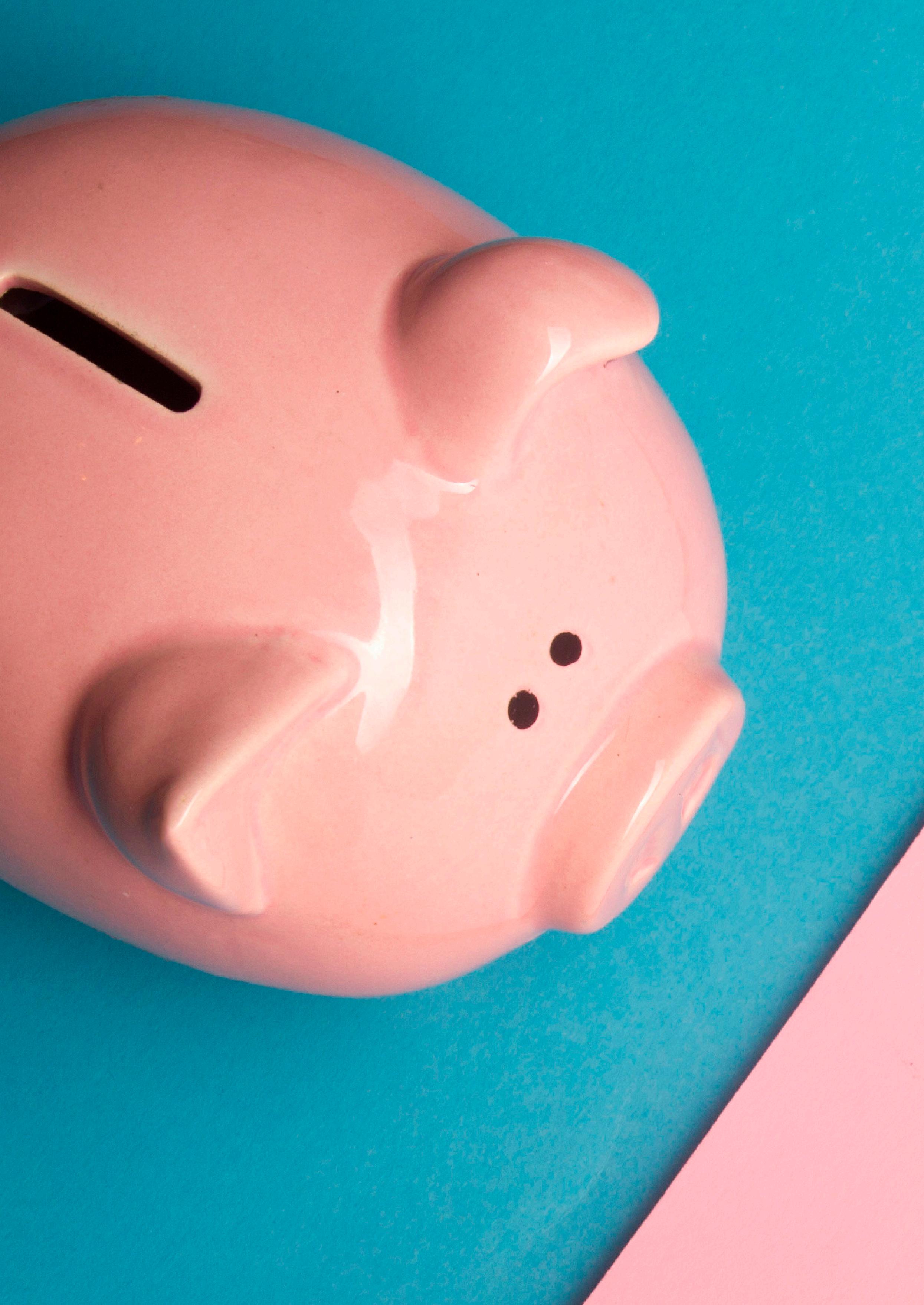
7 minute read
Investing in a net-zero future
Continuing to upgrade pipelines to advance safety is an ongoing priority for natural gas utilities, says Christina Sames, Senior Vice President for Safety, Operations, and Security, The American Gas Association (AGA), USA.
merican natural gas utilities deliver essential energy to customers and communities safely and reliably. The US Department of Energy estimates that US natural gas will remain between half and one-third the price of other fuels through 2050, ensuring that Americans have access to affordable energy to meet their needs.
Thanks to continual investment in reliability and safety by utilities, natural gas is the most dependable form of energy, with only one in 800 customers experiencing an unplanned gas outage in any given year, compared to at least one outage per year for nearly all customers of electric distribution systems. This incredible reliability is made possible by a commitment to the industry’s number one priority – safety. One of the greatest priorities of this commitment to safety is helping ensure the structural integrity of natural gas pipelines.
The continuous investment in pipeline safety, reliability and innovation has helped maintain a safe and reliable distribution system. Utilities are consistently modernising their systems to help ensure continued safe and reliable service, and in parallel driving down emissions – so much that distribution system emissions declined by more than 69% from 1990 to 2020, a trend that continues today.
Part of the modernisation process includes applying integrity management to help keep natural gas transportation systems safe and reliable. Operators consider the age and material of the pipeline, the method of construction, the characteristics of the natural gas that is transported, and the potential for corrosion or other issues.
Efforts to maintain the integrity of pipelines should be understood as having two goals: helping ensure that infrastructure can meet all demands safely, and that our infrastructure can meet the fuel needs of the future. For example, in some cases, fuel blends with a high hydrogen content can temporarily compromise metal via embrittlement whilst for other pipelines, external water or corrosive byproduct can pose a corrosion risk. These are things that utilities pay attention to as they work on maintaining the safety of systems for customers and communities.
Natural gas pipelines are made from a variety of materials. In the US, customer piping inside the house is primarily copper, while the other side of the meter is mostly polymer or steel. Pipelines buried under streets can be iron, steel, plastics or PVC, while major supply pipelines are typically carbon steel, used specifically for high pressures.
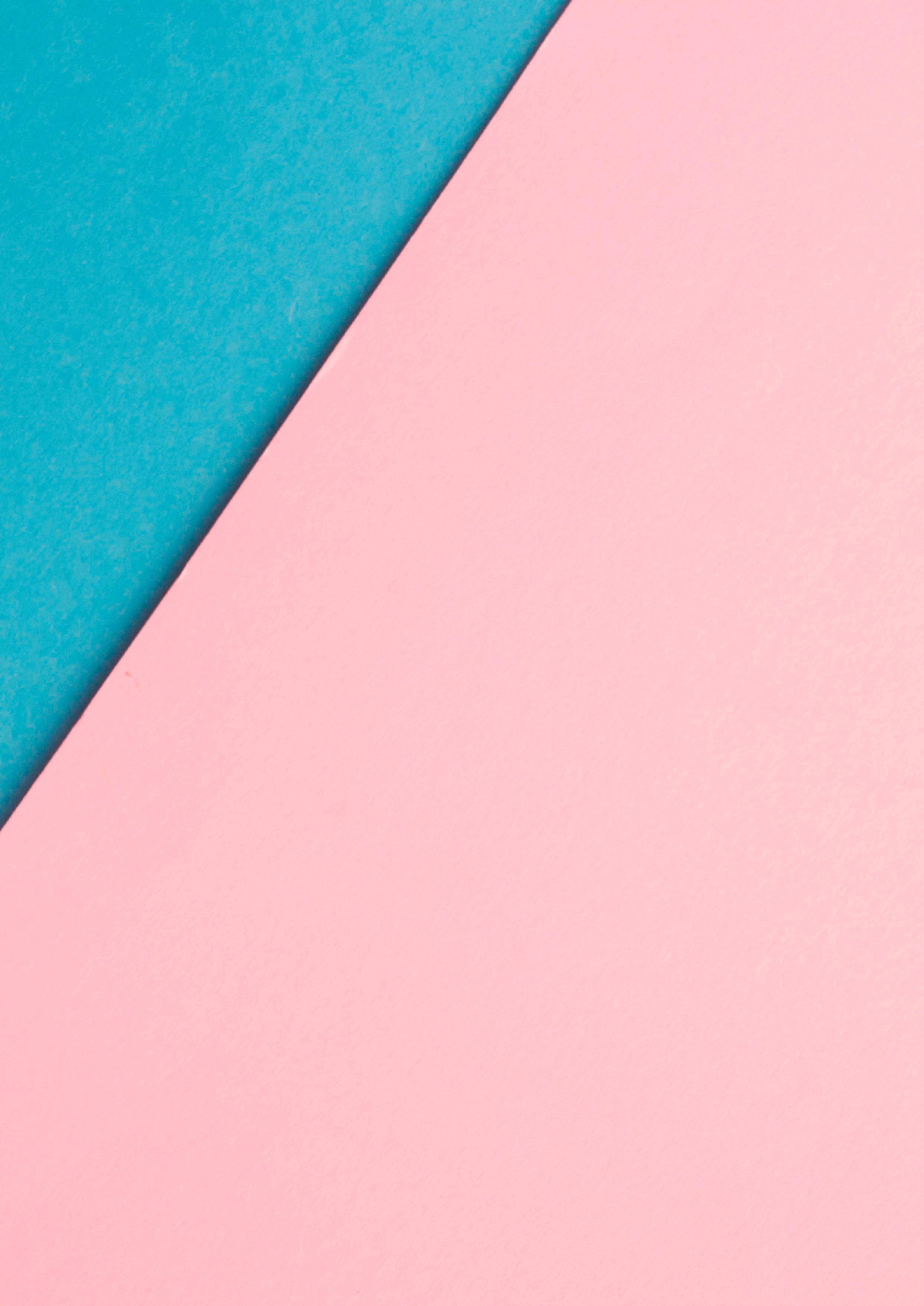
Iron pipelines According to the US Department of Transportation’s Pipeline and Hazardous Materials Safety Administration (PHMSA), approximately 60% of the total mileage in distribution pipelines is plastic, 38% is steel, and the remainder consists of cast, wrought and ductile iron pipes.1 With more than 3.1 million miles (5 million km) of natural gas pipelines in the US and Canada, including 2.6 million miles (4.2 million km) of local utility distribution lines, the range of materials used in the construction of pipelines means that there is no such thing as a one-size-fits-all approach to maintaining the integrity of pipelines.
While less than 2% of the distribution system today is made of iron pipelines, there are still segments in select parts of the US that consist of iron. Many early pipelines were made of iron with mechanically coupled joints incorporating fibrous materials to ensure an airtight seal. Natural gas utilities have invested heavily in replacing such pipes with more modern materials that incorporate advanced polymers or high-grade steel, especially in areas that are using higher pressures.
Exposure to groundwater can be an issue for some pipelines. The modern interstate system operates at significantly higher pressures than some earlier pipelines were designed for. This poses some unique challenges for some materials, like a build up of byproduct that is not present in geologic natural gas, because of the nature of the materials and casting methods. However, these unique challenges do not always mandate replacement – there are additional safety measures available. Frequently, iron pipelines will incorporate cathodic protection, where an electric current helps prevent corrosion on the surface through electro-chemistry. And for lower pressure systems, iron pipelines can continue to provide reliable supplies of natural gas safely and affordably.
‘Pipe within a pipe’ As the industry continues to modernise pipelines, many utility companies are turning to the ‘pipe within a pipe’ method. This method installs a flexible plastic liner into an existing pipeline. ‘Pipe within a pipe’ enables pipelines to operate at significantly higher pressures than otherwise possible. A higher-pressure system allows the same volume of pipeline to transport increased volumes of gas, improving the performance of the system in high demand areas.
An internal liner also allows for pipelines constructed from materials prone to hydrogen embrittlement to transport hydrogen safely and reliably. The US Environmental Protection Agency (EPA) has stated that the costs of this are significantly lower than excavating and replacing with new materials.
Continuing to upgrade pipelines to advance safety is an ongoing priority for natural gas utilities. Most existing pipeline infrastructure can operate on a gas blend containing up to 20% hydrogen without major modifications, and without incurring any significant embrittlement risks across all components of the natural gas distribution system. When hydrogen is added to a higher pressure, higher flow, steel pipeline’s fuel mix at levels above 20% of the total volume of gas within the pipeline, it increases the possibility that the pipeline could experience material embrittlement and potential leaks.
Helping ensure that these pipelines can handle increasing concentrations of hydrogen is worth the investment. Among the advantages of the US’s extensive natural gas network is that the infrastructure can be used for both geologic natural gas and other renewable sources of energy. Renewable natural gas (RNG), as well as carbon-neutral green hydrogen, will continue to be a part of the nation’s fuel mix as it works towards a cleaner energy future. The Biden Administration recently approved and started to disburse US$8 billion in funding for renewable hydrogen hubs, a move that will likely lead to more hydrogen production and more hydrogen blending. Further, a variety of carbon-neutral synthetic natural gases (SNG) create more opportunities for using power-togas technologies. Safety will continue to be the absolute top priority as these fuels are incorporated into the gas distribution system with increasing regularity, and in greater percentages of the total blend.
When the ‘pipe within a pipe’ method is not ideal, or when more modern materials and larger capacity is beneficial, pipelines can be replaced entirely using a variety of materials. For transportation pipelines, this usually means steel. For distribution pipelines past the city gate, the replacement pipelines are typically plastic, such as PVC.
Safety and reliability Since 1990, North American natural gas utilities have more than tripled the miles of pipelines made from more modern materials. Carbon steel or stainless-steel pipelines can be rubberised or treated with specialised corrosion and embrittlement-resistant paints. Like iron pipelines, steel pipelines also typically incorporate cathodic protection. PVC and other modern plastics do not corrode at all and are capable of operating at high pressures. This makes them excellent choices for local distribution networks, which is why polymers represent 60% of the total pipeline mileage, a percentage that is only likely to increase.
Utilities are consistently modernising their systems to help ensure continued safe and reliable service, and in parallel this is driving down emissions. One secret of the success of US natural gas utilities in providing such a safe and reliable natural gas distribution system is an extensive system of peer review, and a culture of open sharing of safety information. The American Gas Association (AGA) Peer Review Program is a voluntary safety and operational practices programme that allows participating companies to be reviewed by their peers, share leading practices, and identify opportunities to better serve customers and communities. Each review features a panel of fellow gas utility professionals from North America who provide the company with feedback to help enhance its safety and efficiency.
Natural gas is key to achieving our nation’s energy future while protecting our energy security today, and the distribution system is at the heart of it all. Efforts to help ensure system integrity are important both to continue to ensure safety, and to reach the US’s environmental goals. AGA’s study, ‘Net-Zero Emissions Opportunities for Gas Utilities’, identifies a variety of pathways to net-zero greenhouse emissions for the natural gas utility sector, and continued investment in modernising and upgrading distribution pipelines is key to those pathways.2 A safe and reliable distribution system is key to ensuring that the natural gas industry continues to deliver environmentally friendly, affordable, and reliable energy to Americans every day.
References
1. www.phmsa.dot.gov/data-and-statistics/pipeline/pipeline-mileage-andfacilities 2. www.aga.org/research/reports/net-zero-emissions-opportunities-for-gasutilities
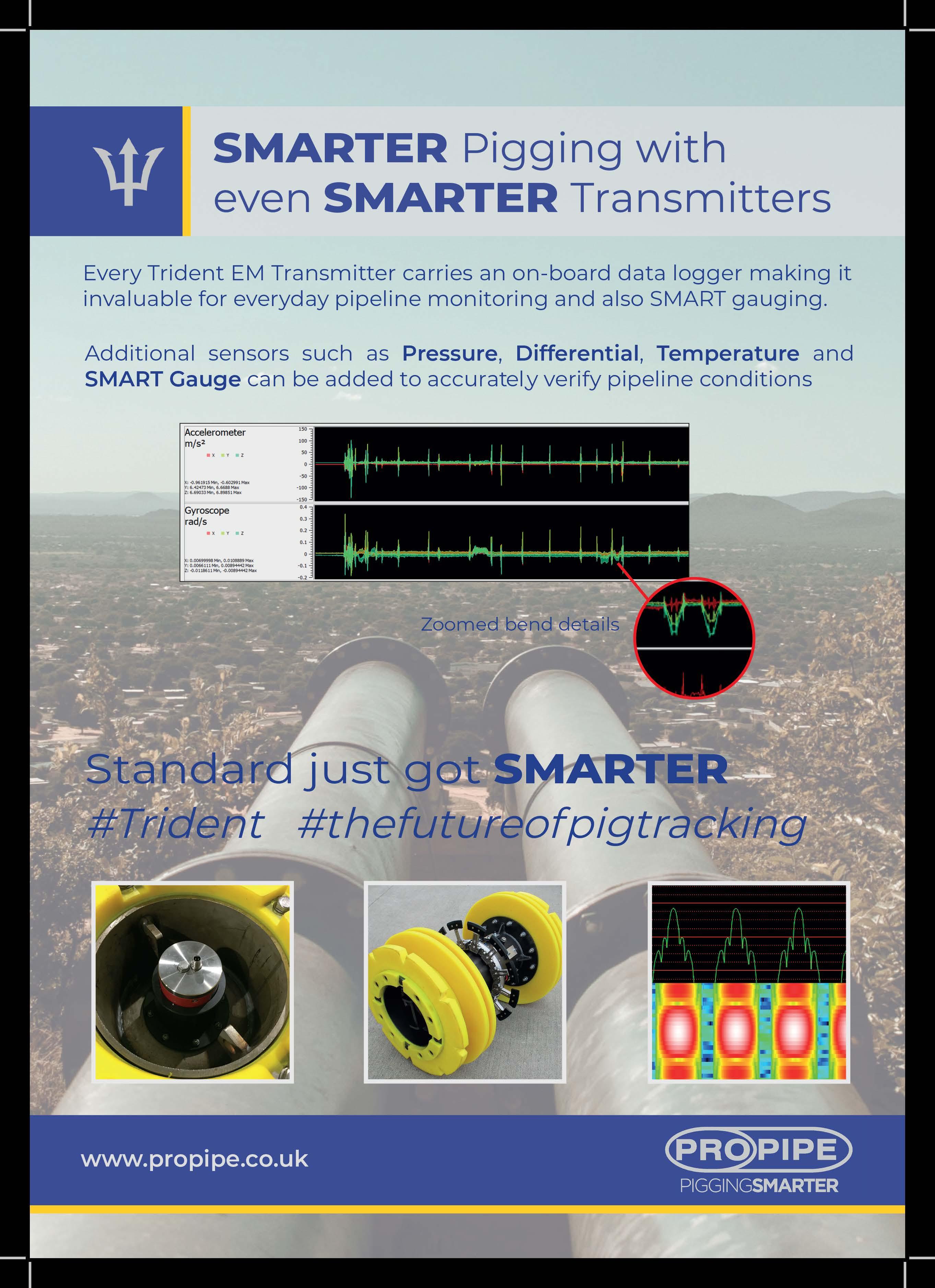