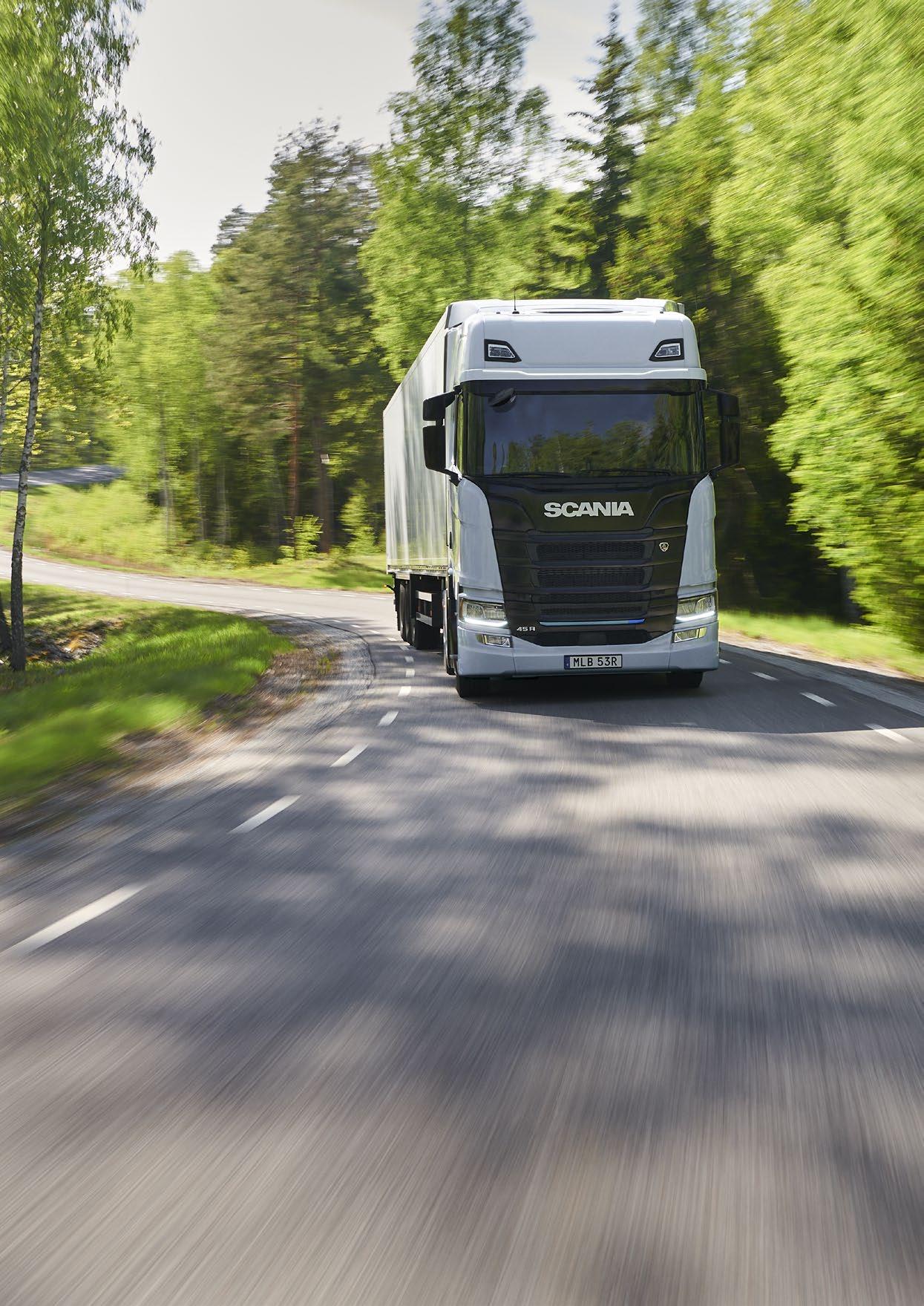
3 minute read
Scania and Proton Engineering join forces for electrification journey
Proton Engineering
Proton Engineering is the chosen partner as Scania embarks on its great transition to electrified vehicles. Camilla Linderberg, Scania’s sourcing manager promises a fast-moving journey with many exciting curves along the way. “This project will place completely new demands on our suppliers in terms of speed, flexibility and feedback.”
The electrification of freight and passenger transport is key to society’s green transition. As one of the world’s leading manufacturers of heavy goods vehicles and buses, Swedish company Scania is one of the driving forces behind this transition.

“We are currently running a major electrification project that encompasses all types of vehicles: electric trucks, electric buses, as well as charging infrastructure. The idea is that we will be able to help our customers future-proof their vehicle fleet. As part of this project, Proton Engineering has been nominated for the delivery of a great many articles," says Camilla Linderberg, sourcing manager at Scania in Södertälje.
Linderberg has been working in purchasing in Scania’s truck business for seven years, the last two with a focus on projects.
“I also worked as a prototype buyer for a period, meaning that I have had contact with Proton Engineering since I started at Scania. We are delighted to have such a versatile supplier that can offer series and prototype production.”
Continual change
Although Scania and Proton Engineering have been collaborating since the 1960s, with the new electrification project they are stepping into a new era together. The order is for series production of components for Scania’s new electric trucks, with the focus on pipes, Proton Engineering’s main area of expertise. At the same time, the company has also been entrusted with the production of prototypes for Scania’s new electric buses. Linderberg notes that the transition from traditional internal combustion engines to electricity will affect the entire supply chain.
“One of the challenges is that this is the first time we've done this. We simply cannot see the full picture. Our work is therefore based on the strategy of continuous improvement throughout the project. We are well aware that there will be changes, something that also places high demands on suppliers. They must be very flexible and able to make changes to components as and when we update the design. They must be committed and quick to communicate, so we don’t lose momentum anywhere along the supply chain. This means that they in turn must keep their a tight rein on their subcontractors. Naturally, we need all articles in place for a truck to roll off the production line.”
Positive energy
Proton Engineering’s team in Skillingaryd welcome the challenge and are looking forward to the change. “It will be all go – all the time,” says project manager Jonathan Bardh, who works in sales in Skillingaryd.
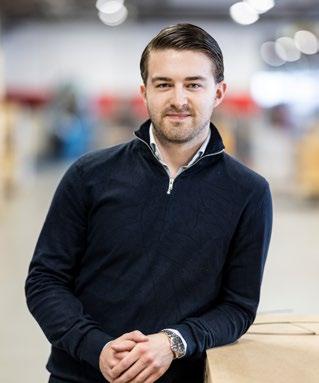
“There will be many changes, which means that each series will be shorter. This presents a challenge for all subcontractors in the automotive industry, where we are used to having long series rolling off the production line over an extended period. There will be constant product development. If we don’t keep pace and see whats coming, we won’t be able to keep up.”
Bardh agrees wholeheartedly that communication skills are just as important as engineering skills and product knowledge.
“The road to receiving an order is long and it has involved many meetings, inquiries and negotiations. In my experience, our dialogue with Scania is characterised by transparency and honesty from both sides and I believe that this has been important to our collaboration. My responsibility is to act as the link between Proton Engineering and
Scania and I would say that we are in touch on an almost daily basis. Then, of course, we maintain a close dialogue internally here at Proton. We really are a close-knit team that takes on the challenge together. This project has generated a lot of positive energy.”
Reducing carbon footprints, thinking more locally Linderberg is at pains to point out that, for Scania, a procurement is never simply about the price.
“We take a helicopter view. We consider many parameters: price, lead times and reliability, feedback, quality and sustainability management. Sustainability is a very important issue for us and our customers. We already rank our suppliers on sustainability and we are preparing more in-depth collaboration with our suppliers to further reduce carbon footprints.”
Given the global situation and the aftermath of the pandemic, Scania has also begun to think locally.
“This implies focusing more on local suppliers, and by that I mean not only in Sweden but around Europe. We are dependent on having suppliers who can deliver quickly. Of course, rising logistics costs also have an impact.”

“An exciting journey”
“This is just the beginning of an exciting journey and I am happy for Proton Engineering’s sake that they have jumped aboard. Here at Scania, we believe that it is vital to have suppliers who are not lagging behind but understand that their customers want and are prepared to keep up with the times,” says Linderberg.