
3 minute read
It should be so safe that our children could work here!”
That’s how unequivocal they are about safety at quick coupling specialist CEJN in Skövde. JL Safety is CEJN’s longstanding machine safety partner.
To ensure machine safety in conjunction with designing new and refurbishing existing production lines, the company has a wellestablished collaboration with JL Safety. CEJN has also chosen to use Cedoc software, which along with JL Safety is part of the Proton Group’s Edge business area.
“From a production engineering perspective, we are in a unique position. CEJN steps in when many others have given up. When the customer is stuck and needs something out of the ordinary, they come to us. This means that we have designed a production process based on high mix, low volume – and vice versa in some ranges –which will be a combination of automation and manual production," explains Johan Magnusson.
Founded in 1955, quick connect coupling specialist CEJN is now a global brand. With sales offices in 17 countries and representation in many more, you can find CEJN’s products in many different applications all over the world. Still, the company’s head office, R&D and all production remains in Skövde, Sweden.
“You might say that CEJN’s products are everywhere in everyday life, even where one might least expect it,” says Johan Magnusson, technical manager of the assembly group at CEJN.
“We are good at transporting different media through quick couplings and systems. Compressed air is one example; our quick couplings are found in compressed air systems and hose reels. Hydraulic oil is another medium where we offer quick couplings for both medium and high pressure hydraulics, such as plant and bolt preload.
We are also big in liquid cooling – in server halls, for example – and in wind power, where our products are used in cooling systems for converters and in the hydraulic couplings that secure the entire wind turbine. Now I think about it, I’m sure our quick couplings have also played a role in the manufacture of the large rotors as well, as they are used in the compressed air systems that powered polishing machines.”
Collaborative robots
One of the secrets behind CEJN's success is that the company has always had the courage and willingness to adopt new production techniques.
While, when faced with the transition, many others hesitated, CEJN was quick to switch to a hybrid model with collaborative robots.
“When we chose to do so in 2014, many others were hesitant, partly due to uncertainty about how to assess risk. JL Safety, however, was alert to developments. They realised that this was something new to Swedish industry and accompanied us on the journey. This was an amazing success that, among other things, resulted in a robot network.”
A self-learning organisation
Robert Turesson is a production engineer at CEJN and the person who works most often with JL Safety on various projects. His main point of contact is machine safety specialist Kenneth Ahllund.
“We view JL Safety as our competence resource, supporting us in both small and large projects. I usually design in CAD. Kenneth will then step in an make a risk assessment together with the project group. In fact, one of the major projects we carried out together was awarded the 2019 Swedish Assembly Award. JL Safety was very much involved in and contributed to the project,” says Robert, who points out that the learning process is very much part of the strategy.
“All of the issues we resolve along the way are entered into a database, meaning that we can consult ourselves on these issues and constantly develop in the field of machine safety. Collaboration with JL Safety provides safety at detail level but also keeps CEJN updated on standards and ensures that we make a correct assessment that is consistent across different project managers and end users. Thanks to this collaboration, we feel secure when we put a CE label on the machines that we install or refurbish for our own use.”
“Genuine
commitment”
For his part, JL Safety’s Kenneth Ahllund, enjoys the teamwork of collaborating with CEJN to the fullest.
“My job is most enjoyable when I can work with customers with a genuine interest in machine safety and who see the benefits of it, not least from a sustainability perspective. A safe workplace is an attractive workplace. The gang at CEJN are fond of saying that their production should be so safe that they would consider allowing their children to work here. I think that’s a nice way to put it.”
CEJN & JL SAFETY OFFER SOME TIPS
The most common problem is that various types of guards are missing, something that can be difficult to detect for both the producer and the person rebuilding the machine. Watch out for crushing, cutting and other injury risks.
Double-check electrical safety – an area that is often overlooked.
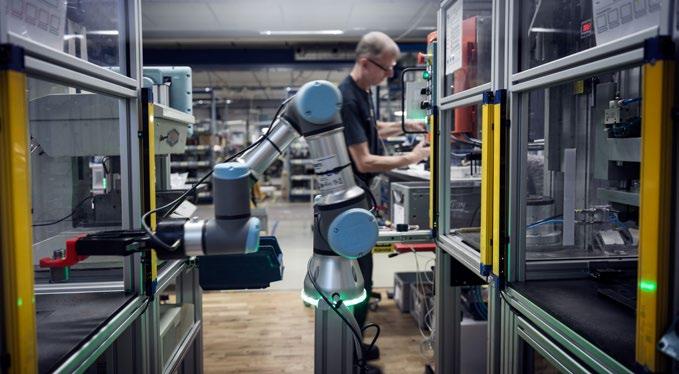