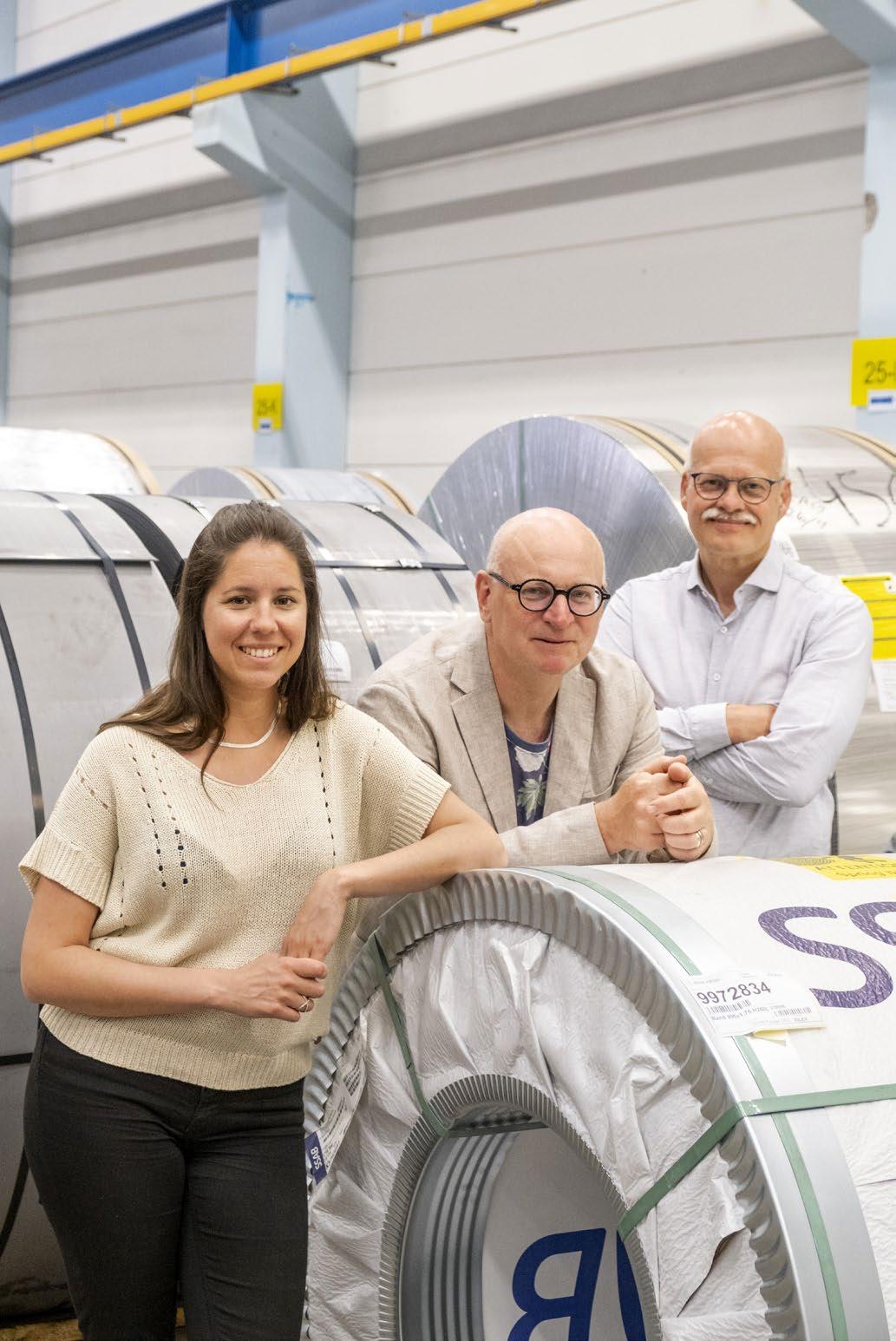
4 minute read
Sustainability must never become a paper tiger”
Proton Finishing’s sustainability developer Sandra Vatn, sales manager Anders Olsson and Jan Strandesjö, quality and environment manager at Beslag & Metall, are at the forefront of delivering climate-impactcalculated components to the automotive industry.
Customers of Proton Finishing can now find a calculation of the climate footprint for surface treating their products in their quote. The calculations cover all processes at production line level for each individual item. Jan Strandesjö, quality and environment manager at Beslag & Metall, is absolutely delighted with the new arrangement.
“We are really pleased to be able to take this step together!”
Over recent years, Proton Finishing has set a number of highly ambitious, some might say overreaching, goals designed to lead the surface treatment industry into the future. One of them was to become the first company in the industry to offer customers climate footprint calculations. And now, they are there. Proton Finishing can now report the climate footprint of all of its production lines.
“We can report the climate footprint of a product based on the production line it was manufactured on. All we need from the customer is the size of the area being treated,” explains Sandra Vatn, sustainability developer at Proton Finishing.
“It’s been tough”
While it may sound relatively simple, it has required the combined forces of all production units.
“A great deal of data needs to be unearthed concerning our processes. The first stage was difficult, as we decided to split it at production line level. Of course, it would have been much easier to just calculate the total for the entire plant – but customers are interested in their particular products. To create customer and climate benefits, we were forced to do our homework. And once all the data is available and a method decided on, it’s easy,” says Vatn, who is keen to point out the work is also highly significant for Proton Finishing’s own improvement work.
“We have gained a fantastic basis for our own sustainability work with prioritised measures.”
Sustainability pioneers
Proton Finishing’s initiative was just what Beslag & Metall in Ekenässjön was looking for. The company is a market leader in stamped sheet metal components for the automotive industry. Customers include Scania, Volvo Trucks and Volvo Cars.

“Proton Finishing is our surface treatment partner alongside our own paint shop. We do the large volumes of power coating in our own paint shop in Ulricehamn. Proton Finishing helps us with electrolytic surface treatment, as well as some painting,” says Jan Strandesjö, quality and sustainability manager at Beslag & Metall.
Beslag & Metall currently uses five of Proton Finishing’s six production units and Strandesjö is enthusiastic about the fact that climate footprint has been calculated at production line level.
“Beslag & Metall is a third-generation family business and we have a long tradition of developing alongside our customers – not least when it comes to environmental efforts. We have been certified in compliance with ISO 14001 for over 20 years and we are used to being audited for sustainability requirements. As such, we were well-prepared when the automotive industry began to work actively on sustainability issues,” explains Strandesjö.
Right now, intensive efforts are underway to increase the percentage of fossil-free materials and to further improve energy efficiency. Naturally, the roof is equipped with solar panels and in the gigantic press – the largest in Europe and in itself worth a visit to Ekenässjön – braking energy is recovered and returned to the system.
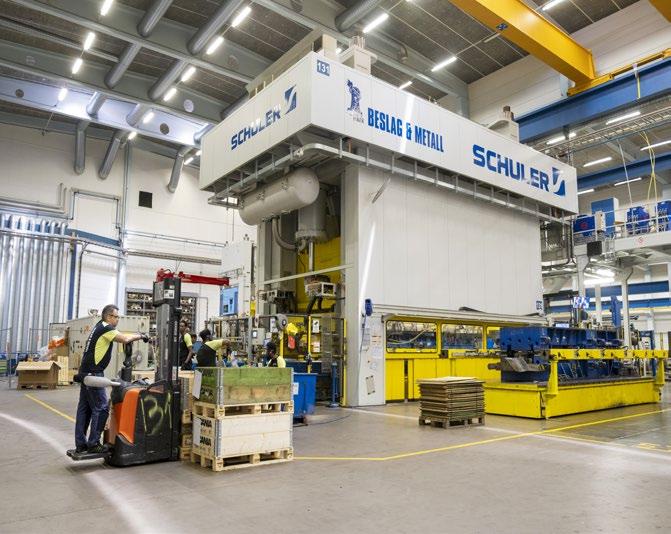
“The fact is, when we commissioned the press in 2015, it made no impression whatsoever on the electricity grid, despite the fact that it is such an energy-intensive process. This is mainly due to the energy recovery and, today, we are very grateful that we were so forward-thinking!”
“Inundated with questions”
Strandesjö sees Proton Finishing’s initiative as another opportunity for the company to remain one step ahead through close collaboration between subcontractors.
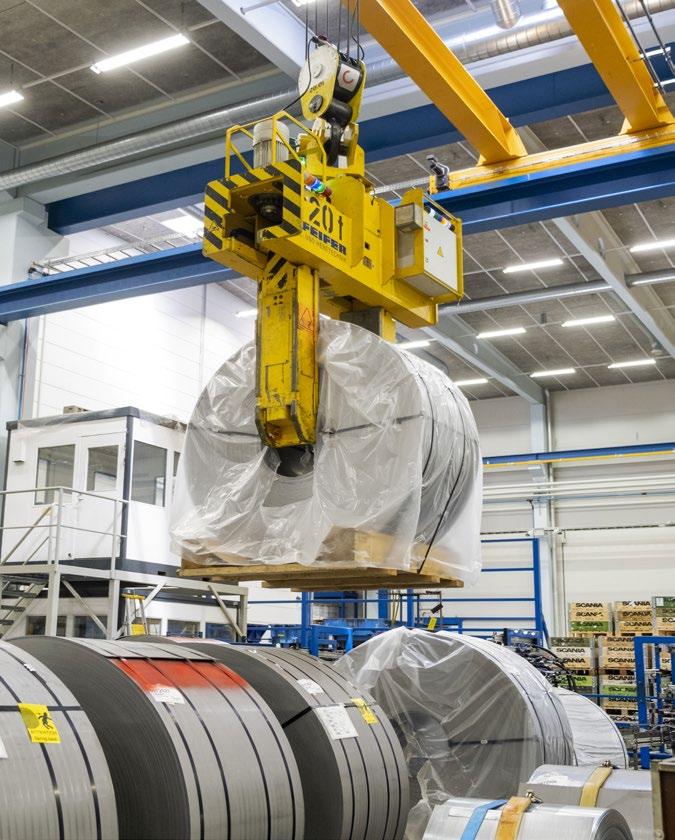
“Right now, we are being inundated with questions about CO2 emissions from our customers. We have made our own efforts to map the climate footprint of our operations and, naturally, we look on it very positively when our suppliers are able to do the same thing. Proton Finishing reports its climate footprint in a highly skilled manner and the response from our customers have been very positive. In fact, one of them stated that we are the first company to be able to present results in this way, which is, of course, the result of good teamwork,” says Strandesjö, who believes that active sustainability work and concrete results – such as climate footprint calculations – have become a competitive advantage.
“We recently won an order from Scandia worth SEK 150 million and high quality, high delivery capacity and successful sustainability work were decisive.”
New tendering standard
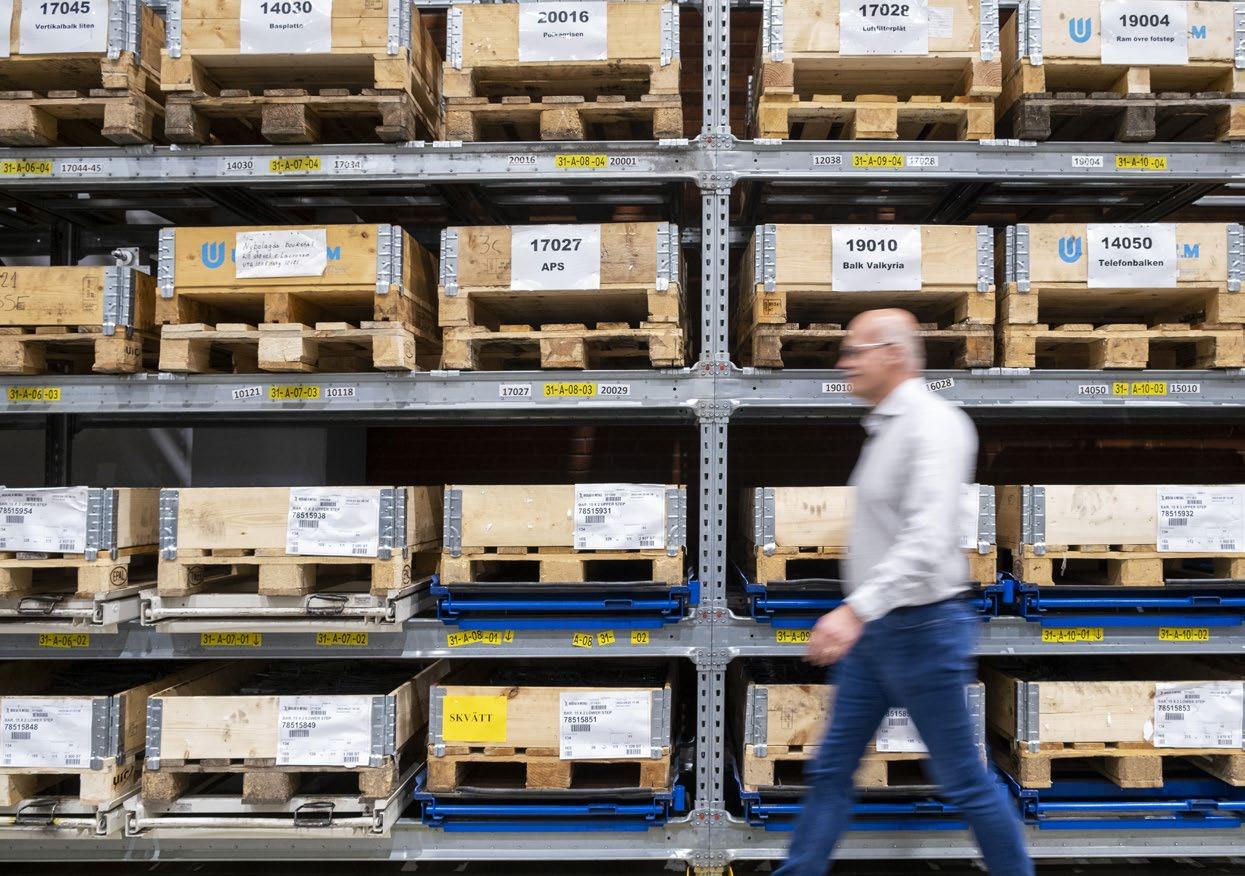
Jan Strandesjö notes that collaboration
“between subcontractors” is crucial, not only to common success but also to the development of the industry as a whole.
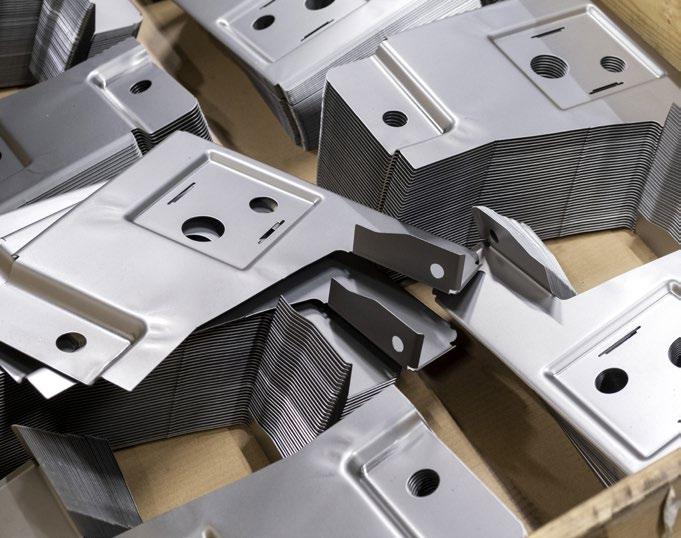
“It is vital that sustainability never becomes a paper tiger without any real benefit. And at Beslag & Metall and Proton Finishing, we have succeeded in creating that benefit together. To work sustainably is to create an economically justifiable business. The moment you avoid consuming a resource, you have actually saved money,” says Strandesjö. Anders Olsson, sales manager at Proton Finishing, agrees.
“In all honesty, it feels great to get there first – and to earn the customer’s appreciation for what we’ve done. Even potential customers seem to have picked up on it and we are receiving many positive reactions and curious inquiries. The next planned step is to report details of climate footprint at the tendering stage, giving customers an even better basis on which to make decisions.
“It’s a matter of collaboration and working together. When we collaborate, it brings us together and motivates us to trust one another, so that we can get the work done and achieve optimal results. And we do it together.”
Inga Petreikyte, quality and environment manager,

“It’s about give and take, everyone getting a piece of the cake.”
“To me, it means that we have good team spirit.”