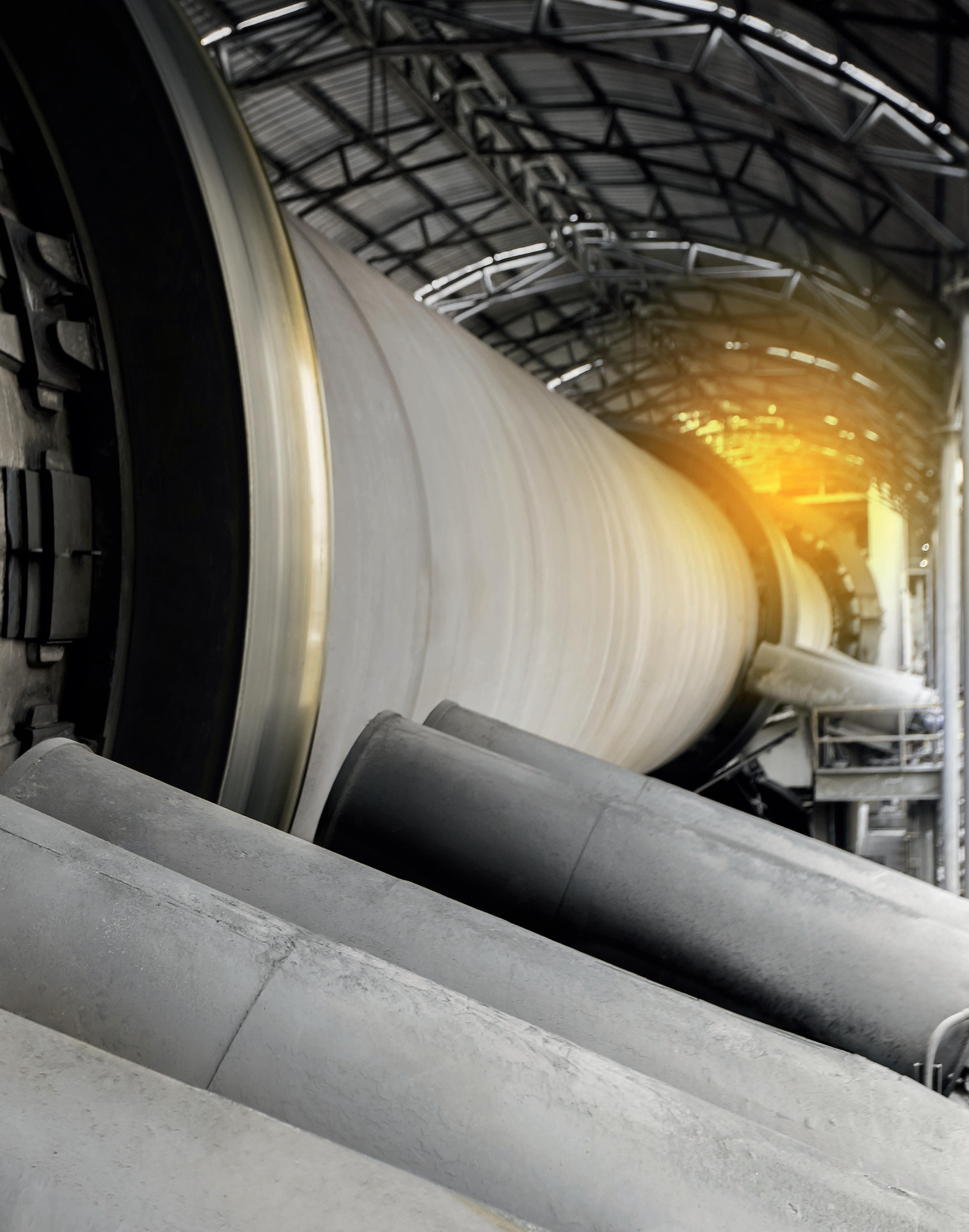
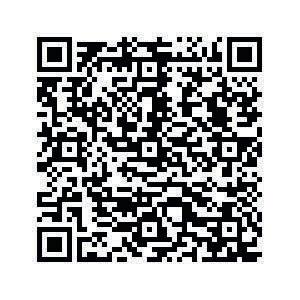
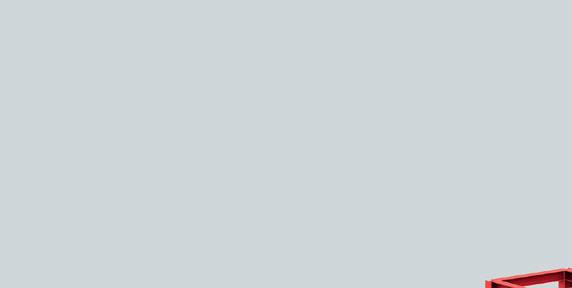
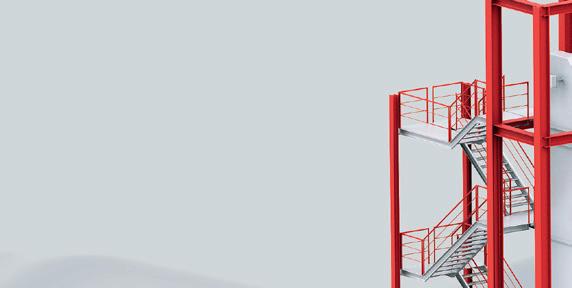
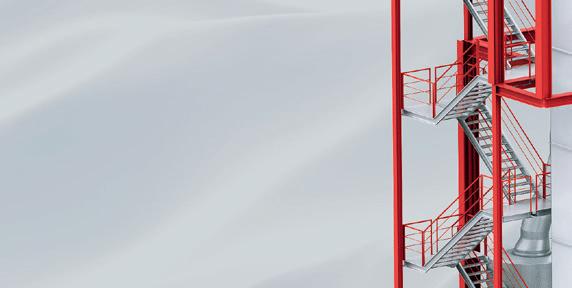
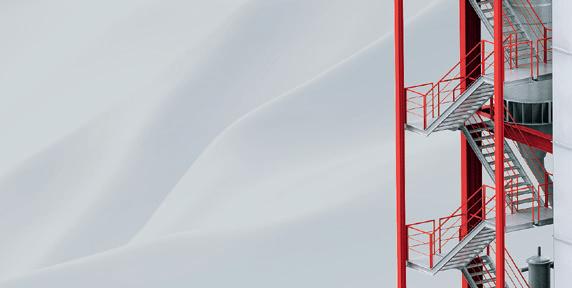
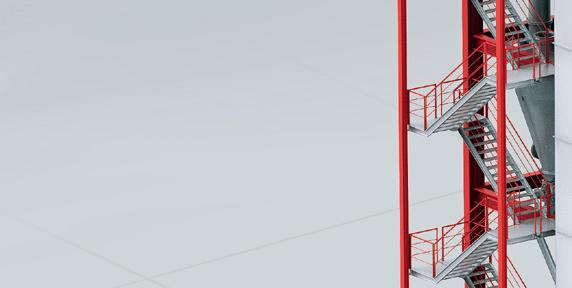
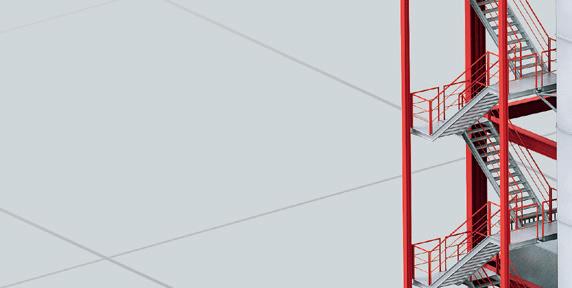
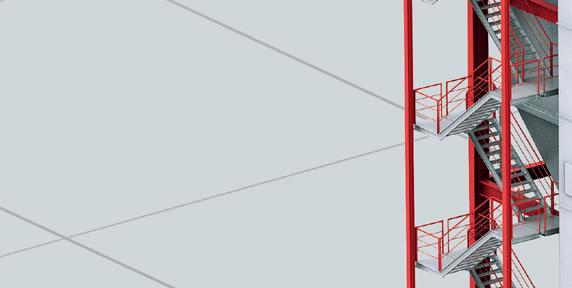
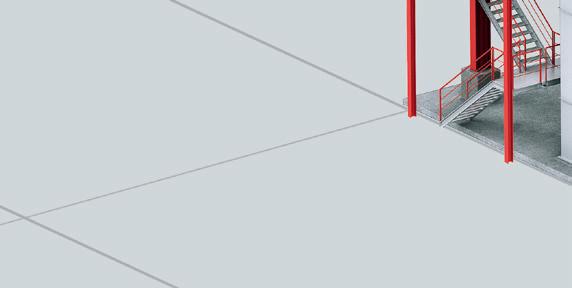
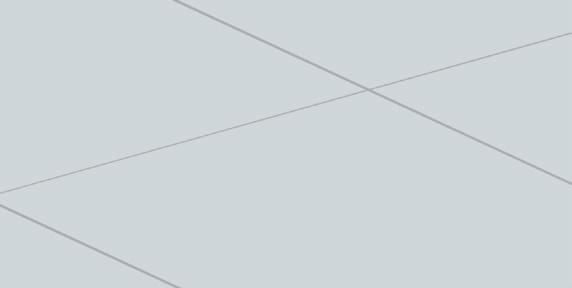
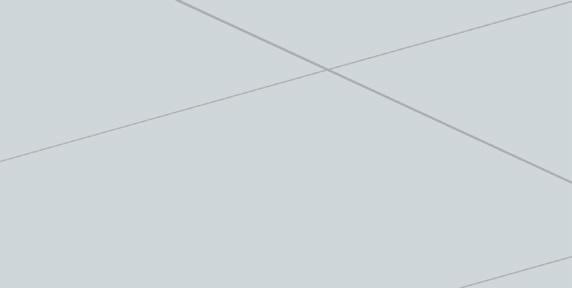
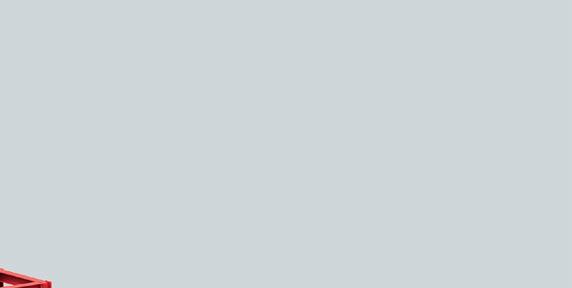


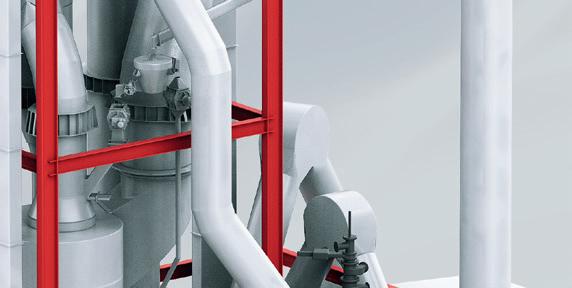
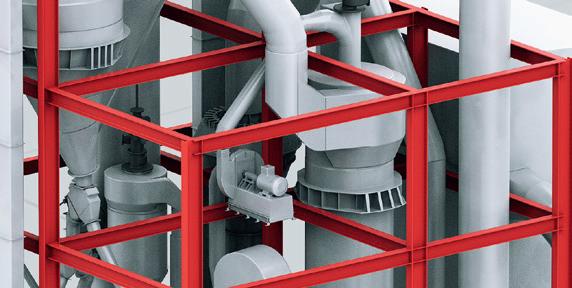
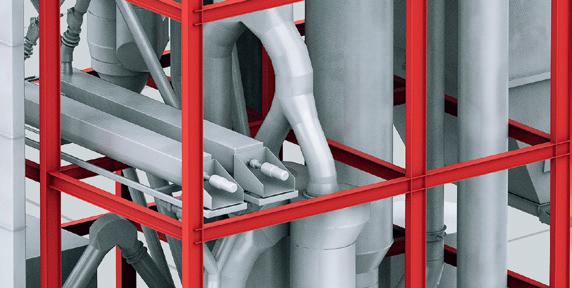
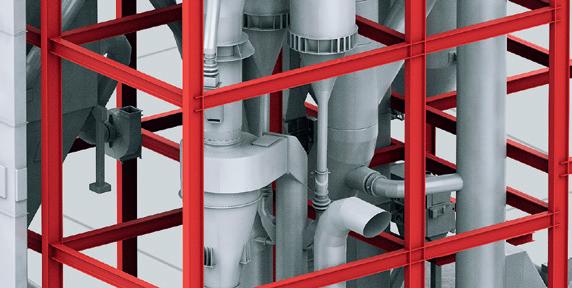
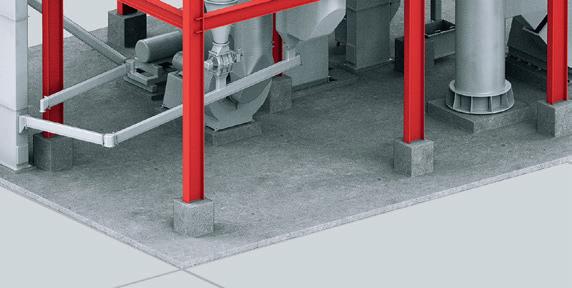
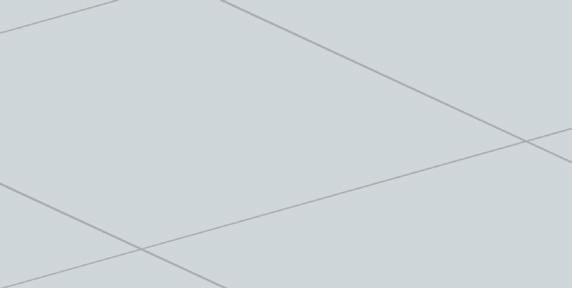
Rotary calciner for upgrades
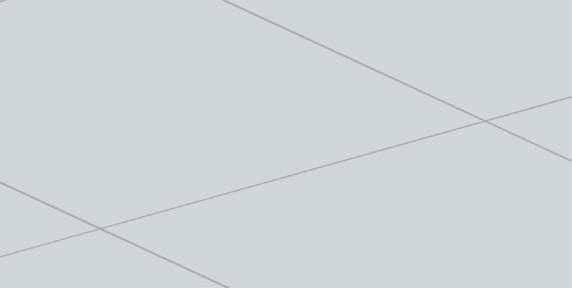
Based on the familiar principals of clinker production, rotary clay calciners are ideal for mothballed clinker production lines.
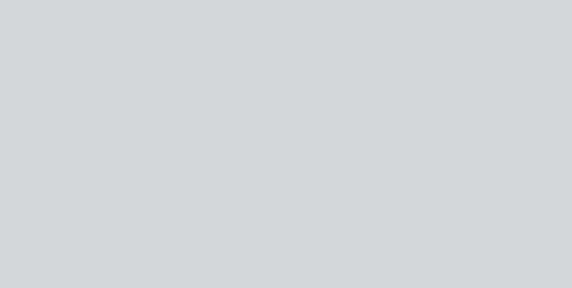
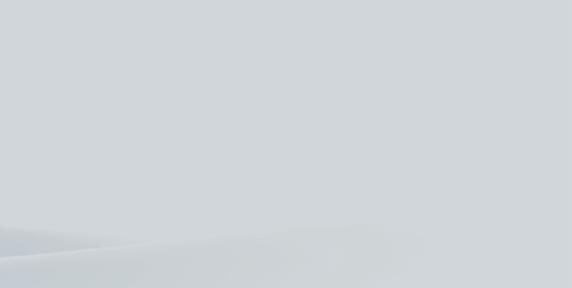
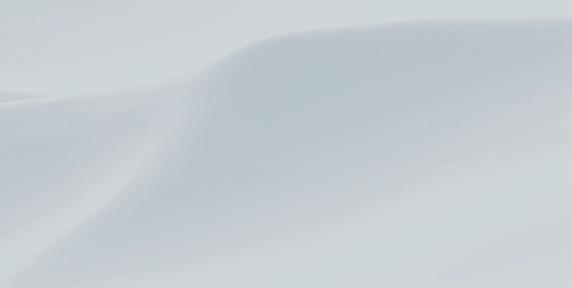
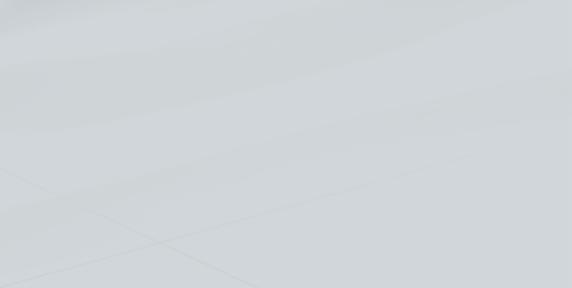
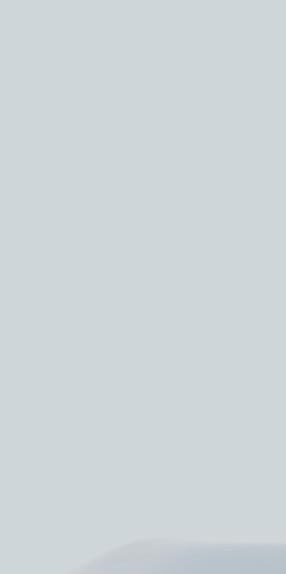
Rotary calciner for upgrades
Based on the familiar principals of clinker production, rotary clay calciners are ideal for mothballed clinker production lines.
Cement producers around the world are pursuing clay calcination as part of e orts to cut the carbon intensity of cement.
But how best to implement these projects?
That depends on a range of site-specific factors.
Our clay calcination solutions have been developed from proven components and processes to deliver a high-quality Portland cement substitute. And they come backed by our advanced process and plant engineering skills to ensure they deliver the best possible results for your application.
We can also combine them with our leading alternative fuel solutions to further reduce carbon emissions. So, when you’re looking for your clay calcination partner, think KHD.
And let’s deliver Cement beyond Carbon together. www.khd.com/clay-calcination
Flash calciner for new projects
Ideal for greenfield projects, our flash calciner delivers cost-e ective clay calcination, including for very sticky clays and clays with up to 40% moisture.
Benefit from extra AF potential
Alternative fuel solutions like the Pyrorotor® o er signifcant extra benefits with regards to emission reduction.
Our clay calcination solutions produce material that is the same color as ordinary cement –thanks to advanced process control. No additional processes required.
03 Comment
05 News
ACHIEVING NET ZERO
10 The Blended Cement Boom
DIGITALISATION
56 Unlocking AI’s Cement Potential
Isabel Rask, alcemy, explores how well-designed interfaces are key to overcoming AI adoption challenges in the cement industry and ultimately driving decarbonisation efforts.
62 Digitally Decarbonising Cement
Mike Ireland, Portland Cement Association (PCA), examines the opportunities and challenges arising from the growing demand for blended cements in the US.
15 Affordable Actions For Clean Cement
Elliot Mari, Industrial Transition Accelerator (ITA), outlines some affordable policies for decarbonising the cement industry.
20 Disruption Through Startups
Eduardo Gomez, CRH Ventures, explains why partnering with startups is key to the decarbonisation revolution.
24 The Carbon Solution
Rob Cumming, Lafarge Canada (East), explores how a ‘silver buckshot’ approach can achieve net-zero concrete without the high costs of CCS or e-fuels.
31 The Blueprint for Cement’s Carbon Crusade
Bodil Recke, ABB Process Industries, discusses the strategies driving the cement industry’s transition to sustainability.
SCMs & LOW CARBON CEMENTS
36 Partnering For Progress
Olivier Guise, Ecocem, discusses how collaboration and scalable low-carbon solutions can accelerate the cement industry’s path to net zero.
42 Scaling Up Low Carbon Cement
David Hughes, Material Evolution, explores the benefits of ultra-low carbon cement in transforming the built environment.
49 Crucial Clay Activation Conditions
Mylène Krebs, Jean-Michel Charmet, and Damien Chudeau, Fives FCB, discuss the key factors influencing the calcination process and present insights from a calcination test centre in Northern France.
53 Ashes To Innovation In Concrete
Grant Quasha, Eco Materials Technologies, reveals how the innovative use of coal ash and other supplementary cementitious materials is helping the concrete industry reduce its carbon footprint and improve performance.
Pascal Gaillot, Yokogawa Europe, explains how the integration of digital technologies and decarbonisation strategies is preparing the cement industry for the future.
67 The AI Advantage
Molly Pace, Imubit, explains how closed loop AI optimisation is reshaping cement manufacturing by boosting efficiency, reducing emissions, and enabling real-time process control.
CARBON CAPTURE, UTILISATION, & STORAGE
72 The Enablers And Disablers of CCUS
Rohan Dighe, Ismael Justo-Reinoso, Tania Alvarez, and Peter Findlay, Wood Mackenzie, consider a range of factors that could impact the deployment of CCUS in cement production.
77 Consolidating Carbon Capture
Jeffrey Tyska, Honeywell, highlights how advanced carbon capture technologies can help cement producers significantly reduce CO2 emissions and achieve their decarbonisation goals.
81 CCS 101
Katherine Romanak, The University of Texas at Austin, underscores the crucial role that carbon capture and storage (CCS) will play in driving decarbonisation within the cement industry.
85 Mastering Emissions With Membranes
Cool Planet Technologies discusses the implementation of advanced membrane carbon capture technology in the cement and lime industries.
High-performance lubricants from Klüber Lubrication offer opportunities to increase uptime and lower specific energy consumption. Saving energy is top of the agenda for most cement plants these days. Lubricant and service solutions from Klüber Lubrication can help operators to reduce costs – while increasing the sustainability of their plant. Get in touch to learn more about increasing the availability of kilns, mills, coolers, crushers and compressors whilst evidently saving energy and reducing cost. Visit: www.klueber.com/cement
rod.hardy@palladianpublications.com
Sales Manager: Ian Lewis ian.lewis@palladianpublications.com
Sales Executive: Sophie Birss sophie.birss@palladianpublications.com
Head of Events: Louise Cameron louise.cameron@palladianpublications.com
Digital Events Coordinator: Merili Jurivete merili.jurivete@palladianpublications.com
Digital Content Coordinator: Kristian Ilasko kristian.ilasko@palladianpublications.com
Junior Video Assistant: Amélie Meury-Cashman amelie.meury-cashman@palladianpublications.com
Digital Administrator: Nicole Harman-Smith nicole.harman-smith@palladianpublications.com
Administration Manager: Laura White laura.white@palladianpublications.com
Reprints reprints@worldcement.com
DAVID BIZLEY, SENIOR EDITOR
Hello Dear Reader, and welcome to the March 2025 issue of WorldCement.
I hope you’re keen to get reading because this is no ordinary issue. Of course, all the usual aspects are here – regional industry analysis, technical insights, case studies, and the latest news. However, a glance at the Contents page should highlight a common theme: decarbonisation.
So, why have we made this choice? Well, aside from the importance of the topic, it’s finally time for the 2025 edition of our flagship decarbonisation focused conference: EnviroTech – The Gateway To Green Cement. This issue has been commissioned from the ground-up to act as something of a companion piece for the show. Throughout the following pages, you’ll hear from cement producers, industry associations, and technology providers as they provide their insights and expertise on a range of decarbonisation-related topics – insights and expertise that are needed now more than ever.
Looking back to my comment from the March 2024 issue of WorldCement(published just prior to our first EnviroTech conference), I noted how the cement industry found itself caught between the twin challenges of building the world of the future, whilst also helping to ensure that same world remained liveable.
CBP019982
Annual subscription (published monthly): £160 UK including postage/£175 (€245) overseas (postage airmail)/US$280 USA/Canada (postage airmail). Two year subscription (published monthly): £256 UK including postage/£280 (€392) overseas (postage airmail)/US$448 USA/Canada (postage airmail). Claims for non receipt of issues must be made within 4 months of publication of the issue or they will not be honoured without charge.
Applicable only to USA and Canada: WORLD CEMENT (ISSN No: 0263-6050, USPS No: 020-996) is published monthly by Palladian Publications, GBR and is distributed in the USA by Asendia USA, 17B S Middlesex Ave, Monroe NJ 08831.
Periodicals postage paid at Philadelphia, PA and additional mailing offices. POSTMASTER: send address changes to World Cement, 701C Ashland Ave, Folcroft PA 19032
Copyright © Palladian Publications Ltd 2025. All rights reserved. No part of this publication may be reproduced, stored in a retrieval system, or transmitted in any form or by any means, electronic, mechanical, photocopying, recording or otherwise, without the prior permission of the copyright owner. All views expressed in this journal are those of the respective contributors and are not necessarily the opinions of the publisher, neither do the publishers endorse any of the claims made in the articles or the advertisements. Uncaptioned images courtesy of Adobe Stock. Printed in the UK.
Palladian Publications Ltd 15 South Street, Farnham, Surrey GU9 7QU, UK Tel +44 (0)1252 718999
Email: mail@worldcement.com Website: www.worldcement.com
As I write this a year later, those twin challenges remain. Cement and, by extension, concrete are still the only building materials capable of meeting the world’s infrastructure demands. And the clock is ticking, ever faster, when it comes to tackling climate change. I mentioned last month how 2024 is now officially the hottest year on record according the UN. And, as Katherine Romanak (Research Professor for the University of Texas), points out in her article on pg 81: “If we continue with our current policies, we are on a path towards a global temperature rise of 3.1˚C by the end of the century.”
It’s clear that action is needed now – from industry, from government, from every level of society. And, by being responsible for the oft-quoted figure of 7% of global CO2 emissions, the cement industry has a golden opportunity to play a lead role in combatting this global crisis. Thankfully, the industry has grasped this opportunity with both hands. Progress continues to be made on multiple fronts, with new developments showcased throughout this issue, all moving the industry forwards, toward a greener future.
For those of you reading this at our venue in Athens, then:
You’ll be able to hear more about the latest developments in cement’s decarbonisation journey in-person from our line-up of expert presenters and panellists. You’ll also have ample opportunity to share your own insights, build relationships, and collaborate at our multiple networking events.
And for those of you who weren’t able to join us, stay tuned for highlights from this year’s edition of EnviroTech. And perhaps consider registering your interest for our 2026 outing here: https://bit.ly/EnviroTech2026
Meanwhile, wherever you are, I hope you enjoy the issue. Until next time: Αντίο.
Molins receives a visit from President Salvador Illa at Sant Vicenç dels Horts
Molins welcomed the President of the Generalitat of Catalonia, Salvador Illa, to its headquarters in Sant Vicenç dels Horts (Barcelona). During the meeting, Molins highlighted its commitment to decarbonisation and shared the progress made in its Sustainability Roadmap plan, which outlines the path to reducing its CO2 emissions by 20% by 2030.
This plan accelerates the efforts Molins has been undertaking since 1990, with the ultimate goal of supplying carbon-neutral concrete by 2050.
During the meeting, Molins highlighted the ongoing sustainability projects, such as its alternative raw materials (MPA) plant, which enabled the reuse of more than 93 000 t of construction and demolition waste in 2024.
Additionally, Molins delved into innovative initiatives it is developing, including energy efficiency projects aimed at reducing thermal consumption and CO2 emissions at its plants, as well as projects from its artificial intelligence laboratory focused on industrial applications.
Marcos Cela, CEO of Molins, emphasised Molins commitment to decarbonising the cement sector: “At Molins, we have been driving concrete initiatives for years to accelerate the transition toward a more sustainable industry. We are aware that the goal is highly ambitious, but at the same time, we know that, as a society, we cannot afford to aim for anything less. That is why we continue to push forward with cutting-edge innovation projects that will allow us to develop new solutions. The visit of President Salvador Illa has been an excellent opportunity to share our progress and reaffirm our commitment to sustainable industrial development.”
The visit also included the presence of Government Delegate Pilar Díaz and the Mayor of Sant Vicenç dels Horts, Miguel Comino, alongside President Illa. Representing Molins were its President, Juan Molins, and CEO, Marcos Cela, along with Salvador Fernández, Executive Vice President Cement & RMC Spain & Mexico; Carlos Martínez, Chief Strategy & Sustainability Officer; and Ignacio Machimbarrena, Chief Innovation Officer.
Holcim & Gebr. Pfeiffer collaborate on GO4ZERO green cement project.
Gebr. Pfeiffer has received an order to supply a vertical roller mill of the type MVR 5000 R-4. The mill is intended for the new 4800 tpd kiln line of Holcim (Belgique) SA in the existing Obourg cement plant in Belgium.
Holcim (Belgique) SA has chosen Gebr. Pfeiffer's ultra-modern grinding technology for its GO4ZERO green cement project. A vertical roller mill of the type MVR 5000 R-4 will be used for cement raw material grinding. The mill will grind 370 tph of cement raw material to a fineness of ≤ 15% R to 0.090 mm. At the same time, the cement raw material is dried in the mill from a feed moisture content of approximately 4% to a residual moisture content of < 0.7%.
In addition to efficient comminution and the associated high power density, MVR mills are also characterised by very smooth running and very low pressure drop. These features increase the technical availability and reduce both emissions and specific operating costs. In this project, the mill is integrated into the pioneering 'oxyfuel operation', with all the resulting requirements. This is, for example, the longest possible uninterrupted mill operation, to achieve the highest possible efficiency in the subsequent 'CO2 capture process'. The mill will be equipped with a SLS 4000 VR classifier.
Gebr. Pfeiffer is very pleased to be able to contribute again to reducing the carbon footprint. The contract is being handled by the Chinese general contractor CBMI. The MVR mill is expected to be put into service in the second half of 2025.
thyssenkrupp Polysius and SaltX to develop emission-free facilities
thyssenkrupp Polysius and SaltX have signed a letter of intent (LOI) to jointly develop the next generation of fully electrified production facilities. This partnership aims to scale innovative technologies and advance the decarbonisation of the industry. New technologies, fresh ideas, and exciting opportunities were the focus of a workshop between thyssenkrupp Polysius and SaltX, an innovative start-up from Sweden driving the electrification of calciners.
Together, they discussed potential collaborations and the integration of this groundbreaking concept into various business areas.
bauma.de/en/trade-fair
IEEE-IAS/PCA Cement Conference
04 – 08 May, 2025 Birmingham, AL., USA cementconference.org
CEMENTTECH 2025
15 – 17 May, 2025 Hefei, China www.cementtech.org
Carbon Capture Technology Expo North America
25 – 26 June, 2025 Houston, TX., USA www.ccus-expo.com
POWTECH
23 – 25 September, 2025 Nürnberg, Germany www.powtech-technopharm.com
As part of this collaboration, SaltX's patented electric arc calciner (EAC) technology will be integrated into thyssenkrupp Polysius' green system solutions. The EAC process enables the electric calcination of materials, replaces fossil fuels with renewable energy, and isolates the released carbon dioxide, resulting in an emission-free production process.
Dr. Luc Rudowski, Head of Innovation at thyssenkrupp Polysius, stated: “The partnership with SaltX is a significant step towards a sustainable industry. By integrating the electric arc calciner technology, we can expand our portfolio of green solutions and offer our customers innovative and environmentally friendly production methods. This collaboration is an important milestone on the path to decarbonising the cement and lime industry.” The electrification of calciners could be a game-changing technology for both thyssenkrupp Polysius and the entire industry. There is great potential in the areas of cement, lime, and direct-air-capture (DAC). Cement is a key sector where sustainable technologies are becoming increasingly important. In the lime sector, electrification could bring new efficiency and environmental benefits. DAC is an innovative process for capturing CO2 directly from the ambient air.
Lina Jorheden, CEO of SaltX, added: “The collaboration with thyssenkrupp Polysius is of great importance to effectively implement our technology and drastically reduce CO2 emissions in the industry. Together, we can set new standards and offer our customers fully electrified and emission-free production facilities.”
Lukas Schoeneck, Head of Green Solutions at thyssenkrupp Polysius, commented: “This partnership is based on mutual trust and shared goals. Both sides benefit from the collaboration by combining our strengths and developing innovative solutions that are both ecologically and economically advantageous.”
Materials Processing institute unveils £1 million sustainable cement and concrete centre
The Materials Processing Institute (MPI) is taking a significant step in supporting the construction industry’s drive toward decarbonisation with the opening of its £1 million Sustainable Cement and Concrete Centre (SCCC) later this month.
Supported by MPI’s Advanced Materials Characterisation Centre, The SCCC will focus on cutting-edge research and material development, including novel formulations for low-carbon cement and concrete and the use of electric arc furnace (EAF) slags in aggregate and clinker production. It will also provide consultancy services to further support clients to accelerate innovation, offering expertise and project management from concept through to pilot stage production.
MPI hosted a meeting of the Cement Standards and Technical Group of the Mineral Products Association (MPA). Delegates were given an exclusive, advanced tour of the facility, showcasing its advanced capabilities to drive sustainability within the built environment.
Process improvement is like sailing. With an experienced partner, you can achieve more.
Optimizing processes and maximizing efficiency is important to remain competitive. We are the partner that helps you master yield, quality, and compliance. With real-time inline insights and close monitoring of crucial parameters, we support manufacturers to optimize processes, reduce waste, and increase yield.
Terry Walsh, CEO of MPI, said: “The SCCC is a critical step in supporting the UK construction industry’s journey to net zero. Cement and concrete are the backbone of our built environment, and by focusing on decarbonising, we can significantly reduce emissions across the sector. This facility demonstrates our commitment to sustainability, providing the tools, expertise, and innovation required to enable a greener future through fuel switching, low-carbon cements and concretes, and innovations such as carbon capture, utilisation, and storage (CCUS) technology.
Roger Griffiths, Manager – Innovation Projects of the MPA, commented: “MPI’s investment in this facility will help support cement and concrete research and testing to strengthen the UK’s position as a leader in sustainable construction innovation.”
Concrete and cement play a vital role in the UK economy, with over 90 million t used annually. The industry contributes £18 billion to GDP and supports 3.5 million jobs, underpinning critical infrastructure and housing. Decarbonising this essential material is a significant opportunity to reduce emissions, ensuring sustainability and resilience in the construction sector.
The SCCC is a key part of the broader EconoMISER programme, led by the Foundation Industries Sustainability Consortium (FISC), which aims to accelerate the decarbonisation of the UK’s foundation industries. It builds on MPI’s role as a national leader in research and innovation, and its track record in delivering transformational change across the sector.
Titan Cement International SA have announced that its Belgian subsidiary, Titan America SA, parent of its US operations, has priced its initial public offering (IPO) of 24 000 000 common shares at a price to the public of US$16.00 per share.
The IPO consists of 9 000 000 new common shares to be issued and sold by Titan America and 15 000 000 existing common shares to be sold by Titan Cement International SA. Titan Cement International SA has granted the underwriters a 30-day option to purchase up to an additional 3 600 000 common shares to cover over-allotments, if any, at the initial public offering price, less underwriting discounts and commissions.
Titan America’s common shares are expected to begin trading on the New York Stock Exchange
under the ticker symbol 'TTAM' on February 7, 2025. The offering is expected to close on February 10, 2025, subject to the satisfaction of customary closing conditions.
Titan America expects to receive net proceeds of approximately US$136 800 000, after deducting underwriting discounts and commissions, which will be used for capital expenditures and other general corporate purposes, including to fund investments in technologies and Titan America’s growth strategies and to pursue strategic acquisitions that complement Titan America’s business.
Titan Cement International SA expects to receive net proceeds of approximately US$228 000 000, after deducting underwriting discounts and commissions.
After the completion of the IPO, Titan Cement International SA is expected to own 160 362 465 common shares of Titan America, representing 87% of the total outstanding common shares (or 156 762 465 common shares, representing 85% of the total outstanding common shares, if the underwriters exercise in full their over-allotment option).
Citigroup and Goldman Sachs & Co. LLC (in alphabetical order) are acting as joint lead book-running managers for the IPO. BofA Securities, BNP Paribas, Jefferies, HSBC, Societe Generale, and Stifel are acting as bookrunners for the IPO.
The Innovandi Open Innovation Challenge 2025 will unite start-ups with leading global cement and concrete manufacturers to collaborate on cutting-edge solutions for low-carbon concrete.
The Open Challenge is looking for start-ups from around the world working on next generation materials towards net zero concrete, e.g. low-carbon admixtures, supplementary cementitious materials (SCMs), activators, or binders.
Thomas Guillot, Chief Executive of the GCCA, said: “Advanced production methods which are decarbonising our sector are already being used in cement and concrete production in many parts of the world. Through the Innovandi Open Challenge, start-ups can bring in even newer ideas and further accelerate our industry’s push."
Mike Ireland, Portland Cement Association (PCA), examines the opportunities and challenges arising from the growing demand for blended cements in the US.
The demand for lower-carbon cements in the US has quickly grown from a trickle to a flood, as sustainability continues to emerge as a key metric for end users on par with resilience and reliability. In a short time, the market has shifted significantly, with more advanced cement blends being developed for the future.
In some areas of the US, 100% of the cement currently being produced is portland-limestone cement (PLC). The rest of the country is moving in a similar direction, making blended cement the new default for modern construction projects. This blended material carries substantial
environmental benefits, with up to 10% less embodied carbon than traditional portland cement. PLC offers a way for concrete producers to achieve a lower-carbon footprint, much like fly ash and slag cement have done for decades.
The transition to using greener cements has been underway for many years, but the pace has dramatically picked up recently as more producers, contractors, engineers, and architects have gained experience and confidence working with PLC. In 2020, blended cements like PLC represented about 3% of the 100 million metric t of cement consumed annually in the US. By 2024, blended cements grew to more than half of the total US cement consumption.
With this shift came significant climate benefits. In 2023, replacing traditional portland cement with PLC resulted in more than 3.9 million metric t of carbon avoided. That is roughly equivalent to a year’s worth of emissions from one coal-fired power plant, according to the US Environmental Protection Agency.
While traditional portland cement has long dominated the construction and infrastructure market in the US, blended cements offer an opportunity to maintain ambitious climate goals of net zero building without adding costs to projects. Traditional portland cement was patented almost 200 years ago, and challenges today call for new solutions.
In addition, those who have worked with PLC are realising benefits such as a lighter colour, which can be advantageous in certain architectural uses, and similar, or even improved, performance. A primary advantage is that PLC also offers carbon reduction with the ability to meet the same proven performance as traditional cement.
Contractors start with the same amount of PLC to replace portland cement, then test the mixture to confirm fresh and hardened properties. As the quantity of PLC produced in the US continues to grow, so does the number of projects it is being used in – and there are now numerous examples across the country that showcase the successes of blended cements.
A prominent example of PLC being at the centre of a new project’s design is the new US$64 million training facility for the WNBA’s Seattle Storm. In construction, all the cement used was Type IL: the project used ASTM C595 Type IL PLC produced by Ash Grove Cement, a CRH company. As the team plays in Seattle’s Climate Pledge Arena, in a city that passed new building performance standards to reach net zero by 2050, sustainability was a critical key metric, leading the contractors to use PLC throughout the structure. The completed project not only exceeded LEED Gold standards but was also named a winner in the National Ready Mixed Concrete Association’s (NRMCA) 2024 Concrete Innovation Awards.
This same commitment to sustainability and responsible building was the driver behind the decision by the designers of Drexel University’s new Health Sciences Building in West Philadelphia to not only use PLC from Heidelberg Materials, but also source concrete materials locally. Some phases of the project used up to 25% Class F fly ash as a supplemental cementitious material to further reduce CO2 emissions from concrete by up to 35%.
There has also been an increase in the number of roadway and other paving projects using PLC to reduce emissions without compromising performance. PLC was recently used in a project reconstructing a 4 mile stretch of California’s Highway 101, which Caltrans estimates will cut emissions by 28 000 tpy – the equivalent of taking more than 6000 cars off the road.
Beyond California, several other state Departments of Transportation have had success placing PLC concrete pavements for more than a decade. 2024 was a watershed year as all 50 state DOTs and the District of Columbia approved PLC for their projects, paving the way for this material to be used in transportation infrastructure across the US.
PLC has also been used in dam projects, such as the Gross Reservoir Expansion Project in Colorado, where it was the material used to produce nearly 1 million cubic yards of roller-compacted concrete (RCC) and conventional concrete. The use of PLC will avoid more than 5600 metric t of CO2. PLC also has its own ASTM standard and is permitted for use in airport construction projects by the Federal Aviation Administration.
In the near term, this dramatic shift in the market will continue as PLC is consistently taking over applications where traditional portland cement once reigned. Helping end-users transition to PLC and other blended cements will remain a top priority for the Portland Cement Association (PCA), including assisting with adoption, serving as a source of information, communicating why this change is worthwhile, and educating the rest of the supply chain on PLC best practices. PCA represents more than 75% of US cement production capacity and is actively engaged with both the NRMCA and the American Society of Concrete Contractors (ASCC) to help everyone who works with PLC execute high-quality results that match performance requirements.
Looking to the future, there is an opportunity for more widespread adoption of ternary-blend alternatives. Ternary blends use a third ingredient to further reduce embodied carbon and lower overall environmental impacts. They can also help producers take advantage of locally available, abundant materials.
The rehabilitation of a highway exit in upstate New York is a useful case study in how ternary cement systems are being used in real world settings. Cold Spring Construction used a ternary cement blend on an I-86 bridge structure in Coopers Plains, NY, with a cementitious system comprised of a binary Type 1P
cement (6% silica fume) blended with 20% Class F fly ash. As part of construction work to rehabilitate exit 42 of the highway, the project included reconstruction of the bridge and adjacent roads as well as drainage and box culvert replacement. All concrete was mixed at a central mix plant with locally sourced materials for the ternary blend, including crushed gravel and river sand from a contractor in nearby Erwin, NY. Initial and final sets occurred at 5.76 hrs and 6.72 hrs, respectively, with hardened properties showing 3160 psi compressive strength at seven days and 3970 psi compressive strength at 28 days. The contractor reported no difficulties with using this particular blend.
PCA is actively looking for other projects using ternary cements so the industry can learn from on-the-ground experience. The association also works to educate regulators, concrete producers, and other decision-makers on how these cements are performing and what testing is needed. A key challenge to increasing consideration of blended cements is regulatory lag that doesn’t keep up with the pace of innovation.
How are teams overcoming these challenges?
A well-trafficked stretch of road in Henry County, Tennessee, provided the Tennessee Department of Transportation (TDOT) with the opportunity to work with suppliers to use PLC with a 25% fly ash replacement. This project relied on 450 trial batches to confirm compressive strength at 28 days (4000 psi), noting little-to-no difference between PLC and their typical mixes. As a result, TDOT reduced the carbon footprint for several bridge decks while repairing the bridge with concrete that possessed the required properties.
In conversations with regulators and others, it is critical to continue focusing on how the market is shifting from prescriptive specifications to performance-based specifications. As more projects consider ternary cement systems, trial batching and field verification will remain the best method to determine the performance of a concrete mixture. Trial batching should evaluate factors such as compressive strength, slump/water demand, slump loss, setting time, air content, strength development, and bleeding. Additionally, speciality mixes are tested in a subset of trial batches for factors like sulfate resistance, chloride resistance, shrinkage, and more.
The shift toward lower-carbon cement is coming from both suppliers and users. An increasing number of projects is taking advantage of incentives available to lower the carbon footprint of construction. As of 2024, 13 states have implemented 'Buy Clean' initiatives to reduce the embodied carbon of construction materials. Similar to efforts involving PLC, PCA will work across the value chain to educate about these new ternary options. It will be especially critical for these blends to be included in new sustainable construction codes and considered for inclusion in
green rating systems to inform better decisions for longer-term, sustainable projects.
The cement industry in the US has a longstanding commitment to reduce the carbon impact of products, pledging to reach carbon neutrality by 2050. As materials continue to evolve, it is possible there will also be widespread usage of quaternary blends that offer further environmental benefits and cost savings to construction projects. For this to gain traction, regulation will need to be nimble enough to capture the latest, state-of-the-art materials. In the private sector, industry leaders will need to remain focused on combatting institutional inertia and providing guidance on testing so new blends can be considered.
It is also important to avoid relying on older materials when newer options are cleaner and perform just as well. Some of the most exciting projects with quaternary blends will be pushed forward by innovative companies at the forefront of change, such as tech giants committed to net-zero goals. These cutting-edge projects can serve as important proof points for the advantages of new cementitious material mixes and help the rest of the US tap into available resources, setting a global standard for a sustainable future.
It is clear that achieving carbon neutrality across the value chain by 2050 will require a deep and lasting commitment from both the industry and its customers. These new cement blends remain a major part of the puzzle.
Concrete – made with cement – is central to the American built environment, with 88 million t of cement and 400 million t of concrete produced in the US in 2023. The cement, concrete, and related industries directly and indirectly employ nearly 600 000 people and contribute US$150 billion to the US economy. By working with partners across the value chain, the industry can reach carbon neutrality while continuing to provide the buildings, roads, and runways people rely on to lead productive lives across the country and around the globe.
Michael 'Mike' Ireland is the President and CEO of the Portland Cement Association (PCA). Previously, Mike was Associate Executive Director of the American Society of Mechanical Engineers (ASME), as well as CEO of two other professional associations. He is a seasoned association executive, with expertise in all phases of organisational management, including executive leadership, marketing and communications, workforce development, philanthropy and fundraising, and membership development. Throughout his career, he has been known for fostering a culture of camaraderie and customer focus, thanks to his sense of creativity and ability to help organisations positively navigate strategic change.
Unlike some other sectors, such as petrochemicals or heavy transportation, it is fair to say that the technological pathway to deep decarbonisation of cement production has now crystallised around fundamentals. Although their relative importance fluctuates, global and regional cement roadmaps all acknowledge the need for:
� More efficient use of cement and concrete.
� Switching from fossil fuels to waste and biomass to generate heat.
� Reducing the average clinker content through the use of supplementary cementitious materials (SCMs).
� Carbon capture, either for utilisation or storage (CCUS), to tackle residual emissions.
Publications have also evidenced the massive investments needed to transform the cement industry, especially due to CCUS. While most in the industry believe that public funding will be needed to drive the transition, many early policy options with little or no direct financial support can be adopted. This article will illustrate three of these potentially impactful policies that require limited financial effort.
Some types of SCMs are already commonly used for cement blending (e.g. limestone filler, blast furnace slag, pozzolans) and other very promising sources are emerging (e.g. calcined clay, recycled concrete, reclaimed coal fly ash). While blended cements usually do not pose a major technical challenge and can find areas to compete with ordinary portland cement, they are still far from their full potential deployment. Their penetration in the construction market has often been impeded by a slow evolution of building codes and product standards which tends to reflect the conservative nature of public and private stakeholders in the industry. Government intervention should focus on transitioning from the traditional recipe-based to the performance-based approach whereby
SCMs and blended cements can be introduced to the market when demonstrating certain performance criteria. The Rocky Mountain Institute (RMI) has recently published a guide with very practical recommendations for developing performance standards and specifications for concrete. Besides, given the high cost of CCUS and its slow deployment, reducing clinker production through SCMs will only alleviate the future reliance on carbon capture to address residual emissions.
Landfilling is a common waste management practice in many jurisdictions. Yet some materials such as tyres, textiles, foams, sawdust, or agricultural residues have a valuable energy content and a fraction of biogenic carbon that can contribute to climate mitigation. Thanks to very high temperatures, cement manufacturing has the ability to process such waste and destroy most residuals which are potentially hazardous. Many manufacturers already resort to alternative waste fuels owing to attractive economics (e.g. in the EU, more than 40% of the thermal energy comes from waste and biomass) but changes in regulation can further support the phase-out of fossil fuels. Implementing waste legislation to divert waste streams from simple disposal and recognising co-processing as a viable waste management solution would further support the reduction of fossil fuel use in the sector. For instance, the cement industry in Poland rapidly increased its average thermal substitution rate to 45% in 2011 and more than 60% in 2017 partly due to strong enforcement of waste regulations, particularly those related to landfilling. In oil producing and refining regions, such as the Middle East, oil sludges used in well drilling are often disposed of in dedicated lagoons.
These sludges are still largely recoverable and can be used as fuels for clinker manufacturing.
Cement is probably one of the most promising candidates to be stimulated through Green public procurement (GPP) policies, with the public sector accounting for 40% to 60% of concrete sales globally. Public buyers can leverage their purchase power by imposing more stringent sustainability criteria in their projects and, especially, limits on embedded carbon emissions in materials. The Industrial Deep Decarbonisation Initiative (IDDI) has been collecting national commitments to procure low-carbon construction materials under the Green Public Procurement Pledge to encourage this practice globally. Promoting the use of novel blended cements and chemistries in public construction through GPP is essential to showcase their technical performance and create the market confidence they often lack. By absorbing the higher initial cost, governments can also contribute to create lead markets that should trigger economies of scale once green demand has sufficiently aggregated.
Although it is not the focus of this article, it is worth mentioning that GPP criteria can be calibrated to reinforce the economics of CCUS. More generally, demand-side policy measures (as presented in the Green Demand Policy Playbook published by the ITA at COP29) are essential to stimulate early adoption of green materials.
A case study published by Ramboll in November 2024 on the construction of a new school building in Zürich, Switzerland, concluded that the inclusion of GPP criteria has allowed the reduction of embodied emissions from concrete use by almost 25% for a modest 2% increase in cost (the so-called 'green premium'), compared to a business-as-usual scenario.
CCUS probably represents the most challenging, yet indispensable, piece of the cement net zero journey. However, a series of other solutions (totalling about 50% of the cumulative GHG emissions savings between 2022 and 2050 according to the MPP Net Zero scenario for the cement industry) can be deployed more rapidly to put the industry on track to the 2030 target. As hurdles are mostly linked to the regulatory framework and industry conservatism, rather than economics, some well-calibrated policy measures entailing limited public money can be taken to stimulate these levers.
Eduardo Gomez, CRH Ventures, explains why partnering with startups is key to the decarbonisation revolution.
The importance of innovation and emerging technologies to drive progress in reducing carbon emissions, optimising the use of resources, and delivering process efficiencies has never been greater. While the adoption rate and impact of innovation is increasing, there remains huge scope for more transformative strategies as the industry responds to the changing needs of customers and society.
At CRH, constant innovation is key to improving processes and developing new technologies that play a crucial role in the journey to net-zero. The company's commitment to innovation, alongside other corporations and governments, is critical in order to accelerate and provide resources for large-scale change. There is also a growing recognition of the importance of working with industry startups, whose challenger mindset helps rethink, reimagine, and reinvent systems, processes, and technologies.
The industry is rich in expertise and knowledge, with a proven track record showing that sustainability and profitability can go hand in hand. Embedding innovation is vital in converting challenges into value-creation opportunities. Ideas and innovation are emerging from various sources, including businesses, academia, and startups. However, the real challenge lies in converting these ideas and small-scale technologies into large-scale, economically viable solutions. Combining the entrepreneurial spirit and determination shared by startups and those in the cement industry already addressing decarbonisation, with the scale, weight, and backing from the established industry players, is one of the most impactful ways to advance the development of viable sustainable solutions.
Innovation in areas such as AI-driven material optimisation, alternative cementitious materials, and novel production
methods is now supporting the cement decarbonisation journey. Capable of demonstrating real impact, startups in this space are attracting growing interest from institutional and strategic investors as their solutions offer the potential for long-term cost savings, enhanced performance, and a competitive edge in a rapidly evolving market. However, the construction industry’s complex systems of standards and regulations can make for a challenging environment to deliver transformative ideas. Startups are known for their ingenuity and courage, often pushing the boundaries of what is possible. They need assistance in navigating the complex industry landscape and in scaling solutions which require significant capital investment, regulatory approval, and widespread adoption – substantial hurdles for small ventures. At CRH, there is a strong belief in the importance of playing a key role in accelerating the most promising innovations and technologies, whether through partnerships or funding. Accelerators and incubators focused on climate-tech also play a vital role in bridging the gap between early-stage innovation and large-scale implementation.
Interest from construction technology (ConTech) startups willing to tackle the industry's challenges is directly linked to the significant growth in funding from institutional and strategic investors. As a result, collaboration between those who own and operate the assets and those bringing forward new outside thinking to transform them is increasingly recognised as the most effective and efficient way forward. CRH is playing an important role in embedding this way of working, partnering with startups on a range of technologies, material innovations, and new processes designed to deliver a more sustainable built environment. For example, CRH has invested in AICrete – a company using AI to better predict recipe formulations for concrete and optimise the amount of cement used. Results from a pilot project indicate potential savings of 3.5% on material costs, and an average 5% reduction in carbon emissions. Through a focus on resource efficiency and circularity, CRH is also working with partners to advance the development of new and novel materials, as well as the use of non-traditional materials, in the cement manufacturing process. Carbon Upcycling Technologies is able to transform local industrial by-products into high-performing supplementary cementitious materials (SCMs), which can reduce the clinker factor and associated embodied carbon. The Canadian startup has used 30 different feedstocks in its process so far, including fly ash, glass, biomass, volcanic rocks, natural pozzolans, metal mine tailings, aggregate fines, silicates, and clays. With the transformation process taking place in-situ at cement plants, there is the additional benefit of logistical environmental performance gains.
The commercialisation of breakthrough technology that avoids both mineral and fossil fuel emission sources in the cement manufacturing process is also advancing. Massachusetts-based Sublime Systems, for example, is at the forefront of developing an innovative electrochemical, near-ambient-temperature approach to cement production. This technology aims to replace traditional kiln processes and achieve a 90% reduction in cement’s CO2 emissions at full commercial scale. By utilising calcium-rich minerals and industrial byproducts like slags and kiln dusts, Sublime Systems produces a material that is a novel alternative to traditional portland cement.
For new and emerging technologies like these to realise their potential in accelerating the decarbonisation of the industry, they must be encouraged and combined with the strategic advantages and expertise of the leading building materials companies.
The path to decarbonisation in the industry requires collaboration and a concerted effort from all stakeholders. Startups, established companies, investors, and policymakers must work together to drive innovation and investment.
While the backdrop to scaling new technologies and innovations which support industry and government decarbonisation ambitions is complex and challenging, it also presents unparalleled opportunities. The key to success lies in driving forward innovative thinking and delivery, supported by strategic partnerships between industry leaders and startups which can ensure that promising technologies receive the funding, expertise, and market access needed to scale effectively.
CRH Ventures are committed to fostering collaboration and investing strategically in ConTech and climate technology startups. Doing so means CRH can continue to develop new, cutting-edge mutually beneficial partnerships to accelerate decarbonisation and enable safer, smarter, and more sustainable construction.
Eduardo Gomez is the Head of CRH Ventures, where he leads efforts in investing and partnering with innovative startups across the construction value chain. With a strong background in venture capital and a passion for sustainable development, Eduardo is dedicated to fostering long-term partnerships that drive the development of sustainable solutions. Under his leadership, CRH Ventures focuses on making the construction industry safer, smarter, more efficient, and more resilient. Eduardo holds a degree in Engineering and an MBA, and he brings over 15 years of experience in the industry to his role.
Rob Cumming, Lafarge Canada (East), explores how a 'silver buckshot' approach can achieve net-zero concrete without the high costs of CCS or e-fuels.
As the cold, hard reality of the expense of carbon sequestration weighs heavily on the industry’s shoulders, it is important to question whether it truly is the ultimate solution. Geologic sequestration projects, or their even more expensive cousin ‘sustainable’ e-fuels, are high stakes ventures with significant electricity and water needs – and eye watering costs – with no benefits beyond decarbonisation (as important as that is).
Has this question been approached from the wrong angle? Cement is an engineering-intensive industry, and 'big problems call for big technical solutions' is the rallying cry. Or, as often heard, the only proven, full scale solutions are carbon capture & storage (CCS) or sustainable e-fuels (fuels made by combining H2 with captured CO2).
But what if the perspective shifts to that of the concrete user – those needing concrete for buildings, infrastructure, or other applications?
Perhaps key performance indicators (KPI) should focus on kg/m3 of delivered concrete, which ties nicely into customer KPIs of kg/m2 of floorspace or kg/km of highway. ‘What gets measured gets done’ is a proven management mantra, and so the selection of the KPIs will steer the entire strategy.
Can net zero concrete in buildings and infrastructure be achieved without relying on CCS or e-fuels by rethinking final products from the buyer's perspective?
Can a ‘silver buckshot’ approach – targeting multiple solutions – be more effective than searching for a single 'silver bullet' to decarbonise the industry?
The silver buckshot approach
There are a number of decarbonisation strategies that make sense even without monetising the carbon benefit attained. These include energy efficiency measures, replacing fossil fuels with lower carbon fuels (often financed by waste tipping fees), new low
clinker content formulations, and new cementitious products. Even electrification is becoming a low cost choice in multiple applications. These investments can be considered 'no regrets' investments, even in uncertain times where decarbonisation policies are in political flux. Carbon pricing systems or tax credits can make them even more profitable. Adding smart design practices in collaboration with the builder can further decarbonise the final building. In a recent collaboration between The Daniels Corporation and Lafarge Canada (East), a 25% reduction in carbon in the delivered concrete was achieved simply by identifying where schedule slack in non-critical path project components could be tolerated and applying a smart mix design strategy.
Thirty five different mix designs were used to accomplish this reduction, with no impact on the building’s schedule.
Some net zero roadmaps, like the 'Concrete Zero Roadmap' prepared by the Cement Association of Canada (CAC), show that a combination of all of the above ‘no regrets’ measures could reduce the carbon content of new buildings and infrastructure by two thirds, much of this at low or no cost. Certainly nowhere near the cost of CCUS, which is well over US$100/t of CO2.
How about measures that come with a cost? If the last measure in a net zero strategy is CCS at over US$100/t of CO2, then this opens the door to solutions that are still expensive, but less so in comparison. Many other solutions with lower costs than CCUS have yet to be fully explored. Plants that have installed CCS or e-fuel systems may find themselves competing against plants that have pursued a different, multi-path approach to achieving net-zero status, at much lower costs.
Some examples of these multi-path solutions are provided in this article, and innovators who forsee the future need for decarbonisation are actively working on these solutions. It is worth noting that many of these alternative solutions produce sellable products in addition to their decarbonisation benefits, and their environmental benefits contibute to the industry’s overall decarbonisation efforts (not always the case in CCS and e-fuels strategies).
There are a number of sources of calcium that are already in the oxide form and so do not produce CO2 during cement production. Natural minerals such as wollastonite, serpentine, and olivine may be able to play a partial role in the formulation of clinker. Of course, the mineral resources may not be co-located near the cement plant and a processing step may be needed, but in comparison to CCS & e-fuel costs these added
by providing a new process optimization solution: CemAI Process Optimizer . Combining the power of AI/ML with cement-specific expertise, CemAI Process Optimizer enables a step-change in production volumes, energy efficiency and consistent quality output.
Predictive Maintenance & Real-Time Optimization are now in your hands.
Please
info@cemai.com | +1 (502) 322 0433
costs could be much lower. In other cases, waste materials from other industries and mining operations may provide many of the necessary minerals needed for traditional clinker production, often at a much lower cost than virgin minerals. Concrete rubble is already being used as a raw material in cement production. Solidia Technologies continues to explore alternative cement formulations, similar to wollastonite, which produce cement and resulting concrete that cure with CO2
Mineralised aggregates in concrete
Mineralisation can be defined as the reaction of CO2 with metal oxide bearing materials (e.g. Ca, Mg, Fe) to form insoluble carbonates. An example of one chemical reaction (for wollastonite) is provided below:
CaSiO3 + CO2 → CaCO3 + SiO2 + 90 kJ/mol CO2
Carbonation terminology is often used in this context but typically refers to the natural consumption of CO2 by concrete in buildings.
‘Negative carbon’ mineralised aggregate products in a cubic metre of concrete can fully or partially balance out or offset remaining embodied carbon content after other measures have been implemented. Akin to the natural carbonation of CO2 in-situ in buildings, concrete rubble through an industrialised process can be used to absorb CO2 from cement production (or any CO2 producing source). The resulting negative carbon aggregate can then be used in mix designs or road construction, etc. This is already being done by Switzerland based Neustark.
All mineralisation strategies face one major achilles heel: the need for a supply of geomass to chemically react with CO2. The IPCC has defined RCO2 as a metric to define the ratio of the mass of mineral needed to the mass of CO2 captured at 100% efficiency. In the case of crushed concrete rubble, the practical RCO2 ratio is around 20, meaning that 20 million t of concrete rubble are required to absorb 1 million t of CO2. Mineralisation has some advantages:
� The capture and utilisation occur in a single step, in contrast to technologies which require capture first and then a subsequent reaction step.
� Mineralisation is an exothermic reaction and occurs naturally.
� The need for expensive flue gas cleaning and conditioning to enable capture is non-existent or less critical given the nature of the process itself and the final product produced.
� Any biogenic carbon in a flue gas, from biomass fuels, will further contribute the carbon sequestered in the mineral product.
The aggregate products produced can be sold, and if used in concrete mix designs,they offset CO2 from cement production – potentially even making
advanced concrete products carbon-negative in the future.
Start-ups are active in this space. A short list of companies includes: BluePlanet, Carbon8, Carbon Upcycling, Fortera, Carbfix, Hyperion, and Solidia.
Neutral or negative carbon filler in concrete
A number of emerging technologies produce materials that can be added to concrete as a filler. An example is the use of biochar, which exploits the biogenic nature of the char to effectively sequester CO2 in concrete, offsetting in whole or in part CO2 from cement production. Other aggregates that do not have cementitious properties but provide other mix design benefits can be used as well and synergistically reduce clinker content. Global norms and standards need to evolve to unleash the maximum benefit these creative mix designs can achieve in terms of low cost decarbonisation. Even under the current standards, the Lafarge – Daniels example noted earlier achieved a 25% reduction, and as standards evolve further, this capability will continue to grow.
Carbon removal through mineralisation and other pathways
There are already companies selling minerals for agricultural use that not only provide nutrients but also naturally remove CO2 from the air through mineralisation. Three examples include:
� UNDO, which uses wollastonite in an agricultural additive which contributes minerals to the soil, enhancing soil quality while also absorbing CO2 over time in a natural weathering process, which is monitored and credibly accounted for to allow the sale of removal offsets.
� A non-mineralisation example is CarbonRun, which treats acidified rivers through the addition of finely ground limestone, restoring fish habitats and forming a bicarbonate, in another form of carbon removal. Both of these examples demonstrate the use of aggregates to address decarbonisation.
� Ottawa based Hyperion is producing precipitated calcium carbonate, a high value aggregate product used in a wide variety of applications, including toothpaste and paint. Hyperion relies on chemical feedstocks rather than mineral geomass. In this case the CO2 will come from industrial sources.
When decarbonisation is viewed from the customer perspective, transportation emissions become relevant. Without a doubt clinker production remains the lion's share of CO2 emitted in the supply and delivery of concrete to the customer, but other sources add up and must also be managed to deliver a net zero product for customer projects. Electric ready-mix trucks are already in use in Europe.
For example, Holcim has committed to purchasing 1000 trucks for its European operations. As battery costs come down, this trend will spread to other parts of the world.
The case for silver buckshot in meeting concrete buyer net zero needs
It is easy to dismiss any individual solution presented above as 'just a small solution' or reject it as 'too expensive'. Strangely though, in the context of cost, published net zero strategies for the cement and concrete industry list CCUS as the final technology to be deployed. CCUS is the universal black box piece in the puzzle of net zero roadmaps. Interestingly, the KPI used by most cement producers is kg of CO2/t of cementitious product produced. This metric ignores a wide swath of the available solutions noted earlier and is not a great fit with the KPIs of the industry’s customers.
It is quite conceivable that, through a combination of known low- and moderate cost solutions, the concentration of CO2 embodied in a delivered cubic metre of concrete in a few years can be reduced by over two thirds when compared to historical concrete – as shown in many net zero roadmaps. The use of higher cost but negative carbon mix components could offset that cubic metre, turning it into a net zero product. This pathway would not rely on big bets such as CCS and e-fuels, but rather on dozens of small solutions which collectively add and subtract to net zero. If the alternative is a US$100/t of CO2 solution, as is the case with CCS and sustainable fuels, this seems a smarter approach.
The industry must revisit offsets – but in a narrow, credible way. The outcry when the Science Based Targets Initiative proposed allowing offsets in net zero strategies was widely noted. Perhaps a more focused offset strategy, one that is a) strictly for use within the industry and b) includes removal technologies that use products from within the industry itself.
This would necessitate excluding avoidance offsets and broad-based nature based offsets. A ‘book and claim’ market system, similar to the airline industry, could be an effective model. This system would be restricted to concrete industry players and would incorporate supply chain data accounting, tallying up the decarbonisation strategies leading to the delivered cubic metre of concrete, including only those offsets that meet the specified criteria.
It is possible that net zero can be achieved without CCS and e-fuels by taking a concrete buyer’s perspective, using a kg/m3 of delivered product KPI, and thus contributing to the affordability of decarbonised critical housing and infrastructure needs.
From individual components to upgrades to complete plants, InterCem provides customized solutions for operators and investors of cement plants all over the world. InterCem is therefore also the right partner for you when it comes to planning, detailed engineering, project management of greenfield projects and conversion/modernization of production plants.
Contact us: The InterCem professionals will also find the right solution for your requirements.
ementtech
May 15-17, 2025
Organizer:
China Building Materials Federation
China Cement Association
CCPIT Building Materials Sub-council
Exhibition/Conference/Plant Tour/City Walk
---Your direct gateway to China cement market
Bodil Recke, ABB Process Industries, discusses the strategies driving the cement industry's transition to sustainability.
Cement is integral to economic growth, and demand is on the rise as urbanisation increases and infrastructure projects escalate worldwide. However, with cement production responsible for around 7% of global CO2 emissions,1 the industry must reconcile its necessity with its environmental impact. Addressing this challenge means rethinking the fundamentals
of cement production, from energy sources to material composition. Emerging strategies, including electrification, carbon capture, alternative materials, and digitalisation are shaping the path toward sustainability.
Decarbonisation demands an integrated approach that considers the entire value chain, from raw material extraction to final application. It goes beyond the
implementation of isolated technological solutions, instead requiring a comprehensive shift in process efficiency, material usage, and policy alignment.
For decades, cement production has depended on fossil fuels to power the high temperatures required for clinker formation. The initial step to move away from this has been to replace fossil fuels with various waste materials, like plastics or agricultural waste. Electrification is one of the most discussed strategies for decarbonising cement production as it involves shifting energy inputs from fossil fuels to electricity, ideally from renewable sources. However, the transition to electrification is complex and presents various operational challenges. At the heart of cement production, cement kilns require continuous high temperatures, which grid-based electricity alone cannot reliably supply in many parts of the world. The volatility of electricity supply, particularly in regions where the grid remains heavily reliant on coal, creates significant risk. Electrification could help reduce direct emissions by switching to cleaner electricity, but there are still complexities related to energy reliability, cost, and scalability that remain.
While renewable energy sources are central to this transition, direct partnerships are becoming critical. By securing dedicated renewable energy supplies as partners, cement plants can reduce their exposure to fluctuating energy costs and instabilities in the grid. This could stabilise the energy input costs in cement production while reducing emissions from energy consumption. Coupled with robust energy storage systems for continuity and reliability, electrification can significantly reduce emissions. From electric plasma-based calcination and rotary kiln electrification to electric arc calciners capable of reaching the necessary high temperatures, electrification also offers a cleaner means of processing raw materials.
Electrification has emerged as a strategy for decarbonising cement production as it offers an opportunity to shift away from fossil fuels. Ongoing developments in technologies such as electric
plasma-based calcination and rotary kiln electrification provide alternatives to the traditionally fuelled kilns. Alternatively, electric arc calciners, capable of reaching the high temperatures needed for cement production, offer a cleaner means of processing raw materials.
Decarbonisation through electrification is one strand of the solution which must be considered alongside its operational and infrastructural challenges. Replacing fossil-fuel-fired kilns with electric alternatives can generate the necessary heat cement manufacturers need while significantly cutting back on emissions. However, a shift in energy policy and infrastructure development is required to overcome energy supply volatility and cost considerations.
Transitioning from traditional fossil fuels to alternative energy sources, such as biomass or municipal waste, is a viable avenue for reducing emissions in cement production. However, these alternative fuels (AFs) have distinct combustion characteristics that can affect process stability. Biomass and waste-based fuels typically have lower energy content compared to coal, and their combustion can result in inconsistent temperatures and potentially affect the chemistry or increase emissions of certain pollutants.
To mitigate these issues, cement producers must invest in modifying kiln technologies and optimising their combustion processes to ensure that AFs can be used effectively without compromising the quality of the final product. Furthermore, this fuel substitution must be accompanied by broader energy efficiency improvements across cement production.
Rather than implementing isolated upgrades, cement producers should consider the adoption of a plant-wide strategy for optimising energy use. This could include integrating renewable energy sources, improving energy storage, and ensuring that heat recovery systems are used to their full potential.
Despite advancements in cleaner energy, some emissions in cement production remain unavoidable. The calcination process, involving the transformation of limestone into clinker, releases substantial amounts of CO2 as a natural byproduct. As these emissions are inherent to the chemical reaction, capturing them at the source becomes essential. This is where CCUS technologies come into play.
CCUS technologies offer a way to mitigate emissions, as demonstrated by the cement plants in the industry already piloting CCUS systems that capture CO2 from kiln flue gases before it enters the atmosphere. This captured carbon can either be stored underground in geological formations or repurposed for industrial applications, such as synthetic aggregate production or carbon-infused concrete curing. However, for CCUS to be implemented at scale, investments in carbon transportation and
storage infrastructure are necessary. Industry collaboration is driving these initiatives forward, laying the groundwork for a future where carbon capture might become a standard feature of cement plants. Cement producers can also look to integrate CCUS with other industrial sectors to increase its viability. Captured CO2 can be used in chemical processes, contributing to the circular economy by turning emissions into valuable inputs. For example, research into mineral carbonation explores how captured CO2 can react with industrial byproducts to create new construction materials, permanently storing carbon while producing commercially viable products. The economic feasibility of these applications depends on continued investment and policy support, underscoring the importance of cross-industry collaboration.
Modifying cement’s composition is a more direct approach to reducing the industry’s carbon footprint. Clinker, the key binding component of cement, is also its most emission-intensive ingredient. Reducing the clinker factor by incorporating supplementary cementitious materials (SCMs) provides an achievable means of lowering emissions without compromising structural integrity.
As industries such as coal-fired power plants and steel production transition towards cleaner processes, the availability of traditional SCMs may decrease. This creates a challenge for the cement industry, which has traditionally relied on waste products from other industries to meet its demand for supplementary materials. To overcome this, the cement industry must invest in developing new supplementary materials that are not reliant on industrial byproducts. Alternatives such as calcined clay and other natural pozzolans have long been explored as clinker substitutes and can also enhance cement performance in specific applications while reducing the overall carbon footprint.
Research into alternative binders continues across the industry, with innovations in blended cement
formulations allowing for greater customisation based on performance needs. Shifting toward performance-based cement standards, rather than ingredient-based requirements, would further enable wider adoption of low-carbon alternatives. Additionally, repurposing recycled concrete as aggregate offers another opportunity to reduce raw material consumption, closing the loop on cement production.
One of the most promising approaches to reducing the environmental impact of cement production is adopting a circular economy model. Recycling concrete from demolition and reusing materials such as aggregates and cementitious components has the potential to reduce the need for raw materials. However, the challenges are not only technical but logistical as well. While the potential for circularity in cement is significant, the industry must first implement large-scale recycling programmes to keep up with demand.
Technologies and systems need to be developed to make the recycling process more efficient. This includes grinding, sorting, cleaning, and reprocessing recycled concrete and other materials. The logistics of collecting and transporting these materials for reuse in cement production also need to be streamlined to ensure that they are cost-effective and scalable.
Another critical element of circularity is the development of closed-loop systems, where the waste generated from cement plants or construction sites is systematically reused, reducing the need for new resources. Adopting circularity in cement production will not only reduce carbon emissions but will also enhance resource efficiency, ensuring a more sustainable material flow within the construction industry.
While technological solutions exist, the decarbonisation of cement production also relies on the policy frameworks and investment structures that incentivise long-term change. No single company or sector can achieve meaningful decarbonisation in isolation. A transition towards low-carbon cement production necessitates broad collaboration among cement producers, technology developers, policymakers, and construction firms. Cross-industry cooperation is already yielding innovative solutions, with companies jointly investing in electrification, CCUS, and digitalisation.
Policymakers play a crucial role in shaping the regulatory landscape for sustainable cement production. Clear regulatory frameworks and long-term policy stability are also essential in creating predictability for cement manufacturers, allowing the industry to make the long-term investments in sustainable technology. The alternative to clear, stable
policy runs the risk of creating hesitancy within the industry, slowing down decarbonisation efforts. Additionally, establishing standardised emissions reporting frameworks allows companies to benchmark their progress, share best practices, and collectively push the industry toward decarbonisation goals. The shift toward performance-based cement standards also holds promise, enabling manufacturers to innovate while ensuring product integrity and structural performance.
Decarbonisation presents significant challenges in the cement industry, but with the right strategies, the sector can meet its sustainability targets. Electrification, CCUS, alternative materials, and process optimisation are the individual steps that, when combined, can provide the industry with a solid foundation to achieve these goals.
The path forward is complex, and there is a need for action. Cement manufacturers who act now will position themselves as leaders in the transition to a low-carbon economy, securing their place in the future of sustainable construction. The question is not whether the cement industry can decarbonise, but how it should leverage the tools and solutions available to accelerate the transition.
1. 'WCA supports full decarbonisation of the cement industry', World Cement Association – https://www. worldcementassociation.org/about-us/sustainability
Bodil Recke joined ABB in September 2024 and has over two decades of experience in the cement industry. With broad expertise in both operational efficiency and environmentally sustainable solutions, her career has evolved from focusing on cost reduction to addressing the urgent need for decarbonisation in cement production. Bodil's vision for the future emphasises the critical role of collaboration across the value chain, ranging from cement production to concrete manufacturing and recycling. She believes that achieving significant progress in reducing CO2 emissions will require a diverse set of solutions tailored to local contexts, including raw materials, green energy sources, and digital automation.
Passionate about contributing to a more sustainable world, Bodil sees her role at ABB as a unique opportunity to drive environmentally friendly innovations that support the cement industry’s journey toward net zero emissions. Her work not only aims to reduce the environmental footprint of cement products but also ensures that the industry continues to meet the global demand for infrastructure, improving the quality of life for people across the globe.
GEA Waste Heat Recovery units are tailored systems that combine proven ORC technology with an innovative heat recovery concept to harvest most of the waste heat out of the cement process & transform it into electricity.
Smaller carbon footprint, waste energy reuse, cost optimization and higher overall efficiency are only some of its advantages.
Learn more, get in touch: gea.com/contact
Olivier Guise, Ecocem, discusses how collaboration and scalable low-carbon solutions can accelerate the cement industry's path to net zero.
he buildings and construction sector faces a crucial challenge in reducing its carbon emissions, and despite advancements, the current pace of change is still too slow.
Accounting for 37% of global emissions, the sector is at a crossroads. The EU's latest 'Copernicus Climate Change Service' report confirmed 2024 as the warmest on record and the first year ever to exceed the 1.5˚C above pre-industrial levels in the annual average temperature, reinforcing the urgency with which emissions reduction must be accelerated.
Cement is one of the largest contributors to the construction industry’s emissions – accounting for
almost 8% of global CO2 alone. According to the International Energy Agency (IEA), there needs to be an annual 3% reduction in the industry’s emissions, if the industry is to align with the net zero scenario.
While there is widespread investment in innovation – including research into alternative materials and processes – many of the proposed solutions to get the industry to net zero, including carbon capture, utilisation, and storage (CCUS), mean increased production costs. And despite some clear advancements, such as the electrification of heating processes during the manufacture of cement, the industry is not yet fully addressing the core carbon issue: clinker. Clinker is the primary reactive ingredient in cement and is responsible for approximately two-thirds of its carbon emissions – primarily due to the calcination process, when limestone is burned to produce clinker and releases CO2
The reality is simple: unless CO2 production is avoided, which can only be done by dramatically reducing the amount of clinker in cement and concrete production, net zero will remain a distant dream.
To reduce clinker volumes, the industry must embrace new thinking and approaches. The cement sector is – quite rightly – highly regulated to ensure the safety of any construction in which cement and concrete are used. However, the industry is a conservative one, slow to adopt new technologies and reliant on traditional practices. Adopting the widest possible range of viable, emerging technologies as fast as possible is essential to tackle the emissions crisis.
Cement and concrete technologies have advanced significantly in recent years, making it possible to use half the amount of cement in concrete compared with historical levels, while still maintaining essential performance metrics in the concrete it is used to make, namely workability, strength, and durability. Halving the amount of cement produced means halving the CO2 associated with cement production. The industry’s footprint can be reduced even further, up to 70%, by maximising the use of locally available alternative materials, known as supplementary cementitious materials (SCMs). The more SCMs incorporated, the greater the positive impact will be.
Low-carbon cement is not new. What is new is the ability to scale these cements using a variety of readily available SCMs. Industry reluctance
toengage with these solutions has been rooted in the belief that there are not sufficient volumes of these SCMs available to make a real impact. This is no longer the case.
Low-carbon cement production without a substantial green premium Encouragingly, technologies which tackle the volume of clinker in cement without the need for huge additional cost are becoming more widely used. One such example is ACT from Ecocem, which works at a cost of around at around €10 – €18 per t of CO2 avoided, compared to €175 for CCS. One of ACT’s key advantages is its ability to be manufactured in existing cement plants without requiring significant additional capital investment. This 'drop-in' solution makes it both cost-effective and scalable, offering a low-barrier entry for cement producers aiming to reduce their carbon footprint.
ACT has been validated by a number of partners, including Cemex France, which has been testing and using ACT at several of its ready-mix plants. Furthermore, ACT has already been successfully poured at pilot sites in France, Belgium, and the UK. ACT gained the ETA certification in Brussels in February 2024 and is on target to obtain further national accreditations during the course of 2025 and beyond. It is supported by the backing of key national and regional policymakers, with financial grants received from the French Government (France 2030), the Région Hauts-de-France and the Communauté Urbaine de Dunkerque (Dunkirk territory).
Cracking the science and manufacturing challenges is only one part of the equation. Government, industry, and policymakers have a crucial role to play in accelerating the adoption and use of low-carbon cements as part of the mix of solutions that will achieve net zero.
Strong and clear policy making has the power to drive change and the adoption of a range of technologies. EU mechanisms such as the Carbon Border Adjustment Mechanism (CBAM) and the Emissions Trading Scheme (ETS) are already driving emissions reductions across sectors, including cement. However policy needs to do more. Currently, from the perspective of the cement and concrete industry, policy in Europe is focused on a single solution: carbon capture. And while carbon capture is certainly part of the mix it is not a silver bullet. It is expensive and will take a long time to reap rewards. It is estimated that connecting over 200 cement installations to CO2 storage sites will cost up to €175 per t of CO2 avoided. Even if the cost can be reduced, it would take almost two decades to deliver any tangible environmental benefits.
A policy focus on enabling multiple solutions, much as the energy industry has done, can accelerate development and widespread adoption of low-carbon cement, quickly, cost-efficiently, and with the potential to scale-up across the globe.
Against this backdrop, however, funding allocations for sustainable cement industry solutions needs to be more balanced. Currently, money is disproportionately allocated towards methods like CCUS. Since 2021, Europe’s Innovation Fund has awarded €2.1 billion in grants to the cement sector, of which 99.6% are related to CCUS focused initiatives. As of yet no allocation has been made to accelerating the delivery of low-carbon cement solutions. Even a very small percentage of this funding if awarded to the cement market for innovation purposes would turbo charge development and the delivery to market of low-carbon cement solutions. It would spread the industry’s risk substantially and at minimal additional cost.
Additionally, green public procurement (GPP), which accounts for 40 – 45% of cement purchases in Europe, offers significant leverage to promote low-carbon cement use and drive change. As governments implement mandates for low-carbon materials, such as in Ireland, the demand for these products will increase.
Standards drive action. Building materials are rightly subject to stringent standards to prioritise safety. However, standards have fallen behind the rate of technological development in the industry. Europe needs to shift from recipe-based to performance-based cement and concrete standards to ensure a level-playing field for all products and technologies.
The ongoing CPR Acquis process is currently centred on cement standards. However, the proposed standard falls short of expectations for a performance-based approach. The current scope only addresses existing cements and those already approved through the EOTA process, leaving no provision for innovative or novel materials. In fact, this narrow scope has the potential to delay the introduction of any innovation to the market by seven years, since new materials will be required to go through the EOTA process at the EU level. Followed by approvals from national standardisation committees for inclusion in national annexes, this consequently limits their integration into the broader market.
For low-clinker, low-carbon cement to achieve widespread adoption in the cement industry, collaboration with large and established businesses is key. Strategic partnerships enable the sharing of knowledge, resources, and expertise, which are
vital in bringing new technologies to market. They accelerate and facilitate change at scale.
One such partnership is the recently announced agreement between TITAN Group, an international cement and building materials producer, and Ecocem. This partnership aims to co-develop and deploy a version of ACT, which will be optimised for use across TITAN’s portfolio for years to come.
Ecocem is delighted to be working with a business which shares their passion and commitment for the rapid and substantial reduction of carbon emissions from cement manufacturing. Importantly, the partnership has the potential to accelerate the use of SCMs with ACT technology and create new global opportunities.
Partnerships with global players in the wider construction sector are also being struck. Cemex France has been a key partner, testing and scaling ACT as the shift from lab to live projects occurs.
Most recently Bouygues Construction announced a partnership with Ecocem. The long-term goal is to roll-out ACT low-carbon cement across Bouygues Construction’s portfolio of projects, following an intense period which will evaluate ACT’s use in range of deployments, including a full sale construction mockup at Bouygues Construction’s Scale One® facility.
This commitment to validating and developing Ecocem’s ACT technology by major players in the cement and construction industries marks a decisive turning point in the decarbonisation of the construction sector.
The low-carbon cement market is expected to grow from US$30.15 billion in 2023 to US$47.32 billion by 2028, according to The Business Research Company. This trajectory reflects the broader shift within the construction sector, with a growing focus on sustainability and the integration of more eco-friendly practices across the supply chain.
Many corporate leaders and policymakers across the construction value chain recognise the need for an unwavering commitment to use more sustainable and efficient approaches across the industry in order to ultimately achieve net zero.
However, for that to happen, less innovation in isolation and more collaboration between different parties is needed. Going further and faster to tackle the industry’s challenges as a collective is essential. The greatest prize will be delivering a scalable low-carbon, low-cost cement solution that can be adopted worldwide.
Emerging economies cannot afford to adopt expensive carbon reduction strategies, and since these nations are responsible for 90% of CO2 emissions from cement and concrete, this is a prize worth winning.
Only then will truly scalable solutions be delivered that can be used globally, both now and for many years to come.
PSCL’s Laboratory Data Management System (LDMS) integrates your chemistry quality monitoring in one easy-to-use package. And as an ongoing subscription, it’s kind to your cashflow.
The world leader in quality monitoring, automation and logistics solutions for the cement industry
David Hughes, Material Evolution, explores the benefits of ultra-low carbon cement in transforming the built environment.
The cement industry is on the cusp of a significant transformation, driven by the need to tackle the massive carbon emissions associated with the industry. Environmental concerns, increasing government regulation, and innovation are aligning to push the US$400 billion cement industry toward a greener future.
However, real-world adoption remains low. This is due to the (rightly) risk-averse nature of the construction industry, which remains cautious about replacing a product that has many hundreds of years of demonstrated performance. It will take innovation and industry collaboration to unlock the green cement industry at scale. Material Evolution’s new ultra-low carbon cement product may provide the key.
The ultra-low carbon cement product, MevoCem, represents an innovation in the
cement industry, combining sustainability and cutting-edge technology to address the pressing challenges of traditional cement production, supply, and performance.
The environmental impact of ordinary portland cement (OPC) production is profound, contributing approximately 8% of global CO2 emissions. Beyond carbon emissions, OPC manufacturing is resource-intensive, relying heavily on extractive processes that deplete finite natural resources. Construction as a whole consumes 32% of the world’s natural resources and generates 25% of total solid waste.
Material Evolution addresses these challenges by focusing on alternative feedstocks. By harnessing untapped and underutilised waste materials, such as mineral and construction waste rich in silica and
alumina, MevoCem significantly reduces dependency on virgin resources. The use of alternative feedstocks and a novel production pathway enables the product to achieve up to 85% reduction in carbon emissions compared to OPC.
The development of MevoCem hinges on three core technological innovations:
� Alkali fusion technology: Material Evolution’s process enables the transformation of industrial by-products and waste materials into reactive supplementary cementitious materials (SCMs) without requiring heat, drastically reducing energy consumption and CO2 emissions. The technology is a mechano-chemical process which increases the number of reactive sites in the precursor materials and induces solid state fusion with chemical activators. This leads to a one-part 52.5N cement solution that only requires water to be added, but still achieves high early strengths of minimum 12 MPa at day 1, increasing to 35 MPa depending on the powder content and water-cement ratio used.
� Artificial intelligence (AI) and predictive modelling: Material Evolution uses advanced computational tools to analyse and optimise cement compositions, ensuring consistent quality and efficiency across production batches. The company's formulation prediction tool, for example, can predict compressive strength performance based on mineral feedstock composition and optimise for activator ratios with >90% accuracy.
� Scalability: MevoCem’s production process bridges the gap from laboratory research to industrial-scale application, enabling widespread adoption. The Mevo A1 production facility exemplifies the scalability of the technology. Constructed in just 8 months, this facility sets a new standard for ultra-low carbon cement production. The A1 facility is situated in Llay, Wrexham, at the site of CCP Building Products, a producer of precast concrete blocks. This innovative co-location integrates cement and concrete production within a single site, significantly reducing the carbon footprint of the final product by minimising transport needs.
One of the key advantages unlocked with MevoCem is its optimised water-cement ratio, which is critical for balancing workability, strength, and durability. Technical and customer trials have revealed that reduced water-cement ratios create a denser microstructure, which enhances durability and resistance to environmental factors. AACMs and geopolymers create robust, interlocking 3D mesh structures, in contrast to the crystalline structure of traditional OPC cement. This microstructure not only enhances durability and chemical resistance but also increases flexural strength, allowing for the use of thinner slabs
without compromising performance. This innovation supports material efficiency, reducing overall cement and aggregate requirements in construction projects.
Additionally, MevoCem demonstrates superior flowability compared to OPC at equivalent water-cement ratios, simplifying application and ensuring consistent performance. The reduced water demand and reduced section thickness requirements align with Material Evolution’s holistic sustainability goals, lowering overall resource consumption during construction.
Figures 2 and 3 show results from laboratory trials utilising the MevoCem product in a ready-mix design to demonstrate the impact of the water-cement ratio. Figure 2 shows the effect that increasing the water-cement ratio has on initial slump value and
early day 1 strength at a range of powder contents (350, 400, and 450 kg/m3). It is possible to tune the water-cement ratio for each powder content to obtain day 1 strengths of more than 20 MPa while still achieving S4 slump classification (>170 mm as indicated by the dashed blue line), therefore not sacrificing workability. Furthermore, most of the water-cement ratios investigated can satisfy the S3 slump class while achieving at least 15 MPa day 1 strength – suitable for stripping and handling precast products at an early age.
Figure 3 highlights the strength development for each powder content at a range of water-cement ratios, where almost all of the samples tested achieved greater than 50 MPa at day 28. It is possible to obtain finished products of C50 strength classification at 400 kg/m3 and 450 kg/m3 powder content with an initial S4 slump, and of C60 strength classification at 450 kg/m3 powder content with an S3 initial slump.
When compared to a CEM III/A cement, MevoCem offers clear advantages in water-cement ratio, flowability, and strength development. CEM III/A, defined under the European cement standard EN 197-1, contains 36 – 65% ground granulated blast furnace slag (GGBS) blended with portland cement clinker. Typically, CEM III/A requires a water-cement ratio of 0.50 – 0.55 to achieve adequate workability, often resulting in slower early strength development. It has compressive strengths of approximately 8 – 12 MPa at day 1, depending on the mix design and curing conditions, and workability can be limited without the use of chemical admixtures.
MevoCem shows effective flowability even at lower water-cement ratios, typically around 0.35 – 0.40, ensuring ease of application without the need for admixtures. This reduced water demand also enhances the material's microstructure, leading to higher day 1 strengths, and day 28 strengths consistently above 50 MPa, regardless of curing conditions. Unlike CEM III/A, which relies on extended curing times for strength gain, MevoCem provides rapid strength development, making it particularly well-suited for precast applications and accelerated construction timelines.
Additionally, using an increased powder content of the product does not incur the disadvantages associated with OPC. The heat of hydration of MevoCem is low, resulting in reduced water loss due to evaporation, and thus eliminating plastic shrinkage. Problems that may occur due to thermal build up associated with pouring large structures are minimised, and thermal cracking is also eliminated.
These advantages were seen in recent production trials. The trial, conducted in partnership with Ready Mix Tees Valley,
Together beyond lubrication.
successfully showcased MevoCem in a ready-mix application, showing that the product can directly replace OPC while maintaining high performance, workability, and durability – plus an 85% reduction in CO2 emissions.
The trial underscored how MevoCem can act as an alternative to conventional binders without requiring retooling at batching plants.
Designed to meet S4 slump class standards, the one-part activated solution did not require the handling of large quantities of chemical activators, improving health and safety while ensuring seamless integration within existing plant and infrastructure. This trial underscores the practicality and performance of green cement, addressing longstanding concerns around quality and adaptability.
A key driver behind this initiative is the increasing demand for low-carbon construction materials. In partnership with Ready Mix Tees Valley, Material Evolution is integrating carbon-negative aggregate with its innovative binder, pushing the boundaries of sustainable concrete solutions. As regulatory pressures mount and industry stakeholders seek credible pathways to reduce embodied carbon, the success of this trial marked a pivotal step toward widespread adoption of low-carbon alternatives.
The concrete slab was finished with a power float, achieving a smooth and durable surface without any issues related to setting time, surface integrity, or finish quality. Despite being poured on a warm windy day, the slab showed no bleed or plastic shrinkage cracking. The low heat of hydration and enhanced water holding within the geopolymer gel reduced water mobility and migration.
Beyond the site trial, the product has been tested to EAD 040287-00-0404, a rigorous standard simulating 25 years of UK weathering through freeze/thaw cycles. This confirms its resilience under challenging conditions.
Material Evolution’s £7.6 million MEVOCRETE
Project has been instrumental in defining Material Evolution's future trajectory. By collaborating with Teesside University and the Materials Processing
Institute, the project successfully demonstrated the integration of alternative feedstocks into a scalable supply chain. This collaboration included rigorous testing and validation of new feedstocks in partnership with LKAB, leading to the identification of materials that meet both performance and sustainability benchmarks. These feedstocks are now being scaled for commercial use in the UK and internationally.
Beyond supply chain innovation, the project played a crucial role in advancing the company's net zero cement solutions. By leveraging cutting-edge research with Teesside University, significant progress was made in carbon capture integration into Material Evolution’s cement product. This approach not only reduces the carbon footprint of cement production, but also offers a pathway to actively sequester CO2 within construction materials.
The Mevocrete project emphasised the importance of collaboration across academia and industry. Partnerships with leading institutions and businesses enabled the scaling of laboratory findings to industrial applications, ensuring the practical viability of these innovations. Current efforts focus on expanding the supply chain globally, reinforcing the scalability and impact of Material Evolution’s solutions.
Without commercial and operational progress, however, technical innovation will not be able to scale from lab to industry.
To address this, the Material Evolution team has built and commissioned an industrial-scale facility to produce the MevoCem product. The Mevo A1 production facility in Wrexham, Wales, has the capacity to produce 120 000 tpy, making it the UK’s largest producer of ultra-low carbon cement. The plant produced its first batch of ultra-low carbon cement in October 2024 on schedule and just eight months after construction work began onsite.
The 120 m2 plant was designed to combine and react waste feedstocks using lean manufacturing techniques.
Material is transported around the plant using state-of-the-art material handling processes, allowing its overall footprint to be far smaller than the average UK cement factory. By using a modular design, the Mevo A1 production facility is flexible to the supply chain and raw materials required, allowing for adaptation to new cement technology and innovation.
Material Evolution continues to collaborate with on-site partners, CCP – a subsidiary of SigmaRoc – and other commercial partners to develop the full supply chain, including deploying products into real world ready-mix and precast applications.
Mylène Krebs, Jean-Michel Charmet, and Damien Chudeau, Fives FCB, discuss the key factors influencing the calcination process and present insights from a calcination test centre in Northern France.
The calcination of clay is a transformative process, unlocking its potential as a reactive supplementary cementitious material (SCM).
At Fives FCB, the Cement and Minerals division of Fives Group, a dedicated calcination pilot has been operational since 2021. Equipped with advanced technologies, the facility enables precise parameter optimisation for a wide range of clays. This article examines the major calcination parameters, the performance of two distinct calcination technologies, and considerations for assessing clay suitability.
Calcination equipment and methods
The Fives FCB test centre houses two calcination technologies:
� Flash calciner: Featuring the four independent process steps (i.e. heat generation, calcination, colour control, and final cooling) as in Fives' industrial plants. This technology ensures the best overall
performance and versatility across a wide range of clay qualities. It can be operated up to 1300˚C, extending the use of flash calcination to other types of materials.
� Rotary kiln: A 4 m long rotary kiln providing residence time of 30 min., suitable for producing both calcined clay and clinker.
To date, dozens of materials have been tested, resulting in a robust database of 150 samples.
Optimising the calcination process requires attention to three principal factors:
� Temperature:
» Insufficient heating results in incomplete dehydroxylation, reducing reactivity.
» Excessive heating induces sintering and crystallisation reactions, creating unreactive phases.
� Particle size distribution:
» The proper grinding sequence has a strong influence on process efficiency.
» In flash process, preliminary grinding to a d50 in a range of 30 µm to 40 µm often strikes a balance, minimising operational issues like clogging and reducing the need for subsequent grinding.
� Residence time:
» Residence time varies significantly between technologies. Flash calciners enable short residence times (sec.), while rotary kilns require prolonged durations (30 min.). Optimal residence time correlates with particle size and ensures uniform calcination.
A systematic survey of flash calcination parameters was conducted using the Taguchi method (Figure 2), a robust statistical approach to experimental design. The study evaluated the influence of the three key factors – temperature, residence time, and particle fineness – each tested at three distinct levels. This factorial design resulted in a total of 18 tests, carefully structured to assess the interactions and individual effects of these parameters. The reactivity of the calcined clay was measured using the modified Chapelle Test, following the NF P18-513 standard. This methodology ensures reliable and reproducible insights into the optimisation of calcination conditions for maximising clay reactivity.
The primary determinant of the calcination process efficiency and outcome is the particle size distribution of the clay. Finer particles ensure higher reactivity and consistency in the final product, as they promote uniform heat transfer and complete dehydroxylation during calcination. Conversely, coarse particles often
result in insufficient calcination, leading to a lower reactivity of the material. It is important to note that increasing the temperature or prolonging the residence time cannot fully compensate for the challenges posed by coarse particles. Such adjustments may lead to energy inefficiencies and undesirable transformations, such as the formation of unreactive phases – by sintering or crystallisation reactions. Therefore, achieving an optimal particle size distribution before calcination is critical for maximising reactivity and process efficiency.
The Fives FCB test centre has performed comparative studies on identical clays using both technologies. Key observations include:
� Rotary kilns:
» Advantages: adaptable for retrofitting existing kilns.
» Limitations: difficulties to achieve uniform particle calcination.
� Flash calciners:
» Advantages: precise control over temperature and residence time; suitable for fine clays.
» Performance: tests confirm superior reactivity of clays calcined in flash calciners compared to rotary kilns.
As seen in Figure 3, the optimal reactivity is obtained with flash calcination at a temperature between 750˚C and 800˚C. The x-axis (calcination temperature) has been correctly set between the flash and the kiln tests by comparing with the LOI of the final product as an image of the calcination rate. The reactivity of calcined product (y-axis) has been measured performing R3 tests based on bound water. On average, the reactivity is 16% higher with flash technology compared to kiln technology. It should be noted that this conclusion on reactivity results from the comparison between the rotary kiln and the flash calciners is quite important. Indeed, final product reactivity is a key criteria for a new clay calcination plant, other important features being the energy consumption or the design efficiency related to colour control or emissions. Those tests confirm the higher efficiency of the flash calciner compared to the rotary kiln. As in every modern cement plant, calcination is performed by a flash calciner, and the kiln being used for final clinkerisation. Indeed, clay activation by dehydroxylation – consisting in breaking OH bound in the mineral structure – is a very fast kinetic process that fits perfectly with a flash calciner. It does not require the combination of several chemical components by solid-solid or solid-liquid reactions like in the clinkerisation. Thus, a long residence time at the activation temperature, as in a rotary kiln, is not necessary
and can even be harmful for reactivity as sintering reactions may occur.
In the context of clay calcination, certain aspects can be controlled – such as the calcination parameters outlined earlier – while others, like the characteristics of the clay quarry, are more challenging to alter. A detailed evaluation of the clay is essential to determine its suitability as a candidate for calcination. Reactivity is primarily derived from kaolin, though pure kaolin is rare.
Most clays are complex mixtures of minerals, including quartz, kaolinite, illite, smectite, which can be identified through X-ray diffraction (XRD) analysis. Additionally, the chemical composition, determined via X-ray fluorescence (XRF), must be analysed to identify elements such as iron or carbonates that may impact reactivity. Thermogravimetric and differential calorimetry analysis (TGA/DSC) is also crucial for assessing the clay's thermal behaviour and suitability.
Based on extensive database insights, the suitability of a clay has been preliminarily evaluated at Fives FCB by examining the total clay content, ensuring that the loss on ignition (LOI) from dehydroxylation is sufficient, and analysing the ratios of Al2O3 to SiO2
If some parameters are suboptimal, processes such as clay beneficiation or quartz removal may be employed to enhance its quality. However, any conclusions regarding the clay's potential must ultimately be validated through pilot-scale calcination testing to ensure optimal performance.
Fives FCB is implementing a new clay calcination unit in Germany. Rohrdorfer Zement, operating cement plants both in Germany and Austria, is actively implementing its road map to carbon neutrality by 2038. Clay calcination shall play an important role in this road map. First step will consist of testing different clays and different cement recipes.
To do so, Rohrdorfer Zement entrusted Fives FCB for the engineering, supply, and erection of a 50 tpd reliable flash calcination unit equipped with high efficiency colour control (Figure 5). Erection is under progress and commissioning scheduled for mid-2025.
Optimising clay calcination demands a systematic approach, balancing temperature, particle size, and residence time. Flash calcination emerges as a preferred technology for most applications, offering superior control and reactivity. Nonetheless, detailed assessments of clay mineralogy and chemistry are indispensable for choosing a suitable material and tailoring calcination strategies.
Grant Quasha, Eco Materials Technologies, reveals how the innovative use of coal ash and other supplementary cementitious materials is helping the concrete industry reduce its carbon footprint and improve performance.
Much of the world’s infrastructure – highways, bridges, dams, tunnels, and buildings – is built with concrete. Comprised of aggregate, water, and cement, concrete is economical, strong, and durable. These traits have made concrete the most-used substance in the world after water and, by far, the most popular construction material.
From an environmental perspective, however, concrete has a significant drawback: its carbon footprint. Cement – the binding ingredient in most concrete mixes – accounts for about 8% of all man-made greenhouse gas emissions worldwide. Every tonne of cement manufactured, produces nearly the same amount of CO2, and global cement production is expected to top 6 billion metric t by 2050. With the climate change threat tied to increasing levels of carbon-dioxide emissions in the atmosphere, governments, researchers, and
cement manufacturers are looking for solutions to help decarbonise the concrete industry.
For decades, builders have replaced a portion of the portland cement used to produce concrete with coal ash – chiefly for the performance characteristics it imparts to both fresh and finished concrete. Such benefits include increased strength, workability, and durability, as well as lower permeability and heat of hydration. As climate concerns have come to the forefront, however, coal ash is increasingly being specified for its ability to lower concrete’s carbon footprint. Each t of coal ash used to replace portland cement in concrete production saves almost 1 t of CO2 from entering the earth’s atmosphere. In 2022 alone, beneficial use of coal ash in concrete delivered approximately 11 million t of CO2 reduction.
Coal ash has traditionally been sourced directly from operating coal plants. However, as coal generators continue to be retired, previously disposed ash – now stored in landfills and surface impoundments throughout the country – has become an increasingly important supply of this material. The American Coal Ash Association estimates that there are approximately 2 billion t of coal ash stored in this manner.
Eco Material Technologies, the largest supplier of coal ash and other advanced supplementary
cementitious materials (SCMs) in the US, is at the forefront of decarbonising the built environment. The company has developed multiple green cement products that can be manufactured with significantly lower carbon emissions than portland cement, and which can substitute for cement in even higher proportions than traditional SCMs. Researchers, chemists, and R&D experts at Eco’s Georgia-based Materials Testing and Research Facility (MTRF) work behind the scenes to develop these low-carbon cement alternatives from coal ash as well as natural and other industrial-based pozzolans.
Located near Cartersville, Georgia, Eco's AASHTO-accredited cementitious materials and concrete laboratory is one of two company research facilities tasked with validating the quality of potential coal ash deposits and ensuring the high performance and quality of the final products. The facility’s 1700 ft2 concrete lab enables Eco Material to test SCMs in their intended final product, concrete. Lab technicians perform concrete testing according to ASTM C192 to determine the effects of SCMs in slump, set time, finishability, and workability in fresh concrete. Additionally, the team tests the compressive strength, permeability, and other durability qualities in hardened concrete. Each year, the MTRF team processes more than 3500 samples of coal combustion products, pozzolans, and building products. In addition, MTRF staff conduct an array of concrete testing services for aggregates, cements, alkali-aggregate reactivity analysis, concrete sulfate testing, hardened concrete petrography, and more. MTRF's technical service representatives (TSRs) work with customers to prepare and test concrete trial batches to demonstrate the value of each SCM. The lab works with both as-produced and beneficiated coal combustion products.
The lab’s team of American Concrete Institute (ACI)-certified personnel includes a senior research manager, chemical technician, lab manager, multiple lab technicians, a quality assurance manager, physical lab supervisor, R&D associate, geologist, and a lab support coordinator. Eco also has three full-time technical services managers available to customers and employees as needed, providing technical support and managing testing and C618 certifications for 62 coal ash and natural pozzolan sources.
MTRF utilises a range of advanced technological equipment to examine all aspects of coal combustion products stored in landfills and ponds, from particle size and pozzolanic properties to reactivity and detection of potential impurities.
Eco’s high-tech tools include a particle size analyser, optical microscope, scanning electron microscope, thermogravimetric analyser, calorimeter, infrared carbon analyser, specific surface area analyser, X-ray diffractometer, and more. MTRF’s physical testing capabilities include ASTM C109, C311, C1012, C1260, and C1567, among others.
In addition to supporting Eco’s existing business by ensuring the quality of products and providing technical services to clients and partners, MTRF plays the key role of discovering, researching, evaluating, vetting, and developing new supplementary cementitious materials that contribute to concrete decarbonisation once they are deployed in the market. In 2016, MTRF started conducting R&D on the potential of harvested fly ash and ground bottom ash to be used as SCMs in concrete.
This played a crucial role in developing MTRF’s fly ash harvesting and bottom ash processing plants in Washingtonville, Pennsylvania, and Franklin, Texas, that began operations in 2018 and 2023, respectively. These efforts required not just research and development on these materials, but also the involvement of the MTRF team to drive specification changes to ASTM C618 that were vital to the successful commercial rollout of these products. MTRF also supported the successful development of two more SCM processing plants: a natural pozzolan facility in Arizona and a harvesting plant in Georgia. Because of MTRF’s efforts, Eco Material is now on track to have 8 SCM processing plants by the end of 2025.
In July 2025, Eco will expand its facility into a comprehensive 16 400 ft2 research centre, representing an US$8 million investment. The state-of-the-art expansion will drive innovation in the utilisation of harvested ashes, green cement products, and natural and other industrial-based pozzolans. New facilities will include an 11 000 ft2 building housing current pilot-scale technologies, offices, a conference room, material storage, and additional space to expand for future innovations in the business.
By investing in research and testing, Eco Material is demonstrating its commitment to developing environmentally friendly alternatives to portland cement that improve the performance and longevity of concrete, restore disposal sites to their natural condition, and achieve significant reductions in greenhouse gas emissions for the concrete sector.
Grant Quasha is CEO of Eco Material Technologies, a leading producer of sustainable cementitious materials and near-zero-carbon cement replacement products in North America.
With over 50 years of experience, DI MATTEO has set many standards in the business of handling alternative fuels.
Products like the innovative
• ODM-MultiFUEL-System
• ODM-WeighTUBE® RWS
• ODM-Docking station BOX
• ODM-Injector rotary valve IZS and various state-of-the-art screw conveyors are worldwide in operation.
Isabel Rask, alcemy, explores how well-designed interfaces are key to overcoming AI adoption challenges in the cement industry and ultimately driving decarbonisation efforts.
Though the term artificial intelligence (AI) was first coined in 1956, AI has rapidly gained popularity over the past 10 years.
A well-established buzzword in the startup space of the 2010s, the release of ChatGPT and other generative AI models in November 2022 launched the technology into the mainstream. Not one to be left behind, the cement industry has similarly embraced AI with open arms. From conferences like Envirotech 2024 to company roadmaps, AI is seemingly everywhere within the cement industry, with the promise to help the sector tackle its greatest challenge in recent memory: decarbonisation.
However, while research has shown that AI in the cement industry has proven potential to help producers reduce costs and emissions,1 this article will examine AI’s rise in the industry with a
critical lens. Specifically, this article will discuss the role of a well-designed interface in coordinating industry experts and technology for maximum results, exploring the steps required beyond the AI itself to ensure successful adoption. Using the German tech company alcemy as a case study, this article will also explore the factors necessary for effective cement AI implementation.
AI’s interface
Though the term AI is used in a variety of contexts, its most common definition includes all computer-based systems that perform tasks traditionally thought to require human intelligence.2 This could be anything from understanding speech to, in the case of the cement industry, making decisions on how to best run a
cement plant. Every AI system utilises at least some algorithms, step-by-step processes that take input and provide output. These algorithms are what allow the AI to adapt to different situations by recognising patterns and making decisions in real-time.
However, algorithms alone are not enough to make an AI system function effectively. Beyond the computer, infrastructure and security measures needed to protect data, a well-designed interface is key to reaping the full benefits of AI adoption. Often broadly defined, the interface is the point where the end user interacts with the technology and typically includes the user interface (UI) and user experience (UX) design that makes the technology easy and intuitive to use. An interface allows users to both receive and give information to the AI system, adjusting their own behaviour based on its recommendations and providing feedback.
While AI algorithms are often the focus of keynote speeches and white papers, the AI interface fundamentally defines the effectiveness of adoption, as the insights available without a well-designed interface will be limited. A great interface can mean the difference between effectively connecting
experienced team members in the plant with AI insights to optimise production and simply having another screen open. In a recent Boston Consulting Group (BCG) report titled 'Where’s the Value in AI', the firm estimates that approximately 70% of AI-based challenges relate to people and processes. The report goes on to explain that “too often, companies make the mistake of prioritising technical issues over the human ones – which helps explain why many of them do not achieve the results they are looking for.” While an effective interface can help solve many of these problems, building one can require significantly more effort than the AI algorithms themselves due to the deep understanding of the user’s end goals required.
As already discussed, a well-designed interface can be the key to unlocking AI’s full potential in cement production. One company that has successfully implemented this approach is alcemy, a German AI company focused on decarbonising the cement and concrete industries. Over the past six years, the firm has quickly expanded to over 10 countries and partnered with more than a third of all German cement plants. alcemy offers two solutions for the value chain: 'alcemy for cement' and 'alcemy for concrete', each designed to address specific challenges within cement and concrete plants, respectively. While these tools are designed to be compatible with one another, this article will focus on alcemy for cement, highlighting how effective interface design can drive effective AI adoption and decarbonisation in the cement industry. alcemy for cement is an AI web application that predicts the 2- and 28-day strengths for different cement recipes. Based on the predicted compressive strength, alcemy’s algorithms recommend an optimal steering fineness to ensure the quality of the end product. While the AI side of alcemy’s technology is managed by machine learning engineers who oversee regular algorithm
retrainings and data cleanup, multiple other team members focus exclusively on designing an intuitive interface aligned with user needs.
According to Sebastian Lesser, alcemy’s Head Cement Product Manager, “alcemy for cement isn’t just about providing accurate predictions – it’s about delivering a seamless user experience that integrates into your existing workflows. While building AI models is one challenge, creating a system that is intuitive, actionable, and deeply aligned with the realities of cement production is what truly drives value. We’ve worked hand-in-hand with industry leaders to ensure that our solution feels like a natural extension of your team, enabling faster decision-making and immediate impact. It’s not just the AI – it’s the ease of using it that sets us apart.”
With this philosophy in mind, alcemy’s engineering team has designed specific views tailored to different user groups, creating an effective bridge between the AI and the users.
Designed for the control room, the heart of a cement plant's
operations, alcemy’s steering view displays the most recent fineness recommendations from the AI algorithms along with a small subset of laboratory data selected by the user themselves (Figure 1).
As control room operators and production personnel are often managing a large quantity of information at once, this interface is designed to show only the most vital information from the AI. By not overwhelming the user, alcemy’s steering view aims to facilitate fast decision making and a smooth continuation of production day-to-day.
However, alcemy’s AI offers significantly more insights beyond the most recent fineness recommendation. The analysis view, for example, is designed for quality control managers as well as executives to facilitate the long-term improvement of operations, with additional information from the AI needed to evaluate production over time (Figure 2). Users can see not only how the compressive strength and fineness recommendations changed over time, but also note the accuracy of the AI’s predictions for previous samples, creating trust and transparency in the system. When more detail is needed, users can scroll down and view how individual laboratory values changed across samples (Figure 3).
This data, though not calculated by the AI algorithms, is displayed within the 'alcemy for cement' web app so that users only have to check one application for these insights. This interface ensures that the user can easily access information relevant to their decision making within a single programme. Additionally, the laboratory view makes it easy for users to spot sample outliers, allowing for quick and accurate root cause analysis.
Through offering various easy-to-access views, alcemy’s interface design empowers cement producers to reap the sustainability and financial benefits of the AI for decarbonisation. By enabling users to see production in real-time and produce at a quality optimum, team members can lower their clinker factors after fully understanding their current cement production trends. For example, alcemy customers have removed 1 – 3% clinker from previously optimised recipes in the first year of implementation, with some reaching 5% reduction as the partnership continues. In addition, producers can also increase their use of alternative fuels and novel SCMs, as the alcemy interface allows them to track and adapt to fluctuations in real time. Thomas Sievert, Head of Quality at Dyckerhoff Germany, commented on the alcemy software by stating: “With alcemy, we are ahead of our time.
It is a powerful tool that provides us with the necessary information much earlier and enables us to proactively manage operations even in times of constant change. We have already achieved considerable savings and reduced the clinker content.” alcemy’s interface design and its success in decarbonising and reducing costs in the cement industry are not a coincidence: rather, the interface is vital to ensuring that the AI insights can be effectively used and applied.
Outlook: interface design in the cement industry and beyond
There is no one set of rules for a well-functioning interface, and continued success will require adaptation to changing needs and purposes. For example, alcemy has applied similar AI-driven interface principles to its 'alcemy for concrete' solution, which addresses challenges unique to concrete users. Unlike cement production, where decisions are often made in a control room setting, concrete operations demand flexibility and mobility. To meet this need, alcemy’s concrete application includes a mobile-friendly interface that allows users to access AI insights on the go (Figure 4).
However, one thing remains clear: as AI adoption in the cement industry continues to grow, companies that prioritise integration into existing expertise via well-designed interfaces stand to reap the greatest rewards, both in terms of efficiency and decarbonisation. By using alcemy for cement as a case study, the demonstration has been made that the industry as a whole must ensure that AI is not simply a buzzword but a tool that truly enables smoother decision-making and more sustainable operations. AI’s success should not be measured solely by its technical capabilities, but by how effectively its insights are applied in practice. Looking forward, the cement sector has an opportunity to lead in industrial AI adoption, but only if innovation is matched with a deep understanding of the people who use it. Those who bridge this gap with effective interfaces among other tools will help define the role of AI in the cement industry.
1. de BELLEFONDS, N., CHARANJA, T., FRANKE, M., APOTHEKER, J., et al., 'Where's the Value in AI?', Boston Consulting Group, 2024 – https://www.bcg.com/ publications/2024/wheres-value-in-ai
2. MANNING, C., 'Artificial intelligence definitions', Stanford University, Human-Centered Artificial Intelligence (HAI), 2020 – https://hai.stanford.edu/sites/ default/files/2020-09/AI-Definitions-HAI.pdf
3. FELDMANN, R., 'Artificial intelligence helps cut emissions and costs in cement plants', McKinsey & Company, 2019 – https://www.mckinsey.com/industries/ chemicals/our-insights/artificial-intelligence-helps-cutemissions-and-costs-in-cement-plants
• High accuracy through patented dual wavelength pyrometric technology
• Better image quality through high-definition optics and 1080p resolution
• Modular design for ease of serviceability
• Enhanced user interface to simplify operations
• Greater flexibility with support of up to two cameras/displays
• Added security and auditability with Windows 10 network compatibility
Pascal Gaillot, Yokogawa Europe, explains how the integration of digital technologies and decarbonisation strategies is preparing the cement industry for the future.
Cement production plays a crucial role in modern infrastructure. It drives the construction of buildings, roads, and bridges that support global economic development. However, this important industry also faces a major challenge: it is one of the largest industrial emitters of greenhouse gases, accounting for around 7 – 8% of global CO2 emissions. As the world moves towards more sustainable practices, the cement industry must find innovative ways to balance growth demand with environmental responsibility. Two transformative trends, digitalisation and decarbonisation, will reshape the industry and provide new opportunities for efficiency, sustainability, and growth.
The cement production process: a short overview
The cement production process begins with the extraction of raw materials, such as limestone and clay, from quarries. These materials are then crushed and mixed to form a raw meal, which is fed into a kiln where temperatures exceed 1400˚C. In this high-temperature environment, the chemical
transformation known as calcination takes place, creating clinker, the main component of cement. The clinker is cooled and mixed with gypsum and other additives before being ground into the fine powder, known as cement.
Although the process is simple, it is very energy-intensive. The kiln phase, in particular, is responsible for the majority of carbon dioxide (CO2) emissions in cement production, both through burning fossil fuels and the chemical reaction during the deacidification of limestone. One parameter that is often mentioned in this context is the specific CO2 emission. This describes how much CO2 is emitted during the production of one ton of cement.
According to the German Emissions Trading Authority (DEHSt), the value in 2018 was around 0.59. This results in CO2 emissions of 590 kg/t of cement. In 2018, a total of around 33.7 million t of the building material was produced in Germany.
In addition, the grinding and mixing processes consume significant amounts of electricity, making energy efficiency an important issue. Understanding these emission hotspots is the first step in addressing the environmental impact of cement production.
Globally, the cement industry is both a cornerstone of development and a major source of environmental setbacks. Demand for cement continues to rise, driven by urbanisation and the expansion of infrastructure in emerging countries. At the same time, the industry is under increasing pressure to reduce its environmental footprint. Regulatory frameworks like the UN SDGs or the EU taxonomy, consumer expectations from around the globe, and investor interest in sustainable investment are forcing companies to adopt more sustainable practices.
Challenges such as fluctuating raw material prices, complex supply chains, and strict emissions standards are making the industry's path more difficult. However, these challenges also offer opportunities for innovation and change. Companies that successfully navigate this environment can gain a competitive advantage while contributing to global climate goals.
Digitalisation represents a paradigm shift in the way cement is produced, managed, and distributed.
By using advanced technologies such as the internet of things (IoT), artificial intelligence (AI) and machine learning, companies can optimise their processes and improve sustainability.
Process optimisation is a key application of digital technology. Sensors embedded in equipment and pipelines – such as flow meters, temperature and pressure sensors, or high-end laser-sensor-systems like Yokogawa’s tunable diode laser spectrometers (TDLS) in combustion areas – gather real-time data on combustion gases to identify inefficiencies and reduce energy consumption while improving product quality. Predictive maintenance systems use AI to predict equipment failure, allowing companies to proactively address issues and minimise downtime.
Digital twins, virtual replicas of physical processes, allow operators to simulate and optimise production scenarios without interrupting actual operations.
Systems like Visual MESA® Greenhouse Gas Emissions Management (VM-GEM), which, amongst other things, can autonomously control processes based on stoichiometric calculations while taking into account weather forecasts, market trends or things like supply/energy contacts, are valuable for improving energy efficiency while reducing waste. In addition, digital platforms are transforming supply chain management by increasing transparency, streamlining logistics, and reducing costs. These advances not only improve operational efficiency, but also set the stage for more sustainable practices, which Yokogawa can support with a huge range of solutions.
in the cement industry
Decarbonisation is the cornerstone of the cement industry's sustainability efforts. Reducing CO2
emissions requires a multi-layered approach that considers both direct and indirect sources of emissions.
One of the most promising strategies is the use of alternative fuels (AFs). By replacing coal and petroleum coke with biomass or waste-derived fuels, companies can significantly reduce their dependence on fossil fuels. Measures to increase energy efficiency, such as modernising furnaces and introducing advanced grinding technologies, also play a crucial role in minimising emissions.
Carbon capture, utilisation, and storage (CCUS) technologies are becoming increasingly popular for tackling emissions at the source. These systems capture CO2 from flue gases and either store it underground or reuse it for other industrial processes like sustainable aviation fuel (SAF). Clinker substitution is another effective strategy, where additional cementitious materials such as fly ash or slag replace some of the clinker in cement production, reducing emissions from calcination.
Different connections come into play further along the supply chain. Slag produced during ore processing can make concrete more climate-friendly and reduce the need for CO2-intensive cement. Yokogawa has been assured that up to 40% of cement can be replaced by a finely ground waste product from silicon manganese production without
compromising concrete’s stability, shown by a pilot test in Norway. The slag concrete could save up to 95% of CO2 emissions that would otherwise be caused by the cement content. Even if, of course, this initially reduces the volume of cement production and does not contribute to cement manufacturers’ sales, it is still a big step for sustainability and, more precisely, for decarbonisation. But this is a different story.
Renewable energy is also becoming a key component of decarbonisation. Many cement plants are investing in solar, wind, and hydro power to meet their electricity needs and further reduce their carbon footprint. Case studies from industry leaders demonstrate the feasibility of these approaches and illustrate how innovation can add both environmental and economic benefits.
The intersection of digitalisation and decarbonisation offers unprecedented opportunities for the cement industry. Digital tools provide the data and insights needed to implement effective decarbonisation strategies. For example, real-time monitoring systems like VM-GEM can track energy consumption and emissions, enabling companies to identify areas for improvement and create reports for CO2 audits that
meet the regulations at the customer's location. A first-class system can even make the audit itself easier, as a 'certified calculation method' (certified by TÜV Rheinland under ISO14068), such as VM-GEM, can significantly reduce audit times and audit checks. Through advanced analytics, production parameters can be optimised to reduce waste and emissions while maintaining product quality.
Digitalisation also facilitates the integration of renewable energy sources and CCUS technologies into existing processes. By simulating different scenarios using digital twins, companies can assess the feasibility and impact of different decarbonisation initiatives. These tools provide decision-makers with actionable insights and make it easier to align sustainability goals with operational priorities.
Combining digitalisation and decarbonisation offers long-term benefits. Companies can achieve significant cost savings through improved efficiency and reduced energy consumption. In addition, alignment with sustainability goals enhances brand reputation, attracts environmentally conscious customers, and opens access to green financing opportunities.
Despite its potential, the transition to a more digitalised and sustainable cement industry is not without its challenges. High upfront costs for digital and decarbonisation technologies can be an obstacle, especially for smaller companies. In addition, implementing these technologies requires a skilled workforce, which necessitates investment in education and training.
Regulatory uncertainties and market pressures also complicate the transition. Companies must navigate a complex landscape of emissions standards, carbon pricing mechanisms, and reporting requirements. However, these challenges also present
significant opportunities. Innovation-driven growth, partnerships with technology providers, and access to green incentives can help companies overcome initial hurdles and achieve long-term benefits.
The cement industry’s future lies in its ability to adapt to changing requirements and embrace innovation. Emerging technologies such as AI, advanced materials, and next-generation CCUS systems can revolutionise production processes and further reduce emissions. Collaboration between stakeholders, including governments, industry, and research institutions, will be crucial for accelerating this change. Main automation contractors with the know-how and background like Yokogawa can provide the digital platforms and data required for sustainable operation and optimisation. Yokogawa are typically the link between all parties and have a fundamental knowledge about IT-OT, data protocols, how to collect the data, and how to interpret the data from all automation levels.
Policy frameworks and incentives can also play a crucial role in promoting change. Support for research and development, subsidies for green technologies, and clear regulatory guidelines can help align industry efforts with global climate goals. By taking proactive steps now, the cement industry can position itself as a leader in sustainability and innovation.
Cement production is at a crossroads and faces the dual challenge of meeting growing demand while reducing its environmental impact. Digitalisation and decarbonisation offer powerful tools to overcome these challenges. They enable the industry to optimise its operations, reduce emissions, and improve sustainability. By embracing these transformative trends, the cement industry can pave the way for a more sustainable and prosperous future, balancing economic growth with environmental responsibility.
Molly Pace, Imubit, explains how closed loop AI optimisation is reshaping cement manufacturing by boosting efficiency, reducing emissions, and enabling real-time process control.
Cement manufacturing, a cornerstone of global infrastructure, is undergoing a significant transformation driven by the need to improve energy efficiency and reduce emissions. This change comes as the industry faces mounting pressure to address its environmental footprint; it is currently responsible for approximately 8% of global CO2 emissions. A key enabler in this transformation is a new closed loop AI optimisation (AIO)
approach, which offers a fresh perspective on process control and online optimisation. The most significant operational challenges facing cement plants today are multi-faceted, encompassing raw material availability and variability. Unpredictable volumes, inconsistent frequency, and fluctuating quality of supply lead to irregular clinker quality, reduced plant productivity, and elevated emissions. Furthermore, ageing equipment compounds
these issues throughout production campaigns, as wear and tear on critical components of the cement manufacturing process progressively diminishes production capacity and process efficiency.
Variability in raw material quality is particularly problematic in cement production, as it can lead to mechanical, environmental, operational, and safety challenges. Fluctuations in raw material quality directly affect the chemical
Figure 1. Unfiltered relationship matrix (top, grey) shows all possible values of each relationship learned by the AI model during training. Filtered relationship matrix (bottom, red) highlights the nonlinear relationship between natural gas flow and kiln NOx calling out behaviour of other variable pairs when this relationship is negative.
reactions involved in clinker formation, which, in turn, influence the overall quality of clinker production.
Similarly, variability in the type and quality of fuel can disrupt the temperature profile and heat distribution in the kiln, causing over-burning or under-burning of clinker and adversely impacting its quality and reactivity. Additionally, changes in ambient conditions and humidity can influence the hydration reaction of the cement product and the efficiency of heat transfer during the process.
The path to a low carbon future Decarbonising cement production centres on minimising CO2 emissions generated during the calcination process.
A key lever in this effort is reducing the clinker factor – the percentage of clinker used in cement production. However, the two primary challenges here are maintaining throughput demand and adhering to product quality standards, both of which directly affect profitability.
Clinker factor reduction is achieved by substituting clinker with other raw materials or industrial by-products, collectively known as
While increasing the proportion of SCMs lowers the clinker factor, it often compromises cement performance, particularly mortar strength.
This issue can be mitigated by enhancing cement fineness or increasing clinker reactivity, both of which significantly impact the cement grinding process.
Higher cement fineness demands greater energy consumption to grind clinker into fine powder.
Conversely, using more reactive clinker facilitates easier grindability at higher fineness targets due to its mineralogical composition, particularly its high alite (C3S) content. This is crucial for counteracting the mortar strength reduction associated with higher SCM usage.
Alternative fuels (AF) also play a pivotal role in decarbonising the industry, as approximately 40% of cement industry CO2 emissions stem from fossil fuel use. Introducing and sustaining AFs in the production process, known as co-processing, is vital for strengthening the circular economy.
While other decarbonisation methods aim to reduce specific gross emissions (the total amount of CO2 emitted per tonne of cement),
Traditional methods, such as model predictive control (MPC), have long played a vital role in stabilising plant operations. However, these systems rely on fixed models and often require manual intervention, making them less effective in addressing the complexities of modern cement production. Enter closed loop AIO, a system designed to adapt in real-time to the dynamic conditions of a cement plant. By leveraging advanced machine learning techniques, AIO redefines operational efficiency and sustainability.
Closed loop AIO presents significant opportunities for data-driven decision-making, surpassing the limitations of MPC, which relies on predefined relationships. This advanced optimisation approach evolves alongside the site, pushing the plant to achieve a continually higher state of optimisation.
Closed loop AIO systems can support the cement industry's decarbonisation goals in two key ways. Firstly, they provide deeper insights into the relationships between process variables (Figure 1) and the carbon emission costs of various operational modes. For instance, operating at half production capacity does not necessarily halve emissions. Secondly, they enable carbon emission costs to be integrated into the economic objective function that guides optimisation strategies.
Cement manufacturing processes are inherently complex, involving multiple variables such as fuel composition, kiln feed, and ambient conditions. While MPC has improved stability, its limitations become evident in highly variable environments.
Closed loop AIO addresses these challenges using reinforcement learning to learn from a plant’s history. Unlike traditional systems operating within predefined boundaries, AIO simulates both historical and never before seen process conditions, enabling plants to maintain optimal performance under fluctuating conditions.
This adaptability is critical for an industry striving to meet ambitious decarbonisation targets.
Imubit’s 'Optimising Brain', an AIO solution, provides real-time insights that enhance both productivity and sustainability. By integrating with existing infrastructure, the system optimises critical components such as kilns, coolers, and preheaters.
The AIO creates a digital twin of the plant, learning from historical data to make decisions that improve efficiency while reducing emissions – a level of insight that was previously unattainable.
One significant advantage of AIO is its ability to minimise reliance on manual intervention, which has become increasingly important as the industry faces a skills gap. With experienced operators retiring, AIO helps standardise optimisation techniques, ensuring consistent performance across shifts and locations.
The adoption of AIO by a top global cement company exemplifies how the technology can be effectively implemented. Imubit selected one of its most optimised plants as a pilot site to test AIO’s capabilities.
The pilot highlighted several key outcomes, including reduced fuel consumption, lower CO2 emissions, and enhanced production flexibility. By creating a plant simulator for operator training, Imubit also hopes to address workforce turnover, ensuring newer operators can quickly onboard and adapt to the demands of modern cement production.
The broader implications of AIO extend beyond operational efficiency. The technology aligns with the industry's sustainability goals by optimising the use of AFs and improving energy management.
Collaboration between operators and AI systems has been a cornerstone of Imubit’s success. By combining human expertise with machine intelligence, Imubit has improved plant performance and enhanced operator satisfaction. This partnership underscores the potential of AIO to serve as a transformative tool for the cement industry.
As the cement sector navigates the dual challenges of decarbonisation and operational complexity, closed loop AIO emerges as a practical solution. Its ability to adapt to changing conditions and deliver real-time insights positions it as a key driver of efficiency and sustainability. Imubit’s experience demonstrates that AIO is not merely a replacement for traditional systems but a complementary enhancement that unlocks new performance levels.
The journey toward widespread adoption of AIO in cement manufacturing is just beginning. AIO represents a significant step forward for an industry at the crossroads of tradition and innovation by addressing immediate operational needs while supporting long-term sustainability goals.
Through careful implementation and a commitment to collaboration, the cement sector can harness technology to build a more efficient and environmentally responsible future.
Cement is a crucial element of modern development, but its production is carbon-intensive: the industry emits 2.4 Gtpy CO2, nearly 7% of global anthropogenic CO2 emissions and over 25% of all industrial emissions.
Most industrial emissions are a consequence of burning fossil fuels for process heat, but cement production exhibits a different emissions profile. Around 60% of cement-related emissions come from the chemical process of calcining limestone to produce clinker, with the balance coming from fuel burning and electricity use.
Because most cement emissions come from calcination and not from heat production, some decarbonisation approaches that work in other industrial applications – biomass or hydrogen firing and electrification – will not be sufficient to decarbonise cement production. While efficiency improvements and process modifications will certainly produce some reduction in carbon intensity, carbon capture, utilisation, and storage (CCUS) remains the only method ready for deployment that can enable full decarbonisation of the cement value chain.
Cement production differs from other manufacturing processes in a few ways that make applying CCUS uniquely challenging. Cement is relatively inexpensive: regional variations exist, but market prices hover around US$50 – 70/t. Additionally, cement tends to be locally produced and consumed. This means that unlike manufacturing plants in other industries, which may capitalise on economies of scale by maximising plant capacity and co-locating near transport channels, cement plants vary more in size and are dispersed globally.
The effect of this on CCUS deployment is twofold. Firstly, CCUS costs will cause a proportionally large increase in the price passed on to customers due to cement’s low sale price. Secondly, because plants are dispersed and of varying capacities, there will be limited scale benefits driving down per tonne decarbonisation costs when installing CCUS equipment.
Cement production is also concentrated heavily in a small number of countries; China and India together produce nearly 60% of the world’s cement. This means that meaningful decarbonisation of the global cement value chain is predicated on Chinese and Indian policy support for CCUS deployment. This support is essentially non-existent today.
Regardless, cement producers around the world are beginning to experience pressure (albeit to varying extents) to decarbonise their production. In this article, Wood Mackenzie’s CCUS and carbon markets research will be utilised to articulate the CCUS options available to producers, quantify the economics of deploying CCUS in cement production, and predict the factors that could enable at-scale deployment of CCUS for cement decarbonisation.
The CCUS toolbox presents multiple pathways
Sample cement plant emissions with inlaid pie chart showing general emissions source distribution.
Potential relative contribution of various approaches to overall cement decarbonisation.
Several possible CCUS pathways exist for cement producers to consider. A producer’s optimal approach will vary based on several factors, including access to nearby transport infrastructure, favourable subsurface geology for CO2 storage, regulatory support for a specific pathway, technology readiness, and many others.
Today, amine absorption is the most used CO2 capture platform. The technology uses an amine solvent to absorb CO2 from waste gas. CO2 is then stripped from the amine solution using heat input of roughly 3 GJ/t CO2, producing a high-purity CO2 stream and a solvent recycle loop. Process equipment used in amine absorption typically benefits from increases in scale, exhibiting power law-type reductions in per-unit cost as plant size increases. The total cost of post-combustion amine absorption ranges from US$80 – 120/t CO2, equivalent to a roughly US$50 – 75 increase per t of cement produced.
Cement decarbonisation via CCUS and CO2 removal pathways.
Announced cement CCUS projects by status and capacity by region, with select projects highlighted.
Startups and established companies alike are developing technologies and manufacturing approaches that promise to reduce these costs. Approaches like modularisation of capture equipment could enable capital cost reductions, especially for smaller cement facilities, through repetitive manufacturing of smaller units. Various next-generation platforms, including CO2 adsorption, solids looping, and advanced solvents promise significant reductions in both capital and energy consumption costs. However, cement’s tight profit margins mean that even with precipitous declines in the cost of capture technologies, producers will require significant revenues through government subsidies or other streams to stay cost competitive.
Most announced capture capacity is destined for sequestration in saline aquifer formations. For such storage, developers have two main options: direct onsite CO2
storage at the project facility or transportation of captured CO2 to storage hubs. If a cement facility is located directly above favourable geology for subsurface CO2 storage, a producer may choose to develop their own, onsite CO2 sequestration project. Benefits of this approach include lower cost due to limited need for pipeline construction and faster deployment, since a producer may not need to wait for a storage hub to come online. In some cases, however, factors including complex regulatory and permitting processes, high costs of drilling, and lack of in-house expertise in subsurface operation could make hub transport and storage a more attractive option. Storage hubs are designed to take emissions from distributed sources and sequester them in one location. These hubs are particularly advantageous in places where favourable subsurface geology is limited, permitting barriers are high, and government support for hub projects makes costs more competitive. Generally, if a cement producer chooses to use hub storage, a fee-toll will be assessed to the producer for the transport and storage of CO2 emissions. Today, these fee-tolls vary by region and range between US$20 – 60/t CO2 stored. These costs are expected to fall significantly over time. Enhanced oil recovery presents a third option for permanent sequestration of CO2 with the added benefit of producing additional revenues for the emitter. While this pathway has received limited support in some government policy schemes, Wood Mackenzie’s research shows that CCS-EOR could more efficiently decarbonise global industry per dollar invested due to the use of existing reservoirs and the displacement of higher emitting sources of crude oil.
Instead of storing CO2 underground, cement producers may choose to convert captured CO2 into products sold for supplementary revenues. While CO2 utilisation pathways are generally still early in development, some applications could be ready for near- and mid-term deployment. One such application is the conversion of CO2 to limestone (CaCO3) via mineralisation, which is already cost-competitive with traditional high-purity limestone production. While further development is needed to make CO2 mineralisation cost-competitive as a lower-purity concrete additive pathway, the market for such additives exceeds 500 million tpy and could provide supplementary revenues to support carbon capture in the mid-to long-term.
Other utilisation pathways, like e-hydrocarbon and carbon-based materials production, are very expensive today and need significant development before at-scale deployment is cost-competitive. Additionally, unlike CO2 mineralisation, these pathways do not result in permanent sequestration of CO2 and thus limit the decarbonisation credit that can be claimed by a cement producer.
Producers may instead choose to purchase carbon removal credits to offset their emissions. These credits could come from nature-based solutions like afforestation or engineered approaches such as direct air capture (DAC), bioenergy with carbon capture and storage (BECCS), and biochar. Engineered removals tend to be regarded as ‘higher quality’ versus nature-based removals, but technologies like DAC and BECCS are extremely expensive and limited in capacity today. DAC credit prices exceed US$600/t CO2, though prices are expected to fall to roughly US$200/t by the mid-2030s.
Removal credit purchases could enable cement producers to selectively decarbonise portions of their output if some demand for ‘green cement’ materialises from buyers willing to pay a premium. Cement producers may also be able to generate a small quantity of removals credits by firing biomass fuel in their kilns and capturing the generated CO2 with an associated CCS facility.
While a range of policy mechanisms including incentives, carbon taxes, and direct funding have been proposed and implemented, few currently available
Cement production and CCUS policy readiness by country, with policy readiness scores for China & India highlighted.
Representative cement CCS project costs and revenue across geographies (2.4 million tpy cement facility).
are sufficient to fully offset the cost of CCUS for cement production.
The US 45Q tax credit of US$85/t CO2 is broadly considered the most certain CCUS incentive in the world but is not sufficient to offset costs. For this reason, the US Department of Energy has announced supplementary project grants (US$300 – 500 million) to spur development of some projects with the hope that first-of-a-kind builds will drive costs down over time. In Canada, federal and provincial grants and credits paired with carbon tax avoidance can be sufficient to support some projects, though political and market uncertainty in carbon pricing and grant disbursements complicates project economics.
In Europe, support comes both from incentives and from penalty avoidance. Mechanisms like the EU Innovation Fund, UK industrial carbon capture model, and country-level support for transport and storage hubs have resulted in several cement CCUS project announcements. Additionally, EU ETS projections indicate that penalty avoidance could provide a strong, partial incentive for cement producers to implement CCUS, though this penalty avoidance will likely result in a cost passed on to customers.
However, the effect of North American and European policy support is insignificant when considering the challenge of decarbonising global cement production. Nearly half the world’s cement is produced in China, where support for CCUS deployment is currently extremely limited. Developments like NDRC Notice 733 (a 2024 document outlining China’s initial cement decarbonisation roadmap), China United Cement’s startup of a 0.2 million tpy CO2 oxyfuel combustion with CCS+EOR project, and small project announcements from other major producers indicate some progress.
But policy support strong enough to decarbonise a significant portion of China’s 1.9 billion tpy of cement production has yet to materialise. The policy landscape in India, the world’s second largest producer of cement, tells a similar story.
Project economics highlight CCUS uncertainties and opportunities
Regional variations in cost and policy support translate into CCUS project economics that look dramatically different by geography.
Wood Mackenzie’s CCUS valuations methodology enables robust cross-geography project modelling. Applying this methodology shows a few key trends illustrating the economics of applying CCUS to cement production.
The clearest conclusion is that CCUS is expensive today – installation of the technology in a large-scale cement facility roughly doubles the overall cost
of production before considering government incentives. While technology advancements will drive these costs down, implementing CCUS will inevitably result in costlier cement.
The mechanisms used to pay for this costlier cement vary dramatically by region. In North America, support takes the form of CAPEX grants, tax credits, and (in Canada) carbon tax avoidance.
The sum of these incentives in almost all cases does not generate sufficient revenue for breakeven and a significant price premium from the consumer is still needed. The uncertainty of CAPEX grants and Canadian carbon tax value adds risk to the project’s economics, which is reflected in the assumed cost of capital.
European costs are higher, largely due to costlier transport and storage resulting from onerous regulations and limited onshore CO2 storage capacity. Carbon tax avoidance produces most revenue in the region; while this is certainly an incentive to decarbonise, the cost of doing so will be passed on to customers. Both the EU and UK have project grant programmes applicable to cement CCUS, but these are limited to a few projects.
Asian costs are lower, but essentially no incentives exist today to drive CCUS deployment. Again, most emission reductions in the cement value chain will need to come from China and India, but without strong government support, widespread decarbonisation cannot occur.
Price premiums paid by customers seeking ‘green cement’ could contribute some revenues, but no evidence exists that a liquid, at-scale market for such premiums will materialise in the near term.
Technological advancements and strong government support could enable widespread CCUS deployment
While today’s cement CCUS economics seem dour, it is important to recognise the nascency of many advanced technologies in development. Much like other technologies – solar power, hydraulic fracturing, microchip manufacturing – CCUS platforms will develop given time and deployment capital.
Many of these platforms exhibit technically sound pathways toward meaningfully reducing capital and operating costs.
However, even with tremendous cost reduction, government support will be crucial at facilitating both the impetus for decarbonisation and the support necessary to deploy new technology at scale.
As governments and technologists work in lockstep to enable widespread deployment, cement producers must be ready to navigate the technological and economic realities of decarbonising with CCUS.
Jeffrey Tyska, Honeywell, highlights how advanced carbon capture technologies can help cement producers significantly reduce CO2 emissions and achieve their decarbonisation goals.
Decarbonising the cement industry is crucial to limiting global warming to 1.5˚C, a target set by the United Nations. According to the GCCA 2050 Cement and Concrete Industry Roadmap, cement producers will have to fully decarbonise by 2050 to meet this goal.1 This decarbonisation will require major CO2 reductions.2 While improved efficiency and savings in cement clinker production will also help reduce emissions, perhaps the most promising method of
reducing carbon emissions from cement plants is carbon capture. By 2050, over 1 Gt/year of CO2 will need to be captured by cement producers, which is a more than 400% increase from the 2030 goal of 258 million tpy.3 Honeywell UOP has a portfolio of carbon capture solutions that can help producers achieve these goals while also helping to minimise energy usage and cost of capture. These include solvent, adsorbent, and cryogenic CO2 capture solutions.
Traditional solvents such as MEA (monoethanolamine) have been used for over 80 years to capture acid gases such as CO2 in natural gas plants,4 however they face significant
challenges in flue gas services due to large regeneration energy requirements, tall absorbers, and high rates of solvent degradation in the presence of oxygen. Honeywell UOP’s Advanced Solvent Carbon Capture technology (ASCC) was developed in collaboration with the University of Texas at Austin to help address these challenges and provide a cost-effective solution for carbon capture. ASCC uses a proprietary solvent in tandem with a high-pressure stripper and a novel heat exchange flow scheme (as seen in Figures 1 and 2) to mitigate the effect of these challenges. The solvent enables a high mass transfer rate, leading to shorter and less expensive absorbers. The solvent also has high thermal stability, enabling high regeneration pressures of 4 – 6 bar(g). The high regeneration pressure significantly reduces the amount of electricity required to compress the captured CO2 to the desired product pressure for sequestration, while also lowering the CAPEX required for CO2 compression. Both the solvent and novel heat exchange scheme enable low regeneration energy requirements, typically from 2.1 – 2.4 GJ/MT CO2. While flue gas conditioning is generally required to manage contaminants such as NO2, the ASCC solvent is more resistant to oxidative degradation than many other solvents, leading to reduced makeup requirements and less reclaiming.
The ASCC solvent has been tested for over 8500 hours at the National Carbon Capture Center (NCCC) in Wilsonville, Alabama using flue gas CO2 concentrations of 4 – 12 vol% and a variety of contaminant concentrations, with higher concentration testing performed at University of Texas. The testing has included a skid specific to the unique heat exchange set up for ASCC, along with the high-pressure stripper setup. The unit has demonstrated low rates of solvent degradation and low energy consumption along with testing metallurgy, effects of contaminants, and emissions. The unit has demonstrated solvent emissions under 1 ppmv and produces CO2 with less than 1 ppmv of SOx and NOx content.6
The ASCC solvent is also being tested at Technology Centre Mongstad (TCM) in Norway on residue fluid catalytic cracker (RFCC) and steam boiler flue gases, further demonstrating ASCC’s ability to efficiently capture CO2 from a variety of sources.
ASCC has been selected for multiple Department of Energy (DOE) funded FEED studies, and Korean conglomerate SK E&S recently selected ASCC to help demonstrate CO2 capture viability at a natural gas power plant.7
While ASCC units often use steam to regenerate the solvent, they can also be configured to run using only electricity. This novel design reduces electricity usage in multiple ways, as seen in Figure 4. This includes utilising a heat pump that can efficiently recover heat from a variety of sources in the unit. The design and heat pump fluid allow for a high coefficient of performance (C.O.P.), lowering the unit’s overall energy requirements. Additional energy from the regenerator is recovered by utilising compression to further improve heat recovery in the unit. The energy performance of the e-ASCC is competitive and should be considered where project or site specifics make sense.
Honeywell UOP also offers the UOP CO2 fractionation Process Unit for carbon capture. This unit combines Honeywell UOP’s pressure swing adsorption (PSA) and CO2 fractionation technologies to provide a low energy and cost-effective solution for CO2 capture. The benefits of the UOP CO2 fractionation process include low energy usage, an inherently all-electric design, less pretreatment required than most solvent systems, and a liquid CO2 product. The energy usage per tonne of CO2 product depends on the flue gas composition due to the need for flue gas compression. The energy decreases significantly with increasing CO2 concentration, especially above 15 vol% CO2 on a dry basis. For cement plants with high CO2 concentrations, energy usage can be attractive while maintaining over 95% recovery.8 The significant variation in energy usage with varying inlet CO2 concentration contrasts with chemical solvent systems, which are less sensitive to the inlet CO2 concentration. The lack of solvent also enables less flue gas pretreatment for most cement flue gas, lowering the overall cost of capture. The liquid CO2 product from the cryogenic tower is a key differentiator for customers who need to produce a liquid product, as liquefying CO2 vapour can be energy intensive. In addition, the amount of power required to produce a dense phase CO2 product is greatly reduced versus solvent systems, as the energy required to pump the CO2 is much less than what is required to compress it.
Honeywell UOP has a CO2 fractionation process unit with over 10 years of commercial operating experience on natural gas and has used this experience to help guide the design of the post-combustion CO2 fractionation process unit. The operating UOP CO2 fractionation process unit has demonstrated high recovery (>95%) during operation. Honeywell UOP has also delivered over 1100 PSA systems within
the last half century, with user reported operating data confirming onstream reliability claims of up to 99.95%.9
Another way to help reduce the energy usage of a cement plant is to utilise an oxyfuel configuration. Air is separated into nitrogen and oxygen rich streams, and the oxygen rich stream is used for combustion in the cement plant in place of air. This design helps concentrate the CO2 in the flue gas, significantly decreasing the downstream compressor power required and increasing the partial pressure of CO2 to the CO2 fractionation section. In most cases, an oxyfuel plant will only require cryogenic
Sensitivity to CO2 concentration
Flue gas pretreatment req.
Energy required to separate CO2
Solvent required? Yes No
Flue gas compression required? Blower only Yes
Product state 4 – 6 bar(g) vapour Liquid
Good option for oxyfuel? No Yes
All electric solution available? Yes Yes
High purity CO2 product? Yes
separation, and recoveries well above 98% can be achieved by adding an additional PSA. CO2 may be recycled back to the kiln if needed. The oxyfuel system typically requires larger expenditures in the cement plant but results in a simpler carbon capture solution with lower utility requirements and lower CAPEX.
Adsorbents for dehydration
Dehydration is key for carbon capture. For solvent systems, it is typically required on the overhead CO2 product to ensure that the CO2 meets product specifications. For CO2 fractionation systems, a dehydration unit is required to avoid ice formation and to ensure the product meets the desired specifications. Honeywell UOP’s molecular sieve process technology has been used in over 2400 units worldwide, including dehydrating streams with high concentrations of CO2.
As described, Honeywell UOP is able to offer multiple types of carbon capture solutions, including the solvent based ASCC and the CO2 fractionation process unit. Furthermore, the all electric ASCC unit enables multiple types of all electric carbon capture solutions to be offered. By having multiple efficient carbon capture offerings, Honeywell UOP can tailor the carbon capture solution to a cement plant’s flue gas composition and site constraints.
Capturing carbon from cement plants is key in reaching net zero emissions goals and minimising the extent of global warming. There are multiple approaches to capturing CO2 from cement plants, all of which have unique benefits. Honeywell UOP has a dynamic suite of carbon capture technologies that can be tailored to meet the preferences and requirements of individual cement plants.
ASCC is a solvent solution that has low energy requirements due to its unique solvent, high pressure stripping, and a patented heat exchange flow scheme. It has demonstrated very low solvent emissions while also ensuring less than 1 ppm of SOx and NOx in the product. The unique solvent also allows for shorter absorbers than first generation solvents such as MEA. ASCC can be designed as a steam regenerated system or an all-electric system, depending on customer preference.
Honeywell UOP’s CO2 fractionation system allows for efficient CO2 capture via pressure swing adsorption and cryogenic fractionation. This system lowers the amount of flue gas conditioning needed compared to traditional solvent systems and is a great option for high NOx flue gas. The liquid product is inherent to the design of the unit and can help greatly reduce
utilities where a liquid or dense phase CO2 product is required.
When oxyfuel combustion is considered for cement kilns, a simpler and lower energy carbon capture design can be used. Honeywell UOP’s CO2 fractionation system is a good fit for the high concentrations of CO2 in the flue gas and can minimise energy while producing a liquid product.
Honeywell UOP’s MOLSIV dehydration unit can be used in CO2 fractionation units or CO2 product from solvent systems such as ASCC. This adsorbent can reduce water content of the gas to less than 1 ppmv and performs well even with high CO2 concentrations in the gas.
Honeywell UOP has developed a leading position in separations by providing advanced technology in gas treating (including CO2 removal), membranes, absorption, cryogenics, distillation, and heat transfer. Honeywell UOP has demonstrated ASCC technology through over 8500 hours of operating at NCCC, is testing the solvent at TCM, has commercial experience with CO2 fractionation on a natural gas unit, and has commercial experience with MOLSIV dehydration in high CO2 gas feeds.
This experience and wide range of technologies helps ensure an efficient solution can be found for cement plants looking to decrease their CO2 emissions.
1. 'Technology Brief: Carbon Neutral Energy Intensive Industries' – https://unece.org/sites/default/files/2022-11/ Industry%20brief_EN_2.pdf
2. 'COP27: UN report shows pathways to carbonneutrality in “energy intensive” steel, chemicals and cement industries', 2022 – https://unece.org/media/ press/372890
3. 'CCUS in the transition to net-zero emissions' – https:// www.iea.org/reports/ccus-in-clean-energy-transitions/ ccus-in-the-transition-to-net-zero-emissions
4. 'An Introduction to CO2 Separation and Capture Technologies',1999 – https://sequestration.mit.edu/pdf/ introduction_to_capture.pdf
5. Technology Centre Mongstad – www.tcmda.com
6. Based on internal data from solvent testing at the National Carbon Capture Center in 2023
7. 'Honeywell To Collaborate With SK E&S To Deploy Carbon Capture Technology Across Korea And Southeast Asia', 2023 – https://www.prnewswire.com/apac/newsreleases/honeywell-to-collaborate-with-sk-es-to-deploycarbon-capture-technology-across-korea-and-southeastasia-301941319.html
8. Based on internal study for cement flue gas
9. Based on reliability data from the 2010 North American User Meeting feedback. 99.95% (1 shutdown/yr) achieved with a preventative maintenance project versus 99.8% (2 – 6 shutdowns/yr) without a preventive maintenance programme.
Katherine Romanak, The University of Texas at Austin, underscores the crucial role that carbon capture and storage (CCS) will play in driving decarbonisation within the cement industry.
The cement industry is crunching the numbers, and the verdict is in: the future of cement hinges on the industry’s ability to decarbonise, and decarbonisation will be impossible without carbon capture and storage (CCS).
The industry's large carbon footprint stems from two main sources: the energy required to reach the high temperatures needed for production, and the chemical reactions involved in making cement and concrete. While improving energy efficiency and switching to alternative fuels (AFs) are steps in the right direction, they are not enough to make a dent in the deep decarbonisation targets needed. Even with all the potential innovations – such as better efficiency in clinker, cement, binders, and concrete production, smarter plant design, greener electricity, and more CO2 absorption into concrete – the industry
still faces the harsh reality that more than a third of the emissions will remain stubbornly unaddressed (GCCA Decarbonisation Roadmap).
This is where CCS technology enters the scene, and not everyone supports it. So, let's dive into this technology a bit to separate fact from fiction.
What is CCS and how does it work?
CCS stops carbon dioxide emissions at any industrial point source. It works on any facility with a flu stack that emits waste gases which include CO2. This includes: power generation, gas processing, chemical production, waste incineration, iron and steel production, and importantly, cement production; the list goes on and on. Each year, these processes dump billions of tonnes of carbon into the atmosphere. To mitigate this using CCS, the CO2 is scrubbed out of the waste gas stream, compressed into a liquid-like substance, transported to a suitable location, and injected deep into the Earth – at least 800 m deep but more commonly thousands of metres deep for permanent disposal. As the carbon was previously locked away in the earth (e.g. oil, gas, limestone, ores) we want to 'put it back' where it came from, to keep it out of the active carbon cycle on Earth where it greatly affects climate.
But the overwhelming truth is that even if all emissions stopped tomorrow, because too much CO2 has already been put into the air, it still needs to be removed from the atmosphere to stop the effects of climate change. CCS can be used for this as well, either through using bioenergy with CCS (BECCS) or direct air capture and storage (DAC). BECCS involves capturing CO2 from bioenergy processes, where sustainably sourced biomass is converted into energy, and then storing it underground. This method not only generates energy but also removes CO2 from the atmosphere through the photosynthesis of the biomass, making it a negative emissions technology. On the other hand, DAC uses large fans to draw in ambient air and extract CO2 through chemical processes, which is then stored safely underground. Both BECCS and DAC rely on capture, transport, and geologic storage, providing durable and permanent disposal for reducing atmospheric CO2 levels. These applications of the capture portion of CCS technology are less mature than flu stack capture, but are being developed with the realisation that we are orders of magnitude away from our climate targets and the crisis at hand is urgent!
Yes, that's right! In order to reach global climate targets we need to scale up all technologies (efficiency, renewables, fuel switching, nuclear, CCS, terrestrial, and engineered sinks) by order of magnitude from their current levels. According to the UNEP Emissions Gap Report 2024, the current trajectory is alarming. If we continue with our current policies, we are on a path towards a global temperature rise of 3.1˚C by the
end of the century. Even with full implementation of current pledges and promises, the temperature rise is still projected to be between 2.6 – 2.8˚C, far from the Paris Agreement targets of limiting warming to well below 2˚C, with efforts to limit it to 1.5˚C. This highlights the urgent need for increased ambition and immediate action to close the emissions gap and prevent the worst impacts of climate change.
This is why the cement industry’s push to decarbonise is so critically important. The need to reach net zero emissions has never been more urgent, and the task is huge. The ticking clock is becoming deafening. I believe if the scale of the challenge were fully understood, there would likely be less nitpicking over individual technologies and more encouragement for the development of all viable solutions.
Sadly, this is not the case, especially when it comes to CCS, a sorely misunderstood technology. Even though CCS plays a uniquely important role in emissions mitigation, many people are either underor mis-informed about the technology. In many ways that is understandable. It is a large, complex multi-disciplinary technology that people have a hard time grasping and therefore tend to lump in with the other more polluting technologies that it is designed to clean up. With 75% of global emissions currently produced by the burning of fossil fuel, many people link CCS to fossil fuel use, believing that its only purpose is to help oil companies continue their polluting activities. Generally, these folks want to end fossil fuel use tomorrow and in order to make that happen they demand no CCS.
This leads to wide skepticism about CCS, with many believing it is unproven, non-existent, too expensive, dirty, or unsafe – a so-called ‘unicorn’ technology. They worry about its safety, potential leaks, and the consequences if it does leak. These fears stem from the fact that many communities living near other toxic industries have suffered a history of environmental injustice. Adding to the distrust is the anti-fossil fuels movement, which sees CCS solely as a tactic to keep fossil fuels in play. On one side, climate change deniers downplay the urgency of the issue, while on the other, climate activists reject CCS, arguing it just prolongs fossil fuel use. This divide fuels a wave of misinformation, with sensational headlines about CO2 well leaks and claims that CCS is unproven, despite decades of successful research and implementation.
The public may not be fully aware of the extensive work and proven track record of CCS technology. It was deeply considered and scrutinised for almost a decade within the UNFCCC, the global treaty on combatting climate change, before being formally incorporated by consensus of some 197 countries as an accepted mitigation strategy in 2011 at COP 17. This simply could not happen for a ‘unicorn technology’. The technology has been proven
through decades of prior research and development and now deployment.
The questions that people are asking now about the safety and efficacy of CCS are the same ones I was asking 18 years ago as an environmental geochemist researching CCS. After starting a family while finishing my PhD, I left science to focus on raising my family. When I returned to the workforce in 2007 CCS was being looked at seriously in the United States, and The University of Texas at Austin’s Bureau of Economic Geology was looking for researchers to study the safety efficacy and potential environmental impacts of geologic CO2 storage. This group was at the forefront of CO2 geologic storage research, developing scientific methods to store and monitor the subsurface behaviour of CO2, ensuring it stays put, and understanding the environmental impacts in the slight chance that it leaks. What sets us apart is our extensive project experience. We've been in the field, putting CO2 in the ground and monitoring its behaviour – boots on the ground handling CO2 for two decades.
Our journey began in the late 1990s with Dr. Susan Hovorka leading the Frio test a small-scale project, injecting about 1000 t of CO2 into a saline aquifer. These early efforts laid the groundwork for The US ‘Regional Carbon Sequestration Partnership Program’ which divided the country and parts of Canada into seven regions and funded research institutions across the country to identify potential CO2 storage formations. This programme progressed from white paper studies to demonstration projects, where CO2 was injected and monitored in the subsurface, reaching up to 1 million tpy at various research projects around the country. Eventually, this activity led to commercial deployment at sites injecting as much as 1.6 million metric tpy – fully monitored and safely stored.
At this point, despite what some headlines might say, the world has stored and monitored more than 200 million t of CO2 safely with no negative impacts on groundwater, the environment, or any CO2 release from storage back into the atmosphere. According to the Global CCS Institute, the world currently has over 50 projects currently storing about 50 million t of CO2 per year and this is being upscaled by 102% year on year. Now, the US is developing sites that can store 50 million t to manage large US emissions, and other countries in Europe, Australia, Canada, UK, and South East Asia are ramping up their efforts to deploy CCS. In fact, a few commercial CCS projects have been running globally for decades. For instance, the Sleipner project in Norway has been storing CO2 since 1996 (>25 million metric t stored), and the Snøhvit project in the Barents Sea since 2008 (>10 million metric t stored). The Weyburn field has been injecting since 2000 with a total of over 30 million metric t stored, and in West Texas, the SACROC CO2-enhanced
oil recovery (CO2-EOR) field has been operational since 1972 and has stored over 80 million t of CO2 And while it is true that the benefits of storing CO2 through CO2-EOR are lessened by the additional oil that is produced during the process, the fact that an CO2-EOR site needs a pipeline to supply CO2 to the operation is significant. If it were possible, those companies would pull the CO2 out of the reservoir and recycle it but the rocks naturally hold onto it.
The process of storing CO2 underground
CO2 is essentially compressed into a liquid-like and injected into the earth through wells similar to oil and gas wells. Just like oil and gas is trapped in the subsurface for millions of years, so too is CO2. It is not stored in caves or caverns, but in between the grains of the rock where salty water and sometimes oil and gas naturally reside.
By regulation, CO2 is only stored in geologic formations that would never be used for anything else and are far from any potable sources of drinking water. It is stored in formations that have the porosity and permeability to accept the CO2 and are overlain by what we call ‘confining systems’ or rocks that have little permeability and porosity which prevent any upwards movement of the CO2 to the surface. Fortunately, this is a common sequence in underground formations.
CO2 is sticky in the subsurface. It gets trapped in the pores, similar to how mayonnaise clings to a piece of bread. If you spread mayonnaise on bread and then tried to scrape it off, you'd find it almost impossible because the mayonnaise would remain stuck in the bread's pores. With CO2 similarly stuck in the pores of the rock, the permanence of geological storage is a key advantage. While storing CO2 in plants and soil is important and might last around 100 years, CO2 storage in geological formations for thousands to hundreds of thousands of years. This longevity makes CCS a vital component of emissions reduction strategies. Another significant advantage is the large volumes of CO2 that can be accommodated. Current estimates show that the world has several orders of magnitude more space underground than is needed to store the world's emissions.
Groundwater protection is a concern I hear a lot about. That is something the global research community looked at thoroughly. It is a precious resource and an important question to ask! So, the scientific community attacked it head on for two decades.
CO2 geological storage sites have never leaked, nor impacted groundwater resources, so researchers have used multiple approaches to study potential impacts. We have looked at natural analogues – or places where CO2 naturally occurs in the subsurface to understand its long-term behaviour. We have used industrial analogues, such as CO2-enhanced oil production (CO2-EOR) sites, to learn about CO2
handling, injection, and storage. Computational models have been used to simulate CO2 transport in reservoirs and aquifers, and laboratory experiments have been used to observe CO2 behaviour under controlled conditions.
Perhaps one of the most useful and direct ways of studying potential leakage is to make it happen on purpose. Near-surface controlled releases involve injecting CO2 into shallow aquifers (tens of feet below ground surface) at rates that would intentionally cause surface flux. Then global scientists would use these sites to test tools, approaches, and technologies to monitor and assess environment impact. There have been about 17 of these experiments done around the world, most onshore with 2 experiments conducted offshore. These have provided many significant research outcomes.
What we found is that CO2 in drinking water is not a problem in itself. We pay slightly more for sparkling water than for still water, and it is completely safe to drink. Our concern was that if CO2 were to reach a drinking water aquifers or surface ecosystems it would form carbonic acid which could quickly dissolve rocks, releasing ions and impurities into groundwater. However, decades of research have consistently shown that the concentration of these ions are never significant enough to meaningfully impact groundwater quality. Environmental recovery is swift either once groundwater moves beyond CO2's influence, or if CO2 inputs stop or are mitigated. As pH stabilises, metals are readsorbed onto mineral surfaces and can co-precipitate with minerals, significantly reducing trace metal concentrations in water. These natural processes are so proficient that they maintain metal concentrations at trace levels which are inconsequential to drinking water quality. It is exactly these natural processes that make the impacts of CO2 in the environment so benign. CO2 is a natural component of every ecosystem on Earth, present in water, soil, and air. Plants and microbes have evolved natural mechanisms to uptake CO2, which helps in limiting its environmental impact. We consume CO2 in beverages like soda, sparkling water, and champagne so it is not a toxic waste but one whose quantities must be managed. Whereas CO2 must be viewed as a ‘waste product’ that causes harm when too much of it enters the atmosphere, CCS must be viewed as a necessary component of our waste management strategy. Just as we pay for trash removal, we must manage CO2 as a waste product, even though in itself it is a friendly molecule.
Nothing is without risk and as we scale up the technology there will evidently be mishaps that we will learn from. The main risks associated with CCS, such as induced seismicity and potential leakage
through old wells, are well understood and can be mitigated through engineering and regulatory measures. Global regulations, established since the IPCC Greenhouse Gas Guidelines in 2006 – 2007, ensure that CO2 remains securely stored. Rigorous site selection, risk assessment, and continuous monitoring are integral to the permitting process, making CO2 storage one of the safest subsurface activities.
Effective CCS deployment requires not only scientific and technical expertise but also community engagement and supportive policies. In our activities there is a strong emphasis on involving local communities in CCS projects, addressing their concerns, and ensuring that the benefits of these projects are shared.
Policy support is also crucial. Incentives such as tax credits can make CCS projects financially viable and encourage broader adoption. Cap and trade systems, or regulations requiring the disposal of CO2 are sorely needed and essential for making CCS economically viable. Currently, CO2 capture from dilute flue streams remains costly, but ongoing technological improvements and numerous demonstration projects are bringing significant cost reductions. Various capture technologies, such as post-combustion capture, chemical absorption, direct separation, oxyfuel, calcium looping, and others are being demonstrated and tested worldwide.
The cement industry's commitment to CCS is starting to advance at an impressive pace. According to the GCCSI 2024 Global Status of CCS Report, there are currently 30 CCS projects under development at cement plants across North America, Europe, and China. Notably, the Qingzhou Oxy-fuel CCS project in China is already operational, while the Brevik Cement Plant in Norway is under construction. Should all of these developing and conceptual projects achieve their targets, they are poised to enhance global emissions reduction through CCS by 29 million metric tpy – a commendable beginning for the cement industry's sustainability efforts.
I have heard the cement industry referred to as the ‘glue of society’ because It literally forms the foundations of our world. As the industry continues to build essential infrastructure, embracing CCS technology will enable its sustainability into the future.
Deploying CCS is crucial for mitigating the environmental impact of cement production emissions, but it is a formidable task for the industry. Armed with science-based factual information on CCS, the industry can move forward with confidence. Decarbonatisation of cement and concrete is possible with CCS and will enable the industry to remain the cornerstone of a more resilient world for generations to come.
Cool
Many companies operating in emission intensive industries are working to solve the challenges represented by large-scale decarbonisation. However, to succesfully navigate the journey, there are many obstacles to overcome.
The cement and lime industries have limited direct experience with carbon capture, utilisation, and storage (CCUS), given its relative infancy and the limited number of CCUS technologies available today. Combine this with regulatory, transport, utilisation and market uncertainties and it is clear that industry leaders still have a highly complex series of challenges to solve.
Many emitters are going through a process of technology selection involving multiple technologies in order to better understand the dynamics of a nascent sector. The choices made and the timing of deployment are critical to the success of large-scale, successful businesses. Move too quickly or choose the wrong technology, and company returns could suffer, giving competitors an advantage. Conversely, delaying too long may result in missed market opportunities, with emissions regulations potentially forcing the closure of several plants.
The first mover advantages for those that partner with optimal solution providers delivering low-cost
capture across full scale deployments could shine the light on the industry’s future winners.
A variety of technologies exist today, albeit at differing technology readiness levels (TRL). Most of these technologies are hampered by at least one or more major hurdle, including:
� Energy consumption.
� Plant footprints.
� Emissions during use.
� Scalability (techno-operational limits to maximum operational capacities).
� Resilience to varying operating conditions of industrial processes.
� Regulatory uncertainties.
Membranes have been used for gas separation for many years, however in recent years, there have been considerable advances in membrane technology used for CO2 separation and capture. Membrane based carbon capture systems, while not yet as advanced as some of the solvent-based options, now appear to represent an increasingly interesting and competitive set of performance criteria. Within the field of membranes, there are now several distinct and quite different technologies emerging too.
Cool Planet Technologies has developed a highly effective solution: a diffusion membrane carbon
capture system which is on the cusp of solving many of the industry’s challenges. This innovative solution has gained industry attention as the company is working closely with industrial partners, including Holcim and CRH in cement, and Carmeuse in lime, to evaluate, scale, and deploy its advanced technology.
Collaborating with Hereon, the leading German R&D institute focused on membrane research, Cool Planet has developed a scalable, modular system using the advanced, class leading PolyActive™ membrane and a unique in-house designed compact capture module. This solution can be deployed in a scalable manner ranging from 10 000 tpy to installations in excess of 1 000 000 tpy.
PolyActive membranes have been systematically developed both in the laboratory and in the field for some 15 years. The membrane has an excellent optimisation of selectivity (the preferential selection of CO2 in comparison to other gases) and permeability (the volume of CO2 that flows through the membrane in a given time).
PolyActive is a thin film composite membrane produced as flat sheets. It is a solution diffusion membrane, meaning the transportation of CO2 through the membrane occurs via pressure gradient driven diffusion as opposed to facilitated transport membranes, where a chemical reaction takes place in the membrane.
Consequentially, the membrane is highly resilient to typical industrial flue gas compositions, which include compounds such as NOx and SOx. Unlike facilitated transport membranes, PolyActive is also tolerant to varying operating conditions, enabling its application across a wider variety of industrial settings and locations, where changing operating conditions and seasonal temperature fluctuations pose significant challenges for alternative technologies. Cool Planet’s capture plants have fast turndown, turn-up, and response times, accommodating operational fluctuations, including the cyclical nature of lime plant operations.
Cool Planet and Hereon have an ongoing research and development programme together to further
develop and enhance the properties of the membrane and capture process.
Carbon capture is not always part of a cement or lime company’s core business. Cool Planet works with emitters to provide a compact, highly energy efficient end of pipe carbon capture solution capable of meeting pipeline, sequestration, and even food grade specifications. The membrane system offers a competitive advantage for flue gases with CO2 concentrations of 10% and higher, using significantly less energy than amine-based capture systems. Crucially, the process does not use solvents, which can generate emissions during their use and require disposal afterward.
Cool Planet’s engineering teams collaborate closely, from first concept to delivering an operational plant. While the solution is already economically advantageous, company engineers can work with emitters to ascertain if higher CO2 concentrations could be realised from plant adaption and/or integration with the emitter’s plant to drive even greater efficiencies. For example, benefits can be gained by reducing false air in a plant, leading to increased CO2 in the flue and higher capture plant efficiency. Lime operations can benefit from oxygen enrichment in the combustion process, which significantly raises CO2 concentrations in the flue gas, resulting in more efficient capture operation, lower footprint, and reduced costs.
Cool Planet can also offer advice to emitters throughout the establishment of the capture, offtake, and sequestration/utilisation chain. Finally, the company can also provide ongoing operational support and maintenance for the project on an ongoing basis. The capture process is at its core a simple three step process (Figure 1).
The pre-processing is designed by Cool Planet and is tailored specifically to the characteristics of the emitter’s flue gas emissions, utilising proven ‘off the shelf’ technology. The typical pre-treatment unit cools the flue gas and removes the particulates to ensure optimal conditions for input into the membrane separation units.
The membranes are packed into high-density, low-cost cartridges and modules jointly developed by Cool Planet and Hereon, which fit into a standard 40 ft (12 m) ISO container. Capture capacity is scalable and can be readily increased by adding additional membrane containers. These membrane modules can be arranged in series or cascade depending on the operational requirements and project objectives with respect to recovery and
product purity. Energy recovery is also integrated into the capture process.
Post-processing and purification of the captured CO2 is designed by Cool Planet and tailored to the emitter’s requirements. Again, proven ‘off-the-shelf’ technology is used, ensuring the captured CO2 meets the necessary specifications for onward transportation, sequestration, or utilisation. As no chemicals are used in the capture process, there are no residual chemicals to remove afterward.
Onsite space for retrofit capture plants is often limited at many cement and lime plants, and the installation of a tall tower required by conventional capture technologies may not be feasible. The compact and low-rise footprint of Cool Planet’s capture solution helps to overcome these space issues, and the structure of the plant also allows for flexibility in arranging the capture plant around existing facilities. The capture plant is self-contained and has no requirement for waste heat from the cement/lime plant for efficient operations, avoiding the extra complexity and cost that this can entail.
Plants are also designed to operate, if required, continuously for up to 5 – 7 years to match operational maintenance cycle of some lime plants. On changeout, the membrane cartridge is replaced in its entirety to reduce downtime and a new cartridge with the latest generation of membranes is loaded. This results in existing users of the technology benefit from Cool Planet’s ongoing membrane R&D programme and avoids emitters being potentially encumbered by outdated capture technology.
Capture plants operate primarily in an autonomous mode, with control and monitoring systems fully integrated into the existing control rooms of cement and lime plants. The straightforward nature of the technology relieves plant operators of the requirement of specialist knowledge to operate the capture plant on a day-to-day basis.
While some technologies are still in the laboratory phase of demonstration, Cool Planet’s capture technology has over 15 years of R&D and testing through five pilot projects in coal fired power, cement, and steel. A plant attached to a gas boiler is now entering its eleventh year of operation.
Importantly, a modular design allows for a phased approach to carbon capture deployment. This approach enables emitters to make stepwise progress toward decarbonisation while markets develop transportation and utilisation options. Whilst emitters are still working with the dilemmas of technology selection, a phased approach to carbon capture deployment is often the optimal technical and economic solution incorporating risk mitigation.
This is especially important for early adopters as CO2 export infrastructure is still currently underdeveloped. The use of export pipelines with associated send or pay commitments to shippers and sequestrators may be required, which for a full-scale deployment will consume significant credit capacity.
Cool Planet is currently working on scaling projects, including:
� 100 000 tpy plant, forecast to be operational in cement by 2028.
� 100 000 tpy plant, forecast to be operational in lime by 2030.
� 800 000 tpy plant, forecast to be operational in cement by 2030.
The company is also participating in the new EU-funded Project ICO2NIC, which aims to capture and valorise waste CO2, making CCU economically viable. The ICO2NIC consortium will establish a comprehensive value chain, from the CO2 emitter, Tüpras, to the end consumers Procter & Gamble and Tüpras. Cool Planet’s role in this consortium is to capture CO2 with a cement plant that is utilising the 4th generation of membrane modules
To ensure a sufficient supply of high-quality PolyActive membrane and modules for this rapid scaling programme, Cool Planet is investing in its own highly automated production facility in Europe. The output from this manufacturing facility will be capable of supplying sufficient membrane to decarbonise several major cements plants a year.
In 2022, Cool Planet conducted a pilot at Holcim’s Höver cement plant in Germany, which was reported by Holcim as having “extraordinarily positive results…”.
Consequently, construction is now underway for a commercial plant at Höver to capture 10 000 tpy, with operations expected to commence in late 2025.
The plant will capture CO2 from the flue gas, which will then be processed through an on-site liquefaction plant. Cool Planet will also conduct a pre-operational demonstration of its 3rd generation membrane module at a test site in Grimsby, UK, in Q2 2025.
Despite the many challenges society is facing in tackling climate change, it is clear that both industrial emitters and those developing carbon capture solutions are making great progress in developing low-cost, efficient, compact, and robust solutions. While there are still many hurdles to overcome, it is clear that there is a bright future ahead for hard to abate industries.
ABC www.abc.org.uk
AUMUND www.aumund.com
Cachapuz www.cachapuz.com
CemAI cemai.com
Cementtech www.cementtech.org
Chryso www.chryso.com
Climate Earth climateearth.com
DI MATTEO www.dimatteo.de
Dracyon Corp. www.dracyoncorp.com
Endress + Hauser www.endress.com
ES Processing www.es-processing.com
Euromecc www.euromecc.com
Fives www.fivesgroup.com
GEA
www.gea.com
Geometrica www.geometrica.com
Honeywell UOP uop.honeywell.com
IEEE-IAS/PCA Cement Conference www.cementconference.org
InterCem Engineering www.intercem.de
KHD Humboldt Wedag www.khd.com
Klüber Lubrication www.klueber.com
Mirion Technologies www.mirion.com
Optimitive www.optimitive.com
PSCL www.pscl.com
Rieter Morando www.rietermorando.com
SiloConnect www.nanolike.com/siloconnect
SOMA Coordenadas Industrial www.soma-industrial.com
Starlinger www.starlinger.com
Technip Energies www.ten.com
May 4-8
Diverse technical training, including 17 technical paper presentations and seven training module sessions
Roundtable discussions on three timely industry topics
Panel discussions on supply chain & logistics and government affairs with PCA members and staff
Keynote speaker Paul Chadwick, award-winning comic book creator of Concrete
Enhanced plant tour includes visits to National Cement Company of Alabama, Inc. (Ragland Plant) and Reworld (alternative fuel provider)
®
Keep cement production GREEN and the skies clear with a Geometrica dome.