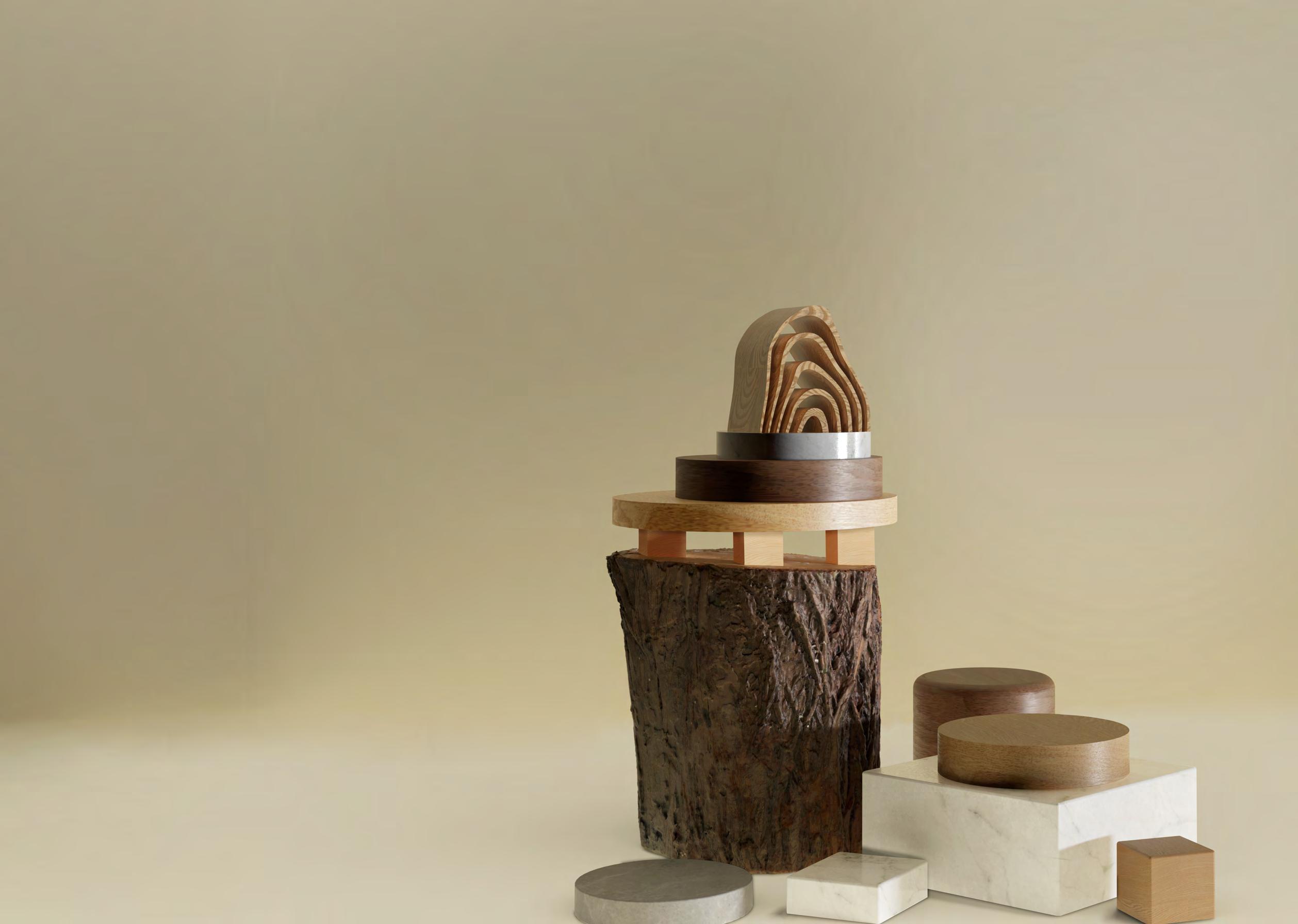
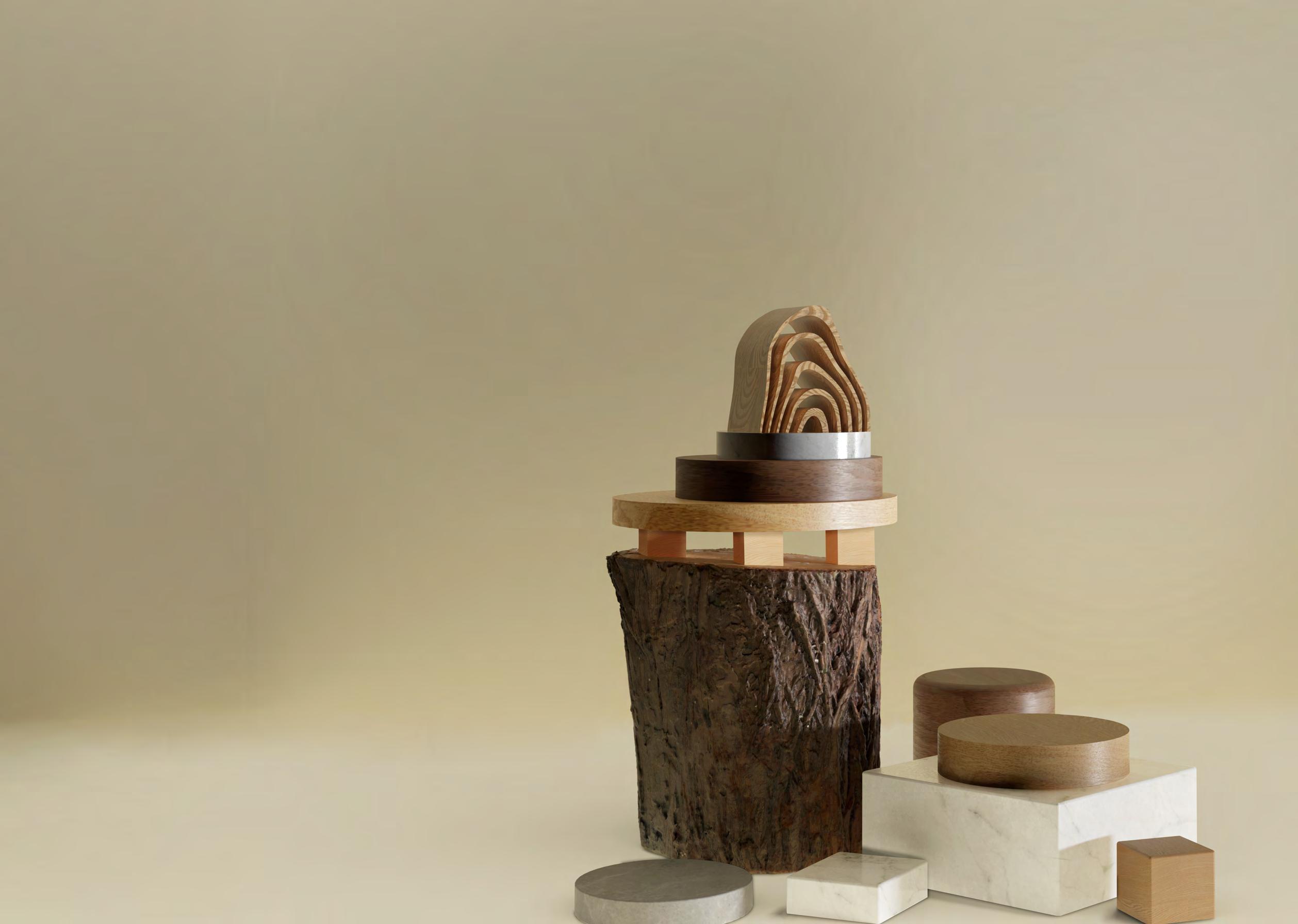
Nature Inspired Paper Foils
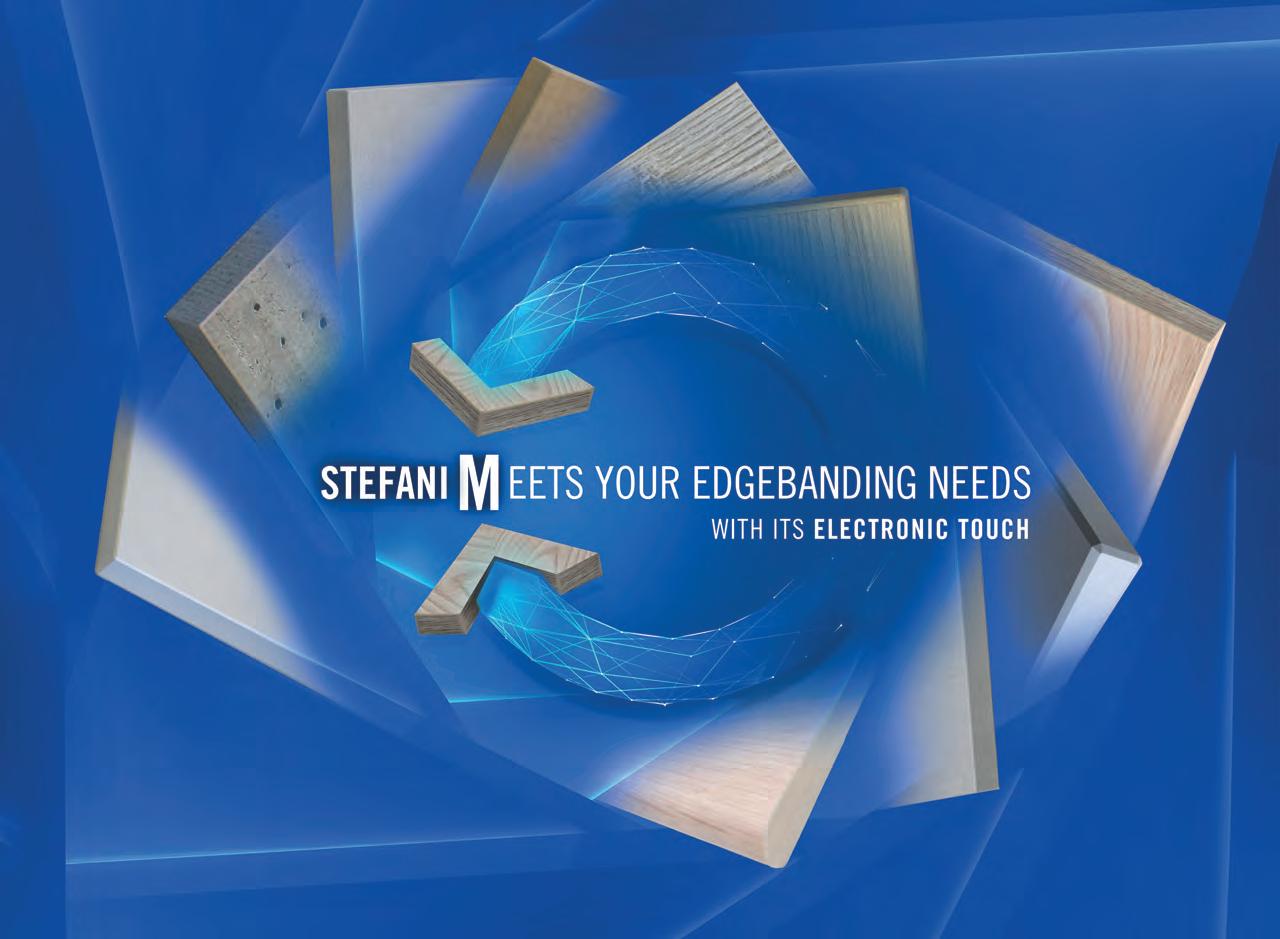
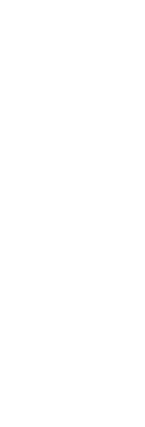
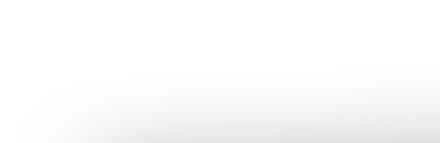
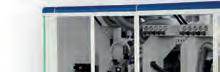
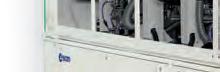
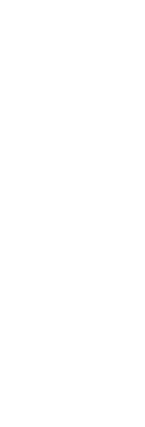
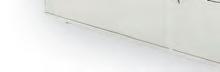
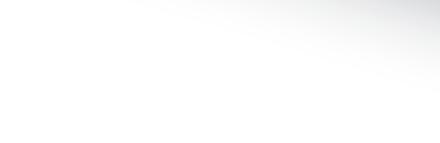
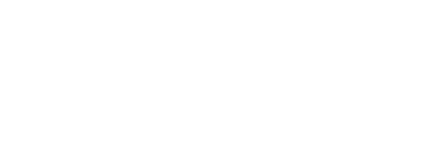
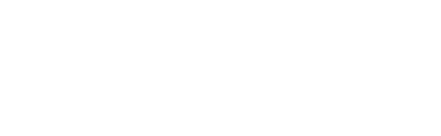
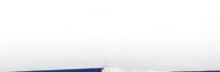
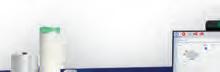
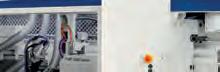
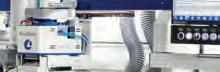
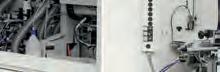
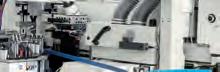

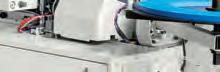
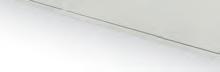
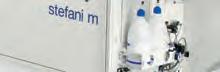
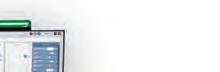
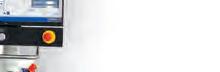
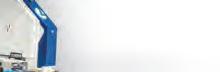
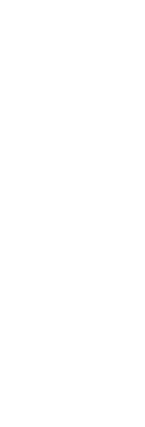
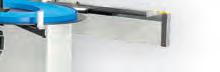
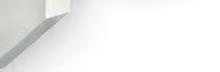
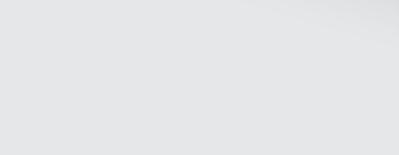

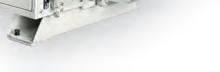
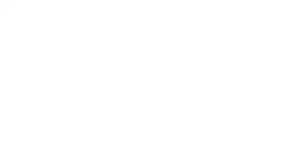
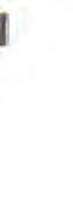
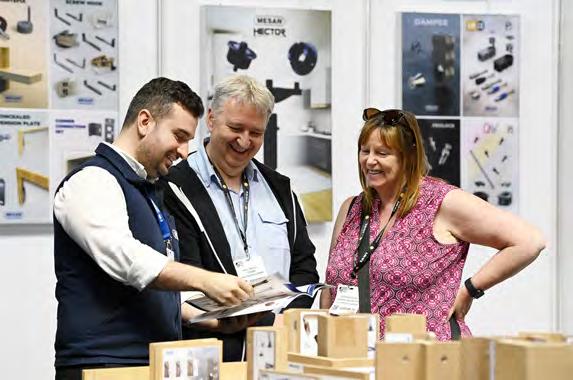

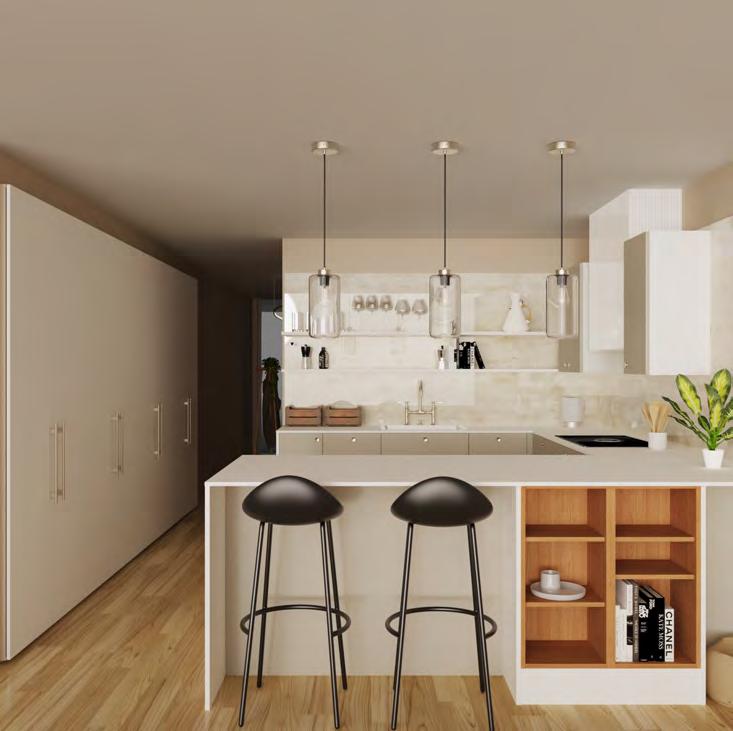
Blum Introduces MERIVOBOX
Professional Woodworking Expo

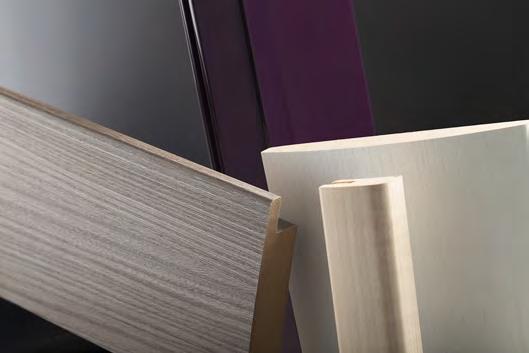

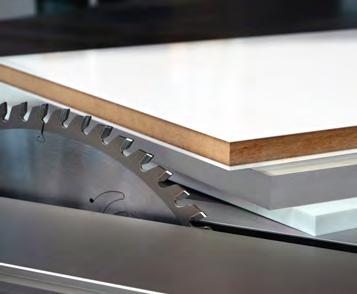
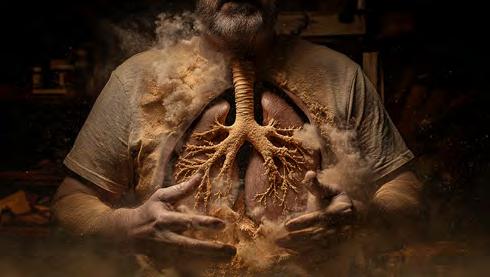
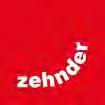
Intercoat Paints Urges Industry-Wide Transition To Water-Based Coatings
Mirka’s Tailored Approach To Upskilling Industry Professionals
Introducing TAKA: Italian Excellence In Adhesive Innovation
Osmo Recommends: Find The Perfect Finish For Your Project Titus: Full Solutions For Cabinet Hardware Crocodile Packaging Enhances Reliability And Efficiency With HOMAG Ranheat - The Heat Is On Experience The Adler Advantage Only From Elmbridge
Leitz: Panel & Beam Saw Blades
Clean Air Solutions: The Air We Breathe Is Rarely A Problem. Until It Is Biesse Builds On LIGNA 2025 Success British Woodworking Federation Awards – Call For Entries
TM – Keep It Simple, Stupid
Elevate Your Panels With Dp-Decor Extractly Delivers On Time, And On Budget
WEINIG Connect 2025
The Power Of Change
Events Blum Ligna Panelco - Sustainable Innovation with Saviola Group
40 years with Chemique Adhesives
Harrison Collier Future-Proofs Production With HOMAG
Hoffmann Technology - Precision & Efficiency In Fire Door Production
Ligna Review
SCM At Ligna 2025
Combilift Launches Two Groundbreaking Solutions At Ligna 2025
Free Tooling Health check with Leitz Biesse & The
Reproduction of articles: All material appearing in Panel & Joinery Production is strictly copyright, and all rights are reserved.
No part of the publication may be copied or transmitted in any form whatsoever, including photocopying without prior permission of the publishers.
Publishers note: The editorial opinions expressed in Panel & Joinery Production are not necessarily those of the publishers, who shall be under no liablity with respect to any article published herein.
Blum introduces new MERIVOBOX solution to the UK
Blum, a leader in innovative furnishing solutions, has introduced MERIVOBOX to the UK market, a unique, modular, single platform drawer box solution.
Designed to combine maximum flexibility with ultimate creativity, MERIVOBOX offers a number of applications, all from one single running platform.
With multiple design options and a modern, slim profile, the new solution inspires an extensive range of applications around the home.
Perfect for furniture makers looking for the opportunity to offer more creativity without adding complexity, MERIVOBOX is built on a flexible platform that makes it incredibly simple to manufacture and assemble drawers and pull-outs to meet every demand. Krystyna Threlfall, Marketing Manager for Blum UK, commented: “Understanding our customer’s needs has always lived at the heart of Blum and the launch of MERIVOBOX is an example of us doing just that.
“We know there is an increasing need to differentiate in an ever-evolving market, whilst the requirement to work efficiently remains key to enabling business success. This is a tension felt by many, for which MERIVOBOX can provide the solution.”
MERIVOBOX is the brand’s first drawer box launch in the UK since 2019. It successfully complements Blum’s existing range which includes TANDEMBOX, a tried, tested and trusted design and LEGRABOX, the ultimate design for elegance and sophistication.
Krystyna continued: “Collectively, these products not only set the standard in quality and design, but they also offer a mix of solutions that can fulfil the needs of many. We’re very proud to introduce MERIVOBOX to our portfolio and to offer something fresh and flexible that promotes new design ideas.”
Why MERIVOBOX?
• Built on an ideal, single running platform solution
• Multiple design options to enable creative solutions
• Suited to an extensive range of applications around the home
• Slimmer profile for improved aesthetics and greater flexibility
• One drawer side, countless opportunities
Centred around creativity, the new product is now available, enabling new ideas and more flexibility than has been seen before.
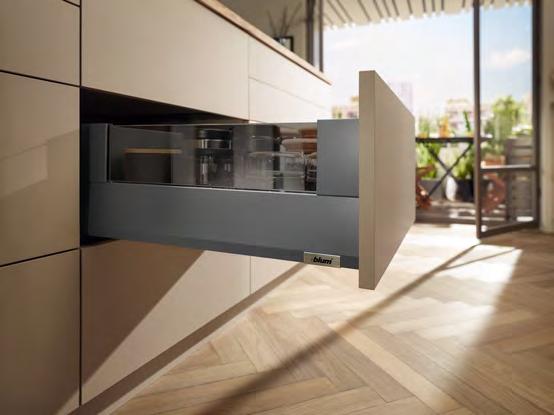
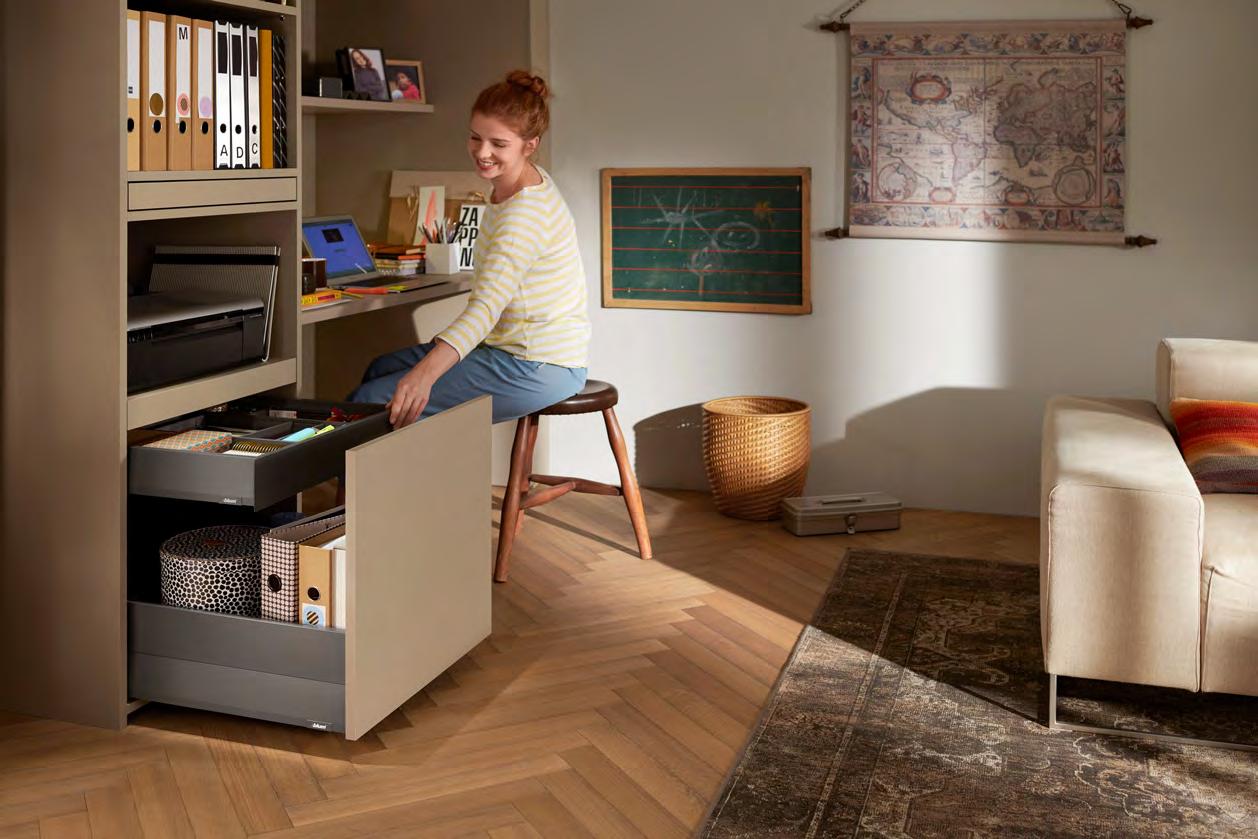
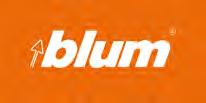
LAMINATED WOOD
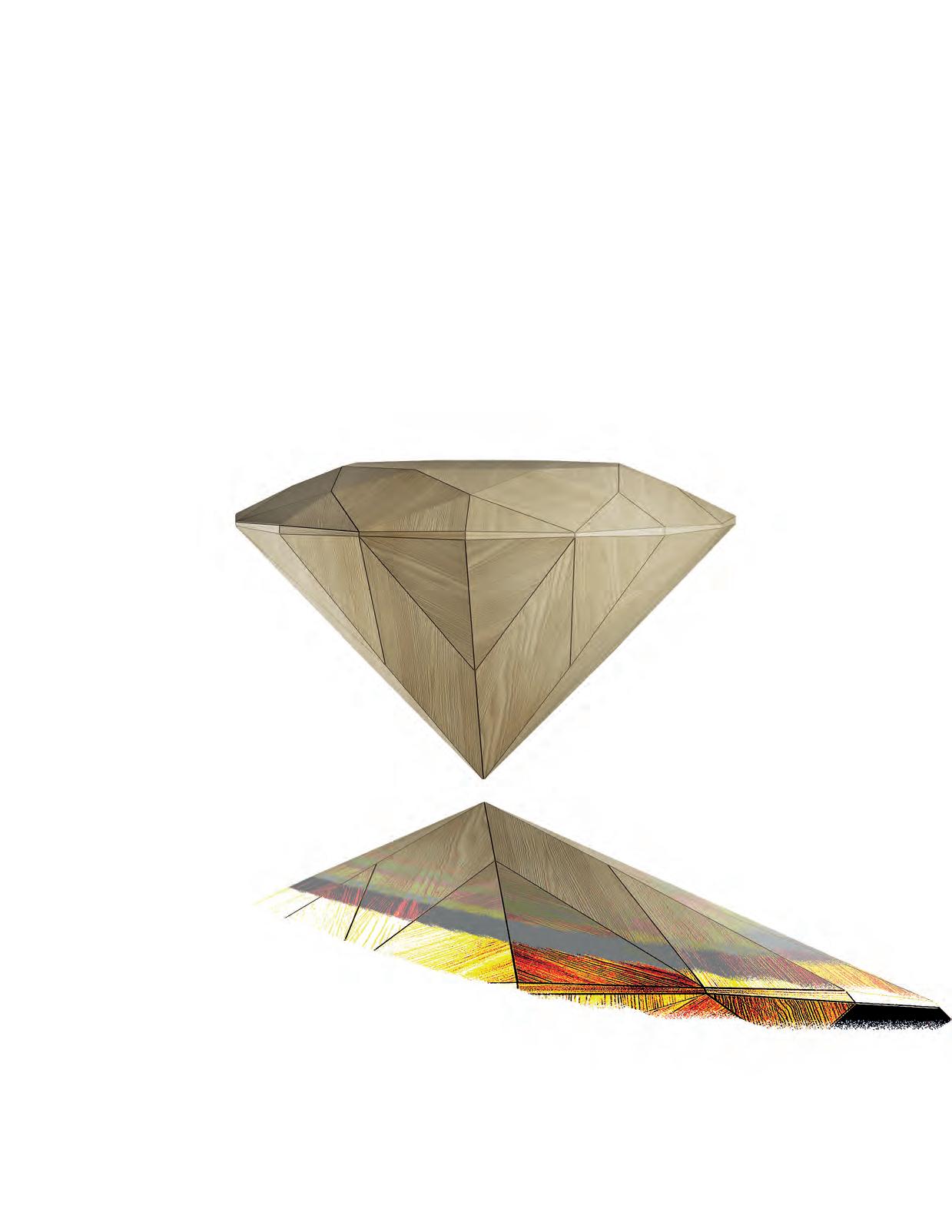
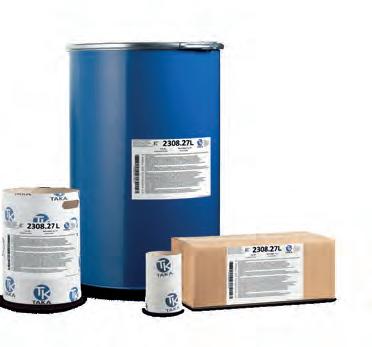
By using Taka adhesives, you not only ensure the durability and bonding quality of your wood lamination, but you also contribute to the reduction of carbon dioxide emissions thanks to the new sustainable adhesives range. These adhesives are formulated with a minimum content of 20% bio-based raw materials. All raw materials are certified and sourced from suppliers who spouse sustainable growth objectives.
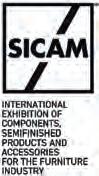
EVENT
Momentum builds for Professional Woodworking Expo 2026
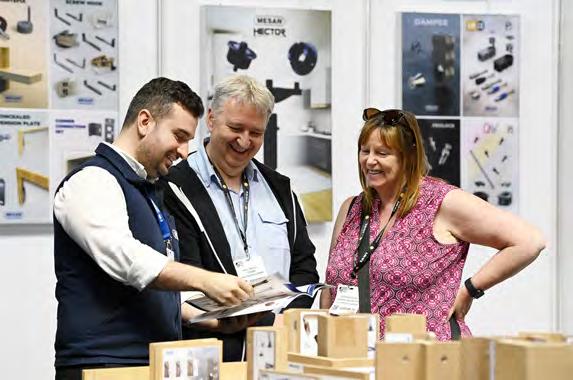
Professional Woodworking Expo 2026 continues to go from strength to strength as the UK’s dedicated event for woodworking and joinery professionals. Taking place from 17 to 19 May 2026 at the NEC Birmingham, the show is firmly establishing itself as the key platform for professionals to connect with suppliers, discover innovation, and grow their businesses.
Following the successful evolution of the Materials and Finishes Show, the rebranded PWE reflects a clear demand for a focused and high-quality showcase tailored specifically to the woodworking and joinery manufacturing sector. With expert guidance from a dedicated advisory board, the event will deliver curated content, practical training, and technical demonstrations shaped by real insight from across the industry.
The Professional Woodworking Expo advisory board, made up of experienced professionals and respected voices from across the woodworking and joinery landscape, is playing a key role in refining the 2026 programme. Their knowledge and industry perspective are helping to shape seminar content, ensure relevance, and spotlight emerging trends.
Names such as Robin Clevett, presenter, carpenter and joiner, Mark Stevens, Director for Health and Safety at Didac Ltd, Adam the Welsh Woodworker, Owen Dare, Founder of OT Dare Joinery Consultants, Andy Ball, Co-Founder, The Joinery Network, and more will help lead the Advisory Board for next year’s show.
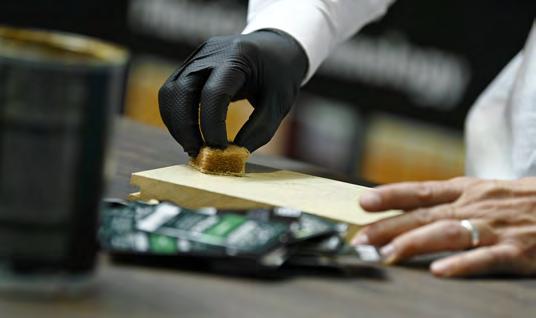
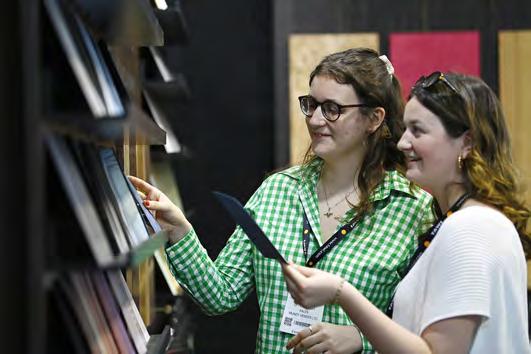
More than 6,000 woodworking professionals from across the UK and Ireland are expected to attend across three days, with over 200 leading exhibitors showcasing machinery, tools, software, coatings, finishes, and workshop essentials. The show offers a powerful opportunity for businesses to do face-to-face business, share best practice, and find the solutions they need to move forward.
The latest exhibitors to join the 2026 line-up include IMA Schelling, Festool, SawStop, Doucet, and ScanHugger. They join returning names such as Ostermann, AMS, VWM, Leitz Tooling, Elmbridge UK, and Mirka, reinforcing PWE’s position as the essential destination for professional woodworkers. Event Director David Todd commented: “We are proud to see Professional Woodworking Expo continuing to grow and gain momentum within the sector. With such strong support from exhibitors, visitors, and our advisory board, we are confident that the 2026 edition will offer more value, more connections, and more opportunities than ever before.”
Key features of PWE 2026 include:
• More than 6,000 woodworking and joinery professionals expected
• Over 200 exhibiting brands from across the supply chain
• Live demonstrations and hands-on product testing
• Technical seminar sessions, peer-to-peer learning, and business networking
• Curated content shaped by a dedicated and experienced advisory board
Stand space is in high demand and selling fast. To secure a prime location and maximise your exposure at the UK’s leading woodworking event, act now.
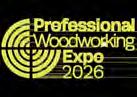
To exhibit contact: Jeff.Downton@montgomerygroup.com.
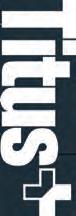
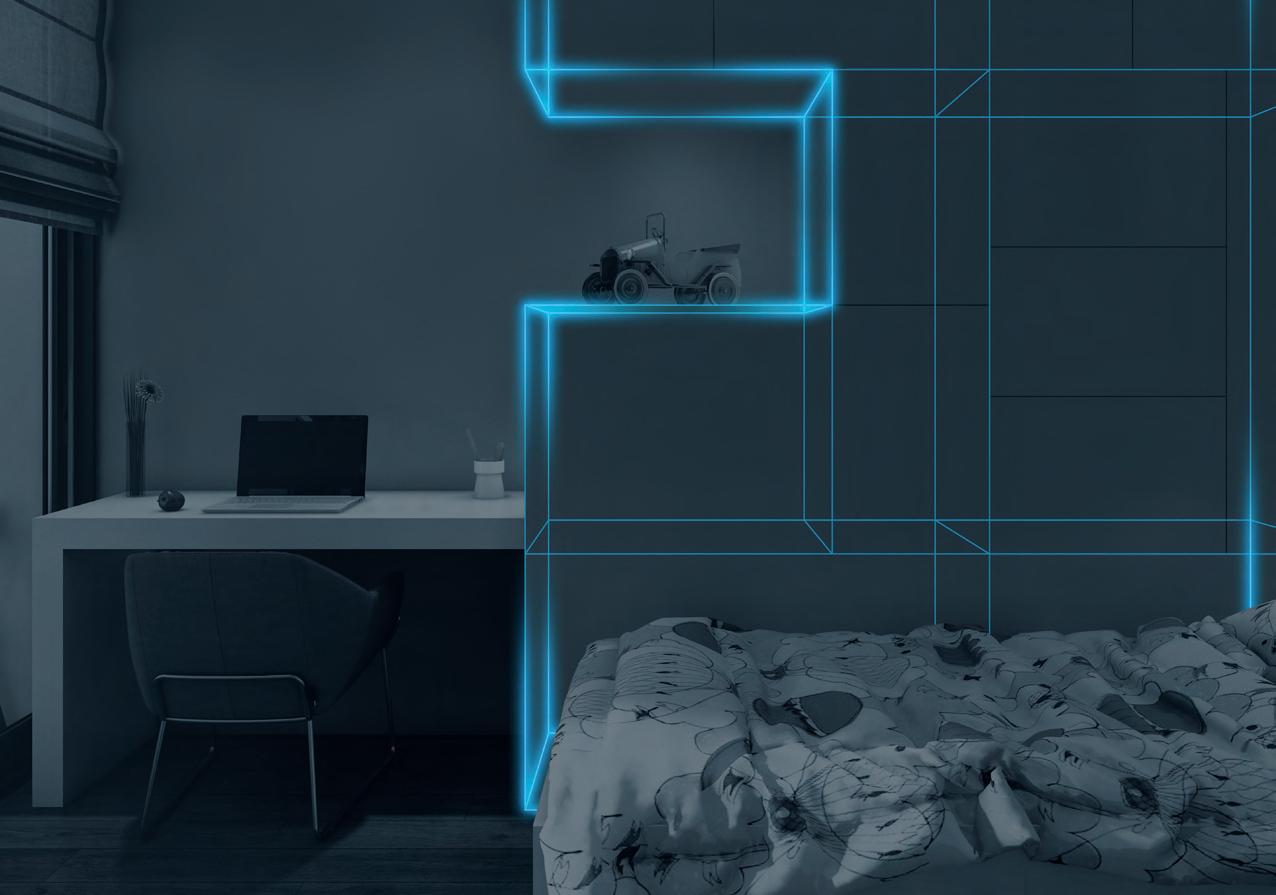
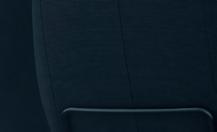
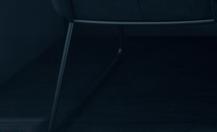
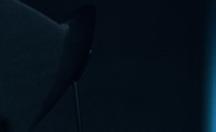
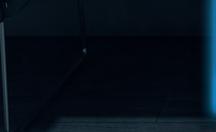

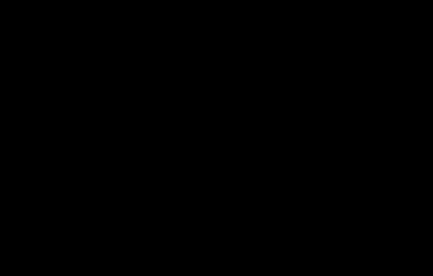
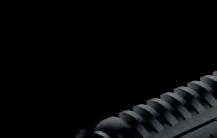
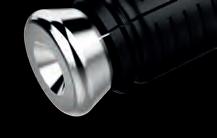
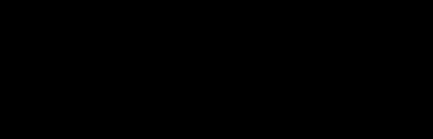
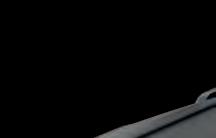
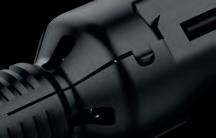
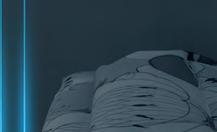
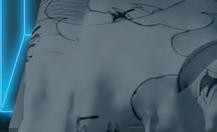
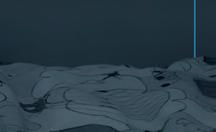
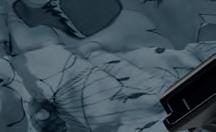

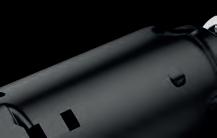
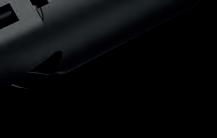
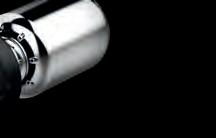
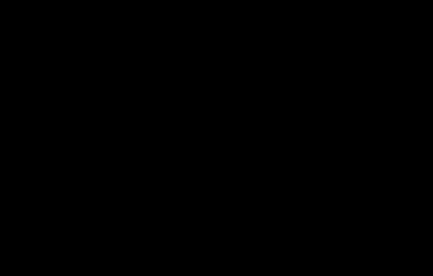
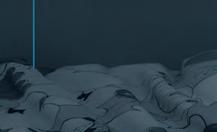
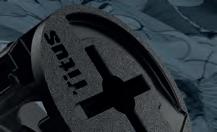
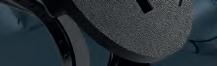
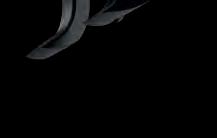
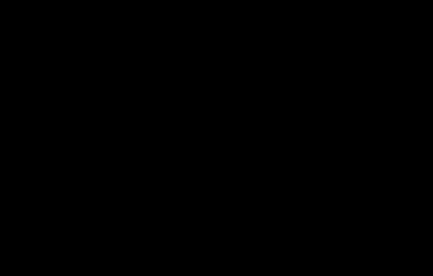

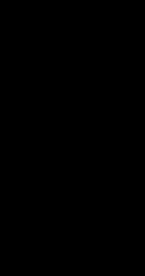
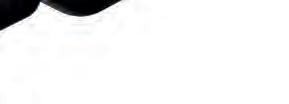
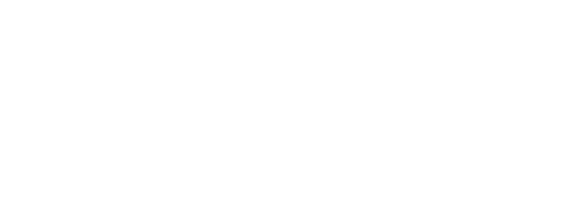


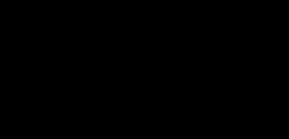
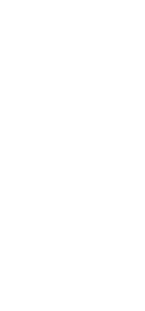
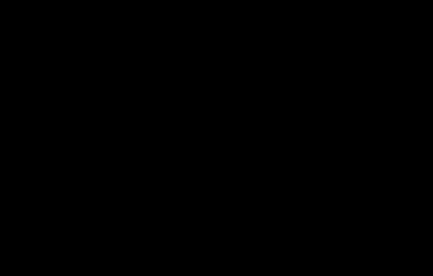
Intercoat Paints urges industry-wide transition to water-based coatings — Where doing the right thing makes business sense
UK-based pioneers in environmentally responsible coating solutions, Intercoat Industrial Paints is urging professionals in the coatings, manufacturing, and construction sectors to fast-track their shift away from solvent-based paints and embrace advanced water-based alternatives. The company points to rising environmental pressures, tougher regulations, and solid business incentives as reasons for acting now.
While solvent-based coatings have long been the industry standard — often relied on for their durability — they are also known for releasing hazardous chemicals such as VOCs (volatile organic compounds) and formaldehydes. Intercoat’s message is clear: the latest water-based technologies are now capable of matching or outperforming their solventbased counterparts, without the harmful side effects.
“We’re well past the point of gradual change,” said Michael Vann, Managing Director at Intercoat Paints. “Businesses that genuinely value environmental, social and governance principles — and want to remain profitable — need to reconsider their coating systems. Adopting water-based options is no longer just a sustainable choice; it’s a commercially wise one.”
Why Water-Based Is the Smarter Option
Intercoat’s most recent innovations in water-based coatings - aren’t just environmentally safer — they’re engineered to handle real-world demands. The company’s formulations are designed for faster drying, easier application, and reliable performance across a wide range of uses.
“Our research and development team has pushed the boundaries of what water-based products can do,” comments Marketing Manager Anita Chumber. The company shared in a joint statement. “The coatings we’re delivering today stick better, last longer, and covers more evenly — all while significantly cutting down on VOC emissions and worker exposure to hazardous materials.”
Real-World Business Benefits
Switching to water-based products comes with practical, bottom-line improvements. Intercoat outlines several key gains companies can expect:
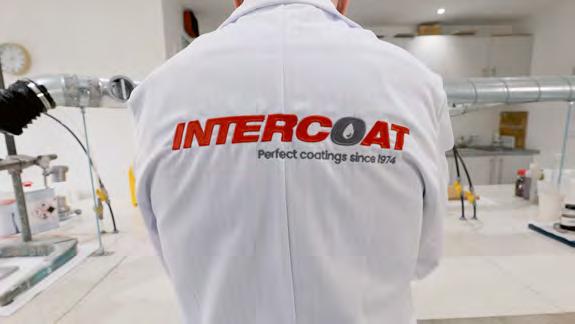
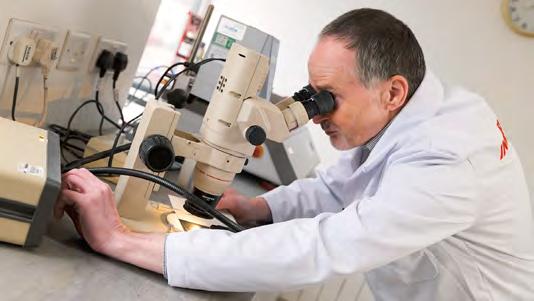
• Lower Insurance Costs: Less flammability and lower toxicity translate to reduced risk profiles.
• Faster Turnaround: Shorter drying times speed up project delivery.
• Regulatory Ease: New coatings help companies stay compliant as laws around emissions and safety tighten.
• Operational Efficiency: Water clean-up, safer handling, and fewer safety procedures reduce day-to-day complications and costs.
• Safer Work Environments: Reduced fumes and health risks support employee well-being.
• Reputation & Trust: Companies seen to be leading on sustainability earn more trust from clients and consumers.
• Simplified Waste Handling: Disposal is less costly and less hazardous when dealing with water-based leftovers.
• No external factory storage requirements.
“Clients are increasingly looking for suppliers who can prove they’re environmentally responsible,” Michael Vann added. “Firms that make the switch early will stand out and stay ahead as both market expectations and legislation evolve.”
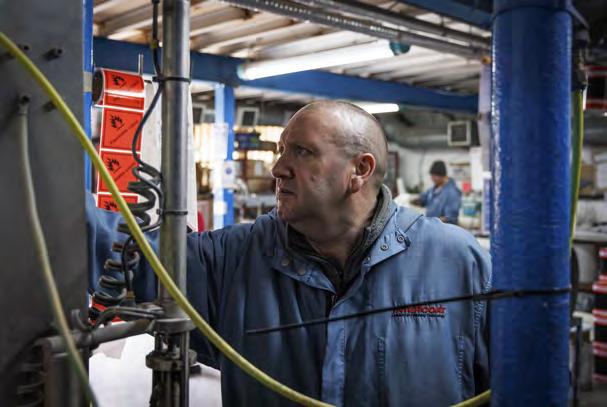
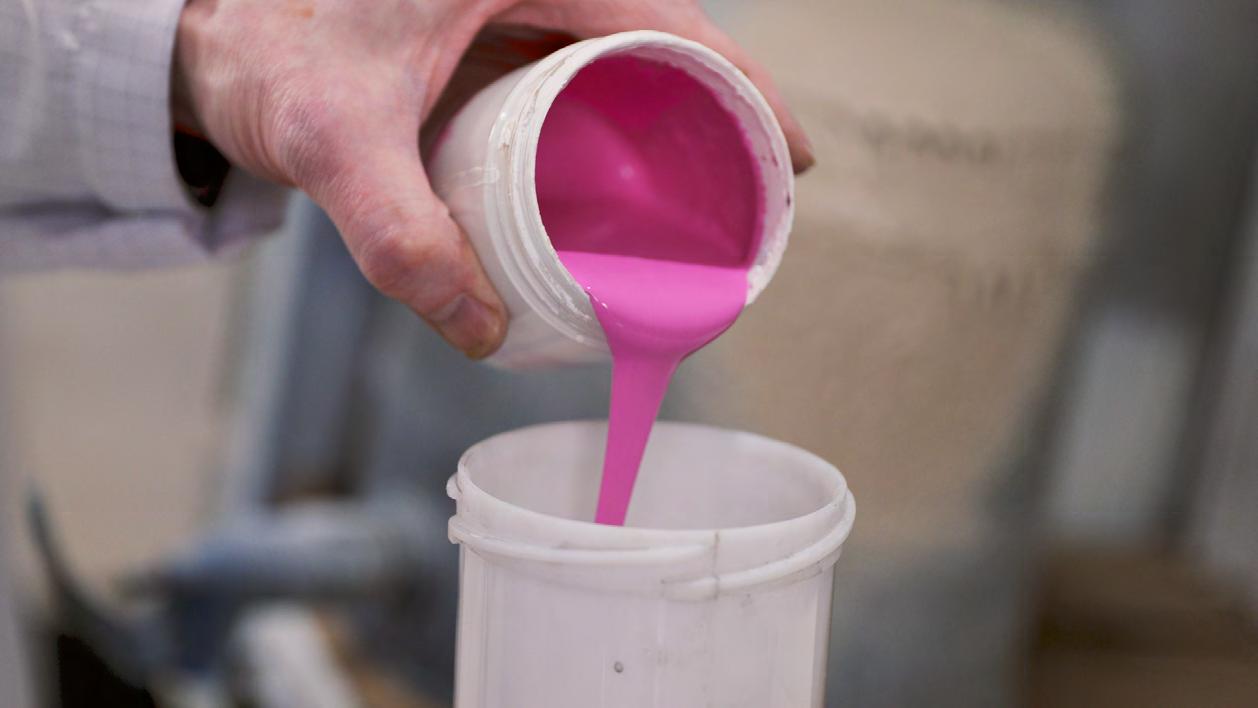
This September 2025, Intercoat is opening its doors for a series of Open Days designed to support companies making the transition from solvent-based to water-based coatings.
Anita Chumber, Marketing Manager at Intercoat, commented: “There’s a growing demand for sustainable practices in our industry, and Intercoat is proud to be leading that change. These Open Days are a great opportunity for businesses to experience firsthand how water-based coatings can meet performance demands while supporting environmental goals.”
What Attendees Can Expect:
• Meet-the-Team: Speak directly with the chemists and engineers behind Intercoat’s technologies.
• Product Showcases: Preview the Aqualine range and see the coatings in real-time use.
• Live Demonstrations: Watch how these products behave during actual application and drying cycles.
• Q&A Sessions: Ask technical questions and get straightforward answers.
• Switching Support: Learn how to transition away from solvent-based products smoothly.
• Industry Networking: Meet others facing similar challenges and exploring similar solutions.
• Myth Busting: Get clarity on common misconceptions about water-based coatings.
“We’ve seen a lot of hesitation based on outdated assumptions,” said Colin Tilly, Technical Service Manager at Intercoat. “Our Open Days are about showing the industry that modern water-based coatings are just as tough, just as good-looking, with quicker drying times and safer to use — for people and the planet.”
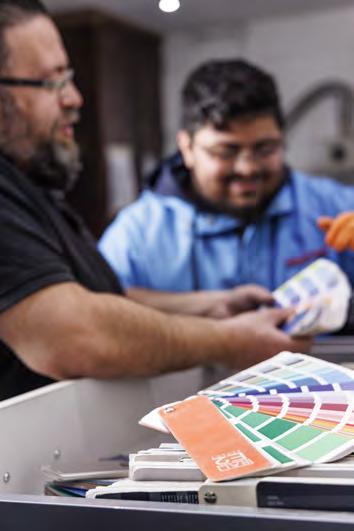
As environmental awareness increases and regulatory frameworks tighten across the globe, Intercoat believes the future of the coatings industry depends on bold action and innovative thinking.
“Responsibility and profitability aren’t in conflict anymore,” Mr Vann concluded. “Companies that lead on sustainability will also lead in customer loyalty, operational savings, and long-term growth.”
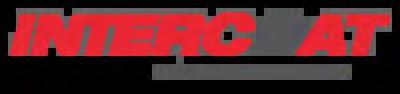
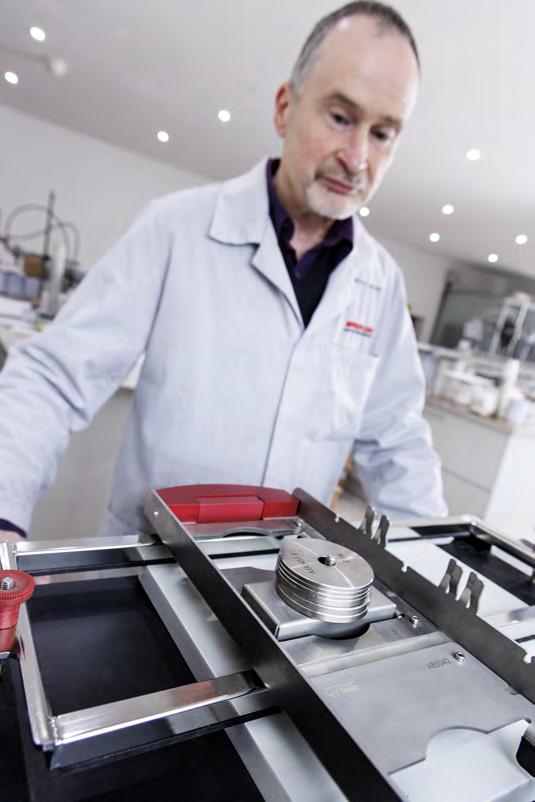
INDUSTRY Training for tomorrow: Mirka ’s tailored approach to upskilling industry professionals
As tools and job requirements continue to evolve, it is more important than ever for businesses to upskill their workforce. This comes in the form of training that equips participants with the essential skills and knowledge needed to meet the constantly changing demands of the industry. As a business, Mirka recognises that the evolution is ongoing, and it means that Mirka’s training programme needs to be fluid to ensure it meets the needs of the customer as well as aligning with what is going on in the sector.
According to Neil Newbrook, business sector manager wood, at Mirka UK, “Our training programmes deliver significant value in the short, medium and long term to businesses as well as the industry. The training is a key part of the full service offering we provide our customers, and the process is pretty simple. We meet with the customer to assess their current sanding and polishing processes which then leads to an action plan that involves staff training and implementation of recommended working practices. Even after the training is completed, Mirka will continue to follow up with regular contact or on-site support. We know this approach works because it allows our technical team to tailor each programme to the needs of the business to ensure their requirements are met instead of it being a onesize-fits-all approach.
“With our training, we also use a ‘Train the Trainer’ method which has been designed so that Mirka’s technical team trains a member of the customer team and they can then train new starters on specific Mirka tools and processes or carry out refreshers for any staff that need it.
“Where the training takes place is just as important as the training itself, so we ensure that it is done where the workforce feel comfortable. Our team knows there are benefits to running the courses on site or at our training centre in Milton Keynes.
However, it is left in the hands of the customer to decide where it takes place. For on site, the customer has the familiarity of their usual surroundings, which enables Mirka’s experienced technicians to highlight how their own specific products or processes would work in an environment they are familiar with. When Mirka takes the training away from the workshop floor to its training centre, participants can take part in classroom-based learning, before having their hands-on experience with the relevant tools, abrasives and solutions. One of the main takeaways we have seen by bringing it to the Mirka Training Centre is that without the distractions of the normal work environment, the attendees tend to ask more questions, which, in turn, leads to more discussion points being covered during the training programme.
“Overall, training is something that should be carried out on a regular basis to ensure the workforce has the knowledge and skills to use tools at an optimal level to perform the work efficiently. This will lead to increased productivity when it comes to the work cycle and the potential to open up new avenues for the business.”
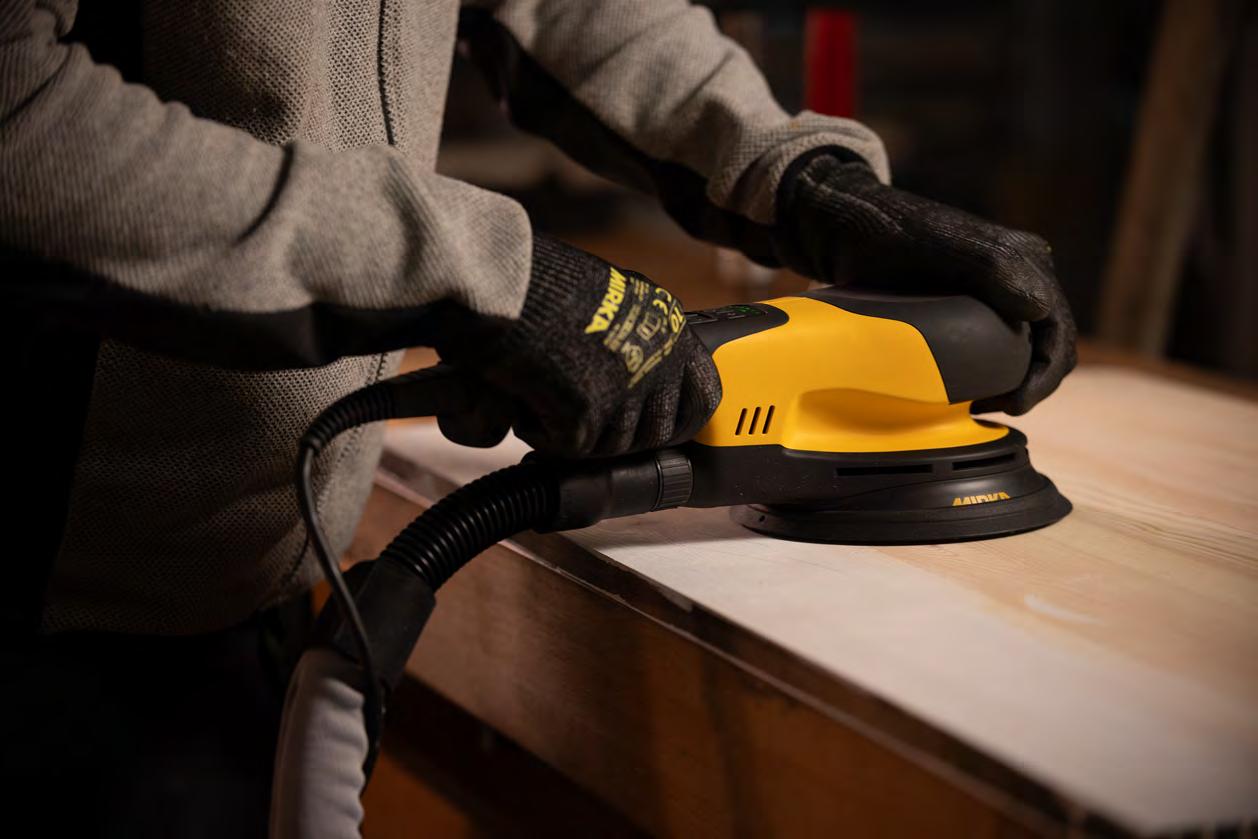
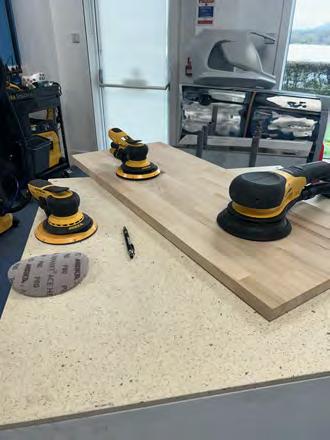
Connecting lightweight panels effortlessly
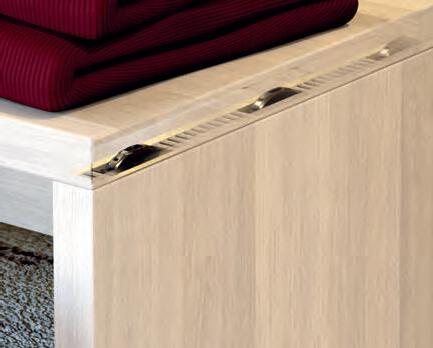
LC P-16
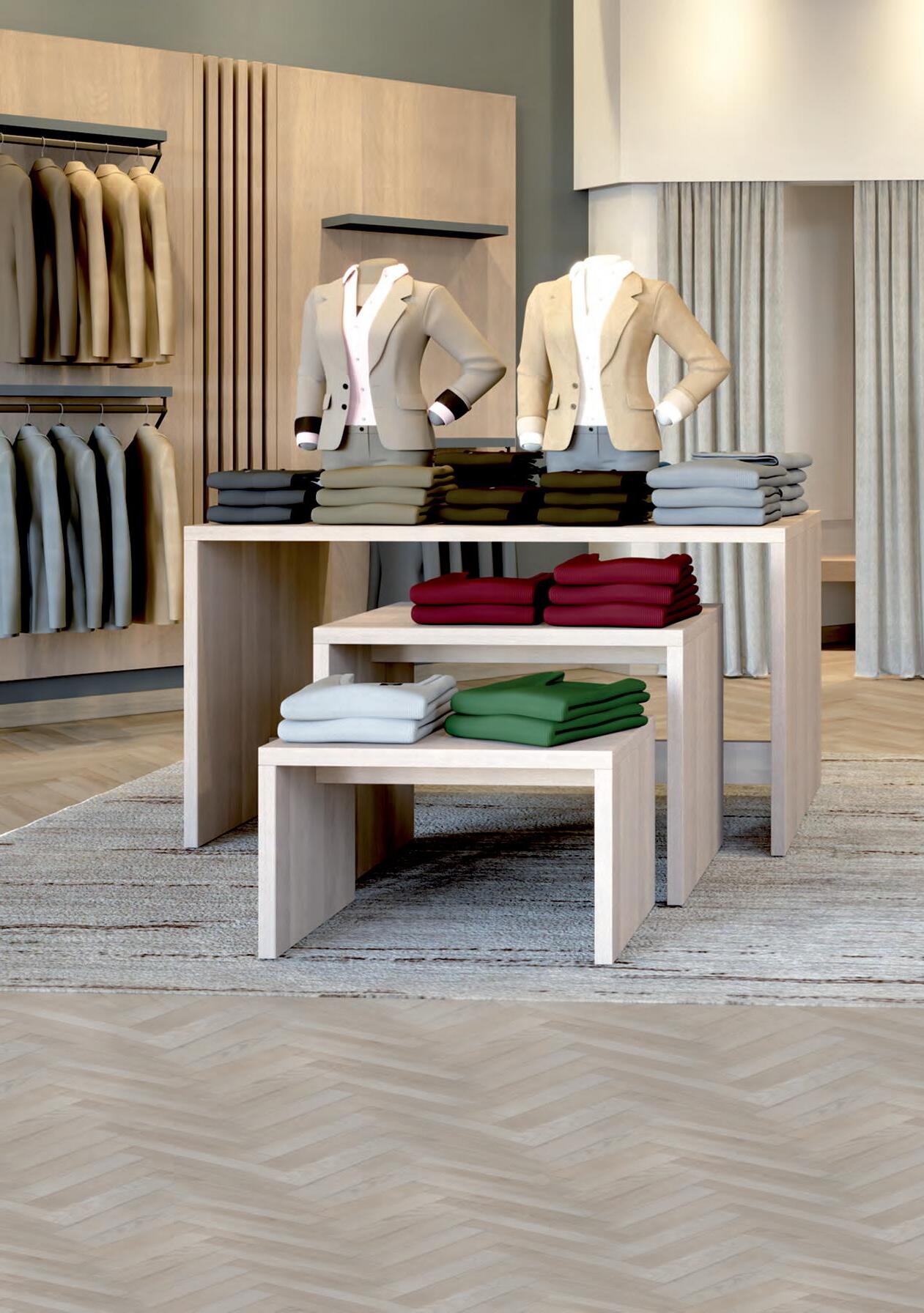
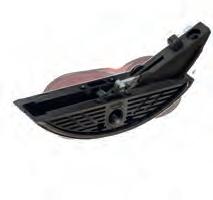
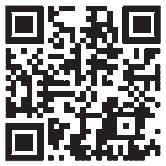
Joining system for lightweight panels without the need for concealed timber edges
– Time-saving anchoring directly in the surface layer
– Suitable for use with Clamex P-14, Clamex P-14 Flexus, Clamex P-14 CNC
– Three product sizes for applications in various lightweight panels
Introducing TAKA : Italian excellence in adhesive innovation
Nestled in the historic town of Marostica, in the heart of Italy’s Veneto region, TAKA Srl stands as a beacon of innovation and craftsmanship in the world of industrial adhesives. With over two decades of experience and roots that trace back to the 1950s in the chemical sector, TAKA has evolved into a global reference point for highperformance hot melt polyurethane adhesives (HMPUR).
A Legacy of Innovation and Specialization
Founded in 2003, TAKA quickly distinguished itself through a commitment to engineering excellence and customer-centric innovation. Today, the company specializes exclusively in the development and production of next-generation reactive HMPUR adhesives, designed for demanding industrial applications—particularly in the furniture and interior design sectors. These adhesives offer superior bonding performance and exceptional resistance to water, humidity, and temperature fluctuations.
Customer-Centric Development and Testing
A key strength of TAKA lies in its close collaboration with customers. Many of its adhesive solutions are co-developed with clients to meet specific production challenges and performance requirements. This customer-driven approach is supported by TAKA’s in-house application laboratory, a state-of-the-art facility where adhesives are tested directly on customer profiles and panels. Within this lab, TAKA simulates real-world conditions to evaluate long-term durability, edge bonding strength, hydrolysis resistance, and more. Equipped with advanced testing instruments, the lab ensures that every formulation is validated not only for immediate performance but also for its ability to withstand the test of time.
Integrated Production and Global Reach
TAKA’s fully integrated production process spans four plants, including one dedicated to polyester synthesis and another housing one of Europe’s most advanced adhesive manufacturing lines. This vertical integration ensures consistent quality and allows for the development of unique, tailor-made solutions that go beyond what is possible with off-the-shelf raw materials.
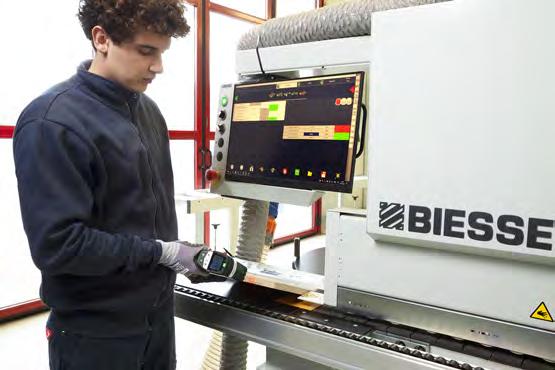
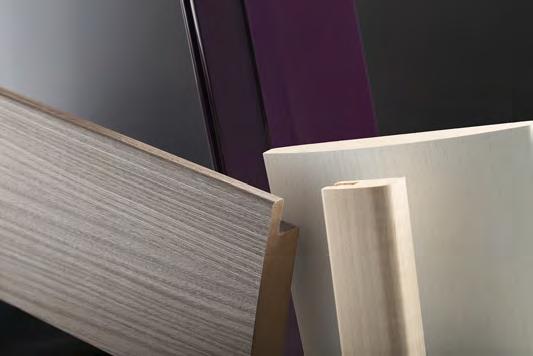
A Group Committed to Knowledge and Sustainability
TAKA is part of the TAKA-WPR Group, which also includes WPR, a leader in lamination technologies. Together, they have established the TAKA-WPR Academy, a certified training hub that shares decades of expertise with customers worldwide, helping them optimize production and elevate quality standards.
Knowledge That Sticks: The TAKA-WPR Academy
TAKA firmly believes that having the right adhesive is only part of the equation—true bonding excellence comes from understanding the entire application process. That’s why, in 2016, the company established the TAKA-WPR Academy, a dedicated training hub designed to transfer technical knowhow and optimize production systems.
The Academy offers a wide range of training modules, from standard programs to fully customized sessions tailored to each customer’s needs. These include production audits, operator training, and advanced workshops for line managers and in-house trainers. The goal is to empower customers with the knowledge needed to achieve consistent, high-quality results.
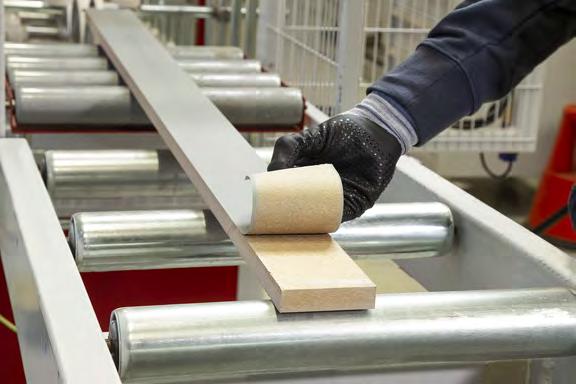
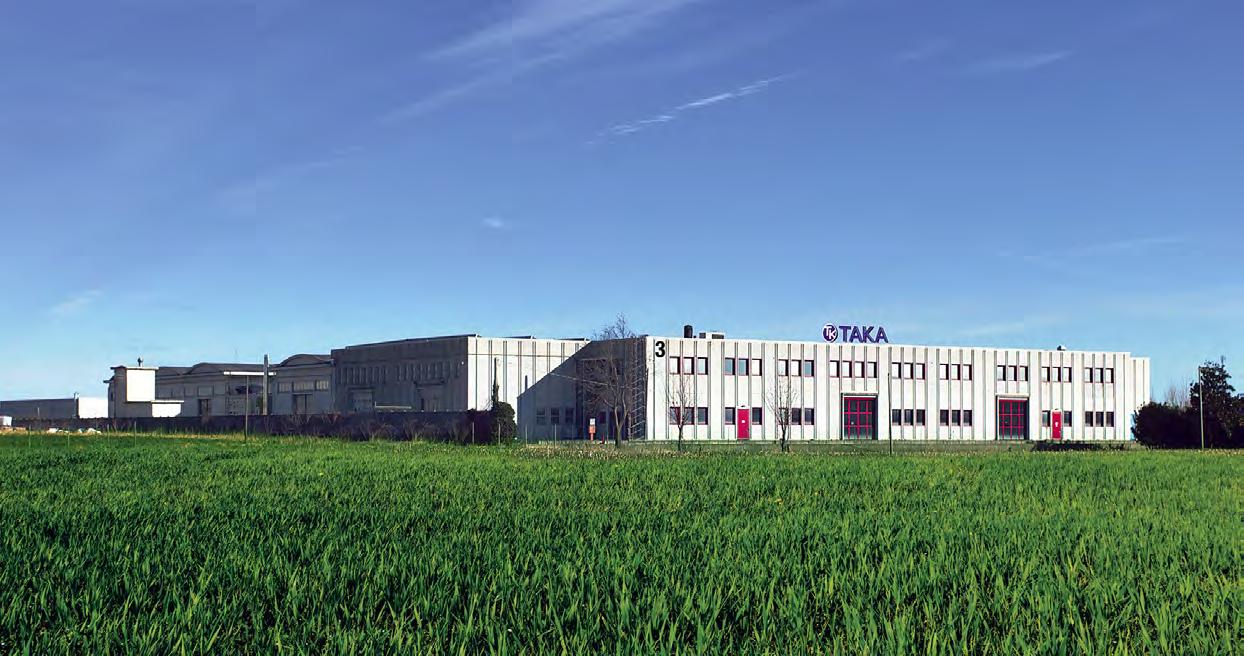
By combining technical training with real-world testing in internal laboratory, the TAKA-WPR Academy strengthens customer partnerships and helps companies align their processes, people, and performance with the highest industry standards.
The Advantages of HMPUR Adhesives and TAKA’s Core Product Families
At the heart of TAKA’s innovation lies its mastery of HMPUR (Hot Melt Polyurethane Reactive) adhesives—an advanced bonding technology that has become the gold standard in modern furniture manufacturing. Unlike traditional adhesives, HMPUR systems cure through a chemical reaction with ambient moisture, resulting in bonds that are not only strong and durable but also resistant to water, heat, and solvents. This makes them ideal for applications where longterm performance and aesthetic precision are essential.
TAKA’s HMPUR adhesives offer several key advantages: Superior bond strength and long-lasting durability
• Zero-joint finish for seamless aesthetics
• Thermal stability for consistent performance, even in intermittent production
• Micro-emission formulations with monomeric isocyanate content below 0.1%, ensuring safety and regulatory compliance
• Bio-based options with up to 20% renewable raw materials, supporting sustainable manufacturing
TAKA’s product portfolio is structured around three specialized families; each tailored to a specific application:
1. Edgebanding Adhesives
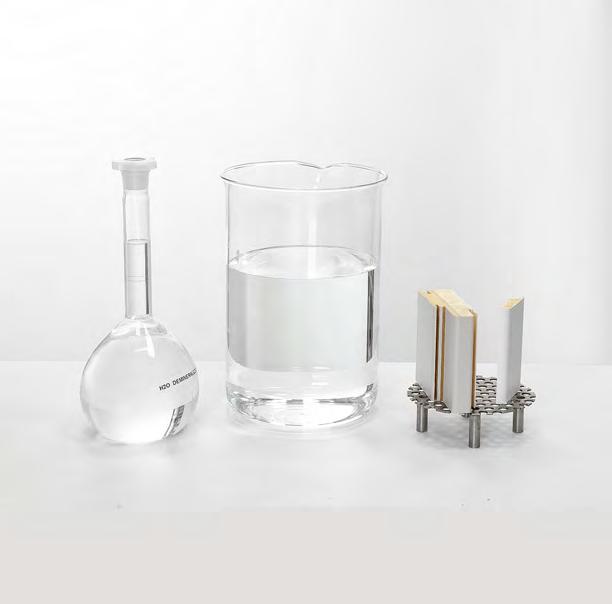
2. Profile Wrapping Adhesives
Engineered for wrapping complex geometries such as skirting boards, frames, and moldings, these adhesives ensure flawless adhesion on glossy or super-matte surfaces. Their versatility and thermal stability make them suitable for a wide array of decorative foils and substrates, including wood, plastic, and metal.
3. Panel Lamination Adhesives
These adhesives are optimized for flat lamination of furniture panels, doors, wall elements, and flooring. They provide smooth, defect-free finishes on materials like MDF, HDF, particle board, CPL, HPL, and decorative papers. With specialized formulations for different production needs, they combine aesthetic excellence with environmental responsibility.
Designed for bonding edges on wood-based panels, these adhesives are compatible with a wide range of materials including PVC, PP, ABS, melamine, wood veneers, and aluminum. They deliver strong initial tack, invisible glue lines, and are available in various colors to match panel aesthetics. Ideal for both artisanal and industrial use, they also include bio-based and micro-emission variants.
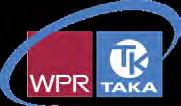
UNLOCK EVERY INCH OF YOUR STORAGE SPACE!
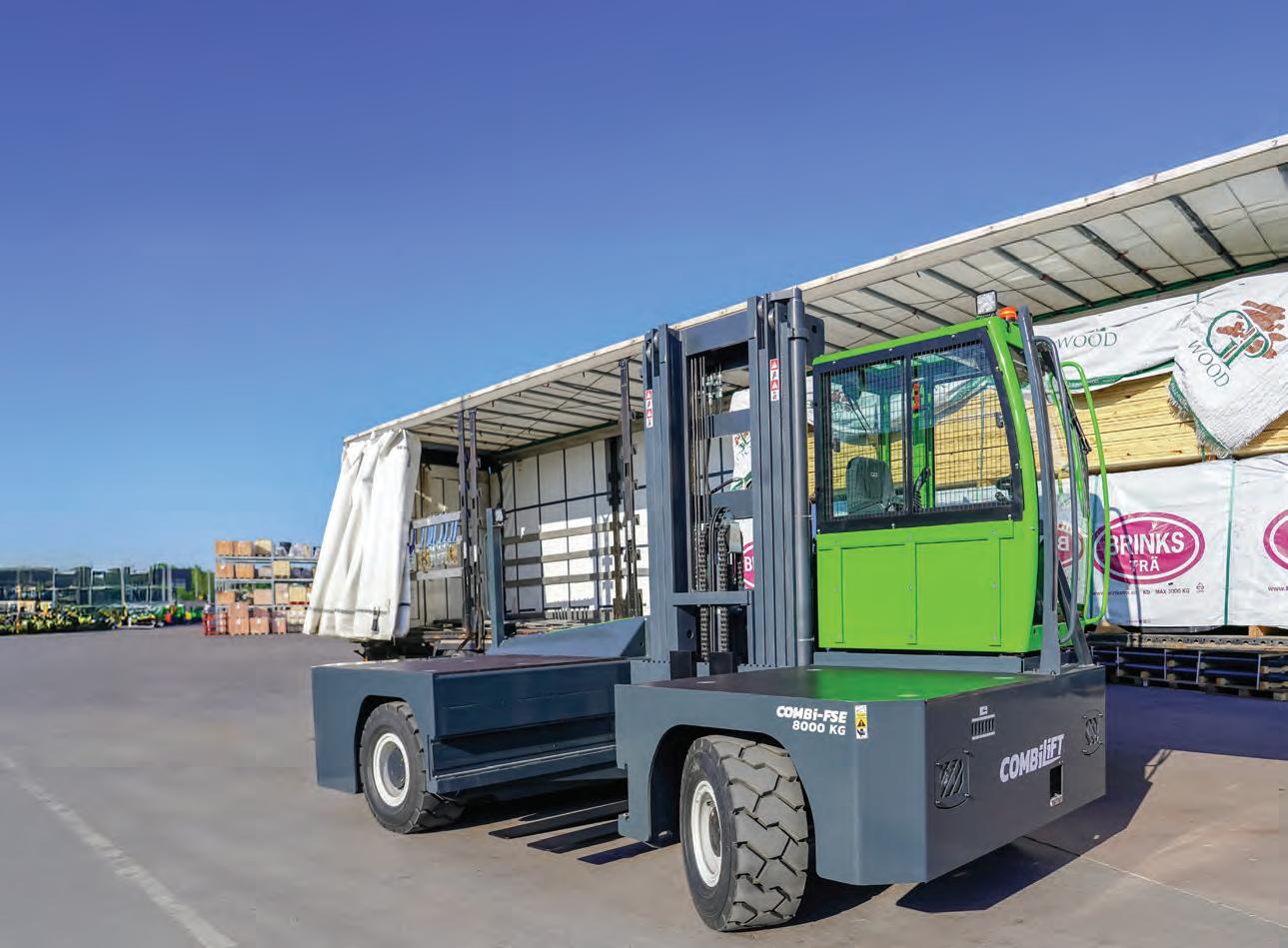
ENHANCE THE SAFETY, STORAGE AND EFFICIENCY OF YOUR LOGISTICS WITH COMBILIFT
For 25 years, Combilift has been revolutionising the way companies handle and store goods. We help companies of all sizes and from every industry to maximise the capacity, safety and efficiency of their warehouse and storage facilities.
Our pioneering product range of multidirectional, articulated and pedestrian forklifts, straddle carriers and container loaders allows you to manoeuvre long loads safely, reduce aisle widths and increase the amount of space available for storage.
CONTACT US TODAY
To find out how Combilift can help you unlock every inch of your storage space.
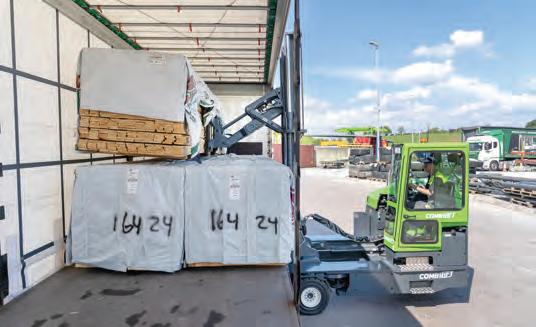
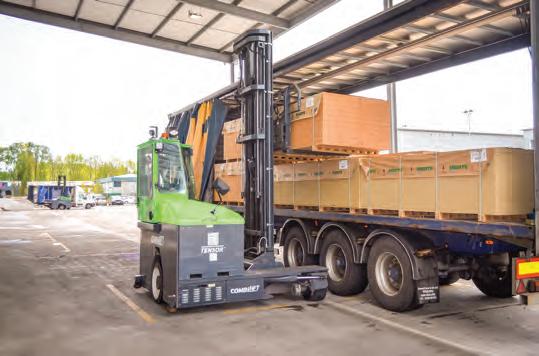
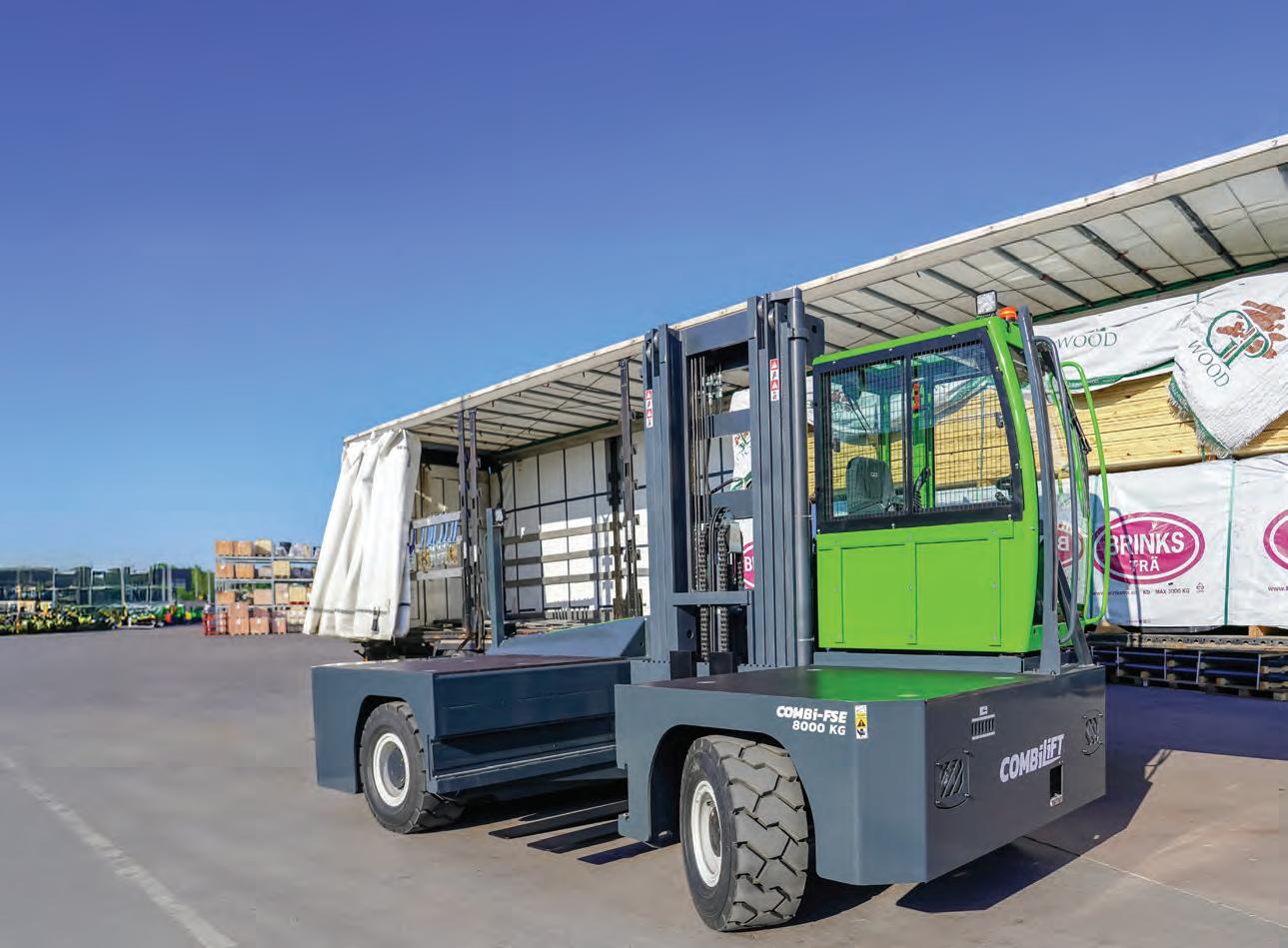
Osmo Recommends: Find the perfect finish for your project
Are you seeking expert advice to help you choose the ideal wood finish? Look no further.
At Osmo, we understand the inherent beauty and enduring appeal of wood. For over a century, we’ve been dedicated to developing premium wood finishes that not only protect and preserve this timeless material but also enhance its unique character.
With such a wide variety of finishes available — and an even broader range of wood species, each with its own specific needs and characteristics — selecting the right product can feel like navigating a minefield.
That’s why we’ve developed the “Osmo Recommends” app: a comprehensive tool designed to guide you through every possible scenario, ensuring you get the right product and finish for your project — first time.
Whether you’re working with interior surfaces such as flooring, worktops, or internal joinery, or tackling exterior applications like decking, fencing, or cladding, the app provides tailored recommendations to suit your needs. From traditional clear finishes that enhance the wood’s natural colour, to tinted transparent options that let the grain show through, to more opaque finishes for a bold, intensive look — we’ve got it all covered.
The app doesn’t just help you choose the right finish. It also offers expert advice on surface preparation, specific to
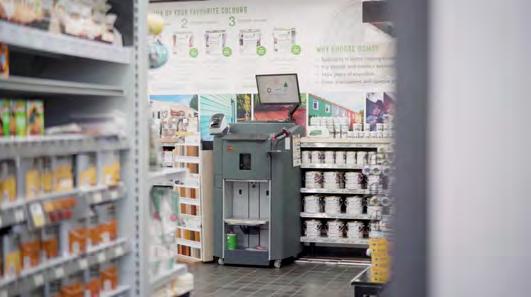
both the product and the wood species in question. You’ll also receive comprehensive recommendations for ongoing cleaning and maintenance, so your wood stays beautiful for years to come.
For extra support, the app features a handy Help & Advice section, ensuring we’re with you every step of the way — whether you need guidance during application or encounter one of those rare but tricky challenges.
With Osmo’s range of high-quality finishes and expert-led recommendations, you can achieve stunning, long-lasting results with confidence. Download today! Available on the Apple App Store and Google Play Store.
Osmo – Good for Wood.
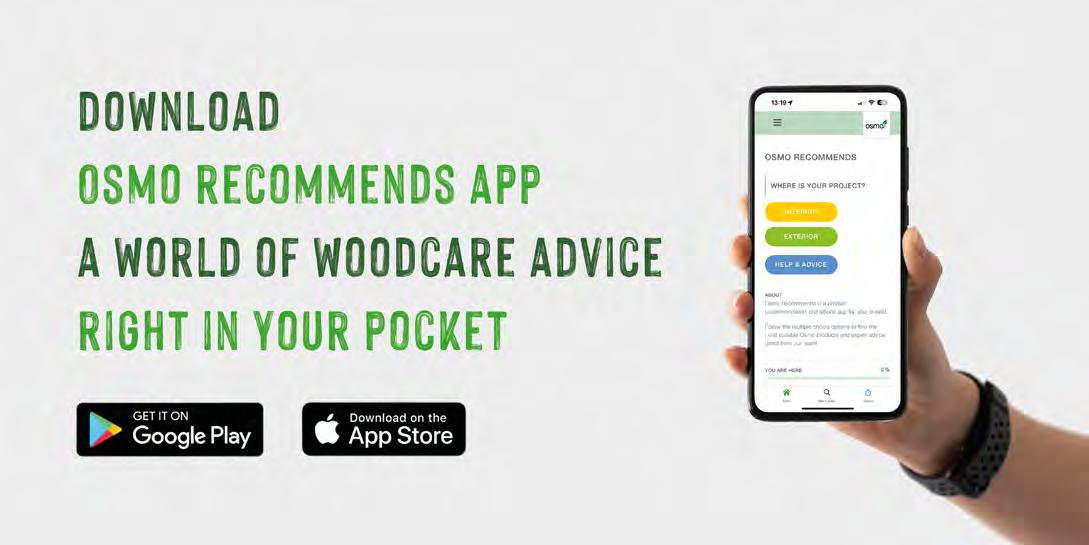
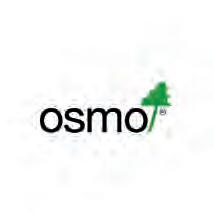
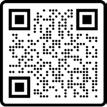
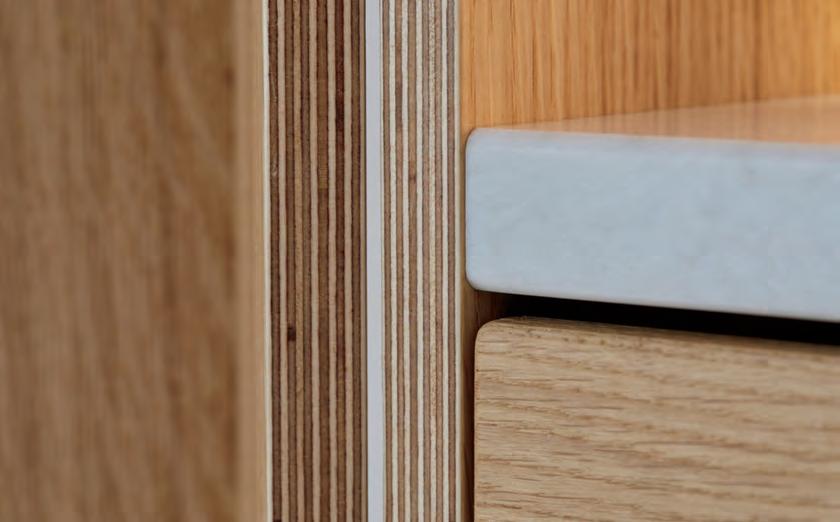
Titus: Full solutions for cabinet hardware
Reliability, innovation, and technical expertise are vital in cabinet manufacturing. Titus, a leading component manufacturer specialising in the development and production of cabinet hardware and hydraulic dampers, has consistently demonstrated its commitment to these values. It offers an unparalleled range of products and services to support cabinet makers in creating high-quality, durable, and aesthetically pleasing furniture.
Comprehensive product range for every application
Titus offers a wide range of hardware solutions that cater to its customers’ diverse needs. The product portfolio includes connectors, hinges, drawer boxes, and sliding systems, among others. With such an extensive range of products, cabinet manufacturers can source all their hardware requirements from Titus, a single and reliable supplier. This helps streamline procurement processes and ensures consistency in quality across projects.
Titus’ product range is designed to cater to the evolving needs of the industry. Take, for example, the innovative T-type PressTo hinges. These hinges feature a tool-less cup fixing system that enables quick and easy mounting, along with a unique anyway clip that ensures consistent and reliable soft-close action. The T-type-i 170 hinges go a step further, allowing cabinet doors to open to a full 170 degrees, providing unobstructed access to cabinet interiors while maintaining exceptional stability throughout their operating range.
Titus’ Tekform Slimline Tacto drawers are the perfect choice for those seeking a sleek, modern aesthetic. These doublewall drawers, designed for handleless cabinets, incorporate an activator that facilitates smooth push opening and reliable soft closing. The slim design optimises storage space without compromising performance, making it ideal for minimalist cabinet designs.
When it comes to cabinet construction, the Quickfit TL5 ‘Full Metal Jacket’ cabinet connectors are in a league of their own. These all-metal dowels offer high resistance to pullout and feature tool-free insertion with a uniform 5 mm drilling pattern. The Quickfit TL5 dowels create solid, reliable joints that don’t loosen over time, even when repeatedly disassembled and reassembled. Their high tolerance for drilling inaccuracies ensures the longevity and structural integrity of your cabinets.
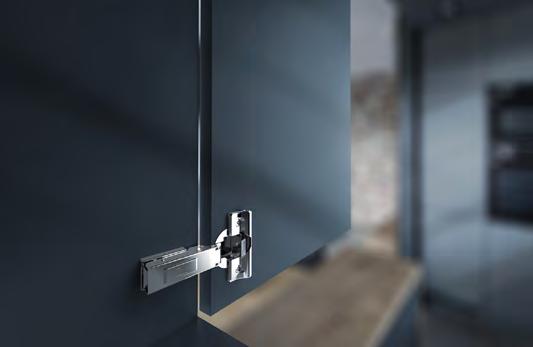
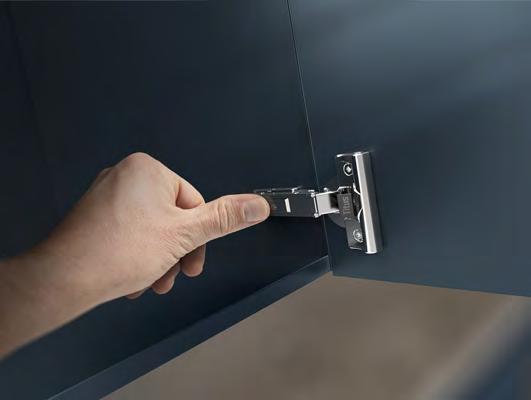
Uncompromising quality and rigorous testing
Titus’ commitment to quality is evident in every product they manufacture. All Titus products undergo stringent in-house testing, as well as evaluation by external, independent testing companies. This comprehensive approach ensures that each component meets or exceeds established industry standards, giving you the confidence that the hardware you use is fit for purpose and built to last.
Titus’ state-of-the-art manufacturing facilities employ the latest technology and adhere to the highest quality control standards. From raw material selection to final product inspection, every step of the manufacturing process is carefully monitored to ensure consistent quality and performance. This attention to detail sets Titus apart and guarantees that your cabinets will stand the test of time.
Expert technical support and guidance
In addition to its exceptional product offerings, Titus provides unparalleled technical support to its customers. The company understands that cabinet-making requires precision engineering and consistent performance, and even the most well-designed hardware can present challenges during installation or use. That’s why Titus has a dedicated technical support team comprising experienced professionals with in-depth knowledge of the company’s products and their applications.
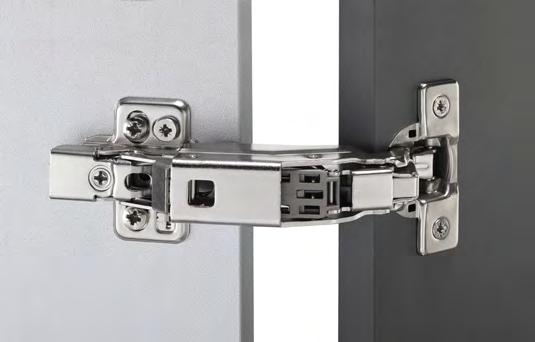
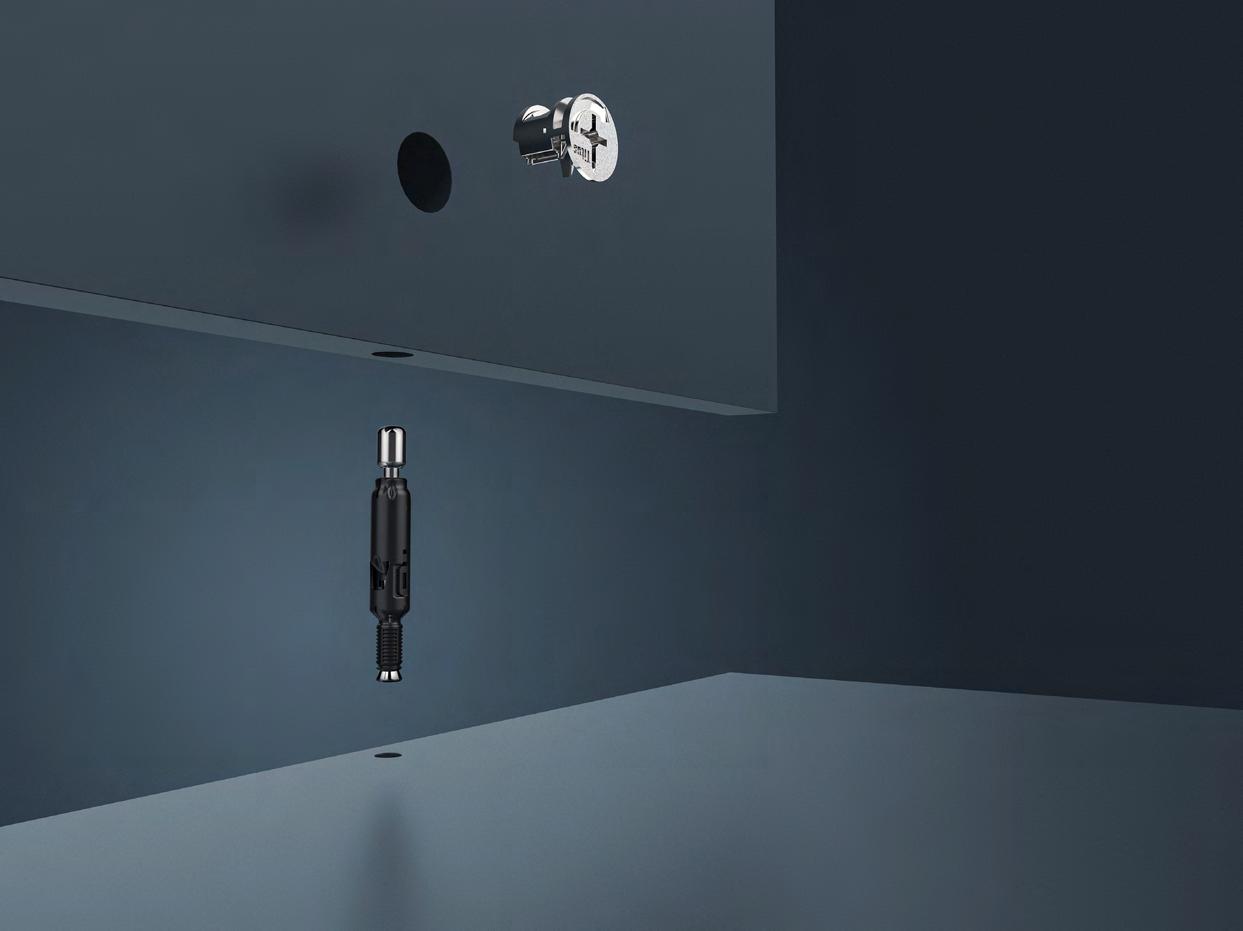
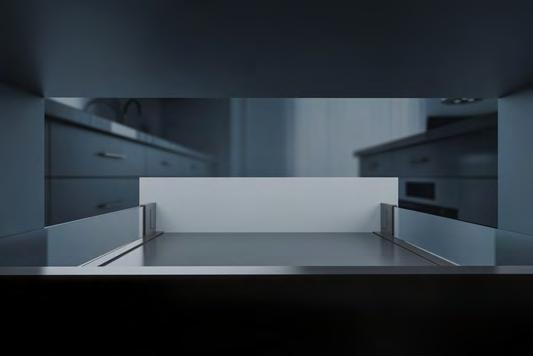
Titus’ technical support team works closely with cabinet makers to provide guidance on product selection, installation best practices, and troubleshooting. Whether you need assistance choosing the right hardware for your project or require support optimising your manufacturing processes, Titus’ experts are always ready to help. They are committed to ensuring that you have the knowledge and resources you need to achieve optimal results and maintain the highest quality standards in your production.
Trusted partner in furniture and cabinet hardware
Titus is not just a hardware supplier. They are a trusted partner who is invested in your success. With an unwavering commitment to innovation, quality, and customer support, Titus enables cabinet manufacturers to create products that exceed expectations and stand the test of time. When you choose Titus, you are not just getting top-quality hardware, but you are also gaining a partner who understands your
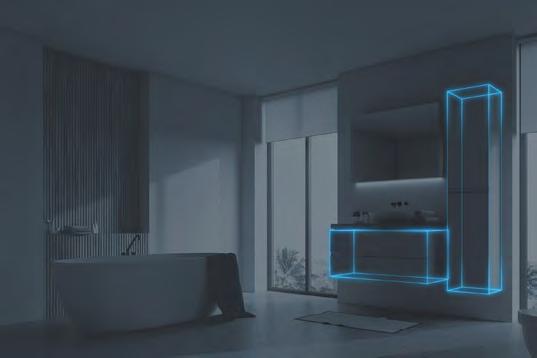
needs and is dedicated to helping you achieve your goals. In today’s highly competitive market, having a reliable and innovative hardware supplier is crucial to staying ahead of the curve. Titus offers a comprehensive range of products, uncompromising quality, and expert technical support, making them the perfect choice for cabinet manufacturers who strive for excellence. By choosing Titus, cabinet manufacturers can have the peace of mind that comes with knowing their components are not only fit for purpose but also backed by a company committed to their success every step of the way.
CASE STUDY
Cutting with confidence: Crocodile Packaging enhances reliability and efficiency with HOMAG SAWTEQ S-300
In 1991, Crocodile Packaging began its journey as a family business, responding to a growing demand for bespoke industrial packaging. Over thirty years and several million tons of cut timber later, it has remained a family business, and from its base in Swindon, has built a global reputation for its top-quality wooden packaging products.
Now, as part of a broader strategy to optimise and expand its operations, Crocodile Packaging has taken a significant first step by investing in HOMAG’s SAWTEQ S-300 beam saw.
The need for an upgrade Crocodile Packaging has a long-standing history with HOMAG, previously using two HOLZMA saws (HOLZMA being part of the HOMAG family). One of these machines had been in operation for nearly 12 years, reliably cutting vast amounts of timber.
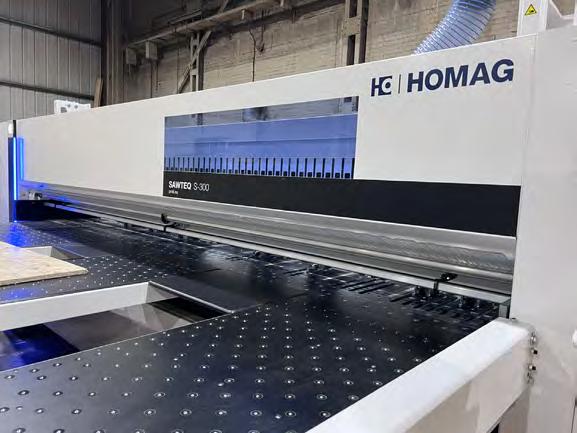
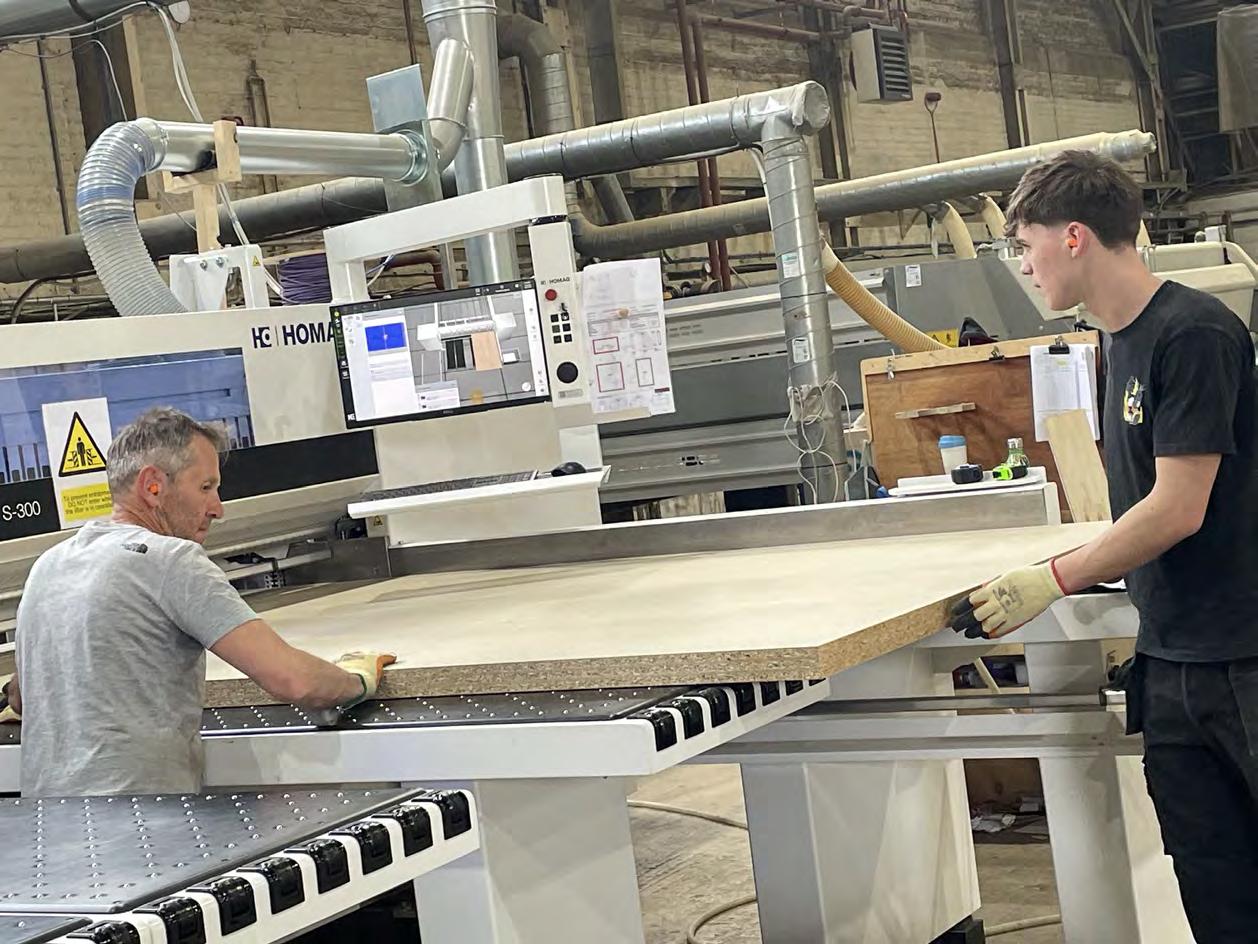
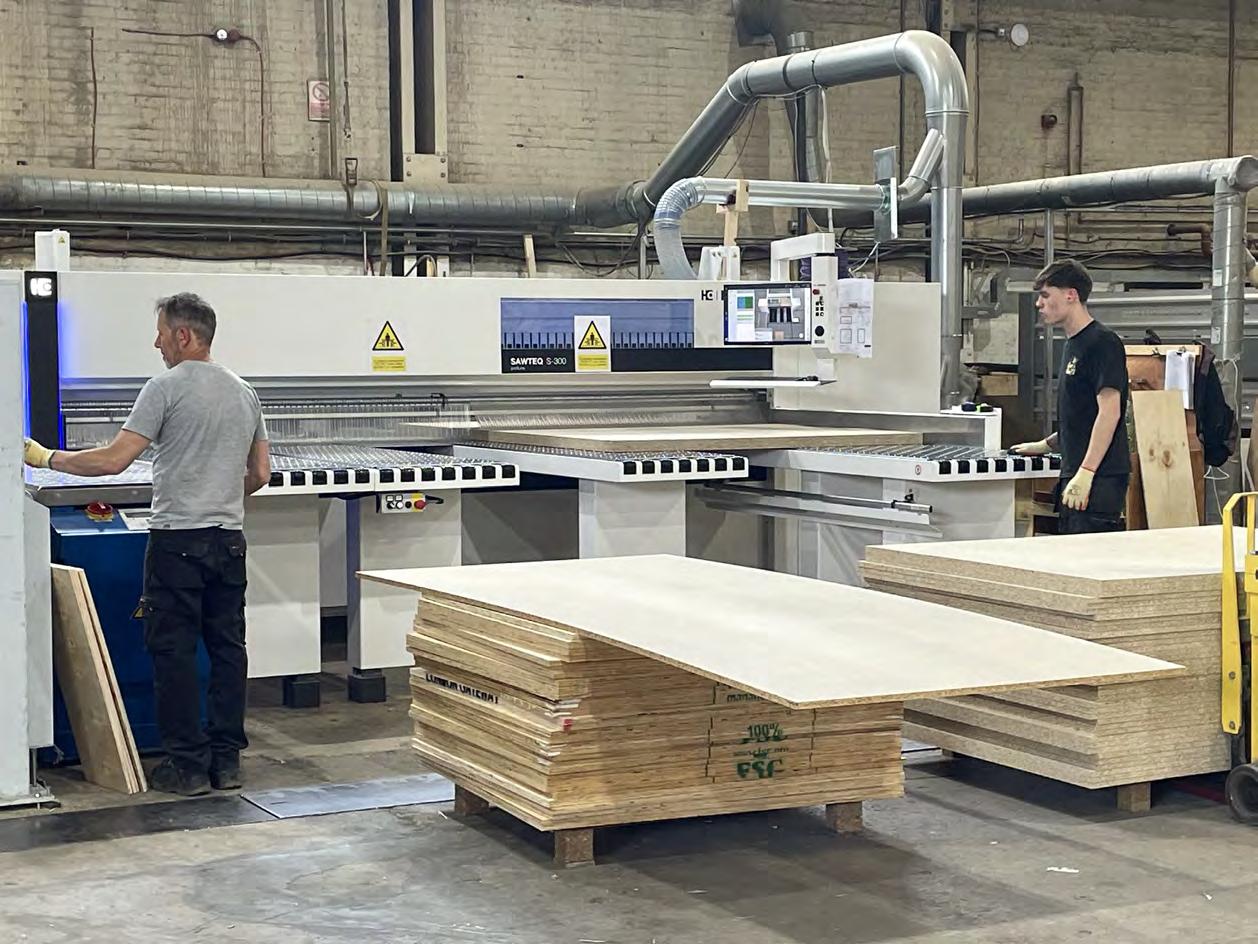
“We recently worked out that we’d cut 16,000 tons of timber on our HOLZMA saw over a nine-year period – and that was a second-hand machine. That’s quite a testament to the quality of the brand,” explains Quentin Philip, Managing Director at Crocodile Packaging. “But the software on the old saw was becoming unsupported by Microsoft, so we made the decision to upgrade before we ran into major issues.”
Choosing HOMAG
Crocodile Packaging conducted a thorough review of three leading saw manufacturers before ultimately choosing to stay with HOMAG. “The quality and reliability of HOMAG, both in terms of the company and their machines, is hard to beat,” Quentin says. “We worked closely with Simon Durant from the HOMAG sales team to assess all the options and settled on the SAWTEQ S-300 as the best fit for our needs.”
A key factor in the decision was HOMAG’s latest CADmatic 5 software, which offers a 3D assistance graphic for operators, intuitive controls that reduce training time, and seamless tapio connectivity for cloud-based software integration.
An easy transition
Although there were minor logistical challenges with part deliveries, HOMAG handled the situation efficiently, ensuring a smooth installation process. “The saw was up and running in no time, and HOMAG trained four of our saw technicians, ensuring they were comfortable with everything.
“The transition was seamless. Almost immediately we felt more productive… and as our familiarity with the machine has grown, we’ve found more and more ways to optimise our operation.”
He also highlights the ease of use across generations of workers. “We have a 20-year-old saw technician and others in their 50s, and they all got to grips with the new tech with
HOMAG’s training – so now we have a good age range of people competent with the machine.”
Enhanced reliability, accuracy, and efficiency
Since implementing the SAWTEQ S-300, Crocodile Packaging has seen noticeable improvements in its operations. “The biggest benefit is reliability,” Quentin states. “Last year, we faced downtime waiting for spare parts for our old machines. Now, with tapio connectivity, we can run remote diagnostics – though we haven’t needed it yet because the saw has been so dependable.”
Additionally, the precision of the SAWTEQ S-300 has proven invaluable. “As a packaging manufacturer, accuracy is critical, and this beam saw delivers exactly what we need,” Quentin adds.
A strong partnership for the future
Crocodile Packaging’s relationship with HOMAG extends beyond the initial investment. “The service has been excellent – and it is ongoing,” Quentin says. “We’ve had post-installation visits from the initial installer, check-ins from Simon Durant, and even refresher training from Nick to help us brush up on a couple of bits.”
Quentin Philip concludes, “This level of support has really solidified our confidence that HOMAG is the right partner for us as we look to the future. The working relationship we’ve got with the sales team is first class, and they’re going to help us look at how HOMAG can help us further optimise and expand our operation.”
Ranheat: The
heat is on
Chris Franklin Chairman at Ranheat Engineering Ltd. a leading UK manufacturer of wood combustion equipmencontinues his series of articles exclusively for Panel and Joinery Production. This edition he writes about uses for heat from your Wood-waste boiler or heater during the summer months when space heating is not required.
There are several uses that waste heat produced by boilers and heaters in the summer can be used, we must bear in mind that the wood-waste from a wood manufacturing process, is a waste and for the manufacturing process to continue the wood-waste still needs to be dealt with and disposed of for the factory to run.
Recent changes have occurred in the use of fine dusts mainly, but not exclusively, in it’s use in agricultural animal bedding. The introduction of these fine dusts is no longer acceptable in Agricultural animal bedding.
So here are the options:
• Send it to landfill.
• Burn it and reject the heat to atmosphere.
• Produce Briquettes for storing and use in the winter.
• Use the heat for process loads such as drying waterbased paint finishes.
• Use in kilning processes either for kiln drying or heat treatment (pallets)
• Produce electricity.
• Produce cooling for the factory.
The seven options above are the most obvious but not exclusive uses of wood-waste during non-heating periods.
Let’s look at for and against for each method.
Send it to landfill
This is the simplest but probably the most expensive as you will need to pay the site taking the waste to pay the landfill tax as well as transport costs plus gate charges to take the material. Fine dusts such as MDF “flour” may have to be bagged first.
Burn it and reject the heat to atmosphere. Sounds bad for the environment but decomposing woodwaste in landfill gives off 25 times more greenhouse gases than combustion.
Produce Briquettes for storing and use in the winter. Making briquettes uses a lot of electricity and as there is no binding agent when stored they tend to go back to dust 100% dust briquettes are not the best. You have to ask yourself am I making product from wood or am I a fuel supplier?
Use the heat for process loads such as drying waterbased paint finishes.
Great if you have a paint-line or extensive painting facility.
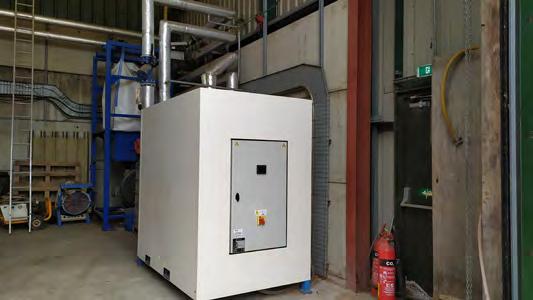
Use in kilning processes either for kiln drying or heat treatment (pallets)
Kilns are expensive to buy and kiln drying of timber is a specialist process, If you make pallets then possibly a “nobrainer”.
Produce electricity.
Can be expensive but if you have enough wood-waste could be viable. Mainly using the ORC method (Organic Rankine Cycle) or possibly a Sterling engine for small scale production.
Produce cooling for the factory.
Not as silly as it sounds but might be used abroad in hotter countries as cooling in the summer can cost more than heating in the winter.
So these are the various ways that your wood-waste could be used in the summer. Probably too late for this year but worth a look for 2026 and the summers do seem to be getting hotter.
As well as the boiler/heater system design considerations there are also the permitting requirements for burning wood-waste at any time of the year:
• All wood-waste burning operations require a permit to burn waste that is a by-product of a wood machining process even if burning Virgin Timber.
• The systems are divided into 3 ranges, up to 50kgs/hr. up to 90 kgs/hr and over 90kgs/hr. There are 3 different permits or exemptions one for each size.
• All installations must have planning permission for the chimney (or written permitted development)
• All installations need chimney height approval from environmental health.
All of these permits and permissions must be in place before the installation goes ahead.
All installations must meet the guidance as laid down in the MCPD (Medium Combustion Plants Directive)
Unlike previous legislation the MCPD is retrospective, and will apply to all installations by 2030, Plants over 5MW had to comply by 1st January 2025 and plants under 5MW have until 2030.
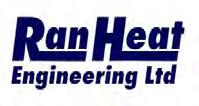
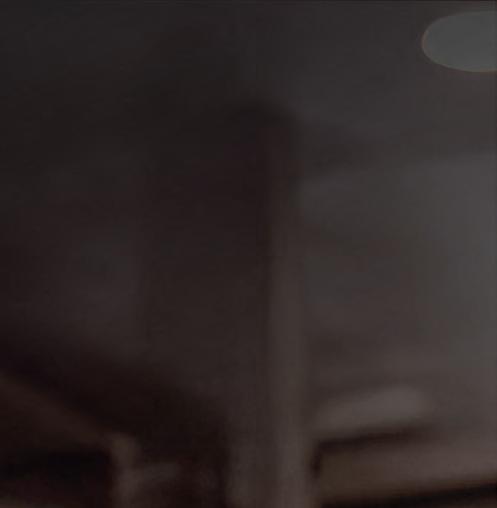
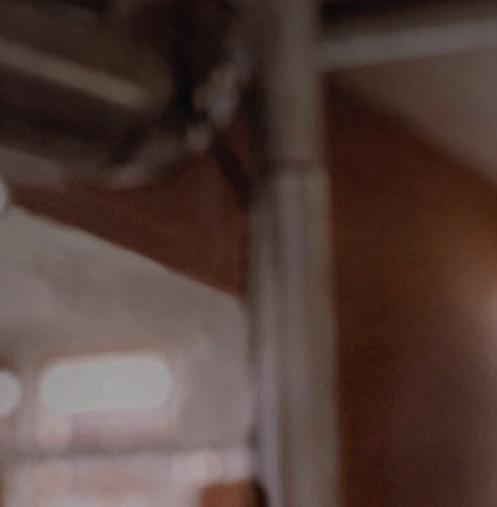
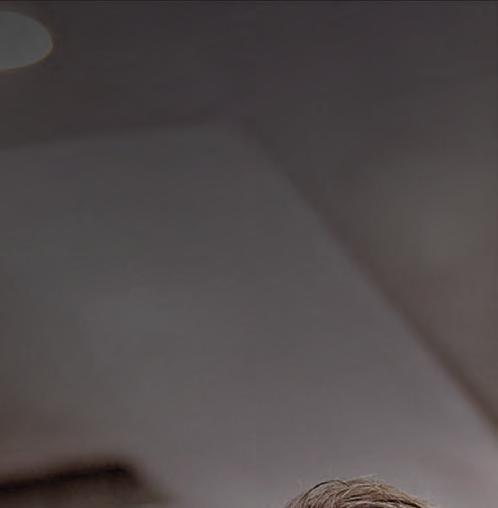
ARE YOU STILL PLANING OR ARE YOU ALREADY CUBEING?
THE SOLID PLANE CUBE SET UP, SWITCH ON, REA DY.
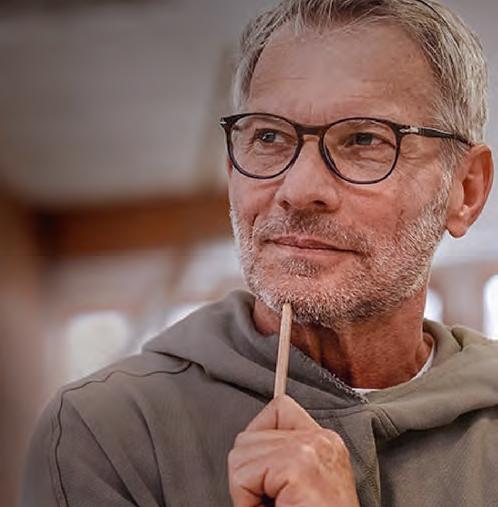

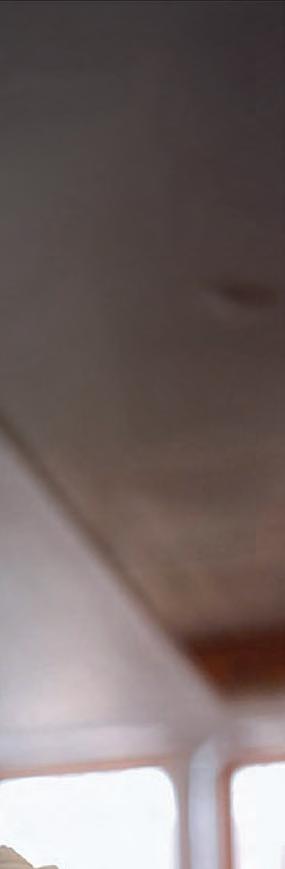
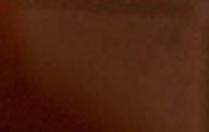
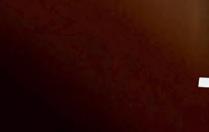
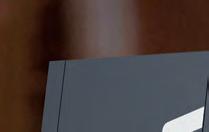
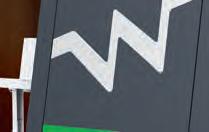


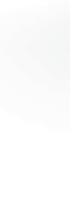
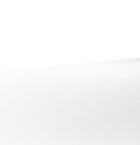
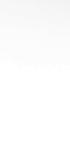


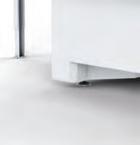



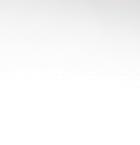
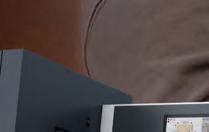
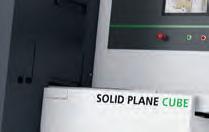
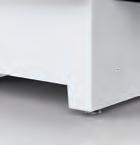
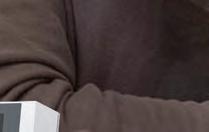
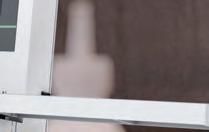

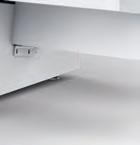
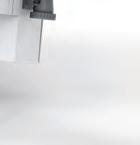
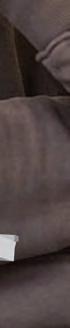
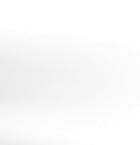
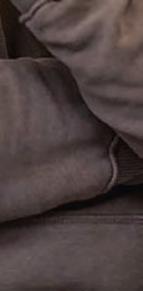
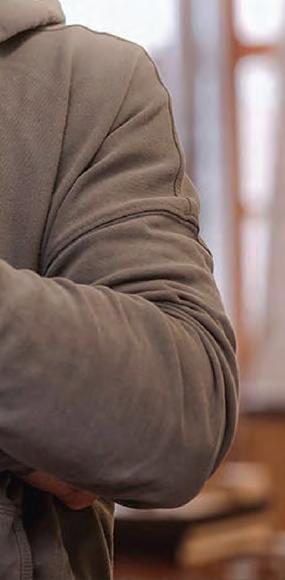

cube3.weinig.
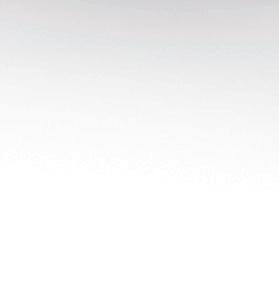
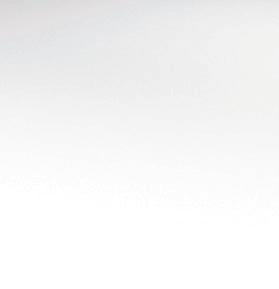
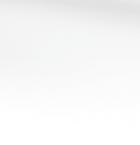
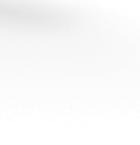
Experience the Adler advantage only from Elmbridge
What if your coating system didn’t just meet your specifications but exceeded every expectation?
For years professional joiners, interior specialists and manufacturers across the UK have relied on the long-standing partnership between Adler and Elmbridge UK for performance and support. And they have delivered, with quality products and excellent service.
Adler’s premium wood coatings, backed by Elmbridge’s technical expertise and support have become a go-to solution for customers that demand quality and consistency. A partnership that provides one of the most advanced coatings available.
As Adler’s exclusive UK coatings distributor, Elmbridge brings more than just product to the table. Their deep understanding of the wood and joinery sector ensures customers get the right system from specification through to application. From first consultations to a full spray demonstration and comprehensive training they make sure every system is matched to the demands of the job.
Performance without compromise
A comprehensive range of Adler products is available from Elmbridge, but there are two products at the heart of their offer: Bluefin Isospeed and Pigmocryl. Water-based primer and topcoats that form their popular two-step coating system.
Adler’s Bluefin Isospeed is a water-based polyurethane primer, ideal for use on interior furniture, kitchens and panels. Designed for efficiency without compromise, Isospeed is a quick drying lacquer
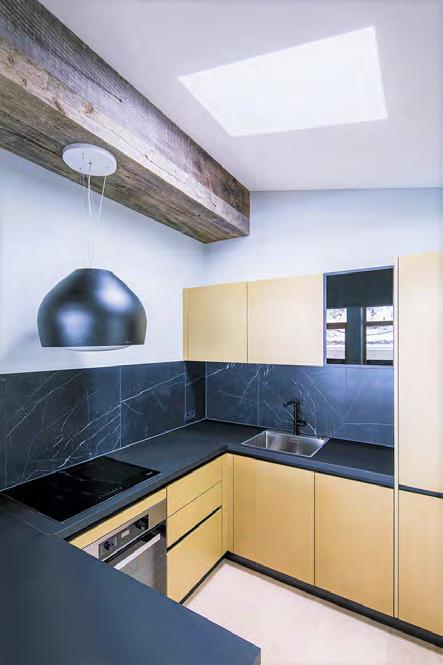
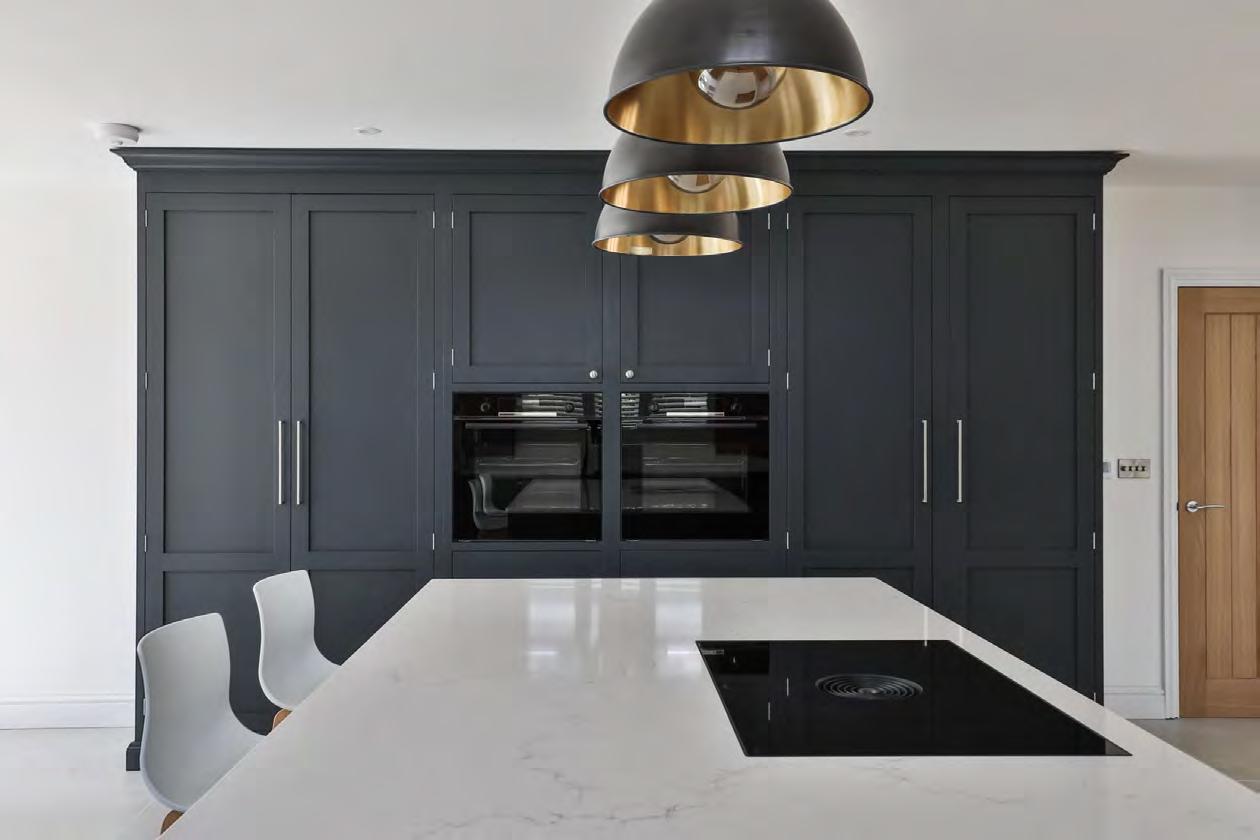
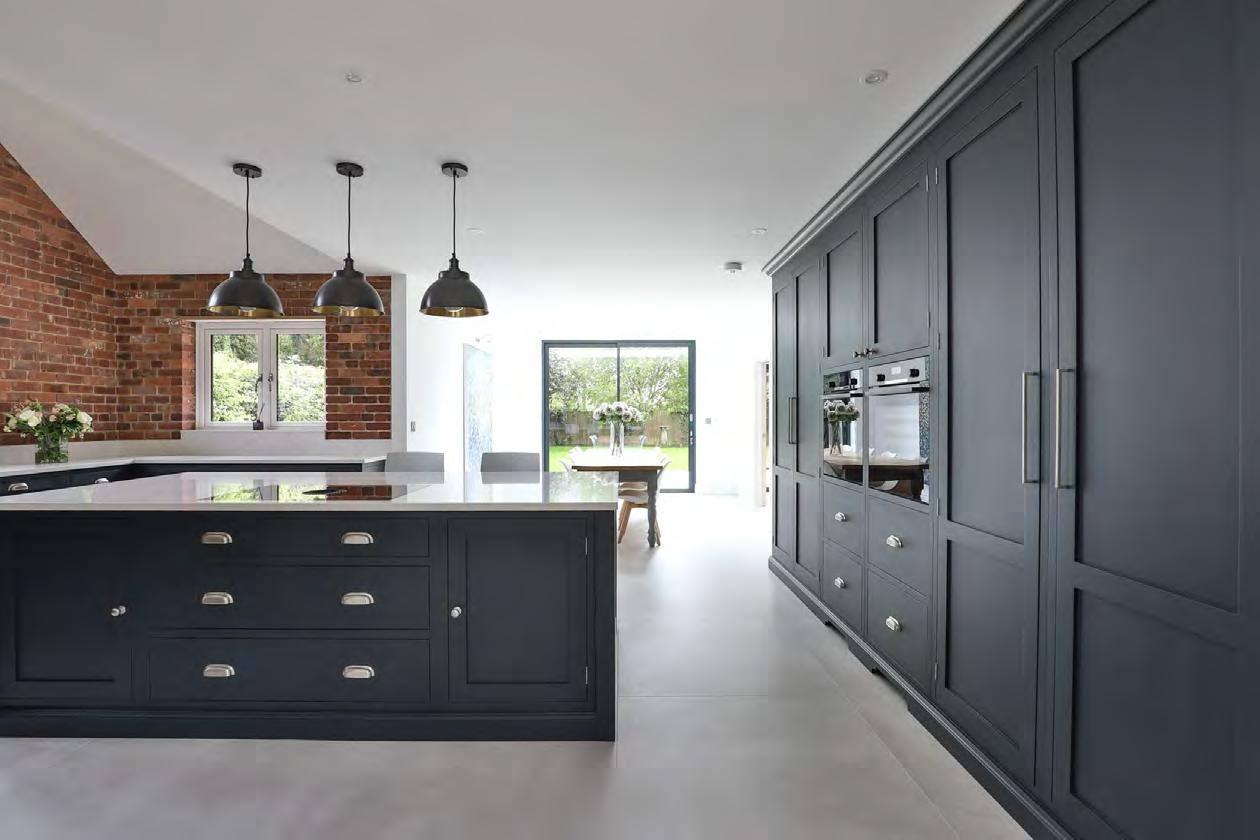
mechanical resistance, making it popular in production lines where throughput and finish quality are equally critical. The best results are achieved when it is applied with an air assisted spray gun at high temperature.
An optional 5% catalyst is also available, allowing its use with solvent based products.
The next step in the coating system is Pigmocryl, a waterbased acrylic topcoat developed for vibrant, uniform colour across wood and MDF substrates. A fast-drying coating that that also has strong mechanical resistance, and it can also be applied directly to the timber to showcase an open grain finish. Pigmocryl also has a high resistance to light, ensuring long term colour stability.
These Adler coatings offer some of the best water-based opacity available today, thanks to colours formulated from four different based materials and 16 colourants, a step above the industry norm.
Sustainability is central to Adler’s approach, with a focus on water-based, low-VOC coatings that support cleaner, safer working environments. From formulation to production, they are committed to reducing environmental impact without compromising performance.
Precision Colour Tinting
Isospeed and Pigmocryl like most Adler products are fully tintable. Elmbridge’s in-house colour matching service uses Adler mixing systems to tint to almost any shade to a high standard of accuracy. From established colour systems or matching to existing surfaces Elmbridge ensures consistency, speed and control throughout.
Using advanced X-Rite spectrophotometers, colours are matched precisely to customer requirements. A final check by their quality control team confirms each sample matches before it is approved for delivery.
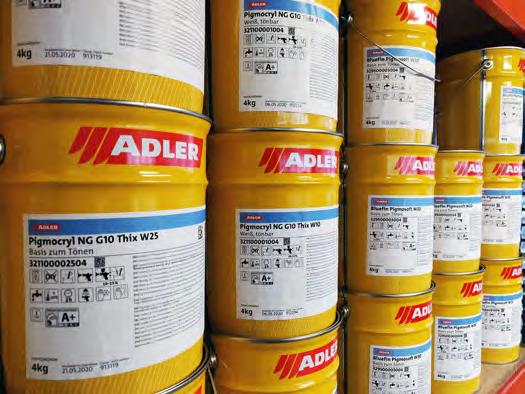
Design without limits
The Adler range extends beyond traditional coatings. Its range of special effects can unlock a world of creative possibilities. Metallic options add depth and lustre to the wood substrate, while concrete-look coatings and antique patinas bring character to bespoke surfaces. These finishes give designers and fabricators the tools to stand out, all with the performance and reliability Adler is known for.
For customers looking to enhance the natural beauty of timber with added depth and character, Adler’s Arova Spritzbeize offers an excellent solution. This water-based stain delivers even, vibrant tones across a variety of hard and soft woods, making it ideal for use with high-end furniture and various interiors. It’s easy to apply and designed for consistent absorption. It forms a perfect base for topcoats, giving wood surfaces a warm, refined finish.
Expert support. Next day delivery
It is not just the exceptional Adler product range; it is the Elmbridge service that comes with it. From a first enquiry the team offers full technical support to make sure you have the right system for your application. With onsite knowledge and our experienced in-house customer service team, Elmbridge is there to help every step of your journey.
For professionals looking for a wood coatings partner that delivers on quality, service and support Adler and Elmbridge is the solution you need.
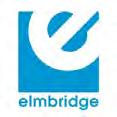
Leitz: Panel & beam saw blades
How Saw Blade Technology Impacts Productivity, Finish Quality and Operating Costs
The vast majority of British woodworkers, especially in furniture and joinery production, use panel or beam saws daily. But for many machinists, utilising the wrong saw blade technology has meant they are not using their machinery to the fullest and maximising it’s productivity. Equipping your machinery with the correct sawblade for its application can have drastic impacts on your productivity, finish quality and also tooling costs.
As the global leader in woodworking tools and saw blades, Leitz tooling has engineered a series of specialist blades to improve productivity on beam and panel saws. Leitz has solutions for improving productivity, cost-efficiency, finish quality and processing advanced materials like solid surface.
RazorCut and RazorCut PLUS For Productivity:
When panel processing with sawblades, cutting stacked panels can often lead to dramatic decreases in cycle times. The Leitz RazorCut saw blade is engineered for highperformance stacked panel processing. Designed for fast feed speeds and achieving up to 50% better productivity than standard carbide saw blades, the RazorCut can machine panel stacks to finish cut quality. This dramatically reduces the need for post-processing or second operations and the innovative geometry reduces noise when machining by -4 dB(A) for more comfortable machining. When SD Manufacturing invested in RazorCut sawblades, they saw their productivity almost triple. MD David Donaghue weighs in “The investment has also resulted in an increase in production output from 20 metres per minute to 50 metres per minute, more than doubling the feed speed, a marked improvement to the quality of finish and a near-zero changeover downtime. In the past 6 months alone, we have increased our panel processing production by at least 30%”.
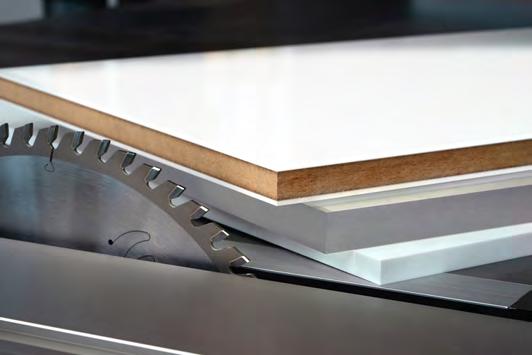
BrillianceCut To Eliminate Post-Processing in Plastics and Solid Surface:
For furniture and kitchen manufacturers, solid surface & plastic sawing can present big challenges when finishing. The incorrect sawblade can cause scratching or melting on the workpiece when sizing, leading to increased cycle times and costly rectifications. The Leitz BrillianceCut sawblades were designed for two reasons: to eliminate reworking and to provide a high cost efficiency. Thanks to an innovative tooth geometry and filled laser ornaments, the BrillianceCut processes plastics like PIMMA and PC or solid surface such as Corian® and Varicor® to finish cut quality. This leads to massive cost and time savings by eliminating the need for reworking the cut edge. The blade is also very sustainable and cost effective with up to 20 sharpens before end of life. In-built vibration reduction also extends the tool life and maintains precision when cutting.
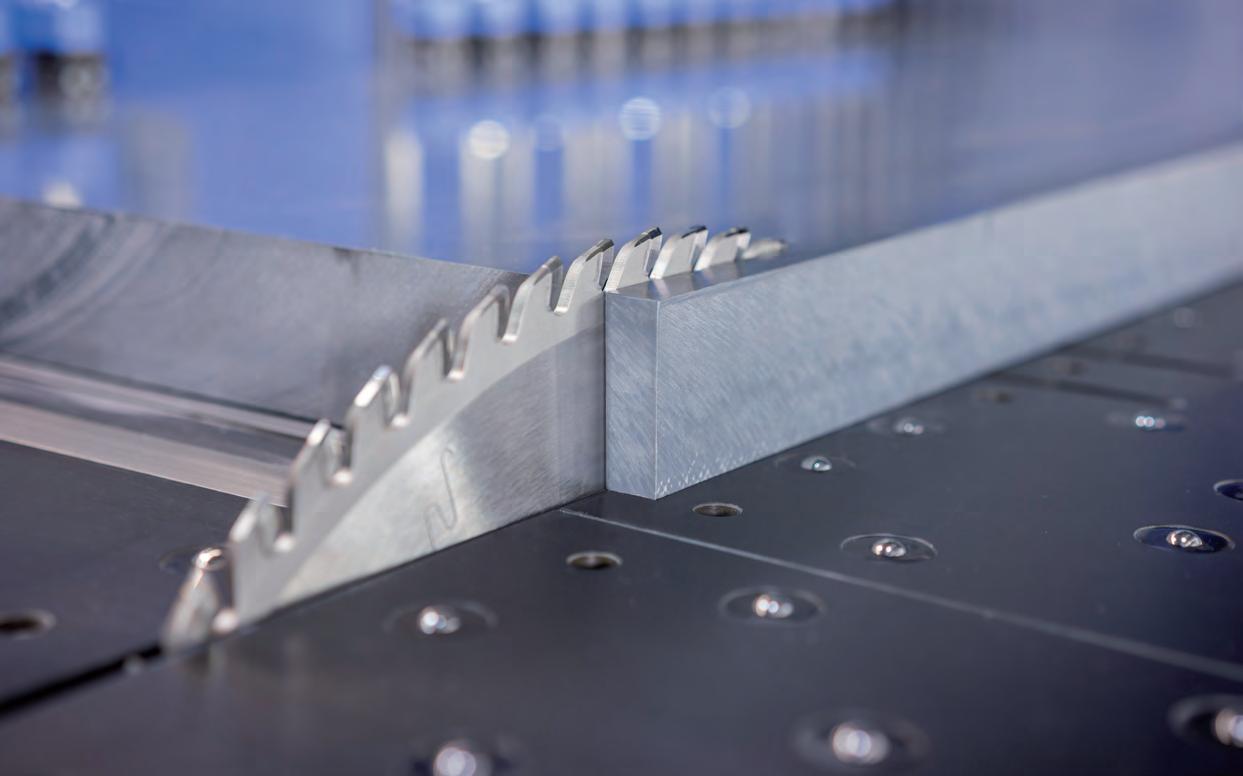
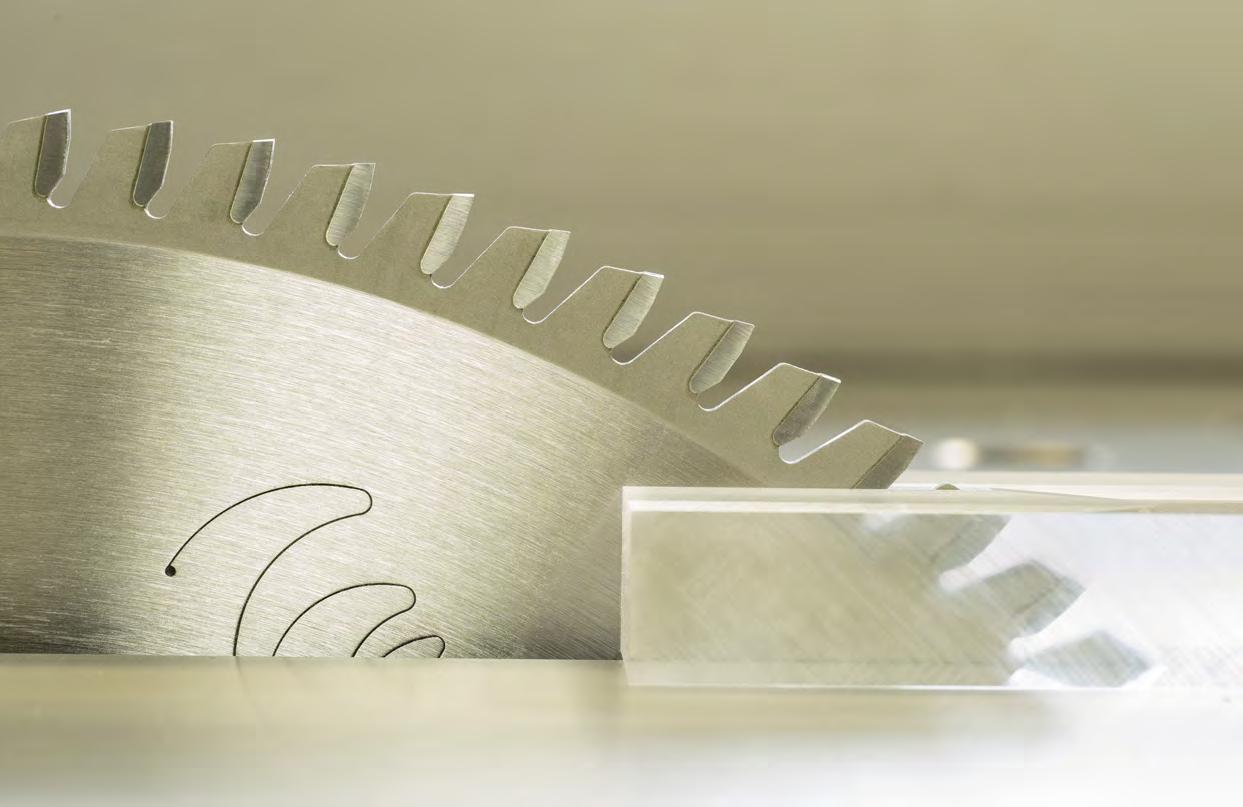
WhisperCut for Economical Machining:
The WhisperCut sawblade from Leitz is another economical solution for panel and beam saws. First engineered in 2017, WhisperCut saw blades have been continually developed as an economic solution to processing a variety of panel materials. Tipped with high-grade diamond for exceptional tool life, the WhisperCut achieves 15x longer lifetime than carbide tipped sawblades. Its Vibration reduction technology reduces noise output by -6 dB(A) when idling and further supports long tool life and precision cutting. The high stability of the tool body makes it Ideally suitable for mitre cuts and provides excellent cutting quality in laminated panels, gluelam and compact laminated panels due to a unique grouped teeth design. Ideal for workshops concerned about noise or HSE compliance, the blade also requires less power than other diamond saw blades due to reduce cutting forces.
Scoring Saw Blades For Improved Finish Quality & Flexibility:
Scoring sawblades are a crucial but often overlooked aspect when sizing panels, the scoring blade makes a shallow cut on the underside of the workpiece before the main blade reaches it. The result is a perfectly clean, chip-free edge on both the top and bottom surfaces of the cut. This is vital for materials like melamine faced chipboard that will be
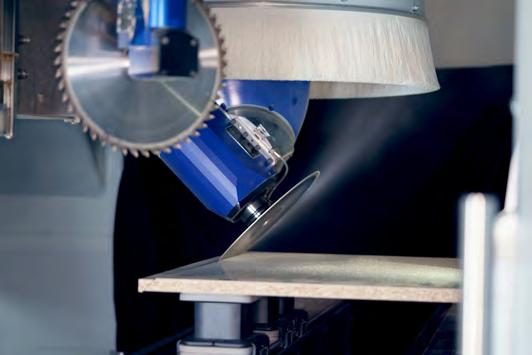
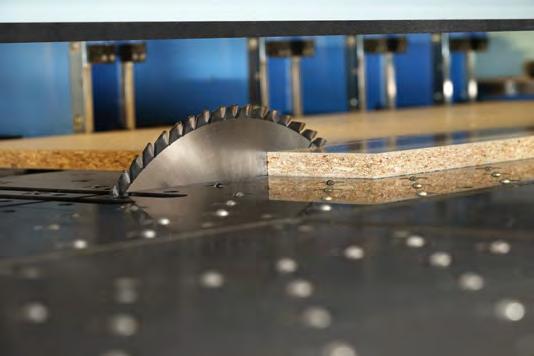
exposed or edged with banding. Leitz tooling understands the importance of this process and its impact on assembly. Leitz scoring sawblades improve productivity thanks to their long tool life, manufactured from high-grade carbide from our own carbide factory, Leit scoring sawblades provide exceptional tool life coupled with fast feed rates and high quality finishes. The scorers are also available with an adjustable cutting width, thanks to a 2-part design featuring spacers. Scoring sawblades increase the tool life for the main saw blade too.
Leitz Tooling is the global market leader in woodworking technology and saw blades, with new innovations and developments being made every year. Equipped with the UK’s most advanced saw blade sharpening setup to date, Leitz service offers unparalleled quality and surface finish. We always take the minimum cutting material, ensuring that your saw blades get the maximum number of sharpens. If you are looking for high-performance saw blades for your machinery, need high quality tool & saw sharpening or technical advice.
Zehnder Clear Air Solutions: The air we breathe is rarely a problem. Until it is.
In the woodworking industry, dust is simply part of the job. It’s a symbol of something being made, shaped, brought to life. Most people barely think twice about it – until the moment it can’t be ignored. That’s when a persistent cough becomes more than just a nuisance. That’s when another employee heads home early, complaining of a tight chest. That’s when you realise the real danger isn’t the dust you can see, but the invisible particles that linger long after the work stops.
The unspoken risk in every workshop
Across woodworking shops in the UK, extraction systems hum and COSHH files are up to date. PPE hangs on hooks, ready for use. On the surface, everything appears safe and compliant.
And yet – the air isn’t clean. Not really.
Zehnder Clean Air Solutions recently conducted a series of air quality measurements in real workshops – not just at the bench, but in places you wouldn’t expect to matterwalkways. The results can be shocking.
In many areas, the air pollution was higher than directly next to the machines. Dust migrates, drifts, and accumulates in places where no one wears protection – because no one expects to need it.
“Because, the air we breathe is rarely a problem. Until It is.”
So what’s really going on?
Many in the woodworking industry assume that having dust extraction in place means the problem is solved. But that’s exactly the issue, as local extraction only captures dust at the source. It can’t deal with what escapes and plenty of fine particles do slip through. The most dangerous ones are often the smallest, lingering unseen in the air long after the work stops.
They float. They drift. They linger – long after the sawing stops.
Even workers using protective gear aren’t completely safe. Why? Because masks aren’t always worn properly, sometimes aren’t worn at all and often can’t filter the tiniest particles (those smaller than 2.5 microns).
We call this Pedestrianism
It’s a term we’ve coined to describe the exposure of people who aren’t even handling wood – people walking through, working near, or simply sharing the same building. Designers. Admin teams. Clients.
They don’t saw, sand, or sweep – but they inhale the same air.
The tragedy is: it looks clean. It smells safe. It feels compliant. But compliance doesn’t equal protection. And dust doesn’t need permission to do harm.
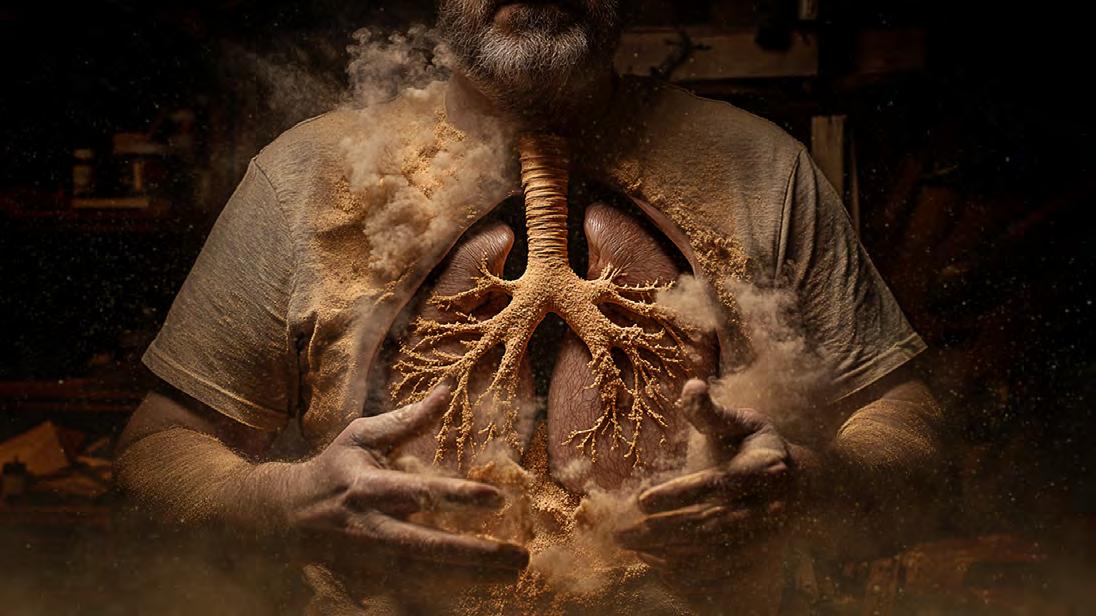

Case in point: when Dovetailors discovered the invisible risk Dovetailors, a bespoke woodworking company in Leeds, experienced this hidden danger first-hand. Despite having LEV systems and a clean workshop, they found fine dust drifting into walkways and offices, affecting staff who were not even on the machines. “You could actually taste what material was being cut,” shared their lead furniture maker.
Realising the unseen risks of pedestrian exposure, they installed an industrial air cleaning system to address the dust LEV could not capture. The result was an immediate improvement in air quality, creating a healthier environment for everyone, not just those on the tools, and demonstrating that clean air requires more than visible compliance
A new standard for safety
It’s time to stop accepting dust as “just part of the job.” Because dust that you can’t see is still dust that can do damage.
Our campaign doesn’t aim to scold. It’s here to inform, support, and help woodworking businesses across the UK take their next step forward.
We’ve created a practical guide: “Sawdust and safety” – a free download packed with insights, realworld stats and easy-to-understand actions any workshop can take.
Because health shouldn’t be a matter of luck – or legal minimums.
About Zehnder Clean Air Solutions
Zehnder Clean Air Solutions is a global leader in workplace air quality management.
With over two decades of experience, we specialise in providing innovative air purification solutions that create cleaner, healthier, and safer working environments. Our advanced systems remove harmful airborne particles, improving employee wellbeing, operational efficiency, and overall productivity. We are dedicated to making a measurable difference in the lives of workers and supporting businesses to thrive by prioritising clean air.
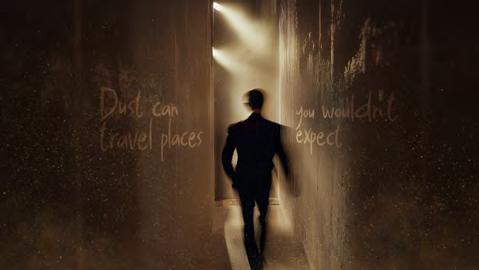
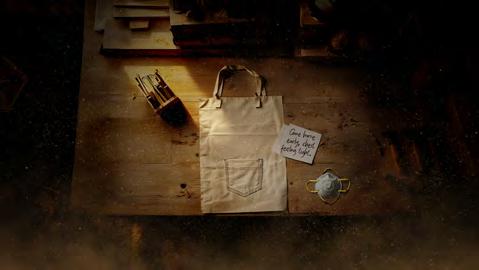
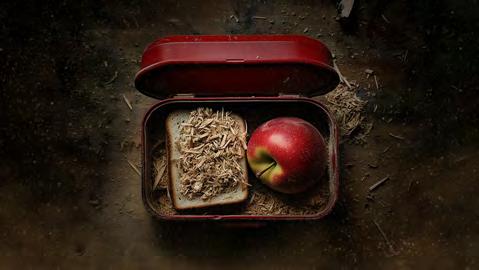
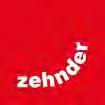
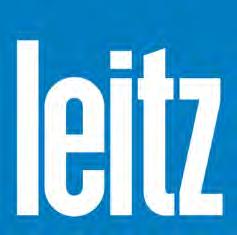
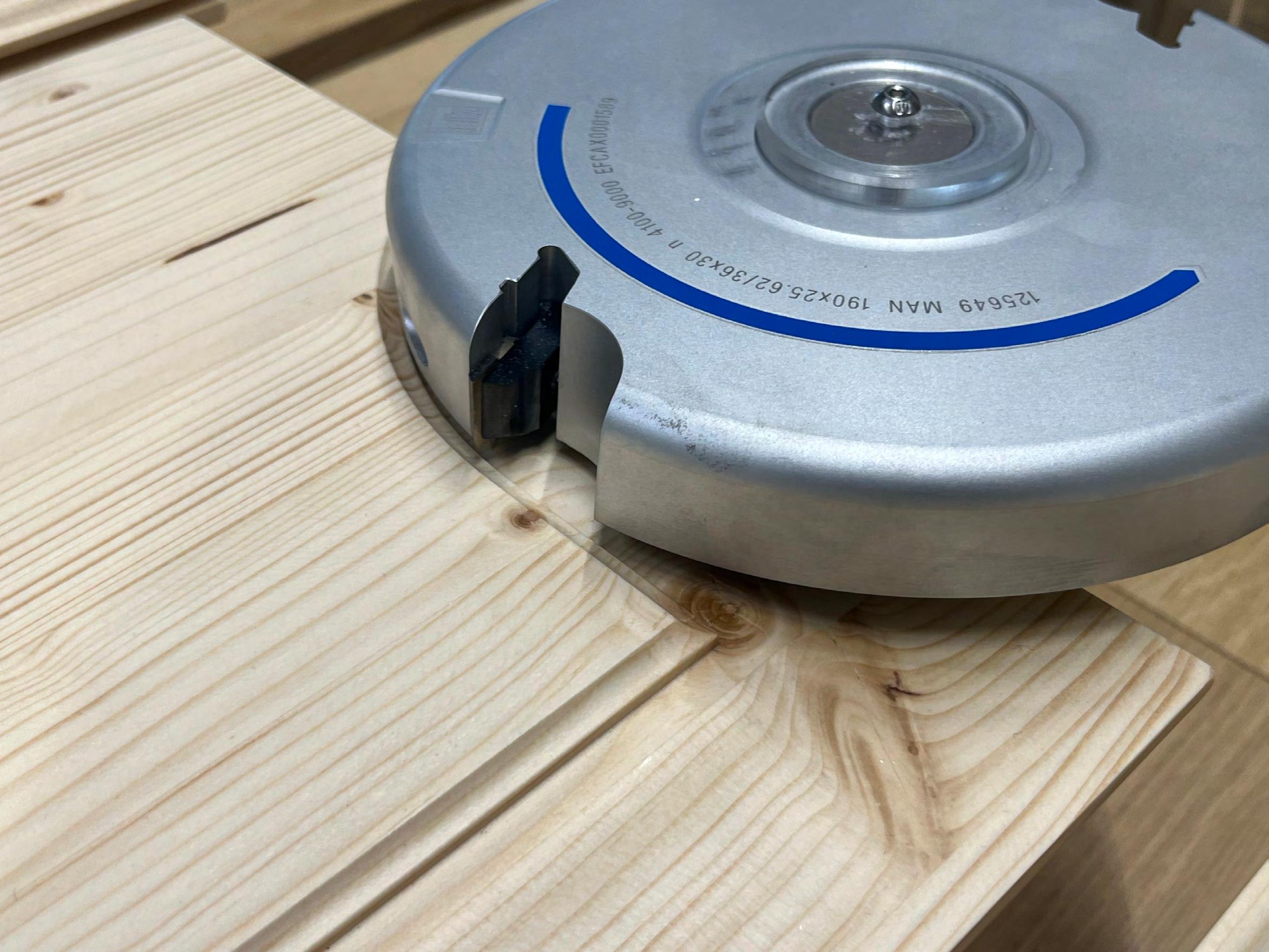
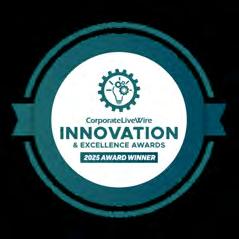
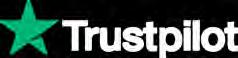

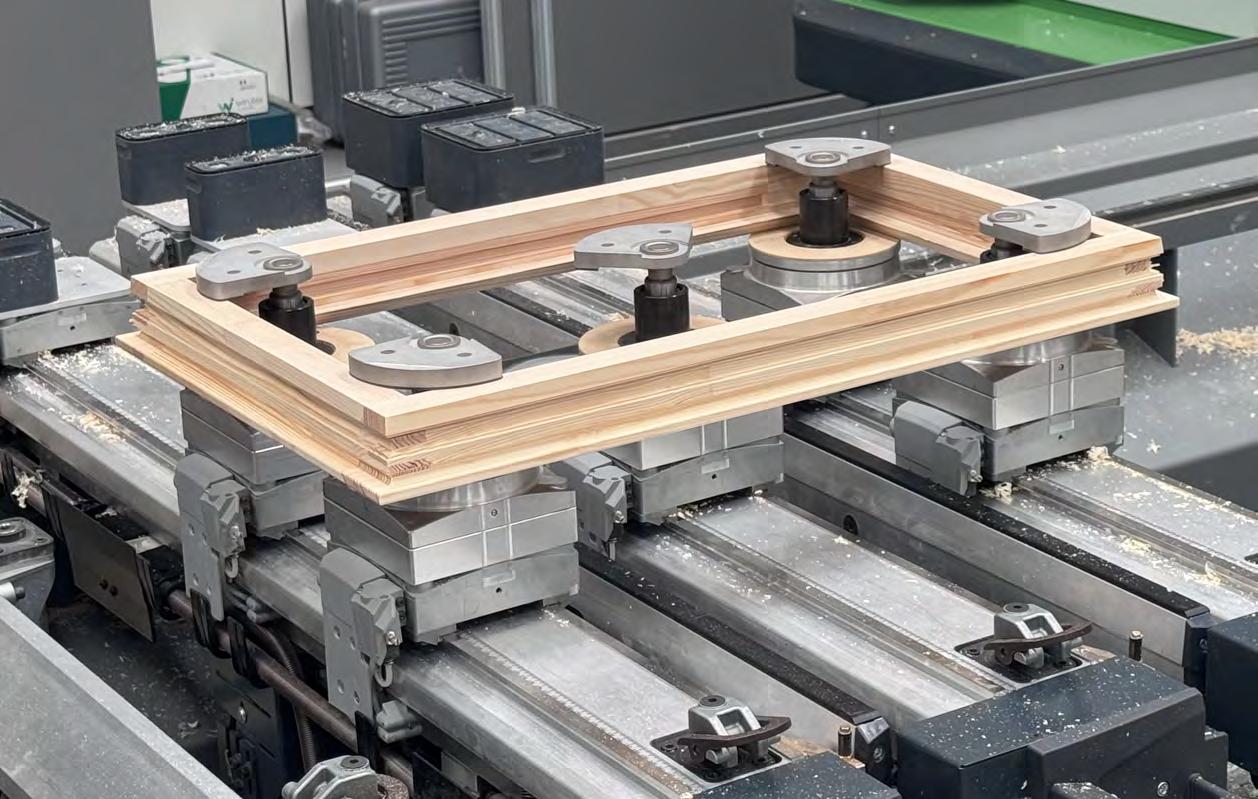
Biesse builds on LIGNA 2025 success
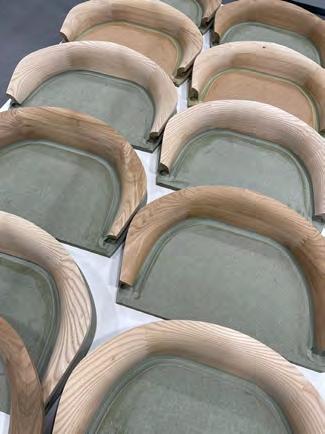
Multi-Material Capabilities and Solid Wood Expertise in the UK Showroom
Following a standout appearance at LIGNA 2025, Biesse UK is continuing the momentum by showcasing the powerful Rover Multi Up M G at their UK showroom, reinforcing the company’s commitment to delivering reliability, multi-material solutions while continuing to thrive in the woodworking sector.
At LIGNA, Biesse celebrated a milestone event with the launch of Biesse Technic, a brand dedicated to fully integrated production lines across wood, glass, and stone. This marked the company’s bold step in expanding its multimaterial footprint, providing innovative solutions to meet the evolving demands of global manufacturing.
While Biesse is rapidly growing in multi-material capabilities, wood remains at the core of its expertise. The company’s solid wood processing credentials continue to be a key focus in the UK, particularly with the Rover Multi Up M G, a versatile machine capable of crafting window frame production and high-precision solid wood processing. Thanks to strong partnerships with Leitz Tooling and The Joinery Network, Biesse is uniquely positioned to offer complete, end-to-end solutions for manufacturers working in solid wood window and door production.
Designed for flexibility and high productivity, the Rover Multi Up M G allows manufacturers to handle their processes from solid wood shaping to nesting panel work, providing consistently high processing standards but also reducing carbon footprint. This machine is multi-functional and continues to efficiently keep up with business’s growing demands.
“Our investment in multi-material solutions is accelerating, but we remain deeply committed to supporting the woodworking industry,” says Mike Moran, Sales Director UK&I at Biesse. “With our solid wood expertise, the backing of trusted partners like Leitz Tooling and The Joinery Network, and the advanced capabilities of machines like the Rover Multi Up M G, we’re well-positioned to support the next generation of UK manufacturers.”
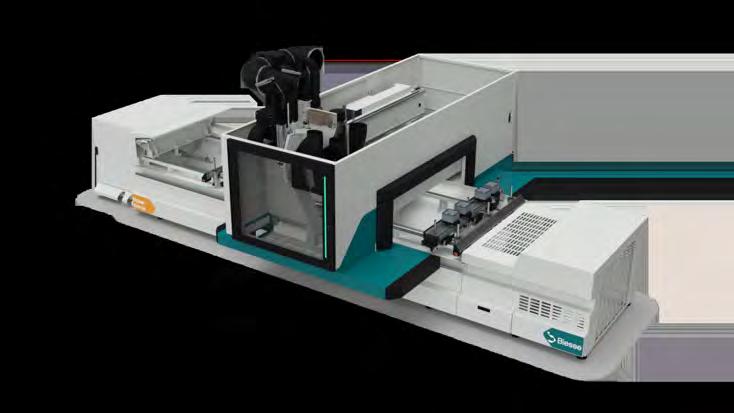
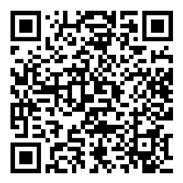
To book your demo at the Biesse UK showroom scan QR code or click: www.biesse.com/gb/en/events/event-detail/?eventId=232
British Woodworking Federation Awards - Call for entries
Entries are now open for the British Woodworking Federation (BWF) Awards – a celebration of the individuals, skills, projects, and manufacturing excellence which have driven the woodworking and joinery sector forward over the last year.
The prestigious annual awards are now in their 17th year and will see the event return to the Kimpton Fitzroy London.
Helen Hewitt, Chief Executive of the BWF, said: “Last year’s launch of the BWF Sustainability Award exceeded all expectations, becoming our most entered category. By encouraging our customers and the broader construction industry to embrace timber’s potential as a high-performance, low-carbon material, we can support Government initiatives such as the Timber in Construction Roadmap and Future Homes Hub, and deliver beautiful, responsibly sourced products.
Entries for this year’s BWF Awards close on Friday 15th August at 5pm. Those shortlisted will be invited to attend the prestigious BWF Awards Dinner on Friday 21st November.
Businesses can nominate themselves or be nominated by a client or supplier, and there are no limits on the number of free to enter categories that can be entered.
BWF Woodworking Project of the Year Award –Sponsored by Anker Stuy Coatings
Recognising innovation and the very best in design, application and ability in joinery manufacture. Judges are looking for a project that demonstrates excellence in woodworking and joinery, exceeding usual requirements of joinery products.
BWF Innovation Award – Sponsored by Teknos
Recognising excellence in technical innovation, product development, design, manufacturing or application. The judges are looking for a product or process development that showcases or extends the opportunity and application of timber joinery by overcoming technical or process difficulties or by introducing new concepts to produce the desired joinery solution.
BWF Health and Safety Award – Available to sponsor
This award acknowledges an individual or collective effort, or initiative, which has made a notable difference to the health and safety practices and culture within a business. The judges are looking for an initiative or action that has improved safety in an organisation.
BWF Rising Star Award – Sponsored by NFU Mutual
This award recognises an individual whose dedication and hard work has made a real difference to either the organisation in which they work, or to the wider woodworking and joinery community. The judges are looking for an individual who goes the ‘extra mile’ to ensure that customers receive the best possible experience and has had a positive impact on the performance or efficiency of the business.
BWF Heritage Project of the Year Award – Sponsored by Impra Wood Protection
Recognising excellence in a conservation, restoration or renovation application, for this award the judges are looking for a heritage joinery project that demonstrates excellence in woodworking/joinery, and evidence that the company contributed to the conservation, restoration or renovation of a heritage project.
BWF Sustainability Award – Sponsored by Remmers UK Ltd
This award recognises outstanding projects, initiatives or individuals that demonstrate a commitment to improving the company’s environmental sustainability performance. The judges are looking for organisations or individuals that have identified and secured lasting sustainability improvements, demonstrated through evidence that sustainable environmental improvements have been made, and committed to continually improving sustainability through clear processes.
BWF Apprentice of the Year Award – Sponsored by CITB
Celebrates the achievements of all apprentices within the woodworking businesses. The judges are looking for quality of work to agreed quality targets and standards, a safetyfirst attitude and extraordinary commitment that has added value to the apprentice’s place of work.


To enquire about sponsorship opportunities, which are open to members and non-members, please contact: Gemma Price:gemma.price@bwf.org.uk
www.bwf.org.uk/bwf-awards-2025/
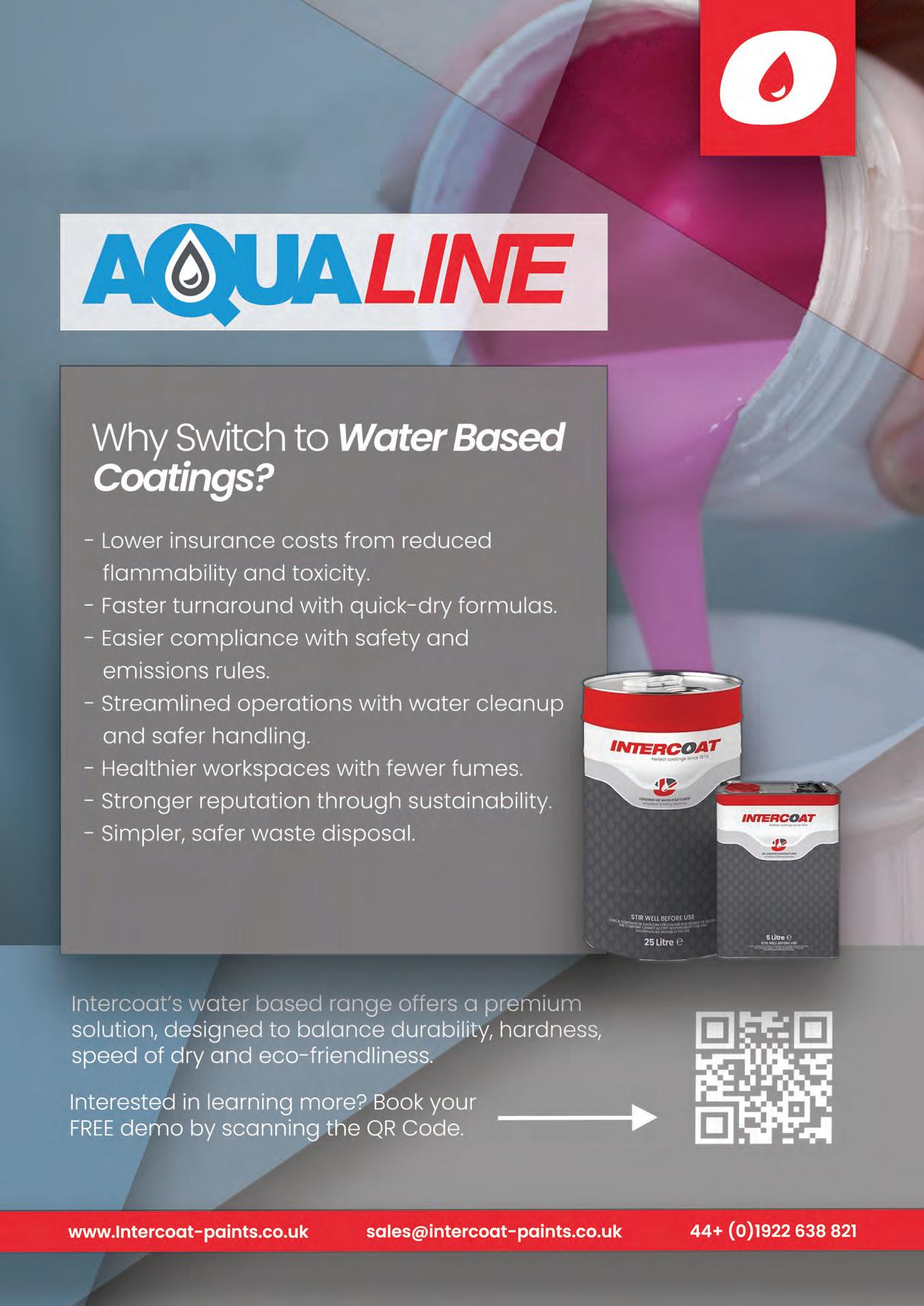
CASE STUDY
Keep it simple, stupid.
Technology vs growth. Often, the two seem intrinsically linked but why do so many manufacturers think this way? Take Strebig’s Compact vertical panel saw. The flexible, entry-level panel saw offers the precision and quality you’d expect from a Swiss-made machine but without a plethora of features you’ll probably never need. In the words of Ian Sabin, Production Manager at Birmingham Joinery, the Compact is, “small but perfectly formed.” So, why did the Birmingham-based fire door manufacturer decide to replace its 20 year old Striebig Compact with its modern-day equivalent? The answer is simply, simplicity.
“Our business model has been slowly developing over the last few years,” explains Ian. “We’re putting more emphasis than ever on large commercial projects with universities, hospitals and schools. With this move has come the necessary investment in new machinery but for us, fulfilling larger orders like this doesn’t automatically require high levels of automation and technology. I’m a firm believer in keeping things as simple as possible and brands like Striebig are helping us achieve this.”
“Our old Compact was in use for a least five hours a day, every day – cutting 44mm and 54mm thick chipboard and solid timer door cores up to 8 x 4 in size,” explains Ian. “The saw was the starting point of our production and it was an essential part of our operation. It was easy to set-uptraining took minutes, not days – and it required very little maintenance throughout its lifetime. But like everything, age simply caught up with it and it was time for it to go into retirement.”
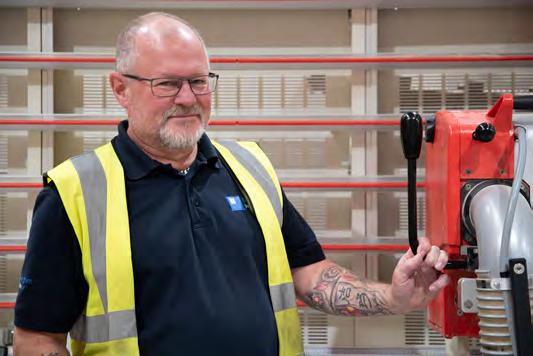
Ian briefly looked at other saw brands and flirted with the idea of a beam saw but the new generation Compact was refreshingly simple to use and, with the added benefit of a digital read-out system for horizontal and vertical cuts, was a contemporary replica of the old saw.
“It just made sense to me,” admits Ian. “It included everything I needed and nothing that I didn’t.” He continues, “A beam saw would have taken up a lot more space and we’d have used no more than a third of its capacity. It would have also come with a lot of technology we simply didn’t need but would have ended up paying for. If you know you can invest in a smaller, cheaper machine like a Compact and still have the ability to increase productivity and efficiencies, why wouldn’t you?”
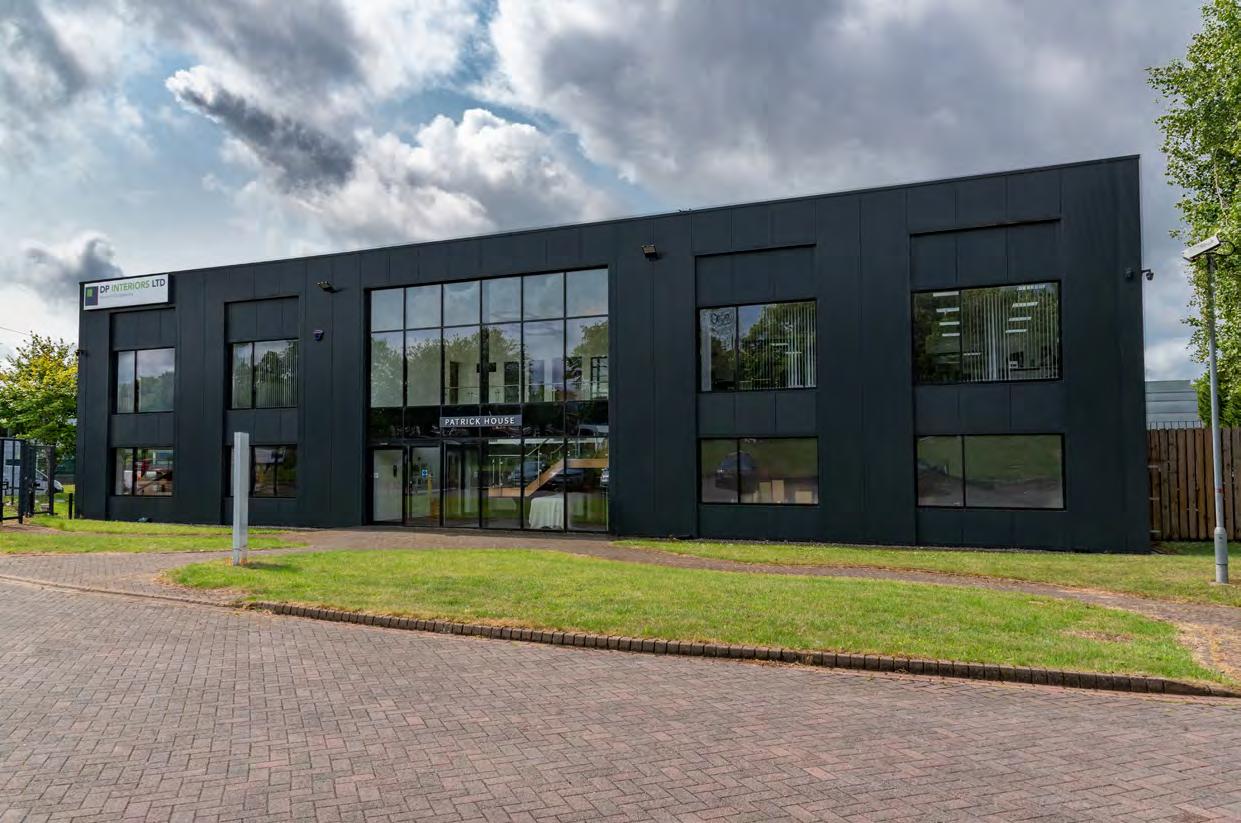
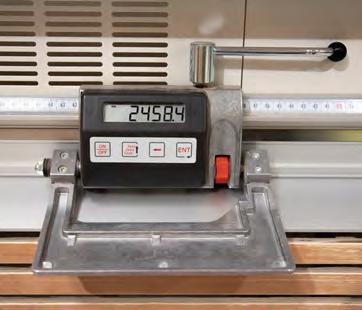
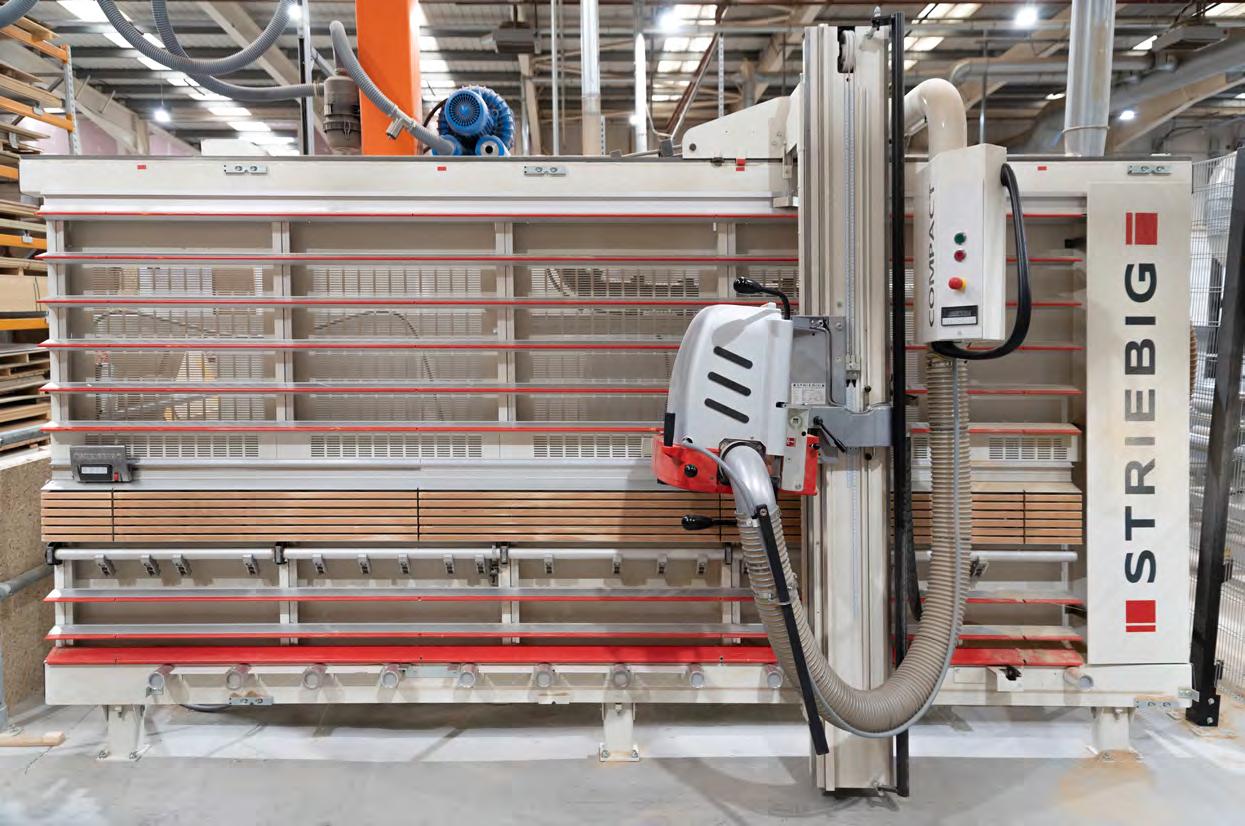
The Striebig Compact, which feeds Birmingham Joinery’s Homag Edgebander with new return system and new Homag CNC router, fits neatly into its predecessors blueprint and now fully calibrated, cuts anywhere between 30-50 sheets per day, with up to three cuts per sheet. Ian adds, “We installed new lifting equipment at the same time to reduce panel handling and speed up production. The operation is now easier from start to finish and we’ve seen big improvements in material waste.”
The Compact also offers the fuss-free user experience Ian required. “We wanted to keep this part of our manufacturing as simple as possible, allowing us to hire entry-level workers to run the machine efficiently.”
Ian admits the digital read-out has also been a useful feature. “Of course we could have continued to perform each cut without one but it certainly helps keep mistakes and material waste under wraps. We train our team to measure, cut and measure again but mistakes happen and if they’re not picked up at source, it can be an issue. The digital read-out is a great secondary check. You know if the number shown on the read-out if wrong, the cut will be too. It couldn’t be clearer.”
Ian continues, “Although we’ve been using Striebig saws for over two decades now, it’s funny to think how few times we’ve needed to get in touch with TM Machinery. It’s a testament to the build quality of these machines. When we have needed something, we find TM Machinery to be very responsive and if a visit is needed, they come within 24 hours. That’s exactly the kind of suppliers we want to work with.”
Ian adds, “The Compact has helped us to grow and modernise our production without overcomplicating it. We’re now easily fulling orders of over 1800 door sets at a time and we still have room to grow further. Like its predecessor, it remains a valuable workhouse for us and we look forward to many more years of use.”
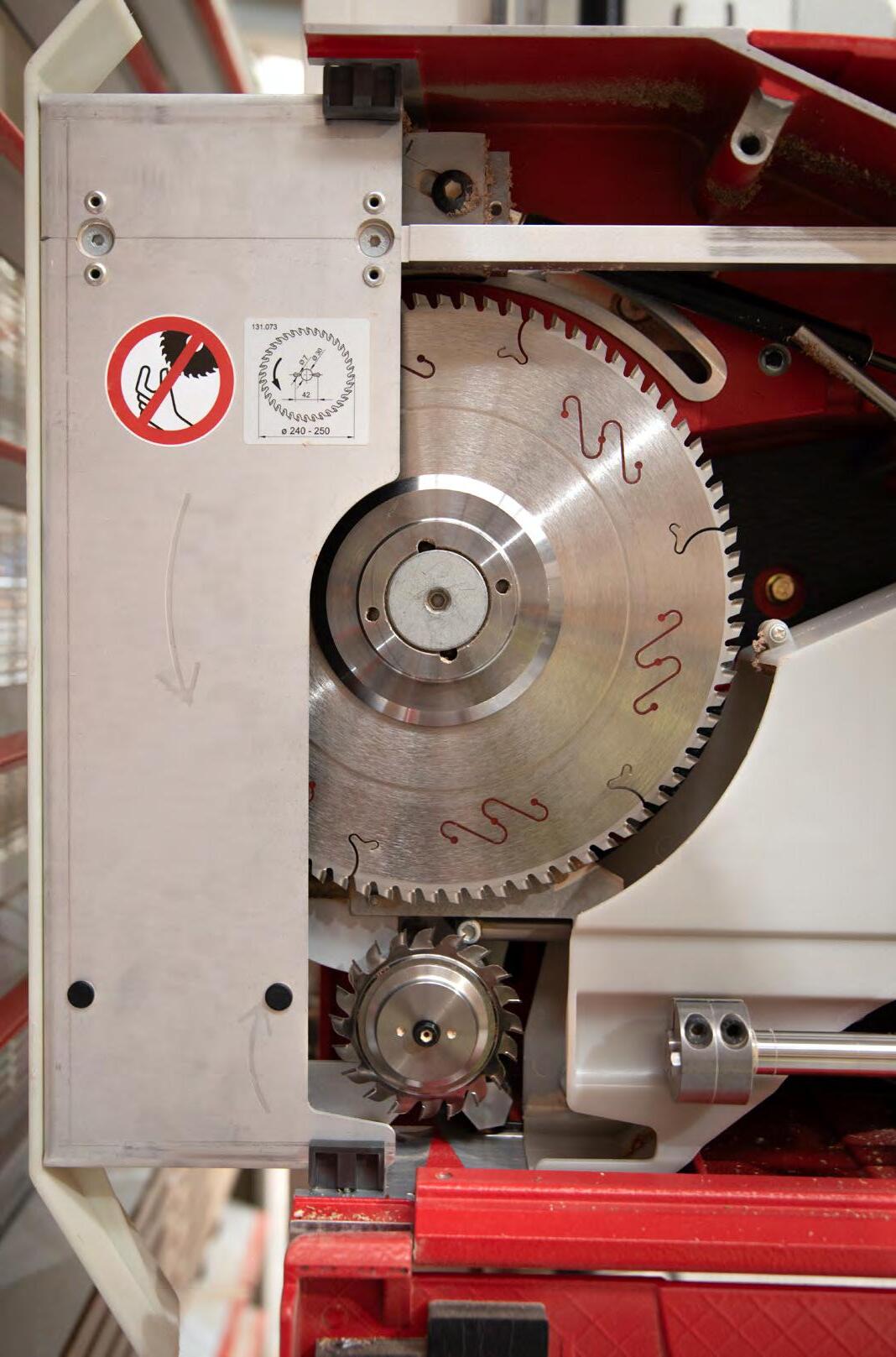
Elevate your panels with dp-decor
Elevating interiors with dp-decor: high-performance decorative foils by Decorative Panels Lamination
dp-decor, from Decorative Panels Lamination, is the original, trusted paper foil range from the dp-group, offering a sophisticated alternative to real wood veneers. It brings together premium design aesthetics and advanced material engineering to deliver surfaces that truly impress both visually and to the touch.
At Decorative Panels Lamination, dp-decor is supplied expertly laminated to a wide range of wood-based substrates, ensuring consistent quality, ease of machining, and efficient processing for joinery manufacturers and fit-out specialists. Meanwhile, the foil itself remains perfectly suited for profile wrapping, offering added flexibility for detailed component work.
A carefully curated collection, dp-decor features realistic woodgrains, vivid unicolours, and imaginative fantasy patterns, developed with leading global print houses. Each design is thoughtfully selected to align with contemporary interior trends, enabling clients to create everything from calming, natureinspired spaces to bold, statement-driven environments.
dp-decor is engineered for performance. Manufactured to meet rigorous FIRA 6250 and BS 6222 standards, it’s ideal for heavy-duty use across furniture, shopfitting, kitchens, bedrooms, bathrooms, hospitality venues, educational settings, healthcare, and wider commercial interiors. Where hygiene is critical, dp-decor can also be specified with optional Biomaster antimicrobial technology, which inhibits bacterial growth by up to 99.99%.
Produced at Decorative Panels Lamination’s advanced UK facility, dp-decor is designed to support volume production with consistent quality, quick exstock availability, and reliable lead times. Ideal for furniture manufacturers and large-scale interior projects, it combines on-trend aesthetics with proven durability—making it the dependable choice for delivering beautiful, robust surfaces efficiently.
Explore the dp-decor range for yourself: order samples online or visit our dedicated marketing suite in Elland, West Yorkshire.
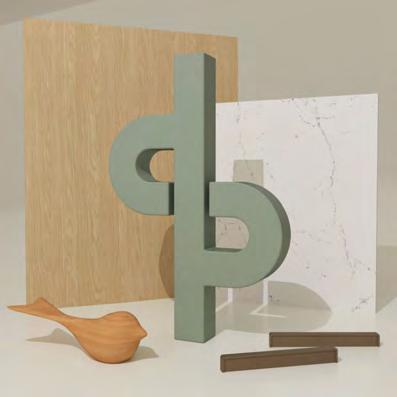
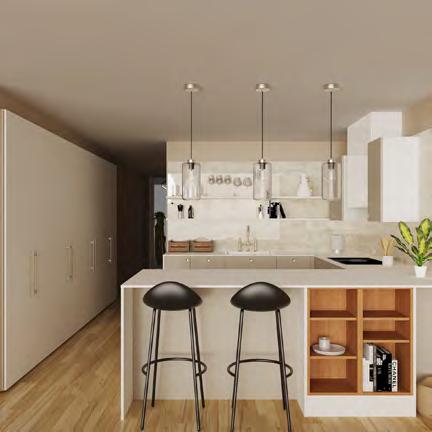
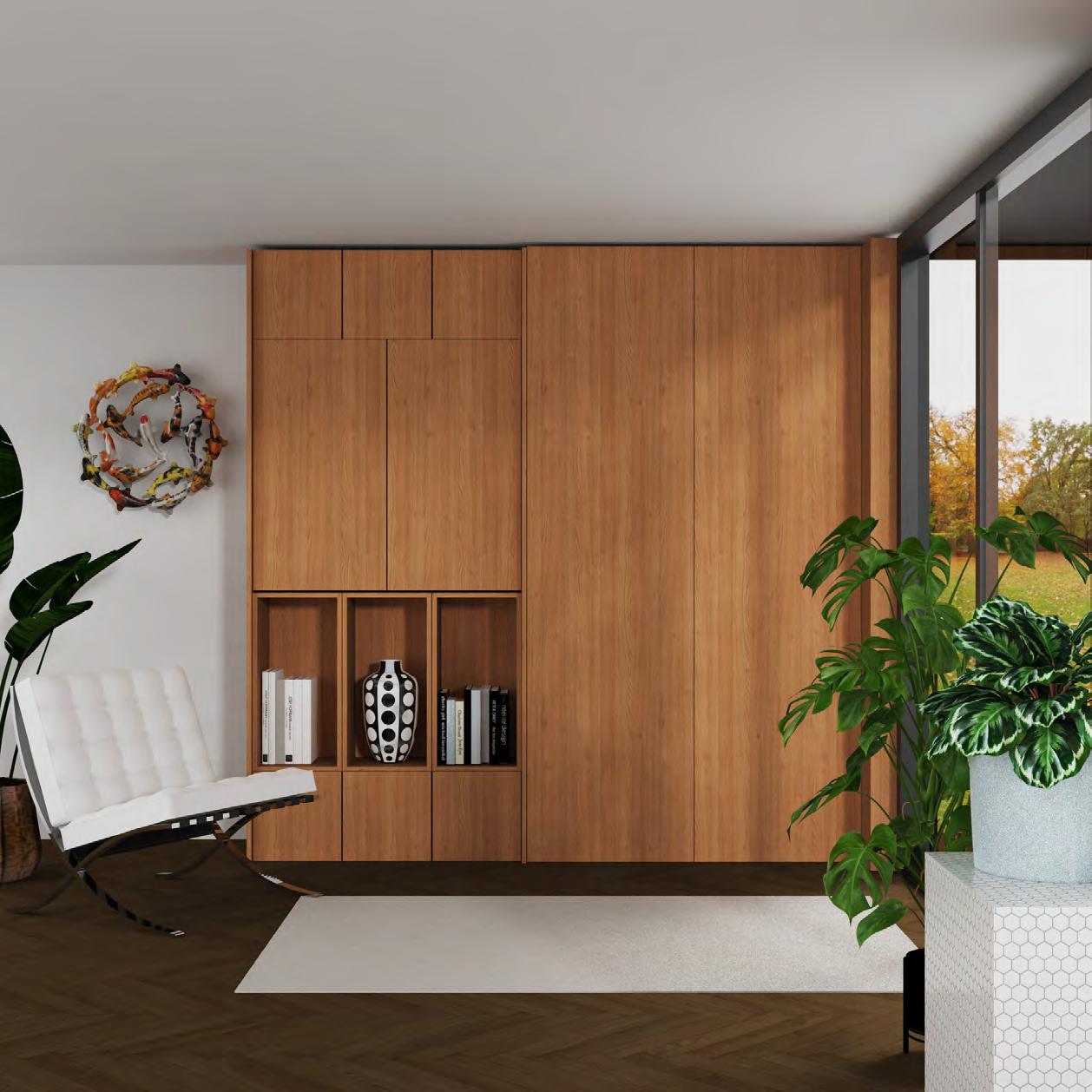
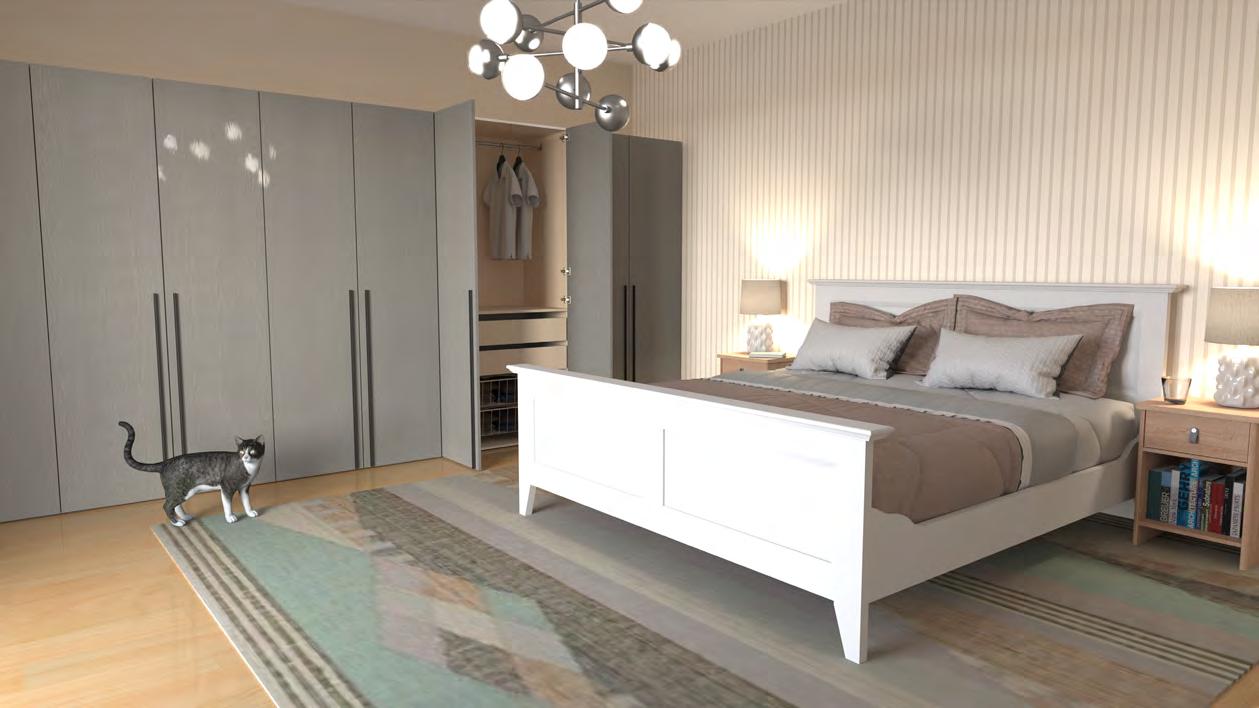
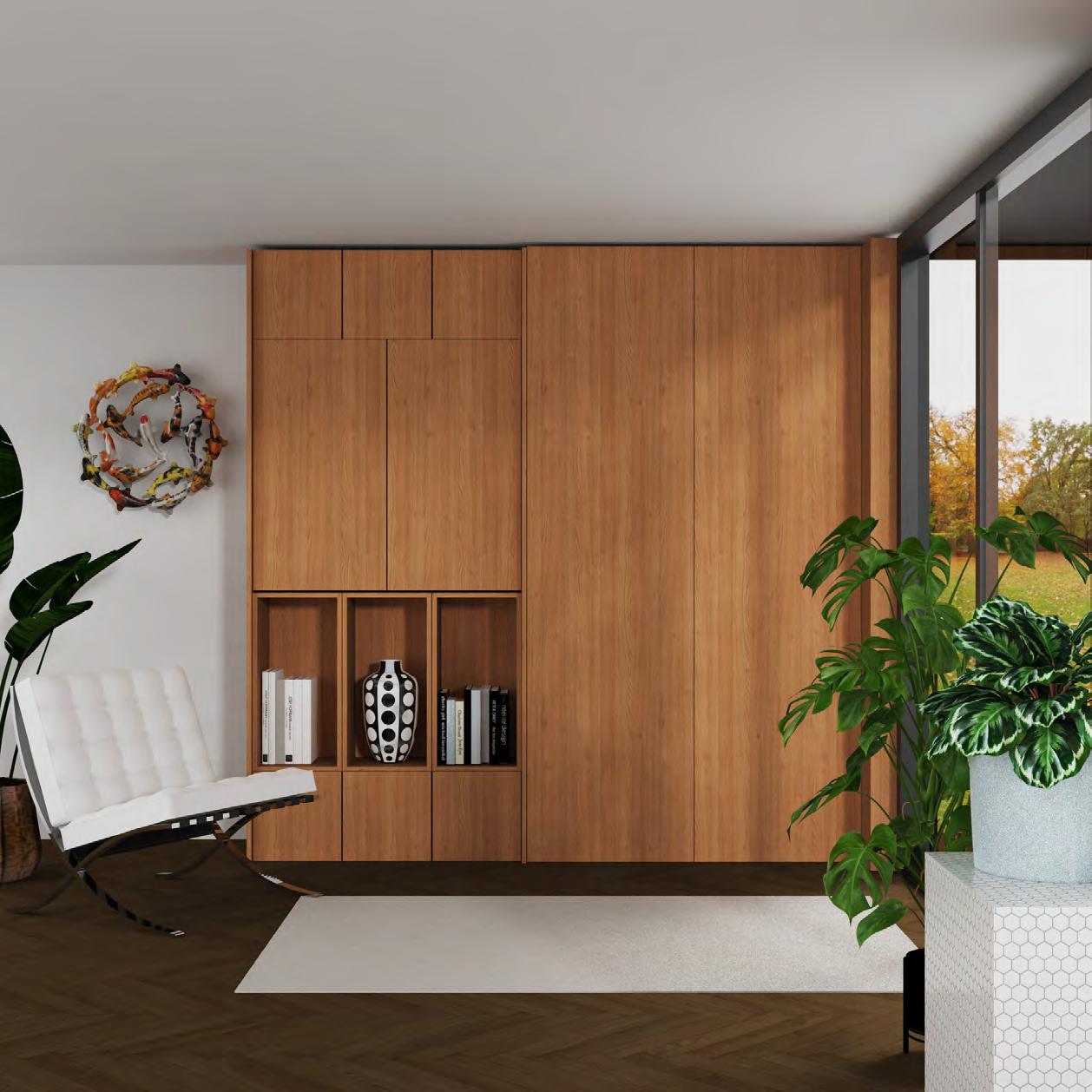
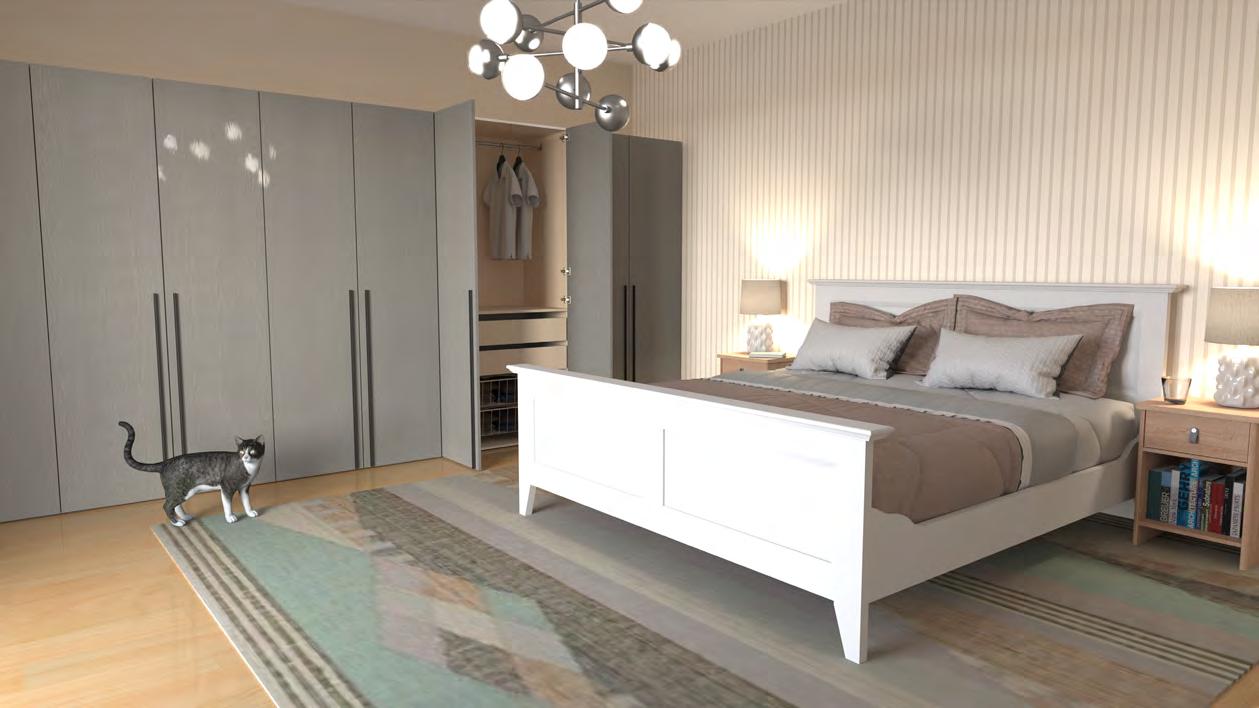
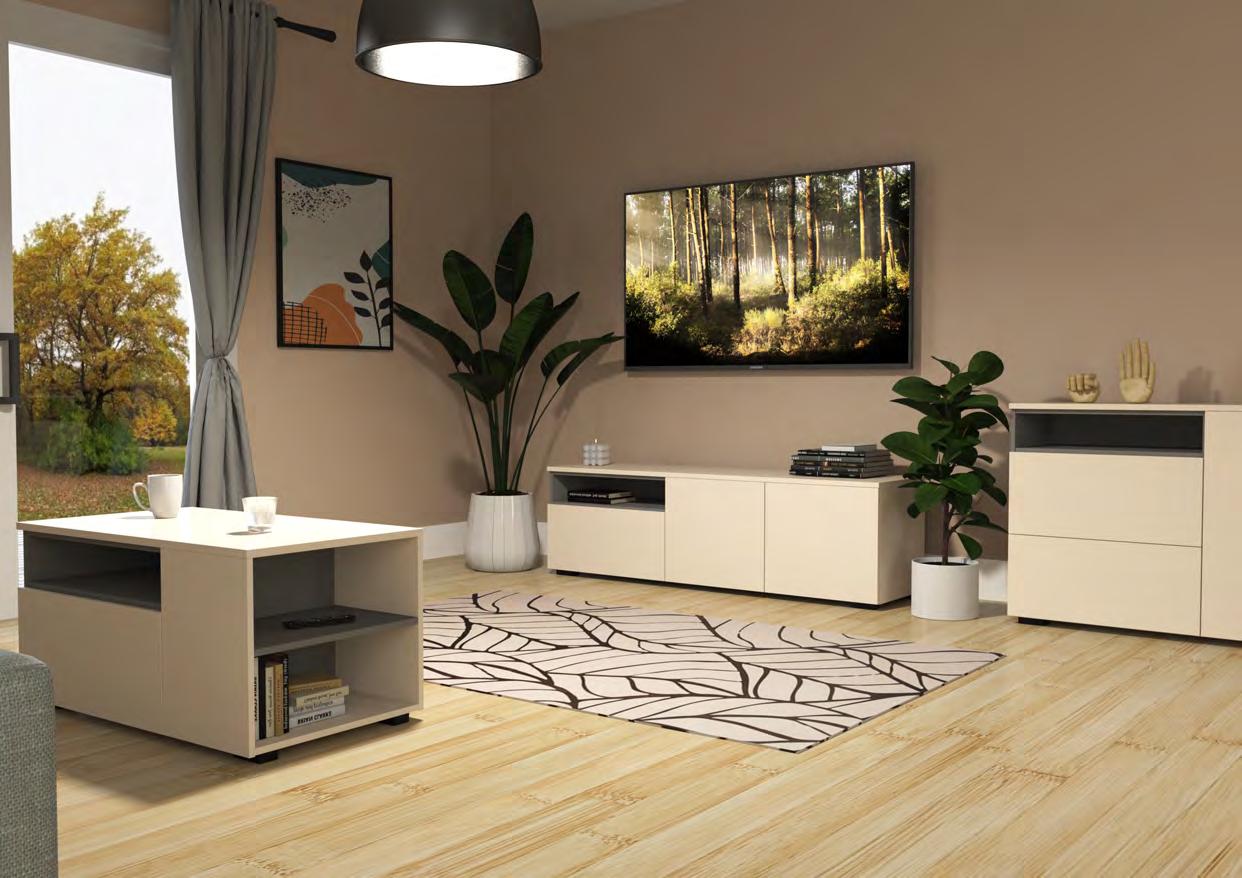
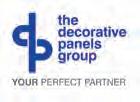
CASE STUDY Extractly delivers on time, and on budget
Extractly Limited have recently completed the installation of a 20,000m3/hr dust waste extraction system, with a super-quick turnaround, for a leading furniture manufacturer.
Established in 2015, by Managing Director Martin Clarke, Cotswold Panel Products Ltd manufactures bespoke panel components and produces panel-based built furniture for the hospitality, events and exhibition markets, corporate office spaces, educational establishments, along with POS items for retail businesses and other specialised commercial markets. With Martin at the helm, the company is still very much a family-run business renowned for quality and attention to detail; delivering a high level of customer service, with a personal touch.
Over the past decade Martin’s dedicated team has continually driven the company forward; achieving consistently solid sales growth, which has demanded a continuous programme of investment in cutting-edge machinery to deliver ever greater capacity – which has, of course, continually necessitated bigger and better premises to accommodate it all. Martin’s latest plans for the company involved moving production just over the border (around 7 miles, as the crow flies), from a semi-rural site in Gloucestershire to their new 20,000 sq. ft. facility on the north west outskirts of Evesham, in Worcestershire.
“Our relocation has actually been on the cards for around 2 years” Martin explained, “but, unfortunately, plans to move to another property we’d earmarked fell through at a late stage; we’d even got as far as going out to tender for the installation of a new dust extraction system.” Extractly Ltd had previously carried out a relatively minor addition to the extraction system at the company’s former location and, impressed with the service provided, and the engineers’ work on site, Martin had included Extractly Limited on the shortlist for installation of a new extraction system.
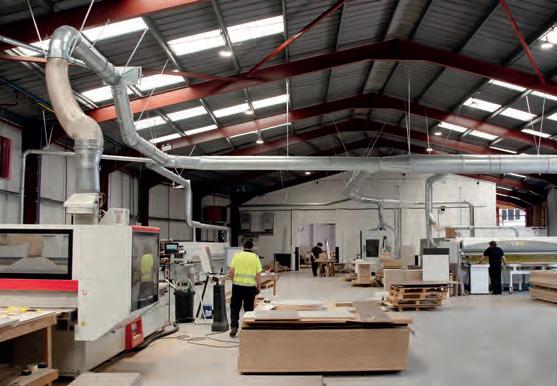
The company’s new 20,000 sq. ft. facility provides space for efficient workflow and potential for future expansion
Although that move was ultimately scuppered, the decision had already been taken to award the contract to Extractly; based on their industry knowledge, their understanding of the requirements, their proposed budget for the project, and their commitment to completion of the installation within a tight deadline. “So, when the Evesham property came across our radar at the beginning of the year,” Martin continued, “I was more than happy to invite Extractly to put together a new proposal, again for a complete installation, but based on our updated requirements.”
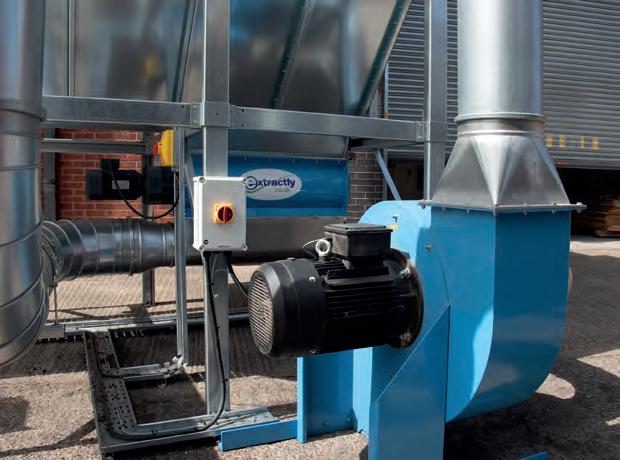
“We were delighted to have another opportunity to work with Cotswold Panel Products,” says Graham Seymour, Extractly’s sales engineer on the project, “and this installation was straight out of the textbook.” The new location presented an opportunity for production flow to be organised much more effectively, and also affords Martin plenty of capacity to increase output and accommodate further machinery acquisitions. “The factory was being completely refurbished ahead of the move,” says Graham, “so, with no production schedules to work around, we had virtually free rein to install the most efficient extraction system to meet the demands of the company’s current range of high-speed machinery, with a margin of spare capacity available for future expansion.”
The system currently extracts from an externally-sited chipper, along with 10 other production machines, of varying capacity; from edge sander to edgebander, and drilling machines to CNC machining centres. The main 45kW fan delivers dust and chip-laden air to the Aagaard ASF 2 DAK XL ATEX filter unit which houses over 160m3 of filter material to capture extracted woodwaste from the air flow.
Heavier waste material drops into the hopper section, at the base of the unit, where it’s continually gathered up by scrapers on a chain conveyor and, above the filtration section, three 1.5kW regeneration fans operate intermittently to remove the finer dust from the filter material. All of the collected waste is discharged
Dust and chips are discharged from the filter unit via a rotary valve, then a 15kW transport fan delivers it to the waste container
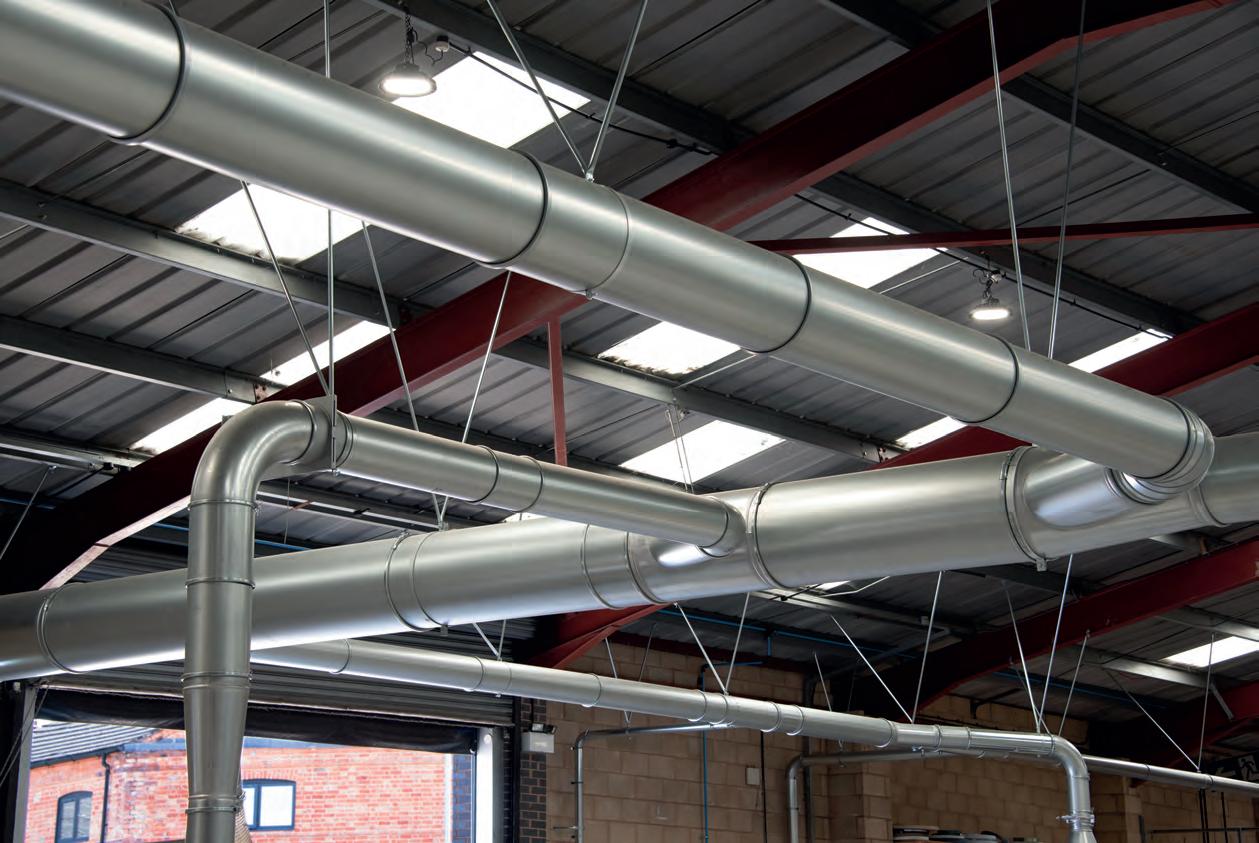
Nordfab’s QF galvanised steel ductwork installed throughout connects all machines to the extraction system and, in the unlikely event of an explosion occurring in the filter unit, an ATEX-certified nonreturn valve ensures that resultant pressure and flames are restricted from travelling back down the ductwork and into the factory.
“Extractly have delivered a really neat and efficient installation for us,” Martin concludes, “and I couldn’t fault the professional manner in which the project was executed. The entire installation was completed in under a week; allowing us to move straight in with machinery and get back to full production again in under 10 days.”
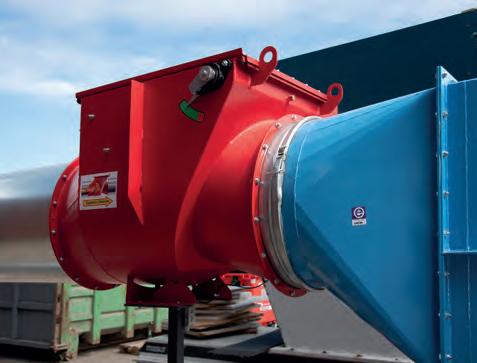
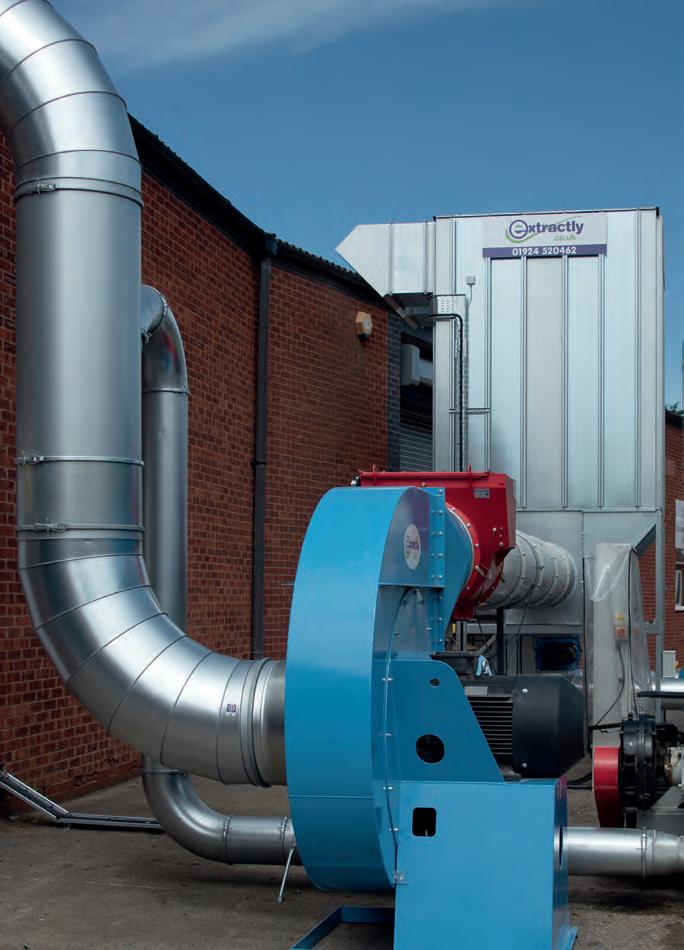
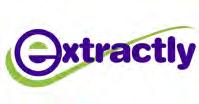
Galvanised steel QF ductwork throughout the factory connects all machines to the extraction system
The Aagaard ASF 2 DAK XL ATEX filter unit is powered by a 45kW main fan to provide an airflow capacity of 20,000m3/hr
EVENTS WEINIG Connect 2025: An industry event for the joinery and timber manufacturing community
21–23 October 2025
WEINIG UK Showroom, Abingdon
This October, WEINIG UK invites the joinery and timber manufacturing community to its Abingdon showroom for WEINIG Connect 2025. A three-day event showcasing how fully integrated profiling and moulding systems can transform productivity, precision and performance across workshops of all sizes.
Building on the success of last year’s Performing with Powermat series, this year’s event taking place 21–23 October, will demonstrate how digital planning, CNC tool preparation, and advanced moulding technology can be brought together to boost output, improve consistency, and keep machinery running smoothly and reliably.
WEINIG System Plus
Today’s timber processors and joinery professionals face increasing pressure to deliver greater accuracy and flexibility, particularly when dealing with shorter runs and a wider mix of profiles. A core focus of WEINIG Connect 2025 will be System Plus, a fully integrated production solution that streamlines every stage from design to finished profile. WEINIG System Plus brings together four key technologies into a seamless, closed-loop workflow:
• APP PROFILE MASTER – for profile design and digital planning
• SOLID GRIND 1000 P – precision CNC grinder for repeatable tool production
• SOLID PRESET 1000 – for fast, accurate tool measurement and setup
• SOLID PROFILE P1500 (Powermat 1500) – high-speed moulder for precise profiling
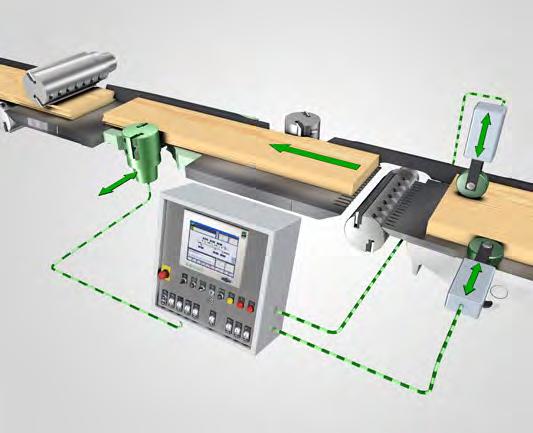
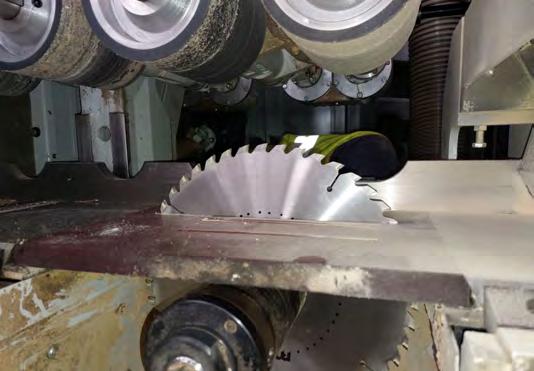
By integrating these technologies, the system eliminates manual guesswork, reduces setup time and ensures consistent quality, whether producing complex bespoke profiles, or managing high-volume runs. It’s a compelling solution for operations looking to balance flexibility with efficiency.
Live Demonstrations
More than just a machinery showcase, WEINIG Connect 2025 offers a valuable opportunity for joinery and manufacturing professionals to gain insight from WEINIG’s expert demonstration team. Across the three-day event, visitors can take part in focused sessions and live demos that explore smarter, more effective approaches to modern timber processing.
Key topics will include:
• How to optimise tool preparation through CNC grinding
• Speeding up moulder setup using digital tool data
• Ensuring profile repeatability from batch to batch
• Selecting the right systems to support growth and improve production flow
Alongside the System Plus setup, visitors will also be able to explore and interact with other solutions from the WEINIG range, including:
• SOLID GRIND 960 P – a manual grinder for flexible profile tool production
• SOLID GRIND 980 S – a fully automatic straight knife grinder ideal for planer blocks
• SOLID PROFILE P500 – compact moulder for varied or smaller-scale production
• SOLID PLANE CUBE – best-selling planer known for its simplicity and reliability
• Timber ripping solutions – helping streamline raw material preparation ahead of profiling
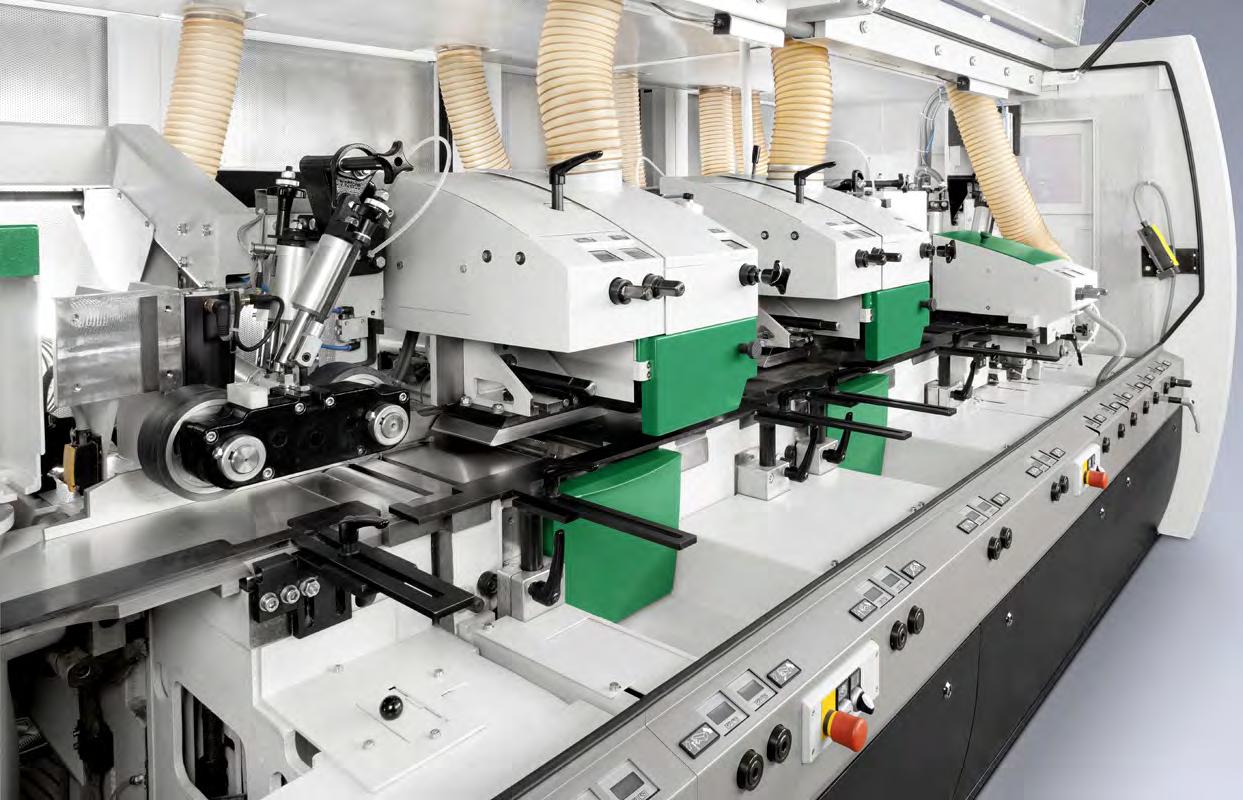
Together, these demonstrations offer a clear view of how WEINIG’s product ecosystem can help companies reduce waste, improve accuracy and achieve better throughput in even the most demanding production environments.
Strengthening the Future of Timber Processing
Looking ahead to 2026, WEINIG UK is placing increasing emphasis on supporting British manufacturers with tailored events, training programmes and intelligent technical support.
Commenting on the event, WEINIG UK, Managing Director Malcolm Cuthbertson said:
“We’re committed to offering our customers more than just machinery. We deliver integrated thinking and expert guidance to help woodworking professionals get the very best from their production.
“Events like WEINIG Connect allow us to share knowledge and help businesses embrace change, adopt smarter tooling processes, and stay competitive in a demanding market.
“We want to help companies build resilience into their operations by adopting systems that reduce waste, improve precision, and allow for fast, flexible production.”
Why Attend WEINIG Connect 2025?
For manufacturers, joiners, and mill operators seeking practical solutions to modern production challenges, WEINIG Connect 2025 offers a rare opportunity to experience first-hand how integrated systems can unlock new efficiencies, improve accuracy, and support long-term growth.
Whether you’re looking to improve moulder setup times, upgrade your toolroom, or explore how digital planning can future-proof your workflow, this event delivers the insight and expertise needed to move forward with confidence.
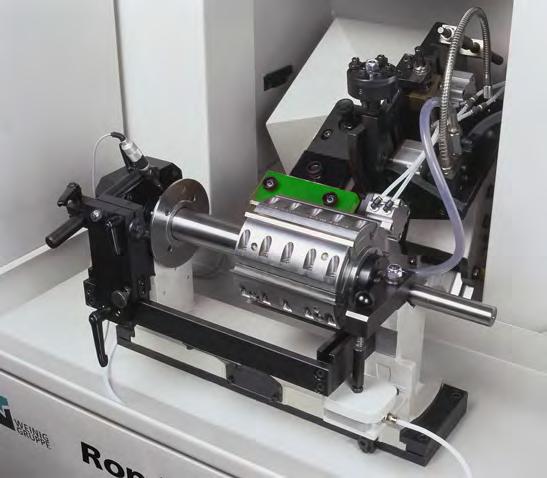
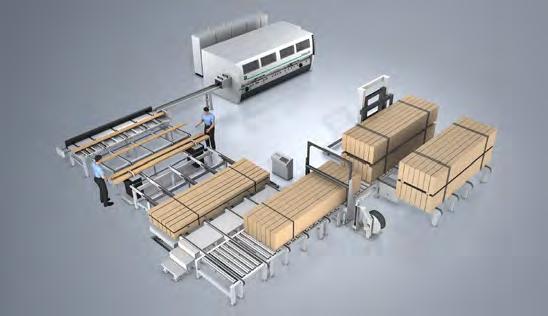
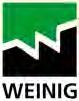
POLYCRYSTALLINE DIAMOND TIPPED SAW BLADES
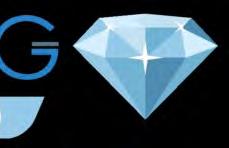
Made to order to suit any machine.
Beam Saws, Panel Sizing, Grooving, Special Saws
Improved Superior Quality Finish
Much Greater Lifespan
6mm Depth of PCD on all Blades
DIA 50mm to 600mm
Any number of Teeth
Any Tooth Geometry
TO CUT VIRTUALLY ANY MATERIAL
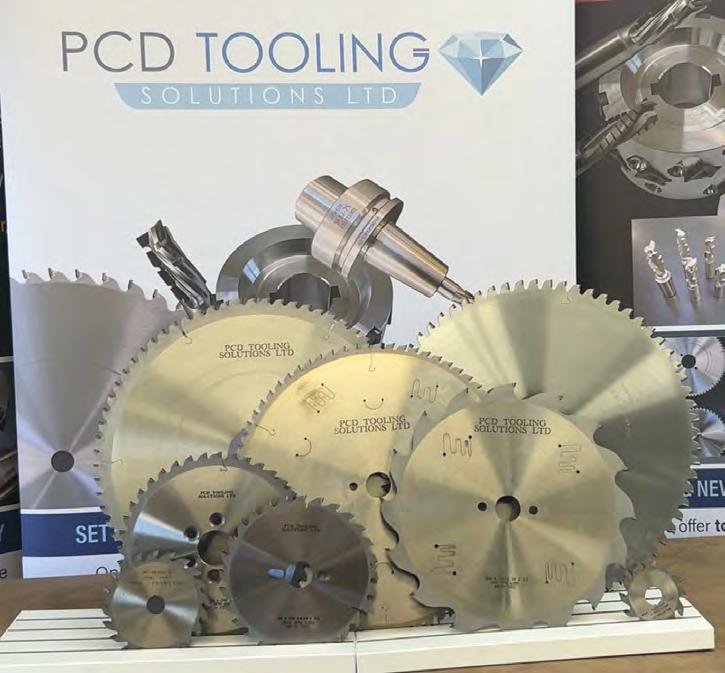

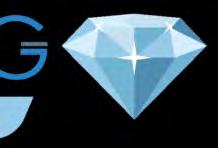
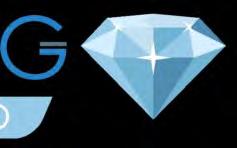
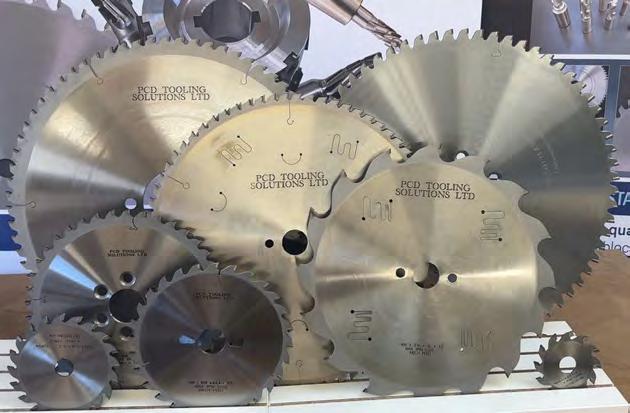
Manufactured in Yorkshire, with all materials from UK Suppliers.
Excellent Performance on:-
Hardwoods
MFC
MDF
Chipboard
Veneers
Laminates
Plywood
Trespa
Corian
Ceramics
GRP
Cement Partical
Insulation
Plastics
Non Ferrous Metals
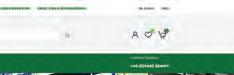
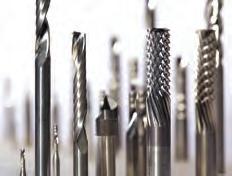


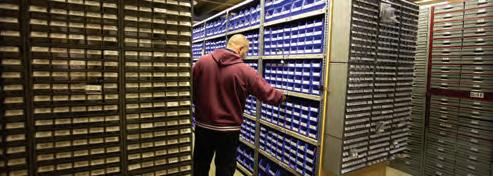
Castle Pocket Routers
TSM22 Pocket Router
The most popular Pocket Router in the Castle range has been re-designed with a new lift up table top.
This long established and widely used model continues to provide the quickest and strongest method for kitchen and bedroom carcass manufacture, retail display stands and other interior fitting applications. Other models available see www.ataeng.com
Router Cutters
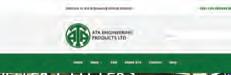
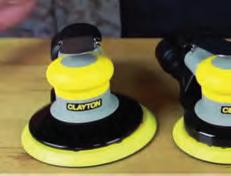

Dustless Made Simple
A comprehensive range of routing cutters in HSS, Carbide tipped and solid carbide to suit a wide variety of applications in aerospace, woodworking, plastics and composites. Enquiries welcomed for special cutters.
Extensive Stock ATA carry an extensive stock of cutters, tool holders and collets, for next day delivery.
ATA Engineering Products Ltd Unit B, ATA House, Boundary Way, Hemel Hempstead, Herts, HP2 7SS t: 01442 264411 e: sales@ataeng.com www.ataeng.com
Clayton Associates was established in 1984, has become an industry leader in hazardous control solutions. Starting with Jim Clayton’s first vacuum for asbestos removal, the company began a legacy of innovation, constantly improving and enhancing the product line to best meet needs of workers in woodworking, automotive, aerospace, and industrial applications.
Extensive range of Router Cutters in stock www.atacuttershop.com
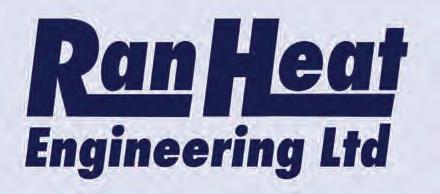
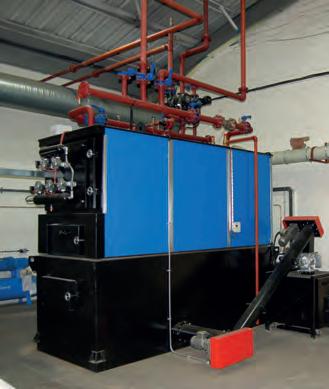
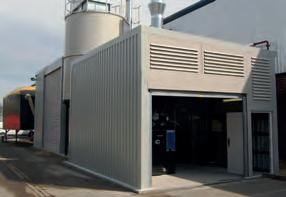
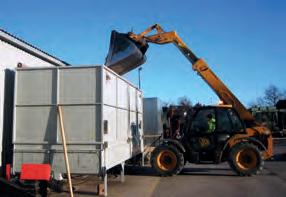
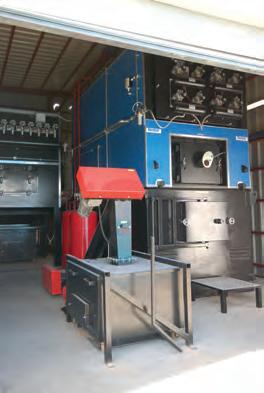
CASE STUDY The power of change
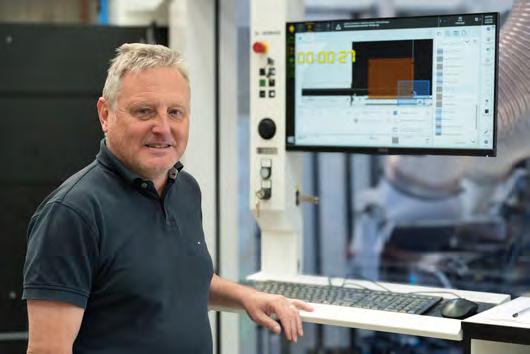
In March 2025, bespoke contract furniture manufacturer, Witley Jones embarked on its biggest challenge yet: to find a new, innovative fixing that could withstand the rigours of school life, whilst maintaining the elegant aesthetics expected from luxury retail giants.
A seasoned furniture provider for some of the most prestigious schools in the UK, the company’s more recent partnership with one of Europe’s biggest shop fitting companies led Managing Director, Simon Downes to look at new ways to improve both his products and production. “Moving away from metal cam and dowels had been on my mind for some time – they’re difficult to hide and don’t offer a sleek look – but I knew it would be a root and branch change for the company,” says Simon.
“At peak times, we can machine up to 800 sheets per week so we couldn’t afford to make any wrong moves.” But, as a volume manufacturer working on fit-out projects that are often in excess of £500,000 – each with its own strict completion deadline – he had a lot of questions: Where do you start when looking to integrate a new fixing into your production? How long will it take?
“From the very beginning, everything seemed to be pointing to Lamello and their Cabineo X CNC fixing,” recalled Simon. “A casual chat with an industry friend ended up in a conversation about Lamello. The trade magazine I was reading featured a story on Lamello and a demonstration on a Drillteq vertical drilling machine at Homag UK’s showroom was done using Lamello’s CNC fixings.
“Very quickly, Lamello felt like a good fit for the business and everyone had positive things to say about them, but I needed to involve the entire team in this decision. I am lucky in the sense that I have a very progressive workforce, but we needed to test the Lamello theory and prove to all involved it was the right move. Did it offer the aesthetics we wanted? Did it offer the brute strength we needed? And, could we integrate this fixing into our production without costly delays?”
Simon already knew the Cabineo X worked seamlessly with his new HOMAG Drillteq thanks to his earlier demonstration on a P-system-ready CNC that he subsequently went on to buy out of the showroom. Once up and running, Simon’s
team was ready to put Lamello to the test. “We designed two desks: one with metal cams and dowels and the other using Lamello’s Cabineo X. We cut, edged, drilled and assembled each design and then tried our best to break them. Lamello’s design remained intact.”
The testing didn’t stop there. “We then created two key items in our school range that were more prone to damage. We mocked them up on Cabinet Vision and made them using Kronospan’s particle board and Lamello’s Cabineo X fixings. We then sent them to FIRA for testing. They passed everything with no advisories. Impressive. Another tick in the box.”
Then came the cost calculations. “While cost isn’t always at the forefront of my mind, it is never far from it,” says Simon. “There’s always a concern when trialling new things that you could end up trying to reinvent the wheel and spend excessive amounts doing so. But the fact of the matter is, there were reasons why metal cam and dowels weren’t working for us any longer – aesthetics being a major consideration – so we needed to adapt what we were doing and streamline our manufacturing for the good of the business. The cost between metal cam and dowels and Lamello fixings was not that dissimilar and due to their strength, we could use fewer Lamello fixings without impacting on the furniture’s integrity.
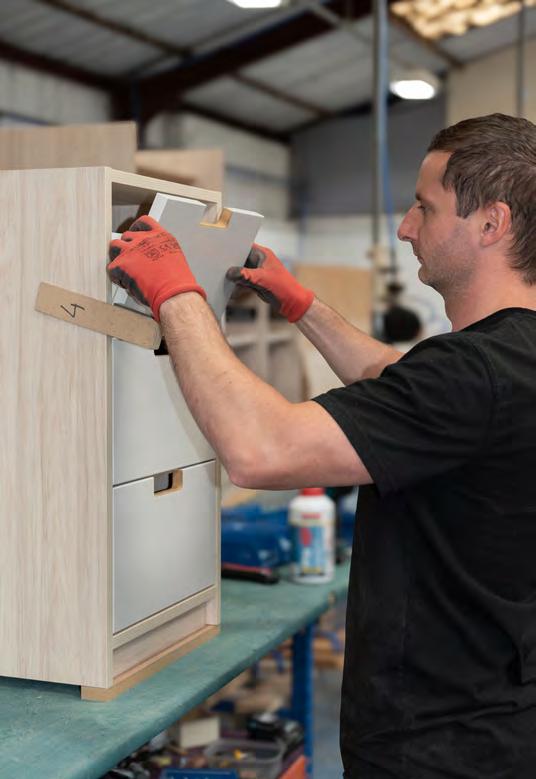
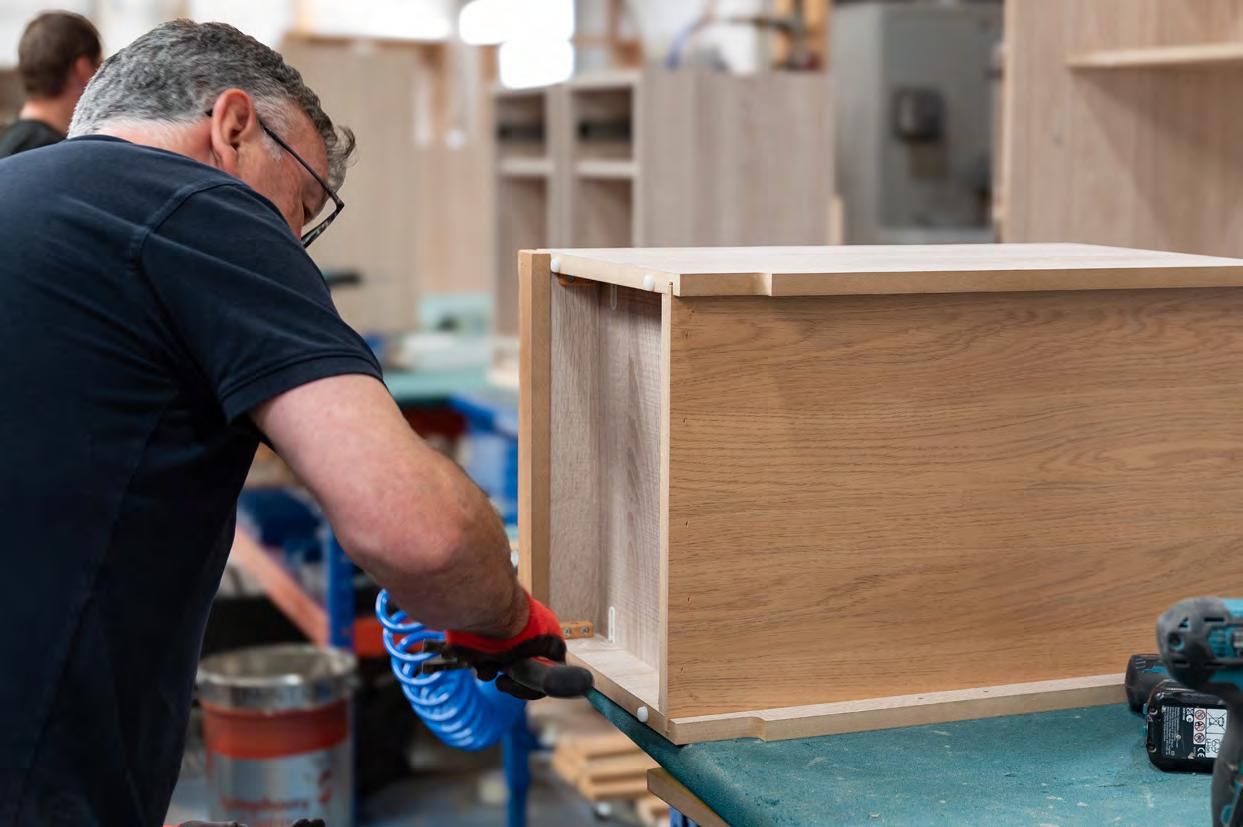
difference it would make to production. It took seven seconds longer to drill the three holes required than it did to machine cam and dowel holes but we knew this could be reduced if using an aggregate. Also, considering how quick they were to assemble, those seconds paled into insignificance.”
Fast forward three months and Simon has just placed his third order with Lamello and is on track to exceed 100,000 fixings this year alone.
“We’ve used them extensively since March and we’ve had zero comeback. They’ve even helped us rethink designs we’ve been manufacturing for some time and allowed us to create new items. Take our modular bunk beds as an example: we create single beds for schools that can be made into a bunk bed as and when required. All the parts are stored within the frame of the single bed. We now use Lamello fixings to dismantle and reassemble these beds multiple times because they remain strong time after time. They also make assembly of bulky items like wardrobes quick and easy on site.”
They’re also helping Simon with his sustainability pledge: “We’re winning public contracts because of our sustainable credentials,” he says. “Whilst our aim has always been to supply aesthetically pleasing furniture, longevity matters. That’s why we offer a 10-year guarantee on all our furniture. Lamello’s longevity is helping us to maintain our pledge. Teamed with our new HOMAG machine – which can optimise the cut, edge and drill process on boards larger than 8x4 – and particle board from Kronospan that can be recycled seven times in its lifespan, we have the ability to produce furniture that can be used far longer than 10 years, maybe even 20!
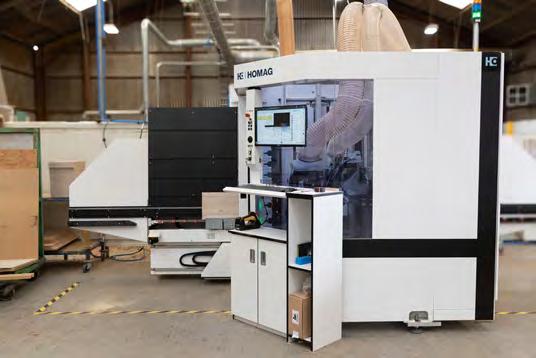
“Now, imagine if we can recycle our customer’s furniture at the end of its 20-year lifespan seven times over and create new furniture from it. This would mean we could produce furniture for 140 years without needing to chop down another tree. Now that’s proper carbon capturing!”
Simon admits the integration of Lamello into the family-run businesses has revolutionised not just their products but his team’s mindset, too. “I try and empower my team to come up with new ideas and find ways to incorporate different fixings into our furniture. Our mentality cannot be We’ve always done it this way. It must be What if we did it this way? This attitude is helping our business succeed. “We’ve found working with Lamello, Cabinet Vision and HOMAG exceptionally easy throughout this transition. The integration of the new fixings has been seamless and everyone involved has been supportive. This is just the tip of the iceberg for us. We have a long way to go, but I know this investment will help us move the business forward. Lamello’s ethos centres on growing and evolving. We’re very similar in that respect and I’m excited to see what is next for us.
“I’ve been in business over 30 years and if I have learned anything, it’s that if your business doesn’t innovate, you’ll only go backwards. My advice to anyone looking to make the leap and move away from cam and dowels is: open your mind to new possibilities and leave no stone unturned. Old habits die hard. Break the mould and make the change. It’ll be worth it.”
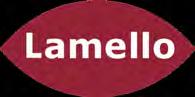
EVENTS
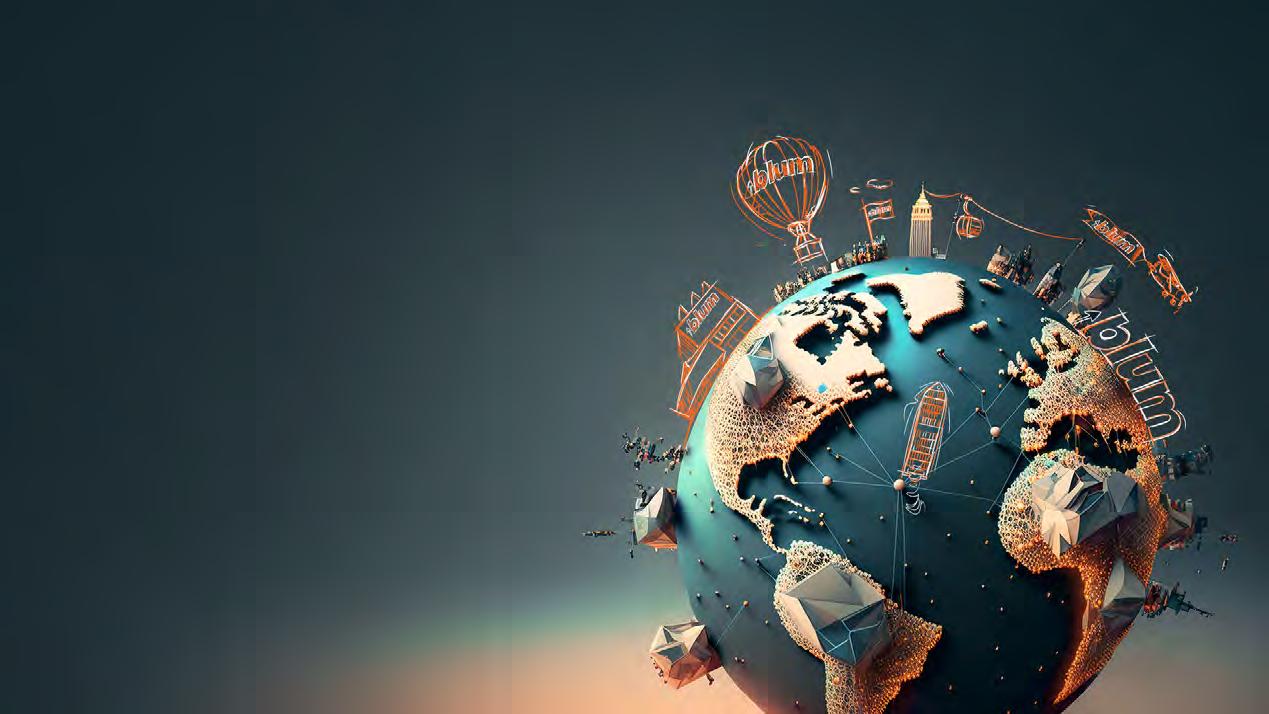
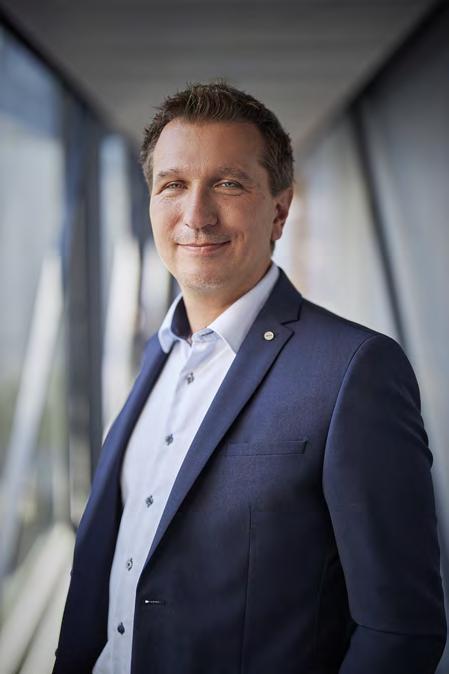
Blum takes visitors around the world in 80 minutes at interzum 2025 trade fair
Inspired by novelist Jules Verne, visitors to Blum’s stand at the interzum 2025 trade fair in Cologne, Germany, were taken on a trip around the world in just 80 minutes. Among the belongings packed by the Austrian manufacturer of fittings for this extraordinary journey were new products for all living spaces, useful services and international trends. Expanding on its interzum 2023 “FOR EVERYONE” concept, which showcased different living environments for a range of living situations, this year the company added “EVERYWHERE” to its thinking — giving visitors the chance to discover ideas and furniture, inspired by real-life applications from all around the world.
“As a global company, we are always thinking about different living habits and requirements. In some cases, this requires us to find tailored solutions or even to rethink our existing products for new applications. This means it is important to think outside the box and really listen to our customers,” explained Philipp Blum, Managing Director of the Blum Group, before elaborating further: “With this in mind, we drew inspiration for our trade fair stand from our customers around the world. Our aim was to inspire visitors to our stand in the same way and trigger some interesting discussions.”
The world tour at Blum’s stand took just 80 minutes and the stand was split into three different sections. Kitchens and bathrooms were divided into three focal areas: “Inspirational Design” for inspiring furniture, “Creative Design” for creative
and practical applications and “Effective Design” for extraefficient living solutions. It gave interested attendees the opportunity to explore different living situations, such as a large kitchen in America, a compact bathroom in a city in Asia, and practical wardrobes designed for European fashionistas.
In addition to Blum’s ‘For everyone, everywhere’ focus at interzum 2025, the family-run business once again demonstrated its commitment to a sustainable future. The key theme for the trade fair was “Rethinking Resources” and, in line with this, the manufacturer of fittings chose to shine a spotlight on the circular economy.
This display involved interactivity which allowed visitors to become part of the experience and find out more about the five closed material cycles at Blum.
By sorting its steel scrap by type, Blum makes a significant contribution to reducing its carbon footprint, and with fun interactive elements for visitors to get involved in – including a mini-golf course – the fittings specialist illustrated the recycling path for its main raw material, steel.
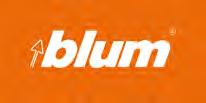
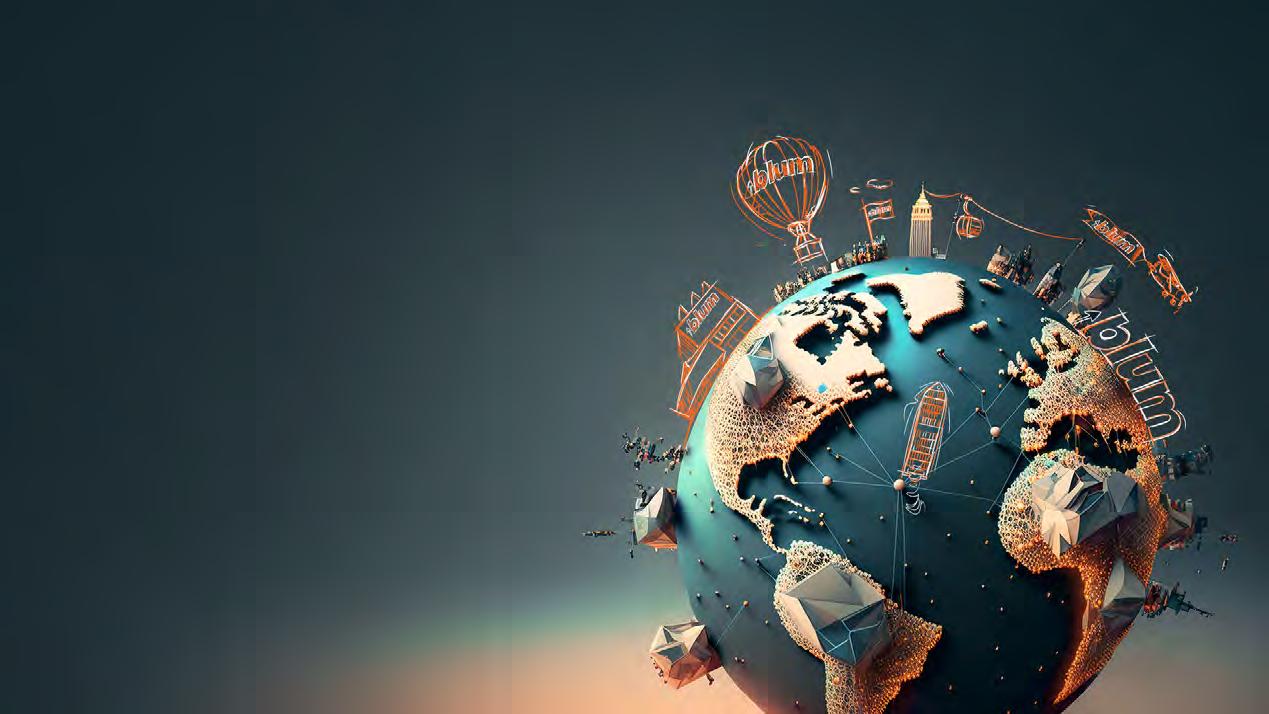
looking for Professional woodcare advice?
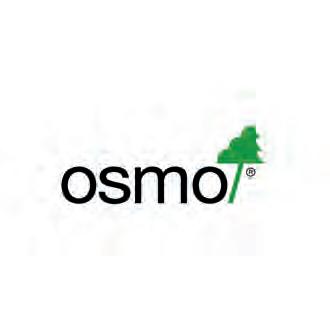
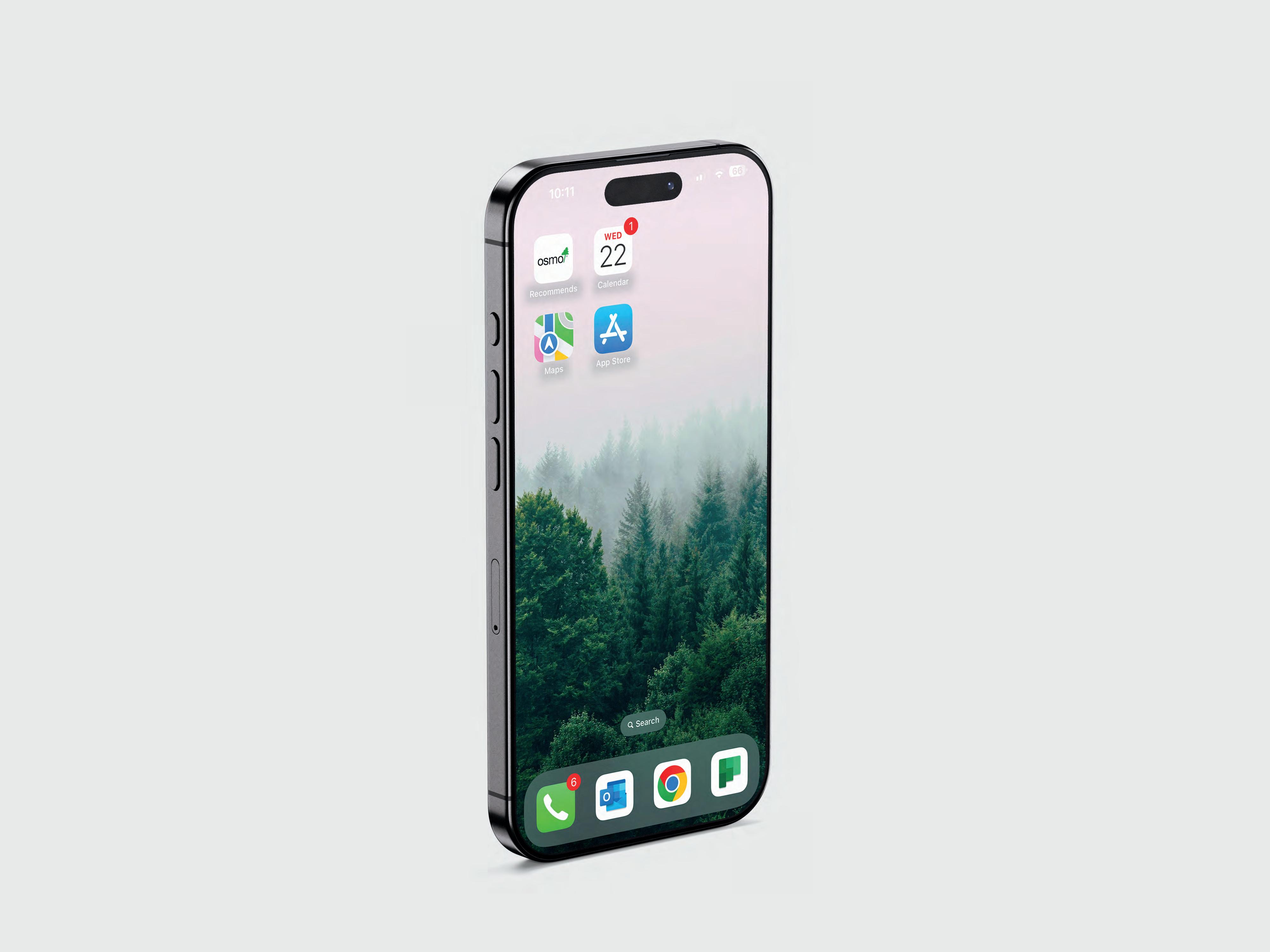
Download the Osmo Recommends app to access a wealth of product expertise in one convenient place. Let us recommend you with the perfect product for your next project!
download osmo recommends
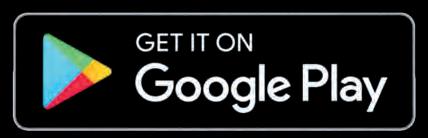
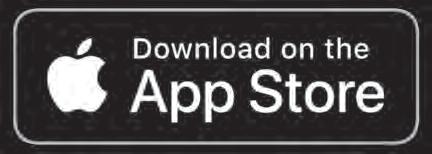
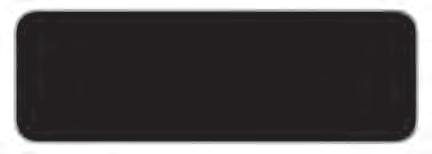
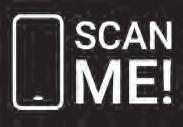
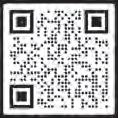
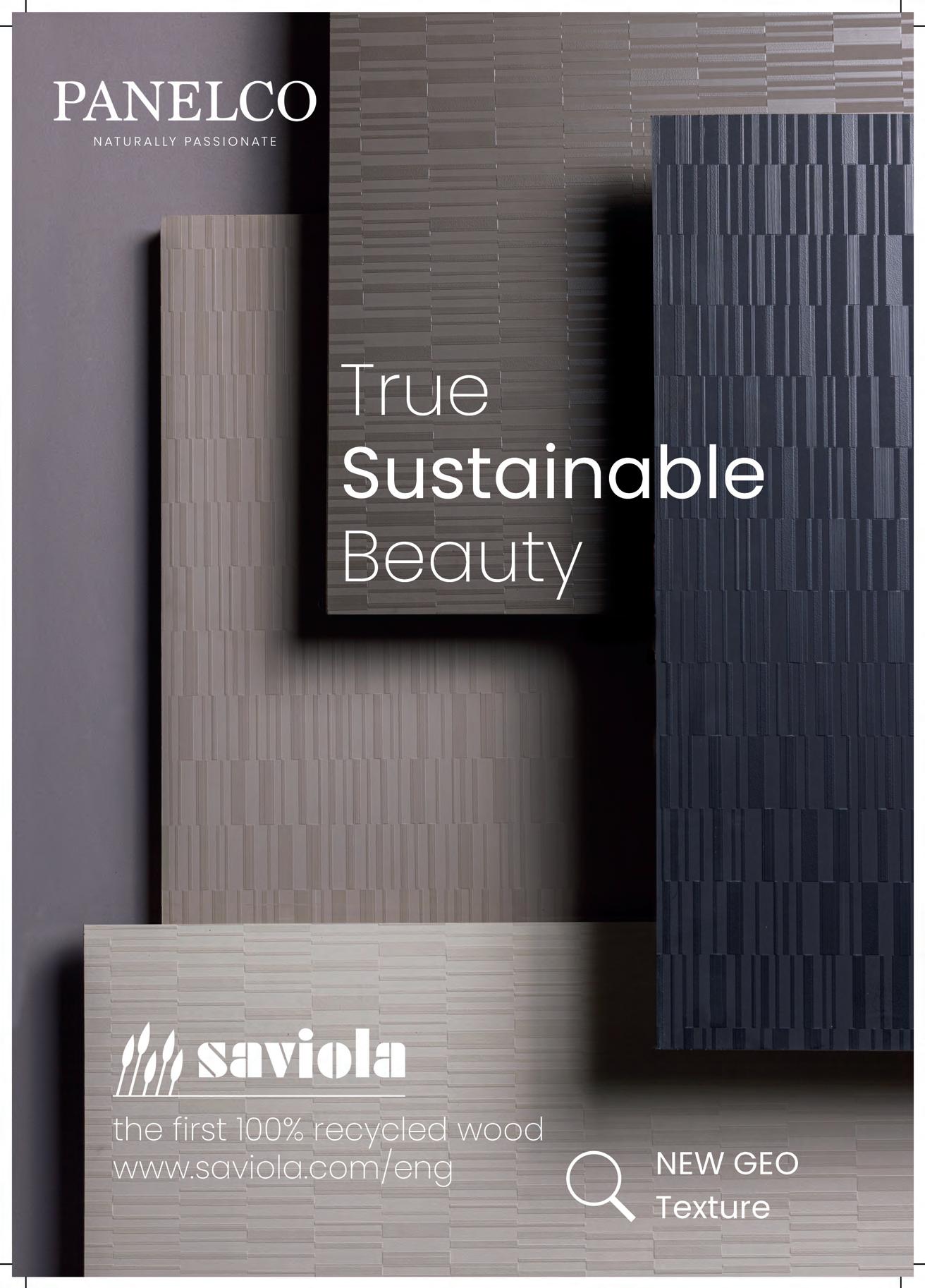
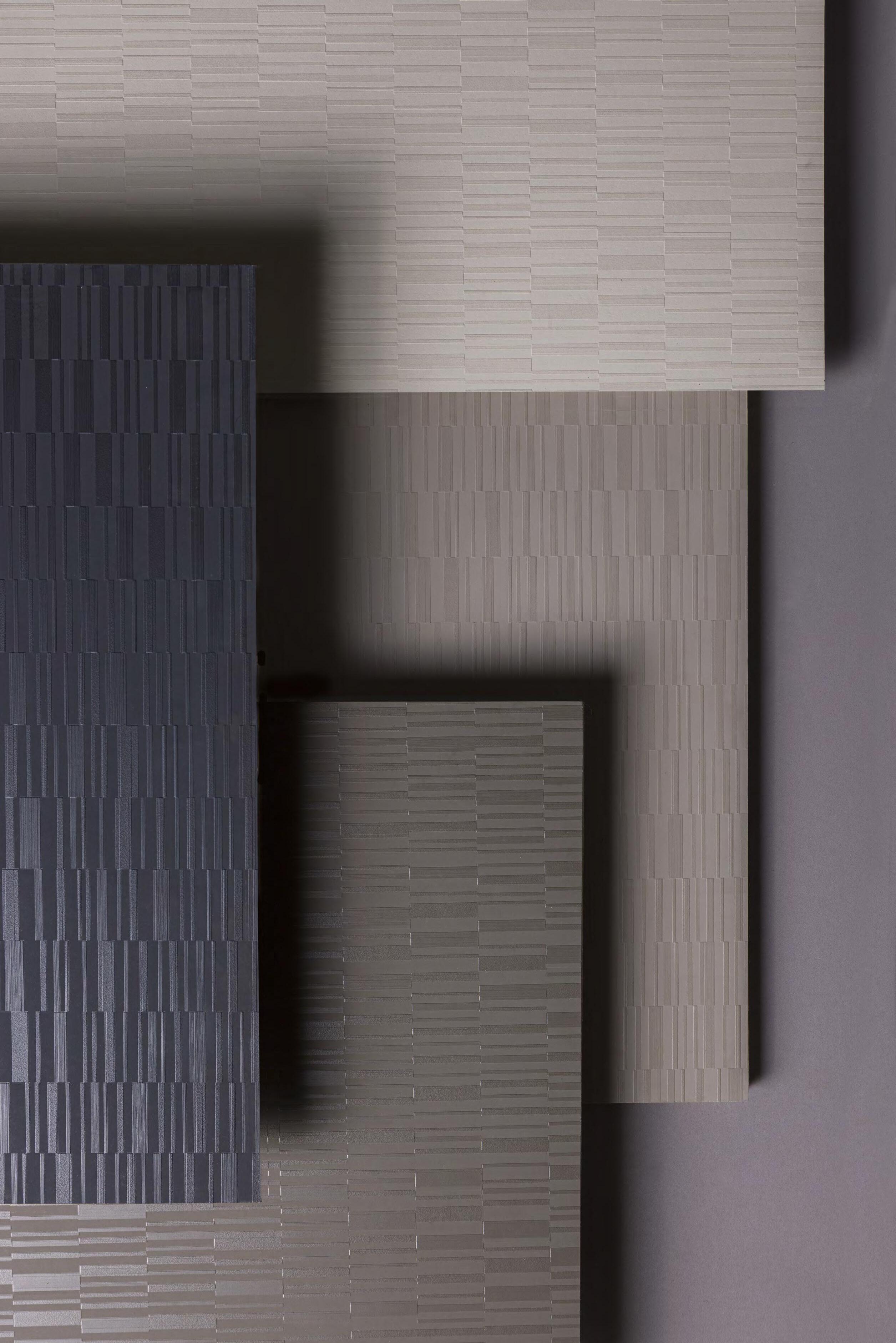
Sustainable InnovationThe tree-free future of furniture
Saviola Group is the largest Italian producer of panels made from 100% regenerated wood and one of the global leaders in the industry. Saviola successfully reintegrates materials into the circular economy every year thanks to its integrated system, reinforcing its commitment to sustainability and innovation.
Saviola works closely with its UK partner, Panelco, and continues to redefine the intersection of design and sustainability, proving that beauty and responsibility can coexist seamlessly in the modern design world. Saviola consistently drives design trends and innovative finishes, creating sophisticated aesthetics, and this has always been a focus of the ever-strengthening partnership.
The latest decorative panels can be used in many target fields, including residential, hotel, retail, furniture, and shopfitting. The unique and diverse finishes set themselves apart with their cutting-edge design and contemporary aesthetics.
Recent design trends show a strong resurgence of geometric patterns, and Saviola has responded by presenting GEO, the finish with a bold statement. Distinctive and eyecatching, this textured finish will enhance any space with its immediate visual impact, which again reinforces the brand’s reputation for trend-forward solutions. It is ideal for use with natural woodgrains and solid colours for collaborative schemes with luxury appeal.
Saviola’s commitment to sustainable design paired with refined surfaces is a partnership that fits seamlessly into the Panelco profile of always thinking ahead.
SAVIOLA’S OFFICIAL DISTRIBUTOR IN THE UK
In partnership with Saviola, Panelco is updating the UK Trend A Porter collection. The collection will still feature 46 decors but incorporate the latest stunning designs handpicked for you to show the most up-todate innovative designs. This collaboration guarantees a premium, diverse collection, all with unique designs and textures, elevating surfaces with depth and elegance while staying true to Saviola’s commitment to sustainable design.
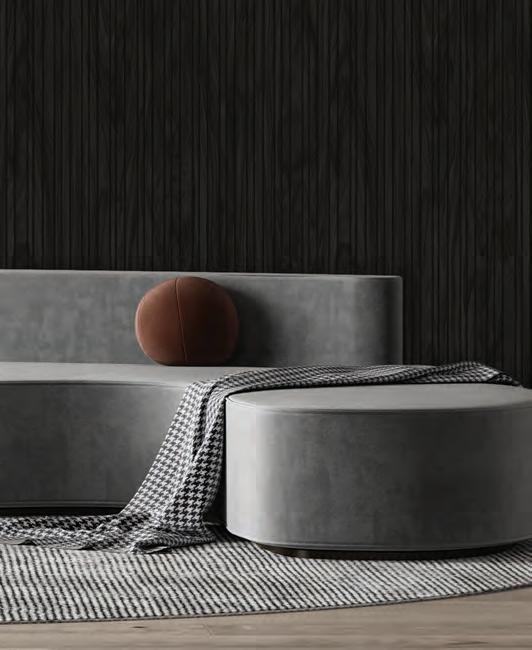
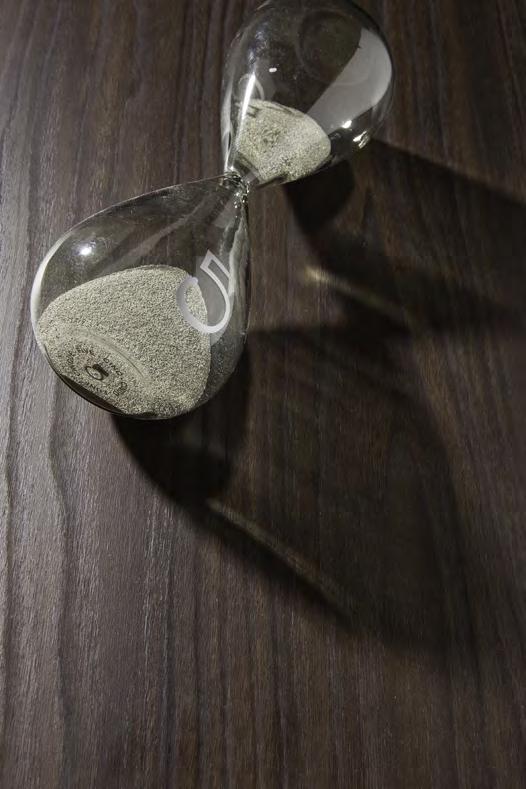
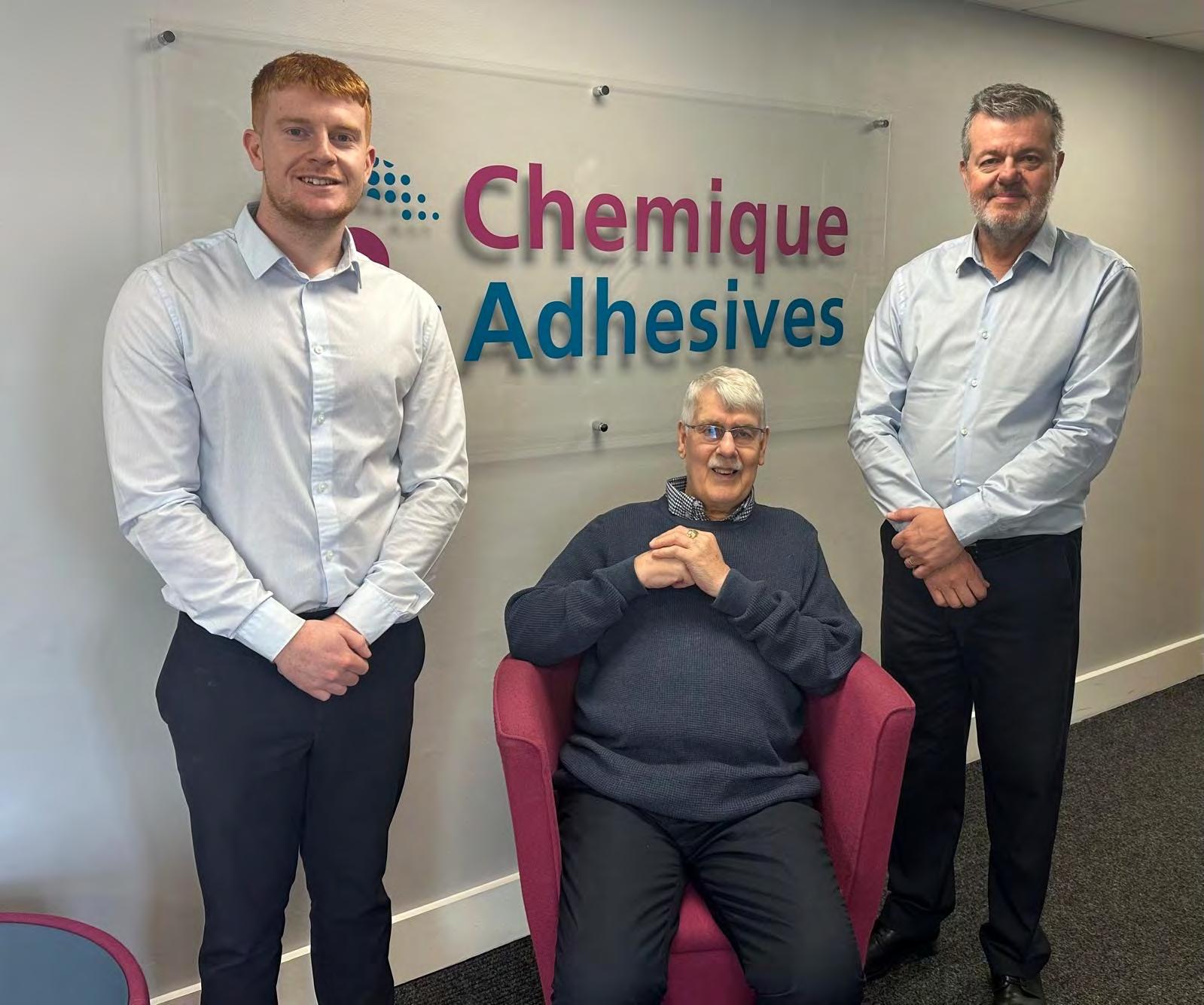
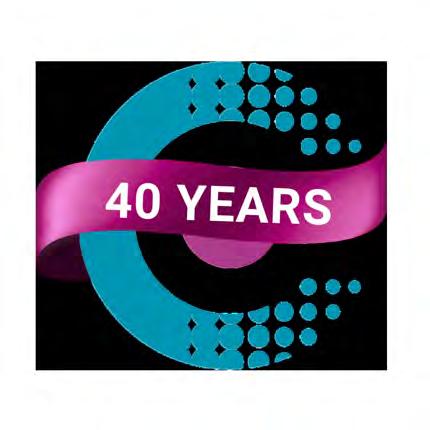
Chemique Adhesives Celebrates 40 years of excellence in adhesive manufacturing
This year marks the 40th anniversary of Chemique Adhesives, a leading UK manufacturer of high-performance industrial adhesives and adhesive application equipment. For four decades and across three generations, Chemique Adhesives has proudly remained a family-owned business built on ingenuity, quality, and exceptional service. Founded in 1985 in Aldridge, West Midlands, UK, from the vision of former CEO Mick McMullen, the company has experienced significant growth and emerged as a leader in industrial adhesive solutions.
Over the years, the company has expanded its portfolio of specialist adhesives, now providing advanced bonding solutions to a diverse range of industries, including artificial turf, foam, furniture, panel lamination, and raised access flooring. Additionally, its toll manufacturing service has established partnerships with many leading international adhesive companies, allowing for the delivery of quality products across the UK, Ireland, Europe, the Middle East, and the USA.
Stuart Francis, managing director at Chemique Adhesives comments, “From our humble beginnings to becoming an industry leader in the adhesives market, we have remained dedicated to developing cutting-edge bonding systems tailored to the evolving needs of our customers. This anniversary is a testament to our customers, old and new, and the dedication of our exceptional team, whose efforts have been instrumental in our growth and continue to shape our vision for the future.”
Throughout the decades, the company has achieved several key milestones. The 1990s saw a site expansion, the introduction of Solfre - a revolutionary range of one and twopart polyurethane adhesives and the launch of ProAqua – a breakthrough in water-based adhesive technology.
During the 2000s, the company achieved ISO 90001 and ISO 14001 certifications, strengthening its commitment to quality and environmental responsibility. Building on a successful period of growth in the US market, Chemique Adhesives Inc. was founded in Atlanta, Georgia, in 2005. Now celebrating its 20th year, the company continues to uphold the same proven techniques and principles from its UK origins.
In recent years, Chemique Adhesives has made significant investments to expand its operations, including a new manufacturing and warehouse facility. In 2023, this expansion was further supported by the acquisition of cutting-edge manufacturing equipment, which has boosted production, improving both capacity and workflow. Looking ahead, the company anticipates further developments and continued growth while maintaining the values that have been the foundation of its success for the past forty years. Here’s to the next chapter!
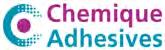

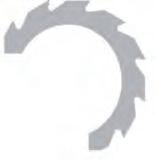
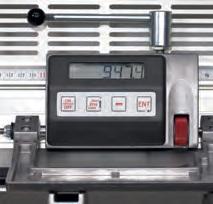
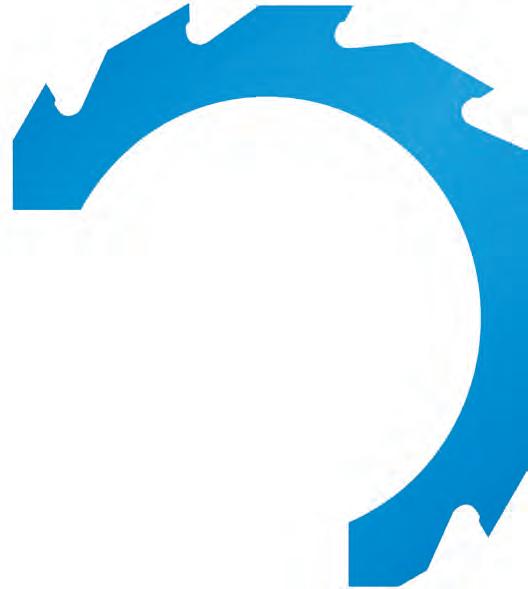
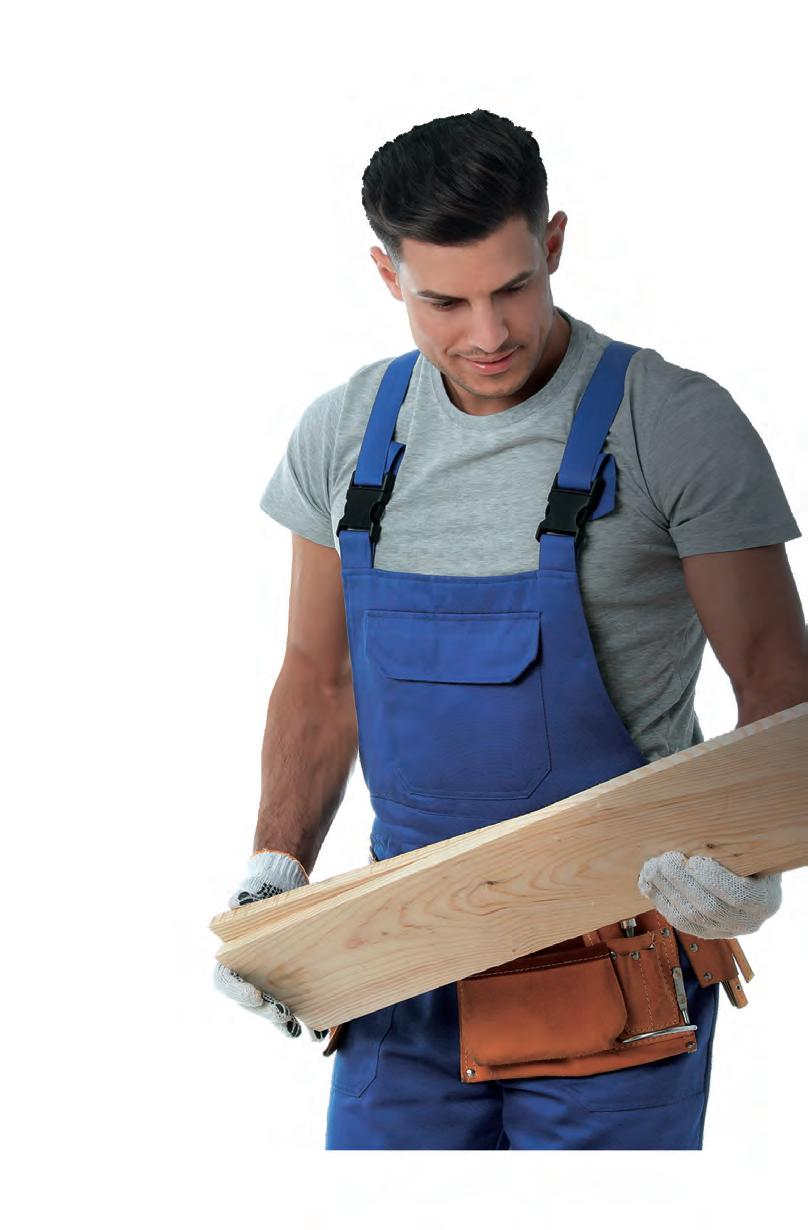
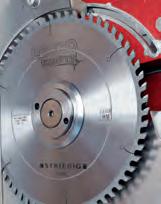
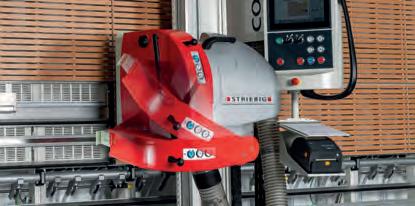
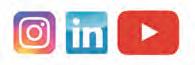
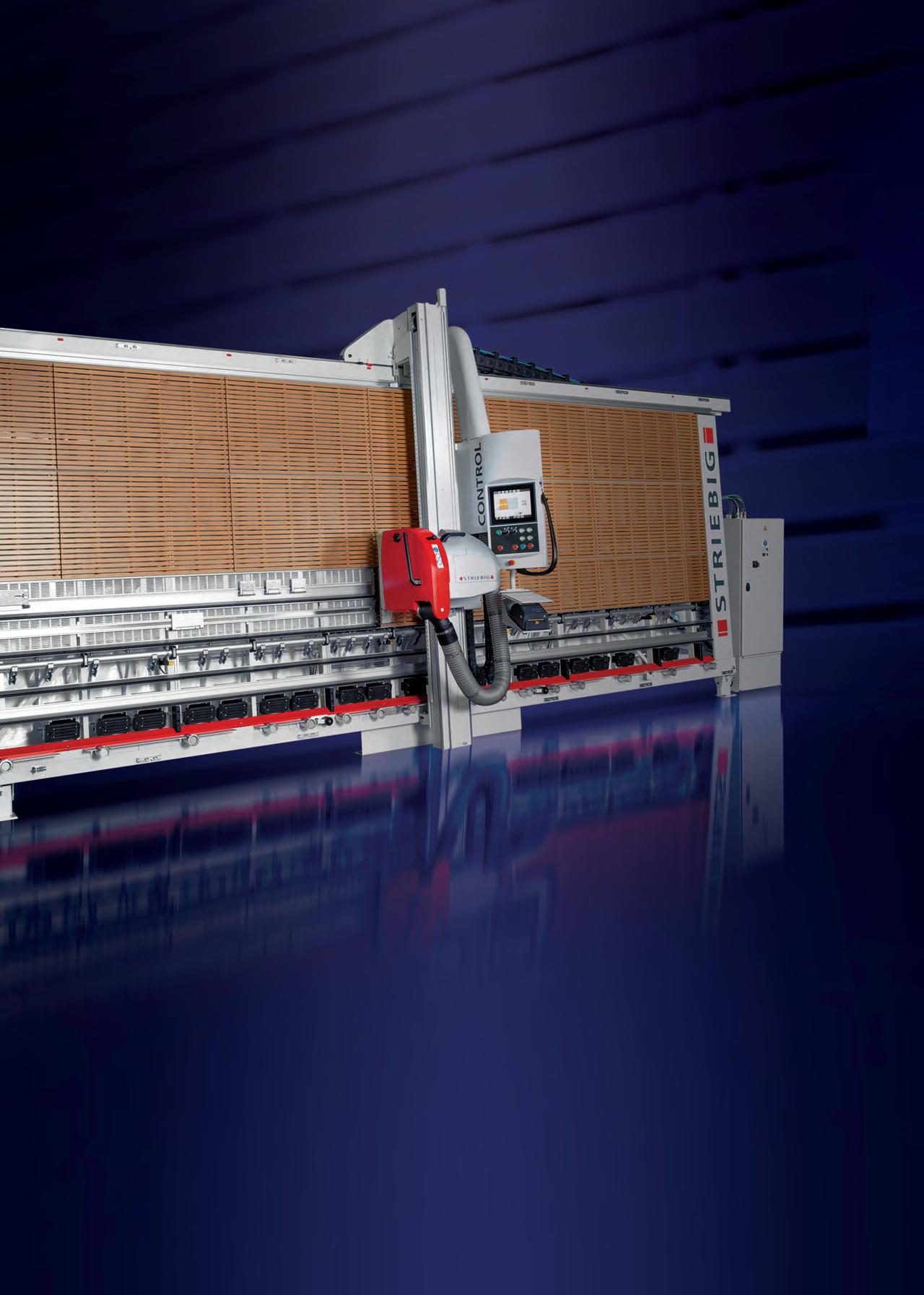
CASE STUDY
Harrison Collier future-proofs production with HOMAG CNC upgrades
Harrison Collier, designer and manufacturer of bespoke interior cabinetry, was established in 1990 by Managing Director Simon Harrison in a small Cheshire barn. From those humble beginnings it has climbed to the top of its niche, serving a discerning clientele and working closely with interior designers, architects, developers, and private clients across the UK specialising in full house installation projects.
Operating from a 14,000 sq ft purpose-built facility in Prescot, Merseyside, Harrison Collier has a 30-strong team and delivers an end-to-end service – from design and CAD drawings to manufacture, finishing, and installation. It’s a company that goes from strength to strength, and with this in mind, they turned to HOMAG for their latest investment.
The need for new machinery
“The times were changing, our business was growing, and so we decided it was time to upgrade our machinery,” explains Simon. “We already had a couple of older HOMAG machines – a Vantage nesting CNC and a BHX 050 – that had been reliable for over a decade. But technology has moved on and it was time we moved with it.”
Why HOMAG?
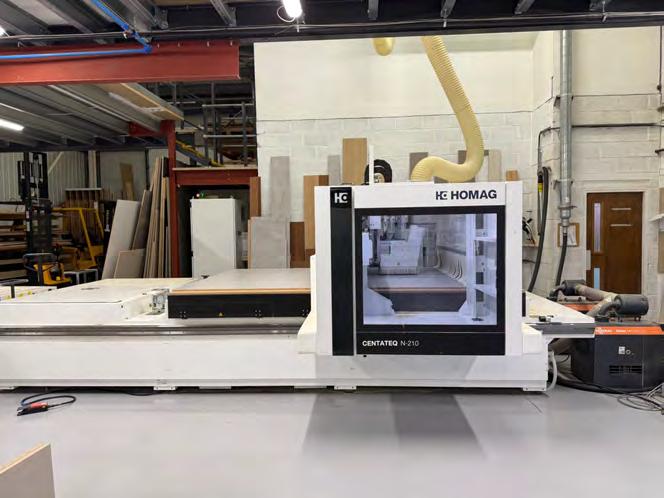
The choice of supplier was straightforward. “We’ve used HOMAG machines for years and they’ve always served us well. There was never really a question of looking elsewhere.”
Their long-standing relationship with Jon Lawman from HOMAG made the process even easier. “We spoke to Jon about what upgrades would suit us best. What really excited us was learning we could integrate our Lamello jointing system with the new CNCs.”
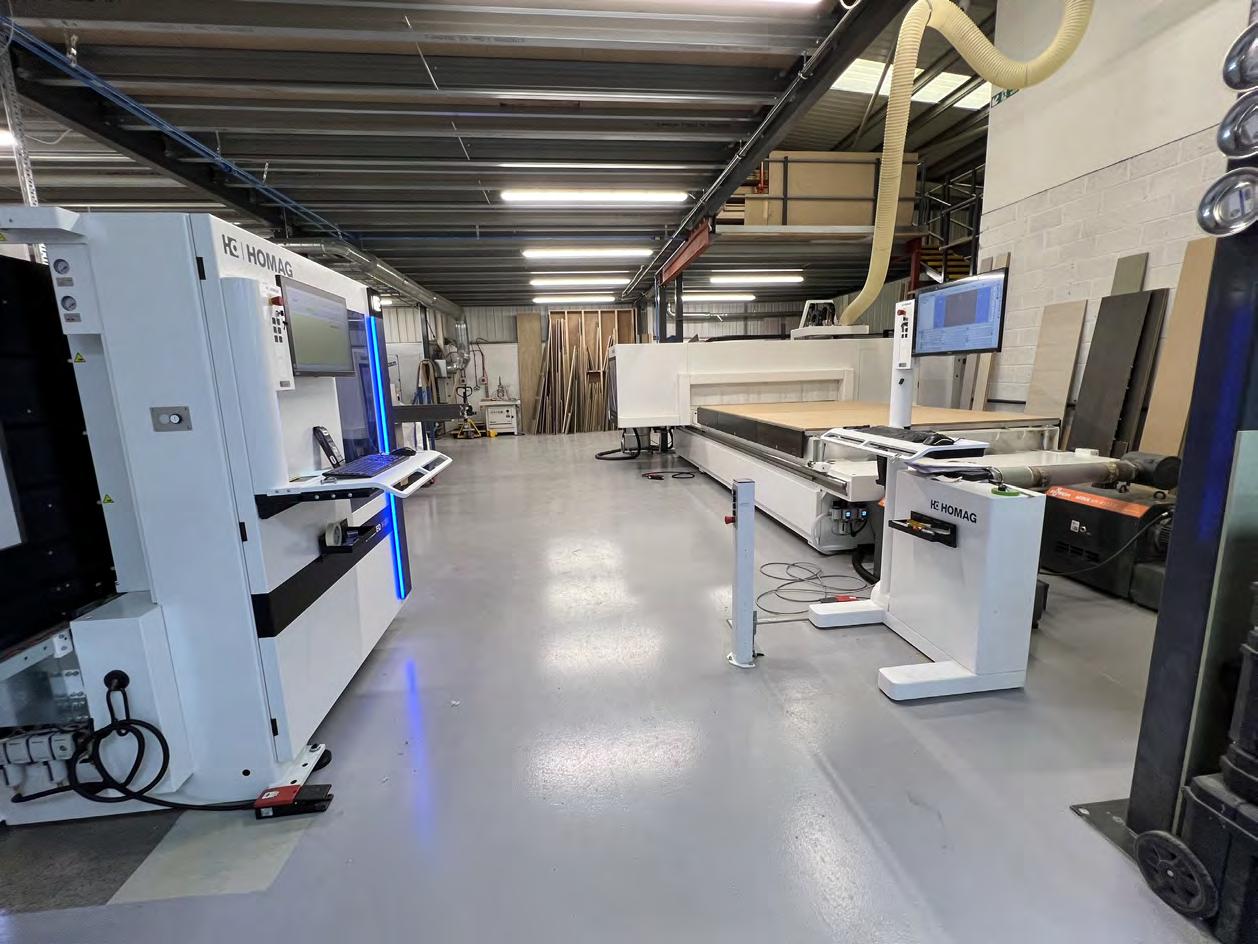
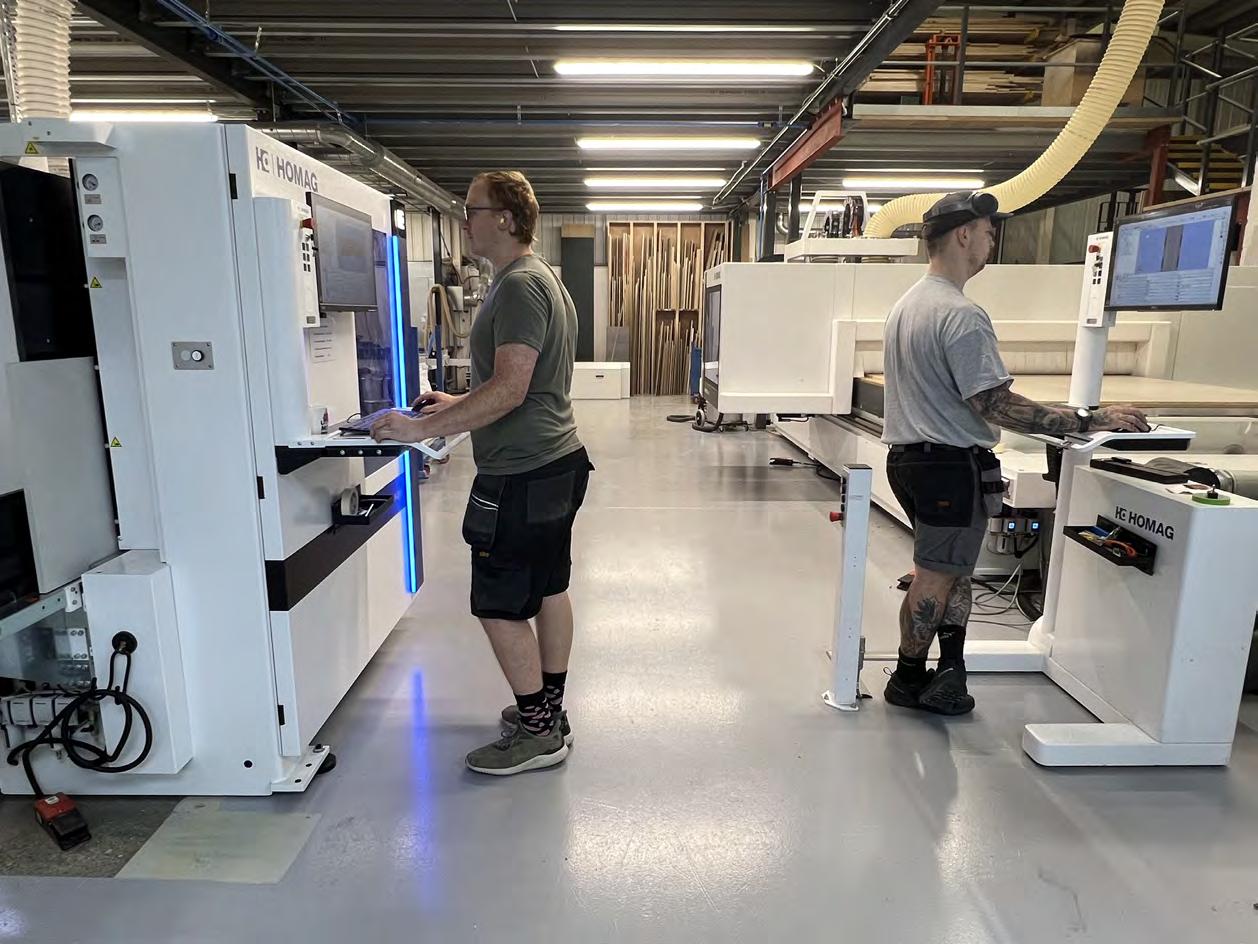
Simon and his team had purchased a handheld Lamello unit a few years earlier. “It worked an absolute treat,” he says. “Then, once we’d decided on the CENTATEQ N-210 and DRILLTEQ V-200, we found out HOMAG could integrate Lamello through their woodWOP software. That was a complete game-changer.”
Installation & training
“Delivery was bang on time and caused minimal disruption – can’t ask for more than that,” says Simon. Four team members were sent to HOMAG’s Castle Donnington showroom for training. “They had a great trip, got to grips with the basics, and were ready to go as soon as the machines were installed. These CNCs are incredibly intuitive – the lads took to them like ducks to water.”
Operational improvements
The benefits of the upgrade were immediate. “The Lamello integration alone has made us far more efficient,” says Simon. “Aside from that, the general upgrades in the technology are working wonders for our operation. We have a lot more flexibility with these machines, and they’re so user-friendly that more members of staff can operate them, which has increased capacity.”
The company also benefits from remote programming. “We can now programme jobs from the office, sending the CNCs complicated instructions from the comfort of a chair at the click of a button. It saves a lot of time and effort and really just simplifies the manufacturing process.
“And of course, the finish of the products produced with these CNCs is second to none. Quality is everything to us, so it’s great knowing our machines deliver it without fail.”
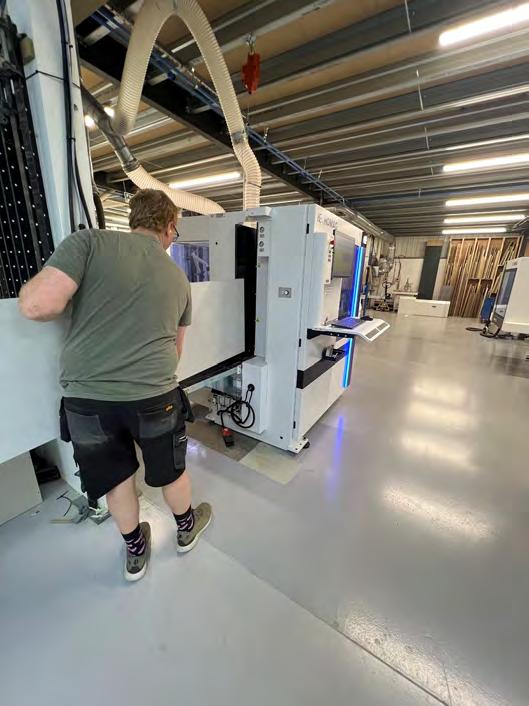
Working with HOMAG
“We can’t fault HOMAG’s service,” says Simon. “If something goes wrong, they deal with it quickly. And with the Lamello integration, they really went the extra mile. They’re a firstrate supplier.”
Looking ahead
“We’re not looking to expand further for the time being,” Simon adds. “We’re happy with our space and our niche. This investment was about making the most of what we’ve got – being as efficient as possible while continuing to deliver exceptional work. With these new HOMAG CNCs, we’re confident we’ll be doing just that for many years to come.”
CASE STUDY
Achieving precision and efficiency in fire door production with Hoffmann technology
Ahmarra Streamlines Glazing Cassette Manufacturing
Using
Hoffmann MU3-PD Router
Ahmarra Door Solutions continues to lead the way in fire door manufacturing by investing in high-performance machinery. Their latest additions— a double mitre saw and the Hoffmann MU3-PD Pneumatic Router—have significantly enhanced the production of glazing cassettes, achieving exceptional precision and efficiency.
The Importance of Glazing Cassettes in Fire Doors
Glazing cassettes are integral to fire doors, housing vision panels that allow light through while preserving fire resistance. Precision in constructing these cassettes is critical—not only to meet fire safety standards but also to ensure visual quality. Mitre joints must be clean and accurate to maintain structural integrity and visual appeal, particularly as vision panels are often at eye level. Flaws in angle or finish can undermine both safety and aesthetics. Ahmarra understands that achieving this precision requires not just craftsmanship but the right tools. That’s why they’ve chosen the Hoffmann MU3-PD Pneumatic Router as a cornerstone of their glazing cassette production.
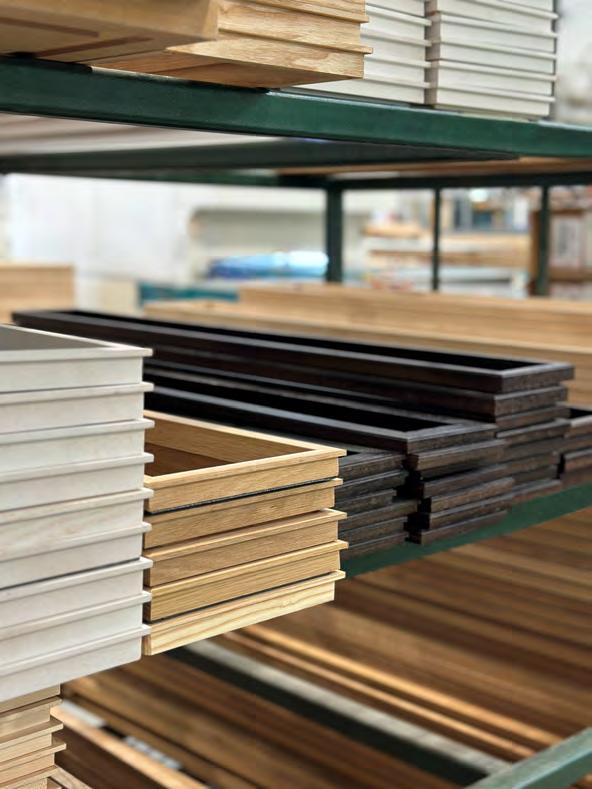
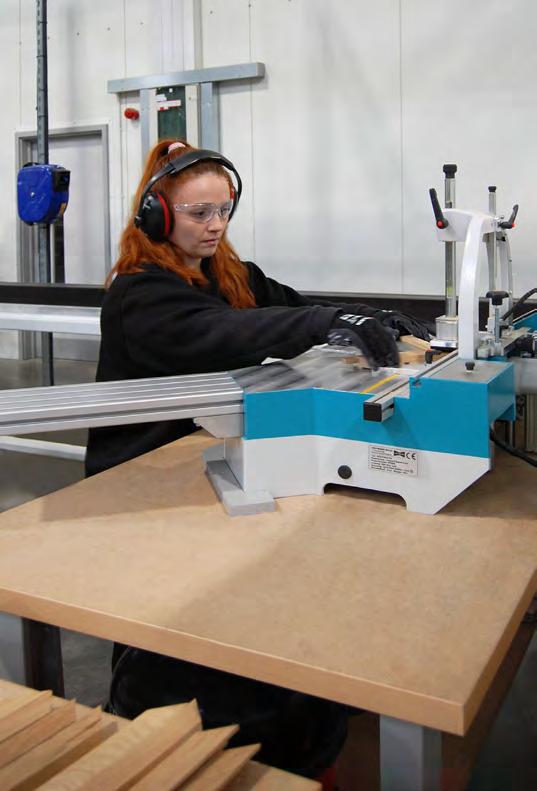
Cutting with Accuracy: The Double
production process begins with Jack, a
operator at Ahmarra, using a double mitre saw to cut timber glazing beads. This saw delivers consistent 45° cuts essential for creating clean, reliable mitre joints. Each cut component is precisely shaped and ready for the next stage—dovetail routing.
The Hoffmann MU3-PD: Core of the Joinery Process
Once cut, pieces move to the Hoffmann MU3-PD. Becca, another experienced technician, uses the router to cut dovetail slots into the corners of the frame components. These dovetail joints are key to ensuring strength and durability—particularly under the stress of fire exposure. The process is straightforward and efficient: glue is applied to the mitre faces, Hoffmann Dovetail Keys are inserted into the routed slots, and the components are drawn together into a tight, permanent joint. The result is a strong, stable cassette frame—without the need for clamping tables or extended curing times. Frames can be finished immediately after assembly.
Mitre Saw
The
skilled
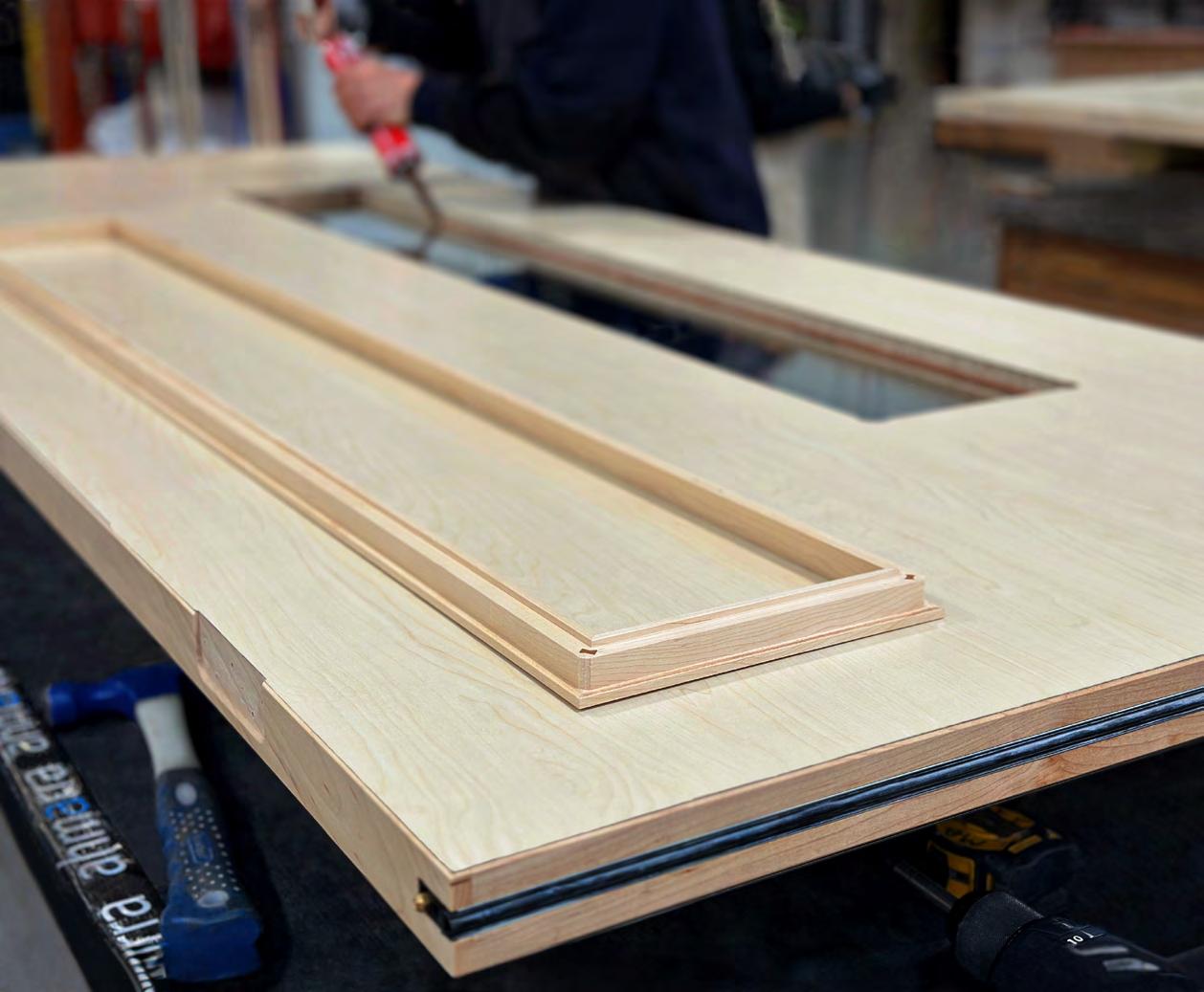
Designed for high-throughput production, the MU3-PD features pneumatic clamping and foot-pedal operation, allowing fast and repeatable processing. Its precise, automated controls—complete with a digital two-axis display—ensure each dovetail slot is machined to exact specifications. This consistency is vital for large-scale production without sacrificing quality.
Certified Strength and Safety
Hoffmann Dovetail Keys used in the MU3-PD are tested to BS 476: Part 22: 1987, confirming their compliance with UK fire resistance standards. This gives assurance that each cassette not only looks good but also contributes to the overall fire performance of the door, maintaining integrity under fire conditions.
Benefits of the Hoffmann MU3-PD for Fire Door Manufacturers
• High Precision: Ensures exact slotting for tight-fitting dovetail joints.
• Speed: Pneumatic clamping and foot control support fast, continuous production.
• Versatility: Suitable for various joinery applications beyond glazing cassettes.
• Cost-Effective: Reduces labour and finishing time, material waste, and tool wear.
• Compliance: Supports fire-rated construction to meet building safety regulations.
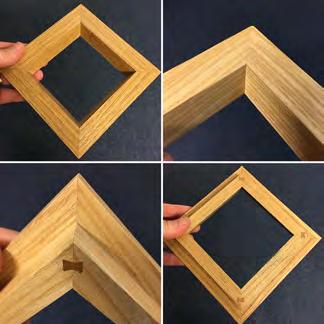
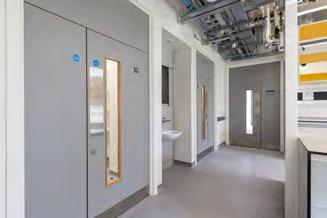
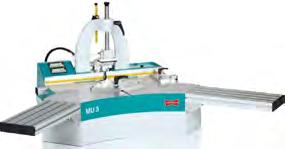
As fire safety standards continue to evolve, precision and compliance are more crucial than ever. Ahmarra’s investment in the MU3-PD reflects their commitment to innovation, quality, and performance. By integrating the double mitre saw and Hoffmann MU3-PD into their workflow, Ahmarra produces reliable, aesthetically refined glazing cassettes—delivering peace of mind to their customers and end users.
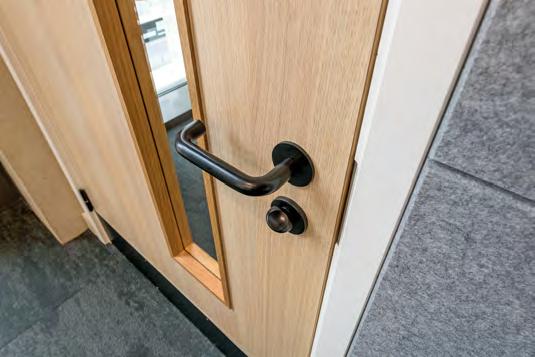
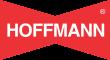
LIGNA 2025 inspires and motivates the industry
In its 50th anniversary year, LIGNA 2025 once again proved to be the leading platform for the international woodworking community, featuring 1,433 exhibitors from 49 countries. From May 26 to 30, it brought together the global woodworking and wood processing industry in Hanover, provided a significant boost to the sector, ignited fresh momentum, and laid the foundation for future investments.
“LIGNA has impressively reaffirmed its unique position as the world’s leading trade fair for the industry. Around 78,000 visitors from 156 countries came to Hanover –putting us on par with the previous event in 2023. Given the circumstances, that is a strong result,” said Dr. Jochen Köckler, CEO at Deutsche Messe AG. “Despite all the benefits of digitalization, nothing can replace the experience of seeing machines in live operation at a trade fair. I would like to thank all LIGNA exhibitors who demonstrated this so clearly here,” Köckler continued, adding: “The combination of innovation, technological progress, and passion is the best foundation for renewed investment.”
The proportion of trade visitors at LIGNA 2025 was 93 percent, with 60 percent of them holding management positions – 44 percent of those in top management.
Whether in forestry, sawmilling, production, manufacturing, or craft industries, exhibitors presented solutions spanning the entire value chain, showing how current challenges can
be addressed and turned into opportunities. The spotlight was on digitalization, automation, artificial intelligence, smart production, sustainable and climate-friendly construction using wood and wood-based materials, and the responsible, future-oriented use of wood as a resource.
Köckler stated: “What makes LIGNA unique worldwide is its role as an international marketplace for the woodworking and wood processing industry. This is where global supply meets international demand. With 56 percent of visitors coming from abroad, LIGNA clearly demonstrates that it is the undisputed world’s leading trade fair for the industry and enables global business at the highest level.” The largest groups of international visitors came from Poland, Italy, and Austria, followed by the Netherlands, France, and Belgium.
Markus Hüllmann, Chairman of the Executive Board of the VDMA Woodworking Machinery Association, also gave a positive assessment of LIGNA 2025: “We had a successful LIGNA that provided motivation and momentum in an otherwise uncertain environment. The situation differs across segments and manufacturers, but everyone here in Hannover discussed important projects and recharged their batteries. For some, this even resulted in unexpected orders at their stands – which gives us confidence that the industry will quickly bounce back.”
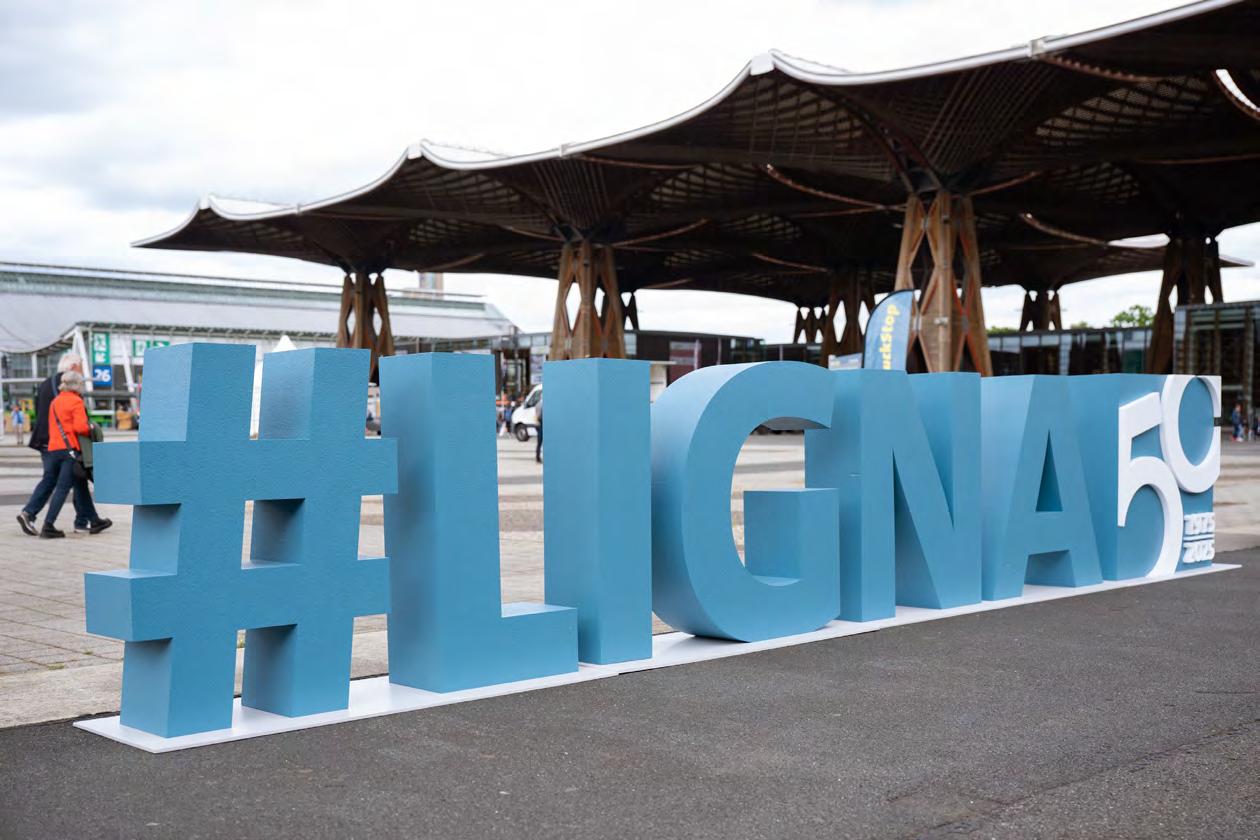
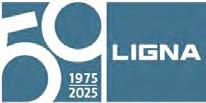
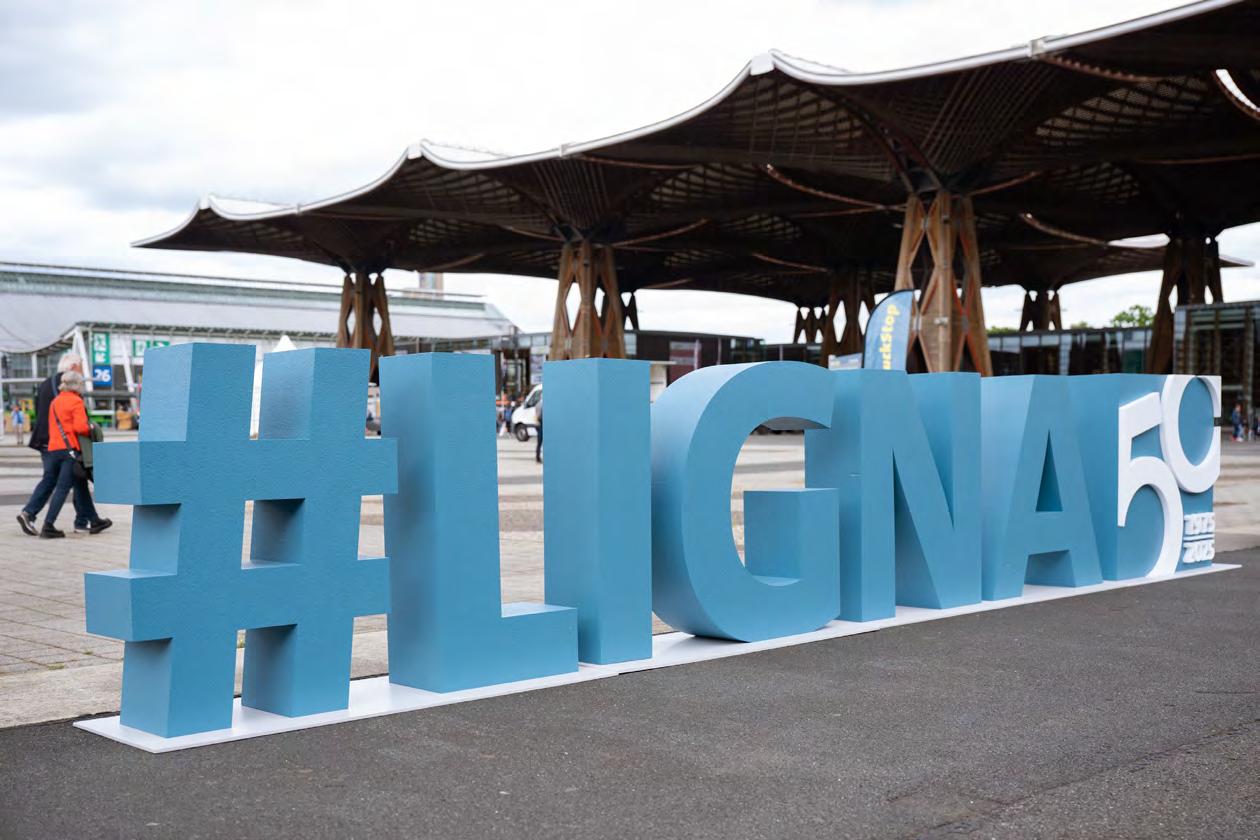

The UK’s sole coatings distributor of
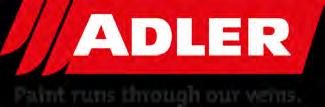
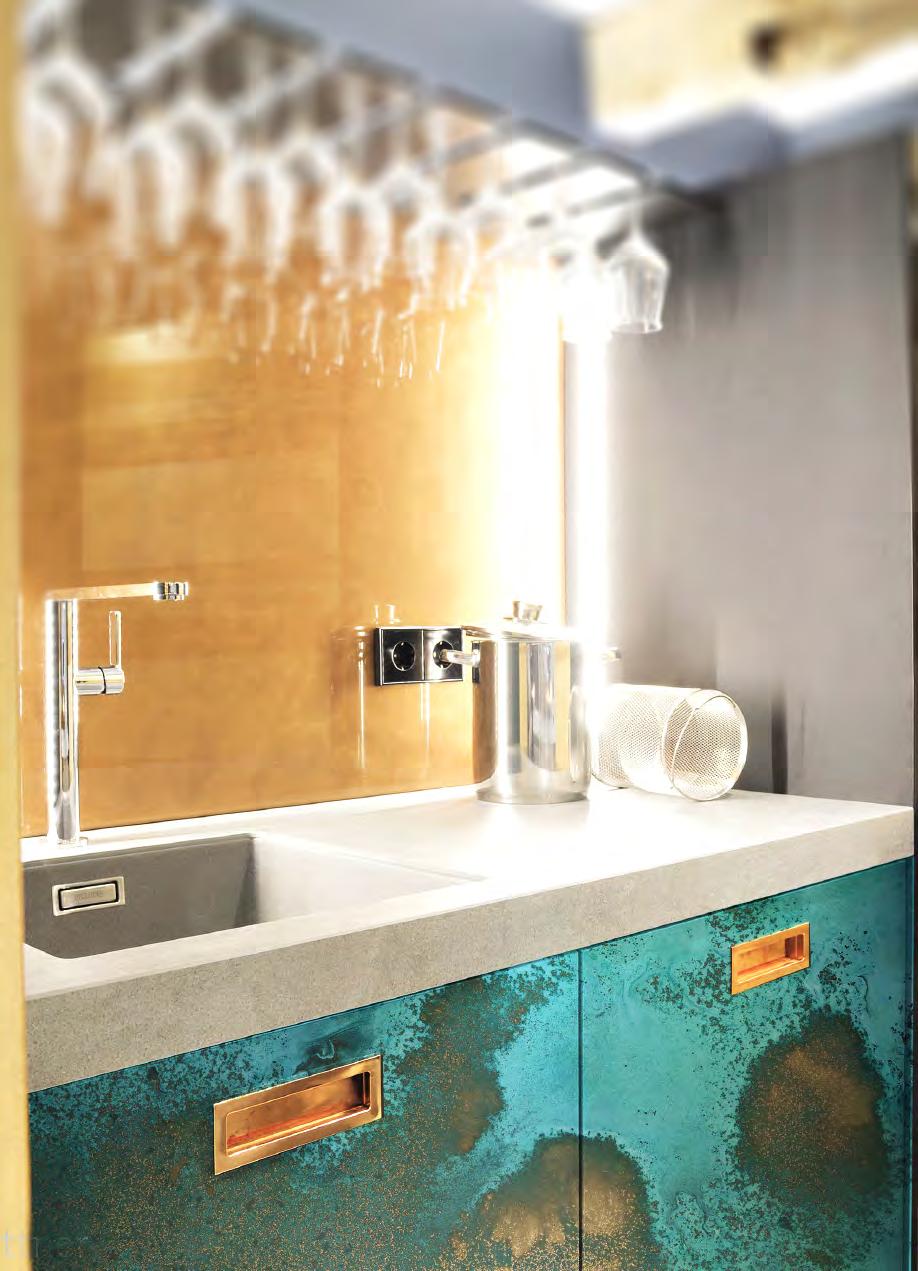
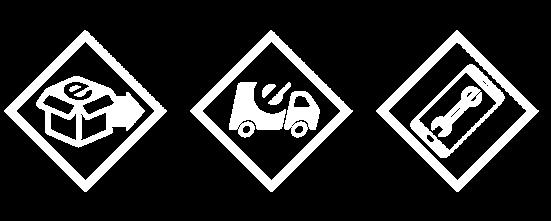
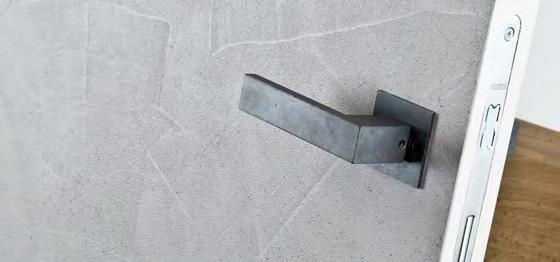
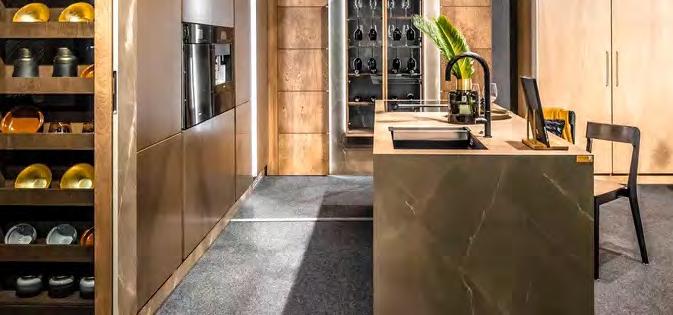
Special Effects
Incredible Real Metal, Oxide, Concrete, Briliant Metallic effects and more for interior wood finishing. Professional coating effects for stunning results.
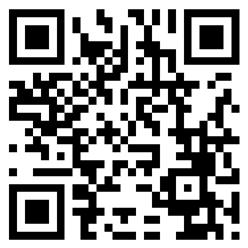
Learn more about our special effect range
SCM at LIGNA 2025: outstanding results and technological breakthroughs
SCM closed Ligna 2025 on a high note, reporting strong attendance and a marked increase in business opportunities compared to 2023. Thousands of visitors from over 100 countries attended the event, with notable representation from the DACH region, as well as Northern and Eastern Europe.
Welcoming thousands of professionals, SCM’s participation reflected a vibrant and forward-thinking wood industry. The company’s success at the event included strong deal flow, new international contacts, and growing momentum across key markets such as North and South America, and Europe. With 78,000 attendees overall, the show reaffirmed the sector’s openness to innovation despite global macroeconomic pressures.
Occupying over 3,300 square meters, SCM reinforced its role as a strategic business partner across the entire production cycle. Its Hall 13 stand presented a vision that went beyond machinery, highlighting integrated solutions aimed at improving process efficiency, quality, and cost-effectiveness. The display combined cutting-edge technology, digital services, and hands-on demonstrations.
SCM’s 350 experts and more than 100 dealers welcomed attendees with typical “Made in Italy” hospitality and the commercial network showed strong engagement at the preshow meeting on May 25.
New solutions: Engineering and Stand-Alone SCM’s engineering solutions drew particular attention, including edge-banding innovations from Tecno Logica. Stand-alone machines in timber construction, surface treatment, and solid wood machining also stood out.
“Despite the complexity of the global scenario, we came to Ligna with tangible, high-value innovations for our customers,” stated Pietro Gheller, SCM Division Director.
“We invest 7% of our turnover in R&D and after-sales services, which have become the true key to supporting our customers’ business growth.”
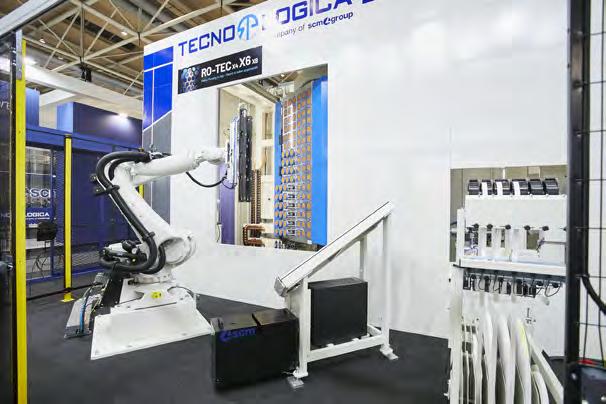
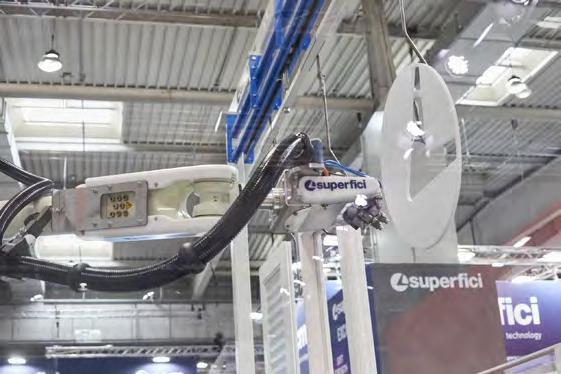
Digital services and systems: the power of connectivity
Digital innovation was a core theme, with SCM showcasing connected machines that enable proactive, data-driven service. These systems reduce downtime and boost productivity by anticipating issues before they escalate.
Key highlights included:
• WinMES: SCM’s factory management system, acting as the digital production brain, connects machines, people, and materials in real time to optimize traceability and coordination.
• MyPortal: The newest version supports fleet monitoring, energy usage tracking, tool management, maintenance scheduling, and service tickets.
• Smart Spindle: A predictive tool using real-time sensor data to prevent mechanical failures and optimize machining.
• Cybersecurity Solutions: Addressing growing industrial IT security demands.
• Solutions Library and a technical training portal offering e-learning and digital twin simulations round out the digital ecosystem.
These innovations are offered as part of modular service bundles, customized to support every production stage from start-up to preventive maintenance.
SCM and Tecno Logica: a new paradigm in industrial automation
In response to skilled labour shortages, SCM highlighted automation as a growth priority. A standout was the RO-TEC X6 edgebander at Tecno Logica’s stand—a multifunctional work centre featuring a rotary table and a new automation concept inspired by the automotive sector, enabling vertical part processing via a carousel setup.
SCM closed 2024 with €900 million in turnover, 90% of which came from exports with the Wood Division accounting for €600 million.
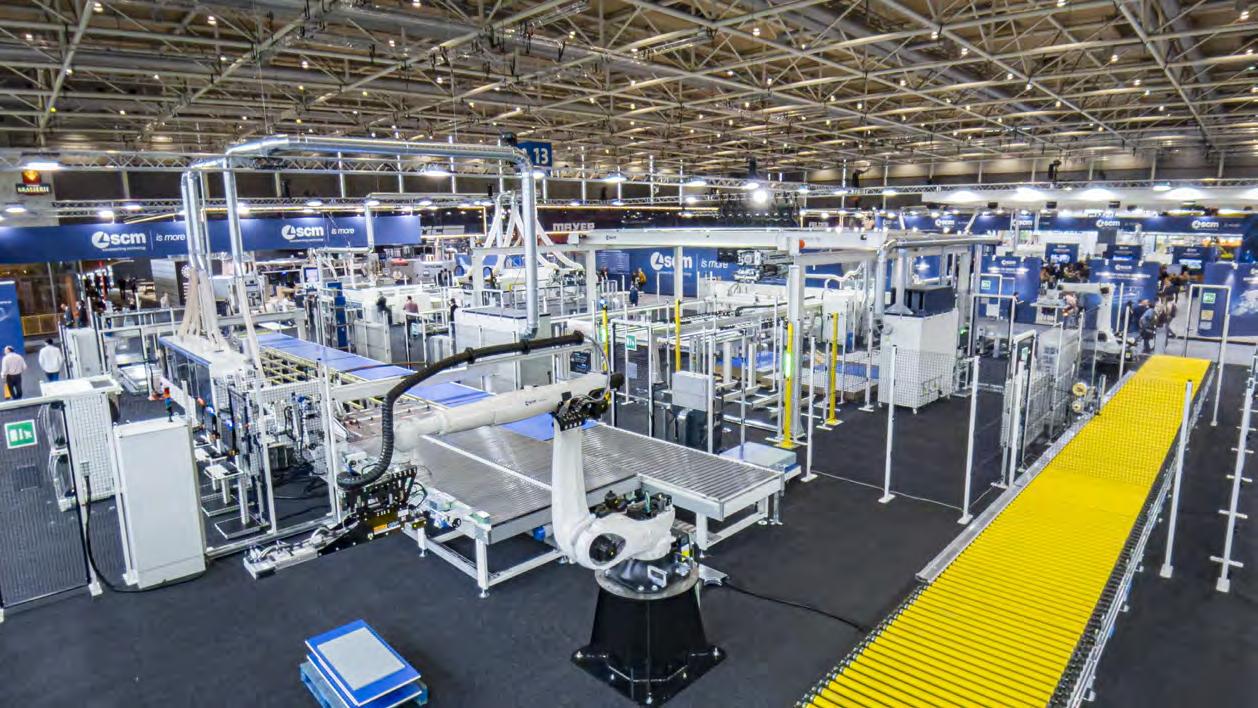
components per shift. The line included:
• gabbiani a2 angular panel saw with flexstore hp storage
• Outfeed robot and automatic labeller
• stefani cell E edge-banding system
• morbidelli fx100 CNC drilling cell (Ligna debut)
Timber Construction: CLT and Beam Processing
Debuting at Ligna, the oikos xs 650 supports flexible processing of beams up to 650x310 mm. Enhanced by Maestro lab beam&wall software, it offers improved programming and performance.
Also presented was the celaschi xl, a double-end profiler designed for CLT, highlighting SCM’s focus on sustainable building technologies.
Surface Treatment: from sanding to finishing
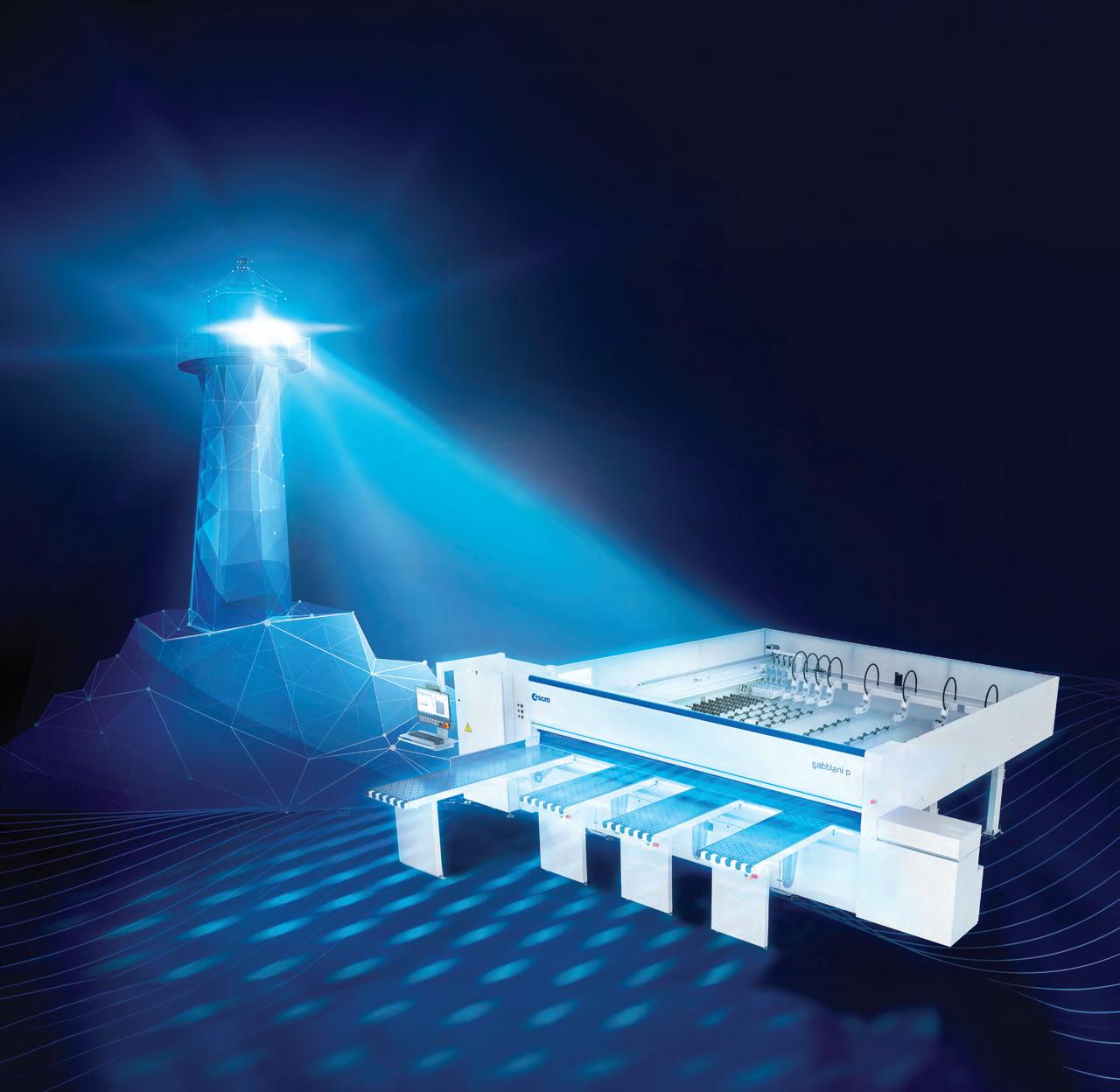
SCM’s finishing solutions offered a wide array of on-trend surface capabilities. A show highlight was the dmc system tc, an automatic sanding-calibrating machine featuring a CO2 laser engraving unit for creating 3D textures on wood, MDF, and other surfaces.
The Superfici range also debuted upgrades:
• maestro painting robot with advanced software for doors and windows
• mini spraying machine with integrated color-change system
• valtorta f1 roller coater with new roller tech for shaped surfaces
CNC and Solid Wood Innovations
SCM unveiled the morbidelli x50 nesting CNC in its new ProSpace configuration, featuring:
• Spoilboard Management System (SMS) for improved handling
• High Grip Vacuum table for small-piece hold
• SCM-patented spoilboard panel reducing waste by 90%
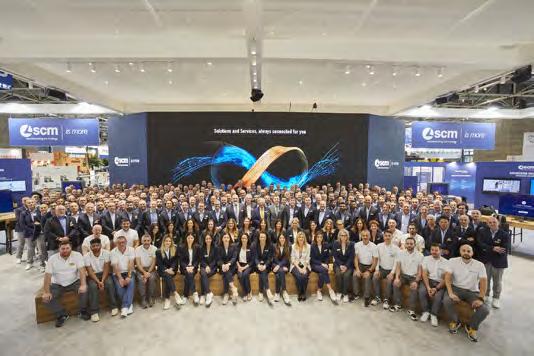
The accord 500 CNC received updates like Optizone, an asymmetric machining tool connected to Maestro lab, and the Quadro 35 chain tool changer for fast, space-efficient tool access.
The gabbiani pt95 beam saw, suitable for batch-one or mass production, includes top-tier features like a Flexcut unit, powerful blade motors, and LED-guided loading systems.
Edgebanding and Moulding Advances
The new stefani m edge bander was unveiled as a highly configurable machine that balances precision with userfriendliness, ideal for both stand-alone and integrated use. Features like fully automatic setup and touch-based control enhance quality and repeatability.
In solid wood machining, the topset xxl throughfeed moulder impressed with increased working sections, customizable layouts, and spindle speeds up to 12,000 rpm for optimal performance.
Compact and Versatile Joinery Machines
SCM introduced new circular saws:
• evocut 350i: A compact saw with tilt cutting up to 46°, programmed via the “eye-S” panel.
• nova si 4 and minimax si 4: Versatile saws with a 10year guaranteed sliding carriage and optional Quick Lock squaring frame for fast setup changes.
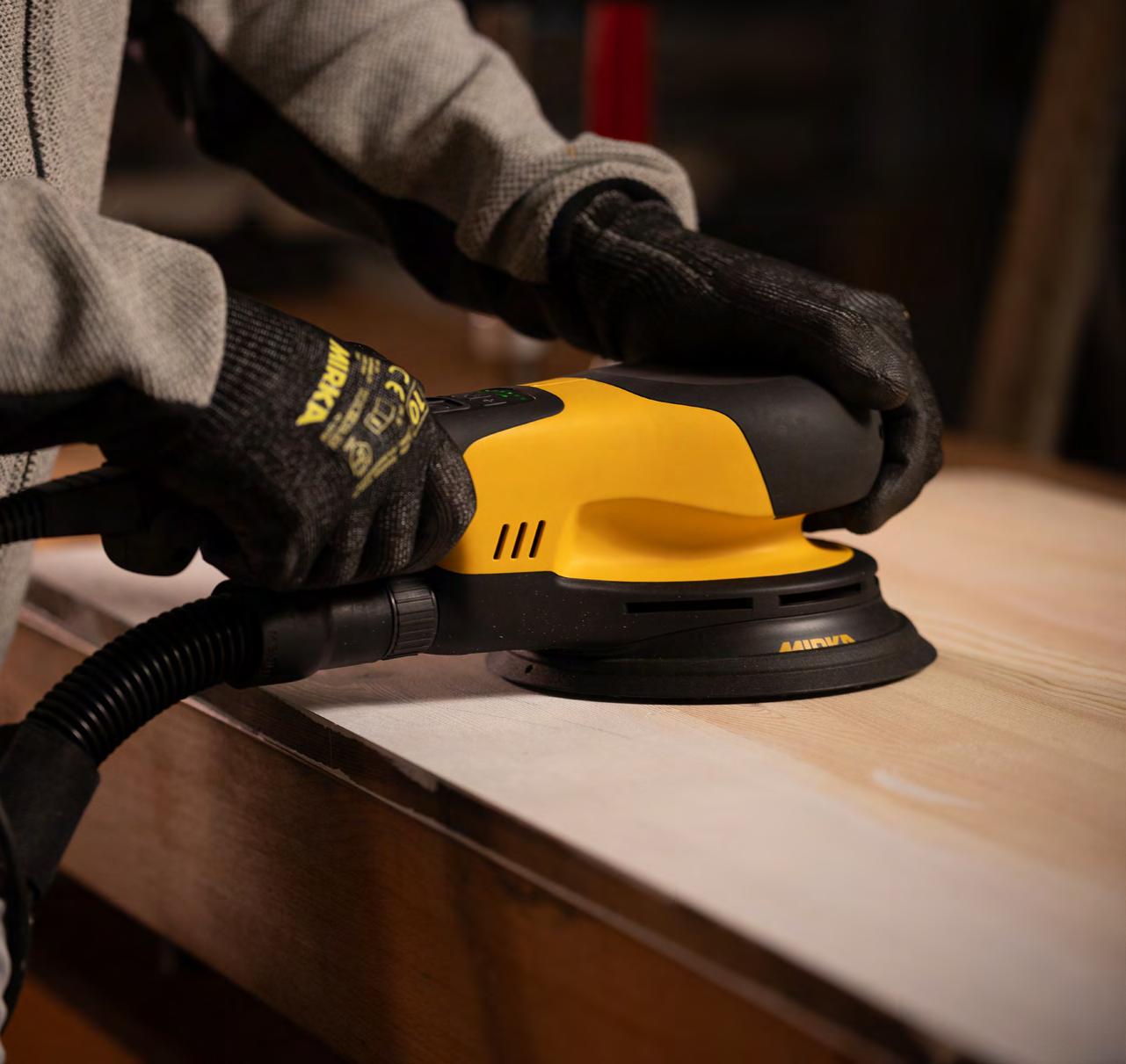
Mirka® DEROS RS 600 is a rotary sander designed for heavy-duty, coarse sanding applications. Its lightweight, compact design provides a smooth operation and enhances user comfort and productivity. The Mirka® DEROS RS is the perfect solution to tackle paint removal, furniture restoration, cabinetry, solid surface and wooden flooring projects with ease. For further information or to arrange a demonstration, please contact Customer Services on 01908 866100.
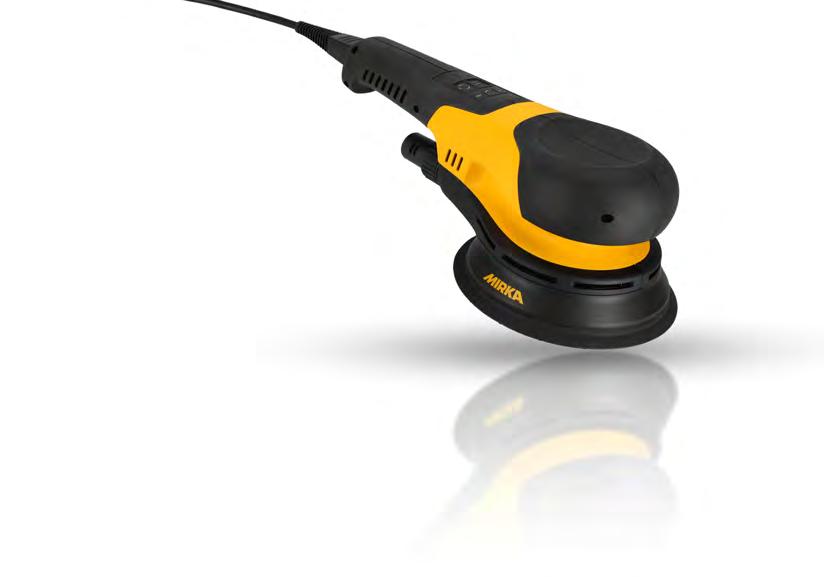
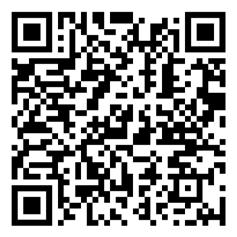
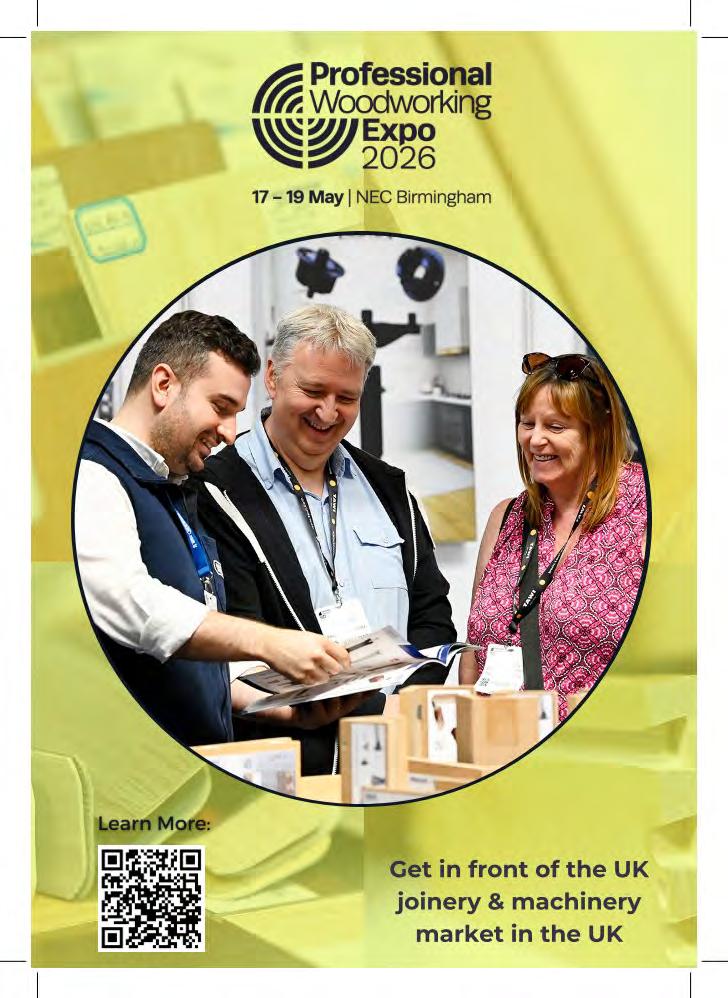
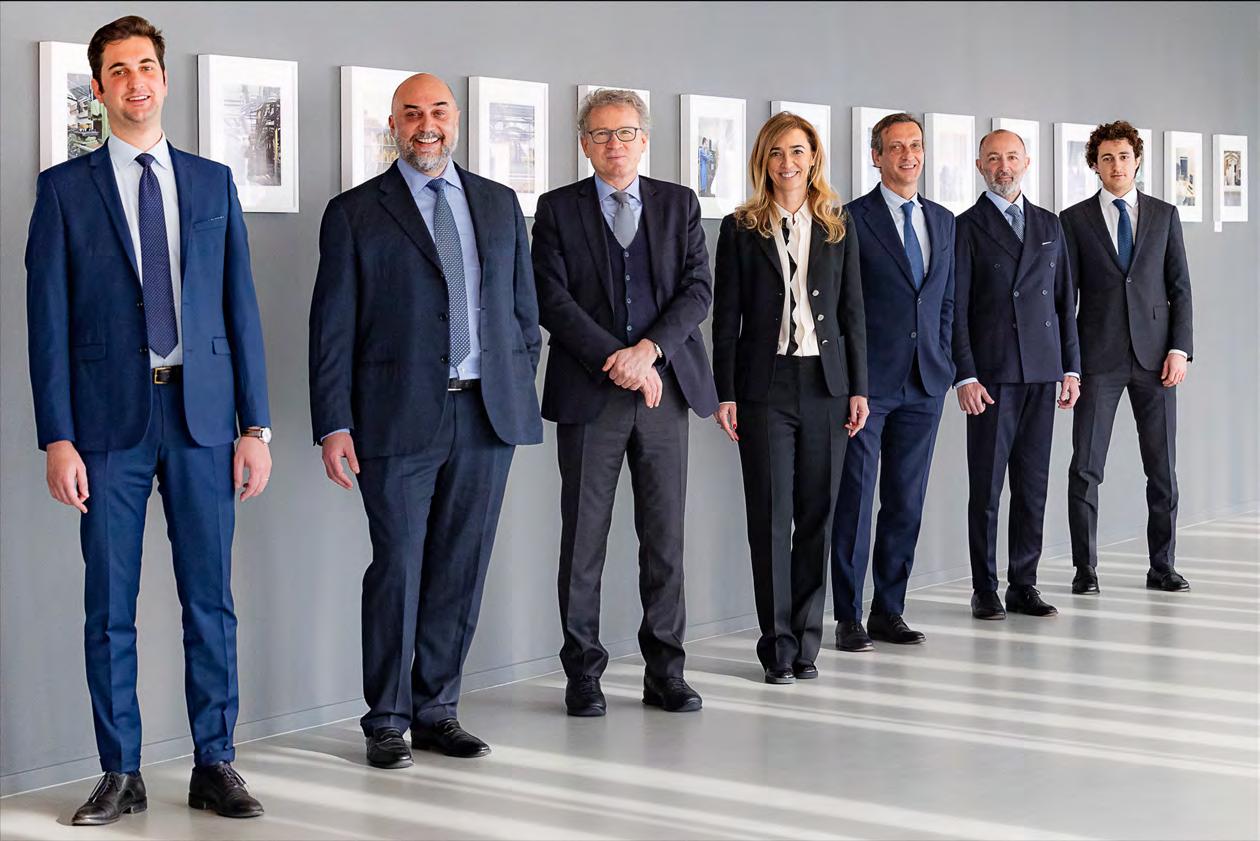
Scm Group: new board appointments
Board of Directors for 2025 - 2027 appointed and €900 million turnover
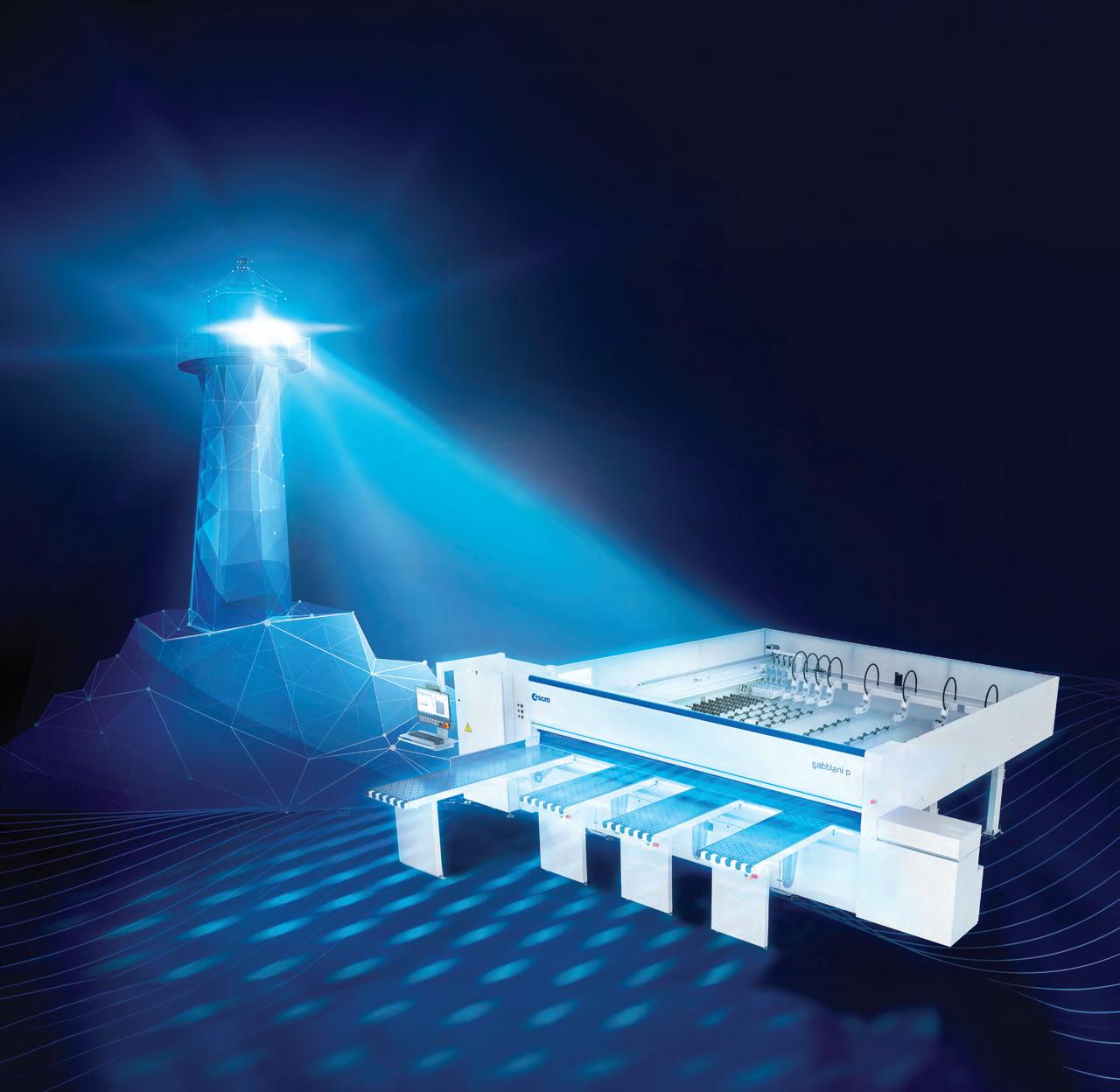
The shareholders’ meeting of Scm Group S.p.A. convened to appoint the new Board of Directors, the President, and the Honorary President, as well as to approve the financial statements as of December 31, 2024.
The new Board of Directors is composed as follows: Enrico Aureli (President), Andrea Aureli (Vice President), Giovanni Gemmani (Vice President), Marco Mancini (Chief Executive Officer), and board members Valentina Aureli, Luca Franceschini, and Martino Gemmani.
The shareholders also appointed Adriano Aureli as Honorary President.
The shareholders expressed their gratitude to the outgoing President Andrea Aureli and the outgoing Honorary President Alfredo Aureli for their valuable contributions during their respective terms.
The Group’s consolidated financial statements were also approved, showing revenues of €900 million as of December 31, 2024.
“Once again, over the past year, the macroeconomic environment has remained highly complex and uncertain for our business sectors and for the manufacturing industry as a whole, due to well-known geopolitical and economic challenges,” said Marco Mancini, CEO of Scm Group.
“Despite these critical issues, the Group continued to invest in expanding its presence in new business areas through two significant acquisitions: Tecno Logica, a specialist in the development of cutting-edge, fully integrated, high-mix and high-productivity technological solutions, and Mecal Machinery, a leader in machinery for processing aluminum profiles.”
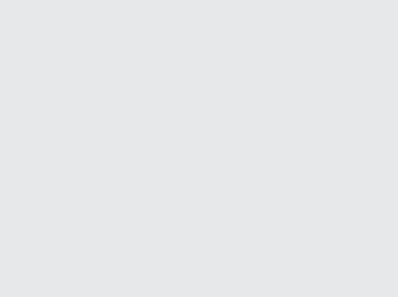
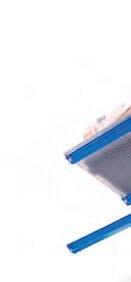
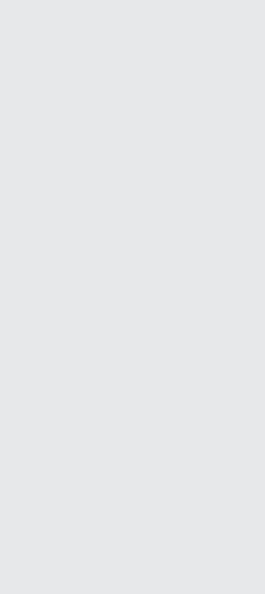
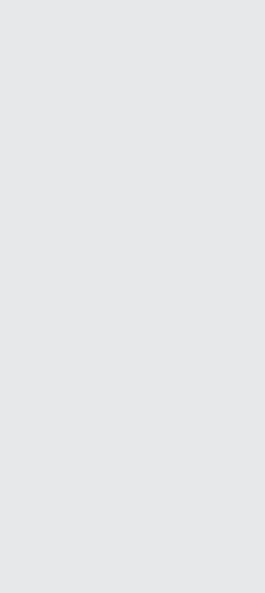
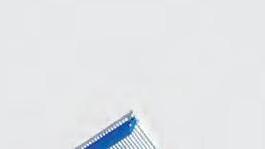
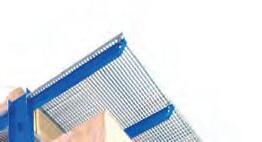
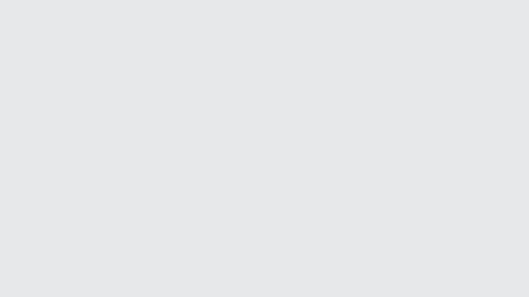
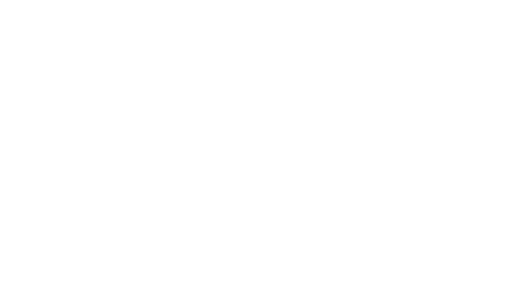
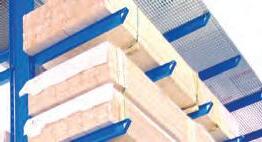
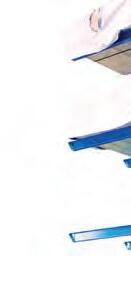
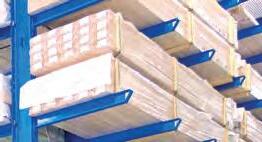
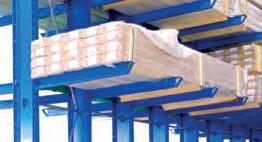
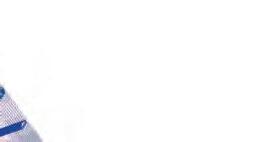
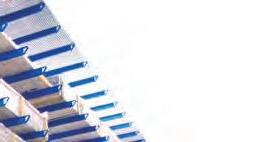
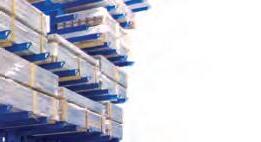
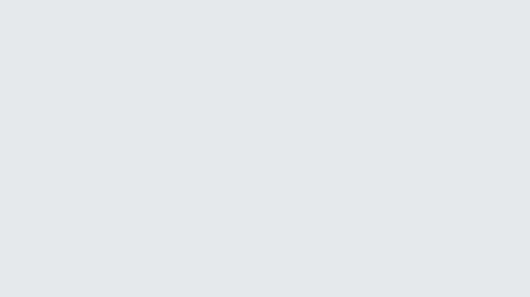
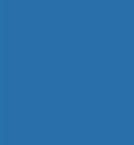
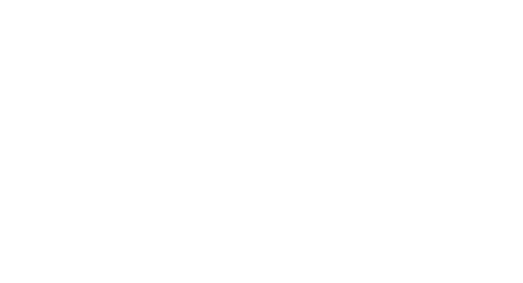
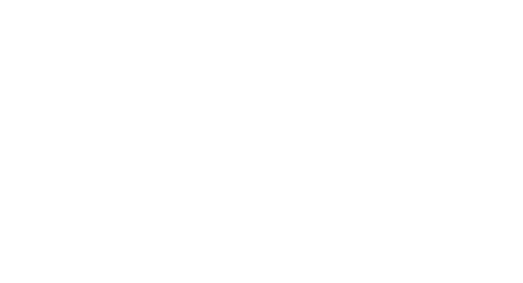
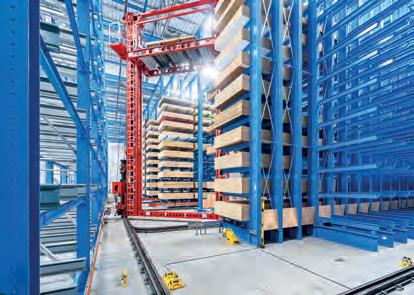
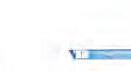

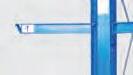
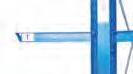


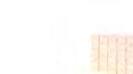
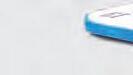


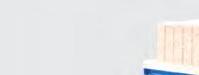
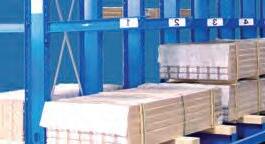
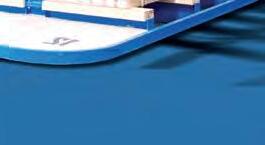
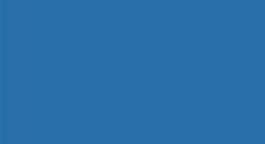
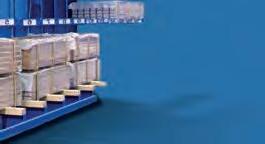
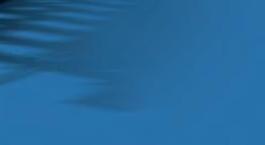
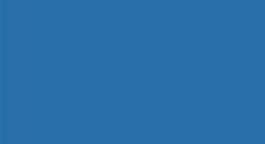

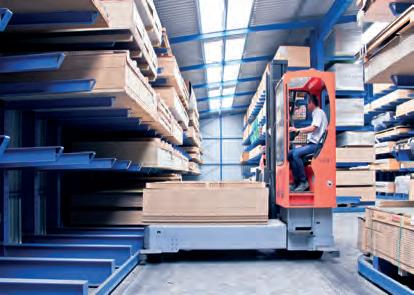
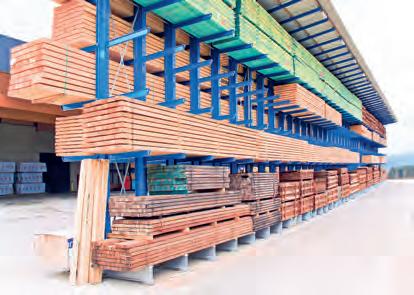
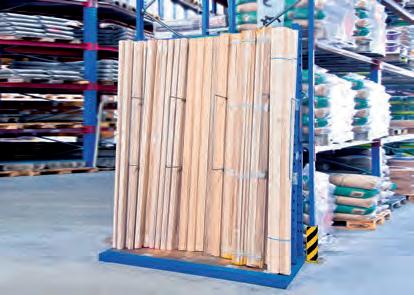
Combilift launches two groundbreaking solutions at LIGNA 2025
The New 8T Electric Sideloader and Combi Load Xtender Bring Unmatched Efficiency and Safety to Long-Load Operations
Timber yards, panel product suppliers, and sawmill operations face ever-increasing pressure to handle long and heavy loads more safely, more efficiently, and with less environmental impact. At Ligna 2025, Combilift unveiled two major innovations designed specifically with these industry challenges in mind: the new Combi-FSE 8000 and the Combi Load Xtender.
Combi-FSE 8000 – Heavy-Duty Electric Sideloader for Long Loads
The latest addition to Combilift’s four-wheel electric sideloader range, the Combi-FSE 8000, offers an 8-tonne lift capacity — ideal for handling structural timber, packs of sawn wood, panels, or engineered wood products in confined indoor or outdoor environments.
Key timber-focused benefits include:
• Powerful, Emission-Free Operation: Twin 18kW drive motors provide the torque and responsiveness required for heavy packs, with all-electric performance suited for indoor timber stores.
• Patented Traction and Steering: Designed for yearround reliability in muddy or uneven yard conditions.
• Unrivalled Operator Visibility: The under-deck battery position and expansive glazing allow operators a clear
line of sight, especially when reversing in narrow racking aisles or busy sawmill loading areas.
• Quick Battery Change: Ideal for multi-shift operations in busy timber yards.
Fleet managers also benefit from Combi-Connect, Combilift’s advanced telematics system for real-time machine performance tracking and maintenance planning.
Combi Load Xtender – Game-Changing One-Side Loading for Timber Yards
Unveiled alongside the sideloader, the Combi Load Xtender is a new pantograph-style load extender that enables complete loading and unloading of trailers or rail wagons from a single side — a major advantage in timber yards where space is tight or trailer access is limited.
For timber operations, the Xtender delivers:
• One-Side Access: Load full packs of timber from one side only, removing the need to move trailers or access both sides.
• Ultra low mechanism height: Its ultra-compact design ensures smooth movement and full functionality below standard trailer height without interference.
• Enhanced Safety: Operators can load securely against the far closed side of the trailer, reducing the risk of products falling and keeping personnel out of busy traffic zones.
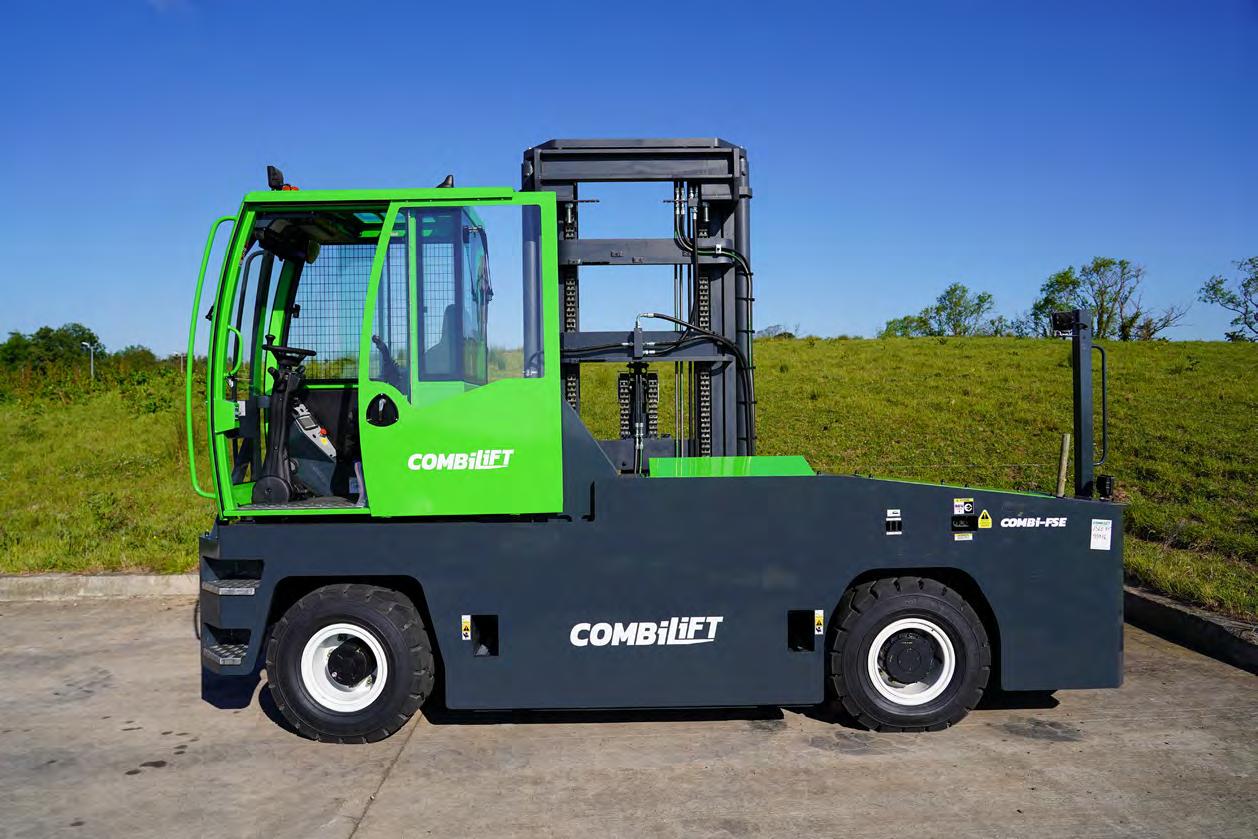
Purpose-Built for the Timber Industry
“These new solutions were developed in direct response to what we’re hearing from the timber sector,” said Martin McVicar, CEO, Combilift. “Customers need to move larger loads in tighter spaces with greater safety and lower emissions. The FSE 8000 and Combi Load Xtender do just that — and they’re backed by Combilift’s proven track record in long-load innovation.”
Both products are now available for order, with live demonstrations running throughout Ligna 2025.
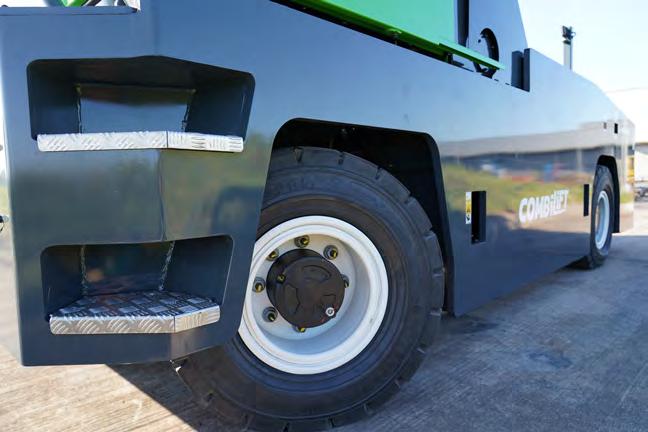
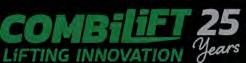
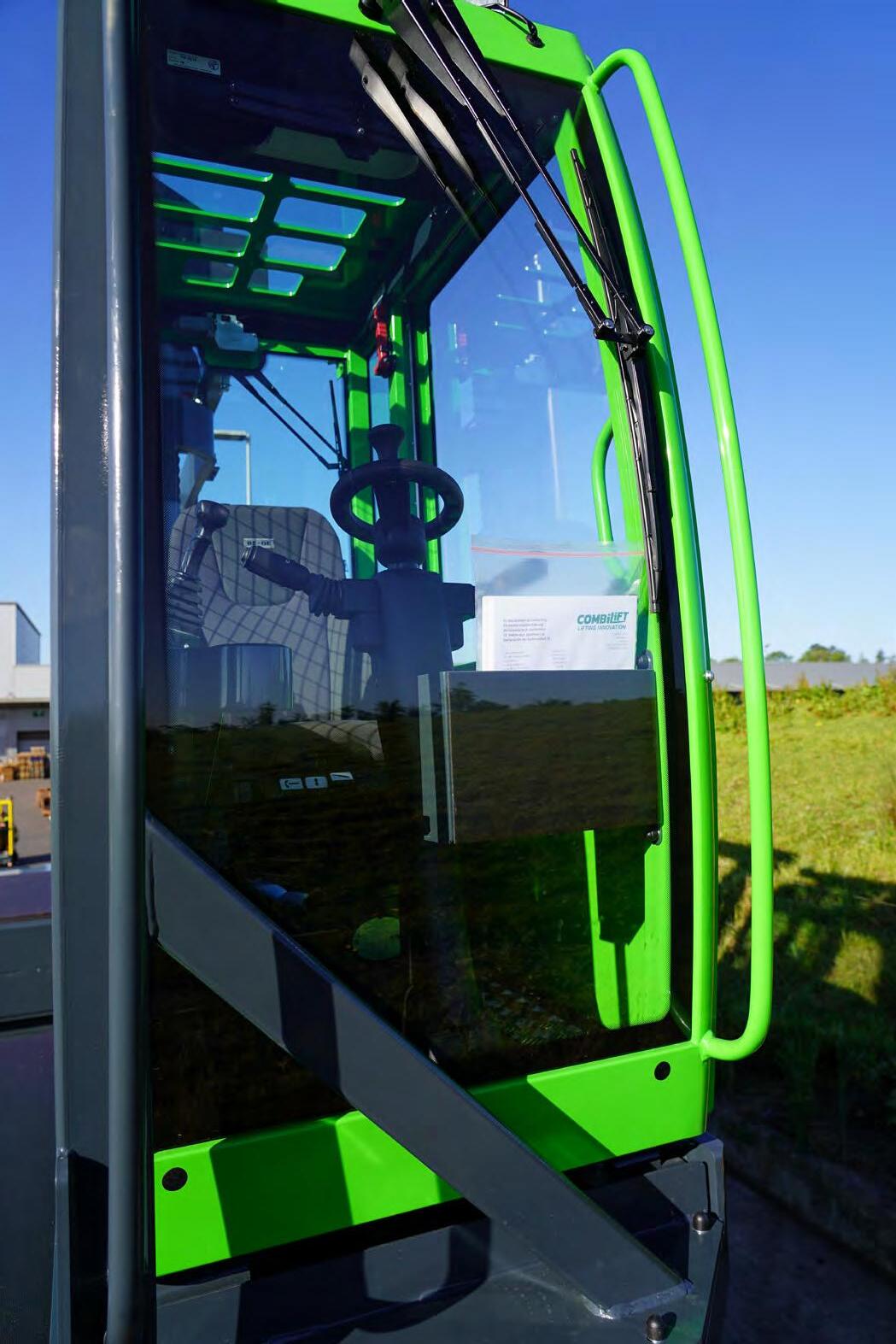
www.combilift.com/fse-8000/ www.combilift.com/combi-load-xtender/
Combilift receives its 3rd Red Dot Win
The recently launched Combi-CB70E earns global recognition for its ergonomic design, performance, and sustainability at the prestigious Red Dot Design Awards 2025
Irish-based manufacturer Combilift, a global leader in multi-directional and customised handling solutions, has been awarded the prestigious Red Dot Award for Product Design 2025 for its Combi-CB70E, highcapacity, electric-powered multidirectional forklift, developed to meet the needs of heavy-duty, long-load handling in more sustainable ways.
The Red Dot Award, one of the most internationally renowned design competitions, recognises excellence in design quality and innovation, and is no stranger to Combilift’s exceptional vision to shaping the future of the Commercial Vehicles Industry. This award completes a hat trick for Combilift who previously won a Red Dot for the Combi-WR and ‘Best of the Best’ for the Combi-CB4. Combilift’s Combi-CB70E impressed the international jury with its new ergonomic design, environmental credentials, and ability to enhance operator comfort and productivity in demanding industrial settings.
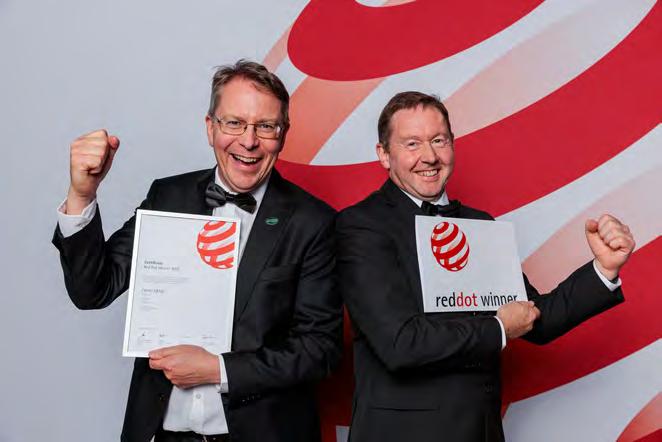
Martin McVicar, CEO and Co-founder of Combilift, commented: “We are delighted to receive our third Red Dot Award this year for the Combi-CB70E. Our design and engineering teams have been striving to provide solutions that are not only functional and safe but also reflect excellence in industrial design. Our customers increasingly demand electric alternatives that don’t compromise on performance, and the CB70E is exactly that.”
www.combilift.com/combi-cb70e/
Free tooling health check offer for joinery & furniture manufacturers
As a leader in woodworking technical expertise , Leitz Tooling is launching a new initiative and offering free tooling reviews to all joinery and furniture manufacturers.
A tooling review provides a valuable opportunity to make sure your tooling is legal, safe and efficient. Technical representatives from Leitz will visit your workshop and analyse your tooling, ensuring it is fit for purpose and making recommendations.
In addition to checking safety and legal compliance, Leitz will also check your tools are correct for their application and optimised correctly. Leitz can look at manufacturing challenges such as long cycle times, noise & dust and improving finish quality and make recommendations for improvement. Leitz can also analyse your machining strategies to ensure you are using the most efficient production methods available. Looking at your tooling, Leitz can recommend new tools to reduce downtime or streamline manufacturing processes.
Business Owners and Managing Directors are legally responsible for the tooling used in their business, do you know if you are safe and complaint? Are you at risk?
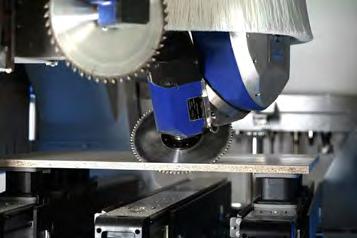
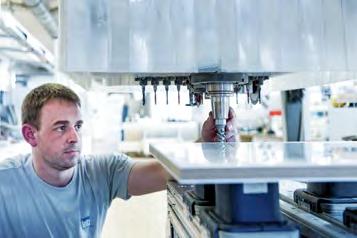
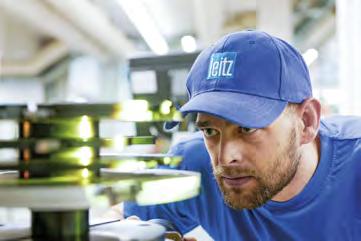
Tooling Review Benefits:
• Peace of mind. Prevent possible incidents and eliminate unhealthy practices.
• Ensuring all of your tooling is legally compliant and safe.
• Check your tooling is correct for current application and materials used.
• Check your tooling is optimised - reduce waste and cycle times.
• Check your machining strategies are right for your applications – improve finish and productivity.
• Feedback and recommendations on tool maintenance and sharpening frequency.
• Identify areas for process improvement.
This check is completely free of charge to Joinery Network members and following the check, a full report and recommendations will be provided to the business for your consideration.
Availability is based on demand, so contact Leitz today to book in your tooling review.
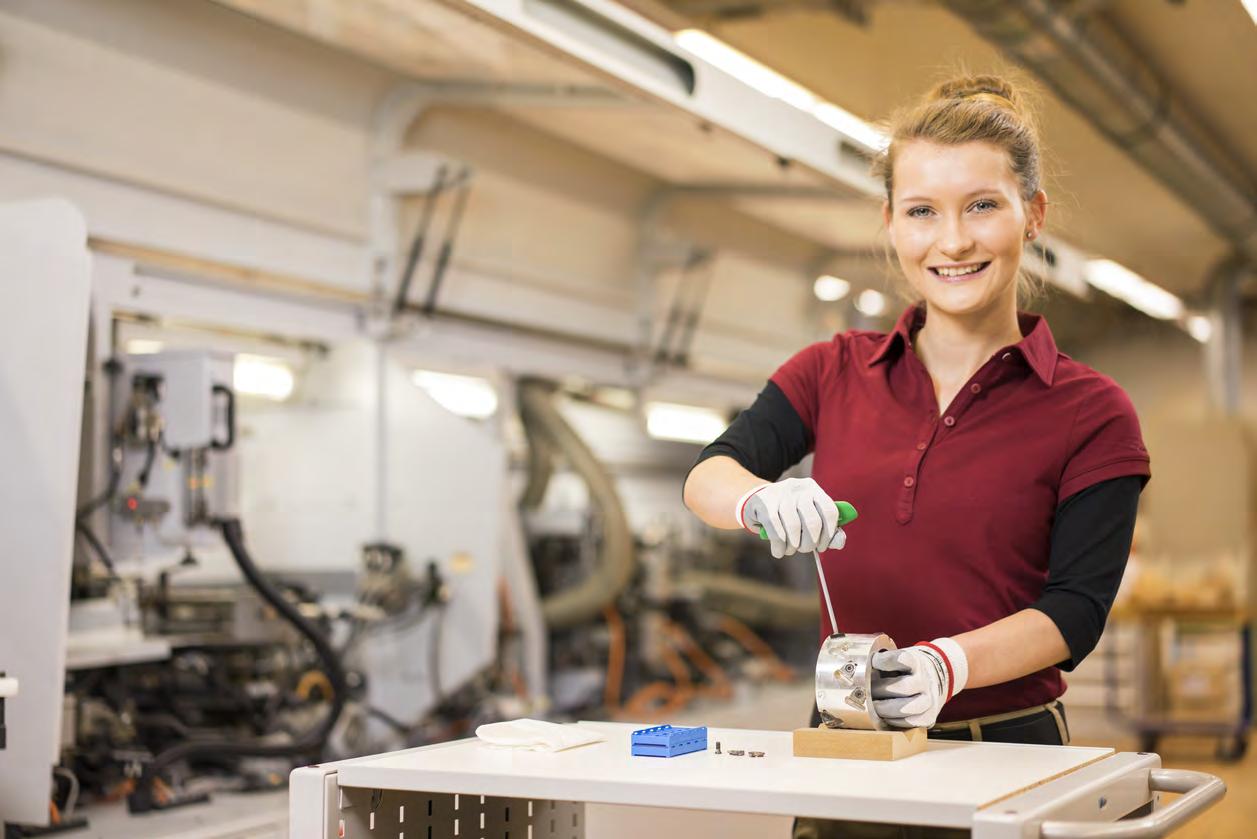
Biesse & The Joinery Network team up
Join Them For A Window & Door Manufacturing Technology Event At Biesse HQ
Biesse, Leitz & The Joinery Network
invite you learn how to grow your timber window & door business with high-performance machining and the innovative Lignum window and door system.
Open to all manufacturers, this open day is an ideal introduction into timber window and door manufacturing. For current manufacturers, this CNC focused event is the perfect place to introduce yourself to the industry-disrupting Lignum tooling system for timber windows and doors. Take advantage of our combined knowledge and learn how to build profit into your business with impactful machinery, tooling and technical support.
The Lignum system is all about efficiency and productivity, helping you to grow and scale your business. The system has also been engineered for compliance with building regulations, lowering barriers to entry and allowing joiners to compete for bigger contracts in all markets.
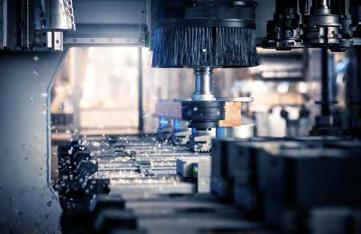
What To Expect At The Biesse & Joinery Network Event:
• Lignum CNC demonstration: Watch us manufacture a sash window efficiently using a Biesse CNC from the Rover range. Could you eliminate test cuts and avoid sanding?
• Passivglass demonstration: Discover the impact of Passivglass and learn about this new glazing product and how It competes with traditional methods like triple or double glazing.
• Talk to timber and joinery specialists about building more profit into your products.
• Talk to experts from across the Industry: Biesse, Leitz, The Joinery Network, BJ Waller, Teknos, JoinerySoft, Excel Finance and more…
• The Joinery Network Expert Market Place & technical support.
• A great opportunity to network with your peers, in your industry.
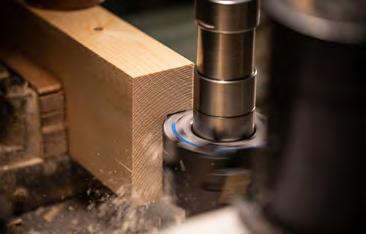
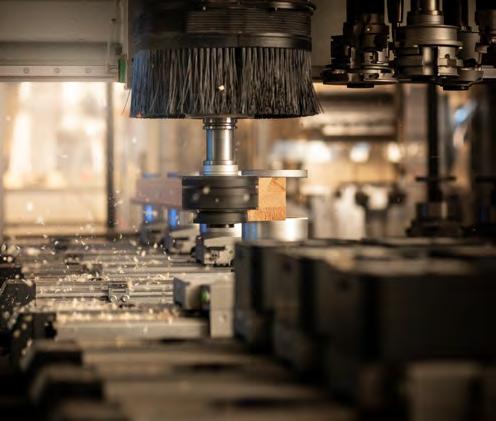
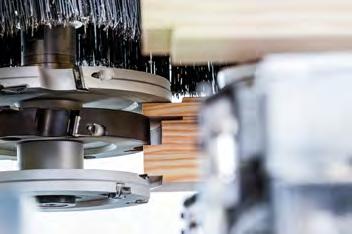
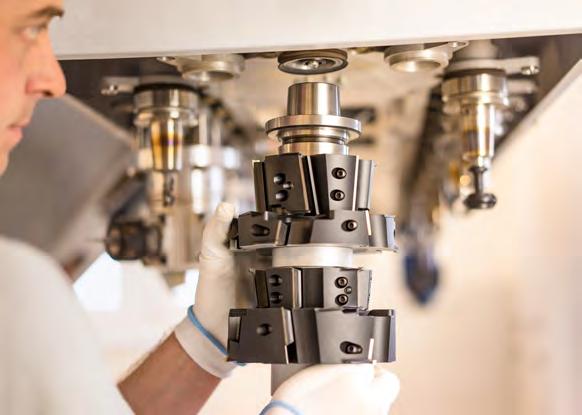
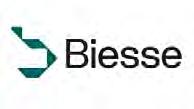
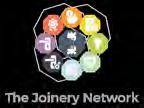
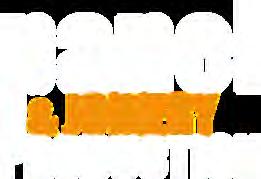

Share Your Stories
We invite you to share your latest case studies, product updates, or any other exciting news for us to promote across the PJP publishing network.
Editorial Features - included in our bi-monthly magazine, online web articles, social media platforms and e-newsletter.
Targeted e-Shots - deliver targeted messages to a highly relevant and engaged audience.
Event Promo Packages - encourage attendance through our unique online database and social media presence.
Contact the team at PJP to find out more at info@p-j-production.com
The PJP Network ensures we are delivering industry updates to our readers across Print, Email, Online and Social Media. PJP e-Newsletter - Subscribe Now
Subscribe now to receive all the latest industry news, new products, compelling case studies and industry events.
Delivered bi-weekly, our carefully curated updates will help to keep you well informed of all the latest news and updates from the wood
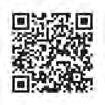
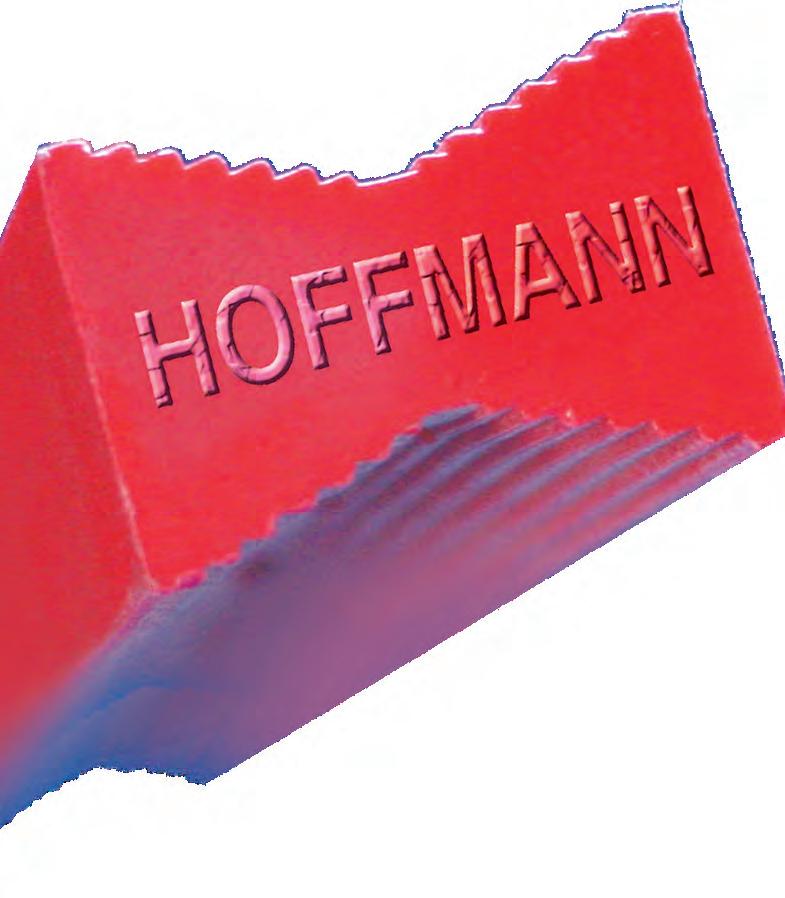
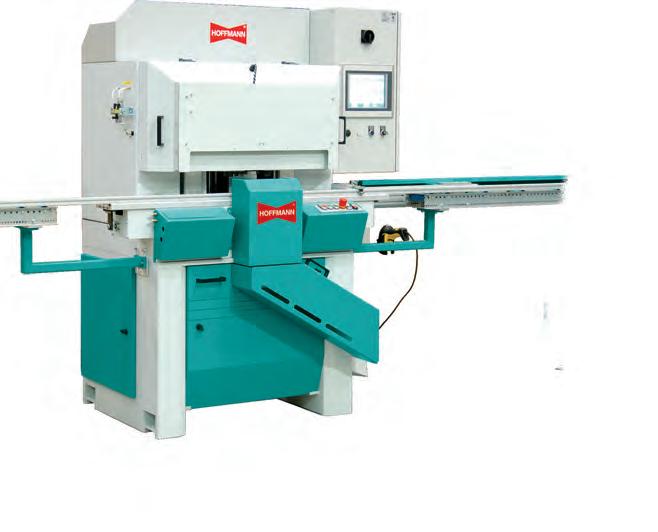
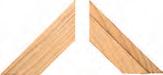
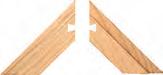
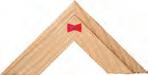
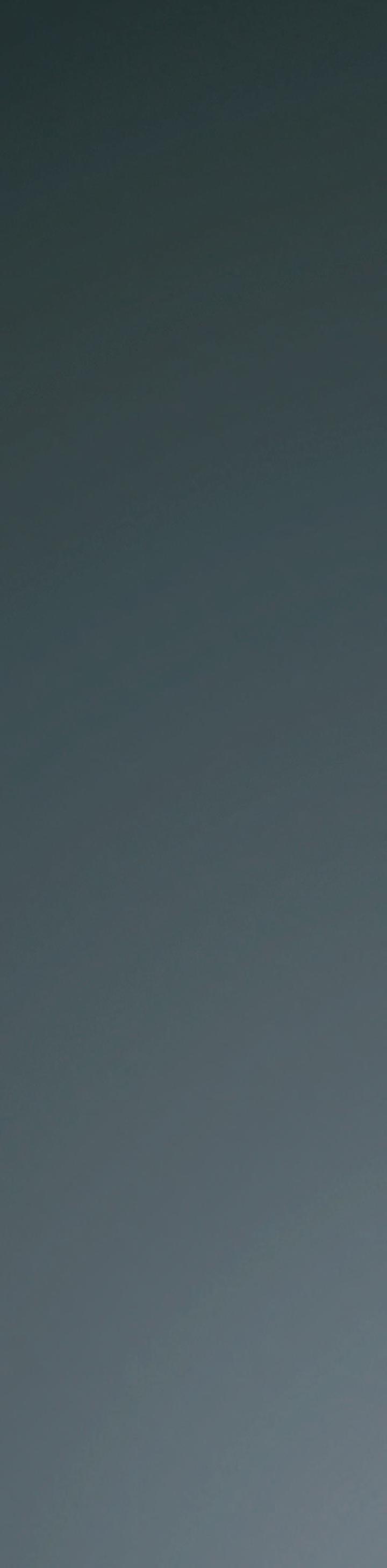
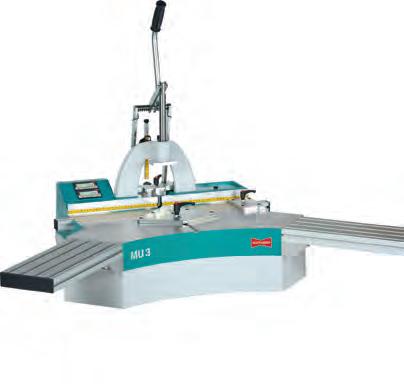
AXYZ WARDJet UK Open House AXYZ UK HQ, Telford, UK
(AWFS) Association of Woodworking & Furnishings Suppliers Fair Las Vegas
Saudi Wood Expo RICEC Riyadh, Saudi Arabia
London Design Festival London, UK
Design London Shoreditch EC1 London, UK
Biesse & The Joinery Network Biesse Group UK, Daventry
Woodtech Woodtech | Tüyap Fair and Congress Centre, Istanbul
SICAM 2025 Pordenone Fiere, Italy
WEINIG Connect 2025 WEINIG UK Showroom, Abingdon, UK
British Woodworking Federation Annual Awards Kimpton London Hotel
Surface Design Show Business Design Centre, London
Eurobois EurExpo, Lyon, France
Fimma + Maderalia Fiera Valencia, Spain 17 May - 19 May
Professional Woodworking Expo NEC, Birmingham, UK
Clerkenwell Design Week EC1 London, UK
International Woodworking Fair Georgia World Congress Centre, USA
dp-decor is the original and trusted paper foil range from Decorative Panels Lamination - developed as a cost-effective yet visually stunning alternative to real wood veneers.
The collection features an extensive selection of woodgrain, unicolour, and fantasy designs, developed in partnership with leading global print houses.
www.decorativepanels.co.uk
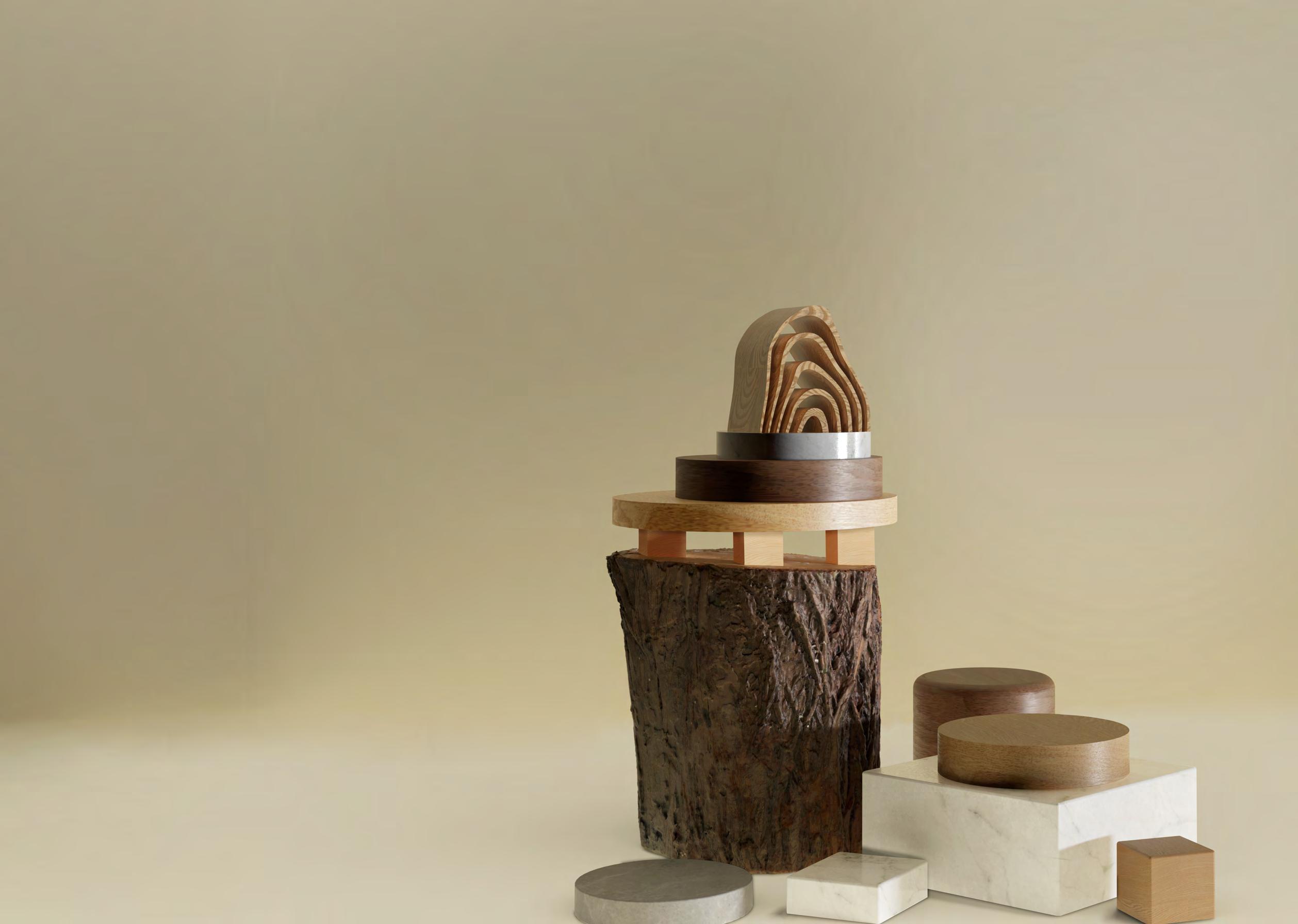
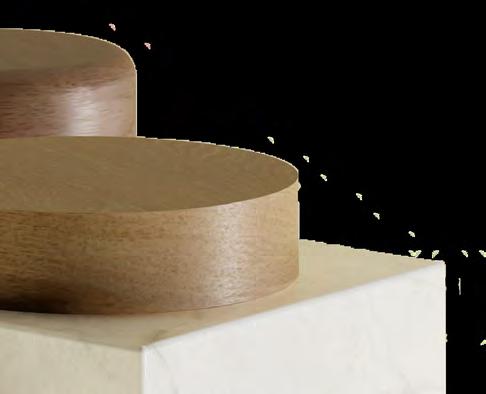
