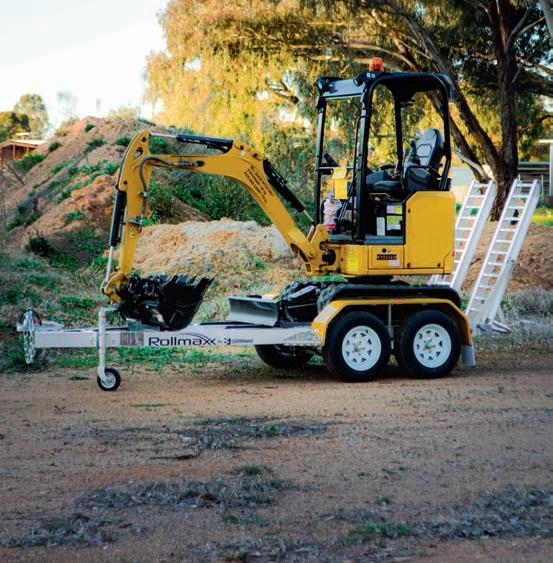
4 minute read
DDT: Plan your route with the DDT exhibitor map
Left: Sureweld recently released its new ‘Nexxgen’ Rollmaxx trailer range
moving on up
Developing and manufacturing Australian products to help Australian operators move better has been the core of Sureweld’s mission for 45 years, and the company isn’t stopping now
Sureweld started out in 1976 as a small welding and fabrication business mainly servicing the agricultural industry and based in Lilydale, Victoria.
But since developing an aluminium loading ramp concept for a few machine operators in the early 1980s, the company has grown to become the recognised benchmark in aluminium ramps and plant trailers for the construction and transportation industries.
Today, Sureweld has 30 different standard models suitable for machines weighing from 1.5T–11.5T, built at its Wangaratta production facilities – with custom models also available.
When the transportation industry came knocking at the door for their aluminium ramps, it was an amazing opportunity for Sureweld to collaborate with large truck body manufacturers, and freight firms.
Having a customisable walkboard configuration revolutionised the transportation and small freight field, says Sureweld. The easy to handle, lightweight ramps become an easy solution for removalists and the bespoke sizing makes it a ‘go-to’ for truck body builders incorporating them into their designs.
Since then, Sureweld has moved onto vehicle wheel riser ramps, built in accordance with Australian Standard AS. 2640:2016, popular with companies such as Aldi and Toll Group for under vehicle inspection, washing and servicing.
When support is needed most, Sureweld knows a thing or two about service. Having used qualified engineering and sophistic technology in the design of its products, Sureweld knows the parts of its products and understands how they are used. Provision of spare parts and service for an urgent situation has never been an issue, but rather key to its success in the marketplace.
In the early 2000’s Sureweld added a range of aluminium plant trailers – Rollmaxx Trailers – to its product offering, with civil contractor Paul Kaspersenn saying: “A Sureweld aluminium plant trailer is an invaluable asset; it makes the transportation of my machinery safe and practical.”
Rollmaxx aluminium plant trailers allow greater flexibility in the transportation of mini earthmoving equipment, with their impressively low tare weights allowing for higher payloads.
With the release of its new ‘Nexxgen’ Rollmaxx trailer range, contractors and hire companies have just been given the best of both worlds.
Utilising exclusively approved componentry, coupled with the trusted Sureweld service and ‘know-how’, towing machinery just got a whole lot easier.
With both a steel and aluminum option, Sureweld has mastered a higher allowable payload of 2,200kg, using a mechanical override braking system.
This opens up a highway of possibility for hire companies that usually would require trailers of this size to have an electronically-controlled braking system.
“We understand that this isn’t the first trailer of this nature in the Australian marketplace,” says Sureweld managing director Carl Hansen, “but we can say that we are the very first Australian made and owned company to master it.”
Priding itself on its local manufacturing processes, Sureweld can offer the spare parts and fast service when it is needed, making repairs and maintenance as seamless as possible.
As the fleet manager of a large multinational hire company describes it: “[Sureweld] provides an excellent Aussie-made product that is backed up by trusted Aussie service.”
Now incorporating the tagline ‘Move Better’, Sureweld is dedicated to helping move its clients’ machinery with ease. Reach out on 1800 787 005 to see how Sureweld can meet your transportation needs.
Action packed
Come watch the FlipScreen demo at the
Diesel Dirt & Turf Expo
FlipScreen is the world’s best high volume, patented, screening bucket that inexpensively and efficiently screens any material, on-site, for any industry, states FlipScreen.
The FlipScreen is made to suit any size of excavator, loader, skid steer or tractor, with zero daily maintenance on new direct-drive models.
FlipScreens are replacing trommels and screening plants as they screen more, at greater profits, are a portion of the cost and have lower operating expenses. One carrier machine and a quarry is operational, says FlipScreen.
Grizzly screens become obsolete when faced with an attachment that handles the material once and saves on time.
FlipScreen is truly portable, reduces hauling and labour costs and provides rapid, easy separation of any material, including vegetation, rocks, scrap metal and anything you can scoop up.
All industries requiring a primary separation process benefit. From large mines to local landscape businesses, FlipScreen has reinvigorated the way sites are operated, it says.
Screen wet material with no hassles as the optional brush kit clears the mesh on every rotation. You can even mix concrete with FlipScreen’s mixing screen. The mixer removes the need for multiple attachments and equipment.
Find out more at www.flipscreen.net
Come watch the Flipscreen Demo at the Diesel, Dirt & Turf Expo from the 9th to the 11th April!
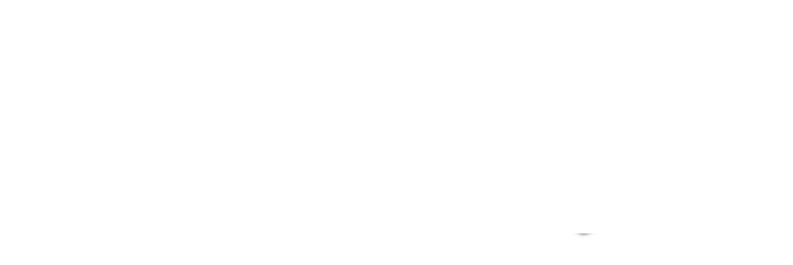
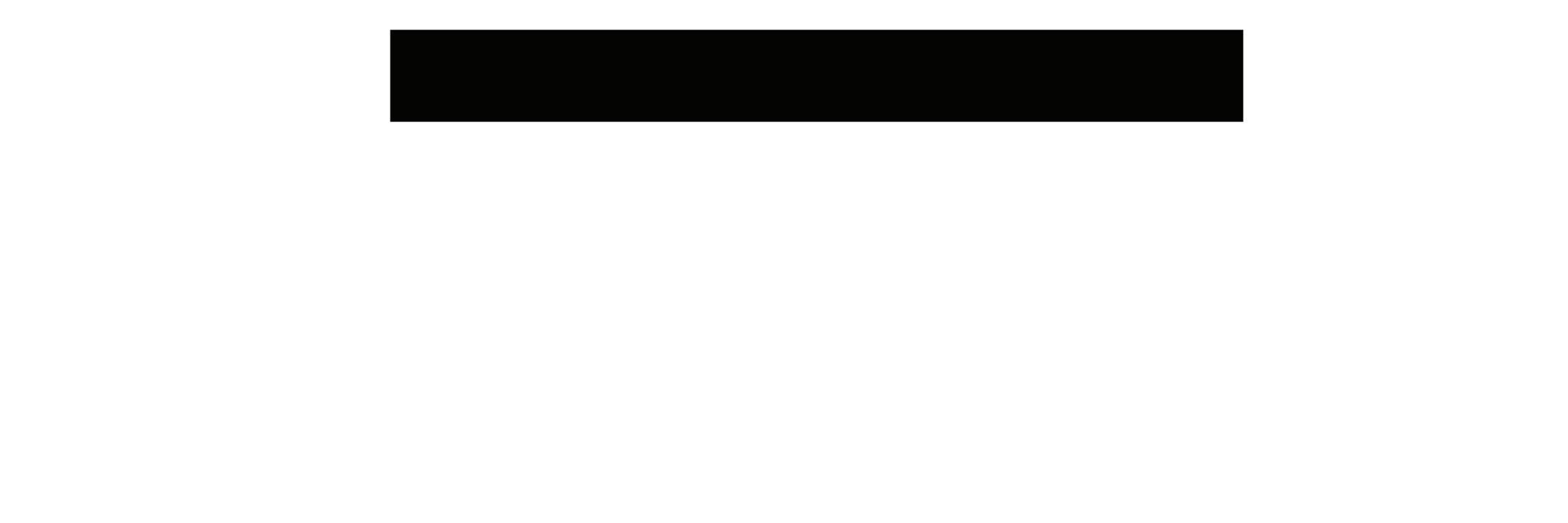
www.flipscreen.net | 02 9055 7756 | info@flipscreen.net Hitches, Buckets, Wear Parts

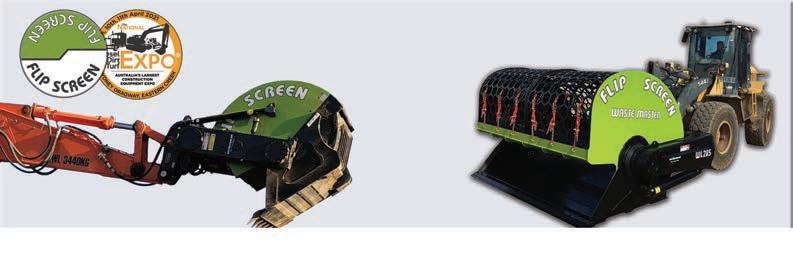
Genuine Value, Genuine Service, Genuine ANT.
Your best choice for Earthmoving Attachments and Wear parts
Great Savings. Uncompromising quality
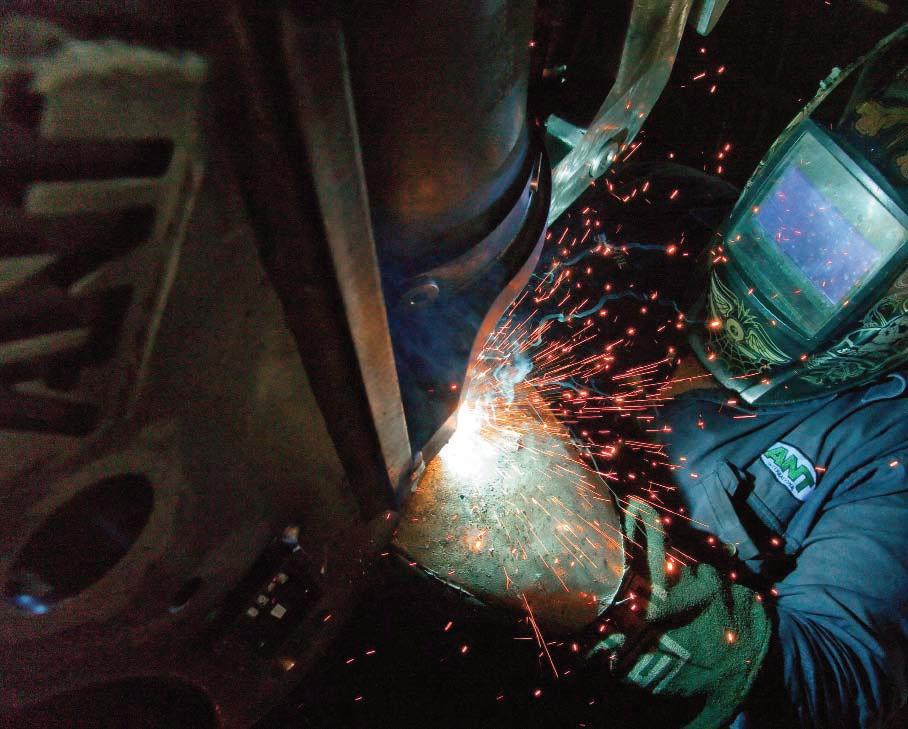