Circular Design Primer for Interiors
Acknowledgements
Leigh Christy and Yehia Madkour, Project Directors
Jesce Walz, Author, Principal Investigator
Kimberly Seigel, Project Manager
Content Contributors:
Perkins&Will London
Simon Bone, Asif Din, Grant Spencer, and Adam Strudwick
Featured projects:
5 Bank Street, European Bank for Reconstruction and Development
Netflix London
Perkins&Will Washington D.C.
David Cordell, Brittany McNairy
Featured projects:
Greenpeace Headquarters
U.S. Green Building Council Headquarters
Perkins&Will Vancouver
Amy Brander, Rufina Wu
Featured project: Our Vancouver Studio
Schmidt Hammer Lassen (SHL)
Helena Christensen, Enlai Hooi
Featured content:
Visual and written contributions
About Perkins&Will
Innovation starts with inquiry. In our never-ending quest for knowledge, we push limits, take risks, investigate, and discover.
Perkins&Will, an interdisciplinary, research-based architecture and design firm, was founded in 1935 on the belief that design has the power to transform lives. Our research is inspired by our practice, and our practice is informed by our research.
We believe that research holds the key to greater project performance. Our researchers and designers work in partnership from project start to completion. We constantly ask ourselves, “What if?” “What’s next?” This makes our ideas clearer, our designs smarter, our teams happier, and allows us to innovate to achieve our clients' goals and further best practices in design.
www.perkinswill.com
Abstract
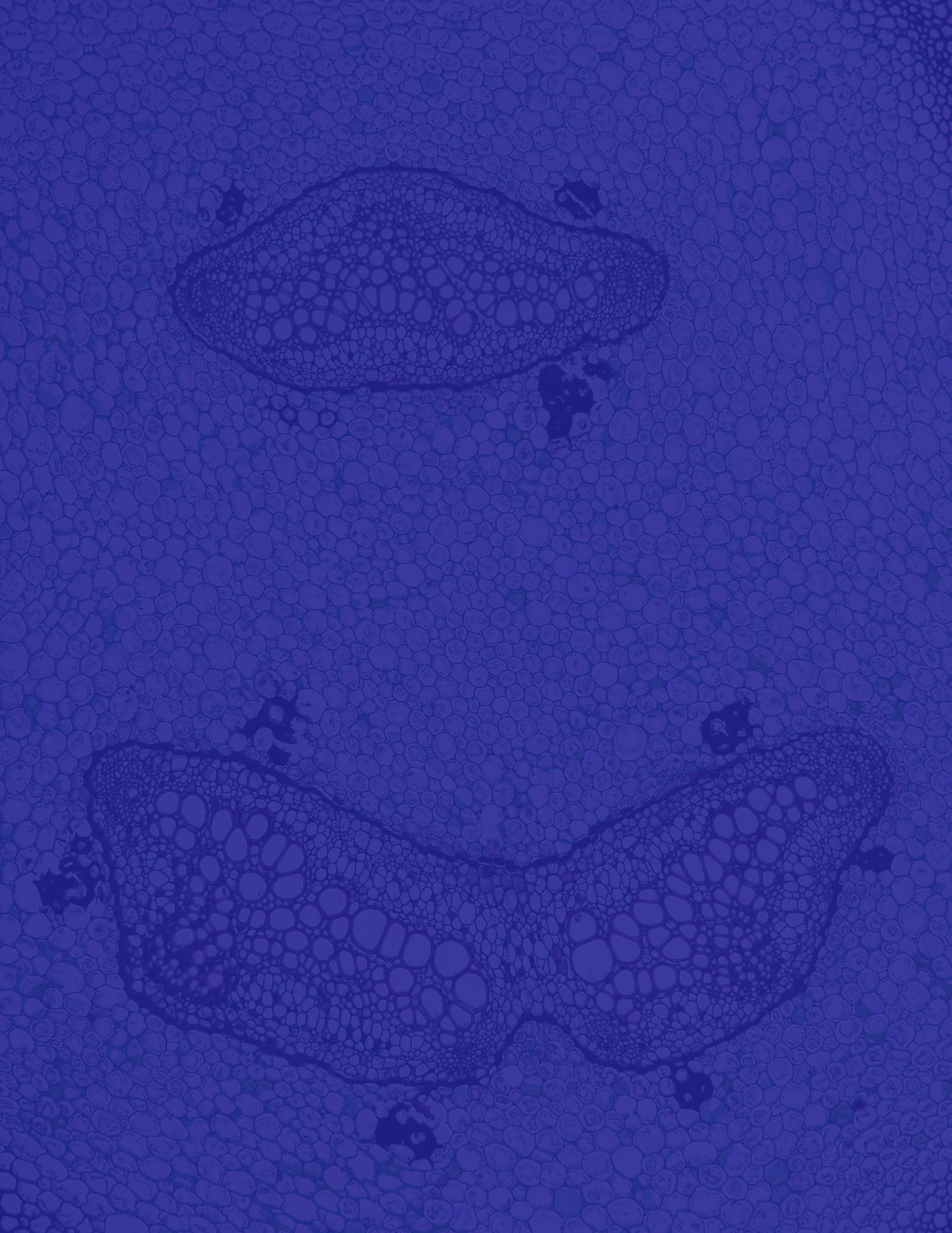
The Circular Design Primer for Interiors distills best practices in circular design from projects across our global practice, making a circular approach more accessible for design teams. While the principles presented here are inspired by commercial interiors, they can be applied to projects of all scales.
Circular design is a powerful way to reduce environmental impacts because it minimizes emissions and waste while unlocking the latent economic value of building materials. By pairing material optimization and reuse with adaptable space planning, it maximizes the long-term utility of building materials as assets.
While reuse is foundational to carbon-conscious design, widespread adoption faces challenges, as the infrastructure needed to support a circular economy is still evolving. This primer helps teams navigate these obstacles, integrate circularity into their design processes, and prioritize high-impact strategies tailored to each project’s needs and context.
Beyond individual projects, circular design fosters industrywide change. Every project that implements circular strategies can shape systems to make it easier for future projects to follow suit. Five example projects show how teams have met ambitious sustainability goals and set new precedents for broader adoption of circular outcomes.
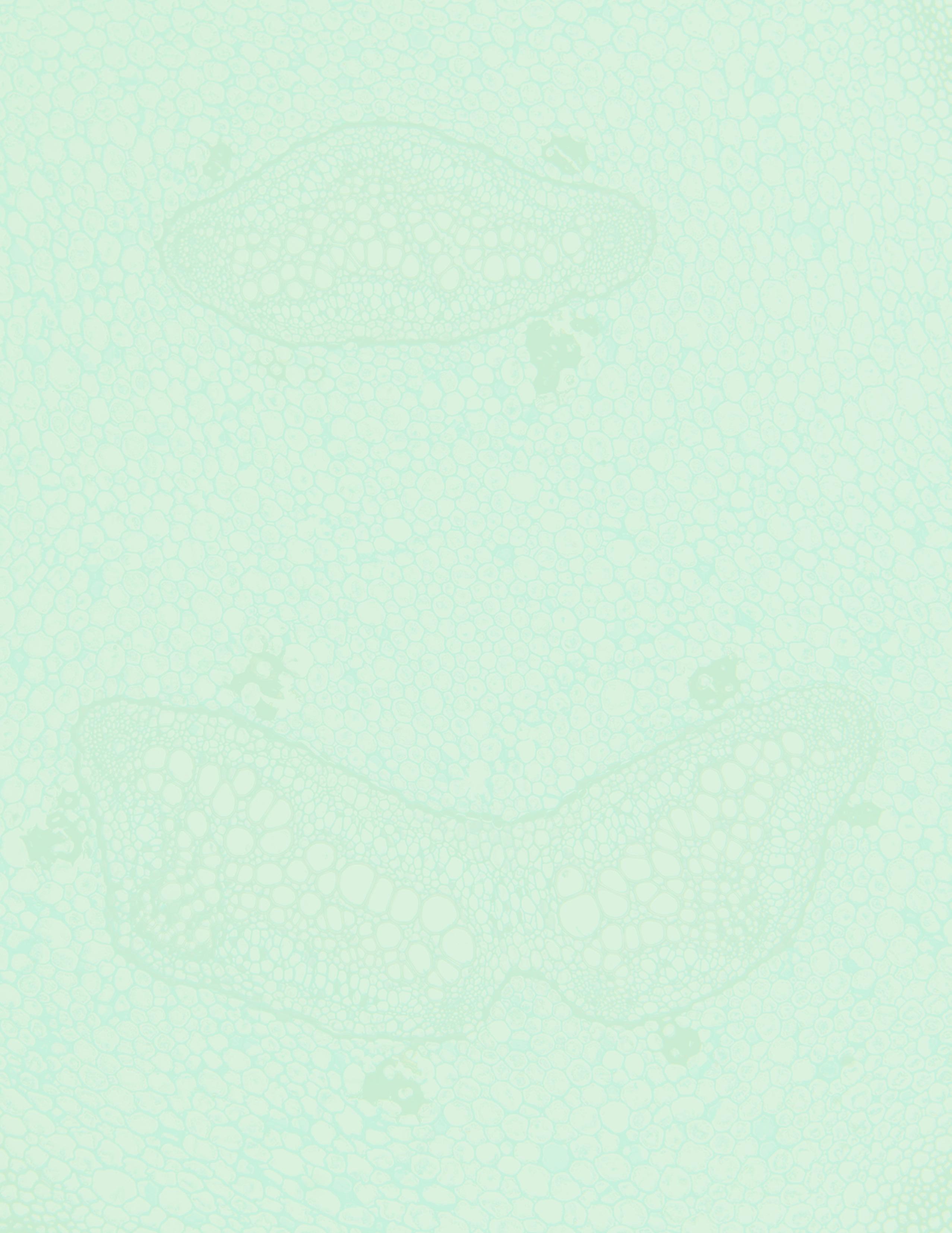
Executive Summary
Nothing is ever truly created from scratch. Materials are tangible resources that can be shaped, relocated, and repurposed. While their perceived value shifts with changing needs and sentiment, their physical worth remains.1
Interior architecture is designed to meet the ever-evolving needs of people and businesses. However, repeated interior fitouts tailored to specific requirements can generate as much carbon over a building’s lifespan as its structure and enclosure. This cycle not only harms the environment but also diminishes the long-term value of materials.
Circular Design Primer for Interiors
leverages the power of design to uncover, track, and maximize the value of projects’ partitions, furnishings, and other materials as enduring assets.
It provides a framework for teams to integrate circular principles into interior architecture, offering overarching guidelines, practical strategies, and real-world examples.
Instead of constantly replacing interior elements, we recommend viewing each project as a “bank of materials,” a collection of elements designed to adapt and retain value over time. While traditional linear models equate change and newness with increased value, which often leads to waste, a circular mindset, in contrast, embraces preservation and reuse as fundamental design strategies.
While “keep things as they are” may seem antithetical to design, a circular approach views maintaining present value while enhancing a space as a design challenge.
In a circular economy, a designer’s role evolves to include actions like assessing existing spaces and elements, integrating each existing element at its highest value before modifying it or sourcing new materials, and documenting and archiving elements for future use. Prioritizing reuse and material stewardship unlocks multiple benefits, from cost and carbon savings to waste reduction, local economic support, and a deeper connection to materials.
Designers who pursue a circular approach will cultivate a rich understanding of materials as investments in future reuse, viewing each material as a seed that is planted for harvest in 5, 15, or even 60+ years.
This means designing for adaptability and ensuring information about materials is recorded, tracked, and transferred as spaces change. A well-coordinated team can proactively plan for how materials are sourced, procured, installed, used, and eventually repurposed, delivering a project that will be admired and cared for by its occupants over time.
This Design
1. Refuse: evaluate what’s needed
2. Rethink: design for future uses
3. Reduce: share, lease, and optimize
4. Reuse: work with existing materials
5. Repair: maintain and reuse in-place
Future Design Cycles
6. Refresh: rearrange modular elements
7. Remanufacture: disassemble and re-make
8. Repurpose: transform or upcycle
9. Recycle: when re-utilization is not viable
10. Recover: for nutrients or energy
Getting Started with Circular Design
Circular design can begin with small, intentional actions, such as sourcing reused elements and designing assemblies without adhesives or nails.
Teams can start by asking:
nj What do we really need?
nj What do we already have?
nj What can we do with what we have?
nj Where can we source what we don’t have?
nj How can these materials be reused in the future?
To apply circularity at scale, broader challenges must be addressed.
Designing a Circular Future
The most ambitious projects embed circular design goals into their basis of design, revisiting them iteratively from concept through project completion. The scope of coordination extends to include the full design team, the client’s stakeholder group (including occupants, operations and maintenance), suppliers, and subcontractors.
This primer supports circular design through a collaborative and iterative process. It begins by outlining circular design principles, then provides tools for teams to align around a shared vision and assess progress throughout the design process. Strategies and real-world examples are organized across four key scales: Systems, Spaces, Materials, and Assemblies, each spanning the design stages to offer a comprehensive framework for implementation.
Alongside design challenges, this primer also addresses systemic barriers to circularity. Even with a coordinated team, broader infrastructure gaps can create hurdles. This guide offers strategies for fostering positive feedback loops, where each project contributes to strengthening material reuse ecosystems, making it easier for future projects to adopt circular practices.
The processes outlined in this primer are part of a larger movement toward foundational change in interior design. By collaborating with contractors and suppliers, design teams can influence material manufacturing, sourcing, and procurement, making circular design more accessible across the building industry. By engaging in this way, each project becomes a blueprint for the future, accelerating the shift to a circular economy while delivering exceptional design outcomes.
Circular Strategies
The strategies outlined in this primer offer an array of opportunities for any project to engage circular design.
Survey these with the full project team, and consider which strategies are the best fit for your project. Identify key strategies to pursue and align an approach to realize them through the design and delivery process. Dig in for more details as needed and track the team’s progress throughout the design process to achieve a more circular outcome.
Process
Getting Started
Consider typical high-impact actions and elements at project outset.
Aesthetic Harmonization
Develop an aesthetic and spatial quality that prioritizes positive values over visual noise.
Collaboration Structure
Work with the project team, client, and other stakeholders to explore new possibilities. Allow shared goals to guide decisions.
Critical Assessments
Workshops
Establish a collective vision and revisit progress frequently throughout the design process.
Target Setting
Set specific, measurable targets early in the design process and consider aligning with certifications or frameworks.
Measure & Report
Use life cycle assessment (LCA) to identify priority areas of focus for impact reduction.
Compare Options
Consider the present cost, future value, and carbon, health and other impacts of each design option.
Systems
Process, not Projects
Explore ways to affect change and contribute to a circular economy beyond the bounds of the project.
Circularity Ecosystem
Map regional resources to locate services, facilities, and organizations that can support circular design in your project’s context.
Ownership Assessment
Share, borrow, or lease, elements and look for material takeback programs.
Material Passport
Develop an inventory of the project’s materials w/ guidance for deconstruction and reuse.
Digital Twin
Replicate the project virtually to enable precise assessment and planning.
Spaces
Lease Assessment
Find spaces with existing materials on-site, extend lease periods, and plan for transitions.
DfA and Bespoke Beauty
Design for adaptation with modular and demountable elements; balance this with fixed, or “bespoke,” spaces.
DfL
Design for longevity to support resilience of spaces and materials.
Use = Need
Conserve resources. Use space planning to reduce energy use and design to omit excess “stuff.”
Gamification
Engage occupants with dashboards, sensors or other feedback systems.
Materials
Less, but Better
Select fewer, but higherquality materials.
Decommissioning Audit
Maximize utilization of existing materials.
Resource Mapping
Categorize existing materials, assess their value, and determine how to incorporate them.
Circular Sourcing
Identify and procure reused materials from a variety of sources.
Material Evaluation
Assess reused materials for suitability and determine the most efficient approach to incorporate each material.
Procurement and Specifications
Plan to acquire reused elements and adjust specs. to align with circular sourcing.
Assemblies
Design for Harvest
Plan for the next use of each element.
DfD
Design for disassembly and future reuse.
DfMA
Design for manufacture and assembly; leverage the benefits of off-site fabrication.
Misfit Materials
Embrace variation and prioritize reuse of scrap materials.
Reclaim & Assemble
Process reused materials into new assemblies, maximizing value and minimizing modifications.
Circular Assembly Guidance
Review guidance for circular design of specific assembly types.
Core Concepts
Why Circular Design?
Why Circular Design?
Circularity creates a positive feedback loop of value.
Spatially, circularity represents an opportunity to distill a pragmatic and innovative design sensibility that prioritizes honest expression and added value of materials over time. Socially, reusing building elements can tell a story and add to the character of a space. Economically, circular design expands markets by activating existing materials’ monetary value and generating local entrepreneurial opportunities. Environmentally, circularity reduces resource extraction, carbon, waste, and other ecological impacts.
Of these values, circular design’s ability to reduce the built environment’s ecological impacts is paramount.
As a global society, we have exceeded planetary boundaries associated with both climate change and biodiversity loss.2 The pattern that led to this point is alarming: In 2024 alone, we extracted 106.6 billion tons of raw material from the earth3 and emitted over 53 billion tons of greenhouse gas emissions (GHGs).4 Across all solid waste types, we produce over 25 billion tons of waste each year. Total global waste generation is expected to increase to at least 45 billion tons by 2050.5
Approximately half of these extracted materials are used in the built environment. In turn, building, construction and demolition are estimated to generate 40% of global GHG emissions and a third of the world’s waste.6 This escalating cycle of depletion, production, and pollution is fundamentally unsustainable, yet the building and design industry’s current approach depends on and supports it.
In contrast, a circular economy shifts focus from extraction to using existing assets. A circular approach conserves resources, supports local economies, is the core component of carbon reduction strategy, and can promote natural systems’ regeneration.
Every opportunity to practice circularity makes a difference, both now and for our future, as each kilogram of carbon dioxide that is emitted today requires thousands of years to cycle out of the atmosphere.7 However, realizing circular design, and in turn circular economy, is no small task.
Circular frameworks are the building industry’s next paradigm shift in the journey towards responsible, resilient, and regenerative design. This shift begins with fostering a design culture that acknowledges the impacts of designing with new materials; prioritizes reuse of existing building elements; and plans beyond today, designing for the use, reuse, and next life of each element over time.
Annual Extraction and Emissions, with Atmospheric CO2
Image: Adapted and compiled from multiple data sources.8 Note that different emissions and extraction data are shown together to visualize relationships, not to compare magnitude.
Global Annual Waste Generation
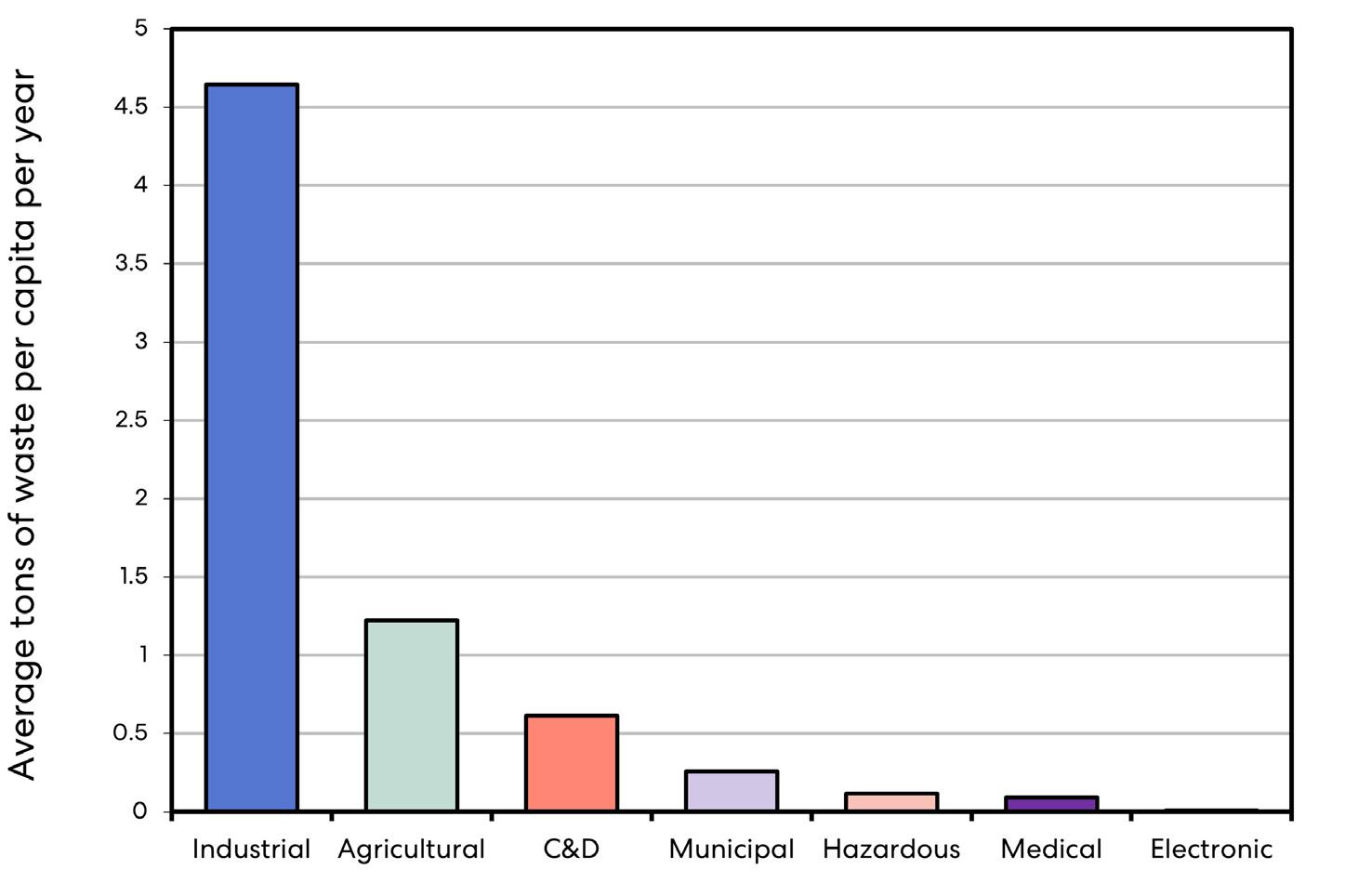
The built environment is responsible for construction and demolition (C&D) waste as well as a portion of industrial waste (from product manufacturing)
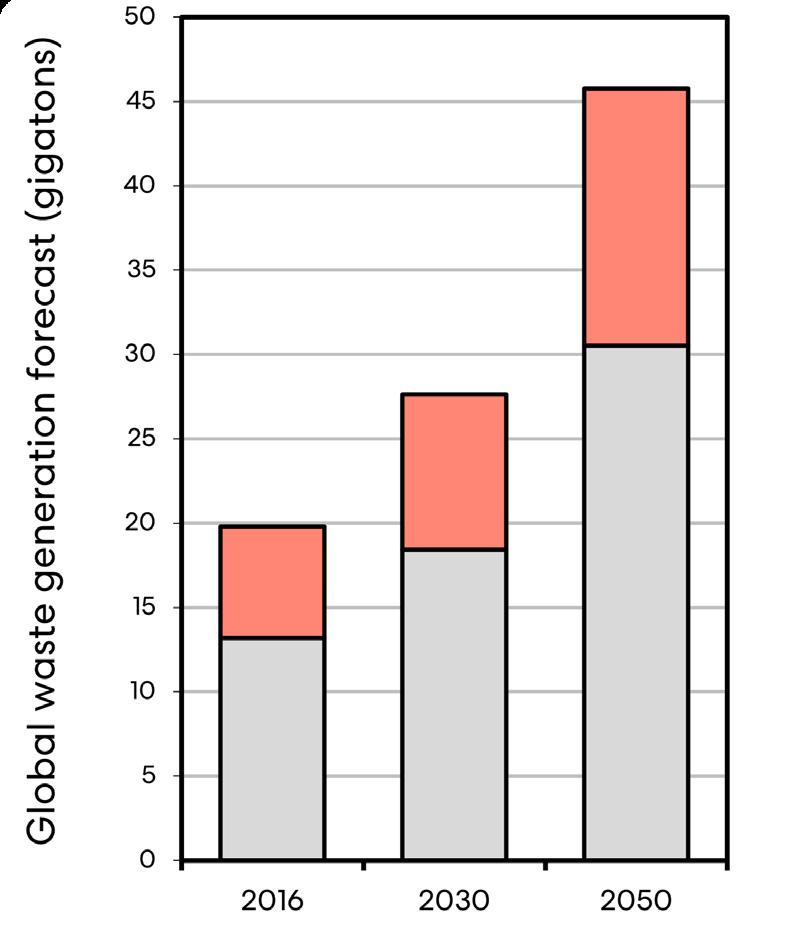
Why Interiors?
Interior design plays a crucial role in the broader context of circular architecture.
Interior refit projects inherently support circularity by reusing existing structures, thus aligning with whole-building reuse strategies. At the same time, the frequency of material “turnover” associated with refitting interior spaces results in an aggregation of carbon and waste impacts over time. After just four cycles of fitout and refit, the embodied carbon impact of a building’s interior fixtures, finishes, and furnishings (FF&E) can equate to that of the building’s core and shell.11 This reality highlights the urgent need to apply circular principles to interior projects to prevent unnecessary environmental impact.
Interiors projects often move at a rapid pace, yet even under tight schedules, teams can integrate circular strategies by distilling an approach that prioritizes essential elements, mindful sourcing, and design for reuse. The demand for flexible spaces is growing as organizations increasingly seek environments that can evolve with their changing needs. By designing interiors that are both adaptable and reusable, teams can meet these demands while promoting stewardship of material resources. In essence, circular outcomes add value to projects in a way that is good for business and good for our planet.

How does a circular design project differ from a linear project?
Context. Circular design is in large part about the interplay between the project site and specific materials that become available. The specific conditions of a project, including location, brief, and access to and availability of resources, will affect the scope of what circular design actions are possible for each individual project as well as how these actions are realized.
Multi-scalar mindset. Circular design projects are connected more by mindset and approach than by a prescribed process. Circular design strategies can manifest at many scales, including space planning, material sourcing, methods of assembling components, and even at a socioeconomic scale. This primer outlines strategies across these scales to support teams’ engagement with a circular design process.
Present value. A core tenet of circular design is the goal of maintaining materials at their present value for as long as possible prior to modifying or even transforming them. While “keep things as they are” may seem antithetical to design, a circular approach views maintaining present value while enhancing a space as a design challenge, and uses this as the starting point for other design decisions.
Future value. Circular design development includes planning for both the current and next lives of the project’s elements. This requires design for repair, refurbishment, adaptability, disassembly, and reassembly in future use cycles. Elements must be also be designed to break down into discreet components that will retain their maximum value when elements can no longer be serviced. These measures, accompanied by planning with project stakeholders for ownership and maintenance, increase long-term value and transform the design into a space that is also a bank of material assets.
Stakeholder team. Circular design requires curiosity, communication, and diligence. It is not a solo game, but a team sport that requires active engagement with potential suppliers, fabricators, and the full project team. The most effective circular design projects begin with an early onboarding process to establish a shared vision among the project’s stakeholders. These include owners, occupants, and operators of the space. Establishing an integrated and inclusive approach from a project’s outset incites an innovative mindset to support the project’s goals.
Timing. In circular design, the timeline of a project evolves to accommodate improvisation. Project owners and teams must challenge their thinking by reconsidering the length of lease periods, adapting expectations for timing of when materials may be sourced, and simultaneously designing for present and future uses of materials and assemblies.
This is the next project. Circular design is a call to action for every project to promote change in the building industry. Any team can explore the strategies outlined in this primer, select appropriate strategies to focus on, and contribute to adoption of circular practices in decommissioning, sourcing, design, and (re)construction, so that future projects can engage more fluidly in a circular economy.
The Circular Economy
Circular design is supported by advanced underpinning frameworks, originating in the broader context of circular economy. Circular economy is rooted in the idea of decoupling economic growth from economic development and focuses on the goal of keeping materials and assemblies in use at their highest potential value over time. The Ellen MacArthur Foundation cites these principles as the basis of the circular economy:
14
The remainder of this primer references several of the elements in the chart to the right, with a focus on actions for design.
“Underpinned by a transition to renewable energy and materials, the circular economy is a resilient system that is good for business, people, and the environment.” 13
Circularity and Related Concepts
In practice, the principles of circularity overlap with many other sustainable and ethical design goals. The field can be noisy, with new terms and frameworks arising frequently. To reduce ambiguity, the following chart compiles some of the most recognized concepts and relates them to the tools and frameworks that have arisen to support them, contextualizing relationships among these concepts.
This is by no means comprehensive, but it creates clarity about the function and interrelation of these terms. Additionally, understanding the overlapping priorities between sustainability, circularity, and regenerative design may reveal an entry point for further exploration of circular design in a project that is already exploring related goals.
Understanding the overlapping priorities between sustainability, circularity, and regenerative design may reveal an entry point for further exploration of circular design in a project that is already exploring related goals.
Material Banks
Buildings as Material Banks (BaMB) is a framework that supports the transition to a circular economy with a strong value case. BaMB leverages the value of existing assets to advance circularity and decrease waste.15 The BaMB concept can be coupled with the hierarchy of the “10 R’s” (page right), as each of these approaches prioritizes rightsizing, optimization, and low-impact strategies to minimize expenditure and maximize materials' value over time.
The outcome is a project that is also a repository of high-quality material assets that are easy to take apart and recover, leading to both cost and carbon benefit. When proposing circular design strategies, designers must leverage these benefits, making a shift from viewing a design as “a final product” to engaging clients in the ownership of a bank of material assets.
Design teams may also involve quantity surveyors and materials or cost consultants to support the integration of circular and economic factors into design decisions. To facilitate design optimization and increase the value of a project’s elements, explore these questions in early design:
What elements does the design really need? Omit or optimize elements wherever viable.
What resources are available? Source reused, refurbished, or remanufactured elements.
What must be added? Add to the system asneeded through circular sourcing and design elements in a way that will allow them to be appreciated and reused in the future.
How long will elements last? Design durable elements for adaptability and reuse. Extending service life reduces the impacts of waste and replacement and increases the likelihood of longterm value retention.
How do these actions add value? Establish cost and carbon values for circular design decisions (optimization, reuse, and future reuse/resale) to support an understanding of the project as a material bank.
The 10 “Rs”
The “R” strategies are a set of propositions for material use that expand circular thinking beyond “reduce, reuse, recycle.” Circular design maximizes optimization via R0: Refuse, R1: Rethink, and R2: Reduce, and includes planning for use stage, extended use(s), and end of use outcomes for each material.
Together,
these strategies reinforce the possibility for materials to come from existing or discarded products, rather than new materials.
The “R” strategies introduce the concept of “loops,” or ways resources can be sent back into the system for a new purpose. They are typically broken down into three scales across the 10 R Strategies. Shorter loops relate to more immediate reuse of materials and provide more control over circularity. Longer loops require planning and systemic support, or even institutional change, to be realized.
Omitted or very short loops
Right-size the program and optimize product design and manufacturing; most effective and verifiable.
Short loops
Reuse elements and extend their service life through continued use; requires planning and coordination.
Medium loops
Remake elements for their same function or identify new applications for them; more resource intensive.
Long loops
Extract resources from materials after more direct reuse is no longer possible.
Omitted or Very Short Loops
Strategize & optimize: core technology innovation
The “R Ladder”
The
R
Ladder is a primary tool for prioritizing circular design options.
Strategies higher on the ladder are most effective at reducing the need for new resources. Importantly, this tool should be used to design for both “now” and for “next.” This means designing the current project using low-impact strategies and designing for each element in the project to travel through the R Ladder over its life span.
Short Loops
Maintain present value: Revenue model innovation
Medium Loops
Transform for new use: Product design innovation
Long Loops
Plan for post-use: Diversion and processing innovation Waste
Exiting the circular system 9. Recover
Process
From Project to Process
Circularity incites a shift from designing a project to designing a process.
A linear process involves curating a set of elements that are then specified, priced, procured, and installed. A team may have sustainability goals for those elements, but they are typically composed of extracted materials and installed without a plan for their future use when the design is complete.
A circular process transforms the design into a container for a kit of parts and includes instructions for using the kit and its parts in the future. Other sustainability metrics integrate with circularity, but circular design and economy promote closed loop systems first and foremost. Circularity adds complexity to the design process. Actions like material sourcing and planning for future reuse may span the stages of the design process rather than adhering to set milestones.
This section of the primer provides an overview of how circular strategies can integrate with stages of a typical design process. Subsequent sections outline circular strategies across four scales of interior design:
Systems: Each project exists within a set of systems. These include the project’s physical context, ownership structure, and the greater socioeconomic and ecological context. Systems strategies address both conceptual and technical systems for material take-back and tracking.
Spaces: Occupants may rotate through the project’s physical location over time. The project, in turn may move to other locations in the future. Spatial strategies address flexible and modular design as well as the composition, quality, and uses of space within the design.
Materials: A circular material palette is informed by the sources and quantities of reused components that are available to the team. Material strategies focus on circular sourcing of design elements as well as planning for how those materials will be specified, procured and incorporated in a design.
Assemblies: Assembly strategies support maintenance and reuse of existing elements, fabrication of new assemblies with reused or new materials, and fabrication methods to increase efficiency, flexibility and future reuse and disassembly.
The strategies to follow provide entry points into the circular design process. Collaborate with your project team to assess whether and how each strategy may apply to your project, develop a plan to respond to priority strategies, and revisit progress throughout the design process to realize circular outcomes.
Linear Material Flows
Linear Material Flows
Linear Material Flows
EXTRACT & EMIT
Extract and Emit Waste
EXTRACT & EMIT
WASTE
WASTE
SYSTEM : Finite resources
STRUCTURE : 30-100 years
SYSTEM : Finite resources
SKIN : 20+ years
STRUCTURE : 30-100 years
SPACE PLAN : 3-40 years
SKIN : 20+ years
MATERIALS : 1 day-100+ years
SPACE PLAN : 3-40 years
ASSEMBLIES : 3-40 years
MATERIALS : 1 day-100+ years
ASSEMBLIES : 3-40 years
Circular Material Flows
Circular Material Flows
Circular Material Flows
RETHINK, REDUCE, REUSE
MAINTAIN & TRANSFORM
MAINTAIN & TRANSFORM
Maintain and Transform
SYSTEM : Renewable resources
STRUCTURE : 100-300 years
SYSTEM : Renewable resources
SKIN : Servicable
STRUCTURE : 100-300 years
SPACE PLAN : Adaptable
SKIN : Servicable
MATERIALS : Reused
SPACE PLAN : Adaptable
ASSEMBLIES : DfL/DfD
MATERIALS : Reused
ASSEMBLIES : DfL/DfD
Rethink, Reduce, Reuse
RETHINK, REDUCE, REUSE
Circularity in Practice
Circularity can seem abstract until it is applied through practice. Ultimately, circular design is realized both by working through and adapting the design process. Design drawings, coordination meetings, finish schedules, specifications, and shop drawings are tools to further circular design goals.
The process map to the right outlines key actions that are associated with each of the four scales of design that are explored in this primer, and it overlays these with the stages of the design process. Together, these actions support the goals of minimizing waste, maximizing reuse, and supporting materials’ long-term value.
Ideally, as many of these efforts should be applied as possible. However, this map is not intended to be a definitive or static resource. Actions may occur more periodically than visualized here, or they may occur in different design stages. Use the map as a guide to assist in planning and modify it according to your project’s scope and context.
What are the project’s goals and context?
What is needed?
What is available?
How can it be used?
Where can remaining elements be sourced?
How can planning reduce future impacts?
How will components be joined and fabricated?
What documentation is required?
Which elements of the construction process require verification? What goals did the project achieve?
Where will next steps be communicated?
Circular Design Process Map
Systems
Spaces Materials Assemblies
Harmonize design aesthetic w/ circularity goals, assess the project's context, & align the full team around project drivers.
Kick off the project. Hold a workshop to identify priority strategies; establish a workshopping cadence & coordination structure.
Set targets and establish a decision matrix, digital execution plan, and templates for progress tracking & material passporting.
Circularity ecosystem mapping
Ownership assessment
Engage and build upon local circularity resources to strengthen circular economy and contribute to systems change
Lease assessment; minimize white boxing & ID "end of lease" pathways
Design for Longevity (DfL)
Fixed (bespoke) vs. Flexible (modular) space plan
Resource conservation plan
If existing space: decommissioning audit & resource mapping on-site
Resource mapping off-site
Establish a procurement plan with the GC; continue to ID and propose circular sourcing options throughout the design process
If existing space: Plan for refurbishment and integration, resale, or donation of existing elements
Select & apply assembly strategies to maximize long-term value & minimize new inputs & waste (e.g. DfL, DfA, DfMA, DfD)
Measure & Report: Run an LCA to identify focus areas; report on cost, carbon, & sourcing; adjust course to align with targets.
Survey the supply chain for innovative opportunities
Coordinate material passporting and/or digital twin
Staging plan for migration from an existing space and/or storage of reused elements
Explore gamification
Refine carbon requirements & decommissioning plan
Coordinate DfA & DfD with shop drawings
Finalize specifications and end-of-life instructions Plan for installation and DfA/DfD with contractors
Confirm Progress: update reporting per selected metrics & targets; adjust the project as needed to align w/ targets.
Construction Reports: monthly reports to stakeholders on the construction & build-out as compared to agreed upon targets.
Finalize material passport and/or digital twin; transfer to client + O&M
Protect existing builtin components during construction
Follow the decommissioning plan to maximize reuse; verify submittals
Verify fabrication & installation; update docs. to include as-builts
Final Report: demonstrate the project's current & future impacts; offset if needed for net-zero targets.
Communicate details about the project's optimal use and plans for future treatment of its elements to key stakeholders.
Share lessons learned to benefit other projects; celebrate the project's successes with all stakeholders & the project team.
Getting Started
Key strategies for circular interiors will vary greatly among projects based on the brief, context, and design intent. To get started, teams may take these typically high-impact considerations into account at the outset of the design process:
High-Impact Actions
01 ― Location selection and pre-lease evaluation. Work with clients to identify spaces to lease that already have usable materials in place. Work with the space owner to perform a decommissioning audit, map existing materials to determine what to keep vs. reuse elsewhere, and eliminate additional pre-lease placeholder materials.
02 ― Design for harvest. Begin design with the intent of “harvesting,” or removing and reusing, all the project’s elements at the end of this design’s use cycle. Employ design for durability, modularity, and ease of assembly and disassembly and provide the client team with documentation to facilitate this future harvest.
03 ― Share, lease, and reuse elements. Search for alternatives to owning assets directly wherever viable. This may include sharing or reservation systems. Leasing packages are also common for furnishings, carpeting, and other elements. Couple this with sourcing reused, rather than new, elements. This may require steps like rewarranting elements or working to remove the stigma of refurbished materials.
04 ― Assess and reduce embodied carbon. Measurement supports management. Identify your specific project’s highest impact elements using life cycle assessment (LCA). Use the circular strategies in this primer to reduce these elements’ impacts and share progress with the team to reach quantifiable percent reduction targets.
05 ― Transparency. Carbon and waste are not the only metrics to consider. Select new elements that can verify compliance with material health, supply chain equity, and biodiversity protection standards.
High-Impact Elements
06 ― Furnishings. Furniture from virgin resources contributes to 30% or more of the carbon footprint of a commercial building over its lifespan.18 Source reused or leased furnishings. Sell decommissioned furniture or donate it to an exchange service.
07 ― Metals. Interiors projects may include structural metal, as well as trim, doors, panels, mullions, and other metal finishes and furnishings. These are carbon-intensive to produce. Teams should both look for reused metal elements and right-size member profiles, gauges, and spacing between periodic elements like studs, channels, and clips. If reuse is not possible, source 100% recycled content and always design metal-based elements for disassembly and reuse.
08 ― Partitions, wall finishes, and floor finishes. These are frequently modified during refit, compounding their impacts. Minimize layers of material and identify modular or leased options where viable. Couple this with design for adaptation and reuse.
09 ― Raised access flooring. Omit raised flooring if possible or attempt to secure it from a reused source. For new products, preference non-metallic products like calcium silicate. Plan to take raised flooring to the next space at end of lease or negotiate to leave it in place and design it for future reuse.
10 ― Vinyl, PVC, foam, & fossil fuel-based materials. These have negative human health and environmental impacts and are non-renewable. Identify elements that typically consist of a fossil-based material (such as insulation, upholstery padding, flooring, etc.) and select substitutes that come from renewable sources or consist of 100% recycled content
Aesthetic Harmonization
The he most sustainable buildings are those that are fully utilized and vibrant, balancing efficiency and sustainability with spaces that people genuinely want to use and maintain.
Cultivate a design approach that acknowledges that audiences are more accepting and attracted to an aesthetic and spatial quality that prioritizes positive values over visual or other signals. Consider the value of characteristics like patina, use of whole, simple materials, and story of a material’s source or assembly + disassembly methods.
Circular design outcomes should be lean and able to maintain value over time. This doesn’t require a minimalist or a patchwork aesthetic. Reused materials may blend in seamlessly or become featured elements. While there are limitless approaches to expressing circularity, a circular design sensibility is often marked by:
nj Awareness and expression of what things are made of and where they come from
nj Use of natural materials and reused elements
nj A legible hierarchy of elements that are designed in response to use patterns
nj Careful consideration of how components fit together and planning for what can be done with them in the future
nj An elegant, reductivist design that retains value as an asset over time
When proposing strategies to achieve circular design goals, ensure that occupant and owner experience is a central consideration. The full team, including the contractor, should be involved early to understand client drivers and align around the outcomes of the kickoff and target-setting process.
Throughout the design process, the team must harmonize design themes and space planning decisions with circular strategies to develop a design that resonates with the client’s aesthetic and functional priorities.
Collaboration Structure
A project team’s approach to the design process is as important as arriving at circular outcomes. A positive collaborative experience helps achieve success for this project and translates that success to future endeavors.
Teams must allow project goals to guide their decisions and be willing to consider new possibilities.
This requires maintaining momentum while leaving room for experimentation and failure. There are many reasons that a single option may not be viable (supply, timing, price, complexity), so it is essential to be diligent in exploring a variety of sourcing and fabrication options.
To maximize potential to incorporate circular strategies, avoid generalized suggestions and questions that have “yes/no” answers. Instead, identify and introduce specific opportunities that are aligned to the project’s context, such as, “We’ve located a local supplier that uses urban waste wood to produce dimensional lumber and millwork. Can we assess them as a potential casework fabricator?”
Circular design opportunities can be challenging to track due to moving pieces like quantity and timing of material availability or the need for refurbishment or adaptation prior to installation.
For each proposed circular element in the project:
nj Establish a decision matrix to evaluate whether it is viable to incorporate each element.
nj Identify potential obstacles or accommodations that may be required.
nj Delegate and track actions like procurement coordination, staging, refurbishment, and testing or certification.
An open and responsive design process coupled with a nimble coordination structure will empower the whole team to identify opportunities, work through technical challenges, resolve potential conflicts, and realize circular outcomes.
Critical Assessments
The circular design process is guided by a variety of assessments that occur across project stages.
During the brief stage, the team must engage in early exploration of the project’s basis and context. Establish a deep understanding of the project’s spatial, cultural, and functional dimensions, alongside the client’s aspirations and the surrounding environment’s unique characteristics. These will inform priority strategies.
Critical assessments also include development of matrices, workshops, and spatial analyses to guide design decisions, and periodic impact reporting to verify progress. Comprehensive evaluation and structured follow-through ensure that all relevant parameters are understood.
These qualitative and quantitative assessments must be approached as interconnected threads that inform the project’s conceptual narrative and guide integration of circular principles throughout the design process.
Set the Stage: Harmonize design aesthetic with circularity goals, assess the project's context, and align the full team around the project drivers
Kick off: Hold a workshop to identify priority strategies; establish a workshopping cadence and coordination structure
Set Targets: Establish a decision matrix, digital execution plan, and templates for progress tracking and material passporting
Measure and Report: Run an LCA to identify focus area; report on cost, carbon, and sourcing; adjust course to align with targets
Construction Report: Monthly reports to stakeholders on the construction and build-out as compared to agreed-upon targets
Confirm Progress: Update reporting per selected metrics and targets; adjust the project as needed to align with targets
Final Report: Demonstrate the project's current and future impacts; offset if needed for net-zero targets
Stakeholder Communication: Share details about the project's optimal use and plans for future treatment of its elements to key stakeholders
Lessons Learned: Share insights to benefit other projects; celebrate the project's successes with all stakeholders and the project team
Target Setting Workshops
Circular strategy workshops can help establish a collective design vision and achieve circular goals throughout a project.
Schedule a goal-setting workshop as early as possible and follow it up with a cadence of subsequent workshops that are integrated into the design process.
Topics may include:
Early goal-setting workshop
nj Outline the brief, project goals and drivers, and circular design aspirations with the client and team.
nj Assess the project brief alongside the “short loops” strategies in the “R Ladder” (refuse, rethink, and reduce). Consider what interventions and elements are really necessary for the project.
nj Review the circular design strategies that are outlined in this primer and organize them according to project relevance.
nj Select a set of strategies to prioritize for the project.
nj Identify clear goals in response to the priority strategies.
nj Consider referencing an existing resource, like the templates provided in the “Circular Buildings Toolkit,” to inform an engaging workshop format.19
Follow-through workshops
nj Establish a project execution plan and tracking system. Review decision matrices and templates for progress tracking with the team and delegate responsibility for tracking as applicable.
nj Meet frequently with consultants (including the contractor) to work through each material type and assembly, identifying circular sourcing opportunities and design for disassembly requirements.
nj Host thought experiments like designating a project element and going through each “R” in the R Ladder over the course of 30 minutes to identify the most impactful ways to make that element more circular.
nj Revisit the team’s priority circular design strategies and milestone reports in project meetings and presentations.
nj Maintain a record to track progress and tasks associated with specific circular goals or materials.
Target-setting is a critical step to ensure alignment with sustainability goals and accountability to realize measurable circular design outcomes. Establishing clear focus areas provides a road map for the team to direct efforts and resources, ensuring that circularity is integrated meaningfully.
Certifications and frameworks
Certifications and frameworks play a pivotal role in establishing clear, actionable goals for circularity.
Interiors projects might target:
nj Cradle-to-Cradle (C2C): For materials and products that meet stringent criteria for health, recycling, and sustainability. Prioritize C2C silver or better.
nj Living Product Challenge: A broad, yet ambitious standard for regenerative materials and products.
nj Global Recycled Standard (GRS): Verifies percent recycled content in products (20% minimum) and includes health and equity considerations.
nj American Institute of Architects (AIA) Materials Pledge: Architecture industry commitment to support materials that support equity and human, social, ecosystem, and climate health alongside circularity.
nj LEED or BREEAM: For broader sustainability goals, including resource efficiency, materials reuse, and waste reduction.
nj Level(s) Framework: A European system focused on life cycle assessments, material use, and circularity principles.
Specific, measurable targets
Once focus topics and frameworks are identified, the project team sets specific, measurable targets like:
nj Material reuse targets: A percentage of reused materials incorporated into the project
nj Carbon footprint goals: Reductions in embodied carbon compared to baseline standards
nj Adaptability objectives: Minimum requirements for reconfiguration capacity in space planning
nj Waste diversion rates: Goals for waste minimized during construction and end-of-life deconstruction
Measure and Report
Life cycle assessment (LCA) is a standardized method for measuring an element’s environmental impacts throughout its life cycle. Perform an LCA at the end of schematic design to identify the project’s top 20 highest embodied carbon elements and focus on these for circular decision-making. Update the LCA throughout the design process to validate results against the project’s targets.
Environmental product declarations (EPDs) are third-party verified, standardized documents that report on products’ embodied carbon impacts. It is common for two similar products to have very different carbon impacts from one another, so EPDs are an important way to identify lowercarbon products. Where new elements are required, use product-specific EPDs to select and specify products.
An interiors embodied carbon assessment often requires a synthesis of approaches, as teams may not model all interior finishes, and many LCA programs do not yet include data for elements like furnishings.
A team may capture interior elements’ impacts by:
nj Partitions and finishes: Either include these elements in a building information model (BIM) and use a BIMbased LCA program to assess impacts or compile a bill of materials from drawings and pricing and translate this into an LCA program.
nj Furnishings and other elements: Select products that have EPDs and use these to estimate impacts. For elements that do not have EPDs, use material takeoffs to model impacts or use generic industry estimates. While data is less available for elements like FF&E, circular design strategies may be effectively applied to any design element (with or without data).
nj Reused elements: Although reused elements have low to no upfront impact, including them in the LCA helps track their use, replacement, and end-of-life impacts.

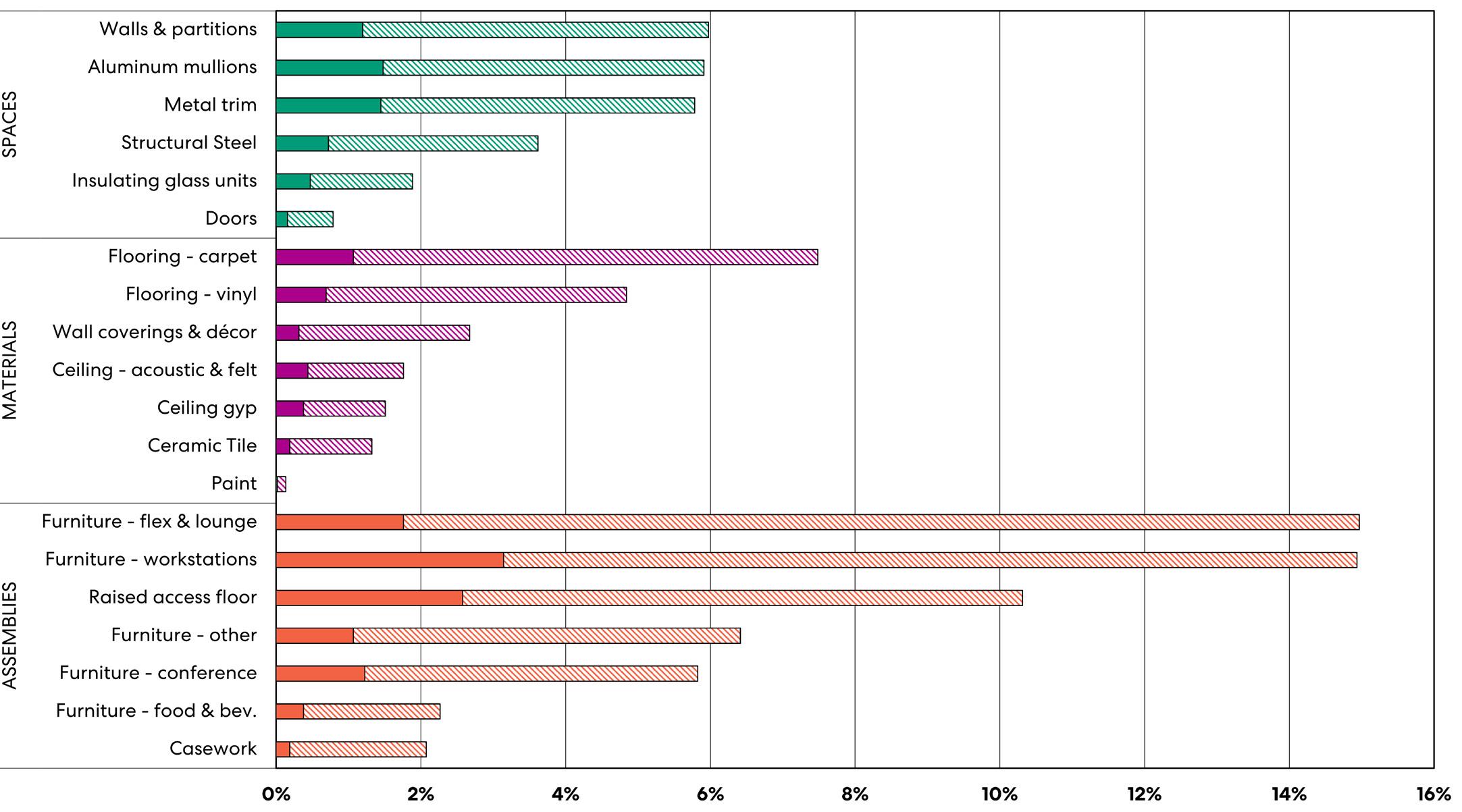
Quantitative Comparison
Compare Options
Carbon is only one factor to consider when comparing the impacts of design options. Other serious factors, ranging from cost to supply chain equity to chemicals of concern, must be considered as well. Assessing elements through various lenses encourages design teams to develop a compass to inform design that maximizes circular, economic, social, and sustainability value over time.
Quantitative comparisons may include service life, present cost, and future value of materials alongside carbon impacts. A quantity or cost surveyor may be able to support quantitative data collection. Metrics for comparison should include:
nj Weight: kilograms or pounds
nj Quantity: amount of material per unit
nj Global warming potential (GWP): carbon dioxide equivalent emissions (kg CO2e) per unit
nj Present cost: local currency units
nj Future value: local currency units
nj Distance from site: kilometers or miles
Life Cycle Cost Analysis (LCCA) is a process that can be used to compare design options that have different initial, operational, and end-of-use costs. LCCA takes all financial costs of owning an asset over its entire lifespan into account and can help teams to understand which options result in the highest net value over time.20
Qualitative comparisons should assess industry values such as human health (avoiding toxic ingredients), equity, and biodiversity alongside circularity metrics like capacity for reuse, repair, and remanufacturing. There are a range of ways to assess this. The easiest is to rely on comprehensive certifications that address circularity as well as other factors, like C2C (silver and above) or ILFI’s Living Product Challenge.
A magnitude-based approach can also be used to compare disparate variables. This approach leverages contextual information to assign a “magnitude of impact” to each variable. For instance, when comparing the human health, water use, and carbon impacts of design options, the magnitude of impact assigned to “water use” should relate to water resiliency and supply levels at the physical locations of the design options’ manufacturing facilities.
Qualitative Comparison
Water use Gallons 5
Upfront carbon kg CO2e 2
Service life Years 5
Image and Chart: Perkins&Will
Some options sourced from regions experiencing drought
All options are low GWP per their product category
Some options are neither durable nor recyclable
As the team compares design options, ensure that elements being compared are “functionally equivalent.” This means that each option serves the same purpose and meets the same performance criteria, and that the quantity of each option can be assessed with the same unit of measurement. For instance, the team might assess 1 m2 of paper wall covering applied over gypsum with adhesive and compare the impacts of this assembly to 1 m2 of wall tile with backer board and grout.
Netflix London
London, UK
Client: Netflix
Size: 90,000 sf, 8,361 m2
Completion Date: 2022
Sustainability: BREAM Outstanding, Net-Zero Carbon
Lead Contractor: ISG Construction
CLT Stair Fabricator: Xylotek
Sustainability Consultant: Introba
Key Circular Strategies: Material reuse and iterative life cycle assessment (LCA) to inform impact reduction
High-Level Findings
Inspired by Netflix’s culture of transparency, trust, and storytelling, this project features a bold and engaging design centered around a “Kaleidoscope” narrative and grounded by the desire to support a collaborative and inclusive workplace. The project’s focus on collaboration extended to the procurement process, as the project team worked across disciplines from early analysis through procurement to realize the project’s goals for circular design, flexibility, adaptation, health, and resilience.
Process
Close collaboration between Netflix and the full team began in early design and increased to weekly meetings as the design progressed. This frequent collaboration helped develop an ambitious narrative, goals, and key elements. This structure freed up coordination meetings to be more focused and area-specific. LCA was another key part of the team’s process. They began assessment in early design, identified the project’s top 20 carbon contributors, and selected opportunities to reduce each of the highest impact elements through design and procurement. The top 20 elements in an LCA tend to account for most of the impacts within the scope of study, so isolating these elements and treating each one as an action item is an excellent practice.

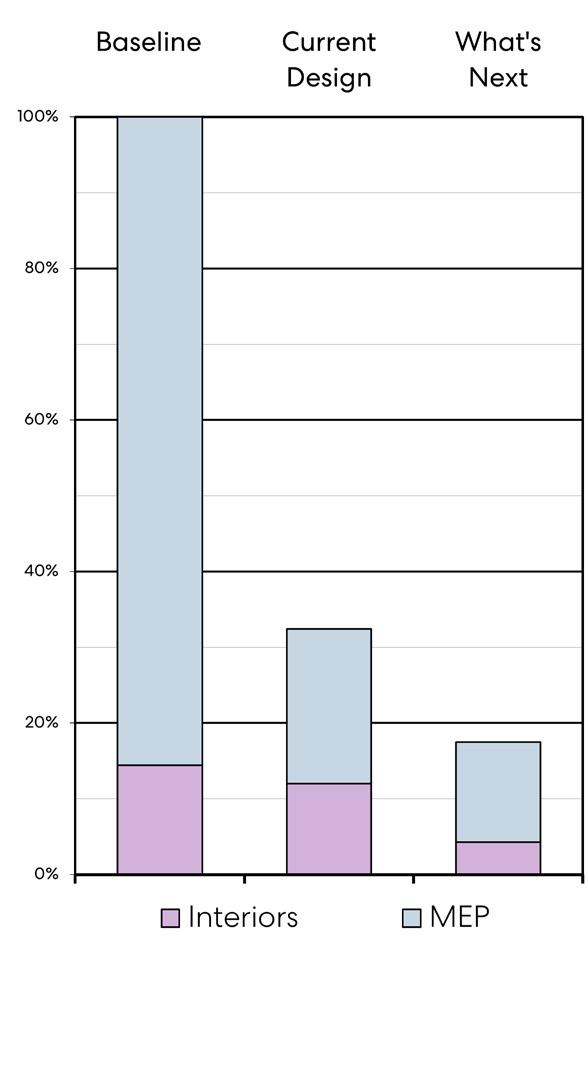
System
The team’s advanced approach to assessment went on to influence future projects. In addition to interior partitions, finishes, and furnishings, Perkins&Will assessed transportation and construction/installation impacts and collaborated with Introba to assess and reduce the embodied carbon impacts of the project’s mechanical equipment. This is an important precedent for future projects, as LCA data for furniture and equipment is still evolving.
The team’s subsequent recommendations to reduce impacts addressed cost and carbon and responded to the design narrative. The team also went beyond reduction recommendations for this project, establishing a further-reaching set of recommendations for future, or “next,” projects, which have informed standards for Perkins&Will, Netflix, and other entities.
Space
A mixture of settings breaks down the scale of the space. The plan is divided into “neighborhoods” located along the full length of the building, with built rooms separating open collaboration areas. The project features flexible space planning, with rooms designed to be arranged in multiple configurations (lounge, office, or meeting room).
Material
The team surveyed the existing fitout and identified opportunities to reuse an array of elements, including equipment, raised flooring, lighting, casework, and banquettes. Intent for reuse was communicated with the contractor, who in turn worked with partner companies to repurpose as many materials as possible, both on-site and off-site. The team used the project’s LCA as well as health declarations, EPDs, and labels like C2C gold to specify healthy, low-carbon materials and products (like timber instead of aluminum or steel).
Assembly
In addition to reusing assemblies from the existing fitout, the project required reused or refurbished workstations and furniture. The team procured furniture from takeback and leasing schemes as well as second-hand, vintage, and local sources. A key feature of the project is a 6-story cross-laminated timber (CLT) central stair that was designed for disassembly (DfD) from carbon-storing materials. The stair’s handrails are made from salvaged wood from the existing fitout’s door frames.

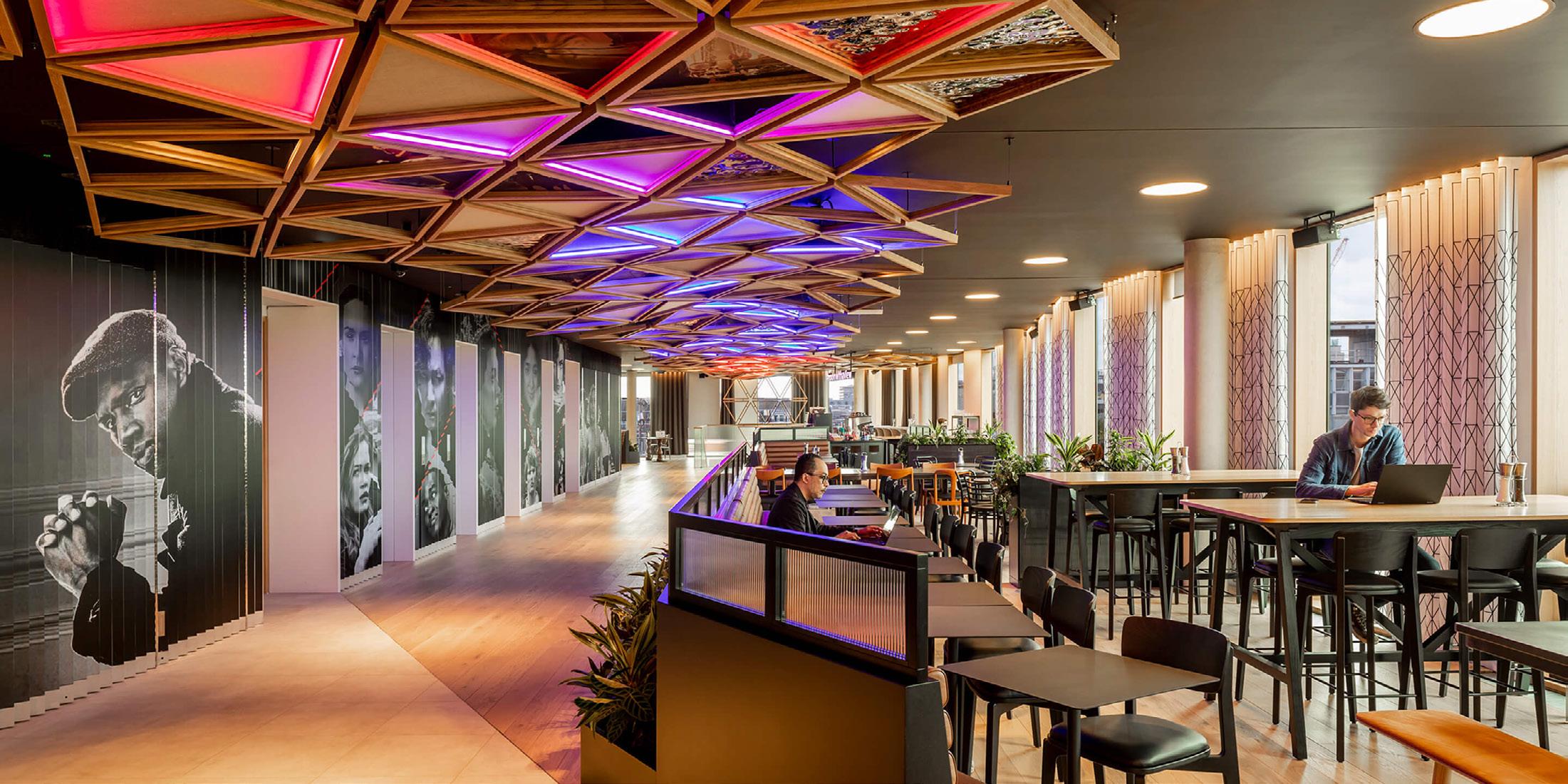
Process, not Projects
Incorporating circular design into architectural projects goes beyond the realm of innovative design. An important goal is to affect change beyond the bounds of one project to expand resources and make it easier for future teams to engage in a circular process.
Consider how the approach and findings from this project can have a positive impact on the whole industry, not just one project. Explore available opportunities to strengthen the circular economy from your project’s context and plan to share learnings from your project with the industry.
Circularity ecosystem mapping
Ownership assessment
Engage and build upon local circularity resources to strengthen circular economy and contribute to systems change
Survey the supply chain for innovative sourcing, mfg., fabrication, and tracking opportunities
Coordinate development of material passport and/or digital twin
Finalize the material passport and/or digital twin; transfer these to the client and O&M team, providing instructions for their use over time
Circularity Ecosystem
Not all approaches will be feasible in all places. The infrastructure, services and actors that support circular design and decision-making are at different maturity levels in different places globally. The transition from a linear to a circular economy involves anticipating and addressing layers of systems-level change. Designers must understand the types of systems that are emerging to support the circular economy, as integrating emerging initiatives into our design processes can further enhance our effectiveness.
“What we are trying to do is create a matchmaking service, not unlike dating apps, between people who have materials available for reuse and buyers, developers and skilled workers familiar with disassembly and reassembly, and other services within circular construction.”
Catherine De Wolf 21
The examples to the right illustrate systems-based efforts to bolster and streamline a circular economy for building materials.
Circular design projects should perform research to understand what resources are in place to support their efforts. Teams can also add resources to centralized directories to inform future projects and strengthen emerging initiatives.
Consider these resources and search for initiatives to support circular design in your project’s region:
1. Materials passports: Documentation to track materials over their life cycles, making it easier to maintain and reuse them in the future. While passports are most frequently developed manually by project teams, technologically integrated options are emerging, such as physically tagging materials and linking them to a database with maintenance and reuse instructions. Centralized passporting initiatives have also been piloted at an industry scale.
2. Deconstruction services: Contractors or third-party services that decommission spaces rather than demolish them. Some of these entities run their own storage and exchange services, reselling materials directly. Services may include full building salvaging, interior decommissioning, or customized deconstruction.
3. Materials exchanges: Developing and supporting materials exchanges can facilitate the flow of reusable resources. These exchanges act as platforms where surplus materials can be traded, reducing waste and promoting resource efficiency. Storage solutions and just-in-time systems for material transfer are vital to increasing efficiency of sourcing reused products and materials. Examples include central clearing houses that manage material exchanges, ensuring that resources are effectively redistributed, as well as manufacturers who work with clients to track and take back, remanufacture, and resell used products.
4. Directories: Databases of contractors, collectors and providers of reused materials, and products with takeback schemes can improve accessibility to resources and information and foster collaboration with manufacturers.

Image: All for Reuse, Ecosystem Map.22 Note that other, similar tools exist for contexts outside of North America.
The example directory above comes from the US based organization “All for Reuse,” and includes an interactive option for site visitors to suggest additions to the map. Similar resources exist or are emerging in other markets, including the “European Circular Economy Stakeholder Platform.”
5. Policy: Policies are emerging to reduce material waste and support reuse. These may include requirements for waste-stream diversion, incentives or code requirements to reuse rather than build new, and pilot projects to explore deconstruction, materials storage, or resale.
6. Educational resources: Many organizations and networks support circular economy initiatives. These groups hold conferences and informal meetings and create educational collateral. Organizations may also train providers, contribute to workforce development, offer seed funding to develop infrastructure, or provide direct consulting services to support teams.
Ownership Assessment
Sharing resources is a crucial way to achieve the shortest “loops” in the R Ladder, (refuse, rethink, reduce).
There are many approaches to sharing, yet sharing is often overlooked as a circular design strategy.
Consider the assets planned for acquisition in the project and assess which elements must be owned directly by the project. For all other elements, review the ownership models below, which are organized from “most shared” to “less shared,” and explore opportunities to secure elements via alternative approaches to ownership.
Alternative Ownership Models:
1. Fully shared: Can infrequently used equipment or supplies be shared among building occupants or space tenants? Does the project include spaces or durable components that can be shared? Can publicly shared resources like transit, green space, or community / recreation spaces be utilized instead of creating private resources?
2. Reserve and borrow: Can elements be borrowed from a local resource, like a tool or equipment library, when needed? Can meeting rooms or desks be reserved to maximize space utilization and flexibility?
3. Lease or rent: Many elements can be leased from a supplier for a fixed duration. Co-working spaces and bike or car share are established options, but other items are leasable as well. Can elements like FF&E, modular meeting rooms, or even carpeting be leased and sent back to the manufacturer for future reuse at the end of the lease?
4. Product as a service (PaaS): PaaS elements are offered in subscription models with services such as maintenance, repair, or software attached. This approach supports the circular economy and extends the suppliers’ financial and operational responsibility for their products to include life cycle costs, such as renewal and repurposing.
5. Material takeback: Some manufacturers offer material takeback programs for purchased assets. When selecting a product based on material takeback, verify that manufacturers with these programs have also established “secondary market offerings.” This is one way to help ensure that materials will in fact be reused or recycled into new products.
6. Own or co-own: Items or spaces that are frequently individually used, that require investment to fit to a specialized purpose, or that are less durable may require direct ownership.
Digital Twin Material Passport
Material passports provide a structure to support circular operations and future reuse. Collaborate with the contractor to develop an inventory with guidance for maintenance and deconstruction for each type of element across its life cycle stages. This may be a digital document or part of an advanced tracking system. Engage the client and their operations and maintenance team to socialize the passport while the project is in development and provide training and hand over at project completion.
Items to Track in a Material Passport
Explore the benefits of technology that virtually represents the physical project, such as a digital twin or individual asset twins. A digital twin—a virtual replica of the physical project—enhances circularity by enabling precise planning, visualization, and life cycle analysis during schematic design. It allows teams to optimize design choices and predict impact outcomes. A digital twin is a powerful tool for refining circular strategies early in the design process and may integrate with a material passport.
Product
Overview
General Information
nj Element type and function (e.g. ceiling finishes)
nj Install location(s)
nj Specific Product
nj Manufacturer
nj Product image
nj Description of product characteristics (e.g., panel size, thickness, color)
nj General material type(s)
Product Specifications
nj Past uses if reused
nj Performance criteria
nj Certifications (e.g. C2C Gold)
nj Recycled content %
nj Recyclable content
nj Composite? (y/n)
nj Environmental Product Declarations
nj Health declarations
Key Contacts
nj Manufacturer or fabricator
nj Maintenance contractor
nj Leasing entity or takeback contact Maintenance
nj Warranty information
nj Product as a Service (PaaS) agreements
nj Lease agreements & requirements
nj Cleaning protocols & maintenance requirements
nj Component breakdown (material types and %'s)
nj Fixing type (e.g. joined, screwed, glued, hung) Operations and Maintenance
Adaptation and Decommissioning
nj Manufacturer takeback scheme info. & instructions
nj Level of deconstructability
nj Deconstruction narrative
nj Deconstruction details
nj Links to assembly / disassembly guides
nj Storage and stacking requirements
nj Other decommissioning considerations
nj End-of-life pathway (e.g., reuse, takeback, recycling, recovery, or landfill)
nj Waste stream type or other compliance information
nj Recycling options
nj Reuse possibilities
Our Vancouver Studio
Vancouver, B.C.
Client: Perkins&Will
Size: 13,875 ft2, 1,289 m2
Completion Date: 2024
Sustainability: RESET Air and targeting WELL Platinum
Lead Contractor: Turner Construction
Millwork: Uppercase (bespoke remanufactured furniture); Toso Woodworks (refabricated workstations)
Key Circular Strategies: Translated materials from an existing material bank and used LCA and EPDs to reduce carbon impacts
Our Living Design framework informed the development of our new Vancouver studio.23 Reducing embodied carbon and construction waste were primary drivers for the project’s site selection and fitout. The studio’s base building, Arthur Erickson Place, is a 1968 heritage tower that has achieved CaGBC Zero Carbon Building— Performance Standard™ and LEED Platinum® certifications, an example of alignment with our Green Operations Plan.24
Process
We followed a multifaceted approach to carbon reduction, challenging ourselves to see how much carbon we could cut. This began with reusing and refabricating elements from the existing space. The project’s material types and quantities were then optimized through LCA, and lowcarbon products were selected using EPDs. The LCA was updated at each design stage, and the final study reflects the impacts of the project’s reused and installed products. This process resulted in an impact reduction of more than 50% from the project’s baseline design. The design outcome is healthy, low-carbon, and respects the aesthetic of Arthur Erickson Place. It also reduces the need for new inputs by maintaining exposed elements and is composed of legible materials.

System
Our team was well-equipped to reuse elements from our existing space, as it was designed more than 20 years ago for deconstruction. We worked to give components from our space a second life through disassembly and refabrication.
This required early onboarding with a contractor so that a deconstruction strategy could be included in the construction timeline. It also required effort to find a millwork fabricator who was willing to work with existing materials that are inherently inconsistent and accompanied by potential unknowns.
While most of studio’s existing materials were repurposed for our new space, some elements found new lives beyond. Heritage Office Services provided in-kind support by delivering unused metal shelving components to a local non-profit organization, where they will be reused in an upcoming interior restoration project.
Space
The whole studio had to be on board to treat the space that we were actively working from as our material bank. It was a logistical challenge to slowly deconstruct a still-functioning studio over the course of three months, but the transition was eased by capacity for remote work, shared aspirations, and acceptance of operational and budget flexibility by the leadership team.
Material
The studio’s material palette is an extension of the existing materials that we incorporated. We even hand-transplanted vegetation from the living wall in the original studio to a wall in the new space. The materiality of the project lends itself to a nonprecious workplace that supports creative exploration. While the space is new, the materials are recognizable and invoke a sense of collaborative contribution to circular design.
Assembly
Existing desks, casework, shelving, and tabletops were repurposed from the previous studio space. These had been fastened mechanically, making it easy to separate each component, and were made from plywood with exposed edges. This “thru”’ or solid material was easy to cut and re-shape to suit new functions. The team created a 3D model of each element to design refabricated items for the new space. The furniture fabricator then ensured that the pieces would be compatible with standard parts and reshaped the material into desks, tabletops, shelving, and planters.

Material Bank Inventory
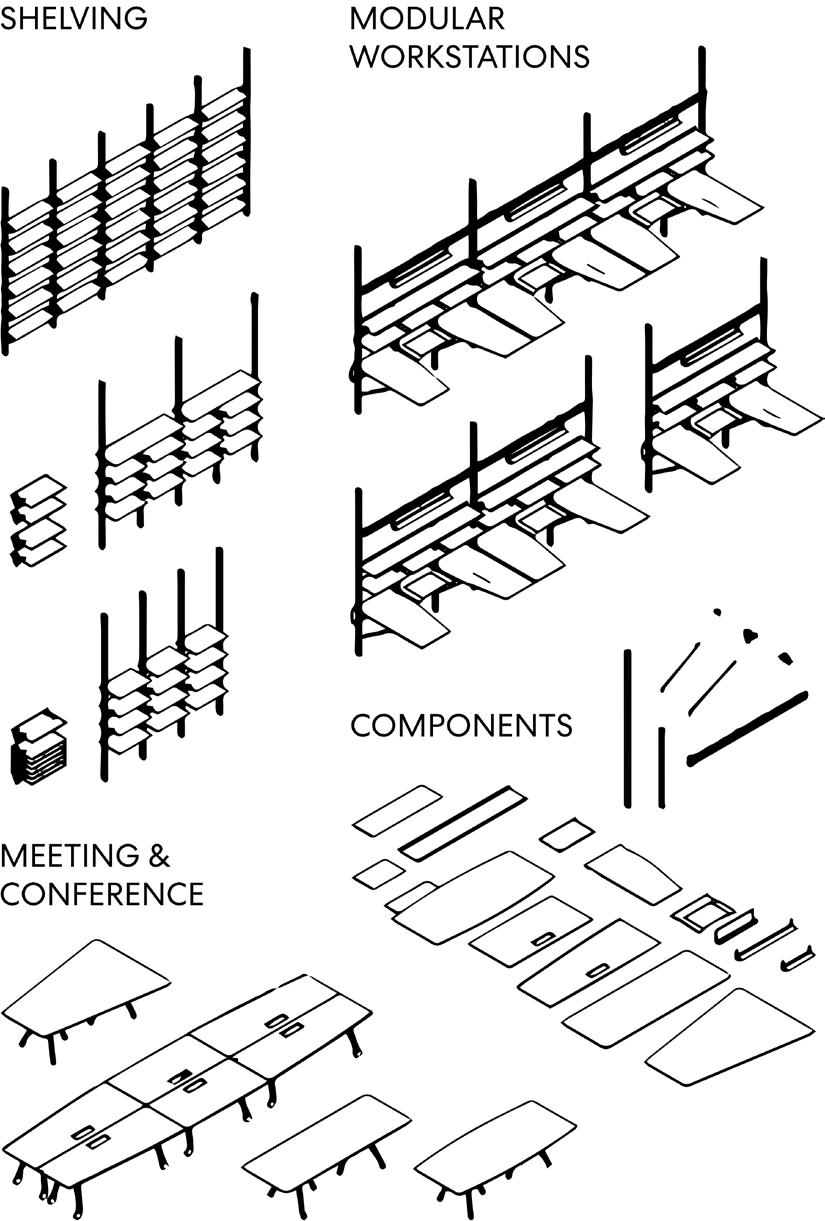

Spaces Lease Assessment
The needs of people and businesses are constantly evolving.
Occupants’ needs are fluid, yet built spaces are traditionally static. Therefore, designing for adaptability, disassembly, and other circular economy principles is good for ecology and good for business.
Spatial strategies for circular design emphasize flexibility and adaptability at the scale of the building or space to support a variety needs, optimize operations, and “future-proof” spaces. These strategies accommodate changes without requiring significant alterations, thereby reducing the financial and carbon cost of renovation and extending the project’s life span.
Lease assessment: minimize white boxing and identify “end of lease” pathways
Design for Longevity (DfL)
Fixed (bespoke) vs. flexible (modular) space plan
Resource conservation plan
Staging plan for migration from existing space and/or storage of reused elements
Explore gamification
Review the lease assessment and protect existing built-in components during construction; ensure that attachments to these are reversible
Transitions between tenants are typically accompanied by waste and other environmental impacts, as items are discarded when a lease period ends, and new temporary materials are sometimes installed to attract new tenants. Explore the following parameters to minimize waste between tenants.
Lease duration: Can the lease duration be extended? Select longer lease durations to reduce waste and other impacts that occur with each move and fitout.
Pre-fit site evaluation: What is already in place? Is a space with a salvageable existing fitout available? Document the pre-fit state of the space. Negotiate with the space manager / owner to leave any existing elements that may be useful in place and work these into the design.
Eliminate white boxing. How will the space be prepared prior to fitout construction? Establish an agreement that no “CAT A” elements (like pre-fit materials like partitions, ceiling and floor finishes, and temporary fixtures) are to be installed unless they are to remain a part of the design.
End-of-lease plan: In what state should the project be left after the lease ends? Which elements must be removed and which must stay on site?
nj Create a set of project plans that highlight elements to be removed vs. elements that must stay on-site.
nj Plan for the next use of all elements that must eventually be removed. Refer to Design for Adaptation (DfA) in this section and Design for Disassembly (DfD) in section 7, “Assemblies” of this primer for guidance on design for multiple use cycles.
nj If the space includes durable or built-in elements that will remain on-site (for example, partitions or casework), protect these during construction and ensure that any connections or attachments to these elements are designed to be reversible and serviceable.
Three scenarios for lease length and embodied carbon impact of interior fitouts over 60 years
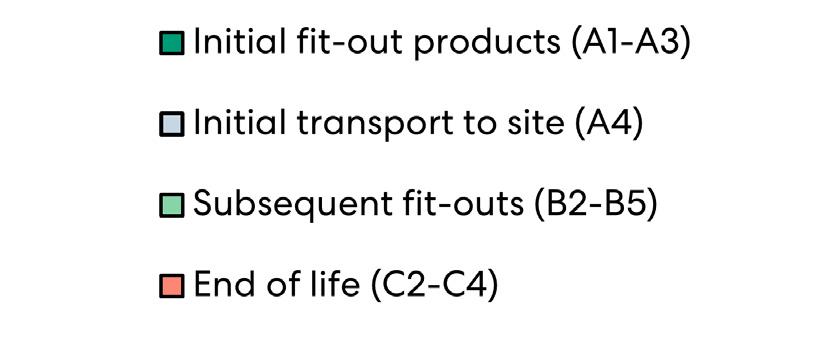
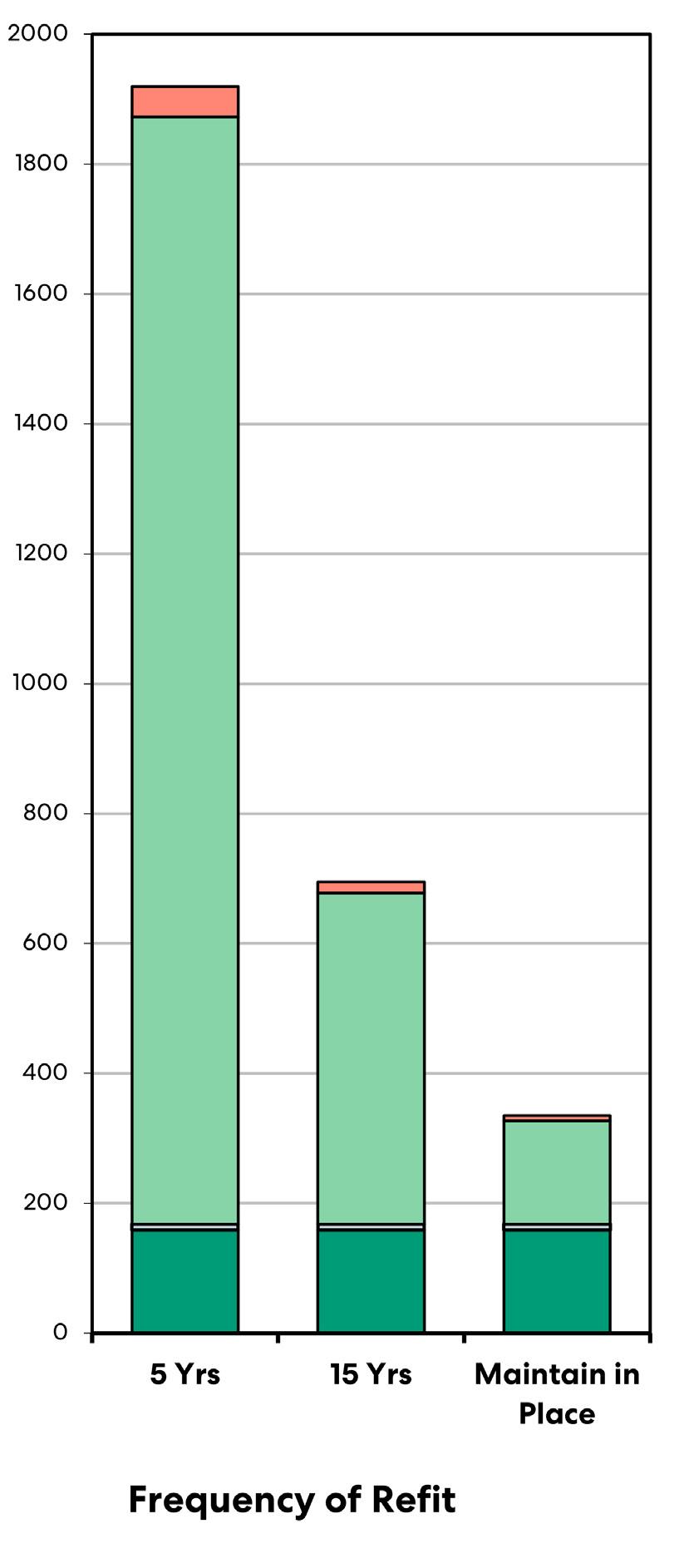
The cumulative impacts of interior architectural elements over time are tied to how frequently they are replaced. The comparison on this page explores three scenarios for the embodied carbon impact of one company’s commercial interior fitouts over 60 years. In this example, a full refit or new build every five years has 2.8 times the impact of refitting every 15 years, and 5.7 times the impact of staying in one space and replacing materials over time according to their typical service lives.
5-Year Lease Length (12 Refits)
2.8 x the embodied carbon of updating every 15 years.
5.7 x the embodied carbon of incremental updates without full refits.
15-Year Lease Length (4 Refits)
2.1 x the embodied carbon of incremental updates without full refits.
Maintain in Place: No Full Refits
Design for Adaptation (DfA)
Adaptation pertains to both a project’s spaces and its elements. Adaptive elements incorporate flexible, demountable design approaches to support ease of reconfiguration and enable low-impact modification through future use cycles. Adaptive spaces are designed to support planning for today, enhance the utility of a design over time, and provide an enduring framework to accommodate future flexibility and change.
At the spatial scale, DfA introduces a mixture of flexible, adaptable, and fixed zones to space planning. These zones are characterized by:
Flexible spaces: Highly flexible components that can be moved by users and/or facilities management that will enable multiple configurations.
Adaptable spaces: Planned adaptability, for instance, zoning areas of the space plan to allow for future change that could be implemented without closing down the space.
Fixed spaces: New fixed spaces require planning, permitting, design, and external construction work to be implemented. Existing fixed spaces include those that can’t be moved (like egress and services) or that are already built in from a previous use.
A functional benefit of including a distribution of space types is that an individual will be able to easily see and locate an asset that they need. Balance this sightlineoriented approach by incorporating adaptable components such as screening and modular rooms to break up open areas, create vistas, and ensure that people feel supported.
Adaptable Components
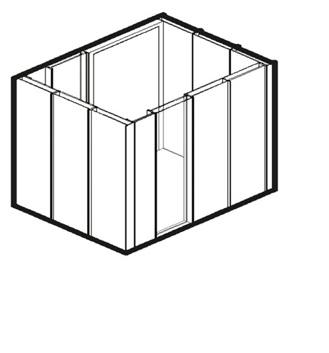
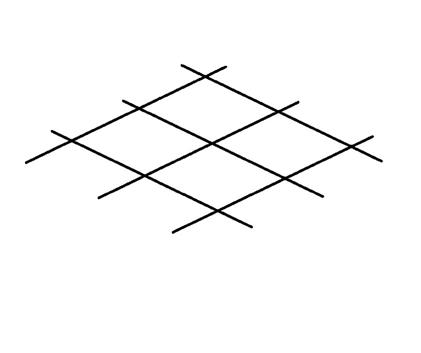
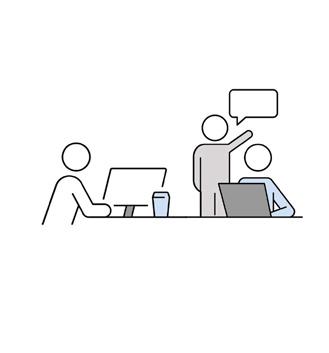
DfA can be layered into the space planning and test fit process. Outline and determine locations for flexible, adaptive, and fixed spaces by following these steps:
1. Define space types and activities that the project’s occupants will engage in across varying periods of time (hourly, weekly, during major transitions), collaborating with the client and stakeholder team.
2. Explore the needs associated with various space types and identify key parameters to include in planning, such as focused vs. social space, acoustic requirements, occupancy loads at varying times of day, etc.
3. As parameters are established, outline layouts that visualize how the design can incorporate adaptive zoning.
4. Test modular and adaptive design strategies that can evolve with changes across these uses and activities. Adaptive strategies typically apply to ceilings, floors, services, rooms, partitions, and furniture.
5. Plan for modular design with a “plug and play” system, using the building grid as a framework for adding components that are designed to be relocated, removed, stored or reused in future spaces.
6. Assess whether fixed spaces can be designed to serve multiple uses as needs and occupants change. For example, can the same module and quality of space be used for a lounge, office, or small meeting room?
7. Distribute flexible zones throughout the project area that include assets like modular rooms, workstations, alternative work settings, refreshment points, and collaborative or focus spaces.
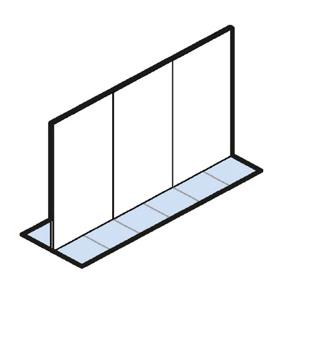
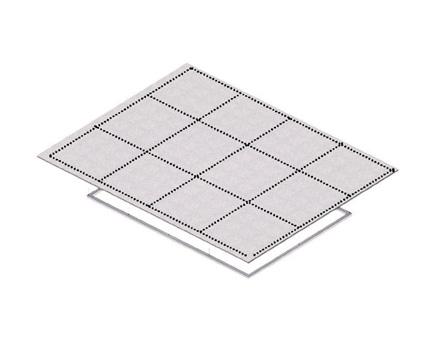
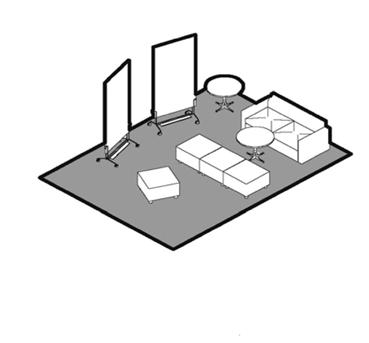
nj Furniture moves
nj Typical meeting room setup
nj Collaboration tables
nj Lunch & learns
nj Pin-up / design walls
nj Event set up
Adaptive Planning Using the Grid as a Baseline:
Adaptable Zone
Adaptable Zone
nj Technology / AV
nj Change to use of room
nj Signage / wayfinding
nj Specialized dept. needs
nj Stack reshuffle
nj Renovation
The following strategies dovetail with DfA to address durability over time and space-related approaches to resource conservation:
Design for Longevity (DfL)
DfL applies to multiple scales of building elements (spaces, materials, and assemblies). Spatial longevity can be achieved by designing layouts and elements that remain relevant, functional, and resilient to changes in use, ensuring enduring value over time. Configure spaces to facilitate ease of maintenance, repair, and refurbishment with minimal financial and carbon investment.
Whether a project’s components are fixed or flexible, select high-quality materials whose strength and service life is appropriate to their intended application. In the spirit of “right to repair,” components that may wear or break with use should be replaceable or reparable, allowing for maintenance without requiring fullscale replacement
Use = Need
Conserve resources through consideration of occupants’ use patterns over time. Implement flexible planning to design spaces that can be shared, reserved, or fully shut down to conserve energy when not in use. Reduce plug loads, adapt thermal comfort ranges, and omit excess “stuff” like kitchenware and office equipment.
Gamification
Implement game mechanics strategies to engage the occupants of the space. Dashboards, sensors, and other feedback systems can increase participation and reward good behaviors like reducing energy, waste, or water use.
Balance Modular Structures with Bespoke Beauty
Flexible and modular structures are efficient yet are typically standardized for ease of manufacturing and repair. Balance these with purpose-built and unique elements that provide character.
Assess the following and incorporate a variety of modular and fixed, or “bespoke,” spaces throughout the project:
Modular spaces play an important part in circular design by providing a system whereby components can be separated and recombined. Modular components allow for simplified maintenance and upgrades, ensuring that parts of the building can be exchanged or reconfigured without disrupting the whole.
To ensure circular use, modular elements should either be movable as whole assemblies or designed as a kit of parts that are easy to disconnect and reassemble. For example, modular meeting rooms can be standardized for easy repair and remanufacture, and then they become assets.
Bespoke rooms have fixed configurations and are typically located at the perimeter or core of the building. This space type provides flexibility for larger groups within enclosed spaces and may contain feature or non-standard elements. Per DfL best practices, these spaces should be designed for durability and ease of maintenance over time. Fixed and bespoke spaces must also provide enough flexibility to accommodate changes of use during space shuffles and lease transitions.
Occupancy flexibility: Assess potential fluctuations in occupancy or needs for changes of use over time. Use occupant studies to assist in planning modular vs. fixed zones.
What can be standardized? Determine what elements in the project can reasonably be standardized and what features must be bespoke. Prioritize modular spaces where appropriate.
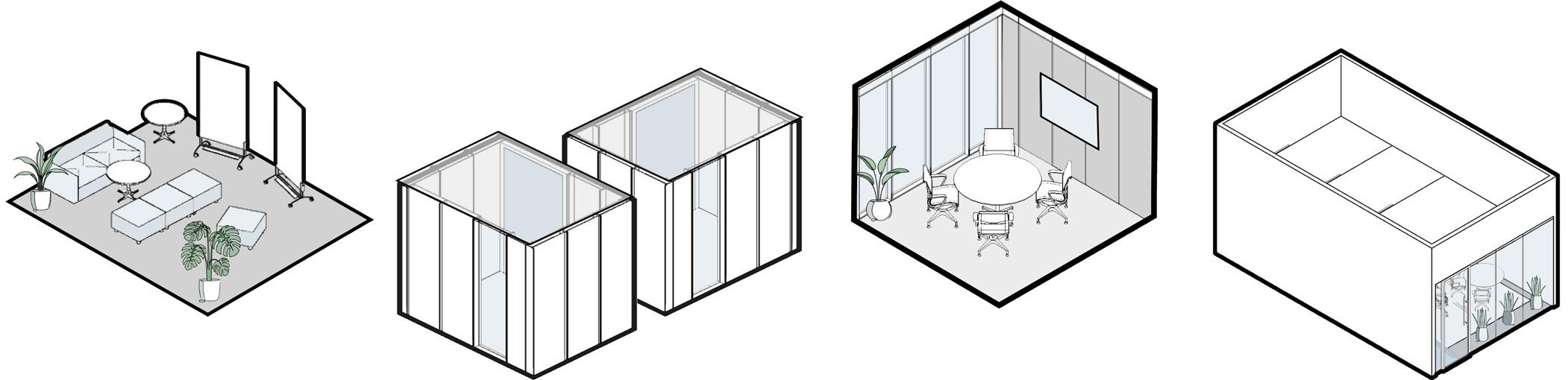
Considerations for
Modular, 'off the shelf' rooms
Recommended for:
nj Ease of construction and high precision commissioning of key functions like acoustics, ventilation, and thermal controls
nj Future adaptability and change
nj Rooms with a smaller occupancy of 4-6 people
Benefits:
nj Integrated ceilings, lighting, and tested acoustic systems make modular rooms a versatile solution with comparable upfront costs to bespoke rooms.
nj Simple typical construction consists of metal frame (or timber) and glazing. Each module’s materiality is contained to traceable fabrication sources, making transparency and carbon and health assessments straightforward.
nj Offers a level of customized / bespoke design. Must be high enough quality enough to meet technical requirements and retain value as an asset over time.
nj Offers flexibility in construction and future adaptability. Units should be designed for multiple use cycles and deconstructability.
nj Modular rooms may connect to building management system (BMS).
Considerations for Built, 'bespoke' rooms
Recommended for:
nj Perimeter and core conditions
nj Custom elements that can't be standardized
nj Rooms with 8+ person occupancy
Benefits:
nj Any size / configuration is possible.
nj Acoustics can be customized to accommodate specific applications.
nj Ability to integrate complex AV and ceiling systems.
nj Typically constructed of drywall, metal studs, insulation, and glazing, but can be optimized or customized to include lower carbon products without the constraint of working through a sole fabricator.
nj Easy to build into a grid using modular and DfL principles to maximize reuse.
nj Integrated and fully serviced rooms with individual services and controls.
USGBC Headquarters
Washington, D.C.
Client: U.S. Green Building Council (USGBC)
Size: 13,535 ft2, 1,257 m2
Completion Date: 2021
Sustainability: LEED ID+C v4.1 Platinum; WELL v2 Platinum; TRUE Net Zero Waste
Lead Contractor: HITT Contracting
Key Circular Strategies: Optimization and rightsizing through space planning; use of existing elements as a material bank
The new headquarters of the U.S. Green Building Council (USGBC) in Washington, DC, is the first project in the world to receive three Platinum certifications from the Green Building Certification Inc. (GBCI): LEED ID+C, WELL, and TRUE. The design embodies the USGBC’s brand and mission to reduce the negative impacts of the built environment while promoting health and wellbeing. In response to the organization’s evolving space needs, the office footprint was reduced and consolidated. The remaining area was divided into a refresh of the staff workspace and a new public-facing collaboration area.
Process
The design team aligned around ambitious targets right from the start, beginning with the project brief. Viewing this project as an opportunity to showcase the concept of using USGBC’s previous headquarters as a material bank, the team not only reused elements but also featured them to share knowledge, reinforce the project’s circular design narrative, and ensure their continued use over time. For example, the team worked with the contractor on-site to reconfigure and retain components from the original space’s wood feature wall and USGBC logo, making this into the backdrop to the public space.
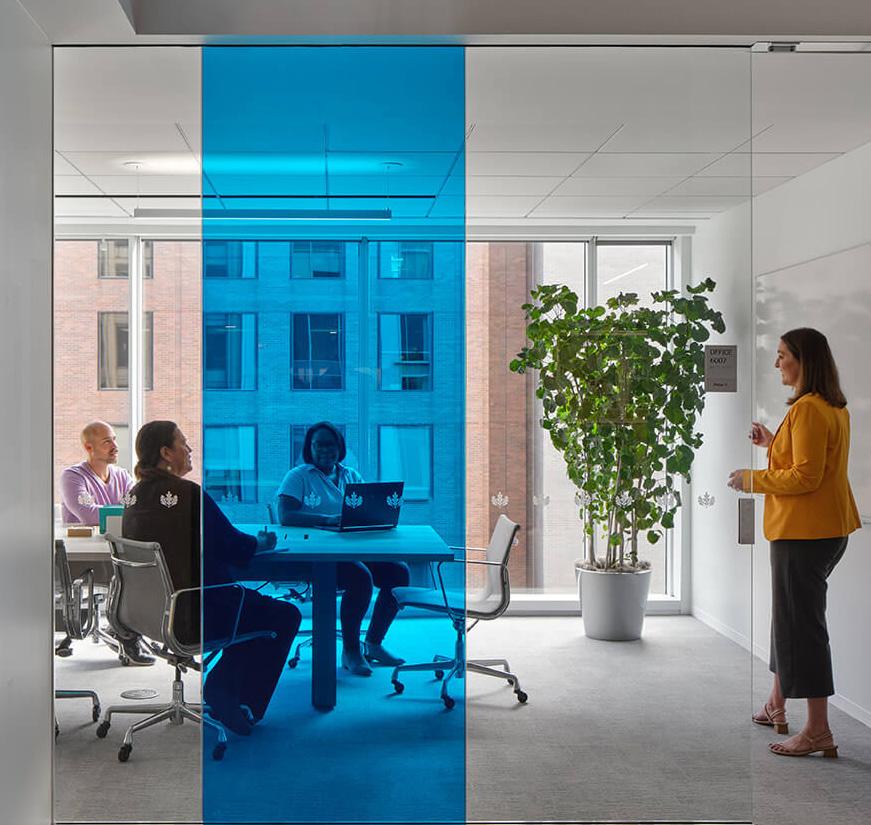
System
The design features a public-facing Knowledge Library. This resource showcases the full inventory of innovative products and materials installed in the project, including an assortment of elements from reused sources.
The project leveraged our early partnership with Building Transparency in the development of the Embodied Carbon in Construction Calculator (the “EC3” tool). Our D.C. studio used EC3 in conjunction with life cycle assessment (LCA), refining the studio’s process for reducing embodied carbon in interiors. LCA was used for design option comparison and full project assessment, and EC3 was used to research and specify products with low embodied carbon impact based on EPDs. Use of EPDs is an important contributor to systemic change, as these documents incentivize transparency and competition to develop lower-impact products.
Space
The project team leaned into preserving the project’s durable and fixed elements and minimizing alteration to them during construction. As a part of optimizing the project’s footprint, the space plan prioritized preserving existing offices and partitions. Open office areas were reconfigured with existing workstation components and ancillary furniture.
Material
The team salvaged existing elements for reuse wherever possible. The scope of reuse included partitions, finishes, fixtures, equipment, and furnishings. Where possible, new materials were specified as carbon neutral and carbon negative, and non-toxic materials were required by the project’s basis of design and certification targets. These combined strategies resulted in the reuse of more than 90% of existing furnishings and a 44% reduction in embodied carbon from a typical fitout of similar size and scope.
Assembly
The project salvaged full assemblies, leaving them in place where possible and restoring them as needed. These included ceiling systems, glass and gypsum partitions, doors, and furniture. Reused furnishings included workstations, task chairs, ancillary tables and chairs, and conference tables and chairs. Many reconfigured partitions incorporated salvaged millwork and colored laminated glass from the previous layout to create fresh focal elements in the new space.


Materials
Good design is as little design as possible. Less, but better – because it concentrates on the essential aspects.
― Dieter Rams25
A project’s material palette sets the stage for its circular design outcomes. Distill the design to focus on fewer, but higher-quality materials, prioritizing innovative, well-detailed materials that are good for the environment.
Reduce the superfluous use of layers and products and affirm the value of the project’s components as a bank of materials. For required materials, prioritize reuse of existing resources. This means surveying the field, testing materials’ integrity, and engaging with the contractor and sub-contractors to ensure that best practices and innovative approaches to material procurement are woven into the project.
If existing space: decommissioning audit and resource mapping on-site
Resource mapping off-site
Establish a procurement plan with the GC; continue to identify and propose circular sourcing options throughout the design process
Refine carbon and transparency requirements and decommissioning plan
Finalize specs. and end-of-life instructions
Follow the decommissioning plan to maximize reuse, takeback, salvage, and diversion; verify submittals
Decommissioning Audit
When selecting materials for any project, start with what’s on hand. If the site has existing materials, perform a decommissioning audit to assess existing materials’ potential uses. Each existing element may be useful for someone, so any decision to recycle or send materials to a landfill must be justified. Maximize reuse of existing materials, either on-site within the current design or off-site, by identifying new owners or redistributors.
Key considerations for a decommissioning audit include:
nj Timing: Ideally, the audit occurs before the tenant signs a new lease or before the space is prepared, so that any reusable materials on-site can be retained.
nj Takeback: Explore whether existing elements are associated with takeback programs. In some cases, like carpeting, a manufacturer may have a program for material retrieval, but the product and program must be identified for this to occur.
nj Responsibilities: As a part of the audit, identify what actions are needed to ensure that decommissioning occurs as intended. Deconstruction can extend decommissioning timelines, but this can be reduced with planning. If deconstruction is written into the demolition contractor’s bid, the contractor may be responsible for finding new users for existing materials. Some general contractors offer reuse programs, while others adapt their approach with each project.
nj Proximity to site: Locations or entities that could use the project’s elements are typically local. If the team is looking to sell or donate items, begin with a search for platforms, programs, or organizations within the region.
nj Documenting: Methodologies like 3D laser scanning, photogrammetry, and physically tagging elements can assist in auditing materials and preparing for next steps.
Resource Mapping Exercise
Resource Mapping
Resource mapping is a foundational step to align with circular principles and inform decision-making. It may follow a decommissioning audit on-site or may also be conducted to assess available resources at other off-site locations.
The mapping process involves dividing the building’s existing components into material types (for example, concrete, glass, and carpet) as well as assembly types like casework, partitions, and ceiling or floor systems. The value of these elements is determined through key metrics like weight, embodied carbon, and economic value. This granular approach allows for a deeper understanding of the building’s material composition and its potential for transformation.
nj Examine the weight of materials to reveal the physical scale of resources and help teams identify which materials and components carry the most significance in terms of reuse, refabrication, or salvage potential.
nj Evaluate embodied carbon to highlight the environmental impact of each material, allowing for targeted strategies to reduce emissions and prioritize low-carbon solutions.
nj Assess economic value to underscore the financial implications of material selection and guide decisions that maximize resource efficiency and project value.
Circular Sourcing
Circular design projects typically procure reused materials from multiple sources, as a myriad of pathways may lead to suitable materials.
Work through these examples and challenge the team: How many of the project's materials can come from reused sources?*
One-off Sources
nj Existing materials from the project site
nj Materials from an off-site previously leased space
nj Materials from other projects in the client’s portfolio
nj Materials from other project sites
nj Salvaged materials from local resale listings
Vendor Sources
nj A contractor who sorts, stores, and supplies decommissioned / reused elements
nj A supplier who remanufactures products and sells them as refurbished or recertified
nj A company that leases reused elements
nj A manufacturer who makes new products out of reused material (remanufacturing or upcycling)
Material Exchange Marketplaces
Exchange marketplaces are programs or platforms where materials and building elements can find new life in other projects. These may include local architectural salvage or resale vendors, or they may be online platforms with regional reach. In either case, these resources facilitate the exchange of surplus, salvaged, or reclaimed materials, enabling broader and more interconnected access to reused elements.
Urban Mining
Cities’ waste materials include concrete, bricks, stone, steel reinforcements, wood, roofing materials, copper and aluminum. Urban mining focuses on recovery and reuse of these long-lived materials, which may be sourced through municipal programs, recycling facilities, or local organizations.
* Sources for reused materials may also be used to identify new homes for existing materials that are present on a project site but cannot be used in the current design.
Material Evaluation
Once reused elements are identified, they may be inspected to assess their value and determine how to utilize them. Tools for testing include:
Spatial Assessment
nj Visual inspection: survey materials for design attributes, fixing methods, and general condition.
nj Dimensioning: take physical measurements to understand elements' size in relation to one another (where uniform size may be desired) or in relation to a space where they may be installed.
nj Matterport LiDAR scanning: create a precise spatial mapping, documentation and visualization.
Structural Assessment
nj Magnetic stud finding: find stud locations and analyze framing.
nj Schmidt hammer: assess strength or hardness of concrete, stone, brick, or mortar.
nj Fatigue testing: assess integrity after repeated loading cycles to understand durability and resistance to failure.
nj Tensile, impact, or compression testing: measure strength under tension, toughness under shock. or resistance to crushing (requires special equipment).
Thermal and Moisture Assessment
nj Moisture metering: monitor moisture content.
nj IGU tightness testing: evaluate seal integrity and energy efficiency.
nj Freeze spray: identify punctured windows and puncture locations.
nj Thermal imaging camera: test for thermal insulation deficiencies, moisture intrusion.
Certification
nj Recertification or warranty: suppliers may offer certifications, and in some cases, extended warranties can be negotiated.
nj Upfront certification: some reused elements may be certified by third-party entities to verify integrity (for example, certified refurbished), safety, or sustainability and circularity criteria.
Approaches to Reuse
As sourcing options are identified, assess potential applications and reuse strategies for each material that may be incorporated. Reusability assessment begins with evaluating available materials’ condition to determine their potential for continued use, and follows by categorizing materials according to their suitability for different circular pathways, including:
nj Direct reuse: repurposing materials/elements in their current form with minimal processing.
nj Deconstruction: carefully dismantling components to preserve their integrity for reuse.
nj Upcycling: enhancing the value or functionality of materials through creative innovation.
nj Recycling: breaking materials down into raw inputs for new production.
nj Downcycling: extending a material’s life via conversion to lower-value applications (less ideal).
Identify the most circular approach to reusing for each element, prioritizing direct reuse of materials “as they are” to retain their present value.
Then adapt, transform, or upcycle if alterations are needed for reused materials to be incorporated. While recycling, downcycling, and recovery are more effective than waste, they represent “longer loops” and require more industrial support and energy to realize, so decisions to recycle rather than reuse should be justified.
Where direct reuse is not possible, creating higher-value products from lower-value materials offers significant opportunities for resource efficiency as well as new streams of value-add revenue. Strategies like upcycling encourage creative reuses of materials that differ from their original purpose or form. Upcycling focuses on taking materials that might otherwise become a part of the recycling or waste stream and transforming them into new materials that hold quality and value due to their creative approach and environmental benefits.
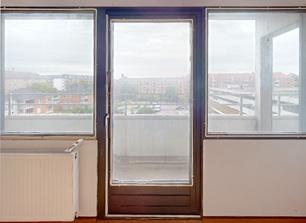


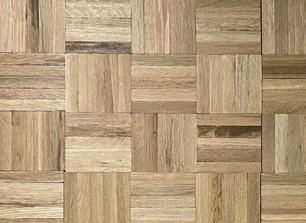
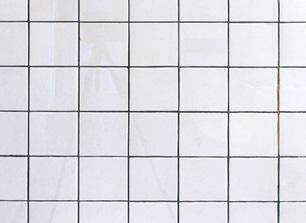
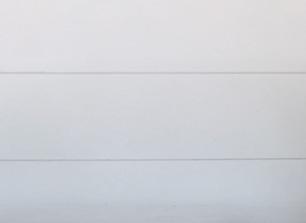


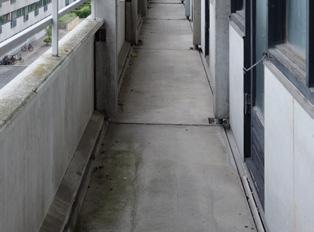
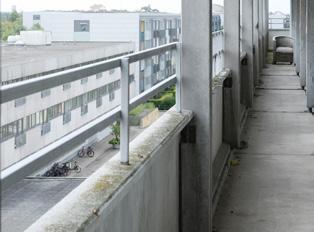

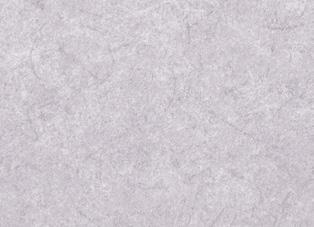

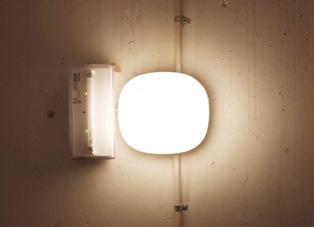
Technical or Biological?
In assessing materials’ value, it is important to understand that materials typically fall into one of two categories:
nj Technical materials; e.g., metal and plastics
nj Biological materials; i.e., organic and plant-based
Primary difference between these is that they are metabolized differently at their end-of-life.26 Technical materials are typically more durable, yet this means that they don’t “go away” easily. Care should be taken to select technical materials that are non-toxic, reusable, and recyclable, preventing waste and pollution. These are best used for durable and long-lived applications and should be designed for adaptation and disassembly.
While biological materials can be reusable and long-lived, in some cases they typically have shorter life spans. These materials come from renewable resources and can return nutrients back to the environment at their end-of-life. Select biological materials for elements that have shorter life spans and prioritize sustainable sourcing to ensure that these materials are derived from healthy ecologies.
Each material or assembly should be accompanied by clear instructions for sourcing, repurposing, and processing at end of use. Composite elements that hybridize biological and technical materials must be detailed so that these materials are separable to maximize the benefits of each material type’s ideal end-of-life pathway.
Procurement Planning
In a circular project, material procurement can begin in conceptual design and extend into construction. This is because some circular materials may need to be acquired as they become available, which could happen at any point in the design process.
A procurement plan is essential to evolve the design from sourcing possibilities to purchased and installed elements.
This plan serves as a strategic road map to guide the acquisition of materials, components, and services. It is also a framework to ensure that aspirations for reuse are actionable and practical, reducing the risk of misalignment later in the design or construction/ installation process.
Key considerations for procurement planning include:
nj Material availability and lead times: factor the projected availability of specific materials into the project timeline. If space is available, storing and staging reused materials on-site can support timely and efficient project execution.
nj Supplier partnerships: establish relationships with manufacturers or vendors who share circular values and can support reuse or take-back programs, for instance, a fabricator who is willing to work with reclaimed materials or a vendor who identifies and supplies reused elements.
nj Refurbishment or certification requirements: reused, reclaimed or leased elements may require screening, testing, repair, certification, or extended warranties to avoid liability issues and ensure reliability over time.
See the “testing” recommendations to page-right for examples.
nj End of life documentation: develop a plan to collect and create instructions to guide future deconstruction, reuse, or recycling. This documentation could focus on instructions for operations, maintenance, and “next steps” for key elements, or, it could take the form of a full material passport for each element in the project.
Specification Criteria
Requirements and specifications translate circularity objectives into actionable, measurable standards and serve as a critical reference for all stakeholders. These documents ensure that the project’s elements meet sustainability goals while aligning with practical construction and operational needs.
While specification development may occur later in the design process for a typical (linear) project, a circular design project may require early development of specification language to ensure that the project’s contractor has authority to source reused, reclaimed, leased, or other alternative materials.
Look for specification language that might prevent the contractor from sourcing reused elements and modify this to maintain key performance requirements while allowing for reuse.
Specifications should detail:
nj Reused elements: allowances or requirements for the contractor to source reused materials and any key requirements for reused materials to be acceptable for each application.
nj Expected durability and reusability: measures to ensure that materials and components perform reliably throughout their life cycle while remaining suitable for future reuse or recycling
nj Circular design criteria: modular systems, adaptability measures, reversible joinery, separability of technical and biological materials, and disassembly requirements
nj Alignment with certification standards: requirements for transparency documentation, certifications, or other verifiable metrics
nj Procurement preferences: Importantly, projects that require competitive bidding can establish circular performance criteria (such as percent reused or recycled content, product-specific embodied carbon impacts, waste diversion rates, certifications, etc.) to target preferred suppliers and ensure that substitutions comply with the project’s circularity goals.
By combining circular sourcing networks, reusability assessments, and strategic planning, teams can develop a circular materials approach that supports the project’s goals. This combined effort fosters collaboration, innovation, and resource efficiency, ensuring that materials and building elements are viewed not as waste but as valuable assets within a regenerative design framework.
Material Suitability Assessment
Potential Materials Performance Criteria

Storefront Requirements: Durability
Opacity “Quiet” aesthetic
Glazing Requirements:
Transparency
Large dimensions
Safety (toughened)
Same UV filters, etc.
Terrace Base Requirements: Weather-resistance
Opacity
Pedestrian safety Durability
Approved Materials

Greenpeace Headquarters
Washington, D.C.
Client: Greenpeace USA
Size: 18,700 ft2, 1,737 m2
Completion Date: 2022
Sustainability: Address the project’s full life cycle, from pre-design through future use and end-of-use impacts
Lead Contractor: Davis Construction
Key Circular Strategies: Pre-lease assessment to identify a space that had a usable existing fitout; reuse and design for disassembly
Greenpeace’s new office embodies the organization’s mission to reverse the detrimental impacts of climate change on our planet and society through advocacy and leadership. The new space was conceived as a prototype for climate-responsible interior fitouts, demonstrating approaches to reducing embodied carbon within a modest budget. The design marries technical approach and Greenpeace’s mission in the concept of a mobius loop: All things are part of a larger cycle, and it is our responsibility as environmental stewards to improve it for a better future. It highlights the notion of time as a nonlinear continuum, symbolizing the past, present, and future.
Process
Conventional design and construction practices often fail to address the full life cycle of building products. Greenpeace strove to shift this pattern from the inception of its new headquarters. Rather than build out a new space, the team collaborated during site selection to identify a space that was recently vacated by another tenant and in like-new condition.
The general contractor was onboarded in schematic design, allowing the team to maximize material reuse on-site, salvage off-site materials, and design for disassembly (DfD). Where new products were required, the project team sourced lower-carbon options using EPDs. Through this comprehensive process, Greenpeace’s new headquarters achieved an impressive 54% reduction in embodied carbon from its baseline LCA.

System
The general contractor went above and beyond to support sourcing reused materials from the project site and beyond. Sources included materials from another local project that was undergoing demolition as well as from the contractor’s own office renovation. While this collaboration was successful, the team’s research into reusing existing elements, salvaging materials, and specifying low-carbon products uncovered a gap between manufacturers offering material reclamation programs and contractors removing materials from a site. The team went on to address this through a research effort, “Closing the Loop on the Circular Economy,” 28 which created a resource for designers to facilitate connections between manufacturers, contractors, clients, and building owners.
Space
The design team surveyed the existing space and focused on identifying elements of the current layout to incorporate into the new space plan or reuse on-site. Wood walls, glass partitions and doors, divisible conference rooms, and operable partitions within the conference rooms were salvaged. Where possible, ceiling and floor finishes were reused, and millwork from existing pantries was utilized for the layout of the new staff café and coffee areas.
Material
The team placed a strong priority on reused materials, first from on-site and then from multiple off-site locations. The project sourced and incorporated the following reused elements:
nj Ceiling tile and grid
nj Electrical back boxes
nj Floor finishes
nj Insulation
nj Millwork
nj Non-structural metal framing
nj Partitions
nj Solid Core Wood Doors
nj Wood blocking
nj Wood Ceiling
nj Wood feature wall
Assembly
The team collaborated with the general contractor and created architectural details to facilitate future adaptation and disassembly of the project’s elements and to ensure ease of future salvage or recycling. Wood end caps on partial height partitions were salvaged from the general contractor’s office renovation, cut to size, and refinished by the millworker for reuse as wood ceiling slats and feature walls. The team worked closely with a local millworker to develop DfD details using mechanical fasteners, a Unistrut frame, wood cross-bracing, and hanger screws for the ceiling assembly.
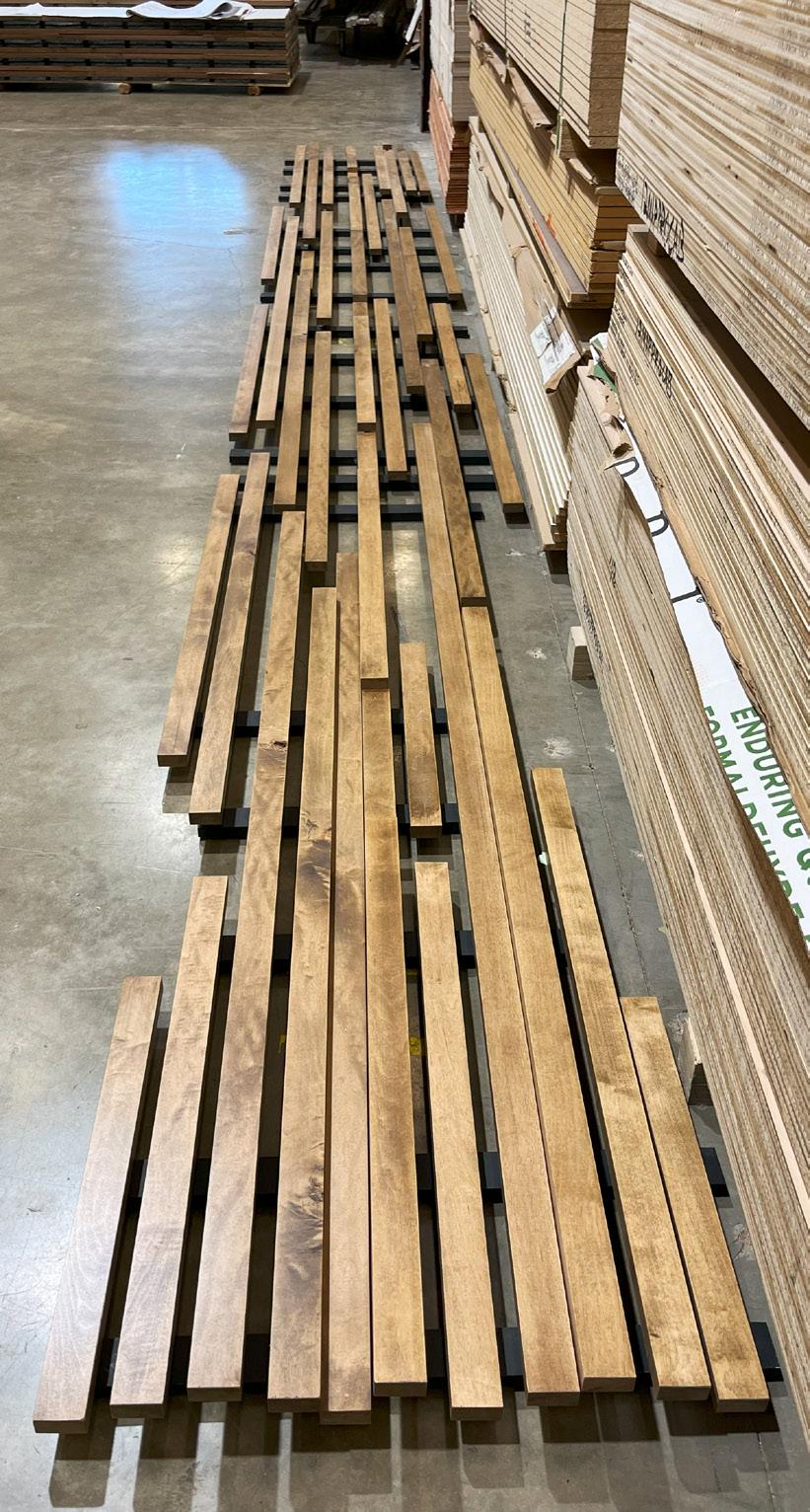
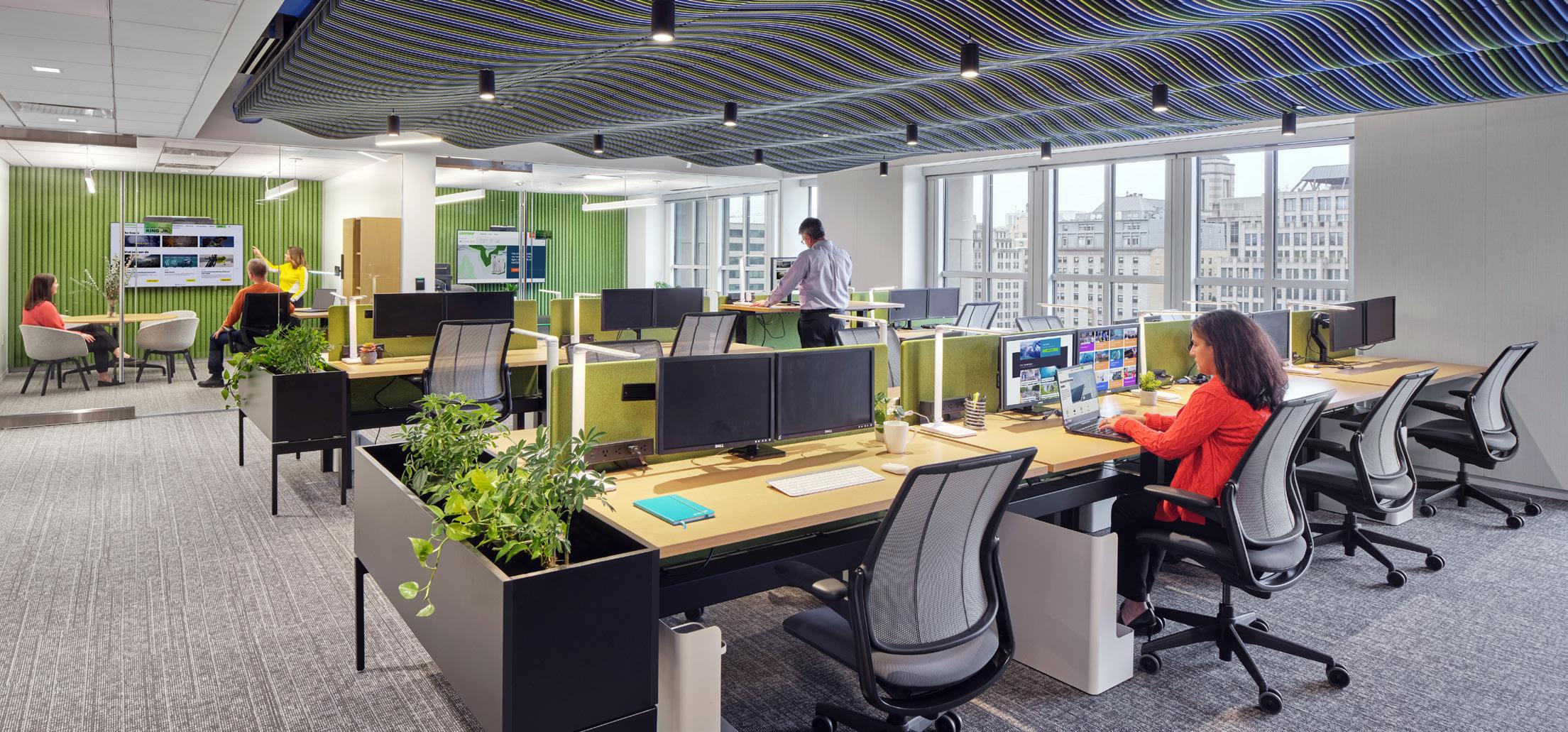
Assemblies
Design Beginnings, Not Endings
Design, and all life, exists in a closed system where resources are finite and nothing truly “new” is created. As such, the primary task of circular design is to align with this reality by focusing on reusing resources and encouraging reconfiguration of a project’s elements across a range of different purposes over time.
Circular assembly strategies support teams in integrating reused materials into a project’s assemblies and in designing for “next” or future outcomes of its elements. These strategies leverage composition, craft, connections, and detailing to support the sustainable use and reuse of each assembly.
If existing space: plan for refurbishment and integration, resale, or donation of existing elements
Design for Harvest
While exploring circular assembly methods, imagine design as a parallel to the acts of gardening and foraging. All materials to be installed, whether reused or new, are akin to “seeds” to be sown for future harvests. By designing for the next use of each material and assembly, the project becomes a “crop” of resources that will be cultivated through use and can be harvested in future design cycles.
Many strategies to plan for future uses of assemblies are variations on a theme, designing for longevity, adaptability, manufacture and assembly, and ultimately, disassembly and reuse. These strategies overlap and use common language and actions.
Select and apply assembly strategies to maximize long-term value and minimize new inputs and waste (e.g., DfA, DfL, DfD)
Coordinate DfA and DfD w/ shop drawings
Plan for installation, DfA, and DfD contractors
It’s up to each team to determine what strategy is right for their project; however, these themes are part of a greater whole. The overarching intent across these variations is for each of a design’s components to serve its highest use through multiple use cycles through its end-of-life.
To achieve this, assembly strategies employ joinery and construction methods to support ease of maintenance and reversible construction. This approach makes each assembly versatile, scalable, reusable, and ultimately separable into discreet materials, allowing each element to retain its value and utility across future applications.
Adapt to changes while verifying fabrication and installation requirements; update documentation to include as-built drawings
Design for Disassembly (DfD)
DfD involves designing for deconstruction before it occurs, using reversible construction techniques so they can be efficiently dismantled without damage to their components. DfD elements are intended to be relocated and reused over time, and eventually can be separated into parts for refabrication, recycling, or recovery.
Designers can begin the process of DfD by detailing each assembly’s form and joinery to minimize waste and ensure reversible assembly. Beyond this, realizing ease of disassembly requires coordination with the contractor and sub-contractors or fabricators, as the finer details of reversible joinery are often described in shop drawings. The design team must convey DfD requirements and review all drawings and submittals to ensure that design intent and fabrication processes are aligned. If applicable, the team may also need to consult with structural to assess DfD potential for structural modifications.
Guidance and documentation can help to ensure that DfD elements are used as intended over time. This may include instructions in the project specs, drawings, or a full material passport. Working backwards through an element’s assembly instructions should result in deconstruction. As such, it should be viable to provide disassembly drawings by reversing the project’s assembly drawings.
Exploring the Use of Salvaged Wood in Assemblies
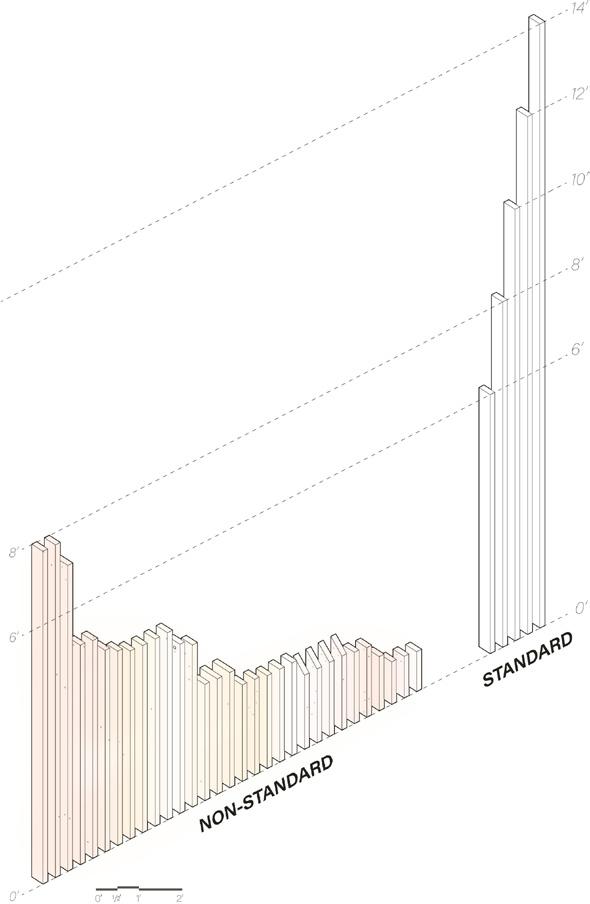
Design for Manufacture and Assembly (DfMA)
DfMA is centered on creating prefabricated components that are easy to produce, assemble, disassemble, relocate, reconfigure, and replace. Prefabrication increases offsite construction, reducing energy demands and waste while optimizing quantity and costs through efficient manufacturing. DfMA components foster scalability, facilitate reuse, and can include design for modularity, adaptation, and disassembly.29
Misfit Materials
Adopt an aesthetic approach that embraces variation. When identifying reused materials to incorporate into assemblies, instead of using high-integrity reclaimed elements, explore designing with non-standard, scrap, or visually inconsistent materials that are unlikely to be used as whole elements for another purpose.
For example, standard dimensions of reclaimed lumber can be resold or reused as dimensional lumber; it does not need to be transformed or upcycled. Where whole or standardized materials are required, incorporate these in a way that maintains their integrity and dimensions so they can be reused in a standard way in future projects.

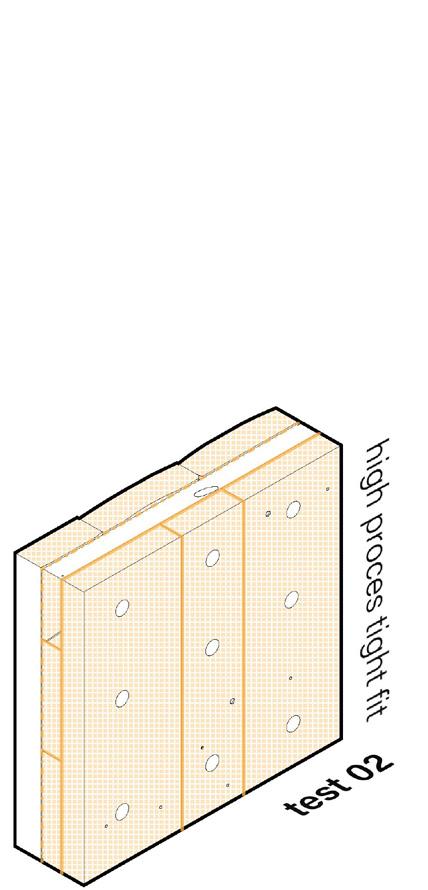
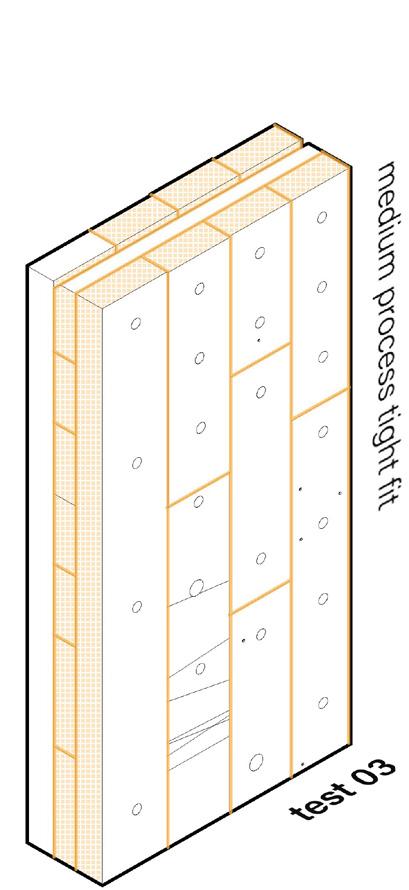
Image: Testing fabrication of doweled cross laminated timber (dCLT) with reclaimed wood. Source: Prototyping Secondary Lumber Networks Local Feasibility of Waste Wood for Reuse in Mass Timber. Gulon, M. (2025).30
Reclaim and Assemble
There are diverse approaches to guide the integration of existing material assets into the project’s assemblies. These aim to retain the existing value of each reused element while giving it new life that is tailored to its condition, characteristics, and potential.
Map these strategies to each of the project’s reused assets and cross reference them with the project’s requirements for new assemblies to identify optimal ways to incorporate each asset into a useful component that integrates reused materials.
Clean & Protect
Preserve materials that are in good condition and can be directly reused with minimal intervention.
Cut & Transform
Modify materials to adapt them, extending their functionality and value.
Remove & Reuse
Disassemble into constituent materials / components and repurpose for a new use.
These strategies begin to establish a design and technical language to describe approaches to realizing “next uses” for existing elements. Apply these and other fabrication methods to create functional, beautiful designs that integrate existing materials into a project’s assemblies.
Reclaiming Concrete

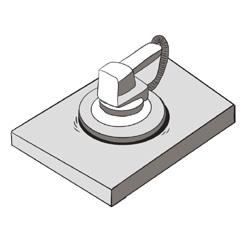
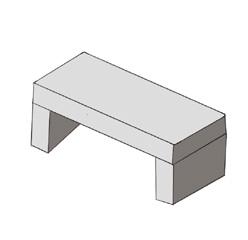
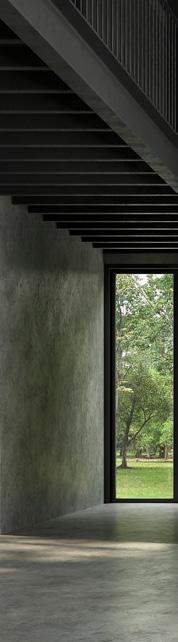

Reclaimed Furniture
Cutting concrete for reclaimed furniture involves using saws with diamond blades to slice the material into precise shapes, ensuring smooth edges and durability and safety. Processing Cut & Transform Reuse strategy Reclaim
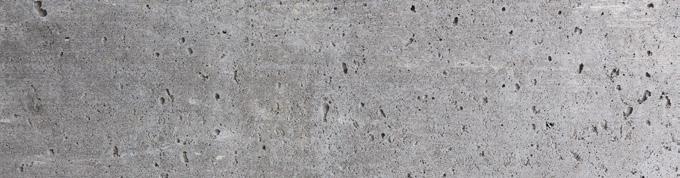
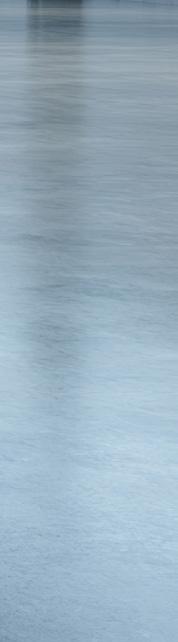
Repurposing Glass
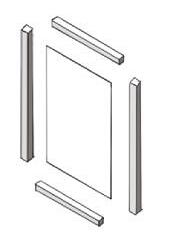
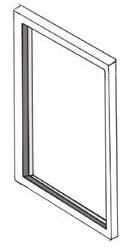


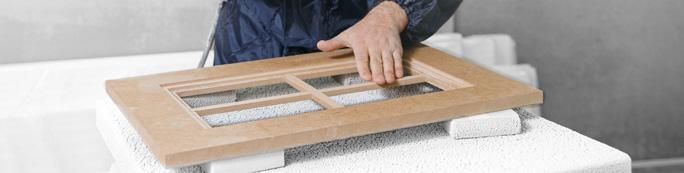
Exterior-to-Interior
Processing Cut & Transform Reuse strategy Repurpose
Testing exterior windows for repurposing as interior windows involves assessing and reinforcing their frames and seals to meet indoor pressure standards and aesthetic requirements.
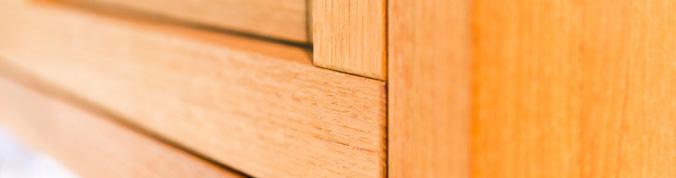
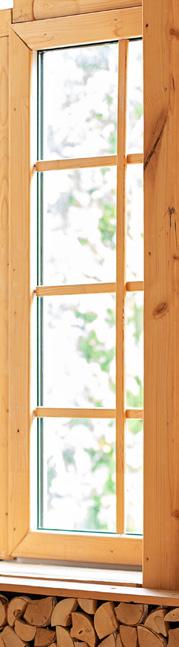
Transforming Carpet
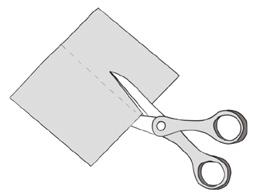


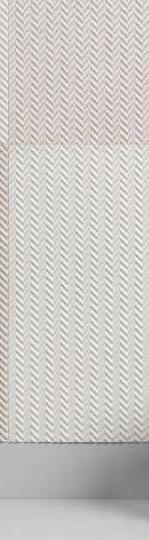
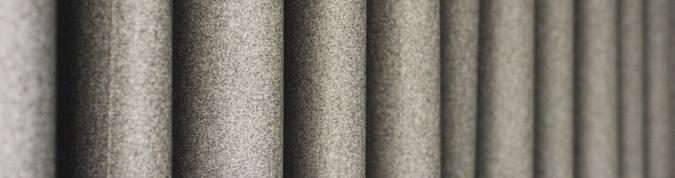
Acoustic Walls
Processing Cut & Transform Reuse strategy Transform
Cutting carpet to create acoustic tiles requires measuring and slicing sections to size, then backing or finishing the edges to prevent fraying and enhance sound-absorbing properties. Elements may also formed to enhance their dimensional quality.
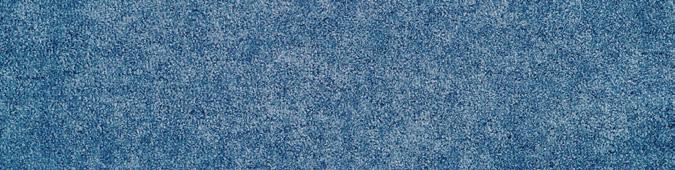

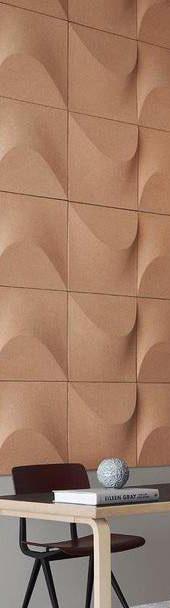
Circular Assembly Guidance
The following suggestions cross-reference common categories of assemblies with strategies that have been outlined in this primer to provide overarching guidance for impact reduction and circular design.
Per the early guidance in the “Critical Assessments” section of this primer, hold frequent workshops as well as targeted check-ins to work through each of the project’s elements and identify circular sources for each.
Casework
Does the project site have existing casework that can be reused, reconfigured or refabricated? Casework may also be available from other sites or salvage suppliers. In assessing reused casework, carefully assess repairs or modifications that may be required and plan with the contractor(s) accordingly.
For casework, preference durable wood-based products and ensure that composite products don’t include toxic chemicals like formaldehyde. Reduce laminations, veneers, and coatings. Design with dimensions that relate to the size of sheet materials and avoid perforations or cut-outs in panels to maximize future reusability. Design for durability, disassembly, and modularity so that casework may be modified and reused over time.
Ceilings Systems
Work through the project’s plans and reflected ceiling plans to develop a space plan for ceiling treatments. Which areas of the project can be designed without any ceiling materials? Which require aesthetic ceilings? Where are sound-masking treatments necessary? Which areas will allow for salvaged, reused, or refurbished ceiling materials?
Preference panelized ceiling systems built with sturdy materials that won’t be damaged when they are disassembled and moved, rather than continuous surfaces like gypsum that are easily damaged. Standardize ceiling panel grids; avoid bespoke forms and perforations that are less flexible for reuse.
Floor Assemblies
Review the project’s plans and identify locations where floor finishes could be reused, omitted, or installed with salvaged material. For flooring that is required:
nj Procure leased flooring, or flooring products that are supported by manufacturer takeback programs. Verify that manufacturers who offer takeback are reusing or recycling their material into new products.
nj Evaluate whether flooring substrates are needed. Include each layer of substrate when comparing the carbon and cost impacts of design options for flooring assemblies. Where substrate is required, look for biological or lowcarbon products.
nj Select modular, low-carbon, and healthy flooring. Consider using biological products like solid wood flooring, linoleum, or cork. Where technical products are needed, look for low-fire tile or flooring products with high recycled content and low carbon footprints.
nj Avoid toxic flooring materials like vinyl, tire-derived rubber, PFA based sealers, phthalates, and PVC.31
nj If raised access flooring is required, search for reused options and either design it to move to a future space or be left in place for future tenants. If reused products are unavailable, look for non-metallic products such as calcium silicate raised access flooring.
nj Design and install flooring for disassembly and reuse. Eliminate adhesives and nails in favor of mechanical or even magnetic fixings and use modular tile systems instead of sheet materials.
Partitions
Work through the space plan to review existing on-site partitions and identify which areas of the design will allow for salvaged, reused, refurbished, or modular (demountable) partition materials. Prioritize reuse of existing partitions wherever possible and take care not to damage them during construction. Partitions should be designed for disassembly regardless of whether they are flexible, modular, designed for adaptation, or fixed in place.
Per the guidance in the “Spaces” section of this primer, overlay partition design with space planning activities to assess which spaces should be able to “flex” with moveable partitions to allow opening of smaller spaces into larger rooms, and which walls require higher levels of acoustic rating. Design each partition type according to its level of flexibility, considering either durable design for reuse place or modular design for ease of reconfiguration.
Other considerations for partition design include:
Acoustic & fabric panels
nj Develop a space plan and determine where sound masking or aesthetic treatments are required. Avoid excess materials.
nj Design with distinct layers and joinery that can be disassembled or purchase modular acoustic systems that are designed for reuse.
nj Prioritize reused and recycled content in metal framing and fabrics.
nj Select fabrics that are overstock, upcycled, or have Cradle to Cradle or other healthy materials declarations.
Doors
nj Use reclaimed or bio-based doors where possible.
nj Fire doors may be sourced from reused elements but will require testing. A project may work with suppliers to test a select set of doors from a batch so that the others may be bulk certified for reuse.
Glazed partitions
nj Avoid sealants.
nj Look for reclaimed or recycled glass.
nj Avoid composites and coatings that would make glazing difficult to recycle in the future.
Interior structure
nj Explore wood framing for wall construction in place of metal framing. Where metal is used, select lighter gauge studs with wider spacing between members.
nj If the project involves stairs, explore creating these as a feature, using reclaimed materials or timber.
nj Consult with a structural engineer to ensure that all structural modifications are designed for disassembly.
Insulation
nj Eliminate the use of insulation with HFC blowing agents, which are often found in XPS and spray foam.
nj Preference biological insulation materials: wood fiber, cellulose, hemp, expanded cork, or recycled fabric.
Teams may narrow down areas of focus by common high-impact materials and actions and
by
running an LCA to identify their project's top 20 highest embodied carbon materials
or
assemblies based on the project's design and material quantities.
Furnishings, Fixtures, and Equipment
Develop a schedule and assess all furnishings, fixtures, and equipment (FF&E) through the “R Ladder” and consider: How can quantities of FF&E elements be optimized through creative space planning? What can be supplied from reused sources? How can each element be installed for disassembly and reuse?
Furnishings
Two pieces of furniture that serve the same function may be made from completely different materials and assembled in a variety of ways. For instance, a “chair” could be a wooden Danish chair or a cushioned recliner. Consider what functions are really needed and focus on pared-down selections composed of low-impact base materials.
nj Carbon impact: Furniture and replacement furnishings over time are often the primary source of impact in interiors projects. Prioritize reusing furnishings wherever possible.
nj Underutilized furniture: Investigate whether underutilized furniture owned by a client may be available to be transferred to the current design. Reusing desks, tables, workstations, and other elements results in significant carbon and cost savings.
nj Reused furniture: Reused furniture may also come directly from a reused furniture supplier or may be leased.
nj Dealer packages: Some furniture dealers are beginning to deliver sustainable FF&E packages; the team may survey dealer packages, develop a short list of agreed upon dealers, and engage in a dealer-driven program.
nj Decommissioning alternatives: Any decommissioned furniture could be sold or donated to a furniture exchange service.
nj Standardization: Task chairs and desks can be standardized so they can be repaired and remanufactured and remain assets in the project’s material bank.
nj Transparency labels: Transparency labels are becoming more common for furnishings. Prioritize pieces that can demonstrate simple, low-carbon, healthy materials that can be separated into distinct elements in the future.
Fixtures and Equipment
MEP and portable energy-using equipment relate to both embodied and operational carbon. Work with the project’s engineers to optimize equipment quantities, adapt space planning and individual equipment types for energy conservation, and apply DfL and DfD principles.
Bio-Based Materials
Where new elements are required, prioritize durable renewable materials, biopolymers, and other non-toxic materials. These options are readily available for lighting, blinds, casework, and other FF&E elements.
Ensure that these are accompanied by sourcing requirements in specs (for instance, certified wood is readily available for furniture and lighting scale elements). Verify that the design of bio-based materials allows for separability to promote renewable metabolism at end-of-life.
Right to Repair
nj Warranties and right to repair are important considerations for FF&E. Research whether each element is reparable, as the right to repair is crucial to maintaining multi-component elements over time.
nj If elements are reused, assess whether testing is required, ensure that warranties are agreeable to clients, and negotiate an extended warrantee period if desired.
nj Ensure that casework is reparable and able to be disassembled / reassembled. Pay attention to joinery and look for opportunities to use whole panels in consistent forms can be repurposed for other uses in the future.
Joinery and Fixing
Design all joinery for disassembly. Express the design as a kit of parts or building blocks.
Design with reversible fixings involves:
1. Adhesives: Avoid glues and sealants. Separating glued elements is challenging and may involve damaging multiple layers rather than allowing them to be reused. Where adhesives are required, use easily dissolvable or removable binders.
2. Joints: Design with non-mechanical joinery wherever possible. Ensure that joints are dimensionally appropriate and structurally sound.
3. Fasteners: Use screws, bolts, cleats, clips, pins, and straps instead of nails.
4. Standardization: Use common and similar fasteners. Avoid custom shapes and sizes or proprietary connections that will be difficult to repair or replace, as reliance on highly customized connections can lead to an entire assembly becoming unusable if one of those connections break.
5. Mortar: Use lime mortar; this is a historic material and is different from Portland limestone cement or “Portland cement.” Cement is impossible to disassemble, and because it is stronger than the surrounding bricks, it allows the brick to wear down while the cement stays in place, weakening masonry façades and structures.
6. Panels: Whole panels can be repurposed in the future. Avoid custom cutouts and shapes that are built for only one purpose. If an assembly uses sheet material, design to maintain as much of the area as possible so it may be reused in the future.
7. Get creative: Explore expressive fixing methods. Consider creative options, including distinctive wood joinery, weaving or knot tying, and magnets.
Joinery Do's and Don'ts
Use easily dissolvable or removable binders
Explore creative fixing methods
Avoid excess layers and lamination
5 Bank Street
London, United Kingdom
Client: European Bank for Reconstruction and Development (EBRD)
Size: 366,000 ft2, 34,003 m2
Completion Date: 2022
Sustainability: WELL Certified Platinum; BREAM Outstanding
Lead Contractor: Overbury
Key Circular Strategies: Stakeholder engagement, design for disassembly and reconfiguration, and extensive material passporting
The EBRD and its new home at 5 Bank Street have challenged the status quo and set a new benchmark for office design. The project began with EBRD’s strong ambitions to create a bestin-class workplace, striking a balance between human-centric and planet-conscious design. Circular design was a core part of the project brief; the team wove circularity and the EBRD’s other goals together to develop a bespoke sustainability character based on five factors:
1. Social Network
2. Human Interactions
3. Physical Assets
4. Natural Environment
5. Economic Aspects Process
5 Bank Street is an exemplar of collaboration and co-creation with staff and stakeholders. The client united the project team around clear sustainability and diversity, equity, and inclusion goals. The full team aligned around a manifesto at the project’s outset, working to exceed expectations through change management, the design, construction, and procurement process, and occupation. To support the project’s long-term goals and prepare for project handover, operations, and maintenance, the EBRD launched an internal communications campaign, engaging staff and other project stakeholders with the narrative of change throughout the design and delivery process.
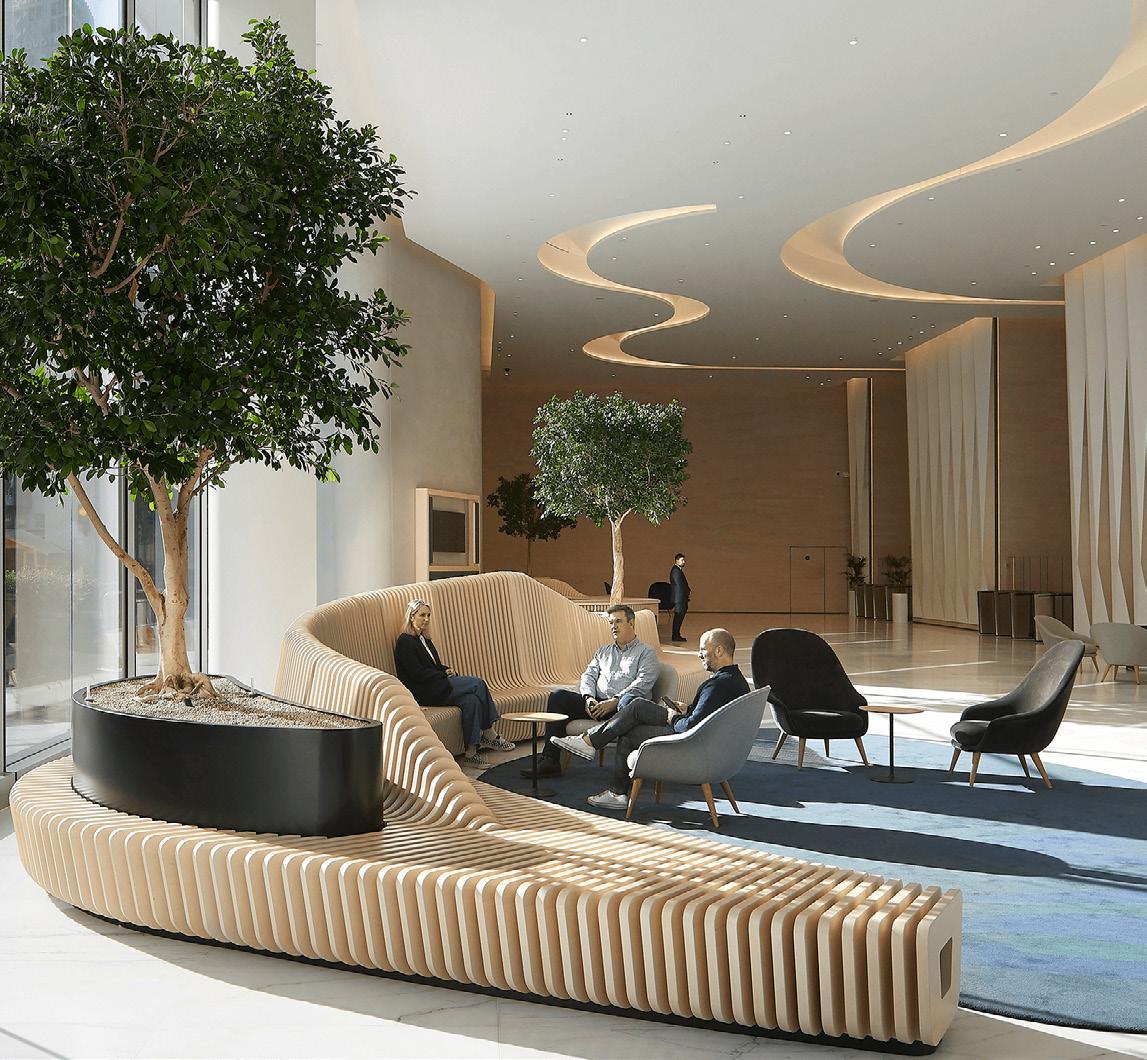
System
In support of the EBRD project’s circularity goals, the contractor, Overbury, developed a comprehensive “Deconstruction Guide” in partnership with the project team. This guide serves in place of a material passporting system, and covers each installed product, from flooring to modular partitions to duct work.
The guide allows future users (i.e., maintenance, stripout, and fitout contractors) to make more informed and strategic decisions. The deconstruction guide is split into sections by element type, where contact details for the sub-contractor and material takeback schemes are listed. Each element then includes information on product certification schemes, cleaning and maintenance, a breakdown of components, information on attachment types (for example, screwed, taped, or hung), level of deconstructability, and end-of-life or next use instructions.
Space
The project is designed as a “living organism,” composed of a variety of spaces that are delineated with modular elements and designed for adaptation. The energy and forms of these spaces are inspired by ecology.
nj Open spaces, like the entry or cafeteria, use themes of weaving and curvature to delineate between open space and corridor.
nj Prospect and refuge spaces evoke the feeling of sitting under a tree canopy or being in a cocoon.
nj Cellular spaces can be reconfigured to host a variety of programs, such as large offices, small meeting areas, and wellness rooms.
Material
The EBRD team focused on valuing each material as an asset and designing with simple, elegant materials. Unnecessary veneers, paint, and other layers were omitted. Embodied carbon reduction, material health, and supply chain equity were all key factors in material selection and specification.
Assembly
The project’s furniture and casework are a “kit of parts” designed to ensure ease of use as well as reuse. The team designed with traditional mechanical fixings and developed creative attachment methods like adhering floor coverings with magnets. Many elements are composed of modules; for example, the curvilinear reception seating components are connected by a spine and can be reconfigured in the future.

Modular Reception Seating
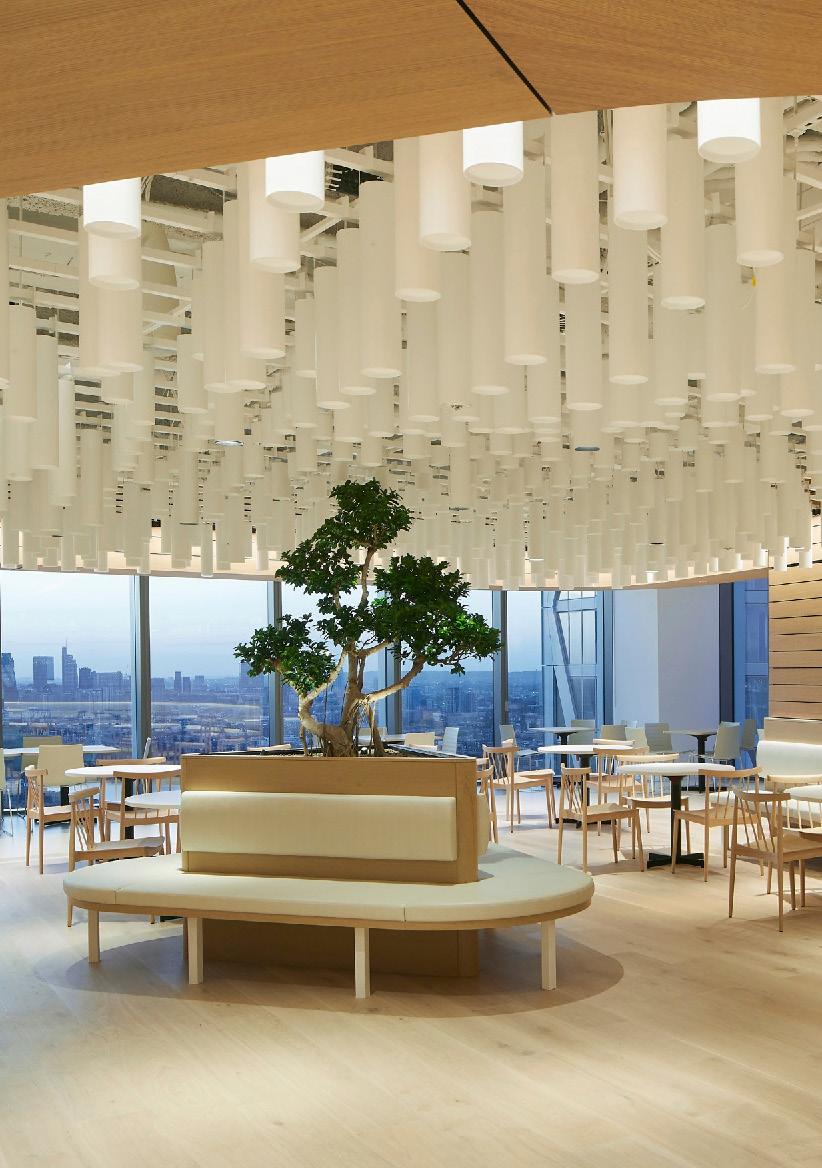
Acknowledgements
Special thanks to our Perkins&Will London studio leaders, who developed and tested many of the processes and strategies that inspired this primer. These include:
Simon Bone
Linzi Cassels
Asif Din
Mehmet Ermiya
Cesar Herrera
Siobhan O'Leary
Grant Spencer
Adam Strudwick
Our London studio's 2020 commitment to pursue net-zero interiors, accompanied by their “Net Zero Now. Interiors” report, set a precedent for circular design in interior architecture. The report can be found at: perkinswill.com/net-zero-now-interiors
End Notes
1 Adapted from Camplisson, E., BuchDohrmann, J. (2024). Upcycling in Practice, Practicing Upcycling. Perkins&Will Research.
2 Planetary boundaries. (n.d.). Stockholm Resilience. Retrieved from https://www.stockholmresilience. org/research/planetary-boundaries. html
3 Schandl, H., et al. (2024). Global material flows and resource productivity: The 2024 update. Journal of Industrial Ecology, 28 (6), 2012–2031. https://doi.org/10.1111/ jiec.13593
4 GHG emissions of all world countries. (n.d.). Europa.eu. Retrieved from https://edgar.jrc.ec.europa.eu/ report_2024
5 Total global solid waste generation statistics vary and must be assembled from a variety of sources. These statistics tend to be limited to “municipal solid waste” - but other waste streams, such as industrial waste, are much more significant. Three sources that account for both municipal solid waste and other waste generation include:
‒ Platform for Accelerating the Circular Economy. (2021). Circularity Gap Report 2021 . p. 49. Retrieved from https://circularitygap.world/2021
‒ Maalouf, A., Mavropoulos, A. (2022). Re-assessing global municipal solid waste generation. Waste Management and Research. Retrieved from https://www.researchgate. net/publication/358126678_Reassessing_global_municipal_ solid_waste_generation
‒ Kaza,S., et al. (2024). What a Waste 2.0 : A Global Snapshot of Solid Waste Management to 2050 (English). Urban Development Series Washington, D.C.: World
Bank Group. pp. 36-37. Retrieved from http://documents. worldbank.org/curated/ en/697271544470229584/ What-a-Waste-2-0-A-GlobalSnapshot-of-Solid-WasteManagement-to-2050
Note: Municipal waste generation per capita is estimated to be 1/18th of industrial waste generation, per Kaza,S., et al. (2024). p. 37.
6 Miller, N. (2022). The industry creating a third of the world’s waste. BBC. Retrieved from https://www. bbc.com/future/article/20211215the-buildings-made-from-rubbish
7 Climate Change Indicators: Greenhouse Gases. (N.d.). US EPA. Retrieved from https://www. epa.gov/climate-indicators/ greenhouse-gases
8 Data sources for the “ Global Annual Extraction & Emissions” chart:
‒ CO2 concentrations & emissions: Global atmospheric carbon dioxide compared to annual emissions (1751-2022), adapted from original by Dr. Howard Diamond (NOAA ARL). (n.d.). Climate.gov. Retrieved from https://www.climate.gov/ media/14596
‒ GHG emissions data: Jones, et al., with major processing by Our World in Data. (2024). “Annual greenhouse gas emissions including land use” [dataset]. Jones, et al., “National contributions to climate change 2024.2” [original data]. Retrieved from https://ourworldindata.org/ grapher/total-ghg-emissions
‒ Extraction data, 1850-1970: Krausmann, et al. “Long-term Trends in Global Material and Energy Use,” in Social Ecology: Society-Nature Relations across Time and Space, ed.
Haberl, et al. (Switzerland: Springer, 2016). retrieved from https://www.researchgate.net/ publication/304816638_LongTerm_Trends_in_Global_Material_ and_Energy_Use
‒ Extraction data, 1970-2024: Schandl, H., et al (2024).
9 Kaza,S., et al. (2024).
10 Maalouf, A., Mavropoulos, A. (2022).
11 Treloar, GJ., Et al. (1999). Embodied energy analysis of fixtures, fittings and furniture in office buildings, Facilities, Volume 17 (issue 11), pp. 403-409. Retrieved from https://www. academia.edu/18481731/Embodied_ energy_analysis_of_fixtures_fittings_ and_furniture_in_office_buildings
12 We adapted the data for the “Impact of Interior Refits” chart from Treloar, G.J., et al. (1999). It is worth noting that this paper was published in 1999 and that carbon contribution analyses can vary widely due to considerations like grid factor, system boundary, and product-specific impacts. However, its findings fall within with the ranges of impact observed in several recent Perkins&Will case studies, so we selected this data source due to its continued relevance and its publicly available methodology.
13 Circular economy introduction. (n.d.). Ellen MacArthur Foundation. Retrieved from https://www. ellenmacarthurfoundation.org/ topics/circular-economy-introduction
14 Circular economy introduction. (n.d.). Ellen MacArthur Foundation.
15 About bamb. (2019). Buildings as Material Banks. Retrieved from https://www.bamb2020.eu/ about-bamb/
16 The R Ladder has evolved over time through many contributors. The 10 R’s are expressed in “Figure 1. Levels of Circularity, the 10 R’s,” which can be found in: Cramer, J., The Raw Materials Transition in the Amsterdam Metropolitan Area: Added Value for the Economy, Well-Being and the Environment, 2017, 59, 3, 14-21. Retrieved from https://doi.org/10.1080 /00139157.2017.1301167
17 Brand, S. (1994). How Buildings Learn: What Happens After They're Built. New York: Viking Press.
18 Treloar, GJ. Et al, (1999). Embodied energy analysis of fixtures, fittings and furniture in office buildings, Facilities, Volume 17 (Issue 11), pp. 403-409. Retrieved from https://www. academia.edu/18481731/Embodied_ energy_analysis_of_fixtures_fittings_ and_furniture_in_office_buildings
19 Workshop templates from the Circular Buildings Toolkit, a free resource created by ARUP and the Ellen MacArthur Foundation, can be accessed at https://ce-toolkit.dhub. arup.com/workshop
20 Life-Cycle Cost Analysis (LCCA). (n.d.). Retrieved from https:// www.wbdg.org/resources/ life-cycle-cost-analysis-lcca
21 Marani, M. (2024). Continuing Education: Circular Construction. Retrieved from https://www. architecturalrecord.com/ articles/16929-continuing-educationcircular-construction
22 All for Reuse, Ecosystem Map. Retrieved from www.allforreuse.org/ ecosystem-map, Open Street Map
23 Perkins&Will. (2024). Living Design. Retrieved from https://perkinswill. com/living-design/
24 Perkins&Will. (2023). Green Operations Plan. Retrieved from https://perkinswill.com/ green-operations-plan/
25 A well-known paraphrasing of Dieter Rams’ design philosophy, elaborated upon in: Rams, D. (2010). Less, but better. Gestalten.
26 Cradle-to-cradle design. (2024). Retrieved from https://en.wikipedia. org/wiki/Cradle-to-cradle_design
27 Camplisson, E., Buch-Dohrmann, J. (2024).Upcycling in Practice, Practicing Upcycling. Perkins&Will Research.
28 Cordell, D., McNairy, B., Pendorf J. (2022).Closing the Loop on the Circular Economy. Perkins&Will Research. Retrieved from https://research. perkinswill.com/projects/closing-theloop-on-the-circular-economy/
29 Ghaffarian, M, Gjata, E. et.al. Perkins&Will. (2024). Design for Manufacture and Assembly - A Primer. Retrieved from https://issuu.com/ perkinswillvan/docs/perkinswilldesign_for_manufacture_and_ assembly-a_
30 Gulon. M. (2025). Prototyping Secondary Lumber Networks Local Feasibility of Waste Wood for Reuse in Mass Timber. AIA, ASCA. To be published in 2025 and retrievable at: https://www.acsa-arch.org/ proceedings-index
31 McGrath, T, Seigel K., et. al. Perkins&Will. (2022). Embodied Carbon and Material Health in Gypsum Drywall and Flooring. Perkins&Will. Retrieved from issuu.com/perkinswill/docs/ white-paper_carbon-health_final
General Note: Some phrasing, text refinements, and editing were assisted by ChatGPT, an AI language model by OpenAI, in February 2025. Retrieved from https://openai.com/chatgpt.