Scaling Innovation
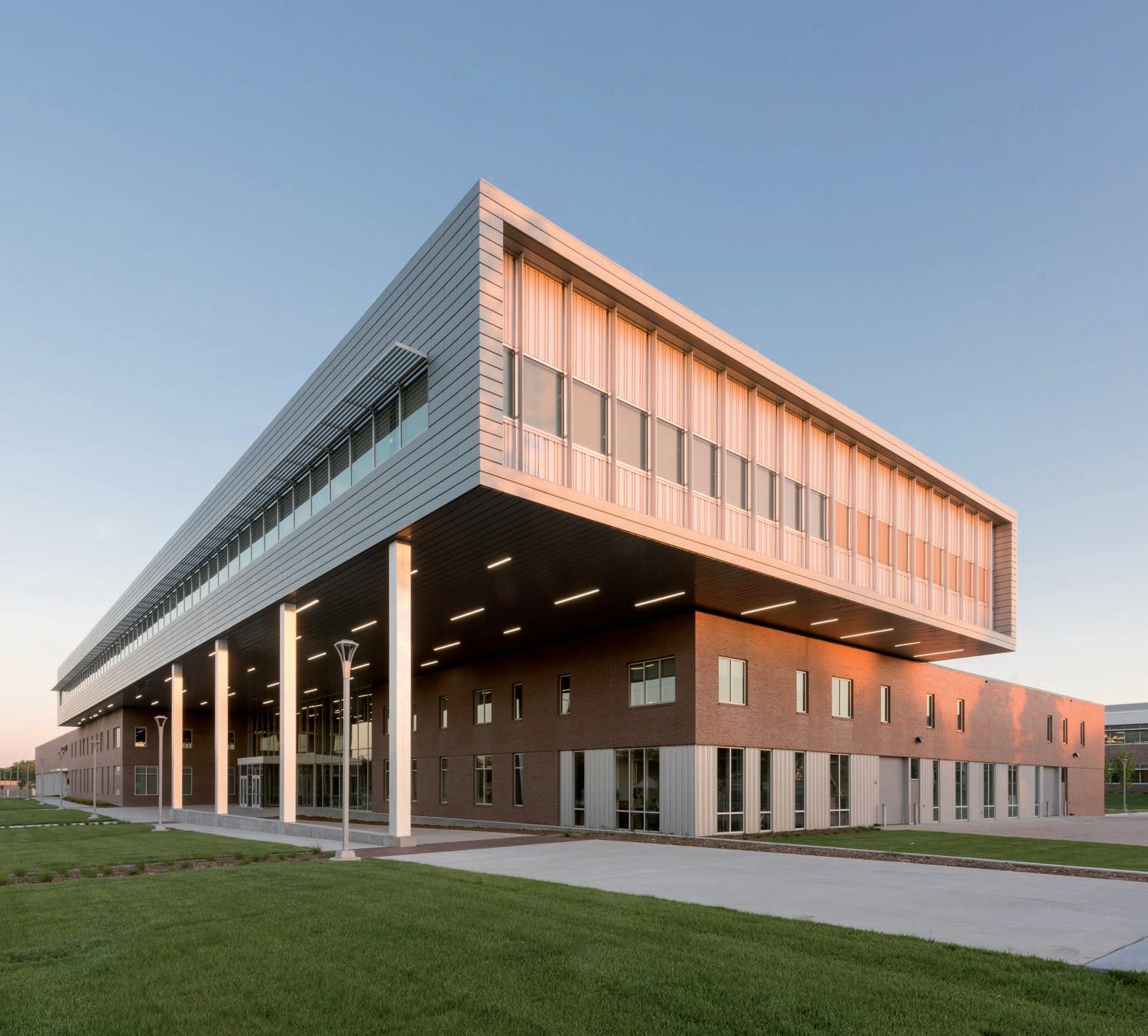
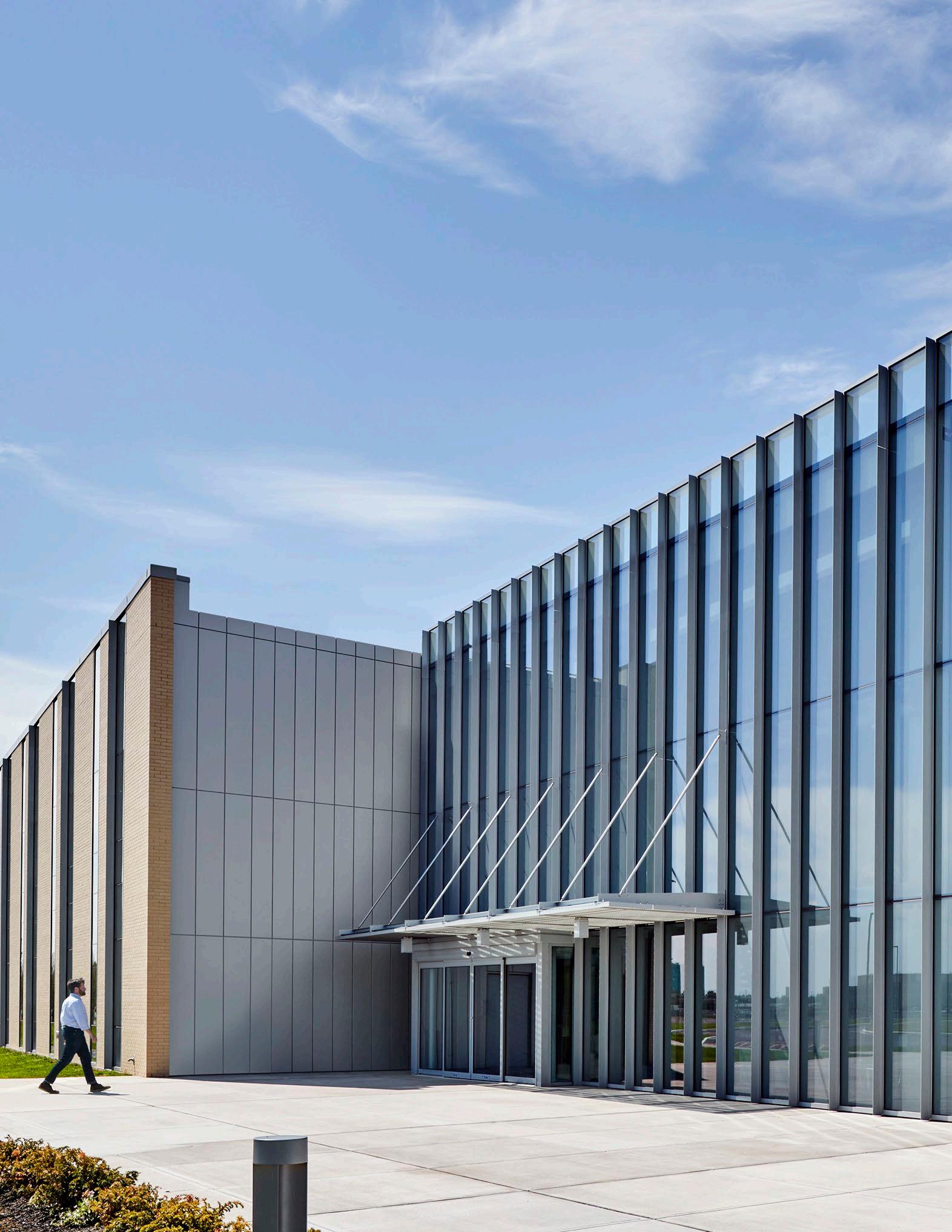
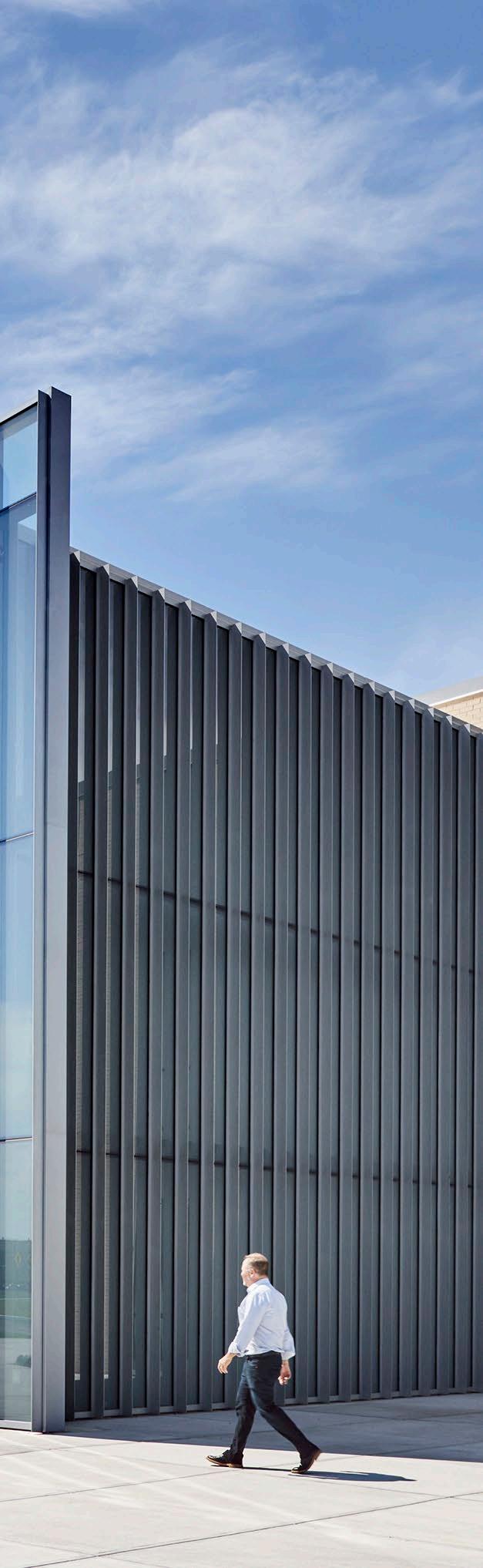
Introduction ― 4
University Research Facilities ― 12
Industrial Manufacturing ― 20
Career and Technical Education ― 30
Our Team ― 38
Introduction ― 4
University Research Facilities ― 12
Industrial Manufacturing ― 20
Career and Technical Education ― 30
Our Team ― 38
The face of manufacturing is rapidly evolving, both domestically and internationally. The constant flow of new discoveries in such diverse fields as aerospace, medicine, energy, and computing, along with increasing pressures of global competition, are challenging industry to more speedily translate emerging scientific and engineering discoveries into novel and marketable products, systems, and services.
In response, Advanced Manufacturing (AM) leverages a variety of cutting-edge technologies in novel ways, such as robotics, 3D printing, artificial intelligence, and high-performance computing, often employing new materials enabled by advancements in biology, chemistry, metallurgy, and nanotechnology. Along the way, AM pioneers innovative processes, often using established techniques in new ways, or adapting them to new domains. ↑
Industry and government policy makers in the United States, Canada, and many other countries have recognized that meeting this challenge requires establishing a comprehensive ecosystem of Advanced Manufacturing that includes new models of industry/ university research collaboration, engineering education, and workforce skills development.
From revolutionary cell and gene therapies (CGT), to clean energy, the success of every emerging medical and technological advancement depends on our ability to create products at scale. Commercial viability hinges on an efficient supply chain and manufacturing infrastructure, operated by a skilled workforce, that can bring technologies or therapies to market. Perkins&Will is at the forefront of helping industrial and educational clients align their facilities to their roles in the Advanced Manufacturing ecosystem, buiding the structures and systems that can scale to meet global demand.
←
National Institutes of Health, E-Wing, Washington, D.C.
In recent years, global industrial economies have put a renewed emphasis on innovative manufacturing technologies. This has required investments in every stage of Advanced Manufacturing, including workforce skills training, AM integration into engineering education, and cutting-edge research. These can only come from effective collaboration between universities and industry, combining the advantages of basic discovery and skills development with an understanding of real-world issues around market demand and scaleup. Our experience in the educational market helps us anticipate the future of research and manufacturing; we’re building for today, and planning for what will best position us for the future.
Government agencies are not only enduse customers, but are also instrumental in setting policies to remove obstacles and making critical connections between institutions and the private sector.
The ecosystem operates as a cyclical feedback loop, with industry informing education and research, which in turn provide a pipeline of knowledge and talent to industry.
Understand the project’s position in the ecosystem.
Knowing whether a facility will support teaching, research, or production is critical for efficient programming and design. Higher education and CTE facilites work best with established “typologies” of standard laboratory types, which range in capability. Balancing a mix of these spaces is a pathway to affordable but robust environments. For developers of multi-tenant industrial facilities, early discussions with potential anchor tenants is vital to the success of the project, as their needs will define the required attributes and degree of flexibility of the facility.
Identify the major technologies or modes of production.
Different technologies have different demands for equipment and facility capabilities. It is not a one-size-fits-all model. Some common and emerging AM technologies include: subtractive and additive manufacturing; forging, forming, or casting; coatings and surface engineering; composite materials; robotics and automated manufacturing systems; remanufacturing; structural and materials testing; and digital analytics of producting processes.
Align on a long-term, flexible planning strategy.
The most successful projects balance cost with capability; visibility with security; and nearterm needs with long-term flexibility. Simplicity and regularity of the building’s structural frame, space planning, and systems distribution strategy will provide a readily adaptable facility for future generations. A “change-friendly” building is framed around a wellconsidered range of functional capabilities, and provides a secure and welcoming work environment.
W. Plaster
Higher education institutions are inherently convergent and interdisciplinary. They requires facilities that are readily adaptable to everchanging experimental needs. This is especially true for research facilities that have a focus on Advanced Manufacturing.
Client: Commonwealth Center for Advanced Manufacturing, University of Virginia Foundation
Size: 63,000 square feet
Completion Date: 2012
Awards:
Award in Architecture, AIA, DC Chapter, 2014
Design Excellence Award, Institutional, AIA, Northern Virginia, 2014
Honor Award, AIA, Potomac Valley, 2013
Best of Best, Global Best Projects Award, Engineering News Record, 2013
Best Manufacturing Project, Engineering News Record, Mid-Atlantic, 2013
CCAM’s collaborative model joins academic research with best-in-class manufacturers for accelerated product innovations.
CCAM is a research collaboration between the University of Virginia, Virginia Tech, Virginia State University, and manufacturing companies worldwide, including Rolls Royce North America. The 63,000 square foot (5,850 square meter) state-of-the-art facility has been designed for manufacturers to collaborate with faculty and students from Virginia’s top research and teaching institutions to perform advanced research in surface engineering, additive manufacturing, and adaptive automation systems.
CCAM houses engineering and computational labs, as well as a large high-bay space for prototypical manufacturing processes, including thermal spraying, directed vapor disposition, and multi-axis milling. The facilities also include core laboratories for materials preparation, surface characterization, and computer visualization, as well as conferencing and amenity spaces for CCAM employees and visitors.
By pooling resources of universities and member companies, the CCAM offers a new model for accelerating the transitions of research breakthroughs into product development and manufacturing techniques. The founding companies involved with this facility and its initial research operations include Canon Virginia Inc., Chromalloy, Northrup Grumman, Rolls-Royce North America, Sandvik Coromant, and Siemens.
“The unanimous consensus is that the facility is truly world-class. Researchers will appreciate the efficient layout, the catwalk, the communal areas, and the high bay space...the building is the perfect blend of high tech and industrial, without being soulless.”
Pace Lochte, UVA Director of Regional Business Development
Client: Missouri University of Science and Technology
Size: 118,000 square feet
Completion Date: October 2025
The Missouri Protoplex is a reflection of the statewide ecosystem of manufacturing and technology it serves. It unites industry and academia to conduct research on new materials and methods; prototype; test new manufacturing processes; develop workforce competencies; and solve the multi-disciplinary problems required to bring integrated cyber-physical manufacturing systems into practical use.
This building will seed a new Missouri University of Science and Technology innovation campus and serve as a gateway to the main campus. Its gently-curving south-facing façade follows a bend in the adjacent interstate highway and references an existing arch bridge that connects the innovation campus to the main campus.
The building materials and overall expression reflect the high-tech nature of the Advanced Manufacturing research and development occurring within.
Client: Wichita State University Size: 142,661 square feet
Completion Date: 2016
Construction Cost: $34.7million Awards: Excellence in Architecture, Honor Award, AIA Wichita Design Awards, 2017
― WHAT IT IS A functioning co-location for partnerships between students, faculty, the university, private businesses, and public organizations.
Wichita State University is focused on being at the forefront of technological and engineering advances in the business world. They challenged our team to create a space that would facilitate important opportunities and partnerships between students, faculty, the university, private businesses, and public organizations.
We systematically designed the Experiential Engineering Building (EEB) to advance the University’s needs by creating highly collaborative spaces as well as state-of-the-art instructional, research, and office space. Programs held at the EEB include the Technology Transfer program, allowing for expansion support for entrepreneurial development of technology-based businesses, and the Experiential Learning program, essential to support and grow Wichita as an engineering hub for the United States. As the first of four future buildings, the Experiential Engineering Building offers high visibility to attract donors, draw expertise, and inspire the university’s youth.
↑ Research facilities at the EEB are specially aligned with Wichita’s Advanced Manufacturing economy.
Low-emitting materials were used inside in combination with lots of natural daylight to provide healthy learning and research environments.
With a focus on efficiency, scalability, and precision, we design state-of-the-art environments that optimize workflow, enhance safety, and drive technological breakthroughs.
Princeton West Innovation Campus has identified an opportunity in the growing market sectors of bioscience and biomanufacturing. To tap into that momentum, they plan to build three new cGMP biomanufacturing buildings on underutilized locations around their campus. The design phase focuses on creating a clear and inspiring vision for these new facilities that can build enough momentum with potential tenants to generate a viable project.
We begin with an empathetic focus on the needs of the diverse range of people the project will accommodate. Solutions focus on universal equitable experience and inclusivity; potential employees have a high degree of choice in the marketplace, and are looking for a workplace that supports an active and healthy lifestyle. This project aims to provide a competitive mix of attractive amenities that fuel tenant interest.
The project plans to restore the natural ecosystem on each site in service of all life. This will benefit people through environmental stewardship, but will also benefit the plants, animals, pollinators, and birds.
Client: SANY
Size: 400,000 square feet
Completion Date: 2012
The SANY Office & Assembly Building in Peachtree City serves as the North American Headquarters for a China-based heavy equipment manufacturer. The first phase of a 228-acre site master plan, the 360,000 square foot assembly building and integrated 60,000 square foot three-level office consolidates visitor, executive, and employee amenity areas in a single unique location that limits the land disturbance on site, while maximizing future expansion opportunities. The office component is integrated into the northeast corner of the assembly building, adjacent to the entry drive.
A three-story, point-supported glass atrium anchors the corner and allows for impressive views in and out of the space. Flowing canopies provide shade to the east-facing atrium and visually weave the relationship from floor to floor, from east elevation to north and from inside to outside.
A waveform design symbolically references the country of origin, and the journey that components take across the ocean to the Port of Savannah for assembly at the facility.
The first floor of the office component welcomes visitors through the atrium and allows direct access into the assembly plant for tours. A state-of-the-art equipment logistic center, also on the first floor, allows tracking and diagnostics of all equipment in North and South America. The second floor contains Sany’s temporary corporate offices, while the third floor houses the company’s research and development center.
Client: RTX (formerly United Technologies) Size: 150,000 square feet
Sustainability: LEED Gold ®
Completion Date: 2017
The atrium is strategically positioned between lab and research office space to provide a physical connection between lab and office functions and help foster a collaborative work environment. Demountable walls provide flexibility for an array of user groups, enabling rapid changes and the ability to accommodate them. Modularity and related planning concepts will further influence campus expansion and flexibility in developing new technologies and processes. ― WHAT IT IS
This signature facility unifies the existing collection of loosely connected buildings and creates a new campus entrance that expresses a strong identity. A highly visible and transparent 2-story atrium space provides collaboration zones and meeting space and functions as a showcase where RTRC products are displayed, which further reinforces the brand.
The new building is designed to achieve 45% reduction in energy use compared to base code. From the building’s high-performance envelope, to energy efficient lighting and fixtures, the design strives to meet RTRC’s sustainability goals.
RTRC incorporates sustainable design features such as under carpet flat wire to provide electric power and data cabling to work stations, daylight harvesting with solar tubes and LED lighting controls. The steel used in the 50,000 square foot new construction project is made from 90% recycled materials. Sustainable design features extend to the exterior of the building and include landscaping with indigenous plants that do not require irrigation and twelve electric vehicle charging stations for use by employees that drive zero/low emission vehicles.
The Cara project creates a new generation of highly secure research spaces that are flexible, transparent, and foster collaboration. The design incorporates the guiding principles that were developed during the master planning process, which established a clear vision for future projects on RTRC’s campus.
Brooklyn, New York
Client: NYCEDC
Size: 200,000 square feet
Completion Date: 2027
The Brooklyn Army Terminal (BAT) opened in 1918 and served as the largest military supply base in the U.S. through World War II. Today, BAT continues to impact New York’s working waterfront by serving as a nexus of modern industrial businesses and entrepreneurs.
The New York City Economic Development Corporation (NYCEDC) has enlisted a consortium of partners to develop and design a cutting-edge innovation hub at the Brooklyn Army Terminal (BAT) in Sunset Park, as part of a long-term commitment to developing the city’s green economy. Called BATWorks, this new facility will transform a significant portion of the historic site into an innovation incubator for emerging businesses, primarily in the clean tech and energy sectors.
The hub will transform a proposed 200,000 square feet across multiple interior levels and an outdoor courtyard. When complete, these spaces will provide a wide range of start-ups—including emerging market innovators, small- and medium-sized companies, and growth-stage and commercialization-stage companies—with fit-for-purpose space to build products, rapidly prototype new technology, and carry out product research and development.
The innovation hub will support 150 startups over 10 years, generate $2.6 billion in economic impact, and provide local workforce training and job placement programs by providing co-working, incubation, lab prototyping, and trial assembly facilities.
Career and Technical Education (CTE) aligns the needs of employers with workforce and talent development. These facilies house a range of programs that train workers in skills to meet the unique demands of the Advanced Manufacturing economy.
Springfield, Missouri
Client: Ozarks Technical Community College Size: 122,000 square feet
Cost: $26,000,000 Completion: 2023
The Future is Here
The new 117,000 square foot, two-story Robert W. Plaster Center for Advanced Manufacturing (PMC) serves as the regional hub for Advanced Manufacturing and technologyrelated education and training. The design for the PMC includes specialized hands-on learning environments, flexible and collaborative classrooms, customizable simulation training centers, long-distance learning space, research and development labs, designated process-improvement space, business incubation test centers, and a large high-bay environment for industry-led projects. The PMC offers shortand longer-term training opportunities that cover a breadth of industry specializations, and focus on the future of the Advanced Manufacturing industry, highly technical processes, and employment.
―
Occupying a key site at the campus edge, the PMC is a signature building that reflects OTC’s critical role in providing skilled talent for Missouri’s Advanced Manufacturing industries. Fronting one of Springfield’s main thoroughfares, the 500’ long high-bay space offers views into PMC’s main programs including Industrial Systems, Precision Manufacturing, Collaborative Projects, and Industry Partner Space. Alongside the highbay, a two-story wing accommodates other lab space including Network Technologies, Digital Design, and Rapid Prototyping. To enhance the visitor experience, a choreographed “parade route” helps OTC lead prospective students and industry recruiters through the facility.
Toronto, Ontario
― WHAT IT IS A multi-disciplinary research facility where students work interactively with industry partners set in the heart of one of Ontario’s largest polytechnic Colleges.
Designed to connect students, community and industry partners in an environment that supports entrepreneurship and environmental stewardship, the Barrett Centre for Technology Innovation (BCTI) is the flagship facility for Humber College’s Applied Research and Innovation program. Through its radical program, signature architectural expression, and cutting-edge performance the building establishes a new focal point for student life at Humber, creates a gateway onto the College’s north campus, and celebrates the unique identity and growing reputation of applied research at Humber.
“The Centre will be a game changer for students. Working on multiple projects with different partners links what they’re doing here with the careers ahead of them. It instills confidence as well as skills.”
― DARREN LAWLESS, DEAN OF APPLIED RESEARCH AND INNOVATION, HUMBER COLLEGE
Typical makerspace with flexible exposed ceiling grid.
Generous transparency along the central spine of the building invite views into the various project rooms and makerspaces. Open ceilings allow ease of access to the various systems of the building for maximum flexibility.
The BCTI encourages learning outside the classroom by omitting classrooms entirely. Instead, flexible project modules provide space for students, faculty and industry partners to research, fabricate and explore together. Supported by fabrication and technical zones, these modules are equipped with flexible power, data and pneumatics, movable partitions, ubiquitous technology, and embedded meeting rooms and storage areas, making the building into a dynamic learning warehouse that can be easily re-configured to serve a range of project types and scales.
Client: Greenville County Schools
Size: 227,907 square feet
Completion Date: 2021
Awards: Merit Award, Excellence in School Building and Design, Association for Learning Environments, 2021
Citation, New Construction/Substantial Renovation over 5,000 SF, AIA South Carolina, 2024
Completed by Perkins&Will as Design Architect in association with Craig Gaulden Davis as Architect of Record.
The school is organized around a 2-story lobby with primary entrances on the upper level. The phase 1 Academic Wing houses; Studios, Science Labs and spaces that support the Advanced Manufacturing Lab. Student Commons and Distributed Professional areas are located at the center of the Academic Wing. A 675-seat Performing Arts theater shares the Dining Commons for break out space during functions. Choir and Band spaces are located adjacent to the Performing Arts Theater.
The new high school integrates Advanced Manufacturing into the curriculum to introduce students to skillsets for careers that are currently underserved in the community. The facility planning embeds the Advanced Manufacturing labs within the core curriculum classes to encourage hands-on, interdisciplinary learning.
“The building itself becomes an integral part, a teaching tool, for the way the program is set up.”
― DR. W. BURKE ROYSTER, SUPERINTENDENT OF GREENVILLE COUNTY SCHOOLS
― Our Team
We believe in cross-disciplinary advancement in design. Our fimwide expertise is part of our toolkit of design resources.
Areas of Practice
Adaptive Transformation
Advisory Services
Aviation
Branded Environments
Corporate and Commercial
Cultural and Civic
Federal
Health
Health Education
Higher Education
Hospitality
K-12 Education
Landscape Architecture
Residential
Science and Technology
Sports, Recreation, and
Entertainment
Transportation
Urban Design
Workplace
Curious, agile, and adaptable, we craft solutions that inspire our clients and their communities, create positive long-term environmental, economic, and social change, and set new paradigms for the future.
Perkins&Will, founded in 1935, is an interdisciplinary architecture and design firm with 2,700 professionals working out of 32 design studios worldwide. Having designed more than 50 million square feet of science and technology facilities in the past ten years, our designs embrace flexibility, scalability, and resilience— anticipating future technologies, workflows, and challenges yet to emerge to ensure today’s facilities are ready for the discoveries of tomorrow. Perkins&Will has worked with over 400 colleges and universities across the country and around the globe, and is recognized for our unparalleled expertise in designing higher education and science facilities. More broadly, our research park master planning projectsnew hubs of research and innovation around the world - are attracting scientists, knowledge workers, students, startups and incubators with lively spaces to live, learn, work, play, and collaborate. With more than 50 research and innovation parks around the globe, our urban design solutions generate long term economic, social, and environmental value for private and public clients and communities.
nj Leaders in Engineering & Advanced Manufacturing Design Deep experience in creating state-of-the-art facilities that drive innovation.
nj Depth of Experience in Higher Education Research Facilities Renowned for our expertise in designing cutting-edge research spaces for colleges and universities.
nj Proven Track Record – Consistently delivering commercial development and program-dependent projects on time and on budget
nj Experts in Innovation Campus Planning – Strategic, forward-thinking planning that fosters collaboration and growth.
nj Comprehensive, Multidisciplinary Approach – A uniquely integrated team of planners, innovators, and designers.
→
George Mason University, Mason Innovation Exchange (MIX)
FAIRFAX, VA
The MIX provides facilities that support acquisition of making and fabrication skills by students, in collaboration with faculty and industry.
↓→
Humber College, Barrett Centre for Technology Innovation
ONTARIO, CA
The BCTI has a series of flexible module spaces for short-term and long-term project work, where students, faculty, and industry partners can research, fabricate, and explore together. Net Zero Energy, LEED ® Platinum.