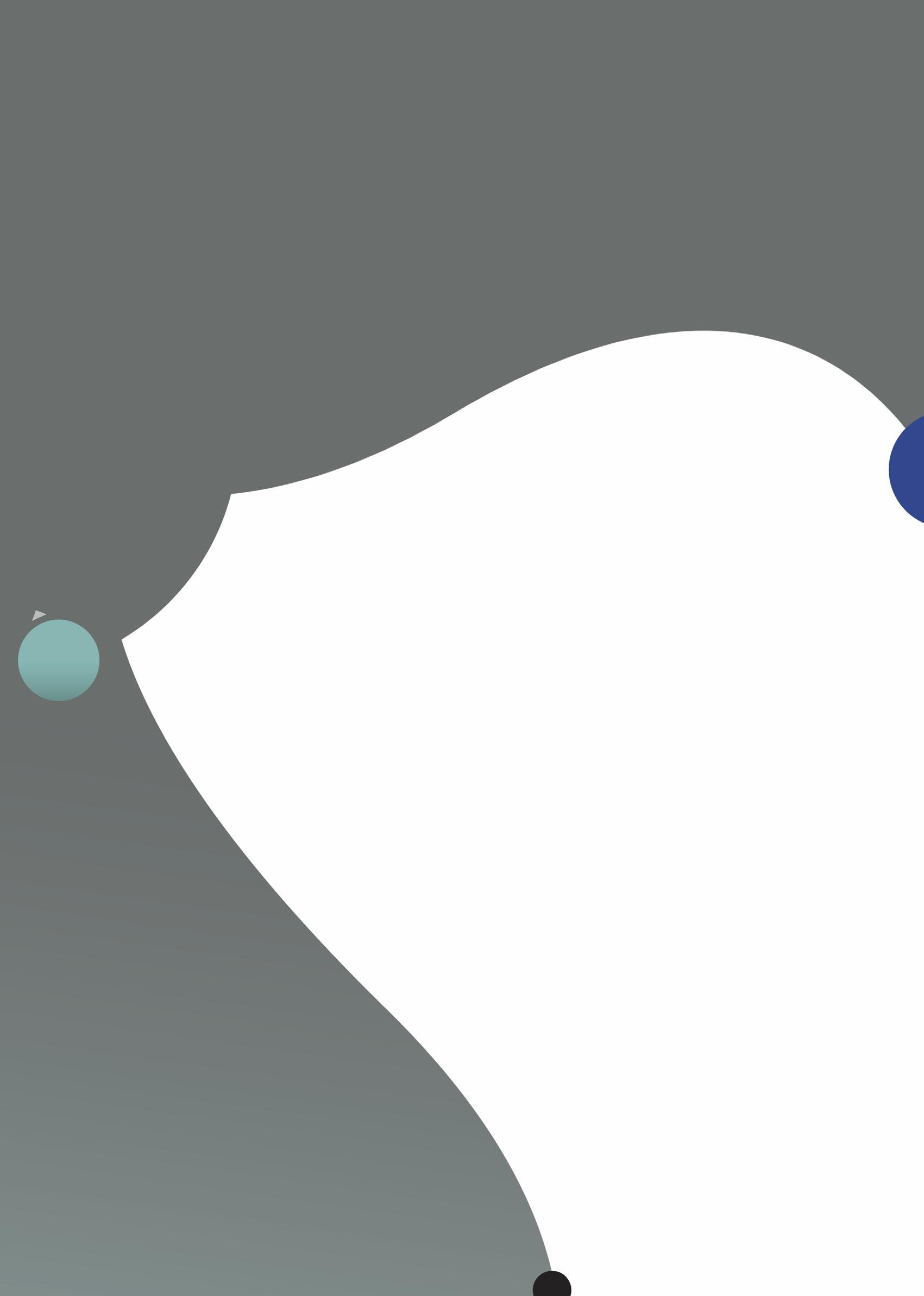



QUPAQ is the leading global provider of tray denesting and handling solutions for food producers. Developing market-leading technology, the company helps customers reduce manual tray handling with automated solutions, ‘safely, simply and profitably.’ Hannah Barnett learnt more about what this means from CEO Kim Weidemann.
Tray denesting is the process of separating trays that are stacked together, then placed on a conveyor for individual loading. In manufacturing operations that load products in trays, filling rates can only be increased as quickly as trays can be separated and placed under the loading device.
QUPAQ, in its current form, is relatively new, having changed name from Intech in April 2022. This was to reflect the 2021 merger of Intech and the denesting division of seafood processing company Carsoe. QUPAQ seeks to combine the best of both, with a product portfolio that includes the leader in electrical denesting equipment, INTRAY, and the leader in pneumatic denesting equipment, ANYTRAY. The company developed and pioneered both denesting technologies and will continue to do so.
QUPAQ CEO Kim Weidemann explained the rationale behind the merger: “We wanted to create a bigger player with lots of growth potential. And to go beyond denesting and
expand into the whole packaging operation. Once you have loaded food products in the container or tray, you could make it into a full logistical operation, packing the filled
and sealed trays in boxes ready for shipment. That's basically the logic of it. Combining the two divisions gave us a broader product programme and new possibilities, because we took the best from both worlds and brought them together.”
Annually, QUPAQ currently denests and handles over ten billion trays for food packing across more than 50 markets. The company sells its automation systems to food producers, integrators and re-sellers worldwide. Its product portfolio comprises the world’s largest modular range of denesters, conveyors and related equipment for efficient tray handling.
End customers includes the biggest manufacturers in the world: Nestlé, Tyson Foods, Mondel e - z, Tönnies, Cargill, Hilcona, Bonduelle, Martinez, Hubers and many more.
Headquartered in Brønderslev, Denmark, QUPAQ employs around 100 people. “In 2021, we opened a sales office in Germany,” said Mr Weidemann, “and we are currently working on establishing premises in the US to further open that market and have boots on the ground. We have a lot of outsourced processes in the neighbourhood, and we are thereby quite agile in our production set up.”
According to Mr Weidemann, QUPAQ is a company with a global reach: “We are stretching our market globally and are right now supplying machines in Australia and Argentina. I think you will find most of our products on all continents. We also have a good number of partners selling our machines. They are mainly in Europe, but we have the ambition to further expand our partner network to the rest of the world.
“We're working with a lot of integrators who are buying our machines to be a part of their production lines. We work both as a white label supplier, but also as a branded product.”
Perhaps the most significant result of the merger is the range and quality of denesting possibilities now on offer. As Mr Weidemann put it: “We are flexible, and now we can offer both a pneumatic and a servo solution.”
One of QUPAQ’s flagship products, the INTRAY Step Loader, is designed to automatically denest trays and gently load various product types directly, with the possibility
2.5 million
More than 2.5 million portions of minced meat are packed every day on QUPAQ production lines.
of several individual loads in the same tray. This enables the slicer to load cheese and salami into the same tray.” The Step Loader offers an in-line compact solution to handle high capacities at high speeds, due to an innovative tray handling design.
The other significant machine is the ANYTRAY pneumatic denester. It is designed for production flows of up to 120 trays per minute, the go-to choice for food producers who want the full advantages of packing automation.
“We have fast changeover times when shifting to other tray sizes,” Mr Weidemann explained, “and we have very good run times on the machines. They are quite steady in their performance; they don't demand a lot of maintenance or spare parts. They are simple and quite easy to operate, to maintain and to wash down. So, both in operation and hygiene we are excelling.”
There has no doubt been a lot of exciting activity happening at QUPAQ in the last few years. But has the company been impacted by disruptions in the global supply chain?
“There's been some turbulence,” Mr Weidemann reflected, “mostly on
the electrical side, where the supply chain is long, and we depend on supplies from large electronic companies. But we haven't been hard hit. I think it looks like things are easing up and I don't think that will be a major challenge going forward.”
The company is not standing still. Like any successful business, it is constantly looking for ways to adapt, evolve and innovate.
“We’re still discovering new ideas,” said Mr Weidemann. “Like ‘how we can better assist our clients with their ease of operation?’ We are looking into what the next generation of denesters will deliver. And then, ‘what about the next generation of loading systems? What do they look like?’ Then I think we will do improvements on the sales-tools we give to our partners, to ease their inter -
action with us as a company. To make things smoother.”
QUPAQ have delivered several customtailored solutions including elevators, where the trays are loaded into the buffer from a different floor, high-speed solutions with 320 products loaded per minute and several unique handling solutions. All based on off-the-shelf technology customised for specific applications.
As the CEO pointed out, since the merger, QUPAQ is a still new company. But the results seem to be paying dividends. “Succeeding in this and monitoring the progress from day-today, week-to-week, month-to-month, is very fulfilling,” Mr Weidemann concluded. “We have seen steady improvement of the company processes. It is quite cool to watch and to be a part of.” n