

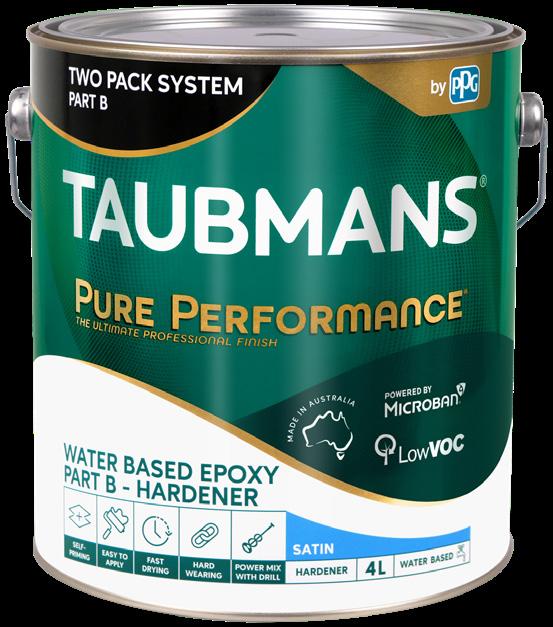
Taubmans® Pure Performance® Water Based Epoxy Two Pack is a high performing two pack water based epoxy designed to give an excellent protective finish to new and old concrete. Water Based Epoxy is selfpriming and can be used in factories, educational facilities, and garage floors* due to excellent alkali, chemical and mar resistance and surface hardness.
With Microban® anti-microbial technology incorporated into the coating, Water Based Epoxy is also suitable for high humidity areas and where an added level of protection and cleanliness is needed for your peace of mind.
With Microban, Water Based Epoxy helps prevent the growth of mould and mildew on your floors.
* Due to the wide variety of tyre chemical composition, the contact between tyres and coating may result in tyre staining.
MICROBAN® INCORPORATED INTO THE COATING
PRE-TINTED TO AS N35 LIGHT GREY
A POPULAR SMOOTH SATIN FINISH
LOW VOC AND LOW ODOUR
EXCELLENT OPACITY AND HIDING POWER
HARDWEARING WITH EXCELLENT ADHESION RESISTANCE
EXCELLENT FLOW PROPERTIES AND EASY APPLICATION
A PENETRATIVE FORMULA
SELF PRIMING ON CONCRETE FLOORS
FAST DRYING
BLEACH AND ALKALI RESISTANCE
CAN BE USED WITH ANTI-SLIP ADDITIVE
Mixing ratio: 1.1 by volume. Power mix Part A and Part B with drill individually and then again when combined.
The new Taubmans Pure Performance Water Based Epoxy has been designed to give a tough and durable protective coating for concrete floors. This product is available in a combined 16L and 8L size for both large commercial and small residential jobs.
Pure Performance Water Based Epoxy is in uniquely designed packaging with additional space available for mixing ease. When the Hardener is added into the larger Base container, there is space left for adding water and for drill mixing to help keep mess to a minimum. A third container for mixing is not needed unlike with other two-part products.
Taubmans Pure Performance Water Based Epoxy covers new and old cement and previously painted floor coatings in a variety of residential and commercial situations. With a high opacity finish, in a popular light grey, Water Based Epoxy is the perfect choice for application where a protective, low VOC, quick, and easy application floor coating is needed to cover visually unpleasant concrete floors.
Microban® is the trusted global leader in antimicrobial technology.
For over 35 years, Microban® has redefined clean with protection that lives on by offering antimicrobial solutions in over 50 countries. Microban® and Taubmans work together to provide effective antibacterial and antifungal benefits and solutions that are built into the paint during the manufacturing process. By inhibiting the growth of mould and mildew painted surfaces are kept cleaner and longer-lasting.
This means Pure Performance Water Based Epoxy with Microban® is ideal for use in hospitals, health or aged care facilities, educational facilities, and commercial buildings.
Why use antimicrobial technology?
• Microban® enables a cleaner, fresher and more hygienic surface during and after painting
• Painted surface remains antimicrobial for its expected lifetimeantibacterial and antifungal properties will not wash away
• Helps prevent stain-causing microbes so you can leave a job with confidence
• An added level of cleanliness protection for your customer’s peace of mind
• 24/7 product protection
The GBCA is a not-for-profit organisation committed to developing a sustainable property industry for Australia and encourages the adoption of green building practices.
The GBCA launched Green Star in 2003. Green star is Australia’s largest voluntary and truly holistic sustainability rating system for buildings, fitouts and communities. It aims to transform the built environment by reducing the impact of climate change, enhancing our health & quality of life, restoring and protecting our planet’s biodiversity and ecosystems, driving resilient outcomes for buildings, fitouts, and communities, contributing to market transformation and a sustainable economy.
Taubmans Pure Performance Water Based Epoxy Supports Green Building Council Australia ‘Green Star’ rating tools:
• Green Star – Design & As Built
o Indoor Environment Quality – Credit 13 Indoor Pollutants
• Green Star – Interiors
o Indoor Environment Quality – Credit 12 Indoor Pollutants
Finish Satin depending on surface and application method
Colour Pretinted to AS N35 Light Grey
Parts Part A Base and Part B Hardener
Mix ratio Part A 1 : 1 Part B by volume. Power mix with drill
Substrate Bare or previously coated old or new interior concrete
Humidity
Below 80%. High humidity can reduce sheen level and mar resistance
VOC 30 grams/litre
Temperature 10º - 35ºC. Minimum surface temperature should be at least 3ºC above dew point
Coverage 6-10m2 p/ltr
Application tools
Good quality brush and roller. Can be sprayed
Pot Life 1 hour at 25ºC
Recoat Time 4 hours to 7 days
Light Traffic Time 24 hours
Normal Traffic Time 7 days
Clean-up Water. Flush application tool immediately and thoroughly after use with water
Slip Rating AS 4586-2013
With White Knight® Ultra Pave® Grip Additive applied as per instructions, Water Based Epoxy is able to achieve P5/R12
Concrete moisture content below 5.5%
Taubmans Pure Performance Water Based Epoxy has been developed to work by itself or with a suitable anti-slip additive to increase slip resistance.
If you need a higher slip resistant floor for your project, Water Based Epoxy is recommended to be used in conjunction with White Knight Ultra Pave Grip Additive. Together, this will give a R12 / P5 result when tested to AS 4586-2013 and applied to the final coat as per additive instructions.
For recommended slip resistance for your project please review the latest National Construction Code.
AS 4586-2013 APPENDIX A (WET PENDULUM TEST)
AS 4586-2013 APPENDIX D (OIL-WET INCLINING PLATFORM TEST)
Preparation
Surfaces must be clean, dry, sound, and free from all surface contamination including loose or flaking paint and salt deposits.
Repair surface defects such as cracks or holes with a suitable filler.
A test patch is recommended prior to first coat.
For new concrete, allow concrete to cure for a minimum of 28 days.
Areas of grease, oil or dirt need to be cleaned by washing with mild detergent or with a suitable solvent.
To get a uniform surface profile, use acid etching, power tool cleaning, grinding, or abrasive blast cleaning. Thorough removal of dust is required by vacuum cleaning.
Thin down product by up to 20% with clean water for the first coat to aid penetration followed by two non-thinned coats.
Areas of grease, oil or dirt need to be cleaned by washing with mild detergent or with a suitable solvent.
To get a uniform surface profile and improve adhesion, use power tool cleaning or abrasive blast cleaning. Ensure existing sealers or curing compounds have been removed, and an absorbent concrete substrate is achieved. Thorough removal of dust is required by vacuum cleaning
If abrasive cleaning exposes areas of bare concrete, refer to Bare Concrete instructions.
• Power stir Part A and Part B separately for at least 2 minutes each.
• Add parts A & B together (1:1 ratio by volume) and power stir for at least 2 minutes at a high speed without causing excess foaming. Improper mixing can result in product failure.
• If water is added to thin, continue to power stir for an additional minute.
• Pot life is 1 hour at 25ºC. Do not use after 1 hour as this can result in gloss inconsistency and performance failure.
• A test patch is highly recommended before full application.
• Apply two coats of the mixed epoxy using a good quality brush or floor roller. Stir paint continuously during application.
• Depending on the absorption rate of the concrete, extra coats may be required to produce the desired finish.
• Apply first coat using an airless sprayer using a 17-21 thousand spray tip at 2000 psi.
• Back roll first coat, if required second coat can be back rolled.
• Depending on the absorption rate of the concrete, extra coats may be required to produce the desired finish.
• Do not allow the mixed paint parts to remain in hoses, gun, or spray equipment.
• Flush application tools immediately and thoroughly after use with water to help prevent blockages.
• After mixing and a prolonged break, it is recommended to recommence work with freshly mixed paint.
• Once the base and hardener have been mixed together, they should not be resealed.
There is no need to dispose of application tools prior to the application of the second coat which is common with traditional solvent based epoxies.
Troubleshooting
If I have any product left in the tin after it is mixed can I keep it for another day?
If the parts A and B are mixed together you cannot keep this as it will start to harden after 1 hour and become solid in the tin. After a prolonged break, it is recommended to recommence work with freshly mixed paint.
Can Pure Performance Water Based Epoxy be used outside?
This epoxy can only be used outside with a suitable UV resistant topcoat.
Can I hand mix?
No, you must power stir with a drill as improper mixing may result in product failure, poor drying, or a patchy finish.
How do I clean the floor once it is complete?
After 7 days, clean fresh water or diluted bleach can be used for cleaning.
Can I apply over wood / plaster board / plaster / metal?
No, this epoxy is only suitable for concrete and previously painted concrete.
Why is my floor patchy and the gloss level inconsistent?
The cause of this is likely to be improper mixing or the wrong grinding shoes have been used. Please contact customer service for more information or refer to the Technical Datasheet.
Do I need to acid etch first?
Acid etch is only recommened on bare concrete. However, for best results you can alternatively use grinding, power tool cleaning or abrasive blast cleaning to get a uniform surface on bare concrete. See application pages for more detail.
Do I need a primer first?
No, a 20% water-diluted first coat can be used as a primer layer on bare concrete. For pre-coated substrates, no primer is required, please follow the instruction on back of pack or the Technical Datasheet.
Why is the epoxy peeling off the floor?
It is likely that not all surface contaminates were removed before application or improper mixing has occurred. Please ensure the floors are clean and sound before application. A test patch is highly recommended before full application.
Why is the epoxy not drying properly?
Either too little hardener was used, Water Based Epoxy is 1:1 ratio by volume, or improper mixing occurred. Power mixing Part A, Part B, and then combined for 2 minutes each helps ensure a thorough blending of the epoxy.