
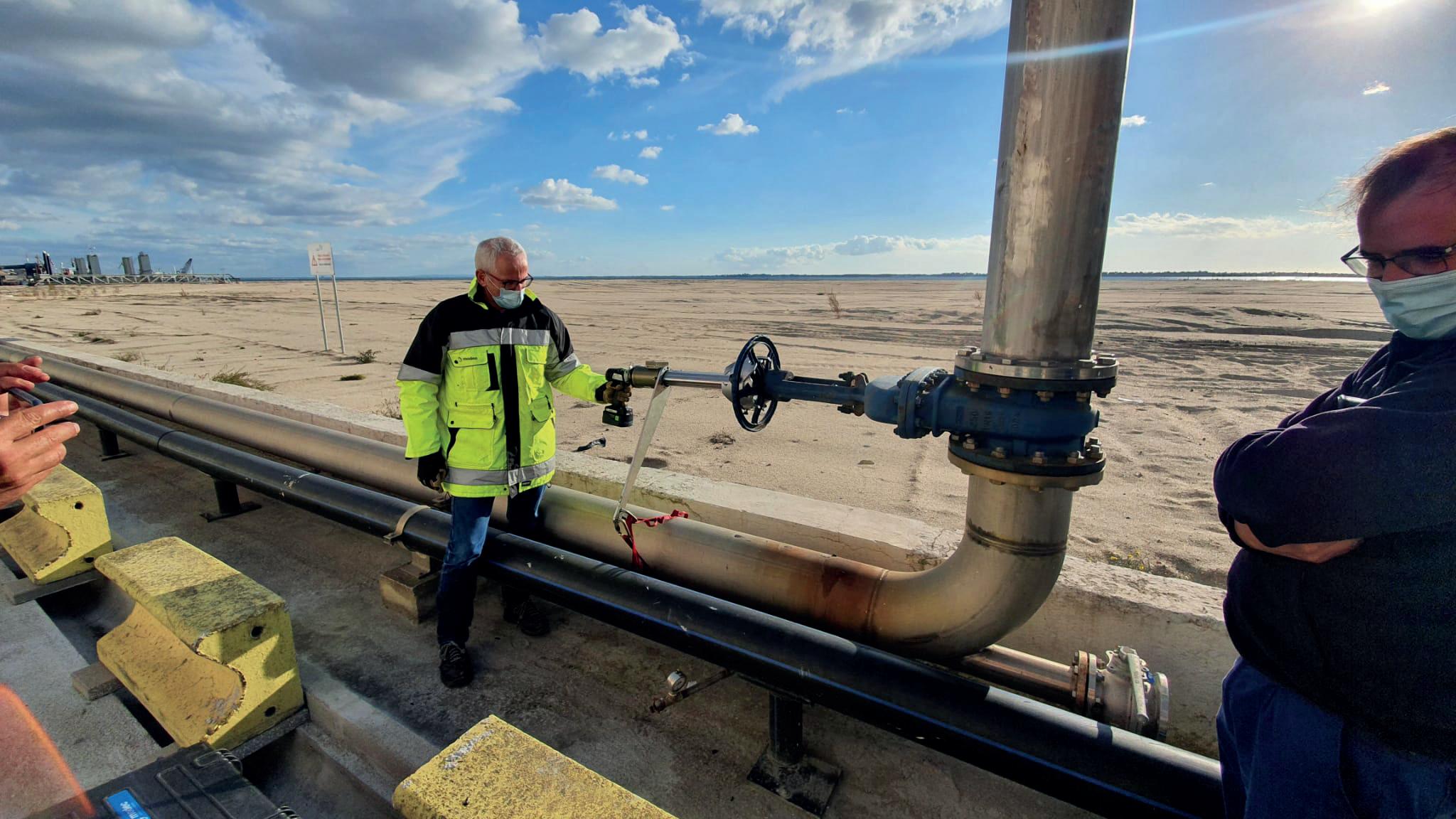
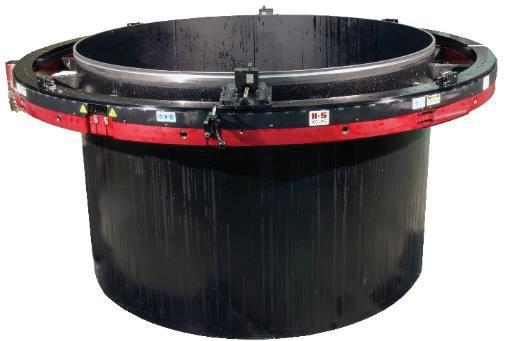
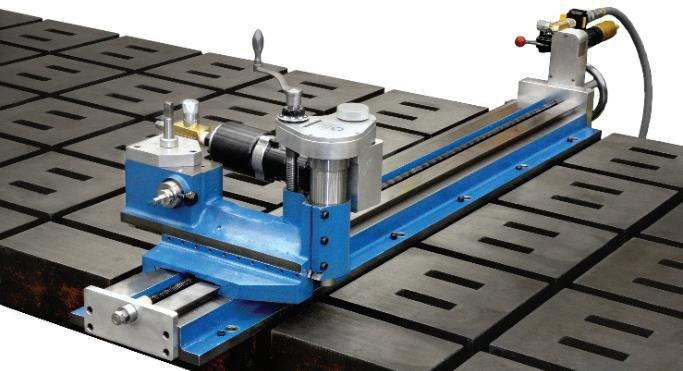
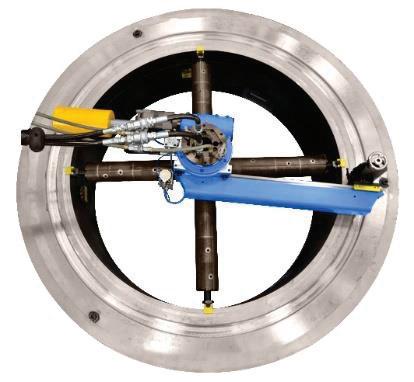
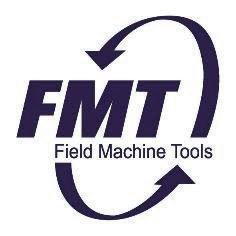
ABN: 36 426 734 954
C/- The Commons, 36–38 Gipps St, Collingwood VIC 3066
P: (03) 9988 4950 monkeymedia.com.au
info@monkeymedia.com.au miningmagazine.com.au info@miningmagazine.com.au
Editor
Assistant
ABN: 36 426 734 954
C/- The Commons, 36–38 Gipps St, Collingwood VIC 3066
P: (03) 9988 4950 monkeymedia.com.au
info@monkeymedia.com.au miningmagazine.com.au info@miningmagazine.com.au
Editor
Assistant
With 2023 and the holiday festivities well and truly behind us, we’re starting this year off with a bang.
Crammed full of the latest industry news, insights and thought leadership – I’d like to warmly welcome you back to Australia’s resources sector with the first edition of Mining Magazine for 2024.
The industry is off to a rockier start than anticipated, with an influx of lower cost nickel supply from other countries causing global market disruption and resulting in six operating nickel facilities either reducing operations or going into care and maintenance.
Design
Jacqueline
National
Rima
Brett
Radhika
Marketing
Isabella
Digital
Publisher
Managing
ISSN: 2653-634X
Despite this, the adaptability and resilience of the industry has shone through, with nickel earning a spot on the Critical Minerals List and nickel companies being given the opportunity to unlock billions of dollars in Commonwealth funding.
2024 is forecast to be a significant year for the industry and in this edition of Mining, Deloitte offers insight into the key trends it expects will shape and impact the industry over the next 12 to 18 months.
We spoke to former Western Australian Mines and Petroleum Minister, Bill Johnston, about how the industry has changed throughout his decades-long career and the challenges lying on the horizon for the state's mining and resources industry.
Incorporating innovative technologies into mining operations continues to pique the interest of the industry, and this edition includes input from Sydney University’s Australian Centre for Robotics about the significant opportunities for automation and AI in mining.
Mine rehabilitation is still a prevalent topic of conversation for the industry’s key players and with a new CSIRO report estimating the closure of almost 240 Australian mines by 2040, we investigate solutions to help the industry to overcome the challenges associated with mine closure.
With additional features on mining in outer space and how virtual reality can significantly enhance worker training, safety, and operational efficiency in the mining industry, Mining Autumn is bursting with the latest topics that are rocking the mining industry.
As always, if there’s a topic, project, technology or challenge you’d like to read in future editions, please feel free to flick me an email – I’d love to hear from you.
Rebecca Todesco EditorDrop Rebecca a line at rebecca.todesco@monkeymedia.net.au
Following his November 2023 announcement to retire from Cabinet, Mining Magazine sat down with former Western Australian Mines and Petroleum Minister, Bill Johnston, to reflect on his time in the role and what’s in store for the resources sector.
Entering 2024, the mining and metals industry finds itself at the centre of a complex matrix of challenges and opportunities, expectations and demands.
It is hard to believe that less than 20 years ago there was very little automation on even the world's largest, most complex mines. The resources sector of today is a pioneer in the development and adoption of robotics, automation and artificial intelligence systems, and while much has been achieved there is still much more to be done.
Various Virtual Reality (VR) and Augmented Reality (AR) technologies have the potential to significantly enhance worker training, safety, and operational efficiency in the mining industry.
The last decade has seen an increased focus on the escalating prevalence of mine dust lung disease in both mining and the engineered stone industries. A new dust testing methodology has been developed by the Minerals Industry Safety and Health Centre (MISHC) at The University of Queensland (UQ) to provide insight into dust exposure to better protect workers from mine dust lung diseases such as black lung and silicosis.
Choosing the right pump for applications in the mining industry is essential to ensuring efficient and reliable operations, cost effectiveness and safety for the workers and environment. Knowing which type – either diesel-driven or electric-driven – is suitable for a particular application is critically important.
Aboriginal business owner Derek Flucker highlights how Traditional Owners, First Nations companies and the resource sector working together will protect Indigenous culture. This will secure a meaningful future for First Nations people and prevent the destruction of the world’s oldest living culture, so events like the eradication of Juukan Gorge are never repeated.
The night sky has long captured the fascination and imagination of countless generations but it seems that for ensuing generations it may also hold the future of the mining industry.
With tens of thousands of Australian mines awaiting rehabilitation and a new report estimating the closure of almost 240 Australian mines by 2040, it is more important than ever to explore innovative solutions for the mining industry to overcome closure challenges as it simultaneously leads the way in the path to net zero.
The waste generated from mining operations is one of the largest waste streams in the world, and there can be catastrophic consequences if it’s not handled properly. Knowing this, a team at Flinders University is sifting through tonnes of mining waste to address this problem head-on.
The first copper concentrate has been produced at a copper mine in Adelaide’s southeast, marking a significant milestone for the project following its successful commissioning.
The commissioning and production of copper at Hillgrove Resources’ Kanmantoo plant was achieved within the targeted time frame of Q1 2024.
Hillgrove is now positioned as one of the few pure play copper producers on the ASX, with first revenues from sales of the copper concentrate received in February.
Hillgrove said there is significant opportunity to grow the resource and therefore mine life, as evidenced by:
♦ The substantial JORC Exploration Target at the Project of 60 – 100Mt at 0.9 per cent to 1.2 per cent copper (Cu) and 0.1g/t to 0.2 g/t gold (Au)
♦ Recent drilling results, including:
» 36.6m at 3.35 per cent Cu from 43m downhole in East Kavanagh
» 45.4m at 1.19 per cent Cu and 0.12g/t Au from Spitfire from 428.5m downhole
» 40m at 1.2 per cent Cu from 43m downhole in Central Kavanagh
» 33.23m at 1.46 per cent Cu from 42m downhole in East Kavanagh
Mains power was established to the underground operation resulting in a substantial circa 65 per cent cost reduction to power use from circa $0.40 per kilowatt hour to circa $0.13 per kilowatt hour.
Furthermore, connection to the South Australian power grid, which is supplied by over 70 per cent renewable energy generation, substantially reduces Kanmantoo’s carbon footprint.
Hillgrove CEO and Managing Director, Lachlan Wallace, said, “First copper production from the Kanmantoo underground operation, and the transition to cashflow generation, is a watershed moment for the company.”
Mr Wallace said that mine output and copper production was expected to continue to ramp up as the planned additional work areas are established underground.
“Completing this transition from explorer to producer makes Hillgrove Resources one of only a few copper producers on the ASX, and doing so in eight months highlights the company’s capability to deliver on stated objectives.
“Operations will be bedded down at Kanmantoo as we ramp up to steady stage production, and our attention will turn to growing the business by converting future exploration and development opportunities.”
Mr Wallace said the project was well-positioned to take advantage of the anticipated growth in demand for copper as the world continues to decarbonise through electrification.
“To leverage our position as a copper producer into the future, we are actively seeking to grow both the mine life and the annual copper production profile through exploration, starting with our substantial 60-100 million tonne exploration target within close proximity to the underutilised processing plant, including the recently discovered Kanmantoo Deeps target.”
The FS10i is a universal flow switch and flow monitor designed for simple insertion into 13mm or larger diameter pipes and square ducts. The unit is suitable for either liquid or air/gas applications. Fast responding, the unit is highly repeatable to both increasing and decreasing flow rate changes.
The standard 1A relay trip point is easily set in the field for low or high trip points and the trip and reset points can be further tuned with hysteresis and time delay adjustments. Also included standard is a 4-20mA trending output of the flow rate for connection to ancillary controls or alarm systems.
The FS10i includes a 10-LED array which provides both an indication that the trip point has been exceeded – in which the LED flashes on and off – and of relative flow rate (ten per cent increments) across the flow range.
The FS10i provides best-in-class features for installation in rugged duty, and long-life in industrial plants, processes and large buildings. Its flow sensor’s thermowells are constructed of highly corrosion resistant Hastelloy C-22, meaning it will operate in fluid temperatures up to 121 degrees Celsius.
The FS10i boasts an IP protection rating to IP67, optional global agency approvals for installation in Division 2/Zone 2 locations and it is the only unit in its price range to carry a SIL 2 compliance rating.
The fact that it has no moving parts that can clog and requires no routine maintenance offers users time and cost savings over any mechanical-technology based flow switch on the market.
Fluid Components International (FCI) are represented in Australia by AMS Instrumentation & Calibration.
ANew South Wales coal mine was issued a prohibition notice, banning any further mining of coal onsite due to ongoing safety concerns.
The NSW Resources Regulator had been working closely with the operator of Russell Vale coal mine since an initial frictional ignition event in April 2022.
The prohibition notice was to remain in place until the Regulator was satisfied appropriate safety measures had been carried out at the site.
Following investigations into numerous incidents at the mine and the scrutiny from the Regulator, it was later announced that the Russell Vale Colliery would close, affecting approximately 145 employees.
The environmental authority (EA) application for Whitehaven Winchester South coal mine was approved by the Queensland Government’s Department of Environment, Science and Innovation.
The project was assessed through an environmental impact statement managed by the Coordinator-General, who issued an evaluation report in November 2023, recommending the project proceed subject to the stated conditions and recommendations.
The EA application was publicly notified and five submissions were received by the department – all of which were considered in the assessment process.
The department said that it would issue a notice of the decision, including reasons, to Whitehaven and the five submitters by 14 February 2024.
Whitehaven and the submitters would have the opportunity to object to the department’s decision and request that the project be referred to the Land Court.
The objection period was 20 business days from receipt of the notice of decision.
Queensland environmental groups did not welcome the approval, with the Queensland Conservation Council (QCC) saying that it was a terrible decision that would impact Queenslanders still clearing up from storms, fires and floods made worse by climate change.
The QCC also said that as the largest proposed greenfield coal mine in Australia, Winchester South had the potential to release 583 million tonnes of CO2e emissions, posing a threat to Australia’s climate, nature and the health of its communities.
QCC Director, Dave Copeman, said that the Queensland Government put Queenslanders at further risk by approving the mine.
“Despite the continuous environmental disasters we have witnessed in the past months across Queensland, the Queensland Government’s decision to greenlight this project shows that their approvals process must change.
“Instead of protecting Queenslanders from the worst impacts of climate change, they are adding fuel to the fire for short-term gains.
“The climate science is clear, we must end the use of coal urgently if we are to meet our climate targets and keep Queenslanders safe from the worsening impact of climate change. We are dangerously close to likely tipping points in our global climate systems.
“As an open cut mine, once they start extracting coal, it will be too late to reduce the methane that will be released into the atmosphere continuously for generations, turbocharging climate change.”
sharp decline in nickel prices led to closures in two key Australian nickel operations.
Wyloo Metals, owned by iron ore billionaire Andrew Forrest, announced that its Kambalda nickel operations will be put on care and maintenance from the end of May due to low nickel prices.
Following this, BHP announced that it would pause part of its Kambalda processing operations in June, cutting 20 roles in Western Australia. Wyloo Metals
supplies ore to BHP’s Kambalda nickel concentrator.
Wyloo’s CEO, Luca Giacovazzi, said in a statement to the ABC, “The decision to temporarily pause our operations in the current nickel market will allow us to develop and assess these options as we move towards our long-term strategy to mine and process nickel from our own facilities in Kambalda and Kwinana.”
BHP’s Nickel West asset president, Jessica Farrell, told the ABC that “the decision by Wyloo to suspend its operations means it will no longer be
viable to continue operating parts of the Kambalda concentrator from mid-year. BHP will transition the Kambalda concentrator’s crushing, milling and flotation circuits into care and maintenance from June 2024.”
Fortescue announced that a change of name was approved for the company after being accepted by shareholders at the Annual General Meeting of the company held on 21 November.
Formerly known as Fortescue Metals Group, the company is now called Fortescue on the ASX, with the ASX ticker code remaining unchanged as FMG.
Fortescue said that the change of name was intended to reflect the diversification of Fortescue’s operations as an integrated green technology, energy and metals company.
Construction of a vanadium electrolyte manufacturing facility in Western Australia is now complete.
Australian Vanadium Limited (AVL) announced the completion of the facility, located in the northern suburbs of Perth. The facility has been designed to produce up to 33MWh per year of high purity electrolyte for vanadium flow batteries (VFBs).
CEO of AVL, Graham Arvidson, said, “We are pleased to have been able to successfully and safely execute another segment of our ‘pit to battery’ strategy through the construction of Western Australia’s first vanadium electrolyte manufacturing facility.”
The construction of the facility was supported by a $3.6 million Modern Manufacturing Initiative grant by the Federal Government, which demonstrates the value of investing in domestic downstream processing capability, allowing more value from Western Australia’s battery mineral endowment to be captured and retained in Australia.
Construction of the facility was undertaken by Western Australian-based engineering company Primero Group
and was completed without injury. AVL issued a certificate of practical completion to Primero Group, which allowed for the formal handover of the facility from the construction team to the commissioning team.
“We are grateful to the teams at Primero and USV for their contributions in delivering a facility that is the first of its kind for Western Australia,” Mr Arvidson said.
The vanadium electrolyte manufacturing facility utilises proven electrolyte manufacturing technology licensed from US Vanadium LLC exclusively to AVL in Australia and New Zealand. Using this technology greatly reduced the development risk for the facility.
USV will assist with commissioning of the facility, which was anticipated to be completed in early 2024.
The vanadium electrolyte produced by the facility will initially be employed in the VFB projects being developed by AVL’s wholly owned subsidiary, VSUN Energy Pty Ltd, and will allow AVL to qualify its product with key global VFB manufacturers.
Demand for vanadium electrolyte within the region is expected to grow rapidly over the coming years. According to Guidehouse Insights, “Asia Pacific leads significantly, with a compound annual growth rate (CAGR) of 25.7 per cent for revenue and 37.4 per cent for energy capacity. By 2031, it is estimated that Asia Pacific will reach around 14.5GWh of annual VFB energy capacity.”
Construction and subsequent operation of the facility ensures that AVL remains engaged with downstream aspects of the vanadium and VFB markets.
Vanadium pentoxide for electrolyte manufacture will initially be sourced from USV, prior to supply being available from the AVL’s Australian Vanadium Project in Western Australia. The experience gained from the construction of the vanadium electrolyte manufacturing facility is anticipated to be of great use in the construction of the Australian Vanadium Project.
“Production of AVL’s first vanadium electrolyte will position AVL to become a trusted supplier for battery projects in Australia and the wider region,” Mr Arvidson said.
Your industry personnel roundup – here we cover who’s moved where, which boardrooms have been shaken-up and the new leaders making big decisions in organisations across the industry.
In December 2023, Pilbara Minerals announced the appointment of a new Non-Executive Chair, with Kathleen Conlon assuming the position from 1 January 2024 after retiring as Chair of Lynas Rare Earth. Ms Conlon took over from Anthony Kiernan, who retired on 31 January 2024 after seven years in the role, including seeing Pilbara Minerals through its transition from a lithium developer to a lithium producer.
For BHP, the new year came with a new executive leadership team, with the announcement of a number of updates in December 2023 to come into effect in the first quarter.
On 1 March, Vandita Pant commenced as the new Chief Financial Officer (CFO), having worked for BHP since 2016 – most recently in the capacity of Chief Commercial Officer (CCO). The previous CFO, David Lamont, will remain with BHP until February 2025 as a Senior Executive Officer in an advisory and projects capacity.
Ragnar Udd took over as CCO from 1 March 2024, departing his previous role as President Americas.
Other updates to the BHP team include the appointment of Brandon Craig as the new President Americas, commencing on 1 March, and Johan van Jaarsveld as Chief Technical Officer, who also stepped into the role on 1 March 2024.
On 11 January 2024, Dr Luke Mortimer commenced his role as the new Chief Executive Officer of Kalamazoo Resources. Dr Mortimer joined Kalamazoo in 2019 as the Exploration Manager and played a role in Kalamazoo’s acquisition and development of lithium exploration assets.
Dr Mortimer took over from Luke Reinehr, who co-founded Kalamazoo and has served as CEO since 2019. Mr Reinehr will continue as Executive Chairman of Kalamazoo.
Another company who made changes to its board and leadership team is Mineral Resources (MinRes).
In February 2024, Jacqueline McGill was appointed as an Independent Non-Executive Director to its Board, with a background as a highly credentialed mining executive and gender equity champion and a long career in the commodities sector. Another change to the MinRes Board in February was the resignation of Independent Non-Executive Director, Kelvin Flynn, who served for 14 years, including nine years as the chair of the Audit and Risk Committee.
Finally for MinRes, Jenna Mazza was appointed joint Company Secretary, having joined the company in 2014, working across a variety of senior legal roles, most recently as General Manager, Corporate Legal.
The increasing uptake of battery technology is a critical step in supporting traditionally emissionsheavy industries to decarbonise their operations, but it won’t be conventional lithium batteries driving technology for the future.
Toshiba’s SCiBTM technology is a transformative force in the battery market. Unlike conventional lithium batteries, a SCiBTM cell utilises a lithium titanium oxide (LTO) in its anode. This chemistry means that if SCiBTM cells are pierced or damaged, the anode material transitions from a conductive phase to a high-resistance phase. This is key to limiting the flow of energy and preventing thermal runaway and subsequent combustion. Essentially, SCiBTM cells are self-protecting, which is a gamechanging development.
Additionally, using an LTO anode means no possibility of lithium deposition or membrane-puncturing dendrite growth – meaning SCiBTM is exceedingly robust and far safer over time.
Toshiba have been manufacturing SCiBTM since 2010, with zero cell recalls or CPL (Contract/Product Liability) accidents – a claim that conventional lithium batteries can’t make.
Optimising the total lifespan and cost of ownership for battery technology are crucial factors in the decarbonisation process –another area where SCiBTM technology excels.
Compared to conventional lithium batteries, SCiBTM cells have a typical lifespan of more than 20,000 cycles. Even after the 20,000 cycle point they still retain 80 per cent of their original capacity. This means that after reaching the end of the first application, they can receive a second life where weight isn’t a factor, such as stationary solar support, creating a provable asset long into the future.
An exciting development for the technology is its rapid charging capabilities. With a high C-rate, charge times are measured in minutes, not hours, and an entire system can be charged to 80 per cent capacity in just six minutes and fully charged in ten minutes.
This is key for easy adoption. If a vehicle requires multi-hour charging times, workers must carefully plan their usage to ensure availability, but if their vehicle rapidly charges in the time it takes for a coffee break, this downtime disappears.
With exceptional safety, improved lifespan and rapid charging, SCiBTM technology has the capability to be the cornerstone of a business’ decarbonisation plan. The Australian mining industry has started to take notice, with SCiBTM systems already deployed in underground electric vehicles.
More than just fleet electrification, there are also flow-on effects – faster charging enables a smaller fleet, fewer charging stations and more efficient use of the vehicles on hand. It allows businesses to improve safety onsite, while vastly reducing capital costs at the same time.
Does this signal the end for conventional lithium batteries? Not yet. As decarbonisation efforts ramp up across industry, they will still be used in low-challenge applications where low charge rates or lower lifetime is required. However, for operations that require rapid charging, uncompromising safety and extreme longevity, SCiBTM technology will lead the way.
While traditional trade publications have quality audiences and high levels of trust, they can lack the full range of services to guarantee a return on your investment. And while traditional marketing agencies offer the latest marketing techniques, they don’t have the audience or the industry understanding the B2B sector needs.
Monkey Media is the missing link that brings together a trusted brand and powerful audience, with a complete agency offering.
TO FIND OUT MORE SCAN THE QR CODE NOW
Following his November 2023 announcement to retire from Cabinet, Mining Magazine sat down with former Western Australian Mines and Petroleum Minister, Bill Johnston, to reflect on his time in the role and what’s in store for the resources sector.
Mining Magazine (MM): Can you give us a bit of insight into what led to your decision to step down?
Bill Johnston (BJ): After the 2021 election, I spoke to thenPremier McGowan and explained that I thought that seven years was plenty of time to be a minister, and I wanted to step away from Cabinet before Christmas 2023 so that I could return to the back bench and see out my term in Parliament. In that role, I thought that was the best way forward for myself and for the party.
When Roger Cook took over in June of last year, I met with him and explained that was my intention. I feel that I've made a significant contribution and it was time for somebody else to have a try and for me to get ready for the next phase of my life.
MM: How have things changed over the decades your political career has spanned?
BJ: I've been thinking about that quite a lot lately. Over the last 25 years, social media has changed the landscape of politics. It encourages extremists and unfortunately, the media follows the social media line. It's harder to explain complex issues in the public arena now than it was 25 years ago and because of the reduction in the number of journalists, there's less analysis of politics and more opinion. I think that's been the biggest change.
MM: Have your expectations of politics changed over the course of your career? And if so, how?
BJ: My expectation of politics hasn't changed. I've always thought that politics is about achieving the best outcomes for the community and in particular for working people. But I do think there's less rigorous analysis of politics now than there was in the past.
MM: The mining and resources industry has played such an important role and will continue to play an important role in the state economy, and the nation's economy. With this in mind, how did it feel to take on the role of Minister for Mines and Petroleum back in 2017?
BJ: It was an extraordinary privilege to be given that responsibility and I felt the weight of needing to provide proper leadership to the industry. I know how important the industry is to all Australians, even if they don't necessarily understand it themselves.
Who wouldn't want to be the Minister for Mines and Petroleum in the world's number one mining jurisdiction? I always had the view that it was a rare privilege to have such a fabulous job, and I wanted to make the most of it each day.
MM: It has been a big year for the Western Australian resources industry, with the environmental approval system being overhauled and the Aboriginal Cultural Heritage Act being repealed. What challenges do you think lie on the horizon for the state's mining and resources industry?
BJ: When I talk to people, the number one thing that they raise at the moment, of course, is skilled labour. Making sure we've got enough people to execute all the projects that are out there is very critical. But the number one issue for the mining
sector is always exploration. That's why, as Minister, I always gave strong encouragement to the exploration sector because if you don't make new discoveries, you won't have future mining.
Along with the Government of Western Australia, we've always tried to strongly support the exploration sector. That's why we invested strongly in pre-competitive data projects and also in the exploration incentive scheme and the co-funded drilling activities. Continuing to support exploration activity is going to be the number one thing here in Western Australia.
MM: Other than exploration, what are you hoping to see more of in Western Australia and Australia's mining industry in the future?
BJ: I'm really looking forward to continued expansion of the downstream processing of battery minerals here in Western Australia and nationally. This is a real opportunity as the demand for these new materials grows. We're not competing with other existing jurisdictions. It's all about where the growth in the processing infrastructure is built.
Whilst there are many challenges here in Western Australia, I'm confident that we'll see continued success in the midstream sector of the battery and critical minerals industry.
MM: What impact are you hoping that your time as Mines and Petroleum Minister has had on the industry?
BJ: I'm not too concerned about legacy. I just hope that people respected the fact that I wanted to listen to the needs of the industry and respond to the things that are occurring.
Obviously, we had the global pandemic during my time in the role, and government and industry worked very closely together to make sure that the industry here in Western Australia was able to continue to operate. At a time when we thought that there was going to be a major economic dislocation, we were able to keep the industry strong, which kept Western Australia strong, and that supported Australia's rapid return from the impacts of COVID-19. That was a really critical element that the government and industry executed together. I think everybody in the sector can be proud of the work that was done during that time.
MM: What are some of the biggest challenges you faced throughout not only your time as Mines and Petroleum Minister, but your years in politics and Cabinet as a whole?
BJ: The COVID-19 global pandemic was extraordinary. I think when we were in opposition thinking about what it would be like to be in government, we ran a lot of scenarios, but we did forget to run the global pandemic scenario. But politics is a complicated business. It's about compromise, and you can't do everything that you'd like to do. So over the last 25 years with my involvement in politics, I've been very pleased to work with some outstanding Western Australians and support them in their work like Dr. Geoff Gallop, Alan Carpenter, McGowan and now Roger Cook as Premier for the state.
That's been a rare privilege to be able to work so closely with these outstanding Western Australians to try and make the state an even better place to live.
during your political career has been?
BJ: I think that's for other people to judge. I'm very proud of the work that I've done alongside the mining industry to keep the industry strong and to develop the exploration sector. When I came into the job, just over half of exploration activity in Australia was being done here in Western Australia and now nearly two-thirds of exploration activity is here in Western Australia. And in 2022, we had a record high level of employment.
I support the mining industry because it supports the global transition to net zero and allows people in other parts of the world to move out of poverty. But it also provides 135,000 high-skill, high-wage jobs, which is exactly what I got involved in politics to support.
MM: The mines and petroleum portfolio has been taken on by David Michael; what advice would you give to him as he takes on this new responsibility?
BJ: I'm really pleased that Roger Cook gave the portfolio to David. I think he's a great guy. We've known each other for a long period of time. I think he'll do an excellent job because he's prepared to listen. The advice I gave to him when we met up just after Christmas was that he should pay attention to what people are saying and listen. I think that's what I've tried to do in my time. I think that if David takes that approach of listening to people in the sector, making sure he understands what the challenges are, I think that will set him up very well for the future.
BJ: In the Cannington community, it's really pleasing to see a number of projects coming together at the minute. One of those is the Lynwood Senior High School refurbishment. It's an older school. We've had nearly $20 million spent on it. Of course, the big issue at the moment is seeing the massive new rail infrastructure going in that's improving the connectivity in the Cannington community, particularly removing three levelcrossings that used to divide the suburbs and cause traffic chaos. That's a great personal achievement.
There's always more to be done, but I'm very pleased that the plans for the community here in Cannington have been working to improve the community's situation.
MM: Is there anything you'd like to add?
BJ: I just want to emphasise again that I've considered it a rare privilege to be able to be Minister for Mines and Petroleum. I've enjoyed every part of it. I shadowed for four years before I became Minister, so I've worked very hard to listen to the industry and make sure that I understand, to the best I can, the industry's needs. I know that I don't always do exactly what the industry wants, but I hope people understood that all my decisions were designed to improve the outcomes for Western Australians.
We produce Linear Motion Screens (HLS) and Circular Motion Screen (HKS) with a maximum length of 10,000mm and a maximum width of 4,000mm.
We also deliver Banana Screens, Dewatering Screens and Hot Screens for material up to 1,000 °C.
With a working moment of up to 15,000kgcm, our drive system exciters are also compatible with other brands.
Large-scale projects in Australia must adhere to a range of stringent requirements and regulations. When it comes to meeting these demands, it helps to form partnerships with Australia-based companies, securing local products and joining forces with teams who understand unique project demands.
Australia is a tempting location for large-scale projects, but companies can face lengthy delays due to supply chain disruptions and waiting for international equipment deliveries. Companies can avoid these delays and showcase their commitment to high-quality work by pairing with local companies and suppliers.
SAACKE Australia has been involved in combustion technology for more than 90 years and is considered a world leader in the field. Its products meet the highest industrial and ecological standards and as a specialist, it plans, develops and produces burners and system solutions for industrial thermal processes.
When SAACKE Australia was presented with the opportunity to create gas manifolds for use on a lithium project in Australia, taking on the project was a no-brainer. To deliver the project, SAACKE Australia’s goal was to source a local supplier of fittings that ensured it met the Australian standards and customer specifications.
A key factor in supplier selection was that SAACKE required delivery within a tight time frame. It also sought a supplier that could ensure a high-quality product. With these requirements in mind, the VIS-LOK® products from Ibex Australia attracted the attention of SAACKE Australia. Not only did VIS-LOK appear to be perfect for use in gas manifolds, SAACKE was also impressed with Ibex’s local supply and extensive customer support.
The solution delivering results
SAACKE used Ibex Australia’s VIS-LOK Stainless Steel compression fittings, as
“Fabian and the team at Ibex have always gone out of their way to make sure we get prompt deliveries and product support. The VIS-LOK system gives us a visual indication of correct tube fitment and tightness, unlike the inspection gauge we have used in the past on other brands. Pricing of VISLOK Fittings and Seamless Tube is very competitive and is an added bonus.
"I have no problem recommending this product to anyone considering a move away from the traditional suppliers.”
– Peter Carlino, Workshop Manager at SAACKE Australia
well as the VIS-LOK Seamless Stainless Steel Instrumentation Tube. Ibex Australia’s seamless tube is dual certified 316/316L, dual specified A269/A213, and is used extensively in many industries and applications, including lithium projects.
VIS-LOK Stainless Steel Compression Fittings offer an innovative design that allows for a quick and easy installation. The fittings are suitable for a range of applications, including use in gas manifolds on lithium projects. VIS-LOK requires no inspection gauge or markers and eliminates over and under tightening issues with its unique check-ring system.
Ibex Australia’s VIS-LOK products not only met the requirements of the project, but the Seamless Stainless Steel tube arrived already annealed, saving SAACKE time and making the project more efficient.
Ibex Australia is a family-owned and operated business with more than 30 years of experience delivering smarter, safer industrial stainless steel piping solutions. Ibex Australia prides itself on delivering excellence in product reliability, responsiveness and technical knowledge.
At Ibex Australia, we know that efficiency is crucial in the mining industry. That's why we offer fast, clean, and safe industrial piping systems that eliminate hot works and passivation.
With our commitment to quality, timely delivery, and responsive customer service, Ibex is your trusted partner in delivering exceptional results and boosting your bottom line.
Experience the difference with Ibex Australia.
Entering 2024, the mining and metals industry finds itself at the centre of a complex matrix of challenges and opportunities, expectations and demands.
In 2023, the geopolitical environment, which was already complex and heated, deteriorated further. Meanwhile, record levels of catastrophic weather events underscored the need for urgent action on climate change.
The global economy, already severely disrupted by the pandemic, remains challenged by levels of inflation not seen in decades and skill shortages plague many advanced economies, handicapping growth.
Meanwhile, despite mining companies' efforts to improve transparency and adopt responsible mining methods, the industry is still battling an image problem and is failing to articulate a clear sense of purpose in the face of shifting public sentiment. And of course, last year was the year that generative AI (Gen AI) truly arrived, with governments, the private sector and the public realising the immense economic opportunities and challenges the technology presents.
In Deloitte’s 2024 Tracking the Trends report, we identify the key trends that we believe will shape and impact the industry over the next 12 to 18 months.
In Australia, we find the following trends particularly relevant to mining and metals operators.
Navigating global uncertainty – building capacity to thrive in the face of disruption
The disruption of the COVID-19 pandemic has given way to the kind of complex and tense geopolitical environment we have not seen in decades, which is disrupting business-as-usual operations and creating considerable uncertainty.
During 2023, the Russia-Ukraine war continued to disrupt commodity markets, impacting supplies of everything from nickel to fertiliser. This conflict has now been compounded by a deterioration of the security situation in the Middle East that has the potential to destabilise both commodity markets and global shipping routes that underpin supply chains.
While geopolitical tensions approach boiling point, the rapid pace of technological advancement continues unabated as a notable increase in extreme weather throughout the year underscored the risks posed by climate change and the need for action at a global scale.
Critical mineral supply chains find themselves at the intersection of global geopolitical uncertainty and the push towards net zero goals. The mining of these essential minerals is heavily concentrated in specific geographical regions, with Australia dominating lithium production, China leading in graphite and rare earths and the Democratic Republic of Congo in cobalt.
However, the processing stage is even more geographically concentrated, with China accounting for more than 50 per cent of the world's refined supply of various critical minerals. It’s not hard to figure out that these supply chains are susceptible to geopolitical risks, posing a potential threat to the speed of the energy transition unless diversification efforts are expedited. In response to this landscape, businesses are shifting away from vertical integration towards an ecosystem approach. The growing complexity of these networks means that changes in markets, politics, and regulations have far-reaching impacts across industries, sectors, geographies, and suppliers.
We are also seeing dynamic strategic planning emerging as a key solution to navigate this evolving terrain. A dynamic strategy allows businesses to proactively adapt to changing scenarios, minimising operational threats and capitalising on new opportunities by incorporating flexibility and innovation into decision-making processes.
A higher emphasis on scenario planning further aids in testing strategies in a hypothetical environment before making decisions. Encouraging executives to immerse themselves in hypothetical yet plausible scenarios provides valuable insights into how organisations might need to adapt to potential future developments.
Dealmaking for future-focused growth – rethinking minerals and metals investments
This growing complexity is prompting key stakeholders to rethink how they invest in minerals and metals and position themselves for the future.
The proof is the numbers – mergers and acquisitions (M&A) activity totalled USD$88.2 billion in value across 288 deals in 2023, a level of activity not observed in a decade. This has been driven by the need for traditional minerals and metals players to increase their exposure to critical minerals or metals key to the transition to net zero – think BHP's acquisition of OZ Minerals, which increased the mining giant’s exposure to nickel and copper.
Other players prioritise organic growth into new markets while companies with portfolios centred on high-emission commodities are exploring ways to enhance investment appeal as environmental, social, and governance (ESG) concerns increasingly become a priority for both institutional and retail investors.
This shifting investor sentiment combined with major energy, resources, and industrial players adopting firm net zero targets requires executives and directors to put an ESG lens over everything they do.
ESG imperatives are leading key players into unusual alliances and partnerships. Globally, governments are also emerging as a crucial source of investment for not just ESG-focused initiatives, but also projects that enhance sovereign energy and minerals security.
For instance, the US Government's Inflation Reduction Act and the European Union's Critical Raw Materials Act are injecting substantial funds into critical minerals projects that will see the onshoring of parts of the manufacturing process for products crucial to the net zero transition, like lithium batteries.
In Australia, the Federal Government has announced a significant expansion in critical minerals financing, doubling the capacity of the critical minerals facility to support mining and processing projects.
Where government money flows, investor money follows. Organisations that put an ESG lens over everything they do and look outside the traditional partnerships and alliances box will, in the long run, prove to be more resilient.
Working toward net zero – building capacity and futureproofing ESG strategies for a credible transition
According to the UN, the world is in danger of falling short of its goal of limiting the global temperature rise to 1.5 degrees by the end of the century and could overshoot that target by as
much as one degree. The environmental and economic effects of this would be catastrophic.
Research by the Deloitte Economics Institute has found that, if left unchecked, climate change could create USD$178 trillion in global economic losses between 2021 and 2070. Conversely, a coordinated effort in climate change mitigation could deliver an additional 300 million jobs by 2050 and boost the economy by more than USD$43 trillion by 2070.
The private sector has a pivotal role to play in ensuring we not only avoid the catastrophic consequences of missing our climate goals, but that we also capitalise on the economic opportunity inherent in the transition to net zero. But first they need the capacity to do so.
A potential first step organisations can take is to think beyond mere emissions reduction. ‘Climate Related Transition Plans’ (CTAP) are a useful framework for laying out holistic decarbonisation targets over the short, medium and long
term by integrating capital allocation frameworks, operational impacts, and portfolio optimisation.
In addition to holistic plans, leaders should also look at what action is truly ‘credible’, recognising that standards may vary across sectors and geographies based on technological, physical dependencies, and equitable transition principles. It is good practice to stay abreast of evolving regulatory frameworks and socio-environmental shifts in their operational jurisdictions.
It is also important that leaders learn how to navigate ESG-focused disputes as scrutiny around global corporate climate disclosures and ESG grows around the world. Avoiding accusations of greenwashing necessitates ethical dealings and collaborative efforts with customers, suppliers, regulators, traditional owners, and competitors.
The true challenge in the transition to a net zero economy lies in swiftly ramping up supply to decarbonise economies before critical climate tipping points are surpassed. However, lengthy approval processes for critical projects endanger the ability of our industry to do all it can to help reach net zero.
S&P Global notes that the average mine takes 15.7 years to reach commercial production, emphasising the need for expedited processes. The industry should look at how it can take a collaborative approach with government to balance appropriate regulation against streamlining approvals and enhancing overall competitiveness.
The industry also needs to make strides to engage in effective project prioritisation, considering factors like power supply, water availability, and infrastructure. Economic relationships with Indigenous rights holders present both challenges and opportunities, highlighting the importance of not just mandated consultation but establishing effective voluntary collaborations. Integrating Indigenous knowledge systems into project design fosters direct community participation, addressing concerns promptly and lowering barriers to approvals.
Addressing workforce challenges through a skills-based approach – equipping mining and metals companies for the future
Lowering development approval times is a pointless exercise if the industry does not possess workers with the right skills. Skills shortages are emerging as a permanent, not a transitory, issue for the metals and mining sector and will not simply go away if the global labour market – currently running hot –cools down.
Solving this problem will require the industry to tackle the specific structural issues causing workforce challenges while keeping an eye on broader employment trends, like the importance of Diversity, Equity and Inclusion (DEI) and modern work.
The mining and metals industry grapples with the challenge of attracting talent, particularly among younger generations. According to the Australian Geoscience Council, the number of students completing geoscience degrees plunged more than 40 per cent in the eight years to 2021. Meanwhile, the Australasian Institute of Mining and Metals Industry reports that the number of mining engineer graduates more than halved between 2011 and 2020.
It has been suggested that the industry has an image problem among young people, who highly prioritise environmental and ethical concerns when searching for an employer. Despite notable strides in environmental and social commitments, the industry must evolve to appeal to the values-driven Gen Z and
millennials and articulate a clear purpose that champions the worthwhile contributions the industry makes to clean energy, global food security, and economic development.
We also must make strides to rework industry education programs, specifically by focusing on micro-credentialing, as it makes it easier for workers interested in joining the industry to gain necessary skills. It will also make upskilling easier – a necessary development in a fast-changing industry. Collaboration between industry players and universities is vital for developing relevant courses, curricula, and credentials.
A focus on workforce well-being is also important, and DEI initiatives play a central role. While the mining and metals industry is gradually becoming more diverse, a focus on systemic changes and supportive structures is necessary to reap the full benefits of diverse workforces.
Achieving gender balance, as seen at BHP's South Flank iron ore mine where women make up 40 per cent of the front-line workforce, is essential to attracting and retaining talent.
Bringing Generative AI into mining and metals –capitalising on current and future opportunities
2023 will be remembered as the year of Gen AI. While its initial impact was noticeable in consumer-facing sectors, Gen AI holds immense potential for industrial and enterprise applications and could help the mining and metals industry solve many challenges.
Realising these benefits will involve the industry overcoming its inherent conservatism. Many companies are recognising the potential of Gen AI to introduce contextual awareness and human-like decision-making into workflows, fundamentally altering business operations.
Understanding potential use cases is crucial. In the near term, Gen AI is expected to impact workforce productivity and efficiency, enhancing back-office tasks and aiding developers in code writing.
Longer term, virtual ‘field assistants’ could improve safety, bridge knowledge gaps, and guide new recruits through processes. Gen AI's simulation and modelling capabilities may support supply chain resilience and optimisation in the near future.
One of Gen AI's crucial capabilities is facilitating deeper interactions with data, an asset for mining and metals businesses that want to be as efficient as possible. Despite previous digital transformation efforts, some companies struggle with data accessibility, and Gen AI platforms offer a solution to this challenge.
While Gen AI platforms are still evolving, their capabilities are advancing rapidly. Exploring and implementing Gen AI now could provide valuable insights, allowing organisations to adapt and evolve alongside the advancing technology.
It is clear that mining and metals companies will continue to play a critical role in the energy transition.
In 2024, miners must keep advocating for the critical role minerals play in addressing climate challenges. They must lead the way purposefully to a sustainable future by addressing supply shortages and ESG challenges, and adopting emerging technologies, all while attracting the best and brightest talent to the industry. If they can, the future looks bright..
Elphinstone is excited to introduce the new E15 model to the Elphinstone Underground Hard Rock Mining Support Vehicle range. T he lo w-profile E15 is a welcome addition to the existing range of E10 (formerly W R810) s upport vehicles, both base platforms s haring a h igh l evel o f i nterchangeability of p arts and c omponents. Built to thrive in the harsh underground e nvironment, the new E15 provides o utstanding r ide and handling w ith e xcellent manoeuvrability and turning c ircle.
For more information scan the QR code or email sales@elphinstone.com
Continued demand for commodities and minerals is ensuring Australia’s resources industry remains a driving force in the nation's economy. To maximise output and operations, mine owners and operators need to partner with companies that offer high-quality products and services.
The remoteness and isolation of many Australian mine sites present a unique combination of challenges and when it comes to selecting equipment and machinery, operators want to know they’re pairing with companies that understand the challenges they’re up against.
When choosing who to partner with, mine owners and operators seek experienced companies who understand the characteristics of mining applications and offer products that can meet these challenges head-on.
Since 1995, R&J Batteries has been committed to delivering a superior product range combined with exceptional customer service. This dedication has seen R&J Batteries become one of the fastest growing battery companies in the country.
Today, R&J Batteries has over 29 company-owned stores and a footprint of more than 10,000 experienced stockists and distributors across Australia and New Zealand, cementing its standing as a trusted provider of high-quality products.
More than just selling batteries to customers, R&J Batteries backs its products, including the OPTIMA® batteries range, featuring a series of colour-coded, high-performance AGM batteries known as REDTOP®, YELLOWTOP® and BLUETOP®. The RED, YELLOW and BLUE top batteries cater for Automotive, Deep cycle and Marine applications respectively.
The unique Spiralcell Technology® in OPTIMA’s range permits more tightly compressed cells within the battery, which extends the battery’s life and gives it superior vibration resistance. As well as this, each model is 99.99 per cent pure lead and features solid cast inter-cell connections for increased durability and maximum plate height.
These features allow the battery to live up to twice as long as traditional batteries. The extreme applications and unique requirements of mine site trucks demand more from a battery and with both deep-cycle and starting capabilities with patented Spiralcell Technology, OPTIMA YELLOWTOP batteries can rise to the challenge and fulfil those needs.
A high-performance, heavy-duty battery solution
OPTIMA’s AGM batteries are the perfect fit for extreme applications, making it the ideal choice for mining equipment, military vehicles, emergency services, road transport and agricultural machinery. OTPIMA’s YELLOWTOP battery in particular is highly regarded in the mining industry for its performance capabilities in extreme applications.
Reliable batteries with a long service life – such as OPTIMA YELLOWTOP – are crucial to mitigating onsite downtime. Fulfilling a dual purpose, YELLOWTOP batteries deliver both reliable starting power and repeated deep cycling for applications packed with accessories.
With its deep cycle characteristics and extreme resistance to vibration, the YELLOWTOP provides performance vehicles with the repetitive power they need in a unique spill-proof package.
Other key benefits of OPTIMA YELLOWTOP batteries include up to three-times longer service life, 15-times more resistance to vibration, leak proof, mountable in virtually any position, maintenance-free, and more than 300 discharge/ recharge cycles.
The YELLOWTOP is one of the few truly dual-use car batteries on the market. This high-performance, heavy-duty battery is also suitable for accessory-packed vehicles. Its low internal resistance provides more consistent power output and faster recharge times.
R&J Batteries is your OPTIMA Batteries distributor in Australia with 24 branches and a strong network of more than 10,000 stockists across the nation. For more information about OPTIMA Batteries, visit rjbatt.com.au or call 1300 769 282
• High Performance Capabilities
• AGM Battery Design
• Up to 3x Longer Battery Life
• 15x More Vibration Resistant
• 99.99% Pure Lead
• Spiralcell Technology®
A key characteristic of a strong, successful and reliable business is its ability to secure and establish strong industry partnerships to deliver its customers with the best quality equipment and service.
In a strategic move to reinforce its commitment to excellence, CAPS Australia proudly announced its recent collaboration with Mitsubishi Heavy Industries Engine System Asia (MHIES-A) as the official Australian distributor for the esteemed Mitsubishi MGS Generator Series.
The partnership was solidified during an official signing ceremony held at CAPS Australia's headquarters in Perth, where representatives from MHIES-A were given a comprehensive tour of the in-house engineering facilities.
This collaboration marks a significant milestone for CAPS and is a testament to its standing as a respected industry player.
Renowned for reliability, efficiency, and robust performance, the Mitsubishi Generator Series provides power solutions across diverse industries and applications. At the core of its excellence are Mitsubishi Heavy Industries diesel engines, meticulously crafted in Japan to deliver outstanding performance, fuel efficiency, and reduced emissions, reflecting a balanced blend of cost-effectiveness and environmental sustainability.
CAPS’ National Sales Manager – Power Generation, Nestor DeNiese, said this collaboration is incredibly significant to CAPS.
“This partnership is a perfect alignment with CAPS Australia’s objective to offer valuable and effective solutions to the Australian mining sector. With shorter lead times due to the vertical integration and, more importantly, a reliable product, CAPS aims to propel progress and innovation in the region and beyond.”
The MGS-R Series, ranging from 455 to 3025kVA, emerges as an indispensable component in powering mission-critical systems for mining operations, data centres, and essential infrastructure.
Compliant with ISO8528 G3 transient performance standards, it holds certifications such as Data Centre Tier III/Tier IV from the Uptime Institute, along with ANSI/TIA-942 ratings ranging from Rated 1 to Rated 4.
This series is engineered with quick-start ability within ten seconds and 100 per cent one-step load capability, demonstrating its reliability in demanding situations. Moreover, the MGS-R Series adheres to seismic design codes, ensuring approval for use in seismic applications.
Setting the Mitsubishi Generator Series apart is its commitment to environmental responsibility. All MGS-R products are Hydrogenated Vegetable Oil (HVO) compatible –reducing the overall environmental impact and contributing to a cleaner, more sustainable future.
CAPS Australia, now the official Australian distributor for the Mitsubishi Generator Series, is poised to deliver top-tier power solutions through this alliance with MHIES-A. This partnership underscores CAPS's dedication to providing innovative and reliable power solutions to the Australian market.
CAPS Australia specialises in end-to-end solutions. Its in-house engineering allows the company to design, supply, and install bespoke, purpose-built systems to clients with specialised applications, and state-of-the-art factory acceptance test bays assure quality and compliance.
As an independent company with the flexibility to search globally for the best products that are price competitive, technologically advanced, and best serve Australian manufacturers, CAPS works alongside world-renowned partner brands to deliver peace of mind and ensure production continuity.
With ten branches nationwide and 24/7 service for maintenance and emergency breakdowns, CAPS makes it easy to get expert advice when you need it – leading the industry in service and solutions.
Ingersoll Rand, CAPS and Hertz brand electric compressors available as oil-flooded or oil-free.
Air recievers, air dryers, fuel tanks, blowers and gas generators specifically designed for rental allowing versatility and transport protection.
02
AIRMAN compressors customised to mine-site specifications as standard.
04 AIR TREATMENT & SPECIALIST EQUIPMENT
CAPS offers mine-spec skid packages as standard to better accommodate safety and performance in extreme conditions.
Quality AIRMAN generators from 100-300kVA are built tough and easy to use and maintain.
It is hard to believe that less than 20 years ago there was very little automation on even the world's largest, most complex mines. The resources sector of today is a pioneer in the development and adoption of robotics, automation, and artificial intelligence systems, and while much has been achieved there is still much more to be done.
The transformation of this sector since the mid2000s, to its position today as a global standard for industrial field robotics and automation, is truly remarkable.
Perhaps less well-known is that Australian innovation, scientific breakthroughs, and industry research collaborations with Australian universities have been a significant driver of this transformation. These achievements are proof that Australia does not need to be a passenger in global innovation but can instead be a leader in the development and export of robotic and automation technologies.
In the early 2000s, academics at the Australian Centre for Robotics (ACFR) at the University of Sydney, made groundbreaking contributions to a technology known as Simultaneous Localisation and Mapping (SLAM). SLAM gives a robot the ability to reconstruct the physical world around it in real-time and orient itself within that reconstruction – much like humans do every day, navigating and operating within their surrounding environment.
Until this point, robotic systems in industry had been largely confined to structured environments, like factory floors, where the scenario and tasks are controlled and predictable. The development of SLAM meant robotic systems could now interact with the unstructured ‘real-world’ and led to an explosion of Australian innovation in industry, with the most notable being in the resources sector.
In the mid-2000s, ACFR academics published a series of papers articulating the vision of an autonomous remotely operated mine. These seminal works and engineering contributions left a lasting legacy and helped propel the Australian mining industry to the forefront in terms of technology investment and adoption.
These innovations also led to an enduring industry research partnership – the Rio Tinto Centre for Mine Automation (RTCMA) between Rio Tinto and the ACFR, which formed in 2007 and is still around 15 years later.
Through this partnership, ACFR researchers and Rio Tinto Engineers have pioneered numerous industry-leading innovations. In the robotics and automation of physical assets, the group has developed autonomous drills, light vehicles, surveying platforms and geological data collection tools. At the fleet level, autonomous train scheduling, truck dispatch systems, haul-road network mapping and material movement planning across a complex mine network.
The proprietary Mine Automation System, or MAS, fuses data from disparate vendors and internally-developed systems to provide a centralised, real-time source of truth, allowing observations of the activities in the mine and providing analysis, insights and support for intelligent decision-making from across the globe.
Professor Ian Manchester, Director, Australian Centre for Robotics; Director, Australian Robotic Inspection and Asset Management Hub. School of Aerospace, Mechanical and Mechatronic Engineering, University of Sydney, and Dr Andrew Hill, Director of the Rio Tinto Centre for Mine Automation, Australian Centre for Robotics, University of Sydney
Data fusion has also been employed in orebody modelling, using probabilistic models to combine complementary datasets as they become available, providing more accurate representations of ore bodies aiding in the planning and design of mine pits.
These innovations only scratch the surface of what is possible.
Striving for completely autonomous operation
It is worth noting for the purpose of this article, that while automation in the resources sector is considered a global standard, we are still very much at the beginning of this journey. We are still yet to meet the inflection point where mines are wholly designed for automation, rather than the incremental automation of processes in a value chain previously undertaken by people.
In other words, a way of looking at mine automation for much of the past two decades is that it has centred on automating equipment that was designed for humans. But what does a mine and its equipment look like if it is designed for completely autonomous operation from inception?
The various answers to this question involve radically different operational modes, safety considerations, and more specialised and efficient equipment.
A popular example of this we use at the ACFR is haul trucks. On first impression one might assume that these tremendous vehicles are as large as they are because it is the most effective way to transport large volumes of crude unprocessed material, but this is not the case. They are large primarily to cater to the constraints of a human operator workforce. Namely, this is a highly-skilled but small workforce creating a potential bottleneck or a point of critical failure, should enough drivers be unavailable simultaneously.
To ensure there are no disruptions to throughput, larger trucks are required to cater to the economics of a small workforce. But if these trucks and other related load and haul equipment are no longer operated by humans, do they still need to be this large? The answer is ‘No’.
When we think about a fully autonomous haulage fleet the economics actually favour a smaller vehicle as they have standard dimensions and standard parts, are easier for mechanics to maintain and can drive on standard sized roads that require less maintenance.
When we think like this about the future of mining, examples abound.
Major assets – such as those found on mine sites – require constant inspection, maintenance and repair. This work is almost exclusively done by people and for major industry, this means a whole suite of considerations need to be accommodated into asset design.
Important elements need to be accessible not only for inspection, but designed in such a way that they can be safely repaired by an operator. Stairs, railings, safety cages and restricted areas add a layer of complexity to an operation that would not be required if operations were fully autonomous. Furthermore, many operations have such large safety exclusion areas that they must be completely stopped and isolated to just facilitate visual inspections by operators.
For a mine the scale of those found in the Pilbara, this work stoppage can rapidly accrue millions of dollars in lost production time, and inefficiencies up- and downstream.
There is a tremendous opportunity for future mine processing assets and facilities to be designed free of these safety constraints; where operations and robotic maintenance platforms are co-designed for a fully automated, more efficient system.
The ACFR is leading the development of this novel technology in partnership with over a dozen industry partners, Queensland University of Technology (QUT) and Australian National University (ANU) through the newly-created Australian Robotics Inspection and Asset Management (ARIAM) Hub. ARIAM was created to address the impending post-war ‘infrastructure cliff’. As major assets approach the end of their life it is becoming increasingly clear the development of novel robotic and intelligent systems will be essential to their management, now and into the future.
This is also true for the resources sector where mines operate on the timescale of decades, requiring constant inspections and maintenance, as discussed above. ARIAM partners like Nexxis, Abyss Solutions, Emesent and partner resource companies are working to develop novel robotic systems for asset management that take humans out of harm's way, providing more regular and reliable inspection data in the process.
An area ARIAM is focusing on where we see tremendous innovation potential is ‘whole-of-operations’ optimisation and decision-making for large, dynamic industries such as manufacturing, construction, shipbuilding, transport, and the resources sector to name a few.
Mines such as those found in the Pilbara, and their downstream supply chains, are of a size and complexity so vast it is simply not possible for human based decisionmaking across all aspects of an operation to result in efficient production and utilisation of resources.
Mining operations are often segmented or ‘silos’, each with its own priorities. While segments do of course work together to achieve a main objective, without a comprehensive real-time evaluation of an entire operation and the state of each segment within the value chain, it is impossible to efficiently determine
operational priorities on a granular level at any given moment. For example, the goal of a load-haul operation in one area is to get ore out of the pit as quickly as possible. But if the grade is lower than expected, this will need to be blended with other material. The ‘local’ solution will be to move an excavator to adjust the blend, at the cost of productivity in this shift. But it may be more efficient to stockpile in another load-haul operation with a higher grade, elsewhere in the network of mines, or at the point of sale via penalties/discounts.
It is easy to see how inefficiencies can cascade downstream, compounding opportunity costs at every step. The globally optimal solution can only be determined if the entire value chain is well tracked and modelled, and sophisticated decisionmaking tools are developed to analyse the situation and potential range of actions. Robotics are essential to achieving this vision as a means of collecting the continuous, high-quality data these systems require.
Pushing to meet net zero
Optimisation will become increasingly important as we move into a decarbonised resources sector.
Rio Tinto, BHP, Fortescue and many other major resource companies have already committed to net zero by 2050. The significance of these commitments is perhaps underestimated, not only because the resources sector is responsible for such a large proportion of global emissions, but because the scale and complexity of such a transition is typically underappreciated.
Optimisation will be important; firstly because it will reduce energy consumption by minimising waste, but even more importantly because optimisation will support the design and operation decisions of future mines powered by a completely different energy matrix.
Current design and operations are based entirely on the availability of rapidly deployable energy produced by fossil fuels, but the assumption of constant nameplate power availability will not always hold with renewable energy supply.
So what does a mine powered by renewable energy look like and how does it operate? Can operations be scaled seasonally, daily, or even on the scale of hours to milliseconds, to minimise energy storage costs, or will the generation and transmission infrastructure dictate the schedule? How will the scale of energy infrastructure required be constructed in only a few years?
Optimisation is perfectly placed to help industry make these decisions when systems are complex and ambiguous. Additionally, automation will be a huge competitive advantage for the design, construction, maintenance, and material recycling of a renewable energy matrix. For this reason, the transition
of the resources sector to net zero is possibly the greatest opportunity for robotics, automation, and AI innovation.
Many of the opportunities mentioned so far will require additional steps as part of longer-term planning commitments and thinking, and these additional steps are no less exciting or important.
One such step that is central to the ARIAM mission is emphasising the value and need for broader, more comprehensive data collection and sharing when dealing with complex assets and operations. This is especially relevant to mine operations and essential to developing the mines of the future. We cannot optimise what we cannot model, and modelling depends on high-quality data.
Resource companies are amongst the biggest companies in the country and for some, the world. But when we compare data collection and utilisation practises with the world's largest tech companies like Amazon, Meta, Apple, Google, Microsoft and others, the disparity becomes clear. Although an extreme example between vastly different businesses, the analogy is valuable just the same.
These companies are famous for the amount of data they collect, how they value it, and use it strategically. The general principle is to collect as much data as possible, knowing that its value will become apparent as new analytics and products are developed. It is this mindset that has allowed Apple to develop the most sophisticated and efficient ‘just-in-time' supply chains in the world, where components from numerous manufacturers, or the subsequent iPhone or laptop, are stationary for no more than a few hours at any stage in the supply chain to the moment it lands in a customer's hand.
When we think of resources companies through this lens, they aren’t all that different – large, complex operations, with constantly competing priorities and objectives on a global scale. It is especially true given the timescales of mine operations, measured in decades. There is no reason the resources sector cannot operate in the same league as these tech giants, but in order to achieve this, the sector needs to embrace and value data collection the same way the technology sector has. At ARIAM we strongly believe robotics will be central to achieving this as they are the mediators between digital and physical worlds, simultaneously collecting data to construct digital twins of their environment, and using the insights derived from this data to take action in the real world.
It is an exciting time for robotics, automation and artificial intelligence in the resources sector. The sector has already been successful with its adoption of this technology, to the point that one would be forgiven for thinking it is ‘mission accomplished’.
In reality, what has been achieved is a solid foundation from which the mines of the future and all the novel technology that comes with it can be developed and that is something industry can be truly excited about.
The Australian Centre for Robotics (formerly known as the Australian Centre for Field Robotics) is Australia’s largest robotics group and is a global leader in robotics research. Our research tackles deep scientific problems in core robotics technology such as sensing and perception, mapping and insights, planning, control, modelling and optimisation, learning, complex dynamic systems, as well as their applications in complex cyber-physical environments. The ACFR has a long and distinguished history of delivering first in world robotics capabilities to major industry including in resources, agriculture, aerospace and freight logistics sectors. The ACFR is also the lead organisation for the new Australian Robotic Inspection and Asset Management Hub (ARIAM Hub).
It’s no secret that Australia’s mine sites are home to some of the harshest, most unforgiving conditions in the country. Mine site vehicles and equipment are on the front line of operations and often bear the brunt of the extreme temperatures, dusty locations and continuous operation.
Taking care of equipment and vehicles is key to prolonging life cycles and when it comes to maintenance it helps to take a proactive approach. Many in the industry understand and make the effort to protect against the wear and tear that vehicle exteriors suffer on Australian mine sites, but this foresight often comes at the expense of interiors.
Although providing a safe haven from the extreme outside environment, mine site vehicle interiors can very quickly deteriorate from frequent use.
Whether it’s fabric tears from gear rolling around in the back, stains from the countless coffees needed for shift work or bringing abrasive material and dirt inside from hopping in and out in dirty boots, vehicle interiors are often quick to look a little worse for wear.
Damage to vehicle interiors often requires expensive repairs and can have a serious impact on a vehicle’s resale value, costing thousands of dollars on sale day. Seat covers are a surefire way to safeguard against occupational wear and tear and an easy way to save money.
Proudly Australian-owned and made specifically for Australian conditions, Black Duck understands the unique demands of Australia’s mining industry. Operating in Western Australia – the heart of Australia’s mining industry – Black Duck prides itself on pioneering product development to ensure its premium seat covers offer vehicles the heavy-duty protection they need while still complying with all health and safety requirements. Offering seat covers in two tried and tested materials – Canvas and exclusive 4Elements – for a wide range of vehicle makes and models, the Black Duck team provides in-depth local knowledge and understanding of the unique and harsh Australian climate, meaning its products are designed and built tough to last.
The company’s top-of-the-range seat covers are tailor-made and practical, ensuring users retain access to buttons, levers, adjusters and cup holders – enabling full functionality without sacrificing productivity.
To ensure continued high quality and high performance, Black Duck’s seat covers undergo rigorous assessment and trials.
Seat cover fabrics and manufacturing techniques are tested against nationally-recognised methods for safety and performance. The covers are also airbag compliant, with all airbag-compatible patterns dynamically tested to ensure they suit a wide range of vehicles and allow for the unobstructed deployment of airbags in the case of an emergency.
Black Duck started as a family business in 1984, specialising in new and used furniture, automotive reupholstery, canvas swags and tarpaulins. The idea to do seat covers came from a local farmer who approached the family and asked if they could manufacture a seat cover for his tractor. The rest is history, with 2024 marking 40 years of serving the mining industry.
Black Duck is there to protect the inside, so you can get outside.
Various Virtual Reality (VR) and Augmented Reality (AR) technologies have the potential to significantly enhance worker training, safety, and operational efficiency in the mining industry.
The adoption of VR technology in the resources industry offers many benefits including improved safety training, reduced risks to trainees, more efficient skill development, and cost savings by reducing the need for physical equipment or offering remote training.
The mining industry is leveraging immersive VR experiences to revolutionise training and the upskilling of its workforce. These VR experiences are often created using a virtual world that meticulously replicates various aspects of mining operations.
There are specific benefits VR brings to training and upskilling, in particular:
♦ Virtual environments are safe environments – reduces the risk of training in high-risk tasks, machinery, or operations
♦ Virtual training is mobile and repeatable – reduces the cost, while maintaining consistency, with highquality training
♦ Virtual activities can be simulated – training for specific fringe case scenarios/events
Using state-of-the-art technology, trainees are immersed in lifelike scenarios and provided hands-on experience without any real-world risk. Training simulations in VR offer a safe and controlled environment where trainees learn to recognise, respond to, and mitigate various hazards and challenges found in real mining environments. This approach involves creating 3D virtual environments that precisely model terrain, equipment, structures, and geological formations.
Trainees wear VR headsets – also called head mounted displays or HMDs – providing them with a 3D visual display and spatial audio, enhancing the sense of immersion.
To further engage trainees, VR systems use spatial tracking, allowing sensors and cameras to track head and hand movements in real-time, therefore enabling accurate human interaction within the virtual environment. Interactions can be monitored and used in reporting for formative or summative assessments to meet competencies and skills outcomes.
VR training is far superior to conventional classroom teaching due to the immersive nature of VR, which ensures that a trainee is fully engaged in the simulated situation. Whether it's for equipment operation or emergency response training, VR experiences and simulations ensure individuals gain valuable skills while guaranteeing safety.
The mining industry has various applications for VR technology in the areas of training simulations, safety training, and high-risk task planning. Immersive training simulators for mobile plant and equipment operators create a safe and realistic environment for training without requiring actual equipment.
Safety training scenarios simulate hazardous situations and emergency responses, ultimately enhancing preparedness and reducing the potential for errors and confusion in the event of real-world incidents. Drill and blast planning simulations enable precise planning and execution, leading to cost savings and improved safety.
Safety checks and inspections using VR and AR technologies can assist in remote inspection and maintenance. This allows experts to guide onsite personnel through complex machinery maintenance and inspection tasks.
Defects can be identified, images can be taken and uploaded to in-house asset management systems for immediate tracking and action. Operator assistance is provided through wearable AR devices, such as smart glasses, offering real-time data and enhancing decision-making.
VR technology is particularly effective for process-driven tasks and high-consequence activities, with datadriven improvement possibilities and multilingual options.
While VR technology offers numerous benefits, the mining industry faces various challenges and barriers to its widespread adoption.
These include high initial costs associated with implementing VR solutions, such as the cost of hardware,
software, and facilitator training. This may deter smaller mining companies and businesses operating in the mining and resources industries. The technical complexity of setting up and maintaining VR and AR systems can pose challenges, as mining companies may initially lack in-house expertise.
Integrating VR and AR with existing mining systems and processes can be intricate, necessitating investments in software and IT infrastructure for compatibility and data exchange. The sensitive data involved in mining operations requires robust data security and privacy measures to protect information held in VR and AR systems.
In addition, limited internet connectivity in remote mining sites can hinder the implementation of VR technology, necessitating investments in alternative connectivity solutions.
Content creation for VR and AR that accurately simulates mining environments and hazards can be time-consuming and costly, prompting some companies to consider outsourcing. It takes considerable time and company
investment to ensure that subject matter experts are engaged to assist in the development of high-quality and accurate training simulations.
Mining is a heavily regulated industry, requiring technology to comply with safety and environmental regulations. Hardware and software updates are essential, as VR and AR technologies evolve rapidly. Environmental impact considerations, such as the disposal of hardware, require sustainable practices and recycling efforts.
Resistance to technological change is common across industries, necessitating management efforts, training, and education to address this issue. Cultural acceptance of VR and AR may require time and effort, with pilot projects and employee involvement facilitating acceptance.
Implementing VR and AR on a larger scale can be challenging, making gradual scaling through pilot projects a viable strategy. Monitoring and assessing the effectiveness of VR and AR applications is crucial, involving regular assessments and user feedback for refinement.
The statistics from PWC’s study1 on the effectiveness of VR in training highlight the remarkable impact VR technology can have on learning outcomes.
Participants who underwent VR training were reported to be 275 per cent more confident in applying what they learned, indicating a significant boost in their practical skills. The study also revealed that VR training is, on average, four-times faster than traditional classroom and theoretical training, making it an efficient and time-saving approach.
Furthermore, VR learners were found to be four-times more focused than those using standard e-learning platforms, emphasising the engagement and immersion that VR training can offer.
In practical experience, the effectiveness of VR training becomes even more evident. VR can significantly lower the infrastructure and resource costs and requirements for training programs.
Traditional training often requires dedicated physical spaces, such as classrooms or training centres, which can be expensive to lease, maintain, and equip. Training in VR eliminates the need for physical training spaces.
Participants can engage in VR training from anywhere, reducing travel expenses, including transportation, accommodation, and per diem costs. Training simulations can be reused indefinitely, allowing multiple trainees to go through the same scenarios. This is more cost-effective than
each
a
batch of trainees needs instruction.
VR also offers scalability for training modules, making it particularly beneficial for industries with high turnover rates or those that require rapid onboarding. The high level of realism in VR training scenarios allows trainees to practice skills and encounter challenges closely resembling real-life mining conditions, enhancing training effectiveness, and bringing workers to site faster and betterequipped to deal with situations onsite.
VR training ensures that every trainee experiences the same scenarios and content, resulting in more consistent training outcomes. This reduces the need for multiple trainers, who may interpret or deliver training content differently, and minimises the risk of costly errors due to inconsistent training.
The immersive nature of VR accelerates learning and improves skill retention, with adaptive learning based on trainee performance. VR systems can collect data on trainee performance, enabling tailored instruction and data-driven improvement. As a result, VR is a powerful and efficient tool for training, resulting in improved confidence, engagement, and cost savings.
The use of virtual environments (e.g., Digital Twins)
Virtual environments, or Digital Twins, play a pivotal role in providing effective VR experiences for the mining industry. Digital Twins replicate mining
environments and scenarios offering a diverse range of applications.
This includes:
♦ Immersive training simulators for heavy machinery operators
♦ Safety training simulations to prepare mining staff for hazardous situations and emergency responses
♦ Remote inspection and maintenance guidance provided through augmented and virtual reality (AR/VR) technologies
♦ Precise simulation of drilling and blasting operations
♦ Real-time operator assistance using wearable AR devices
♦ Data visualisation
♦ Manufacturer and detailed product displays
♦ 3D machinery manuals
♦ Collaborative design and planning
♦ Scaffolded training modules
Bringing 4D environments to life
Digital Twins, as dynamic models, can go beyond traditional 3D representations by incorporating the element of time (or 4D – referring to the fourth dimension). In doing so, stakeholders can simulate and observe how a project may evolve over its entire life cycle.
This has emerged as a powerful tool for enhancing the planning and execution of complex infrastructure projects. A significant benefit of 4D visualisations is the ability to help project managers and engineers identify potential issues before specific mining activities begin.
By simulating the entire process and visualising how various elements interact over time, teams can detect clashes, conflicts, or delays in the project schedule. This early detection of issues empowers project managers to make informed decisions, mitigate risks, and optimise resource allocation, ultimately resulting in more cost-effective and efficient project delivery.
Another key advantage of 4D visualisations is the ability to enhance communication and collaboration among project stakeholders.
By providing a comprehensive and intuitive representation of the project's progress and outcomes, these visualisations make it easier for both technical and non-technical individuals to understand the intricacies of a mining project. This helps to foster improved collaboration between stakeholders such as architects, engineers, contractors, and internal/external clients, ensuring everyone is on the same page and reducing the likelihood of miscommunication or misunderstandings.
4D visualisations can also serve as a valuable marketing and public relations tool, as it enables project teams to present their plans and progress in a visually compelling manner, garnering support from local communities and regulatory bodies.
Digital twins and the use of 4D visualisations offer a holistic view of infrastructure projects, facilitating better decision-making, improved collaboration, and enhanced stakeholder engagement, all of which contribute to the successful and efficient execution of projects.
The future of VR technology and simulations in the mining industry appears promising, with continued growth expected. As technology improves and becomes more affordable, VR will become more deeply integrated into training and safety programs.
Advancements in haptic feedback and realistic simulations are expected to further enhance the effectiveness of training, ensuring mining personnel are better prepared for the complexities and hazards of their work.
VR technology is set to play an increasingly crucial role in enhancing training, operational efficiency, and safety within the mining industry, positioning itself as a valuable asset for the sector's ongoing development.
The last decade has seen an increased focus on the escalating prevalence of mine dust lung disease in both the mining and engineered stone industries. A new dust testing methodology has been developed by the Minerals Industry Safety and Health Centre (MISHC) at The University of Queensland (UQ) to provide insight into dust exposure to better protect workers from mine dust lung diseases such as black lung and silicosis.
The alarming rate of silicosis diagnoses in the mining and engineered stone industries has resulted in Australian governments unanimously agreeing to implement a prohibition on the use, supply, and manufacture of engineered stone from 1 July 2024.
The ruling comes after a significant number of new cases have been diagnosed – including young workers with less than a decade of experience in the industry. In Queensland alone, there have been 885 reported cases of Queensland workers being diagnosed with dust-related lung diseases since 2019, mostly in the mining and quarrying, construction and manufacturing industries.
Worker exposure to particulates is currently monitored on a total mass basis via gravimetric analysis. Digging deeper into the details, it's evident that the story goes beyond just mass.
The new methodology developed by MISHC is able to take an in-depth look at particle characteristics such as size, shape, and mineral makeup. The method also found interesting patterns in the way particles agglomerate – or group together – which wasn’t a factor that was even considered a few years ago.
We can no longer sweep the dust under the rug; it is evident that the size and shape of the particulate matter can affect its potential impact on human health.
In mining, the prevalence rates of disease can vary widely between regions, even with the same exposure standards. This was evident in British Coal, and is still an issue in Central Appalachia, in the US, where one in five miners are diagnosed with a mine dust lung disease. These regional variations have led researchers to look at the specifics of what in the dust is causing high rates of diseases in some areas, but not others.
Researchers within MISHC and the Mineral Characterisation Research Facility – which are both part of UQ’s Sustainable Minerals Institute (SMI) – developed the methodology for
characterising respirable and inhalable dust samples using scanning electron microscopy with energy dispersive spectra on the Mineral Liberation Analyser (MLA).
The MLA was also originally developed at SMI, specifically in its Julius Kruttschnitt Mineral Research Centre, for the analysis of samples for minerals processing. Instead of analysing core samples or bulk samples, the MLA is now able to analyse respirable dust collected on a filter paper by a respirable cyclone – similar to the way dust exposure samples are taken.
The MLA provides detailed information on each particle measured on the filter – including the size and shape of the particle – and produces a mineral map of the particle showing the shape and relative contributions of the different mineralogies present in the particle.
Understanding what is in the mine environment is an important precursor to understanding the actual health hazard posed by the dust in different locations.
Lung tissue studies have shown that the size of dust particles can change how much reactivity the dust produces in the lung tissue, particularly for respirable crystalline silica. It’s also become evident that certain contaminants within the dust can produce much more reactivity. Understanding the characterisation of dust can also serve as an input to methods to mitigate exposure.
Multiple dust samples from numerous mining operations have already been analysed using the MLA.
The refined MLA Method was recently published in the Journal Minerals in a paper entitled Method for the Analysis of Respirable Airborne Particulates on Filter Using the Mineral Liberation Analyser1. The method has been successful in showing the variety of mineralogical components and particle size distributions present in various areas of the mines.
The research found a range of mineralogies present in tested coal samples and for some mines, surprisingly little of the ‘coal dust’ was found to actually be coal.
The MLA can detect up to 42 different mineralogies present, with the 12 most abundant mineralogies shown in Figure 2.
The research has found that for underground coal mines the average size of particles can vary substantially between mines and, to a lesser extent, there are even variations within the mine.
The overall size distributions of the dust can be calculated by the MLA based on the measurements of the individual particles, which are of the actual particle diameter, not aerodynamic equivalent diameter.
For the coal mines, the overall particle size distributions seem to follow a pattern as shown in Figure 3 with the midface of the longwall (MF – long dashed lines) being the finest dust, while the maingate (MG – solid lines) is somewhat coarser and the continuous miner section is the coarsest dust (CM – short dashed lines).
These findings mean it may be possible for a worker to be exposed to a significant number of sub 1 micron particles that do not add up to enough mass to exceed the eight-hour time-weighted average exposure limit, but can still pose a significant hazard. While in other mines, workers may be exposed to larger particles where far fewer are penetrating into the lungs, but account for a significant portion of the mass in compliance sampling.
The differences in particle size may also affect the behaviour of the dust particles in current dust control methodologies. Mine sites with in-depth knowledge on particle sizes and mineralogy can help tailor more effective dust control systems. With the level of detail available, it is possible to see how effective dust control measures are on the various sizes of silica particles present.
The MLA characterisation data also shows that respirable particles are more mineralogically complex than initially thought. The particles look to be agglomerating at this small size producing multiple mineralogies in one particle – not just particles of single mineralogies as was initially thought.
This figure (Figure 4) shows false colour images of silica particles showing different agglomeration patterns from three different mines. The agglomeration patterns can vary between mines with the following patterns showing:
♦ Agglomeration with aluminosilicates such as orthoclase and muscovite
♦ Agglomeration with carbon particles, either coal or diesel particulate matter
♦ Mostly free silica
When these particles are inhaled, the variations in chemical composition can affect how the body reacts with them.
There can be several sources of dust in a mine besides the cutting of the coal seam and these can be attributed to causes
including vehicle traffic though the mine, the mining of roof or floor rock or rider seams, stone dusting activities and other activities in the mine such as shovelling.
Performing sampling in actual mining conditions picks up the contributions from all these sources, which in some instances can be significant. As well as this, the samples conducted in the study were taken in a variety of underground locations including at the maingate and midface of the longwall, around the continuous miners, on the shuttle car, in belt roadways and during secondary recovery activities.
Within MISHC, there is ongoing work to characterise the dust present in different mining environments to better understand how the chemical components, particle sizes and shape contribute to the health effects.
A range of underground coal and metal mines have been sampled to date, with recruitment currently in surface coal mines and engineered stone. One of the goals of the research is to build a database of dust exposures so industry can start to understand the detail of these exposures for a range of workers, and provide more details into the actual exposures of these similar exposure groups.
To address the escalating rates of mine dust lung diseases, MISHC has pioneered a groundbreaking dust testing methodology. Traditional mass-based monitoring is no longer sufficient, and MISHC's approach – utilising the MLA – examines particle characteristics, revealing patterns in agglomeration previously overlooked. The research not only identifies variations in particle sizes within and between mines but also emphasises the potential health risks posed by submicron particles.
The ultimate goal in establishing a dust database is to provide detailed insights into the specific dust exposures faced by different worker groups, in order to make more informed decisions on exposure and control.
It is crucial for stakeholders, industry leaders, and policymakers to support and engage with these initiatives to ensure a safer and healthier future for mining communities. Uniting in the pursuit of knowledge, awareness and actionable measures to protect miners from mine dust lung diseases can enable industry to prioritise the wellbeing of those contributing to the mining industry and safeguard their health against the rise of dust-related diseases.
Choosing the right pump for applications in the mining industry is essential to ensuring efficient and reliable operations, cost effectiveness and safety for the workers and environment. Knowing which type – either dieseldriven or electric-driven – is suitable for a particular application is critically important.
There are a wide range of applications in the mining sector that require pumps, including raw water supply, dewatering, transporting slurry and tailings, leach and drainage solutions, chemical dosing, transporting process water, truck washing, and dust suppression. Broadly, there are two categories of pumps that can be used; diesel-driven and electric-driven.
Traditionally, mining operations have relied on diesel-driven pumps due in part to the remote location of mine sites and the flexibility of easily moving the equipment around. While diesel-driven pumps continue to be a popular choice, electric-driven pumps are starting to be accepted as a versatile choice that offers environmental benefits and are cheaper to run with increasing prices for diesel.
Electric-driven pumps are ideal where continuous operation is required onsite. As long as they can remain connected to a stable, continuous power supply, they can run continuously without damage or failure. This feature means they are the first choice for applications that need to operate for more than 20 minutes per cycle, such as dewatering and industrial processes.
These pumps are portable, easy to handle, and can offer a small site footprint, making them suited to groundwater applications. They are also useful in applications where diesel pumps cannot be used, such as in underground mines, where emissions are not allowed, and at high altitudes.
Electric-driven pumps are available in a variety of performances and can generally handle higher flow rates and head than diesel-driven pumps. For example, medium-to-large electric submersible pumps typically have a power rating up to 80kW and manage flows up to 20,000L per minute with a head of 85m.
Electric-driven pumps are very versatile, making them a good choice for mine sites as they can adapt to the ever changing needs of the site. For example, when paired with a variable frequency drive (VFD) the speed can be adjusted so that it can be used for multiple applications, meeting varying duty points to achieve the efficiency and performance specifications of each application. VFDs also allow electric-driven pumps to
operate over a larger operating range on the performance curve.
With ESG integration becoming a focus in mine sites over recent years, along with concern about global warming and more stringent environmental regulations, electric-driven pumps provide a cleaner and more environmentally friendly option.
Diesel-driven pumps produce greenhouse gas emissions from burning fossil fuels, and spontaneous combustion from non-exhaust emissions and leaks are safety and environmental concerns. Spillages of fuel not only cause harm to flora, fauna and the environment, but it is also a safety hazard and can result in costly clean-up.
On the other hand, electric-drive pumps – especially those powered by solar, wind or other renewable energy sources – have a much lower environmental impact and eliminate the risk of fuel spillages.
Ease of maintenance
Electric-driven pumps can be extremely durable, with high wear resistance. These parts tend to be easy to maintain, for example, submersible pumps with their modular construction allow for simplified maintenance procedures, with some models also offering onsite servicing and parts replacement kits.
When paired with advanced controllers with data monitoring capabilities, the end user will be notified when service intervention is required, allowing for preventative maintenance without additional labour to manually check the pump.
Diesel-driven pumps are designed to handle high volumes of water discharge, with discharge diameters for centrifugal pumps typically ranging from 75-200mm. They can work with clean or dirty water, as well as handle trash and fibrous materials.
When designed with features such as semi-open impellers and an abrasionresistant pump casing, submersible diesel pumps can handle solids up to 76mm in size. This makes them ideal for transporting or raising water with large abrasion solids such as for quarry site dewatering and floodwater.
Fully automatic, self-priming diesel centrifugal pumps are the choice for fast dewatering solutions on sites where there
is no other power source available. Their transportation and storage handling at remote sites is also made easier if they are equipped with forklift slots and a lifting eye.
Some pumps can also be equipped with an extra-large fuel tank to allow them to run for longer periods of time, reducing interruptions to work in order to refuel. Diesel-driven pumps are not suitable for use in high altitudes as it negatively affects performance and efficiency due to the lower pressure. Furthermore, as the oxygen levels thin, a wider throttle opening would be needed to pull in an adequate amount of air, resulting in more fuel being burned. They should also avoid being used in areas where there is a high risk that the fuel could spark an explosion, or where a spillage could harm wildlife or contaminate drinking water.
These pumps have a typical operating flow between 50-830m³/h, with a head of up to 51m. They are also able to operate in a variable speed range, allowing them to cover different applications and flow/ head combinations.
Diesel-driven pumps are built for endurance and reliability. Compared to electric-driven pumps, they require more frequent maintenance, and operations need to be interrupted for refuelling, which delays work and increases the final cost. However, new techniques have reduced the amount of maintenance required, with oil and filter changes only needed every 250-300 hours and they can run without maintenance for up to 1,500 hours and still have factory warranty.
Both diesel and electric-driven pumps have benefits for mine sites depending on specific site requirements. While electric-driven pumps have a cost benefit across the life cycle of the pump in terms of maintenance and fuel, diesel-driven pumps remain the better choice in a number of circumstances.
One of the key determining factors for which type to choose is the operating conditions. If there is no access to power onsite, diesel-powered pumps are likely to be the better option due to the additional cost of needing a generator.
Furthermore, if onsite power is not available across the mine site to allow an electric-driven pump to be used in multiple areas or applications, it may not be as cost-effective as a diesel-driven pump.
Diesel-driven pumps are also a good choice when it will be used across a site for temporary applications as installing permanent power to all the locations of temporary jobs within a site or sites is not a cost-effective solution.
However, where there is onsite power and it is cost-effective, electric-driven pumps can provide a better return on investment, as well as a more environmentally-friendly and safer option for mine operations.
know
importance of choosing
E mpowering your mine operations with Roto’s high pressure flexible shaft series pumps. Unleash the solution that challenges excess wate r, ensuring safe and efficient operations ; the Underground Maintena n ce Engineers’ Choice for ground water control.
Features:
• Robust construction for prolonged life and reliable performance
• Adaptable for challenging underground environments, available in fixed station configurations for single lift or staging along with portable packaged solutions
• Forge a direct connection with the manufacturer, ensuring personalised support,
A key focus for the Western Australian mining industry is mine rehabilitation, and there are a variety of practices underway to ensure that closed and abandoned mines don’t pose a risk to Australia’s natural environment or local communities.
The Western Australian Government’s Department of Energy, Mines, Industry Regulation and Safety (DEMIRS) has released the 2022-23 yearly report for its Mining Rehabilitation Fund (MRF) and Abandoned Mines Program (AMP), and outlined the primary projects and achievements of the partnership over the last year.
Introduced in 2013, the MRF was the state’s first dedicated and perpetual fund for the rehabilitation and management of historical abandoned mines. Created as a pooled fund, Western Australian mining operators contribute yearly – ensuring that the community doesn’t have to pay for the rehabilitation of
MRF contributions are used in circumstances where efforts to enforce the obligations of tenement holders/operators to rehabilitate mines are unsuccessful. The recovery of costs may still be sought from any former operator that fails to meet their
A spokesperson for DEMIRS said that an important part of the annual report is the information about MRF levies assessed and paid, compliance activities and a summary of the data reported.
“As the fund has matured, industry has become more familiar with the reporting process, which has resulted in close to 100 per cent compliance with annual reporting obligations.”
The Department spokesperson said that where levies are payable, there are very few instances of non-payment – which is significant considering the more than 4,000 reports industry lodges each year, with close to 600 levy payments required.
DEMIRS’s annual report provides valuable information on the management of the MRF and enables the Western Australia Government to consider and approve the projected revenue and expenditure for the MRF through the State Budget each year.
As well as monitoring contributions, the Department spokesperson said the report allows the Department to share the progress of AMP project work, which is fully funded through Mining Rehabilitation Fund Act of 2012.
As a requirement of the MRF, all tenement holders are required to provide DEMIRS with accurate information of the types and areas of ground disturbance for each tenement.
This data is collected to calculate the annual mining rehabilitation levy but it also allows DEMIRS to understand the type and extent of ground disturbance on mining Act tenure
The released MRF data is available to the public to filter and search by type of disturbance and tenement type. It can be used to gain a detailed picture of mining and exploration activities in a particular area, including the scale of disturbance on tenements that may be the subject of a potential purchase.
“Another key aspect of the MRF yearly report is the outline of the fund’s key activities and achievements, including those undertaken by the AMP.
“The department’s actions are designed to keep industry and the public informed about how the MRF is being managed and how well it is achieving its aims.
“The report includes summary information derived from the assessment data that holders provide in their online MRF reports. DEMIRS collates data for individual tenements for the report, making comparisons with the combined information provided in previous years.”
The spokesperson explained that although the MRF does not absolve tenement holders and mine operators from their legal obligation to conduct rehabilitation works on a tenement, it does include an incentive for mine operators to gradually rehabilitate mining disturbances whenever feasible.
“If an area of disturbance is undergoing rehabilitation and has reached the point where all necessary earthworks are completed, that area – unless it is related to exploration – can typically be classified as 'land under rehabilitation' and attract a lower levy calculation.”
The DEMIRS spokesperson said that the industry’s compliance with annual reporting requirements and payment obligations has improved each year and that DEMIRS continues to fine tune its compliance reviews and update guidance to support reporting.
The principal funds are available for abandoned mines across the state in circumstances where the tenement holder/ operator (that contributed levies to the MRF) has failed to meet rehabilitation obligations and efforts to recover funds from the holder/operator have been unsuccessful. The work carried out by the AMP has been prioritised on a risk basis, with consideration to significant risks to the community and environment.
The report outlined major progress made on the AMP’s Ellendale project, the largest contract undertaken by
Australia, mining at the Ellendale Diamond Mine site commenced in 2002 and continued until Kimberley Diamond Company entered into administration in October 2015. Ellendale was declared an abandoned mine site in December 2015.
The first phase of significant safety works have been completed with the removal and clean-up of all obsolete infrastructure and equipment across the former
Notable achievements
recordable injuries or incidents, as well as the removal of all waste
The report also explores the AMP’s several key actions to reduce community and environmental risks associated with the Donnybrook Shafts project area completed in collaboration with the Department of Biodiversity, Conservation and Attractions (DBCA).
The report says the AMP achieved significant milestones during the 2022-23 financial year, with the successful completion of the Ellendale Deconstruction project and completion of the rehabilitation works on the Donnybrook Shafts project.
AMP projects funded from MRF interest earnings continued to be closely managed due to the impact of historic low interest rates, with a significant focus on project spend.
While a number of projects remained on hold during this reporting period, recent interest rate rises enabled this area of the program to be re-evaluated, with planned progression on prioritised MRF interest-funded projects underway.
The spokesperson said that the 2023 yearly report shows a significant increase in the number of active projects compared to previous years.
“Interest earnings on the MRF have gradually increased over the past year, enabling the re-initiation of several AMP projects that were previously on hold.”
To inform the 2022-23 report, mining rehabilitation levies totalling $42.8 million were assessed, representing a 9.2 per cent increase from the previous year.
The MRF compliance team reviewed 1,665 tenements and found 203 tenements required amendments to their submission. The outcomes of the annual compliance plan resulted in additional levy payments of $376,508.77 and refunds of $13,071.40.
As at 30 June 2023, the net balance of funds was $291.2 million including $3.1 million in net interest.
In May 2018, DBCA reported old mine workings within a section of Argyle Forest Block to the AMP. The area is located approximately 2km south of Donnybrook and was prospected and mined for gold between 1897 and 1903.
A number of additional shafts adjacent to the project area – presenting an ongoing safety risk to forestry workers and the community – were assessed by geotechnical experts in February 2022, in addition to a previously unknown shaft reported to the AMP and DBCA by members of the public.
Earthworks to rehabilitate shaft features were undertaken in November 2022, with eleven shaft features backfilled with granular material to eliminate safety risks to the community.
In August 2023, the Western Australian Government announced that the MRF would be undergoing a review, as mandated in the Mining Rehabilitation Fund Act.
The Act requires that the fund be reviewed within ten years of its commencement, to ensure that it continues to meet its objectives and has sufficient financial resources available.
A summary of the findings will be released when the review is complete, outlining where the fund is succeeding and where it may need to be adjusted, so that it remains fit for purpose and continues to provide meaningful benefits to Western Australia’s rehabilitation efforts and keeps the mining industry financially responsible for works – not ratepayers.
The legacy of mining activities can often endure long after a mine has closed. Identification and mitigation of environmental and social risks, and identification of potential opportunities to transition a mining community away from mining and into other income streams from the outset is a necessity for the industry, government and community. Early closure planning and robust iterative mine closure plans are essential to secure the long-term viability, social licence to operate and environmental health of mining operations.
The Mine Land Rehabilitation Authority (MLRA) works closely with industry, government and community to facilitate good rehabilitation outcomes for the rehabilitation of declared mines in Victoria.
The legislation governing mining in Victoria is the Mineral Resources (Sustainable Development) Act 1990. It defines a declared mine as a mine or quarry in Victoria declared by the Minister to have geotechnical or hydrogeological factors within that pose a significant risk to public safety, the environment or infrastructure.
A common misconception is that mine rehabilitation commences only after a mine has reached or is reaching its end-of-life, but MLRA’s Technical Director, Antonia Scrase, said that the closure
planning process should start the moment the project is being designed, and that closure options and costings need to be considered from pre-feasibility stage onwards. If closure is not considered at these early stages, options will be severely restricted and there is a potential that opportunities will be missed, with end closure costs far exceeding expectations.
With current mechanisms for long-term costs used by mining companies, it is often seen as fortuitous for companies to push closure costs further into the future. Therefore, delaying the work that needs to be done to understand the many underlying issues and hurdles to achieving closure, as well as potentially delaying progressive rehabilitation, and reducing the overall risks and costs of final closure.
“This approach can leave little room for adaptation of rehabilitation techniques or focus which can reduce options and increase project costs,” Ms Scrase said.
It is therefore vital that all viable closure options are well understood and costed at the early stages. Closure planning needs to allow for the ongoing operational, legislation, social and environmental changes that occur during the mine’s life cycle.
Definitions of mine rehabilitation success are site specific, but generally most mine companies or landowners are seeking to leave physically and chemically
Modern mining practices have seen an increased demand for sustainable resource extraction and environmental stewardship, including the effective rehabilitation of mine sites and their surrounding environment upon closure. Planning for rehabilitation is critical and needs to be factored into all stages of a mine life cycle, from project inception and pre-feasibility onwards.
stable, safe and sustainable environments – where the asset/land is not sterilised but able to be re-used for sequential land uses, driving new economies. The rehabilitated mines should assist in the transition of mining communities away from mining economies.
Mining companies usually define success of rehabilitation through closure objectives and closure criteria. These are often physical parameters that can be demonstrated and checked off as part of a process, which leads to surrender/ relinquishment of the mining licence. But true success potentially comes further down the line, when the land has transitioned to other non-mining land uses and mining is a distant memory.
Below are some examples of “good” or “successful” rehabilitation projects, although the true level of success of each example will only be possible to gauge in due course:
This example has been created from a closed mine and the mine operator was no longer involved in the site. After some significant time through collaborative community leadership, the site has been rehabilitated and is now a tourist attraction.1
This location is considered to be on the pathway to having fully transitioned from a coal industrial landscape into a tourist location with many different thriving tourist businesses.2
This site has been rehabilitated by the mining company and it has achieved its closure criteria and is on the pathway to the relinquishment of its mining licence.3
This location is often deemed a mine closure success, due to its incorporating tourism attractions. Again, the rehabilitation was not undertaken by the mining company and occurred some period of time after mining had ceased.4
“It’s worth noting that in the cases of Collie and the Eden Project, success has come after the mining company has exited and other entities have stepped into the void,” Ms Scrase said.
“It is interesting that the Eden Project has now formed from the success of the Eden Project Cornwall. The Eden Project now seeks to invest in the redevelopment of further industrial and mine closure projects around the world, including the Eden Project in Anglesea Victoria, which it is aiming to support the concept for a world class eco-tourism attraction on the site of a former coal mine.”
Also worth noting in these ‘successful’ examples is that they are largely collaborative projects – between the landowners/mine companies, government and community. Mining companies are unlikely to be able to achieve successful transitions to new economies without collaboration between other interested parties and government.
Rather than being created at a project’s inception and then forgotten about, mine closure plans are meant to be dynamic documents and are required to undergo regular review and updating with new information. As time and the project progresses, the plans should be refined to ensure they reflect the most up-to-date knowledge relevant to the development and rehabilitation status of the mine.
A closure plan is a multidisciplinary document which includes many technical aspects, including environmental and social elements. The documents are usually relatively long and complex by the end of mining, so it is important for readers’ understanding to summarise the whole project upfront – setting out what the plan is trying to achieve, how it will get there and how it will demonstrate its success.
“When developing a mine closure plan, companies should refer to their local and national legislation and best practice guidelines. All states and nations have different requirements for their closure plans. Unless companies understand and close out these requirements, mine rehabilitation and mine licence relinquishment/surrender is unlikely to ever be achieved,” Ms Scrase said.
There are several key elements that appear to cross state and international guidelines for mine closure planning and preparing mine closure plans. These are well detailed in the ICMM Closure Guidelines and generally include but are not limited to:
♦ Closure vision, principles and objectives
♦ Post-closure landforms and potential land uses
♦ Legislated requirements, obligations and commitments
♦ Knowledge base
♦ Stakeholder engagement
♦ Closure risk and opportunities assessments
♦ Closure criteria (success criteria)
♦ Closure execution
♦ Monitoring and maintenance
♦ Closure costs
♦ Relinquishment
Mine closure planning is evidencebased and therefore transparency and provision of relevant technical studies and designs are key.
“When developing their plan, it is wise for companies to engage with government early and attempt to bring them on the journey of closure. Leaving government and stakeholder engagement to late in the day will undoubtedly raise questions that could have been answered along the closure road to rehabilitation.”
As an independent non-regulatory authority, the MLRA serves as a source of information for declared mine rehabilitation in Victoria, and is also a statutory referral agency on all Declared Mine Rehabilitation Plans. The MLRA also sits on the Technical Reference Group (TRG) for the Environmental Effects Statement process that the declared mines may have to go through as part of getting approval for the closure/ rehabilitation plans.
The MLRA is there to facilitate good rehabilitation outcomes for Declared Mines in Victoria.
“Currently there are three declared mines in Victoria, all located in the Latrobe Valley. The MLRA also provides a source of unbiased information and education to the wider community on mine rehabilitation,” Ms Scrase said.
“In order to facilitate good rehabilitation outcomes, the MLRA assists in legislative clarification and change, providing advice to government and industry on mine closure planning and rehabilitation.
“Once mine licensees have achieved closure criteria, paid into the Declared Mine Fund (DMF) and have surrendered the licences, the land is registered by the MLRA on to the Declared Mine Land Register.
“The mining licence no longer exists and the landowner takes responsibility for any ongoing monitoring and maintenance work associated with the historic mining activities. At this point, the MLRA will take on administration of the DMF and either be responsible for ensuring the landowner takes on the post-closure monitoring and maintenance work or by becoming the next landowner and undertaking the work.
“In this area, Victoria is starting to develop mechanisms for managing the residual liabilities aimed to limit financial impact on future generations.”
Mining’s social licence to operate is intrinsically linked to how mining companies are seen to perform in a number of ways, particularly being seen/known to be able to close and rehabilitate mines to a suitable standard.
As community and government have become more aware of mine closure and the ongoing costs associated, it becomes even more important to achieve the transition of mines to a new state that does not drain resources from future generations. This transition can only be achieved through collaboration between mining companies, government, community and interested parties.
1. Alex (2023). From a coal mine to a world-class recreational lake. [online] The Chamber of Minerals and Energy of Western Australia. Available at: https://www.cmewa.com.au/safer-smarter-cleaner/articles/ from-a-coal-mine-to-a-world-class-recreational-lake/ [Accessed 16 February 2024].
2. Germany: The Ruhr Region’s Pivot from Coal Mining to a Hub of Green Industry and Expertise. (2021). www.wri.org. [online] Available at: https://www.wri.org/update/germany-ruhr-regions-pivot-coalmining-hub-green-industry-and-expertise. (Accessed 16 February 2024).
3. Bhp.com. (2023). Closure and water management at Beenup. [online] Available at: https://www.bhp.com/news/case-studies/2018/08/closure-and-water-management-at-beenup. (Accessed 16 February 2024)
4. The Eden Project. (n.d.). Visit Eden. [online] Available at: https://www.edenproject.com/visit. (Accessed 16 February 2024)
Aboriginal business owner Derek Flucker highlights how Traditional Owners, First Nations companies and the resource sector working together will protect Indigenous culture. This will secure a meaningful future for First Nations people and prevent the destruction of the world’s oldest living culture, so events like the eradication of Juukan Gorge are never repeated.
For more than 30 years, Derek Flucker has been involved in the mining industry, witnessing first-hand the change and growth in the way that the mining sector and First Nations communities interact and work with each other.
As the Managing Director of two companies –RBY Projects and Manaji Projects – Mr Flucker has been long involved in the industry, as a business development specialist, General Manager and Managing Director, so he has a broad perspective on the industry and First Nations communities.
“RBY Projects does civil construction, maintenance and rehabilitation activities where Coal Seam Gas activities occur,” Mr Flucker said. “We'll go in, undertake the civil works during the construction phase and undertake the rehab once the construction is finished.
“Manaji Projects does the cultural heritage clearance work. So, where activities are happening on Country, the Traditional Owners go in and make sure that their cultural areas are not being disturbed. And if they are, they come up with plans and ways to manage these areas or cultural objects. This model ensures the two parties walk together through the process when development occurs on their land.
“Having Indigenous businesses in the sector, such as mine, has been really important in terms of ensuring Traditional Owners feel comfortable, supported and are in a safe space when they do their work on Country. Traditionally, the engagement with Traditional Owners has occurred via the big resource sector companies and for Traditional Owners this is a conflict of interest.
“The resource sector’s main interest is extracting the resources from the ground. Finding a balance between Traditional Owner interests and resource extraction is difficult to achieve.”
Mr Flucker said having First Nations people working out in the field also provided a ‘good story’ to the wider public that challenged the stereotype of Aboriginal people as welfare recipients.
“This is great for our community to have role models out there working and protecting Country and feeding their families.”
Giving back to the local community is a priority for Mr Flucker and is a key driver of the work his companies do – the people they employ, the services they provide and the investment the companies have in those communities.
When Mr Flucker started his first joint venture Aboriginalowned business some 25 years ago, it struck him that there were very few Aboriginal businesses in the resource sector and in business generally.
“It was quite lonely in the space as I didn’t grow up with wealth or having role models that went into business.”
In 2005, Aboriginal Enterprises in Mining, Energy and Exploration (AEMEE) was established with a focus on gaining a true market share for Indigenous businesses within the resource sector and developing and connecting First Nations businesses with real opportunities.
“AEMEE came along; it was developed to help bring people together, help guide policy and help guide the government in making decisions around mining projects. You've got a lot of communities that are sitting on the back door of these projects, and a lot of the work was bypassing the local people. Many of these communities were living in third world conditions, with little to no employment opportunities and relying on government money to survive. AEMEE went about changing the sector to ensure this work was getting distributed to First Nations people.”
As well as giving a voice to the First Nations community, it served to bring people already involved in the mining industry together.
“It gave me and other Aboriginal businesses a family that were doing a similar thing, so we felt connected; we felt as though we were part of something that was quite important for our communities.”
Mr Flucker currently serves as a Chairperson for AEMEE and has fulfilled this role since 2010 – he understands the significant role the enterprise has played in First Nations engagement in the resources sector, and the continued role it will play in the years to come.
“As it is today, the mining sector is the biggest economic driver for Aboriginal people in Australia, so it's been great to be part of AEMEE,” he said.
Reviving the conversation
Since its inception in 2005, AEMEE has strived to bring members together and address key issues at inclusive and informative events and conferences, including the Annual AEMEE Conference.
Although COVID-19 put a pause on in-person events for a few years, the Annual AEMEE conference was held in Cairns for the first time since the COVID-19 pandemic in September 2023. Mr Flucker said that the feel and energy in the room was the best he’s seen for a very long time.
“We had a lot of new players from various sectors there and a lot of new businesses. We had a number of the big mining companies attend but we had mostly Indigenous businesses – it was great to hear their stories and the positivity that they're providing for their communities and their families.
“For us, it was just a real energy boost for our community that work in the industry, and it was great to see them all there.”
One of the key points in the conference agenda was bringing Traditional Owners and mining companies together to discuss the ways to protect Aboriginal heritage sites going forward, including getting Traditional Owners from Juukan Gorge and Rio Tinto together to present on the topic.
“I understand it was the first public forum where the Traditional Owners for Juukan Gorge were able to speak on the matter and we really enjoyed having them there and getting their insights on how they see the future for their people. They
have started some great initiatives with Rio and I believe the conference attendees learnt a lot from their experiences,” Mr Flucker said.
“It was really good to hear both sides of the story including how both parties were able to move forward from the situation to ensure it doesn’t happen again.”
He said Rio Tinto had drawn on the support of AEMEE to help with their engagement with Aboriginal businesses.
“During the process, Rio Tinto was taking a holistic approach. They weren't just looking at the cultural heritage incident, they were looking at how they can do better with Indigenous groups generally from economic, social and cultural perspectives.”
Key stakeholder engagement: from the beginning
The conference focused on brainstorming how to protect cultural heritage and ways to prevent something like Juukan Gorge from happening again.
“Major items on discussion were about early consultation, early involvement, getting consent, and where there are mistakes, owning up to them. Where mistakes occur it’s about both parties developing joint improvement plans for the future and making each other accountable to agreements and change.
“That was a pretty key message throughout the whole thing.”
Another clear message that emerged from the conference was the importance of giving Traditional Owners engagement in all aspects of the mine, not just the cultural heritage engagement.
This engagement needed to be at the planning phases of the mine and building in economic, social, and cultural programs to be delivered at all stages.
“We see it too often that First Nation people are engaged too late in the process, or they are only engaged on certain aspects of the project,” Mr Flucker said.
He said discussions that occurred at the conference helped to show that if companies involve Indigenous people early and on more than just cultural heritage, there was a better relationship between parties for the duration of the project.
“There are some major social issues happening in communities including high suicide rates, negative health statistics and major deficiencies in education. Aboriginal people want to be at the forefront to improve these areas. Resource
projects provide the potential income and jobs to improve the negative statistics in these communities.”
Those striving for better outcomes and better engagement have found themselves at the mercy of legislation and government bodies. To avoid a repeat of Juukan Gorge, the Aboriginal Cultural Heritage Act was introduced in 2023, but in August, Western Australian Premier Roger Cook repealed the laws and restored the 1972 legislation.
Mr Flucker said that in this situation “we've taken a number of steps forward, and then we've taken a number of steps back”.
“From an AEMEE point of view it’s unacceptable to see this legislation reverted to the archaic legislation of the past. We’re one of the players that are working with the government and the mining companies to make sure we have better legislation, to make sure these things don’t occur. And if we go back to what was happening in ‘72, we’re going to get repeats of what has already occurred, which has been a major issue for the Aboriginal community, Australia and its reputation internationally.
“The government needs to change their paradigm and put the shoe on the other foot. If they introduced legislation which could potentially lead to the destruction of English churches or sites important to the colonial history of Australia there would be major public backlash, but this legislation has been treated very differently,” Mr Flucker said.
Mr Flucker is optimistic about the future and what effective communication and engagement between Traditional Owners and mining companies could look like. The three keys are respecting each other, seeing each other as partners to developing land and working together to achieve each other’s goals.
“We need to ensure that we can still have a strong mining industry, but we need to make sure that both the mining and the Indigenous sector can work together.
“This sector has grown significantly from twenty-five years ago when I started. We’ve made mistakes. The mining companies made mistakes and Indigenous groups made mistakes, but to see this sector grow for Indigenous groups and the economic
impact that it's having on Indigenous Australia, we want to ensure that continues.
“But we also want to make sure that our culture and heritage is protected, and we all learn from situations where our culture and heritage has been adversely affected.”
“25 years ago, we had less than a handful of Aboriginal businesses in the sector and now we have thousands of businesses in the sector being the biggest economic driver for First Nations people.
“Over the past three years Rio, BHP and Fortescue have had major spending increases in terms of contracts being given to Aboriginal businesses, some doubling their spend. This is not a handout mentality, as the mining industry now relies on the First Nations businesses to be successful as without them many projects would be at risk. We now have Aboriginal businesses running and managing their own mines which was unthinkable ten years ago.
“In terms of AEMEE, well, it's an exciting time ahead for the future. We have just appointed our inaugural CEO to lead out a range of activities, events, and projects to further build on and strengthen our presence and role within the sector. This will mean cultivating new opportunities, strengthening partnerships, and establishing pathways within the industry to benefit Indigenous businesses, ensuring our collective growth and success in the future.”
The mining industry continues to be one of the driving forces for the nation’s successful economy and Mr Flucker said that mining companies and Indigenous groups need to work together to help the Australian resources sector meet increasing mineral and resources demand in Australia and across the world. First Nations people want to be partners in the economic future of Australia on the national and world stage but they also want to ensure the economic future of their own families and communities.
“First Nations people also have obligations to their lores and culture which have to be respected and the drive for a successful resource sector cannot be done at the detriment of lore and culture. This is achievable and has been achieved in the majority of projects across Australia and I am confident the sector will continue to prosper where everybody can achieve their desired goals.”
The night sky has long captured the fascination and imagination of countless generations but it seems that for ensuing generations it may also hold the future of the mining industry.
Mining: the word alone conjures up images of mineral-rich earth, drilling deep into the dirt and digging pits of mammoth proportions, but there are some in the Australian resources sector who believe that terrestrial mining might one day share the spotlight with mining of a different sort.
The knowledge that Earth’s offerings are finite and may one day cease altogether has been at the back of the industry’s mind for some time, prompting the search for alternative methods to bolster Australia’s mineral supply.
Deep sea mining is one method that has come into the spotlight in recent years, but it could be that the answers to the mining industry’s future lie not in the depths of the sea, but off earth entirely.
The University of New South Wales’ (UNSW) Professor Andrew Dempster is one individual who thinks that the sky is no longer the limit for Australia’s mining industry.
A Professor with the School of Electrical Engineering and Telecommunications and Director of the Australian Centre for Space Engineering Research (ACSER), Professor Dempster often collaborates with Professor Serkan Saydam at UNSW's School of Mineral and Energy Resources Engineering on the topic, with the pair thinking that off-earth mining could play a large role in Australia’s mining industry in the not so distant future.
But those hoping to see astronauts in high-vis and hard hats are going to be sorely disappointed.
“Mining in space, at least initially, will look a lot different to mining on earth,” Professor Dempster said.
“The extreme environment is the biggest differentiator, with space mining needing to operate in low gravity, low pressure, high radiation, extremes of temperature, absence of water, and at a great distance from Earth.
“For those same reasons, it is likely that it will also need to be autonomous, with minimum human interaction.”
Mr Dempster said that the places industry is currently looking at are the moon, Mars, and asteroids, with each presenting a unique combination of extreme environmental factors.
As is to be expected, there are a number of distinctive issues and challenges that arise when considering off-earth mining feasibility.
“Off-earth mining is a problemrich environment, which is great for researchers but less good for investors who are looking for certainty – hence our research focus on risk reduction. The problems are also full-spectrum. An investor needs to know a series of things that at present are unknowns. For example, ‘will I own what I dig up?’”
According to Professor Dempster, there is a slow and measured process underway in the United Nations to try and formulate a legal framework, but that it is bound to be overtaken by events, resulting in a phase where things are progressing in an unregulated fashion. As well as this, some countries have legislation that they say covers the moon, but whether or not these claims can hold up is questionable.
“Business cases are difficult to make as there is uncertainty in almost all aspects of the business, and there is a very large valley of death associated with simultaneously growing both supply and demand; why create a refuelling station when no one needs topping up versus why design a machine that can be refuelled if there is no supply?
“Environmental and ethical issues have yet to be adequately debated – like the recent Navajo Nation objections to flying human remains to the moon. We are yet to have considered enough implications of what is being proposed. All of that still leaves the technical and engineering developments that are required, and these are many.”
Learning of galactic proportions
Professor Dempster said that the mining industry and the space industry have plenty to learn from one another.
“The space and mining industries have a lot in common: they both deal with long time frames and large expenditures, and they have highly structured development methods recognised across their industries. However, those methods are not similar, and communication between the industries is poor, making ‘learning’ from the other more difficult than you might think.”
According to Professor Dempster, areas where both industries have interests include autonomous robotics, semiautonomy in systems with high latency, materials handling, mineral processing, mine/mission planning, system engineering, business case development, social licence, sustainability, and more.
“We try and cover all these bases in our own research,” Professor Dempster said.
“Our work at UNSW has the motivation: reducing the risk perceived by an
investor in a space resources venture. The more one pays attention to that aim, the more it becomes obvious that the mindset required may not come from the space industry, which has a number of drawbacks – its history of being driven by large agencies and large prime contractors, often emphasising science for its own sake, and its focus on missions, rather than businesses.”
Professor Dempster said that the Australian mining industry has a lot to offer in the area of space resources and that there are a number of ways that the mining industry can get involved.
“The Australian Space Agency’s Moon to Mars program has funded a lunar rover – recently named Roo-ver – which assists in what the space industry calls In-Situ Resource Utilisation (ISRU), in this case moving regolith (soil) around on the moon.
“Also, Australian Remote Operations in Space and on Earth (AROSE) is a consortium that is focussed on this exact area. It works with stakeholders in the mining industry and informs them of how to contribute to and benefit from space.”
According to Professor Dempster, experts have always argued that Australia needs a niche in space and the country’s history of strength in mining makes space resources an obvious choice of niche. Additionally, the Australian mining sector already has a leadership position globally when it comes to technology, which Professor Dempster said could be jeopardised if Australia fails to participate in space resources.
“The fact that the current Federal Government has decided space is a partisan issue, and pulled funding out of this rapidly-growing sector, is likely to be just a bump in the road. There are several Australian start-ups who are really starting to make their mark and bad policy making seems not to be affecting them. The sector will continue to grow regardless.”
And grow it has, with rapid progress in the last decade. UNSW has hosted the Off-Earth Mining Forum since 2013, providing a platform for experts interested in the topic and bringing together the two industries.
“When we started there was lots of speculation about whether mining would concentrate on asteroids or whether platinum group metals were the way to go but over the years, a strong focus moved to the moon and water and we
have now seen India land its rover at the lunar south pole in its Chandrayaan-3 mission, and we have a new lunar launch service, Vulcan Centaur, carrying the first commercial lander to the moon, Astrobotic’s Peregrine.
“These are fantastic technological contributions, but if you were to try and explain to a mining engineer how they fit into the feasibility study process, you couldn’t do it effectively because the work does not fit into how miners expect mines to develop.”
Despite the history of holding the OEMF at UNSW’s campus on the east coast of Australia, the 2023 event took place in Perth.
“We thought it was time we engaged more directly with the mining industry. Happily, over 50 per cent of attendees were from mining companies so in that sense, we feel we succeeded.”
However, even with the high percentage of mining company attendees at the 2023 event, Professor Dempster said that at present the engagement is with enthusiastic mining individuals rather than mining companies.
“There’s still work to be done. The event itself has always attracted high-level speakers who present on very exciting missions such as the Japanese Hyabusa-2 mission to return a sample from an asteroid.
“We also had a keynote from Colorado School of Mines’ Dr Kevin Cannon on regolith mining techniques. There were presentations on Australian missions, automation, and system engineering. Whereas the usual format was more universal, and reporting of progress, this one was quite directed to be of interest mainly to miners.”
According to Mr Dempster, despite the potential of off-earth mining, space mining will not replace terrestrial mining and rather than causing the industry to turn completely to the skies, it will instead complement terrestrial mining opportunities.
“From a miner’s point of view, it’s the value added that makes a space project interesting.
“Terrestrial mining will increasingly take place in remote settings, so many lessons learned from space mining projects can be immediately applied on earth. By trying to solve the hard problem, a series of easier, immediately applicable problems can be solved on the way.”
The next OEMF will be held in Sydney with another Perth event to follow in a year or two.
The Enabling mine closures and transitions: Opportunities for Australian industry report, released in November 2023.
Image credit: CSIRO.
With tens of thousands of Australian mines awaiting rehabilitation and a new report estimating the closure of almost 240 Australian mines by 2040, it is more important than ever to explore innovative solutions for the mining industry to overcome closure challenges as it simultaneously leads the way in the path to net zero.
Mining has been a key element of Australia’s economic development since 1802 when the very first shipment of coal was exported. As the country has grown and evolved, so too has the mining sector.
With more mines across the country coming to the end of their lives and growing demand for innovative closure and rehabilitation solutions, Australia has the potential to become a global leader in the space.
Australia’s mining industry will play a critical role in achieving the Federal Government’s goal of net zero by 2050.
A greener future will require a change in the resources mined in Australia as priorities shift in favour of clean and renewable energy. This will mean the development of new mines and the retirement of old mines.
Mine closure is a normal part of the mine life cycle, however, it can have mixed impacts on the environment and on communities if not handled in accordance with standards and frameworks specifically designed to support mining closure and rehabilitation.
With limited examples of successful mine relinquishment and repurposing in Australia, there is a growing demand for solutions that support the mining sector to address accompanying challenges such as effective engagement with stakeholders, mineral and non-mineral waste, resource recovery and the physical condition of the mine site.
Providing solutions to such challenges and enabling smooth mine closures or transitions will assist the industry in achieving optimal social, environmental and economic outcomes once a mine’s resources are no longer required.
CSIRO Futures, the strategic and economic advisory arm of CSIRO – Australia’s national science agency – works with forward-thinking industry and government organisations to tackle the industry’s most important challenges.
CSIRO partnered with the Cooperative Research Centre for Transformation in Mining Economies (CRC TiME) to develop a report that explores the growth opportunities for Australian businesses to supply equipment, technology and services-based solutions to address the challenges that mine closures present to the industry.
The report, Enabling mine closures and transitions: Opportunities for Australian industry, was released in November 2023.
CSIRO Futures’ Senior Manager, Dominic Banfield, said that CSIRO wanted to ensure the report was co-developed with industry to accurately reflect the current mine closure
challenges and define clear opportunities for Australian business to help.
“We undertook targeted interviews and workshops with stakeholders between April and September 2023, engaging various participants across the mine closure and transitions value chain. This included mine closure practitioners, mine closure solutions (MCS) providers, government organisations, industry bodies, researchers, and thought leaders.”
Mr Banfield said that the insights from the consultations were supported by desktop research and further validated in two workshops.
“Our team also undertook novel economic and market sizing analysis to explore the potential scale of expenditure of mine closure and related markets in Australia. This analysis utilised mining industry databases, market research data, and input from industry experts.”
2040 forecast: ten per cent of Australian mines to close
The report identified almost 240 mines that are projected to close by 2040, which is more than ten per cent of the approximately 2,200 current operational mines across the country.
Mr Banfield said that mining is a temporary land use, and that every single mine across the country is destined to cease operations at some point.
CRC TiME’s CEO, Dr Guy Boggs, said that all mines are based on finite resources and with the wave of mining investment over recent decades, it is natural that some will be coming to the end of their lives.
“It’s also important to recognise that the report provides a point of time estimate, noting that mine life at individual sites may change based on new resource discovery, market changes and other factors,” Dr Boggs said.
The estimate is based on projected closure dates sourced from a market intelligence database.
The report highlights the importance and potential of Australia's mine closure solutions industry.
It marks the first public release of information outlining the opportunities for Australian businesses to play a role in addressing mine closure challenges and aims to support industry growth by exploring the scope of the opportunities, the diversity of solutions required, and identifying enabling actions for industry development.
“This industry will be key to improving post-mining outcomes and capturing the economic opportunity associated with mine rehabilitation and closure,” Mr Banfield said.
CSIRO has estimated that the projected closure of 240 mines in Australia will create over $4 billion of annual expenditure on the broad range of activities associated with mine closure and rehabilitation.
“This expenditure represents a demand for equipment, technology and service solutions that optimise mine closure and transitions to both reduce closure costs and create better environmental and social outcomes,” Mr Banfield said.
Dr Boggs said that a key takeaway of the report is the diversity, span and scale of services, technology and equipment that is required for mine closure.
In addition to the demand for rehabilitation solutions that ensure the long-term safety and stability of the site, the report also identified growing opportunities for solutions that:
♦ Facilitate effective engagement and equitable partnerships with communities and other stakeholders
♦ Apply waste hierarchy principles to reduce ongoing liabilities and generate value from mine waste
♦ Facilitate the transition of mine sites to valuable postclosure land uses
The report identifies both existing and emerging opportunities, and highlights the ways in which Australian businesses can offer new and emerging solutions for the challenges that arise when mines close.
“Through focused consultations and workshops, the project identified collaborative actions for MCS providers, miners and the government to address barriers to the growth of Australia’s MCS industry,” Mr Banfield said.
By utilising the potential of its industry to commercialise and export solutions and supporting best practice mine closures and transition outcomes, Australia has the potential to emerge as a prominent exporter of mine closure and rehabilitation expertise.
Mr Banfield said that a coordinated approach to unlocking the industry’s potential will be key to Australia becoming a global leader in MCS provision.
The report suggested that to position themselves for export success, MCS providers can develop cost-effective solutions with validated performance, interoperability across mine sites and alignment with global best practices.
Mr Banfield said that to foster this potential, Australia must create an environment that encourages innovation, supports the business development of SMEs and attracts new market entrants.
“Initiatives promoting collaborative investment in developing solutions for common challenges, along with opportunities to test and demonstrate these solutions, can be facilitated through joint efforts by both the government and the mining sector.”
Mr Banfield said that by leveraging its strong reputation as a mining nation with robust environmental standards and performance benchmarks, Australia can export locally developed solutions to countries that are anticipated to see substantial mine closure.
Mr Banfield said that exporting to countries such as China, Canada, the US, South Africa and Mexico, all of which are expected to experience increased mine closures in the coming decades, will “further establish Australia as a global leader in mine closure and rehabilitation services”.
Dr Boggs said that the report confirms there is a huge opportunity for Australia to leverage its world-leading METS sector to develop a distinct identity for local, Indigenous and Australian businesses delivering mine closure and transition solutions.
“From a CRC TiME perspective, we think the Australian Government’s commitment to develop a roadmap to grow the oil and gas decommissioning sector will be powerful and could present huge opportunity for the MCS sector.”
The Enabling mine closures and transitions report also acknowledges an increasing need for mining transition solutions.
Dr Boggs said that the scale of development over recent decades means that demand for equipment, technology and services for activities to achieve positive outcomes at the end of mine life is growing.
“Indigenous and regional communities rightly expect that decisions by governments and companies about post-mining landscapes as well as investment to support local economic transformations will be made with them.”
Dr Boggs said another change is a broader rethink and recognition of the value of mine waste, mined lands and mining infrastructure for new purposes – for example, the reprocessing of tailings to extract minerals, or the numerous instances of pumped hydro energy production being considered in pit voids.
Mr Banfield said that CSIRO attributes the surge in demand for mine transition solutions to a number of factors, primarily stemming from increasing recognition of the importance of successful post-mining outcomes by the mining sector, community and government.
“Additionally, evolving community expectations for positive social and environmental outcomes are shaping regulatory requirements, industry best practices, and the decision-making of mining companies.”
Mr Banfield said the report will hopefully raise awareness in the mining industry of the opportunities presented by mine closure and transitions, foster greater investment and support in solutions.
“This extends to providing greater support for existing and emerging mine closure solution businesses, both within the sector and across different industries which may offer viable solutions.”
Additionally, Mr Banfield said that CSIRO hopes the report will offer a clearer direction on how miners, MCS providers and the government can collaborate and align themselves, contributing to the creation of a sustainable industry.
“Fostering a sustainable mine closure solutions industry is crucial for establishing Australian best practices, industry cultures and frameworks that support innovative solutions, ultimately leading to positive environmental, social and economic outcomes.”
Dr Boggs said the response to the report has exceeded expectations, with inquiries from all over the world from people within and external to the sector.
CRC TiME has integrated the findings of the report into its work, particularly to highlight the scale of opportunity for regions, Indigenous communities and Australia in the shift from viewing mine closure as a requirement or liability.
Mr Banfield said that the Enabling mine closures and transitions report can be used by stakeholders in industry, research and government that are unfamiliar with the opportunities and challenges of mine closure to identify ways that they could make meaningful contributions to mine closures and transitions.
Dr Boggs said that a critical step for industry is to see mine closure through a similar lens to project development, requiring a similar whole-of-organisation approach and procurement policies that support innovation and the engagement of local, regional and Australian businesses.
Over the next 12 months, CRC TiME said it will be working with its partners and the broader industry and with governments and regional and First Nations organisations to raise awareness of the opportunities that exist in MCS and transitions.
Mr Banfield said that mine closure needs to be reframed as an opportunity and not just a liability and that doing so will protect the sector for a productive and effective future.
“This will be enabled by the growing community of passionate and skilled people solving the challenges of mine closures and transitions.”
Even with the projected closure of more than 200 mines in the next two decades, the mining industry remains at the core of Australia’s economy and an integral part of the nation’s transition to clean energy.
Closure is a key part of a mine’s life cycle and with demand for innovative solutions to closure and transition continuing to grow, Australia has the potential to become a global leader in MCS expertise.
The waste generated from mining operations is one of the largest waste streams in the world, and there can be catastrophic consequences if it’s not handled properly. Knowing this, a team at Flinders University is sifting through tonnes of mining waste to address this problem head-on.
Acid and metalliferous drainage, also known as acid mine drainage or AMD, is the outflow of acidic and/or metalliferous water into the environment. This occurs when rock containing sulphide minerals (predominantly pyrite) is exposed to water and oxygen, causing them to break down and oxidise, triggering a chemical reaction which produces sulphuric acid. This usually occurs when earth is disturbed and rock containing pyrite is brought to the surface.
This is especially problematic at mine sites, when the smaller grain size of crushed waste rock and tailings and high pyrite content produce more acid than the natural environment can neutralise.
This outflow can result in the release of acid into surrounding water systems which can, in turn, dissolve rock and leach metals and acid into the environment. This damage is not only longterm, but can be costly to remedy. That is why it’s essential to assess the potential of AMD across a mine’s lifespan during the planning stage of a project.
A major $10 million dollar, five-year initiative called ‘Improved Prediction, Remediation and Closure of Acid and Neutral Metalliferous Drainage (AMD/NMD) Sites by Examination of Mine Waste Behaviour at the Meso-scale’ is taking place at Flinders University, with Professor Sarah Harmer at the helm.
The project is funded through Cooperative Research Centre Transformations in Mining Economies and involves Adjunct Professor Andrea Gerson from Blue Minerals Consultancy, the University of Queensland, the University of Windsor, eight mining and METS companies, Minerals Research Institute of Western Australia (MRIWA), the Department of Agriculture, Water and the Environment (DAWE) and International Network for Acid Prevention (INAP).
The project is centred on scaling-up innovative methods for acid mine drainage assessment and remediation and water and ecosystem decontamination. Professor Harmer’s team is also looking at other methods to improve both mine site closures and mining’s impact on the landscape.
Acknowledging AMD at an early stage
Professor Harmer stressed that a critical element of AMD management is that it should take place proactively, not
retrospectively – meaning that management should start during greenfield mine development based on geochemical testing of waste rock and tailings.
“Although at this stage there is no mine or mill, waste rock geochemistry can be determined from exploration core samples obtained to forecast the deposit value elements. This can then enable block modelling of potentially acid forming and non-acid forming strata and lithography.”
A geochemical understanding of the tailings can be undertaken through test work on pilot plant process residues.
“Understanding how these mine wastes will react to prolonged weathering, in terms of both acid and metalliferous drainage, enables planning for appropriate segregation and deposition during operations. This has high potential to reduce water treatment costs prior to site discharge during operations, enable effective emergency closure if required and greatly reduce the cost on final closure.”
The consequences of improper AMD management can be farreaching, extending beyond just environmental to also impact companies financially, with mine waste materials often getting in the way of mine closures.
“AMD can significantly restrict a company’s capacity to relinquish a site, whether to a private party or government agency, after mine closure due to residual liabilities and risk,” Professor Harmer said.
Alternatives for companies are either to go through an approved closure process while maintaining ownership and liability, or to place the mine in care and maintenance with the option for future re-opening. Adjunct Professor Gerson said that these options, however, come with varying degrees of environmental and legal responsibility, and all require appropriate judicial approvals.
“They also all come with some degree of cost with relinquishment frequently requiring the greatest capital expenditure particularly where insufficient planning has taken place.”
Adjunct Professor Gerson explained that, as an example, a roadblock to successful closure and relinquishment of a mine
site can be the lack of planning of final landforms, such that potentially AMD materials are not sufficiently encapsulated within benign wastes1
“There are numerous challenges faced by industry in its ability to manage AMD, which stem from the complexity of understanding AMD processes, coupled with evolving regulatory requirements.”
Professor Harmer attributes a lack of consistent site AMD management/investment, constant tension between short-term profit and long-term remediation costs with less clear financial benefits, everchanging mine personnel and a lack of effective record keeping as having hampered effective AMD management.
Another challenge lies in correctly forecasting acid and metalliferous drainage. Accurate predictions of AMD enable effective mitigation strategies that result in minimal downstream impact on flora, fauna and human utilisation. On the other hand, the incorrect prediction of AMD can mean the associated company has to undertake water treatment prior to discharge, resulting in a liability of potentially hundreds of millions of dollars.
“Accurate prediction requires not just the bulk assessment of detrimental metals and/or acidification and neutralisation capacities, but an understanding of their rates of release. Static testing may indicate low acid drainage risk, but acid drainage may still occur due to greater rate of release of acidity than neutralisation. Relinquishment is only viable if the acid generation rate is matched by the neutralisation rate in the long-term.”
Professor Harmer said that there has been a long record of incorrect AMD forecasting in the industry to date.
“Much of this is not formally documented; however a survey undertaken to determine the accuracy of prediction of water quality at hard rock mines indicated a low level of predictive capability2. Where the mines were close to water resources and had significant potential for acid and/or metalliferous drainage about 75 per cent underestimated the impacts of operational water quality in the environmental impact statement predictions.”
According to Professor Harmer, the Flinders University AMD meso-scale project has several themes that merge to a common purpose for improving the assessment and remediation of mine waste for mine closure.
“The project aims to provide links between prediction, scaleup and residual risk. For prediction of waste management, there are potential improvements, utilising both detailed mineralogy and microbiological assessment of waste for acid generation capacity and remediation of mine waste.
“The project aims to bridge the gap between lab-scale standardised tests and mine site implementation through emphasis on meso-scale testing of mine waste at more than one tonne.
“A more complete focus on control at source can influence early changes to process flowsheet and mine planning with the potential to reduce residual risk through improved mine and process design. The link to prediction, scale up and residual risk is key to the project success.”
The value of this project lies in:
♦ Improved forecasting of AMD risk
♦ Identification of resources for AMD prevention, reduction, and control at source enabling a progressive shift away from downstream water treatment approaches
♦ Environmentally sustainable, reduced rates of AMD release through implementation of source control strategies, both microbial and geochemical
♦ Testing of prediction and control strategies through scale-up from laboratory to mesoscale and for potential demonstration in sponsor mine site trials
♦ Improved block modelling of non-acid forming (NAF) and potential acid forming (PAF) rock zones for green and brown field sites
♦ Better waste rock dump planning and construction, and improved flowsheet and process planning for reduced residual risk and AMD prevention planning in operation and closure
Professor Harmer said that project partners have identified multiple sites of interest in Australia, the US, Canada and Mongolia – covering a range of climatic conditions from the desert to cool and wet to sub-arctic.
“These sites cover the evolutionary range for closure planning from green field, working mine to legacy. To date, 12 sites have been chosen in collaboration with industry partners and detailed scopes of work for each site have been established and approved.
“Project sampling techniques for mineralogical and microbial analysis have been developed and are being added to a new AMD/NMD Test Handbook. Mineralogical and microbiological characterisation of principal nominated wastes is well underway and has provided insight into the complexity of microbial life on mine sites.
“The design of both laboratory based and mesoscale tests has been completed. Kinetic column testing of principal nominated waste with agreed weathering parameters has begun. A new mesoscale facility has been completed at Flinders University where mesoscale kinetic leach testing has started. The initial studies are defining potential remediation strategies for each site.”
Professor Harmer expects that the results generated from the study will be high-quality and will help produce transformative change for the utilisation of post-mining land.
“The results will impact policy and community practice across Australia and internationally through industry and government collaboration, while widespread dissemination of state-of-theart practice will inform ecosystem restoration and mine-site closure standards.”
Professor Harmer said that dissemination of project outcomes will be provided through the new AMD/NMD Handbook, with collaboration with government bodies ensuring that the results will be disseminated broadly.
“Further utilisation of the research findings will be carried out through engineered large-scale trials on mine sites of the companies involved in the project. This will ensure that the project’s outcomes reach the target audience and are commercialised for productive usage and greater impact.”
At its core, the mining industry is cyclical, so it makes sense that new life can be found in the discarded remnants and forgotten waste piles of previous mining operations. Once dismissed as worthless and scraps, tailings and other mine waste are now increasingly emerging as an opportunity for industry to reclaim valuable minerals.
Around the world, governments and organisations are predicting that the rise in clean energy technology will supercharge demand for critical minerals. It is expected that to meet this critical minerals demand, new mines around Australia will need to be developed.
However, Geoscience Australia’s Jane Thorne said that with such long lead times in the creation of new mines, from discovery to development, meeting the predicted demand should also include recovery and recycling innovations.
Incorporating recovery and recycling innovations would include rethinking the value proposition of existing mine tailings and rock dumps, in a bid to unlock the potential of oncediscarded critical minerals and diversify supply chains.
“Mine waste potentially contains significant amounts of previously overlooked minerals and materials that are today considered critical and/or strategic.”
Ms Thorne said that reprocessing material previously excavated during mining operations could give new life to old mining towns, create jobs, rejuvenate local economies and potentially lead to improved environmental outcomes.
“With Australia’s long history in mining, our waste material could contain considerable quantities of valuable critical minerals and strategic materials that were previously of limited economic interest. This got us thinking, what are the opportunities for critical mineral recovery from mine waste and, importantly, how can Geoscience Australia support these opportunities?”
The lack of a national mine waste database is what spurred Geoscience Australia into action.
A comprehensive mine waste directory
Work began in 2021 and in May 2023 the Atlas of Australian Mine Waste was launched by Geoscience Australia as part of the Geoscience Australia-led Exploring for the Future program. The Atlas is an interactive, online spatial mapping tool that offers accurate information on known mine tailings, waste rock, smelter residues and other related mine waste materials in Australia.
“Geoscience Australia wanted to create a national Atlas that would support Australia’s commitment to net zero emissions by 2050 and contribute to Australia’s world-leading environmental, social and governance standards.”
Ms Thorne said the Atlas is intended to be a tool used to identify and support the sustainable and economic recovery of critical minerals from prospective mine waste sites and the management of their environmental legacy.
The interactive nature of the Atlas allows users to zoom in to see specific features and read a summary of publicly known information about a waste type, how it is stored and which mine, refinery or smelter it came from. Additional information for individual sites such as the associated mineral system and geochemistry will be added as it becomes available.
To create the Atlas and help industry realise the potential in mine waste, Geoscience Australia partnered with researchers at the School of Engineering at RMIT University and the Sustainable Minerals Institute at The University of Queensland. The partnership combined Geoscience Australia’s world-class mineral resource and mineral systems understanding with world-leading mine waste research conducted by the universities.
“Together, we set about building a comprehensive understanding of mine waste distribution across the nation to generate Australia’s first national inventory – the Atlas of Australian Mine Waste. This is one of the first national datasets in the world focussed on mineral resource potential in mine waste.
“The Atlas helps identify potential new opportunities for critical minerals supply from individual mine waste sites –whether that be reprocessing tailings or reassessing the viability of old waste rock dumps with new extraction techniques in mind."
The Atlas currently includes more than 1,400 storage facilities across Australia.
Data collection processes
According to Ms Thorne, populating the Atlas with mine waste locations is just the first step in helping industry realise the potential for sourcing critical minerals and strategic materials from mine waste.
“Realising the potential value of Australia’s mine waste requires a thorough understanding of the chemical and mineral characteristics of the different types of waste from around the country.”
Together with its partners, Geoscience Australia undertook a nation-wide mine waste sampling and analysis campaign in partnership with the state and territory geological surveys.
“Building on an approach pioneered by The University of Queensland and the Geological Survey of Queensland, this project is assessing representative sites of different deposit and mineral system types to support mine waste recycling across Australia.
“As part of the Exploring for the Future program, the researchers have sampled waste at 19 sites across Australia in order to understand the geochemical and mineral composition of these sites and determine what strategic materials and critical minerals they may contain.
“With complementary state- and territory-funded programs, over 90 mine waste sites across Australia are being
similarly assessed for their metal content, concentrations and composition.”
Ms Thorne said this national consistent approach allows the results to be incorporated into the Atlas and improves confidence in the data.
Prior to this undertaking, a national dataset recording Australia’s mine waste sites did not exist.
“No project is without its challenges. You can probably imagine the sheer number of datapoints and range of datasets we needed to bring together to create this.
“Together with our university, state and territory government partners, we gathered and standardised the existing information into a single national dataset. We then went about filling the knowledge gaps and populating previously unknown sites using publicly available information in conjunction with expertise from our researchers and our partners.”
Ms Thorne attributes the success of the on-ground, national sampling campaign to the support and willingness of mining companies who provided researchers with access to their mine waste.
“Fortunately, as this project and state and territory mine waste programs have built momentum, there is greater enthusiasm for the sampling campaign. This has also led to a broader national discussion about the potential valorisation of mine waste.”
Ms Thorne said that one of the most pleasing outcomes has been the way the project has brought together a diverse range of experts and stakeholders from industry, academia and government to help build the critical mass and national momentum needed to ensure that Australia can make the most of its mine waste opportunities as a nation.
“The work has also enabled Geoscience Australia to provide leadership internationally, engaging with partners through established programs – including the Critical Minerals Mapping Initiative with the US and Canada – to establish consistent approaches in sampling and mine waste data management and enabling us to develop a more rapid understanding of critical mineral and strategic materials potential in our tailings and rock dumps globally.”
Following its launch, industry is encouraged to make use of the dataset, and there are a number of ways it can do so.
“By providing detailed information about individual mine waste sites and their associated deposits, the Atlas can be used to investigate potential critical mineral associations and provide greater understanding of the current management status of the waste sites across Australia from one location.”
Ms Thorne said the results of the sampling and analysis campaign are being progressively released and will be incorporated into the Atlas over the next six months.
“When combined, the Atlas of Australian Mine Waste is a pre-competitive toolbox, provided by the Australian Government, seeking to support mineral recovery through mine waste recycling. It provides data, information and new thinking to help inform and de-risk further investigations and investment decisions.
“Our focus is now shifting to understanding the viability of reprocessing mine waste. This includes an assessment of potential environmental, social and governance outcomes as well as legislative considerations. Understanding mineral grade and character will be fundamental to determining how mine waste sites can be economically reprocessed.”
“We are incredibly grateful to the mining community for getting involved and supporting this world-leading project.”
Horizontal directional drilling offers a superior solution for pipe and well-screen installation in the mining and energy industry.
This method is highly accurate, sustainable, and efficient, providing the least disruptive way to transfer, dewater, power machinery, and extract materials from hard-to-reach locations.
It’s a better environmental, whole-of-life cost installation method that protects the surrounding environment and saves you money.
AHD Trenchless is Australia’s most experienced horizontal directional drilling contractor – visit www.ahdtrenchless.com.au to learn how we can help you.