PERI scope
Formwork | Scaffolding | Engineering
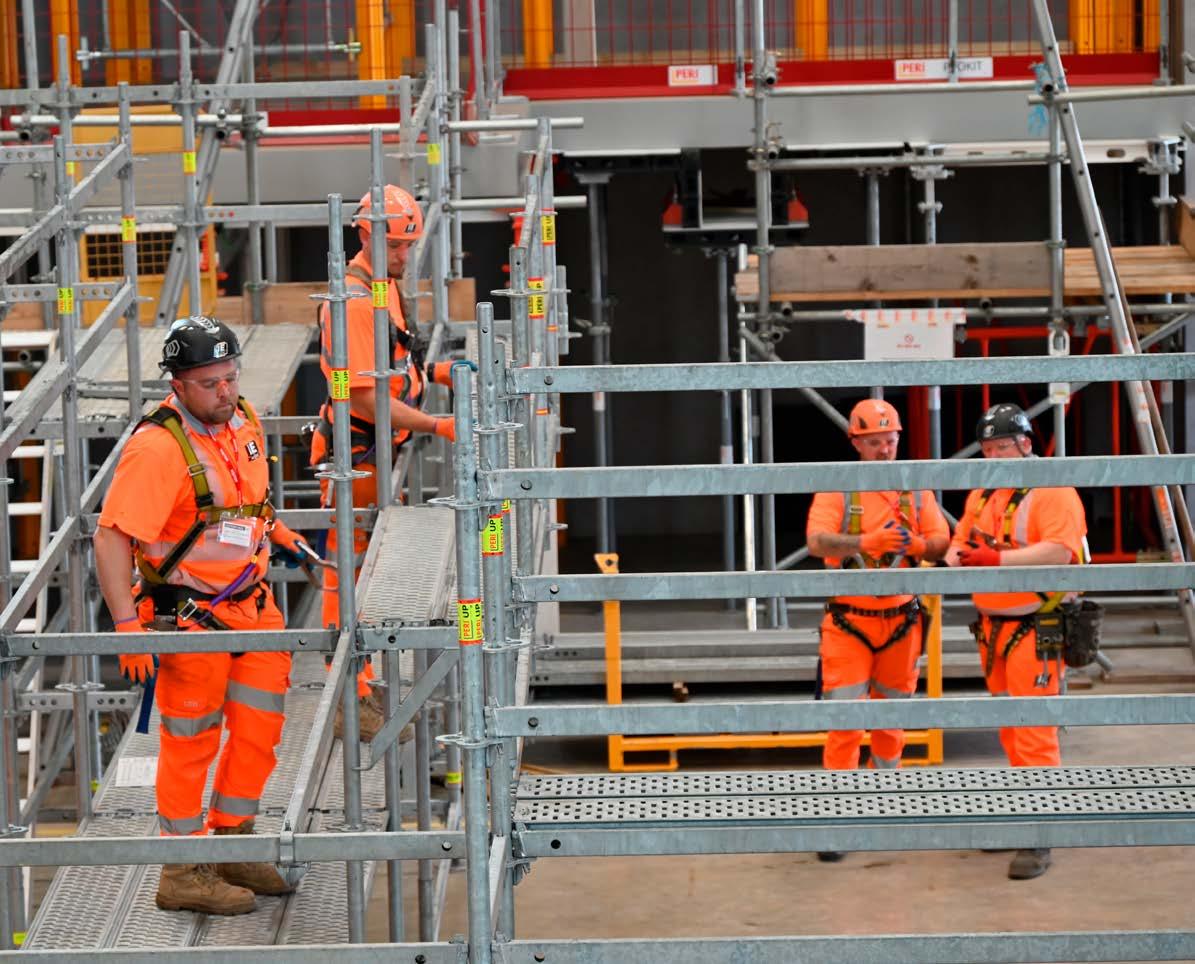
In Focus
From tube and fitting to system scaffolding
Find out why IE Access is making the switch
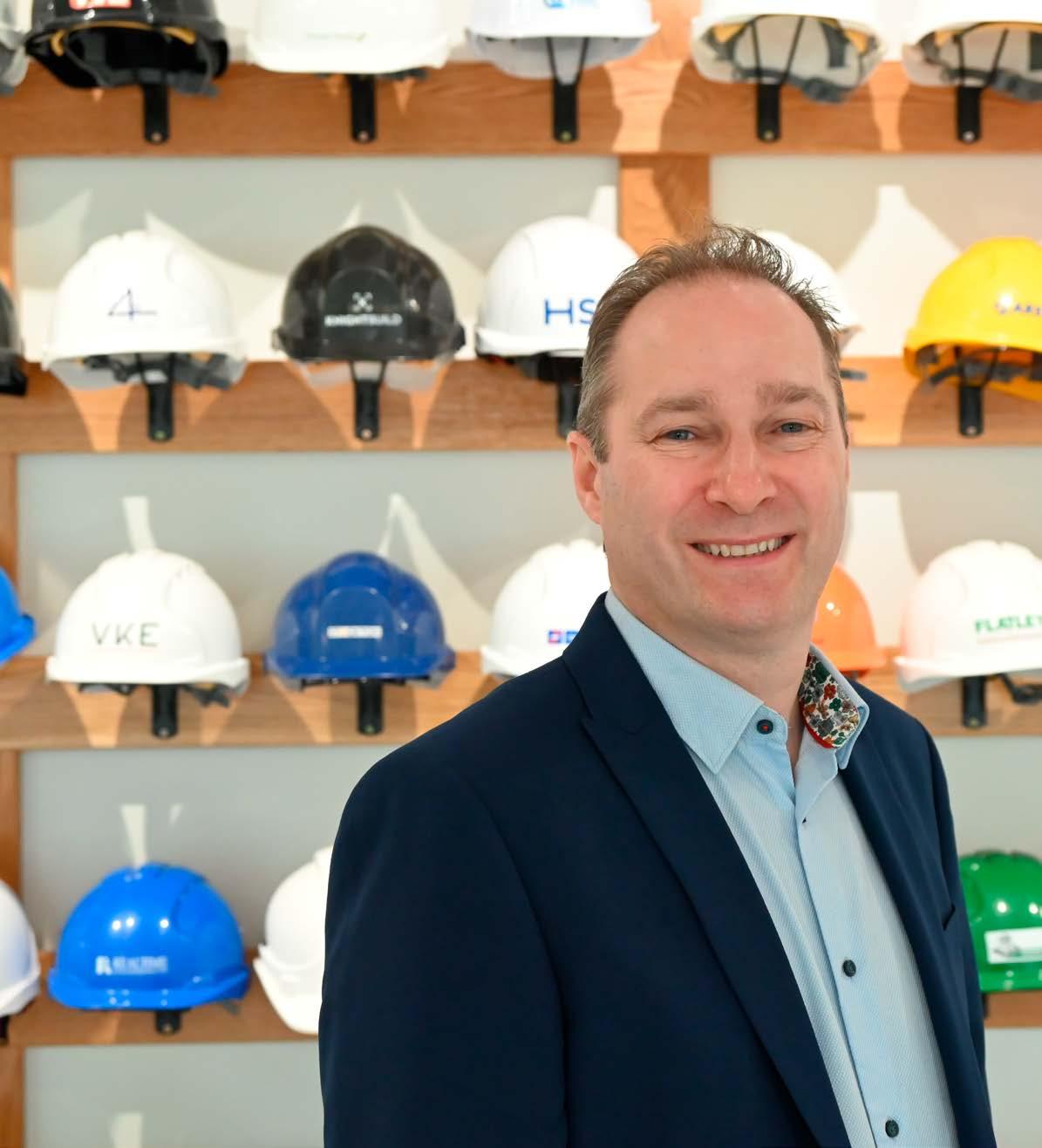

Find out why IE Access is making the switch
Welcome to the summer issue of PERIscope 2024.
We’ve had an eventful few months since our last edition! We hosted our largest customer event of the year at Wyboston Lakes, where guests enjoyed a day of exhilarating and relaxing activities away from their daily routines. The event was truly memorable, and we extend our heartfelt thanks to our customers who took the time out to join us.
Our products have received an equal amount of attention too – Our Construction Accessories team exhibited at the Concrete Expo in May and the MPA Precast and Masonry Expo in June to showcase the benefits of BECOSTOP – a permanent waterstop which is earning its place on construction sites in both the residential and infrastructure sectors. You can read more about this product on page 10.
To top off our events, we recently celebrated 35 years of PERI UK. Employees across our six offices tucked into a celebratory lunch to mark the occasion. It was fantastic to see so many of our talented team members come together.
In Q2, we announced our acquisition of Mabey Hire, which will unlock cross-selling opportunities for both brands. We are thrilled to offer our customers an even wider range of infrastructure and renovation products, expanding the possibilities when choosing PERI as their temporary works supplier.
We aim to make people, products, and processes more efficient across everything we do. To achieve this, we are increasing our focus on training, which we feel plays a crucial role in enhancing site efficiency and, more importantly, safety.
Whether it’s scaffolding or formwork training, our courses have had a positive impact on site teams and their projects. On page 12, we explore the dangers associated with inadequate training for site operatives and demonstrate how investing in product training can substantially reduce these risks.
In this issue, you will discover how training has also played a big part in IE Access’s journey from tube and fitting to system scaffolding. It was great to see senior management team members attending the SSPTS PERI UP Flex course at our Brentwood training facility alongside their employees, reinforcing their strong commitment to health and safety – you can read more about this on page 6.
If you’d like further information about the training courses we offer, please visit our website or get in touch with our instructors at training@peri.ltd.uk.
Thank you for your continued support and business! We understand that the market remains challenging at the moment, and we truly appreciate your loyalty. We wish you an enjoyable summer holiday season and hope you find some time to relax and recharge your batteries during this time.
I hope you enjoy the issue!
Gary Horne PERI UK Sales Director
Editor
PERI Ltd.
Formwork
Scaffolding Engineering
Market Harborough Road
Clifton upon Dunsmore
Rugby CV23 0AN United Kingdom
Responsible PERI UK
Editor-in-chief
Jinal Kansara
Editing and graphics
Dekany Design
Photos PERI UK
Neil Terry Design & Print
Copyright
The photos used in this brochure feature certain situations at particular moments on various construction sites. Additional images, e.g. regarding safety and anchor details, cannot always be considered as conclusive or final. These are subject to the risk assessment carried out by the contractor.
© PERI GmbH
Read our interview with the directors of IE Access to find out why the business is switching from tube and fitting to system scaffolding.
8 Accelerating the construction of a 2m thick basement slab using permanent stopends
One Liverpool Street, London
10 A powerful combination to help you form construction joints faster
Explore the benefits of using BECOSTOP and CEMflex together.
12 What are the risks of not training site operatives?
We’re on a mission to make formwork and climbing system training mandatory across all construction sites. Find out what we think the 7 biggest risks are and how training can prevent them.
14 News
Find out the latest updates in our infrastructure segment
During their recent two-day CISRS SSPTS PERI UP Flex course, we spoke to IE Access’s Managing Director – Charlie Wheeler and Operations Director – Paul Corfield to understand why they decided to make the switch from tube and fitting to system scaffolding. Both directors, who have used tube and fitting since their early days in the industry as trainee scaffolders, share how the transition will accelerate their ambitious plans for growth.
What does IE Access stand for and what does growth look like for the company?
IE Access: We pride ourselves on providing our clients with quality scaffolding solutions for their projects. We’ve got a proven record of delivering high-profile and technically challenging projects nationwide.
Currently, we’re working hard to secure further projects in the infrastructure sector, including more industrial work where we can provide long-term support for clients. At the same time, we’re taking more scaffolders on and growing our in-house expertise.
You’ve used tube and fitting predominantly over the last 30 years, why make the change now?
IE Access: We’re continuously looking to improve as an industry leader, offering safer and more efficient solutions to our clients at every opportunity. Health and safety is a top priority for us, especially when you consider the nature of our work and the heights our team are working at. As well as ensuring our team are safe, we have a greater responsibility to protect the general public whenever they are in proximity to one of our projects.
Technology in the industry is evolving, and we need to keep up with these changes. Adopting system scaffolding is a step in the right direction, as we continue to improve safety standards and build times on every project. This is both internally driven, but also a result of adapting to the shift in what is important to our clients and the work they are doing.
When we think about safety and topical issues in the industry, using fully metal non-combustible materials is a no-brainer.
Why is product training important for the journey you’re on?
We don’t sub-contract labour for any project. By employing scaffolders directly, we have a better understanding of our team’s capabilities when they are out on site. Training is at the core of building a stronger team and it starts with management. That’s why we decided to attend the two-day CISRS course along with our workforce – it’s important for us to understand the products our scaffolders are using so we can offer the right support.
Going from tube and fitting to system is a big step, so getting hands-on and learning from product experts was the best way to facilitate the transition and get our team to see the long-term benefits.
The training we received will also be valuable throughout the pre-construction process. We know the PERI UP Flex system’s capabilities, which means we can advise clients on buildability and what can be achieved early on.
For scaffolders that have used tube and fitting for so long, did you have any misconceptions about system scaffolding?
There is a popular misconception that system scaffolding is just for square buildings, but it’s actually very versatile. Many of the structures we’ve built during the training disproves our preconceptions too.
We are currently working on a few industrial sites. We are having to get around a lot of pipework and other obstacles and that’s where we feel the PERI system does offer that versatility and removes the need for ducking under components. It surpasses systems featuring round ledgers too, as PERI UP’s rectangular ledgers enable you to board in any direction.
Training has definitely helped overcome some of the worries and misconceptions the team had. Coming to PERI’s site and seeing the scaffolding structures in their exhibition hall was an eye-opener. The team got a feel for how much lighter the system was and how it reduced manual labour compared to tube and fitting.
We continue to have a busy summer ahead with exciting projects to come. We’ve recently finished working on our first F1 event, providing media access at Silverstone using PERI UP of course. It’s a fantastic product and we look forward to working with the PERI team on the next project.
Located directly over the London Underground’s Metropolitan line and Crossrail line, One Liverpool Street is a 10-storey of fice and retail scheme funded by Aviva and TfL.
Our customer required a stopend solution to facilitate the construction of the ground slab and prevent concrete outflow throughout the build of the basement. With a 2m slab thickness, traditional shuttering was not practical due to the size of the excavation that would be required.
Traditional shuttering would need extensive propping and a supporting frame, which would need to be removed and rebuilt once the pour was complete. Site space was tight, with a live underground railway line neighbouring the basement and work starting on the floor above simultaneously. With limited time and space to build timber shuttering, the John F Hunt project team were looking for a more efficient solution to speed up the concreting process and conserve space on site.
By introducing our permanent stopend solution, BECOSTOP, we were able to reduce the installation time and eliminate the removal process altogether. In partnership with Richter, we provided a full temporary works design inclusive of CAT 2 checks which enabled the site team to achieve a rate of rise of 350mm per hour.
Installation was simplified by using tying wire as a time-saving alternative to clamps when connecting the units to the rebar. By delivering bespoke BECOSTOP shutters to site, the units were ready to assemble from the pallet without any additional cutting or adjustments required – a big advantage considering the site limitations.
The perforations on the mesh effectively minimised grout leakage between pours, while our innovative spacer strip, BECOSPACE, ensured zero grout leakage in the cover zone.
Using permanent stopends also helped to reduce material and save vital workspace on site, as external props were not required.
With BECOSTOP’s key profile, our customer was able to achieve full reinforcement continuity, resulting in stronger construction joints.
John F Hunt
Danious Sountharajah, Project Engineer
“There is no mechanical scabbling required, which is a big advantage as the surface of the product is designed to create strong connections between joints. Installation was smooth, as we could secure the BECOSTOP panels by using tying wire with no welding involved.”
For over 50 years, we’ve offered an extensive range of formwork systems, scaffolding, and engineering services, all designed to help you deliver construction projects more efficiently, more quickly and always more safely.
But did you know we now offer a carefully selected range of construction accessories, that complement our products and add value to every project?
Thanks to System Plus, various applications and tasks on site can be improved, whether it’s transporting material up a building, forming footings with ease or a stop-end system for the installation of concrete joints, our accessories will optimise the way you build.
In this article we look at how combining two accessories, BECOSTOP and CEMflex will ensure the smoothest and cost-efficient formation of high-quality concrete structures. First, we’ll briefly consider each product and its benefits in isolation.
This permanent stop-end system provides full continuity of reinforcement for the installation of construction joints. BECOSTOP allows consecutive bays to be poured on consecutive days, which could deliver a four or five-day advantage when casting deep reinforced slabs.
It comes to site ready to install, with a full temporary works design provided, including structural design and CAT checks. The strength and consistency of the construction joints are key benefits of BECOSTOP, which also ensures that the diameter of the reinforcement steel does not need to be increased.
The steel BECOSTOP panels utilise a unique trapezoidal profile which allows for full 100% bearing capacity according to EC2. The design limits the flow of concrete, which significantly reduces the pressure on these stop-end units and requires a lower concrete pour pressure, which in some cases can be reduced by 50%.
BECOSTOP avoids the risk of leaving a day joint with a low bearing capacity when multiple pours are needed. Whilst poor joints can compromise the structural integrity of the concrete, those formed without remedial work to create a stronger bond, reduce the
slab’s durability and increase the risk of water ingress, which can lead to the corrosion of the reinforcement steel.
The BECOSTOP panels are fixed to the rebar cage using inexpensive tying wire and the skills of site labourers, with no extra supports needed for the panels, which self-support up to 1.5m. But what about waterproofing the structure? This is where CEMflex leads the way.
CEMflex is one of the most highly effective and innovative waterproofing systems on the market, designed for sealing vertical and horizontal joints in concrete structures, providing a physical and chemical barrier, with an unlimited sealing capacity.
The system can be easily assembled together with the reinforcement or simply put into fresh concrete, easily bent or cut to suit the needs of the project. Installation of CEMflex is quicker too, as overlaps are simply fixed together with a clip, removing the need to bond or weld them.
CEMflex ensures that concrete structures, foundation slabs and tunnels are completely waterproof. It functions as an active and passive barrier for the transmission of water at the construction joint, with a life expectancy of 100 years.
The 2m-long steel plates of CEMflex are coated with a unique product that on closer inspection has a rough surface that takes the surface area from approximately 1m to 100m to significantly increase the quality of the bond to the concrete.
This unique coating crystallises on contact with the wet concrete and expands into every crack and every pore during the drying process to provide a long-lasting waterproof seal – it can be left uncovered overnight without any adverse reaction, unlike some simple bentonite products
Backed by rigorous testing and a track record of success, our clients trust CEMflex for its reliable performance and genuine adaptability. This combination allows for on-site customisation to meet the specific waterproofing demands of any concrete structure.
CEMflex not only helps streamline any installation, but the associated reduction in labour costs, makes it a cost-effective choice without compromising quality. Choosing CEMflex ensures concrete structures are shielded against water intrusion, which increases their longevity.
great when combined
Both BECOSTOP and CEMflex were developed independently of each other to address different issues. BECOSTOP was designed to provide project managers with a modern, more costeffective alternative to outdated timber shuttering and shoring for pouring concrete slabs.
Recognising the need to waterproof joints to prevent water ingress through concrete and the more expensive, harder to fit and outdated products available, CEMflex was developed to work in tandem with BECOSTOP to deliver the quickest, most efficient method to waterproof concrete structures.
BECOSTOP and CEMflex can both be fitted successfully by site labourers, without the need for specialist skills or tools, which makes for a more costeffective solution.
No special preparation is required and no welding or additional protection tapes are needed to form an effective joint. Corners and wall intersections are easily formed by hand, thanks to the high malleability of CEMflex and with the crystallisation coating all around the plate, it is easy to install the plates correctly.
Specifying BECOSTOP is already saving time on site for many contractors and including CEMflex as the waterproofing solution will bring down the required time from preparation to successful pour even further. After all, time saved is money saved.
It is time the industry considered concrete pouring and waterproofing as a single solution, made easier with complementary products that are easy to install, bring quality to every installation and make the process more efficient.
BECOSTOP and CEMflex are fit-andforget products that offer genuine peace of mind for project managers and installers working on large concrete pours. Such quality might cost more initially, but when installation and remedial costs are considered this winning combination will save a fortune over the life of a project.
What are the risks of not training site operatives?
We recognise the numerous and significant risks posed by an untrained workforce. Here at PERI UK, we continue to push the case for mandatory training for those tasked with erecting formwork and climbing formwork systems.
In this article we look at the potential risks of putting individuals with no appropriate training, under pressure to erect formwork systems and climbing formwork systems at great height, on constrained sites, in busy public spaces.
1) All climbing systems involve working at height
Working at height clearly increases the risk, especially when operatives have not been trained and are not competent to operate the machinery. Given that climbing systems are typically used on buildings higher than four storeys, it’s clear there are significant dangers for those operating them, workers on lower levels, and the public on the ground.
2) Skills gap in your workforce
With staff turnover rates across the construction industry running at around 20% [5% higher than the rate across all industries], there is a risk that when workers leave, they do not pass their knowledge and experience to others in the team. With no information passed down or gaps in the instructions provided, workers without training may not have the required knowledge to operate climbing systems efficiently or safely, such as the correct lifting techniques and points.
3) Inefficient workforce
Those without the appropriate training will not be as efficient when erecting formwork or climbing formwork systems, as they may take more time to learn on the job, often adopting a ‘trial and error’ approach that can waste time and also impact the important assembly and striking process. With training, operatives are immediately comfortable with the process, whereas those without training can spend valuable time looking at assembly brochures or drawings and waiting for confirmation from others.
Sites that are more complex or specify certain finishes may not achieve the desired outcome, as the way formwork is used and handled will impact the quality of the concrete and the finish. Weak form joints, offsets or poor facing material, are just a few of the problems that can be avoided with good quality training, which will also reduce the potential for expensive remedial work.
Key players in the industry are beginning to understand and benefit from the training we offer on the erection of formwork and climbing formwork systems, actively enrolling their teams. Given that around 90% of all infrastructure projects require this type of training, it’s vital that every contractor recognises the positive impact of training to ensure they remain competitive.
Here at PERI, we strive to develop innovative products that not only do the job for which they are designed, but where possible are easy to lift and move around site. But as with many construction-related tasks, without the appropriate training, there remains the risk of personal injury to the individual or their colleagues, caused by poor technique and a lack of knowledge.
Damages caused by incorrect use can be costly to repair for contractors renting equipment. In all cases, prevention is better than cure.
For example, there is a right way and a wrong way of starting out from a fixed position when using SKYDECK formwork. This involves using different sized MRK frames and components like our dropheads and propheads. Formwork training covers these aspects, so operatives know what to use in any given scenario.
No training is ever a waste. And it is important for contractors to understand that without a training certificate it is difficult to assess a site operative’s competency and their ability to erect formwork and climbing formwork systems efficiently and safely, which increases the risk of injury, damage and the need for remedial work.
Whilst our training programmes address the use of formwork systems in general, there are additional risks presented when untrained operatives install climbing formwork, in addition to those outlined on the previous page.
Firstly, it is critical to know exactly where and how climbing components sit on the structure. Climbing rails need to be installed in the correct orientation and these are often installed upside down, which then requires them to be removed and reinstalled with spacers. With the appropriate professional training, this time-consuming error can be avoided.
Much of the training is general in nature to ensure whatever formwork or climbing formwork system is being used, workers will know how to move it, handle it and install it safely.
However, there are also specific details given that ensure best practice is adhered to, such as the PERI systems having different anchor sizes depending on the climbing system being used. If the wrong anchors are installed it can be dangerous and remedial work can cause unnecessary delays.
Operatives need to know how many climbing shoes the rail needs to be locked into, which are the components that the rail feeds through as it ascends.
If this is not done correctly or the rail is locked into fewer shoes as detailed in the training, then the entire system will be less secure, with the potential to tip into the building. It is also important to understand what the correct lifting position is.
Having looked at the risks of working with climbing formwork systems, it is also important to understand how the training improves site safety and the personal safety of those installing and working on climbing formwork systems.
Climbing formwork systems typically have external platforms (visible on the outside) and internal platforms. External platforms are stronger, due to their contact with the built/concrete structure and most often need to ascend before the internal platforms. This is a simple, but often overlooked aspect of working with climbing systems.
Climbing formwork systems have in-built safety features which need to be engaged correctly, such as the safety pins found on our internal platforms, which need to be locked in place prior to operation.
Guardrail posts (a safety component used to provide edge protection) must be installed with a specified number of bolts and screws, all of which must be mounted correctly to ensure safe working on the platform. Again, opting for a cheaper alternative poses a risk to those on the platform and those working below.
As use of modular formwork and climbing formwork systems increases, to enhance productivity, safety and the quality of concrete construction, it follows that training in their use will become more important.
As part of our commitment to greater site safety, we have developed training courses to minimise the risk of injury, improve efficiency, increase productivity and reduce the risk of damage to the equipment.
In May this year, we announced the acquisition of Mabey Hire – a specialist in groundworks support, propping and jacking for renovation and temporary bridges. With synergies in culture, a strong reputation for engineering and professionalism combined with a clear segment fit, Mabey Hire was the perfect brand to complement and strengthen our position in the infrastructure sector.
“Together,wewillworktoachievecross-sellingopportunities toofferourcustomersanevenbroaderrangeofinfrastructure and renovation products and continue the drive to always provide the best possible service to our customers ”
IanHayes | Managing Director PERI UK
HS2 Bromford Tunnel
Work is progressing at high speed across the HS2 scheme. We’re grateful to be on this exciting journey, supporting multiple sites across the 140milerailroute.Oneofthesesites is Bromford Tunnel, where we are supporting the construction oftheAerodynamicBox.We’ve engineered a bespoke solution thatnotonlyformstheconcrete structure but also transports a 25-tonne rebar cage into each casting position. Don’t miss the full story in the next issue of PERIscope for an in-depth look at how we worked with our customer, Balfour Beatty VINCI, to deliver this solution.
Rye Meads STW
In addition to the rail sector, we’ve been busy in other areas of infrastructure. Our PERI UP Flex scaffolding system was designed to serve multiple purposes throughout the upgrade of the Rye Meads wastewater treatment tank in Harlow, which is being delivered by Gel Engineering. You can see the internal scaffold providing access into the 10m-deep tank here.