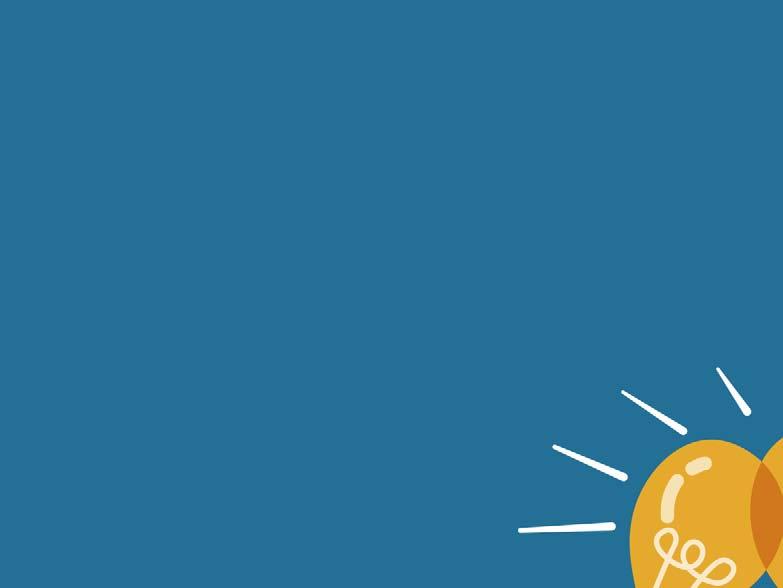
13 minute read
Smart surveys
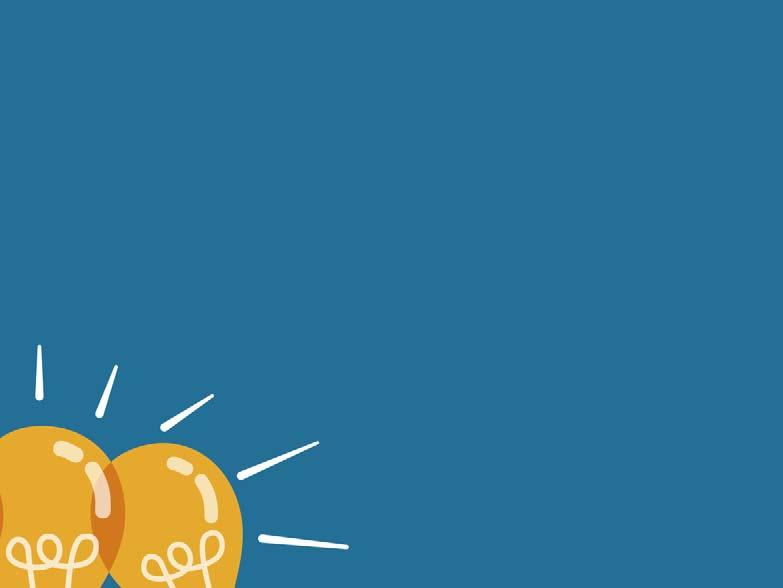
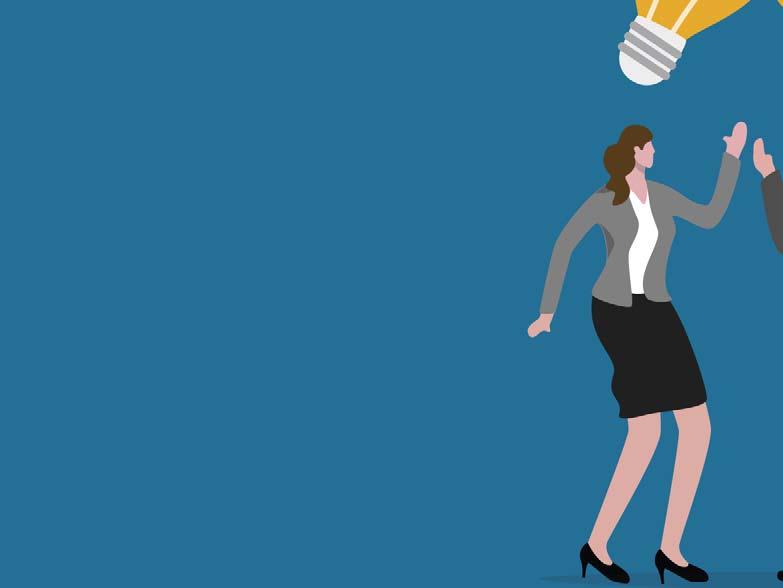
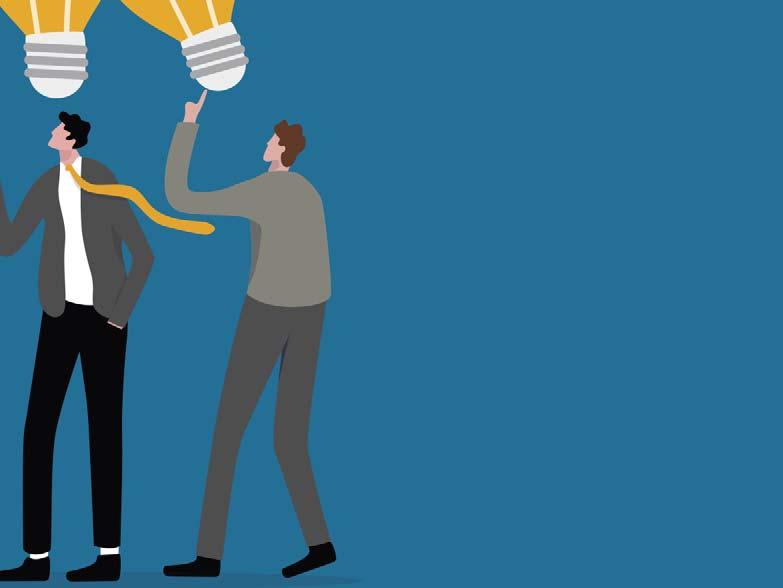
Kaveh Ebrahimi, Fluor Ltd, and Cristiana Nascimento, Fluor B.V., provide an engineering perspective on the best practices for successful modern surveys of existing equipment.
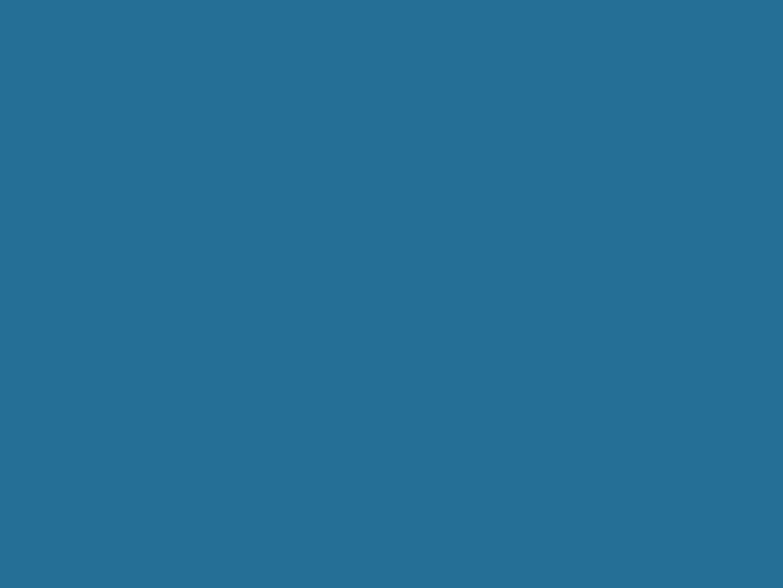
Understanding the status of existing and operating equipment in a process plant greatly assists plant owners/operators as well as engineering contractors to assess the integrity of equipment, risks associated with their continued operation and to decide the correct approach for any planned maintenance, modifi cations or upgrade of equipment. Many process plants around the world suffer from poorly recorded documentations for existing equipment. This is usually because of continuous expansions, repairs or alterations made on the equipment without correct on-site recording or updating of as-built documentations, or due to insuffi cient transfer of information from old to new owners/operators of process plants. In order to get a better view of existing facilities and equipment, traditional as well as modern survey methods such as 3D laser scans or drone investigations can be very benefi cial in providing valuable data to engineers. A full step-by-step survey of existing equipment can provide useful information on topics such as: Exact dimensions to facilitate replacements. Unrecorded changes of modifications on the existing equipment. Performance issues. Failures. Re-calibration requirements. Change of process operating parameters. Change of access routes. Vibration. Signs of leakage. Insulation deterioration. Denting or distortion.
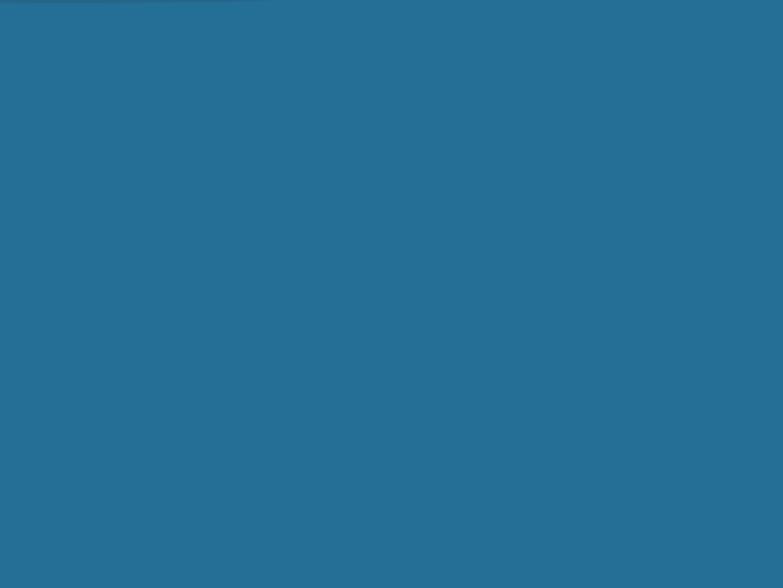
Any survey can be a challenging activity in a large operating plant, and without a well-thought process, it may not provide the reliable data required by engineering contractors or plant owners/operators. Even worse, it can provide wrong or inaccurate impressions about the status of existing facilities or equipment.
Any engineering contractor in charge of the survey process usually has a key role in how a survey is planned, conducted and reported. The engineering contractor’s experience with the plant process scheme, its pinch points and the survey process, combined with their input for making sound engineering decisions is critical for success.
This article attempts to provide a systematic guideline to engineering contractors in charge of surveys on existing equipment, and explain how best to plan and execute surveys in operating plants or during planned turnarounds. The guidance provided can be used for plant surveys in different sections of process industries, such as: upstream, midstream, downstream, petrochemical, etc.
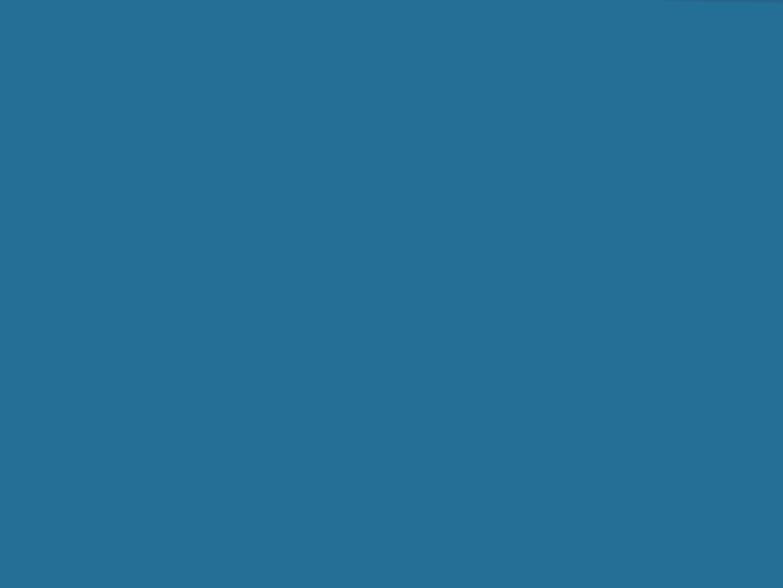

Figure 1. Survey steps.
Survey steps
Figure 1 provides an overview of various identifi ed steps for the survey of existing equipment at an operating plant or during planned turnarounds.
Due to the geographically diverse nature of the process industry, survey of equipment may need to be performed in any part of the globe. Therefore, in addition to the steps mentioned in Figure 1, it must be emphasised that when working in any region, the engineering contractor in charge of the survey programme and its assigned surveyor should be prepared and willing to work in the local language, and in accordance with local laws and customs, which may vary widely. Certainly, it helps if the engineering contractor has local offi ces which can be trusted to have knowledge of local rules, regulations and customs.
Data gathering
To effectively carry out a survey programme for existing equipment, an early data gathering exercise should be performed by the engineering contractor in charge. This will help the engineers identify any missing or mismatching data which require confi rmation or the main areas of concern from owner/operating personnel.
Usually, two distinct types of data can be gathered: active and archived data, as well as operating personnel data and information which may or may not have been formalised on any document.
During the data gathering exercise, it would help to organise a meeting with operating personnel of the plant and share ideas with them.
Scope and purpose definition
The engineering contractor in charge of survey activities should clearly defi ne the scope of the survey. Ideally, the survey scope should encompass the current immediate need for a given equipment as well as any potential future long-term programme to upgrade, modify or revamp the facilities.
The purpose of the survey may be clear to the engineer in charge of the investigations, but not so to the surveying team. It is usually of great help if the purpose of the survey is clearly defi ned, as this will help the surveying team understand why certain checks are necessary for any given equipment, or it may even result in the surveying team suggesting extra checks that may not have been fully requested.
This step of the survey process is better to be conducted along with the next step, which is selecting the survey method. This is because once the engineering contractor reviews the available data and information, they usually have a few ideas about how the equipment survey should be conducted, and this can be refl ected in the scope and purpose defi nition.
Selection of survey method
Depending on the scope of the survey and following the discussions with the owner/operator, the suitable survey method or methods can be selected. Correct selection of the survey method also requires consideration of the time available and accuracy level of the information required. For a large scale dimensional survey, Table 1 may provide a comparison between three commonly used survey methods.
3D laser scans
3D laser scans have become a popular method in the process industry for the survey of existing assets.
The level of accuracy, resolution, reliability, cost effi ciency and ease of handling achieved by laser scanner technology-based systems make them particularly suitable to carry out dimensional checks in various industrial sectors.
The success of the 3D laser scan survey and the resulting point cloud is highly dependent on setting the right expectations and discussing them in advance with the company providing the service. Questions such as the ones listed in Table 2 should be addressed to ensure the adequacy of the service being requested.
The quality of the point cloud that is delivered should ultimately be the responsibility of the company providing the scanning service, but there are validation checks that the engineering contractor may resort to or request in order to guarantee that the data provided is correct. Table 3 provides some examples for this purpose.
Planning
Any successful survey must be planned well in advance. Deciding on when to mobilise people to site usually requires a multi-discipline review and discussion with various stakeholders, including: surveyor, operation and maintenance personnel, the engineering team, suppliers (who may have a view on repair methods or replacement parts required), regulatory offi ces, and others.
The areas that are off-limits for any surveys during plant operations should be identifi ed, and surveys for those parts perhaps timed at planned shutdowns or turnarounds.
Table 1. Comparison of different dimensional surveys
Direct inspection 3D laser scanning Aerial photogrammetric
Area
Small Medium Medium to large
Schedule
Speed
Usually acceptable for small areas only Medium Medium
Slow Fast Fast
Quality
Medium High High Recommended for Small areas and easy access Medium areas and speed Large areas and difficult access
Table 2. Examples of questions/coordination points for a suitable 3D laser scan request
Address within the engineering contractor team
• What is the aim of the scan? • What needs to be seen and checked? • What is the level of detail and desired accuracy that the scans should have? • What resolution should the total 3D scan have?
Discuss/coordinate with point cloud supplier (beforehand)
• Request different datasets, not only the export file for a specific drawingsoftware, but also software independent data • Request the recorded raw data and any specific software registration
Table 3. Examples of 3D scan data quality checks
Checks performed by the engineering contractor
• Whether the scan plan (requested with the order) has been followed • Properties of the scans and scanners used (e.g. to confirm that the apparatus used was calibrated) • Whether the scans have the requested resolution and accuracy
Permits and preparations
Almost all modern process industry plants globally have strict permit-to-work systems in place, through which any potentially hazardous work carried out at site is controlled and recorded. Permit-to-work is also usually the main method of communication between plant management, surveyors, operators and anyone responsible for carrying out potentially hazardous work.
The engineering contractor in charge of the survey should identify steps required in order to have permits ready on time for the survey process. Depending on the type of permit-to-work, it may need a series of authorisations or endorsements in order to be valid and, therefore, it is benefi cial that preparations are carried out beforehand to make the people involved aware of the nature and timing of surveys being proposed for the equipment.
These need to be clarifi ed with the owner/operator of the plant prior to making preparations to mobilise personnel and equipment to site.
In addition to permit-to-work procedures, there are also safety trainings that might be specifi c to a certain client or country, and these also need to be addressed in preparations for any survey.
Checks requested from the laser scan contractor
Surveying during turnarounds may require careful coordinating with other works and contractors which are going to be present at site. Figure 2 provides a brief overview of what factors can have an infl uence on planning for the survey.
Modern survey methods such as 3D laser scans are usually non-intrusive and quickly done, and therefore they can be performed in most operating plants after receiving the right permits. But other types of surveys or inspections, such as ultrasonic thickness measurements, may require access to components or equipment which are operating at high temperatures, and during operation it may not be safe or feasible to access them. However, paradoxically, surveying the equipment during shutdowns may not necessarily result in detecting the anomalies in equipment operation. Therefore, the engineering contractor in charge has a key role in assessing the
situation based on safety, economics and technical risks associated with performing surveys whilst the equipment is in operation. • Analysis of the registration report (not Perform survey just supply of the report itself) At this point, the surveyors should be briefed • Analysis of point cloud cuts (e.g. by and provided with a plan of action to start means of vertical and horizontal cuts, as this makes it possible to check if the points are shifted) their survey process. Each surveyor usually has a preferred way of measuring and • Overlapping point cloud cuts, by recording data, but they should all be attributing different colours to the required to transfer the data in a pre-agreed point cloud cuts format to the engineering contractor in charge of the survey process. Surveyors shall work in a coordinated manner so as not to miss any part of the scope or perform duplicate surveys. The site operation team may need to allocate experienced escorts to the surveyors, so they can access permitted areas whilst walking through the plant. Some of the key aspects that need to be addressed whilst performing any survey are summarised in Table 4.
Survey report
Findings from survey programmes need to be reported in a clear format in order to be helpful for the engineering team. It is benefi cial if a list of assumptions is also included in the report that can be later referred to. Pictures in the report should be captioned, numbered and described in the report. Use of pictures without any explanation should be avoided.
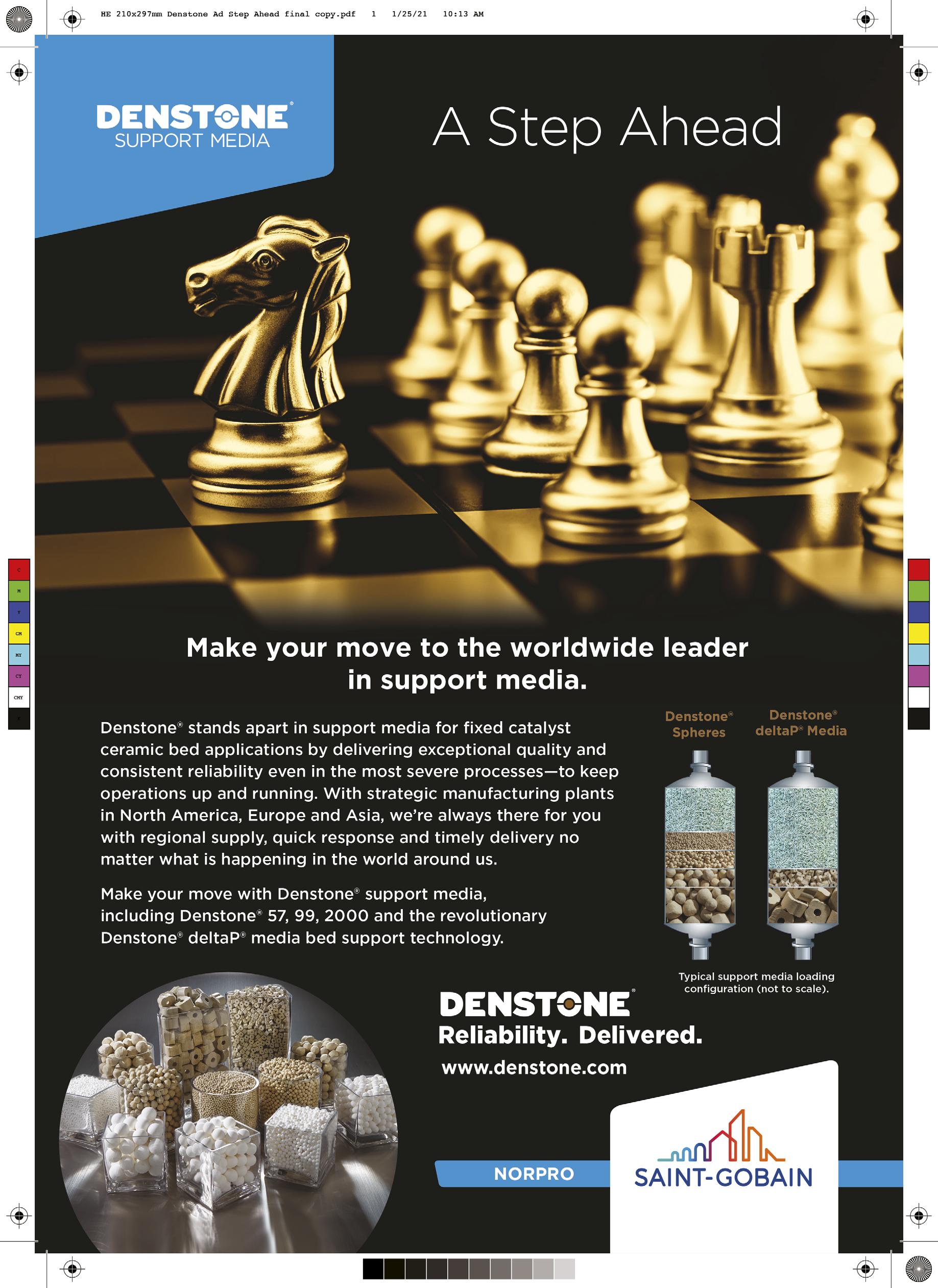
Any abnormalities found in equipment during survey should be reported in an easy to understand way by the engineering team.
If there have been limitations in surveying any part of the equipment, these should also be clearly reported.
It is also a recommended practice that the surveyor team is experienced enough to provide their comment about the best possible action to be taken.
Recommendation
It is the engineering contractor’s responsibility to provide the owner/operator with its advice on the next steps that need to be taken. The recommendation always needs to take into consideration the reason for the performance of the survey in the fi rst place, as well as the fi ndings that have been reported in the survey report.
It is possible that certain issues found during the survey could be solved or mitigated by taking different approaches. It is, therefore, important to describe all identifi ed options and evaluate each one based on its merits to resolve the issue.
The proposed options must refl ect a technical understanding of the equipment and of the process in which it is involved, as well as demonstrate an understanding for the specifi c business and the organisation (time and commercial constraints). Any identifi ed limitations to the proposed solutions and to how to put them into effect should be mentioned at this stage. Suggestions on how to overcome those limitations should also be provided.
At the end, the recommendation should clearly indicate the engineering contractor’s opinion of which is the best solution for the issue at hand. All steps required to move towards implementation, as well as the responsible party for taking each action, should be clearly identifi ed. If required, the identifi ed actions can be categorised by priority.
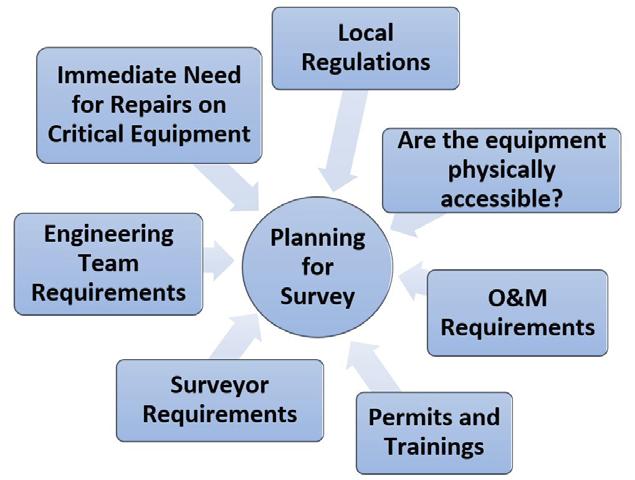
Figure 2. Planning for survey.
Table 4. Recommended practices for performing surveys
Survey type Recommendation
Visual inspections Ask surveyors to report anything unusual associated with equipment, including but not limited to: vibration, signs of leakage, unusual loud or rattling noises, excessive dusts on equipment, damage to insulation or coating, loose or missing bolts, deterioration, relief device having opened, distortion, denting, instrument reading anomalies (high or low pressure drops), presence of rust stain, and even sighting of bird nests
Dimensional or angular measurements
Clearly define the required units of measurements. Without correct definition of units of measurements, the survey results may need further time-consuming conversion (with potential errors) to preferred units
Update of data
The last step of a survey is always the update of documentation with the information gathered. It is therefore important to understand and discuss with the owner/operator how the data should be updated, what their expectations are in terms of documentation, which drawing software is used, whom within their structure is responsible for maintaining and uploading the information, and ultimately discuss who should be responsible for updating existing documents: should it be part of the deliverables of the engineering contractor or should it be done by the owner/operator team themselves? It is also important to understand that this step, here identifi ed as the closing step of the survey performance cycle, may be the starting point of the activities of a new project, where the data regarding an existing equipment needs to be gathered in order to assess the existing (and up to date) information.
Conclusion
Survey of existing equipment in any process plant is benefi cial to provide critical information to the owner/operator of the plant. The information resulting from equipment surveys can assist and shape the decision-making process for future investments in upgrades or maintenance procedures. In order for a survey programme to be successful, thorough planning and organisation of its various key activities is essential. This article has tried to provide an overview on key issues during different stages of survey programmes.
3D laser scans The surveyor should have the necessary tools and software to convert the gathered data to user friendly 3D or CAD models which can be imported to engineering contractor’s modelling software Camera or drone surveys The object should be in focus, not blurred or obstructed by other items
Ultrasonic thickness measurements
Check for excessive corrosion or deviation from existing as-built drawings
Bibliography
1. FARROW, G. ‘Laser Scanning of Revamps: a review of benefits, best practices and emerging opportunities in laser-enabled revamp projects’, Digital Refining, (October 2014). 2. Guidelines for the Conduct of Oil, Gas & Petrochemical Risk
Engineering Surveys, published by LMA, (2015). 3. ‘Guidance on Permit to Work Systems’, Health and Safety
Executive, (2005). 4. BARRETT, R., et al., ‘Permits Around the World’, IChemE Symposium
Series No. 158, (2012).