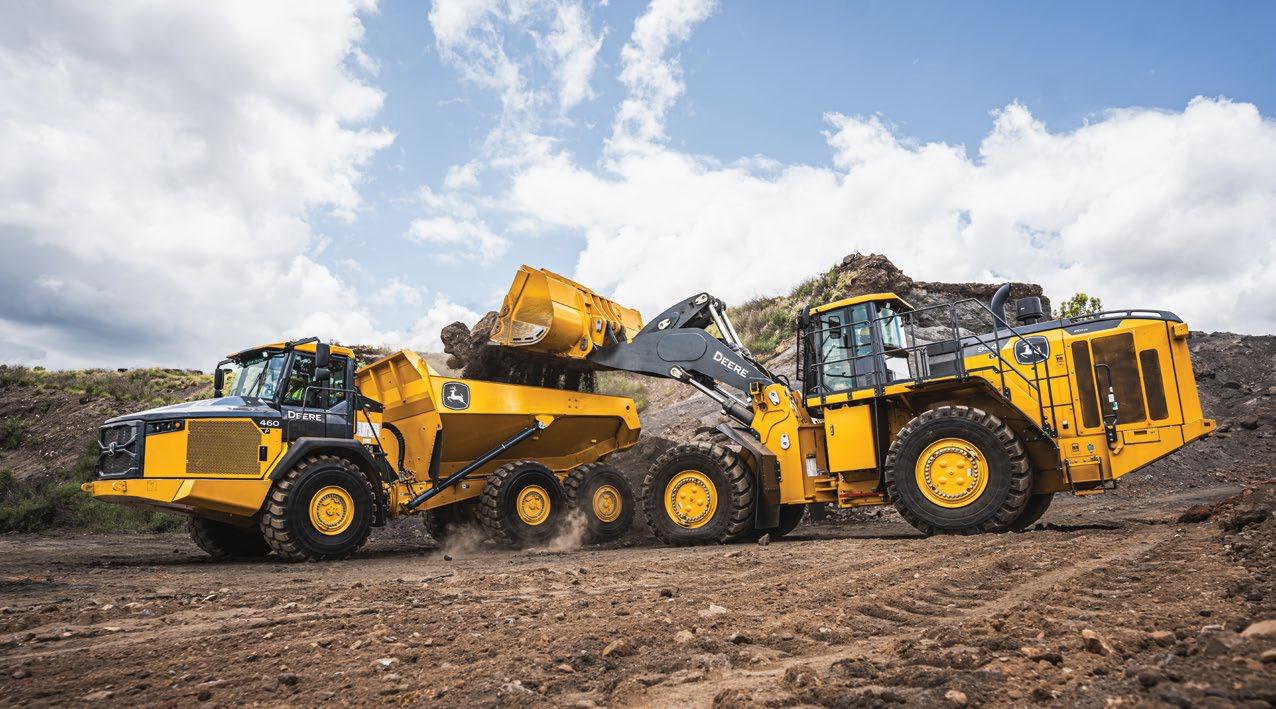
combines a John Deere 13,5L engine with advanced electric drive components.
This hybrid-electric drivetrain not only delivers exceptional power but also enhances fuel efficiency. The E-Drive system allows the 944 X-Tier to burn 13-33% less fuel compared to conventional drive loaders in typical applications, significantly reducing operational costs and environmental impact.
Why John Deere?
Lewcor currently runs a total of 105 ADTs in its fleet, spread across three brands and size ranges. “In the 45-t category, the John Deere machine has done particularly well in terms of performance and reliability. We keep track of the various important parameters through JDLink™ Connect and Operations Centre, the John Deere connectivity service that allows us to view critical and timely information about our machines, and to move data wirelessly and effortlessly. From a fuel efficiency perspective, we find John Deere to be a fierce competitor and one of the cheaper machines to run,” says Lewis.
Contract mining is a fast-paced operating environment, stresses Lewis, and machine reliability is one of the principal keys to success. In fact, he says, a machine that passes the reliability test must be able to run at least 500-600 hours a month, which translates into 20 hours a day, “without much assistance”. However, if there is an issue, the supplier must be able to help rectify it timeously to minimise downtime.
“Not too many machines or brands in the market can achieve the 500-600 hours a month benchmark
and there are even fewer brands that can do it without good aftermarket service. That is where we separate good suppliers from bad ones. In this instance, AFGRI has passed the test with flying colours. I also commend top management’s involvement, which is a key consideration for us. It puts us at ease that we are making a big financial commitment and we have the necessary backing for the long haul,” says Lewis.
Other factors
Commenting on other key considerations when making buying decisions, Lewis highlights financing as one of the principal ones. In fact, the availability of captive finance from the original equipment manufacturer (OEM) or supplier holds a 60% influence in the whole decision-making process.
60%
Captive finance, says Lewis, eliminates the need to seek financing from external financial institutions, simplifying the purchase process. He also notes that mainstream banks’ appetite for risk, especially when it comes to financing yellow metal equipment, is at its lowest.
“Because we run a multi-brand fleet, we have adopted an internal audit and scoring system. Some of the factors to take into account include price of the machine, operator comfort, fuel efficiency, aftermarket support, tonnes per hour and trading values, amongst others,” he says.
Based on these factors, Lewis believes that John Deere has hit the mark, and given the commitment from both the OEM and the dealer, Lewcor will likely end up boosting its John Deere fleet to 100 machines in the near future. a
The availability of captive finance from the OEM or supplier holds a 60% influence in the Lewcor’s decision-making process

E-Drive Technology
Maximized Productivity THE 944 X Crush Costs. Cut Carbon.
The John Deere 944 X-Tier Wheel Loader features an advanced E-Drive system, replacing traditional transmissions with electric wheel motors for 30% lower fuel use and 50–60% lower rebuild costs.

Lower Cost of Ownership

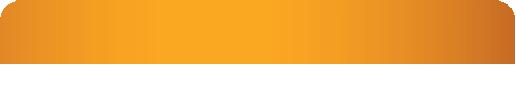
8 YEAR/20,000 HOUR
ELECTRIC-DRIVE COMPONENTS WARRANTY
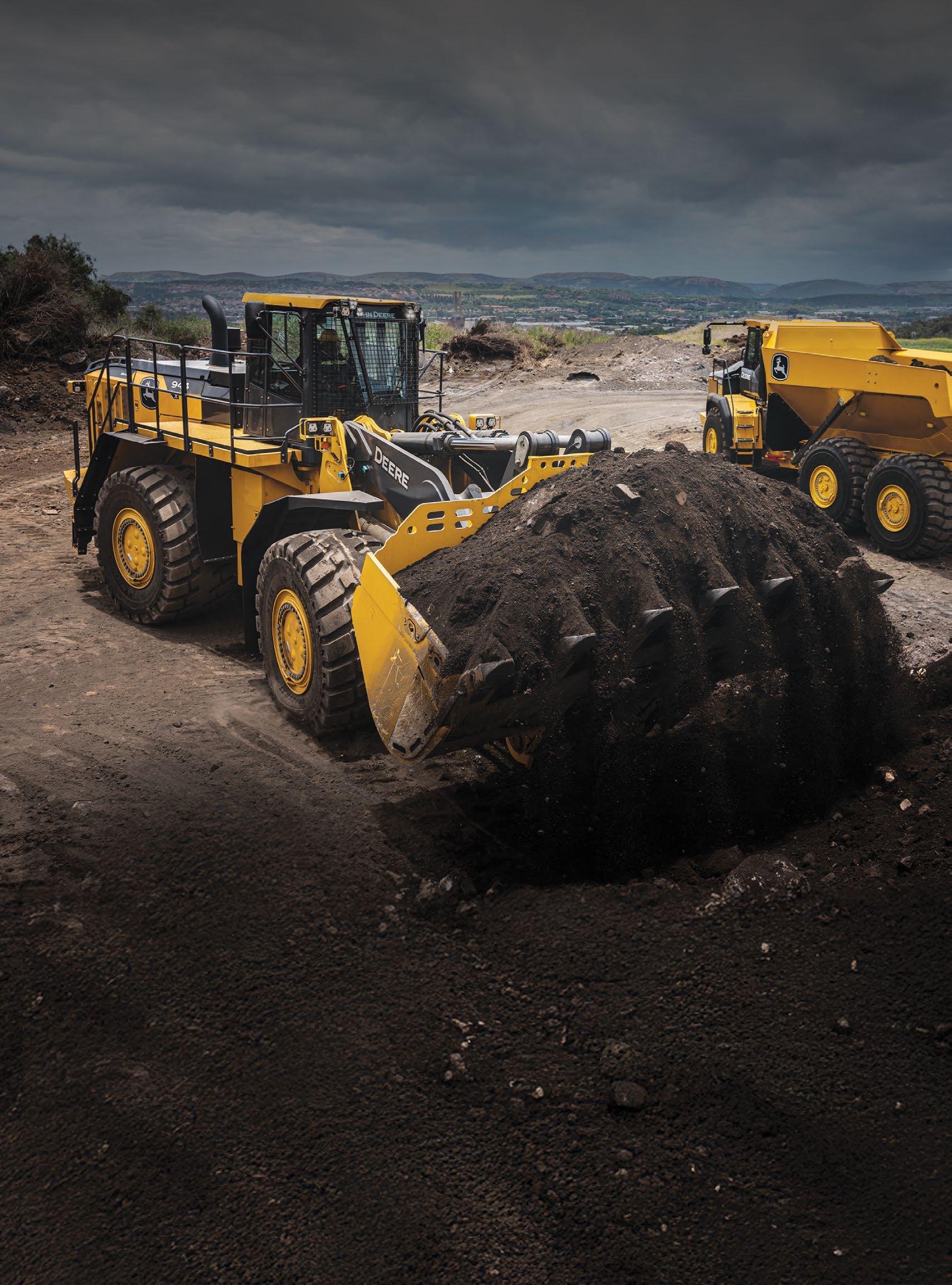
*Terms and conditions apply. (Available at https://www.deere.africa/en/) https://www.deere.africa/en/construction/ I cfjohndeereame@johndeere.com I Customer care: 0800 983 821 JohnDeereAME JohnDeere JohnDeereAfrica
NEW INDUSTRY TRENDS
The IQSA Conference, an annual staple on the local quarrying sector’s calendar, returns on April 3-4, 2025 in Durban, South Africa. Ahead of the event, Quarrying Africa speaks to some of the members of the supply chain about a number of new trends they have identified in the quarrying sector and how the industry can navigate the changing landscape. By Munesu Shoko.
There are several trends currently shaping the quarrying industry in South Africa. According to Brad Castle, product manager at Bell Equipment, global trends in the quarrying sector include stricter safety and environmental regulations, adoption of automation/digitalisation, skills shortage and rising operational costs. The same trends, he says, are being experienced in South Africa, although there is a greater appetite for digitalisation than automation at this stage.
The same view is shared by Ivan van Heerden, MD of Dynamic Weigh Systems, who says that there
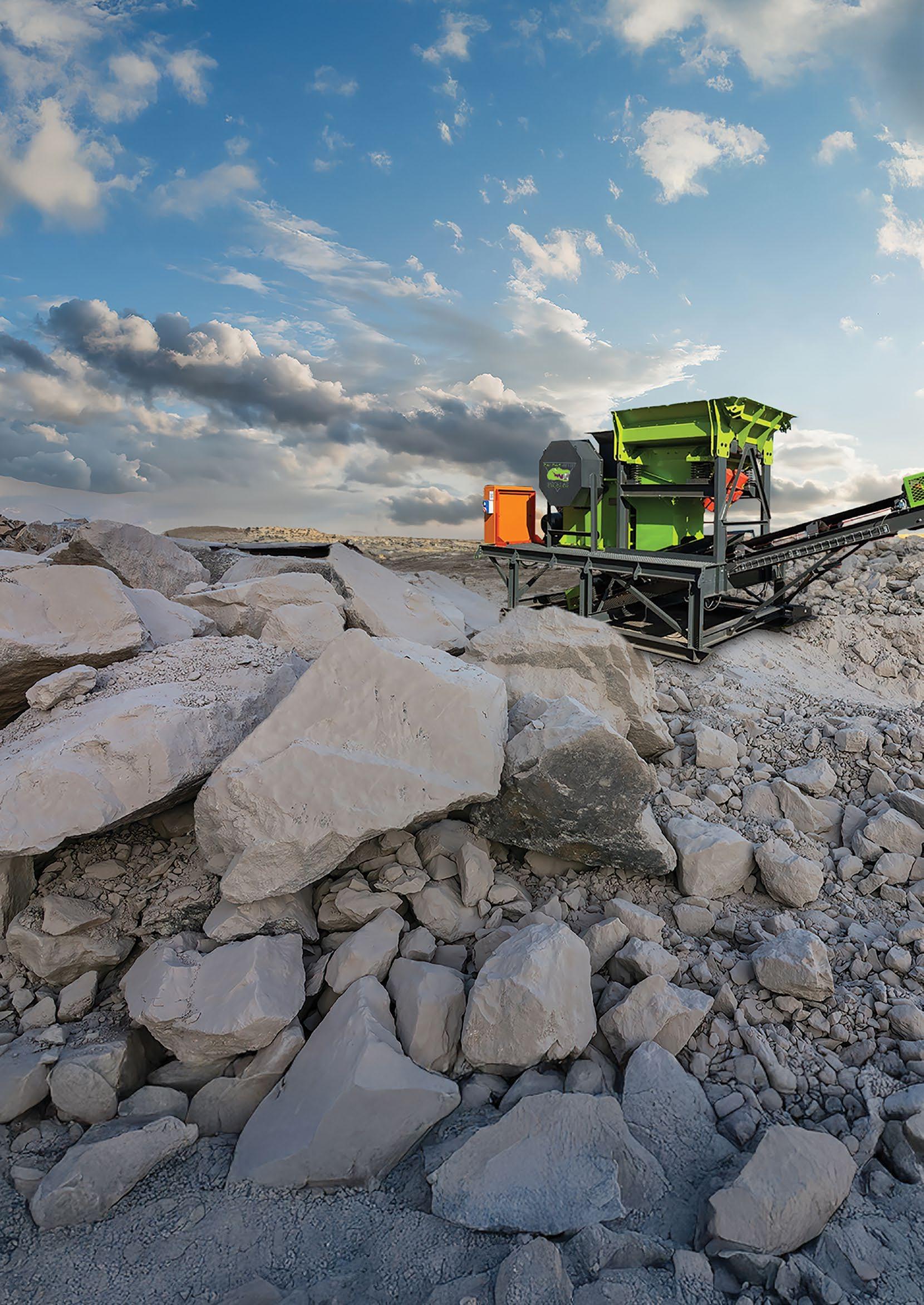
has been an increased focus on efficiency and costsaving. Efficiency in quarries is vital for maximising profitability, minimising waste and ensuring sustainability by optimising resource utilisation, as well as improving overall production.
“By utilising new technologies and making data-driven decisions, as well as investing in operator education, quarries can win the efficiency battle at their operations,” says Van Heerden. “As the industry seeks to drive efficiencies, we see a growing uptake of onboard weighing solutions. However, the adoption at this stage seems to be limited to wheel loaders. We will use the coming
4x4
Bell Equipment will use the IQSA Conference to highlight its niche Bell 4x4 articulated dump truck range, which comprises the B30E 4x4, B45E 4x4 and the B60E 4x4
Caldas for Crushers Wears Spares will use this year’s show to showcase its latest product range, particularly the ready-to-operate, entry-level portable comminution equipment.
Customers can have peace of mind knowing that they have guaranteed backup support from Caldas, a partner that has proven itself over the past 30 years
KEY TAKEAWAYS
Global trends in the quarrying sector include stricter safety and environmental regulations, adoption of automation/digitalisation, skills shortage and rising operational costs
There has been a definite move to place more focus on sustainability, thus reducing the industry’s impact on the environment
There is an emergence of new-generation young entrepreneurs, particularly from previously disadvantaged communities, coming to the fore
By utilising new technologies and making datadriven decisions, as well as investing in operator education, quarries can win the efficiency battle at their operations
conference to highlight an array of other solutions that allow for an entirely integrated approach from face to loadout.”
Rui Caldas, CEO of Caldas for Crushers Wears Spares, has observed the emergence of new-generation young entrepreneurs, particularly from previously disadvantaged communities, coming to the fore. He has also seen a trend where big holding groups are diversifying their traditional construction materials businesses by entering into the mainstream production of commodities.
Pieter Uys, business development manager at Multotec, says there has been a definite move to place more focus on sustainability, thus reducing the industry’s impact on the environment. Quarries, he adds, are also increasingly implementing new technologies, particularly digitalisation and automation, to increase efficiency and boost production.
Commenting on how the industry can navigate new changes, Uys says, “I believe the best way to navigate the trends is to embrace change, not fight it, as well as learning from past experiences. At Multotec we draw valuable lessons from over 50 years of experience in screening.”
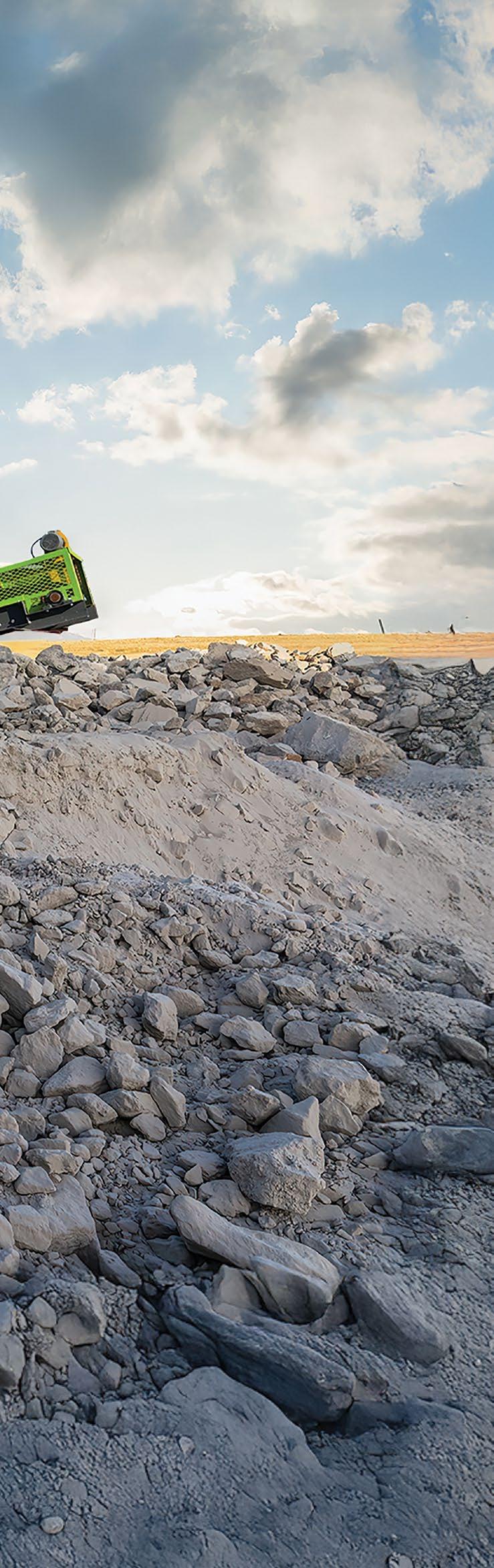
Key exhibits
To help quarries meet their new operational obligations, Multotec will use the IQSA Conference to showcase numerous screening solutions. These include, but are not limited to, some of the company’s newest product developments in fine screening.
One of the solutions the company will highlight is the Multotec side-tension MBV mats. A key feature of these mats is their modularity, meaning that only areas that have failed need to be replaced, instead of replacing the whole large sheet because of failures in smaller areas of the screening deck. This presents a major cost saving, while reducing downtime.
“The once-off tensioning is another major feature of the side-tension MBV mats. These mats are only tensioned on initial installation, thereafter, you only replace the MBV strip/s that has/have been damaged without releasing and tensioning the whole mat again. This has a major reduction on downtime and the labour component related to changing out screening media,” says Uys.
In addition, the Multotec MBV mats are renowned for their self-cleansing properties. Because of the elliptical movement of these mats while in motion, they clean
Bell Equipment will use the show to highlight its niche Bell 4x4 articulated dump truck range, which includes the B30E 4x4.
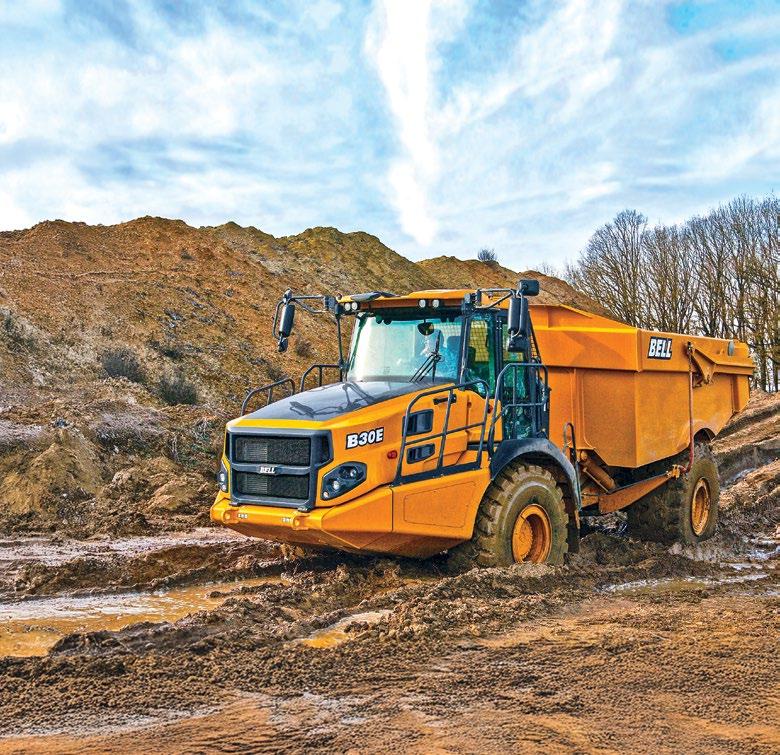
themselves, leading to less blinding and pegging. The resultant effect is a reduction in downtime and labour costs as the need for constantly cleaning screening media is reduced drastically.
Another product to be showcased at the show consists of the MultoSensepanels. With real-time monitoring of vibration patterns, it is easy to promptly identify issues such as loose, damaged or missing screen panels. Another benefit is the early detection of mechanical issues, including damage to cross-members and stringers, as well as exciter motor and counterweight imbalances, helping to prevent unexpected breakdowns.
The MultoSense panels ensure continuous measurement of wear on screening media, providing predictive insights into maintenance scheduling and timely replacement. In addition, the immediate identification of pegging and blinding occurrences enables proactive maintenance interventions to sustain optimal throughput.
“Multotec’s sensor-equipped screening panels represent a significant technological advancement in the quarrying and mining industry. By offering real-time monitoring and predictive maintenance insights, these innovative sensors help optimise screening performance, minimise downtime and enhance overall plant efficiency,” says Uys.
Caldas for Crushers Wears Spares will use this year’s show to showcase its latest product range, particularly the ready-to-operate, entry-level portable comminution equipment. “These plants offer low capital investment, immediate availability, they are simple to transport and require low skill levels. Customers can also have peace of mind knowing that they have guaranteed backup support from a partner that has proven itself over the past 30 years,” says Caldas.
According to Van Heerden, DWS will be using IQSA 2025 to introduce its new Bluetooth beacons which automatically select the stockpile being used during loading, thus removing the need for operator input.
Bell offering
Bell Equipment will use the show to highlight its niche Bell 4x4 articulated dump truck (ADT) range, which comprises the B30E 4x4, B45E 4x4 and the B60E 4x4. Operating Bell 4x4s in quarrying, says Castle, has been proven to reduce production costs through shorter cycle times, reduced
fuel burn and minimal wear on haul roads – all of which translate into increased production and profit.
“One of our long-standing quarrying customers has seen significant gains from their fleet of eight Bell B30E 4x4 ADTs since the end of 2023. The company traditionally used 30-tonne (t) haulage vehicles in its quarrying operations, as well as traditional 6x6 Bell B30D models and various other sizes of Bell E-series ADTs.
“The client has found the Bell B30E 4x4 to be of great benefit for many reasons. By having only two axles, the truck can turn in tighter circles than that of a six-wheeled machine. There is also less scuffing on the road, which promotes longer tyre life and less wear on haul roads. Through the analysis of differential and final drive oils, the customer also discovered that scuffing induces strain through the drivetrains of traditional six-wheeled ADTs, a problem they do not have with the 4x4,” says Castle.
Despite their shorter bin, the 4x4 trucks carry the same loads as the 6x6 model ADTs, which is 28 t on average. Having a slightly shorter body length that is offset by the wider body of the bin, and no centre axle, the Bell B30E 4x4 ADTs can negotiate sharp turns found in quarries better than their 6x6, three-axle counterparts.
“The Bell B30E 4x4 ADTs made an immediate impact on the customer’s production, especially in terms of shortening cycle times. At this particular customer’s site, the trucks have comfortably shaved off one minute off a ten-minute cycle,” says Castle. “The customer noticed that the B30E 4x4 ADTs were also lighter on fuel, which has a direct effect on lower production cost per tonne of any material they move,” adds Castle.
In addition, Bell Equipment pioneered the production of ADTs that are Level 9-ready, meaning the vehicles can accept the installation of proximity detection systems (PDS) and collision avoidance systems (CAS) without the need for any modifications, helping the industry to comply with the Department of Mineral and Petroleum Resources’ PDS/CAS regulations. More importantly, customers can retrofit PDS technology to their older Bell ADTs.
“All Bell ADTs offer industry-leading production, machine protection and safety features such as the PDS-ready platform that integrates with third-party systems. In terms of safety and machine protection, our trucks feature keyless start, Hill Assist to
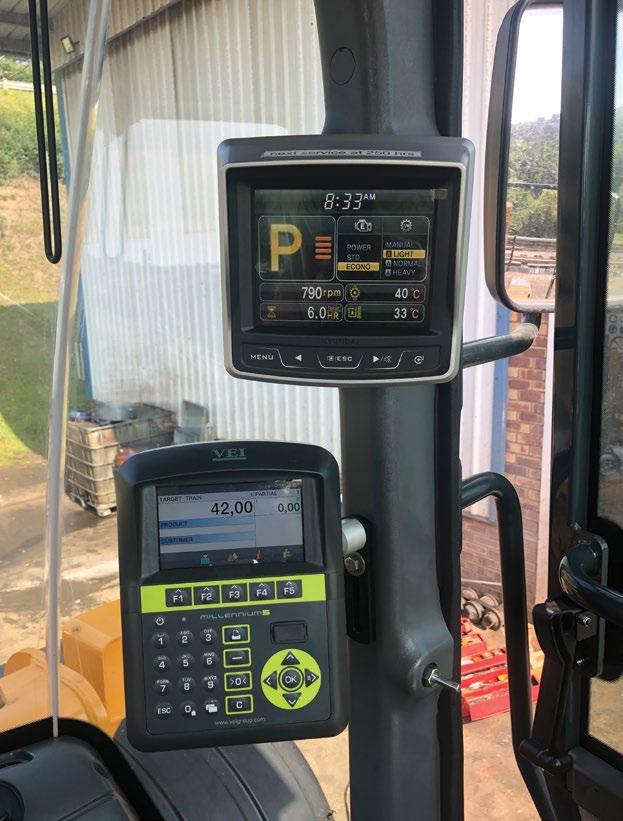
prevent rollback on slopes, as well as Tip Safe to prevent rollovers due to unsafe tipping angles,” explains Castle.
In addition, Bell offers one of the most accurate onboard weighing systems on the market, which comprises three weighing points and has proven to be accurate to 5%, irrespective of the amount and distribution of the material being loaded.
“Onboard weighing is an integral feature of our Bell Fleetm@tic® telematics system that makes it possible to provide customers with useful production information, including payload, fuel consumption and tip cycle data to monitor and maximise their operational and fleet efficiencies,” says Castle.
Excitement brewing
Ahead of the 2025 IQSA Conference, several original equipment manufacturers (OEMs) interviewed by Quarrying Africa expressed their excitement at exhibiting at this year’s show. “It is a great privilege to be associated with such great industry organisations such as IQSA and ASPASA, with whom I have personally been linked since 1991,” says Caldas.
“Multotec is excited, privileged and honoured to engage with our quarrying customers at this year’s IQSA Conference, while together we navigate, explore and
CRUSHERS. WEARS. SPARES.

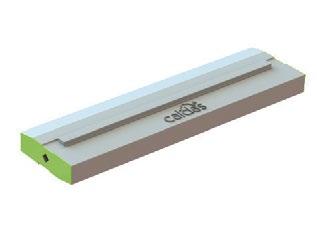
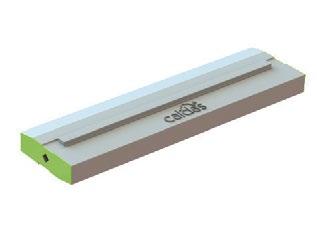
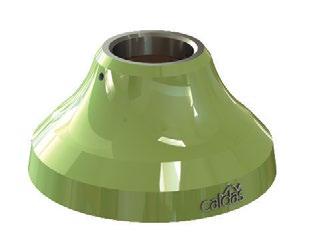
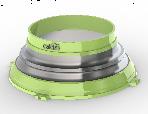
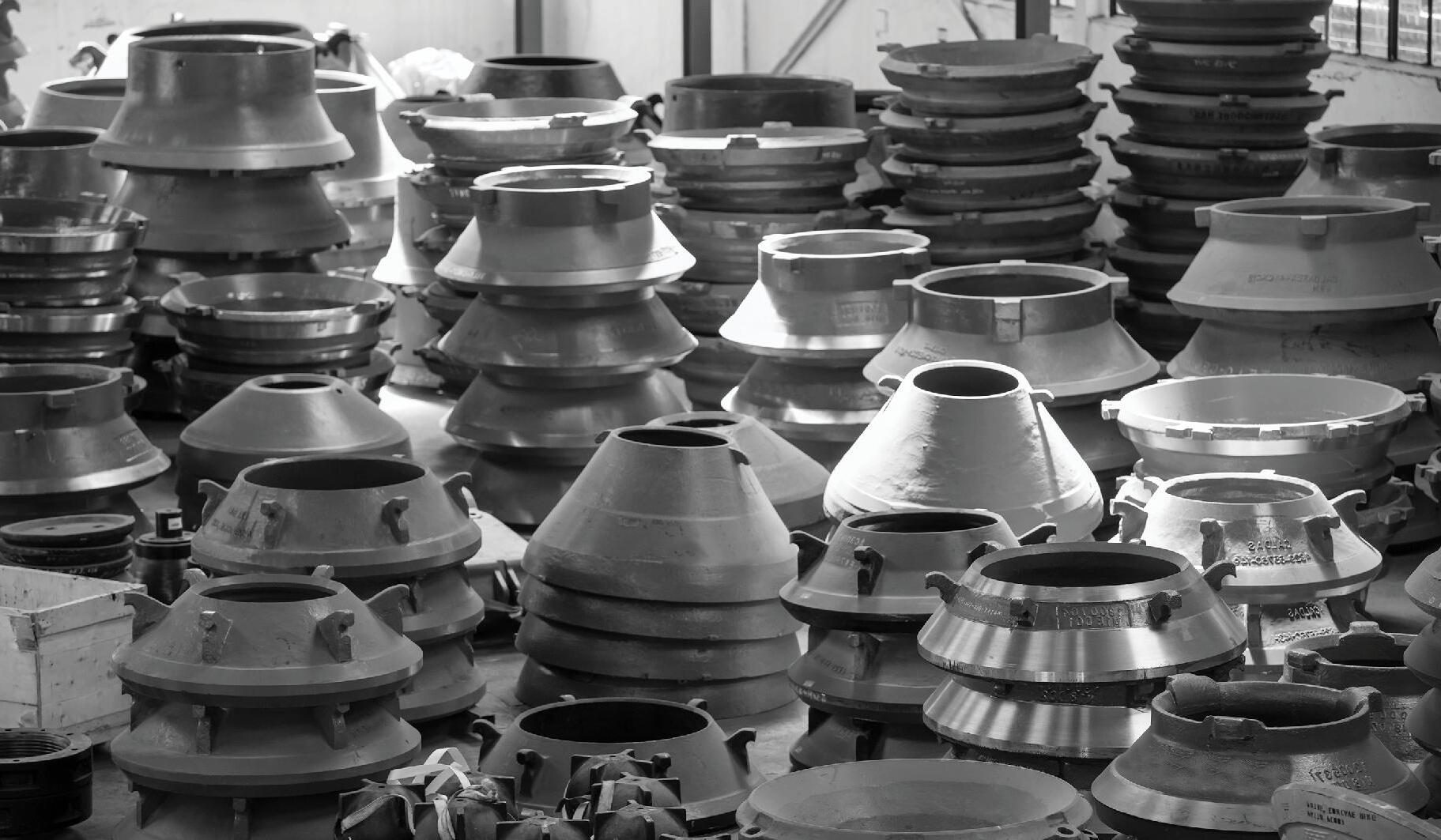
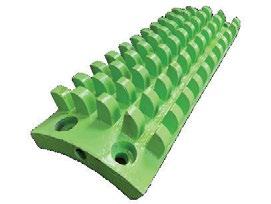
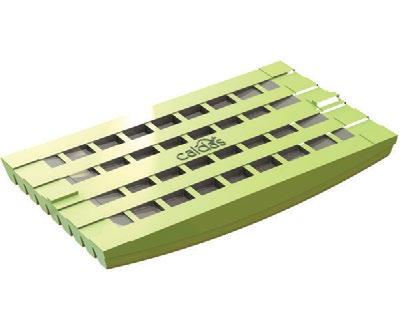


conquer the changing landscape that faces the industry,” says Uys.
Castle says Bell Equipment is a proud, long-standing Associate Member of ASPASA, a partner association to IQSA. “Our local sales and distribution network, Bell Equipment Sales South Africa (BESSA), is a B-BBEE Level 1 company that offers a range of load and haul, as well as crushing and screening solutions from the world’s leading equipment brands, including Bell, Kobelco, JCB and Finlay,” explains Castle.
With ADTs suited for all sizes of quarry operations –from the Bell B18E to the B60E 4x4 – Bell has a range of JCB wheel loaders and Kobelco excavators that are matched to provide the lowest cost per tonne loading solutions. JCB telehandlers and skid steers are also useful utility solutions for machine maintenance and housekeeping under conveyor systems respectively, while the Bell tri-wheeler forklifts and JCB backhoe loaders are versatile general housekeeping tools.
“The Finlay range of crushing plants comprises jaw, impact and cone crushers, complemented by horizontal, incline and scalping screeners. In addition, the choice of two-tracked stacking conveyors delivers operational cost-reduction, site efficiency and improved material quality through reduced handling in certain applications,” concludes Castle. a

A key feature of the MBV Mats from Multotec is their modularity, meaning that only areas that have failed need to be replaced.
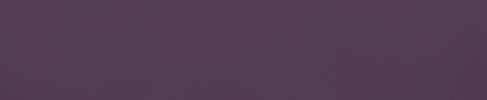


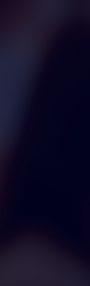
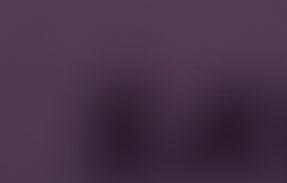
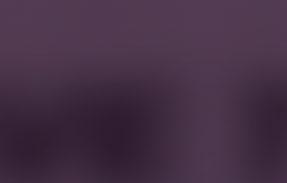
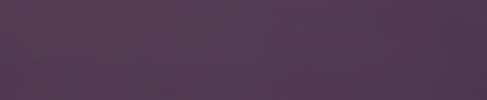
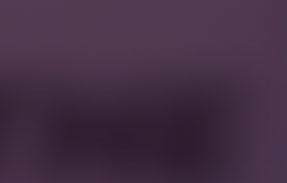

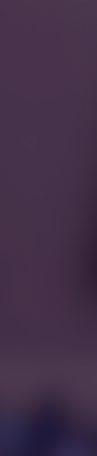
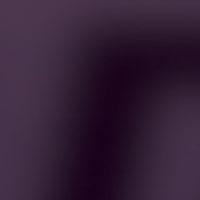
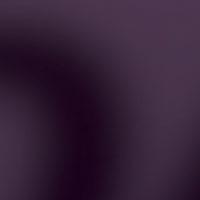
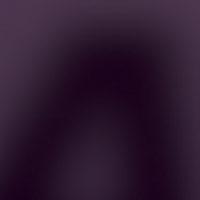
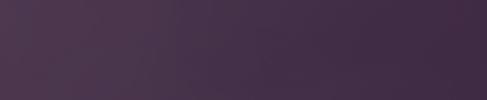
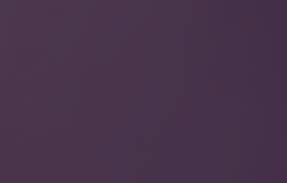

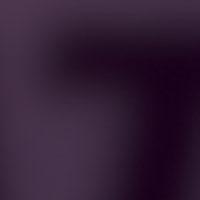
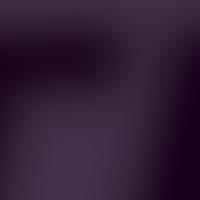

SAVE THE DATE
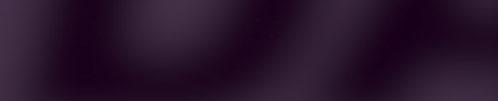
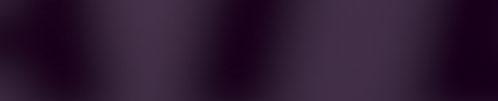
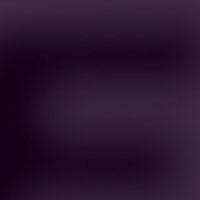
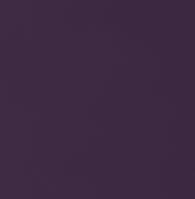
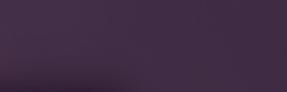

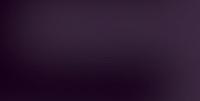

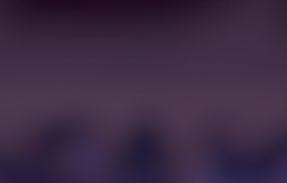
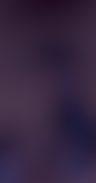
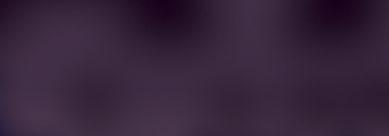
3 - 4 APRIL 2025
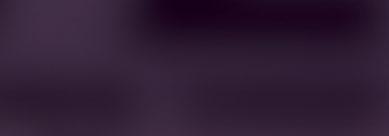
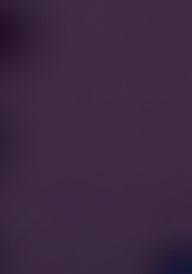
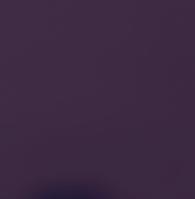
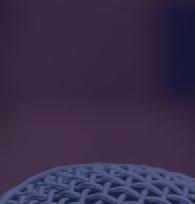

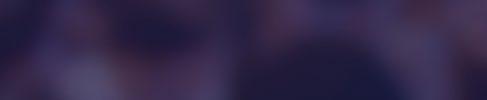
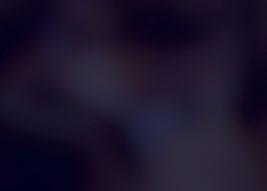

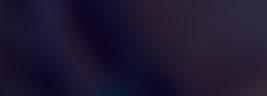
THE CONFERENCE will feature 2 Keynote speakers as well as 14 Quarry industry speakers. This will include presen tations from our Young Professionals within the industry.
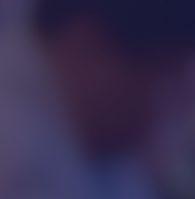
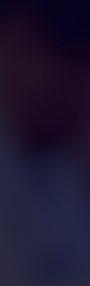
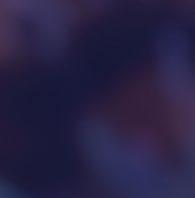

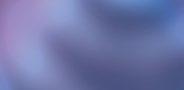
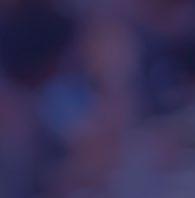
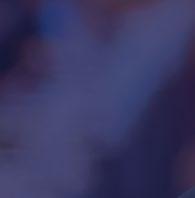
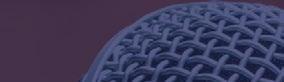

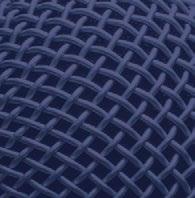

Our theme for this year is “Navigating a changing landscape”.As our world changes, so does our technology. As technology evolves, companies and employees will need to continuously upskill and reskill to stay relevant. presen-
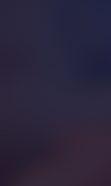
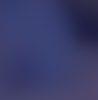
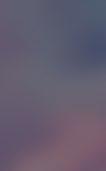

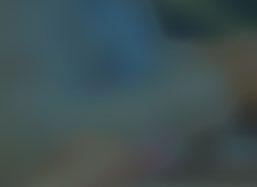
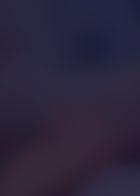
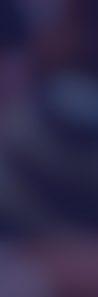
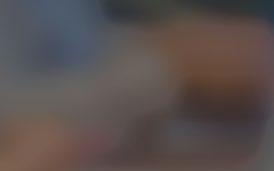
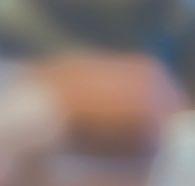
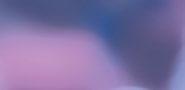
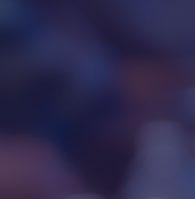
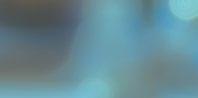


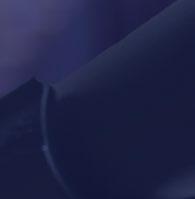
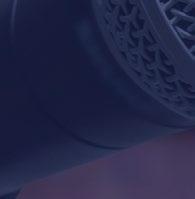
EXHIBITION. A static Exhibition will be staged and will be open for the duration of the Conference. This will give the delegates an opportunity to view the latest technology in the quarrying industry from the top Industry suppliers.


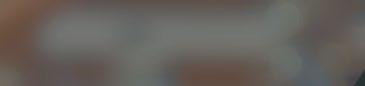
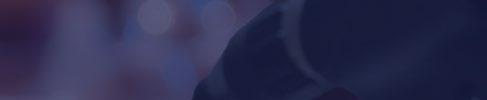

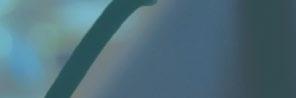
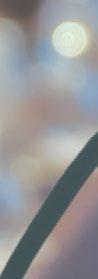
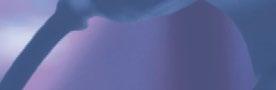
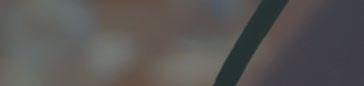
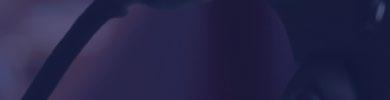
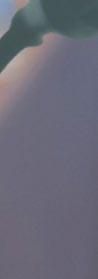
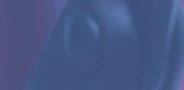


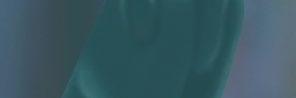
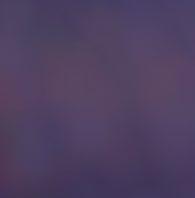
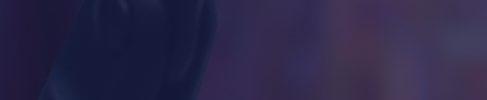
Venue: SCAN QR CODE FOR DIRECTIONS
Elangeni Hotel Snell Parade, Durban, KwaZulu-Natal
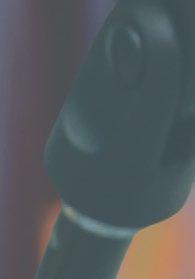
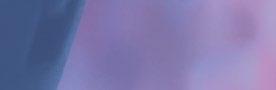


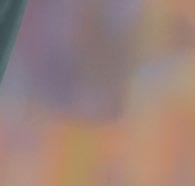
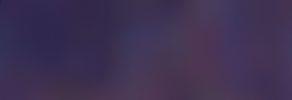
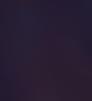
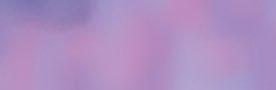

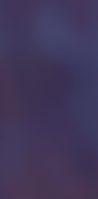
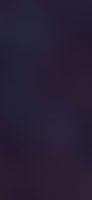

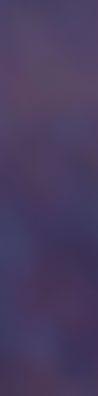


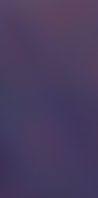
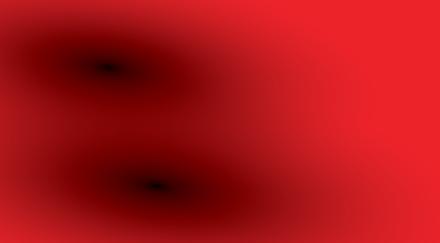

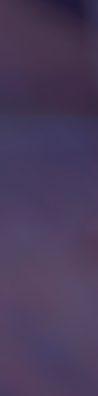
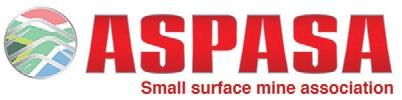

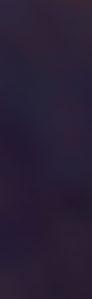















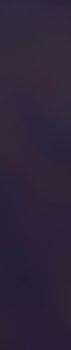
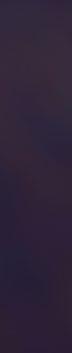

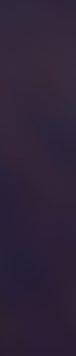
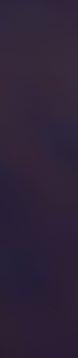
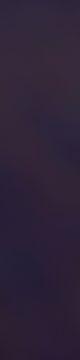
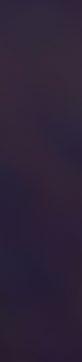
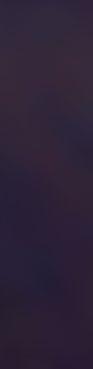
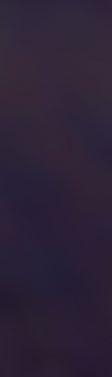
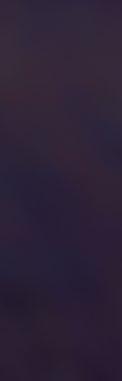
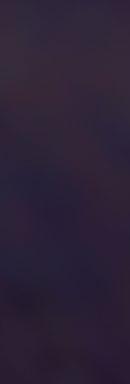
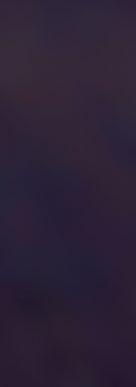



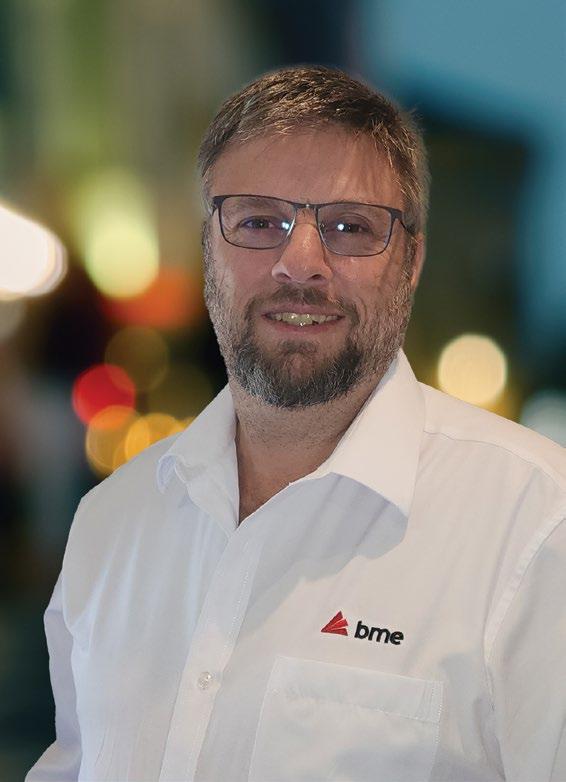
BME is shaping the future of quarry blasting by integrating innovative technology, sustainability-focused explosives and intelligent blast designs. We are helping the quarrying industry navigate its evolving challenges with confidence.
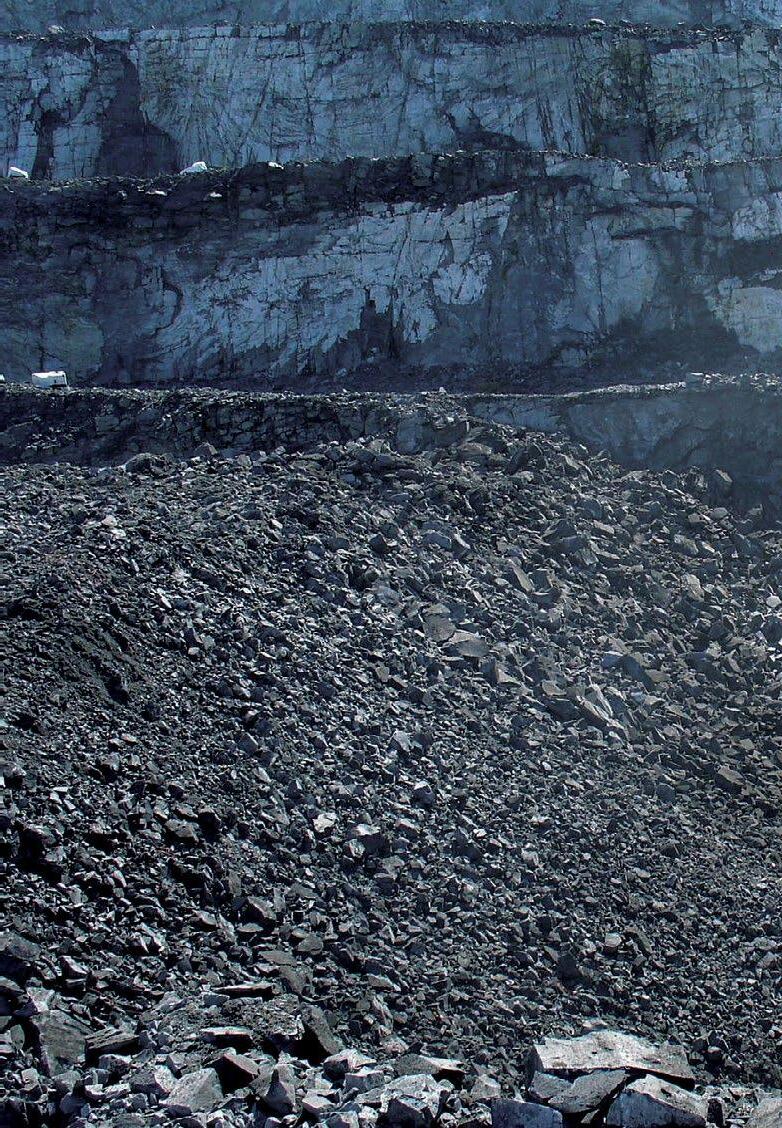
Well controlled energy and optimal blast design can deliver blasting to specification with optimal results.
KEY POINTS
Due to the expansion of cities and communities, quarries that were once located in remote areas are now increasingly surrounded by residential neighbourhoods, commercial districts and industrial zones
Issues such as noise pollution, dust emissions, ground vibrations and the risk of fly rock have become critical challenges for both quarry operators and the surrounding communities
Implementing real-time monitoring systems for air quality, noise levels and ground vibrations can help operators stay compliant with regulations and address issues before they escalate
At the upcoming IQSA Conference, BME will showcase its AXXIS Silver initiation system, specifically designed for quarries and other smaller mining operations
ADAPTING TO THE CHANGING ENVIRONMENT
Like many other sectors of the economy, the quarrying sector is undergoing an intense period of change. Hennie van Niekerk, regional manager: Technical at BME, a leading provider of blasting solutions, discusses some of the major trends in the industry and how quarry operators can adapt and respond to this shift. By Munesu Shoko.
As the quarrying sector continues to shift in line with new trends shaping the industry, this year’s Institute of Quarrying South Africa (IQSA) Conference will cast the spotlight on “Navigating a Changing Landscape”. According to Van Niekerk, there are several new trends that are shaping the industry, from environmental to safety concerns, amongst others.
With the expansion of cities and communities, he says, quarries that were once located in remote areas are now increasingly surrounded by residential

Hennie van Niekerk, regional manager: Technical at BME
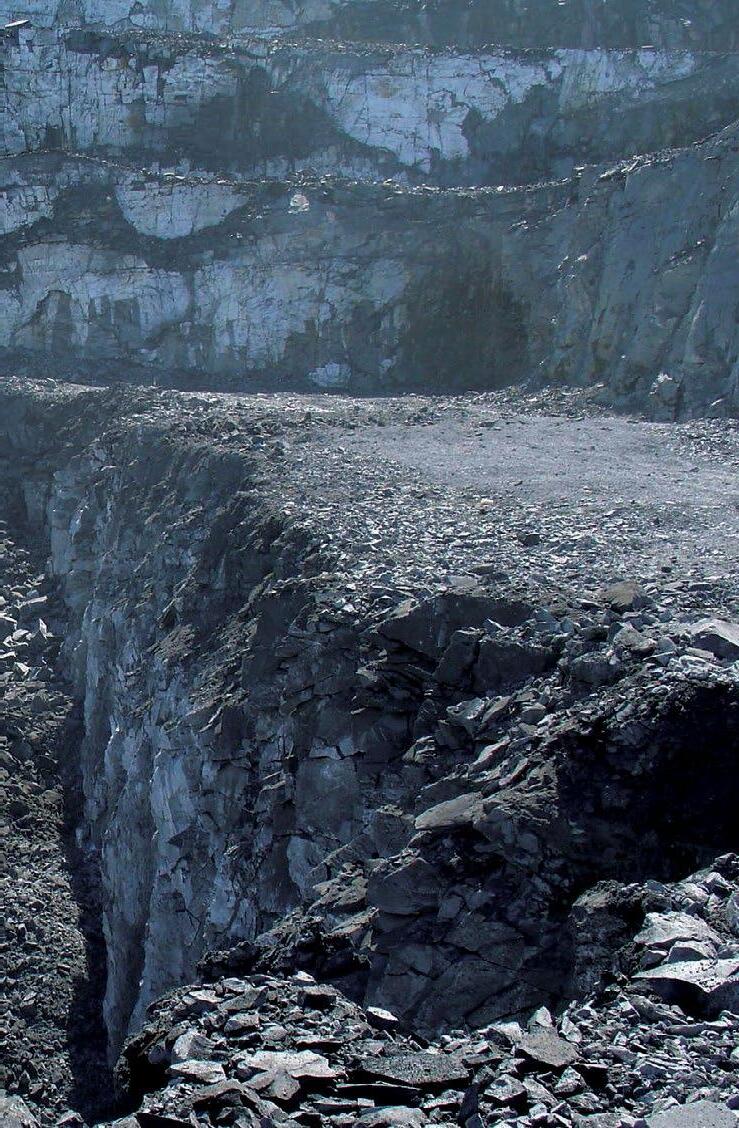
3-4
At the upcoming IQSA Conference, to be held in Durban on April 3-4, 2025, BME will highlight a number of innovative blasting solutions that can help the industry navigate the changing operational environment
1 600
The AXXIS Silver is designed for up to 1 600 detonators – 800 per blast box, which is more than enough for the quarrying industry’s blasting requirements
15
The AXXIS Silver’s programmability of up to 15 seconds with 1-millisecond intervals allows for blast designs to be precision-designed, resulting in better fragmentation
neighbourhoods, commercial districts and industrial zones. As a result, concerns over environmental impact and public safety have grown significantly.
“Issues such as noise pollution, dust emissions, ground vibrations and the risk of fly rock have become critical challenges for both quarry operators and the surrounding communities. To address these concerns, the industry has had to adapt by implementing innovative blasting design changes and adopting more sustainable practices,” says Van Niekerk.
Stricter environmental regulations, he adds, have driven the development of dust suppression technologies, noise reduction measures and controlled blasting techniques to minimise disturbances. Additionally, advancements in automation, digital monitoring and sustainable resource management have played a key role in improving operational efficiency, while reducing the environmental footprint of quarrying activities.

Efficient use of explosives energy can result in good fragmentation and uniformity.
“In addition to the environmental restrictions, competition in the industry has created a costconscious approach. To be competitive, a quarry needs to be responsible with all aspects of its operations. This has created the need for value-added initiatives to re-evaluate all aspects of the mining value chain and optimise efficiencies,” Van Niekerk explains.
Adapting to changes
As urban expansion continues to bring communities closer to quarry operations, Van Niekerk urges that the industry must adopt proactive strategies to balance production efficiency with environmental and social responsibility. To successfully navigate these challenges, quarry operators can focus on a number of key areas, including innovation, adopting new and advanced technologies, community engagement and corporate responsibility, as well as workforce training and safety initiatives, amongst others.
In terms of advanced technologies, automation and digital monitoring are fast becoming central to successful operations. Implementing real-time monitoring systems for air quality, noise levels and ground vibrations can help operators stay compliant with regulations and address issues before they escalate.
Poor use of energy and initiation timing can cause back- and side break that negatively influence productivity, safety and efficiency.

As part of the technology drive, adoption of controlled blasting techniques is key to ensuring safety. Precision blasting and the use of electronic detonation systems can minimise fly rock, reduce vibrations and improve overall safety. In addition, dust management on roads, water misting systems, noise barriers and enclosed processing equipment can help reduce the impact on nearby communities.
The importance of community engagement and corporate responsibility cannot be reiterated enough as communities encroach on quarry operations. Engaging with local communities through public forums, regular updates and open dialogue can help build trust and address concerns. Investing in local infrastructure, employment and educational initiatives can also strengthen relationships with neighbouring communities.
While regulatory compliance and operating costs are at the forefront of every operation, adopting newer technologies can help companies remain abreast of the evolving environmental and safety regulations to ensure smoother operations.
With continuous investments in workforce training and safety initiatives, quarries can also respond better to the new challenges confronting their businesses. “Continuous education on environmental compliance, new technologies and safety protocols ensures a well-equipped workforce,” says Van Niekerk. “Implementing strict workplace safety guidelines, personal protective equipment (PPE) standards and emergency response plans can also minimise workplace hazards.”
By embracing these strategies, he adds, the quarrying industry can continue to operate efficiently, while reducing its environmental footprint and maintaining positive relationships with surrounding communities.
Solutions on display
At the upcoming IQSA Conference, to be held in Durban on April 3-4, 2025, BME will highlight a number of innovative blasting solutions that can help the industry navigate the changing operational environment.
“As a leading provider of blasting solutions, we recognise the challenges facing the quarrying industry due to increasing environmental regulations, community concerns and operational efficiency demands. We are excited
to showcase a range of advanced blasting solutions and value-added initiatives designed to enhance safety, minimise environmental impact and optimise productivity,” says Van Niekerk.
To reinforce the need for precision electronic blasting systems, BME will showcase its AXXIS Silver™ initiation system, specifically designed for quarries and other smaller mining operations. The AXXIS Silver is a costeffective electronic blasting solution for operations with less demanding blasting needs.
Some of the key features of the AXXIS Silver include advanced electronic initiation for precise timing and sequencing, programmable delay intervals for optimal fragmentation and remote monitoring and initiation capabilities. This provides several benefits for quarries, including the reduction of ground vibrations and fly rock, thus minimising the impact on surrounding communities; improved fragmentation, leading to better downstream processing efficiency; and enhanced safety through remote detonation and real-time monitoring.
The AXXIS Silver is designed for up to 1 600 detonators – 800 per blast box, which is more than enough for the quarrying industry’s blasting requirements. The accuracy of detonation delays has been enhanced to less than 1 millisecond at the maximum firing time for consistent quality blasting that results in optimal rock fragmentation. The programmability of 15 seconds with 1-millisecond intervals allows for blast designs to be precision-designed, resulting in better fragmentation.
Value-added initiatives
In addition, BME will showcase its value-added initiatives and blast optimisation solutions, which form part of its Global Blasting Technical Services. These include blast audit and assessments, predictive modelling for blast performance, blast simulation tools, blast impact and performance measurements, as well as integrated compliance tracking and reporting.
By utilising these services, quarries can reduce their environmental impact by optimising charge placement and detonation timing, ensure regulatory compliance and improve operating costs and efficiency by minimising explosive usage to gain maximising yield.
In addition, the company will also highlight its advanced training and safety programmes. These include hands-on and virtual reality (VR) driver safety modules, compliance workshops for regulatory adherence and onsite expert consultation and risk assessment. The benefits for quarries include reduced accidents and human errors in blasting operations, improved workforce competence with up-to-date best practices and strong compliance with industry safety standards.
“BME is shaping the future of quarry blasting by integrating innovative technology, sustainability-focused explosives and intelligent blast designs. We are helping the quarrying industry navigate its evolving challenges with confidence. Our goal is to enhance safety, improve efficiency and ensure environmental responsibility – all while maintaining optimal operational performance,” concludes Van Niekerk. a

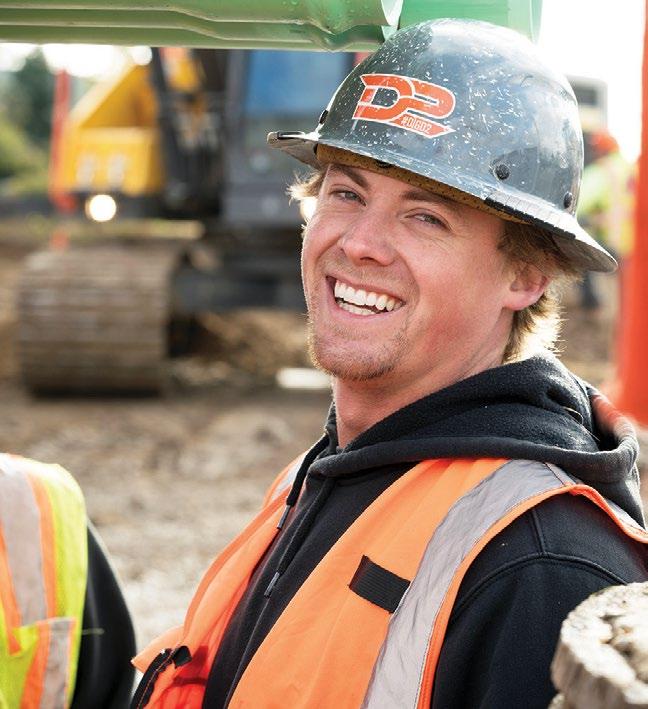
EXPANDING HORIZONS
Following its appointment to distribute a selected range of XCMG mining equipment in South Africa, Kiboko Group is expanding its horizons by adding equipment sales to its contract mining and equipment rental businesses.
Speaking to Quarrying Africa, CEO Nhlakanipho Ngcobo says the XCMG distributorship allows the company to not only supply and support a globally proven product, but also to ease barriers to market entry for upcoming mining contractors by availing flexible equipment solutions. By Munesu Shoko.
Kiboko Projects, a South African headquartered equipment management company, together with its principal, XCMG, ranked the fourth biggest construction equipment manufacturer on the 2023 Yellow Table (which compiles the sales for the world’s top 50 OEMs), used the recently ended Mining Indaba to announce their partnership.
The partnership sees Kiboko Group assuming the distributorship of a selected range of XCMG mining equipment to the South African mining industry. The range, says Ngcobo, has been carefully selected to meet the requirements of both mining houses and contract mining companies. Initially, Kiboko will bring in XCMG rigid dump trucks in the 100-tonne (t) to 260-t range. These will be complemented by a line of excavators in the 80-400-t range. In addition to new equipment sales, Kiboko will also acquire some of the XCMG equipment for its own rental divisions.
Transformative partnership
Having ventured into the world of entrepreneurship ten years ago, though initially involved in construction, Ngcobo has always had a special interest in mining. The 2020 surge in demand for commodities, particularly coal, as global economies started to recover, offered a perfect platform for Ngcobo to venture into mining,
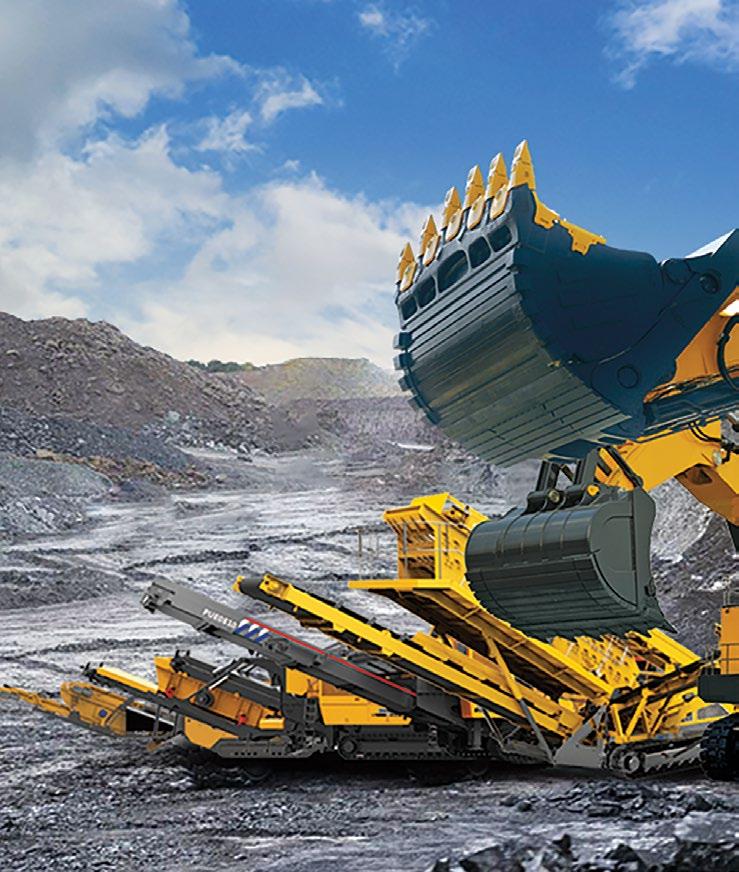
initially in contract mining, before expanding the offering with a mining equipment rental division. With a strong understanding of the struggles associated with starting a contract mining business in South Africa, Ngcobo believes the market has a high barrier to entry due to obstacles such as high start-up costs which are exacerbated by the lack of financing, especially in the case of start-ups with little to no credit record. He thus seeks to play a transformative role in the market by providing solutions that speak directly to this group of customers.
4th
“Our partnership with XCMG is groundbreaking, especially for upcoming contract miners who struggle to get a foothold in this market. Affording equipment as a start-up is a major hurdle, and I have first-hand experience of the struggles. In most cases, upcoming companies have to rely on third-parties who often ‘charge an arm and a leg’ for their equipment, which makes it difficult for upcoming contractors to be profitable and grow their businesses so as to be in the position to afford their own equipment,” he says.
To plug this gap, Kiboko is partnering with reputable financial institutions to provide funding for upcoming mining contractors. “For example, we have partnered with a reputable bank to offer a rent-to-buy model, which offers the benefit of flexibility and reduced upfront
XCMG was ranked the fourth largest construction equipment manufacturer on the 2023 Yellow Table
Kiboko Group has assumed the distributorship of a selected range of XCMG mining equipment to the South African mining industry.
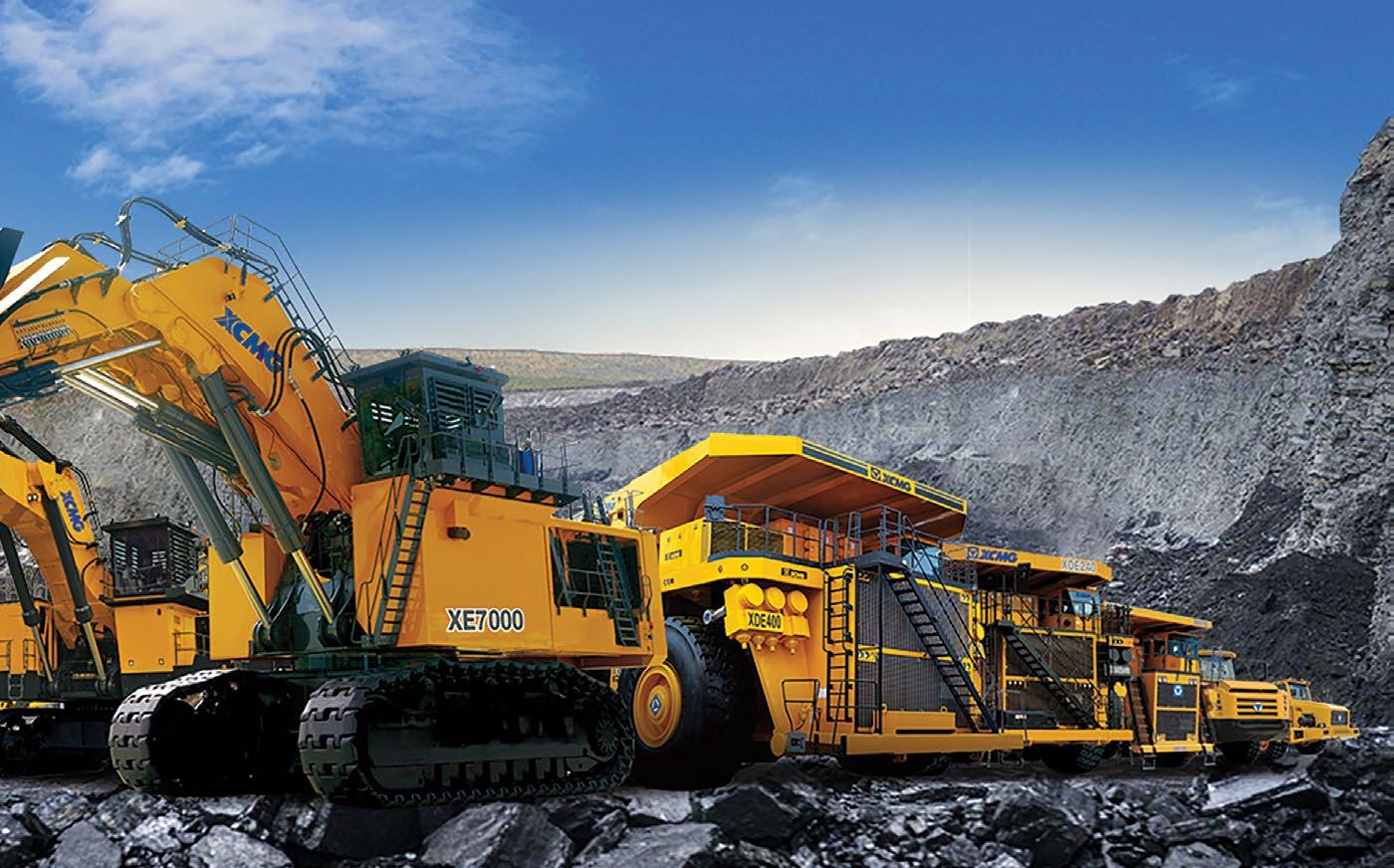
100-260 t
Initially, Kiboko will bring in XCMG rigid dump trucks in the 100-tonne (t) to 260-t range
80-400 t
Kiboko will also offer a complementary line of excavators in the 80-400-t range
2007
XCMG is a globally recognised brand that has made its mark in South Africa since its arrival back in 2007
costs, along with improved cash flow for these young companies,” he says.
Why XCMG?
Before opting to supply the XCMG range of equipment, Kiboko went on a fact-finding mission in China. The company met with XCMG in China and also visited a couple of mines running XCMG equipment. Impressed by the equipment’s performance and resilience in some of the most taxing operating conditions, Kiboko decided to enter into a distributorship with XCMG.
Apart from the build quality of the equipment, Ngcobo and his team were impressed by the wide range that XCMG has to offer. In addition, he says, XCMG is a globally recognised brand that has also made its mark in South Africa since its arrival in 2007.
“We have initially selected a few items from the XCMG catalogue to supply and support in the local market. Based on how we grow the initial offering, we will probably consider expanding the range with more models in the future,” says Ngcobo.
As an organisation driven by innovation, demonstrated
KEY POINTS
Following its appointment to distribute a selected range of XCMG mining equipment in South Africa, Kiboko Group is expanding its horizons by adding equipment sales to its contract mining and equipment rental businesses
The partnership sees Kiboko Group assuming the distributorship of a selected range of XCMG mining equipment to the South African mining industry
Kiboko is partnering with reputable financial institutions to provide flexible equipment financing for upcoming mining contractors
The company has invested in a new office and workshop on a 4-hectare site strategically located along the busy R21 highway in Centurion
Kiboko will bring in XCMG rigid dump trucks in the 100-260 tonne range, as well as a line of excavators in the 80-400-t range.
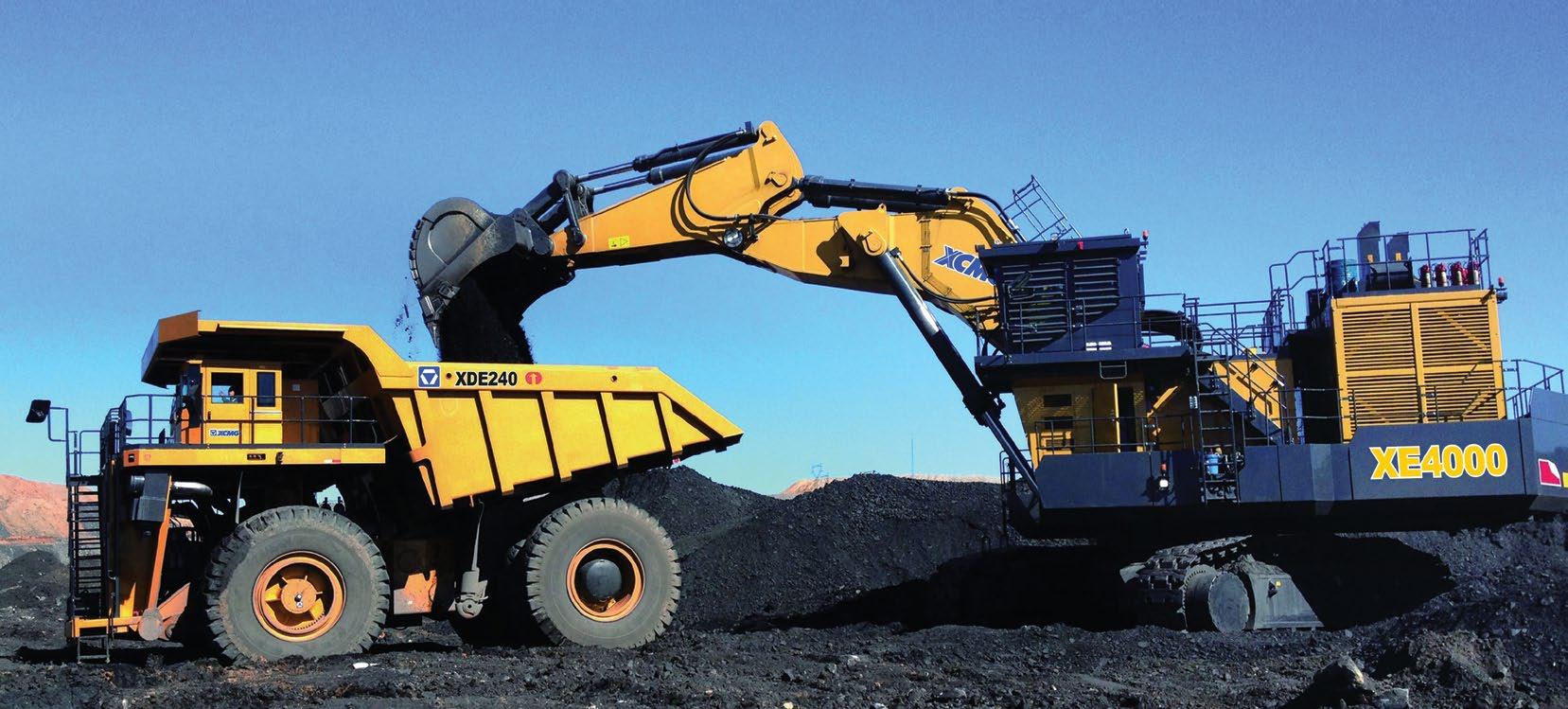
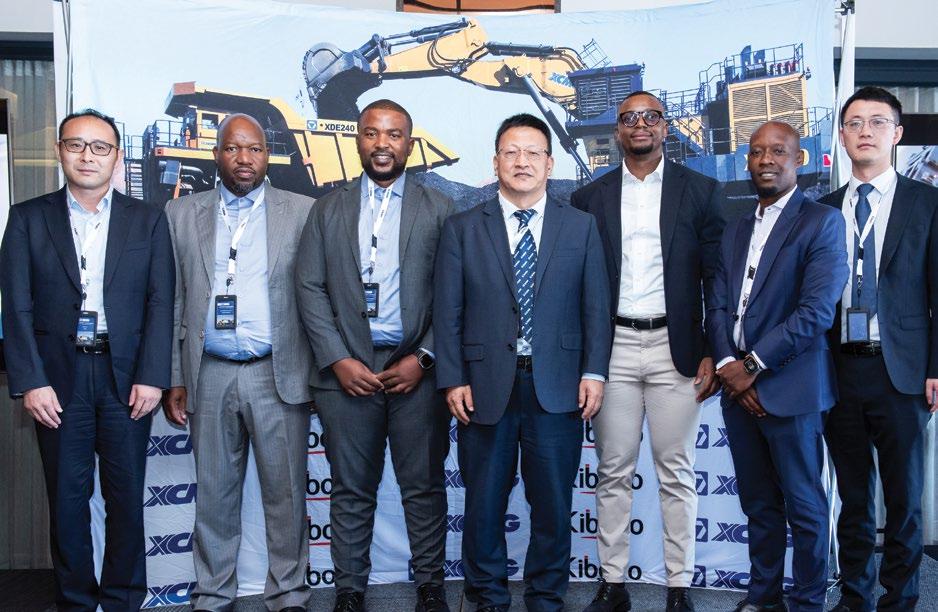
by its in-house AI-driven predictive maintenance, remote diagnostics and automated performance technology, Kiboko is encouraged by the strides that XCMG has made in the fields of automation and electromobility – key trends that address the mining sector’s quest for zero harm and sustainability.
“XCMG has gone the automation route further than most other premium original equipment manufacturers (OEMs). While automation technology is seemingly premature for our market needs, it will at some point become relevant as the local mining sector adapts to the new operational realities. While it is not feasible to automate the whole fleet, we believe that driverless trucks are the answer
for risky environments such as where highwalls exist. This allows companies to take people out of harm’s way,” explains Ngcobo.
To be competitive, Kiboko will place value on lower total cost of ownership (TCO) for its XCMG customers. The efficient nature of the machines already provides for the building blocks to ensure lower TCO. This is complemented by their proven reliability, which not only ensures uptime but also high equipment availability.
According to Ngcobo, the days in which Chinese equipment was viewed with disdain are long gone. Chinese OEMs have proven to be real innovators fighting for a larger share of the global capital equipment market. Placed among the top four best-selling
construction equipment manufacturers globally, XCMG has proven its mettle among global giants. The stigma around Chinese products, he adds, has also been dispelled by the fact that companies such as XCMG run globally renowned components such as Cummins and MTU engines.
Strong support structure
For Kiboko, a good reputation is crucial, and it fosters trust, credibility and longterm success, says Ngcobo, which is why the company is investing heavily in its support structures. “We will first focus on a few product lines to allow us to perfect our aftermarket service. We have also invested in a new office and workshop on a 4-hectare site strategically located along the busy R21 highway in Centurion. This facility affords us ample space to pull in large 260-t dump trucks for service, while its strategic location allows for easy access to the major highways,” says Ngcobo. This support infrastructure will be complemented by a large investment in parts to ensure high availability. In addition to Kiboko’s own parts holding, XCMG already has a large parts warehouse in Kempton Park, near Johannesburg. Kiboko technicians are undergoing OEM training to equip them with the necessary skills to look after the XCMG equipment. The company will also send some personnel to the XCMG factory in China for further training.
“We will leave no stone unturned to ensure that we adequately support our customers. Having been on the other side of the ‘fence’, operating a large fleet of equipment, we understand customer pain points and their support needs. We are therefore well geared to take good care of our customers,” concludes Ngcobo. a
Kiboko Group and XCMG used the recently ended Mining Indaba to announce their partnership.
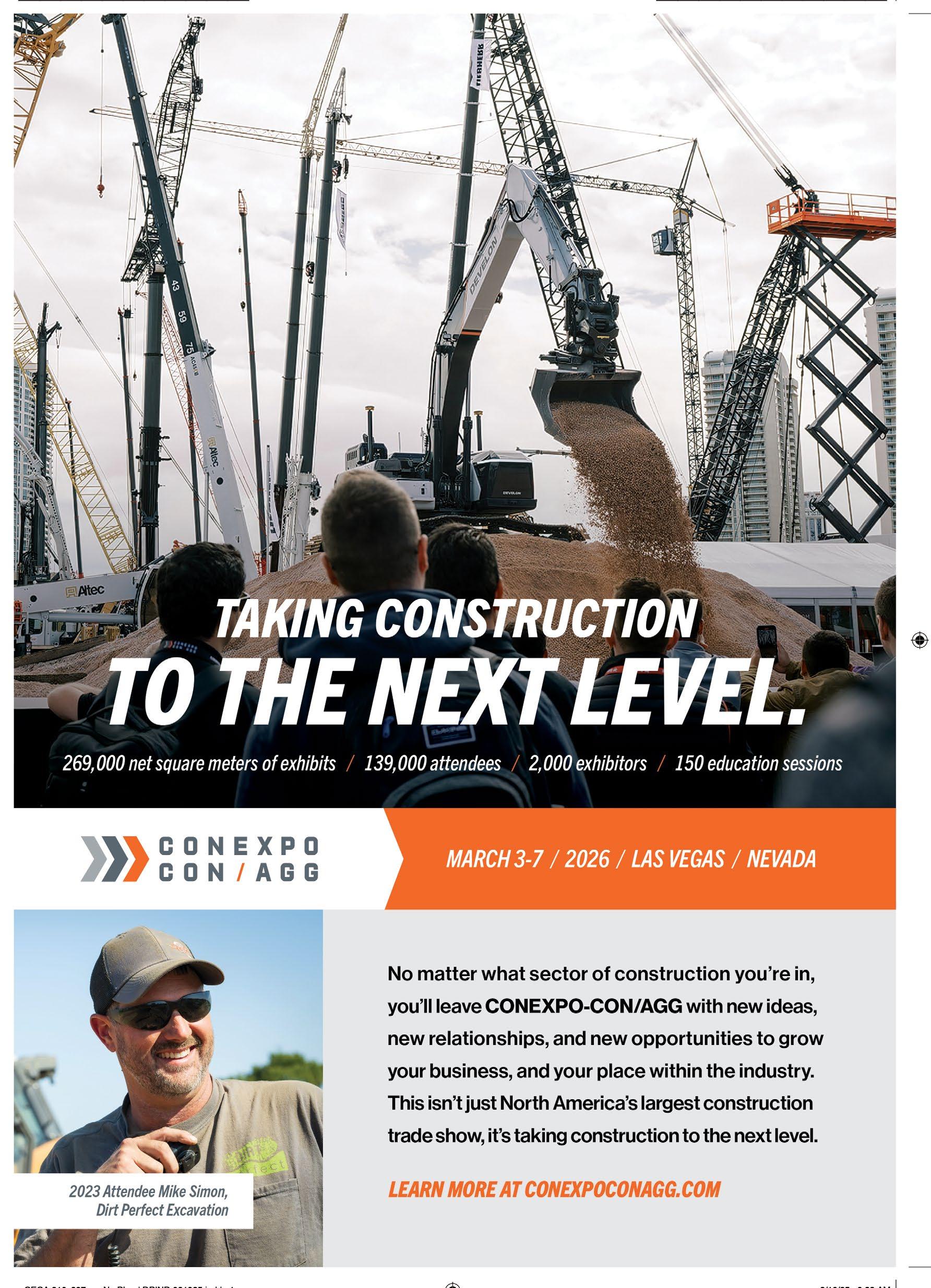

The Research and Development Centre will enable the continual improvement of Dunlop Belting Products’ 100% locally-manufactured products.
ADDRESSING TOMORROW’S CHALLENGES, TODAY
To manufacture products suited to withstand its client’s harsh operating environment, South Africa’s largest majority black-owned and part black woman-owned conveyor belt manufacturer, Dunlop Belting Products (DBP), launched a world-class research and development (R&D) centre in November 2024. The centre is said to be the first of its kind in Africa for the conveyor belt industry and will enable the continual improvement of DBP’s 100% locally-manufactured conveyor belt products, as well as manufacturing techniques and capabilities. By Chantelle Kotze.
Located at the company’s manufacturing facility in Benoni on Johannesburg’s East Rand, the R&D centre forms an integral part of DBP’s growth and development objectives, enabling it to maintain its position as Africa’s largest conveyor belt manufacturer.
“The R&D Centre provides a space for innovation, in which DBP can perform rigorous testing aimed at improving and refining its existing products, and create novel conveyor belt compounds that are lighter, stronger, safer and more efficient in moving bulk materials over long distances in demanding conditions,” Vicky Naidoo, technical manager for DBP, explains.
Despite having relied on the R&D work carried out at Dunlop’s Germany-based facilities to inform the development of its products in the past (due to the company’s former ownership structure), DBP always held the vision of establishing a local R&D facility capable of
undertaking credible and meaningful R&D work.
Capitalising on the visits to Dunlop’s R&D facilities, DBP’s technical team used these learnings to start informally developing and testing improved compounds at its SABS ISO 9001:2015 accredited production facility in Benoni that could meet the unique challenges faced by its customers in Africa.
“Based on the amount of informal inhouse R&D that was taking place, we took the decision to formalise this and invest in creating a purpose-built R&D centre in which our technical team could innovate,”
11/2024
Dunlop Belting Products launched a purpose-built research and development (R&D) centre in Benoni in November 2024
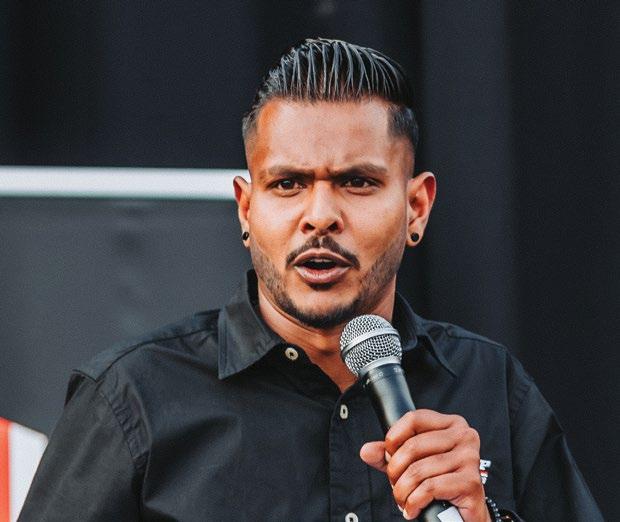
R1,2-billion
Nearly R1,2-billion worth of conveyor belts are imported into South Africa each year and comprise mostly cheaper Chinese products which pose a significant threat to the domestic conveyor belt sector

“ “
The R&D Centre provides a space for innovation, in which Dunlop Belting Products can perform rigorous testing aimed at improving and refining its existing products.
Based on the amount of informal in-house R&D that was taking place, we took the decision to formalise this and invest in creating a purpose-built R&D Centre in which our technical team could innovate.
KEY POINTS
Dunlop Belting Products launched its Research and Development Centre to conduct rigorous in-house research and testing aimed at improving and refining its existing conveyor belt products
The R&D Centre aims to overcome industry challenges such as weight, strength, energy efficiency as well as client-specific challenges with the aim of developing smarter, more efficient solutions for its customers
The company plans to further grow its footprint in the rest of Africa and further afield into parts of Europe, as well as Russia and Kazakhstan
To counter the threat of cheaper imported conveyor belts, DBP is collaborating with the International Trade Administration Commission of South Africa to address import duties that limit the competitiveness of the local conveyor belt industry
Mbuso Thabethe, CEO of Dunlop Belting Products, told Quarrying Africa on the sidelines of the launch of the R&D Centre.
With its commissioning, the R&D Centre provides a space for DBP to work towards its objective of developing ‘conveyor belts of the future’ that can address industry challenges such as weight, strength, energy efficiency and more, Thabethe notes.
Further, Thabethe points out that the R&D Centre, together with the company’s training academy, will serve as a platform to actively attract and encourage specialist young talent to the conveyor belt industry. This will contribute towards overcoming the challenge of youth unemployment, poverty and inequality in South Africa.
Challenges into operational solutions
DBP has evolved the way it conducts its business to align with changing consumer demands by increasing its focus on safety and sustainability. In line with this
Vicky Naidoo, technical manager at Dunlop Belting Products
Mbuso Thabethe, CEO of Dunlop Belting Products
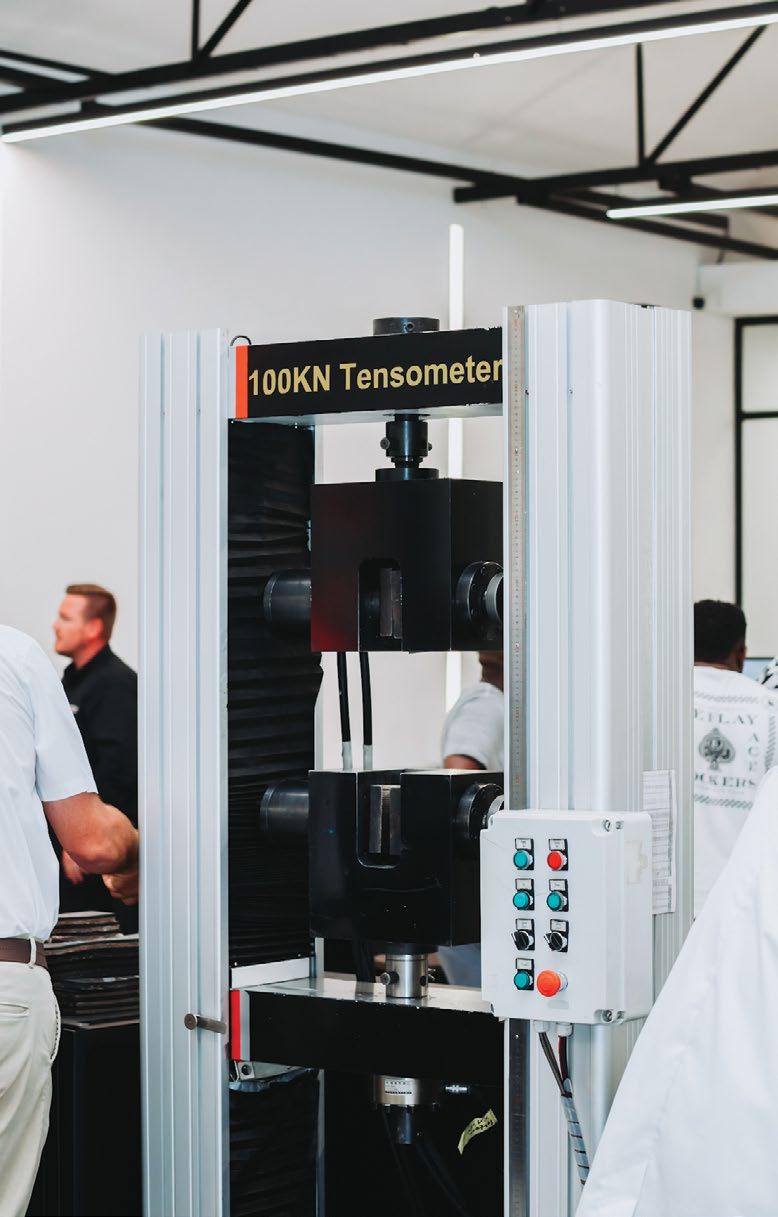
The company undertakes several safety and performance tests to ensure that its products meet SANS quality standards.
approach, the R&D Centre enables the company to explore new materials, test the latest and best technologies and develop smarter, more efficient solutions for its customers, explains Naidoo.
The Centre, adds Naidoo, seeks to address the mining sector, power generation sector and maritime port’s most pressing challenges of reducing energy consumption, improving system longevity, minimising environmental impact and enhancing worker safety.
The safety and performance testing includes several fire retardancy tests to improve the fire safety performance of the conveyor belts and in turn mitigate fire safety hazards in the industries in which the belts will be deployed.
The tests include finger-burn testing to test fire retardancy and the time it takes to extinguish a fire; drum friction testing to determine heat and fire resistance of the belt when exposed to drum friction; and midscale and large-scale fire propagation testing to test the rate at which a fire propagates along a belt. This large scale test is conducted in a replica underground mine tunnel, with the test conforming to global standards, Naidoo elaborates.
The R&D Centre also conducts toxicity testing as a way to measure harmful gases emitted when a conveyor is burning. In addition, ozone testing is aimed at testing the belt’s resistance to UV rays from the sun, while cold resistance testing facilitates the testing of different rubber compounds in cold conditions and the tensile strength of the compound. Cut and gouge testing determines the forces that a belt can withstand from falling material at transfer points, whilst low rolling resistance testing allows for testing of the energy efficiency of a belt.
Naidoo explains that the Centre is also equipped to undertake simulation testing using several purpose-built conveyor systems capable of simulating real-world operational scenarios to test conveyor belt endurance and fatigue. This is often used to test belt or equipment failures at certain sections on the conveyor system, to diagnose belt tracking and troughability issues, identify flaws in belting designs and perform dynamic belt splicing testing, he points out.
Safety and performance testing
DBP ensures that its conveyor belt products consistently meet current SANS quality standards. To achieve this, the company extracts, prepares and tests samples from every conveyor belt it manufactures.
All of DBP’s conveyor belts undergo the following tests:
• abrasion testing, which tests the volumetric loss that a conveyor belt undergoes in order to ensure it conforms to the SANS specification;
• tensometer testing for all destructive testing, including breaking and adhesion strength;
• rheometer testing, which measures the flow characteristics and behaviour of the rubber in an effort better to understand the cure times during vulcanisation;
• troughability testing, to ensure that the conveyor belt conforms to customers’ troughing needs;
• yarn testing, which includes yarn twisting and yarn assembly, to determine how much yarn is needed for a conveyor belt carcass; and
• electrical conductivity testing, to confirm the amount of electricity a conveyor belt can absorb before it dissipates a charge.
The R&D Centre is said to be the first of its kind in Africa for the conveyor belt industry.
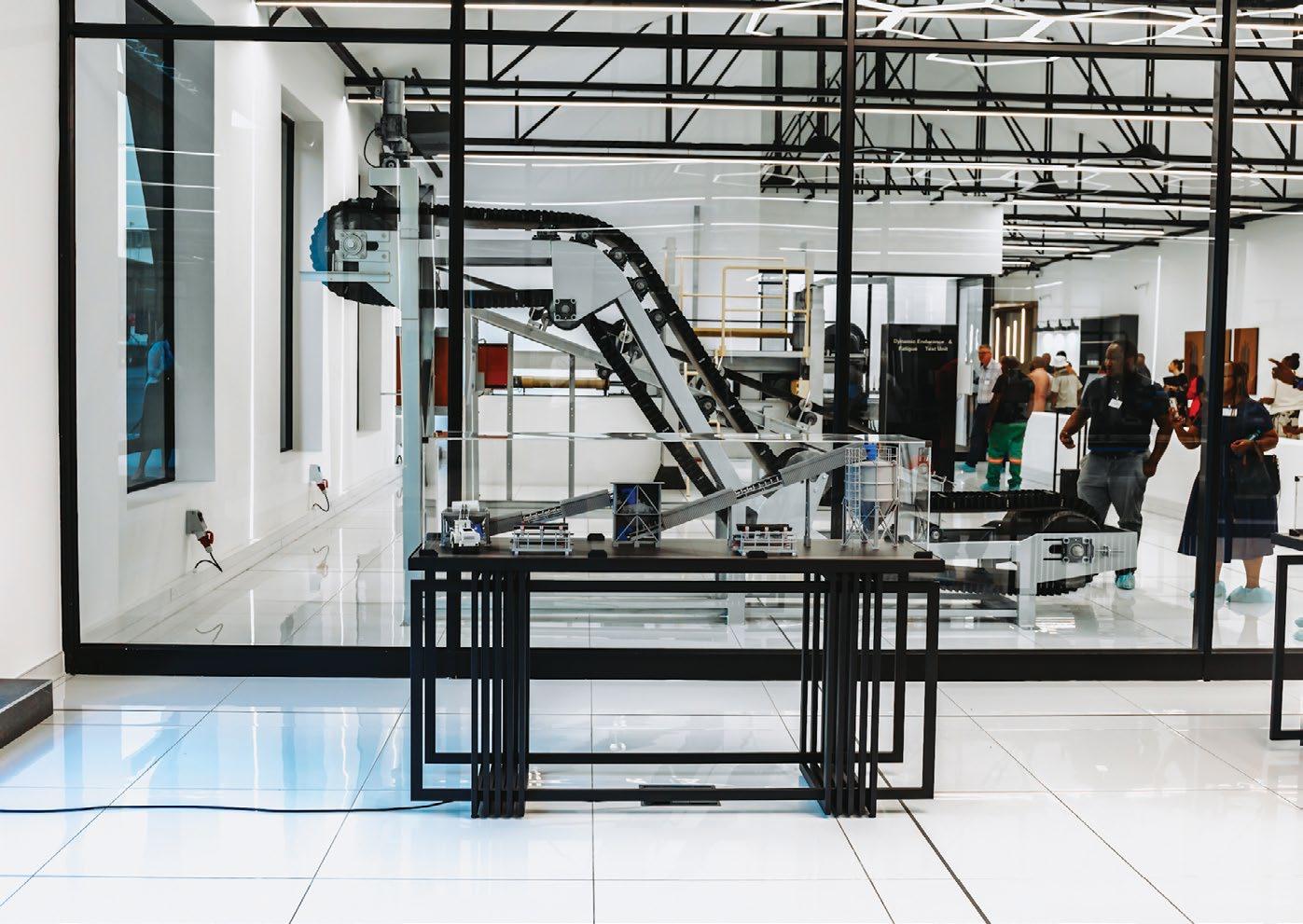
Moreover, the company also has steel cord-specific belt testing. These tests include air penetration testing that ensures each and every steel filament within the steel cord is embedded with rubber during manufacture, for better adhesion and strength of the conveyor belt; as well as dynamic cyclic endurance testing – to test the fatigue resistance of the steel cord within the belt, ensuring it is able to handle tension under load.
9001:2015
Capitalising on the visits to Dunlop’s R&D facilities in Germany, DBP’s technical team used these learnings to start informally developing and testing improved compounds at its SABS ISO 9001:2015 accredited production facility in Benoni
“In-process samples are extracted and tested throughout each stage of the manufacturing process, while the final product is also tested before being dispatched to customers,” Naidoo says.
Naidoo, who was closely involved in the establishment of the Centre, explains that the facility houses a testing laboratory, which was previously located in the company’s old test facility which is currently used to test sample preparation.
Overcoming the threat of imports
Despite DBP’s promising growth opportunities, competing with nearly R1,2-billion in annual conveyor belt imports to South Africa – which comprise mostly
cheaper Chinese products, poses a significant threat to the domestic conveyor belt sector, highlights Thabethe.
To overcome this threat, DBP is working closely with the International Trade Administration Commission of South Africa to address the issue of import duties which are currently hindering the competitiveness of the domestic conveyor belt sector.
By challenging the levying of import duties on raw materials, such as steel cord rods, which cannot be procured locally due to the absence of in-country manufacturing capability, it is hoped that the competitiveness of the local conveyor belt sector will improve.
Despite the prevalence of Chinese imported conveyor belts at African mines, Thabethe believes the quality of DBP’s product – due to improved and more innovative compounds, together with shorter lead times and distance to market – stands the company in good stead to compete with cheaper imports.
“Customers seem willing to pay a slight premium for a quality product and the convenience of faster delivery,” he concludes. a
AfriSam
AfriSam is a leading construction materials group in southern Africa. Since establishing its first cement plant in 1934, the company has grown into a formidable construction materials group with operations in South Africa, Lesotho and Eswatini.
www.afrisam.co.za
Babcock
Through several business units, Babcock offers a range of products and services, including construction and mining equipment, engineering solutions for steam generation and power plants, crane hire and gear rental, industrial generators, welding equipment and DAF truck sales and service.
www.babcock.co.za
Booyco Electronics
With more than 16 years of experience in Proximity Detection Systems solutions, Booyco Electronics has supplied over 6 500 sets of mining vehicle equipment installations across southern Africa, as well as more than 55 000 pedestrian RFID installations.
www.booyco-electronics.co.za
Bunting
Bunting’s range of magnetic separators and metal detectors for quarries and mines ensures the protection of crushers, screens and conveyors. Overband magnets, suspension magnets and pulley magnets automatically remove tramp ferrous metal from conveyed quarried rock. www.bunting-redditch.com
IPR
IPR is recognised across the SADC region as the pump, heavy duty slurry handling and dredging specialist operating in underground and surface mining, quarrying, construction, wastewater, petrochemical and oil and gas sectors. www.pumprental.co.za
Loadtech
LOADTECH Load cells Onboard Weighing are specialists in onboard weighing providing complete solutions onboard your heavy goods vehicle, primarily in the application of load cell and transducer systems for payload protection and accuracy in the commercial vehicle sector. www.loadtech.co.za
JBI Industrial Solutions
JBI Industrial Solutions specialises in a diverse range of weighing systems in partnership with PFREUNDT GmbH. We provide solutions for both mobile and static weighing needs. The PFREUNDT weighing systems are versatile and deliver significant benefits across various industries, including extraction, disposal, recycling, industry and agriculture.
www.jbisolutions.co.za
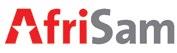
Pilot Crushtec International
Pilot Crushtec International (Pty) Ltd is South Africa’s leading supplier of mobile and semi-mobile crushing, screening, recycling, sand washing, stockpiling, compacting and material handling solutions. www.pilotcrushtec.com
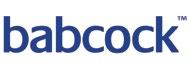
Sandvik
As a world-leading mining equipment manufacturer, Sandvik Mining and Rock Solutions is committed to improving your productivity and profitability. Our products and services provide you maximum value in terms of performance, quality, safety, flexibility and total economy. www.rocktechnology.sandvik/en/

Astec
Astec Industries has been a global leader in providing innovative Rock to Road™ solutions since 1972, specialising in equipment for asphalt road building and aggregate processing. www.astecindustries.com

John Deere
John Deere offers a comprehensive range of construction equipment, including ADT’s, excavators, loaders, dozers, graders, skid steers and TLB’s, designed to enhance productivity, efficiency, and performance on job sites of all sizes. www.deere.africa/en/construction

Lintec & Linhoff
Lintec & Linnhoff is a global manufacturer and distributor of leading-edge solutions for the asphalt and concrete industries under the Lintec and Linnhoff brand names. Its products include asphalt mixing plants, concrete batching plants, pavement related technologies, and specialist concrete cooling solutions.
www.lintec-linnhoff.com
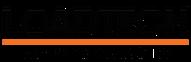
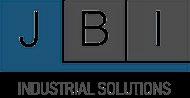
Weir Minerals
Weir Minerals Africa offers a wide range of equipment solutions including pumps, hydrocyclones, valves, dewatering equipment, wear-resistant linings, rubber products, screens and crushers – backed throughout the product lifecycle by high levels of aftermarket support.
www.global.weir
SANY
Sany Southern Africa is a subsidiary of Sany Group, a leading manufacturer of construction, mining and port machinery with over 20 R&D centres and manufacturing bases all over the world. www.sanysouthafrica.com

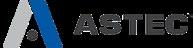

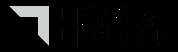

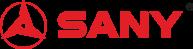
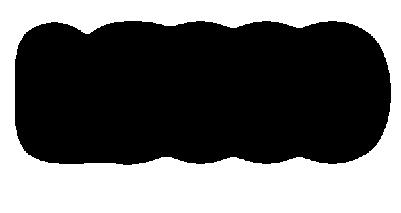
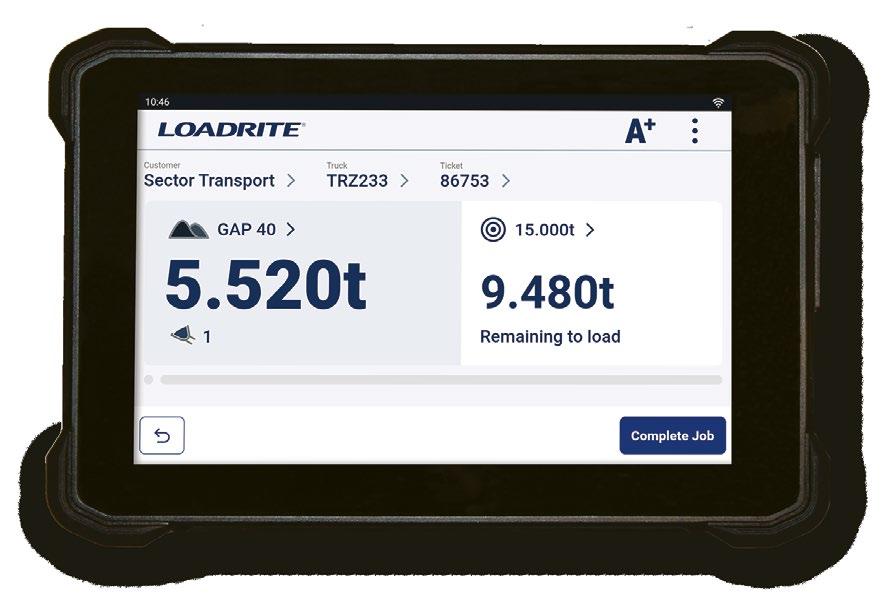
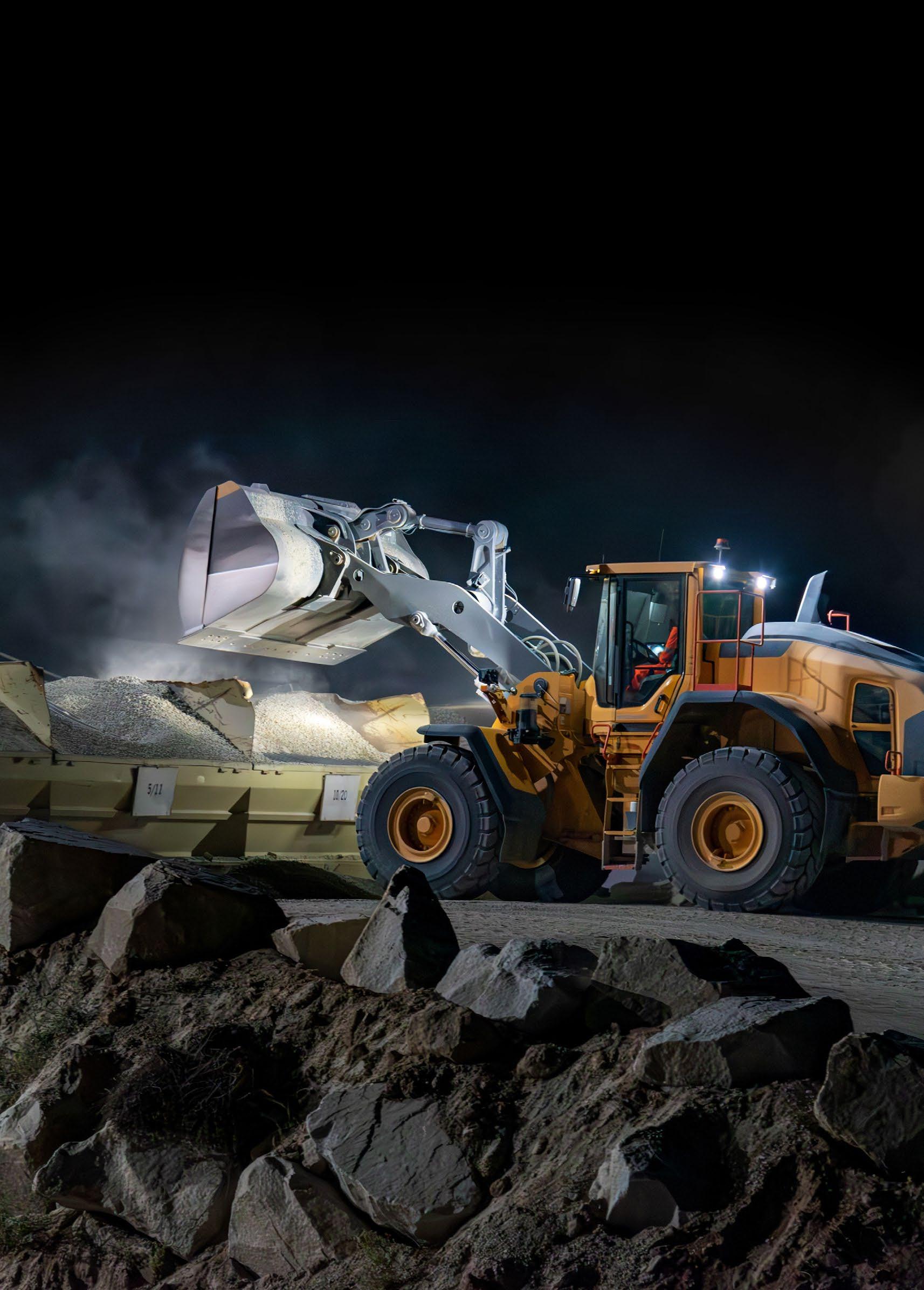
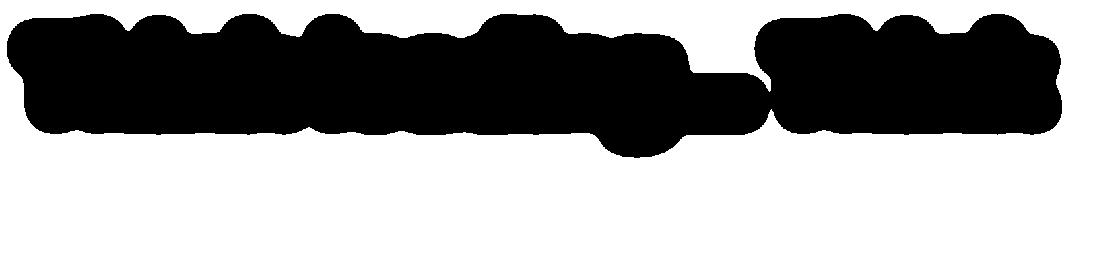
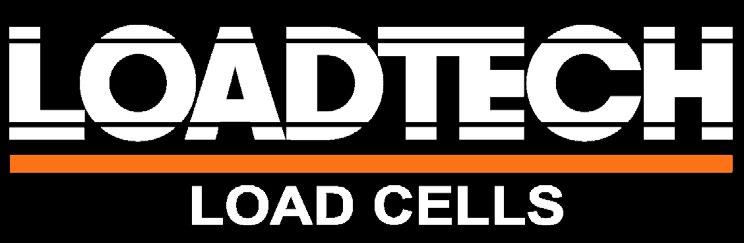
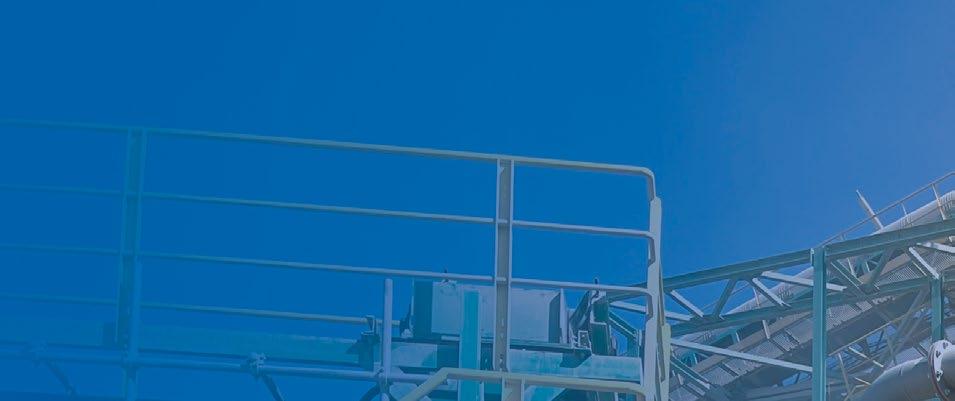

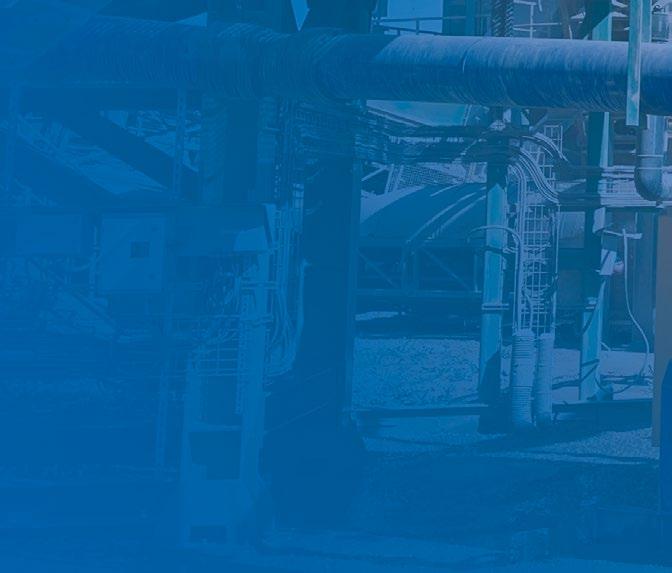
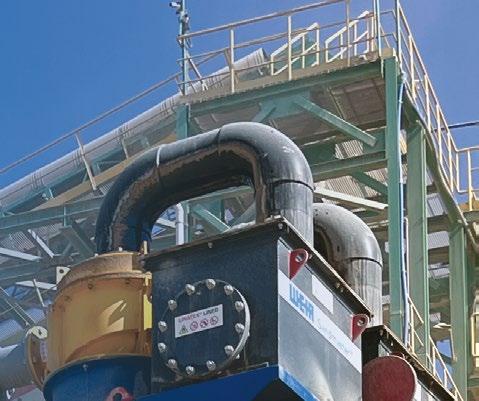

Compact wash plants producing fine and coarse sands
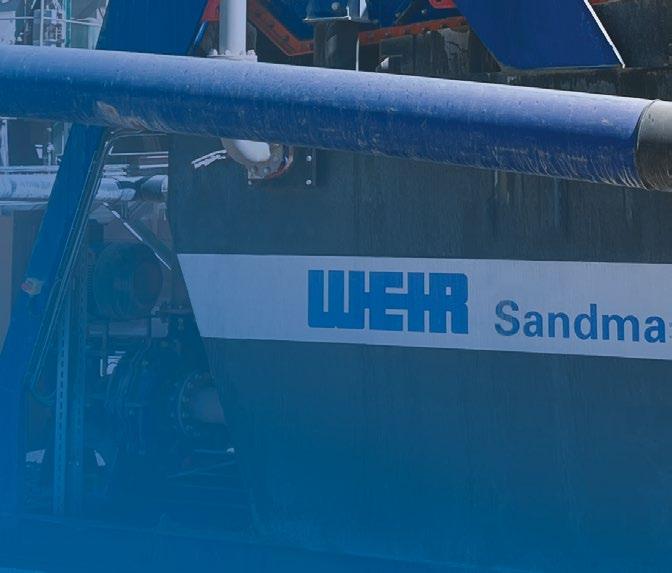

Using advanced WARMAN®, LINATEX® and CAVEX® technology.
Washing is critical to aggregate and sand production. Weir’s SANDMASTER™ washing equipment uses some of our most advanced technology like WARMAN® pumps, LINATEX® premium rubber products, and CAVEX® hydrocyclones, to produce a portable sand wash plant that can be easy to assemble, maintain and operate — for new entrants or highly experienced sand producers working in the toughest washing and scrubbing applications.
Our range of SANDMASTER™ sand wash plants are fully supported by Weir’s unrivalled global service network to meet your needs. www.global.weir/Sandmaster
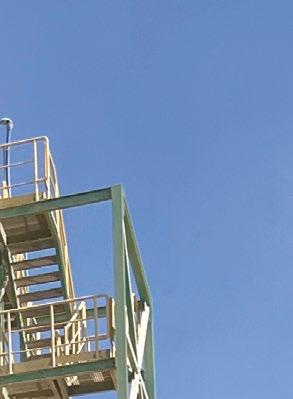
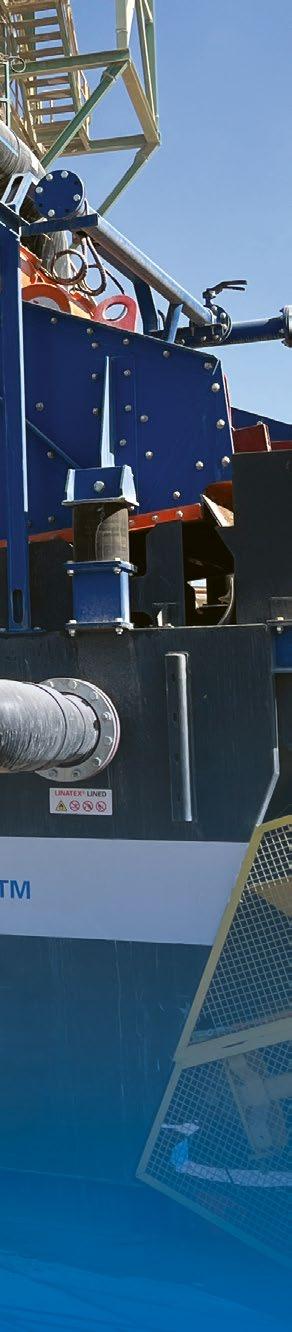